Плазменная сварка и плазмотроны прямого, косвенного действия
Для плазменной дуги характерны крайне высокая температура (до 30000°С) и широкий диапазон регулирования технологических свойств.
По сравнению с аргонодуговой сваркой плазменная сварка отличается более высокой проплавляющей способностью. Это дает ей следующие преимущества:
- повышенную производительность;
- меньшую зону термического влияния;
- более низкие деформации при сварке;
- пониженный расход защитных газов;
- более высокую стабильность горения дуги;
- меньшую чувствительность качества шва от изменения длины дуги (ввиду её неизменной геометрии по длине (рисунок 1).
Рис. 1. Плазменная (сжатая) дуга, горящая на графит
Плазмотроны прямого и косвенного действия
Плазменную дугу получают при помощи устройства под названием плазмотрон. Есть два способа подключения плазмотрона: для генерации дуги прямого действия (рис.
Плазмотроны, подключаемые для генерации дуги, называют плазмотронами прямого действия, а для генерации плазменной струи — косвенного действия. Часто плазмотроны косвенного действия конструктивно отличаются от плазмотронов прямого действия системой охлаждения соплового узла плазмотрона. У первых она более эффективна.
Принцип действия и конструкция плазмотронов
В плазмотронах прямого действия плазменная дуга возбуждается между вмонтированным в газовую камеру стержневым — как правило, вольфрамовым — электродом и свариваемым изделием. Сопло электрически нейтрально от электродного (катодного) узла и служит для сжатия и стабилизации дуги.
В плазмотронах косвенного действия плазменная дуга создается между электродом и соплом, а поток плазмы выдувает плазменную струю.
Рис. 2. Схемы плазмообразования
Для плазменной сварки металлов обычно применяют плазмотроны с дугой прямого действия.
Сжатие столба дуги происходит следующим образом: рабочий газ, проходящий через столб дуги, нагревается, ионизируется и выходит из сопла плазмотрона в виде плазменной струи.
Плазменная дуга прямого действия по форме почти цилиндрическая и немного расширяется у поверхности изделия.
Плазменная дуга косвенного действия (струя) по форме представляет собой ярко выраженный конус с вершиной, обращенной к изделию и окруженной факелом.
Слой газа, омывающий столб дуги снаружи, остается относительно холодным, образуя тепловую и электрическую изоляцию между плазменной дугой и каналом сопла. Плотность тока дуги в плазмотронах достигает 100 А/мм2, а температура — 15000–30000 °С.
Особенности дуг прямого и косвенного действия
У плазмотрона с дугой прямого действия плазменная струя совмещена со столбом дуги — в отличие от плазмотрона с дугой косвенного действия. Это значит, что для первого плазмотрона характерна более высокая температура и тепловая мощность.
Процесс возбуждения дуги непосредственно между электродом и изделием осуществить трудно. Поэтому сначала возбуждается дуга между электродом и соплом (дежурная), а когда ее факел касается изделия, происходит автоматическое зажигание основной дуги между электродом и изделием.
Дежурная дуга отключается при устойчивом горении основной дуги. Обычно дежурная дуга питается от того же источника, что и основная, через токоограничивающие сопротивления.
В плазмотронах с дугой прямого действия в изделие вводится дополнительное тепло за счет электронного тока. КПД таких плазмотронов значительно выше, чем у плазмотронов с дугой косвенного действия. Поэтому плазмотроны с дугой прямого действия лучше применять для сварки, резки, наплавки, а плазмотроны с дугой косвенного действия — для напыления, нагрева и т.п.
Плазменная дуга может быть использована:
- при сварке тонколистового материала толщиной менее 1 мм, включая тугоплавкие металлы;
- при сварке металлов с неметаллами;
- для наплавки и нанесения покрытий путем расплавления электронной или дополнительно подаваемой в дугу присадочной проволоки;
- для пайки;
- разделительной резки и поверхностной обработки различных металлов.
Похожие статьи
Товары по теме
Информация о методе плазменная сварка
Плазменная сварка представляет собой способ сваривания металлов с использованием плазменного потока. Главной особенностью плазменной сваркой является возможность достижения более высоких температур, чем при стандартной дуговой сварке. Это обеспечивает лучшие условия проплавления металла во время работы.
Плазменная сварка является одним из самых современных и инновационных методов сваривания материалов. Широкие возможности применения обеспечиваются благодаря ряду преимуществ:
- возможность ведения процесса с использованием высоких температур,
- снижение чувствительности процесса к длине дуги,
- горение дуги даже на малых токах,
- повышенная скорость ведения процесса,
- увеличенный коэффициент полезного действия,
- возможность работы с материалами толщиной до 1см,
- точный контроль глубины провара,
- практические полное отсутствие шлаков и отходов в ходе работы,
- простота в установке и использовании оборудования.
Главным недостатком плазменной сварки является высокая стоимость оборудования и работы. Несмотря на простоту установки и использования плазмотрона оборудование требует тщательного ухода, регулярной чистки. Горелка и электрод плазмотрона должны меняться своевременно, чтобы избежать проблем в работе оборудования. Также необходимо тщательно следить за температурой процесса и оборудования, чтобы избежать перегрева. Специалисты, работающие с плазмотроном, должны пройти специальное обучение. Оператор плазмотрона должен иметь определенные знания и навыки.
Все недостатки легко нивелируются достоинствами плазменной сварки. Высокая эффективность и повышенная производительность перевешивают понесенные затраты на оборудование и обучение персонала. В результате же компания получает первоклассных специалистов, обученных работать на самом современном оборудовании для ведения плазменной сварки.
Область применения плазменной сварки
Плазменная сварка подходит для работы практически с любыми видами металлов и сплавов, в том числе для:
- титана и его сплавов,
- алюминия и его сплавов,
- магния и его сплавов,
- меди и ее сплавов,
- вольфрама,
- высоколегированных, низколегированных или нелегированных сталей,
- чугуна,
- сплавов никеля,
- различных неэлектропроводных металлов,
- других разнородных металлов.
В первую очередь плазменная сварка применяться на промышленных предприятиях. Это объясняется высокой стоимостью плазмотрона и необходимостью специального обучения персонала. Для индивидуального или бытового применения плазменная сварка может оказаться слишком затратным методом работы.
В промышленности плазменная сварка может применяться практически во всех отраслях. Особое применение плазменная сварка находит в отраслях, предъявляющих высокие требования к качеству сварного соединения и точности работы, например, в приборостроении, авиакосмической отрасли, медицинской отрасли и многих других.
Техника проведения и оборудование для плазменной сварки
Стандартно оборудование для плазменной сварки состоит из плазменной горелки, вольфрамового электрода, системы охлаждения, системы подачи газа и сопла плазмы. Для образования плазмы используется специальный газ – аргон, смесь аргона с водородом, кислород или азот. Сама плазма способна разогреваться до 30 000 Система охлаждения нужна для контроля этой температуры и удержания ее не выше 8 000oC.
При подаче тока на конце электрода образуется электрическая дуга. Аргон, попадая в зону дуги, образует плазму, нагревается и ионизируется. Тепловое расширение увеличивает объем газа в 50-100 раз. Аргон начинает истекать из сопла плазмотрона. Основным источником энергии для сварки является тепловая энергия газа и энергия ионизированных частиц газа.
Сварка может проводиться плазменной дугой при сварке прямого действия или плазменной струей при сварке косвенного действия. При прямой сварке плазменная дуга горит между электродом и свариваемым изделием. При косвенной сварке плазменная струя горит между соплом плазмотрона и электродом.
По величине тока различают микроплазменную сварку (при токах 0,1-0,25А), сварку на средних токах (до 150А) или сварку на больших токах (свыше 150А). Сварка на больших токах обеспечивает полных прожог металла.
Плазменная сварка — Плазма и газ-резка, сварка, напыление
Требования предъявляемые к плазматронамПри конструировании плазмотронов, предназначенных для различных видов обработки материалов следует учитывать ряд общих требований, предъявляемых к ним:
- Плазмотрон должен обеспечивать многократное надежное зажигание и стабильное горение плазменной дуги в заданном диапазоне рабочих токов и напряжений. Это требование удовлетворяется при определенных соотношениях между диаметром электрода, сопла, длиной последнего, и зазором между ними, а также при правильном конструктивном решении узла формирования и стабилизации дуги.
- Элементы, наиболее подверженные действию тепла (электрод, сопло), должны выдерживать длительную тепловую нагрузку при максимальной мощности плазмотрона. Это требование выполняется при правильном выборе материала теплонапряженных элементов и си-стемы их охлаждения.
- Электрическая изоляция между электродами и соплом должна быть рассчитана на максимальное напряжение, возникающее на дуговом промежутке при возбуждении дуги и ее обрыве. При возбуждении дуги с помощью осциллятора это напряжение составляет 2-5 кв в диапазоне частот 0,3-1 Мгц.
- Элементы водяных и газовых коммуникаций плазмотрона (шланги, уплотнения, прокладки и пр.) должны выдерживать давление не ниже 10 атм.
- Для обеспечения маневренности плазмотрона подсоединяемые к нему шланги и электрические провода должны быть гибкими и прочными.
- Плазмотрон должен быть технологичным в изготовлении, в ремонте и удобным в эксплуатации. Особо важно обеспечить легкость его разборки и сборки и возможность быстрой замены наиболее часто изнашиваемых деталей (катода и сопла).
- Конструкция плазмотрона должна быть экономичной, т. е. должна предусматривать возможность применения недифицитных материалов для его изготовления и обеспечивать минимальное потребление охлаждающей воды, рабочего газа и минимальные потери тепла.
- К плазмотронам предъявляется и ряд специальных требований, обусловленных особенностями технологического процесса.
- Плазмотроны для сварки и наплавки должны обеспечивать надежную защиту шва от вредного воздействия окружающей среды, плазмотроны для напыления — высокие скорость течения и теплосодержание плазменной струи при минимальной ее загрязненности продуктами эрозии электродов, плазмотроны для резки — высокую концентрацию теплового потока плазменной струи. Ручной плазменный резак должен быть легким и удобным в обращении.
- отсутствие любых водо-, электро- или газоподводящих шлангов в рабочем пространстве печи;
- водоохлаждение всех металлических частей;
- защита от излучения всех уплотнений и неметаллических деталей водоохлаждаемыми или термоизоляционными экранами;
- возможность ввода плазмотрона в печную камеру через уплотнение.
В ряде случаев выдвигаются особые требования к системе управления плазмотроном, к способу его охлаждения, к защите от воздействия окружающей среды, к повышенной надежности его в условиях работы на поточной линии и др.
Плазматроны: схемы, классификация
При создании плазмотрона первым шагом является составление схемы его устройства. Исходя из особенностей технологического процесса и условий работы плазмотрона выбираем систему его охлаждения, род тока, плазмообразующую среду, вид и материал электрода, способ стабилизации дуги, перемещения ее электродных пятен и т. д. Различные варианты схем плазмотронов удобнее всего представить в виде классификации (рис.). Данная классификация составлена таким образом, что один из вариантов каждого подраздела является необходимым составным элементом общей схемы плазмотрона любого типа.
В первую очередь все плазмотроны разделяются на две группы по виду дуги (см. рис.): плазмотроны с дугой прямого и косвенного действия (схемы 1 и 2). Различие тепловых свойств обоих типов плазмотронов и области их применения уже рассматривались выше.
рис. 1 Классификация плазмотронов по критериям
По системе охлаждения электрода и сопла плазмотроны также делятся на два основных типа: с воздушным и с водяным охлаждением (схемы 3, 4). Теплоемкость воды намного выше теплоемкости воздуха и других газов. Поэтому наиболее эффективной и распространенной является водяная система охлаждения, при которой допускаются высокие тепловые нагрузки на электрод и сопло, т. е. обеспечивается нормальная работа плазмотрона при больших токах и высокой степени обжатия плазменной дуги. Однако водяное охлаждение несколько усложняет конструкцию плазмотрона, утяжеляет его из-за наличия водоподводящих шлангов и удорожает эксплуатацию плазменной установки. Чистота воды существенно влияет на эффективность теплоотвода. При больших расходах воды плазменную установку целесообразно оснащать циркуляционной системой охлаждения с использованием дистиллированной воды во избежание образования накипи. Система воздушного охлаждения ввиду низкой эффективности применяется реже, главным образом для охлаждения малоамперных плазменных горелок и ручных плазменных резаков, предназначенных для монтажных работ в зимних условиях. В таких резаках рабочий ток обычно не превышает 300-400 а. В обеих системах охлаждающая среда чаще всего проходит последовательно электродный и сопловой узел через изолирующий корпус плазмотрона. При этом существенную роль с точки зрения эффективности охлаждения играет профиль полостей охлаждения, температура и давление поступающей в плазмотрон охлаждающей среды. Основная задача при выборе системы охлаждения состоит в том, чтобы обеспечить максимальную интенсивность отвода тепла стенками сопла, так как чем выше величина теплового потока, отводимого соплом, тем круче температурный градиент газовой прослойки между столбом дуги и стенками канала сопла и, следовательно, тем выше плотность тока и мощность столба дуги.
рис. 2 Классификация плазмотронов по методам стабилизации дуги
Плазмотроны можно классифицировать и по способу стабилизации дуги. Система стабилизации дуги, обеспечивающая сжатие столба и строгую фиксацию его по оси электрода и сопла плазмотрона, является наиболее важным элементом плазмотрона. Существуют три вида стабилизации дуги: газовая, водяная и магнитная. Наиболее простой и распространенной является газовая стабилизация, при которой наружный холодный слой рабочего плазмообразующего газа, омывая стенки столба дуги, охлаждает и сжимает его. При этом в зависимости от способа подачи газа (вдоль или перпендикулярно оси столба) газовая стабилизация может быть аксиальной или вихревой (схемы 5, 6). Наибольшее обжатие дуги достигается при вихревой ее стабилизации, поэтому этот способ используется главным образом в плазмотронах для резки и напыления. При аксиальной стабилизации поток газа, обдувающего столб дуги, имеет более спокойный, ламинарный характер, что обеспечивает лучшие условия защиты нагреваемого изделия от воздействия окружающей среды. Поэтому аксиальная стабилизация применяется в плазмотронах для сварки и наплавки.
Иногда применяют двойную стабилизацию дуги (схема 7), при которой сочетается аксиальная подача газа через первичное и вихревая подача через вторичное сопло или наоборот. Столб дуги можно стабилизировать, омывая его водяной струей (схема 8). Образуемый из струи водяной пар служит плазмообразующей средой. При водяной стабилизации можно достигнуть наиболее высокой степени сжатия и температуры столба дуги до 50 000 °К. Однако присутствие паров воды вблизи катодной области приводит к интенсивному сгоранию электродов из любых материалов. В плазмотронах с водяной стабилизацией, предназначенных для резки, используется графитовый электрод, автоматически перемещаемый по мере его сгорания. Плазмотроны с водяной стабилизацией отличаются сложностью конструкции, малой надежностью системы автоматического регулирования подачи электрода и сложностью способов возбуждения дуги. Магнитная стабилизация (схема 9), при которой создается продольное магнитное поле, сжимающее столб дуги, менее эффективно, чем газовая и водяная.
Кроме того, надетый на сопло соленоид усложняет конструкцию плазмотрона. Преимущество способа магнитной стабилизации состоит в возможности регулирования степени сжатия столба дуги независимо от расхода рабочего газа, в то время как при газовой и водяной стабилизации рабочий газ является одновременно плазмообразующим и стабилизирующим. На практике наложение продольного магнитного поля применяется не столько для стабилизации дуги, сколько для вращения ее анодного пятна по внутренним стенкам сопла с целью повышения стойкости последнего. Например, в плазмотронах, применяемых для напыления, магнитное вращение анодного пятна газовихревым способом позволяет значительно снизить эрозию сопла и, следовательно, загрязненность плазменной струи.
Классификация плазмотронов по виду электрода
По виду электрода-катода плазмотроны постоянного тока можно разделить на две группы: плазмотроны со стержневым и плазмотроны с распределенным катодом.В плазмотронах со стержневым катодом, катодное пятно фиксируется на торце электрода, а в плазмотронах с распределенным катодом — интенсивно перемещается с помощью газовихревого или магнитного вращения по развитой поверхности электрода.
В плазмотронах для обработки металлов применяются в основном стержневые катоды, подразделяемые на три основных вида: расходуемый, газозащищенный и пленкозащитный (схемы 1, 2, 3).
Расходуемый, чаще всего графитовый, электрод был показан в схеме плазмотрона с водяной стабилизацией. Несмотря на то, что графит обладает высокой температурой плавления, при нагревании до этой температуры он не плавится, а возгоняется, чем и обусловлен его повышенный расход.
Газозащищенный вольфрамовый электрод — самый распространенный из всех видов электродов. При работе в инертной (аргон, гелий) и восстановительной (азот, водород) средах катод из тугоплавкого вольфрамового стержня при нагрузке 15-20 а/мм2 практически не расходуется. Вольфрамовый катод по сравнению с графитовым значительно прочнее и обладает во много раз большей электропроводностью.
Для улучшения условий работы катоды дуговых плазмотронов изготовляют из вольфрама с небольшой добавкой окиси тория или лантана (1,5-2%). Существует мнение, что торированные вольфрамовые электроды обладают некоторой радиационной способностью, поэтому в последнее время чаще используются лантанированные вольфрамовые электроды. Примеси окиси тория или лантана повышают эмиссионные свойства вольфрамового катода (работа выхода электронов понижается с 4,5 до 2,63 эв), что обеспечивает лучшие условия зажигания, более высокую допустимую плотность тока и устойчивость горения дуги. Кроме того, вольфрам с указанными добавками имеет температуру рекристаллизации на 600° К выше, чем чистый вольфрам и, следовательно, сохраняет волокнистое строение и пластичность до более высокой температуры. Однако стойкость вольфрамового электрода при добавлении кислорода к газовой среде в связи с образованием летучих соединений резко снижается. Например, в плазмотронах, применяемых для резки, при использовании технического азота, содержащего 3-5% О2, на вольфрамовом катоде через 2-3 ч работы при токе 300-400 а образуется кратер, смещение центра которого относительно оси сопла вызывает соответствующее смещение столба дуги и приводит к явлению двойного дугообразования. Поэтому при работе с кислородосодержащей плазмообразующей средой в первичное сопло подается аргон, защищающий вольфрамовый электрод от воздействия рабочего кислородосодержащего газа, подаваемого во вторичное сопло.
Система с двойным газовым потоком имеет существенные недостатки. При использовании дешевого рабочего газа, например воздуха, все же остается необходимость в использовании дефицитного аргона. При этом усложняется конструкция плазмотрона и ухудшается нагрев рабочего газа, так как наиболее эффективно газ нагревается вблизи катодной области. Сравнительно недавно появился новый вид катода — пленкозащитный стержневой катод, обладающий высокой стойкостью в газах, содержащих кислород (в воздухе, углекислом газе, техническом азоте). Он представляет собой стержень из циркония или его сплавов, запрессованный в медной обойме. Механизм работы такого электрода должен быть еще детально изучен, но можно уже считать установленным, что достаточно высокая термостойкость циркония, имеющего относительно низкую температуру плавления (2125° К), в значительной мере обусловлена образованием стойкой тугоплавкой пленки из его окислов и нитридов, защищающей чистый цирконий от испарения. Тугоплавкие соединения, образующие пленку, при обычных температурах являются диэлектриками, а при температурах, близких к температуре плавления (3200° К), теряют свои диэлектрические свойства и становятся проводниками с ионной проводимостью (σ >= 1 ом-1*см-1).
Таким образом, стойкость циркониевого катода определяется его термохимическим взаимодействием с плазмообразующей средой. Не-обходимыми условиями, обеспечивающими высокую стойкость катода, является наличие в составе газовой среды кислорода и азота, а также такая интенсивность его охлаждения, при которой температура катодного пятна не превышала бы температуру разложения туго-плавких соединений. Эрозия циркониевого катода резко повышается при большем процентном содержании кислорода, чем в воздухе (более 20%) и особенно при наличии в газовой среде водорода. Особо важное значение с точки зрения повышения стойкости циркониевого катода имеет его конструкция и система охлаждения. В настоящее время в плазмотронах для воздушно-плазменной резки достигнута вполне удовлетворительная стойкость циркониевого катода при работе на токах до 400 а. Применение пленкозащитного электрода в плазмотронах переменного тока исключается ввиду его активного разрушения в полупериоды обратной полярности. Особенностью работы циркониевой вставки является постепенное углубление ее нижнего основания в медную обойму по мере эрозии.
Циркониевая вставка расходуется главным образом при включении дуги, очевидно, вследствие разрушения пленки от термоудара. При определенном углублении нижней поверхности вставки последующее зажигание дуги осуществляется с медной обоймы, поэтому для перемещения катодного пятна на циркониевую вставку и для жесткой фиксации его необходимо применять газовихревую или магнитную стабилизацию дуги, обеспечивающую строгую соосность столба дуги с электродом и соплом плазмотрона. При использовании циркониевого электрода допускается большая плотность тока, достигающая 80-100 а/мм2, чем при использовании вольфрамового электрода. При работе плазмотрона с окислительной плазмообразующей средой на больших токах (1000 а и выше) используются разнообразные виды распределенных катодов, наиболее распространенными из которых являются полый, дисковый и кольцевой (схемы 4, 5 и 6). Недостатками распределенных катодов являются сложность их конструкции, трудность равномерного перемещения катодного пятна по всей поверхности электрода, низкая стабильность горения дуги, возрастание напряжения прикатодной области дуги и связанное с этим увеличение потерь мощности в электроде.
Поэтому в плазмотронах для обработки металлов распределенные катоды не нашли практического применения. Существует классификация плазмотронов и по плазмообразующей среде. Состав плазмообразующей среды диктуется технологическим процессом и в свою очередь является определяющим фактором при выборе схемы плазмотрона.
По химическому воздействию на обрабатываемое изделие и электроды плазмотрона все плазмообразующие среды можно разделить на три большие группы: инертная, восстановительная и окислительная. Физические свойства и оценка роли каждого из плазмообразующих газов уже рассматривались выше.
Классификация плазмотронов по роду тока
По роду тока плазмотроны отличаются наибольшим разнообразием вариантов. Поэтому рассмотрим лишь основные из них. Подавляющее большинство плазмотронов для обработки металлов выполняется на постоянном токе прямой полярности (схема 1). Это объясняется, прежде всего, физической особенностью дуги, заключающейся в том, что на аноде дуги выделяется большее количество тепла, чем на катоде. Тепловая мощность, выделяемая в электроде плазмотрона, в отличие от плавящегося электрода сварочной дуги является не только бесполезной, но и вредной. Наименьшую тепловую нагрузку несет электрод, являющийся катодом. Достаточно отметить, что предельно допустимая токовая нагрузка на лантанированный вольфрамовый электрод на переменном токе примерно в два раза, а на обратной полярности при использовании постоянного тока в десять раз ниже, чем на прямой полярности. Поэтому плазмотроны постоянного тока имеют наиболее высокий коэффициент полезного использования мощности. Столб интенсивно сжатой дуги должен быть жестко стабилизирован по оси электрода и сопла плазмотрона. При смене полярности электрода эта стабилизация нарушается, поэтому дугу переменного тока сжать труднее, чем дугу постоянного тока.
Важным преимуществом плазмотронов постоянного тока по сравнению с плазмотронами переменного тока является большая стабильность горения дуги. Прохождение тока через нуль может вызвать погасание дуги, поэтому обычно напряжение холостого хода источника питания переменным током не менее чем вдвое превышает рабочее напряжение дуги. При питании плазмотронов постоянным током можно достичь отношения uд/uxx равного 0,8-0,9. Следовательно, при одинаковой мощности дуги установленная мощность и габариты источника постоянного тока меньше, чем мощность и габариты источника переменного тока. Кроме того, источник постоянного тока обеспечивает равномерную загрузку трехфазной сети. Существовавшая раньше проблема выпрямления постоянного тока в настоящее время практически решена благодаря созданию и широкому выпуску электропромышленностью мощных малогабаритных полупроводниковых вентилей. Первоначальные затраты и расходы на эксплуатацию плазменных установок переменного и постоянного тока приблизительно равны. Поэтому с учетом перечисленных выше преимуществ для большинства процессов обработки материалов целесообразно применять плазмотроны постоянного тока. Плазмотроны переменного тока применяются в ряде случаев в силу технологических требований процесса. Например, плазменную сварку алюминиевых сплавов необходимо вести на переменном токе, так как в периоды обратной полярности за счет действия эффекта катодного распыления разрушается тугоплавкая пленка окиси алюминия, препятствующая нормальному процессу сплавления металла.
При плазменной плавке в случае параллельной работы нескольких мощных плазмотронов постоянного тока на общую ванну-анод возникает трудноустранимое магнитное взаимодействие между дугами. Поэтому в этих условиях могут быть использованы плазмотроны переменного тока. В этом случае целесообразно использовать плазмотроны в количестве, кратном трем, что обеспечивает равномерную загрузку трехфазной сети. Рассмотрим три основные схемы плазмотронов переменного тока. На схемах 2 и 3 плазмотроны питаются от однофазного трансформатора. В схеме 3 осуществлена вентильная коммутация тока таким образом, что электрод функционирует только как катод (в полупериод прямой полярности), а сопло — как анод (в полупериод обратной полярности). При такой схеме обеспечивается большая стойкость вольфрамового электрода. Однако с увеличением тока ухудшаются условия работы сопла, а при работе на токах ниже определенного предела (~150 а) нарушается стабильность горения дуги. На схеме 4 плазмотрон питается от трехфазного трансформатора. В этом случае обеспечивается высокая стабильность горения дуги, однако электроды и сопло находятся в сравнительно тяжелых условиях работы. Кроме того, значительно усложняется конструкция плазмотрона. В целях повышения стабильности горения дуги переменного тока некоторые плазмотроны выполняют комбинированными. В этом случае основную дугу переменного тока прямого действия стабилизируют вспомогательной маломощной дугой постоянного тока, горящей либо между электродом и соплом (схема 5), либо между двумя соплами (схема 6), одно из которых (катод) является формирующим. Второе сопло (анод) выполняется с большим внутренним диаметром. Благодаря этому оно подвержено меньшему тепловому воздействию столба основной дуги.
Наряду с дуговыми плазмотронами, работающими на переменном токе промышленной частоты, за последнее время были разработаны высокочастотные (ВЧ) и сверхвысокочастотные (СВЧ) плазмотроны [7, 8]. Принцип работы высокочастотного индуктивного или безэлектродного плазмотрона (схема 7) заключается в нагреве газа до состояния плазмы в электромагнитном поле индуктора. Для этого в полость индуктора, питаемого от высокочастотного генератора (частотой 1-40 Мгц, напряжением до 10 кв и мощностью до 50 кВт), помещается трубка из термостойкого изолирующего материала, например, кварца. В трубку подается плазмообразующий газ и кратковременно вводится металлический или графитовый пруток. Последний раскаляется под действием поля индуктора и вызывает нагрев и первоначальную ио-низацию окружающего газа. Когда электропроводность газа возрастает до определенной величины, начинается интенсивный его нагрев и ионизация вихревыми токами, создаваемыми полем индуктора. После развития самостоятельного кольцевого разряда пруток удаляется из полости трубки. Продуваемый через трубку газ, проходя через кольцевой разряд, нагревается и истекает в виде плазменной струи, температура которой достигает 15 000-20 000° К, а скорость истечения в десятки раз меньше, чем скорость истечения плазменной струи дуговых плазмотронов. Высокочастотная энергия сравнительно дорога, высокочастотные генераторы сложны и имеют ограниченную мощность.
Поэтому очень чистый (ввиду отсутствия электродов) и мягкий факел индукционного плазмотрона нашел применение для обработки особо чистых тугоплавких порошковых материалов, выращивания монокристаллов и других специальных процессов, не требующих высокой производительности.
В сверхвысокочастотных (СВЧ), или электронных плазмотронах, газ также нагревается электромагнитным полем, создаваемым электродом-излучателем (схема 8). Плазменный высокочастотный факел возникает у электрода при остроконечной форме электрода и высокой напряженности поля вблизи него. В высоковольтном и сверхвысокочастотном электрическом поле свободные электроны ускоряются и приобретают такую кинетическую энергию, что при столкновении с частицами газа вызывают их диссоциацию и ионизацию. Электрод плазмотрона подключен к магнетронному генератору частотой 2000-3000 Мгц и мощностью 2-5 кет. Плазменный факел электронного плазмотрона интересен тем, что в нем нет термического равновесия: температура электронов на порядок выше температуры ионов и свободных атомов. Например, при температуре факела 3500° К электронная температура достигает 35 000° К. Такая высокая температура электронов позволяет проводить в плазменной струе химические реакции синтеза некоторых специальных материалов.
Сварка сжатой дугой — Сварка металлов
Сварка сжатой дугой
Категория:
Сварка металлов
Сварка сжатой дугой
Сущность способа состоит в том, что сечение плазменной струи уменьшается по сравнению со свободной струей под действием магнитных полей, обдуванием потоками газа или распыленной жидкости, пропусканием струи через сопло. Данный способ является наиболее важным и распространенным (рис. 1).
В дуге между неплавящимся электродом и нагреваемым изделием располагается сопло, представляющее собой металлическую или графитную пластинку с калиброванным отверстием-каналом, через которое проходит плазменная струя, образуемая дуговым разрядом. Дуга может быть прямого действия (замкнут контакт, разомкнут), косвенного действия (замкнут, разомкнут) и смешанного действия (замкнуты контакты). При замыкании контакта 6 ток идет через сопротивление.
Рис. 1. Сварка сжатой дугой
Рис. 2. Плазменная сварочная горелка
Обычно для плазменной сварки используют горелку, часто называемую плазматроном (рис. 2). В горелку подается одновременно два независимых потока 1 — плазмообразующий и 2 — защитный. В обоих потоках может быть один и тот же газ, например аргон; могут быть и разные газы, например 1 — аргон и 2 — азот – водород. Поток подает газ для образования плазмы; расход и скорость газа небольшие. С увеличением скорости газа усиливается расплавляющее действие плазменной струи и глубина расплавления основного металла. При значительном увеличении скорости газа расплавление металла может стать сквозным, металл выдувается из ванны и процесс сварки может перейти к резку металла.
Внешний поток защищает сварочную ванну и зону сварки от воздействия атмосферного воздуха; кроме того, он обжимает плазменную струю за пределами сопла и может придавать ей цилиндрическую или коническую форму. Свободная струя, вышедшая из сопла, постепенно расширяется по мере удаления от среза сопла. Поток в случае дуги косвенного действия может сводить конец факела на острие, что иногда целесообразно технологически, поэтому защитный поток называют также формирующим или фокусирующим.
Питание горелки производится от обычных источников постоянного тока с падающей характеристикой на прямой полярности (минус на вольфрамовом электроде). Для сварки алюминия и его сплавов имеются положительные результаты применения переменного тока с использованием эффекта катодного распыления для очистки поверхности алюминия.
Для зажигания дуги используется генератор высокочастотного тока — осциллятор. Если используется дуга прямого действия с анодом на изделии, то сначала зажигается вспомогательная дуга между катодом и соплом, ток вспомогательной дуги ограничивается сопротивлением, толчки тока смягчаются конденсатором. Плазменная сварка начинает получать промышленное применение обычно как автоматическая или полуавтоматическая, причем автоматы и полуавтоматы для дуговой сварки легко могут быть приспособлены для плазменной с соответствующей заменой горелки. К преимуществам плазменной сварки можно отнести повышение производительности, уменьшение расхода присадочного металла, расширение возможности стыковой сварки металла без скоса кромок (толщиной до 15 мм) или с уменьшением разделки, малую чувствительность к колебаниям длины дуги, устранение включений вольфрама в наплавленном металле.
При значительных толщинах металла возможна многослойная сварка. Сварку можно вести и на вертикальной поверхности. Струя плазмы отличается большой жесткостью и устойчивостью. Обратная сторона стыковых швов защищается аргоном, вдуваемым в коробчатую подкладку (рис. 3). Плазменная сварка с Дугой косвенного действия пригодна не только для металлов, но и для неэлектропроводных материалов (стекла, керамика и т.п.).
Рис. 3. Защита обратной стороны шва
Для сварки особо малых толщин металла, от десятков микрон до 1 мм, мелких и мельчайших деталей успешно используется разновидность плазменной сварки, известная под названием микроплазменная сварка, или сварка игольчатой дугой, потому, что здесь струя плазмы диаметром 1,5—2 мм, заканчивается острием. Токи применяются 0,1—10 а, расход газа 10—30 л/ч, диаметр сопла 0,8 мм. Формирующий газ придает плазменной струе форму иглы.
Особенно легкая и портативная горелка питается от источника постоянного тока, высокочастотный ток не применяется для упрощения аппаратуры.
Вспомогательная дуга горит все время и зажигается замыканием контакта внутри горелки. Можно работать дугой как прямого, так и косвенного действия; дуга весьма устойчива и постоянна, легко зажигается при наличии постоянно горящей вспомогательной дуги. Дуга поддерживается довольно длинной, около 10—12 мм, и случайные колебания длины дуги порядка ±1 мм не оказывают заметного влияния на качество сварки. Способ весьма эффективен для сварки очень тонких листов, проволок и т. п. При питании от специальных источников постоянного тока можно получить устойчивую сварочную дугу уже при токе 0,5 а. Плазменный факел с острым игольчатым концом и нечувствительностью к колебаниям длины дуги до ±1 мм делает работу весьма надежной и очертания швов точными и аккуратными. Микроплазменная сварка успешно используется при соединении фольги, проволок, изготовлении сильфонов, при соединении проволочных сеток и т. п.
Реклама:
Читать далее:
Электрошлаковая сварка
Статьи по теме:
Плазменная сварка и резка — Энциклопедия по машиностроению XXL
Производительность процесса плазменной сварки и резки зависит от эффективной тепловой мощности плазменной струи, которая определяется силой тока, напряжением на дуге, составом и расходом газа, диаметром и длиной мундштука, расстоянием его до поверхности детали и скоростью перемещения горелки. Для обеспе- [c.135]Пост для ручной плазменной сварки и резки. [c.136]
Какие применяются способы сжатия дуги при плазменной сварке и резке [c.139]
Основные технологические применения Ме-дуг — сварка и резка плавящимся электродом, а W-дуг — сварка неплавящимся электродом, плазменная сварка и резка, напыление.
[c.93]
Водород (Н2) — это горючий газ, не имеющий цвета, запаха и вкуса. Смеси его с кислородом и воздухом взрывоопасны, поэтому при использовании водорода необходимо соблюдать особую осторожность, тщательно проверять на плотность все соединения газового тракта помещения, в которых производится сварка, должны хорошо проветриваться. Б зависимости от способа получения водород выпускают по ГОСТ 3022-80 трех марок А, Б и В, с содержанием водорода от 95 до 99,99 %. Хранят и транспортируют водород в стальных баллонах под давлением 15 МПа. Применяют водород для составления плазмообразующих смесей при плазменной сварке и резке. [c.157]
Плазменная сварка и резка металлов. При плазменной сварке основным источником для нагрева и расплавления металлов является плазма, т. е. смесь электрически нейтральных молекул газа и электрически заряженных частиц — электронов и положительных ионов. Плазму получают в специальных плазменных горелках при про-
[c. 333]
ПЛАЗМЕННАЯ СВАРКА И РЕЗКА [c.368]
Плазменная сварка и резка металлов. При плазменной сварке основным источником для нагрева и расплавления металлов является плазма, т. е. смесь электрически нейтральных молекул газа и электрически заряженных частиц — электронов и положительных ионов. Плазменной струей можно производить сварку, резку, пайку, напыление, термообработку различных металлов и сплавов, обрабатывать неметаллические материалы (керамику, стекло). Температура плазмы может достигать 20 ООО—30 ООО °С. Для сварки металлов особо малых толщин, мелких и мельчайших деталей применяют микро-плазменную сварку или сварку игольчатой дугой (струя плазмы диаметром 1,5—2 мм заканчивается острием). [c.163]
Защитные и плазмообразующие газы. Газы используют при ручной дуговой сварке неплавящимся электродом, плазменной сварке и резке, термической резке. [c.73]
Неплавящиеся электроды применяют главным образом для сварки в защитном газе и плазменной сварки и резки. Неплавящимися электродами служат вольфрамовая проволока — прутки. Вольфрам-— тугоплавкий металл, температура его плавления достигает 4500 °С, поэтому при сварке его расход незначителен. Применение вольфрамовых электродов позволяет осуществлять аргонодуговую сварку различных высоколегированных сталей и цветных металлов без присадочного или с присадочным материалом, обеспечивая при этом хорошую защиту зоны сварки инертным газом. ГОСТ 23949—80 предусматривает несколько марок вольфрамовых электродов
[c.148]
Очень перспективны плазменная сварка и резка металлов. Газ, нагреваемый дуговым разрядом, продувается через калиброванный канал сопла малого диаметра в особой плазменной горелке, или плазмотроне. Температура газа повышается до 20 000—30 000° С. Выходящая из плазмотрона тонкая струя очень горячей плазмы позволяет получить чрезвычайно концентрированный нагрев. [c.9]
Быстрыми темпами, особенно за последние годы, внедряются в промышленность нашей страны новые прогрессивные методы сварки сварка порошковой и голой легированной проволокой, сварка трением, холодная сварка, сварка электронным лучом, плазменная сварка и резка и др. Плазменная резка полностью разрешила проблему резки цветных металлов и высоколегированных сталей.
[c.5]
Особенности сжатой дуги. Для концентрации тепла дуги и повы- Ц шения ее температуры столб дуги сжимают с помощью специальной конструкции сопла плазменной горелки или потока газа. В этом случае уменьшается площадь поперечного сечения столба дуги, а температура дуговой плазмы повышается за счет увеличения числа упругих соударений частиц (электронов, ионов и др.). Сжатая дуга й применяется для плазменной сварки и резки металлов. [c.17]
ГЛАВА 12 АППАРАТЫ И УСТАНОВКИ ДЛЯ ПЛАЗМЕННОЙ СВАРКИ И РЕЗКИ [c.181]
Плазменная сварка и резка 182 204 [c.204]
Плазменную сварку и резку применяют при изготовлении воздуховодов на поточной линии (см. гл. 4). Кроме того, плазменную сварку в аргоне используют при изго- [c.213]
Применение плазмы как теплоносителя связано с процессами сварки и резки металлов. Поскольку макс, темп-ра в хим. горелках Дуговой разряд позволяет создать плазму с темп-рой в 3—4 раза выше, к-рая при соприкосновении с металлом расплавляет его. Плазменные методы сварки и резки металлов обеспечивают более высокую уд. производительность, качество продукта, дают меньше отходов, но требуют больших затрат энергии и более дорогого оборудования.
[c.354]
Плазменная струя представляет собой независимый источник теплоты, позволяющий в широких пределах изменять степень нагрева и глубину проплавления поверхности заготовок. Тепловая мощность плазменной струи ограничена, и ее применяют для сварки и резки тонких металлических листов и неэлектропроводящих материалов, а также для напыления тугоплавких материалов на поверхность заготовок. Горелки, предназначенные для сварки, снабжены вторым концентрическим соплом 6, через которое подается защитный газ. [c.240]
Какие разновидности плазменных источников нагрева применяют для сварки и резки материалов
[c. 241]
СВАРКА И РЕЗКА ПЛАЗМЕННОЙ СТРУЕЙ [c.145]
Сущность способа. Плазма — ионизированный газ, содержащий электрически заряженные частицы и способный проводить ток. Ионизация газа происходит при его нагреве. Степень ионизации тем выше, чем выше температура газа. В центральной части сварочной дуги газ нагрет до температур 5000. .. 30 ООО °С, имеет высокую электропроводность, ярко светится и представляет собой типичную плазму. Плазменную струю, используемую для сварки и резки, получают в специальных плазмотронах, в которых нагревание газа и его ионизация осуществляются дуговым разрядом в специальных камерах. [c.145]
Сущность и техника сварки и резки плазменной струей. [c.167]
Вольфрамовые электроды применяются при дуговой сварке в инертных газах — аргоне и гелии, а также при плазменных процессах сварки и резки, наплавки и напыления. Их выпускают в соответствии с ГОСТ 23949—80 из чистого вольфрама и вольфрама с активирующими присадками (диоксид тория, оксиды лантана и иттрия). Размеры электродов, предельные отклонения и химический состав должны соответствовать указанным в табл. 4.6.
[c.90]
Плазменная струя прямого действия (рис. П1.4.12, б), когда дуга горит между катодом и деталью, получила. наибольшее применение при сварке и резке металлов. В этом случае наибольшее количество тепла выделяется на детали. [c.157]
Для получения ионизированного потока газов обычно используют дуговой разряд 1 1(рис. 159), возникающий между вольфрамовым электродом 2 и соплом специальной горелки 3. Дуга горит в замкнутом цилиндрическом канале 4, стенки которого интенсивно охлаждаются водой. Через этот канал под давлением подают инертный газ. Вследствие сжатия газового проводника силами магнитного поля и наружного охлаждения столба дуги стенками канала происходит обжатие ионизированного потока. В результате появляется центральная тонкая струя 5 с высокой степенью ионизации, большим избыточным давлением и температурой, достигающей 10000— 30000° С.
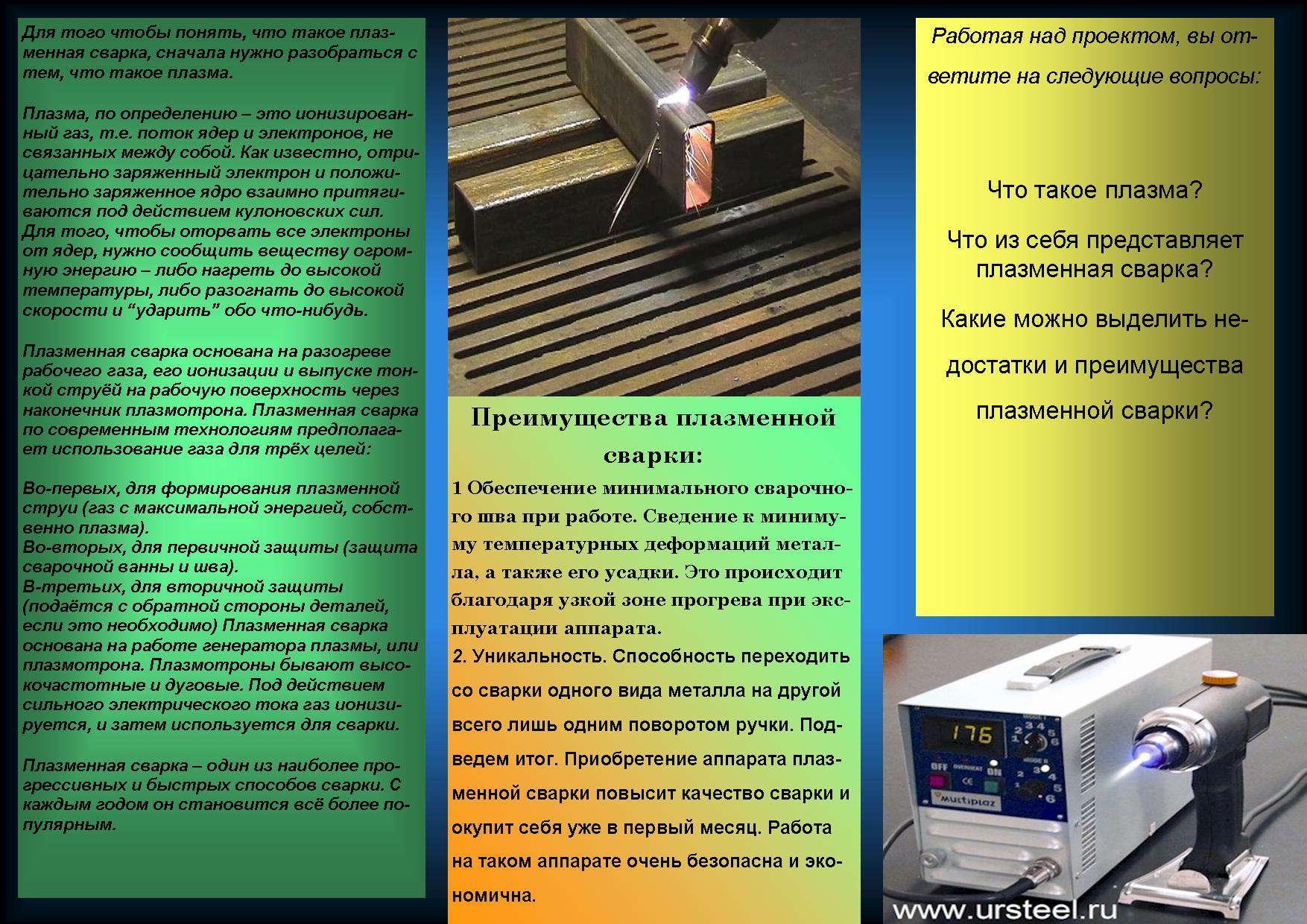
В настоящее время осцилляторы находят применение не только при обычной ручной дуговой сварке на переменном токе, но и при газоэлектрической (аргоно-дуговой сварке, сварке и резке плазменной дугой), [c.114]
При ручной сварке неплавящимся электродом, плазменной сварке и резке применяется аргон — инертный газ, не способный к химическим реакциям и практически не растворимый в металлах негорючий и невзрыво-оиасный. Он не образует взрывчатых смесей с воздухом. Будучи тяжелее воздуха, аргон обеспечивает хорошую защиту сварочной ванны. Аргон перевозят в цельнотянутых баллонах при давлении 15 МПа. Баллон содержит около 6 м газообразного аргона, окрашен в серый цвет и имеет в верхней части черную надпись Аргон чистый . Используется также аргон в смеси с водородом и азотом. Смесь из 90 % аргона и 10 % водорода употребляется при сварке тонкого металла, обеспечивая увеличение скорости сварки, уменьшение зоны термического влияния, количества выгораемых легирующих элементов и остаточных деформаций. Смесь аргона с
[c.73]
Источники питания дуги классифицируют по следующим признакам роду тока —на источники постоянного и переменного тока общепромышленного назначения количеству одновременно подключаемых сварочных постов — на однопостовые и многопостовые назначению — на источники для ручной дуговой сваркн покрытыми электродами автоматической и механизированной сварки под флюсом сваркн в защитных газах электрошлаковой сварки плазменной сварки и резки источники специального назначения (для сварки трехфазной дугой, импульснодуговой сварки и др. ) принципу действия и конструктивному исполнению специализированные источники питания в установках.
[c.112]
Сущсственны.м недостатком плазменной сварки и резки является малая. стойкость сопел плазматрона, которые разрушаются от тепловой нагрузки или от двойной дуги, возникающей в плазматро-не прямого действия (между соплом и изделием). [c.317]
К самостоятельным работам на высоте >5 м допускаются сварщики III разр., обследованные медицинской комиссией и не имеющие противопоказаний терапевта, невропатолога, окулиста и отоларинголога. Особое внимание обращается на состояние вестибулярного аппарата. Женщины-сварщицы не допускаются к сварке в закрытых емкостях, на сооружениях (башнях, мачтах) высотой >10 м, к верхолазным работам, а также к плазменной сварке и резке. В период беременности и кормления детей женщины должны переводиться на работу, не связанную с процессами сварки. [c.413]
Плазменная сварка и резка металлов. Источником местного нагрева при этом виде сварки служит плазменная струя. Плазмой называют высокотемпературный ионизирующийся газ. Минимальной температурой, при которой начинается самопроизвольная (автоматическая) ионизация, является температура свыше 5500°С. В сварочной практике применяются плазменные струи с температурами 5500-30000°С. На рис. 10, а схематически представлен процесс получения плазменной струи. Питание осуществляется от источника постоянного тока Е. Минус подводится к электроду 4, плюс-к соплу 2. Дуга 5 горит между электродом и соплом и выдувается газовой смесью с образованием струи плазмы 1. В горелках для сварки плазменной дугой (рис. 10,6) одним из электродов является обрабатываемый материал.
[c.11]
Дуговую плазменную струю для сварки и резки получают по двум основпым схемам (рис. 53). При плазменной струе прямого действия изделие включено в сварочную цепь дуги, атстивные пятна которой располагаются па вольфрамовом электроде и изделии. При плазменной струе косвенного действия активные пятна дуги находятся на вольфрамовом электроде и внутренней или боковой поверхности сопла. Плазмообразующий газ мон ет служить также и защитой расплавленного металла от воздуха. В некоторых случаях для защиты расплавленного металла используют подачу отдельной струи специального, более дешевого за-п1,итного газа. Газ, перемещающийся вдоль степок сопла, менее ионизирован и имеет пониженную температуру. Благодаря этому предупреждается расплавление сопла. Однако болынинство илаз-менных горелок имеет дополнительное водяное охлаждение.
[c.65]
Максимальная температура обычной сварочной дуги, горящей в чистом гелии = 24,59 В), составляет 810X246 = 19 845°. При наличии в дуге паров других элементов эффективный потенциал уменьшается и соответственно снижается температура дуги. Поэтому возникает вопрос, почему же при сварке и резке плазменной струей в некоторых случаях получают температуру 30 000° и более. Это как будто противоречит вышеуказанному. Но в действительности никакого противоречия нет. Температура столба дуги-плазмы зависит от многих факторов, в том числе от упругих соударений частиц в ней. Чем их больше, тем выше температура. Представим себе, что мы каким-то путем (подачей газа по бокам столба или размещением дуги в постороннем магнитном поле) заставим столб дуги сжаться, т. е. уменьшить свое сечение. Так как сварочный ток не меняется, количество электродов, проходящих по сечению столба дуги, не изменится, а количество упругих и неупругих соударений увеличится. Плазма становится более высокотемпературной и в определенных условиях может достигать ранее указанных температур.
[c.134]
Дуговую плазменную струю для сварки и резки получают по двум основным схемам. При плазменной струе прямого действия изделие включено в сварочную цепь дуги, активные пятна которой располагаются на электроде и изделии. При плазменной сфуе косвенного действия активные пятна дуги находятся на электроде и внутренней или боковой по- [c.145]
Оборудование для сварки плавлением основного металла или для собственно сварки плавлением дуговой сварки и наплавки элек-трошлаковой сварки (ЭШС) и наплавки газовой сварки, наплавки и резки электроннолучевой сварки (в высоком вакууме, в промежуточном и вне вакуума) и специальных видов сварки, наплавки и резки, в том числе плазменной сварки, наплавки и резки, микроплаз-менной сварки, ударной конденсаторной сварки, дуговой конденсаторной сварки, сварки контактным плавлением, сварки и резки под водой, сварки и резки в космосе, лазерной сварки, наплавки и резки, сварки световым лучом. термитной сварки, сваркопайки, воздушно-дуговой резки некоторых способов сварки полимерных материалов.
[c.11]
Динамика плазмы занимается изучением движений ионизованных газов в электрических и магнитных полях. Динамика плазмы находит все большее число приложений в астро- и геофизике, в проблеме термоядерных реакций, в задаче прямого преобразования тепловой энергии в электрическую, для получения высокоскоростных газовых струй в плазменных и ионных реактивных двигателях и аэродинамических трубах, при создании плазматронов для химического синтеза, сварки и резки металлов и т. д. С течениями плазмы мы сталкиваемся при движении спутников в ионосфере и при входе аппаратов в атмосферу с космическими скоростями. [c.433]
Плазменно-дуговая сварка и резка. Струя дуговой плазмы представляет собой поток сильно ионизированного (электропроводного) газа, содержащего примерно одинаковые количества положительно и отрицательно заряженных частиц и имеющего температуру 10 ООО—20 000° С и выше. Для получения плазменной струи применяют специальную горелку, в наконечник которой вставлен вольфрамовый электрод, обдуваемый газом, выходящим через сопло, охлаждаемое водой. Дуга горит между электродом и разрезаемым или свариваемым металлом (дуга прямого действия). Вытекающая из сопла струя газа образует сжатую высокотемпературную плазменную дугу, которой сваривают и разре-
[c.12]
Плазменная дуга. Статьи компании «»Black Wolf»»
Основой плазменной резки является плазменная дуга. Она характеризуется довольно высокой температурой (до 30000 С) и большим диапазоном управления ее технологических свойств.
По сравнению с аргонодуговой сваркой плазменная сварка имеет преимущества из-за того, что имеет более высокую проплавляющую способность . Вот некоторые из преимуществ:
более высокая стабильность горения дуги;
зона термического влияния — меньше;
деформации при сварке гораздо меньше;
повышенная производительность;
пониженный расход защитных газов;
Плазменная дуга образуется устройством, которое называется плазмотроном. Есть два способа подсоединения плазмотрона: для генерации дуги косвенного действия, называемой плазменной струёй и для генерации дуги прямого действия.
Плазмотроны, которые подключают для генерации плазменной струи, называются плазмотронами косвенного действия, а подключение для генерации дуги — прямого действия. Конструкция плазмотронов косвенного действия отличаются от конструкции плазмотронов прямого действия. Этим отличием является система охлаждения соплового узла плазмотрона, она более эффективна у плазмотронов косвенного действия.
Плазменная дуга, в плазмотронах прямого действия, создается между стержневым электродом, который, как правило, сделан из вольфрама и вмонтирован в газовую камеру, и свариваемым изделием. Сопло имеет нейтральный заряд от электродного (катодного) узла и используется только для стабилизации и сжатия дуги.
плазменная дуга ,В плазмотронах косвенного действия возбуждается между соплом и электродом, а поток плазмы воспроизводит плазменную струю.
Для плазменной сварки металлов чаще всего используют плазмотроны с дугой прямого действия.
Сжатие столба дуги происходит таким образом: рабочий газ, который проходит через столб дуги, нагревается, тем самым ионизируется и выходит из сопла плазмотрона как плазменная струя.
Плазменная дуга прямого действия характеризуется практически цилиндрической формой, которая слегка расширяется у поверхности изделия.
Плазменная дуга косвенного действия , также называемая струей, характеризуется формой с вершиной, которая обращена к изделию и окружена так называемым факелом. Слой газа, который омывает столб дуги снаружи, практически холодный, тем самым образуя электрическую и тепловую изоляцию между каналом сопла и плазменной дугой. Температура дуги в плазмотронах достигает 15000 — 30000 С, а плотность тока-100 А/мм2.
Плазменная струя, которая истекает из плазматрона прямого действия, накладывается на столб дуги, чем отличается от плазматронов косвенного действия и потому имеет более высокую тепловую мощность и температуру.
Очень трудно создать дугу непосредственно между изделием и электродом. Из-за этого часто сначала создается плазменная дуга между электродом и соплом (ее часто называют дежурной), а затем при касании факела дежурной дуги к изделию происходит зажигание конечной дуги между электродом и изделием. Дежурная дуга отключается, после того, как конечная начинает стабильно гореть.
В плазмотронах прямого действия КПД значительно выше, чем у плазмотронов косвенного действия. Из-за этого плазмотроны с дугой прямого действия как правило применяют для наплавки, сварки, резки, а плазмотроны с дугой косвенного действия применяют в основном для напыления, нагрева и т.п.
Плазменная дуга часто используется:
для пайки;
при сварке металлов с неметаллами;
при сварке материала, толщина которого менее 1 мм, включая тугоплавкие металлы;
разделительной резки и поверхностной обработки различных металлов.
для того, чтобы наплавлять и наносить покрытия ,расплавляя электронную или дополнительно подаваемую в дугу проволоку;
Плазменная сварка металла. Микроплазменная сварка. Плазмотрон схема.
Плазменная сварка
Плазменная сварка — плазменная струя, применяемая для сварки, представляет собой направленный поток частиц или полностью ионизированного газа, имеющего температуру 10000…200000С. Плазму получают в плазменных горелках (плазмотронах), пропуская газ через столб сжатой дуги. В качестве плазмообразующих газов применяют азот, аргон, водород, гелий, воздух и их смеси.
Применяют два основных плазменных источника нагрева: плазменную струю, выделенную из столба косвенной дуги и плазменную дугу, в которых дуга прямого действия совмещена с плазменной струей.
Плазменная струя представляет собой независимый источник теплоты, позволяющий в широких пределах изменять степень нагрева и глубину проплавления поверхности заготовок. Тепловая мощность плазменной струи ограничена, и ее применяют для сварки и резки тонких металлических листов и неэлектропроводящих материалов, для напыления тугоплавких материалов.
Плазменная дуга обладает большой тепловой мощностью, имеет более широкое применение: для сварки высоколегированной стали, сплавов титана, никеля, молибдена, вольфрама. Плазменную дугу применяют для резки материалов (меди, алюминия), наплавки тугоплавких материалов на поверхность.
Плазменной дугой можно сваривать металл толщиной до 10 мм без разделки кромок и применения присадочного материала. Так как плазменная дуга обладает высокой стабильностью, то обеспечивается повышенное качество сварных швов. Это позволяет выполнять микроплазменную сварку металла толщиной 0,025…0,8 мм.
Рисунок 1 — Плазмотрон схема
Работа плазмотрона в режиме:
А — прямой полярности; Б — дуги косвенного действия (сопло 4 выполняет одновременно роль анода)
Принцип действия плазмотрона, питающаяся от источника 1, заключается в том, что дуга между электродом 2 и изделием 3 проходит через очень маленькое сопло 4. Именно проходя через сопло 4 плазмообразующий газ сжимает дугу. Защитное сопло 5 плазмотрона защищает зону горения от окружающего воздуха. Плазмообразующий и защитный газы проходят по двум независящим друг от друга каналам. В качестве плазмообразующего газа используют инертные газы (гелий, аргон) если речь идет о сварке изделий. Если же предполагается резка металлов, то основу плазмообразующего газа составляет очищенный от примесей воздух.
В зависимости от материала изделия плазменную сварку проводят на постоянном токе прямой полярности или в импульсном режиме. Для этого плазмотрон соединяют с источником питания 1 постоянного тока или источником питания, обеспечивающим импульсный режим.
Микроплазменная сварка
Разновидностью плазменной сварки является микроплазменная сварка. По конструкции это тот же плазмотрон, но меньших размеров. Микроплазменная сварка позволяет соединять различные материалы, сплавы, даже неметаллические изделия (пластмассы, диэлектрические материалы) вплоть до текстильных изделий. Устройство плазмотрона для микроплазменной сварки показано на рисунке 2.
Рисунок 2 — Плазмотрон для микроплазменной сварки
В корпусе 2 закреплен электрод 1 с помощью цанги 3. Корпус вставляется в верхний каркас 4. Сам каркас соединен с нижним каркасом б через керамическую втулку 5. Вставленный во внутреннюю часть сопла 8 наконечник 7 соединен с нижним каркасом 6. Электрод 1 зажимается в цанге 3 с помощью гайки 9 и специальной втулки 11. Внутренняя конструкция плазмотрона заключена в изолирующий корпус 10, который сверху закрывается колпачком 12.
Для проведения плазменной и микроплазменной сварки в настоящее время применяются следующие установки: УПС-501, УПС-804 и УПС-301 для плазменной сварки и установка А-1342 — для микроплазменной сварки.
Главный недостаток плазменной сварки – недолговечность горелок-плазмотронов.
Что такое плазменная сварка? — Сварочный штаб
Процесс дуговой сварки, плазменная сварка (PAW) в чем-то похож на сварку TIG, поскольку дуга создается между сфокусированным вольфрамовым электродом и объектом. Однако плазменную дугу можно изолировать от оболочки защитного газа, поместив электрод внутрь корпуса горелки.
Вместо этого плазма проталкивается через тонкостенное медное сопло, ограничивающее дугу.
Что такое плазменная сварка?
Сварка или центральная дуга горит между деталью и вольфрамовым электродом при плазменной сварке.В качестве альтернативы, между вольфрамовым электродом и соплом с сильным влажным охлаждением горит нечто, называемое «пилотной дугой», с максимальной силой тока 3-30 А.
Кроме того, между соплом и электродом проходит плазменный газ (обычно аргон). Это немного вытесняет пилотную дугу из сопла, поэтому ее можно использовать в качестве электромагнитной «вспышки».
Вспомогательная дуга полимеризует контур контура, и с чрезвычайно высокой надежностью основная дуга теперь может быть активирована без высокочастотного контакта.
Различные физические эффекты (охлаждающий эффект сопла, электромагнитные эффекты) обеспечивают сужение дуги, типичное для плазменной сварки. Ванна расплава защищена безопасным газом, который подается между внешним соплом защитного газа и плазменными соплами.
Смеси чистого аргона или метана с водородом или гелием могут использоваться в качестве безопасного метана.
Подобно другим традиционным методам дуговой сварки, плазменная дуга имеет немного более высокую плотность энергии и меньшее расстояние между лучами.
Хотя диаметр дуги TIG расширяется от кончика электрода до заготовки под углом 45 °, диаметр плазменной дуги увеличивается лишь незначительно и имеет форму столба.
Принцип работы плазменной сварки
В атмосфере нейтрального газа, генерирующего плазму, подвод энергии, необходимой для сварки, поддерживается за счет электрической дуги. Эта дуга, образованная между плавким электродом и изготовленными деталями, нагнетается соплом, которое пневматически и механически сжимает ее.
- Превосходный внешний вид
- Сокращение времени подготовки к сборке за счет исключения снятия фаски со слоев до 10 мм
- Правдивая манипуляция
- Качество стыков: 100-процентная точность рентгеновских лучей благодаря максимальному и частому проникновению
- Соблюдение химической структуры вяжущего
- Уменьшение зоны теплового воздействия за счет сжатия дуги
Основы плазменно-дуговой сварки (PAW)
В процессе дуговой сварки, PAW, используется электрод из неплавящегося вольфрама или вольфрамового сплава, что-то вроде GTAW.Основное различие между этими двумя сварочными процессами заключается в том, что электрод в PAW закреплен консолью в сопле, которое служит для подавления дуги.
Через ограничивающее сопло плазменный газ ионизируется и выходит из сопла с высокой скоростью.
Плазменный газ сам по себе недостаточен для защиты атмосферы от расплавленного сварочного потока. Следовательно, защитный газ подается вокруг плазменной базы, как и при GTAW.
Выходная мощность плазменного газа немного ниже, чем у защитного газа, чтобы уменьшить турбулентность
Для поддержания равномерного размера пятна и плотности энергии конусообразная форма газовой вольфрамовой дуги требует использования устройства контроля напряжения дуги (AVC) или длины дуги (ALC) для автоматической сварки.В PAW ограниченная дуга приводит к более высокой столбчатой дуге.
Это снижает влияние вариации длины дуги на плотность энергии и снижает потребность в AVC или ALC. Преимущество отрезания электрода в сопле состоит в том, что уменьшается контакт с электродом.
Обычно электрода хватает на всю смену производства без пескоструйной обработки.
Еще одна особенность PAW — это способ зажигания дуги. Обычно ток высокой частоты (ВЧ) используется для создания вспомогательной дуги между медным соплом и электродом.
HF отключается после начала вспомогательной дуги. Ток вспомогательной дуги обычно фиксируется на одном уровне или может быть установлен на одном из двух этапов, обычно от 2 до 15 ампер.
Дуга передается на сварку и является составной частью электрической цепи. Поскольку дуга образуется до того, как будет сделан сварной шов, начало дуговой сварки обычно бывает довольно точным.
Во время сварки пилотная дуга остается включенной, и горелка может выполнить следующий шов, не требуя дополнительной высокочастотной сварки.
Может быть полезен для сварки в роботизированных приложениях, где высокочастотный электромагнитный шум может взаимодействовать с автоматизированными системами управления. Следствием пилотной дуги является то, что для нее требуются плазменные горелки с водяным охлаждением, особенно для приложений с минимальным током.
Различные режимы работы PAW
Изменяя расход плазменного газа и диаметр ствола, можно выполнять следующие три режима работы.
Микроплазменная сварка
Микроплазма применяется для сварки тонких листов (до 0.Толщиной 1 мм), а также для деталей из сетки и проволоки. Прямая дуга, похожая на шприц, сводит к минимуму блуждающие дуги и смещение.
Среднетоковая сварка
Это альтернатива традиционному TIG при использовании в режиме плавления. Преимущества заключаются в большей инфильтрации (из-за более высокого потока плазменного газа), лучшей устойчивости к загрязнениям подложки, таким как покрытия (электрод находится внутри горелки), и улучшенной устойчивости к различиям в зазоре между заготовкой и электродом без значительных изменений в энергозатратах. .
Сварка замочной скважины
За счет увеличения сварочного тока и потока плазменного газа создается действительно сильный плазменный луч, который может обеспечить полное погружение в материал, например, при лучевой или лазерной сварке. Во время сварки создается замочная скважина, которая медленно проходит через металл, а расплавленная сварочная ванна движется позади, создавая сварной шов под факторами поверхностного натяжения.
Этот метод можно использовать для сварки более толстых материалов за один процесс (до 10 мм нержавеющей стали).
Плазменная дуга обычно обрабатывается с помощью фирменного источника питания постоянного постоянного тока (провисания). Так как специальная система горелки и независимые потоки плазмы и защитного газа являются источником ее специфических функциональных характеристик, пульт управления плазмой может быть подключен к традиционному источнику питания TIG.
Он также предоставляет плазменные системы собственного производства.
Хотя для активации дуги используется HF, она сначала возникает между плазменным соплом и электродом.Эта «вспомогательная» дуга сохраняется внутри корпуса горелки до тех пор, пока не переместится к заготовке, необходимой для сварки.
Устройство вспомогательной дуги гарантирует стабильное начало дуги, а поскольку вспомогательная дуга сохраняется между сварными швами, оно устраняет необходимость в повторном зажигании высокочастотной дуги, которое может вызвать электрические помехи.
Электродом, используемым во время плазменной фазы, является вольфрам с 2% тория, а медь является плазменным соплом. Диаметр отверстия плазменного сопла имеет жизненно важное значение, а диаметр отверстия слишком мал для текущей стадии, а скорость потока плазменного газа может вызвать значительное окисление сопла или даже его возгорание.
Для плазменного газа обычное соотношение газов — аргон с аргоном или аргоном плюс от двух до пяти процентов водорода в качестве защитного материала. В качестве плазменного газа можно использовать гелий.
Однако из-за его высокой температуры это снижает текущий рейтинг сопла. Меньшая масса гелия также может затруднить режим замочной скважины.
Комбинации гелия и аргона используются в таких материалах, как медь, в качестве защитного газа.
Общие сведения о различных типах плазменной сварки (PAW)
Теперь, когда мы знаем основы плазменной сварки, мы можем перейти к различным типам плазменно-дуговой сварки, используемым сегодня.Ниже приведены две категории плазменной сварки:
Переданная PAW
Эта система PAW использует постоянный ток с постоянным напряжением. Кроме того, в этой форме металл может быть связан с выводом + ve , а вольфрамовый электрод может быть связан с выводом -ve .
Дуга образует вольфрамовый электрод, а также участок работы. Для этого вида процесса и дуга, и плазма движутся к секции работы, что увеличивает мощность нагрева техники.
Этот вид PAW можно использовать для соединения прочных листов.
Непереданная PAW
В этом процессе PAW используется постоянный ток прямой полярности. Кроме того, в этом процессе можно подключить сопло к наконечнику + ve и связать вольфрамовый электрод с наконечником -ve .
Дуга возникает внутри горелки между вольфрамовым электродом и соплом, что способствует ионизации газа внутри горелки. Кроме того, резак должен пропускать ионизированный газ, чтобы идти дальше.
Этот стиль PAW можно использовать для соединения тонких листов.
Это два разных типа дуговой сварки лапой, которые можно использовать для сварки. Вы можете выбрать правильный метод плазменно-дуговой сварки для ваших приложений, учитывая процесс / этап, связанный с каждым типом плазменной сварки.
Обсудив типы плазменной сварки, мы можем перейти к преимуществам и недостаткам плазменной сварки.
Преимущества и недостатки плазменной сварки
Несмотря на то, что плазменная дуговая сварка (или плазменно-дуговая сварка) часто игнорируется в производстве стали, алюминия или нержавеющей стали, несмотря на то, что она используется в приложениях с высокой степенью достоверности, таких как аэрокосмическая, электронная, автомобильная и медицинская промышленность, поскольку это гораздо больше сложный и требует более дорогостоящего набора инструментов по сравнению с другими процессами дуги.
Объяснение игнорируемого затруднительного положения заключается в том, что лапа работает немного медленнее по сравнению с другими методами сварки, такими как сварка лазерным лучом (LBW).
ОднакоPAW не самый медленный из всех. Это быстрее, чем GTAW (газовая дуговая сварка вольфрамом), которая также известна как TIG или инертный газ. Кроме того, PAW обеспечивает сварку с минимальными затратами, тогда как LBW была первым вариантом.
УPAW также есть свои плюсы и минусы, включая металлопрокат, гибку металла, лазерную резку и т. Д.По правде говоря, PAW намного медленнее, чем LBW.
Интенсивность может быть в пять раз больше, чем достигается PAW, в зависимости от лазера, используемого в LBW. Однако, когда вы обнаружите затраты на сварку, PAW намного более экономичен, чем LBW и некоторые другие методы сварки.
Вот почему PAW все еще используется в обработке металлов как экономичная альтернатива дорогостоящей LBW, где высокое качество и высокая скорость не являются обязательными. Однако у PAW есть обратная сторона, заключающаяся в большем тепловложении.
Позволяет образовывать более широкие сварные швы и некоторые термически затронутые области, а также LBW и EBW. Это создает большую нестабильность, а также приводит к повреждению механических свойств.
Тем не менее, PAW имеет преимущество перед ними помимо экономической эффективности. Именно сопротивление стыковке зазоров, а также неровностей обеспечивает использование PAW в производстве металла.
Хотя дуга ограничена, столб плазмы имеет значительно больший диаметр, чем пучок. Следовательно, легче создавать наполнители с PAW, чем с LBW или EBW.
Что касается контраста между PAW и GTAW, PAW имеет серьезный недостаток — сложность. Фактически, как вы узнаете, рентабельность GTAW выше.
По сравнению с конической газовой вольфрамовой дугой, тонкая дуга для плазменно-дуговой сварки менее устойчива к неровностям стыка. Тем не менее, тонкая дуга микроплазмы легко сохраняется при более низком уровне тока, что дает ей небольшое преимущество перед GTAW.
PAW имеет немного более низкий предел тока, который составляет почти одну десятую GTAW.Это наряду с эффективным зажиганием дуги делает плазменно-дуговую сварку идеальным вариантом для многих приложений с меньшей чувствительностью, таких как медицина и электроника.
PAW также имеет более высокие преимущества по сравнению с GTAW. По этой причине активация сварных швов в режиме «замочная скважина» при плазменной дуговой сварке может привести к полному проплавлению всего за один проход более мелкого материала.
PAW устраняет необходимость в дорогостоящих совместных подготовительных работах и устраняет необходимость в наполнителе.Кроме того, большую часть материала можно сваривать с помощью DCEN (отрицательный электрод постоянного тока) с помощью плазменно-дуговой сварки.
Несмотря на свою сложность и медлительность, PAW все еще используется, и легко понять, почему.
Выше мы обсудили некоторые причины использования плазменной сварки, а также причины, по которым ее следует избегать. Вы можете решить, использовать ли плазменную сварку или нет, в зависимости от того, что вы хотите получить от процесса сварки.
Чтобы облегчить вам выбор, мы быстро перечислим основные преимущества и недостатки не только плазменной сварки (PAW), но и плазменной резки.
Преимущества плазменной резки
Ниже приводится список основных преимуществ использования плазменной резки:
- Быстрая автоматизация
- Остается крошечный пропил
- Можно резать любые металлы
- Плавная толщина 150 мм
- Резка быстрее (примерно в 5-10 раз), чем газокислородная
Недостатки плазменной резки
Ниже приводится список основных недостатков плазменной резки:
- Большие первоначальные инвестиционные затраты
- Большая область, подверженная воздействию тепла
- Система также вызывает заусенцы
- Поверхность шероховатая
- Создает дым и шум
- Сложно построить острые углы
Преимущества PAW
Ниже приводится список основных преимуществ использования PAW:
- Зона воздействия тепла меньше по сравнению с GTAW
- Архитектура резака обеспечивает большую мощность дуги
- Высокая температура плазмы и повышенная теплоемкость допускают воздействие замочной скважины и обеспечивают полную инфильтрацию нескольких стыков при однопроходной сварке.
- Увеличенная тепловая и плазменная струя позволяет увеличить скорость переноса
- Такой подход обеспечивает более свободное наблюдение и контроль сварного шва.
Недостатки PAW
Ниже приводится список основных недостатков PAW:
- Горелка тяжелая, поэтому ручная сварка очень сложна и требует обучения
- По сравнению с EBW и LBW, он обеспечивает более широкие сварные швы и зоны термического влияния
- Система генерирует более высокий уровень шума в диапазоне около 100 дБ
- Системы плазменной сварки очень дороги; следовательно, он будет иметь более высокие стартовые затраты
- Генерирует ультрафиолетовое и инфракрасное излучение
- Для проведения плазменной сварки требуется обучение и специализация
Вот и все — преимущества и недостатки плазменной резки и плазменной сварки (PAW).Основываясь на этой информации, вы можете решить, стоит ли использовать плазменную сварку для вашей конкретной области применения.
Применение плазменной сварки
Один из наиболее распространенных вопросов о плазменной сварке после «что такое плазменная сварка» — это «где можно использовать плазменную сварку?» Ниже перечислены основные области применения плазменной сварки:
- Используется для особого покрытия лопатки турбины
- Может использоваться в таких секторах, как морская и авиакосмическая промышленность.
- PAW используется в основном для ремонта инструментов, придания формы и окраски
- Этот вид сварки применяется в основном в электронной промышленности
- Используется для соединения нержавеющих труб и трубок вместе
Этот список не является исчерпывающим, и существуют другие области применения плазменной сварки.
Сводка
Что такое плазменная сварка? Приведенная выше информация — это все, что нужно знать о плазменной сварке.
Из приведенных выше деталей мы можем сделать вывод, что метод плазменно-дуговой сварки в равной степени подходит для ручных, автоматизированных приложений, в дополнение к различным операциям, охватывающим сварку листового металла в больших объемах и сварку кухонного оборудования, автоматический ремонт лопастей реактивного двигателя до прецизионная сварка медицинского оборудования.
Похожие сообщения:
Plasma Welding — обзор
16.3.1.11 J Плазменная сварка и резка
Плазменно-дуговая сварка была разработана на основе сварки TIG путем размещения узкого отверстия вокруг дуги и подачи небольшого потока аргона через отверстие (рисунок 16.80). Суженная дуга диссоциирует газообразный аргон на положительно и отрицательно заряженные электроны, образуя плазму. Когда плазменный газ уходит от столба дуги, он снова образует нейтральные атомы и отдает свою энергию в виде тепла.
Рисунок 16.80. Плазменная сварка
Между вольфрамовым электродом и медным отверстием с водяным охлаждением возникает слаботочная вспомогательная дуга.Газ аргон, протекающий через отверстие, ионизируется и инициирует первичную дугу между вольфрамовым электродом и основным металлом при увеличении тока. Дуга и зона сварки защищены газом, протекающим через внешнее сопло. Защитный газ состоит из аргона, гелия или газовых смесей аргона с водородом или гелием.
Обычная вольфрамовая дуга имеет температуру приблизительно 11 000 ° C, но сжатая дуга плазменной горелки может достигать 20 000 ° C. Струя высокотемпературного ионизированного газа отдает свою энергию при контакте с основным металлом и, таким образом, увеличивает энергию вольфрамовой дуги.Таким образом получается сварной шов с глубоким проплавлением с высоким отношением глубины к ширине с минимальной деформацией основного металла. Термин «замочная скважина» используется для описания формы отверстия, образованного в основном металле при сварке стыкового соединения с близким квадратным краем. Когда горелка перемещается по стыку, расплавленный металл течет по краям отверстия и затвердевает в задней части отверстия. Расплавленный металл по бокам отверстия удерживается на месте за счет поверхностного натяжения и давления паров металла в отверстии.
Сварка со шпонкой может использоваться для обработки углеродистых, низколегированных и нержавеющих сталей толщиной 2,5-10 мм и алюминиевых сплавов до 20 мм. Скорость сварки обычно на 50–150% выше, чем скорость сварки TIG.
Слаботочным вариантом процесса является микроплазменная дуговая сварка, которая используется для прецизионной сварки тонких листов толщиной от 0,025 до 1,5 мм при токе 0,1-10 А. Плазменная дуга намного стабильнее, чем сварка TIG. дуга, которая имеет тенденцию отклоняться от соединительной линии при малых токах.
Плазменная резка Если ток и потоки газа увеличиваются в достаточной степени, расплавленный металл, образующийся вокруг замочной скважины, выбрасывается на дно отверстия, и когда плазменный резак перемещается по заготовке, образуется разрез. Плазменная резка особенно подходит для резки цветных металлов, таких как алюминий, медь и никель, а также их сплавов, которые трудно разрезать в пламени кислородного газа. Для резки большинства цветных металлов в качестве плазменного газа используются азот, смеси азота с водородом или смеси аргона с водородом.Вторичный защитный газ, подаваемый через сопло, окружающее сопло плазменного газа, выбирается в соответствии с разрезаемым материалом. Для низкоуглеродистой и нержавеющей стали это может быть CO 2 , а для алюминия — смесь аргона с водородом. Иногда вода используется вместо вспомогательного защитного газа, а в другом варианте технологического процесса вода впрыскивается вокруг конца сопла плазменного газа, что позволяет концентрировать плазменное пламя и обеспечивать более высокие скорости резки.
Плазменная резка может использоваться для подготовки кромок листов (т. Е. Снятия фаски) и для фигурной резки. Процесс можно использовать вручную, или резак может быть установлен на механизированном режущем оборудовании, аналогичном тому, которое используется для газовой резки. Углеродистые стали толщиной до 75 мм можно резать плазменной резкой быстрее, чем кислородно-топливным газом, а при толщине металла до 25 мм скорость резки может быть в пять раз выше.
Важным изменением процесса является использование сжатого воздуха для плазменного газа без подачи какого-либо дополнительного защитного газа.Использование сжатого воздуха вместо воды для охлаждения позволяет сделать горелку более простой.
Доступны небольшие ручные плазменные горелки, которые находят все более широкое применение при резке листового металла (например, в мастерских по ремонту двигателей). Для получения дополнительной информации обратитесь к ссылке 40.
Процесс плазменной сварки: принципы работы
Процесс плазменно-дуговой сварки обычно сравнивают с процессом газовой вольфрамовой дуги.
Если электрическая дуга между вольфрамовым электродом и изделием сужается в области поперечного сечения, ее температура повышается, поскольку по ней проходит такой же ток.
Эта сжатая дуга называется плазмой или четвертым состоянием материи.
Этот процесс основан на ионизирующем газе, который происходит при высоких температурах. Когда ионизированный газ может проводить электричество. Затем газ используется для передачи электрической дуги на свариваемую деталь. Сильный жар дуги сваривает или сплавляет два куска металла вместе.
Выбранный газ — аргон плюс вторичный газ гелий, смесь аргона с водородом или аргон. Вторичный газ защищает сварочную ванну, как и при других сварочных процессах.Это снижает степень окисления сварного шва.
Плазменная горелка содержит электрод из вольфрама, помещенный в сопло из меди. Наконечник насадки имеет небольшое отверстие. Дуга зажигается между электродом и концом сопла. Затем дуга передается на свариваемый материал.
Небольшое отверстие заставляет газ проходить через «суженное отверстие или отверстие». Это концентрирует тепло на относительно небольшой площади.Способность направлять концентрированное тепло таким образом позволяет сварщику производить сварной шов очень высокого качества.
В результате получается процесс, который обеспечивает более высокую скорость сварки, меньшую деформацию, более однородные сварные швы, меньшее разбрызгивание и больший контроль области сварки, снижая риск повреждения любых близлежащих термочувствительных компонентов. Расходные материалы тоже имеют долгий срок службы.
Видео о процессе плазменно-дуговой сварки
Режимы работы процесса плазменной сварки
Плазменно-дуговая сваркаСуществует два режима работы процесса плазменной сварки: непереносимая дуга и перенесенная дуга.
- Режим дуги без переноса : В режиме без переноса ток проходит от электрода внутри горелки к соплу, содержащему отверстие, и обратно к источнику питания. Он используется для плазменного напыления или тепловыделения неметаллов.
- Режим перенесенной дуги : В режиме перенесенной дуги ток передается от вольфрамового электрода внутри сварочной горелки через отверстие к заготовке и обратно к источнику питания.
Разница между этими двумя режимами работы показана на рисунке 10-37 ниже.Режим перенесенной дуги используется для сварки металлов. Для сравнения показан процесс газовой вольфрамовой дуги.
Перенесенная и непереносимая плазменные дуги — Рис. 10-37Как образуется плазма
Плазма создается за счет сжатия электрической дуги, проходящей через отверстие сопла. Горячие ионизированные газы также пропускаются через это отверстие. Плазма имеет жесткую столбчатую форму и имеет параллельные стороны, поэтому она не вспыхивает так же, как газовая вольфрамовая дуга.Эта высокотемпературная дуга, направленная на изделие, расплавляет поверхность основного металла и присадочный металл, добавляемый для сварки. Таким образом, плазма действует как чрезвычайно высокотемпературный источник тепла, образуя сварочную лужу. Это похоже на газовую вольфрамовую дугу. Однако более высокотемпературная плазма заставляет это происходить быстрее и называется режимом плавления. На Рис. 10-36 показано поперечное сечение головки плазменной горелки.
Высокая температура плазменной или суженной дуги и высокоскоростная плазменная струя обеспечивают повышенную скорость теплопередачи по сравнению с дугой газовой вольфрамовой дугой при использовании одного и того же тока.Это приводит к более высокой скорости сварки и более глубокому провару. Этот метод работы используется для сварки очень тонких материалов. и для сварки многопроходных канавок, сварных и угловых швов.
Процесс сварки замочной скважины
Еще один метод использования процесса плазменной сварки — это метод сварки «замочная скважина». Плазменная струя проникает через заготовку и образует отверстие или замочную скважину. Поверхностное натяжение заставляет расплавленный основной металл обтекать замочную скважину, образуя сварной шов.Метод замочной скважины можно использовать только для стыков, в которых плазма может проходить через стык. Он используется для неблагородных металлов толщиной от 1/16 до 1/2 дюйма (от 1,6 до 12,0 мм). На него влияет состав основного металла и сварочные газы. Метод замочной скважины предусматривает сварку с полным проплавлением за один проход, которую можно выполнять вручную или автоматически во всех положениях.
Совместное проектирование
Конструкция шарнира основана на толщине металла и определяется двумя способами работы.
- Метод «замочной скважины» : Для метода «замочная скважина» конструкция соединения ограничивается типами с полным проникновением. Предпочтительной конструкцией соединения является квадратная канавка без минимального корневого отверстия. Для корневых проходов, особенно на толстостенных трубах, используется U-образная канавка. Лицевая поверхность корня должна быть 1/8 дюйма (3,2 мм), чтобы обеспечить полное проникновение в замочную скважину.
- Метод плавления : Для метода плавления при сварке тонкой толщины от 0,020 дюйма (0,500 мм) до 0.Металл 100 дюймов (2.500 мм) следует использовать сварной шов с квадратной канавкой. Для сварки фольги толщиной от 0,005 дюйма (0,130 мм) до 0,020 дюйма (0,0500 мм) следует использовать краевое фланцевое соединение. Фланцы расплавляются, чтобы обеспечить присадочный металл для сварного шва.
При использовании режима плавления для толстых материалов можно использовать ту же общую деталь соединения, что и при дуговой сварке защищенным металлическим электродом и дуговой сварке вольфрамовым электродом. Его можно использовать для угловых швов, фланцевых швов, всех типов швов с разделкой кромок и т. Д., а также для соединений внахлест с использованием дуговой точечной и дуговой сварки. На рис. 10-38 показаны различные конструкции соединений, которые можно сваривать с помощью процесса плазменной дуги.
Различные соединения для плазменной дуги — Рисунок — 10-38 Сварочная цепьи ток
Сварочная схема для процесса плазменной сварки более сложна, чем для дуговой сварки вольфрамовым электродом в газе.
Требуется дополнительный компонент в качестве цепи управления, помогающий запускать и останавливать плазменную дугу. Используется тот же источник питания.
Есть две газовые системы: одна для подачи плазменного газа, а вторая для защитного газа.
Сварочная схема для плазменной сварки показана на рисунке 10-39. Используется постоянный ток типа постоянного тока (ПС). Переменный ток используется только для нескольких приложений.
Принципиальная схема плазменно-дуговой сварки (плазменная сварка) — рисунок 10-39Советы по использованию процесса
Вольфрамовый электрод должен быть точно отцентрован и расположен относительно отверстия в сопле. Ток вспомогательной дуги должен поддерживаться достаточно низким, достаточно высоким, чтобы поддерживать стабильную вспомогательную дугу.При сварке очень тонких материалов из фольги вспомогательная дуга может быть всем, что необходимо.
Когда присадочный металл используется как часть процесса плазменной сварки, он добавляется так же, как при газовой вольфрамовой дуговой сварке. Однако чем больше расстояние от резака до детали, тем больше свободы для добавления присадочного металла. Оборудование необходимо правильно отрегулировать, чтобы защитный газ и плазменный газ были в правильных пропорциях. Также необходимо использовать подходящие газы.
Тепловая нагрузка важна.Плазменный газовый поток также имеет важное значение. Эти факторы показаны на рисунке 10-40.
Качество плазменной сварки и общие неисправности — Рисунок 10-40Присадочный металл и другое оборудование
Присадочный металл обычно используется в процессе плазменной сварки, за исключением сварки самых тонких металлов. Состав присадочного металла должен соответствовать основному металлу. Размер стержня присадочного металла зависит от толщины основного металла и сварочного тока. Наполнитель обычно добавляется в лужу вручную, но может добавляться автоматически.
Защитный газ
Инертный газ, аргон, гелий или их смесь, используется для защиты области дуги от атмосферы. Аргон более распространен, потому что он тяжелее и обеспечивает лучшую защиту при более низких расходах. Для плоской и вертикальной сварки достаточно расхода защитного газа от 15 до 30 куб. Футов в час (от 7 до 14 литров в минуту).
Сварка над головой требует немного большей скорости потока. Аргон используется в качестве плазменного газа с расходом 1 куб. Фут в час (0.5 литров в минуту) до 5 кубических футов в час (2,4 литра в минуту) для сварки, в зависимости от размера горелки и области применения. Активные газы не рекомендуются для плазменного газа. Кроме того, требуется охлаждающая вода.
Качество, скорость осаждения и переменные
Качество процесса плазменной сварки чрезвычайно высокое и обычно выше, чем у сварных швов газовой вольфрамовой дугой, потому что вероятность появления вольфрамовых включений в сварном шве мала или отсутствует. Скорость наплавки при плазменно-дуговой сварке несколько выше, чем при газовой вольфрамовой сварке, и показана кривой на рисунке 10-41.
Графики сварки для процесса плазменной дуги показаны данными в таблице 10-5.
Скорость наплавки при плазменной сварке — Рисунок 10-41Параметры процесса плазменной сварки показаны на рисунке 10-41. Большинство переменных, показанных для плазменной дуги, аналогичны другим процессам дуговой сварки. Есть два исключения: поток плазменного газа и диаметр отверстия в сопле.
Основные переменные оказывают существенное влияние на процесс. Второстепенные переменные обычно устанавливаются в оптимальных условиях для данного приложения.Все переменные должны присутствовать в процедуре сварки.
Такие переменные, как угол и отклонение электрода и тип электрода, считаются фиксированными для данного приложения.
Процесс плазменной сварки реагирует на эти переменные иначе, чем процесс газовой вольфрамовой дуги.
Зазор, или расстояние от резака до детали, менее чувствителен для плазмы, но угол резака при сварке деталей разной толщины более важен, чем при сварке газовой вольфрамовой дугой.
График процедуры плазменно-дуговой сварки Применение вручную — Таблица 10-5Варианты процесса
Сварочный ток может быть импульсным, чтобы получить те же преимущества, которые дает импульсная сварка при дуговой сварке вольфрамовым электродом. Сильный импульс тока используется для максимального проникновения, но не работает постоянно, чтобы обеспечить затвердевание металла. Это дает более легко управляемую лужу для работы вне рабочего места. Импульсный режим может выполняться тем же аппаратом, который используется для дуговой сварки вольфрамовым электродом в газе.
Способ подачи присадочной проволоки
Метод плазменной подачи присадочной проволоки практически такой же, как и при дуговой сварке вольфрамовым электродом в газе. Можно использовать концепцию «горячей проволоки». Это означает, что к присадочной проволоке подается ток низкого напряжения для ее предварительного нагрева перед попаданием в сварочную ванну.
Программно-плазменная дуговая сварка
Программируемую сварку также можно использовать для процесса плазменной сварки таким же образом, как и для дуговой сварки вольфрамовым электродом в газе.Используется тот же источник питания со способностями к программированию, что дает преимущества для определенных видов работ. Сложность программирования зависит от потребностей конкретного приложения. Помимо программирования сварочного тока, часто необходимо программировать поток плазменного газа. Это особенно важно при закрытии замочной скважины, которая требуется для выполнения корневого прохода сварного шва, соединяющего два отрезка трубы.
5 фактов о плазменно-дуговой сварке
Хотя дуговая сварка в среде защитного металла (SMAW) является наиболее распространенным типом сварочного процесса, существуют и другие способы сварки, в том числе плазменная дуга.Как следует из названия, здесь используется плазменная сварочная горелка. Плазменная дуговая сварка по-прежнему основана на электрической дуге, которая возникает между электродами, но она также включает плазму. По мере того, как плазма нагревается, она проходит через узкое сопло на кончике резака. Сегодня мы собираемся изучить пять важных фактов о плазменно-дуговой сварке, некоторые из которых могут вас удивить.
# 1) Может достигать 50000 градусов по Фаренгейту
Сказать, что плазменная сварка горячая, — ничего не сказать.В зависимости от конкретного типа используемого плазменного резака, а также его настроек, температура может достигать 50 000 градусов по Фаренгейту. Чтобы представить это число в перспективе, температура SMAW обычно достигает всего 10 000 градусов по Фаренгейту. Таким образом, можно с уверенностью сказать, что плазменная дуговая сварка примерно в пять раз горячее, чем другие, более традиционные сварочные процессы.
# 2) Плазма выходит из факела почти со скоростью звука
Плазма, используемая при плазменной сварке, не просто горячая; это быстро.Когда плазма выходит из сопла горелки, она достигает скорости, почти равной скорости звука (1 Мах). Сочетание тепла и скорости позволяет плазме плавить большинство материалов, включая алюминий, медь, сталь, латунь, железо и другие.
# 3) Плазма на самом деле газ
Некоторые люди предполагают, что плазма, используемая при плазменно-дуговой сварке, является жидкостью, но это не всегда так. На самом деле это газ. Когда электрический ток активируется, плазменный газ ионизируется, тем самым увеличивая его проводимость.В этом случае электрический ток может свободно протекать через плазму недавно ионизированного газа.
# 4) Изобретен в 1950-х
Плазменная дуговая сварка берет свое начало в 1950-х годах, когда ее впервые применил американский инженер Роберт Гейдж. В то время не существовало эффективного процесса сварки для резки как тонких, так и толстых металлов. Новое изобретение Гейджа решило эту проблему, представив новый универсальный сварочный процесс. Эта технология, известная как плазменная сварка, позволила ускорить и повысить эффективность процессов сварки, а также резки в обрабатывающей промышленности.
# 5) Существуют горелки для плазменно-дуговой сварки переменным и постоянным током
Не все горелки для плазменной сварки работают на постоянном токе (DC). Некоторые вместо этого используют переменный ток (AC). Однако из этих двух типов резаки постоянного тока являются наиболее распространенными. По сравнению с горелками переменного тока они производят меньше шума, обеспечивают лучший контроль, потребляют меньше электродного материала и более энергоэффективны.
Нет тегов для этого сообщения.Разница между дуговыми горелками с переносом и без переноса дуги
Тепловая плазма — это ионная форма вещества, получаемая при нагревании подходящего газа до очень высокой температуры.Плазма состоит из возбужденных ионов газовых атомов и свободных электронов (таким образом, плазма может проводить электричество). Локальная температура плазмы может достигать 30 000 ° C и даже больше. Такая высокая температура может практически расплавить и испарить любой материал независимо от его физического состояния. Искусственно созданная управляемая струя высокотемпературной плазмы может использоваться для нескольких целей, включая резку или механическую обработку, сварку, нанесение покрытия, термообработку и т. Д. Во всех этих процессах тепло плазменной струи по-разному используется для достижения намеченной цели.Однако основным требованием для такой активности является суженная струя высокотемпературной плазмы, текущая с большой скоростью. Для искусственного создания плазмы плазмообразующий газ (может быть воздух, водород, аргон или азот) вводится в газовую камеру с высокой скоростью потока (1 — 5 м 3 / ч). Газовая камера содержит вольфрамовый электрод, который соединен с отрицательной клеммой (катодом) источника постоянного тока. Положительный вывод источника питания может быть подключен как к заготовке, так и к соплу газовой камеры.Исходя из этого, плазмотрон (плазмотрон) можно разделить на плазмотрон с переносной дугой и плазмотрон с переносной дугой.
В плазменной горелке с переносом дуги заготовка является неотъемлемой частью электрической цепи. Следовательно, положительный вывод источника питания постоянного тока подключается к заготовке (в то время как электрод остается подключенным к отрицательному выводу). Не нужно упоминать, что заготовка должна быть электропроводной. Когда на два вывода подается достаточное напряжение (около 200 В), между электродом и заготовкой через небольшое отверстие сопла образуется длинная электрическая дуга.Поскольку трудно установить дугу непосредственно между электродом и деталью (из-за зазора 5-10 мм), вспомогательная дуга возникает между электродом и соплом в начале работы на очень короткий период. Плазмообразующий газ, закачиваемый в газовую камеру, выходит через небольшое сопловое отверстие, окружающее электрическую дугу. Благодаря высокой температуре дуги газ автоматически превращается в плазму и выходит из сопла в виде струи, окончательно ударяясь о заготовку.Плазменная горелка с переносимой дугой также известна как плазменная горелка с прямой дугой , поскольку электрическое соединение выполняется непосредственно между электродом и заготовкой. Проблема с этой компоновкой возникает, когда заготовка не является электропроводной. В таких случаях медное сопло подключается к положительному выводу (аноду) источника постоянного тока, в то время как соединение с заготовкой не выполняется. Такое устройство известно как плазменный резак с непереносимой дугой или плазменный резак с непрямой дугой .Здесь между электродом и соплом образуется электрическая дуга. Однако плазмообразующий газ с силой направляет дугу в небольшое отверстие сопла, в то время как сам преобразуется в плазму и выходит из сопла в виде высокотемпературной высокоскоростной струи. Различные сходства и различия между перенесенным и непереносимым плазменным резаком приведены ниже в виде таблицы.
- В обоих случаях обязательно используется электрод для высвобождения электронов. Этому электроду придана отрицательная полярность (катод).
- Обе дуговые системы основаны на постоянном токе. Напряжение остается около 200 В, а ток может достигать 1000 А.
- Плазмообразующий газ (например, воздух, водород, аргон или азот) также требуется для непрерывной подачи в газовую камеру независимо от типа плазменной горелки. использовал.
- В обоих случаях электрическая дуга обеспечивает тепло, необходимое для образования плазмы.
- Независимо от типа горелки, работа плазменного луча очень шумная. Соответственно, при эксплуатации плазменных машин необходимо использовать соответствующие средства индивидуальной защиты.
Плазменная горелка с переносом дуги | Плазменная горелка с переносной дугой |
---|---|
Электрическая дуга образуется между электродом и заготовкой. Однако в начале работы между электродом и соплом возникает вспомогательная дуга на очень короткий период. | Электрическая дуга образуется между электродом и соплом, и одна и та же дуга сохраняется на протяжении всей операции. |
Здесь заготовка сделана анодом (положительный вывод источника постоянного тока), а сопло остается электрически нейтральным. Катод — всегда медный электрод. | Здесь деталь остается электрически нейтральной, а сопло выполнено анодом. Как обычно, катодом всегда является медный электрод. |
Плазмотрон с прямой дугой может применяться только к электропроводящим деталям. | Плазменный резак с косвенной дугой можно использовать для любой заготовки, независимо от ее электропроводности.Однако это предпочтительно для непроводящих материалов. |
Прямая дуга имеет относительно более высокий электротермический КПД (85 — 95%). | Непрямая дуга имеет сравнительно низкий электротермический КПД (65 — 75%). |
Прямая дуга в подавляющем большинстве используется для механической обработки (или резки), сварки, наплавки, переплавки и напыления. | Непрямая дуга предпочтительна для газопламенного напыления, сфероидизирующей термообработки, обработки руды и т. Д. |
Плазменная горелка с переносом дуги также известна как «Плазменная горелка с прямой дугой», потому что дуга поддерживается непосредственно между электродом и заготовкой. | Плазменная горелка с непередаваемой дугой также известна как «Плазменная горелка с косвенной дугой», потому что дуга не поддерживается между электродом и заготовкой, хотя заготовка получает тепло. |
- Современные технологии дуговой сварки от Ador Welding Limited (Оксфорд и IBH Publishing Company Pvt. Ltd.).
- Нетрадиционная обработка. П. К. Мишра (издательство «Нароса»).
Что такое плазменно-дуговая сварка?
Плазменно-дуговая сварка — чрезвычайно популярный процесс, используемый промышленными сварщиками.Фактически, как известно любому профессиональному сварщику, плазменная сварка имеет довольно широкий спектр применения.
При плазменной сварке ваш инженер может выполнить глубоких и узких швов на высоких скоростях .
Этот процесс, который часто называют PAW, включает в себя коалесценцию (или соединение) металлов посредством нагрева заготовки с помощью ограниченной дуги. Это называется переходной дугой. Также можно сформировать промежуток между сужающей насадкой и электродом.Это называется процессом непереносимой дуги, то есть ваша заготовка не становится частью электрической цепи.
Способ, которым происходит экранирование, напрямую связан с горячим ионизированным газом, который выходит из отверстия. Часто он дополняется другими источниками защитного газа. Во многих случаях защитный газ состоит из смеси разных газов или инертного газа определенного типа.
В этом процессе можно использовать (или не использовать) давление.Также возможно подавать или не поставлять присадочный металл.
Назначение плазменно-дуговой сварки
Основная цель этого процесса — помочь увеличить уровень полной энергии контролируемым образом дуговой плазмы. Это достигается за счет использования специального газового сопла вокруг вольфрамового электрода, которое работает от источника питания DCEN (отрицательный электрод постоянного тока).
Преимущества PAW
Преимущества процесса плазменно-дуговой сварки по сравнению с системой дуговой сварки газом вольфрамовым электродом обусловлены тем фактом, что процесс плазменно-дуговой сварки имеет гораздо более высокую концентрацию энергии.Более высокая температура и скорость фактической плазменной струи создают гораздо более высокое теплосодержание.
Другое преимущество связано с тем, что жесткая столбчатая дуга (или фактическая форма плазмы) не вызовет вспышку , что происходит с газовой вольфрамовой дугой.
Использование и аутсорсинг плазменной сварки
Информирование — лучший способ понять плазменную сварку. Чтобы научиться правильно управлять этим процессом, требуется специальная подготовка, и если у вас нет надлежащей подготовки или опыта, это может привести к серьезным проблемам и дорогостоящим ошибкам.Это также может привести к травмам, поэтому убедитесь, что вы прошли необходимое обучение, прежде чем приступать к сварке этого типа.
Если у вас нет персонала или обучения для этого процесса сварки, найдите производителя листового металла, который сделает . Многие имеют в штате сварщиков, сертифицированных AWS.
Другие типы сварки
Хотите убедиться, что вы выбираете правильные типы сварки для своих проектов? Посмотрите это сравнение сварки MIG и сварки TIG.У них тоже есть масса полезных приложений!
Сравнение плазменно-дуговой сварки с переносом и без переноса
Плазменно-дуговая сварка работает с использованием ионизирующих газов при высоких температурах. Горячие ионизированные газы обычно называют плазмой. Ионизированный газ, проводящий электричество, переносит электрическую дугу на сварочную поверхность. Сверхвысокая температура дуги сваривает две металлические детали вместе.
Плазменно-дуговая сварка почти аналогична процессу газовой вольфрамовой дуги.Электрическая дуга возникает между заготовкой, а площадь поперечного сечения сужается, что приводит к повышению температуры.
Что такое плазменная дуговая сварка с переносом?
В этом процессе используется постоянный ток прямой полярности. Заготовка подключается к положительной клемме, а вольфрамовый электрод — к отрицательной клемме. Между заготовкой и вольфрамовым электродом поддерживается дуга. Нагрев коаксиального газа поддерживает его в плазменном состоянии.
Как дуга, так и плазма передаются на заготовку, чтобы ускорить процесс нагрева.
В этом процессе используется плазменная дуга высокой плотности, которая проводит через ионизацию газообразного аргона, проходящего через электрическую дугу. Переносимая дуга дросселируется для достижения высоких температур, создавая плазменный столб с температурами от 8000 до 18000 градусов Цельсия.
Применение плазменно-дуговой сварки с переносом газа
Этот процесс подходит для деталей, подверженных износу или коррозии.Плазменная дуговая сварка с переносом применяется в следующих процессах:
- Матричные штампы
- пластифицирующий шнек
- изготовление гидроцилиндров
- изготовление форм и принадлежностей для стекольной промышленности
- Лезвия и ножи ковочные промышленные
- производство автомобильной арматуры
Преимущества плазменно-дуговой сварки
Сварщики и инженеры отдают предпочтение плазменной сварке. Некоторые из преимуществ плазменно-дуговой сварки:
Высокий уровень качества конструкции
Плазменная дуговая сварка с переносом тока отличается от других методов сварки.Он поддерживает металлургическую однородность, а контролируемое проплавление позволяет наносить покрытие за один проход, что обеспечивает высококачественную сварку.
Высокая скорость сварки
Дуговая сварка с переносом тока позволяет сваривать до 500 мм в минуту, что больше, чем сварка TIG с холодной проволокой. Если вам нужен быстрый процесс сварки, это может быть идеальным вариантом для вас.
Высокая энергоэффективность
Высокая скорость сварки ограничивает добавление тепла, что позволяет значительно экономить электроэнергию.В среднем 12кВт электроэнергии позволяют откладывать шесть тысяч металла в час. Кроме того, эта энергия снижает деформацию металлических деталей, сохраняя при этом металлургическую структуру.
Низкое загрязнение
По сравнению с традиционными методами сварки, дуговая сварка с переносом газа производит дым с низким уровнем загрязнения атмосферы.
Что такое плазменно-дуговая сварка без переноса?
В этом процессе плазмотрон имеет два электрода, задний и передний.Постоянный ток (DC) между двумя электродами создает плазму йодированного газа, которая сжимается на конце горелки.
Тепло, выделяемое при сварке непередаваемой плазменной дугой, более рассеяно, чем переданная плазменная дуга. Это делает процесс дуговой сварки без переноса тока пригодным для широкого спектра применений. Ток течет от электрода внутри горелки к соплу с отверстием и обратно к источнику питания.
Преимущества плазменно-дуговой сварки без переноса
Этот процесс подходит для больших площадей за счет плазменного напыления.К его основным достоинствам можно отнести следующее:
Точная сварка тонких металлических листов
Одним из преимуществ этого процесса является получение точных сварных швов.