Билет № 10 Тестирование по экзаменационным билетам сварщика
Билет № 10
Инструкция
- Выберите один из вариантов в каждом из 10 вопросов;
- Нажмите на кнопку «Показать результат»;
- Скрипт не покажет результат, пока Вы не ответите на все вопросы;
- Загляните в окно рядом с номером задания. Если ответ правильный, то там (+). Если Вы ошиблись, там (-).
- За каждый правильный ответ начисляется 1 балл;
- Оценки: менее 5 баллов — НЕУДОВЛЕТВОРИТЕЛЬНО, от 5 но менее 7.5 — УДОВЛЕТВОРИТЕЛЬНО, 7.5 и менее 10 — ХОРОШО, 10 — ОТЛИЧНО;
- Чтобы сбросить результат тестирования, нажать кнопку «Сбросить ответы»;
- В каких условиях рекомендуется хранить электроды?
В сухом отапливаемом помещении при температуре не ниже +15 и влажности воздуха не более 50 %.
В складском помещении при температуре выше 00С.
В ящиках, в упакованном виде. - Какие дефекты могут быть в сварном шве, если притупление кромок превышает рекомендуемую величину?
Возможно появление непровара корня шва.
Возможно появление холодных трещин.
Возможно появление пористости. - С какой целью источники питания сварочной дуги для ручной дуговой сварки имеют напряжение холостого хода выше, чем напряжение на дуге при сварке?
Для увеличения глубины проплавления в начале шва.
Для улучшения возбуждения дуги.
Для уменьшения разбрызгивания металла. - Какие углеродистые и низколегированные стали необходимо подогревать при сварке?
С эквивалентным содержанием углерода более 0,5 %.
С содержанием серы и фосфора более 0,05 % каждого. С содержанием кремния и марганца до 0,5…1,5 % каждого. - Какие способы резки рекомендуется применять для подготовки деталей из аустенитных сталей?
Кислородная.
Кислородно-флюсовая, плазменно-дуговая, механическая.
Воздушно-дуговая - Что входит в понятие металлургической свариваемости металлов?
Влияние на свариваемость химического состава металла и отсутствие дефектов в результате химического взаимодействия элементов в сварочной ванне и кристаллизующемся металле шва.
Влияние на свариваемость способа сварки и возможность появления дефектов в результате воздействия термического цикла на сварочную ванну и кристаллизующейся металл шва. - Какие сварочные деформации называют остаточными?
Деформации, появляющиеся во время сварки.
Деформации, появляющиеся по окончании сварки.
Деформации, образующиеся под действием эксплуатационных нагрузок. - Допускаются ли трещины в сварных швах при сварке низколегированных сталей?
Допускается, если их длина не превышает толщины металла шва.
Допускается, если концы трещины после сварки заварить газовой сваркой.
Трещины всех видов и направлений не допускаются. - Какой род тока более опасен при поражении человека электрическими токами при напряжении 220В?
Переменный ток 50 Гц.
Постоянный ток.
Ток высокой частоты. - Какими индивидуальными средствами должен обеспечиваться сварщик при выполнении потолочной сварки?
Поясом безопасности.
Беретом и рукавицами.
Нарукавниками, шлемом и пелеринами.
Трещины кристаллизационные в сталях — Энциклопедия по машиностроению XXL
Кремний способствует появлению горячих трещин в швах углеродистых сталей, однако в меньшей степени, чем углерод. В чисто аустенитных хромоникелевых швах кремний более опасен в отношении возникновения кристаллизационных трещин, чем в швах углеродистой стали. Оптимальное содержание кремния обеспечивает устранение пористости, но не вызывает снижения стойкости металла против образования трещин. В свариваемых углеродистых и низколегированных конструкционных сталях должно содержаться 0,15… 0,6 % кремния.Горячие трещины образуются непосредственно в сварном шве в процессе кристаллизации, когда металл находится в двухфазном состоянии. Причинами их возникновения являются кристаллизационные усадочные напряжения, а также образование сегрегаций примесей (серы, фосфора, кислорода), ослабляющих связи между формирующимися зернами.

В отличие, от кристаллизационных (горячих) холодные трещины образуются в сварных соединениях при невысоких температурах (ниже 200°С). Особенностью холодных трещин является замедленный характер их развития. Холодные трещины в основном зарождаются по истечении некоторого времени после сварки и затем медленно, на протяжении нескольких часов и даже суток, распространяются по глубине и длине. Холодные трещины — это типичный дефект сварных соединений из средне- и высоколегированных сталей. Холодные трещины в металле шва появляются, главным образом, в том случае, когда по содержанию углерода и легирующих элементов металл шва близок к составу основного металла. Эти трещины имеют такой же вид, как и кристаллизационные. Холодные трещины залегают в металле шва и в околошовной зоне.
Накопленный за последние годы опыт изготовления сварных конструкций из технически чистого никеля показал, что при его сварке возникает целый ряд серьезных трудностей, связанных прежде всего с большой склонностью металла швов к образованию кристаллизационных трещин. Главной причиной появления кристаллизационных трещин в металле шва является образование легкоплавкой сульфидной эвтектики N1—N 5.
Если деформационная способность металла кромки в период остывания зависит от отношения объемов твердой и жидкой фаз. размеров и форм кристаллитов, характера структуры и субструктуры, то пластичность его в основном определяется химическим составом сплава. В частности, трещинообразование хромоникелевых сталей усиливается с увеличением в них суммарного содержания хрома и никеля. Поэтому стали по степени возрастания склочности их к трещинообразованию обычно располагают в следующей последовательности 18-8, 25-15, 25-20 и 15-35. С другой стороны, ряд исследователей считает, что склонность к возникновению кристаллизационных трещин определяется в основном не суммарным содержанием хрома и никеля в сплаве, а соотношением между ферритообразующими и аустенитообразующими элементами, т.

Низколегированные стали повышенной прочности поставляются по ГОСТ 5058—65 и 5520—69, а также по различным техническим условиям. Повышение предела прочности и текучести углеродистой стали обеспечивается только увеличением концентрации углерода, что ухудшает свариваемость. Нередко в швах конструкций из стали с повышенным содержанием углерода (свыше 0,3%) возникают кристаллизационные трещины, которые в процессе эксплуатации могут развиваться и быть причиной разрушения. [c.139]
Так как растворимость фосфора в аустените меньше, чем в феррите, опасность образования кристаллизационных трещин от фосфора значительно больше в аустенитных швах. Наиболее опасен фосфор для швов с чисто аустенитной структурой. Если же на ранних стадиях кристаллизации металла шва кроме аустенита образуется и феррит, опасность образования трещин значительно уменьшается, так как большая часть фосфора растворяется в металле.
В отличие от кристаллизационных трещин холодные трещины образуются в сварных соединениях при остывании их до относительно невысоких температур, как правило, ниже 200° С. К этому времени металл шва и околошовной зоны приобретает высокие упругие свойства, присущие ему при нормальных температурах. Холодные трещины являются типичным дефектом сварных соединений из среднелегированных и высоколегированных сталей перлитного и мартенситного классов. Значительно реже они возникают в соединениях из низколегированных ферритно-перлитных сталей и высоколегированных сталей аустенитного класса. Ввиду преимущественного возникновения холодных трещин в соединениях из восприимчивых к закалке мартенситных и перлитных сталей трещины этого типа иногда называют закалочными. Холодные трещины наиболее часто поражают околошовную зону и реже металл шва.
239]
Для ручной сварки среднеуглеродистых сталей применяют электроды с фтористо-кальциевым покрытием УОНИ-13/55 и УОНИ-13/45, обеспечивающие достаточную прочность и высокую стойкость металла шва против образования кристаллизационных трещин. Чтобы избежать образования малопластичных и хрупких закалочных структур в околошовной зоне, при сварке среднеуглеродистых сталей следует замедлить остывание изделий путем снижения скорости сварки, предварительного подогрева металла, сварки двумя и более раздвинутыми дугами. Чем больше содержание углерода в стали, тем выше должна быть температура подогрева металла при сварке. Даже при использовании всех указанных приемов сварные соединения на среднеуглеродистой стали чаще всего получаются недостаточно пластичными, так как закалка основного металла в околошовной зоне полностью не предотвращается. Если к сварному соединению предъявляются требования высокой пластичности, то для выравнивания свойств приходится применять последующую термообработку, чаще всего закалку с отпуском.
[c.492]
К трудностям электроннолучевой сварки среднелегированных сталей средних и больших толщин относится чувствительность к повышенному содержанию в основном металле углерода, легирующих элементов и газов, в частности кислорода. Так, например, при сварке сталей толщиной более 30 мм с содержанием более 0,2%С в швах возникают кристаллизационные трещины. Если содержание кислорода в стали превышает 0,02%, электроннолучевая сварка становится практически невозможной из-за повышенного [c.566]
Понижение окружающей температуры и увеличение содержания углерода в стали уменьшает стойкость к образованию кристаллизационных трещин при этом оказывается полезным применение предварительного подогрева. [c.290]
С увеличением ширины и толщины свариваемых элементов повышается их сопротивляемость деформациям. Это способствует увеличению реакции связей, напряжений и вероятности образования трещин в процессе сварки. На фиг. 53, а изображена зависимость склонности к образованию кристаллизационных трещин соединений в стык малоуглеродистых сталей от ширины соединяемых элементов на фиг. 53, б от толщины полки. С ростом ширины соединяемых элементов до 150 мм сопротивляемость образованию трещин падает. Увеличение ширины элементов свыше 150 мм не оказывает заметного влияния на изменение сопротивляемости швов образованию трещин. Увеличение толщины полки повышает возможность трещинообразования.
[c.124]
Образование хрупких разрушений. Эксплуатация сварных конструкций показывает, что иногда в них образуются трещины. Нередки случаи, когда трещины, обнаруженные в эксплуатации, представляют собой кристаллизационные трещины, возникшие в швах при их наложении и раскрывшиеся спустя длительный промежуток времени в результате растягивающих напряжений и низкой температуры. В сварных конструкциях, работающих при переменных нагрузках, усталостные трещины образуются в сварных швах, в околошовных зонах, в основном металле, в местах концентрации напряжений (в зависимости от формы и конструкций соединений, рода материала, термической об работки и т. д.). Трещины в сварных конструкциях образуются также и при отсутствии первичных разрушений и переменных напряжений. Подобного рода трещины называют хрупкими. Иногда образование хрупких трещин в сварных конструкциях объясняется влиянием собственных остаточных напряжений, вызванных сваркой. В гл. VII было показано, что величины остаточных напряжений в сварных соединениях из углеродистых и других сталей почти всегда достигают предела текучести металла, а в некоторых случаях превышают его.
[c.213]
Углеродистые эвтектики в ряде случаев не оказывают значительного влияния на эксплуатационные характеристики металла. Поэтому можно обеспечить повышение стойкости против образования кристаллизационных трещин, создавая в металле композиции, обеспечивающие достаточное количество углеродистых эвтектик, в частности, применительно к аустенитным хромоникелевым -сталям — углеродисто-ниобиевых эвтектик [66, 84, 125]. [c.57]
НИИ серы в стали можно исключить кристаллизационные трещины, но механические свойства таких швов окажутся весьма низкими.
[c.321]
Горячие трещины — хрупкие межкристаллитные разрушения, возникающие в процессе затвердевания сварочной ванны под действием напряжений усадки. Горячие трещины появляются чаще всего при кристаллизации последних порций жидкой фазы, поэтому другое название таких трещин — кристаллизационные. Повышенную склонность к образованию горячих трещин при сварке обнаруживают аустенитные стали, сплавы никеля, алюминия, меди. [c.69]
Сера — вредная примесь в сталях. Повышение содержания серы в металле шва резко снижает его стойкость против кристаллизационных трещин. Сера практически нерастворима в твердом железе, а поэтому находится в стали в виде сульфидных включений. Причина образования кристаллизационных трещин в присутствии серы — образование легкоплавких сульфидных прослоек, располагающихся по границам кристаллитов металла шва. [c.69]
Углерод — важнейший элемент, определяющий структуру и свойства сварных соединений и поведение при эксплуатации. Вместе с тем углерод оказывает резко отрицательное влияние на стойкость металла шва против кристаллизационных трещин. При сварке углеродистых и низколегированных сталей углерод усиливает вредное действие серы. При сварке высоколегированных сталей углерод способствует образованию по границам кристаллитов легкоплавких эвтектик карбидного происхождения, что также снижает стойкость швов против кристаллизационных трещин. Критическое содержание углерода зависит от конструкции узла, наличия или отсутствия предварительного подогрева, формы швов и содержания в стали других элементов, в первую очередь серы.
[c.70]
При высоком содержании марганца в металле шва в присутствии углерода возможно возникновение кристаллизационных трещин, вызванных образованием легкоплавкой карбидной эвтектики. В связи с этим в зависимости от концентрации марганец оказывает двойственное влияние на стойкость швов против образования кристаллизационных трещин. Так, например, повышение содержания марганца до 2,5 % в сварных швах, содержащих 0,10. ..0,12% С, оказывает положительное влияние на стойкость против образования горячих трещин. Содержание марганца в пределах 2,5…4% не оказывает влияния, а дальнейшее повышение его содержания уменьшает стойкость металла шва против образования трещин. В сталях с содержанием углерода 0,13…0,2% полезное влияние марганца сказывается при меньших концентрациях ([c.71]
Предварительный подогрев стыков в условиях низких температур обычно предназначается для предотвращения возникновения кристаллизационных трещин и уменьшения остаточных напряжений. Для сравнения склонности малоуглеродистых и низколегированных сталей к образованию кристаллизационных трещин [97] были предложены следующие формулы определения эквивалентного содержания углерода (Сак). [c.73]
Одним из основных факторов, определяющих свариваемость аустенитных сталей, является склонность аустенитного металла шва к горячим (кристаллизационным) трещинам при сварке. Эти трещины, природа которых до настоящего времени полностью не выяснена, наиболее часто встречаются в швах, имеющих чисто аустенитную структуру без выделений второй фазы (фиг. 13). Поэтому одним из наиболее эффективных средств борьбы с горячими трещинами является переход к двухфазной структуре металла шва. В качестве второй фазы наиболее часто используется ферритная фаза. Аусте-нитно-ферритный двухфазный металл шва (фиг. 13, б), обеспечиваемый при использовании наиболее широко применяемых в настоящее время электродов (табл. 6), в отличие от чисто аустенитного металла шва, не склонен в условиях сварки к горячим трещинам и обладает высокой технологической прочностью даже при выполнении жестких швов большой толщины. По уровню жаропрочности швы, выполненные аустенитно-ферритными электродами, приближаются к аустенитным сталям первой группы. Длительная прочность сварных соединений аустенитных сталей первой группы также в большинстве случаев близка к соответствующим показателям для основного металла.
[c.35]
Металл шва, соответствующий области А, имеет однофазную аусте-нитную структуру, весьма склонную к образованию горячих трещин кристаллизационного и подсолидусного типа.

При выборе материалов для сварки аустенитных сталей различного легирования главное требование — исключить образование горячих трещин кристаллизационного и подсолидусного типа (см. рис. 10.6, б), а также локальных разрушений и снижение коррозионной стойкости. Сварку сталей с малым запасом аустенитности производят электродами (табл. 10.8), обеспечивающими в шве 4. .. 6 % ферритной фазы. Однако при сварке различных стабильно-аустенитных коррозионно-стойких сталей, как правило, не допускается в швах наличия ферритной фазы. Необходимо применять сварочные материалы, обеспечивающие швы с однородной аустенитной структурой без горячих трещин, что достигается легированием их молибденом, марганцем и азотом, например
[c.401]
В свою очередь появление дефектов кратерного происхождения (кристаллизационные трещины, возникающие в кратерах свариваемых валиков-слоев при обрывах сварочной дуги) связано с повышенным содержанием углерода в металле шва. Таким образом, сварочнотермическая технология выполнения сварных соединений паропроводов из такой стали является достаточно сложной и требует высокой организационно-технологической культуры выполнения. [c.322]
МПа, S > 20 %. Свариваемость стали всесторонне и глубоко исследована в США, Японии, Германии и в других странах. Установлена ее нечувствительность к горячим (кристаллизационным) трещинам даже при сварке толстостенных паропроводных труб (диаметром 600 х 150 мм) и возможность устранения склонности сварных соединений к холодным и термическим трещинам (например, путем снижения содержания фосфора в стали до Р Коэффициент прочности сварных соединений Фо) = 0,75. .. 0,85 для температур 595. .. 620 °С. Повреждение образцов при испытании на длительную прочность происходит в ЗТВр сварного соединения по механизму ползучести с развитием трещин типа IV.
[c.324]
Сварка храмоникелевых аустенитных сталей связана с рядом трудностей, обусловленных онецифическими свойствами этих сталей. Повышенный коэффициент расширения при малой теплопроводности опособствует созданию значительных сварочных напряжений, величина которых в некоторых случаях достигает предела текучести металла. При сварке эти стали проявляют повышенную склонность к образованию горячих трещин. Так как горячие трещины возникают в процессе кристаллизации металла, их называют также кристаллизационными трещинами. [c.134]
Повышение содфжания углерода в сталях вызывает значительные трудности при их сварке. Это связано с необходимостью создания условий, предотвращающих образование малопластичных закалочных структур и трещин в околошовной зоне, понижение стойкости металла шва против появления кристаллизационных трещин и обеспечивающих равнопрочность металлов шва и основного.
[c.127]
Кремний способствует образованию кристаллизационных трещин в швах на углеродистых сталях. Однако его вредное действие в этом отношении значительно слабее, чем углерода. В чисто аустенитных хромоникелевых швах кремний более опасен в отно шении образования кристаллизационных трещин, чем в швах углеродистой стали. Это об словлено выделением на границах кристаллитов пленок силицидов и других легкоплавких неметаллических соединений. Появление ферритной составляющей в структуре аустенитных швов повышае их стойкость против образования трещин. [c.232]
Главной причиной появления кристаллизационных трещин в металле никелевого шва является образование легкоплавкой сульфидной эвтектики N1—N15. Поэтому в основном металле содержание серы ограничивается 0,001%, что в 10—50 раз ниже, чем допустимое содержание ее в стали. Наличие марганца, связывающего серу в тугоплавкое соединение Мп5, ослабляет ее вредное влияние. На этом основано применение присадочных проволок НМц2,5 и НМц5, содержащих около 2,5 и 5% Мп соответственно.
[c.674]
Швы, сваренные на низкоуглеродистых сталях всеми способами сварки, обладают удовлетворительной стойкостью против образования кристаллизационных трещин. Это обусловлено низким содержанием в них углерода. Однако при сварке на углеродистых сталях с содержанием >0,20 % С угловых швов и валика корня шва в многослойных швах, особенно с повышенным зазором, возможно появление в металле шва кристаллизационных трещин, что связано в основном с неблагоприятной формой провара (узкой, глубокой). Все )тлеродистые стали хорошо свариваются всеми способами сварки плавлением. Обычно не имеется затруднений, связанньк с возможностью возникновения холодных трещин, вызванных образованием в шве или ОШЗ закалочных структур. Однако в сталях, содержащих углерод >0,25 % С или повышенное количество марганца, вероятность появления холодных трещин в указанных зонах повышается, особенно с ростом скорости охлаждения (повышение толщины металла, сварка при отрицательных температурах, сварка швами малого сечения и др. ). В этих условиях предупреждение трещин достигается предварительным подогревом до 120…200 °С. Предварительная и последующая термическая обработка на низкоуглеродистых сталях, использующихся в ответственных конструкциях, служит для этой цели, а также позволяет получить необходимые механические свойства сварных соединений (высокую прочность или пластичность либо их необходимое сочетание).
[c.17]
Дефекты сварных соединений, выполненных электрошлаковой сваркой. Горячие, или кристаллизационные, трещины (рис. 223, а) в металле шва образуются главным образом вследствие повышенного содержания углерода в стали. Появлению трещин способствует также чрезмерно большой или малый коэффициент формы шва (отно- [c.330]
Горячие, или кристаллизационные, трещины рис. 145, а) в металле шва образуются главным образом вследствие повышенного содержания углерода в стали. Появлению грещин способствует также чрезмерно большой или малый коэф-
[c. 243]
По данным Б. И. Медовара, повышенная склонность к ликвации примесей по границам зерен в высоколегированных сталях приводит к тому, что в этих зонах образуются более легкоплавкие прослойки с меньшей прочностью при температурах кристаллизации, когда ранее закристаллизовавшиеся части приобрели достаточную прочность. Под влиянием усадочных напряжений в них возникают надрывы, переходящие в межкристаллитную трещину. В аустенитном металле сварных швов с транскристаллит-ным строением такая трещина может поразить весь шов, проходя по непрерывной межзеренной границе. В связи с рассмотренным для предотвращения появления кристаллизационных трещин в металле аустенитных швов можно использовать особо чистые по сере и фосфору свариваемые стали и присадочные материалы. Хорошо зарекомендовали себя аустенитные стали, рафинированные электрошлаковым переплавом или каким-либо другим методом. Поскольку в процессе сварки нельзя обеспечить снижение содержания фосфора, ибо это достигается окислением, а в стали имеются более легко окисляющиеся элементы, содержание фосфора в свариваемой стали и присадочных материалах ограничивают 0,01 % и избегают использования флюсов и электродных покрытий, способных загрязнять металл шва вредными примесями.
[c.273]
Помимо горячих кристаллизационных трещин в сварных швах аустенитных сталей могут возникать горячие высокотемпературные полигонизационные трещины, образующиеся в довольно узком интервале температур, находящемся несколько ниже температуры кристаллизации. Б. А. Мовчан показал, что в литом аустенитном металле при достаточно медленном охлаждении после кристаллизации дефекты кристаллического строения начинают мигрировать, сосредоточиваясь с образованием полигональных границ субзерен. Эти полигональные границы в отдельных местах могут совпадать со старыми границами аустенитных кристаллитов, с участками сосредоточения примесей, здесь могут зарождаться трещины под влиянием напряжений, вызываемых усадкой металла. Для подавления образования таких трещин можно увеличивать скорость охлаждения с тем, чтобы не дать развиться полигонизации. Уменьшение опасности появления полигонизационных трещин может быть достигнуто специальным легированием, уменьшающим подвижность полигонизационных границ.
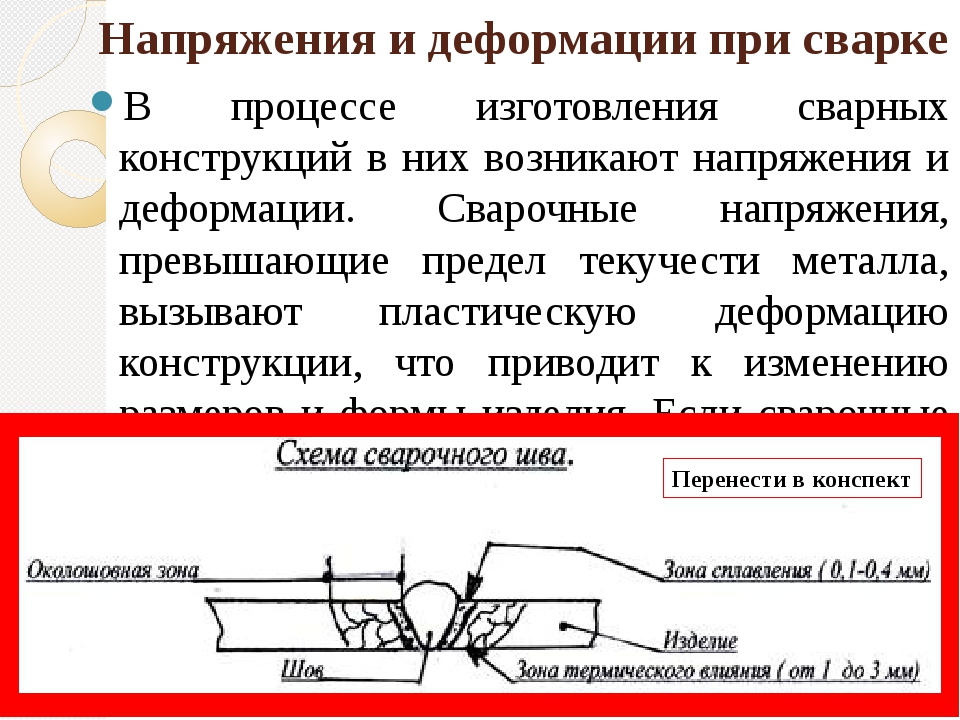
Кремний способствует образованию кристаллизационных трешин в швах углеродистых сталей, однако его вредное влияние значительно слабее, чем углерода. В чисто аустенитных хромоникелевых щвах кремний более опасен в отношении образования кристаллизационных трещин, чем в швах углеродистой стали. Это [c.70]
Трещины при сварке. Различают три вида трещин, образующихся при сварке аустенитных сталей кристаллизационные, подсолидусные и холодные [4]. Первые два вида объединяют названием горячие трещины . Природа трещин описана в гл. 6. [c.276]
По степени раскисления сталь изготовляют кипящей, спокойной н полуспокойной (соответствующие индексы кп , сн и пс ). Кипящую сталь, содерн ащую не более 0,07% Si, получают при неполном раскислении металла. Сталь характеризуется резко выраженной неравномерностью распределения серы и фосфора по толщине проката. Местная повышенная концентрация серы может привести к образованию кристаллизационных трещин в шве и околошовной зоне. Кипящая сталь склонна к старению в околошовной зоне и переходу в хрупкое состояние при отрицательных температурах. В спокойной стали, содержащей не ыенев 0,12% Si, распределени(3 серы и фосфора более равномерно. Эти стали менее склонны к старению. Полуспокопная сталь занимает проме куточное положение мел ду кипящей и спокойной сталью.
[c.204]
Свариваемость рассматриваемых сталей и сплавов затрудняется мпогокомпонеитностью их легирования и разнообразием условий эксплуатации сварных конструкций (коррозионная стойкость, жаростойкость или жаропрочность). Общей сложностью сварки является предупреждение образования в шве и околошовной зоне кристаллизационных горячих трещин, имеющих межкристаллит-пый характер, наблюдаемых в виде мельчайших микронадрывов и трещин. Горячие трещины могут возникнуть и при термообработке или работе конструкции нри повышенных температурах. Образование горячих трещин наибо,лее характерно для крупнозернистой структуры металла шва, особенно выраженной в многослойных швах, когда кристаллы последующего слоя продолжают кристаллы предыдущего слоя.
[c.286]
В работе Д. Сефериана [96] как наиболее эффективный технологический прием для предотвращения кристаллизационных трещин и повышения пластичности сварного соединения рекомендуется предварительный подогрев стыков. Пункт 4.22 СниП III Г—66 регламентирует технологию сварочных работ при температурах ниже — 30°С только с предварительным подогревом стыка и прилегающей к нему зоны шириной 200—250 мм до температуры 150—200°С. Между тем назначение предварительного подогрева для всех без исключения марок сталей и типов конструкций может привести к неоправданному увеличению технологического цикла, а в некоторых случаях — к снижению хладостойкости соединения. [c.73]
Чем выше эквивалентное содержание углерода, тем больше вероятность образования трещины. С. А. Островской дана классификация наиболее употребляемых малоуглеродистых и низколегированных сталей. В соответствии с этой классификацией сталь 09Г2С признана одной из лучших по стойкости к образованию кристаллизационных трещин.
[c.73]
Для сварки аустенитных сталей второй группы с перлитными сталями аустенитно-ферритные электроды применены быть не могут, так как в данном случае, как и в однородных соединениях аустенитных сталей (п. 4), в участках шва, примыкающих к аустенитной составляющей, будет получена однофазная аустенитная структура и в них могут образовываться кристаллизационные трещины. Поэтому для указанных сварных соединений следует применять электроды, обеспечивающие однофазную аустенитную структуру, стойкую против трещин. В настоящее время наибольшее распространение имеют электроды с повышенным содержанием молибдена на базе проволоки типа Х15Н25М6 (марок ЦТ-10, НИАТ-5). Структурное состояние наплавленного металла типа XI5Н25М6 определяется точкой D на диаграмме. Эти же электроды желательно использовать и в сварных соединениях аустенитных сталей первой группы с перлитными сталями. [c.46]
Трещины. Макро-, мнкро- и субмпкроскопические трещины являются характерными дефектами фасонных отливок из легированных и углеродистых сталей, цветных сплавов и высокопрочных чугунов. Природа и механизм образования некоторых видов трещин еще полностью не изучены, особенно слабо изучены микро- и субмпкроскопические трещины. Этот вид дефектов обусловлен главным образом технологическими особенностями приготовления, заливки и кристаллизации жидкого металла, условиями охлаждения и взаимодействия жидкого металла и отливки с литейной формой, учет которых представляет большие трудности. В настоящее время наиболее полно изучены кристаллизационные трещины, зарождение и развитие которых происходят в эффективном интервале кристаллизации.
[c.93]
ВОПРОС 16. Что входит в понятие металлургической свариваемости металлов?
1. Влияние на свариваемость химического состава металла и отсутствие дефектов в результате химического взаимодействия элементов в сварочной ванне и кристаллизующемся металле шва.
2. Влияние на свариваемость способа сварки и возможность появления дефектов в результате воздействия термического цикла на сварочную ванну и кристаллизующейся металл шва.
3. Влияние на свариваемость объема сварочной ванны и кристаллизующегося металла шва.
ВОПРОС 17. Какие сварочные деформации называют остаточными?
1. Деформации, появляющиеся во время сварки.
2. Деформации, появляющиеся по окончании сварки.
3. Деформации, образующиеся под действием эксплуатационных нагрузок.
ВОПРОС 18. Допускаются ли трещины в сварных швах при сварке низколегированных сталей?
1. Допускается, если их длина не превышает толщины металла шва.
2. Допускается, если концы трещины после сварки заварить газовой сваркой.
3. Не допускаются.
ВОПРОС 19. Какой род тока более опасен при поражении человека электрическими токами при напряжении 220В?
1. Переменный ток 50 Гц.
2. Постоянный ток.
3. Ток высокой частоты.
ВОПРОС 20. Какими индивидуальными средствами должен обеспечиваться сварщик при выполнении потолочной сварки?
1. Поясом безопасности.
2. Беретом и рукавицами.
3. Нарукавниками, шлемом и пелеринами.
БИЛЕТ 6
ВОПРОС 1. В каком из перечисленных ниже ответов наиболее полно указано назначение электродного покрытия?
1. Упрощает возбуждение дуги, увеличивает коэффициент расплавления металла электродного стержня и глубину проплавления металла.
2. Повышает устойчивость горения дуги, образует комбинированную газо-шлаковую защиту расплавленного электродного металла и сварочной ванны, легирует и рафинирует металл шва, улучшает формирование шва.
3. Защищает металл стержня электрода от окисления, улучшает санитарно-гигиенические условия работы сварщика.
ВОПРОС 2. Какой буквой русского алфавита обозначают кремний и кобальт в маркировке стали?
1. Кремний — К, кобальт — Т.
2. Кремний — Т, кобальт — М.
3. Кремний — С, кобальт — К.
ВОПРОС 3. Какие стали относятся к группе углеродистых сталей?
1. Ст3сп5, Сталь10, Сталь15, 20Л, 20К, 22К.
2. 45Х25Н20, 15ГС, 09Г2С.
3. 08Х14МФ, 1Х12В2МФ, 25Х30Н.
ВОПРОС 4. Укажите правильное название источников постоянного тока
1. Сварочные выпрямители, генераторы, агрегаты.
2. Специализированные сварочные установки.
3. Трансформаторы.
ВОПРОС 5. Для чего служит трансформатор?
1. Для преобразования частоты переменного тока
2. Для преобразования напряжения электрической сети
3. Для преобразования напряжения электрической сети при постоянной силе тока.
ВОПРОС 6. Какие параметры необходимо контролировать после выполнения подготовки деталей и сборочных единиц под сварку?
1. Форму, размеры и качество подготовки кромок; правильность выполнения переходов от одного сечения к другому; другие характеристики и размеры, контроль которых предусмотрен ПКД или ПТД.
2. Форму и размеры расточки или раздачи труб; качество зачистки подготовленных под сварку кромок; химический состав металла.
3. Все параметры, указанные в п.п. 1 и 2.
ВОПРОС 7. Для какой группы сталей применяют при сварке электроды типов Э50, Э50А, Э42А, Э55?
1. Для сварки конструкционных сталей повышенной и высокой прочности.
2. Для сварки углеродистых конструкционных сталей.
3. Для сварки высоколегированных сталей.
ВОПРОС 8. Что обозначает в маркировке типов электродов буква «А», например Э42А?
1. Пониженное содержание легирующих элементов.
2. Пониженное содержание углерода.
3. Повышенные пластические свойства наплавленного металла.
ВОПРОС 9. Нужен ли предварительный подогрев для сварки хорошо свариваемых малоуглеродистых и сталей толщиной менее 30 мм?
1. Нужен.
2. Не нужен.
3. По усмотрению руководителя работ.
ВОПРОС 10. Каким инструментом определяют соответствие ширины шва стандартным требованиям?
1. Шаблоном сварщика
2. Линейкой.
3 . Штангенциркулем.
Различные дефекты сварных соединенийГазовые поры образуются в случае применения отсыревших электродов, большой скорости сварки и длинной дуги, загрязненных кромок разделки, недостаточной защиты шва при сварке в защитных газах. Равномерная пористость обычно возникает при постоянно действующих факторах — загрязненность свариваемых кромок (ржавчина, масло, влага), непостоянная толщина покрытия электродов, влажные электроды. Поры могут быть одиночными, в виде цепочки по продольной оси шва или отдельных групп, равномерно распределенных по шву. Одиночные поры образуются за счет действия случайных факторов — колебания напряжения в сети, местного дефекта в покрытии электрода, случайном удлинении дуги. В рассмотренных причинах появления пор и кроются меры по их предотвращению. Существуют однако и другие способы, которые могут уменьшить порообразование. На стадии появления газовых зародышей вероятность нх возникновения будет снижаться в случае применения обратной полярности при сварке на постоянном токе, снижения температуры металла сварочной ванны, устранения или снижения интенсивности перемешивания металла в сварочной ванне, уменьшения числа газов и их содержания в металле, отсутствия неметаллических включений в металле. Рост пузырьков газа будет затруднен при уменьшении интенсивности перемешивания металла, повышении внешнего давления, снижении содержания газов в металле. При многослойной сварке скорость роста газовых пузырьков уменьшается при снижении температуры металла сварочной ванны, введении в металл компонентов, повышающих его вязкость. Удалению газовых пузырьков из металла сварочной ванны способствует увеличение ширины сварочной ванны, повышение интенсивности перемешивания металла сварочной ванны, снижение вязкости металла и шлака. Поры являются причиной усталостных разрушений в угловых, стыковых и в поперечных швах (по отношению к действующей нагрузке) с высокими растягивающими остаточными напряжениями. Поэтому в сварных швах трубопроводов высокого давления не допускаются одиночная пора, сплошная цепочка или сетка пор (независимо от длины и площади) размером более 5 % толщины стенки трубы при ее толщине до 20 мм и свыше 1 мм при большей толщине и наличии двух и более пор на 100 мм сварного шва. Неметаллические включения (рис. 88), представляющие пустоты в металле шва, заполненные неметаллическими веществами (шлаками, окислами), как правило, присутствуют в металле сварных швов. Их состав, количество, размер, форма и распределение в металле шва могут оказать заметное влияние на механические свойства сварных соединений. Неметаллические включения можно разделить на включения, которые образуются в металле сварочной ванны в результате различных физико-химических процессов, и на включения, вносящиеся в сварочную ванну извне. Большинство неметаллических включений относится к первой группе и их образованию способствует обогащение жидкого металла примесями вследствие ликвационных явлений и понижение совместной растворимости примесей при охлаждении металла сварочной ванны. Извне неметаллические включения могут быть внесены в результате перехода в сварочную ванну части расплавленного покрытия в виде отдельных капель или вместе с электродным металлом за счет перехода окислов (соединение металла с кислородом), находящихся на поверхности свариваемых деталей, или неполного удаления шлаковой корки с поверхности предыдущего валика. Рис. 89. Трещины в сварных швах и соединениях Наиболее действенным средством, способствующим устранению неметаллических включений в сварном шве, является исключение или сильное снижение содержания в металле шва кислорода, азота и серы. Рис. 88. Шлаковые включения по подрезу кромки в многослойном шве Наиболее опасными дефектами в сварном соединении являются трещины (рис. 89). Появлению трещин в металле шва могут способствовать поры и неметаллические включения. Процесс разрушения начинается с образования зародышевой трещины, поэтому наличие в металле трещин является фактором, предрасполагающим к разрушению. Кристаллизационные трещины образуются под действием сварочных напряжений в тот период, когда сварочная ванна представляет собой двухфазную систему: кристаллы — расплав. Холодные трещины являются довольно распространенным дефектом. Для них характерно замедленное развитие в начальной стадии. Обычно они зарождаются спустя некоторое время после сварки и, достигнув «которой критической длины, могут расти с огромной скоростью. Скорость роста на заключительном этапе разрушения определяется величиной действующего напряжения, температурой, скоростью нагружения. Наибольшие значения скорости роста трещин достигаются при динамическом нагружении в условиях низких температур и при большом запасе упругой энергии. В заключение следует отметить, что появлению трещин способствует сварка при низких температурах, сварка конструкционных легированных сталей в жестко закрепленных конструкциях, использование сварочного тока повышенной плотности при наложении первого слоя многослойного шва толстостенных изделий, чрезмерное нагромождение швов (многочисленные накладки, ребра жесткости и т. п.) для усиления конструкции, высокая скорость охлаждения при сварке углеродистых сталей, склонных к закалке на воздухе. Наряду с трещинами к наиболее опасным дефектам относят непровары (рис. 90), которые представляют собой несплавление основного металла с наплавленным или незаполнение расплавленным металлом разделки шва. Непровары первого вида чаще всего наблюдаются по толщине основного металла и в вершине углового шва. Формирование сварного шва происходит за небольшой промежуток времени, поэтомна процесс образования непроваров будет влиять и скорость заполнения расплавленным металлом разделки кромок свариваемых деталей. Разрушение конструкций чаще всего начинается от дефектов, возникающих в сварном соединении или основном металле. Влияние дефектов на свойства сварных соединений определяется величиной и формой дефектов, частотой их повторения, материалом конструкций, условиями эксплуатации и характером нагрузки. Опасность дефектов наряду с влиянием их собственных характеристик зависит от множества конструктивных и эксплуатационных факторов. Так, влияние дефектов, представляющих собой концентраторы напряжений, во многом будет зависеть от распределения остаточных и рабочих напряжений, возникающих в процессе эксплуатации. Из дефектов сварных соединений наиболее опасными являются трещины. Трещины ослабляют сечение швов или свариваемых элементов и тем самым уменьшают статическую прочность соединений. Являясь концентраторами напряжений, они, кроме того, существенно уменьшают динамическую прочность сварных соединений. Увеличение размеров трещин, образовавшихся при сварке, может привести к разрушению конструкции во время эксплуатации. Трещины опасны еще и тем, что, являясь дефектами плоского типа, трудно обнаруживаются рентгенографическими методами контроля. Поэтому наличие трещин в сварных соединениях не допускается. По иному на сварные конструкции влияют поры. Многие исследователи считают, что до некоторого предела наличие пор в металле шва практически не снижает его статическую прочность. Для низкоуглеродистых сталей этот предел составляет около 10 % площади поперечного сечения шва, для перлитных сталей — 6—8%; для алюминиевых сплавов — 3,6%- Однако поры снижают не только статическую прочность сварного соединения, а, являясь концентраторами напряжений, могут вызвать снижение выносливости сварного соединения. В этом случае особенно опасным является наличие пор в зонах растягивающих остаточных напряжений. Растягивающие остаточные напряжения особенно велики в поверхностных слоях металла, поэтому опасность разрушения возрастает, если поры будут расположены близко к поверхности. Но сварные соединения могут разрушаться и из-за наличия внутренних пор, если они расположены в зонах высоких растягивающих остаточных напряжений. Неметаллические включения, содержащиеся в металле шва, также оказывают заметное влияние на механические свойства сварного соединения. Это влияние существенно зависит от величины, формы и места расположения включений, так как они являются концентраторами напряжений. Установлено, что шлаковые включения площадью до 10% площади поперечного сечения шва предел прочности металла шва почти не изменяют. Однако при работе в агрессивных средах даже при статическом нагружении наличие шлаковых включений в сварном шве снижает долговечность конструкции. Неметаллические включения могут способствовать образованию других дефектов. Так, сульфидные включения, которые часто имеют температуру плавления ниже температуры кристаллизации металла, служат причиной появления горячих трещин, а наличие нитридов (соединение металла с азотом) увеличивает склонность металла шва к старению. Результаты исследования показывают, что при статической нагрузке для пластичных материалов влияние величины непровара на уменьшение прочности прямо пропорционально относительной глубине непровара или его площади. Для малопластичных и высокопрочных материалов, а также при динамической или вибрационной нагрузках пропорциональность между потерей работоспособности и величиной дефекта нарушается. Непровар оказывает большое влияние на ударную прочность металла сварных швов. По данным Института электросварки им. Е. О. Патона непровар в 10% толщины сварного соединения может на 50% снизить усталостную прочность, а непровар в 40—50% снижает пределы выносливости стали в 2,5 раза. Однако наружные дефекты также оказывают серьезное влияние на работоспособность сварных конструкций. Опасным наружным дефектом является подрез. Он не допускается в конструкциях, работающих на выносливость. Подрезы небольшой протяженности, ослабляющие сечение не более чем на 5% в конструкциях, работающих под действием статических нагрузок, на прочность конструкций не оказывают заметного влияния. Однако суммарное влияние подреза и увеличения растягивающих остаточных напряжений может привести к снижению предела выносливости вдвое. Усиление шва не снижает статическую прочность, но сильно влияет на вибрационную прочность сварного соединения. Чем больше усиление шва, а следовательно, меньше угол перехода от основного металла к наплавленному, тем сильнее снижается предел выносливости. Поэтому чрезмерное усиление сварного шва может привести к ликвидации тех преимуществ, которые получены от оптимизации технологического процесса по улучшению качества наплавляемого металла в сварных соединениях, работающих при динамических, вибрационных нагрузках. Наплывы также снижают выносливость конструкций, являясь концентраторами напряжений. Наплавы большой протяженности нередко сопровождаются непроварами. У трубопроводов для горючих, токсичных и сжиженных газов сварные швы бракуют, если обнаружены трещины любых размеров и направлений, свищи, сетки или цепочки пор, шлаковые или другие инородные включения, непровар в корне шва, межваликовые несплавления. Кроме того, бракуют сварные швы, имеющие непровар при одностороннем шве без подкладного кольца, глубиной более 10 % толщины стенки трубы, если она не превышает 20 мм, и глубиной более 2 мм при толщине стенки свыше 20 мм, а также бракуют швы, имеющие одиночные поры, включения вольфрама размером свыше 10 % толщины стенки, если толщина не превышает 20 мм, и размером более 2 мм, если толщина стенки свыше 20 мм, в количестве более трех на каждые 100 мм шва. Примерно такими же являются браковочные признаки для трубопроводов высокого давления. В сварных соединениях стальных конструкций промышленных и гражданских зданий и сооружений допускаются непровары по сечению швов в соединениях, доступных сварке с двух сторон, глубиной до 5 % толщины металла, но не более 2 мм при длине непровара не более 50 мм и общей длине участков непровара не более 200 мм на 1 м шва. Кроме того, возможны непровары в соединениях, доступных сварке с одной стороны (без подкладок), глубиной до 15% толщины металла, если она не превышает 20 мм. Допускается суммарная величина непровара, шлаковых включений и пор, расположенных отдельно или цепочкой, не превышающая в рассматриваемом сечении при двусторонней сварке 10%) толщины свариваемого металла, но не более 2 мм, и при односторонней сварке без подкладок—15%, но не более 3 мм. Читать далее: |
ДЕФЕКТЫ И КОНТРОЛЬ КАЧЕСТВА. СВАРНЫХ СОЕДИНЕНИЙ
Дефекты сварных соединений, выполненных
с дополнительным порошкообразным присадочным
металлом
Наличие в сварных соединениях дефектов, т. е. несоответствия соединений требованиям нормативной документации, может привести к их разрушению, разрушению всей конструкции, аварии на производстве. Поэтому увеличение затрат на вспомогательные и основные технологические операции с целью снижения вероятности образования дефектов экономически оправдывается. В зависимости от характера, расположения дефектов, способа их воздействия на сварное соединение они подразделяются на группы. По месту расположения дефекты бывают наружные (прожоги, подрезы, наплывы, неравномерность шва, усиленные и ослабленные швы, крупная чешуйчатость, кратеры, непровары по кромке, наружные поры и трещины) и внутренние (шлаковые включения, непровар в корне шва, внутренние трещины и поры, пережог металла). Сварке с порошкообразным присадочным металлом присущи дефекты, встречающиеся как при обычных способах сварки, так и некоторые специфические. Несплавление в вершине шва (рис. 64, а) образуется из-за недостаточного напряжения на дуге. Отсутствие проплавления (рис. 64,6) появляется из-за недостаточной силы сварочного тока. Смещение шва с одной из кромок (рис. 64, в) происходит в результате неправильного направления электрода, при этом противоположная кромка оплавляется чрезмерно. В тавровых соединениях с большой раз-
Рис. 64 Дефекты сварных соединений, характерные для сварки с порошкообразным присадочным металлом а — несплавление в вершине шва; б — отсутствие проплавления: в — смешение шва с одной из кромок; г — несплавление в середине шва |
носїью толщин элементов увеличивается опасность перегрева вертикальной стенки. Несплавление в середине шва (рис. 64, г)—дефект наиболее серьезный, так как его можно выявить только с помощью физических методов контроля. Этот дефект указывает на недостаточную мощность сварочной дуги (сварочного тока) или на слишком большое количество порошкообразного присадочного металла. При электро — шлаковой сварке смещение электрода от оси зазора может вызвать несплавление по одной из кромок.
Этот же дефект образуется при подаче большего количества, чем это требуется, порошкообразного присадочного металла. Непровар у поверхности свариваемых элементов наблюдается при смещении электрода от оси сварного соединения к одному из медных ползунов.
По степени влияния на сварное изделие дефекты бывают критические, значительные и малозначительные. Наличие критического дефекта исключает применение сварной конструкции. Значительный дефект существенно влияет на качество сварной конструкции, но не является критическим. Малозначительный дефект не оказывает заметного влияния на качество конструкции. Рассмотрим основные дефекты сварных соединений и причины их образования.
Непровар — местное несплавление между основным и наплавленным металлами или отдельными слоями при многослойной сварке резко снижает механические показатели сварного соединения, отрицательно влияет на его пластичность и может, являясь концентратором напряжений, привести к образованию трещин. Причиной непровара может быть отсутствие зазора, большое притупление, небольшой угол разделки кромок, неправильный режим сварки или его нарушение, неточное направление конца электродной проволоки, отсутствие в конце и начале сварки технологических пластин, неправильное возобновление процесса сварки после перерыва. При электрошлаковой сварке встречается непровар трех видов: у поверхности свариваемого металла, по середине шва, по одной или обеим кромкам, В первом случае непровар образуется при недостаточном времени остановки у ползунов или снижении напряжения на одном из электродов, увеличении расстояния между крайним положением электрода и ползуном. Непровар по середине шва при сварке 2—3 электродами появляется при чрезмерном расстоянии между соседними электродами. Непровар по одной из кромок образуется при смещении электрода от оси зазора, по двум — из-за малой ширины шва, большой скорости подачи электродной проволоки, резкого увеличения глубины шлаковой ванны и большой толщины электродного металла.
Поры — заполненные газом полости круглой, вытянутой или другой формы в металле сварного шва, располагающиеся цепочкой по оси шва или отдельными группками, образуются по ряду причин, которые можно разделить на две группы. К первой относятся причины, непосредственно зависящие от сварщика,— окалина, ржавчина, масло, краска на свариваемых кромках, влажный флюс или электрод с влажным покрытием, большая скорость сварки, при которой нарушается газовая защита металла сварочной ванны. Ко второй относятся причины, заложенные в технологии сварки,— азот, водород и окись углерода, образую — щиеся в результате отклонения химического состава металла шва от заданного из-за снижения в нем кремния и марганца по причине применения несоответствующей электродной проволоки или уменьшения глубины проплавления. При электрошлаковой сварке металл шва более стоек против порообразования по сравнению с электродуговой сваркой. Поры в этом случае не выходят на поверхность и располагаются по сечению шва без определенного порядка или скапливаются в отдельные группы. В случае применения порошкообразного присадочного металла при автоматизированной сварке под флюсом существенно уменьшается порообразование и появление несплошностей. Поры не допустимы в сварных швах аппаратуры, работающей под давлением и вакуумом, или предназначенной для транспортировки и хранения жидких и газообразных продуктов.
Трещины — наиболее опасные и недопустимые дефекты в сварных соединениях. Трещины бывают горячие и холодные. Горячие трещины зарождаются в процессе первичной кристаллизации и развиваются при остывании металла. На их появление влияет химический состав металла шва, величина и скорость действующих в процессе кристаллизации металла шва растягивающих напряжений, форма сварочной ванны, величина первичных кристаллитов. Элементы, входящие в металл шва, по-разному влияют на стойкость против горячих трещин. Сера и фосфор являются вредными примесями. Сера переходит в металл шва из основного металла и сварочных материалов. Поэтому практический интерес представляет применение флюсов, способствующих переходу серы из сварочной ванны в шлак. Фосфор является причиной образования горячих трещин в сварных швах некоторых среднелегированных сталей, а наиболее опасен —для швов с чисто аустенитной структурой. В большой степени способствует образованию горячих трещин углерод, попадая в металл шва из основного металла и сварочных материалов. Поэтому уменьшение доли основного металла и применение электродной проволоки с низким содержанием углерода позволяет снизить его содержание в металле шва. Кремний способствует образованию трещин в сварных швах из углеродистой стали и особенно опасен в швах из аустенитной хромоникелевой стали. При сварке углеродистых и низколегированных сталей никель не оказывает отрицательного влияния, а у других сталей, усиливая вредное влияние серы при его содержании более 1—2%, способствует образованию горячих трещин. Кислород повышает стойкость металла шва против образования горячих трещин, вызываемых серой, и снижает ударную вязкость металла шва при сварке углеродистых и низколегированных сталей. Повышение скорости сварки, снижение сварочного тока, увеличение числа слоев в шве, колебание электрода и металла сварочной ванны приводят к увеличению скорости кристаллизации и образованию мелкозернистой структуры, что увеличивает стойкость металла шва против образования горячих трещин. Этому же способствует применяемый технологический прием — изменение формы провара (отношение ширины шва к глубине его проплавления). При автоматизированной сварке под флюсом коэффициент формы провара должен быть равен 1—2, электрошлаковой — 2,5—5. Для предотвращения образования горячих трещин рекомендуется использовать способы и режимы сварки, обеспечивающие минимальное тепловложение. С этой точки зрения большими возможностями обладает сварка с дополнительным порошкообразным присадочным металлом, позволяющая уменьшить удельное тепло — вложение, что приводит к улучшению термического цикла сварки. Это, в свою очередь, улучшает структуру металла сварного соединения, условия кристаллизации и механические свойства. Уменьшение тепловложения способствует также снижению сварочных деформаций. В итоге повышается сопротивляемость образованию горячих и холодных трещин.
Кроме того, уменьшение доли основного металла в ме — халле сварного шва позволяет снизить в нем содер жание углерода, что, в свою очередь, повышает стойкость металла шва против образования горячих трещин. Применение порошкообразного, присадочного металла при электрошлаковон сварке, создавая благоприятный тепловой режим, уменьшает склонность швов к горячим и усадочным трещинам.* К образованию усадочных дефектов могут привести вынужденные остановки сварочного автомата. В таких случаях до возобновления сварки конец ранее выполненного шва на длину 100 мм необходимо обязательно удалить.
Холодные трещины образуются при остывании металла сварных соединений ниже 200 °С. Основным видом холодных трещин являются околошовные трещины. Появлению холодных трещин способствует повышенное содержание углерода и водорода в металле шва, а причиной их образования являются сварочные напряжения, внешние нагрузки и закалочные явления.
Шлаковые включения — заполнение шлаком несплошности в металле шва,— являясь концентраторами напряжений и ослабляя сечение шва. уменьшают его прочность. Они образуются из-за наличия грязи, окалины и ржавчины на свариваемых кромках, из-за неполного удаления шлака при многослойной сварке, некачественных электродов, когда кусочки электродного покрытия попадают в сварочную ванну. При электрошлаковой сварке шлаковые включения образуются по кромке соединений в местах резкого изменения ширины провара или в виде прослойки между основным металлом и металлом шва. При несплавлении шлаковые включения образуются из-за большой глубины шлаковой ванны, повышенной теплопроводности основного металла или применения тугоплавкого флюса.
Рассмотрим теперь дефекты формирования сварных швов.
Прожоги — сквозные отверстия в сварном шве из-за вытекания металла сварочной ванны — являются недопустимыми дефектами. Они образуются при наличии большого зазора, отсутствия притупления, плохого поджатия флюсовой подушки, заниженной скорости сварки или завышенного сварочного тока.
Кратеры — углубления в металле сварочной
ванны, образующиеся после резкого обрыва дуги,— уменьшают сечение шва и могут явиться очагами образования трещин. Для предупреждения появления кратеров необходимо применять технологические пластины, а при их отсутствии при ручной сварке кратер следует тщательно заварить, обрывая дугу на уже заваренном участке сварного шва.
Подрез — углубление в основном металле вдоль сварного шва. с одной или двух сторон — существенно снижает прочность сварного соединения у конструкций с вибрационными нагрузками. Суммарное влияние подреза и увеличение растягивающих остаточных напряжений может привести к снижению предела выносливости сварной конструкции вдвое. Глубина подреза может достичь нескольких миллиметров. Устранить подрезы можно, уменьшив скорость кристаллизации или увеличив скорость заполнения углубления металлом. Обычно снижают скорость кристаллизации за счет уменьшения скорости сварки, предварительного подогрева деталей или применения многоэлектродной сварки. Причиной подрезов может быть большая сила сварочного тока, повышенное напряжение на дуге, смещение электрода относительно оси шва, неудобное пространственное положение при сварке, небрежность или недостаточная квалификация сварщика. Устранение этих недостатков предотвратит появление подрезов. При элекгрошлаковой сварке подрезы образуются из-за плохого охлаждения ползунов, увеличения продолжительности их остановки в конечном положении.
Неравномерность ширины шва при автоматизированной сварке появляется из-за нарушения скорости подачи электродной проволоки или скорости сварки. Значительные изменения ширины сварного шва могут привести к непровару, так как они сопровождаются изменением глубины провара.
Наплывы — натекания жидкого металла на кромки нерасплавленного основного металла — образуются при неправильном режиме сварки или большом слое окалины на свариваемых кромках. Наплывы могут сопровождаться скрытыми непроварами кромок, поэтому их следует срубать, а места эти подваривать.
Деформация сварной конструкци и—
это один из видов дефектов. Расширение и сжатие металла при сварке затруднено, так как нагреваемый участок со всех сторон окружен холодным металлом, размеры которого не изменяются. Это вызывает возникновение в конструкции остаточных напряжений. Когда значения сварочных напряжений достигнут предела текучести, они вызовут пластическую деформацию, что приведет к изменению размеров и формы сварной конструкции, т. е. произойдет коробление — деформация конструкции. Если остаточные деформации достигнут заметной величины, то они могут привести к неисправимому браку. Когда деформация конструкции выходит за допускаемые пределы, применяют ее правку.
Наличие дефектов в сварных соединениях еще не определяет потерю их работоспособности. Однако дефекты могут существенно снижать ее, и даже при определенных условиях приводят к разрушению сварных конструкций. В конструкциях, эксплуатируемых при статических и динамических нагрузках, одни и те же дефекты по-разному влияют на сварное соединение. При статической нагрузке основное влияние на прочность конструкции оказывает относительная величина дефекта, если материал сварного соединения имеет большой запас пластичности. При температурах ниже —60 °С прочность определяется уже интенсивностью напряжений в зоне дефекта. При динамических нагрузках прочность сварных соединений определяется их сопротивлением усталостным напряжениям. Различные дефекты по-разному влияют на прочность сварных конструкций. Как правило, наличие трещин любой величины, являющихся концентраторами внутренних напряжений, легко распространяющихся в глубь металла и ослабляющих сечение швов, и тем самым уменьшающих статическую прочность соединений, не допускается в сварных конструкциях. Трещины опасны еще и тем, что, являясь дефектами плоского типа, трудно обнаруживаются рентгенографическими методами контроля. Непровары, поры, шлаковые включения, подрезы, создавая концентрацию напряжений, снижают срок эксплуатации конструкций. Виды, количество и размеры допускаемых дефектов зависят от назначения конструкции.
Наряду с трещинами наиболее опасными дефектами являются непровары. Исследованиями установлено, что при статической нагрузке для пластичных материалов влияние величины непровара на уменьшение прочности прямо пропорционально относительной глубине непровара или его площади. По данным института электросварки им. Е. О. Патона, непровар в 10% толщины свариваемого металла может снизить усталостную прочность наполовину, а непровар в 40—50% снижает предел выносливости стали в 2,5 раза. В сварных соединениях стальных конструкций промышленных и гражданских зданий и сооружений допускаются непровары по сечению шва в соединениях: доступных сварке с двух сторон глубиной до 5% толщины металла, но не более 2 мм при длине непровара не более 50 мм и общей длине участков непровара не более 200 мм на 1 м шва; доступных сварке с одной стороны (без подкладок) глубиной до 15% толщины металла, если она не превышает 20 мм, и не свыше 3 мм при толщине более 20 мм.
Поры, снижая статическую прочность сварного соединения, являются концентраторами напряжений и могут вызвать снижение предела выносливости сварного соединения. Поры становятся очагами усталостных разрушений в первую очередь в угловых, стыковых и поперечных шаах с высокими растягивающими остаточными напряжениями. Однако многие исследователи считают, что до некоторого предела наличие пор в металле сварного шва практически не снижает его статическую прочность. Для низкоуглеродистых сталей этот предел составляет около 10% площади поперечного сечения шва, для перлитных сталей 6—8%, для алюминиевых сплавов 3,6%. Заметное влияние на механические свойства сварного соединения оказывают шлаковые включения, степень влияния которых зависит от формы, величины и места расположения включений и обусловливается тем, что включения становятся концентраторами напряжений. Считается, что шлаковые включения площадью до 10% площади поперечного сечения шва почти не изменяют предел прочности металла шва. Однако шлаковые включения могут способствовать появлению трещин и увеличивать склонность металла шва к старению, а также снижают долговечность конструкций при работе в агрессивных средах. В сварных соединениях стальных конструкций промышленных и гражданских сооружений допускается суммарная величина неррова — ра, пор и шлаковых включений, расположенных отдельно или цепочкой, не превышающая в рассматриваемом сечении 10% толщины свариваемого металла, но не более 2 мм, и при односторонней сварке без подкладок — 15%, но не более 3 мм.
Существенное влияние на работоспособность сварных конструкций оказывают также наружные дефекты. Подрезы небольшой протяженности, ослабляющие сечение конструкции, работающей под действием статических нагрузок. не’более 5%, заметного влияния на прочность конструкций не оказывают. Однако они являются опасным дефектом и не допускаются в конструкциях, работающих на выносливость. Суммарное влияние подреза и увеличение растягивающих остаточных напряжений может привести к снижению предела выносливости вдвое. Наплывы также снижают выносливость конструкций, являясь концентраторами напряжений. Наплывы большой протяженности нередко сопровождаются непроварами.
В основном, как показывает эксплуатация сварных конструкций, сварочные напряжения и деформации не снижают несущей способности конструкций. Однако в некоторых случаях изменение размеров и формы конструкций снижает их работоспособность и портит внешний вид. Искривление продольной оси элементов конструкций, работающих на сжатие, местное выпучивание, грибовидность полок колонн и балок могут привести к потере устойчивости и разрушению всей конструкции.
Наряду с размерами дефектов и местом их расположения на работоспособность сварной конструкции влияет способ устранения дефектов и число исправлений одного и того же участка. Поэтому устранение дефектов производится в строгом соответствии с назна чением конструкции. Чем ответственнее конструкция, тем более жесткие требования к удалению дефектных участков сварных швов.
В сварных швах конструкций промышленных и гражданских сооружений при устранении дефектов следует придерживаться следующих правил:
перерывы швов и кратеры завариваются;
швы с трещинами, а также с непроварами и
другими дефектами, превышающими допустимые нормы, удаляются на длину дефектного места с припуском в 10 мм е каждой стороны и завариваются вновь;
при удалении трещин концы их засверливаются;
подрезы основного металла, превышающие допустимые размеры, зачищаются и завариваются с последующей зачисткой, обеспечивающей плавный переход от наплавленного металла к основному.
Для устранения деформаций, величины которых выходят за пределы допустимых, применяют термический, механический или термомеханический способы. При термическом способе производят нагрев газовыми горелками деформированных участков, при механическом — прикладывают усилия к дефектным участкам с помощью домкратов, винтовых прессов или других механизмов, создающих статическую или ударную нагрузки. Термомеханический способ сочетает в себе местный нагрев с приложением статической нагрузки. Внутренние напряжения r сварных соединениях уменьшают при помощи предварительного, сопутствующего нагрева места сварки, последующей термической обработки, проковки или обкатки сварных швов.
Рекомендации по подогреву при сварке толстостенных металлоконструкций карьерных экскаваторов Текст научной статьи по специальности «Технологии материалов»
УДК 621. 172.18
РЕКОМЕНДАЦИИ ПО ПОДОГРЕВУ ПРИ СВАРКЕ ТОЛСТОСТЕННЫХ МЕТАЛЛОКОНСТРУКЦИЙ КАРЬЕРНЫХ ЭКСКАВАТОРОВ
© А.П. Макаров1, А.Н. Шевченко2
Иркутский национальный исследовательский технический университет, 664074, Россия, г. Иркутск, ул. Лермонтова, 83.
Даны практические рекомендации при сварке низколегированных и низкоуглеродистых сталей деталей и металлоконструкций рабочего оборудования карьерных экскаваторов. Рекомендации касаются выбора присадочного материала, исходя из требований прочности и вязкости, предъявляемых к сварочному соединению. Установлены рациональные соотношения толщины свариваемого металла от температуры подогрева и числа сварочных швов. Исполнение приведенных рекомендаций технологии сварки низколегированных и низкоуглеродистых сталей позволяет обеспечить сопротивляемость сварных соединений и зоны термического влияния образованию холодных трещин, хрупкому разрушению и ударной вязкости до регламентируемого уровня. Ключевые слова: сварка; рукоять; экскаватор; сварные валики; электрод; трещиностойкость.
RECOMMENDATIONS ON HEATING UNDER MINE EXCAVATOR HEAVY-WEIGHT METAL
STRUCTURE WELDING
A.P. Makarov, A.N. Shevchenko
Irkutsk National Research Technical University, 83 Lermontov St., Irkutsk, 664074, Russia.
Practical recommendations are given for welding of low alloy and low-carbon steel parts and metal structures of mine excavator working equipment. The recommendations deal with the choice of welding filler on the basis of strength and toughness requirements imposed on welded joints. Rational ratios of weld metal thickness to heating temperature and number of welds are determined. Implementation of given recommendations for the technology of welding low alloy and low-carbon steels ensures the resistance of weld joints and heat affected zone to cold cracking, brittle fracture and notch toughness to the regulated level.
Keywords: welding; bucket arm; mine excavator; weld beads; electrode; crack resistance.
Для обеспечения качественного сварного соединения необходимо исключить наличие водорода, вызывающего трещины в зоне сварки.
Кромки соединения до сварки должны быть чистыми и сухими. Допускается использовать только сухие присадочные материалы и электроды. При сварке деталей большой толщины сварку необходимо проводить при повышенной температуре. Предлагаемая зависимость сварки и толщины металла (рис. 1) предназначена для низколегированных и низкоуглеродистых сталей: 09Г2С; 30ХГС и т.п.
Контроль температуры осуществляется одним из самых удобных способов — с помощью термоиндикаторных мелов на поверхности, обратной нагреваемой (рис. 2).
При сложнонагруженных элементах в конструкции, какими являются узлы и детали рабочего оборудования экскаваторов, и при сварке в сырую погоду рекомендуется ближайший к представленному повышенный уровень температуры.
Определение числа сварных валиков при многопроходной сварке толстостенных конструкций производят, когда необходимо, чтобы ударная вязкость сварного соединения равнялась ударной вязкости основного металла. При этом рекомендуется соблюдение следующего практического правила:
Число сварных валиков =
_ толщина сварного металла х 2 ■ = 5
1
Макаров Анатолий Павлович, кандидат технических наук, доцент кафедры горных машин и электромеханических систем, тел.: (3952) 405085, e-mail: [email protected]
Makarov Anatoly, Candidate of technical sciences, Associate Professor of the Department of Mining Machinery and Electromechanical Systems, tel.: (3952) 405085, e-mail: [email protected]
2Шевченко Алексей Николаевич, кандидат технических наук, доцент кафедры горных машин и электромеханических систем, тел.: (3952) 405069, 79646541034, e-mail: [email protected]
Shevchenko Alexey, Candidate of technical sciences, Associate Professor of the Department of Mining Machinery and Electromechanical Systems, tel.: (3952) 405069, 79646541034, e-mail: [email protected]
Балку рукояти экскаватора ЭКГ-15 толщиной 51,5 мм рекомендуется сваривать не менее чем десятью валиками, поскольку сварка производится с У-образной разделкой кромок (рис. 3). Так, стыковой
шов двадцатимиллиметрового металла заваривают, по меньшей мере, восемью валиками (рис. 4). При снижении требований по ударной вязкости допускается уменьшение числа сварных валиков.
50 200
I Температура, С
10 20 I I 30 I W 50 60 I I I
Толщина сварныхкролюк, мм Рис. 1. Зависимость температуры подогрева от толщины металла
Рис. 2. Сварка соединения встык (натяжные окна ЭКГ-15): 1- места подогрева;
2 — места замера температуры
Рис. 3. Разрез свариваемой балки рукояти ЭКГ-15. Стыковка при У-образной разделке кромок под 45
1, 2 — места замера температур
Рис. 4. Расположение сварных валиков при сварке металла толщиной 20 мм
a
кЛж
+ 1
+ 1 1 1
+ 1 1 1 |
+ / Л) ^ 1 1 120 LO 1 1 1 50] 1 .60
Толщина металла мм
Рис. 5. Зависимость подводимого к сварочному шву тепла от толщины металла
При сварке низкоуглеродистых сталей около сварочной ванны образуется мягкая зона, ширина которой меняется в зависимости от количества и продолжительности вводимого тепла. При умеренном вводе тепла мягкая зона достаточно узкая, никак не влияющая на твердость сварного соединения. График на рис. 5 показывает оптимальное количество тепла, вводимого в сварочный шов, в зависимости от толщины металла (зависимость получена эмпирически на основе опыта практического применения подогрева толстостенных низкоуглеродистых сталей).
При выборе присадочного металла (электрода) следует исходить из требований по прочности и вязкости, предъявляемых к сварному соединению, а также из существующих напряжений в свариваемой детали. В большинстве случаев рекомендуются «мягкие» присадочные металлы, и к этому следует стремиться, чтобы избежать повышенной твердости и хрупкости сварного шва. Применение электрода с показателями предела прочности оВ и предела текучести оТ ниже, чем основной металл, позволяет более пластично формировать сварочный шов при охлаждении, а также
уменьшить вероятность возникновения дополнительных напряжений в сварочном соединении и избежать как горячих, так и холодных трещин. Более мягкий присадочный металл должен всегда использоваться при наплавке валиков в корне многослойного сварного шва и в стыковых соединениях, поскольку от наплавленного металла не требуется одной и той же прочности с основным металлом, кроме случаев, когда присадочный металл в силу конструктивных особенностей нагрузки детали должен иметь одинаковую прочность с основным металлом при наплавке валиков в корне.
Всегда необходимо стремиться выбрать такие присадочные металлы и способы сварки, которые по возможности обеспечат более низкий уровень содержания водорода. Электроды с покрытием должны обязательно быть высушенными, суммарная влажность их покрытия не должна превышать 5-10 мл на каждые 100 гр. электродов.
Для снижения вероятности появления холодных трещин эффективно использовать предварительный и сопутствующий подогрев. В практике ремонта в полевых условиях при сварочных работах ответ-
ственных узлов и деталей горного оборудования применяются специальные брезентовые палатки, которые устанавливают непосредственно на свариваемый участок крупногабаритной детали, что позволяет укрыть сварщика и свариваемую деталь экскаватора от различных атмосферных осадков. К тому же это обеспечивает необходимую температуру воздуха вокруг как наплавляемого, так и остывающего сварного шва.
Для определения температуры подогрева стали с целью предотвращения образования холодных трещин в зависимости от содержания в ней химических элементов и толщины свариваемых кромок рекомендуется использовать график Эрен-берга. По графику установлено, что необходимая температура подогрева возрастает с увеличением степени легированности стали и толщины свариваемого металла.
При разработке технологии сварки низколегированных сталей типа 09Г2С, 08ГДНФЛ и других необходимо учитывать то обстоятельство, что при уменьшении погонной энергии и увеличении интенсивности охлаждения в металле шва и в зоне термического влияния (ЗТВ) возрастает вероятность распада аустенита с образованием закалочных структур. При этом установлено, что снижается сопротивляемость сварных соединений образованию холодных трещин и хрупкому разрушению. При повышенных погонных энергиях наблюдается рост зерна аустенита и образуется крупнозернистая ферритно-перлитная структура с пониженной ударной вязкостью.
Технология ручной дуговой сварки низкоуглеродистых сталей не отличается от соответствующей технологии сварки низколегированных сталей, из которой изготовлены почти все детали рабочего оборудования и базовые узлы карьерных экскаваторов.
Сварку низколегированных сталей осуществляют электродами типа Э46А и Э50А, что обеспечивает повышенную хла-достойкость металла шва, а порог хладноломкости составляет -50°С. Фтористо-
кальциевое покрытие электродов позволяет достигать более высокой стойкости против образования кристаллизационных трещин и повышенной пластичности по сравнению с электродами других типов.
Балку рукояти, двуногую стойку, нижнюю, верхнюю секции стрелы карьерных экскаваторов, изготовленных из стали 09Г2С, рекомендуют сваривать электродами УОНИ 13/55, К5А, АНО-11 (тип 50А). Все кольцевые швы указанных деталей, работающих при температуре до -70°С, выполняют электродами ВСН-3 (тип Э50АФ) с фтористо-кальциевым покрытием.
Электрошлаковая сварка сталей толщиной свыше 30 мм осуществляется, как правило, с последующей или сопутствующей нормализацией с условно повышенной ударной вязкости металла шва и ЗТВ до регламентируемого уровня. Сварку стали 09Г2С осуществляют с применением флюса АН-8 и сварочных проволок Св-08ГС или Св-10Г2. Режимы термообработки аналогичны низкоуглеродистым сталям.
Для кольцевых швов трубных конструкций с толщиной стенки до 100 мм при температуре эксплуатации ниже -40°С (сталь 09Г2С) в соответствии с ОСТ 291-81 допускается применять электрошлаковую сварку с регулированием термических циклов в сочетании с последующим отпуском. При этом удается не только обеспечить равнопрочность, но и достаточно высокий уровень сопротивления сварных соединений хрупкому разрушению без применения последующей высокотемпературной термообработки. Это особенно важно для сварки балок рукояти и двуногих стоек экскаваторов ЭКГ-10, ЭКГ-15, ремонт которых даже в условиях цеха сопряжен с большими трудностями, связанными с качественной термообработки.
В условиях ремонтных мастерских АК «АЛРОСА» (рис. 6, 7) по специально разработанной технологии сварки металлоконструкций удалось получить довольно высокие механические характеристики сварочных швов деталей рабочего оборудования карьерных экскаваторов.а-превращении. Отмеченное препятствует протеканию коррозионных процессов, а уменьшение размеров карбидных частиц, играющих роль коллекторов водорода, тормозит катодную реакцию при эксплуатации соединений в коррозионно-активных средах.
Особенностью термоупрочненных сталей является их склонность к разупрочнению при сварке.
Рис. 7. Балка рукояти ЭКГ-10 после сварки
Примечание. Кй — максимальный КИН цикла, при котором трещина не развивается на протяжении заданного числа циклов, (Н/м3)/2; Кс — наибольший КИН цикла, при котором наступает излом образца, (циклическая вязкость разрушения), (Н/м3)/2; ОМ — основной металл; МШ — металл шва; ЗС — зона сплавления; ЗТВ — зона термического влияния; КДЦТ — кинетическая диаграмма циклической трещиностойкости.
Характеристики циклической трещиностойкости сталей и сварных соединений _металлоконструкций карьерных экскаваторов_
Марка стали Зона сварки Асимметрия цикла нагрузки, R Температура испытаний, °С Kth, Mna-M1/2 Kfc, Mna-M1/2
09Г2С ОМ 0,7 20 -70 3,8 6,4 20,3 -19,6
0,1 20 -70 5,8 12,1 20,6 27,6
МШ 0,7 20 -70 4,9 6,4 17,8 10,4
ЗС 0,7 20 -70 4,9 5,9 20,7 17,4
ЗТВ 0,7 20 -70 4,9 5,9 19,2 11,7
КДЦТ — — 3,8 10,4
10ХСНД ОМ 0,7 20 -70 3,5 5,9 20 22,4
МШ 0,7 20 -70 5,5 6,4 20,0 15,8
ЗС 0,7 20 -70 3,7 6,4 20,3 20,7
ЗТВ 0,7 20 -70 4,3 5,6 19,6 11,2
КДЦТ — — 3,5 11,2
Применение сопутствующего охлаждения позволяет обеспечить равнопроч-ность сварных соединений с основным термоупрочненным металлом и повысить их сопротивление хрупкому разрушению.40 металла шва — с 120 до 720, а металла околошовного участка — с 80 до 420 КДж/м2.
Статья поступила 16.04.2015 г.
Библиографический список
1. Макаров А.П. Развитие усталостных трещин в металлоконструкциях экскаваторов // Вестник ИрГТУ. 2011. № 11 (58). С. 105-109.
Способ предупреждения образования холодных трещин в сварных соединениях из углеродистых и низколегированных сталей при сварке на заданных режимах
Изобретение относится к области сварочной техники, а именно к оценке требований к химическому составу углеродистых и низколегированных сталей, обеспечивающих отсутствие склонности к образованию холодных трещин и требуемый комплекс механических характеристик сварного соединения при выполнении сварки на заданных режимах. Предварительно для группы сталей выбранного класса определяют критические скорости охлаждения металла околошовного участка сварного соединения в интервале температур 800-500°С, соответствующие предельно допустимому значению показателя склонности каждой стали группы к образованию холодных трещин в околошовном участке сварного соединения. В качестве указанного показателя используют максимально допустимый процент мартенсита в структуре околошовного участка сварного соединения или предельно допустимое значение твердости околошовного участка сварного соединения. Определяют значения эквивалентного углерода для каждой стали и строят график зависимости между критическими скоростями охлаждения и эквивалентным углеродом для указанной группы сталей. Наносят на полученный график значение скорости охлаждения околошовного участка сварного соединения, соответствующее заданному способу и режимам сварки, и определяют по графику критическое значение эквивалентного углерода для сталей указанной группы выбранного класса. Для сварки на заданном режиме используют стали, эквивалентный углерод которых не превышает определенного критического значения. Повышается надежность предупреждения образования холодных трещин с достижением заданных механических свойства металла околошовного участка сварного соединения. 1 ил., 2 табл.
Изобретение относится к области сварочной техники, в частности к оценке требований к химическому составу углеродистых и низколегированных сталей, обеспечивающих отсутствие склонности к образованию холодных трещин и требуемый комплекс механических характеристик сварного соединения при выполнении сварки на заданных режимах.
Известен способ оценки влияния режимов сварки на стойкость стали к образованию холодных трещин путем проведения испытаний крупномасштабных образцов, заключающийся в том, что производят разрушение конструкции и фиксируют напряженное состояние сварного соединения с помощью тензорезисторов (см. RU 2065347, B23K 31/12, 1992).
Однако известный способ при отрицательном результате испытаний не позволяет определить требования к химическому составу сталей, которые могут быть использованы на указанных сочетаниях режимов сварки.
Известен способ предупреждения образования холодных трещин в сварных соединениях из углеродистых и низколегированных сталей при сварке на заданных режимах, базирующийся на расчете величины эквивалентного углерода (Сэкв или Рсм), обеспечивающей отсутствие холодных трещин в сварном соединении исходя из требований к химическому составу стали в зависимости от температуры предварительного или сопутствующего подогрева в процессе сварки (см. Строительные нормы и правила (СНиП) 2.05.06-85 «Магистральные трубопроводы»).
В известном способе при использовании в качестве эквивалентного углерода Сэкв, предполагается, что:
— проведение сварки без подогрева допускается для сталей химический состав которых соответствует Сэкв≤0,4%;
— сварка с подогревом в диапазоне температур от 50 до 200°С проводится на сталях, химический состав которых соответствует Сэкв=0,4-0,45%.
При определении эквивалентного углерода по Рсм считается, что сварка без подогрева допустима для сталей, химический состав которых дает значение Рсм не превышающее 0,23.
Недостатком указанного способа является то, что при определении требований к химическому составу стали, обеспечивающему отсутствие холодных трещин, учитывается только температура предварительного и сопутствующего подогрева и не принимается во внимание влияние других режимов сварочного процесса, таких как сила тока и скорость сварки.
Кроме того, способ не позволяет получить информацию о количественной взаимосвязи между режимами применяемых сварочных процессов и соответствующего им критического значения эквивалентного углерода, определяющего химический состав стали, обеспечивающий стойкость против образования холодных трещин, и, соответственно, получение требуемого комплекса механических свойств сварного соединения.
В основу настоящего изобретения положена задача создания способа предупреждения образования холодных трещин в сварных соединениях из углеродистых и низколегированных сталей при сварке на заданных режимах, обеспечивающего повышение надежности предупреждения образования холодных трещин и достижение заданных механических свойств металла околошовного участка (ОШУ) сварного соединения за счет учета взаимосвязи критического значения эквивалентного углерода (Сэкв или Рсм) со скоростью охлаждения металла зоны термического влияния (ЗТВ) сварного соединения в интервале температур 800-500°С
(w8-5).
Поставленная задача достигается тем, что способ предупреждения образования холодных трещин в сварных соединениях из углеродистых и низколегированных сталей при сварке на заданных режимах заключается в том, что предварительно для группы сталей выбранного класса определяют критические скорости охлаждения металла околошовного участка сварного соединения в интервале температур 800-500°С, соответствующие предельно допустимому значению показателя склонности каждой стали группы к образованию холодных трещин в околошовном участке сварного соединения, в качестве которого используют максимально допустимый процент мартенсита в структуре околошовного участка сварного соединения или предельно допустимое значение твердости околошовного участка сварного соединения, определяют значения эквивалентного углерода для каждой стали и строят график зависимости между критическими скоростями охлаждения и эквивалентным углеродом для указанной группы сталей, наносят на полученный график значение скорости охлаждения околошовного участка сварного соединения, соответствующее заданному способу и режимам сварки, определяют по графику критическое значение эквивалентного углерода для сталей указанной группы выбранного класса и используют для сварки на заданном режиме стали, эквивалентный углерод которых не превышает определенного критического значения.
Способ осуществляют следующим образом.
На основе анализа исходных анизотермических и структурных диаграмм для рассматриваемой группы сталей определяют критические скорости охлаждения w8-5, при которых в металле ЗТВ сварных соединений каждой из выбранных сталей достигается предельно допустимое значение выбранного показателя склонности стали к образованию холодных трещин, в качестве которого может быть использован:
либо максимально допустимый % мартенсита в структуре ОШУ ЗТВ сварного соединения;
либо предельно допустимые значения механических свойств ОШУ ЗТВ сварного соединения (твердость, ударная вязкость).
С использованием расчетных формул для определения эквивалентного углерода выбираемой в зависимости от химического состава рассматриваемой группы сталей рассчитывают значения эквивалентного углерода (Сэкв или Рсм) для каждой стали (см. табл. 1).
С использованием полученных значений Сэкв или Рсм для каждой стали из рассматриваемой группы и предварительно определенных экспериментальных путем соответствующих им критических значений скорости охлаждения определяют зависимость: скорость охлаждения — эквивалент углерода. Наносят на полученную диаграмму значение скорости охлаждения (w8-5) ЗТВ сварного соединения, соответствующее заданному способу сварки и используемому сочетанию режимов, и определяют критическое значение эквивалентного углерода для сталей рассматриваемой группы, гарантирующее отсутствие холодных трещин в ЗТВ сварного соединения.
Определение критических скоростей охлаждения проводят с использованием предварительно построенных по ГОСТ 23870 («Свариваемость сталей. Метод оценки влияния сварки плавлением на основной металл») для металла околошовного участка сварного соединения структурных диаграмм или анизотермических (термокинетических) диаграмм распада аустенита с нанесенными на них значениями изменения твердости в зависимости от скорости охлаждения в интервале температур 800-500°С. По указанным диаграммам определяют скорость охлаждения, обеспечившую формирование в металле околошовного участка сварного соединения или 50% мартенсита или твердость, равную, например, 350 HV. Это значение скорости охлаждения принимают за критическое для данной стали.
Ниже приведен пример реализации предлагаемого изобретения при сварке корневого прохода кольцевых стыков трубопроводов, изготовленных из стали категории прочности Х80, выполненного методом ручной дуговой сварки с погонной энергией 1,6 кДж/мм при подогреве 50°С и обеспечивающего скорость охлаждении
w8-5 металла ЗТВ сварного соединения 60°С/с.
1. Сталь категории прочности Х80 относится к классу низколегированных сталей системы легирования Si-Mn. Отличительной особенностью их химического состава от традиционных кремне-марганцевых трубных сталей является пониженное содержание углерода и дополнительное микролегирование сильными карбидообразующими элементами. В качестве показателя, обеспечивающего отсутствие холодных трещин и требуемые свойства ЗТВ сварного соединения для отобранной группы сталей, было выбрано предельно допустимое значение твердости ОШУ ЗТВ сварного соединения, равное 300 HV.
По экспериментальным данным были определены критические величины скорости охлаждения для каждой стали из рассматриваемой группы, при которых в металле ЗТВ сварного соединения достигается предельно допустимая твердость не более 300 HV. В табл. 2, содержащей данные о химическом составе, значениях эквивалентного углерода и критических скоростях охлаждения для кремнемаргенцевых сталей, обобщены сведения по сталям, химический состав которых близок к сталям категории прочности Х80.
2. По формуле 6 из табл. 1 были рассчитаны значения эквивалентного углерода (Сэкв) для всех сталей из рассматриваемой группы, также представленные в табл. 2.
3. С использованием найденных значений была построена зависимость: скорость охлаждения, обеспечивающая твердость металла ЗТВ сварного соединения не выше 300 HV — эквивалент углерода (чертеж).
Сопоставляя полученный график со значением скорости охлаждения w8-5, характеризующим заданный режим сварки и равным 60°С/с, получим, что проведение сварки на указанных режимах с гарантированным обеспечением твердости металла ЗТВ сварного соединения не выше 300 HV, возможно на сталях, эквивалент углерода которых не превышает критического значения, равного 0,36.
Предлагаемый способ позволяет определить критическое значение эквивалентного углерода для углеродистых и низколегированных сталей исходя из требований по обеспечению стойкости сварных соединений к образованию холодных трещин и механических свойств металла ЗТВ на уровне нормативных требований, в зависимости от скорости охлаждения (w8-5), соответствующей выбранному способу и режимам сварки.
Способ предупреждения образования холодных трещин в сварных соединениях из углеродистых и низколегированных сталей при сварке на заданных режимах, при котором предварительно для группы сталей выбранного класса определяют критические скорости охлаждения металла околошовного участка сварного соединения в интервале температур 800-500°С, соответствующие предельно допустимому значению показателя склонности каждой стали группы к образованию холодных трещин в околошовном участке сварного соединения, в качестве которого используют максимально допустимый процент мартенсита в структуре околошовного участка сварного соединения или предельно допустимое значение твердости околошовного участка сварного соединения, определяют значения эквивалентного углерода для каждой стали и строят график зависимости между критическими скоростями охлаждения и эквивалентным углеродом для указанной группы сталей, наносят на полученный график значение скорости охлаждения околошовного участка сварного соединения, соответствующее заданному способу и режимам сварки, определяют по графику критическое значение эквивалентного углерода для сталей указанной группы выбранного класса и используют для сварки на заданном режиме стали, эквивалентный углерод которых не превышает определенного критического значения.
Предотвращение образования холодных трещин при сварке
Когда сварка более прочных стальных материалов, водородное холодное растрескивание (HACC) — это реальная проблема. HACC характеризуется трещинами, которые образуются в сварном шве и / или нагреваются. зона воздействия основного металла после снижения температуры сварного изделия. С участием адекватные сварочные процедуры и уход во время сварки, HACC в значительной степени может быть устранено.
The WelderDestiny Compass: еженедельная подписка на электронный журнал
Вы можете посмотреть прошлые выпуски «The WelderDestiny Compass», щелкнув здесь.
Аналог.
условия:
- Водород Вспомогательное холодное растрескивание. (HACC)
- Водородный крекинг.
- Холодное растрескивание. Под холодным крекингом понимается тот факт, что водородный крекинг имеет место только при сварной шов относительно холодный.
- Отсроченное растрескивание. Водородный крекинг может быть задерживается на много часов. Иногда до 72 часов, хотя это необычный. Гораздо более типичным было бы около 12 часов.
Что такое холодный крекинг с водородом?
Там
представляют собой ряд различных механизмов, предложенных для холодного крекинга с водородом. Учитывая, что
существует множество различных «теорий», я уверен, вы можете себе представить, что
единого принятого механизма нет.
А
широко распространенная теория состоит в том, что атомы водорода диффундируют через металл, и
собираются в «пробелах» в микроструктуре металла. Обычно это было бы
на включениях в металле и на границах зерен металла.Однажды
атомарный водород собирается, он превращается в молекулярный водород (h3)
или даже вступает в реакцию с углеродом с образованием метана в тех точках, где он собирается.
Как только водород больше не существует как отдельный атом, он становится слишком большим.
легко диффундировать через металлическую структуру. Со временем все больше и больше
водород накапливается и приводит к чрезмерному «давлению» в этих очень локализованных
точки. Утверждается, что давление может стать настолько большим, что в результате
в материале, «раскалывающемся». Это расщепление под давлением вызвало
водородом тогда рассматривается как водородный крекинг.Есть проблемы с этим
теория, если рассматривать ее изолированно.
Другой
теория состоит в том, что водород собирается вокруг включений в металле, таких как
карбидные включения. Когда материал затем медленно пластифицируется
деформация (может присутствовать при усадке сварных швов при их остывании до помещения).
температуры) атомы водорода «увлекаются» движущимися дефектами (называемыми
дислокации) до тех пор, пока атомы водорода не будут эффективно закреплять дислокации. Когда
это происходит, пластическая деформация больше не может происходить, и материал
действует хрупко.Важно отметить, что пластичность металлов
из-за движения вывихов. Если вывихи больше не могут двигаться, то
пластичности больше нет.
Независимо
точного механизма, мы знаем, что водородное растрескивание происходит, когда все
соблюдены следующие условия:
- Наличие атомарный водород: При дуговой сварке почти всегда присутствует водород. настоящее время. В основном это происходит из-за загрязнения влаги или углеводорода.
- Наличие растягивающее напряжение: При отсутствии напряжения водородное растрескивание не принимает место. Во время сварки почти всегда возникают высокие напряжения из-за термическая усадка шва при охлаждении. Любые концентраторы напряжений, такие как Дефекты сварного шва будут иметь тенденцию локально увеличивать уровни напряжений.
- А чувствительная микроструктура: Некоторые структуры материала, такие как «аустенит» (Нержавеющие стали 304 и 316 являются аустенитными материалами при комнатной температуре) не подвержен водородному растрескиванию.Наиболее восприимчивые микроструктуры: те, которые твердые и хрупкие. Высокопрочные стали обычно имеют такие конструкции. Поэтому закаленные сварные швы углеродистых и низколегированных сталей также восприимчив к водородному растрескиванию.
- А достаточно низкая температура: Растрескивание происходит только ниже температуры, при которой водород не так легко диффундирует. Обычно предел около 100 ° C. допустимо, хотя в очень неблагоприятных условиях водородный холодный крекинг (HACC) может произойти при температурах немного выше этой.
Предотвращение холодного крекинга с водородом (HACC)
В
По сути, любая мера, которая устраняет одно из 4 условий, показанных выше, будет
исключить водородное растрескивание. Ниже приведен список типичных шагов, которые можно
принято, для устранения HACC:
- Уменьшить уровень водорода: Некоторые сварочные процессы, такие как газовая дуговая сварка вольфрамом (GTAW) по своей природе являются низким содержанием водорода.В случае процессов флюсования, таких как Дуговая сварка защищенного металла (SMAW — также называемая сваркой палкой) флюсом составляющие могут быть составлены с низким содержанием влаги. Это дальше усиливается за счет «запекания» электродов для удаления как можно большего количества влаги. возможный.
- Применить относительно высокий предварительный нагрев свариваемого материала: Это обычно приводит к при более низких скоростях охлаждения сварного шва и зоны термического влияния (ЗТВ) и в целом приводит к более жесткой микроструктуре.
- Обслуживание относительно высокая температура между проходами: Если температура сварного шва и зона термического влияния поддерживается выше примерно 100 ° C, для типичных структурных стали, даже в промежутке между сварочными швами, тогда температура не опуститесь достаточно низко, чтобы произошло «холодное растрескивание». Для сталей повышенной прочности возможно, потребуется повысить температуру до 150 ° C.
- Применить пост-нагрев: В этом методе высокая температура предварительного нагрева и промежуточного прохода сохраняется во время сварки.После завершения сварки температура все еще остается на прежнем уровне. поддерживается в течение определенного периода времени. Это называется «пост-тепло». Во время этого поста тепла, водороду, который наносит вред, дается время, чтобы «прогреться» из материала, снижение уровней водорода, доступного, чтобы привести к водородному крекингу.
- Обслуживание высокое тепловложение при сварке: Высокое тепловложение — это просто еще один способ сказать что количество энергии, прикладываемой при сварке, велико. Тепловая нагрузка составляет обычно измеряется как напряжение, умноженное на силу тока, разделенное на сварку Скорость путешествия.Высокое тепловложение обычно приводит к более медленной скорости охлаждения, что обычно приводит к более пластичной микроструктуре. Кроме того, есть немного более длительное время при повышенной температуре, что позволяет большему количеству водорода «запечь» до того, как температура станет достаточно низкой, чтобы позволить холодному растрескиванию происходить.
- Использование материал, который вряд ли образует твердые, хрупкие микроструктуры: Обычно это достигается за счет использования материалов с низким содержанием углерода. Современные сталелитейные заводы удается получить высокую прочность материала с низким содержанием углерода, используя термомеханически управляемый процесс (TMCP) при прокатке стали до окончательная форма.
- Использование присадочный металл, более слабый, чем свариваемый основной металл: Если сварной шов металл значительно слабее основного металла и очень пластичен, тогда когда сварной шов подвергается напряжению, пластическая деформация в значительной степени ограничивается металл шва, а не основной металл. Поскольку металл шва не имеет чувствительной микроструктуры, водородное растрескивание маловероятно. Очевидно это означает, что сварной шов слабее основного металла, поэтому сварной шов не в полной мере использовать прочность материала.Чтобы преодолеть это, более слабый сварной шов металл обычно используется только для одного или двух сварных швов, а остальная часть сварного шва прогоны выполняются с присадочным металлом излишне подходящего размера. Это работает, потому что водород растрескивание наиболее распространено в сварном шве при небольшом поперечном сечении. Один раз сварной шов становится «достаточно толстым», он подвергается гораздо меньшей пластической деформации при воздействии термических напряжений, поэтому вероятность водородного растрескивания составляет уменьшенный.
- Обеспечить что время задержки между сварочными работами сведено к минимуму: Поскольку водородное растрескивание имеет тенденцию чтобы быть механизмом, зависящим от времени, вероятность растрескивания может быть уменьшена за счет обеспечение следующего цикла сварки, в результате которого температура сварного шва повысится. снова, помещается до того, как сварной шов успеет остыть, и для водород накапливается вокруг включений в материале.Самый критический временная задержка между первым и вторым циклами сварки. По этой причине вторую сварку часто называют «горячим проходом». Идея в том, что этот проход его необходимо нанести как можно скорее, пока сварной шов еще «горячий». Этот горячий проход также нагревает сварной шов до температуры, выше которой водород может быть «выжжен» из сварного шва. Как правило, если время от начало корневого прохода, до начала горячего прохода может быть меньше, чем 8 минут, то водородное растрескивание маловероятно.Иногда это достигается одновременное выполнение нескольких сварочных работ несколькими сварщиками.
- Использование из аустенитного присадочного металла: Это необычно, но хорошо работает, если нет проблемы с использованием аустенитного наплавленного металла. Это работает, потому что аустенитный сварочный металл может «растворить» весь водород, который реально возникать во время сварки. Это означает, что вождения не так много сила для проталкивания водорода в основной металл, поэтому водородное растрескивание маловероятно.К сожалению, у этого есть ряд недостатков. В Во-первых, типичные сварочные металлы серии 300 слабее, чем высокопрочные. стали, поэтому для повышения прочности необходимо использовать аустенитные наполнители с высоким содержанием никеля. соответствие. Эти наполнители дорогие. Типичная нержавеющая сталь серии 300 материалы также подвержены коррозионному растрескиванию под напряжением в определенных среды, поэтому они не подходят для этих приложений. Другой проблема — гальваническая коррозия, которая может возникнуть, когда углеродистые стали и коррозионно-стойкие сплавы контактируют в агрессивной среде.
- Уменьшить приложенные напряжения на сварном шве, насколько это возможно, пока вам не удастся наплавьте относительно толстое поперечное сечение сварного шва: В качестве примера при выполнении сварка трубопровода, выравнивающие зажимы, удерживающие соединение вместе, не удаляется до тех пор, пока не будет нанесена большая часть сварного шва. Другой пример — обеспечить наилучшая возможная стыковка концов труб при сварке. Чем хуже подгонка, тем больше напряжения, которые испытывает сварной шов, особенно в корне область сварного шва.Другой пример — завершить сварку перед перемещением сварной шов. Если труба перемещается после того, как был пройден только корневой участок осажденного, тогда напряжения должны быть достаточно высокими, чтобы привести к водородному растрескиванию.
Холодное растрескивание с водородом при сварке трубопроводов
Когда
при прокладке магистральных трубопроводов обычно выполняются тысячи сварных швов
обязательный. В этих условиях высокопроизводительные сварочные технологии являются
важный. Экономия времени на 10% при выполнении такого большого количества сварных швов очень выгодна.
с экономической точки зрения.Один из традиционных способов достижения высоких
Производительность при сварке этих трубопроводов заключается в использовании целлюлозных
электроды с процессом дуговой сварки защищенного металла (SMAW).
Пока
большинство сварных швов магистральных трубопроводов в наши дни выполняются автоматизированной сваркой,
трубопроводов по-прежнему используют целлюлозные электроды для «врезных» сварных швов.
Причина в том, что у целлюлозных электродов очень проникающая дуга, поэтому они
хорошо подходят для выполнения корневых проходов на трубах. Шлак тоже быстрый
замораживание, позволяющее использовать последовательность сварки вертикально вниз.Это далее
увеличивает скорость и производительность сварки.
большая проблема с целлюлозными электродами заключается в том, что они зависят от влаги в
покрытие флюсом, чтобы обеспечить эти преимущества. По замыслу целлюлозные электроды
приводят к присутствию большого количества водорода. Следует признать, что когда
сварка электродами из целлюлозы всегда присутствует достаточно водорода для
приводит к водородному растрескиванию, если присутствуют все другие факторы.
В
Помимо высокой производительности сварки, экономичность трубопроводов, как правило, благоприятствует использованию
высокопрочных трубопроводных сталей. (Тогда трубопровод может быть тоньше.) Такой высокий
Прочностные стали обычно более склонны к водородному растрескиванию, чем низко
стали бы прочнее. Благодаря такому сочетанию высокопрочных сталей
сварены методами сварки с высоким содержанием водорода, холодное растрескивание под водородом
(HACC) уделяет большое внимание трубопроводным проектам. Фактически, большинство кросс-кантри
В правилах трубопроводов большое внимание уделяется параметрам сварки, которые могут привести к
водородный крекинг.По этой причине в этих правилах сварки, как правило, много
важные переменные, которые не рассматриваются в других правилах сварки. Это также
Важно отметить, что большинство современных сталей для трубопроводов термомеханически
Стали с контролируемым технологическим процессом (TMCP), повышающие стойкость сталей к
водородный крекинг.
Это
важно отметить, что в наши дни есть альтернативы целлюлозному
электроды, но часто конкретная экономика проекта трубопровода все еще может
подтолкнуть инженеров-проектировщиков к использованию целлюлозных электродов.
В
в случае подводных трубопроводов использование целлюлозных электродов обычно не допускается.
разрешается. Это потому, что временные задержки обычно указываются между сварными швами.
завершение и начало неразрушающего контроля (NDT) при сварке
с процессом сварки с высоким содержанием водорода. Типичные минимальные временные задержки между
завершение сварки и начало неразрушающего контроля займет 48 часов при использовании
целлюлозные электроды. Это сделано потому, что у вас будет достаточно времени, чтобы убедиться, что
что если произойдет холодное крекинг с водородом (HACC), то это произойдет.
фактически происходят до проведения тестирования.При сварке на трубоукладочной барже
такие временные задержки добавят огромных затрат на операцию по укладке трубопровода. Технически и
Поэтому с экономической точки зрения использование целлюлозных электродов просто нецелесообразно.
Ресурсы для снижения риска HACC
Как
водородный крекинг может иметь тяжелые последствия для безопасности и экономики.
многочисленные документы, которые могут помочь нам снизить вероятность образования водорода
растрескивание. Часто используемые ресурсы:
- Сварка Технологический институт Австралии (WTIA) Техническое примечание 1.
- Австралийский Стандарт на сварку трубопроводов для газа и сжиженного газа, AS / NZS 2885.2, Приложение E.
- Американский Кодекс по сварке конструкций Общества сварщиков AWS D1.1, приложение H.
- Европейский Стандарт рекомендаций по сварке ферритных сталей, EN 1011-2 Приложение C.
Кроме того
стандарты, упомянутые выше, есть много книг, посвященных сварке
сталей без водородного растрескивания, но с использованием одного из указанных выше стандартов
вероятно будет достаточно для большинства обстоятельств.
The WelderDestiny Compass: еженедельная подписка на электронный журнал
Вы можете посмотреть прошлые выпуски «The WelderDestiny Compass», щелкнув здесь.
Водородный крекинг | Металлургия для чайников
Что такое водородный крекинг?
Водородный крекинг также известен как холодный крекинг или замедленный крекинг. Основная особенность этого типа трещины заключается в том, что она возникает в ферритных свариваемых сталях и обычно возникает сразу после сварки или через короткое время после сварки, но обычно в течение 48 часов.Механизм начинается с одиночных атомов водорода, диффундирующих через металл.
При высоких температурах повышенная растворимость водорода позволяет водороду диффундировать в металл (или водород может диффундировать при низкой температуре, чему способствует градиент концентрации). Когда эти атомы водорода воссоединяются в крошечных пустотах металлической матрицы с образованием молекул водорода, они создают давление изнутри полости, в которой они находятся. Это давление может увеличиваться до уровней, при которых металл имеет пониженную пластичность и прочность на разрыв, вплоть до точки, при которой он растрескивается (водородное растрескивание, или HIC).Наиболее подвержены высокопрочные и низколегированные стали, никелевые и титановые сплавы. Незакопленное железо также восприимчиво.
Водородные трещины обычно могут иметь следующие характеристики:
- В сталях C-Mn трещина обычно возникает в зоне термического влияния (HAZ), но также может распространяться на металл сварного шва.
- Трещины также могут возникать в валике сварного шва, обычно перпендикулярно направлению сварки под углом 45 ° к поверхности шва.Они почти прямо, по неровной дороге.
- В низколегированных сталях трещины могут располагаться поперек сварного шва, перпендикулярно поверхности сварного шва, но не разветвляться и быть плоскими (плоский дефект).
При разрыве сварного шва поверхность трещин обычно не окисляется, даже если они разрушаются, что указывает на то, что они образовались, когда сварной шов был при температуре окружающей среды или близкой к ней.Легкий синий оттенок может быть заметен в результате предварительного нагрева или нагрева при сварке.
Водородные трещины, возникающие в ЗТВ и металле сварного шва. (Обратите внимание, что не ожидается, что показанный тип трещин образуется в одном и том же сварном изделии.)
Трещины, возникающие в ЗТВ, обычно связаны с крупнозернистой областью. Трещины могут быть межкристаллитными, трансгранулярными или смешанными. Межкристаллитные трещины чаще возникают в более твердых структурах ЗТВ, образованных в низколегированных и высокоуглеродистых сталях.Трансгранулярное растрескивание чаще встречается в стальных конструкциях из C-Mn. При угловой сварке трещины в ЗТВ обычно связаны с корнем шва и параллельны шву. В стыковых швах трещины ЗТВ обычно ориентированы параллельно сварному шву.
Типичные повреждения, вызванные водородным растрескиванием стенок трубопровода, выявленные в результате ультразвукового контроля
Есть три фактора, которые могут вызвать водородное растрескивание:
- Водород, образующийся в процессе сварки или при загрязнении области сварного шва.
- Твердая хрупкая структура, склонная к растрескиванию.
- Остаточные растягивающие напряжения, действующие на сварное соединение (ограничение).
- Трещины вызваны диффузией водорода к сильно нагруженной закаленной части сварного изделия.
В C-Mn сталях, поскольку существует больший риск образования хрупкой микроструктуры в ЗТВ, большая часть водородных трещин, вероятно, находится в основном металле.При правильном выборе электродов металл шва будет иметь более низкое содержание углерода, чем основной металл, и, следовательно, более низкий углеродный эквивалент (CE). Однако поперечные трещины в металле сварного шва могут возникать, особенно при сварке толстых секций.
Трещина по крупнозернистой структуре в ЗТВ
В низколегированных сталях, поскольку структура металла сварного шва более восприимчива, чем ЗТВ, в сварном шве могут быть обнаружены трещины. Есть три фактора, которые могут вызвать водородное растрескивание:
- Водород, образующийся в процессе сварки или при загрязнении области сварного шва.
- Твердая хрупкая структура, склонная к растрескиванию.
- Остаточные растягивающие напряжения, действующие на сварное соединение (ограничение).
- Трещины вызваны диффузией водорода к сильно нагруженной закаленной части сварного изделия.
В стали C-Mn, поскольку существует больший риск образования хрупкой микроструктуры в ЗТВ, большая часть водородных трещин, вероятно, находится в основном металле.При правильном выборе электродов металл шва будет иметь более низкое содержание углерода, чем основной металл, и, следовательно, более низкий углеродный эквивалент (CE). Однако поперечные трещины в металле сварного шва могут возникать, особенно при сварке толстых секций.
Соответствующее сообщение
- Знаете ли вы о водородной хрупкости?
Водородное охрупчивание — это процесс, при котором различные металлы, в первую очередь высокопрочная сталь, становятся хрупкими и … - Осадочное упрочнение
Осадочное упрочнение, также называемое старением, представляет собой метод термообработки, используемый для повышения текучести сила… - Что такое металл?
Металл — это элемент, соединение или сплав, который хорошо проводит как электричество, так и тепло. … - Как сваривать титан?
Титан и большинство титановых сплавов легко поддаются сварке с использованием нескольких сварочных процессов. … - Неисправность вала направляющего ролика
Часть вышедшего из строя вала «направляющего ролика» была отправлена на анализ неисправности (Рисунок 1). Этот вал предназначен для …
Зона термического влияния — обзор
СТАЛИ С НИЗКОЛЕГОВЫМИ СТАЛАМИ
В целом, применение различных процессов сварки одинаково как для низколегированных, так и для низколегированных сталей, главное отличие состоит в том, что выбор расходных материалов для низколегированных сталей может быть большим ограничено.Ручная дуговая сварка металлом и дуговая сварка под флюсом наиболее широко используются в промышленности для низколегированных сталей, расходные материалы для первого процесса приведены в Таблице 33.12.
Таблица 33.12. РУЧНЫЕ МЕТАЛЛИЧЕСКИЕ ДУГОВЫЕ ЭЛЕКТРОДЫ ДЛЯ НИЗКОЛАПНЫХ СТАЛЕЙ (EN 1599: 1997, EN 757: 1997)
Код состава | Элемент , вес.% | ||||||||||||||||
---|---|---|---|---|---|---|---|---|---|---|---|---|---|---|---|---|---|
C | Si | Cr | Mo | S | P | ||||||||||||
Mo-сталь | |||||||||||||||||
.10 макс. | 0,60 макс. | 0,75–1,20 | — | — | 0,40–0,70 | 0,030 макс. | — | 0,40–0,70 | 0,030 макс. | 0,035 макс. | |||||||
Cr – Mo сталь | |||||||||||||||||
1CrMoLB * | 0,05 макс.50–1,20 | — | 1,0–1,8 | 0,40–0,70 | 0,025 макс. | 0,025 макс. | |||||||||||
1CrMoB * | 0,10 макс. 1,0–1,5 | 0,40–0,70 | 0,030 макс. | 0,035 макс. | |||||||||||||
1CrMoR | 0,10 макс.030 макс. | 0,035 макс. | |||||||||||||||
2CrMoLB * | макс. 0,05 | 0,50 макс. | 0,50–1,20 | — | 2,0–2,5 | 0,90–1,20 | макс. | ||||||||||
2CrMoB * | макс. 0,10 | макс. 0,50 | 0,75–1,20 | — | 2,0–2,5 | 0,90–1,20 | 0,030 макс.10 макс. | 0,30 макс. | 0,35 мин. | — | 2,0–2,5 | 0,90–1,20 | 0,030 макс. | 0,035 макс | |||
5CrMoB | 0,10 макс. | — | 4,0–6,0 | 0,40–0,70 | макс. 0,030 | 0,035 макс. | |||||||||||
7CrMoB | макс. 0,10 | 0,60 макс. | 0,50–1,00 | 40–0,70 | макс. 0,030 | 0,035 макс. | |||||||||||
9CrMoB | макс. 0,10 | 0,60 макс. | 0,50–1,00 | — | 8,0–10,0 | макс. | |||||||||||
12CrMoB a | 0,23 макс. | 0,80 макс. | 0,30–1,00 | 0,3–0,8 | 11,0–12,5 | 0,80–1,20 | 0,0251 макс. б0.23 макс. | 0,80 макс. | 0,30–1,00 | — | 11,0–13,0 | 0,80–1,20 | 0,030 макс. | 0,030 макс. | |||
12CrMoWVB | макс. 0,50–1,00 | 0,3–0,8 | 11,0–13,0 | 0,80–1,20 | 0,030 макс. | 0,030 макс. 0.07 макс. | 0,60 макс. | 0,30–1,10 | 0,80–1,20 | — | — | 0,030 макс. | 0,030 макс. 2,00–2,75 | — | — | макс. 0,030 | макс. 0,030 |
3NiLB | 0,07 макс.030 макс. | 0,030 макс. | |||||||||||||||
1NiB | 0,10 макс. | 0,80 макс. | 0,50–1,20 | 0,80–1,10 | — | — | 0,030 макс. 0,10 макс | 0,80 макс | 0,50–1,20 | 2,00–2,75 | — | — | 0,030 макс | 0,035 макс | |||
3NiB | 0,10 макс | 50–1,202,80–3,50 | — | — | 0,030 макс. | 0,035 макс. | |||||||||||
1NiC | макс. 0,15 | 0,80 макс. — | 0,030 макс. | 0,035 макс. | |||||||||||||
2NiC | макс. 0,15 | 0,80 макс. | 0,50–1,20 | 2,00–2,75 | — | — | макс. Mn – Mo сталь | ||||||||||
MnMoB | 0.10 макс | 0,80 макс | 1,20–1,80 | — | — | 0,25–0,45 | 0,025 макс | 0,025 макс | |||||||||
2MnMoB | 0,10 макс | —— | 0,25–0,45 | 0,025 макс | 0,025 макс | ||||||||||||
Высокопрочная сталь | |||||||||||||||||
M10 макс. | 0,80 макс. | 0,60–1,20 | 1,00–1,80 | — | — | 0,030 макс | 0,035 макс | ||||||||||
NiMoB | 0,101 макс. 1,20–1,90 | — | 0,20–0,50 | макс. 0,030 | макс. 0,035 | ||||||||||||
1NiMoC | макс. 0,18 | 0,80 макс.20–0,50 | макс. 0,030 | 0,035 макс. | |||||||||||||
2NiCrMoB | макс. 0,10 | 0,80 макс. | 1,30–2,20 | 1,50–2,50 | 0,70–1,50 | 0,70–1,50 | 0,035 макс.
Следует понимать, что в зоне термического влияния (HAZ) вокруг сварного шва может наблюдаться очень высокая скорость охлаждения. В частности, из легированных сталей могут быть получены твердые микроструктуры ЗТВ, имеющие высокую склонность к растрескиванию под действием остаточных сварочных напряжений, а также водорода, улавливаемого во время операции сварки.Необходимость избежать образования трещин, вызванных водородом, является основным фактором при выборе условий сварки для низколегированных сталей.
На растрескивание ЗТВ в ферритных сталях влияют следующие взаимосвязанные переменные:
- 1.
Состав стали и поведение при трансформации.
- 2.
Процесс сварки и тип расходных материалов.
- 3.
Энергозатраты сварочного процесса и температура предварительного нагрева.
- 4.
Ограничитель сустава.
Как правило, более высоколегированные стали имеют большую склонность к растрескиванию из-за их более низкой температуры превращения и образования более твердых продуктов превращения. На практике важными аспектами трансформационного поведения стали являются способность стали к закалке и склонность закаленной структуры к растрескиванию.
И закаливаемость, и восприимчивость обычно возрастают с увеличением содержания углерода и легирующих элементов.Доминирующий эффект углерода был признан путем эмпирического вывода формул углеродного эквивалента (CE), которые предназначены для описания свариваемости стали. Широко используемая формула для углеродисто-марганцевых конструкционных сталей согласно BS 4360: 1986 выглядит следующим образом:
CE = C + Mn6 + Cu + Ni15 + Cr + Mo + V5
Это соотношение признано Международным институтом сварки и ISO. Также можно рассмотреть следующее:
Pcm = C + Si30 + Mn + Cu + Cr20 + Ni60 + Mo15 + V10 + 5BCEN = C + A (C) [Si24 + Mn6 + Cu15 + Ni20 + Cr + Mo + V + Nb5 + 5B]
, где
A (C) = 0.75 + 0,25tanh [20 (C − 0,12)]
Формула Pcm была получена в первую очередь для высокопрочных низколегированных сталей, в то время как соотношение CEN признает нелинейный вклад углерода в прокаливаемость и риск растрескивания при более высоких уровнях углерода. При повышенном CE необходимы более строгие меры предосторожности, чтобы избежать растрескивания. Следует понимать, что такие формулы применимы только к конкретным композициям, используемым при их определении, и не применимы повсеместно.
Риск растрескивания ЗТВ сильно зависит от содержания водорода в свежеосажденном металле сварного шва.Что касается ручной дуговой сварки металлическим электродом, риск растрескивания в конкретной стали ниже, когда используются электроды с низким содержанием водорода, а не обычные рутиловые электроды, особенно если первые электроды сушат при температурах выше примерно 300 ° C. Процессы сварки под флюсом и дуговой разряд в среде защитного газа могут приводить к образованию отложений металла сварных швов с содержанием водорода, сравнимым или меньшим, чем у основных электродов, и с помощью этих процессов возможно некоторое смягчение условий сварки при условии использования чистых сухих расходных материалов .Типичные уровни водорода в металле сварного шва, определенные в соответствии с процедурами, указанными в BS 6693, приведены в Таблице 33.13.
Таблица 33.13. ТИПИЧНОЕ СОДЕРЖАНИЕ ВОДОРОДА ДЛЯ РАЗЛИЧНЫХ СТАЛЬНЫХ СВАРОЧНЫХ МЕТАЛЛОВ (EN 499: 1994)
Тип сварочного металла | Диапазон содержания водорода (мл на 100 г наплавленного металла ) | 0 | Класс | C | 70–100 |
---|---|---|---|---|---|
Классификация R | 20–35 | ||||
Классификация B (высушенная при 100–150 ° C) | 10–15 | ||||
Классификация B (запеченная при 350–450 ° C) † | 3–10 | ||||
Дуга под флюсом | 5 * -25 | ||||
Металлическая дуга в газовой среде (Ar или CO 2 ) | 3 * -10 9050 | Порошковая CO 2 : основной флюс | 3–5 | ||
Рутиловый флюс | 5–15 |
Температурные условия, преобладающие во время сварки, контролируются по одной или обеим из двух причин.Во-первых, контролируя скорость охлаждения, часто можно определить продукт превращения после сварки. Во-вторых, растрескивания можно избежать, поддерживая зону сварного шва при температуре около 250 ° C (когда эффект охрупчивания водородом незначителен) в течение достаточного периода времени, чтобы водород диффундировал из уязвимых областей.
Для данной геометрии сварного шва повышенное тепловложение во время сварки приведет к более низкой скорости охлаждения. Во многих материалах такого снижения скорости охлаждения будет достаточно, чтобы избежать превращения в твердые, восприимчивые микроструктуры.Повышенного тепловложения можно добиться за счет увеличения сварочного тока или напряжения или за счет уменьшения скорости движения. Если растрескивание невозможно контролировать путем увеличения подводимой энергии, можно применить предварительный нагрев для снижения скорости охлаждения после сварки. Температура предварительного нагрева, необходимая в конкретном случае, будет зависеть от состава материала, ограничений соединения и используемого процесса сварки, но обычно она находится в диапазоне 100–250 ° C. В многопроходных сварных швах температура предварительного нагрева должна поддерживаться между циклами сварки как промежуточная температура.
Сдерживание соединения может быть определено как сопротивление деформации, которое снимает напряжение при сварке сужением. Сдержанность, как правило, увеличивается с увеличением толщины соединяемых компонентов. Увеличение размера материала также увеличит скорость охлаждения сварного шва за счет увеличения радиатора. Тип соединения имеет большое значение при определении количества путей, по которым тепло может отводиться от сварного шва, а влияние геометрии соединения на условия охлаждения можно описать параметром «комбинированная толщина».Комбинированная толщина — это общая толщина материала в мм, через которую тепло может отводиться от сварного шва, как указано в Таблице 33.14.
Таблица 33.14. ОПРЕДЕЛЕНИЕ КОМБИНИРОВАННОЙ ТОЛЩИНЫ
Если есть сомнения относительно риска растрескивания в данной ситуации, следует рекомендовать проведение процедурных испытаний.
Было обнаружено, что с углеродомарганцевыми конструкционными сталями можно избежать растрескивания за счет контроля условий сварки, чтобы микроструктура в ЗТВ была не выше критического значения.При использовании материалов для ручной дуговой сварки металла с относительно высоким водородным потенциалом твердость HAZ не должна превышать 350 HV. Для материалов с низким содержанием водорода или сварки CO 2 подходит твердость 400 HV или даже выше. На рисунке 33.1 представлена номограмма для материала с классом CE, определенного, как указано выше, с указанием условий сварки, при которых критическая твердость не превышается и можно избежать образования трещин. Делается поправка на использование процессов с разными водородными потенциалами и на общую толщину сварного шва.Для предполагаемого процесса сварки выбирается соответствующая шкала CE. От CE рассматриваемого материала проводится вертикальная линия, пересекающая заданную температуру предварительного нагрева. От этого пересечения проводится линия по горизонтали до соответствующей комбинированной толщины, а затем по вертикали вниз, чтобы определить минимальную подводимую энергию дуги, необходимую во время сварки, чтобы избежать превышения критической твердости. Аналогичным образом, исходя из материала, толщины и энергии дуги, можно определить минимальную температуру предварительного нагрева.Следует сделать дополнительную ссылку на EN 1011-1: 1998, EN 1011-2: 2001. Одно предостережение заключается в том, что критическая твердость для предотвращения растрескивания немного зависит от углеродного эквивалента. Рекомендуется соблюдать осторожность при нанесении рисунка 33.1 на стали с CE <0,40 для сварных швов, которые должны быть выполнены без предварительного нагрева.
Рисунок 33.1. Условия сварки мягких сталей и C – Mn .
Для получения дополнительной информации, см. N. Bailey, Met. Констр. & amp; Brit.Weld J. , 1970, 2 , 442.
Шкала CE A: Нормальные сварочные процессы; Твердость HAZ ограничена до 350 HV, шкала CE B: процессы сварки с низким содержанием водорода; Твердость HAZ ограничена до 400 HV,
CE Шкала C: Процессы сварки с очень низким содержанием водорода; Твердость HAZ ограничена до 450 HV.
Подход CE к формулированию сварочных процедур неприменим при CE выше 0,6. Для низколегированных сталей можно классифицировать склонность к растрескиванию в ЗТВ в соответствии с их поведением при трансформации.В таблице 33.15 показаны пять общих классификаций вместе с кратким описанием мер предосторожности, необходимых для предотвращения растрескивания. Соответствующие температуры предварительного нагрева и промежуточного прохода для сталей классов 4 и 5 указаны на рисунке 33.2. Более точное определение поведения невозможно, поскольку склонность к растрескиванию не связана однозначно с твердостью, в то время как влияние геометрии соединения не может быть адекватно количественно определено для этих материалов.
Таблица 33.15. КЛАССИФИКАЦИЯ СТАЛЕЙ С НИЗКИМ ЛЕГКИМ
Класс | Прокаливаемость | Склонность к растрескиванию HAZ | Примеры | 9028 9028 9028 | 9028 Нет | Низкоуглеродистая сталь | Нет | |||||||||||
---|---|---|---|---|---|---|---|---|---|---|---|---|---|---|---|---|---|---|
2 | Низкая | Низкая |
| Тонкие профили, нет; с более толстыми секциями, более низкое H 2 процессы, высокая погонная энергия и некоторый предварительный нагрев — все это является преимуществом | ||||||||||||||
3 | Низкая | Высокая (двойной мартенсит) | Среднеуглеродистые стали, например 080M30, 080M40 * | Производство немартенситной HAZ более важно, чем с низким содержанием водорода.Используйте высокие тепловложения и предварительный нагрев 250–350 ° C | ||||||||||||||
4 | Высокий | Низкоуглеродистый (мартенсит с низким содержанием углерода) | Низкоуглеродистые, низколегированные высокопрочные стали, например 9% Ni HY80, стали C – Mn в толстых сечениях | Процессы с низким содержанием водорода, повышенное тепловложение и, как правило, требуется некоторый предварительный нагрев | ||||||||||||||
5 | Высокий | Высокий (сдвоенный мартенсит или бейнитные составляющие) |
| Температура предварительного нагрева и промежуточного прохода в диапазоне 200–350 ° C. (Возможно использование 150 ° C в тонких сечениях.) Рекомендуется термообработка после сварки |
Для получения дополнительной информации, см. T. Boniszewski и R. G. Baker, Proc. Вторая конференция Содружества по сварке, Институт сварки, Лондон, 1965, Статья M5.
Рисунок 33.2. Предлагаемые условия предварительного нагрева для процедурных испытаний сталей классов 4 и 5 таблицы 33.15.
В целом металлы сварных швов, используемые для мягких и низколегированных сталей, содержат гораздо меньше углерода, чем основной материал, и, как следствие, менее подвержены водородному растрескиванию, чем HAZ. Факторы, указанные выше для HAZ, тем не менее применимы, и в некоторых случаях могут потребоваться меры предосторожности, чтобы избежать водородного растрескивания металла сварного шва.
Ликвидационное растрескивание ЗТВ
Другой проблемой при сварке ферритных сталей является растрескивание, связанное с ликвацией неметаллических фаз на предшествующих границах зерен аустенита в ЗТВ под действием термических напряжений в этой зоне.Восприимчивость в основном зависит от относительных количеств серы, углерода, марганца и фосфора в стали, а в простых сплавах железо с углеродом проблема становится значительной при содержании углерода выше примерно 0,2%. При таком содержании углерода соотношение марганца к сере должно составлять не менее 20: 1, чтобы избежать проблемы, а при более высоком содержании углерода это соотношение может достигать 30: 1 или 50: 1.
Пластинчатый разрыв
Пластинчатый разрыв может возникнуть в соединениях, в которых граница плавления сварного шва параллельна поверхности пластины, а остаточные напряжения растяжения действуют по всей толщине пластины.Растрескивание обычно носит ступенчатый характер и связано с включениями, которые свертываются в плоскую форму во время изготовления листа. Такие включения приводят к снижению пластичности в направлении толщины листа. Пластинчатый разрыв обычно не возникает в пластине с пластичностью по всей толщине более 20% уменьшения площади (RA). Между 10 и 20% RA он может встречаться в сильно ограниченных случаях, таких как полностью проникающие форсунки. Если пластичность ниже 10% RA, трещины могут образовываться даже в относительно слабо закрепленных Т-образных соединениях.Пластинчатые разрывы были обнаружены в пластинах толщиной от 10 до 175 мм, но не являются обычным явлением при толщине менее 25 мм. Если опыт работы с конкретным материалом и конфигурацией соединения указывает на риск разрыва ламелей, необходимо уделить внимание конструкции соединения и процедуре сварки, чтобы уменьшить эффект ограничения и гарантировать, что граница плавления сварного шва проходит через возможные плоскости ослабления в материал.
Растрескивание при снятии напряжения
Ряд ферритных сталей может подвергаться растрескиванию при снятии напряжения или повторном нагреве.Растрескивание является межкристаллитным и возникает в ЗТВ, когда закрепленные соединения подвергаются термообработке после сварки. Проблема аналогична проблеме с аустенитными сталями, рассматриваемым ниже, и возникает в первую очередь в сплавах, демонстрирующих вторичное упрочнение. В настоящее время поведение трещин невозможно предсказать с какой-либо точностью. О растрескивании не сообщалось в сплавах, таких как стали 2¼ Cr / 1Mo или ½ Mo / B при толщине менее 75 мм, или в сплавах ½ Cr / ½ Mo / V при толщине менее 18 мм. Риск растрескивания можно снизить за счет правки сварного шва для уменьшения локальной концентрации напряжений и контролируемых процедур термообработки.
Руководство по сварке нержавеющей стали и никелевых сплавов
Руководство по сварке нержавеющей стали и никелевых сплавов
Сварка нержавеющих сталей и никелевых сплавов — это чистота и правильный выбор присадочного металла. Эти рекомендации предназначены для пошагового содействия успешной сварке нержавеющих сталей и никелевых сплавов.
Шаг 1. Выбор сплава присадочного металла для процесса сварки
Если оба основных металла одинаковые , используйте сплав основного металла в качестве ориентира.Например, при соединении 316L с 316L используйте присадочный металл 316L. Прошлый опыт может показать преимущественную коррозию сварного шва, и в этом случае может потребоваться увеличение содержания сплава. Необходимо внимательно рассмотреть вопрос о том, насколько далеко подниматься, чтобы не допустить чрезмерного легирования, вызывающего гальваническую коррозию.
Для сварки разнородных стыков (пример; нержавеющая сталь с углеродистой сталью)
Замечание: отказ может произойти из-за низколегированных смесей, если выбран неправильный присадочный металл или если степень разбавления слишком высока.Самым распространенным видом отказа является растрескивание, но также возможно охрупчивание сварного шва.
Поэтому правильный выбор сплава и техника сварки имеют решающее значение для успешной сварки:
- НЕ используйте низколегированные электроды для соединения низколегированной стали с нержавеющей сталью. Это приведет к появлению хрупких сварных швов.
- НЕ используйте присадочную проволоку из низколегированной нержавеющей стали для соединения низколегированной и нержавеющей стали. В результате этого могут стать хрупкие сварные швы из-за образования мартенсита.
- ИСПОЛЬЗУЮТ сплавы с повышенной легкостью, такие как 309 и 312, которые разработаны специально для этой цели.
Для соединений из разнородных нержавеющих и нержавеющих или никель-никелевых соединений см. Руководство по соединению разнородных материалов. Как правило, лучше всего использовать присадочный металл, предназначенный для более высоколегированного из двух. Например, при соединении основных металлов 304L с 316L используйте присадочный металл 316L.
При соединении нержавеющей стали со сплавами на основе никеля всегда используйте присадочные металлы на основе никеля.
- ЗАПРЕЩАЕТСЯ использовать присадочные материалы из нержавеющей стали для соединения нержавеющей стали со сплавами на основе никеля, поскольку существует очень высокий риск растрескивания по средней линии.Это происходит из-за разбавления никелевой стороны соединения. Более высокое содержание никеля в наплавленном нержавеющем шве создает дисбаланс в составе, повышая чувствительность к растрескиванию.
Шаг 2: Выбор параметров сварки для процесса сварки
Параметры сварки должны быть выбраны таким образом, чтобы обеспечить максимально низкое тепловложение, чтобы минимизировать деформацию. Термическая деформация может быть достаточно высокой, чтобы перегрузить основные материалы и вызвать растрескивание под напряжением.
Тепловая нагрузка = (А x Вольт x 60) / Скорость движения.Более низкие значения силы тока или напряжения приводят к меньшему тепловложению. Более высокая скорость перемещения, например, бусинок стрингера, по сравнению с ткачеством, дает меньшее тепловложение.
Отрегулируйте силу тока или напряжение для оптимизации:
- Стабильность дуги
- Проникновение (более низкое напряжение имеет тенденцию к меньшему проникновению)
- Брызги (используйте либо более низкую подачу проволоки, либо более высокое напряжение)
- Подрез (более высокое напряжение имеет тенденцию к увеличению подреза. В качестве альтернативы уменьшите скорость перемещения, чтобы расплавленная сварочная ванна могла заполнить поднутрение)
- Разбавление (меньшее проплавление дает меньшее разбавление)
Используйте сварочную технику с короткой длиной дуги, чтобы минимизировать выгорание легирующих элементов.
Шаг 3: Правильная подготовка шва
ЗАГРЯЗНЕНИЕ
Удалите или устраните все возможные источники загрязнения, включая продукты коррозии: грязь, масло, жир, окалину, краски и маркировочные краски, которые могут содержать хлориды.
Если используются средства, предотвращающие разбрызгивание, используйте материалы, специально разработанные для нержавеющих сталей. Остерегайтесь масел в сжатом воздухе, если они используются для охлаждения или сушки сварных швов.
Обратите внимание, что при обезжиривании могут появиться загрязняющие вещества, нарушающие сварку, а также образоваться опасные ядовитые газы.
Не смешивайте нержавеющую сталь и углеродистую сталь, чтобы избежать загрязнения железом. Частицы железа вызывают локальную коррозию.
ВЛАГА И ТЕМПЕРАТУРА ОСНОВНОГО МЕТАЛЛА
Удалите конденсат. Во избежание конденсации дайте сварным деталям, хранящимся на открытом воздухе, нагреться до температуры окружающей среды. Проверить влажность защитных газов.
ПЛАЗМЕННАЯ РЕЗКА
Финишная шлифовка для очистки металла, стыков, полученных плазменной резкой или процессов с использованием азота или воздуха в плазме.Это может привести к азотированию шва, которое может вызвать ржавление в зоне термического влияния готового шва.
Используйте чистые абразивные материалы, предназначенные для нержавеющих сталей.
ПРЕДУПРЕЖДАЮЩЕЕ ИСКАЖЕНИЕ
Нержавеющие стали имеют коэффициент теплового расширения на 50% больше, чем углеродистые стали. Никелевые сплавы расширяются в меньшей степени. Используйте частые прихваты или пропустите сварку, чтобы снизить напряжение. Сведите к минимуму методы ткачества, которые приводят к снижению скорости движения и увеличению тепловложения. Бусины стрингера наиболее востребованы при сварке нержавеющей стали или сплавов на основе никеля.
Узкие щели
Избегайте узких щелей. Корневой зазор должен как минимум равняться диаметру электрода. Это особенно важно при сварке дуплексных нержавеющих сталей и сплавов на основе никеля, которые имеют тенденцию иметь плохие характеристики текучести сварного шва, что приводит к отсутствию плавления или поднутрения.
Шаг 4: Очистка после сварки
Это очень важный шаг. Целью очистки после сварки является обеспечение должным образом сформированной пленки оксида хрома на поверхности для обеспечения оптимальной коррозионной стойкости: чем ровнее поверхность, тем выше коррозионная стойкость.Тепло от сварки способно разрушить хром на поверхности, что может привести к коррозии. Чтобы избежать ржавчины, очень важно удалить обедненную хромом зону с помощью химической или механической очистки после сварки.
Настоятельно рекомендуется использовать щетки из нержавеющей стали и другие инструменты, чтобы избежать попадания частиц железа на поверхность, которые могут вызвать ржавчину.
МЕТОДЫ ОЧИСТКИ
ЭЛЕКТРОЛИТИЧЕСКАЯ ПОЛИРОВКА
Это лучший метод, но он медленный и дорогой.
PICKLING
Азотная и плавиковая кислота. Наряду с гладкой поверхностью этот метод обеспечивает оптимальную коррозионную стойкость и устраняет поверхностные дефекты. Избегайте чрезмерного травления, которое приведет к шероховатости поверхности. Обратите внимание, что побочные продукты травления должны быть должным образом нейтрализованы и утилизированы в соответствии с местными экологическими нормативами. Затравленный сварной элемент одновременно пассивируется. Растворы для пассивации не так эффективны для удаления загрязнений, как растворы для травления.
ШЛИФОВКА
Коррозионная стойкость зависит от чистоты поверхности.
МЕХАНИЧЕСКАЯ ПОЛИРОВКА
Практически такая же эффективная, как и электролитическая полировка, в зависимости от используемой зернистости: чем мельче поверхность, тем выше коррозионная стойкость.
ЩЕТКА
Это подходящий метод, если используются чистые щетки из нержавеющей стали.
Пескоструйная обработка
Используйте незагрязненные среды. Избегайте чрезмерной струйной очистки, которая может привести к грубой отделке.
Особые требования к никелю и супераустенитным сплавам
Наплавленные сварные швы стандартной серии 300 содержат определенный уровень феррита, который помогает подавить микротрещины. Микротрещины могут переходить в непрерывные трещины, которые обычно наблюдаются в центре сварного шва. Микротрещины обычно вызываются пленками жидкости с низкой температурой плавления на границах зерен затвердевающего сварного шва в сочетании с высокой скоростью теплового расширения. Феррит служит для увеличения площади границ зерен, тем самым уменьшая количество легкоплавких интерметаллидов.
Поскольку никель и супераустенитные сплавы не содержат феррита, они более подвержены растрескиванию. Чтобы снизить риск растрескивания, может быть полезно следующее:
КОНСТРУКЦИЯ СОЕДИНЕНИЯ
Из-за более высокого содержания никеля течение сварочной ванны имеет тенденцию быть более медленным. Чтобы предотвратить отсутствие плавления, рекомендуется использовать более широкие углы стыков и большие корневые отверстия, чем обычно используются в нержавеющих сталях.
ТЕПЛОПОДХОД
Чем меньше подвод тепла, тем меньше подверженность растрескиванию.Использование расходных материалов меньшего диаметра с меньшим током является выгодным. Обычно предпочтительна максимальная погонная энергия 25 кДж / дюйм (1 кДж / мм).
BEADSHAPE
Следует избегать вогнутого контура валика. Предпочтительны плоские или слегка выпуклые сварные швы.
ТЕМПЕРАТУРА МЕЖДУ ПРОХОДОМ
При сварке сплавов, не содержащих феррит, предпочтительна более низкая температура промежуточного прохода, что снижает термические напряжения. Рекомендуется максимальная температура промежуточного прохода 300 ° F (150 ° C).
Особые рекомендации для дуплексных нержавеющих сталей
Дуплексные сплавы сильно отличаются от стандартных нержавеющих сталей. Они содержат примерно по 50% феррита и аустенита. При неправильной сварке этот класс сплавов может быть подвержен образованию хрупких фаз или образованию выделений, которые могут вызвать точечную коррозию. Признавая это и правильно соблюдая рекомендуемые процедуры, можно легко получить механически прочную и устойчивую к коррозии продукцию.
Exaton предоставляет рекомендации по сварке для успешного соединения дуплексных материалов основы.
Вообще говоря, необходимо соблюдать следующие параметры:
КОНСТРУКЦИЯ СОЕДИНЕНИЯ
Из-за медленной природы ферритных материалов течение сварочной ванны имеет тенденцию быть вялым. Чтобы предотвратить отсутствие плавления, рекомендуется использовать более широкие углы стыков и большие корневые отверстия, чем обычно используются в нержавеющих сталях. Более подробную информацию см. В Руководстве по сварке Exaton.
ВЫБОР ЭКРАНИРУЮЩЕГО И ПОДДЕРЖИВАЮЩЕГО ГАЗА
Из-за свойств ферритных материалов поток в сварочной ванне вялый. Это можно компенсировать правильным выбором защитного газа, который также может улучшить баланс аустенита и феррита. Выбор защитного газа может положительно повлиять на коррозионную стойкость.
Более подробную информацию см. В Руководстве по сварке Exaton.
ПОДАЧА ТЕПЛА
Для достижения оптимального соотношения феррита и аустенита необходимо надлежащим образом контролировать подвод тепла.Рекомендуемый диапазон тепловложения зависит от марки производимой дуплексной нержавеющей стали. Более подробную информацию см. В Руководстве по сварке Exaton.
INTERPASS TEMPERATURE
Для дуплексных сплавов рекомендуются определенные температуры промежуточного прохода для предотвращения образования хрупких интерметаллических фаз. Правильная температура между проходами зависит от марки сварки и толщины основного металла. Более подробную информацию см. В Руководстве по сварке Exaton.
Сварка ферритных сталей
Ферритные сплавы нержавеющей стали по своей природе имеют тенденцию к медленной сварке из-за их плохих характеристик текучести.
Exaton разработала специальные химические составы для нескольких марок ферритных нержавеющих сталей, чтобы улучшить это состояние. Свяжитесь с Exaton для получения дополнительной информации.
Сварной шов
Для многих промышленных применений необходимо поддерживать относительно высокое давление в соответствии с различными нормами для сосудов высокого давления, такими как ASME.В то же время для продления срока службы сосуда требуется защита от коррозии.
Распространенным решением является изготовление емкости из высокопрочной низколегированной стали и плакирование емкости с помощью различных высоколегированных материалов с использованием различных процессов. Обычно используются такие процессы, как MIG, TIG, SMAW и SAW с использованием неизолированной проволоки или комбинации проволоки и флюса. В последние несколько десятилетий использование ленточных электродов стало все более и более обычным явлением как для сварки под флюсом, так и для электрошлакового процесса.
ЭСАБ разработал обширную линейку расходуемых проволок, лент и флюсов, которые позволяют получать полностью легированные сварные швы всего за один слой со скоростью наплавки, превышающей 90 фунтов / час (40 кг / час).
Как правило, для получения механически прочного наплавленного покрытия необходимо нанести первый слой с использованием сверхлегкого сварочного материала. Последующие слои могут быть получены с использованием присадочного металла с желаемым химическим составом окончательного осаждения.
Обратитесь к торговому представителю Exaton, чтобы узнать больше о сплавах, доступных в сочетании с проволокой, лентой или флюсом.
Свариваемость стали | Металлический пресс от onlinemetals.com
Виды стали
По данным Американского института железа и стали (AISI), сталь делится на четыре основные группы в зависимости от химического состава. Каждая группа различается по содержанию углерода и, следовательно, обладает разной свариваемостью. К четырем группам относятся углеродистая сталь, легированная сталь, нержавеющая сталь и инструментальная сталь.
Углеродистая сталь
Легкость сварки углеродистой стали во многом зависит от количества присутствующего углерода.По мере увеличения содержания углерода свариваемость имеет тенденцию к снижению. Это связано с тем, что увеличение твердости делает сталь более склонной к растрескиванию. Однако большинство углеродистых сталей по-прежнему поддаются сварке.
Низкоуглеродистая сталь (низкоуглеродистая сталь)
Эти стали обычно содержат менее 0,3% углерода и до 0,4% марганца. Низкоуглеродистые стали с содержанием углерода 0,15-0,3% и марганца до 0,9% обладают хорошей свариваемостью. Идеально подходят те, у которых менее 0,2% углерода.
До тех пор, пока содержание примесей остается низким, эти металлы редко вызывают проблемы во время процесса сварки.Стали с содержанием углерода более 0,25% склонны к растрескиванию в определенных областях применения. И наоборот, стали с содержанием углерода менее 0,12% могут иметь пористость. Любую низкоуглеродистую сталь можно сваривать, используя любой из обычных способов сварки. Но стали с большим содержанием углерода лучше всего сваривать с низким содержанием водорода или с наполнителями с низким содержанием водорода.
Сталь среднеуглеродистая
Среднеуглеродистые стали содержат 0,30–0,60% углерода и 0,60–1,65% марганца. Они прочнее низкоуглеродистой стали, но их труднее сваривать.Это потому, что они более склонны к растрескиванию. Среднеуглеродистые стали всегда следует сваривать с использованием процесса сварки с низким содержанием водорода или контролируемых водородных наполнителей.
Высокоуглеродистая сталь (инструментальная углеродистая сталь)
Высокоуглеродистая сталь содержит 0,60–1,0% углерода и 0,30–0,90% марганца. Они очень твердые и прочные, но также плохо свариваются, и их трудно сваривать без образования трещин.
После термообработки они становятся чрезвычайно твердыми и хрупкими. При сварке высокоуглеродистые стали требуют предварительного нагрева, тщательного контроля температуры между проходами и снятия напряжений после сварки.При сварке этих сталей необходимы процессы с низким содержанием водорода и присадки с низким содержанием водорода.
Углеродисто-марганцевые стали Углеродисто-марганцевые сталисодержат 0,15-0,5% углерода и 1,0-1,7% марганца. Обычно эти стали поддаются сварке, хотя для некоторых сталей требуется контроль предварительного нагрева и подводимой теплоты. При сварке углеродисто-марганцевых сталей с повышенным содержанием углерода рекомендуется использовать процессы сварки с низким содержанием водорода или контролируемые водородные наполнители.
Как и другие углеродистые стали, многие низколегированные стали пригодны для сварки.Но их свариваемость снова зависит от содержания углерода. В частности, свариваемость легированных сталей зависит от углеродного эквивалента его легирующих добавок: марганца, хрома, молибдена, ванадия и никеля.
Как избежать растрескивания в алюминиевых сплавах
Большинство сплавов на основе алюминия можно успешно сваривать дуговой сваркой без проблем, связанных с растрескиванием, однако, использование наиболее подходящего присадочного сплава и проведение операции сварки с использованием надлежащим образом разработанной и испытанной процедуры сварки имеет большое значение для успеха .Чтобы оценить потенциальные проблемы, связанные с растрескиванием, необходимо понимать множество различных алюминиевых сплавов и их различные характеристики. Эти предварительные знания помогут избежать ситуаций взлома.Механизм первичного растрескивания в сварных швах алюминия
Существует ряд механизмов растрескивания, связанных со сваркой металлических сплавов. Одним из наиболее известных является водородный крекинг, также называемый холодным крекингом.Водородное растрескивание часто является серьезной проблемой при сварке углеродистых сталей и высокопрочных низколегированных сталей. Однако при сварке алюминиевых сплавов водородное растрескивание возникнуть не может.
Горячее растрескивание является причиной почти всех трещин в сварных алюминиевых деталях. Горячее растрескивание — это механизм высокотемпературного растрескивания, который в основном зависит от того, как системы металлических сплавов затвердевают. Этот механизм растрескивания также известен как горячая непродолжительность, горячее растрескивание, кристаллизационное растрескивание и ликвационное растрескивание.
Есть три области, которые могут существенно повлиять на вероятность возникновения горячих трещин в алюминиевой сварной конструкции.Они чувствительны к химическому составу основного сплава, выбору и использованию наиболее подходящего присадочного сплава и выбору наиболее подходящей конструкции соединения.
Кривые чувствительности к растрескиванию алюминия (рис. 1) помогают понять, почему сварные швы алюминия растрескиваются и как выбор присадочного сплава и конструкции соединения могут влиять на чувствительность к трещинам. На диаграмме показано влияние четырех различных добавок сплава — кремния (Si), меди (Cu), магния (Mg) и силицида магния (Mg 2 Si) — на чувствительность алюминия к растрескиванию.Кривые чувствительности к трещинам (рис. 1) показывают, что при добавлении небольших количеств легирующих элементов чувствительность к трещинам становится более высокой, достигает максимума, а затем падает до относительно низких уровней. Изучив кривые чувствительности к трещинам, легко понять, что большинство сплавов на основе алюминия, считающихся несвариваемыми автогенно (без добавления присадочного сплава), имеют химический состав на пиках чувствительности к трещинам или около них. Кроме того, на рисунке показаны сплавы с низкими характеристиками растрескивания, химический состав которых находится далеко от пиков чувствительности к образованию трещин.
На основании этих фактов становится ясно, что трещиностойкость сплава на основе алюминия в первую очередь зависит от его химического состава. Используя те же принципы, можно сделать вывод, что чувствительность к растрескиванию алюминиевого сварного шва, который обычно состоит как из основного сплава, так и из присадочного сплава, также зависит от его химического состава.
Учитывая важность химии для чувствительности алюминиевого сварного шва к растрескиванию, применяются два основных принципа, которые могут снизить вероятность возникновения горячих трещин.Во-первых, при сварке основных сплавов с низкой чувствительностью к растрескиванию всегда используйте присадочный сплав аналогичного химического состава. Во-вторых, при сварке основных сплавов, которые имеют высокую чувствительность к трещинам, используйте присадочный сплав с химическим составом, отличным от химического состава основного сплава, чтобы создать химический состав металла сварного шва, который имеет низкую чувствительность к трещинам. При рассмотрении сварки наиболее часто используемых сплавов на алюминиевой основе серии 5xxx (Al-Mg) и серии 6xxx (Al-Mg-Si) эти принципы четко проиллюстрированы.
Сплавы серии 5xxx (Al-Mg)
Большинство базовых сплавов 5xxx, которые содержат около 5% Mg, демонстрируют низкую чувствительность к образованию трещин.Часто свариваемые автогенно (без присадочного сплава), эти сплавы легко сваривать с присадочным сплавом, который имеет немного больше Mg, чем основной сплав. Это может обеспечить сварной шов с превосходной трещиностойкостью и температурой затвердевания немного ниже, чем у основного сплава. Эти сплавы не следует сваривать с присадочным сплавом серии 4ххх, поскольку в сварном шве могут образоваться определенные количества силицида магния и образование соединения с нежелательными механическими свойствами.
В эту группу входят базовые сплавы, такие как 5052, содержание Mg в которых очень близко к пику чувствительности к трещинам.В случае основного сплава 5052 с содержанием Mg около 2,5% определенно избегайте автогенной сварки. Сплавы на основе Mg с содержанием Mg менее 2,5%, такие как 5052, можно сваривать как с присадочными сплавами 4xxx, такими как 4043 или 4047, так и с присадочными сплавами 5xxx, такими как 5356. При сварке основных сплавов с содержанием Mg менее 2,5% необходимо: изменить химический состав затвердевающего сварного шва от высокого пикового уровня трещин основного сплава. Мы изменяем химический состав сварного шва, выбирая присадочный сплав с гораздо более высоким содержанием Mg, например 5356 (5.0% Mg) или с добавлением кремния в случае 4043.
Сплавы серии 6xxx (Al-Mg-Si)
Сплавы на основе алюминия / магния / кремния (серия 6xxx) очень чувствительны к образованию трещин, поскольку большинство этих сплавов содержат приблизительно 1,0% силицида магния (Mg 2 Si), что близко к пику кривой чувствительности к трещинам при затвердевании. Содержание Mg 2 Si в этих материалах является основной причиной отсутствия присадочных сплавов серии 6xxx.Использование присадочного сплава серии 6xxx или автогенная сварка неизбежно вызовут проблемы с растрескиванием (см. Рис. 2). Во время дуговой сварки склонность этих сплавов к растрескиванию доводится до приемлемого уровня путем разбавления основного материала избыточным магнием (за счет использования присадочных сплавов Al-Mg серии 5xxx) или избыточного кремния (за счет использования сплавов Al- 4xxx серии Al- Si-присадочные сплавы).
Особая осторожность необходима при сварке TIG (GTAW) тонких участков этого типа материала. Часто возможно произвести сварку, особенно на внешних угловых соединениях, без добавления присадочного материала, путем плавления обоих краев основного материала вместе.Однако в большинстве случаев дуговой сварки с этим основным материалом требуется добавление присадочного материала для создания однородных сварных швов без трещин. Одним из возможных исключений может быть противодействие механизму растрескивания путем поддержания сжимающего усилия на деталях во время операции сварки. Это требует специальных методов изготовления и рассмотрения. По этой причине метод редко используется.
Наиболее подходящий и успешный метод, используемый для предотвращения растрескивания в основных материалах серии 6xxx, заключается в добавлении соответствующего присадочного сплава во время операции сварки.
Другими соображениями при сварке этой группы сплавов (6xxx) являются влияние конструкции соединения на разбавление основного сплава и присадочного сплава, а также профиль сварного шва, связанный с склонностью к растрескиванию. Сварные швы с квадратными канавками в этом материале чрезвычайно уязвимы для растрескивания, потому что очень мало присадочного сплава смешивается с основным материалом во время сварки. Часто бывает необходимо оценить использование подготовки сварного шва с V-образной канавкой, которая добавит больше присадочного сплава в сварочную смесь металла и снизит чувствительность к образованию трещин.Кроме того, вогнутые угловые швы с уменьшенной толщиной горловины и вогнутые корневые проходы в стыковых швах могут иметь тенденцию к растрескиванию (см. Рис. 3).
Дополнительные сведения
Кривые чувствительности к растрескиванию служат отличным ориентиром для определения вероятности образования горячих трещин, однако есть и другие вопросы, которые необходимо учитывать, чтобы понять растрескивание в алюминиевых сплавах. Одной из этих проблем является влияние легирующих элементов, отличных от основных легирующих элементов, рассматриваемых в кривых чувствительности к трещинам.Несомненно, некоторые сплавы на основе алюминия могут быть трудными для сварки и вызывать проблемы с растрескиванием, особенно без полного понимания их свойств и / или при неправильном обращении. Фактически, некоторые сплавы на основе алюминия непригодны для дуговой сварки, и по этой причине их обычно соединяют механически с помощью клепок или болтов. Эти алюминиевые сплавы трудно поддаются дуговой сварке без проблем во время и / или после сварки. Эти проблемы обычно связаны с растрескиванием, чаще всего с горячим растрескиванием, а иногда и с коррозионным растрескиванием под напряжением (SCC).
Алюминиевые сплавы, которые относятся к этой категории трудных для сварки, можно разделить на различные группы. Всегда помните о небольшом количестве алюминиевых сплавов, предназначенных для обработки, а не свариваемости. Такими сплавами являются 2011 и 6262, которые содержат 0,20-0,6 Bi, 0,20-0,6 Pb и 0,40-0,7 Bi, 0,40-0,7 Pb соответственно. Добавление элементов (висмута и свинца) к этим материалам обеспечивает отличное стружкообразование в этих сплавах, не требующих механической обработки. Однако из-за низких температур затвердевания они могут серьезно снизить возможность получения качественных сварных швов в этих материалах.В дополнение к сплавам для свободной механической обработки, упомянутым выше, многие другие алюминиевые сплавы могут быть весьма восприимчивыми к горячему растрескиванию при дуговой сварке. Эти сплавы обычно подвергаются термообработке и чаще всего встречаются в группах материалов серии 2ххх (Al-Cu) и серии 7ххх (Al-Zn).
Чтобы понять, почему некоторые из этих сплавов непригодны для дуговой сварки, необходимо рассмотреть причины, по которым некоторые алюминиевые сплавы могут быть более восприимчивыми к горячему растрескиванию.
Горячее растрескивание, или растрескивание при затвердевании, возникает в алюминиевых сварных швах при высоких уровнях термического напряжения и усадки при затвердевании, когда сварной шов подвергается различной степени затвердевания.Сочетание механических, термических и металлургических факторов влияет на чувствительность любого алюминиевого сплава к образованию горячих трещин. Комбинируя различные легирующие элементы, были разработаны многие высокоэффективные термически обрабатываемые алюминиевые сплавы для улучшения механических свойств материалов. В некоторых случаях комбинация требуемых легирующих элементов позволила получить материалы с высокой чувствительностью к образованию горячих трещин.
Когерентность Диапазон
Возможно, наиболее важным фактором, влияющим на чувствительность алюминиевых сварных швов к горячим трещинам, является температурный диапазон когерентности дендритов, а также тип и количество жидкости, доступной во время процесса замораживания.Когерентность возникает, когда дендриты начинают сцепляться друг с другом, так что расплавленный материал начинает образовывать мягкую стадию.
Диапазон когерентности — это температура между образованием когерентных взаимосвязанных дендритов и температурой солидуса. Чем шире диапазон когерентности, тем более вероятно возникновение горячего растрескивания из-за накапливающейся деформации затвердевания между взаимосвязанными дендритами.
Сплавы серии 2ххх (Al-Cu)
Чувствительность к образованию горячих трещин в сплавах Al-Cu увеличивается при добавлении примерно 3% Cu; однако затем он снижается до относительно низкого уровня — 4.5% Cu и выше. Сплав 2219 с 6,3% Cu показывает хорошее сопротивление горячему растрескиванию из-за его относительно узкого диапазона когерентности. Сплав 2024 содержит примерно 4,5% меди, что вызывает ощущение относительно низкой чувствительности к образованию трещин. Однако сплав 2024 также содержит небольшое количество магния (Mg). Небольшое количество Mg в этом сплаве снижает температуру солидуса, но не влияет на температуру когерентности; следовательно, увеличивается диапазон когерентности и возрастает склонность к образованию горячих трещин.Проблема при сварке 2024 заключается в том, что высокая температура операции сварки позволит сегрегацию легирующих компонентов на границах зерен, а присутствие Mg, как указано выше, снизит температуру солидуса. Поскольку эти легирующие компоненты имеют более низкие фазы плавления, напряжение затвердевания может вызвать растрескивание на границах зерен и / или создать условия внутри материала, способствующие коррозионному растрескиванию под напряжением позже. Высокое тепловложение во время сварки, повторяющиеся проходы сварного шва и большие размеры сварных швов — все это может увеличить проблему сегрегации границ зерен (сегрегация зависит от температуры и времени) и последующей тенденции к растрескиванию.
Сплавы серии 7xxx (Al-Zn)
Сплавы серии 7xxx, с учетом свариваемости, содержат две отдельные группы: типы Al-Zn-Mg и Al-Zn-Mg-Cu.
Сплавы Al-Zn-Mg , такие как 7005, будут лучше сопротивляться горячему растрескиванию и демонстрировать лучшие характеристики соединения, чем сплавы Al-Zn-Mg-Cu, такие как 7075. Содержание Mg в этой группе (Al-Zn-Mg) сплавы обычно повышают чувствительность к растрескиванию. Однако добавление Zr для уменьшения размера зерна эффективно снижает тенденцию к растрескиванию.Эта группа сплавов легко сваривается с присадочными сплавами с высоким содержанием магния, такими как 5356, что гарантирует, что сварной шов содержит достаточно магния для предотвращения растрескивания. Рекомендация присадочных сплавов на основе кремния, таких как 4043, для этих сплавов нежелательна, поскольку избыточный Si, вводимый присадочным сплавом, может привести к образованию чрезмерного количества хрупких частиц Mg 2 Si в сварном шве.
Сплавы Al-Zn-Mg-Cu , такие как 7075, содержат небольшое количество меди.Небольшие количества Cu вместе с Mg расширяют диапазон когерентности и, следовательно, увеличивают чувствительность к трещинам. Подобная ситуация может возникнуть с этими материалами, как и со сплавами типа 2024. Напряжение затвердевания может вызвать растрескивание на границах зерен и / или создать в материале состояние, способствующее коррозионному растрескиванию под напряжением позже.
Будьте в курсе:
Проблема повышенной подверженности горячему растрескиванию из-за увеличения диапазона когерентности не ограничивается сваркой этих более восприимчивых основных сплавов, таких как 2024 и 7075.Чувствительность к образованию трещин может быть значительно увеличена при сварке несовместимых разнородных основных сплавов (которые обычно легко свариваются сами с собой) и / или путем выбора несовместимого присадочного сплава. Например, путем соединения идеально свариваемого основного сплава серии 2xxx с идеально свариваемым основным сплавом серии 5xxx или использования присадочного сплава серии 5xxx для сварки основного сплава серии 2xxx или присадочного сплава серии 2xxx на базовом сплаве серии 5xxx, мы можем создать такой же сценарий. Если мы смешиваем во время сварки высокое содержание Cu и высокое содержание Mg, мы можем расширить диапазон когерентности и, следовательно, повысить чувствительность к образованию трещин.
Резюме:
Избегайте горячего растрескивания алюминиевых сплавов, применяя один или несколько из следующих подходящих принципов:
- Избегайте чрезвычайно чувствительных к растрескиванию основных материалов, которые обычно считаются несвариваемыми.
- Используйте таблицу выбора подходящего присадочного сплава для выбора наиболее подходящего присадочного сплава для конкретного основного сплава, тем самым избегая критических диапазонов химического состава (диапазонов чувствительности к трещинам) в сварном шве.
- Выберите присадочный сплав с точкой затвердевания, близкой или ниже точки затвердевания основного материала.
- Выберите наиболее подходящую подготовку кромки и корневой зазор, чтобы допустить добавление достаточного количества присадочного материала, таким образом создавая химический состав металла сварного шва за пределами критического диапазона химического состава.
- Чтобы противодействовать растрескиванию, используйте хорошо зарекомендовавшие себя присадочные сплавы с добавлением измельчителей зерна, таких как титан или цирконий.
- Используйте максимально возможную скорость сварки. Чем быстрее проводится сварка, тем выше скорость охлаждения и тем меньше времени сварка находится в диапазоне температур горячего растрескивания.
- Старайтесь использовать последовательности и методы сварки и сборки, которые минимизируют ограничение, уменьшают остаточное напряжение и обеспечивают сварные швы приемлемого профиля.
- Приложите сжимающую силу к сварному соединению во время сварки, чтобы противодействовать механизму растрескивания.
Рис. 1. На этом рисунке показано влияние четырех различных добавок сплава на трещиностойкость алюминия
.Рис. 2 Вот два сварных шва GTAW (TIG), выполненных бок о бок на опорной плите 6061-T6.
1. Верхний сварной шов был наплавлен без присадочного сплава, а затем подвергнут испытанию на проникновение жидкости. Метод испытаний выявил множество мелких линейных признаков (трещин) на поверхности сварного шва.
2. Нижний шов, выполненный также без присадочного сплава, использовал более высокий ток и меньшую скорость перемещения. Чрезмерное тепловложение во время сварки этого валика привело к возникновению гораздо большего напряжения в сварном шве, что привело к гораздо более очевидной ситуации растрескивания. Как легко видеть, без испытания проникающей жидкостью большая продольная трещина образовалась по центру сварного шва.
Вывод состоит в том, что можно ожидать горячего растрескивания той или иной формы, если основные сплавы серии 6ххх сваривать без добавления присадочного материала.
Рис. 3. На этом рисунке показаны два окончания углового шва в углу сварной конструкции. Трещины видны в обоих кратерах прекращения. Также видны трещины по центру обоих сварных швов. Причина этого горячего растрескивания — нежелательный профиль сварного шва из-за плохой техники сварки.Уменьшение толщины шва на окончании и для части углового шва позволило напряжениям, возникающим во время сварки, разрушить сварной шов.
Напряжения при сварке и растрескивание: Maine Welding Company
В этом разделе *** объясняются сварочные напряжения и их влияние на образование трещин ***. Факторы, связанные с разрушением сварных деталей, включают напряжения сварного шва, растрескивание, деформацию сварного шва, ламеллярный разрыв, хрупкое разрушение, усталостное растрескивание, конструкцию сварного шва и дефекты сварного шва.
Когда к свариваемому металлу добавляют сварочный металл, это, по сути, литой металл. При охлаждении металл сварного шва сжимается в большей степени, чем основной металл, контактирующий со сварным швом, и, поскольку он прочно сплавлен, оказывает волочильное действие. Это действие волочения создает напряжения в сварном шве и вокруг него, которые могут вызвать коробление, коробление, остаточные напряжения или другие дефекты.
Снятие напряжения — это процесс снижения остаточных напряжений или уменьшения их интенсивности. Если свариваемые детали закреплены слишком прочно, чтобы допускать движение, или не нагреваются равномерно во время операции сварки, возникают напряжения из-за усадки металла сварного шва в месте соединения.Детали, которые не могут двигаться, чтобы допускать расширение и сжатие, должны равномерно нагреваться во время сварочной операции. После завершения сварки необходимо снять напряжение. Эти меры предосторожности важны при сварке алюминия, чугуна, высокоуглеродистой стали и других хрупких металлов или металлов с низкой прочностью при температурах непосредственно ниже точки плавления. Пластичные материалы, такие как бронза, латунь, медь и низкоуглеродистая сталь, деформируются или растягиваются в пластичных или мягких условиях и менее склонны к растрескиванию.Однако они могут иметь нежелательные напряжения, которые могут ослабить готовый сварной шов.
Когда напряжения, приложенные к соединению, превышают предел текучести, соединение будет пластично деформироваться, так что напряжения будут снижены до предела текучести. Это нормально для простых конструкций, в которых напряжения в одном направлении возникают на деталях из пластичных материалов. Усадочные напряжения из-за нормального нагрева и охлаждения действительно возникают во всех трех измерениях. В тонкой плоской пластине напряжения растяжения возникают под прямым углом.По мере того, как плита становится толще или в очень толстых материалах, напряжения возникают в трех направлениях.
Когда простые напряжения прикладываются к тонким, хрупким материалам, материал будет хрупким при растяжении, и излом будет демонстрировать небольшую податливость или ее отсутствие. В таких случаях у материала нет предела текучести, поскольку предел текучести и предел прочности почти одинаковы. Отказы, происходящие без пластической деформации, известны как хрупкие отказы. Когда в пластичном материале возникают два или более напряжения, и особенно когда напряжения возникают в трех направлениях в толстом материале, может возникнуть хрупкое разрушение.
Остаточные напряжения также возникают в отливках, поковках и горячекатаных профилях. В поковках и отливках остаточные напряжения возникают в результате возникающего дифференциального охлаждения. Сначала охлаждается внешняя часть детали, а более толстая внутренняя часть охлаждается значительно быстрее. По мере остывания детали сжимаются и набирают прочность, так что ранее остывшие части испытывают сжимающую нагрузку, а части, которые позже остывают, переходят в режим растягивающего напряжения. В сложных частях напряжения могут вызвать коробление.
Остаточные напряжения не всегда вредны. Они могут не иметь эффекта или могут положительно сказаться на сроке службы деталей. Обычно внешние волокна детали подвергаются растягивающей нагрузке, и, таким образом, при остаточной сжимающей нагрузке существует тенденция к нейтрализации напряжения во внешних волокнах детали. Пример использования остаточного напряжения — горячая посадка деталей. Типичным примером является охлаждение подшипников скольжения, чтобы вставить их в обработанные отверстия и дать им возможность расшириться до нормального размера, чтобы удерживать их в нужном месте.Подшипники скольжения используются для тяжелой, медленной техники и подвергаются сжимающей остаточной нагрузке, удерживая их в отверстии. Большие роликовые подшипники обычно устанавливаются на валы путем нагревания, чтобы они немного расширились, чтобы они поместились на валу, а затем дать им остыть для получения плотной сборки.
Остаточные напряжения возникают во всех сварных швах. Наиболее распространенный метод измерения напряжения — это изготовление образцов сварных швов с последующей обработкой определенных количеств металла, которые выдерживают растягивающее напряжение в сварном шве и рядом с ним.Затем измеряется происходящее движение. Другой метод — использование меток сетки или точек данных на поверхности сварных деталей, которые можно измерить в нескольких направлениях. Делаются разрезы для уменьшения или снятия остаточных напряжений с определенных частей сварного соединения, после чего измерения проводятся снова. Величина движения зависит от величины напряжений. Третий метод использует очень маленькие тензодатчики. Сварная деталь постепенно механически отрезается от прилегающих участков, чтобы определить изменение внутренних напряжений.С помощью этих методов можно установить закономерности и фактически определить величину напряжений в деталях, которые были вызваны тепловым воздействием сварных швов.
На рисунке 6-53 показаны остаточные напряжения в кромочном сварном шве. Металл, прилегающий к сварному шву, имеет тенденцию расширяться во всех направлениях при нагревании сварочной дугой. Этот металл удерживается прилегающим к нему холодным металлом и в течение этого периода нагрева слегка опрокидывается или немного увеличивается в толщине. Когда металл сварного шва начинает остывать, зона высадки пытается сжаться, но снова сдерживается более холодным металлом.Это приводит к тому, что нагретая зона становится напряженной. Когда сварной шов остынет до комнатной температуры, металл шва и прилегающий основной металл испытывают растягивающие напряжения, близкие к пределу текучести. Следовательно, есть часть, которая сжимается, а за ней еще одна зона растягивающего напряжения. Две кромки испытывают остаточное напряжение растяжения, а центр — остаточное напряжение сжатия, как показано.
Остаточные напряжения в стыковом сварном шве из относительно тонкой пластины проанализировать сложнее.Это связано с тем, что напряжения возникают в продольном направлении сварного шва и перпендикулярно оси сварного шва. Остаточные напряжения внутри сварного шва являются растягивающими в продольном направлении сварного шва, а величина соответствует пределу текучести металла. Основной металл, прилегающий к сварному шву, также имеет предел текучести, параллельно сварному шву и по большей части длины сварного шва. При удалении от сварного шва в основной металл остаточные напряжения быстро падают до нуля, а для сохранения баланса переходят на сжатие.Это показано на рисунке 6-54. Остаточные напряжения в сварном шве под прямым углом к оси сварного шва являются растягивающими в центре пластины и сжимающими на концах. Для более толстых материалов, когда сварные швы выполняются многопроходными, соотношение иное из-за большого количества проходов источника тепла. За исключением однопроходных простых конструкций соединений, остаточные напряжения сжатия и растяжения можно только оценить.
По мере выполнения каждого сварного шва он будет сжиматься по мере затвердевания и набирать прочность по мере охлаждения металла.Когда он сжимается, он имеет тенденцию тянуть, и это создает растягивающие напряжения в сварном шве и рядом с ним. Вдали от сварного шва или валика металл должен оставаться в равновесии, и поэтому возникают сжимающие напряжения. В более тяжелых сварных конструкциях, когда задействовано ограничение, движение невозможно, а остаточные напряжения имеют более высокую величину. В многопроходном сварном шве с одной канавкой первый сварной шов или корневой проход изначально создает растягивающее напряжение. Второй, третий и четвертый проходы сжимаются и вызывают сжимающую нагрузку в корневом проходе.По мере выполнения проходов до завершения сварки верхние проходы будут испытывать растягивающую нагрузку, центр пластины — сжатие, а корневой проход будет иметь остаточное напряжение растяжения.
Остаточные напряжения можно уменьшить несколькими способами, как описано ниже:
Если сварной шов подвергается нагрузке, превышающей его предел текучести, произойдет прочностная пластическая деформация, и напряжения будут более однородными, но все же будут находиться на пределе текучести металла. Это не устранит остаточные напряжения, но создаст более однородную картину напряжений.Другой способ снизить высокие или пиковые остаточные напряжения — это нагружать или растягивать сварной шов путем нагрева соседних участков, вызывая их расширение. Тепло снижает предел текучести металла сварного шва, а расширение будет способствовать снижению пиковых остаточных напряжений в сварном шве. Этот метод также делает картину напряжений в зоне сварного шва более однородной.
Высокие остаточные напряжения можно снизить термической обработкой для снятия напряжений. При термической обработке сварная деталь равномерно нагревается до повышенной температуры, при которой предел текучести металла значительно снижается.Затем сварной детали дают медленно и равномерно остыть, чтобы разница температур между деталями была незначительной. Охлаждение будет равномерным, и внутри сварного соединения будет развиваться однородная картина с низким напряжением.
Высокотемпературный предварительный нагрев также может снизить остаточное напряжение, поскольку вся сварная деталь находится при относительно высокой температуре и будет охлаждаться более или менее равномерно от этой температуры и, таким образом, снизит пиковые остаточные напряжения.
Остаточные напряжения также способствуют растрескиванию сварного шва.Растрескивание сварного шва иногда происходит во время изготовления сварного изделия или вскоре после его завершения. Трещины возникают по многим причинам и могут возникать спустя годы после завершения сварки. Трещины — это наиболее серьезные дефекты, возникающие в сварных швах или сварных соединениях сварных деталей. Трещины недопустимы в большинстве сварных деталей, особенно в тех, которые подвержены воздействию низких температур, когда повреждение сварного соединения угрожает жизни.
Растрескивание сварного шва, возникающее во время или вскоре после изготовления сварного изделия, может быть классифицировано как горячее или холодное растрескивание.Кроме того, сварной шов может растрескаться в металле сварного шва или в основном металле, прилегающем к металлу сварного шва, обычно в зоне термического влияния.
Сварные швы трескаются по разным причинам, в том числе по следующим:
- Недостаточное поперечное сечение металла шва для выдерживания соответствующих нагрузок.
- Недостаточная пластичность металла сварного шва, чтобы поддаваться действию напряжений.
- Растрескивание под бортом из-за поглощения водорода в отверждаемом основном материале.
Сдерживающие и остаточные напряжения являются основными причинами растрескивания сварного шва во время изготовления сварного изделия.Ограничение сварного шва может быть обусловлено несколькими факторами, включая жесткость или жесткость самого сварного изделия. Металл сварного шва дает усадку при охлаждении, и если свариваемые детали не могут двигаться относительно друг друга, а металл шва имеет недостаточную пластичность, это приведет к трещине. Движение сварных швов может вызвать высокие нагрузки на другие сварные швы и привести к их растрескиванию во время изготовления. Следует использовать более пластичный присадочный материал или сварной шов следует выполнять с достаточной площадью поперечного сечения, чтобы по мере охлаждения он обладал достаточной прочностью, чтобы противостоять тенденции к растрескиванию.Типичные трещины сварного шва возникают в корневом проходе, когда детали не могут двигаться.
Быстрое охлаждение наплавленного металла также вызывает растрескивание сварного шва. Если соединяемый основной металл холодный, а сварной шов небольшой, он быстро остынет. Также быстро произойдет усадка, и может произойти растрескивание. Если соединяемые детали предварительно даже немного нагреть, скорость охлаждения будет ниже, и растрескивание может быть устранено.
Содержание сплава или углерода в основном материале также может повлиять на растрескивание.Когда сварной шов выполняется с использованием основного материала с более высоким содержанием углерода или более высокого сплава, определенное количество основного материала расплавляется и смешивается с электродом для получения металла шва. Получаемый металл шва имеет более высокое содержание углерода и сплава. Он может иметь более высокую прочность, но менее пластичен. По мере усадки он может не обладать достаточной пластичностью, чтобы вызвать пластическую деформацию, и может произойти растрескивание.
Поглощение водорода в металле шва и в зоне термического влияния также может вызвать растрескивание. При использовании покрытых целлюлозой электродов или когда водород присутствует из-за влажного газа, влажного флюса или углеводородных материалов на поверхности, водород в атмосфере дуги будет поглощаться расплавленным металлом сварного шва и прилегающим к нему высокотемпературным основным металлом.По мере того как металл остывает, он отторгает водород, и при достаточной сдержанности может произойти растрескивание. Этот тип растрескивания можно уменьшить, увеличив предварительный нагрев, уменьшив ограничение и исключив водород из атмосферы дуги.
Причиной появления трещин в зоне термического влияния или замедленного образования обычно является накопление водорода в металле сварного шва и в зоне термического влияния основного металла. Причиной также может быть наличие материалов с более высоким содержанием углерода или высоколегированного сплава в основном металле.При сварке высоколегированных или высокоуглеродистых сталей можно использовать технику нанесения масла для предотвращения растрескивания. Это включает наплавку поверхности сварного шва соединения металлом сварного шва, содержание углерода или сплава которого намного ниже, чем в основном металле. Затем между нанесенным наплавочным материалом выполняется сварной шов, который позволяет избежать поглощения углерода и сплава в металле сварного шва, поэтому осаждение сварного шва становится более пластичным. Общая прочность соединения должна быть достаточно большой, чтобы соответствовать проектным требованиям. Растрескивание под валиком можно уменьшить за счет использования процессов с низким содержанием водорода и присадочных металлов.Использование предварительного нагрева снижает скорость охлаждения, что снижает вероятность растрескивания.
Методы снятия напряжений
Снятие напряжений в стальных сварных швах может быть достигнуто путем предварительного нагрева от 800 до 1450 ° F (от 427 до 788 ° C), в зависимости от материала, а затем медленного охлаждения. Охлаждение при некоторых условиях может длиться от 10 до 12 часов. Небольшие детали, такие как сваренные встык быстрорежущие наконечники инструмента, можно отжечь, поместив их в ящик из огнестойкого материала и охладив в течение 24 часов.В случае низкоуглеродистой стали, снимающей напряжение, обычной практикой является нагрев готового сварного шва в течение 1 часа на каждые 1,00 дюйма (2,54 см) толщины. Исходя из этого, сталь толщиной 1/4 дюйма (0,64 см) следует предварительно нагреть в течение 15 минут при температуре снятия напряжений.
Прокаливание — это еще один метод снятия напряжения на готовом сварном шве, обычно с помощью сжатого воздуха и инструмента для черновой или упрочняющей обработки. Однако чрезмерное упрочнение может вызвать хрупкость или упрочнение готового сварного шва и фактически вызвать растрескивание.
Предварительный нагрев во многих случаях облегчает сварку. Он предотвращает растрескивание в зоне термического влияния, особенно при первых проходах металла шва. При использовании надлежащего времени и температуры предварительного нагрева скорость охлаждения существенно снижается, чтобы предотвратить образование твердого мартенсита, вызывающего растрескивание. В Таблице 6-1 перечислены температуры предварительного нагрева определенных металлов.
Потребность в предварительном нагреве стали и других металлов увеличивается при следующих условиях:
- Когда температура детали или окружающей атмосферы равна или ниже точки замерзания.
- Когда диаметр сварочного стержня мал по сравнению с толщиной соединяемого металла.
- При высокой скорости сварки.
- При сложной форме и конструкции свариваемых деталей.
- При большой разнице масс свариваемых деталей.
- При сварке сталей с высоким содержанием углерода, низким содержанием марганца или других сплавов.
- При сварке сталь имеет тенденцию к затвердеванию при охлаждении на воздухе от температуры сварки.
Для снятия напряжения и уменьшения растрескивания можно использовать следующие общие процедуры:
- Используйте шов из пластичного металла.
- Избегайте чрезмерно высоких ограничений или остаточных напряжений.
- Измените процедуры сварки, чтобы уменьшить ограничения.
- Используйте низколегированные и низкоуглеродистые материалы.
- Уменьшите скорость охлаждения за счет предварительного нагрева.
- Используйте процессы сварки с низким содержанием водорода и присадочные металлы.