Газовая резка металла — технология обработки, устройства, рекомендации
Газовая резка металла (кислородная/автогенная) – процесс разрезания стальных и металлических изделии/заготовок кислородным потоком, который подается из специального аппарата. Суть процедуры раскроя заключается в горении металла, с помощью газовой смеси и кислорода, подаваемых на обрабатываемый элемент. Предварительно изделие нагревается до 1300 градусов открытым пламенем, затем подается кислородная струя, разрезающая металл в соответствии со схемой. Современная технология газовой резки позволяет производить раскрой листа любой конфигурации толщиной до 300 мм, в отдельных случаях до 1000 мм.
Основные методы резки металла газом
Копьевая резка — с помощью данной операции производится обработка нержавейки, чугуна и низкоуглеродистой стали больших диаметров. Суть резки заключается в том, что копье разогревается до температуры плавления и прижимается к разрезаемой заготовке.

Кислородно-флюсовая резка используется для работы с высоколегированными хромистыми и хромоникелевыми сплавами. Данный способ характеризуется тем, что в струю газа (кислорода) начинает вводится порошкообразный флюс, он служит дополнительным источником тепла.
Воздушно-дуговая резка основана на расплавлении металла посредством электрической дуги. При использовании данного метода газ подается вдоль всего электрода.
Резка пропаном выполняется при необходимости раскроя титана, низколегированных и низкоуглеродистых стальных сплавов.
Оборудование данного типа не может раскроить металл толще 300 мм.
Толщина материала, см | Пробивание, сек. | Ширина реза, см | Расход пропана, м3 | Расход кислорода, м3 |
---|---|---|---|---|
0,4 | От 5 до 8 | 0,25 | 0,035 | 0,289 |
1,0 | От 8 до 13 | 0,3 | 0,041 | 0,415 |
2,0 | От 13 до 18 | 0,4 | 0,051 | 0,623 |
4,0 | От 22 до 28 | 0,45 | 0,071 | 1,037 |
6,0 | От 25 до 30 | 0,5 | 0,071 | 1,461 |
Как рассчитать стоимость услуги за метр
При расчете стоимости в рассмотрение принимается: толщина металла, максимальный размер детали, ширина реза, кромка, особенности конфигурации, исходный материал – черный или цветной металл, а также предусмотрена резка под углом.
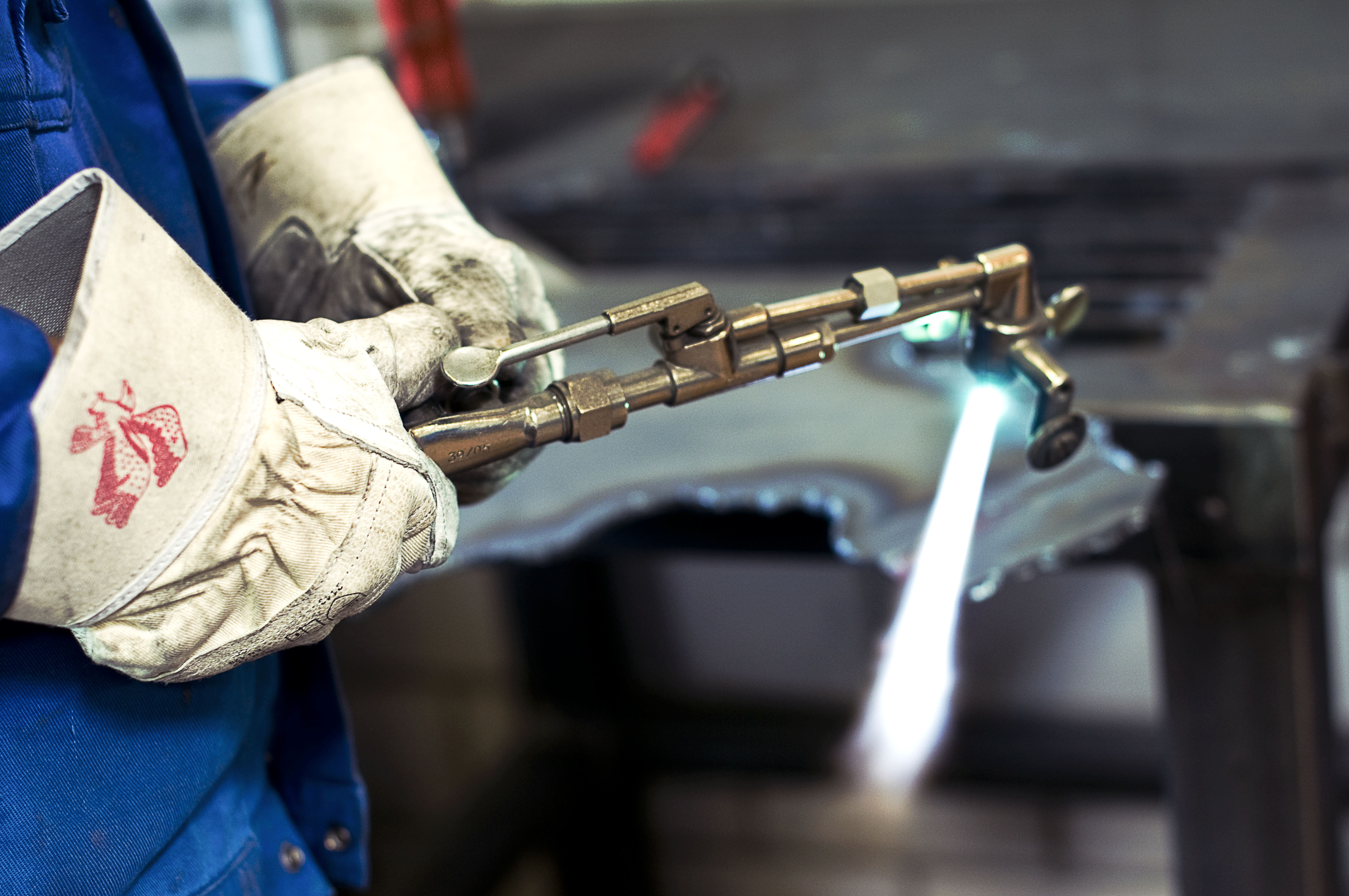
Расход газа при резке металла
Рабочий диапазон, мм | Резательное сопло NX | Кислород (давление, bar) | Горючий газ (давление, bar) | Кислород (потребление, m3/h) | Горючий газ (потребление, m3/h) |
---|---|---|---|---|---|
3-5 | 000 NX | 1,0-2,0 | 0,5 | 1,5-2,0 | 0,20 |
5-10 | 00 NX | 1,5-2,0 | 0,5 | 2,0-3,0 | 0,30 |
10-15 | 0 NX | 2,0-3,0 | 0,5 | 3,0-3,5 | 0,35 |
15-25 | 1 NX | 2,5-3,5 | 0,5 | 3,5-4,5 | 0,40 |
25-50 | 2 NX | 3,5-4,0 | 0,5 | 4,0-4,8 | 0,40 |
50-75 | 3 NX | 3,0-4,5 | 0,5 | 5,0-6,5 | 0,40 |
75-150 | 4 NX | 3,5-5,5 | 0,5 | 6,5-9,5 | 0,50 |
150-200 | 5 NX | 4,5-5,5 | 0,5 | 10,0-14,0 | 0,60 |
200-300 | 6 NX | 5,5-6,5 | 0,5 | 15,0-19,0 | 0,70 |
Особенности резки в размер
Газовая резка позволяет проводить фигурный раскрой листа.
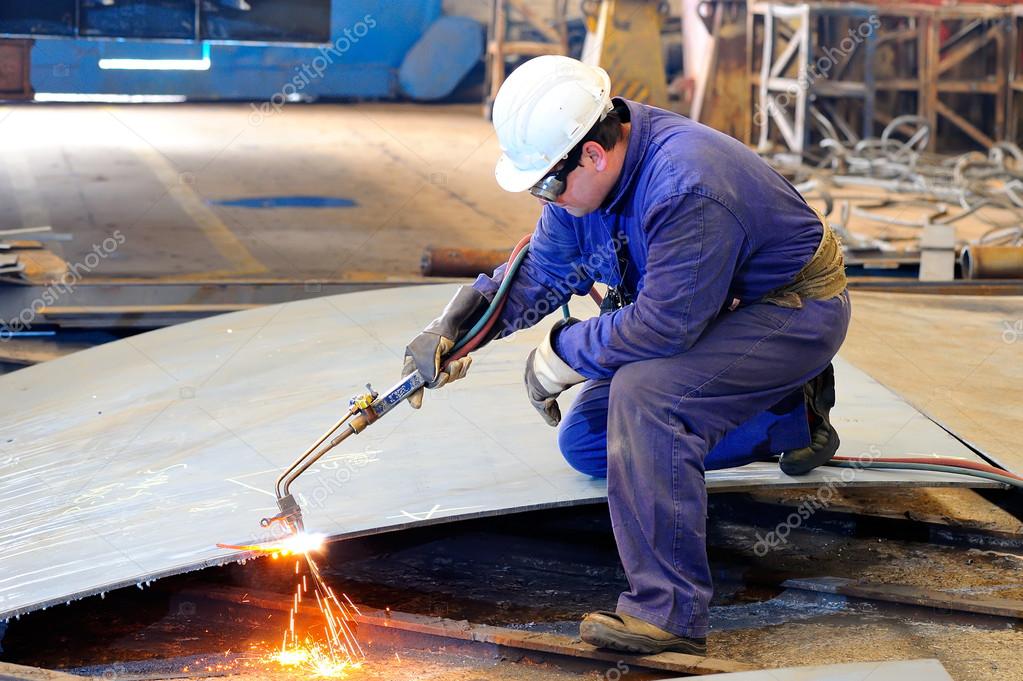
Преимущества метода газовой резки
- ● быстрота и универсальность
- ● оптимальная стоимость и высокое качество
- ● любой уровень сложности
- ● любая конфигурация реза
- ● возможность работы с металлом разной толщины
Возможность деформации
Деформация — обычное явление, если на металл оказывается термическое воздействие. Исправить дефекты можно с помощью вальцовки, обжига, предварительного закрепления изделия, также не стоит превышать допустимую скорость обработки.
Процесс раскроя металла
● Резка начинается с точки, от которой должен идти разрез.
● Эта точка разогревается до температуры 1000-1300 С.
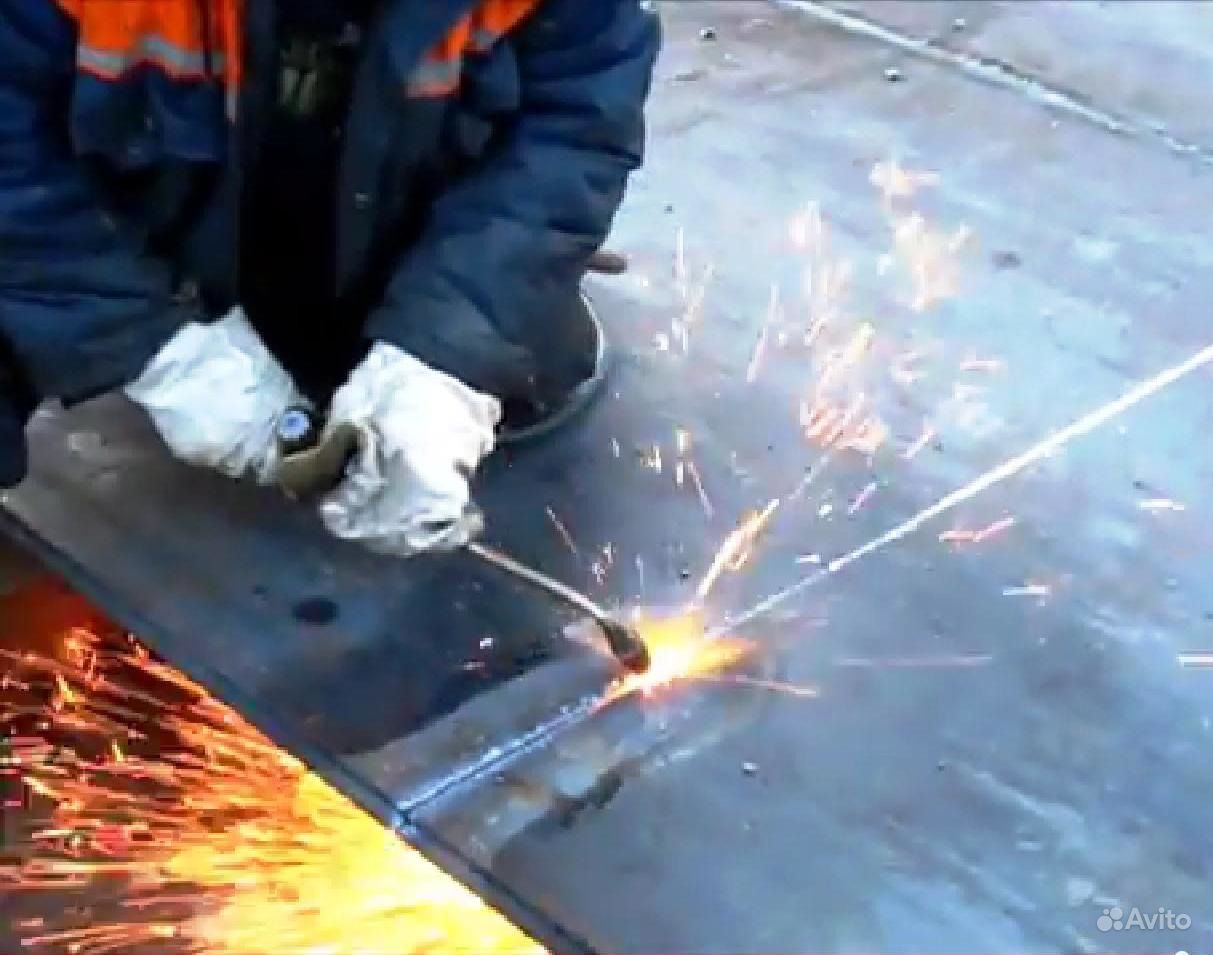
● Резак плвно ведется по линии (угол — 84-85 градусов), сторона — противоположная от резки.
Устройство ручного газового резака
Устройство инжекторного резака
От чего зависит расход газа:
● квалификации мастера
● технических характеристик оборудования
● вида и толщины разрезаемой детали
● глубины и ширины реза
Технология кислородной резки металла — определение, техника
Кислородная резка металла – это термический способ разрезания металла с помощью газового пламени. В подаваемой струе кислорода разрезаемый металл сгорает, одновременно с этим процессом сгорают и выделяемые оксиды. Для поддержания стабильного процесса используют горючие газы – ацителен, пропан-бутановую смесь, МАФ, а также в отдельных случаях – пары бензина и керосина.
Технология кислородной резки
Исходя из особенностей обрабатываемой поверхности, ее формы и самой основы материала, различают несколько видов кислородной резки:
- • скоростная, нормальная и кислородно-флюсовая, предназначены для прямолинейной и фигурной резки;
- • строжка поверхности и канавок, обточка – используют в поверхностных обработках;
- • кислородное копье и струя – применяют в сверлении и прожигании.

Резка металла кислородом под водой
Данный вид обработки используется только при необходимости проведения специальных операций: спасательных, строительных, аварийных, подъемных. Резаком для подводной резки можно кроить стальные сплавы толщиной до 70 мм, находясь при этом на глубине до 30 м. Бензокислородный резак может работать со сталью, толщина которой достигает 100 мм.
По типу разреза подразделяются на:
Особенности кислородной резки труб
Ручной способ кислородного раскроя применяется для обработки торцов трубопровода перед сварочными работами, для удаления дефектов. Операция может выполняться в любом пространственном положении. Для ее выполнения применяют вставные и универсальные резаки. Настройка режима зависит от толщины обрабатываемого изделия.
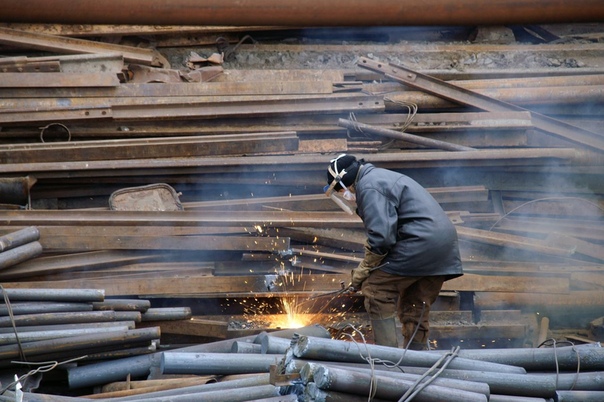
Классификация оборудования для резки кислородом
По способу обработки резка бывает ручная и механизированная. Существуют ручные резаки, работа которых характеризуется достаточно высокой точностьюю Они подразделяются на универсальные, специальные, для фигурного и прямого раскроя. При необходимости обработки больших объемов металла рационально использовать переносные аппараты «Гугарк», большие партии одинаковых изделий успешно вырезаются с помощью шарнирных машин АСШ-86. Промышленные предприятия чаще всего используют портально-консольные устройства.
Особенности рабочего процесса
Резка, как и другой рабочие процесс, требует внимательности и соблюдения техники безопасности:
- • запрещено проводить подогрев металла одним только сжиженным газом;
- • запрещено использовать жидкое горючее в газосварочных работах;
- • при работе в закрытых помещениях должны быть предусмотрены вентиляционные системы;
- • баллоны с сжиженным газом должны располагаться на расстоянии не менее 5 м от газосварочных работ.
Сталь | Характеристика разрезаемости |
---|---|
Высокоуглеродистая | При содержании углерода свыше 0,3% до 1% резка затруднена и требуется предварительный подогрев стали до 300-700С. При содержании углерода более 1-1,2% резка невозможна |
Среднеуглеродистая | С увеличением содержания углерода от 0,3 до 0,7% резка осложняется |
Низкоуглеродистая | При содержании углерода до 0,3% резка без затруднений |
Как подготовить поверхность перед резкой
Перед проведением раскроя металла кислородом необходимо очистить поверхность от коррозии, грязи, масляных пятен и окалин. Если резка выполняется вручную, достаточно всего лишь очистить место реза плазменным резаком. Если процесс механизирован, то листы правят на вальцовочных аппаратах, а очищают с помощью химических или дробеструйных работ.
Чертеж устройства ручного ацетилено-кислородного резака
- 1 — головка резака;
- 2 — трубки;
- 3 — вентиль;
- 4 — кислородный вентиль;
- 5 — кислородный ниппель;
- 6 — ацетиленовый ниппель;
- 7 — рукоятка;
- 8 — корпус;
- 9 — ацетиленовый вентиль;
- 10 — инжектор;
- 11 — накидная гайка;
- 12 — смесительная камера;
- 13 — трубка.
Резка алюминия газом: важные нюансы технологии
Вопросы, рассмотренные в материале:
- Суть процесса газовой резки
- 4 способа резки металла газом
- Технологию кислородно-флюсовой резки алюминия
- Не менее востребованные способы резки алюминия плазмой и лазером
- Газ для лазерной резки алюминия
- Газы для плазменной резки алюминия
Резка алюминия газом – достаточно сложный процесс, имеющий массу нюансов. Дело в том, что применять обычный для данного метода обработки металла кислород тут не представляется возможным, так как последний просто не выделяет нужного количества тепла.
Выход из ситуации был найден с появлением кислородно-флюсовой резки, подробнее о которой мы расскажем в нашей статье. Кроме того, не следует забывать, что методы лазерной и плазменной резки для обработки алюминия также предполагают использование специальных газов.
Суть процесса газовой резки
Процесс резки алюминия газом заключается в нагревании заготовки до температуры около +1 100 °С и последующей подаче в зону реза кислородной струи. При взаимодействии газа с нагретым металлом происходит его воспламенение. Необходимым для раскроя условием является постоянное и стабильное поступление газовой струи. Кроме того, температура горения металла должна быть ниже температуры плавления. Иначе возникнут сложности с удалением из рабочей области частиц, которые расплавились, но не сгорели.
Резка алюминия газом происходит в результате сгорания металла в газовой среде. Операция выполняется с помощью резака, обеспечивающего подачу смеси с нужными пропорциями газа (паров жидкого топлива) и кислородных масс. Резак необходим также для воспламенения газовоздушной смеси и отдельной подачи кислорода в зону реза.
Резка алюминия газом – высокопроизводительный термический способ обработки, позволяющий работать с металлами любой толщины. Ежедневная выработка газосварщика может составлять несколько тонн продукции. К достоинствам этого способа обработки металлов специалисты относят автономность от электрического оборудования. Это важно, так как многие работы ведутся в условиях и на объектах, где источники питания отсутствуют.
Рекомендовано к прочтению
С помощью ручного газокислородного оборудования можно выполнять резку различных металлов. Исключение составляют латунь, нержавеющая сталь, медь и алюминий.
4 способа резки металла газом
Существует несколько методов газовой резки металлов. Разница между ними состоит в используемых для работы газах. Выбор того или иного способа зависит от стоящей перед резчиком задачи. При наличии возможности подключения к питанию можно выбрать кислородно-электрическую дуговую резку. Для работы с низкоуглеродистыми сталями больше подходит газовоздушная смесь с пропаном.
На практике чаще всего применяются следующие виды резки:
- Воздушно-дуговая резка.
Суть высокоэффективной кислородно-электрической дуговой резки заключается в расплавлении металла электрической дугой с последующим удалением из зоны реза частиц расплавленного металла воздушной струей. Подача газа при этом способе обработки выполняется вдоль электрода. Минус способа заключается в небольшой глубине разреза, в то время как его ширина может быть любой.
- Резка пропаном.
Широко распространена резка металлов пропаном и кислородом, однако при использовании этих газов существует ограничение по видам обрабатываемых металлов. Способ подходит для титановых сплавов, низкоуглеродистых и низколегированных сталей. При содержании в сплаве свыше 1 % углерода или легирующих элементов пропановая резка не рекомендуется. Пропан может быть заменен другими газами, например, метаном, ацетиленом и др.
- Копьевая резка.
Кислородно-копьевым способом режут габаритные стальные массивы, технологические производственные отходы и аварийные скрапы. Резка характеризуется увеличенной скоростью обработки. При этом методе используется высокоэнергетичная струя, снижающая расход стальных копий. Высокая скорость процесса обусловлена полным и быстрым сгоранием металла.
- Кислородно-флюсовая резка.
Отличительная черта кислородно-флюсовой резки металлов состоит в подаче в зону реза дополнительного компонента – порошкообразного флюса. Он используется для обеспечения большей податливости обрабатываемого материала в процессе обработки.
Технология кислородно-флюсовой резки алюминия
Результативность кислородно-флюсовой резки металлов на 15–20 % выше за счет мощного пламени и отсутствия необходимости в дополнительном прогревании заготовок. Этот способ является намного более эффективным в сравнении с применяемыми ранее. Благодаря высокой скорости обработки получаются чистые высококачественные края среза. Используемый в процессе флюс обладает высокими термомеханическими или механическими свойствами.
Кислородно-флюсовая резка используется для работы с:
- высоколегированными сталями, содержащими хром и никель, частицы которых при сварке образуют тугоплавкие окислы, не удаляющиеся под воздействием кислородной струи;
- с чугуном и цветными металлами, чувствительным к перепадам температур.
Флюсы могут быть следующих видов:
- алюминиевыми и железными порошками;
- кварцевым песком;
- керамическими (силикокальцием и ферросилицием) для работы с низколегированными сталями;
- феррофосфором, подходящим для резки заготовок из цветных металлов.
Кислородно-флюсовая резка алюминия и других металлов возможна как вручную, так и при помощи специального оборудования. Конструкция последнего состоит из резака, флюсопитателя, передатчика, подающего флюс в резак.
В устройствах для кислородно-флюсовой резки используется металлорежущий инструмент большего диаметра, чем в оборудовании для раскроя с помощью одного кислорода. Газовая среда образуется окислителями, пропаном, азотом, флюсонесущими газами, углекислым газом. Для ручной резки используется специальное устройство – копьедержатель. Машинная обработка выполняется при помощи портальных автоматических устройств и установок. Устройства для ручной и автоматической резки подходят для работы со сталями, чугуном, бетоном, алюминием, различными сплавами цветных металлов.
При работе кислородно-флюсовым способом необходимо рассчитать флюсовый состав для резки заготовки из определенного металла по диаграмме состояния, получения шлакового состава, имеющего минимальную температуру плавления и вязкость. Резаки, используемые при этом способе, отличаются от приспособлений для кислородной резки каналами для подачи газа, имеющими меньший диаметр. Техника раскроя аналогична кислородному способу, но с более мощным пламенем (15–20 %), позволяющим флюсу нагреться до возгорания.
Высокая теплопроводность цветных металлов (латуни, бронзы, медных сплавов) затрудняет работу с ними. Тепла, выделяемого кислородом, недостаточно для резки деталей из цветмета. Для работы с ними к кислороду и флюсовому порошку добавляют дополнительное вещество – феррофосфор. Прежде чем приступить к резке заготовки, ее нагревают до температуры +300…+400 °С. При работе необходимо пользоваться респираторными масками, поскольку выделяемые в процессе раскроя пары вредны для здоровья.
Не менее востребованные способы резки алюминия плазмой и лазером
- Лазерная резка.
Для этого типа резки необходим лазерный резонатор, возбуждающий узконаправленный луч с волной необходимой длины. Луч направляется на обозначенную линию реза и расплавляет металл заготовки за счет сконцентрированной в нем энергии.
Достоинства резки алюминия лазером заключаются в:
- высокой производительности;
- возможности получать детали необходимого размера и конфигурации без дальнейшей доработки;
- отсутствии деформаций кромок среза;
- возможности создавать изделия различной, в том числе сложной, конфигурации.
К такому способу прибегают при необходимости выполнения в заготовках отверстий сложной формы, соблюдения точных размеров допуска и посадки. Благодаря отсутствию контакта с обрабатываемым металлом не происходит его деформация в процессе резки. Суть обработки состоит в передаче импульсного лазерного излучения, возбуждаемого при помощи волоконной, газовой или углекислотной лазерной установки.
- Плазменная резка.
Для создания плазменного потока используется ионизация электрической дугой поступающего под давлением газа. Ионизированный газ (водород, азот, аргон) нагревается до нескольких тысяч градусов по Цельсию. На алюминий и другие металлы оказывается кратковременное высокотемпературное воздействие, расплавленные частицы удаляются из зоны разреза мгновенно.
Достоинства плазменной резки алюминия заключаются в:
- экономичности;
- возможности резать металлы толщиной 200 и более миллиметров;
- высокой производительности;
- широком спектре подвергаемых обработке металлов и сплавов;
- отличном качестве изделий;
- возможности получения изделий сложной конфигурации – как при серийном производстве, так и по индивидуальным чертежам.
При резке газом алюминия и других металлов выбор газа осуществляется исходя из толщины разрезаемой заготовки: менее 20 мм – используется азот, менее 100 мм –смесь азота с водородом, более 100 мм – смесь аргона и водорода.
Газ для лазерной резки алюминия
При лазерной обработке металлов используют 4 вида вспомогательных газов:
- кислород, являющийся активным газом;
- азот, относящийся к условно инертным;
- аргон и гелий – настоящие инертные;
- атмосферный воздух.
Однако лазерная резка именно алюминия выполняется с помощью условно инертного азота, который участвует в химических реакциях, но не является окислителем. А при работе с большинством металлов специалисты стараются не допускать реакций окисления и горения.
Помимо того, что азот не вступает в реакции окисления в области разреза, он вытесняет из нее содержащий кислород атмосферный воздух. Таким образом, О2 также не вызывает окисления краев разреза.
Кислород при резке алюминия газом отрицательно влияет на качество обработки, не позволяя получить чистые и ровные кромки разреза. Выполняя раскрой алюминия с помощью О2, можно получить неровные края с множеством заусенцев. Некоторое время назад он использовался для резки алюминия, так как не существовало более мощного оборудования.Затем неровные кромки изделий обрабатывали механически, повышая их качество. Однако дополнительная механическая обработка увеличивала затрачиваемое на производство время и, соответственно, повышала стоимость готовой продукции.
В настоящее время используется более мощное оборудование, применение азота позволяет сразу получить разрез высокого качества, не требующий дальнейшей обработки кромок. Этот газ подходит для резки алюминия, нержавеющих, высоколегированных сталей, никеля.
Газы для плазменной резки алюминия
Качественный раскрой цветных металлов получается в результате именно плазменной резки. Плазма, с помощью которой выполняют обработку алюминия и его сплавов, образуется за счет использования неактивных газов: водорода, аргона или азота.
Активные газы, например, воздух и кислород, используются для работы с черными металлами.
Резка алюминия газом с использованием плазмореза возможна при толщине заготовок не более 70 мм.
Не подходят для работы с алюминием газовые смеси, в состав которых входят азот и аргон, поскольку они предназначены для обработки высоколегированных сталей толщиной 50 мм.
Резка алюминия чистым азотом возможна, если речь идет о раскрое деталей, толщина которых не превышает 20 мм.
Использование азота и водорода позволяет осуществлять раскрой алюминия и его сплавов при толщине заготовок 100 мм.
Смесь аргона с водородом используется для раскроя заготовок из алюминия толщиной более 100 мм. Содержание водорода в составе должно быть максимум 20 %, в этом случае он обеспечит стабильную горящую дугу.
Качественная серийная резка алюминия газом выполняется с помощью станков с ЧПУ.
Алюминий обладает специфическими характеристиками, что обуславливает необходимость использования иной технологии обработки, чем при раскрое стали. Мастеру необходимо правильно подобрать способ резки, верно выставить исходные параметры (если раскрой осуществляется с помощью автоматизированного оборудования), проконтролировать процесс. Пластичность и вязкость этого металла не позволяют ошибаться в расчетах.
Почему следует обращаться именно к нам
Мы с уважением относимся ко всем клиентам и одинаково скрупулезно выполняем задания любого объема.
Наши производственные мощности позволяют обрабатывать различные материалы:
- цветные металлы;
- чугун;
- нержавеющую сталь.
При выполнении заказа наши специалисты применяют все известные способы механической обработки металла. Современное оборудование последнего поколения дает возможность добиваться максимального соответствия изначальным чертежам.
Для того чтобы приблизить заготовку к предъявленному заказчиком эскизу, наши специалисты используют универсальное оборудование, предназначенное для ювелирной заточки инструмента для особо сложных операций. В наших производственных цехах металл становится пластичным материалом, из которого можно выполнить любую заготовку.
Преимуществом обращения к нашим специалистам является соблюдение ими ГОСТа и всех технологических нормативов. На каждом этапе работы ведется жесткий контроль качества, поэтому мы гарантируем клиентам добросовестно выполненный продукт.
Благодаря опыту наших мастеров на выходе получается образцовое изделие, отвечающее самым взыскательным требованиям. При этом мы отталкиваемся от мощной материальной базы и ориентируемся на инновационные технологические наработки.
Мы работаем с заказчиками со всех регионов России. Если вы хотите сделать заказ на металлообработку, наши менеджеры готовы выслушать все условия. В случае необходимости клиенту предоставляется бесплатная профильная консультация.
Резка трубы газом: способы и оборудование
Вопросы, рассмотренные в материале:
- Что такое резка трубы газом
- Основные методы резки трубы газом
- Какое оборудование применяется для резки трубы газом
- Пошаговую инструкцию по резке трубы газом
- Какие машины применяются при резке трубы газом
Резка трубы газом востребована на рынке металлообработки, так как является одним из наиболее применимых способов резки. Посредством такого метода разрезаются трубы любого диаметра с толщиной стенок до 300 мм.
Существуют разные способы резки трубы с применением газа, для этого используется различное оборудование. О том, как осуществляется данный процесс и какие нюансы необходимо учитывать при подготовке и выполнении работ, читайте далее.
Что такое резка трубы газом
Газовая резка металла (кислородная/автогенная) представляет собой процесс разрезания стальных или металлических заготовок поступающим из специального аппарата кислородным потоком. Металл раскраивается и режется за счет высокотемпературной смеси горючего газа и кислорода, которая подается на обрабатываемый участок изделия.
Сначала заготовку нагревают до температуры +1 300 °С за счет воздействия открытого пламени, после чего на нее направляют кислородную струю, разрезающую металл согласно заданной схеме. Благодаря современным технологиям работать можно с металлическими листами толщиной до 300 мм, а в ряде случаев и до 1 000 мм, независимо от их конфигурации.
При резке газом незначительное количество металла сгорает. Образующиеся под воздействием кислорода окислы (шлак) выдуваются из заготовки кислородной струей.
Резка труб газом подходит для работы с теми металлами, которые под воздействием кислорода воспламеняются при более низкой температуре, чем температура плавления. В качестве примера такого материала можно привести низкоуглеродистую сталь, плавящуюся при температуре +1 500 °С, а воспламеняющуюся при +1 300 °С. Аналогичным образом ведут себя некоторые другие металлы и сплавы, бетон и железобетон. У других металлов (алюминия, чугуна, меди, нержавеющей стали, ряда цветных металлов) температура плавления ниже температуры горения.
Резка труб газом характеризуется:
- невысокой стоимостью;
- отсутствием необходимости в дополнительной обработке краев разреза;
- возможностью обработки изделий под разными углами;
- работой с изделиями независимо от их толщины, включая трубы большого диаметра.
В процессе обработки используются два вида газов: кислород, с помощью которого и выполняется резка металла, и горючий газ (пропан, ацетилен, нефтяной газ, метан, бензин), использующийся для нагрева заготовки.
Рекомендовано к прочтению
Основные методы резки трубы газом
- Копьевая резка.
Такой метод резки труб газом подходит для изделий большого диаметра, изготовленных из чугуна, нержавеющей и низкоуглеродистой стали. В основе метода лежит прижимание к обрабатываемой поверхности копья, нагретого до температуры плавления материала заготовки. Широко применяется в таких сферах, как машиностроение и металлургия.
- Кислородно-флюсовая резка.
Для резки труб, изготовленных из высоколегированных хромистых и хромоникелевых сплавов, используется кислородно-флюсовый способ. Его отличительной чертой является введение в струю кислорода порошкообразного флюса, выступающего в качестве дополнительного источника нагрева.
- Воздушно-дуговая резка.
Трубы разрезаются электрической дугой. Газ при этом поступает вдоль электрода.
- Резка пропаном.
Обработка титановых заготовок, труб, выполненных из низколегированных и низкоуглеродистых стальных сплавов, осуществляется с использованием пропана. Максимальная толщина обрабатываемых изделий не может превышать 300 мм.
В процессе кислородной резки некоторое количество материала сгорает, образуя окислы (шлак), выдуваемые кислородной струей. Этот способ используется для металлов, которые воспламеняются при более низкой температуре, чем температура их плавления.
Например, низкоуглеродистая сталь плавится при температуре +1 500 °С, в то время как гореть она начинает уже при +1 350 °С. У большей части высоколегированных сталей и цветных металлов, чугуна температура горения превышает температуру плавления.
Для поставки кислорода используются стальные баллоны голубого цвета объемом 40 л и весом 67 кг. Кислород в баллонах сжижен под давлением 150 кгс/см2.
Для поставки ацетилена используются баллоны белого цвета объемом 40 л или 50 л, диаметром 219 мм, весом 52 кг или 64 кг соответственно. На баллоны наносится надпись «Ацетилен». Газ сжижен под давлением 16 кгс/см2. Кроме того, возможно получение газа из карбида кальция при помощи ацетиленовых генераторов. Для получения 230–280 л газа необходим 1 кг карбида кальция.
Помимо ацетилена, при кислородной резке используются пропанобутановая смесь, метан, пары керосина, бензина.
Поскольку отличительной чертой смеси горючих газов с воздухом и кислородом является их взрывоопасность, резка труб газом должна выполняться в хорошо проветриваемых и вентилируемых помещениях.
В процессе добычи и переработки нефти и нефтяных газов образуются пропанобутановые смеси, используемые при кислородной резке. Газовая смесь сжижается под давлением от 1 до 8 кгс/см2. Для хранения и транспортировки используются тонкостенные стальные баллоны красного цвета объемом 40–55 л, в которых газ находится под давлением не более 17 кгс/см2.
Испарение 1 кг сжиженной газовой смеси приводит к образованию 500 л газа.
Основу природных газов, которые получаются при разработке газовых месторождений, составляет метан с небольшой примесью других газов (соотношение составляет примерно 90 % метана и 10 % иных примесей). Чаще всего газы поставляют на места использования по газопроводам, реже – транспортируют в баллонах красного цвета.
Для ацетилено-кислородной сварки и резки труб газом необходимы:
- ацетиленовые генераторы или баллоны с газом;
- кислородные баллоны;
- редукторы, снижающие давление;
- газовые горелки или резаки.
Ацетиленовые генераторы преобразуют карбид кальция в ацетилен под воздействием воды.
Кислород и горючий газ смешиваются в газосварочных горелках в пропорциях, обеспечивающих устойчивое сварочное пламя. В зависимости от принципа действия горелки могут быть инжекторными и безынжекторными.
В отличие от горелок, резаки для кислородной обработки труб дополнены трубкой и вентилем режущего кислорода, а также специальной головкой с несколькими соплами. Резаки классифицируются в зависимости от используемого газа (могут быть ацетиленовыми, для газов, используемых вместо ацетилена, для жидких горючих), а также в зависимости от принципа действия (могут быть инжекторными и безынжекторными).
Чаще всего для резки труб газом пользуются универсальными ацетилено-кислородными устройствами РР53, а также вставными ацетилено-кислородными резаками РГС53 и РГМ53, дополняющими горелки ГС53 и ГСМ53. С помощью вставных резаков облегчается выполнение монтажных и строительных работ, требующих попеременного применения как сварки, так и резки.
Для снижения и поддержания давления сжиженного газа в баллоне до необходимого для работы уровня используются редукторы.
Какое оборудование применяется для резки трубы газом
Обработку металлов выполняют ручным и автоматизированным способами. В первом случае применяется оборудование, предназначенное для резки труб газом.
Газопламенная резка труб производится ручным способом по разметке при помощи специального оборудования, а также на автоматических станках. Для ручной обработки используются ручные ацетилено-кислородные, бензино- и керосинокислородные резаки. Данный процесс достаточно трудоемок и требует от мастера высокой квалификации.
Для заготовок, полученных в результате ручной резки труб газом, характерны неровные края, неправильные углы и формы фасок под сварку. В связи с этим соединение труб и деталей затруднено. По окончании ручного процесса необходима дополнительная обработка кромок, в течение которой им придается нужная форма и размеры. Такая обработка осуществляется с помощью пневматических зубил, шлифовальных машинок и напильников.
Автоматическая резка труб газом более эффективна. Во время обработки используются специальные полуавтоматические приспособления или станки. Такие установки отличаются простыми конструкциями, легкостью обслуживания, небольшим весом, что позволяет пользоваться ими не только в стационарных условиях.
При оборудовании цехов трубозаготовительных баз и заводов используют стационарные станки, предназначенные для резки труб газом.
Принцип работы станка заключается в следующем. Пневмоцилиндр прижимает обрабатываемую заготовку верхним роликом к ведущим роликам фрикционного вращателя. Такое оборудование позволяет работать с трубами разного диаметра без перенастройки. Резак, расположенный на одном рычаге с верхним прижимным роликом, автоматически подводится и отводится от детали.
Эффективность и производительность оборудования увеличена за счет автоматизации основных и вспомогательных операций. Управление станком осуществляется с общего пульта мастером-газорезчиком.
Если необходима магистральная прокладка труб, используется автоматизированное оборудование с несколькими режущими головками. Такой способ обработки отличается высокой точностью и скоростью работы.
Самое простое оборудование, позволяющее выполнять газовую резку труб, включает:
- газовую горелку;
- регулятор давления;
- шланги;
- смесители;
- газовые баллоны.
Газосварочная горелка представляет собой резак, смешивающий кислород и горючий газ в нужном соотношении, создающий и поддерживающий постоянное пламя для резки.
Резак оснащен специальной головкой с определенным количеством сопел. Внешние сопла смешивают горючий газ (ацетилен, пропан, метан) и кислород, нагревая заготовку до нужной температуры. Центральное – подает кислородную струю, разрезающую трубу.
Обработка невозможна без газовых баллонов (кислородного и с горючим газом), двухслойных резиновых шлангов диаметром от 6 до 12 мм, подающих газ. Шланги рассчитаны на воздействие температуры до -30…- 35 °С.
Пошаговая инструкция по резке трубы газом
Резка труб газом требует предварительной подготовки, снижающей вероятность повреждения оборудования, заготовок, травмирования резчика.
Подготовка включает:
- Визуальный осмотр баллонов, соединительных шлангов, крепежных элементов, горелки. Оборудование не должно иметь внешних повреждений, видимых дефектов.
- Оценку запаха воздуха, позволяющая определить утечку газа. Горелка соединяется с баллонами шлангами, зажимаемыми хомутами. Горючий газ не должен прорываться из емкостей.
- Осмотр резиновых уплотнителей. Наличие трещин, измененная форма требует немедленной замены их новыми.
- Визуальный осмотр баллонов и другого оборудования, в процессе которого необходимо установить отсутствие жировых пятен, потеков масла. Даже незначительное количество масла может спровоцировать взрыв.
Резку труб газом осуществляют в соответствии с инструкцией. Необходимо:
- открыть кислородный вентиль;
- открыть вентиль на баллоне с горючим газом;
- поджечь газовую струю, выходящую из сопла горелки;
- отрегулировать скорость газового потока при помощи вентилей;
- нагреть металлическую заготовку до изменения ее цвета на соломенный;
- открыть кислородное сопло на горелке и выполнить непосредственно резку;
- после обработки в первую очередь перекрыть баллон с горючим газом, затем с кислородом.
Какие машины применяются при резке трубы газом
Аппаратура для резки труб газом должна быть:
- портативной, иметь небольшие размеры;
- разборной;
- простой в обслуживании;
- позволять работать при минимуме обслуживающего персонала.
Один из недорогих станков – «Орбита» – позволяет работать как в стационарном цехе, так и на производственных участках.
Среди иностранных аппаратов стоит отметить немецкие станки ZINSER, выпускаемые как с ручным, так и с электрическим приводом.
Аппараты серии CG2 (к примеру, CG2-11G, CG2-11 и т. п.) схожи со станками «Орбита», но у них нет направляющих бандажей.
Важно иметь в виду, что при отсутствии опыта работы с подобным оборудованием его самостоятельное использование для резки труб газом может быть опасным, поэтому оптимальным вариантом будет обращение к специалистам.
Почему следует обращаться именно к нам
Мы с уважением относимся ко всем клиентам и одинаково скрупулезно выполняем задания любого объема.
Наши производственные мощности позволяют обрабатывать различные материалы:
- цветные металлы;
- чугун;
- нержавеющую сталь.
При выполнении заказа наши специалисты применяют все известные способы механической обработки металла. Современное оборудование последнего поколения дает возможность добиваться максимального соответствия изначальным чертежам.
Для того чтобы приблизить заготовку к предъявленному заказчиком эскизу, наши специалисты используют универсальное оборудование, предназначенное для ювелирной заточки инструмента для особо сложных операций. В наших производственных цехах металл становится пластичным материалом, из которого можно выполнить любую заготовку.
Преимуществом обращения к нашим специалистам является соблюдение ими ГОСТа и всех технологических нормативов. На каждом этапе работы ведется жесткий контроль качества, поэтому мы гарантируем клиентам добросовестно выполненный продукт.
Благодаря опыту наших мастеров на выходе получается образцовое изделие, отвечающее самым взыскательным требованиям. При этом мы отталкиваемся от мощной материальной базы и ориентируемся на инновационные технологические наработки.
Мы работаем с заказчиками со всех регионов России. Если вы хотите сделать заказ на металлообработку, наши менеджеры готовы выслушать все условия. В случае необходимости клиенту предоставляется бесплатная профильная консультация.
это, по металлу, воздушная, станок, ручная, с ЧПУ, принцип работы, инверторная, ремонт аппаратов – Газовая сварка на Svarka.guru
Плазменная резка – это современный метод теплового разделения металлических заготовок. Метод основан на использовании энергии ионизированного газа и отличается исключительно высокой температурой струи (до 30 тысяч градусов), позволяющей быстро и точно резать самые тугоплавкие сплавы и металлы.
Газоплазменная резка используется как на больших стационарных станках, так и в ручных установках ограниченной мощности.
Что представляет собой процесс?
Для ионизации потока газа используются два фактора:
- электродуга;
- сужение сопла в месте истечения, существенно поднимающее давление в струе.
Под таким воздействием атомы газа теряют электроны со своих орбит, превращаясь в положительно заряженные ионы. Сами электроны служат отрицательно заряженными ионами. Вещество превращается в плазму, разогретую до очень высоких температур.
Плазменная струя направляется на заготовку, испаряет металл в зоне контакта и выносит его за пределы зоны разреза.
Сравнение с лазерной
Плазменная и лазерная резка металла — это два наиболее современных способа раскроя.
Лазерный раскрой металла основан на действии высокоэнергетического светового луча, сконцентрированного в очень узкий пучок. Луч лазера испаряет молекулы, после него остается очень тонкий и гладкий разрез.
Толщина заготовки для современных лазерных резаков ограничена 20 мм. При этом они демонстрируют высокую производительность.
Лазерная резка благодаря высокой концентрации энергии очень мало разогревает заготовку, сводя к минимуму тепловые деформации, особенно для тонколистовых деталей.
Плазмообразующие газы
Газы для плазменной резки делятся на две группы. К перовой относятся инертные и малоактивные, такие, как аргон, азот, водород, реже аммиак и гелий. Ко второй — активные газы: кислород, углекислый газ, водяной пар, подготовленный воздух.
Применимость газов и их смесей для резки.Подготовка воздушных масс заключается в тщательной фильтрации от механических загрязнений и удалении частиц масла и воды на сепараторах.
Принцип работы
Принцип действия плазменного резака основан на использовании высокой тепловой энергии ионизированного газа, или плазмы. Для ее получения струю газа подвергают резкому сжатию, одновременно на нее воздействуют электродугой. Дуга разжигается между центральным вольфрамовым электродом и соплом, либо между электродом и заготовкой. Поток плазмы направляют в зону разреза, там он испаряет узкую область металла, формируя линию разделки. Во избежание перегрева в сопло встроена система жидкостного охлаждения.
Резак прямого действия
Предварительная дуга будет зажигаться между заготовкой и вольфрамовым электродом. Она ионизирует газ, и далее рабочий разряд идет уже через него. Применяется для резки металлов, имеющих высокую проводимость.
Прямое (слева) и косвенное (справа) действие.Косвенного
Таким способом можно резать низкопроводящие металлы и даже диэлектрические материалы. Дуга разжигается между центральным неплавким электродом и латунным соплом. На заготовку действует только поток плазмы. Такие плазмотроны обходятся дороже и при покупке, и в эксплуатации.
Преимущества
Плазменный резак обладает следующими достоинствами:
- справляется с любыми металлами и сплавами, в том числе самыми тугоплавкими;
- высокая скорость резки;
- высокая точность, уступающая лишь лазерной;
- рез под углом, фигурная резка;
- возможность работы с любой толщиной заготовки;
- минимум отходов и вредных выделений;
- высокая безопасность работы.
Присущ методу и ряд недостатков:
- цена оборудования;
- дорогостоящее обслуживание и ремонт аппаратов;
- высокая шумность во время работы.
Тем не менее, сопоставляя выгоды и недостатки, все больше предприятий и частных мастерских делают свой выбор в пользу прогрессивного метода раскроя.
Какое оборудование применяют?
Применяется две большие группы плазморезательного оборудования:
- Индустриальные установки для раскроя листовых заготовок. Это высоко автоматизированные комплексы, работающие под программным управлением. Плазменные резаки крепятся на подвижных порталах или на манипуляторах.
- Ручной плазменный резак по металлу. Устройство размером со средний инверторный аппарат, справляется с листом в 1-2 см толщиной. Линией реза управляет рука оператора. Портативный резак снабжен также системой осушения и отделения масла из воздуха.
Выбор аппарата
Чтобы правильно выбрать оборудование, нужно исходить из своих потребностей. Для их оценки нужно спрогнозировать объем и номенклатуру работ, которые будут выполняться с помощью резака.
При ограниченном объеме работ подойдет инвертор для плазменной резки. Он экономичен, компактен, легко переносится к месту работы. Однако такие устройства перегреваются и требуют периодического охлаждения.
Для серьезной работы в течение всей смены потребуется трансформаторное устройство. Оно обладает серьезными массогабаритными характеристиками и может разрезать заготовки большой толщины.
По мощности
Потребляемая мощность определяет максимальный рабочий ток, и, следовательно, максимальную толщину раскраиваемых заготовок. Детали до 3 см поддадутся резаку с током 90 ампер. Более солидные детали потребуют от 100 до 170 ампер.
Соответственно мощности подбирается форма и размер наконечника сопла.
По времени и скорости разрезания материала
Скорость резания зависит от следующих факторов:
- материал заготовки;
- ее толщина;
- рабочий ток.
Так, алюминий будет разрезан существенно быстрее стали.
[stextbox id=’alert’]Если скорость резания — критически важный параметр, нужно уделить внимание времени беспрерывной работы устройства.[/stextbox]
Горелка
Мощность горелки следует выбирать, исходя из оценок объемов работы и средней продолжительности разреза. Ее должно хватать для того, чтобы успеть выполнить этот разрез за один прием, между двумя стадиями охлаждения.
Сопло опытные резчики советуют брать медное, оно лучше других материалов охлаждается.
Рукоятка должна удобно лежать в руке и снабжена съемным ограничителем, поддерживающим постоянное расстояние до детали.
Для непродолжительного раскроя тонколистовых заготовок подойдет воздушная горелка. Для работы с толстыми деталями лучше выбрать азотную.
Внешние характеристики
Если места разрезов удалены друг от друга, как это, например, происходит при демонтаже металлоконструкций, важными параметрами становятся масса и размеры устройства.
Свойства технологии
Аппараты профессионального и бытового класса имеют сходные конструкции и принцип действия:
- розжиг начальной электрической дуги;
- ионизация газовой струи;
- применение скоростного потока плазмы для резки металла.
Для технологии свойственны:
- Температура струи. Для цветных металлов и их сплавов устанавливают 5 тысяч оС, для высокотемпературных стальных сплавов- максимальное значение в 30 тысяч оС.
- Скорость истечения струи. Меняется в диапазоне 450-1600 метров в секунду. Определяется материалом и толщиной детали, криволинейностью линии реза.
- Ширина реза. Определяется типом сопла.
- Скорость резания. Достигает 6-7 метров в минуту.
[stextbox id=’warning’]С ростом толщины заготовки ширина реза увеличивается, а скорость уменьшается.[/stextbox]
Качество поверхности
Определяется квалификацией резчика и нормативными документами. Качество важно для последующей сварки. Задаются следующие параметры:
- отклонение линии реза от перпендикуляра к поверхности;
- оплавление кромки;
- класс шероховатости.
Качество поверхности после плазменной резки уступает только лазерной.
Виды
Различают следующие подвиды метода:
- Обычная. В качестве плазмообразующего газа применяется подготовленный воздух. Используется для обычной конструкционной низкоуглеродистой стали.
- Водная. Создаваемая водная завеса способствует охлаждению сопла и защищает рез от контакта с кислородом воздуха. Применяется для высоколегированных сплавов.
- В защитной газовой среде. Плазмообразующий инертный (или малоактивный) газ создает защитную атмосферу, предотвращающую. доступ воздуха к линии разреза. Используется для цветных и легких металлов, а также их сплавов.
По способу создания дуги и воздействия плазмы на материал заготовки различают также плазменно-дуговую и струйную резку.
Лазерноплазменная
Этот метод состоит в совместном применении плазменного пучка и лазерного луча в одной горелке. Лазерная установка применяется при раскрое заготовок не толще 6 мм. Если нужно разделать более серьезные детали, в ход идет плазменный резак. Такие станки выгодны небольшим предприятиям с широкой номенклатурой и средним объемом заказов. Они снабжены системой ЧПУ, позволяющей использовать компьютерные программы построения оптимальных раскроев. Единая решетка для размещения листов позволяет экономить время на подготовительно- завершающих операциях.
Области применения
Технология активно используется в следующих областях:
- раскрой листового металла;
- раскрой профильного проката;
- демонтаж металлоконструкций;
- художественная резка по металлу, создание декоративных изделий.
Раскрой заготовок применяется во всех машиностроительных отраслях, производстве сложных строительных конструкций и транспортных средств.
С увеличением выпуска ручных плазморезов их цена становится доступна и домашним мастерам, выполняющим много операций по разделке или демонтажу.
Точность и скорость резания
Точность и скорость резания не находятся в однозначной зависимости друг от друга. Если вести горелку слишком быстро, возможны частичные непрорезы. Если же, наоборот, задерживать ее на каких-либо участках, они будут перегреваться и может случиться прожог или термическая деформация.
Опытный и квалифицированный резчик выбирает скорость работы, исходя из материала заготовки и ее толщины. Он ведет горелку с постоянной скоростью, ровно и на постоянном расстоянии от детали.
Нормальной является конусность разреза от 3 до 10о. Допускается также оплавление кромок в начале линии.
Обработка цветных сплавов
При разделке цветных металлов и их сплавов следует соблюдать следующие рекомендации:
- Алюминий. При грубой скоростной разделке заготовок не толще 7 см в качестве газа применяется подготовленный воздух. Если нужно улучшенное качество поверхности реза или толщина доходит до 10 см, используют азот. Для деталей толще 10 см применяют аргонно-водородную смесь.
- Медь. Также рекомендована смесь аргона и водорода.
- Титан. Ввиду тугоплавкости металла и его сплавов, а также их высокой химической активности нагретого титана приходится применять аргон либо гелий.
Если же требуется особо точный раскрой или проводится формирование изделий со сложной пространственной формой, все чаще прибегают к лазерной резке цветных металлов.
Тонкости процесса раскроя металла
Главная тонкость в ходе плазменной резки — это выбор и поддержание правильного расстоянии от горелки до заготовки. При его занижении увеличивается ширина разреза и область температурного воздействия. Это может вызвать появление термических деформаций.
При пробивке сквозных отверстий расстояние увеличивают до 20-25 мм, далее горелку подводят на рабочую дистанцию.
Рабочий ток следует выставлять минимально возможный для стабильного горения дуги и плазменного пучка. Превышение минимальных значений ведет к повышенному расходу газа и износу сопел.
Как пользоваться плазморезкой?
Опытные резчики сформулировали ряд рекомендаций для облегчения освоения технологии начинающим мастерами:
- строго соблюдать постоянное расстояние от горелки до заготовки;
- при необходимости пользоваться упором, крепящимся сбоку на горелке и ограничивающим зазор;
- вести горелку равномерно, без рывков, с заданной скоростью;
- следить за перпендикулярностью плазменного пучка к поверхности детали отклонения приводят к снижению качества поверхности разреза;
- следить за пучком искр, вылетающих с тыльной стороны детали, если их мало или они пропали — металл прорезается не полностью и надо корректировать режим резки;
После завершения разреза горелку необходимо наклонить, чтобы дать выйти газам, скопившимся в шланге.
Газокислородная резка
Сущность процесса заключается в сгорании металла в струе химически чистого кислорода, с последующим удалением этой струёй продуктов окисления из зоны реза (выдуывом).
Условия для газовой резки
- Температура плавления металла должна быть выше температуры его воспламенения в кислороде. (Для Ст.З температура плавления −1539°С, а температура воспламенения — 1100-1200°С.) Углерод заметно снижает температуру плавления. Поэтому высокоуглеродистые стали и чугуны резать обычным резаком невозможно.
- Температура плавления металла должна быть выше температуры плавления его окислов. Иначе пленка окислов будет препятствовать доступу кислорода к металлу и горения (резки) не будет. (Окисел хрома имеет температуру плавления 2270°С, а температура плавления для Ст.З −1539°С).
- Окислы, образующиеся при резке должны быть достаточно жидко-текучими. При их избытке они налипают на кромки реза, и удалить их очень трудно (Окислы кремния, хрома и др. обладают высокой вязкостью). И можно потратить очень много времени причем малорезультативно на их удаление.
- Металл должен плохо проводить тепло, иначе тепла от пламени не хватит, чтобы нагреть кромку перед началом резки.
Качество резки
На качество резки влияет:
- расход кислорода. Недостаток кислорода приводит к неполному окислению металла и не интенсивному удалению окислов; а избыток — к охлаждению и выносу тепла из зоны резки.
- чистота кислорода. Снижение чистоты влияет на качество кромок реза; Чем ниже чистота, тем больше налипает трудноотделимого шлака на нижней кромке реза.
- мощность подогревающего пламени; В зависимости от состава смеси пламя бывает окислительным, нормальным и науглероживающим. Окислительное — для резки стали толщиной 3–8 мм. Нормальное — для толщин 10–100 мм. Науглероживающее — для больших толщин.
- общая длина пламени должна быть больше толщины разрезаемого металла.
Скорость резки
При малой скорости — оплавляются кромки, при большой скорости — неразрезание металла из-за отставания кислородной струи.
Правильность выбора скорости можно определите визуально по направлению пучка искр, выходящих из нижней стороны реза (см. рис).
Подготовка к резке металла
Весь металл, поступающий на ручную резку, должен быть тщательно очищен от окалины, ржавчины, краски, масел, благи и других загрязнений, которые могут привести к снижению скорости резки и ухудшению качества обработки кромок.
Под воздействием пламени некоторые загрязнения выгорают, образуя газообразные продукты, которые засасываются в зону реза, смешиваются с кислородом и ухудшают условия сгорания металла. Загрязнения на нижней кромке реза разогреваются до высоких температур и способствуют налипанию шлака.
Подготовка оборудования для резки
Обрабатываемый металл уложите в удобное положение, предпочтение отдается всегда нижнему.
При необходимости резку можно проводить во всех положениях. Для того чтобы расплавленный шлак свободно вытекал из зоны реза, под разогреваемым листом должно быть свободное пространство L (мм), L = S/2 + 100, де S — толщина разрезаемого металла, мм; В зависимости от толщины разрезаемого металла установите необходимые внутренний и наружный мундштуки. |
Перед тем как зажечь резак
Убедитесь в исправности оборудования и проверьте:
а) герметичность присоединения рукавов, всех разъемных и паяных соединений;
б) убедитесь в наличии инжекции.
Осмотр резака
Осмотр резака на примере Р1 «ДОНМЕТ» 150П
Внимание! В случае появления непрерывных хлопков или обратного удара, быстро закрыть вентили горючего газа, затем кислорода и охладить резак. После возникновения обратного удара прочистить и продуть инжектор, смесительную камеру и мундштуки, подтянуть мундштуки и гайки, проверить герметичность резака.
Запрещается!
- Продолжать работы в случае возникновения обратного удара пламени; при невозможности регулировки состава пламени по горючему газу или выявления неисправности аппаратуры, приборов и защитных средств, нарушения крепления баллонов.
- Держать во время работы рукава на плечах, ногах, под мышками или обмотанными вокруг пояса.
- Перемещаться с зажженным пламенем резака. Выполнять резку сосудов, находящихся под давлением или содержащим легко воспламеняющиеся и взрывчатые вещества.
- Оставлять резак с зажженным пламенем при вынужденном прекращении работ или удалении рабочего от рабочего места.
Резка металла
Для того чтобы получить качественный рез, выполните порядок действий, указанный на рисунке.
После окончания резки
- Закройте кислородный вентиль, и затем вентиль горючего газа на резаке. Если сделать в обратном порядке, то может произойти «хлопок». «Хлопок» отбрасывает углеродистую сажу назад в горелку и может со временем частично забить газовые проходы.
- Закройте вентили на баллонах.
- Откройте кислородный вентиль на стволе резака. Выпустите кислород из системы. Закройте кислородный вентиль резака.
- Поверните регулировочный винт на редукторе кислорода против часовой стрелки, чтобы освободить пружину.
- Откройте вентиль горючего газа ствола резака. Выпустите газ из системы. Закройте газовый вентиль резака.
- Повернуть регулировочный винт на редукторе горючего газа против часовой стрелки, чтобы освободить пружину.
- Проверьте манометры высокого давления на редукторах через несколько минут, чтобы убедиться, что вентили баллона полностью закрыты.
- Содержите резак в чистоте, периодически очищайте мундштуки от нагара и брызг металла.
- Отсоедините резак от рукавов.
- Аккуратно сверните рукава.
- Уберите с рабочего места инструменты и средства индивидуальной защиты.
- Уберите рабочее место от шлака, обрезков металла и прочего мусора
- По окончании работ не покидайте рабочее место, не убедившись в отсутствии очага, способного вызвать пожар на месте проведения работы.
типов резаков | Он все еще работает
Пол Новак
Сварщик за работой изображение Сергея Костюценко с Fotolia.comВ процессах, связанных с резкой металла, используются различные методы удаления материала с металла, чтобы отделить желаемые части металла от нежелательных. В дополнение к механическим методам, которые используют пилы по металлу, сверла и шлифовальные машины для удаления материала, для резки могут использоваться тепло и электрическая энергия. Эти методы обладают преимуществами быстрого резания твердых металлов и снижения износа используемых инструментов.
Кислородно-ацетиленовые горелки
Кислородно-ацетиленовые горелки режут металл, используя кислород для сжигания металла. Ацетиленовое пламя нагревает металл до температуры воспламенения, а затем добавляет кислород, чтобы повысить температуру пламени и выжечь удаляемый металл. Теплота кислородного пламени заставляет элементы в металле под пламенем окисляться в результате химической реакции. Давление кислородного пламени, выходящего из горелки, отталкивает обожженный металл от пути резания и приводит к отделению металла.Кислородно-ацетиленовые горелки работают только с металлами, которые легко окисляются, за исключением меди и алюминия.
Плазменный резак
Плазменный резак использует ионизированный газ, выпускаемый с высокой скоростью из небольшого отверстия для плавления металла. Ионизированный газ проводит электрическую энергию от горелки к металлу, который воспламеняет ионизированный газ и создает плазму. Перегретая плазма плавит металл на своем пути, и высокое давление газа, когда он выходит из резака, сдувает расплавленный металл с пути резания, разделяя металл.Плазменные резаки полагаются на механическую резку металла путем плавления и отвода расплавленного металла от рабочей зоны, а не на сжигание металла, что делает плазменные резаки эффективными для любого металла, который будет проводить электричество.
Лазерная резка
Лазерные резаки расплавляют металл на пути тонкого, плотно сфокусированного луча интенсивной энергии, нагревая сильно локализованную область, которая плавит и испаряет металл, с которым соприкасается. Материал, сгоревший или расплавленный лазером, затем либо уносится газами под высоким давлением, либо испаряется, что приводит к отделению металла.Лазерные резаки чаще всего управляются компьютером для получения чистого и точного разреза и используются там, где необходима точная и сложная резка металлов и других материалов.
Еще статьи
▷ Продажа машин для газовой резки
Оборудование для газовой резки
Сравнение газовой резки и газовой сварки
Кусок металла, разрезаемый газовой горелкойПроцесс газовой резки — это процедура термической резки металла, при которой тепловая энергия, производимая кислородным пламенем и пламенем горящего газа (ацетилена, пропана или природного газа), используется для резки металла.Это старейшая процедура, применяемая в промышленности с 1908 года. Процесс газовой резки противоположен газовой сварке, которая представляет собой процесс соединения металлов путем приложения тепла, создаваемого газовым пламенем. Машины газовой резки, такие как газорезательная машина с ЧПУ и автоматическая газорезательная машина, используют ацетилен и кислород для предварительного нагрева металла до докрасна, а затем используют чистый кислород для сжигания предварительно нагретого металла. Поскольку это достигается за счет окисления, он эффективен только для металлов, таких как низкоуглеродистая сталь и низколегированные стали, которые легко окисляются при этой температуре.Инструменты для газовой резки можно использовать для резки толщиной от 2/8 ″ до 12 ″.
Работа газорезательного аппарата
Резка листового металла газовым резакомОборудование и принадлежности для газокислородной резки такие же, как и для газовой сварки, за исключением того, что вы используете газовый резак в комплекте с комплект газовой резки, вместо сварочной горелки. Основное различие между резаком и сварочной горелкой заключается в том, что резак имеет дополнительную трубку для кислорода высокого давления, а также режущий наконечник или сопло.В наконечнике имеется центральное отверстие, через которое проходит струя чистого кислорода. Смешанный кислород и ацетилен проходят через отверстия, окружающие центральные отверстия для пламени предварительного нагрева. Количество отверстий для оксиацетиленового пламени варьируется от 2 до 6, в зависимости от цели, для которой используется наконечник. Резак управляется спусковым крючком или рычажным клапаном. Резак снабжен сменными наконечниками для резки стали толщиной от менее ¼ ”до более чем 12,0”. Газовая резка может производиться вручную или с помощью машины, называемой газорезательной машиной.Ручная резка используется для общих работ и для резки по прямой. При машинной резке резак устанавливается на рельсе, и оба рельса и резак могут перемещаться одновременно по двум взаимно перпендикулярным осям в горизонтальной плоскости с помощью серводвигателей. Роботизированные кислородно-топливные резаки позволяют производить практически любую форму из больших стальных листов. Предусмотрена возможность удержания более одного резака, чтобы можно было резать большое количество одинаковых деталей одновременно.
Области применения газовой резки
- Газовая резка будет полезна только для тех материалов, которые легко окисляются, а оксиды имеют более низкие температуры плавления, чем металлы.Поэтому он наиболее широко используется для черных металлов.
- Кислородная резка не может применяться для таких материалов, как алюминий, бронза, нержавеющая сталь, которые имеют тенденцию сопротивляться окислению.
- Резка высокоуглеродистых сталей и чугунов требует особого внимания из-за образования зоны термического влияния (ЗТВ), в которой происходит структурное преобразование.
▷ Продажа оборудования для газовой резки
Оборудование для газовой резки
Сравнение газовой резки иГазовая сварка
Кусок металла, разрезаемый газовой горелкойПроцесс газовой резки — это процедура термической резки металла, при которой тепловая энергия, производимая пламенем кислородного пламени и горящего газа (ацетилена, пропана или природного газа), используется для резки металл. Это старейшая процедура, применяемая в промышленности с 1908 года. Процесс газовой резки противоположен газовой сварке, которая представляет собой процесс соединения металлов путем приложения тепла, создаваемого газовым пламенем. Машины газовой резки, такие как газорезательная машина с ЧПУ и автоматическая газорезательная машина, используют ацетилен и кислород для предварительного нагрева металла до докрасна, а затем используют чистый кислород для сжигания предварительно нагретого металла.Поскольку это достигается за счет окисления, он эффективен только для металлов, таких как низкоуглеродистая сталь и низколегированные стали, которые легко окисляются при этой температуре. Инструменты для газовой резки можно использовать для резки толщиной от 2/8 ″ до 12 ″.
Работа газорезательного аппарата
Резка листового металла газовым резакомОборудование и принадлежности для газокислородной резки такие же, как и для газовой сварки, за исключением того, что вы используете газовый резак в комплекте с комплект газовой резки, вместо сварочной горелки.Основное различие между резаком и сварочной горелкой заключается в том, что резак имеет дополнительную трубку для кислорода высокого давления, а также режущий наконечник или сопло. В наконечнике имеется центральное отверстие, через которое проходит струя чистого кислорода. Смешанный кислород и ацетилен проходят через отверстия, окружающие центральные отверстия для пламени предварительного нагрева. Количество отверстий для оксиацетиленового пламени варьируется от 2 до 6, в зависимости от цели, для которой используется наконечник. Резак управляется спусковым крючком или рычажным клапаном.Резак снабжен сменными наконечниками для резки стали толщиной от менее ¼ ”до более чем 12,0”. Газовая резка может производиться вручную или с помощью машины, называемой газорезательной машиной. Ручная резка используется для общих работ и для резки по прямой. При машинной резке резак устанавливается на рельсе, и оба рельса и резак могут перемещаться одновременно по двум взаимно перпендикулярным осям в горизонтальной плоскости с помощью серводвигателей. Роботизированные кислородно-топливные резаки позволяют производить практически любую форму из больших стальных листов.Предусмотрена возможность удержания более одного резака, чтобы можно было резать большое количество одинаковых деталей одновременно.
Области применения газовой резки
- Газовая резка будет полезна только для тех материалов, которые легко окисляются, а оксиды имеют более низкие температуры плавления, чем металлы. Поэтому он наиболее широко используется для черных металлов.