Сталь химическое пассивирование — Справочник химика 21
Основной объем производства труб приходится на горячекатаные трубы и сварные. Химическая обработка горячекатаных труб из нержавеющих сталей включает травление с целью удаления окалины, травление для выявления дефектов, пассивирование труб, обезжиривание. [c.75]ХИМИЧЕСКОЕ ПАССИВИРОВАНИЕ СТАЛИ 8 ВОДЕ ВЫСОКОЙ ЧИСТОТЫ [c.122]
Большое значение для коррозионных процессов имеет способность металла образовывать на поверхности прочные оксидные пленки. Так, алюминий окисляется легче железа, но он более стоек к коррозии, так как окисляясь кислородом воздуха, покрывается плотной пленкой оксида. На этом явлении основана пассивация металлов, заключающаяся в обработке их поверхности окислителями, в результате чего на поверхности металла образуется чрезвычайно тонкая и плотная пленка, препятствующая оррозии.
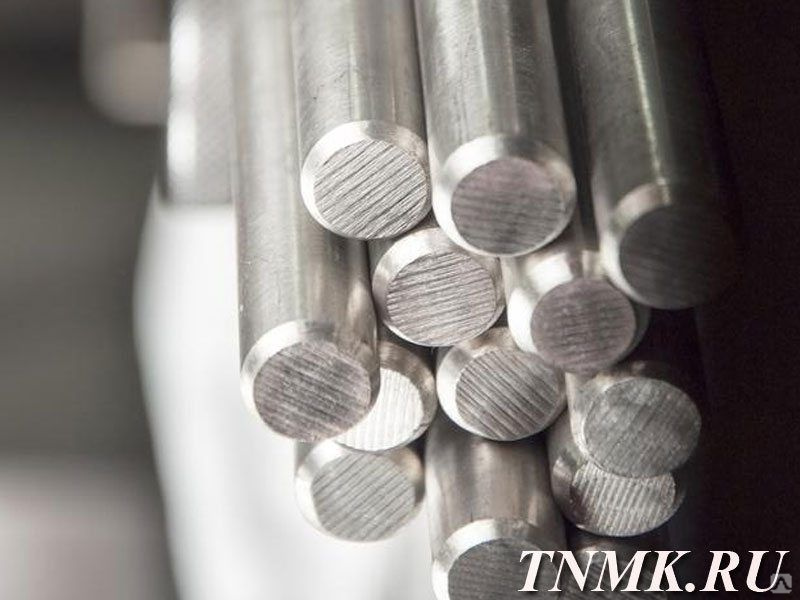
Однако нередко наблюдаются случаи, когда вновь образовавшееся химическое соединение образует на твердой поверхности сорбента столь прочную пленку, что через нее дальнейший доступ молекул газа вглубь сорбента совершенно прекращается, и таким образом хемосорбция приобретает кажущийся адсорбционный характер. В качестве примера можно привести процесс пассивирования стали путем азотирования ее поверхности, сопровождающегося образованием на этой поверхности тонкой и прочной пленки из нитрида железа.
Дальнейшее повышение химической стойкости хромоникелевых сталей в ряде агрессивных сред достигается введением молибдена. Характерной особенностью молибдена является его способность к пассивированию как в окислительных, так и в [c.119]
Для химического пассивирования малоуглеродистой стали рекомендуется 9—10-процентный раствор бихромата калия. При комнатной температуре обработку ведут в течение 1 ч, а при 60° С — в течение 20 мин. Лучшие результаты дает последовательная обработка изделий сначала в течение 10 мин в 20-процентном растворе хромового ангидрида при комнатной температуре и затем после промывки в 10-процентном растворе бихромата калия при 60° С.
Пассивирование поверхности стальных изделий с целью кратковременной защиты их от воздействия окружающей среды проводят химической или электрохимической обработкой в кислых или щелочных растворах. Эффективность такого метода защиты от коррозии определяется условиями пассивирования, составом металла, а также состоянием его поверхности. Наибольшее повышение стойкости против коррозии достигается при пассивировании легированных сталей, причем длительность защитного действия пассивных пленок значительно больше, чем при обработке углеродистых сталей.
Кислород в качестве агента для химического пассивирования стали имеет ряд преимуществ перед пероксидом водорода а именно эффективность действия пероксида водорода значительно ниже из-за быстрого термического разложения его при температуре 100—120 °С, в присутствии пероксида водорода значительно интенсивнее корродируют стеллитовые облицовки внутренних поверхностей промышленного оборудования, применение кислорода более экономично. [c.125]
При подготовке металла к окраске могут применяться многие способы очистки механический, химический, электрохимический, с применением ультразвука и др. Наряду с этим хорошей подготовкой под окраску стали является фосфатирование, для алюминия — оксидирование, для медных и покрытых медью изделий — пассивирование в растворах — пассиваторах. [c.264]
Основные виды хромовых покрытий молочное, блестящее, матовое и черное. Покрытия характеризуются высокой химической стойкостью, термостойкостью, склонностью к пассивированию на воздухе, устойчивостью в условиях тропического климата, способностью к растрескиванию в виде сетки и неравномерностью распределения по поверхности.
Кривая / соответствует режиму растворения железо (II) — активное . Процесс начинается при потенциале около —350 мВ, по достижении этого потенциала кривая резко поднимается вверх. Железо переходит в раствор в виде Ре , Кривая 3 характеризует режим растворения железо (И) — частично пассивированное , Поскольку проба пассивирована, то для ее растворения требуется значительно больший потенциал, а именно 500 мВ, Железо и в этом случае переходит в раствор в виде Ре , Некоторые химически стойкие сорта стали пассивируются в такой сильной степени, что для их растворения требуются очень высокие потенциалы (кривая 5). Железо по мере его растворения окисляется до железа (П1)—так называемый процесс железо (П1) — активное растворение .
Никелевые покрытия. Химическая устойчивость никеля в различных средах обусловлена сильно выраженной способностью его к пассивированию. Никелевые покрытия защищают стальные изделия от коррозии только механически при отсутствии в них пор. Эти покрытия используют для защиты от коррозии деталей из стали и цветных металлов (медь и ее сплавы), декоративной отделки поверхности, а также для повышения износостойкости трущихся поверхностей. Никелевые покрытия нашли широкое применение в машиностроении, приборостроении, радиотехнической и автомобильной промышленности.
Скорость растворения сплавов зависит главным образом от их состава, электрохимической активности и электрохимических эквивалентов компонентов, составляющих сплав, а также от физико-химических параметров электролита. При увеличении содержания в сплаве хрома затрудняется нарущение его пассивного состояния при воздействии галоидных анионов [193]. Вследствие различия электрохимических эквивалентов компонентов сплава, их потенциалов растворения и способности к пассивированию во многих случаях при ЭХО происходит увеличение в поверхностном слое содержания более электроположительных составляющих (например, никеля, меди, молибдена). При этом в анодной поляризационной характеристике сплава может наблюдаться несколько участков, соответствующих пассивации его различных компонентов [178]. Это обусловливает необходимость обеспечения приблизительно одинаковой скорости растворения всех основных компонентов сплава при подборе электролита. Определенное влияние на процесс анодного растворения кроме химического состава сплава оказывает и его структура. Связь производительности электрохимической обработки сталей с их микроструктурой показана в работе [127]. При анодном растворении жаропрочных сплавов на никелевой основе отмечалось преимущественное растворение (растравливание) границ зерен вследствие их относительно более высокой активности.
Химическое пассивирование металлов как метод предупреждения кислородной коррозии в воде высокой чистоты, теоретически обоснованный и разработанный Я. М. Колотыркиным, Т. X. Маргуловой, Г. М. Флорианович и О. И. Мартыновой [32, 47, 66], представляет практический интерес для защиты оборудования из стали и алюминия на химических производствах. Этот метод борьбы с коррозией применяется на многих объектах промышленности, использующих в качестве рабочей среды воду высокой чистоты [67]. Метод позволяет снижать концентрацию гидроксидов железа в теплоносителе с 20 до 4— 7 М кг/кг и ликвидировать коррозию как при низких, так и при высоких температурах.
Наконец, в процессах хемосорбции возможны, как это установил Н. А. Шилов, случаи образования так называемых поверхностных соединений, когда между поверхностными атомами адсорбента и атомами адсорбтива устанавливается химическая связь однако в результате ее не образуется новой фазы и нового химического соединения, которое можно было бы выделить особо, так как поверхностные атомы адсорбента продолжают сохранять связь и с остальными глубже лежащими его атомами.
Стали типа 18-8 устойчивы в азотной кислоте до 60%-ной концентрации при температурах кипения. Кроме растворов азотной кислоты, эти стали устойчивы в химически чистой фосфорной кислоте до 15%-ной концентрации, 1в большинстве органических соединений, не содержащих ионов хлора в сернокислых и других солях. Коррозионная стойкость хромо никелевых сталей может быть повышена путем легирования их молибденом, медью, кремнием и другими элементами. При легировании молибденом склонность сталей к пассивированию увеличивается (снижается ток пассивации и ток в пассивном состоянии), повышается устойчивость пассивного состояния. Стали типа 18-12, легированные молибденом, устойчивы в средах, содержащих хлор-ионы (при невысоких температурах), в органических кислотах (уксусной, муравьиной), в средах целлюлозно-будмажной промышленности и др. Л. И. Посысаевой, А. А. Бабаковым и В. А. Петровской [86, с.623] было показано, что введение 2,7% Мо в стали, содержащие 20, 24, 28% N1 и 18, 21 и 24% Сг повышает их стойкость в растворах фосфорной кислоты и в экстракционной фосфорной кислоте (Р2О5—32%, Р-—2%, 50Г—1,6%) при 68—70°С. [c.207]
Защита от коррозии имеет исключительно важное значение для черных металлов—железа, чугуна и стали, так как эти металлы имеют наибольшее распространение в технике и быту, но в силу своих физико-химических свойств наиболее подвержены действию коррозии. Ряд цветных металлов и сплавов — алюминий, магний, медь, бронза, латунь и другие также подвергаются коррозии, но в значительно меньшей мере, чем черные металлы, и тоже в некоторых случаях подвергаются защитным покрытиям более стойкими металлами, бесцветными или цветными лаками, а также оксидированию и пассивированию. [c.50]
Борьба с коррозией является народнохозяйственной задачей, поэтому исследования теории коррозии и проведение мероприятий по защите металлов от разрушения имеют первостепенное значение. Защита металлов от коррозии производится путем нанесения металлических покрытий из более стойких в данной среде металлов, нанесения лаков, красок, пластмасс и т. д. Среди различных методов защиты все большее значение приобретает пассивирование металлов. Некоторые металлы (Ре, N1, Сг, А1 и др.) в определенных условиях (состава и концентрации среды, Г, р) переходят в состояние высокой химической устойчивости, тогда как в исходных условиях ведут себя, как химически неустойчивые. Так, если железо погрузить в раствор разбавленной НМОз, то наблюдается интенсивное растворение металла. Однако при достижении некоторого предельного значения концентрации кислоты растворение металла прекращается и наблюдается переход его в пассивное состояние. При этом потенциал железа становится более положительным. Железо после пребывания в концентрированной азотной кислоте очень медленно растворяется при погружении его в разбавленную кислоту. Необходимые условия пассивирования зависят от состава и структуры металла.
Небольшие добавки к железу никеля, хрома, ванадия способствуют его переходу в пассивное состояние на воздухе. Это свойство лежит в основе получения нержавеющих сталей. Пассив- ное состояние вызывают окислители и окислительные процессы. [c.270]
В настоящее время переход металла в пассивное состояние чаще всего объясняют образованием на его поверхности хемосорбнрованного слоя атомов кислорода, т. е. химически соединенного с поверхностными атомами металла. При этом атомы кислорода могут покрывать как всю поверхность металла, так и часть ее. При пассивации потенциал металла сильно облагораживается, т. е. делается более положительным. Пассивированием объясняют коррозионную стойкость нержавеющих сталей (сплавов). [c.249]
Для химического полирования хромистых и хромоникелевых нержавеющих сталей, а также углеродистых сталей готовят раствор фосфорной кислоты, который медленно нагревают до 250° С, при этом фосфорная кислота частично переходит в пирофосфорную. Реакция продолжается 1,5 ч (ее окончание определяют по прекращению выделения газа). Затем кислоту быстро охлаждают и добавляют около 10% серной кислоты. Чем больше содержание углерода в стали, тем меньше добавляют кислоты. Полирование проводят при 200° С в течение 1—10 мин. После пассивирования, электролитического или химического полирования необходима нейтрализация остатков кислоты на деталях, которую производят в 1—3 % -ном растворе кальцинированной соды с последующей промывкой и сушкой. [c.105]
Неметаллические неорганические покрытия, наносимые на детали нз коррэзионностойких сталей. Химические пассивные покрытия. Коррозионная стойкость деталей из коррозионностойких сталей определяется качеством пассивных покрытий. Качество пассивного покрытия определяется полнотой удаления окалины, содержанием хрома в поверхностном слое и технологие пассивирования. [c.705]
Применение анодной защиты позволяет в качестве конструкционного материала для оборудования химической промышленности использовать различные нержавеющие стали и титан, хорошо пассивирующиеся во многих средах. Приложенный анодный ток ускоряет наступление пассивности, способствует ее сохранению продолжительное время, позволяет подобрать условия оптимального пассивирования, а в ряде случаев использовать более низколегированные стали. [c.69]
По сравнению с покрытиями Со—Р, которые используют главным образом при изготовлении магнитных полуфабрикатов, сплав Ni—Р оказывается значительно менее пригодным для таких целей. Однако он имеет очевидное преимущество при решении вопроса об антикоррозионной защите деталей. Пористость покрытия толщиною 8—10 мкм такая же, как электролитического никеля толщиною 18—20 мкм. Антикоррозионные свойства сплавов, формированных в кислых растворах, лучше, чем в щелочных. Для уменьшения пористости и повыщения защитной способности покрытий рекомендуется применять двухслойное никелевое покрытие, причем перед осаждением второго слоя — проводить протирку поверхности никеля кашицей венской извести и активацию в НС1 (1 1). Таким путем число пор уменьшается в 42—45 раз [141, с. 100]. Весьма эффективной является пассивация однослойного покрытия в растворе, содержащем 60 мл/л Н3РО4 (плотность 1,7 кг/дм ) и 50 г/л СгОз, при 50—60 °С в течение 6 мин [143]. Дополнительной защитой может служить гидрофобизация пассивированного покрытия препаратом ГФЖ 136-41 по технологии, указанной далее применительно к оксидным покрытиям на стали. Стойкость против коррозии деталей, имеющих покрытие химическим никелем толщиною 3 мкм, подвергшейся пассивации, не уступает стойкости образцов с таким же покрытием толщиною 24 мкм, не подвергавшимся дополнительной обработке. [c.209]
В некоторых случаях процесс поглощения вещества, начавшись на поверхности, распространяется в глубь поглотителя. Такие процессы можно разделить на три класса абсорбция, хемосорбция и капиллярная конденсация. Примером абсорбции может служить поглощение платиной или палладием водорода-При хемосорбции происходит химическое взаимодействие сорбтива с сорбентом с образованием нового химического вещества. Например, СОг, приведенное в соприкосновение с порошком СаО, химически взаимодействует с последним с образованием новой твердой фазы — СаСОз. Этот процесс постепенно распространяется в глубину зерен порошка, давая там то же самое химическое соединение — СаСОз. При хемосорбции новая фаза может и не появляться, например, при взаимодействии газообразного аммиака с водой образуется гидроокись аммония, но число фаз в системе не изменяется. Наконец, в процессах хемосорбции возможны, как это установил Н. А. Шилов, случаи образования так называемых поверхностных соединений, когда между поверхностными атомами адсорбента и атомами адсорбтива устанавливается химическая связь, однако новой фазы и нового химического соединения, которое можно было бы выделить, не возникает. Такие поверхностные соединения образуются на границе соприкосновения угля и стали с кислородом воздуха, обусловливая в последнем случае пассивирование металла. Капиллярная конденсация наблю 1ается при контакте пористых сорбентов с парами легко конденсирующихся веществ.
Капиллярная конденсация может происходить только при определенной температуре, давлении и при достаточном смачивании жидким сорбтивом поверхности стенок капилляра. Из курса физики известно, что, если жидкость смачивает стенки капилляра, то при одной и той же температуре, давление насыщенного пара над вогнутой поверхностью жидкости меньше давления пара над плоской поверхностью той же жидкости. В результате этих различий, пар, ненасыщенный по отношению к плоской поверхности, может оказаться насыщенным и даже пересыщенным по отношению к вогнутой поверхности, тогда пар начнет конденсироваться над мениском и капилляры будут заполняться жидкостью. Таким образом, капиллярная конденсация происходит не под действием адсорбционных сил, а является результатом притяжения молекул пара к поверхности мениска жидкости в мелких порах, где имеется пониженное давление пара. Капиллярная конденсация играет значительную роль в водном режиме почв. [c.281]
Футеровку из пентапласта применяют для защиты ванн хромирования, химического никелирования, травления, пассивирования. На ряде предприятий используют ванны, изготовленные из листового пентапласта толщиной 2—3 мм (ТУ 6-05-041-707—79). Пентапластовую емкость помещают в обрешетку из полос нержавеющей стали и опускают в пароводяную рубашку. [c.300]
Химическая устойчивость сплавов железо — хром и, в частности, нержавеющих сталей целиком основана на их пассивировании. Из компонентов нержавеющий сталей легче гхего лассивируется хром, заметно слабее никель и железо. Хром, находясь в твердом растворе с железом, в значительной мере повышает стойкость железа к шаосивированию. Чем больше в сплаве хрома, тем легче наступает пассивность и тем труднее сталь переходит в активное состояние. [c.476]
Что такое пассивирование нержавеющих сталей и зачем его делать?
Пассивирование, или пассивация, металла в общем понятии – это способ обработки поверхности материала, при котором появляются тонкие солевые и оксидные плёнки. Такое покрытие защищает сталь от воздействий кислорода и других агрессивных химических веществ. Нержавейка сама по себе является антикоррозийной сталью с инактивированной поверхностью. Необходимо ли в этом случае пассивирование?
Коррозия нержавеющей стали
Металл содержит в себе много добавок в виде кобальта, никеля, титана и др. Чем больше в нержавеющей стали хрома, тем выше её антикоррозийные свойства. Если эта цифра равна 12–13%, то металл выдержит воздействие атмосферных окислителей. При 17% сталь уже будет стойкой к более агрессивным средам, например, к соляной, серной или азотной кислоте. Кроме состава и пропорций, антикоррозийные свойства достигаются при наличии оксидной плёнки на однородной поверхности металла. Если она прерывиста, химический состав неоднороден, то защитные свойства вполне могут нарушиться. Нержавеющие стали подвергаются коррозии по таким причинам:
- некачественный сварной шов;
- отсутствие полировки после сварки;
- чистка изделия железной щёткой;
- попадание частиц другого металла во время обработки;
- использование инструмента, который соприкасался до этого с обычным металлом.
После чистки изделия необходимо проверить, не остались ли металлические частицы и железная пыль, не повредилась ли оксидная плёнка. Пассивирование особенно актуально проводить после работы со сваркой. Для этого используются химические кислотные растворы. Сварочный шов является самым слабым местом у нержавейки, в процессе обработки запускаются изменения на уровне кристаллической решётки материала.
Сталь могут испортить чистящие средства. Если говорить о бытовых, то это, например, хлорсодержащие препараты. Ржавчина в таких случаях распространяется по всей поверхности. Крепёжные элементы подвергаются коррозии при очень плотном соприкосновении с другими деталями. Поэтому контакт нержавейки с другими металлами должен исключаться.
Определить места с появившимися вкраплениями коррозии просто: нужно намочить водой изделие и дать постоять несколько часов. Второй вариант – это использование реактивов, от воздействия которых участки с ржавлением приобретут синий цвет.
Способ пассивирования
Верхний слой металлических изделий вступает во взаимодействие с кислородом, водой и другими веществами. Чтобы предотвратить реакцию атомов, необходимо сделать поверхность стали пассивной. Есть металлы, которые совсем не нуждаются в такой обработке. Это золото и платина, они химически инертны, не подвергаются ржавлению.
Восстановление антикоррозийных свойств с переводом поверхности в пассивное состояние заключается в покрытии стали разными видами плёнок (сульфатные, оксидные, фосфатные). Лёгкой обработки изделий будет достаточно, чтобы препятствовать коррозии. Пассивирование может проводиться и с помощью кислорода, который погружается в поры на поверхности металла.
Сплавы по-разному реагируют на химические вещества. Использование металла как анода при электрохимической пассивации позволяет добиться желаемого результата. Такая технология способна окрашивать и тонировать металл. При разных концентрациях компонентов можно добиться любой толщины и степени шероховатости защитной плёнки. Пассивирование не проводят, если нержавеющая сталь не будет использоваться в условиях агрессивных сред.
Как применять пассивацию
Очень часто используемый метод включает применение азотной кислоты, которая и формирует оксидную плёнку. Возможно добавление бихромата натрия. Химический состав, температура нагревания и время выдержки будут зависеть от марки стали. Обработка швов после сваривания проводится по той же технологии, но сначала они зачищаются щёткой и шлифуются.
Технологический процесс должен проводиться с точным соблюдением всех условий, тогда толщина плёнки будет равномерной. Пассивирование необходимо металлическим изделиям из нержавейки, так как обеспечить идеальные условия эксплуатации для них практически невозможно. Конструкции из труб, крепежи, элементы корпусов, механизмы, находящиеся в морской воде, и другие детали, будут нуждаться в дополнительной защите – пассивации. Все перечисленные изделия и нержавеющий металлопрокат можно приобрести в компании «Ориннокс», которая поставляет продукцию предприятиям химического и транспортного машиностроения, торгового и пищевого оборудования.
Сталь химическое пассивирование — Энциклопедия по машиностроению XXL
ХИМИЧЕСКОЕ ПАССИВИРОВАНИЕ СТАЛИ 8 ВОДЕ ВЫСОКОЙ ЧИСТОТЫ [c.122]Для улучшения свинчиваемости нержавеющих сталей применяют химическое пассивирование (Хим. Пас.). [c.125]
Для химического пассивирования малоуглеродистой стали рекомендуется 9—10-процентный раствор бихромата калия. При комнатной температуре обработку ведут в течение 1 ч, а при 60° С — в течение 20 мин. Лучшие результаты дает последовательная обработка изделий сначала в течение 10 мин в 20-процентном растворе хромового ангидрида при комнатной температуре и затем после промывки в 10-процентном растворе бихромата калия при 60° С. [c.15]
Скорость растворения сплавов зависит главным образом от их состава, электрохимической активности и электрохимических эквивалентов компонентов, составляющих сплав, а также от физико-химических параметров электролита. При увеличении содержания в сплаве хрома затрудняется нарущение его пассивного состояния при воздействии галоидных анионов [193]. Вследствие различия электрохимических эквивалентов компонентов сплава, их потенциалов растворения и способности к пассивированию во многих случаях при ЭХО происходит увеличение в поверхностном слое содержания более электроположительных составляющих (например, никеля, меди, молибдена). При этом в анодной поляризационной характеристике сплава может наблюдаться несколько участков, соответствующих пассивации его различных компонентов [178]. Это обусловливает необходимость обеспечения приблизительно одинаковой скорости растворения всех основных компонентов сплава при подборе электролита. Определенное влияние на процесс анодного растворения кроме химического состава сплава оказывает и его структура. Связь производительности электрохимической обработки сталей с их микроструктурой показана в работе [127]. При анодном растворении жаропрочных сплавов на никелевой основе отмечалось преимущественное растворение (растравливание) границ зерен вследствие их относительно более высокой активности. В зависимости от природы фаз, составляющих данный сплав, существенно различаются параметры возникающих на них пленок [117]. [c.34]
При подготовке металла к окраске могут применяться многие способы очистки механический, химический, электрохимический, с применением ультразвука и др. Наряду с этим хорошей подготовкой под окраску стали является фосфатирование, для алюминия — оксидирование, для медных и покрытых медью изделий — пассивирование в растворах — пассиваторах. [c.264]
Пассивирование поверхности стальных изделий с целью кратковременной защиты их от воздействия окружающей среды проводят химической или электрохимической обработкой в кислых или щелочных растворах. Эффективность такого метода защиты от коррозии определяется условиями пассивирования, составом металла, а также состоянием его поверхности. Наибольшее повышение стойкости против коррозии достигается при пассивировании легированных сталей, причем длительность защитного действия пассивных пленок значительно больше, чем при обработке углеродистых сталей. [c.14]
Дальнейшее повышение химической стойкости хромоникелевых сталей в ряде агрессивных сред достигается введением молибдена. Характерной особенностью молибдена является его способность к пассивированию как в окислительных, так и в [c.119]
Для химического полирования хромистых и хромоникелевых нержавеющих сталей, а также углеродистых сталей готовят раствор фосфорной кислоты, который медленно нагревают до 250° С, при этом фосфорная кислота частично переходит в пирофосфорную. Реакция продолжается 1,5 ч (ее окончание определяют по прекращению выделения газа). Затем кислоту быстро охлаждают и добавляют около 10% серной кислоты. Чем больше содержание углерода в стали, тем меньше добавляют кислоты. Полирование проводят при 200° С в течение 1—10 мин. После пассивирования, электролитического или химического полирования необходима нейтрализация остатков кислоты иа деталях, которую производят в 1—3 % -ном растворе кальцинированной соды с последующей промывкой и сушкой. [c.105]
Для металлизации рекомендуется использовать проволоку напыляемого металла диаметром 1,5 мм. Значительно реже детали из углеродистых и низколегированных сталей перед окраской защищают гальваническим цинком (с хроматным пассивированием) или оловом, а также никелем, который, как правило, наносят в ваннах химического никелирования. [c.123]
То же, при концентрации 30- 100 г/л и / 500 А, (химическое оксидирование алюминия и магния) Химическая обработка стали в растворах хромовой кислоты и ее солей при > 50°С (пассивирование, травление, наполнение в хромпике и др). [c.176]
Химическое пассивирование металлов как метод предупреждения кислородной коррозии в воде высокой чистоты, теоретически обоснованный и разработанный Я. М. Колотыркиным, Т. X. Маргуловой, Г. М. Флорианович и О. И. Мартыновой [32, 47, 66], представляет практический интерес для защиты оборудования из стали и алюминия на химических производствах. Этот метод борьбы с коррозией применяется на многих объектах промышленности, использующих в качестве рабочей среды воду высокой чистоты [67]. Метод позволяет снижать концентрацию гидроксидов железа в теплоносителе с 20 до 4— 7 мкг/кг и ликвидировать коррозию как при низких, так и при высоких температурах. [c.122]
Кислород в качестве агента для химического пассивирования стали имеет ряд преимуществ перед пероксидом водорода а именво эффективность действия пероксида водорода значительно ниже из-за быстрого термического разложения его при температуре 100—120 °С, в присутствии пероксида водорода значительно интенсивнее корродируют стеллитовые облицовки внутренних поверхностей промышленного оборудования, применение кислорода более экономично. [c.125]
Стали типа 18-8 устойчивы в азотной кислоте до 60%-ной концентрации при температурах кипеиия. Кроме растворов азотной кислоты, эти стали устойчивы в химически чистой фосфорной кислоте до 15%-ной концентрации, 1в большинстве органических соединений, не содержащих ионов хлора в сернокислых и других солях. Коррозионная стойкость хромоникелевых сталей может быть повышена путем легирования их молибденом, медью, -кремнием и другими элементами. При легировании молибденом склонность сталей к пассивированию увеличивается (снижается ток пассивации и ток в пассивном состоянии), повышается устойчивость пассивного состояния. Стали типа 18-12, легированные молибденом, устойчивы в средах, содержащих хлор-ионы (при невысоких температурах), в органических кислотах (уксусной, муравьиной), в средах целлюлозно-будмажной (Промышленности и др. Л. И. Посысаевой, А. А. Бабаковым и В. А. Петровской [86, с.623] было показано, что введение 2,7% Мо в стали, содержащие 20, 24, 28% N1 и 18, 21 и 24% Сг повышает их стойкость в растворах фосфорной кислоты и в экстракционной фосфорной кислоте (Р2О5—32%, Р-—2%, 1,6%) при 68—70°С. [c.207]
Применение анодной защиты позволяет в качестве конструкционного материала для оборудования химической промышленности использовать различные нержавеющие стали и титан, хорошо пассивирующиеся во многих средах. Приложенный анодный ток ускоряет наступление пассивности, способствует ее сохранению продолжительное время, позволяет подобрать условия оптимального пассивирования, а в ряде случаев использовать более низколегированные стали. [c.69]
Химическое травление нержавеющих и высоколегированных сталей. Наиболее простым химическим методом снятия окалины с деталей из хромистых сталей типа 1X13 и 2X13 является травление в 20%-ном растворе соляной кислоты при 15—25° С с последующим удалением разрыхленной окалины стальными щетками и пассивированием в 10%-но.м растворе азотной кислоты при 15—25° С с повторной очисткой стальными щетками. [c.932]
Ультразвуковое» травление особенно эффективно для очистки поверхностей мелких и тонкостенных деталей, а также деталей сложной конфигуращш с ограниченным доступом к паяемой поверхности. Травильный шлам с поверхностей деталей из сталей, бериллнсвой бронзы, титана и сплавов на его основе удаляют следующими способами химическим в растворах, составы которых и режимы обработки приведены в табл. 27 электрохимическим (для сталей) в растворах для обезжиривания по режиму температура раствора 15—35°С, продолжительность обработки 5—10 мин, анодная плотность тока 3—10 А/дм механической очистки — для углеродистых, низко- и среднелегированных сталей путем обдува кварцевым и металлическим песком, для коррозиоиностойких сталей — электрокорундовым порошком или нейтральной солью (сернокислый калий) с последующим пассивированием. [c.106]
По сравнению с покрытиями Со—Р, которые используют главным образом при изготовлении магнитных полуфабрикатов, сплав Ni—Р оказывается значительно менее пригодным для таких целей. Однако он имеет очевидное преимущество при решении вопроса об антикоррозионной защите деталей. Пористость покрытия толщиною 8—10 мкм такая же, как электролитического никеля толщиною 18—20 мкм. Антикоррозионные свойства сплавов, формированных в кислых растворах, лучше, чем в щелочных. Для уменьшения пористости и повыщения защитной способности покрытий рекомендуется применять двухслойное никелевое покрытие, причем перед осаждением второго слоя — проводить протирку поверхности никеля кашицей венской извести и активацию в НС1 (1 1). Таким путем число пор уменьшается в 42—45 раз [141, с. 100]. Весьма эффективной является пассивация однослойного покрытия в растворе, содержащем 60 мл/л Н3РО4 (плотность 1,7 кг/дм ) и 50 г/л СгОз, при 50—60 °С в течение 6 мин [143]. Дополнительной защитой может служить гидрофобизация пассивированного покрытия препаратом ГФЖ 136-41 по технологии, указанной далее применительно к оксидным покрытиям на стали. Стойкость против коррозии деталей, имеющих покрытие химическим никелем толщиною 3 мкм, подвергшейся пассивации, не уступает стойкости образцов с таким же покрытием толщиною 24 мкм, не подвергавшимся дополнительной обработке. [c.209]
Соединения Сг +(Н2Сг04 и ее сати) широко используются в различных технологических процессах гальванического производства, при химическом травлении и пассивировании поверхности деталей из обычной, оцинкованной и кадмированной стали, медных сплавов при гальванопокрытиях и электрополировании стальных деталей, а таклсе электрохимическом анодировании деталей из алюминия. Соединения Сг + относятся к классу токсичных, чрезвычайно опасных веществ. В сточных водах Сг[c.217]
Поляризацией называется уменьшение начальной разности потенциалов коррозионного микроэлемента при прохождении через его электрического тока, причем потенциал анода смещается в положительную сторону (анодная поляризация), потенциал катода — в отрицательную. Электродные процессы, уменьшающие поляризацию, называются процессами деполяризации (анодная и катодная деполяризация). Явления поляризации тормозят работу микроэлемента и уменьшают скорость электрохимической коррозии в их отсутствии электрохимическая коррозия протекала бы во много раз быстрее. Анодный процесс в коррозионном микроэлементе распадается на стадии растворение металла с образованием ионов, повышение концентрации ионов непосредственно у поверхности, возникновение на поверхности пассивных пленок ш их разрушение. Слабая коррозия нержавеющих сталей в растворах солей при доступе воздуха и в азотной кислоте определяется торможением анодного процесса вследств1И1а пассивирования анодных участков. Повышение концентрации ионов у поверхности вызывает концентрационную поляризацию в соответствии с формулой (1), пассивность — химическую поляризацию [c.891]
Аустенитные стали наилучшую коррозионную стойкость приобретают после закалки ва чистый аустенит, т. е. когда весь хром и другие легирующие присадки находятся в твердом растворе. Отпуск при 450—800° сообщает хромоникелевым аустенитным сталям в ряде случаев склонность к межкристаллитной коррозии вследствие местного обеднения твердого раствора хромом по границам зерев. Хром сообщает стал также способность к пассивированию в окислительных средах, в результате чего хромистые стал приобретают высокую коррозионную стойкость в ряде химически агрессивных сред. [c.916]
Существующие методы химической очистки включают этапы предварительного щелочения (обезжиривания), удаления прокатной окалины или кислотной очистки и пассивирования металла. Первый этап обычно осуществляется слабым (раствором щелочи и детергента, но в последнее время для этой цели успешно используют только детергент. Применение NaOH считается нежелательным из-за вредного действия его на аустенитные стали. [c.89]
Химическая устойчивость сплавов железо — хром и, в частности, нержавеющих сталей целиком основана на их пассивировании. Из компонентов нержавеющий сталей легче гхего пассивируется хром, заметно слабее никель и железо. Хром, находясь в твердом растворе с железом, в значительной мере повышает стойкость железа к пассивированию. Чем больше в сплаве хрома, тем легче наступает пассивность и тем труднее сталь переходит в активное состояние. [c.476]
Пассивация (пассивирование) металлов: технология и методы
Несмотря на то, что нержавеющая сталь отличается высокой устойчивостью к коррозии, дополнительная защита, которую позволяет получить такая технологическая операция, как пассивация, для нее желательна. В отдельных случаях, когда большому риску развития коррозии подвержены даже изделия, изготовленные из нержавеющей стали, необходимость в выполнении такой процедуры не вызывает сомнений.
Примеры нержавеющих поверхностей, подвергнутых коррозии, и результаты проведенной пассивации
Чем обусловлена высокая коррозионная устойчивость нержавеющих сталей
Суть такого явления, как коррозия, состоит в том, что поверхность металла под воздействием негативных внешних факторов и окружающей среды начинает разрушаться. Что характерно, коррозия из-за постоянного окисления поражает металл слой за слоем, постепенно разрушая внутреннюю структуру стали. Во многих случаях локализовать пораженные участки внутренней структуры металла уже не имеет смысла, поэтому стальные изделия приходится заменять на новые.
Пассивирование (или пассивация) как технология, позволяющая обеспечить надежную защиту стали от коррозии, лежит в основе создания такого уникального металла, каким является нержавеющая сталь. В химическом составе преимущественного большинства сталей, относящихся к нержавеющей категории, могут содержаться различные элементы:
- никель;
- молибден;
- кобальт;
- ниобий;
- марганец.
Однако основным легирующим элементом таких сталей, количество которого в их составе может варьироваться в пределах 12–20%, является хром. Добавление различных легирующих элементов в состав нержавеющих сталей позволяет придать им требуемые физико-химические характеристики, но именно хром отвечает за коррозионную устойчивость стального сплава.
Влияние хрома на свойства нержавеющей стали
Нержавеющие стальные сплавы, в составе которых содержится 12% хрома, проявляют высокую коррозионную устойчивость только при взаимодействии с окружающим воздухом. Если количество хрома в химическом составе нержавеющей стали увеличить до 17%, то изделия из нее смогут спокойно взаимодействовать с азотной кислотой, не утрачивая при этом своих эксплуатационных характеристик.
Чтобы сделать металл устойчивым к еще более агрессивным средам, к числу которых относятся соляная, серная и другие кислоты, в нем не только увеличивают количественное содержание хрома, но и добавляют в его состав такие элементы, как медь, молибден, никель и др. Иными словами, выполняют пассивирование металла, то есть увеличивают его пассивность к коррозионным процессам.
В процессе пассивации зоны сварочного шва образуется прочная пленка
Пассивация, при которой в химический состав нержавеющей стали добавляют соответствующие легирующие элементы, – это не единственное условие высокой коррозионной устойчивости металла. Чтобы защитные свойства нержавеющей стали оставались на высоком уровне, оксидная пленка на ее поверхности, состоящая преимущественно из оксида хрома, должна быть целой, иметь однородный химический состав и толщину.
Причины возникновения коррозии
Несмотря на то, что в химическом составе нержавеющей стали должны содержаться пассиваторы, значительно повышающие ее коррозионную устойчивость, ее поверхность и внутренняя структура могут подвергаться коррозии.
Основной причиной, по которой нержавеющая сталь начинает разрушаться, является недостаточное или неравномерное содержание в ее химическом составе хрома. Вызвать коррозию также может контакт с металлом, который отличается значительно меньшей устойчивостью к окислению. Часто подвергаются разрушению изделия из нержавейки, которые были соединены между собой по технологии сварки.
Коррозия труб полотенцесушителя, возникшая по причине недобросовестного исполнения сварочного шва производителем
Что характерно, даже если нержавеющая сталь отличается очень высоким качеством, после сварки она может покрыться слоем ржавчины. Чтобы избежать таких негативных явлений, сварные швы, при помощи которых выполнено соединение изделий из нержавейки, необходимо тщательно зачищать и полировать. Такая процедура позволяет удалить с поверхности сварного шва и самих изделий из нержавейки остатки менее устойчивого к коррозии металла, который был использован для выполнения сварочных работ.
Очень часто на поверхность нержавейки частички менее устойчивого к коррозии металла попадают и в тех случаях, когда его обработка выполняется в непосредственной близости от стальных изделий. Так, если рядом пилят, шлифуют или выполняют другие виды обработки обычного металла, то его частички, попав на нержавеющую сталь, обязательно станут источниками ее коррозии. На нержавейке они могут появиться и в том случае, если вы решите выполнить ее обработку инструментом, который до этого взаимодействовал с обычным металлом. Именно поэтому инструменты, особенно относящиеся к режущему типу, желательно использовать для выполнения обработки только однотипных материалов.
Коррозия вытяжки из нержавеющей стали, произошедшая вследствие чистки изделия железной щеткой
Однако, конечно, наиболее критичным местом на поверхности изделий из нержавейки с точки зрения возникновения и развития коррозионных процессов является сварной шов. Именно поэтому важны не только тщательная зачистка, шлифовка и полировка места сформированного сварного соединения, но и его пассивация, для чего используются различные кислотные растворы.
Пассивация (химическое пассивирование), как правило, выполняется с применением раствора, основу которого составляет азотная кислота. Обработка таким раствором тщательно подготовленного участка изделия из нержавеющей стали позволяет сформировать оксидную пленку, отличающуюся высокой пассивностью к коррозионным процессам.
Обработка сварных соединений на нержавейке, после которой и выполняется химическое пассивирование, осуществляется при помощи металлической щетки и шлифовальной машинки. При этом, как уже говорилось выше, важно следить за тем, чтобы используемые при пассивации инструменты не реагировали до этого с обычным металлом, частички которого могут стать источником развития коррозионных процессов.
Чтобы проверить, не присутствует ли на поверхности нержавейки включений обычного металла, можно воспользоваться двумя способами.
Обработка водным раствором азотной кислоты и ферроцианида калияМеста на поверхности изделия, на которых присутствуют включения свободного железа, после выполнения такой обработки сразу окрасятся в синий цвет. Следует отметить, что такой способ проверки используют преимущественно в условиях производственных лабораторий.
Смачивание обычной водойИзделие выдерживают в таком состоянии на протяжении нескольких часов. Если на нержавейке присутствуют включения свободного железа, то участки с такими включениями начнут покрываться ржавчиной.
Виды коррозии
Несмотря на то, что коррозионный процесс приводит практически к одинаковым последствиям, причины, ее вызывающие, могут быть различными. Наиболее частой причиной коррозии изделий из нержавейки, используемых в бытовых условиях, является применение для их чистки средств, содержащих в своем химическом составе значительное количество хлора. Такие средства активно способствуют разрушению оксидной пленки на металле, что приводит к развитию коррозионного процесса на всей его поверхности (т.е. общей коррозии).
Щелевая коррозия нержавейки возникает в тех случаях, когда детали из такого металла длительное время соприкасаются между собой. Коррозия данного типа, что характерно, часто начинает развиваться в местах крепежа. Различают также точечную коррозию, которую часто называют питтинговой. Она возникает в тех случаях, когда оксидная пленка на нержавейке повреждена механическим способом.
Коррозия нержавейки под водой проявляется в большей степени в местах соединения деталей
Если нержавейка контактирует с разнородным для нее металлом в токопроводящей среде, начинает развиваться коррозия, которая получила название гальванической. Этому процессу наиболее подвержены изделия из нержавеющих сталей, эксплуатируемые в морской воде и при этом контактирующие с металлами, отличающимися меньшей степенью легирования.
Межкристаллитная коррозия – очень распространенное явление, возникающее в тех случаях, когда изделие из нержавеющей стали было подвергнуто значительному перегреву. При сильном нагреве (свыше 500°) на границах кристаллической решетки нержавеющей стали формируются карбиды хрома и железа, которые и становятся причиной снижения прочности металла.
Коррозия нержавеющей стали может возникать из-за применения хлоросодержащих чистящих составов
Различают также эрозивную коррозию, которая возникает, если нержавейка постоянно находится под воздействием абразивной среды. Постоянно воздействуя на поверхность металла, частички такой среды разрушают защитную оксидную пленку, которая не успевает восстанавливаться.
Пассивирование нержавейки
Обеспечить такие условия эксплуатации изделий из нержавеющей стали, чтобы они не контактировали с другими металлами и агрессивными средами, а также не подвергались механическим повреждениям, практически невозможно. Именно поэтому необходима упомянутая выше технологическая операция – пассивирование. Дополнительную степень защиты, которую обеспечивает пассивирование (пассивация), часто стараются обеспечить:
- трубным конструкциям из нержавейки;
- крепежным элементам;
- корпусным элементам конструкций и механизмов, эксплуатируемых в морской воде.
Между тем пассивация не всегда целесообразна даже для изделий подобного назначения.
Пассивирование сварочного шва нержавейки
Пассивирование, хотя и является методом обработки нержавеющей стали, способным обеспечить ее дополнительной защитой от коррозии, во многих случаях является нецелесообразным и даже может ухудшить защитные свойства стали. Поэтому прежде чем выполнять пассивацию, следует проанализировать условия, в которых будет эксплуатироваться изделие, чтобы однозначно решить, нужна ли его поверхности дополнительная защита.
Пассивация, если решение о ее выполнении принято, должна обеспечивать получение цельного и равномерного по толщине защитного слоя, что достигается строгим соблюдением технологического процесса. Как правило, пассивацию выполняют в тех случаях, когда дополнительная защита необходима внешней, а не внутренней поверхности изделия из нержавеющей стали.
Суть такого процесса, как пассивация, заключается в том, что поверхность изделия из нержавеющей стали обрабатывают специальным раствором, основу которого составляет азотная, а в некоторых случаях и лимонная кислота. Иногда такой раствор могут дополнять незначительным количеством (2-6%) бихромата натрия. Химический состав такого раствора, а также такие параметры, как температура нагрева и время выдержки, зависят от марки обрабатываемой нержавеющей стали.
Оценка статьи:
Загрузка…Поделиться с друзьями:
1 | Ацетатальдегид | A | A | C | A | A | A | A | A | A | A | A | A | A | A | A | A |
2 | Ацетатная кислота, без воздуха | C | C | C | C | C | C | A | A | A | A | A | A | A | A | A | A |
3 | Ацетатная кислота, насыщенная воздухом | C | C | C | C | B | B | A | A | A | A | C | A | A | A | A | A |
4 | Ацетон | B | A | A | A | A | A | A | A | A | A | A | A | A | A | A | A |
5 | Ацетилен | A | A | A | A | A | A | A | A | A | A | A | A | A | A | A | A |
6 | Спирты | A | A | A | A | A | A | A | A | A | A | A | A | A | A | A | A |
7 | Сульфат алюминия | C | C | C | C | B | A | A | A | A | A | B | A | A | A | A | A |
8 | Аммиак | A | C | A | A | A | A | A | A | A | A | A | A | A | A | A | A |
9 | Нашатырь | C | C | C | C | C | C | B | A | A | A | B | A | A | B | A | A |
10 | Аммиак едкий | A | C | A | A | A | A | A | A | A | A | C | A | A | A | A | B |
11 | Аммиачная селитра | B | C | B | B | A | A | A | A | A | A | C | A | A | A | C | A |
12 |
Фосфат аммония |
B | B | C | B | B | A | A | A | A | A | B | A | A | A | A | A |
13 |
Сульфат аммония |
C | C | C | C | B | B | A | A | A | A | A | A | A | A | A | A |
14 |
Сульфит аммония |
C | C | C | C | A | A | A | A | A | A | C | A | A | A | A | A |
15 | Анилин | C | C | C | C | A | A | A | A | A | A | B | A | A | A | A | A |
16 | Асфальт, битум | A | A | A | A | A | A | A | A | A | A | A | A | A | A | A | A |
17 | Пиво | A | A | B | B | A | A | A | A | A | A | A | A | A | A | A | A |
18 | Бензол | A | A | A | A | A | A | A | A | A | A | A | A | A | A | A | A |
19 | Бензойная кислота | A | A | C | C | A | A | A | A | A | A | A | A | A | A | A | A |
20 | Борная кислота | C | B | C | C | A | A | A | A | A | A | B | A | A | A | A | A |
21 | Бром сухой | C | C | C | C | B | B | B | A | A | A | A | A | A | A | C | C |
22 | Бром влажный | C | C | C | C | C | C | C | C | C | C | A | A | A | C | C | C |
23 | Бутан | A | A | A | A | A | A | A | A | A | A | A | A | A | A | A | A |
24 | Хлорид кальция | C | C | B | C | C | B | B | A | A | A | A | A | A | A | A | A |
25 | Гипохлорит кальция | C | C | C | C | C | C | C | A | A | A | C | A | B | B | A | A |
26 |
Диоксид углерода сухой |
A | A | A | A | A | A | A | A | A | A | A | A | A | A | A | A |
27 | Диоксид углерода влажный | A | B | C | C | A | A | A | A | A | A | B | A | A | A | A | A |
28 | Дисульфид углерода | C | C | A | B | B | A | A | A | A | A | A | A | A | A | A | A |
29 | Угольная кислота | A | B | C | C | A | A | A | A | A | A | A | A | A | A | A | A |
30 | Тетрахлорид углерода | A | A | B | B | A | A | A | A | A | A | A | A | A | A | A | A |
31 | Хлор сухой | C | C | A | C | B | B | B | A | A | A | A | A | A | A | C | A |
32 | Хлор влажный | C | C | C | C | C | C | C | C | C | C | B | B | B | C | A | A |
33 | Хромовая кислота | C | C | C | C | C | C | C | B | A | C | C | A | B | C | A | A |
34 | Лимонная кислота | B | C | C | C | B | B | A | A | A | A | A | A | A | A | A | A |
35 | Коксовая кислота | C | B | A | A | A | A | A | A | A | A | B | A | A | A | A | A |
36 | Сульфат меди | C | C | C | C | C | C | B | A | A | A | C | A | A | C | A | A |
37 | Хлопковое масло | A | A | A | A | A | A | A | A | A | A | A | A | A | A | A | A |
38 | Креозот | C | C | A | A | A | A | A | A | A | A | A | A | A | A | A | A |
39 | Даутерм | A | A | A | A | A | A | A | A | A | A | A | A | A | A | A | A |
40 | Этан | A | A | A | A | A | A | A | A | A | A | A | A | A | A | A | A |
41 | Эфир | A | A | B | A | A | A | A | A | A | A | A | A | A | A | A | A |
42 | Этилхлорид | C | B | C | C | B | B | B | A | A | A | A | A | A | A | A | A |
43 | Этилен | A | A | A | A | A | A | A | A | A | A | A | A | A | A | A | A |
44 | Этиленгликоль | A | A | A | A | A | A | A | A | A | A | A | A | A | A | A | A |
45 | Хлорид железа | C | C | C | C | C | C | C | C | B | C | C | A | C | C | A | A |
46 | Фтор сухой | B | B | A | C | B | B | B | A | A | A | A | A | A | A | C | C |
47 | Фтор влажный | C | C | C | C | C | C | C | C | C | C | B | B | B | C | C | C |
48 | Формальдегид | A | A | B | A | A | A | A | A | A | A | A | A | A | A | A | A |
49 | Муравьиная кислота | B | C | C | C | C | C | B | A | A | A | C | A | B | B | C | A |
50 | Фреон влажный | C | C | B | C | B | B | A | A | A | A | A | A | A | A | A | A |
51 | Фреон сухой | A | A | B | A | A | A | A | A | A | A | A | A | A | A | A | A |
52 | Фурфурал | A | A | A | B | A | A | A | A | A | A | A | A | A | A | A | A |
53 | Бензин стабильный | A | A | A | A | A | A | A | A | A | A | A | A | A | A | A | A |
54 | Глюкоза | A | A | A | A | A | A | A | C | A | A | A | A | A | A | A | A |
55 | Соляная кислота, насыщенная воздухом | C | C | C | C | C | C | C | C | C | C | C | B | A | C | С | A |
56 | Соляная кислота, без воздуха | C | C | C | C | C | C | C | C | C | C | C | B | A | C | С | A |
57 | Плавиковая кислота, насыщенная воздухом | C | C | C | C | C | C | C | C | C | C | B | B | B | C | С | C |
58 | Плавиковая кислота, без воздуха | C | C | C | C | C | C | C | C | C | C | A | B | B | C | С | C |
59 | Водород | A | A | A | C | B | A | A | A | A | A | A | A | A | A | С | A |
60 | Перекись водорода | A | C | C | C | B | A | A | A | A | A | C | A | C | A | A | A |
61 | Сероводород | C | C | C | C | C | A | A | A | A | A | A | A | A | A | A | A |
62 | Йод | C | C | C | C | C | A | A | A | A | A | C | A | A | A | С | B |
63 | Гидроксид магния | B | B | A | A | A | A | A | A | A | A | A | A | A | A | A | A |
64 | Ртуть | C | C | A | A | A | A | A | A | A | A | B | A | A | A | С | A |
65 | Метанол | A | A | A | A | A | A | A | A | A | A | A | A | A | A | A | A |
66 | Метилэтилгликоль | A | A | A | A | A | A | A | A | A | A | A | A | A | A | A | A |
67 | Молоко | A | A | C | A | A | A | A | A | A | A | A | A | A | A | A | A |
68 | Природный газ | A | A | A | A | A | A | A | A | A | A | A | A | A | A | A | A |
69 | Азотная кислота | C | C | C | C | A | A | A | A | A | A | C | B | C | С | A | A |
70 | Олеиновая кислота | C | C | C | B | B | B | A | A | A | A | A | A | A | A | A | A |
71 | Щавелевая кислота | C | C | C | C | B | B | B | A | A | A | B | A | A | B | С | A |
72 | Кислород | C | A | C | C | B | B | B | B | B | B | A | B | B | B | С | C |
73 | Минеральное масло | A | A | A | A | A | A | A | A | A | A | A | A | A | A | A | |
74 | Фосфорная кислота, насыщенная воздухом | C | C | C | C | B | A | A | A | A | A | C | A | A | A | С | A |
75 | Фосфорная кислота, без воздуха | C | C | C | C | B | B | B | A | A | A | B | A | A | B | С | A |
76 | Пикриновая кислота | C | C | C | C | B | B | A | A | A | A | C | A | A | A | A | A |
77 | Углекислый калий/ карбонат калия | C | C | B | B | A | A | A | A | A | A | A | A | A | A | A | A |
78 | Хлорид калия | C | C | B | C | C | B | B | A | A | A | A | A | A | A | A | A |
79 | Гидроксид калия | C | C | B | B | A | A | A | A | A | A | A | A | A | A | A | A |
80 | Пропан | A | A | A | A | A | A | A | A | A | A | A | A | A | A | A | A |
81 | Канифоль, смола | A | A | B | A | A | A | A | A | A | A | A | A | A | A | A | A |
82 | Нитрат серебра | C | C | C | C | B | A | A | A | A | A | C | A | A | A | A | A |
83 | Ацетат натрия | A | A | A | A | A | A | A | A | A | A | A | A | A | A | A | A |
84 | Карбонат натрия | C | C | A | B | A | A | A | A | A | A | A | A | A | A | A | A |
85 | Хлорид натрия | С | A | C | C | B | B | B | A | A | A | A | A | A | A | A | A |
86 | Декагидрат хромата натрия | A | A | A | A | A | A | A | A | A | A | A | A | A | A | A | A |
87 | Гидроксид натрия | С | С | A | B | B | B | A | A | A | A | A | A | A | A | A | A |
88 | Гипохлорит натрия | C | C | C | C | C | C | C | C | C | C | C | A | B | C | A | A |
89 | Тиосульфат натрия | C | C | C | C | B | B | A | A | A | A | A | A | A | A | A | A |
90 | Хлорид олова | C | C | C | C | C | C | B | A | A | A | C | A | A | B | A | A |
91 | Водяной пар | A | A | A | A | A | A | A | A | A | A | A | A | A | A | A | A |
92 | Стеариновая (октадекановая) кислота | C | B | B | B | B | A | A | A | A | A | A | A | A | B | A | A |
93 | Сера | A | B | A | A | A | A | A | A | A | A | A | A | A | A | A | A |
94 | Диоксид серы сухой | C | C | C | C | C | C | B | A | A | A | C | A | A | B | A | A |
95 | Триоксид серы сухой | C | C | C | C | C | C | B | A | A | A | B | A | A | B | A | A |
96 | Серная кислота, насыщенная воздухом | C | C | C | C | C | C | C | A | A | A | C | A | C | B | С | A |
97 | Серная кислота, без воздуха | C | C | C | C | C | C | C | A | A | A | B | A | A | B | С | A |
98 | Сернистая кислота | C | C | C | C | C | B | B | A | A | A | C | A | A | B | A | A |
99 | Деготь | A | A | A | A | A | A | A | A | A | A | A | A | A | A | A | A |
100 | Трихлорэтилен | B | B | B | B | B | B | A | A | A | A | A | A | A | A | A | A |
101 | Скипидар | A | A | B | A | A | A | A | A | A | A | A | A | A | A | A | A |
102 | Уксус | B | B | C | C | A | A | A | A | A | A | A | A | A | A | A | A |
103 | Вода химочищенная | A | A | A | A | A | A | A | A | A | A | A | A | A | C | A | A |
104 | Вода дистиллированная | A | A | C | C | A | A | A | A | A | A | A | A | A | A | A | A |
105 | Вода морская — в сухпутной РФ малоизвестно, но исключительно малоприятная среда, применимость — «относительная» |
С | A | C | C | C | C | B | A | A | A | A | A | A | A | A | A |
106 | Виски, водка, вино | A | A | C | C | A | A | A | A | A | A | A | A | A | A | A | A |
107 | Хлорид цинка | C | C | C | C | C | C | C | B | B | B | A | A | A | B | A | A |
108 | Сульфат цинка | С | С | С | С | А | А | А | А | А | А | А | А | А | А | А | А |
РД 302-07-19-92 Пассивирование заготовок, отливок, узлов и деталей трубопроводной арматуры из коррозионностойких сталей и сплавов. Типовые технологические процессы
РД 302-07-19-92
РУКОВОДЯЩИЙ ДОКУМЕНТ
ПАССИВИРОВАНИЕ ЗАГОТОВОК, ОТЛИВОК, УЗЛОВ И ДЕТАЛЕЙ ТРУБОПРОВОДНОЙ АРМАТУРЫ ИЗ КОРРОЗИОННОСТОЙКИХ СТАЛЕЙ И СПЛАВОВ. ТИПОВЫЕ ТЕХНОЛОГИЧЕСКИЕ ПРОЦЕССЫ
Дата введения 1994-01-01
ИНФОРМАЦИОННЫЕ ДАННЫЕ
1. РАЗРАБОТАН НПОА «Знамя труда» им. И.И.Лепсе исполнители: Ольховская С.Г.; Краснянский Б.Г.; Мещеряков А.В.
2. УТВЕРЖДЕН И ВВЕДЕН В ДЕЙСТВИЕ листом утверждения от 15.12.92 г.
Зарегистрирован за N 19.
3. ВЗАМЕН ОСТ 26-07-2035-81.
4. Ссылочные нормативно-технические документы.
Обозначение НТД, на который дана ссылка | Номер пункта, подпункта, перечисления, приложения |
1 | 2 |
ГОСТ 201-76 | 2.1.4; 4.1 |
ГОСТ 443-76* | 4.1 |
________________ * На территории Российской Федерации документ не действует. Действует ТУ 38.401-67-108-92, являющиеся авторской разработкой. За дополнительной информацией обратитесь по ссылке, здесь и далее по тексту — Примечание изготовителя базы данных. | |
ГОСТ 701-89 | 2.1.6; 2.1.13.5; 2.3.9; 4.1 |
ГОСТ 2263-79 | 2.1.4; 4.1 |
ГОСТ 5100-85 | 4.1 |
ГОСТ 6552-80 | 2.1.4; 4.1 |
ГОСТ 6552-80* | 4.1 |
________________ | |
ГОСТ 9175-77* | 4.1 |
______________ * Вероятно ошибка оригинала. Следует читать: ГОСТ 9179-77, здесь и далее по тексту. — Примечание изготовителя базы данных. | |
ГОСТ 10484-78 | 2.1.13.5; 4.1 |
ГОСТ 12966-85 | 4.1 |
ГОСТ 12.3.008-75 | 7.1 |
ГОСТ 13078-78 | 2.1.4; 4.1 |
ГОСТ 17299-78 | 4.1 |
ГОСТ 23844-79 | 4.1 |
СОГЛАСОВАНО Представитель ПЗ 953 Мустафин Ю.А. «14» декабря 1992 г. |
ЛИСТ УТВЕРЖДЕНИЯ
ПАССИВИРОВАНИЕ ЗАГОТОВОК, ОТЛИВОК, УЗЛОВ И ДЕТАЛЕЙ ТРУБОПРОВОДНОЙ АРМАТУРЫ ИЗ КОРРОЗИОННОСТОЙКИХ СТАЛЕЙ И СПЛАВОВ. ТИПОВЫЕ ТЕХНОЛОГИЧЕСКИЕ ПРОЦЕССЫ
РД 302-07-19-92
Первый зам. директора ЦКБА | В.А.Айриев |
Зам. главного инженера | Э.А.Макаров |
Зам. директора НТИЦ | Р.И.Хасанов |
Начальник отдела 161 | А.А.Косарев |
Начальник отдела 933 | С.Г.Ольховская |
Начальник сектора отд. 933 | Б.Г.Краснянский |
Ведущий инженер-технолог отд. 933 | А.В.Мещеряков |
Настоящий документ распространяется на процессы химического пассивирования и травления заготовок, отливок, деталей и узлов трубопроводной арматуры, изготовленных из коррозионностойких сталей и сплавов.
Руководящий документ устанавливает последовательность выполнения и параметры основных технологических операций, входящих в процесс химического пассивирования в зависимости от вида и материала заготовок, деталей и узлов, а также требования, предъявляемые к качеству обработанной поверхности, способы приготовления и корректировки растворов, меры, обеспечивающие экологическую безопасность применяемой технологии.
1. ОБЩИЕ ПОЛОЖЕНИЯ
1.1. Химическое пассивирование поверхности заготовок, деталей и узлов арматуры, изготовленных из коррозионностойких сталей и сплавов производится с целью:
- очистки поверхности от окалины, окислов;
- улучшения внешнего вида, осветления поверхности;
- повышения коррозионной стойкости;
- выявления дефектов отливок, сварных швов и наплавленного металла.
Процесс пассивирования заключается в растворении химическим способом вкреплений частиц углеродистого материала после удаления окалины механическим способом и в формировании тонкой защитной пленки на поверхностях коррозионностойкого материала, либо в размягчении окалины химическим способом с последующим ее удалением неметаллическими щетками.
1.2. Химическое пассивирование назначается в том случае, когда конструкция детали или узла обеспечивает полное удаление остатков кислоты при последующей промывке. При наличии в деталях, узлах карманов, узких каналов, глухих гладких и резьбовых отверстий, не позволяющих полностью удалить остатки кислоты, а также на сборках трубопроводов (труба, штуцер, гайка), имеющих разные марки сталей, химическая обработка, включая операции травления и пассивирования, не производится.
1.3. В зависимости от назначения изделий, типа узлов и деталей, марки материала, из которых они изготовлены, устанавливается вид химической обработки по одному из режимов, рекомендуемых настоящим руководящим документом.
1.4. Необходимость химической обработки деталей и узлов арматуры должна быть указана в чертежах. В технических требованиях чертежа делается запись по типу: «Покрытие — Хим. пас. по режим I». При использовании химической обработки для осветления, травления и пр. в литейном, кузнечно-штамповочном, сварочном и сильфонном производстве в технологической документации должна быть произведена аналогичная запись.
1.5. Для предотвращения образования трудноудаляемой окалины и пригаров детали, подлежащие химическому пассивированию, перед термообработкой, сваркой и другими операциями, связанными с нагревом, необходимо очистить от смазки и прочих жировых загрязнений.
2. РЕЖИМЫ ХИМИЧЕСКОГО ПАССИВИРОВАНИЯ УЗЛОВ И ДЕТАЛЕЙ АРМАТУРЫ
2.1. Режим I. Химическое пассивирование деталей и узлов из коррозионностойких сталей.
2.1.1. Химическому пассивированию по режиму I подвергаются литые, кованные, штампованные и сварные заготовки, детали и узлы арматуры, изготовленные из сталей следующих марок 10Х18Н9Л, 12Х18Н9ТЛ, 12Х18Н12М3ТЛ, 16Х18Н12С4ТЮЛ, 07Х20Н25МЗД2ТЛ, 05Х18АН5ФЛ, 12X17, 14X17h3, 07X16Н4Б, 07Х21Г7АН5, 08X18h20T, 12Х18Н9Т, 10X18H9, 12Х18H9, 15Х18Н12С4ТЮ, Х32Н8, 06ХН28МДТ, 10Х17Н13МЗТ, сплава XH60BТ, a также детали из указанных марок с наплавками стеллитом ВЗК, ЦН6, ЦН6М-67, ЦН6Л, ЦН12-67, ЦН12М-67, УОНИ-13/h2-BК, 06Х20Н10МЗДЗС4Л.
2.1.2. Детали, сборки и заготовки, включая отливки, поковки, штамповки подвергаются обработке по следующей технологической схеме:
2.1.3. Механическая очистка включает в себя дробеметную и дробеструйную обработку, обработку абразивными кругами и крацщетками.
Дробеметная обработка производится в дробеметных камерах. Очистка производится литой дробью марки ДЧЛ. В дробеструйных аппаратах используется металлическая дробь или металлический песок различных фракций от 0,15 до 1,00 мм. Зернистость дроби и давление воздуха в дробеструйных аппаратах выбирают в зависимости от толщины стенок обрабатываемых деталей и состояния поверхности. Резьбу и другие поверхности, не подлежащие механической очистке, изолируют при помощи резиновых насадок и колец.
Интервал времени между дробеметной (дробеструйной) обработкой и последующей пассивацией не должен превышать более 8 часов.
Примечание. При использовании для механической очистки нержавеющих материалов (дробь, крацщетки), при условии полной очистки от окалины заготовок, деталей и узлов, допускается операции химической пассивации не производить.
2.1.4. Химическое обезжиривание производится в растворе следующего состава:
а) натр едкий по ГОСТ 2263-79 | — 50-70 г/л |
б) сода кальцинированная по ГОСТ 5100-85 | — 30-40 г/л |
в) тринатрийфосфат по ГОСТ 201-76 | — 15-20 г/л |
г) жидкое стекло натриевое по ГОСТ 13078-78* | — 5 г/л |
________________
* На территории Российской Федерации документ не действует. Действует ГОСТ 13078-81. — Примечание изготовителя базы данных.
Температура раствора — 50-70 °С
Время выдержки — 15-20 мин.
Примечания: 1. Электрохимическое обезжиривание может производиться в ванне того же состава при плотности тока от 5 до 10 А/дм, температуре от 60 до 70 °С.
2. Допускается использовать другие составы растворов, обеспечивающие полное обезжиривание обрабатываемой поверхности.
2.1.5. После обезжиривания детали промыть в горячей проточной воде при температуре от 70 до 90 °С, а затем в холодной проточной воде. Минимальная продолжительность промывки — 20 сек.
2.1.6. Пассивирование заготовок, деталей и узлов из вышеперечисленных марок сталей производится в растворе следующего состава:
кислота азотная концентрированная по ГОСТ 701-89 — 250-350 г/л.
Температура раствора — 18-30 °С.
Время выдержки от 0,5 до 2,0 часов (в зависимости от состояния поверхности),
2.1.7. Нейтрализация деталей производится в растворе, содержащем 50 г/л кальцинированной соды, при комнатной температуре. В случае, если промывка в холодной воде, а затем в горячей гарантируют качественную отмывку деталей от кислоты (качество отмывки проверяется с помощью универсальной индикаторной бумаги), операция нейтрализации может быть опущена.
2.1.8. После пассивирования и последующей нейтрализации детали тщательно промываются многократным погружением в ванну с холодной проточной водой (не менее 3-х раз), а затем промываются в ванне с горячей проточной водой при температуре 60-90 °С.
2.1.9. Литые заготовки с трудноудаляемой окалиной из сталей марок 15Х18Н12С4ТЮ и 12X18H9, а также заготовки из других сталей при неудовлетворительном состоянии поверхности после пассивирования проходят весь цикл обработки, начиная с дробеструйной, повторно.
2.1.10. При химической обработке деталей и узлов, имеющих наплавку стеллитом ВЗК, ЦН6, ЦН6М-67, ЦН6Л, ЦН12-67, ЦН12М-67, УОНИ-13/Н1-БК, и 06Х20Н10МЗД3СЛ6 припуск на механическую обработку наплавки и прилегающих к ней поверхностей должен быть не менее 2,5 мм на сторону и должен охватывать как наплавку, так и прилегающие к ней поверхности на ширине 5 мм от наплавки, а при ширине поверхности менее 5 мм — по всей ширине поверхности.
Поверхности, связанные с наплавками и определенные жесткими допусками (соосность, параллельность), механически обрабатываются после химической обработки.
2.1.11. Сушка производится одним из трех способов:
- на воздухе при комнатной температуре;
- в сушильном шкафу или калорифере при температуре от 50 до 80 °С;
- обдувкой теплым сжатым воздухом, очищенным от пыли, влаги и масла.
2.1.12. После сушки производится визуальный контроль состояния внешней поверхности обработанных заготовок, отливок деталей и узлов в соответствии с разделом 5. При неудовлетворительном состоянии поверхности заготовок, деталей и узлов все технологические операции производятся повторно.
2.1.13. В тех случаях, когда удаление окалины механическим способом невозможно (чистовые детали после термообработки) следует производить травление в азотно-плавиковых растворах.
2.1.13.1. Травление обеспечивает химическое удаление окалины и окисных пленок после операций, связанных с термическим воздействием с образованием окислов (наплавки, сварки и термообработки).
2.1.13.2. Травлению подвергаются детали и узлы из сталей марок, перечисленных в п.2.1.1 за исключением сталей с содержанием никеля менее 8%, например 14Х17Н2, 12X17.
2.1.13.3. Технологическая схема процесса травления состоит из следующих последовательно производимых операций.
2.1.13.4. Операции химического обезжиривания и последующей промывки производятся согласно п.п.2.1.4, 2.1.5.
2.1.13.5. Травление деталей и узлов производится в растворе следующего состава:
а) кислота азотная концентрированная по ГОСТ 701-89 | — 150-250 г/л |
б) кислота фтористоводородная по ГОСТ 10484-78 | — 50-80 г/л |
Температура раствора 18-30 °С.
Время выдержки от 0,3 до 10 часов в зависимости от состояния поверхности металла и концентрации кислоты в ванне.
2.1.13.6. При обработке деталей, имеющих наплавки, необходимо учитывать требования, изложенные в п.2.1.10 настоящего РД.
2.1.13.7. Операция нейтрализации производится в соответствий с п.2.1.7.
2.1.13.8. Промывочная операция после травления и нейтрализации производится многократным погружением в ванну с холодной водой.
2.1.13.9. Окалина, размягченная в процессе травления, травильный шлам с поверхности удаляются тщательной очисткой неметаллическими щетками и смывом водой.
Если в результате очистки щетками не удается удалить окалину и шлам, то необходимо повторно обработать детали в растворе травления.
2.1.13.10. Промывка после очистки шлама производится в горячей проточной воде при температуре от 70 до 90 °С.
2.1.13.11. Сушка производится согласно п.2.1.11.
2.1.13.12. Контрольные операции производятся согласно п.2.1.12.
2.1.13.12. После травления в азотно-плавиковом растворе пассивирование допускается не производить.
2.2. Режим II. Химическое пассивирование деталей арматуры, предназначенной для спецпродуктов.
2.2.1. Химическому пассивированию по режиму II подвергаются изделия в собранном виде из сталей марок 08X18h20T, 12X18H9T и 14X17h3, предназначенные для работы в среде со спецпродуктами (типа 030 и амидола).
Химическое пассивирование по режиму II обеспечивает тщательную очистку от масел, продуктов окисления стали (пленок, окалины и других) и придает ей каталическую инертность при работе со спецпродуктами.
2.2.2. Перед химическим пассивированием сварные швы и околошовные зоны деталей подвергаются механической очистке с целью полного удаления окалины и остатков флюса.
2.2.3. Детали и узлы, входящие в состав арматуры, предназначенной для работы со спецпродуктами, перед пассивированием по режиму II должны быть полностью химически обработаны по режиму I, а сильфонные сборки (в зависимости от типа сильфонов) — по режимам III или IV настоящего стандарта.
2.2.4. Химическое пассивирование по режиму II включает в себя следующие операции:
2.2.5. При сборке рабочие поверхности деталей арматуры должны быть защищены от загрязнений; с этой целью необходимо обеспечить чистоту рабочего места, инструмента, используемой ветоши и пр.
2.2.6. Для обезжиривания собранные изделия заливаются хладоном с выдержкой в течение от 10 до 15 минут. Вместо хладона для обезжиривания арматуры под продукт 030 допускается применять ацетон, а под продукт амидол — бензин «Калоша».
2.2.7. После слива растворителя производится сушка арматуры продувкой теплым фильтрованным воздухом (температура от 50 до 60 °С) до полного удаления растворителя.
2.2.11.* Пассивирование под продукт 030 представляет собой операцию промывки собранной и обезжиренной арматуры 30-процентным раствором спецпродукта. Пассивирование производится непосредственно перед началом эксплуатации арматуры.
_______________
* Нумерация соответствует оригиналу. — Примечание изготовителя базы данных.
После сборки и обезжиривания арматура под амидол не пассивируется из-за токсичности и взрывоопасности продукта. Пассивирование производится амидолом только в составе агрегата или системы, на которых она установлена.
2.2.12. Для предохранения внутренних полостей арматуры от загрязнений при транспортировке и хранении ее патрубки должны быть закрыты заглушками в соответствии с конструкторской документацией.
2.3. Режим III. Химическое пассивирование сильфонных сборок с многослойными сильфонами.
2.3.1. Химическому пассивированию по режиму III подвергаются наружные поверхности сборок с многослойными сильфонами, имеющие детали из коррозионностойких сталей марок 08X18h20T, 10X17h23M3T, ХН60ВТ, XН35BT.
Цель обработки — повысить коррозионную стойкость деталей путем удаления с их поверхности следов углеродистой стали от металлических крацщеток и режущего инструмента и образования пассивной пленки.
2.3.2. Сварные швы на сильфонных сборках, поступающих на химическую обработку, не должны иметь трещин, наплавок, прожогов, непроваренных кратеров, подрезов, пор и шлаковых включений.
2.3.3. Химическая обработка сильфонных сборок должна производиться так, чтобы гарантировать внутренние полости их от попадания химических растворов.
2.3.4. Технологическая схема обработки деталей по режиму III состоит из следующих последовательно производимых операций:
2.3.5. Операции химического обезжиривания производятся по п.2.1.4. При использовании для обезжиривания горячего щелочного раствора следует учитывать, что на верхних фланцах сильфонных сборок, которые не подвергаются обработке во избежание попадания в сильфоны используемых щелочных растворов, может выкристаллизоваться белый налет щелочи, который впоследствии должен быть удален протиркой ветошью, смоченной раствором фосфорной кислоты в спирте (200 мл фосфорной кислоты на литр этилового спирта).
2.3.6. Операции промывки после обезжиривания производятся в соответствии с п.2.1.5.
2.3.7. Травление производится в растворе, содержащем от 150 до 200 г/л фосфорной кислоты при температуре от 70 до 80 °С, продолжительность травления — от 15 до 25 минут.
2.3.8. После травления сильфонные сборки подвергаются промывке в холодной проточной воде с обработкой волосяными щетками.
2.3.9. Пассивирование производится в растворе, содержащем от 200 до 300 г/л азотной кислоты ГОСТ 701-78*, при температуре от 18 до 30 °С в течение 20 минут.
_______________
* На территории Российской Федерации документ не действует. Действует ГОСТ 701-89. — Примечание изготовителя базы данных.
2.3.10. После пассивирования сильфонные сборки промываются в холодной проточной воде.
2.3.11. Для нейтрализации остатков кислоты промытые детали погружаются на период от 15 до 20 минут в растворе, содержащий от 20 до 30 г/л кальцинированной соды; температура раствора — от 15 до 30 °С.
2.3.12. По окончании нейтрализации сборки промываются в горячей проточной воде со встряхиванием, температура воды — от 70 до 90 °С.
2.3.13. Промывка в холодной проточной воде производится путем многократного (не менее трех раз) погружения сильфонной сборки в ванну до нейтральной реакции промывной воды, оставшейся на поверхности сильфонных сборок, по универсальной индикаторной бумаге.
При использовании для промывочных операций воды хозяйственно-питьевого и промышленного водоснабжения или природной жесткой воды с общей жесткостью (сумма временной и постоянной жесткости) свыше 1,5 мг-экв/л (до 40 мг окиси кальция в литре воды) детали перед сушкой должны промываться в конденсате или дистиллированной воде с температурой от 80 до 100 °С, время выдержки — 0,5 мин.
2.3.14. Сушка сильфонных сборок осуществляется обдувкой горячим сжатым фильтрованным воздухом с последующей протиркой сильфонов бязью и промывкой в этиловом спирте.
Примечание. Допускается сушку производить в калорифере при температуре 50-80 °С с последующей протиркой сильфонов бязью.
2.4. Режим IV. Химическая обработка сильфонных сборок с однослойными сильфонами.
2.4.1. Химической обработке по режиму IV подвергаются наружные поверхности сильфонных сборок с однослойными сильфонами, в том числе имеющие швы короткоимпульсной контактной сварки.
2.4.2. Сильфонные сборки, обрабатываемые по режиму IV, должны быть предохранены от попадания во внутренние полости всех используемых растворов.
2.4.3. Технологическая схема обработки по режиму IV состоит из следующих последовательно производимых операций:
2.4.4. Операция обезжиривания производится по п.2.1.4.
2.4.5. Промывки после обезжиривания производятся по п.2.1.5.
2.4.6. Химическое пассивирование сильфонных сборок с однослойными сильфонами производится в растворе, содержащем 300 г/л азотной кислоты, при температуре от 15 до 25 °С в течение 3 часов.
2.4.7. После пассивирования сборки промываются в холодной проточной воде.
2.4.8. Операции нейтрализации, последующей промывки, сушки выполняются по п.п.2.3.9-2.3.12.
3. ОБОРУДОВАНИЕ ДЛЯ ХИМИЧЕСКОЙ ОБРАБОТКИ ДЕТАЛЕЙ И УЗЛОВ АРМАТУРЫ
3.1. Для подготовительных операций, операций промывки и нейтрализации используется типовое для гальванических участков оборудование. Процессы ведутся в стационарных ваннах.
3.2. Ванны для процессов пассивирования, травления в азотно-плавиковой смеси и промывные ванны, а также подвесные корзины рекомендуется изготавливать из листовой нержавеющей стали типа 08Х18Н9Т (толщина листа от 5 до 6 мм).
3.3. Ванны пассивирования, травления в азотно-плавиковой смеси должны быть оснащены бортовыми отсосами из нержавеющей стали или винипласта.
3.4. Для проведения полного комплекса операций на участке должна быть площадка для шланговой промывки, монтажные столы, сушильные шкафы или калориферы.
3.5. Участок должен быть оснащен подъемно-транспортным оборудованием (кран-балки, тельферы) и другими средствами механизации.
4. КОНТРОЛЬ И КОРРЕКТИРОВАНИЕ РАСТВОРОВ
4.1. Применяемые реактивы должны удовлетворять требованиям следующих стандартов:
кислота азотная (концентрированная) | — по ГОСТ 701-89 |
кислота ортофосфорная термическая | — по ГОСТ 6552-80 |
кислота фтористоводородная | — по ГОСТ 10484-78 |
сода кальцинированная техническая | — по ГОСТ 5100-85 |
натр едкий технический | — по ГОСТ 2263-79 |
тринатрийфосфат | — по ГОСТ 201-76 |
стекло натриевое жидкое | — по ГОСТ 13078-81 |
спирт этиловый технический | — по ГОСТ 17299-78 |
хладон 113 | — по ГОСТ 23844-79 |
бензин «Калоша» | — по ГОСТ 443-76 |
ацетон | — по ГОСТ 2768-84 |
известь строительная | — по ГОСТ 9175-77* |
______________ * Вероятно ошибка оригинала. Следует читать: ГОСТ 9179-77. — Примечание изготовителя базы данных. | |
алюминия сульфат технический | — по ГОСТ 12966-85 |
4.2. Применяемый при обезжиривании щелочной раствор при длительном использовании подвергается химическому анализу на основные компоненты не реже I раза в 2 недели; если концентрация не соответствует предложенному составу, то раствор корректируют.
4.3. Анализ травильных и пассивирующих растворов производится не реже I раза в неделю на основные составные компоненты и наличие ионов железа; накопление железа отрицательно сказывается на качестве отделки обрабатываемых деталей: появляются темные окисные пленки и затравы; при накоплении железа 20 г/л и более (в пересчете на металлическое) — раствор следует сменить.
4.4. Корректирование растворов производится по данным химического анализа путем добавления недостающих компонентов; при уменьшении содержания в растворах травления и пассивирования азотной кислоты возникает опасность точечного травления поверхности деталей.
4.5. Не реже одного раза в сутки корректируется рН нейтрализирующего раствора; раствор пригоден для дальнейшего использования при рН не менее 6.
5. ТЕХНИЧЕСКИЕ ТРЕБОВАНИЯ К КАЧЕСТВУ ОБРАБАТЫВАЕМЫХ ПОВЕРХНОСТЕЙ
5.1. Пассивные пленки должны быть бесцветными.
5.2. На поверхности химически обработанных деталей не допускается:
а) следы неотмытых солей;
б) растравливание поверхности деталей;
в) непрозрачные окрашенные окисные пленки;
г) продукты коррозии;
д) остатки окалины, кроме указанных п.5.3.
5.3. На поверхности химически обработанных деталей допускаются:
а) следы механической обработки деталей;
б) незначительные риски, забоины, царапины и другие повреждения поверхности, которые имелись до пассивации;
в) цвета побежалости различных оттенков в зоне сварки и местах гибки;
г) светлые матовые пятна в местах удаления продуктов коррозии;
д) следы от потеков воды;
е) остатки окалины в виде отдельных черных точек или их скопления на поверхности металла, не удаляемые механическим складыванием* стальной иглой.
_________________
* Текст документа соответствует оригиналу. — Примечание изготовителя базы данных.
5.4. Пассивированные детали контролируются визуально по состоянию поверхности и внешнему виду.
6. ОБЕЗВРЕЖИВАНИЕ ОТРАБОТАННЫХ РАСТВОРОВ ПАССИВИРОВАНИЯ, ТРАВЛЕНИЯ И ПРОМЫВНЫХ СТОЧНЫХ ВОД
6.1. Отработанные растворы пассивирования, промывные сточные воды и другие отработанные растворы, не содержащие фтор-ионы, обрабатываются по стандартной технологии, принятой для реагентной очистки.
Вышеуказанные растворы и промывные воды следует подщелачивать (10% раствором кальцинированной соды или 5-10% раствором извести) до значений рН=9,5-9,7. При этом кислота, содержащаяся в растворах, нейтрализуется, а растворенные тяжелые металлы выпадают в осадок, который оседает в отстойниках.
6.2. При использовании травильных растворов на основе фтористоводородной кислоты, требуются дополнительные меры, уменьшающие сброс фтор-ионов в сточные воды.
6.2.1. В технологическую цепь необходимо включить ванну улавливания после ванны травления, которая позволит в несколько раз снизить концентрацию фтор-ионов в промывных водах.
6.2.2. Обезвреживание отработанных травильных растворов и растворов ванны улавливания производится известью до значения рН=10,5-11,0 обрабатываемого раствора. Далее производится отстаивание растворов, после чего остаточная концентрация фтор-ионов составляет 20-40 мг/л.
6.2.3. Дальнейшее снижение содержания концентрации фтор-ионов в обезвреженных растворах и в промывных сточных водах до значений ПДК (0,2-1,0 мг/л в зависимости от региональных требований) достигается за счет разбавления стоков другими сточными водами.
6.2.4. При отсутствии возможности разбавления фторосодержащих стоков для дальнейшего понижения концентрации фтор-ионов используется дополнительная обработка сточных вод раствором трикальцийфосфата (Ca(PO)) — 500 мг/л или раствором сернокислого алюминия (Al(SO)) — 350-400 мг/л.
6.2.5. Время перемешивания сточной воды с раствором трикальцийфосфата составляет 15 минут, а с раствором сернокислого алюминия — 1,5 часа. Время отстаивания в первом случае — 1,0 час, во втором случае — 1,5 часа, а величина рН 6-7,5 в обоих случаях.
6.2.6. Для обезвреживания наиболее концентрированных растворов травления на первом этапе обезвреживания следует использовать известь — пушонку или 20% раствор известкового молока.
6.3. Осадки, полученные при обезвреживании отработанных растворов и промывных вод, подлежат обезвоживанию вместе с другими гальваническими осадками и захоронению в специально отведенных для этого местах.
7. ТРЕБОВАНИЯ БЕЗОПАСНОСТИ
7.1. Требования безопасности — по ГОСТ 12.3.008-75.
Пассивация нержавеющей стали, формирование защитного слоя электрохимическим способом
В этом материале расскажем почему важна пассивация зоны сварных швов на нержавеющей стали
Нержавеющая сталь способна противостоять коррозии благодаря пассивному слою оксида хрома, который образуется на ее поверхности. Формирование этого защитного слоя называется пассивацией. Механическое воздействие, истирание, травление или перегрев (вызванный сваркой) разрушают этот защитный слой, что в дальнейшем подвергает металл коррозии.
Пассивный слой формируется, когда атомы хрома, содержащийся в нержавеющей стали, вступают в контакт с атомами кислорода в воздухе. Эта химическая реакция образует пассивный слой оксида хрома, который защищает поверхность нержавеющей стали. Для формирования плотного и равномерного пассивного слоя оксида хрома поверхность исходного материала должна быть идеально чистой.
Механическое воздействие, термическая обработка, сварка, сильные кислоты и гальваническое загрязнение повреждают слой оксида хрома и приводят к нежелательному окислению поврежденных участков нержавеющей стали.
В частности, после процессов сварки нержавеющей стали, чтобы полностью восстановить коррозионную стойкость стали, необходимо удалить термический слой, или по другому — цвета побежалости, вызванные перегревом нержавеющей стали в процессе сварки, а также другие поверхностные загрязнения. Для того существует специальный аппарат для электрохимической очистки сварных швов ISOJET ® Cleaner 5.
ISOJET ® Cleaner 5 — это безопасная, эффективная и быстрая система электрохимической очистки нержавеющей стали. Скорость очистки сварных швов с помощью этой системы составляет 90-150 см. в минуту.
Аппарат ISOJET ® Cleaner 5 сочетает в себе очищающую способность электрического тока с одновременно пассивирующими нержавеющую сталь свойствами электролита ISOL C.
Пассивация нержавеющей стали мгновенно начинается после того, как электрохимический процесс очистки завершен. Обычно для завершения и стабилизации пассивного слоя зоны сварного шва требуется от 24 до 48 часов.
Что это такое и как оно работает?
Частота повторной пассивирования — обычно это достигается пропусканием через систему пассивирующей кислоты — зависит от того, насколько жесткими являются условия обработки и насколько агрессивны обрабатываемые химические вещества.
Некоторые переработчики повторно пассивируют один раз в год, но другие могут делать это чаще, потому что их продукты, например, сделанные из помидоров, содержат много хлоридов и коррозионных кислот. Некоторая вода, используемая при обработке, естественно, с высоким содержанием хлоридов и плохо влияет на пассивный слой.Фирмы, занимающиеся поставками химикатов, предлагают наборы для тестирования на предмет наличия свободной поверхности железа. Если обнаружен высокий уровень, возможно, пора пассивировать.
Пассивация нержавеющей стали по сравнению с травлением
Травление — это процесс, который часто путают с пассивацией, но он служит разным целям. Оба они направлены на повышение коррозионной стойкости нержавеющей стали и других сплавов за счет создания эффективного пассивного слоя из оксида хрома.
В то время как недогрев во время сварки может вызвать плохое проплавление сварного шва, перегрев может отрицательно повлиять на физические свойства и химический состав нержавеющих сталей и других сплавов. Он может окислять составляющие металлы, в результате чего металл приобретает различные цвета от желтого до коричневого и синего в зависимости от температуры, которой они подвергались, и от толщины окисленного слоя. Это изменение цвета называется «тепловым оттенком».
В нержавеющих сталях и других сплавах, где хром играет центральную роль в коррозионной стойкости, область теплового оттенка означает, что хром был истощен с поверхности металла и недоступен для образования пассивного слоя.Следовательно, поврежденный окисленный слой должен быть удален, чтобы повторно обнажить сплав в его первоначальной, устойчивой к коррозии форме .
Таким образом, в то время как пассивация включает создание нового слоя, травление удаляет поврежденный слой, после чего можно проводить пассивацию.
Как и пассивация, травление выполняется химическими веществами — обычно растворами азотной или плавиковой кислоты — причем кислоты гораздо более агрессивны. Травление также может быть выполнено электрополировкой (когда металл погружается в раствор, пропускающий электрический ток, который удаляет очень тонкий слой поверхности металла) или механическим удалением , которое может оставлять мелкие загрязняющие частицы.
Что такое процесс пассивации?
Что такое процесс пассивации?
Как определено в стандарте MIL-STD-753C, процесс пассивации — это процесс окончательной обработки / очистки, используемый для удаления железа с поверхности коррозионно-стойких стальных деталей, так что достигается более равномерное формирование пассивной поверхности, что повышает коррозионную стойкость.
Нержавеющая сталь отличается от других металлов тем, что по мере приближения к поверхности состав металла фактически меняется.В процессе пассивации свободное железо удаляется с поверхности в раствор, оставляя более высокий уровень хрома. Обычно считается, что хорошим соотношением хрома к железу является 1,5: 1 или выше.
Что такое пассивация?
Пассивация — это химическая обработка нержавеющей стали и других сплавов, повышающая способность обработанных поверхностей противостоять коррозии.
Пассивированные оборудование и системы обладают множеством преимуществ:
Состав из нержавеющей стали
Чтобы понять пассивацию нержавеющей стали, очень важно взглянуть на саму нержавеющую сталь.Все нержавеющие стали — это сплавы железа, никеля и хрома. Хром составляет не менее 10% металла. Именно этот элемент придает нержавеющей стали устойчивость к коррозии. Часто производители стали добавляют молибден, чтобы улучшить защитные характеристики хрома для применения в высококоррозионных или высокотемпературных условиях.
Помимо химического состава металла, его состав варьируется в разных слоях, из которых состоит нержавеющая сталь. На поверхности находится пассивный слой, который иногда называют пассивной пленкой, который отвечает за обеспечение коррозионной стойкости.Это очень тонкий слой высокостабильных атомов металла, который нелегко подвергается коррозии или ржавчине. Это всего лишь несколько атомных слоев толщиной, в которых отношение хрома к железу (Cr / Fe) составляет по крайней мере 1,5: 1. Хром связывается с кислородом, образуя химически инертную «пассивную» поверхность.
На рисунке ниже показан очень тонкий пассивный слой на внешней поверхности металла:
Ниже пассивного слоя находится переходная область, где никель находится в более высоких концентрациях.Как и пассивная пленка, ее толщина составляет всего 3-4 атомных слоя. Никель в этом разделе защищает пассивную пленку, предотвращая химические реакции с железом в нижележащем слое. Он также действует как защитный барьер для основного металла, который составляет большую часть нержавеющей стали. Процентное содержание хрома, никеля и железа зависит от предполагаемого использования изделия.
Зачем нужно пассивировать?
Хотя пассивация происходит естественным образом в коррозионно-стойких и богатых хромом сплавах, при надлежащих условиях новый корпус или деталь из нержавеющей стали необходимо пассивировать перед вводом в эксплуатацию.Изготовление, механическая обработка и сварка оставляют после себя загрязнения, такие как оксиды металлов, включения, производственный мусор и постороннее железо, тем самым ставя под угрозу естественную способность металла противостоять коррозии.
Как работает пассивация?
Химическая пассивация улучшает химический состав пассивного слоя за счет увеличения отношения очень стабильных атомов хрома к более химически активным атомам железа в верхних трех-пяти атомных слоях поверхности металла. Это обогащение можно количественно измерить с помощью различных методов, включая оже-электро-спектроскопию (AES), электронную спектроскопию для химического анализа (ESCA) и энергодисперсионный рентгеновский анализ (EDX).Наиболее часто используемые данные, полученные с помощью этих методов для оценки пассивного слоя, — это отношение хрома к железу и глубина улучшения.
Текущие методики пассивации
Astro Pak использует множество различных методов пассивации, в том числе:
- Погружение резервуара — Обычно выполняется на объекте Astro Pak и рекомендуется для одновременной обработки всех производственных поверхностей для обеспечения однородности отделки и оптимальной коррозионной стойкости.
- Циркуляция — химический раствор циркулирует по системе трубопроводов и особенно рекомендуется для трубопроводов, по которым будут проходить коррозионные жидкости.
- Нанесение распылением — Может быть выполнено в Astro Pak или на объекте заказчика, и предпочтительно для обработки на месте, но необходимы надлежащая утилизация кислоты и меры безопасности.
- Нанесение геля — Ручная обработка может выполняться путем нанесения паст или гелей на поверхность. Это полезно для точечной обработки сварных швов и других сложных участков, требующих ручной обработки.
Услуги и возможности Astro Pak
ПассивацияUltrapass осуществляется в наших современных чистых помещениях и в местах с высокой степенью чистоты для клиентов. В зависимости от требований конкретной площадки можно использовать азотную кислоту, а также хелатирующие агенты с лимонной кислотой. Очистка и пассивация могут быть предоставлены для пусконаладочных работ при новом строительстве или работ по техническому обслуживанию и останову. В плановом порядке обеспечивается немедленное реагирование на аварийные отключения и критические коммунальные службы.Пассивация выполняется в сочетании с травлением дефектов зоны сварного шва, удалением коррозионных окрашивающих пленок и новыми дополнениями или заменой оборудования. Профессиональный консалтинг, проводимый нашими известными отраслевыми экспертами с многолетним опытом, приносит пользу нашим клиентам в решении их сложных вопросов.
Что такое пассивация нержавеющей стали?
Коррозионная стойкость имеет решающее значение для металла, используемого в различных сферах, где загрязнение может иметь разрушительные последствия во время производства или конечного использования продукта.Хотя необработанная нержавеющая сталь начинается с высокого уровня коррозионной стойкости, поверхностное загрязнение консистентной смазкой и маслом, мусором и химическими веществами обычно присутствует на деталях и компонентах после обработки. Процесс пассивации удаляет эти загрязнения с целью повышения коррозионной стойкости металлических компонентов.
Что такое пассивация нержавеющей стали?
Пассивация — это неэлектролитический финишный процесс, используемый для улучшения коррозии и стойкости к ржавчине компонентов из нержавеющей стали после изготовления.В состав нержавеющей стали входят железо, хром и ряд других цветных металлов, в зависимости от конкретного сплава.
Ржавчина требует присутствия железа, поэтому удаление молекул железа с поверхности металла создает преобладание молекул хрома, которые по своей природе инертны. Присутствие большого количества молекул хрома создает толстую, не относительную и пассивную поверхность, на которой не может легко образоваться ржавчина.
Процессы пассивации
Сплавы нержавеющей стали обычно начинаются с хорошего уровня коррозионной стойкости, уровень которой варьируется в зависимости от их молекулярного состава.Чтобы еще больше повысить это сопротивление, пассивация включает три этапа:
Шаг 1. Очистка компонентов
Процесс пассивации начинается с тщательной очистки детали из нержавеющей стали, удаления любых поверхностных масел, химикатов или мусора, оставшихся после обработки. Без этого этапа процесса посторонние предметы на поверхности металла ограничат эффективность пассивации.
Шаг 2. Погружение в кислотную ванну
Погружение детали в кислотную ванну после очистки для удаления любых свободных частиц железа с ее поверхности.На этом этапе процесса используются три общих подхода.
Азотно-кислотная ванна
Азотная кислота — это традиционный подход к пассивации, обеспечивающий наиболее эффективное молекулярное перераспределение молекулярной структуры поверхности металла. Однако у азотной кислоты есть некоторые недостатки, связанные с ее классификацией как опасный материал. Он не только требует особого обращения, но и выделяет токсичные газы, опасен для окружающей среды и может потребовать более длительного времени обработки.
Азотная кислота с ванной с бихроматом натрия
В некоторых сплавах добавление дихромата натрия к азотной кислоте усиливает или ускоряет процесс пассивации. Дихромат натрия увеличивает опасность принятия ванн с азотной кислотой, поэтому это менее распространенный вариант.
Ванна с лимонной кислотой
Более безопасная альтернатива пассивации азотной кислотой — лимонная кислота. Лимонная кислота не требует особого обращения, не выделяет токсичных газов и является экологически чистым вариантом.Пассивация лимонной кислотой изо всех сил пыталась завоевать популярность, потому что ее соединения рисковали органическим ростом и плесенью, но инновации последних лет устранили эти проблемы, сделав ее экономичной и экологически чистой альтернативой.
Независимо от применяемого подхода, этот процесс погружения или купания вызывает химическую реакцию на поверхности компонента, добавляя тонкий слой оксидной пленки с минимальным присутствием или отсутствием молекул железа, восстанавливая коррозионную стойкость металла до состояния исходного материала. .
Шаг 3. Тестирование и сертификация
Тестирование после процесса пассивации обеспечивает проверку эффективности процесса пассивации и подтверждает соответствие ASTM, Mil-Spec и другим различным отраслевым стандартам.
Преимущества и приложения
Пассивирование дает множество преимуществ, в том числе:
- Удаление остатков загрязнений после обработки
- Повышенная коррозионная стойкость
- Сниженный риск загрязнения во время производственных процессов
- Повышенная производительность компонентов
- Увеличенный срок межремонтными интервалами
Эти преимущества пассивации универсальны в широком спектре отраслей промышленности и во многих областях применения, в которых используются некоррозионные свойства нержавеющей стали, в том числе:
- Техника тяжелая (подшипники шариковые, крепеж)
- Аэрокосмическая промышленность и авиационные компоненты
- Медицинские (ортопедические имплантаты, хирургические инструменты)
- Фармацевтическая промышленность (насосы, фитинги и компоненты, используемые в производстве)
- Армия (огнестрельное оружие, военная техника)
- Энергетика (распределение и передача электроэнергии)
Пассивация нержавеющей стали от FZE Manufacturing
Ржавчина и другие виды коррозии на поверхностях из нержавеющей стали со временем могут привести к разрушительным последствиям.Процесс пассивации устраняет угрозу коррозионного загрязнения, восстанавливая резистивные свойства обработанных компонентов до исходного состояния их сплава.
Свяжитесь с нами, чтобы узнать больше об услугах по пассивации нержавеющей стали от FZE Manufacturing Solutions или запросить расценки для конкретных потребностей вашей организации.
Будет ли эта нержавеющая сталь ржаветь?
Автоматическая рука электрохимически очищает, чтобы обеспечить полную пассивацию сварного шва из нержавеющей стали.
В мире производства нержавеющей стали нержавеющая сталь должна означать именно это — нержавеющую сталь. Тем не менее, производители нередко жалуются на появление ржавчины после ввода в эксплуатацию или установки компонентов. Такой ремонт на месте может быть дорогостоящим. Для клиентов это может означать головную боль и дорогостоящие задержки. Ржавчина вредна для бизнеса, поэтому пассивация необходима. В химии и технике пассивация относится к материалу, который становится пассивным или менее подверженным влиянию окружающей среды.
Что делает нержавеющую сталь нержавеющей? Одним словом хром. Нержавеющая сталь — это сплав железа с минимум 10,5% хрома. Хром образует тонкий слой оксида на поверхности стали — «пассивный» слой, который предотвращает поверхностную коррозию.
Пассивация — важный процесс при производстве и обеспечении качества различных марок нержавеющей стали. Он начинается сразу после полного удаления поверхностных загрязнений. Для получения однородного и стабильного пассивного слоя в нержавеющей стали обычно требуется от 24 до 48 часов, но пассивация может происходить только в определенных условиях.Нередко пассивный оксидный слой нержавеющей стали подвергается повреждениям в результате любого количества механических, промышленных и экологических процессов. Вот почему пассивация является заключительным этапом в производстве деталей из нержавеющей стали.
Что могло пойти не так?
Нержавеющая сталь отличается от углеродистой стали количеством присутствующего хрома. Незащищенная углеродистая сталь ржавеет под воздействием воздуха и влаги. Эта пленка оксида железа (ржавчина) является «активной» и ускоряет коррозию, облегчая образование большего количества оксида железа.
Нержавеющая сталь содержит достаточно хрома для пассивирования за счет образования на ее поверхности инертной пленки оксида хрома. Но пассивация происходит только в том случае, если доля хрома достаточно высока и присутствует кислород.
Увеличение количества хрома увеличивает устойчивость к коррозии. Нержавеющая сталь также содержит различные количества углерода, кремния и марганца. Добавленные элементы, такие как никель и молибден, могут придавать другие полезные свойства, такие как улучшенная формуемость и повышенная коррозионная стойкость.
Некоторые металлы, такие как золото и титан, самопассивируются. Открытые поверхностные атомы легко вступают в реакцию с кислородом окружающего воздуха с образованием стабильного слоя пассивного оксида металла. Тем не менее, если на таких металлах используются стальные инструменты, на поверхности могут остаться следы свободного железа (трехвалентного материала), что приведет к коррозии железа. То же самое и с нержавеющей сталью.
Для пассивирования поверхности из нержавеющей стали не должны содержать загрязняющих веществ, например, свободного железа. Чистая поверхность позволяет хрому реагировать с кислородом окружающего воздуха с образованием инертного или пассивного слоя оксида хрома на поверхности металла.Микропокрытие из оксида хрома действует как барьер между железосодержащим сплавом и окружающим воздухом.
Очистка для включения пассивации
Сварка создает зону термического влияния и тепловой оттенок, в котором изменяется структура сплава нержавеющей стали. Тепловой оттенок — это утолщение естественного оксидного слоя на поверхности нержавеющей стали. Когда на нержавеющей стали формируются оттенки теплого цвета, хром вытягивается из-под поверхности металла, образуя поверхностный слой оксида, богатого хромом.
Это оставляет металл чуть ниже поверхности с более низким уровнем хрома, что может отрицательно сказаться на коррозионной стойкости. Тепловое окрашивание — это серьезное загрязнение, которое необходимо удалить с поверхности не только из эстетических соображений, но и для того, чтобы нержавеющая сталь могла самостоятельно пассивироваться.
Техник электрохимически очищает кольцевой сварной шов на катаной секции из нержавеющей стали, чтобы обеспечить полную пассивацию.
Пескоструйная обработка удаляет тепловой оттенок, но загрязняет нержавеющую сталь. Шлифовка, хотя и является эффективным методом удаления теплового оттенка, оставляет следы свободного железа, которые вызывают точечную коррозию и коррозию. Удаление свободного железа требует химической обработки едкими кислотами.
Существует несколько методов очистки для пассивации. Однако из-за ограничений безопасности, бюджета и окружающей среды не все подходят для производителей. Методы включают обработку материала кислотными растворами, в том числе травильными пастами и гелями, которые очищают металлическую поверхность от загрязнений, содержащих свободное железо.Обратите внимание, что эти пасты содержат кислоты, которые могут быть опасными для окружающей среды и оператора.
Другой метод включает электрохимическую очистку и полировку. Этот процесс удаляет тепловой оттенок и другие загрязнения, в том числе больше железа и никеля, оставляя поверхности с высоким содержанием хрома. Электрополировка воздействует на выступы и скругления на поверхности материала и увеличивает долю хрома на поверхности. Эта техника существенно влияет на внешний вид нержавеющей стали, увеличивая блеск и яркость, изменяя измеренную шероховатость только примерно на 30 процентов.
Некоторые системы очистки и полировки сварных швов используют пищевые кислоты и электричество для удаления теплового оттенка и могут обеспечить химическую пассивацию деталей из нержавеющей стали в соответствии с определением ASTM International.
Валидация методов пассивации и испытаний
Невозможно переоценить важность валидации пассивации поверхностей из нержавеющей стали. Невозможно обнаружить невооруженным глазом, пассивация указывает на наличие защитного слоя оксида хрома на поверхности нержавеющей стали.Это важный ингредиент, который гарантирует устойчивость нержавеющей стали к коррозии.
Итак, как изготовитель может гарантировать, что нержавеющая сталь действительно полностью пассивирована? Существует множество тестов, и ASTM International описывает передовой опыт в своих стандартах. В частности, стандарт ASTM A380 описывает передовые методы очистки, удаления накипи и пассивации деталей, оборудования и систем из нержавеющей стали. Стандарт ASTM A967 описывает испытания с критериями приемки, чтобы продемонстрировать успешность процедур пассивации.
Далее следуют различные тесты на пассивацию. Однако знайте, что не все эти испытания подходят для всех марок нержавеющей стали.
Испытание на погружение в воду. Испытание на погружение в воду обнаруживает анодное поверхностное загрязнение нержавеющей стали, в том числе свободное железо. В ходе испытания пассивированные компоненты подвергаются воздействию дистиллированной воды с интервалами в один час погружения в воду и одного часа без погружения в течение как минимум 24 часов.
Хотя вода легко доступна, доступ к специализированным погружным камерам может потребовать значительных капиталовложений.Вода должна быть чистой, дистиллированной и не содержать химикатов, что может потребовать дорогостоящего водопровода. Неправильная сантехника может ложно указать на следы железа на проверенных поверхностях. Неисправные компоненты требуют доработки и дальнейшей дезактивации. А чтобы соответствовать стандарту ASTM, цикл испытаний должен составлять не менее 24 часов.
Испытание солевым туманом. Испытание в солевом тумане — это ускоренное лабораторное испытание, обеспечивающее контролируемую коррозионную среду для определения коррозионной стойкости нержавеющих сталей.Он подвергает компоненты воздействию солевого тумана (тумана) с 5-процентным раствором хлорида натрия в испытательной камере, нагретой до 95 градусов по Фаренгейту. Продолжительность испытания короткая, поэтому он не идеален для оценки поведения материала, особенно нержавеющей стали, подверженного воздействию коррозионные элементы в естественной среде.
Пассивация позволяет нержавеющей стали образовывать защитный оксидный слой на поверхности материала.
Испытание также имеет ограниченное применение при сравнении коррозионной стойкости различных марок нержавеющей стали, например, при установлении рейтинга или количественной оценке различий в коррозионной стойкости.Коррозионные условия испытания фиксированы и не могут быть скорректированы с учетом удельной коррозионной стойкости определенных марок.
Для испытания требуется специализированное лабораторное оборудование, в том числе камера влажности, которая может не подходить для крупных компонентов из нержавеющей стали. Более того, вышедшие из строя компоненты требуют доработки и дальнейшей дезактивации.
Тест на высокую влажность. Тест на высокую влажность обнаруживает свободное железо или любые другие поверхностные анодные загрязнения на нержавеющей стали. Он выполняется в камере влажности, способной поддерживать влажность 97 (± 3) процентов при температуре 100 (± 5) градусов по Фаренгейту в течение как минимум 24 часов.
Образец для испытаний приемлем, если нет следов ржавчины или другой коррозии. Чтобы соответствовать стандартам ASTM, компоненты необходимо погрузить в ацетон или метиловый спирт, а затем высушить в инертной атмосфере или осушенном контейнере.
Для этого теста также требуется специализированное лабораторное оборудование и камера влажности, что опять же может не подходить для крупных компонентов из нержавеющей стали. Испытания не могут быть адаптированы к различным маркам нержавеющей стали, а стандарт ASTM требует, по крайней мере, 24-часового цикла испытаний.И, как и в других тестах, вышедшие из строя компоненты требуют доработки и дальнейшей дезактивации.
Тест на сульфат меди. Тест на сульфат меди редко применяется в пищевой промышленности из-за его токсичности. Фактически, ASTM запрещает использование этого теста на компонентах из нержавеющей стали, «предназначенных для использования в пищевой промышленности».
Испытание, для которого требуются водные растворы сульфата меди «возрастом не более двух недель», используется для определенных марок аустенитных, мартенситных, ферритных и дисперсионно-упрочненных сталей, содержащих не менее 16 процентов хрома.
Тест с феррицианидом калия и азотной кислотой. Это рекомендуется, когда требуется обнаружение очень малых количеств свободного железа на аустенитных нержавеющих сталях серий 200 и 300. Как и в случае теста на сульфат меди, ASTM запрещает использование этого теста на компонентах из нержавеющей стали, используемых в пищевой промышленности. Он не рекомендуется для ферритных или мартенситных сталей из-за ложных срабатываний на эти материалы. Также раствор для тестирования необходимо готовить ежедневно.
Новая альтернатива: испытание потенциала холостого хода
Разработанный в рамках портативной системы, которую можно использовать в работе, этот тест определяет стабильность и толщину пассивного слоя оксида хрома из нержавеющей стали.Тест измеряет проводимость в двух точках, при этом ток проходит через жидкость в датчике, что помогает сделать измерение максимально точным.
Устройство отображает числовое значение, которое описывает качество пассивного слоя оксида хрома. Положительное значение указывает на то, что образец пассивирован, а отрицательное значение указывает на то, что это не так. Чем выше значение, тем толще и прочнее пассивный слой.
Испытательное устройство, работающее по принципу потенциала разомкнутой цепи, проверяет, что изделие из нержавеющей стали полностью пассивировано.
Вопросы пассивации
Надлежащая пассивация и испытания обеспечивают документацию — будь то ручную или цифровую — критически важную для любого производителя, специализирующегося на нержавеющей стали. Надлежащая документация служит важным документом, свидетельствующим о том, что заготовки были испытаны на пассивацию.
Пассивирование нержавеющих сталей — основная проблема производителей, сварщиков и производителей, которые покупают, продают или работают с повсеместно распространенными и необходимыми материалами. Благодаря тестерам пассивации компании имеют в своем арсенале инструменты для ускорения, обнаружения и измерения пассивации, а также снижения затрат, связанных с переделкой бракованной продукции из нержавеющей стали.
Джонатан Доувилль — старший менеджер по продукции, R&D International, в Walter Surface Technologies, 810 Day Hill Road, Windsor, CT 06095, 860-298-1100. Изображения любезно предоставлены Walter Surface Technologies.
Ваш путеводитель по пассивации нержавеющей стали
КлиентыMarlin часто хотят узнать больше о различных вариантах отделки, которые производственная группа использует для изготовления корзин из стальной проволоки на заказ. Одна из наиболее часто используемых отделок, которую Marlin Steel применяет для своих корзин по индивидуальному заказу, — это пассивированная отделка.Пассивированная отделка часто указывается для корзин из нержавеющей стали, потому что этот процесс может улучшить химическую стойкость нержавеющей стали.
Но как работает пассивация нержавеющей стали и чем она отличается от других видов отделки, например, электрополировки?
Как работает процесс пассивации нержавеющей стали?
Некоторые особенности пассивации нержавеющей стали, такие как точное сочетание используемых химикатов, могут различаться в зависимости от используемого стального сплава — то, что помогает одному сплаву, может повредить другой, поэтому процесс требует частой настройки.Однако основной процесс обычно состоит из тех же широких шагов:
- Загрузите деталь или детали, которые нужно пассивировать, в другой контейнер (обычно в корзину из проволочной сетки, специально предназначенную для данной операции).
- Погрузите контейнер и его содержимое в химическую ванну (обычно ванну с лимонной или азотной кислотой).
- Дайте деталям постоять в ванне на время и при температуре, указанной для этого сплава.
- Выньте детали из ванны и высушите их, чтобы удалить излишки химикатов.
Когда детали из нержавеющей стали находятся в кислотной ванне, кислота начнет удалять свободное железо и другие загрязнения с поверхности детали. В зависимости от очищаемого сплава и конкретной используемой химической ванны это может улучшить защитный оксидный слой детали из нержавеющей стали, делая ее более устойчивой к химическому воздействию в некоторых ситуациях.
Хотя процесс пассивации может значительно изменить устойчивость детали к ржавчине, он не меняет существенно внешний вид готовой детали.Это одно из основных различий между пассивацией и электрополировкой. Детали, подвергнутые электрополировке, легко узнать по их гладкой блестящей поверхности.
Существует два основных типа пассивации: пассивация азотной кислотой и травление.
Что такое пассивация азотной кислотой?
Пассивация на основе азотной кислоты — один из самых основных методов пассивации. Здесь проволока из нержавеющей стали или листовой металл погружают в ванну с окислительной азотной кислотой.Эта ванна с мягкой кислотой удаляет некоторые свободные молекулы железа и другие посторонние вещества с поверхности стали, одновременно способствуя развитию пассивного оксидного слоя.
Однако этот процесс не удаляет тепловой оттенок, ожоги сварных швов или оксидную окалину с поверхности стали.
Что такое травление?
Травление очень похоже на основной процесс пассивации, поскольку для очистки поверхности стали используется ванна с кислотными химикатами.Однако там, где в основном процессе пассивации используется слабая азотная кислота, при травлении используется более интенсивная химическая смесь, такая как фтористоводородная кислота.
Эта более сильная кислота удаляет поверхностный слой стали, удаляя загрязнения, ожоги от сварных швов и свободные молекулы железа, оставляя гладкую матовую поверхность.
Что нужно знать о процессах пассивации, таких как азотная кислота и травление?
Эти два процесса стоят примерно одинаково и могут помочь удалить примеси и повысить прочность пассивного оксидного слоя нержавеющей стали.
Кстати, важно знать точный сплав обрабатываемой нержавеющей стали, прежде чем выбирать процесс пассивирования. Это связано с тем, что использование неправильного раствора для вашей нержавеющей стали может привести к повреждению стали, а не к ее улучшению.
Например, сравните нержавеющую сталь 304 и 430 для процессов пассивации. Каждый из них позволяет иметь разные уровни стойкости к азотной кислоте и другим коррозионным веществам, а это означает, что для одной из них может потребоваться более сильная ванна с азотной кислотой, чем для другой, для обеспечения надлежащей пассивации нержавеющей стали.Следует отметить, что аустенитные нержавеющие стали (например, нержавеющая сталь марки 304), как правило, имеют более высокое содержание хрома, чем мартенситные нержавеющие стали (например, нержавеющая сталь марки 430), что делает аустенитный сплав более устойчивым к коррозии и точечной коррозии.
Каковы некоторые ограничения пассивации?
Перед пассивированием деталей из нержавеющей стали следует учесть несколько моментов, в том числе:
- Сварные детали могут не подходить для пассивации .Процесс пассивации не так эффективен при удалении загрязнений из зон сварки, как некоторые процессы.
- Необходима индивидуальная настройка химической ванны. Температура и тип кислоты, используемой в химической ванне в процессе пассивации, должны быть отрегулированы для конкретного пассивируемого стального сплава. Это увеличивает стоимость и сложность процесса по сравнению с электрополировкой.
- Некоторые сплавы не пассивируются. Некоторые сплавы нержавеющей стали с низким содержанием хрома и никеля могут быть повреждены кислотной ванной.Как таковые, они не могут быть пассивированы.
- Отделка будет выглядеть практически так же. В отличие от электрополировки, при которой удаляется поверхностный слой детали для получения гладкой блестящей поверхности, пассивация не сильно меняет внешний вид детали. Итак, если целью является создание гладкой, антипригарной поверхности, то процесс пассивации не будет идеальным.
Основные преимущества пассивации нержавеющей стали заключаются в том, что она может повысить устойчивость деталей из нержавеющей стали к ржавчине и что ее установка дешевле, чем электрополировка.Однако важно сбалансировать эти преимущества с преимуществами использования электрополировки или специальных покрытий для отделки детали.
Электрополировка нержавеющей стали
Подобно процессам пассивации, перечисленным выше, электрополировка включает использование химической ванны. Однако, в отличие от двух процессов, описанных выше, при электрополировке используется ванна с электролитом и , пропускающая электрический ток для растворения поверхностного слоя металла, оставляя микроскопически гладкую блестящую поверхность.
Гладкость новой поверхности делает ее почти идеально антипригарной, поскольку процесс электрополировки устраняет почти все микроскопические дефекты, на которые обычно прилипает мусор. Дополнительным преимуществом этого является упрощение очистки и дезинфекции электрополированной детали.
Преимущества электрополировки нержавеющей стали
- Удаление заусенцев. Благодаря активному удалению поверхностного слоя детали, электрополировка удаляет многие заусенцы и заусенцы, которые могли пропустить другие процессы отделки.
- Снижение усталости деталей. Электрополировка устраняет поверхностные трещины и сводит к минимуму усталостные трещины, которые возникают на микроскопическом уровне в процессе производства. Это помогает снизить усталость детали и создать более прочную и долговечную деталь.
- Уменьшение истирания / заедания. Из-за микроскопической гладкости, обеспечиваемой электрополировкой, этот процесс часто используется производителями для обработки нитей материала для предотвращения истирания и заедания в хрупких механизмах.
- Единый внешний вид. Электрополировка удаляет со стали многие следы сварных швов и прожогов, которые оставит после себя более мягкий процесс пассивации. Это обеспечивает эстетическое улучшение некоторых производимых деталей.
- Простота управления. Электрополировка может применяться к различным сплавам нержавеющей стали, не требуя особой настройки настройки. Это делает электрополировку лучшим вариантом для производственных установок, которые обрабатывают многочисленные виды сплавов нержавеющей стали, например, когда производителю часто приходится выбирать между нержавеющей сталью 304 или 430 для различных применений.
Самый большой недостаток процесса электрополировки заключается в том, что он может стоить немного дороже, чем стандартный процесс пассивации. Кроме того, электрополировка существенно не изменяет защитный оксидный слой стали так же, как пассивация.
Однако электрополировка остается предпочтительным вариантом обработки, когда состояние поверхности детали является основной проблемой — в основном потому, что она создает поверхность более высокого качества по сравнению с пассивацией. Например, как пищевая, так и фармацевтическая промышленность предпочитают электрополированные поверхности из нержавеющей стали, потому что микроскопически гладкую поверхность невероятно легко чистить и стерилизовать по сравнению со стандартной металлической отделкой 2B.
При правильной отделке производительность проволочной корзины или другой металлической формы по индивидуальному заказу может быть значительно улучшена.
Создание специальной проволочной корзины для пассивирующего хирургического оборудования
Процессы пассивации могут быть очень грубыми для корзин и лотков, через которые проходят детали. Когда одна компания-производитель медицинских товаров заказала проволочную корзину на заказ для процесса пассивации и ультразвуковой очистки деталей, инженеры Marlin Steel использовали проверенный процесс, чтобы конструкция корзины идеально соответствовала их потребностям:
Шаг 1. Сбор информации о процессе пассивации клиента
Конкретный состав кислот и других элементов процесса пассивации может изменяться в зависимости от типа пассивируемого стального сплава.Из-за этого, когда Marlin Steel получает задание создать нестандартную проволочную корзину или лоток для пассивирования хирургического оборудования или других предметов, Marlin всегда начинает с запроса специфики процесса пассивации.
Для этого комбинированного процесса пассивации / ультразвуковой очистки важно знать:
- Размеры системы пассивирования . Размер бака и отверстия для вставки / извлечения корзин являются важной информацией для разработки индивидуальной корзины для пассивации.
- Конкретные химические вещества, используемые в процессе . Пассивация — это не универсальный процесс. В зависимости от пассивируемого металла можно использовать разные химические вещества. Чем жестче химикаты, тем жестче должна быть корзина.
- Размеры и вес детали . Размеры деталей будут влиять на размер и форму корзины. Чем крупнее и тяжелее детали, тем крупнее и прочнее должна быть корзина.Для тяжелых условий эксплуатации часто требуется стальная проволока большего сечения.
- Продолжительность процесса пассивации . Как долго корзина будет погружена в пассивирующую жидкость? Чем дольше корзины будут погружены в воду, тем больший ущерб может нанести процесс пассивации. Для особо длительных процессов требуются чрезвычайно устойчивые к коррозии сплавы.
- Сила ультразвуковых волн, используемых в процессе очистки . От того, насколько мощен ультразвуковой генератор, напрямую зависит, какому напряжению подвергается корзина во время ультразвуковой очистки.Для более высоких частот ультразвука требуются более прочные корзины, что обычно означает более толстую проволоку и более тщательную сварку.
Эта информация окажется жизненно важной для понимания того, какой дизайн корзины лучше всего подходит для нужд клиента.
Шаг 2: виртуальная проверка конструкции корзины для экономии времени и исключения ошибок
Традиционно создание идеальной проволочной корзины для ультразвуковой очистки и пассивации было долгим и трудоемким процессом. Корзины будут составляться с использованием логики «наилучшего предположения», основанной на том, что работало для аналогичных проектов в прошлом.Затем физический прототип будет отправлен заказчику и подвергнут серии стресс-тестов в течение нескольких недель или месяцев. Если бы проблемы были обнаружены, корзину пришлось бы перепроектировать, чтобы процесс начался с самого начала.
У этого метода есть несколько проблем:
- Срок поставки. Создание физического прототипа происходит очень медленно и может значительно отодвинуть сроки изготовления.
- Стоимость прототипов. Металл для корзин, расходы на транспортировку и потерю производственного времени из-за отсутствия жизнеспособной корзины — все это имеет свои затраты, сокращая операционные бюджеты.
- Сложность определения основной причины отказа корзины. При испытаниях физического прототипа иногда бывает трудно быть на 100% уверенным в причине отказа корзины. Не повлияла ли химическая коррозия на прочность корзины на разрыв? Или это вызвано действием ультразвуковой вибрации? Знание причины сбоя является обязательным условием для исправления таких сбоев в будущем.
Чтобы сэкономить время и ресурсы на поиске идеального дизайна корзины, Marlin Steel использует более быструю и эффективную форму тестирования, которая использует программное обеспечение для моделирования физики для виртуального тестирования конструкции.
За считанные минуты команда инженеров Marlin может смоделировать годы использования, не тратя ни единого кубического дюйма стали на прототип. Более того, если деталь выходит из строя при моделировании физики, причина отказа автоматически регистрируется и сообщается команде.Поскольку инженер знает причину сбоя, ему легче решить проблему.
Например, если корзина выходит из строя из-за сильных вибраций, разносящих ее на части в сварных швах, эти соединения можно изменить, чтобы они были более устойчивыми к вибрационным нагрузкам. Или, если виновата коррозия, то материалы, из которых изготовлена корзина, можно было бы изменить, чтобы сделать ее более стойкой.
Шаг 3: Обеспечение постоянного качества с помощью автоматизации производства
Дизайн может быть технически совершенным, но это не имеет значения, если конечный продукт не произведен в соответствии с установленными стандартами.Создание согласованной детали, которая может соответствовать жестким допускам, является одной из самых больших проблем в любом индивидуальном производственном приложении.
Вот почему Marlin Steel использует передовую автоматизацию производства для создания своих заказных корзин и лотков из стальной проволоки для клиентов из медицинской промышленности. Эти производственные роботы могут работать изо дня в день, не утомляя и не отвлекаясь. Это позволяет им постоянно производить детали с точностью до миллиметра.
Единообразие инструментов автоматизации производства помогает свести к минимуму процент брака деталей, помогая Marlin увеличить производительность при одновременном снижении затрат на утилизированные корзины.
Благодаря инвестициям Marlin в программное обеспечение для моделирования физики и автоматизацию производства — в дополнение к сбору подробной информации о процессе пассивации клиента — создание идеальных индивидуальных проволочных корзин для процесса пассивации и ультразвуковой очистки было простым. Это позволило Марлину за пару недель выполнить то, что компании без этих инструментов потребовалось бы несколько месяцев.
Долговечность пассивной корзины и общая стоимость владения
Процессы пассивации могут быть очень жесткими для используемых в них корзин.Это может привести к сокращению срока службы, поскольку корзины изнашиваются химическими веществами, используемыми для удаления верхнего слоя свободных молекул железа с ваших деталей.
Время, в течение которого корзина может прослужить в процессе пассивации, может существенно повлиять на общую стоимость владения.
Например, у вас есть выбор из двух разных корзин:
- Корзина «A» едва удовлетворяет минимальным требованиям, предъявляемым к работе, и имеет средний срок полезного использования 8 месяцев.По прошествии этих 8 месяцев качество корзины слишком велико, чтобы ее можно было безопасно использовать с вашим оборудованием для пассивации.
- Корзина «B» сконструирована таким образом, чтобы значительно превосходить минимальные требования, необходимые для вашего процесса пассивации, и имеет средний срок службы 4+ лет. Однако корзина B стоит в 2,5 раза дороже корзины A.
В этом теоретическом примере 10 единиц корзины A будут стоить 2000 долларов, а 10 единиц корзины B будут стоить 5000 долларов. В краткосрочной перспективе корзина A может показаться более выгодной покупкой, но в конечном итоге корзина A будет стоить намного дороже, чем корзина B.
Допустим, вы используете тот же процесс пассивации в течение следующих 8 лет. За это время корзина A будет стоить 24 000 долларов, потому что вам придется покупать корзины 12 раз по цене 2 000 долларов каждый раз. За тот же период времени корзину B нужно было бы купить только дважды по цене 5000 долларов, на общую сумму 10000 долларов.
Это делает более дорогую, но долговечную корзину гораздо более доступной в долгосрочной перспективе.
Если вам нужна корзина из нержавеющей стали для пассивации, помните о характере процесса пассивации и ожидаемом сроке службы корзин для пассивации, которые вы заказываете, необходимы для управления затратами.
Узнайте, как Marlin Steel обеспечивает высокое качество и быструю разработку для пассивирующих корзин из нержавеющей стали и многих других специальных применений, обратившись к инженеру-механику.
Пассивация нержавеющей стали: нужна ли она?
Во многих отраслях промышленности используется нержавеющая сталь, поскольку она устойчива к коррозии и выдерживает высокую степень износа. Нержавеющая сталь во многом обязана пассивацией — химическим процессом, в ходе которого кислоты удаляют излишки железа с поверхности материала, в результате чего образуется инертный оксидный слой, защищающий сталь от ржавления.
Многие производственные и промышленные организации, включая ASTM, ASME, SAE, SEMI и FDA, ввели строгие положения, регулирующие надлежащую пассивацию нержавеющей стали. Поскольку нержавеющая сталь продолжает оставаться важным элементом во многих областях строительства, производства, транспортировки и пищевой промышленности, пассивирование стали в соответствии с нормативными требованиями имеет первостепенное значение для создания надежных продуктов.
Но что такое пассивация и почему она так важна?
Понимание процесса пассивации и ее преимуществ
Пассивация — это процесс, с помощью которого рабочие делают металлические поверхности «пассивными» или более невосприимчивыми к коррозионным элементам, с которыми они могут столкнуться.Эта химическая обработка увеличивает свойства коррозионной стойкости самых разных металлов, металлоидов и металлических сплавов, таких как:
- Сталь
- Алюминий
- Медь
Как это работает?
Рабочие обычно используют хром для пассивирования металлических сплавов, потому что он очень хорошо сопротивляется коррозии. После погружения металлических компонентов в кислотную ванну с азотной или лимонной кислотой хром связывается с кислородом, образуя химически инертный пассивный слой или тонкую пленку на металлических поверхностях.Эта тонкая пленка предотвращает химические реакции, приводящие к ржавчине или коррозии.
Преимущества пассивации
Пассивация приносит металлам четыре основных преимущества:
- Повышает коррозионную стойкость
- Удаляет поверхностные загрязнения, оставшиеся от процессов фрезерования
- Снижает риск загрязнения продукта
- Увеличивает срок службы между интервалами обслуживания
Пассивация нержавеющей стали: зачем это нужно?
Сплавы нержавеющей стали состоят из железа, никеля и хрома в различных соотношениях каждого элемента, и эти соотношения определяют марку стали.В случаях, когда требуется, чтобы сталь выдерживала экстремальные температуры или повышенный уровень коррозионных агентов, сталевары добавляют в хром молибден для улучшения его защитных свойств.
Компоненты из нержавеющей стали подвергаются такой же обработке в кислотной ванне, как описано выше, что создает пассивную поверхность, предотвращающую реакцию железа с кислородом с образованием ржавчины.
После обработки на деталях из нержавеющей стали часто остается свободное железо, которое может привести к загрязнению заготовки.Пассивирование очищает эти загрязнения и создает необходимый пассивный слой, который делает нержавеющую сталь такой универсальной. Применяя передовые методы пассивации, предприятия могут добиться хороших результатов в различных областях применения.
Решения по производству высококачественной стали в Durco Manufacturing
Durco Manufacturing предоставляет эти услуги и стремится соответствовать и превосходить стандарты пассивации, установленные для каждой области применения нержавеющей стали.
Помимо полного набора услуг по пассивации нержавеющей стали, мы также работаем с другими важными промышленными металлами, такими как алюминий и медь.Свяжитесь с нами сегодня, чтобы узнать больше о наших процессах пассивации и их преимуществах для вашего следующего проекта.
Пассивирование корпусов, деталей и компонентов из нержавеющей стали
Пассивация
Видео с техническими советами по Protocase
Краткое видео о пассивации
Protocase предлагает внутреннюю пассивацию всех корпусов, деталей и панелей из нержавеющей стали.
Что такое пассивация?
Пассивация — это процесс обработки нержавеющей стали лимонной кислотой для удаления свободного железа с поверхности металла. Когда поверхностное железо удаляется, наносится пассивная поверхностная пленка, состоящая из оксидов хрома / никеля.
Когда нержавеющая сталь подвергается воздействию воздуха, оксиды хрома / никеля вступают в реакцию с кислородом с образованием оксидного слоя, защищающего остальную часть стали от коррозии.
Почему выбирают пассивацию?
Если нержавеющая сталь не окрашена, она ржавеет из-за присущих ей свойств.Пассивация максимизирует коррозионную стойкость нержавеющей стали.
Если вы выбираете чистую металлическую отделку, пассивация потребуется после того, как детали будут очищены щеткой в соответствии с вашими требованиями.
Если вы выберете порошковое покрытие для корпуса, детали или панели из нержавеющей стали, пассивация не потребуется, потому что после нанесения порошкового покрытия нержавеющая сталь не подвергнется коррозии.
Однако, если вы маскируете определенные области своей детали из нержавеющей стали для электропроводности (или по другим причинам), вы можете потребовать пассивацию маскированных областей перед нанесением порошкового покрытия, чтобы маскированные области не окислялись.
Что можно пассивировать?
Protocase предлагает пассивирование по умолчанию для всех имеющихся на складе продуктов из нержавеющей стали:
- • Листовой металл из нержавеющей стали 304
- • Пруток круглого сечения из нержавеющей стали 304
Мы автоматически применим пассивацию к любым не имеющимся на складе проектам из нержавеющей стали.