Проверка качества сварочных швов в системе неразрушающего контроля
Ультразвуковое обследование сварных соединений металлоконструкций.
Контроль проводился в соответствии с требованиями ГОСТ 14782-86.
Объект контроля: сварные соединения усиливающих деталей 7-4 в переходе из 2-го строения в 14-ое,1-й этаж.
СХЕМА ОБЪЕКТА КОНТРОЛЯ №1
ФОТО ОБЪЕКТА КОНТРОЛЯ №1
РЕЗУЛЬТАТЫ КОНТРОЛЯ ОБЪЕКТА КОНТРОЛЯ №1
№ П.П. |
№ Сварного соединения |
Типо размер соединения, мм |
Контроле доступность |
Оценка, балл |
Примечание |
1 |
1 |
5 |
1ДК |
Не годен |
Присутствуют недопустимые дефекты |
2 |
2 |
5 |
1ДК |
Годен |
|
3 |
1а |
5 |
1ДК |
Не годен |
Присутствуют недопустимые дефекты |
4 |
2а |
5 |
1ДК |
Годен |
|
Проверка сварного шва — сопровождение и завершение сварочных работ
Всесторонний и полный контроль сварных швов – ключевой компонент обеспечения надёжного и качественного соединения деталей в узел и работоспособности обследуемого объекта. Правильная оценка качества шва важна всегда, но в ответственных соединениях параметры шва нормируются. Регламентируется и контроль этого типа соединений.
Нормы государственных стандартов, отраслевые нормы задают все необходимые требования к сварке
- Обработку кромок и деталей
- Сварочные материалы и технологии
- Регламент контроля.
Вот почему качество объекта, в котором предусмотрена сварка, закладывается на стадии проектирования. Грамотный дизайн конструкции любого объекта предусматривает удобство выполнения сварочных работ, обработку швов и их контроль, а впоследствии – антикоррозионные и отделочные мероприятия. Таким образом, качество сварного шва определяется до начала его исполнения — грамотным дизайнерским и конструкторским решением.
Качество сварного соединения
Соединения металлических деталей сваркой играют различную роль в общей работе конструкции.
Измерение геометрии сварного шва
Во многих конструкциях использованы такие соединения сваркой, деформации и разрушение которых приведут к незначительным негативным явлениям без угрозы людям и без серьёзных убытков. Такие соединения должны соответствовать нормам самого общего характера. Проверка таких швов выполняется в общем порядке, без детального анализа и полной проверки.
Важная часть сварочной технологии – точная настройка режима каждой операции. Такое уточнение режима сварки реализуется выполнением пробных швов с использованием проектных материалов для будущего соединения. Эти образцы можно подвергать любому виду контроля, в том числе – со вскрытием (разрезкой) швов для анализа. Пробы позволяет уточнить параметры тока, проверить точность выбора электродов или других сварочных материалов.
Вся подготовительная работа значительно уменьшает риск брака в выполнении соединений сваркой, а
Порядок проверки сварных соединений
Порядок выполнения оценки качества сварных соединений приблизительно одинаков для всех случаев применения технологии сварки. Проверку выполняют таким образом:
- Выполненный участок шва зачищают от шлака и окалины, а при необходимости – обрабатывают раствором кислоты для получения однородной поверхности шва
- Выполняют визуальный осмотр и замеры параметров шва
- Производят инструментальную проверку качества шва согласно регламенту, предусмотренному нормами для изготавливаемого изделия или конструкции.
На практике первые фазы такого контроля проводят в процессе выполнения сварки. Специалист-сварщик проверяет выполнение операции, добиваясь достаточного уровня качества, для чего требуется контролировать параметры сечения шва (величину катета), его длину и другие требования, например – к выполнению прерывистого шва.
Магнитный метод проверки образца сварного шва
Только добившись полного выполнения технологических требований, сварщик объявляет шов выполненным и предъявляет его к проверке, зачистив от шлака и окалины. На практике исполнение важных и ответственных швов делается в присутствии специалистов, отвечающих за качество такой работы. Эти специалисты выполняют текущий контроль процесса сварки, корректируют этот процесс, контролируют его.
Хорошая организация сварочных работ, участие в них компетентных специалистов нужного уровня обеспечивают высокое качество, которое почти всегда подтверждается точным инструментальным контролем.
Особенности контроля сварочных работ
Выполняемый контроль сварных соединений преследует цель не только выяснить качество шва, но и его соответствие особенным требованиям узла, изделия или конструкции, для которой он выполнен. Одно из основных таких требований – герметичность шва и его способность выдержать давление.
Особенности некоторых изделий, изготавливаемых с применением сварки таковы, что контроль под давлением осуществить невозможно. В таком случае эта проверка откладывается на момент испытания полностью готового объекта. Так поступают при испытаниях ёмкостей и трубопроводов, работающих под высоким давлением. Дефекты швов, обнаруженные при испытании давлением, исправляют и проверяют качество повторным испытанием.
Одна из главных особенностей проверки качества сварных соединений заключается в необходимости контролировать весь процесс, от разделки кромок до зачистки готового шва от шлака и окалины. Отчасти такая необходимость объясняется тем, что сварку выполняет один человек и надёжность многих сложных, дорогостоящих и опасных конструкций нельзя оставлять в зависимости от одного, самого ответственного исполнителя или подрядчика.
Небольшая группа специалистов, в которую хорошо включать инженера, способна обеспечить хорошую поддержку непосредственному исполнителю сварочных работ, квалификация которого в самом лучшем случае ограничена практическими навыками. В такой группе могут приниматься более точные решения о корректировке режима сварки, что в конечном итоге отражается на качестве готового шва. Важна мотивация сварщика и всей группы, заинтересованных в качественном выполнении сварочных работ.
Осмотр и замеры сварочных швов
При выполнении серьёзных, ответственных сварочных операций к контролю шва относят проверку разделки кромок соединяемых деталей, от которых зависит соответствие всей операции проектным требованиям.
Цель первой стадии контроля сварных соединений – проверка параметров шва и обнаружение видимых изъянов, а также – признаков внутренних дефектов. Вот что проверяет эксперт, выполняющий такую работу:
- Делаются замеры длины шва
- Шаблоном проверяют профиль (сечение) шва
- Оценивается равномерность шва, его внешний вид, свидетельствующий о качестве наплавленного металла
- Шов тщательно осматривается на предмет поиска непроваров, подрезов, следов обрыва дуги — основных дефектов сварочной технологии
- Уточняется характер последующих фаз контроля, учитывающих требования норм и характер операции.
Внешний вид шва многое говорит опытному специалисту, неспроста некоторые швы подвергают самому придирчивому контролю. В случае обнаружения недопустимого брака шов срезают или вырубают, после чего выполняют заново. Есть изделия и конструкции, в которых повторное выполнение сварочной операции не допускается, такие детали и узлы изготавливают заново.
Сварщик выполняет первые этапы визуального контроля в процессе сварки шва
Значительные дефекты, обнаруженные визуально, являются достаточным основанием для признания шва браком, другие виды диагностики при этом не требуются. После исправления дефектов проверку сварных швов выполняют заново.
Ультразвуковой контроль сварки
Проверка сварочных швов ультразвуковой аппаратурой – самый распространённый метод неразрушающего контроля соединений такого рода. Это объясняется самыми широкими возможностями такой аппаратуры, простотой и безопасностью её работы, пригодностью для применения в полевых условиях.
Ультразвуковые дефектоскопы предназначены для обнаружения мест с нарушением цельности и плотности металла, для поиска трещин, пустот, каверн, включений шлака и других дефектов.
Магнитная проверка швов
Ещё один достаточно распространённый способ контроля качества сварных швов основан на использовании свойств магнитного поля, на состоянии которого отражаются внутренние дефекты сварного соединения. Этот метод особенно хорош в стационарных условиях производства, но есть и портативная аппаратура для его применения «на выезде».
В зоне проверки выполненной сварки создаётся сильное магнитное поле, а на поверхность шва наносят мелкодисперсную смесь или взвесь со стальными опилками, которые занимают характерное положение, отражающее состояние магнитного поля в необходимом месте.
На равномерном фоне такого изображения отчётливо видны места, где магнитное поле неравномерно – это и есть место расположения дефекта или брака. Одно из важных достоинств этого метода – его наглядность и простота. Рисунок характера магнитного поля, отображённый на поверхности сварочных швов детали можно сфотографировать и включить в документацию о выполнении контроля.
Капиллярный контроль
Ещё один хороший способ проверки качества сварки – капиллярный контроль, который в старые времена назывался керосиновой пробой. Суть этого метода заключается в том, что керосин, обладающий очень высокой степенью текучести, способен проникать в самые тонкие зазоры и трещины, где он потом обнаруживается с помощью специальных вспомогательных материалов.
Эта технология применяется и сейчас, причём в старинном виде, с использованием керосина и мела, который наносят на обследуемое место. На поверхности, покрытой мелом, проявляются следы керосина, сохранившегося в дефектных местах – трещинах шва.
Интересны особенности выполнения сплошного шва нахлестом. Такая технология формирования стыка листовых материалов или заготовок приводит к образованию небольшого промежутка между двумя швами, расположенными с обеих сторон плоскостного (в пределах ограниченного участка) по характеру объекта.
Для выполнения капиллярного контроля проникающую жидкость, керосин или пенетрант закачивают в этот промежуток под небольшим давлением через специально сделанное для этого отверстие. Следы проникновения пенетранта стараются обнаружить с одной, иногда – с обеих сторон фрагмента объекта.
Так же работает и современная замена керосину – пенетрант, который сохраняется в трещинах, полостях и прочих дефектных местах. Кстати, во многих современных составах для капиллярного анализа пенетрант либо содержит керосин, либо является полноценным керосином с добавками.
Теоретически возможны ситуации, при которых керосиновая проба может не отреагировать на наличие полостей в теле шва, но вероятность такого дефекта ничтожна.
Сварка рельсов
Рельсы железнодорожных и трамвайных путей соединяют сваркой на сложных узлах пересечений и разветвлений, а также – для уменьшения количества стыков. Для этого применяют три основные технологии:
- Обычная ручная дуговая сварка электродом
- Контактная сварка, в том числе — в виде газопрессовой технологии
- Термитная сварка – оригинальная технология, аналогичная процессу плавки и литья.
В особенных условиях протяжённых рельсовых путей используют специальные передвижные установки, представляющие собой мобильный сварочный пост, в составе которого есть и аппаратура неразрушающего контроля сварных швов и стыков. Такая организация сварки и её проверки важна для оперативного выполнения всех работ. Скорость сооружения или ремонта рельсового пути – важный фактор экономического характера.
Другие методы проверки качества сварки
В производственных, а иногда – в полевых условиях применяют и другие методы контроля сварных швов. Ограничения в их использовании обусловлены дороговизной, громоздкой или опасной аппаратурой. Вот несколько таких методов:
- Радиационный (рентгенографический) контроль, использование которого ограничивает дороговизна и опасность радиационного поражения для человека. Точность и наглядный характер этой проверки не позволяют отказаться от его применения
- Проверка высоким давлением – этот метод применим только для испытания объектов, формирующих замкнутый порожний объём.
Места, где шов «пропускает», обнаруживаются при помощи обычного мыльного раствора
- Испытание герметичности аммиаком – эта методика, применяемая для проверки герметичности швов, имеет ограниченное применение из-за опасности аммиака для человека, однако отличается очень высокой точностью. Идея такой проверки состоит в том, что пары аммиака, которым удаётся проникнуть в самых малых количествах через обследуемый шов, вступают в реакцию с индикаторным составом с обратной стороны.
Технологии проверки качества сварных швов приблизительно одинаковы для всех видов свариваемых материалов:
- Стали
- Нержавеющей стали
- Алюминия
- Чугуна
и некоторых других цветных металлов. Наибольшие сложности вызывает проверка результатов ручной дуговой сварки электродами, немного проще проверить результаты газосварки.
Более высокое качество сварного шва обеспечивает сварка полуавтоматом, выполняемая в среде углекислого газа. Настолько же качественными получаются швы, выполненные во многих современных технологиях автоматической сварки. Швы, выполненные в атмосфере аргона, отличаются мизерным количеством шлака и окалины, полноценным составом наплавляемого металла. Проверка таких сварочных соединений показывает лучшие, чем при ручной сварке электродами, результаты.
Общее качество сварочных работ принципиально выше на отлаженных производственных участках и линиях, работающих в стационарном режиме. В таком же постоянном, стационарном режиме работает и система контроля сварных соединений. Количество дефектов и брака в таких производственных условиях минимально.
Такой поточный режим применяют при изготовлении многих изделий и деталей в разных отраслях. Качественная наладка постоянного, стабильного режима сварки – гарантия высокого качества. В такой технологии серийного стационарного производства можно изготавливать даже крупноразмерные строительные конструкции.
В полевой обстановке, на стройплощадке, условия выполнения сварочных работ хуже, чем в производственном цеху, уровень качества швов также не так высок. Проверка в полевых условиях сложнее. Эти и многие другие факторы учитывают при разработке проектов тех объектов, где применяется сварка, а качественно запроектированный объект всегда будет доведён до завершения.
Механические испытания сварных соединений — Справочник химика 21
Простейшие механические испытания сварного соединения с целью получения таких его характеристик, как предел прочности, относительное удлинение, угол изгиба, производят прн помощи портативной машины с разрывным усилием 200 кН. [c.103]Механические испытания сварных соединений производят для проверки соответствия их прочности и пластических свойств техническим условиям. Основные виды механических испытаний — испытания на растяжение, ударную вязкость, загиб или сплющивание. [c.129]
Контроль сварных соединений проводят в соответствии с требованиями Правил устройства и безопасной эксплуатации сосудов, работающих под давлением .
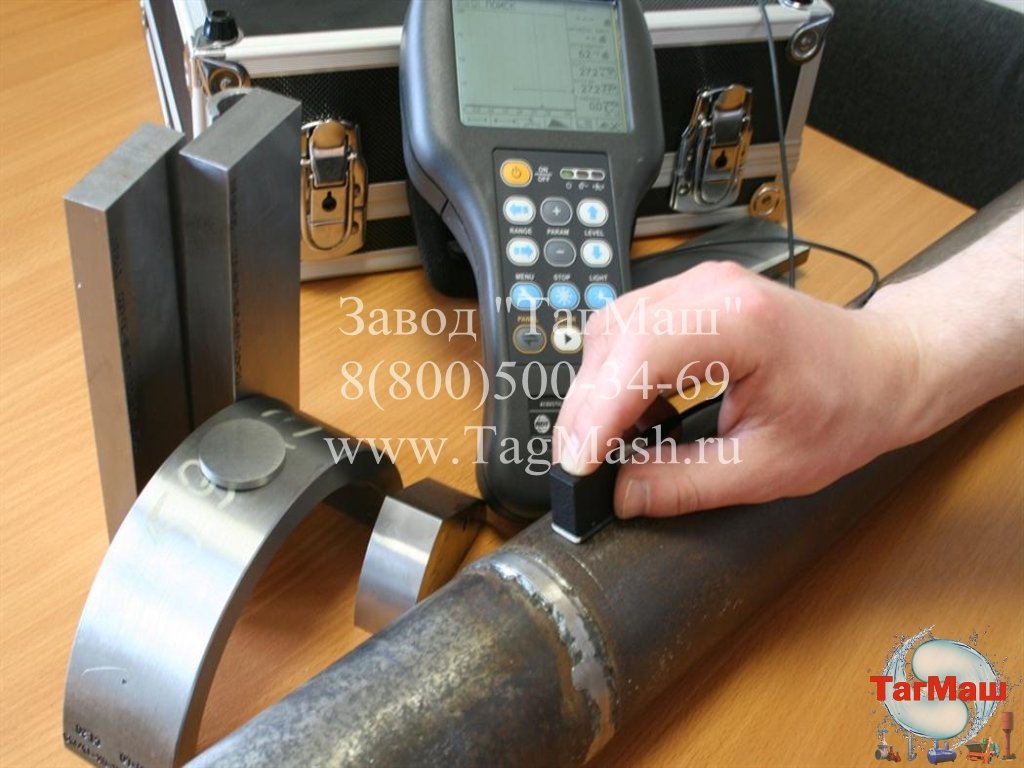
В табл. 176 даиы результаты механических испытаний сварных соединений, [c.183]
Результаты механических испытаний сварных соединений должны удовлетворять требованиям табл. 7.8. [c.111]
Форма и размеры образцов для механических испытаний сварных соединений должны соответствовать действующим стандартам [c.76]
До настоящего времени еще не разработаны единые условия механических испытаний сварных соединений пластмасс. Методы прочностных испытаний, принятые для металлов, не могут быть целиком перенесены на испытания пластмасс и их сварных соединений. Поэтому многие организации при разработке технологии сварки пластмасс разраб
Проверка непроницаемости сварных швов и соединений
Рекомендуем приобрести:
Установки для автоматической сварки продольных швов обечаек — в наличии на складе!
Высокая производительность, удобство, простота в управлении и надежность в эксплуатации.
Сварочные экраны и защитные шторки — в наличии на складе!
Защита от излучения при сварке и резке. Большой выбор.
Доставка по всей России!
Сварные швы и соединения ответственных изделий и сооружений должны быть непроницаемыми для различных жидкостей и газов Неплотности в швах снижают их прочность при вибрационных нагрузках, уменьшают коррозионную стойкость, вызывают утечку хранимых и транспортируемых продуктов и создают недопустимые условия эксплуатации сварных конструкций.
Контроль непроницаемости сварных соединений проводят в соответствии с ГОСТ 3242-79, включая следующие виды испытаний: керосином, обдувом, аммиаком, воздушным давлением, гидравлическим давлением, наливом и поливом.
Кроме этого, непроницаемость сварных соединений определяют вакуумным методом и газоэлектрическими течеискателями.
Перед проведением испытаний должны быть устранены все дефекты, выявленные внешним осмотром.
Испытание керосином основано на способности многих жидкостей подниматься по капиллярным трубкам, какими в сварных швах являются сквозные поры и трещины. Керосин обладает высокой смачивающей способностью и сравнительно малой вязкостью, что обеспечивает большой эффект этого способа контроля. Например, в отличие от воды (полярная жидкость) керосин под действием поверхностных сил проникает в мельчайшие (10-3 — 2,10-4 мм) неплотности в металле.
Испытание сварных соединений керосином проводят следующим образом. После внешнего осмотра простукивают молотком или подвергают вибрации основной металл на расстоянии 30—40 мм от шва и тщательно очищают сварное соединение от шлака, ржавчины, масла и других загрязнений. Такое простукивание или вибрация способствует лучшему удалению шлака и развитию несквозных дефектов в сквозные.
Затем с помощью пульверизатора сварные швы покрывают меловым раствором (350—450 г молотого мела или каолина на 1 л воды) с той стороны, которая более доступна для осмотра.
После высыхания мелового раствора другую сторону шва обильно смачивают керосином и выдерживают в течение определенного времени.
Исходя из экспериментальных данных Института электросварки им. Е. О. Патона, Всесоюзного научно-исследовательского института строительства трубопроводов и ряда монтажных организаций время выдержки под керосином обычно устанавливают не менее 12 ч при окружающей температуре выше 0° и не менее 24 ч — при температуре ниже 0°.
Ввиду того что при повышении температуры вязкость керосина уменьшается и скорость проникания его через неплотности шва увеличивается, для сокращения времени контроля рекомендуется швы перед испытанием нагревать до температуры 60—70° С. В этом случае время выдержки под керосином сокращается до 1,5—2 ч. Керосин наносят в процессе испытания 3—5 раз.
Соединения внахлестку, у которых один шов сплошной, а второй прерывистый, опрыскивают струей керосина под давлением co стороны прерывистого шва. Соединения внахлестку, сваренные сплошным швом с обеих сторон, испытывают керосином путем нагнетания его под давлением в межнахлесточное пространство через специально просверленное отверстие.
О наличии пор, свищей, сквозных трещин и непроваров свидетельствуют жирные желтые точки или полоски керосина на меловом слое, которые с течением времени расплываются в пятна. Поэтому необходимо тщательно следить за появлением первых точек или полосок и своевременно отмечать границы дефектных участков.
Обнаруженные дефекты устраняют, после чего сварной шов подвергают повторному контролю.
Для лучшего наблюдения за керосиновыми пятнами применяют керосин, окрашенный в красный цвет краской «Судан-III» в количестве 2,5—3 г на литр.
Эффективность контроля непроницаемости сварных швов с помощью керосина можно повысить, применяя дополнительно продувку швов сжатым воздухом под давлением 3—4 кгс/см2, разрежение атмосферного воздуха с меловой стороны шва при помощи специальных камер, вибрацию швов. Все эти меры ускоряют проникание керосина через неплотности.
С помощью керосина выявляют не только сквозные, но и поверхностные дефекты. Для этого поверхность контролируемого сварного соединения после тщательной очистки обезжиривают бензином или ацетоном и обильно смачивают окрашенным керосином. По истечении 15—20 мин керосин вытирают или смывают 5%-ным водным раствором кальцинированной соды с последующим просушиванием. Затем на поверхность сварного соединения при помощи пульверизатора наносят тонкий слой разведенного в воде мела (или каолина).
Когда мел высохнет, изделие около шва обстукивают молотком, а сам шов прогревают горячим воздухом. При этом керосин, задержавшийся ранее на дефектных участках (в случае их наличия), просачивается на меловую краску в виде пятен и полосок, по которым судят об имеющихся дефектах.
При испытании обдувом одну сторону сварного шва промазывают мыльным раствором (вода 1 л, мыло хозяйственное 100 г), а другую — обдувают сжатым воздухом, подаваемым по гибкому шлангу с наконечником под давлением 4—5 кгс/см2. Расстояние между наконечником и швом должно быть не более 50 мм.
Если испытание проводят при температуре ниже 0° С, мыльный раствор готовят с частичной заменой воды спиртом (до 60%) или с применением незамерзающей жидкости, растворяющей мыло.
Сквозные дефекты обнаруживают по появлению пузырей на промазанной мыльным раствором стороне шва.
В основу испытания аммиаком положено свойство некоторых индикаторов, например спирто-водного раствора фенолфталеина или водного раствора азотнокислой ртути, изменять окраску под воздействием щелочей, в данном случае сжиженного аммиака.
Перед началом испытаний тщательно очищают металлической щеткой сварное соединение от шлака, ржавчины, масла и других загрязнений. Если сварку вели электродами с обмазкой основного типа, то швы, кроме того, промывают водой, иначе остатки щелочных шлаков будут реагировать в процессе испытания с индикатором, изменяя его окраску.
После такой подготовки на одну сторону шва укладывают бумажную ленту или светлую ткань, пропитанную 5%-ным раствором азотнокислой ртути (индикатором), а с другой стороны создают давление аммиака.
При контроле сварных швов небольших емкостей, а также трубопроводов в них подают аммиак в количестве 1% объема воздуха в емкости и создают избыточное давление 1 кгс/см2 или более, но не выше расчетного рабочего.
При контроле отдельных участков шва над ними устанавливают герметичную камеру, в которой создают давление аммиака.
В обоих случаях спустя 1—5 мин аммиак, проникая через неплотности сварного шва, окрашивает пропитанную индикатором бумагу или ткань в серебристо-черный цвет. Скорость и интенсивность окраски, а также величина пятен характеризуют размеры дефектов, границы которых отмечают мелом или краской.
При использовании в качестве индикатора спирто-водного раствора фенолфталеина его тонкой струей льют на контролируемый шов. Если в шве имеются неплотности, аммиак проходит через них и окрашивает раствор фенолфталеина в ярко-красный цвет с фиолетовым оттенком.
Для испытания сварных швов днищ резервуаров или газгольдеров аммиак подают в пространство между днищем и основанием по трубкам с отверстиями и создают избыточное давление 8 — 10 мм вод. ст. Поливая швы спирто-водным раствором фенолфталеина, определяют неплотности в сварных швах и устраняют их.
Испытанию давлением газа подвергают емкости и трубопроводы, работающие под давлением, с целью контроля общей непроницаемости сварной конструкции.
Малогабаритные изделия герметизируют газонепроницаемыми заглушками и полностью погружают в ванну с водой. Затем в изделие через редуктор от воздушной сети или из баллона подают газ (воздух, азот, инертные газы) под давлением, величина которого на 10—20% больше величины рабочего. Имеющиеся неплотности определяют по появлению пузырьков газа в воде.
Крупногабаритные сварные изделия испытывают следующим образом. После герметизации в них создают испытательное давление и промазывают сварные швы мыльным раствором (100 г мыла на 1 л воды). Появление мыльных пузырей на промазанной поверхности свидетельствует о проницаемости шва.
Величину давления и время выдержки под ним устанавливают в соответствии с техническими условиями.
При испытании сжатыми газами следует тщательно соблюдать правила техники безопасности. Работы должны проводиться в изолированном помещении с ограждениями (на случай взрыва). Трубопроводы испытывают отдельными изолированными участками с предупредительными знаками об опасности. Гидравлическим давлением проверяют прочность и плотность сварных соединений различных емкостей, котлов паропроводов, водопроводов, газопроводов и других сварных конструкций, работающих под высоким давлением.
Перед испытанием сварное изделие герметизируют водонепроницаемыми заглушками, обтирают или обдувают сжатым воздухом сварные швы до получения сухой поверхности.
После полного заполнения изделия водой с помощью насоса или гидравлического пресса создают избыточное контрольное давление, величину которого принимают в соответствии со стандартами, инструкциями или техническими условиями (обычно в 1,5—2 раза больше рабочего). В процессе испытания давление определяют по проверенным и опломбированным манометрам.
В самой высокой точке испытываемого изделия устанавливают контрольную заглушку на резьбе для наблюдения за заполнением всего объема водой и выпуском воздуха в атмосферу. В противном случае не исключено образование воздушной подушки, находящейся под большим давлением, что может привести к разрыву изделия в процессе испытания.
По истечении 5—6 мин давление уменьшают до рабочего, а околошовную зону слегка обстукивают молотком на расстоянии 15—20 мм от края шва. Боек молотка должен быть круглым, чтобы не повредить основной металл изделия.
Проницаемость сварных швов и места сквозных дефектов устанавливают по снижению испытательного давления и появлению течи или просачиванию воды в виде капель, а также по запотеванию поверхности шва или вблизи него.
Во избежание ошибочных выводов следует иметь в виду, что при температуре воды в сосуде ниже температуры воздуха в помещении возможно полное запотевание всей поверхности металла испытуемого изделия. Кроме того, уменьшение испытательного давления не всегда указывает на наличие дефектов, а может быть вызвано неплотностями в нагнетательной системе, присоединительной арматуре, заглушках.
Недостатками этого способа контроля являются необходимость в источниках водоснабжения и трудности, возникающие при испытаниях в зимнее время на открытом воздухе.
Вертикальные резервуары для хранения нефти и нефтепродуктов, газгольдеры и другие крупные емкости испытывают наливом воды.
До испытания сварные швы тщательно обтирают ветошью или обдувают воздухом до получения сухой поверхности. Затем емкость заполняют водой и наблюдают за сварными швами и падением уровня воды. Продолжительность испытания, необходимого для осмотра всех швов, составляет от 2 до 24 ч в соответствии с техническими условиями. Если в течение этого времени не обнаружено пропусков воды и уровень ее не снизился, емкость считают выдержавшей испытание.
Категорически запрещается обстукивать сварные швы резервуаров, газгольдеров и других крупных емкостей в процессе испытания во избежание их разрушения. Испытание проводится при температуре окружающего воздуха не ниже 0° С и температуре воды не ниже +5° С.
Когда швов немного, их непроницаемость определяют, полива одну сторону шва водой из брандспойта под давлением 1—10 кгс/см2, устанавливаемым техническими условиями. Одновременно осматривают противоположную сухую сторону шва.
Проницаемость сварных швов и места дефектов определяют, следя за появлением течи, просачиванием воды в виде капель, запотеванием поверхности шва или вблизи его.
Вакуумный контроль сварных швов применяют в тех случаях, когда применение других способов почему-либо исключено. В частности, этот метод широко применяется при контроле сварных днищ резервуаров, газгольдеров, цистерн, гидроизоляционных ящиков. Он позволяет обнаружить отдельные поры диаметром до 0,004— 0,005 мм, а производительность при его использовании достигает 40—60 м сварных швов в час.
Вакуум создают при помощи переносной вакуум-камеры, которую устанавливают на наиболее доступной стороне проверяемого участка шва.
В зависимости от формы контролируемого изделия и типа соединения применяются плоские, угловые и кольцевые вакуум-камеры.
Механизированная вакуум-тележка укомплектована набором переносных вакуум-камер, позволяющих контролировать различные типы сварных соединений во всех пространственных положениях.
Контроль швов газоэлектрическими течеискателями. В настоящее время применяют два вида газоэлектрических течеискателей: гелиевые и галоидные.
Чувствительность газоэлектрических течеискателей к выявлению неплотностей в швах очень высока, но ввиду сложности конструкции и значительной стоимости изготовления их применяют только для контроля особо ответственных сварных конструкций.
Принцип работы гелиевого течеискателя основан на высокой способности гелия при определенном вакууме проходить сквозь неплотности сварных швов.
В зависимости от конфигурации и объема испытуемой сварной конструкции контроль неплотностей швов гелиевыми течеискателями производят следующими методами.
а) Контроль избыточным давлением состоит в том, что испытуемую емкость помещают в газонепроницаемую металлическую камеру, соединенную с насосами течеискателя. Внутри камеры создают вакуум, а в емкость подают под давлением гелий. При наличии сквозных дефектов в сварных швах гелий проникает в камеру и попадает в течеискатель, где фиксируется одновременно миллиамперметром и звуковым сигналом.
По окончании испытаний гелий перекачивают в другую емкость, подготовленную для контроля, или в резервуар для хранения.
б) При контроле с помощью гелиевой камеры вакуум создают в испытуемой емкости, а гелий подают в газонепроницаемую камеру. Если в сварных швах имеются неплотности, то гелий просачивается в испытуемый сосуд и попадает в течеискатель.
в) Метод установки специальной герметичной камеры-муфты применяют в основном для испытания стыков трубопроводов.
Камеру соединяют с насосом течеискателя, создают в ней вакуум и подают в трубопровод гелий. При наличии неплотностей в сварных швах гелий попадает в течеискатель и вызывает сигнал.
Эти три метода являются наиболее чувствительными к выявлению неплотностей в сварных швах, но не определяют место их расположения. С этой целью применяют обдувание струей гелия наружной поверхности испытуемой емкости, в которой создают вакуум. Места неплотностей фиксируют по сигналу течеискателя, соединенного с емкостью.
Для более точного определения расположения дефектных участков используют специальный щуп-улавливатель, соединенный с течеискателем. Щуп перемещают вдоль швов по наружной поверхности емкости, в которой находится гелий под давлением выше атмосферного. Малейшая неплотность в шве тотчас же фиксируется течеискателем.
Гелиевые течеискатели применяются для обнаружения неплотностей в сварных швах трубопроводов, находящихся под землей. Для этого над трубопроводами пробуривают несколько скважин, в которые опускают специальный щуп-улавливатель, а в каждую трубу подают гелий. Примерное место течи определяют в зависимости от того, какая из скважин показывает максимальную концентрацию гелия.
ГОСТ Р ИСО 17641-1-2011 Испытания разрушающие сварных швов металлических материалов.
Испытания на сопротивляемость образованию горячих трещин в сварных соединениях. Процессы дуговой сварки. Часть 1. Общие положения
Текст ГОСТ Р ИСО 17641-1-2011 Испытания разрушающие сварных швов металлических материалов. Испытания на сопротивляемость образованию горячих трещин в сварных соединениях. Процессы дуговой сварки. Часть 1. Общие положения
ФЕДЕРАЛЬНОЕ АГЕНТСТВО
ПО ТЕХНИЧЕСКОМУ РЕГУЛИРОВАНИЮ И МЕТРОЛОГИИ
НАЦИОНАЛЬНЫЙ | ГОСТ Р ИСО |
ИСПЫТАНИЯ РАЗРУШАЮЩИЕ СВАРНЫХ
ШВОВ МЕТАЛЛИЧЕСКИХ МАТЕРИАЛОВ
Испытания на сопротивляемость образованию
горячих трещин в сварных соединениях.
Процессыдуговойсварки
Часть 1
Общиеположения
ISO 17641-1:2004
Destructive tests on welds in metallic materials — Hot cracking tests for weldments
— Arc welding processes — Part 1: General
(IDT)
Москва Стандартинформ 2012 |
Предисловие
Цели и принципы стандартизации в Российской Федерации установлены Федеральным законом от 27 декабря 2002 г. № 184-ФЗ «О техническом регулировании», а правила применения национальных стандартов Российской Федерации — ГОСТ Р 1.0-2004 «Стандартизация в Российской Федерации. Основные положения»
Сведения о стандарте
1 ПОДГОТОВЛЕН Федеральным государственным учреждением «Научно-учебный центр «Сварка и контроль» при МГТУ им. Н.Э. Баумана» (ФГУ НУЦСК при МГТУ им. Н.Э. Баумана), Национальным агентством контроля и сварки (НАКС) на основе собственного аутентичного перевода на русский язык стандарта, указанного в пункте 4
2 ВНЕСЕН Техническим комитетом по стандартизации ТК 364 «Сварка и родственные процессы»
3 УТВЕРЖДЕН И ВВЕДЕН В ДЕЙСТВИЕ Приказом Федерального агентства по техническому регулированию и метрологии от 30 ноября 2011 г. № 661-ст
4 Настоящий стандарт идентичен международному стандарту ИСО 17641-1:2004 «Разрушающие испытания сварных швов металлических материалов. Испытания на сопротивляемость образованию горячих трещин в сварных соединениях. Процессы дуговой сварки. Часть 1. Общие положения» (ISO 17641-1:2004 «Destructive tests on welds in metallic materials — Hot cracking tests for weldments — Arc welding processes — Part 1: General»)
При применении настоящего стандарта рекомендуется использовать вместо ссылочных международных стандартов соответствующие им национальные стандарты Российской Федерации, сведения о которых приведены в дополнительном приложении ДА
5 ВВЕДЕН ВПЕРВЫЕ
Информация об изменениях к настоящему стандарту публикуется в ежегодно издаваемом информационном указателе «Национальные стандарты», а текст изменений и поправок — в ежемесячно издаваемых информационных указателях «Национальные стандарты». В случае пересмотра (замены) или отмены настоящего стандарта соответствующее уведомление будет опубликовано в ежемесячно издаваемом информационном указателе «Национальные стандарты». Соответствующая информация, уведомление и тексты размещаются также в информационной системе общего пользования — на официальном сайте Федерального агентства по техническому регулированию и метрологии в сети Интернет
СОДЕРЖАНИЕ
1 Область применения. 3 2 Нормативные ссылки. 3 3 Термины и определения. 3 4 Показатели, обозначения и единицы измерения. 4 5 Основы теории образования горячих трещин. 4 6 Виды испытаний. 5 7 Описание испытаний. 5 8 Применения. 6 Приложение ДА (справочное) Сведения о соответствии ссылочных международных стандартов ссылочным национальным стандартам Российской Федерации. 7 |
Введение
ИСО 17641-1 подготовлен Европейским комитетом по стандартизации (СЕН) в сотрудничестве с техническим комитетом ИСО/ТК 44 «Сварка и родственные процессы», подкомитетом ПК 5 «Испытания и контроль сварных швов» в соответствии с Соглашением о техническом сотрудничестве между ИСО и СЕН (Венское Соглашение).
ИСО 17641 состоит из следующих частей под общим наименованием «Разрушающие испытания сварных швов металлических материалов. Испытания на сопротивляемость образованию горячих трещин в сварных соединениях. Процессы дуговой сварки»:
— часть 1. Общие положения;
— часть 2. Испытания с естественной жесткостью;
— часть 3. Испытания с приложением внешней нагрузки (технический отчет).
НАЦИОНАЛЬНЫЙ СТАНДАРТ РОССИЙСКОЙ ФЕДЕРАЦИИ
ИСПЫТАНИЯ РАЗРУШАЮЩИЕ СВАРНЫХ ШВОВ МЕТАЛЛИЧЕСКИХ МАТЕРИАЛОВ
Испытания на сопротивляемость образованию горячих трещин в сварных соединениях.
Процессы дуговойсварки
Часть 1
Общие положения
Destructive tests on welds in metallic materials. Hot cracking tests for weldments.
Arc welding processes. Part 1. General
Дата введения — 2013-01-01
1 Область применения
Настоящий стандарт содержит основные положения, касающиеся образования горячих трещин в металле сварного шва и основном металле, и испытания, применяемые для оценки сопротивляемости образованию этих трещин при дуговой сварке.
Часть 2 (испытания с естественной жесткостью) устанавливает испытания, которые следует использовать для оценки сопротивляемости образованию горячих трещин металла сварного шва. Деформации, вызывающие образование трещин, создаются за счет жесткости сварного узла.
Часть 3 (испытания с приложением внешней нагрузки) описывает испытания, которые могут быть использованы для оценки сопротивляемости образованию горячих трещин основного металла и металла сварного шва. Деформации, вызывающие образование трещин, создаются путем нагружения испытуемого образца внешней силой.
Примечание — Испытания, приведенные в части 3, требуют использования нестандартного специального оборудования. Лаборатории применяют разные процедуры, условия испытаний и размеры образцов. Поэтому, хотя воспроизводимость внутри одной лаборатории обычно является хорошей, при испытаниях в разных лабораториях иногда возможны расхождения.
2 Нормативные ссылки
В настоящем стандарте использованы нормативные ссылки на следующие международные стандарты. Для датированных ссылок последующие поправки или изменения любых из этих публикаций действительны для настоящего стандарта только после введения поправок и изменений к нему.
ЕН ИСО 17641-2:2005 Разрушающие испытания швов на металлических материалах. Испытания свариваемых деталей на горячее растрескивание в процессе дуговой сварки. Часть 2. Самоограничивающие испытания (ISO 17641-2:2005)
EN ISO 17641-2:2005 Destructive tests on welds in metallic materials — Hot cracking tests for weldments — Arc welding processes — Part 2: Self-restraint tests (ISO 17641-2:2005)
СЕН ИСО/ТО 17641-3:2005 Разрушающие испытания сварных швов металлических материалов. Испытания на сопротивляемость образованию горячих трещин в сварных соединениях. Процессы дуговой сварки. Часть 3. Испытания с приложением внешней нагрузки (ИСО/ТО 17641-3:2005)
CEN ISO/TR 17641-3:2005 Destructive tests on welds in metallic materials — Hot cracking tests for weldments — Arc welding processes — Part 3: Externally loaded tests (ISO/TR 17641-3:2005)
3 Термины и определения
В настоящем стандарте применены следующие термины с соответствующими определениями:
3.1 горячие трещины (hot cracks): Нарушения сплошности материала, происходящие при высокой температуре вдоль границ зерен (дендритные границы), когда деформация или темп деформации превышают определенный уровень.
Примечание — Мелкие трещины, видимые только при увеличении более чем в 50 раз, часто рассматриваются как микротрещины.
3.1.1 кристаллизационные трещины (solidification cracks): Горячие трещины, образующиеся при кристаллизации жидкой фазы металла сварного шва.
Примечание — Обычно они выходят на поверхность сварного шва, но иногда могут быть под поверхностью.
3.1.2 ликвационные трещины (liquation cracks): Горячие трещины, образующиеся при расплавлении ликватов в зоне термического влияния (ЗТВ) основного металла или в многопроходных швах, когда наплавленный металл повторно нагревается при выполнении последующих проходов сварки.
3.1.3 трещины, вызванные падением пластичности (ductility dip cracks): Горячие трещины, образующиеся при сварке из-за снижения высокотемпературной пластичности. Как и ликвационные трещины они могут возникать в ЗТВ или в многопроходных швах.
3.2 испытания с естественной жесткостью (self-restraint tests): Испытания, при которых деформация шва образца происходит за счет напряжений, возникающих при сварке жестко закрепленного узла.
3.3 испытания с приложением внешней нагрузки (externally loaded tests): Испытания, при которых деформация шва образца происходит за счет напряжений, возникающих под действием внешней силы, создаваемой специальным испытательным оборудованием.
4 Показатели, обозначения и единицы измерения
Примененные в стандарте показатели, обозначения и единицы измерения приведены в таблице 1.
Таблица 1 — Показатели, обозначения и единицы измерения
Обозначение | Показатель | Единица измерения |
MSI(TT) | Показатель склонности к возникновению микротрещин (испытание на растяжение)a | мм/мм |
MSI(LBT) | Показатель склонности к возникновению микротрещин (испытание на продольный изгиб)b | мм/мм |
Ltot | Суммарная длина всех обнаруженных в образце горячих трещин | мм |
Vcrit | Критическая скорость деформации для возникновения первой горячей трещины | мм/с |
BTR | Температурный интервал хрупкости, т.е. разница между NST и DTR (см. СЕН ИСО/ТО 17641-3:2003, рисунок 2) | К |
a MSI = LMF/L0 ∙ d ∙ π b MSI = LMF/b ∙ l0 |
5 Основы теории образования горячих трещин
Горячие трещины возникают в сварном шве и ЗТВ основного материала, когда деформации, развивающиеся при охлаждении сварного соединения или под действием извне, превосходят пластичность металла в определенной зоне сварного соединения. Они имеют размеры от очень малых ликвационных трещин (длиной менее 1 мм) в ЗТВ или многопроходных швах до крупных кристаллизационных трещин, которые могут распространяться на всю длину сварных соединений.
Примечание 1 — Эти трещины не следует путать с холодными трещинами, которые всегда возникают при температурах ниже 200 °С.
Горячие трещины не ограничиваются конкретными системами сплавов. Они могут возникать в сталях, в том числе коррозионно-стойких, сплавах на основе никеля, меди и алюминия. Причин возникновения горячих трещин много, но обычно они возникают, когда локальная пластичность недостаточна для противодействия развивающимся сварочным деформациям. Недостаток пластичности может зависеть от свойств микроструктуры и ориентации (по отношению к направлению деформирования) и в некоторых случаях от присутствия хрупких включений и прослоек с низкой температурой плавления. В этом отношении некоторые системы сплавов очень чувствительны к присутствию примесей, таких как сера, фосфор, свинец и другие. Общепризнано, что аустенитные однофазные микроструктуры, особенно металла сварного шва, в том или ином виде склонны к горячему растрескиванию. Содержание примесей в таких сталях и сплавах влияет на возникновение трещин.
Примечание 2 — Точный механизм образования горячих трещин пока полностью не выяснен.
6 Виды испытаний
6.1 Испытания с естественной жесткостью
Эти испытания зависят от жесткости (закрепления) сварного узла, в результате которой возникает деформация, достаточная для возникновения трещин. Испытания с естественной жесткостью включают в себя испытания:
a) заключающиеся в сварке жестко закрепленного узла и непосредственной проверке испытуемого шва на наличие трещин;
b) заключающиеся в сварке стыкового сварного шва с полным проплавлением, из которого вырезают образец, подвергаемый дополнительной деформации для обнаружения ранее возникших горячих трещин (особенно микротрещин), облегчения выявления их направления и размеров. Для разрушения после сварки применяют растяжение или изгиб. Они не предназначены для инициирования новых трещин.
Испытания под действием сварочных напряжений пригодны только для оценки горячих трещин металла сварного шва.
6.2 Испытания с приложением внешней нагрузки
Эти испытания предусматривают внешнее нагружение образца во время процесса сварки или уже сваренного образца, который одновременно нагревают и нагружают.
Испытания с приложением внешней нагрузки включают в себя испытания:
a) при которых нагрузка прикладывается при выполнении сварного шва;
b) при которых сварной шов повторно нагревается и одновременно нагружается, чтобы получить возможность оценки склонности к возникновению трещин.
Эти испытания внешней нагрузкой пригодны для оценки образования горячих трещин металла сварного шва, основного металла и зоны термического влияния.
7 Описание испытаний
7.1 Испытания с естественной жесткостью
7.1.1 Общие положения
Подробности процедур испытания приведены в ЕН ИСО 17641-2.
7.1.2 Испытание на сопротивляемость образованию горячих трещин в шве таврового соединения (T-joint weld cracking test)
Процедура испытания предназначена для оценки склонности к возникновению кристаллизационных трещин металла однопроходного углового сварного шва. Применяют три типа образца с увеличивающейся от образца к образцу жесткостью, которая обеспечивается увеличением толщины листа и/или применением в испытуемом узле ребер жесткости. Оценка является по существу качественной, поскольку прямое измерение сварочных напряжений недоступно. Оценка основывается на длине и положении трещин (если они есть) в испытуемом сварном шве.
7.1.3 Испытание растяжением металла сварного шва (weld metal tensile test)
Это испытание предназначено для оценки сопротивляемости металла сварного шва, вырезанного из стыкового соединения, образованию ликвационных трещин и трещин, вызванных падением пластичности. Разрушение цилиндрического образца, вырезанного из стыкового шва, открывает трещины, возникшие при сварке. При проверке соседней с изломом области трещины могут быть обнаружены и измерены.
Примечание — См. ЕН ИСО 17641-2, рисунки 2 и 3.
7.1.4 Испытание продольным изгибом (longitudinal bend test)
Это испытание предназначено для оценки сопротивляемости образованию трещин при кристаллизации, ликвации и падении пластичности наплавленного металла стыковых швов. Изгиб продольных образцов, вырезанных из стыкового шва, открывает возникшие при сварке трещины, которые могут быть обнаружены и измерены.
Примечание — См. ЕН ИСО 17641-2, рисунки 4 и 5.
7.2 Испытания с приложением внешней нагрузки
7.2.1 Общие положения
Подробности процедур испытания приведены в СЕН ИСО/ТО 17641-3.
7.2.2 Испытание растяжением с нагревом (hot tensile test)
Сопротивляемость образованию горячих трещин определяют путем выполнения испытания растяжением с нагревом, имитирующим сварочный термический цикл. Чтобы оценить сопротивляемость образованию кристаллизационных и ликвационных трещин используют разные процедуры и размеры образцов:
a) чтобы моделировать возникновение кристаллизационных трещин, образец нагревают до температуры плавления, а зажимы оборудования фиксируют образец таким образом, что усадочная деформация металла вызывает образование трещин;
b) чтобы моделировать возникновение ликвационных трещин, серию образцов нагревают до температуры чуть ниже температуры солидуса, а оценка сопротивляемости образованию трещин основывается на испытании некоторого числа образцов для построения кривой пластичности при высоких температурах.
7.2.3 Испытание нагрузкой, действующей вдоль сварного шва (varestraint test) и испытание нагрузкой, действующей поперек сварного шва (transvarestraint test)
Испытания нагрузкой, действующей вдоль и поперек сварного шва, используют для определения сопротивляемости образованию горячих трещин путем нагружения образца одновременно с его сваркой.
При испытании нагрузкой, действующей вдоль сварного шва, нагрузку прикладывают в направлении, совпадающем с осью сварного шва. Испытание дает возможность оценки возникновения кристаллизационных, ликвационных трещин и трещин, возникающих из-за падения пластичности металла.
При испытании нагрузкой, действующей поперек сварного шва, нагрузку прикладывают в поперечном по отношению к оси сварного шва направлении. Испытание применяют для оценки сопротивляемости образованию только кристаллизационных трещин. В заданный момент выполнения сварочной операции производят нагружение образца путем его изгиба вокруг оправки определенной формы. По завершении испытания визуально оценивают и измеряют трещинообразование. Сопротивляемость образованию трещин оценивают по длине трещин на стороне, подвергшейся растяжению.
7.2.4 Испытание регулируемым растяжением плоского образца (controlled flat tensile test)
Это испытание проводят путем растяжения одного плоского образца, который растягивают в продольном направлении в испытательном оборудовании, обеспечивающим линейное увеличение скорости нагружения. Управляемая нагрузка прикладывается во время выполнения сварного шва. Скорость растяжения, вызывающая горячее растрескивание, характеризуется как критическая скорость растяжения и используется в качестве меры сопротивляемости образованию горячих трещин.
8 Применения
Возможные применения различных испытаний изложены в таблицах 2 и 3.
Таблица 2 — Испытания на сопротивляемость образованию горячих трещин на образцах с естественной жесткостью и их применение
Тип испытания | Вид трещин | Результат | Применение |
Испытание на сопротивляемость образованию горячих трещин в сварном шве таврового соединения | Кристаллизационные | Качественный | Сертификация сварочных материалов. Сертификационное испытание сварочных материалов |
Испытание растяжением металла сварного шва | Кристаллизационные | Качественный или количественный, если используется показатель чувствительности к возникновению микротрещин MSI(tt) | Аттестация процедуры сварки. Испытание образца изготовленного изделия. Сертификация сварочных материалов. Сертификационное испытание сварочных материалов |
Ликвационные | |||
Возникающие из-за падения пластичности металла | |||
Испытание продольным изгибом | Кристаллизационные | Качественный или количественный, если используется MSI(LBT) | Аттестация процедуры сварки. Испытание образца изготовленного изделия. Сертификация сварочных материалов. Сертификационное испытание сварочных материалов |
Ликвационные | |||
Возникающие из-за падения пластичности металла |
Таблица 3 — Испытания на сопротивляемость образованию горячих трещин на образцах с приложением внешней нагрузки и их применение
Тип испытания | Вид трещин | Результат | Применение |
Испытание нагрузкой, действующей вдоль сварного шва | Кристаллизационные | Ltot BTR | Основной материал, выбор и сертификация. Металл сварного шва, выбор и сертификация. Процедуры сварки |
Ликвационные | Ltot | ||
Возникающие из-за падения пластичности металла | Ltot | ||
Испытание нагрузкой, действующей поперек сварного шва | Кристаллизационные | Ltot | Выбор металла сварного шва. Процедуры сварки |
Испытание регулируемым растяжением плоского образца | Кристаллизационные | Vcrit | Выбор материала. Узлы с многопроходными сварными швами. Процедуры сварки. Сочетания материалов |
Ликвационные | Vcrit | ||
Возникающие из-за падения пластичности металла | Vcrit | ||
Испытание растяжением с нагревом | Кристаллизационные | BTR | Выбор и сертификация материала |
Ликвационные | BTR |
Приложение ДА
(справочное)
Сведения о соответствии ссылочных международных стандартов
ссылочным национальным стандартам Российской Федерации
Таблица ДА.1
Обозначение ссылочного международного стандарта | Степень соответствия | Обозначение и наименование соответствующего национального стандарта |
ЕНИСО 17641-2:2005 | — | * |
СЕН ИСО/ТО 17641-3:2003 | — | * |
* Соответствующий национальный стандарт отсутствует. До его утверждения рекомендуется использовать перевод на русский язык данного международного стандарта. Перевод данного международного стандарта находится в Национальном агентстве контроля и сварки (НАКС). |
Ключевые слова: сварные швы, дуговая сварка, горячие трещины, испытания
Контроль качества сварных швов
Контроль качества сварных швов
Для своевременного выявления дефектов необходим тщательный и систематический контроль сварных соединений трубопроводов на всех стадиях производства сварки. В зависимости от требований проекта или технических условий контроль сварных соединений технологических трубопроводов осуществляется путем наружного осмотра всех стыков, механических испытаний и физических методов контроля (металлографического исследования, просвечивания рентгеновскими или гамма-лучами, ультразвука, магнитографического способа), а также проверки плотности сварных стыков гидравлическим или пневматическим испытанием. В отдельных случаях в зависимости от материала труб и назначения трубопровода сварные швы проверяют на коррозионную стойкость.
Наружному осмотру подвергают каждый сваренный стык трубопровода. Путем осмотра выявляют внешние дефекты шва: наплывы, подрезы, кратеры, прожоги, трещины, свищи, наружные поры.
Механические испытания сварных соединений производят, чтобы определить их прочность и пластичность. Обязательными, видами механических испытаний являются испытания на растяжение, загиб или сплющивание и на ударную вязкость. Для проведения механических испытаний каждый сварщик одновременно со сваркой трубопровода осуществляет сварку контрольных (пробных) стыков, из которых вырезают образцы. Механические испытания контрольных стыков выполняют только при сварке трубопроводов, подведомственных органам Госгортехнадзора, на газопроводах, подведомственных органам газовой инспекции, а также на внутризаводских трубопроводах, транспортирующих огне- и взрывоопасные или токсичные газообразные и жидкие продукты. Механические испытания производят в соответствии с ГОСТ 6996—54.
Металлографическое исследование осуществляют, чтобы определить структуру металла шва и околошовной зоны, выявить в сварном шве газовые или шлаковые включения, волосяные трещины, непровары. При металлографическом исследовании проверяют излом сварного шва и определяют его макро- и микроструктуру. Эти исследования обязательны только для паропроводов первой и второй категорий, подведомственных Госгортехнадзору, и трубопроводов специального назначения. Исследованию подвергаются образцы, вырезанные из контрольного стыка.
Просвечивание рентгено- и гамма-лучами — наиболее распространенный способ контроля сварных швов без разрушения. Просвечивание позволяет обнаружить внутренние дефекты сварки — трещины, непровар, шлаковые включения и поры. Для просвечивания сварных швов применяют стационарные (РУП-200, РУП-400-5) и переносные (РУП-120-5-1 иИРА-1д) рентгеновские установки. Стационарные установки из-за больших габаритных размеров используют на заводах и в лабораториях; переносные — в монтажных условиях.
Гамма-лучи возникают в результате процессов, происходящих при распаде ядер элементов или изотопов, обладающих искусственной или естественной радиоактивностью. Эти лучи способны проникать через слой металла значительной толщины и действовать на рентгенопленку, приложенную к шву с обратной стороны. В тех местах, где имеются дефекты, поглощение лучей металлом будет меньше, и они окажут более сильное воздействие на эмульсию пленки. В данном месте на пленке появится темное пятно, по форме соответствующее дефекту шва. Для просвечивания пользуются гамма-лучами радиоактивных элементов цезия-137,. туллия-170, кобальта-60, иридия-192, европия-152. Для просвечивания радиоактивные вещества, излучающие гамма-лучи, помещают в специальные ампулы, заключенные в свинцовые кожухи (контейнеры). Рентгеновское и гамма-просвечивание проводят в соответствии с ГОСТ 7512—55. Недостатком способа контроля гамма-лучами является его вредность, требующая особых мер к охране людей от их воздействия.
Магнитографический способ контроля сварных швов основан на принципе изменения магнитного рассеивания, возникающего во время намагничивания контролируемого изделия в местах расположения дефектов. Особенностью этого способа является «запись» обнаруживаемых дефектов на специальную магнитофонную пленку (ленту).
Данный способ контроля применяют для труб толщиной до 20 мм, он позволяет четко выявить такие дефекты сварных швов, как продольные трещины, непровар, шлаковые включения и поры.
Ультразвуковой способ контроля сварных швов основан на различном отражении направленного пучка высокочастотных звуковых колебаний от металла (сварного шва) и имеющихся в нем дефектов.
Ультразвуковой контроль применяют для труб с внутренним диаметром 80 мм и более и стенками толщиной свыше 10 мм. Наибольшее применение для контроля нашли ультразвуковые дефектоскопы УЗД-7Н, НИИМ-5 и УЗД-39.
Недостатком данного способа контроля является то, что он позволяет определить лишь место дефекта, а не его характер.
Контролю физическими методами подвергают наихудшие стыки из отобранных по внешнему осмотру, в количестве:
Для трубопроводов I и II категорий…………………….. 3%
Для трубопроводов III категории ……………………….. 2%
Для трубопроводов IV категории…………………………. 1%
Количество стыков определяется от общего числа сваренных каждым сварщиком стыков, но оно должно быть не менее одного. Контролю необходимо подвергать весь периметр стыка.
При физических методах контроля сварные швы полагается браковать, если в них обнаружены следующие дефекты: трещины любых размеров; непровар глубиной более 15% от толщины стенки трубы, если она не превышает 20 мм, а при толщине стенки свыше 20 мм — более 3 мм; шлаковые включения и поры глубиной более 10% от толщины стенки трубы, если она не превышает 20 мм и 3 мм — при толщине стенки свыше 20 мм; скопления включений и пор в виде сплошной сетки дефектов в шве независимо от их глубины. Шлаковые включения глубиной до 10% от толщины стенки и длиной не более 30 мм, а также скопления пор длиной не более 15 мм не являются признаками брака.
Исправление дефектов сварных стыков трубопроводов допускается, если при условном диаметре трубопровода до 100 мм длина трещин меньше 20 мм и при условном диаметре свыше 100 мм — меньше 50 мм, а также если протяженность участков с недопустимыми дефектами меньше ¼окружности стыка. В процессе исправления необходимо вырубить дефектные места и вновь их заварить. В остальных случаях дефектный стык должен быть удален из трубопровода и на его место вварена катушка. Все подвергавшиеся исправлению участки стыков должны быть проверены физическими методами контроля.
1. Какие применяют способы контроля сварных швов?
2. В чем сущность просвечивания гамма-лучами? Какие радиоактивные элементы используются при этом?
3. Как производится исправление дефектов сварного шва?
Все материалы раздела «Сварка труб» :
● Способы сварки трубопроводов и виды сварных соединений
● Подготовка труб под сварку
● Технология газовой сварки и резки
● Кислородно-флюсовая и дуговая резка
● Технология ручной электродуговой сварки, электроды
● Источники питания сварочной дуги
● Автоматическая и полуавтоматическая сварка под флюсом
● Автоматическая и полуавтоматическая сварка в защитных газах
● Сварка трубопроводов из легированной стали
● Сварка трубопроводов высокого давления, термообработка сварных соединений
● Сварка трубопроводов из алюминия и его сплавов, из меди и ее сплавов
● Пайка трубопроводов, дефекты сварных швов
● Контроль качества сварных швов
● Виды сварки и применяемое оборудование
● Сварка и склеивание винипластовых труб
● Сварка полиэтиленовых трубопроводов
● Правила техники безопасности при резке и сварке трубопроводов
ГОСТ ISO 22826-2017 Испытания разрушающие сварных швов металлических материалов. Испытания на твердость узких сварных соединений, выполненных лазерной и электронно-лучевой сваркой (определение твердости по Виккерсу и Кнупу)
ГОСТ ISO 22826-2017
МКС 25.160.40
Дата введения 2019-03-01
Предисловие
Цели, основные принципы и основной порядок проведения работ по межгосударственной стандартизации установлены в ГОСТ 1.0-2015 «Межгосударственная система стандартизации. Основные положения» и ГОСТ 1.2-2015 «Межгосударственная система стандартизации. Стандарты межгосударственные, правила и рекомендации по межгосударственной стандартизации. Правила разработки, принятия, обновления и отмены»
Сведения о стандарте
1 ПОДГОТОВЛЕН Обществом с ограниченной ответственностью «Национальная экспертно-диагностическая компания» (ООО «НЭДК») на основе собственного перевода на русский язык англоязычной версии стандарта, указанного в пункте 5
2 ВНЕСЕН Техническим комитетом по стандартизации ТК 364 «Сварка и родственные процессы»
3 ПРИНЯТ Межгосударственным советом по стандартизации, метрологии и сертификации (протокол от 30 ноября 2017 г. N 52)
За принятие проголосовали:
Краткое наименование страны | Код страны | Сокращенное наименование национального органа по стандартизации |
Азербайджан | AZ | Азстандарт |
Армения | AM | Минэкономики Республики Армения |
Беларусь | BY | Госстандарт Республики Беларусь |
Грузия | GE | Грузстандарт |
Казахстан | KZ | Госстандарт Республики Казахстан |
Киргизия | KG | Кыргызстандарт |
Молдова | MD | Институт стандартизации Молдовы |
Россия | RU | Росстандарт |
Таджикистан | TJ | Таджикстандарт |
Туркменистан | TM | Главгосслужба «Туркменстандартлары» |
Узбекистан | UZ | Узстандарт |
Украина | UA | Минэкономразвития Украины |
4 Приказом Федерального агентства по техническому регулированию и метрологии от 23 октября 2018 г. N 822-ст межгосударственный стандарт ГОСТ ISO 22826-2017 введен в действие в качестве национального стандарта Российской Федерации с 1 марта 2019 г.
5 Настоящий стандарт идентичен международному стандарту ISO 22826:2005* «Испытания разрушающие сварных швов металлических материалов. Испытания на твердость узких сварных соединений, выполненных лазерной и электронно-лучевой сваркой (определение твердости по Виккерсу и Кнупу)» [«Destructive tests on welds in metallic materials — Hardness testing of narrow joints welded by laser and electron beam (Vickers and Knoop hardness tests)», IDT].
________________
* Доступ к международным и зарубежным документам, упомянутым в тексте, можно получить, обратившись в Службу поддержки пользователей. — Примечание изготовителя базы данных.
Международный стандарт разработан Техническим комитетом по стандартизации ISO/TC 44 «Сварка и родственные процессы», подкомитетом SC 5.
При применении настоящего стандарта рекомендуется использовать вместо ссылочных международных стандартов соответствующие им межгосударственные стандарты, сведения о которых приведены в дополнительном приложении ДА
6 ВВЕДЕН ВПЕРВЫЕ
Информация об изменениях к настоящему стандарту публикуется в ежегодном информационном указателе «Национальные стандарты«, а текст изменений и поправок — в ежемесячном информационном указателе «Национальные стандарты«. В случае пересмотра (замены) или отмены настоящего стандарта соответствующее уведомление будет опубликовано в ежемесячном информационном указателе «Национальные стандарты«. Соответствующая информация, уведомление и тексты размещаются также в информационной системе общего пользования — на официальном сайте Федерального агентства по техническому регулированию и метрологии в сети Интернет (www.gost.ru)
1 Область применения
Настоящий стандарт устанавливает специальные требования к определению твердости поперечных сечений узких сварных соединений металлических материалов, выполненных лазерной и электронно-лучевой сваркой. Настоящий стандарт распространяется на методы измерения твердости по шкалам Виккерса и Кнупа в соответствии с ISO 6507-1 и ISO 4545 при нагрузках от 0,098 до 98 Н (от HV 0,01 до HV 10) для испытания твердости по Виккерсу и при нагрузке до 9,8 Н (только до НК 1) для испытания твердости по Кнупу.
Настоящий стандарт распространяется на сварные швы, выполненные с присадочной проволокой или без присадочной проволоки. Настоящий стандарт не относится к испытаниям сварных соединений, полученных с помощью гибридной лазерно-дуговой сварки.
Для определения твердости сечений неузких сварных соединений применяют ISO 9015-1 и ISO 9015-2.
2 Нормативные ссылки
Для применения настоящего стандарта необходимы следующие ссылочные документы*. Для недатированных ссылок применяют последнее издание ссылочного документа (включая все изменения к нему):
________________
* Таблицу соответствия национальных стандартов международным см. по ссылке. — Примечание изготовителя базы данных.
ISO 4545 Metallic materials — Hardness test — Knoop test (Материалы металлические. Испытание на твердость. Определение твердости по Кнупу)
________________
В настоящее время действует ISO 4545-1 «Материалы металлические. Определение твердости по Кнупу. Часть 1. Метод испытаний».
ISO 4546 Metallic materials — Hardness test — Verification of Knoop hardness testing machines (Материалы металлические. Испытание на твердость. Проверка приборов для определения твердости по Кнупу)
________________
В настоящее время действует ISO 4545-2 «Материалы металлические. Определение твердости по Кнупу. Часть 2. Проверка и калибровка испытательного оборудования».
ISO 4547 Metallic materials — Hardness test — Calibration of standardized blocks to be used for Knoop hardness testing machines (Материалы металлические. Испытание на твердость. Калибровка аттестованных образцов, используемых для определения твердости по Кнупу)
________________
В настоящее время действует ISO 4545-3 «Материалы металлические. Определение твердости по Кнупу. Часть 3. Калибровка эталонных образцов».
ISO 6507-1 Metallic materials — Vickers hardness test — Part 1: Test method (Металлы и сплавы. Испытания на твердость по Виккерсу. Часть 1. Метод измерения)
ISO 6507-2 Metallic materials — Vickers hardness test — Part 2: Verification and calibration of testing machines (Материалы металлические. Определение твердости по Виккерсу. Часть 2. Поверка и калибровка испытательных машин)
ISO 6507-3 Metallic materials — Vickers hardness test — Part 3: Calibration of reference blocks (Металлические материалы. Определение твердости по Виккерсу. Часть 3. Калибровка контрольных образцов)
ISO 10250 Metallic materials — Hardness testing — Tables of Knoop hardness values for use in tests made on flat surfaces (Материалы металлические. Определение твердости. Таблицы значений твердости по Кнупу для испытаний на плоских поверхностях)
________________
В настоящее время действует ISO 4545-4 «Материалы металлические. Определение твердости. Часть 4. Таблица значений твердости по Кнупу для испытаний на плоских поверхностях».
ISO/ТR 16060 Destructive tests on welds in metallic materials — Etchants for macroscopic and microscopic examination (Испытания разрушающие сварных швов металлических материалов. Реактивы для травления при макро- и микроскопическом исследовании)
3 Общие положения
Испытания на твердость по Виккерсу проводят в соответствии с ISO 6507-1, ISO 6507-2 и ISO 6507-3, испытания на твердость по Кнупу проводят в соответствии с ISO 4545, ISO 4546 и ISO 4547.
Испытания на твердость проводят для определения диапазона значений твердости в основном металле (или в двух металлах для разнородного соединения металлов), в зоне термического влияния и в металле сварного шва. Измеряют твердость по отдельным отпечаткам или по группам отпечатков (испытания типа Е) и по ряду расположенных отпечатков (испытания типа R).
Испытания проводят при температуре (23±5)°C. Если испытания проводят при температуре за пределами этого диапазона, то это должно быть оговорено в протоколе испытаний.
На результаты измерения микротвердости влияет вибрация, поэтому измерения следует проводить в месте, свободном от вибрации.
4 Обозначения
В настоящем стандарте применены обозначения, приведенные в таблице 1.
Таблица 1 — Обозначения
Обозначение | Определение | Единица измерения |
HAZ | Зона термического влияния | — |
E | Отдельный отпечаток | — |
R | Ряд (линия) отпечатков | — |
HV | Твердость по Виккерсу | |
HK | Твердость по Кнупу | |
L | Расстояние между центрами отпечатков | мм |
M | Рекомендуемое расстояние между центрами отпечатков в ряду | мм |
W | Расстояние между центрами отпечатков в зоне термического влияния и линии сплавления | мм |
Длина диагонали отпечатка при измерении твердости по Виккерсу | мм | |
Длина длинной диагонали отпечатка при измерении твердости по Кнупу | мм | |
Длина короткой диагонали отпечатка при измерении твердости по Кнупу | мм | |
h | Глубина проплавления | мм |
t | Толщина образца для испытания | мм |
См. ISO 6507-1. См. ISO 4545 и ISO 10250. |
5 Подготовка образцов для испытаний
Образцы для испытаний на твердость должны быть подготовлены в соответствии с ISO 6507-1 или ISO 4545.
Образец изготавливают с применением механической резки, как правило, поперек сварного шва. Эту операцию и последующую подготовку поверхности проводят, исключая нагрев до высокой температуры, чтобы не вызывать разупрочнение или упрочнение поверхности.
Поверхность образцов, подвергаемых испытанию, должна быть надлежащим образом подготовлена и протравлена в соответствии с ISO/ТО 16060, чтобы для различных зон сварного соединения измерения длин диагоналей отпечатков были выполнены с достаточной точностью.
6 Испытания
6.1 Общие требования
На рисунке 1 показаны области для размещения групп отпечатков. Номера 1 и 2 относятся к металлу сварного шва, номера от 3 до 6 к HAZ и номера 7 и 8 — к основному металлу.
1, 2 — металл сварного шва; 3, 4, 5, 6 — зоны термического влияния HAZ; 7, 8 — основной металл; а — ось сварного шва; b — линия сплавления
Рисунок 1 — Расположение групп отпечатков для определения твердости по Виккерсу и Кнупу
Если тип сварного соединения отличается от приведенного в примерах, должна быть проведена процедура испытания, соответствующая этому типу соединения.
6.2 Тип испытаний
Испытания на твердость следует проводить по отпечаткам, расположенным в соответствии с рисунками 2 и 3 для испытаний по типу Е и в соответствии с рисунками 4 и 5 для испытаний по типу R. Тип испытания определяет лицо, проводящее испытания, если не указано иное. Тип испытания должен быть указан.
6.3 Подготовка к испытанию
Если толщина основного металла t или глубина проплавления h не более 4 мм, то отпечатки на металле сварного шва и в зоне термического влияния HAZ должны быть расположены на линии по центру толщины образца, т.е. t/2, или по центру глубины проплавления, т.е. h/2 , как показано на рисунках 2, а) и 2, с).
Если t или h больше 4 мм, то отпечатки следует располагать на линиях на расстоянии не более 2 мм от верхней поверхности образца и от нижней границы сварного шва (нижней границы проплавления), как показано на рисунках 2, b) и 2, d). В случае двусторонних угловых швов с полным проплавлением отпечатки следует располагать в центральной части зоны перекрытия в соответствии с рисунком 2, d).
а) Расположение отпечатков при глубине проплавления h4 мм
b) Расположение отпечатков при глубине проплавления h>4 мм
с) Расположение отпечатков при глубине проплавления h или t4 мм
d) Расположение отпечатков при глубине проплавления h или t>4 мм
1, 2 — металл сварного шва; 3, 4, 5, 6 — зона термического влияния HAZ; 7, 8 — основной металл; а — ось сварного шва; b — линия сплавления
Рисунок 2 — Расположение отпечатков для тонких и толстых пластин — испытание типа Е
Для закаливаемых черных металлов расстояние между центром любого отпечатка и краем образца должно быть:
— не менее 2,5 длины средней диагонали отпечатка для измерения твердости по Виккерсу;
— равно длине короткой диагонали отпечатка для измерения твердости по Кнупу.
Для незакаливаемых черных и цветных металлов расстояние между центром любого отпечатка и краем образца должно быть:
— не менее трех длин средней диагонали отпечатка при измерении твердости по Виккерсу;
— равно длине короткой диагонали отпечатка для измерения твердости по Кнупу.
Расстояние L между центрами двух соседних отпечатков должно соответствовать данным, приведенным в таблице 2 для испытания типа Е, и данным, приведенным в таблице 4 для испытания типа R.
Примечание — Рекомендуется прикладывать на протяжении всего испытания одну и ту же нагрузку для испытаний сварного шва.
Таблица 2 — Расстояние L между центрами отпечатков (испытание типа Е)
Метод измерения твердости | Основной металл | Расстояние между центрами отпечатков L |
Испытание по Виккерсу (HV) | Закаливаемые черные металлы | |
Незакаливаемые черные и цветные металлы | ||
Испытание по Кнупу (HK) | Закаливаемые черные металлы | в направлении длинной диагонали в направлении короткой диагонали |
Незакаливаемые черные и цветные металлы | в направлении длинной диагонали в направлении короткой диагонали |
6.4 Отдельные отпечатки (испытание типа Е)
6.4.1 Испытания на твердость металла сварного шва
Испытания на твердость металла сварного шва следует проводить не менее чем в трех точках: в центре и в верхней и нижней областях и/или на левой и правой сторонах, как показано на рисунке 3. Твердость измеряют по всем отпечаткам. Для больших значений нагрузки при проведении испытаний по Виккерсу, например 49 Н (HV 5) и 98 Н (HV 10), число отпечатков может быть уменьшено.
Длина диагонали отпечатка или при определении твердости металла сварного шва должна составлять не более 1/10 ширины металла шва, подлежащего измерению. Испытательные нагрузки и значения твердости приведены в таблице 3.
Примечание — Длина диагонали отпечатков для каждой испытательной нагрузки и твердости материала приведена в таблице А.1 для испытания твердости по Виккерсу и в таблице А.2 — для испытания твердости по Кнупу.
6.4.2 Испытания на твердость в зоне термического влияния HAZ
Испытания на твердость в HAZ следует проводить в трех точках вдоль линии сплавления, как показано на рисунках 3, а) и 3, b).
Испытательная нагрузка при определении твердости в зоне HAZ должна быть такой же, как и для измерения твердости металла сварного шва. В случае определения твердости HAZ расстояние между линией, соединяющей центры отпечатков, и линией сплавления не должно быть меньше, чем 0,5 или 0,5 , и не должно превышать длину отпечатка или 2
Обзорыseam test — интернет-магазины и отзывы на seam test на AliExpress
Отличные новости !!! Вы попали в нужное место для проверки швов. К настоящему времени вы уже знаете, что что бы вы ни искали, вы обязательно найдете это на AliExpress. У нас буквально тысячи отличных продуктов во всех товарных категориях. Ищете ли вы товары высокого класса или дешевые и недорогие оптовые закупки, мы гарантируем, что он есть на AliExpress.
Вы найдете официальные магазины торговых марок наряду с небольшими независимыми продавцами со скидками, каждый из которых предлагает быструю доставку и надежные, а также удобные и безопасные способы оплаты, независимо от того, сколько вы решите потратить.
AliExpress никогда не уступит по выбору, качеству и цене.Каждый день вы будете находить новые онлайн-предложения, скидки в магазинах и возможность сэкономить еще больше, собирая купоны. Но вам, возможно, придется действовать быстро, поскольку этот тест на лучший шов должен в кратчайшие сроки стать одним из самых востребованных бестселлеров. Подумайте, как вам будут завидовать друзья, когда вы скажете им, что прошли тест на Алиэкспресс. Благодаря самым низким ценам в Интернете, дешевым тарифам на доставку и возможности получения на месте вы можете еще больше сэкономить.
Если вы все еще не уверены в тесте на швы и думаете о выборе аналогичного товара, AliExpress — отличное место для сравнения цен и продавцов.Мы поможем вам решить, стоит ли доплачивать за высококлассную версию или вы получаете столь же выгодную сделку, приобретая более дешевую вещь. А если вы просто хотите побаловать себя и потратиться на самую дорогую версию, AliExpress всегда позаботится о том, чтобы вы могли получить лучшую цену за свои деньги, даже сообщая вам, когда вам будет лучше дождаться начала рекламной акции. и ожидаемая экономия.AliExpress гордится тем, что у вас всегда есть осознанный выбор при покупке в одном из сотен магазинов и продавцов на нашей платформе.Реальные покупатели оценивают качество обслуживания, цену и качество каждого магазина и продавца. Кроме того, вы можете узнать рейтинги магазина или отдельных продавцов, а также сравнить цены, доставку и скидки на один и тот же продукт, прочитав комментарии и отзывы, оставленные пользователями. Каждая покупка имеет звездный рейтинг и часто имеет комментарии, оставленные предыдущими клиентами, описывающими их опыт транзакций, поэтому вы можете покупать с уверенностью каждый раз. Короче говоря, вам не нужно верить нам на слово — просто слушайте миллионы наших довольных клиентов.
А если вы новичок на AliExpress, мы откроем вам секрет. Непосредственно перед тем, как вы нажмете «купить сейчас» в процессе транзакции, найдите время, чтобы проверить купоны — и вы сэкономите еще больше. Вы можете найти купоны магазина, купоны AliExpress или собирать купоны каждый день, играя в игры в приложении AliExpress. Вместе с бесплатной доставкой, которую предлагают большинство продавцов на нашем сайте, мы думаем, вы согласитесь, что вы получите этот тест на шов по самой выгодной цене.
У нас всегда есть новейшие технологии, новейшие тенденции и самые обсуждаемые лейблы. На AliExpress отличное качество, цена и сервис всегда в стандартной комплектации. Начните самый лучший шоппинг прямо здесь.
Обзоры на сварной шов— интернет-магазины и отзывы на сварной шов на AliExpress
Отличные новости !!! Вы находитесь в нужном месте для сварки швов.К настоящему времени вы уже знаете, что что бы вы ни искали, вы обязательно найдете это на AliExpress. У нас буквально тысячи отличных продуктов во всех товарных категориях. Ищете ли вы товары высокого класса или дешевые и недорогие оптовые закупки, мы гарантируем, что он есть на AliExpress.
Вы найдете официальные магазины торговых марок наряду с небольшими независимыми продавцами со скидками, каждый из которых предлагает быструю доставку и надежные, а также удобные и безопасные способы оплаты, независимо от того, сколько вы решите потратить.
AliExpress никогда не уступит по выбору, качеству и цене. Каждый день вы будете находить новые онлайн-предложения, скидки в магазинах и возможность сэкономить еще больше, собирая купоны. Но вам, возможно, придется действовать быстро, поскольку этот верхний шов в кратчайшие сроки станет одним из самых востребованных бестселлеров. Подумайте, как вам будут завидовать друзья, когда вы скажете им, что сделали шов на AliExpress.Благодаря самым низким ценам в Интернете, дешевым тарифам на доставку и возможности получения на месте вы можете еще больше сэкономить.
Если вы все еще не уверены в сварке швов и думаете о выборе аналогичного товара, AliExpress — отличное место для сравнения цен и продавцов. Мы поможем вам решить, стоит ли доплачивать за высококлассную версию или вы получаете столь же выгодную сделку, приобретая более дешевую вещь.А если вы просто хотите побаловать себя и потратиться на самую дорогую версию, AliExpress всегда позаботится о том, чтобы вы могли получить лучшую цену за свои деньги, даже сообщая вам, когда вам будет лучше дождаться начала рекламной акции. и ожидаемая экономия.AliExpress гордится тем, что у вас всегда есть осознанный выбор при покупке в одном из сотен магазинов и продавцов на нашей платформе. Реальные покупатели оценивают качество обслуживания, цену и качество каждого магазина и продавца.Кроме того, вы можете узнать рейтинги магазина или отдельных продавцов, а также сравнить цены, доставку и скидки на один и тот же продукт, прочитав комментарии и отзывы, оставленные пользователями. Каждая покупка имеет звездный рейтинг и часто имеет комментарии, оставленные предыдущими клиентами, описывающими их опыт транзакций, поэтому вы можете покупать с уверенностью каждый раз. Короче говоря, вам не нужно верить нам на слово — просто слушайте миллионы наших довольных клиентов.
А если вы новичок на AliExpress, мы откроем вам секрет.Непосредственно перед тем, как вы нажмете «купить сейчас» в процессе транзакции, найдите время, чтобы проверить купоны — и вы сэкономите еще больше. Вы можете найти купоны магазина, купоны AliExpress или собирать купоны каждый день, играя в игры в приложении AliExpress. Вместе с бесплатной доставкой, которую предлагают большинство продавцов на нашем сайте, вы сможете приобрести сварной шов по самой выгодной цене.
У нас всегда есть новейшие технологии, новейшие тенденции и самые обсуждаемые лейблы.На AliExpress отличное качество, цена и сервис всегда в стандартной комплектации. Начните самый лучший шоппинг прямо здесь.
AATCC TM6 | Устойчивость цвета к кислотам и щелочам |
AATCC TM8 | Устойчивость цвета к изгибу: Crockmeter |
AATCC TM15 | Устойчивость к потоотделению |
AATCC TM16.1 | Устойчивость к свету: на открытом воздухе |
AATCC TM16.2 | Устойчивость цвета к свету: угольная дуга |
AATCC TM16.3 | Цветостойкость к свету: Xenon-Arc |
AATCC TM17 | Смачивающие вещества, оценка |
AATCC TM20 | Анализ волокна: качественный |
AATCC TM20A | Анализ волокна: количественный |
AATCC TM22 | Водоотталкивающая способность: спрей |
AATCC TM23 | Стойкость цвета к дымовым газам |
AATCC TM26 | Старение текстильных изделий, окрашенных серой: ускоренное |
AATCC TM27 | Смачивающие агенты: оценка смачивающих агентов |
AATCC TM30 | Противогрибковая активность, оценка текстильных материалов: устойчивость текстильных материалов к плесени и гниению |
AATCC TM35 | Водонепроницаемость: дождь |
AATCC TM42 | Водонепроницаемость: проницаемость при ударе |
AATCC TM43 | Смачивающие агенты для мерсеризации |
AATCC TM61 | Стойкость цвета к отмывке: ускоренная |
AATCC TM66 | Восстановление складок на тканых тканях: угол восстановления |
AATCC TM70 | Водоотталкивающая способность-опрокидывающаяся банка Динамическое поглощение |
AATCC TM76 | Электрическое поверхностное сопротивление тканей |
AATCC TM79 | Впитывающая способность текстиля |
AATCC TM81 | pH водного экстракта из влажных обработанных текстильных материалов |
AATCC TM82 | Текучесть дисперсий целлюлозы из беленой хлопковой ткани |
AATCC TM84 | Электрическое сопротивление пряжи |