Как изогнуть железный лист без гибочного станка » Изобретения и самоделки
В процессе строительства дома или дачи зачастую появляется необходимость в оборудовании водостоков, канализации, каркасов из металла.
При изготовлении подобных изделий необходимо придать плоской заготовке необходимую пространственную форму. Советы опытных мастеров, как загнуть лист металла в домашних условиях, позволят изготавливать конструкции хорошего качества, которые прослужат долгое время. Для работы не понадобится гибочный станок, обойдемся небольшим набором инструментов, которые есть в мастерской.
Существует простой способ сделать это и без специальных приспособлений наподобие листогиба.
Товары для изобретателей. Осенние скидки до 60%🔥Перейти в магазин Ссылка.Что понадобится для сгибания листа
Понадобятся измерительные инструменты, болгарка с камнями толщиной 1 мм и 2 мм. Для техники безопасности требуется иметь специальные очки. Гнуть будем листовую сталь толщиной 2 мм, размеры подбираются в зависимости от чистой длины и ширины с учетом величины подгибов.
Технология загиба листового материала
Процесс рассмотрим на примере изготовления крышки для коптильни. Толщина листа в нашем случае 2 мм.
Сделайте разметку на листе. На каждый изгиб предусмотрено 35 мм, для загиба рекомендуется вычесть из этого размера по 4 мм. Соответственно, на листе надо нарисовать прямоугольник 508×308 мм, изгибы получатся длиной по 31 мм. Под линейку проведите линии.
Чтобы лист можно было легко согнуть, необходимо прорезать небольшие канавки. Наденьте защитные очки или маску и болгаркой ровно пройдитесь по линиям, глубина резания примерно один миллиметр, но не более. Толщина диска 1 мм.
Поменяйте диск на 2,5 мм и еще раз пройдитесь по линиям. Пользоваться двумя дисками надо по двум причинам.
- Тонким диском намного легче работать, он дает ровный срез, проще контролировать глубину.
- Широкий диск увеличивает пропил, что позволяет загибать металл без упора о кромки.
Прорежьте одну сторону угла, полностью они срезаются после изгиба.
Приступайте к гибке листа. Точно по линии пропиливания положите его на профиль, согните вначале одну сторону, затем противоположную.
Обстукивайте постепенно по всей длине, гните медленно, не пытайтесь сделать сразу большой угол.
Повторите операции с оставшимися краями листа. Если линия получилась не идеальной, то поставьте деталь на ребро и подровняйте проблемные места.
Проверьте изделие. Все в норме – отрежьте болгаркой оставшиеся хвостики.
Проварите места срезов на углах. Болгаркой уберите окалину, потеки металла и острые края, придайте товарный вид.
Заключение
Ровным изгиб получается за счет предварительного прорезания, по этим линиям металл гнется намного быстрее, а толстые края не деформируются. Таким методом можно гнуть толстые листы под различные изделия.
Смотрите видео
youtube.com/embed/5lsxJNJ3Vgg?feature=oembed» frameborder=»0″ allowfullscreen=»allowfullscreen» data-mce-fragment=»1″>
https://sdelaysam-svoimirukami.ru/
Как сделать трубу из жести без станка
Домашние мастера придумали много способов сгибания металлического листа в трубу без применения станка.
Предлагаем вариант с применением походящей по размерам болванки. Делают её из старой трубы подходящего диаметра.
Лист металла раскладывают на полу, отрезают от него кусок нужной длины. Чтобы определить нужный размер, требуемый диаметр трубы умножают на 3,14 и прибавляют 30 мм на шов.
К болванке с двух сторон приваривают перпендикулярно одна к другой по паре трубок. В их отверстия должен свободно вставляться лом.
Рекомендация мастера: способом сгибания металлического листа при помощи болванки удобно изготавливать трубы не более метра в длину.
Чтобы воспользоваться приспособлением, потребуются усилия трех человек. Болванку укладывают на край листа. Один человек встает сверху, двое других накручивают металл на болванку, проворачивая лом на 90 градусов.
Всю длину листа скручивают таким способом, оставшийся край подбивают молотком. Шов закрепляют при помощи сварки.
Видео:
Нужно учесть, что радиус сгиба листового металла зависит от его толщины и способа изготовления. Горячекатаная сталь больше подходит для труб, из холодного проката изготавливают профильные изделия.
Гибка листового металла — технология процесса
Гибка листового металла — одна из распространенных операций холодного и горячего деформирования. Она отличается малой энергоемкостью.
Гибка листового металла — одна из распространенных операций холодного и горячего деформирования. Она отличается малой энергоемкостью, и при правильной разработке техпроцесса позволяет успешно производить из плоских заготовок пространственные изделия различной формы и размеров.
Классификация и особенности процесса
В соответствии с поставленными задачами технология гибки листового металла разрабатывается для следующих вариантов:
- Одноугловая (называемая иногда V-образной гибкой).
- Двухугловая или П-образная гибка.
- Многоугловая гибка.
- Радиусная гибка листового металла (закатка) — получение изделий типа петель, хомутов из оцинковки и пр.
Усилия при гибке невелики, поэтому ее преимущественно выполняют в холодном состоянии. Исключение составляет гибка стального листа из малопластичных металлов. К ним относятся дюралюминий, высокоуглеродистые стали (содержащие дополнительно значительный процент марганца и кремния), а также титан и его сплавы. Их, а также заготовки из толстолистового металла толщиной более 12…16 мм, гнут преимущественно вгорячую.
Гибку сочетают с прочими операциями листовой штамповки: резку и гибку, с вырубкой или пробивкой сочетают довольно часто. Поэтому для изготовления сложных многомерных деталей широко используются штампы, рассчитанные на несколько переходов.
Особым случаем гибки листового металла считается гибка с растяжением, которую используют для получения длинных и узких деталей с большими радиусами гибки.
В зависимости от размера и вида заготовки, а также требуемых характеристик продукции после деформирования, в качестве гибочного оборудования используются:
- Вертикальные листогибочные прессы с механическим или гидравлическим приводом;
- Горизонтальные гидропрессы с двумя ползунами;
- Кузнечные бульдозеры — горизонтально-гибочные машины;
- Трубо- и профилегибы;
- Универсально-гибочные автоматы.
Для получения уникальных по форме и размерам конструкций, в частности, котлов турбин и т.п., применяют и экзотические технологии гибки листовой стали, например, энергией взрыва. В противоположность этому, вопрос — как гнуть жесть — не вызывает сложностей, поскольку пластичность этого материала — весьма высокая.
Характерная особенность листогибочных машин — сниженные скорости деформирования, увеличенные размеры штампового пространства, сравнительно небольшие показатели энергопотребления. Последнее является основанием для широкого производства ручных гибочных станков, предназначенных для деформации оцинкованного материала. Они особо популярны в небольших мастерских, а также у индивидуальных пользователей.
Несмотря на кажущуюся простоту технологии, баланс напряжений и деформаций состояния в заготовке определить затруднительно. В процессе изгиба материала в нем возникают напряжения, вначале — упругие, а далее — пластические. При этом гибка листового материала отличается значительной неравномерностью деформации: она более интенсивна в углах гибки, и практически незаметна у торцов листовой заготовки. Гибка тонколистового металла отличается тем, что внутренние его слои сжимаются, а наружные — растягиваются. Условную линию, которая разделяет эти зоны, называют нейтральным слоем, и его точное определение является одним из условий бездефектной гибки.
В процессе изгиба металлопрокат получает следующие искажения формы:
- Изменение толщины, особенно для толстолистовых заготовок;
- Распружинивание/пружинение — самопроизвольное изменение конечного угла гибки;
- Складкообразование металлического листа;
- Появление линий течения металла.
Все эти обстоятельства необходимо учитывать, разрабатывая технологический процесс штамповки.
Этапы и последовательность технологии
Здесь, и в дальнейшем речь пойдет о процессах штамповки листового металла в холодном состоянии.
Разработка проводится в следующей последовательности:
- Анализируется конструкция детали.
- Рассчитывается усилие и работа процесса.
- Подбирается типоразмер производственного оборудования.
- Разрабатывается чертеж исходной заготовки.
- Рассчитываются переходы деформирования.
- Проектируется технологическая оснастка.
Анализ соответствия возможностей исходного материала необходим для того, чтобы выяснить его пригодность для штамповки по размерам, приведенным на чертеже готовой детали. Этап выполняют по следующим позициям:
- Проверка пластических способностей металла и сопоставление результата с уровнем напряжений, которые возникают при гибке. Для малопластичных металлов и сплавов процесс приходится дробить на несколько переходов, а между ними планировать межоперационный отжиг, который повышает пластичность;
- Возможность получения радиуса гиба, при котором не произойдет трещинообразования материала;
- Определение вероятных искажений профиля или толщины заготовки после обработки давлением, особенно при сложных контурах у детали;
По результатам анализа иногда принимают решение о замене исходного материала на более пластичный, о необходимости предварительной разупрочняющей термической обработки, либо используют подогрев заготовки перед деформацией.
Обязательным пунктом при разработке технологического процесса считается расчет минимально допустимого угла гибки, радиуса гибки и угла пружинения.
Радиус гибки rmin вычисляют с учетом пластичности металла заготовки, соотношения ее размеров и скорости, с которой будет проводиться деформирование (гидропрессы, с их пониженными скоростями передвижения ползуна, предпочтительнее более скоростных механических прессов). При уменьшении значения rmin все металлы претерпевают так называемое утонение — уменьшение первоначальной толщины заготовки. Интенсивность утонения определяет коэффициент утонения λ, %, который показывает, на сколько уменьшится толщина конечного изделия. Если это значение оказывается более критичного, то исходную толщину s металла заготовки приходится увеличивать.
Для малоуглеродистых листовых сталей соответствие между вышеуказанными параметрами приведено в таблице (см. табл. 1).
Таблица 1
Таким образом, при определенных условиях металл заготовки может даже несколько выпучиваться.
Не менее важным является и определение минимального радиуса гибки, который также зависит от исходной толщины металла, расположения волокон проката и пластичности материала (см. табл. 2). В том случае, когда радиус гиба слишком мал, то наружные волокна стали могут разрываться, что нарушает целостность готового изделия. Поэтому минимальные радиусы принято отсчитывать по наибольшим деформациям крайних частей заготовки, с учетом относительного сужения ψ деформируемого материала (устанавливается по таблицам). При этом учитывают также и величину деформации заготовки. Например, при малых деформациях используют зависимость
а при больших деформациях — более точное уравнение вида
Таблица 2
Эффект вероятного пружинения можно учесть при помощи данных по фактическим углам пружинения β, которые приведены в таблице 3. Данные в таблице соответствуют условиям одноугловой гибки.
Таблица 3
Определение усилия гибки
Силовые параметры гибки зависят от пластичности металла и интенсивности его упрочнения в ходе деформировании.

Для расчета силовых параметров уточняют, как будет выполняться деформирование. Оно возможно изгибающим моментом, когда заготовка укладывается по фиксаторам/упорам, и далее деформируется свободно, либо усилием, когда в завершающий момент процесса полуфабрикат опирается на рабочую поверхность матрицы. Свободная гибка проще и менее энергоемка, зато гибка с калибровкой дает возможность получать более точные детали.
Если упрочнение металла невелико (например, гнется изделие из алюминия, либо малоуглеродистой стали), то момент можно вычислить по зависимости:
где σт — предел текучести материала заготовки перед штамповкой.
Больший угол гиба (свыше 450) должен учитывать интенсивность упрочнения заготовки, которая зависит от размеров ее поперечного сечения:
где b — ширина заготовки.
Для расчета значений технологического усилия Р используют следующие зависимости. При одноугловой свободной гибке
, где
Как согнуть металлическую полосу без потери прочности
Как согнуть металлическую полосу без потери прочности и добиться точности конфигурации знают не все. Чтобы не изобретать велосипед — читайте наши советы!
При работе с металлом часто приходится иметь дело с изготовлением изделий из стальной полосы — скоб, хомутов, кронштейнов. Но как согнуть металлическую полосу без потери прочности и добиться необходимой точности конфигурации знают не все. Тем не менее, это достаточно простая операция, которая не требует инструментов особой сложности. Только в случае гибки полосы на ребро необходимо довольно сложное приспособление, которое самому изготовить непросто.
Гибка полосы под углом (60, 90, 1200…) в сторону плоскости производится на обычных слесарных тисках, если требуется изготовить единичное изделие или несколько штук. В случае мелкосерийного производства понадобится станок для гибки металлической полосы. При необходимости его можно сделать своими руками.
Гибка полосы при помощи тисков
Сначала рассмотрим вариант гибки на слесарных тисках под углом 900. Для этого необходим брусок квадратного сечения из стали. Зажимаем полосу вместе с бруском таким образом, чтобы брусок находился со стороны неподвижной губки тисков и выступал над верхней кромкой на 1-2 см.
После того, как такой «сэндвич» будет крепко зажат, берем обычный молоток и легкими ударами загибаем полосу в сторону бруска. Если требуется, чтобы поверхность загиба не имела повреждений от ударов, то нужно использовать медную или латунную прокладку, по которой будем наносить удары молотком, а уже от нее усилие будет передаваться на полосу.
Таким образом можно согнуть полосу под любым углом, важно только подобрать опорный брусок с нужным углом среза. Без такой твердой опоры добиться нужного угла будет очень трудно.
Похожие операции производятся и при изготовлении хомутов, только в этом случае в роли матрицы используем толстостенную трубу или пруток нужного диаметра. Как и в случае с прямоугольной гибкой, удары молотком наносятся в сторону неподвижной губки тисков. Такая гибка полосы — процесс медленный и требует аккуратности.
Гибка полосы в кольцо
Более сложная операция — гибка полосы на кольцо. Здесь необходим небольшой и несложный в изготовлении станок, например, как показанный на видео . Он состоит из опорной плиты на которой закреплены три ролика — два опорных и один приводной, на рукоятке длиной 30-40 мм. Приводной ролик может перемещаться вдоль горизонтальной оси и прижимать полосу к опорным. Один из опорных роликов должен иметь возможность сдвигаться перпендикулярно направлению прижима.
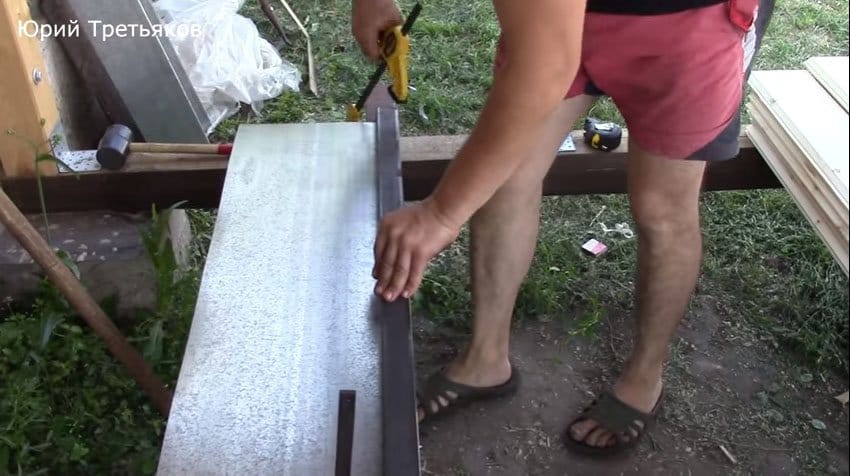
Полоса помещается между роликов и прижимается с помощью винтового механизма. При вращении приводного ролика полоса начинает двигаться между ним и опорными и загибаться в сторону привода. После полного прохода полосы получается практически идеальное кольцо. Если сделать рукоятку телескопической, чтобы можно были сделать длиннее плечо, то можно выполнять гибку на кольцо полосы практически любой толщины без особых физических усилий.
Такой самодельный станок для гибки полосы практически ничем не отличается от заводского. При правильном выборе металла для роликов и прижимного устройства, мелкосерийное производство, например для изготовления декоративных оград, ворот или каркасов козырьков и навесов, возможно даже в домашнем гараже, не говоря уже о слесарной мастерской.
Гибка полосы на ребро
Сложнее сделать станок для гибки на ребро. При изготовлении металлического декора такая операция требуется довольно часто. Принцип действия такого приспособления похож на описанный выше, но гибка стальной полосы на ребро требует значительно больших усилий, поэтому прижимной ролик не вращается , а движется на рычаге возвратно-поступательно. Кроме того, на линии подачи полосы необходимо установить прижимное устройство, чтобы полоса удерживалась в нужном положении. Этим приспособлением может служить обычная прижимная колодка на болтах или шпильках с прорезью, сквозь которую и будет проходить полоса.
Если гибка производится часто на полосах различной ширины, то нужно сделать несколько колодок с прорезями, соответствующими тому калибру, который обрабатывается.
Но самодельный инструмент, при всей своей привлекательности и дешевизне, все же уступает промышленному, функционал которого значительно выше.
Ручной инструмент производится в виде универсальных приспособлений, в которых только меняются насадки и рычаги, или в виде целых наборов, где каждый механизм выполняет только одну, максимум две функции. Примером такого комплекта может служить «Холодная ковка» промышленного изготовления.
Инструменты для гибки металлической полосы промышленного изготовления имеют перед самодельными то преимущество, что сделаны они из специальных марок стали и при гибке заготовок достаточно большой толщины не будут деформироваться. Они легко настраиваются на необходимые размеры и не требуют изготовления новых оправок и матриц каждый раз, когда необходимо изменить диаметр или угол загиба.
При этом их стоимость не слишком высока даже для домашнего мастера. Поиск необходимых деталей для самодельного станка, сборка, подгонка и настройка будет стоить не намного меньше, даже в случае надлежащей слесарной квалификации. Если не покупать самые дешевые инструменты, то работать станки для гибки будут на протяжении десятилетий.
Операции с листовым металлом — Гибка и родственные процессы
1 Операции с листовым металлом — Гибка и родственные процессы Р. Чандрамули Заместитель декана по исследованиям Университет SASTRA, Танджавур
2 Содержание 1.Ключ викторины … Ошибка! Закладка не определена.
3 1. Гибка и связанные процессы: 1.1 Гибка листового металла Гибка листов и пластин широко используется при формовании таких деталей, как гофры, фланцы и т. Д. Гибка — это операция формования, при которой листовой металл подвергается изгибающему напряжению, в результате чего плоский Прямой лист превращается в изогнутый лист. Лист пластически деформируется без изменения толщины.Для гибки используются матрица и пуансон. Если используются v-образная матрица и пуансон, гибка называется v-образной гибкой. Если лист сгибается по краю с помощью протирочного штампа, это называется краевым изгибом. В этом процессе один конец листа удерживается как консоль с помощью нажимной подушки, а другой конец деформируется пуансоном, который перемещается вертикально вниз, сгибая лист. Обычно загиб кромок выполняется так, чтобы получить угол 90 o. Во время изгиба полосы материал за пределами нейтральной оси подвергается растягивающему напряжению.Материал внутри подвергается сжимающему напряжению. Радиус изгиба R — это радиус кривизны гнутого листа внутри изгиба. Нейтральная ось остается в центре толщины листа для упругого изгиба. Однако при пластическом изгибе нейтральная ось смещается внутрь изгиба. Скорость удлинения внешних волокон больше, чем скорость сокращения внутренних волокон. Следовательно, на изгибе происходит уменьшение толщины.
4 Рис. Операции V-образной гибки и гибки кромок U-образная гибка.swf V-Bending.swf Рис. A: Анимации U-образного и V-образного изгиба 1.2 Теория изгиба: При пластическом изгибе мы игнорируем уменьшение толщины. Поэтому мы предполагаем, что нейтральная ось остается в центре толщины листа. Рассмотрим лист толщиной t, подвергаемый изгибу так, чтобы он был изогнут до радиуса кривизны R. Мы можем не учитывать деформацию в направлении ширины. Пусть будет угол изгиба. Допуск на изгиб — это длина дуги нейтральной оси в области изгиба. Это важный параметр дизайна.Он задается формулой: Lb = (R + kt), где k — постоянная величина, равная 0,5 для идеального изгиба: нейтральная ось остается в центре. K = от 0,33 до 0,5 для R <2t или R> 2t. соответственно. Мы можем записать деформацию внешнего или внутреннего волокна как (оба равны): e = При фактическом изгибе внешние волокна растягиваются больше, чем внутренние волокна сжимаются. Эта разница в деформации между внешними и внутренними волокнами увеличивается с уменьшением радиуса изгиба или уменьшением R / t. За пределами определенного минимального значения R / t растягивающая деформация внешнего волокна может достигать настолько высокого значения, что материал снаружи начинает трескаться.Конкретный радиус появления трещин на
5 Наружная поверхность гнутого листа называется минимальным радиусом изгиба. Обычно указывается в единицах толщины листа, t. В следующей таблице указаны минимальные радиусы для некоторых материалов: Таблица 1.2.1: Минимальный радиус гибки Материал Мягкие закаленные алюминиевые сплавы 0 6 т. Низкоуглеродистая сталь 0,5 т. 4 т. Титановые сплавы 2.5t 4t Обратите внимание, что минимальный радиус изгиба, равный нулю, означает, что лист можно сгибать сам по себе. Чтобы получить выражение для минимального радиуса изгиба, истинную деформацию материала во время испытания на одноосное растяжение при разрушении можно приравнять к деформации при изгибе. ln (ao / af) = ln (1 + e) = ln (1+) Отсюда получаем: R / t минимум =, где r — уменьшение площади листа при изгибе. Или Rmin / t = 50 / r 1, где r выражается как процент уменьшения площади. Это выражение применимо для уменьшения площади менее 0.2. Для уменьшения площади на 50% R = 0, что означает, что материал может складываться сам по себе.
6 R / t% уменьшения площади при растяжении Рис. Минимальный радиус изгиба в зависимости от уменьшения площади в процентах На приведенном выше графике показано изменение минимального радиуса изгиба относительно уменьшения площади в процентах. Рис. Терминология и геометрия гибки При гибке очень важную роль играет пластичность листового металла.Если пластичность ниже, минимальный радиус изгиба больше. Точно так же состояние двухосного напряжения в области изгиба может также снизить пластичность внешних волокон. Для больших значений отношения ширины к толщине (w / t) листа можно ожидать состояния двухосного напряжения. Состояние двухосности достигается, когда w / t достигает значения 8. Большее отношение w / t снижает критическую деформацию, необходимую для разрушения. В результате радиус изгиба будет больше. Узкие листы растрескиваются по краям, потому что напряженное состояние вдоль края более двухосное, чем в центре.Более широкие листы, когда подвергаются большему радиусу изгиба, растрескиваются в центре, потому что центр подвергается более двухосному состоянию напряжения.
Для увеличения минимального радиуса листы полируют или шлифуют.
7 Способность подвергаться изгибу, называемая изгибаемостью, может быть улучшена путем воздействия на материал гидростатического напряжения. Это улучшает пластичность (уменьшение площади в процентах).Воздействие сжимающего напряжения на внешние волокна также может повысить изгибаемость. Шероховатые края листа ухудшают сгибаемость, поскольку острые края могут легко потрескаться во время сгибания. Холодная обработка кромок также может привести к растрескиванию. Растрескивание кромок также может происходить из-за включений или анизотропии материала из-за таких операций, как прокатка на нем. 1.3 Пружинность: упругое восстановление листа после снятия изгибающей нагрузки называется пружинящим возвратом. Даже после пластической деформации в пластичных материалах может происходить небольшое упругое восстановление после снятия нагрузки.При изгибе пружинение уменьшает угол изгиба. Точно так же радиус изгиба после упругого возврата больше. Пружинность будет больше для материалов с более низким модулем упругости и более высоким пределом текучести. Пружинная отдача увеличивается для листа с более высоким отношением ширины к толщине, поскольку напряженное состояние является двухосным или плоским. После снятия нагрузки при изгибе радиус изгиба изменяется. Однако припуск на изгиб не меняется. Следовательно, мы имеем: Lb = (Ri + t / 2) = (Rf + t / 2) Или, K = / = K — коэффициент упругого возврата, Ri — начальный радиус кривизны перед снятием нагрузки, Rf — радиус кривизны прогнуться после отпускания груза.K = 1 указывает на отсутствие упругого возврата. K = 0 означает полное упругое восстановление, как в пружинах. Пружинность зависит от отношения R / t. По мере увеличения отношения упругая отдача также увеличивается, на что указывает уменьшение значения K на графике ниже. Пружина назад или K Увеличивающаяся отдача
8 R / t Рис. Зависимость коэффициента упругого возврата от радиуса изгиба Отрицательное пружинение — это ситуация, в которой угол изгиба становится больше после снятия нагрузки.Отрицательная возвратная пружина происходит при v-образном изгибе. После снятия нагрузки материал прогибается внутрь из-за больших деформаций. Еще одно выражение для упругого возврата с точки зрения радиуса изгиба: пружинение уменьшается с уменьшением предела текучести. Изгиб — это один из способов компенсации упругого возврата. Другой способ заключается в том, что лист подвергается сжимающему напряжению, создаваемому между штампом и пуансоном перед изгибом. Это называется дно. Высокая температура также может снизить упругость, так как снижается предел текучести. Изгиб с растяжением, при котором лист подвергается растягивающему напряжению во время изгиба, также может уменьшить упругую отдачу.Это связано с тем, что избыточное растягивающее напряжение, прикладываемое во время растяжения, снижает изгибающий момент при изгибе. 1.
4 Сила изгиба: Сила, необходимая для изгиба листа толщиной t, длиной L, до радиуса R, определяется как: F = tan (Максимальное усилие изгиба определяется как: Fmax = kutslt 2 / W, где UTS — предел прочности на разрыв материала, W — ширина отверстия матрицы, k принимает значения от 1,2 до 1,33 для гибки в форме v-образной формы и от 0,3 до 0,4 для протирки.
9 1.5 Другие процессы гибки. Длинные и узкие листы металла обычно формуются или сгибаются до требуемых форм с использованием гидравлического или механического пресса. Простая длинная матрица и инструмент, а также материалы матрицы из чугуна или углеродистой стали делают этот процесс формования листогибочным прессом очень широко используемым. Гибка на воздухе — это свободное сгибание листов между верхним валком или пуансоном и нижним штампом. При гибке валков пара валков поддерживает гибку листа, а верхний валок прикладывает усилие гибки. При непрерывной валковой гибке, называемой профилированием, используется серия валков. Полоса или лист пропускается через валки, выполняя поэтапную гибку. С помощью этого процесса можно формировать панели, рамы, каналы и т. Д. Валки изготовлены из серого чугуна и хромированы. Основное усилие при профилировании — это изгиб, а не сжатие, как при прокатке. Скручивание или скручивание: в этом процессе край листа сгибается в круглую или другую контурную форму самого штампа или формируется в завиток с помощью одного штампа или пары штампов. Отбортовка концов листа улучшает его жесткость за счет увеличения момента инерции на краях.Петли являются примерами для вышивки бисером. Подгибание относится к процессу гибки, при котором конец листа сгибается сам в себя, чтобы увеличить жесткость или защитить край листа или избежать острого края. Сшивание — это сборка двух подшитых концов листов для образования стыка листов. Двойные швы используются для водонепроницаемых или воздухонепроницаемых соединений, например, в контейнерах для пищевых продуктов. U-образные формы, гофры, каналы, трубы могут быть сформированы путем гибки листового металла до определенной формы с использованием пары фигурных штампов.
Отбортовка: отбортовка кромок листов на 90 градусов для повышения их жесткости или для сборки называется отбортовкой. Если угол изгиба меньше 90 градусов, это называется развальцовкой. При отбортовке отбортовки задействованы кольцевые напряжения сжатия или растяжения. Фланцы также могут быть изготовлены путем совмещения пробивки листа пуансоном с последующим расширением прошитой кромки с помощью расширительного пуансона. Этот процесс называется ямочкой. Иногда также используется пробивной пробой в форме пули.
10 1.6 Сгибание труб: сгибание трубок сложнее, чем листов, потому что трубки имеют тенденцию к складыванию или могут разрушиться, если подвергаются нагрузкам при изгибе. Когда труба подвергается изгибу, стенка трубы на внешней стороне изгиба подвергается растягивающему напряжению, тогда как внутренняя часть изгиба подвергается сжатию. В результате стенка трубы утончается снаружи и утолщается внутри изгиба. Чрезмерное сжимающее напряжение внутри изгиба приводит к появлению морщин или складок. Обычно трубы загибают после заполнения песком изнутри.Заполнение песком предотвращает коробление трубы при изгибе. При гибке трубы обычно используются внутренние гибкие оправки или заглушки. Для толстых трубок могут не требоваться внутренние заливки или заглушки. Различные методы гибки труб, такие как гибка с вытяжкой, гибка с растяжением и гибка сжатием, показаны на рисунке ниже: Минимальный радиус изгиба обычно в 1,5 раза превышает диаметр трубки для тонкостенных труб с использованием внутренних оправок. Минимальный радиус изгиба при гибке толстостенных труб без оправок в 3 раза больше диаметра трубы.Пример: определенный листовой металл (предел прочности = 500 МПа, E = 200 ГПа), имеющий толщину 3 мм и ширину 40 мм, подвергают гибке в v-образной матрице с отверстием 22 мм. Остальные размеры указаны на рисунке. Какой размер заготовки и сила изгиба требуются? Пропускание без учета пружинения o 5 30 На рисунке видно, что угол изгиба = 60 o Длину заготовки можно определить как: L = Допуск на изгиб Допуск на изгиб определяется по формуле:
11 фунтов = (Ri + t / 2) = (Rf + t / 2) = 6. 8 мм L = 76,8 мм Теперь силу изгиба можно определить из выражения: Fmax = kutslt 2 / W k = 1,33 F = 1,33X300X76,8X9 / 22 = N
Процесс формовки листового металла Глава 7
Презентация на тему: «Процесс формования листового металла Глава 7» — стенограмма презентации:
1 Процесс формовки листового металла Глава 7
2 Процесс формовки листового металла Глава 7
Введение Операции формовки листового металла позволяют производить широкий спектр потребительских и промышленных товаров, таких как металлические столы, бытовая техника, фюзеляжи самолетов, кузова автомобилей и кухонная утварь. Формовка листового металла, также называемая прессованием, штамповкой или штамповкой, является одним из наиболее важных процессов металлообработки, начиная с 5000 г. до н.э., когда домашняя утварь, ювелирные изделия и другие предметы изготавливались путем ковки и штамповки металлов, таких как золото, серебро и медь. По сравнению с деталями, изготовленными методом литья или ковки, детали из листового металла обладают такими преимуществами, как легкий вес и универсальность формы.
3 Процесс формования листового металла Глава 7
Введение Формование листа, в отличие от процессов объемной деформации, включает в себя заготовки с высоким отношением площади поверхности к толщине, такие как колпаки противней.Листовой металл изготавливается методом прокатки. Если лист тонкий, он обычно свертывается после прокатки, если толстый, он доступен в виде плоских листов или пластин, которые могут быть размотаны и сплющены перед их формированием. При типичной операции формования сначала вырезают заготовку подходящих размеров из большого листа, обычно это делается с помощью процесса резки.
4 Характеристики процессов формовки листового металла
5 Листовой металл — характеристики и формуемость
Формование листового металла обычно осуществляется за счет растягивающих усилий, так как в противном случае приложение внешних сжимающих сил может привести к короблению, складыванию и складкам листа.В некоторых процессах объемной деформации толщина заготовки изменяется для изготовления детали, тогда как в процессе формования листа любое изменение толщины обычно происходит из-за растяжения листа под действием растягивающих напряжений. Поэтому следует избегать резкого уменьшения толщины при формовании листового металла, поскольку они могут привести к образованию шейки и разрушению, как это происходит при испытании на растяжение.
6 Листовой металл — Характеристики и формуемость
Механика всей формовки листа в основном состоит из растяжения и гибки, некоторые параметры существенно влияют на общую операцию.Это: относительное удлинение; относительное удлинение; относительное удлинение; анизотропия; размер зерна. Остаточное напряжение.
7 Характеристики процессов формовки листового металла
Удлинение: когда образец подвергается растяжению, он сначала претерпевает равномерное удлинение до UTS, после чего начинает сужаться. Затем за этим удлинением следует неравномерное удлинение до разрушения образца.Поскольку лист будет растягиваться во время процесса формования, таким образом, желательно высокое равномерное удлинение для хорошей формуемости,
Что такое обработка листового металла —
- Дом
- Около keyboard_arrow_right
- keyboard_arrow_left Назад
- История — Как мы сюда попали?
- FAQ — Работа с листовым металлом
- Как с нами связаться
- Что такое обработка листового металла
- Светотехническая промышленность
- Положения и условия
- Оценка риска коронавируса COVID-19
- Список растений keyboard_arrow_right
- keyboard_arrow_left Задний
- Угловой надрез и надрез
- Уборочное оборудование
- Эдвардс Пирсон PR3
- Fly Прессы и прессовые работы
- Guifil PE 6-16 Гибка с ЧПУ
- Устройство для вставки втулок / шпилек Haeger
- Высокоскоростная распиловка алюминия
- Лазерная резка листового металла
- Power Press и прессовые работы
- Работа с листовым прокатом
- Safan e-brake гибка с ЧПУ
- Safan Гильотина и резка
- Уголок, труба и пруток
- Точечная сварка листового металла
- Сварка листового металла шпильками
- Trumpf 200R / 3000R Пуансон с ЧПУ
- Trumpf 7036 — гибка с ЧПУ
- Процессы сварочного производства
- Программное обеспечение Radan CAD / CAM
- Программное обеспечение для производства P4W
- Инструмент keyboard_arrow_right
- keyboard_arrow_left Назад
- Что такое лазерная резка?
- Стандартный 2D инструмент Trumpf
- Нестандартный инструмент Trumpf 2D
- Что такое гибка с ЧПУ?
- Что такое штамповка с ЧПУ?
- Гибочный стол с ЧПУ — U-образный гиб
- Гибочный стол с ЧПУ — Z-образный изгиб
- Гибочный стол с ЧПУ — одинарный
- Стол для сгибания — Маленькие джогглы
Проектные данные - keyboard_arrow_right
- keyboard_arrow_left Назад
- Мягкая сталь и ее методы обработки
- Нержавеющая сталь и ее отделка
- Алюминий и его обработка
- Краска и порошковое покрытие
- Размеры изгиба и положение отверстий
- Правила штамповки листового металла
- Толщина листового металла
- Таблица преобразования манометров
- Метрические сверла для нарезания резьбы
- Обозначения на сварочных чертежах
- Производство листового металла в сборе
- Производство коробок
- Изготовление кронштейнов
- Блог
- Галерея
- Контакт
Научные принципы
Научные принципыСостав металлов:
Металлы составляют около двух третей всех элементов и около 24% массы планеты.Они повсюду вокруг нас в таких формах, как стальные конструкции, медная проволока, алюминиевая фольга и золотые украшения. Металлы широко используются из-за их свойств: прочности, пластичности, высокой температуры плавления, теплопроводности и электропроводности, а также вязкости.
Эти свойства также дают ключ к разгадке структуры металлов. Как и все элементы, металлы состоят из атомов. Прочность металлов предполагает, что эти атомы удерживаются вместе прочными связями. Эти связи также должны позволять атомам двигаться; иначе как металл можно было забивать в листы или вытягивать в проволоку? Разумной моделью будет модель, в которой атомы удерживаются вместе прочными, но делокализованными связями.
Склеивание
Такие связи могут образовываться между атомами металлов, которые имеют низкую электроотрицательность и не сильно притягивают свои валентные электроны. Это позволило бы наиболее удаленным электронам быть общими для всех окружающих атомов, в результате чего положительные ионы ( катионов, ) были окружены морем электронов (иногда называемым электронным облаком).
Рисунок 1: Металлическое соединение .Поскольку эти валентные электроны являются общими для всех атомов, они не считаются связанными с каким-либо одним атомом.Это сильно отличается от ионных или ковалентных связей, где электроны удерживаются одним или двумя атомами. Таким образом, металлическая связь получается прочной и однородной. Поскольку электроны притягиваются ко многим атомам, они обладают значительной подвижностью, что обеспечивает хорошую теплопроводность и электропроводность металлов.
Выше точки плавления металлы являются жидкостями, их атомы расположены беспорядочно и относительно свободно перемещаются. Однако при охлаждении ниже точки плавления металлы перестраиваются, образуя упорядоченные кристаллические структуры.
Рисунок 2: Расположение атомов в жидкости и твердом теле.Кристаллы
Для образования наиболее прочных металлических связей металлы упаковываются как можно плотнее. Возможны несколько вариантов упаковки. Вместо атомов представьте шарики, которые нужно упаковать в коробку. Шарики помещали на дно коробки аккуратными упорядоченными рядами, а затем начинали второй слой. Второй слой шариков нельзя размещать непосредственно поверх других шариков, поэтому ряды шариков в этом слое перемещаются в промежутки между шариками первого слоя.Первый слой мрамора может быть обозначен как A, а второй слой как B, давая двум слоям обозначение AB.
Слой «A» | Слой «B» | AB упаковка |
---|
Укладка мрамора в третий слой требует решения. Снова ряды атомов будут гнездиться в полостях между атомами во втором слое, но существуют две возможности.Если ряды мрамора уложены так, что они находятся непосредственно над первым слоем (A), то расположение можно описать как ABA. Такое устройство насадки с чередующимися слоями будет обозначено как ABABAB. Такое расположение ABAB называется гексагональной плотной упаковкой (HCP).
Если ряды атомов упакованы в этом третьем слое так, чтобы они не лежали над атомами в слое A или B, то третий слой называется C. Эта последовательность упаковки будет обозначена ABCABC и также известна как гранецентрированный кубик (ГЦК).Оба устройства обеспечивают максимально плотную упаковку сфер, оставляя пустой лишь около четверти доступного пространства.
Наименьший повторяющийся массив атомов в кристалле называется элементарной ячейкой. Третье распространенное устройство упаковки в металлах, объемно-центрированная кубическая (ОЦК) элементарная ячейка, имеет атомы в каждом из восьми углов куба плюс один атом в центре куба. Поскольку каждый из угловых атомов является углом другого куба, угловые атомы в каждой элементарной ячейке будут разделены между восемью элементарными ячейками.Элементарная ячейка ОЦК состоит из двух атомов, одного в центре и восьми восьмых от углов.
В схеме FCC также есть восемь атомов в углах элементарной ячейки и по одному центру на каждой из граней. Атом в грани делится с соседней ячейкой. Элементарные ячейки FCC состоят из четырех атомов, восемь восьмых по углам и шесть половин на гранях. В таблице 1 показаны стабильные кристаллические структуры при комнатной температуре для нескольких элементарных металлов.
Таблица 1: Кристаллическая структура некоторых металлов (при комнатной температуре)Алюминий | FCC | Никель | FCC | ||||
---|---|---|---|---|---|---|---|
Кадмий | HCP | Ниобий | 9024 B9024FCC | ||||
Кобальт | HCP | Серебро | FCC | ||||
Медь | FCC |
| |||||
Железо | BCC | Цинк | HCP | ||||
Свинец | FCC |
Структуры элементарных ячеек определяют некоторые свойства металлов.Например, структуры FCC с большей вероятностью будут пластичными, чем BCC (объемно-центрированная кубическая) или HCP (гексагональная плотноупакованная). На рисунке 4 показаны элементарные ячейки FCC и BCC. (См. Активность кристаллической структуры)
Телоцентрированный кубический | Лицоцентрированный кубический |
---|
Когда атомы расплавленного металла начинают собираться вместе, образуя кристаллическую решетку в точке замерзания, группы этих атомов образуют крошечные кристаллы.Эти крошечные кристаллы увеличиваются в размере за счет постепенного добавления атомов. Получающееся в результате твердое вещество представляет собой не один кристалл, а на самом деле множество более мелких кристаллов, называемых зернами. Эти зерна растут до тех пор, пока не столкнутся с соседними растущими кристаллами. Образовавшаяся между ними граница раздела называется границей зерен. Иногда зерна бывают достаточно большими, чтобы их можно было увидеть под обычным световым микроскопом или даже невооруженным глазом. Блестки, которые видны на недавно оцинкованном металле, представляют собой зерна. (См. Модель активности металлов с помощью частиц). На рисунке 5 показан типичный вид металлической поверхности с множеством зерен или кристаллов.
Рисунок 5: Зерна и границы зерен для металла.Дефекты кристалла:
Металлические кристаллы не идеальны. Иногда встречаются пустые места, называемые вакансиями, где отсутствует атом. Другим распространенным дефектом металлов являются дислокации, которые представляют собой линии дефектного соединения. На рисунке 6 показан один тип дислокации.
Рис. 6: Поперечное сечение краевого вывиха, выходящего на страницу. Обратите внимание, как плоскость в центре заканчивается внутри кристалла.Эти и другие дефекты, а также наличие зерен и границ зерен определяют многие механические свойства металлов. Когда к металлу прикладывается напряжение, возникают дислокации, которые перемещаются, позволяя металлу деформироваться.
Механические свойства:
Когда к металлам прикладываются небольшие нагрузки (напряжения), они деформируются и возвращаются к своей исходной форме при снятии нагрузки. Сгибание стального листа является примером, когда скрепления изгибаются или растягиваются только на небольшой процент.Это называется упругой деформацией и включает временное растяжение или искривление связей между атомами.
Рисунок 7: Упругая деформация металлического стержня.При приложении более высоких напряжений возникает остаточная (пластическая) деформация. Например, если скрепку сильно согнуть, а затем отпустить, она останется частично согнутой. Эта пластическая деформация включает разрыв связей, часто в результате движения дислокаций. См. Рис. 8. Дислокации легко перемещаются в металлах из-за делокализованной связи, но не перемещаются легко в керамике.Это во многом объясняет, почему металлы пластичны, а керамика - хрупка.
Рисунок 8: Движение дислокации в кристалле.Если поместить под слишком большое напряжение, металлы будут механически разрушаться или ломаться. Со временем это также может быть результатом множества небольших нагрузок. Наиболее частая причина (около 80%) выхода металла из строя - усталость. Благодаря приложению и снятию небольших напряжений (до миллионов раз) по мере использования металла в нем образуются небольшие трещины, которые медленно растут.Со временем металл деформируется или ломается (ломается). (См. Раздел «Обработка металлов»)
Обработка:
В промышленности расплавленный металл охлаждают для образования твердого тела. Затем твердому металлу механически формируют конкретный продукт. Очень важно, как выполняются эти этапы, поскольку нагрев и пластическая деформация могут сильно повлиять на механические свойства металла.
Влияние размера зерна:
Давно известно, что свойства некоторых металлов могут быть изменены термической обработкой.Зерна в металлах имеют тенденцию увеличиваться в размерах при нагревании металла. Зерно может увеличиваться в размерах за счет миграции атомов из другого зерна, которые в конечном итоге могут исчезнуть. Дислокации не могут легко пересекать границы зерен, поэтому размер зерен определяет, насколько легко дислокации могут перемещаться. Как и ожидалось, металлы с мелкими зернами прочнее, но менее пластичны. На рис. 5 показан пример зеренной структуры металлов.
Закалка и закалка:
Есть много способов термической обработки металлов.Отжиг - это процесс размягчения, при котором металлы нагревают, а затем дают медленно остыть. Большинство сталей можно закалить путем нагрева и закалки (быстрого охлаждения). Этот процесс использовался довольно рано в истории обработки стали. Фактически, считалось, что биологические жидкости являются лучшими гасящими жидкостями, и иногда использовалась моча. В некоторых древних цивилизациях раскаленные лезвия меча иногда вонзались в тела несчастных заключенных! Сегодня металлы закаливают в воде или масле.На самом деле закалка в растворах соленой воды происходит быстрее, поэтому древние не совсем ошибались.
В результате закалки металл становится очень твердым, но при этом хрупким. Осторожно нагревая закаленный металл и давая ему медленно остыть, вы получите металл, который останется твердым, но менее хрупким. Этот процесс известен как темперирование. (См. «Обработка металлов»). Это приводит к появлению большого количества мелких выделений Fe 3 C в стали, которые блокируют движение дислокаций, тем самым обеспечивая упрочнение.
Холодная обработка:
Поскольку пластическая деформация возникает в результате движения дислокаций, металлы можно упрочнять, предотвращая это движение. Когда металл изгибается или приобретает форму, возникают и перемещаются дислокации. По мере увеличения количества дислокаций в кристалле они будут запутываться или скрепляться и не смогут двигаться. Это укрепит металл и усложнит его деформацию. Этот процесс известен как холодная обработка. При более высоких температурах дислокации могут перестраиваться, поэтому упрочнение не происходит.
Можно попробовать со скрепкой. Разогните скрепку и несколько раз согните одну из прямых частей вперед-назад. Представьте себе, что происходит на атомарном уровне. Обратите внимание, что металл сложнее согнуть в одном и том же месте. Вывихи образовались и запутались, увеличивая прочность. Скрепка со временем сломается на изгибе. Очевидно, что холодная обработка работает только до определенной степени! Слишком большая деформация приводит к спутыванию дислокаций, которые не могут двигаться, поэтому металл вместо этого ломается.
Нагрев устраняет последствия холодной обработки. При нагревании холоднодеформированных металлов происходит перекристаллизация. Новые зерна образуются и растут, чтобы потреблять холодно обработанную часть. В новых зернах меньше дислокаций, и восстанавливаются первоначальные свойства.
Сплавы:
Наличие в металле других элементов также может изменить его свойства, иногда резко. Расположение и вид связи в металлах позволяет добавлять в структуру другие элементы, образуя смеси металлов, называемые сплавами.Даже если добавленные элементы являются неметаллами, сплавы могут иметь металлические свойства.
Медные сплавы начали производить в самом начале нашей истории. Бронза, сплав меди и олова, была первым известным сплавом. Его было легко получить, просто добавив олово к расплавленной меди. Орудия и оружие из этого сплава были прочнее, чем из чистой меди. Добавление цинка к меди дает еще один сплав - латунь. Хотя латунь труднее производить, чем бронзу, она была известна и в древние времена.(См. «Золотая» Пенни Активность) Типичный состав некоторых сплавов приведен в Таблице 2.
Таблица 2: Состав нескольких сплавов.Сплав | Состав |
---|---|
Латунь | Медь, цинк |
Бронза | Медь, цинк, олово | 9025
Припой | Свинец, олово |
Alnico | Алюминий, никель, кобальт, железо |
Чугун | Железо, углерод, марганец, кремний |
Сталь небольшое количество легирующих элементов) | |
Нержавеющая сталь | Железо, хром, никель |
Сплавы представляют собой смеси, и их процентный состав может варьироваться.Это полезно, потому что свойствами сплавов можно управлять, варьируя состав. Например, электрикам нужен припой с другими свойствами, чем у сантехников. Электрический припой очень быстро затвердевает, образуя почти мгновенное соединение. Это будет непрактично для сантехников, которым нужно время, чтобы установить соединение. Электрический припой содержит около 60% олова, тогда как припой для сантехников - около 30%.
Первоначально олово содержало свинец, а поскольку олово использовалось для изготовления тарелок и кубков, вероятно, оно было источником отравления свинцом.Изготовленный сегодня олово не содержит свинца. Расширение знаний о свойствах металлов также приводит к созданию новых сплавов. Некоторые латуни образуют сплавы с памятью формы, которые можно сгибать и возвращать к своей исходной форме при осторожном нагревании. Цинковые сплавы, используемые в качестве покрытия на стали, замедляют коррозию (оцинкованная сталь). Сплавы кадмия находят широкое применение в солнечных элементах. Способность мельхиора противостоять образованию отложений делает его полезным в садках в рыбоводстве.
Чугун и сталь:
Углеродистые стали различаются по процентному содержанию углерода.Количество углерода влияет на свойства стали и ее пригодность для конкретного использования. Стали редко содержат более 1% углерода. Конструкционная сталь содержит около 0,1-0,2% углерода по весу; это делает его немного более пластичным и менее склонным к разрушению во время землетрясений. Сталь, используемая для изготовления инструментов, содержит около 0,5-1% углерода, что делает ее более твердой и износостойкой. Чугун содержит от 2,5 до 4% углерода и находит применение в недорогих приложениях, где его хрупкость не является проблемой. Удивительно, но чистое железо чрезвычайно мягкое и используется редко.Увеличение количества углерода приводит к увеличению твердости металла, как показано на следующем графике. В медленно охлаждаемых сталях углерод увеличивает количество твердого Fe 3 C; в закаленных сталях он также увеличивает твердость и прочность материала.
Рис. 9: Зависимость твердости стали от% углерода. Рисунок 10: железо BCC, показывающее расположение межузельных атомов углерода.Заколки для бобби и скрепки обрабатываются практически одинаково, но содержат разное количество углерода.Заколки и скрепки изготовлены из холоднокатанной стальной проволоки. Скрепка, содержащая мало углерода, в основном состоит из чистого Fe с некоторым количеством частиц Fe 3 C. Шпилька для бобби содержит больше углерода и, следовательно, содержит большее количество Fe 3 C, что делает ее намного более твердой и прочной.
Свойства стали могут быть адаптированы для специальных целей путем добавления в сплав других металлов. Титан, ванадий, молибден и марганец входят в число металлов, добавляемых к этим специальным сталям.Нержавеющая сталь содержит минимум 12% хрома, который останавливает дальнейшее окисление, образуя защитный оксид на поверхности.
Коррозия:
Коррозия металлов может быть серьезной проблемой, особенно для долговременных конструкций, таких как автомобили, мосты и корабли. В большинстве случаев коррозия носит электрохимический (гальванический) характер. Для возникновения коррозии должны присутствовать анод (более легко окисляемая область) и катод (менее легко окисляемая область). Это могут быть разные типы металлов или просто разные участки одного и того же металла.Также должен присутствовать какой-то электролит, который может обеспечивать перенос электронов. Коррозия включает высвобождение электронов на аноде из-за высокого окислительного потенциала атомов на аноде. Когда электроны высвобождаются, образуются катионы металлов, и металл распадается. Одновременно катод, который имеет больший восстановительный потенциал, принимает электроны, либо образуя отрицательные ионы, либо нейтрализуя положительные ионы.
В случае ряда активности или электродвижущей силы металл, такой как цинк, реагирует с водородом и служит как анодом, так и катодом.(См. Активность серии действий) Уравнение этой реакции:
2 Zn + 2 H + -> 2 Zn 2+ + H 2Пузырьки водорода на катоде при разрушении анода. Неровности поверхности, наличие примесей, ориентация зерен, локализованные напряжения и вариации окружающей среды - вот некоторые из факторов, определяющих, почему один кусок металла может служить обоими электродами. Например, головка и острие гвоздя обработаны холодным способом и могут служить анодом, а корпус - катодом.(См. Коррозия от активности железа)
Хотя окисление на аноде и восстановление на катоде - одновременные процессы, коррозия обычно происходит на аноде. Катод почти никогда не разрушается. В 1824 году Дэви разработал метод защиты корпусов кораблей от коррозии с помощью цинка, который можно периодически заменять. Цинк более активен, чем сталь в корпусе, и будет служить анодом и подвергаться коррозии; им приносят в жертву защиту стальной конструкции. Сталь, которая была бы и анодом, и катодом, обычно служит катодом.Это называется катодной защитой. Трубопроводы также защищены более активным металлическим магнием. Иногда электрические токи поддерживаются в коротких отрезках трубопроводов с такой же металлической проволокой, которая используется в качестве жертвенного анода.
Коррозия - серьезная проблема, которую необходимо решить для эффективного использования металлов. Железо соединяется с кислородом воздуха, образуя оксид железа (ржавчину), в конечном итоге разрушая полезность металла. (См. Дополнительно: действие химического подогревателя рук). К счастью, некоторые металлы, такие как алюминий и хром, образуют защитное оксидное покрытие, предотвращающее дальнейшее окисление (коррозию).Точно так же медь соединяется с серой и кислородом, образуя знакомую зеленую патину.
Понимание химического состава металлов приводит к разработке методов уменьшения и предотвращения коррозии. Атомы хрома примерно того же размера, что и атомы железа, и могут замещать их в кристаллах железа. Хром образует оксидный слой, который позволяет нержавеющей стали противостоять коррозии. Металлы можно окрашивать или покрывать другими металлами; оцинкованная (оцинкованная) сталь является примером. Когда эти два металла используются вместе, более активный цинк корродирует, жертвуя собой ради сохранения стали.
Металлические руды:
Золото, серебро и медь были первыми металлами, которые использовали, потому что они находятся в свободном или элементарном состоянии. Большинство металлов, встречающихся в природе, сочетаются с другими элементами, такими как кислород и сера. Энергия необходима для извлечения металлов из этих соединений или руд. Исторически сложилось так, что легкость, с которой данный металл может быть извлечена из руды, наряду с доступностью, определялась при его использовании, отсюда и раннее использование меди, олова и железа.Формулы для некоторых руд приведены ниже:
Гематит | Fe 2 O 3 | Рутил | TiO 2 | |||||
---|---|---|---|---|---|---|---|---|
Магнетит | Fe 3 O 4 Z | Пирит | FeS 2 | Касситерит | SnO 2 | | ||
Халькоцит | Cu 2 S | Боксит | 9024 9024 9024 9024 9024 O246 9024 O246 9024 O2 | Галена | PbS |
Эти руды представляют собой ионные соединения, в которых металлы существуют в виде положительных ионов.Например, степень окисления железа в гематите +3; степень окисления меди в халькоците +1. Извлечение металлов из их руд представляет собой окислительно-восстановительную (окислительно-восстановительную) реакцию. В элементарном состоянии металлы состоят из атомов, а не ионов. Поскольку у атомов нет общего заряда, ионы металлов в реакции приобретают электроны; они уменьшены.
Общая реакция восстановления меди из халькоцита:
Cu 2 S + O 2 + Энергия -> 2 Cu + SO 2Это только общая реакция.Весь процесс не так прост. Восстановление металлов из их руд обычно требует ряда химических и механических процессов. Обычно они энергетически дороги, потребляют большое количество тепла и / или электроэнергии. Например, около пяти процентов электроэнергии, потребляемой в Соединенных Штатах, используется для производства алюминия. Изготовление алюминиевой консервной банки, начиная с руды, стоит примерно в сто раз дороже, чем плавление и образование переработанного алюминия. Извлечение металлов из руд может также приводить к образованию загрязняющих веществ, таких как диоксид серы, указанный выше.По возможности, переработка и переработка металлов имеет смысл.
Относительная сложность извлечения металлов из руд указывает на то, что это их предпочтительное состояние. После удаления из руд и в элементарном состоянии большинство металлов проявляют значительную тенденцию реагировать с кислородом и серой и возвращаться в свое естественное состояние; они разъедают! При коррозии металл окисляется. Он теряет электроны, становясь положительным ионом. (См. Раздел "Коррозия металлов")
Сводка по металлам
Металлы обладают полезными свойствами, включая прочность, пластичность, высокие температуры плавления, термическую и электрическую проводимость и ударную вязкость.Они широко используются в конструкциях и электротехнике. Понимание структуры металлов может помочь нам понять их свойства.
Атомы металлов связаны друг с другом прочными делокализованными связями. Эти связи образуются облаком валентных электронов, которые разделяются между положительными ионами (катионами) металлов в кристаллической решетке. В таком расположении валентные электроны обладают значительной подвижностью и могут легко проводить тепло и электричество. В кристаллической решетке атомы металлов плотно упакованы вместе, чтобы максимизировать прочность связей.Настоящий кусок металла состоит из множества крошечных кристаллов, называемых зернами, которые касаются границ зерен.
Из-за делокализованной природы связей атомы металла могут скользить мимо друг друга, когда металл деформируется, вместо того, чтобы разрушаться, как хрупкий материал. Это движение атомов осуществляется за счет образования и движения дислокаций в решетке. Методы обработки, которые изменяют связь между атомами или влияют на количество или подвижность дислокаций, могут иметь большое влияние на механические свойства металла.
Упругая деформация металла - это небольшое изменение формы при низком напряжении, которое можно восстановить после снятия напряжения. Этот тип деформации включает растяжение металлических связей, но атомы не скользят друг мимо друга. Пластическая деформация возникает, когда напряжение достаточно для постоянной деформации металла. Этот тип деформации включает разрыв связей, обычно за счет движения дислокаций.
Пластическая деформация приводит к образованию большего количества дислокаций в металлической решетке.Это может привести к снижению подвижности этих дислокаций из-за их тенденции запутываться или скрепляться. Пластическая деформация при температурах, достаточно низких, чтобы атомы не могли перегруппироваться (холодная обработка), может упрочнять металл в результате этого эффекта. Одним из побочных эффектов является то, что металл становится более хрупким. При использовании металла трещины имеют тенденцию образовываться и расти, что в конечном итоге приводит к его разрушению или разрушению.
Дислокации не могут легко пересекать границы зерен. Если металл нагреть, зерна могут стать больше, а материал станет мягче.Нагревание металла и быстрое охлаждение (закалка) с последующим мягким нагревом (отпуском) приводит к более твердому материалу из-за образования множества мелких выделений Fe 3 C, которые блокируют дислокации.
Смешивание металлов с другими металлами или неметаллами может привести к получению сплавов с желаемыми свойствами. Сталь, образованная из железа и углерода, может существенно различаться по твердости в зависимости от количества добавленного углерода и способа ее обработки. Некоторые сплавы обладают более высокой устойчивостью к коррозии.
Коррозия - основная проблема большинства металлов. Это окислительно-восстановительная реакция, в которой атомы металла образуют ионы, вызывающие ослабление металла. Один из методов, который был разработан для борьбы с коррозией в конструкциях, включает прикрепление расходуемого анода, сделанного из металла с более высоким окислительным потенциалом. В этом случае анод подвергается коррозии, оставляя катод, конструктивную часть, неповрежденным. Образование защитного покрытия на внешней стороне металла также может противостоять коррозии.Стали, содержащие металлический хром, образуют защитное покрытие из оксида хрома. Алюминий также устойчив к коррозии благодаря образованию прочного оксидного покрытия. Медь образует знакомую зеленую патину, реагируя с серой и кислородом в воздухе.
В природе можно найти лишь несколько чистых металлов. Большинство металлов существует в виде руд, соединений металла с кислородом или серой. Для отделения чистого металла от руды часто требуется большое количество энергии в виде тепла и / или электричества. Из-за такого большого расхода энергии имеет смысл по возможности утилизировать металлы.
Вопросы для обсуждения
1. Как руды добываются из земли?
2. Назовите 4 сплава и металлы, из которых они сделаны.
3. Какое влияние оказывает «холодная обработка» на металлы?
4. Какой процесс делает металлы твердыми, но хрупкими?
5. Какой процесс делает металлы более мягкими и удобными в обработке?
6. Назовите три метода уменьшения коррозии.
7. Дайте 2 ценных результата переработки.
Проблема
Предположим, что радиус одного атома железа равен 1,24 ангстрем (1 ангстрем = 1 x 10 -8 см). Какой была бы плотность объемно-центрированного кубического (ОЦК) железа в граммах на кубический сантиметр? Подсказка: найдите массу и объем одной элементарной ячейки. Не забудьте считать только долю каждого атома в ячейке.
Добавочный номер:
Максимальная растворимость углерода в железе ОЦК составляет один атом на каждые 5000 атомов железа.Какой будет плотность стали при максимальном растворении углерода?
Решение
= m / V = # атомов x (масса / атом) / объем ячейки
В ОЦК-железе на элементарную ячейку приходится два атома железа. (8 х 1/8 + 1)
Один атом железа имеет массу 55,85 а.е.м. или 9,27 x 10 -23 граммов.
Общая масса одной элементарной ячейки составляет 1,85 x 10 -22 граммов.