Как самому сделать станок для холодной ковки
Придать приусадебному участку респектабельный вид можно без затрат больших денежных средств. Для этого достаточно установить кованые металлические элементы ограды, смонтировать кованые садовые скамейки, закрепить фонари и светильники, выковать подставки под вазоны, мангалы, детали для беседки. Дешевым способом изготовления предметов интерьера и экстерьера является холодная ковка в профессиональной или бытовой кузне.
Производство фигурных элементов
Для кустарных мастерских изготовление художественных элементов вполне доступно, если в наличии имеется оборудование для холодной ковки, к основным компонентам которого относится станок специальной конструкции. Кованые металлические детали можно изготавливать в домашней кузне, если имеются чертежи станков для холодной ковки, своими руками умельцы способны собрать от 3 до 5 вариантов из доступных компонентов.
Прежде чем собирать самодельные станки и приспособления для холодной ковки, специалисты рекомендуют изучить технологический процесс и приемы изготовления фигурных элементов без применения оборудования и оснастки.
Что такое холодная ковка
От горячей гибки холодная художественная ковка отличается способом обработки заготовки. Сделать красивую поделку при помощи горячей поковки можно только после предварительного разогрева металла. Холодную деталь наклепывают серией ударов молотом с протяжкой по длине полосы. Физическое воздействие изменяет структуру материала, увеличивает прочность верхнего слоя, оставляя сердцевину эластичной и устойчивой к излому.
Ускорить производственный процесс помогают списанные рельсы, колесные бандажи и буфера железнодорожных вагонов, используемых при изготовлении гибочного приспособления «улитка». Простой чертеж «улитки» для холодной ковки поможет из подручных материалов собрать приспособление с экономным и безопасным ручным приводом. Простая конструкция состоит из следующих компонентов:
- гибочного рычага;
- ворота или поворотного лемеха;
- лекала;
- обводного ролика.
К положительным свойствам станка-твистера «улитка» относятся следующие факторы: оборудование может устанавливаться в любом месте, вертикальная компонента обладает минимальной рабочей нагрузкой, горизонтальная нагрузка передается на опору из стального профиля. Поворот лемеха можно осуществлять одной рукой, вторая рука поджимает прут арматуры или полосу металла.
Простые механические станки для ковки металла позволяют сгибать спирали с числом витков до 5 шт. Чтобы правильно собрать станок «улитка», необходимо изучить принцип действия оборудования и способ сборки основных узлов, среди которых основными является:
- каркас из металлического уголка и швеллера или трубы с толстыми стенками;
- столешница из двух круглых стальных плит толщиной более 4 мм;
- основной вал, закрепленный в центральной части станка между кругами столешницы с помощью согнутых под прямым углом треугольников.
Для вала можно использовать толстостенную трубу;
- рычаг для сгибания прутка, закрепленный к валу кольцом.
Рычажная «улитка» обладает уникальным свойством, благодаря которому получают завитки с ограниченным в размерах ядром из полосы металла, уложенного плашмя. Избежать образования вертикальной волны на заготовке помогает установка вертикального ролика с ребордой. Рабочий процесс требует затраты времени, рычаг должен подаваться короткими подвижками.
Монтаж деталей «улитки»
В зависимости от квалификации кузнеца в рабочем процессе могут принимать участие станки для ковки одного из трех вариантов приспособлений.
Вариант первый относится к простым устройствам, в котором контур спирали протачивается или приваривается на поверхности столешницы.
Вариант второй предусматривает изготовление «улитки» из разборных частей

Третий вариант станка состоит из разборных сегментов для производства модулей с разным вариантом спирали. Модули выполняются из отдельных фрагментов металла с наваренными частями «улитки».
Независимо от варианта исполнения станки холодной ковки монтируются одинаковым способом. В начальном этапе необходимо оборудовать место под каркас, ножки которого бетонируются в специально подготовленном фундаменте.
На следующем этапе по контуру каркаса приваривается основной круг столешницы, с помощью треугольников монтируется вал, закрепляется вращающийся рычаг. К верхнему отделу вала приваривается второй круг столешницы, на которую устанавливаются сегменты спирали «улитки».
«Гнутик» в качестве приспособления
В техническом словаре «гнутиками» называются все гибочные станки для холодной ковки металла. Меняя в станке с ручным управлением ролики и клинья, можно регулировать угол загиба металла, шаг и высоту волны. Шаблон для ковки завитков строятся по принципу математической спирали, основанной на формах природного происхождения: раковина улитки, скрипичный ключ, гриф скрипки и пр.
«Гнутик» промышленного производства позволяет изготавливать детали, которые на станке домашней сборки ковать не представляется возможным. Комплектующие детали оборудования и сменный инструмент должны изготавливаться по точным размерам и обрабатываться на профессиональном оборудовании.
Профессиональные кузнецы рекомендуют купить готовый «гнутик». Такое приспособление управляется просто, пригодится для производства сварных конструкций из труб небольшого диаметра, прутка, арматуры, стальной полосы в домашних условиях.
Простейшим приспособлением для художественной ковки холодным способом также является доска с проставками, в качестве которых могут служить болты М24. Устройство легко справляется с металлической полосой толщиной до 6 мм
Станок «Улитка» для холодной ковки своими руками используется большинством мастеров в работе над оригинальными изделиями из проката. Кузнечный бизнес чаще всего основан на изготовлении кованых изделий, где присутствуют детали в виде оригинальных петель.
Входные ворота в стиле XVII-XIX веков невозможно представить без завитков, вензелей и других оригинальных элементов. Они не только украшают, умелые мастера могли создавать из металла письменные приветствия. Сложные изогнутые фрагменты используются в качестве усилителей на заборах, входных группах, перилах ограждений и других декоративных изделиях. Сложные профили придают ажурность конструкциям.
Приспособления для изгибания металлических элементов «Улитка»
Чтобы производить изгибы заготовок по определенным параметрам используют вспомогательные кондукторы, получившие название «Улитка».
Если выполнять подобную работу только за счет физической силы кузнеца, то работник довольно быстро устанет. Его производительность снизится до нуля. А при наличии вспомогательного механического помощника, можно производить сотни заготовок за смену.
Нужно учитывать, что гибка заготовок – это промежуточный этап в изготовлении сложных конструкций. Их еще нужно установить в нужном месте и приварить. Только тогда будет получен промежуточный результат. Потом потребуется окраска и монтаж изделия по месту заказа. На все операции потребуется не только время, н и физическая сила мастера.
Конструктивно приспособление может быть:
- Неразборным, тогда на нем будет производиться изгибание деталей только на определенные длины. Получаемая спираль имеет определенные ограничения в использовании.
- Сборным (присутствуют дополнительные фрагменты для увеличения продолжительности гиба), и на приспособлении можно производить догибание длинных деталей. Будут получены крупноразмерные детали.
Для работы с деталями из профильной трубы небольших номеров некоторые изготавливают приспособления с ручным исполнением. В них предусматривают использование рычагов, помогающих продвигать заготовку вокруг оправки. Готовые детали снимают с торца, слегка ослабив натяжение.
Технология изготовления приспособления «Улитка»
Упрощенно технологический процесс изготовления станка «Улитка» своими руками можно представить в виде ряда последовательных операций.
- На листе бумаги вычерчивается профиль изделия, который требуется изготовить. При вычерчивании выдерживаются размеры изделия. Чертеж нужен только для получения профиля самой детали. Внимание! При проработке учитываются толщина заготовки. Нужен зазор не менее 3…4 мм, тогда изделия можно снять после его изгибания в приспособлении.
- Для большинства станков изготавливают центральный упор. В нем будет фиксироваться начало.
- Разные мастера используют свои приемы фиксации, поэтому изделия у них можно отличить по почерку.
- Из стального листа вырезается опорная пластина. К ней будет привариваться центр, а также спираль. Толщина пластины должна быть не менее 3 мм, так как будут прилагаться значительные усилия. Размер пластины в будущем определит и параметры завитка.
- Пользуясь чертежом спирали, изгибается из полосы заготовка. При ее гибке контролируются параметры. Чем точнее будет изготовлен этот элемент, тем проще будет выполнять изготовление элементов для кузнечных изделий. Внимание! При необходимости изготовления завитков с количеством витков более одного нужно срезать полосу спирали по диагонали. Поэтому используют полосу значительно ширины. Минимальный размер соответствует высоте профиля, который собираются гнуть на станке.
- Приспособление размещают на специальной стойке, чтобы легче формировать готовые изделия.
Для небольших по размеру деталей удобно размещать на вертикальной стойке.
- Чтобы проще выполнять работу приваривают ручку. Ее устанавливают с обратной стороны, чтобы не мешала устанавливать и снимать заготовки.
Пошаговое изготовление малогабаритного ручного станка для изготовления завитков
Небольшой станок предназначен для изготовления завитков из полосового проката шириной 20…30 мм. Его несложно сделать самому.
Центр
Сначала изготавливается центр. Для этого отпиливается небольшой фрагмент из кругляка. Заготовку фиксируют в тисках, размечают линию реза. С помощью отрезного диска и углошлифовальной машинки (УШМ) отпиливается заготовка.
Она имеет диаметр 38 мм. Боковая поверхность дополнительно не обрабатывается.
Длина центра составляет 28 мм. Можно и немного больше, но для изгибания полосы шириной 30 мм этого достаточно.
На сверлильном станке сверлится отверстие Ø 8 мм. Его располагают эксцентрично. Такое положение обусловлено тем, что нужно изготовить фиксатор для конца заготовки.
Прорисовывается профиль, который следует удалить с помощью отрезного и зачистного дисков, устанавливаемых на болгарке. Заготовку крепят в тисках и удаляют излишки металла.
Лепестковыми дисками поверхность защищается так, чтобы осуществлялся плавный переход между разными поверхностями фиксатора.
Чтобы в дальнейшем проще фиксировать конец заготовки, нужно просверлить отверстие. Его располагают на радиальной поверхности центра. Сверлится отверстие под резьбу М10.
С помощью набора метчиков нарезается внутренняя резьба. Здесь будет использоваться винт без головки. После фиксации заготовки он спрячется внутри металла центра.
К опорной пластине толщиной 4 мм приваривается центр. На этом работа с его изготовлением завершается.
Изготовление приспособления
Для удобства работы с приспособлением к обратной стороне пластины приваривается вал. Вращая его в специальной оправке, будут вращать улитку.
Наружную поверхность нужно обточить, чтобы сварные швы не мешали свободному облеганию будущих заготовок.
Будущая спираль прорисовывается на пластине. Создается контур, куда ее в дальнейшем приварят.
Из полосы толщиной 4 мм изгибают спираль. Она должна соответствовать проекту.
После проверки спирали по шаблону излишки обрезаются, а саму спираль приваривают к пластине и к центру.
В качестве стойки используется профильная труба 40·40 мм со стенкой 3 мм. На ней сверлят отверстия для крепления элементов станка. С помощью опорных площадок фиксируют подготовленные части.
С обратной стороны видна ручка. Ее закрепили к валу с помощью подшипника. Подготовленная «Улитка» может вращаться.
Проводится проверка работоспособности. За ручку выполняется поворот спирали вокруг оси центра.
Изготовление простейшей детали на станке
Отрезают заготовку из полосовой стали в нужный размер. Этот размер обычно уточняют, прорисовывая готовое изделие и его составляющие элементы.
Свободный конец устанавливают в центр спирали. С помощью внутреннего винта производится фиксация заготовки.
Выполняется поворот «Улитки». Заготовка плотно прижимается к направляющим. Тут требуется прилагать определенные усилия, чтобы получать нужный профиль изделия.
Проворачивая приспособление дальше, осуществляют изготовление завитка. При необходимости вставляют другой конец заготовки и производят изготовление замкнутого или разомкнутого завитка.
Обычно другой конец не остается прямым. Его тоже изгибают. Поэтому различают внутренние и наружные обратные завитки. На самом приспособлении с помощью маркера или мела делают отметки. По ним ориентируются, когда изготавливают завитки с требуемыми параметрами.
Как гнуть профильную трубу на станке «Улитка»?
Если попытаться изгибать профильную трубу без специальной подготовки, то сварной шов разойдется. Получится брак.
Кузнецы с большим опытом работы изготавливают более сложные станки для изготовления своих изделий. Они дополнительно оснащают «Улитку» съемными элементами.
Пошаговый технологический процесс изготовления обратного завитка на станке «Улитка»
На прокатных роликах производится последовательный обжим трубы. Образуются выступающие ребра, а сварной шов остается внутри слоя, смещенного к центру.
На параллельных эксцентричных вальцах выполняется обжатие концов трубы. Она становится похожей на полосу. В таком виде ее проще фиксировать на станке.
В специальном приспособлении формируется хвостовик. Теперь заготовки будут фиксироваться на станке одним движением.
Заготовку фиксируют в центре. Там имеется паз, который закрепляет хвостовик. Видно, что спираль имеет равномерный спуск по высоте.
После фиксации хвостовика включается электродвигатель. Начинается формование детали.
Петля образуется при касании заготовки в специальный опорный элемент. Его чаще называют опорным валом. Чтобы снизить усилие, его оснащают подшипником. Деталь свободно проворачивается вокруг опоры.
Часть спирали образована. Но при необходимости обрабатывать на большую длину, будет установлен съемный элемент.
Формируется заготовка и с другого конца. Здесь мастер определяет, в какую сторону производить изгибание детали.
Для продолжения работы устанавливается съемный элемент сборной «Улитки».
Теперь можно формировать загиб деталей большого размера.
Даже длинные заготовки легко изгибаются по заданным размерам. На рабочих элементах делают метки. По ним ориентируются, сколько нужно гнуть.
С обратной стороны выполняют дополнительный изгиб детали.
Дорабатывается изделие с обеих сторон.
Готовая деталь имеет законченный вид. Если нужно, то хвостовики будут спилены. Тогда никто не догадается, как выполнялась фиксация заготовок.
Если нужно изготовить маленькую деталь, то используют другую «Улитку». У опытных мастеров их несколько штук.
Примеры изделий с завитками
Оригинальный козырек над входом в здание:
При оформлении французского балкона оригинальные завитки придают ажурный вид всему изделию.
На лестничном пролете завитки выглядят весьма оригинально.
Используя одни завитки, изготавливают опоры для скамьи, а также в том же стиле создают решетку для камина.
На винтовой лестнице видна рука отличного мастера. Не всякий сумеет сделать подобное изделие.
В створке ворот присутствуют элементы, изготовленные на станке «Улитка». Тяжелое изделие прибрело особую легкость.
Легкая лестница в стиле Хай-тек. Она может украсить не только загородный дом. Современные дворцы при минимализме конструкции могут иметь отличный вид.
Простор для творчества не ограничен. Многие кузнецы являются настоящими художниками. Они украшают мир вокруг себя.
Видео: “Улитка” – холодная ковка своими руками.
Производство металлических деталей требует специального оборудования, способного создавать усилие, формирующее конфигурацию предмета. Как вариант, можно приобрести относительно недорогие приспособления. Однако, нетрудно самостоятельно сделать практически любой станок для холодной ковки своими руками.
Что потребуется для этого мы рассмотрим по ходу нашей статьи.
Особенности оборудования
Конечно, если позволяет бюджет, можно особо не осложнять себе жизнь и приобрести универсальное оборудование для холодной ковки металла. Причем такой станок в себе совмещает все отдельные ручные приспособления. Но довольно не маленькая стоимость такого верстака делает его недоступным для многих домашних мастерских.
Какие можно сделать приспособления для холодной ковки своими руками и что на них производить?
Для основания собственной мастерской по обработке металла вполне достаточно основной шестерки станков: гнутика, твистера, фонарика, объемника, улитки, и волны.
Эти станки-самоделки способны обрабатывать основные типы материалов, использующихся в технологии холодной металлообработки: квадраты, прутки (сечением до 14 миллиметров) и стальную полосу, толщиной 3-6 мм с шириной в диапазоне 25-ти миллиметров.Приспособления, сделанные самостоятельно, осуществляют те же операции, как и заводское оборудование: гибку, кручение или прессование без потери качества.
Также на самодельном ручном станке вполне реально производить основные элементы изделий холодной ковки: завитки, волюту, корзинки,требуемые для дальнейшей сборки готовой продукции. Причем само кузнечное оборудование компактно, его можно без проблем разместить в гаражной мастерской.
Обучиться работать, имея инструмент для холодной ковки, очень просто. Здесь не требуются специальные знания о свойствах металла и его дальнейшей обработке (отжига, отпуска или закалки). Процесс обучения и производства практически безопасен, оборудование и материалы не работают с высокими температурами, а рабочие механизмы очень простые.
Единственный недостаток в холодной ковке металла и работе на ручном оборудовании — это возможность брака при допущенных ошибках. Но главная проблема заключается в том, что дефекты очень трудно исправить. Бракованные элементы можно будет подправить лишь путем разогрева металл в горне или на горелке.
Самыми простыми для самостоятельной сборки будут: улитки, гнутики и твистеры. Они не требуют наличия дорогостоящих инструментов. Потребуется лишь сварка, инструмент для резки, чертежи с материалами и немного понятия в механике.
Итак, как сделать самодельные станки для холодной ковки своими руками?
Сборка разных типов оборудования
Для начального этапа обустройства мастерской по холодной металлообработке потребуется три основных приспособления: гнутик, твистер и улитка. Какие элементы можно производить на них?
Гнутик — это устройство, намного упрощающее гибку детали и производство изгибов любой формы.
Он с легкостью обрабатывает прокат в виде стальной полосы и прутка с размерами 12×12 миллиметров. Кроме угловых деталей гнутик может создавать детали с конфигурацией в виде дуги.
Твистер служит для закручивания длинной заготовки вокруг своей оси в продольную спираль. В горячей ковке есть подобный инструмент — вороток. Твистер похож на это приспособление по своему устройству. Это станина, на которой закреплен ворот с крутящейся головкой и ползунок, ограничивающий и фиксирующий нужную длину детали. Закрученные на таком оборудовании детали — частый элемент, использующийся для сборки оконных решеток, заборов, перил и прочих видов ограждений.
Если на твистер установить дополнительные приспособы в виде вала, то он будет способен производить объемные корзинки.
Улитка, пожалуй, самый известный ручной станок для холодной ковки. На ее кондукторе производят волюту и различные закрученные вокруг оси детали. Собранное устройство состоит из своеобразной станины (круглой/квадратной) на нее закрепляют кондуктор (спираль) и ролик с ручным приводом в виде рычага. Нажимая на приводной рычаг и подавая заготовку, можно без проблем закрутить любой тип спирали.
Главное при изготовлении ручного оборудования для холодной ковки металла — соблюдение трех основных принципов:
- Длина рычажного привода рассчитывается так, чтобы создавалось достаточное усилие на металл.
- Комплектующие установок лучше всего делать сборными или подвижными, тогда можно будет без проблем регулировать размеры производимых элементов.
- Все детали кондукторы изготавливаются с достаточным запасом прочности, а соединения должны быть качественными.
Соблюдая такие принципы, изготовить нормальное оборудование для металлообработки с отличной работоспособностью вполне осуществимо.
Перечисленные три установки с механизмом, работающим вручную, позволяют производить большинство наименований продукции без разогрева металла.
Сборка гнутика
Такой станок для холодной ковки имеет широкое применение. С помощью его можно изгибать детали любой конфигурации. Устройство довольно простое, состоит из основы, на которой смонтированы ролики, клина (задающий изгиб) и рычагов управления. Сам станок может быть выполненным в вертикальном или горизонтальном исполнении.
Самостоятельно проще сделать горизонтальный тип.
- Нужно подготовить станину, в которой сверлятся посадочные отверстия под крепление роликов, клина и рычага.
- Клин должен двигаться вдоль станины (управляется нажатием на нижний рычаг). Его положение должно быть сменным, так можно будет регулировать угол и крутизну изгиба. Для этого его лучше сделать на винтовой резьбе, ввинчивая которую меняют расстояние клина.
- Верхний рычаг используется для придания заготовке формы дуги.
Посмотрев видео, можно понять как работает такой станок и принцип его устройства
Изготовление улитки
На фото показаны основные части приспособления холодной ковки улитки. Формирование элемента происходит за счет специального кондуктора, завитого спиралью (улитки). Эта часть, желательно, должна быть двусоставной. Изготовление станка следующее.
- Подготавливается станина круглой, либо квадратной, формы.
На ее изготовление лучше использовать металл 5-6 мм.
- В основании сверлятся отверстия под крепление кондуктора (двух его частей) и рабочего рычага.
- Сбоку монтируется вращающийся ролик, который будет задавать движение заготовке.
- Рычаг должен обладать достаточной прочностью, его можно изготовить из соответствующего профиля или трубы (с толстыми стенками).
- Кондуктор делается из толстого металла, изогнутого по спирали. В нем делают отверстия под крепежные болты.
Ниже представлены фото чертежей кондуктора и самого устройства.
Для более понятного принципа работы такого оборудования посмотрите предоставленное видео:
Сделанные ручные станки для холодной ковки своими руками с такой конструкцией вполне способны изгибать прутки и квадраты разного сечения вплоть до 14 миллиметров.
Стоит помнить, что большее усилие на толстую заготовку можно создать при помощи более длинного рычага, поэтому можно предусмотреть дополнительно удлинитель для такого привода.
Существуют и другие варианты улитки. Например, с приводом в виде ворота, расположенного в горизонтальной плоскости. Схематические чертежи такого устройства приведены на фото ниже.
Как сделать твистер
Твистер (или торсион) имеет горизонтальное расположение частей. Состоит из станины, на которой крепят вороток с вращающейся головкой, и ползунка, жестко фиксирующий заготовку и регулирующий длину изделия.
- Сначала нужно подготовить верстак (стол), где будет закреплено устройство.
- Станину можно изготовить из прочной двутавровой балки или любого другого материала, обладающего достаточной прочностью. Ее длина выбирается в зависимости от параметров обрабатываемых заготовок.
- По станине изготавливается ползунок. Его нижняя часть должна двигаться вдоль устройства и фиксироваться в нужном положении. Для крепления можно высверлить отверстия под болты. Часть, где будет вставляться заготовка, может быть выполнена под ее размер (сквозное отверстие) или изготовлена из тисков.
- Ворот с вращающейся головкой можно также сделать под конкретную заготовку или использовать патрон от токарного станка (небольших размеров)
- На стол установка монтируется так, чтобы край стола не мешал крутить вороток.
Как и в случае с улиткой, длина рычага определяет усилие, которое создается на обрабатываемый металл.
Если изготовить дополнительное крепление для вала, то на таком торсионе можно будет производить объемные корзинки, закручивая на шаблон пруток.
Принцип работы станка показан на видео:
Изучив информацию, можно изготовить и такие приспособления, как волна (волнообразные элементы), фонарик (корзинки) или объемник (объемные элементы с изогнутыми в разных плоскостях деталями).
Если есть возможность, то некоторые из этих станков можно сделать с электрическим приводом, установив для этого двигатель с соответствующей мощностью.
А что вы можете добавить к этому материалу из своего личного опыта по изготовлению оборудования для холодной ковки? Насколько проблемно сделать станок холодной ковки своими руками и какие материалы при этом использовать? Присоединяйтесь к обсуждению в комментариях к статье и поделитесь своими наработками.
Чертеж простого станка для холодной ковки металла своими руками — как сделать ручное самодельное оборудование —
Станок для холодной ковки своими руками: чертежи и инструкции
Известными, благодаря наружному виду, считаются металлические изделия, которые сделаны методом ковки. Такой декор отличается ценой, поэтому не каждый может заказать их себе. Однако, помимо горячей технологии ковки, необходимой для изготовления деталей из металла, существует и холодная. Последний вариант есть возможность сделать самому, для этих целей потребуется изготовить станок для холодной ковки собственноручно.
Устройство станков для ковки по холодному типу
Конструкция станковЛюбой прибор для проведения ковки холодным способом обладает характерными чертами и качествами. Чтобы сделать качественный станок для холодной ковки своими руками, важно выяснить, как он устроен.
- Гибочные. Изменяя положение роликов и клиньев, изменяются габариты волн и изгибов. Из-за этого изгибаются прутья до 1,6 см.
Единственным недостатком применяемого механизма станет невозможность изготовления его самому.
- Твистер. Снабжен спецшаблоном, к нему придавливают используемую металлическую часть. Сохранность шаблона обеспечивается упорным рогом.
- Основание с проставками. Прибор помогает делать любые узоры. Конструкция отличается простотой, основой является пластиной из материала высокого качества, куда вкручиваются проставки на определенной дистанции. Этот тип прибора эффективен для металла в толщину 0,6 см.
- Улитки. Изделие является пластинкой-основой, где расположен спецвиток. Его применяют как шаблон для обрабатываемой детали. Характерной чертой станет то, что «улитка»-шаблон разделена на фрагменты, закрепленные друг с другом с помощью соединительных спецэлементов. Это даст возможность при работе шаблону менять форму, ввиду чего будут созданы разнообразные волны и изгибы. Для изготовления такого станка потребуется выбирать крайне надежный материал, которой не будет гнуться по прошествии времени.
- Торсионный станок. Подобное приспособление эффективно для винтового скручивания прута. Устройство делают из цилиндрического металлического каркаса и 2 фиксирующих элементов. Принцип работы заключается в том, что прутья помещают в крепежные элементы. С одной стороны их зажимают, а с другой закручивают до необходимых размеров винтовой волны.
Важно! До того, как создать устройство, необходимо ознакомиться с чертежами станка для холодной ковки.
Разновидности и назначение станков для ковки
Механизм облегчит работы вручную и создать уникальные изделия. Для ковки холодным методом мастера применяют различное оборудование, которое минимизирует физ. усилия человека и позволяет провести такие основные действия:
- согнуть профиль под необходимым углом;
- изготовить спирали либо завитки;
- скрутить детали вдоль.
Различные механизмы помогают создавать уникальные конструкции, художественное полотно для беседки, декор для скамьи в парке, прочие предметы разнообразного предназначения.
Декор-станки дают возможность создавать схожие по форме и параметрам детали за короткий временной интервал, помогают уменьшить их себестоимость и сроки изготовления.
Такие станки бывают профильными (выполняют лишь одно действие) и универсальными. Выделяют такие спецстанки:
- гнутики;
- улитки;
- торсионы;
- штамповочные.
Универсальные модели состоят из компонентов спецтехники в разных комбинациях.
Станок «улитка»
«Улитка»Алгоритм сборки станка для холодной ковки своими руками не вызовет сложностей. Во время создания улитки вероятны 3 типа конструкции, и то относительные. Каждый специалист делает завиток, спираль и изгиб изделия по-своему.
По виду исполнения механизмы бывают 3 видов:
- монолитные с фиксированным шаблоном изгиба;
- со съемным изгибом, дающим возможность делать различные завитки;
- с разборными составляющими завитка и крутящейся столешницей, чтобы получать сложные профили изгиба.
Монтаж станка начинают с конструирования основных узлов приспособления:
- Каркас. Механизм должен быть изготовлен из металла. Древесина совсем непригодна для сборки прибора: продолжительные и чрезмерные нагрузки разрушают дерево за несколько использований. Как основной материал используется уголок, трубы с толстой стенкой либо швеллер.
- Столешница. Ее изготавливают из плиты из металла, которая вырезана в форме окружности, по толщине 0,4 см. Из такой плиты вырезают вторую столешницу, которая повторит по форме первую. На последней располагаются составляющие, производят изгибы заготовок. При холодной ковке столешница будет принимать большую нагрузку, потому не требуется экономить и создавать ее из тонколистового железа.
- Главный вал и рычаг. Вал расположен посередине, его окружают столешницы. Фиксируется к каркасу 4 треугольниками. Механизм сделан из трубы с толстой стенкой нужного диаметра. Рычаг крепят к валу посредством кольца и вращают вокруг его оси.
Вспомогательно на него устанавливают ролик, чтобы сгибать прутья.
Станок торсионный
Обыкновенное скручивание ряд пользователей осуществляют, не используя станок. Зажимается одно окончание детали в тисках, а второе обращается благодаря стандартному вороту. При такой методике обрабатываемая заготовка скручивается, однако иногда и вытягивается. Во избежание этого, сооружается направляющая конструкция в качестве желоба. Необходимо учитывать:
- протяженность желобка – он не может быть длиннее детали, уменьшаемой во время деформации;
- ширину желобка – требуется, чтобы он вдвое был шире изделия, поскольку в процессе деформации оно увеличится.
Возможно достичь ожидаемых результатов без оборудования – в таких целях потребуется приложить усилия и потратить большое количество времени. Те, кто предпочитает собрать необходимое устройство, должны спроектировать такую спецтехнику.
Торсионный станокСборка такого станка собственноручно возможна в 2 вариациях: стандартная и универсальная. Первая станет улучшенным способом работ с тисками, а вторая предоставит шанс создавать уникальные детали.
Главное рабочее усилие, которое требуется, чтобы деформировать материал, принимает опора, потому основание создаваемого устройства должно отличаться высокой прочностью. В таких целях используется двутавр либо 2 швеллера, которые сварены друг с другом. Устойчивости для каркаса добавляют лапы, которые приварены к устройству. Затем возможно изготавливать остальные элементы – заднюю бабку и шпиндель.
В узлах механизма из профильной трубы своими руками находятся патроны, назначением которых станет их размещение внутри заготовки. Они должны обладать прочными фиксаторами (для надежного крепления). Ввиду уменьшения длины используемого изделия во время скручивания заднюю бабку выполняют скользящей. Допустимо сооружать ее из тисков, закрепляя на основании посредством болтов.
Подвижный элемент шпинделя проворачивают при помощи ручки, которая предусматривает наличие нескольких рычажков, имеющих необходимую длину для гашения прилагаемых усилий.
Сборка торсионного прибораВажно! Возможно добавить втулки из резины, чтобы защитить руки от скольжения.
Основным различием в алгоритме монтажа универсального прибора станет устройство подвижного элемента. Он предполагает винтовую подачу при изготовлении фонарей, фиксируется с помощью стандартного скручивания. Потому активный элемент снабжается 2 шпинделями. В этом варианте для скользящей бабки требуется фиксирующий винт.
Когда нужно сделать деталь, которая скручена лишь на конкретном фрагменте, к прибору добавляют ограничители. Их изготавливают по принципу задней бабки – присутствуют спецзажимы и есть опция скольжения.
Работы в такой ситуации крайне утомительны, получение изделий высокого качества представляет собой трудоемкий процесс. Потому оснащение электрическим приводом изделия станет наилучшим решением.
Станок «гнутик»
Приспособление отличается эффективностью, массивностью, простотой монтажа. Но существенным минусом станет то, что сложно отыскать и подогнать детали. Назначением устройства станет сгибание под различными углами детали, потому понадобится прикладывать значительные усилия на, следовательно, требования к монтажу станут выше.
Для каркаса приспособления подбирают толстую раму из стали. Следует учитывать, что устройство крепится к столу. В основном делается крепеж с помощью болтового соединения, к примеру, как в тисках. В середине рамы есть направляющая, отличающаяся подвижностью. Ее приводят в действие с помощью эксцентрикового механизма, фиксируемого на раме-каркасе. Вспомогательно устанавливаются 3 упора, которые создают необычную «вилку» – это рабочие составляющие устройства. С учетом профиля сгиба они меняются: круглые валы – чтобы выполнить волну, «молоток» – чтобы формировать углы.
«Гнутик»Рабочие комплектующие изготавливаются лишь из особой стали. Они будут отвечать за прочность всей конструкции. Чтобы обрабатывать и подгонять изделия, понадобятся непосредственно спецнавыки и соответствующие инструменты. Потому, когда присутствуют трудности в заказе, при покупке либо изготовлении главных узлов, то рекомендуется приобрести устройство в магазине. Его цена не слишком высока, однако он может дополнительно использоваться, чтобы сгибать трубы.
Станок «волна»
Более логично называть рассматриваемое изделие управляемой волной. Устройство оснащается 2 стальными дисками в диаметре 14 см. Они фиксируются посредством болтов к столешнице. На основном диске закрепляется ось, которая вращает универсальный вороток.
Управлять рассматриваемым приспособлением нужно, меняя дистанцию меж дисков. Во время обкатывания воротом прута формируется узор. Когда прут снимают с кондуктора, образуется узор со второй стороны.
«Волна»Станок — пресс
Чтобы формировать наконечники прутьев, потребуется воспользоваться прессом. Рассматриваемое устройство функционирует аналогично маховику: изначально вращается штанга с грузиками, отводится винтовой боек до конца назад. Затем вставляется внутрь гнезда другой штамп и ставится обрабатываемое изделие. После, штанга быстро раскрутится в противоположный бок. Боек будет бить по хвостовой части штампа, вследствие чего образуется усилие необходимое в целях штамповки.
Детали, которые изготовлены методом холодной ковки, соединяют 2 методами:
- Сварка — изделия приваривают, окалину стачивают «болгаркой» либо иным оборудованием.
- Хомуты — подобный тип соединения выглядит значительно ярче.
Окрашивают заготовки, применяя спецэмали либо краски из акрила.
ПрессКак сделать своими руками станок для холодной ковки
Для монтажа станка для холодной ковки своими руками потребуется осуществить следующие действия:
- Сначала собирается стойка, выступающая в качестве опоры. В этих целях каждый элемент (фрагменты трубы аналогичных размеров и сочленения с верхней и нижней стороны) соединяются в одно целое. Устройство снаружи напоминает табуретку. Монтажные работы производят, используя сварочный аппарат, нарезку — применяя пилу.
- Теперь требуется нарезать металлические листы. Получатся круги одинакового диаметра и 4 треугольника, которые имеют одинаковые стороны. Треугольные составляющие привариваются к нижней части конструкции так, чтобы вышло что-то схожее с пирамидой.
Основание с более широкой площадью приваривается к центру вырезанного круга.
- 4 планки, расположенные по горизонтали, присоединяются к окружности с приваренным элементом. Подобное осуществляется, применяя болты (используют дрель для сверления отверстий).
- Последующим действием станет изготовление рукоятки. Требуется использовать 2 прута разной длины. Определяются их габариты методом соотношения с диаметра и окружности. Первый прут долен совпасть по размерам, второй несколько превышать его параметры. Во время сгибания первого прута требуется соблюсти необходимый угол. После этого углы привариваются между собой, затем вниз вваривается третий прут. Должна присутствовать перемычка меж начальных двух отрезков, к ним присоединяют спецрычаг.
- Подшипник для разнообразия направлений в приспособлении прикрепляется к окончанию приваренного рычага, к отрезку, который находится в нижней половине устройства. Верхний отрез играет роль крепления для металлической катушки (монтируется по горизонтали, помогает сгибать металл).
Снизу отрезка, где находится свободное окончание, проделывается отверстие.
- Завершающим шагом изготовления станет монтаж изготовленной рукоятки с элементом, который напоминает «пирамиду». Фиксируются такие детали после одевания рукоятки механизма с помощью гайки большого диаметра. На нее заранее приваривается круг из металла, дающий возможность закрепить шаблон. Затем «улитку» необходимо присоединить, используя сварочный аппарат. Теперь механизм будет готов к эксплуатации.
Соблюдая несложный алгоритм действий, домашний специалист или мастер сможет создать устройство высокого качества.
Для создания механизма самому требуется быть внимательным в процессе проектирования чертежей и произведения необходимых расчетов. В других моментах алгоритм изготовления простой. Установив принцип работы прибора, возможно придумать ему оригинальные вариации, способствующие улучшению обрабатываемых заготовок.
Кузнечное оборудование: станок для холодной ковки своими руками — RMNT
Холодная ковка невозможна без специального кузнечного оборудования. Давайте рассмотрим виды приспособлений и фигуры, которые можно получить с их помощью. Мы подготовили для вас чертежи и тематические видео. Также рассмотрим последовательность изготовления станка для холодной ковки своими руками.
Если вы только собираетесь организовать мастерскую холодной ковки и хотите избежать больших расходов, то самостоятельное изготовление станков и приспособлений поможет создать свой маленький бизнес без чрезмерных затрат.
Основные приспособления и станки
Станки для холодной ковки предназначены в основном для гибки по дуге или углом, а также для скручивания. Они могут быть ручные или с электрическим приводом.
Основные виды станков и приспособлений для холодной ковки:
- «Гнутик»
- «Твистер»
- «Улитка»
- «Глобус»
- «Волна»
- «Фонарик»
Приспособление «Гнутик»
Покупной или сделанный самостоятельно «Гнутик» — универсальное приспособление, позволяющее получить дугу или угол из прута. Он представляет собой основание с ползуном, на котором закреплен упор с углом (90° или другим по необходимости) и двумя цилиндрическими неподвижными упорами. Перемещая ползун и угловой упор, прут сгибается под углом.
Приспособление может быть выполнено на горизонтальной или вертикальной платформе.
Аксонометрия приспособления «Гнутик» — вертикальное расположение
Чтобы смасштабировать размеры, приводим чертёж нижней планки этого «Гнутика».
Планка нижняя
Это приспособление — универсальное. С помощью насадок на нем можно не только гнуть, но и резать, и пробивать отверстия. Но это уже будет следующим шагом.
Получение дуги на «Гнутике»
Получение угла на «Гнутике»
Так выглядит самодельный «Гнутик»:
Приспособление «Твистер»
«Твистер» — инструмент для скручивания прутков, в основном квадратного сечения, вдоль продольной оси. Это несложное приспособление может быть ручным и с электроприводом. Принцип действия: закрепляются оба конца прута, потом одно крепление начинает проворачиваться, скручивая металл до необходимой формы.
Внешний вид покупного ручного «Твистера»
Посмотрите фото самодельного «Твистера» с электроприводом, собранного с использованием электрооборудования бывшего в употреблении:
Для изготовления «Фонариков» и «Шишек» существует специальный станок, но для начала можно использовать и «Твистер», как это показано на видео (англоязычное, но всё предельно понятно).
Видео 1. Как сделать заготовку под «Фонарик» на «Твистере»
Приспособление «Улитка»
Инструмент «Улитка» предназначен для получения завитков (или спиралей) и «валют» (S-образных деталей). Встречаются различные конструкции.
Один из вариантов конструкции: 1 — лемех улитки; 2 — основа станка; 3 — прижимной валик; 4 — рычаг для управления прижимным валиком; 5 — крепление основы; 6 — палец для фиксации лемехов; 7 — паз для прижиного валика; 8 — ось рычага управления; 9 — пружина для прижатия валика; 10 — фиксатор для заготовки; 11 — ведущий лемех улитки; 12 — основная ось; 13 — рычаги
В результате должно получиться такое приспособление:
Ещё одна лёгкая конструкция, чтобы гнуть прокат сечением до 12 мм:
1 — сегмент улитки; 2 — эксцентрик; 3 — ручка; 4 — основание; 5 — направляющие полозья; 6 — ось; 7 — ползун; 8 — гайка оси; 9 — ось крепления ролика; 10 — ролик; 11 — приводная ось; 12 — направляющая эксцентрика; 13 — центральный сегмент улитки; 14 — барашек эксцентрика; 15 — основная ножка; 16 — соединительный штифт сегментов улитки; 17 — корректирующий винт; 18 — соединительное ухо сегментов улитки
Часто приспособление «Улитка» делают на опоре, особенно если гнуть нужно толстый прокат.
Несколько полезных видеоматериалов по самодельных станкам «Улиткам».
Вариант с массивным основанием на опоре:
Видео 2. Изготовление основания
Видео 3. Изготовление улитки
Видео 4. Работа станка
Вариант настольного приспособления:
Видео 5. Часть 1
Видео 5. Часть 2
Подробнее о таких конструкциях мы поговорим ниже.
Приспособление «Глобус»
Такое устройство внешне похоже на школьный транспортир и предназначено для изготовления дуг с большим радиусом изгиба из полосы, квадрата, круга или шестигранника. Сначала загибом фиксируется один конец заготовки, потом она изгибается по всей длине по шаблону. Принцип действия чем-то похож на работу закаточной машинки для консервации.
Внешний вид приспособления
Видео 6. Работа на «Глобусе»
Пользуясь исключительно мускульной силой, дугу большого диаметра можно изготовить на шаблоне, прикрученном или приваренном к верстаку. На нём хорошо гнуть полосу, трубу тонкостенную и т. д.
Шаблон
Приспособление «Волна»
Получить волнообразные изделия из заготовки круглого, квадратного, шестигранного сечения или трубки можно на приспособлении «Волна». Деформация заготовки происходит между вертикальными валками прокручиванием.
Приспособление волна и полученные изделия
Видео 7. Приспособление в действии
Приспособление «Фонарик»
На этом станке изготавливают заготовки элементов «Фонарики» или «Шишки», которые могут состоять из 4-х, 6-ти, 8-ми и более прутков. По принципу действия станок похож на «Твистер», но тут заготовки изгибаются вокруг направляющего вала, что формирует более правильную и точную конфигурацию изделия.
Приспособление «Фонарик»
Видео 8. Работа приспособления для изготовления «Фонарик»
Приспособление для холодной ковки элемента «Хомут»
Элемент холодной ковки «Хомут» предназначен для фиксирования между собой других элементов конструкции.
Приспособление для гибки «Хомута» можно выполнить по прилагаемым чертежам.
Приспособления для выполнения «гусиной лапки»
«Гусиная лапка» — расплющивание с нанесением красивых насечек концов заготовок для придания большей изящности конструкции или с целью уменьшения толщины для различных соединений.
Концы элементов оформлены «гусиной лапкой»
Эту операцию можно выполнить при помощи станка с матрицей или приспособлением и тяжелым кузнечным молотом на наковальне. Оба варианта мы даем в виде видеоматериалов.
Видео 9. Станок для изготовления «гусиной лапки»
Видео 10. Приспособления для ковки «гусиных лапок»
youtube.com/embed/HL0aAjztrsI?rel=1&fs=1″ frameborder=»0″ allow=»accelerometer; autoplay; encrypted-media; gyroscope; picture-in-picture»/>
Видео 11. Подробный процесс изготовления штампа
Ниже прокатный станок для выполнения той же операции.
Станок для прокатки «гусиной лапки» (расстояние между вальцами регулируется). Материалы для прокатного станка: шестерни и валы — запчасти от комбайна б/у
Принцип действия
Изготовление «Улитки» с приводом
«Улитка» с электроприводом облегчает изготовление завитков и «валют». Особенно это ценно, когда работа не «для души», а для изготовления большого количества однотипных изделий на потоке при работе на заказ.
Ниже приведены этапы сборки станка для гиба прута максимальным сечением 10х10 мм. Двигатель мощностью 0,5 КВт/1000 об/мин работает при этом на пределе своих возможностей. Выполняет 6 оборотов вала в минуту. Сегменты улитки выточены из круглой болванки Ст.45 без термообработки высотой 25 мм и толщиной 20 мм. Улитка насажена на вал на подшипниках от заднего колеса мотоцикла — 7204. Поддерживающий ролик закреплён жёстко в пазу. Между двигателем и редуктором установлены шкивы.
Ниже приведены чертежи сегментов улитки.
Элемент улитки 1
Элемент улитки 2
Элемент улитки 3
Центральный элемент улитки
Для более массивного прута (от 12 мм) мощность двигателя должна составлять более киловатта. На фотографиях ниже представлен станок с двигателем мощностью 2,2 кВт, 1000 об/мин, дающий выход на валу около 10 об/мин. Это уже станок для профессионального использования. Применён бывший в употреблении редуктор, матрица вырезана из заготовки толщиной 30 мм — самый трудоёмкий процесс.
Для холодной ковки ещё понадобятся наковальня и молот. Горн не нужен, он требуется только для горячей ковки.
Совет! Перед началом работ начертите эскиз будущей конструкции в натуральную величину. Это поможет корректировать элементы и не запутаться при сборке.
рмнт.ру
Станок для холодной художественной ковки своими руками: чертеж, инструкция и видео
Самодельный станок для холодной ковки может пригодиться, если вам нравиться мастерить и вы не прочь сделать своими руками что-то красивое для загородной усадьбы, домашнего интерьера, для подарков близким и родным людям или просто для души.Величественный внешний вид изделий, сделанных способом ковки, манит изящными линиями и завораживает взоры. Издревле, во всех лучших домах, можно было непременно увидеть такие украшения, как металлические ажурные завитушки. Да и сегодня, когда разработано огромное количество всевозможных материалов и технологий, кованые изделия не потеряли своей актуальности.Изделия, изготовленные с помощью ковки, используются в дизайне наряду со стеклянными, пластиковыми и иными элементами декора. Ковка металла происходит холодным или горячим способом. Для выполнения процесса горячей ковки нужно выполнить множество особых условий, потому ей очень сложно заниматься в домашних условиях. Более доступным способом является художественная холодная ковка. Научиться ей намного проще, а при желании можно сделать самодельные станки для холодной ковки своими руками.
Процесс холодной ковки
При холодном варианте ковки потребуется два основных процесса:
Чтобы провести данные мероприятия, не нужно сообщать металлу какую-то температуру. Но определенная термообработка все-таки должна происходить между этапами работ.Необязательно иметь в своем распоряжении полноценные станки для художественной ковки, часто любители изготавливают инструменты своими руками. С помощью самодельного оборудования можно придавать заготовкам всевозможные причудливые формы. Нужно только обзавестись определенными навыками работы. Поэтому готовьтесь к тому, что для того, чтобы согнуть требуемую фигуру, будут необходимы чертежи и немалые усилия. Выполнение работ возможно только с использованием сырья необходимой толщины.
Изделия, которые получаются с помощью самодельного станка для холодной ковки, намного крепче тех, которые выполняются или отливаются с помощью штамповки. Так происходит за счет того, что металлические прутья, которые проходят через оснастку, прессуются вместе с приданием им необходимой формы. При этом способе ковки нужно не допускать ошибок, так как они практически не исправляемы. С приобретением навыков вы сможете создавать своими руками привлекательные и замечательные изделия.
С помощью самодельного станка для холодной ковки, можно изготавливать такие изделия, как:
- элементы вроде балконных козырьков, поручней для лестницы;
- решетки на окна;
- ограды и заборы;
- мебель для дома – столы, стулья, кровати;
- элементы, которые используются в дизайне дома: обрешетки каминов, треноги для цветов.

При обработке большой партии однотипных изделий своими руками все можно сделать при помощи трафаретов и чертежа. Так удается значительно уменьшить трудозатраты и сократить время изготовления. Иногда детали необходимо нагреть, прогревание делают на участках стыков, чтобы не было кривизны. Новичкам рекомендуется перед выполнением работ тщательно продумать план изготовления, нелишним будет видео урок и выполнить чертеж будущего изделия.
Инструменты и оборудование
Ручной станок для выполнения холодной ковки включает ряд элементов. Необходимые приспособления, которые понадобятся для работы:
- твистер;
- улитка;
- гнутик;
- волна;
- глобус;
- фонарик.
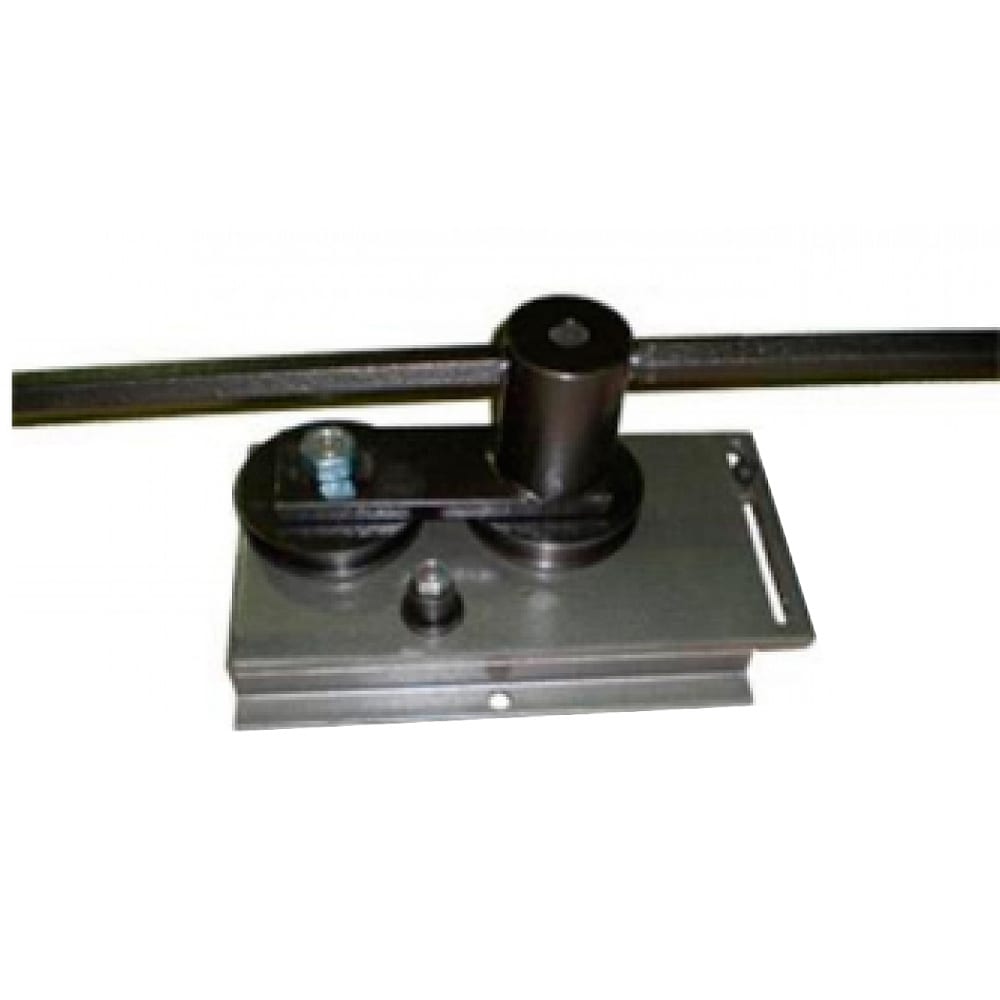
Главным инструментом для работы будет гнутик, который используется для изменения формы металла. Его функция — изгиб детали под необходимым углом или изгиб дуг с различным радиусом.
Улитка используется, как правило, для свивания в спирали стальных прутов. Это оснастка для сгибания прутков, полос, трубок, квадратов и профилей до формы спирали, изделий с различными формами и радиусом. Во время использования этого инструмента можно не ограничивать в радиусе создаваемую спираль и сделать ту величину, которая требуется.
Инструмент «фонарик» необходим для сгибания металлических деталей. С помощью него обрабатывают металлические прутки, сечение которых менее 30 мм, или квадратные профили сечением менее 16 мм.
При помощи такого устройства, как волна, делают волнообразно выгнутые элементы. Применяют его и для обработки труб, которые имеют шестигранное или круглое сечение.
Твистер похож чем-то на фонарик. При помощи этих двух инструментов можно выкручивать прутья вокруг оси.
С помощью глобуса можно выполнить большую дугу из профильного прута толщиной до 12 мм. Причем концы заготовки также плавно сгибаются.
Этот инструмент для холодной ковки абсолютно не сложный, поэтому зачастую можно увидеть и самодельный. Заводскому он почти ни в чем не уступает.
Станки для ковки
Зачастую при работе, сделать станки для холодной ковки своими руками представляется гораздо целесообразней. Так как не каждый элемент можно полноценно обработать с помощью лишь ручного оборудования для ковки. Да и цена этого оборудования довольно большая, даже когда речь идет о простейшем станке улитке.Если домашний умелец сделает какое-то изделие на самостоятельно изготовленном кондукторе, то вещь будет уникальной, хотя по некоторым параметрам и будет уступать той, которая сделана в заводских условиях. Если планируется делать большое количество деталей с помощью холодной ковки, то лучше всего сделать кондуктор с электромотором. Так вы облегчите себе рабочий процесс.
Полезным будет предусмотреть изготовление на станке основных видов работ – вытяжки, гибки и закручиваний. Эти устройства можно объединить во время создания кондуктора своими руками.
Во время вытяжки изделию придается определенная форма. Для чего ее нужно пропустить через валики или пресс, причем сечение исходного сырья уменьшится.
Процесс гибки состоит в том, что деталь гнут под требуемым углом. Выполнить эту операцию можно с помощью шаблонов. Они делаются таким образом: подготавливается чертеж изделия, по которому после делается шаблон. На стальную пластину приварите завитушку, после этот лист крепится на станке в держателе. Окончание заготовки устанавливают в прорезь, второй конец фиксируется. С помощью рычага происходит воздействие на один конец изделия, которое нужно протащить по всем изгибам пластины, используемой в роли шаблона.
Делая шаблон, сварочный шов нужно проводить с внешней стороны, иначе он будет мешать при дальнейшей эксплуатации изделия.
Часто мастера сами собирают простые устройства, с помощью которых можно изготавливать довольно оригинальные изделия. Тут все зависит от опыта мастера. Рассмотрим одну из таких самодельных моделей, чтобы понять сам принцип.
Станок «Улитка» для ковки своими руками
С помощью этого станка домашние мастера выполняют всевозможные кольца и спирали, завитушки, волны. Чтобы сделать этого рода станок, нужно действовать согласно чертежам и технологии, которая включает в себя ряд этапов.Прежде чем делать любые приспособления, ручные инструменты или станки для художественной ковки, требуется выполнение графических изображений, шаблонов, эскизов, чертежей будущего приспособления.
Чтобы более точно получилась разметка, лучше всего пользоваться миллиметровой бумагой. Нарисуйте на ней спираль, у которой постепенно увеличивается радиус витков. Между витками нужно соблюдать одинаковый шаг. Нужно сказать, что это условие необходимо соблюдать только в случаях, если нужна симметричность узоров, как правило, делают не более 4 шт.
Также учитывайте и то, какие будут заготовки, с которым нужно работать. Дистанцию между витками нужно сделать так, чтобы она немного превышала диаметр металлических прутьев, иначе сложно будет доставать из станка готовое изделие.
Для рабочей поверхности будет необходимо листовое железо. Толщина в четыре миллиметра вполне хватит. Определение размеров происходит на основании габаритов необходимых деталей. Чтобы сделать форму, потребуется листовой металл в виде полос толщиной три миллиметра. С этим материалом можно работать с помощью ручных инструментов. Его просто выгибают по шаблону в спираль с помощью плоскогубцев.Чтобы создать полноценный процесс работы, необходимо сделать надежную фиксацию одного конца изделия. Тут понадобится кусок прута, который равен ширине полос. Для фиксации рабочей площадки потребуется верстак. Часто в роли стойки используют кусок толстостенной трубы. Главное – обеспечить максимальную фиксацию, так как при холодной ковке усилия прилагаются довольно большие.
Сборка станка
Чтобы сделать любой станок для холодной ковки, существует множество вариантов. Можно его изготовить разборным, монолитным или сплошным. При монолитной конструкции устройство целиком или части «Улитки» привариваются к площадке.По длине конструкции можно приварить небольшие кусочки прутков с расстоянием 5-6 см, в рабочей площадке для них нужно сделать специальные отверстия. Не забывайте тщательно крепить концы изделий, которые будете выгибать.
Холодная ковка является особенно популярной среди начинающих в кузнечном деле. Для изготовления изделий этим способом не нужно ни хорошо оборудованной мастерской (можно обойтись гаражом или сараем), ни обладания большим опытом, не нужны особые знания о поведении металлов. Что касается приспособлений, то все необходимые станки и инструменты можно изготавливать своими руками в домашних условиях.
размеры, эксплуатация, изготовление своими руками
Люди занимаются обработкой металла не одно тысячелетие. Известно две основных технологии обработки — горячая и холодная ковка. Первый метод требует использования нагревательного оборудования для плавки или разогрева металла. Вторая технология выполняется с помощью специального оборудования. Станки для холодной ковки — это простые конструкции, которые можно изготовить самому.
Станок для холодной ковкиПроцесс холодной ковки
Холодная ковка — простой технологический процесс обработки металла. Кузнец изгибает детали используя ручные установки. Работа проводится с помощью рычагов, которые уменьшают человеческое усилие, передаваемое на материал. На выходе получаются более прочные изделия, чем при отливке. При холодной ковке станок одновременно гнёт и прессует заготовки.
Изменение формы металлических деталей без нагревания применяется при изготовлении:
Оборудование для сгибания металлических заготовок позволяет создавать изделия разной формы. Сложные металлоконструкции изготавливаются из отдельных деталей с помощью сварочного аппарата.
Виды станков
Существуют разные виды кузнечных станков, с помощью которых можно изменять металлические заготовки. Это конструкции рычажного типа, которые можно собрать самостоятельно. Для этого нужно разобраться в принципе работы отдельных моделей.
Улитка
Это ручной агрегат для создания завитков, спиралей из металлического прута. Самодельные станки улитка для холодной ковки присутствуют во многих мастерских. Чтобы сгибать заготовки малого размера, используется специальный кулачковый механизм.
Торсионный
Приспособления для холодной ковки, с помощью которых скручивают металлические прутья разного размера. Кузнец может изгибать по спирали один прут или объединять несколько в один. Представляет собой литое основание, на котором закрепляются два вида тисков. Одни неподвижные с воротом, вторые передвигаются по основанию. Тиски предназначены для закрепления прутьев. Далее кузнец закручивает ворот до нужного положения.
Чтобы скручивать несколько заготовок вместе, используется оборудование с установленными двигателями. Такие конструкции снижают усилия человека при работе с заготовками до минимума. Механизированные агрегаты эффективнее изгибают металлические детали.
Гнутик
Это ручной станок для ковки металла. Считается основным механизмом для сгибания прутьев под разными углами. Конструкция станка для ковки металла представляет собой металлическое основание, на котором закрепляются два неподвижных вала, а между ними подвижная деталь. С помощью подвижного элемента кузнец выбирает угол, по которому будет сгибаться заготовка.
Станок гнутикВолна
Ручное оборудование. Позволяет изгибать металлические заготовки по форме волны. Представляет собой ряд металлических дисков, которые расположены по одной прямой. Расстояние между ними может изменяться зависимо от требуемых изгибов волн.
Пресс
Чтобы делать плоские окончания на металлических изделиях, используется самодельный пресс. Он представляет собой два диска, которые объединяются между собой системой шестерней. Арматура закрепляется одним концом между дисками. Кузнец начинает вращение с помощью ручки.
Изготовление
Сборка самодельных станков для холодной ковки своими руками не доставляет больших трудностей. Сделать станок для холодной ковки своими руками можно в несколько этапов:
- Подготовить чертежи. Если это многофункциональный универсальный станок, схемы отдельных элементов можно найти в интернете. Объединить их на одном рисунке, обозначить места скрепления, проводов.
Нельзя забывать про указание размеров.
- Подготовить инструменты, расходные материалы. Например, для изготовления улитки понадобится кулачковый механизм, спираль из твердосплавного металла. Для волны нужны металлические диски, для торсиона — тиски.
- Следующий этап — сборка конструкции, на которой будут закрепляться другие детали. Чтобы соединить металлические детали, необходимо использовать сварочный аппарат. Швы зачищаются с помощью болгарки, покрываются защитным составом.
- На готовой конструкции закрепляются подвижные элементы, которые будут взаимодействовать непосредственно с заготовкой.
- Прежде чем начинать работать нужно проверить надёжность креплений.
Несмотря на многообразие чертежей и инструкций, часто качество самодельных станков оставляет желать лучшего, а учитывая количество потраченного времени, многие выбирают вариант покупки заводского оборудования.
Цены на станки для холодной ковки сейчас на очень низком уровне благодаря компании Stancraft, которая разработала и запустила в массовую продажу универсальный комплект ручных станков, что бы их мог позволить себе любой дачник.
На их официальном сайте stancraft.ru есть такие станки, как «Улитка», «Торсион+Корзинка», «Гнутик», «Профилегиб». Если Вам хочется максимально быстро начать работать на станках, самый простой способ — заказать на сайте stancraft.ru.
Эксплуатация
Чтобы не испортить материал и оборудование, нужно знать ряд особенностей. Кузнецы дают такие рекомендации:
- Прежде чем начинать работать нужно проверить целостность крепёжных элементов.
- Подвижные детали необходимо периодически смазывать моторным маслом. Это обеспечит надёжную работу оборудования.
- Чтобы проще было изгибать заготовки из металла, можно делать предварительное разогревание материала.
- При сгибании деталей движения должны быть плавными. Самодельные станки не настолько надёжны как покупное оборудование.
- Нельзя надеяться на высокую точность самодельного агрегата.
После сваривания металлических элементов конструкции нужно зачистить швы. Покрыть их антикоррозийным составом. На самодельном оборудовании для холодной ковки изготавливаются отдельные детали металлоконструкции. Кузнец располагает их на рабочем столе так, как они будут расположены в готовом изделии. После этого он должен соединить их с помощью сварочного аппарата.
Самодельные станки для холодной ковки популярны в частных мастерских, гаражах. Кузнецы изготавливают с их помощью разные кованые изделия сложной формы. Для сборки не нужно обладать дополнительными навыками. Достаточно сделать чертёж, подготовить материалы, инструменты, провести поэтапную сборку.
самодельные кондукторы, матрицы и другие инструменты, изготовление из профтруб и не только; гибка, сварка, сборка; видео
Кованая настенная вешалка-полка, украшенная листьями и завитками. Фото Царская Ковка
Кованые завитки являются универсальными декоративными элементами, применяющимися для дополнения дизайна разнообразных по форме изделий. Для изготовления деталей подобного типа используется механизированное оборудование, а также ручные инструменты и приспособления. Некоторое оснащение продается по достаточно высоким ценам. Но существует также возможность изготовления (сборки) оборудования своими руками.
Изготовление самодельных вертикальных устройств из металла, профтрубы и других материалов, видео
Производство станков любого типа своими руками представляет собой сложное дело. Изготовление составных частей устройства, а также сборку следует осуществлять внимательно. Корректность гарантирует качество изготовляемых элементов и предметов из металла.
Как сделать улитку с электропроприводом и без, для холодной ковки и гибки завитков, волют, запятых
- Стол выполняется из стали, к нему с нижней части приваривается труба, к которой в свою очередь крепится подвижный рычаг, сделанный из профильной трубы 45х25, толщина стенок – 1,5 мм.
- Данная часть станка крепится к ножкам, опорам.
- К рычагу крепится дополнительная регулируемая часть, дополнительно усиленная угольником.
- В ровной поверхности, где предварительно сделаны отверстия, крепятся оправки (кондукторы), выполненные из квадратного прутка с сечением в 10 мм. и полосы.
- Изготовление оправок осуществляется по рисунку.
- Несколько отверстий позволяют располагать оправки разным образом, что позволяет гнуть элементы разных конфигураций и размера.
- Мастер демонстрирует процесс изготовления элементов.
Ручные инструменты и приспособления для изготовления кованых завитков
Изготовление ручных инструментов требует меньших затрат времени и расходных материалов. Подобные приспособления имеют более простое строение.
Матрица
- Для изготовления приспособления потребуется кусок швеллера длиной 25 см.: покупная или выточенная самостоятельно петля с диаметром 22 м. с втулкой из двух видов труб и элемента сложной формы, а также еще одной петли.
- Лекало подобного типа позволяет производить волюты разных размеров.
Кондуктор
- Для изготовления кондуктора потребуется полоса длиной 60 см. и шириной – 4 см.; кусок жести 16 на 16 см., толщина – 3 мм.; кусок угольника; небольшие вырезанные из рессоры элементы с закругленными углами и снятыми фасками. Из малых деталей сваривается деталь с углом в 90 градусов, для крепления заготовок при гибке.
- На полосе прорисовывается наклонная линия, часть заготовки позже будет удаляться.
- Полоса слегка гнется, к ней приваривается малый угольник, после этого гибка продолжается.
- Спираль крепится к основанию, к куску жести.
- Кондуктор фиксируется в тисках, лишняя часть обрезается болгаркой.
- С нижней части основания приваривается угольник, обеспечивающий крепление изделия в тисках.
Другое оборудование для ковки
Весь перечень оснащения для холодной ковки следует разделять на четыре отдельные категории, критерием для классификации выступает уровень автоматизации.
- Универсальное оборудование представляет собой автоматические или в некоторых случаях ручные установки, позволяющие обрабатывать заготовки с разным сечением. Такие многофункциональные машины служат заменой целому набору ручных устройств, использующихся для гибки профильных труб, квадратных и круглых прутков.
Важным достоинством подобных машин является возможность выпуска различных по форме элементов.
Станок для ковки Ажур-1М. Фото КовкаПРО
- Станки для холодной ковки предназначены для облегчения ручного труда. В перечень устройств кроме улитки входят гнутик, волна, твистер, глобус. Каждый агрегат предназначен для изготовления определенного вида элементов. Рычажное (ручное) управление позволяет снизить трудозатраты, но не исключить их совсем. Ручные станки применяются мастерами, которые занимаются ковкой в качестве хобби, так как производительность данных устройств не слишком высока. Для улучшения технических характеристик необходимо оснастить агрегат электродвигателем.
Станок для холодной ковки типа Волна
- Инструменты представляют собой простые предметы, ковка выполняется вручную, посредством применения силы. К инструментам относятся тяжелый молоток (кувалда), клещи, вилки.
Вилка кузнечная
- Приспособления являются более сложными предметами, представляют собой механизмы, к которым относятся кондуктор, шаблоны, лекала, оправки.
Самодельные модели, изготовление, как сделать, размеры
Кроме устройства типа улитка возможно также изготовить самостоятельно и другие станки для холодной ковки: фонарик, волна и прочие, в том числе и электрические. Приспособления в большинстве случаев делают своими руками. Самодельные модели разных видов и размеров позволяют осуществлять процесс холодной ковки своими руками и выпускать элементы необходимых конфигураций.
Купить
Исполнители, не уверенные в собственных навыках, имеют возможность приобрести станки для ковки заводского производства. Предприятия предлагают широкий выбор моделей ручных устройств: улитки, волны, фонарики, твистеры, прессы, гнутики, а также универсального оснащения.
Китайская машина для горячей и холодной штамповки, Китайские производители и поставщики станков для горячей и холодной штамповки на Alibaba.com
Механический ковочный пресс с управлением от ПЛК 200тонн с механическим кузнечно-прессовым прессом с ПЛК 200тонн Механический кузнечно-прессовый пресс с ПЛК 200тонн Фотографии Технические характеристики КОД АРТ. 800 1250 Ход слайда S мм 80120140160180 Ход слайда Фиксированный об / мин Время / мин 100 80 70 60 50 Переменный (опционально) об / мин Время / мин 60-100 50-80 45-70 40-60 35-50 Макс.Высота затвора матрицы h4 мм 250 270300320350 Регулировка высоты затвора матрицы t мм 50 60 70 80 90 Глубина горловины C1 мм 210 225 270 310350 Расстояние между колоннами d1 мм 450 515 560 610 670 Размер нижнего салазок FB b мм 250 340 400 460 520 LR a мм 360 410 480 540 620 Диаметр отверстия хвостовика d мм 40 50 50 50 70 Глубина I мм 65 60 70 65 90 Размер надрессорной балки FB D мм 400 440 520 600 680 LR C мм 720 825 930 950 1100 Толщина h5 мм 80 110130140155 Диаметр отверстия в кровати ¢ мм 150150150180200 Габаритные размеры FB A мм 1496 1585 1540 1765 2040 LR B мм 945 1075 1200 1200 1320 Высота H мм 2120 2391 2570 2725 3035 Мощность двигателя кВт 3 5.5 5,5 7,5 11 Вес (приблизительный) кг 2450 3550 5150 6450 9550 КОД АРТ. ЕДИНИЦА Jh41-160 Jh41-200 Jh41-250 Jh41-315 Jh41-400 Номинальная нагрузка Pe кН 1600 2000 2500 3150 4000 Ход скольжения S мм 200 220 220 220 250 Ход слайдов Фиксированный об / мин Время / мин 45 45 30 30 30 Переменный (опционально) об / мин Время / мин 30-45 25-45 20-30 20-30 20-30 Макс.
Высота закрытия штампа h4 мм 400 450 500 500 550 Регулировка высоты закрытия штампа t мм 100 110 120 120 120 Глубина горловины C1 мм 400 430 450 450 490 Расстояние между колоннами d1 мм 736 910 980 980 1050 Размер нижней части скольжения FB b мм 580 650 700 700 750 LR a мм 700880950950 1020 Диаметр отверстия под хвостовик Диаметр d мм 70 70 70 70 70 Глубина I мм 100100130130130 Размер надрессорной балки FB D мм 760840880880950 LR C мм 1175 1390 1500 1540 1700 Толщина h5 мм 165 180 190 190 210 Диаметр отверстия в кровати ¢ мм 220 250 270 270 290 Габаритные размеры FB A мм 2305 2600 2660 2720 2850 LR B мм 1420 1540 1640 1680 1750 Высота H мм 3215 3800 3865 3865 4150 Мощность двигателя кВт 15 18.5 22 30 37 Вес (приблизительный) кг 13600 19200 23200 26600 31600 Описание Ковочный пресс 200тонн Характеристики: 1. Стальной сварной корпус, закалка, высокая жесткость, точность и стабильность; 2. Вертикально расположенный коленчатый вал, компактная конструкция; 3. Коленчатый вал подвергается шлифованию после высокочастотной закалки; 4.
Удлиненная прямоугольная направляющая с поверхностью из бронзовой пластины; 5. Пневматический цилиндр с двойной балансировкой, который уравновешивает ползун и вес штампа для снижения шума и ударов; 6. управление PLC и импортный двойной предохранительный клапан; 7.Мокрое сцепление и гидравлический предохранитель от перегрузки.
Станок для холодной штамповки болта
Машина для холодной штамповки болта
Описание продукта
Применение формирователя холодной штамповки
Машина для холодной штамповки использует метод холодной штамповки, подходит для производства всех видов винтов, Специальная машина для обработки шурупов по дереву, внутренняя шестиугольная, вогнутая шестиугольная заклепочная заготовка. Машина может автоматически завершать подачу, правку, резку, формовку, штамповку.
Характеристики формирователя холодного болта
(1) Идеальный дизайн, простота в эксплуатации.
(2) Конструкция салазок с одной направляющей позволяет машине работать с высокой скоростью, а эффективность производства также высока.
(3) Основной монтажный комплект наших машин изготовлен из высококачественного материала, подвергнутого термообработке с высокой стойкостью к истиранию и низкой деформацией, машина долговечна и долговечна.
(4) Холодная высадка Машина использует систему принудительной подачи масла , чтобы убедиться, что все компоненты машины работают в пленках состояния масла, и машина может быть долговечной в течение длительного времени.
(5) Ключевые компоненты наших машин импортируются, и все они соответствуют всем требованиям к высокой точности, высокой твердости и устойчивости к истиранию.
(6) Конструкция для выталкивания наружной формы, которая решает проблему блокировки винтов при спуске.
Поточный процесс станка для изготовления шурупов по дереву
Грубая линия → Проволока → Заголовок → Накатка резьбы → Термическая обработка → Покрытие (цвет) → Упаковка
(1). Протяните грубую линию к необходимому участку линии.(Волочильный станок)
(2). Отрегулируйте, изготовьте и сформируйте головку винта на высадочной машине. (Станок для нарезки резьбы)
(3). Отшлифуйте зуб на резьбонакатном станке и полностью сформируйте винт (Нарезной станок)
(4). Обрабатывайте шнек-полуфабрикат термической обработкой согласно стандарту (печь для термообработки)
(5). В соответствии с требованиями, технологическое покрытие и т. Д. (Цинкование)
(6). Упаковка и с завода
Формовщик холодного болта Подробное шоу:
000 000 000 000 000Упаковка и доставка
Упаковка: В стандартном деревянном ящике для экспорта
в течение 150002 дней после доставки .Условия оплаты :. 30% T / T при предоплате, оставшаяся сумма должна быть оплачена после того, как мы закончим производство. (Мы возьмем для проверки фотографии машин и упаковки)
У нас есть собственный фарвард. Мы можем своевременно проверить информацию о доставке. Вы также можете использовать свой экспедитор. Мы свяжемся с ним как можно скорее.
Информация о компании
Мы производитель, а не торговая компания.
Основанная в 1990 году компания Xingtai JUDU Technology Co., ООО специализируется на производстве всех видов оборудования. В то же время мы можем производить по желанию наших клиентов. Эта продукция экспортировалась в США, Германию, Пакистан и Австралию.
Емкость:
Основные рынки | Общая выручка | |||
Африка | 24% | 9015 9015 Южный Восток 9015 9015 Юг | ||
Южная Америка | 9% | |||
Восточная Азия | 10% | |||
Северо-Восточная Азия | 8% | |||
Европа | 7% |
Основные рынки | Общая выручка | |||
Африка | 24% | 9015 9015 Южный Восток 9015 9015 Юг | ||
Южная Америка | 9% | |||
Восточная Азия | 10% | |||
Северо-Восточная Азия | 8% | |||
Европа | 7% |
Чертеж простого станка для холодной ковки металла своими руками — как сделать ручное самодельное оборудование —
- Чертежи станков для изготовления элементов холодной ковки
- Самодельные станки и приспособления для холодной художественной ковки без нагрева: чертежи, инструмент, лекало
- как сделать изделия из металла, изготовление элементов, как посчитать длину заготовок, профильная труба и другие необходимые материалы
- Холодная ковка своими руками: чертежи, станок, изделия, инструкция
- Горячие продажи горячей штамповки металлических деталей холодной ковки согласно чертежам
- 0 Срок службы Более 20 лет Ваш рисунок — наша миссия.
Ваше требование — это наша цель. Мы ориентируемся на то, что вы хотите! Выставка литья по выплавляемым моделям Процесс обработки Наш процесс обработки Методы испытаний Наша фабрика показать Даньдун Хенгруи расположен в городе Даньдун, который является самым красивым приграничным городом.Здесь мы находимся недалеко от шоссе Данда, примерно в 5 км от порта Дадунган и в 12 км от аэропорта Даньдун, где наземный, морской и воздушный транспорт очень удобен. Здесь приятный климат и хорошие пейзажи, мы можем увидеть Корейскую Народно-Демократическую Республику за рекой Ялу. Отображение сертификата Отображение нашего сертификата Почему выбирают нас? Преимущества: 1.Опытный поставщик сланцевых изделий » 2. Профессиональная команда дизайнеров и отдел продаж для ваших услуг; 3. 9-летний поставщик золота alibaba, фабрика, признанная CE / ISO9001 и т. Д .; 4. Обслуживание 7 * 24 для вас , Все вопросы будут решены в течение 24 часов. Вы получаете выгоду: 1. Стабильное качество —— Благодаря хорошим материалам и технике 2.
Более низкая цена —— Не самая дешевая, но самая низкая при том же качестве 3.Хорошее обслуживание —— Удовлетворительное обслуживание до и после продажи 4. Срок поставки —— 30-45 дней для массового производства . Горячая штамповка деталей из металла холодной штамповки по чертежам
- G5 Gt55 Карбид вольфрама высшего качества умирает для холодной штамповки пресс-форм
- Горячие продажи горячей штамповки металлических деталей холодной ковки согласно чертежам
Чертежи станков для изготовления элементов холодной ковки
Станки для ковки являются хорошим инструментом для художественных и творческих людей, у которых есть желание создать что-то красивое и индивидуальное в своем доме, чтобы подчеркнуть интерьер, а может сделать хороший подарок своими руками для важных людей. Существует два способа ковки металла. Чтобы сковать что-то способом горячей ковки необходимо произвести множество приготовлений и действий, поэтому дома проще всего ручная ковка дается, пользуясь способом холодной ковки. Период обучения такому процессу не занимает много времени, к тому же есть реальная возможность сконструировать станок своими руками
Начало холодной ковки самодельными станками.
Холодная ковка своими руками требует два обязательных действия – пресс и гнутье. Для совершения всех этих действий придавать определенную температуру для металла нет необходимости, но все равно необходимо провести термообработку.
Чтобы сконструировать что-то своими руками, уже не обязательно иметь специальные станки для художественной ковки, теперь можно создать станки для ковки металла в домашних условиях. Но без опыта работы с такими инструментами все равно не справиться. Чтобы вся работа была успешной, нужно пользоваться металлами определенной толщины.
Самодельный станок для холодной ковки запросто можно использовать для создания конструкций, которые будут значительно прочнее, нежели те, которые были изготовлены штамповкой. Кованые изделия своими руками получаться высококачественными, когда будет все сделано верно и без ошибок, ведь исправить их очень сложно. После нескольких работ, благодаря полученному опыту, можно начать делать превосходные конструкции, используя самодельные станки и приспособления для холодной ковки.
При изготовлении большого количества одинаковых металлических конструкций лучшего всего воспользоваться чертежами, приготовленными заранее. Чертежи на станки для холодной ковки своими руками заготавливаются заблаговременно. В некоторых случаях деталь лучше будет прогревать, чтобы избавиться от дефектов в последующем. Тем, кто не так давно начал использовать самодельные станки для холодной ковки для начала стоило бы продумать план работ, а так же приобрести необходимые навыки. Не лишней тут будет помощь различных видео уроков в сети интернет, а так же специальных курсов.
Компоненты станка и необходимые инструменты. Станок для ковки своими руками состоит из определенных устройств. Среди которых обязательно должны быть:
1. гнутик;
2. улитка;
3. волна;
4. глобус;
5. твистер;
6. фонарик;
Этими приспособлениями пользоваться лучше всего. Улитка для холодной ковки своими руками понадобиться для сплетения стальных прутьев. Можно ознакомиться с фото, чтобы лучше разглядеть конструкцию и пример деталей. Кузнечное оборудование для холодной ковки металла отыгрывает важную роль в работе. Основным инструментом во время работу будет гнутик. Это весьма простой элемент.
Чтобы обработать трубы с шестигранным и круглым сечением используют «волну». «Фонариком» сгибают металлические прутья, а твистер чем-то на него похож, весьма удобное преспособление. Глобусом делается большая дуга из профильных прутьев.
Станки холодной ковки в большей мере выгоднее всего сделать самому, ведь далеко не все можно обработать ручными инструментами, а цена за станок для художественной ковки очень высока. Когда мастер за счет своих навыков с помощью своего оборудование создаст конструкцию, она будет неповторимой и особенной, пускай в чем-то и будет не такой качественной, как заводская. При изготовлении большого количества деталей, правильно будет создать кодуктор на электромоторе. Это облегчает процесс работы.
В процессе вытяжки конструкция приобретает определённую форму. Поэтому она должна пройти через пресс, после чего сечения первостепенного материала станет меньше. Под гибкой подразумевается создание гнута в нужном угле. Для этого понадобятся шаблоны. Фото чертежей кованных изделий своими руками приготавливается заранее из которого и будет сделан шаблон. К стальной пластине прикрепляется завитушка, а сам лист закрепляется в держателе станка. В конце заготовке размещается прорезь, другой же конец закрепляется на месте. Используя рычаг, происходит влияние на окончание конструкции, которое необходимо провести по каждому изгибу пластины, которая используется как шаблон.
Видео самодельного станка по загибанию балясин.
Многие опытные изготовители собственноручно собирают несложные механизмы, которые позволяют создавать уникальные конструкции. На это влияет стаж работы. Чертежи на станки для холодной ковки своими руками можно в достаточном количестве найти в интернете, как и фото изделий холодной ковки, которые можно получить в итоге. Фотография такого оборудования позволяет выполнить мастеру чертеж с нуля, если у него есть опыт.
Можно рассмотреть станок «Улитка». Используя его можно создавать различные спирали или волны. Для создания такого станка нужно иметь чертежи на станок для холодной ковки своими руками такого типа, а так же делать все в соответствии с технологией. Рабочая поверхность должна состоять из листового металла. 4 мм толщины будет достаточно. Размеры устанавливаются исходя из габарита детали. Для придания форму необходим листовой металл в толщину 3 мм и в виде полос. Он выгибается по шаблону плоскогубцами и получается спираль.
Для создания нормального процесса работы нужно хорошо зафиксировать один из концов детали. В этом поможет прут, равный ширине полос. Чтобы зафиксировать рабочую площадку нужно будет использовать верстак. Основная цель всего – придать максимальной неподвижности детали, потому что во время холодной ковки нужно приложить большие усилия.
Перед началом изготовления любого станка для холодной ковки, инструментами для ручной работы нужны шаблоны, эскизы и различные чертежи, в том числе и чертеж на оборудование для холодной ковки своими руками.
Придать более хорошую точность разметке можно за счет миллиметровой бумаги. Нужно нарисовать на ней спираль, где будут увеличиваться витки в радиусе. Между ними нужно должным образом соблюдать равную дистанцию. Такое условие будет обязательным только для создания симметричных узоров.
Конструирование станка.
Для создания любого станка можно использовать несколько вариантов на выбор – разборный, монолитный или сплошной. По все длине бедующего станка рекомендуется приварить маленькие прутки. На рабочей площадке для этого стоит просверлить специальные дырки. Требуется хорошо закрепить концы деталей, которые будут выгибаться. Такой способ ковки очень популярен у новичков кузнечного дела.
Используя станок для холодной ковки металла, сделанного своими руками, неопытный мастер сможет изготовить кованые балконные козырьки, поручни для лестниц, различные решетки для окон, заборы, многочисленную мебель для дома, ограждения, различные кованые аксессуары и предметы декора, которые дополняют интерьер помещений, на подобии решеток под камины. Это хороший вариант для начинающих специалистов.
Коллекция чертежей станков для холодной ковки.
Чертеж для улитки с лемехом.
На чертеже представлено устройство гибочной улитки с лемехом и правила работы с ним
Самодельные станки и приспособления для холодной художественной ковки без нагрева: чертежи, инструмент, лекало
Придать приусадебному участку респектабельный вид можно без затрат больших денежных средств. Для этого достаточно установить кованые металлические элементы ограды, смонтировать кованые садовые скамейки, закрепить фонари и светильники, выковать подставки под вазоны, мангалы, детали для беседки. Дешевым способом изготовления предметов интерьера и экстерьера является холодная ковка в профессиональной или бытовой кузне.
Производство фигурных элементов
Для кустарных мастерских изготовление художественных элементов вполне доступно, если в наличии имеется оборудование для холодной ковки, к основным компонентам которого относится станок специальной конструкции. Кованые металлические детали можно изготавливать в домашней кузне, если имеются чертежи станков для холодной ковки, своими руками умельцы способны собрать от 3 до 5 вариантов из доступных компонентов.
Прежде чем собирать самодельные станки и приспособления для холодной ковки, специалисты рекомендуют изучить технологический процесс и приемы изготовления фигурных элементов без применения оборудования и оснастки. Научиться создавать красивые вещи своими руками просто, достаточно получить минимальные навыки по работе с арматурой и листовым материалом.
Что такое холодная ковка
От горячей гибки холодная художественная ковка отличается способом обработки заготовки.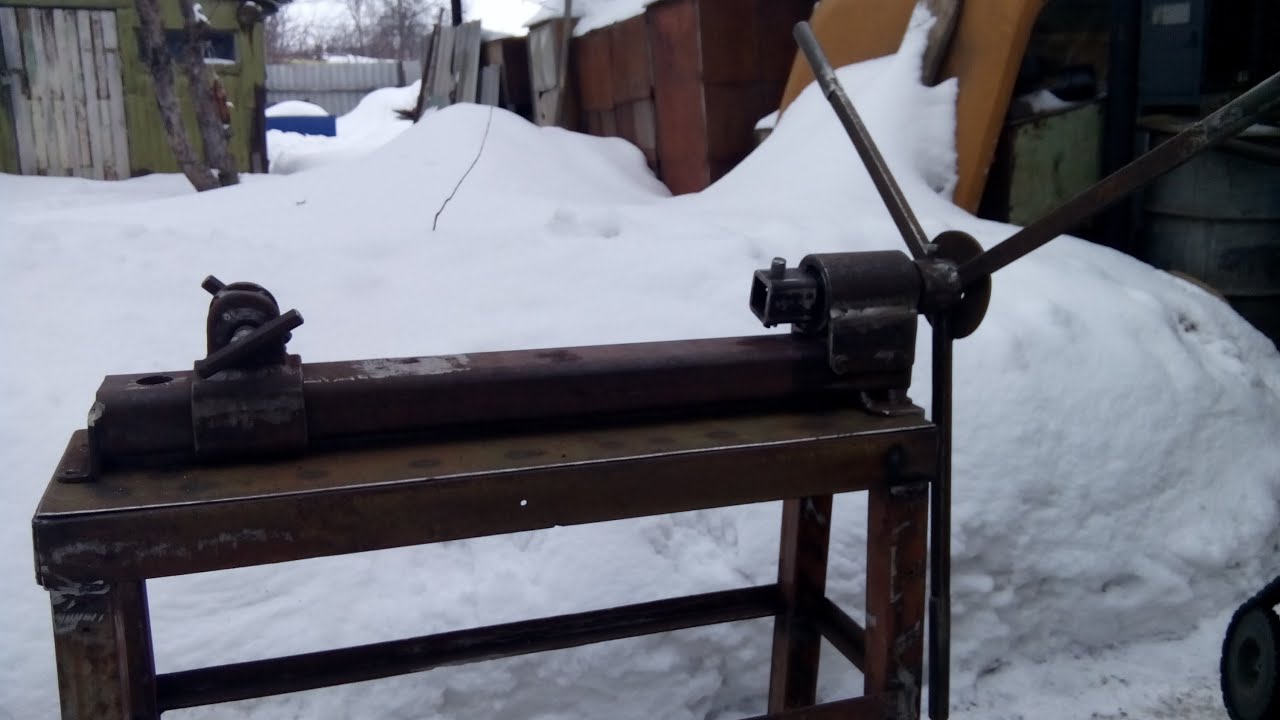
Ускорить производственный процесс помогают списанные рельсы, колесные бандажи и буфера железнодорожных вагонов, используемых при изготовлении гибочного приспособления «улитка». Простой чертеж «улитки» для холодной ковки поможет из подручных материалов собрать приспособление с экономным и безопасным ручным приводом. Простая конструкция состоит из следующих компонентов:
- гибочного рычага;
- ворота или поворотного лемеха;
- лекала;
- обводного ролика.

Простые механические станки для ковки металла позволяют сгибать спирали с числом витков до 5 шт. Чтобы правильно собрать станок «улитка», необходимо изучить принцип действия оборудования и способ сборки основных узлов, среди которых основными является:
- каркас из металлического уголка и швеллера или трубы с толстыми стенками;
- столешница из двух круглых стальных плит толщиной более 4 мм;
- основной вал, закрепленный в центральной части станка между кругами столешницы с помощью согнутых под прямым углом треугольников. Для вала можно использовать толстостенную трубу;
- рычаг для сгибания прутка, закрепленный к валу кольцом.
Рычажная «улитка» обладает уникальным свойством, благодаря которому получают завитки с ограниченным в размерах ядром из полосы металла, уложенного плашмя. Избежать образования вертикальной волны на заготовке помогает установка вертикального ролика с ребордой.
Рабочий процесс требует затраты времени, рычаг должен подаваться короткими подвижками.
Монтаж деталей «улитки»
В зависимости от квалификации кузнеца в рабочем процессе могут принимать участие станки для ковки одного из трех вариантов приспособлений.
Вариант первый относится к простым устройствам, в котором контур спирали протачивается или приваривается на поверхности столешницы.
Вариант второй предусматривает изготовление «улитки» из разборных частей. По длине контура кузнечной разметки устраиваются отверстия с внутренней резьбой, по шаблону вырезаются металлические накладки с отверстиями под болты. Для закрепления сегментов на столешнице применяются болты или упоры, конструкция позволяет изготавливать заготовки с разным радиусом завитков «улитки» не используя нагрев прутка.
Третий вариант станка состоит из разборных сегментов для производства модулей с разным вариантом спирали. Модули выполняются из отдельных фрагментов металла с наваренными частями «улитки».
Независимо от варианта исполнения станки холодной ковки монтируются одинаковым способом. В начальном этапе необходимо оборудовать место под каркас, ножки которого бетонируются в специально подготовленном фундаменте.
На следующем этапе по контуру каркаса приваривается основной круг столешницы, с помощью треугольников монтируется вал, закрепляется вращающийся рычаг. К верхнему отделу вала приваривается второй круг столешницы, на которую устанавливаются сегменты спирали «улитки».
«Гнутик» в качестве приспособления
В техническом словаре «гнутиками» называются все гибочные станки для холодной ковки металла. Меняя в станке с ручным управлением ролики и клинья, можно регулировать угол загиба металла, шаг и высоту волны. Шаблон для ковки завитков строятся по принципу математической спирали, основанной на формах природного происхождения: раковина улитки, скрипичный ключ, гриф скрипки и пр.
«Гнутик» промышленного производства позволяет изготавливать детали, которые на станке домашней сборки ковать не представляется возможным. Комплектующие детали оборудования и сменный инструмент должны изготавливаться по точным размерам и обрабатываться на профессиональном оборудовании.
Профессиональные кузнецы рекомендуют купить готовый «гнутик». Такое приспособление управляется просто, пригодится для производства сварных конструкций из труб небольшого диаметра, прутка, арматуры, стальной полосы в домашних условиях.
Простейшим приспособлением для художественной ковки холодным способом также является доска с проставками, в качестве которых могут служить болты М24. Устройство легко справляется с металлической полосой толщиной до 6 мм
Originally posted 2018-07-04 07:43:44.
как сделать изделия из металла, изготовление элементов, как посчитать длину заготовок, профильная труба и другие необходимые материалы
На данной странице вы найдете сведения по теме “холодная ковка своими руками”, а также ссылки на другие страницы нашего сайта, которые связаны с данной темой. Читайте подробную информацию ниже, чтобы узнать больше, переходите, пожалуйста, по интересующим вас ссылкам, в конце страницы дан список страниц с этой меткой.
В металлообработке, в основном в заготовительном производстве, используется технологическая операция ковка. Формообразование заготовки при выполнении этой операции производится обработкой давлением. Деформация металла становится возможной при нагреве его до определенной температуры.
Однако некоторые технологические операции, например гибка заготовок, возможно выполнить без нагрева. Материалом для таких работ являются пластичные малоуглеродистые стали, медь, латунь, дюралюминий и другие сплавы, обладающие свойством легко деформироваться. Такой вид обработки объединили под названием холодная ковка, хотя в чистом виде она ковкой не является. Применение эта технология нашла в изготовлении художественных изделий своими руками. Особенности холодной ковки разбираются в этой статье.
Оборудование для ковки металла в домашних условиях
Без специального (иногда универсального) оборудования, станков и оснастки получить изделия художественной формы не получится. Гибка, прессование, нанесение рисунка на поверхность изделия производится с помощью ручных или машинных приспособлений. В домашних условиях применяются следующие виды станков для холодной ковки.
- Гнутик. Приспособление предназначено для изгиба проката или полосы на угол произвольной величины. Эксцентриковый привод, гибочный штамп и закаленные ролики смонтированы на прочном основании. При необходимости к этому ручному станку добавляется дополнительная оснастка.
Станок для холодной ковки PROMA Gnutik 0005
- Улитка. Создает из проката изделия в виде спирали, находящейся в одной плоскости. Основным элементом конструкции является кондуктор, который выполняется в форме завитка, напоминающего улитку. Под каждый вид спирали изготавливается свой кондуктор.
Станок типа улитка PROMA. Фото ВсеИнструменты.ру
- Твистер. Приспособление дает возможность закручивать прутки вокруг своей оси. Заготовка фиксируется во вращающейся головке и ползунке и при помощи рукоятки закручивается на нужную величину. При скручивании длина заготовки уменьшается, поэтому ползунок должен иметь возможность передвижения вдоль оси.
Станок для холодной ковки типа Твистер Blacksmith M3-TR
Для получения качественных изделий закручивание прутков вокруг своей оси лучше производить на механизированном оборудовании. Твистер, в составе с электромотором и червячным редуктором, дает равномерную дозированную нагрузку, какую нельзя обеспечить ручной. При этом значительно облегчает усилия, которых требуется достаточно много при закручивании прутков.
- Фонарик. Представляет собой переплетение прутков в форме вытянутых по винтовой поверхности спиралей.
По аналогии с твистером, конструкция состоит из вращающейся головки и ползунка. Добавляется вставка в виде вала, на которую ложится пруток при намотке.
Станок для ковки PROMA Корзинка Фонарик. Фото ВсеИнструменты.ру
- Волна. Ручное приспособление создает узоры в виде набегающих волн. Между двумя роликами и упором пропускается пруток. Подвижный ролик, обкатываясь по неподвижному, создает на прутке изгиб в виде волны. Длину волны изменяют, увеличивая/уменьшая расстояние между роликами.
Станок для холодной ковки типа Волна
- Глобус. Заготовка изгибается по дуге. Концы также гнутся в зависимости от фантазий автора. Основой для приспособления служит шаблон в виде дуги. На ручке расположен ролик, который при ее движении обкатывает дугу. Заготовка, расположенная между роликом и шаблоном, принимает требуемую форму.
Станок глобус (объемник) для холодной ковки. Фото КовкаПРО
Своими руками
Сварочный аппарат с зарядным устройством «SSVA-160-2».
Как видно из описания конструкции ручных станков, изготовить их своими руками вполне доступно. Для выполнения работ потребуются следующие материалы и инструменты:
Помимо навыков слесаря надо обладать квалификацией хорошего сварщика. Качественный сварной шов является залогом прочности любого вида станков для холодной ковки: улитка, фонарик, глобус и прочие.
Инструменты и приспособления в большинстве случаев собираются самостоятельно.
Купить
При объемах производства, соизмеримых с масштабами небольшого предприятия, возможно рассмотреть приобретение оборудования, выполняющего все виды работ холодной ковки. В случае стабильной номенклатуры изделий дорогостоящий ручной станок: улитка, гнутик или любой другой – окупится за счет более производительной работы.
Станок для холодной ковки типа Улитка Stalex SBG-30. Фото КовкаПРО
Необходимые расходные материалы: профильные трубы, прутки и прочие
Основными материалами, из которых выполняются изделия методом холодной ковки, являются:
- сплошной круглый пруток;
- профильный прокат;
- металлическая лента;
- квадратный пруток (на картинке).
При работе своими руками используют небольшие типоразмеры заготовок, где не требуется применять большие усилия. Так, например, квадратный пруток — 10-12 мм., металлическая лента толщиной около 3 мм. Из этих материалов легко подготовить заготовки для операций холодной ковки: не требуется особых трудозатрат, чтобы отрезать в нужный размер.
Как сделать различные изделия
Технология холодной ковки позволяет изготавливать изогнутые и витые детали разнообразной формы. Дизайнер, обладающий художественным вкусом, способен создать из них оригинальные композиции. Ограды и решетки, навесы и крылечки, столики и скамейки – многие из них выполнены с помощью холодной ковки, привнося в свой дизайн признаки художественного произведения.
Для начинающего приоритетом будет освоить изготовление декоративных завитков. Они являются основой для изготовления большинства изделий холодной ковки. Поэтому в первую очередь надо овладеть производством на станке улитка.
Создание завитка для балясины на самодельном кондукторе
Далее, с целью увеличения разнообразия продукции, изучить и применить на практике станок твистер. Остальные ручные приспособления внедрять по мере роста мастерства и увеличения видов продукции.
Справка. С образцами изделий холодной ковки, выполненными профессионалами, можно ознакомиться на сайтах компаний из раздела «Где купить или заказать».Сделай сам: подставки для цветов
Обзор посвящен самостоятельному изготовлению оконной цветочницы (балкончика) с завитками и патинированием. Подробная инструкция представлена здесь.
Изготовление узоров
Обзор посвящен изготовлению фигурных балясин, служащих узором для лестничных перил. Гибка квадратов выполняется на самодельном кондукторе.
Изготовление элементов, как делать
Начинать изготовление нужно с эскиза элемента. Если это возможно, то выполнить его в натуральную величину.
Холодная ковка и сварка, решетка из завитков с хомутами
В зависимости от имеющегося оборудования подбирается материал. Ручная оснастка не может согнуть пруток толще 14 мм.
На специальной оснастке изготавливаются:
Технология изготовления основана на трех основных операциях: вытяжка, гибка, кручение.
Сборку элементов в единую композицию собирают при помощи заклепок, хомутов или сварки. Сварка самый простой и эффективный способ.
При окончательной отделке изделие зачищают и наносят декоративное покрытие.
Длина, размеры заготовок
Важно! Для изготовления элементов холодной ковкой необходимо правильно рассчитать размеры заготовки. Ошибку при выполнении работы исправить будет зачастую невозможно.С помощью эскиза, выполненного в натуральную величину, легко рассчитать длину заготовки. На линию, образующую контур элемента, наложить мягкую проволоку. Размер длины вытянутой проволоки будет соответствовать размеру развертки элемента. Если добавить небольшой припуск, то получим размер заготовки.
Для измерения длины кривых линий применяется прибор под названием курвиметр. Зубчатым колесиком повторяют путь кривой, а на шкале выносится искомый показатель.
В проектировании деталей все больше применяются компьютерные программы. В них закладываются данные, которые оказывают влияние на геометрию детали при обработке холодной ковкой. Такая программа выдает готовые размеры заготовки.
Завитки
В видеообзоре представлен процесс гибки круглых прутков диаметром 10 мм. Мастером используется станок типа улитка со съемными кондукторами разных форм и размеров.
Цветы
В обзоре представлен полная и подробная инструкция изготовления цветка: от прорисовки элемента на металле до крепления детали в общую композицию.
Розы
В видео представлен процесс изготовления розы по методу холодной ковки, с помощью бумажных шаблонов, самодельных ножниц по металлу, двери, болгарки, электродов, а также дополнительных инструментов и приспособлений, сделанных из подручных средств.
Фонарики
Инструкция по гибке круглых (диаметр 6 мм.) и квадратных (6х6 мм.) прутков на станке фонарик для изготовления одноименных элементов.
Холодная ковка своими руками: чертежи, станок, изделия, инструкция
Человеку, неравнодушному к кованым изделиям, можно только позавидовать. У него есть все необходимое для воплощения самых смелых проектов оформления. Приспособления для изготовления элементов холодной ковки можно приобрести в готовом виде или изготовить своими руками, но в том или ином случае, вы можете быть уверенны, что работать с ними будет удобно и просто. При этом большой физической силы не потребуется, все что нужно, это нажимать на нужные кнопки и поворачивать своевременно специальные рычаги.
Единственное, что нужно помнить, это то, что изготовление кованых изделий холодным способом требует соблюдения строгих правил и последовательности. Другими словами, холодная ковка — это поэтапный технологический процесс, при котором происходит деформация металлических заготовок, в зависимости от нужного проекта. Чтобы иметь большее представление об этой работе, необходимо разобраться, каких видов бывает ковка, как называются популярные кованые элементы и как выглядит изготовление кованых изделий своими руками.
Содержание статьи
Виды холодной ковки
При изготовлении металлических изделий можно выделить 7 видов холодной ковки. Это своего рода этапы создания элементов, которые нужно выполнять при работе с заготовками.
Всю работу необходимо проводить в соответствии с требованиями и правилами, в противном случае надеяться на получение красивого кованого изделия не стоит.
Самым главным этапом является ковка заготовок из металла. Это самый большой, ответственный, сложный и серьезный процесс, поэтому к нему нужно отнестись очень внимательно. Холодная ковка может быть нескольких видов:
- Осадка — она выполняется под высоким давлением. Это нужно для того, чтобы увеличить заготовку по бокам, за счет уменьшения ее высоты.
- Протяжка — этот этап выполняется путем нагревания металлической детали с последующей обработкой ее молотком. Это нужно для того, чтобы уменьшить площадь поперечного сечения за счет увеличения длины металлического прута.
- Прошивка — этот этап подразумевает проделывание отверстий внутри заготовки. При выполнении такой работы можно получить отверстия разного диаметра и длины.
Она бывает открытой и закрытой.
Осадка и протяжка делает структуру металлической заготовки более хрупкой, поэтому дальнейшая работа должна проводиться очень аккуратно, чтобы не допустить поломки той или иной части конструкции.
- Штамповка — на этом этапе происходит пластичная деформация металла, что приводит к изменению формы или размера заготовки. Штамповка может быть объемной или листовой. При первом варианте работы выполняются под давлением. В этом случае деталь нагревается и подвергается прессованию до нужных размеров. Этот метод больше подходит для производственных масштабов, когда нужно изготовить большую партию одинаковых элементов. Листовая штамповка отличается от первого варианта тем, что детали производят из листового железа. Этот метод подходит для изготовления мелких или средних деталей, при этом они будут отличаться высоким качеством и прочностью.
- Прессование — на этом этапе происходит повышение плотности металлической заготовки и изменение ее формы, за счет высокого давления.
Прессование может быть прямым и обратным. При прямом способе происходит выдавливание металлических заготовок через различные отверстия, что приводит к получению различных прутьев, труб и профилей. При обратном прессовании металлические изделия располагают в специальном формуляре, при этом давление подается в обратном направлении.
- Волочение — это процесс протягивания металла, только уже прессованного, через специальную матрицу. При этом способе обработки можно получить различные фасонные профиля, проволоку или тонкие трубы.
- Прокатка — это заключительный этап обработки, при котором задействован закон силы трения. При трении специальных валиков о металлическую поверхность происходит деформация заготовки. Прокатка может быть нескольких видов, в зависимости от способа вращения валиков:
- продольная — при которой вращение валиков происходит в разные стороны. Это приводит к постепенному обжиманию и удлинению металлической детали. Таким способом производится листовое и ленточное железо;
- поперечная — при которой движение валиков происходит в одном направлении.
Это приводит к деформации заготовки в поперечном направлении. Этим методом изготовлены цилиндрические шестеренки с накатными зубцами;
- винтовая — при которой расположение валиков выполнено под углом друг к другу. В этом случае заготовка проходит одновременно два валика с поступательным и вращательным движением, что позволяет получить небольшой зазор, в который и попадает металл. Таким способом получают трубные заготовки, «гильзы».
Приспособления для холодной ковки
Изготовление кованых изделий холодным способом предусматривает использование нескольких приспособлений или станков. Как было сказано выше, их можно приобрести, или изготовить своими руками, но для начала, давайте разберемся, какие детали можно получить при помощи различных станков.
- Улитка — такой механизм применяется в том случае, если металлической заготовке нужно придать спиралевидную форму. В большинстве случаев такой механизм крепят на стальную толстую плиту либо делают съемной.
Сама плита должна быть достаточно прочной, а допустимая ее толщина не должна быть меньше 4 мм.
Для изделий, изготавливаемых своими руками, придется изготовить специальные шаблоны, которые позволяют создавать элементы различной формы и величины.
Как работать с механизмом улитка, можно посмотреть на предложенном видео:
- Универсальный механизм — он позволяет выполнять несколько функций, резку, клепку и формирование металлических изделий. Кстати, такое устройство легко можно собрать своими руками, что в значительной степени сэкономит ваш бюджет.
- Гнутик — такой механизм позволяет создать дуговую деформацию металлической детали. Но здесь нужно провести точные расчеты и замеры, чтобы не ошибиться с радиусом изгиба.
- Твистер — механизм этого плана позволяет сгибать заготовку по продольной оси уже готового изделия. Принцип действия такого механизма заключается в том, чтобы изогнуть изделие, зажав его с одной и другой стороны.
При этом вращающаяся рукоятка позволит произвести скручивание детали.
- Волна — механизм такого плана позволяет получать волнообразные детали из металлических заготовок. На таком станке принято изготавливать решетки «Боярские» или «Волна».
- Штамповый пресс — название говорит само за себя. Такой механизм позволяет наносить на металлические детали штампы с различными резными элементами. В арсенале каждого мастера должны быть несколько таких штампов, тогда и готовые изделия будут более разнообразными. Принцип его действия очень прост, под действием давления на металлических элементах остаются четкие отпечатки с шаблонов.
- Механический узел — этот механизм позволяет изгибать металлические прутья в круг. При этом диаметр таких изделий может быть разным. Поэтому в арсенале мастеров такое приспособление незаменимо.
Холодная ковка своими руками, пошаговая инструкция и советы специалистов
Как это ни странно, но кованые изделия можно изготовить даже в домашних условиях. Конечно, они не будут столь вычурными, как элементы горячим способом изготовления, но в качестве декоративного оформления им нет равных. Все что вам нужно, это несколько приспособлений, описанных выше, материалы и самое главное, желание. Остальное — это соблюдение технологии.
Процесс изготовления состоит из нескольких этапов:
- Первое, что вам нужно сделать, это нарисовать эскиз будущего изделия. Если вы только учитесь, попробуйте соорудить что-то элементарное, и только потом беритесь за большие объемы. Что касается эскиза, то на нем нужно отразить все нюансы будущей конструкции, рисунок, нужные детали и размеры. Здесь же продумайте, сможете ли вы выполнить задуманные элементы на вашем оборудовании? Каждый механизм предназначен для выполнения одной функции, но не всех сразу.
- Второе, о чем нужно подумать, это как правильно рассчитать материал. Если вы задумали изготовить подставку для цветов из элементов холодной ковки, то нужно подготовить железную трубу и металлические полосы, а для ворот или забора перечень материалов будет намного шире.
Начиная работу, проверьте еще раз ваши расчеты, даже небольшая погрешность может испортить внешний вид готового изделия, не говоря уже о том, что оно может не подойти по размеру к задуманной композиции. Исправлять и подгонять готовые детали всегда сложнее, гораздо проще несколько раз все проверить.
- Теперь можно приступать к изготовлению самих деталей. Для этого возьмите подходящий механизм и заготовку и выполните нужное количество кованых элементов.
После изготовления всех деталей можно начинать собирать задуманную композицию. Для крепления лучше использовать сварку, но и переусердствовать с ней не стоит, чтобы не повредить более мелкие элементы.
Финальным этапом будет обработка готового изделия, которая подразумевает шлифовку и покраску готовой композиции.
Желательно, чтобы покраске предшествовала грунтовка изделия, тогда оно вам прослужит очень долго.Если вы взялись за изготовление кованых элементов холодным способом, то вы наверно изучили рынок цен и оценили ваши финансовые возможности. Если нет, то сначала обратите внимание на стоимость материалов, необходимого оборудования и способы обработки готового изделия. Но в любом случае изделие, изготовленное своими руками, стоит всех затрат. А снизить их можно на оборудовании, если изготовить его своими руками.
Похожие статьи
Горячие продажи горячей штамповки металлических деталей холодной ковки согласно чертежам
Горячая продажа Горячая штамповка Металлические детали холодной штамповки согласно чертежам
Наименование продукта | Горячая формовка металла Детали по чертежам | |
Стандарты | По чертежам клиентов | |
Материал | — литая сталь — 9000 — литой алюминий — медный литой — ковкий чугун — серый чугун — поковка | |
Технология | — литье в песчаные формы — смола sa nd литье — точное литье | |
Давление | — механические детали — автомобильные детали — части сельскохозяйственной техники — корпус цилиндра, корпус насоса, корпус клапана — аксессуары для напорных трубопроводов | |
Давление | PN1. | |
Допуск | +/- 0,01 мм | |
Инспекция | Профессиональное качество | Более 20 лет |
Ваш рисунок — наша миссия.
Ваше требование — это наша цель.
Мы ориентируемся на то, что вы хотите!
Выставка литья по выплавляемым моделям
Процесс обработки
Наш процесс обработки
Методы испытаний
Наша фабрика показать
Даньдун Хенгруи расположен в городе Даньдун, который является самым красивым приграничным городом.Здесь мы находимся недалеко от шоссе Данда, примерно в 5 км от порта Дадунган и в 12 км от аэропорта Даньдун, где наземный, морской и воздушный транспорт очень удобен. Здесь приятный климат и хорошие пейзажи, мы можем увидеть Корейскую Народно-Демократическую Республику за рекой Ялу.
Отображение сертификата
Отображение нашего сертификата
Почему выбирают нас?
Преимущества:
1.Опытный поставщик сланцевых изделий »
2. Профессиональная команда дизайнеров и отдел продаж для ваших услуг;
3. 9-летний поставщик золота alibaba, фабрика, признанная CE / ISO9001 и т. Д .;
4. Обслуживание 7 * 24 для вас , Все вопросы будут решены в течение 24 часов.
Вы получаете выгоду:
1. Стабильное качество —— Благодаря хорошим материалам и технике
2. Более низкая цена —— Не самая дешевая, но самая низкая при том же качестве
3.Хорошее обслуживание —— Удовлетворительное обслуживание до и после продажи
4. Срок поставки —— 30-45 дней для массового производства
.Горячая штамповка деталей из металла холодной штамповки по чертежам
высокое качество и низкая цена
, пожалуйста, свяжитесь с нами, если у вас возникли проблемы
Название позиции | Горячая штамповка Металлические детали холодной штамповки по чертежам |
Продукция общего назначения Область применения / обслуживания | Металлические детали для транспортных средств, сельскохозяйственных машин, строительных машин, транспортного оборудования, системы клапанов и насосов, металлических деталей сельскохозяйственных машин, кронштейна двигателя, кронштейна шасси грузового автомобиля, коробки передач, корпуса редуктора, крышки шестерни, вала, шлицевого вала, шкива, фланца, соединительная труба, труба, гидравлический клапан, корпус клапана, штуцер, фланец, колесо, маховик, корпус масляного насоса, корпус стартера, корпус насоса охлаждающей жидкости, вал трансмиссии, шестерня передачи, звездочка, цепи и т. |
Основная заготовка Процесс изготовления кованых деталей | Ковка, пресс |
Допуск заготовок | +/- 0,3 ~ +/- 2 мм |
Применимый материал | Углеродистая сталь, низкоуглеродистая сталь, среднеуглеродистая сталь, 40Cr, 20CrMnTi, 20CrNiMo и т. Д. |
Размер / размеры поковки | 142 мм — 300 мм или по требованию заказчика |
Масса заготовок | Диапазон от 0.1кг-1000кг |
Применимый процесс обработки | Обработка с ЧПУ / токарная обработка / фрезерование / токарная обработка / растачивание / сверление / нарезание резьбы / протяжка / развертывание и т. Д. |
Допуск обработки | От 0,005 мм-0,01 мм-0,1 мм |
Качество обработанной поверхности | Ra 0,8-Ra3,2 по требованию заказчика |
Применяемая термообработка | Нормализация, закалка и отпуск, цементирование, азотирование, азотирование углерода, индукционная закалка |
Применимая обработка поверхности | Дробеструйная очистка / пескоструйная обработка, полировка, пассивация поверхности, окраска грунтовкой, порошковое покрытие, ED-покрытие, хромирование, цинкование, покрытие Dacromat, чистовая окраска, |
MOQ | Для кованых деталей: 1 тонна Для обработки: 50 шт. |
Время выполнения | 45 дней с момента получения депозита для ковки |
Hangzhou Chinabase Machinery Co., Ltd представляет собой группу заводов, предоставляющих клиентам комплексные решения по передаче электроэнергии и промышленной продукции. Мы можем поставлять широкий спектр продукции, включая цепи, звездочки, клиновые и клиновые шкивы, зубчатый ремень и шкивы зубчатого ремня, шестерни, редукторы скорости, двигатели, стойки, муфты и многие другие детали, такие как блокирующий узел, коническая втулка, направляющая цепи, воротник вала, ограничитель крутящего момента, кулачковая муфта, универсальный шарнир, основание двигателя и ползун двигателя, конец штока, вилка, резиновая опора и т. д.Изготовляем специальные детали по чертежам и / или образцам.
.G5 Gt55 Карбид вольфрама высшего качества умирает для холодной штамповки пресс-форм
G5 GT55 Высококачественные штампы для волочения из карбида вольфрама Формы для холодной штамповки формы
Технические характеристики
1. Матрица для ковки из карбида вольфрама YG8 YG 11 YG16C
2. Высокое качество с точностью и полировкой
3. Различные типы
3. Различные типы 4. 19-летний опыт работы с карбидом вольфрама
Процесс производства карбида вольфрама Штамп
1. Вскоре после подтверждения заказа продукты из карбида вольфрама начнут готовить порошок RTP в соответствии с требованиями заказчика с помощью нашей влажной -шлифовальный станок
2, Перед массовым производством нам необходимо провести пробное прессование и спекание с использованием каждой формы, и мы проверяем внешний вид и размеры образцов штампов из карбида вольфрама с помощью микрометра, проектора и т. д.для обеспечения выполнения требований чертежей перед серийным производством
3, Массовое производство, прессование сырья для придания формы заготовкам, и все заготовки штампов из карбида вольфрама должны пройти полуфабрикатную проверку
4, Затем спекайте заготовки до отделки (HIP) и проверяйте готовую матрицу из карбида вольфрама, у нас есть 10 комплектов вакуумных печей для спекания и 2 комплекта HIP на заводе, что обеспечивает лучшее качество и производственную мощность.
5, 1).Очистка / галтовка предназначена для улучшения внешнего вида матрицы из карбида вольфрама.
2). Матрица из карбида вольфрама может быть отшлифована в соответствии с требованиями к допускам заказчика.
Размер
ТИП | некоторый размер матрицы крепежа из карбида вольфрама | ||
d | D | L | |
BD0101015 | 10 | 1 | 15 |
BD0171230 | 12 | 1.7 | 30 |
BD0211015 | 10 | 2,1 | 15 |
BD0211230 | 12 | 2,1 | 30 |
BD0241015 | 10 | 2,4 | 15 | 53 | 900 BD0291425 | 14 | 2,9 | 35 |
BD0291640 | 16 | 2,9 | 40 |
.![]() | … | … | .. |
Класс | Рекомендуемые характеристики и применение | ||||||||||
Плотность | TRS | Твердость | |||||||||
г / см3 | МПа | HRA | |||||||||
A | 13,5 | 3000 | 83,5 | Хорошая износостойкость и высокая прочность на изгиб. Primariy для штампов для формирования гаек и штампов для штамповки с высокой ударопрочностью. | |||||||
YM11 | 14,4 | 2420 | 88,5 | Формовочные или штамповочные матрицы для металлических порошков и неметаллических порошков. | |||||||
YM15 | 14,0 | 2500 | 87,5 | Для изготовления штампов для волочения трубок и стержней для окрашивания с высоким коэффициентом сжимаемости; штамповка, штамповка , штамповка инструментов при больших нагрузках. | |||||||
YM20 | 13,5 | 2800 | 85.5 | Для изготовления штампов для деталей часов, пружинных пластин музыкальных инструментов, банок для теста , стальных малогабаритных шариков, винтов, резьбовых крышек. | |||||||
ML32 | 13,9 | 2750 | 85,5 | Ударопрочные штампы для ковки | |||||||
ML35 | 13,7 | 2800 | 84,5 | Поковки ударопрочные, штампы для горячей штамповки и ролики. | |||||||
ML40 | 13.5 | 2850 | 83,5 | Плашки для прочного или ударопрочного применения. | |||||||
ML50 | 13,3 | 2900 | 83,0 | Плашки для штамповки гаек и штампы для ковки с высокой ударопрочностью. | |||||||
ML60 | 13,1 | 2950 | 82,5 | Плашки и ролики сборщика болтов из нержавеющей стали.![]() | |||||||
ML90 | 13,3 | 3200 | 82,0 | Формовочные штампы с завинчивающейся крышкой с высокой ударопрочностью (ковочные штампы с максимальной ударопрочностью). | |||||||
Другие марки могут быть предложены по требованию клиентов |
Класс и применение
марка | Равно | / см 3 ) | TRS (Н / мм2) | Ремень | ИСПОЛЬЗУЙТЕ |
YG11C YG11C | 14.35 | 2200 | 87,6 | Формовочные или штамповочные матрицы для металлических и неметаллических порошков. | |
YG15 | K40 | 14,0 | 2300 | 86,5 | Для изготовления штампов для волочения стальных труб и стержней с большой степенью сжатия штамповочный инструмент. . |
YG15C | K40 | 14.0 | 2500 | 85 | |
YG18C | K40 | 13,7 | 2700 | 84,5 900 dies 53 Сопротивление горячему удару ковочные штампы и ролики. | |
YG20 | K40 | 13,5 | 2400 | 4 | Для различных штампов, изготовленных методом холодной штамповки, холодной штамповки и горячей штамповки. |
YG20C | K40 | 13,4 | 2600 | 81-82 | устойчивое к износу или удару |
Сертификаты предприятий
Являясь одним из самых профессиональных производителей карбида вольфрама в Китае, Zhuzhou Ming Ri Cemented Carbide Co., Ltd поставляет широкий спектр высококачественной продукции для клиентов
по всему миру с принципом управления «стабильное качество и надежное сотрудничество».
Мы прошли ISO9001: 2000 в 2003 году и постоянно улучшаем качество. Мы всегда стараемся изо всех сил предоставлять нашим клиентам высокое качество, лучшую цену и удовлетворительные услуги.
Почему выбирают нас?
1. В Чжучжоу Мингри самый богатый ассортимент штампов для холодной штамповки.
2. Более 19 лет стабильных отношений с нашими клиентами.
3. Самая современная инструментальная мастерская.
4. Самая большая производственная мощность и самая быстрая доставка.
5. Самые надежные испытательные машины для всех спецификаций.
6. Лучшее и надежное послепродажное обслуживание.
Здравствуйте, узнайте больше об отправке эффективного запроса по электронной почте
удобно для вас и сэкономит время для всех.
Упаковка | Картон и внутренний пластиковый ящик. |
Доставка | UPS, TNT, EMS, FedEx, DHL или по вашему запросу. |
Введение
Компания Zhuzhou Mingri Tungsten Carbide Co., Ltd. была основана в мае 2001 года с инвестициями в размере 40 миллионов юаней. У нас есть современная производственная линия и много технических специалистов.
Zhuzhou MingRi Cemented carbide co., Ltd находится в родном городе карбида вольфрама, удобная транспортная развязка, из аэропорта Чанша всего 40 минут, Ухань всего 1,5 часа, из Гуанчжоу всего 2 часа. Благоприятная периферийная среда для производства цементированного карбида является естественным барьером. Удобное движение для завтрашней интернационализации проложило широкую дорогу.
Мы получили отзывы от наших реальных клиентов, спасибо за вашу поддержку и понимание.
Мы специализируемся на различных продуктах из карбида вольфрама. Наша продукция продается в Великобритании, Европе, Японии, Корее, Тайване и Юго-Восточной Азии.
Мы стремимся к долгосрочным деловым отношениям со всеми клиентами и надеемся, что станем вашим лучшим поставщиком карбида.
Основные продукты
.Горячие продажи горячей штамповки металлических деталей холодной ковки согласно чертежам
Горячие продажи горячей штамповки металлических деталей
Описание продукта
мы можем изготовить с чертежом или образцом все, что вы хотите. Высочайшее качество и самая низкая цена
* Категория: детали для литья
* техпроцесс: поковка по выплавляемым моделям, литье. Сварка, мехобработка
* Материал: латунь / медь / бронза
* OEM приемлемый
* обработка: обрабатывающий центр с ЧПУ
* проверка: современное испытательное оборудование, включая КИМ, машину для испытания на разрыв, твердомер, спектрометр, тестер паралллета и т. Д.
Название продукта | Горячие продажи горячих штамповок для холодной штамповки металлических деталей |
материал | сталь |
Цена | на основе предоставленного чертежа или образца |
Оплата | L / C, T / T, Western Union, MoneyGram |
сертификат | ISO9001 / TS16949 |
OEM | приемлемо |
Поцесс | прецизионное литье, ковка, обработка с чпу, сварка |
Упаковка и доставка
Горячие продажи горячей штамповки металлических деталей упаковки
1. Катон упаковка
2. деревянный ящик упаковка
3. упаковка на поддонах
4. как требование
Информация о компании
наша мастерская в основном включает: 1. литейный цех
2. кузнечный цех
3. Цех обработки ЧПУ
Сертификаты
гарантия качества
Сертификация: ISO9001 / TS16949
Дизайнер: Технические специалисты берут на себя ответственность за создание чертежей по образцу, предлагаемому клиентами.
Литье: Автоматическая производственная линия, включающая: смешивание, формование и заливку песка.
Обработка: Обрабатывающий центр с ЧПУ.
Требования к испытаниям: Каждая деталь должна быть строго проверена, например. Испытание на динамическое сопротивление, испытание на скачкообразную нагрузку и испытание химического состава тигля и т. Д.
Первичный соревновательный
Передовая международная технология литья
Сложное машинное оборудование
По желанию заказчика необходимо заказать спецификацию
Гарантия стандарта качества OEM
Стандартный материал согласно техническому чертежу
Многолетняя история производства и экспорта
Уровень конкурентоспособной цены
Положительные отзывы клиентов из-за рубежа и внутри страны
контактная информация
Qingdao hengze locomotive equipment co. , ООО
адрес: индустриальный парк Нангуань, офис подрайона Санлихэ.
jiaohzou qingdao, провинция Шандун, Китай
контактное лицо: лян
тел: 0086-15066421570
кв: 1092641322
Whatsup 86-15066421570
в чате: lljxdq
.Как сделать станок для холодной ковки самому?
Готовые станки для холодной ковки стоят дорого. Заводской станок сделан по точным чертежам и работать на нем можно только с заготовками из металла определенного сечения. Мастера давно решили эти две проблемы, изготавливая оснащение своими руками. Как самому сделать станок улитку или гнутик, расскажем нашим читателям.
Преимущества самодельного оснащения
Художественные кованые изделия интересны, когда элементы изготовлены по собственным эскизам. Штамповка, собранная на заводских станках, мало чем отличается друг от друга. Настоящий мастер имеет свой почерк. Сделать металлический элемент, отличный от стандартных, можно только на станке, который собран своими руками.
Конечно, самодельный станок будет уступать по некоторым характеристикам заводскому устройству, но для холодной свалки в домашних условиях подойдет. Перед сборкой необходимо определиться, какая форма деталей будет необходима, а так же как часто будет использоваться оборудование. Важны и другие факторы:
- Для изготовления нескольких деталей раз в год целесообразнее собрать ручной механизм. Если холодная сварка настоящее хобби или бизнес, собирайте станок с электродвигателем. Он упростит работу и сэкономит время.
- На станке предусматривается виды работ: сгибание, закручивание или вытяжка. Для этого понадобятся валики, металлические бруски. Подробнее схему можно рассмотреть на фото в статье.
Все работы на одном станке можно выполнить только используя различные формы. Рассмотри как изготовить самые популярные для своих работ.
Форма Улитка
При помощи улитки можно изготовить завитые элементы ковки или волнистые. Изготовление осуществляется этапами:
- Рисуем на миллиметровке шаблон улитки.
Рисунок спирали выполняется от меньшей окружности к большей. Между окружностями делается шаг, равный 100– 150 мм. Симметричность и точность рисунка у каждого мастера индивидуальны, так как спираль может быть круглой, вытянутой. Завитков стандартно от 2 до 4 шт. Ширина шага завитка на рисунке должна быть толще сечения прутка, который будет обрабатываться. Иначе достать готовую деталь будет сложно.
- Изготавливается столешница или рабочая поверхность для холодной ковки. Сделать ее можно при помощи листовой стали, шириной не меньше 3–4 мм. Зависит от тяжести формы.
- Форму сгибают по эскизу, при помощи ручного инструмента (плоскогубцев), из полоски металла толщиной не меньше 3 мм. Если взять материал толще, то работать вручную с ним будет сложно.
- Для того чтобы деталь ковки во время обработки не выскакивала из формы, один ее конец крепят внутри. Сделать крепление можно из кусочка арматуры, длинной равной ширине формы. Кусочек арматуры просто вставляют внутрь и закрепляют тисками либо сваркой.
- Рабочую поверхность нужно установить на хорошо стоящую столешницу. Отлично подойдет верстак или стойка из толстостенной трубы. Главное, разместить оборудование так, чтобы он не мешал при выполнении других работ. Если размер рабочего помещения маленький, вместо стойки снизу к конструкции крепится шестигранная гайка большого сечения. Ее просто зажимают в мощные тески и работают. Но надо понимать, что холодная ковка потребует некоторых усилий, поэтому конструкция должна стоять жестко.
- Форма крепится к листу железа жестко, при помощи сварки.
Сборка деталей и соединение
Модель станка для холодной сварки может быть монолитной или разбираться по запчастям. Монолитная конструкция более прочная, но занимает много места. Улитку приваривают к рабочей поверхности при помощи металлических прутков: отрезают кусочки по 1–2 см и привариваются по столешнице в заданной форме с шагом 4 см. Между прутками высверливается отверстие под форму. Между собой детали соединяют сваркой. Это самый простой способ крепления. Существуют различные варианты, все зависит от фантази хозяина.
Внимание: Все сварочные работы выполняются снизу детали так, чтобы швы не мешали при изгибе элемента. К столу форму тоже приваривают снизу. Все лишние неровности приведут к некачественному и неровному сгибу элементов холодной ковки.
Изготовление формы гнутика
Гнутик необходим в холодной ковке для изготовления загнутых углом деталей. Угол сгиба должен быть регулируемый. Готовый станок состоит из основной неподвижной детали с отверстием, куда вставляется пруток и столешницы.
Для изготовления неподвижной детали с различными отверстиями по диаметру подойдет толстый лист железа. В нем проделываются необходимые отверстия. Диаметр отверстий зависит от того, с какими толщиной прутиками будет осуществляться холодная сварка.
Главное, жестко закрепить форму на станке, так как для сгиба нужны не маленькие усилия.
Перед тем как сделать оборудование для холодной ковки дома, рекомендуем читателю ознакомиться поближе с заводским оборудованием. Схемы есть в интернете. “Голь на выдумку ловка», и придумать из чего и как изготовить станок своими руками, сможет любой хозяин с головой. Для работ используйте готовые схемы из статьи или начертите сами. Каждый элемент нужно несколько раз измерить, иначе необходимой жесткости не будет. Если у вас достаточно терпения и мастерство позволяет, соберите станок для ковки своими руками. Для остальных, рекомендуем присмотреться к заводским моделям, цена от 150 000. Зато нервы и время будут сэкономлены.
Похожие статьиСамодельный станок для холодной ковки улитка.
После первых проб и не большего опыта в холодной ковке, решил я смастерить небольшой ручной станок для холодной ковки улитка, который будет превращать профиль, квадрат или полосу в красивые спиральные завитки. Идею такого типа станка я увидел в необъятных просторах интернета, устройство просто и ясно как светлый день, а вот над исполнением пришлось подумать и посмотреть завалявшиеся железки в гараже.
Заглянув в гараж увидел маховик от москвича 412 — то что надо, отталкиваясь от него я начал собирать станок.В металлоломе нашел ступицу, не знаю от чего, но мне она как раз подошла, в принципе ее можно было бы самостоятельно сделать из вала и трубы подходящих под диаметр подшипников. Остальные элементы как трубы, уголки, полосы, профиля у меня были и я начал сборку.
Начал я с подготовки маховика вырезал из листа 8 мм круг равный внутренней части маховика сделал защиту от проворота и нарезал резьбу в маховике дабы сделать кондуктор съемным.После по нарисованному эскизу выгнул спираль кондуктора из полосы толщиной 5 мм прикинул на маховик и разбил ее на 2 части малую и большую.Малую часть приварил к внутреннему кругу, а большую продолжил на маховике засверлив в маховике отверстия по внутреннему кругу спирали , а к самой спирали приварили шпильки, теперь кондуктор съемный.
Теперь я начал сборку, приварил маховик к внутренней части ступицы, к ней же приварил уже изготовленную опору из флянца (от газовых труб) тощиной около 18 мм и трубы диаметром 20 сантиметров (точно уже не помню), опора у меня крепилась к забетонированному в землю столбу и станок я решил сделать съемный , так как у меня не было желания и материала делать для него громоздкую раму которая потом занимала много место в гараже. К внешней части ступицы я приварил ручку которая была собрана в основном из полос толщиной 8 мм у основания ступицы ,а ближе к ручке труба на ней я сделал телескопический механизм с фиксатором на котором в конце установлен подшипник котрый уже будет давить на на заготовку и огибать ее вокруг кондуктора (улитки).
На видео все наглядно представленно и рассказано.
Из чего был сделан Самодельный станок улитка.
А здесь уже небольшое видео работы
Самодельный станок для холодной ковки улитка.
Всем ровных завитков и удачи!
Понравилось это:
Нравится Загрузка. ..
чертежи и видео — Обзоры оборудования для бизнеса
Самостоятельно изготовленные станки для холодной ковки окупятся довольно быстро, ведь при их изготовлении чрезмерных затрат не потребуется. Это поможет вам в короткие сроки организовать свой небольшой бизнес — мастерскую по производству изделий холодной ковки. Если возможности сделать оборудование для ковки своими руками у вас нет, тогда можно купить готовое:
Но? если вы все-таки решили самостоятельно своими руками сделать оборудование для холодной ковки, то какие же станки вам потребуются для работы:
- Улитка
- Гнутик
- Твистер
- Фонарик
- Волна
- Объемная
В этой статье мы более подробно остановимся на оснастке Гнутик — как самостоятельно изготовить данный станок.
Оснастка Гнутик для холодной ковки — важный элемент всей работы. С его помощью происходит сгибание металла, причем угол сгиба мастер может выбирать самостоятельно. Также Гнутик применяется для сгибания дуг с разными радиусами. Станок Гнутик представляет собой основание с ползуном. На ползуне Гнутика закреплены упоры — с углом и цилиндрические неподвижные упоры. Для сгибания металлического прутка под углом нужно переместить ползун и угловой упор. Для того чтобы сделать дугу необходим третий цилиндр, расположенный напротив углового упора.
На фото, расположенном ниже, представлен чертеж нижней планки оснастки Гнутик.
Более «полный» чертеж оснастки Гнутик для холодной ковки представлен в видеоролике «Чертеж Гнутика своими руками». По словам мастера, в данный чертеж станка Гнутик внесены изменения по улучшению качества оснастки.
Следующее видео показывает работу станка Гнутик, сделанного своими руками. На станке изготавливают различные геометрические фигуры — змейку, ромб, квадрат, элемент сердечко, элемент кольцо, заготовку для элемента хомут и другие.
Оборудование для гибки различного проката представлено на следующем видеоролике. По словам автора, оборудование гнет квадрат до 14 мм, круг и арматуру до 16 мм, полосу до 30 мм.
Самодельный станок для холодной ковки
Холодная ковка – это изгибание металлопроката без доведения металла до высоких температур. Для этих целей используют несложные приспособления, которые возможно изготовить самому в домашних условиях. Такие самодельные станки для холодной ковки могут быть универсальными или приспособленными только под одну операцию. Они могут быть с ручным или электрическим приводом.
В вопросе выбора привода для такого оборудования нужно учесть толщину обрабатываемого проката. Изгибать прут вручную имеет смысл при не большой толщине. Не смотря на то, что в продаже есть несложные ручные станки для холодной ковки с насадками, большинство из них не выдерживают частого использования и считаются игрушечными прототипами реальных станков, на которых можно делать бизнес. С другой стороны профессиональное оборудование стоит немалых денег, и организация небольшого частного производства по изготовлению кованых изделий будет чрезвычайно затратным. Поэтому многие нашли для себя выгодным изготовить самодельный станок для ковки металла под свои нужды и возможности.
Весь принцип холодного формирования узоров из квадратного или круглого прута обычно сводится к концентрическому скручиванию. Это может быть скручивание вокруг продольной оси заготовки (торсировка) или навивка круглой плоской спирали вокруг воображаемого центра (завиток). Возможно также нанесение матричного отпечатка с помощью пресса. Полученные таким способом детали сваривают в общую композицию будущего изделия. Применением в кузнечном деле методов холодной ковки добиваются большего геометрического соответствия одинаковых деталей и повышают экономическую выгоду.
Самой распространённой формой изгиба кованых изделий являются завитки. Для их формирования самодельный станок холодной ковки должен обеспечивать плавную контролируемую навивку прута на спиралевидный шаблон. Оптимальный вариант – получить вращение меньше 10 об/мин. Если скорость вращения будет больше, то тяжело поймать момент, когда следует остановить навивку.
Понижение оборотов достигается с помощью редукторов или ременной передачи. Большинство редукторов имеют ограничения по количеству принимаемых оборотов до 1500 об/мин, поэтому если электродвигатель высоко оборотистый, можно сделать ступенчатое понижение скорости. Для этого перед редуктором можно добавить ременную передачу. Эта мера позволит также предохранить кинематическую систему от перегруза. Многие энтузиасты, которые собирали станки для ковки своими руками, использовали и цепную передачу, но судя по отзывам, для плавного пуска привода нужна компенсация в виде шкивов. В случае экстремального усилия ремень сгладит его кратковременной пробуксовкой.
Для самодельных станков нет стандартов по рекомендуемой мощности электроприводов. Обычно сборка делается из того, что под рукой, однако для создания хорошего усилия при изгибании толстого металла мощность электродвигателя должна быть не только приемлемой, но и должна иметь небольшой запас. Как известно, при подключении трёхфазного двигателя в бытовую сеть теряется до 50% мощности, поэтому при отсутствии 380 вольт нужно учесть все потери.
Шаблоны для гибки завитков (улиток, волют) можно изготовить из полосы 4х25 мм. Для этого её сворачивают в спираль и приваривают к круглой пластине толщиной 6мм. Это если работать с квадратом 12х12 мм. Для более толстого металла вместо пластины стоит применить квадрат. Крепление к валу можно сделать на резьбовом соединении, а лучше использовать фланцы. Все насадки в таком случае изготавливают с четырьмя отверстиями под болтовое соединение, а второй фланец приваривается к муфте и крепится к валу.
youtube.com/v/bgX-G_SSmmk?version=3&hl=ru_RU&rel=0″ type=»application/x-shockwave-flash»>
Свежие записи:
Чертежи шаблонов для холодной ковки. Как сделать станок для холодной ковки
своими рукамиАрхитекторы и дизайнеры часто используют в своей работе кованые элементы. Элегантно и благородно смотрятся ажурные металлические решетки, покрывающие камины или красивые балясины на лестнице.
Если вы умеете выполнять ковку и научитесь этому ремеслу, то сможете создавать оригинальные изделия самостоятельно.
Это занятие подойдет всем, кто любит заниматься физическим трудом и готов познакомиться с технологией и особенностями выбора металла.
Что нужно знать о ковке?
Ковка — это процесс обработки специальной заготовки. Его цель — придать металлу нужные размеры и форму. Различают горячую ковку и холодную.
Мастеру необходимо познакомиться с обеими разновидностями, чтобы знать достоинства и недостатки каждой.
Метод горячей штамповки
При горячем способе металлическая преформа сильно нагревается. В результате металл становится пластичным.Горячая ковка придает заготовке желаемые размеры и желаемую форму. Мастеру доступны различные варианты работы.
У нагрева металлической заготовки тоже есть недостатки. В первую очередь необходимо оборудовать специальную комнату. Вам нужно будет купить кузнечную кузницу, для которой нужно будет покупать топливо.
Необходимо соблюдать правила пожарной безопасности, важно, чтобы мастер умел работать с огнем.
Имея представление о температурных режимах, используемых в процессе ковки, вы легко можете выбрать нужный вид ковки.
Метод холодной штамповки
Холодная штамповка — трудоемкий процесс. Чтобы получить требуемую форму металлической заготовки, ее гнут, обжимают и сваривают. Техника выполнения несколько проще по сравнению с горячим методом.
Мастерская не требует много места, и для ее обустройства не нужно будет покупать специальный рог, достаточно купить кузнечный станок.
Производственный процесс продукта предполагает работу с полуфабрикатами заводского изготовления.Если была допущена ошибка, то исправить ее невозможно.
Выбрать металл
Для ручной ковки подходят металлы с определенными свойствами. Чем пластичнее металл, тем легче изменить его форму. Однако пластичность неразрывно связана с прочностью.
Увеличение показателя одной характеристики неизбежно влечет за собой уменьшение другой. Покупая заготовку, мастер должен точно знать, каков ее состав.
Мастера изготавливают декоративные элементы ковки из меди, стали, дюралюминия или латуни.Кроме того, также могут использоваться сплавы. Информацию о металлах, которые легко подделать, можно найти в Марочнике стали и сплавов.
Какие инструменты нужны для ковки?
Инвентарь варьируется в зависимости от метода ковки. Кузнечная кузница с наковальней, для горячей ковки понадобятся молотки с клещами.
Для холодного способа понадобится инструмент Gnutik, позволяющий сгибать заготовку под углом, и станок Snail для ковки, который можно сделать самостоятельно.Последний станок позволяет создавать декоративные элементы с формой в виде спирали.
Примечание!
Помимо основных инструментов для холодного метода можно использовать «Фонарик», «Волна», «Твистер», станок для кольцевания и другие.
Современный рынок предлагает промышленные машины, предназначенные для выполнения технологических операций. На фото ковки вы можете увидеть изделие, изготовленное на станке Master 2 фирмы MAH.
Ручная ковка
Чтобы заготовка приобрела желаемую форму, мастер должен применять в своей работе различные приемы и приемы. Вам нужно будет приобретать различные инструменты и осваивать различные технологии.
Метод холодной ковки не требует от мастера особых усилий. В работе выделяются следующие этапы:
- создание рисунка или наброска декоративного элемента;
- заготовка заготовок;
- процесс ковки.
Сегодня рисунок можно сделать с помощью компьютерной программы самостоятельно или заказать у профессионалов. Проект позволит еще до начала работ рассчитать, сколько металлических заготовок нужно закупить.
Примечание!
Основные кованые элементы представлены следующими группами:
- Лапы. Концу металлического стержня придают определенную форму.
- кудрей. Концы стержня можно загнуть в одну или две стороны.
- Кольца.Элементы декора изготавливаются из прутьев квадратного или круглого сечения.
- Торсион. Характеризуется винтовой закруткой по оси.
Используются 3 общепринятые технологии: волочение, гибка и скручивание.
- Вытяжка позволяет увеличивать длину металлической заготовки, уменьшая значение ее поперечного сечения.
- Гибка дает возможность изгибать любую часть заготовки под углом.
- Скручивание — технология, при которой заготовка скручивается по оси.Для скручивания используется машина Twister.
Все элементы собираются вместе и фиксируются сваркой. Эти операции выполняются на специальном столе. Самодельная холодная ковка не требует особых навыков.
Ковка своими руками фото
Примечание!
Люди давно заметили, что нагретому в кузнице металлу можно придать практически любую форму. Кованые изделия прекрасно смотрятся в любом интерьере.Они могут быть элементом декора как деревянных, так и каменных коттеджей.
Среди владельцев частных домов вряд ли найдется человек, который не хотел бы иметь кованый забор, перила или лестницу. Но, несмотря на множество преимуществ, изделия, полученные с помощью горячей ковки — процесса, при котором металл становится пластичным под воздействием высокой температуры, доступны далеко не всем из-за высокой цены. Есть альтернатива — холодная ковка металла. Его главное преимущество — не только невысокая цена, но и доступность техники для самостоятельного повторения.
Холодная ковка металла — это процесс, при котором металл не подвергается нагреву, а форма изделия придается за счет его гибки, опрессовки и сварки из нескольких заготовок.
Некоторые специалисты считают название «холодная ковка» не совсем правильным. По их мнению, ковкой можно назвать только процесс пластической деформации горячего металла. Но название этого метода обработки металла прижилось. Более того, пользователи считают, что в некоторых случаях холодная ковка металла может стать достойной заменой горячей ковке.Так ли это на самом деле мы расскажем в сегодняшней статье.
Особенности холодной ковки
Бытует мнение, что изделия, полученные путем гибки, получаются однообразными, больше похожими на заводскую штамповку на резьбе. Однако практика показывает, что при правильном подходе с помощью холодной ковки можно создавать настоящие авторские произведения.
Чаще всего методом холодной ковки металла делают:
- решетки оконные;
- элементов козырьков, перил и навесов для входной группы;
- декоративные элементы для ворот и калиток;
- фигурные ножки для столов и стульев;
- элементов декора: подставки для цветов, решетки для каминов, обрамление картин, зеркала и др.
Для художественной горячей ковки металла выпускаются изделия, полученные методом холодной деформации на специальном оборудовании, впоследствии свариваемые в одно целое: элементы ограждения, ограждения или калитки. Тем более, что непосвященный человек не сразу поймет, как было подделано это изделие.
Goblin 2 пользователь FORUMHOUSE
На мой взгляд, кованые элементы, изготовленные методом холодной деформации (гибки), выглядят не хуже, чем такие же элементы, сделанные вручную — горячей ковкой.И они дешевле.
Холмофф пользователь FORUMHOUSE
Холодная штамповка металла позволяет на достаточно простом комплекте оборудования создавать типовые элементы — торсионы, катаные пики, спирали, элементы пространственного изгиба. А затем, комбинируя этот набор (примерно из 10-15 типов типовых элементов) для создания изделий со сложным рисунком. Освоить процесс гибки сможет любой человек, владеющий слесарным инструментом, было бы желание.
Обычные геометрические формы в сочетании с завитками и волнами могут очень красиво смотреться в металле, ведь любой сложнейший узор состоит из множества простых элементов.
Существенным преимуществом холодной ковки металла перед горячей ковкой является высокая производительность. Для работы не требуется много места. Нет необходимости обустраивать и разжигать рог, кузницу, молот на наковальне. Меняя только фурнитуру, можно быстро создавать самые разные элементы, но для соединения узлов потребуется хорошее владение сварочным делом.
Холмофф пользователь FORUMHOUSE
Однажды я сделал холодную ковку и научился готовить в полуавтомате за два дня.
Для получения хорошего результата процесс холодной ковки металла следует разделить на несколько последовательных этапов:
- Идея и постановка задачи.
- Концептуальные зарисовки от руки на бумаге.
- Точный рисунок продукта вручную или в графической программе.
- Разбивка всего изделия на отдельные простых элементов .
- Рисование или печать на принтере единиц продукции в натуральную величину.
Некоторые принтеры поддерживают печать плакатов, то есть печатают части большого изображения на листах A4, после чего их можно только склеить.
- Расчет необходимого количества материала.
- Изготовление отдельных элементов.
- Шлифовка и сборка (сварка) отдельных элементов в единой конструкции.
Несмотря на кажущуюся простоту, практика холодной ковки металла требует вдумчивого подхода и грамотного расчета всех деталей будущего изделия.Специалисты FORUMHOUSE советуют — для визуализации идеи предварительно изготовить отдельные блоки из проволоки реального размера . Это поможет понять, как различные элементы будут сочетаться друг с другом и вовремя исправить ошибки, или найти более удачное сочетание узоров и отдельных элементов.
К основным элементам, полученным методом холодной ковки металла, относятся:
- Лапы и козырьки. Эти элементы выкатываются из металлического прутка.
- Локоны.Включают: завиток, червяк и улитку. У волута, или, как его еще называют, рогалики, концы загибают в одну сторону. Маленький червяк выглядит как знак $. Улитка похожа на запятую.
- Кольца изготавливаются из прутка круглой или квадратной формы, намотанного на специальную оправку. Получается своеобразная металлическая пружина, которую потом нарезают кольцами.
- Торсион. Один из самых распространенных элементов. Получается скручиванием одного или нескольких стержней.
Все вышеперечисленные элементы можно выполнить, объединив всего три технологических процесса.
1. Капюшон. Благодаря этому процессу за счет уменьшения поперечного сечения заготовки увеличивается ее длина. Таким образом обычно получаются лапки и пики, для чего металл помещается в специальный прокатный или опрессовочный станок. Пропуская заготовку через ролики и постепенно уменьшая расстояние между ними, материал раскатывается. Также на валики могут наноситься рельефные насечки, которые придают поверхности заготовки определенную фактуру.
2. Торсион. Металл (полосы или стержни) скручивают вдоль своей оси. Вы можете скрутить одну, две, три и более заготовок. Для этого один конец заготовки (или заготовок) помещается в тиски, а другой начинает поворачиваться по оси. Если скрутить несколько стержней, а затем сжать их, прилагая усилие по оси, то они разойдутся по дуге. Получается утолщение из плетеных стержней под названием «Фонарик» или «Корзина».
3. Гибка.Металл гнут на специальном станке по шаблонам.
Для гибки металла в разных плоскостях необходимо простейшее оборудование и простые станки. На рынке имеется множество машин для холодной ковки. Но из-за высокой цены их приобретение оправдано только в том случае, если планируется дальнейшая прибыль. Начинающий мастер, занимающийся холодной ковкой «под себя», вполне может согнуть металл.
Сначала можно обойтись простыми кондукторами и оправками, вставленными в обычные настольные тиски.Сделать кручение можно, зажав конец заготовки в тисках, затем надев на него трубу, и, используя хомут, закрутить заготовку по своей оси.
Alexei62 пользователь FORUMHOUSE
Все инструменты для холодной ковки (кроме сварочного аппарата) могут быть изготовлены из подручных средств.
Для холодной ковки металла чаще всего используются следующие инструменты:
- Gnoot. С его помощью заготовка изгибается под определенным углом.
- Улитка.С его помощью заготовка сгибается по спирали. Изменяя шаблоны, вы можете изменить радиус изгиба.
- Фонарик. Он напоминает токарный инструмент.
С помощью этого инструмента металлические заготовки переплетаются между собой, чтобы получить одноименный элемент.
- Волна. Принцип действия этого средства понятен из названия. С его помощью металлу придается волнистая поверхность. Расстояние между «гребнями» волн и их высоту можно регулировать в зависимости от настроек машины.
- Твистер. Скручивает полосу или брус по продольной оси.
Принцип работы всех вышеперечисленных машин очень прост. Он основан на приложении определенной силы к заготовке через рычаги, приводящей к деформации металла. Гибка металла на станках ручная. Для облегчения труда некоторые станки оснащены электродвигателями, что увеличивает их стоимость. Многие домашние мастера предпочитают изготавливать станки для холодной ковки своими руками.Также с появлением опыта и увеличением сложности изделий необходимо оснащать станки разнообразными аксессуарами — шаблонами, кондукторами, упорами, упорами.
Большой простор для творчества. Каждый мастер делает адаптацию под свои задачи. Важно соблюдать принцип разумной достаточности. Самые красивые изделия можно сделать с помощью минимум приспособлений.
Секреты холодной ковки
Один из главных вопросов начинающих мастеров: «Какой металл подходит для холодной ковки.«По мнению форумчан, нужно не тратить время и ходить по местным металлобазам, а также знакомиться со списком, который они предлагают. Для холодной ковки используется самый распространенный« черный »металл. Погонный размер для полос шириной 14 и 16 мм, толщиной 2-4 мм. Пруток — квадрат со стороной до 10 мм. Такой материал легче гнуть. Более толстый материал, полоса 20х4 мм и т. д., сначала будет иметь на разрез.
Горячая ковка известна человеку с тех пор, как он начал обрабатывать и применять металлы в своей жизни.До изобретения штамповочных и металлорежущих станков горячая ковка и литье были единственными способами производства инструментов и оружия, домашней утвари и ювелирных изделий.
Чтобы освоить традиционное кузнечное дело, нужно было долго учиться и набираться опыта. Изделия кузнеца оказались очень трудоемкими и уникальными, это несомненный плюс для искусства и столь же очевидный недостаток там, где требуется большое количество идентичных изделий.
К недостаткам горячей штамповки относятся:
- высокая сложность
- высокие требования к квалификации мастера,
- низкая повторяемость изделий.
Метод холодной ковки лишен недостатков. В его основе лежит свойство металлов изменять свою форму в определенных пределах под действием механической силы. Технология применима к круглому и квадратному прутку, металлической полосе, трубам и прокату различного профиля. Несколько основных операций, такие как
- изгиб заготовки под заданным углом и заданным радиусом,
- формирование завитков и спиралей,
- скручивание одной или нескольких заготовок по продольной оси
и сочетание полученных деталей позволяет создавать кружевные ограждения, беседки, скамейки, предметы декора и быта в разумные сроки и по доступной цене, в разы, а то и в десятки раз ниже, чем при использовании горячей ковки. .
При этом все элементы будут абсолютно одинаковыми по форме и размеру, что особенно важно при формировании из них узоров и орнаментов.
Для получения основных элементов используют специальные станки.
- Гнутик — один из самых популярных. Он позволяет сгибать брус под заданным углом и заданным радиусом, в том числе в виде волны.
- Улитка используется для скручивания конца стержня или трубы в спираль.
- Торсионный стержень предназначен для скручивания стержня вдоль его продольной оси.
Если вы планируете выпускать продукцию большими сериями, то вам понадобится станок для промышленного производства. Обладает высокими характеристиками, достаточным ресурсом, оснащен электроприводом достаточной мощности, сочетающим в себе гнут, улитку и торсион. Продвинутые производители оснащают свои агрегаты полуавтоматическими приставками, а роль сотрудника сводится к установке необходимой оправки, закреплению заготовки и запуску программы.
Сама система контролирует скорость подачи, усилие прижима формовочного ролика, начало и конец формования.
Если для начала вы планируете просто познакомиться с технологией холодной штамповки, потрогать ее руками, то можно сделать устройство начального уровня самостоятельно, сэкономив значительные суммы, так как промышленные агрегаты приближаются к цене автомобиля.
Станок
Одна из несложных конструкций самодельного гнутика состоит из следующих деталей:
- Массивное основание с проточкой.
- Подвижный упор, перемещаемый по пазу червячной передачей
- Два фиксированных упора, закрепленных на основании.
Крепление «Гнутик»
Ролики на фиксированных упорах взаимозаменяемы, чтобы можно было гнуть стержни и трубы под разными углами и радиусами. На подвижном упоре также фиксируется съемный ролик или клин, в зависимости от желаемой формы изгиба.
Пока прямая заготовка зажимается неподвижными упорами и, вращая привод червячного механизма изгиба, подводят к ней подвижный упор — клин или ролик.
Продолжая вращать привод, согните заготовку на нужный угол.
Сделать комара для холодной ковки своими руками вполне реально, достаточно строго следовать чертежу, соблюдая размеры и припуски.
Сложности в домашней мастерской могут возникнуть при фрезеровании высокопрочной стали и сверлении в ней отверстий.
Если такого оборудования в цехе еще нет, то лучше оформить заказ на основные детали гайки в производстве — сверлом и лобзиком этого не сделать.
Соединение и покраска деталей
Для сборки деталей нужного дизайна необходимо предусмотреть ровное свободное пространство — на полу или на столе, в зависимости от размера. Перед сваркой и покраской детали лучше отшлифовать, чтобы удалить ржавчину, и очистить поверхность. Пескоструйный агрегат также можно изготовить самостоятельно из использованного газового баллона, пары насадок и кранов. В качестве форсунки можно использовать керамический корпус использованной свечи зажигания.
Для этого достаточно владеть навыками сварочного и слесарного дела.
После пескоструйной обработки детали раскладываются на месте сборки. Для удобства работы можно использовать штанги-накладки. После того, как детали расставлены, стоит еще раз проверить соответствие их расположения чертежу. Далее, зафиксировав зажимами ключевые элементы конструкции, точечная сварка должна прижать их друг к другу. В последний раз проверяя размеры, углы и взаимное расположение, можно приступать к сварке всех необходимых швов.
После сварки необходимо очистить окалину проволочными щетками, закрепленными в дрели, а в труднодоступных местах вручную.Дизайн готов к покраске. В зависимости от выбранных грунтовок и финишного покрытия, а также от способа нанесения, сборка укладывается на амортизирующие планки или устанавливается вертикально с временными упорами.
Конструкции с высокой плотностью деталей удобно красить из пульверизатора, для редкой решетки, для уменьшения потерь краски придется вооружиться кистью.
Холоднокованые изделия
Холодной штамповкой производятся различные изделия.Это, прежде всего, элементы решеток и заборов — как сами штанги, так и поперечины, вершины и украшения. С расстояния в несколько метров ее сложно отличить от кованой решетки. Любую решетку оживят завитки и спирали, складывающиеся в замысловатые узоры и орнаменты. Таким образом, обычный забор, помимо утилитарного назначения, приобретает еще и художественную ценность. Для этого потребуются гайка, улитка и торсион.
Кованые подставки для фонарей, перила для мостов через пруды, навесы и веранды, столы и скамейки прекрасно смотрятся на придомовой территории.Да и саму беседку неплохо сделать из кованого бруса. Неожиданная для сурового металла легкость и воздушность придадут ему завитки и спирали, а закрученные опоры подчеркнут желание встать.
Сегодня широко распространены кованые мангалы, которые эстетично дополняют бытовое назначение.
Сам мангал теряется среди навеса, узорчатых стен и опор, украшен завитками крыши.
Очень популярны детали балюстрад, лестничных перил и балконов.Завитки и спирали здесь тоже широко используются не только как украшение, но и как структурный элемент. Очень уместно смотрится балясина, закрученная по продольной оси, а угловые опоры часто делают из нескольких скрученных между собой стержней. Также на торсионе делают так называемый «фонарик» — несколько стержней, изогнутых по спирали, соединенных концами сваркой.
Следующее направление применения холодной ковки — это детали декора помещений и мебели.Дверные ручки и защелки, каминные инструменты и вешалки, стойки для зонтов и карнизы для штор и портьер — здесь широко используются мелкие завитки и перекрученные штанги.
Мебель изготавливается как садовая, не боящаяся осадков и смены времен года, так и домашняя, сочетающая металл с деревом и тканью.
Кованые изделия в архитектуре и дизайне интерьеров уже давно пользуются большой популярностью. Кованые из металла решетки на окнах и для каминов, ограды или балясины лестниц всегда выглядят элегантно и привлекательно.Сегодня, несмотря на современные технологии обработки металла, как никогда популярны кованые изделия из металла. Конечно, ковка металла своими руками — задача не из легких, а без должной подготовки сделать красивое кованое изделие сложно. Но тем, кто хочет овладеть этим старинным ремеслом и готов к тяжелому физическому труду, придется познакомиться с видами и технологией ковки металла, понять, как ковка используется в металлах, понять процесс ковки и уметь обращаться с кузнечным инструментом.
Поковка металлическая
Ковка металла — это процесс обработки металлической заготовки для придания ей определенной формы и размера. На самом деле существует два вида ковки — холодная и горячая. Выполняя ручную ковку металла, необходимо разбираться в обоих видах ковки, поскольку у каждого есть свои достоинства и недостатки.
Во время горячей ковки заготовка нагревается до определенной температуры, при которой металл теряет прочность и становится пластичным. Высокая пластичность — главное преимущество горячей штамповки. Он позволяет легко придать металлической заготовке определенную форму и размер. Также горячая ковка позволяет использовать большинство технологий ковки, что благоприятно сказывается на разнообразии вариантов работы.
Но у металлического обогрева есть свои недостатки. В первую очередь, это необходимость оборудовать специальный кузнечный очаг и стоимость топлива для него. Это может стать настоящей проблемой для тех, кто хочет заняться горячей ковкой металла своими руками в городских условиях.К тому же работа с огнем — занятие достаточно опасное и требует повышенной пожарной безопасности. Еще один фактор, который может существенно повлиять на выбор типа ковки, — это конкретные знания температурного режима ковки металла.
В отличие от горячей ковки, холодная ковка металла не требует оборудования пода для нагрева металла. Вся суть холодной ковки заключается в формовании металлической заготовки путем гибки, опрессовки и сварки. Холодную ковку реализовать несколько проще, а для оснащения цеха не требуется много места.Весь процесс создания готового продукта не требует использования высоких температур, что очень положительно сказывается на общей безопасности.
Но у холодной ковки есть один существенный недостаток. Вся работа должна выполняться с определенными готовыми полуфабрикатами без возможности исправить свою ошибку. Конечно, это касается не всех работ по холодной ковке, но в большинстве случаев поврежденная заготовка подходит только для металлолома или учебного пособия.
В любом случае, независимо от типа ковки, необходимо достаточно внимательно ознакомиться с рядом важных моментов.В первую очередь, это касается металлов и температурных режимов их плавки и ковки. Во-вторых, нужно знать и понимать технологию ковки металла. Ниже мы рассмотрим, какие технологические приемы используются для ковки и как они используются в работе.
Поковка металлическая
Ручная ковка металла — довольно трудоемкая и сложная задача, требующая использования определенных металлов, а точнее металлов с определенными характеристиками. Для ручной холодной или горячей ковки важнейшей характеристикой является пластичность металла, ведь именно от нее зависит простота и удобство изменения формы заготовки.Но стоит отметить, что пластичность и прочность металла взаимосвязаны. При увеличении одной из этих характеристик вторая уменьшается. Поэтому так важно понимать характеристики металла и знать состав обрабатываемой детали.
Важно! Есть и другие, не менее важные характеристики металлов. Но поскольку мы рассматриваем ковку декоративных изделий, таких как решетки каминов, балясин, заборов и т. Д., Нет необходимости акцентировать внимание на износостойкости, устойчивости к покраснению и так далее, а также на легирующих элементах.
Для декоративной ковки используются следующие металлы: медь, латунь, дюралюминий, сталь, а также другие сплавы меди, магния, алюминия и никеля. Фактически, для ручной ковки используется мягкий ковкий металл, которому можно легко согнуть или придать определенную форму. Чтобы выбрать самый легкий пластичный металл, вам нужно присмотреться к Marochnik Steel and Alloys. В нем вы можете найти подробное описание всех металлов и сплавов с их характеристиками и составом.
Несмотря на то, что самый ковкий металл — это медь и ее сплавы, мастера предпочитают использовать черные металлы для холодной и горячей ковки. Такая позиция обусловлена высокой стоимостью цветных металлов. Ведь на ковку из металла цена больше зависит от стоимости исходной заготовки, и приобрести забор или балясины из меди может позволить себе далеко не каждый. Выбирая для ковки мягкий черный металл, необходимо ориентироваться на сталь с минимальным содержанием углерода около 0.25%. А также с минимальным количеством вредных примесей, таких как хром, молибден, сера и фосфор. Кроме того, следует избегать использования конструкционных и инструментальных сталей с высоким содержанием углерода от 0,2% до 1,35%. Такие стали наименее пластичны и трудны для сварки.
При выборе того или иного металла необходимо использовать Марочник стали и сплавов. Но если доступа к нему нет, то для определения содержания углерода в стали можно воспользоваться приведенными ниже таблицами. Сам процесс определения довольно простой, достаточно поднести заготовку к работающей точилке и посмотреть на сноп искр, а потом сравнить с показателями в таблице.
Сегодня, благодаря промышленному производству металла, отпала необходимость создавать заготовки своими руками. В современных кузницах для холодной ковки используются уже готовые заводские изделия. Чаще всего используются заготовки следующих размеров: 30×45 мм, 40×45 мм, 10×10 мм, 12×12 мм, стержни сечением 10 мм, 12 мм, 16 мм, 25 мм, 30 мм, 50 мм, листовой металл с толщиной от 3,5 до 6 мм, круглые трубы 1/2 «, 3/4», 1 «, профильные трубы от 20×20 мм до 30×30 мм.
Инструмент для ковки металла
Любая работа по ковке металла невозможна без специального инструмента.Кузнечное оборудование для горячей штамповки довольно разнообразно и включает в себя наковальню, кузницу, различные молотки, клещи и другое. Инструмент для холодной ковки несколько проще и состоит из нескольких специальных станков. Конечно, современный инструмент, такой как сварочный аппарат, шлифовальный станок и шлифовальный станок, используется как в холодной, так и в горячей ковке. Зная предназначение инструмента, вы сможете правильно выполнить любую работу.
Инструмент для горячей штамповки
- Гудок . Без горячей ковки не обойтись. Ведь именно в нем можно нагреть заготовку до температуры 1400 ° С.По большей части печь представляет собой печь, рассчитанную на высокие температуры и с обдувом.
- Наковальня . Этот инструмент является опорой, на которой выполняется ковка. Сама наковальня бывает нескольких видов, среди которых наиболее популярной является наковальня с двумя рогами массой 200 кг. Но вес может колебаться от 150 до 350 кг.
- Шпера . При выполнении различной художественной и декоративной ковки используются шперы. Их много разных видов, и каждый мастер может сделать их для себя.Общей чертой любых шпереков является то, что они вставляются в квадратное отверстие наковальни или закрепляются в деревянном бревне. На фото ниже представлены самые распространенные шперы.
- Кувалда и Ручной тормоз . Это основной инструмент кузнеца. Кувалда весит от 4 до 8 кг и используется для нанесения сильных ударов. В зависимости от вида работ и толщины заготовки подбирается и вес кувалды. Ручник весит от 0.От 5 до 2 кг. Используется для доработки продукта.
- Клещи . Горновые клещи — второй по важности инструмент. Без них невозможно провести горячую заготовку для обработки. Для определенного профиля и размера заготовки существует несколько видов клещей. На фото ниже представлены клещевые клещи различной формы.
- Молотки фасонные . При выполнении художественной ковки требуется создание криволинейных заготовок или заготовок определенной формы.Для этого используются фасонные молотки. Они могут быть как нижними, на которых производится обработка, так и верхними. Вариантов фасонных молотков много и у каждого мастера свои. На фото ниже показан основной вспомогательный инструмент.
В дополнение к описанным выше используются различные измерительные инструменты, такие как обычная рулетка , двойной штангенциркуль , кузнечный уголок , образцы и калибры . Выбор кузнечного инструмента огромен, весь перечень сложен, поэтому у каждого мастера свой набор только необходимых и часто используемых инструментов.
Инструмент для холодной штамповки
- Гнутик (фото внизу). Это основной инструмент для холодной ковки. Как следует из названия, он позволяет сгибать металлическую заготовку под определенным углом. Кроме того, гайка позволяет создавать элементы дуги определенного радиуса.
- Улитка . Имя говорит само за себя. С помощью улитки можно создавать различные элементы декора в форме спирали. Спираль изготавливается под определенный узор, который при необходимости можно поменять на другой, с меньшим или большим радиусом.
- Фонарик . Эта машина предназначена для создания одноименного декоративного элемента.
- Волна . Позволяет создавать волнообразные элементы. При протягивании стержня через этот станок на выходе получается красивая синусоидальная заготовка.
- Твистер . По принципу действия этот станок похож на Фонарик, но в отличие от него крутилка только скручивает заготовку по оси.
- Кольцевой станок . Как и во всех предыдущих машинах, название говорит само за себя.
Помимо вышеперечисленного, существуют еще универсальные станки для клепки, резки, опрессовки и придания объема. Все описанные выше машины можно изготовить как самостоятельно, так и приобрести в магазине. Конечно, самодельные приспособления для холодной ковки будут несколько уступать по качеству заводским, но это компенсируется уникальностью элементов, созданных с их помощью.Для изготовления машин холодной ковки чертежи можно найти как в свободном доступе, так и купить у специалистов.
Важно! Машины холодной ковки могут быть ручными или оснащаться электродвигателями. Несмотря на наличие зубчатых передач, ручная холодная ковка — довольно трудоемкая и длительная задача, и для получения больших объемов кованых элементов лучше оборудовать станок электродвигателем.
Отдельно стоит упомянуть промышленные станки для холодной ковки.На аналогичные станки холодной ковки цены порядка 6000 у.е., но на одном таком станке можно выполнять практически все технологические операции холодной ковки. Примером может служить машина Master 2 фирмы MAN. На видео, показывающем холодную ковку, вы можете увидеть возможности этого станка.
Металлическая ковка своими руками
В процессе ковки используются различные приемы и методы ковки, чтобы придать заготовке определенную форму. Для выполнения каждого из них используется определенная технология и инструмент для ковки металла.Технология ковки металла горячим и холодным способами существенно отличается. Как уже отмечалось, горячая ковка требует нагрева заготовки для изменения ее формы, а при холодной ковке заготовка только изгибается. Исходя из этого, выделяют основные технологические приемы, зная которые можно смело браться за ковку металла своими руками.
Металлическая ковка своими руками
Холодная ковка своими руками довольно проста и не требует особых усилий. Все работы разделены на несколько этапов: создание эскиза или чертежа будущего изделия, закупка материалов и собственно процесс ковки металла.
Рисунок может быть создан в специальной компьютерной программе, куплен готовым или нарисован вручную. Вы можете найти чертежи для холодной ковки. Для этого достаточно обратиться к мастерам, занимающимся ковкой несколько лет, и попросить один-два чертежа для обучения. На самом деле рисунок преследует несколько целей. Во-первых, чтобы знать, какие элементы нужно будет изготовить методом холодной ковки. Во-вторых, имея такой проект на руках, можно рассчитать количество и вид металлических заготовок, таких как прутки, профильные трубы и так далее.В-третьих, потребуется чертеж, чтобы собрать все элементы в единое целое.
Отдельно необходимо рассмотреть элементы холодной ковки, составляющие проект. Сегодня можно встретить довольно много разных кованых элементов, но все они могут быть объединены в несколько классических групп.
- Лапы . Этот элемент представляет собой раскатанный в той или иной форме конец металлического стержня. В эту группу входят так называемые Пики. Несмотря на заостренный конец, козырьки выполнены по аналогичной технологии.
- Кудри . В эту группу входят несколько общих элементов: завиток, сердечки и улитки. Улитка или Бублик представляет собой стержень, концы которого загнуты в одном направлении. Червячок — стержень, концы которого загнуты в разные стороны. Этот элемент иногда называют «долларом» из-за его сходства со знаком американской валюты. Comma или Snail — простой завиток, один конец которого загнут, а второй прямой.
- Кольца . Создается этот элемент довольно просто: на заготовку станка навинчивается стержень круглого или квадратного сечения, в результате получается пружина, которую потом разрезают на отдельные кольца.
- Торсион . Этот элемент довольно легко узнать по закрутке винта по оси. Вариантов торсионов очень много и один из самых распространенных — такой элемент, как фонарик, а также простой стержень винтовой формы для решетки или забора.
Весь процесс изготовления элементов холодной ковки основан на следующих общепринятых технологиях ковки — гибка, скрутка, волочение.
Вытяжка — это технология, заключающаяся в увеличении длины заготовки за счет уменьшения ее поперечного сечения. При холодной ковке используется один из вариантов вытяжки — прокатка. Именно с его помощью создаются различные лапки и козырьки. Для создания лапок используется специальный прокатный станок.Конец заготовки вводится и затем запускается раскатывающий механизм, в результате конец выравнивается с разгрузкой или без нее. Для изготовления козырька используют пресс. Процедура такая же, но в результате конец раскатывается и прижимается в определенной форме.
Гибка . Эта технология ковки заключается в загибании концов или другой части заготовки под определенным углом. Сама гибка выполняется практически на всех станках для холодной ковки.Процесс гибки можно проследить при изготовлении заготовки на станке Улитка. Сначала конец заготовки помещается внутрь специального шаблона, а затем загибается под определенным углом. Эти работы выполняются на станке Улитка.
Скручивание . Эта технология ковки предполагает скручивание заготовки по оси. При холодной ковке этот процесс можно наблюдать на станке Twister, на котором создаются различные кручения. Для этого один конец заготовки помещают в тиски, а второй конец поворачивают по оси.Отдельно стоит выделить элемент фонарик. Для него используются два и более стержня, которые сначала закручиваются по оси, а затем сжимаются по оси, в результате чего стержни в определенном месте расходятся в стороны.
Сборка всех элементов в единую конструкцию выполняется сваркой на специальном сборочном столе. Сегодня сварочный аппарат является общедоступным и является незаменимым инструментом для современных кузнецов. Самодельная холодная ковка довольно распространена среди начинающих мастеров и частных предпринимателей.Не требует специальных знаний, навыков и больших помещений для работы.
Холодная ковка своими руками: видеоурок
Металлическая ковка своими руками
По сравнению с холодной ручной горячей штамповкой намного сложнее и требует большого опыта в обращении с инструментом и хорошей физической подготовки. Работа проводится в несколько этапов: создание эскиза или чертежа, закупка материалов и ковка.
На самом деле разница между горячей и холодной ковкой заключается в технологических процессах обработки металла.Во-первых, это касается способа обработки. Во-вторых, для горячей ковки можно использовать практически любую металлическую заготовку. Но для удобства принято использовать уже готовые стержни квадратного и круглого сечения. В-третьих, в художественной горячей ковке отсутствуют рамки для элементов готового изделия. Конечно, можно придерживаться создания классических элементов ковки — завитков, лапок, козырька и прочего, но горячая ковка позволяет использовать весь потенциал фантазии мастера, открывающий безграничные возможности.Все изделия для чеканки изготавливаются с использованием следующих технологий обработки металла: осадки, вытяжки, гибки, скручивания, резки, надрезания, тиснения.
Draft используется для ковки металла с целью увеличения поперечного сечения всей заготовки или ее части. При ковке в зависимости от необходимости проводят полный или локальный нагрев заготовки от атмосферных осадков.
Вытяжка заключается в увеличении длины заготовки за счет уменьшения ее поперечного сечения.Это можно сделать как ударом кувалды или ручного тормоза, так и прокаткой металла между валами на машине. В отличие от холодной ковки, создание козырька с помощью вытяжки требует точных и аккуратных движений.
Гибка . Эта операция выполняется для придания заготовке криволинейной формы. При этом следует учитывать, что изгиб толстых заготовок может привести к их перекосу, и чтобы придать первоначальную форму, необходимо выполнить черновую. Для гибки заготовок используются различные шпереки, рожок для наковальни, фасонные молотки и кондукторы.
Скручивание . Эта технология ковки предполагает скручивание заготовки по оси. Как и при холодной ковке, заготовка зажимается в тисках и проворачивается. Но в отличие от холодной ковки, вы можете нагреть заготовку локально, что позволяет легко выполнять локальную скручивание.
Технологии ковки, такие как резка , насечка и рельефная набивка , используемые в художественной ковке с использованием долот. Края горячих заготовок в зависимости от проекта рассекают и скручивают клещами.Также, пока заготовка горячая, на ее поверхности печатается другой узор.
При горячей ковке металла важно знать температурный режим нагрева. Это поможет лучше обработать металл. Ковка черного металла ведется при 800 — 1250 ° С. Конечно, термометром нельзя будет измерить горячую заготовку, а для определения температуры придется ориентироваться по ее цвету. В таблице ниже указаны температура и цвет заготовки из черного металла.
Горячая ковка металла: видеоурок
Ковка металла своими руками — занятие довольно увлекательное, требующее постоянного совершенствования. В первую очередь это касается создания различных художественно-декоративных элементов. Тем, кто только начал заниматься ковкой, придется немало потрудиться, чтобы их работа имела идеальную форму и высокое качество.
Любой мастер, обустраивая домашнюю кузницу, приобретает минимальный набор инструментов и аксессуаров. Но, как правило, простейшие технологические операции с металлическими заготовками производятся только на первом этапе.
С приобретением опыта работы с «железом» появляется и желание, и необходимость заниматься художественной ковкой — это и украшение дома, и дополнительный доход. К сожалению, машины для придания образцам спиральной формы — улитки — в продаже практически нет. Так или иначе, но домашние мастера, как правило, изготавливают его своими руками. Особенности самостоятельного изготовления и сборки мотков для холодной ковки — тема данной статьи.
Характеристики улитки
Автор специально решил обратить внимание читателя на ряд моментов.Это поможет избежать ошибок в будущем. Например, разобравшись с устройством улитки и принципом ее функционирования, кто-то захочет собрать собственное устройство, отличное от тех, чертежи которого будут представлены ниже.
Такой прибор вполне себе (если мы говорим о технике DIY), он позволит изгибать образцы с поперечным сечением (стороной квадрата) не более 10 — 12 мм. Подразумевается модель улитки с «ручным управлением». С более габаритными образцами в повседневной жизни почти никто не занимается.Машину можно улучшить, установив привод и электродвигатель.
Но насколько это рационально для небольшой домашней кузницы?
- Холодная ковка осуществляется на малых скоростях. Резкое изменение геометрии металла приводит к появлению трещин (надрывов).
- Вам нужно будет выбрать не только мощность электродвигателя, но и передаточное число коробки передач. Плюс смонтировать схему автоматики с установкой соответствующих элементов (кнопки, пускатель и так далее).Все это сильно усложняет изготовление станка.
Вывод — для домашней кузницы достаточно улитки, с помощью которой можно гнуть изделия из металла вручную. Каждый, кто разберется во всех нюансах его конструкции и хоть что-то разберется в электротехнике, сможет самостоятельно установить на него электропривод.
Изготовление улиток
Показаны несколько устройств. Примерно так (в основании) и должно получиться.
Сборка улитки своими руками — это один из вариантов самостоятельного проектирования, когда нет смысла давать рекомендации с указанием точных параметров всех комплектующих.Здесь нужно ориентироваться на собственное представление о том, что и как будет гнуться (радиусы, количество витков спирали и так далее). Но если станет ясна суть процесса изготовления, то сама сборка затруднений не вызовет.
Настольное устройство
Процесс холодной штамповки требует больших усилий. Если у вас уже есть готовый верстак, возможно, вам придется его укрепить. При изготовлении улитки с нуля каркас стола делается только из металла — швеллер, уголок, толстостенная труба.
Понятно, что столешница тоже должна быть металлической. Во время работы улитка будет подвергаться как статическим, так и динамическим нагрузкам. Поэтому обычный лист железа не подходит. Только пластина, и не менее 4 мм.
Маркировка и установка «навесного» оборудования
Пожалуй, самый творческий этап работы. Все можно сделать своими руками. Но как, с учетом перспектив или ограничиться выпуском подобных образцов?
Вариант 1.Самый простой. Смысл операции в том, что на столешнице рисуется спиральный контур.
По сути, это набросок будущих фигурных деталей, например, из бруса. После этого достаточно вырезать несколько отрезков из согнутой по радиусу толстой полосы железа. Их приваривают к столешнице, и механизм загибания в основном готов.
Кому-то такое исполнение будет привлекательнее — с цельной полосой.
Но практика показывает, что работать с такой улиткой сложнее.Например, при снятии с него готового изделия возникнут определенные трудности.
Вариант 2. То же, но нарисовано несколько контуров. Вдоль каждого просверливаются отверстия, в которых нарезается резьба. Осталось только подготовить шаблоны для стоп-сегментов. Своими руками их делают, как правило, из плотного картона или фанеры.
Из них металлические колодки, в которых после очередной разметки также просверливаются отверстия под посадочные «гнезда» в плите.Такая конструкция позволит организовать на одном столе производство спиральных заготовок разного радиуса. Вам нужно только, в зависимости от формы сгиба, установить соответствующие сегменты в определенных местах. Их крепление к основанию — болтовое. Можно поступить иначе. Вместо таких упоров ставьте цилиндрические.
Для фиксации притягиваются болтами (снизу пластины) или изготавливаются сразу ножками (+ резьба) и вкручиваются в столешницу. С ними намного удобнее.А если есть, то сделай сам — пару часов сделай.
Вариант 3. Подготовить несколько съемных модулей, которые при необходимости следует менять.
Улитка в сборе
Установлен лемех, прикреплены рычаги, боковой упор. Все это хорошо видно на рисунках.
Все, что есть в сарае (гараже, на чердаке) — отрезы труб, стержни, уголки и тому подобное, пойдет в действие. Если принцип работы улитки понятен, то подсказки больше не нужны.
Проверка здоровья
Это всегда подразумевается, поэтому без комментариев.
В принципе сделать улитку для холодной ковки не так уж и сложно. Более того, для таких устройств нет единого стандарта. Кто-то скажет — не проще ли купить заводскую модель? Во-первых, как уже было сказано, на поиск уйдет много времени. Во-вторых, не факт, что его возможности совпадают с фантазиями мастера. В-третьих, нужно будет облегчить кошелек примерно на 19000 (ручная) и 62000 (электрическая модель) рублей как минимум.
Удачи в изготовлении улитки своими руками!
Холодное формование — это быстрый способ изготовления микродеталей без чипа
Холодное формование — это быстрый процесс, обеспечивающий чистоту поверхности, соблюдение требований жестких допусков и производство готовых к отправке деталей без потерь материала.
Автор: Кип Хэнсон
Участник MICROmanufacturing
Clack-tick-clack-tick-clack-tick-clack-tick. Это звук машины для холодной штамповки с шестью головками, которая выплевывает микрочастицы со скоростью до 200 штук в минуту.Помимо скорости, этот процесс обеспечивает прекрасную отделку поверхности, отвечает требованиям жестких допусков и позволяет производить детали, которые часто уже готовы к отправке. И нет отходов материала, потому что холодная штамповка
не дает стружки.
Холодногнутые детали являются обычными. Посещение секции крепежа в строительном магазине обнаруживает множество примеров, в том числе винты, гайки, болты, заклепки и гвозди. Но холодной штамповкой подвергаются не только крепежные детали. Этот процесс расширяет производственные рамки для создания деталей, в том числе многих микромасштабных, которые нецелесообразно или почти невозможно изготовить другими методами.
Начинается с круглой заготовки
Холодная штамповка включает подачу проволоки или круглой заготовки, обычно с катушки, в высокоскоростную автоматическую возвратно-поступательную машину с одной или несколькими станциями. Станок срезает небольшую часть сырья, чтобы получить заготовку такого же объема, как и готовая деталь.
Затем с помощью набора подающих пальцев, приспособления для захвата и установки или штампа машина подает заготовку в ряд горизонтальных пуансонов и штампов, которые постепенно «шлепают» ее — со скоростью одного удара на станцию - в правильную форму.
Этот многоступенчатый процесс может включать в себя множество операций, таких как чеканка, прошивка, экструзия, резка, обрезка, нарезание резьбы и накатка. За некоторыми исключениями любая операция, которую можно выполнить на токарном станке или фрезере, может быть подвергнута холодной формовке.
Подобно выдавливанию зубной пасты из тюбика, холодное формование заставляет латунь, медь, сталь и даже труднообрабатываемые материалы, такие как инконель, тантал и молибден, попасть в каждую последующую полость штампа. На каждом этапе материал принимает зеркальную форму штампа станции перед переходом к следующей станции.
Поскольку практически нет потерь материала, холодная штамповка особенно полезна при производстве деталей из драгоценных металлов
. Ваш мусорщик может быть недоволен, но из-за отсутствия стружки легче найти микродетали на холодном шаблоне
, чем в поддоне для стружки токарного станка.
Еще одним преимуществом является то, что детали, подвергнутые холодной штамповке, прочнее и долговечнее, чем обработанные детали, потому что поток зерна материала
не прерывается, как при традиционных процессах обработки, таких как фрезерование и токарная обработка.Этот
позволяет создавать сложные формы с соблюдением жестких допусков. (Например, один производитель деталей холодной штамповки придерживается допусков ± 0,0005 дюйма на детали с диаметром 0,010 дюйма.)
Однако, несмотря на многие преимущества, холодная штамповка имеет ограничения. Например, сложно производить холодную формовку деталей
с большим отношением длины к диаметру, поднутрениями или диаметрами «штуцера», а также сложные детали с множеством функций.
Хотите в холодную форму?
Если вы хотите купить машину для холодной штамповки, у вас есть разные варианты: от взлома детской копилки до
покупки старой бывшей в употреблении машины всего за 500 долларов до получения банковского кредита на покупку новой машины. все колокольчики
и свистки, которые могут стоить более 500 000 долларов.
Реальность для большинства магазинов, вероятно, находится где-то посередине. Производители станков холодной штамповки предлагают различные варианты. Например, компания National Machinery LLC из Тиффина, штат Огайо, предлагает широкий спектр предложений от новой машины для микроформования с диаметром проволоки 3 мм до монстра с шестью матрицами, способного обрабатывать материал диаметром 34 мм. заготовка с давлением формования до 600 метрических тонн. National оснащает свои машины такими функциями, как быстросменные инструменты, ЧПУ, механизмы скольжения с нулевым зазором и линейные подачи.
Излишне говорить, что для эффективной холодной штамповки требуется нечто большее, чем просто покупка станка.Холодная штамповка — это искусство, особенно при изготовлении микродеталей. Будьте готовы разработать свои собственные инструменты, процессы и, возможно, собственное оборудование.
Именно этим занимается ведущий производитель медицинских компонентов Deringer-Ney Inc. Эта 200-летняя компания со штаб-квартирой в Вернон-Хиллз, штат Иллинойс, занимается штамповкой, механической обработкой и формованием пластин, а также разрабатывает индивидуальные сплавы драгоценных металлов.
Микроформинг, однако, — сладкое место компании. «Деталь 5 мм — это для нас огромное значение, — сказал Том Шибер, инженер по разработке продукции.«Микро» для нас означает все, что меньше 0,5 мм ».
На своем заводе в Маршалле, Северная Каролина, Deringer-Ney специализируется на формовании микродеталей, включая антенные выводы; штифты исполнительного механизма; медицинские имплантируемые рентгеноконтрастные маркеры; и миниатюрные винты для медицинских и электронных устройств. Он формирует стандартные и дорогие рабочие материалы, включая золото, платину и тантал.
Дерингер-Ней регулярно формует детали размером до 0,25 мм, что всего в три раза больше ширины человеческого волоса.
«Правила меняются, когда вы переходите в микромир», — сказал Гарт Бойд, вице-президент компании по маркетингу.«Например, во время обычной операции холодной штамповки может быть возможно уменьшение диаметра заготовки до 75 процентов. Но когда размер материала меньше 0,5 мм, это уменьшение может быть ограничено лишь 55 процентами из-за ряда ограничений. , включая пластичность материала, точность инструмента и зернистую структуру заготовки ».
Допуски также уменьшаются в зависимости от размера детали. Бойд отметил, что стандартный допуск может составлять ± 0,002 дюйма при диаметре 0,5 дюйма. детали, но деталь 0,5 мм (0,02 дюйма) может иметь допуск ± 0,0002 дюйма.Это уменьшение допуска означает, что инструменты должны быть более точными и лучше выровненными, а качество поверхности и износ инструмента становятся более важными факторами. Дерингер-Ней гораздо чаще контролирует размеры при микроформовании, чем при работе на макроуровне, и чаще заменяет микроинструменты.
Оборудование — еще одна проблема, с которой сталкивается Дерингер-Ней. «Коммерчески доступное оборудование часто не подходит», — сказала Дана Дубук, вице-президент по развитию бизнеса. В результате Дерингер-Ней иногда модифицирует стандартное оборудование для соответствия более жестким допускам и технологическим требованиям — по сути, превращая Chevy в Ferrari.А если это невозможно, компания разрабатывает и производит машины для удовлетворения сложных требований клиентов.
Большие партии деталей, конечно, желательны с точки зрения амортизации инструментов и оборудования, но это не мешает компании Deringer-Ney планировать короткие партии. «Наша минимальная партия — одна штука», — сказал Шибер. Причина в том, что при работе с экзотическими материалами и драгоценными металлами иногда невозможно обработать микродетали традиционным способом. «Покажите оператору швейцарских станков 0.25-миллиметровая деталь, сделанная из тантала, и он просто встряхнет головой и скажет: «Это невозможно», — сказал Шайбер. — Это потому, что некоторые материалы, хотя и идеально подходят для холодной штамповки из-за своей пластичной природы, просто плохо поддаются обработке. . К ним относятся никелевые сплавы, молибден и другие экзотические материалы. Но с помощью микроформования мы можем отшлепывать такие детали в течение всего дня ». Иногда миллионы.
В качестве примера к Дерингер-Ней обратилась компания, производящая медицинское оборудование, с просьбой помочь спроектировать деталь и произвести
нескольких миллионов деталей. ежегодно.Конструкторы Deringer-Ney уже на раннем этапе процесса начали создавать детали
, способствующие холодной штамповке.
«Мы потратили неделю на проектирование детали, а затем они попросили нас изготовить дюжину прототипов деталей из двух видов сырья», — сказал Шайбер. «Мы спроектировали инструмент для холодной формовки с двумя штампами диаметром 1 мм (максимальный диаметр проволоки). Средняя часть детали составляла всего 0,030 дюйма, поэтому диаметр проволоки был немного меньше — 0,0275 дюйма. Мы изготовили пуансоны и матрицы на собственном предприятии и поставили две дюжина деталей за 6 недель.Заказчик проверил детали, остановился на материале и решил внести небольшие изменения в размеры.Мы скорректировали наш процесс и отправили им еще один наперсток с образцами через неделю. Позже мы добавили текстурированную отделку поверхности по косметическим причинам ». Затем Deringer-Ney получила заказ на 250 000 деталей со сроком поставки 2 недели.
У нас дома
Еще одна компания, специализирующаяся на микроформовании, — это Bigelow Components Corp. , Штат Нью-Джерси, в компании есть отдел, занимающийся разработкой инструментов и процессов для эффективного микроформования. «Мы проектируем, производим, термически обрабатываем и обслуживаем все инструменты на месте», — сказал Бретт Харман, президент компании.«Большинство производимых нами деталей представляют собой компоненты, которые входят в более крупную сборку. Они могут быть электронными, электрическими или механическими по своей природе. Что касается заголовка, мы можем производить детали с диаметром проволоки до 0,018 дюйма (0,46 мм)».
Почему бы не использовать винтовой станок? «Холодное формование — это безотказный процесс, обычно его можно выполнять быстрее [чем винтовые станки], а инструменты дешевле», — сказал Харман. Кроме того, многим клиентам Bigelow требуются изделия, изготовленные из бессвинцовых материалов. и материалы, не содержащие серы.Было бы трудно обрабатывать такие детали на многошпиндельном оборудовании, потому что были исключены добавки к материалам, которые способствуют свободной обработке.
«Один из наших заказчиков обрабатывал материал на основе свинца для производства интегральной детали, требующей магнитных свойств для правильного функционирования конечного продукта», — сказал Харман. «Процесс обработки, который они использовали, был медленным, дорогим и оставлял следы отсечки, которые приводили к дефектным компонентам. Мы заменили сырье на низкоуглеродистую сталь из-за его превосходных магнитных свойств и изготовили компонент, который был более стабильным и дефектным. бесплатное и экономичное производство и сборка.»
MICROmanufacturing 1 апреля 2011 г. — Об авторе: Кип Хэнсон — консультант по производству и писатель-фрилансер.
Почему профилирование? — Dahlstrom Roll Form
Существует множество способов производства металлических компонентов, многие из которых мы коснемся ниже на этой странице. Профилирование должно иметь цель и нишу, верно? Вы делаете ставку — это наиболее экономичный производственный процесс для массового производства:
- Уголков
- Каналов (C, J, прямоугольник, шляпа)
- Сложные формы с несколькими изгибами
- Длинные детали с отверстиями
Профилирование также обеспечивает экономичное и простое добавление продольной перфорации . такие функции, как:
- Отверстия
- Пазы Пазы
- Тиснения
Конструирование этих элементов в специальные инструменты устраняет необходимость в медленных, дорогих вторичные операции .Профилирование снижает производственные затраты и значительно сокращает время выполнения заказа — до тех пор, пока подходит обувь.
Преимущества профилирования
Многие преимущества холодного профилирования недоступны иным образом. Конечно, не все в одном пакете. Но мы пока коснулись лишь поверхности.
Давайте развернем полный список преимуществ профилирования:
Поточные элементы
Характер процесса профилирования позволяет добавлять в линию штампованных элементов и тисненых элементов .Ваш производитель может исключить многоэтапные операции, чрезмерное количество отходов и заусенцы.
Гибкость объема заказа
Один из мифов, с которыми сталкивается отрасль, заключается в том, что ее жизнеспособность очень зависит от объема.
Хотя большие объемы, безусловно, являются наиболее рентабельным способом использования профилирования, малые и средние тиражи не обязательно останутся незамеченными. В зависимости от конструкции детали объемов от 10 000 до 20 000 погонных футов в год могут быть рентабельными.
Ваш производитель также может обеспечить экономичный объем заказа. Это позволяет производителю хранить инвентарь и передавать его вам при необходимости. Экономичные запуски увеличивают объем и сокращают время настройки, а вы не работаете всухую.
Ваш производитель может также согласиться со скидкой на небольшие заказы в обмен на более длительный контракт.
Сложные профили со сложным изгибом
Профилегибочный станок подходит для многих других процессов обработки металлов давлением.При помощи небольшой умной инженерии он способен производить широкий диапазон поперечных сечений.
Конструкции с несколькими радиусами изгиба вызывают проблемы при формовке листогибочным прессом по разным причинам. То же самое касается многоугольных деталей — альтернативный процесс приводит к задержкам производства , требуя частой смены инструмента и перезапуска оборудования.
Жесткие, повторяемые допуски
Если ваш производитель знаком с профилегибочными машинами (и не слишком некомпетентен), он будет производить детали высокой точности.
При правильном выполнении профилирование может выдерживать допуски до +/- 0,005 дюйма на определенных сегментах профиля . Общая длина детали может достигать +/- 0,020 дюйма.
При проектировании необходимо учитывать концевую развальцовку и пружинение. Ваш производитель должен понимать, как можно контролировать эти искажения с помощью правильного проектирования и настройки производства.
Вы можете делать большие вещи
С помощью профилирования вы можете изготавливать детали любой длины! Помните, что длина гнутых деталей ограничена только количеством материала под рукой.
Небольшое обслуживание инструмента
Обслуживание инструмента обычно меньше для профилированного профиля, чем для штампованного компонента. Это связано с тем, что профилегибочные машины могут производить детали и элементы в непрерывном движении .
Лучший способ определить объем обслуживания инструмента — это посмотреть объем вашего заказа.
Способен формировать высокопрочные металлы
Не все процессы производства металла могут обрабатывать высокопрочный металл.Или, если они могут, это ценой быстрого повреждения инструмента .
Возможность холодной прокатки высокопрочных материалов, таких как высокопрочная низколегированная (HSLA) сталь, дает вам преимущество перед материалами стандартной прочности, такими как углеродистая сталь 1040. Сталь HSLA отлично подходит для изготовления конструктивных элементов во многих отраслях промышленности.
Право собственности на инструмент
Амортизация затрат позволяет вам сохранить полную собственность на ваш инструмент и избежать скрытых платежей. Вы также получаете:
- Снижение совокупной стоимости владения: Амортизация сразу снижает первоначальные производственные затраты и дает вам возможность делать небольшие платежи.
- Долгосрочная рентабельность инвестиций: Вы платите один раз за инструменты и можете использовать их для других проектов!
- Гибкость: Хотите взять инструмент с собой в другое место? Действуй.
Меньше шансов на ошибку
Профилегибочные машины в 21 веке очень эффективны. Благодаря программному обеспечению САПР машины в высшей степени автоматизированы и требуют меньшего количества рабочей силы. Это означает меньше шансов на ошибку , вызванную человеческим фактором, .
Скорость и адаптируемость являются ключевыми факторами в отраслях с быстрым временем выполнения работ.
Меньше лома
Одним из самых популярных методов профилирования является то, что при профилировании образуется меньше отходов, чем при многих других методах профилирования металла.
Стоимость лома обычно составляет 1-3% от вашей общей стоимости. Это умение вдвойне круто, когда вы работаете с дорогими материалами.
Приложения для профилирования валков
Многие профили продукции сложно изготовить с помощью листогибочного пресса, штамповки или экструзии (подробнее об этом ниже). Эти же приложения можно экономично выполнять при высокой производительности с помощью профилирования.
Это критерии для определения холодной прокатки:
Общие правила
Если ваш проект соответствует хотя бы нескольким из этих ковшей, он может быть идеальным для изготовления профилей:
- Длинные, тонкие формы до 30 футов является обычным явлением)
- Повторяющиеся рисунки пуансонов в семействе деталей различной длины, все с одинаковым профилем
- Средние и большие годовые объемы. Инструменты могут быть дорогими при малых тиражах.
- Эстетические проекты, в которых следы инструментов недопустимы.Постепенный процесс формования фактически устраняет следы инструмента!
- Сложные поперечные сечения
- Глубокие U-образные каналы с узкими отверстиями
Особые области применения
Профилирование идеально подходит для многих отраслей — некоторые очевидны, другие — нет. Многие из этих отраслей используют преимущества профилирования на протяжении десятилетий, в то время как другие все еще изучают его достоинства:
ПерилаМиллионы миль ограждений приобрели свою прочную и прочную форму благодаря профилированию.
Оцинковка перил возможна прямо на заводе. Добавление этого цинкового слоя помогает компоненту оставаться устойчивым в любых условиях.
Монтажные элементы панели солнечных батарейФормованные из рулонов детали составляют каркасную систему , которая удерживает множество солнечных панелей на:
- Коммерческие крыши
- Солнечные электростанции
- Жилые крыши
Американский профилегибочные машины относятся к проектам на рынке солнечной энергии больше, чем к любому другому виду работ.
Строительный каркасБольшинство коммерческих зданий построено не с использованием стальных шпилек в стене, а из гнутых деталей.
Они очень быстро выпускаются компаниями, которые очень привержены этой супер-нишевой отрасли и имеют необходимые специальные сертификаты. Архитектор должен знать, что деталь может соответствовать стандартам и требованиям по нагрузкам, прежде чем он даже рассмотрит это.
НКТПочти все НКТ изготавливаются методом прокатки.Трубопроводы широко используются в производстве бытовой техники, автомобилей, архитектуры и многого другого.
Трубки могут быть квадратными, круглыми, овальными и прямоугольными. При профилировании все трубы свариваются без шва за счет зачистки.
Гнутые трубы изготавливаются из разных металлов. Однако иногда алюминиевые трубки изготавливают методом экструзии.
Сайдинг и кровляВся оболочка здания может быть сделана из гнутых элементов.
Вы увидите много металлических крыш на домах на северо-востоке. Это еще один сырьевой бизнес, в котором доминируют всего несколько профильных компаний.
Прочие конструктивные элементыЭти гнутые гнутые детали требуют большей толщины. Прогоны или Z-образные профили обычно указываются для всех видов конструкций, работающих под большим напряжением.
Типичные области применения в автомобильной промышленности:
- Направляющие рамы
- Бамперы
- Дверные балки
- Дужки крыши
Вы можете заказать оконные стойки и поручни, изготовленные из рулонных деталей.(Стойки представляют собой вертикальные профили, а поручни — это горизонтальные элементы.)
Полая оконная рама сокращает ваши расходы и придает вам элегантный дизайн. Кроме того, вы просто установите его, щелкнув!
Дверные компонентыДверные коробки, кожухи и другие детали могут быть изготовлены с помощью роликов. Существует множество вариантов этого обрамления, доступных для краев, низа и верха вашей двери, в зависимости от того, какой тип оборудования будет использоваться.Формование этих деталей рулоном довольно распространено.
«Стандартные» двери большого объема используют профилирование кромок, верхнего и нижнего обрамления, что приводит к снижению затрат .
Для добавления остекления можно также использовать гнутые детали. Они могут быть установлены заподлицо или внахлест.
Наконец, некоторые поверхности дверей тоже подвергаются прокатке. В таком случае этот шаг обычно выполняется производителем двери, а не третьей стороной.
ЛифтыОтслеживание вала лифта и некоторые структурные компоненты кабины изготавливаются методом профилирования.
Валкообразователи также могут классифицировать элеватор. Внутренние декоративные элементы кабины также подвергаются гнутой форме
.
Здесь задействовано множество профилей профилирования.
Все трубки, входящие в состав теплообменника хладагента , изготовлены из гнутой меди. Множество конструктивных элементов внешней оболочки изготовлено методом прокатки.
В коммерческих хранилищах продуктов этот процесс можно использовать для формирования:
- Отбойные пластины, защищающие от пыли
- Направляющие из нержавеющей стали по краям
- Декоративные планки и карнизы для создания привлекательных витрин в продуктовых магазинах и магазинах повседневного спроса
Любой вид транспорта является целью оптимизации с помощью перехода на гнутые детали.
Конструктивные элементы шасси составляют основную часть отрасли. Это касается как автомобильной, так и строительной отрасли. Вам нужны межкомнатные двери, которые защитят вашего конечного пользователя во время аварии? Используйте гнутые детали.
На прицепах и грузовиках задние элементы конструкции и шасси формируются в рулонах. На внешней стороне корпуса использована декоративная металлическая отделка.
ПоездаВ поездах сайдинг может быть изготовлен из нержавеющей стали гнутой прокаткой. Это распространенный маршрут городского общественного транспорта.
В поездах также используются конструкционные, а также внешние и внутренние декоративные металлические детали, изготовленные методом профилирования.
КораблиЕсть неиспользованный потенциал для декоративных металлических компонентов на судах. Рабочие и правительственные лодки, мы смотрим на вас.
В настоящее время недостаток творчества в мебели из нержавеющей стали внутри. Все это квадратно и приземленно.
Возможности профилирования для кабельной разводки и лотков приводного стола имеются в большом количестве.Их можно повесить по длине корабля для удобства и надежности.
Распределение питанияКабельные лотки, кабельные каналы … они должны быть изготовлены из стали. Почему не прокатанная сталь? Эти изделия, как правило, изготавливаются из оцинкованной стали, с которой легко справляются роллеры.
Медные шины / проводники обычно формуются в рулонах.
Затраты на профилирование
Стоимость профилированных каналов можно проследить до нескольких факторов:
- Сложность формы
- Трудозатраты
- Стоимость сырья
- Оснастка
- Объем заказа
Сложность формы
Сложность профиля и необходимая штамповка будут определять, будут ли добавлены здесь какие-либо затраты.
Высота профиля может увеличивать стоимость инструмента. Для более высоких профилей требуются инструменты для профилирования валков большего диаметра, что увеличивает потребность в инструментальной стали.
Рабочая сила
После того, как линия профилирования установлена, затраты на рабочую силу становятся довольно дешевыми. Профилегибочное формование — это одностадийный процесс, поэтому здесь не требуется человеческого труда.
Стоимость сырья
Самые большие затраты при профилировании — это цена сырья, составляющая 55-70% от окончательной цены.Прелесть этого процесса в том, что производит настолько мало лома , что он составляет всего 1-3% от общей стоимости.
Затраты на инструменты
Затраты на инструменты для профилирования — еще один прискорбный миф об этом процессе.
Во-первых, инструмент для изготовления любого металла может быть дорогим. При разумных покупках инструмент для профилирования валков на не дороже, чем любой другой тип . Вот несколько способов контролировать затраты на инструмент:
- Если ваш производитель участвует в разработке детали, он может оптимизировать деталь для инструмента для профилирования роликов.
- Платежи могут амортизироваться со временем, чтобы избежать высоких первоначальных затрат.
- Ваш производитель может предоставить скидку на инструмент в обмен на обязательство со временем закупить определенное количество деталей.
- Профилегибочный станок, который существует уже давно, возможно, уже имеет инструменты, которые подойдут для вашего проекта.
Объем заказа
Экономическая конкурентоспособность валковой гибки не так зависит от объема заказа, как вы думаете, . Конечно, большие объемы имеют смысл, но некоторые профилегибочные машины могут оптимизировать свой процесс и для небольших заказов.
Почему это не так дорого, как вы думаете
Процесс гибки валков дает множество преимуществ:
1. Бесплатная вставка на линии
После покупки штамповочного инструмента вы эффективно получаете отверстия поставить деталь бесплатно. Форма все равно должна быть сформирована, а процесс штамповки связан и непрерывен.
В отличие от других видов металлообработки, где добавление каких-либо элементов является повторяющимися и совокупными затратами, стоимость рулонной формы зависит от времени работы машины — независимо от того, сколько функций вы используете.
2. Более низкая стоимость детали
Сумма добавленных вами затрат на инструмент возмещается вам за счет более эффективных функций.
Сравните эту окупаемость с многоэтапным цехом:
- Резка детали
- Отнесите ее к прессу или лазерному резчику
- Отнесите к тормозному прессу, где кто-то устанавливает инструмент и сгибает вашу деталь в форму
При использовании профилегибочного станка все это осуществляется непрерывно. Профилирование идеально подходит для повторяемых деталей и процессов.
3. Снижение затрат на рабочую силу
При меньшем количестве задействованных процессов вполне логично, что вы также выиграете от чрезвычайно низких затрат на рабочую силу. Мы говорим о , 6% от общей стоимости проекта, , тогда как в мастерской это 15-20%.
4. Меньше ожидания Примерно
Время выполнения заказа по частям лучше. Мы говорим всего лишь о 10% времени выполнения заказа в этом цехе .
5. Возможность совместной работы по оптимизации детали
Если ваш производитель предлагает помощь в проектировании, это может фактически сэкономить вам деньги за счет оптимизации детали для инструментов и процессов профилирования валков.
Профилирование валков Vs. Конкурирующие процессы
В правильной ситуации ваша компания может воспользоваться профилированием для эффективного производства деталей, подходящих для любой отрасли. Поскольку каждая ситуация уникальна, давайте подробнее рассмотрим плюсы и минусы валковой гибки по сравнению с штамповкой, прессовым торможением, экструзией, литьем и ковкой.
Большинство этих конкурирующих процессов выполняется посредством горячей штамповки. Проблема в том, что горячая штамповка — это очень специализированный процесс на стане .Использование высоких температур и расплавленного продукта требует огромных печей, которых не так много. Покупка оборудования, необходимого для безопасного обращения с жидкой сталью, и поиск опытных специалистов для эксплуатации оборудования — это крупные инвестиции.
А разница в том…
Есть общие различия в конечном результате холодной штамповки и горячей штамповки:
- Скорость и качество обработки: Для горячей стали может потребоваться 50 валков для утонения заготовки. , в то время как для этой же детали может потребоваться 100 проходов при холодной прокатке.Но… с большим количеством валков вы можете получить более жесткие допуски на деталь и более качественный конечный продукт. Это может привести к увеличению затрат, но, возможно, это того стоит для вашего клиента.
- Прочность: Для аналогичных марок холоднокатаный металл может быть прочнее горячекатаного металла из-за наклепа. Если для детали, которая будет формоваться в рулоне, указан горячекатаный лист, вы все равно получите немного дополнительной прочности. Но он не будет соответствовать той прочности, которую вы получили бы, если бы начали со стандартного холоднокатаного материала.
- Использование в конструкциях: Формула стали для двутавровых балок отличается от той, что используется при холодной штамповке. Он менее пластичен и тверже, что затрудняет его изгиб в холодном состоянии.
- Ограничения по размерам: Стальной лист подвергается горячей прокатке только до определенной толщины. Длина гнутых деталей ограничена только количеством материала в рулоне.
Профилирование валков Vs. Штамповка
Штамповка не идеальна для небольших проектов, отчасти потому, что стоимость инструментов для штамповки огромна. При штамповке нельзя формировать длинные детали, и нельзя вносить изменения в рисунок штамповки.
Существуют определенные объемные приложения с простым дизайном, на которые можно наносить штамп. К ним относятся:
- Шестерни
- Двигатели
- Компоненты самолетов
- Электроника
- Телекоммуникации
- Оборудование
- Электроинструменты
- Приборы
- Замки
- Уход за газоном
- Боеприпасы
1
- Освещение Формирование Vs.Листогибочный пресс
- Трубки
- Алюминиевые канистры
- Цилиндры
- Трубопроводы подачи топлива
- Рамы
- Гусеницы
- Рельсы
- Штанги
- Штанги
- Форсунки
- Электроды
- Прототипирование
- Тяжелое оборудование
- Приборы
- Двигатели
- Артиллерия
- Art
- Кожухи и крышки
- Диффузоры
- Клапаны
- Корпуса камер
- Оснастка
- Шестерни
- Рулевые рычаги
- Валы
- Фланцы Клапаны
- Сверла
- Головки
- Крюки
- Шаровые шарниры
- Ракеты
- Шкворни
- 101
- Стержневые балки
- Покупка профилегибочного станка через Интернет
- Наличие у производителя нового оборудования разработки и установки станка под ключ на заказ повлиять на ваш путь.
1. Стоимость оборудования по сравнению с ценой.ROI
Профилегибочное оборудование — это больше, чем просто формовочная машина. Полная линейка включает:
- Погрузочно-разгрузочное оборудование
- Погрузочный кран
- Система разматывания
- Пресс для предварительной перфорации (если в вашем компоненте есть отверстия, пазы или выступы)
- Точная система подачи / управления
- Летающий ускоритель отрезания штампа с элементами управления
- Отрезной пресс подходящего размера
Все эти характеристики линии должны соответствовать вашим формующим инструментам, штампу для предварительного перфорации и режущему штампу.
Стоимость полной системы профилирования может составлять от 200 000 до 2 миллионов долларов в зависимости от сложности вашего семейства компонентов. Большинство собственных систем могут производить только цельный профиль. Типичная линия может производить около 1,5 миллионов погонных футов в год за одну смену.
Если вы планируете приобрести собственную систему профилирования рулонов, лучше всего производить большие объемы, чтобы добиться приличной рентабельности инвестиций.
2. Навыки оператора против. Контроль качества
В отличие от листогибочного оборудования, профилегибочные линии требуют операторов с многолетним опытом для обеспечения высококачественной продукции.Вот лишь некоторые из соображений для каждой линии:
- Толщина и свойства коммерческих металлов сильно различаются
- Прогоны с различными партиями металла требуют точной регулировки для получения ожидаемого профиля
- Необходимо выполнить корректировку с учетом упругого возврата из более твердых металлов
- Для более толстых партий требуется больше места между инструментами для профилирования валков
- Неравное давление на валы для профилирования приведет к скручиванию и изгибу
- Учет растяжения компонентов
- Предотвращение попадания металла в штампы
Может ли ваш штатный оператор покрыть все эти базы? Тебе лучше на это надеяться.
Опытные производители профилированных профилей гарантированно понимают и учитывают эти переменные. Они знают, как полностью использовать свое оборудование. Опытные операторы могут работать с несколькими профилями и металлами на одной линии.
Нанимать специалистов на полный рабочий день для собственных операций очень дорого. И, если вам нужны сервисные подрядчики, у них, вероятно, не будет графиков, отвечающих вашим насущным потребностям. Это подвергает риску вашу цепочку поставок и ваших клиентов.
3.Внутреннее управление запасами Vs. Поставки от поставщика
Контроль над товарно-материальными запасами — основная причина, по которой компании осуществляют проекты по производству профилей для производства рулонов внутри компании. Но как управление запасами соотносится со стоимостью эксплуатации профилегибочного станка? Спросите себя:
- Будет ли линейный оператор работать на полную ставку?
- Большие объемы требуют постоянной работы рабочих групп. Сможет ли ваша компания сбалансировать затраты, объем производства и другие зависимые процессы этой рабочей нагрузки?
Сторонние производители рулонных форм уже имеют сбалансированные системы, обеспечивающие возможность непрерывной прокатки по приемлемой цене.
Они также могут управлять запасами за вас — будь то JIT (своевременная доставка) или поставки с большим запасом по мере необходимости. Чтобы затраты на складские запасы не подкрались к вам, минимизируйте запасы, обеспечивая при этом буфер для изменений спроса. Неопытное управление запасами может привести к дорогостоящим задержкам в цепочке поставок.
Подробнее о рентабельности инвестиций
Поначалу может быть страшно доверять третьей стороне. Если вы взвешиваете, стоит ли аутсорсинг вашего производства, помните, что аутсорсинг только одной детали для U.Поставщик S. может улучшить ROI.
Это не сумасшедший разговор, если вы предложите увеличить количество отправляемых единиц на 20% до 50% ? Вот как и когда это возможно:
Когда обращаться к поставщику за окупаемостью инвестиций
Почти у всех поставщиков есть оборудование и процессы, предназначенные для обеспечения индивидуальных функций, присущих уникальности их продукции. Независимо от того, вносят ли эти функции вклад в уникальную функцию или предлагают клиентам дополнительные возможности, они составляют основное отличие, которое поддерживает их существование.Логично, что инвестиции этих специалистов в…
- Оборудование
- Люди
- Процессы
- Производственные площади
… должны отдавать предпочтение им, а не хранению процессов внутри компании.
Еще одно соображение: какие заказы вы будете выполнять? Товарные позиции в больших объемах могут поставить мертвую хватку на способность вашей организации увеличить количество отгружаемых единиц. Если мощность на линии ограничивается хотя бы одним компонентом с большим объемом , передача этой части на аутсорсинг может экспоненциально увеличить вашу прибыльность.
Прибыльность — это увеличение количества отгружаемых единиц при тех же затратах и существующих инвестициях. Для этого созданы опытные сторонние поставщики.
Таким образом, несмотря на то, что профилирование внутри компании подходит для некоторых компаний, это не рентабельная альтернатива для всех. Для многих контрактный профилегибочный станок обеспечит более высокую рентабельность инвестиций и снизит уровень стресса.
Дальнейшие действия
Если вы решили, что лучше всего передать производство внешнему профилегибочному станку, пора отправиться на охоту! Ищите партнера по профилированию валков, который предложит вам комплексную систему поставок.Правильное соглашение о поставке приведет к:
- Экономия затрат
- Надежность в сроках выполнения заказа и цепочке поставок
- Понимание структуры вашей системы поставок
Удачи в вашей охоте! Если вы не принимаете окончательное решение в своем OEM-производителе , вы можете столкнуться со скептически настроенным начальником. Если ваш проект соответствует хотя бы паре этих критериев использования профилирования, он будет продан:
- Объемы ваших заказов превышают рентабельность ваших текущих процессов.
- Отходы вашего лома вышли из-под контроля.
- Ваш текущий процесс неэффективен.
- Вам нужен больший контроль над процессами и инструментами.
- Вы хотите упростить цепочку поставок с помощью запасов, управляемых поставщиками.
- Вы хотите воспользоваться преимуществами экономичных производственных процессов.
- Вам нужен более экологически чистый продукт.
Будем надеяться, что этот ресурс послужил аргументом в пользу профилирования при производстве компонентов. Если вы хотите лучше понять процесс или у вас есть конкретные вопросы по дизайну, свяжитесь с нами сегодня. Мы работаем над этим с 1904 года , поэтому мы можем быстро определить, какой производственный процесс подходит именно вам.
Процесс холодной штамповки | Преимущества промышленной холодной штамповки
Что такое холодная ковка?
Холодная штамповка — также называемая холодной штамповкой — это тип металлической ковки, который используется в самых разных областях, от автомобильной до электронной и медицинской техники. Холодная штамповка включает формование заготовки, часто называемой «заготовкой», посредством процесса, называемого «деформированием».«
В традиционных процессах ковки металл подвергается воздействию высоких температур. В процессе холодной ковки заготовка подвергается гидравлическому и механическому давлению при комнатной температуре для деформации. Это дает ряд преимуществ для конкретного применения, начиная от улучшенной консистенции до более низких затрат и более эффективного использования материалов.
STS Intelli — компания по холодной штамповке, которая может выполнять проекты любого масштаба. Продолжайте читать, чтобы узнать больше о преимуществах, которые наши услуги по холодной штамповке могут иметь для вашей работы, или свяжитесь напрямую с нашим офисом, чтобы запросить ценовое предложение.
Процесс холодной штамповки
Холодное формование выполняется при комнатной температуре или близкой к ней. При работе с некоторыми металлами для улучшения пластичности применяется некоторое количество тепла, хотя температуры остаются значительно ниже точки рекристаллизации.
Холодная штамповка используется для создания различных форм и деталей. Таким образом, не существует единого стандартного процесса формования заготовок. Вместо этого детали создаются с использованием одного или комбинации следующих методов:
- Прямая экструзия: Прямая экструзия, также известная как прямая экструзия, является наиболее распространенным типом процесса холодной штамповки.В нем к металлической заготовке прикладывают силу, толкая ее в форму, где ей придают форму.
- Обратная экструзия: Обратная экструзия включает использование пуансона для перемещения заготовки в пресс-форму того же размера. Когда заготовка входит в форму, пуансон создает меньшее отверстие и заставляет заготовку формироваться вокруг нее.
- Осадка: При высадке заготовка помещается в более короткую форму. Когда заготовка ударяется о заднюю часть формы, излишки материала выталкиваются вниз, создавая широкий верх.Этот метод чаще всего используется для создания головок крепежа различных размеров.
- Обрезка: Обрезка включает использование штамповочного пресса для срезания лишних материалов с детали, создания более сложных форм с более высоким уровнем допуска.
- Выравнивание и присучивание: Выравнивание и прошивка работают в точности так, как подразумевают их названия: использование штамповочного пресса для создания плоских компонентов или пробивки отверстий в детали без образования металлической стружки.
В дополнение к вышеизложенному, ряд дополнительных процессов может использоваться для формирования очень сложных компонентов различных форм и размеров.STS Intelli может сбрить, сверлить, накрасить или покрасить любой компонент в соответствии с вашими требованиями. Чтобы узнать больше о наших возможностях и обсудить детали вашего проекта с одним из членов нашей команды, свяжитесь напрямую с нашим офисом.
Преимущества холодной штамповки
Каковы основные преимущества холодной штамповки?
Процессы ковки обычно не считаются экологически чистой частью производственного процесса, но холодная ковка, вероятно, является наиболее экологичным процессом такого рода, применяемым сегодня.Для компаний, которые заботятся о сокращении углеродного следа своей продукции, процесс холодной ковки может помочь сократить отходы и снизить потребление энергии по сравнению с альтернативами ковки, использующими тепло.
Другие причины, по которым процесс холодной штамповки является предпочтительным, включают:
- Высокое качество материала поверхности
- Консистенция каждой изготовленной детали
- Эффективное использование материала
Помимо перечисленных выше причин и экологического фактора, холодная штамповка также является одним из наиболее экономичных методов ковки на современном рынке.Например, оценки показывают, что этот процесс может снизить стоимость вашей детали на 40–60%.
Если ваша компания ищет способ массового производства высококачественной продукции с меньшими затратами на производственные операции, холодная ковка — лучший выбор.
Каковы дополнительные преимущества компонентов холодной штамповки?
Процесс холодной штамповки полон преимуществ для производителей. При холодной штамповке меньше отходов.Фактически выход материала составляет почти 100%. При использовании сплавов драгоценных металлов, таких как золото и серебро, стоимость материалов высока. Такой 100% выход приводит к значительной экономии затрат во время процесса холодной штамповки по сравнению с другими методами.
В дополнение к 100% -ному выходу детали холодной штамповки очень стабильны. Другие преимущества холодной штамповки:
- Более высокие скорости и более низкие затраты на инструмент по сравнению с другими процессами обработки
- Лучший контроль над размерами, создание большей однородности формованных деталей
- Меньшее потребление энергии, что помогает снизить выбросы углерода и увеличить экономию
- Создание продукта без особых требований к обработке
- Улучшение свойств металла за счет деформационного упрочнения
- Гладкие детали без заусенцев
При правильной холодной штамповке производитель может рассчитывать на то, что из процесса ковки будет исключен почти весь лом, а также часть без дефектов, складок и других дефектов.Холодная штамповка также позволяет изготавливать детали с жесткими допусками со скоростью 1000 сек в час.
Что это? Преимущества, Процесс, Горячие и холодные, Типы, Соображения
Введение
Это наиболее полное руководство по холодной штамповке, доступное в Интернете.
В этой статье рассматриваются следующие темы:
- Что такое холодная ковка и как она работает
- Преимущества и недостатки холодной штамповки
- Горячая штамповка vs.холодная ковка
- Металлы и оборудование / машины бывшие в употреблении
- Холодная штамповка
- И многое другое …
от компании Anderson ShumakerГлава первая — Что такое холодная штамповка и как она работает?
Холодная штамповка — это процесс формовки и производства металла, при котором пруток вставляется в штамп и сжимается во второй закрытой штампе.Процесс завершается при комнатной температуре или ниже температуры рекристаллизации металла для придания металлу желаемой формы или конфигурации.
Холодная штамповка — это эффективный и экономичный процесс деформирования металла для производства больших объемов деталей по низкой цене. Существует три метода холодной ковки, которые различаются в зависимости от температуры, которые могут быть холодными, теплыми или горячими и включают использование молотков, штампов или прессов для придавать форму, сжимать, деформировать и катить металлы.Холодную ковку не следует путать с механической обработкой или литьем, поскольку конечный результат — более прочный и качественный продукт.
В отличие от горячей или горячей штамповки, холодная штамповка формирует и деформирует пруток при комнатной температуре с использованием локализованного сжимающего усилия. В зависимости от требований к конструкции детали заготовка может проходить через несколько штампов или подвергаться ударам несколько раз подряд для достижения правильной формы.
Глава вторая — Как работает холодная штамповка
Низкая стоимость холодной ковки обусловлена снижением трудозатрат и устранением вторичной обработки.Детали производятся быстро и эффективно со скоростью до 1000 штук в час, что снижает удельную стоимость. Производство просто заключается в том, чтобы вставить металлическую деталь и позволить машинам быстро и экономично выполнить работу.
Готовые изделия из холодной штамповки имеют идеальную поверхность и улучшенную стабильность размеров, как показано на изображении ниже. Различные процессы повышают прочность и долговечность заготовки, позволяя производить долговечные изделия или детали.
Процесс холодной штамповки —
Этап 1: Смазка
— Перед ковкой заготовку обрабатывают смазкой, чтобы предотвратить ее прилипание к матрице и сохранить ее прохладной во время процесса штамповки, поскольку при деформации могут возникать температуры от 250 ° до 450 °.
Шаг 2: Вставка металлической детали
— Металлическая деталь помещается на матрицу, имеющую форму последней детали.Матрица может иметь две секции, одна из которых прикреплена к молотку, а другая — под заготовкой. Молоток — это верхняя часть и ударный механизм, создающий силу для деформации металлической детали.
Шаг 3: Ход
— Удар по заготовке или ход может производиться тремя механизмами — гидравлическим, пневматическим или механическим. Каждый из этих методов направляет вал с молотком на нем с большой силой вниз на заготовку для создания желаемой формы.Это происходит с точностью до миллисекунд. В некоторых случаях молоток может потребоваться несколько раз подряд для получения точного контура и формы.
Шаг 4: Вспышка
— Вспышка — это лишний металл, который находится вокруг матрицы или набора штампов. Он выступает из корпуса поковки в виде тонкой пластины в месте соединения штампов и удаляется во время обрезки. Вспышка ограничивает поток металла, обеспечивая идеальное впечатление. Наличие вспышки необходимо для того, чтобы металл полностью заполнил матрицу.
Шаг 5: Удаление детали
— Метод удаления детали зависит от типа процесса. Большинство современных производителей используют автоматику для удаления детали конвейером или рукой робота. Это еще одна мера экономии, которая устраняет необходимость в транспортировке материалов.
Шаг 6: После формирования
— Как и в случае с другими частями процесса, это может принимать различные формы. Для деталей, требующих одного штампа и одного хода, деталь обрезается и отправляется на отгрузку.В случае деталей, которые имеют несколько граней, они перемещаются в другие процессы штамповки для добавления элементов. Перемещение штампа от станции к станции обычно автоматизировано. С более крупными деталями используются другие механизированные методы, которые могут включать подъемник, вилочный погрузчик или кран.
Глава третья — Преимущества холодной ковки
В этой главе подробно обсуждается шесть основных преимуществ холодной кромки. В их числе:
- Рентабельность
- Более быстрое производство
- Экологичность
- Превосходная производительность продукта
- Высокая производительность
- Большой выбор металлов
Приведенная ниже информация описывает некоторые преимущества холодной ковки и причины ее широкого использования.В третьей главе сравниваются холодная и горячая штамповка, а также преимущества каждой из них.
Рентабельность:Холодная штамповка — это низкая стоимость за счет 3 факторов — предварительной обработки, температуры и чистовой обработки. В других методах формования металла заготовка должна подвергаться некоторой форме предварительной обработки, такой как нагрев. Печи, обжиговые печи или электричество обычно используются для повышения температуры металла выше точки его рекристаллизации.Они дороги в обслуживании, производят загрязняющие вещества и требуют много времени.
При холодной штамповке после обработки заготовка становится законченной и требует минимальной обработки, что снижает затраты на рабочую силу.
Холодная штамповка позволяет экономить до 70% производственных затрат, так как очень мало отходов и лома.
Ускоренное производство:Холодная штамповка — это простой процесс, при котором заготовка помещается непосредственно в кузнечный станок для мгновенного изготовления готовой детали.Современные производители используют автоматику для загрузки заготовки и снятия ее с пресса. Как вы можете видеть на этом видео, металл загружается в станок, обрабатывается и перемещается дальше. Время между входом и окончанием составляет менее секунды.
Экологичность:Основная причина, по которой холодная ковка является экологически чистой, заключается в устранении потребности в тепле, поскольку дым и дым из печей вызывают значительные выбросы углерода.Это также снижает стоимость, поскольку производителям не нужно устанавливать оборудование для фильтрации и очистки воздуха.
Превосходная производительность продукта:Холодная штамповка позволяет получать изделия с превосходными характеристиками, поскольку она изменяет структуру зерна заготовки в соответствии с конфигурацией конечной детали.
Устраняет возможные негативные реакции:Обработка металла может создать множество потенциальных проблем.Холодная ковка устраняет некоторые отрицательные эффекты, такие как усталостная пористость, за счет увеличения общей прочности металла и устранения риска потери целостности материала.
Повышенное качество и долгий срок службы:Холоднокованые детали способны выдерживать высокие нагрузки. Когда заготовка выходит за пределы ее предела текучести или упругости, она все еще может сохранять свою измененную форму.
Сохранение допусков детали:Критические и строгие допуски деталей поддерживаются на протяжении всего производственного цикла.Они воспроизведены до мельчайших деталей, так что каждая часть является точной копией первой.
Свобода дизайна:В отличие от других процессов, холодная штамповка дает свободу проектирования, когда можно создавать сложные контуры и формы, которые потребуют множества различных и дорогостоящих вторичных методов в других процессах.
Высокая производительность:Хотя могут быть различия между методами производства холодной штамповки, высокая производственная скорость холодной штамповки позволяет производить от 50 до более 400 штук в минуту.Единственное, что влияет на скорость процесса, — это размер детали.
Большой выбор металлов:Можно ковать широкий спектр металлов, в том числе твердые, такие как углеродистая сталь, легированная сталь и нержавеющая сталь, а также мягкие металлы, такие как алюминий, латунь и медь.
Разнообразие болтов холодной ковки из различных металловНа этом изображении представлены образцы болтов, изготовленных методом холодной штамповки.Каждый из различных болтов был сделан из разного металла. В комплекте идут из меди, латуни, алюминия и стали.
Глава четвертая — Горячая и холодная ковка
Разница между горячей ковкой и холодной ковкой заключается в температуре: холодная ковка деформирует и нагружает металлы при комнатной температуре, в то время как горячая ковка нагревает металлы вблизи их точек плавления.
Ключом к температурному диапазону является рекристаллизация: холодная штамповка проводится перед рекристаллизацией, а горячая штамповка нагревает металл выше точки рекристаллизации.
Выбор холодной ковки или горячей ковки зависит от:
- A Производители оборудования и обработки: Производители специализируются на том или ином процессе, чтобы максимально использовать свое оборудование.
- Потребительский запрос: На этапе проектирования деталей инженеры принимают решение относительно наилучшего процесса производства своих конструкций, поскольку холодная и горячая ковка имеет свои ограничения.
- Типы производимых деталей: Часто ограничения относительно выбора правильного процесса определяются конструкцией детали, поскольку определенные детали могут быть подвергнуты только горячей штамповке, в то время как другие идеально подходят для холодной штамповки. Конструкции деталей, изготовленных методом холодной ковки, просты, без сложных деталей, в то время как горячая штамповка позволяет получать изделия с очень точными мелкими деталями.
- Требование более низкой стоимости: По возможности производители выбирают холодную ковку, поскольку она требует меньшего количества оборудования и не включает нагрев, что значительно снижает общую стоимость производства.
Горячая штамповка
Горячая ковка выполняется при исключительно высоких температурах от 700 ° C или 1292 ° F до 1000 ° C или 1832 ° F. Повышенные температуры помогают избежать деформации и упрочнения, а также снижают поток напряжений и количество энергии, необходимое для деформации. и профилировать металлы. После остывания металлы сохраняют свою деформированную форму. В процессе формования используются гидравлические, пневматические и механические прессы.
Характеристики горячей штамповки:
Плашки или пресс-формы:Одной из основных статей расходов на горячую штамповку является стоимость изготовления штампов и форм, изготовленных из усиленной стали, выдерживающей экстремальные температуры, способной противостоять усталости и обладающих пластичностью, ударной вязкостью и прочностью на разрыв.
Формы горячей штамповки:Хотя многие методы горячей штамповки похожи на методы холодной штамповки, другие методы включают в себя газовую формовку, закалку в штампе, формовку вытяжкой и изотермическую обработку.
Температура металла:Тип процесса определяет температуру металла при формовании.В некоторых процессах металл полностью расплавляется и выливается в форму или проталкивается через матрицу. В других случаях его отжигают и формуют с помощью штампа или пресс-формы под давлением и сжатием.
Опасные факторы окружающей среды:Самый большой недостаток — это количество загрязняющих веществ, образующихся в процессе нагрева. Это была серьезная проблема с момента ее возникновения во время первой промышленной революции, и производители постоянно сталкивались с этой проблемой на протяжении многих лет.На видео ниже показано количество образовавшегося дыма.
Пресс горячей штамповки 1000 тонн: смазка для штампов на масляной основе
Обогрев металлов:Детали необходимо нагреть выше точки рекристаллизации, которая намного превышает 300 ° F и может доходить до 1000 градусов. Для достижения соответствующей температуры требуются большие печи или обжиговые печи.
Время проведения:Сложный характер горячей штамповки требует времени для нагрева металла, его обработки и охлаждения. Хотя фактическая штамповка, деформация или формование занимает примерно столько же времени, что и холодная ковка, процессы нагрева и охлаждения требуют тщательного ухода и управления в течение длительных периодов времени.
Результаты горячей штамповки:Нагрев и охлаждение металлов увеличивает их прочность, ударную вязкость и пластичность, но снижает их твердость.В процессе охлаждения металлы могут коробиться и терять форму.
Масштабирование:Горячая штамповка может вызвать окисление, которое приводит к образованию окалины, которое может обесцветить поверхность металла, что затрудняет чистовую обработку.
Чистовая обработка:Детали необходимо обработать, чтобы устранить деформации, дефекты и ошибки в процессе нагрева. Эти вторичные операции трудоемки и требуют нескольких видов специализированного оборудования.
Холодная штамповка
Температура, при которой происходит ковка, отличает холодную ковку от горячей. Для горячей штамповки деталь нагревают до температуры выше точки рекристаллизации, что изменяет ее микроструктуру. Когда он нагревается, его внутреннее напряжение и прочность устраняются, что делает его более пластичным. Холодная ковка не требует нагрева, позволяя металлу сохранять свою прочность и микроструктуру.
Характеристики холодной поковки следующие:
Температура формовки:Металлы формуются при комнатной температуре ниже точки их рекристаллизации, что позволяет снизить затраты и избежать расходов на печи.
Скорость:Скорость варьируется от семи штук в минуту для машин небольшого объема до 400 штук в минуту для машин большого объема.
Оборудование:Холодная штамповка выполняется на станках, предназначенных для придания формы металлу, включая выжимку, гибку, резку и волочение. Оборудование доступно в широком диапазоне цен в зависимости от количества техники и ее размеров.
Стоимость:Экономия средств за счет материала и скорости. Экономия материала достигается за счет небольшого количества производимого лома — до 70%.Поскольку детали производятся очень быстро, стоимость единицы продукции значительно ниже.
Факторы окружающей среды:Никаких выбросов или загрязняющих веществ не происходит, как это видно на этой машине от Stalcop ниже. Все замкнуто и замкнуто. Углерод и другие загрязнители исключаются, поскольку нет необходимости нагревать металл.
Результат холодной ковки:Как видно на диаграмме ниже, структура зерен металлов перестроена, чтобы следовать за потоком конечной детали, что устраняет усталостную пористость, увеличивает прочность на сдвиг и снижает любой риск целостности материала.Напрягая металл, он становится прочнее и эластичнее. Недостатком является то, что после холодной ковки металл теряет пластичность и становится более хрупким.
Масштабирование:Перед ковкой металла важно удалить любые накипи, такие как ржавчина или коррозия, которые могут образоваться во время хранения. Если не снимать, деталь будет иметь такой же износ, как при горячей штамповке.
Чистовая обработка:Требуется минимальная отделка.После обработки деталь готова к использованию или отправке.
Недостатки холодной штамповки
Холодная ковка не идеальна. Как и для любого метода производства, для холодной ковки существуют ограничения и ограничения, которые необходимо учитывать, прежде чем выбирать ее для своего следующего производственного проекта.
- В больших объемах можно производить только простые формы и дизайн.Уникальные, необычные или замысловатые узоры не поддаются холодной ковке. Уровни деформации и качества формования ограничены, а металлы, полученные методом холодной ковки, обладают меньшей пластичностью.
- Изменение зернистости металла придает ему дополнительную прочность, но может вызвать остаточное напряжение.
- Некоторые методы холодной ковки требуют термической обработки для устранения возможных трещин или упрочнения при ползучести.
- Существует ограничение на типы металлов, которые можно подвергать холодной ковке. Не следует выбирать материалы с низкой пластичностью и чувствительностью к деформационному упрочнению, поскольку они теряют пластичность и ломаются под действием растягивающего напряжения. Могут использоваться только металлы с твердостью HRC 44 по шкале Роквелла.
- Производственные процессы требуют большого усилия для создания необходимой силы сжатия и давления.Хотя добавление гидравлики и пневматики уменьшило размер оборудования, оно не уменьшило количество потребляемой мощности машин.
- Инструменты, штампы и формы должны быть специально спроектированы, а также достаточно прочными и прочными, чтобы выдерживать постоянную повторяющуюся силу.
Глава пятая — Процессы холодной штамповки
Развитие различных технологий и достижений в области обработки металлов привело к появлению нескольких методов холодной обработки металлов давлением.Каждая из них предназначена для разных целей, но все они предназначены для эффективного и быстрого производства продукции без необходимости вторичной отделки.
Восемь наиболее распространенных процессов холодной штамповки:
- Гибка
- Холодная прокатка
- Матрица закрытая
- Рисунок
- Экструзия
- Открытая матрица
- Кольцо поковка
- Обжимной
Как я буду обсуждать в конце этой главы, существует больше процессов, чем только перечисленные.Описания ниже предоставляют вам базовые данные для начального понимания различных методов.
Кроме того, очень важным аспектом процесса холодной штамповки является тип используемой смазки. Двумя наиболее распространенными являются фосфат цинка или какое-либо полимерное покрытие. Хотя холодная ковка выполняется при комнатной температуре, в процессе гибки и формовки температура металлов повышается. Смазка может предотвратить ошибки и предотвратить прилипание заготовки к матрице и продлить срок службы инструментов.
Производители смазочных материалов предлагают широкий выбор продуктов для каждого типа процесса холодной штамповки. Изображены графитовые смазки, но доступны типы без графита, а также покрытия из алюмината кальция, фторида алюминия и фосфата.
Обычные методы холодной ковки:
Гибка —Гибка выполняется с использованием пресса и штампа, когда заготовка прижимается к формовочному инструменту.Его также называют прокаткой пирамиды и иногда используют для подготовки детали к другому процессу холодной штамповки. Заготовка растягивается по одной оси, образуя угол.
Холодная прокатка —Прокатка — это процесс формования, при котором металл пропускается через пару вращающихся роликов для пластической деформации, вызванной сжимающей силой. Напряжения сжатия вызывают трение между валками и поверхностью металлической заготовки.Обычно используется для обработки стали.
Закрытая матрица —При штамповке в закрытых штампах заготовке придают форму путем последовательных механических ударов после того, как ее поместили между двумя половинами штампа. Поскольку молоток ударяет по заготовке несколько раз, некоторые производители называют штамповку в закрытых штампах штамповкой. При ударе по металлу он течет в полости матрицы, изменяя ее форму.
Чертеж —Вытяжка — это протягивание заготовки через матрицу за счет усилия на разрыв, приложенного на выходе из матрицы. По мере протягивания заготовки происходит уменьшение площади поперечного сечения с увеличением ее длины. Формованные металлы имеют более точные допуски по размерам, чем полученные прокаткой.
Экструзия —Заготовка или заготовка проталкивается через матрицу ниже сжимающего усилия, имеющего профиль конечной детали.После прохождения его обрезают до необходимой длины, готовят к отправке или отправляют для дальнейшей обработки. Усилие, прилагаемое при холодной экструзии, может достигать 20 000 кН или 2007 тонн. Экструзия может производиться вперед, назад или в обоих направлениях.
Прямая экструзия — металл проталкивается вперед через матрицу.
Обратная экструзия — металл входит в матрицу в обратном направлении, образуя отверстия или чашки, в результате чего дно становится толще его сторон.
Боковое выдавливание — сила прикладывается сбоку, сбоку к направлению выдавливания, чтобы добавить в профиль второй элемент.
Открытый штамп:Для открытой штамповки используются две плоские штампы без предварительно вырезанного профиля. Заготовке постепенно придают форму с помощью нескольких процессов, позволяющих производить широкий диапазон форм и размеров. Он в основном используется с конструкциями, включающими большие металлические компоненты, требующие высочайшей структурной целостности.Деформация достигается перемещением заготовки.
Выдавливание, также известное как калибровка, представляет собой форму обработки в открытом штампе, при которой сила прикладывается на небольшом расстоянии, обеспечивая точную размерную отделку.
Кольцо поковка —При ковке в виде кольца в середине штампуется круглая заготовка, чтобы получить форму пончика. По мере того как пробитая деталь вращается, она ударяется и сжимается.В результате производятся бесшовные кольца идеального диаметра и прочности.
Обжимка —Обжимка или радиальная ковка — это деформация заготовки, при которой две части подходят друг к другу. Он автоматизирован и отличается высокой надежностью. Есть два типа обжатия: трубчатая и радиальная. Обжатие трубок похоже на экструзию, когда заготовка проталкивается через матрицу. При радиальной обжимке молоток проталкивает заготовку через две или более матрицы.
Когда вы начнете поиск производителя холодной штамповки, вы найдете больше методов, чем семь описанных здесь. Базовое понимание нескольких возможных методов поможет вам авторитетно и разумно говорить с продюсерами, а также уметь интерпретировать их жаргон.
Как и любой современный метод производства, вы обнаружите, что холодная штамповка постоянно развивается по мере развития новых технологий и методов.Важным и растущим фактором является добавление автоматизации и робототехники, которые быстро меняют облик отрасли. Специалист по ковке может указать вам правильное направление, чтобы найти процесс, который наилучшим образом соответствует вашим потребностям.
Глава шестая — Оборудование и машины для холодной штамповки
Оборудование и станки для холодной штамповки бывают трех видов — гидравлические, пневматические и механические.Хотя некоторые поставщики специализируются только на одном типе, вы обнаружите, что у большинства есть несколько вариантов в зависимости от цены и типа операции. Технология и автоматизация являются общими, как вы можете видеть на рисунке ниже, который представляет собой пресс для холодной штамповки с сервоприводом от Marvel Machinery. Отрисовки дизайна деталей создаются с помощью инженерного программного обеспечения, такого как САПР.
Есть требования, которым должны соответствовать машины, чтобы их можно было использовать для холодной ковки.
- Force — Процессы холодной штамповки зависят от огромного усилия. Подключенное к нему оборудование должно быть способно поглощать эту силу и рассеивать ее.
- Balance — Машины должны быть статически и динамически сбалансированы по массе, чтобы уменьшить вибрацию и повысить производительность.
- Долговечность во времени — Независимо от метода холодной ковки, для каждого из них требуется многократное усилие.Чтобы машина прослужила долго, она должна выдерживать эту силу.
- Несколько операций — Современные машины для холодной штамповки или формовки, называемые коллектором, выполняют от одной до нескольких операций за один процесс. Это необходимо, поскольку существует ограниченная степень деформации, которую можно выполнить за один ход.
Виды оборудования для холодной штамповки:
Гидравлический штамповочный молот —Гидравлический штамповочный молот разработан для обеспечения максимальной силы при минимальных затратах.Он может производить широкий ассортимент оттисков из различных штампов. Он работает с использованием инженерных концепций гидравлики, когда несжимаемая жидкость находится в цилиндре. Когда жидкость сжимается поршнем, вал с прикрепленной матрицей опускается на заготовку.
Винтовой пресс —Винтовой пресс используется для большой деформации из-за низкой скорости прессования. Его можно использовать для штампов без заусенцев и поковок с длинными прутками.Конфигурация винтового пресса позволяет использовать его для однопроходных штампов, которые включают гибку и окончательную штамповку. Электродвигатель обеспечивает вращение винта, который прижимает матрицу к заготовке.
Высокоскоростной пресс с С-образной рамой —Конструкция с С-образной рамой подходит для операций формовки, штамповки, гибки и многопрессовки. Они бывают с одним или двумя кривошипами, с усилием штамповки от 110 до 400 тонн и ходом скольжения от 110 до 280 мм.Они могут работать с высотой штампа от 435 до 600 мм и могут использоваться для производства мелких деталей.
Пневматический силовой пресс —Пневматический приводной пресс может выполнять весь спектр функций штамповки. Они оснащены фрикционной муфтой и тормозом с пневматическим приводом. Мощность пресса создается воздушным компрессором, который прижимает ковочный молот к заготовке за счет давления воздуха в цилиндре с поршнем.
Механический холодный пресс —Из разновидностей машин холодной ковки механическая версия становится наименее используемой, поскольку они должны быть очень большими для обеспечения необходимого усилия.У них есть маховик, накапливающий энергию от двигателя. Когда маховик приводится в действие, он вдавливает молоток или трамбовку на матрицу. Он может обеспечивать мощность в течение нескольких оборотов, но должен работать на холостом ходу, чтобы восстановить мощность своего двигателя, прежде чем он сможет продолжить свои циклы.
Из множества разновидностей оборудования для холодной штамповки наиболее распространенными являются гидравлические и пневматические, поскольку они занимают меньше места, могут обеспечивать различное усилие и являются программируемыми. Когда вы исследуете свой выбор для производства, лучше всего знать, какие типы оборудования имеет производитель, поскольку современное оборудование с большей вероятностью будет производить детали более высокого качества.
Холодная ковка предлагает широкий выбор металла для проекта. Различные разновидности включают твердые металлы, такие как углеродистая сталь, легированная сталь и нержавеющая сталь. Алюминий, латунь, медь, кремний и магний — мягкие металлы, которые можно использовать. Единственное требование к любому металлу — это его твердость 44 HRC или ниже по шкале Роквелла.
Медь —Медь — отличный металл для холодной ковки, поскольку она очень пластичная и ковкая.Ему можно придать форму, согнуть или потянуть с небольшим усилием, а детали из него устойчивы к коррозии и ржавчине.
Алюминий —Алюминий — это цветной металл, который очень легкий и имеет низкую плотность. Он имеет температуру плавления 1220 ° F, податлив, устойчив к ржавчине и коррозии.
Углеродистая сталь —Углеродистая сталь представляет собой сплав железа и углерода.Различные сорта зависят от количества углерода, смешанного с железом. Он обладает исключительной прочностью и пластичностью.
Нержавеющая сталь —Нержавеющая сталь стала одним из наиболее часто используемых металлов благодаря своей коррозионной стойкости, внешнему виду и прочности. Хотя термин нержавеющая сталь обычно используется для описания любой стали, имеющей свои характеристики, нержавеющая сталь бывает разных марок в зависимости от содержания в ней сплава.
Стали для холодной ковки —
Низкоуглеродистые стали с содержанием углерода 0.От 1% до 0,25%. Холодная ковка улучшает деформационное упрочнение стали, устраняя необходимость в аустенизации, закалке или отжиге.
Соображения при выборе металла:Металлы, пригодные для холодной штамповки Подходящий сплав Характеристика деформируемости в холодном состоянии Медь Отлично Золото, серебро и большинство их сплавов Отлично Латунь — Картридж Латунь Хорошо Платина, палладий, тантал и их сплавы Большинство из них формуются холодным способом. Титан и его сплавы Чистый Ti и сплавы с высокой пластичностью, да, но сплавы типа 6-4 подходят только для горячей головы. Никель и его сплавы Чистый Ni — да, сплавы с относительным удлинением при комнатной температуре 20% и более — да. Чугун и сталь Чистое железо, да. Стали, в зависимости от стали. Многие из них поддаются холодному формованию.
Данные с сайта https://www.deringerney.comСамое логичное и важное, что вы можете сделать, выбирая металл для проекта, — это провести исследование.Каждый тип металла по-разному реагирует на пластификацию и деформацию. Выбранный вами металл должен соответствовать его конечному использованию и требуемой прочности. Если вы проконсультируетесь со специалистом по кузнечному делу, вы получите ценную информацию, которая поможет вам сделать правильный выбор.
Глава восьмая — Применение холодной штамповки
Холодная штамповка позволяет получать формы любого размера с высокой точностью размеров и структурной точностью.Экономическая эффективность и скорость холодной ковки сделали ее самой популярной производственной альтернативой.
Холодная штамповка отвечает требованиям современной промышленности, потому что:
- Максимальное использование сырья: Основное вложение для любой операции — сырье. В процессе холодной ковки очень мало отходов. Вспышку и обрезку можно вернуть в производственный процесс.
- Снижает затраты: Поскольку детали производятся быстро, стоимость единицы продукции очень низкая, что делает конечные продукты более прибыльными и менее дорогими в производстве.
- Производит высококачественные детали: Холодная штамповка увеличивает прочность и долговечность деталей и изделий, гарантируя их долгий срок службы. Структура и характеристики фасонного изделия не меняются, обеспечивая превосходную точность размеров.
Применения, в которых используются детали холодной ковки:
Автомобили —Высокая прочность, надежность, качество и доступная цена сделали холодную штамповку очень привлекательной для автомобилестроения.Холоднокованые детали устанавливаются в местах высоких нагрузок из-за их превосходной ударопрочности. Такие компоненты, как трансмиссии, приводные валы, стойки или амортизаторы, изготавливаются методом холодной ковки. На схеме ниже показаны некоторые детали ходовой части автомобиля, изготовленные методом холодной штамповки.
Ручной инструмент и скобяные изделия —Соединители, такие как гвозди, болты, заклепки и гайки, производятся методом холодной ковки в течение многих лет. Низкие допуски и превосходная точность размеров — вот почему производители ручных инструментов предпочитают холодную ковку другим методам, например, механической обработке.
Военные —Военные имеют очень строгие правила в отношении военной техники и выбирают холодную штамповку для производства гильз, пуль и другой военной техники. Детали обладают высокой надежностью и работоспособностью в условиях кризиса. Низкие допуски и прочность деталей делают их идеальными для боевого оружия.
Производство зубчатых колес —Холодная штамповка используется для производства зубчатых колес, поскольку она устраняет необходимость в нарезании зубчатых колес.Зубчатые колеса могут быть изготовлены из заготовок менее 50 мм или профилированы с использованием витой проволоки. Для снятия остаточных напряжений и наклепа может потребоваться некоторый отжиг. Важным преимуществом зубчатых колес холодной ковки является то, насколько плавно и бесшумно они зацепляются.
Заключение
- Холодная штамповка позволяет получать металлы с низкими допусками и высокой точностью размеров при очень низкой стоимости и больших объемах.
- Холодная штамповка быстро и быстро создает готовые детали, которые сразу становятся доступными и готовыми. Производители
- предложат вам широкий выбор процессов для производства именно той детали, которая вам нужна, с использованием самого современного и технически совершенного оборудования.
- У вас будет широкий выбор металлов для завершения вашего проекта от закаленной стали и нержавеющей стали до меди и алюминия.
- У вас будет очень мало ограничений на количество продуктов, которые вы можете производить из устойчивых к нагрузкам компонентов вашего автомобиля, заклепок, шестерен и рабочих инструментов.
- Сравнивая холодную и горячую штамповку, вы обнаружите, что холодная штамповка занимает меньше времени и дает более прочные и долговечные детали и изделия.
Как построить кузницу
.
POP Projects — это коллекция новых и классических проектов из более чем столетней коллекции Popular Mechanics .Овладейте навыками, получите рекомендации по инструментам и, что наиболее важно, создайте что-то свое.
Если вы хотите работать с металлом, есть одна вещь, с которой вам придется столкнуться: вам нужно тепло. С его помощью вы можете заставить самый прочный металл подчиниться своей воле. Без него вы никогда не получите полного мастерства над этим трудным материалом.
На протяжении многих лет меня разочаровывала моя неспособность работать с горячей сталью. Я скрепил металл болтами, сварил и припаял. Но я не мог его сформировать, и такие большие участки механического царства были для меня недоступны.
Но кузнечное дело никогда не было чуждым. Мой отец — металлург, потомок кузнецов XIX века. Родился в Германии в семье судостроителей, чьи кузницы разбрасывали искры по берегам реки Эльбы и Северного моря. Я вырос в сельском Коннектикуте среди механиков-янки, которые могли что-нибудь выковать, обработать, построить что угодно, что угодно починить — и я всю жизнь пытался соответствовать стандартам тех старожилов. Было нетрудно наконец решиться сделать еще один шаг и научиться некоторым кузнечным навыкам.
Строительство кузницы
Популярная механика
Может быть, из-за того, что наша промышленность по производству дымовых труб находится в упадке, все большее число американцев чувствуют потребность в ремонте металлообработки в домашних мастерских. Ассоциация художников-кузнецов Северной Америки насчитывает в своем составе 4000 любителей и профессионалов. По некоторым оценкам, сегодня в этой стране больше кузнецов, чем в 1800-х годах.И вам не придется долго копаться, чтобы найти десятки веб-сайтов, предлагающих дружелюбные — даже страстные — советы мастеров, а также оборудование, от наковальни и клещей до пневматических молотов.
Сначала мне понадобилась кузница. Я рассматривал возможность покупки модели с газовым двигателем, но факт был в том, что я хотел построить свою собственную. Поэтому я остановился на дизайне, который можно реализовать днем, используя детали, купленные в домашнем центре, на кладовой и в магазине автозапчастей. Кузница будет сжигать уголь, а не газ, чтобы все было проще.И у дизайна было еще одно достоинство, по крайней мере, с моей точки зрения. Он был основан на планах, опубликованных в журнале Popular Mechanics в июле 1941 года.
Популярная механика
Я заручился помощью Майка Аллена, бывшего старшего автомобильного редактора журнала Popular Mechanics и опытного слесаря. Он взглянул на старые планы и сказал: «Конечно, мы можем построить это». В течение нескольких дней в доме Майка и в магазине за ним кипела активность, когда парень из UPS быстро доставил 275-фунтовую наковальню, инструменты, материалы и четыре 50-фунтовых ящика кузнечного угля, отправленные из Пенсильвании.
Когда припасы были поданы, мы приступили к строительству кузницы, начиная с ее стенда. Я вырезал стальные детали и передал их Майку, который разложил их в цехе, скрепил их вместе и временно прихватывал небольшими стальными шариками.
Закрепив подставку, он поднял маску и протянул мне сварочный пистолет: «Возьми его отсюда». Я надел маску и продолжил с того места, где он остановился. Пока я работал, Майк склонился над моим плечом и давал советы.«Получите больше сварочного металла на вертикальных поверхностях», — сказал он. «Вы получаете слишком много брызг; уменьшите скорость движения и вылет электрода». Когда мне стало трудно видеть сквозь сварочные блики и дым, он сказал: «Разберитесь с этим. Смотрите на сварочную лужу, а не на дугу». За эти полчаса я узнал о сварке больше, чем за годы дурачения в одиночку.
Несколько кузнечных инструментов, которые вам понадобятся
Щипцы для челюсти кузнеца
Калибурн
Кузнечный молот, 48 унций
Отвес
Шаровой молоток на 40 унций
Кузница: Раковина из нержавеющей стали с двумя чашами служит центром нашей кузнечной установки.Один бассейн заполнен водой, образуя закалочную емкость. Другой облицован печным цементом, а затем облицован огнеупорным кирпичом, уложенным на месте без раствора. Чугунная крышка сливного отверстия в полу, расположенная над сливом раковины, образует фурму — отверстие, через которое поток воздуха (подаваемый производственным вакуумом) входит в угольный пласт снизу.
Огнеупорный цемент, кирпич: Огнеупорная глина Rutland Black Furnace Цемент был затерт в раковину, чтобы защитить ее. Огнеупорный кирпич продается в кладочных центрах.
Forge Fuel: Penn Keystone Coal продает кузнечный уголь на основе битумного и антрацита чистого горения в 50-фунтовых мешках, защищенных картонной коробкой.Один фунт дает удивительные 14 373 БТЕ.
Колпак и вентиляционное отверстие: Листовой металл 20 калибра и 5-дюйм. оцинкованная дымовая труба образовывала вытяжку и вентиляционное отверстие кузницы. Материалы обычно доступны в домашних центрах.
После того, как мы завершили стенд, мы приклепали листовой металл к вытяжке и сделали дымоход из 5-футового куска дымохода. Затем мы затерли в раковину тугоплавкий цемент (из тех, что используются в печах). Мы проложили стальные и ПВХ трубы от слива к выходному отверстию на заводском вакууме.Одна и та же линия будет подавать воздух как в раковину (для разведения огня), так и через Y-образное соединение в другую трубу, ведущую в дымоход (чтобы помочь вытягивать дым вверх и прочь). Мы установили клапан, чтобы направить воздух туда, куда нам нужно.
Мы также разрезали обработанные давлением пиломатериалы 4 x 4, чтобы сделать блок для наковальни, затем подняли наковальню на блок, используя буксирный ремень, прикрепленный к электрической лебедке, установленной на потолке. Наконец, мы забили стальной плоский приклад толщиной 1/8 дюйма в ленты, чтобы прикрепить наковальню к блоку.Поверьте, 15 минут, потраченных на обстрел холодного оружия, могут убедить любого в необходимости кузницы.
Теперь нам просто нужно было дать цементу в печи затвердеть в течение ночи.
Поджигание угля
Я прибыл в магазин Майка рано утром и обнаружил, что он возится с чашкой кофе в руке и еще одной, недавно налитой, ожидающей меня на верстаке. «Готовы к огню?» он спросил.
Мы вынесли кузницу на улицу и при легком осеннем ветре использовали пропановую горелку, чтобы поджечь крошащуюся транспортную бумагу и растопку, отколовшуюся от поддона, на котором была отправлена наковальня.Когда огонь стал ярким и горячим, мы уговорили его углем и с тревогой наблюдали, как он испускает слабый желто-зеленый, сернистый дым. Мы добавили топлива. Огонь тлел упорно, но, когда мы свернули на нашем сверхмощного вакууме, взрыв воздуха сбил нашу маленькую угольную кучу из положения. Мы оттолкнули тлеющие куски стальным стержнем и попробовали снова, но безуспешно.
Пару минут спустя мы вытащили металл и обнаружили, что он просто стал светло-голубым — тепла все еще недостаточно.
Майк взял воздушный шланг и сопло из своего компрессора в магазине и слегка потянул. Теперь уголь начал светиться. Мы добавили еще топлива, и дым почти исчез. Мы снова включили магазинный пылесос. При этом из кузницы раздался впечатляющий шум, и центр угольной насыпи покраснел, как светофор. Несколько мгновений спустя ярко-желтое пламя вырвалось из горючего, а затем над ним возникло призрачное синее сияние. Пока он парил, синий свет выглядел как живое существо.
Как только уголь стал хорошо гореть сам по себе, я взял кусок металлолома из цеха и затолкал сталь в вулканический горючий слой. Пару минут спустя мы вытащили металл и обнаружили, что он просто стал голубым — тепла все еще недостаточно. Майк повернул клапан, чтобы весь выходящий из вакуума воздух устремился в огонь, питая пламя. (Отсюда старый кузнечный термин «полный взрыв».) Мы с трепетом наблюдали, как в центре угля образовалось желто-белое свечение, а сталь потерялась в ярком свете.Свет был слишком интенсивным, чтобы смотреть на него без затемненных защитных очков.
Работа со сталью
Через пару минут я взял щипцы и вынул сталь. Конец теперь светился ярко-желтым и извергал искры — температура, должно быть, была около 1900 F. Я положил металл на край наковальни и взял наш кузнечный молот весом 48 унций. Достаточно нескольких ударов, чтобы штанга аккуратно изогнулась.
После десятилетий борьбы с ножовками и заклепочными пистолетами я не могу передать, как приятно было приложить молоток к раскаленной стали и согнуть ее, как замазку.Механическое правосудие восторжествовало.
Последовал долгий день, когда мы с Майком практиковали основы старинного кузнечного ремесла: сгибание, сплющивание, скручивание, сужение и опрокидывание — удары по прутку для утолщения и увеличения его горячего конца. Мы использовали угловое железо, чтобы сформировать лучший инструмент для работы с углем, который я видел — изогнутую огненную кочергу, достойную кузнечной мастерской верфи. И мы почувствовали себя достаточно смелыми, чтобы попробовать свои силы в изготовлении долота для сноса из прутка инструментальной стали диаметром 3/4 дюйма — высокоуглеродистого материала, намного более прочного, чем те, что продаются в строительных магазинах.Нам пришлось трижды дать стали пропитаться огнем в кузнице и несколько минут размахивать молотком, прежде чем она начала подтачиваться.
На закате мы остановили работу и дали топливному слою остыть до пепла. Мы подметали цех и складывали инструменты на ночь, уже планируя будущие проекты. Научиться кузнечному делу и основам кузнечного дела за два дня было хорошей работой. Но у Майка были планы на змеевидную железную стойку для хранения мотоциклетных шлемов, а я хотел еще раз создать свои собственные инструменты, специально разработанные для моих нужд.
Вот как я представляю себе, что железный век начался в доисторические времена, в кузнице, подобной той, которую археологи нашли разбросанной по всей Африке и на Ближнем Востоке. Какому-то парню нужен был инструмент получше, и он придумал, как его сделать.
Было темно, когда я опустился на сиденье машины и направился домой. Когда я выехал на шоссе и попал в пробку, я по-новому увидел задние фонари впереди идущих машин. Только сегодня вечером они не доставляли хлопот. Они были похожи на гигантский слой раскаленных углей, ожидающий своей стали.
Этот контент создается и поддерживается третьей стороной и импортируется на эту страницу, чтобы помочь пользователям указать свои адреса электронной почты. Вы можете найти дополнительную информацию об этом и подобном контенте на сайте piano.io.
Что такое гидроформинг своими руками? — Jones Metal Products
Когда мы смотрим на то, что это такое гидроформование, это процесс изготовления и формовки металла, который позволяет формовать различные металлы, такие как нержавеющая сталь, латунь и алюминий.В целом, этот процесс является довольно рентабельным, когда речь идет о производстве, благодаря использованию штампов и инструментов в больших производственных партиях. Но можно задать вопрос: что такое гидроформовка своими руками? Это то же самое, что и профессиональная гидроформовка и в чем отличия?
Самостоятельная гидроформовка упоминалась во многих сообщениях на форумах и в видеороликах на YouTube за последние несколько лет, предлагая альтернативу профессиональным услугам гидроформинга. Детали профессионального качества находят свое применение в проектах «сделай сам», выполняемых домашними строителями, хотя уровень профессионального гидроформования с использованием штампов и инструментов еще не совсем достижим для домашних строителей.Когда дело доходит до гидроформинга своими руками, они нашли способы создавать детали дома с помощью экономных методов, использующих инструменты и вещи, которые могут быть у вас дома.
Что такое гидроформинг своими руками?
Гидроформование своими руками — это процесс изготовления и формовки металла, выполняемый дома с использованием инструментов и материалов, доступных в домашних условиях. Поскольку гидроформовочные прессы часто выходят за пределы ценового диапазона для частных лиц, гидроформование своими руками стало популярным методом для многих строителей. Эти строители варьируются от людей, которые хотят создавать детали небольших самолетов для своих собственных проектов, до тех, кто хочет гидроформовать более крупные металлические детали для использования в различных проектах.
Самодельная гидроформовкаприменялась строителями дома по-разному, с использованием самодельных прессов и даже мойок высокого давления, которые могут быть у вас в собственном гараже.
Один из способов гидроформовки своими руками — это использование блока резины, помещенного в стальной ящик с матрицей и гидравлическим прессом, который был приобретен у Harbor Freight. Используемая коробка была создана вручную, а самодельную прессовую установку можно использовать для изготовления деталей, необходимых для любого проекта, который хочет выполнить домашний строитель.
Другой домашний метод гидроформовки своими руками включает в себя сварку листового металла желаемой формы, добавление трубного фитинга к детали и использование мойки высокого давления для создания гидроформованных металлических деталей. Форма, созданная путем сваривания листового металла, может в конечном итоге создать несколько интересных деталей для гидроформовки своими руками.
Поскольку при гидроформовке действительно используется вода за счет равномерного распределения давления по металлу внутри формы, эти методы гидроформинга своими руками, безусловно, представляют собой интересный вариант профессиональных услуг гидроформинга, доступных на рынке.
Важно отметить, что домашние методы могут представлять опасность и для строителя дома. Как и в случае с любым процессом домашнего строительства, создание собственных методов может быть опасно для вас и других.
Разнообразные видеоролики YouTube предлагают пошаговые инструкции по созданию собственных процессов гидроформинга своими руками в домашних условиях, которые могут быть особенно полезны при ответе на вопрос «что такое гидроформование своими руками?».
Различные доступные ресурсы показывают, что гидроформовка своими руками может быть сложной задачей.Разработка собственного штампа и фактическое использование процесса формовки может сводиться к искусству. Метод проб и ошибок, безусловно, является ключевым фактором в обучении гидроформингу своими руками. Маленькие и простые детали часто могут быть лучшим способом начать работу, прежде чем переходить к более сложным и крупным деталям.
Некоторые детали, которые домашние строители потенциально могут создать с помощью гидроформинга своими руками, включают:
- Колена
- Конусы
- Предметы искусства и дизайна
- Рамы велосипедные
- Детали малой авиамодели
- Шестерни
- Зажимы
Если вы рассматриваете услуги гидроформинга помимо гидроформинга своими руками, рассмотрите возможность обращения в Jones Metal.
Листогибочный пресс имеет некоторые из недостатков штамповки, а также некоторые недостатки.
Листогибочный пресс также не подходит для более длинных деталей. Также он не превосходит сложные изгибы, углы и радиусы.
Отличие заключается в том, что на самом деле он намного лучше для заказов с небольшим объемом, чем для заказов с большим объемом.
Как правило, листогибочный пресс дает противоречивые результаты. Никогда не знаешь, когда у тебя останется царапин и других следов инструмента .
К гибочным прессам относятся детали из листового металла.
Профилирование валков Vs. Экструзия
Теперь все становится немного интереснее. Экструдирование немного более конкурентоспособно с профилированием, чем наши первые два участника.
Во-первых, плохо. При крупносерийном производстве экструзионное оборудование и инструменты могут быть очень дорогими. Все требует вторичной обработки, и нет дополнительных операций, которые можно было бы выполнять в оперативном режиме.
Экструзия — это еще один процесс, ограниченный размерами компонентов. Следует учитывать длину детали; тонких компонентов — тоже вызов .
Тем не менее, нет недостатка в областях, в которых экструзия предпочтительнее, чем детали, формованные прокаткой, особенно при работе с алюминием. Структурные формы часто изготавливаются с помощью горячей прокатки (сочетание экструзии и прокатки) для достижения хорошего баланса веса и прочности.
Помимо структурных компонентов, приложения для экструзии включают:
Профилирование валков Vs.Литье
Литье часто препятствует конкуренции со стороны порошковой металлургии, но бывают также случаи, когда прокатка сталкивается с ним.
С точки зрения эффективности литье не подходит для больших партий. С точки зрения качества, он производит детали с высокой пористостью — что, в зависимости от вашего применения, может быть большим запретом.
Вот области применения, в которых литье становится жизнеспособным:
Профилирование валков Vs.Ковка
Тепло, возникающее при ковке, приводит к очень твердым компонентам. Иногда это хорошо; в других случаях это буквальный рецепт неудачи. Высокая твердость отлично подходит для деталей, которые должны противостоять вмятинам и царапинам. Но с твердостью приходит хрупкость — компоненты с высокой твердостью имеют низкую ударопрочность, что делает их опасными для некоторых транспортных проектов.
Итак, где же стоит посмотреть поковки?
Делаем это внутри компании Vs.Аутсорсинг
Возможно, вы пришли к выводу, что профилирование хорошо подходит для вашего проекта. Если да, то что теперь?
Нужно принять решение — делать это самому или использовать контрактный прокатный станок.
Внедрение процессов профилирования в ваш бизнес — сложное вложение. Это больше, чем просто покупка профилегибочного станка, который можно включать и выключать по мере необходимости. Существуют дополнительные затраты и риски, которые многие предприятия, не специализирующиеся на профилировании, не могут понять — пока не станет слишком поздно.
Это не значит, что вы не можете этого сделать. Ваш уровень успеха просто зависит от ваших конкретных операций, потребностей и целей.
У вас есть три варианта: