Точный расчет количества электродов, необходимых для сварки – это один из самых важных моментов при подготовке к сварочным работам. От точности расчетов зависит результат сварочного процесса, эффективность и правильность распределения денег на покупку расходных материалов. Чтобы правильно рассчитывать необходимую массу электродов, нужно учитывать следующие параметры:
Норма расхода электродов в сварочном процессе – это максимальное количество расходуемого при производстве продукции материала, если соблюдаются все необходимые технологические требования. Существует несколько способов, которые помогают точно рассчитывать расход электродов. Самым популярным методом для расчета является подсчет массы наплавленного металла. По этому методу результат расчета расхода электродов выводится в килограммах. Чтобы рассчитать расход электродов по этому методу, можно воспользоваться формулой: Н = М * К(расх.). М – масса наплавленного металла, К(расх.) – коэффициент расхода электродов. Массу наплавленного металла можно узнать, если посчитать площадь сечения сварочного шва и умножить ее на длину шва и густоту металла. Коэффициент расхода электродов можно узнать ниже:
Теперь проведем расчеты. Теперь перейдем к теме вельдолетов. Вельдолет – это усилитель, который применяется в качестве отводного патрубка для случаев, когда нужно соединить трубопровод. Вельдолеты отличаются высоким уровнем безопасности и надежностью эксплуатации. Их используют для соединений, где высокая температура, а в условиях эксплуатации соединение будет подвергаться высокому давлению. Основные способы соединения с помощью вельдолетов – это стыковая сварка, сваривание внахлест или резьбовое соединение. Рассчитать расход электродов при сварке вельдолетов можно с помощью все той же формулы: Н = М * К(расх.). |
Расчет норм расхода сварочных материалов при сварке корпуса цистерны замещения
Расчет сварочных материалов производится по РД5.УЕИА.2585-88 [44]
Уровень механизации сварочных работ при совершенствовании технологического процесса составляет 75%, из которых объемы применения автоматической сварки составляют 28%, а полуавтоматической сварки 72%.
Суммарная масса наплавленного металла , кг, определяется по формуле
, (6.1)
где — масса свариваемого проката, т;
— норматив массы наплавленного металла на тонну свариваемого проката, кг;
.
Для выполнения плавных сопряжений сварного шва и усилений обварки конструкций суммарная масса наплавленного металла , кг, увеличивается на 5 %
.
Масса наплавленного металла при выполнении прихваток составляет 10 % от общей массы наплавленного металла
.
Масса металла, наплавленного проволокой при автоматической и полуавтоматической сварке , кг, определяется по формуле
, (6.2)
где А – уровень механизации, %;
.
С учетом прихваток масса металла, наплавленного проволокой при автоматической и полуавтоматической сварке , кг, составит
.
Масса металла, наплавленного автоматической сваркой под слоем флюса и полуавтоматической в среде углекислого газа, распределяется в соответствии с долей участия данного способа сварки на данном предприятии.
Масса металла, наплавленного автоматической сваркой под слоем флюса , кг, определяется по формуле
, (6.3)
.
Масса металла, наплавленного полуавтоматической сваркой в среде углекислого газа , кг, определяется по формуле (6.3)
.
, (6.4)
где — коэффициент перехода от массы наплавленного металла к расходу сварочных материалов в соответствии с приложением 6 [44];
Норма расхода порошковой проволоки марки ПП-А22/9H, кг, определяется по формуле (6.4)
.
Норма расхода проволоки марки Св – 09Х16Н25М6АФ для автоматической сварки H, кг, определяется по формуле (6.4)
.
Норма расхода флюса марки 48-ОФ-6М H, кг, определяется по формуле (6.4)
.
Норма расхода двуокиси углеродаH, кг, определяется по формуле (6.
.
Норма расхода аргонаH, кг, определяется по формуле (6.4)
.
Масса металла, наплавленного ручной дуговой сваркой ,кг, при совершенствовании технологии определяется по формуле
, (6.5)
.
Норма расхода электродов , кг, для изготовления конструкций на заказ в целом при совершенствовании технологии определяется по формуле
, (6.6)
.
Электроды ЭА-48М/22 для подварки корня шва при совершенствовании технологии составляют 30% от общего расхода электродов
.
Норма расхода электродов , кг, для изготовления конструкций на заказ в целом по существующей технологии определяется по формуле
, (6.7)
.
Электроды ЭА-48М/22 для подварки корня шва по существующей технологии составляют 30% от общего расхода электродов
.
Масса наплавленного металла при выполнении плавных сопряжений , кг, вычисляется по формуле
, (6.8)
.
Норма расхода электродов марки ЭВИ-1 для оплавления сварных швов , кг, вычисляется по формуле
, (6.9)
.
Норма расхода проволоки Св – 09Х16Н25М6АФ для ручной аргонодуговой наплавки , кг, вычисляется по формуле (6.9)
.
Норма расхода аргонадля оплавления сварных швов , кг, определяется по формуле (6.9)
.
Определение потребности в сварочных материалах
Потребность цеха, участка и всего предприятия в электродах и сварочной проволоке для выполнения заданного объема работ можно определить по количеству наплавленного металла.
Расход электродов Qэл (кг) определяют по формуле
Qэл = QнКэ,
где Qэл — масса наплавленного металла, определяемая по сечению и длине шва, кг; Кэ — коэффициент расхода электродов, учитывающий массу обмазки и потерн на огарки, разбрызгивание, угар металла.
Расход проволоки Qпр при автоматической сварке под флюсом и сварке в среде защитных газов принимается равным массе наплавленного металла, умноженной на коэффициент потерь:
Qпр = QнКп,
где Кп — коэффициент потерь проволоки на угар и разбрызгивание. Для сварки под флюсом Кп принимают равным 1,02— 1,05; для сварки в среде защитных газов — 1,08—1,15.
Расход флюса принимается равным расходу сварочной проволоки, а расход углекислого газа в зависимости от условий выполнения работ, конфигурации свариваемых изделий и преобладающего количества угловых или стыковых швов берется ориентировочно от 0,6 до 1,1 массы, израсходованной на сварку сварочной проволоки, или 120—240 л/мин.
Расход электроэнергии в киловатт-часах определяют по массе наплавленного металла через показатель удельного расхода электроэнергии на 1 кг наплавленного металла. Этот показатель зависит от рода тока (при сварке на постоянном токе расход энергии больше, чем при сварке на переменном) и времени работы источника тока на холостом ходу (чем больше работает источник без нагрузки, тем больше расход электроэнергии на 1 кг наплавленного металла).
Ориентировочно можно принимать расход электроэнергии при сварке на переменном токе 3—4 кВт·ч/кг и при сварке на постоянном токе 4—6 кВт·ч/кг. Однако при выборе сварочного тока следует отдавать предпочтение постоянному (и лучше от выпрямителя) как более технологичному.
Существенная экономия материальных и энергетических ресурсов при выполнении сварочных работ возможна на основе сокращения удельного расхода наплавленного металла при изготовлении металлических конструкций.
Экономия наплавленного металла производится на основе осуществления конкретных мероприятий, обеспечивающих:
повышение уровня механизации и автоматизации сварочных работ;
повышение эффективности использования сварочных материалов;
повышение качества подготовки полуфабрикатов и сборки конструкций;
повышение качества сварочных работ;
расширение применения неразрушающих методов контроля;
обучение сварщиков передовым методам труда;
улучшение учета расходования сварочных материалов.
Сварочные материалы следует выдавать на рабочее место в количествах, необходимых для односменной работы и хранить в условиях, предохраняющих их от воздействия влаги и повреждений.
Расход электродов при сварке
Подсчет расхода электродов при сварке — процедура необходимая на стадии планирования сварочных работ. Для того чтобы правильно рассчитать необходимое количество электродов, следует взять во внимание такие основные факторы как масса наплавленного металла, норма расхода сварочных электродов и длина шва. Корректные расчеты позволяют сделать процесс более эффективным и результативным.
Расход электродов при сварке – величина, которую должны рассчитывать специалисты, которые будут выполнять необходимые сварочные работы. Это нужно для того, чтобы расчеты были выполнены в соответствии нюансами будущих сварочных работ.
Стоит сказать, что для того, чтобы рассчитать расход электродов при сварке, существует множество методик. Во многих странах приобрела популярность и широкое использование методика определения необходимого количества электродов по массе наплавленного металла. Именно по этой причине единица измерения электродов – это килограммы. Количество электродов, необходимых для сварочных работ, определяется согласно формуле — Н=М*Красх. М – это масса наплавленного металла (измеряется в килограммах), Красх — коэффициент расхода электродов.
Чтобы определить массу наплавленного металла, необходимо площадь поперечного сечения наплавленного металла умножить на плотность и на длину шва.
При расчете коэффициента расхода электродов при сварке следует учитывать такие критерии как угар, разбрызгивание, длина огарка. Эти нормативы зависят от марки используемых электродов. В среднем этот показатель составляет 1,6. Стоит учитывать, что при работе с нержавеющими и жаропрочными деталями, этот коэффициент может увеличиться до 1,8.
Существует еще одна формула, в которой учитываются эти показатели. Выглядит расчет этого нормированного показателя следующим образом: N=QH+q1+q2. В этой формуле QH – это показатель массы наплавленного металла, q1 — это потери на разбрызгивание и угар; q2 — потери на огарки электродов.
Если нет возможности рассчитать теоретическое количество по массе, то следует прибегнуть к практическим расчетам. В этом случае следует произвести сваривание металлических элементов определенным количеством необходимой марки электродов. Во время сварки следует применять тот же тип сварочного соединения, режима сварочного тока и пространственного положения сварки, что и для последующих работ. После этого следует определить длину шва и рассчитать нужное количество электродов для сварки.
Поскольку приобретение электродов – это значительная статья расходов любых сварочных работ, возникает вопрос, как можно сэкономить расход электродов при сварке? Главное – чтобы тип, показатели силы тока и напряжения электродов четко соответствовали виду сварочных работ, для которых они применяются.
Также необходимо применять автоматическую и полуавтоматическую сварку. Эти виды сварки позволяют уменьшить расход электродов при сварке за счет меньшего процента разбрызгивания. Если при ручной сварке этот показатель составляет 5%, то при автоматической и полуавтоматической – меньше 3%.
Купить ПВЛ просечно-вытяжной лист в Алматы
Источник: nanolife.info
Расход проволоки при сварке полуавтоматом
Расход сварочной проволоки — Ковка, сварка, кузнечное дело
Механизированный сварочный процесс легированной проволокой в среде углекислого газа получил широкое распространение в разных отраслях народного хозяйства. Это обуславливается его технико-экономическими преимуществами в сравнении, прежде всего, с ручным сварочным процессом покрытыми электродами, а в ряде случаев, также и сварочным процессом под флюсом (сварка короткими швами).
Расходование газа и легированной проволоки достигли больших объемов, а также имеют тенденцию к устойчивому росту. Широкое распространение в последнее время получило использование смеси аргона и углекислого газа (75-80%Аг + 20-25% СО2). Сварочный процесс в газовой смеси обладает лучшими технологическими характеристиками. Рациональное использование расходных сварочных материалов является важным моментом в развитии сварочного производства.
Расход сварочной проволоки и защитных газов являются важными составляющими резерва экономии в разработке и внедрению прогрессивных нормативов использования расходных сварочных материалов. Реализация этого способна обеспечить экономию затрат при производстве продукции и следовательно, поспособствует повышению ее конкурентоспособности.
Расчет расхода сварочной проволоки
- При сварке полуавтоматом расход сварочной проволоки зависит от свариваемого металла, диаметра проволоки, характеристик сварочного полуавтомата, отсутствия или наличия защитного газа.
- Обычно расход проволоки не превышает 1,5 процента от массы свариваемой конструкции.
Необходимо, также отметить, что ее расход от 2 до 6 процентов больше веса наплавляемого металла с учетом угара металла и отходов в процессе выполнения сварки.
- Нормы расхода по конкретному виду проволоки на один метр шва можно определить по соотношению M = HР ∙ KР, где, М – масса наплавляемого материала, которая дифференцирована по толщине металла и виду сварочного соединения, КР – коэффициент расходования проволоки, который определяется по специальным таблицам, в зависимости от диаметра сварочной проволоки и ее типа он может меняться.
- По количеству наплавленного материала для выполнения конкретного объема работ определяется потребность участка, цеха и всего предприятия в сварочной проволоке.
kovka-svarka.net
Расчет норм расхода сварочных материалов, страница 2
Величина Кур определяется экспериментально, путем наплавки валика на пластину или расчетным методом по формуле:
Кур = 100 / Кп,
где Кп – коэффициент перехода металла электрода в шов, %;
Значение величины Кп указывается в паспорте электрода.
Величина Ког определяется по формуле:
Ког = Lэ / Lэ · lо,
где Lэ – полная длина электрода по ГОСТ 9466, мм;
lо – длина огарка по ГОСТ 9466, мм.
Величина Кпокр определяется экспериментально или рассчитывается по формуле:
Кпокр = (100 +q) / 100,
где q – коэффициент массы покрытия, указанный в паспорте электрода, %.
Значение коэффициентов Кур, Ког, К покр, Кп зависят от марки, диаметра применяемых электродов и приведены в /1/.
2.2 Полуавтоматическая сварка в среде углекислого газа
Норматив расхода сварочной проволоки при полуавтоматической сварке плавящимся электродом в среде углекислого газа устанавливается исходя из массы наплавленного металла, технологических потерь и отходов и определяется по формуле (1). Величина технологических потерь сварочной проволоки не должна превышать 15%.
Норматив расхода сварочной проволоки принимается равным массе наплавленного металла с коэффициентом потерь Кпр=1,15. При сварке швов малой протяженности (l=0,3м) коэффициент Кпр следует принимать равным 1,3 на кг наплавленного металла.
Норматив расхода углеродистого газа при сварке устанавливается в зависимости от массы наплавленного металла и определяется по формуле (1).
Коэффициент расхода углекислого газа Кг учитывает расход газа на сварку и определяется по часовому расходу и времени сварки, с учетом неизбежных технологических потерь газа на продувку системы, утечку из-за не плотностей присоединения шлангов и остатка в баллоне (цистерне), а также расхода газа на все виды прихваточных работ.
В зависимости от условий выполнения сварки, на основании опытно-производственных данных заводов, величина коэффициента расхода углекислого газа Кг на 1 кг наплавленного металла устанавливается следующая:
— при сварке в закрытых помещениях (цехах), где отсутствует сильный воздухообмен, Кг=1,6кг;
— при сварке на открытых площадках; где имеют место неблагоприятные атмосферные условия (сильный ветер, сильные морозы и т. д.), Кг = 3,0-4,0кг;
— при сварке швов малой протяженностью (l=0,3м) и прерывистых Кг=2,0кг.
2.3 Полуавтоматическая и автоматическая сварка под слоем флюса
Норматив расхода сварочной проволоки определяется исходя из массы наплавленного металла и технологических потерь и определяется по формуле (1).
Сумма всех технологических потерь сварочной проволоки составляет 3% от массы наплавленного металла, следовательно, коэффициент потерь Кпр равен 1,03.
Нормативы расхода флюса входит расход флюса на образование шлаковой корки и технологические потери его на рассыпание, и распыление в процессе сварки и при замене использованного флюса новым.
Нормативы расхода флюса определяется по формуле (1).
Коэффициент расхода флюса Кф (в зависимости от способа сварки и толщины свариваемого металла) приведены в табл.3
Для электрошлаковой сварки конструкций коэффициенты расхода сварочной проволоки и флюса на 1 кг наплавленного металла принимаются следующие:
— для электродной проволоки Кпр=1,05
— для флюса Кф=0,1
Таблица 3
Величина коэффициентов расхода флюса
Марка флюса | Способ сварки | Коэффициент расхода флюса Кф |
ОСЦ-45 АН-348А | Автоматическая сварка под флюсом: на весу на флюсомедной проволоке на флюсовой подушке | 1,2 1,3 1,35 |
ОСЦ-45М АН-348М | Полуавтоматическая сварка | 1,6-1,72 |
2. 4 Электродуговая сварка конструкций из алюминиевых сплавов
Нормативы расхода вольфрамовых электродов, сварочной проволоки и защитного газа при ручной электродуговой, полуавтоматической и автоматической сварках плавящимся и неплавящимся электродом в среде защитных газов учитывают массу наплавленного металла и неизбежные потери, и отходы материалов в процессе сварки.
Норматив расхода сварочных материалов (электродов, проволоки и защитных газов) определяются по формуле (1).
Значение коэффициентов расхода сварочных материалов на 1 кг расплавленного и наплавленного металла для различных способов сварки и сварочных материалов приведены в табл. 4.
Таблица 4
Величины коэффициентов К при различных способах сварки
Способ сварки | Коэффициент перехода от массы наплавленного металла к расходу сварочных материалов | ||
Вольфрамовых электродов | Присадочной проволоки | Аргона м3 | |
Ручная неплавящимся электродом Автоматическая неплавящимся электродом Полуавтоматическая и автоматическая плавящимся электродом | 0,02 0,018 — | 1,25 1,05 1,15 | 3,0 2,6 2,8 |
2. 5 электродуговая сварка конструкций из титановых сплавов
Нормативы расхода вольфрамовых электродов, присадочной проволоки и защитных газов при ручной, полуавтоматической и автоматической сваркой плавящимся и неплавящимся электродами устанавливаются по массе наплавленного металла с учетом неизбежных технологических потерь и отходов материалов при сварке и определяются по формуле (1).
Значение коэффициентов К расхода сварочных материалов на 1 кг расплавленного и наплавленного металлов в зависимости от способа сварки и толщины свариваемого металла приведены в табл.5,6.
При приварке набора к полотнам толщиной до 6 мм включительно, а также при сварке пересекающихся полослбульб норматив расхода газа на поддув с обратной стороны шва необходимо удвоить.
3. Расчета расхода горючих газов при термической резке
Расход газов (кислорода, ацетилена, пропан-бутана и т.д.) при термической резко листового и профильного прокатов определяется по формуле.
Н = N·L + N·V·t·n = N(L + V·t·n),
где Н- расход газа на вырезку детали, л;
N- норматив расхода газа на 1 погонный метр заданной толщины, л/м;
L – расчетная длина реза на одну деталь, м;
V – скорость резки, м/ мин;
t – время нагрева перед пробивкой отверстия, мин. ;
n – число подогревов в начале резки на одну деталь.
Нормативы расхода, скорости резки, времени нагрева приведены /1/.
4.Расчет расхода электроэнергии при электродуговой сварке
vunivere.ru
Расход проволоки при сварке, ее преимущества и принципы выбора
Трубопроводный транспорт мира – одна из новых отраслей в транспортной сфере. Но за время своего существования этот вид транспорта уже успел показать себя как экономически выгодный и наименее затратный. О мировом трубопроводном транспорте и пойдет речь в этой статье.
Добыча серебра в России имеет неплохие показатели. По ним мы занимаем не последнее место в мировом рейтинге. Но вот насколько добыча серебра выгодна для экономики страны и какие дивиденды приносит, мы узнаем из этой статьи.
Металлургическая отрасль – одна из самых важнейших в экономике большинства стран, и Бразилия не исключение. В этой статье познакомим вас с металлургией Бразилии: ее реалиями и перспективами. Посмотрим, какое место эта страна занимает на мировом рынке.
stalevarim.ru
Полуавтоматическая сварка — советы от мастера
С каждым годом дуговая механизированная («полуавтоматическая») сварка плавящимся электродом MIG/MAG становится все более популярной, медленно, но верно вытесняя ручную дуговую сварку покрытыми электродами. Этому способствует появление доступных сварочных полуавтоматов, обеспечивающих качественную, производительную сварку как омедненными проволоками сплошного сечения, так и порошковыми самозащитными сварочными проволоками. Современный сварочный полуавтомат инверторного типа позволяет в полной мере реализовать все преимущества механизированной сварки плавящимся электродом:
- возможность сварки как тонкостенных, так и толстостенных изделий;
- повышение производительности труда;
- «длинные» швы;
- снижение себестоимости сварочных работ;
- высокий коэффициент наплавки, малые потери на угар и разбрызгивание;
- сварка сложных стыков сварщиками низкой квалификации, новичками;
- безопасная работа – ток не поступает до момента поджига;
- отсутствие значительных деформаций свариваемых деталей ввиду меньшего тепловложения;
Важной особенностью многих сварочных полуавтоматов инверторного типа является возможность ручной дуговой сварки штучным электродом (ММА). Приобретая оборудование такого типа, Вы получаете в свое распоряжение универсальный инструмент, позволяющий выполнять обширный спектр сварочных работ.
Особый интерес для частного хозяйства, небольших производств, автомастерских представляет собой использование именно сварочных порошковых самозащитных проволок, ввиду того, что их применение позволяет исключить использование тяжелых баллонов с защитным газом, редукторов и шлангов. Порошковая проволока представляет собой трубчатый электрод с порошкообразным наполнителем – сердечником. Входящие в состав сердечника проволок компоненты при нагреве в сварочной дуге создают необходимую шлаковую и газовую защиту расплавленного металла. Порошковые проволоки позволяют в широких пределах варьировать своим составом и свойствами, ввиду чего сфера их применения практически не имеет ограничений. Как правило, оболочкой порошковой проволоки служит углеродистая сталь, а сердечник представляет собой смесь металлов, сплавов, а также шлакообразующих, газообразующих материалов, стабилизаторов дуги и специальных добавок. Многие при использовании впервые сварочной порошковой самозащитной проволоки жалуются на повышенное разбрызгивание, трудности с качественным формированием сварного шва. Все это проходит с опытом или в более сжатые сроки благодаря возможности точной настройки сварочного аппарата с помощью параметров индуктивности, сварочного тока, напряжения на дуге. Для устойчивого процесса сварки скорость подачи проволоки должна быть примерно равна скорости ее плавления.
Остановимся подробнее на такой крайне полезной функции, как регулировка индуктивности. Для уменьшения разбрызгивания металла во время сварки необходимо сделать плавным сжимающее усилие, возникающее при коротком замыкании. Достигается это с помощью введения в источник сварочного тока регулируемой индуктивности. Максимальная величина сжимающего усилия определяется уровнем тока короткого замыкания, который зависит от конструкции блока питания. Величина индуктивности регулирует скорость нарастания сжимающего усилия. При малой индуктивности капля металла будет быстро и сильно сжата — электрод начинает брызгать (капельный перенос). При большой индуктивности увеличивается время отделения капли, и она плавно переходит в сварочную ванну (струйный перенос). Сварной шов получается более гладким и чистым.
Достаточно часто используется и «классическая» механизированная сварка плавящимся электродом в среде защитных газов. Плавящимся электродом в этом случае является сварочная проволока. В этом случае Вам потребуется баллон с защитным газом (углекислота CO2 или ее смесь с аргоном Ar+CO2), редуктор с расходомером и газовый рукав. Дополнительно, для работы в холодное время года, понадобится и подогреватель газа во избежание перемерзания газосварочного оборудования. Углекислый газ при сварке малоуглеродистых и низколегированных сталей способствует устранению пористости сварных швов. При добавке в количестве 15-25% к аргону повышает стабильность дуги и улучшает формирование шва при сварке, что особенно важно при сварке тонколистовых сталей. Поэтому, рекомендуем Вам использовать газовую смесь – коргон, фогон. Важным недостатком при использовании смеси является ее повышенный расход по сравнению с чистой углекислотой. Расход защитного газа обычно составляет 8-12 л/мин, однако может и отличаться от этих цифр как в большую, так и в меньшую сторону, ввиду различных конструкций газовых сопел горелок, погодных условий и т.д. Наилучшая защита расплавленного металла обеспечивается при ламинарном характере течения газового потока, формирующегося при выходе из сопла горелки. После окончания сварки на большинстве бюджетных сварочных полуавтоматов защитный газ поступает в зону сварки еще в течение 1 с (post gas) для лучшей защиты.
Нельзя не упомянуть о том, что использование более прогрессивного сварочного аппарата, которым и является полуавтомат по сравнению с обычным сварочным источником для ручной дуговой сварки, накладывает повышенные требования по уходу за оборудованием. В обязательном порядке необходимо содержать сварочный аппарат в чистоте, регулярно продувать механизм подачи проволоки и внутренний направляющий канал горелки. Следите за состоянием контактного наконечника и сопла, не допускайте перегиба шланга горелки. Притупляйте напильником острый край проволоки и снимайте токоподводящий наконечник перед ее заправкой в горелку (особенно это касается сплошной проволоки) во избежание повреждения внутреннего направляющего канала. Порошковую проволоку после выполнения сварочных работ рекомендуется снимать и хранить в полиэтилене ввиду возможного образования коррозии. Под порошковую проволоку необходимо устанавливать меньшую степень сдавливания прижимным роликом (обычно это 1-2 деление), иначе существует вероятность «закусывания» проволоки.
Будьте внимательны и при операциях по заправке проволоки в подающее устройство и сварочную горелку. Случайное нажатие на кнопку подачи проволоки на подающем механизме или горелке может привести к травмам. Из-за мощного механизма подачи сплошная проволока легко протыкает пальцы и кисти рук. Не направляйте на себя горелку при протяжке проволоки!
Рекомендуем приобретать сварочное оборудование и расходные материалы в ТД «Дока», так как мы предлагаем продукцию очень хорошего качества по низким ценам.
В ТД «Дока» с продаже представлена качественная сварочная порошковая самозащитная проволока E71T-GS диаметром 0,8 мм в катушках по 0,45; 0,8; 1 и 5 кг, позволяющая вести сварку во всех пространственных положениях, обеспечивая высокое качества шва при минимальном разбрызгивании.
Также Всегда в наличии для Вас сплошная омедненная сварочная проволока ER 70S-6 (аналог СВ-08Г2С-О) диаметром 0,8; 1; 1,2; 1,6 мм в катушках по 5 и 15 кг.
Копирование контента без указания ссылки на первоисточник ЗАПРЕЩЕНО.
www.tddoka.ru
Сварочные электроды | Электроды от Электродгруп | Производство электродов МР, УОНИ, ОЗС, АНО,
На этапе планирования сварочных работ важнейшей процедурой является расчет расхода электродов для сварки. Данная процедура осуществляется с учетом таких показателей, как нормы расхода сварочных электродов, масса наплавленного металла, длина шва и других параметров. От корректного расчета расходов напрямую зависит эффективность и результативность процесса, а также распределение выделенного на осуществление работ бюджета.
Осуществлять расчет расхода электродов должны непосредственно специалисты, которые будут осуществлять сварочные работы. Доскональное знание тонкостей процесса и ориентирование в марках электродов для сварки позволит избежать каких-либо ошибок в проведении расчета.
Существуют множество методик расчета необходимого количества сварочных электродов. К основной, широко используемой во всех странах, методике относится определение количества необходимых электродов по массе наплавленного металла. Именно по этому единицей измерения электродов считаются килограммы.
Необходимое количество электродов определяется по формуле:
Н=М*Красх.,
где М – масса наплавленного металла в килограммах;
а, Красх. – коэффициент расхода электродов.
Показатель М – масса наплавленного металла, определяется исходя из площади поперечного сечения наплавленного металла помноженное на плотность (к примеру для углеродистых и низколегированных сталей плотность примерно равна 7,85 г/см3) и на длину шва.
Коэффициент расхода электродов учитывающий разбрызгивание, угар и длину огарка, определяется исходя из нормативов, для каждой марки электродов отдельно:
Таб. Норма расхода электродовРасход электродов на 1 кг наплавленного металла, кг | Марка электродов |
1,7 | МР-3, АНО-4, Т–590, ОЗЧ-2 |
1,65 | МР-3 СИНИЕ, ОЗС-12, ОЗС-4, АНО-21, АНО-6 |
1,6 | УОНИ 13/45, УОНИ 13/55, ОЗЛ-6, ЦЛ–11 |
1,5 | ОЗС-6 |
при этом длинна электрода 450 мм и огарок не более 50 мм.
В случае если нет возможности рассчитать теоретическое количество по массе можно прибегнуть к практическому. В таком случае необходимо произвести сваривание двух металлических частей определенным количеством необходимой марки электродов. При этом применить такой же тип сварочного соединения, выбор пространственного положением сварки и режимом сварочного тока, как и в последующих работах. После чего можно определить длину шва и спрогнозировать необходимое количество электродов для сварки.
Расход электродов при сваркеРасход сварочных электродов – основной параметр, влияющий на планирование работ и закупку комплектующих для сварки. Рассчитав уровень расхода, и произведя закупку электродов с учетом непредвиденных обстоятельств, можно не волноваться о качестве и удобстве проведения сварочных работ.
таблица, нормы расхода при сварочных работах на тонну металла
На чтение 12 мин Просмотров 56. 9к. Опубликовано Обновлено
Одним из важных показателей является расход электродов на 1 метр шва, который приводится в специальных таблицах. Эти данные позволяют производить расчет сметы.
В подсчете необходимо учитывать множество нюансов, поэтому его делает опытный сварщик, разбирающийся в марках материалов и в методиках сварки. От правильности выполнения расчета будут зависеть экономические показатели всего проекта.
Что влияет на расход?
Важной составляющей любого производственного процесса является правильно спланированный расход сварочных материалов. Это необходимо в предварительном расчете сметы, что позволит заранее оценить финансовые затраты.
Особенно важно знать нормы расхода во время строительства крупных объектов. На столь больших масштабных производствах даже незначительная экономия материала в каждой отдельной задаче может существенно снизить экономические затраты.
В этих целей было создано понятие затрат на 1 м шва. Оно позволяет сварщикам ориентироваться в стоимости работ, которые необходимо выполнить. Кроме того, это позволит нормировать количество стержней на объем материала.
Стоит отметить, что в бытовых условиях подобные оценки не нужны. Ведь маленький объем работ создания соединений каких-либо металлических изделий не принесет существенных затрат при перерасходе материала.
Кроме того среди множества показателей, есть такие, которые в наибольшей степени влияют на потери. Их важно знать, ведь это поможет в будущем сэкономить деньги.
К ним относятся:
- масса наплавки материала на шов;
- длительность и глубина соединения;
- общая масса наплавки;
- тип сварки.
Как определить затраты сварочных материалов?
Существует множество специализированных формул, позволяющих теоретически рассчитать, какая должна быть норма расхода электродов. Среди них можно выделить несколько самых распространенных способов.
Первый метод основан на применении специального коэффициента расхода стержней. Он позволяет также определить затраты сварочных материалов:
H=M*K
здесь М – масса свариваемой металлической конструкции, К – специальный коэффициент, который можно взять из справочника. Его величина находится в интервале от 1,5 до 1,9.
Второй метод – расчет, включающий физические свойства стержней и материалов. С его помощью можно определить массу наплавленного металла.
Данный способ также предполагает использование табличных коэффициентов, которые можно взять из специализированных справочников. Кроме того необходимо выполнить замер шва.
Подсчет определяется формулой:
G=F*L*M
где F – площадь поперечного сечения, L – длина шва; M – масса одного кубического сантиметра проволоки.
Как видно, данный расчет количества электродов подразумевает выполнение предварительных тестовых работ.
После того, как они будут сделаны, мастер производит следующие действия:
- осуществляет измерение огарка;
- учитывает параметры : напряжение и силу тока;
- замеряет длину соединения, полученного после сварки.
Таким образом, можно рассчитать нормативы, показывающие, сколько необходимо затратить на один шов свариваемых материалов. К ним также необходимо отнести затраты рабочего газа, например, ацетилена и кислорода, арматуры или других металлических частей.
В результате станет возможным подсчет всех экономических затрат.
Высчитываем затраты присадочного материала в штуках
В сварке используют различные присадочные материалы, которые также могут со временем заканчиваться. В связи с этим важно знать расход сварочной проволоки, использующейся во время соединения металлических частей изделий.
Данная информация необходима по нескольким причинам. Во-первых, появляется возможность заблаговременно рассчитать нужное количество проволоки. Во-вторых, расчет затрат каждого отдельного метода работы покажет, какой именно способ будет наиболее выгодным с экономической точки зрения.
Важно иметь в виду, что у каждого типа присадки есть свой коэффициент наплавки. Так как для качественного выполнения соединения важно, чтобы оно выполнялось непрерывно, затраты материалов нужно знать заранее.
Стоит учитывать, что значение данного параметра зависит от вида сварки. Можно самостоятельно научиться делать подобные расчеты, но в целях экономии времени были созданы онлайн сервисы, которые позволяют свести вычисления к автоматизму.
Таким образом, данный критерий не менее важен, чем коэффициент расхода электродов.
Расход – важное понятие, характеризующее необходимый объем материалов для формирования соединения на определенном участке. Иначе говоря, он включает в себя все этапы работы, в том числе и подготовку, чтобы технологический процесс был выполнен в соответствии с высокими стандартами.
У всех видов сварки также существуют свои показатели расхода, будь-то или обычная газовая. Везде есть свои нюансы, которые влияют на количество затрачиваемого материала.
Ради удобства простых расчетов можно воспользоваться онлайн сервисами и определить затраты, например, у аргонодуговой сварки на калькуляторе. Стоит брать во внимание и изделия, с которыми осуществляется работа. У сварки труб или листов будут разные параметры.
После того, как произведены расчеты, можно составлять смету или же просто оценить размер необходимых затрат.
Не стоит забывать о том, что после покупки стержней часть из них может оказаться бракованной. В связи с этим необходимо учитывать возможность списания учитывать это в подсчете.
Как снизить потери?
Характеристики стыковых соединений.
Рассчитать расход электродов – это лишь один из способов оценки затрат. Во время работы материала может понадобиться больше ожидаемой нормы по многим причинам.
Например, более третьей части может пойти на разбрызгивание и огарки. Расход во время варки на 1 кг наплавленного металла зависит от их типа. Например, у жаропрочных и нержавеющих сталей его значение составляет 1,8.
Кроме того, нормы расхода электродов на 1 стык зависят и от вида работы. На сварку трубопроводов уйдет не столько же материала за час работы, как на соединение листового материала.
Стоит иметь в виду, что не только расход электродов на 1 м шва или на 1 тонну влияет на затраты. Необходимо учитывать и списание материалов на производстве.
Поскольку финансовая сторона вопроса является очень важной составляющей в любом деле, то возможность снижения затрат очень актуальна. Существует два способа экономии: технический и организационный.
Самым простым и доступным методом экономии является использование оптимальных параметров сварки. Каждый тип работ предполагает использование соответствующих материалом и режимов, если соблюдать все условия, тогда электроды не будут «гореть».
Использование и автомата экономит потери на разбрызгивании более двух процентов.
Стоит также отдавать предпочтение стержням с высокой эффективностью, что снизит потери. Также они должны быть с высоким коэффициентом наплавки. Так что правильный выбор материалов – важная составляющая экономии.
Обобщая все вышесказанное, можно сделать вывод, что точное и правильное соблюдение технологии сварочного процесса, а также выбор оптимальных параметров, является залогом экономии средств.
Таблицы
Нормы расхода сварочных материалов определяются с использованием коэффициента. Данный параметр берется из специальных таблиц. Если необходимо определить расход электродов, например, в сварке труб, тогда следует воспользоваться таблицей.
В целях упрощения расчетов можно использовать уже готовые таблицы, в которых приводятся готовые данные. На производстве использовать подобный материал существенно проще, чем выполнять каждый раз новые вычисления.
Нормы покрытыми стержнями приведены в таблицах ниже.
Норма на 1 стык.
Размер трубы, мм | Масса наплавленного металла, г | Электроды по группам, г | Код строки | ||||
II | III | IV | V | VI | |||
45´3 | 21 | 37 | 40 | 42 | 44 | 47 | 1 |
45´4 | 28 | 50 | 54 | 57 | 61 | 64 | 2 |
57´3 | 27 | 57 | 60 | 54 | 67 | 60 | 3 |
57´4 | 36 | 64 | 69 | 73 | 77 | 82 | 4 |
76´5 | 61 | 108 | 108 | 123 | 130 | 137 | 5 |
Норма на 1 м шва.
Толщ. стенки, мм | Масса наплавленного металла, г | Эл-ды по группам, гр | Код строки | ||||
II | III | IV | V | VI | |||
3 | 152 | 269 | 286 | 305 | 322 | 340 | 1 |
4 | 207 | 368 | 393 | 417 | 442 | 466 | 2 |
5 | 262 | 465 | 497 | 527 | 558 | 590 | 3 |
Затраты на формирование вертикальных стыков трубопроводов, со скошенными кромками
1 м шва.
Толщина стенки, мм | Масса наплавленного металла, г | Эл-ды по группам, гр | Код строки | ||||
II | III | IV | V | VI | |||
3 | 201 | 366 | 390 | 415 | 439 | 464 | 1 |
4 | 249 | 453 | 484 | 514 | 544 | 574 | 2 |
5 | 330 | 600 | 640 | 680 | 820 | 760 | 3 |
6 | 474 | 861 | 918 | 975 | 1033 | 1090 | 4 |
8 | 651 | 1182 | 1261 | 1410 | 1419 | 1498 | 5 |
10 | 885 | 1607 | 1714 | 1821 | 1928 | 2035 | 6 |
12 | 1166 | 2116 | 2257 | 2398 | 2539 | 2680 | 7 |
15 | 1893 | 3436 | 3665 | 3894 | 4123 | 4352 | 8 |
16 | 2081 | 3778 | 4030 | 4281 | 4533 | 4785 | 9 |
18 | 2297 | 4532 | 4834 | 5136 | 5438 | 5740 | 10 |
1 стык.
Размер трубы, мм | Вес напл. металла, г | Эл-ды, г | Код строки | ||||
II | III | IV | V | VI | |||
45´3 | 27 | 60 | 54 | 58 | 61 | 64 | 1 |
45´4 | 34 | 62 | 66 | 70 | 74 | 79 | 2 |
57´3 | 35 | 64 | 69 | 73 | 77 | 82 | 3 |
57´4 | 44 | 79 | 85 | 90 | 95 | 100 | 4 |
76´5 | 77 | 140 | 149 | 158 | 168 | 177 | 5 |
89´6 | 130 | 235 | 251 | 266 | 282 | 298 | 6 |
108´6 | 158 | 287 | 306 | 325 | 344 | 363 | 7 |
133´6 | 195 | 354 | 377 | 401 | 425 | 448 | 8 |
133´8 | 268 | 483 | 516 | 548 | 580 | 613 | 9 |
159´6 | 234 | 424 | 453 | 481 | 509 | 537 | 10 |
159´8 | 320 | 580 | 619 | 658 | 697 | 735 | 11 |
219´6 | 323 | 586 | 625 | 664 | 703 | 742 | 12 |
219´8 | 442 | 803 | 856 | 910 | 963 | 1017 | 13 |
219´10 | 599 | 1088 | 1160 | 1233 | 1305 | 1376 | 14 |
219´12 | 787 | 1428 | 1523 | 1619 | 1714 | 1809 | 15 |
273´8 | 553 | 1003 | 1071 | 1138 | 1205 | 1272 | 16 |
273´10 | 750 | 1361 | 1452 | 1542 | 1633 | 1724 | 17 |
273´12 | 985 | 1788 | 1907 | 2026 | 2145 | 2265 | 18 |
273´15 | 1592 | 2890 | 3082 | 3275 | 3467 | 3660 | 19 |
325´8 | 659 | 1196 | 1276 | 1357 | 1436 | 1516 | 20 |
325´10 | 894 | 1623 | 1731 | 1839 | 1947 | 2055 | 21 |
325´12 | 1175 | 2133 | 2275 | 2417 | 2559 | 2701 | 22 |
325´15 | 1902 | 3453 | 3683 | 3913 | 4144 | 4374 | 23 |
377´8 | 765 | 1389 | 1482 | 1576 | 1667 | 1760 | 24 |
377´10 | 1039 | 1885 | 2010 | 2136 | 2261 | 2387 | 25 |
377´12 | 1365 | 2478 | 2643 | 2808 | 2973 | 3138 | 26 |
377´15 | 2211 | 4013 | 4281 | 4548 | 4816 | 5083 | 27 |
426´10 | 1175 | 2132 | 2274 | 2416 | 2558 | 2700 | 28 |
426´12 | 1545 | 2804 | 2990 | 3177 | 3364 | 3551 | 29 |
426´16 | 2759 | 4991 | 5324 | 5655 | 5988 | 6321 | 30 |
465´18 | 3598 | 6531 | 6966 | 7401 | 7836 | 8271 | 31 |
Горизонтальные соединения трубопроводов со скосом одной кромки
1 м шва.
Толщина стенки, мм | Вес напл. металла, гр | Электроды, гр | Код строки | ||||
II | III | IV | V | VI | |||
3 | 232 | 411 | 438 | 466 | 493 | 521 | 1 |
4 | 299 | 529 | 564 | 599 | 635 | 670 | 2 |
5 | 384 | 680 | 724 | 770 | 816 | 861 | 3 |
6 | 470 | 832 | 887 | 943 | 998 | 1054 | 4 |
8 | 832 | 1474 | 1573 | 1671 | 1769 | 1868 | 5 |
10 | 1110 | 1965 | 2096 | 2227 | 2358 | 2489 | 6 |
12 | 1562 | 2765 | 2949 | 3133 | 3318 | 3502 | 7 |
15 | 2137 | 3782 | 4034 | 4287 | 4539 | 4791 | 8 |
16 | 2348 | 4157 | 4434 | 4712 | 4989 | 5266 | 9 |
18 | 2786 | 4931 | 5260 | 5588 | 5917 | 6246 | 10 |
1 стык.
Размер трубы, мм | Вес напл. металла, гр | Эл-ды, гр | Код строки | ||||
II | III | IV | V | VI | |||
57´3 | 41 | 72 | 77 | 82 | 87 | 92 | 1 |
57´4 | 53 | 93 | 99 | 105 | 111 | 117 | 2 |
76´5 | 89 | 158 | 169 | 179 | 190 | 201 | 3 |
89´6 | 128 | 227 | 242 | 257 | 272 | 288 | 4 |
108´6 | 157 | 277 | 295 | 314 | 332 | 351 | 5 |
133´6 | 193 | 342 | 365 | 388 | 410 | 433 | 6 |
133´8 | 341 | 603 | 643 | 683 | 723 | 764 | 7 |
159´6 | 232 | 410 | 437 | 465 | 492 | 520 | 8 |
159´8 | 482 | 724 | 772 | 820 | 869 | 917 | 9 |
219´6 | 320 | 567 | 604 | 642 | 680 | 718 | 10 |
219´8 | 565 | 1001 | 1068 | 1135 | 1201 | 1268 | 11 |
219´10 | 751 | 1330 | 1419 | 1508 | 1596 | 1685 | 12 |
219´12 | 1054 | 1866 | 1991 | 2115 | 2240 | 2364 | 13 |
273´8 | 1707 | 1251 | 1335 | 1419 | 1502 | 1586 | 14 |
273´10 | 940 | 1664 | 1775 | 1886 | 1997 | 2108 | 15 |
273´12 | 1320 | 2336 | 2492 | 2647 | 2804 | 2959 | 16 |
273´15 | 1797 | 3181 | 3393 | 3605 | 3817 | 4029 | 17 |
325´8 | 843 | 1492 | 1592 | 1691 | 1790 | 1890 | 18 |
325´10 | 1121 | 1985 | 2117 | 2249 | 2382 | 2514 | 19 |
325´12 | 1575 | 2787 | 2973 | 3158 | 3344 | 3530 | 20 |
325´15 | 2147 | 3801 | 4064 | 4308 | 4562 | 4815 | 21 |
377´10 | 1302 | 2035 | 2459 | 2612 | 2766 | 2920 | 22 |
377´12 | 1829 | 3238 | 3530 | 3669 | 3885 | 4101 | 23 |
377´16 | 2741 | 4851 | 5174 | 5449 | 5822 | 6145 | 24 |
465´18 | 4015 | 7106 | 7580 | 8052 | 8526 | 9000 | 25 |
С19 вертикальных стыков со скосом кромок
1 м шва.
Толщ. ст., мм | Вес напл. металла, гр | Эл-ды, гр | Код строки | ||||
II | III | IV | V | VI | |||
3 | 201 | 366 | 390 | 415 | 439 | 464 | 1 |
4 | 260 | 472 | 503 | 535 | 566 | 598 | 2 |
5 | 329 | 599 | 639 | 679 | 719 | 759 | 3 |
6 | 464 | 842 | 898 | 955 | 1011 | 1067 | 4 |
8 | 670 | 1216 | 1297 | 1378 | 1459 | 1540 | 5 |
10 | 974 | 1768 | 1885 | 2004 | 2121 | 2240 | 6 |
12 | 1250 | 2269 | 2420 | 2571 | 2722 | 2874 | 7 |
15 | 2010 | 3649 | 3894 | 4137 | 4380 | 4623 | 8 |
16 | 2204 | 4000 | 4266 | 4534 | 4800 | 5067 | 9 |
18 | 2615 | 4748 | 5063 | 5378 | 5695 | 6011 | 10 |
1 стык.
Размер трубы, мм | Вес напл. металла, гр | Эл-ды, гр | Код строки | ||||
II | III | IV | V | VI | |||
45´3 | 27 | 50 | 54 | 58 | 61 | 64 | 1 |
45´4 | 36 | 65 | 69 | 73 | 77 | 82 | 2 |
57´3 | 35 | 64 | 69 | 73 | 77 | 82 | 3 |
57´4 | 46 | 83 | 88 | 94 | 99 | 105 | 4 |
76´5 | 77 | 140 | 149 | 158 | 167 | 177 | 5 |
89´6 | 127 | 230 | 245 | 261 | 276 | 291 | 6 |
108´6 | 154 | 280 | 299 | 318 | 337 | 355 | 7 |
133´6 | 191 | 346 | 369 | 392 | 415 | 438 | 8 |
133´8 | 274 | 497 | 530 | 564 | 597 | 630 | 9 |
159´6 | 229 | 415 | 443 | 471 | 498 | 526 | 10 |
159´8 | 329 | 597 | 637 | 677 | 716 | 756 | 11 |
219´6 | 216 | 573 | 611 | 650 | 683 | 727 | 12 |
219´8 | 455 | 826 | 881 | 936 | 991 | 1046 | 13 |
219´10 | 659 | 1197 | 1276 | 1357 | 1436 | 1516 | 14 |
219´12 | 844 | 1532 | 1633 | 1735 | 1837 | 1940 | 15 |
273´8 | 569 | 1032 | 1101 | 1170 | 1239 | 1307 | 16 |
273´10 | 825 | 1497 | 1597 | 1697 | 1796 | 1897 | 17 |
273´12 | 1056 | 1917 | 2045 | 2172 | 2300 | 2428 | 18 |
273´15 | 1691 | 3069 | 3275 | 3479 | 3684 | 3880 | 19 |
325´8 | 678 | 1231 | 1313 | 1394 | 1476 | 1580 | 20 |
325´10 | 984 | 1786 | 1904 | 2024 | 2142 | 2262 | 21 |
325´12 | 1260 | 2287 | 2449 | 2592 | 2744 | 2897 | 22 |
325´15 | 2020 | 3667 | 3913 | 4158 | 4402 | 4646 | 23 |
377´10 | 1143 | 2074 | 2211 | 2351 | 2488 | 2627 | 24 |
377´12 | 1464 | 2657 | 2834 | 3011 | 3187 | 3365 | 25 |
377´15 | 2348 | 4262 | 4548 | 4832 | 5116 | 5400 | 26 |
426´10 | 1292 | 2346 | 2501 | 2659 | 2815 | 2972 | 27 |
426´12 | 1656 | 3006 | 3206 | 3407 | 3607 | 3808 | 28 |
426´16 | 2911 | 5284 | 5635 | 5989 | 6341 | 6693 | 29 |
465´18 | 3768 | 6839 | 7296 | 7750 | 8206 | 8662 | 30 |
Соединения С52 вертикальных стыков трубопроводов с криволинейным скосом кромок
1 м шва.
Толщ. ст., мм | Вес напл. металла, гр | Эл-ды, гр | Код строки | ||||
II | III | IV | V | VI | |||
10 | 551 | 1371 | 1462 | 1554 | 1645 | 1737 | 1 |
12 | 1164 | 2112 | 2253 | 2394 | 2534 | 2675 | 2 |
15 | 1606 | 2915 | 3109 | 3303 | 3497 | 3692 | 3 |
16 | 1755 | 3185 | 3397 | 3609 | 3821 | 4034 | 4 |
18 | 2085 | 3785 | 4037 | 4289 | 4541 | 4794 | 5 |
20 | 2409 | 4373 | 4664 | 4956 | 5247 | 5539 | 6 |
22 | 2763 | 5015 | 5349 | 5683 | 6017 | 6352 | 7 |
1 стык.
Размеры трубы, мм | Вес напл-ого металла, гр | Эл-ды, гр | Номер п/п | ||||
II | III | IV | V | VI | |||
1 | 2 | 3 | 4 | 5 | 6 | 7 | 8 |
133´10 | 310 | 562 | 599 | 637 | 675 | 712 | 1 |
159´10 | 370 | 672 | 716 | 762 | 806 | 851 | 2 |
159´12 | 570 | 1035 | 1104 | 1173 | 1242 | 1311 | 3 |
219´10 | 514 | 932 | 994 | 1057 | 1119 | 1181 | 4 |
219´12 | 791 | 1436 | 1532 | 1628 | 1723 | 1819 | 6 |
219´16 | 1176 | 2134 | 2276 | 2418 | 2560 | 2703 | 6 |
273´10 | 642 | 1165 | 1248 | 1321 | 1398 | 1476 | 7 |
273´12 | 989 | 1795 | 1915 | 2035 | 2154 | 2274 | 8 |
273´15 | 1349 | 2449 | 2612 | 2775 | 2938 | 3101 | 9 |
273´20 | 2024 | 3673 | 3918 | 4163 | 4430 | 4653 | 10 |
325´10 | 763 | 1385 | 1477 | 1570 | 1682 | 1754 | 11 |
325´12 | 1175 | 2133 | 2276 | 2418 | 2559 | 2702 | 12 |
325´15 | 1622 | 2944 | 3140 | 3336 | 3532 | 3729 | 13 |
325´18 | 2085 | 3785 | 4037 | 4289 | 4541 | 4794 | 14 |
377´10 | 891 | 1618 | 1725 | 1834 | 1941 | 2080 | 15 |
377´12 | 1361 | 2471 | 2636 | 2881 | 2965 | 3130 | 16 |
377´15 | 1879 | 3411 | 3638 | 3865 | 4092 | 4320 | 17 |
377´18 | 2440 | 4429 | 4723 | 5018 | 5313 | 5609 | 18 |
426´10 | 1004 | 1823 | 1945 | 2067 | 2188 | 2310 | 19 |
426´12 | 1548 | 2809 | 2997 | 3184 | 3370 | 3558 | 20 |
426´16 | 2316 | 4204 | 4484 | 4764 | 5044 | 5325 | 21 |
426´20 | 3180 | 5772 | 6157 | 6542 | 6962 | 7312 | 22 |
465´18 | 3003 | 5450 | 5813 | 6176 | 6539 | 6903 | 23 |
465´22 | 3979 | 7222 | 7703 | 8184 | 8665 | 9153 | 24 |
С53 вертикальные стыки трубопроводов с криволинейным скосом
1 м шва.
Толщ. ст., мм | Масса напл. металла, гр | Эл-ды, гр | Номер п/п | ||||
II | III | IV | V | VI | |||
16 | 1566 | 2843 | 3032 | 3221 | 3411 | 3600 | 1 |
18 | 1958 | 3554 | 3790 | 4027 | 4264 | 4501 | 8 |
20 | 2314 | 4200 | 4480 | 4760 | 5040 | 5320 | 3 |
22 | 2681 | 4866 | 5190 | 5515 | 5839 | 6164 | 4 |
1 стык.
Размер трубы, мм | Вес нап-ного металла, г | Эл-ды по группам, г | Код строки | ||||
II | III | IV | V | VI | |||
219´16 | 1053 | 1911 | 2038 | 2165 | 2292 | 2419 | 1 |
273´20 | 1940 | 3521 | 3756 | 3991 | 4226 | 4460 | 2 |
325´18 | 1958 | 3554 | 3790 | 4027 | 4264 | 4501 | 3 |
377´18 | 2281 | 4140 | 4415 | 4691 | 4967 | 5243 | 4 |
426´16 | 2070 | 3758 | 4008 | 4258 | 4509 | 4759 | 6 |
426´20 | 3052 | 5539 | 5908 | 6278 | 6647 | 7016 | 6 |
465´18 | 2822 | 5122 | 5463 | 5804 | 6146 | 6487 | 7 |
465´22 | 3855 | 6998 | 7464 | 7931 | 8397 | 8864 | 8 |
Соединения У7 угловые фланцев с трубой
1 м шва.
Толщ. ст., м | Масса напл. металла, гр | Эл-ды по группам, гр | Строки п/п | ||||
II | III | IV | V | VI | |||
3 | 129 | 234 | 250 | 265 | 281 | 297 | 1 |
4 | 186 | 333 | 360 | 383 | 405 | 428 | 2 |
5 | 272 | 494 | 527 | 559 | 592 | 625 | 3 |
6 | 366 | 664 | 709 | 753 | 797 | 841 | 4 |
8 | 494 | 897 | 956 | 1016 | 1076 | 1136 | 6 |
10 | 626 | 1136 | 1212 | 1288 | 1363 | 1439 | 6 |
12 | 775 | 1407 | 1500 | 1594 | 1688 | 1782 | 7 |
15 | 941 | 1708 | 1822 | 1936 | 2049 | 2163 | 8 |
1 фланец.
Размеры трубы, мм | Вес напл. металла, гр | Эл-ды по группам, гр | Номер | ||||
II | III | IV | V | VI | |||
25´3 | 10 | 18 | 20 | 21 | 22 | 23 | 1 |
32´3 | 13 | 23 | 25 | 27 | 28 | 30 | 2 |
38´3 | 15 | 28 | 30 | 32 | 33 | 35 | 3 |
45´4 | 26 | 48 | 51 | 64 | 57 | 60 | 4 |
57´4 | 33 | 60 | 64 | 68 | 72 | 77 | 5 |
76´5 | 65 | 118 | 126 | 133 | 141 | 149 | 6 |
89´6 | 102 | 186 | 198 | 210 | 223 | 235 | 7 |
108´6 | 124 | 225 | 240 | 255 | 270 | 285 | 8 |
133´6 | 152 | 277 | 296 | 314 | 333 | 351 | 9 |
133´8 | 206 | 375 | 399 | 424 | 449 | 474 | 10 |
159´6 | 182 | 331 | 354 | 376 | 398 | 420 | 11 |
159´8 | 247 | 448 | 477 | 507 | 537 | 567 | 12 |
219´6 | 252 | 457 | 487 | 518 | 548 | 578 | 13 |
219´8 | 340 | 617 | 657 | 699 | 740 | 781 | 14 |
219´10 | 430 | 781 | 833 | 886 | 937 | 989 | 15 |
219´12 | 533 | 967 | 1031 | 1096 | 1161 | 1225 | 16 |
273´6 | 313 | 569 | 608 | 645 | 683 | 721 | 17 |
273´8 | 424 | 769 | 819 | 871 | 922 | 974 | 18 |
273´10 | 536 | 974 | 1039 | 1104 | 1168 | 1233 | 19 |
273´12 | 664 | 1206 | 1286 | 1366 | 1447 | 1528 | 20 |
325´8 | 504 | 915 | 976 | 1037 | 1098 | 1159 | 21 |
325´10 | 639 | 1159 | 1237 | 1314 | 1391 | 1468 | 22 |
325´12 | 791 | 1436 | 1531 | 1627 | 1723 | 1818 | 23 |
325´15 | 944 | 1743 | 1859 | 1976 | 2091 | 2207 | 24 |
377´8 | 585 | 1062 | 1132 | 1203 | 1274 | 1345 | 25 |
377´10 | 741 | 1345 | 1435 | 1525 | 1613 | 1703 | 26 |
377´12 | 918 | 1666 | 1776 | 1887 | 1998 | 2109 | 27 |
377´15 | 1114 | 2022 | 2157 | 2292 | 2426 | 2560 | 28 |
426´10 | 837 | 1520 | 1621 | 1723 | 1823 | 1925 | 29 |
426´12 | 1037 | 1882 | 2006 | 2132 | 2258 | 2384 | 30 |
426´15 | 1260 | 2285 | 2437 | 2590 | 2741 | 2893 | 31 |
Угловые У8 фланцы с трубой с симметричным скосом одной кромки
1 м шва.
Толщ. ст., мм | Вес напл. металла, г | Эл-ды по группам, г | Номер п/п | ||||
II | III | IV | V | VI | |||
3 | 90 | 163 | 174 | 185 | 196 | 207 | 1 |
4 | 165 | 299 | 319 | 339 | 359 | 379 | 2 |
5 | 285 | 517 | 552 | 586 | 621 | 655 | 3 |
6 | 411 | 746 | 796 | 845 | 895 | 945 | 4 |
8 | 592 | 1076 | 1148 | 1220 | 1292 | 1363 | 5 |
10 | 770 | 1398 | 1491 | 1584 | 1677 | 1770 | 6 |
12 | 970 | 1761 | 1878 | 1995 | 2113 | 2230 | 7 |
15 | 1192 | 2163 | 2308 | 2452 | 2596 | 2740 | 8 |
Угловые У8 фланцы.
1 м шва.
Толщ. ст., мм | Вес напл. металла, грамм | Эл-ды, грамм | Номер п/п | ||||
II | III | IV | V | VI | |||
3 | 91 | 136 | 146 | 155 | 164 | 173 | 1 |
4 | 148 | 222 | 237 | 252 | 266 | 281 | 2 |
5 | 218 | 327 | 349 | 371 | 392 | 414 | 3 |
1 патрубок.
Размеры патрубка, ми | Масса напл. металла, грамм | Эл-ды, грамм | Номер п/п | ||||
II | III | IV | V | VI | |||
25´3 | 9 | 13 | 14 | 15 | 16 | 17 | 1 |
32´3 | 11 | 17 | 18 | 19 | 20 | 21 | 2 |
38´3 | 13 | 20 | 21 | 23 | 24 | 25 | 3 |
45´4 | 26 | 39 | 41 | 44 | 46 | 49 | 4 |
57´4 | 33 | 49 | 52 | 55 | 59 | 62 | 5 |
76´5 | 64 | 96 | 102 | 109 | 115 | 121 | 6 |
Нормы для ручной аргонодуговой сварки приведены в таблицах ниже.
Вертикальные соединения С2 трубопроводов
1 м шва.
Толщ. ст., мм | Масса напл. металла, г | Проволока сварочная, г | Стержень вольфрамовый неплавящийся, г | Аргон, л | Номер п/п | |
сварка | поддув | |||||
2 | 44 | 54 | 1,064 | 107 | 70,4 | 1 |
3 | 45 | 56 | 1,103 | 110 | 72,0 | 2 |
1 стык.
Размеры трубы, мм | Масса напл. металла, грамм | Проволока сварочная, грамм | Стержень вольфрамовый неплавящийся, мг | Аргон, л | Номер п/п | |
сварка | поддув | |||||
25´2 | 3 | 4 | 80 | 7,3 | 4,8 | 1 |
25´3 | 3 | 4 | 82 | 7,3 | 4,8 | 2 |
32´2 | 4 | 5 | 103 | 9,8 | 6,4 | 3 |
32´3 | 4 | 5 | 107 | 10,0 | 6,5 | 4 |
38´2 | 5 | 6 | 123 | 12,2 | 8,0 | 5 |
38´3 | 6 | 7 | 128 | 14,6 | 9,6 | 6 |
45´2 | 7 | 8 | 147 | 17,1 | 11,2 | 7 |
45´3 | 7 | 8 | 152 | 17,1 | 11,2 | 8 |
57´3 | 8 | 10 | 194 | 19,5 | 12,8 | 9 |
Вертикальные соединения С17 трубопроводов со скосом кромки
1 м соединения.
Толщ. ст., мм | Вес напл. вещества, грамм | Проволока сварочная, грамм | Вольфрамовый неплавящийся, мг | Аргон, л | Номер п/п | |
сварка | поддув | |||||
3 | 117 | 145 | 2305 | 285,5 | 18,7 | 1 |
4 | 154 | 191 | 3034 | 375,7 | 18,7 | 2 |
5 | 190 | 236 | 3743 | 463,4 | 48,0 | 3 |
6 | 253 | 314 | 4984 | 617,3 | 48,0 | 4 |
1 стык.
Размеры трубы, мм | Масса напл. вещества, грамм | Проволока сварочная, грамм | Вольфрамовый неплавящийся, мг | Аргон, л | Номер п/п | |
сварка | поддув | |||||
25´3 | 9 | 11 | 173 | 22,0 | 1,5 | 1 |
32´3 | 11 | 14 | 224 | 26,8 | 1,8 | 2 |
38´3 | 14 | 17 | 267 | 34,2 | 2,3 | 3 |
45´4 | 21 | 26 | 416 | 51,2 | 2,7 | 4 |
57´4 | 27 | 33 | 531 | 65,9 | 3,5 | 6 |
76´5 | 44 | 55 | 872 | 107,4 | 8,6 | 6 |
89´6 | 69 | 86 | 1366 | 168,4 | 13,4 | 7 |
108´6 | 84 | 106 | 1660 | 205,0 | 16,3 | 8 |
133´6 | 104 | 129 | 2048 | 253,8 | 20,0 | 9 |
159´6 | 125 | 155 | 2457 | 305,0 | 24,0 | 10 |
219´6 | 172 | 214 | 3394 | 419,7 | 33,0 | 11 |
273´6 | 215 | 267 | 4241 | 524,6 | 41,2 | 12 |
С18 вертикальные стыки трубопроводов
1 м соединения.
Толщ. ст., мм | Масса наплавленного металла, г | Проволока сварочная, г | Вольфрамовый неплавящийся, мг | Аргон, л | Номер |
2 | 146 | 182 | 2896 | 356,2 | 1 |
3 | 199 | 247 | 3920 | 485,6 | 2 |
4 | 250 | 310 | 4930 | 610,0 | 3 |
5 | 330 | 409 | 6501 | 805,2 | 4 |
6 | 473 | 588 | 9338 | 1154,1 | 6 |
1 стык.
Размеры трубы, мм | Масса наплавленного металла, грамм | Проволока сварочная, грамм | Вольфрамовый неплавящийся, мг | Аргон, л | Код строки |
на сварку | |||||
25´2 | 11 | 14 | 217 | 26,8 | 1 |
25´3 | 15 | 19 | 294 | 36,6 | 2 |
32´2 | 14 | 18 | 281 | 34,2 | 3 |
32´3 | 19 | 24 | 380 | 46,4 | 4 |
38´2 | 17 | 21 | 336 | 41,5 | 5 |
38´3 | 23 | 29 | 455 | 57,1 | 6 |
45´2 | 21 | 25 | 400 | 51,2 | 7 |
45´4 | 35 | 43 | 675 | 85,4 | 8 |
57´4 | 44 | 54 | 863 | 107,4 | 9 |
76´5 | 76 | 95 | 1515 | 185,4 | 10 |
89´6 | 130 | 161 | 2549 | 317,2 | 11 |
108´6 | 158 | 196 | 3110 | 385,5 | 12 |
133´6 | 195 | 242 | 3838 | 475,8 | 13 |
159´6 | 233 | 290 | 4604 | 568,5 | 14 |
219´6 | 322 | 400 | 6359 | 785,7 | 15 |
273´6 | 402 | 500 | 7947 | 980,9 | 16 |
Соединения С5 вертикальных стыков трубопроводов без скоса
1 м шва.
Толщина стенки, мм | Масса наплавленного металла, грамм | Проволока сварочная, грамм | Вольфрамовый неплавящийся, мг | Аргон, л | Номер строки |
2 | 87 | 108 | 1714 | 212,3 | 1 |
3 | 106 | 132 | 2110 | 258,6 | 2 |
1 стык.
Камеры трубы, мм | Масса наплавленного металла, грамм | Проволока сварочная, грамм | Стержень вольфрамовый неплавящийся, мг | Аргон, л | Номер строки |
25´2 | 6 | 8 | 129 | 14,6 | 1 |
25´3 | 8 | 10 | 180 | 19,5 | 2 |
32´2 | 9 | 11 | 166 | 22,0 | 3 |
32´3 | 10 | 13 | 233 | 24,4 | 4 |
38´2 | 10 | 13 | 233 | 24,4 | 5 |
38´3 | 12 | 15 | 278 | 29,3 | 6 |
45´2 | 12 | 15 | 278 | 29,3 | 7 |
46´3 | 14 | 18 | 331 | 34,2 | 8 |
57´3 | 18 | 23 | 422 | 56,1 | 9 |
Соединения С19 вертикальных стыков трубопроводов со скосом кромок
1 м соединения.
Толщина стенки, мм | Масса наплавленного металла, кг | Проволока сварочная, кг | Эл-д вольфрамовый неплавящийся, г | Аргон, л | Номер строки |
2 | 0,146 | 0,182 | 2,896 | 356,2 | 01 |
3 | 0,199 | 0,247 | 3,920 | 485,6 | 02 |
4 | 0,259 | 0,322 | 5,122 | 632,0 | 03 |
5 | 0,329 | 0,409 | 6,501 | 802,8 | 04 |
6 | 0,463 | 0,575 | 9,141 | 1129,7 | 06 |
1 стык.
Размеры трубы, мм | Вес наплавленного металла, грамм | Проволока сварочная, грамм | Эл-д вольфрамовый неплавящийся, мг | Аргон, л | Номер строки |
25´2 | 11 | 14 | 217 | 26,8 | 1 |
25´3 | 15 | 19 | 294 | 36,6 | 2 |
32´2 | 14 | 18 | 281 | 34,2 | 3 |
32´3 | 19 | 24 | 380 | 46,4 | 4 |
38´2 | 17 | 21 | 336 | 41,5 | 5 |
38´3 | 23 | 29 | 455 | 56,1 | 6 |
45´2 | 20 | 25 | 400 | 48,8 | 7 |
45´4 | 35 | 44 | 537 | 85,4 | 8 |
57´4 | 45 | 56 | 896 | 109,8 | 9 |
76´5 | 76 | 95 | 1515 | 185,4 | 10 |
89´6 | 126 | 157 | 2495 | 307,4 | 11 |
108´6 | 156 | 192 | 3044 | 378,2 | 12 |
133´6 | 190 | 236 | 3757 | 463,6 | 13 |
159´6 | 229 | 284 | 4507 | 558,8 | 10 |
219´6 | 315 | 392 | 6225 | 768,6 | 14 |
273´6 | 394 | 489 | 7779 | 961,4 | 15 |
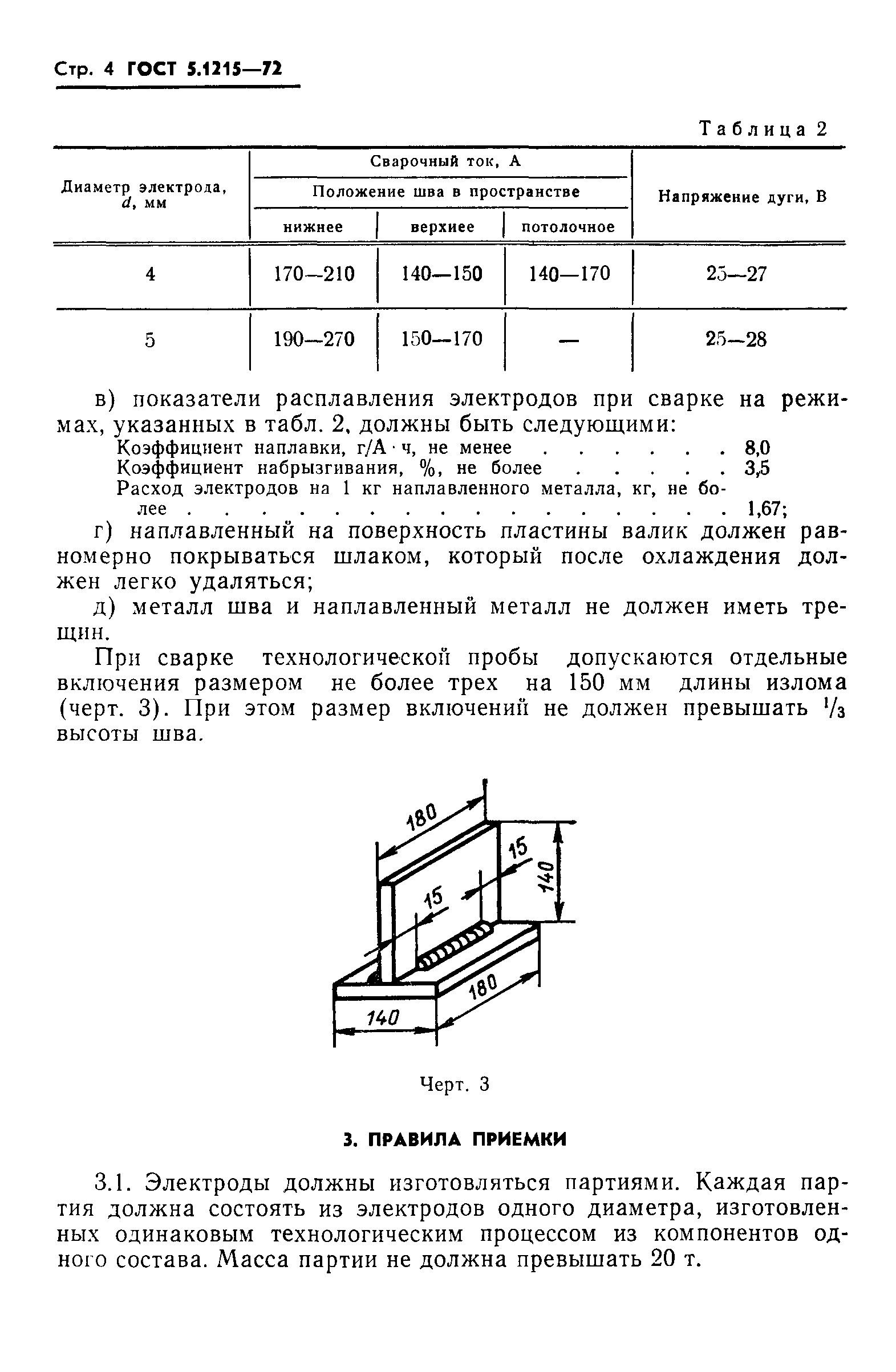
Приведенные выше таблицы позволяют определить расход электродов на стык, метр или на тонну металла. Расход флюса при автоматической сварке обычно составляет 20% по массе от расхода сварочной проволоки.
Таким образом, становится понятно, как рассчитать количество электродов в каждой конкретной задаче.
Итог
Расход электродов при сварке – важный параметр, который позволяет заблаговременно сделать экономическую оценку выполняемых работ. Рассчитанный показатель позволит определить затраты на тонну металлоконструкций или же на одно соединение.
Важно понимать, что данное значение соответствует идеальным условиям сварки, и оно может отличаться от реального. В связи с этим в расчет количества электродов необходимо закладывать их дополнительное количество, так как аттестация может выявить, что часть из них непригодна.
Расчет необходимого веса сварочного металла
Расчет требований к металлу сварного шва кажется сложным, но в большинстве случаев этого не должно быть. Если не считать компьютерной программы, которая рассчитывает это за вас, самый простой способ — использовать таблицы из «Руководства по процедурам дуговой сварки». В Таблице 12-1 приведены данные для расчета веса сварочного металла, необходимого на один фут соединения. В нем есть информация об угловых швах (которые также можно использовать для нахлеста) и сварных швах с разделкой кромок.Все, что вам нужно знать, это детали соединения (размер ножек, угол скоса, корень и т. Д.). Если у вас нет таблиц из Руководства по процедурам, вы можете относительно легко выполнить все эти вычисления вручную. Взгляните на нашу публикацию «Расчет требований к металлу сварного шва вручную
Мы получаем звонки от клиентов, которые спрашивают о требованиях к металлу сварных швов для заявленных ими работ. Когда мы разговариваем с заказчиком, мы спрашиваем общее количество сварных швов в дюймах (или футах), тип и размеры сварного шва. Нам также необходимо знать, какой процесс используется для учета эффективности электродов, когда мы сообщаем им, сколько продукта нужно покупать.
Клиент недавно предоставил нам эту информацию:
У меня есть сборка с сорока пятью угловыми сварными швами 3/16 дюйма и длиной 3 дюйма. Он также имеет семнадцать угловых швов диаметром ¼ дюйма и длиной 4,5 дюйма. По контракту мы должны построить 3200 из них. Сколько фунтов миграционной проволоки нам нужно для этой работы?
Мы переходим к таблицам в «Руководстве по процедурам» и видим, что для скругления 3/16 дюйма с плоской поверхностью нам нужно 0,072 фунта сварочного металла на фут соединения. Мы также видим, что для филе ”необходимое количество равно 0.129 фунтов на фут сустава. Эти значения включают 10% -ный допуск на сварку. Однако учтите, что это очень небольшая надбавка. Если ваше филе 3/16 дюйма оказывается равным дюйма, значит, вы перевариваете на 77%!
Таблица 12-1 в Руководстве по процедурам дуговой сварки помогает определить потребность в металле сварного шва на основе геометрии соединения.
Итого:
45 сварных швов по 3 дюйма = 135 дюймов = 11,25 фута -> при 0,072 фунта / фут, это дает 0,81 фунта на сборку
17 сварных швов x 4. 5 дюймов каждый = 76,5 дюйма = 6,375 фута -> @ 0,129 фунта / фут, это дает 0,82 фунта на сборку.
В сумме получается 1,63 фунта на деталь. А для изготовления 3200 деталей нам потребуется 5216 фунтов сварочного металла. Поскольку процесс, который они будут использовать, — это GMAW, и в этом случае они собирались использовать режим короткого замыкания для переноса металла, мы смотрим эффективность проволоки и видим, что она составляет 95%. Мы разделим весь необходимый металл сварного шва на коэффициент полезного действия 5 216 / 0,95, и это дает нам количество сварочной проволоки, которое необходимо купить, которое в данном случае составляет 5 491 фунт.
Если бы эту работу выполняли с помощью стержневого электрода, нам нужно было бы использовать КПД 65% (намного ниже из-за потерь на шлейфах, шлака и брызг). В этом случае нам потребуется 8 024 фунта. Никогда не забудьте указать КПД электрода, иначе могут возникнуть проблемы.
Если у вас нет таблицы, такой как в Руководстве по процедуре, и вам нужен быстрый ответ, вы всегда можете использовать карандаш, бумагу и математику средней школы, чтобы получить эту информацию. Взгляните на нашу публикацию о том, как это сделать: Расчет требований к металлу сварного шва вручную
Массообмен и внешний вид электрода с покрытием из нержавеющей стали 316L при дуговой сварке защищенного металла
Дж.К. Липпольд, Д.Дж. Котецки: Сварка и металлургия нержавеющих сталей, , 1-е изд., John Wiley & Sons, Inc., Хобокен, Нью-Джерси, 2005 г., стр. 1–229.
Google Scholar
М. Турски, Я.А. Фрэнсис, П.Р. Харрелл, С.К. Бейт, С. Хиллер и П.Дж. Уизерс: Int. J. Press. Весс. Пип. , 2012, т. 89, стр. 9–18.
Артикул Google Scholar
К. Боннет: в Металлургия и механика сварки , Р. Блондо, изд., John Wiley & Sons, Хобокен, Нью-Джерси, 2008 г., стр. 169–204.
Р. Цинь и Г. Он: Металл. Матер. Пер. А , 2013, т. 44A, стр. 1475–84.
Артикул Google Scholar

Х. Лю: Сварка, металлургия и свариваемость , Machinery Industry Press, Пекин, 2007, стр. 59–64 (на китайском языке).
W. Zhang: Welding Metallurgy , Machinery Industry Press, Пекин, 1999, стр. 55–57 (на китайском языке).
P.K. Растоги, Б. Шах, А. Синха и П. Кулькарни: Br. Корр. J. , 1994, т. 29. С. 178–80.
Артикул Google Scholar
AWS D18.2 Руководство по уровням обесцвечивания сварных швов на внутренней стороне трубы из аустенитной нержавеющей стали , Американское сварочное общество, Майами, Флорида, 2009.
E.M. Westin, C.-O.A. Ольссон и С. Герцман: Corr. Sci. , 2008, т. 50. С. 2620–34.
Артикул Google Scholar
К. Пауэлл и Д. Джордан: Производство нержавеющей стали для водного хозяйства , Справочник, серия № 11026, Институт никеля, Дарем, Северная Каролина.
С. Тернер и Ф.П.А. Робинсон: Коррозия , 1989, т. 49. С. 710–16.
Артикул Google Scholar
К. Асами и К. Хашимото: Corr. Sci. , 1979, т. 19. С. 1007–17.
Google Scholar
H.J.T. Ellingham: J. Soc. Chem. Инд , 1944, т. 63. С. 125–33.
Артикул Google Scholar
F.D. Ричардсон и Дж.E. Jeffes: J. Iron Steel Res. Int. , 1948, т. 160. С. 261–70.
Google Scholar
N.N. Гринвуд и А. Эрншоу: Химия элементов, , 2-е изд., Баттерворт-Хайнеманн, Оксфорд, Соединенное Королевство, 1997, стр. 328–61 и 1040–62.
S. Kou: Welding Metallurgy , 2-е изд., John Wiley & Sons, Hoboken, NJ, 2003, стр. 65–98.
Google Scholar
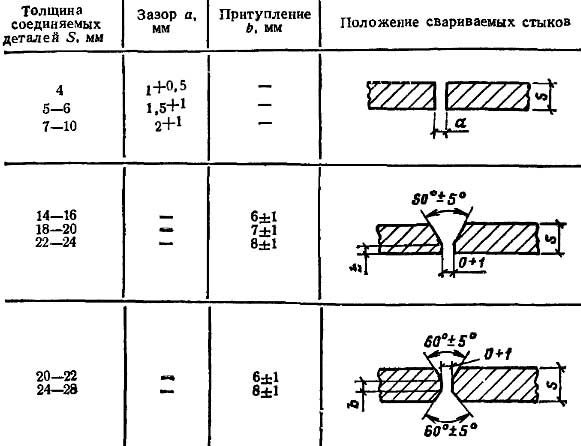
Ю. Накадзима и М. Мукаи: ISIJ Int. , 1993, т. 33. С. 109–15.
Артикул Google Scholar
С. Накамура, Ф. Цукихаси и Н. Сано: ISIJ Int. , 1993, т. 33. С. 53–58.
Артикул Google Scholar
Md.I. Хан: Сварка. Sci. Technol. , 1-е изд., New Age International Ltd., Нью-Дели, 2007, стр.69–96.
Р. В. Месслер: Принципы сварки , Wiley-VCH Verlag GmbH & Co. KGaA, Вайнхайм, 2004 г., стр. 270–90.
Google Scholar
Д. Стародуб, Е.П. Гусев, Э. Гарфункель и Т. Густафссон: Surf. Rev. Lett. , 1999, т. 6. С. 45–52.
Артикул Google Scholar
Х. Ли и У. Чен: Corr.Наук, 2010, т. 52. С. 2481–88.
Артикул Google Scholar

Чжан: Теория и технология сварочных материалов , Metallurgical Industry Press, Пекин, 2002, стр. 85–86.
Google Scholar
Справочник — Расчеты
Справочник — Расчеты 2 0,5 » 0,5 дюйма (А) ВЫСОТА (B) ОСНОВАНИЕ Объем сварного шва =.5B х А х 12 Вес стали = 0,283 фунта на куб. в. Вес сварного шва = (0,5 х 0,5) х 0,5 х 12 х 0,283 = 0,424 фунта РАСЧЕТ ВЕС НА СТУПКУ ФИЛЕЙНОЙ СВАРКИ В угловой шов, показанный ниже, площадь поперечного сечения (треугольник) равна в половину базы, умноженной на высота, объем сварного шва равен площади, умноженной на длину, а тогда вес сварного шва равен объем, умноженный на вес материала (стали) на кубический дюйм.Этот пример относится к угловому сварному шву с без подкрепления. Аналогичные расчеты можно произвести для стыковых или нахлесточных соединений. Эффективность осаждения Эффективность осаждения электрода или сварочная проволока указывает на ту часть продукта, которую вы можете ожидается наплавка как металл шва.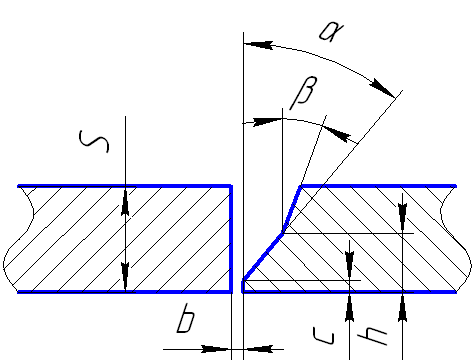
Определения терминов сварки
Абразивный
Шлак, используемый для очистки или придания шероховатости поверхности.
Активный флюс
Флюс для сварки под флюсом, количество элементов, осажденных в металле шва, зависит от условий сварки, в первую очередь от напряжения дуги.
Клейкое соединение
Поверхности, затвердевающие с образованием клеевого соединения.
Резка угольной дугой на воздухе
Процесс дуговой резки, при котором металлы, подлежащие резке, плавятся под действием тепла угольной дуги, а расплавленный металл удаляется струей воздуха.
Цельносварной образец для испытаний металла
Испытательный образец с редукционной частью, полностью состоящей из металла сварного шва.
Легирование
Добавление металла или сплава к другому металлу или сплаву.
Переменный ток (AC)
Электрический ток, который периодически меняет направление, обычно много раз в секунду.
Отожженное состояние
Металл или сплав, нагретый и затем охлажденный для снятия внутренних напряжений и уменьшения хрупкости материала.
Arc Blow
Отклонение электрической дуги от нормального пути из-за магнитных сил.
Дуговая резка
Группа процессов термической резки, при которой металл разрезается или удаляется путем плавления с теплом дуги между электродом и заготовкой.
Arc Force
Осевая сила, создаваемая дуговой плазмой.
Дуговая строжка
Процедура дуговой резки, используемая для формирования скоса или канавки.
Длина дуги
Расстояние от кончика электрода или проволоки до обрабатываемой детали.
Arc Time
Время, в течение которого поддерживается дуга.
Напряжение дуги
Напряжение на сварочной дуге.
Дуговая сварка
Группа сварочных процессов, при которых происходит слияние металлов путем нагрева их дугой, с приложением давления или без него, с использованием присадочного металла или без него.
Эффективность наплавки дуговой сваркой (%)
Отношение веса наплавленного присадочного металла к весу расплавленного присадочного металла.
Электрод для дуговой сварки
Часть сварочной системы, через которую проходит ток, который заканчивается на дуге.
После сварки
Состояние металла шва после завершения сварки и до любой последующей термической или механической обработки.
Сварка атомарным водородом
Процесс дуговой сварки, при котором происходит слияние металлов путем их нагрева с помощью электрической дуги, поддерживаемой между двумя металлическими электродами в атмосфере водорода.
Аустенитный
Состоит в основном из гамма-железа с углеродом в растворе.
Автогенная сварка
Сварка плавлением, выполненная без добавления присадочного металла.
Автоматический
Управление процессом с помощью оборудования, которое не требует наблюдения за сваркой или не требует ручной регулировки органов управления оборудованием.
Задняя строжка
Удаление металла шва и основного металла с другой стороны частично сварного соединения для обеспечения полного проплавления при последующей сварке с этой стороны.
Backfire
Мгновенное падение пламени в сварочный или режущий наконечник с последующим возобновлением или полным исчезновением пламени.
Сварка с обратной стороны
Метод сварки, при которой сварочная горелка или пистолет направлена противоположно направлению сварки.
Основа
Материал (основной металл, металл сварного шва или гранулированный материал), размещаемый в основании сварного соединения с целью поддержки расплавленного металла сварного шва.
Backing Gas
Защитный газ, используемый на нижней стороне сварного шва для защиты от атмосферного загрязнения.
Опорное кольцо
Подложка в виде кольца, обычно используется при сварке труб.
Последовательность обратного шага
Продольная последовательность, в которой приращения сварного шва наносятся в направлении, противоположном процессу сварки соединения.
Основной металл (материал)
Металл (материал) для сварки, пайки, пайки или резки. См. Также подложку.
Радиус изгиба
Радиус кривизны на изгибе образца или области изгиба формованной детали. Измерено на внутренней стороне изгиба.
Фаска
Подготовка кромки под углом.
Заготовка
Процесс резки материала по размеру для более управляемой обработки.
Сварка припоем
Метод сварки с использованием присадочного металла, имеющего температуру ликвидуса выше 840 ° F (450 ° C) и ниже солидуса основных металлов.
Пайка
Группа сварочных процессов, при которых происходит слияние материалов путем их нагрева до подходящей температуры и использования присадочного металла, имеющего ликвидус выше 840 ° F (450 ° C) и ниже солидуса основных материалов. . Наполнитель распределяется между плотно прилегающими поверхностями стыка за счет капиллярного притяжения.
Заусенец
Неровный гребень, кромка, выступ или участок, оставшийся на металле после резки, сверления, перфорации или штамповки.
Смазка
Форма наплавки, при которой наплавлен один или несколько слоев металла шва (например, наплавка высоколегированного металла на стальной основной металл, который должен быть приварен к разному основному металлу). Нанесение масла обеспечивает подходящий переходный сварной шов для последующего завершения стыкового шва на поверхности канавки одного элемента.
Стыковое соединение
Соединение между двумя элементами, лежащими в одной плоскости.
Развал
Отклонение от прямолинейности кромки, обычно наибольшее отклонение боковой кромки от прямой.
Cap Pass
Последний проход сварного соединения.
Газ-носитель
При термическом напылении газ, используемый для переноса порошкообразных материалов из дозатора порошка или бункера к пистолету.
Капиллярное действие
Действие, при котором поверхность жидкости поднимается или опускается в месте контакта с твердым телом, поскольку молекулы жидкости притягиваются друг к другу и к молекулам твердого тела.
Облицовка
Тонкая (> 0.04 «) слой материала, нанесенный на основной материал для повышения коррозионной или износостойкости детали.
Плакированный металл
Композитный металл, содержащий два или три слоя, которые были сварены вместе. Сварка могла быть выполнена валиком. сварка, дуговая сварка, литье, тяжелое химическое напыление или тяжелое гальваническое покрытие.
Coalescence
Объединение множества материалов в одно тело
Coherent
Движение в унисон.
Cold Lap
Неполное сплавление или перекрытие.
Коллиматор
Для визуализации параллелей определенной линии или направления.
Complete Fusion
Сплав, который произошел по всем поверхностям основного материала, предназначенным для сварки, а также между всеми слоями и проходами.
Полное проникновение в стык
Включение в стык, при котором металл сварного шва полностью заполняет канавку и сплавлен с основным металлом по всей его толщине.
Источник питания постоянного тока
Источник питания для дуговой сварки с вольт-амперной выходной характеристикой, обеспечивающий небольшое изменение сварочного тока при большом изменении напряжения дуги.
Источник питания постоянного напряжения
Источник питания для дуговой сварки с вольт-амперной выходной характеристикой, обеспечивающий большое изменение сварочного тока при небольшом изменении напряжения дуги.
Контактная трубка
Компонент системы, передающий ток от горелки к непрерывному электроду.
Сопротивление контактов
Сопротивление в омах между контактами реле, переключателя или другого устройства, когда контакты соприкасаются друг с другом.
Контактная трубка
Устройство, передающее ток на непрерывный электрод.
Электрод с покрытием
Электрод из присадочного металла, используемый при дуговой сварке защищенным металлом, состоящий из сердечника из металлической проволоки с покрытием из флюса.
Кратер
При дуговой сварке — углубление на поверхности сварного шва.
Crater Crack
Трещина в кратере сварного шва.
Криогенный
Относится к низким температурам, обычно -200 o (-130 o) или ниже.
Приставка для резки
Устройство для преобразования газокислородной сварочной горелки в газокислородную резак.
Баллон
Переносной контейнер, используемый для транспортировки и хранения сжатого газа.
Дефект
Непрерывность или неоднородности, которые по своей природе или накопленному эффекту (например, общая длина трещины) приводят к тому, что деталь или продукт не могут соответствовать минимальным применимым стандартам приемки или спецификациям.
Плотность
Отношение веса вещества к единице объема; например масса твердого вещества, жидкости или газа на единицу объема при определенной температуре.
Наплавленный металл
Присадочный металл, добавленный во время сварки, пайки или пайки.
Эффективность наплавки
При дуговой сварке — отношение веса наплавленного металла к чистому весу израсходованного присадочного металла, без учета заглушек.
Скорость наплавки
Вес материала, нанесенного за единицу времени.Обычно он выражается в фунтах / час (фунт / час) или килограммах в час (кг / час).
Глубина плавления
Расстояние, на которое сплав распространяется в основной металл или предыдущий проход от поверхности, расплавленной во время сварки.
Точка росы
Температура и давление, при которых начинается сжижение пара. Обычно применяется для конденсации влаги из водяного пара в атмосфере.
Разбавление
Изменение химического состава сварочного присадочного материала, вызванное примесью основного материала или ранее нанесенного сварочного материала в наплавленный сварной шов.Обычно он измеряется процентным содержанием основного материала или ранее нанесенного сварочного материала в сварном шве.
Постоянный ток
Электрический ток, протекающий в одном направлении.
Отрицательный электрод постоянного тока (DCEN)
Расположение выводов для дуговой сварки на постоянном токе, при котором электрод является отрицательным полюсом, а деталь — положительным полюсом сварочной дуги.
Положительный электрод постоянного тока (DCEP)
Расположение выводов для дуговой сварки на постоянном токе, при котором электрод является положительным полюсом, а деталь — отрицательным полюсом сварочной дуги.
Рабочий цикл
Процент времени в течение периода времени, в течение которого источник питания может работать с номинальной мощностью без перегрева.
Динамическая нагрузка
Сила, прилагаемая движущимся телом к элементу сопротивления, обычно в относительно коротком интервале времени.
Удлинитель электрода
Длина электрода, выступающая за конец контактной трубки.
Держатель электрода
Процесс сварки, при котором происходит слияние металлов с теплом, полученным от концентрированного луча, состоящего в основном из высокоскоростных электронов.
Электронно-лучевая сварка
Процесс сварки, приводящий к слиянию металлов с расплавленным шлаком, при котором плавится присадочный металл и поверхности свариваемого изделия. Расплавленная сварочная ванна защищена шлаком, который перемещается по всему поперечному сечению соединения по мере выполнения сварки.
Электрошлаковая сварка
Процесс сварки, приводящий к слиянию металлов с расплавленным шлаком, при котором плавится присадочный металл и поверхности свариваемого изделия.Расплавленная сварочная ванна защищена шлаком, который перемещается по всему поперечному сечению соединения по мере выполнения сварки.
Состав эвтектоидов
Смесь фаз, состав которых определяется точкой эвтектоида в твердой области диаграммы равновесия, и чьи составляющие образуются в результате эвтектоидной реакции.
Лицевая поверхность
Поверхности материалов, контактирующие друг с другом и соединяемые или собирающиеся соединиться вместе.
Присадочный материал
Материал, добавляемый при сварке, пайке или пайке.
Угловой сварной шов
Сварной шов с приблизительно треугольным поперечным сечением, который соединяет две поверхности приблизительно под прямым углом друг к другу внахлест, Т-образное соединение или угловое соединение.
Фильтровальная пластина
Прозрачная пластина, тонированная в различной темноте, для использования в защитных очках, шлемах и щитках для рук для защиты рабочих от вредного ультрафиолетового, инфракрасного и видимого излучения.
Распыление пламенем
Процесс термического напыления с использованием пламени кислородно-топливного газа в качестве источника тепла для плавления материала покрытия.
Диапазон воспламеняемости
Диапазон, в котором газ при нормальной температуре (NTP) образует горючую смесь с воздухом.
Положение при сварке в плоскости
Положение при сварке, при котором ось сварного шва приблизительно горизонтальна, а поверхность сварного шва расположена приблизительно в горизонтальной плоскости.
Flashback
Спад пламени в смесительную камеру горелки или позади нее.
Пламегаситель
Устройство, ограничивающее повреждение от вспышки, предотвращая распространение фронта пламени за пределы точки, в которой установлен пламегаситель.
Мигающий
Сильный выброс мелких металлических частиц из-за дуги во время стыковой сварки оплавлением.
Flux
Материал, используемый для предотвращения, растворения или облегчения удаления оксидов и других нежелательных поверхностных веществ.
Дуговая сварка порошковой проволокой (FCAW)
Процесс дуговой сварки, при котором происходит слияние металлов с помощью трубчатого электрода.Защитный газ можно использовать или не использовать.
Сварка трением
Процесс сварки твердым телом, при котором происходит слияние материала за счет тепла, полученного в результате механически вызванного скользящего движения между трущимися поверхностями. Рабочие части удерживаются вместе под давлением.
Сварка трением с перемешиванием
Процесс сварки в твердом состоянии, при котором происходит слияние материала за счет тепла, полученного в результате механически индуцированного вращательного движения между плотно стыкованными поверхностями.Рабочие части удерживаются вместе под давлением.
Сварка вперед
Техника сварки, при которой сварочные горелки или горелка направлены в направлении сварки.
Fusion
Плавление вместе присадочного металла и основного металла (подложки) или только основного металла, которое приводит к слиянию.
Газовая дуговая сварка металла (GMAW)
Процесс дуговой сварки, при котором дуга возникает между электродом из сплошного присадочного металла и сварочной ванной.Требуется экранирование от внешнего источника газа.
Газовая дуговая сварка вольфрамом (GTAW)
Процесс дуговой сварки, при котором дуга возникает между вольфрамовым электродом (неплавящимся) и сварочной ванной. В процессе используется защитный газ, подаваемый извне.
Газовая сварка
Сварка теплом газокислородного пламени с добавлением присадочного металла или давлением или без него.
Ток перехода от шарового распыления к распылению
В режиме GMAW / Spray Transfer значение, при котором перенос электродного металла изменяется с шарового на распылительный режим по мере увеличения сварочного тока для любого заданного диаметра электрода.
Globular Transfer
При дуговой сварке тип переноса металла, при котором расплавленный присадочный металл переносится по дуге большими каплями.
Сварной шов с разделкой кромкой
Сварной шов, выполненный в канавке между двумя элементами. Примеры: одинарный V, одинарный U, одинарный J, двойной скос и т. Д.
Hard-Facing
Наплавка на рабочем месте для уменьшения износа.
Зона термического влияния
Та часть основного металла, обычно прилегающая к зоне сварного шва, механические свойства или микроструктура которой были изменены теплом сварки.
Герметично
Герметично. Гетерогенный
Смесь фаз, например: жидкость-пар или твердое тело-жидкость-пар.
Горячая трещина
Трещина, образовавшаяся при температурах, близких к завершению затвердевания сварного шва.
Горячий проход
При сварке труб второй проход, который проходит над корневым проходом.
Наклонное положение
При сварке труб ось трубы находится под углом 45 градусов к горизонтальному положению и остается неподвижной.
Неполное сплавление
Нарушение сплошности сварного шва, при котором сплавление металла сварного шва и соединения или прилегающих валиков сварного шва не происходит.
Неполное проникновение в стык
Состояние сварного шва с разделкой кромок, при котором металл сварного шва не выходит на толщину стыка.
Инертный газ
Газ, который обычно химически не соединяется с основным металлом или присадочным металлом.
Межкристаллитное проникновение
Проникновение присадочного металла по границам зерен основного металла.
Межпроходная температура
В многопроходном сварном шве температура области сварки между проходами.
Ионизационный потенциал
Напряжение, необходимое для ионизации (добавления или удаления электронов) материала.
Соединение
Место соединения элементов или кромок элементов, которые должны быть соединены или были соединены.
пропил
Ширина пропила, полученного в процессе резки.
Keyhole
Метод сварки, при котором концентрированный источник тепла полностью проникает через заготовку, образуя отверстие на передней кромке расплавленного металла шва.По мере продвижения источника тепла расплавленный металл заполняет отверстие за отверстием, образуя сварной шов.
Соединение внахлест
Соединение между двумя перекрывающимися элементами в параллельных плоскостях.
Лазер
Устройство, обеспечивающее концентрированный когерентный световой луч. Лазер — это аббревиатура от Light Amplification by Stimulated Emission of Radiation.
Резка лазерным лучом
Процесс, при котором материал разделяется теплом от концентрированного когерентного луча, падающего на заготовку.
Сварка лазерным лучом
Процесс плавления материала с помощью тепла от концентрированного когерентного луча, падающего на соединяемые элементы.
Ветвь углового сварного шва
Расстояние от основания стыка до носка углового сварного шва.
Ликвидус
Самая низкая температура, при которой металл или сплав полностью жидкие.
Оправка
Металлический стержень, служащий стержнем, вокруг которого отливаются, кованы или прессуются другие металлы, образуя истинное центральное отверстие.
Коллектор
Множественный коллектор для соединения источников газа или жидкости с точками распределения.
Мартенситный
Межузельный сверхнасыщенный твердый раствор углерода в железе с объемноцентрированной тетрагональной решеткой.
Ручная сварка
Процесс сварки, при котором горелкой или электрододержателем управляют вручную. MIG
См. Раздел «Газовая дуговая сварка металла» (GMAW).
Механическое соединение
Прилипание нанесенного термическим напылением покрытия к шероховатой поверхности за счет сцепления частиц.
Механизированная сварка
Сварка с использованием оборудования, при котором требуется ручная регулировка органов управления в ответ на изменения в процессе сварки. Горелка или электрододержатель удерживается механическим устройством.
Диапазон плавления
Диапазон температур между солидусом и ликвидусом.
Melt-Through
Видимая арматура, создаваемая на противоположной стороне сварного шва с одной стороны.
Дуговая сварка с металлическим сердечником
Процесс трубчатого электрода, при котором полая конфигурация содержит легирующие материалы.
Электрод с металлическим сердечником
Композитный трубчатый электрод, состоящий из металлической оболочки и сердечника из различных порошкообразных материалов, образующих не более чем островки шлака на поверхности сварного шва. Требуется внешнее экранирование.
Молекулярная масса
Сумма атомных масс всех составляющих атомов в молекуле элемента или соединения.
Монохроматический
Цвет поверхности, излучающей свет, содержащий чрезвычайно малый диапазон длин волн.
Нейтральное пламя
Пламя кислородно-топливного газа, которое не является ни окислительным, ни восстанавливающим.
Напряжение холостого хода
Напряжение между выходными клеммами сварочного аппарата при отсутствии тока в сварочной цепи.
Orifice Gas
При плазменной дуговой сварке и резке — газ, который направляется в горелку и окружает электрод. Он ионизируется в дуге с образованием плазмы и выходит из отверстия в сопле горелки в виде плазменной струи.
Окислительное пламя
Пламя кислородно-топливного газа, обладающее окислительным действием (избыток кислорода).
Прокаливание
Механическая обработка металлов ударными ударами.
Pilot Arc
Слаботочная непрерывная дуга между электродом и сужающим соплом плазменной горелки, которая ионизирует газ и облегчает зажигание сварочной дуги.
Плазма
Газ, который был нагрет, по крайней мере, до частично ионизированного состояния, что позволяет ему проводить электрический ток.
Плазменно-дуговая резка (PAC)
Процесс дуговой резки с использованием суженной дуги для удаления расплавленного металла с помощью высокоскоростной струи ионизированного газа из сужающего отверстия.
Плазменно-дуговая сварка (PAW)
Процесс дуговой сварки, в котором используется сжатая дуга между неплавящимся электродом и сварочной ванной (переносимая дуга) или между электродом и сужающимся соплом (непереносимая дуга). Экранирование обеспечивается ионизированным газом, выходящим из горелки.
Плазменное напыление (PSP)
Процесс термического напыления, в котором непередаваемая дуга используется для создания дуговой плазмы для плавления и продвижения материала наплавки к подложке.
Сварной шов с заглушкой
Круговой сварной шов, выполненный через отверстие в одном элементе внахлестку или тройника.
Пористость
Дырчатый разрыв, образованный захватом газа во время затвердевания.
Последующий нагрев
Нагревание сборки после сварки, пайки, пайки, термического напыления или резки.
Термическая обработка после сварки
Любая термообработка после сварки.
Преформа
Начальное прессование металлического порошка, которое образует прессовку.
Предварительный нагрев
Нагревание основного металла непосредственно перед сваркой, пайкой, пайкой, термическим напылением или резкой.
Температура предварительного нагрева
Температура основного металла непосредственно перед началом сварки.
Квалификация процедуры
Демонстрация того, что производственный процесс, такой как сварка, выполненный по определенной процедуре, может соответствовать заданным стандартам.
Техника с вытяжным пистолетом
То же, что при сварке сзади.
Импульсная силовая сварка
Любой метод дуговой сварки, при котором мощность циклически программируется на импульс, чтобы можно было использовать эффективные, но кратковременные значения параметра. Такие кратковременные значения существенно отличаются от среднего значения параметра. Эквивалентные термины — сварка импульсным напряжением или импульсным током.
Импульсная сварка распылением
Вариант процесса дуговой сварки, в котором импульсный ток обеспечивает перенос металла распылением при средних токах, равных или меньших, чем ток перехода от глобулярного к распылению.
Угол толкания
Угол перемещения, при котором электрод указывает в направлении движения.
Угол наклона
Наклон ножа от конца до конца.
Уменьшение пламени
Газовое пламя, которое имеет уменьшающий эффект из-за наличия избытка топлива.
Армирование
Сварите металл на лицевой стороне или у основания, превышающий количество металла, необходимого для заполнения стыка.
Остаточное напряжение
Напряжение, остающееся в конструкции или элементе в результате термической и / или механической обработки.Напряжение возникает при сварке плавлением в первую очередь потому, что расплавленный материал сжимается при охлаждении от солидуса до комнатной температуры.
Обратная полярность
Расположение выводов для дуговой сварки на постоянном токе с работой в качестве отрицательного полюса и электрода в качестве положительного полюса сварочной дуги.
Корневое отверстие
Разделение на стыке основания между заготовками.
Корневая трещина
Трещина в корне сварного шва.
Самозащитная порошковая сварка (FCAW-S)
Вариант процесса дуговой сварки порошковой проволокой, при котором защитный газ получают исключительно из флюса внутри электрода.
Дуговая сварка защищенного металла (SMAW)
Процесс, при котором выполняется сварка за счет тепла от электрической дуги между покрытым флюсом металлическим электродом и изделием. Экранирование возникает из-за разложения покрытия электрода.
Защитный газ
Защитный газ, используемый для предотвращения загрязнения атмосферы.
Пайка
Процесс соединения с использованием присадочного металла с температурой ликвидуса менее 840 ° F и ниже солидуса основного металла.
Сварка в твердом состоянии
Группа сварочных процессов, при которых происходит коалесценция при температурах существенно ниже точки плавления соединяемых основных материалов без добавления припоя. Давление нельзя использовать.
Solidus
Самая высокая температура, при которой металл или сплав становится полностью твердым.
Брызги
Частицы металла, выброшенные во время сварки, которые не являются частью сварного шва.
Распылительный перенос
При дуговой сварке тип переноса металла, при котором расплавленный присадочный металл перемещается в осевом направлении через дугу небольшими каплями.
Стандартные температура и давление (STP)
Принятая на международном уровне эталонная база, при которой стандартная температура составляет 0 ° C (32 ° f), а стандартное давление составляет одну атмосферу или 14,6960 фунтов на квадратный дюйм.
Вылет
Длина нерасплавленного электрода, выступающего за конец контактной трубки в процессах непрерывной сварки.
Прямая полярность
Дуговая сварка постоянным током, когда работа является положительным полюсом.
Термическая обработка для снятия напряжений
Равномерный нагрев сварной детали до температуры, достаточной для снятия большей части остаточных напряжений.
Растрескивание при снятии напряжения
Трещины в металле шва или в зоне термического влияния во время послесварочной термообработки или эксплуатации при высоких температурах.
Струнный валик
Сварной валик, сделанный без поперечного перемещения сварочной дуги.
Дуговая сварка под флюсом
Процесс, при котором происходит сварка с использованием тепла, выделяемого электрической дугой, между неизолированным металлическим электродом и изделием. Одеяло из гранулированного плавкого флюса экранирует дугу.
Субстрат
Любой материал, на который наносится напыление методом термического напыления.
Synergistic
Действие, при котором общий эффект двух активных компонентов в смеси больше, чем сумма их индивидуальных эффектов.
Прихваточный шов
Сварочный шов, предназначенный для удержания частей сварной конструкции в правильном положении до тех пор, пока не будут выполнены окончательные сварные швы.
Tenacious
Сплоченный, прочный.
Прочность на растяжение
Максимальное напряжение, которое материал, подвергающийся растягивающей нагрузке, может выдержать без разрыва.
Теплопроводность
Количество тепла, проходящего через материал.
Термическое напыление
Группа процессов, в которых мелкодисперсные металлические или неметаллические материалы осаждаются в расплавленном или полурасплавленном состоянии с образованием покрытия.
Термические напряжения
Напряжения в металле, возникающие в результате неравномерного распределения температуры.
Thermionic
Эмиссия электронов в результате нагрева.
Горловина
При сварке — область между руками сварщика сопротивлением. В прессе — расстояние от центральной линии слайда до рамы, в прессе с разрывной рамкой.
Сварка TIG
См. Раздел Газовая вольфрамовая дуговая сварка (GTAW).
Расстояние зазора резака
Расстояние от внешней поверхности сопла резака до обрабатываемой детали.
Перенесенная дуга
При плазменно-дуговой сварке плазменная дуга возникает между электродом и заготовкой.
Трещина под бортом
Трещина в зоне термического влияния, как правило, не распространяется на поверхность основного металла.
Канавка
Канавка, вплавленная в опорную пластину рядом с носком сварного шва или корнем сварного шва, осталась незаполненной металлом сварного шва.
Давление пара
Давление пара при достижении состояния равновесия между жидкостью, твердым телом или раствором и его паром.Когда давление пара жидкости превышает давление пара в ограничивающей атмосфере, обычно говорят, что жидкость кипит.
Вязкость
Сопротивление текучей среды (жидкости или газа) течению.
Свариваемость
Способность материала свариваться в условиях изготовления, налагаемых на конкретную, подходящим образом спроектированную структуру, и удовлетворительно работать в предполагаемой эксплуатации.
Сварной шов
Металл, нанесенный на стык в результате технологической обработки и использованной присадочной проволоки.
Сварочные провода
Вывод заготовки и вывод электрода в цепи дуговой сварки.
Сварочная проволока
Форма сварочного присадочного металла, обычно упакованная в виде катушек или катушек, которая может проводить или не проводить электрический ток в зависимости от используемого процесса сварки.
Металл сварного шва
Часть сварного шва плавлением, полностью расплавленная во время сварки.
Сварной проход
Однократная сварка вдоль стыка.Результатом прохода является сварной валик или слой.
Сварочная ванна
Локализованный объем расплавленного металла в сварном шве до его затвердевания в качестве металла шва.
Сварочная ванна
Нестандартный термин для обозначения сварочной ванны.
Армирование сварного шва
Наплавленный металл сверх количества, необходимого для заполнения стыка.
Последовательность сварки
Порядок нанесения валиков сварного шва на сварную деталь.
Смачивание
Явление, при котором жидкий присадочный металл или флюс растекается и прилипает тонким непрерывным слоем к твердому основному металлу.
Скорость подачи проволоки
Скорость, с которой расходуется проволока при сварке.
Рабочий поводок
Электрический проводник между источником тока дуговой сварки и изделием.
Сварка — SteelConstruction.info
Сварка — это основная деятельность на заводе-изготовителе, которую осуществляют квалифицированные специалисты, работающие в системе управления качеством сварки под контролем ответственного координатора сварки. Он используется для подготовки стыков к подключению в магазине и на месте, а также для крепления других приспособлений и фурнитуры.На заводе-изготовителе для различных видов деятельности используются разные методы сварки.
По сути, в процессе сварки используется электрическая дуга для выработки тепла для плавления основного материала в соединении. Отдельный присадочный материал, поставляемый в качестве расходуемого электрода, также плавится и соединяется с основным материалом, образуя расплавленную сварочную ванну. По мере продвижения сварки вдоль стыка сварочная ванна затвердевает, сплавляя основной металл и металл сварного шва. Для заполнения стыка или нарастания сварного шва до проектного размера может потребоваться несколько проходов или проходов.
Сварка
(Изображение любезно предоставлено William Haley Engineering Ltd.)
[вверх] Принципы дуговой сварки металлическим электродом
Терминология области сварного шва
Сварка — это сложное взаимодействие физических и химических наук. Правильное определение металлургических требований и разумное практическое применение являются предпосылкой для успешной сварки плавлением.
В процессе дуговой сварки металлическим электродом используется электрическая дуга для выработки тепла для плавления основного материала в соединении. Отдельный присадочный материал, поставляемый в качестве расходуемого электрода, также плавится и соединяется с основным материалом, образуя расплавленную сварочную ванну. Сварочная ванна подвержена атмосферному загрязнению и, следовательно, нуждается в защите во время критической фазы замерзания жидкости и твердого тела. Защита достигается либо за счет использования защитного газа, за счет покрытия бассейна инертным шлаком, либо за счет комбинации обоих действий.
В процессах с защитным газом от удаленного источника поступает газ, который подается на сварочную дугу через горелку или горелку. Газ окружает дугу и эффективно исключает атмосферу. Точный контроль необходим для поддержания подачи газа с соответствующей скоростью потока, так как слишком большое количество может вызвать турбулентность и засасывать воздух, а также может быть настолько же вредным, насколько и слишком маленьким.
В некоторых процессах используется флюс, который плавится в дуге для образования шлакового покрытия, которое, в свою очередь, покрывает сварочную ванну и защищает ее во время замерзания.Шлак также затвердевает и самораспускается или легко удаляется легким скалыванием. Действие плавления флюса также создает газовый экран для защиты.
По мере того, как сварка продолжается вдоль стыка, сварочная ванна затвердевает, сплавляя основной металл и металл сварного шва. Для заполнения стыка или нарастания сварного шва до проектного размера может потребоваться несколько проходов или проходов.
Тепло от сварки вызывает металлургические изменения в основном материале, непосредственно примыкающем к границе или линии плавления.Эта область изменения известна как зона термического влияния (HAZ). Общая терминология, используемая в области сварного шва, проиллюстрирована справа вверху.
Сварочные операции требуют надлежащего технологического контроля со стороны компетентных сварщиков, чтобы гарантировать достижение проектных характеристик, минимизировать риск дефектных соединений, вызванных низким качеством сварки, и предотвратить образование склонных к образованию трещин микроструктур в ЗТВ.
[вверх] Типы сварных соединений
Большинство конструкционных сварных соединений выполняется на заводе-изготовителе и описывается как стыковые или угловые швы.Сварка на месте также возможна, и руководство по вопросам сварки на месте доступно в GN 7.01.
[вверху] Стыковые швы
Макрос клиновидного стыкового шва
(Изображение любезно предоставлено Mabey Bridge Ltd.)
Стыковые сварные швы обычно представляют собой стыковые соединения в прокатных профилях или стыковые соединения листов на стенках и фланцах, чтобы приспособиться к изменению толщины или восполнить доступный материал по длине.Положения этих стыковых швов допускаются при проектировании, хотя ограничения доступности материалов или схема монтажа могут потребовать согласования различных или дополнительных сварных швов. Тройники, приваренные встык, могут потребоваться, если при поперечных соединениях возникают значительные нагрузки или усталость.
Стыковые швы — это сварные швы с полным или частичным проплавлением, выполняемые между материалами со скошенными или скошенными кромками. Стыковые швы с полным проплавлением предназначены для передачи всей прочности сечения.Как правило, эти соединения можно сваривать с одной стороны, но по мере увеличения толщины материала желательна сварка с обеих сторон, чтобы уравновесить эффекты деформации, с операцией обратной строжки и / или обратной шлифовки в процессе для обеспечения целостности корень шва. Односторонние стыковые сварные швы с подкладными полосами из керамической или прочной стали обычно используются для соединения больших площадей пластин (например, стальных пластин настила) и там, где есть закрытые коробчатые секции, трубы или элементы жесткости, к которым можно получить доступ для сварки только с одного боковая сторона.Расчетная толщина горловины определяет глубину проплавления, необходимую для швов с частичным проплавлением. Обратите внимание, что соображения усталости могут ограничивать использование сварных швов с частичным проплавлением, особенно на мостах. Руководство по подготовке к сварке доступно в GN 5.01.
Необходимо приложить все усилия, чтобы избежать стыковой сварки приспособлений из-за затрат, связанных с подготовкой, временем сварки, более высоким уровнем квалификации сварщика и более строгими и трудоемкими требованиями к испытаниям. Кроме того, стыковые швы имеют тенденцию иметь большие объемы наплавленного металла шва; это увеличивает эффект усадки сварного шва и приводит к более высокому уровню остаточных напряжений в соединении.Чтобы уравновесить усадку и распределить остаточное напряжение, минимизируя таким образом деформацию, необходима тщательная последовательность сварочных операций.
Иногда бывает необходимо обработать стыковые сварные швы заподлицо по причинам усталости, или для улучшения дренажа стальных балок, устойчивых к атмосферным воздействиям, или для улучшения режима испытаний. Следует избегать зачистки заподлицо только по эстетическим причинам, потому что трудно обработать поверхность, чтобы она соответствовала смежной поверхности после прокатки, и результат часто более визуально заметен, чем исходный сварной шов.Кроме того, шлифование представляет собой дополнительную опасность для здоровья и безопасности, которую лучше избегать по мере возможности. Правка стыковых сварных швов до заподлицо обычно не требуется для строительных стальных конструкций, поскольку обычно они не подвержены усталости.
- Пример обработанного стыкового шва с гладкой поверхностью и сливными пластинами
(изображения любезно предоставлены Mabey Bridge Ltd.)
[вверху] Угловые швы
Макрос однопроходного углового сварного шва
(Изображение любезно предоставлено Mabey Bridge Ltd.)
В большинстве сварных соединений в зданиях и мостах используются угловые швы, обычно в форме тройника. Обычно они включают в себя концевую пластину, ребро жесткости, подшипники и соединения распорок с прокатными секциями или плоскими балками, а также соединения стенки с фланцами на самих пластинчатых балках. Их относительно просто подготовить, сварить и испытать в обычных конфигурациях, при этом главным соображением является сборка стыков.
В S275 полная прочность сталей также развивается в угловых сварных швах и сварных швах с частичным проплавлением с вышележащими угловыми швами при условии, что такие сварные швы симметричны, выполнены с использованием правильных расходных материалов и сумма сварных швов равна толщине элемента, который сварные швы стыкуются.
Размеры сварных швов должны быть указаны на чертежах проекта вместе с любыми специальными требованиями классификации усталости. BS EN ISO 22553 [1] предписывает правила использования символов для детализации сварных соединений на чертежах.
Обращается внимание на тот факт, что в традиционной британской практике для определения размера углового сварного шва обычно используется длина ветви, но это не универсально: в европейской практике используется толщина горловины, а в стандарте BS EN 1993-1-8 [2] [2] дает требования относительно размера горла, а не длины ноги.Проектировщик должен быть осторожен, чтобы убедиться, что ясно, какой размер указан, и что все стороны должны знать, что было указано.
[вверх] Процессы
Важными факторами, которые подрядчик по изготовлению металлоконструкций должен учитывать при выборе процесса сварки, являются способность выполнять проектные требования и, с точки зрения производительности, скорость наплавки, которая может быть достигнута, а также рабочий цикл или эффективность процесса. (Эффективность — это отношение фактического времени сварки или дуги к общему времени, в течение которого сварщик или оператор занят выполнением сварочной задачи.Общее время включает настройку оборудования, очистку и проверку выполненного шва.)
Ниже описаны четыре основных процесса сварки, которые регулярно используются при производстве стальных конструкций в Великобритании. Номера процессов определены в BS EN ISO 4063 [3] . Разновидности этих процессов были разработаны для соответствия методикам и возможностям отдельных производителей, и другие процессы также имеют место для конкретных приложений, но выходят за рамки данной статьи.
[вверх] Металлоактивная газовая сварка (MAG), процесс 135
Сварка MAG
(Изображение любезно предоставлено Kiernan Structural Steel Ltd.)
MAG-сварка сплошным проволочным электродом — это наиболее широко используемый процесс с ручным управлением для заводских производственных работ; иногда это называют полуавтоматической сваркой или сваркой CO 2 . Сплошной проволочный электрод из сплошной проволоки пропускается через устройство подачи проволоки к «пистолету», который обычно удерживает и управляет оператором. Питание подается от источника выпрямителя или инвертора по соединительным кабелям к устройству подачи проволоки и кабелю горелки; электрическое подключение к проводу осуществляется через контактный наконечник на конце пистолета.Дуга защищена защитным газом, который направляется в зону сварки через кожух или сопло, окружающее контактный наконечник. Защитные газы обычно представляют собой смесь аргона, диоксида углерода и, возможно, кислорода или гелия.
Хорошая производительность наплавки и рабочий цикл можно ожидать от процесса, который также можно механизировать с помощью простых моторизованных кареток. Газовая защита может быть сдувана сквозняками, что может вызвать пористость и возможные вредные металлургические изменения в металле сварного шва.Таким образом, этот процесс лучше подходит для заводского производства, хотя он используется на месте, где могут быть предусмотрены эффективные укрытия. Он также более эффективен в плоском и горизонтальном положениях; Сварные швы в других положениях наплавляются с более низкими параметрами напряжения и силы тока и более подвержены дефектам плавления.
Металлоактивная газовая сварка (МАГ), процесс 135
Металлоактивная газовая сварка (MAG), процесс 135
MAG-сварка электродом с флюсовой сердцевиной, процесс 136 представляет собой разновидность, в которой используется то же оборудование, что и MAG-сварка, за исключением того, что плавящийся проволочный электрод имеет форму трубки малого диаметра, заполненной флюсом.Преимущество использования этих проволок заключается в том, что можно использовать более высокие скорости наплавки, особенно при сварке в вертикальном положении (между двумя вертикальными поверхностями) или в верхнем положении. Наличие тонкого шлака помогает преодолевать силу тяжести и позволяет наносить сварные швы в местах с относительно высокими током и напряжением, тем самым уменьшая возможность дефектов плавления. Добавки флюса также влияют на химию сварного шва и, таким образом, улучшают механические свойства соединения.
[вверху] Ручная дуговая сварка металлом (MMA), процесс 111
Этот процесс остается наиболее универсальным из всех сварочных процессов, но его использование в современной мастерской ограничено.Трансформаторы переменного тока, выпрямители постоянного тока или инверторы подают электроэнергию по кабелю на электрододержатель или клещи. Проволочный электрод с флюсовым покрытием (или «стержень») вставляется в держатель, и сварочная дуга возникает на кончике электрода, когда он ударяется о заготовку. На острие электрода плавится, образуя ванну расплава, которая сливается с основным материалом, образуя сварной шов. Флюс также плавится, образуя защитный шлак и создавая газовый экран, предотвращающий загрязнение сварочной ванны по мере ее затвердевания.Добавки флюса и сердечник электрода используются для влияния на химический состав и механические свойства сварного шва.
Обычно используются электроды с основным покрытием, контролируемым водородом. Эти электроды необходимо хранить и обращаться с ними в соответствии с рекомендациями производителя расходных материалов, чтобы сохранить их низкие водородные характеристики. Это достигается либо путем использования сушильных шкафов и подогреваемых колчанов для хранения и обработки продукта, либо путем приобретения электродов в герметичных упаковках, специально разработанных для поддержания низкого уровня водорода.
Недостатками процесса являются относительно низкая скорость осаждения и высокий уровень отходов, связанных с непригодными для использования концевыми штырями электродов. Тем не менее, он остается основным процессом для сварки на стройплощадке и для труднодоступных мест, где громоздкое оборудование не подходит.
Ручная дуговая сварка металлом (MMA), процесс 111
Ручная дуговая сварка металлом (MMA), процесс 111
[вверх] Дуговая сварка под флюсом (SAW), процесс 121
Оперативная сварка под флюсом
(Изображение предоставлено Mabey Bridge Ltd.)
Это, вероятно, наиболее широко используемый процесс для сварки угловых швов перемычки между стенкой и фланцем и стыковых сварных швов на линии толстой пластины для получения отрезков фланца и стенки. В процессе процесса непрерывный провод подается через контактный наконечник, где он обеспечивает электрический контакт с мощностью от выпрямителя, в зону сварки, где он изгибается и образует ванну расплава. Сварочная ванна заполняется флюсом, подаваемым из бункера. Флюс, непосредственно покрывающий расплавленную сварочную ванну, плавится, образуя шлак и защищая сварной шов во время затвердевания; излишки флюса собираются и повторно используются.По мере остывания шва шлак замерзает и отслаивается, оставляя высококачественные профильные швы.
Этот процесс по своей природе более безопасен, чем другие процессы, так как дуга полностью покрывается во время сварки, отсюда и термин дуга под флюсом. Это также означает, что требования к личной защите меньше. Высокая производительность наплавки — особенность процесса, поскольку он обычно механизируется на портальных установках, тракторах или другом специализированном оборудовании. Это позволяет контролировать параметры и дает рекомендации по точному размещению сварных швов.
Сварка под флюсом (SAW), процесс 121
Сварка под флюсом (SAW), технологическая 121
[вверху] Приварка шпилек методом вытяжной дуги, процесс 783
Композитные мосты требуют приваривания соединителей со срезной шпилькой к верхнему фланцу пластинчатых или коробчатых балок и в других местах, где требуется композитное воздействие стали на бетон, например.грамм. на интегральных абатментах. В зданиях композитные балки требуют приваривания соединителей срезных шпилек к элементам либо непосредственно к верхнему фланцу, либо чаще через постоянный настил из оцинкованной стали на композитных полах, где верхний фланец балки остается неокрашенным.
Сварка шпильки на балке моста
(Изображение любезно предоставлено Mabey Bridge Ltd.)Сварка сквозных шпилек
(Изображение любезно предоставлено Structural Metal Decks Ltd.)
Метод приварки шпилек известен как процесс с натянутой дугой, и требуется специальное оборудование в виде мощного выпрямителя и специального пистолета. Шпильки загружаются в пистолет, и при электрическом контакте с изделием концы с наконечниками изгибаются и плавятся. Продолжительность дуги рассчитывается так, чтобы между концом шпильки и основным материалом установилось расплавленное состояние. В нужный момент пистолет погружает шпильку в сварочную ванну.Керамическая манжета окружает шпильку для защиты и поддержки сварочной ванны, стабилизации дуги и формовки смещенной сварочной ванны для формирования сварной манжеты. Когда сварной шов затвердевает, обойма отслаивается. У удовлетворительных сварных швов обычно есть правильная, яркая и чистая втулка, полностью охватывающая шпильку.
Приварка шпилек методом вытяжной дуги 783
[вверху] Спецификации процедуры сварки
Чертежи детализируют конструктивную форму, выбор материала и указывают сварные соединения.Подрядчик по изготовлению металлоконструкций выбирает методы сварки каждой конфигурации стыка, обеспечивающие требуемые характеристики. Прочность, вязкость разрушения, пластичность и усталость являются важными металлургическими и механическими свойствами, которые необходимо учитывать. Тип соединения, положение сварки, производительность и требования к ресурсам влияют на выбор подходящего процесса сварки.
Выбранный метод представлен в спецификации процедуры сварки (WPS), в которой подробно описывается информация, необходимая для инструктирования и руководства сварщиками, чтобы обеспечить повторяемость характеристик для каждой конфигурации соединения.Пример формата WPS показан в Приложении A стандарта BS EN ISO 15609-1 [4] . Подрядчики по изготовлению металлоконструкций могут иметь свой собственный корпоративный шаблон, но все они включают важную информацию, позволяющую передать сварщику надлежащие инструкции.
Необходимо подкрепить WPS свидетельством удовлетворительных испытаний процедуры в виде протокола аттестации процедуры сварки (WPQR), подготовленного в соответствии с BS EN ISO 15614-1 [5] . Введение этого стандарта гласит, что испытания процедуры сварки, проведенные в соответствии с прежними национальными стандартами и спецификациями, не аннулируются при условии их технической эквивалентности; Для этого могут потребоваться дополнительные тесты.Крупные британские подрядчики по изготовлению металлоконструкций имеют предварительную квалификацию сварочных процедур, позволяющих производить удовлетворительные сварные швы в большинстве конфигураций стыков, которые могут встретиться в сталелитейном строительстве и в мостовой промышленности.
В случаях, когда данные предыдущих испытаний не актуальны, необходимо провести испытание процедуры сварки, чтобы установить и подтвердить пригодность предлагаемого WPS.
Руководство по стандартным спецификациям процедуры сварки для стальных конструкций доступно в публикации BCSA No.58/18.
[вверху] Процедура испытаний
BS EN ISO 15614-1 [5] описывает условия для проведения испытаний процедуры сварки и пределы действия в пределах квалификационных диапазонов, указанных в стандарте. Координатор сварки подготавливает предварительную спецификацию процедуры сварки (pWPS), которая является первоначальным предложением для проведения испытания процедуры. Для каждой конфигурации стыка, будь то стыковой или угловой сварной шов, учитывается марка и толщина материала, а также ожидаемые допуски посадки, которые могут быть достигнуты на практике.Выбор процесса определяется методом сборки, положением сварки и тем, является ли механизация жизнеспособным предложением для повышения производительности и обеспечения постоянного качества сварки. Размеры подготовки швов зависят от выбора процесса, любых ограничений доступа и толщины материала.
Расходные материалы выбираются из соображений совместимости с марками материалов и достижения указанных механических свойств, в первую очередь с точки зрения прочности и ударной вязкости. Для сталей марки S355 и выше используются продукты с водородным контролем.
Риск водородного растрескивания, пластинчатого разрыва, растрескивания при затвердевании или любой другой потенциальной проблемы оценивается не только с целью проведения испытания, но и для предполагаемого применения процедуры сварки в проекте. Соответствующие меры, такие как предварительный или последующий нагрев, включены в pWPS.
Контроль искажений обеспечивается правильной последовательностью сварки. При необходимости вводятся обратная строжка и / или обратное шлифование для достижения целостности корневого шва.
Приведены диапазоны сварочного напряжения, тока и скорости для определения оптимальных условий сварки.
Допустимые диапазоны групп материалов, толщины и типа соединения в пределах спецификации тщательно рассматриваются, чтобы максимально использовать pWPS. Подготавливают испытательные пластины достаточного размера для извлечения образцов для механических испытаний, включая образцы для любых дополнительных испытаний, указанных или необходимых для повышения применимости процедуры.
Пластины и pWPS предъявляются сварщику; испытание проводится в присутствии эксперта (обычно из независимого проверяющего органа), и ведется запись фактических параметров сварки вместе с любыми необходимыми изменениями процедуры.
Завершенные испытания передаются независимому эксперту для визуального осмотра и неразрушающего контроля в соответствии с таблицей 1 Стандарта. Удовлетворительные испытательные пластины затем отправляются на разрушающий контроль, опять же в соответствии с таблицей 1. Неразрушающие методы контроля, как правило, включают ультразвуковой контроль для объемного контроля и контроль магнитных частиц для выявления дефектов поверхности.
Пример испытательного образца процедуры сварки
(Изображение любезно предоставлено Mabey Bridge Ltd.)
Существует ряд дополнительных стандартов, детализирующих подготовку, обработку и испытания всех типов образцов для разрушающих испытаний. Обычно специализированные лаборатории организуют подготовку образцов для испытаний и проводят фактические механические испытания и составление отчетов. Типичные образцы для стыкового сварного шва пластины включают испытания на поперечное растяжение, испытания на поперечный изгиб, испытания на удар и образец для макроэкспертизы, на котором проводится испытание на твердость.Для испытаний на удар минимальные требования к поглощению энергии и температура испытания обычно такие же, как и для основного материала в соединении. Целесообразно испытать все сварочные процедуры до предела возможного применения, чтобы избежать повторения подобных испытаний в будущем.
Завершенные результаты испытаний заносятся в протокол аттестации процедуры сварки (WPQR), утверждаемый экзаменатором. Типичный формат показан в Приложении B стандарта BS EN ISO 15614-1 [5] .
Существует дополнительное общее требование, касающееся испытаний процедуры сварки, согласно которому, если грунтовки для краски должны быть нанесены на работу до изготовления, они должны наноситься на образец материала, используемого для испытаний. На практике требуется тщательный контроль толщины краски, чтобы избежать дефектов сварки.
BS EN ISO 14555 [6] описывает метод процедуры тестирования соединителей шпилек, приваренных дуговой сваркой. Стандарт включает требования к испытаниям, необходимым для подтверждения целостности сварных швов шпилек, а также устанавливает требования к производственным испытаниям для контроля приваривания шпилек в процессе.Допускается также квалификация, основанная на предыдущем опыте, и большинство подрядчиков по изготовлению стальных конструкций могут предоставить доказательства, подтверждающие это.
Дополнительное руководство по испытаниям процедуры сварки доступно в GN 4.02.
[вверху] Водородный крекинг
Растрескивание может привести к хрупкому разрушению соединения с потенциально катастрофическими последствиями. Водородное (или холодное) растрескивание может происходить в области основного металла, прилегающей к границе плавления сварного шва, известной как зона термического влияния (HAZ).Разрушение металла сварного шва также может быть вызвано определенными условиями. Механизмы, вызывающие отказ, сложны и подробно описаны в специальных текстах.
Рекомендуемые методы предотвращения растрескивания водородом / HAZ описаны в BS EN 1011-2 [7] , приложение C. Эти методы определяют уровень предварительного нагрева для изменения скорости охлаждения, что дает время водороду для миграции на поверхность. и ускользнуть (особенно если поддерживается в виде пост-нагревания после завершения соединения) вместо того, чтобы застревать в жестких, напряженных зонах.Предварительный нагрев не препятствует образованию микроструктур, подверженных образованию трещин; он просто снижает один из факторов, водород, так что растрескивания не происходит. Предварительный нагрев также снижает термический шок.
Подставки для подогрева
(Изображение любезно предоставлено Mabey Bridge Ltd.)
Одним из параметров, необходимых для расчета предварительного нагрева, является подвод тепла. Заметным изменением в стандарте является отказ от термина «энергия дуги» в пользу тепловложения для описания энергии, вводимой в сварной шов на единицу длины прогона.Расчет подводимого тепла основан на сварочном напряжении, токе и скорости движения и включает коэффициент теплового КПД; формула подробно описана в BS EN 1011-1 [8] .
Высокая ограниченность и повышенные значения углеродного эквивалента, связанные с более толстыми листами и более высокими марками стали, могут потребовать более строгого контроля процедур. Опытные подрядчики по изготовлению металлоконструкций могут выполнить эту дополнительную операцию и соответственно учесть ее.
BS EN 1011-2 [7] подтверждает, что наиболее эффективной гарантией предотвращения водородного растрескивания является снижение поступления водорода в металл шва из сварочных материалов.Процессы с изначально низким водородным потенциалом эффективны как часть стратегии, так же как и принятие строгих процедур хранения и обращения с электродами с водородным контролем. Данные и рекомендации поставщиков расходных материалов служат руководством для обеспечения минимально возможных уровней водорода для типа продукта, выбранного в процедуре.
Дополнительные информативные приложения к BS EN 1011-2 [7] описывают влияние условий сварки на ударную вязкость и твердость в ЗТВ и дают полезные советы по предотвращению растрескивания при затвердевании и разрыва пластин.
Дополнительное руководство по крекингу водородом / HAZ доступно в GN 6.04.
[вверх] Квалификация сварщика
Квалифицированный сварщик
(Изображение предоставлено Mabey Bridge Ltd.)
BS EN 1090-2 [9] требует, чтобы сварщики имели квалификацию в соответствии с BS EN ISO 9606-1 [10] . Этот стандарт предписывает испытания для аттестации сварщиков в зависимости от процесса, расходных материалов, типа соединения, положения сварки и материала.Сварщики, прошедшие успешные испытания процедуры, автоматически получают одобрение в пределах квалификационных диапазонов, установленных стандартом. Сварщики должны быть аттестованы в соответствии с BS EN ISO 14732 [11] , когда сварка полностью механизирована или автоматизирована. В этом стандарте особое внимание уделяется проверке способности оператора настраивать и настраивать оборудование до и во время сварки.
Квалификация сварщика ограничена по времени и требует подтверждения действительности в зависимости от продолжительности работы, участия в работе соответствующего технического характера и удовлетворительной работы.Продление квалификации сварщика зависит от зарегистрированных подтверждающих свидетельств, демонстрирующих продолжающуюся удовлетворительную работу в пределах исходного диапазона испытаний, и доказательства должны включать либо объемные разрушающие испытания, либо разрушающие испытания. Успех всех сварочных операций зависит от персонала, имеющего соответствующую подготовку и регулярного контроля компетентности посредством инспекций и испытаний.
[вверх] Инспекция и испытания
BS EN 1090-2 [9] устанавливает объем проверки до, во время и после сварки и дает критерии приемки, связанные с классом исполнения.Большинство испытаний являются неразрушающими; Разрушающие испытания проводятся только на отводных плитах.
[вверх] Неразрушающий контроль
Контроль сварных швов с помощью магнитных частиц (MPI)
(Изображение любезно предоставлено Mabey Bridge Ltd.)
Неразрушающий контроль проводится в соответствии с принципами BS EN ISO 17635 [12] . Для стальных конструкций основными методами являются визуальный контроль после сварки (см. GN 6.06), магнитопорошковый контроль (обычно сокращенно MPI или MT) для поверхностного контроля сварных швов (см. GN 6.02) и ультразвуковой контроль (UT) для подповерхностного контроля сварных швов (см. GN 6.03). Радиографические испытания также упоминаются в BS EN 1090-2 [9] . Радиография требует строгого контроля за здоровьем и безопасностью; это относительно медленно и требует специального оборудования. Использование этого метода в стальных конструкциях снизилось по сравнению с более безопасным и портативным оборудованием, связанным с UT.Безопасные запретные зоны требуются на работах и на месте во время проведения рентгенографии. Однако рентгенографию можно использовать для уточнения природы, размеров или степени множественных внутренних дефектов, обнаруженных с помощью ультразвука.
Технические специалисты с признанной подготовкой и квалификацией в соответствии с BS EN ISO 9712 [13] требуются для всех методов неразрушающего контроля.
BS EN 1090-2 [9] требует, чтобы все сварные швы подвергались визуальному контролю по всей их длине.С практической точки зрения сварные швы следует визуально осматривать сразу после сварки, чтобы гарантировать своевременное устранение очевидных дефектов поверхности.
Дальнейшие требования к неразрушающему контролю основаны на эксплуатационных методах и требуют более строгого исследования первых пяти соединений новых технических требований к процедуре сварки, чтобы установить, что процедура способна производить сварные швы соответствующего качества при внедрении в производство. Затем указываются дополнительные неразрушающие испытания, основанные на типах соединений, а не на конкретных критических соединениях.Цель состоит в том, чтобы опробовать различные сварные швы в зависимости от типа соединения, марки материала, сварочного оборудования и работы сварщиков и, таким образом, поддерживать общий мониторинг производительности.
Если указано частичное или процентное обследование, руководство по выбору продолжительности испытания дано в BS EN ISO 17635 [12] ; при обнаружении недопустимых разрывов площадь исследования соответственно увеличивается.
BS EN 1090-2 [9] также включает в таблицу минимальное время выдержки перед дополнительным неразрушающим контролем на основе размера сварного шва, подводимой теплоты и марки материала.
Признавая, что там, где требования к усталостной прочности более обременительны и требуется более строгая проверка, BS EN 1090-2 [9] действительно предусматривает спецификацию выполнения проекта для определения конкретных соединений для более высокого уровня проверки вместе с объемом и метод тестирования.
Для класса EXC3 критерием приемлемости дефектов сварного шва является уровень качества B стандарта BS EN ISO 5817 [14] . Там, где необходимо достичь повышенного уровня качества для удовлетворения конкретных требований к усталостной прочности, BS EN 1090-2 [9] дает дополнительные критерии приемлемости с точки зрения категории деталей в BS EN 1993-1-9 [15] для расположения сварного шва.
Как правило, дополнительные критерии приемки практически не достижимы при обычном производстве. Стандартные испытания процедуры сварки и квалификационные испытания сварщика не оцениваются по требованиям этого уровня. Если необходимо достичь такого уровня качества, требования должны быть сосредоточены на соответствующих деталях соединения, чтобы подрядчик имел возможность подготовить спецификации процедуры сварки, квалифицировать сварщиков и разработать соответствующие методы контроля и испытаний.
Неразрушающий контроль
[наверх] Разрушающий контроль
В стандарте BS EN 1090-2 [9] нет требований о проведении разрушающих испытаний поперечных соединений в натяжных фланцах. Тем не менее, объем для определения конкретных соединений для проверки позволит в спецификации проекта испытать, например, образцы от «стекающих» пластин, прикрепленных к встроенным стыковым сварным швам. Дополнительно производственные испытания могут быть указаны для: марок стали выше S460; угловые швы, в которых используются характеристики глубокого проплавления сварочного процесса; для мостовидных ортотропных настилов, где требуется макросъемка для проверки проплавления сварного шва; и на соединениях ребер жесткости с соединительными пластинами.
[вверх] Производственные испытания приварки шпилек
Испытание на изгиб приварной шпильки
(Изображение любезно предоставлено Mabey Bridge Ltd.)
Сварные шпильки для соединителей, работающих на сдвиг, исследуются и испытываются в соответствии с BS EN ISO 14555 [6] . Стандарт подчеркивает необходимость контроля процесса до, во время и после сварки. Предпроизводственные испытания используются для подтверждения процедуры сварки и, в зависимости от области применения, включают испытания на изгиб, испытания на растяжение, испытания на крутящий момент, макросъемку и радиографическое обследование.
Производственные испытания сварных швов также необходимы для приварки шпилек с дугой протяжки. Они должны выполняться производителем до начала сварочных работ на конструкции или группе аналогичных конструкций и / или после определенного количества сварных швов. Каждое испытание должно состоять как минимум из 10 сварных шпилек и быть испытано / оценено в соответствии с требованиями BS EN ISO 14555 [6] . Количество требуемых тестов должно быть указано в спецификации контракта.
[вверх] Качество сварки
Влияние дефектов на характеристики сварных соединений зависит от приложенной нагрузки и свойств материала.Эффект также может зависеть от точного расположения и ориентации дефекта, а также от таких факторов, как рабочая среда и температура. Основное влияние дефектов сварного шва на эксплуатационные характеристики стальных конструкций заключается в повышении риска разрушения из-за усталости или хрупкого разрушения.
Типы дефектов сварки можно разделить на одну из нескольких общих рубрик:
- Трещины.
- Плоские дефекты, кроме трещин, например непробиваемость, отсутствие плавления.
- Включения шлака.
- Пористость, поры.
- Поднутрения или дефекты профиля.
Трещины или плоские дефекты, проникающие через поверхность, потенциально являются наиболее серьезными. Включения вкрапленного шлака и пористость вряд ли станут причиной разрушения, если только они не будут чрезмерными. Подрезание обычно не является серьезной проблемой, если не существует значительных растягивающих напряжений поперек стыка.
Путем выбора класса исполнения в BS EN 1090-2 [9] устанавливаются критерии приемки, при превышении которых дефект считается дефектом.
Если дефекты обнаружены в результате осмотра и испытаний во время производства, вероятно, потребуется обработка после сварки (см. GN 5.02) или другие меры по исправлению положения, хотя во многих случаях конкретный дефект может быть оценен по концепции « пригодность по назначению ». Такое принятие зависит от фактических уровней напряжения и значимости усталости на месте. Это вопрос для быстрой консультации между подрядчиком по изготовлению металлоконструкций и проектировщиком, поскольку, если это приемлемо, можно избежать дорогостоящего ремонта (и возможности появления дополнительных дефектов или деформации).
Руководство по контролю качества сварных швов и контролю сварных швов доступно в BCSA № 54/12 и GN 6.01.
[вверх] Список литературы
- ↑ BS EN ISO 22553: 2019, Сварка и родственные процессы. Символическое изображение на чертежах. Сварные соединения. BSI.
- ↑ BS EN 1993-1-8: 2005, Еврокод 3. Проектирование стальных конструкций. Дизайн стыков, BSI
- ↑ BS EN ISO 4063: 2010, Сварка и родственные процессы. Номенклатура процессов и ссылочные номера, BSI
- ↑ BS EN ISO 15609-1: 2019, Технические требования и квалификация процедур сварки металлических материалов.Спецификация процедуры сварки. Дуговая сварка, BSI
- ↑ 5,0 5,1 5,2 BS EN ISO 15614-1: 2017 + A1: 2019, Технические требования и квалификация процедур сварки металлических материалов. Испытание процедуры сварки. Дуговая и газовая сварка сталей и дуговая сварка никеля и никелевых сплавов, BSI
- ↑ 6,0 6,1 6,2 BS EN ISO 14555: 2017, Сварка. Дуговая сварка металлических материалов, BSI
- ↑ 7.0 7,1 7,2 BS EN 1011-2: 2001, Сварка. Рекомендации по сварке металлических материалов. Дуговая сварка ферритных сталей, BSI
- ↑ BS EN 1011-1: 2009, Сварка. Рекомендации по сварке металлических материалов. Общее руководство по дуговой сварке, BSI
- ↑ 9,0 9,1 9,2 9,3 9,4 9,5 9,6 9,7 9,8 BS EN 1090-2: 2018, Изготовление металлоконструкций и алюминиевых конструкций.Технические требования к стальным конструкциям, BSI
- ↑ BS EN ISO 9606-1: 2017 Квалификационные испытания сварщиков. Сварка плавлением. Стали, BSI
- ↑ BS EN ISO 14732: 2013. Сварочный персонал. Квалификационные испытания сварщиков и наладчиков для механизированной и автоматической сварки металлических материалов BSI
- ↑ 12,0 12,1 BS EN ISO 17635: 2016, Неразрушающий контроль сварных швов. Общие правила для металлических материалов, BSI
- ↑ BS EN ISO 9712: 2012.Неразрушающий контроль. Квалификация и аттестация персонала по неразрушающему контролю, BSI
- ↑ BS EN ISO 5817: 2014, Сварка. Соединения, сваренные плавлением из стали, никеля, титана и их сплавов (за исключением лучевой сварки). Уровни качества для выявления недостатков, BSI
- ↑ BS EN 1993-1-9: 2005, Еврокод 3. Проектирование стальных конструкций. Усталость, BSI
[вверх] Ресурсы
- Стальные здания, 2003 г. (Публикация № 35/03), BCSA
- Стальные мосты: практический подход к проектированию для эффективного изготовления и строительства, 2010 г. (Публикация №51/10), BCSA
- Национальные технические условия на стальные конструкции (7-е издание), 2020 г. (Публикация № 62/20), BCSA
- Типовые спецификации процедуры сварки металлоконструкций — Второе издание, 2018 г. (Публикация № 58/18), BCSA
- Высокопрочные стали для применения в конструкциях: Руководство по изготовлению и сварке, 2020 г. (Публикация № 62/20), BCSA
- Руководство по контролю сварных швов для металлоконструкций, 2012 г. (Публикация № 54/12), BCSA
- Хенди, К.Р.; Ильес, округ Колумбия (2015) Steel Bridge Group: Рекомендации по передовой практике в строительстве стальных мостов (6-й выпуск). (P185). SCI
[вверх] Дополнительная литература
- Руководство проектировщика металлоконструкций (7-е издание), 2011 г., глава 26 — Сварные швы и проектирование для сварки, Институт стальных конструкций.
[вверху] См. Также
Массовая доля металла сварного шва для различных элементов (выбор)
Die nachhaltige Nutzung von Bodenflächen in der Land- und Forstwirtschaft unter ökologischen Aspekten ist, ebenso wie die ökonomische Betriebsführung, eine der landbehr- dieudenstreender.Die Fülle der Gesetze und Zertifizierungen, wie z.B. das FSC-Gütesiegel, führen heute dazu, dass die Anforderungen an die neuzeitlichen Agrar- und Forstgeräte immer weiter zu niedrigeren Bodenbelastungen unter Steigerung der Nutzlasten führen. Durch diese neuen gesetzlichen Rahmenbedingungen und dem Wunsch nach einer erhöhten Produktivität sowie der Verringerung der Bodenverdichtung wird der Druck, Leichtbau auch bei forst- und agrarwirtschaftlichen Maschinöhten umzuze. Dabei spielt auch der Wunsch nach immer größeren Nutzlasten für eine gesteigerte Produktivität eine entscheidende Rolle.Hierfür ist die Einführung von Leichtbauaspekten und eine funktionale Werkstoffauswahl eine Möglichkeit. Ум Дас Зил етег Leichtbaustrategie цу erreichen вирда nachfolgend systematische Анализ сделайте дер Einflussfaktoren AUf фильеры Festigkeit фон Schweißverbindungen унтер unterschiedlichen Lastarten (statisch, zyklisch унд schlagartig-dynamisch) durchgeführt мкм умирают Gewichtsreduktion über funktionale Werkstoffauswahl сделайте унд сделайте gezielte Modifikation фон Schweißzusatzwerkstoffen цу erreichen. Bei der funktionalen Werkstoffauswahl wird davon ausgegangen, dass sich das Verhalten von verschiedenen Stählen, entsprechend ihrer Chemischen Zusammensetzung, der Gefügeausprägung und der Herstellungsmetatzeitz, unstanddenchensmetatzen, img.Ziel der Arbeit ist es, durch das dargestellte Vorgehen, die Grundlagen für eine Gewichtsreduktion von Rahmenkonstruktionen in der Agrartechnik, mit dem Fokus auf schweißtechnische Verbindungen und deren Festigkeiten evensterungendenden%. Байм detaillierten Vergleich дер Verbindungseigenschaften фон ZWEI unterschiedlichen Feinkornbaustahlgruppen мкм funktionale Werkstoffauswahl сделайте für Leichtbaupotentiale identifizieren унд цу charakterisieren können, zeigte Сечь, Дасс Trotz vergleichbarer mechanischer Ausgangseigenschaften signifikante Unterschiede им Gefüge VOR унд нах дем Schweißen vorhanden Синд.Diese führen dazu, dass sich nach dem Schweißen deutlich andere Eigenschaften einstellen und so für eine der Stahlgruppen deutlich höhere zyklische Lasten ertragbar sind. Des Weiteren konnte über die Erarbeitung einer weiteren Methodik zur Verbesserung der Mechanischen Eigenschaften der Schweißverbindung unter statischen, zyklischen und Dynamisch-schlagartigen Belastungen unter Modifkeation des Schweißzustechtzwerkstungen. Hierzu wurde gezielt die Fließfähigkeit der Schmelze durch eine Oberflächenbeschichtung mit Titan beeinflusst und dadurch die geometrische Kerbwirkung am Nahtübergang vermindert.Ауф Основа дер erhöhten Technischen Dauerfestigkeit унтер zyklischer Последняя унд дем Erfüllen дер в фильеру Verbindungen gestellten statischen унд dynamisch-schlagartigen Festigkeitsanforderungen, IST Эйн Leichtbaupotential фон deutlich über 50% hinsichtlich де Rahmengewichts в дер Agrartechnik antizipierbar, да в Jedem Fall умирают Grundwerkstofffestigkeit erreicht Werden Одер gängige Auslegungskriterien um mehr als 50% überschritten werden.
Расчет затрат на сварку и объяснение времени
Расчет затрат и времени на сварку важен, потому что сварка может составлять значительную часть затрат на изготовление сварных конструкций и составные части.Зная, как оценить объем наплавленного шва, и типичное время, необходимое для выполнения сварки, важно для подготовки расценки, а также планировать графики.
The WelderDestiny Compass: еженедельная подписка на электронный журнал
Вы можете посмотреть прошлые выпуски «The WelderDestiny Compass», щелкнув здесь.
Сварка газо-вольфрамовой дуговой сваркой (GTAW): GTAW обычно представляет собой процесс с низкой скоростью наплавки.
Там
доступно множество ресурсов, которые подходят к вопросам, связанным с расчетом затрат на сварку, с разных точек зрения,
поэтому важно отметить, что есть несколько способов получить ответ.Подход, использованный на этой веб-странице, является относительно фундаментальным подходом, который
должны быть легко изменены для использования в большинстве случаев. Для расчета затрат и времени на сварку необходимо выполнить следующие действия:
- Рассчитать объем наплавленного металла. По сути, это основано на сварном шве. подготовка и длина сварного шва.
- Рассчитать масса наплавленного металла шва, основанная на плотности конкретный материал, с которым вы работаете.
- Применить рассчитанный «коэффициент восстановления» массы сварного шва для оценки общего количества необходимых сварочных материалов. (Некоторые расходные материалы будут потрачены впустую и будут не попадать в сустав. Например, в случае дуги из экранированного металла При сварке (SMAW) будут потери в огне, шлак и разбрызгивание.)
- На основании по массе необходимых сварочных материалов, теперь вы сможете узнать стоимость сварочных присадочных металлов, получив соответствующее предложение от вашего поставщик присадочного металла.Это не учитывает «дополнительные» расходные материалы. например, защитный газ, шлифовальные диски и т. д. оплачивается отдельно в зависимости от типа работы, которую вы будете выполнять.
- Рассчитать время, необходимое для осаждения необходимой массы сварочного металла, на основе скорость наплавки для конкретного сварочного процесса, который вы будете использовать. Этот значение предполагает 100% -ное время «горения дуги».
- Применить «коэффициент дуги», чтобы учесть тот факт, что ни один сварщик никогда не сваривает на 100% времени.Бывают случаи, когда ему / ей нужно удалить заглушку и заменить другим электродом или выполнить шлифовку или другую очистку между сварными швами. пробежек и т. д. Очевидно, что этот коэффициент будет разным для каждого сварщика, но вы можете начните с типичного принятого в отрасли значения и уточните его для своих конкретный бизнес или проект. (Ваш бизнес может быть более или менее эффективным чем в среднем по отрасли, или конкретная работа может быть более сложной, что приводит к уменьшению дуги в процентах. Это часто бывает при техническом обслуживании. тип работы)
- Это теперь сообщит вам, сколько «человеко-часов» потребуется для выполнения работы.
- На основе в человеко-часах вы можете оценить время, которое потребуется для завершить работу, решив, сколько сварщиков будут одновременно выполнять сварку время.
- На основе при расчете человеко-часов и сделанном вами предположении о количестве сварщики одновременно сваривают, вы можете прикинуть, сколько сварщиков вам нужно, и как долго. При расчете затрат на рабочую силу на данном этапе не забудьте добавить надбавку на помощников, а также «непродуктивное время» связанных с системами и процессами вашей компании.(Подумайте о встречах по безопасности, утренние встречи, кружки качества, инспекции безопасности или другие административные процессов.)
- Каждый бизнес также будет иметь некоторую надбавку на «накладные расходы», основанную на общем времени работа возьму. При этом учитываются затраты на управление, качество контрольный персонал, оборудование, косвенные расходные материалы и т. д. Эти накладные расходы будет отличаться для каждой компании, а также будет сильно различаться между разными отрасли. Иногда оценщик просто использует коэффициент, основанный на затратах. рассчитано выше (например,грамм. Умножьте рассчитанные затраты на 1,5, чтобы учесть накладные расходы.), а иногда это будет «ставка накладных расходов», основанная на количестве человеко-часы на сварку. (например, 50 долларов США на накладные расходы в человеко-часе.)
Имейте в виду, что в этом обсуждении расчета затрат на сварку рассматривается только операция сварки. Не принимает во внимание
затрат, связанных с материалами или производством / строительством котлов.
Сметные пакеты для расчета затрат на сварку
Расчет затрат и времени на сварку, очевидно, займет довольно много времени, если нам придется пересчитывать основы для каждого
оцените, что вам нужно сделать, поэтому у большинства предприятий будут какие-то автоматизированные
оценочная система. Существует ряд обобщенных коммерческих оценок.
доступны пакеты, которые можно использовать практически для любого вида работы. В
Недостатком большинства этих обобщенных систем оценивания является то, что
методика расчета затрат и времени на сварку не включена достаточно подробно.В этой ситуации расчет времени и затрат на сварку обычно включается в более специализированную оценку.
приложения, ориентированные на сварочные операции.
Многие
поэтому у предприятий есть комбинация пакетов коммерческой оценки,
в сочетании с набором электронных таблиц, чтобы предоставить некоторые данные для
коммерческий сметный пакет. Очевидно, что некоторые компании просто используют выборку
электронных таблиц, чтобы сделать их оценки, которые будут включать расчет затрат и времени на сварку.Это особенно актуально для небольших
предприятия.
Помощь с расчетом затрат на сварку и времени
Кому
помочь вам с расчетом затрат и времени на сварку, мы предоставили электронную таблицу
который выполняет расчеты объема и времени сварки. Вы можете скачать электронную таблицу, нажав здесь. Хотя я старался создать электронную таблицу, которая делает достаточно точные вычисления, WelderDestiny не несет никакой ответственности за ответы, которые вы получите из этой таблицы.Пожалуйста, используйте на свой страх и риск.
Кому
помочь вам на правильном пути, ниже приведены некоторые объяснения того, как использовать
таблица для расчета затрат и времени на сварку. Электронная таблица содержит два листа.
Первый рабочий лист касается косых, стыковых и угловых швов. Вторая сделка
с соединениями TYK. Соединения TYK рассматриваются отдельно, потому что их много
Сложнее рассчитать объем сварного шва.
Указания по расчету затрат и времени на сварку для стыковой скругленной кромки.
рабочий лист:
- В рабочий лист «Скругление стыка со скосом», детали сварного шва фиксируются вверху левая сторона.
- В В первом столбце описаны 5 различных типов подготовки к сварке. (Подготовка каждого сварного шва была воспроизведена 4 раза, чтобы вы могли ввести больше чем по одному каждого типа, если необходимо.) Он выделен желтым.
- следующие 5 столбцов относятся к разным параметрам, связанным с разными подготовка к сварке. Здесь вы вводите необработанные размерные данные для расчеты. Эти столбцы выделены голубым. Чтобы исключить любые в строке расчетов, убедитесь, что значение в столбце «Длина» равно нуль.(В настоящее время введены типичные значения, чтобы предложить некоторые Обратите внимание на единицы измерения, используемые для различных размеров. Этот рабочий лист заполнен в единицах СИ. Если будет достаточно спроса, я воспроизведет это в имперских единицах, хотя это будет довольно легко для вас чтобы внести эти изменения самостоятельно.
- следующие 4 столбца — это результаты вычислений. (Обратите внимание, что если вы измените что-либо в этих столбцах, тогда расчеты будут затронуты, так что будьте осторожный.) В расчетах здесь учтены размерные данные, вдоль с присадочным металлом и деталями сварки ниже на левой стороне рабочий лист. Эти столбцы выделены светло-зеленым.
- Эскизы показаны различные варианты подготовки к сварке и соответствующие размеры. включены справа и под таблицей расчетов.
- детали присадочного металла вводятся в выделенные голубым цветом ячейки на слева под таблицей расчетов.
- сведения о сварке вводятся в выделенные голубым цветом ячейки под детали наполнителя.
- Ниже детали сварки — это список терминов, используемых в рабочем листе.
- Кому в правом нижнем углу листа, в соответствии с деталями-заполнителями, типовые значения, которые можно использовать для различных сварочных процессов и материалов. Чуть выше находится пара «быстрых калькуляторов» для пересчета фунтов на час в килограмм в час и дюймы в миллиметры.
- Кому внизу рабочего листа есть много справочных материалов, которые помогут сделать решения относительно скорости осаждения и эффективности.Пожалуйста, позаботьтесь о единиц, поскольку некоторые ссылки даны в имперских единицах, а некоторые — в единицах СИ. Вы можете использовать «быстрые калькуляторы» для перевода любых единиц измерения, перед вводом значений в рабочий лист.
- В результаты расчетов на листе суммируются в строке «Итого», которая было выделено жирным красным шрифтом. Общая потребность в наполнителе, включая припуск на процент восстановления металла шва указан в «Total Filler Обязательная »ячейка.
Пожалуйста
обратите внимание, что размерные данные, введенные в рабочий лист, будут подвергнуты
значения, введенные в сведения о присадке и сведения о сварке, чтобы получить
необходимые расчеты. Это означает, что вы можете иметь дело только с одним наполнителем.
металл и единый процесс сварки за раз. Это действительно усложняет расчет затрат и времени на сварку для многопроцессорных сварных швов, но все же может
осуществляется следующим образом:
- Первый применяйте размерные и сварочные данные, как если бы вы приваривали только корень процесс.Например, если корневой отросток будет длиной 1000 мм, 4 мм Толстый слой газовой вольфрамо-дуговой сварки (GTAW) на листе толщиной 20 мм под углом 60 ° включенный угловой одинарный шов Vee с корневым зазором 4 мм, введите: a = 30; b = 2; Т = 4; h = 0; Длина = 1. (Убедитесь, что вы ввели необходимое Значения GTAW в разделах о присадочных деталях и деталях сварки.)
- Далее, примените размеры и детали сварки, как если бы вы только сваривали наполнитель и крышка процесса. Если мы собираемся сварить оставшуюся часть описанного стыка в пункте выше с процессом дуговой сварки порошковой проволокой (FCAW), тогда мы будем введите следующую информацию для раздела FCAW: a = 30; b = 5; (Это приблизительное значение того, каким был бы «корневой зазор», если бы мы удалили GTAW раздел.) Т = 16; (Толщина пластины 20 мм минус 4 мм для корневого отростка.) H = 3 мм; (Примерное значение высоты арматуры цоколя.) Длина = 1 (Убедитесь, что вы ввели необходимые значения FCAW в сведениях о наполнителе и детали сварки секций.)
- В Значения присадочного металла и человеко-часов, рассчитанные по двум указанным выше пунктам, могут затем использоваться надлежащим образом для выполнения остальной части сметы затрат и времени расчеты.
В
Рекомендации по расчету затрат и времени на сварку для рабочего листа «Соединения TYK» следующие:
- Это рабочий лист предназначен для Т-образных и Y-образных соединений между двумя секциями труб. пересекающиеся в единой плоскости.Неплоские пересечения труб и К-образные стыки которые пересекаются в узле, потребуют некоторых модификаций для получения точных ответы, хотя ответы не будут слишком далекими.
- Вкл. В верхней левой части рабочего листа у нас есть основная информация о размерах. Это в значительной степени зависит от диаметра меньшего элемента и угла, который меньший член совпадает с основным.
- голубые ячейки — это места, где нужно ввести необходимую информацию.
- светло-зеленые ячейки отображают рассчитанную информацию.Как правило, вы не хочу возиться с зелеными клетками.
- Ниже информация о размерах в верхнем левом углу — это место, где наполнитель информация введена. (В голубых ячейках.)
- Для рабочий лист TYK Joints вам необходимо ввести информацию для корня и «Основные» сварочные процессы. Это позволяет выполнить весь расчет за один идти, когда у вас разные процессы для рута и наполнителя / шапки. если ты только один процесс, затем введите толщину корня 0 мм.
- Ниже разделы, посвященные присадке и сварке, на рабочем листе — это «TYK Подробная информация о сварном шве ». Это матрица, которая дополнительно определяет детали подготовки к сварке для различных частей сварного шва.
- Только введите соответствующую размерную информацию в ячейки, которые были выделено голубым. Ячейки, выделенные светло-зеленым цветом, рассчитываются значения, так что не связывайтесь с этими ячейками.
- Кому помочь в выборе подходящих деталей сварного шва. четыре эскиза включены в правую часть рабочего листа.(Деталь 36; Деталь 37; Деталь 38; Деталь 39)
- Вы необходимо выбрать один ряд «Носок сварного шва», один ряд «Стороны сварного шва» и один ряд «Пятка сварного шва». Сварка »для использования в расчетах. Вы выбираете это, помещая 1 (Да) или 0 (Нет) в соответствующей ячейке столбца «G» матрицы деталей сварного шва. Руководствоваться описания в столбце A и углы, указанные в столбце B. (Обратите внимание, что это основан на деталях, приведенных в AWS D1.1, но вам необходимо выбрать наиболее подходящий сварные детали.
- Пожалуйста не обращайте внимания на выделенный серым блок в правом нижнем углу рабочий лист.Это используется для встроенных вычислений. Если вы возитесь с этим клетки, вы получите неправильные ответы.
- Расчетное количество присадочного металла и человеко-часы указаны под сварным швом. подробная информация и выделена розовым цветом.
- Пожалуйста прочтите раздел «Примечания» в левой нижней части рабочего листа, чтобы узнать, дальнейшее руководство по использованию рабочего листа.
Автор
используя прилагаемые рабочие листы, вы сможете получить необходимую сварку
расходные материалы и трудозатраты на сварку, необходимые для выполнения более высокого уровня
смета расходов на сварочные работы.
The WelderDestiny Compass: еженедельная подписка на электронный журнал
Вы можете посмотреть прошлые выпуски «The WelderDestiny Compass», щелкнув здесь.