Как происходит сварка
Чтобы начать рабочий процесс, сварщик касается электродом металла. Быстро отводит его от него на 3мм. От соприкосновения вспыхивает дуга. Длина ее равна расстоянию удаления от электрода. Поднимая и опуская прибор, усиливается или уменьшается сила плавки и температура дуги. Работы требуют соблюдения техники безопасности. Лицо закрывается щитком.
Есть другой способ образования дуги. Сварщик проводит по металлу электродом, затем отводит прибор в сторону на нужное расстояние. Образуется электрическая дуга.
Качество шва
От размера дуги зависит качество шва. Лучший результат получается при короткой дуге. Она не дает металлу разбрызгиваться, т.е. сохраняет его в большем объеме, при меньшей деформации. Электрод плавится при короткой дуге спокойно, без вспышек. Пучок искр ровный. Глубина при такой дуге получается больше. Если дуга длиннее, то электрод быстрее окисляется, сильнее разбрызгивается. Шов получается неровным, с оксидами и наплывами.
Длину дуги можно контролировать по звуку, издаваемому оборудованием. Оптимальная длина сопровождается равномерным звуком на одной ноте. Длинной дугой издается резкий тон, прерывающийся. Иногда слышатся звуки, похожие на хлопки, взрывы.
Дуга может прерваться. Тогда процесс повторяется, важно не оставить провал там, глее произошел разрыв.
Некоторые мастера при сваривании сложных деталей, ответственных за работу техники мест, зажигают дугу вне зоны сваривания. Они стремятся не допустить ожога металлической поверхности. Зажигание вне зоны сложнее, его смогут выполнить только квалифицированные работники.
Метод подвода дуги к изделию магнитным способом:
- отклонение влево;
- нормальное;
- отклонение вправо;
- влияние ферромагнитной массы железа.
Шов – это прочность скрепления. Поэтому одним из основных умений сварщика можно считать умение манипулировать электродом. Мастер перемещает электрод по металлу, видит шов, меняет его форму и размеры.
Режимы сварки и размеры шва
Режим сваривания – показатель проваривания металла. Математически это можно представить в виде формулы: отношение ширины шва к глубине. Ручная сварка предоставляет в этом широкие возможности. Шов можно получить как достаточно широкий, так и минимально узкий. Тип шва при этом не зависит от размера:
- угловой;
- стыковой;
- накладной.
Параметры и коэффициенты подачи тока
В ручной сварке важна сила тока. От ее увеличении зависит глубина проникновения в металл, проплав получается только при нужном токе. поэтому важно заранее просчитать необходимый коэффициент силы тока. Чем плотнее металл, тем больший проплав. Род электрического тока также имеет значение.
- Постоянный ток дает узкий шов;
- Увеличение напряжения увеличивает шов.
Поэтому выбираются электроды разных диаметров наконечника.
Уменьшение электрода сокращает горение дуги, увеличивает глубина проплава, сокращается ширина.
Изменение напряжения используется активно в автоматической сварке, он позволяет регулировать наплавку.
Сварка в защитных газах
Процесс заключается в том, что в дуговую область поступант газ, который явлеяется ее защитой. Газ становится изолятором расплавленного металла от воздуха.
Виды такой сварки:
- активные газы;
- смеси газов;
- струйная газовая защита.
В комплект для сварочных работ входит следующая техника:
- трансформаторы;
- инверторы;
- блоки питания;
- горелки;
- маски или щитки;
- газовое оборудование.
ГОСТ
По межгосударственному стандарту ручная сварка имеет утвержденный ГОСТ – 5264-80.
Стандарт распространяется на конструктивные элементы, указывает размеры. Характеристики по ГОСТу дают следующие данные:
- Тип соединения;
- Форму подготовленных краев деталей;
- Характер получаемого шва;
- Форма поперечного сечения;
- Толщина деталей.
В ГОСТе дается условное обозначение каждого типа соединения. Изучив документ, сварщик легко сориентируется в чертежах, самостоятельно разрабатывает требования к сварным конструкциям. Есть четкие требования, каким по размерам и форме должен быть шов:
- при одинаковых поверхностях;
- разных металлов;
- разная толщина изделий.
Применять стандарт сможет сварщик с любым уровнем образования. Его соблюдение станет гарантом получения отличного качества сварки.
подготовка кромок, цветных, как отличить от шлака, толстого, как нагреть электросваркой, детали и изделия из сплавов, индукционная – Определенных металлов на Svarka.guru
Сварка металлов изобретена людьми немногим позже, чем сама металлообработка. Уже древние кузнецы умели создать из отдельных железных изделий единое целое.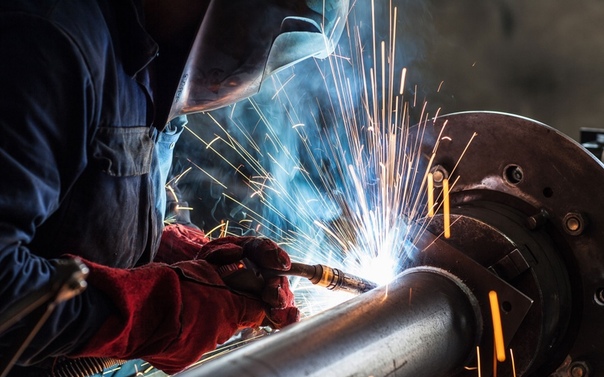
Ее используют на производстве, в быту, при изготовлении строительных конструкций и автомобилей, деталей механизмов, украшений. Выполняют под водой и в космическом пространстве.
Современные технологии позволяют достигать такой прочности полученного изделия, как если бы оно изначально было цельным.
Свариваемость металлов изучают профильные институты разных стран мира, а сварщик одна из самых востребованных сегодня рабочих профессий.
Основные понятия процесса
Добиваются соединения тремя методами:
- Термическим, расплавляя металл самих соединяемых деталей, либо дополнительной присадки.
Пример — распространенная дуговая и газовая, лазером, струей плазмы. Сюда относится и пайка.
- Термомеханическим, при котором изделия раскаляют, после чего сжимают либо выполняют проковку. Это самый древний способ, которым владели кузнецы уже пятого тысячелетия до Н.Э. Кроме ковки это диффузионная сварка, контактная, индукционно-прессовая.
- Механическим методом изделия сваривают, подвергая различным воздействиям без специального нагрева. Пример — ультразвуковые методики, соединения взрывом, трением, давлением.
Второй и третий методы применяют на промышленных линиях, при серийных выпусках, а также для изготовления уникальных изделий.
Не зависимо от используемой методики, существует всего две разновидности процесса:
- Бесшовный, когда соединяется металл непосредственно самих деталей.
- С образованием шва. При этом применяют вспомогательные присадки. Они могут как точно соответствовать основному металлу, так и отличаться. Пример — соединение стали медным электродом, пайка оловом, все виды сварки с использованием плавкого электрода.
История
До второй половины XIX единственным методом сварных соединений была ковка, а также пайка
[stextbox id=’info’]Пайка отличается тем, что при ней не происходит расплав кромок соединяемых деталей. Это своего рода «склеивание», где роль клеящего состава играет расплавленный металл.[/stextbox]
Настоящая революция сварочных процессов началась с открытием процесса электрической дуги. Для соединения деталей ее сумели применить русские инженеры. Методику дуговой сварки угольными электродами изобрел Н.Н. Бенардос, а спустя буквально несколько месяцев, Н. Г. Славянов сумел выполнить первое соединение металлов плавящимся электродом.
Настоящим сварочным бумом отмечен век XX. Французские инженеры изобрели газовую сварку, в 1956 г. токарь А. И. Чудиков сумел соединить вращающиеся на токарном станке детали трением. К концу 60-х люди узнали, как сварить металл лазером. Примерно тогда же появились промышленные аппараты плазменного напыления, сварка индукционная, диффузионная и пр.
Основные способы
На сегодня насчитывается более 150 различных способов сварных работ. Отличаясь деталями, все они входят в несколько основных категорий, которые мы вкратце рассмотрим.
Электродуговая
Наиболее распространенная на сегодня технология. Ее разделяют на два основных типа: неплавящимся и плавким электродом.
Оба они основаны на температурном воздействии вольтовой дуги. В первом случае задача как нагреть металл электросваркой решается с помощью тугоплавкого электрода из вольфрама. Сам он не плавится, а только образует дугу, формируя сварочную ванну из материала самих деталей либо с добавлением присадки.
Последнюю вносят рукой, как сварочный пруток, либо автоматической подачей, как тонкую проволоку.
Во втором варианте дуга образуется между свариваемым металлом и плавящимся электродом. Последний одновременно служит для формирования шва, который образуется струйным переносом его металла.
Для концентрации дуги, а также образования защитного слоя, металлический стержень покрывают слоем специальной обмазки. К обмазке так же добавляют ряд компонентов, перенос которых улучшает качество шва.
[stextbox id=’info’]Впервые синтетический рутил, основу обмазки большинства видов электродов, был получен при разработке технологии изготовления белой краски: титановых белил, в 50-х годах прошлого века. Сегодня этот метод является основным источником для электродной промышленности.[/stextbox]
Чтобы защитить расплав от окисления на сварочную зону через горелку подают поток газа. В зависимости от его свойств различают:- Сварку в углекислом газе. Как правило ведут полуавтоматическими инверторами. Скорость сварки полуавтоматом в зависимости от толщины металла, диктует и необходимый объем подачи углекислоты. Таким способом сваривают тонколистовой металл, скажем, при ремонтах кузова автомобиля.
- Соединение в среде инертных газов аргона, либо гелия. К примеру, так варят трубопроводы из нержавейки, алюминия, специальных сплавов.
- Сварку в активном газе.
Оборудование, которыми ведут работы отличаются устройством, но как правило это различного типа трансформаторы и генераторы.
Методика дуговой сварки универсальна, позволяет как варить тонкий металл полуавтоматом, так и соединять толстостенные стальные трубы ручным способом.
Автоматическая под флюсом
Сварочный флюс представляет собой порошок из различных веществ. Его задача двойная:
- Защитить расплав металла от окисления.
- Внести в соединение вещества для усиления прочности стыка.
Процесс происходит следующим образом.
Предварительно подготовленные детали фиксируют на специальном стенде. После этого, на место стыка специальной трубкой подают слой флюса, образующего длинный холмик. За ней идет сварочная головка, образующая дугу. Далее может следовать еще одна трубка, засасывающая не использованный порошок флюса.
Работа ведется неплавящимся или плавящимся электродом. Флюс при этом частично расплавляется. Как отличить металл от шлака при сварке задача не ставится: после завершения работы, достаточно простучать шов, чтобы шлаковая корка, образованная расплавом флюса, отскочила.
Электрошлаковая
При сходстве технологии под флюсом, отличие процесса принципиально. Температура тут создается расплавом специального состава, куда помимо металла входит токопроводящий шлак.Расплав поддерживается проходящим через него электрическим током. При этом, прогрев ведется сразу по всей длине соединения.
Металл образующий соединительный шов одновременно является плавким электродом, подающим ток в расплав. Это может быть проволока, пластина, либо трубчатый мундштук.
Постепенный нагрев и такое же плавное охлаждение исключает перекаливание изделия, не создает дополнительных напряжений.
Метод требует специфического оборудования и выполняется в заводских условиях. Зато, ему доступна сварка толстого металла, сразу на весь массив деталей.
Электронно-лучевая и плазменная, диффузионная и контактная
При различии методов и принципов соединений изделий все эти виды объединяет отсутствие вольтовой дуги (либо ее особая разновидность, как при сварке плазменной). Более того, при контактной технологии дуга нежелательна.
Электронно-лучевое соединение деталей впервые получили еще в 50-е годы. Процесс схож с соединением лазером, но вместо луча фотонов выступает направленный пучок электронов. Таким способом возможно, как соединять крохотные детали, размеры которых измеряются долями миллиметра, так производить сварку листового металла размером в десятки квадратных метров.
[stextbox id=’info’]Обязательное требование процесса, специфическая особенность электронно-лучевой технологии — помещение соединяемых деталей в вакуум. Поэтому, этому типу сварки ученые пророчат будущее как основной технологии при сборке конструкций космических станций и кораблей.[/stextbox]
Сварка плазменная подходит для работы с тугоплавкими металлами. В отличие от электрической дуги, температура которой 6-7 тыс. градусов Цельсия, в потоке плазмы жар достигает 30000ºС. Кроме соединения, процесс позволяет выполнять напыление разнородных металлов.Диффузная сварка основана на взаимопроникновении атомов металлов плотно сжатых, предварительно нагретых деталей. Этот процесс, называемый диффузией, дал название методу. Эффективен метод в сложных случаях, к примеру с его помощью выполняется сварка цветных металлов.
Сварка контактная также относится к соединению давлением. При сжатии деталей в месте контакта проходит импульс эл. тока, который обеспечивает связь.
Холодное сваривание деталей и индукционный способ
Основа холодной сварки: деформация соединяемых деталей. Иначе — холодная ковка. При всей привлекательности метода (отсутствие эл. тока) с его помощью удается соединять только неокисляющиеся детали.
Индукционный способ является полной противоположностью холодному. Детали греют, причем не пламенем или дугой, а высокочастотным электромагнитным полем. При этом сварные изделия из металла прогреваются на значительную глубину.
Способ технологичен, поэтому применяется, к примеру, на автоматизированных. трубопрокатных линиях.
Как свариваются разные металлы и сплавы?
Особым качеством металлов является такое понятие как свариваемость, то есть способность соединятся сваркой с помощью того, или иного метода. Зависеть она может от многих причин: химический состав, специфические свойства металла либо сплава, методика подготовки деталей под сварку и многое другое.
ГОСТ разделяет это свойство на следующие группы, свариваемые:
- хорошо;
- удовлетворительно;
- ограниченно;
- плохо.
- окисная пленка, препятствующая контакту;
- наличие легирующих добавок, в частности углерода делающих шов хрупким и непрочным.
Свариваемость улучшают предварительной специфической подготовкой металла к сварке.
Особенно сложны в отношении свариваемости цветные металлы, каждый со своей спецификой.
Процедура
Хотя технология создания сварных соединений отличается, во всех случаях процесс начинается с подготовительных операций. Для дуговых методов это подготовка кромок под сварку, или как говорят, их разделка. Для холодной ковки — тщательная зачистка (вплоть до полировки) соединяемых деталей и т.п. Подготовка может включать очистку от грязи, обезжиривание.
Еще одно негативное явление, объединяющее все виды сварочных контактов — температурные деформации и напряжения.
Борются с этим по-разному. В некоторых случаях изделия заранее фиксируют струбцинами. Еще один распространенный способ — термическая обработка готового изделия: нагрев с последующим медленным охлаждением (отпуск).
В заключение
Мы рассмотрели далеко не все виды и способы сварки. Кроме того, постоянно развиваются существующие технологии, изобретаются новые.
При этом технологические решения диктуются задачами. В одном случае вопрос стоит как правильно сварить байпас из металла отопительной системы квартиры используя простейший ручной способ, в другом — создать сверхточное изделие для авиапромышленности. Соответственно подход требуется разный.
На смену существующим, неизбежно придут новые методы, более быстрые и надежные.
Механические виды сварки
Содержание страницы
К механическим видам сварки относятся холодная и ультразвуковая сварка, а также сварка трением и взрывом.
1. Холодная сварка
Данный вид сварки применяют для соединения очень пластичных металлов (алюминия и его сплавов, меди, свинца, олова и др.)(рис. 1).
Холодная сварка – сварка давлением при значительной пластической деформации без нагрева свариваемых частей внешними источниками теплоты. Подразделяется на три вида: точечную, шовную и стыковую.
Рис. 1. Схема холодной сварки
Точечной холодной сваркой соединяют внахлёстку листовые материалы или в стык (рис. 2).
Рис. 2. Схемы холодной сварки усилиями, нормальными к поверхности соединения: а, б – внахлёстку; в, г – встык; 1, 2 – свариваемые детали; 3 – прижимы
Холодной сваркой в основном сваривают однородные или неоднородные металлы и сплавы, обладающие высокой пластичностью при нормальной температуре. Высокопрочные металлы и сплавы холодной сваркой не сваривают, так как для этого требуются очень большие удельные усилия, которые практически трудно осуществить.
Хорошо свариваются сплавы алюминия, кадмия, свинца, меди, никеля, золота, серебра, цинка и тому подобные металлы и сплавы. К преимуществу этого способа относятся малый расход энергии, незначительное изменение свойств металла, высокая производительность, возможность автоматизации.
Для соединения холодной точечной сваркой могут быть использованы любые прессы (винтовые, гидравлические, рычажные, эксцентриковые), кроме того специализированные установки для стыковой холодной сварки (рис. 3).
Рис. 3. Электропневматический аппарат для сварки прутьев, проволоки и полосы цветных металлов диаметром от 5 до 12,5 мм (а) и длина сваренных медных и алюминиевых прутьев (б)
Шовной холодной сваркой соединяют листовые материалы непрерывным швом (рис. 4).
Рис. 4. Схема шовной холодной сваркой: 1 – свариваемый металл; 2 – опорные ролики; 3 – ролики-пуансоны (выступы)
Стыковой холодной сваркой соединяют стержни по поверхности стыкуемых торцов.
Рис. 5 Сварка трением
При сварке трением используется превращение механической энергии в тепловую. При вращении металлических заготовок 1 одна относительно другой одна установлена в неподвижном зажиме 2, а вторая в подвижном зажиме 3 (рис. 5), их торцы разогреваются вследствие трения поверхностей соприкосновения. Разогрев производят до пластического состояния, а затем прикладывают осевое усилие Р. Образование сварного соединения происходит в результате возникновения металлических связей между контактирующими поверхностями. Окисные пленки, имеющиеся на металлических поверхностях в точке соединения, разрушаются трением и удаляются в результате пластической деформации в радиальных направлениях. Основными параметрами процесса сварки трением являются: скорость относительного перемещения свариваемых поверхностей; величина удельного давления, прилагаемого к свариваемым поверхностям; величина пластической деформации, т. е. осадки.
Необходимый для сварки нагрев при прочих равных условиях обусловлен скоростью вращения и величиной осевого усилия.
2. Ультразвуковая сварка
Сварка давлением, осуществляемая при воздействии ультразвуковых колебаний, называется ультразвуковой сваркой (УЗС) (рис. 6). Реализация УЗС состоит в приложении высокочастотных колебаний (16 – 20 кГц) к свариваемым заготовкам. В заготовках возникают касательные напряжения, вызывающие пластическую деформацию материала свариваемых поверхностей. В месте соединения развивается повышенная температура (0,4 – 0,6) Тпл, зависящая от свойств свариваемых материалов. Эта температура способствует возникновению пластического состояния свариваемых материалов и их соединению. В месте сварки в процессе охлаждения формируются совместные кристаллы, обеспечивающие прочность сварного соединения. Одновременно под действием ультразвука разрушаются оксидные плёнки на поверхностях заготовок, что также облегчает получения соединения.
Рис. 6. а – схема ультразвуковой сварки, где: 1 – преобразователь; 2 – трансформатор; 3 – рабочий инструмент; 4 – наконечник; 5 – свариваемое изделие; 6 – опора; б – ультразвуковая сварка по контуру, где: 1 – волновод; 2 – сменный полый штифт; 3 – сменный прижимной штифт; 4 – прижимная опора; 5 – свариваемое изделие
Технологические возможности УЗС: соединение металлов без снятия поверхностных плёнок и расплавления; особенно хорошая свариваемость чистого и сверхчистого алюминия, меди, серебра; соединение тончайшей металлической фольги со стеклом и керамикой. Ультрозвуком свариваются большинство известных термопластичных полимеров. Для ряда полимеров УЗС является единственно возможным надёжным способом соединения. При УЗС в принципе нет ограничений по нижнему пределу свариваемых толщин различных металлов. Возможно также соединение с существенным перепадом толщин и свойств свариваемых материалов (например, в соединение металл – стекло может быть отношение 1 : 1000 и больше). Для УЗС также характерны малая энергоёмкость; возможность питания нескольких сварочных головок от одного генератора и возможность выноса их на значительное растояние; простота автомотизации процесса работы колебательной системы; гигиеничность процесса.
Методы УЗС применяют в приборостроении, радиоэлектронике, авиационной промышленности. На рис. 7 показана одна из промышленных установок для ультрозвуковой сварки.
Рис. 7. Ультразвуковая сварка плёнки
3. Сварка взрывом
Сварку взрывом можно отнести к видам сварки с оплавлением при кратковременном нагреве на воздухе, так как на отдельных участках наблюдаются зоны металла, нагретые до оплавления. Однако на других участках температура может быть не высока, и здесь процесс приближается к холодной сварке.
При осуществлении сварки взрывом химическая энергия превращения заряда взрывчатого вещества (ВВ) в газообразные продукты взрыва трансформируется в механическую энергию их расширения, сообщая одной из свариваемых заготовок большую скорость перемещения. Кинетическая энергия соударения движущейся части с поверхностью неподвижной части
затрачивается на работу совместной пластической деформации контактирующих слоёв металла, приводящей к образованию сварного соединения. Работа пластической деформации сопровождается выделением теплоты, за счёт которой вследствие адиабатического характера процесс при больших скоростях металл в зоне соединения может разогреваться до высоких температур (вплоть до оплавления локальных объёмов). Большинство технологических схем сварки основано на использовании направленного (кумулятивного) взрыва (рис. 8).
Рис. 8. Схема сварки взрывом: 1 – детонатор; 2 – взрывчатое вещество; 3 и 4 – свариваемые заготовки; 5 – основание; h – зазор между заготовками; Н – толщина слоя взрывчатого вещества
Прочность соединений, выполненных сваркой взрывом, выше прочности соединяемых материалов. Перспективы и области применения сварки взрывом определяются возможностью создания в твёрдой фазе прочных соединений за счёт поверхностных металлических связей без развития объёмной диффузии вследствие скоротечности процесса на больших (20 м2), практически неограниченных площадях. Это позволяет применять сварку взрывом при изготовлении заготовок для проката биметалла, плакирования поверхностей конструкционных сталей металлами и сплавами с особыми физическими и химическими свойствами, при сварке заготовок из разнородных материалов. Целесообразно сочетание сварки взрывом со штамповкой и ковкой. На рис. 9 зафиксирована удачная фотография сварки взрывом в полевых условиях.
В настоящее время открываются широкие возможности применения сварки взрывом для создания композиций с промежуточными слоями, играющими при нагревах роль диффузионных барьеров между основными и промежуточными слоями. А также для повышения прочности и работоспособности таких переходников с помощью контактного упрочнения промежуточных слоёв при уменьшении их относительной толщины в неограниченных пределах.
Рис. 9. Сварка взрывом на открытой площадке ЗАО «Импульсные технологии»
Просмотров: 614
Основные сведения о металлах, применяемых в сварке — Студопедия.Нет
Сталь – это сплав железа с углеродом, количество которого должно быть не более 2%.Классификация сталей:
· По способу производства: конверторная, мартеновская, электросталь.
· По степени раскисления: кипящая (кп), полуспокойная (пс), спокойная (СП).
· По химическому составу: углеродистая (низко-, средне-, высокоуглеродистая) и легированная (низко-, средне- и высоко-)
· По назначению: обыкновенного качества, качественная конструкционная, строительная, инструментальная, котельная, судостроительная.
· По особым свойствам: не ржавеющая, жаростойкая, жаропрочная.
Классификация углеродистых и легированных сталей:
· По химическому составу: углеродистая (низко-, средне-, высокоуглеродистая) и легированная (низко-, средне- и высоко-)
· По назначению: обыкновенного качества, качественная конструкционная, строительная, инструментальная, котельная, судостроительная.
· По особым свойствам: нержавеющая, жаростойкая, жаропрочная.
Режим работы источников питания.
К параметрам режима работы электросварочного оборудования относя:
-номинальный сварочный ток,
-напряжение рабочее и холостого хода,
-продолжительность включения (ПВ),
— продолжительность нагрузки (ПН),
— продолжительность работы (ПР).
Металл для резки разделяют по толщине на 3 группы: толщ. до 5 мм, толщ. 5-300мм, толщ. более 300 мм. Параметрами резки являются:
-расход газа и вид подогревающего пламени,
-давление режущего кислорода,
-скорость резки.
Расход газа увеличивается с увеличением толщины разрезаемого металла, цвет подогревающего пламени для малых и средних толщин должен быть нормальный, а для больших толщин изменяется на желто-зеленый (науглероживающее).
Давление режущего кислорода составляет 2-3 Атм для тонких и толстых металлов, а для металлов средней толщины увеличивается пропорционально увеличению толщин металла.
Скорость резки металла уменьшается с увеличением толщины металла.
4. Причины возникновения горячих трещин и меры предупреждения.
При сварке легированных сталей появляются следующие трудности:
· Пористость,
· Перегрев металла и закалочные структуры из-за пониженной теплопроводности,
· Холодные и горячие трещины,
· Склонность к деформациям.
Чтобы избежать появления трещин необходимо жестко соблюдать технологию сварки: организовать предварительный подогрев металла до температуры 250-350град., вести сварку на больших скоростях, после сварки нужна термообработка в виде нормализации. Можно так же измельчать структуру за счет введения Мо или Si.
Действие электротока на человека.
Неправильная эксплуатация электрооборудования способна создать опасность поражения электротоком, который воздействует на сердце, нервную систему, мышцы.
Очень опасен для жизни человека ток силой 0,04А, а ток силой 0,05А обязательно приведет к тяжелым последствиям.
Билет №2
Физические и химические свойства металлов.
К физическим свойствам сталей относят:
—плотность – это масса вещества, заключенная в единицу объема;
—теплопроводность – это способность Ме передавать теплоту от более нагретых участков к менее нагретым,
—электропроводность – это способность Ме пропускать электроток
К химическим свойствам сталей относят:
—окисляемость – это способность вещества соединяться с кислородом;
—коррозионная стойкость – это способность Ме не окисляться и не вступать в химические реакции с окружающими веществами;
— жаростойкость – это способность стали не окисляться при высокой температуре;
— жаропрочность – это способность стали сохранять прочность при высокой температуре.
Источники питания классифицируют по следующим признакам:
· По роду тока, (постоянного и переменного тока)
· По количеству одновременно подключаемых постов,
· По назначению, (для ручной, п/а, автоматической сварки)
· По принципу действия,
· По конструктивному исполнению,
· Специализированные.
Источники питания дуги имеют общую маркировку:
· —первая буква – название ИП (Т,В,П,Г),
· —вторая буква – дуговая сварка,
· —третья буква – способ сварки (К,Ф,Г,У),
· —четвертая буква – количество постов (М),
· —первые две цифры – номинальный ток в сотнях ампер,
· —третья цифра – модификация,
Преобразователь представляет собой комбинацию асинхронного трехфазного двигателя переменного тока и сварочного генератора постоянного тока. Преобразователь используются для ручной дуговой сварки в углекислом газе в цеховых условиях. Они имеют жесткую или падающую характеристику.
1.3 Основные виды сварки металлов
Холодная сварка. Осуществляется при значительной пластической деформации без внешнего нагрева соединяемых частей. Если две (рис. 1.1) свариваемые пластины 2 и 3, наложенные друг на друга
внахлестку, обжать шайбами 1 и 4, исключающими выпучивание пластин при их деформировании, и затем вдавливать в пластины пуансоны 5 и 6, изготовленные из более твердого металла, то выдавливаемый пуансонами объем металла приведет к значительному деформированию металла в окружающей зоне. По мере вдавливания
пуансонов деформации будут увеличиваться и начнется течение металла, в частности вблизи поверхностей раздела пластин 2 и 3. Если
Рис. 1.1. Схема холодной сварки.
эти поверхности предварительно очищены от жировых загрязнений, а окисные пленки окажутся разрушенными при течении металла, то во многих участках в области деформации чистые ювенильные поверхности пластин 2 и 3 придут в соприкосновение, при котором между ними возникнут металлические связи. Степень деформации, которая приведет к такому схватыванию, зависит от свойств металла, свойств окисных пленок и др.
Холодной сваркой можно соединить только весьма пластичные металлы. При этом могут быть получены соединения внахлестку и встык.
Ультразвуковая сварка. Условия разрушения поверхностных окисных пленок и вступления в контакт ювенильных поверхностей могут быть получены не только общим деформированием значительного объема, но и местной деформацией поверхностей у границы раздела пластин, которые должны быть сварены. Это достигается введением в металл ультразвуковых колебаний.
Генератор 1 (рис. 1.2,а) и рабочий инструмент 2 вводят ультразвуковые колебания небольшой амплитуды в свариваемое изделие (детали 3 и 4). Если мощность ультразвуковых колебаний (обычно при частоте 8000 – 15000 Гц) окажется достаточной, то это приведет к разрушению окислов, некоторому местному повышению температуры (термопарами отмечается температура 200 – 350 С0) и свариванию. Обычно ультразвуковую сварку применяют для соединения относительно
Рис. 1.2. Схема ультразвуковой сварки (а) и сварки взрывом (б)
тонких элементов или тонкостенного элемента с толстостенным.
Сварка взрывом. Осуществляется соударением быстродвижущихся частей при начальной нормальной (комнатной) температуре. Нижний лист 4 (рис. 1.2,б) укладывается на жесткое основание, а верхний лист 3 устанавливается с некоторым углом (2 – 150) и на его поверхности равномерно размещается необходимое количество взрывчатого вещества 2. Для осуществления сварки взрыв инициируется запалом 1. Взрывная волна, распространяясь по поверхности, создает большое давление р и «метает» верхний лист на нижний, осуществляя сварку по их контактирующим поверхностям. Очистка поверхностей осуществляется кумулятивной газовой струей, имеющей огромные давления рк (до млн. кгс/см2 или 1011 Н/м2) и весьма большую скорость ( 6000 м/с). Зона деформации при сварке относительно невелика и составляет до 100 – 300 параметров кристаллической решетки. Детали значительных размеров (например, листы с поверхностью сварки в м2) обычно сваривают на полигонах. Малогабаритные изделия можно сваривать в специальных камерах.
Кузнечная сварка. Этот вид сварки является самым древним.
После разогрева в горне (обычно при сжигании твердого или жидкого топлива) металла 1 (рис.1.3) до температуры сварочного жара осуществляют сварочную операцию ручной (кувалдой) или механизированной (специальным устройством 2) проковкой. В результате нагрева и в течение времени между нагревом и проковкой поверхности, подлежащие сварке, покрываются толстым слоем
Рис. 1.3. Схема кузнечной сварки.
окислов. Для получения хорошего соединения поверхности должны быть очищены. Предварительная очистка обычно осуществляется удалением окислов механическим способом. Для удаления оставшихся окислов применяется их флюсование. Например, при сварке сталей, когда пленка окислов состоит в основном из закиси железа (FeO), для флюсования применяют песок (SiO2). При этом понижается температура комплексного соединения FeO*SiO2 или (FeO)2*SiO2 в сравнении FeO; окислы в жидком виде выдавливаются при проковке, позволяя получать более качественное соединение. Однако в ряде случаев в сварном соединении все же остается некоторое количество окислов.
В настоящее время кузнечная сварка имеет ограниченное применение.
Газопрессовая сварка. Принцип газопрессовой сварки аналогичен кузнечной, однако для нагрева металла используют пламя газообразных горючих, которое более легко регулируется и дает возможность осуществлять нагрев металла более локализовано, в определенном месте.
Газопрессовую сварку можно проводить как с последовательным нагревом от участка к участку соответственно с их проковкой или статическим сдавливанием, так и с нагревом всего сечения свариваемых элементов с одновременным сжатием. Во втором случае можно применить как боковой, так и торцевой нагрев (пламя направляется параллельно оси свариваемых элементов, перпендикулярно к нагреваемым поверхностям кромок, подлежащих свариванию, или вдоль их оси). В случае бокового нагрева возможно сдавливание при продолжающемся воздействии пламени, а при торцевом – пламя перед сдавливанием должно быть удалено. Так как при удалении пламени кромки быстро окисляются кислородом воздуха, их следует нагревать до поверхностного оплавления, чтобы окислы выдавливались вместе с жидким металлом. Этот вид сварки применяется при выполнении стыков трубопроводов и ряда деталей железнодорожного транспорта, изготавливаемых из углеродистых сталей.
Контактная сварка. Принцип нагрева при контактной сварке заключается в выделении тепла при прохождении электрического тока по любому электрическому сопротивлению.
Q = 0,24IUt = 0,24I2Rt.
В последовательной цепи на участке большего сопротивления (каким является место контакта двух подлежащих сварке поверхностей) выделяется большее количество тепла. Выбором соответствующей мощности сварочной машины можно обеспечить сварку деталей быстрым (0,003 – 10 с) их нагревом и последующим сжатием. Обычно нагрев осуществляется переменным током
Рис. 1.4. Схемы контактной сварки.
применением силовых понижающих трансформаторов. Различают три основных вида контактной сварки: стыковая, точечная и шовная.
Стыковая контактная сварка (рис. 1.4, а). Осуществляется по двум схемам: сварка сопротивлением и сварка оплавлением.
При сварке сопротивлением подлежащие сварке детали 1 и 2 соосно зажимают в неподвижном 3 и подвижном зажимных устройствах (губках) машины. Далее детали приводят в контакт друг с другом с давлением Р и включают трансформатор 5 посредством контактора 6. Проходящий по деталям электрический ток, разогревает их в зоне контакта. Металл в этой размягчается и происходит осадка – пластическое деформирование нагретого объема для осуществления сварки.
При сварке оплавлением напряжение на свариваемые детали подают до того как они сведены, т.е. когда между торцами заготовок есть зазор. При медленном сближении деталей появляется контакт то в одной, то в другой точках, приводя к быстрому их оплавлению. Такой процесс приводит к постепенному оплавлению всей поверхности. В нужный момент контактор 6 выключает ток и поверхности нагретых элементов сдавливают. При этом выдавливаются остатки жидкости и освобожденные от нее твердые, нагретые до пластического состояния объемы металла свариваются.
Точечная контактная сварка (рис. 1.4, б) осуществляется для соединения элементов внахлестку. Свариваемые листы 2 и 3 зажимают неподвижным 4 и подвижным 1 электродами машины. При включении трансформатора 5 контактором 6 выделяется тепло вблизи внутренних контактных поверхностей деталей и часть металла расплавляется , образуя ядро литого металла 7. После выключения тока и увеличения давления Р осуществляется затвердевание жидкого металла и местное сваривание в районе литой точки.
Шовная контактная сварка (рис. 1.4, в) осуществляется так же, как и точечная, обеспечивая получение не только прочного, но и сплошного герметического шва. Это достигается последовательной постановкой ряда точек с частичным перекрытием последующей точки предыдущей. Свариваемые элементы 2 и 3 зажимают между электродами 1, 4, выполненными в виде дисков. Диски, вращаясь, протаскивают свариваемые элементы между собой, а периодическое включение и выключение тока приводит к последовательной сварке точек.
Индукционная сварка (рис. 1.5). Нагрев металла до сварочной температуры осуществляется с помощью специальных индукторов 3, питаемых от источников тока 4 высокой частоты. Форма индуктора должна соответствовать форме нагреваемого изделия. .
Рис. 1.5. Схема индукционной сварки.
Диффузионная сварка. При сварке различных химически активных материалов необходимо максимально исключить возможность их взаимодействия с атмосферой в период выполнения сварочной операции. Это достигается применением вакуума; свариваемые изделия помещают в специальную камеру, из которой насосами удаляют воздух до получения вакуума 10-3 – 10-5 мм. рт. ст. После достижения такого вакуума осуществляют нагрев изделия индуктором и дают сварочное давление.
Вакуум предохраняет от окисления свариваемые поверхности, обеспечивает распад окислов, находящихся на поверхностях. Одновременно происходит удаление адсорбированных газов. Это позволяет получать качественные соединения ряда металлов и металлов с неметаллами при относительно небольшой пластической деформации вблизи места соединения.
Термитная сварка. При термитной сварке источником тепла является экзотермическая реакция (с выделением тепла) взаимодействия порошкообразных окисла и элемента с большей активностью (сродством) к кислороду. Например, если в тигель из огнеупорного материала поместить смешанные порошки алюминия и закиси железа и создать местный нагрев до 7500 С, то начнется реакция
Fe2O3 + 2Al = Al2O3 + 2Fe + Q,
которая распространяется на весь объем порошка и в оптимальных условиях полученные продукты реакции (Al2O3, Fe) теоретически должны нагреться до 30000 С. Практически эта температура оказывается ниже и составляет около 2200 – 24000 С, при которой и железо и окись алюминия расплавлены и как несмешивающиеся жидкости разделяются по плотности (жидкое железо собирается у дна тигля, а Al2O3 – в верней его чести). Аккумулированный такой жидкостью запас тепла может быть использован для сварки давлением или плавлением.
Область применения термитной сварки среди прочих видов сварки относительно невелика.
Газовая сварка. Это сварка плавлением, при которой источником тепла является высокотемпературное пламя горючих газов в смеси с кислородом. В качестве горючих газов применяют ацетилен, водород, природный газ (метан), пары керосина пропанобутановую смесь.
Кромки двух листов 1 и 2 (двух деталей) (рис. 1.6) подвергаются местному нагреву сосредоточенным пламенем 3 до расплавления. Образовавшаяся ванна 4 контактирует с кромками обоих листов. После образования ванны пламя перемещают по линии стыка листов в направлении стрелки V, металл под пламенем расплавляется, а позади пламени в связи с охлаждением – затвердевать. Этот затвердевший металл и образует сварной шов 5 между исходными листами (деталями). Подобрав соответственно режим (мощность пламени, скорость его относительного перемещения по кромкам листов) можно получить необходимое проплавление металла и, следовательно, рабочее сечение шва.
Обычно для швов, которые должны обеспечить прочность, сопоставимую с прочностью свариваемых элементов, требуется получить сквозное проплавление соединяемых деталей (на всю их толщину). Если толщина металла велика и обеспечить сквозное проплавление трудно, то кромки под сварку обрабатывают со скосом и полученную разделку заполняют добавочным расплавленным присадочным металлом 6. Этот присадочный металл обычно представляет собой прутки (стержни), подаваемые в пламя, расплавляющиеся в нем и пополняющие сварочную ванну.
Рис. 1.6. Схема газовой сварки.
Для различной толщины свариваемого металла применяют различную удельную мощность сварочного пламени, которая характеризуется часовым расходом ацетилена в литрах, приходящимся на 1 мм толщины свариваемого металла.
В процессе сварки пламя не только расплавляет металл, но и защищает расплавленную ванну от вредного влияния кислорода и азота атмосферного воздуха. Поэтому при сварке необходимо, чтобы расплавленный основной металл и конец присадочного металла находились все время в восстановительной зоне пламени. Изменением угла наклона горелки к поверхности свариваемого металла можно изменить интенсивность расплавления свариваемого металла. Наиболее интенсивно металл расплавляется при перпендикулярном расположении горелки.
При необходимости горелка может передвигаться по направлению сварки или прямолинейно, или с поперечными и круговыми движениями.
1.4 Кислородная резка
Кислородная резка основана на сгорании металла в струе кислорода. Металл при резке нагревают пламенем, который образуется при сгорании горючего газа в кислороде. Кислород, сжигающий металл, называют режущим. В процессе резки струю режущего кислорода подают к месту реза отдельно от кислорода, идущего на образование горючей смеси для подогрева металла. Касаясь нагретого металла, режущая струя кислорода интенсивно окисляет и сжигает его верхние слои. Процесс окисления верхних слоев металла сопровождается выделением большого количества тепла, которое идет на прогрев нижних слоев металла. Процесс сгорания разрезаемого металла распространяется на всю толщину, образующиеся окислы выдуваются из места реза струей режущего кислорода.
Металл, подвергаемый резке кислородом, должен удовлетворять следующим требованиям: температура воспламенения металла в кислороде должна быть ниже температуры его плавления, окислы металла должны иметь температуру плавления ниже, чем температура плавления самого металла, и обладать хорошей жидкотекучестью, металл не должен обладать высокой теплопроводностью.
1.5 Электродуговая сварка
При дуговой сварке нагрев металла осуществляется электрической дугой. При устойчивом длительном протекании тока через ионизированный газовый промежуток между двумя электродами, подсоединенными к источнику питания, выделяется тепловая и световая энергия. Температура, развиваемая в дуге, может быть очень высокой, значительно превышающей температуру плавления свариваемых металлов.
Сварка дугой косвенного действия. Осуществляется нагревом металла дугой, горящей между двумя неплавящимися электродами, подключенными к различным полюсам источника электрической энергии. Свариваемое изделие в электрическую цепь не включено. Дуга горит независимо от свариваемого изделия. Нагретые газы столба дуги контактируют с поверхностью металла, нагревают его и, при достаточной мощности дуги, расплавляют. Сварка может выполняться как без добавочного присадочного металла, так и с применением присадки, подаваемой в дугу в виде прутка.
Сварка неплавящимся электродом. Выполнятся, когда свариваемое изделие включено в цепь дуги и является одним из ее полюсов. Второй полюс дуги находится на неплавящемся электроде. (Сварка на прямой и обратной полярности, на переменном токе.) Эффективность при этом способе значительно выше, чем при сварке дугой косвенного действия, при одинаковой электрической мощности дуги.
Сварка плавящимся электродом. Выполнятся по такой же схеме, как и при неплавящемся электроде (изделие включено в цепь дуги и является одним из полюсов). Электрод является металлическим, интенсивно расплавляется дугой, и обеспечивает введение в сварочную ванну дополнительного (наплавленного) металла.
Этот вид сварки является наиболее эффективным видом сварки плавлением и в связи с этим имеет наибольшее распространение в промышленности при изготовлении и ремонте металлических конструкций.
Разновидности сварки плавящимся электродом.
1.Ручная дуговая сварка (РДС) – когда сварка осуществляется специальными штучными электродами с обмазкой для защиты дуги и сварочной ванны. Подача электрода в зону плавления и перемещение электрода вдоль шва осуществляется сварщиком вручную.
Для изготовления электродов должны быть правильно подобраны электродная проволока и состав покрытия электродов. Марки проволоки имеют условное обозначение, например Св-08ГА: первые две буквы означают, что эта проволока сварочная, следующие за ними цифры и буквы характеризуют содержание различных элементов в металле проволоки – первые две цифры – выраженная в сотых долях процента массовая доля углерода, в данной марке она равна 0,08%. Буква Г указывает на содержание в проволоке марганца, в данном случае 0,8 – 1,1%, а буква А – на изготовление ее высококачественной стали с уменьшенным содержанием вредных примесей (серы и фосфора). В других марках после первых двух цифр, указывающих на содержание углерода, ставятся буквы и цифры: обозначают содержание отдельных элементов, цифры – их массовою долю в процентах.
Табл. Обозначение элементов в марках электродной проволоки.
Элемент | Буквенное обозначение | Элемент | Буквенное Обозначение |
Азот | А | Кремний | С |
Ниобий | Б | Титан | Т |
Вольфрам | В | Ванадий | Ф |
Марганец | Г | Хром | Х |
Медь | Д | Цирконий | Ц |
Молибден | М | Алюминий | Ю |
Никель | Н |
В проволоке Св-10Х11ВМФН содержится в процентах: углерода 0,1; хрома 10 – 12; вольфрама 1 – 1,4; молибдена 1 – 1,3; ванадия 0,25 – 0,5; никеля 0,9 – 1,1.
В состав покрытия входят ряд материалов, которые выполняют определенные функции при сварке. Покрытие образуется из хорошо размолотых и перемешанных материалов, связанных жидким стеклом и нанесенных на стержни под давлением. Применяемые для электродного покрытия материалы разделяют на группы в соответствии с их функциями.
К материалам, образующим шлак, относятся полевой шпат, кремнезем, магнезит, мрамор др.
К газообразующим материалам относятся минералы, которые кроме шлака образуют защитный газ – это мрамор, магнезит и др. Кроме того, в состав покрытия вводят органические вещества – крахмал, целлюлозу, древесную муку и др., которые выделяют только защитный газ.
Важную роль играют стабилизирующие вещества, предназначенные для обеспечения устойчивости горения дуги. К ним относятся соединения щелочных и щелочноземельных металлов калия, натрия, кальция и др.
Для восстановления окисленного в процессе сварки металла применяют специальные раскислители, к которым относятся ферросплавы – ферромарганец, ферросилиций, ферротитан и др. Эти же ферросплавы служат легирующими материалами, которые увеличивают содержание марганца, титана и др. элементов в металле шва. Кроме того, для легирования иногда используют порошкообразные металлы. В покрытие также вводят пластификаторы, улучшающие его пластические свойства.
Согласно ГОСТ 9467—75 электроды подразделяются на типы. ГОСТ предусматривает 14 типов электродов для конструкционных сталей и 9 типов для теплоустойчивых сталей. Типы электродов для сварки конструкционных сталей обозначают буквой Э, после которой следуют цифры минимального временного сопротивления наплавленного этим электродом металла в кгс/мм2, например электроды Э42 должны гарантировать минимальное временное сопротивление 420 МПа. Буква А, стоящая после цифр (например, Э46А) означает, что электроды этого типа обеспечивают более высокие пластические свойства наплавленного металла, чем без буквы А. Типы электродов для сварки теплоустойчивых сталей также обозначают буквой Э, после которой следуют буквы и цифры, характеризующие химический состав наплавленного металла.
Каждому типу электродов может соответствовать несколько марок электродов. Марка электродов характеризуется определенным составом покрытия, маркой электродного стержня, технологическими свойствами, свойствами металла шва.
Условное обозначение электродов для сварки конструкционных сталей состоит из обозначения марки электрода, типа электрода, диаметра стержня, типа покрытия и номера ГОСТа. Например, УОНИ-13/45-Э42А-4,0-Ф ГОСТ 9467—75 расшифровывается: УОНИ-13/45 – марка электрода; Э42А – тип электрода; 4,0 – диаметр электродного стержня в мм; Ф – фтористо-кальциевый тип покрытия.
2. Полуавтоматическая сварка – подача электрода в зону плавления осуществляется автоматически, а перемещение вдоль шва – вручную.
3. Автоматическая сварка – подача электрода и в зону плавления и перемещение вдоль шва осуществляется автоматически.
Сварка плавящимся электродом может выполняться:
а) открытой дугой, когда в область дуги не подается защитный газ или флюс; зона дуги доступна наблюдению. Защита от воздействия воздуха часто осуществляется специальными веществами (газообразующими, шлакообразующими), вносимыми с электродом обычно в виде покрытия;
б) дугой под флюсом, когда место горения закрыто порошкообразным флюсом, расплавляющимся теплом дуги и образующим шлак; в этом случае дуга не видна – она горит в пространстве (газовой полсти), изолированном от окружающей среды слоем шлака и нерасплавившегося порошкообразного флюса.
В) дугой, защищенной от воздуха специальной газовой защитой, например углекислым или инертными газами. Этот способ называют сваркой в защитных газах.
Плазменная обработка металлов.
Для получения плазменной дуги служит устройство, называемое плазмотроном. Существует два типа плазмотронов – с дугой прямого и с дугой косвенного действия.
Рис. 1.7. Схема устройства плазмотрона.
В плазмотронах прямого действия (рис.1.7) плазменная дуга создается между стержневым электродом 1, вмонтированным в газовую камеру 2, и обрабатываемым изделием 4. Сопло 3 электрически нейтрально и служит для сжатия и стабилизации дуги.
В плазмотронах косвенного действия плазменная дуга создается между электродом 1 и соплом 3.
Сжатие столба дуги происходит следующим образом: рабочий газ, проходящий через столб дуги, нагревается, ионизируется и выходит из сопла плазмотрона в виде плазменной струи. Слой газа, омывающий столб газа снаружи, остается относительно холодным, образуя тепловую и электрическую изоляцию между плазменной дугой и каналом сопла. Плотность тока в плазмотронах достигает 100 А/мм2, а температура 15000 – 300000 С.
Процесс возбуждения дуги непосредственно между электродом и изделием осуществить очень трудно. В связи с этим вначале возбуждается дуга между электродом и соплом (дежурная), а затем при касании ее факела изделия происходит автоматическое зажигание основной дуги между электродом и изделием. После возбуждения основной дуги дежурная дуга отключается. Дежурная дуга питается от того же источника через токоограничивающее сопротивление.
В плазмотронах с дугой прямого действия в изделие вводится дополнительное тепло за счет электрического тока и к.п.д. их значительно выше, чем у плазмотронов косвенного действия. В связи с этим плазмотроны с дугой прямого действия целесообразно применять для сварки, резки, наплавки, а плазмотроны с дугой косвенного действия – для напыления, нагрева и т.д.
Электрошлаковая сварка. Процесс идет в пространстве, ограниченном кромками свариваемой детали и ползунами (рис. 1.8). Тепло в шлаковой ванне выделяется за счет прохождения в ней тока Iш. В холодном состоянии шлак практически не электропроводен. Поэтому для наведения шлаковой ванны сначала возбуждают дугу, которая расплавляет флюс, образуется шлаковая ванна, которая гасит дугу, в результате чего начинается шлаковый процесс. В результате тепловыделения в шлаке увеличивается его электропроводность. Объем расплавленного шлака увеличивается, и весь ток от электрода 5 к свариваемому изделию 1 будет проходить через шлаковую ванну 3. Вследствие выделения тепла в шлаковой ванне расплавляются электрод 5 и кромка свариваемого изделия 1, образуя металлическую ванну 2. Для предотвращения вытекания расплавленного металла и шлака применяют специальные медные формирующие устройства 4 (ползуны).
Этот способ применяется для сварки металлов достаточно большой толщины, причем шов выполняется на всю толщину свариваемого металла за один проход. В промышленности освоена сварка изделий с толщиной металла в месте выполненного шва около 1 м.
Электроннолучевая сварка. Сварка осуществляется в вакуумной камере при давлении 10-1 – 10-5 мм рт.ст. (1.3 – 0,0013 Па). Тепло в изделии, подлежащее сварке, выделяется в результате торможения электронов направленного электронного луча. Луч формируется в специальной электронной пушке, имеющей нагреваемый катод (эмиттер). Питание пушки осуществляется от высоковольтного выпрямителя. Фокусировка пучка электронов обеспечивается воздействием электромагнитных полей специальной фокусирующей электромагнитной линзы.
Выполнение сварных швов на изделии заданной длины и направления обеспечивается перемещением сварочного стола при помощи привода, или электронного луча вследствие перемещения пушки, или отклонения луча с помощью электромагнитной отклоняющей системы.
Рис. 1.8. Схема электрошлаковой сварки, 1 – сваренное изделие; 2 – жидкий металл; 3 – шлаковая ванна; 4 – ползуны; 5 – электрод; 6 – скользящий контакт.
Этот способ применяется при изготовлении изделий из легкоокисляющихся или тугоплавких металлов. Он может обеспечить высокие скорости сварки и малые деформации свариваемых изделий.
Лазерная сварка . В 1960 – 1961гг. появились первые лабораторные макеты оптических квантовых генераторов (ОКГ) или так называемые лазеры. В настоящее время лазерная сварка находит применение в приборостроении.
В соответствии с квантовой теорией энергия элементарных излучателей может изменяться только скачками, кратными некоторому значению, постоянному для данной частоты излучения. Минимальная порция энергии называется квантом энергии
w = h,
где h – постоянная Планка (6,625*10-34 В*А*с2), γ – частота излучения.
В любой микросистеме, включающей в себя молекулы, атомы, ионы и электроны, их движение и ориентация соответствуют дискретному ряду энергий – энергетическим состояниям или уровням. Внешние источники энергии, взаимодействуя с микросистемой, изменяют ее внутреннюю энергию. При этом частицы совершают переход с одного энергетического уровня на другой (возбуждаются). Для перевода активных частиц из равновесного в возбужденное состояние служат источники возбуждения, которые называются генераторами накачки. Они могут воздействовать на активное вещество следующими основными способами:
световым полем;
потоком электронов;
потоком радиоактивных частиц;
химическим возбуждением.
Рис. 1.9. Схема энергетических Рис. 1.10. Принципиальная блок-
уровней ионов хрома в рубине. Схема действия ОКГ.
1 – источник питания; 2 – источник возбуждения; 3 – электромагнитное поле; 4 – активное вещество; 5 – полупрозрачное зеркало, образующее открытый резонатор.
Наиболее применимы системы возбуждения световым полем, состоящие из источника света – газоразрядной лампы «накачки» спирального или карандашного типа и рефлектора. Источником питания обычно является конденсатор большой мощности, заряжаемый от выпрямителя.
Механизм возбуждения и излучения показан на примере трехуровневого лазера, где в качестве активного вещества используется синтетический рубин с примесью хрома. (рис. 1.9 и 1.10). При освещении кристалла рубина белым или зеленым светом ионы хрома возбуждаются и переходят на высший уровень 2, поглощая энергию зеленой части спектра. Уровень 2 нестабилен и частицы быстро совершают безизлучательный переход на промежуточный (метастабильный) уровень 3, где может находиться значительное число частиц. При воздействии на кристалл слабого излучения соответствующей частоты или при переходе хотя бы одной из частиц на низший уровень все частицы с промежуточного уровня совершают переход ( = 6943 А – красный цвет) на основной уровень 1 синфазно. Это и создает когерентное излучение, монохроматическое, так как уровень 3 узкий.
Узконаправленность и резонансное усиление энергии достигается с помощью объемного резонатора, имеющего два строго параллельных зеркала, например, торцы кристалла, между которыми тысячекратно отражаются световые лучи. В ОКГ одно из зеркал делается полупрозрачным, и через него происходит выход излучения.
Энергия, излучаемая в современных лазерах, составляет величины от единиц до сотен Дж. Плотность энергии до ста Дж./мм2.
Вопросы для самопроверки к разделу 1.
1.Чем обеспечивается монолитность твердых тел?
2.Чем обеспечивается связь атомов твердых тел?
3.Перечислите виды элементарных связей атомов в твердых телах.
4.Перечислите условия установления взаимосвязи между поверхностями двух кусков металла, приводящие к возможности получения свойств в месте связи, сопоставимых со свойствами целого металла.
5.За счет чего достигается адгезионный контакт и активация поверхности при сварке плавлением?
6.За счет чего достигается адгезионный контакт и активация поверхности при сварке давлением?
7.Дайте определение понятия сварка металлов.
8.Какие существуют принципы классификации видов сварки металлов?
9.Приведите примеры классификации видов сварки по виду затрачиваемой энергии.
10.Как классифицируются виды сварки по состоянию металла в сварочной зоне в момент сварки?
11.Каковы особенности применения различных видов сварки?
12.Кратко охарактеризуйте следующие виды сварки: холодная сварка; ультразвуковая сварка; кузнечная и газопрессовая сварка; контактная сварка; индукционная сварка; газовая сварка; дуговая сварка и ее разновидности; электрошлаковая сварка; сварка электронным лучом; лазерная сварка.
Новые технологии сварки металлов
Современная цивилизация многим обязана процессу сварки. Без сварочных элементов мы не получили бы транспорта, огромных строений, технологических конструкций, мобильных телефонов и пр. Несмотря на то, что этот физический процесс применяется много столетий, он не останавливает своего прогресса. Учёные многих стран продолжают исследовать и совершенствовать сварочные механизмы, применять новые приёмы и производить революционные открытия в этой сфере.
Новые технологии позволяют добиться более совершенного результата с использованием минимальных ресурсов. Разработки, появляющиеся ежегодно, делают возможным сварку тех материалов, которые раньше оставались за границами данной технологии.
Основные инновационные направления
Все разработки в данной области направлены на то, чтобы улучшить основные показатели процесса с наименьшими затратами:
- снижение коррозии и коробления металлов во время эксплуатации;
- повышение скорости выполнения сварочного процесса;
- облегчение зачистки мест соединения или обеспечение отсутствия такой необходимости;
- минимальный расход материалов;
- облегчённое и упрощенное управление процессом;
- способность соединения самых тонких листов металла различных марок.
Портативные аппараты
Такие типы сварочных аппаратов позволили вывести сварку на новый – бытовой — уровень. Если до изобретения портативных устройств подобные работы выполнялись преимущественно профессионалами с высокой квалификацией, то портативная техника позволила применять их и дома.
Современные сварочные аппараты
Во-первых, такие аппараты очень лёгкие по весу, в связи с чем их удобно транспортировать. Во-вторых, производители снабдили их полным готовым для использования комплектом, не забыв о системе подачи электродов (проволоки весом до 10 кг).
Главным усовершенствованием можно считать то, что в аппарат вмонтирована система цифрового управления. На дисплее каждый может указать основные параметры сварки: диаметр закладываемой проволоки, тип газа и т.д. На основании введённых данных портативный аппарат самостоятельно настраивается и выполняет сварку на достаточном для непроизводственных сварных швов уровне.
Усовершенствованные горелки
Самым примитивным звеном во время сварки считается газовая горелка, но даже небольшие изменения этого элемента позволили значительно улучшить качество выполняемой работы. Современные конструкции горелок производят не только из новых материалов, но имеют другой диаметр выходного отверстия, которое способно работать с нестандартными температурами и создавать необходимое давление.
Предлагаемые учёными газовые горелки стали безредукторными и высокодинамичными, при помощи их даже во время продолжительного процесса на самых высоких температурах можно получить идеально ровное пламя, в котором не будут появляться факелы, вспышки и хлопки. Из-за таких инноваций работа сварщика не требует частых остановок, что позволяет выполнить больший объём работ за то же самое время.
Разработаны агрегаты с многочисленными соплами, которые используются для соединения труб большого диаметра. Ширина пламени при использовании линейных горелок может достигать нескольких метров. Эта технология часто применяется для соединения деталей под водой или в воздухе, где существует острая необходимость в резком сокращении времени выполнения работ.
Гибридная лазерная технология
Такой способ был разработан для автомобилестроения, но нашёл применение и в других промышленных отраслях. Гибридный лазер используют для получения качественных швов при соединении тугоплавких сортов стали при совмещении с диоксидом углерода. Это позволяет получить идеальные сварные швы при точном управлении мощности лазерного излучения в пределах 1,5 – 4,0 кВт.
Ещё одной особенностью, присущей гибридной лазерной технологии, является высочайшая скорость плавящегося электрода и выполняемых работ – от 40 до 450 м/час. С такими же показателями можно обрабатывать тончайшие листы, изготовленные из автомобильной стали, что стало причиной финансовой поддержки и усовершенствования этой разработки ведущими автомобильными корпорациями.
Двухдуговая сварка
Такая методика была разработана для крупногабаритных конструкций, в изготовлении которых задействованы толстые листы закаливающейся стали таких марок как 30ХГСА. Способ основан на том, что при двухдуговом воздействии одномоментно применяются проволоки двух разных типов, имеющие в составе легирующие (сверхпрочные) компоненты. Диаметр таких электродов – 5 мм.
Для обеспечения устойчивого горения дуги при двухдуговой сварке необходим керамический флюс, созданный на основе керамики марки АНК-51А. Именно с керамическим флюсом данный способ показывает самый высокий результат и формирование идеальной сварной поверхности.
Щадящая методика
Для определённых работ была разработана новая щадящая технология, которая очень высокорезультативна, но отличается низкой себестоимостью. Во время процесса применяют специальные смеси защитных газов: диоксид углерода в соединении с аргоном или смесь аргона, диоксида углерода и кислорода. По сравнению с традиционным применением обособленного диоксида углерода, получаемый шов выходит более гладким и безупречным.
Ещё одним позитивным моментом является значительное удешевление сварочного процесса: на равный объём выполненных соединений расходуется меньшее количество проволочных электродов. Экономия составляет около 20%, что в промышленных масштабах представляет собой значительную сумму. Кроме того, во время сварочного процесса переход к деталям, поддающимся сварке, становится очень постепенным и плавным. Профессиональные сварщики, которые были задействованы в начальных тестах щадящей методики, подчеркнули, что разбрызгивание электродных металлов при многокомпонентной смеси газов значительно уменьшается.
Двухкомпонентная методика
Этот новый метод, который получил широкое распространение в развитых странах за короткий промежуток времени, обязан своим появлением запуску новых скоростных составов на железных дорогах. Двухкомпонентная технология является модифицированным вариантом литьевого способа. Она разрешила достичь результатов, которые раньше считались взаимоисключающими: обеспечить высочайшую пластичность шовного соединения, не ухудшив при этом износоустойчивость металла в месте сварного шва.
Технически двухкомпонентная методика выполняется сложно, поскольку требует особой подготовки: на месте проведения работ должна быть расплавленная сталь, которая аккуратно помещается в жидком виде в зазор между рельсами. Для того, чтобы придать соединению внушительную вязкость, применяется плавка с низколегированными компонентами. Износостойкость увеличивается посредством использования керамических флюсов, которые позволяют после заполнения сварного стыка вывести легирующие добавки из процесса. Керамика разрушается под действием высокой температуры, а добавки, укрепляющие соединение, застывают на поверхности, обеспечивая длительную эксплуатацию без трещин и деформаций.
Орбитальная аргонодуговая технология
Эта технология нашла применение в аэрокосмической отрасли, в автомобилестроении и полупроводниковой промышленности. Такая методика является высокоспецифичной и применяется для объектов со сложным конструктивным контуром. Впервые она была разработана 50 лет назад, но её значительно усовершенствовали, применив вольфрамовый электрод.
Главным преимуществом орбитальной аргонодуговой вольфрамовой сварки является то, что расход активирующего флюса при таком методе рекордно низкий: на 1 м сварного шва расходуется всего 1г флюса. Это делает возможным проводить процесс при пониженном токе, что уменьшает не только объём, но и вес сварочной ванны. При этом качество соединения регулируется в режиме реального времени посредством корректировки давления дуги.
Такой методикой успешно пользуются при необходимости соединить жаропрочные, высокопрочные сплавы, углеродистые стали, титан, медь и никель.
Технология СМТ
Эта методика основана на холодном переносе металлов. Когда говорят о холодном переносе, в виду не имеют реально низкую температуру, просто она значительно ниже, чем при классических вариантах.
Главное отличие заключается в том, что заготовки и зона будущего шва не прогреваются до максимальных значений, поэтому тепловложение в области обработки в разы уменьшается. Из-за того, что металл точечно не перегревается, не происходит сильная деформация. Работа электрода основана на контролируемом коротком замыкании, которое прекращается быстрым отодвиганием проволоки из зоны действия разряда и быстрого повторного его возвращения (до 70 раз в секунду).
Применение СМТ-сварки осуществляется через автоматизированные системы, которые дают очень однородные и качественные швы на местах соединения оцинкованных или стальных листов с алюминиевыми сплавами.
В данном случае сварка ведётся короткозамкнутой дугой с систематическими прерываниями. В результате такой системы шов атакуется горячими и холодными импульсами, что позволяет снизить давление в районе вхождения дуги. По такому же принципу снижается разбрызгивание при переносе металлов.
Таким образом, при помощи СМТ-сварки был достигнут стандарт, который ранее считался только теоретическим. Это стало возможным из-за контроля короткого замыкания и полного отсутствия разноса брызг, что резко снижает необходимость послесварочной механической обработки.
Плазменная сварка
Этот метод делает возможной сварку металлов разной толщины, начиная от самых тонких листов и заканчивая глубиной шва до 20 см. Плазменная технология позволяет одновременно с выполнением сварочных работ производить резку.
В основе плазменного метода находится ионизированный газ, который полностью заполняет пространство между двумя электродами. Именно через этот газ проходит электрическая дуга определённой мощности, обеспечивая очень сильный эффект.
Использование плазменного генератора представляет собой сложный процесс, требующий высокого профессионализма и профессиональных навыков, поэтому использовать его в бытовых целях не получится. Внутри генератора возникает многофункциональная сварочная система, которая может использоваться в узкоспециализированных сферах.
Технология компьютерного моделирования
Самое современное направление в сварочных технологиях по праву отводится компьютерному моделированию. Оно одинаково целесообразно для выполнения соединений самых мелких деталей со сложными контурами и для масштабных работ, где необходимо управление огромными площадями и множеством сварочных аппаратов.
Если раньше объёмные работы выполнялись при использовании многих аппаратов или целым сварочным комплексом, то компьютерное моделирование позволяет иметь одну функциональную единицу с разветвлённой периферией, оснащённой множеством горелок и насадок.
Полная автоматизация позволяет внедрять принципиально новые способы сварочных работ, которые недоступны для большинства сварщиков. Сами сварщики в таком случае функционально превращаются в операторов, задающих компьютеру все необходимые параметры, на основании которых программа задаёт оптимальные значения и контролирует процесс. Такой подход значительно повышает результат выполняемой работы.
Компьютерное моделирование сварочного процесса
Новые технологии вывели сварку на совершенно новый уровень, который позволяет выполнять сварочный процесс в рекордные сроки с минимальными трудозатратами и максимальным результатом. В то же время, прогресс не стоит на месте, поэтому вполне возможно, что в ближайшем будущем появятся системы, которые будут работать автономно, практически без участия людей. Разработки подобных проектов уже ведутся, и в том случае, если испытания увенчаются успехом, скоро человечество сможет получить новые масштабы и концепции сварочных производств.
Комплексная модель явления переноса при дуговой сварке металлическим газом
1. Введение
Дуговая сварка металлическим электродом в газовой среде (GMAW) является наиболее широко используемым процессом соединения благодаря своей способности обеспечивать высококачественные сварные швы для широкого диапазона черных металлов. и цветные сплавы по низкой цене и высокой скорости. Как показано на рис. 1, GMAW — это процесс дуговой сварки, в котором используется дуговая плазма между непрерывно подаваемым электродом из присадочного металла и заготовкой для плавления электрода и заготовки.Расплавленный присадочный металл образует капли и откладывается на частично расплавленной заготовке, образуя сварочную ванну. Сварочная ванна затвердевает, чтобы связать детали после удаления дуги. Защитный газ подается через газовое сопло, чтобы защитить расплавленный металл от азота и кислорода в воздухе. GMAW также широко известен как металлический инертный газ (MIG), поскольку в качестве защитного газа часто используются инертные газы аргон и гелий. Также используется активный защитный газ, содержащий кислород и диоксид углерода, и поэтому процесс GMAW также называется активным газом металла (MAG).Постоянный ток обычно используется с присадочной проволокой в качестве анодного электрода для увеличения скорости плавления проволоки. GMAW можно легко адаптировать для высокоскоростной роботизированной сварки, жесткой автоматизации и полуавтоматической сварки.
Рис. 1.
Схематическое изображение системы GMAW с расчетной областью, показанной внутри кадра.
GMAW — это сложный процесс с тремя основными связующими событиями: (1) эволюция дуговой плазмы, (2) динамический процесс образования, отделения и падения капель на сварочную ванну и (3) динамика сварки бассейн под воздействием дуговой плазмы и периодическим падением капель.Стабильность процесса GMAW и качество сварки зависят от многих параметров процесса, таких как сварочный ток, сварочное напряжение, скорость подачи проволоки, материал и размер проволоки, длина дуги, расстояние между контактной трубкой и заготовкой, материал и толщина заготовки, защитный газ. свойства, расход защитного газа, скорость сварки и т. д. Выбор этих параметров сварки и обработки основан на обширных экспериментах и является дорогостоящим методом проб и ошибок. Поэтому огромные исследовательские усилия были направлены на разработку математических моделей процесса GMAW, чтобы выявить лежащие в основе физики сварки и предоставить основные сведения о параметрах процесса для оптимизации процесса и предотвращения дефектов.Из-за сложности процесса сварки и связанных с ним числовых трудностей многие числовые модели в литературе упростили процесс GMAW и сосредоточились только на одном или двух событиях. Многие работы по образованию капель [1–8] и динамике сварочной ванны [9–29] не включали плазму дуги. Сейчас больше работ посвящено изучению дуговой плазмы и ее влиянию на перенос металла [30–41] и динамику сварочной ванны [41–49].
В этих упрощенных моделях образование капель рассматривается как изолированный процесс в электроде.Влияние дуговой плазмы рассматривается как граничные условия с предполагаемыми распределениями, такими как линейные распределения плотности тока [1–3] или гауссовы распределения для плотности тока и теплового потока [6–8].
Эффекты падения капель на сварочную ванну были значительно упрощены в качестве граничных условий при моделировании динамики сварочной ванны многими исследователями [9–21]. Поверхность сварочной ванны предполагалась плоской [9–14] или моделировалась с граничными координатами [13–15].Динамическое падение капли на сварочную ванну не учитывалось [13], оно рассматривается как столб жидкости [14] или цилиндрический объемный источник тепла [15–19], воздействующий на сварочную ванну во многих моделях сварочной ванны. Только в последних моделях [20–29] моделировалось динамическое взаимодействие капель, падающих на сварочную ванну, включая эффекты теплопередачи и потока жидкости, и отслеживалась деформированная свободная поверхность сварочной ванны. Тем не менее, все они применяли предполагаемые граничные условия тока, теплового потока и давления дуги на поверхности сварочной ванны, а также аппроксимировали столкновение капли с предполагаемой формой, объемом и температурой капли, а также частотой и скоростью столкновения.
Практически во всех вышеупомянутых исследованиях взаимодействие дуговой плазмы с плавлением электрода, образованием и переносом капель и динамикой сварочной ванны не учитывалось. В качестве граничных условий на поверхности электрода [1–6] и поверхности сварочной ванны [15–29] были приняты линейная или гауссова плотность тока и тепловой поток. Однако поверхность заготовки сильно деформируется, и профиль электрода быстро меняется, что сильно влияет на поток дуговой плазмы и, таким образом, изменяет ток, тепловой поток и распределение импульса на поверхностях электрода и заготовки.Кроме того, дуговая плазма может сильно искажаться, когда между острием электрода и поверхностью сварочной ванны имеются свободные капли, как это наблюдалось в экспериментальных исследованиях [30–32]. Разработано несколько моделей [33–39] для изучения динамического взаимодействия дуговой плазмы с образованием капли. Однако капля удалялась, когда она отделялась от кончика электрода или достигла заготовки. Динамика сварочной ванны также не учитывалась, и заготовка рассматривалась как плоская пластина.Некоторые недавние модели [40–43] включали в себя дуговую плазму, присадочную проволоку и заготовку для изучения прямого взаимодействия трех доменов. Однако они не являются полностью связанными моделями, поскольку перенос капель в дуге по-прежнему основывается на эмпирической формулировке для расчета силы сопротивления плазмы в [43] или столкновение капли не моделируется в [40–42].
Авторы разработали полностью связанную комплексную модель GMAW [44–52], которая включает в себя весь процесс сварки — эволюцию дуговой плазмы, плавление электрода, образование и отрыв капель, перенос капель в дуге, падение капли на сварочную поверхность. сварочная ванна, а также динамика и затвердевание сварочной ванны.Метод объема жидкости (VOF) использовался для отслеживания границы раздела дуговой плазмы и металла. Температура, давление, скорость, электрическое и магнитное поля рассчитываются во всей вычислительной области, включая дугу, присадочную проволоку и заготовку, без использования предполагаемых распределений тепла, тока и давления на границах раздела. В следующих разделах сначала представлена комплексная математическая модель для моделирования физики GMAW, а затем представлены результаты расчетов, показывающие эволюцию дуговой плазмы и ее динамическое взаимодействие с образованием, отрывом, переносом и столкновением капель, а также динамика сварочной ванны.
Понимание несплошностей сварного шва
Первоочередная задача сварщика в любом виде работы — обеспечение прочности сварного шва. По этой причине для инспектора, осматривающего сварной шов, важно иметь возможность обнаружить множество неоднородностей сварного шва, в том числе:
- Пористость.
- Неполный сплав.
- Неполное проплавление шва.
- Недопустимые сварные профили.
- Растрескивание.
Первым шагом к пониманию неоднородностей сварного шва является изучение терминологии сварки.
Неоднородность определяется как нарушение типичной структуры материала, например, отсутствие однородности его механических, металлургических или физических характеристик. Нарушение непрерывности может быть результатом дефекта, но не обязательно дефектом.
Дефект , с другой стороны, представляет собой разрыв, который по своей природе или накопленному эффекту (например, общей длине трещины) делает деталь или продукт неспособными соответствовать минимальным применимым стандартам приемки или техническим условиям.Дефект приводит к браку детали или продукта.
Поскольку мы изучаем эти явления вне требований конкретных правил или стандартов сварки и не обсуждаем их ограничения в терминах этих документов, мы будем использовать слово несплошность для их описания. Первый тип несплошностей сварного шва мы » Все адреса — пористость.
Пористость
Пористость определяется как неоднородность полого типа, образованная захватом газа во время затвердевания. Эти захваченные газы в расплавленном сварном шве могут образовывать пузырьки или карманы по мере затвердевания сварного шва.
Четыре основные причины присутствия газов, вызывающих пористость:
- Грязный основной материал, загрязненный углеводородами, такими как масло, смазка или краска.
- Влага на стыковой поверхности или электроде в виде воды или гидратированных оксидов или утечка воды из плохо обслуживаемых систем охлаждения, которые могут вносить водород в процесс сварки.
- Недостаточная или неправильная защита из-за недостаточной скорости потока защитного газа; газ, загрязненный из его источника или из его системы доставки; или ветер или сквозняк, которые не позволяют газу должным образом защищать расплавленный металл шва.
- Неправильные условия или методы сварки.
- Пористость часто классифицируется по ее форме и распределению в сварном шве, например, равномерно или беспорядочно, кластерно или линейно. Каждое из этих распределений пористости может иметь разные уровни приемлемости в пределах сварочного кодекса или стандарта.
Наиболее практичными методами контроля или устранения пористости являются использование чистых основных материалов, надлежащее хранение незагрязненных сварочных материалов, надлежащее техническое обслуживание сварочного оборудования, использование проверенных процедур сварки и сварка в приемлемых условиях окружающей среды.
Неполное сплавление и неполное проникновение в стык
Поскольку эти термины иногда используются неправильно, важно понимать разницу между этими двумя неоднородностями сварного шва.
Неполное плавление — это несплошность сварного шва, при которой не происходит плавление между металлом шва и поверхностями плавления или прилегающими сварными швами. Это отсутствие плавления может возникать в любом месте сварного шва и присутствовать в угловых швах или швах с разделкой кромок.
Неполное сплавление может произойти, если температура основного материала или ранее наплавленного металла шва не повышается до его точки плавления во время процесса сварки.Неполное плавление часто наблюдается на одном участке углового шва и вызвано неправильным углом сварки, в результате чего тепло распределяется неравномерно между обеими сторонами стыка.
Это также может быть вызвано оксидами или другим посторонним материалом на поверхности основного материала.
Неполное проплавление стыка — это разрыв в сварном шве с разделкой кромок, в котором металл сварного шва не выходит на толщину стыка. Это неспособность присадочного или основного металла полностью заполнить основание сварного шва.
Некоторые частые причины неполного проплавления шва — плохая конструкция сварного шва с разделкой кромок или подгонка, не подходящая для условий сварки. Неполное проплавление шва может произойти, если размеры поверхности корня слишком велики, отверстие в корне слишком мало или угол наклона сварного шва с V-образной канавкой слишком мал. Все эти проблемы конструкции соединения ограничивают способность сварного шва проникать через толщину соединения.
Неполный провар соединения можно предотвратить с помощью правильной конструкции соединения и подгонки в соответствии с требованиями процедуры сварки.
Понимание этих неоднородностей сварных швов поможет инспекторам по сварке выявить их и, что более важно, предотвратить их появление в процессе производства. Использование контроля сварки в качестве профилактического инструмента в рамках системы качества более эффективно, чем использование его только как метод оценки для отделения плохих сварных швов от хороших.
Неприемлемые профили сварного шва
Профиль завершенного сварного шва может существенно повлиять на характеристики этого сварного шва в процессе эксплуатации. Инспекторы по сварке должны выявлять несплошности посредством визуального осмотра и оценивать их приемку или отклонение в соответствии с применимыми правилами сварки или стандартными критериями приемки.
Неприемлемые профили сварного шва могут вызвать уменьшение толщины основного материала, уменьшение размера сварного шва или концентрации напряжений на поверхности сварного шва или листа. Эти типы несплошностей сварного шва часто серьезно ухудшают общие характеристики сварного компонента в эксплуатации.
Некоторые неоднородности профиля сварного шва — это подрез, перекрытие, недостаточный срез и чрезмерная выпуклость. Подрезание определяется как канавка, проплавленная в основном металле рядом с носком сварного шва или корнем сварного шва, и оставленная незаполненной металлом сварного шва.
Термин выточка описывает два особых состояния. Первый — это расплавление основного материала на боковой стенке сварного шва с разделкой кромок на краю валика, в результате чего в боковой стенке образуется острая выемка в области, где должен быть нанесен следующий валик. Этот тип поднутрения может захватывать включения внутри выемки, которые затем могут быть покрыты последующим наплавленным валиком.
Это состояние обычно можно исправить шлифованием выемки перед нанесением следующего валика.Однако, если подрез небольшой, опытному сварщику, который знает, на какую глубину проникнет дуга, возможно, не потребуется его удалять. Подрез на боковой стенке шва с разделкой кромок не повлияет на готовый шов, если условие исправлено до нанесения следующего валика.
Второе условие — уменьшение толщины основного металла на линии, где сварной валик на последнем слое металла шва сцепляется с поверхностью основного металла. Это положение известно как основание сварного шва. Это может произойти на угловом сварном шве или стыковом шве.
Допустимая величина поднутрения на поверхности завершенного сварного шва обычно указывается в используемых сварочных нормах или стандартах. Необходимо строго соблюдать требования к максимально допустимым поднутрениям для завершенных сварных швов, поскольку чрезмерные подрезы могут серьезно повлиять на характеристики сварного шва, особенно если он подвергается усталостной нагрузке в процессе эксплуатации.
Оба типа поднутрения обычно возникают из-за неправильной техники сварки, неправильного позиционирования электродов или неправильной скорости движения.Высокий ток и длинная дуга увеличивают вероятность подрезания.
Перекрытие. Перекрытие определяется как выступ металла сварного шва за выступ или основание сварного шва. Это состояние возникает в угловых сварных швах и стыковых соединениях и приводит к образованию зазубрин на носке сварного шва, что нежелательно из-за концентрации в них результирующих напряжений под нагрузкой. Это нарушение непрерывности может быть вызвано неправильной техникой сварки или недостаточным током.
Недостаточное горло. Недостаточная горловина обычно возникает в профилях углового шва и стыкового соединения, которые являются вогнутыми.Избыточная вогнутость уменьшает толщину шва, что значительно снижает прочность сварного шва. Это состояние обычно вызвано чрезмерным сварочным током или длиной дуги.
Чрезмерная выпуклость. Чрезмерная выпуклость может привести к образованию надрезов в зоне сварки и, как следствие, к концентрации напряжений под нагрузкой. По этой причине в некоторых нормах и стандартах указывается максимально допустимая выпуклость профиля сварного шва. Недостаточный ток или неправильная сварочная техника обычно вызывают это состояние.
Трещины
Трещины в сварном изделии, вероятно, являются самым опасным из всех дефектов сварного шва. Поскольку в сварке используется так много материалов и применений, растрескивание — сложная тема.
Чувствительность к растрескиванию основного материала может быть связана с его химическим составом и склонностью к образованию элементов, снижающих его пластичность. Чрезмерные напряжения в сварном шве, особенно если материал чувствителен к трещинам, могут вызвать растрескивание.
Сама операция сварки может создавать напряжения внутри и вокруг сварного шва, вызывая экстремальный локальный нагрев, расширение и сжатие.
Трещины часто возникают из-за концентрации напряжений вблизи неоднородностей в сварных швах и основном металле, а также возле механических надрезов в конструкции сварной детали. Водородное охрупчивание, состояние, которое вызывает потерю пластичности и существует в металле сварного шва из-за поглощения водорода, может способствовать образованию трещин в некоторых материалах.
Горячие и холодные трещины. Трещины подразделяются на два типа: горячие и холодные.
Горячие трещины возникают при повышенных температурах, распространяются между зернами материала и обычно образуются во время затвердевания металла шва.
Холодные трещины возникают после затвердевания сварного шва под действием напряжений и распространяются как между зернами, так и через зерна. Холодные трещины в стали иногда называют замедленными трещинами и часто связаны с водородным охрупчиванием.
Горячие трещины и холодные трещины могут быть далее классифицированы как трещины основного материала и трещины металла сварного шва.
Трещины основного материала. Растрескивание в зоне термического влияния (HAZ) чаще всего происходит с основным материалом, который может быть упрочнен. Высокая твердость и низкая пластичность в ЗТВ часто являются результатом металлургической реакции на термические циклы сварки. В ферритных сталях твердость увеличивается, а пластичность уменьшается с увеличением содержания углерода и более высокой скоростью охлаждения.
Твердость HAZ зависит от способности основного материала к упрочнению, которая, в свою очередь, зависит от химического состава основного материала.Углерод оказывает преимущественное влияние на прокаливаемость стали. Например, чугун содержит от 2 до 4,5 процентов углерода, что придает сплаву высокую твердость и низкую пластичность. Сварка этого материала без серьезного учета скорости охлаждения и остаточного напряжения неизбежно приведет к растрескиванию основного материала.
Трещины сварного металла. Трещины в металле сварного шва можно разделить на три типа:
- Поперечные, которые перпендикулярны направлению сварного шва.
- Продольные, которые проходят в том же направлении, что и сварной шов, и часто ограничиваются его центром.Этот тип трещины может быть продолжением трещины, которая первоначально возникла в конце сварного шва.
- Кратер, который может образоваться в результате резкого прекращения сварки, если кратер не заполнен металлом шва. Эти трещины обычно имеют звездообразную форму и сначала доходят только до края кратера. Однако они могут перерасти в продольные трещины сварного шва.
Работа с трещинами. Трещины являются недопустимыми неоднородностями и ухудшают характеристики сварки. Трещина по своей природе острая на концах, поэтому действует как концентрация напряжений.Эффект концентрации напряжения трещины больше, чем у большинства других несплошностей.
Трещины имеют тенденцию к распространению, что способствует разрушению сварного шва под напряжением. Независимо от их размера, трещины не допускаются в сварных деталях, которые регулируются большинством производственных норм. Их необходимо удалить шлифованием или строжкой, а выемку заполнить прочным металлом сварного шва.
Успешные процедуры сварки включают меры контроля, необходимые для преодоления тенденции к образованию трещин.К таким элементам управления относятся температура предварительного нагрева, температура между проходами, тип и подготовка расходных материалов, а также термообработка после сварки.
Инспекторы по сварке несут ответственность за оценку этих процедурных контролей во время инспекций, чтобы гарантировать, что сварка выполняется для минимизации возможности растрескивания сварных швов.
Обнаружение и оценка несплошностей
Разрывы сварного шва часто обнаруживаются при визуальном осмотре. Некоторые из них обнаруживаются с помощью методов контроля, таких как рентгенография, ультразвуковое исследование, проникающая жидкость и магнитопорошковый контроль.
Максимально допустимые ограничения для этих неоднородностей зависят от требований к характеристикам сварного компонента и указаны в соответствующих правилах сварки, стандарте или спецификации. Инспектор по сварке часто требуется для определения степени несплошностей и установления их приемлемости или отклонения на основе соответствующих критериев приемки.
Тони Андерсон — менеджер по техническим услугам в AlcoTec Wire Corp., 2750 Aero Park Drive, Traverse City, MI 49686-9263, 800-228-0750, факс 231-941-9154, tanderson @ alcotec.com, www.alcotec.com. AlcoTec Wire Corp. — производитель алюминиевой сварочной проволоки.
Примечания к тексту —
1. впечатляющих прорывов 䳿, ()
2. порог ,
3. случайный процесс ()
4. IBM
Упражнение 7. Ответьте на вопросы.
1. О чем этот текст? 2. Что такое явление сверхпроводимости? 3.Кто первым открыл это явление? 4. Какие вы знаете ученых, которые работали в области сверхпроводимости? 5. Какие материалы являются лучшими сверхпроводниками? 6. Можно ли вернуть сверхпроводящие материалы в нормальное состояние? 7. Как это сделать? 8. В каких областях науки и техники можно использовать явление сверхпроводимости?
Упражнение 8. Переведите словосочетания на украинский язык.
выдающихся ученых, мировые достижения, революция в технологии и промышленности, мощные высокоскоростные компьютеры, электрические характеристики, переменный ток, чтобы превратить новые материалы в полезные продукты, сильное магнитное поле, уникальные свойства, чтобы объяснить эту теорию, фундаментальную теорию сверхпроводимости, чтобы внести большой вклад, электромагнитные свойства, специальный керамический материал, сверхтвердые сплавы.
Упражнение 9. Скажите, верны эти утверждения или нет. В ответе используйте фразы: Совершенно верно. Вы правы. Совершенно верно. Боюсь, это не совсем так. Как раз наоборот. Насколько я помню.
1. Последние достижения в области сверхпроводимости означают революцию в технологии и промышленности. 2. Когда-то считалось, что сверхпроводники физически невозможны. 3. Достижения в области сверхпроводимости нельзя сравнивать с открытиями, которые привели к электронике и ядерной энергетике.4. Удельное электрическое сопротивление ртутной проволоки исчезает при охлаждении ниже 4K. 5. Сверхпроводящий материал нельзя вернуть в нормальное состояние. 6. Ландау и Гинзбург представили модель, которая оказалась полезной для понимания электромагнитного поля сверхпроводников. 7. Ученые из IBM обнаружили керамический материал, который стал сверхпроводником при температуре 23К. 8. Возможное техническое использование высокотемпературной сверхпроводимости маловероятно и практически невозможно.
Упражнение 10. Переведите предложения с субъективным инфинитивным комплексом. на украинский
A 1. На лекциях студенты Кембриджа должны носить халаты. 2. Сообщается, что были разработаны первые карманные цветные телевизоры. 3. Ожидается, что на смену нынешним самолетам через несколько лет придет новая модель гиперзвукового самолета. 4. Сообщается, что в ряде американских компаний ведутся интенсивные исследования оптико-электронных компьютеров. 5. Известно, что метод записи информации на кристалл с помощью лазера был разработан украинским исследователем.6. Ожидается, что в ближайшем будущем годовой объем производства персональных компьютеров достигнет миллионов. 7. Лазер, как известно, представляет собой устройство, создающее интенсивный световой луч за счет усиления излучения. 8. Оптическая технология оказалась рентабельной. 9. Сообщается, что был произведен оптический эквивалент транзистора.
Б . 1. Наша сегодняшняя жизнь кажется совершенно невозможной без телефона, радио и телевидения. 2. На сегодняшний день принцип работы радио кажется довольно простым.3. Известно, что термин «радар» состоит из первых букв слова «радио», «обнаружение и дальность». 4. Получается, что это отражает его основной принцип — быть загрязненным с момента начала работы Байкальского завода.
Упражнение 11. Сравните пары предложений. Переведите на украинский ..
1. Разработчики сообщают о новом пилотируемом корабле, способном погружаться на глубину 21 000 футов. Сообщается, что новый пилотируемый корабль сможет погружаться на глубину 21 000 футов.
2. Мы знаем, что радионавигационные станции должны быть расположены в разных местах по всему миру, чтобы направлять пилотов. Радионавигационные станции, как известно, расположены по всему миру, чтобы направлять пилотов.
3. Люди считали дирижабли слишком медленными и ненадежными, поэтому долгое время их не использовали. Дирижабли считались медленными и ненадежными.
4. Эксперты ожидают, что новый подводный аппарат будет перемещаться по дну океана, как спортивный автомобиль.Ожидается, что новый подводный аппарат будет перемещаться по дну океана, как спортивный автомобиль.
5. Ученые многих стран считают гребные двигатели гораздо более экономичными. Пропеллерные двигатели считаются гораздо более экономичными.
6. Мы знаем, что винтовые самолеты летают медленнее реактивных самолетов, поэтому был построен новый вентиляторный двигатель с пропеллером. Но поскольку винтовые самолеты, как известно, летают медленнее, чем реактивные, был построен новый вентиляторный двигатель с пропеллером.
Упражнение 12. Переведите эти предложения. Найдите предложения с субъективным инфинитивным комплексом.
1. Явление сверхпроводимости, по-видимому, было открыто еще в 1911 году. 2. До 1911 года сверхпроводимость считалась невозможной. 3. Недавние открытия в области сверхпроводимости заставили ученых искать новый проводящий материал и находить практическое применение феномену. 4. Последние достижения в области сверхпроводимости, несомненно, произведут революцию в технологии и промышленности.5. Рекомендации физиков позволят принять необходимые меры по защите воздуха от загрязнения. 6. Лазеры, несомненно, выполняют некоторые работы лучше и при гораздо меньших затратах, чем другие устройства. 7. М. Фарадей предположил, что луч света меняет свою поляризацию, проходя через намагниченный кристалл. 8. Сверхпроводники, вероятно, найдут применение, о котором мы даже не думаем в настоящее время. 9. Голландский физик обнаружил, что сверхпроводящий материал возвращается в нормальное состояние при приложении сильного магнитного поля.10. Свойства материала, полученного в космосе, оказываются намного лучше, чем у материала, произведенного на Земле. 11. Есть перспективы использования лазеров для дальней связи и для передачи энергии на космические станции. 12. Было обнаружено, что электрическое сопротивление ртутного провода исчезает при охлаждении до -269 0 C. 13. Дополнительные радиопередатчики позволяют пилоту приближаться к аэропорту, наблюдая за его полетными приборами. 14. Похоже, что существует множество сплавов и соединений, которые при определенных условиях становятся сверхпроводниками.
Упражнение 13 . Измените следующие предложения в соответствии с образцом и переведите их на украинский язык.
Модель: Мы знаем, что медь, серебро, алюминий и другие металлы являются хорошими проводниками электричества. Известно, что медь, серебро, алюминий и другие металлы являются хорошими проводниками электричества.
1. Мы знаем, что сверхпроводящие диоды используются в различных отраслях промышленности. 2. Мы знаем, что электроны легко выходят из полупроводника в особых условиях.3. Оказалось, что сверхпроводники обладают неожиданными свойствами. 4. Известно, что полупроводники бывают p-типа и n-типа. 5. Известно, что этот ученый и многие его сотрудники внесли большой вклад в физику сверхпроводников. 6. Предполагается, что электрон движется с большой скоростью.
Упражнение 14. Составляйте предложения из двух частей.
1. Последние достижения в исследованиях сверхпроводимости | 1.фундаментальная теория для объяснения этого неожиданного явления. |
2. Их можно сравнить с | 2. обнаружили, что удельное электрическое сопротивление ртути исчезает при охлаждении до температуры 4 Кельвина. |
3. Сверхпроводимость известна | 3. К развитию теории сверхпроводимости. |
4. При проведении низкотемпературных исследований он | 4.были открыты голландским физиком. |
5. В течение 59 лет после открытия не было | 5. Имеет большое значение для науки и техники. |
6. В 1950-е годы большой вклад внесли российские и американские физики. | 6. С момента открытия сверхпроводящей металлической керамики. |
7. Особенно активными стали исследования в области сверхпроводимости. | 7.открытия в физике, которые привели к развитию электроники и ядерной энергетики. |
Exercise 15. Переведите следующие предложения. Обратите внимание на слова, выделенные жирным шрифтом.
1. Климат в этой части мира является наиболее подходящим для проживания людей. Это ни ни слишком жарко, ни ни слишком холодно. 2. Многие лазеры испускают невидимое излучение или инфракрасное, или ультрафиолетовое .3. На по обе стороны от экватора находится тропическая зона. 4. Можно разделить все страны на классы: развитые и развивающиеся. Различные критерии могут использоваться для включения конкретной страны в или из двух категорий. 5. Такие спутники могут содержать или телекамер, или фотоаппаратуры для передачи изображений на Землю. 6. Полупроводники — это , ни хорошие проводники, ни , ни хорошие изоляторы .7. Энергия не может быть , ни ни создан, ни ни уничтожен. 8. Материя не может , ни появиться, ни , ни исчезнуть сама по себе. 9. Наибольшая часть вещества на Земле — это или жидкий, или газ. 10. Кремний и германий могут быть изготовлены из полупроводников или p-типа, или n-типа. 11. Материя может существовать в или из четырех состояний твердого, жидкого, газообразного или плазменных состояний.
Задача. Прочитать и перевести текст
Текст 15Б.
Новая надежда на энергию .
Недавно было обнаружено, что некоторые керамические материалы являются сверхпроводниками. Сверхпроводящая керамика — это вещества, которые могут передавать электрические токи без потери энергии при температурах намного выше, чем у обычных сверхпроводников (то есть при температуре жидкого азота).
Одним из применений новых сверхпроводников будет замена тех, которые нуждаются в экстремальном холоде жидкого гелия, огромных сверхпроводящих электромагнитах, используемых в исследованиях ядерного магнитного резонанса, ускорении атомных частиц и исследовательских реакторах.
Другие типы электромагнитов из сверхпроводников могут быть использованы для снижения стоимости производства и хранения электроэнергии. На такое использование может потребоваться 10 лет исследований, более быстрое использование, вероятно, будет в электронике.
По оценкам исследователей, крошечные, но чрезвычайно мощные высокоскоростные компьютеры, использующие сверхпроводники, могут появиться через три-пять лет. Далее 300 миль в час. поезда, плавающие на магнитных подушках, которые сейчас существуют в качестве прототипов, но на их совершенствование может уйти не менее десяти лет.Линии электропередач, которые могут удовлетворить потребности города в электроэнергии с помощью сверхпроводящих кабелей, могут быть в будущем еще дальше.
Между тем ученые всего мира пытаются превратить новые материалы в полезные продукты. Среди наиболее примечательных — тонкая пленка микрон, которая пропускает полезное количество электрического тока без потери сверхпроводимости. Пленка может быть использована в микроскопических схемах современных компьютеров в качестве высокоскоростного пути между компьютерными микросхемами.
Известно, что несколько стран очень активны в исследованиях сверхпроводников.Например, Соединенные Штаты тратят миллионы долларов на такие исследования, большая часть из которых используется в военных целях: ускорители снарядов, лазеры, двигательные установки кораблей и подводных лодок.
:
- Примечания к тексту
- Примечания к тексту
- Примечания к тексту
- Примечания к тексту
- Примечания к тексту
- Примечания к тексту
- Примечания к тексту
- Примечания к тексту
- Примечания к тексту
- Примечания к тексту
- Примечания к тексту
Что такое термопара? — Определение, принцип работы, конструкция, преимущества и недостатки
Определение: Термопара — это устройство для измерения температуры.Он используется для измерения температуры в одной конкретной точке. Другими словами, это тип датчика, который используется для измерения температуры в виде электрического тока или ЭДС.
Термопара состоит из двух проволок из разных металлов, сваренных на концах. Сваренная часть создавала стык, где обычно измеряли температуру. Изменение температуры провода вызывает появление напряжения.
Принцип работы термопары
Принцип работы термопары зависит от трех эффектов.
Обратный эффект — Обратный эффект возникает между двумя разными металлами. Когда тепло подводится к любому из металлов, электроны начинают переходить от горячего металла к холодному. Таким образом, в цепи возникает постоянный ток.
Короче говоря, — это явление, при котором разница температур между двумя разными металлами вызывает разность потенциалов между ними . Эффект Зее-Бека производит небольшие напряжения на один градус температуры.
Эффект Пельтье — Эффект Пельтье противоположен эффекту Зеебека. Эффект Пельтье утверждает, что разница температур может быть создана между любыми двумя разными проводниками путем приложения разности потенциалов между ними.
Эффект Томпсона — эффект Томпсона утверждает, что , когда два разнородных металла соединяются вместе, и если они создают два соединения, тогда напряжение индуцирует всю длину проводника из-за градиента температуры .Температурный градиент — это физический термин, который показывает направление и скорость изменения температуры в определенном месте.
Конструкция термопары
Термопара состоит из двух разнородных металлов. Эти металлы свариваются в месте соединения. Это соединение считается точкой измерения. Точки соединения подразделяются на три типа.
- Незаземленный переход — В незаземленном переходе проводники полностью изолированы от защитной оболочки .Используется для работ с высоким давлением. Основное преимущество использования такого типа перехода заключается в том, что он снижает влияние паразитного магнитного поля.
- Заземленный переход — В таком переходе металл и защитная оболочка свариваются друг с другом. Заземленный переход используется для измерения температуры в агрессивной среде. Этот переход обеспечивает устойчивость к шуму.
- Открытое соединение — Такой тип соединения используется там, где требуется быстрое срабатывание.Открытый спай используется для измерения температуры газа.
Материал, из которого изготовлена термопара, зависит от диапазона измерения температуры.
Работа термопары
Схема термопары показана на рисунке ниже. Схема состоит из двух разнородных металлов. Эти металлы соединены вместе таким образом, что образуют два соединения. Металлы прикрепляются к стыку посредством сварки.
Пусть P и Q — два спая термопар.T 1 и T 2 — температуры на стыках. Поскольку температуры спаев отличаются друг от друга, в цепи генерируется ЭДС.
Если температура на стыке становится одинаковой, в цепи генерируется равная и противоположная ЭДС, и через нее протекает нулевой ток. Если температуры перехода становятся неравными, в цепи возникает разность потенциалов. Величина индукции ЭДС в цепи зависит от типа материала, из которого изготовлена термопара.Полный ток, протекающий по цепи, измеряется измерительными приборами.
ЭДС, наводимая в цепи термопары, определяется уравнением где Δθ — разница температур между горячим спаем термопары и эталонным спаем термопары.
а, б — константы
Измерение выхода термопары
Выходная ЭДС, полученная от термопар, может быть измерена следующими методами.
- Мультиметр — это более простой метод измерения выходной ЭДС термопары. Мультиметр подключается к холодным спаям термопары . Прогиб стрелки мультиметра равен току, протекающему через счетчик.
- Потенциометр — Выход термопары также можно измерить с помощью потенциометра постоянного тока.
- Усилитель с устройствами вывода — Выходной сигнал, получаемый от термопар, усиливается через усилитель и затем подается на регистрирующий или индикаторный прибор.
Преимущества термопары
Ниже приведены преимущества термопар.
- Термопара дешевле, чем другие приборы для измерения температуры.
- Термопара имеет быстрое время отклика.
- Имеет широкий температурный диапазон.
Недостатки термопар
- Термопара имеет низкую точность.
- Повторная калибровка термопары затруднена.
Никелевый сплав, сплав платина / родий, сплав вольфрама / рения, хромель-золото, сплав железа — это названия сплавов, используемых для изготовления термопары.
Что такое магнетизм? | Магнитные поля и магнитная сила
Магнетизм — это один из аспектов комбинированной электромагнитной силы. Это относится к физическим явлениям, возникающим из-за силы, вызванной магнитами, объектами, которые создают поля, которые притягивают или отталкивают другие объекты.
Согласно веб-сайту HyperPhysics Университета штата Джорджия, магнитное поле действует на частицы в поле за счет силы Лоренца. Движение электрически заряженных частиц порождает магнетизм.Сила, действующая на электрически заряженную частицу в магнитном поле, зависит от величины заряда, скорости частицы и силы магнитного поля.
Все материалы обладают магнетизмом, некоторые сильнее, чем другие. Постоянные магниты, сделанные из таких материалов, как железо, испытывают сильнейшее воздействие, известное как ферромагнетизм. За редким исключением, это единственная форма магнетизма, достаточно сильная, чтобы ее могли почувствовать люди.
Противоположности притягиваются
Магнитные поля генерируются вращающимися электрическими зарядами, согласно HyperPhysics.Все электроны обладают свойством углового момента или спина. Большинство электронов имеют тенденцию образовывать пары, в которых один из них имеет «спин вверх», а другой — «спин вниз», в соответствии с принципом исключения Паули, согласно которому два электрона не могут находиться в одном и том же энергетическом состоянии одновременно. В этом случае их магнитные поля имеют противоположные стороны, поэтому они компенсируют друг друга. Однако некоторые атомы содержат один или несколько неспаренных электронов, спин которых может создавать направленное магнитное поле. Направление их вращения определяет направление магнитного поля, согласно Ресурсному центру неразрушающего контроля (NDT).Когда значительное большинство неспаренных электронов выровнены своими спинами в одном направлении, они объединяются, чтобы создать магнитное поле, достаточно сильное, чтобы его можно было почувствовать в макроскопическом масштабе.
Источники магнитного поля дипольные, с северным и южным магнитными полюсами. По словам Джозефа Беккера из Университета Сан-Хосе, противоположные полюса (северный и южный) притягиваются, а аналогичные полюса (северный и северный или южный и южный) отталкиваются. Это создает тороидальное поле или поле в форме пончика, поскольку направление поля распространяется наружу от северного полюса и входит через южный полюс.
Земля сама по себе является гигантским магнитом. Согласно HyperPhysics, планета получает свое магнитное поле от циркулирующих электрических токов внутри расплавленного металлического ядра. Компас указывает на север, потому что маленькая магнитная стрелка в нем подвешена, так что он может свободно вращаться внутри корпуса, выравниваясь с магнитным полем планеты. Как ни парадоксально, то, что мы называем Северным магнитным полюсом, на самом деле является южным магнитным полюсом, потому что он притягивает северные магнитные полюса стрелок компаса.
Ферромагнетизм
Если выравнивание неспаренных электронов продолжается без приложения внешнего магнитного поля или электрического тока, образуется постоянный магнит. Постоянные магниты — результат ферромагнетизма. Приставка «ферро» относится к железу, потому что постоянный магнетизм впервые наблюдался в форме естественной железной руды, называемой магнетитом, Fe 3 O 4 . Кусочки магнетита можно найти разбросанными на поверхности земли или рядом с ней, и иногда они намагничиваются.Эти встречающиеся в природе магниты называются магнитными камнями. «Мы до сих пор не уверены в их происхождении, но большинство ученых считают, что магнитный камень — это магнетит, пораженный молнией», — говорится в сообщении Университета Аризоны.
Вскоре люди узнали, что можно намагнитить железную иглу, поглаживая ее магнитом, в результате чего большая часть неспаренных электронов в игле выстраивается в одном направлении. По данным НАСА, примерно в 1000 году нашей эры китайцы обнаружили, что магнит, плавающий в чаше с водой, всегда выстраивался в направлении север-юг.Таким образом, магнитный компас стал огромным помощником в навигации, особенно днем и ночью, когда звезды были скрыты облаками.
Было обнаружено, что другие металлы, помимо железа, обладают ферромагнитными свойствами. К ним относятся никель, кобальт и некоторые редкоземельные металлы, такие как самарий или неодим, которые используются для создания сверхпрочных постоянных магнитов.
Другие формы магнетизма
Магнетизм принимает множество других форм, но, за исключением ферромагнетизма, они обычно слишком слабы, чтобы их можно было наблюдать за исключением чувствительных лабораторных приборов или при очень низких температурах.Диамагнетизм был впервые открыт в 1778 году Антоном Бругнамсом, который использовал постоянные магниты в поисках материалов, содержащих железо. По словам Джеральда Кюстлера, широко опубликованного независимого немецкого исследователя и изобретателя, в своей статье «Диамагнитная левитация — исторические вехи», опубликованной в Румынском журнале технических наук, Бругнамс заметил: «Только темный и почти фиолетовый висмут проявлял конкретное явление в исследовании; когда я положил его кусок на круглый лист бумаги, плавающий на воде, он оттолкнулся обоими полюсами магнита.
Было установлено, что висмут обладает самым сильным диамагнетизмом из всех элементов, но, как обнаружил Майкл Фарадей в 1845 году, это свойство всей материи отталкиваться магнитным полем.
Диамагнетизм вызван орбитальным движением электронов, создающих крошечные токовые петли, которые создают слабые магнитные поля, согласно HyperPhysics. Когда к материалу прикладывается внешнее магнитное поле, эти токовые петли имеют тенденцию выравниваться таким образом, чтобы противостоять приложенному полю.Это приводит к тому, что все материалы отталкиваются постоянным магнитом; однако результирующая сила обычно слишком мала, чтобы быть заметной. Однако есть некоторые заметные исключения.
Пиролитический углерод, вещество, похожее на графит, демонстрирует даже более сильный диамагнетизм, чем висмут, хотя и только вдоль одной оси, и фактически может подниматься над сверхсильным редкоземельным магнитом. Некоторые сверхпроводящие материалы демонстрируют даже более сильный диамагнетизм ниже своей критической температуры, поэтому над ними можно левитировать редкоземельные магниты.(Теоретически из-за их взаимного отталкивания один может левитировать над другим.)
Парамагнетизм возникает, когда материал временно становится магнитным при помещении в магнитное поле и возвращается в немагнитное состояние, как только внешнее поле удаляется. При приложении магнитного поля некоторые из неспаренных электронных спинов выравниваются с полем и преодолевают противоположную силу, создаваемую диамагнетизмом. Однако, по словам Дэниела Марша, профессора физики Южного государственного университета Миссури, эффект заметен только при очень низких температурах.
Другие, более сложные формы включают антиферромагнетизм, при котором магнитные поля атомов или молекул выстраиваются рядом друг с другом; и поведение спинового стекла, в котором участвуют как ферромагнитные, так и антиферромагнитные взаимодействия. Кроме того, ферримагнетизм можно рассматривать как комбинацию ферромагнетизма и антиферромагнетизма из-за многих общих черт между ними, но, по данным Калифорнийского университета в Дэвисе, он все же имеет свою уникальность.
Электромагнетизм
Когда провод перемещается в магнитном поле, поле индуцирует в проводе ток.И наоборот, магнитное поле создается движущимся электрическим зарядом. Это соответствует закону индукции Фарадея, который лежит в основе электромагнитов, электродвигателей и генераторов. Заряд, движущийся по прямой линии, как по прямому проводу, создает магнитное поле, которое вращается вокруг провода по спирали. Когда этот провод превращается в петлю, поле приобретает форму пончика или тора. Согласно Справочнику по магнитной записи (Springer, 1998) Marvin Cameras, это магнитное поле можно значительно усилить, поместив ферромагнитный металлический сердечник внутри катушки.
В некоторых приложениях постоянный ток используется для создания постоянного поля в одном направлении, которое можно включать и выключать вместе с током. Это поле может затем отклонить подвижный железный рычаг, вызывая слышимый щелчок. Это основа телеграфа, изобретенного в 1830-х годах Сэмюэлем Ф. Б. Морзе, который позволял осуществлять связь на большие расстояния по проводам с использованием двоичного кода, основанного на импульсах большой и малой длительности. Импульсы посылались опытными операторами, которые быстро включали и выключали ток с помощью подпружиненного переключателя с мгновенным контактом или ключа.Другой оператор на принимающей стороне затем переводил слышимые щелчки обратно в буквы и слова.
Катушка вокруг магнита также может двигаться по шаблону с изменяющейся частотой и амплитудой, чтобы индуцировать ток в катушке. Это основа для ряда устройств, в первую очередь для микрофона. Звук заставляет диафрагму двигаться внутрь и наружу с волнами переменного давления. Если диафрагма соединена с подвижной магнитной катушкой вокруг магнитопровода, она будет производить переменный ток, аналогичный падающим звуковым волнам.Затем этот электрический сигнал может быть усилен, записан или передан по желанию. Крошечные сверхсильные магниты из редкоземельных элементов сейчас используются для изготовления миниатюрных микрофонов для сотовых телефонов, сообщил Марш Live Science.
Когда этот модулированный электрический сигнал подается на катушку, он создает колеблющееся магнитное поле, которое заставляет катушку входить и выходить по магнитному сердечнику по той же схеме. Затем катушка прикрепляется к подвижному диффузору динамика, чтобы он мог воспроизводить звуковые волны в воздухе.Первым практическим применением микрофона и динамика был телефон, запатентованный Александром Грэмом Беллом в 1876 году. Хотя эта технология была усовершенствована и усовершенствована, она все еще является основой для записи и воспроизведения звука.
Применения электромагнитов почти бесчисленны. Закон индукции Фарадея составляет основу многих аспектов нашего современного общества, включая не только электродвигатели и генераторы, но и электромагниты всех размеров. Тот же принцип, который используется гигантским краном для подъема старых автомобилей на свалку металлолома, также используется для выравнивания микроскопических магнитных частиц на жестком диске компьютера для хранения двоичных данных, и каждый день разрабатываются новые приложения.
Штатный писатель Таня Льюис внесла свой вклад в этот отчет.
Дополнительные ресурсы
Прочтите и переведите текст. Химия — изучение веществ
ХИМИЯ
Химия — это изучение веществ. Химики исследуют свойства веществ, из которых состоит Вселенная, и их поведение в различных условиях. Они пытаются объяснить поведение вещества с точки зрения его структуры и состава.Химики также стремятся понять химические изменения. Эти изменения связаны с изменениями химического состава вещества. Комбинация железа с кислородом из воздуха, образующая ржавчину, представляет собой химическое изменение. Вещества также могут претерпевать физические изменения без изменения своего химического состава. Вода изменяется физически, но не химически, когда она замерзает.
Химики много узнали о химических веществах и процессах, происходящих в природе, и создали много полезных веществ, которые не встречаются в природе, поэтому они значительно улучшили жизнь людей.
Химия изучает многие вещества. Вещества сильно различаются по свойствам, структуре и составу. Методы, которые используют химики, и вопросы, на которые они пытаются ответить, также сильно различаются.
Самыми основными химическими веществами являются химические элементы. Они являются строительными блоками всех других веществ. Каждый химический элемент состоит только из одного вида атомов. Известно, что на Земле существует 91 элемент. Дополнительные 20 элементов изготовлены искусственно.Электрические силы на атомном уровне создают химические связи, которые соединяют два или более атомов вместе, образуя молекулы. Некоторые молекулы состоят из атомов одного элемента. Когда атомы двух или более разных элементов соединяются вместе, они образуют химическое соединение. Вода — это соединение двух атомов водорода и одного атома кислорода. Соединения образуются или разлагаются в результате химических реакций. Все химические реакции включают образование или разрушение химических связей.
Химия включает в себя следующие науки.
Аналитическая химия определяет идентичность и количество каждого элемента или соединения, присутствующего в веществе. Качественный анализ связан с определением типов элементов или соединений в образце. Количественный анализ показывает количество присутствующих элементов. Методы аналитической химии включают использование спектроскопа, масс-спектрографа, рентгеновской трубки, ультрафиолетовой флуоресценции и радиоизотопов.
Биохимия — это исследование химического состава живого вещества и химических процессов, происходящих в живых организмах.Эта область особенно важна в сельском хозяйстве, биологии, бактериологии, фармакологии, медицине и стоматологии.
Химическая инженерия — это комбинация химии и инженерии, которая развивает или улучшает промышленные процессы для получения коммерческих количеств желаемых химикатов, которые были произведены только в небольших количествах или в лаборатории.
Коллоидная химия — это исследование поведения частиц вещества, которые больше обычных молекул, но меньше объектов, которые можно увидеть в лучший оптический микроскоп.Частицы этого диапазона размеров (от 10 до 2 000 А в диаметре) обладают множеством уникальных свойств. Инструменты, используемые в этой области, включают ультрацентрифугу, ультрамикроскоп и электронный микроскоп.
Электрохимия — это исследование химических реакций, которые производятся или производятся электрическим током. Также изучается электропроводность растворов и явления, возникающие при наложении электродов. Электрохимия предоставляет методы химического анализа и производства химикатов электрическими средствами.
Неорганическая химия — это изучение всех элементов и соединений, не содержащих углерод. К ним относятся металлы, галогены и щелочи.
Ядерная химия — это изучение радиоактивности, атомного ядра и ядерных реакций, а также разработка приложений для радиоактивных изотопов в медицине и промышленности.
Органическая химия — это изучение углерода и его соединений. На углеродные соединения приходится около 96 процентов (около шести с половиной миллионов) всех известных соединений.Среди углеродных соединений, изученных химиками-органиками, есть ткани растений и животных, нефть, углеводы, белки, пластмассы и каучук.
Физическая химия — это применение физических методов к изучению химических проблем. В это поле входят атомная и молекулярная структура; теория скоростей реакции; механизм реакций; химические равновесия; энергетические изменения в реакциях; теории твердых тел, жидкостей, газов, плазмы и растворов; электрохимия; радиоактивность.
IV. Развитие языка.
1. Заполните пропуски словами из списка.
свойства, изменение, происходят, содержат, количество, связь, соединение, частица, уникальный, реакция, раствор, равновесие
1. Все химические элементы различаются по своим физическим и химическим свойствам
2. Попадание ртути в воду может привести к очень негативным последствиям.
3.Natural … был уничтожен из-за государственных экспериментов с экосистемами.
4. Этот экземпляр …, я ничего подобного не видел.
5. Два этих элемента имеют ионную …, поэтому вместе они образуют очень стабильное сложное вещество.
6. Будьте очень осторожны при работе с … соляной кислотой, вы можете обжечься.
7. Когда различные элементы связываются вместе, они подвергаются химическому ….
8.Наука химия … много разных, но, тем не менее, очень важных областей.
9. Когда фармацевт готовит лекарство, он должен думать не только о …, но и о качестве.
10. В результате многие последующие изменения могут ….
2. Ответьте на следующие вопросы.
1. Что такое химия?
2. Что изучают химики?
3. Что такое химические изменения?
4.В чем разница между химическими и физическими изменениями?
5. Чем химические элементы отличаются друг от друга?
6. Сколько элементов на Земле: природных и искусственно синтезированных?
7. Что такое аналитическая химия? Почему важно изучать количественный и качественный анализ?
8. Для каких профессий биохимия особенно важна?
9. Какие инструменты используются в коллоидной химии?
10.В чем разница между органической, неорганической химией и биохимией?
В. Разговор.
1. Задавайте вопросы вместо ответов. Затем попарно разыгрывайте диалог.
— _____________________________________________________?
— Химия — это изучение веществ.
— _____________________________________________________ ?
— Есть много областей химии, аналитической химии, биохимии, химической технологии, органической и неорганической химии, электрохимии.
— ____________________________________________________?
— Аналитическая химия определяет идентичность и количество каждого
элемент или соединение, присутствующее в веществе.
— ____________________________________________________?
— Биохимия — это изучение химического состава живого вещества и химических процессов, происходящих в живых организмах.
— _______________________________________________________?
— Неорганическая химия — это изучение всех элементов и соединений, не содержащих углерод.К ним относятся металлы, галогены и щелочи. Органическая химия — это изучение углерода и его соединений.
— ________________________________?
— Ядерная химия — это изучение радиоактивности, атомного ядра и ядерных реакций, а также разработка приложений для радиоактивных изотопов в медицине и промышленности.
— __________________________________________________________?
— Физическая химия — это применение физических методов к изучению химических проблем.
2. Сообщите как можно больше информации о:
направления химии;
возможности карьерного роста в разных областях химии;
современных раздела химии, таких как биохимия и химическая инженерия.
Органическая химия.
.