Принцип работы плазмореза | Строительный портал
Плазменная резка широко используется в различных отраслях промышленности: машиностроении, судостроении, изготовлении рекламы, коммунальной сфере, изготовлении металлоконструкций и в других отраслях. К тому же, в частной мастерской плазморез тоже может пригодиться. Ведь с помощью него можно быстро и качественно разрезать любой токопроводящий материал, а также некоторые нетокопроводящие материалы – пластик, камень и дерево. Разрезать трубы, листовой металл, выполнить фигурный рез или изготовить деталь можно просто, быстро и удобно с помощью технологии плазменной резки. Рез выполняется высокотемпературной плазменной дугой, для создания которой нужен лишь источник тока, резак и воздух. Чтобы работа с плазморезом давалась легко, а рез получался красивым и ровным, не мешает узнать принцип работы плазмореза, который даст базовое понятие, как можно управлять процессом резки.
- Устройство плазмореза
- Параметры плазмореза
- Плазморез своими руками
- ЧПУ плазморез своими руками
Устройство плазмореза
Аппарат под названием «плазморез» состоит из нескольких элементов: источника питания, плазменного резака/плазмотрона, воздушного компрессора и кабель-шлангового пакета.
Источник питания для плазмореза подает на плазмотрон определенную силу тока. Может представлять собой трансформатор или инвертор.
Трансформаторы более увесисты, потребляют больше энергии, но зато менее чувствительны к перепадам напряжения, и с помощью них можно разрезать заготовки большей толщины.
Инверторы легче, дешевле, экономнее в плане энергопотребления, но при этом позволяют разрезать заготовки меньшей толщины. Поэтому их используют на маленьких производствах и в частных мастерских. Также КПД инверторных плазморезов на 30 % больше, чем у трансформаторных, у них стабильнее горит дуга. Пригождаются они и для работы в труднодоступных местах.
Плазмотрон или как его еще называют «плазменный резак» является главным элементом плазмореза. В некоторых источниках можно встретить упоминание плазмотрона в таком контексте, что можно подумать будто «плазмотрон» и «плазморез» идентичные понятия. На самом деле это не так: плазмотрон – это непосредственно резак, с помощью которого разрезается заготовка.
Основными элементами плазменного резака/плазмотрона являются сопло, электрод, охладитель/изолятор между ними и канал для подачи сжатого воздуха.
Схема плазмореза наглядно демонстрирует расположение всех элементов плазмореза.
Внутри корпуса плазмотрона находится электрод, который служит для возбуждения электрической дуги. Он может быть изготовлен из гафния, циркония, бериллия или тория. Эти металлы приемлемы для воздушно-плазменной резки потому, что в процессе работы на их поверхности образуются тугоплавкие оксиды, препятствующие разрушению электрода. Тем не менее, используют не все эти металлы, потому что оксиды некоторых из них могут нанести вред здоровью оператора. Например, оксид тория – токсичен, а оксид бериллия – радиоактивен. Поэтому самым распространенным металлом для изготовления электродов плазмотрона является гафний. Реже – другие металлы.
Сопло плазмотрона обжимает и формирует плазменную струю, которая вырывается из выходного канала и разрезает заготовку. От размера сопла зависят возможности и характеристики плазмореза, а также технология работы с ним. Зависимость такая: от диаметра сопла зависит, какой объем воздуха может через него пройти за единицу времени, а от объема воздуха зависят ширина реза, скорость охлаждения и скорость работы плазмотрона. Чаще всего сопло плазмотрона имеет диаметр 3 мм. Длина сопла тоже важный параметр: чем длиннее сопло, тем аккуратнее и качественнее рез. Но с этим надо быть поаккуратнее. Слишком длинное сопло быстрее разрушается.
Компрессор для плазмореза необходим для подачи воздуха. Технология плазменной резки подразумевает использование газов: плазмообразующих и защитных. В аппаратах плазменной резки, рассчитанных на силу тока до 200 А, используется только сжатый воздух, и для создания плазмы, и для охлаждения. Такого аппарата достаточно для разрезания заготовок 50 мм толщиной. Промышленный станок плазменной резки использует другие газы – гелий, аргон, кислород, водород, азот, а также их смеси.
Кабель-шланговый пакет соединяет источник питания, компрессор и плазмотрон. По электрическому кабелю подается ток от трансформатора или инвертора для возбуждения электрической дуги, а по шлангу идет сжатый воздух, который необходим для образования плазмы внутри плазмотрона. Более детально, что именно происходит в плазмотроне, расскажем ниже.
Принцип работы плазмореза
Как только нажимается кнопка розжига, источник питания (трансформатор или инвертор) начинает подавать на плазмотрон токи высокой частоты. В результате внутри плазмотрона возникает дежурная электрическая дуга, температура которой 6000 – 8000 °С. Дежурная дуга зажигается
После возникновения дежурной дуги в камеру начинает поступать сжатый воздух. Он вырывается из патрубка, проходит через электрическую дугу, вследствие чего нагревается и увеличивается в объеме в 50 – 100 раз. Помимо этого воздух ионизируется и перестает быть диэлектриком, приобретая токопроводящие свойства.
Суженное к низу сопло плазмотрона обжимает воздух, формирует из него поток, который со скоростью 2 – 3 м/с вырывается из сопла. Температура воздуха в этот момент может достигать 25000 – 30000 °С. Именно этот высокотемпературный ионизированный воздух и является в данном случае
В тот момент, когда плазма вырывается из сопла и соприкасается с поверхностью обрабатываемого металла, зажигается режущая дуга, а дежурная дуга гаснет. Режущая/рабочая дуга разогревает обрабатываемую заготовку в месте реза – локально. Металл плавится, появляется рез. На поверхности разрезаемого металла появляются частички расплавленного только что металла, которые сдуваются с нее потоком воздуха, вырывающегося из сопла. Это самая простая технология плазменной резки металла.
Катодное пятно плазменной дуги должно располагаться строго по центру электрода/катода. Чтобы это обеспечить, используется так называемая вихревая или тангенциальная подача сжатого воздуха. Если вихревая подача нарушена, то катодное пятно смещается относительно центра электрода вместе с плазменной дугой. Это может привести к неприятным последствиям: плазменная дуга будет гореть нестабильно, может образовываться две дуги одновременно, а в худшем случае – плазмотрон может выйти из строя.
Если увеличить расход воздуха, то скорость плазменного потока увеличится, также увеличится и скорость резки. Если же увеличить диаметр сопла, то скорость уменьшится и увеличится ширина реза. Скорость плазменного потока примерно равна 800 м/с при токе 250 А.
Скорость реза – тоже важный параметр. Чем она больше, тем тоньше рез. Если скорость маленькая, то ширина реза увеличивается. Если увеличивается сила тока, происходит то же самое – ширина реза увеличивается. Все эти тонкости относятся уже непосредственно к технологии работы с плазморезом.
Параметры плазмореза
Все аппараты плазменной резки можно разделить на две категории: ручные плазморезы и аппараты машинной резки.
Ручные плазморезы используются в быту, на маленьких производствах и в частных мастерских для изготовления и обработки деталей. Основная их особенность в том, что плазмотрон держит в руках оператор, он ведет резак по линии будущего реза, держа его на весу. В итоге рез получается хоть и ровным, но не идеальным. Да и производительность такой технологии маленькая. Чтобы рез получился более ровным, без наплывов и окалины, для ведения плазмотрона используется специальный упор, который одевается на сопло. Упор прижимается к поверхности обрабатываемой заготовки и остается только вести резак, не переживая за то, соблюдается ли необходимое расстояние между заготовкой и соплом.
На ручной плазморез цена зависит от его характеристик: максимальной силы тока, толщины обрабатываемой заготовки и универсальности. Например, существуют модели, которые можно использовать не только для резки металлов, но и для сварки. Их можно отличить по маркировке:
- CUT – разрезание;
- TIG – аргонодуговая сварка;
- MMA – дуговая сварка штучным электродом.
Например, плазморез FoxWeld Plasma 43 Multi совмещает все перечисленные функции. Его стоимость 530 – 550 у.е. Характеристики, касающиеся плазменной резки: сила тока – 60 А, толщина заготовки – до 11 мм.
Кстати, сила тока и толщина заготовки – основные параметры, по которым подбирается плазморез. И они взаимосвязаны.
Чем больше сила тока, тем сильнее плазменная дуга, которая быстрее расплавляет металл. Выбирая плазморез для конкретных нужд, необходимо точно знать, какой металл придется обрабатывать и какой толщины. В приведенной ниже таблице указано, какая сила тока нужна для разрезания 1 мм металла. Обратите внимание, что для обработки цветных металлов требуется большая сила тока. Учтите это, когда будете смотреть на характеристики плазмореза в магазине, на аппарате указана толщина заготовки из черного металла. Если вы планируете резать медь или другой цветной металл, лучше рассчитайте необходимую силу тока самостоятельно.
Например, если требуется разрезать медь толщиной 2 мм, то необходимо 6 А умножить на 2 мм, получим плазморез с силой тока 12 А. Если требуется разрезать сталь толщиной 2 мм, то умножаем 4 А на 2 мм, получаем силу тока 8 А. Только берите аппарат плазменной резки с запасом, так как указанные характеристики являются максимальными, а не номинальными. На них можно работать только непродолжительное время.
Станок с ЧПУ плазменной резки используется на производственных предприятиях для изготовления деталей или обработки заготовок. ЧПУ означает числовое программное управление. Станок работает по заданной программе с минимальным участием оператора, что максимально исключает человеческий фактор на производстве и увеличивает производительность в разы. Качество реза машинным аппаратом идеально, не требуется дополнительная обработка кромок. А самое главное – фигурные резы и исключительная точность. Достаточно ввести в программу схему реза и аппарат может выполнить любую замысловатую фигуру с идеальной точностью. На станок плазменной резки цена значительно выше, чем на ручной плазморез. Во-первых, используется большой трансформатор. Во-вторых, специальный стол, портал и направляющие. В зависимости от сложности и размеров аппарата цена может быть от 3000 у.е. до 20000 у.е.
Аппараты машинной плазменной резки используют для охлаждения воду, поэтому могут работать всю смену без перерыва. Так называемый ПВ (продолжительность включения) равен 100 %. Хотя у ручных аппаратов он может быть и 40 %, что означает следующее: 4 минуты плазморез работает, а 6 минут ему необходимо для того, чтобы остыть.
Плазморез своими руками
Наиболее разумно будет приобрести плазморез готовый, заводского исполнения. В таких аппаратах все учтено, отрегулировано и работает максимально идеально. Но некоторые умельцы «Кулибины» умудряются смастерить плазморез своими руками. Результаты получаются не очень удовлетворительными, так как качество реза хромает. В качестве примера приведем урезанный вариант, как можно сделать плазморез самостоятельно. Сразу оговоримся, что схема далека от идеала и лишь дает общее понятие процесса.
Итак, трансформатор для плазмореза должен быть с падающей ВАХ.
Пример на фото: первичная обмотка – снизу, вторичная – сверху. Напряжение – 260 В. Сечение обмотки – 45 мм2, каждая шина 6 мм2. Если установить силу тока на 40 А напряжение падает до 100 В. У дросселя также сечение 40 мм2, наматывался той же шиной, всего около 250 витков.
Для работы нужен воздушный компрессор, естественно, заводского исполнения. В данном случае использовался агрегат производительностью 350 л/мин.
Самодельный плазморез – схема работы.
Плазмотрон лучше приобрести заводской, он обойдется примерно в 150 – 200 у.е. В данном примере плазмотрон изготавливался самостоятельно: медное сопло (5 у.е.) и гафниевый электрод (3 у.е.), остальное «кустарщина». За счет чего расходники быстро вышли из строя.
Схема работает так: на резаке находится кнопка пуск, при ее нажатии реле (р1) подает на блок управления напряжение, реле (р2) подает напряжение на трансформатор, затем пускает воздух для продувки плазмотрона. Воздух осушает камеру плазмотрона от возможного конденсата и выдувает все лишнее, на это у него есть 2 – 3 секунды. Именно с такой задержкой срабатывает реле (р3), которое подает питание на электрод для поджига дуги. Затем включается осциллятор, который ионизирует пространство между электродом и соплом, как результат загорается дежурная дуга. Далее плазмотрон подносится к изделию и загорается режущая/рабочая дуга между электродом и заготовкой. Реле геркона отключает сопло и поджиг. Согласно данной схеме, если режущая дуга внезапно погаснет, например, если сопло попало в отверстие в металле, то реле геркона снова подключит поджиг и спустя несколько секунд (2 – 3) загорится дежурная дуга, а затем режущая. Все это при условии, что кнопка «пуск» не отпускается. Реле (р4) пускает воздух в сопло с задержкой, после того, как отпустили кнопку «пуск» и режущая дуга погасла. Все эти предосторожности необходимы для того, чтобы продлить ресурс сопла и электрода.
Самостоятельное изготовление плазмореза в «домашних» условиях дает возможность изрядно сэкономить, но о качестве реза говорить не приходится. Хотя если за работу возьмется инженер, то результат может быть даже лучше заводского исполнения.
ЧПУ плазморез своими руками
Станок плазменной резки с ЧПУ может позволить себе не каждое предприятие, ведь его стоимость может достигать 15000 – 20000 у.е. Довольно часто такие организации заказывают выполнение работ плазменной резки на специальных предприятиях, но это тоже обходится недешево, особенно если объемы работ большие. Но ведь так хочется свой новый станок плазменной резки, а средств не хватает.
Помимо известных профильных заводов есть предприятия, которые занимаются производством станков плазменной резки, закупая лишь профильные детали и узлы, а все остальное изготавливают самостоятельно. В качестве примера мы расскажем, как делают станки плазменной резки с ЧПУ инженеры в производственном цеху.
Составляющие станка плазменной резки своими руками:
- Стол 1270х2540 мм;
- Ременная передача;
- Шаговые детали;
- Линейные направляющие HIWIN;
- Система, управляющая высотой факела THC;
- Блок управления;
- Стойка-терминал, в котором находится блок управления ЧПУ, стоит отдельно.
Характеристики станка:
- Скорость перемещения по столу 15 м/мин;
- Точность установки позиции плазмотрона 0,125 мм;
- Если использовать аппарат Powermax 65, то скорость реза будет 40 м/мин для 6 мм заготовки или 5 м/мин для заготовки толщиной 19 мм.
На подобный станок плазменной резки металла цена будет около 13000 у.е., не включая источник плазмы, который придется приобрести отдельно – 900 у.е.
Для изготовления такого станка комплектующие заказываются отдельно, а затем все собирается самостоятельно по такой схеме:
- Готовится основание для сварки стола, оно должно быть строго горизонтальным, это очень важно, лучше проверить уровнем.
- Сваривается рама станка в виде стола. Можно использовать трубы квадратного сечения. Вертикальные «ноги» необходимо усилить укосинами.
- Рама покрывается грунтовкой и краской, чтобы защитить от коррозии.
- Изготавливаются опоры для станка. Материал опор – дюраль, болты 14 мм, гайки лучше приварить к болтам.
- Сваривается водяной стол.
- Устанавливаются крепления для реек и ставятся рейки. Для реек используется металл в виде полосы 40 мм.
- Устанавливаются линейные направляющие.
- Корпус стола зашивается листовым железом и окрашивается.
- Устанавливается портал на направляющие.
- На портал устанавливается двигатель и концевые индуктивные датчики.
- Устанавливаются рельсовые направляющие, зубчастая рейка и двигатель оси Y.
- Устанавливаются направляющие и двигатель на оси Z.
- Устанавливается датчик поверхности металла.
- Устанавливается кран для слива воды из стола, ограничители для портала, чтобы не съехал со стола.
- Устанавливаются кабель-каналы Y,Z и X.
- Все провода прячутся в гофру.
- Устанавливается механизированная горелка.
- Далее изготавливается терминал с ЧПУ. Сначала сваривается корпус.
- В корпус терминала с ЧПУ устанавливается монитор, клавиатура, модуль ТНС и кнопки к нему.
Все, станок плазменной резки с ЧПУ готов.
Несмотря на то, что плазморез имеет достаточно простое устройство, все же не стоит браться за его изготовление без серьезных познаний в сварочном деле и большого опыта. Новичку проще заплатить за готовое изделие. А вот инженеры, желающие воплотить свои знания и умения в домашних условиях, что называется «на коленке», могут попробовать создать плазморез своими руками от начала и до конца.
принцип работы, что им можно делать и как резать металл
Плазменная резка – одна из наиболее современных эффективных технологий, позволяющая работать с металлом, а также с некоторыми материалами, не проводящими ток, в том числе древесиной, пластиком и камнем.
Неудивительно, что метод пользуется спросом и активно применяется в различных сферах деятельности, в ЖКХ, в строительстве, промышленности. Главным устройством во всем процессе является плазморез, продуцирующий дугу, сформированную плазмой огромной температуры.
Дуга позволяет вести работу с высокой точностью, проводить раскрой не только по прямым линиям, но и формировать сложные фигуры.
Чтобы разобраться в тонкостях всего процесса, рассмотрим подробнее конструкцию устройства, а также основные принципы, на которых построено его функционирование.
Конструкция
Плазморезка сформирована следующими элементами:
1. Элемент питания, который отвечает за подачу тока той или иной силы. В качестве элемента применяют либо трансформаторы, либо инверторы.
Первый вариант характеризуется значительной массой, зато почти неуязвим для колебаний напряжения, а также дает возможность осуществлять рез металлических заготовок огромной толщины.
Инвертор – хороший выбор в том случае, если манипуляции ведутся с не слишком толстыми заготовками. Они экономичны в отношении потребления энергии, характеризуются высоким КПД и рекомендуются для использования в частном хозяйстве.
2. Плазмотрон. Основной элемент, посредством которого и ведется рез.
Корпус детали скрывает электрод, отвечающий за формирование мощной дуги. Сделан электрод из тугоплавкого металла, благодаря чему исключены его деформации и разрушения вследствие высокотемпературных нагрузок. Как правило, используется гафний, как наиболее прочный и безопасный материал.
На конце находится сопло, формирующее струю плазмы, с легкостью разрезающую заготовку.
Производительность и мощность устройства, во многом, определяется именно диаметром сопла. Чем шире сопло, тем больше воздуха оно пропускает за единицу времени, а увеличение объемов воздуха непосредственно увеличивает производительность. Наиболее распространенный диаметр – 3 миллиметра.
Точность работы зависит от конфигурации сопла, для проведения наиболее тонкой работы следует подбирать удлиненный элемент.
3. Компрессор. Его главная задача – нагнетание воздуха, без которого плазменный резак по металлу просто не может функционировать. Процесс построен на использовании газа для формирования плазменной струи и защиты.
Если сила тока устройства ограничена 200А, то необходим просто сжатый воздух, его достаточно и для отвода лишнего тепла, и для формирования струи. Такая модель – оптимальное решение в случаях, когда режутся заготовки не толще 5 сантиметров.
Установки промышленного типа используют не обычный сжатый воздух, а концентрированные газовые смеси на основе гелия, водорода, азота.
4. Комплекс кабелей и шлангов соединяет все модули между собой. Шланги транспортируют сжатый воздух, кабеля передают электрический ток.
Смотрите полезное видео, устройство и как работает плазменная резка:
Рабочий принцип
Теперь изучим непосредственно принцип работы устройства.
Когда оператор нажимает на клавишу розжига, элемент питания подает ток на плазмотрон. Это приводит к формированию первичной дуги огромной температуры, которая составляет от 6 до 8 тысяч градусов.
Формирование дуги между наконечником электрода и сопла происходит из-за того, что крайне трудно добиться такого результата непосредственно между заготовкой и электродом. Более того, если работа ведется с материалом, характеризующимся изолирующими свойствами, это просто невозможно.
Когда сформирована первичная дуга, к ней подается воздушная смесь. Данный воздух контактирует с ней, его температура растет, а объем – увеличивается, причем увеличение может быть даже стократным. Вдобавок к этому, воздух теряет свои диэлектрические свойства, ионизируется.
За счет того, что сопло имеет сужение к своему окончанию, воздушный поток разгоняется до 2-3 метров в секунду и вырывается наружу, имея температуру почти в 30 тысяч градусов. Из-за высокой степени ионизации и огромной температуры воздух называется плазмой, показатель электрической проводимости которой равняется этому параметру у обрабатываемого металла.
В момент соприкосновения с обрабатываемой поверхностью первичная дуга угасает, а дальнейшая работа ведется уже за счет вновь образованной режущей дуги. Именно она плавит или прожигает материал. Рез получается ровным, так как мощный воздушный поток сдувает с поверхности все появляющиеся частички.
Такое описание того, как работает система, является наиболее простым и распространенным.
Области применения
Теперь рассмотрим, что им можно делать:
- Оперативный рез больших объемов материалов.
- Изготовление листовых деталей, характеризующихся сложностью геометрии, вплоть до ювелирной и приборостроительной отрасли, где требуется максимальное соответствие исходным чертежам.
Штамповка в такой ситуации не применяется, так как данная технология, хоть и дешево, не обеспечивает достаточной точности. Плазморез же, несмотря на огромную температуру струи, нагревает обрабатываемый элемент точечно, что полностью исключает вероятность температурной деформации.
- Монтаж металлических конструкций. Плазморез исключает нужду в применении баллонов со сжатым кислородом и ацетиленом, что повышает степень безопасности и удобства, в особенности, если дело касается осуществления операций на высоте.
- Рез сталей высокой степени легирования. Механические способы в данном случае не подходят, так как прочность сталей огромна, инструмент, способный эффективно резать листы на их основе, будет стоить очень дорого, а изнашиваться – очень быстро.
Получается, что сферы использования разнообразны. Выполнение в металлических листах отверстий любой конфигурации, резка труб, уголков и заготовок другого сечения, обработка кромок кованых изделий с целью “спаивания” металла и закрытия его структуры – для всего этого плазморез подходит оптимально.
Основные инструкции
Несколько правил, позволяющие понять, как резать плазморезом эффективно и безопасно:
- Необходимо контролировать расположение катодного пятна, оно должно соответствовать центру электрода. Достигается такая точность вихревой подачей воздуха. Отклонения в подаче приводят к тому, что происходит смещение плазменной дуги, она теряет стабильность горения. В некоторых случаях формируется вторая дуга, а в самой сложной ситуации устройство просто ломается.
- Контроль над воздушным расходом дает возможность корректировать скорость потока плазмы, варьировать производительность.
- Скорость реза напрямую влияет на толщину. Чем выше скорость, тем тоньше рез, ее уменьшение увеличивает ширину. Аналогичных результатов, большей ширины, можно достичь и увеличением силы тока.
Смотрите видео-урок работы плазморезом:
Заключение
Итак, мы разобрались, что такое плазморез.
Можно сделать вывод, что в ситуации, когда вам регулярно приходится работать с металлическими элементами, резать арматуру, трубы или другие детали, его помощь окажется полезной. Так что расходы на его покупку будут полностью компенсированы удобством и эффективностью дальнейшей работы.
Плазморез из инвертора: Инструкция +Видео
Плазморез: принцип действия, устройство, инструкция по применению
Что представляет собой плазморез и по какому принципу он работает? Если говорить про данный инструмент, то стоит сразу отметить, что это тот прибор, который используют сварщики, причем далеко не все. Для единоразового использования такой инструмент никогда и нигде не применяют. По этой причине есть инструменты, при помощи которых есть возможность проводить отрезные операции, и при этом не прибегать к использованию дорогого варианта, а именно болгарки. Но если требования к объему и скорости проводимого процесса ужесточенные, то вам никак не обойтись без использования плазмореза.
Именно по этой причине его используют в машиностроительной индустрии, при изготовлении больших конструкций из металла, для резки труб и всего остального.
Разновидности резаков и назначение каждого из них
Много при выборе плазменного резака будет зависеть от того, в какой области вы планируете его использовать. Дело в том, что конструктивные особенности всех видов сильно отличаются между собой – у каждого устройства свой тип зажигания дуги, а также мощность охлаждающей системы.
- Инструменты, которые работают в среде газов защитного типа – водород, аргон, гелий, азот и прочие. Такие газы имеют восстанавливающие свойства.
- Резаки, которые работают в среде газов окисления. Такие обычное насыщают посредством кислорода.
- Приборы, которые используют для работ со смесями.
- Резаки, которые работают в стабилизаторах жидкостно-газового типа.
- Устройства, которые работают с магнитной и водной стабилизацией. Это особый инструмент, который очень редко используют, поэтому его достаточно трудно найти в свободной продаже.
Есть и другая классификация, которая помогает разделить и купить плазморез по виду оборудования, которое используется для работ.
- Инверторные – вариант, признанный экономичным, может разрешать детали из металла с толщиной до 3 см.
- Трансформаторные – такие устройства способны производить резку металла с толщиной до 8 см, вариант сам по себе менее экономичный.
По типу контакта устройства можно поделить на две группы – бесконтактные и контактные. По названию уже легко понять, какие есть методы использования плазменного резака. В первом случае для устройства не требуется контакта с обрабатываемым металлом, причем толщина заготовки может быть любой, тогда как во втором случае требуется контакт с металлом, и его толщина должна быть не меньше 1,8 см.
Еще одна категория – тип использования и возможность питания от электрической энергии. в этом случае есть вде позиции – бытовой резак, который работает от сети с переменным током и стандартным напряжением 220 В, и промышленный, который можно подключать лишь к трехфазной питающей сети с напряжением в 380 В.
Обратите внимание, что даже те резаки, которые имеют минимальную мощность, будут от 4 кВт. По этой причине при его подключении к бытовой электросети для начала удостоверьтесь, что она точно выдержит такую нагрузку.
Такая нагрузка не является единственной, так как в системе резки плазменным устройство используют охлаждение, и для этого в комплект к стандартному оборудованию идет компрессор, который тоже будет работать от сети. Учитывайте и его мощность при подключении к домашнему питанию.
Устройство
Самому названию уже понятно, что процесс резки металла выполняется благодаря плазме, причем последняя представляет собой ионизированный газ с высокой проводимостью электротока. Чем выше будет температура газа, тем выше будет проводимость, а сила разрезания увеличится в значительной мере. Для процесса резки металла используют также воздушно-плазменную дугу. Учтите, что в данном случае ток уже будет иметь непосредственное воздействие на поверхности из металла.
Получается, что принцип действия устройства такой:
- Металл расплавляют.
- Его жидкое состояние выдувают из зоны среза.
Ручной плазморез состоит из:
- Блока питания – это может быть инвертор или сварочный трансформатор.
- Шлангов.
- Резака, который изредка называют плазмотроном.
- Компрессора.
Не будет лишним разобраться, чтобы понять конструктивные особенности резака. Внутри устройства находится установленный электрод, который сделан из редкого металла, например, из гафния, бериллия, циркония и прочего. Почему именно эти металлы? Дело в том, что при нагревании на поверхности данного электрода образуются тугоплавкие виды оксидов. Она являются своеобразной защитой электрода, которая будет обеспечивать целостность материала, т.е. не разрушать. Чаще всего в плазменных резаках устанавливают гафниевые электроды, потому что данный металл не является токсичным и радиоактивным, как, к примеру, бериллий.
Важное значение в конструкции играет сопло – именно через него плазма попадает на резку. Именно от него и будут зависеть основные параметры устройства, а точнее от толщины и длины сопла. Т диаметра будет зависеть мощность потока плазмы, а значит, и скорость среза и ширина срезанной канавки. Конечно, от этого будет зависеть еще и скорость охлаждения. Чаще всего на резаках устанавливают сопло, диаметр которого равен 0,3 см. Длина будет прямопропорционально влиять на качестве среза – чем длиннее, тем лучше. Учтите, что очень длинное сопло будет быстро выходить из строя.
Схема работы плазмореза
Итак, когда вы нажимаете на кнопку розжига, источник электрической энергии автоматически включается, и в резак попадает высокочастотный ток. Из-за этого появляется дежурная дуга между электродом и наконечником сопла. Температура дуги составляет от +6 000 до +8 000 градусов. Следует обратить внимание на то, что дуга между разрезаемым металлом и электродом появляется не сразу, на это требуется время.
После этого в камеру резака начинает поступать воздух, находившийся в компрессоре (сжатый). Воздух начинает нагреваться при прохождении через камеру, в которой расположена дежурная дуга, и его становится больше в 100 раз. Помимо этого он начинает ионизироваться, по сути, превращаясь в токопроводящую среду, хотя воздух сам по себе является диэлектриком.
Сопло, которое сужено до 0,3 см создает плазменный поток, который вылетает из резака с большой скоростью (от 2 до 3 метров в секунду). Температура воздуха, который стал ионизированным, достигает до +30 000 градусов. С такой температурой воздух по проводимости становится таким же, как и проводимость металла. Как только плазма попадает на обрабатываемую поверхность, дежурная дуга выключается, но вместо нее включается рабочая. Плавление металлической заготовки производится в месте среза, откуда жидкий металл сдувается воздухом, который попадает в зону среза. Это и есть схема резки.
Правила выбора инструмента
Люди, которые работали с плазморезом, отметят, что чем больше сила тока, попадающего на электрод, тем быстрее будет процесс. Но есть и некоторые условия, на которые будут влиять и остальные параметры оборудования. Сюда отнесем толщину среза и тип металла. От таких параметров будет зависеть, какое оборудование для работы выбрать, а именно такой из параметров, как сила тока. Чтобы разрезать лист меди с толщиной в 0.2 см, вам нужен будет плазменный резак с силой тока в 12 А.
Обратите внимание, советуем покупать оборудование, которое будет иметь запас силы тока. Обычно указанные параметры при покупке максимальные, а значит, работать на них получится непродолжительное время.
Преимущества и недостатки
Перед тем как сделать выбор и решить, купить плазморез или нет, следует узнать обо всех отрицательных и положительных сторонах оборудования. Так, например, в домашних условиях данное устройство заменимо болгаркой.
Итак, преимущества следующие:
- Резка на большой скорости, а значит, на процесс будет затрачено не так много времени. По сравнению с остальными режущими инструментами (к примеру, с кислородной горелкой) скорость выше в целых 6 раз. Он уступает только лазерной резке.
- При помощи плазменного устройства можно разрезать заготовки с большой толщиной, а это не всегда под силу даже болгарке.
- Может разрезать любые виды металлов, главное, чтобы был правильно выставлен режим работы.
- Минимальный этап подготовки – поверхности деталей можно зачищать от грязи, ржавчины, масляных пятен, но в этом нет никакого смысла, так как это не помеха для резки.
- Точность среза высокая, качество тоже. Для ручных устройств чтобы улучшить точность среза часто используют специальные упоры, которые не будут давать резаку смещаться по плоскости. В итоге получается срез без наплывов, тонкий и ровный.
- Небольшая температура нагревания, исключение – зона среза, поэтому заготовки не подвергаются деформации.
- Возможность фигурного среза, и хотя таким качеством могут похвастаться и остальные инструменты, но, например, после использования кислородной горелки придется шлифовать края среза и убирать подтеки металла.
- Проводимая операция безопасна на 100%, так как нет ни одного газового баллона в комплекте к оборудованию.
Недостатки:
- Высокая стоимость оборудования.
- Допустимо работать лишь одним резаком.
- Следует выдерживать направление плазмы аккурат перпендикулярно плоскости обрабатываемой детали. На данный момент в продаже появились аппараты, который могут резать под углом от 15 до 50 градусов.
- Толщина изделия для разрезания ограничена, поэтому самые мощные экземпляры могут резать металл, толщина которого 10 см. При помощи кислородной горелки вы сможете порезать металл с толщиной в 50 см.
И, тем не менее, плазморез как устройство достаточно востребован. Ручные виды часто используют, но лишь в небольших предприятиях, где нужно выполнять большие объемы резки и к качестве реза предъявлены жесткие требования.
Плазменный резак своими руками: принцип действия, конструкция, сборка
Создавать плазменный резак своими руками весьма выгодно благодаря простой конструкции и применению доступных комплектующих. Они уступают по функциональности промышленным моделям, но позволяют выполнять основные виды резки металла с не меньшей эффективностью и качеством.

Для чего нужен плазморез?
Плазморез позволяет обрабатывать различные металлы при температурах 25–30 тыс. градусов с высокой скоростью, точностью, качеством. Он является прямым конкурентом лазерной обработки, но имеет более простую конструкцию, неприхотлив в обслуживании, эксплуатации, ремонте.
Плазменная резка используется для нарезания металлических заготовок с формами различной сложности. За счёт защитной газовой атмосферы при нагреве не образуются сложные металлические соединения, свойства которых отличаются от требуемых.
Принцип действия
Работа плазмореза основана на поджиге электрической дуги, в которую подаётся под давлением инертный газ, прогреваемый в замкнутом объёме до состояния плазмы, а затем поступающий прямо на поверхность разрезаемого металла. Направленная струя газа формируется в результате его перегрева внутри закрытой ёмкости при создании избыточного давления.
Когда электроды прикладываются к поверхности металла, создаётся вторая дуга, мощность которой превышает первоначальную в несколько раз. В ней плазменный поток ускоряется до 1,5 км/с. Комбинация высокой температуры дуги с потоком плазмы позволяет резать металлические заготовки, толщина разреза которых зависит от параметров сопла.
В плазморезах косвенного действия создаётся только плазменная направленная струя, способная резать не только металлы, но и непроводящие ток материалы. Однако их самостоятельное изготовление сложно, так как требуется точный расчёт параметров конструкции, подбора характеристик, настройки.
Инвертор или трансформатор
Чтобы получить плазму, нужно подключать качественные источники питания. Это могут быть трансформаторы или инверторы.
Сделать плазморез из инвертора выгодно благодаря компактности, точности подстроек тока, напряжения, контроля электрических параметров, экономному потреблению электроэнергии. Он имеет ограничение по току до 70 А, но мощности хватает для выполнения типичных работ по обработке металла.
Недостатком инвертора являются высокие требования к качеству питания, что не позволяет их применять в сетях с перепадами напряжения без подключения к стабилизаторам.
Трансформаторы лишены недостатка инвертора, более надёжны в эксплуатации, неприхотливы в обслуживании. Но при этом они имеют большие габариты, вес, высокое потребление электроэнергии. Ограничение по току достигает 180 А, в зависимости от количества витков, диаметра используемой проволоки.

Конструкция
Конструкция плазменного резака состоит из следующих компонент:
- Плазмотрон, предназначенный для формирования плазменной струи. Имеет сложную конструкцию, изготавливается из тугоплавкого металла. Требуется подбор таких параметров: диаметра сопла, длины резака, угла подачи сжатого воздуха в область формирования плазмы.
- Источник питания предназначен для поджига дуги. Должен иметь стабильные параметры по току и напряжению. Подбирают в зависимости от максимальной величины выходного тока, габаритов, размеров и веса.
- Осциллятор, используемый для упрощения розжига дуги, стабилизации её горения. Имеет простую схему, поэтому может быть собран самостоятельно либо приобретён в сборе.
- Компрессор для создания потока воздуха, подаваемого для охлаждения горелки, формирования направленного потока плазмы. Подходит практически любая модель. Чтобы не попала влага, потребуется установить осушитель.
- Медный кабель с зажимом на конце для подключения массы.
- Кабель-шланг, предназначенный для подключения горелки и поджига электрической дуги, а также для подачи сжатого воздуха. Может быть изготовлен путём укладки кабеля и кислородной трубки внутри поливочной гибкой трубки.
Необходимые комплектующие
Перед сборкой резака потребуется подготовить следующие комплектующие:
- источник питания;
- резак или плазмотрон;
- компрессор с осушителем или фильтром;
- осциллятор;
- электроды;
- шланги;
- кабели.
Подбор блока питания
Выбор источника электроэнергии для плазменной установки выполняется с учётом следующих критериев:
- максимальной толщины и типа разрезаемого металла;
- длительности проведения работ, времени горения дуги;
- требований к параметрам плазмы;
- стабильности тока, напряжения питающей сети;
- требований безопасности;
- необходимости расширения функциональности плазмореза.

Плазмотрон
Поскольку плазмотрон используется для генерации плазмы, к подбору его параметров нужно подходить грамотно. Важные параметры:
- стойкость к рабочим температурам;
- удобство пуска, настройки, остановки работы оборудования;
- небольшой вес, компактные размеры;
- срок службы;
- требования к обслуживанию;
- ремонтопригодность.
По типу стабилизации дуги плазмотроны бывают газового, водяного и магнитного вида.
При работе важно своевременно заменять электроды, чтобы максимально продлить срок службы сопла. Понять необходимость данной процедуры можно по ухудшению качества резки: нарушение точности, появлению поверхностных волн. Важно не перегревать плазмотрон, поскольку это может повлечь серьёзные поломки.
Для создания плазмотрона потребуются следующие детали:
- рукоятка из материала с низкой теплопроводностью, в которой есть отверстия под провода для электрода, трубок для газа;
- пусковая кнопка;
- подходящие по параметрам электроды;
- сопло нужного диаметра;
- изолятор;
- пружина для соблюдения расстояния от сопла до разрезаемого металла;
- наконечник с защитой от брызг расплавленного металла;
- завихритель потока;
- специальная насадка.
Осциллятор
Осциллятор применяется для выработки токов высокой частоты. Работает в режимах коротких импульсов или постоянного горения дуги. Предназначен для быстрого запуска плазмореза.
Конструктивно состоит из следующих элементов:
- выпрямителя;
- конденсаторов;
- блока питания;
- управляющей микросхемы;
- импульсного модуля;
- повышающего трансформатора;
- контроллера напряжения.
Электроды
Выбор электродов определяется на основе рабочих режимов резки, типа металла, требований к качеству работ. Для эксплуатации в небольших мастерских рекомендуется приобретать гафниевые электроды. Бериллиевые или ториевые могут формировать токсичные соединения.
Компрессор и кабель шланги
Модель компрессора подбирается на основе его технических параметров, требований к конструкции плазмореза. Он используется для создания воздушных потоков внутри рабочих каналов, охлаждения компонентов оборудования при непрерывной работе. Для регулировки подачи воздуха на выходе из компрессора устанавливается электрический клапан.
Внутри шлангов размещают кабель, трубку для сжатого воздуха. На массовом кабеле располагают щуп для обеспечения контакта с разрезаемым металлом и поджига стабильной дуги.
Достоинства самодельного аппарата
Преимущества создания плазмореза своими руками:
- простота конструкции;
- лёгкость обслуживания;
- подбор оптимальных параметров оборудования;
- ремонтопригодность.
Самодельные аппараты отличаются высокой скоростью сборки, так как существует много доступных для освоения схем. Они неприхотливы в эксплуатации, позволяют резать практически любые виды металлов, могут быть легко разобраны для транспортировки или хранения.
Сборка
Пошаговая сборка выполняется в такой последовательности:
- К источнику питания подключается кабель питания электродов.
- С компрессором соединяется шланг для подачи сжатого воздуха.
- Кабель массы подключается к соответствующей клемме источника питания.
- Плазмотрон подсоединяется к кабелю и шлангу.
Когда изготовление плазмореза завершено, необходимо убедиться в правильности сборки, плотности контактов, соблюдении правил техники безопасности.

Проверка плазмореза
Проверка станка для плазменной резки, изготовленного своими руками, выполняется в несколько этапов:
- принимаются необходимые меры безопасности — одевается защитная одежда, обеспечивается хорошая проветриваемость места, убираются возгораемые материалы;
- подаётся питание на электрод, проверяется формирование дуги, стабильность, размер;
- включается компрессор, подаётся через шланг сжатый воздух, при наличии утечек производится герметизация;
- после формирования плазмы выполняется резка металла толщиной 2 мм — в случае успеха сборка считается завершённой, обнаруженные проблемы устраняются.
Доработка инвертора
Доработать инвертор до плазмореза можно путём подключения в электрическую цепь осциллятора. Существует два способа подсоединения:
- параллельное, используемое для сварки на токах различной величины;
- последовательное, ток сварки ограничен параметрами устанавливаемого блокировочного конденсатора.
Недостатками параллельного подключения являются:
- чтобы получить высокое напряжение, требуется применять осциллятор соответствующей мощности;
- при падении напряжения на обмотке трансформатора, используемого в качестве источника питания, велика вероятность повреждения всех подключённых устройств;
- высокочастотные токи в обмотках трансформатора создают помехи в электросетях.
Выбор подключения зависит от типа свариваемых металлов, их параметров, ограничений подключённого источника питания. То есть учитываются возможные негативные последствия.
устройство, принцип действия, выбор, какой лучше
Что такое плазморез, как работает он? Если говорить об этом инструменте, то необходимо отметить, что он является прибором, который использует достаточно узкий круг сварщиков. Для одноразового применения плазменный резак нигде и никогда не применяется. Потому что существуют инструменты, с помощью которых можно провести отрезные операции, не прибегая к дорогому варианту, к примеру, болгаркой.
Но если требования к скорости и объему проводимых процессов достаточно жесткие, то без плазмореза не обойтись. Поэтому его используют в машиностроительной промышленности, в изготовлении больших металлических конструкций, при резке труб и прочего.
Виды плазменных резаков и их назначение
На вопрос, как выбрать плазморез, необходимо ответить так, все будет зависеть от того, в какой области вы его собираетесь использовать. Потому что конструктивные особенности у разных видов сильно отличаются, у всех у них разный тип зажигания дуги и различная мощность системы охлаждения.
- Инструменты, работающие в среде защитных газов: аргон, водород, азот, гелий и так далее. Эти газы обладают восстановительными свойствами.
- Резаки, работающие в среде окислительных газов. Газы обычно насыщаются кислородом.
- Приборы, работающие со смесями.
- Плазменные резаки, работающие в стабилизаторах газожидкостного типа.
- Плазморезы, работающие со стабилизацией водной и магнитной. Специфичный инструмент, который редко используется, поэтому в свободной продаже трудно найти.
Существует еще одна классификация, которая делит плазморезы по виду используемого оборудования.
- Инверторные. Экономичный вариант, который может резать металлические детали толщиною до 30 мм.
- Трансформаторные. Производит резку металлов толщиною до 80 мм, менее экономичный вариант.
По типу контакта плазморезы делятся на контактные и бесконтактные. Из названий можно понять метод использования плазменного резака. В первом случае для него необходим контакт с обрабатываемым металлом, поэтому с его помощью можно отрезать изделия толщиною не более 18 мм. Во втором такого контакта не должно быть, зато толщина отрезаемой металлической заготовки может быть максимально возможной.
И еще один вид разделения – это по типу использования и возможностях потребления электроэнергии. Здесь две позиции: бытовой, работающий от сети переменного тока под напряжением 220 вольт, и промышленные (профессиональные), подключаемые к трехфазной питающей сети напряжением 380 вольт.
Внимание! Даже самый маломощный бытовой резак плазменного типа обладает мощностью 4 кВт. Поэтому при подключении его в бытовую электрическую сеть, необходимо удостовериться, что она сможет выдержать такую нагрузку.
Но данная нагрузка не единственная. В системе плазменной резки используется охлаждение, для чего в комплект к основному оборудованию прилагается компрессор, который также работает от электросети. И его мощность нужно учитывать, подключаясь к бытовой питающей сети.
Устройство плазмореза
Само название уже информирует о том, что резка металлов производится с помощью плазмы. А плазма – это ионизированный газ, который обладает высокой проводимостью электрического тока. И чем выше температура этого газа, тем выше проводимость, а значит, сила резки увеличивается.
Для процессов резки металлов используют воздушно-плазменную дугу. При этом электрический ток имеет непосредственное воздействие на металлические поверхности. То есть, принцип работы плазмореза такой:
- Плавление металла.
- Выдувание его жидкого состояния из зоны среза.
Состоит плазменный резак из:
- источника питания – это может быть сварочный трансформатор или инвертор;
- самого резака, который иногда называют плазмотроном;
- компрессора;
- шлангов.
Важно понять конструктивные особенности самого резака. Внутри него вставлен электрод, изготовленный из редких металлов, таких как бериллий, гафний, цирконий и так далее. Почему именно они? Потому что в процессе нагревания на поверхности такого электрода образуются тугоплавкие оксиды. Они своеобразная защита самого электрода, которая обеспечивает целостность материала, то есть, не разрушается. Но чаще всего в плазменных резаках устанавливаются электроды из гафния, потому что он не токсичен, как торий, и нерадиоактивен, как бериллий.
Немаловажное значение в конструкции резака играет и сопло, через который подается плазма на резку. Именно от него и зависят основные характеристики оборудования. А точнее сказать, от его диаметра и длины. От диаметра зависит мощность плазменного потока, а соответственно и быстрота среза и ширины срезанной канавки. Конечно, от этого зависит и скорость охлаждения заготовки. Чаще всего на резаках плазменной резки устанавливается сопло диаметром 3 мм. Длина сопла влияет на качество среза. Чем оно длиннее, тем качество выше. Хотя очень длинное сопло быстро выходит из строя.
Схема работы плазменной резки
При нажатии на кнопку розжига автоматически включается источник электроэнергии, который подает в резак ток высокой частоты. Появляется так называемая дежурная дуга между наконечником сопла и электродом. Температура дуги – 6000-8000С. Необходимо обратить внимание, что сразу дуга между электродом и разрезаемым металлом не образуется, на это надо время.
После чего в камеру резака начинает поступать воздух из компрессора, он сжатый. При прохождении через камеру, где располагается дежурная дуга, воздух нагревается и увеличивается в сто раз. К тому же он начинает ионизироваться, то есть, превращается в токопроводящую среду, хотя сам по себе воздух – это диэлектрик.
Суженное до 3 мм сопло создает поток плазмы, который с большой скоростью вылетает из резака. Скорость – 2-3 м/с. Температура ионизированного воздуха достигает огромной величины – до 30000С. При такой температуре воздух по проводимости электрического тока приближается к проводимости металла.
Как только плазма касается обрабатываемой металлической поверхности, дежурная дуга выключается, а рабочая включается. Производится плавление металлической заготовки в месте среза, откуда жидкий металл сдувается подающим в зону среза воздухом. Вот такая элементарная схема принципа работы плазменной резки.
Как правильно выбрать инструмент для плазменной резки
Любой работавший с плазменной резкой сварщик отметит, что чем выше сила подающего на электрод тока, тем быстрее проходит процесс. Но есть определенные условия, на которые влияют и другие параметры оборудования.
Тип металла и толщина среза. От этих параметров будет зависеть выбор оборудования, с которым придется работать. А именно такой параметр, как сила тока. Внизу таблица соотношений.
Вид металла | Сила тока для резки металлического листа толщиною 1 мм, А |
---|---|
Цветные металлы | 6 |
Черные металлы и нержавейка | 4 |
Чтобы разрезать медный лист толщиною 2 мм, потребуется резак плазменный с силой тока 12 А. И так далее.
Внимание! Рекомендуется приобретать оборудование с запасом силы тока. Потому что указанные параметры в таблице являются максимальными, а с ними работать можно лишь незначительное время.
Достоинства и недостатки
Перед тем как принять решение о приобретение плазменного резака, нужно ознакомиться со всеми положительными и отрицательными сторонами этого оборудования. Ведь, к примеру, в домашних условиях его может заменить обычная болгарка.
Итак, плюсы использования резака для плазменной резки металлов.
- Большая скорость резки, соответственно уменьшение времени на этот процесс. По сравнению с другими режущими инструментами (кислородная горелка, например) скорость выше в шесть раз. Уступает только лазерной резке.
- С помощью плазменного инструмента можно резать толстые заготовки, что иногда не под силу болгарке.
- Режет любые виды металлов. Главное – правильно выставить режим работы.
- Минимальный подготовительный этап. Зачищать поверхности деталей от ржавчины, грязи, масляных пятен нет никакого смысла. Они для резки не помеха.
- Высочайшая точность среза и высокое его качество. Для ручных агрегатов для точности среза используются специальные упоры, которые не дают резаку смещаться в плоскости. Срез получается без наплывов, ровным и тонким.
- Невысокая температура нагрева, кроме зоны среза, поэтому заготовки не деформируются.
- Возможность фигурного среза. И хотя этим могут похвастаться и другие режущие инструменты, но, к примеру, после кислородной горелки придется края среза шлифовать и убирать подтеки металла.
- Стопроцентная безопасность проводимых операций, ведь никаких газовых баллонов в комплекте оборудования нет.
Минусы:
- Высокая цена оборудования.
- Возможность работать только одним резаком.
- Необходимо направление плазмы выдерживать строго перпендикулярно плоскости обрабатываемой детали. Правда, сегодня можно приобрести аппараты, которые режут изделия под разными углами: 15-50°.
- Толщина разрезаемого изделия ограничена, потому что самые мощные плазморезы могут разрезать металл толщиною 100 мм. С помощью кислородной горелки можно резать толщину 500 мм.
И все же плазморезы сегодня достаточно востребованы. Ручные часто используются в небольших цехах, где требуется провести большой объем резки металлов, и где к качеству разреза предъявляются жесткие требования. Обязательно посмотрите видео, которое специально размещено на этой странице сайта.
Поделись с друзьями
0
0
0
1
Плазменный резак – что это такое, устройство, принцип работы, характеристики, что можно резать?
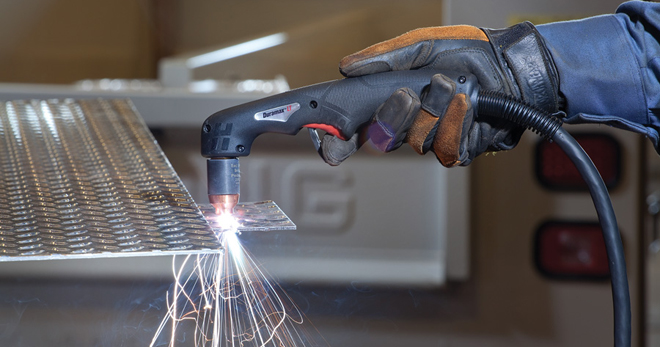
Резка металла на производстве и дома считается сложным процессом, для которого необходимы специальные инструменты и приспособления, одним из них является плазменный резак, который помогает быстро и безопасно выполнить раскрой металлических изделий любой сложности.
Что такое плазменный резак?
Не каждая кислородная горелка справляется с резкой любых типов металла. Некоторые виды стали, например, нержавейку, можно обработать при помощи плазменного резака, это устройство, которое использует возможности плазменно-дуговой резки. Идеальный ровный срез без зазубрин и «наплывов» возможно получить при использовании плазмореза. Благодаря универсальности и отличным характеристикам станки, работающие по принципу плазменной резки, могут легко справиться с самыми капризными материалами:
- листовым металлом;
- трубами разного диаметра;
- чугуном;
- сталью.
Устройство плазменного резака
Сложное электрическое устройство, которое способно создавать плазму, необходимую для резки металла – плазморез, состоит из определенных узлов. Некоторые модели оснащаются узлом завихрения, который сжимает газовую дугу для ее стабилизации. Основные составляющие аппарата для плазменной резки:
- система подачи газа и воды;
- дуговая камера;
- изолятор;
- сопло;
- электродержатель.
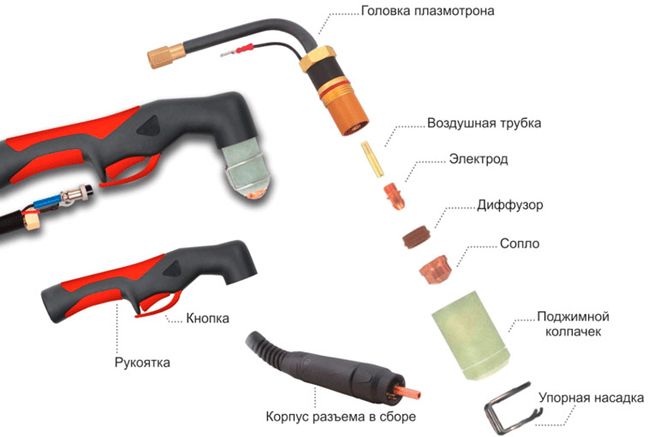
Принцип работы плазменного резака
Объяснить за счет чего в аппарате для резки металла образуется плазма, способная разрезать самый прочный металл, непросто. Чтобы понять, как работает плазморез, надо разобраться в его устройстве. При попадании электрического заряда в газ образуется плазма – ионизированный поток воздуха высокой температуры, доходящей до 20000-30000°С. Для охлаждения системы подается вода или специальный газ. После попадания вспомогательного разряда между соплом плазмореза и катодом возникает факел, который режет металл, разрушает твердые камни, наносит разнообразные покрытия.
Плазменный резак – характеристики
Главные технические характеристики устройств для резки металла необходимо знать, чтобы разбираться в видах моделей и понимать, чем они отличаются. Информация о параметрах аппаратов для плазменной резки должна содержать:
- Силу тока – основной показатель, влияющий на толщину металла, с которым может работать инструмент, и на скорость работы устройства. Рассчитать необходимую величину силы тока можно самостоятельно, если умножить толщину сплава в миллиметрах на 4, например, для плазменной резки листа металла толщиной 20 мм нужен резак мощностью 80 А.
- Продолжительность включения измеряется в %, для примера можно сказать, что работа плазменного резака с характеристиками ПВ 60% должна составлять 6 мин., а следующие 4 мин. агрегат должен отдыхать. Профессиональные модели плазморезов имеют ПВ от 80%, домашние недорогие устройства – около 50%.
- Тип питания агрегата бывает различным. В продаже имеются модели станков, которым требуется двух- или трехфазная сеть, 380 В требуется профессиональным трехфазным моделям. Обычные, работающие на параметрах домашних 220 В, приборы более удобны в использовании.
Что можно резать плазморезом?
В различных сферах производства специалисты по достоинству оценили характеристики ручного плазмореза, которым можно осуществлять разные работы: быстро и качественно раскроить большой объем металлических изделий, изготовить любые сложные геометрические формы с максимальным соответствием исходным чертежам. Современная и эффективная плазменная резка способна работать не только с металлами, но и с материалами, которые не проводят электрический ток:
- камнем;
- деревом;
- пластиком.
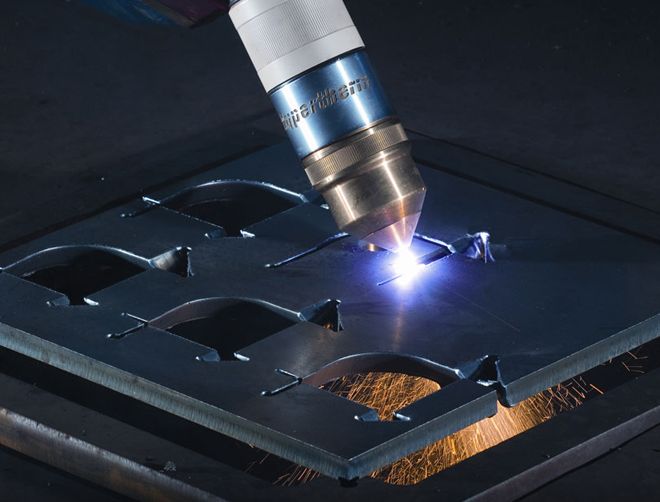
Плюсы и минусы плазмореза
Выбирая приспособление для эффективной работы с металлом, домашним мастерам предстоит сделать нелегкий выбор и решить, чему отдать предпочтение – плазменному резаку по металлу или обычной газовой горелке. Неоспоримые преимущества, которыми обладает плазменный резак, известны:
- высокая производительность и мощность;
- качественная обработка материала;
- универсальность;
- безопасность;
- экологичность.
Недостатком плазморезов считаются:
- высокая стоимость агрегата;
- ограничение толщины материала;
- невозможность работать двумя станками одновременно.
Виды плазменных резаков
Огромный ассортимент моделей резаков представлен в профессиональных магазинах электротоваров. Отличаются ручные плазменные резаки друг от друга многими параметрами. Какой тип агрегата выбрать – переносной или стационарный, программируемый или ручной – зависит от конкретных потребностей владельца. Разделяются плазменные резаки на следующие виды:
- по типу энергопотребления – на трансформаторные и инверторные модели;
- по виду контакта – на бесконтактные и контактные;
- по типу работы – на ручные и с ЧПУ.
Газ для плазмореза
Плазмообразующие газы – отдельный ряд среди химических элементов. В аппарате плазменной резки металла применяются различные газы и их смеси, от которых зависит качество работы. Физические свойства газов – атомная масса, теплопроводность, химическая активность влияют на показатели работы плазморезов. Смешивание газов – процесс непростой, и зависит от толщины металла, типа стали и других параметров. Хорошо зарекомендовали себя в работе смеси аргона и азота с водородом. Смесь азота и кислорода применяется для многих видов металла и считается самым экономичным вариантом.
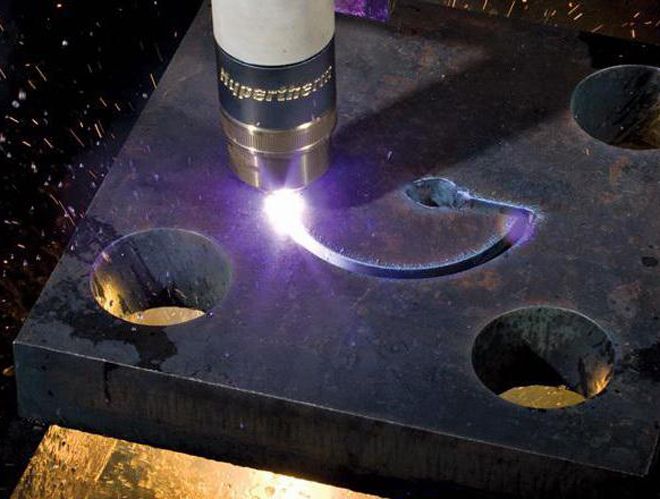
Как выбрать плазменный резак?
Оптимизация рабочего процесса на производстве и дома – важное условие качественного результата. Выбирать машину для плазменной резки следует обдуманно. Чтобы не ошибиться с покупкой, специалисты рекомендуют ответить на несколько вопросов.
- С каким металлом предстоит работать? Для медных, латунных, алюминиевых, сплавов идеально подойдет плазморез с мощностью 6 А. Для работы с черными металлами и нержавейкой хватит мощности 4А.
- В каких условиях будет работать устройство? Для продолжительной работы лучше выбирать резаки с внешней компрессорной подачей воздуха. Для небольших мастерских подойдет плазморез с внутренним компрессором.
- Как часто планируется менять расходные материалы? Следует учитывать, что электроды и сопло – детали, которые нуждаются в периодической замене, и частота их изнашивания зависит от длительности и мощности работы резака. Выбирая плазморез необходимо убедиться, что расходные материалы имеются в магазине в наличии или под заказ.
Рейтинг плазменных резаков
Простота использования, компактность, универсальность – основные параметры, за которые профессионалы любят работать с плазменными резаками. ТОП-3 лучших моделей выглядит следующим образом.
- Переносной плазменный резак «Ресанта» инверторного типа работает быстро, точно и качественно. Сила тока регулируется плавно, существует система автоподжига дуги. Работает устройство от сети 220 В, необходим источник сжатого воздуха. Удобная ручка позволяет легко переносить плазморез, вентиляционные отверстия в корпусе помогают системе не перегреться, понятные индикаторы делают управление легким.
- «Сварог CUT 100» – плазменный резак последнего поколения, который хорошо зарекомендовал себя на рынке. Способность разрезать металл толщиной до 35-ти мм, защита от перегрева, безопасность сделали данную модель востребованной среди покупателей. Сжатый воздух и трехфазная сеть 380 В необходимы для работы устройства. Недостатком называют высокую стоимость аппарата.
- «Aurora Pro airforce 100» – агрегат необходимый там, где осуществляется плазменная обработка материалов. Мобильность, высокое качество работы, встроенные транзисторы улучшенного качества, многоступенчатая защита – бесспорные плюсы устройства.
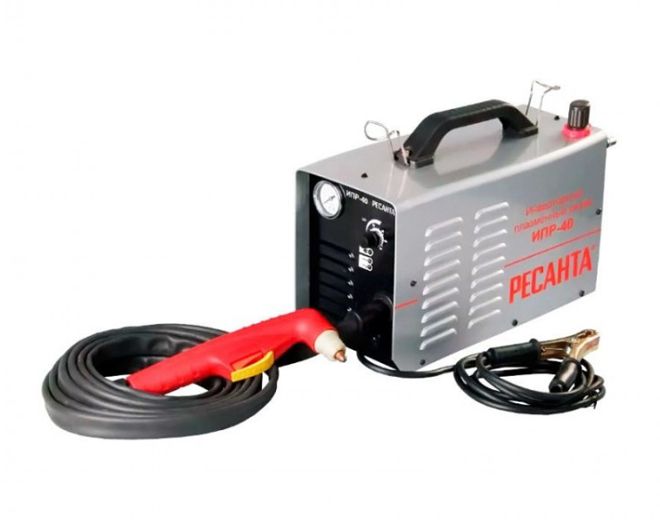
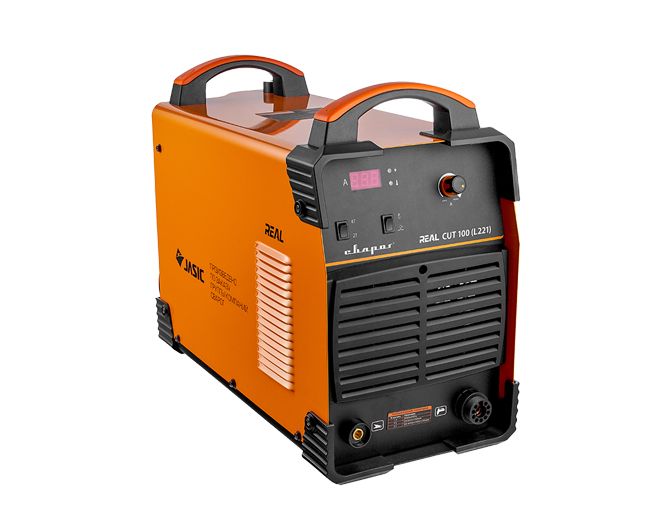
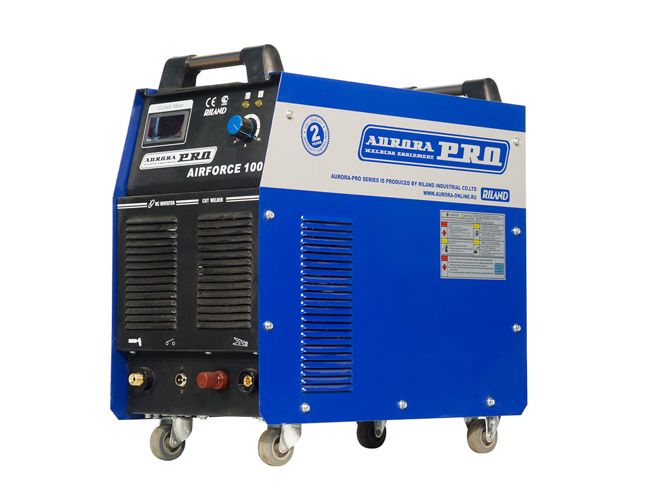
Как пользоваться плазморезом?
Плазменная резка – процесс несложный. Соблюдение простых правил необходимо для получения качественного результата. Во время работы плазморезом следует соблюдать пошаговую инструкцию:
- Перед началом работы необходимо защитить себя, надев специальную одежду и очки. Помещение должно быть оснащено вытяжкой, на лицо можно надеть маску.
- Чтобы избежать травм, до работы следует проверить все электрические шнуры на отсутствие повреждений, убедиться в соответствии тока с необходимыми параметрами резака.
- Плазморез нужно подключить к сети и источнику сжатого воздуха.
- Заготовка должна быть очищена от грязи, краски и других покрытий.
- В зависимости от толщины материала подобрать оптимальную силу тока и скорость резания.
- Резак продуть газом, через 30-40 сек. выполнить розжиг пилотной, а после нее – рабочей дуги.
- Держа сопло под углом 90° к заготовке, аккуратно провести по намеченной траектории.
- Работать необходимо, соблюдая режим ПВ – продолжительности включения.
- После работы отключить аппарат в обратной последовательности.
Плазменный резак своими руками
Если денег на качественный станок для резки металла нет, можно сделать плазморез своими руками, имея несколько необходимых составляющих, самый главный – это источник питания, обладающий необходимыми характеристиками. Для этих целей отлично подходит сварочный инверторный аппарат. Компрессор средней мощности для подачи воздуха стоит купить в магазине. Другие важные составляющие плазменного резака можно изготовить из подручных материалов:
- Для горелки нужна ручка от мощного паяльника. Через отверстие в середине будет подводиться сжатый воздух и ток.
- Кнопку пуска лучше сделать крупной.
- Электроды из гафния и набор сопл следует купить в магазине.
- Сборка плазмотрона проста: за ручкой размещается металлическая трубка, внутри нее – катод, покрытый изоляцией, следом на резьбе располагается сопло.
- К самодельному плазмотрону подключается компрессор и источник питания.
- Работать с самодельным устройством следует аккуратно, соблюдая технику безопасности и не допуская перегревания.
особенности, принцип работы, преимущества и недостатки
Плазменную резку очень часто используют в таких отраслях промышленности, как судостроение, машиностроение, а также при изготовлении металлоконструкций, коммунальной сфере и т. п. Кроме этого, плазморез довольно часто используется в частной мастерской. С его помощью быстро и качественно разрезают любой материал, проводящий ток, и некоторые нетокопроводящие материалы – дерево, камень и пластик.
Технология плазменной резки позволяет разрезать листовой металл и трубы, выполнять фигурный рез или изготавливать детали. Работа осуществляется при помощи высокотемпературной плазменной дуги. Чтобы ее создать, потребуется только источник тока, воздух и резак. Чтобы работа выполнялась довольно легко, а рез получался ровным и красивым, следует выяснить, как осуществляется принцип работы плазменной резки.
Как устроен плазморез
Этот аппарат состоит из следующих элементов:
- источник питания;
- воздушный компрессор;
- плазменный резак или плазмотрон;
- кабель-шланговый пакет.
Источник питания для аппарата плазменной резки осуществляет подачу на плазмотрон определенной силы тока. Представляет собой инвертор или трансформатор.
Инверторы довольно легкие, в плане энергопотребления экономные, по цене недорогие, однако, способны разрезать заготовки небольшой толщины. Из-за этого их применяют только в частных мастерских и на маленьких производствах. У инверторных плазморезов КПД на 30% больше, чем у трансформаторных и у них лучше горит дуга. Часто используют их для работ в труднодоступных местах.
Трансформаторы гораздо увесистее, тратят много энергии, но при этом имеют меньшую чувствительность к перепадам напряжения, и с их помощью разрезают заготовки большой толщины.
Плазменный резак считается главным элементом плазмореза. Его основными элементами являются:
- сопло;
- охладитель/изолятор;
- канал, необходимый для подачи сжатого воздуха;
- электрод.
Компрессор требуется для подачи воздуха. Принцип работы плазменной резки предусматривает применение защитных и плазмообразующих газов. Для аппаратов, которые рассчитаны на силу тока до 200 А, применяется только сжатый воздух как для охлаждения, так и для создания плазмы. Они способны разрезать заготовки толщиной в 50 мм.
Кабель-шланговый пакет используется для соединения компрессора, источника питания и плазмотрона. По электрическому кабелю от инвертора или трансформатора начинает поступать ток для возбуждения электрической дуги, а по шлангу осуществляется подача сжатого воздуха, который требуется для возникновения внутри плазмотрона плазмы.
Принцип работы
При нажатии на кнопку розжига начинается подача тока высокой частоты от источника питания (инвертора или трансформатора). В результате этого внутри плазмотрона образуется дежурная электрическая дуга, температура которой достигает 8 тыс. градусов. Столб этой дуги начинает заполнять весь канал.
После того как возникла дежурная дуга, в камеру начинает поступать сжатый воздух. Вырываясь из патрубка, он проходит через электрическую дугу, нагревается, при этом увеличиваясь в объеме в 50 или 100 раз. Кроме того, воздух начинает ионизироваться и перестает быть диэлектриком, приобретая свойства проводить ток.
Сопло плазмотрона, суженное книзу, обжимает воздух, создавая из него поток, которое начинает вырываться оттуда со скоростью 2 – 3 м/с. В этом момент температура воздуха часто достигает 30 тыс. градусов. Именно такой раскаленный ионизированный воздух и является плазмой.
В то время, когда плазма начинает вырываться из сопла, происходит ее соприкосновение с поверхностью обрабатываемого металла, дежурная дуга в этот момент гаснет, а зажигается режущая. Она начинает разогревать заготовку в месте реза. Металл в результате этого плавится и появляется рез. На поверхности разрезаемого металла образуются небольшие частички расплавленного металла, сдуваемые с нее потоком воздуха. Таким образом осуществляется работа плазмотрона.
Преимущества плазменной резки
Работы по резке металла часто осуществляются на стройплощадке, в мастерской или цеху. Можно использовать для этого автоген, но не всех это устраивает. Если объем работ, связанный с резкой металла, слишком большой, а требования, предъявляемые к качеству реза, очень высоки, то следует подумать о том, чтобы использовать плазменный резак, имеющим следующие достоинства:
- Если мощность подобрана правильно, то аппарат плазменной резки позволяет в 10 раз повысить производительность. Такой параметр позволяет плазморезу уступить только промышленной лазерной установке, однако, он значительно выигрывает в себестоимости. Целесообразно с экономической точки зрения применять пламенную резку для металла, имеющего толщину до 50 – 60 мм.
Универсальность. С помощью плазменной резки обрабатываются чугун, медь, сталь, алюминий и прочий металл. Необходимо просто выбрать оптимальную мощность и выставить конкретное давление воздуха.
- Высокое качество реза. Аппараты плазменной резки способны обеспечить минимальную ширину реза и кромки без перекаливания, наплывов и грата практически без дополнительной обработки. Кроме того, достаточно важен такой момент, что зона нагрева материала в несколько раз меньше, чем при использовании автогена. А так как термическое воздействие минимально на участке реза, то и деформация от этого вырезанных деталей будет незначительной, даже если они имеют небольшую толщину.
- Не происходит существенного загрязнения окружающей среды. С экономической точки зрения, если имеются большие объемы работ, то плазменная резка гораздо выгоднее кислородной или механической. Во всех остальных случаях учитывают не материалы, а трудоемкость использования.
Недостатки плазменной резки
Недостатки в работе плазменной резки тоже имеются. Первый из них – максимально допустимая толщина реза довольно небольшая, и у самых мощных агрегатов она редко бывает больше 80 – 100 мм.
Следующий недостаток – достаточно жесткие требования, предъявляемые к отклонению от перпендикулярности реза. Угол отклонения не должен быть больше 10 – 50 градусов и зависит это от толщины детали. Если случается выход за эти пределы, то возникает довольно существенное расширение реза, что в результате влечет за собой быстрый износ расходных материалов.
Кроме того, рабочее оборудование довольно сложное, что делает совершенно невозможным использование двух резаков одновременно, которые подключаются к одному аппарату.
Заключение
Принцип работы плазменной резки довольно прост. Кроме того, аппарат, который используется для этого, имеет большое количество преимуществ, в несколько раз превосходящие имеющиеся недостатки. Если его правильно эксплуатировать, то можно существенно сэкономить время и получить качественный результат.
Оцените статью: Поделитесь с друзьями!Как работает плазменный резак
Что такое плазма?
Чтобы правильно объяснить, как работает плазменный резак, мы должны начать с ответа на основной вопрос: «Что такое плазма? Проще говоря, плазма — это четвертое состояние вещества. Обычно мы думаем о материи, имеющей три состояния: твердое, жидкое и газообразное. Материя переходит из одного состояния в другое посредством введения энергии, например тепла. Например, вода переходит из твердого (лед) в жидкое состояние при приложении определенного количества тепла.Если уровень тепла увеличится, он снова изменится с жидкости на газ (пар). Теперь, если уровень тепла снова увеличится, газы, составляющие пар, станут ионизированными и электропроводящими, превратившись в плазму. Плазменный резак будет использовать этот электропроводящий газ для передачи энергии от источника питания к любому проводящему материалу, в результате чего процесс резки будет более чистым и быстрым, чем при использовании кислородного топлива.
Формирование плазменной дуги начинается, когда газ, такой как кислород, азот, аргон или даже производственный воздух, пропускается через небольшое отверстие сопла внутри горелки.Электрическая дуга, генерируемая от внешнего источника питания, затем вводится в этот газовый поток под высоким давлением, в результате чего возникает то, что обычно называют «плазменной струей». Плазменная струя сразу достигает температуры до 40000 ° F, быстро пробивая заготовку и сдувая расплавленный материал.
Компоненты плазменной системы
Источник питания — Источник питания для плазменной резки преобразует одно- или трехфазное сетевое напряжение переменного тока в плавное постоянное напряжение постоянного тока в диапазоне от 200 до 400 В постоянного тока.Это постоянное напряжение отвечает за поддержание плазменной дуги на всем протяжении резки. Он также регулирует требуемый выходной ток в зависимости от типа и толщины обрабатываемого материала.
- Консоль зажигания дуги
— Схема ASC вырабатывает переменное напряжение приблизительно 5000 В переменного тока на частоте 2 МГц, которое создает искру внутри плазменной горелки для создания плазменной дуги.
- Плазменный резак
— Плазменный резак предназначен для обеспечения правильного выравнивания и охлаждения расходных деталей.Основными расходными деталями, необходимыми для генерации плазменной дуги, являются электрод, вихревое кольцо и сопло. Дополнительный защитный колпачок может использоваться для дальнейшего улучшения качества резки, а все части удерживаются вместе внутренними и внешними удерживающими колпачками.
Подавляющее большинство систем плазменной резки сегодня можно разделить на обычные или прецизионные категории.
![]() | В обычных плазменных системах в качестве плазменного газа обычно используется производственный воздух, а форма плазменной дуги в основном определяется отверстием сопла.Примерная сила тока плазменной дуги этого типа составляет 12-20K ампер на квадратный дюйм. Во всех портативных системах используется обычная плазма, и она все еще используется в некоторых механизированных приложениях, где допуски деталей более приемлемы. | |
![]() | Системы прецизионной плазменной резки (с высокой плотностью тока) спроектированы и спроектированы так, чтобы производить резку с максимальной резкостью и высочайшим качеством, достижимую с помощью плазмы.Конструкции резака и расходных деталей более сложны, и в комплект входят дополнительные детали для дальнейшего сжатия и формы дуги. Прецизионная плазменная дуга составляет приблизительно 40-50 кОм на квадратный дюйм. Несколько газов, таких как кислород, воздух высокой чистоты, азот и смесь водорода / аргона / азота, используются в качестве плазменного газа для получения оптимальных результатов на множестве проводящих материалов. |
Ручной режим В типичной ручной плазменной системе, такой как наша Tomahawk® Air Plasma, расходные части электрода и сопла контактируют друг с другом внутри резака в выключенном состоянии.При нажатии на спусковой крючок источник питания вырабатывает постоянный ток, который течет через это соединение, а также инициирует поток плазменного газа. Как только плазменный газ (сжатый воздух) создает достаточное давление, электрод и сопло раздвигаются, что вызывает электрическую искру, которая превращает воздух в плазменную струю. Затем поток постоянного тока переключается с электрода на сопло, на путь между электродом и заготовкой. Этот ток и воздушный поток продолжаются до тех пор, пока спусковой крючок не будет отпущен. | ![]() |
Прецизионная плазменная установка
Внутри прецизионного плазменного резака электрод и сопло не соприкасаются, а изолированы друг от друга закручивающим кольцом с небольшими вентиляционными отверстиями, которые преобразуют предварительный поток / плазменный газ в вихрь. Когда на источник питания подается команда пуска, он генерирует до 400 В постоянного тока напряжения холостого хода и запускает предварительную подачу газа через шланг, подсоединенный к горелке.Сопло временно подключается к положительному потенциалу источника питания через цепь вспомогательной дуги, а электрод находится на отрицательном полюсе.
Затем из пульта запуска дуги генерируется высокочастотная искра, которая заставляет плазменный газ становиться ионизированным и электропроводящим, в результате чего возникает путь тока от электрода к соплу, и создается пилотная плазменная дуга.
Как только вспомогательная дуга контактирует с заготовкой (которая подключается к заземлению через планки режущего стола), путь тока смещается от электрода к заготовке, высокочастотная дуга отключается, и цепь вспомогательной дуги размыкается. .
Затем источник питания увеличивает постоянный ток до значения силы тока резания, выбранного оператором, и заменяет газ предварительной подачи оптимальным плазменным газом для разрезаемого материала. Также используется вторичный защитный газ, который выходит за пределы сопла через защитный колпачок.
Форма защитного колпачка и диаметр его отверстия заставляют защитный газ еще больше сжимать плазменную дугу, что приводит к более чистому срезу с очень малыми углами скоса и меньшим пропилом.
Основы плазменной резки
Основы плазменной резки
Процесс плазменной резки
- Плазменная резка — это самый быстрый процесс резки углеродистой, алюминиевой или нержавеющей стали.
- Плазменная резка может сочетаться с гидроабразивной или кислородной резкой одной и той же детали.
- Плазменная резка может использоваться для точной резки материала толщиной до 6 дюймов из нержавеющей стали. ЭСАБ изобрел плазменную резку в 1955 году, и мы никогда не прекращали разработки способов сделать устройства плазменной резки лучше и проще.Последние инновации ЭСАБ в автоматизации процесса плазменной резки увеличивают объемы производства с неизменно высоким качеством резки каждый раз … независимо от уровня квалификации оператора:
Плазменная дуга
Характеристики Плазма определяется у Вебстера как «совокупность заряженных частиц …, содержащих примерно равное количество положительных ионов и электронов и обладающих некоторыми свойствами газа, но отличающихся от газа тем, что является хорошим проводником электричества …»
Для дуговой резки плазму также можно определить как электрически нагретый газовый поток.Газовый поток нагревается до такой высокой температуры, что становится ионизированным. Ионизированный газ по определению может свободно обмениваться электронами между атомами. Это движение электронов позволяет газу переносить режущий ток.
В плазменной горелке используется сопло из сплава меди, которое сужает поток ионизированного газа и фокусирует энергию на небольшом поперечном сечении. Принцип такой же, как при использовании увеличительного стекла для концентрации солнечной энергии для создания сильного тепла.
Газ, протекающий через сопло, также служит средой для удаления расплавленного металла, нагретого ионизированным газом.Приблизительно 30% газа фактически ионизируется (при оптимальных условиях), тогда как оставшиеся 70% газового потока используются для удаления материала и охлаждения.
Завихрение газа
Закрутка газа способствует резке несколькими способами. Закрутка увеличивает охлаждение. Атомы неионизированного газа тяжелее / холоднее и выбрасываются за пределы вращающегося газового потока. Этот холодный барьер защищает медное сопло. По мере увеличения силы тока степень ионизации увеличивается (изменяется соотношение 30/70%), а охлаждение уменьшается, сокращая срок службы сопла.Сопла предназначены для работы в определенном диапазоне тока (ампер).
Вихревой газ улучшает качество резки.
Если плазменный газ не закручивается, в результате будет получен скос с обеих сторон реза. Закручивая газ, дуга равномерно распределяется по одной стороне разреза. Если направление завихрения меняется на противоположное (от CW к CCW), сторона квадрата изменится. Когда ионизированный газ (плазменная дуга) закручивается, электрическая дуга равномерно прикрепляется к передней кромке разреза.Эти многочисленные точки крепления обеспечивают более равномерное распределение мощности по заготовке. Это выравнивание мощности сверху вниз приводит к получению более квадратной стороны. Другая сторона имеет фаску от 5 до 8 градусов.
Введение защитного газа будет дополнительно сужать и охлаждать сопло. Этот газ впрыскивается в поток плазмы после процесса ионизации на кончике сопла.
Впрыск воды улучшает качество резки и охлаждает сопло. Закручивая воду в том же направлении, что и газ, а затем впрыскивая ее в точку выхода дуги из сопла, дуга еще больше сужается.Когда холодная вода вступает в контакт с высокотемпературной дугой, между дугой и отверстием сопла образуется слой пара. Действие этого барьера можно продемонстрировать, если нагреть сковороду и налить на нее воду. Сразу же маленькие капельки воды будут танцевать на поверхности кастрюли вместо того, чтобы испаряться. Эти водяные шарики защищены пароизоляционными свойствами, которые образуются при контакте воды с поддоном. Для правильной работы впрыска воды температура воды должна оставаться ниже 70 градусов по Фаренгейту.Состояние, известное как пленочное кипение, возникает, если температура поднимается выше этой точки. В результате возникает нестабильная дуга, сокращается срок службы сопла и ухудшается качество резки.
Запуск плазменной дуги
Внутри корпуса резака есть три основных компонента.
- Электрод
- Газовая заслонка (завихритель)
- Сопло
Эти предметы называются расходными материалами. Они расходуются с течением времени в процессе плазменной резки и подлежат замене.Детали резака ESAB PT-36 показаны выше. Другие факелы могут выглядеть иначе, но у всех есть части, которые функционируют как 3 основных перечисленных выше. Обратитесь к руководству по эксплуатации резака, чтобы узнать точную конфигурацию деталей.
Электрод подключен к отрицательной стороне источника питания постоянного тока плазмы. Форсунка подключена к положительной стороне, но электрически изолирована с помощью нормально разомкнутого реле.
При подаче на систему плазменной резки пускового сигнала происходит следующее:
- Главный контактор в источнике питания возбуждает, создавая высокое отрицательное напряжение на электроде.
- Газ начинает поступать к горелке и закручивается перегородкой.
- Нормально разомкнутые контакты в цепи форсунки замыкаются, обеспечивая путь к положительной стороне источника питания.
- Высокочастотный генератор создает потенциал высокой частоты-высокого напряжения между электродом и соплом. Это заставляет небольшую искру прыгать между соплом и электродом, ионизируя путь через газ.
- Вдоль этого ионизированного пути между электродом и соплом начинает протекать большая дуга постоянного тока.Это называется вспомогательной дугой.
- Пилотная дуга выдувается из сопла потоком газа и контактирует с заготовкой.
- Основная дуга создается, когда вспомогательная дуга переходит на рабочий материал (если горелка расположена достаточно близко). Реле форсунки размыкается при отключении форсунки от цепи. Установлено состояние перенесенной дуги.
- После размыкания реле сопла основная дуга увеличивается до режущей силы.
Двойная дуга
Двойная дуга — это состояние, при котором сопло остается в плазменном контуре.Как описано выше, сопло должно находиться в цепи только во время фазы вспомогательной дуги. Если оставить в цепи, сопло будет пропускать режущий ток, который его разрушит.
Возникновение двойной дуги:
- Постоянный пирс. Горелка должна быть расположена достаточно близко к обрабатываемой детали, чтобы вспомогательная дуга касалась пластины, чтобы основная дуга могла переноситься. Брызги прожига выбрасываются под небольшим углом во время начального прожига. Когда дуга проникает в материал, брызги становятся более вертикальными.Этот мусор может соединить пластину и сопло, удерживая сопло в цепи, даже когда реле размыкается, чтобы удалить его. Этот сценарий может повредить переднюю часть резака.
- Горелка контактирует с пластиной. Резка тонких материалов. Все системы автоматического позиционирования резака используют некоторый метод определения начальной высоты для позиционирования резака над пластиной. Один из методов — это метод касания и втягивания. Горелка перемещается, пока не соприкасается с пластиной, и возвращается на начальную высоту с помощью таймера или кодировщика.Если прикосновение не распознается должным образом, резак может оставаться в контакте с материалом из-за подпружинения или деформации материала. Сопло останется в плазменном контуре с током резки, повредив его.
- Неисправность вспомогательной дуги. Это может произойти, если цепи реле вспомогательной дуги не удается снять сопло. Это может произойти либо с закороченным реле, либо с резистором. И снова сопло пропускает больше тока, чем предполагалось, что приводит к его повреждению.
Предотвращение двойной дуги
Двойная дуга обычно возникает во время процесса прожига.
Некоторые методы, которые могут помочь избежать двойной дуги:
- Ползучесть. Режущий станок запрограммирован на пониженную скорость, чтобы начать движение станка при переносе дуги. Эта скорость обычно составляет от 5 до 10% от нормальной скорости резания и рассчитана на определенный период времени. В это время из сопла выбрасываются пронзительные брызги. Это снижает вероятность возникновения двойной дуги.
- Факел поднимается при прожиге стоя. При переносе дуги резак начинает отрываться от заготовки.Это позволяет разбрызгивателям вылетать из сопла. Это втягивание продолжается в течение определенного периода времени, а затем снижается до необходимой высоты резки после того, как машина движется со скоростью резки.
- Пробивка с более высокой начальной высотой (пробивка стоя), чем обычно. Это позволяет прожигающим брызгам не попадать в сопло, что снижает вероятность образования двойной дуги. Этот способ профилактики наименее эффективен.
Параметры плазменного процесса
Все параметры плазменной резки должны тщательно контролироваться для достижения максимального качества резки, максимального срока службы сопла / электрода и максимальной производительности.Между ними должен соблюдаться баланс.
Газ
Чистота газа
Чистота газа важна для хорошего качества резки и длительного срока службы электрода. Минимальные требования к чистоте азота 99,995% и 99,5% кислорода. Если уровень чистоты ниже рекомендуемого минимума, может произойти следующее.
- Неспособность дуги проникать в тонкие материалы при любом уровне тока.
- Качество резки зависит от степени загрязнения.
- Чрезвычайно короткий срок службы электрода.
- При резке N2 появление остатков черной пленки на торце электрода и в отверстии сопла. Чем сильнее загрязнение, тем больше остатков. Если газ чистый, электрод и отверстие сопла приобретут вид пескоструйной обработки.
Давление / расход газа
Каждая форсунка рассчитана на работу при оптимальном токе в зависимости от заданного давления / расхода газа. Повышение этого давления может привести к сокращению срока службы электрода.Об этом свидетельствует появление отверстий на вольфрамовой вставке. При использовании азота возникнет проблема с запуском горелки. Если горелка не запускается при высоком давлении, может наблюдаться разбрызгивание вспомогательной дуги. Там, где высокое давление газа может создать проблемы, низкий расход газа обычно приводит к отказу двойной дуги.
Вода
Чистота воды
Для плазменного процесса с впрыском воды требуется деионизированная и фильтрованная вода. Взвешенные твердые частицы, растворенные минералы и другие факторы влияют на проводимость воды и срок службы форсунки и увеличивают возможность высокочастотных помех.
Давление / расход воды для резки
Расход воды для резки должен быть установлен на количество, указанное в документации по резаку. Чрезмерный поток воды приведет к сокращению срока службы электрода и нестабильной дуге. Низкий расход воды приведет к недостаточному охлаждению, влияющему на срок службы сопла.
пропил
Пропила — это ширина материала (перпендикулярного резаку и оси резки), удаляемого в процессе плазменной резки. Kerf зависит от трех основных переменных.
- Скорость резания. Более высокая скорость резания при постоянных других переменных приведет к более узкому пропилу. Прорезь будет продолжать сужаться, пока не произойдет потеря пропила. Более низкая скорость движения приведет к более широкому пропилу, пока не произойдет пропадание дуги.
- Режущая сила тока. Увеличение силы тока резки при постоянных двух других переменных приведет к более широкому пропилу. Продолжая увеличивать ток, пропил будет увеличиваться до тех пор, пока сопло не будет разрушено. Снижение силы тока приведет к более узкому пропилу и более положительному углу среза до тех пор, пока проплавление не будет потеряно.
- Противостояние. Зазор — это расстояние между резаком и заготовкой после прожига (во время резки). В большинстве современных систем используется система обратной связи по напряжению дуги. Увеличение напряжения дуги увеличивает расстояние зазора и расширяет пропил. Продолжение увеличения противостояния в конечном итоге приведет к потере резания. Уменьшение зазора приведет к более узкому пропилу и, в конечном итоге, к потере пропила.
Напряжение дуги
Напряжение дуги не является независимой переменной.
Зависит от:
- Ток (в амперах)
- Размер сопла
- Противостояние
- Расход режущего газа
- Расход воды для отсечки (если применимо)
- Скорость резания
Газы, необходимые для большинства приложений, — это пусковой газ, защитный газ и режущий газ. В некоторых ситуациях требуется второй защитный газ. Результаты меняются в зависимости от различных комбинаций азота, кислорода, воздуха, метана и H-35 (комбинация 35% водорода — 65% аргона).Для плазменной маркировки используется газообразный аргон. Тип и толщина материала, качество резки, скорость и стоимость производства — это переменные, которые следует учитывать при выборе комбинаций газов. Все газы не подходят для некоторых применений и горелок. Обратитесь к документации по горелкам для получения дополнительной информации.
Решение ESAB
Плазменная система m3ESAB полностью автоматизирует процесс плазменной резки, упрощая настройку всех параметров процесса, описанных выше, и обеспечивает стабильное качество резки.
.Как работает плазменный резак
Что такое плазма?
Чтобы правильно объяснить, как работает плазменный резак, мы должны начать с ответа на основной вопрос: «Что такое плазма? Проще говоря, плазма — это четвертое состояние вещества. Обычно мы думаем о материи, имеющей три состояния: твердое, жидкое и газообразное. Материя переходит из одного состояния в другое посредством введения энергии, например тепла. Например, вода переходит из твердого (лед) в жидкое состояние при приложении определенного количества тепла.Если уровень тепла увеличится, он снова изменится с жидкости на газ (пар). Теперь, если уровень тепла снова увеличится, газы, составляющие пар, станут ионизированными и электропроводящими, превратившись в плазму. Плазменный резак будет использовать этот электропроводящий газ для передачи энергии от источника питания к любому проводящему материалу, в результате чего процесс резки будет более чистым и быстрым, чем при использовании кислородного топлива.
Формирование плазменной дуги начинается, когда газ, такой как кислород, азот, аргон или даже производственный воздух, пропускается через небольшое отверстие сопла внутри горелки.Электрическая дуга, генерируемая от внешнего источника питания, затем вводится в этот газовый поток под высоким давлением, в результате чего возникает то, что обычно называют «плазменной струей». Плазменная струя сразу достигает температуры до 22000 ° C, быстро пробивая заготовку и сдувая расплавленный материал.
Компоненты плазменной системы
Источник питания — Источник питания для плазменной резки преобразует одно- или трехфазное сетевое напряжение переменного тока в плавное постоянное напряжение постоянного тока в диапазоне от 200 до 400 В постоянного тока.Это постоянное напряжение отвечает за поддержание плазменной дуги на всем протяжении резки. Он также регулирует требуемый выходной ток в зависимости от типа и толщины обрабатываемого материала.
- Консоль зажигания дуги
— Схема ASC вырабатывает переменное напряжение приблизительно 5000 В переменного тока на частоте 2 МГц, которое создает искру внутри плазменной горелки для создания плазменной дуги.
- Плазменный резак
— Плазменный резак предназначен для обеспечения правильного выравнивания и охлаждения расходных деталей.Основными расходными деталями, необходимыми для генерации плазменной дуги, являются электрод, вихревое кольцо и сопло. Дополнительный защитный колпачок может использоваться для дальнейшего улучшения качества резки, а все части удерживаются вместе внутренними и внешними удерживающими колпачками.
Подавляющее большинство систем плазменной резки сегодня можно разделить на обычные или прецизионные категории.
![]() | В обычных плазменных системах в качестве плазменного газа обычно используется производственный воздух, а форма плазменной дуги в основном определяется отверстием сопла.Примерная сила тока плазменной дуги этого типа составляет 12-20K ампер на квадратный дюйм. Во всех портативных системах используется обычная плазма, и она все еще используется в некоторых механизированных приложениях, где допуски деталей более приемлемы. | |
![]() | Системы прецизионной плазменной резки (с высокой плотностью тока) спроектированы и спроектированы так, чтобы производить резку с максимальной резкостью и высочайшим качеством, достижимую с помощью плазмы.Конструкции резака и расходных деталей более сложны, и в комплект входят дополнительные детали для дальнейшего сжатия и формы дуги. Прецизионная плазменная дуга составляет приблизительно 40-50 кОм на квадратный дюйм. Несколько газов, таких как кислород, воздух высокой чистоты, азот и смесь водорода / аргона / азота, используются в качестве плазменного газа для получения оптимальных результатов на множестве проводящих материалов. |
Ручной режим В типичной ручной плазменной системе, такой как наша Tomahawk® Air Plasma, расходные части электрода и сопла контактируют друг с другом внутри резака в выключенном состоянии.При нажатии на спусковой крючок источник питания вырабатывает постоянный ток, который течет через это соединение, а также инициирует поток плазменного газа. Как только плазменный газ (сжатый воздух) создает достаточное давление, электрод и сопло раздвигаются, что вызывает электрическую искру, которая превращает воздух в плазменную струю. Затем поток постоянного тока переключается с электрода на сопло, на путь между электродом и заготовкой. Этот ток и воздушный поток продолжаются до тех пор, пока спусковой крючок не будет отпущен. | ![]() |
Прецизионная плазменная установка
Внутри прецизионного плазменного резака электрод и сопло не соприкасаются, а изолированы друг от друга закручивающим кольцом с небольшими вентиляционными отверстиями, которые преобразуют предварительный поток / плазменный газ в вихрь. Когда на источник питания подается команда пуска, он генерирует до 400 В постоянного тока напряжения холостого хода и запускает предварительную подачу газа через шланг, подсоединенный к горелке.Сопло временно подключается к положительному потенциалу источника питания через цепь вспомогательной дуги, а электрод находится на отрицательном полюсе.
Затем из пульта запуска дуги генерируется высокочастотная искра, которая заставляет плазменный газ становиться ионизированным и электропроводящим, в результате чего возникает путь тока от электрода к соплу, и создается пилотная плазменная дуга.
Как только вспомогательная дуга контактирует с заготовкой (которая подключается к заземлению через планки режущего стола), путь тока смещается от электрода к заготовке, высокочастотная дуга отключается, и цепь вспомогательной дуги размыкается. .
Затем источник питания увеличивает постоянный ток до значения силы тока резания, выбранного оператором, и заменяет газ предварительной подачи оптимальным плазменным газом для разрезаемого материала. Также используется вторичный защитный газ, который выходит за пределы сопла через защитный колпачок.
Форма защитного колпачка и диаметр его отверстия заставляют защитный газ еще больше сжимать плазменную дугу, что приводит к более чистому срезу с очень малыми углами скоса и меньшим пропилом.
Принцип работы машины плазменной резки
4600 долларов США.00–9600 долларов США / Устанавливать | 1 компл. / Компл. Принцип работы машины для плазменной резки (мин. Заказ)
- Перевозка:
- Служба поддержки Морские перевозки