Плазморез своими руками
Плазменная резка – достаточно востребованная операция, особенно, когда дело касается резки толстых металлических деталей или заготовок. Процесс происходит быстро, кромки металла остаются ровными. Но такой аппарат стоит недешево. Поэтому многие умельцы изготавливают для себя плазморез своими руками из разных видов оборудования, соединив их в одну конструкцию. Схема соединения их проста, главное – правильно подобрать приборы по необходимым техническим характеристикам.
Основы плазменной резки
В основе плазменной резки лежит ионизированный газ, который вылетает из сопла горелки с большой скоростью. Этот газ и есть та самая плазма. Что она делает.
- По сути, это ионизированная среда является отличным проводником электрического тока, который от электрода поступает к металлической заготовке.
- Плазма нагревает металл до необходимой температуры.
- Она же сдувает расплавленный металл, освобождает пространство реза.
Значит, чтобы создать плазму, необходим газ и источник электроэнергии. И эти две составляющие должны соединиться в одном месте. Поэтому оборудование плазменной резки состоит из баллона с газом, источника электроэнергии повышенной силы и резака, в котором установлен электрод.
Конструкция резака изготовлена таким образом, чтобы вокруг электрода проходил газ и в нагретом от электрода виде вырывался наружу через небольшое отверстие. Небольшой диаметр отверстия и давление газа создают необходимую скорость плазме. При изготовлении самодельной плазменной резки нужно просто приобрести готовый резак и не думать над его созданием. Потому что в нем уже все продумано, плюс заводской вариант – это гарантия безопасности.
Что касается газа, то от всех вариантов давно уже отказались, оставив сжатый воздух. Получить его можно сегодня очень просто – приобрести и установить компрессор.
Есть определенные условия, которые гарантируют качество резки плазмой.
- Сила тока на электроде не должна быть меньше 250 А.
- Сжатый воздух должен подаваться на резак со скоростью в пределах 800 м/сек.
Как сделать плазморез своими руками
Основы плазменной резки понятны, конструкция плазмореза тоже ясна, можно приступать к его сборке. Кстати, для этого не нужны специальные чертежи.
Итак, что будет необходимо.
- Нужно найти источник электроэнергии. Самый простой вариант – это сварочный трансформатор или инвертор. По многим причинам инвертор лучше. К примеру, у него стабильное значение тока, без перепадов. Он экономичнее в плане потребления электроэнергии. Обратить внимание придется на ток, который выдает сварочный аппарат. Его значение не должно быть меньше 250 ампер.
- Источник сжатого воздуха. Здесь без изменений – компрессор. Но какой? Основной параметр – давление воздуха. На него и надо будет обратить внимание. 2,0-2,5 атм. – будет нормально.
- Резак можно приобрести в магазине. И это будет идеальным решением. Если есть в наличии резак для аргонной сварки, то и его можно переделать под плазменную резку.
- Комплект шлангов и кабелей, для соединения всех частей самодельного плазмореза. Опять-таки комплект можно приобрести в магазине, как единый соединяющий элемент.
Вот четыре элемента, с помощью которых собирается самодельный плазморез.
Вспомогательные элементы и материалы
На что еще необходимо обратить внимание, собирая аппарат плазменной резки своими руками. Как уже было сказано выше, основная характеристика плазменного резака – это диаметр его отверстия. Каких размеров он должен быть, чтобы качество реза было максимальным. Специалисты считают, что диаметр в 30 мм – оптимальный размер. Поэтому, покупая резак в магазине, нужно обратить внимание, есть ли в его комплекте сопло с таким отверстием.
К тому же надо подбирать сопло со значительной длиной. Именно этот размер дает возможность струе сжатого воздуха набрать необходимую скорость. От чего рез металла получается аккуратным, а сам процесс резки быстрым и легким. Но не стоит приобретать сопло уж очень большой длины. Такое приспособление быстро разрушается под действием высоких температур.
Что касается выбора электрода для плазмореза, то тут необходимо обратить внимание на сплав, из которого он изготовлен. К примеру, если в сплав входит бериллий, то это радиоактивное вещество. Работать с такими электродами долго не рекомендуется. Если в сплав входит торий, то при высоких температурах он выделяет токсичные вещества. Идеальный электрод для плазменной резки, в сплав которого входит гафний.
Проверка плазмореза
Итак, шланги соединяют резак и компрессор, кабель резак и инвертор. Теперь необходимо проверить, а работает ли собранная конструкция. Включаются все агрегаты, на резаке нажимается кнопка подачи электроэнергии на электрод. При этом образуется дуга с температурой 6000-8000С. Она проскакивает между металлом электрода и сопла.
После этого начинает подаваться в резак сжатый воздух. Проходя через сопло и нагреваясь от электрической дуги, он резко расширяется в десять раз и при этом приобретает токопроводящие свойства. То есть, получается ионизированный газ.
Он проходит через суженное сопло, при этом приобретая скорость в пределах 2-3 м/сек. А вот температура плазмы повышается до 25000-30000С. Самое важное, что дуга, с помощью которой был разогрет сжатый воздух и превращен в плазму, гаснет, как только плазма начинает воздействовать на металлическую заготовку, подготовленную к резке. Но тут же включается вторая, так называемая рабочая дуга, которая на металл действует локально. Именно в зону реза. Поэтому металл режется только в этой зоне.
Если при проверке работы плазменного резака у вас получилось разрезать металл толщиною не меньше 20 мм, то все элементы новой конструкции, собранной своими руками, были подобраны правильно. Необходимо обратить внимание, что заготовки толщиною более 20 мм плазморез из инвертора не режет. У него просто не хватает мощности. Чтобы резать металл большей толщины, придется использовать трансформатор.
Внимание! Любые работы, связанные с использование плазменной резки, должны проводиться в защитной одежде и перчатках.
Полезные советы
Существует много моментов, которые обязательно сказываются на работе агрегата.
- Приобретать, например, большой компрессор нет необходимости. Но 2-2,5 атмосфер при большом объеме работ может не хватить. Выход из положения – установить на компрессоре ресивер. Он работает, как аккумулятор, накопляющий давление в сжатом воздухе. Для этого дела можно приспособить, к примеру, болоны от тормозной системы большегрузных машин. Вариант на самом деле простой. Объем у баллона большой, и его должно хватить на длительный промежуток времени.
- Чтобы давление воздуха было стабильным и одинаковым, на выходе ресивера нужно установить редуктор.
- Чтобы сделать мобильную версию станка, можно изготовить тележку небольших размеров.
Ведь все элементы плазмореза – небольшие по габаритам приспособления. Конечно, о мобильности придется забыть, если станок изготовлен на основе сварочного трансформатора. Слишком он большой и тяжелый.
- Если нет возможности купить готовый комплект шланг-кабель, то можно его сделать самостоятельно. Нужно сварочный кабель и шланг высокого давления объединить в один рукав и поместить их в единую оболочку. К примеру, в обычный шланг большего диаметра. Сделанный таким образом комплект просто не будет мешаться под ногами, что очень важно при проведении резки металлов.
Сделать свой собственный плазморез совсем несложно. Конечно, надо будет получить необходимую информацию, изучить ее, обязательно рекомендуется посмотреть обучающее видео. И после этого правильно подобрать все элементы точно под необходимые параметры. Кстати, собранный плазморез на основе серийного инвертора дает возможность не только проводить плазменную резку металлов, но и плазменную сварку, что увеличивает функциональность агрегата.
Поделись с друзьями
1
0
0
0
Плазморез своими руками из инверторной сварки
Чтобы сделать самодельный плазморез понадобятся: источник постоянного тока, плазмотрон, осциллятор, компрессор, шланги подключения, кабеля питания.
Резка листового металла плазмой обычно применяется на крупных производствах для изготовления сложных по конфигурации деталей. Резать на промышленных станках можно любые металлы — сталь обычную и нержавеющую, алюминий, медь, латунь, сверхтвердые сплавы. Плазморез своими руками сделать тоже можно, причем вполне работоспособную конструкцию, правда с несколько ограниченными возможностями.
Для крупносерийного производства она будет непригодна, но вырезать несколько деталей в слесарной мастерской, металлообрабатывающем цехе или в домашних условиях, в гараже, например, всегда получится. При этом по сложности конфигурации и твердости обрабатываемого металла ограничений практически нет. Ограничения касаются толщины металла, размеров листа и скорости резания.
Что нужно для плазмореза
Проще всего построить плазменный аппарат для резки на базе инверторного сварочного аппарата. Плазморез своими руками из инвертора отличается относительно простой конструкцией, работоспособностью, доступностью основных узлов и деталей. Которые нет возможности купить, можно сделать самостоятельно в условиях мастерской средней оснащенности оборудованием.
Самодельный аппарат плазменной резки не оборудуется ЧПУ — в этом его недостаток и преимущество. Недостаток состоит в том, что сложно изготовить две абсолютно точные детали при управлении вручную. Даже мелкие серии заготовок будут в чем-то отличаться.
Преимущество же состоит в том, что один из самых дорогостоящих узлов не придется покупать. Сделать его под силу не каждому инженеру высшей квалификации, а собирать из готовых узлов — то же, что покупать новое устройство. Для мобильного резака ЧПУ не нужно, в силу других задач, которые он выполняет.
Главными составными частями самодельного плазмореза являются:
- источник постоянного тока;
- плазмотрон;
- осциллятор
- компрессор или баллон со сжатым газом;
- шланги подключения;
- кабеля питания.
Как видно, ничего особо сложного в состав аппарата не входит. Но сложности начинаются при ближайшем рассмотрении характеристик того или иного узла.
Источник тока
Особенности плазменной резки требуют, чтобы сила тока находилась по меньшей мере на уровне сварочного аппарата средней мощности.
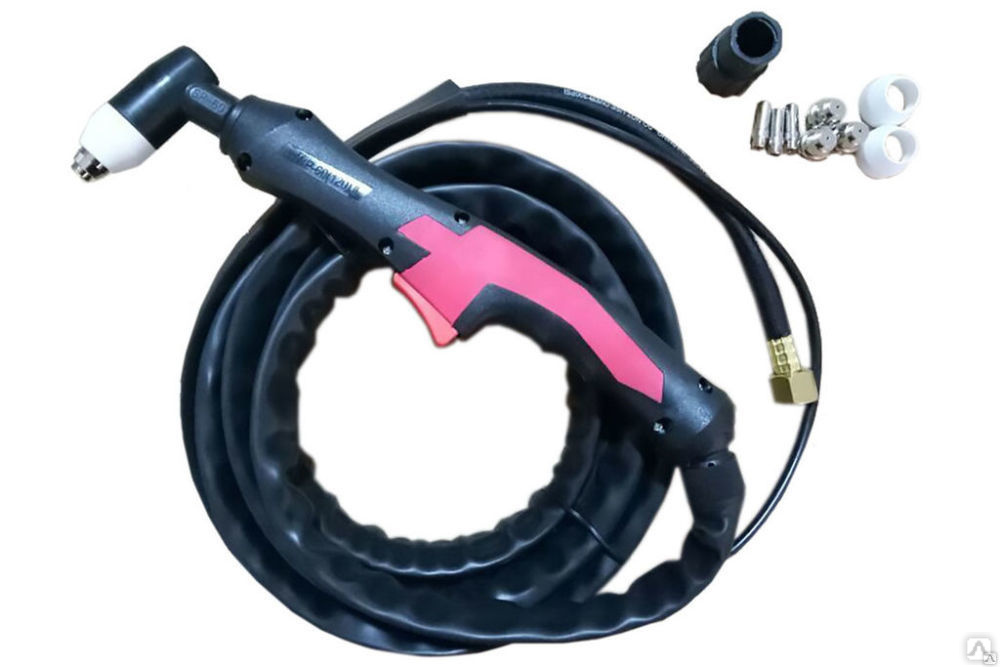
Кроме того, трансформаторы отличаются невысоким КПД, что приведет к повышенному расходу электроэнергии при резке металла. Схема с использованием инвертора несколько проще и удобнее в эксплуатации, как и выгоднее по затратам энергии. Из сварочного инвертора получится довольно компактный плазморез, который без труда справиться с резкой металла толщиной до 25-30 мм. Именно для таких толщин применяются и промышленные установки. Плазменный резак на трансформаторе сможет обрабатывать более толстые заготовки, но это требуется реже. Все преимущества плазменной резки проявляются именно на тонких и сверхтонких листах. Это:
- точность линии;
- гладкость кромок;
- отсутствие брызг металла;
- нет перегретых зон вблизи места взаимодействия дуги и металла.
Самодельный плазморез собирается на базе любого инверторного аппарата для сварки. Количество режимов работы не имеет значения — нужен только постоянный ток силой более 30А.
Плазмотрон
Второй по важности элемент плазмореза. Рассмотрим коротко принцип его работы. Плазменный резак состоит из двух электродов, один из которых, основной, сделан из тугоплавкого металла, вторым является сопло. Обычно его делают из меди. Катодом служит основной электрод, анодом сопло, а при работе — обрабатываемая токопроводящая деталь.
В данном случае мы рассматриваем плазмотрон прямого действия для резки металлов. Дуга возникает между резаком и обрабатываемой деталью. Существуют еще плазмотроны косвенного действия, которые режут плазменной струей, но о них будет сказано ниже. Плазморез из инвертора рассчитан на прямое действие.
Кроме электрода и сопла, которые являются расходными материалами и могут заменяться по мере износа, в корпусе плазмотрона есть изолятор, разделяющий катодный и анодный узлы и небольшая камера, в которой подаваемый газ завихрятся. В сопле конической или полусферической сделано тонкое отверстие, сквозь которое вырывается раскаленный до температуры 5000-3000 0С газ.
Плазмотрон прямого действия
Подается в камеру газ из баллона или от компрессора по шлангу, совмещенному с кабелями питания, которые образуют шлангово-кабельный пакет. Они соединены в одном изоляционном рукаве, или соединены в виде жгута. Газ поступает в камеру через прямой патрубок, расположенный сверху или сбоку вихревой камеры, которая нужна, чтобы рабочая среда перемещалась только в одну сторону.
Как работает плазмотрон
Газ, поступая под давлением в пространство между соплом (анодом) и электродом (катодом) спокойно проходит в рабочее отверстие и уходит в атмосферу. При включении осциллятора, устройства вырабатывающего импульсный высокочастотный ток, между электродами возникает дуга, которая называется предварительной и нагревает газ, находящийся в ограниченном пространстве камеры сгорания. Температура нагрева столь высока, что он переходит в другой вид физического состояния — плазму.

Этот вид материального состояния отличается тем, что практически все атомы ионизированы, то есть электрически заряженные. Кроме того, давление в камере резко возрастает и газ вырывается наружу в виде раскаленной струи. При поднесении плазмотрона к детали, возникает вторая дуга, более мощная. Если сила тока от осциллятора равна 30-60 А, то рабочая дуга возникает при 180-200 А.
Эта дуга дополнительно разогревает газ, которые разгоняется под действием электрических сил до чрезвычайно высокой скорости — до 1500 м/с. Комбинированное действие высокой температуры плазмы и скорости движения разрезает металл по очень тонкой линии. Толщина разреза зависит от свойств сопла.
По-другому работает плазмотрон косвенного действия, в нем в качестве основного анода выступает сопло. Из резака вырывается не дуга, а поток плазмы — струя, которая и режет не токопроводящие вещества. Оборудование-самоделка с такими плазмотронами работает очень редко.
Из–за сложности устройства плазмотрона и тончайших настроек изготовить его практически невозможно самостоятельно, несмотря на простые чертежи, которые есть в интернете. Он работает под высокими давлениями и температурами и становится попросту опасным, если что-то сделать не так. Плазморез по чертежам своими руками можно собрать из готовых деталей, которые продаются в магазинах сварочного оборудования. Но, как и большинство машин и механизмов, сборка из комплектующих стоит дороже, чем готовый резак в сборе.
Осциллятор
Это своеобразный стартер, служащий для запуска предварительной дуги. Для разбирающихся в электронике схема его несложна. Функциональная схема выглядит так:
Функциональная схема осциллятора
А электрическая примерно так (один из вариантов):
Электрическая схема осциллятора
Как выглядит и работает самодельный осциллятор видно на видео. Если сборкой электросхем и поиском деталей нет времени заниматься, воспользуйтесь осцилляторами заводского изготовления, например ВСД-02. Его характеристики лучше всего подходят для работы с инвертором. Подсоединяется осциллятор в схему питания плазмотрона параллельно или последовательно, в зависимости от требований инструкции конкретного прибора.
Рабочий газ
Перед тем, как сделать плазморез, следует очертить предварительную сферу его применения. Если вы собираетесь работать только с черными металлами, то обойтись можно только компрессором. Для меди, титана и латуни потребуется азот, а резка алюминия происходит в смеси азота с водородом. Высоколегированные стали режутся в аргоновой атмосфере. В этом случае аппарат рассчитывается еще и под сжатый газ.
Сборка устройства
Ввиду достаточной сложности и многочисленности компонентов аппарата плазменной резки, его трудно разместить в переносном корпусе или ящике. Лучше всего использовать складскую тележку для перевозки товаров. На ней можно компактно расположить инвертор, баллоны или компрессор, кабельно-шланговую группу. В пределах цеха или мастерской перемещать их очень легко. Если потребуется выезд на другой объект, то все можно загрузить в прицеп легкового автомобиля.
самодельный, подробно, схемы и чертежи – Виды сварочных аппаратов на Svarka.guru
Для любителей постоянно мастерить полезные и красивые вещи из металла, кроме сварки периодически требуется резать металл. Можно изготовить плазморез из сварочного инвертора своими руками.Не стоит покупать дополнительное дорогое оборудование, которое будет редко использоваться. Плазморез возможно сделать из трансформатора, но он будет тяжелый и энергоемкий.
Для чего нужен?
Каждому специалисту периодически приходится выкраивать детали из листа. Делать это механической обработкой, значит перевести в стружку много металла. Покупать дорогое оборудование ради использования раз в неделю несколько минут, не имеет смысла. Выход – изготовить плазменный резак своими руками. Переделывать можно разные типы выпрямителей:
Работать будет любой аппарат. Оптимальный вариант, для любителей мастерить, изготовление самодельного плазмореза из сварочного инвертора. При использовании газовой резки производительность ниже, ширина реза больше.
[stextbox id=’warning’]Основное преимущество плазмореза — использование обычного воздуха. Давление создает компрессор. Нет риска взрыва или отравления, как при работе с пропаном, кислородом и другими газами.[/stextbox]
Толщина разрезаемого листа на бытовом оборудовании с током до 200А ограничена 40 – 50 мм. Для строительства дома и работы в домашней мастерской этой мощности хватает. Полупрофессиональный инвертор настраивается на толщину до 100 мм.Легкому и мощному оборудованию достаточно подсоединить компрессор и обычный держак заменить на плазмотрон, своими руками сделанный и купленный готовым. Оснастка оборудования легко меняется, и плазморезы инверторные превращаются в обычные аппараты, на которых производится сварка.
Принцип работы горелки
Плазменная резка своими руками происходит за счет превращения потока воздуха, проходящего через электрическую дугу, в плазму с температурой 3000 – 6000⁰C. Металл мгновенно расплавляется на ограниченном участке и выдувается. Принцип работы аналогичен газовой резке.
Образование плазмы
Инвертор создает постоянный ток большого значения. На конце электрода образуется дуга. В сопло под давлением поступает газ. Он проходит по спирали вокруг электрода. Образуется завихрение, движущееся с большой скоростью. В держак воздух поступает холодный. Двигаясь вокруг электрода, он его охлаждает и одновременно нагревается сам. В дуге он подходит уже подогретый.
На выходе струя газа становится тонкой. При соединении с горячей дугой, воздух нагревается ею и превращается в плазму, увеличиваясь в объеме в 20 – 30 раз. Вращение потока вокруг электрода делает струю тонкой.
Резка
Плазменная горелка, сделанная своими руками, подносится к металлу. Горячая плазма быстро расплавляет металл на малом участке. Воздушный поток выдувает расплав, образуя отверстие. При перемещении резака за ним остается узкая полоска разрезанного насквозь листа.Тонкий аккуратный рез получается при расположении плазмореза из инвертора под прямым углом к разрезаемой поверхности. Чем больше угол наклона, тем шире полоса реза.
Для производства строжки поверхности детали, плазменный резак по металлу, сделанный своими руками, наклоняется к снимаемой поверхности под острым углом в 5 – 10⁰. Пламя нагревает верхний слой, воздух выдувает жидкий металл.
Аппараты прямого действия
Прямого действия плазменные резаки по металлу, сделанные своими руками, работают с образованием дуги между деталью и электродом. Резать таким способом можно только токопроводящие металлы.
На деталь крепится зажим «+» от сварочного автомата. На электрод подается «–». На выходе из сопла наконечника образуется дуга между металлом и электродом. На нее направлен воздух.
Косвенного
Плазморез, собранный своими руками из инвертора, может работать по принципу косвенного действия. Минус подается на наконечник. Дуга возникает независимо от наличия токопроводящей детали. Резаком косвенного действия режут любые материалы, включая фанеру, пластик, оргстекло. Струя плазмы образуется тоньше.Сложность изготовления плазмотрона косвенного действия своими руками, демонстрируют схемы и чертежи. В небольшой наконечник длиной около 20 мм необходимо поместить воздушное охлаждение и надежно изолировать детали друг от друга.
[stextbox id=’info’]Руководитель конструкторского бюро по проектированию сварочного оборудования, оснастки и инструмента завода САИК Твердохлебов И. Г.: «В плазмотроне используют не привычный электрод, сделанный из прутка проволоки и покрытый флюсом. Сердечник расположен внутри горелки и не выходят за пределы сопла. Электрическая дуга в аппаратах прямого действия загорается бесконтактно и превращается на выходе из сопла в плазму. Резак косвенного действия выдувает горячую струю независимо от расположения материала и его электропроводности. Можно отжигать медные кольца и опаливать древесину».[/stextbox]
Источник тока
Если вопрос выбора типа источника питания не принципиальный, следует предпочесть инвертор. Легкий малогабаритный аппарат работает от бытового источника тока 220В. Он легко регулируется, потребляет мало электроэнергии. Большинство сварочных бытовых инверторов имеют рабочий коэффициент 50% и выше. Они имеют систему охлаждения. Платы мало греются, по сравнению с устройством другого оборудования.В качестве источника питания используется трансформатор, преобразующий электрический переменный ток в сварочный. Он более мощный, позволяет резать металл до 100 мм. Переделать трансформатор проще, чем другие выпрямители. Он имеет ряд недостатков для применения его в бытовых условиях:
- тяжелый;
- габаритный;
- работает от трехфазного тока 380В;
- потребляет много электроэнергии;
- низкий КПД.
Для массового производства партий однотипных деталей в мастерских и цехах, изготавливаются плазморезы из сварочного автомата своими руками.
Типовая конструкция
В список оборудования для изготовления плазмореза своими руками из инвертора входят:
- инвертор;
- компрессор;
- плазмотрон.
Пошаговый план создания плазмореза начинается со сборки плазмотрона. Самоделка включает в себя несколько деталей, требующих высокой точности изготовления. Все их можно купить готовые:
- в центре электрод из тугоплавкого металла;
- электродная втулка держит электрод и закручивает воздух;
- изоляционная втулка закрывает электрод от контакта с водой;
- фторопластовый корпус;
- сопло.
Самоделка требует аккуратности и точного изготовления всех деталей.
АПР-91 – схема переделки
Подробный чертеж для изготовления плазмореза показан для инвертора АПР-91. Специалисты считают эту модель наиболее удобной для переделки.
Кроме инвертора и компрессора, в изготовлении плазмореза используется много деталей. От самого плазмотрона, до подведенных к нему кабелей и шланга.
Электроды и кабель
Электроды подбираются их тугоплавких металлов: бериллий, ванадий, вольфрам. Они должны выдерживать температуру дуги и не разрушаться длительное время. Длина их относительно ширины 1,5 – 1,8. Длинные детали будут быстро сгорать.
Кабель обеспечивает равномерную подачу тока в зону образования плазмы. Он должен иметь сечение от 12 мм2, хорошую изоляцию.
Шланги воздушные от компрессора до держака подключаются для высокого давления.
Вентиляция
Инструкция по безопасным приемам работы требует, чтобы вентиляция в обязательном порядке присутствовала. Вытяжку наклонной конструкции должна располагаться на высоте 35 см от плоскости реза. Мощность вытяжного оборудования регулируется таким образом, чтобы весь дым от горящего металла втягивался системой. При этом не должно быть завихрений в рабочей зоне.
Сборка аппарата
Собирать следует начинать с плазмотрона. Узел требует точности и правильного подбора деталей. Если резать придется постоянно, необходимо иметь запасные электрод и сопло, они быстро сгорают.
Шланг и кабеля подключают сначала к оборудованию, затем к резаку. Только после этого можно инвертор подключать к сети.
Советы по эксплуатации самодельного плазмореза
Перед началом работы следует позаботиться о безопасности. Рядом должны находиться средства пожаротушения электрических приборов:
- ящик с песком;
- пенный или углекислотный огнетушитель;
- емкость с водой
График работы следует соблюдать указанный на инверторе. Оборудование должно остывать положенное ему время.
Без заземления работать нельзя.
Резать металл следует на специальном верстаке. Сварщик должен стоять или сидеть в удобной позе.
как сделать плазморез из сварочного инвертора или трансформатора, подробные схемы или чертежи для этого
Плазморез, в том числе и самодельный, успешно применяется для выполнения всевозможный работ как на производстве, так и дома.
Это устройство незаменимо в тех ситуациях, когда необходимо выполнить точный, тонкий и качественный разрез металлических заготовок.
Изготовить рабочий плазморез из сварочного инвертора своими руками не такая уж и сложная задача, как на первый взгляд может показаться. Для того чтобы реализовать данную идею, нужно приготовить все необходимые детали такого устройства:
- Резак плазменный (или по другому — плазмотрон)
- Инвертор сварочный или трансформатор
- Компрессор, с помощью которого будет создаваться воздушная струя, необходимая для формирования и охлаждения потока плазмы.
- Кабели и шланги для объединения всех конструктивных элементов устройства в одну систему.
Отдельные модели плазменных резаков с точки зрения их функциональности позволяют применять их в качестве сварочного аппарата. Такая сварка выполняется в защитном газе аргона.
При выборе источника питания для самодельного плазмотрона важно обратить внимание на величину тока, который может генерировать такой источник.
Чаще всего для этого выбирают инвертор, который обеспечивает высокую стабильность процесса плазменной резки и позволяет более экономно использовать энергию. В отличие от сварочного трансформатора, обладает компактными размерами и небольшим весом, инвертор удобнее в использовании.
Единственным недостатком использования инверторных плазменных резаков является сложность резки слишком толстых заготовок с их помощью.
При сборке самодельного агрегата для выполнения плазменной резки вы можете использовать готовые схемы, которые легко найти в Интернете.
Используя готовую схему при сборке такого устройства, очень важно строго её придерживаться, а также обратить особое внимание на соответствие конструктивных элементов друг другу.
Схемы плазмореза на примере аппарата АПР-91
В качестве примера при изучении принципиальной электрической схемы, мы будем использовать устройство для плазменной резки APR-91.
Принципиальная схема силовой части плазмореза! Принципиальная схема управления плазмореза.
Детали самодельного устройства для плазменной резки
Первое, что вам нужно найти для изготовления самодельного плазменного резака, это источник питания, в котором будет генерировать электрический ток с необходимыми характеристиками. Обычно для этого используют сварочные инверторные аппараты, что объясняется рядом их преимуществ.
Благодаря своим техническим характеристикам, подобное оборудование способно обеспечить высокую стабильность генерируемого напряжения, что положительно сказывается на качестве резки.
Работать с инверторами гораздо удобнее, что объясняется не только их компактными размерами и небольшим весом, но и простотой настройки и эксплуатации.
Благодаря своей компактности и малому весу плазменные резаки на основе инверторов могут использоваться при работе даже в самых трудных местах, что исключено для громоздких и тяжелых сварочных трансформаторов. Большим преимуществом инверторных источников питания является их высокая эффективность. Это делает их очень экономичными с точки зрения энергопотребления устройств.
В некоторых случаях источником питания для плазменного резака может быть сварочный трансформатор, но его использование чревато значительным энергопотреблением. Следует также учитывать, что любой сварочный трансформатор характеризуется большими габаритами и значительным весом.
Основным элементом аппарата, предназначенного для резки металла плазменной струей, является плазменный резак. Этот элемент оборудования обеспечивает качество резки, а также эффективность ее выполнения.
Для формирования воздушного потока, который будет преобразован в высокотемпературную плазменную струю, в конструкции плазменного резака используется специальный компрессор. Электрический ток от инвертора и поток воздуха от компрессора поступают в плазменный резак с помощью пакета кабельных шлангов.
Центральным рабочим элементом плазменного резака является плазменная горелка, конструкция которой состоит из следующих элементов:
- Сопла
- Канала, по которому подается струя воздуха
- Электрода
- Изолятора, который параллельно выполняет функцию охлаждения
Конструкция плазменного резака и советы по его изготовлению
Некоторые из вышеперечисленных материалов при нагревании могут выделять соединения, опасные для здоровья человека, этот момент следует учитывать при выборе типа электрода. Таким образом, при использовании бериллия образуются радиоактивные оксиды, и при испарении тория в сочетании с кислородом образуются опасные токсичные вещества. Совершенно безопасным материалом для изготовления электродов для плазменной горелки является гафний.
За формирование плазменной струи, с помощью которой и производится резка, отвечает сопло. Его производству следует уделить серьезное внимание, так как качество рабочего процесса зависит от характеристик этого элемента.
Самым оптимальным является сопло, диаметр которого равен 30 мм. От длины этой детали, зависит аккуратность и качество исполнения реза. Однако слишком длинное сопло также не следует делать, так как в данном случае оно быстро разрушается.
Как было упомянуто выше, в конструкцию плазмореза обязательно входит компрессор, который формирует и подает воздух в сопло. Последнее необходимо не только для формирования струи высокотемпературной плазмы, но и для того что бы охлаждать элементов аппарата.
Применение сжатого воздуха в качестве рабочей и охлаждающей среды, а также инвертора, который формирует рабочий ток 200 А, позволяет эффективно резать металлические детали, толщина которых не превышает 50 мм.
Для подготовки аппарата плазменной резки к работе, нужно соединить плазмотрон с инвертором и компрессором. Для решения этой задачи применяются пакеты кабельных шлангов, который используют следующим образом.
- Кабель, через который будет подаваться электрический ток, соединяет инвертор и электрод плазменной резки.
- Шланг подачи сжатого воздуха соединяет выход компрессора и плазменную горелку, в которой из входящего воздушного потока будет образовываться плазменная струя.
Основные особенности работы плазмореза
Чтобы сделать плазменный резак, используя инвертор для его изготовления, необходимо понять, как работает такое устройство.
После включения инвертора электрический ток от него начинает течь к электроду, что приводит к воспламенению электрической дуги. Температура дуги, горящей между рабочим электродом и металлическим наконечником сопла, составляет около 6000–8000 градусов.
После зажигания дуги сжатый воздух подается в камеру сопла, которая проходит строго через электрический разряд. Электрическая дуга нагревает и ионизирует воздушный поток, проходящий через нее. В результате его объем увеличивается в сотни раз, и он становится способным проводить электрический ток.
С помощью сопла плазменного резака из проводящего воздушного потока формируется плазменная струя, температура которой активно поднимается и может достигать 25-30 тысяч градусов.
Скорость потока плазмы, благодаря которой осуществляется резка металлических деталей, на выходе из сопла составляет около 2-3 метров в секунду.
В тот момент, когда плазменная струя контактирует с поверхностью металлической детали, электрический ток от электрода начинает протекать через нее, и начальная дуга гаснет. Новая дуга, которая горит между электродом и заготовкой, называется резкой.
Характерной особенностью плазменной резки является то, что обрабатываемый металл плавится только в том месте, где на него влияет поток плазмы. Вот почему очень важно, чтобы место плазменного воздействия было строго в центре рабочего электрода.
Если мы пренебрегаем этим требованием, то можем столкнуться с тем фактом, что воздушно-плазменный поток будет нарушен, в следствии чего, качество резки значительно ухудшится.
Чтобы удовлетворить эти важные требования, используйте специальный (тангенциальный) принцип подачи воздуха к соплу.
Также необходимо следить, что бы два плазменных потока не образовывались одновременно, за места одного. Возникновение такой ситуации, которая приводит к несоблюдению режимов и правил технологического процесса, может привести к выходу из строя инвертора.
Важным параметром плазменной резки является скорость воздушного потока, которая не должна быть слишком большой. Хорошее качество реза и скорость его выполнения обеспечиваются скоростью воздушной струи, равной 800 м/с. В этом случае ток, протекающий от инверторного блока, не должен превышать 250 А.
При выполнении работ на таких режимах следует учитывать тот факт, что в этом случае поток воздуха, используемого для формирования потока плазмы, будет увеличиваться.
Самостоятельно изготовить плазменный резак не так уж и сложно, для этого нужно изучить нужный теоретический материал, просмотреть обучающее видео и правильно подобрать все необходимые детали. При наличии в домашнем пользовании подобного аппарата, изготовленного на основе заводского инвертора, может выполнять не только качественную резку металла, но и плазменную сварку!
В том случае если у вас в пользовании нет инвертора, можно изготовить плазморез, взяв за основу сварочный трансформатор, в таком случае вам придется смириться с его большими габаритами и не малым весом. Так же, плазморез, сделанный на основе трансформатора, будет иметь не очень хорошую мобильностью и переносить его с места на место будет проблематично!
Источник: https://kavmaster.ru/plazmorez-iz-invertora-svoimi-rukami/
Плазменный резак своими руками: самодельный плазморез из сварочного инвертора
Плазменные резаки активно используются в мастерских и предприятиях, связанных с цветными металлами. Большинство небольших предприятий применяют в работе плазменный резак, изготовленный своими руками.
Плазменный резак хорошо себя показывает при разрезе цветных металлов, поскольку позволяет локально прогревать изделия и не деформировать их. Самостоятельное производство резаков обусловлено высокой стоимостью профессионального оборудования. В процессе изготовления подобного инструмента используются комплектующие от других электроприборов.
Особенности и назначение плазменного резака
Инвертор плазменной резки используется для выполнения работ как в домашних, так и в промышленных условиях. Существует несколько видов плазморезов для работы с различными типами металлов.
Различают:
- Плазморезы, работающие в среде инертных газов, например, аргона, гелия или азота.
- Инструменты, работающие в среде окислителей, например, кислорода.
- Аппаратура, предназначенная для работы со смешанными атмосферами.
- Резаки, работающие в газожидкостных стабилизаторах.
- Устройства, работающие с водной или магнитной стабилизацией. Это самый редкий вид резаков, который практически невозможно найти в свободной продаже.
Плазменный резак или плазматрон – это основная часть плазменной резки, отвечающая за непосредственную нарезку металла.
Большинство инверторных плазменных резаков состоят из:
- форсунки;
- электрода;
- защитного колпачка;
- сопла;
- шланга;
- головки резака;
- ручки;
- роликового упора.
Принцип действия простого полуавтоматического плазмореза состоит в следующем: рабочий газ вокруг плазмотрона прогревается до очень высоких температур, при которых происходит возникновение плазмы, проводящей электричество.
Затем, ток, идущий через ионизированный газ, разрезает металл путем локального плавления. После этого струя плазмы снимает остатки расплавленного металла и получается аккуратный срез.
По виду воздействия на металл различают такие виды плазматронов:
- Аппараты косвенного действия. Данный вид плазматронов не пропускает через себя ток и пригоден лишь в одном случае – для резки неметаллических изделий.
- Плазменная резка прямого действия. Применяется для разрезки металлов путем образования плазменной струи.
Конструкция плазменного резака и рекомендации по работе с ним серьезно разнятся в зависимости от типа устройства.
Делаем плазменный резак своими руками
Плазменная резка своими руками может быть изготовлена в домашних условиях. Неподъемная стоимость на профессиональное оборудование и ограниченное количество представленных на рынке моделей вынуждают умельцев собирать плазморез из сварочного инвертора своими руками. Самодельный плазморез можно выполнить при условии наличия всех необходимых компонентов.
Перед тем как сделать плазморежущую установку, необходимо подготовить следующие комплектующие:
- Компрессор. Деталь необходима для подачи воздушного потока под давлением.
- Плазмотрон. Изделие используется при непосредственной резке металла.
- Электроды. Применяются для розжига дуги и создания плазмы.
- Изолятор. Предохраняет электроды от перегрева при выполнении плазменной резки металла.
- Сопло. Деталь, размер которой определяет возможности всего плазмореза, собранного своими руками из инвертора.
- Сварочный инвертор. Источник постоянного тока для установки. Может быть заменен сварочным трансформатором.
Трансформаторные источники постоянного тока характеризуются следующими недостатками:
- высокое потребление электрической энергии;
- большие габариты;
- труднодоступность.
К преимуществам такого источника питания можно отнести:
- низкую чувствительность к перепадам напряжения;
- большую мощность;
- высокую надежность.
Инверторы, в качестве блока питания плазмореза можно использовать, если необходимо:
- сконструировать небольшой аппарат;
- собрать качественный плазморез с высоким коэффициентом полезного действия и стабильной дугой.
Благодаря доступности и легкости инверторного блока питания плазморезы на его основе могут быть сконструированы в домашних условиях. К недостаткам инвертора можно отнести лишь сравнительно малую мощность струи. Из-за этого толщина металлической заготовки, разрезаемой инверторным плазморезом, серьезно ограничена. Одной из главнейших частей плазмореза является ручной резак.
Сборка данного элемента аппаратуры для резки металла осуществляется из таких компонентов:
- рукоять с пропилами для прокладки проводов;
- кнопка запуска горелки на основе газовой плазмы;
- электроды;
- система завихрения потоков;
- наконечник, защищающий оператора от брызг расплавленного металла;
- пружина для обеспечения необходимого расстояния между соплом и металлом;
- насадки для снятия окалин и нагара.
Резка металла различной толщины осуществляется путем смены сопел в плазмотроне. В большинстве конструкций плазмотрона, сопла закрепляются специальной гайкой, с диаметром, позволяющим пропустить конусный наконечник и зажать широкую часть элемента.
После сопла располагаются электроды и изоляция. Для получения возможности усиления дуги при необходимости в конструкцию плазматрона включают завихритель воздушных потоков.
Сделанные своими руками плазморезы на основе инверторного источника питания являются достаточно мобильными. Благодаря малым габаритам такую аппаратуру можно использовать даже в самых труднодоступных местах.
Чертежи
В глобальной сети интернет имеется множество различных чертежей плазменного резака. Проще всего изготовить плазморез в домашних условиях, используя инверторный источник постоянного тока.
Наиболее ходовой технический чертеж резака на основе плазменной дуги включает следующие компоненты:
- Электрод. На данный элемент подается напряжение от источника питания для осуществления ионизации окружающего газа. Как правило, в качестве электрода используются тугоплавкие металлы, образующие прочный окисел. В большинстве случаев конструкторы сварочных аппаратов используют гафний, цирконий или титан. Лучшим выбором материала электрода для домашнего использования является гафний.
- Сопло. Компонент автоматического плазменный сварочного аппарата формирует струю из ионизированного газа и пропускает воздух, охлаждающий электрод.
- Охладитель. Элемент используется для отвода тепла от сопла, поскольку при работе температура плазмы может достигать 30 000 градусов Цельсия.
Большинство схем аппарата плазменной резки подразумевают такой алгоритм работы резака на основе струи ионизированного газа:
- Первое нажатие на кнопку пуск включает реле, подающее питание на блок управления аппаратом.
- Второе реле подает ток на инвертор и подключает электрический клапан продувки горелки.
- Мощный поток воздуха попадает в камеру горелки и очищает ее.
- Через определенный промежуток времени, задаваемый резисторами, срабатывает третье реле и подает питание на электроды установки.
- Запускается осциллятор, благодаря которому производится ионизация рабочего газа, находящегося между катодом и анодом. На данном этапе возникает дежурная дуга.
- При поднесении дуги к металлической детали зажигается дуга между плазмотроном и поверхностью, называющаяся рабочей.
- Отключение подачи тока для розжига дуги при помощи специального геркона.
- Проведение резальных или сварочных работ. В случае пропажи дуги, реле геркона вновь включает ток и разжигает дежурную струю плазмы.
- При завершении работ после отключения дуги, четвертое реле запускает компрессор, воздух которого охлаждает сопло и удаляет остатки сгоревшего металла.
Что нам понадобится?
Для создания аппарата плазменной сварки необходимо обзавестись:
- источником постоянного тока;
- плазмотроном.
В состав последнего входят:
- сопло;
- электроды;
- изолятор;
- компрессор мощностью 2-2.5 атмосферы.
Большинство современных мастеров изготавливают плазменную сварку, подключаемую к инверторному блоку питания. Сконструированный при помощи данных компонентов плазмотрон для ручной воздушной резки работает следующим образом: нажатие на управляющую кнопку зажигает электрическую дугу между соплом и электродом.
Сборка инвертора
В случае, если фабричного инвертора нет в наличии, можно собрать самодельный.
Инверторы для резаков на основе газовой плазмы, как правило, имеют в строении такие комплектующие:
- блок питания;
- драйвера силовых ключей;
- силовой блок.
Сборка инвертора для плазморезов или сварочного оборудования не может обойтись без необходимых инструментов в виде:
- набора отверток;
- паяльника;
- ножа;
- ножовки по металлу;
- крепежных элементов резьбового типа;
- медных проводов;
- текстолита;
- слюды.
Блок питания самодельного инвертора для плазменной резки собирается на базе ферритового сердечника и должен иметь четыре обмотки:
- первичную, состоящую из 100 витков проволоки, толщиной 0.3 миллиметра;
- первая вторичная из 15 витков кабеля с толщиной 1 миллиметр;
- вторая вторичная из 15 витков проволоки 0.2 миллиметра;
- третья вторичная из 20 витков 0.3 миллиметровой проволоки.
Силовой блок самодельного инвертора должен состоять из специального трансформатора. Для создания данного элемента следует подобрать два сердечника и намотать на них медную проволоку толщиной 0.25 миллиметров.
Отдельного упоминания стоит система охлаждения, без которой инверторный блок питания плазмотрона может быстро выйти из строя.
Рекомендации по работе
При работе на аппарате плазменной резки для достижения наилучших результатов нужно соблюдать рекомендации:
- регулярно проверять правильность направления струи газовой плазмы;
- проверять правильность выбора аппаратуры в соответствии с толщиной металлического изделия;
- следить за состоянием расходных деталей плазмотрона;
- следить за соблюдением расстояния между плазменной струей и обрабатываемым изделием;
- всегда проверять используемую скорость резки, чтобы избежать возникновения окалин;
- время от времени диагностировать состояние системы подвода рабочего газа;
- исключить вибрацию электрического плазмотрона;
- поддерживать чистоту и аккуратность на рабочем месте.
Заключение
Аппаратура для плазменной резки – это незаменимый инструмент для аккуратной нарезки металлических изделий. Благодаря продуманной конструкции плазмотроны обеспечивают быстрый, ровный и качественный порез металлических листов без необходимости последующей обработки поверхностей.
Большинство рукоделов из небольших мастерских предпочитают своими руками собирать мини резаки для работы с не толстым металлом. Как правило, самостоятельно сделанный плазморез по характеристикам и качеству работы не отличается от заводских моделей.
Источник: https://tutsvarka.ru/oborudovanie/plazmennyj-rezak-svoimi-rukami
Как из сварочного инвертора сделать плазморез своими руками? Рекомендации по изготовлению!
Отслужившие детали различных машины и инструментов отлично подходят для изготовления полезных в домашнем хозяйстве устройств своими руками. Если есть в наличии ненужный сварочный инвертор, то из него можно сделать самодельный плазморез.
О том, каким образом превратить прибор для сваривания металла в устройство, которое способно разрезать прочный материал, будет подробно рассказано в этой статье.
Преимущество плазмореза перед газовым резаком
Одним из самых простых устройств для резки металла является газовый резак. Такой прибор стоит небольших денег и расходные материалы к нему также недороги. Но при выполнении газосварочных работ происходит нагрев слишком большой площади металла.
По этой причине материалы, обладающие большой теплопроводностью могут покоробиться и изменить цвет. Как в месте плавления металла, так и на значительном удалении от термического воздействия пламени горелки.
Преимущество плазмореза заключается в том, что удаётся получить очень тонкую струю раскалённого газа, которая будет воздействовать на небольшую площадь поверхности, что позволит значительно уменьшить нагрев детали.
Принцип работы плазмореза
Изготовить плазморез самостоятельно, не разбираясь в принципе работы этого устройства практически невозможно.
Процесс образования плазмы происходит в результате:
- Подачи электрического тока в горелку.
- Между электродами (катод и анод) горелки возникает электрическая дуга.
- Воздух под давлением подаётся в горелку и «выдувает» дугу наружу, при этом значительно увеличивая её температуру.
- К разрезаемому металлу подключается кабель «массы», поэтому ионизируемое пламя как бы замыкает о поверхность материала.
В результате получается высокоэффективное устройство для разрезания различных металлов. В том числе тех, которые обладают повышенными показателями теплопроводности.
Детали для самодельного устройства
Плазморез из сварочного инвертора своими руками изготавливается из следующих деталей.
- Плазмотрон. Эта деталь в конструкции плазмореза является наиболее важной.
Даже при наличии необходимого по силе электрического тока и давления газа, дугу не удастся получить, если внутренние электроды будут неправильно расположены. А отверстие для подачи воздуха будет иметь неподходящий диаметр.
Стоит такая деталь довольно дорого, поэтому домашние мастера предпочитают изготавливать горелки самостоятельно из подручных деталей.
- Источник тока. В самодельном плазморезе источником тока будет сварочный инвертор.
- Компрессор. Чтобы обеспечить длительную подачу сжатого воздуха в плазмотрон необходимо приобрести компрессор средней мощности.
Также потребуются для самодельного плазмореза купить достаточное количество медных проводов большого диаметра. Для подключения «массы» к разрезаемой детали и обеспечения плазмотрона необходимым количеством электроэнергии.
Самостоятельное изготовление плазмотрона
Горелка или плазмотрон может быть изготовлена из подручных материалов. Чтобы собрать этот элемент самодельного плазмореза понадобятся:
- ручка;
- кнопка пуска;
- специальный электрод;
- сопло;
- изолятор.
Для изготовления самодельного плазмотрона идеально подойдёт ручка от мощного паяльника. Как правило, такая деталь имеет серединное отверстие, через которое и будут подводиться электрический ток и сжатый воздух.
Кнопку лучше использовать достаточно большую, чтобы во время работы пользоваться устройством было максимально комфортно.
Электроды потребуется приобрести в магазине. Для самостоятельного изготовления плазмотрона лучше выбирать изделия, изготовленные из гафния. Для работы с металлами различной толщины потребуется также купить набор сопл.
Изготавливается плазмотрон в такой последовательности:
- Сразу за ручкой помещается металлическая трубка, покрытая изнутри фторопластом.
- Внутри трубки размещается электрод, который почти по всей длине закрыт высокотемпературной изоляцией.
- За электродом устанавливается с помощью резьбового соединения сопло подходящего диаметра.
Плазмотрон готов к использованию. Ещё для работы устройства потребуется подключить для подачи воздуха шланг от компрессора и электрический провод от инвертора.
Источник тока
В качестве источника электроэнергии можно использовать сварочный инвертор со следующими показателями:
- напряжение питания – 220 В;
- мощность – от 4 кВт;
- возможность регулировки тока от 20 – 40 А.
Сборка плазмореза
Когда отдельные детали плазмореза будут готовы, можно приступить к сборке. Чтобы работать с самодельным устройством было максимально комфортно, необходимо свести к минимуму количество тянущихся за ручкой проводов и шлангов.
Для более компактного размещения рабочего провода его помещают внутри шланга, по которому производится подача сжатого воздуха. Провод надёжно подсоединяется к электроду, при этом шланг также должен быть подключён к горелке без образования зазоров.
Другой контакт от инвертора будет подключаться к разрезаемой детали в качестве «массы» поэтому его следует оборудовать клеммой типа «крокодил».
Процесс разрезания металла с помощью плазменного резака очень прост. После подачи электричества образуется электрическая дуга. Момент образования запала регулируется кнопкой, которая была ранее установлена на ручке плазмотрона. Воздух подаётся от компрессора по шлангу и раздувает дугу, тем самым увеличивая её температуру, которая может достигать 8000ºС.
Для того чтобы затушить дугу достаточно отпустить кнопку на ручке. Таким образом горелка будет работать только в тот момент, когда необходимо разрезать металл, что сведёт к минимуму эффект перегрева, к которому самодельные изделия очень чувствительны.
Советы и рекомендации
Важно не только знать, как переделать инвертор в плазморез, но и как сделать работу такого устройства максимально эффективной и безопасной.
Далее будут приведены несколько рекомендаций. Придерживаясь которых можно избежать наиболее распространённых ошибок при изготовлении и использовании самодельного устройства:
- Перед тем как приступить к изготовлению из сварочного инвертора устройства для резки металлов, следует наметить на бумаге основные элементы такой системы. Самостоятельно изготовленные чертежи и схемы позволят в процессе работы не допустить досадных ошибок, которые наиболее часто бывают вызваны обычной невнимательностью.
- Несмотря на то, что плазменный резак имеет очень узкое пламя, которое не слишком разогревает даже металлы обладающие повышенной теплопроводностью, рекомендуется при работе с алюминиевыми изделиями использовать в качестве распыляющего газа неон или аргон, которые не позволят окислиться поверхности, подвергнувшейся воздействию высокой температуры.
- Чтобы максимально сократить время на изготовление плазмореза рекомендуется приобрести готовую горелку для газового резака. Такое изделие позволит максимально эффективно и безопасно работать с металлом.
- При использовании самодельного плазмореза необходимо придерживаться основных правил техники безопасности. Прежде всего, следует обеспечить защиту от воздействия электричества и брызг расплавленного металла. Для этой цели используются специальная обувь, перчатки и фартук. Также необходимо надевать защитные очки, которые позволят предохранить зрение от воздействия ультрафиолетовых лучей. В процессе резки металла выделяется большое количество вредных для здоровья веществ, поэтому рекомендуется защищать органы дыхания с помощью респиратора.
Источник: https://plavitmetall.ru/oborudovanie/plazmorez-iz-svarochnogo-invertora-svoimi-rukami.html
Как сделать плазморез из сварочного инвертора?
Плазморез — это приспособление, необходимое каждому домашнему умельцу. Без него невозможна быстрая резка металлов и изготовление самоделок. Современные плазморезы можно купить в любом крупном городе, вот только их стоимость не всегда бывает приемлемой.
Качественный агрегат стоит как минимум 300$, и не всякий сварщик готов отдавать за него такую сумму. А покупать дешевый плазморез тоже нет смысла, поскольку он вряд ли выдержит даже редкие попытки резать металл, не говоря уже о постоянном использовании.
К тому же, заводской плазморез трудно чинить и обслуживать в домашних условиях. Покупной плазморез сложно устроен, и порой вмешательства в его конструктив могут привести к потере гарантии. Эту проблему можно решить двумя способами: покупкой б/у аппарата или сборкой самодельного плазмореза.
Мы считаем, что при нечастом использовании есть смысл изготовить плазморез самому. Самодельный плазморез из сварочного инвертора или трансформатора хорошо справляется даже с резкой толстых металлов, и в этом вы сможете убедиться сами.
Эта статья о том, что такое плазменная резка, какового устройство плазмореза и как сконструировать такой прибор своими руками.
Общая информация
Чтобы понимать принцип работы плазмореза, необходимо разбираться в самой технологии резки. Итак, плазменная резка — это способ обработки металла, в основе которого лежит применение плазмы в качестве резца. Плазма — это ионизированный газ.
У плазменной резки есть множество преимуществ по сравнению с другими технологиями:
- Можно резать любые металлы вне зависимости от их состава и особенностей
- Резка плазмой осуществляется в два раза быстрее, чем при использовании газопламенной технологии. Это особенно заметно при резке тонких деталей
- Детали не деформируются при резке, поскольку в процессе область реза нагревается
- Рез получается очень аккуратным и чистым
- Для резки не нужно использовать газовый баллон, поэтому повышается безопасность работ
- С помощью плазмореза можно выполнять фигурную резку без ограничений по форме и размеру
- Плазморез можно использовать не только с металлическими деталями.
Существуют различные типы плазморезов. Мы не будем перечислять их в рамках этой статьи. Скажем лишь, что они могут быть инверторными и трансформаторными. Применение инверторной технологии позволяет изготовить плазморез для сварки тонких деталей. Трансформаторный плазморез более универсален и подходит для толстых деталей.
Устройство плазмореза
Итак, теперь вы знаете, что для резки плазморезом используется плазма — ионизированный газ. Плазма обладает крайне высокой степенью проводимости электрического тока. При этом степень проводимости увеличивается со степенью нагрева плазмы. Это значит, что чем выше температура плазмы, тем больше сила резки.
Для выполнения резки применяют не чистую плазму, а воздушно-плазменную дугу. Электрический ток напрямую воздействует на металл, формируя рез. Для тех, кто хочет знать больше подробностей, мы поясним.
Плазморез формирует воздушно-плазменную дугу, которую сварщик должен направить в зону резки. Металл начнет медленно нагреваться, а вскоре и плавиться. Затем металл, находясь в жидком состоянии, выдувается из зоны резки.
Стандартный плазморез состоит из нескольких компонентов. Самый главный — это инвертор или трансформатор, который играет роль источника питания. Также необходим компрессор и сам резак, который также называют плазматроном.
Отдельно обратим внимание на конструктив плазмотрона. Внутри резака присутствует электрод, который изготавливается из циркония, бериллия, гафния и других редких металлов.
При нагревании на поверхности такого электрода образовываются тугоплавкие оксиды, которые защищают сам электрод от разрушения. Это одна из причин, почему не стоит изготавливать резак своими руками. Лучше приобрести его в магазине.
Также обратите внимание на сопло, которое напрямую участвует при подаче воздушно-плазменной дуги. Сопло может иметь различную длину и диаметр. Подбирая диаметр, определитесь, как быстро будете выполнять резку. Чем больше диаметр, тем больше и плазменный поток, а значит и резка происходит быстрее. Мы рекомендуем использовать сопло диаметром 3 мм. Оно наиболее универсально.
Что касается длины, то здесь важно соблюдать золотую середину. Чем длиннее сопло, тем быстрее оно выходит из строя. Но при этом качество реза заметно выше. Приобретите сопла разной длины и поэкспериментируйте. Выберите для себя оптимальное.
Как сделать плазморез
Как вы заметили, заголовок нашей статьи звучит так: «Как сделать плазморез из сварочного инвертора». Это один из самых частых запросов по данной теме. Но спешим вас огорчить: собирать плазморез из инвертора своими руками — это не самая лучшая идея. Точнее так: использовать инвертор в качестве источника тока в самодельном плазморезе — это неэффективное и дорогое занятие. И вот почему.
Стандартный инвертор работает от сети 220В. Для резки очень тонкого металла этого может быть достаточно, но для выполнения более сложных работ вам понадобится источник, работающий от 380В. Для этих целей годится трансформатор. Кроме того, в плазморезе поджиг дуги контактный, а его невозможно сделать дома при использовании инвертора в качестве «донора».
Также учитывайте, что нельзя взять просто самый дешевый инвертор и сделать из него плазморез. Вам понадобится достаточно мощный и качественный аппарат, стоимостью минимум 150-200$.
Что уже составляет половину или более от цены заводского плазмореза. Дополнительно вам понадобится плазмотрон и клапан. В итоге общая стоимость такой самоделки составит те самые 300$, которые просят за новый плазморез в магазине.
Вердикт: сделать дешевый плазморез из инвертора невозможно. Переделка ММА-аппарата в резак целесообразна только в том случае, если вам просто нравится мастерить все своими руками, а не покупать готовое.
Ну а если вы просто хотите сделать недорогой плазморез, то целесообразнее изготовить плазменный резак из обычного трансформатора. Трансформатор — это самый простой источник тока. В нем нет никаких электронных компонентов, поэтому он наиболее надежен.
Самодельный плазморез из трансформатора будет работать даже при перепадах напряжения. А благодаря большой мощности от сможет резать толстый металл. Единственный недостаток — это большие габариты и вес такого плазмореза. К тому же, он будет потреблять немало электроэнергии.
Что такое сварочный трансформатор?
Ниже видео о том, как смастерить плазморез из сварочного трансформатора своими руками. А также подробные схемы от одного из умельцев, найденные в открытом доступе.
Мы не рекомендуем собираться своими руками плазмотрон (он же резак). Это невыгодно и сложно. Себестоимость самодельного резака будет близка к себестоимости магазинного. Так что лучше соберите «начинку» плазмореза, а все комплектующие докупите.
Вместо заключения
Как видите, чтобы сделать плазморез из сварочного инвертора своими руками, необходимо потратиться. И в большинстве случаев эта трата нецелесообразна, поскольку разница в цене между самодельным плазморезом и заводским будет несущественной. Мы рекомендуем изготавливать плазморез из трансформатора. Так вы получите недорогой аппарат, способный варить толстые и тонкие металлы, что удобно в быту.
Плазморез, изготовленный из трансформатора, прослужит вам долгие годы. Он надежен и прост в применении, а его ремонт не ударит по кошельку. Словом, плазморез из трансформатора — это оптимальный вариант для домашнего мастера. Для его сборки не нужны дорогостоящие комплектующие, что крайне важно.
Источник: https://zen.yandex.ru/media/id/5bf3137cd8320000adc8b015/5c472820a600e200adaab4b4
Плазморез своими руками из инвертора – делаем самодельный плазменный резак
Изготовить рабочий плазморез из сварочного инвертора своими руками не такая уж и сложная задача, как на первый взгляд может показаться. Для того чтобы реализовать данную идею, нужно приготовить все необходимые детали такого устройства:
- Резак плазменный (или по другому — плазмотрон)
- Инвертор сварочный или трансформатор
- Компрессор, с помощью которого будет создаваться воздушная струя, необходимая для формирования и охлаждения потока плазмы.
- Кабели и шланги для объединения всех конструктивных элементов устройства в одну систему.
Плазморез, в том числе и самодельный, успешно применяется для выполнения всевозможный работ как на производстве, так и дома.
Это устройство незаменимо в тех ситуациях, когда необходимо выполнить точный, тонкий и качественный разрез металлических заготовок.
Отдельные модели плазменных резаков с точки зрения их функциональности позволяют применять их в качестве сварочного аппарата. Такая сварка выполняется в защитном газе аргона.
Обратный кабель и газовый шланг для плазменной резки!
При выборе источника питания для самодельного плазмотрона важно обратить внимание на величину тока, который может генерировать такой источник.
Чаще всего для этого выбирают инвертор, который обеспечивает высокую стабильность процесса плазменной резки и позволяет более экономно использовать энергию. В отличие от сварочного трансформатора, обладает компактными размерами и небольшим весом, инвертор удобнее в использовании.
Единственным недостатком использования инверторных плазменных резаков является сложность резки слишком толстых заготовок с их помощью.
На фото горелка от плазменного резака ABIPLAS и ее составные части!
При сборке самодельного агрегата для выполнения плазменной резки вы можете использовать готовые схемы, которые легко найти в Интернете.
Кроме того, в Интернете есть видео о том, как изготовить плазморез своими руками.
Используя готовую схему при сборке такого устройства, очень важно строго её придерживаться, а также обратить особое внимание на соответствие конструктивных элементов друг другу.
Схемы плазмореза на примере аппарата АПР-91
В качестве примера при изучении принципиальной электрической схемы, мы будем использовать устройство для плазменной резки APR-91.
Принципиальная схема силовой части плазмореза! Принципиальная схема управления плазмореза Принципиальная схема осциллятора!
Детали самодельного устройства для плазменной резки
Первое, что вам нужно найти для изготовления самодельного плазменного резака, это источник питания, в котором будет генерировать электрический ток с необходимыми характеристиками. Обычно для этого используют сварочные инверторные аппараты, что объясняется рядом их преимуществ.
Благодаря своим техническим характеристикам, подобное оборудование способно обеспечить высокую стабильность генерируемого напряжения, что положительно сказывается на качестве резки.
Работать с инверторами гораздо удобнее, что объясняется не только их компактными размерами и небольшим весом, но и простотой настройки и эксплуатации.
Принцип работы устройства для плазменной резки!
Благодаря своей компактности и малому весу плазменные резаки на основе инверторов могут использоваться при работе даже в самых трудных местах, что исключено для громоздких и тяжелых сварочных трансформаторов. Большим преимуществом инверторных источников питания является их высокая эффективность. Это делает их очень экономичными с точки зрения энергопотребления устройств.
В некоторых случаях источником питания для плазменного резака может быть сварочный трансформатор, но его использование чревато значительным энергопотреблением. Следует также учитывать, что любой сварочный трансформатор характеризуется большими габаритами и значительным весом.
Основным элементом аппарата, предназначенного для резки металла плазменной струей, является плазменный резак. Этот элемент оборудования обеспечивает качество резки, а также эффективность ее выполнения.
Размер и форма плазменной струи полностью зависит от диаметра сопла!
Для формирования воздушного потока, который будет преобразован в высокотемпературную плазменную струю, в конструкции плазменного резака используется специальный компрессор. Электрический ток от инвертора и поток воздуха от компрессора поступают в плазменный резак с помощью пакета кабельных шлангов.
Центральным рабочим элементом плазменного резака является плазменная горелка, конструкция которой состоит из следующих элементов:
- Сопла
- Канала, по которому подается струя воздуха
- Электрода
- Изолятора, который параллельно выполняет функцию охлаждения
Конструкция плазменного резака и советы по его изготовлению
Сменные насадки для плазмотрона
Некоторые из вышеперечисленных материалов при нагревании могут выделять соединения, опасные для здоровья человека, этот момент следует учитывать при выборе типа электрода. Таким образом, при использовании бериллия образуются радиоактивные оксиды, и при испарении тория в сочетании с кислородом образуются опасные токсичные вещества. Совершенно безопасным материалом для изготовления электродов для плазменной горелки является гафний.
За формирование плазменной струи, с помощью которой и производится резка, отвечает сопло. Его производству следует уделить серьезное внимание, так как качество рабочего процесса зависит от характеристик этого элемента.
Устройство сопла плазменной горелки
Самым оптимальным является сопло, диаметр которого равен 30 мм. От длины этой детали, зависит аккуратность и качество исполнения реза. Однако слишком длинное сопло также не следует делать, так как в данном случае оно быстро разрушается.
Как было упомянуто выше, в конструкцию плазмореза обязательно входит компрессор, который формирует и подает воздух в сопло.
Последнее необходимо не только для формирования струи высокотемпературной плазмы, но и для того что бы охлаждать элементов аппарата.
Применение сжатого воздуха в качестве рабочей и охлаждающей среды, а также инвертора, который формирует рабочий ток 200 А, позволяет эффективно резать металлические детали, толщина которых не превышает 50 мм.
Таблица выбора газа для плазменной резки металлов!
Для подготовки аппарата плазменной резки к работе, нужно соединить плазмотрон с инвертором и компрессором. Для решения этой задачи применяются пакеты кабельных шлангов, который используют следующим образом.
- Кабель, через который будет подаваться электрический ток, соединяет инвертор и электрод плазменной резки.
- Шланг подачи сжатого воздуха соединяет выход компрессора и плазменную горелку, в которой из входящего воздушного потока будет образовываться плазменная струя.
Основные особенности работы плазмореза
Чтобы сделать плазменный резак, используя инвертор для его изготовления, необходимо понять, как работает такое устройство.
После включения инвертора электрический ток от него начинает течь к электроду, что приводит к воспламенению электрической дуги. Температура дуги, горящей между рабочим электродом и металлическим наконечником сопла, составляет около 6000–8000 градусов.
После зажигания дуги сжатый воздух подается в камеру сопла, которая проходит строго через электрический разряд. Электрическая дуга нагревает и ионизирует воздушный поток, проходящий через нее.
В результате его объем увеличивается в сотни раз, и он становится способным проводить электрический ток.
С помощью сопла плазменного резака из проводящего воздушного потока формируется плазменная струя, температура которой активно поднимается и может достигать 25-30 тысяч градусов.
Скорость потока плазмы, благодаря которой осуществляется резка металлических деталей, на выходе из сопла составляет около 2-3 метров в секунду.
В тот момент, когда плазменная струя контактирует с поверхностью металлической детали, электрический ток от электрода начинает протекать через нее, и начальная дуга гаснет. Новая дуга, которая горит между электродом и заготовкой, называется резкой.
Характерной особенностью плазменной резки является то, что обрабатываемый металл плавится только в том месте, где на него влияет поток плазмы. Вот почему очень важно, чтобы место плазменного воздействия было строго в центре рабочего электрода.
Если мы пренебрегаем этим требованием, то можем столкнуться с тем фактом, что воздушно-плазменный поток будет нарушен, в следствии чего, качество резки значительно ухудшится.
Чтобы удовлетворить эти важные требования, используйте специальный (тангенциальный) принцип подачи воздуха к соплу.
Также необходимо следить, что бы два плазменных потока не образовывались одновременно, за места одного. Возникновение такой ситуации, которая приводит к несоблюдению режимов и правил технологического процесса, может привести к выходу из строя инвертора.
Основные параметры плазменной резки разных металлов.
Важным параметром плазменной резки является скорость воздушного потока, которая не должна быть слишком большой. Хорошее качество реза и скорость его выполнения обеспечиваются скоростью воздушной струи, равной 800 м/с.
В этом случае ток, протекающий от инверторного блока, не должен превышать 250 А.
При выполнении работ на таких режимах следует учитывать тот факт, что в этом случае поток воздуха, используемого для формирования потока плазмы, будет увеличиваться.
Самостоятельно изготовить плазменный резак не так уж и сложно, для этого нужно изучить нужный теоретический материал, просмотреть обучающее видео и правильно подобрать все необходимые детали. При наличии в домашнем пользовании подобного аппарата, изготовленного на основе заводского инвертора, может выполнять не только качественную резку металла, но и плазменную сварку!
В том случае если у вас в пользовании нет инвертора, можно изготовить плазморез, взяв за основу сварочный трансформатор, в таком случае вам придется смириться с его большими габаритами и не малым весом. Так же, плазморез, сделанный на основе трансформатора, будет иметь не очень хорошую мобильностью и переносить его с места на место будет проблематично!
Источник: https://kavmaster.ru/plazmorez-iz-invertora-svoimi-rukami/
Плазменный резак своими руками: самодельный празморез из сварочного инвертора
Плазменные резаки активно используются в мастерских и предприятиях, связанных с цветными металлами. Большинство небольших предприятий применяют в работе плазменный резак, изготовленный своими руками.
Плазменный резак хорошо себя показывает при разрезе цветных металлов, поскольку позволяет локально прогревать изделия и не деформировать их. Самостоятельное производство резаков обусловлено высокой стоимостью профессионального оборудования.
В процессе изготовления подобного инструмента используются комплектующие от других электроприборов.
Особенности и назначение плазменного резака
Инвертор плазменной резки используется для выполнения работ как в домашних, так и в промышленных условиях. Существует несколько видов плазморезов для работы с различными типами металлов.
Различают:
- Плазморезы, работающие в среде инертных газов, например, аргона, гелия или азота.
- Инструменты, работающие в среде окислителей, например, кислорода.
- Аппаратура, предназначенная для работы со смешанными атмосферами.
- Резаки, работающие в газожидкостных стабилизаторах.
- Устройства, работающие с водной или магнитной стабилизацией. Это самый редкий вид резаков, который практически невозможно найти в свободной продаже.
Плазменный резак или плазматрон – это основная часть плазменной резки, отвечающая за непосредственную нарезку металла.
Плазменный резак в разборе.
Большинство инверторных плазменных резаков состоят из:
- форсунки;
- электрода;
- защитного колпачка;
- сопла;
- шланга;
- головки резака;
- ручки;
- роликового упора.
Принцип действия простого полуавтоматического плазмореза состоит в следующем: рабочий газ вокруг плазмотрона прогревается до очень высоких температур, при которых происходит возникновение плазмы, проводящей электричество.
Затем, ток, идущий через ионизированный газ, разрезает металл путем локального плавления. После этого струя плазмы снимает остатки расплавленного металла и получается аккуратный срез.
По виду воздействия на металл различают такие виды плазматронов:
- Аппараты косвенного действия.
Данный вид плазматронов не пропускает через себя ток и пригоден лишь в одном случае – для резки неметаллических изделий. - Плазменная резка прямого действия.
Применяется для разрезки металлов путем образования плазменной струи.
Конструкция плазменного резака и рекомендации по работе с ним серьезно разнятся в зависимости от типа устройства.
Делаем плазменный резак своими руками
Плазменная резка своими руками может быть изготовлена в домашних условиях. Неподъемная стоимость на профессиональное оборудование и ограниченное количество представленных на рынке моделей вынуждают умельцев собирать плазморез из сварочного инвертора своими руками.
Самодельный плазморез можно выполнить при условии наличия всех необходимых компонентов.
Перед тем как сделать плазморежущую установку, необходимо подготовить следующие комплектующие:
- Компрессор.
Деталь необходима для подачи воздушного потока под давлением. - Плазмотрон.
Изделие используется при непосредственной резке металла. - Электроды.
Применяются для розжига дуги и создания плазмы. - Изолятор.
Предохраняет электроды от перегрева при выполнении плазменной резки металла. - Сопло.
Деталь, размер которой определяет возможности всего плазмореза, собранного своими руками из инвертора. - Сварочный инвертор.
Источник постоянного тока для установки. Может быть заменен сварочным трансформатором.
Схема работы плазменного резака.
Трансформаторные источники постоянного тока характеризуются следующими недостатками:
- высокое потребление электрической энергии;
- большие габариты;
- труднодоступность.
К преимуществам такого источника питания можно отнести:
- низкую чувствительность к перепадам напряжения;
- большую мощность;
- высокую надежность.
Инверторы, в качестве блока питания плазмореза можно использовать, если необходимо:
- сконструировать небольшой аппарат;
- собрать качественный плазморез с высоким коэффициентом полезного действия и стабильной дугой.
Благодаря доступности и легкости инверторного блока питания плазморезы на его основе могут быть сконструированы в домашних условиях. К недостаткам инвертора можно отнести лишь сравнительно малую мощность струи. Из-за этого толщина металлической заготовки, разрезаемой инверторным плазморезом, серьезно ограничена.
Одной из главнейших частей плазмореза является ручной резак.
Сборка данного элемента аппаратуры для резки металла осуществляется из таких компонентов:
- рукоять с пропилами для прокладки проводов;
- кнопка запуска горелки на основе газовой плазмы;
- электроды;
- система завихрения потоков;
- наконечник, защищающий оператора от брызг расплавленного металла;
- пружина для обеспечения необходимого расстояния между соплом и металлом;
- насадки для снятия окалин и нагара.
Резка металла различной толщины осуществляется путем смены сопел в плазмотроне. В большинстве конструкций плазмотрона, сопла закрепляются специальной гайкой, с диаметром, позволяющим пропустить конусный наконечник и зажать широкую часть элемента.
После сопла располагаются электроды и изоляция. Для получения возможности усиления дуги при необходимости в конструкцию плазматрона включают завихритель воздушных потоков.
Сделанные своими руками плазморезы на основе инверторного источника питания являются достаточно мобильными. Благодаря малым габаритам такую аппаратуру можно использовать даже в самых труднодоступных местах.
Чертежи
В глобальной сети интернет имеется множество различных чертежей плазменного резака. Проще всего изготовить плазморез в домашних условиях, используя инверторный источник постоянного тока.
Электрическая схема плазмореза.
Наиболее ходовой технический чертеж резака на основе плазменной дуги включает следующие компоненты:
- Электрод.
На данный элемент подается напряжение от источника питания для осуществления ионизации окружающего газа. Как правило, в качестве электрода используются тугоплавкие металлы, образующие прочный окисел. В большинстве случаев конструкторы сварочных аппаратов используют гафний, цирконий или титан. Лучшим выбором материала электрода для домашнего использования является гафний. - Сопло.
Компонент автоматического плазменный сварочного аппарата формирует струю из ионизированного газа и пропускает воздух, охлаждающий электрод. - Охладитель.
Элемент используется для отвода тепла от сопла, поскольку при работе температура плазмы может достигать 30 000 градусов Цельсия.
Большинство схем аппарата плазменной резки подразумевают такой алгоритм работы резака на основе струи ионизированного газа:
- Первое нажатие на кнопку пуск включает реле, подающее питание на блок управления аппаратом.
- Второе реле подает ток на инвертор и подключает электрический клапан продувки горелки.
- Мощный поток воздуха попадает в камеру горелки и очищает ее.
- Через определенный промежуток времени, задаваемый резисторами, срабатывает третье реле и подает питание на электроды установки.
- Запускается осциллятор, благодаря которому производится ионизация рабочего газа, находящегося между катодом и анодом. На данном этапе возникает дежурная дуга.
- При поднесении дуги к металлической детали зажигается дуга между плазмотроном и поверхностью, называющаяся рабочей.
- Отключение подачи тока для розжига дуги при помощи специального геркона.
- Проведение резальных или сварочных работ. В случае пропажи дуги, реле геркона вновь включает ток и разжигает дежурную струю плазмы.
- При завершении работ после отключения дуги, четвертое реле запускает компрессор, воздух которого охлаждает сопло и удаляет остатки сгоревшего металла.
Что нам понадобится?
Чертеж плазменного резака.
Для создания аппарата плазменной сварки необходимо обзавестись:
- источником постоянного тока;
- плазмотроном.
В состав последнего входят:
- сопло;
- электроды;
- изолятор;
- компрессор мощностью 2-2.5 атмосферы.
Большинство современных мастеров изготавливают плазменную сварку, подключаемую к инверторному блоку питания. Сконструированный при помощи данных компонентов плазмотрон для ручной воздушной резки работает следующим образом: нажатие на управляющую кнопку зажигает электрическую дугу между соплом и электродом.
Сборка инвертора
В случае, если фабричного инвертора нет в наличии, можно собрать самодельный.
Инверторы для резаков на основе газовой плазмы, как правило, имеют в строении такие комплектующие:
- блок питания;
- драйвера силовых ключей;
- силовой блок.
Плазменная горелка в разрезе.
Сборка инвертора для плазморезов или сварочного оборудования не может обойтись без необходимых инструментов в виде:
- набора отверток;
- паяльника;
- ножа;
- ножовки по металлу;
- крепежных элементов резьбового типа;
- медных проводов;
- текстолита;
- слюды.
Блок питания самодельного инвертора для плазменной резки собирается на базе ферритового сердечника и должен иметь четыре обмотки:
- первичную, состоящую из 100 витков проволоки, толщиной 0.3 миллиметра;
- первая вторичная из 15 витков кабеля с толщиной 1 миллиметр;
- вторая вторичная из 15 витков проволоки 0.2 миллиметра;
- третья вторичная из 20 витков 0.3 миллиметровой проволоки.
Силовой блок самодельного инвертора должен состоять из специального трансформатора. Для создания данного элемента следует подобрать два сердечника и намотать на них медную проволоку толщиной 0.25 миллиметров.
Отдельного упоминания стоит система охлаждения, без которой инверторный блок питания плазмотрона может быстро выйти из строя.
Рекомендации по работе
Чертеж технологии плазменной резки.
При работе на аппарате плазменной резки для достижения наилучших результатов нужно соблюдать рекомендации:
- регулярно проверять правильность направления струи газовой плазмы;
- проверять правильность выбора аппаратуры в соответствии с толщиной металлического изделия;
- следить за состоянием расходных деталей плазмотрона;
- следить за соблюдением расстояния между плазменной струей и обрабатываемым изделием;
- всегда проверять используемую скорость резки, чтобы избежать возникновения окалин;
- время от времени диагностировать состояние системы подвода рабочего газа;
- исключить вибрацию электрического плазмотрона;
- поддерживать чистоту и аккуратность на рабочем месте.
Заключение
Аппаратура для плазменной резки – это незаменимый инструмент для аккуратной нарезки металлических изделий. Благодаря продуманной конструкции плазмотроны обеспечивают быстрый, ровный и качественный порез металлических листов без необходимости последующей обработки поверхностей.
Большинство рукоделов из небольших мастерских предпочитают своими руками собирать мини резаки для работы с не толстым металлом. Как правило, самостоятельно сделанный плазморез по характеристикам и качеству работы не отличается от заводских моделей.
Источник: https://tutsvarka.ru/oborudovanie/plazmennyj-rezak-svoimi-rukami
Как самостоятельно сделать плазморез из инвертора
- В отличие от сварочного трансформатора, инвертор отличается компактностью, малым весом и высоким КПД, что объясняет его популярность в домашних мастерских, небольших гаражах и цехах.
- Он позволяет закрывать большинство потребностей в сварочных работах, но для качественной резки требуется лазерный аппарат или плазморез.
Универсальный аппарат для сварки
Лазерное оборудование очень дорогое, плазморез тоже стоит недешево. Плазменная резка и сварка металла небольшой толщины имеет прекрасные характеристики, недостижимые при использовании электросварки. При этом силовой блок у плазмореза и сварочного аппарата для электродуговой сварки во многом имеют одинаковые характеристики.
Возникает желание сэкономить, и при небольшой доработке использовать его и для плазменной резки. Оказалось, что это возможно, и можно встретить много способов переделки сварочных аппаратов, в том числе инверторных, в плазморезы.
Аппарат плазменной резки представляет собой тот же сварочный инвертор с осциллятором и плазмотроном, кабелем массы с зажимом и внешним или внутренним компрессором. Часто компрессор используется внешний и в комплект поставки не входит.
Если у владельца сварочного инвертора имеется еще и компрессор, то можно получить самодельный плазморез, приобретя плазмотрон и сделав осциллятор. В итоге получится универсальный сварочный аппарат.
Принцип работы горелки
Работа аппарата плазменной сварки и резки (плазмореза) основана на использовании в качестве режущего или сваривающего инструмента плазмы, четвертого состояния вещества.
Для ее получения требуется высокая температура и газ под высоким давлением. При создании между анодом и катодом горелки электрической дуги в ней поддерживается температура в несколько тысяч градусов.
Образование плазмы
Если пропустить при таких условиях через дугу струю газа, то он ионизируется, расширится в объеме в несколько сотен раз и нагреется до температуры в 20-30 тысяч °C, превращаясь в плазму. Высокая температура почти мгновенно расплавляет любой металл.
В отличие от кумулятивного снаряда процесс образования плазмы в плазмотроне регулируемый.
Анод и катод в резаке плазмореза находятся на расстоянии нескольких миллиметров друг от друга. Осциллятор вырабатывает импульсный ток большой величины и частоты, пропускает его между анодом и катодом, что приводит к возникновению электрической дуги.
После этого через дугу пропускается газ, который ионизируется. Так как все происходит в замкнутой камере с одним выходным отверстием, то получившаяся плазма с огромной скоростью вырывается наружу.
На выходе горелки плазмореза она достигает температуры 30000 ° и плавит любой металл. Перед началом работ к заготовке с помощью мощного зажима подсоединяется провод массы.
Когда плазма достигает заготовки, то электрический ток начинает течь через кабель массы и плазма достигает максимальной мощности. Ток доходит до 200-250 А. Цепь анод – катод разрывается с помощью реле.
Резка
При пропадании основной дуги плазмореза, эта цепь опять включается, не давая исчезнуть плазме. Плазма играет роль электрода в электродуговой сварке, она проводит ток, а благодаря своим свойствам создает в области соприкосновения с металлом область с высокой температурой.
Площадь соприкосновения струи плазмы и металла маленькая, температура высокая, нагрев происходит очень быстро, поэтому практически отсутствуют напряжения и деформации заготовки.
Срез получается ровный, тонкий не требующий последующей обработки. Под напором сжатого воздуха, который используется в качестве рабочего тела плазмы, жидкий металл выдувается и получается рез высокого качества.
При использовании инертных газов с помощью плазмореза можно проводить качественную сварку без вредного воздействия водорода.
Плазмотрон своими руками
При изготовлении плазмореза из сварочного инвертора своими руками самой сложной частью работ является производство качественной режущей головки (плазмотрона).
Инструменты и материалы
Если делать плазменный резак своими руками, то легче использовать в качестве рабочего тела воздух. Для изготовления понадобятся:
- рукоятка, в которой должны поместиться кабель и трубка для подачи воздуха;
- пусковая кнопка горелки плазмореза;
- изолирующая втулка;
- электрод горелки плазмореза;
- устройство завихрения воздушного потока;
- набор сопел различного диаметра для резки металлов различного вида и толщины;
- защитный наконечник от брызг жидкого металла;
- ограничительная пружина для поддержания одинакового зазора между соплом горелки плазмореза и разрезаемым металлом;
- насадки для снятия фасок.
Расходные материалы плазмореза в виде сопел, электрода стоит купить в магазине сварочного оборудования. Они в процессе резки и сварки выгорают, поэтому имеет смысл приобретать по несколько штук на каждый диаметр сопла.
Чем тоньше металл для резки, тем меньше должно быть отверстие сопла горелки плазмореза. Чем толще металл, тем больше отверстие сопла. Наиболее часто используется сопло с диаметром 3 мм, оно перекрывает большой диапазон толщин и видов металлов.
Сборка
Сопла горелки плазмореза прикрепляются прижимной гайкой. Непосредственно за ним располагается электрод и изолирующая втулка, которая не позволяет возникнуть дуге в ненужном месте устройства.
Затем расположен завихритель потока, который направляет его в нужную точку. Вся конструкция помещается во фторопластовый и металлический корпус. К выходу трубки на ручке горелки плазмореза приваривается патрубок для подсоединения воздушного шланга.
Электроды и кабель
Для плазмотрона требуется специальный электрод из тугоплавкого материала. Обычно их изготавливают из тория, бериллия, гафния и циркония. Их применяют из-за образования при нагреве тугоплавких окислов на поверхности электрода, что увеличивает длительность его работы.
При использовании в домашних условиях предпочтительней применение электродов из гафния и циркония. При резке металла они не вырабатывают токсичных веществ в отличие от тория и бериллия.
Кабель от инвертора и шланг от компрессора к горелке плазмореза нужно прокладывать в одной гофрированной трубе или шланге, что обеспечит охлаждение кабеля в случае его нагрева и удобство в работе.
Сечение медного провода нужно выбрать не менее 5-6 мм2. Зажим на конце провода должен обеспечивать надежный контакт с металлической деталью, в противном случае дуга с дежурной не перекинется на основную дугу.
Компрессор на выходе должен иметь редуктор для получения нормированного давления на плазмотроне.
Варианты прямого и косвенного действия
Конструкция горелки плазмореза довольно сложная, выполнить в домашних условиях даже при наличии различных станков и инструментов сложно без высокой квалификации работника. Поэтому изготовление деталей плазмотрона нужно поручить специалистам, а еще лучше приобрести в магазине. Выше была описана горелка плазмотрона прямого действия, она может резать только металлы.
Существуют плазморезы с головками косвенного действия. Они способны резать и неметаллические материалы. В них роль анода выполняет сопло, и электрическая дуга находится внутри горелки плазмореза, наружу под давлением выходит только плазменная струя.
При простоте конструкции устройство требует очень точных настроек, в самодеятельном изготовлении практически не применяется.
Доработка инвертора
Для использования инверторного источника питания для плазмореза его нужно доработать. К нему нужно подключить осциллятор с блоком управления, который будет выполнять функцию пускателя, поджигающего дугу.
Схем осцилляторов встречается довольно много, но принцип действия один. При запуске осциллятора между анодом и катодом проходят высоковольтные импульсы, которые ионизируют воздух между контактами. Это приводит к снижению сопротивления и вызывает возникновение электрической дуги.
Затем включается газовый электроклапан и под давлением воздух начинает проходить между анодом и катодом через электрическую дугу. Превращаясь в плазму и достигая металлической заготовки, струя замыкает цепь через нее и кабель массы.
Основной ток величиной примерно 200 А начинает течь по новой электрической цепи. Это вызывает срабатывание датчика тока, что приводит к отключению осциллятора. Функциональная схема осциллятора изображена на рисунке.
Функциональная схема осциллятора
В случае отсутствия опыта работы с электрическими схемами можно воспользоваться осциллятором заводского производства типа ВСД-02. В зависимости от инструкции по подключению они присоединяются последовательно или параллельно в схему питания плазмотрона.
Перед изготовлением плазмореза, необходимо определить предварительно с какими металлами, и какой толщины хотите работать. Для работы с черным металлом достаточно компрессора.
Для резки цветных металлов потребуется азот, высоколегированной стали нужен аргон. В связи с этим, возможно, потребуется тележка для перевозки газовых баллонов и понижающие редукторы.
Как любое оборудование и инструмент, сварочный аппарат с плазменной головкой требует определенной сноровки от пользователя. Движение резака должно быть равномерным, скорость зависит от толщины металла и его вида.
Медленное движение приводит к образованию широкого реза с неровными краями. Быстрое перемещение приведет к тому, что металл прорезается не во всех местах. При должной сноровке можно получить качественный и ровный срез.
Источник: https://svaring.com/welding/apparaty/plazmorez-iz-svarochnogo-invertora-svoimi-rukami
Как из сварочного инвертора сделать плазморез своими руками? Рекомендации по изготовлению!
Отслужившие детали различных машины и инструментов отлично подходят для изготовления полезных в домашнем хозяйстве устройств своими руками. Если есть в наличии ненужный сварочный инвертор, то из него можно сделать самодельный плазморез.
О том, каким образом превратить прибор для сваривания металла в устройство, которое способно разрезать прочный материал, будет подробно рассказано в этой статье.
Преимущество плазмореза перед газовым резаком
Одним из самых простых устройств для резки металла является газовый резак. Такой прибор стоит небольших денег и расходные материалы к нему также недороги. Но при выполнении газосварочных работ происходит нагрев слишком большой площади металла.
По этой причине материалы, обладающие большой теплопроводностью могут покоробиться и изменить цвет. Как в месте плавления металла, так и на значительном удалении от термического воздействия пламени горелки.
Преимущество плазмореза заключается в том, что удаётся получить очень тонкую струю раскалённого газа, которая будет воздействовать на небольшую площадь поверхности, что позволит значительно уменьшить нагрев детали.
Принцип работы плазмореза
Изготовить плазморез самостоятельно, не разбираясь в принципе работы этого устройства практически невозможно.
Процесс образования плазмы происходит в результате:
- Подачи электрического тока в горелку.
- Между электродами (катод и анод) горелки возникает электрическая дуга.
- Воздух под давлением подаётся в горелку и «выдувает» дугу наружу, при этом значительно увеличивая её температуру.
- К разрезаемому металлу подключается кабель «массы», поэтому ионизируемое пламя как бы замыкает о поверхность материала.
В результате получается высокоэффективное устройство для разрезания различных металлов. В том числе тех, которые обладают повышенными показателями теплопроводности.
Смотрите видео, где в доступной форме показано что такое плазменная резка и как она работает:
Детали для самодельного устройства
Плазморез из сварочного инвертора своими руками изготавливается из следующих деталей.
1. Плазмотрон. Эта деталь в конструкции плазмореза является наиболее важной.
Даже при наличии необходимого по силе электрического тока и давления газа, дугу не удастся получить, если внутренние электроды будут неправильно расположены. А отверстие для подачи воздуха будет иметь неподходящий диаметр.
Стоит такая деталь довольно дорого, поэтому домашние мастера предпочитают изготавливать горелки самостоятельно из подручных деталей.
2. Источник тока. В самодельном плазморезе источником тока будет сварочный инвертор.
3. Компрессор. Чтобы обеспечить длительную подачу сжатого воздуха в плазмотрон необходимо приобрести компрессор средней мощности.
Узнайте из этого видео, как выбрать компрессор для плазменной резки:
Также потребуются для самодельного плазмореза купить достаточное количество медных проводов большого диаметра. Для подключения «массы» к разрезаемой детали и обеспечения плазмотрона необходимым количеством электроэнергии.
Самостоятельное изготовление плазмотрона
Горелка или плазмотрон может быть изготовлена из подручных материалов. Чтобы собрать этот элемент самодельного плазмореза понадобятся:
- ручка;
- кнопка пуска;
- специальный электрод;
- сопло;
- изолятор.
Для изготовления самодельного плазмотрона идеально подойдёт ручка от мощного паяльника. Как правило, такая деталь имеет серединное отверстие, через которое и будут подводиться электрический ток и сжатый воздух.
Кнопку лучше использовать достаточно большую, чтобы во время работы пользоваться устройством было максимально комфортно.
Электроды потребуется приобрести в магазине. Для самостоятельного изготовления плазмотрона лучше выбирать изделия, изготовленные из гафния.
Для работы с металлами различной толщины потребуется также купить набор сопл.
Изготавливается плазмотрон в такой последовательности:
- Сразу за ручкой помещается металлическая трубка, покрытая изнутри фторопластом.
- Внутри трубки размещается электрод, который почти по всей длине закрыт высокотемпературной изоляцией.
- За электродом устанавливается с помощью резьбового соединения сопло подходящего диаметра.
Плазмотрон готов к использованию. Ещё для работы устройства потребуется подключить для подачи воздуха шланг от компрессора и электрический провод от инвертора.
Посмотрите видео, где человек рассказывает, как он пытался сделать плазмотрон:
Источник тока
В качестве источника электроэнергии можно использовать сварочный инвертор со следующими показателями:
- напряжение питания – 220 В;
- мощность – от 4 кВт;
- возможность регулировки тока от 20 – 40 А.
Сборка плазмореза
Когда отдельные детали плазмореза будут готовы, можно приступить к сборке. Чтобы работать с самодельным устройством было максимально комфортно, необходимо свести к минимуму количество тянущихся за ручкой проводов и шлангов.
Для более компактного размещения рабочего провода его помещают внутри шланга, по которому производится подача сжатого воздуха. Провод надёжно подсоединяется к электроду, при этом шланг также должен быть подключён к горелке без образования зазоров.
- Другой контакт от инвертора будет подключаться к разрезаемой детали в качестве «массы» поэтому его следует оборудовать клеммой типа «крокодил».
- Из этого видео вы узнаете, как самому сделать шланг пакет, шлейф для плазмореза:
Процесс разрезания металла с помощью плазменного резака очень прост. После подачи электричества образуется электрическая дуга. Момент образования запала регулируется кнопкой, которая была ранее установлена на ручке плазмотрона. Воздух подаётся от компрессора по шлангу и раздувает дугу, тем самым увеличивая её температуру, которая может достигать 8000ºС.
Для того чтобы затушить дугу достаточно отпустить кнопку на ручке. Таким образом горелка будет работать только в тот момент, когда необходимо разрезать металл, что сведёт к минимуму эффект перегрева, к которому самодельные изделия очень чувствительны.
Интересное видео про плазморез своими руками и из чего он состоит:
Советы и рекомендации
Важно не только знать, как переделать инвертор в плазморез, но и как сделать работу такого устройства максимально эффективной и безопасной.
Далее будут приведены несколько рекомендаций. Придерживаясь которых можно избежать наиболее распространённых ошибок при изготовлении и использовании самодельного устройства:
- Перед тем как приступить к изготовлению из сварочного инвертора устройства для резки металлов, следует наметить на бумаге основные элементы такой системы. Самостоятельно изготовленные чертежи и схемы позволят в процессе работы не допустить досадных ошибок, которые наиболее часто бывают вызваны обычной невнимательностью.
- Несмотря на то, что плазменный резак имеет очень узкое пламя, которое не слишком разогревает даже металлы обладающие повышенной теплопроводностью, рекомендуется при работе с алюминиевыми изделиями использовать в качестве распыляющего газа неон или аргон, которые не позволят окислиться поверхности, подвергнувшейся воздействию высокой температуры.
- Чтобы максимально сократить время на изготовление плазмореза рекомендуется приобрести готовую горелку для газового резака. Такое изделие позволит максимально эффективно и безопасно работать с металлом.
- При использовании самодельного плазмореза необходимо придерживаться основных правил техники безопасности. Прежде всего, следует обеспечить защиту от воздействия электричества и брызг расплавленного металла. Для этой цели используются специальная обувь, перчатки и фартук. Также необходимо надевать защитные очки, которые позволят предохранить зрение от воздействия ультрафиолетовых лучей. В процессе резки металла выделяется большое количество вредных для здоровья веществ, поэтому рекомендуется защищать органы дыхания с помощью респиратора.
О том, как из инвертора сделать плазморез своими руками подробно рассказано в этой статье. Перед началом изготовления плазменного резака рекомендуется проверить работоспособность инвертора.
(1
Источник: https://plavitmetall.ru/oborudovanie/plazmorez-iz-svarochnogo-invertora-svoimi-rukami.html
Изготовление плазменного резака из инвертора своими руками
До недавнего времени, когда в домашних условиях возникала необходимость в резке металлических заготовок для различных нужд, у домашнего мастера выбор был не очень большим. Либо УШМ (угловая шлифовальная машина, в простонародье «болгарка»), либо газовый резак.
Но прогресс не стоит на месте, и относительно недавно для широких масс стало доступно принципиально иное средство для резки металла, более эффективное и удобное в эксплуатации. Речь идёт о плазменном резаке или, как его ещё иногда называют, плазморезе. Учитывая высокую стоимость бытовых плазменных резаков заводского изготовления вполне рациональной выглядит идея попытаться собрать этот прибор в домашних условиях. А для того чтобы убедиться в целесообразности этой идеи, можно сравнить технологические особенности производимых работ с помощью вышеперечисленных приспособлений.
- УШМ (угловая шлифовальная машина). Обеспечивает очень хороший уровень реза, но только в том случае, когда речь идёт о прямолинейной резке металла. Выполнить с помощью «болгарки» фигурный рез практически невозможно.
- Газовый резак. Обеспечивает возможность фигурного реза, но с очень низким качеством. Края реза получаются неровные, рваные, с кусочками расплавленного металла. Как правило, при толщине металла более 5−7 мм резать становится очень тяжело или практически невозможно.
- Плазморез. Обеспечивает высококачественный, идеально чистый шов практически любой конфигурации и толщины. Положительным моментом применения плазмореза является полное отсутствие остаточной деформации металла после окончания процесса резки, чего нельзя сказать о двух первых способах.
Самодельный плазморез
Сборка плазмореза в домашних условиях очень напоминает собирание конструктора. Дело в том, что все без исключения составные элементы плазмореза относятся к достаточно сложным технологическим изделиям. Изготовление этих элементов в домашних условиях с нуля не только требует очень глубоких познаний в данном предмете и соответствующего дорогостоящего оборудования, но и является небезопасным в плане здоровья домашнего мастера.
Например, температура внутри камеры сгорания плазмотрона составляет порядка 20000−30000 градусов. Поэтому лучше купить элементы, из которых состоит плазморез, уже готовыми, с гарантией высокой надёжности, чем пытаться сделать дома из подручных средств и тем самым подвергать опасности не только свою жизнь, но и жизнь своих близких.
Совсем ничего не понимающим в металлообработке необходимо знать хотя бы элементарные вещи, например, то, что лазерный резак по металлу и плазменный резак по металлу — это не одно и то же.
Составляющие элементы
Любой плазморез состоит из следующих элементов:
- Источник постоянного тока. Для этих целей можно использовать либо сварочный трансформатор, либо сварочный инвертор. О преимуществах и недостатках того и другого поговорим ниже.
- Осциллятор. Выполняет роль стартера, который запускает предварительную дугу. Оптимальный вариант — осциллятор заводского изготовления марки ВСД-02. Как самостоятельно изготовить осциллятор читайте здесь.
- Источник сжатого воздуха. Компрессор мощностью 2.00−3.00 атм и выше, в зависимости от мощности аппарата.
- Резак, он же плазмотрон. Приобретается в готовом виде в соответствующем магазине. В крайнем случае можно взять резак для аргонной сварки и путём незначительных доработок переделать его в плазмотрон.
- Комплект соответствующих шлангов для подвода газовой смеси к камере сгорания.
- Комплект электрических кабелей для подвода электричества к трансформатору.
Инвертор или трансформатор
И у того, и у другого есть как положительные стороны, так и отрицательные. В конечном итоге выбор происходит в пользу конкретного устройства исходя из технических задач, которые ставятся перед будущим плазморезом.
Сварочный инвертор-полуавтомат
Наиболее оптимальное решение для личного гаража или небольшой мастерской.
- Относительно малый вес, некрупные габариты и минимальное количество потребляемой электроэнергии.
- Качество реза у инверторного плазмореза выше за счёт более высококачественной дуги.
- Крайняя чувствительность к качеству подаваемой на него электроэнергии. Частые перепады напряжения в сети способны просто убить ваш инвертор за очень короткий промежуток времени, и никакая система защиты в этом случае не поможет.
- Небольшая мощность, что не позволяет резать толстые листы металла.
Сварочный трансформатор
Более подходит для стационарных условий крупных мастерских или заводов.
- Никогда не выходят из строя в случае даже сильного падения напряжения в сети. В этом плане они более надёжны.
- Более длительный рабочий цикл (период работы без перерыва).
- Не имеют ограничения по мощности, поэтому можно резать металл практически любой толщины.
- Очень высокая масса, большие габариты и высокое энергопотребление.
Исходя из этих сравнительных характеристик домашние мастера чаще всего склоняются в сторону плазмореза из инвертора, собранного своими руками на базе сварочного инвертора.
Плазмотрон или резак
Основными компонентами плазморезки являются: два электрода, изолятор, разделяющий катодный и анодный узлы, и камера завихрения газовой смеси.
- Один из электродов является основным и изготавливается из тугоплавкого металла типа тория, циркония или бериллия. Но все эти металлы, точнее, продукты их взаимодействия с высокими температурами, являются крайне вредными для здоровья. Поэтому оптимальным вариантом будет изготовление электрода из другого тугоплавкого метала — гафния, который абсолютно безвреден.
- Вторым электродом является сопло. Оно, как правило, изготавливается из меди. В сопле имеется очень тонкое отверстие, через которое раскалённый газ вырывается наружу. Периодически этот элемент требует своей замены в силу того, что постоянно находится в зоне запредельно высоких температур. Поэтому оптимальным является иметь не одно сопло, чтобы в случае необходимости можно было быстро заменить вышедшее из строя.
- Газ под давлением подаётся в камеру завихрения через прямой патрубок, расположенный сверху или сбоку от камеры. Предварительно нагнетается необходимое давление с помощью компрессора.
Принцип работы плазмотрона
Под давлением газ поступает в пространство между соплом и электродом. В момент включения осциллятора, в результате возникновения высокочастотного импульсного тока, между двумя электродами возникает электрическая дуга. Эта дуга носит название предварительной, и её задача — разогреть газ, находящийся в камере сгорания. Температура разогретого газа в камере относительно невысокая — порядка 5000−7000 градусов.
После того как предварительная дуга заполнит собой всё сопло, с помощью компрессора увеличивают давление подаваемого сжатого воздуха, в результате начинает происходить ионизация газа. Как следствие этого, газ расширяется в объёме, становится сверхпроводимым и разогревается до запредельно высоких температур порядка 20000−30000 градусов. Иными словами, газ превращается с плазму.
Под большим давлением плазма вырывается через узкое отверстие сопла наружу. В момент соприкосновения потока плазмы с поверхностью металла возникает вторая дуга — основная, или классическая. Роль второго электрода в этом случае берёт на себя сама плазма. Плазменная дуга мгновенно расплавляет металл в точке контакта. Под сильным напором сжатого воздуха расплавленный металл мгновенно выдувается, и в результате остаётся чистый рез.
Существуют два базовых условия, при соблюдении которых получается качественная резка с помощью плазмы:
- Ток, подаваемый на электрод, должен обладать силой не менее 250 А.
- Сжатый воздух подаётся в камеру сгорания со скоростью не менее 800−900 м/с.
Сложность изготовления плазмотрона
Схемы, чертежи для изготовления плазмореза своими руками очень легко найти в Интернете. Но плазменный резак очень сложно устроен и, кроме того, требует очень тонких настроек перед непосредственной эксплуатацией. Несмотря на обилие в Интернете соответствующих рекомендаций, чертежей и видеороликов, сделать плазмотрон дома технически крайне сложно. А если учесть, что затея эта ещё и крайне опасная для здоровья, то лучше от неё совсем отказаться и воспользоваться услугами «Али Экспресса» или ближайшего специализированного магазина.
Сборка из готовых комплектуюущих
Необходимо подключить сопло плазмореза к инвертору и компрессору. Осуществляется это посредством так называемого кабель-шлангового пакета. Оптимальным будет использовать для этих целей специальные зажимы и клемы, которые легко фиксируются и также легко снимаются.
Перед тем как начинается сборка, необходимо окончательно убедиться в совместимости всех комплектующих.
Порядок сборки достаточно прост:
- Инвертор посредством электрического кабеля соединяется с электродом плазмореза.
- Компрессор с помощью специального шланга присоединяется к рабочей камере плазмореза.
Практические рекомендации
Даже при сборке из уже готовых комплектующих цена конечного продукта будет на несколько порядков меньше, чем если покупать готовый плазменный резак. После того как аппарат будет собран и станок будет готов к работе, нужно позаботиться о расходных материалах и некоторых аспектах эксплуатации устройства.
- Необходимо приобрести заранее несколько комплектов резиновых прокладок, которые используются при подключении шланга подачи сжатого воздуха.
- Самой быстроразрушающейся деталью в плазменном резаке является медное сопло. Кроме того, толщина реза напрямую зависит от диаметра отверстия в сопле. Поэтому комплект медных сопел с разным диаметром выходного отверстия должен обязательно быть в запасе.
- Необходимо достаточно точно определиться с задачами, которые стоят перед будущим плазморезом, и исходя из этого заранее подобрать соответствующую мощность инвертора. Учитывая высокую цену на инверторы, будет очень накладно эксплуатировать плазморез, обладающий излишней мощностью.
- Необходимо всегда помнить, что температура рабочего участка плазмы составляет 20000−30000 градусов. Это крайне опасно и может привести к ЧП, если работающий плазморез окажется в руках несмышлёного ребёнка или психически невменяемого человека.
- Крайне важно в процессе работы правильное образование вихревого потока. В противном случае во время работы плазменной горелки может образоваться так называемая двойная дуга, что может привести к разрушению устройства. Поэтому очень важно использовать плазменные резаки, изготовленные в заводских условиях, с соблюдением всех необходимых технических стандартов.
О том, как выбрать плазморез можно прочитать здесь.
О том, как выбрать плазморез можно прочитать здесь.
О том, как выбрать плазморез можно прочитать здесь.
Как сделать плазменный резак своими руками у себя дома?
Последнее обновление: вторник, 25 февраля 2020 г.
Знаете ли вы , как сделать себе дома плазменный резак ? Если вы не подозреваете об этом факте, то самое время попробовать что-нибудь по-настоящему интересное.
Инженеры-подражатели найдут это потрясающим, когда они успешно сделают проект.
Что такое мини-плазменный резак?
Для вашего удобства мини-установка для плазменной резки не что иное, как специализированный станок, но это руководство поможет вам узнать о том, что вы можете легко сделать дома.
Чтобы сделать этот плазменный резак своими руками, вам понадобится набор оборудования. Однако плазма относится к дуге огня, которую необходимо поддерживать при резке металлических листов.
Хотя установки плазменной резки различаются от типа к типу, от номинала к требованиям, их основной принцип работы одинаков во всем, что касается точной резки металлических листов.
Однако давайте перейдем к изучению , как сделать плазменный резак своими руками у себя дома.
Вещи, которые вам потребуются:
Есть несколько вещей, которые вам нужно будет подготовить в соответствии с этим руководством о том, как сделать самодельный плазменный резак.
Не волнуйтесь, все, что вам понадобится, обязательно будет в вашем доме.
Получите эти вещи сначала у себя
- зарядное устройство (с выходом постоянного тока и номиналом до 20+ вольт, если возможно)
- карандаш (не слишком длинный и не слишком короткий, лучше, если это HB и 0,7 мм в диаметре)
- медных проводов малого диаметра и короткой длины, достаточно ленты,
- металлического листа (лучше всего, если вы можете собрать любую фольгу),
- источник питания переменного тока.
Как сделать из них плазменный резак своими руками?
Выполните следующие действия, чтобы сделать плазменный резак:
- Сначала возьмите адаптер постоянного тока и подключите два провода к двум выходным клеммам выходного разъема адаптера.
- Возьмите один из самых прочных грифелей HB.
- Подсоедините карандаш к положительной части выходного провода адаптера, а фольгу — к отрицательной клемме выходного провода адаптера.
- Теперь возьмитесь за проволоку, которой крепится грифель карандаша.Прокрутите и поцарапайте провод вниз до фольги, и вы увидите, что бумага разрезается до тех мест, где она касается бумаги.
Ознакомьтесь с тем, как использовать плазменный резак с ЧПУ
Каков принцип работы этого самодельного плазменного резака?
Вывод карандаша подсоединяется к положительному выводу, а фольга — к отрицательному выводу из выводов адаптера.
Когда эти две части соприкасаются, электрическая цепь замыкается и, таким образом, точка соединения нагревается.
Температура выше точки плавления фольги, но не карандаша.
Вот почему грифель карандаша останется почти таким же, но фольговая бумага расплавится, что в конечном итоге кажется, что вы очень легко разрезаете фольгу.
В этом секрет этого самодельного плазменного резака.
Меры безопасности перед изготовлением и использованием устройства плазменной резки своими руками:
Перед тем, как приступить к изучению данного руководства по изготовлению устройства плазменной резки, обязательно запомните следующие термины:
- Убедитесь, что вы подключили последний источник питания в последнюю очередь, после выполнения всех остальных шагов из этого руководства по изготовлению самодельного плазменного резака.
- Перед обмоткой проводов вокруг выходного гнезда адаптера убедитесь, что соединения подключены. Также не забывайте сильно наматывать ленту, чтобы соединения были плотными.
- При резке фольги не касайтесь фольги и грифеля карандаша напрямую. Несмотря на то, что он питается от постоянного тока, величина уровня мощности может сильно шокировать.
Подробности смотрите в этом видео: (Источник: Youtube)
Заключение
Если у вас дома есть все необходимое, почему бы не сделать что-нибудь настолько интересное?
Изготовление плазменного резака своими руками в домашних условиях даст вам представление о том, как резать толстые металлические листы в промышленности.Кроме того, это также расширит ваши знания с целью их дальнейшего развития.
Подробнее: Обзор 10 лучших плазменных резаков 2020
Как построить собственный плазменный резак своими руками НЕ?
Этот вопрос часто задают на многих сварочных площадках, промышленных форумах и форумах DIY. Мы также понимаем, что покупка нового устройства плазменной резки может быть довольно дорогостоящим. Вот почему люди чувствуют необходимость построить собственный станок для плазменной резки с нуля, считая, что это легко. Правда в том, что … если у вас нет опыта или квалификации для работы с электроникой и электрическими деталями, вам даже не следует задавать этот вопрос … пусть даже построит плазменный резак с нуля.
Давайте посмотрим правде в глаза, когда вы работаете с электрическим оборудованием, устройствами, запчастями или даже аксессуарами, всегда есть риск, что вы или кто-то из окружающих можете получить травму. Это просто не та область, в которой люди должны заниматься, если они не являются лицензированными электриками или кем-то, кто имеет квалификацию для работы с электричеством, напряжением, током или чем-либо подобным … включая очень мощную плазменную струю.
Итак, как построить собственный плазменный резак?
По правде говоря … мы провели много исследований по этой конкретной теме, и, к нашему удивлению (или не очень), ни один из этих так называемых сайтов или форумов DIY не может предоставить достаточно четких инструкций, руководств или руководств для позволяет читателям и зрителям правильно следить.Конечно, они скажут вам купить то и это… соединить этот кусок с другим, сварить его и так далее. Однако ни один из этих веб-сайтов не может дать четкого описания различных вариантов работы с определенными компонентами и связанных с этим опасностей, особенно если они касаются или подключаются к неправильной области…. ОЧЕНЬ ОПАСНО !!!
А как насчет этих обучающих видео с YouTube?
Да, на YouTube есть много видеороликов, которые предоставляют так называемые учебные пособия о том, как создавать определенные вещи, и некоторые из них могут быть действительно красивыми и простыми в использовании (например, как построить свой собственный диван, шкаф, журнальный столик в саду. сарай и т. д.), но вы должны помнить, что большинство этих видеороликов своими руками основаны на предметах, с которыми не опасно взаимодействовать.Даже если есть видео, которое показывает вам, что именно делать, всегда есть шанс, что создатель (или режиссер) видео упустил важные вещи, включая предупреждения при работе с определенными материалами. Помнить! Вы играете с электричеством и, возможно, с огнем… вот !!!
Стоит ли тратить время на строительство с нуля?
Прежде чем мы расскажем вам миллион причин, почему вам не следует строить установку для плазменной резки своими руками, почему бы нам не потратить некоторое время и не подумать, действительно ли стоит потратить ваше время, деньги и усилия на ее создание с нуля.Посмотрим правде в глаза, внутренние компоненты машины плазменной резки очень сложны, и есть много деталей, которые вы должны купить в местном хозяйственном магазине, чтобы даже начать. На самом деле… покупка всех этих проводов, деталей, компонентов, необходимых деталей и принадлежностей может занять очень много времени и не так рентабельно. Это особенно верно, если вы понятия не имеете, что покупаете, потому что велика вероятность, что вы проведете день с продавцом, и он мало чем поможет, потому что то, о чем вы спрашиваете, действительно будет слишком техническим, чтобы они могли справиться или рекомендую.
Да! НЕ РЕКОМЕНДУЕМ Плазменные резаки своими руками!
Наш вывод: да, мы не рекомендуем людям строить собственные плазменные резаки, потому что это просто не стоит вашего времени, особенно с учетом рисков, связанных с игрой с электричеством. Серьезно, небольшая ошибка, просчет или даже неправильное понимание инструкций, которым вы следуете, могут иметь тяжелые… если не смертельные последствия! Подумайте об этом, вы действительно играете с огнем здесь, и если вы не будете осторожны … вы можете сжечь свой гараж, бизнес, мастерскую или даже собственный дом.Не говоря уже о том, чтобы подвергнуть себя и своих близких серьезной опасности.
Итак … зачем ставить себя в такую ситуацию, когда можно легко купить его у надежного продавца за пару сотен баксов?
Да! Если вы не используете его для тяжелой промышленной резки металла, скорее всего, вам не понадобится слишком дорогой плазменный резак. За несколько сотен долларов вы можете приобрести тот, который изготовлен надежным производителем с надлежащей информацией, инструкциями, меню и руководящими принципами, и обычно он также имеет несколько лет гарантии.Этого должно хватить для большинства приложений.
Чтобы узнать, какой из них подходит вам, просто ознакомьтесь с нашими обзорами плазменных резаков для получения дополнительной информации!
Помните! Ваша жизнь, время и благополучие определенно стоит больше, чем несколько сотен долларов, поэтому, пожалуйста, не играйте с огнем!
Вернуться к руководству по покупке
Каковы лучшие советы по изготовлению плазменного резака своими руками?
Возможно, лучший и самый важный совет при изготовлении устройства для плазменной резки своими руками — это проявлять особую осторожность.Любой человек, выполняющий задачу по изготовлению собственного плазменного резака своими руками, должен хорошо разбираться в электронике в целях безопасности. Этот конкретный проект DIY включает в себя множество электрических компонентов, а также газы под высоким давлением. Хотя доступны некоторые планы для самостоятельной сборки, необходимы определенные инструменты и материалы.
Плазменные резаки могут быть чрезвычайно опасными и должны быть изготовлены только из специальных материалов.Трудно найти какие-либо чертежи для установки плазменной резки своими руками, потому что это высокотехнологичный инструмент, конструкция которого уже проверена и не требует доработки. Для сравнения: если человек хочет построить картинг, ему не нужно переделывать колесо или двигатель внутреннего сгорания. Все, что ему нужно сделать, это следовать существующему дизайну.
Имея это в виду, домашний мастер также должен понимать, что он не может реально получить все компоненты DIY плазменного резака из материалов DIY.Например, режущий наконечник или головка имеет специально разработанную конфигурацию, которая выдерживает токи большой мощности и сжатые газы. Практически все планы, сделанные своими руками, включают контактную информацию, которая направляет читателя к источникам, где он может купить режущее сопло. Почти наверняка домашнему мастеру потребуется вложить средства в режущее сопло для этого проекта плазменной резки.
Крафтер своими руками просто не может воспроизвести несколько других компонентов внутри насадки.Медные наконечники, керамические изоляторы, диффузоры и, в некоторых моделях, ламинированные вольфрамовые электроды — все это находится внутри плазменной резки. В сфере металлообработки они известны как «расходные материалы» и требуют периодической замены в зависимости от интенсивности использования плазменной резаки.
Когда дело доходит до проектов «сделай сам», установка плазменной резки «сделай сам» может оказаться одним из самых сложных и потенциально одним из самых опасных проектов, которые можно предпринять.Температуры, возникающие в процессе плазменной резки, могут достигать 30 000 ° F (16 649 ° C). Регулирование давления газа — еще одна неотъемлемая опасность, потому что скорость этих перегретых газов может достигать 20 000 футов в секунду (6096 метров в секунду).
Профессионал в этой области советует, что любому, кто собирается создать установку для плазменной резки своими руками, необходим высокий уровень знаний в области электроники, понимание того, как работают машины плазменной резки, и источник деталей, которые просто невозможно изготовить из набора материалов для самостоятельной работы, в частности резак и его расходные материалы.Большинство планов, предлагаемых в Интернете, предполагают подготовку к инвестициям на сумму до 300 долларов США (USD). По совпадению, бывшие в употреблении и маломощные устройства плазменной резки, как правило, доступны примерно за одинаковую сумму — без каких-либо рисков.
Советы и рекомендации по плазменной резке для начинающих
Новейшие
- [9 ноября 2020 г.] Какие тиски для скамьи самые сильные? Потребовалось сломать их, чтобы узнать… Продукты и обзоры
- [9 ноября 2020 г.] Какой аккумуляторный храповой ключ 3/8 ″ самый лучший? Продукты и обзоры
- [4 ноября 2020 г.] Как превратить железнодорожные пути в самодельную наковальню. Проекты «сделай сам»
- [4 ноября 2020 г.] Как на заказ нарисовать и нанести аэрографом реалистичный череп и полосатое пламя Как сделать и своими руками
- [3 ноября 2020 г.] В погоне за мечтами и штурмом Бонневилль Образ жизни с горячим стержнем
- [2 ноября 2020 г.] Как правильно выполнять сварку ~ Дуговая сварка экранированного металла (SMAW) Начальный уровень Практическое руководство
- [2 ноября , 2020] Как адаптировать ЛЮБОЙ двигатель к ЛЮБОЙ трансмиссии How To & DIY
- [30 октября 2020 г.] Традиционные справочники Hot Rod, которые у вас должны быть Техническая информация
- [30 октября 2020 г.] Проект Chevrolet Bel Air Restomod 1956 г. Автор Chip Foose Design Сборки и примеры
- [29 октября 2020 г.] Двухтактный Chevy Apache Monster Truck от WelderUp ’58 Build Bio and Drive Аттракционы и Roadkillers
- [29 октября 2020 г.] Золотая Сахара ~ Джордж Баррис построил шоу-кар стоимостью 1 миллион долларов Аттракционы и Roadkillers
- [29 октября 2020 г.] Восстановление разрушенного гаража Gas Monkey Garage 1976 Chevrolet C10 Сборки и примеры
- [Октябрь 28, 2020] Построен, чтобы уничтожить ~ 1941 General Motors Rat Rod Prerunner Rides & Roadkillers
- [26 октября 2020 г.] Незавершенные проекты ~ Когда вы можете позволить себе только половину Hot Rod Идеи
- [23 октября 2020 г.] Как сделать Нанесите на двигатель и мелкие детали для предотвращения ржавчины черный оксид How To & DIY
- [21 октября 2020 г.] Как нарисовать Candy Metal-Flake Panel Graphics How To & DIY
- [20 октября 2020 г.] Известный Roadrunner, Хеми Юте и близкий к аресту Hot Rod Lifestyle
- [15 октября 2020 г.] Полная перестройка Dodge Challenger 1970 года за считанные минуты! Сборки и примеры
- [14 октября 2020 г.] Чип Фуз оптимизирует концептуальные автомобили Corvette 1963 года и дизайн
- [
DIY Plasma Cutter LinuxCNC THC —
YouTube
Резак Prolox 60 с Trafimet Ergocut s45, 30A, 1500 мм / мин, сталь 2 мм.Сделай сам THC (THC-300) с LinuxCNC. Функция напряжения в LinuxCNC в данный момент не используется. ЖК-дисплей немного тормозит;)
Взаимодействие с другими людьмиС гордостью хочу представить вам мой плазменный роутер. Извините, но я не предоставляю чертежи. — Мне очень жаль. Маршрутизатор с ременным приводом от шаговых двигателей
YouTube
Вырубные ножницы очень полезны, поскольку они используются для удаления части трубки, чтобы точно установить ее на другую трубку, не оставляя зазора между ними и s
YouTube
Посетите мой новый сайт, чтобы получить кучу информации обо всех моих сборках.https://www.cymbalukdesigns.com Следуйте за мной на Instagram https://www.instagram.com/stefancymbaluk/ F
YouTube
В этом 11-минутном видео показаны основные моменты 97-минутного DVD «Основы бисероплетения». Более подробную информацию о сварке и металлообработке Вы можете получить на нашем сайте
.YouTube
Ссылки на Мои файлы и САПР находятся по адресу: https://www.patreon.com/russtuff Я давно хотел снять это видео, и вот оно наконец! Машина s
YouTube
В этом видео вы видите небольшой фрезерный станок, который оснащен 4-й осью, которая может действовать как токарный станок или как ось A для одновременного фрезерования.См. Также Compl
YouTube
Я никогда раньше не пользовался плазменным резаком и купил его у Fee-Bay за 235 долларов + 30 долларов с доставкой, этот маленький аппарат очень хорош.
YouTube
Máquina Plasma CNC fabricada pela Metalique Plasma CNC, Sorocaba SP. Maquina de excelente custo beneficio, leve, especial para chapas finas (0,5 мм) или гроссас
YouTube
Инструкции и файл образа SD-карты: http: // bb-lcnc.blogspot.com/ После моего успеха с BeagleBone White и ядром 3.2 я потратил некоторое время на выяснение ho
YouTube
Чак Томази навещает своего приятеля, который построил себе плазменный резак
YouTube
Proma Compact THC по цене 250 долларов — это нижняя часть линейки регуляторов высоты резака. Он просто контролирует напряжение, используемое для генерации плазменной дуги, сравнивает
YouTube
Обзор плазменного резака Cut 50 Я получил пару писем с вопросом о дешевых плазменных резаках eBay из Китая за 229 долларов.Так что я потратил капусту и купил Колоссал
YouTube
Прототип 6-осевого гексапода (платформа Стюарта) под управлением LinuxCNC (EMC2). Компоненты: шпиндель 2,2 кВт с водяным охлаждением, 24000 об / мин, с инвертором, 60EM-DHT-
YouTube
Ранний прогресс в моем домашнем плазменном столе с ЧПУ. Двигатели на 275 унций, приводы Gecko, направляющие V-образной гусеницы и открытая тяга ремня ГРМ.ПОСМОТРЕТЬ МОЙ ПОЛЬЗОВАТЕЛЬСКИЙ КАНАЛ «mgerm
YouTube
Токарка — аваны делают ЧПУ. Процедура тестирования NGCGUI. Zapraszam do wspólnego majsterkowania — Częstochowa, okolice i nie tylko — тел. 343636223
YouTube
Посетите мой новый сайт, чтобы получить кучу информации обо всех моих сборках. https://www.cymbalukdesigns.com Моя старая машина запускает какой-то код. Linuxcnc с Proma THC. Эверласт
YouTube
Прецизионный плазменный стол с ЧПУ для резки декоративной решетки.Сталь калибра 16 на глубине 150 дюймов в минуту. Быстрая скорость составляет 1000 фунтов в минуту, а ускорение — 50 дюймов / сек / сек. Посетите precisionplas
YouTube
Краткое видео, как мой самодельный фрезерный станок с ЧПУ, вырезанный из лучшего зажима для фрезера, взамен сделанного мной. Я создаю свой дизайн в Google SketchUp и использую
YouTube
В этом видео рассматривается установка плазменной резки. Он демонстрирует настройку и работу плазменного резака.Он начинается с обсуждения важности сохранения влажности
.YouTube
Связанное сообщение в блоге http://www.tangentaudio.com/?p=727 Много деталей, охватывающих всю электронику, на которой работает мой переделанный фрезерный станок с ЧПУ. Несколько уникальных
YouTube
Плазменный резак с ЧПУ— Boomle.com
CNC Gas Oxyfuel Flame Plasma Cutting Table от Newlin Machinery — отличный вариант для A CNC Plasma резак может резать любой металл.Путем нанесения через ускоренную струю горячей плазмы резал …
toolsfocus.com> Лучший плазменный стол с ЧПУ на 2020 год | инструменты
CNC Plasma Cutters , CNC Plasma Cutting Machine for Sale — Blue …
CNC Plasma Cutter 0005 также имеет преимущества быстрой резки 0005. , гладкая поверхность среза, небольшое тепловое искажение и деформация.Лучше, чем газовая резка металла , плазменная резка мало …
elephant-cnc.com> Плазменные резаки с ЧПУ, Станки плазменной резки с ЧПУ
Доступный ЧПУ Плазменный Фрезы | CNC Plasma Столы … — STYLECNC
stylecnc.com> Доступные плазменные резаки с ЧПУ | Плазма с ЧПУ
Построить CNC Plasma Cutter за 3000 $ | Марка
Makezine.com> Построить плазменный резак с ЧПУ за 3000 долларов |
ЧПУ Плазменный Резак | PlasCUT-1350 с Hypertherm Powermax
CNC плазменный Резак для стальных листов, алюминия, латуни и нержавеющей стали. Плазменный резак Станок High-Z PlusCut-1350 поставляется с мощным плазменным резаком Hypertherm Powermax , …
cnc-step.com> Плазменный резак с ЧПУ | PlasCUT-1350 с Hypertherm
Что такое CNC плазменный станок Cutter ? — Quora
A CNC Plasma Cutter — это промышленный станок для резки металла , используемый для резки листового металла сложной формы.Я собираюсь разбить это на 2 части: « CNC » и « Plasma cutter » CNC означает Computer …
quora.com> Что такое станок плазменной резки с ЧПУ? —
чпу плазма продукты на продажу | eBay
Cnc плазменный резак 4X2 фута 1 доступный, требует термодинамики Hypertherm-parweld. Alpha CNC плазменный резак 1.5×3 м (5 футов x 10 футов) стол для резки Hypertherm Powermax 45XP.
ebay.co.uk> плазменные изделия с чпу для продажи |
CNC Plasma Cutter Project Картинная галерея — PlasmaSpider.com | Forum
Massey Ferguson 6700 TractorDIY CNC Plasma Контроллер
Plasmaspider.com> Галерея изображений проекта плазменной резки с ЧПУ —
Найдите отличные предложения на eBay для cnc Plasma Cutter .