Подрез сварного шва фото
Все встречающиеся дефекты швов можно разделить на три группы. В статье для большей наглядности представлены сварочные швы (фото) и их изъяны:
1. Наружные, к которым относятся наплывы, трещины, подрезы, не заваренный кратер, свищ и поверхностное окисление; 2. Внутренние — механические примеси, наличие пор, непровары, оксидные и вольфрамовые включения, перегрев и пережог металла; 3. Сквозные дефекты представлены прожогами.
Кратко разберём основные характеристики перечисленных изъянов, а также причины, которые могут их вызывать.
Дефекты швов при сварочных работах
Наплывы
Этот дефект возникает при накатывании расплавленного металла на основной. Но при этом они не образуют единую структуру соединения. Причинами наплывов может стать окалина на кромках или недостаточный прогрев обрабатываемой поверхности из-за малой силы подаваемого тока.
Трещины
Данные дефекты сварочных швов являются самыми опасными, так как способны быстро привести к разрушению конструкций.
- холодные трещины появляются в момент остывания шва после сварки в результате снижения прочности металла во время сварочного напряжения. Причинами их появлений становятся влажные швы или используемые материалы.
- горячие трещины образуются, когда температура металла достигает 1100–13000С. В этот момент его пластические свойства резко снижаются, и начинается процесс кристаллизации. Если в металле повышенное содержание кремния, фосфора, серы, никеля или водорода, то на границах кристаллических решёток образуются микроскопические разрывы, которые быстро распространяться и вдоль шва, и поперёк него.
Трещины появляются при неправильном закреплении деталей, нарушении технологии процесса сварки, использовании некачественных или неподходящих электродов или быстром охлаждении поверхности.
Подрезы
Подрезы представляют собой небольшие углубления, образованные там, где проходит граница сварного шва и основного металла. Возникают они в результате большой силы подаваемого тока. Во время сварки угловых швов может произойти смещение электрода. Это приводит к стеканию расплавленного металла на горизонтальную полку и меняет катет сварочного шва, что влечёт за собой образование подрезов.
Кратеры
Кратеры являются углублениями, возникающими в момент резкого обрыва сварочной дуги. Они уменьшают сечение шва и снижают его прочность.
Свищи
Свищи представляют собой полости, образованные в швах во время сварки. Они снижают прочность соединения и приводят к появлению трещин. Свищи возникают в результате недостаточной обработки поверхности или плохого качества используемой присадочной проволоки.
Непровар
Непровары — это дефекты сварочных швов, которые проявляются отсутствием местного несплавления основного и наплавленного металла.
Причинами могут служить наличие на кромках окалины, масляных пятен или ржавчины, снижение силы тока, а также большой скорости сварки.
Во время вибрации конструкции непровары снижают её прочность от 40 до 70 процентов.
Посторонние включения
К посторонним включениям относят шлак, окислы металлов, вольфрам и другие механические примеси. Они образуются, если режим сварки выбран неправильно, зачистка металла проведена не качественно или было произведено его быстрое охлаждение. Данный дефект приводит к уменьшению диаметра сечения шва и снижению его прочности.
Перегрев и пережог металла
Пережог и перегрев возникают в результате подачи большого сварочного тока или при малой скорости сварки. Они приводят к хрупкости металла и снижению его ударной вязкости.
Прожог
Проверка сварочных швов должна начинаться с осмотра на наличие прожогов, представляющих собой сквозные отверстия в сварочных отверстиях. Возникают они при подаче тока большой силы при малой скорости сварки или при резком обрыве подачи защитного газа.
Контроль сварочных швов осуществляется несколькими способами в зависимости от того происходит ли процесс разрушения сварного соединения или нет.
Методы контроля
Существует два вида методов контроля качества сварки. К ним относятся неразрушающие и разрушающие методы.
Главным неразрушающим методом является внешний осмотр, затем следует проверка на герметичность, наличие поверхностных и скрытых дефектов.
Разрушающие методы включают в себя различные испытания, проводимые с контрольными образцами для получения полной характеристики швов. Особое внимание заслуживает корень шва сварка. Она должна быть проведена особо тщательно, так как от неё зависит качество всех последующих работ.
Сварочные швы фото показывают, как выглядят описанные дефекты работы для того, чтобы облегчить их распознавание и дальнейшее устранение.
Еще по этой теме на нашем сайте:
- Сколько стоят сварочные работы — цена за шов от хорошего сварщика
Очень востребованными во многих сферах стали такие работы, как сварочные. Применяются они и в строительстве, и в быту. У каждого может возникнуть необходимость в проведении.
Сварка медных проводов своими руками — используем графитовые электроды для сварки
Что такое соединение электропроводки, известно любому мужчине. Каждый хоть раз в жизни сталкивался с выполнением такой работы, как сварка медных проводов своими руками. И все.
Кислородные баллоны для сварки — какой должна быть сварочная смесь в баллонах
Нормы и требования к сварочным постам
Оборудовать место для проведения работ, связанных с огнем, нужно так, чтобы не создавалось опасности для окружающих и для самого сварщика. Взрывоопасные и пожароопасные комнаты сразу.
Изъян, называемый подрезом, это углубление, образующееся рядом со швом. Из-за уменьшения толщины металла на месте дефекта снижается прочность сварного соединения. Внешне подрезы выглядят как усадочные канавки по всей длине шва или на отдельных участках.
Причины возникновения
Чаще всего изъяны, называемые подрезами, получаются у неопытных сварщиков при неправильном выборе тока. Также причиной могут стать:
- плохая смачиваемость металла заготовок;
- изменение длины дуги при наложении сварного шва;
- значительные отклонения электрода от оси стыка;
- неудобное для сварки расположение заготовок;
- некачественная подготовка кромок;
- завышение скорости проведения работы;
- неправильный угол наклона электрода.
Способы предотвращения подрезов сварных швов
Риск образования дефектов сводится к минимуму, если подготовка стыка выполнена в полном объеме, а сварка проводится с соблюдением технологических правил:
- Чтобы не было подреза на сварном шве, заготовки для улучшения смачиваемости предварительно подогревают. Это улучшает растекание жидкого металла по ширине стыка, снижает вероятность образования очагов напряженности.
- При неправильном положении электрода дефекты появляются из-за неравномерного нагрева кромок.
При соединении разных по толщине деталей большую часть тепла направляют на толстую кромку. Углеродистую сталь сваривают, наклоняя электрод углом вперед.
- При повышенной скорости сварки металл в центральной части шва быстро остывает, создавая по краям усадочные канавки. Однако чрезмерное снижение скорости не избавляет от проблемы. Поэтому оптимальное значение выбирают в соответствии с маркой свариваемого железа.
- Вероятность образования огрехов значительно возрастает при неверном выборе защитного газа. Углеродистую сталь сваривают в среде из смеси инертного и углекислого газа. Для работы с другими материалами тип газа выбирают в зависимости от вида свариваемого металла.
- У неопытных сварщиков дефекты чаще всего появляются при нарушении правил проведения сварочных работ. Когда диаметр электрода меньше ширины шва, приходится делать поперечные движения с большой амплитудой. После такой сварки образование подрезов неизбежно. Поэтому по возможности нужно уменьшать ширину соединения или сваривать его несколькими проходами.
Чтобы не было перегрева основного металла, рабочий ток устанавливают в соответствии с толщиной заготовок. Сварку выполняют короткой дугой с постоянной скоростью. - При наложении вертикальных швов огрехи образуются из-за сложности заполнения пространства стыка расплавленным металлом. Поэтому соединение заготовок, если есть такая возможность, следует выполнять в горизонтальном положении с меньшим расходом электродов. Чтобы исключить образование подрезов, угловые швы накладывают способом «в лодочку».
- Лучшим способом для предотвращения подрезов считается создание сварных соединений инверторами с функциями MIG/MAG. Кроме усадочных канавок эти аппараты позволяют избежать появления других изъянов на сварных швах.
Устранение подрезов
Для устранения такого дефекта участок изъяна очищают от шлака и грязи, а затем заваривают тонким швом. Желательно, чтобы у электрода был высокий показатель смачиваемости. Однако при этом увеличивается потребность в расходных материалах. Чтобы избежать непредусмотренных затрат, подрезы в сварных швах устраняют аргонодуговой сваркой неплавящимся электродом. После нагрева огрех замазывают расплавленным металлом. Однако такой метод исправления не рекомендуется, если соединение было выполнено другим видом сварки, так как внутри могут быть поры, посторонние включения и пр. Чтобы прочность не уменьшалась, участки сварного соединения с многочисленными подрезами вырубают или вырезают до основного металла и переваривают. Размер удаляемой части должен превышать длину изъяна на 1- 2 см с каждой стороны.
После исправления сварные соединения проходят повторную проверку. При выявлении дефектов отправляются на доработку. Один и тот же участок допускается исправлять в зависимости от сорта стали не более 2 — 3 раз. Это связано с изменением характеристик металла после повторной сварки. При исправлении следует учитывать, что при усилении сварного соединения снижается стойкость к вибрации.
Допускаются ли подрезы в сварных швах
Смонтированные конструкции принимают в эксплуатацию, если размеры подрезов в сварных швах не превышают указанных в ГОСТ30242-97 норм. Окончательное решение принимают после рассмотрения следующих факторов:
- размер конструкции и длина шва;
- как дефект влияет на прочность изделия с учетом начального и остаточного напряжения;
- вид и параметры изъяна;
- характеристики подреза по текучести, сопротивляемости, вязкости, пластичности;
- в каких условиях будет эксплуатироваться смонтированная конструкция;
- степень влияния дефекта на функциональность.
Прибор для замера изъянов должен иметь необходимый предел измерения. Поэтому следует внимательно изучить инструкцию, чтобы знать его возможности. Прибором с пределом до 5 мм не получится с необходимой точностью измерить дефект до 2 мм.
Даже у многоопытных сварщиков случаются подрезы, поэтому новичкам не следует расстраиваться, если не все швы получаются идеальными. Чтобы снизить количество огрехов в период обучения сварку лучше выполнять многофункциональными инверторами. Дополнительные опции такого оборудования компенсируют недостаток опыта.
Имеющиеся фактические дефекты на металлическом изделии усложняют принцип использования конструкции по прямому назначению. Но, если грамотно и профессионально провести устранение дефекта, например подрез дефект сварного шва, то можно добиться отличных результатов механических и физических свойств материала. Чаще всего подрез сварного шва признается явным изъяном технологического процесса, который возникает от естественного перегрева металла, или места, где образован шов, так называемая технологическая усадка на кромках, которые происходят в процессе плавления. Чаще всего этот эффект возникает тогда, когда сварщик использует высокую скорость проведения сварочных мероприятий, а также в случае нарушения технологических процессов сварки, например, есть место появления высокого сварочного тока.
Кроме этого, неправильный угол наклона изделия, создаёт направление зоны горения дуги сварочного аппарата в места с тонкими краями, что в свою очередь создаёт технологическую глубину подреза сварного шва. В результате, в естественной газовой среде, при достаточно высоких температурах можно сжечь металл, а это, приводит к нарушению прочности конструкционного строения металла.
Как образуются дефекты?
Попробуем разобраться, что такое подрез сварочного шва и как он влияет на физическую природу строения металла. Сам подрез является конструкционным углублением внутри основного металла, имеющий расположение по краям готового сварного шва. Чаще всего такой дефект возникает по причине появления излишнего показателя силы сварочного тока в рабочем процессе варки или пайки металла. Также причины подреза сварного шва вызваны неконтролируемой длиной электрической дуги. В данном случае длина сварного шва неестественным образом увеличиться, а края готовых кромок сильно оплавятся.
На представленных фото подрез сварного шва можно заметить, если видны смещения электрода к самой видимой и близкой части горизонтальной стенки. При этом сама вертикальная стенка оплавляется максимально быстро, чем горизонтальная. Расплавленный в данном случае металл мгновенно стекается по горизонтальной части. В этом случае возникает допуск подреза сварного шва на вертикальной части, а в горизонтальной плоскости образуются наплывы.
Способы предотвращения появления дефектов
Несмотря на то, что есть определённый технологический регламент контроля дефекта ГОСТ 30242-97 подреза сварного шва, рекомендуется все же предотвратить эти явления, соблюдая минимальные требования, в числе которых представлены следующие:
- Соблюдение температурного режима. Как известно, подрез сварного шва это процесс, который получаете в результате перегрева, и высокие показатели силы тока, являются основными причинами увеличения температуры и образования подреза.
- Угол наклона. Нередко в качестве дефекта служит банальное несоблюдение рабочего угла наклона, который имеет свои характеристики. Используйте рекомендуемый угол наклона, а высокую температуру сварки направляйте в зону, где есть более толстый слой металла.
Таким образом, вы сумеете придерживать требуемые нормы подреза сварного шва.
- Скорость. Быстрая скорость сварки приводит к тому, что допускается подрез сварного шва. В результате дефекты будут очевидными, а это в свою очередь негативно сказывается на характеристиках прочности соединения. Рекомендуем попробовать свои силы и научиться выстраивать скорость проведения сварочных работ.
работать умеренно, не допускать высоких скоростей работы, но и медленная работа не даёт нужного результата.»
- Правильный выбор газа. Дополнительным отрицательным моментом работы в среде газа MAG-сварки, станет неправильный выбор экранирующего газа, который ставит перед собой проблему — допускаются ли подрезы сварных швов. Правильный выбор типа газа, а также его соответствие с металлами, станет гарантией качества проведённой работы. Для углеродистых сталей оптимальным вариантом станет двуокись углерода, а лучше в сочетании с различными группами инертных газов.
- Соблюдение технологии сварки.
В ряде случаев предусматривается что подрез сварного шва можно замерить с помощью специальных слесарных инструментов, которые есть у каждого сварщика. В процессе сварки используйте только тот диаметр электродов, который является оптимальным для данного класса или группы металлов. Если нет возможности исключить полностью подрез, то используйте оптимальную рабочую зону шва. В крайнем случае, допускается использование многопроходных швов.
- Правильное рабочее положение. Некоторые сварщики допускают оплошность в виде того, что сварка осуществляется в горизонтальном положении. Это случай создаёт определённую усадку на металле, точнее на ее кромках. Самым оптимальным вариантом в данном случае является вертикальное положение свариваемых деталей. Здесь же вы получите дополнительный плюс в виде адекватного расходования электрода в процессе сварки.
- Использование многофункциональных систем сварки. При необходимости, используйте не только MAG-сварку, а аналог типа MIG. Это в конечном итоге даст хороший результат и меньше всего будут заметны дефекты сварки в целом.
Смело комбинируйте различные варианты сварочных аппаратов в рабочем процессе.
Допускаются ли подрезы в сварных швах
В силу ряда причин допускается использование подреза сварных швов, которые чаще всего вынуждены использовать в сложных конструкционных решениях. Для точного определения надобности наличия подреза, учитываются следующие факторы:
- Естественные габаритные размеры металлоконструкции, а также размеры сварного шва.
- Какое фактическое напряжение возникает внутри металлоконструкции, учитываются как начальное, так и остаточное напряжение.
- Общий вид имеющегося сварного дефекта, описание и характеристика.
- Механические параметры дефекта (текучесть, сопротивление, вязкость, пластичность и т.д.).
- Условия эксплуатации металлоконструкции, чаще всего определяются по параметрам состояния окружающей среды.
- Функциональная пригодность в дальнейшем изделия.
При выборе прибора для измерения, учитываем возможности устройства. Если прибор имеет предел измерения 5 мм, то невозможно точно определить данные дефекта с диаметром менее 2 мм. Внимательно изучите инструкцию прибора, и правильно производите измерение параметра глубины дефекта. Учитываем также общее состояние металлоконструкции, уставший металл верный признак того, что подрез сварного шва будет неэффективным по многим параметрам.
причины появления, допуск, нормы, ГОСТ
Имеющиеся фактические дефекты на металлическом изделии усложняют принцип использования конструкции по прямому назначению. Но, если грамотно и профессионально провести устранение дефекта, например подрез дефект сварного шва, то можно добиться отличных результатов механических и физических свойств материала. Чаще всего подрез сварного шва признается явным изъяном технологического процесса, который возникает от естественного перегрева металла, или места, где образован шов, так называемая технологическая усадка на кромках, которые происходят в процессе плавления. Чаще всего этот эффект возникает тогда, когда сварщик использует высокую скорость проведения сварочных мероприятий, а также в случае нарушения технологических процессов сварки, например, есть место появления высокого сварочного тока.
Кроме этого, неправильный угол наклона изделия, создаёт направление зоны горения дуги сварочного аппарата в места с тонкими краями, что в свою очередь создаёт технологическую глубину подреза сварного шва. В результате, в естественной газовой среде, при достаточно высоких температурах можно сжечь металл, а это, приводит к нарушению прочности конструкционного строения металла.
Пример подреза сварного шва
Как образуются дефекты?
Попробуем разобраться, что такое подрез сварочного шва и как он влияет на физическую природу строения металла. Сам подрез является конструкционным углублением внутри основного металла, имеющий расположение по краям готового сварного шва. Чаще всего такой дефект возникает по причине появления излишнего показателя силы сварочного тока в рабочем процессе варки или пайки металла. Также причины подреза сварного шва вызваны неконтролируемой длиной электрической дуги. В данном случае длина сварного шва неестественным образом увеличиться, а края готовых кромок сильно оплавятся.
Внешний вид подреза сварного шва
На представленных фото подрез сварного шва можно заметить, если видны смещения электрода к самой видимой и близкой части горизонтальной стенки. При этом сама вертикальная стенка оплавляется максимально быстро, чем горизонтальная. Расплавленный в данном случае металл мгновенно стекается по горизонтальной части. В этом случае возникает допуск подреза сварного шва на вертикальной части, а в горизонтальной плоскости образуются наплывы.
Способы предотвращения появления дефектов
Несмотря на то, что есть определённый технологический регламент контроля дефекта ГОСТ 30242-97 подреза сварного шва, рекомендуется все же предотвратить эти явления, соблюдая минимальные требования, в числе которых представлены следующие:
- Соблюдение температурного режима. Как известно, подрез сварного шва это процесс, который получаете в результате перегрева, и высокие показатели силы тока, являются основными причинами увеличения температуры и образования подреза.
- Угол наклона. Нередко в качестве дефекта служит банальное несоблюдение рабочего угла наклона, который имеет свои характеристики. Используйте рекомендуемый угол наклона, а высокую температуру сварки направляйте в зону, где есть более толстый слой металла. Таким образом, вы сумеете придерживать требуемые нормы подреза сварного шва.
- Скорость. Быстрая скорость сварки приводит к тому, что допускается подрез сварного шва. В результате дефекты будут очевидными, а это в свою очередь негативно сказывается на характеристиках прочности соединения. Рекомендуем попробовать свои силы и научиться выстраивать скорость проведения сварочных работ.
«Важно,
работать умеренно, не допускать высоких скоростей работы, но и медленная работа не даёт нужного результата.»
- Правильный выбор газа. Дополнительным отрицательным моментом работы в среде газа MAG-сварки, станет неправильный выбор экранирующего газа, который ставит перед собой проблему – допускаются ли подрезы сварных швов.
Правильный выбор типа газа, а также его соответствие с металлами, станет гарантией качества проведённой работы. Для углеродистых сталей оптимальным вариантом станет двуокись углерода, а лучше в сочетании с различными группами инертных газов.
- Соблюдение технологии сварки. В ряде случаев предусматривается что подрез сварного шва можно замерить с помощью специальных слесарных инструментов, которые есть у каждого сварщика. В процессе сварки используйте только тот диаметр электродов, который является оптимальным для данного класса или группы металлов. Если нет возможности исключить полностью подрез, то используйте оптимальную рабочую зону шва. В крайнем случае, допускается использование многопроходных швов.
- Правильное рабочее положение. Некоторые сварщики допускают оплошность в виде того, что сварка осуществляется в горизонтальном положении. Это случай создаёт определённую усадку на металле, точнее на ее кромках. Самым оптимальным вариантом в данном случае является вертикальное положение свариваемых деталей.
Здесь же вы получите дополнительный плюс в виде адекватного расходования электрода в процессе сварки.
- Использование многофункциональных систем сварки. При необходимости, используйте не только MAG-сварку, а аналог типа MIG. Это в конечном итоге даст хороший результат и меньше всего будут заметны дефекты сварки в целом. Смело комбинируйте различные варианты сварочных аппаратов в рабочем процессе.
Допускаются ли подрезы в сварных швах
В силу ряда причин допускается использование подреза сварных швов, которые чаще всего вынуждены использовать в сложных конструкционных решениях. Для точного определения надобности наличия подреза, учитываются следующие факторы:
- Естественные габаритные размеры металлоконструкции, а также размеры сварного шва.
- Какое фактическое напряжение возникает внутри металлоконструкции, учитываются как начальное, так и остаточное напряжение.
- Общий вид имеющегося сварного дефекта, описание и характеристика.
- Механические параметры дефекта (текучесть, сопротивление, вязкость, пластичность и т.
д.).
- Условия эксплуатации металлоконструкции, чаще всего определяются по параметрам состояния окружающей среды.
- Функциональная пригодность в дальнейшем изделия.
При выборе прибора для измерения, учитываем возможности устройства. Если прибор имеет предел измерения 5 мм, то невозможно точно определить данные дефекта с диаметром менее 2 мм. Внимательно изучите инструкцию прибора, и правильно производите измерение параметра глубины дефекта. Учитываем также общее состояние металлоконструкции, уставший металл верный признак того, что подрез сварного шва будет неэффективным по многим параметрам.
Подрез сварного шва и 7 способов его предотвращения
Дефекты сварочных соединений часто усложняют нам жизнь. Подрез сварного шва или усадочная канавка является изъяном, характеризующимся образованием канавки возле корня одностороннего сварного шва из-за перегрева основного металла или металла шва (усадка на кромках при сплавлении). Это происходит, когда сварщик пытается варить с высоким сварочным напряжением или при быстрой скорости сварки. Кроме того, неправильный угол наклона направляет дугу в сторону более тонких краев, где перегрев может сжечь металл. Способствовать такому дефекту сварочных соединений может неправильное использование защитной газовой атмосферы, нарушение техники сварки, положение свариваемого предмета и т.д.
Усадочные канавки всегда были серьезной проблемой в отраслях промышленности связанных со сваркой и обработкой сталей. Были предприняты усилия чтобы решить эту проблему в последние годы. Ниже приведены советы, которые эффективно помогают упреждать или снижать частоту этого явления.
Соответствующее нагревание
Подрез сварного шва чаще всего вызывают высокие тепловые очаги, возникающие впоследствии прохода вблизи кромок. Это может привести к перегреву и плавлению вблизи корня шва. Для предотвращения дефектов необходимо проявлять большую осторожность при сварке металлов за счет уменьшения силы тока при приближении к более тонким и свободным краям.
Положение электрода при сварке.
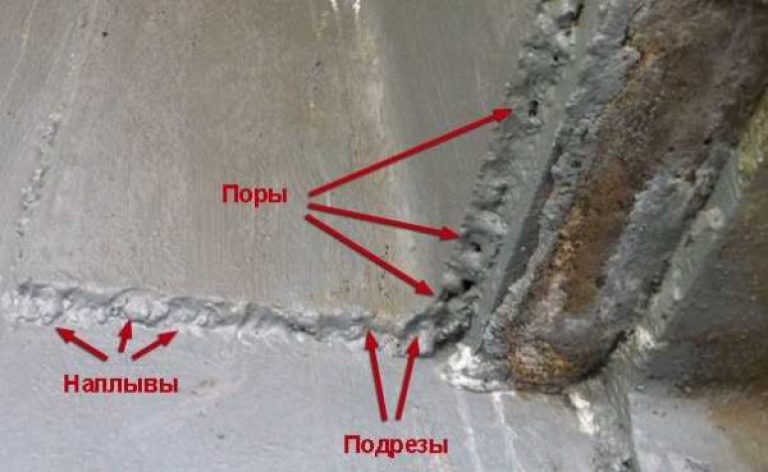
Ошибочный угол при сварочных работах часто играет особо важную роль для появления дефектов такого рода. Даже один проход с неправильным углом, который направляет больше тепла свободным краям, способствует склонности сварного шва к появлению усадочных канавок. Во избежание проблем понадобится просто использовать правильные углы, дабы направить больше тепла в сторону более толстых компонентов по сравнению со свободными краями.
Умеренная скорость сварки
Изготовление сварного шва с высокой скоростью плавления, является еще одной большой причиной усадки на кромках. При этом некоторая часть исходного базового металла вдавливается в нижнюю центральную часть сварочной ванны и из-за быстрого отвердевания оставляет углубление по краям. Рекомендуется проводить сварочные работы умеренным темпом. Не стоит забывать: медленная скорость также негативно скажется на результате работ и не даст удовлетворительных результатов.
Корректный выбор защитного газа
В случае MAG-сварки (Metal Active Gas), неправильный выбор экранирующего газа может стать одной из основных причин появления подреза сварного шва. Правильный состав газа в соответствии с требованиями по типу материала и его толщине обеспечат хороший результат. При сварке углеродистых сталей лучше всего применять двуокись углерода в сочетании с инертными газами.
Правильная технология сварки
Подрез сварного шва или усадочные канавки часто возникают при попытке сварщика сделать сварной шов с чрезмерным поперечным перемещением электрода при сварке. Кодексы и нормы по стандартам требуют рекомендуемой ширины шовной зоны в зависимости от размера электрода. Размер шва при сварке не должен быть более приемлемого предела, иначе в противном случае шов может быть склонен к подрезам. Для того, чтобы не допустить этого, нужно стремиться либо уменьшить размер шовной зоны или делать многопроходные швы.
Правильное положение предмета в пространстве
Некоторые сварщики пытаются делать угловые швы не в горизонтальном положении, а в вертикальном, что способствует усадке на кромках. В этом случае депрессивные формы образуются из-за недостаточного заполнения металлом кромок стыка. Для предотвращения, по возможности, попытайтесь варить в горизонтальном положении, чтобы обеспечить адекватное потребление электрода.
Использование многофункциональных систем сварки
Применение многофункциональных аппаратов для MIG/MAG сварки предусматривает упомянутые выше предупреждения и позволяет выполнять тонкие сварные швы с улучшенными механическими свойствами. Таким образом, подрез сварного шва лучше всего предотвращает данный метод. Соблюдая все указанные правила, сварщик минимизирует вероятность негативных последствий и дефекты сварных швов такого рода в крайнем случае будут минимальными.
Подрез при сварке
Подрез – это дефект в виде канавки вдоль шва на металле. Обычно возникают при слишком длинной дуге или недостаточном напряжении. Шов становится широким, температуры дуги для прогрева не хватает. Металл по краям быстро застывает, образуя эти канавки. Исправляется он более короткой дугой или корректировкой силы тока в большую сторону. При слишком высокой скорости сварки и повышенном напряжении сварной шов образуется «горбатым». Из-за быстрого затвердевания сварочной ванны также образуются подрезы. Уменьшение скорости сварки постепенно сокращает размер подреза и в конечном итоге устраняет этот дефект.
При угловом или тавровом соединении подрез образуется из-за того, что электрод больше направлен на вертикальную плоскость. Тогда металл стекает вниз, снова образуется канавка, но уже по другой причине: слишком сильном нагреве вертикальной части шва. Устраняется он снижением силы тока и/или укорочением дуги.
Наиболее часто подрезы возникают при сварке угловых швов и первых слоев многослойных стыковых швов.
Подрез приводит к резкой концентрации напряжений в тех случаях, когда он расположен перпендикулярно к направлению главных напряжений, действующих на сварное соединение. Для конструкций, работающих при вибрационных нагрузках, подрез существенно снижает прочность сварного соединения.
Устранение подреза производится наплавкой небольшого тонкого шва по линии этого дефекта.
В силу ряда причин допускается использование подреза сварных швов, которые чаще всего вынуждены использовать в сложных конструкционных решениях. Для точного определения необходимости устранения подреза, учитываются следующие факторы:
- Естественные габаритные размеры металлоконструкции, а также размеры сварного шва.
- Какое фактическое напряжение возникает внутри металлоконструкции, учитываются как начальное, так и остаточное напряжение.
- Общий вид имеющегося сварного дефекта, описание и характеристика.
- Механические параметры дефекта (текучесть, сопротивление, вязкость, пластичность и т.д.).
- Условия эксплуатации металлоконструкции, чаще всего определяются по параметрам состояния окружающей среды.
- Функциональная пригодность в дальнейшем изделия.
Непровар сварного шва фото — Морской флот
- наружные, к основным из которых относятся: трещины, подрезы, наплывы, кратеры;
- внутренние, среди которых чаще всего встречаются: пористость, непровары и посторонние включения;
- сквозные – трещины, прожоги.
Причинами возникновения дефектов могут быть различные обстоятельства: низкое качество свариваемого металла, неисправное или некачественное оборудование, неверный выбор сварочных материалов, нарушение технологии сварки или неправильный выбор режима, недостаточная квалификация сварщика.
Основные дефекты сварки, их характеристика, причины возникновения и способы исправления
Чаще всего причиной образования трещин является несоблюдение технологии сварки (например, неправильное расположение швов, приводящее к возникновению концентрации напряжения), неверный выбор сварочных материалов, резкое охлаждение конструкции. Способствует их возникновению также повышенное содержание в шве углерода и различных примесей – кремния, никеля, серы, водорода, фосфора.
Исправление трещины заключается в рассверливании ее начала и конца, с целью исключения дальнейшего распространения, удалении шва (вырубанию или вырезанию) и заваривании.
Подрезы. Подрезы – это углубления (канавки) в месте перехода «основной металл-сварной шов». Подрезы встречаются довольно часто. Их отрицательное действие выражается в уменьшении сечения шва и возникновении очага концентрации напряжения. И то и другое ослабляет шов. Подрезы возникают из-за повышенной величины сварочного тока. Чаще всего этот дефект образуется в горизонтальных швах. Устраняют его наплавкой тонкого шва по линии подреза.
Наплывы. Наплывы возникают, когда расплавленный металл натекает на основной, но не образует с ним гомогенного соединения. Дефект шва возникает по разным причинам – при недостаточном прогреве основного металла вследствие малого тока, из-за наличия окалины на свариваемых кромках, препятствующей сплавлению, излишнего количества присадочного материала. Устраняются наплывы срезанием с проверкой наличия непровара в этом месте.
Прожоги. Прожогами называют дефекты сварки, проявляющиеся в сквозном проплавлении и вытекании жидкого металла через сквозное отверстие в шве. При этом обычно с другой стороны образуется натек. Прожоги возникают из-за чрезмерно высокого сварочного тока, недостаточной скорости перемещения электрода, большого зазора между кромками металла, слишком малой толщины подкладки или ее неплотного прилегания к основному металлу. Исправляют дефект зачисткой и последующей заваркой.
Непровар. Непровары – это локальные несплавления наплавленного металла с основным, или слоев шва между собой. К этому дефекту относят и незаполнение сечения шва. Непровары существенно снижают прочность шва и могут явиться причиной разрушения конструкции.
Дефект возникает из-за заниженного сварочного тока, неправильной подготовки кромок, излишне высокой скорости сварки, наличия на кромках свариваемых деталей посторонних веществ (окалины, ржавчины, шлака) и загрязнений. При исправлении нужно вырезать зону непровара и заварить её.
Кратеры. Это дефекты в виде углубления, возникающего в результате обрыва сварочной дуги. Кратеры снижают прочность шва из-за уменьшения его сечения. В них могут находиться усадочные рыхлости, способствующие образованию трещин. Кратеры надлежит вырезать до основного металла и заварить.
Свищи. Свищами называют дефекты швов в виде полости. Как и кратеры, они уменьшают прочность шва и способствуют развитию трещин. Способ исправления обычный – вырезка дефектного места и заварка.
Посторонние включения. Включения могут состоять из различных веществ – шлака, вольфрама, окислов металлов и пр. Шлаковые включения образуются тогда, когда шлак не успевает всплыть на поверхность металла и остается внутри него. Это происходит при неправильном режиме сварки (завышенной скорости, например), плохой зачистке свариваемого металла или предыдущего слоя при многослойной сварке.
Вольфрамовые включения возникают при сварке вольфрамовым электродом, окисные – из-за плохой растворимости окислов и чрезмерно быстрого охлаждения.
Все виды включений уменьшают сечение шва и образуют очаг концентрации напряжения, снижая тем самым прочность соединения. Дефект устраняют вырезкой и завариванием.
Пористость. Пористость – это полости, заполненные газами. Они возникают из-за интенсивного газообразования внутри металла, при котором газовые пузырьки остаются в металле после его затвердевания. Размеры пор могут быть микроскопическими или достигать нескольких миллиметров. Нередко возникает целое скопление пор в сочетании со свищами и раковинами.
Возникновению пор способствует наличие загрязнений и посторонних веществ на поверхности свариваемого металла, высокое содержание углерода в присадочном материале и основном металле, слишком высокая скорость сварки, из-за которой газы не успевают выйти наружу, повышенная влажность электродов. Как и прочие дефекты, пористость снижет прочность сварного шва. Зону с ней необходимо вырезать до основного металла и заварить.
Перегрев и пережог металла. Пережог и перегрев возникают из-за чрезмерно большого сварочного тока или малой скорости сварки. При перегреве размеры зерен металла в шве и околошовной зоне увеличиваются, в результате чего снижаются прочностные характеристики сварного соединения, главным образом – ударная вязкость. Перегрев устраняется термической обработкой изделия.
Пережог представляет собой более опасный дефект, чем перегрев. Пережженный металл становится хрупким из-за наличия окисленных зерен, обладающих малым взаимным сцеплением. Причины пережога те же самые, что и перегрева, а кроме этого еще и недостаточная защита расплавленного металла от азота и кислорода воздуха. Пережженный металл необходимо полностью вырезать и заварить это место заново.
Дефе́кты сварны́х соедине́ний — любые отклонения от заданных нормативными документами параметров соединений при сварке, образовавшиеся вследствие нарушения требований к сварочным материалам, подготовке, сборке и сварке соединяемых элементов, термической и механической обработке сварных соединений и конструкции в целом.
Содержание
Основные причины [ править | править код ]
По данным американского общества инженеров-механиков (ASME) причины дефектов сварки распределены следующим образом: 45 % — ошибки выбора технологии сварки, 32 % — ошибки сварщика, 12 % — сбои в работе сварочного оборудования, 10 % — неподходящие сварочные материалы, 1 % — прочее [1] .
Классификация по геометрии [ править | править код ]
Классификация дефектов изложена в ГОСТ 30242-97 «Дефекты соединений при сварке металлов плавлением. Классификация, обозначение и определения» [2] , а также в ГОСТ Р ИСО 6520-1-2012 «Классификация дефектов геометрии и сплошности в металлических материалах. Часть 1. Сварка плавлением» [3] , которые соответствуют стандарту ISO 6520 [4] .
Дефекты соединений при сварке разделяются на шесть групп:
- Трещины — несплошности, вызванная местным разрывом шва, который может возникнуть в результате охлаждения или действия нагрузок.
- Полости и поры — несплошность произвольной формы, образованная газами, задержанными в расплавленном металле, которая не имеет углов.
- Твёрдые включения — твёрдые инородные вещества металлического или неметаллического происхождения в металле сварного шва.
- Несплавления и непровары — отсутствие соединения между металлом сварного шва и основным металлом или между отдельными валиками сварного шва.
- Нарушение формы шва — отклонение формы наружных поверхностей сварного шва или геометрии соединения от установленного значения.
- Прочие дефекты — все дефекты, которые не могут быть включены в перечисленные выше группы.
Трещины [ править | править код ]
Трещины возникающие в соединениях при сварке могут располагаться в металле сварного шва, в зоне термического влияния, в основном металле.
В зависимости от ориентации трещины делятся на:
- продольные (ориентированные параллельно оси сварного шва). Преимущественно обуславливаются высокими усадочными напряжениями[5] .
- поперечные (ориентированные поперек оси сварного шва). Как правило, образуются в результате продольной усадки металла с низкой пластичностью и, обычно, неглубоки.
- радиальные (радиально расходящиеся из одной точки)
Кроме того, отдельно выделяют следующие виды трещин:
- размещённые в кратере сварного шва
- групповые и раздельные
- групповые разветвлённые
- микротрещины, обнаруживаемые физическими методами при не менее чем 50-кратном увеличении.
Методами снижения трещинообразования при сварке являются:
- прокаливание флюсов перед сваркой;
- предварительный подогрев заготовок от 250 до 450 °С;
- сваривание в режиме с оптимальными параметрами;
- медленное охлаждение металла после сварки;
- проведение после сварки мягкого отжига для снятия остаточных напряжений.
Полости и поры [ править | править код ]
Возникновение этих дефектов преимущественно обуславливается газами, задержанными в расплавленном металле. По расположению они подразделяться на:
- равномерно распределённые по сварному шву;
- расположенные скоплением;
- расположенные цепочкой.
К полостям также относятся свищи — продолговатые трубчатые полости, вызванные выделением газа, и усадочные раковины — полости, которые образуются вследствие усадки при затвердевании. Частным случаем усадочной раковины является кратер — не заваренная усадочная раковина в конце валика сварного шва.
Твёрдые включения [ править | править код ]
Выделяют следующие виды твёрдых включений:
- шлаковые включения — линейные, разобщённые, прочие;
- флюсовые включения — линейные, разобщённые, прочие;
- оксидные включения;
- металлические включения — вольфрамовые, медные, из другого металла.
Несплавления и непровары [ править | править код ]
Выделяют следующие типы несплавлений или отсутствий соединения между металлом шва и основным металлом либо между отдельными валиками сварного шва [6] :
- по боковой поверхности;
- между валиками;
- в корне сварного шва.
Термином непровар или неполный провар, называют несплавление основного металла на участке или по всей длине шва, появляющееся из-за неспособности расплавленного металла проникнуть в корень соединения, заполняя зазор между деталями.
Нарушение формы шва [ править | править код ]
К нарушениям формы шва по ГОСТ 30242-97 относятся:
- подрезы — продольные углубления на наружной поверхности валика шва.
- усадочные канавки — подрезы со стороны корня одностороннего шва из-за усадки вдоль его границы.
- превышения выпуклости стыкового и углового швов
- превышение проплава — избыток наплавленного металла на обратной стороне стыкового сварного шва.
- неправильный профиль шва — угол между поверхностью основного металла и плоскостью, касательной к поверхности шва, меньше нормального значения.
- наплав — избыток наплавленного металла шва, натёкший на поверхность основного металла.
- линейное и угловое смещения свариваемых элементов — смещение между свариваемыми элементами при их параллельном расположении на разном уровне (линейное) или расположение кромок элементов под углом (угловое).
- натёк — металл шва, не имеющий сплавления с соединяемой поверхностью и образовавшийся в результате перераспределения наплавленного металла шва под действием силы тяжести. Натёки часто возникают при сварке угловых швов или стыковых швов в горизонтальном положении.
- прожог — вытекание металла сварочной ванны, приводящее к образованию в шве сквозного отверстия.
- не полностью заполненная разделка кромок
- чрезмерная асимметрия углового шва — значительное превышение размеров одного катета над другим.
- неравномерная ширина шва
- неровная поверхность
- вогнутость корня сварного шва — неглубокая канавка со стороны корня шва, возникшая из-за усадки.
Содержание
Дефекты сварных швов – это, прежде всего, различные несплошности в металле шва, ухудшающие его качество. При оценке свариваемости стали исходят, главным образом, из того, что металл сварного шва должен быть сплошным. И все образования, которые делают сварной шов неоднородным, принято считать дефектами. Различают следующие виды дефектов сварного шва: микро- и макротрещины (горячие и холодные), непровары, поры, различные включения.
Внутренние и наружные дефекты сварных швов
Самый распространённый метод классификации дефектов сварки – по их месту расположения. Согласно этой классификации, различают внутренние и наружные сварные дефекты. Наружные выходят на поверхность шва и околошовной зоны, а внутренние располагаются внутри соединения, не выходя на поверхность. Из этого следует, что один и тот же вид дефектов (например, трещины или поры) может быть как внутренним (если располагается внутри), так и наружным (если выходит на поверхность).
Наружные сварные дефекты
К наружным дефектам сварных соединений относят неравномерность формы сварного шва из-за неправильного его формирования, подрезы шва, прожоги свариваемого металла, наплывы, трещины, поры и другие дефекты, которые располагаются на поверхности металла. Все они выявляются при внешнем визуальном осмотре сварного соединения. Ниже по тексту перечислены и показаны распространённые виды наружных дефектов.
Внутренние сварные дефекты
К внутренним дефектам сварных соединений, согласно ГОСТ23055, относятся неметаллические, шлаковые и оксидные включения, непровары и несплавления металла, а также поры и трещины, не выходящие на поверхность металла. Для того, чтобы выявить подобные дефекты, на практике применяются методы неразрушающего контроля сварки. Ниже по тексту рассказывается о часто встречающихся видах внутренних дефектов.
Дефекты формирования шва
Дефекты формирования сварных швов проявляются в неравномерности их формы (см. рисунок справа). Формируются они из-за непостоянных режимов сварки, непостоянного зазора между свариваемыми кромками и неравномерного угла скоса кромок. Несоответствие фактической формы шва требуемой может проявится вследствие неверной техники ручной дуговой сварки, из-за неправильного расположения электрода относительно сварных кромок.
Подобный дефект может проявиться и при других видах сварки. Например, при автоматической сварке причиной появления такого дефекта могут стать проскальзывание сварочной проволоки в подающем механизме, перепад напряжения в сети, попадание расплавленного металла в зазоры и др.
Непровар сварного шва
Чаще всего, непровары в сварных швах происходят в тех случаях, когда между сварными кромками небольшие зазоры, при большом притуплении кромок, а также при наличии на них загрязнений, при неправильном положении электрода или сварочной проволоки относительно свариваемых кромок, при недостаточной силе сварочного тока и при завышенной скорости сварки.
Очень часто непровары образуются в корне шва (схема а) и б) ни рисунке слева и схемы в) и г) на рисунке). При автоматической сварке под флюсом непровары, в большинстве случаев, формируются в начале сварного шва. Чтобы предотвратить их появление, сварку рекомендуется производить на специальных подкладках. Непровары – одни из самых опасных дефектов для сварного соединения.
Подрезы сварных швов
Подрезы сварных швов формируются на поверхности соединения. Подрезы – это углубления в основном металле, расположенные по краям сварного шва. Они появляются из-за излишне большой силы сварочного тока и из-за большой длины электрической дуги, т.к. в этом случае ширина сварного увеличивается и края сварных кромок оплавляются сильнее.
При сварке угловых швов подрезы, чаще всего, получаются при смещении электрода очень близко к горизонтальной стенке. При этом вертикальная стенка оплавляется быстрее, чем плавится горизонтальная и расплавленный металл стекает по горизонтальной кромке вниз. В этом случае, на вертикальной стенке образуются подрезы, а на горизонтальной – наплывы (схема б) на рисунке справа).
Прожоги сварных швов
К прожогам сварного шва относятся сквозное проплавление основного или наплавленного металла (см. рисунок слева). Прожоги образуются при излишне большой силе сварочного тока и при малых скоростях сварки. Причинами прожогов могут также стать большой зазор между свариваемыми кромками или недостаточное их притупление.
В большинстве случаев, прожоги получаются при сварке тонкого металла, а также при наплавке первого слоя многослойного шва. Причинами прожогов может быть недостаточное поджатие металлической подкладки или флюсовой подушки.
Наплывы сварных швов
Наплывы в сварных швах формируются при натекании расплавленного металла из жидкой металлической ванны на холодный основной металл (см. рисунок справа). Наиболее часто наплывы случаются в процессе дуговой сварки в защитных газах при сварке горизонтальных швов на вертикальной поверхности. Причинами наплывов является большая сила сварочного тока, неправильное положение электрода при сварке, излишняя длина электрической дуги.
Кратеры сварных швов и усадочные раковины
Кратеры в сварных швах образуются при обрыве электрической дуги. Кратеры в сварных швах имеют вид углублений в застывшем металле. При автоматизированных способах сварки выполнение сварного шва завершают на выводной планке, и кратер образуется на ней. При случайном обрыве электрической дуги в процессе сварки, получившийся кратер необходимо заплавить.
Усадочными раковинами называют полости, которые появляются в результате усадки сварочной ванны при её затвердевании. Появляются усадочные раковины из-за того, что при охлаждении объём металла уменьшается и он «проседает».
Поры в сварных швах
Поры в сварных швах образуются при быстром остывании расплавленного металла из-за того, что газы, присутствующие в сварочной ванне, не успевают выйти из неё наружу и остаются в застывшем металле в виде пузырьков. Поры могут быть как внутренними сварными дефектами (схемы б) на рисунке справа), так и и наружными (схема а) на рисунке), выходящими на поверхность. Наружные поры называются свищами.
Величина пор может быть различной, от нескольких микрометров до нескольких миллиметров. Чаще всего они имеют сферическую форму. Причинами образования газовых пор в сварных швах могут стать присутствие ржавчины, окалины, масляных плёнок и другие загрязнений на сварных кромках, на сварочной проволоке или на присадочных материалах.
Причинами образования пор могут служить, также, применение влажных, не прокаленных электродов и флюсов, недостаточная чистота защитных газов и присутствие в ней вредных примесей. Также поры возникают при очень большой скорости сварки, из-за чего газовая защита зоны сварки может стать менее неэффективной. Поры в сварных швах появляются и при повышенном содержании углерода в составе свариваемого металла и при неверно подобранной марки сварочной проволоки. В особенности, если сварка производится в среде углекислого газа.
Несплавления сварных швов
Несплавления в сварных швах появляются в том случае, если нет их проплавления с основным, или ранее наплавленным металлом.
Причиной несплавлений могут стать плохая подготовка металла под сварку (отсутствие, или плохая зачистка), большая длина сварочной дуги, недостаточная сила сварочного тока и большая скорость выполнения сварочных работ.
Шлаковые включения в сварных швах
Шлаковыми, неметаллическими или оксидными включениями в сварном шве принято называть небольшие пространства в металле, в которых находятся неметаллические вещества. Величина включений может быть довольно значительной и составлять несколько миллиметров.
Обычно шлаковые включения обладают объёмной вытянутой формой, но, в некоторых случаях они могут быть и круглыми, и плоскими. Часто шлаковые включения находятся по границам между основным металлом и наплавленным. При выполнении многослойных швов, формирование шлаковых включений часто происходит по границам между отдельными слоями.
Причиной образования шлаковых включений могут стать наличие загрязнений на сварочных кромках (ржавчины, шлака и др.), слишком маленькая сила сварочного тока, и излишне большая скорость сварки.
Трещины в сварных швах, их виды
Трещины в сварных швах представляют наибольшую опасность для сварного соединения. Трещины могут относиться как к внутренним дефектам (схема б) на рисунке слева), так и к наружным (схема а) на рисунке). Трещины очень часто образуются при сварке высокоуглеродистых сталей, а также при сварке высоколегированных сталей.
Различают несколько видов сварных трещин:
1. Горячие трещины при сварке. К ним относятся микротрещины и макротрещины, которые образуются в металле шва или зоне термического влияния во время охлаждения при высоких температурах, порядка 800-900°C.
2. Холодные трещины при сварке. Холодные трещины (можно встретить название замедленные) вызываются водородом и появляются, как правило, после сварки, при температурах, не превышающих 200-300°C.
3. Отпускные трещины. Трещины такого вида образуются после окончания сварки, во время последующей термообработки сварного соединения.
4. Ламелярные трещины. Особенность такого типа трещин в том, что зарождаются они при высоких температурах, но развиваются уже в холодном состоянии металла. Ламелярные трещины могут развиться, например, из горячих микротрещин.
Классифицировать такие дефекты сварных соединений, как трещины, достаточно сложно из-за того, что очень часто выявленные трещины не являются трещинами какого-либо одного типа. К примеру, может возникнуть горячая микротрещина, но развиваться она будет как холодная, при низких температурах и под воздействием водорода. То же самое относится к отпускным трещинам и к ламелярным.
Виды дефектов сварных соединений, в зависимости от их формы
Существующие дефекты сварных швов по их форме можно разделить на два вида. Это плоскостные дефекты и пространственные дефекты. К плоскостным дефектам относятся горячие и холодные трещины, непровары сварного шва.
К пространственным относятся различные шлаковые включения, поры, пузырьки от газов и все виды неправильно выполненного сварного шва (подрезы, прожоги, неверная конфигурация, смещение и др.).
Плоскостные дефекты сварного шва представляют наибольшую опасность для соединения, в целом. И существующие типы трещин, в зависимости от температуры, при которой они появляются, можно разделить ещё на несколько видов, о которых сказано выше по тексту.
Виды сварных дефектов, в зависимости от причин их возникновения
При сварке плавлением, возникающие дефекты сварных соединений, в зависимости от причин их возникновения, можно разделить на два вида. Первый вид дефектов связан с металлургическими процессами при сварке и с тепловыми явлениями, которые протекают в результате образования и кристаллизации сварочной ванны и остывания сварного соединения. К этим дефектам относятся горячие и холодные трещины в металле и зоне термического влияния, поры в металле, неметаллические включения, а также несоответствие свойств наплавленного металла и околошовной зоны заданным параметрам.
Второй вид дефектов включает в себя их виды, причиной которых является нарушение выбранных режимов сварки, нарушения при подготовке сварных элементов и при их сборке, неисправности сварочного оборудования, недостаточный профессионализм сварщика, а также другие нарушения технологии сварки. К дефектам такого типа относятся несоответствие фактических размеров швов требуемым. Это такие дефекты, как непровары, подрезы, незаплавленные кратеры, прожоги свариваемого металла.
Допустимые и недопустимые дефекты в сварных швах
Дефекты, появившиеся при сварке, в той или иной степени, влияют на работоспособность сварного соединения. И принимая решение о пригодности, или непригодности данного сварного соединения, учитывают все факторы, которые могут повлиять на допустимость или недопустимость дефекта в сварном шве. При этом принимают во внимание такие обстоятельства, как:
Геометрия и габариты сварной конструкции, в целом, и дефектного сварного соединения, в частности.
Напряжения, возникающие в конструкции. При этом, учитывают не только действие максимальных распределённых нагрузок, но и действие остаточных напряжений при сварке.
Вид сварного дефекта. А также его величина и место его возникновения.
Механические свойства сварного соединения. Это предел прочности, текучесть, ударная вязкость, пластичность, сопротивляемость коррозии, сопротивление усталостному разрушению и т.д.
Условия, при которых изделие эксплуатируется. В основном, это характер окружающей среды.
Функции, которые должно выполнять изделие. Существует даже такой термин: «пригодность для данной цели». Т.е. один и тот же дефект в сварном шве может быть допустим для выполнения одной задачи, и недопустим для выполнения другой.
Для принятия решения о допустимости дефектов того, или иного типа и величины, необходимо, чтобы измерительная способность прибора для контроля дефектов была выше, чем допустимая величина дефекта. Т.е., если в сварном шве допускаются дефекты, величиной не более 2мм, то нельзя использовать для контроля этого шва прибор, с измерительной способностью 5мм.
Для того, чтобы определить максимальную величину допустимого дефекта, необходимо иметь ввиду, что дефекты сварных швов увеличивают, главным образом, способность стали к усталостному и хрупкому разрушению.
Для разрушений такого вида, наибольшую опасность представляют плоскостные дефекты (микротрещины, макротрещины, непровары). В случае их выявления, нужно обратить внимание не только на максимальные размеры отдельно взятых дефектов, но и на их взаимное расположение и на их количество.
Опасность плоскостных дефектов заключается в том, что они являются концентраторами высоких напряжений из-за отсутствия радиуса закругления у трещин. Пространственные дефекты, такие, как поры, газовые пузыри или какие-либо включения имеют какой-либо радиус закругления, поэтому, представляют собой меньшую опасность, даже при большем количестве.
При маленьком закруглении у основания трещины, для того, чтобы оценить действующие в ней напряжения, применяют коэффициент интенсивности напряжений К1, позволяющий оценить механику разрушения. Коэффициент интенсивности напряжений возможно определить в том случае, если напряжение, необходимое для разрушения, меньше предела текучести материала. Определяется он по формуле:
где а – величина (высота) наружного дефекта, или половина величины внутреннего дефекта;
б m – напряжение при растяжении;
б в – напряжение при изгибе;
Мm и Мв – коэффициенты, величина которых определяется отношением величины дефекта к толщине детали и расположением дефекта;
Q – коэффициент, зависящий от формы дефекта.
Для сварных соединений, не подвергаемых отжигу после сварки, с целью уменьшения внутренних напряжений, для оценки допустимости сварных дефектов необходимо использовать расчёт критического раскрытия трещины (COD). Вычисление коэффициента К1, или нахождение величины критического раскрытия, даёт возможность с высокой точностью определить величину возможного допустимого дефекта сварного шва.
Дефекты сварных швов (схема). О сварке и сварочном оборудовании.
Причинами возникновения дефектов могут быть различные обстоятельства: низкое качество свариваемого металла, неисправное или некачественное оборудование, неверный выбор сварочных материалов, нарушение технологии сварки или неправильный выбор режима, недостаточная квалификация сварщика.
Все виды дефектов швов подразделяют на три группы:
- наружные, к основным из которых относятся: трещины, подрезы, наплывы, кратеры;
- внутренние, среди которых чаще всего встречаются: пористость, непровары и посторонние включения;
- сквозные — трещины, прожоги.
Основные дефекты сварки, их характеристика, причины возникновения и способы исправления
Трещины. Это наиболее опасные дефекты сварки, способные привести к практически мгновенному разрушению сваренных конструкций с самыми трагическими последствиям. Трещины различаются по размерам (микро- и макротрещины) и времени возникновения (в процессе сварки или после нее).
Чаще всего причиной образования трещин является несоблюдение технологии сварки (например, неправильное расположение швов, приводящее к возникновению концентрации напряжения), неверный выбор сварочных материалов, резкое охлаждение конструкции. Способствует их возникновению также повышенное содержание в шве углерода и различных примесей — кремния, никеля, серы, водорода, фосфора.
Исправление трещины заключается в рассверливании ее начала и конца, с целью исключения дальнейшего распространения, удалении шва (вырубанию или вырезанию) и заваривании.
Подрезы. Подрезы — это углубления (канавки) в месте перехода «основной металл-сварной шов». Подрезы встречаются довольно часто. Их отрицательное действие выражается в уменьшении сечения шва и возникновении очага концентрации напряжения. И то и другое ослабляет шов. Подрезы возникают из-за повышенной величины сварочного тока. Чаще всего этот дефект образуется в горизонтальных швах. Устраняют его наплавкой тонкого шва по линии подреза.
Подрезы сварного шва
Наплывы. Наплывы возникают, когда расплавленный металл натекает на основной, но не образует с ним гомогенного соединения. Дефект шва возникает по разным причинам — при недостаточном прогреве основного металла вследствие малого тока, из-за наличия окалины на свариваемых кромках, препятствующей сплавлению, излишнего количества присадочного материала. Устраняются наплывы срезанием с проверкой наличия непровара в этом месте.
Наплыв сварного шва
Прожоги. Прожогами называют дефекты сварки, проявляющиеся в сквозном проплавлении и вытекании жидкого металла через сквозное отверстие в шве. При этом обычно с другой стороны образуется натек. Прожоги возникают из-за чрезмерно высокого сварочного тока, недостаточной скорости перемещения электрода, большого зазора между кромками металла, слишком малой толщины подкладки или ее неплотного прилегания к основному металлу. Исправляют дефект зачисткой и последующей заваркой.
Прожог сварного соединения
Непровар. Непровары — это локальные несплавления наплавленного металла с основным, или слоев шва между собой. К этому дефекту относят и незаполнение сечения шва. Непровары существенно снижают прочность шва и могут явиться причиной разрушения конструкции.
Незаполнение и непровар шва
Дефект возникает из-за заниженного сварочного тока, неправильной подготовки кромок, излишне высокой скорости сварки, наличия на кромках свариваемых деталей посторонних веществ (окалины, ржавчины, шлака) и загрязнений. При исправлении нужно вырезать зону непровара и заварить её.
Кратеры. Это дефекты в виде углубления, возникающего в результате обрыва сварочной дуги. Кратеры снижают прочность шва из-за уменьшения его сечения. В них могут находиться усадочные рыхлости, способствующие образованию трещин. Кратеры надлежит вырезать до основного металла и заварить.
Кратер сварочного шва
Свищи. Свищами называют дефекты швов в виде полости. Как и кратеры, они уменьшают прочность шва и способствуют развитию трещин. Способ исправления обычный — вырезка дефектного места и заварка.
Свищи сварных швов
Посторонние включения. Включения могут состоять из различных веществ — шлака, вольфрама, окислов металлов и пр. Шлаковые включения образуются тогда, когда шлак не успевает всплыть на поверхность металла и остается внутри него. Это происходит при неправильном режиме сварки (завышенной скорости, например), плохой зачистке свариваемого металла или предыдущего слоя при многослойной сварке.
Посторонние включения сварного соединения
Вольфрамовые включения возникают при сварке вольфрамовым электродом, окисные — из-за плохой растворимости окислов и чрезмерно быстрого охлаждения.
Все виды включений уменьшают сечение шва и образуют очаг концентрации напряжения, снижая тем самым прочность соединения. Дефект устраняют вырезкой и завариванием.
Пористость. Пористость — это полости, заполненные газами. Они возникают из-за интенсивного газообразования внутри металла, при котором газовые пузырьки остаются в металле после его затвердевания. Размеры пор могут быть микроскопическими или достигать нескольких миллиметров. Нередко возникает целое скопление пор в сочетании со свищами и раковинами.
Пористость в сварном шве
Возникновению пор способствует наличие загрязнений и посторонних веществ на поверхности свариваемого металла, высокое содержание углерода в присадочном материале и основном металле, слишком высокая скорость сварки, из-за которой газы не успевают выйти наружу, повышенная влажность электродов. Как и прочие дефекты, пористость снижет прочность сварного шва. Зону с ней необходимо вырезать до основного металла и заварить.
Перегрев и пережог металла. Пережог и перегрев возникают из-за чрезмерно большого сварочного тока или малой скорости сварки. При перегреве размеры зерен металла в шве и околошовной зоне увеличиваются, в результате чего снижаются прочностные характеристики сварного соединения, главным образом — ударная вязкость. Перегрев устраняется термической обработкой изделия.
Пережог представляет собой более опасный дефект, чем перегрев. Пережженный металл становится хрупким из-за наличия окисленных зерен, обладающих малым взаимным сцеплением. Причины пережога те же самые, что и перегрева, а кроме этого еще и недостаточная защита расплавленного металла от азота и кислорода воздуха. Пережженный металл необходимо полностью вырезать и заварить это место заново.
Пережог металла шва
Распространенные дефекты сварных швов и методы их контроля
Время чтения: ≈12 минут
Не важно, какую технологию вы выбрали для выполнения сварочных работ. Дефекты могут возникнуть в любом случае, что при ручной дуговой сварке, что при сварке под флюсом с применением автоматического сварочного аппарата. Появление дефектов связано либо с неопытностью сварщика, либо с неправильно выбранным режимом сварки, либо с недостаточно тщательным контролем качества.
Поэтому важно предотвращать дефекты и контроль качества сварных соединений должен проводится после выполнения каждой сварочной операции. В этой статье мы подробно расскажем, какие существуют распространенные дефекты сварных швов. И какие методы контроля можно использовать, чтобы обнаружить их.
Содержание статьи
Распространенные дефекты
Любой опытный сварщик скажет вам, что существуют многочисленные виды дефектов сварных швов. Их можно разделить на две категории — наружные и внутренние. Наружные дефекты сварных швов можно обнаружить прямо на поверхности шва с помощью специального инструмента (например, лупы) или хорошего зрения. Внутренние дефекты сварных швов визуально не видны и для их обнаружения нужно использовать особые методики контроля качества. О них мы расскажем ближе к концу. А пока дефекты.
В рамках этой статьи мы не будем перечислять все возможные дефекты, а расскажем только о самых распространенных. Итак, ниже наша краткая классификация дефектов сварных швов.
Непровар
Непровар в сварном шве — один из самых часто встречающихся дефектов у новичков. Представляет собой небольшой участок с недостаточно проваренным металлом. Основные причины образования непроваров — слишком длинная сварочная дуга, недостаточная сила тока или обе ошибки одновременно.
У новичков непровары образуются в том случае, если была выполнена неправильная разделка кромок или если сварка велась слишком быстро. Как не трудно догадаться, чтобы предотвратить непровар сварного шва нужно подобрать оптимальный режим сварки, варить не слишком быстро и на короткой дуге.
Подрез
Если вы когда-либо варили тавровый или нахлесточный шов, то наверняка могли заметить небольшие углубления вдоль сторон сварного валика. Это и есть подрезы. Частая причина образования подрезов — слишком быстрая сварка или неправильно подобранное напряжение сварочной дуги. Также подрезы порой возникают из-за слишком длинной дуги.
Читайте также: Исправление дефектов сварки
Некоторые новички спрашивают: «Допускаются ли подрезы сварных швов?». Да, но только в очень сложных конструкциях, где подрезов не избежать. В подобных ситуациях подрезы называют просто «допустимые дефекты сварных швов». В остальных случаях это недопустимые дефекты.
Наплыв
Наплыв в сварном шве в 95% случаев свидетельствует о том, что вы неправильно настроили режим сварки или недостаточно тщательно зачистили кромки. Очевидно, что для предотвращения образования дефекта нужно правильно настроить силу сварочного тока и немного повысить напряжение дуги.
Прожог
Прожог сварного шва — это сквозное отверстие в сварном соединении, которое вы можете обнаружить невооруженным глазом. Прожоги образуются из-за медленной сварки. В одном месте концентрируется слишком большая температура и металл плавится больше, чем должен. Главная опасность прожогов — существенное снижение прочности шва.
Понизьте сварочный ток и ускорьте формирование шва. Только так вы сможете предотвратить появление прожогов. Уделите особое внимание, если варите алюминий. У него очень высокая теплопроводность, при этом низкая температура плавления. Так что получить прожог на алюминиевой заготовке проще простого.
Кратер
Кратер — это воронка небольшого размера, расположенная прямо на валике шва. Чаще всего в самом его конце. Образуется из-за резкого обрыва дуги. Ведите дугу плавно и оканчивайте сварку постепенно. Если на вашем сварочном аппарате есть специальный режим предотвращения образования кратеров, то включите его.
Горячая или холодная трещина
Трещины в сварных швах — также один из самых часто встречающихся дефектов. Трещины бывают холодными и горячими. Горячие образуются во время сварки, а холодные — после. Горячие трещины образовываются при несовместимости электрода/присадочной проволоки и свариваемого металла. Иногда трещины могут образоваться при попытке заварить кратер, о котором мы говорили выше. Проверяйте, чтобы состав присадочного материала и металла был идентичен.
Читайте также: Способы предотвращения горячих трещин
С холодными трещинами все проще. Они образовываются только в том случае, если шов слишком хрупкий и не выдерживает механической нагрузки. Единственный способ предотвратить появление холодных трещин — соблюдать технологию сварки и работать профессионально. Горячие и холодные трещины могут быть как внутренними (скрытыми от глаз), так и наружными.
Поры
Что такое пора в сварке? Пора (а чаще всего поры) — это небольшие углубления в структуре шва. Могут быть поверхностными или внутренними. Представьте муравейник, который пронизывают множественные ходы. Вот то же самое происходит и со швом. Поры без сомнения можно назвать самым частым дефектом из всех возможных.
Если в ходе процесса образовались поры в сварном шве, значит вы с самого начала все делали неправильно. Скорее всего, вы недостаточно тщательно зачистили кромки и не защитили шов от попадания кислорода. А подобные ошибки совершают только те, кто только-только начал свое знакомство со сваркой. На работайте на сквозняке и проверяйте качество электродов/исправность горелки/исправность системы подачи газа.
Методы контроля качества
Что ж, теперь вы знаете самые распространенные дефекты сварных соединений и причины их возникновения. Теперь давайте поговорим о методах контроля. Мы расскажем вам о самых часто применяемых и эффективных. Это визуально-измерительный контроль, радиационный и ультразвуковой контроль.
Визуально-измерительный контроль
Визуально-измерительный контроль (ВИК) — это самый простой и самый старый способ оценки качества сварного соединения. Из названия понятно, что в ходе этого контроля используется визуальное наблюдение и измерительные приборы. Под визуальным наблюдением подразумевается простой осмотр шва невооруженным глазом или с помощью лупы. В отдельных случаях используют микроскопы. А в качестве измерительных инструментов чаще всего применяют обычные линейки. Это самый доступный и недорогой метод контроля, поскольку инструменты стоят недорого и такому контролю можно обучить самого сварщика, выполняющего работу. Предприятию даже не нужно нанимать отдельных специалистов для проведения этого контроля.
Сейчас в магазинах продаются специальные наборы со всеми необходимыми инструментами и даже подробно инструкцией, как проводить контроль. Вам достаточно один раз прочесть брошюру, все запомнить и вы уже можете провести такой контроль самостоятельно. Но, несмотря на все плюсы, есть у ВИК большой недостаток — значительное влияние человеческого фактора на результат контроля. Вся ответственность ложится на плечи человека. И если он в силу объективных или субъективных причин не сможет выполнить контроль качественно, то есть вероятность брака.
Радиационный контроль
Радиационный контроль (его также называют радиографическим) — очень интересный метод контроля, который основан на применение рентгеновских лучей. Да, как при рентген-диагностике в поликлинике. Деталь повещается в специальный аппарат (или аппарат устанавливается на деталь), затем сквозь металл пропускают рентгеновское излучение и на выходе получают снимок, на котором видны все дефекты сварки. Эта технология наверняка известна вам давно.
Нетрудно догадаться, что подобная диагностика крайне эффективна. На снимке видны малейшие дефекты, которые невозможно обнаружить любым другим способом. Особенно, если снимок выполняется с применением компьютера, на котором потом можно детально рассмотреть все изъяны сварки. Но при работе с рентгенографом необходимо соблюдать повышенную технику безопасности. Частицы радиации могут заражать воздух, из-за чего он становится токопроводимым. А о возможном вреде для здоровья и говорить не приходится. Так что к выполнению радиационного контроля должны быть допущены только хорошо обученные сотрудники.
Ультразвуковой контроль
Ультразвуковая дефектоскопия сварных швов (он же ультразвуковой контроль качества или просто УЗК сварных швов) — метод контроля, который во многом схож с выше описанным радиационным. Только вот вместо рентгеновских лучей здесь используются ультразвуковые волны. Для фиксации результата используется ультразвуковой дефектоскоп для контроля сварных соединений.
Суть его работы проста. На поверхность шва посылаются ультразвуковые волны, которые проходят сквозь металл. Проходят не полностью, часть лучей отражается и возвращается обратно. Если у шва есть какой-либо дефект, то отразившиеся и вернувшиеся назад волны будут ослаблены и искажены. Проще говоря, они будут отличаться от тех, что были пущены вначале проведения контроля. Все эти изменения как раз и фиксирует дефектоскоп.
Читайте также: Неразрушающий контроль сварных соединений
Ультразвуковой контроль используется очень часто. Для его проведения можно установить большой стационарный дефектоскоп в отдельном кабинете, а можно приобрести компактную модель для выездной диагностики. И эта компактная модель сможет дать вполне объективный результата. С помощью дефектоскопа можно не только узнать местонахождение дефекта, но и его размеры. Но нужно учитывать, что дефектоскопы стоят дорого и для работы с ними нужно дополнительно обучать персонал. Или искать специалиста «на стороне».
Вместо заключения
Дефекты сварных швов и соединений бывают разными, но суть всегда одна — они так или иначе нарушают эксплуатационные характеристики готового изделия. Чтобы их избежать необходимо как можно больше практиковаться, правильно настраивать режим сварки и не забывать о контроле качества. Проведение ультразвукового контроля занимает считанные минуты, а в результате вы получаете объективную картину и можете трезво оценить качество своей работы.
Что такое подрезка при сварке? (Причины и профилактика)
Подрезы — обычная проблема для сварщиков, поэтому я подумал, что напишу статью для тех, кто плохо знаком со сваркой. Сварочные дефекты могут быть любого размера, формы и степени. Дефекты сварки обычно связаны с применением или материалом, но есть и другие причины возникновения дефектов, например, подрезы.
Итак, что такое подрезка при сварке? Поднутрение — это канавка, которая образуется в основном металле рядом с носком или корнем сварного шва.Подрезание происходит, когда металл сварного шва не может заполнить эту область с канавками. Это приводит к слабому сварному шву, который может иметь трещины вдоль кромок сварного шва.
Подрезание — обычное дело и дорогостоящее. Это приводит к снижению производительности и снижению скорости. Это проблема, которую случайно может создать даже самый опытный сварщик. Сварщики могут избавиться от дефектов сварки и быстро вернуться к работе несколькими способами.
В этой статье я расскажу о причинах подрезов, о том, как можно предотвратить подрезы и как исправить некоторые распространенные проблемы с поднутрениями.
Каковы основные причины поднутрения?Подрезы — одна из основных проблем, снижающих качество сварки. Предотвращение таких проблем, как подрезы и их последствия, означает экономию времени и денег на сварочных операциях.
Поднутрение обычно возникает из-за перегрева и неправильной техники сварки.- Подрезание может быть вызвано выдержкой большой длины дуги.
- Еще одна частая причина подрезки — неправильный подбор газовой защиты.
- Кроме того, поднутрение может произойти, если сварщик пытается быстро сварить большим сварочным током.
- Ржавчина также может вызвать подрезы, поэтому предварительная надлежащая подготовка может помочь устранить проблему.
- Неправильный угол электрода.
Поднутрение стали всегда было серьезной проблемой в сталелитейной промышленности, и в последние годы было приложено много усилий для решения проблемы поднутрения.
Поднутрение обычно происходит, когда основной материал и металл шва не плавятся должным образом во время процедуры сварки.Другими словами, это происходит, когда не удается заполнить гофрированный участок металлом шва.
Когда возникает этот сварочный дефект, слабый источник склонен к растрескиванию.
Итак, что вы можете сделать с поднутрением?
Как предотвратить подрезы1.
Точный подвод тепла Одной из наиболее важных причин подрезов во время сварки является использование сильного нагрева во время работы вблизи свободных кромок. Это вызывает плавление основного металла или металла предыдущего шва. Чтобы избежать этого, уменьшите сварочный ток, что может потребовать уменьшения скорости дуги. Также обращайте внимание на температуру сварки при приближении к свободным и более тонким кромкам.
Быстрая сварка — еще одна причина появления поднутрений. При слишком быстрой сварке часть основного металла становится расплавленным металлом, и ему невозможно вернуть первоначальную форму из-за быстрого затвердевания. Это создает углубление по краям. Самая идеальная скорость сварки — средняя.Очень медленная сварка не дает удовлетворительных результатов. Опять же, слишком быстрая скорость может вызвать такие проблемы, как подрезание.
3. Правильный угол и размер электрода Знание углов сварки играет жизненно важную роль в безошибочной сварке. Если один из сварщиков нагревает свободные кромки под неправильным углом, вероятно, образуется поднутрение. Не забудьте направить тепло к краям и участкам с более толстыми компонентами по сравнению со свободными краями. Вам также следует избегать использования электрода большего размера, чем необходимо. Поднутрение может быть получено, если размер расплавленного металла становится слишком большим для толщины листа.
Плетение используется для регулирования нагрева в сварочной ванне. Обязательно сделайте паузу с каждой стороны сварного шва, чтобы предотвратить подрезку кромок. Другими словами, когда сварщик выполняет сварочную операцию с использованием техники быстрого плетения, может возникнуть проблема подреза.При использовании плетения держите воздуховод за боковую стенку паза. Грязная рабочая поверхность — еще одна частая причина недостаточности сварки. Правильная и тщательная очистка поверхности до и во время сварки — отличный способ добиться успеха в сварке.
5. Выбор газовой защиты Выбор неправильной газовой защиты во время сварки также является одной из основных причин появления поднутрений. Правильный состав газа соответствует типу материала, производным источникам и толщине. Например, использование диоксида углерода с инертными газами обеспечивает качественные результаты при сварке углеродистой стали. При необходимости увеличьте поток защитного газа в регуляторе, чтобы снизить вероятность образования поднутрений.
Иногда сварка в горизонтальном и вертикальном положении может вызвать сварочные порезы. Неправильное положение при сварке может привести к поднутрению из-за недостаточной металлической заливки соединительных кромок. Чтобы избежать этого, старайтесь выполнять сварку на ровной поверхности.
7. Использование технологии многопроходной сваркиЭто лучший вариант для уменьшения количества нижних сегментов или поднутрений во время сварки. Многооперационная техника решает все вышеупомянутые проблемы. Это помогает генерировать хорошие ресурсы с улучшенными механическими свойствами.
8. Используйте правильную скорость движения Использование слишком высокой скорости движения может вызвать поднутрение. Чтобы предотвратить эту проблему, следите за тем, сколько переплетения используется, внимательно наблюдайте за скоростью сварки и старайтесь не держать электрод рядом с вертикальной пластиной при попытке выполнить горизонтальный угловой шов.
Поднутрение может возникнуть, если напряжение дуги слишком длинное или слишком высокое. Еще раз, слишком много тепла в одной области приводит к поднутрениям.
Как исправить проблемы с поднутрениемПоднутрение можно исправить, поместив бортик стрингера на всю длину поднутрения. При необходимости вы можете растушевать его болгаркой, чтобы получить желаемый профиль сварного шва.
Как правило, поднутрения не требуется исправлять, если они не превышают 0.Глубиной 5 мм. В листе из низкоуглеродистой стали их можно оставить нескорректированными, если они имеют толщину 10 мм, но не более 1 мм в глубину.
Что такое внутренняя подрезка? Эта статья в основном посвящена внешнему апперкоту, который является основным видом апперкота.
Внутренний подрез, или корневой подрез, обычно возникает в стыковом сварном шве рядом с основным металлом. Они возникают рядом с корнем сварного шва.
При сварке труб внутренние апперкоты могут образовываться около внутренней части трубы рядом с узким краем.
Другой тип внутренней поднутрения может быть обнаружен внутри сварного шва. Это воспринимается как бороздка, оставленная возле боковой стенки в верхней части корневого шва.
Внутренние апперкоты фиксируются приварными валиками, которые располагаются в зоне сварки. Эти валики могут образовывать включения в сварном шве.
Методы предотвращения внутренней сварки аналогичны обычным методам предотвращения апперкотов. Уделяйте особое внимание корням, чтобы избежать внутренних апперкотов.
Заключение
Поднутрение образуется, когда нет зазоров в соединении между металлами во время сварки.Подрезы в основном возникают из-за чрезмерного распространения тепла, которое создает зазоры и углубления в сварном шве. Плохая техника также является одной из основных причин появления поднутрений.
Это явление ослабляет источник и в дальнейшем может вызвать растрескивание. Есть много разных причин подрезки. Некоторые поднутрения можно оставить в покое, но некоторые могут потребовать ремонта.
У вас есть какие-нибудь приемы, которыми вы хотели бы поделиться? Дайте нам знать в комментариях ниже. Не забудьте ознакомиться со всеми нашими проектами по изготовлению металлических изделий и планами по производству оборудования. Если вы хотите расширить возможности своего цеха по изготовлению металлических изделий, вы обязательно захотите это проверить.
Причины дефектов GMAW
Правильное определение причины дефектов сварного шва и правильное лечение могут помочь сварщикам свести к минимуму время простоя и связанные с ним расходы. Дефекты сварных швов бывают всех форм, размеров и степени серьезности. Тем не менее, одно верно независимо от приложения или материала, на котором они возникают: они являются распространенной и дорогостоящей причиной простоев и снижения производительности. Это также явление, с которым может столкнуться даже самый опытный сварщик.
В частности, в процессе GMAW может появиться несколько типичных дефектов сварного шва. От пористости до поднутрения и прожига — у каждого есть несколько причин. К счастью, существует множество способов лечения, которые могут помочь сварщикам свести к минимуму разочарование из-за дефектов сварного шва и быстрее вернуться к работе.
Пористость
Когда газ задерживается на поверхности или внутри металла шва, возникает пористость. Как и другие дефекты сварного шва, пористость приводит к слабому сварному шву, который необходимо отшлифовать и обработать заново.
Пористость, как показано здесь, чаще всего является результатом недостаточного защитного газа. Увеличение потока газа и / или обеспечение герметичности газовых шланговили пистолета GMAW может помочь решить проблему.
Причины: Как правило, недостаточный или загрязненный защитный газ является причиной пористости. Использование сопла, которое слишком мало для данной области применения, или сопла, полного сварочных брызг, также может вызвать этот дефект сварки. Дополнительной причиной является грязный основной металл и / или выход сварочной проволоки слишком далеко за пределы сопла.В теплые дни потоки воздуха от охлаждающих вентиляторов могут нарушить оболочку защитного газа вокруг сварочной ванны, создавая эту проблему. Другой частой причиной является плохое уплотнение или неплотное соединение в канале защитного газа через сварочный пистолет. Любая утечка газа может привести к попаданию воздуха в поток газа.
Лечение: Чтобы исправить пористость, убедитесь, что имеется достаточный поток газа (увеличивая его по мере необходимости), и замените все поврежденные газовые шланги или компоненты пистолета GMAW, которые могут вызывать утечки.Кроме того, поместите сварочный экран вокруг рабочей зоны, если сварка ведется снаружи или в зоне с особенно сильным сквозняком внутри. Убедитесь, что используемая форсунка достаточно велика для применения, и замените ее на более крупную, если это не так. Удалите из сопла скопившиеся брызги. Вытяните сварочную проволоку не более чем на 1/2 дюйма за сопло и перед сваркой убедитесь, что основной металл чистый. Снижение скорости движения для обеспечения большего покрытия защитным газом также может уменьшить пористость, так же как и сохранение сопла в пределах от 1/4 до 1/2 дюйма от основного металла во время сварки.
Прожигать
Как следует из названия, прожиг происходит, когда металл сварного шва полностью проникает через основной металл, по существу «прожигая» его. Это наиболее распространено на тонких материалах, особенно на тех, которые составляют 1/4 дюйма или меньше. Другой дефект сварного шва, чрезмерный провар (слишком большое проникновение в сварное соединение), очень часто может привести к прожогу.
Причины: Избыточное тепло — основная причина прожога. Наличие слишком большого корневого отверстия на сварном шве также может привести к прожогу.
Способы устранения: в случае прожога можно решить проблему, снизив напряжение или скорость подачи проволоки. Также помогает увеличение скорости движения, особенно при сварке алюминия, который склонен к нагреву. Если предполагаемой причиной прожога является широкое отверстие в корне, увеличение длины проволоки и / или использование техники плетения во время сварки может помочь минимизировать тепловложение и вероятность прожога.
Неполное проникновение в сустав (отсутствие проникновения)
Неполное или непроваренное соединение, как показано на этом микроскопическом изображении, обычно является результатом недостаточного тепловложения.Увеличение скорости подачи проволоки и / или напряжения, а также снижение скорости движения могут помочь решить проблему. (Изображение любезно предоставлено компанией Hobart Brothers)Неполный провар или отсутствие проплавления возникает в результате неглубокого проплавления металла шва и основного металла, а не полного проплавления стыка. Это часто может привести к растрескиванию сварного шва и разрушению соединения.
Причины: Недостаточное тепловложение и неправильная подготовка шва являются основными причинами неполного проплавления шва. Смесь защитного газа и диаметр проволоки также могут иметь значение.
Лечение: Существует несколько способов лечения неполного провара соединения, включая использование более высокой скорости подачи проволоки и / или напряжения. Уменьшение скорости перемещения также позволяет большему количеству сварочного металла проникать в соединение, равно как и правильная подготовка и проектирование соединения. Соединение должно позволять сварщику поддерживать надлежащее удлинение сварочной проволоки (не более 1/2 дюйма от сопла) и при этом иметь доступ к нижней части сварного соединения.Убедитесь, что защитный газ или газовая смесь, тип и диаметр проволоки рекомендованы для применения.
Подрезка
Поднутрение — это бороздка или кратер, возникающий у носка сварного шва. Когда возникает этот дефект сварного шва, металл шва не может заполнить эту желобчатую область, что приводит к слабому сварному шву, который склонен к растрескиванию вдоль пальцев.
Причины: Чрезмерный нагрев, а также неправильная сварка могут привести к подрезанию сварного шва.
Лечение: снижение сварочного тока и напряжения — первый шаг к устранению недорезов. Использование техники плетения, при которой сварщик немного останавливается с каждой стороны сварного шва, также может помочь предотвратить этот дефект сварного шва. Дополнительные меры включают снижение скорости движения до уровня, позволяющего сварочному металлу полностью заполнять шов, и регулировку угла пистолета GMAW, чтобы он был направлен более прямо в сторону сварного шва.
Горячее крекинг
Горячие трещины обычно появляются по длине сварного шва или непосредственно рядом с ним почти сразу после затвердевания сварочной ванны.Этот дефект сварного шва возникает при температуре выше 1000 градусов по Фаренгейту (538 по Цельсию). Существует несколько вариантов горячего растрескивания, включая осевую линию, форму валика и кратерные трещины.
Причины: Горячее растрескивание может возникнуть по нескольким причинам. К ним относятся плохая подгонка или конструкция соединения, создание слишком тонких сварных швов и сварка при слишком высоких напряжениях. Высокий уровень примесей основного металла также может вызвать этот дефект сварного шва. В некоторых случаях проблемы могут быть вызваны высоким содержанием определенных сплавов (например, бора) в присадочных металлах.
Отверждение. Правильная конструкция шва и правильная подгонка деталей — один из способов предотвратить образование горячих трещин, так как сварочная лужа остается подходящего размера и сводится к минимуму вероятность того, что горловина сварного шва будет слишком тонкой. В случае кратерного растрескивания, в частности, использование техники обратной засыпки (подпора для полного заполнения шва) может минимизировать растрескивание за счет увеличения толщины горловины сварного шва кратера. Тщательный выбор присадочного металла и защитного газа также является обязательным.
Неполное слияние
Это микроскопическое изображение показывает неполное сплавление с обеих сторон сварного шва.Этот дефект сварного шва, который обычно возникает из-за неправильного угла наклона пистолета, можно частично исправить, поддерживая угол наклона пистолета от нуля до 15 градусов и удерживая дугу на передней кромке сварочной ванны.
Когда металл сварного шва не может полностью сплавиться с основным металлом или с предыдущим наплавленным валиком в многопроходных приложениях, может произойти неполное сплавление. Некоторые люди также называют этот дефект сварного шва холодным наплавлением или отсутствием плавления.
Причины: Чаще всего причиной неполного плавления является неправильный угол наклона пистолета, хотя загрязнения на основном металле также могут вызвать этот дефект сварного шва.В некоторых случаях причиной может быть недостаточное количество тепла.
Лечение: Во-первых, тщательно очистите основной металл перед сваркой, убедившись, что на нем нет грязи, масла, жира или другого мусора. Затем сварщики должны расположить пистолет GMAW под углом от нуля до 15 градусов, чтобы получить полный доступ к канавке сварного соединения и удерживать дугу на передней кромке сварочной ванны. При необходимости увеличьте скорость движения, чтобы дуга не выходила слишком далеко за сварочную ванну. Для соединений, требующих техники плетения, удерживание дуги на боковой стенке на мгновение может помочь предотвратить неполное соединение.Также убедитесь, что подводимого тепла достаточно для полного плавления металла шва и основного металла. Увеличьте диапазон напряжения и при необходимости отрегулируйте скорость подачи проволоки, чтобы завершить сварку.
Помните, что даже самые опытные сварщики могут столкнуться с дефектами сварного шва. Ключом к тому, чтобы они не влияли на производительность и увеличивали затраты на сварку, является как можно более быстрое выявление и устранение проблем. Правильное обслуживание сварочного оборудования также является обязательным.Отремонтируйте или замените изношенные или дефектные элементы.
Сварка TIG: когда внешний вид имеет значение
Газовая дуговая сварка вольфрамом (GTAW) — это процесс, который чаще всего используется для соответствия высоким эстетическим стандартам и стандартам качества. Это самый сложный из сварочных процессов, для освоения которого требуется значительная практика. Оценить качество сварки TIG часто так же просто, как оценить внешний вид валика. Помимо более сложных форм контроля, простой визуальный осмотр сварного шва может многое сказать о его качестве.Из-за своей простоты визуальный осмотр сварки часто может быть самым простым для выполнения и, как правило, наименее затратным. При правильном проведении такой контроль обычно является эффективным методом поддержания приемлемого качества сварки, предотвращения проблем при сварке и обеспечения прочности и долговечности сварных швов.
Как визуально отличить хороший сварной шов от плохого, и что нужно сделать, чтобы сделать плохой шов хорошим?
GTAW: основные принципы
Во-первых, рассмотрите следующие основные принципы, необходимые для получения хорошего сварного шва с помощью любого из сварочных процессов:
- Убедитесь, что основной материал и наполнитель чистые и не содержат ржавчины, краски, масла или оксидов.
При необходимости очистите материал шлифовальной машиной, проволочным колесом или проволочной щеткой перед началом сварки.
- Определите подходящие расходные материалы в зависимости от типа и толщины материала. Выберите электрод и размер электрода подходящего размера и правильно подготовьте острие электрода. Убедитесь также, что вы выбрали правильный защитный газ и полярность.
- Убедитесь, что ваше рабочее место хорошо освещено и хорошо вентилируется.
- Проверьте надежность заземления.
- Используйте таблицу параметров сварки, чтобы определить необходимое напряжение и силу тока в зависимости от материала, который вы свариваете.
- Для GTAW важно, чтобы источник питания имел хороший контроль тока в нижнем диапазоне. Это необходимо для поддержания стабильной дуги и особенно важно при сварке тонкостенных материалов. Современная инверторная технология особенно полезна для GTAW по нескольким причинам. Стабильность дуги контролируется постоянно и точно.
Инверторы также обладают улучшенными сварочными характеристиками.Кроме того, они намного меньше, легче и портативнее, чем сварочные аппараты для трансформаторов.
Назначение сварного шва — создать прочное соединение с основным материалом, обеспечивающее достаточное проплавление или плавление. Красивый сварной шов — чистый и того же цвета, что и основной металл, как внутри, так и снаружи. Ширина борта должна быть одинаковой и иметь привлекательный профиль поверхности лица. Края сварного шва должны иметь плавный переход в основной металл без поднутрения (дефект, который проявляется в виде канавки в основном материале).
Поверхность профиля сварного шва с разделкой кромок должна быть плоской или иметь минимальную выпуклость. Профиль скругления может быть вогнутым, плоским или минимально выпуклым. Угловой шов, полученный без присадочного материала, будет иметь вогнутую поверхность.
Вообще говоря, плохой вид сварного шва не означает, что это так. Допускаются небольшие участки пористости вместе с небольшими поднутрениями. Неравномерно расположенные нахлёстки борта обычно подходят.
Плохой сварной шов — сварной шов с высокой вероятностью выхода из строя — будет иметь следующие контрольные характеристики.
Выгорание. Теплообразование в сварном шве и основном материале вызывает выгорание или чрезмерное проплавление в конце сварного шва. Чтобы избежать выгорания, начните сначала с левой стороны заготовки, сварите примерно на дюйм, а затем остановитесь. Начните снова с правой стороны и перекрывайте первый сварной шов.
Современное сварочное оборудование помогает свести к минимуму вероятность перегорания. Технология импульсной сварки обеспечивает более контролируемый подвод тепла и ширину валика, что помогает снизить вероятность выгорания.Эта технология особенно полезна при сварке сплавов на основе никеля, таких как INCONEL® и нержавеющая сталь, которые особенно чувствительны к тепловыделению.
Без присадочного металла. Даже при сварке тонкого материала обычно необходимо добавить присадочный материал. Опускайте конец стержня в переднюю кромку сварочной ванны и из нее примерно на каждые ¼ дюйма хода и внимательно следите за тем, чтобы не наложить кусочки присадочного металла на старый, не расплавленный основной металл. Никогда не тяните конец стержня слишком далеко от лужи.
Красивый сварной шов чистый и того же цвета, что и основной металл, как внутри, так и снаружи. JulAug14PWT.
Хорошее практическое правило — оставаться в зоне действия защитного газа. Это предотвращает образование оксида на стержне и сохраняет конец стержня горячим. Не нагретый стержень или слишком глубокое погружение стержня в лужу приведет к тому, что лужа остынет, что приведет к непоследовательности борта. Добавление нужного количества наполнителя в нужное время позволит добиться однородной бусинки правильных пропорций.
Неверный размер присадочного металла. Диаметр присадочного металла должен быть примерно такой же толщины, как и толщина основного материала. Если вы используете присадочный пруток увеличенного размера, скорее всего, процесс не будет генерировать достаточно тепловой энергии, чтобы достаточно быстро повысить его температуру, чтобы он плавно плавился в сварочной ванне. Пруток, который слишком мал для технологического процесса, будет израсходован так быстро, что также будет невозможно получить однородный сварной шов.
Кроме того, стержень присадочного металла должен быть из того же семейства металлов, что и основной материал.Например, для основного материала из низкоуглеродистой стали требуется стержень из низкоуглеродистого присадочного металла. Также важно учитывать служебное применение сварного шва, например создание точки износа на коленчатом валу. Вал относится к семейству срединных углеродов, поэтому стержень присадочного электрода должен быть подобран соответствующим образом.
Неверная сила тока . Неправильная сила тока может быть двоякой: она может быть слишком низкой (низкая) или слишком высокой (высокая). Слишком низкая сила тока приведет к образованию высоких, узких и неустойчивых бусинок, которые не слились должным образом с основным металлом.Сварочную ванну будет сложно запустить и переместить.
Слишком высокая сила тока приведет к получению широкого плоского валика без четкого рисунка валика. Скорее всего, он будет перегрет до такой степени, что металл станет хрупким, что является причиной разрушения сварного шва.
Включения вольфрама. Включение вольфрама вызвано погружением вольфрамового электрода в сварочную ванну или прикосновением стержня присадочного металла к вольфраму во время сварки.
Рассеянные включения вольфрама являются результатом использования вольфрамового электрода, который слишком мал для пропускаемого тока, что приводит к попаданию небольших кусочков вольфрама в сварочную ванну.
Пористость. Пористость возникает, когда грязь или масло на основном материале испаряется и образует газовый карман в сварочной ванне. Обязательно тщательно очистите зону сварного шва. Кроме того, защищайте поток защитного газа от ветра или сквозняков, которые могут унести защитный газ из сварочной ванны и вызвать пористость.
Защитный газ также должен быть настроен правильно. Часто сварщики используют большее давление защитного газа, чем необходимо, что создает турбулентность. Турбулентность втягивает внешнюю атмосферу в сварочную ванну, загрязняя расплавленный металл.Это создает пористость так же, как и слишком низкое давление защитного газа. Более того, слишком длинная дуга неэффективна и увеличивает разбрызгивание, поэтому важно, чтобы дуга была как можно короче.
Подрезка. Подрезание обычно является побочным эффектом установки слишком высокой силы тока или слишком большой длины дуги. Из-за чрезмерной длины дуги и силы тока в основном металле по обеим сторонам валика остаются канавки, что снижает прочность сварного шва. Подрезы также могут возникать при слишком высокой скорости сварочного хода.
Прогар на верхнем сварном шве произошло из-за слишком сильной жары нарастил по всей длине шарик. Вы можете избежать этого, запустив сначала сварной шов с левой стороны и остановка примерно через дюйм. Перезапуск ваш шов с правой стороны и перекрыть первый сварной шов, как показано на нижний шов.
Во избежание подреза уменьшите значение силы тока и, при необходимости, уменьшите скорость движения.Чтобы улучшить смачивание, расположите сварочную горелку или пистолет под небольшим углом к направлению движения. Это поможет сделать переход металла шва в основной металл более гладким.
Избыточное усиление лицевой стороны. Использование большего количества сварочного металла, чем требуется для заполнения сварного шва с канавкой, может привести к избыточному усилению лицевой поверхности. Сварка не сделает сварной шов более прочным. Вместо этого большой сварной шов с увеличенными размерами натягивает края сварного шва или нагружает их во время охлаждения, что, в свою очередь, вызывает растрескивание.Добавляйте только столько присадочного материала, сколько необходимо для получения плоской или слегка выпуклой поверхности шва.
Типы сварочных дефектов и способы их устранения — Weld Guru
Существует несколько распространенных дефектов сварки GMAW (MIG), в том числе:
Сварка алюминия обычно создает больше проблем, чем при работе со сталью, поскольку алюминий лучше проводит тепло и имеет более низкую температуру плавления. Эта комбинация подвергает проекты сварки алюминия таким проблемам, как прогорание и коробление.
Кроме того, в отличие от стали, которую можно сваривать методом перетаскивания или толкания, с алюминием пистолет можно только перетаскивать (также называемый техникой наотмашь).
Дефект сварки GMAW из-за низкого напряжения. Вызывает проблемы с зажиганием дуги, недостаточным проваром и плохим контролем.
Испытание сварных швов GMAW сплошной проволокой
Проволоки с одножильным сердечником бывают разных типов, одни из которых предпочтительны для защиты от кислородного газа, а другие — от комбинации кислорода и аргона.
Проволока с продольным сердечникомGMAW в основном используется при сварке стали зданий, автомобилей, мотоциклов, контейнеров, подвижного состава поездов и строительной техники. Они создают пониженный уровень шлака, что делает его идеальным для многопроходной сварки.
Обычный шарик GMAW (вверху) и то, что называется «горбатым шариком» (внизу). Вызвано чрезмерной скоростью при использовании сплошного провода.1. Проникновение
Отсутствие проникновения
Отсутствие ввода в зону сварки. Это может быть проникновение из-за слишком малого количества тепла. Корректировано с помощью:
- Увеличение скорости подачи проволоки и уменьшение вылета.
- Снижение скорости движения.
- Использование надлежащей техники сварки.
Чрезмерное проникновение
Чрезмерное проникновение обычно вызывает прожиг. Это результат слишком сильного нагрева в зоне сварного шва. Это можно исправить с помощью:
- Уменьшение скорости подачи проволоки и увеличение скорости движения.
- Убедиться, что отверстие в корне и поверхность корня правильные.
- Увеличение вылета при сварке и плетении пистолета.
Профили сварных швов с разной скоростью
При использовании сплошной проволоки в таблице показано влияние различных скоростей сварки на профиль сварки.
2. Усы
Вискеры — это короткие отрезки электродной проволоки, проникающие сквозь сварной шов на корневой стороне соединения. Они вызваны проталкиванием электродной проволоки за переднюю кромку сварочной ванны. Усы можно предотвратить с помощью:
- Уменьшение скорости подачи проволоки и скорости движения.
- Увеличение вылета и плетение ружья.
3. Пустоты
Пустоты иногда называют следами вагонов из-за их сходства с колеями на грунтовой дороге. Их можно продолжать по обе стороны наплавленного металла. Они встречаются при многопроходной сварке. Пустоты можно предотвратить с помощью:
- Избегайте крупнокалиберной коронки и поднутрения.
- Убедиться, что все края заполнены.
- При последующих проходах с использованием немного более высокого напряжения дуги и увеличения скорости движения.
4. Отсутствие Fusion
Отсутствие плавления, также называемое холодным притиркой, в значительной степени является результатом неправильного обращения с резаком, слабого нагрева и более высокой скорости движения. Важно, чтобы дуга была направлена на передний край лужи. Чтобы предотвратить этот дефект, внимательно изучите следующее:
- Направьте дугу так, чтобы она покрывала все области стыка. Сплав должна быть дуга, а не лужа.
- Держите электрод у переднего края лужи.
- Уменьшите размер лужи, если необходимо, уменьшив скорость движения или скорость подачи проволоки.
- Тщательно проверьте текущие значения.
5. Пористость
Пористость или точечные отверстия в сварном шве на стали, вызванные ненадлежащим использованием защитного газа.Самым распространенным дефектом сварных швов, полученных при любом процессе сварки, является пористость. Пористость, которая существует на поверхности сварного шва, легко обнаруживается, но пористость в металле сварного шва под поверхностью необходимо определять с помощью рентгеновских лучей или других методов контроля.Причины наибольшей пористости:
- Загрязнение атмосферой и другими материалами, такими как масло, грязь, ржавчина и краска.
- Изменение физических свойств присадочной проволоки из-за чрезмерного тока.
- Улавливание газа, выделяющегося при затвердевании металла шва.
- Потеря защитного газа из-за слишком быстрого хода.
- Слишком низкий расход защитного газа, не обеспечивающий полной защиты или не втягивающий воздух в зону дуги
- Используется неправильный тип защитного газа.
- Противогаз уносится ветром или сквозняками.
- Неисправности в газовой системе.
- Неправильная техника сварки, чрезмерный вылет, неправильный угол наклона горелки и слишком быстрое извлечение горелки и защитного газа в конце шва.
6. Брызги
Брызги состоят из очень мелких частиц металла на поверхности пластины, прилегающей к области сварного шва.Обычно это вызвано большим током, длинной дугой, нерегулярной и нестабильной дугой, неправильным защитным газом или засорением сопла.
Дефекты сварки из-за высокого напряжения:
Высокое напряжение вызывает плохое управление дугой, плохое и непостоянное проплавление шва.
Сопутствующие : Как уменьшить разбрызгивание при сварке
7. Неровная форма сварного шва
Неправильные сварные швы включают в себя слишком широкие или слишком узкие сварные швы, те, которые имеют чрезмерно выпуклую или вогнутую поверхность, и те, которые имеют грубую неравномерную рябь.Такие характеристики могут быть вызваны неправильным обращением с горелкой, слишком низкой скоростью перемещения, слишком большим или низким током, неправильным напряжением дуги, неправильным вылетом или неправильным защитным газом.
8. Подрезка
Подрезка — это обрезка основного материала по краю сварного шва. Он может присутствовать в сварном шве покровного прохода или при многопроходной сварке. Это состояние обычно является результатом высокого тока, высокого напряжения, чрезмерной скорости движения, низкой скорости подачи проволоки, плохой техники горелки, неправильной газовой защиты или неправильной присадочной проволоки.Чтобы исправить подрезку, перемещайте пистолет из стороны в сторону в стыке. Задержитесь с каждой стороны, прежде чем вернуться к противоположной стороне.
GMAW с порошковой проволокой (FCW)
Существует три основных типа порошковой проволоки:
- рутил: флюс на основе рутила. Известен удобством использования.
- basic: содержат фтористый флюс. Известен стойкостью к трещинам.
- металл: содержит металлический порошок, который становится частью сварного шва, вызывая некоторое покрытие шлака.
Эффективность и качество сварного шва начинается с выбора лучшей сварочной проволоки для конкретной работы.Таблицы, предоставленные производителями, являются практическими, а не абсолютными.
1. Прожигание
Неисправность из-за высокого тока и скорости подачи проволоки:
Если сила тока установлена выше, чем требуется, или если скорость подачи проволоки слишком высокая, могут возникнуть такие проблемы, как плохое зажигание дуги, деформация, прожигание и широкий сварной шов.Прожог может быть вызван следующими причинами:
- Слишком большой ток.
- Чрезмерный зазор между пластинами.
- Скорость движения слишком низкая.
- Слишком большой угол скоса.
- Носик слишком маленький.
- Слишком маленький размер провода.
- Недостаточный прижим или зажим металла.
Неисправность из-за низкого тока и скорости подачи проволоки ниже требуемой:
Если сила тока установлена ниже требуемой, или если скорость подачи проволоки слишком низкая, могут возникнуть такие проблемы, как плохая привязка пальцев ног и выпуклый валик.2. Корона слишком высокая или слишком низкая
Корона сварного шва может быть неправильной по следующим причинам:
- Слишком большой или низкий ток.
- Напряжение слишком высокое или низкое.
- Слишком высокая скорость движения.
- Неправильная подкладка сварного шва.
- Неправильный интервал в сварных швах с подкладкой.
- Заготовка не выровнена.
3. Слишком глубокое или слишком мелкое проникновение
Неисправность из-за низкой скорости движения:
Низкая скорость перемещения сварного шва может способствовать появлению дефектов при сварке методом чеканки, таких как большой сварной шов и прожог.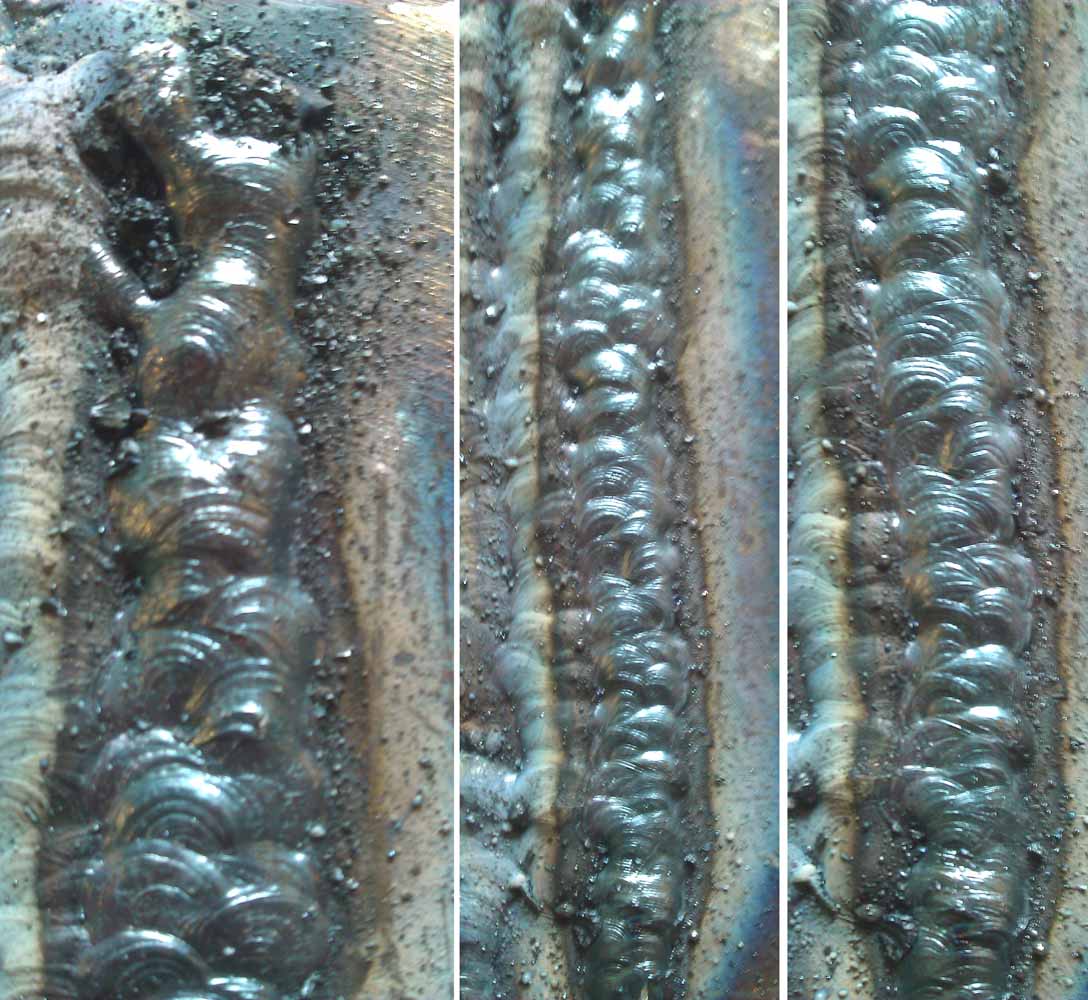
Неправильный провар может быть вызван одним из следующих дефектов сварки GMAW:
- Слишком большой или низкий ток.
- Напряжение слишком высокое или низкое.
- Неправильный зазор между пластинами.
- Неверный размер провода.
- Скорость движения слишком низкая или высокая.
4. Пористость и газовые карманы
Эти дефекты сварки GMAW могут быть результатом любого из следующих действий:
- Флюс слишком мелкий.
- Неправильная очистка.
- Загрязнение основы сварного шва.
- Неправильная установка сварных швов с ручной подкладкой.
- Недостаточное проплавление двойных сварных швов.
5. Узкая и крутая арматура (остроконечная)
Узкие и заостренные арматуры могут быть вызваны следующими дефектами сварки GMAW:
- Недостаточная ширина потока.
- Напряжение слишком низкое.
Укрепление горных хребтов
Если арматура рваная, флюс был слишком глубоким.
Дефект из-за высокой скорости хода сварного шва:
Высокая скорость перемещения может привести к образованию узкого выпуклого валика сварного шва и плохому закреплению на носках сварного шва.Также может стать причиной недостаточного проплавления сварного шва и нестабильности шва.6. Подрезка
Подрезка Дефекты сварки GMAW могут быть вызваны любой из следующих причин:
- Слишком высокая скорость движения.
- Неправильное положение проволоки (угловая сварка).
- Неправильная подкладка сварного шва.
7. Пустоты и трещины
Эти дефекты сварного шва могут быть вызваны любой из следующих причин:
- Неправильное охлаждение.
- Отсутствие предварительного нагрева.
- Неправильная установка.
- Армирование вогнутой формы (угловой шов).
NDE характеристик дефектов сварных швов труб. Специальный отчет, сентябрь 1980 г. (Технический отчет)
Венк С.
, Аллен К. и Уотсон П. Характеристики неразрушающего контроля дефектов сварных швов труб. Специальный доклад, сентябрь 1980 г. . США: Н. П., 1980.
Интернет. DOI: 10,2172 / 6859256.
Венк, С., Allen, C., & Watson, P. Характеристики неразрушающего контроля дефектов сварных швов труб. Специальный доклад, сентябрь 1980 г. . Соединенные Штаты. https://doi.org/10.2172/6859256
Wenk, S., Allen, C., and Watson, P. Mon.
«Характеристики неразрушающего контроля дефектов сварных швов труб. Специальный отчет, сентябрь 1980 г.». Соединенные Штаты. https://doi.org/10.2172/6859256. https://www.osti.gov/servlets/purl/6859256.
@article {osti_6859256,
title = {Характеристики неразрушающего контроля дефектов сварных швов труб. Special report, September 1980},
.
author = {Венк, С., Аллен, К. и Уотсон, П.},
abstractNote = {Оценка неразрушающего контроля (NDE) часто зависит от интерпретации изображений, полученных либо в результате радиографических процессов, либо в результате записи форм электронных сигналов.Этот документ предназначен для облегчения процесса интерпретации путем предоставления сравнительных данных изображений для типовых трубопроводов АЭС. Представлено наглядное сравнение геометрии дефекта сварного шва с сопутствующими результатами рентгенографического и ультразвукового неразрушающего контроля, полученными для нержавеющей стали типа 304, кольцевых стыковых швов 10-дюймовых трубок сортамента 80. Дефекты были намеренно внесены в заводские сварные детали в иллюстративных целях.},
doi = {10.2172 / 6859256},
url = {https: // www.osti.gov/biblio/6859256},
journal = {},
number =,
объем =,
place = {United States},
год = {1980},
месяц = {9}
}
дефектов проплавления сварных швов и упрощение измерений и контроля | Автомобильная и авиакосмическая промышленность | Цифровой микроскоп 4K — примеры применения и решения
Сварка обычно используется при соединении металлических компонентов таких изделий, как автомобили, самолеты, железнодорожные вагоны и корабли. В автомобилях соединение происходит в основном с помощью различных видов дуговой сварки, контактной точечной сварки и лазерной сварки. Эти методы используются в кузовах, рамах, двигателях, трансмиссиях, шасси и других подобных компонентах, к которым прикладывается напряжение во время движения автомобиля. Это придает большое значение расчету прочности сварных швов и контролю качества сварки путем измерения размеров поперечных сечений.
Сварные швы (сварные швы и проплавление), которые соединяют эти основные материалы, хотя они также являются металлическими материалами, включают присадочные материалы (такие как сварочные стержни и сварочные проволоки), которые были расплавлены и затвердели.
При обычной дуговой сварке, например, металлические конструкции непрерывно изменяются не только в металле сварного шва, но и в частях основных материалов, подверженных воздействию тепла сварки. Наряду с этим изменением непрерывно изменяются и механические свойства металлических материалов. С другой стороны, арматура, которая образуется на поверхности сварного шва, имеет неоднородности. Концентрация неоднородности приводит к отклонению механических свойств, вызывая тем самым трещины из-за концентрации напряжений.
При расчете прочности металлических изделий материалы обычно выбираются, принимая нагрузку, которая должна быть приложена к изделиям, и определяя нагрузку, которая должна быть приложена к каждому металлическому материалу. Кроме того, при расчете прочности необходимо учитывать нагрузки, прикладываемые к сварным швам каждого материала, тем самым устанавливая стандарт качества сварки, которого необходимо достичь.
Следовательно, важно проверять качество сварки на основе расчета прочности, измеряя, например, толщину горловины (или поперечное сечение горловины, размер поперечного сечения сварного шва после сварки), длину ветви и Глубина проникновения.Качество сварных швов можно оценить путем макроскопического измерения поперечных сечений после сварки.
Глубина проникновения тесно связана с прочностью соединения. Любые дефекты проплавления сварных швов, такие как несоответствие между глубиной проплавления и основным материалом, сильно повлияют на качество и прочность сварки. На примере стыковой сварки ниже описаны типичные дефекты проплавления.
- Недостаточное проникновение
- Дефект, при котором степень проникновения недостаточна по сравнению с необходимой глубиной проникновения из-за таких факторов, как недостаточное нагревание расплавленного металла.На рисунке показан пример угловой сварки внахлест. При стыковой сварке этот дефект легко возникает на дне канавок. В случае соединения тройника с тонкой пластиной (горизонтального галтеля) проникновение считается недостаточным, если глубина проникновения составляет 20% или меньше от тонкой пластины.
- Неполная сварка
- Дефект, при котором части основного металла не проникли расплавленным металлом. На рисунке показан пример муфты-тройника с тонкой пластиной (горизонтального галтеля).
Этот дефект вызван, например, недостаточным нагревом расплавленного металла и предварительной подачей расплавленного металла. При кольцевой сварке это также вызвано тем, что предыдущие и последующие валики переходят на сварку внахлест до того, как они проникнут в достаточной степени.
Различные канавки также вызывают различный характер проплавления, что приводит к различиям в прочности сварных швов.
- Сварка с проплавлением
- Сварка с полным проплавлением — это метод сварки, при котором канавка соединяемого основного материала объединяется и заделывается расплавленными соединительными материалами (присадочный пруток и сварочная проволока), как при стыковой сварке.
Можно сказать, что сварные швы с полным проплавлением обладают высокой надежностью с точки зрения прочности, поскольку они имеют такое же предел прочности, что и основной материал. С другой стороны, они требуют высокого качества сварки. Особое внимание необходимо уделять концам сварных швов, чтобы предотвратить такие дефекты, как сварные швы с подрезкой.Также важно контролировать и регулировать арматуру, потому что напряжение концентрируется на чрезмерном армировании, вызывая растрескивание или другие подобные проблемы.
- Сварка с частичным проплавлением
- Сварка с частичным проплавлением — это метод, при котором на основном материале создается частичная канавка.В этом методе основной материал сваривается только частично, а сварка с проплавлением сваривает всю толщину листа основного материала. Хотя в целом используется сварка с полным проплавлением, в некоторых случаях требуется сварка с частичным проплавлением, например, когда соединяемые секции переплетаются из-за конструкции и изготовления материалов.
Однако следует соблюдать осторожность при сварке с частичным проплавлением в местах, к которым прилагается изгибающий момент или растягивающее усилие, поскольку сварочная прочность при сварке с частичным проплавлением часто недостаточна. Таким образом, расчет прочности сварных швов, а также измерение и проверка того, соответствуют ли размеры фактического проплавления сварного шва, такие как толщина шва, расчетным условиям, являются особенно важными.
Поперечные сечения сварных швов обычно имеют низкий контраст между проплавлением и основным материалом, поэтому измерения с использованием обычных микроскопов затруднены и приводят к различиям между операторами. Также в случае стереоскопических микроскопов необходимо визуально проверить шкалу и вручную ввести измеренные значения.
Однако в последние годы технический прогресс в цифровых микроскопах решил проблемы обычных микроскопов и значительно изменил четкость проплавления сварного шва и эффективность измерения размеров. Цифровой 4K-микроскоп сверхвысокой четкости KEYENCE серии VHX повышает эффективность контроля проникновения сварных швов благодаря четким изображениям и измерениям размеров, поддерживаемым новейшими линзами высокого разрешения, 4K CMOS, инновациями в освещении и технологиями обработки изображений.
Поперечные сечения сварных швов иногда затрудняют оценку и измерение из-за низкого контраста границ сварных швов как для проплавления, так и для основного материала. Следовательно, эти границы нельзя четко наблюдать с помощью обычного микроскопа.
Цифровой микроскоп 4K серии VHX может четко фиксировать края с помощью изображений 4K с высоким разрешением. Даже для поперечных сечений угловой сварки внахлест, граница между металлом шва и основным материалом которого трудно различить, теперь можно быстро и четко определить четкие граничные края, различия в металлических конструкциях и дефектные участки.
Эти наблюдения устраняют путаницу при обычных измерениях глубины проникновения и сокращают рабочие часы, повышая точность контроля.
Слева: высокое разрешение / справа: нормальное (30x)
Измерение размеров поперечных сечений сварных швов — важная проверка, связанная с прочностью и качеством.Однако с помощью обычного стереоскопического микроскопа трудно судить о точках измерения из-за низкого контраста между основным материалом и шариками. Кроме того, требуется визуальное сопоставление с памятью и ручной ввод полученных значений, что приводит к проблемам, связанным с человеческой ошибкой и усложнением работы.
Благодаря отображению на мониторе изображений с высоким разрешением 4K, которые могут четко отображать границы сварных швов, цифровой микроскоп 4K серии VHX позволяет измерять размеры в 2D таких элементов, как длина ножек, глубина горловины и глубина проплавления, с помощью простого нажатия на точку мера.Вы можете легко и за короткое время выполнять даже высокоточные измерения субмикронного порядка, тем самым значительно сокращая рабочее время.
Кроме того, новейшая функция автоматического определения края предотвращает расхождения в точках измерения между операторами. Кроме того, широкий спектр потребностей в проверке удовлетворяется благодаря функции, которая позволяет пользователям повторять измерения размеров, выбирая измеренные и сохраненные данные из альбома.
Измерение проплавления сварного шва
Также возможно измерение субмикронного порядка.Сварные швы имеют непрерывную неровную форму. Если на поверхности борта имеются (прерывистые) дефекты, такие как недостаточное армирование, перекрытие, поднутрение, ямки и трещины, требуемые механические свойства не могут быть получены, и могут возникнуть трещины. Однако обычные микроскопы не могут сфокусировать всю неровную поверхность валика и не могут предоставить информацию о высоте, необходимую для оценки таких предметов, как арматура.
Цифровой микроскоп 4K серии VHX обеспечивает полностью сфокусированный просмотр и измерение трехмерных размеров объектов с неровной поверхностью.Кроме того, отображая трехмерную форму сварных швов, вы можете не только свободно осматривать форму под разными углами, но также измерять профиль любого поперечного сечения. Поскольку формы и шероховатость можно анализировать, вы также можете проверять брызги, трещины и аналогичные проблемы на поверхности основного материала вокруг сварных швов.
Наблюдение и измерение сварных швов с помощью цифрового микроскопа 4K серии VHX Наблюдение за сварными швами Трехмерные измерения формы и профиля сварных швов Обычно операторам приходилось иметь дело не только со сложными измерениями и проверками, но и с большой рабочей нагрузкой, связанной с созданием отчетов.
Цифровой микроскоп 4K серии VHX оснащен функцией отчета. Вы также можете установить Excel на серии VHX, как на ПК. Предварительная настройка шаблонов позволяет мгновенно вводить не только увеличенные изображения с указанными размерами, но также измеренные значения и оценки «годен / не годен». Эти шаблоны значительно сокращают трудозатраты и трудозатраты, необходимые для создания отчетов.
Серия VHX — это мощный инструмент, который решает проблемы при обычных измерениях и проверках, одновременно повышая эффективность работы.Это достигается благодаря своей четкости, которая может быть достигнута только с изображениями высокого разрешения 4K, получением числовых данных посредством высокоточных измерений, а также сохранением и использованием данных. Он оснащен множеством других расширенных функций, которые ранее не были доступны. Кроме того, предусмотрены многие другие функции для удовлетворения требований к скорости и точности на месте, например, функция плавного масштабирования, которая автоматически изменяет увеличение между 20x и 6000x без замены объектива, режим оптического эффекта тени и функции множественного освещения, которые помогают четко передать мелкие детали неровных поверхностей, а также автоматические шаблоны для повторных измерений.
Для получения дополнительной информации о продукте или запросов, нажимайте кнопки ниже.
Что означает подрезка сварного соединения?
Конкретный код сварки определяет допустимую величину поднутрения.Возможность правильно идентифицировать этот дефект позволяет сварщику принять меры, чтобы избежать подрезов.
Определение подрезов
Поднутрения проявляются в виде канавки в сварочном материале, расположенной непосредственно по краям сварного шва.В точке плавления подрезание уменьшает толщину свариваемого металла. Рентгеновские снимки показывают поднутрение в виде тонкой темной линии, слегка неровной вдоль сварного шва.
Угловая подрезка
При угловой сварке используются два куска металлической пластины для выполнения стыков внахлест, угловых стыков или тавровых стыков. По краю или на носке сварного шва появляется подрез. Компания Esab, производитель сварочных машин и оборудования, сообщает, что подрезы чаще всего наблюдаются при угловых сварных швах внахлест, но также могут наблюдаться при других типах угловых сварных швов.
Внутренняя подрезка
Внутренняя подрезка, также известная как корневая подрезка, возникает при сварке стыкового соединения вдоль основного металла рядом с основанием сварного шва. При сварке труб это внутренняя часть трубы по узкой кромке. Внутри сварного шва обнаруживается другая форма внутренней поднутрения. Он выглядит как канавка, оставленная вдоль боковой стенки в верхней части корневого шва. Когда последующий сварной шов помещается в зону сварного шва, он может образовывать включения в сварном шве. Поднутрение, если оно неправильно отрегулировано, может проявиться на рентгеновских снимках как внутреннее поднутрение.
Наружная подрезка
Наружная подрезка или поднутрение коронки очевидно с внешней стороны стыкового шва. Это выглядит как эрозия или бороздка, идущая по краю сварного шва. Bernard, производитель сварочного оборудования, предостерегает от внешних подрезов, поскольку они ослабляют сварной шов и делают его восприимчивым к растрескиванию по краям сварного шва. (ref 5)
Предотвращение
Подрезы возникают из-за различных условий, включая высокую скорость перемещения, регулировку высокого тока, длинный дуговый зазор и неправильную технику сварки.При слишком быстром движении поверхностное натяжение сварного шва втягивает расплавленный основной металл в сварной шов, что приводит к подрезу.