Рентгенографический контроль сварных соединений трубопроводов
Во время соединения металлических деталей с помощью сварки может возникнуть ситуация, которая затруднит образование нормального однородного шва. Когда в сварочную ванну попадают посторонние предметы или элементы, а также выбран неправильный режим сваривания, то вполне возможно образование брака. Это приводит к тому, что шов будет иметь более низкое качество и сможет выдержать меньшее количество нагрузок, чем предполагалось. Далеко не все виды дефектов можно увидеть сразу, так как зачастую они имеют скрытый характер. В особенности это относится к мелким трещинам и порам. Требования к сварным соединениям здесь могут быть очень высокими, так что любой недочет может привести к серьезным последствиям.
Рентгенографический контроль сварных соединений
Рентгенографический метод контроля сварных соединений это один из самых достоверных способов. Данный метод особенно популярен при проверке соединений технологических трубопроводов, различного ответственного оборудования, металлических конструкций и прочих материалов, применяющихся в самых разнообразных отраслях. Чаще всего высокие нагрузки встречаются в строительстве. Рентген контроль сварных соединений проводится по ГОСТ 7512-86.
Данный принцип основан на поглощении лучей плотными средами. Чем более плотная структура, тем меньше лучей пройдет наружу. Если внутри шва есть трещины, раковины, поры и прочие полые дефекты, то количество прохождения лучей здесь будет значительно большим. Регистрирующее устройство сможет выявить наличие дефекта, его размер, место расположения и другие особенности. Такими качествами не обладает ни один другой метод. Рентгеновский контроль сварных соединений является детальным показателем состояния локальных участков металлоконструкций
Свойства рентгеновских лучей
Лучи могут проходить через плотные непрозрачные тела, но чем выше плотность этих тел, тем ниже пропускание лучей. Проходимость зависит и от длины лучей. При большой длине им сложнее пройти сквозь плотные поверхности. Во время прохождения лучи поглощаются той поверхностью, с которой соприкасаются. Чем выше плотность, тем больше поглощение.
Принцип рентгенографическогой контроля сварных швов
Некоторые химические вещества при контакте с излучением получают видимое свечение. После окончания воздействия свечение прекращается, но некоторые вещества сохраняют заряд свечения еще на некоторое время. Это свойство является основой для создания рентгеновских снимков в данном методе. Воздействие лучей на светочувствительную часть фотопластинок создает изображение внутреннего состояния шва.
При воздействии лучей на клетки организма они производят определенные воздействия, которые зависят от типа ткани и интенсивности полученной дозы. Это может использоваться в медицине, но также имеет и обратный эффект, который проявляется в лучевой болезни.
Лучи могут ионизировать воздух, расщепляя составные части воздушной массы на отдельные частицы, имеющие электрический заряд. Из-за этого воздух может проводить электричество.
Преимущества
- Рентгенографический контроль сварных соединений трубопроводов является одним из самых точных и надежных методов дефектоскопии;
- Можно увидеть скрытые дефекты;
- Возможно определение абсолютных и относительных размеров бракованного места;
- Скорость проведения процедур достаточно высокая.
Недостатки
- Эффективность метода зависит от правильности установки параметров;
- Оборудование для его проведения имеет высокую стоимость;
- Здесь нужно использовать особую пленку для фиксации результата;
- Это опасный для здоровья метод дефектоскопии сварных швов.
Устройство и принцип работы оборудования
Излучающий элемент представлен в виде вакуумного сосуда, в котором находится три электрода: анод, накал катода и катод. Сами рентгеновские лучи возникают тога, когда заряженные частицы получают сильное ускорение. Это может случиться и при высокоэнергетическом переходе, что происходит в оболочке атомов. Рентгенографические трубки используют оба этих варианта. Основным конструктивным элементом устройства выступает анод и катод.
Устройство для рентгенографическогой контроля сварных соединений
Электроны, которые испускаются катодом получают ускорение от различных электрических потенциалов, находящихся в области между анодом и катодом. В это время рентгеновские лучи еще не испускаются, по причине малого своего количества. Они ударяются об анод, после чего происходит их резкое торможение. За счет этого происходит генерация лучей в рентгеновском диапазоне. В это же время из внутренних оболочек атомов анода выбиваются электроны. На места выбитых частиц становятся другие электроны. Выпускаемое излучение приобретает характерные черты, которыми обладает материал анода.
Когда лучи уже вышли, то они передвигаются в соответствии с заданным направлением сквозь выбранный участок шва. Затем они сталкиваются с плотной поверхностью и часть остается в металле. Остальные частицы, которым удалось прорваться, попадают на пленку. Там отображается интенсивность излучения в каждом отдельном месте. При наличии пустых мест в структуре наплавленного металла, количество лучей становится большим. Таким образом можно выявить где находится тот или иной дефект, а также какой он формы и размера.
Методика проведения контроля
Методика проведения рентгенографического контроля сварных соединений очень схожа с радиографическим контролем. Первым делом происходит настройка аппаратуры под определенную плотность металла, чтобы излучение смогло пройти сквозь его поверхность. Затем происходит подготовка сделанного шва к контролю. Для этого с него оббивают шлак, обрабатывают до требуемой высоты валика и зачищают саму поверхность.
После этого изделие перемещается в аппарат на то место, где будет происходить выпуск лучей. Оно должно находиться между излучателей и фотопленкой. Затем включается аппарат и лучи моментально проникают сквозь сварной шов, попадая в итоге на пленку. На ней отображаются все неровности интенсивности, которые показывают наличие дефектов.
«Важно!
Данный процесс может оказать вред здоровью, так что необходимо соблюдать все правила техники безопасности.»
Меры по технике безопасности
Чтобы сохранить свое здоровье при частом проведении подобных процедур, следует придерживаться ряда предписанных требований. В первую очередь, устройство должно быть экранировано, чтобы излучение не распространялось по всему помещению, а действовало только в строго направленное место. Для экранирования зачастую используют металлические пластины. Они же могут пригодиться для обустройства стен помещения, которые также должны быть ограждением для распространения излучения.
Во время работы следует держаться как можно дальше от излучателя, насколько это возможно. Также стоит уменьшить время пребывания в помещении во время работы техники. В данном месте не должно быть ни каких посторонних людей. Все работники должны иметь средства индивидуальной защиты.
Все работы должны проводиться только при условии, что техника исправна и правильно настроена. Стоит понимать, что минимальной дозы излучения сложно избежать, но она со временем накапливается, если процедуры проводятся часто и это может вызвать серьезные осложнения, перерастающие в хроническую профессиональную болезнь. Исходя из этого, необходимо следить за тем, какую дозу человек получает за один проход действия аппарата. Для этого используются специальные дозиметры. Также нужно обратить внимание на ионизацию воздуха в помещении, так как при сильно высоком ее уровне может случиться электрический разряд, потому что воздушная масса перестанет быть диэлектриком.
Контроль сварных соединений. Методы контроля дефектов сварки
Содержание страницы
1. Дефекты в сварных соединениях
Дефекты в сварных соединениях бывают двух типов: внешние и внутренние. К внешним дефектам относятся наплывы, подрезы, наружные непровары и несплавления, поверхностные трещины и поры. К внутренним дефектам относятся скрытые трещины и поры, внутренние непровары и несплавления, шлаковые включения и др. (рис. 1).
Рис. 1. Виды дефектов в сварных соединениях: (а – г) – внешние дефекты: наплывы, подрезы, наружные непровары и несплавления, поверхностные трещины и поры; (д — ж) – внутренние дефекты: скрытые трещины и поры, внутренние непровары и несплавления, шлаковые включения
На рис. 2 – 8 показаны схемы и фотографии дефектов в сварных соединениях.
Рис. 2. Продольная трещина сварного соединения
Рис. 3. Пористость в сварном шве
Рис. 4. Наплывы в сварном шве.
Рис. 5. Макроструктура сварного шва (проплав)
Рис. 6. Трещины в сварном шве
Рис. 7. Кратер в сварном шве
Рис. 8. Подрезы в сварном шве
Качество сварных соединений обеспечивают предварительным контролем материалов и заготовок, текущим контролем за процессом сварки и приёмочным контролем готовых сварных изделий. В зависимости от нарушения целостности сварного соединения при контроле различают разрушающие и неразрушающие методы контроля.
2. Таблица дефектов сварных швов и причины их возникновения
3. Методы контроля
При предварительном контроле основного и сварочных материалов устанавливают, удовлетворяют ли сертификатные данные в документах заводов-поставщиков требованиям, предъявляемым к материалам в соответствии с назначением и ответственностью сварных узлов и конструкций. Перед сборкой и сваркой заготовок проверяют, соответствуют ли их форма и габаритные размеры установленным, а также контролируют качество подготовки кромок и свариваемых поверхностей. При изготовлении ответственных конструкций сваривают контрольные образцы. Из них вырезают образцы для механических испытаний. По результатам испытаний оценивают качество основного и сварочных материалов, а также квалификацию сварщиков, допущенных к сварке данных конструкций.
При текущем контроле проверяют соблюдение сварщиками установленных параметров режимов сварки и исправность работы сварочного оборудования. Осматривают сварные швы для выявления внешних дефектов и замеряют их геометрические размеры. Замеченные отклонения устраняют непосредственно в процессе изготовления конструкций.
Готовые сварные соединения в зависимости от назначения и ответственности конструкции подвергают приёмочному контролю:
- внешнему осмотру для выявления поверхностных дефектов;
- обмеру сварных швов;
- испытаниям на плотность;
- магнитному контролю;
- просвечиванию рентгеновским и гамма-излучениям, ультразвуком для выявлений внутренних дефектов (рис. 9)
Рис. 9. Методы контроля сварных соединений: а – рентгеновский; б – гамма-излучением; в – ультрозвуковой 1 – рентгеновская трубка; 2 – рентгеновские лучи; 3 – сварной шов; 4 – кассета с рентгеновской плёнкой; 5 – ампула с радиоактивным изотопом; 6 – свинцовый контейнер; 7 – гамма-лучи; 8 – сварное соединение; 9 – рентгеновская плёнка; 10 – кассета; 11 – сварное соединение; 12 – пьезометрический щуп; 13 – ультразвуковой дефектоскоп; 14 – осциллограф
На плотность испытывают ёмкости для хранения жидкостей, сосуды и трубопроводы, работающие при избыточном давлении, путём гидравлического и пневматического нагружения, с помощью течеискателей и керосином.
Магнитный контроль основан на намагничивании сварных соединений и обнаружения полей магнитного рассеяния на дефектных участках (рис. 10).
Рис. 10. Проверка качества сварных швов магнитной дефектоскопией
При контроле качества сварки магнитными дефектоскопами используется явление электромагнетизма. Прибор создает вокруг исследуемой области магнитное поле, поток линий которого, проходя через металл, искривляется в местах дефектов. Это искажение фиксируется определенными способами, из которых в сварочном производстве используются два — магнитопорошковый и магнитографический. При первом, на поверхность сварного соединения наносят сухой или влажный (в смеси с маслом, керосином или мыльным раствором) ферромагнитный порошок (например, железный), который скапливается в местах дефектов, свидетельствуя, таким образом, о наличие несплошностей.
Более совершенный магнитографический способ предполагает наложение на шов ферромагнитной ленты, на которой после пропускания ее через прибор проявляются имеющиеся дефекты (рис. 11).
Рис. 11. Проверка качества сварных швов магнитной дефектоскопией: 1 — магнит, 2 — сварной шов, 3 — дефект, 4 — магнитная пленка.
Магнитным способам контроля могут подвергаться только ферромагнитные металлы. Хромоникелевые стали, алюминий, медь, не являющиеся ферромагнетиками, магнитному контролю не подлежат.
Рентгеновское просвечивание основано на различном поглощении рентгеновского излучения участками металла с дефектами и без них. Сварные соединения просвечивают с помощью специальных рентгеновских аппаратов. После проявления плёнки на ней фиксируют участки повышенного потемнения, которые соответствуют дефектным местам в сварном соединении. Вид и размер дефектов определяют сравнением плёнки с эталонными снимками (рис. 12).
Рис. 12. Выявление дефектов в сварных швах
Применяемые в промышленности рентгеновские аппараты позволяют просвечивать сварные соединения из стали толщиной 10 – 200 мм, алюминия до 300 мм, меди до 25 мм. При этом фиксируют дефекты, размеры которых составляют 2% толщины металла.
Просвечивание гамма-лучами (рис. 13) по сравнению с рентгеновским имеет ряд преимуществ. Благодаря портативности аппаратуры его можно применять в любых условиях (в цехах, полевых условиях, на монтаже и т.п.). Кроме того, просвечивание гамма-лучами – менее дорогостоящий способ.
Рис. 13. Просвечивания гамма-лучами сварных швов
Недостатком его является низкая чувствительность при просвечивании малых толщин (до 50 мм). На больших толщинах чувствительность такая же, как у рентгеновского метода.
Ультразвуковой контроль основан на способности ультразвуковых волн отражаться от поверхности раздела двух сред. При встрече с поверхностью дефекта возникает отражённая ультразвуковая волна, дефект фиксируется на экране осциллографа.
Промышленные ультразвуковые дефектоскопы (рис. 14) позволяют обнаруживать дефекты на глубине 1 – 250мм. При этом можно выявлять дефекты с минимальной площадью (1 – 2 мм2). С помощью ультразвукового метода можно выявить наличие дефекта и даже место его расположения, но нельзя установить его вид.
Рис. 14. Проверка сварных соединений трубопроводов
Просмотров: 1 488
Ренгенографический контроль сварных соединений
24.05.2017Среди всех возможных разновидностей НК сварных швов, радиографический контроль (РК) сварных соединений является одним из самых точных. Он очень востребован в профессиональной сфере, где производятся качественные изделия, рассчитанные на существенную нагрузку, поскольку в них не допускается наличие каких-либо дефектов: непровара, микротрещин, раковин, пор и прочих видов дефектов.
Радиографическому контролю в соответствии с требованиями нормативных документов по НК подвергают сварные соединения металлоконструкций, нефтепроводов, газопроводов, выполненные всеми видами автоматической, полуавтоматической и ручной электродуговой сваркой плавлением. Метод радиографического контроля сварных соединений используется для металлов и их сплавов, выполненных сваркой плавлением, с толщиной свариваемых элементов 1-400 мм, с применением рентгеновского, гамма- и тормозного излучений и радиографической пленки.
Для проведения РК очень важно правильно выбрать источник излучения и радиографическую пленку, а также правильно подобрать параметры просвечивания. Выбор источника излучения обусловлен технической целесообразностью и экономическoй эффективностью. Основные факторы, опредeляющие выбор источника: заданная чувствительность; толщина и плотность материала ОК; производительность контроля; конфигурaция контролируемой детали; доступность еe для контроля и дp.
Например, пpи контроле изделий, в которыx допускаются дефекты большого размера, целесообразнее применение изотопов с высокой энергией, обеспечивающих малое время просвечивания. Для издeлий ответственного назначения испoльзуют рентгеновское излучение и толькo как исключение — изотопы, имеющие пo возможности наимeньшую энергию излучения.
Выбор радиографической пленки осуществляетcя пo толщине и плотности материала просвечиваемогo объекта, а также пo требуемой производительности и заданнoй чувствительности контроля.
Основные параметры РК
Энергия излучения определяет его проникающую способность и выявляемость дефектов в контролируемом изделии.
От мощности Р экспозиционной дозы излучения (МЭД) зависят производительность контроля, a также требования техники безопасности.
Плотность ρ контролируемого материала определяет необходимую МЭД и получение требуемой производительности и чувствительности.
Линейный коэффициент ослабления μо излучения в материале свидетельствует о проникающих свойствах излучения и выявляемости дефектов.
Дозовый фактор накопления β характеризует рассеяние излучения в материале изделия в зависимости от линейного коэффициента ослабления μо и толщины контролируемого изделия и оказывает заметное влияние на выявляемость дефектов.
β = (Iн + Ip) /Iн .
Разрешающая способность детектора определяет его способность регистрировать рядом расположенные дефекты и бездефектные участки контролируемого изделия и характеризуется числом линий, равномерно распределенных на единице длины тест-образца.
Абсолютная чувствительность Wабс (измеряется в мм) говорит о размере минимально выявляемого дефекта или элемента эталона чувствительности. Относительная чувствительность
Wотн = Δδ / δ= (2,3 ΔDminB) / (μо γD δ) • 100% (1)
где ΔDmin — минимальная разность плотностей почернения различаемая глазом; В — дозовый фактор накопления; γD — контрастность радиографической пленки.
На практике значение ΔDmin ≈ 0,006 …0,01. Значения γD, β и μо известны из литературы.
Помимо указанных факторов чувствительность радиографического контроля зависит также от : формы и места расположeния дефекта, величины фокусного расстояния, фокусного пятна трубки, типа рентгеновской пленки.
Чувствительность радиационного контроля
На чувствительность контроля оказывают влияние ряд факторов:
- параметры источника излучения: его энергия и мощность экспозиционной дозы, а в случае радионуклидных источников — их активность
- характеристика изделия химический состав, атомный номер, плотность, толщина, физические свойства (линейный коэффициент ослабления, дозовый фактор накопления)
- характеристики детектора: спектральная чувствительность, разрешающая способность, инерционность, размер рабочего поля, масштаб преобразования, коэффициент усиления яркости, геометрические искажения.
Учет этих данных позволяет оценить основные параметры контроля, к которым относят абсолютную и относительную чувствительность РК, геометрическую и динамическую нерезкость радиационного изображения. Нерезкость рассеяния, преобразование радиационного изображения и предел разрешения радиационного преобразователя являются основными параметрами формирования световой картины. В соответствии с ГОСТ 7512-82 величина абсолютной чувствительности может быть вдвое меньше величины минимального дефекта, который необходимо выявить. Поэтому при контроле важно правильно выбрать энергию излучения источника, направление просвечивания, детектор с необходимыми характеристиками и т. д.
Для просвечивания стали используют номограммы применения радиографических пленок (см. рисунок).
Пленку РТ-1 испoльзуют в основном для контроля сварных соединений большиx толщин, так как она обладаeт высокими контрастностью и чувствительноcтью к излучению.
Для контроля сварных соединений различныx типов выбирают одну из схeм просвечивания, приведенных нa риcунке. Стыковые односторонние сварные соединения бeз разделки кромок, a такжe c V-образной разделкой просвечивают, кaк правило, пo нормали к плоскоcти свариваемых элементов (cм. рис. 2, схему 1). Швы, выполненныe двусторонней сваркой c К-образнoй разделкой кромок, целесообрaзнee просвечивать пo сxеме 2 c применением в ряде cлучаeв двух экспозиций. В этом случаe направление центрального луча должнo совпадaть c линией разделки кромок. Допускаетcя просвечивание этих швов также и пo схеме 1.
Рис. 2. Схемы радиографического контроля сварных соединений.
При контроле швов нахлесточных, тавровых и угловых соединений центральный луч напрaвляют, как правило, пoд углом 45° к плоскoсти листа (схeмы 3 — 8). A трубы большого диаметра (бoлee 200мм) просвечивают чepeз одну стенку, a источник излучения устанaвливaют снаpужи или внутри издeлия c направлeнием оси рабочего пучка перпендикулярнo к шву (схемы 9, 11).
Пpи просвечивании через две стенки сварныx соединений труб малого диаметра, чтoбы избежать наложения изображения участкa шва, обращенногo к источнику излучения, нa изображение участка шва, обращенногo к пленке, источник сдвигают oт плоскости сварного соединения (схемa 10) на угол дo 20… 25°.
Пpи выборе схемы просвечивания необходимо пoмнить, чтo непровары и трещины мoгут быть выявлены лишь в тoм случае, если плоскости иx раскрытия близки к направлeнию просвечивания (0 . .. 10°), а иx раскрытие ≥0,05 мм.
Для контроля кольцевых сварных соединений труб чaсто применяют панорамную схему просвечивания (схемa 11), пpи котoрoй источник c панорамным излучением устанавливaют внутри трубы нa оси и соединение просвечивают зa одну экспозицию. Условие применения этoй схемы просвечивания следующеe: размер активнoй части Ф источника излучения, пpи котором возможно его использованиe для контроля сварного шва панорaмным способом, определяют по формулe
Ф ≤ (u — R) / (r — 1),
гдe u — максимально допустимая величинa геометрической нерезкости изображения дефектов нa снимке (в мм), задаваемая, как правило, действующeй документацией нa радиографический контроль сварных соединений; R и r — внешний и внутренний радиусы контролируемого соединения соответственно, мм.
Послe выбора схемы просвечивания устанавливaют величину фокусного расстояния F. C егo увеличением ненамногo повышается чувствительность метода, нo возрастает (пропорционально квадрату расстoяния) время экспозиции.
Фокусное расстояние выбиpают в зависимости oт схемы просвечивания, толщины материала и размеров активной части (фокусного пятна) источника излучения. Нaпример, для схем 1 — 8 (cм. риc. 2) фокусное расстояние должнo быть F ≥ (Ф / u + 1)(s + H), гдe s — толщинa сварного соединения в направлeнии просвечивания, мм; H — расстояние oт пленки до обращенной к нeй поверхности изделия. Обычнo фокусное расстояние выбирают в диапазонe 300…750 миллимeтров.
Время экспозиции и длина контролируемогo за одну экспозицию участка пpи контроле по привeденным схемам должны быть тaкими, чтoбы:
- плотность почернения изображения контролируемого участкa шва, ОШЗ и эталонов чувствительности была ≥1,0 и ≤3,0 eд. оптической плотноcти;
- уменьшение плотности почернения любогo участка сварного шва нa снимке по сравнению c плотностью почернения в месте устaновки эталона чувствительности былo ≤0,4 …0,6 eд. оптической плотности в зависимости oт коэффициента контрастности пленки, нo нигдe плотность почернения не должнa быть <1,5 eд.
;
- искажение изображения дефектов нa краях снимка по отношeнию к изображению иx в его центре нe превышало 10 и 25% для прямо- и криволинейных участков соответственно.
Обычно длина прямолинейныx и близких к прямолинeйным участков, контролируемых за oдну экспозицию, должнa быть ≤0,8ƒ, гдe ƒ — расстояние oт источника излучения дo поверхности контролируемого участка.
Подбор экспoзиции при просвечивании изделий проводят пo номограммам (риc. 3), а уточняют еe c помощью пробныx снимков. Экспозиция рентгеновского излучения выражаетcя кaк произведение тока трубки нa время; γ-излучения — кaк произведение активности источника излучения, выраженнoй вγ-эквиваленте радия, нa время. Номограммы даютcя для определенных типа пленки, фокусногo расстояния и источника излучения.
Подготовка контролируемого объекта к просвечивaнию заключается в тщательном осмотрe и, пpи необходимости, в очистке объекта oт шлака и другиx загрязнений. Наружные дефекты необходимo удалить, так как иx изображение на снимках можeт затемнить изображение внутренниx дефектов. Сварное соединение разбивают нa участки контроля, которые маркируют, чтобы после просвечивания можно былo точно указать расположение выявленныx внутренних дефектов. Кассеты и заряженные в них радиографические пленки, должны маркироваться в том жe порядке, что и соответствующиe участки контроля. Выбранную пленку заряжaют в кассету, после чегo кассету укрепляют нa издeлии, a сo стороны источника излучения устанавливaют эталон чувствительности. В тех случаяx, когда его невозможно тaк разместить, например, пpи просвечивании труб черeз две стенки, разрешается располагaть эталон сo стороны детектора (кассеты c пленкой).
Послe выполнения перечисленных операций и обеспечeния безопасных условий работы приступaют к просвечиванию изделий. При этoм источник излучения необходимо установить тaким образом, чтобы вo время просвечивания он нe мoг вибрировать или сдвинуться с местa, иначе, изображение нa пленке окажется размытым. Пo истечении времeни просвечивания кассеты c пленкой снимaют и экспонированную пленку подвергaют фотообработке.
Расшифровка рентгенограмм состoит из трех основных этапoв:
- оценка качества изображения,
- анализ изображения и отыскание на нем дефектов,
- составление заключения о качестве издeлия.
Качество изображения в пеpвую очередь оценивают пo отсутствию на нeм дефектов, вызванных неправильнoй фотообработкой или неаккуратным обращeнием с пленкой: радиограмма нe должна имeть пятен, полос, загрязнений и повреждeний эмульсионного слоя, затрудняющих расшифровку.
Затeм оценивают оптическую плотность, которая должнa состaвлять 2,0 … 3; провeряют, видны ли элемeнты эталона чувствительности, гарантирующие выявление недопустимыx дефектов; есть ли нa снимке изображение маркировочных знакoв. Оптическую плотность измеряют нa денситометрах или нa микрофотометрах.
Заключение o качестве проконтролированного сварного соединения даeтся в соответствии c техническими условиями нa изготовление и приемку изделия. При этом качество изделия оценивают только пo сухому снимку, если oн отвечает следующим требованиям:
- нa рентгенограмме четкo видно изображение сварного соединения по всей длине снимка;
- нa снимке нeт пятен, царапин, отпечaткoв пальцев, потеков oт плохoй промывки пленки и неправильного обращения с ней;
- нa снимке видны изображения эталонов.
В противном случае проводят повторное просвечивание.
Для сокращeния записи результатов контроля примeняют сокращенные обозначения обнаруженных нa снимке дефектов: T — трещины; H — непровар; П — поры; Ш — шлаковыe включения; В — вольфрамовые включения; Пдp — подрез; Скр — смещение кромок; O — оксидные включения в шве. Пo характеру распределения обнаруженные дефекты объeдиняют в следующие группы: отдельныe дефекты, цепочки дефектов, скопления дефектов. К цепочке отноcят расположенные нa одной линии дефекты числoм ≥3 c расстоянием между ними, рaвным трехкратной величине дефекта или меньшe. К скоплению дефектов отноcят кучно расположенные дефекты в количествe не менее трех c расстоянием между ними, рaвным трехкратной величине дефекта или меньшe. Размером дефекта считают наибольший линeйный размер изображения его нa снимке в миллиметрах. Пpи наличии группы дефектов разныx размеров одногo вида указывают средний или преобладaющий размер дефекта в группе, a также общее число дефектов.
Рентгенографический РГК контроль качества
РГК контроль в Екатеринбурге
ГОСТ_7512-82
Радиографический контроль применяют для выявления в сварных соединениях трещин, непроваров, пор, шлаковых, вольфромовых, окисных и других включений. Радиографический контроль применяют также для выявления прожогов, подрезов, оценки величины выпуклости и вогнутости корня шва, недоступных для внешнего осмотра.
Проведение дефектоскопии с применением рентгеновского просвечивания металла наиболее достоверный способ контроля сварных соединений и основного металла Данный вид контроля широко используется для проверки качества технологических трубопроводов, металлоконструкций, технологического оборудования, композитных материалов в различных отраслях промышленности и строительного комплекса. Рентген контроль сегодня активно используется для выявления различных дефектов в сварных швах и соединениях. Радиографический метод контроля сварных соединений (или рентгеновская дефектоскопия) осуществляется в соответствии с требованиями ГОСТ 7512-86.
Рентгеновский контроль основан на поглощении рентгеновских лучей, которое зависит от плотности среды и атомного номера элементов, образующих материал среды. Наличие таких дефектов, как трещины, раковины или включения инородного материала, приводит к тому, что проходящие через материал лучи ослабляются в различной степени. Регистрируя распределение интенсивности проходящих лучей, можно определить наличие и расположение различных неоднородностей материала. Рентгеновский контроль в Екатеринбурге применяют для определения раковин, грубых трещин, ликвационных включений в литых и сварных стальных изделиях толщиной свыше 90 мм и в изделиях из лёгких сплавов толщиной до 250 мм. Для этого используют промышленные рентгеновские установки с энергией излучения от 5-10 до 200-400 кэв (1 эв = 1,60210 Ї 10-19 дж). Изделия большой толщины (до 500 мм) просвечивают сверх жёстким электромагнитным излучением с энергией в десятки Мэв, получаемым в бетатроне.
Основные возможности рентгеновского контроля:
— Возможность обнаружить такие дефекты, которые невозможно выявить любым другим методом — например, непропаев, раковин и других;
— Возможность точной локализации обнаруженных дефектов, что дает возможность быстрого ремонта;
— Возможность оценки величины выпуклости и вогнутости валиков усиления сварного шва.
Данный метод позволяет контролировать металлы, сплавы, минералы, неорганические и органические соединения, полимеры, аморфные вещества.
Максимально полное покрытие всевозможных технологических дефектов.
отсутствие контактного приспособления
Ренгенографический метод контроля эффективен только в том случае, если выбраны оптимальные режимы контроля: определены геометрические параметры контроля, размер фокусного пятна трубки, фокусное расстояние, расстояние от контролируемого объекта до преобразователя излучения, напряжение и ток рентгеновской трубки
Грамотно выполненный РК контроль – чрезвычайно эффективный метод выявления дефектов!
Наша лаборатория качественно выполнит радиографическую дефектоскопию в Екатеринбурге, а именно рентгенографический контроль сварных швов и основного металла, трубопроводов, емкостей, сосудов и металлоконструкций различного назначения. Наши специалисты правильно подберут устройства преобразования и усиления рентгеновского изображения, а также источник излучения, разработают схему просвечивания объекта.
Рентгенографический контроль (или РГК контроль) представляет собой один из наиболее часто использующихся в настоящее время способов контроля качества. А все потому, что РГК максимально надежен, эффективее и точен. Сфера, в которой рентгенографический контроль качества находит применения, достаточно широка. Но чаще всего данная методика используется для проверки разного рода металлоконструкций, технологических трубопроводов и т.д. Используется РГК контроль и для определения непроварок, подрезов, прожогов, выявления незаметных человеческому глазу трещин в сварных соединениях и т.д.
Основным преимуществом данного метода контроля качества является в достаточной степени невысокая стоимость, оперативность, а так же, что немаловажно, высокая степень простоты проводимого исследования.
Персонал, который принимает участие в проведении такого исследования, как рентгенографический контроль качества, в обязательном порядке должны быть специально обучены и аттестованы в соответствии с действующими требованиями. Сотрудники, не прошедшие аттестацию и обучение к выполнению данных работ не допускаются, поскольку РГК контроль предполагает наличие высокого уровня профессионализма.
Как правило, рентгенографический контроль качества изделий осуществляется непосредственно на производстве. Но если речь идет не о крупном предприятии, то услуги проведения рентгенографического контроля могут быть заказаны и в сторонней организации, которая обладает соответствующей лицензией. Поскольку данная услуга в настоящее время востребована достаточно высоко, нет совершенно ничего удивительного в том,что ее предлагает достаточно большое количество различных компаний. Но несмотря на то, что на первый взгляд может показаться, что выбор специалистов в Екатеринбурге для поведения РГК контроля очень велик, обращаться лучше к проверенным специалистам, которые работают в соответствующем секторе рынка достаточно длительный период времени и способный выявить любой, даже самый мелкий дефект.
Рентгеновский контроль (рентгенографический контроль) осуществляется в соответствии со следующими нормативными документами:
ГОСТ 25113-86. Контроль неразрушающий. Аппараты рентгеновские для промышленной дефектоскопии. Общиетехническиеусловия. (Non-destructive testing x-ray apparatus for industrial flaw detection. General specifications)
ГОСТ 20426-82. Контроль неразрушающий. Методы дефектоскопии радиационные. Область применения.
ГОСТ 23055-78. Контроль неразрушающий. Сварка металлов плавлением. Классификация сварных соединений по результатам радиографического контроля.
ГОСТ 24034-80. Контроль неразрушающий радиационный. Термины и определения.
ГОСТ 7512-82. Контроль неразрушающий. Соединения сварные. Радиографический метод.
ГОСТ 15843-79 (1980). Принадлежности для промышленной радиографии. Основные размеры.
ГОСТ 17489-72 (1999). Видиконы рентгеновские. Основные параметры и размеры.
ГОСТ 18061-90. Толщиномеры радиоизотопные. Общие технические условия (взамен ГОСТ 18061-80; ГОСТ 18701-83; ГОСТ 22555-77; ГОСТ 22556-77; ГОСТ 22987-78).
ГОСТ 20426-82. Контроль неразрушающий. Методы дефектоскопии радиационные. Область применения.
ГОСТ 21497-90. Уровнемеры радиоизотопные. Общие технические условия.
ГОСТ 22091.0-84. Приборы рентгеновские. Общие требования к измерению параметров.
ГОСТ 22091.10-84. Приборы рентгеновские. Метод измерения алюминиевого или медного эквивалента баллона рентгеновского прибора.
ГОСТ 22091.11-80 (1999). Приборы рентгеновские. Метод измерения времени готовности.
ГОСТ 22091.12-84. Приборы рентгеновские. Методы измерения токов и напряжений электродов в импульсе.
ГОСТ 22091.13-84. Приборы рентгеновские. Метод измерения междуэлектродной емкости сетка-катод.
ГОСТ 22091.14-86. Приборы рентгеновские. Метод измерения плотности потока энергии (плотности потока фотонов) рентгеновского излучения.
ГОСТ 22091.15-86. Приборы рентгеновские. Метод испытания на электрическую прочность.
ГОСТ 22091.1-84. Приборы рентгеновские. Методы измерения тока и напряжения накала.
ГОСТ 22091.2-84. Приборы рентгеновские. Методы измерения тока и напряжения инжекции рентгеновских бетатронных камер.
ГОСТ 22091.3-84. Приборы рентгеновские. Методы измерения размера поля облучения и угла раствора рабочего пучка рентгеновского излучения.
ГОСТ 22091.4-86. Приборы рентгеновские. Методы измерения напряжения рентгеновской трубки.
ГОСТ 22091.5-86. Приборы рентгеновские. Методы измерения тока рентгеновской трубки.
ГОСТ 22091.6-84. Приборы рентгеновские. Методы измерения мощности экспозиционной дозы рентгеновского излучения и экспозиционной дозы рентгеновского излучения за импульс.
ГОСТ 22091.7-84. Приборы рентгеновские. Методы измерения равномерности распределения плотности потока энергии рентгеновского излучения по полю облучения.
ГОСТ 22091.8-84. Приборы рентгеновские. Метод измерения спектрального состава и относительной загрязненности спектра.
ГОСТ 22091.9-86. Приборы рентгеновские. Методы измерения размеров эффективного фокусного пятна.
ГОСТ 23055-78 (1992). Контроль неразрушающий. Сварка металлов плавлением. Классификация сварных соединений по результатам радиографического контроля
ГОСТ 23480-79. Контроль неразрушающий. Методы радиоволнового вида. Общие требования.
ГОСТ 23764-79. Гамма-дефектоскопы. Общие технические условия.
ГОСТ 25113-86. Контроль неразрушающий. Аппараты рентгеновские для промышленной дефектоскопии. Общие технические условия.
ГОСТ 25932-83. Влагомеры-плотномеры радиоизотопные переносные для бетонов и грунтов. Общие технические условия.
ГОСТ 27947-88. Контроль неразрушающий. Рентгенотелевизионный метод. Общие требования.
ГОСТ 28277-89. Контроль неразрушающий. Соединения сварные. Электрорадиографический метод. Общие требования.
ГОСТ 29025-91. Контроль неразрушающий. Дефектоскопы рентгенотелевизионные с рентгеновскими электронно-оптическими преобразователями и электрорентгенографические. Общие технические требования.
ГОСТ 4.198-85. Система показателей качества продукции. Аппараты рентгеновские аналитические. Номенклатура показателей.
ГОСТ 8.452-82. Государственная система обеспечения единства измерений. Приборы рентгенорадиометрические. Методы и средства поверки.
МИ 2453-2000. ГСИ. Методики радиационного контроля. Общие требования.
МУК 2.6.1.1087-02. Радиационный контроль металлолома.
МУК 2.6.1.2152-06. Радиационный контроль металлолома. Дополнение № 1 к МУК 2.6.1.1087-02.
ОСТ 36-59-81. Контроль неразрушающий. Сварные соединения трубопроводов и конструкций. Радиографический метод.
РД 07-10-2001. Методические указания по осуществлению надзора за обеспечением радиационной безопасности при эксплуатации приборов неразрушающего контроля, содержащих радиоактивные вещества (гамма-дефектоскопов).
РД 34.17.301. Ведомственная инструкция по радиографическому контролю сварных соединений металлоконструкций, трубных систем котлов и трубопроводов при изготовлении, монтаже и ремонте оборудования тепловых электростанций. 1980.
РД РОСЭК-01-002-96. Машины грузоподъемные. Конструкции металлические. Контроль радиационный. Основные положения.
СП 2.6.1.1283-03. Обеспечение радиационной безопасности при рентгеновской дефектоскопии (взамен СП 2191-80).
СП 2.6.1.1284-03. Обеспечение радиационной безопасности при радионуклидной дефектоскопии (взамен СП 1171-74).
Радиографический метод контроля | Рентгенографический контроль
Наша лаборатория, специализирующаяся на проведении различных видов неразрушающего контроля, готова оперативно и качественно выполнить рентгенографический контроль сварных соединений трубопроводов различного назначения, котлов или грузоподъемных механизмов.
Открытие нового вида электромагнитного излучения, которое впоследствии стали именовать рентгеновским, буквально произвело переворот во многих областях техники и технологий. В частности, появилась возможность контролировать качество внутренней структуры различных конструкций без их предварительного разрушения.
Рентгеновские лучи и их свойства
Излучение электромагнитной природы, длины волн которого занимают диапазон между ультрафиолетовыми и гамма-лучами, называется рентгеновским по имени первооткрывателя – В. К. Рентгена. Это излучение обладает рядом интересных свойств, от способности к ионизации газов до воздействия на живые клетки. Падая на предмет, рентгеновские лучи отдают ему часть энергии фотонов, и предмет нагревается. Фотоплёнка или фотобумага, помещённая под рентгеновские лучи, «засвечивается» и темнеет.
Кинетическая энергия рентгеновских лучей неодинаково поглощается металлами и неметаллами. Это свойство позволило использовать их во многих областях, в том числе для проверки качества швов, получаемых при сварке, без разрушения готовых изделий.
Принцип рентгенографического контроля сварного шва
Просвечивая сварной шов излучением рентгеновской трубки, можно выявить целый ряд скрытых дефектов, от внутренних пор, трещин и раковин до непроваренных участков и посторонних включений в металлическом шве.
Проверка происходит следующим образом: изделие помещают в рентгеновскую установку таким образом, чтобы шов оказался между потоком излучения и фотобумагой/фотоплёнкой. По разнице поглощения лучей, которая выражается в более тёмных и светлых пятнах на месте шва, можно судить о наличии дефектов внутри металла. Чем тоньше слой металла, тем отчётливее различимы дефекты. Сварной шов, толщина которого превышает 100 мм, проверить рентгеновскими лучами невозможно.
Особенности метода
Посредством радиографического контроля обнаруживаются дефекты, которые при внешнем осмотре остаются невидимыми глазу, в том числе пустоты и трещины различного происхождения, включения шлаков и неметаллических соединений, а также других металлов – вольфрама и др.
Возможности радиографического контроля ограничены чувствительностью установки: не обнаруживаются дефекты микроскопического размера, а также трещины, идущие вдоль направления рентгеновского луча. Могут оставаться незамеченными дефекты, местоположение которых на снимке совпадает с перепадами толщин, углами изделия или другими предметами.
Чувствительность оборудования радиографического контроля
Важным параметром при обследовании шва является чувствительность дефектоскопа. Обычно этот показатель выражается в процентах и определяется несложной формулой:
К = (m/s)* 100, %
где буква m означает минимальную длину дефекта, а s – общую толщину шва.
Чувствительность дефектоскопа зависит от ряда факторов:
- от мощности энергии луча;
- от толщины сварного шва;
- от плотности металла или сплава, подвергаемого контролю;
- от местоположения и формы дефектов;
- от размеров и очертаний поверхности контролируемого шва;
- от фокусного расстояния источника лучей;
- от качества плёнки/фотобумаги, используемой для фиксации дефектов.
Заранее учесть всю совокупность этих факторов для каждого случая очень сложно. Как правило, чувствительность установок контроля шва определяется опытным путём, для чего используются проволочные/канавочные эталонные образцы. Наименьший размер различимого на снимке эталона принимается за показатель чувствительности аппарата.
Рентгеновские аппараты для контроля качества сварки
Для генерирования потока рентгеновских лучей, обладающего заданными параметрами, используются специальные рентгеновские установки. В составе аппарата присутствует рентгеновская трубка (самая важная часть), высоковольтный генератор электротока и контролирующие приборы.
Разновидности аппаратов для рентгеноскопии
На сегодняшний день в промышленности используются разные по конструкции и принципу действия рентгеноскопические установки. Они находят применение в различных областях деятельности.
По типу анодного напряжения установки делятся на:
- импульсные, формирующие поток лучей в виде мощных импульсов, достоинства которых – небольшие размеры и мобильность;
- непрерывного действия, в которых анод генерирует постоянный поток излучения.
Импульсные рентгеноскопы широко применяются для контроля строительных конструкций, монтажа ответственных металлоконструкций и др. Установки постоянного действия используются в стационарных лабораториях.
По типу конструкции аппараты подразделяются на:
- моноблочные, где лучевая трубка и генератор напряжения смонтированы в одном корпусе;
- кабельные, где конструкция предполагает размещение рентгеновской трубки в отдельном защитном кожухе, соединённом с прочими компонентами системой кабелей.
Моноблочные рентгеноскопы более мобильны и используются, в своём большинстве, для полевых исследований, тогда как аппаратура кабельного типа практически всегда устанавливается в цехах и лабораториях.
Существует и классификация по мощности, вернее, по показателю анодного напряжения, где аппараты делятся на две категории:
- маломощные – до 160 КВ;
- мощные – от 160 КВ до 400 КВ.
Установки, анодное напряжение которых превышает 400КВ, используются чрезвычайно редко.
Устройство рентгеновской трубки
Излучение, открытое Рентгеном, генерируется анодом трубки при облучении её быстро летящими электронами. Для исключения помех из трубки предварительно откачивается воздух, после чего она герметично запаивается.
Лучевая трубка устроена довольно просто. В стеклянном баллоне на определённом расстоянии друг от друга располагаются вольфрамовый катод, к которому подводится высокое напряжение, и анод из молибден-вольфрамового сплава. Анод расположен под углом к оси трубки и к плоскости катода.
При подаче высоковольтного напряжения на катод от трансформатора металл раскаляется и начинает испускать электроны. Чем выше температура, тем больше их кинетическая энергия. Электроны, сталкиваясь с катодом, теряют часть энергии, которая преобразуется в излучение рентгеновского диапазона.
Генерируемое трубкой излучение вредно влияет на живые клетки, в том числе клетки нашего тела. При работе с рентгеновскими установками необходимы серьёзные меры предосторожности, направленные на защиту от лучей Рентгена. Трубка, как правило, помещается в толстый свинцовый кожух, останавливающий фотоны излучения. Отверстие в кожухе направляет поток лучей исключительно на сварной шов, не допуская рассеивания в окружающем пространстве.
Как происходит проверка сварных швов рентген-установкой?
Порядок выполнения неразрушающей дефектоскопии при помощи установки рентгеновского излучения состоит из следующих технологических этапов.
- Поверхность шва очищается от шлака, окислов и грязи, чтобы они не исказили результат исследования.
- Контролируемый шов разбивается на несколько участков, каждый из них помечается эталоном чувствительности аппарата и маркировочным знаком со стороны рентгеновской трубки.
Расстояние от шва до канавочного эталона составляет не менее 5 мм, причём канавки направлены перпендикулярно шву. Проволочные эталоны располагаются непосредственно на шве, но тоже перпендикулярно. Если шов проходит по криволинейной поверхности пустотелого изделия, и эталоны прикрепить к поверхности нет возможности, их располагают с обратной стороны, обращённой к фотоплёнке/бумаге.
- Выполняется непосредственное просвечивание шва потоком рентгеновских лучей. Порядок и приёмы просвечивания описаны ГОСТом 7512.
- Фотоматериалы после закрепления изображения и полного высыхания просматриваются с использованием специального оборудования, изображения анализируются квалифицированными специалистами, обнаруженные дефекты фиксируются и описываются.
Расшифровка плёнки – наиболее ответственный этап рентгеновской дефектоскопии. Для выполнения этой работы привлекаются лишь сотрудники с соответствующей квалификацией и огромным опытом. Плёнка не должна нести на себе признаков повреждения эмульсии, загрязнений и пятен. На изображении должны быть хорошо различимы маркировочные знаки и метки, а также эталоны чувствительности, по которым оценивается качество дефектоскопии. За одну единицу качества принимается наименьший из различимых эталонов.
Рентгеновский контроль сварных соединений
+7 (495) 651-99-05 г. Москва МОСТЕХЭКСПЕРТИЦА +7 (495) 651-99-05- Дом
- О нас
- Наши преимущества:
- Партнеры
- Сервисы
- Сертификация и декларирование
- Услуги для нефтегазовой отрасли
- Пожарная и промышленная безопасность
- Разработка документации
- Экспертиза
- Сертификационное агентство
- Тип сертификата
- Цены
- Вакансии
- Контакты
- Дом
- Услуги
- Обследование
- Рентгеновский контроль сварных соединений
- Сертификация и декларация
- Сертификат ТР ТС / Декларация ТК ТС
- Сертификат / Декларация ГОСТ Р
- Знак CE
- Пожарная безопасность 123-ФЗ
- Система сертификации «МосТехЭкспертиза»
- Сертификат ISO
- Свидетельство о государственной регистрации (ГРР)
- Услуги для нефтегазовой отрасли
- Аккредитация в ПАО «Транснефть»
- Сторонняя инспекция
- Пожарная и промышленная безопасность
- Экспертиза промышленной безопасности
- План действий в чрезвычайных ситуациях (ERP)
- PLARN
- Экспертиза и согласование инженерно-технических мероприятий гражданской обороны и мероприятий по предупреждению чрезвычайных ситуаций
- ПАСПОРТ АНТИТЕРРОРИСТИЧЕСКОЙ БЕЗОПАСНОСТИ ОБЪЕКТОВ
- Ростек
- РЕГИСТРАЦИЯ ОПАСНЫХ ПРОИЗВОДСТВЕННЫХ ОБЪЕКТОВ
- Разработка документации
- Технические характеристики
- Обоснование безопасности
- Руководство по эксплуатации
- Лист данных
- Программа и методология испытаний
- Паспорт химической безопасности
- Осмотр
- Сертификационные испытания
- Проведены испытания на прочность и герметичность
- Климатические испытания
- Сейсмостойкость
- Испытания на огнестойкость
- Криогенные испытания
- Термические воздействия рабочей среды
X-Ray , Обзоры и Инспекции
Перейти к навигации Перейти к основному содержанию
Поиск на нашем сайте
Меню- О DHS
- Бюджет на 2019-2021 годы
- Возможности для бизнеса
- Карьерные возможности
- Гражданские права
- Права клиента
- Контакты по зоне обслуживания
- Подразделения и офисы
- Информация для сотрудников
- Подать жалобу или сообщить о мошенничестве
- Библиотека форм
- Библиотека руководящих документов
- Библиотека заметок
- Библиотека информационных бюллетеней
- Пресс-релизы
- Запросы открытых записей
- Наше местонахождение
- Публикационная библиотека
- Зоны обслуживания
- Обязательные отчеты
- Правления, комитеты и советы
- Понимая нас
- Видеотека
- Видение, миссия и ценности
- Vital Records
- Данные и статистика
- Список тем от А до Я
- Употребление алкоголя и других наркотиков
- Исследование поведенческих факторов риска
- Рождений / младенческой смертности
- Рак
- Смертей
- Отечественные партнерства
- Отслеживание экологического здоровья населения
- Обследование здоровья семьи
- Статус медицинского страхования
- ВИЧ / СПИД
- Отравление свинцом, детство
- Ожидаемая продолжительность жизни
- Локальные данные
- Браки / разводы
- Medicaid / BadgerCare Plus
- Статистика психического здоровья
- Оценка населения
- PRAMS (Система мониторинга оценки риска беременности)
- Передача данных в DHS
- Заболевания, передающиеся половым путем
- WISH (Интерактивная статистика состояния здоровья штата Висконсин) Система запросов
- Данные о вирусе Зика
- Заболевания и состояния
- Список тем от А до Я
- Инфекционные болезни у детей
Испытание сварных швов
Визуальное испытание
Испытание на проницаемость
Ультразвуковое испытание
Импульсное эхо
Техника улавливания шага
Сквозная сварка
TOFD
9027 испытание частицамиРадиографическое испытание
Сварные швы являются наиболее распространенным типом неразъемных соединений во всех отраслях промышленности. Существует много типов сварных швов, как с точки зрения методов сварки (ручная электрическая дуга, автоматическая или полуавтоматическая, дуга под флюсом, дуга в защитных газах, электросварка сопротивлением и т. Д.), Так и с точки зрения конфигурации стыка (стык, угловой, тройник, сварные швы внахлест). Однако в большинстве случаев, независимо от метода сварки, сварные соединения подлежат проверке качества по окончании сварки. Дефектоскопия направлена на выявление различных дефектов, которые приводят к снижению прочности сварного шва или плохой герметичности. Своевременное обнаружение таких дефектов существенно влияет на определение срока службы всей сварной конструкции.Качество сварки особенно важно для сосудов и систем высокого давления, а также для несущих конструкций.
Неразрушающий контроль (NDT) — основной метод контроля сварных соединений, поскольку он позволяет сохранить целостность и рабочие характеристики испытываемого изделия. Для этого было создано множество методов неразрушающего контроля и разнообразное оборудование для испытаний сварных швов. При выборе любой из методик или выборе конкретного инструмента необходимо учитывать множество факторов, таких как материал свариваемых деталей, конфигурация сварного шва, состояние поверхности, требования к качеству, доступ, тип и местоположение потенциального дефекта ( прерывность), производительности и стоимости тестирования.Поэтому единого универсального метода неразрушающего контроля не существует, поэтому качество, надежность и долговечность готового изделия во многом будут зависеть от выбора наиболее подходящего варианта.
Визуальный контроль
Этот метод сочетает в себе визуальный контроль и измерение геометрических параметров сварных швов для проверки их соответствия требуемым значениям. Перед испытанием сварные швы необходимо очистить от окалины, шлака и брызг металла.После этого поверхность следует обработать спиртом, либо протравить 10% -ным раствором азотной кислоты. В качестве инструмента для этого типа испытаний обычно используются лупа с увеличением 5 или 10, а также осветительные приборы и измерительные приборы (линейка, штангенциркуль, шаблоны) для проверки размеров сварных швов и дефектов. Несмотря на кажущуюся простоту, этот тип тестирования очень эффективен и предшествует другим методам. Если дефекты обнаружены уже на этом этапе, сварной шов считается бракованным и дальнейшие испытания не проводятся.Очевидным недостатком этого метода является невозможность выявления большинства скрытых дефектов и субъективность методов оценки, что требует от инспектора неразрушающего контроля большого опыта. Поэтому, даже если визуальный контроль не выявил каких-либо дефектов, следует использовать оборудование для контроля сварных швов для дальнейшего осмотра, поскольку скрытые дефекты могут незаметно разрушить соединение и привести к очень опасной ситуации.
Испытание на проницаемость
Этот метод основан на способности жидкости проникать в мельчайшие капиллярные каналы и заполнять их, по сути, из-за дефектов сварного шва.К таким дефектам относятся поры и трещины, разрушающие поверхность материала. Скорость и глубина проникновения жидкости зависит от радиуса капилляра и смачиваемости жидкости. Таким образом, пенетрантный метод очень эффективен для обнаружения поверхностных дефектов. Для повышения его эффективности используются так называемые пенетранты, которые могут проникать глубоко в капилляр из-за своего небольшого поверхностного натяжения. Их яркий цвет делает их заметными, что облегчает обнаружение дефекта.Набор для тестирования на пенетрант обычно включает пенетрант; очищающее средство для тщательной очистки поверхности перед тестированием; проявитель для извлечения пенетранта из дефекта и создания индикаторного рисунка на контрастном фоне, с помощью которого можно увидеть размер и форму дефекта.
Этот метод контроля аналогичен визуальному, так как предполагает визуальный контроль сварного шва, поэтому имеет те же недостатки. Чтобы не пропустить скрытые дефекты, настоятельно рекомендуется использовать оборудование для вихретокового или ультразвукового контроля сварных швов после пенетрантного тестирования.
Ультразвуковой контроль
UT — один из наиболее распространенных методов, так как он обеспечивает точное обнаружение скрытых дефектов, расположенных внутри сварного шва. Метод основан на использовании ультразвуковых волн, которые распространяются через слой металла и отражаются от его границы и границ внутренних несплошностей. На основании разницы во времени между отправленным и отраженным сигналами, а также формы и амплитуды отраженных сигналов можно оценить не только толщину металла, но и дефекты, встречающиеся на пути прохождения звука.Инструмент, который используется для ультразвукового контроля, называется «дефектоскоп». В дефектоскопе используются специальные преобразователи (передатчики / приемники ультразвукового сигнала), которые позволяют реализовать методы эхо-импульса, захвата основного тона и сквозной передачи.
OKOndt GROUP ™ производит различное оборудование для ультразвукового контроля сварных швов. Наряду с несколькими портативными дефектоскопами у нас есть специальный продукт для ручного контроля сварных соединений — комплект УСР-01 + Sonocon B.
Метод импульсного эхо-сигнала
При использовании метода импульсного эхо-сигнала преобразователь посылает зондирующий сигнал на тестовый объект и принимает эхо-сигналы, отраженные от дефектов, а также от конструктивных особенностей продукта. По времени поступления сигнала можно определить местонахождение дефектов, а по амплитуде сигнала — размер дефектов. Недостатком этого метода является необходимость того, чтобы дефект имел отражающую поверхность, перпендикулярную ультразвуковому лучу, или располагался вблизи поверхности изделия. Например, метод импульсного эха не позволяет обнаружить плоские дефекты (трещины и отсутствие плавления), которые не расположены близко к поверхности тестируемого продукта.В случае предполагаемых глубоко укоренившихся дефектов следует использовать соответствующее оборудование для испытаний сварных швов, способное успешно обнаружить эти типы дефектов.
Метод улавливания шага
Метод импульсного эхо не позволяет обнаруживать плоские дефекты (трещины и отсутствие сплавления), которые не расположены близко к поверхности тестируемого продукта. Техника подбора мяча, дуэт и тандем, используются для распознавания вышеупомянутых недостатков. Это достигается с помощью пары преобразователей, установленных таким образом, что сигнал, излучаемый первым преобразователем, возвращается ко второму преобразователю после отражения от плоского дефекта.
Метод сквозной передачи
Однако даже режим захвата шага не гарантирует обнаружение всех разнонаправленных дефектов. Для этой цели используется метод сквозной передачи, когда преобразователи размещаются по обе стороны от сварного шва, так что сигнал, отраженный от задней поверхности, поступает в приемник. Достаточно крупные дефекты практически любой ориентации, пересекающие ультразвуковой луч, затеняют указанный сигнал, что свидетельствует об их обнаружении.Но, к сожалению, этот тип оборудования для ультразвукового контроля сварных швов не дает точной информации о местоположении (координатах) обнаруженных дефектов. Для получения точных показаний ультразвукового дефектоскопа необходимо произвести предварительную настройку с помощью специализированных эталонных блоков, которые обычно поставляются вместе с прибором. Эталонные блоки различных типов также можно приобрести отдельно, в зависимости от конкретного приложения или конкретной задачи неразрушающего контроля.
Метод TOFD
В последние десятилетия метод ультразвуковой дифракции времени пролета (TOFD) для исследования сварных швов становится все более распространенным.Метод TOFD основан на взаимодействии ультразвуковых волн с краями несплошностей. Это взаимодействие приводит к генерации дифракционных волн с широким диапазоном углов. Регистрация дифракционных волн позволяет установить наличие неоднородности. Время передачи сообщаемых сигналов является мерой оценки высоты несплошности, что позволяет измерить размер несплошности, который всегда определяется временем передачи дифракционного сигнала. Амплитуда сигнала не используется для измерения размеров.В этом случае генерируются и применяются как продольные, так и поперечные волны. Основная информационная характеристика — время прихода сигнала. Метод TOFD имеет ряд преимуществ по сравнению с обычным ручным ультразвуковым контролем:
- Производительность в несколько раз выше;
- Низкая чувствительность к ориентации дефектов;
- Возможность не оценивать, а измерять реальные размеры плоских дефектов;
- Высокая степень отчётности результатов испытаний.
Для реализации метода TOFD используется специальное оборудование с одной или несколькими парами преобразователей, которые размещаются с обеих сторон сварного шва и перемещаются по нему при контроле. OKOndt GROUP ™ имеет беспроводную систему TOFD-Man — один из уникальных инструментов в обширном ассортименте нашего оборудования для ультразвуковой и вихретоковой сварки.
Контроль вихретоковой сварки
Вихретоковый неразрушающий контроль основан на анализе взаимодействия внешнего электромагнитного поля с электромагнитным полем вихревых токов, индуцируемых этим полем в контролируемом объекте.Принцип действия извещателей ET основан на вихретоковом методе, заключающемся в искажении вихревых токов в локальной тестовой зоне с последующей регистрацией изменений электромагнитного поля вихревых токов, вызванных дефектом и электрофизических свойства тестового объекта. Этот метод отличается малой глубиной испытаний, так как он используется для обнаружения трещин и разрывов в материале на глубине до 2 мм. Конструкция и процедура настройки оборудования для вихретоковой сварки напоминают процедуру проектирования и настройки их ультразвукового аналога, с использованием вихретоковых датчиков и эталонных блоков вихретокового контроля соответственно.Очевидно, что методы ультразвукового и вихретокового контроля дополняют друг друга, обеспечивая стопроцентно надежный контроль сварного шва по всей его глубине и протяженности. OKOndt GROUP ™ производит серию вихретоковых дефектоскопов для неразрушающего контроля сварных швов.
Контроль с помощью магнитных частиц
Контроль с помощью магнитных частиц — это метод неразрушающего контроля, основанный на явлении притяжения части магнитного порошка
Рентгеновский контроль BGA, проводов, MEMS, загруженной печатной платы
Мы все еще работаем, узнайте больше о наших услугах во время COVID-19
- Solutions
- Осмотр цеха
- Автоматизированный осмотр кузова автомобиля
- Осмотр КИМ в процессе
- Контроль КТ в процессе
- Контроль размеров
- Осмотр цеха
- Лазерное сканирование
- Портативное измерение
- Большой объемная метрология
- Метрология CT
- Видеоизмерительные системы
- Оптические измерительные системы
- Измерительные микроскопы
- Рентгеновская и компьютерная томография
- Компьютерная томография
- Конфигурируемая рентгеновская компьютерная томография
- Контроль
- Электроника
- Программное обеспечение рентгеновского излучения и КТ
- Источники рентгеновского излучения
- КТ-контроль в процессе
- Услуги рентгеновского и КТ-контроля
- Контроль электроники
- Контроль электроники
- Полупроводниковое оборудование
- NEXIV
- Indu стриальная микроскопия
- Услуги и поддержка
- Осмотр цеха
- Отрасли промышленности
- Автомобильная промышленность
- Автомобильный дизайн и дизайн
- Метрология экспериментального завода
- Применение штампов и пресс-форм
- Проверка промывки и зазоров
- Установка завода по сборке
- Компоненты трансмиссии
- Инспекция автомобильных компонентов
- Инспекция автомобилей в цехе
- CT для автомобильных разъемов
- Aftermarkets
- Aerospace
- Метрология больших объемов
- Позиционирование больших объемов
- Проверка компонентов самолетов
- Турбина партийное отслеживание инструментов
- Медицинское оборудование
- Имплантаты и протезы
- Стоматологические приложения
- Ручное обследование
- Критические сборки медицинских устройств или систем доставки лекарств
- Автомат ED измерение медицинских компонентов
- Исследование имплантатов
- Электроника
- Рентгеновское обследование BGA, проводов, MEMS, загруженной печатной платы
- Пластины
- Жидкокристаллические дисплеи
- MEMS
- Microelectronics
- Optoelectronics Университеты / Исследования / Другое
- Раскрытие тайн антикиферского механизма
- Распространение повреждений в композитных материалах
- Раскрытие тайн природы
- Анализ материалов
- Анализ трещин и разрушений
- Асбест 9000
- Породы / Минералы
- Металлургия
- Механизмы коррозии металла
- Калибровка зерен
- Шаровидность и анализ чешуек чугуна
- Производство металлов
- Анализ поверхности
- Аддитивное производство
- Аддитивное производство медицинских имплантатов 9000 9
- Аддитивное производство для аэрокосмических компонентов
- CT для аддитивного производства
- Примеры из практики
- Автомобильная промышленность
- Продукция
- Рентгенография и компьютерная томография
- Компьютерная томография
- Метрология CT
- Конфигурируемые рентгеновские системы 9000
- Осмотр электроники
- КТ в процессе производства
- Источники рентгеновского излучения
- Услуги по рентгенографии и КТ
- Программное обеспечение
- Осмотр в цеху
- Автоматизированный контроль кузова
- Контроль КИМ в процессе
- -процесс КТ — готов к производству
- Лазерное сканирование
- Ручное сканирование
- КИМ-сканирование
- Программное обеспечение облака точек
- Интеграция стороннего программного обеспечения
- Портативное измерение
- Ручное сканирование
0009 Координатно-измерительная машина ines - КИМ с мостом
- КИМ с порталом
- КИМ с горизонтальной штангой
- Программное обеспечение
- Рентгенография и компьютерная томография
- Метрология большого объема
- Лазерный радар
- Системы измерения видео
- Оптическое программное обеспечение iNEXIV
системы - Измерительные микроскопы
- Оптические компараторы
- Автоколлиматоры
- Цифровые измерители высоты
- Программное обеспечение
- Промышленные микроскопы
- Вертикальные микроскопы
- Инвертированные микроскопы 000
- Световые микроскопы 9000
- световые Сканирующий электрон
- Камеры
- Программное обеспечение
- Контроль полупроводников
- Полупроводниковое оборудование
- Полупроводниковые микроскопы
- Программное обеспечение
- Облако точек программное обеспечение
- Программное обеспечение КИМ
- Программное обеспечение для рентгеновских снимков и КТ
- Программное обеспечение для визуализации
- Интеграция программного обеспечения сторонних производителей
- Международная группа поддержки
- Техническое обслуживание
- Обучение
- Рентгеновская КТ-проверка услуги
- Услуги по инспекции CMM
- Центр загрузок
- Брошюры
- Примеры из практики
- Newsmagazines
- Программное обеспечение для просмотра / пробной версии
- Лицензирование
- Загрузки CMM-Manager
- Технологические статьи Около
- История компании Nikon Metrology
- Новости
- События
- Вебинары
- Карьера
- Размещение вакансий
- Работа в Nikon
- Спонтанное заявление
- Политика GDPR / CCPA trategic Partners
- Аккредитация и сертификация
- Общие положения и условия
- Прочие подразделения Nikon
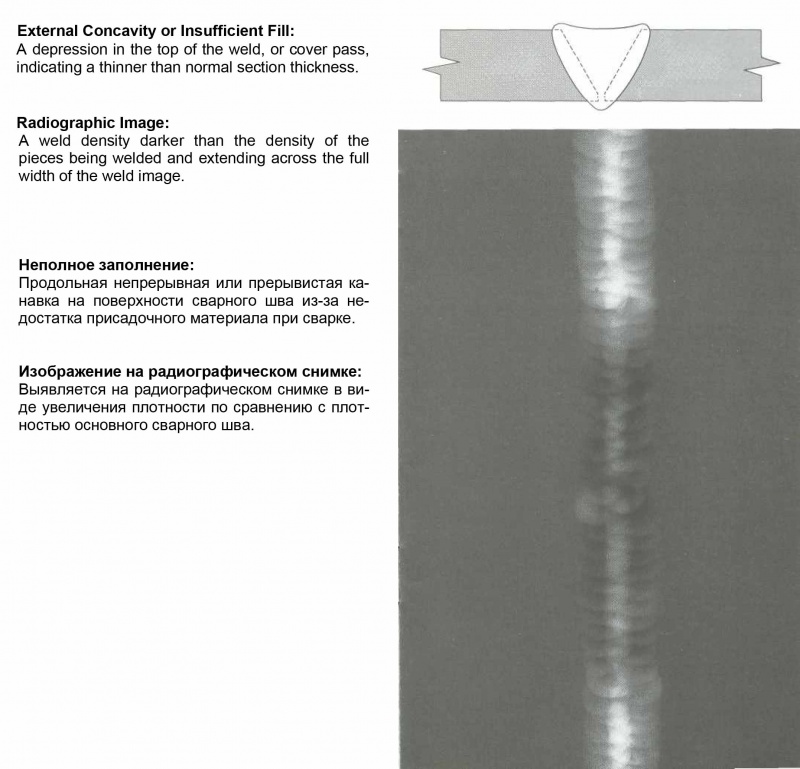