Производство чугуна. Марки чугуна. Технология производства :: SYL.ru
В настоящее время основной способ получения чугуна — плавка железных руд в доменных печах. Для плавки необходим ряд сырых материалов, таких как флюсы, железные или марганцовые руды, а также топливо. В качестве топлива используется кокс, который, по сути, является каменным углем. Роль кокса – обеспечить процесс восстановительной энергией и определенным количеством тепла. Давайте рассмотрим производство чугуна более подробно. Так как это сложный и длительный процесс, то его описание займет много времени.
Топливо для плавки
Как было отмечено выше, в качестве топлива используют кокс. Но, помимо этого, допустимо использование мазута, угольной пыли и природного, а также коксового газов. Тем не менее практически всегда в качестве основного горючего применяют именно кокс. Это вещество, которое образуется при удалении летучих газов из угля при температуре от 900 до 1 200 градусов. Сегодня это единственный вид твердого топлива, который сохраняет свою исходную форму во время движения от колошника к горну. В принципе, к этому материалу выдвигаются жесткие требования, которые касаются механической прочности и жесткости, что нужно для восприятия больших нагрузок в нижней части доменной печи. Крайне важно выдерживать фракцию кокса. Слишком мелкие частицы способствуют газопроницаемости шихты, а слишком большие разрушаются и образуют мелкую фракцию. Помимо этого, необходимо соблюдать определенный процент влажности, что нужно для поддержания теплового режима.
Руды для плавки
В земной коре довольно много железа, однако в чистом виде оно не встречается, его всегда добывают с горными породами в виде различных соединений. Железной рудой можно называть только те породы, из которых с экономической точки зрения выгодно добывать железо посредством плавления в печи. В природе существуют богатые и бедные железные руды. Если говорить с точки зрения металлургической промышленности, то в руде есть ряд полезных добавок, которые необходимы при получении чугуна, – это хром, никель, марганец и другие. Есть и вредные включения: сера, фосфор, медь и т.п. Кроме того, железная руда может делиться на несколько групп в зависимости от минерала:
- красный железняк – 70% железа, 30% кислорода;
- магнитный железняк – 72,4% железа, 27,6% кислорода;
- бурый железняк – до 60% железа;
- шпатовый железняк – до 48,3 % железа.
Логично было бы сделать вывод, что доменное производство чугуна должно предусматривать использование руды из второй группы. Но самой распространенной является первая, поэтому ее чаще и применяют.
Подготовка руды к плавке
Нельзя добыть железную руду из земли и тут же забросить ее в загрузочное устройство доменной печи. Сначала необходимо несколько улучшить технико-экономические показатели, что позволит использовать для получения чугуна относительно бедные руды, которых в земной коре значительно больше. К примеру, увеличение железа в руде всего на 1% приводит к экономии кокса на 2% и к увеличению производительности ДП на 2,5%. На первом этапе руда дробится на фракции, а дальше проходит грохочение. Последнее мероприятие необходимо для разделения железной руды по крупности. Дальше идет усреднение, где выравнивается химический состав. Один из самых важных и сложных этапов – обогащение. Суть процесса заключается в удалении пустых пород с целью увеличения содержания в руде железа. Обычно обогащение проходит в два этапа. Заключительным этапом является окускование, которое нужно для улучшения протекания плавки в доменной печи.
Технология производства
Доменный процесс – это совокупность механических, физических и химико-физических процессов, которые протекают в функционирующей ДП. Загружаемые флюсы, руды и кокс в процессе плавки превращаются в чугун. С точки зрения химии, это окислительно-восстановительный процесс. По сути, из оксидов восстанавливается железо, а восстановители окисляются. Но процесс принято называть восстановительным, так как конечная цель – получить металл.
Основным агрегатом для реализации процесса плавки служит печь (шахтная).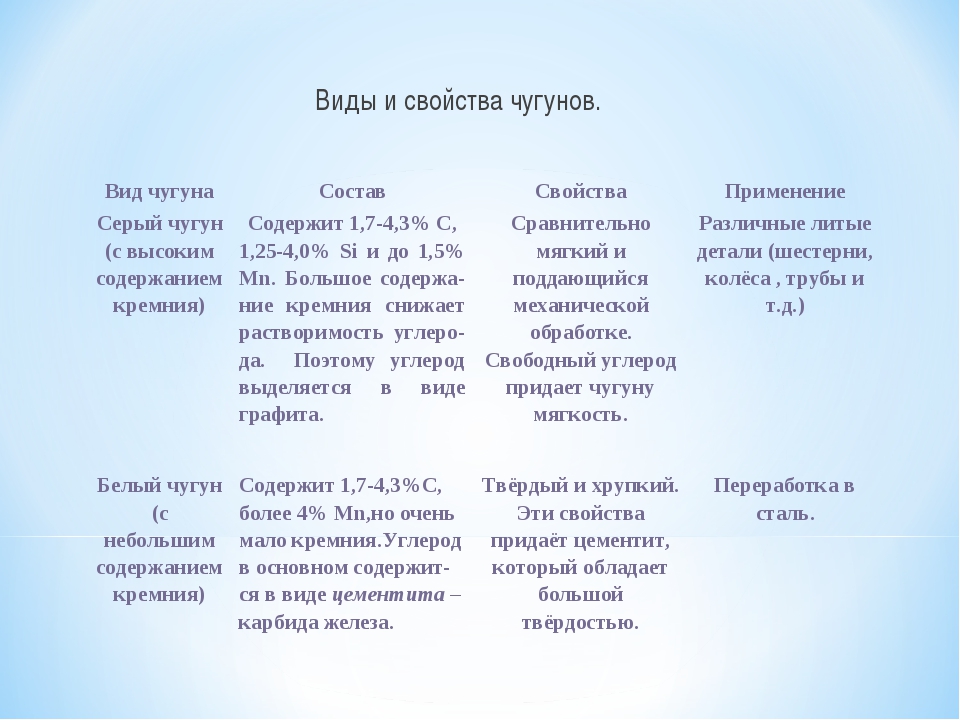
Еще о доменном процессе
Кокс, поступающий непосредственно в горн, имеет температуру порядка 1 500 градусов. В результате в зоне горения образуется смесь газов температурой 2 000 градусов. Он поднимается в верх доменной печи и нагревает опускающиеся к горну материалы. При этом температура газа несколько понижается, примерно до 1700-1600 градусов.
Шихта грузится в колошник порционно. Распространение в ДП происходит слоями. Обычно загружают одну порцию в 5 минут. Перерыв нужен для освобождения места в колошнике. Науглероживание проходит еще в твердом состоянии железа, после температура падает до 1 100 градусов. В этот период заканчивается восстановление железа и начинается окисление кремния, марганца и фосфора. В результате мы имеем науглероженное железо, которое содержит не более 4% углерода. Оно плавится и стекает в горн. Туда же попадает и шлак, но так как удельные массы материалов различные, то они не соединяются. Через чугунную летку выпускают чугун, а через шлаковые летки – шлак. В принципе, это и вся технология производства, описанная вкратце. Сейчас рассмотрим еще один интересный вопрос.
Основные марки чугуна
Чугун – сплав железа с углеродом. Содержание последнего элемента не должно быть меньше 2,14%. Помимо этого, присутствуют и другие элементы, такие как кремний, фосфор, сера и др. Углерод обычно находится или в связанном состоянии (цементит), или же в свободном (графит). Чугун можно поделить на следующие виды:
- Литейный – имеет маркировку Л1-Л6 и ЛР1-ЛР7.
- Передельный чугун – маркируется как П1 и П2. Если материал предназначается для отливок, то это ПЛ1 и ПЛ2. Металл с большим содержанием фосфора обозначается как ПФ1,ПФ2, ПФ3. Помимо этого, есть и высококачественный передельный чугун – ПВК1, ПВК2 и ПВК3.
- Серый – СЧ10, СЧ15, СЧ20,СЧ25, СЧ30 и СЧ35.
- Ковкий чугун – КЧ30-6, ЧК45-7,КЧ65-3 и др. Если после букв стоят цифры, то они обозначают временное усилие на разрыв.
- Легированный чугун, имеющий специальные свойства, обозначается буквой «Ч»;
- Антифрикционный (серый) – АЧС.
Можно говорить о том, что любой вид чугуна имеет свое дальнейшее назначение. К примеру, передельный используется для переделки в сталь и для производства отливок. В это же время марки ПЛ1 и ПЛ2 отправятся в литейный цех, а П1 и П2 будут использованы в сталеплавильном производстве.
Влияние различных соединений на свойства
Независимо от вида и марки чугуна есть ряд элементов, которые значительно влияют на его свойства и технические характеристики. В качестве примера возьмем серый чугун. Повышенное содержание кремния способствует понижению температуры плавления и значительно улучшает его технологические и литейные свойства. По этой простой причине в литейный цех обычно отправляют чугун с большим содержанием этого элемента. А вот марганец – это своего рода противоположность кремнию. Однако он является полезным химическим элементом, так как увеличивает прочность и твердость изделия.
Про науглероживание железа
Восстановленное в ДП железо поглощает в себя самые различные химические элементы и углерод в том числе. Как результат, образуется полноценный чугун. Как только он появляется в твердой форме, сразу же начинается его науглероживание. Сам процесс заметен при относительно невысоких температурах в 400-500 градусов. Кроме того, стоит отметить, что чем больше углерода в составе железа, тем ниже температура плавления. Однако когда металл находится уже в жидком состоянии, процесс протекает несколько интенсивней. Нужно понимать, что после того, как в чугуне будет окончательное количество углерода, изменить это уже будет невозможно. Такие элементы, как марганец и хром, способствуют увеличению содержания углерода, а кремний и фосфор уменьшают его количество.
Немного о литейном производстве
Литье известно человеку уже довольно давно, примерно несколько тысяч лет. Это технологический процесс, позволяющий получить заготовку необходимой формы. Обычно таким способом изготавливают только фасонные детали и заготовки. Суть метода заключается в том, что расплавленный металл или другой материал (пластмасса) выливается в форму, полость которой имеет необходимую конфигурацию будущей детали. Через некоторое время металл застывает и получается заготовка. Она проходит механическую обработку, которая заключается в улучшении качества посадочных поверхностей, получении необходимой шероховатости и т.п. Интересно то, что литейное производство чугуна для промышленного оборудования осуществляется в земле.
Еще кое-что интересное
Стоит обратить ваше внимание на то, что литейное производство использует металл, который был получен в доменной печи. По сути, при вторичной плавке получают изделия с требуемыми свойствами, которые изменяются в плавильной печи. В это же время отливки, химический состав которых оставляют неизменным в литейном производстве, изготавливают крайне редко. В частности это касается чугуна. Когда нужно получить деталь из черного металла, помимо чугуна, в печь загружают ряд модификаторов, флюсов, раскислителей, а также стальной лом и штыковой чугун. Последний нужен для получения стальных и чугунных отливок. Сам же процесс производства чугуна мало чем отличается от доменного производства.
Заключение
Помимо рассмотренных нами, существуют и другие способы производства чугуна. К примеру, плавка в мартеновских печах. Но этот метод морально устарел, так как он слишком энергозатратный, хотя качество металла находится на хорошем уровне. Совсем другое дело – конвертерный способ, который, наоборот, только набирает популярность с каждым годом. К примеру, производство чугуна в России в конвертерах занимает около 30-45% от всего производства. Конвертерный метод обладает рядом существенных преимуществ, одно из них – высокая скорость плавки. Кроме того, из конвертера чугун переливается непосредственно в формы и используется по назначению. Стоит отметить, что остановить ДП невозможно, так как производство непрерывно. В крайнем случае имеет место консервация, при которой кокс тлеет в горне. Если же доменная печь останавливается, то проще построить новую, нежели запустить старую.
Характеристики, свойства, виды и применение чугуна
В идеале сплав чугуна состоит из железа и углерода. Но в него часто входят различного рода присадки, потому что без них сплав был бы ещё более хрупким. Так для увеличения прочности в материал добавляются кремний, марганец, фосфор и серу (не больше 1%).
Наличие в чугуне углерода, процент содержания которого колеблется от 2,14 до 4, способствует исключительной твёрдости материала. Но в то же время именно углерод увеличивает его хрупкость. В практике обычно применяется чугун, содержащий около 3 процентов углерода.
Изделия из чугуна
В некоторые виды чугуна также добавляют специальные примеси, чтобы придать материалу дополнительные свойства. Как правило, это хром, никель и алюминий. Если вам нужно решить вопрос связанный с литьём чугуна, советуем обратиться сюда.
Преимущества чугуна
1) Чугун имеет широкое использование в литейном производстве. У него низкая температура плавления. Она равна примерно 1200 градусов, что ниже показателей стали на 250-300 градусов. Всё потому, что углерод и железо образуют не слишком прочную связь между собой. Благодаря этому, а также плотности 7,2 г/см3 чугун превосходит по литейным свойствам другие материалы, за исключением нескольких разновидностей стали.
2) Ещё одним неоспоримым преимуществом чугуна является его твёрдость. Она достигает 7,5 баллов по шкале Мооса. Этот результат превышает показатели кварца и лишь на 2,5 балла меньше от твёрдости алмаза.
3) Детали из чугуна отличаются долговечностью.
4) Чугун – экологически чистый материал. Поэтому его и применяют для создания посуды, в которой готовится пища. Сплав не включает в себя вредных компонентов и безопасен для здоровья человека.
5) Чугун способен долгое время поддерживать высокую температуру.
Процесс литья чугуна
Недостатки чугуна
1) Из-за значительного части углерода в сплаве материал очень хрупок. А потому он не пригоден для создания деталей, которые будут находиться под давлением.
2) Чугун быстро начнёт покрываться ржавчиной, если на нём длительное время будет собираться вода. Полностью изделие не проржавеет, но может утратить опрятный вид. Поэтому для деталей из чугуна необходимо покрытие для защиты от коррозии.
3) Также изделия всегда отличаются массивностью.
Виды чугуна
1) Белый чугун. Этот сплав приобрёл своё название за светлый оттенок на сколе. Он характеризуется входящим в его состав чрезмерным количеством углерода в виде цементита.
Процент углерода чаще всего выше 3, поэтому белый чугун – материал очень хрупкий и ломкий. Он тяжело плавится и с трудом поддаётся обработке стальными инструментами. В чистом виде его применяют не часто, в основном для деталей, не предназначенных для нагрузок.
Но характеристики материала можно изменить, если добавить в сплав примеси. Обычно для этого используют хром и никель. Полученный материал называется «сормайт», его применяют для нагрева. Основное применение белого чугуна – это отливка ванн.
2) Серый чугун. Эта разновидность чугуна тоже была названа по цвету в месте разлома. Материал используется практически во всех сферах народного хозяйства. Количество углерода в сплаве примерно равно 2,5%. И в отличие от белого, в сером чугуне он содержится также в виде графита.
Применение из чугуна
Материал обладает и пластичностью, и хорошей для чугуна прочностью. Благодаря этому материал применяется в производстве деталей, эксплуатируемых при циклических нагрузках. Из серого чугуна изготавливают втулки, зубчатые шестерёнки, литые конструкции.
3) Ковкий чугун. Для создания этого сплава используют белый чугун. Его подвергают обжигу, что способствует образованию феррита. Этот материал наиболее пластичен. Из него получают шестерни, поршни, подшипники, звенья и ролики конвейерных цепей, муфты, тормозные детали и педали.
4) Высокопрочный чугун. Это вид серого чугуна, в котором графит решётке имеет шаровидную форму. Округлость графита ослабляет кристаллическую решётку, что улучшает механические свойства материала.
Вследствие этого свойственные чугуну характеристики (прочность, удобство литья) дополняются устойчивостью к трещинам и пластичностью, которые близки к показателям стали. Высокопрочным чугуном даже можно заменить все стальные механизмы. Из материала изготавливаются турбопроводы и другие отопительные аппараты.
Применение
1) Чугун незаменим в машиностроении. Большое количество деталей (поршни, шестерни, электродвигатели) производятся именно из него.
2) Ценен чугун и в металлургической отрасли. Он обладает отличными литейными качествами, а также не дорог в цене.
2) Продолжает чугун широко использоваться для создания канализационных труб и сантехники. Из него изготавливаются ванны, отличающиеся долговечностью, раковины и фитинги. Некоторые радиаторы, приобретённые годы назад, всё ещё продолжают служить своим владельцам.
3) Сплав идёт и на производство посуды. Сковородки из чугуна пользуются особой популярностью.
4) Печи из чугуна не только значительно дешевле аналогов, но и не подвержены деформации при нагреве.
5) Также из чугуна создаются декоративные элементы или художественные элементы: ажурные ограды, ворота и решётки.
В последнее время из-за высокой затратности производства чугуна, его использование значительно сократилось. Чтобы облегчить производство, вместо него стали использовать сплавы более лёгкие для изготовления. Эта тенденция продолжается уже несколько лет, и для многих сейчас чугун кажется пережитком прошлого. Но остались отрасли, в которых он пока не сдаёт позиции и по-прежнему крайне необходим. Поэтому полностью отказаться от использования чугуна не представляется возможным.
Применение, свойства и структура белого чугуна
Чугуном называется сплав железа с углеродом и другими элементами. Стоит отметить, что главной особенностью чугуна является именно содержание в справе углерода, минимальное значение которого должно составлять 2,14%. Именно данный показатель содержания углерода в сплаве является точкой предельной растворимости углерода в аустените на диаграмме состояний. Все сплавы, в которых количество углерода ниже, чем 2,14%, называются сталью. Благодаря углероду сплавы железа приобретают твердость, однако, при этом, теряют свою пластичность наряду с вязкостью. Углерод в чугуне присутствует в виде графита или цементита. В зависимости от того, графит какой формы содержится в чугуне графит, различают несколько видов чугуна:
- белый;
- серый;
- ковкий;
- высокопрочный.
Кроме углерода в составе чугуна присутствуют также примеси. Как правило это кремний, марганец, сера, фосфор. Чугун сочетает в себе два качества – с одной стороны это хрупкость, с другой стороны – прочность. Именно это делает чугун незаменимым во многих сферах человеческой деятельности.
Белый чугун в своем составе содержит углеродные соединения — цементиты. Своим названием белые чугуны обязаны характерному белому окрасу и блеску, хорошо видному на изломе. Такой блеск образуется на поверхности чугуна в связи с отсутствием в сплаве больших включений графита. В белом чугуне выявить графит можно только двумя путями – с помощью спектрального анализа или химического.
Состав белого чугуна
Углерод в белом чугуне имеет связанный вид. (Fe3C). Его количественное содержание в данном сплаве определяет следующие виды белого чугуна:
- доэвтектический белый чугун. Для данного чугуна характерно содержание углерода от 2,14% до 4,3%. После полного остывания структура данного чугуна представляет собой структуру перлита, ледебурита (перлит и цементит), а также вторичного цементита;
- эвтектический белый чугун.
Основной характеристикой данного сплава является содержание углерода в количестве 4,3%;
- заэвтектический белый чугун отличается от двух предыдущих видов повышенным содержанием в своем составе углерода – от 4,35% до 6,67%.
Кроме этого, данный сплав также подразделяется на обыкновенный, отбеленный, а также легированный.
Внутренняя структура белого чугуна представлена сплавами двух химических элементов – железа и углерода. Вопреки тому, что производство белого чугуна осуществляется в условиях достаточно высокого температурного режима, он сохраняет мелко зернистую структуру, что, в свою очередь, и дает тот самый характерный белый цвет на изломе детали, выполненной из данного чугуна.
Стоит отметить, что структура доэвтектического сплава всегда присутствует цементит, процентное содержание которого может достигать 100%. Однако, данная ситуация больше характерна для эвтектического металла. А вот заэвтектический вид белого чугуна состоит из эвтектики и первичного цементита.
Представителем таких сплавов является отбеленный чугун, в основе которого находится серый или высокопрочный чугун. В поверхностном слое данного чугуна отмечается высокое процентное содержания ледебурита и перлита. Отбеливание на глубину до 30 мм осуществляется путем быстрого охлаждения. Таким образом добиваются того, что сверху чугун имеет белый цвет, но внутри содержится обыкновенный серый сплав.
В чугуне также могут присутствовать и легированные элементы, такие как хром, никель, алюминий и другие. В зависимости от того, какое количество легируемых элементов содержится в составе чугуна, существуют следующие виды сплавов:
- низколегированные, содержащие в своем составе максимум 2,5% легирующих добавок;
- среднелегированные, в которых процентное содержание легируемых добавок может составлять 10%;
- высоколегированные, которые содержат 10% и более легируемых элементов.
Свойства белого чугуна
Как уже говорилось выше, чугун отличается своей прочностью и хрупкостью одновременно. Однако, данное сочетание качеств придает ему множество уникальных свойств, делающих чугун незаменимым материалом для применения во многих сферах человеческой деятельности.
Среди таких качеств можно выделить следующие:
- высокая твердость;
- высокое удельное сопротивление;
- высокая износостойкость;
- устойчивость к воздействию на материал высоких температур;
- устойчивость к коррозии, а также к различного рода кислотам.
Стоит отметить, что белые чугуны, в которых отмечается пониженное процентное содержание углерода, более устойчивы к воздействию на них высоких температур. Данное свойство применяется с целью уменьшения числа трещин в отливках.
Однако, нет ничего идеального. Не смотря на множество достоинств и уникальность, чугун также обладает и некими недостатками:
- низкие литейные свойства;
- хрупкий;
- отливки и детали из белого чугуна плохо поддаются обработке;
- большая усадка, порой достигающая 2%;
- низкая стойкость к ударам;
- плохая свариваемость.
Применение белого чугуна
В связи с тем, что обыкновенный белый чугун плохо поддается механической и термической обработке, область его применения является достаточно ограниченной. Как правило для изготовления изделий его используют в виде необработанных или частично обработанных отливок.
Однако, все же сплав используется для изготовления габаритных изделий простой конфигурации, а также узлов и агрегатов, постоянно подвергающихся воздействию абразивных материалов. В связи с этим он нашел свое применение в машиностроении, станкостроении, судостроении. Так, белый чугун используется для изготовления корпусов и деталей станков и прокатных станов, шаров для мельниц, приводных и опорных колес. Также он является сырьем для производства некоторых деталей легковых и грузовых автомобилей, тракторов, комбайнов, а также различной габаритной сельскохозяйственной техники. Легирующие элементы, как уже писалось выше, позволяют существенно улучшить сплав, наделяя его специально заданными свойствами.
Стоит отметить, что белый чугун представляет собой сырье, из которого изготавливаются ковкие сорта железоуглеродистых чугунных и стальных сплавов.
Структура, свойства и применение чугунов
⇐ ПредыдущаяСтр 4 из 11Следующая ⇒Чугуны – это сплавы на основе железа, содержащие от 2 до 5 % углерода, а также марганец, кремний и вредные примеси. Это литейный и передельный материал.
Допустимые количества полезных и вредных примесей в чугунах примерно в 5-10 раз больше, чем в сталях.
В зависимости от того, в какой форме содержится углерод, различают следующие виды чугунов: белые, в которых весь углерод связан в карбид железа Fe 12, г).
Рис.12 . Виды чугунов:
а – белый заэвтектический; б – серый; в – ковкий; г – высокопрочный
(б, в, г – структура металлической основы не показана)
Белые чугуны
Излом белого чугуна светлый, блестящий – «белый», отсюда и название. Твердость составляет 450-500HB, материал очень хрупкий и твердый. Резанием (лезвийным инструментом) не обрабатывается, для изготовления деталей не используется.
Применяют отбеленные чугунные детали, у которых сердцевина имеет структуру серого чугуна, а с поверхности есть слой белого чугуна толщиной 5-7 мм.
Для получения структуры белого чугуна в отливке необходимо быстрое охлаждение, а также минимальное содержание кремния и присутствие марганца и хрома («отбеливающих» компонентов).
Главное назначение белого чугуна – передел в ковкий чугун.
Серые чугуны.В сером чугуне весь углерод или его часть находятся в свободном виде – в виде графита. Диаграмма состояния железо – цементит является метастабильной (неравновесной). При очень медленном охлаждении расплавленного чугуна реализуется стабильная, равновесная диаграмма железо – графит. Ее точки и линии смещены чуть влево и вверх.
а б
Рис.13 . Равновесная диаграмма состояния железо-графит (а)
и схема, иллюстрирующая вероятность образования графита и цементита (б)
Графит в сером чугуне – это кристаллы сложной формы – «розетки», растущие из одного центра в виде сильно искривленных лепестков (рис. 70, а). В плоскости шлифа графит виден как отдельные пластинки, прямолинейные или изогнутые, так как плоскость шлифа пересекает графитные лепестки. Такой графит называют пластинчатым.
Металлическая основа серого чугуна может быть ферритной, перлитной или смешанной – феррито-перлитной (рис. 14,б). Излом серого чугуна темно-серого цвета, а в ферритном чугуне, в котором весь углерод содержится в виде графита, – бархатно-черного.
Механические свойства серых чугунов зависят от структуры основы и от количества, формы и размеров графитовых включений. Перлитные серые чугуны тверже и прочнее, ферритные – наименее прочные, феррито-перлитные – имеют промежуточные характеристики. Графит играет роль надрезов, трещин в металлической основе. Прочность графита при растяжении несопоставима с прочностью металла, поэтому пластичность чугунов очень мала (δ ≤ 0,5%), а предел прочности при растяжении значительно ниже, чем у стали. Но на сжатие графит работает хорошо.
Серый чугун – самый дешевый литейный сплав. Имеет высокую жидкотекучесть и малую усадку, что позволяет получать тонкостенные фасонные отливки. Хорошо обрабатывается резанием: дает мелкую сыпучую стружку, графит является твердой смазкой и уменьшает тем самым износ инструмента. Благодаря графиту, в сером чугуне быстро затухают механические колебания, в том числе звуковые, что позволяет уменьшить шум при работе оборудования. Чугун нечувствителен к надрезам на поверхности деталей (в отличие от стали).
Детали из чугуна изготавливают литьем с последующей обработкой резанием. Для получения структуры серого чугуна в отливке сплав должен содержать много кремния и углерода, но мало марганца, чтобы не образовался цементит.
ГОСТ 1412-85 включает 6 основных марок серого чугуна. Чугун – единственный сплав, в марке которого зашифрован не химический состав, а механические свойства. Например, марка СЧ12 означает: серый чугун с пределом прочности при растяжении 120 МПа (12 кг/мм2).
Серые чугуны применяют для изготовления деталей, работающих с небольшими нагрузками, в основном, на сжатие. Это могут быть колонны, опоры, корпуса, станины, крышки, суппорты, зубчатые колеса, канализационные трубы, ванны, батареи.
Высокопрочные чугуны.В высокопрочных чугунах графит имеет шаровидную форму. Они содержат 2,7-3,5 % углерода. Их модифицируют в ковше магнием (0,02-0,08 %). Модификатор не позволяет растущему кристаллу графита принять естественную форму розетки. Атомы магния образуют тонкий слой на поверхности зародыша графита, увеличивая его поверхностную энергию. Стремление системы к минимальной свободной энергии приводит к тому, что графит кристаллизуется в виде шариков (у шара поверхность при заданном объеме минимальна). Металлическая основа может быть такой же, как у серых чугунов (рис. 15).
Такой вид чугунов был создан с целью повышения механических свойства чугуна, сохранив его преимущества перед сталью. Предел прочности при растяжении sВ и относительное удлинение δ у высокопрочных чугунов выше, чем у серых, так как шаровидные включения графита – более мягкие концентраторы напряжения, чем пластинчатые (см. рис. ).
Маркировка высокопрочных чугунов по ГОСТ 7293-85 аналогична маркировке серых. Например, ВЧ90 означает: высокопрочный чугун с пределом прочности при растяжении 900 МПа (90 кг/мм2).
Такие чугуны выдерживают значительные растягивающие нагрузки, поэтому применяются для более ответственных деталей: кузнечно-прессового оборудования, станин прокатных станов, коленчатых валов автомобилей, поршней, вентилей, крыльчаток, распределительных валиков. Отливки из высокопрочного чугуна широко используются в автомобиле- и тракторостроении вместо более дорогих стальных поковок. Их можно подвергать упрочняющей термообработке. Есть смысл выплавлять легированные высокопрочные чугуны для особых условий эксплуатации – с повышенной вязкостью при отрицательных температурах, жаропрочные, коррозионно-стойкие.
Ковкие чугуны.В ковких чугунах графит имеет хлопьевидную форму. Такой графит получается при отжиге белого доэвтектического чугуна с содержанием углерода 2,5-3 %. Его еще называют углеродом отжига.
При нагреве до температур, близких к солидусу, цементит в белом чугуне распадается на исходные компоненты: железо и углерод.
Fe3C → Fe + C.
Режим отжига может быть различным. Во время выдержки при температуре 1000 ºC распадается цементит эвтектики и получается перлитный ковкий чугун (рис. 16, режим а). Если сделать отжиг в две стадии, с выдержкой вначале немного ниже 1147 ºC, а затем чуть ниже температуры перлитного превращения, то на первой стадии распадется цементит эвтектики, а на второй – цементит, входящий в перлит (рис.16, режим б). При таком режиме получается ферритный ковкий чугун, самый мягкий и пластичный (рис. 17, а). Отжиг на ковкий чугун – длительная процедура, он занимает до 70-80 часов. Поэтому ковкий чугун самый дорогой.
Рис. 17. Ферритный (а) и перлитный (б) ковкий чугун
Маркировка ковких чугунов по ГОСТ 1215-92 включает характеристику не только прочности, но и пластичности. Например, КЧ45-7 означает ковкий чугун с пределом прочности при растяжении 450МПа (45 кг/мм2) и относительным удлинением 7%. Но несмотря на повышенную пластичность материала, название «ковкий» – условное, ковать его нельзя.
Ковкие чугуны применяют для мелких деталей, работающих с вибрациями, ударами: крюков, скоб, картеров, ступиц и т.д.
Читайте также:
Белый чугун — это… Что такое Белый чугун?
Белый чугун
Бе́лый чугу́н — вид чугуна, в котором углерод в связанном состоянии в виде цементита, в изломе имеет белый цвет и металлический блеск. В структуре такого чугуна отсутствуют видимые включения графита и лишь незначительная его часть (0,03-0,30 %) обнаруживается тонкими методами химического анализа или визуально при больших увеличениях. Основная металлическая масса белого чугуна состоит из цементитной эвтектики, вторичного и эвтектоидного цементита, а легированного белого чугуна — из сложных карбидов и легированного феррита.
Физико-механические свойства
Отливки белого чугуна обладают износостойкостью, относительной жаростойкостью и коррозионной стойкостью. Наличие в части их сечения структуры, отличной от структуры белого чугуна, понижает эти свойства. Прочность белого чугуна снижается с увеличением содержания в нём углерода, а следовательно, и карбидов. Твёрдость белого чугуна возрастает с ростом доли карбидов в его структуре, а следовательно, и с увеличением содержания углерода.
Наивысшую твёрдость имеет белый чугун с мартенситной структурой основной металлической массы. Коагуляция карбидов резко снижает твёрдость чугуна.
При растворении в карбиде железа примесей и образовании сложных карбидов твёрдость их и белого чугуна повышается. По интенсивности влияния на твёрдость белого чугуна основные и легирующие элементы располагаются в следующей последовательности, начиная с углерода, определяющего количество карбидов и интенсивнее иных элементов увеличивающего твёрдость чугуна.
C — Ni — P — Mn — Cr — Mo — V — Si — Al — Cu — Ti — S.
Действие никеля и марганца, а отчасти хрома и молибдена, обуславливается их влиянием на образование мартенситно — карбидной структуры и содержание их в количествах, соответствующих содержанию в чугуне углерода, обеспечивает максимальную твёрдость белого чугуна.
Особо высокий твёрдостью НВ 800—850 обладает чугун с содержанием 0,7-1,8 % бора. Белый чугун является весьма ценным материалом для деталей, работающих в условиях износа при очень высоких удельных давлениях и преимущественно без смазки.
Прямая зависимость между износостойкостью и твёрдостью отсутствует; твёрдость не определяет износостойкость, но должна учитываться в совокупности со структурой чугуна. Лучшей износостойкостью обладает белый чугун с тонким строением основной металлической массы, в которой в виде отдельных мелких и равномерно распределённых включений или в виде тонкой сетки расположены карбиды, фосфиды и пр.
Структура основной металлической массы определяет и специальные свойства легированного чугуна — его коррозионную стойкость, жаропрочность, электросопротивление.
В зависимости от состава и концентрации легирующих элементов, основная металлическая масса легированного белого чугуна может быть карбидо — аустенитной, карбидо — перлитной и, помимо этого, содержать легированный феррит.
Основным легирующим элементом при этом является хром, связывающий углерод в карбиды хрома и сложные карбиды хрома и железа.
Твёрдые растворы этих карбидов обладают высоким электродным потенциалом, близким к потенциалу второй структурной составляющей основной металлической массы чугуна — хромистого феррита, а возникающие защитные окисные плёнки определяют повышенную коррозионную стойкость высокохромистого белого чугуна.
В присутствии хрома как дополнительного компонента существенно повышается температурная стойкость карбидов в связи со значительным замедлением диффузионных процессов при комплексном легировании.
Эти характерные особенности легированного белого чугуна определили области его использования в зависимости от структуры в качестве нержавеющего и магнитного чугуна и чугуна с высоким электросопротивлением.
Примечания
См. также
Ссылки
Справочник ЗАО УЗЦМ
Легированный чугун: марки, свойства и применение
Легированный чугун — это материал, который производится методом плавки в доменных печах. В нем может находиться разное количество углерода. В зависимости от количественного содержания этого вещества, выделяют два вида чугуна. Первый называют передельным, или белым, а второй — серым, или литейным.
Описание видов чугуна
Первый тип — это передельный чугун. Так называется материал, в котором углерод представлен в виде такого вещества, как цементит. В изломе он имеет белый цвет, откуда и пошло его название. Характеризуется такой чугун высокой твердостью и хрупкостью. Он очень плохо поддается механической обработке. При этом около 80 % всего выплавляемого чугуна является белым. Основное предназначение этого типа материала — это дальнейшая переплавка в сталь.
Серый легированный чугун — это металл, в котором углерод представлен в виде пластичного графита. В изломе его цвет — серый, что также определило его название. Хрупкость и твердость такого чугуна меньше, чем у белого, но при этом он намного лучше поддается механической обработке.
Свойства легированного чугуна этого типа состоят в следующем:
- Во-первых, он отлично сопротивляется нагрузкам сжимающего типа.
- Во-вторых, этот металл нечувствителен к дефектам поверхностного типа, а также отличается тем, что неплохо противостоит усталостному разрушению.
Однако литейный легированный чугун обладает достаточно слабой ударной вязкостью, а также низкой пластичностью. Из-за этих двух недостатков применять такой материал в конструкционных целях достаточно сложно.
Общее описание марок серого чугуна
На сегодняшний день существуют такие марки легированного чугуна серого типа: СЧ 10, СЧ 15, СЧ 18, СЧ 20 и еще несколько других. Буквы СЧ в маркировке обозначают, что это именно серый чугун, а следующие две цифры указывают на предельную нагрузку, которую может выдержать металл при растяжении. Предел прочности в таком случае измеряется в МПа.
Разновидности серого чугуна
Литейный легированный чугун имеет несколько подтипов. Одним из них стал ковкий чугун. Такое условное название получил материал, который отличается тем, что он более мягкий и вязкий, чем серый. Получают его из белого чугуна. Для этого используют процедуру отжига, которая длится достаточно долго. Маркировка здесь примерно такая же, к примеру КЧ 30-6, КЧ 33-8, КЧ 37-12. Буквы указывают на то, что этот чугун ковкий, а следующие две цифры определяют предел прочности на растяжение. А вот что касается последней одной или двух цифр, то они характеризуют максимальное относительное удлинение, которое измеряется в процентах.
Еще один подтип литейного легированного чугуна — модифицированный. Для того чтобы его получить, необходимо добавить к серому специальные элементы. Добавляются такие модификаторы до разливки вещества. В качестве добавок могут использовать алюминий, кремний, кальций и другие. Эти присадки значительно увеличивают количество центров кристаллизации. Другими словами, они способствуют значительному измельчению графита.
Благодаря таким добавкам специальный легированный чугун отличается более высокими прочностными характеристиками, меньшей хрупкостью, повышенной стойкостью к образованию трещин. Стоит добавить, что все лучшие сорта этого сплава получают именно из такого модифицированного материала.
Виды легированного сплава
Что означает легированный чугун? Легирование — это операция по введению в состав материала различных примесей, которые способны улучшить его характеристики. Для чугуна такими добавками стали титан, хром, ванадий и другие. Введение в состав легирующих элементов может увеличить такие характеристики, как прочность, твердость, износостойкость, стойкость к коррозии и множество других.
На сегодняшний день, в зависимости от количества легирующих элементов чугуна, можно выделить три его типа:
- Если присадки содержатся в количестве до 2,5 % от всей массы, то это низколегированный чугун.
- Среднелегированными называют те материалы, содержание веществ в которых находится в пределах от 2,5 до 10 %.
- Последний тип — высоколегированные, если содержание модификаторов суммарно превышает 10 %.
Вещества для легирования, маркировка
По ГОСТу легированный чугун должен содержать определенное количество веществ для использования в определенной сфере. Кроме того, маркировка также является стандартной. К примеру, ЧН15Д7Х — это высокопрочный сплав, в котором содержится 15 % никеля, 7 % меди и примерно 1 % хрома. Как можно заметить, в маркировке легирующие элементы отмечаются одной буквой, после которой идет цифра, указывающая на количественное содержание добавки. Однако может быть и так, что цифра отсутствует, как после хрома. Это означает, что содержание вещества в составе — около 1 %.
Что касается изготовления такого чугуна, то обходится оно достаточно недорого. При этом конечный продукт обладает достаточно высокими эксплуатационными свойствами. Благодаря этим двум факторам область применения описываемого материала постоянно увеличивается.
Виды легированного сплава
Естественно, что добавление в состав какого-либо вещества будет увеличивать какую-либо определенную характеристику. Поэтому различают несколько классов легированных материалов.
Так, чугун может быть износостойким. Материал, относящийся к этой группе, отличается тем, что у него повышенная сопротивляемость к истиранию, которое возникает во время трения поверхности. К этой категории можно отнести антифрикционный и фрикционный чугун. Первый из названных отличается очень низким коэффициентом трения. Благодаря этому основное применение легированного чугуна названного вида — это производство таких деталей, как подшипники скольжения, вкладыши для них и прочие детали со схожими требованиями.
Фрикционный же материал, наоборот, характеризуется достаточно высоким коэффициентом трения, а потому чаще всего он применяется в производстве тормозных устройств для самых разных механизмов, оборудования и т. д.
Нержавеющий чугун
Многие знают о том, что существует металл, который называют нержавеющим. На самом деле, это не совсем точное определение. Просто такие сплавы отличаются тем, что стойкость к коррозии у них достаточно высокая. Наибольшее распространение названный чугун получил в кораблестроении. Если ввести в состав железа более 12 % хрома в качестве легирующего элемента и максимально снизить содержание углерода, то в результате получится именно такой сплав.
Наиболее распространенными его марками стали ЧНХТ, ЧН1ХМД, ЧН15Д7Х2. Они отличаются тем, что сохраняют высокую стойкость к коррозии даже в условиях агрессивной окружающей среды, имеют хорошую сопротивляемость к кавитации и износу в пароводяной среде.
Небольшой, но все же довольно востребованной группой является жаропрочный чугун. Основное преимущество материала заключается в том, что он достаточно плохо поддается окислению, а также отлично сохраняет свои качества в условиях повышенных температур.
Введение меди
В настоящее время все чаще и чаще начинают применять чугун с добавлением меди. Внедрение этой добавки в сплав значительно улучшает его литейные качества. Лучше всего это сказывается на жидкотекучести материала. Кроме этого, значительно уменьшается склонность к появлению трещин и усадочной пористости.
Внедрение 0,5 % Cu (меди) делает чугун достаточно пригодным, чтобы отливать из него такие детали, у которых толщина стенок будет составлять от 10 до 25 мм. Если необходимо увеличить толщину стенок у будущих элементов, то придется повышать и количественное содержание меди, а также ее комплексов. Тут стоит отметить, что эффект от добавления меди можно усилить, если в сплав ввести такие элементы, как сурьма или висмут.
Если же углеродный эквивалент будет увеличиваться, то влияние меди на кристаллизацию графита уменьшается. Легирование чугуна медью может также предотвратить отбеливание в поверхностных слоях, а также значительно повышает твердость к середине. Это довольно заметно при выплавке гильз цилиндров, головок блоков из чугуна и других элементов.
Комплексно-легированный чугун
Для того чтобы успешно выплавлять чугун, который можно использовать для отливки гильз цилиндров, необходимо использовать не только разнообразные ферросплавы, но и индукционную печь. Чтобы осуществлять отливку таких деталей, используется марка ИЧХН4, ЧН1ХМД и ЧНМШ и несколько других типов. Отличительная их особенность заключается в том, что выплавка всех деталей осуществляется в тонкостенный или массивный кокиль.
Игольчатая структура и высокопрочный материал
Небольшая разновидность серого чугуна, который принадлежит к группе износостойких, — это материал с игольчатой структурой. Степень легирования у такого материала достаточно низкая. Содержание в нем кремния и углерода также достаточно низкое. В данном случае количественное содержание таких веществ, как медь, молибден, никель и некоторых других модификаторов, увеличивается в зависимости от требуемой в результате толщины стенок, а также в зависимости от способа литья, который будет использоваться.
Еще одна разновидность — это высокопрочный материал. Это небольшая разновидность серого чугуна, который отличается содержанием шаровидного графита. Для того чтобы получить такую структуру, в сплав необходимо ввести магний, церий и висмут. Добавление именно этих трех легирующих элементов превращает пластичный графит литейного материала в шаровидный. Отличается такой вид тем, что его механические качества значительно выше, чем у других типов чугуна. На сегодняшний день выпускается примерно 10 разнообразных марок сплава названной категории. Такой материал можно отлично использовать в судостроении вместо ковкого типа. А наиболее распространенным видом высокопрочного чугуна является магниевый (с большим количеством магния в составе).
Чугун
О посуде см. Чугунная посуда.
Железо-цементит метастабильная диаграмма.Чугун получают из чушкового чугуна, и хотя он обычно относится к серому чугуну, он также определяет большую группу сплавов на основе железа, которые затвердевают с эвтектикой. Цвет изломанной поверхности можно использовать для идентификации сплава. Белый чугун назван в честь его белой поверхности в момент разрушения из-за примесей карбида, которые позволяют трещинам проходить сквозь них. Серый чугун назван в честь его серой изломанной поверхности, которая возникает из-за того, что чешуйки графита отклоняют проходящую трещину и инициируют бесчисленные новые трещины по мере разрушения материала.
Углерод (C) и кремний (Si) являются основными легирующими элементами в количестве от 2,1 до 4 мас.% И от 1 до 3 мас.% Соответственно. Сплавы железа с меньшим содержанием углерода известны как сталь. Хотя это технически делает эти базовые сплавы тройными сплавами Fe-C-Si, принцип затвердевания чугуна понятен из бинарной фазовой диаграммы железо-углерод.Поскольку составы большинства чугунов находятся около точки эвтектики системы железо-углерод, температуры плавления тесно коррелируют, обычно в диапазоне от 1150 до 1200 ° C (от 2102 до 2192 ° F), что составляет около 300 ° C (572 ° F). F) ниже точки плавления чистого железа.
Чугун имеет тенденцию к хрупкости, за исключением ковкого чугуна. Обладая относительно низкой температурой плавления, хорошей текучестью, литейными качествами, отличной обрабатываемостью, устойчивостью к деформации и износостойкостью, чугуны стали конструкционным материалом с широким спектром применения и используются в трубах, машинах и деталях автомобильной промышленности, таких как цилиндры. головки (снижение использования), блоки цилиндров и коробки передач (снижение использования).Он устойчив к разрушению и ослаблению в результате окисления (ржавчины).
Производство
Чугун получают путем переплавки передельного чугуна, часто вместе с значительным количеством лома и стального лома, и принятия различных мер по удалению нежелательных загрязняющих веществ. Фосфор и сера могут выгореть из расплавленного чугуна, но при этом также выгорит углерод, который необходимо заменить. В зависимости от области применения содержание углерода и кремния регулируется до желаемых уровней, которые могут составлять от 2 до 3.5% и от 1 до 3% соответственно. Затем в расплав добавляются другие элементы, прежде чем окончательная форма будет получена путем литья. [ требуется ссылка ]
Железо иногда плавят в доменных печах особого типа, известных как вагранки, но чаще в электрических индукционных печах. [ необходимая ссылка ] После завершения плавки жидкий чугун выливается в раздаточную печь или ковш.
Типы
Чугунный слив, сливной и вентиляционный трубопроводЛегирующие элементы
Свойства чугуна изменяются за счет добавления различных легирующих элементов или легирующих добавок. После углерода кремний является наиболее важным легирующим агентом, поскольку он вытесняет углерод из раствора. Вместо этого углерод образует графит, в результате чего чугун становится более мягким, уменьшается усадка, прочность и плотность. Сера при добавлении образует сульфид железа, который предотвращает образование графита и увеличивает твердость. Проблема с серой заключается в том, что она делает расплавленный чугун вялым, что вызывает краткосрочные дефекты. Чтобы противодействовать воздействию серы, добавляют марганец, потому что они превращаются в сульфид марганца вместо сульфида железа.Сульфид марганца легче расплава, поэтому он имеет тенденцию всплывать из расплава в шлак. Количество марганца, необходимое для нейтрализации серы, составляет 1,7 × содержание серы + 0,3%. Если добавить больше этого количества марганца, то образуется карбид марганца, который увеличивает твердость и охлаждение, за исключением серого чугуна, где до 1% марганца увеличивает прочность и плотность. [1]
Никель является одним из наиболее распространенных легирующих добавок, поскольку он улучшает структуру перлита и графита, улучшает ударную вязкость и выравнивает разницу в твердости между толщиной сечения. Хром добавляется в ковш в небольших количествах для уменьшения содержания свободного графита, получения холода и потому, что он является мощным стабилизатором карбида; никель часто добавляют вместе. Можно добавить небольшое количество олова вместо 0,5% хрома. Медь добавляется в ковш или в печь в количестве от 0,5 до 2,5% для уменьшения холода, очистки графита и повышения текучести. Молибден добавляется в количестве от 0,3 до 1% для увеличения охлаждения и улучшения структуры графита и перлита; его часто добавляют в сочетании с никелем, медью и хромом для получения высокопрочных чугунов.Титан добавляют в качестве дегазатора и раскислителя, но он также увеличивает текучесть. От 0,15 до 0,5% ванадия добавляют в чугун для стабилизации цементита, увеличения твердости и повышения устойчивости к износу и нагреванию. Цирконий от 0,1 до 0,3% способствует образованию графита, раскислению и увеличению текучести. [1]
В расплавы ковкого чугуна добавляется висмут в диапазоне от 0,002 до 0,01%, чтобы увеличить количество кремния, которое можно добавить. В белое железо бор добавляется для облегчения производства ковкого чугуна; он также снижает эффект огрубления висмута. [1]
Серый чугун
Основная статья: Серый чугун
Серый чугун характеризуется своей графитовой микроструктурой, из-за которой изломы материала приобретают серый цвет. Это наиболее часто используемый чугун и наиболее широко используемый литой материал в зависимости от веса. Большинство чугунов имеют химический состав от 2,5 до 4,0% углерода, от 1 до 3% кремния, а остальное — железо. Серый чугун имеет меньшую прочность на разрыв и ударопрочность, чем сталь, но его прочность на сжатие сопоставима с низко- и среднеуглеродистой сталью.
Белый чугун
Это железо, поверхность трещин которого белая из-за присутствия цементита. При более низком содержании кремния и более быстром охлаждении углерод в белом чугуне выделяется из расплава в виде цементита метастабильной фазы Fe 3 C, а не графита. Цементит, который выделяется из расплава, образует относительно крупные частицы, обычно в эвтектической смеси, где другой фазой является аустенит (который при охлаждении может превратиться в мартенсит).Эти эвтектические карбиды слишком велики, чтобы обеспечить дисперсионное твердение (как в некоторых сталях, где выделения цементита могут препятствовать пластической деформации, препятствуя движению дислокаций через ферритную матрицу). Скорее, они увеличивают объемную твердость чугуна просто за счет своей очень высокой твердости и значительной объемной доли, так что объемная твердость может быть аппроксимирована правилом смесей. В любом случае они предлагают твердость за счет прочности.Поскольку карбид составляет значительную долю материала, белый чугун с полным основанием можно отнести к кермету. Белый чугун слишком хрупок для использования во многих конструктивных элементах, но, обладая хорошей твердостью и устойчивостью к истиранию, а также относительно невысокой стоимостью, он находит применение в таких областях, как износостойкие поверхности (рабочее колесо и спиральная камера) шламовых насосов, гильзы корпуса и подъемные штанги в шаре.
мельницы и мельницы автогенного помола, шары и кольца в измельчителях угля, а также зубья ковша экскаватора (хотя для этого применения более распространена литая среднеуглеродистая мартенситная сталь).
Трудно достаточно быстро охладить толстые отливки, чтобы расплав полностью застыл в виде белого чугуна. Однако быстрое охлаждение может использоваться для затвердевания оболочки из белого чугуна, после чего остальная часть остывает медленнее, образуя сердцевину из серого чугуна. Полученная отливка, называемая охлажденной отливкой , имеет преимущества твердой поверхности и несколько более жесткой внутренней части.
Сплавы белого чугуна с высоким содержанием хрома позволяют отливать массивные отливки (например, рабочее колесо весом 10 тонн) в песчаные формы, т.е.е. не требуется высокая скорость охлаждения, а также обеспечивается впечатляющая стойкость к истиранию. [ требуется ссылка ]
Ковкий чугун
Основная статья: Ковкое железоКовкий чугун сначала представляет собой отливку из белого чугуна, которая затем подвергается термообработке при температуре около 900 ° C (1650 ° F). В этом случае графит отделяется гораздо медленнее, так что поверхностное натяжение успевает превратить его в сфероидальные частицы, а не хлопья. Из-за их более низкого соотношения сторон сфероиды относительно короткие и далеко друг от друга, и имеют меньшее поперечное сечение по сравнению с распространяющейся трещиной или фононом.У них также есть тупые границы, в отличие от чешуек, что снижает проблемы концентрации напряжений, с которыми сталкивается серый чугун. В целом ковкий чугун по своим свойствам больше похож на низкоуглеродистую сталь. Существует предел того, насколько большая деталь может быть отлита из ковкого чугуна, поскольку она сделана из белого чугуна.
Ковкий чугун
Основная статья: Ковкий чугун
Более поздняя разработка — чугун с шаровидным графитом или ковкий чугун . Крошечные количества магния или церия, добавленные к этим сплавам, замедляют рост выделений графита за счет связывания с краями графитовых плоскостей.Наряду с тщательным контролем других элементов и времени, это позволяет углю отделяться в виде сфероидальных частиц по мере затвердевания материала. Свойства аналогичны ковкому чугуну, но можно отливать детали с большим сечением.
Таблица сравнительных качеств чугунов
Имя | Номинальный состав [% по массе] | Форма и состояние | Предел текучести [тыс. Фунтов / кв. Дюйм (0.2% смещение)] | Предел прочности на разрыв [тыс. Фунтов / кв. Дюйм] | Относительное удлинение [% (в 2 дюймах)] | Твердость [шкала Бринелля] | Использует |
---|---|---|---|---|---|---|---|
Серый чугун (ASTM A48) | C 3,4, Si 1,8, Mn 0,5 | Литой | – | 50 | 0,5 | 260 | Блоки цилиндров двигателя, маховики, шестерни, основания станков |
Белый чугун | C 3,4, Si 0,7, Mn 0,6 | Литой (литой) | – | 25 | 0 | 450 | Опорные поверхности |
Ковкий чугун (ASTM A47) | С 2.5, Si 1.0, Mn 0.55 | Литой (отожженный) | 33 | 52 | 12 | 130 | Осевые подшипники, опорные колеса, автомобильные коленчатые валы |
Ковкий чугун или чугун с шаровидным графитом | C 3,4, P 0,1, Mn 0,4, Ni 1,0, Mg 0,06 | Литой | 53 | 70 | 18 | 170 | Шестерни, распредвалы, коленчатые валы |
Ковкий чугун или чугун с шаровидным графитом (ASTM A339) | – | литье (закалка) | 108 | 135 | 5 | 310 | – |
Никель-твердый тип 2 | С 2.7, Si 0,6, Mn 0,5, Ni 4,5, Cr 2,0 | Цельнолитой | – | 55 | – | 550 | Высокопрочные приложения |
Ni-резист типа 2 | C 3,0, Si 2,0, Mn 1,0, Ni 20,0, Cr 2,5 | Литой | – | 27 | 2 | 140 | Устойчивость к нагреву и коррозии |
Историческое использование
Поскольку чугун сравнительно хрупкий, он не подходит для целей, где требуется острый край или гибкость.Он прочен при сжатии, но не при растяжении. Чугун был впервые изобретен в Китае в 4 веке до нашей эры (см. Также: Ду Ши) и разливался в формы для изготовления лемехов и горшков, а также оружия и пагод. [3] На западе, где он не был доступен до конца 14 века, его самые ранние применения включали пушку и дробь. Генрих VIII инициировал отливку пушек в Англии. Вскоре английские металлурги, использующие доменные печи, разработали технику производства чугунных пушек, которые, будучи тяжелее обычных бронзовых пушек, были намного дешевле и позволили Англии лучше вооружить свой флот.Мастера чугуна Weald продолжали производить чугун до 1760-х годов, и вооружение было одним из основных применений чугуна после Реставрации.
Чугунные котлы в то время производились на многих английских домнах. В 1707 году Авраам Дарби запатентовал метод изготовления кастрюль (и чайников) тоньше и, следовательно, дешевле, чем могли бы его конкуренты. Это означало, что его печи Coalbrookdale стали доминирующими поставщиками котлов, и в 1720-х и 1730-х годах к ним присоединилось небольшое количество других доменных печей, работающих на коксе.
Разработка Томасом Ньюкоменом паровой машины открыла новые рынки сбыта чугуна, поскольку чугун был значительно дешевле латуни, из которой первоначально были сделаны цилиндры двигателя. Джон Уилкинсон был великим сторонником чугуна, который, среди прочего, отливал цилиндры для многих улучшенных паровых двигателей Джеймса Ватта до основания литейного завода в Сохо в 1795 году.
Мосты чугунные
Использование чугуна в конструкционных целях началось в конце 1770-х годов, когда Авраам Дарби III построил Железный мост, хотя короткие балки уже использовались, например, в доменных печах в Коулбрукдейле.Затем последовали и другие изобретения, в том числе одно запатентованное Томасом Пейном. Чугунные мосты стали обычным явлением, когда промышленная революция набирала обороты. Томас Телфорд использовал материал для своего моста выше по течению в Билдвас, а затем для акведука через канал в Лонгдон-он-Терн на канале Шрусбери.
За ним последовали Акведук Чирк и Акведук Понцисилльте, которые до сих пор используются после недавних реставраций. Мосты с чугунными балками широко использовались на ранних железных дорогах, таких как мост Уотер-стрит на Манчестерской конечной станции Ливерпульской и Манчестерской железных дорог.Проблемы возникли, когда в мае 1847 года, менее чем через год после открытия, обрушился новый мост, через который проходила железная дорога Честера и Холихеда через реку Ди в Честере. Катастрофа моста Ди была вызвана чрезмерной нагрузкой в центре балки проезжающим поездом, и многие подобные мосты пришлось сносить и восстанавливать, часто из кованого железа. Мост был спроектирован ошибочно: его связывали ремнями из кованого железа, которые, как ошибочно считали, усиливали конструкцию. Центры балок были изогнуты, нижняя кромка находится в напряжении, где чугун, как и кладка, очень непрочен.
Лучше всего использовать чугун для строительства моста, используя арки, чтобы весь материал находился в сжатом состоянии. Чугун, как и кладка, очень прочен на сжатие. Кованое железо, как и большинство других видов железа, а также большинство металлов в целом, обладает прочностью на растяжение, а также прочностью и устойчивостью к разрушению. Отношения между кованым и чугунным железом для структурных целей можно рассматривать как аналог отношений между деревом и камнем.
Тем не менее, чугун продолжал использоваться в несоответствующих конструктивных целях, пока катастрофа на железнодорожном мосту Тей в 1879 году не поставила под сомнение использование этого материала.Важнейшие проушины для удержания анкерных стержней и распорок на мосту Тай были отлиты за одно целое с колоннами, и они вышли из строя на ранних этапах аварии. Кроме того, отверстия для болтов также были отлиты, а не просверлены, так что все напряжение от стяжных стержней было перенесено на угол, а не распределялось по длине отверстия. Новый мост был построен из кованого железа и стали.
Однако произошли и другие обрушения моста, кульминацией которых стало железнодорожное происшествие на Норвудском перекрестке в 1891 году.Тысячи чугунных железнодорожных мостов в конечном итоге были заменены стальными аналогами.
Здания
Основная статья: Чугунная архитектураКолонны из чугуна позволили архитекторам возводить высокие здания без чрезвычайно толстых стен, необходимых для строительства каменных зданий любой высоты. Такая гибкость позволяла высоким зданиям иметь большие окна. В городских центрах, таких как Исторический район Сохо-Чугун в Нью-Йорке, производственные здания и первые универмаги были построены с чугунными колоннами, позволяющими проникать дневному свету.Тонкие чугунные колонны также могут выдерживать вес, для которого в противном случае потребовались бы толстые каменные колонны или опоры, открывая производственные площади на заводах и обзорные линии в церквях и аудиториях. Историческое здание Iron Building в Watervliet, Нью-Йорк, представляет собой чугунное здание.
Текстильные фабрики
Еще одно важное применение было на текстильных фабриках. Воздух фабрик содержал легковоспламеняющиеся волокна пряденного хлопка, конопли или шерсти. В результате текстильные фабрики имели угрожающую тенденцию сгорать.Решением было построить их полностью из негорючих материалов, и было сочтено удобным снабдить здание железным каркасом, в основном из чугуна, вместо легковоспламеняющейся древесины. Первое такое здание было в Дитерингтоне в Шрусбери, Шропшир. Многие другие склады были построены с использованием чугунных колонн и балок, хотя неправильная конструкция, дефектные балки или перегрузка иногда приводили к обрушениям зданий и разрушению конструкций.
Во время промышленной революции чугун также широко использовался для изготовления каркасов и других неподвижных частей машин, включая прядильные, а затем и ткацкие станки на текстильных фабриках. Роберт Темпл (1985). Гений Китая . С. 42–4.
Дополнительная литература
- Джон Глоаг и Дерек Бриджуотер, История чугуна в архитектуре , Аллен и Анвин, Лондон (1948)
- Питер Р. Льюис, Красивый железнодорожный мост Серебристого Тея: повторное исследование катастрофы на мосту Тей 1879 года , Tempus (2004) ISBN 07524 3160 9
- Питер Р. Льюис, Бедствие на Ди: Немезида Роберта Стивенсона 1847 года , Темпус (2007) ISBN 0-7524-4266-2
- Джордж Лэрд, Ричард Гундлах и Клаус Рериг, Справочник по износостойкому чугуну , ASM International (2000) ISBN 0-87433-224-9
Внешние ссылки
Преимущества чугуна — Серый чугун и белый чугун
Типы чугуна Свойства чугуна могут варьироваться в зависимости от добавленных легирующих элементов.Свойства чугуна можно изменять, варьируя легирующие компоненты. Основными легирующими элементами, добавляемыми в чугун, являются углерод и кремний. По количеству добавленных легирующих элементов чугун можно разделить на серый или белый чугун. Их различают по цвету отливки, когда она сломана.
Белый чугун при разрушении позволяет трещине проходить сквозь отливку. С другой стороны, серый чугун отклоняет трещину, но в то же время вызывает множество других трещин из-за наличия структуры графита.Поскольку серый чугун содержит большое количество кремния, он имеет структуру графита, которая придает характеристики, характерные для чугуна. Белый чугун тверже и поэтому хуже обрабатывается, чем серый чугун. Белый чугун также содержит меньше кремния, чем серый чугун. Белый чугун также имеет примеси карбидов.
Кроме того, чугун также можно разделить на ковкий и ковкий. Когда белый чугун нагревается, его свойства меняются, и этот улучшенный вид чугуна называют ковким чугунным чугуном.Когда легирующие элементы, такие как магний или церий, добавляются в чугун при его плавлении, они образуют ковкий чугун с другой структурой по сравнению с другими чугунами.
Серый чугун имеет хорошие литейные свойства, хорошее гашение вибрации, хорошую износостойкость, хорошую обрабатываемость и низкую чувствительность к надрезам. Однако его прочность на растяжение и удлинение очень низкие, поэтому можно производить только некоторые металлические детали с низкими физическими требованиями, такие как защитная крышка, крышка, масляный поддон, маховики, рама, пол, молоток, небольшая ручка, основание, рама, ящик. , нож, станина, седло подшипника, стол, колеса, крышка, насос, клапан, труба, маховик, моторные блоки и т. д.Что касается более высоких марок, серый чугун может выдерживать большую нагрузку и определенную степень герметичности или коррозионной стойкости более важных отливок, таких как цилиндр, шестерня, основание, маховики, станина, блок цилиндров, гильза цилиндра, поршень, коробка передач, тормозное колесо, соединительную пластину, клапан среднего давления и т. д. см. на сайте iron-foundry.com.
Экспериментальное исследование коррозии чугунных труб
Хорошо известно, что коррозия является преобладающим механизмом разрушения чугунных труб, приводящим к уменьшению пропускной способности и окончательному разрушению труб.Чтобы оценить оставшийся срок службы корродированных чугунных труб, необходимо понимать механизмы коррозии в долгосрочной перспективе и разрабатывать модели износа труб. Хотя было проведено множество исследований для определения коррозионного поведения чугуна, было проведено мало исследований, чтобы понять, как чугунные трубы ведут себя в течение более длительного периода времени, чем часы, дни или недели. Настоящая статья направлена на восполнение пробела, касающегося длительного коррозионного поведения чугунных труб в отсутствие исторических данных.В этой статье представлена комплексная экспериментальная программа, в которой коррозионное поведение трех эксцентриковых труб было тщательно исследовано в трех смоделированных условиях эксплуатации. В статье было обнаружено, что локальная коррозия является основной формой коррозии чугунных водопроводных труб. Также было обнаружено, что микроструктура чугунов является ключевым фактором, влияющим на коррозионное поведение чугунных труб. В документе делается вывод о том, что долгосрочные испытания коррозионного поведения чугунных труб могут помочь в разработке моделей коррозионного износа труб для использования при прогнозировании оставшегося срока службы труб.
1. Введение
Чугун уже более 150 лет широко используется во многих промышленных приложениях, таких как водное хозяйство. В результате большая часть водопроводных и распределительных труб в прошлом была преимущественно сделана из чугуна, хотя их производство постепенно прекращается в связи с появлением новых материалов. Закопанные в землю чугунные трубы стареют и изнашиваются во время эксплуатации из-за различных агрессивных сред, окружающих трубы. В зависимости от множества факторов, включая тип чугунных материалов, местную геологию и условия эксплуатации, чугунные трубы изнашиваются с разной скоростью [1, 2].Проблема может еще больше усложняться из-за различий в качестве производимого материала и труб из чугуна, а также из-за большого диапазона диаметров и толщины стенок труб. Для обеспечения безопасности и надежности чугунных труб в эксплуатации необходимо техническое обслуживание и целенаправленная замена изношенных труб. Чтобы разработать экономически эффективную стратегию обслуживания или замены с учетом рисков, необходимо понимать механизмы износа труб и, основываясь на этом понимании, разработать модель для прогнозирования разрушения, чтобы ее могли использовать инженеры. и управление активами как инструмент управления активами чугунных труб.
Хорошо известно, что коррозия является преобладающим механизмом разрушения чугунных труб [2–5], что приводит к уменьшению пропускной способности трубы и, в конечном итоге, к разрушению труб. Из различных форм коррозии коррозионные ямки, в частности, могут действовать как очаги напряжений, приложенных к трубе [3, 4], которые ускоряют износ трубы и последующие разрушения. Следовательно, любая информация о факторах, контролирующих и влияющих на скорость возникновения коррозионных ямок и их проникновения в трубы, имеет особое значение.Более того, для лучшего моделирования вызванного коррозией износа и, что важно, его вклада в отказы труб, необходимо тщательное понимание коррозионного поведения чугунных труб.
Было проведено множество исследований по определению коррозионного поведения чугуна в водной среде различной степени коррозионной активности [6–10]. Большинство этих исследований были результатом работы в течение нескольких часов, дней, недель и, в очень ограниченных случаях, месяцев, и не так много литературы можно найти по долгосрочным исследованиям коррозии, например, годам.В литературе [6, 7] электрохимические параметры образцов чугуна измерялись с использованием метода поляризации постоянного тока. Понимая важность среды и периода воздействия на коррозионное поведение образцов, они рассчитали скорость коррозии образцов в различных испытательных растворах для периода воздействия в 1, 3, 5, 8 и 15 дней. Такие краткосрочные исследования можно использовать для поддержки исследования поверхности излома поврежденной трубы, обеспечивая связь между временем воздействия и наблюдаемой степенью коррозии.В литературе [8, 9] измерены коррозионные свойства образцов чугуна при выдержке в слабощелочных испытательных растворах в течение 124 дней. Ясно, что время выдержки в 124 дня не учитывает долговременное коррозионное поведение образцов. Напротив, некоторые исследования были сосредоточены на трубах, которые подвергались старению в процессе эксплуатации, и исследовали влияние коррозии и коррозионных ямок [2, 11]. В случае заглубленных чугунных труб принято оценивать состояние труб на основе оценки скорости коррозии по возрасту труб, который в большинстве случаев неизвестен.Обзор литературы (см. Ссылки) показывает, что было проведено мало исследований, чтобы понять, как чугунные трубы ведут себя в различных условиях эксплуатации в течение более длительного периода времени, чем часы, дни или недели.
Целью данной статьи является исследование коррозионного поведения чугунных труб в относительно длительной перспективе. Представлена комплексная экспериментальная программа, в которой коррозия трех эксцентриковых труб была тщательно исследована в трех смоделированных условиях эксплуатации с использованием различных методов коррозии.Эксперимент проводился в трех наборах, идущих параллельно друг другу, каждая из которых напоминала условия эксплуатации, в которых трубы были проложены с внешней коррозией трубы. По результатам эксперимента и его результатов исследована морфология продуктов коррозии чугунных труб и определена скорость коррозии. Также в статье охарактеризованы долговременные коррозионные свойства чугунных труб. В статье делается попытка восполнить пробел в отношении долговременного коррозионного поведения чугунных труб при отсутствии исторических данных.
2. Образцы для испытаний
Образцы были взяты из трех бывших водопроводных сетей, обозначенных как трубы 1, 2 и 3. Из каждой трубы были взяты три большие пластины (приблизительно 450 мм на 450 мм), а образцы для испытаний были вырезаны из эти пластины до номинального размера 35 × 25 мм от толщины пластин. На рис. 1 показаны прямоугольные стержни, вырезанные из этих трех пластин, и различная степень графитизации на стержнях. Как можно видеть, трубы в полученном виде демонстрируют ряд условий коррозии, причем смесь общей и более локальной коррозии проявляется как на внешней, так и на внутренней поверхности пластин.Более подробную информацию о размерах, толщине труб и пластинах, вырезанных из этих труб, можно найти в предыдущем исследовании [12].
Информация о степени этих коррозионных ямок представлена в Таблице 1. Общей коррозией в этом случае считается, когда глубина коррозии относительно однородна по ширине образца, в то время как локальная коррозия характеризуется областью проникновения. коррозия, которая возникает в соседних областях почти не затронутого материала.В некоторых случаях очевидно, что эти два типа смешиваются. Трубы 1 и 2 (рисунки 1 (a) и 1 (b)) характеризуются довольно ограниченной общей коррозией, в то время как труба 3 (рисунок 1 (c)) более разрушена и показывает в основном наличие локальной коррозии.
|
Для изучения коррозии чугуна важно знать его микроструктуру. На рис. 2 представлены микрофотографии морфологии микроструктуры труб 1–3.Как можно видеть, на рисунке 2 (a) показана морфология «розеточного» графита типа B, наблюдаемая на трубе 3 с деталями на рисунке 2 (b), на рисунке 2 (c) показана морфология графита типа «коса / серп», наблюдаемая на Труба 2 с деталями на Рисунке 2 (d) и Рисунке 2 (c) показывает смесь типа A и типа B gr
сталь | Состав, свойства, типы, марки и факты
Основной металл: железо
Изучение производства и структурных форм железа от феррита и аустенита до легированной стали.Железная руда — один из самых распространенных элементов на Земле, и одно из основных ее применений — производство стали.В сочетании с углеродом железо полностью меняет свой характер и становится легированной сталью.
Encyclopædia Britannica, Inc. Посмотреть все видео по этой статьеОсновным компонентом стали является железо, металл, который в чистом виде не намного тверже меди. За исключением крайних случаев, железо в твердом состоянии, как и все другие металлы, является поликристаллическим, то есть состоит из множества кристаллов, которые соединяются друг с другом на своих границах. Кристалл — это упорядоченное расположение атомов, которое лучше всего можно представить как сферы, соприкасающиеся друг с другом.Они упорядочены в плоскостях, называемых решетками, которые определенным образом пронизывают друг друга. Для железа структуру решетки лучше всего можно представить в виде единичного куба с восемью атомами железа в углах. Для уникальности стали важна аллотропия железа, то есть его существование в двух кристаллических формах. В объемно-центрированной кубической (ОЦК) конфигурации в центре каждого куба находится дополнительный атом железа. В расположении гранецентрированного куба (ГЦК) есть один дополнительный атом железа в центре каждой из шести граней единичного куба.Существенно, что стороны гранецентрированного куба или расстояния между соседними решетками в ГЦК-схеме примерно на 25 процентов больше, чем в ОЦК-схеме; это означает, что в структуре ГЦК больше места, чем в структуре ОЦК, для удержания посторонних (, т.е. легирующих) атомов в твердом растворе.
Железо имеет аллотропию ОЦК ниже 912 ° C (1674 ° F) и от 1394 ° C (2541 ° F) до его точки плавления 1538 ° C (2800 ° F). Называемое ферритом, железо в его ОЦК-образовании также называется альфа-железом в более низком температурном диапазоне и дельта-железом в более высокотемпературной зоне.Между 912 ° и 1394 ° C железо находится в порядке ГЦК, которое называется аустенитом или гамма-железом. Аллотропное поведение железа сохраняется, за некоторыми исключениями, в стали, даже когда сплав содержит значительные количества других элементов.
Существует также термин бета-железо, который относится не к механическим свойствам, а к сильным магнитным характеристикам железа. При температуре ниже 770 ° C (1420 ° F) железо является ферромагнитным; температуру, выше которой он теряет это свойство, часто называют точкой Кюри.
Получите эксклюзивный доступ к контенту из нашего 1768 First Edition с подпиской. Подпишитесь сегодняВ чистом виде железо мягкое и обычно не используется в качестве конструкционного материала; основной метод его упрочнения и превращения в сталь — добавление небольшого количества углерода. В твердой стали углерод обычно присутствует в двух формах. Либо он находится в твердом растворе в аустените и феррите, либо находится в виде карбида. Форма карбида может быть карбидом железа (Fe 3 C, известный как цементит) или карбидом легирующего элемента, такого как титан.(С другой стороны, в сером чугуне углерод проявляется в виде хлопьев или кластеров графита из-за присутствия кремния, который подавляет образование карбидов.)
Влияние углерода лучше всего иллюстрируется диаграммой равновесия железо-углерод. Линия A-B-C представляет точки ликвидуса (, т.е. температуры, при которых расплавленное железо начинает затвердевать), а линия H-J-E-C представляет точки солидуса (при которых затвердевание завершается). Линия A-B-C указывает на то, что температуры затвердевания снижаются по мере увеличения содержания углерода в расплаве железа.(Это объясняет, почему серый чугун, содержащий более 2 процентов углерода, перерабатывается при гораздо более низких температурах, чем сталь.) Начало жидкой стали, содержащей, например, 0,77 процента углерода (показано вертикальной пунктирной линией на рисунке). затвердеть при температуре около 1475 ° C (2660 ° F) и полностью затвердеть при температуре около 1400 ° C (2550 ° F). С этого момента все кристаллы железа находятся в аустенитном ( т. Е. ГЦК) расположении и содержат весь углерод в твердом растворе. При дальнейшем охлаждении происходит резкое изменение примерно при 727 ° C (1341 ° F), когда кристаллы аустенита превращаются в тонкую пластинчатую структуру, состоящую из чередующихся пластинок феррита и карбида железа.Эта микроструктура называется перлитом, а изменение называется эвтектоидным превращением. Перлит имеет твердость алмазной пирамиды (DPH) приблизительно 200 килограммов-сил на квадратный миллиметр (285 000 фунтов на квадратный дюйм), по сравнению с DPH 70 килограммов-сил на квадратный миллиметр для чистого железа. Охлаждение стали с более низким содержанием углерода (, например, 0,25 процента) приводит к микроструктуре, содержащей около 50 процентов перлита и 50 процентов феррита; он мягче, чем перлит, с DPH около 130.Сталь с содержанием углерода более 0,77 процента, например 1,05 процента, содержит в своей микроструктуре перлит и цементит; он тверже перлита и может иметь DPH 250.
Диаграмма равновесия железо-углерод.
Британская энциклопедия, Inc.Ниобий в чугунах | IntechOpen
2.1. Ниобий в сером чугуне
Использование ниобия в сталях имеет давние традиции; в большинстве случаев он является микролегирующим элементом (<0,1%). Его применение в чугунах не так широко, как в сталях, и одно из основных применений - отливки для изготовления отливок из серого чугуна для автомобильной промышленности.Серый чугун имеет очень низкую способность к изгибу и низкую пластичность из-за наличия чешуек графита, которые действуют как неоднородности, но он имеет низкую температуру разливки, высокую текучесть, низкую усадку от жидкости к твердому и т. Д., Что делает его пригодным. для литья.
Серый чугун с правильным химическим составом может использоваться для блоков цилиндров и головок цилиндров из-за его превосходных свойств термической усталости, в то время как другой химический состав может улучшить его теплопроводность и удельную теплоемкость и может быть использован для роторов дисковых тормозов.
По данным James et al. [33], новые требования к характеристикам и более строгие автомобильные стандарты, двигатели должны работать при более высоких температурах и при более высоком давлении. Эти требования требуют повышения прочности и повышенной стойкости к термической усталости отливок из серого чугуна, особенно в головках цилиндров двигателей из-за их близости к камере сгорания. Во время горения температура в камере может повышаться до 700 ° C, а давление — до 160 МПа. Это тепло может передаваться к головке цилиндров, которая может охлаждаться за счет циркуляции охлаждающей жидкости по каналам в ней.Этот циклический нагрев и охлаждение в сочетании с механическими напряжениями из-за давления на стенку цилиндра делают головку цилиндра очень чувствительной к термической усталости и ползучести. Эти свойства могут быть улучшены за счет добавления элементов в серый чугун.
Молибден и ванадий традиционно использовались в сером чугуне для повышения сопротивления термической усталости. Однако использование ниобия также было исследовано с некоторым успехом [33]. Этот элемент был добавлен как частичный заменитель молибдена (более дорогой элемент) и может присутствовать в сплаве с 0.05 до 0,3% по весу. В структуре могут присутствовать очень небольшие количества карбидов, а основной матрицей является перлит (рис. 12), хотя бейнит и мартенсит могут присутствовать в небольших количествах. Прочность этого литого сплава может достигать 360 МПа. В другой запатентованной работе [34] сообщается об использовании ниобия в количестве от 0,38 до 0,45% и об образовании мелких карбидов, хорошо диспергированных и внедренных в перлитную матрицу, которые снижают износ во время операций торможения.
Замена молибдена ниобием также изучалась в аналогичных серых чугунах для тормозных дисков, но основное внимание уделялось влиянию этого легирующего элемента на малоцикловую усталость [35].Согласно результатам, усталостное поведение сплава улучшается при увеличении количества ниобия и уменьшении количества молибдена. Они пришли к выводу, что ниобий можно заменить молибденом для этого конкретного применения, и предлагают заменить 0,32% Mo на 0,1% Nb. Это преимущество объясняется способностью ниобия очищать эвтектические ячейки и тип графита, измельчением перлита (рис. 13) и выделением мелких карбидов ниобия, которые увеличивают износостойкость. Кроме того, снижается стоимость сплава.
Рис. 12.
(a) Микроструктура серого чугуна с 0,48% Nb, показывающая в основном перлитную матрицу, и (b) EDS частицы карбида, отмеченной стрелкой на (a).
Общие аспекты использования ниобия в сером чугуне указывают на количества ниже 0,5% из-за его высокого сродства к углероду. При таких количествах Найлен [36] подчеркивает, что эффектом этого легирующего элемента является более высокая стабильность аустенита, увеличение микротвердости, небольшое улучшение структуры графита и выделение мелких карбидов.Эти микроструктурные особенности способствуют увеличению предела прочности на разрыв в литом состоянии с 205 МПа для чугуна без ниобия до 270 МПа для чугуна с 0,8% Nb.
Подобные результаты наблюдались также при добавлении до 1,48% Nb в чугуны с высоким содержанием углерода для тормозных дисков [37]. После четкого уточнения графитовой фазы авторы утверждают, что некоторые частицы карбида ниобия могут действовать как гетерогенное зародышеобразование графита в эвтектической реакции. В результате увеличение скорости зародышеобразования привело к улучшенной морфологии графита.Кроме того, уменьшается расстояние между перлитными пластинами, что объясняется снижением температуры эвтектики с добавками ниобия. Эти микроструктурные особенности, в свою очередь, способствуют повышению твердости и износостойкости сплава после добавления ниобия.
Рис. 13.
Улучшение перлитной структуры добавлением ниобия. (а) Серый чугун без ниобия и (б) серый чугун с содержанием Nb 0,32%.
Рис. 14.
Мартенситная матрица в закаленном и отпущенном сером чугуне, содержащем 0.32% Nb.
Влияние ниобия на прочность и износостойкость серого чугуна отмечается только в состоянии после литья, поскольку при закалке и отпуске или аустемплее влияние ниобия сводится к минимуму преобразованной матрицей. Это наблюдалось для высокоуглеродного эквивалента [38] и для заэвтектического серого чугуна [39]. Мартенситная матрица (рис. 14) в условиях закалки и отпуска увеличивает прочность и износостойкость. В случае отпущенного сплава аусферритная структура с 20% остаточного аустенита увеличивает износостойкость за счет эффекта деформационного мартенситного превращения, когда сплав находится в фрикционном контакте.Присутствие карбидов ниобия предотвращает потерю материала во время скольжения за счет усиления матрицы, а графит служит смазкой, снижающей трение. Однако, когда частица карбида высвобождается из матрицы, может иметь место трехчастичное истирание [40]. Подобные результаты наблюдались, если легирующим элементом является титан [41].
Серый чугун также использовался в качестве основного материала для изготовления композитов с железной матрицей, армированной частицами NbC, производимых на месте [42]. Методика заключается в смешивании порошков серого чугуна с ниобиевой проволокой 0.Диаметр 7 мм. Примерно через 25 минут при 1172 ° C ниобиевые проволоки полностью растворились и соединяются с углеродом сплава, образуя небольшие хорошо распределенные карбиды ниобия в железной матрице.
2.2. Ниобий в ковком чугуне
Как упоминалось выше, добавление ниобия в жидкий чугун с высоким содержанием углерода способствует первичному осаждению твердых карбидов ниобия до того, как остальная часть сплава начнет затвердевать. Такое осаждение может вызвать сегрегацию и агломерацию таких частиц, и их обычно удаляют, если они попадают в шлак.Затем добавление ниобия необходимо делать на более поздних стадиях процесса плавления [36].
Рис. 15.
Ковкий чугун после закалки с 0,3% Nb. Обратите внимание на присутствие NbC (отмечен стрелкой) в аусферритной структуре.
Ковкий чугун почти всегда изготавливается для применений, где требуется некоторая вязкость или пластичность, и наличие массивных карбидов считается неблагоприятным признаком для этого конкретного сплава. Увеличение прочности обычно связано с уменьшением пластичности или ударной вязкости сплава.Это особенно верно для ковкого чугуна; всегда желательно увеличить прочность и сохранить хорошую пластичность. Это привело к развитию термической обработки для получения высокопрочных чугунов, а также хорошей пластичности. Конкретной термической обработкой является «закалка», а термообработанные чугуны называются « шипучий чугун с закалкой » (ADI) [43]. Игольчатая структура, полученная при такой термообработке, обеспечивает высокую прочность, но низкую пластичность (обычно менее 5%). На Рисунке 15 показана аусферритная структура, типичная для ADI; в данном случае это ковкий чугун с 0.3% Nb. Обратите внимание на присутствие в структуре частиц NbC (отмечены стрелкой). Такая структура матрицы сводит к минимуму влияние ниобия на прочность и износостойкость чугуна, а также его влияние на усталостные свойства [44].
Однако термообработка всегда требует более высоких производственных затрат и требует много времени. Следовательно, желательно получить желаемые механические свойства сплава в литых условиях путем регулирования процесса затвердевания и / или химического состава.
Выбор термообработки или химических добавок является частным решением каждого литейного завода в соответствии с балансом производственных затрат. В некоторых странах добавление определенного легирующего элемента может быть дешевле, чем термообработка, тогда как в других предпочтительнее проводить термическую обработку. Когда химическое добавление является предпочтительной производственной практикой, добавление одного элемента может способствовать значительному измельчению перлитной составляющей, особенно когда такой элемент растворяется в аустените, способствуя прокаливаемости.
Влияние легирующих элементов на механические свойства высокопрочного чугуна связано с влиянием таких элементов на содержание феррита и перлита в матрице. Легирующие элементы могут увеличивать прочность феррита за счет упрочнения твердого раствора, а также перлита за счет уменьшения межламеллярного расстояния. Они также могут влиять на относительное количество перлита и феррита в результате своего влияния на температуру эвтектоида и кинетику превращения. Усиление, достигаемое легированием, зависит от типа матрицы, поскольку механизмы упрочнения в перлите и феррите не совпадают.В чугунах со смешанными ферритно-перлитными матрицами степень упрочнения зависит от относительного количества феррита и перлита.
Добавление значительных количеств никеля (4%) и молибдена (0,5%) является обычной практикой для производства высокопрочного ковкого чугуна в литых условиях из-за бейнитной матрицы, образованной этими химическими комбинациями. Такая матрица получается благодаря превосходному синергизму этих элементов в улучшении прокаливаемости, как упомянуто выше. Однако стоимость производства может быть высокой, поскольку в большинстве стран это очень дорогие элементы.
Об этом сообщили Kawamoto et al. [45], что добавление карбидообразующих элементов (Mo, V и Ti) в ковкий чугун влияет на механические свойства, влияя на прочность матрицы, а также на состав и дисперсию карбидной фазы. Известно, что ниобий образует чрезвычайно твердый карбид типа MC.
Ниобий добавлен для уменьшения размера зерен аустенита во время затвердевания. Было обнаружено, что это явление происходит из-за образования карбида ниобия, который замедляет рост зерен аустенита.Эти карбиды образуются при высоких температурах и могут служить ядрами для осаждения проэвтектического аустенита, а также, возможно, для эвтектических колоний. Ниобий увеличивает объемную долю эвтектического аустенита, поскольку этот элемент снижает количество углерода, выделяющегося в виде графита во время эвтектического затвердевания. Однако влияние некоторых других элементов в сплаве также изменяет содержание эвтектического углерода (кремния и фосфора), вызывая изменение количества проэвтектического аустенита.
Сообщается, что ниобий в ковких чугунах находится в виде NbC, который образуется на первой стадии затвердевания, во время образования проэвтектического аустенита и перед эвтектической реакцией [46].В конкретной исследовательской работе [47] добавление ниобия в высокопрочный чугун до 0,8% приводило к образованию карбидов ниобия прямоугольной формы, размер и объемная доля которых увеличивались с увеличением содержания ниобия. Частицы размером до 4 мкм были обнаружены в чугунах с добавкой ниобия ниже 0,4%, а частицы размером до 10 мкм наблюдались в чугунах с 0,8% Nb (см. Рисунок 16). Объемная доля NbC для этого более позднего количества ниобия составляла примерно 0,01. Ниобий также способствовал увеличению количества перлита в матрице и уменьшению объемной доли графита.Предполагается, что большая часть содержания ниобия объединяется с образованием NbC, но небольшое количество должно растворяться в матрице, способствуя увеличению образования перлита. Сообщалось об увеличении перлита с 70 до 77% при содержании ниобия 0,8%. Что касается объемной доли графита, то она уменьшилась с 12 до 8% для 0,8% Nb. Поскольку карбиды ниобия образуются до затвердевания эвтектики, они потребляют часть доступного углерода для графитовых конкреций; поэтому наблюдалось уменьшение объема графита после отверждения эвтектики.Такое влияние ниобия на микроструктуру способствовало небольшому увеличению текучести (с 650 до 722 МПа), прочности на разрыв (с 866 до 930 МПа) и твердости (с 27 до 33 HRC), а также снижению пластичности (с 12 до 5%).
Рис. 16.
Ковкий чугун после литья под давлением (a) 0,4% Nb и (b) 0,8% Nb. Обратите внимание на присутствие NbC (указано стрелкой).
2.3. Ниобий в пятнистом чугуне
Основное применение пятнистого чугуна с шаровидным графитом — это валки для горячей прокатки и других износостойких применений.Они содержат как графит, так и карбид (Fe 3 C или M 3 C в зависимости от легирующих элементов). Наличие карбида и графита обеспечивает достаточно хорошую износостойкость. Согласно Nylen [36], есть две стратегии для улучшения характеристик износа для этого типа чугуна: (i) увеличить общую твердость за счет увеличения доли цементита, но сплав становится более чувствительным к растрескиванию, и (ii) увеличить общую твердость. количество карбидов, но с риском нарушить баланс графит / карбид.Комбинация графита и карбида придает сплаву другие важные свойства для этого чугуна: низкую адгезию к трению и хорошее сопротивление термическому растрескиванию, а также хороший модуль упругости [48, 49].
Одна из стратегий улучшения характеристик этих сплавов была сосредоточена на увеличении количества карбидной фазы. Группа AKERS из Швеции работает над добавлением карбидообразующего элемента для увеличения содержания карбидной фазы в крапчатом чугуне и другом чугуне для прокатных станов — ниобии.Однако основные трудности при добавлении ниобия к расплаву железа заключаются в сегрегации частиц во время затвердевания, поскольку эти частицы затвердевают первыми. В этих условиях трудно получить хорошее распределение NbC в сплаве. На рисунке 17 показана микроструктура крапчатого чугуна с 1% Nb, обратите внимание на агломерацию частиц NbC, вызванную сегрегацией во время затвердевания.
Рис. 17.
Пятнистый чугун, демонстрирующий сегрегацию NbC в микроструктуре.
Цель Akers заключалась в разработке более износостойкого материала путем добавления карбидообразующих элементов без потери благоприятных свойств сплава. Это должно быть сделано без нарушения баланса карбид / графит или существенного изменения состава матрицы основного сплава. Присутствие графита в сплаве значительно улучшает способность валка выдерживать термические удары, связанные с горячей прокаткой. Графит также снижает трение между валком и полосой и снижает вероятность приваривания трипса к валку.
Чтобы получить надлежащий баланс графита и карбидов в этих сплавах, некоторые требования были выделены Найленом [36], и они включают следующее: (i) чрезвычайно тщательный выбор плавящегося сырья, (ii) контролируемый условия плавления, (iii) адекватный контроль состава и (iv) эффективные методы внесения, чтобы получить требуемый тип и распределение графита. По его словам, такой правильный баланс может помочь избежать использования более прочных карбидообразующих элементов, которые могут способствовать образованию массивных карбидов в структуре железа.Группа Эйкерса усердно работала над этими действиями, и они пришли к выводу, что использование ниобия в крапчатом утюге имеет огромное будущее.
2.4. Ниобий в белом чугуне
Несомненно, большая часть работ по добавлению ниобия в чугуны была предпринята для белых чугунов, поскольку основное применение этих сплавов находится в области износостойкости, где частицы NbC играют важную роль. роль.
После случайного открытия белого чугуна Робертом Рэнсомом, производителем сельскохозяйственной техники в Ипсвиче, Англия, на рубеже восемнадцатого века [50], искусство производства этого чугуна постепенно превратилось в науку.На момент открытия Рэнсома было известно только, что более твердое и износостойкое железо образуется при быстром охлаждении железа. Кроме того, когда это железо было сломано, поверхность казалась белой, отсюда и название белый чугун. Первоначальные применения этого чугуна в то время были ограничены тонкими сечениями, поскольку для его производства требовалась высокая скорость замораживания. Только в первой половине двадцатого века карбид-стабилизирующая способность хрома была полностью признана с появлением белого чугуна, легированного хромом на 25–30%.Этот новый сплав можно было отлить в белый цвет практически с любым размером профиля, и он был значительно более износостойким, чем нелегированный белый чугун. Впоследствии были введены низшие хромистые чугуны, которые легировали никелем в основном для повышения прокаливаемости [51].
С момента этого открытия так много исследователей постепенно внесли свой вклад в изучение металлургии чугуна и установили взаимосвязь между химическим легированием, технологическими процессами и механическими свойствами, как подчеркнули Табрет и др.[52] в их интересном обзоре. Кроме того, поскольку в настоящее время сплавы белого чугуна представляют собой высоколегированные сложные материалы, они предполагают, что этот сложный химический состав требует глубокого понимания металлургии чугунов во время их производства и обработки. Спецификация ASTM A532 [53] описывает состав используемых стойких к истиранию белых утюгов.
Стандарт ASTM классифицирует эти сплавы как стойкие к истиранию, потому что в горнодобывающей промышленности, которая является основным пользователем, такие утюги используются в различных ситуациях, которые подвержены различным условиям, когда основным механизмом износа является абразивный, т.е. дробление, грохочение и откачка [52].Кроме того, в сталелитейной промышленности чугуны Hi-Cr широко используются для изготовления валков станов горячей прокатки [54], где механизмами повреждения являются истирание матрицы и контактная усталость прокатки [55, 56]. Такой износ поверхности валков вызывает дефекты поверхности полосы [57].
Белые чугуны Hi-Cr основаны на тройной системе Fe-Cr-C. Джексон [58] был одним из первых исследователей, систематически изучавших этот сплав и последовательность его затвердевания. Коммерческие сплавы Hi-Cr часто содержат дополнительные легирующие элементы, такие как молибден, никель, медь и марганец [52], которые могут изменять характеристики затвердевания и количество фаз, присутствующих в сплаве.Например, добавки молибдена способствуют повышению прокаливаемости и предотвращают образование перлита; в таком случае необходим анализ четвертичной системы, как подчеркивает Цю [59]. Однако содержание хрома и углерода являются основными параметрами, описывающими путь затвердевания чугунов Hi-Cr, и тройная система Fe-Cr-C используется для описания первых стадий затвердевания любого промышленного сплава этого типа.
В соответствии с этим, общие композиции идут от 1,8 до 3.5% C и от 12 до 30% Cr. В этих условиях наиболее распространенные сплавы являются доэвтектическими, и путь затвердевания следующий: затвердевание начинается с образования дендритов первичного аустенита, которые растут и отклоняют углерод в направлении междендритных областей; по мере того, как затвердевание прогрессирует, температура понижается, и оставшаяся жидкость становится богаче углеродом, пока не достигнет эвтектического состава. При этой температуре происходит эвтектическая реакция.
Хотя аустенит, образующийся при затвердевании, нестабилен при комнатной температуре, метастабильная аустенитная матрица обычно сохраняется в структуре при температуре окружающей среды.Чаще всего температура M S немного выше температуры окружающей среды, в то время как температура отделки мартенсита M f ниже. Это приводит к некоторому превращению при охлаждении, так что мартенсит может присутствовать в преимущественно аустенитной литой структуре [52].
Микроструктура литого доэвтектического белого чугуна Hi-Cr обычно состоит из дендритов аустенита (с возможным частичным превращением в мартенсит, перлит или бейнит) и междендритной эвтектики карбидов и частично преобразованного аустенита.Пример микроструктуры песчаной отливки 17% Cr-2,6% C-2% Ni-2% Mo приведен на рисунке 18. Оптическая микрофотография показывает, что структура в основном аустенитная с некоторым количеством мартенсита вдоль эвтектических карбидов и в эвтектическая матрица.
Рис. 18.
Литая конструкция из высокохромистого белого чугуна.
Хотя содержание хрома во многих сплавах белого чугуна Hi-Cr довольно высокое (обычно от 12 до 30%), большая часть его сочетается с углеродом в карбидах.Следовательно, содержание хрома, остающегося в матрице, довольно низкое. Например, Laird et al. [60] измерили содержание хрома в матрице всего 9,5% в 17,8% Cr-3% C железе с помощью электронного микрозондового анализа и De Mello et al. [61] получили 9,5% Cr в матрице из 16,1% Cr-3,26% C. Таким же образом Dogan et al. [62] получили значение 16,2% Cr в матрице из 26% Cr-2,76% C. Затем требуются дополнительные легирующие элементы для достижения достаточной прокаливаемости, особенно при больших размерах сечения [63].Наиболее распространенными элементами, используемыми для этих добавок, являются молибден, никель, марганец и медь.
Молибден добавляют в высокохромистые белые чугуны в количестве от 0,5 до 3,5%. Хотя считается, что для эффективности требуются количества более 1% [64], добавление более 3-4% дает мало [65]. Он действует, подавляя образование перлита и увеличивая прокаливаемость [61, 65, 66], эффективно препятствуя выделению вторичного карбида во время охлаждения. Молибден также оказывает синергетический эффект на влияние других легирующих элементов, таких как никель и медь, которые более эффективны в задержке образования перлита, если их добавляют вместе с молибденом [61, 66–69].Часть молибдена в чугунах на конечной стадии затвердевания образует эвтектический карбид типа M 2 C [61, 65, 66, 70–72]. Другое преимущество молибдена состоит в том, что он мало влияет на температуру Ms [73], в то время как большинство элементов имеют тенденцию к снижению температуры Ms, что может приводить к чрезмерной стабилизации аустенита.
Никель, марганец и медь добавляются в эти чугуны в основном для улучшения прокаливаемости. Обычно они встречаются в количестве до 2%. Никель и медь разделены на матрицу [51], в то время как марганец может частично растворяться в матрице и частично отделяться до карбидной фазы, что снижает его эффективность.Эти элементы способствуют снижению температуры Ms аустенита во время охлаждения, и поэтому увеличение содержания сплава часто приводит к увеличению количества аустенита, что, в свою очередь, представляет собой снижение твердости после литья [67]. Когда никель добавляется в железо вместе с молибденом, эффективность улучшения прокаливаемости весьма значительна и предотвращается образование нежелательного перлита [67].
Менее традиционные легирующие элементы, такие как ванадий, вольфрам, титан и ниобий, также добавлялись в сплавы белого железа [45, 46, 64, 70, 74–80].Целью этих добавок обычно является достижение некоторой модификации структуры эвтектического карбида путем получения более твердых карбидов, хотя они могут улучшить прокаливаемость матрицы.
На структуру эвтектического карбида в чугунах Hi-Cr сильно влияет хром, поскольку он является сильным карбидообразующим элементом. Пирс [81] указал, что при увеличении содержания хрома выше 10–12% тип образующегося эвтектического карбида изменяется с M 3 C на M 7 C 3 .Для обоих типов эвтектического карбида увеличение содержания хрома в сплаве увеличивает соотношение хрома к железу как металлических частиц в карбидах [82], а также увеличивает твердость карбида.
Было признано, что возможная стратегия улучшения ударной вязкости сплавов белого чугуна, а также износостойкости в условиях скольжения включает улучшение структуры эвтектического карбида путем получения более мелких, более глобулярных карбидов [81, 83, 84].
Легирующие добавки также использовались для модификации структуры эвтектического карбида [60, 85–94].Обычно попытки изменить структуру эвтектического карбида с помощью легирующих элементов имели ограниченный успех. С этой целью использовался бор в диапазоне 0,1-0,3% [91, 92]. Аргументом является мысль, что присутствие бора в сплавах железа снижает растворимость углерода в аустените; которые могут приводить к более высокому и мелкому выделению карбида во время затвердевания. Влияние кремния и редкоземельных элементов было исследовано в этих утюгах, в случае кремния из-за его влияния на поведение при преобразовании, а в случае редкоземельных элементов из-за его сильного эффекта сегрегации.Воздействие этих элементов на структуру карбида дало противоречивые результаты.
Образование карбида другого типа, такого как карбид ниобия [78] и карбид ванадия [90], хотя и с соответствующими легирующими добавками, было связано с образованием более мелких и круглых карбидов.
Обычно применяемая термообработка для дестабилизации аустенитной матрицы, согласно Пирсу [81], включает выдержку при температуре от 920 до 1060 ° C в течение 1–6 часов. Во время выдержки при этих температурах вторичные карбиды выделяются в матрице, что снижает содержание в ней сплава, особенно количества углерода.Если содержание сплава в аустените слишком низкое, температура M S увеличивается [69], и большее количество аустенита превращается в мартенсит во время последующего охлаждения до комнатной температуры. Для этих сплавов охлаждение на воздухе после дестабилизирующей термообработки обычно является обычной практикой для получения преимущественно мартенситной структуры, и риск растрескивания при быстром охлаждении исключается [81]. На рисунке 19 показана микрофотография структуры дестабилизированного железа Hi-Cr 17% Cr-2,5% C-2% Ni-2% Mo, который выдерживали при 1000 ° C в течение 45 минут и охлаждали на воздухе до комнатной температуры.Структура состоит из эвтектических карбидов, а бывший аустенит превратился в мартенсит и вторичные карбиды.
Рис. 19.
Микроструктура термообработанного белого чугуна с высоким содержанием хрома.
Хотя после дестабилизирующей обработки образуется преимущественно мартенситная матрица, остаточный аустенит может присутствовать в количествах до 35% [95–97]. Согласно Табрету и соавт. [52], объем остаточного аустенита зависит от количества растворенного углерода после дестабилизирующей термообработки.На содержание растворенного углерода в аустените, в свою очередь, влияют состав сплава, время и температура термообработки, а также толщина отливки. С другой стороны, эвтектические карбиды не подвержены влиянию температур дестабилизирующей термообработки.
Широко признана взаимосвязь между объемной твердостью и износостойкостью для большинства сплавов в абразивных условиях; Согласно закону Арчарда , чем тверже материал, тем выше он износостойкость.Однако, как отмечает Tabret et al. [52] имеют пои
Свойства материала
Существительное | Прилагательное | Примеры материалов | |
вес | a легкий материал a тяжелый материал | алюминий, свинец магний, медь | |
гибкость жесткость | a гибкий материал a жесткий материал | тонкие листы металла, пластмассы, камня, чугуна | |
горючесть | горючий материал | резина, пластик | |
пожар сопротивление | негорючий материал | глина, стекло | |
прозрачность | a прозрачный материал | вода, некоторые пластмассы | |
непрозрачность | непрозрачный материал | Камень | |
коррозионная стойкость | коррозионно-стойкий материал материал не устойчив к коррозии | цинк, хром, олово чугун | |
проводимость | хороший кондуктор г. нагреть плохой провод высокая температура | серебристый каучук | |
эластичность | эластичный материал | нейлон | |
пластичность | a пластик материал | медь, алюминий | |
мягкость | a мягкий материал | резина, нейлон | |
твердость — | твердый материал | чугун |
И.Взгляните на эти примеры:
Человек может легко поднять большой рулон
стекловата, но не бетонная балка.
Стекловата — легкая , но бетон —
Человек может гнуть резиновую плитку, но не бетонную плитку.
Резина — это гибкая , а бетон — жесткая.
Дерево может гореть, но бетон не гореть.
Древесина горючая, , бетон негорючая.
Водяной пар может проходить через камень, но не через битум.
Камень — проницаемый, , но битум — — непроницаемый.
Вы можете видеть сквозь стекло, но не сквозь дерево.
Стекло прозрачное , а дерево непрозрачное.
Нержавеющая сталь может противостоять коррозии, а мягкая сталь — нет.
Нержавеющая сталь устойчива к коррозии , но низкоуглеродистая сталь не устойчива к коррозии.
Тепло может легко передаваться через медь, но не через дерево.
Медь является хорошим проводником тепла , а древесина плохо проводит тепло.
Резину можно растянуть или сжать, а затем она вернется к своей первоначальной форме, а глина — нет.
Резина — это эластичная , а глина — это пластмасса.
Битум можно легко поцарапать или поцарапать, стекло — нет. Битумен мягкий , а стекло — твердое .
Посмотрите на эти диаграммы. Сопоставьте буквы A-H на схемах с предложениями ниже:
Теперь дополните эти предложения свойствами:
a) Полиэтиленовая мембрана предотвращает проникновение влаги в бетонный пол.Это означает, что полиэтилен _______.
b) Т-образный алюминиевый профиль может противостоять химическому воздействию, т.е. е. алюминий ..
c) Каменный блок нельзя поднять без использования крана. Это означает, что камень ___________.
г) Крыша из гофрированного железа не может предотвратить нагревание дома солнцем, т.е. е. железо есть.
e) Стекловата может помочь сохранить тепло в доме зимой и прохладу летом, т.е.е. стекловата
е) Керамическая плитка на полу не может быть легко поцарапана людьми, идущими по ней. Это означает, что керамическая плитка ___
г) Асбестовая пленка может использоваться для противопожарной защиты дверей. Другими словами, асбест — это ________.
h) Черные тканевые жалюзи могут использоваться для защиты помещения от света, т. Е. Ткань ________.
II.Составьте предложения о четырех других свойствах материалов из этой таблицы:
Стали Камень Стекло шерсть Кирпич | имеет свойство | хорошая звукоизоляция, хорошая теплоизоляция. высокая прочность на сжатие, высокая прочность на разрыв. | |
Это означает | выдерживает высокие сжимающие силы, он может выдерживать высокие растягивающие усилия, он плохо передает тепло, он не передает звук легко. |
III. Ответьте на следующие вопросы:
Почему для оконных стекол используется стекло?
Потому что стекло такое.
Почему стекловата используется для сохранения тепла в резервуарах для горячей воды?
Потому что стекловата имеет свойство
…
Почему некоторые стали покрываются тонким слоем цинка или ?
Потому что цинк есть…
Почему некоторые противопожарные двери
покрыты листами асбеста?
Поскольку асбест …
Почему некоторые металлические листы
имеют гофрированную форму?
Потому что гофрированная форма
делает лист_
Почему используется бетон для.
колонны строительной конструкции?
Потому что ..
Урок 10
Часть I
Дата: 24.12.2015; просмотр: 2332
.