Импульсная MIG-сварка
Некоторые современные источники питания имеют функцию импульсной сварки. Скорее всего, Вы уже слышали, что этот режим отличается простотой и помогает улучшить качество соединений. Но знали ли Вы, что он также более экономичен? Хотя аппараты для импульсной MIG-сварки требуют более высоких начальных вложений, в долгосрочной перспективе они окупаются за счет снижения общих затрат на сварку.Вот их главные преимущества:
- экономия проволоки и газа
Аппараты для импульсной MIG-сварки более универсальны, так как они позволяют использовать проволоку определенного диаметра с более широким диапазоном скорости подачи. Например, если раньше сварщику приходилось запасаться для различных задач проволокой диаметром 0,9 мм, 1,1 мм и 1,3 мм, то с импульсным аппаратом он может ограничиться диаметром 1,1 мм. Другими словами, вместо двух-трех разных катушек проволоки сварщику понадобится только одна. Это позволит снизить затраты на хранение материалов и простой из-за смены кассет с проволокой.
- Низкое разбрызгивание и дымообразование
По сравнению с традиционными аппаратами, импульсные модели выгодно отличаются низким разбрызгиванием и дымообразованием. Так как благодаря низкому разбрызгиванию в соединение попадет больше наплавленного металла, это делает расход сварочных материалов более эффективным. Также это позволяет тратить меньше времени на очистку поверхности. Низкое дымообразование делает рабочую среду на всем предприятии более безопасной.
- Низкое тепловложение
Для импульсной сварки характерно более контролируемое тепловложение, которое позволяет сократить деформации и улучшить качество и внешний вид шва. Это особенно важно при сварке нержавеющей стали, никеля и других сплавов с высокой чувствительностью к тепловложению.
Импульсная сварка MIG имеет высокую производительность наплавки. Кроме того, аппараты для импульсной сварки универсальнее и проще в обращении по сравнению с другими методами переноса металла, поэтому на обучение сварщика уходит меньше времени.
Высокое качество
Все эти преимущества импульсной сварки обеспечивают высокое качество сварки и стабильность дуги. Кроме того, сварщикам не нужно тратить много времени на вытяжку дыма, очистку поверхности от брызг и шлифовку. При этом не требуется высокая квалификация сварщика.
Что такое импульсная MIG-сварка?
Проще говоря, импульсная MIG-сварка представляет собой метод неконтактного переноса металла из проволоки в сварочную ванну, то есть проволоке вообще не приходится вступать в контакт со сварочной ванной. Это возможно благодаря высокочастотному варьированию величины сварочного тока, что позволяет снизить тепловложение и разбрызгивание по сравнению со струйным и крупнокапельным переносом металла.
При импульсной MIG-сварке в ходе каждого импульса на кончике проволоки формируется капля расплавленного металла. После этого сила тока увеличивается так, чтобы вытолкнуть эту каплю в сварочную ванну. Перемещение этих капель происходит через дугу, по одной капле за импульс.
Чтобы лучше понять этот процесс, взглянем на форму волны сварочного тока. В отличие от сварки на жесткой вольт-амперной характеристике, где сила тока представлена прямой линией, при импульсной MIG-сварке сила тока падает, когда дополнительная энергия не нужна, что позволяет изделию несколько остыть. Эта фаза «остывания» делает импульсный процесс хорошим выбором для сварки тонких материалов при необходимости в минимальных деформациях и для сварки при низкой скорости подачи проволоки.
При формировании капли сила тока возрастает до максимума. Затем начинается фаза фонового тока и ток снижается, благодаря чему снижается тепловложение. При этом для переноса капли необходимо обеспечить подходящую высоту и ширину пика.
Сравнение импульсной MIG-сварки с другими методами переноса металла
Чем импульсная MIG-сварка отличается от других методов переноса металла? Давайте рассмотрим преимущества и недостатки каждого процесса.
Перенос металла короткими замыканиями
В данном режима проволока прикасается к рабочему изделию и вызывает короткое замыкание. Этот вид сварки проходит при самой низкой температуре, но при этом он все же способен обеспечить хорошее сплавление. Перенос металла короткими замыканиями позволяет проводить сварку материалов различной толщины в любых пространственных положениях. Также для него характерна небольшая, быстро затвердевающая сварочная ванна. В качестве недостатков можно назвать ограниченную скорость подачи проволоки и производительность наплавки. В случае материалов большой толщины также существует вероятность «холодных наплывов», вызванных недостатком энергии дуги для полного сплавления металла. Метод коротких замыканий также отличается более интенсивным разбрызгиванием по сравнению с другими методами.
Крупнокапельный перенос металла
Метод крупнокапельного переноса металла по сути представляет собой неконтролируемое короткое замыкание. Его отличает большой объем отделяющегося от проволоки металла. Эти большие капли отделяются от дуги и падают в сварочную ванну. Для этого метода характерны очень сильное разбрызгивание и высокое тепловложение. Кроме того, крупнокапельный перенос металла пригоден только для сварки нижних и горизонтальных угловых соединений. Часто наблюдается недостаточное сплавление из-за того, что брызги искажают сварочную ванну. Вдобавок, крупнокапельный перенос металла считается менее эффективным из-за высокого расхода проволоки.
С другой стороны, крупнокапельный перенос подходит для работ с высокой скоростью подачи проволоки и высокой силой сварочного тока, где требуется полное сплавление толстопрофильных материалов. При этом его можно использовать с недорогим защитным газом CO
Струйный перенос металла
При струйном переносе металла к рабочему изделию выталкивается небольшая капля расплавленного металла. Это процесс на жесткой ВАХ, который требует достаточно высокого тока для непрерывного потока металла с проволоки. Его преимуществами являются высокая производительность наплавки, большая глубина проплавления, хороший внешний вид шва и низкое разбрызгивание.
Недостатки — высокое тепловложение, ограниченное число доступных пространственных положений и склонность к прожиганию тонких материалов.
Импульсная MIG-сварка
Импульсная MIG-сварка — это высокотехнологичный процесс, который совмещает в себе все лучшие черты других видов переноса металла без их недостатков. В отличие от сварки короткими замыканиями, для импульсной MIG-сварки не характерны разбрызгивание и холодные наплывы. Импульсная MIG-сварка доступна в большем числе пространственных положений по сравнению с крупнокапельным или струйным переносом металла, а также имеет намного более эффективный расход проволоки.
Индивидуальная настройка формы волны
Стремясь сделать импульсную MIG-сварку еще совершеннее, компания Линкольн Электрик разработала технологию управления формой волны сварочного тока (Waveform Control Technology®). Она позволяет индивидуально настраивать характеристики тока с учетом особенностей сварочной проволоки и конкретных условий сварки. Благодаря этому источник питания может генерировать сварочный ток с точно заданной формой волны и тем самым обеспечить оптимальное качество сварки в любых условиях. В частности, Вы можете отрегулировать скорость возрастания волны, чтобы изменить скорость переноса капель металла, и убывания волны, чтобы обеспечить достаточное смачивание. Аппараты с поддержкой технологии управления формой волны сварочного тока поставляются с набором предустановленных настроек для большинства стандартных задач.
Выбор оборудования
С тех пор, как оборудование для импульсной MIG-сварки впервые появилось на рынке, оно стало намного совершеннее. В 1980-х она считалась очень сложным процессом, которым могли овладеть только самые квалифицированные сварщики. Тогда оператор должен был помнить все настройки аппарата для каждого диаметра проволоки. Сегодня эта настройка выполняется автоматически благодаря синергетическому управлению. Когда оператор меняет скорость подачи проволоки, синергетическое управление корректирует форму волны и частоту тока.
Синергетическое управление всего одним регулятором позволяет пользоваться аппаратом даже начинающему сварщику. Электроника аппарата даже автоматически подстраивается к изменениям вылета проволоки, ширины зазора или угла наклона горелки.
При выборе оборудования для импульсной MIG-сварки мы рекомендуем руководствоваться следующими соображениями:
1. Выбирайте оборудование, которое позволит реализовать все возможности нового процесса
Если сварщик раньше работал с 300-амперным аппаратом на жесткой ВАХ, не стоит ограничиваться 300-амперным аппаратом для импульсной MIG-сварки. Благодаря более широким возможностям нового процесса Вам может пригодиться аппарат с номинальной мощностью 400А, который позволил бы работать с более широким диапазоном скорости подачи проволоки.
2. Обратите внимание на модели с синергетическим управлением
Как было упомянуто выше, аппараты с синергетическим управлением намного проще в обращении, благодаря чему на обучение новых сварщиков уходит меньше времени.
3. Найдите горелки с функцией быстрого переключения процедур
Так как импульсная MIG-сварка позволяет работать с более широким диапазоном скорости подачи проволоки, стоит подумать о приобретении горелок с функцией быстрого переключения между процедурами. Такие модели позволяют сварщику переключаться между заданными процедурами сварки с различными настройками. Убедитесь в совместимости такой горелки со своим механизмом подачи проволоки.
4. Горелки должны быть подходящего размера
Так как процесс импульсной MIG-сварки пригоден для сварки на более высоком токе и связан с особенно высокими импульсами тока, он может приводить к более сильному нагреву горелки по сравнению с обычной сваркой MIG. По этой причине мы рекомендуем выбрать более крупную горелку для соответствующей силы тока, по возможности с жидкостным охлаждением.
5. При работе на большом расстоянии от источника питания будет полезным контроль напряжения рабочего изделия
Некоторые источники питания имеют функцию замера напряжения в рабочем изделии, которая позволяет улучшить характеристики импульсной сварки при сварке на большом расстоянии от источника питания. Обычно аппарат измеряет напряжение на выходных разъемах, один из которых находится на рабочем изделии, а другой — в механизме подачи проволоки. С данной функцией сварщик получает возможность провести дополнительный датчик к рабочему изделию.
Рекомендации по установке
Монтаж аппаратов для импульсной MIG-сварки несколько отличается от традиционных моделей. Следуйте всем перечисленным в инструкции по эксплуатации мерам предосторожности.
1. Более высокая сила тока требует хорошего заземления.
Перед тем, как приступить к работе, нужно проверить правильность подключения всего сварочного электроборудования.
2. Чтобы сократить индуктивность, рекомендуется использовать кабели небольшой длины
Длину кабелей рекомендуется ограничить 15 метрами. Сматывание кабелей чрезмерной длины вызывает индуктивность. Индуктивность сглаживает импульсы, из-за чего падает их эффективность. Также кабели не рекомендуется обматывать вокруг электропроводящих предметов. Это позволит улучшить эффективность импульсной MIG-сварки.
Заключение
Экономичность, высокое качество, производительность и простота в эксплуатации — все эти факторы делают импульсную MIG-сварку очень привлекательным выбором. Хотя такие модели могут иметь более высокую цену, благодаря уникальным преимуществам этого процесса разница в стоимости быстро окупается. Технологические преимущества этого инновационного процесса позволяют использовать один аппарат для многих задач.
Технология EWM-coldArc® – MIG/MAG-сварка с ограниченным тепловложением
Применение в современном машиностроении металлоконструкций из тонкого металла предъявляет к сварочному оборудованию особые требования, которые не может удовлетворить стандартная сварочная техника. Потребовалась разработка такого сварочного оборудования и технологии, которые могли бы обеспечить получение надежного сварного соединения с минимальным тепловложением.
Компанией EWM был разработан такой сварочный процесс, получивший название coldArc, что означает дословно «холодная дуга». Особенностью этого процесса является то, что процесс идет без дополнительного вмешательства в управление скоростью подачи сварочной проволоки, как это реализовано в оборудовании других производителей сварочной техники. Поэтому при применении технологии coldArc не требуется использование дорогостоящих специализированных сварочных горелок, а применяются стандартные сварочные горелки, подходящие для сварки стандартной MIG/MAG дугой.
EWM-coldArc®: Короткая дуга с минимальным тепловложением для сварки и пайки тонких листов, а также провара корня шва с хорошим перекрытием зазора
К лозунгам современного машиностроения «дальше, выше, быстрее» в последнее время добавился «легче». Это, прежде всего, актуально для автомобилестроения и машиностроения, где малая масса машины позволяет увеличить ресурс изнашивающихся частей. Конечно же, одним из способов снижения массы является применение тонколистового металла и высокопрочных сталей, а также использование легких материалов (алюминия, магния). Тонколистовые конструкции предъявляют к сварочному оборудованию и технологии особые требования при сварке – прочность сварных соединений и ограниченное тепловложение. |
alpha Q |
Минимизированное выделение тепла
- незначительное изменение структуры металла
- снижение деформации
- минимизирована зона термического влияния
- уменьшение зоны цветов побежалости и образования окалины
- применяется для сварки углеродистой, нержавеющей и оцинкованной стали
Применяется во всех пространственных положениях
- контроль сварочной ванны во всех положениях
- замечательное перекрытие зазора делает возможным увеличение допусков в соедидениях
- надежная сварка при неравномерном воздушном зазоре
- надежная сварка в вертикальном и потолочном положениях благодаря оптимальной вязкости сварочной ванны
Процесс без образования брызг
- цифровой контроль переноса металла в сварочную ванну
- сокращение времени на подготовительные операции
- высокое качество лицевых швов — нет необходимости в дополнительной обработке
Непревзойденное перекрытие зазоров при сварке корневых швов
- нет провисания расплавленного материала
- надежный провар даже при смещении кромок
- отсутствие пробивания проволоки насквозь (ёжик)
- корневые проходы на всех толщинах листа во всех пространственных положениях
coldArc + impuls + forceArc
- проварка корня технологией coldArc: полный контроль перехода капли, минимизация дефектов соединения, а также сварка без образования брызг
- заполнение разделки в режиме forceArc, облицовочный шов технологией Impuls
- надежный сварной шов при высокой экономичности
Пайка с минимальным выделением тепла с применением низкотемпературного припоя на основе цинка
- отсутствие повреждения цинкового слоя
- минимальная деформация
- альтернатива сплавам на основе меди сопоставимой прочности
- замечательная антикоррозионная устойчивость
Короткая дуга, традиционная сварка на малой мощности
Стандартная MIG/MAG-сварка короткой дугой осуществима на маленькой силе сварочного тока и небольшом напряжении. При этом переход металла в сварочную ванну осуществляется мелкокапельным переносом, при котором характерны чередующиеся фазы коротких замыканий и фазы горения дуги (см. рис. 1).
Рис. 1 Переход металла в сварочную ванну при сварке короткой дугой
Процесс сварки короткой дугой можно описать так, во время горения дуги на конце электродной проволоки образуется капля расплавленного металла, которая очень быстро вступает в контакт с металла сварочной ванны, в результате чего дуга гаснет. За счет поверхностного натяжения расплавленного металла капля втягивается в сварочную ванну с конца электрода, после разрыва моста из расплавленного металла между электродной проволокой и сварочной ванной зажигается дуга. Что при этом происходит с током и напряжением, показано на рис.1. В начальной стадии короткого замыкания напряжение резко падает, т.к. сопротивление моста из расплавленного металла значительно меньше, чем сопротивление дуги. Одновременно с этим ток начинает возрастать до тока короткого замыкания. Далее перед самым разрывом перемычки между электродной проволокой и сварочной ванной напряжение быстро увеличивается из-за увеличения электрического сопротивления, а сварочный ток при этом спадает очень медленно, из-за индуктивности цени источника питания. Возобновление горения дуги происходит при этом при относительно высоком значении напряжения, из-за этого часть перемычки (моста) взрывообразно испаряется с образованием брызг. Для предотвращения этого необходимо противодействовать росту тока дросселированием сварочной цепи.
При сварке металлоконструкций требующих ограничения по тепловложению, например, при сварке тонких листов с плохой подгонкой друг к другу, может произойти прожог металла, что чаще всего происходит при сварке короткой дугой. При сварке листов с цинковым покрытием, существует вероятность испарения покрытия в околошовной зоне. При сварке высокопрочных сталей при подводе излишнего тепла может произойти разупрочнение. Поэтому, исходя их всего вышеперечисленного, применение обычной короткой дуги не подходит для выполнения сварки материалов чувствительных к теплу.
Способы усовершенствования сварки короткой дугой
На протяжении всей истории сварки проводились многочисленные попытки улучшить горение сварочной дуги после короткого замыкания и ограничения ее теплового вложения в сварочный шов. В 80-х годах осуществлялась попытка уменьшить ток непосредственно перед разрывом перемычки между электродной проволокой и сварочной ванной, и после подвести импульс напряжения для улучшения зажигания дуги. Были получены положительные результаты по уменьшению разбрызгивания, но уменьшить тепловложение не удалось.
Следующим этапом усовершенствования короткой дуги стало применение дуги ChopArc, благодаря которой был достигнут прогресс при MIG/MAG – сварки в диапазоне толщин от 0,8 до 0,2 мм. Была разработана система адаптивного регулирования, оптимизирующая качество процесса сварки в режиме реального времени.
Проводилась попытка решить эту задачу с помощью прерывистой подачи сварочной проволоки, при этом длительность замыкания уменьшалась благодаря оттягиванию сварочной проволоки назад во время короткого замыкания. Таким образом, был достигнут процесс сварки с малым разбрызгиванием и ограниченной мощностью. К недостатку этого технологического решения можно отнести сложность технического решения, т.к. необходим двухтактный привод с 2-я двигателями высокой динамики для подачи сварочной проволоки, поэтому процесс подходит только для автоматической сварки и роботизированной сварки.
EWM-coldArc® – сварка с ограниченным тепловложением
Разработки компании EWM для процесса с малой мощностью без вмешательства в механизм подачи сварочной проволоки привели к созданию процесса, при котором воздействие на сварочную дугу оказывается исключительно источником питания. Этот процесс был назван- coldArc. При нем сварка осуществляется короткой дугой и как следствие характеризуется сменой циклов короткого замыкания и горения дуги. Т.к. напряжение при зажигании дуги является решающим фактором при сварке тонких листов, то оно оказывает решающее влияние на:
- динамику подвода энергии, то есть на фазу дуги,
- фазу короткого замыкания,
- зажигание дуги, рис.
2.
Изменение напряжения идентично изменению при стандартной сварке короткой дугой. Напряжение на дуге является задающим параметром при управлении силой тока.
Рис. 2 Переход металла, изменение напряжения и тока при coldArc
Поскольку напряжение является ведущим параметром, то его необходимо постоянно измерять, оценивать и соответствующим образом реагировать. Благодаря процессу обработки сигналов (DSP) можно резко уменьшить энергию дуги (за 1 мс до зажигания), рис.2. благодаря чему зажигание дуги пройдет без выплесков металла, мягко. Поскольку после зажигания дуги необходимо достаточное количество энергии для образования капли расплавленного металла на конце электрода, то на короткое время сила сварочного тока принудительно увеличивается источником питания. Получается так называемый импульс расплавления. После этого ток снижает до рабочего тока и начинается новая фаза.
Благодаря импульсу после каждого короткого замыкания на конце электродной проволоки образуется большая капля расплавленного металла, что ведет к плавному протеканию процесса и возможности работать в фазах между замыканиями с низкой силой сварочного тока. На рис. 3 показаны кадры высокоскоростного фильма, на которых изображен плавный переход металла в сварочную ванну и легкое зажигание дуги.
Рис. 3 Последовательность перехода металла при coldArc (высокоскоростная съёмка 8000 бит/с)
Что может EWM-coldArc®?
На рис. 4 изображено изменение мощности сварочной дуги при зажигании. Рисунок иллюстрирует преимущества coldArc в сравнении с обычной дуговой сваркой. Видно, что в момент зажигания сварочной дуги напряжение не просто ниже, а оно очень динамично, регулируемо падет и затем, после стабилизации дуги, импульсно повышается до заданного.
Такой процесс может применяться там, где нельзя применить стандартную сварку короткой дугой, например, в машиностроении.
На сегодняшний день толщина листа в автомобильной отрасли постоянно снижается и уже в некоторых случаях достигает 0,3 мм, поэтому становиться невозможным применение стандартной MIG/MAG сварки. Трудно выполнить качественный равномерный шов, если требуется перекрыть большой зазор. Это задача выполнима только для coldArc.
Рис. 4 Динамика напряжения при зажигании дуги coldArc
Уже давно для листов с покрытием используют не сварку, а дуговую пайку. Это позволяет сохранить цинковое покрытие, но могут возникнуть трудности при наличии воздушного зазора. Для решения этой задачи необходима сварка coldArc, которая позволяет перекрывать зазоры.
Спаянные вручную с использованием coldArc оцинкованные листы толщиной 0,8 мм с зазором 4 мм представлены на рис. 5. Дуговая пайка производилась на токе 50 А и напряжении 14,0 В проволокой 1,0 мм CuSi3. Пайка с медным припоем имеет точку плавления ≈ 1000 °C. По сравнению с MIG/MAG — сваркой, здесь в coldArc существенно снижена тепловая нагрузка на цинковое покрытие. Можно получить еще лучший результат, если пайка будет выполняться цинковым припоем – точка плавления ≈ 450 °C. Данный припой можно использовать, если сильно ограничить ток короткого напряжения и значительно снизить общий нагрев. Температура испарения сплава цинка и алюминия составляет ≈ 900 °C, что ниже температуры плавления CuSi3.
Рис. 5 Ручная пайка coldArc оцинкованного листа толщиной 0,8 мм с зазором 4,0 мм проволокой 1,0 мм CuSi3
Поэтому, если не снизить ток короткого замыкания, перемычки короткого замыкания будут взрывообразно испаряться и лёгкий металл шва будет сдуваться. Процесс сварки с помощью дуги coldArc позволил выполнить MIG/MAG пайку с цинковым припоем. На Рис. 6 показано нахлёсточное соединение оцинкованных листов толщиной 0,7 мм, спаянных этим тугоплавким припоем. Как видно на рисунке возле шва и с обратной стороны слой цинка полностью сохранился. В автомобилестроении все чаще применяются соединения стали и алюминия.
Рис. 6 Оцинкованные листы, соединение внахлёстку, пайка coldArc цинковой проволокой
Рис.7. Сварка соединений сталь/алюминий проволокой на основе цинка. Обзорный снимок, микрошлиф, дверь автомобиля
Стандартная сварка данных металлов невозможна, е. к. образуются хрупкие интерметаллические фазы Al-Fe, рис 8.
Рис. 8 Фазовая диаграмма «железо-алюминий»
Из диаграммы рис. 8 видно, что железо и алюминий не растворимы друг в друге. Это типично для любого соотношения компонентов фаз FeAl. Опыты показали, что необходимо ограничивать десятью процентами фазу Al-Fe в расплаве.
Применяя цинк в качестве проволоки, можно выполнять соединения «железо-алюминий», при этом алюминий частично расплавляется, а сталь требует увлажнения перед пайкой. Так возникает соединение, на одной стороне сварное, а на другой — паяное. На рис. 7 показан микрошлиф и снимок такого соединения, выполненного coldArc припоем из цинка.
Для сварки и пайки coldArc не требуется применение специальных горелок, можно пользоваться обычными горелками MIG/MAG.
Другое применение пайки и сварки coldArc на рис. 9-14.
Рис. 9 Оцинкованный стальной лист толщиной 0,7 мм, соединение внахлёстку, пайка coldArc проволокой из цинка диаметром 1,0 мм, скорость 0,35 м/мин. , U=13,5В, I=40A
Рис. 10 Соединение сталь/алюминий, сталь оцинкованная 0,7 мм и AlMg 1,0 мм, соединение внахлёстку, пайка coldArc проволокой из цинка 1,0 мм, скорость 0,35 м/мин, U=13,5В, I=40A
Рис. 11 Соединение сталь/алюминий, сталь оцинкованная 0,7 мм и AlMg 1,0 мм, соединение внахлёстку, пайка coldArc проволокой AlSi5 скорость1,1 м/мин., U=14,5В, I=60A
Рис. 12 Лист стальной, 1,0 мм, стыковое соединение, зазор 1 мм, проволока G4Si1 1,0мм, сварка coldArc, скорость 2,0 м/мин., U=19В, I=136A
Рис. 13. AlMg3, 0,8 мм, соединение внахлёстку, проволока AlSi5 1,0 мм, сварка coldArc, скорость 1,2 м/мин., U=13В, I=55A
Рис. 14 CrNi, 0,5 мм, соединение внахлёстку, 0,8 мм проволока, сварка coldArc, скорость 2,0 м/мин., U=16,5В, I=90A
Видео-материалы по технологии сварки EWM-coldArc®
Читайте также:
Impuls — легкоконтролируемая дуга без короткого замыкания во всем диапазоне сварочного тока для различных положений шва
Контролируемая дуга без короткого замыкания
управляемое распределение тепла благодаря переносу 1 капли в течение 1-го импульса
плавный переход капли также и в материалах с высоким содержанием Ni
стабильная дуга в диапазоне между короткой и струйной дугой
. ..
SuperPuls® — переключение процессов
Комбинация сварочных процессов EWM позволяет расширить возможности сварки
Функция superPuls позволяет осуществлять ручной или автоматический выбор между двумя сварочными точками одного процесса или между следующими комбинациями во время сварки:
…
EWM-rootArc® — MIG/MAG процесс сварки короткой дугой
Процесс обеспечивает качественное соединение деталей по широкому зазору. За счет сварки «мягкой» короткой дугой достигается:
более низкое разбрызгивание по сравнению со стандартной короткой дугой,
хорошее формирование корня шва и охват кромок,
возможность качественной сварки вертикального шва способом на подъем и на спуск,
в комбинации с импульсной дугой исключительная скорость и качество за счет включения режима супер-пульс,
вертикальная сварка без поперечных колебаний,
хорошая авт…
PipeSolution® — сильная дуга для быстрой, безопасной сварки с зазором в корне шва и без, для всех пространственных положений
Абсолютно безопасная сварка корня
Применима для любых толщин металла
Может использоваться во всех положениях для сварки металлических листов и труб
Сварка корня шва без прожогов и снижения скорости
Превосходное формирование корня
Оптимальный охват (форма) шва
Превосходный контроль для позиционной сварки
Безопасное формирование корня также при сварке без зазора
. ..
EWM-forceArc® – сварка с глубоким проваром за счет короткой сжатой дуги
Форсированная дуга с глубоким проплавлением, стабильной направленностью в режиме струйного переноса.
Применение: низкоуглеродистые, низколегированные и высоколегированные стали, а также высокопрочные сорта стали больших толщин.
…
Поделиться ссылкой:
MAG, MIG, TIG, MMA — Основные виды сварочных устройств.
Какой сварочный аппарат стоит купить, а какой нет? Сегодня в продаже много разных аппаратов, что требует дополнительного знакомства с каждым видом сварок, предназначенных для разных типов сварочных работ.
К сожалению, нет универсального инструмента, подходящего для всех применений, поэтому начнем с обзора основных видов и выделим возможности и преимущества каждого из них. Это поможет сузить круг выбора аппарата для конкретных потребностей.
Основные виды сварочных устройств.
Сварка MIG / газовая дуговая сварка/ полуавтоматическая сварка / GMAW /
MIG также называется газовая дуговая
сварка (GMAW) – дуга поддерживается между
сплошным проволочным электродом (проволочный сварочный электрод на катушке ) и
заготовкой. Проволока подается с помощью приводных роликов (механизм подачи
проволоки) в сварочную ванну.
Дуга и сварочная ванна защищены от воздуха потоком инертного газа. Дуга, создаваемая электрическим током между основным металлом и проволокой, плавит проволоку и соединяет ее с металлом, создавая высокопрочный сварной шов, с великолепным внешним видом и незначительной потребностью в очистке.
Сварка МИГ чистая, простая и может использоваться на тонких или толстых листовых металлах, подходит для большинства металлов.
Сварка MAG / газовая дуговая сварка / полуавтоматическая сварка / GMAW /
MAG – это еще один вид газовой дуговой сварки (GMAW). Принцип работы такой, как и в сварке MIG – присадочная проволока с катушки автоматически подается непосредственно к месту сварки через контактную гильзу. Главное отличие сварки MAG – используются активные газы (смесь аргона, углекислого газа и кислорода). Пропорции отдельных газов могут быть скорректированы в соответствии с требованиями к материалу, подлежащему свариванию.
MAG-сварка в основном используется для нелегированных сталей, алюминия и алюминиевых сплавов, а также низколегированной и высоколегированной нержавеющей стали.
Применяется только в закрытых помещениях, так как ветер может сдуть защитный экран ( газ ) и процесс сваривания будет проходить без защиты от окисления, как результат – сварочный шов низкого качества, более чувствителен к коррозии, с низкими несущими показателями.
Дуговая сварка порошковой проволокой / FCAW /
Дуговую сварку порошковой проволокой используют в полуавтоматах MIG/MAG — сварок, с предварительной заменой приводных роликов подачи проволоки и катушки. Сама проволока имеет трубчатую форму и заполнена флюсом и металлическим порошком и нет необходимости во внешнем защитном газе.
Из-за
высокого качества сварки и возможности работы на открытом воздухе, даже в
ветреную погоду, часто используется в строительной промышленности.
FCAW отлично подойдет для сваривания углеродистой стали, нержавеющей сталь и низколегированной стали. Большинство цветных металлов, включая алюминий, сваривать нельзя.
Сварка TIG / газовая вольфрамовая дуговая сварка / GTAW /
Это процесс дуговой сварки, в котором для получения сварного шва используется практически не расходуемый вольфрамовый электрод и присадочная поволока. В процессе сварки сварочным аппаратом TIG дуга прыгает между вольфрамовым электродом и заготовкой, создавая высокую температуру. Экран инертного газа, обычно включающий аргон или другой благородный газ, предотвращает окисление сварного шва. В процессе сварки нет брызг и образования шлака.
Универсальный тип сварки, отлично подходит для тонких профилей из легированной стали, нержавеющей стали и цветных металлов, таких как алюминий, магний и медные сплавы.
Сварка вольфрамовым
инертным газом (TIG) требует
большего мастерства сварщика. Для производства качественных сварных швов, требует
чистой подготовленной поверхности заготовок.
Сварка TIG немного медленнее, чем другие виды дуговой сварки, поэтому время, затрачиваемое на сварку относительно велико.
MMA / ручная электродуговая сварка / SMAW /
Ручная электродуговая сварка – это процесс сварки, при котором электрическая дуга горит между покрытым электродом и заготовкой. Электрод фиксируется в держателе электрода и при касании предполагаемого шва, возникает короткое замыкание, и при отрыве ( электрода ) образуется дуга. От дуги выделяется большая температура, что вызывает быстрое плавление кромок заготовки и электрода. В процессе сварки электрод и его покрытие расплавляются, а шлак растекается над сварочным швом.
Самый эффективный и экономичный вид сварки и может
использоваться внутри и вне помещений. Не требует особой подготовки соединений
перед свариванием, обеспечивая эффективное
сцепление с ржавыми или грязными металлами.
Особенности выбора.
Уделить время и определить основные задачи, с которыми Вы будете сталкиваться наиболее часто, металл с которым будете чаще всего работать – это поможет выбрать наиболее подходящий сварочный аппарат.
Важно понимать, что помимо стоимости аппарата, не забудьте просчитать расходы на защиту глаз и рук при проведении сварочных работ (шлем, перчатки, куртка и т. Д.), и расходные материалы (газ, электроды, электродная проволока).
Please follow and like us:
Область применения сварки MIG/MAG
Сварка методом MIG/MAG – универсальный вид сварки. Возможность автоматической подачи проволоки значительно увеличивает производительность метода. Использование защитных газов позволяет работать со многими видами металлов. В результате MIG/MAG-сварка применяется во многих современных отраслях промышленности, а при соблюдении техники безопасности может использоваться и в бытовом применении.
Сварка MIG/MAG походит для работы с различными видами металлов, включая:
- медь и ее сплавы,
- алюминий и его сплавы,
- магниевые сплавы,
- никель и его сплавы,
- титан и его сплавы,
- нержавеющая сталь различных марок,
- низкоуглеродистая сталь,
- высокоуглеродистая сталь,
- низколегированные стали
- холодно-тянутая сталь,
- катаная сталь.
При этом технология полуавтоматической сварки в защитных газах позволяет сваривать как очень тонкие листы металлов, так и изделия большой толщины. Широкие возможности применения и совместимость с разными металлами позволяет применять сварку методом MIG/MAG в таких отраслях:
- нефтегазовая отрасль,
- производство и обслуживание трубопроводов различного назначения,
- автомобильная промышленность, включая производство и ремонт автомобилей, автозаводы и автомастерские,
- машиностроительная отрасль,
- производство станков и оборудования,судостроение, ремонт и обслуживание кораблей и судов,
- авиакосмическая промышленность,
- приборостроение,
- сельское хозяйство,
- металлургия,
- строительство и многие другие.
Возможности MIG/MAG-сварки применимы не только на крупных промышленных площадках, но и в условиях небольших мастерских для производства и ремонта различных изделий из металла. При условии соблюдения требований безопасности по работе с газом сварка с использованием защитных газов может применяться и в быту.
Полуавтоматическая сварка. Сварка MIG/MAG полуавтоматом
Полуавтоматическая сварка или MIG-MAG сварка.
Сварка полуавтоматом (полуавтоматическая сварка MIG/MAG) — это второй по полурности вид сварки (первый — ручная дуговая сварка MMA), при котором сварка осуществляется с помощью сварочной проволоки, которая автоматически подается в зону сварки, а сам процесс сварки проиходит в среде защитных газов.
Популярности сварки полуавтоматами обусловлена высокой производительностью полуавтоматической сварки и высоким качеством получаемого в процессе сварки полуавтоматом сварного шва.
Что означает аббревеатура MIG/MAG?
MIG – это сварка, в которой используется инертный газ, например, гелий или аргон, или их смеси.
MAG – это сварка, в которой используется активный газ, например, азота или углекислый газ, или их смеси.
Сегодня методы полуавтоматической сварки применяются во всех областях промышленности, в строительстве и производстве. Современное автомобилестроение, судостроение, производство металлоконструкций не возможно представить без сварочных полуавтоматов и полуавтоматической сварки.
Принцип работы сварочного полуавтомата заключается в том, что сварочная проволока автоматически подается в зону сварки, она поступает по кабель каналам через сварочную горелку, которой управляет сварщик. Сварочная проволока выступает в роли токопроводящего электрода и присадочного материала. Процесс сварки осуществляется в среде защитных газов, для защиты сварочной зоны от негативного воздействия внешних факторов и как следствие, сварка качественного сварного шва, изготовление качественного изделия.
В полуавтоматической сварке используют разные источники питания сварочного аппарата, которые работают на постоянном токе: выпрямители и инверторы. Выбор между источникими питания полуавтомата зависит от конкретных условий сварки.
Если сварочный полуавтомат будет использоваться в бытовых условиях, например, дома или в гараже;в небольшом производстве, то лучше выбрать полуавтомат ESAB Caddy® Mig C160i/C200i. Данная модель компактного полуавтомата отличается высокой производительность, надежностью и качеством. Аппарат идеален для кузовного ремонта, для автосервиса.
Если нужен сварочный полуавтомат для постоянной работы, например, для сварки металлоконструкций, металлических изделий, то стоит присмотреться, к серии сварочных полуавтоматов SYNERGIC.PRO2® 170-2-310-4 от немецкой компании REHM. Оборудование REHM — это высококачественный и высокотехнологичный продукт, отличающийся от аналогов, низким энергопотреблением.
Если полуавтомат будет работать в условиях крупного производства или в областях промышленности, где нужны мощные сварочные аппарата, высокой производительности, то стоит опробовать в работе профессиональные сварочные полуавтоматы серий Origo™ Mig от ESAB, SYNERGIC.PRO2® или MEGA.ARC2® от REHM, мощностью до 600A.
Сварочные полуавтоматы в каталоге оборудования для полуавтоматической сварки магазина «ВСЁ ДЛЯ СВАРКИ» компании Сваркомплект.
Полуавтоматическая сварка MIG/MAG от А до Я (Обучение, подготовка, подбор оборудования и материалов, эксплуатация).
Если проанализировать динамику изменений потребления сварочных материалов в мире для различных видов сварки, представленную диаграммой на следующей странице, то видно, что MIG/MAG-сварка показывает самый значительный прирост. Причиной такого роста являются высокая производительность данного процесса сварки, а также простота его автоматизации. Данный рост произошел за счет вытеснения процесса ручной дуговой сварки покрытым электродом, который до этого являлся наиболее широко применимым способом сварки. В настоящее время во всем мире полуавтоматическая сварка MIG/MAG является самым часто применяемым видом сварки.
MIG/MAG-сварка была разработана в 1940 году в США как способ сварки алюминия. В качестве защитного газа использовались аргон или гелий. Для сварки сталей MIG/MAG-процесс не использовался до тех пор, пока не стало ясно, что в качестве защитного газа может использоваться чистая углекислота. Сварка выполнялась только в нижнем пространственном положении, при этом она давала изрядное количество брызг.
Усовершенствование источников питания, а также переход на меньшие диаметры проволок и аргон-углекислотные сварочные смеси позволили значительно снизить количество образующихся брызг и выполнять сварку в различных пространственных положениях.
В промышленном производстве MIG/MAG — процесс начал применяться только с 60-х годов. Однако далее данный вид сварки стал активно развиваться и усовершенствоваться в направлениях связанных с разработкой новых сварочных материалов, источников питания и защитных газов.
Популярность MIG/MAG-процесса с каждым годом неуклонно растет. На сегодняшний день это наиболее часто применяемый вид сварки во всем мире. Причиной тому послужили высокая производительность данного процесса и простота его автоматизации.
Принцип данного процесса сварки заключается в том, что в дугу непрерывно подается металлическая проволока, которая в ней плавиться. В данном случае проволока выполняет функцию, как электрода, так и присадочного материала. Электрическая энергия, необходимая для горения дуги, подается от сварочного источника питания. Сварочная дуга и расплавленный металл от воздействия атмосферы защищаются газом, который может быть как инертным, так и активным. Их отличие в том, что инертный газ не вступает в реакцию с расплавленным металлом. Например, аргон и гелий являются инертными газами. Активные же газы принимают участие в процессах, которые протекают в сварочной дуге и расплавленном металле. Аргон с добавками углекислого газа или кислорода является активным газом. Для получения наилучших результатов, крайне важно, чтобы были правильно установлены все параметры сварки. К основным параметрам MIG/MAG-сварки относятся сварочное напряжение, скорость подачи проволоки и расход защитного газа.
При MIG/MAG, как и при других видах сварки, человек подвергается воздействию ряда неблагоприятных факторов, оказывающих отрицательное воздействие на его здоровье. Поэтому крайне важно уделять серьезное внимание средствам защиты сварщика, чтобы свести к минимуму их влияние. Основными вредными факторами, связанными с MIG/MAG-сваркой, являются выделяемые при данном процессе дымы и газы в сочетании с жестким ультрафиолетовым излучением, исходящим от сварочной дуги. Современные средства защиты позволяют максимально полно изолировать сварщика от воздействия этих вредных факторов на его здоровье. К таким средствам можно отнести сварочные горелки, совмещенные с системой удаления дыма непосредственно из зоны сварки, сварочные маски, позволяющие видеть все, что происходит в процессе подготовки к сварке, но мгновенно затемняющиеся при зажигании дуги, а также системы подачи чистого воздуха в зону дыхания, что практически полностью исключает воздействие выделяемого при сварке озона на здоровье человека.
Принцип сварки
MIG/MAG-процесс относиться к электро-дуговым способам сварки, при котором электрическая дуга используется для плавления основного и присадочного металлов, из расплава которых формируется окончательный сварочный шов. К дуговым методам также относятся ручная сварка покрытым электродом (MMA), сварка в защитном газе неплавящимся вольфрамовым электродом (TIG), плазменная сварка и сварка под флюсом (SAW).
На рисунке схематически представлен принцип дуговой сварки плавящимся электродом в защитном газе (MIG/MAG). Дуга (1) горит между изделием и металлической проволокой, которая непрерывно подается в зону сварки и плавиться. При данном способе металлическая проволока одновременно выполняет функцию, как электрода, так и присадочного материала. Она наматывается на катушку (3) и подается в зону сварки подающими роликами (4) через наплавляющий канал (5), проходящий внутри шланг-пакета (6) сварочной горелки (7). Электрическая энергия на дугу поступает от сварочного источника (8). Сварочный ток на электрод передается через контактное сопло (9) (более известное под названием «контактный наконечник») находящееся внутри сварочной горелки. Обычно на контактное сопло подключается к положительному полюсу сварочного источника, а изделие к минусу. После возбуждения дуги по цепи начинает протекать сварочный ток. Защитный газ (10) подается через газовое сопло (11), расположенное вокруг контактного сопла. Данная конструкция позволяет защитить электрод, дугу и расплавленный металл от воздействия окружающей атмосферы. Защитный газ может быть как инертным, т.е. неактивным и не принимающим участие в процессах, которые протекают в сварочной дуге и сварочной ванне, так и активным. В зависимости от типа защитного газа, процессы сварки подразделяются на MIG (дуговая сварка плавящимся электродом в инертном газе) и MAG (дуговая сварка плавящимся электродом в активном газе).
Общее название этих процессов дуговой сварки плавящимся электродом в защитном газа имеет аббревиатуру GMAW. Данная аббревиатура чаще встречается в США. В случае, когда подача присадочного материала происходит автоматизировано, а перемещение горелки по стыку изделия вручную, данный способ MIG/MAG-сварки сварки обычно называют полуавтоматической.Данный способ сварки достаточно легко автоматизируем за счет применения системы механического перемещения сварочной горелки или самого изделия.
Параметры
При MIG/MAG-сварке процесс задается рядом различных параметров.
Среди них:
• Напряжение на дуге (длина дуги)
• Скорость подачи сварочной проволоки (которая определяет величину сварочного тока)
• Индуктивность (на большинстве источников питания может регулироваться)
• Расход защитного газа
• Скорость сварки
• Угол наклона горелки
• Вылет проволоки (расстояние от контактного наконечника до изделия)
Для получения наилучших результатов данные параметры должны сочетаться друг с другом. Первые три параметра задаются на источнике питания или на подающем механизме. Они подбираются в зависимости от марки основного материала, его толщины, типа разделки кромок, диаметра проволоки, пространственного положения сварки и типа защитного газа. Ориентировочные параметры сварки приведены в таблице.
Данная таблица помогает сварщику правильно подобрать рабочую точку.
Рабочая точка должна попадать в рабочую область, которая определяется комбинацией присадочного материала и защитного газа, при этом тепловая мощность, выделяемая дугой, должна быть правильно подобрана под конкретное изделие. Кроме скорости подачи проволоки, напряжения и защитного газа, на получаемый результат сварки также можно влиять изменением индуктивности источника питания. Принципы подбора этих параметров достаточно детально рассматриваются в последней главе данного справочника. Скорость сварки, угол наклона горелки и вылет электродной проволоки – это параметры, которые сварщик должен сам контролировать в процессе сварки, и их влияние также рассмотрено в последней главе.
Что происходит в дуге?
Самым главным процессом, происходящим при дуговой сварке, является переход плавящегося присадочного материала в сварочную ванну. На характер этого процесса влияют различные факторы, такие как состав защитного газа, ток сварки, напряжение на дуге, материал и диаметр электродной проволоки. В зависимости от этого, процессы подразделяют на перенос металла короткими замыканиями, переходную дугу и струйный перенос присадочного материала. Четвертый тип переноса металла получают при использовании пульсирующего процесса сварки, разновидности MIG/MAG сварки, который все чаще находит применение в последние годы.
Короткая дуга
Процесс сварки с короткими замыканиями дуги является наиболее часто встречающимся типом переноса присадочного материала при MIG/MAG сварке. Сварка «короткой дугой» происходит при достаточно низких значениях дугового напряжения и сварочного тока.
Это означает, что тепловложение в изделие не очень велико, поэтому короткая дуга является предпочтительной при сварке тонкостенных изделий и при сварке в различных пространственных положениях, т.к. размеры расплавленной ванны невелики и она быстро кристаллизуется. В процессе сварки короткой дугой образуются достаточно крупные капли, которые периодически закорачивают дуговой промежуток.
Количество таких коротких замыканий находиться в интервале от 30 до 200 в секунду. В эти моменты дуга исчезает и образуется некоторое количество сварочных брызг. Попадание этих брызг на изделие приводит к тому, что возникает необходимость в его финишной зачистке после сварки. Причем этот отрицательный эффект характерен для всех марок проволок. Правильно настроенная дуга издает равномерно трещащий звук.
Переходная дуга
При небольшом повышении сварочного тока и напряжения, образуется так называемая «переходная дуга». Образующиеся капли имеют различные размеры и могут, как замыкать дуговой промежуток, так и не замыкать его. В результате имеем нестабильную дугу, которая создает большое количество сварочных брызг и дыма. В связи с этим рекомендуют избегать сварку в этой зоне.
Струйный перенос
Когда для конкретного диаметра проволоки и типа защитного газа сварочный ток и напряжение достигают достаточно высоких значений, расплавленный присадочный материал мелкими каплями переходит в сварочную ванну, не замыкая дугового промежутка, см. рис.7. При сварке со струйным переносом, дуга достаточно стабильна и не образуется крупные брызги, которые прилипают к изделию. Данный процесс характеризуется высокой производительностью, а потому его, например, рекомендуют применять для наплавки заполняющих слоев при сварке толстостенных изделий. При этом в изделие вкладывается достаточно много тепловой энергии, и как следствие, расплавленная ванна имеет достаточно большие размеры. Поэтому сварку в режиме струйного переноса рекомендуют выполнять только в нижнем положении.
Короткий пульс
Пульсирующая дуга совмещает в себе преимущества, как короткой дуги, так и струйного переноса – другими словами, тихая стабильная дуга сочетается с достаточно умеренным вложением тепла в изделие. Это достигается благодаря использованию пульсирующего сварочного тока, см. рис. 8. При каждом импульсе этого тока капля отрывается от сварочной проволоки. Благодаря этому капли не замыкают дуговой промежуток, брызги имеют маленький размер, а дуга очень стабильна. Величина дежурного тока невелика, что позволяет поддерживать действующее значение сварочного тока на достаточно низком уровне. Как следствие, тепловложение в изделие не очень велико, что позволяет выполнять сварку в различных пространственных положениях и варить достаточно тонкие пластины.
Преимущества, ограничения и области применения
Основными преимуществами MIG/MAG процесса сварки являются его высокая производительность, относительно низкое
вложение тепла в изделие и простота его автоматизации. В сравнении с процессом сварки покрытым электродом (MMA-сваркой), его более высокая производительность в первую очередь объясняется тем, что нет необходимости тратить время на смену электрода и удаление шлака с наплавленного металла. Кроме того, скорость плавления присадочного материала значительно выше из-за более высокой плотности сварочного тока, протекающего через него. MIG/MAG процесс является одним из наиболее легко приспосабливаемых видов сварки и может применяться для:
- сварки тонких пластин (толщин более 0,5 мм). Чтобы избежать деформаций и короблений при сварке небольших толщин, требуется свести к минимуму удельное тепловложение. При наплавке заполняющих проходов у толстостенных изделий, данный процесс позволяет получить высокие значения производительности.
- сварки всех стандартных конструкционных материалов, таких как низкоуглеродистые, низколегированные и высоколегированные стали, алюминия и его сплавов, а также некоторых других металлов и сплавов.
- сварки во всех пространственных положениях. Благодаря этим преимуществам MIG/MAG процесс нашел широкое применение, как в крупномасштабном производстве, так и в мелком. Он используется в автомобилестроении, сварке строительных и оффшорных конструкций, судостроении и многих других отраслях.
MIG/MAG-сварку можно охарактеризовать одновременно как легко, так и трудно осваиваемый и применяемый вид сварки. Если речь идет просто о сварке двух деталей друг с другом, без каких либо особых требований к свойствам сварного соединения, то данный вид сварки очень прост для применения. С другой стороны, если требуется глубокий провар, не допускаются несплавления или газовые поры и т.п., MIG/MAG процесс требует от сварщика соответствующих знаний и навыков. Также свои ограничения в применяемость данного вида сварки вносит то, что оборудование состоит из нескольких узлов, оно на много дороже и более громоздко в сравнение с оборудованием для MMA- сварки. К тому же, применение данного способа сварки вне цеха весьма ограниченно, т.к. газовая защита весьма чувствительна к сквознякам. Конструкция сварочной горелки в некоторой степени снижает полноту контроля над ситуацией в процессе сварки.
Оборудование
Принципиально MIG/MAG оборудование состоит из следующих узлов: источник питания, подающий механизм, сварочная горелка с кабелем и шланг-пакетом, а также системы подачи защитного газа.
Источники питания
Источник питания обеспечивает систему постоянным током и необходимым уровнем напряжения. По конструкции источники питания можно подразделить на выпрямители со ступенчатым переключением напряжения, тиристорные и инверторные. Источники питания, позволяющие варить пульсирующим сварочным током, как правило, имеют синергетическое управление. Это означает, что сварщику достаточно установить необходимую скорость подачи проволоки и исходную информацию о материале сварочной проволоки, ее диаметре, а также типе защитного газа. Далее источник сам установит необходимые параметры пульсации сварочного тока и соответствующее напряжение. Из параметров сварки на источнике питания задается рабочее напряжение, и, если возможно, величина индуктивности. Напряжение на дуге напрямую связано с длиной дугового промежутка. Чтобы в процессе сварки не происходило колебаний длины сварочной дуги, источник питания должен иметь жесткую или полого падающую внешнюю вольт-амперную характеристику.
Подающие механизмы
Подающий механизм состоит из двух основных узлов, ступицы для установки катушки с проволокой и самой системы подачи. Ступица должна быть оснащена регулируемой тормозной системой, останавливающей вращение катушки в момент прекращения подачи проволоки. Система подачи предназначена для проталкивания электродной проволоки в направляющий канал через шланг-пакет к сварочной горелке. Системы подачи проволоки могут иметь различные варианты конструктивных решений. Например:
- с двумя подающими роликами, когда один является ведущим, а другой прижимным.
- с двумя подающими роликами,получающими привод от одного двигателя
- с четырьмя роликами, получающими привод от одного двигателя
- с четырьмя роликами, получающими привод от двух последовательно включенных двигателей
Общим для всех этих схем является то, что они проталкивают проволоку через шланг-пакет. Также можно встретить комбинацию этих систем, когда электродная проволока проталкивается по системе стандартным подающим механизмом с одной стороны и тянется специальным подающим механизмом, смонтированным на горелке с другой стороны. Эта система, называемая push-pull (тяни-толкай), позволяет использовать более длинные кабеля и шланг-пакеты. Ее также рекомендуют использовать для алюминиевых проволок, т.к. это один из вариантов решения проблемы ее недостаточной жесткости. Размер канавки у подающих роликов должен соответствовать диаметру применяемой проволоки. Некоторые типы роликов имеют канавки под различные диаметры, что позволяет выбирать нужную геометрию канавки изменением положения подающего ролика
Сварка Миг-Маг
Сварка Миг-Маг
Сварка Миг-Маг или сварка в среде СО₂ является основным и наиболее распространенным способом сварки плавлением на машиностроительных предприятиях. Сварка Миг-Маг экономична, обеспечивает достаточно высокое качество швов, особенно при сварке низкоуглеродистых сталей, требует более низкой квалификации сварщика, чем ручная, позволяет выполнить швы в различных пространственных положениях. Наиболее распространена сварка полуавтоматами.
Защитный газ 2, выходя из сопла 1, вытесняет воздух из зоны сварки. Сварочная проволока 3 подается вниз роликами 4, которые вращаются двигателями подающего механизма. Подвод сварочного тока к проволоке осуществляется через скользящий контакт 5. Учитывая, что защитный газ активный и может вступить во взаимодействие с расплавленным металлом, сварка Миг-Маг имеет ряд особенностей. В зоне дуги углекислый газ диссоциирует. Углекислый газ и образовавшийся кислород взаимодействуют с расплавленным металлом сварочной ванны с образованием оксида железа.
Окисление сварочной ванны ухудшает механические свойства шва и, в первую очередь, его пластичность. Для предотвращения этого процесса в сварочную ванну вводят элементы — раскислители, хорошо взаимодействующие с кислородом. Обычно это марганец и кремний. Раскислители выводят в шлак избыток кислорода и на участках сварочной ванны, имеющих пониженную температуру, восстанавливают железо из оксидов. Введение раскислителей в сварочную ванну обычно осуществляется через проволоку. Поэтому при сварке в СО₂ используется сварочная проволока, легированная марганцем и кремнием. При сварке низкоуглеродистых сталей это обычно проволока марки Св08Г2С. Однако, несмотря на введение раскислителей, характеристики пластичности шва получаются несколько ниже, чем при сварке под флюсом или ручной сварке электродами с основным покрытием. Поэтому сварку в СО₂ не рекомендуют использовать для ответственных конструкций, работающих при низких температурах в условиях переменных и ударных нагрузок. Имеет свои особенности и перенос электродного металла при сварке в СО₂. В зоне дуги происходит диссоциация углекислого газа, которая сопровождается поглощением тепла. Кроме того углекислый газ обладает достаточно высокой теплопроводностью. Эти процессы приводят к интенсивному отводу тепла от внешней поверхности дуги, в результате чего она сжимается.
Анодное пятно разогревает только центральную часть капли, не захватывая боковые поверхности проволоки. При сварке в СО₂ интенсивность нагрева дугой ниже, т.к. осуществляется за счет передачи тепла через каплю. При сварке в Ar дуга разогревает непосредственно проволоку, поэтому на ее торце силы поверхностного натяжения ниже и капли отрываются при меньшем весе. Процессу же сварки Миг-Маг характерен перенос электродного металла достаточно крупными каплями.
Улучшить процесс переноса электродного металла и уменьшить размер капель при сварке в СО₂ позволяет введение в сварочную проволоку щелочных и щелочноземельных металлов (цезия, рубина и др.), а также использование импульсных источников питания, позволяющих управлять отрывом капель расплавленного электродного металла.
Читайте также:
Автоматы сварочные
Системы пневматической транспортировки пыли в пылеотсосах
Кожаная маска Нахкис
Особенности конструкций и монтажа пылепроводов
Комплектующие сварочной маски
Соединения для сварки колонн и моментных сварных швов при сварке в полевых условиях
Получите советы по экономии денег и максимальному увеличению производительности и качества сварки в полевых условиях при использовании сварных моментных соединений и стыковых соединений колонн.
Стальные соединения при сварке конструкций
Не секрет, что когда дело доходит до конструкции стальных конструкций, всегда желательно избегать более дорогостоящих и трудоемких сварных соединений в полевых условиях в пользу болтовых соединений. Это еще более верно, когда соединение требует полного проплавления (CJP) шва с разделкой кромок, что особенно характерно для определенных типов соединений с моментом и сращивания колонн.
Использование сварного момента и стыковых соединений колонн в проекте будет сильно различаться в зависимости от нескольких факторов, в том числе места расположения проекта, типа и конструкции самой конструкции.
Независимо от того, потребует ли ваш следующий проект многих из этих типов соединений или только несколько, эти советы помогут вам сэкономить деньги и максимизировать производительность и качество сварки в полевых условиях.
Совет 1. Используйте оборудование подходящего размера для работы
Сварные моментные соединения и стыки колонн отнимают много рабочих часов по сравнению с большинством других сварочных работ в рамках проекта. Чтобы сократить время сварки, многие подрядчики и монтажники выбирают переход на электроды большего размера.
Независимо от того, используете ли вы электросварочные аппараты, сварочное оборудование с приводом от двигателя или их комбинацию, важно иметь аппарат подходящего размера, чтобы с первого раза выполнить работу максимально эффективно.
Слишком часто подрядчики устанавливают максимальное значение на своем сварочном оборудовании. Хотя в этом нет ничего принципиально неправильного, частая работа на максимальных или близких к максимальных возможностях станках означает, что вы, возможно, не получите наилучших характеристик сварки или срока службы оборудования.
Думайте о сварщике как об автомобиле. Если вам нужно разогнаться до 90 миль в час, обычная машина, вероятно, сможет это сделать. Но если вам нужно ездить со скоростью 90 миль в час каждый день, вы, вероятно, переключитесь на более производительный автомобиль. То же самое и со сварочным оборудованием. Тот факт, что машина может сваривать на более высоких диапазонах, не означает, что это лучший вариант в долгосрочной перспективе.
Для большинства работ, вероятно, подойдет машина на 300-400 ампер. Если вы часто свариваете проволокой диаметром более 5/64 дюйма или вам необходимо выполнить много строжки угольной дугой электродами от 1/4 дюйма и более, рассмотрите вариант установки на 500 ампер или более.
Совет 2: переходите с ручной сварки на порошковую сварку
Преимущества сварки порошковой проволокой с самозащитой по сравнению со сваркой штучной сваркой могут показаться очевидными для некоторых, но многие строительные и монтажные компании все еще сваривают все свои многопроходные сварные швы CJP с помощью технологии дуговой сварки (дуговой сварки в среде защитного металла или SMAW). . Ручная сварка отлично подходит для многих применений, но переход на самозащитную порошковую проволоку для проектов, требующих многопроходных сварных швов большего размера, дает несколько преимуществ:
- Скорость наплавки: По сравнению с наиболее часто используемыми 1/8-дюймовыми стержневыми электродами 7018, которые обычно дают производительность наплавки только 3 фунта / час или меньше, сопоставимая порошковая проволока для всех позиций может удвоиться или даже утроиться.
это производство.
- Эффективность наплавки: Это относится к процентной доле электрода, которая фактически попадает в окончательный сварной шов. Вы когда-нибудь задумывались, сколько денег вы бросаете на землю? После каждого сварного шва, независимо от того, полностью или частично использован электрод, оставшийся шлейф электрода обычно оказывается в одном и том же месте — на земле. Это создает беспорядок, который нужно убирать, и вынимает деньги из вашего кармана. Если взять в качестве примера стержневой электрод 7018 диаметром 1/8 дюйма, вам повезет, если вы добьетесь эффективности 70% после учета магнитного потока и потерь на шлейфе.Переход на порошковую проволоку может обеспечить повышение эффективности на 10% или больше благодаря повышенной способности подавать и осаждать расплавленный металл в сварном шве в сочетании с тем фактом, что сварщики могут начинать и останавливать работу в любое время без потерь расходных материалов.
Совет 3.

Когда дело доходит до сварки конструкций самозащитной порошковой проволокой, многие подрядчики используют так называемую проволоку Т-8. Эти проволоки с отрицательной полярностью электродов постоянного тока (DCEN) представляют собой универсальные универсальные проволоки, которые обеспечивают хорошие низкотемпературные удары и могут использоваться для многопроходных сварных швов.
Несмотря на то, что привлекательность использования одного провода для всего проекта понятна, подумайте о переходе на провод T-6 для плоских или горизонтальных сварных швов, подобных тем, которые используются в сварных стыках колонн. Эти провода имеют положительную полярность электродов постоянного тока (DCEP) и обычно дают значительно более высокие скорости осаждения, чем провод T-8. Они также обеспечивают хорошее проникновение и, как правило, также оказывают очень хорошее низкотемпературное воздействие.
Совет 4. Тратьте меньше времени на прогулки
Недавние исследования показали, что в среднем типичный слесарь-слесарь делает четыре поездки обратно к своей машине, чтобы внести коррективы в течение дня. Умножьте это потраченное время на пятидневную рабочую неделю и 50-недельный рабочий год. Предполагая, что каждая поездка в оба конца занимает примерно 15 минут и используя 45 долларов в час в качестве оценки затрат подрядчика на найм слесаря, получаем ежегодную потерю производительности в размере 11250 долларов — просто платите сварщику за то, чтобы он ходил туда-сюда, чтобы внести коррективы. источник питания. Независимо от того, составляют ли ваши производственные затраты половину или вдвое больше, если вы умножите их на всех сварщиков в платежной ведомости, это приведет к значительной трате денег и потере производительности.
Для решения этой проблемы на строительной площадке были внесены некоторые улучшения в разработку передовых технологий дистанционного управления сварочным оборудованием. Технология ArcReach® от Miller Electric Mfg. LLC находится на переднем крае современных возможностей.
Используя только стандартные сварочные кабели и совместимый источник питания, цифровой блок дистанционного управления ArcReach или дополнительные устройства подачи проволоки подключаются прямо к вашему стержневому наконечнику или порошковой горелке. С помощью этих принадлежностей вы можете не только регулировать силу тока, напряжение и другие параметры управления дугой, но также просматривать и настраивать программы и процессы сварки прямо на сварном шве.Это избавляет от необходимости возвращаться к источнику питания или использовать отдельный громоздкий и легко повреждаемый проводной аналоговый пульт дистанционного управления.
Кроме того, на некоторых новейших источниках питания аппарат автоматически компенсирует любое падение напряжения на сварочном кабеле, поэтому все, что вы предварительно настроили на аппарате, — это именно то, что вы получите при дуге. Нет необходимости самостоятельно набирать или вводить правильные параметры.
Заключительные мысли
Если вы давно не вносили изменений или улучшали свою сварочную операцию, подумайте об оценке некоторых из новых решений, представленных сегодня на рынке.Внедрение этих передовых методов для сварных моментных соединений и стыков колонн в полевых условиях требует предварительных затрат времени и денег, но, учитывая, сколько вы, вероятно, оставите на столе, это небольшая цена.
Моментостойкие соединения — SteelConstruction.info
В данной статье рассматриваются моментные моментные соединения, которые используются при проектировании одноэтажных и многоэтажных зданий, в которых используются сплошные рамы.
В статье обсуждаются наиболее часто используемые типы соединений с сопротивлением моменту.Рассматривается использование стандартных соединений для соединений балка-колонна и балка-балка, и представлен обзор процедур проектирования на основе Еврокода 3. Рассматриваются как болтовые, так и сварные соединения. Также представлены соединения колонн и основания колонн.
Типовые болтовые соединения балки с колонной концевой пластины
[вверху] Типы моментных соединений
Моментостойкие соединения используются в многоэтажных несвязных зданиях и в одноэтажных зданиях с портальным каркасом.Соединения в многоэтажных рамах, скорее всего, будут болтовыми, соединениями концевых пластин на всю глубину или соединениями с удлиненными концевыми пластинами. Там, где требуется более глубокое соединение, чтобы обеспечить более крупное плечо рычага для болтов, можно использовать соединение с вытяжкой. Однако, поскольку это приведет к дополнительному производству, этой ситуации следует по возможности избегать.
Для конструкций портальной рамы почти всегда используются соединения с сопротивлением моменту натяжения на карнизе и вершине рамы, так как в дополнение к увеличению сопротивлений соединений, задняя часть увеличивает сопротивление стропила.
Наиболее часто используемые соединения с сопротивлением моменту — это болтовые соединения балки с колонной на концевой пластине; они показаны на рисунке ниже.
Концевая пластина удлиненная с усилением
Вместо болтовых соединений балка с колонной можно использовать сварные соединения. Эти соединения могут обеспечить полную непрерывность момента, но их производство дорого, особенно на месте.Сварные соединения балки с колонной могут быть изготовлены в производственном цехе с помощью болтового стыкового соединения внутри опоры балки в положении с меньшим изгибающим моментом. Сварные соединения также используются при строительстве зданий в сейсмоопасных зонах.
Другие типы соединений с сопротивлением моменту включают:
Один аспект, который не рассматривается в этой статье, — это сварные соединения между
полые секции. Однако руководство по проектированию сварных соединений для полых профилей Celsius®355 и Hybox®355 можно получить в Tata Steel.
[вверх] Совместная классификация
Проектирование стыков в стальных конструкциях в Великобритании регулируется BS EN 1993-1-8 [1] и его национальным приложением [2] .
BS EN 1993-1-8 [1] требует, чтобы соединения классифицировались по жесткости (как жесткие, полужесткие или номинально штифтовые) или по прочности (как полная прочность, частичная прочность или номинально штифтовые). Классификация жесткости актуальна для упругого анализа рам, классификация прочности — для рам, анализируемых пластически.Стандарт определяет модели соединений как простые, полунепрерывные или непрерывные, в зависимости от жесткости и прочности. Сопротивляющиеся моменту соединения обычно бывают жесткими и имеют полную или частичную прочность, и, таким образом, соединения являются непрерывными или полунепрерывными.
В большинстве ситуаций проектная идея заключалась в том, чтобы муфты, сопротивляющиеся моменту, были жесткими и моделировались как таковые при анализе рамы. Если бы соединения были фактически полужесткими, поведение соединения необходимо было бы учитывать при анализе рамы, но UK NA [2] не одобряет этот подход до тех пор, пока не будет накоплен опыт использования численного метода расчета жесткости при вращении. .
Пункт 5.2.2.1 (2) BS EN 1993-1-8 [1] отмечает, что соединение может быть классифицировано на основе экспериментальных данных, опыта предыдущих удовлетворительных характеристик в аналогичных случаях или расчетов, основанных на испытании. свидетельство.
Национальное приложение [2] Великобритании предлагает дополнительные пояснения, а в NA.2.6 комментирует, что соединения разработаны в соответствии с SCI P207 [3] . (версия BS 5950 Зеленой книги по моментным соединениям) могут быть классифицированы в соответствии с рекомендациями в этой публикации.
SCI P207 [3] был обновлен с учетом BS EN 1993-1-8 [1] и был переиздан как SCI P398.
[вверх] Классификация жестких соединений
Соединения правильной пропорции, соответствующие рекомендациям по стандартизации, данным в SCI P398 и рассчитанные только на прочность, обычно можно считать жесткими для соединений в каркасах одноэтажных порталов. Для многоэтажных несвязанных рам жесткость вращения является основополагающей для определения устойчивости рамы.Поэтому проектировщик должен либо оценить жесткость соединения (в соответствии с BS EN 1993-1-8 [1] ) и учесть это при проектировании рамы и оценке устойчивости рамы, либо, если при расчете рамы предполагались жесткие соединения. , убедитесь, что конструкция подключения соответствует этому предположению. Для соединения с торцевой пластиной можно предположить, что соединение является жестким, если удовлетворяются оба следующих требования:
- Использование относительно толстых торцевых пластин и потенциально усиленного фланца колонны
- Сила сдвига стеновой панели колонны не превышает 80% расчетного сопротивления сдвигу.
Если это невозможно, следует использовать более прочную колонну или предусмотреть подходящее усиление.
Если нельзя предположить наличие жесткого соединения, соединение следует считать «полужестким», а гибкость соединений учитывается при оценке устойчивости рамы.
Моментно-резистивные соединения неизменно дороже в изготовлении, чем простые соединения (только срезанные). Хотя стоимость материалов компонентов в соединении (пластин, болтов и т. Д.) Может быть незначительной, моментные соединения обычно требуют большего количества сварки, чем другие соединения.Сварка — дорогостоящая операция, которая также требует осмотра после завершения сварных швов.
Местное усиление увеличивает дополнительные расходы: увеличение сопротивления основных элементов всегда следует рассматривать как экономичную альтернативу. Местное усиление часто затрудняет соединение с малой осью, что увеличивает стоимость.
Закручивания требуют большого количества сварочных работ и поэтому дороги. Когда они используются для увеличения сопротивления элемента, например, в стропилах портальной рамы, их использование оправдано, но бедра могут быть дорогостоящим вариантом, если они предусмотрены только для обеспечения возможности болтового соединения.
[вверху] Стандартные соединения
Несмотря на то, что не существует стандартных соединений с моментным сопротивлением, принципы стандартизации остаются важными для структурной эффективности, рентабельности строительства и безопасности. Обычно рекомендуется следующее руководство, по крайней мере, для целей первоначального проектирования:
- Болты M20 или M24 класса прочности 8.8, с полной резьбой
- Болты с поперечным центром 90 или 100 мм (калибр)
- Болты с шагом 90 мм по вертикали
- Фитинги S275 или S355 (концевые пластины, стыковые пластины и ребра жесткости)
- Торцевые пластины 20 мм с болтами М20; Торцевые пластины 25 мм с болтами M24.
[вверху] Болтовые соединения балки с колонной
Болтовые соединения торцевой пластины между балками и колоннами двутаврового или двутаврового сечения, как показано на рисунке ниже, спроектированы с использованием подхода, описанного в BS EN 1993-1-8 [1] . Болтовые соединения торцевой пластины и соединения вершины, в которых используются аналогичные процедуры проектирования, рассматриваются в разделе, посвященном стыкам.
Типовые болтовые соединения балки с колонной концевой пластины
[вверх] Проектные основы
Усилия в соединении концевой пластины
Сопротивление болтового соединения концевой пластины обеспечивается комбинацией сил растяжения в болтах, прилегающих к одному фланцу, и сил сжатия в подшипнике на другом фланце.Если в балке нет осевой силы, общие силы растяжения и сжатия равны и противоположны. Вертикальному сдвигу противодействуют болты в подшипнике и сдвиг; Обычно считается, что силам сопротивляется, в основном, болтами, примыкающими к компрессионному фланцу. Эти силы схематически показаны на рисунке справа.
В предельном состоянии центр вращения находится на фланце сжатия или рядом с ним, и для простоты конструкции можно предположить, что сопротивление сжатию сосредоточено на уровне центра фланца.
Самый дальний от сжатого фланца ряд болтов будет иметь тенденцию привлекать наибольшую силу натяжения, и в прошлом практика проектирования предполагала «треугольное» распределение сил пропорционально расстоянию от нижнего фланца. Однако, если фланец колонны или концевая пластина достаточно гибки (как определено в NA.2.7 UK NA [2] ), что достигается пластичность, можно использовать полное сопротивление нижних рядов (это иногда его называют «пластическим распределением усилий в ряду болтов»).
- Распределение усилий в болтах
Распределение «Пластик»
[вверх] Метод расчета
Полный метод проектирования соединения концевой пластины обязательно представляет собой итеративную процедуру: выбирается конфигурация болтов и, при необходимости, ребра жесткости; оценивается сопротивление этой конфигурации; затем конфигурацию модифицируют для большей устойчивости или большей экономии, в зависимости от ситуации; Пересмотренная конфигурация повторно оценивается до тех пор, пока не будет достигнуто удовлетворительное решение.
ШАГ 1 | Рассчитайте эффективное сопротивление растяжению рядов болтов. Это включает в себя расчет сопротивления болтов, торцевой пластины, полки колонны, стенки балки и стенки колонны. Эффективное сопротивление для любого ряда может быть таким же, как для изолированного ряда, или как часть группы рядов, или может быть ограничено «треугольным» распределением от уровня сжатого фланца. |
ШАГ 2 | Рассчитайте сопротивления зоны сжатия стенки колонны с учетом силы сдвига в стенке колонны и полки балки. |
ШАГ 3 | Рассчитайте сопротивление сдвигу стенки колонны. |
ШАГ 4 | Если общее сопротивление растяжению превышает сопротивление сжатию (этап 2) или сопротивление сдвигу стенки колонны (этап 3), рассчитайте приведенное эффективное сопротивление растяжению для рядов болтов, если это необходимо для обеспечения равновесия.![]() |
ШАГ 5 | Рассчитайте сопротивление сдвигу рядов болтов. Сопротивление принимается как сумма полного сопротивления сдвигу нижнего ряда (или рядов) болтов (которые, как предполагается, не сопротивляются растяжению) и 28% сопротивления сдвигу болтов в зоне растяжения (при консервативном предположении, что они полностью используются в напряжении). |
ШАГ 6 | Проверьте соответствие всех ребер жесткости конфигурации. |
ШАГ 7 | Убедитесь в правильности сварных швов в соединении. (Обратите внимание, что размеры сварных швов не являются критичными в предыдущих шагах). |
Компоненты, подлежащие оценке в рамках процедуры проектирования
Проверка сопротивления сварного соединения концевой пластины с учетом каждого из компонентов, составляющих соединение, проиллюстрирована на рисунке справа и в прилагаемой таблице ниже.
Зона | Ссылка | Компонент | Процедура |
---|---|---|---|
Напряжение | a | Болт натяжной | Шаг 1а |
б | Гибка торцевой пластины | Шаг 1а | |
c | Изгиб фланца колонны | Шаг 1а | |
д | Натяжение стенки балки | Шаг 1b | |
e | Натяжение полотна колонны | Шаг 1b | |
f | Приварной фланец к концевой пластине | Шаг 7 | |
г | Стенка приварной к торцевой пластине | Шаг 7 | |
Горизонтальные ножницы | ч | Ножницы для стеновых панелей колонны | Шаг 3 |
Сжатие | j | Обжимной фланец балки | Шаг 2 |
к | Балка фланцевая приварная | Шаг 7 | |
I | Стенка колонны | Шаг 2 | |
Вертикальные ножницы | м | Стенка приварной к торцевой пластине | Шаг 7 |
n | Болт ножничный | Шаг 5 | |
п.![]() | Болт опорный (пластина или фланец) | Шаг 5 |
Расчеты, соответствующие этапам проектирования, изложенным выше, подробно описаны в разделе 2 SCI P398.5.
[вверх] Методы усиления
Тщательный выбор элементов во время проектирования часто позволяет избежать необходимости усиления соединения и приведет к созданию более рентабельной конструкции. Однако иногда нет альтернативы усилению одной или нескольких зон соединения. Диапазон используемых ребер жесткости показан на рисунках ниже.
Способы усиления
Тип усиления должен быть выбран таким, чтобы он не конфликтовал с другими компонентами при соединении.Это часто является проблемой с обычными ребрами жесткости, когда вторичные балки соединяются со стенкой колонны.
Обычно существует несколько способов усиления каждой зоны, и многие из них могут способствовать преодолению недостатков в более чем одной области, как показано в таблице ниже.
Тип ребра жесткости колонны | Дефицит | ||||||
---|---|---|---|---|---|---|---|
Лента в натяжении | Фланец в подшипнике | Паутина в сжатом состоянии | Паутина на сдвиг | ||||
| • | • | • | ||||
• | • | • | |||||
Дополнительные пластины стенки | • | • | • | ||||
Диагональные ребра жесткости (N & K) | • | • | • | ||||
Ребра жесткости Морриса | • | • | • | ||||
Опорные пластины фланца | • |
[вверху] Сварные соединения балки с колонной
Целью заводской сварной конструкции является обеспечение того, чтобы соединения главной балки с колонной выполнялись в заводских условиях и могли быть жесткими соединениями полной прочности. Для этого, сохраняя при этом размеры деталей достаточно малыми для транспортировки, к колоннам приваривают короткие отрезки секции балки. Соединение патрубка с остальной частью балки обычно выполняется с помощью болтового соединения крышки. Обратите внимание, что болтовые соединения должны использовать предварительно нагруженные болтовые сборки.
Типовая схема многоэтажного дома показана на рисунке ниже.
Соединения сварной балки с колонной
[вверх] Соединения заводские сварные
Заглушка, приварная заводская
Типичное заводское сварное соединение, как показано на рисунке справа, состоит из короткого отрезка балки, приваренного на заводе к фланцам колонны, и конического патрубка, приваренного к внутреннему профилю колонны на другой оси.Заглушки подготовлены для крепления болтами или приваривания с пластинами крышки, как правило, в местах, где изгибающий момент уменьшился.
Преимущества этого подхода:
- Эффективные моментные соединения с полной прочностью — вся сварка колонны выполняется в контролируемых условиях
- Заготовку можно повернуть, чтобы избежать или минимизировать позиционную сварку.
Недостатки:
- Больше соединений и соответственно более высокие затраты на изготовление
- Заглушки ‘Column Tree’ затрудняют перемещение и транспортировку компонента
- Стыки балок должны быть закреплены болтами или сварены в воздухе на некотором расстоянии от колонны
- Соединительные пластины и болты фланца могут мешать работе с некоторыми типами полов, такими как сборные элементы или металлический настил.
[вверх] Практические соображения
Колонна-манипулятор для приварки заглушек балки к колоннам
Сплошные угловые швы обычно используются для большинства балок малых и средних размеров с фланцами толщиной до 17 мм. Однако многие подрядчики по изготовлению стальных конструкций предпочитают переходить на стыковые швы с частичным проплавлением с наложенными угловыми швами или стыковые швы с полным проплавлением, а не использовать угловые швы более 12 мм.
Чтобы обеспечить хороший доступ для сварки во время изготовления, валы колонн могут быть установлены в специальных манипуляторах и повернуты, чтобы облегчить сварку в нижнем положении к каждой заглушке.
[вверх] Метод расчета
В статически определенных рамах соединение частичной прочности, достаточное для противодействия расчетному моменту, является удовлетворительным. Если рама является статически неопределенной, соединения должны иметь достаточную пластичность, чтобы компенсировать любую неточность расчетного момента, возникающую, например, из-за несовершенства рамы или осадки опор.Для этого сварные швы в соединении должны быть прочными.
ШАГ 1 | Рассчитайте расчетные силы в полках балки на растяжение и сжатие.![]() |
ШАГ 2 | Рассчитайте сопротивления в зоне растяжения и проверьте их соответствие.Если для колонны без жесткости сопротивление неадекватно, определите сопротивление для колонны с жесткостью и проверьте его адекватность. Обычно требуются ребра жесткости фланца колонны. |
ШАГ 3 | Рассчитайте сопротивления в зоне сжатия и проверьте их соответствие. Если для колонны без жесткости сопротивление неадекватно, определите сопротивление для колонны с жесткостью и проверьте его адекватность. |
ШАГ 4 | Проверьте соответствие панели стенки колонны сдвигу.Если неупрочненная панель недостаточна, она может быть усилена, как в случае соединения с торцевой пластиной. |
ШАГ 5 | Проверьте соответствие сварных швов фланцам и стенке. |
Компоненты, подлежащие оценке в рамках процедуры проектирования
Проверка сопротивления соединения сварной балки с колонной с учетом каждого из компонентов, составляющих соединение, показано на рисунке справа и перечислено в прилагаемой таблице ниже.
Зона | Ссылка | Компонент | Процедура |
---|---|---|---|
Напряжение | a | Фланец балки | Шаг 2 |
б | Стенка колонны | Шаг 2 | |
Компрессия | с | Фланец балки | Шаг 3 |
д | Стенка колонны | Шаг 3 | |
Горизонтальные ножницы | и | Ножницы для стеновых панелей колонны | Шаг 4 |
Сварные швы | f, г | Фланцевые швы | Шаг 5 |
ч | Перемычка | Шаг 5 |
Расчеты, соответствующие этапам проектирования, изложенным выше, подробно описаны в SCI P398, Раздел 3. 4.
[вверху] Соединители
Конструкция стыков балок и колонн между двутавровыми или двутавровыми профилями, на которые действуют изгибающий момент, осевое усилие и поперечное усилие сдвига, включает следующие типы стыков:
- Соединения крышки с болтами
- Соединение концевой пластины на болтах
- Соединения сварные.
Конструкция соединенных болтами соединений колонн, которые подвержены преобладающим сжимающим силам, описана в статье о простых соединениях и более подробно в SCI P358.
[вверху] Соединители накладки на болтах
[вверху] Детали подключения
Типовые соединения крышек на болтах
На рисунке показаны типичные соединения крышки с болтовым креплением.
В стыке балок между двумя концами балок остается небольшой зазор. Для небольших секций балки одинарные накладки могут быть достаточными для полок и стенки. Для симметричных поперечных сечений обычно используется симметричное расположение накладок, независимо от относительных величин расчетных усилий во фланцах.
Соединения колонн могут быть опорными или ненесущими. Руководство по проектированию стыков колонн подшипникового типа приведено в SCI P358. Ненесущие стыки колонн могут быть устроены и выполнены как стыки балок.
[вверх] Основа проекта
Стык балки (или стык ненесущей колонны) противостоит сопутствующему расчетному моменту, осевому усилию и сдвигу в балке за счет комбинации сил растяжения и сжатия в накладках фланца и сдвиговых, изгибающих и осевых сил в перемычке. тарелки.
Чтобы получить классификацию жестких соединений, соединения должны быть спроектированы как противоскользящие соединения. Обычно необходимо обеспечить сопротивление скольжению только в SLS (категория B согласно BS EN 1993‑1‑8 [1] , 3.4.1), хотя, если требуется жесткое соединение в ULS, необходимо обеспечить сопротивление скольжению в ULS. (Подключение категории C).
В конструкциях, подвергнутых упругому анализу, стыки болтовых накладок не требуются для обеспечения полной прочности сечения балки, а только для обеспечения достаточного сопротивления расчетным моментам и силам в месте стыка.Однако обратите внимание, что когда стыки расположены в элементе вдали от положения бокового ограничения, необходимо учитывать расчетный изгибающий момент вокруг малой оси сечения, представляющий эффекты второго порядка.
[вверху] Жесткость и непрерывность
Соединения должны иметь достаточную непрерывность по обеим осям. Поэтому фланцевые пластины должны быть, по крайней мере, такими же по ширине и толщине, что и полки балки, и должны выходить на минимальное расстояние, равное ширине полки или 225 мм, по обе стороны от стыка.Минимальные требования к прочности приведены в BS EN 1993-1-8 [1] , пункт 6.2.7.1 (13) и (14). Разработчикам также следует обратиться к примечанию AD393 SCI Advisory Desk.
[вверх] Метод расчета
Процесс проектирования стыка балок включает выбор размеров закрывающих пластин и конфигурации болтов, обеспечивающих достаточное расчетное сопротивление стыка. Этот процесс состоит из нескольких этапов, которые описаны ниже.
ШАГ 1 | Рассчитайте расчетные силы растяжения и сжатия в двух фланцах из-за изгибающего момента и осевой силы (при наличии) в месте стыка.Эти силы можно определить на основе распределения упругих напряжений в сечении балки или, консервативно, игнорируя вклад стенки. |
ШАГ 2 | Определите сопротивления болтов и проверьте их соответствие на фланцах и в стенке.![]() |
ШАГ 3 | Убедитесь, что натяжной фланец соответствует требованиям стыка и заглушек. |
ШАГ 4 | Проверьте соответствие прижимного фланца на стыке и крышках. |
ШАГ 5 | Убедитесь, что существует минимальное сопротивление для непрерывности луча. |
Подлежит проверке соединительные элементы
Вышеупомянутые шаги включают определение значений сопротивления 11 отдельных компонентов болтового соединения, как показано на рисунке справа и перечислено в прилагаемой таблице ниже.
Зона | Ссылка | Компонент | шаг |
---|---|---|---|
Напряжение | a | Крышка (и) фланца | 3 |
б | Болт ножничный | 2 | |
c | Болт подшипник | 2 | |
д | Фланец | 3 | |
Сжатие | и | Фланец | 4 |
f | Крышка (и) фланца | 4 | |
г | Болт ножничный | 2 | |
ч | Болт подшипник | 2 | |
Ножницы | j | Заглушка (и) полотна | 1 |
к | Болт ножничный | 1 | |
л | Болт подшипник | 1 |
Расчеты, соответствующие этапам проектирования, изложенным выше, подробно описаны в разделе 4 SCI P398. 2.
[вверху] Соединения концевых пластин на болтах
[вверху] Детали подключения
Типовые соединения концевой пластины на болтах
Болтовые соединения концевых пластин в виде стыков или вершин в портальных рамах, по сути, являются стороной балки соединений балка-колонна, зеркально отражаясь, образуя пару. Эта форма соединения имеет преимущество перед типом крышки в том, что не требуются болты с предварительным натягом (и, как следствие, необходимая подготовка контактных поверхностей).Однако они менее жесткие, чем детали стыка накладки.
Соединение «бедра на вершине портала» регулярно используется в каркасах одноэтажного портала и обычно считается «жестким» для целей глобального анализа упругости.
[вверх] Метод расчета
Метод проектирования в основном аналогичен описанному для соединений балка-колонна, без оценки сопротивления колонны. Соответствующие шаги и соответствующие вычисления описаны в SCI P398 Раздел 4. 3.
[вверх] Соединение моментов, проходящих через балку
[вверху] Детали подключения
Соединения балки, проходящей через балку, обычно выполняются с помощью соединений торцевой пластины с болтами без предварительного натяжения; типичные детали показаны на рисунке ниже. Болты без предварительного натяга могут использоваться, когда есть только концевые пластины, но когда также используется крышка, следует использовать болты с предварительным натягом, чтобы предотвратить проскальзывание при ULS.
- Типовая балка через стыки балок
[вверх] Метод расчета
Если крышка отсутствует, можно использовать метод проектирования стыков торцевой пластины.Если используется заглушка, она должна быть спроектирована так же, как стыковка заглушки; консервативно можно предположить, что болты концевой пластины несут только вертикальный сдвиг.
Соединение между пластиной и крышкой опорной балкой, как правило, только номинальной, как и момент передается в кручении к опорной балке, как правило, весьма скромный.
Соответствующие шаги и соответствующие вычисления описаны в SCI P398, Раздел 4.4.
[вверх] Сварные соединения
[вверху] Детали подключения
Типовые соединения сварных балок
Сварные стыки в цехах часто используются для соединения более коротких отрезков, поставляемых с заводов или складов.В этих условиях сварные швы неизменно получают «полной прочности» путем стыковой сварки фланцев и стенки. В перемычке могут быть сформированы небольшие угловые отверстия для облегчения сварки фланца.
Типовые сварные соединения колонн
Если соединяемые секции не относятся к одной и той же «прокатке» и, следовательно, незначительно различаются по размеру из-за допусков прокатки, между двумя секциями обычно предусматривается разделительная пластина.При соединении компонентов с другим серийным размером этим методом требуется ребро жесткости стенки в большей части (выровненное с фланцем меньшей части), или может быть предусмотрена вута, соответствующая глубине большего размера.
Соединение на месте может быть выполнено с помощью заглушек, приваренных угловым швом, в качестве альтернативы детали, приваренной встык. В крышках перемычки могут быть предусмотрены болты для временного соединения во время монтажа.
[вверх] Основа проекта
Общие проектные основы для сварных стыков:
- Для статически неопределимых рам, независимо от того, спроектированы ли они пластически или упруго, на фланцах и стенке должны быть выполнены сварные швы полной прочности.
- В статически определенных рамах соединения могут быть спроектированы таким образом, чтобы выдерживать расчетный момент, который меньше, чем сопротивление моменту элемента, и в этом случае:
- Фланцевые сварные швы должны быть рассчитаны на сопротивление силе, равной расчетному моменту, деленному на расстояние между центрами тяжести фланца.
- Сварные швы стенки должны быть спроектированы таким образом, чтобы выдерживать расчетный сдвиг.
- Если есть осевое усилие, оно должно распределяться между фланцами и сварными швами, рассчитанными на эту силу в дополнение к той, которая возникает из-за расчетного момента.
Требование полной прочности для неопределенности необходимо для обеспечения того, чтобы стык был достаточно прочным, чтобы компенсировать любую неточность расчетного момента, возникающую, например, из-за несовершенства рамы, приближений моделирования или осадки опор.
[вверх] Основания колонн
Типичная опорная плита колонны без жесткости
Пример основания колонны, способного передавать момент и осевую силу между стальными элементами и бетонными опорными конструкциями в основании колонн, показан на рисунке слева. Пример показывает столбец базу с неукрепленной опорной плитой. Окоченевшее соединение опорной плиты и основание колонн, отлитое в карманах и другие варианты.Однако жесткие базовые соединения обычно не используются из-за связанных с этим затрат на фундамент.
[вверх] Проектные основы
Конструктивно соединение основания колонны представляет собой болтовое соединение с торцевой пластиной с некоторыми особенностями:
- Осевые силы более важны, чем обычно в соединениях концевых пластин.
- При сжатии расчетное усилие распределяется по площади контакта сталь-бетон, которая определяется прочностью бетона и набивочного раствора или раствора.
- При растяжении сила передается прижимными болтами, закрепленными в бетонном основании.
Как следствие, неподкрепленная опорная плита имеет тенденцию быть очень толстой по сравнению с концевыми плитами соединений балка-колонна.
Чаще всего момент может действовать в любом направлении, и выбираются симметричные детали. Однако могут быть обстоятельства, например некоторые портальные рамы, в которых могут быть уместны асимметричные детали.
Обычно требуется, чтобы соединение передавало горизонтальный сдвиг за счет трения или посредством болтов.Это не разумно, что горизонтальный сдвиг распределяется равномерно на все болты, проходящих через отверстие в клиренсе опорной плиты, если шайба пластина не приварена над болтами в конечном положении. Если горизонтальный сдвиг является большим, сдвиг заглушки приварены к нижней стороне опорной плиты может быть более подходящими. Во всех случаях затирка основания является критической операцией и требует особого внимания.
[вверх] Метод расчета
Процесс проектирования требует итеративного подхода, в котором выбирают пробный базовый размер пластины и конфигурация болта и сопротивлений в диапазоне от комбинированного осевого усилия и момента затем оценки.Соответствующие шаги и соответствующие вычисления описаны в SCI P398, Раздел 5.5.
[наверх] Классификация соединений основания колонны
Жесткость соединения основания, как правило, имеет большее значение для рабочих характеристик рамы, чем другие соединения в конструкции. Большинство незакрепленных опорных пластин существенно жестче, чем типичная деталь концевой пластины. Толщина опорной пластины и предварительного сжатия из колонки способствуют этому.
Однако ни одно базовое соединение не бывает жестче, чем фундамент и, в свою очередь, грунт, на который передается его момент.Многое может зависеть от характеристик этих других компонентов, в том числе от склонности к ползучести при длительной нагрузке. Базовое соединение нельзя рассматривать как «жесткое», если бетонное основание, к которому оно присоединяется, не является относительно жестким. Часто это становится очевидным при осмотре.
[наверх] Список литературы
- ↑ 1,0 1,1 1,2 1,3 1,4 1,5 1,6 1,7 1,8 BS EN 1993-1-8: 2005.Еврокод 3: Проектирование металлоконструкций. Дизайн стыков, BSI
- ↑ 2,0 2,1 2,2 2,3 NA согласно BS EN 1993-1-8: 2005. Национальное приложение Великобритании к Еврокоду 3: Проектирование стальных конструкций. Дизайн стыков, BSI
- ↑ 3,0 3,1 P207 Соединения в стальной конструкции: Моментные соединения, SCI, 1995
[вверх] Дополнительная литература
- Руководство дизайнера по металлу, 7-е издание. Редакторы Б. Дэвисон и Г. В. Оуэнс.Институт стальных конструкций 2012, Глава 28
- Архитектурный дизайн из стали — Требилкок П.
и Лоусон Р. М., опубликованные Spon, 2004 г.
[вверху] Ресурсы
[вверху] См. Также
Обширный обзор практики проектирования и экспериментальных исследований в США, Японии и Европе
7 декабря 2001 г. 10: 0 WSPC / 124-JEE 00059
144 Э. Меле
Попов, Е.П., Пинкни, РБ [1969] » Циклическое изменение текучести в стальных строительных швах », J.
, Struct.Div. ASCE, 95 (ST3), 327–353.
Попов Э. П. и Бертеро В. В. [1973] «Циклическое нагружение стальных балок и соединений»,
J. Struct. Div. ASCE 99 (ST6).
Попов, Э. П., Амин, Н. Р., Луи, Дж. Дж. К. и Стивен, Р. М. [1986] «Циклическое поведение
больших сборок балка-колонна», Engrg. J./AISC,1stquarter,23(1), 9–23.
Попов, Е. П. [1988] «Связи сейсмического момента для MRF», J. Construct. Steel Res. 10,
163–198.
Попов Э.П. и Цай, К. С. [1989] «Характеристики больших сейсмических стальных моментных соединений
при циклических нагрузках», Engrg. J./AISC, 2-я четверть, 9–23.
Попов Э. П. и Блондет М. [1996] «Поведение больших стальных соединений балка-колонна»,
Proc. 11-я Всемирная конф. Earthq. Engrg., Акапулько, Мексика, август, Elsevier
Science Ltd., Paper No. 166.
Попов Е.П., Блондет М. и Степанов Л. [1996] «Применение« собачьих костей »для улучшения
сейсмических свойств стальных соединений », Центр сейсмической инженерии
, Респ.№ UCB / EERC-96/05, Калифорнийский университет, Беркли,
Калифорния.
Roeder, C. W. и Foutch, D. A. [1996] «Экспериментальные результаты для сейсмостойких стальных
соединений моментных рам», J. Struct. Engrg. ASCE 122 (6), 581–588.
Сабол, Т.А., Энгельгардт, М.Д., Отаха, Р.С. и Франк, К.Х. [1996] «Обзор
программы испытаний моментного соединения северного моста AISC», Proc. 11-й WCEE,
World Conf. Earthq. Engrg., Акапулько, Мексика, август, Elsevier Science Ltd.,
Paper No. 857.
Stojadinovic, B. , Goel, S.C. и Lee, K.H. [2000a] «Разработка моментных соединений из стали
после северного моста», Proc. 12-я Всемирная конф. Earthq. Engrg., Auckland,
New Zealand, January, Paper No. 1269.
Stojadinovic, B., Goel, SC, Lee, KH, Margarian, AG и Choi, JH [2000b] “Para-
метрические тесты на неармированные стальные моментные соединения », J. Struct. Engrg. ASCE
126 (1), 40–49.
Тадао, Н., Tetsuya, F. и Keisuke, M. [1997] «При сварке соединений при сборке в цехе
рекомендации по концевым деталям балки в стальных конструкциях2, Proc. STESSA ’97, 2nd
Int. Конф. Стальная конструкция. Seismic Areas, Киото, Япония, август, ред. Маззолани, Ф. М.
и Акияма, Х., 632–639.
Танака, А., Като, Б., Канеко, Х., Сакамото, С., Такахаши, Ю. и Тераока, М. [1997]
«Сейсмическое повреждение стальных соединений между балками и колоннами — оценка из статические
аспектов », Тр.STESSA 1997, 2-й международный Конф. Стальная конструкция. Seismic Areas, Киото,
Япония, август, ред. Маццолани, Ф. М. и Акияма, Х., стр. 856–865.
Таусер Ф., Негро П. и Коломбо А. [1998] «Циклические испытания стальной рамы», JRC
Специальная публикация ELSA № I.98.160, декабрь.
Тераока, М., Мацуо, Ю., Морита, К., Сасаки, С. и Фудзивара, Т. [1997] «Влияние деталей
на конструктивное поведение квадратной трубчатой стальной колонны и Н-образной стальной балки с
смешанное соединение », в« Кобе, повреждение стальных моментных соединений в результате землетрясения »и
, предложенное улучшение» Японского общества стальных конструкций.JSSC Technical
Отчет № 39, июль.
Цай, К.С. и Попов, Е.П. [1988] «Соединения стальных балок и колонн при сейсмическом воздействии на сейсмический момент
систирующих каркасов», Исследовательский центр сейсмической инженерии, Респ. UCB / EERC-88/19,
Калифорнийский университет, Беркли, Калифорния.
Цай К. и Чен К. [1996] «Характеристики моментных соединений балки и колонны из пластичной стали
», Proc. 11-я Всемирная конф. Earthq. Eng., Акапулько, Мексика,
Elsevier Science Ltd., Paper No. 405.
J. Earth. Англ. 2002.06: 111-145. Скачано с www.worldscientific.com
, UNIVERSITA DEGLI STUDI DI NAPOLI FEDERICO II DIPARTIMENTO DI MATEMATICA E APPLICAZIONI — CARLO MIRANDA LIBRARY 14.02.13. Только для личного пользования.
Мы не можем найти эту страницу
(* {{l10n_strings.REQUIRED_FIELD}})
{{l10n_strings.CREATE_NEW_COLLECTION}} *
{{l10n_strings.ADD_COLLECTION_DESCRIPTION}}
{{l10n_strings.COLLECTION_DESCRIPTION}} {{addToCollection.description.length}} / 500 {{l10n_strings.TAGS}} {{$ item}} {{l10n_strings.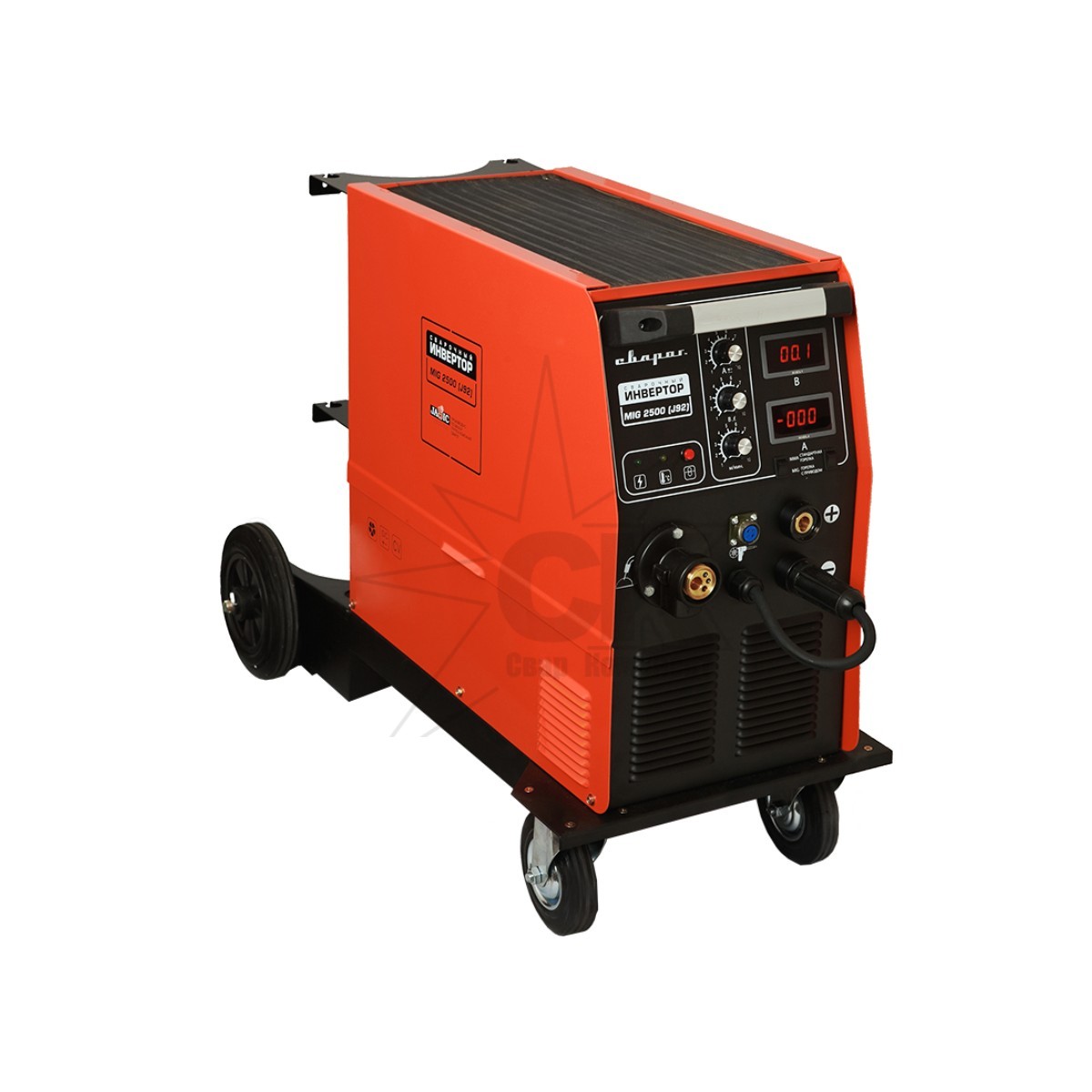
{{l10n_strings.DRAG_TEXT_HELP}}
{{l10n_strings.LANGUAGE}} {{$ select.selected.display}}{{article.content_lang.display}}
{{l10n_strings.AUTHOR}} {{l10n_strings. AUTHOR_TOOLTIP_TEXT}}
Сеймбезопасность сварных стальных зданий с моментным каркасом до северного моста
Это наш второй блог в серии, в которой даются некоторые пояснения к заявлениям, сделанным ранее в этом году в статьях, опубликованных The New York Times, относительно сейсмической опасности и проблем безопасности для высоких зданий, особенно в Сан-Франциско.В этом посте нас интересует вторая статья «В опасности при сильном землетрясении: 39 высотных зданий Сан-Франциско».
В статье сообщается, что «эксперты считают эти стальные высотки до Нортриджа уязвимыми к обрушению только при сильных сотрясениях, вызванных редкими и мощными землетрясениями, подобными тому, что произошло в Сан-Франциско в 1906 году». Хотя это утверждение в целом верно, цель строительных норм и правил до настоящего времени состояла в том, чтобы обеспечить безопасность жизни с небольшой вероятностью обрушения.Для старых зданий с известными дефектами вероятность их обрушения выше. Однако, поскольку сотрясение землетрясения не является равномерным, и даже при сильном сотрясении землетрясения только относительно небольшое количество зданий будет испытывать сотрясения, превышающие уровень MCE, вероятность обрушения на пораженной территории не будет равномерной.
Рис. 1. Схема типичного соединения стального каркаса перед землетрясением до Северного моста. Сварной шов CJP представляет собой непрерывный шов с проплавлением. (Источник: ScientificWorldJournal. В статье также были выявлены основные дефекты сварных стальных зданий с моментом-каркасом, построенных между 1960 и 1994 гг. Типичное соединение каркаса со стальным моментом до Нортриджа (рис. 1) включало болтовое соединение через срезной выступ между колонной и балкой и длинную сплошной сварной шов между полками балки и колонны. Соединения были спроектированы таким образом, чтобы прогибаться при сильном сотрясении и вести себя как пластиковые шарниры, рассеивая энергию землетрясения без потери прочности. Эта текучесть без разрушения предназначена для достижения требования пластичности, которое требует, чтобы люди, находящиеся в здании, могли выйти из сильно поврежденного здания, не подвергаясь опасности обрушения здания.Однако несколько дефектов в этой конструкции были выявлены во время землетрясения в Нортридже 1994 года, в том числе:
- Высокая концентрация напряжений в сварных соединениях
- Сварка с дефектами, при которой не удалось достичь заданной проектной прочности
- Плохо спроектированные и малоразмерные болты, которые не смогли выдержать нагрузки после разрушения сварного участка
Эти дефекты привели к неожиданно ранней податливости и хрупкому разрушению этих соединений. Хотя было очевидно, что эти соединения не работали так, как предполагалось, обнаружение дефектов не обязательно означает, что конструкции не были спроектированы и построены в соответствии со стандартами, действовавшими в то время. Согласно отчету FEMA 350, здания со стальным каркасом, поврежденные землетрясением в Нортридже, соответствовали основным требованиям строительных норм и правил, но не вели себя так, как ожидалось.
Что касается характера повреждений, большинство трещин было ограничено сварным швом между фланцами балки и колонны, при этом болтовая часть соединения оставалась нетронутой.В некоторых случаях часть фланца колонны выдергивалась. В некоторых случаях трещина полностью продвигалась через фланец колонны в стенку, что приводило к ситуации, которая могла привести к обрушению.
Инженеров и владельцев зданий тревожило то, что здание могло выдержать землетрясение без значительных косметических повреждений, но при этом получить значительные структурные повреждения в соединениях моментной рамы. Это говорит о том, что потребность в поперечной и вертикальной силе, которая была разгружена при разрыве стыков, была быстро перераспределена на другие структурные компоненты без заметной деформации здания.Это также предполагает, что эти конструкции обладали некоторой избыточной способностью противостоять полному обрушению, поскольку эти неожиданные трещины вызвали небольшой архитектурный или неструктурный ущерб во время землетрясения в Нортридже.
Учитывая эти наблюдения, можно сделать вывод, что эти стальные здания с моментным каркасом уязвимы для большого экономического ущерба, но полное обрушение всех зданий в результате умеренного землетрясения маловероятно. Согласно модели землетрясения AIR для Соединенных Штатов, вероятность обрушения, вызванного сценарием HayWired, будет меньше 0.1% для стальных конструкций с моментным каркасом, построенных до 1994 г., что согласуется с недавним исследованием сценария USGS HayWired (M7.0), в котором говорится, что «обрушение таких высотных зданий маловероятно в центре Окленда и Сан-Франциско. при землетрясении, таком как главный удар HayWired ».
Разлом Хейворд может в любой момент вызвать следующее крупное землетрясение в районе залива. Прочтите «1868 год: Великое землетрясение в Сан-Франциско»
Применение эффективного полного проплавления Т-образных стыковых швов в моментных сварных соединениях
Guisse S, Jaspart J (1996) Влияние поведения каркаса на конструкцию соединения. В: Соединения в стальных конструкциях III. Пергамон, стр 321–330. https://doi.org/10.1016/B978-008042821-5/50089-4
Wilkinson S, Hurdman G, Crowther A (2006) Моментостойкое соединение для сейсмостойких конструкций. J Constr Steel Res 62 (3): 295–302
Артикул Google ученый
Chen S, Yeh C, Chu J (1996) Соединения балок с колоннами из ковкой стали для сейсмостойкости.J. Struct Eng 122 (11): 1292–1299. https://doi.org/10.1061/(ASCE)0733-9445(1996)122:11(1292)
Статья Google ученый
Тонг Л., Хуанг X, Чжоу Ф., Чен Ю. (2016) Экспериментальные и численные исследования поведения стальных сварных соединений при чрезвычайно низкоцикловом усталостном разрушении. J Constr Steel Res 119: 98–112. https://doi.org/10.1016/j.jcsr.2015.12.015
Статья Google ученый
Дубина Д., Цютина А., Стратан А. (2001) Циклические испытания двусторонних соединений балки с колонной. J. Struct Eng 127 (2): 129–136. https://doi.org/10.1061/(ASCE)0733-9445(2001)127:2(129)
Статья Google ученый
Дубина Д., Стратан А. (2002) Поведение сварных соединений моментных стыков балок рам с колоннами. Eng Struct 24 (11): 1431–1440
Статья Google ученый
Стандарты Новой Зеландии (1997/2001/2007) Стандарт на стальные конструкции. Веллингтон, Новая Зеландия
Европейский стандарт (2005) Еврокод 3: проектирование стальных конструкций. Часть 1–8: конструкция стыков. Утверждено Европейским комитетом по стандартизации (CEN), Брюссель
Американский институт стальных конструкций (2005 г.) Спецификация для зданий из конструкционной стали. Американский национальный институт стандартов, Чикаго, Иллинойс
Google ученый
Steel Construction New Zealand (SCNZ) Steel Connect SCNZ 14.1: 2007 и SCNZ 14.2: 2007. Новая Зеландия
Woerner W, Short A, Ferguson WG (2006) Сейсмические характеристики угловых сварных швов в соединениях, сопротивляющихся моменту. Сварка в мире 50 (5): 51–58. https://doi.org/10.1007/bf03266524
CAS Статья Google ученый
Куробане Ю., Азума К., Макино Ю. (2004) Применимость сварки с пазом PJP к соединениям балка-колонна при сейсмических нагрузках.Соединения в стальных конструкциях V
Saiprasertkit K, Sasaki E, Miki C (2014) Точка зарождения усталостных трещин в несущих крестообразных соединениях в областях мало- и многоцикловой усталости. Int J Fatigue 59: 153–158. https://doi.org/10.1016/j.ijfatigue.2013.09.002
Статья Google ученый
Saiprasertkit K (2014) Оценка усталостной прочности несущих крестообразных соединений в области мало- и многоцикловой усталости на основе концепции эффективной деформации надреза.Сварка в мире 58 (4): 455–467. https://doi.org/10.1007/s40194-014-0129-8
Статья Google ученый
Nie C, Dong P (2012) Определение прочности на сдвиг на основе растягивающего напряжения для угловых швов. Журнал анализа деформации для инженерного проектирования 47 (8): 562–575. https://doi.org/10.1177/0309324712456646
Статья Google ученый
Xing S, Dong P, Threstha A (2016) Анализ перехода к усталостному разрушению в несущих угловых сварных соединениях.Mar Struct 46: 102–126
Статья Google ученый
Xing S, Dong P, Wang P (2017) Количественный критерий определения размеров сварного шва для расчета на усталость несущих угловых сварных соединений. Int J Fatigue 101: 448–458. https://doi.org/10.1016/j.ijfatigue.2017.01.003
Статья Google ученый
Pei X, Dong P (2019) Аналитически сформулированный метод структурной деформации для оценки усталости сварных компонентов с учетом эффектов нелинейного упрочнения.Усталость и разрушение инженерных материалов и конструкций 42 (1): 239–255. https://doi. org/10.1111/ffe.12900
Статья Google ученый
Махин С., Малли Дж., Гамбургер Р. (2002) Обзор программы FEMA / SAC по снижению опасности землетрясений в стальных каркасных конструкциях. Журнал исследований конструкционной стали 58 (5–8): 511–528. https://doi.org/10.1016/S0143-974X(01)00088-8
Статья Google ученый
Миллер Д.К. (1998) Уроки землетрясения в Нортридже. Инженерные сооружения 20 (4): 249–260. doi: http: //dx.doi.org/10.1016/S0141-0296 (97) 00031-X
Ricles JM, Fisher JW, Lu LW, Kaufmann EJ (2002) Разработка улучшенных сварных моментных соединений для сейсмостойкая конструкция. Журнал J Construct Steel Res 58 (5–8): 565–604. https://doi.org/10.1016/S0143-974X(01)00095-5
Статья Google ученый
Накашима М., Иноуэ К., Тада М. (1998) Классификация повреждений стальных зданий, наблюдаемых в результате землетрясения в Хиогокен-Нанбу в 1995 году. Инженерные сооружения 20 (4): 271–281. https://doi.org/10.1016/S0141-0296(97)00019-9
Статья Google ученый
Ватанабэ Э., Сугиура К., Нагата К., Китане Й. (1998) Характеристики и повреждения стальных конструкций во время землетрясения 1995 года Хиогокен-Нанбу. Инженерные сооружения 20 (4): 282–290.https://doi.org/10.1016/S0141-0296(97)00029-1
Статья Google ученый
He J, Yoda T, Takaku H, Liu Y, Chen A, Iura M (2010) Экспериментальное и численное исследование циклического поведения соединений стальных балок с колоннами. Int J Steel Struct 10 (2): 131–146. https://doi.org/10.1007/bf03215825
Статья Google ученый
Мики К., Хирабаяси Ю., Токида Х., Кониси Т., Ягинума Ю. (2003) Детали соединения балки и колонны стальной опоры и их вид усталостного повреждения.Proc Jpn Soc Civil Eng 65: 105–119 (на японском языке)
Google ученый
Мики С., Хирабаяши Ю. (2007) Случаи усталостного повреждения из-за ненадлежащего изготовления стальных мостовых конструкций. Proc Японского общества инженеров-строителей 63 (3): 518–532 (на японском языке)
Google ученый
Морикава Х., Симозато Т., Мики С., Итикава А. (2002) Исследование усталостных трещин в стальных опорах мостов коробчатого сечения и временный ремонт.Proc. Японское общество инженеров-строителей 703: 177–183 (на японском языке)
Google ученый
Lu L-W, Xue M, Kaufmann EJ, Fisher J (1997) Растрескивание, ремонт и повышение пластичности сварных моментных соединений. В: Proceedings, NEHRP Conference and Workshop on Research on the Northridge, California Earthquake, 17 января 1994 г., стр. 637–646
Google ученый
Стоядинович Б., Гоэль С., Ли К., Маргарян А., Чой Дж. (2000) Параметрические испытания неармированных стальных моментных соединений. J. Struct Eng 126 (1): 40–49. https://doi.org/10.1061/(ASCE)0733-9445(2000)126:1(40)
Статья Google ученый
Энгельхардт М. (2000) Циклические испытания сварных неармированных моментных соединений. Неопубликованный отчет, Техасский университет, Остин
Чаттопадхьяй А., Глинка Г., Эль-Зейн М., Циан Дж., Формас Р. (2011) Анализ напряжений и усталости сварных конструкций.Сварка в мире 55 (7): 2–21. https://doi.org/10.1007/bf03321303
Статья Google ученый
Гоял Р., Эль-Зейн М., Глинка Г. (2016) Метод надежного анализа напряжений для прогнозирования усталостной долговечности сварных конструкций. Сварка в мире 60 (2): 299–314. https://doi.org/10.1007/s40194-016-0295-y
Статья Google ученый
Ниеми Э., Фрике В., Мэддокс С. (2006) Подход структурных напряжений в горячих точках к анализу усталости сварных компонентов.vol IIW doc, 13
Scholz W, Clifton C (2000) Улучшенные сварные соединения для сейсмической нагрузки. В: 12-я Всемирная конференция по сейсмостойкости. Новозеландское национальное общество инженерии землетрясений, Силверстрим, Аппер-Хатт, Новая Зеландия
Google ученый
Short A, Woerner W, Voegele G, Moll M (2004) сейсмические характеристики сварных моментных соединений. В: Отчет сварочного центра Новой Зеландии R8-28. Ассоциация исследований тяжелого машиностроения Новой Зеландии (HERA)
Карпенко М., МакКлинток А., Нидермайер Дж. (2013) Рекомендации по проектированию сварных швов для типа сварки мостовых балок, качества и стоимости. Документ, представленный на Steel Innovations 2013, Steel Construction New Zealand (SCNZ)
SAC Joint Venture (1997) Протокол для изготовления, проверки, испытаний и документации испытаний соединения балки и колонны и других экспериментальных образцов. Rep. No. SAC / BD-97, vol 2. Сакраменто, Калифорния
Австралийско-новозеландский стандарт (2014 г.) Сварка конструкционной стали — часть 1: сварка стальных конструкций. Одобрено Советом стандартов Австралии и Советом стандартов Новой Зеландии, опубликовано совместно в Сиднее и Веллингтоне
Австралийско-новозеландский стандарт (2006) Сварочные материалы — трубчатые электроды с сердечником для дуговой сварки металла в среде защитного газа и без защиты газа нелегированных и мелкозернистых сталей — классификация (ISO 17632: 2004, MOD). Одобрено Советом по стандартам Австралии и Советом по стандартам Новой Зеландии, опубликовано совместно в Сиднее и Веллингтоне
Американский национальный стандарт (2010) Сейсмические требования для зданий из стальных конструкций. ANSI / AISC 341-10. Американский институт стальных конструкций, Чикаго (Иллинойс)
Google ученый
Австралийский / новозеландский стандарт (2016 г.) Конструкционная сталь — горячекатаные листы, плиты перекрытия и плиты. Одобрено Советом по стандартам Австралии и Советом по стандартам Новой Зеландии, опубликовано совместно в Сиднее и Веллингтоне
Австралийский стандарт (2003) Методы разрушающего контроля сварных швов в металле. Метод 5.1: макро металлографический тест для исследования поперечного сечения. Утверждено Советом стандартов Австралия, Сидней, Новый Южный Уэльс
Австралийско-новозеландский стандарт (2008) Требования к качеству сварки плавлением металлических материалов — часть 2: комплексные требования к качеству. Одобрено Советом по стандартам Австралии и Советом по стандартам Новой Зеландии, опубликовано совместно в Сиднее и Веллингтоне
% PDF-1.3
%
21 0 объект
>
endobj
xref
21 79
0000000016 00000 н.
0000001928 00000 н.
0000002365 00000 н.
0000002572 00000 н.
0000002942 00000 н.
0000002981 00000 н.
0000003050 00000 н.
0000003127 00000 н.
0000003413 00000 н.
0000003810 00000 н.
0000003831 00000 н. 0000004540 00000 н.
0000004561 00000 н.
0000005109 00000 п.
0000005316 00000 п.
0000005583 00000 н.
0000005604 00000 п.
0000006163 00000 п.
0000006357 00000 п.
0000006727 00000 н.
0000007261 00000 н.
0000007633 00000 н.
0000007967 00000 н.
0000010580 00000 п.
0000012836 00000 п.
0000014487 00000 п.
0000015055 00000 п.
0000015226 00000 п.
0000015549 00000 п.
0000015859 00000 п.
0000016218 00000 п.
0000016395 00000 п.
0000016775 00000 п.
0000017337 00000 п.
0000017581 00000 п.
0000021367 00000 п.
0000021933 00000 п.
0000022292 00000 п.
0000022313 00000 п.
0000022825 00000 п.
0000023274 00000 п.
0000023660 00000 п.
0000024442 00000 п.
0000030081 00000 п.
0000030610 00000 п.
0000030631 00000 п.
0000031492 00000 п.
0000031513 00000 п.
0000032256 00000 п.
0000034152 00000 п.
0000034466 00000 п.
0000035016 00000 п.
0000035180 00000 п.
0000035543 00000 п.
0000035564 00000 п.
0000036379 00000 п.
0000036400 00000 п.
0000037174 00000 п.
0000037357 00000 п.