Соединение разнородных материалов | Сварка и сварщик
Несмотря на значительные трудности сварки, конструкции из разнородных материалов и сплавов в современной технике изготовляют во все большем объеме. Это обусловлено значительными техническими и экономическими преимуществами, которые имеют конструкции из разнородных металлов и сплавов в некоторых технических сооружениях (криогенная техника, энергетические установки, ракетная техника, судостроение, радиоэлектроника).
В конструкциях либо элементах конструкций используют различные комбинации из стали, меди и ее сплавов, алюминия и его сплавов, титана и его сплавов, молибдена, ниобия, тантала.
Для различных пар металлов применяют сварку плавлением и наплавку: дуговую в среде защитных газов неплавящимся и плавящимся электродом, плазменной струёй, толстопокрытыми электродами, под слоем флюса, электронно-лучевую, лазерную.
Для большинства свариваемых пар разнородных металлов или сплавов характерны существенные различия в температуре плавления, плотности, коэффициентах теплофизических свойств, особенно, в коэффициентах линейного расширения.
Для таких металлов, как титан, ниобий, тантал, молибден дополнительные трудности возникают в связи с тем, что при нагреве эти металлы активно взаимодействуют с газами атмосферы. При поглощении газов резко ухудшаются свойства сварных соединений. В большинстве случаев при ограниченной взаимной растворимости для основных комбинаций свариваемых металлов чрезвычайно трудно избежать образования стойких интерметаллических фаз, обладающих высокой твердостью и хрупкостью
В связи с отмеченными особенностями и трудностями сварки разнородных металлов и их сплавов успешно сварить удается отдельные пары металлов способами и приемами, при которых:
1) обеспечивается минимальное время контактирования соединяемых металлов в жидком состоянии, что уменьшает размеры прослоек хрупких интерметаллидов либо даже предотвращает их возникновение;
2) создается надежная защита металла при сварке плавлением от взаимодействия с окружающим воздухом;
3) предотвращается образование хрупких интерметаллидов подбором промежуточных, однородных или комбинированных из разных металлов вставок, хорошо сваривающихся с каждым элементом пары, например, ванадия, тантала, ниобия, бронзы;

Наиболее тонкое регулирование нагрева более тугоплавкого металла свариваемой пары и степени нагрева легкоплавкого металла достигается только при использовании нагрева независимым источником; плазменной струёй и дугой косвенного действия (наплавкой независимой дугой).
Для осуществления быстрого и равномерного контакта свариваемых жидкого и легкоплавкого и нагретого тугоплавкого металлов важное значение имеет состояние поверхности последнего. Невозможно получить соединение, если поверхность тугоплавкого металла загрязнена, окислена, и т.п.
Соединение высоколегированных сталей со средне- или низколегированными и обычными углеродистыми. При сварке таких сталей возникает несколько трудностей. Первая из них заключается в том, что в процессе изготовления сварного соединения или при его эксплуатации в шве часто образуются трещины, которые проходят по его середине или у границы сплавления. Вторая заключается в том, что в зоне оставления может происходить изменения структуры с образованием прослоек, существенно отличающихся от структуры сплавляемых металлов.
Во многих случаях, даже при минимальном проваре, для обеспечения допустимого разбавления наплавленного металла необходимо применять соответствующие сварочные материалы. Для предотвращения трещин, возникающих в металле шва у линии сплавления, разнородные стали необходимо сваривать так, чтобы ширина переходного слоя была минимальной. Это достигается снижением силы сварочного тока и напряжения дуги, а также увеличением скорости сварки.
Одним из основных подходов, направленных на решение вопросов сварки разнородных сталей является получение аустенитного металла шва с высоким содержанием никеля, который обеспечивает вполне стабильную зону сплавления. Преимущество высоконикелевого металла состоит также в близости его коэффициента линейного расширения к этому коэффициенту низко- и среднелегированных сталей. В связи с тем, что никель является дефицитным и довольно дорогим элементом, а также элементом, способствующим образованию горячих трещин в сварном шве, в металле последних целесообразно иметь лишь то количество никеля, которое необходимо для предупреждения образования структурной неоднородности в зоне сплавления с менее легированной сталью.
При сварке перлитных сталей с аустенитными всегда следует применять аустенитные сварочные материалы, обеспечивающие получение наплавленного металла с таким запасом аустенитности, чтобы с учетом расплавления и участия в формировании шва низколегированных составляющих (перлитной стали) обеспечить в высоколегированном шве аустенитную структуру. Приблизительно необходимый состав наплавленного металла для получения шва, обладающего такой структурой может быть определен по диаграмме Шефлера с учетом участия в формировании шва доли основного и дополнительного металлов.
Большой запас аустенитности металла шва позволяет предотвратить образование малопластичных участков с мартенситной структурой в корневых швах и слоях, примыкающих к перлитной стали. Разнородные соединения из перлитной и аустенитной сталей термообработке, как правило, не подвергают, так как режимы термообработки, улучшающие свойства зоны термического влияния одной из свариваемой сталей не оказывают положительного влияния на другую сталь или ухудшают те или иные ее свойства.
Кроме того, из-за разности коэффициентов линейного расширения в перлитной и аустенитной стали высокий отпуск приведет лишь к перераспределению остаточных напряжений, а не к их снятию.
Если сваривается перлитная закаливающаяся сталь с аустенитной, то на кромки закаливающейся стали проводят наплавку аустенитными электродами с предварительным или сопутствующим подогревом, обеспечивающим необходимую скорость охлаждения околошовной зоны. При этом сварочные материалы должны обеспечить получение наплавленного металла с повышенным содержанием никеля. Затем проводят отпуск деталей с наплавленными кромками для устранения закалки в околошовной зоне. После этого детали из перлитной стали с наплавленными кромками сваривают с аустенитной сталью на режимах, оптимальных для последней без предварительного подогрева. При такой технологии отпадает необходимость в последующем отпуске.
При сварке перлитных сталей с 12%-ми хромистыми сталями с целью обеспечения наибольшей пластичности шва применяют сварочные материалы перлитного класса.
При сварке перлитных сталей с 17 … 28%-ми хромистыми сталями использование электродов перлитного класса нецелесообразно из-за чрезмерного легирования хромом из высокохромистой стали и потери им вследствие этого пластичности. Поэтому наиболее подходящими будут сварочные материалы ферритно-аустенитного класса, обеспечивающие достаточную стабильность металла шва даже при наличии значительного проплавления перлитной стали.
Соединение стали одного структурного класса. В практике производства сварных конструкций из сталей одного структурного класса, но разного легирования, к швам не предъявляются требования повышенной прочности или особых свойств, характерных для более легированной стали. Поэтому при выборе сварочных материалов и технологии сварки следует отдать предпочтение материалам и технологии, обычно применяемым для менее легированной стали. Технологические режимы сварки и температуру подогрева следует выбирать по свойствам более легированной стали. При необходимости исключить подогрев можно также производить предварительную наплавку кромок деталей из более легированной стали.
При сварке между собой высокохромистых мартенситных, ферритных и ферритно-аустенитных сталей выбор сварочных материалов должен основываться на необходимости получения швов без трещин и без хрупких участков в них.
При связке 12%-ных хромистых мартенситных сталей с высокохромистыми ферритными и ферритно-аустенитными предпочтительнее выбирать сварочные материалы ферритно-аустенитного класса, т.к. применение ферритных сварочных материалов приводит к получению швов с крупным зерном и низкой пластичностью в исходном состоянии после сварки. В ходе термообработки следует принимать меры к ускоренному охлаждению для предупреждения 475 градусной хрупкости. Так как коэффициенты линейного расширения высокохромистых сталей различных марок и ферритно-аустенитных швов близки, то термообработка приводит к почти полному устранению сварочных напряжений.
При сварке разнородных аустенитных сталей следует иметь в виду повышенную склонность аустенитных швов к образованию горячих трещин. Поэтому при выборе сварочных материалов следует прежде всего исходить из необходимости надежного предотвращения возникновения горячих трещин в шве. Технология сварки этих сталей зависит от соотношения содержания в металле хрома и никеля (запаса аустенитности). Если сваривают разнородные стали с малым запасом аустенитности то можно использовать материалы, рекомендуемые для сварки как одной, так и другой стали. При этом, предупреждение образования в шве горячих трещин обеспечивается получением металла шва с аустенитно-ферритной структурой с регламентированным количеством феррита.
При сварке между собой сталей с большим запасом аустенитности необходимо использовать сварочные материалы, позволяющие получить в шве однородную аустенитную или аустенитно-карбидную структуру при обязательном дополнительном легировании элементами, повышающими стойкость против образования трещин.
Соединение стали с алюминием и его сплавами. Процесс затруднен физико-химическими свойствами алюминия. Выполняется в основном аргонодуговая сварка вольфрамовым электродом. Подготовка стальной детали под сварку предусматривает для стыкового соединения двусторонний скос кромок с углом 70°, так как при таком угле скоса прочность соединения достигает максимальной величины. Свариваемые кромки тщательно очищают механически или пескоструйным способом, или химическим травлением, затем на них наносят активирующее покрытие. Недопустимо применение дробеструйной очистки, так как на поверхности металла остаются окисные включения. Наиболее дешевое покрытие — цинковое, наносимое после механической обработки.
Особенностью сварки алюминия со сталью, по сравнению с обычным процессом аргонодуговой сварки алюминиевых сплавов, является расположение дуги; в начале наплавки первого шва — на присадочном прутке, а в процесс сварки — на присадочном прутке и образующемся валике, так как при длительном воздействии теплоты дуги на поверхность стали происходит преждевременное выгорание покрытия, что препятствует дальнейшему процессу сварки.
После появления начальной части валика дугу нужно зажигать вновь (после перерыва) на алюминиевом валике. При сварке встык дугу ведут по кромке алюминиевой детали, а присадку — по кромке стальной детали, таким образом, что жидкий алюминий натекает на поверхность стали, покрытой цинком или алитированной.
В зависимости от типа соединения при сварке необходимо соблюдать последовательность наложения валиков шва, обеспечивающую необходимое перекрытие. Чередование валиков с лицевой и обратной стороны предотвращает перегрев стальной детали и преждевременное выгорание цинка с ее поверхности.
Важное значение имеет правильный выбор скорости сварки, так как она определяет время взаимодействия жидкого алюминия со сталью, т.е. определяет толщину и стабильность интерметаллидной прослойки. Для первых слоев скорость сварки меньше, чем для последующих, когда сталь достаточно разогрета.
Соединение стали с медью и ее сплавами. В равновесном состоянии при комнатной температуре медь растворяется в а — Fe в количестве до 0,3%, а железо в меди в количестве до 0,2%. Хрупких интерметаллидов не образуется. В связи с большими скоростями охлаждения при сварке в переходном слое образуется пересыщенный твердый раствор меди с железом, но при содержании до 2…2,5% Fe структурно свободное железо не обнаруживается. Граница оплавления между сталью и медью — резкая, с включениями фазы обогащенной железом различного размера Со стороны стали, примыкающей ко шву, размер зерна увеличивается в пределах зоны шириной 1,5… 2,5 мм. Микротвердость зоны оглавления достигает 58… 62 МПа.
Затруднения при сварке и наплавке меди на сталь связаны с ее физико-химическим свойствами, высоким сродством меди к кислороду, низкой температурой плавления меди значительным поглощением жидкой медью газов, различными величинами коэффициентов теплопроводности, линейного расширения и т.д.
Одним из основных возможных дефектов при сварке следует считать образование в стали подслоя меди, трещин заполненных медью или ее сплавами. Указанное явление объясняют расклинивающим действием жидкой меди проникающей в микронадрывы в стали по границам зерен при одновременном действии термических напряжений растяжения.
В углеродистых и низколегированных сталях трещин мало и размеры их невелики, а в сталях, имеющие аустенитную структуру, количество и размеры трещин резко возрастают. Для аустенитных сталей эффективным барьером для упомянутых трещин является введение ферритной фазы. При содержании феррита свыше 30% в хромоникелевой аустенитной стали не наблюдается проникновение меди в сталь. Это объясняется тем, что феррит не смачивается медью и проникновение меди в микронадрывы не происходит.
Медь, латунь и бронза успешно свариваются со сталью всеми способами сварки плавлением на тех же режимах что и стальные детали соответствующих сечений, но дугу со стыка несколько смещают в сторону меди или ее сплавов.
Для соединений меди и ее сплавов со сталью рекомендуется применять аргонодуговую сварку вольфрамовым электродом, а для наплавки цветных металлов на сталь — наплавку плазменной струёй с токоведущей присадочной проволокой. При сварке обеспечивается равнопрочность сварного соединения (по цветному металлу) при действии статической нагрузки. Сварные соединения имеют так же высокую усталостную прочность.
Соединение алюминия и его сплавов с медью. Кроме значительного различия физико-химических свойств алюминия и меди сварка этих металлов затруднена образованием хрупкой интерметаллидной фазы. Обычно сварку выполняют вольфрамовым электродом в аргоне и по слою флюса. Для улучшения процесса сварки на медь после ее очистки необходимо наносить слой покрытия, который активирует поверхность более тугоплавкого металла, улучшает смачиваемость поверхности мели, алюминия. Наилучшим является цинковое покрытие толщиной 50 … 60 мкм, наносимое гальваническим методом. Технология сварки алюминия с медью такая же, как и алюминия со сталью, т.е. дугу смещают на более теплопроводный металл, в данном случае на медь, на 0,5 … 0,6 толщины свариваемого металла. Для обеспечения стабильной прочности сварных соединений по свариваемой кромке меди необходим скос под углом 45 … 60°.
Сварка разнородных металлов
Сварка разнородных металлов
Получение высококачественной сварной конструкции — это сварка идентичных, или же хотя бы похожих по строению металлов. Однако, существует множество случаев, когда сварные конструкции производятся из металлов различных составов и свойств. Причина для того — износ, высокие температуры или другие условия, где от разных частей сварной конструкции требуются разные свойства.
Это создаёт необходимость производства сварных конструкций из разнородных металлов. Такая необходимость возникает в самых разных сферах производства всё чаще. Данная статья написана, чтобы предоставить информацию по успешному составлению комбинаций между некоторыми из более доступных видов металлов.
В случае качественной сварки металлов разнородных видов прочность полученной конструкции примерно совпадает с показателем прочности одного из двух соединяемых металлов, а именно того, чей показатель более низкий. Таким образом, эта система обладает таким пределом прочности и ковкостью, при которых сварочный шов, соединяющий конструкцию, не сможет разойтись. Соединения могут быть произведены между многими видами металлов с помощью разных способов сварки.
Проблема сварки подобных металлов связана с тем, что для таких процессов вначале нужно изучить фазовую диаграмму интерметаллического соединения. Если между выбранными металлами возможна свариваемость, то это объединение будет успешно произведено. В противном случае этого сделать не удастся.
Соединения между металлами необходимо изучить на предмет подверженности коррозии и деформируемости. Микроструктура такого соединения очень важна. Иногда приходится использовать третий металл, чтобы успешно произвести сварку.
Ещё один фактор, который определяет время службы любого соединения двух металлов – коэффициент теплового расширения. Если коэффициенты двух металлов сильно различаются, то оно может вскоре разрушиться.
Помимо прочего, стоит обратить внимание на различие температур плавления металлов. Она также крайне важна, поскольку из-за этой разницы один из металлов будет расплавлен задолго до другого при едином для обоих элементов температурном воздействии. Когда металлы с разными температурами плавления и коэффициентами теплового расширения нужно объединить, то сварочный процесс с высокой тепловой мощностью поможет произвести соединение быстрее, что, несомненно, является преимуществом.
Расстояние на электрохимической шкале показывает устойчивость металлов к коррозии в интерметаллической зоне. Если они расположены далеко, то коррозия станет серьёзной проблемой.
Использование промежуточного металла
В некоторых случаях, как и упоминалось прежде, можно создать сварочную конструкцию из двух металлов, только использовав нечто в качестве переходного материала. Например, при сварке меди со сталью. Такие элементы невозможно сварить напрямую, но, например, никель можно сварить с каждым из них. Таким образом, с помощью промежуточного металла данное объединение будет произведено.
Использование вставки
Ещё объединить разнородные металлы можно использовав композитную вставку между ними. Эта вставка состоит из другого промежуточного объединения между разнородными металлами, совершенного с помощью сварочного процесса, который не требует нагревания.
Процессы сварки для композитных вставок
Далее следует краткое описание сварочных процессов, которые могут использоваться для создания композитных вставок:
• Cварка взрывом
• Холодная сварка
• Ультразвуковая сварка
• Сварка трением
• Сварка сопротивлением высокочастотным током
• Диффузионная сварка
• Перкуссионная сварка
• Лазерная сварка
• Дуговая сварка
Сваривание алюминия с различными металлами
Металлы обладают широким диапазоном температур плавления. У алюминия она составляет примерно 650 градусов Цельсия, у железа — примерно 1538 градусов. Поэтому при плавке алюминий расплавится задолго до стали.
Фазовая диаграмма сварки алюминия с железом показывает, что сплавы железа с алюминием с долей железа более чем 12 % почти не имеют ковкости. Также, у алюминия и железа большая разница между коэффициентом теплового расширения, теплопроводимостью и теплоёмкостью. Это может стать причиной термических напряжений.
Самый действенный способ – использовать алюминиево-стальные (биметаллические) переходные вставки для сваривания сплавов алюминия со сталью при помощи электродуговой сварки.
Еще один способ — покрыть железо металлом, совместимым с алюминием. Успех в этом случае зависит от того, чем покрывается железо, а также толщины слоя и прочности соединения железа и этого металла. Покрыв цинком железо, можно сварить его с алюминием при помощи дуговой сварки. Для сварки алюминия с нержавеющей сталью можно использовать переходные вставки. Также можно использовать вышеупомянутый метод покрытия.
Сваривание алюминия с медью может быть осуществлено с помощью переходной вставки.
Сваривание меди с различными металлами
Медь и её сплавы можно сварить со сплавами железа и с нержавеющей сталью. Для более тонких частей сварочной конструкции можно использовать аргонодуговую сварку с содержащим сплав меди присадочным прутком. Импульсный режим позволяет сделать получение качественного сплава более простой задачей. Дуга должна быть направлена на медную часть конструкции. Для более широких частей конструкции стоит сперва покрыть сталь вышеупомянутым присадочным материалом. Медь следует предварительно нагреть.
Ещё один метод – наплавить медь никельсодержащим электродом. Рекомендуется сделать два слоя. В этом случае её вначале нужно разогреть примерно до 540 градусов Цельсия.
Медь также можно сварить с нержавейкой, а латунь – со сплавами железа.
Сваривание никелевых сплавов с железом.
Никелевые сплавы, такие как монель и инконель могут быть сварены с низколегированной сталью с помощью любого из процессов дуговой сварки с использованием материалов-наполнителей. Таким же образом их можно сварить с нержавейкой, если использовать подходящий электрод.
В случае, если вам понадобится любое сварочное оборудование, материалы, а также квалифицированная консультация — специалисты компании Земля Сварщиков помогут найти ответ и/или наиболее эффектиное решение поставленной задачи.
Технология сварки разнородных сталей
При сварке разнородных сталей одного структурного класса, но различного легирования, как правило, дополнительных требований к выбору способа сварки и режимов не вводят. Это обусловлено тем, что стали имеют близкие теплофизические свойства, а переходные слои в области границ сплавления мало отличаются от металла шва.
При сварке сталей различных структурных классов, особенно перлитной стали с аустенитной, выбирают способ сварки и режимы, обеспечивающие минимальное проплавление соединяемых металлов. Это позволяет получить высоколегированный шов, приближающийся по составу к присадочному металлу.
Во всех случаях сварочные материалы выбирают из условий предотвращения
формирования хрупкого металла шва, а также предотвращения возможности
образования в зоне сплавления хрупких прослоек: кристаллизационных и
диффузионных.
При сварке сталей одного структурного класса в большинстве случаев используют сварочные материалы, близкие по составу к менее легированной стали. В случае выполнения соединений сталей разного структурного класса (например, перлитного с аустенитной) в большинстве случаев используют высоколегированные сварочные материалы, а в некоторых случаях сплавы на никелевой основе, которые позволяют значительно снизить ширину диффузионных прослоек.
Поскольку при сварке легированных сталей в зоне термического влияния возможно
формирование структур закалки, то для предотвращения их образования используют
подогрев. Температуру подогрева назначают исходя из свойств стали, наиболее
склонной к формированию структур закалки. При этом с целью снижения вероятности
формирования диффузионных прослоек назначают минимально допустимую температуру
подогрева. При выборе температуры подогрева необходимо учитывать не только
свойства свариваемых сталей, но и свойства металла шва. В тех случаях, когда в
металле шва возможно образование структур закалки, температуру подогрева
назначают исходя из свойств металла шва. Структуру металла шва обычно оценивают
по структурной диаграмме.
Когда применение подогрева встречает трудности, используют сварочные материалы, обеспечивающие получение аустенитных швов. Пластичный аустенитный шов позволяет снизить внутренние напряжения в зоне сварки и тем самым предотвратить образование холодных трещин. Следует отметить, что аустенитный шов сдвигает температуру мартенситного превращения перлитной (мартенситной) стали в область более высоких температур. Этому способствуют внутренние напряжения, образующиеся из-за различия коэффициентов линейного расширения.
Развитие мартенситного превращения в области высоких температур позволяет
получить более пластичный мартенсит, так как проявляется эффект самоотпуска.
Иногда для исключения подогрева при выполнении соединения используют
предварительную наплавку на сталь, склонную к закалке, слоя незакаливающейся
стали. Наплавку слоя ведут с подогревом или используют отпуск наплавленной
детали. Толщину наплавленного слоя назначают из условий, чтобы в процессе сварки
закаливающаяся сталь в зоне термического влияния не нагревалась выше температуры
А1 (обычно толщина слоя до 9 мм).
В некоторых случаях для придания определенных свойств металлу в зоне соединения разнородных сталей или снятия внутренних напряжений назначают термообработку. Однако необходимо иметь в виду, что снятие внутренних напряжений возможно только в соединении разнородных сталей одного структурного класса. В сварных соединениях разнородных сталей различного структурного класса из-за различия в коэффициентах линейного расширения в результате термообработки величина внутренних напряжений может возрасти. При назначении термообработки соединений из разнородных сталей необходимо провести оценку возможности формирования диффузионных прослоек.
Таким образом, при назначении термообработки необходима всесторонняя оценка
возможных изменений свойств металла в зоне 140 сварного соединения, а также
величины внутренних напряжений. В большинстве сложных случаев термообработку
(обычно отпуск) назначают, если это приводит к получению в зоне сварного
соединения более пластичного металла. Благодаря повышению пластических свойств
снижается вероятность хрупкого разрушения сварного соединения.
Очень часто вместо высокотемпературного отпуска, который приводит к развитию диффузионных прослоек, используют нормализацию, которая позволяет снизить интенсивность развития диффузионных прослоек. Последнее обусловлено, во-первых, снижением скорости диффузии углерода в аустените при нагреве выше точки А3, во-вторых, снижением стойкости карбидов.
Сварка разнородных металлов — Справочник химика 21
Диффузионная сварка. Способом диффузионной сварки в вакууме можно сваривать как однородные, так и разнородные металлы, сплавы и неметаллические материалы, которые трудно или совершенно невозможно сваривать другими способами. Большой экономический эффект достигается при сварке стали и алюминия, титана и стали, чугуна и стали, металлокерамики и стали. [c.350]Возможность сварки разнородных металлов или сплавов зависит от реакций между металлами в зоне плавления, теплопроводности и разницы в коэффициентах теплового расширения обоих материалов.
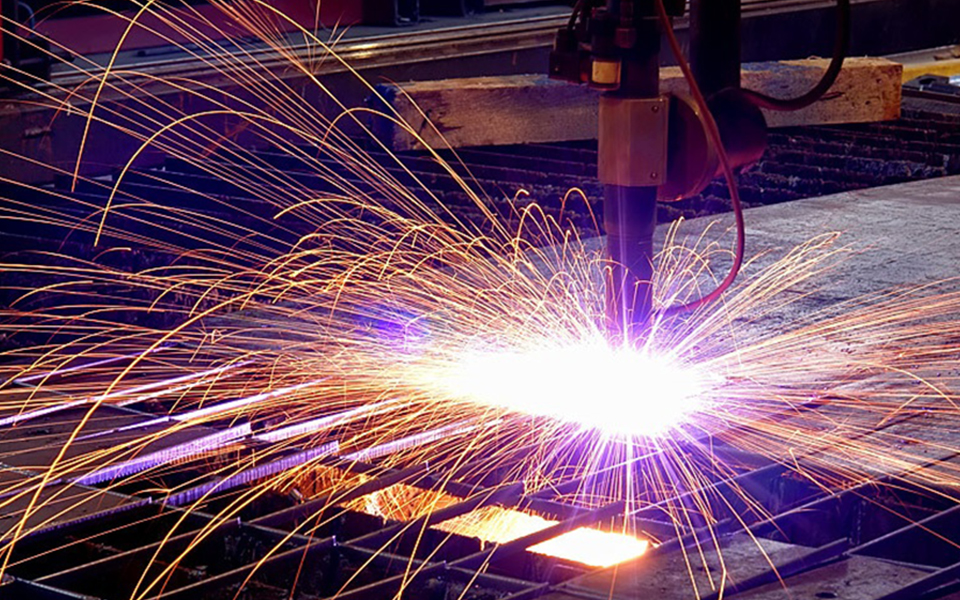
Ниобий и тантал применяют при сварке разнородных металлов, в вакуумной технике и радиоэлектронике. [c.99]
При сварке разнородных металлов во избежание возникновения обычно весьма хрупких интерметаллидов используют несколько промежуточных прослоек в стыке из разных материалов. [c.296]
Механические соединения металлов —сварные, паяные, заклепочные и болтовые — не всегда эффективны. Сварка разнородных металлов — сложный технологический процесс, причем в некоторых случаях, например при сварке магния с алюминием, образуются хрупкие соединения. Затруднительна сварка листов различной толщины. Кроме того, при контакте двух различных металлов возможно образование гальванической пары, способствующей протеканию коррозионных явлений. Сверление отверстий под заклепки и болты увеличивает затраты времени, удорожает производство, наличие отверстий снижает прочность металлических конструкций. Сварные, паяные, заклепочные и болтовые соединения металлов подвержены коррозии, в больщинстве случаев негерметичны и имеют негладкую поверхность. Кроме того, в заклепочных и болтовых соединениях возникает концентрация напряжений в местах расположения болтов и заклепок. [c.190]
Это правило однозначно подтверждается практикой сварки разнородных металлов методами плавления. [c.213]
При сварке разнородных металлов, например обычной малоуглеродистой стали с жаропрочной или нержавеющей, помимо условий свариваемости, необходимо учитывать различие физических свойств материалов — коэффициента линейного расширения, теплопроводности и др. [c.318]
При создании металлических конструкций возникает необходимость соединения различных металлов. Механические соединения — сварные, паяные, заклепочные и болтовые — не всегда эффективны. Известно, что сварка разнородных металлов — очень сложный технологический процесс, а в некоторых случаях, например при сварке магния с алюминием, образуются хрупкие соединения. Затруднительна сварка листов различной толщины. Кроме того, при контакте двух различных металлов возможно образование гальванической пары, способствующей возникновению коррозионных явлений. Пайка легких сплавов еще более сложный, а кроме того и менее надежный способ по сравнению с пайкой сталей. Невозможность полного удаления из некоторых паяных конструкций остаточных флюсов приводит к коррозии металла. Сверление отверстий под заклепки и болты увеличивает затраты времени и удорожает производство. Кроме того, наличие отверстий снижает прочность металлических конструкций.

Определить оптимальное значение доли участия основного металла (уо) при сварке разнородных сталей [c.269]
Металл, используемый для сварки, должен быть высококачественным. По возможности следует применять один вид материала и исключать применение электрохимически разнородных металлов. [c.62]
При эксплуатации производственного оборудования с анодной защитой установлено, что наличие сварных швов, включая швы, соединяющие разнородные металлы, не вызывает ускоренной коррозии. Однако необходимо, чтобы в местах сварки не было трещин и щелей, которые могут явиться причиной развития интенсивной коррозии именно в случае анодной защиты. [c.73]
Контроль биметаллических материалов. Биметаллические материалы состоят из двух разнородных металлов. Их обычно получают прокаткой или сваркой взрывом. [c.607]
Ю. И. Буянов. САП— спеченные алюминиевые пудры. САС— спеченные алюминиевые сплавы. СВАРИВАЕМОСТЬ — свойство материалов, определяющее их пригодность к сварке. Оценивают сопоставлением св-в сварных соединений с одноименными св-вами свариваемого материала или их нормативными значениями, учитывая также экономичность принятого процесса сварки, конструкцию и условия эксплуатации сварного соединения. Понятие С. применяют в основном к металлам, но распространяют его и на стекло, керамику и др. материалы, а также на сварку разнородных материалов (металла со стеклом, металла с графитом и т. п.). С. оценивают применительно к конкретным условиям. Так, под хорошей С. низкоуглеродистой стали, применяемой для изготовления конструкций, эксплуатируемых при [c.331]
При описании технологии изготовления конструкции необходимо обратить большое внимание на методы соединения клепку, сварку, спайку. Рекомендуется приложить инструкции, на основании которых осуществлялись эти операции. Особое внимание следует обратить на контакт различных материалов в конструкции, т. е. на контакты разнородных металлов или металлов и неметаллов. [c.232]
К достоинствам клеевых соединений можно отнести возможность склеивания металлов при комнатной температуре достижение герметичности соединения без применения специальных прокладок, повышенная коррозионная стойкость соединения, так как склеивающее вещество препятствует возникновению электрохимической коррозии простота технологии соединения однородных и разнородных металлов, отсутствие местного ослабления металла, возникающего при сварке от воздействия высоких температур, а в клепаных и болтовых соединениях — за счет отверстий возможность соединения тонколистовых конструкций без их деформации уменьшение массы конструкции и отсутствие необходимости в сложном технологическом оборудовании и высокой квалификации обслуживающего персонала. [c.228]
Как самостоятельный раздел можно выделить локальный спектральный анализ, с помощью которого определяется не средний состав образца, а распределение в нем того или иного элемента. Например, при соединении разнородных металлов сваркой представляет интерес качество сварного шва, глубина и концентрация проникновения одного металла в другой в шве. При анализе горных пород и минералов бывает необходимо знать не только их общий состав, но и состав отдельных вкраплений. Часто возникает необходимость в анализе тонких металлических покрытий, причем в спектре не должны проявляться линии основного металла. Важно знать, как распределяются в сплаве легирующие элементы и т. д. Локальный анализ тоже требует особой техники атомизации, которая мало зависит от объекта анализа. [c.189]
Сварка двухслойных сталей связана с большими трудностями, обусловленными применением различных технологических процессов для сварки основного и плакирующего слоев. В случае сварки двухслойной стали необходимо выполнение требований не только в отношении механической прочности, но и в отношении обеспечения коррозионной стойкости. Определенные трудности при сварке создает наличие в сварном соединении двух разнородных металлов, отличающихся не только по химическому составу, но и по физическим и механическим свойствам. [c.226]
Много ванадия как такового, а также в виде феррованадия используется для улучшения свойств специальных сталей, идущих на изготовление паровозных цилиндров, автомобильных и авиационных моторов, осей и рессор вагонов, пружин, инструментов и т. д. Малое количество ванадия подобно титану и марганцу способствует раскислению, а большое количество увеличивает твердость сплавов. Ниобий и тантал, как дорогие металлы, применяют для легирования сталей только в тех случаях, когда необходима устойчивость по отношению к высокой температуре и активным реагентам. Сплавы алюминия с присадкой ванадия используются как твердые, эластичные и устойчивые к действию морской воды материалы в конструкциях гидросамолетов, глиссеров, подводных лодок. Ниобий и ванадий — частые компоненты жаропрочных сплавов. Ниобий применяют при сварке разнородных металлов. VjOg служит хорошим катализатором для получения серной кислоты контактным методом. Свойства Та О., используются при приготовлении из него хороших электролитических танталовых конденсаторов и выпрямителей, лучших, чем алюминиевые (гл. XI, 3). [c.335]
Механические соединения —сварные, паяные, заклепочные и болтовые — не всегда наиболее эффективны. Известно, что сварка разнородных металлов является очень сложным технологическим процессом, и в некоторых случаях, например при сварке магния с алкуминием, образуются хрупкие соединения. [c.239]
ЦТ-28 Для сварки разнородных металлов (перлитная, хромистая сталь со сплавами на никелевой основе), а также сплавов на никелевой основе марок ХН75Т (ЭИ-435), ХН75ТЮ (ЭИ-437), ХН75М4В4ТЮ2 (ЭИ-765) и аналогичных во всех пространственных положениях постоянным током обратной полярности 80—140 [c.207]
Все однородные материалы обладают физической свариваемостью, т.е, образуют монолитное соединение с химической связью (сталь со сз алью, чугун с чугуном, медь с медью, пластмассы с пластмассами). Не свариваются электрической сваркой плавлением разнородные металлы, не обладающие взаимной растворимостью в идком состоянии свинец-медь, железо-свинец, железо-магний. [c.158]
Термоэлектрический. пирометр (рис. 4-13) состоит из термоэлемента 2 (термопары), соединительных проводов 5 и вторичного прибора гальванометра 8, указывающего температуру измеряемой среды. Термоэлемент состоит из двух проводников разнородных металлов, концы которых сварены. При нагревании места сварки в проводниках возникает электрический ток, сила которого возрастает с повышением температуры. Возникающий в термопаре ток поступает по соединительным проводам в электроизмерительный прибор — гальванометр, шкала 9 которого градиурована в градусах. Стрел- [c.103]
Для сварки разнородных сталей не допускается применение электродов на базе металлов Х25Н13 или Х25Н20 с дополнительным легированием активными карбидообразующими элементами титаном, ниобием, ванадием, вольфрамом (например Х25Н12Т). [c.67]
Изучение структуры и свойств сварных соединений после длительной выдержки (старения) при температурах 250-650°С позволило установить, что разрушение образцов во всех случаях происходит в з. т.в. Это связано с ростсяи зерна, которое увеличивается-до 3-4 балла по сравнению с 7-8 баллом в исходном состоянии. Вздержка при температуре 650°С приводит к собирательной рекристаллизации и направленной диффузии углерода из ферритной в аус-тенитную сталь при сварке разнородных материалов. На поверхности зачищенных сварных соединений и основного металла нет сколь-ко-нибудь значительной окалины. Появляются лишь цвета побежалости. [c.45]
При изготовлении химической аппаратуры из металлов и сплавов в настоящее время основным технологическим процессом является сварка и в ряде случаев пайка. Соединения листового металла склеиванием встык или внахлестку (типы/, 2, 5 и 4 на рис., 13.1) могут быть рекомендованы лишь для разнородных металлов и сплавов, сварка или пайка которых невозможны по технологи изготовления или нерациональны по условиям эксплуатации оборудования. Клеевые соединения листового материала встык (типы 5 и 6 на рис.413,1) широко применяютсж [c. 398]
Для соединения металлов применяются также методы, исключающие (илп допускающие в очень ограниченном масштабе) расплавление основного металла. Супщость этих методов заключается в наплавлении присадочного металла (припоя) на нагретые поверхности, подлежащие соединению. В качестве припоя обычно служат сплавы меди и серебра, и процесс ведется с применением флюсов. При так называемой сварке бронзой (правильнее — сварке латунью) используют местный нагрев и наплавляют присадочный металл (обычно латунь) в зазор между кромками свариваемого изделия при этом может иметь место запотевание основного металла. При пайке твердым припоем расплавленный присадочный металл, не расплавляя основного металла, проникает в зазор между плотно пригнанными кромками за счет действия капиллярных сил. Пайку твердым припоем можно использовать для соединения чугуна, стали, меди и других металлов, а также разнородных металлов. Аналогичным процессом является пайка серебряным припоем, она проводится при температуре красного каления, в качестве припоя используют сплавы серебра с оловом пли серебра с медью. Пайка мягким припоем осуществляется при значительно более низких телшературах (темном калении), и для ее осуществления возможен пшрокий выбор способов нагрева. [c.577]
Наблюдает за правильным монтажом оборудования и коммуникаций, предупреждая ошибки, способствующие возникновению коррозии (замена металла одной марки металлом другой марки, недопустимое сочетание разнородных металлов, неправильная сварка и т. д.). Контролирует качество футеровочных, лакокра- [c.233]
В других случаях, например при сварке разнородных сплавов, картина неоднородности может быть более сложной. Таким образом, сварное соединение представляет собой сложную гетерогенную систему. В связи с этим для сварных соединений характерна повышенная термодинамическая неустойчивость и, следовательно, повышенная чувствительность металла к воздействию агрессивной среды. Наиболее ощутимо влияние термодинамической неустойчивости и неоднородности свойств, вызванной ТФХМВ сварки, проявляется при электрохимической коррозии как в напряженном, так и в ненапряженном состояниях, поэтому остановимся на некоторых характерных особенностях электрохимической коррозии сварных соединений. [c.14]
Использование ультразвука в качестве источника энергии при сварке металлов имеет следующие преимущества перед ранее существовавшими методами сварки отсутствие нагрева значительных объемов металла до температур плавления, в результате чего при ультразвуковой сварке происходит минимальное изменение физико-химических свойств материалов малая электрическая мощность, необходимая для образования сварного соединения, и возможность сварки трудносвариваемых металлов снижение требований к чистоте поверхностей, что дает возможность производить сварку поверхностей плакированных, оксидированных, с лаковым покрытием, воз-. можность сва рки очень малых сечений как двух листов, так и пакета разнородных металлов, а также приварки металлов малых толщин к большим. [c.167]
При сварке разнородных или разнотолщин-ных металлов режимы следует подбирать по более прочному металлу или более тонкому, располагая их в обоих случаях со стороны инструмента. [c.142]
Сварка разнородных материалов Текст научной статьи по специальности «Технологии материалов»
Актуальные проблемы авиации и космонавтики. Технические науки
варов, повышению прочности соединений, уменьшению местных деформаций и др.), позволяет компенсировать недостаток, присущий всем существующим точечным машинам, и тем самым расширить их технологические возможности, а также уменьшить остаточные деформации свариваемых деталей.
Библиографическая ссылка
1. Технология и оборудование контактной сварки / Б. Д. Орлов, Ю. В. Дмитриев, А. А. Чакалев и др. М. : Машиностроение, 1986. .
© Захаров В. В., Козловский С. Н., 2011
УДК 666.655
В. О. Касаткин.
Научный руководитель — А. А. Михеев Сибирский государственный аэрокосмический университет имени академика М. Ф. Решетнева, Красноярск
СВАРКА РАЗНОРОДНЫХ МАТЕРИАЛОВ
Метод диффузионной сварки в вакууме позволяет получать соединения разнородных металлов, отличающихся по своим физико-химическим свойствам, которые не возможно получить другим способом. Технология низкотемпературной диффузионной сварки оличается от «классической» технологии тем, что при соединении деталей между их свариваемыми поверхностями помещается высокоактивная энергонасыщенная промежуточная прокладка на основе ультра дисперсных порошков. Что позволяет снизить основные параметры процесса сварки и сохранить исходные физико-химические и электрофизические свойства материалов.
В связи с бурным развитием наукоемких отраслей, промышленность все больше нуждается в надежных способах соединения только соединения различных металлов, но и металлов со стеклом, пластмассами и разнородных материалов. В настоящее время широко применяются соединения с керамикой.
Метод диффузионной сварки [1] в вакууме позволяет получать соединения разнородных металлов, отличающихся по своим физико-химическим свойствам, которые не возможно получить другим способом, изготавливать изделия из многослойных композитных материалов. Расход энергии при диффузионной сварке в 4…6 раз меньше, чем при сварке плавлением и при контактной сварке. Диффузионная сварка гигиенична: нет вредных излучений, брызг металла, мелкодисперсной пыли, как при многих других способах сварки. Но главное преимущество диффузионной сварки — это возможность образования соединения с минимальной деформацией деталей, не превышающей 5 % [2].
Технология низкотемпературной диффузионной сварки металлических и неметаллических материалов, как в одноименном, так и в разноименном сочетании. Отличие этой технологии от «классической» технологии диффузионной сварки состоит в том, что при соединении деталей между их свариваемыми поверхностями помещается высокоактивная энергонасыщенная промежуточная прокладка на основе ультра дисперсных порошков [3]. Применение такой прокладки по-
зволяет расширить номенклатуру свариваемых материалов, так как промежуточный слой исключает образование хрупких интерметаллидов в зоне соединения, что наблюдается при соединении без прокладки; снизить напряжения в зоне сварки между материалами, отличающимися своими коэффициентам линейного термического расширения; снизить основные параметры процесса сварки: температуру, сварочное давление, время сварки, что позволяет сохранить исходные физико-химические и электрофизические свойства материалов [4].
Библиографические ссылки
1. Диффузионная сварка материалов : справ. / под ред. Н. Ф. Казакова. М. : Машиностроение, 1981.
2. Новиков В. Г., Екимов А. И., Прокопьев С. В. Достижения и перспективы развития диффузионной сварки // Материалы конференции. М. : МДНТП им. Ф. Э. Дзержинского, 1987.
3. Бачин В. А., Квасницкий В. Ф., Котельников Д. И., Новиков В. Г., Полушкин Г. П. Теория, технология и оборудование диффузионной сварки / под общ. ред. В. А. Бачина. М. : Машиностроение, 1991.
4. Новиков В. Г., Екимов А. И., Семичева Л. Г. Способ изготовления пьезоэлементов. Авт. св. СССР. № 963573. МКИВ 06В1/06, 1982, Бюлл.
© Касаткин В. О., Михеев А. А., 2011
АНАЛИЗ ПРОЦЕССА СВАРКИ РАЗНОРОДНЫХ МАТЕРИАЛОВ ПО ДИАГРАММАМ СОСТОЯНИЯ
СВАРКА РАЗНОРОДНЫХ МЕТАЛЛОВ
Определенная температура и иногда давление, необходимые и достаточные для сварки однородных материалов, при сварке разнородных материалов также необходимы, но еще недостаточны. В этом случае материалы обладают различными физико-химическими свойствами, и свойства сварного шва будут определяться свойствами нового материала, который образовался в зоне шва в результате прошедших процессов. Поэтому основная цель при сварке разнородных материалов заключается в направленном регулировании этих процессов [30].
О характере физико-химического взаимодействия между двумя материалами можно судить по соответствующим диаграммам состояния. Эти диаграммы построены для равновесных условий и отвечают стабильному состоянию, между тем как процесс сварки метастабилен. Это обстоятельство необходимо учитывать при пользовании диаграммами состояния, с помощью которых можно представить только первую приближенную схему процесса сварки.
Рассмотрим наиболее характерные случаи сварки двух разнородных материалов с использованием диаграмм состояния.
Многие свариваемые материалы образуют непрерывный ряд твердых растворов. Металлическими сочетаниями, которые образуют непрерывные ряды твердых растворов являются: медь — никель, серебро — золото, никель — платина, хром — молибден, кадмий — магний и др.
Одна из возможных диаграмм такой пары представлена на рис. 1. Пусть материал А плотно под давлением соприкасается с материалом В, и температура на границе соприкасания их постепенно повышается. Вначале, когда температура нагрева не достигла еще значения температуры плавления, но превысила температуру рекристаллизации, в местах контакта соприкасающихся выступов будет про
исходить объединение, срастание зерен обоих материалов с образованием твердого раствора за счет взаимной диффузии материалов А и Б, т. е. начинается процесс сваривания. В создании сварного соединения начнет принимать участие и жидкая фаза, когда температура нагрева достигнет температуры плавления более легкоплавкого материала. По мере повышения температуры количество жидкой фазы увеличивается, и содержание в ней более тугоплавкого материала повышается. Жидкой фазы при некоторой температуре будет вполне достаточно для обеспечения сварки без приложения давления. Глубина области твердого раствора и, следовательно, градиент концентраций будет определяться для данных условий временем и температурой процесса.
Рис. 1. Диаграмма двух свариваемых материалов, образующих непрерывный ряд твердых растворов. |
Б соприкасались идеально |
Если бы материалы А и ровными поверхностями, то для получения полного соединения достаточен был бы одноатомный слой диффузионной зоны. В действительности, из-за неровностей соприкасающихся поверхностей глубина диффузионной зоны гораздо больше.
В пограничных слоях химический состав твердого раствора вследствие продолжающейся диффузии будет несколько отличаться от его состава в средней зоне. При медленной кристаллизации из расплава шов приобретает состав, соответствующий диаграмме на рис. 1. Качество получаемого сварного соединения будет определяться полнотой протекания диффузии соединяемых металлов, т. е. качеством полученного твердого раствора на границе соприкасания.
Несколько иная картина наблюдается при сварке — пайке разнородных металлов. Определяющую роль здесь имеет процесс смачивания — его продолжительность и температурные условия. При кратковременном смачивании в принципе возможно получение качественного соединения. При длительном смачивании протекают сопутствующие процессы — растворение и взаимная диффузия соединяемых металлов, которые не оказывают вредного действия.
Более разнообразная картина получается при сварке плавлением разнородных металлов. Состав и структура шва зависит от соотношения расплавляемых металлов в металле шва, характера перемешивания и скорости остывания жидкого металла. Если при сварке жидкая смесь состоит в основном из более легкоплавкого металла А, то при затвердевании у границ свариваемых металлов будет отлагаться послойно твердый раствор в в противном случае — у границ свариваемых металлов будет отлагаться послойно твердый раствор А в Б переменного состава. В каждом случае сначала выделяется твердый раствор обогащенный более тугоплавким элементом, а затем менее тугоплавким. Быстрое, но недостаточное перемешивание и затем большая скорость охлаждения металла (например, при электроннолучевой сварке) приводят к существенному усложнению структуры шва. Наряду с указанными слоями кристаллизации в металле шва обнаруживаются вихревые образования, слоистая и ячеистая неоднородность [57].
Свариваемые материалы зачастую образуют твердые растворы с ограниченной растворимостью. Как известно, возможны два случая ограниченной растворимости компонентов в твердом состоянии: с образованием эвтектики и с образованием перитектики.
Наиболее характерным является первый случай, для которого типичные сочетания — это сталь — медь (бронза), медь — цинк и др.
При сварке металлов, обладающих ограниченной растворимостью в твердом состоянии, на первом этапе нагрева
протекают также диффузионные процессы. Как только температура достигнет эвтектической, в зонах, расположенных непосредственно на границе, появится жидкая фаза —* эвтектика a — f — (З (рис. 2). При дальнейшем повышении температуры количество жидкой фазы увеличивается и состав ее изменяется.
Рис. 2. Диаграмма двух свариваемых материалов, образующих ограниченную область твердых |
При сварке — пайке такой пары металлов на границе сплавления фиксируется прослойка, представляющая собой твердый раствор на основе более тугоплавкого металла. В случае сварки плавлением обоих металлов структура шва весьма неоднородна*
Наряду с диффузионными участками можно заметить наличие структурно свободных участков более тугоплавкого материала. Для такого типичного сочетания, каким является сталь—медь (бронза), возможны следующие варианты процесса сварки:
а) с направлением источника нагрева на медь (бронзу) —» сварка — пайка. Образующаяся прослойка характеризуется четкими границами (рис. 3, а). Сварное соединение такого типа обладает низкими прочностными и пластическими свойствами и разрушается по диффузионной прослойке;
б) с направлением источника нагрева на сталь—’сварка плавлением. Образующаяся в области сплавления обоих металлов диффузионная прослойка не имеет четких границ с медью, а прорастает в нее в виде вытянутых кристаллов (рис. 3, б).
Наличие переходного слоя с проросшими в бронзу кристаллитами стали препятствует возникновению сплошной диффузионной прослойки, а наличие самых кристаллитов на границе сплавления создает дополнительную механическую
Рис. 3. Микроструктура (х 300) аргонодуговой наплавки бронзы Бр. АМц 9-2 на сталь марки СтЗ:
а — с направлением источника на бронзу; б —* с направлением источника на сталь.
связь меди (бронзы) со сталью. Механические свойства прослойки такого типа намного выше, чем при сварке — пайке. Следует иметь в виду, что для обеспечения высоких механических свойств соединений сварка плавлением меди со сталью должна обеспечивать содержание стали в шве не более 10%.
Многие свариваемые материалы образуют химическое соединение. Образование химического соединения является основным препятствием для получения качественного соединения. Пусть свариваемые материалы образуют сплавы, диаграмма состояния которых изображена на рис. 4. В этом случае кроме твердых растворов а и р в сварном шве образуются химическое соединение эвтектики а + и (3 + у. В условиях сварки образование твердых растворов, а также химического соединения происходит с определенной скоростью и в большой степени зависит от температуры и выдержки. Типичная картина зависимости начала образования химических соединений (интерметаллидов) в твер
до-твердом состоянии для ряда сочетаний металлов (А1—Fe, А1—Ті, Nb—Fe и др.) на примере композиции алюминий — сталь показана на рис. 5. Из этого примера следует, что получение композиционного соединения без прослойки, состоящей из химического соединения, возможно при сравнительно небольших температурах его нагрева. Для этой цели обычно используется давление штамповкой, прокаткой, взрывом и другими методами. При повышении температуры контакта период времени до образования химических соединений резко сокращается.
Рис. 4. Диаграмма свариваемых материалов, образующих химическое соединение. |
В этих условиях получить качественное соединение удается только при сварке—пайке, а в случае значительного проплавления обоих соединяемых
f 575 О 20 НО 60 80 100 120 ПО 160 180 Время, мин Рис. |
наблюдается при сварке— пайке сочетаний металлов никель — алюминий, алюминий — сталь, никель *—• цинк, олово — медь и др. Не все соединяемые материалы могут вступать между собой во взаимодействие с образованием на границе соприкосновения твердого раствора, химического соединения или эвтектики. Может оказаться, что свариваемая пара материалов (например, металл —• металлоид) обладает настолько различными свойствами, что между ними невозможно образование даже эвтектики. В этом случае можно обеспечить процесс сварки, применяя промежуточный материал. Этот третий материал подбирают так, что он может вступить в физико-химическое взаимодействие как с одним, так и с другим соединяемым материалом, или так, что он вступает во взаимодействие с одним материалом, а полученный продукт в свою очередь вступает в реакцию с другим соединяемым материалом.
металлов образуется большое количество химических соединений, повышающих хрупкость шва. Свойства композитного соединения, получаемого при сварке — пайке, во многом определяется толщиной интерметаллидной прослойки, образующейся в стыке. Характерная зависимость скорости роста подобной прослойки приведена на рис. 6
— цинк. Аналогичная закономерность роста прослой — 530 °с ки химических соединений
510 °С
на примере композиции сталь 50 |
Рис. 6. Зависимость скорости роста интерметаллической прослойки от температуры в паре сталь — цинк. |
* Этот промежуточный материал («переходное соединение») готовится методами порошковой металлургии таким образом, что концентрация свариваемых материалов в нем монотонно возрастает (и соответственно снижается для друго
го материала) при переходе от одного края стыка к другому [58].
Используя этот метод, изделия из двух материалов соединяют посредством непрерывного ряда сплавов с целью получения постепенного переходного соединения от одного материала к другому.
Необходимо отметить, что применимость диаграмм состояния для целей сварки ограничена. Диаграмма показывает лишь, какие фазы могут образоваться в равновесных условиях. Однако она не может предсказать, какие фазы появятся в условиях, отличных от равновесных, и в какой форме данная фаза будет присутствовать в сплаве.
Хрупкая компонента может быть совершенно безвредна (или даже действовать как упрочнитель) в случае, если она распределена между зернами сплава в виде мелких включений. Она же может создать угрозу разрушения материала, если присутствует в виде непрерывных полос-строчек по границам зерен или в виде прослойки между двумя металлами,
Сварные соединения алюминий •— медь, алюминий — латунь предназначены для работы в электрических машинах, аппаратах и трансформаторах, которые эксплуатируются в различных атмосферных условиях. Коррозия алюминия при контакте с медными сплавами …
Исследования электрических параметров не дают полной характеристики биметаллических сварных Соединений. И поэтому наряду с измерением токов, потенциалов и поляризаций большое значение для практических целей представляют и исследования коррозионной стойкости в …
Ю. Эванс [40] приводит данные о количественных потерях железа в 1%-ном растворе NaCl, находящегося в контакте с алюминием: Потери железа равны 9,8 мг, а алюминия — 105,9 мг. Цифры показывают, …
Сварка разнородных сталей :: Книги по металлургии
СВАРКА ВЫСОКОЛЕГИРОВАННЫХ РАЗНОРОДНЫХ СТАЛЕЙ
1. Сварка высокохромистых разнородных сталей
В современных металлоконструкциях в ряде случаев возникает необходимость высоколегированные стали сваривать не только со средне- и низколегированными или обычными углеродистыми, но и между собою. При этом необходимо соединять стали разных классов, например высокохромистые мартенситные с ферритными или аустенитными или перечисленные стали со сталями переходного класса (аустенито-ферритными, аустенито-мартенситными и мар-тенсито-ферритными). Сварка таких разнородных сталей имеет свои особенности.
Высоколегированные хромистые стали объединяют стали мар-тенситного, ферритного и мартенсито-ферритного классов. Наиболее распространенными в сварочном производстве являются мартенситные стали 15X11МФ, 18Х11МНФБ, 11Х11Н2В2МФ, 20Х12ВНМФ, 16Х11Н2В2МФ, 20X13, 25Х13Н2, 13Х14НЗВ2ФР; ферритные — 08X13, 12X17, 08Х17Т, 15Х18СЮ и мартенсито-ферритные стали 15Х6СЮ, 15Х12ВНМФ, 18Х12ВМБФР, 12X13, 14Х17Н2. Перечисленные стали мало отличаются по содержанию основных легирующих элементов. Поэтому для их сварки нет надобности применять сварочные материалы, обеспечивающие получение металла шва химического состава, промежуточного между составом свариваемых сталей. Они во всех сочетаниях могут свариваться с применением материалов, предназначенных для сварки любой из используемых в данном соединении стали. В этом состоит первая особенность сварки высокохромистых разнородных сталей.
Основная же особенность сварки рассматриваемых сталей обусловлена тем, что в зоне термического влияния их либо образуется малопластичная структура (мартенситные стали), либо происходит чрезмерный рост зерна, приводящий к значительному снижению ударной вязкости (ферритные стали). Поэтому необходимо принимать меры, исключающие образование околошовных трещин или уменьшающие снижение вязких свойств в зоне термического влияния свариваемой стали, которое здесь не может быть восстановлено даже последующей термической обработкой.
Вероятность образования околошовных трещин, как это следует из гл. I, в значительной мере зависит от степени снижения в зоне термического влияния пластических свойств свариваемой стали. Это снижение зависит от химического состава свариваемой стали, и прежде всего от содержания углерода и легирующих элементов, снижающих температуру у — Μ превращения и упрочняющих твердый раствор. При определенном химическом составе стали вероятность образования околошовных трещин зависит от погонной энергии сварки, т. е. от ее режима. С понижением погонной энергии (снижениетока или повышение скорости сварки) металл околошовной зоны охлаждается быстрее, вследствие чего повышается степень его закалки и поэтому увеличивается вероятность образования околошовных трещин.
Следует отметить, однако, что возможность предотвращения околошовных трещин при сварке сталей мартенситного класса изменением режима сварки ограничена. Поэтому сварка их производится, как правило, с высоким (250—300° С) подогревом, а сварное соединение непосредственно после сварки подвергается отпуску при температуре 700—750° С. Лишь при небольших толщи ,нах (до 10 мм) и при отсутствии жестких закреплений соединяемых элементов сварку мартенситиых сталей можно производить без подогрева. Если эти стали используются в конструкциях, предназначенных для эксплуатации без динамических (ударных) нагрузок, сварку их без подогрева можно производить и при больших толщинах. Но в этом случае необходимо применять сварочные материалы, обеспечивающие получение металла шва аустенитного класса. Однако сварные соединения высокохромистых мартенситиых сталей с аустенитным швом имеют существенный недостаток. Прочность металла их шва значительно ниже прочности свариваемой стали. Кроме того, в зоне сплавления таких соединений в процессе термической обработки возможно такое изменение структуры сплавляемых металлов, которое приводит к снижению работоспособности конструкции. Поэтому сварку сталей мартенситного класса с применением материалов, обеспечивающих получение аустенитного металла шва, рекомендуется производить лишь в конструкциях которые не подвергаются термической обработке, а в случае необходимости — лишь в конструкциях, эксплуатируемых при статических нагрузках без значительных давлений.
Рост зерна в зоне термического влияния высокохромистых сталей ферритного класса зависит от времени пребывания металла этой зоны при температурах выше 1100° С, т. е. прежде всего от по тонной энергии сварки. Чем больше погонная энергия сварки
(выше мощность дуги, меньше скорость сварки), тем больше время пребывания металла зоны термического влияния при температурах, вызывающих рост зерна, тем крупнее образуются зерна. Поэтому конструкции, в которых используются высокохромистые стали ферритного класса, следует сваривать на режимах, обеспечивающих минимально возможную погонную энергию, т. е. максимально снижать ток и максимально повышать скорость сварки.
Время выдержки металла зоны термического влияния при температурах, вызывающих рост зерна, зависит также от степени разогрева выполняемого соединения. Чем выше его разогрев, тем медленнее охлаждается металл зоны термического влияния и тем больше времени пребывает он при температурах, вызывающих рост зерна. По этой причине конструкции, в которых используются высокохромистые ферритные стали, не следует сваривать с подогревом. Более того, многослойную сварку таких конструкций необходимо производить с охлаждением после наложения каждого слоя до минимально возможной температуры, вплоть до комнатной. В случае изготовления конструкции, в которой высокохромистая ферритная сталь должна свариваться со сталью мартенситного класса, сварку которой, как показано выше, следует производить с подогревом, чтобы избежать вредного влияния его на околошовную зону ферритной стали, свариваемые кромки последней облицовываются слоем металла, менее склонного к росту зерна. Толщина этого слоя должна быть не меньше ширины участка перегрева, присущей используемому режиму сварки, т. е. 5—6 мм.
Зачастую конструкции из высокохромистых разнородных сталей должны обладать необходимой коррозионной стойкостью в жидких агрессивных средах. Воздействие же на эти стали термического цикла сварки, для которого характерны высокотемпературный нагрев и быстрое охлаждение, приводит к потере общей коррозионной стойкости в зоне термического влияния и появлению склонности к межкристаллитной коррозии. Поэтому для того, чтобы получить сварное соединение, стойкое против коррозии, его следует подвергать отпуску по режиму, применяемому для обработки стали соединения, требующей более низкой температуры отпуска.
Как уже указывалось, для сварки высокохромистых сталей, особенно мартенситного класса, нередко применяются сварочные материалы, обеспечивающие получение металла шва аустенитной структуры. При изготовлении конструкций, предназначенных для работы в агрессивных средах, следует учитывать, что наплавленный металл аустенитного класса, если он является хромоникелевым сплавом, из-за большого содержания никеля в серосодержащих средах склонен к сульфидной коррозии. Такой наплавленный металл взаимодействует с сернистыми соединениями, образуя сульфиды никеля и эвтектику Ni— Νi3S8. Поэтому для упомянутых конструкций аустенитные материалы, если их использование неизбежно, следует применять другого типа, например, хромомарганцевые.
Что такое сварка разнородных металлов?
Какие факторы нужно учитывать в процессе сварки?
Когда сварщик соединяет два разнородных материала, он должен учитывать несколько факторов, прежде чем выбрать лучший метод сварки и инструменты. Эти факторы зависят от состава металлов, потому что даже сплавы одного и того же металла подпадают под категорию разнородных металлов. Например, углеродистая сталь и нержавеющая сталь имеют разные свойства и требуют такого же планирования, как и сварка разных металлов, таких как медь и алюминий.
Физические и химические свойства — это два из множества факторов, которые должен учитывать сварщик при планировании сварочных работ с разнородными металлами. Узнайте больше об этих факторах и о том, как сварщик может преодолеть различия в металлах, изменив аспекты проекта.
1. Точки плавления металлов
Поскольку при сварке плавлением обычно плавятся некоторые из обоих оснований, температуры плавления обоих металлов играют важную роль в типе выполняемой сварки и используемом присадочном материале.Сварщику необходимо использовать температуру, при которой плавятся оба металла. Высокая температура и быстрая сварка могут уменьшить серьезные проблемы с целостностью готового соединения. Использование методов, которые не плавят металлы, также может преодолеть трудности, связанные с различными точками плавления.
2. Коэффициенты теплового расширения обоих металлов
Коэффициент теплового расширения описывает способ изменения размера объекта при изменении температуры этого объекта. При сварке разнородных металлов коэффициенты теплового расширения каждого металла не должны сильно отличаться, чтобы избежать проблем с готовым сварным швом.
Когда металлы имеют значительные различия в коэффициентах теплового расширения, изменения температуры вокруг сварного соединения могут вызвать чрезмерную деформацию сварного шва. В частности, напряжения будут сосредоточены на интерметаллической зоне, где два металла смешиваются вместе с наполнителем. Сварное соединение имеет большую вероятность термической усталости в этой интерметаллической зоне, особенно в приложениях с большим количеством температурных циклов.
Сварщики, которые соединяют металлы с разными коэффициентами теплового расширения, могут завершить работу с некоторыми изменениями.Чтобы уменьшить вероятность того, что различия в тепловом расширении вызовут термическую усталость в соединении, сварщики могут использовать методы, которые соединяют металлы с минимизацией интерметаллической зоны или которые не требуют плавления обоих металлов.
3. Электрохимические различия
Различия в электрохимии металлов связаны с возможностью коррозии в интерметаллической зоне. Металлы, которые расположены ближе друг к другу по электрохимической шкале, обеспечивают более простой процесс сварки, чем те, которые расположены далеко друг от друга.Коррозия поражает интерметаллическую область, когда электрохимические различия велики. Поиск способов минимизировать интерметаллическую зону может уменьшить проблемы с суставами из-за электрохимических различий.
4. Растворимость каждого металла
Одним из наиболее важных факторов для прочного шва между различными материалами является растворимость каждого металла. В идеале металлы должны интерполироваться друг с другом. Однако некоторые металлы не совместимы таким образом. В таких случаях использование третьего металла, растворимого в обоих, может помочь в создании сварного шва.
Например, использование никеля в качестве промежуточного металла на обеих поверхностях может помочь создать желаемую прочность. Обработка стали и меди слоем никеля перед их сваркой создает сварное соединение, которое соединяет никель с никелем. Поскольку никель является растворимым металлом как для меди, так и для стали, он хорошо прилегает к каждой стороне соединения.
Это использование никеля является одним из примеров использования композитной вставки между разными металлами. Методы сварки без плавления обычно наносят материал вставки на обе поверхности.При сварке деталей композит на обоих краях основных металлов позволяет выполнять сварку аналогично.
5. Окончательное использование сварного компонента
И наконец, применение сварного компонента должно учитывать выбор методов сварки для разнородных материалов. Например, сварная деталь, используемая в котле, может пройти несколько термических циклов, которые проверят прочность сварного шва. Холодные температурные циклы вызывают большую нагрузку на сварное соединение, чем горячие.
Кроме того, для сварных соединений, используемых в контакте с жидкостями электролита, требуется присадочный материал с коррозионной стойкостью, превосходящей оба основных металла. Выбор присадочного материала с более низкой устойчивостью к коррозии может ускорить гальваническую коррозию.
Другой пример применения, затрагивающий компоненты, используемые для сварного соединения, включает добавление износостойких пластин к тяжелому строительному оборудованию. Присадочный металл должен уменьшать растрескивание в зоне термического влияния при одновременном уменьшении нагрузки на соединение.
Окончательное использование также важно, когда один основной металл не будет испытывать таких же температурных изменений, как другой.В котле один основной металл может подвергаться термоциклированию, а другой — нет. Чтобы предотвратить повреждение в этом случае, необходим наполнитель, который одновременно защищает от термической усталости и снимает напряжение.
Как сваривать разнородные металлы?
Для сварки разнородных металлов не существует простого стандартизованного процесса, применимого ко всем ситуациям. Использование нестандартных методов сварки или добавление переходных материалов к поверхностям может быть шагом, который сварщик должен предпринять для успешной сварки.
При таком большом количестве факторов сварщики должны продемонстрировать знание металлов, с которыми они работают, при соединении разнородных металлов. Чтобы избежать проблем, связанных с термической усталостью, растрескиванием сварного шва или другими признаками плохого соединения, всегда консультируйтесь с профессиональным сварщиком при выполнении проектов, требующих соединения разнородных металлов. Опытный сварщик может выбрать лучший метод сварки, материалы и приспособления для удовлетворения требований проекта и свойств металла.
Сварка разнородных металлов — обзор
6 Тенденции в сварке стали, устойчивой к ползучести
Разрушение при ползучести в сварных швах различных сталей является предметом недавнего интереса; Проведено множество исследований возникновения повреждений в многопроходных сварных швах из нержавеющей стали.Предполагается, что разрушение из-за ползучести в сварном шве из нержавеющей стали начинается в области короны, а затем переходит в область корня. В недавних исследованиях было обнаружено, что воздействие высокой температуры в течение длительного времени приводит к укрупнению выделений, которые становятся неэффективными барьерами для движения границ зерен; в результате зернограничное скольжение вызывает зарождение полостей в тройных точках границ зерен или на границе раздела между преципитатом и матрицей. В недавнем исследовании, проведенном для оценки образования полости в аустенитной нержавеющей стали, сваренной плавлением, был использован подробный анализ микроструктуры и анализ методом конечных элементов (15).Наблюдение за микроструктурой поврежденного образца поперечного шва показало, что полости зарождаются в области коронки и распространяются по направлению к области корня. Наблюдение за зарождением и ростом полостей при разном уровне напряжения показало, что зарождение полостей в области коронки может быть приписано неоднородности на микро- и макроуровне, присутствующей в сварном шве. Микронеоднородность в области сплавления происходит из-за различий в морфологии выделений и градиента прочности в области кроны и корня.
Кроме того, геометрия зоны сплавления варьируется от коронки к корневой области и приводит к макронеоднородности. Это вызывает значительный градиент напряжения, что может быть подтверждено анализом методом конечных элементов. Обе эти неоднородности действуют синергетически в образовании сварных полостей, которые инициируют повреждение ползучести в сварном шве нержавеющей стали. Однако микронеоднородность является преобладающим фактором, вызывающим повреждение сварного соединения при высоком уровне напряжения (Vijayanand et al. , 2017).
Недавняя тенденция к повышению эффективности тепловых электростанций проистекает из обязательств по защите окружающей среды и, следовательно, предполагает использование пара при гораздо более высоких температуре и давлении, чем то, что обычно используется в настоящее время.Это требует использования сталей с гораздо более высокой прочностью на разрыв при ползучести, для которых хромомолибденовые стали рассматриваются как потенциальный выбор. Чтобы справиться с этим измененным сценарием рабочей температуры 650 ° C или выше, трубы пароперегревателя в котле должны быть изготовлены из сталей с высокой коррозионной стойкостью, а именно из аустенитных нержавеющих сталей разновидностей AISI 304 H, 316 или 347 H. Таким образом, материал для паровых коллекторов должен быть подвергнут сварке разнородных металлов, особенно нержавеющей стали, которая будет использоваться для труб пароперегревателя котла.Эти трубы пароперегревателя должны быть присоединены к коллекторам пара из хромомолибденовой стали. Следовательно, соединение разнородных материалов из нескольких материалов становится проблемой в обеспечении эксплуатационной надежности.
Чаще всего разнородные металлические соединения между ферритными стойкими к ползучести сталями и аустенитными нержавеющими сталями подвергаются преждевременному разрушению, главным образом из-за разницы в их характеристиках. коэффициент температурного расширения. Для решения этой проблемы модифицированная сталь 9Cr-1Mo соединяется с аустенитной нержавеющей сталью AISI 304 сваркой трением с использованием трех промежуточных слоев Inconel 625, Inconel 600 и Inconel 800 H. Промежуточные слои привариваются одна за другой к Cr-Mo-стали и, наконец, сваркой трением с нержавеющей сталью; это обеспечивает плавный переход теплового коэффициента расширения. При испытании образцов с одним и тремя межслойными сварными швами было обнаружено, что значительное улучшение сопротивления ползучести материала достигается при трехслойной сварке. Кроме того, было обнаружено, что повреждение из-за ползучести происходит из-за роста полостей, что является результатом комбинированного эффекта диффузии и ползучести по степенному закону.Если имеется большая разница в коэффициенте расширения, свойства ползучести разнородного сварного шва сильно ухудшаются (Akram et al ., 2017).
Усовершенствованная сверхсверхкритическая (AUSC) система выработки электроэнергии была разработана для снижения выбросов углекислого газа более чем на 10% по сравнению с традиционной сверхкритической (USC) системой. В соответствии с тенденцией развития, условия пара, как правило, являются жесткими для обычных жаропрочных сталей с содержанием 9% хрома (9Cr), таких как ASME Gr. 91 и 92 стали. Поскольку температура и давление могут возрасти до 973 К и 35 МПа соответственно, сплавы на основе Ni, такие как сплав 617, сплав 263 и сплавы HR 6W на основе Ni-Fe, рассматриваются в качестве материалов-кандидатов для высокотемпературных деталей. , работающие при температуре выше 923 К. Детали, работающие при более низких температурах, работающих при температуре ниже 923 К, будут изготавливаться из усовершенствованных сталей 9Cr, таких как сталь с высоким содержанием B-9Cr и сталь SAVE12AD, чтобы снизить материальные затраты. Поскольку сталь с высоким содержанием B-9Cr, которая была разработана в Национальном институте материаловедения (NIMS), показала превосходную прочность на ползучесть и стабильность микроструктуры не только в основном металле, но и в зоне термического влияния (HAZ) после сварки, она является один кандидатный материал для системы A-USC.Следовательно, при строительстве системы A-USC неизбежны разнородные сварные швы между усовершенствованными сталями 9Cr и сплавами на основе никеля.
Разные сварные швы между жаропрочными сталями с высоким содержанием хрома и сплавами на основе никеля с присадочным металлом на основе никеля ( Для этой цели необходимо будет принять сплав 82). Однако в условиях высокотемпературной ползучести наблюдается разрушение поверхности раздела между сталью и металлом шва. Наблюдения за фрактографией и микроструктурой показали, что разрушение происходит хрупким образом из-за оксидной выемки на дне U-образной канавки.Затем трещина развивалась по линии скрепления пластично с мелкими ямками, где испытания на твердость по микровиккерсу показали заметное разупрочнение стали рядом с линией скрепления. Кроме того, сталь показала гораздо большее общее удлинение и уменьшение площади, чем металл сварного шва, при низких напряжениях в условиях длительной ползучести, что приводило к несоответствию деформации на границе раздела. По результатам можно сделать вывод, что межфазное разрушение между сталями 9Cr и металлом сварного шва сплава 82 инициируется оксидным надрезом и ускоряется за счет разупрочнения и разницы в пластичности сталей и металла шва (Matsunaga et al.
, 2017).
Сварка разнородных материалов позволяет не догадываться
Сварка разнородных металлов может вызвать проблемы, которые могут привести к проблемам с качеством сварки или образованию трещин, поэтому важно выбрать правильный присадочный металл для области применения и следовать основным передовым методам, чтобы добиться успеха.
Необходимость соединения разнородных материалов, таких как низкоуглеродистая сталь с низколегированной сталью или нержавеющая сталь со сталью, обычна во многих отраслях и сферах применения.Однако многие сварщики подходят к сварке разнородных материалов с неопределенностью, так как не понимают, что требуется для создания прочного шва между двумя разными материалами.
Действительно, сварка разнородных металлов может вызвать некоторые проблемы, которые могут повлиять на качество сварки и привести к таким проблемам, как растрескивание. Выбор подходящего присадочного металла для области применения и следование основным передовым методам могут помочь добиться успеха.
Учитывайте все факторы
Недостаток знаний часто является самым большим препятствием для успешной сварки разнородных материалов, и многие сварщики могут просто не знать, с чего начать.
Если присадочный металл металлургически несовместим с обоими основными материалами, это может привести к растрескиванию или снижению прочности сварного шва. Чтобы определить правильный присадочный металл и параметры сварки, ответьте на следующие ключевые вопросы:
- Какие материалы свариваются? В некоторых приложениях, таких как ремонтная сварка, часто бывает трудно точно знать, какие два материала свариваются. Важно иметь некоторое представление о химическом составе материалов; это помогает заполнить пробелы в отношении свойств и характеристик.Перед началом сварки важно понять основные материалы. Общие способы определения химического состава основного материала включают выполнение искрового теста, отправку образца материала для анализа и консультации с оригинальным производителем или чертежами.
Определение основных материалов позволяет выбрать подходящий присадочный металл в зависимости от их химического состава и механических свойств.
- Каковы требования к конструкции готового сварного шва? Понимание условий эксплуатации готовой сварной конструкции также важно для определения правильного присадочного металла.Например, если сварная деталь будет испытывать высокие напряжения или высокие температуры во время эксплуатации, выбор присадочного металла может быть нарушен. Если присадочный металл имеет гораздо более низкие характеристики прочности или коррозионной стойкости, чем основные материалы, готовая сварная деталь может не служить своей цели.
- Требуется предварительный нагрев? Характеристики каждого основного металла также помогают определить требования к температуре предварительного нагрева и промежуточного прохода. Для двух разных материалов может потребоваться разная температура предварительного нагрева, поэтому знание основных металлов помогает определить наилучшую температуру предварительного нагрева.
Каждое приложение следует оценивать индивидуально. Однако практическое правило при сварке материалов с разными рекомендациями по предварительному нагреву обычно заключается в использовании более высокого рекомендуемого предварительного нагрева.
Часто встречаются комбинации для сварки разнородных металлов. Для достижения наилучших результатов рассмотрите следующие передовые практики.
Сварка A36 — A514
Комбинация этих двух сталей часто используется при сварке конструкций, строительства и тяжелого оборудования.A36 — это низкоуглеродистая сталь, обладающая хорошей прочностью и формуемостью. A514 — это высокопрочная сталь, обычно обеспечивающая предел текучести 100 000 фунтов на квадратный дюйм, в зависимости от марки.
Рекомендации по соединению двух сталей с разной прочностью — выбирать присадочный металл на основе прочности материала с более низкой прочностью. Это потому, что прочность сварного шва никогда не будет больше, чем у элемента с наименьшей прочностью. В этом случае выбор присадочного металла будет основываться на свойствах стали A36.Электрод с низким содержанием водорода E7018 Американского общества сварки (AWS), сплошная проволока ER70-6 и порошковая проволока E71T-1 — хорошие варианты для сварки этих двух материалов.
Хотя выбор присадочного металла основан на низколегированном металле, рекомендуется использовать рекомендации по температуре предварительного нагрева и промежуточного прохода для более высокопрочного материала, которым в данном случае будет A514. Это связано с тем, что для более прочного металла более важны надлежащие температуры предварительного нагрева и промежуточного прохода.Неиспользование надлежащих температур предварительного нагрева и промежуточного прохода может привести к таким проблемам, как растрескивание и потеря прочности некоторых материалов.
Соединение нержавеющей стали серии 3ХХ, такой как 308, 309 или 316, с углеродистой сталью — это комбинация, которая применяется во многих областях, включая сварку трубопроводов и конструкций.
Сварка A36 до 4130
Сталь A36 обычно соединяется с AISI 4130 — низколегированной сталью, которая содержит молибден и хром в качестве упрочняющих агентов, особенно при сварке тяжелого оборудования.AISI 4130 обычно используется для таких компонентов, как валы и детали машин.
Опять же, выбор присадочного металла обычно зависит от прочности низколегированного основного металла из двух. Присадочные металлы с низким содержанием водорода, которые обеспечивают предел прочности на разрыв 70-KSI, такие как порошковая проволока E71T-1 и стержневые электроды E7018, обычно являются хорошим выбором для сварки разнородных материалов со сталью A36.
Следует уделить особое внимание тому, чтобы обеспечить соблюдение надлежащих температур предварительного нагрева и промежуточного прохода для материала 4130.Это будет в некоторой степени зависеть от условий термообработки материала. Обычно рекомендуется сваривать 4130 в отожженном состоянии.
Сварка A36 с листом AR
Износостойкий (AR) стальной лист обычно более устойчив к абразивному износу, чем стальной или низколегированный стальной лист, поэтому его часто используют в тяжелом оборудовании и горнодобывающем оборудовании. Пластину AR можно использовать внутри кузова самосвала, например, для продления срока службы в тяжелых условиях.Пластина AR обычно представляет собой закаленную и отпущенную низколегированную сталь, которая предназначена для использования только в качестве износостойкой пластины.
Применения, требующие соединения стали A36 с AR-листом, как правило, просты, но могут потребоваться небольшие предварительные работы перед началом сварки. Поскольку не существует отраслевого стандарта, регулирующего создание и обработку AR-листа, каждый производитель стального листа может производить AR-лист по-своему. В результате химические и механические свойства этого материала часто варьируются в зависимости от производителя и, следовательно, могут иметь разные требования к предварительному нагреву или рекомендации по присадочному металлу.
В то время как присадочные металлы 70-KSI, такие как электроды E7018, часто подходят для этой разнородной сварки, рекомендуется по возможности связываться с производителем пластин AR для получения подробной информации о составе пластины и конкретных требованиях к присадочному металлу и предварительному нагреву.
Сварка нержавеющей стали с углеродистой сталью
Соединение нержавеющей стали серии 3ХХ, такой как 308, 309 или 316, с углеродистой сталью — это комбинация, которая используется во многих областях, включая сварку трубопроводов и конструкций.Нержавеющая сталь часто используется, когда только определенные части конструкции или сварной конструкции требуют коррозионной стойкости или термостойкости; Для этих частей может использоваться нержавеющая сталь, а для остальных — углеродистая сталь.
Стальной лист, устойчивый к истиранию (AR), обычно более устойчив к абразивному износу, чем лист из стали или низколегированной стали, поэтому его часто используют в тяжелом и горнодобывающем оборудовании.
Присадочный металл из нержавеющей стали марки 309 обычно является хорошим вариантом для этой комбинации, поскольку он помогает улучшить трещиностойкость и обеспечивает соответствующий химический состав сварного шва. Из-за своего химического состава нержавеющая сталь более подвержена деформации, чем сталь. Поэтому рекомендуется сохранять как можно более низкое тепловложение при соединении нержавеющей и углеродистой стали.
Лучшие методы для достижения успеха
Многие сварщики могут быть не знакомы с надлежащими методами соединения разнородных материалов. Хорошее место для начала — определить, какие материалы свариваются, будь то низкоуглеродистая сталь, высокоуглеродистая сталь, низколегированная сталь или нержавеющая сталь.Наличие как можно большего количества информации о спецификациях и характеристиках материалов имеет решающее значение для успеха. Выбор подходящего присадочного металла и правильное использование тепла зависят от типа соединяемых материалов и требований к обслуживанию готового продукта.
Калеб Хейвен (Caleb Haven) — инженер по приложениям, CWI, в Хобарте, www.hobartwelders.com.
Соблюдайте осторожность: сварка разнородных металлов
Объединение разных металлов создает несколько проблем, одна из которых иногда решается с помощью «жертвенного анода». «У нас есть несколько лодочников в штате Wiley Metal, и они знакомы с этим термином. Жертвенные аноды используются на лодках, особенно на тех, которые видят соленую воду. Они «притягивают» коррозию и, таким образом, снижают склонность других соединенных металлических деталей к коррозии. Это подчеркивает, что сварка разнородных металлов создает проблемы, которые с самого начала могут быть не очевидны.
Что мы подразумеваем под непохожим?
Если бы мы предложили приваривать оцинкованную сталь к алюминию 6260, некоторые люди могли бы усмехнуться.Однако это можно сделать, как показывают фотографии на веб-сайте EWI. По общему признанию, это крайний пример, но мы получаем больше запросов на соединение разных марок одного и того же типа металла. Хорошим примером может служить сварка низколегированной стали с аустенитной нержавеющей сталью.
По стоимости
Высокопрочный металл стоит дорого, поэтому дизайнеры используют его только там, где это необходимо. Однако это требует, чтобы изготовитель металла соединил металл высокой прочности с металлом меньшей прочности. Это все больше и больше наблюдается в автомобильной промышленности, где компании обращаются к «индивидуальным сварным заготовкам» (TWB’s.)
TWB — это штамповка из стали с относительно низкой прочностью, к которой привариваются высокопрочные вставки. Затем сборка попадает в другой пресс, который превращает ее в конструктивный элемент корпуса. Это позволяет производителю достичь необходимой прочности при использовании минимального количества дорогостоящего высокопрочного металла.
Менее распространенный драйвер — внешний вид. Дизайнер может захотеть использовать нержавеющую сталь на видимых поверхностях, но для экономии денег будет использовать низколегированную сталь в скрытых областях. Для их соединения есть несколько вариантов: крепеж, клеи и, конечно же, сварка.
Объединение вызовов
При сварке разнородных металлов возникают три основные проблемы:
- Различные коэффициенты теплового расширения.
- Другая металлургия.
- Возможность гальванической коррозии.
Тепловое расширение
После предварительного нагрева, а затем сварки разнородных металлов они сжимаются в разной степени по мере остывания. Поскольку сварка соединяет детали вместе, в результате возникают высокие остаточные напряжения, которые вызывают деформацию и даже растрескивание.Снятие напряжения после сварки помогает, но необходимо учитывать разницу в скорости расширения.
Металлургия
Относительная свариваемость двух металлов определяет, насколько легко они соединятся. Свариваемость указывается в различных стандартах, а также может быть выражена в терминах «углеродного эквивалента». Эта сложная формула позволяет сварщику оценить склонность к растрескиванию и определить температуру предварительного нагрева.
Разница в прочности металла влияет на выбор присадочной проволоки.Обычно сварщик выбирает присадку той же прочности, что и более слабый металл, хотя условия эксплуатации готового изделия (особенно воздействие циклических нагрузок) влияют на его решение.
Гальваническая коррозия
Соединение разнородных металлов и их размещение во влажной среде замыкает электрическую цепь. Некоторые металлы легче отдают свои электроны, чем другие, и это позволяет им быстрее корродировать. Хорошим примером являются цинк и латунь: цинк является более «активным» металлом, поэтому при соединении с латунью во влажной среде он будет быстрее подвергаться коррозии.Вот почему, когда латунь используется на лодках для различных фитингов, она соединяется с цинковым анодом, который вместо этого подвергается коррозии.
При соединении разнородных металлов важно учитывать гальваническую коррозию. Если металлы близки с точки зрения их готовности отдавать электроны (аналогично «активным», как определено «гальваническим рядом»), это меньшая проблема, чем если бы они были разными.
Техника сварки
При должном внимании к свариваемости и условиям эксплуатации можно сваривать разнородные марки стали с использованием газовой дуги. По мере того, как они становятся более разными, нужны и другие методы. TWB обычно сваривают, например, лазером, в то время как для сочетаний материалов, таких как алюминий и нержавеющая сталь, используются более новые и более экзотические методы, такие как сварка трением с перемешиванием.
Соединение разнородных материалов — EWI
Инженеры-конструкторы все чаще сталкиваются с необходимостью соединять разнородные материалы, поскольку они ищут новые творческие конструкции или детали со специально разработанными свойствами.Иногда детали требуется высокая термостойкость в одной области и хорошая коррозионная стойкость в другой. Конструкции могут нуждаться в прочности или износостойкости в одной области в сочетании с высокой прочностью в другом месте. Улучшение способности соединять разнородные материалы с измененными свойствами позволяет использовать новые подходы к легким автомобильным конструкциям, совершенствовать методы производства энергии, создавать медицинские продукты и потребительские устройства следующего поколения, а также использовать в других сферах производства и промышленности.
Соединение разнородных материалов можно описать как объединение материалов или комбинаций материалов, которые часто сложнее соединить, чем два куска одного и того же материала или сплавов с незначительными различиями в составе; тем не менее, многие разнородные материалы могут быть успешно соединены с помощью соответствующего процесса соединения и специальных процедур.
С 1970 года было опубликовано более 20 000 статей о соединении разнородных материалов (DMJ). Большая часть исследований DMJ в этот период времени была связана с металлическими системами, наиболее часто используемыми в промышленности, включая углеродистые и низколегированные стали, нержавеющую сталь, никель, медь и алюминиевые сплавы.Также, начиная с 1980-х и 1990-х годов, наблюдается рост исследований DMJ с участием титановых сплавов, керамики, полимеров и композитных материалов. Эти материалы все чаще используются в машиностроении из-за особых требований к характеристикам коррозионной стойкости, высокого отношения прочности к массе, эрозионной стойкости или жаропрочности.
Наша работа с технологиями твердотельного соединения, особенно с сверхмощным ультразвуковым аддитивным производством (VHP / UAM или просто UAM), инерционной сваркой и сваркой трением с перемешиванием, ведет к появлению множества интересных новых разработок и конструкторских возможностей.
При проектировании соединения из разнородных материалов необходимо учитывать ряд факторов, в том числе:
- Конструкция соединения и толщина материала
- Различия в температуре плавления
- Несоответствие теплового расширения-сжатия при соединении и эксплуатации
- Крепежные и ограничивающие воздействия на соединительные напряжения
- Образование хрупких интерметаллических соединений во время соединения, которые могут привести к хрупким соединениям
- Влияние скорости нагрева и охлаждения на микроструктуру соединения, что может повлиять на прочность и точность контроля подводимого тепла
- Необходим для предварительного и последующего нагрева для минимизации напряжений во время сварки и охлаждения
- Потребности в композитных переходных материалах или специальных присадочных материалах при соединении
- Возможность возникновения проблем гальванической коррозии при эксплуатации
Ключевой вывод из долгой истории и опыта EWI в соединении разнородных материалов заключается в том, что ни один процесс или набор параметров обработки не является наилучшим и не подходит для всех ситуаций для всех комбинаций материалов. У каждого процесса есть преимущества и ограничения. Соединение из разнородных материалов лучше всего рассматривать как специальное приложение с уникальными требованиями. Удачные соединения из разнородных металлов часто жизненно важны для технических характеристик и коммерческого успеха конструкции, часто требуя фирменных разработок. По этим причинам в открытой литературе опубликовано относительно немного исследований по соединению разнородных материалов.
Процессы соединения разнородных материалов можно сгруппировать следующим образом:
- Процессы дуговой сварки плавлением: дуговая сварка в среде защитного металла (SMAW), дуговая сварка вольфрамовым электродом (GTAW или TIG), газовая дуговая сварка металлическим электродом (GMAW) и плазменная дуговая сварка (PAW)
- Прочие процессы сварки плавлением: лазерная сварка, контактная точечная и выступающая сварка, наплавка контактным швом, стыковая сварка оплавлением, плазменная дуга и электронно-лучевая сварка
- Процессы соединения в твердом состоянии: сварка трением с перемешиванием, ультразвуковая сварка, сварка трением и инерционная сварка, диффузионная сварка, сварка взрывом и плакирование валков
- Пайка и пайка
- Клейкое соединение
EWI имеет значительный опыт, работая с нашими членами над разработкой методов соединения для широкого спектра разнородных материалов с использованием большинства этих процессов. Наша работа варьируется от небольших, микросварных приложений до крупномасштабных промышленных работ. На рисунке 3 показана наша система сверхмощного / ультразвукового аддитивного производства (UAM). Эта система создает структуры из ленточных материалов с помощью ультразвуковой сварки высокой мощности, выполняя необходимую обработку каждого слоя и обеспечивая возможность создания уникальных структур из разнородных металлов. В качестве примера посмотрите наше видео с этой системой создания декоративных штифтов из меди и алюминия.
EWI также продвигает технологию пайки разнородных материалов с помощью нашего запатентованного активного припоя EWI SonicSolder (TM), который работает в сочетании с процессом ультразвуковой пайки. Ультразвуковая пайка с использованием EWI SonicSolder предлагает преимущества безфлюсовой и бессвинцовой пайки с возможностью соединения трудно смачиваемых материалов.
Чтобы узнать больше, свяжитесь с нами здесь
Обзор методов соединения разнородных материалов
Примечание редактора: эта статья была адаптирована из официального документа «Методы соединения разнородных материалов: металлов и полимеров», Технологический университет Лаппеенранты, Лаппеенранта, Финляндия, 2013.
Растущее распространение полимерных материалов в конструкциях и автомобилях из-за их малого веса, высокой удельной прочности, эластичности и низкой стоимости стимулировало исследования в области сочетания полимеров и металлов в производстве. Детали, изготовленные с применением соединений металл-полимер, сейчас пользуются большим спросом в автомобильной и авиакосмической промышленности.
Одной из целей использования разнородных соединений является повышение гибкости дизайна продукта, чтобы можно было эффективно и функционально использовать различные материалы в зависимости от их конкретных свойств. Сборки металл-полимер сочетают в себе прочность и пластичность металла с физико-химической стойкостью и легкостью полимеров. Металл используется в секциях, где требуется высокая жесткость и прочность, тогда как пластик обладает уникальными химическими свойствами.
Следовательно, важно максимально увеличить совместный вклад каждого материала, чтобы обеспечить оптимальные эксплуатационные характеристики, сохраняя при этом вес и экономичность.
Однако часто бывает трудно соединить разнородные материалы.Поведение таких соединений редко до конца понимают, особенно при использовании методов склеивания и нагрева.
Современные методы соединения металла с пластиком
Для гибридных соединений металлических и полимерных деталей обычно используются несколько методов соединения. Это склеивание, механическое крепление и сварка.
Каждый способ соединения имеет свои преимущества и недостатки. Наиболее подходящий метод будет зависеть от приложения и услуги.
Механическое крепление. Изначально использовавшийся для соединения металла с металлом, механическое крепление теперь используется и для соединения металла с пластиком. Он заключается в использовании зажимных компонентов, таких как винты и заклепки, для образования стыков без сплавления поверхностей стыков. Это требует механических операций, таких как сверление отверстий и нарезание резьбы.
Для соединений металл-пластик существуют различные типы механических технологий соединения, но в настоящее время упор делается на клепку, поскольку она обеспечивает надежное соединение.Для некоторых типов заклепок требуется цикл нагрева, во время которого заклепки нагреваются перед закреплением, так что заклепки сжимаются при охлаждении, плотно зажимая компонент.
Результаты испытаний показали, что при соединении заклепками металлического и полимерного материала процесс зависит от толщины листа и геометрических параметров заклепки, таких как конструкция инструмента и сила заклепки (см. Рисунок 1 ). Поскольку нижний материал подвергается наибольшей деформации, важно, чтобы полимерный материал был помещен под металлический лист.
Конфигурация соединения часто зависит исключительно от условий эксплуатации, например от того, должна ли она быть герметичной. В некоторых случаях соединение может быть спроектировано таким образом, чтобы допускать несоответствие коэффициента теплового расширения во время сборки. Также может быть выполнено соединение, обеспечивающее свободу движения в плоскости, перпендикулярной зажимному элементу.
Механическое крепление остается наиболее часто используемым методом соединения из-за своей простоты. Однако у него есть ограничения, такие как увеличенный вес компонента и концентрация напряжений вокруг отверстий для крепежа, которые снижают прочность и в конечном итоге вызывают коррозию.
Клей . Адгезионное соединение — это метод соединения в твердом состоянии, который основан на формировании межмолекулярных сил между деталями и самим полимерным клеем для образования соединения (см. Рисунок 2 ). Он предполагает использование полимерного клея, который подвергается химической или физической реакции для образования швов.
Использование клеевого соединения металла значительно расширилось в последние годы из-за разработки очень прочных и жестких клеев, которые могут выдерживать как статические, так и переменные нагрузки.Кроме того, они обычно весят меньше механических креплений, что значительно снижает их вес. Кроме того, распределение напряжений во время нагружения однородно.
Однако клеевые соединения могут оказаться проблематичными, потому что клеевые соединения нельзя разобрать без повреждений и могут выделяться вредные выбросы в окружающую среду. Кроме того, стыки подвержены разрушению под воздействием влаги, влажности и температуры и имеют низкое сопротивление в химически активной среде.
Кроме того, склеивание требует тщательной подготовки поверхности. Свойства поверхности детали в адгезивном соединении играют жизненно важную роль в процессе соединения, а прочность соединения и долговечность соединения могут быть значительно улучшены за счет обработки поверхности деталей перед соединением. Во время предварительной обработки поверхности поверхностное натяжение заготовки увеличивается, но угол контакта с водой уменьшается. Типичные методы предварительной обработки поверхности включают очистку растворителем, изменение химического состава поверхности, истирание и другие топографические изменения.
Дополнительным ограничением является то, что клеевые соединения часто выходят из строя мгновенно, а не постепенно. Наиболее важным ограничивающим фактором для склеивания является неопределенность в прогнозировании долговечности такого типа соединения из-за трудностей с проведением надежных неразрушающих испытаний.
Как механическое крепление, так и адгезионное соединение требуют конфигурации стыка внахлест для достижения необходимой прочности стыка, что затем увеличивает вес, толщину и концентрацию напряжений в конструкции.Это ограничение ограничивает использование этих методов соединения.
Это привело к поиску технологии соединения разнородных материалов, которая имеет большую гибкость конструкции и скорость изготовления, чем клеевое соединение и механическое крепление, а также к развитию подходов к сварке.
Сварка. Обычные процессы сварки, такие как дуговая сварка в защитном металлическом корпусе (SMAW), газовая дуговая сварка вольфрамовым электродом (GTAW), газовая дуговая сварка металлическим электродом (GMAW) и дуговая сварка под флюсом (SAW), использовались для сварки разнородных материалов при сварке металла по металлу. суставы.Однако высокие энергозатраты на эти процессы сварки плавлением приводят к металлургической деформации материала, которая препятствует этому применению, а также к соединениям металла с полимером.
Температура плавления металлов чрезвычайно высока по сравнению с температурой плавления полимеров. Следовательно, полимеры имеют тенденцию разрушаться до того, как металлы расплавятся.
Сварку полимеров можно выполнять только на термопластах. Это ограничение существует потому, что переработка термореактивных материалов и химически сшитых эластомеров характеризуется необратимой реакцией сшивания, которая приводит к разрушению; следовательно, им нельзя изменить форму путем нагрева.Термопласты и термопластические эластомеры могут плавиться и размягчаться под действием тепла из-за ослабления вторичных сил Ван-дер-Ваальса и водородных связей между сцепленными полимерными цепями. Это дает возможность повторно формовать термопласты и термопластические эластомеры под воздействием тепла, и, следовательно, их можно сваривать плавлением.
Новые методы сварки или соединение разнородных материалов
Были разработаны многообещающие методы сварки и новые приложения для существующих методов сварки для соединения разнородных материалов — ультразвуковая сварка, лазерная сварка, сварка трением с перемешиванием и точечная сварка трением — как способ решать проблемы, связанные с традиционными методами соединения.Эффективное применение этих сварочных процессов требует понимания их возможностей и ограничений, а также поведения металлов и полимеров.
1. Ультразвуковая сварка. Ультразвуковая сварка — это технология соединения в твердом состоянии, которая инициирует коалесценцию за счет одновременного приложения энергии локализованной высокочастотной вибрации с умеренным усилием зажима (см. Рисунок 3 ).
Этот способ сварки отличается низким энергопотреблением и требует зажима и позиционирования заготовок между сварочным инструментом (сонотродом) и опорой с помощью статической силы.В металле не происходит никаких микроструктурных изменений.
Заготовки могут быть двумя тонкими листами или толстым и тонким листом в простом соединении внахлест или встык, в зависимости от направления подачи энергии упругих колебаний в зону сварки.
Ультразвуковая вибрация может применяться при сварке как металлов, так и пластмасс, но процесс сварки для каждого из них отличается. Фактически полученный сварной шов зависит от того, как ультразвуковая энергия (вибрация) передается в сварной шов.
При ультразвуковой сварке металла направление ультразвуковых колебаний параллельно области сварного шва. Когда осуществляется ультразвуковая сварка металла, фрикционное действие поверхностей заготовки инициирует твердотельное соединение без какого-либо действия плавления заготовки. При сварке пластмасс все наоборот. При ультразвуковой сварке пластмасс направление ультразвуковых колебаний перпендикулярно области сварки (см. , рис. 4, ).
Исследователи экспериментировали с ультразвуковой сваркой алюминиевых листов с термопластическими композитами, армированными углеродным волокном.В их эксперименте изучалась свариваемость алюминиевого сплава 5754 с полимером, армированным углеродным волокном, толщиной 1 мм и 2 мм соответственно. Они заметили, что качественная сварка произошла с амплитудой около 40 мкм в результате смещения термопластической матрицы, армированной углеродным волокном, что привело к лучшему контакту между листовым металлом и волокном.
Они также заметили, что межмолекулярные реакции в зоне сварного шва образуются, когда оксидные слои на листовом металле отслаиваются во время процесса сварки.Полимерная матрица фактически была смещена из зоны сварки, что позволило пластичному алюминию адаптировать углеродные волокна. Это позволило механически заблокировать соединительные слои и, следовательно, повысить прочность соединения.
Наконец, было замечено, что углеродные волокна окружают алюминиевый сплав в результате пластической деформации алюминиевого листа, таким образом создавая успешный сварной шов между металлом и полимером.
2. Лазерная сварка .Лазерная сварка предлагает уникальные производственные возможности. Он дополняет изготовление и обработку стыков, которые раньше было трудно или невозможно выполнить другими методами сварки. Лазерная сварка металлов и полимеров может использоваться для достижения стабильных металлических, химических и ковалентных связей между металлическими и полимерными гибридными компонентами (см. Рисунок 5).
Были предложены методы прямого лазерного соединения металлов и полимеров, обычно известные как лазерное соединение металла и пластика.Граница раздела металл-полимер нагревается падающим лазерным лучом, и температура плавления достигается в пластическом материале в узкой области, прилегающей к границе раздела. Возникающая в результате высокая температура инициирует образование пузырьков в расплавленном пластике вблизи границы раздела, которые распространяются и диффундируют в расплавленную фазу и, следовательно, увеличивают размер шва между пластиком и металлом (см. , рис. 6, ).
Механизм связывания возникает в результате комбинированного влияния химической связи между пленкой оксида металла и атомами углерода полимеров, а также явления физического связывания, возникающего в результате силы Ван-дер-Ваальса и механического связывания.
Преимущества заключаются в очень коротком времени сварки, небольшом тепловложении и высокой адаптируемости процесса. Высокая прочность соединения может быть достигнута при прямом лазерном соединении металла с полимером, и этот метод применим к нескольким металлам, таким как сталь, титан, алюминий и железо.
Следует отметить, однако, что металл не плавится в этом процессе соединения. Ограничениями являются многие параметры, такие как скорость перемещения и мощность сварки, которые влияют на качество и надежность конечного соединения.Лазерная сварка также имеет ограниченную конструктивную гибкость и подходит в основном для соединений внахлест из-за необходимости эффективного поглощения лазерного луча.
Из-за низкой теплопроводности пластмасс это означает, что тепло остается сосредоточенным в зоне взаимодействия материалов. Кроме того, поведение тепла зависит от оптических свойств пластика, которые зависят от его молекулярного состава, таких как цвет пластика и длина волны падающего луча.
3. Сварка трением с перемешиванием . Этот процесс сварки включает три различных этапа: погружение, перемешивание и втягивание. Во время сварки быстро вращающийся инструмент с измерительным штифтом погружается с определенной скоростью в точку перекрытия сварного шва до тех пор, пока заплечик инструмента не коснется верхней детали. Это вызывает пластическую деформацию вокруг штифта.
При традиционной сварке трением с перемешиванием возникают проблемы при сварке пластмасс. Эти проблемы связаны с плохой теплопроводностью и диффузией из макромолекулярной структуры термопластов.
4. Соединение точек трения. Точечное соединение трением представляет собой вариант линейной сварки трением с перемешиванием, за исключением того, что во время соединения отсутствует линейное перемещение инструмента.
Во время точечного соединения трения трение между штифтом и заготовкой генерирует большую часть тепловой энергии для соединения. Присоединение металлов к полимерам в местах трения включает два различных процесса: врезание втулки и врезание пальца.
В рукав погружаясь, заготовки первоначально перекрывается и зажимается между опорной пластиной и зажимного кольца с металлической частью на верхней части полимерной заготовки (см рисунок 7).Затем инициируется вращательное движение втулки и штифта, при этом обе детали вращаются в одном направлении.
В какой-то момент втулка касается верхней металлической заготовки, вызывая нагрев от трения. Одновременно втулка вставляется в металлическую заготовку, пластифицируя металл, и штифт втягивается, что в результате приводит к образованию кольцевого пространства или резервуара. Затем пластифицированный металл выдавливается в созданный резервуар в результате эффекта погружения рукава.
После завершения процесса соединения втулка отводится от металлической поверхности заготовки, и штифт выдавливает захваченный пластифицированный материал обратно в сварной шов. В результате замочная скважина снова заполняется.
Врезание инструмента настраивается таким образом, что врезание происходит только в металлической заготовке. Это делается во избежание повреждения волокнистой арматуры полимерной заготовки, что может снизить прочность соединения. Пластифицированная металлическая заготовка дополнительно деформируется из-за погружения втулки, в результате чего на поверхности полимерной заготовки образуется металлический выступ.
Точечная сварка трением возможна при сварке разнородных металлов, таких как алюминиевый и магниевый сплав.
Возможность сварки трением с перемешиванием соединений металл-полимер до конца не изучена, в основном из-за различий между сваркой трением с перемешиванием металлов и сваркой трением с перемешиванием пластмасс. Низкая теплопроводность полимеров, наряду с их сложной молекулярной структурой, требует изменений в сварочных инструментах и конструкции инструментов. Еще предстоит провести дополнительные исследования, чтобы понять, как можно управлять методом сварки.
Заключение
Из ранее исследованных подходов к сварке ультразвуковая сварка металла с полимером кажется наиболее многообещающим методом для гибридных структур при соединении металлов с полимерами. Между металлической и полимерной частью происходит равномерное перемешивание, что способствует межмолекулярному контакту и механическому сцеплению в зоне сварного шва. Высокая прочность соединения может быть достигнута при относительно низком потреблении энергии и очень коротком времени сварки. Его успешно применяют для соединения металлов и полимеров, армированных волокном.
Точечное соединение трением дает такие же результаты, как и ультразвуковая сварка металла. Однако этот метод соединения успешно применялся только к металлам с низкой температурой плавления, таким как магний и алюминий, и не применим к очень толстым металлам.
Лазерная сварка металлов и полимеров может использоваться для достижения стабильных металлических, химических и ковалентных связей между металлическими и полимерными гибридными компонентами. Однако соединение происходит на границе раздела расплав-твердое тело между пластиком и металлом; металл не плавится.
Процессы сварки металл-полимер перспективны, но все еще находятся в стадии разработки; необходимо провести дополнительные исследования, чтобы эффективно понять их осуществимость и надежность.
Примечание. Ссылки хорошо документированы и многочисленны. Чтобы просмотреть их в оригинальном техническом документе и прочитать подробные исследования, обратитесь к «Методы соединения разнородных материалов: металлы и полимеры» (http://www.ipme.ru/e-journals/RAMS/no_23614/05_23614_kah .pdf), 2013.
Изображения любезно предоставлены авторами, если не указано иное.
Сварка разнородных металлов: что можно и нельзя
Скорее всего, вы слышали страшные истории о сварке разнородных металлов. Принятие правильных мер предосторожности во время этих опасных сварных швов может означать разницу между улучшением вашей системы технологических трубопроводов и причиной долгосрочных головных болей.
К счастью, если вы потратите несколько минут сейчас, чтобы понять опасности и преимущества сварки различных металлов, вы сможете сэкономить время, деньги и производительность в будущем.
В этой статье мы подробно рассмотрим процесс сварки и обозначим, что можно и чего нельзя делать при сварке разнородных металлов.
Почему сварка важна?
Когда все сделано правильно, сварка может творить чудеса. Это позволяет вам изменять конструкции в полевых условиях и поддерживать новые участки трубопроводов без полной замены трубопроводов. Если вам нужно соединить металл, расширить систему трубопроводов или перенаправить поток труб, сварка может быть вашим лучшим вариантом.
Тем не менее, важно по возможности свести количество сварочных работ к минимуму.Приварите нарезку к вашей системе трубопроводов. Это означает, что эти сварные участки, хотя и являются ценными, добавляют трубам слабые места и могут быть уязвимы для коррозии.
Зачем сваривать разнородные металлы?
Возможно, вы уже понимаете опасность объединения разнородных металлов. Поскольку металл может иметь совершенно разные свойства, сплавление неподходящих разнородных металлов вместе может вызвать коррозию или ненадежные соединения.
Однако сам факт того, что металлы обладают разными свойствами, часто вдохновляет сварщиков соединять разнородные металлы.В некоторых случаях выгодно или удобно смешивать и сочетать разные металлы.
Например, вы можете использовать в своей системе алюминий, потому что он легкий и устойчивый к коррозии. Однако алюминий обычно дороже других прочных металлов, таких как сталь. Таким образом, вы можете решить приваривать сталь к алюминию, чтобы сэкономить на расходах или увеличить прочность.
Независимо от комбинации, сварка различных металлов может быть способом максимально эффективно использовать уникальные свойства металла.
Что следует учитывать при сварке разнородных металлов
Сварка разнородных металлов — болезненный процесс. Если вы не будете выполнять сварку осторожно, это может привести к разрушению трубопровода или серьезным проблемам с коррозией. Вот некоторые факторы, которые следует учитывать при сварке разнородных металлов.
Точка плавления: разнородные металлы могут плавиться при совершенно разных температурах. Например, сталь обычно не плавится, пока не нагреется примерно до 1370 ° C (2500 ° F). Алюминий, с другой стороны, начинает плавиться примерно при 660 ° C (1220 ° F).В большинстве случаев вам потребуется изменить технику сварки, чтобы обеспечить плавное плавление и сплавление металлов.
Скорость теплового расширения: когда они нагреваются или охлаждаются, разные металлы расширяются и сжимаются с разной скоростью. Если скорости теплового расширения двух свариваемых металлов будут слишком разными, это может увеличить остаточное напряжение сварной точки. Это означает, что ваше соединение будет противостоять дополнительному давлению и будет более уязвимо для разрывов.
Гальваническая коррозия: Гальваническая коррозия может быстро распространяться и разрушать металл.Эта электрохимическая реакция начинается, когда соединяются металлы с разными анодными и катодными свойствами. Вот почему так важно разделять химически активные металлы с помощью буфера, нейтрального соединения или неметаллической основы.
Конечная среда: окружающая среда металла может значительно повлиять на его долговечность. Например, если незащищенный металл, такой как углеродистая сталь, останется в воздухе с тяжелым содержанием соли, это может вызвать коррозию. Хорошая идея — подумать о том, где будет работать металл, и обо всех коррозионных элементах, с которыми он столкнется.В некоторых случаях на металл может потребоваться защитное покрытие или гальванизация, чтобы избежать коррозии.
Что нужно и что нельзя делать при сварке
Вот краткий обзор передовых методов, которые следует учитывать при сварке разнородных металлов.
До …
Используйте переходные материалы
Если свариваемые металлы имеют разные электрохимические свойства, вы можете разделить их с помощью переходного материала. Это будет препятствовать тому, чтобы благородный металл вытягивал электроны из более основных металлов.
Сварка с ограничением
Какой бы полезной ни была сварка, неплохо помнить, что с каждой сваркой вы увеличиваете вероятность появления слабых мест и коррозии в вашей трубопроводной системе. В некоторых случаях для ограничения сварных швов можно использовать опоры, такие как ремонтные площадки. В других случаях можно использовать башмаки для труб, изнашиваемые прокладки или другие опоры для полного обхода сварки.
Исследовательские металлы
Не уверены, совместимы ли материалы, с которыми вы работаете? Остановитесь и найдите минутку для исследования, прежде чем приступить к сварке.Вот несколько групп, которые предоставляют стандарты для сварочных материалов:
Не …
Прямое подключение несовместимых металлов
Если напрямую соединить металлы с разными электрохимическими свойствами, это может вызвать гальваническую коррозию. Если металлы несовместимы, важно использовать буфер или защитное покрытие для предотвращения коррозии металла.
Недооценка металлических свойств
Помните, металлы могут иметь разные температуры плавления, проводимость, прочность и ковкость.Все эти факторы могут повлиять на долговечность сварного шва и производительность системы трубопроводов.
Исключить альтернативы сварке
Во многих случаях сварка может показаться простым решением. Однако, прежде чем плавить металлические поверхности вашей трубопроводной системы, стоит спросить, есть ли регулируемые опоры или другие творческие альтернативные продукты, которые могут укрепить вашу систему.
Советы по улучшению вашей трубопроводной системы
Хотите быть в курсе последних советов, приемов и секретов увеличения срока службы вашей технологической системы трубопроводов? Подпишитесь на наш блог, чтобы получить инсайдерские советы по опорам для труб и индустрии трубопроводов.