Сварка неповоротных стыков труб при горизонтальном расположении трубы
Темы: Сварка труб, Сварные швы, Ручная дуговая сварка, Сварные соединения.
Сварка этих сварных швов является самым сложным по выполнению и требует особых навыков и высокого мастерства сварщика. Только при твердых навыках в сварке в нижнем положении, сварке вертикальных швов и сварке потолочных швов можно добиться качественной сварки трубы неповоротной в горизонтальном положении. При постоянном поступательном движении электрода необходимо постоянно изменять угол наклона электрода по отношению к поверхности периметра трубы (рис. 1а и 1б, поз. 1-11). Труба делится вертикальной осевой на два участка. По положению сварного шва в пространстве каждый участок можно разбить на три положения:
Другие страницы по теме Сварка неповоротных стыков труб при горизонтальном расположении трубы :
- I-ое — потолочное (поз. электрода с 1 по 3).
- II-ое — вертикальное (поз. электрода с 3 по 8).
- III-e — нижнее (поз. электрода с 8 по 11).
При сварке труб диаметром более 150 мм и толщиной стенки более 6 мм рекомендуется величину сварочного тока подбирать для каждого положения. Сварочный ток на потолочном положении должен быть на 10% выше, чем на вертикальном положении.
Сварка начинается с потолочного положения и заканчивается на нижнем положении.
При оптимальном подборе сварочного тока для каждого положения реко.мендуется сварку производить непрерывно. Сварка ведется только ко роткой дугой. Сварка любого участка начинается с другого участка на 10 20 мм от вертикальной осевой. Длина «замка» (20-40 мм) зависит от диаметра трубы. Чем больше диаметр, тем больше перехлест в «замке», наоборот. При начале сварки с потолочного положения сварку производить «углом назад» (рис. 1а, поз. 1-2), После перехода за осевую сварку производить «углом вперед» (поз. 3-7). При переходе за горизонтальную осевую электрод выравнивать до перпендикулярного положения (поз.
Заканчивать первую половинку шва на 10-15 мм за вертикальной осевой на другом участке.
а) | |
б) |
Рисунок 1.
Валик должен быть «нормальным» по всей длине шва, который достигается определенной скоростью поступательного движения электрода, манипулированием и задержкой на кромках, используя все методы и технику сварки потолочных, вертикальных и нижних швов.
Перед сваркой второй половины (второго участка рис. 1б) — при необходимости зачистить (подрубить) начало сварки в потолочном положении и окончание в нижнем положении до плавного перехода к зазору или предыдущему валику. Сварку второго участка выполнить с той же техникой, что и первый участок.
Сварка корневого валика.
Сварка корневого валика выполняется электродом диаметром 3 мм. Величина сварочного тока в потолочном положении в зависимости от толщины стенки 80-95 А. В зависимости от технических условий рекомендуется выполнить корневой валик по двум вариантам.
Рисунок 2. Сварка корневого валика.
1-й вариант — при сварке труб малого диаметра, когда невозможна подварка обратной стороны корня шва, а по техническим требованиям необходимо обратное формирование валика, то при сварке корневого валика следует добиться качественного формирования обратного валика. Достичь проплавления, особенно в потолочном положении, можно путем постоянной подачи электрода в зазор. Добиваясь проплава внутрь трубы, формирование валика с наружной стороны может получиться «горбатым», что потребует после заварки 1-го участка зачистки «горбатости» шва в потолочном положении.
При сварке вертикальной зоны сварочный ток рекомендуется уменьшить до 75-90 А. Валик выполнять малого сечения, избегая чрезмерного проплавления внутрь трубы. При сварке верхней части трубы (нижнее положение) увеличение сварочного тока до 85-100 А произвести в каждом конкретном случае, не допуская прожога или непровара.
После заварки второй половины трубы второй валик также выполняется электродом диаметром 3 мм, но на повышенном сварочном токе.
2-й вариант — при сварке труб большого диаметра, где доступна и заложена подварка обратного корня шва, в целях производительности не следует обращать такого тщательного внимания на формирование обратного валика. Рекомендуется корневой валик сформировать «нормальным» во всех положениях и с более полным сечением. Это позволит избежать зачистки по наружному шву и применить при сварке второго валика электрод диаметром 4 мм.
Заполнение разделки.
Здесь необходимо применить все методы и технику сварки заполнения разделки, описанную в предыдущих разделах. Сварку труб диаметром менее 150 мм рекомендуется выполнять электродом диаметром 3 мм.
Заполнение разделки труб толщиной стенки более 8 мм происходит неравномерно. Как обычно, отстает нижнее положение. Для выравнивания заполнения разделки необходимо проложить в каждом конкретном случае дополнительные слои в верхней части трубы. Предпоследний слой выполнить так, чтобы глубина незаполненной разделки была не более 2-х мм.
Сварка лицевого слоя.
Рисунок 3. Сварка лицевого слоя.
В зависимости от ширины разделки лицевой слой выполняется за один или несколько проходов. Техника сварки описана в начале раздела и в предыдущих разделах. Особое внимание обратить на поступательное движение электрода, задержку на кромках и шаг манипулирования.
Сварка труб диаметром менее 150 мм и толщиной стенок менее 6 мм, а также в сложных монтажных условиях при отдаленности источника питания от места сварки, в основном, выполняется при одной величине сварочного тока. Рекомендуется сварочный ток подбирать по потолочному положению, величина которого достаточна и для нижнего положения. Во избежание чрезмерного проплавления на подъеме с потолочного положения и в вертикальном положении сварку необходимо вести прерывистым способом. Дугу прерывать на одной из кромок. В зависимости от толщины стенки, зазора и притупления кромок, рекомендуется выполнять прерывистую сварку «мазками» следующим способом:
Рис. 4а — перегрев кромок не допускает длительной задержки электрода. Зажигание рекомендуется производить постоянно на одной из кромок, обрыв дуги (после соединения кромок металлом шва) на другой кромке. Время между обрывом и новым зажиганием дуги должно быть таким, чтобы в месте начала зажигания дуги металл шва не успел полностью закристаллизоваться, а шлак — остыть. После обрыва дуги, описав как бы полукруг в обратном направлении, снова произвести зажигание чуть выше места предыдущего зажигания. Если проследить за торцом электрода, то получается манипулирование по спирали. Слева направо дуга горит, обрыв вправо и на себя, переход справа налево, дуга не горит, затем слева направо, одновременно приближая электрод к месту зажигания, и, пока шлак еще красный, происходит легкое возбуждение дуги и т.д;
Рисунок 4 : точка — зажигание дуги, стрелка — обрыв дуги.
Рис. 4б — когда толщина металла позволяет сделать два и более колебательных движений, затем прервать дугу и возобновить снова.
Нe рекомендуется:
1) зажигание производить на месте, где только что был обрыв дуги;
2) не обрывая до конца дугу, уходить электродом вперед по разделке и затем возвращаться на валик.
Такие методы приводят к большому перегреву и прожогу, к неровности валика по бокам, частому залипанию электрода во время нового зажигания.
- < Сварка угловых соединений
- Сварка неповоротных стыков труб (при расположении трубы под 45°) >
Страница не найдена

Пожалуйста, введите более двух символов
Все результаты поискаТрубопроводы магистральные и промысловые для нефти и газа. Строительство… Роительство в условиях вечной мерзлоты и контроль выполнения работ распространяется на магистральные и промысловые стальные трубопроводы… | Государственный стандарт российской федерации трубопроводы стальные магистральные 621. 643: 006. 354 Группа Г18 | ||
1. На какие магистральные трубопроводы не распространяются требования… На какие магистральные трубопроводы не распространяются требования фнп «Правила безопасности для опасных производственных объектов… | Трубопроводы магистральные и промысловые для нефти и газа. Производство.![]() Разработан общество с ограниченной ответсвтенностью «Трансэнергострой» ООО «Трансэнергострой» | ||
Б 9 Магистральные трубопроводы для транспортировки жидкого аммиака Какой документ, определяющий порядок организации надежного и безопасного ведения технологического процесса, разрабатывается для эксплуатации… | Свод правил В своде Правил изложены технические требования, предъявляемые к полам, рекомендации по проектированию и устройству различных видов… | ||
Свод правил техника пожарная огнетушители требования к эксплуатации Российской Федерации установлены Федеральным законом от 27 декабря 2002 г. N 184-фз «О техническом регулировании», а правила применения… | Профессиональный стандарт КС) и станции охлаждения газа (сог), технологические трубопроводы основного назначения кс и сог (трубопроводы, предназначенные для… | ||
Чрезвычайным ситуациям и ликвидации последствий стихийных бедствий свод правил Российской Федерации установлены Федеральным законом от 27 декабря 2002 г. ![]() | Свод правил системы противопожарной защиты установки пожарной сигнализации Российской Федерации установлены Федеральным законом от 27 декабря 2002 г. N 184-фз «О техническом регулировании», а правила применения… | ||
Чрезвычайным ситуациям и ликвидации последствий стихийных бедствий свод правил Российской Федерации установлены Федеральным законом от 27 декабря 2002 г. №184-фз «О техническом регулировании», а правила применения… | И жилищно-коммунального хозяйства российской федерации свод правил Федерации установлены Федеральным законом от 27 декабря 2002 г. N 184-фз «О техническом регулировании», а правила разработки постановлением… | ||
Министерство регионального развития российской федерации свод правил Федерации установлены Федеральным законом от 27 декабря 2002 г. №184-фз федеральный закон РФ «О техническом регулировании», а правила. ![]() | И жилищно-коммунального хозяйства российской федерации свод правил Фз «О стандартизации в Российской Федерации» и от 27 декабря 2002 г. №184-фз «О техническом регулировании». Порядок разработки сводов… | ||
И жилищно-коммунального хозяйства российской федерации свод правил Российской Федерации установлены Федеральным законом от 27 декабря 2002 г. N 184-фз «О техническом регулировании», а правила разработки… | Свод правил Утвержден и введен в действие приказом Минрегионразвития России от г. № |
Стыки сварка — Справочник химика 21
При подготовке труб к сварке поверхности труб зачищают стальными щетками или шлифовальными машинками на длину 10—30 мм от стыка. Трубы толщиной до 5 мм сваривают без разделки кромок, у толстостенных труб кромки скашивают под углом 15—35°. Угол скоса проверяют шаблоном, а перпендикулярность — угольником. Свариваемые стыки центруют (рис.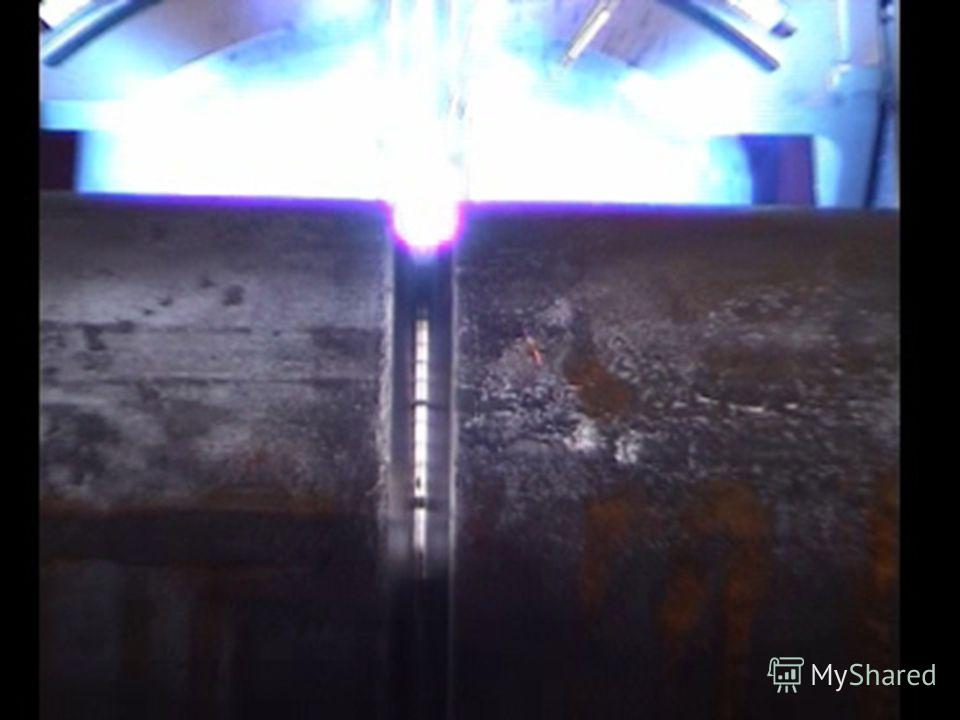
Ряд диаметров. Обечайки корпусов кожухотрубчатых теплообменных аппаратов различных типов и- функционального назначения из черных и цветных металлов и сплавов обычно проектируют цилиндрической формы, предполагая их изготовление путем вальцовки из листового материала и соединения продольного стыка сваркой или пайкой.
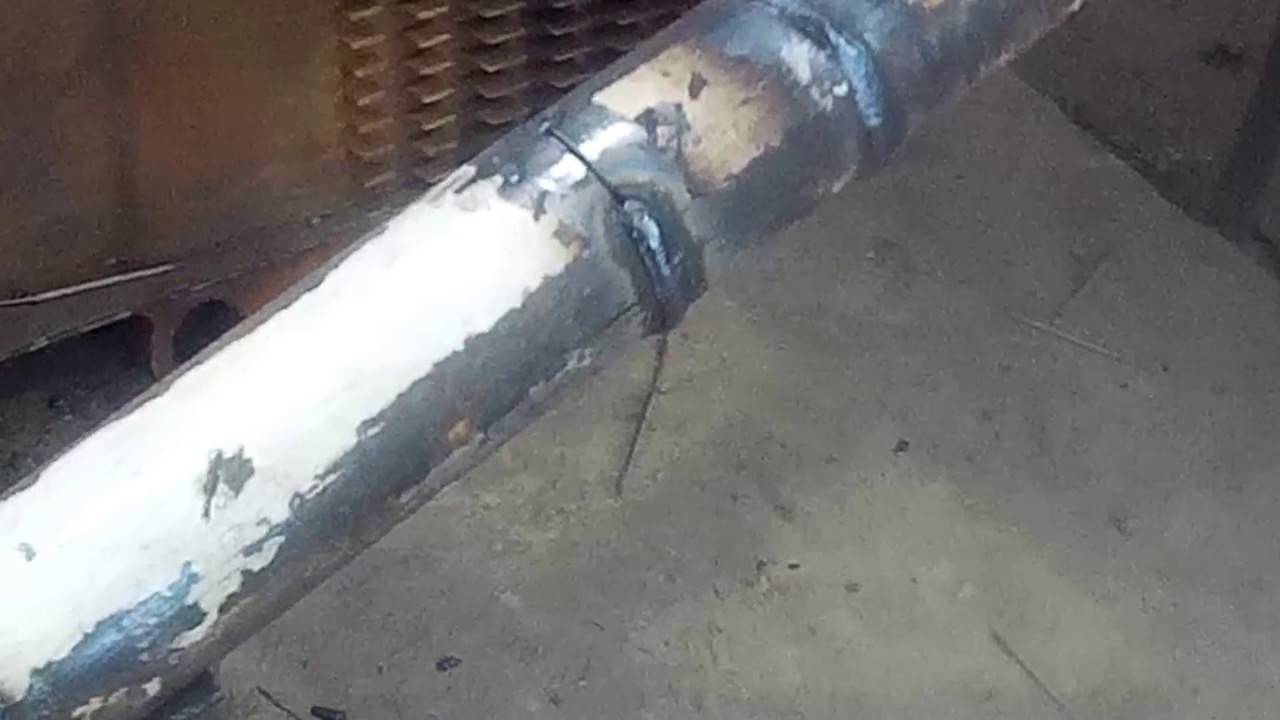
Свальцованные из листов цилиндрические обечайки после соединения стыка сваркой или пайкой проходят технологическую правку (калибровку). Обработка наружной и внутренней поверхностей обечаек на станке обычно не производится. [c.182]
При изготовлении корпуса из карт лист длиной 6—8 м (в зависимости от длины аппарата) обрезается в размер по периметру и изгибается вдоль волокон. Преимущество изготовления корпусов из карт—в резком сокращении трудоемкости сборочных работ (отсутствуют кольцевые стыки) сварка швов, кроме одного замыкающего, производится на плоскости, что улучшает качество [c.33]
Кроме фланцевых соединений (из винипласта или стали) соединение элементов может производиться встык, с дополнительной обваркой пластикатом места стыка сваркой встык с усилением приварной муфтой. Наиболее распространено разъемное соединение на приварных фланцах из винипласта. [c.171]
Сборку и сварку коллекторов осуществляют в такой последовательности устанавливают и приваривают донышки к тройникам, устанавливают и обваривают штуцера, производят сборку трубы с тройниками и прихватывают электросваркой в четырех местах стыки. Сварку стыков трубы с тройниками выполняют при монтаже котла. Осуществляют разметку и сверление отверстий диаметром 38 мм (рис. 10, а). [c.47]
Сварка стыков труб может быть поворотной и неповоротной. Ручная дуговая сварка поворотных стыков труб больших диаметров производится в два или три слоя. Для уменьшения возможности образования грата внутри стыка сварку первого слоя производят способом, указанным на фиг. 34. [c.629]
Первый — это подвесные подмости, служащие для обслуживания монтажных узлов, расположенных на значительной высоте. Эти подмости подвешиваются к конструкциям, с подмостей рабочие могут производить различные операции, как-то заводку элемента и его крепление, рассверловку и клепку монтажных стыков, сварку и т. п. [c.168]
Цилиндрические обечайки из стали, цветных металлов и их сплавов, винипласта при давлении среды в аппарате до 10 МПа изготовляют преимущественно из вальцованных листов с последующей сваркой стыков. Сварка продольных и поперечных швов должна производиться только стыковой. Стыки цилиндрических обечаек из медных и латунных сплавов кроме сварки могут соединяться пайкой. После сварки или пайки стыка цилиндрические обечайки подвергаются правке. [c.42]
Для контроля качества сварных соединений трубопроводов, подлежащих приемке органами Госгортехнадзора или газовой технической инспекцией. Рис. 10—13. каждый сварщик одновременно со сваркой трубопро- Разметка вода обязан сварить контрольный стык. Сварка кон- контрольно-трольных стыков должна производиться в условиях, го стыка одинаковых со сваркой трубопровода, с применением для изготов-тех же материалов и в том же положении, в кото- ления образ-ром выполняются сварщиком стыки свариваемого цов [c.603]
В процессе изготовления узлов и плетей трубопроводов производят систематический пооперационный контроль, чтобы предупредить возможное появление дефектов в сварных соединениях. Проверяют качество исходных материалов, подготовки кромок труб перед сваркой, сборки стыков, сварки. Осматривают электроды, сварочную проволоку, флюсы. При эхом независимо от сертификатов каждую партию электродов подвергают технологическим испытаниям. [c.53]
Удобнее вести сварку вольфрамовым электродом, так как при этом перенос металла в сварочную ванну отсутствует, дуга горит спокойно и расплавленный металл надежно удерживается на кромках стыка. Сварку ведут на постоянном режиме с присадкой или без присадки. При сварке без присадки шов получается более ровный и качественный. [c.76]
После установки и выверки первых двух поясов наружной стенки сваривают вертикальные стыки, горизонтальный и упорный стыки (сварка первого пояса с наружным днищем). [c.276]
При сварке винипластовых труб и деталей не допускается образования воздушных пустот, которые приводят к ослаблению стыка. Сварка считается нормальной, если перед прутком по мере его перемещения движется небольшая волна расплавленной массы материала и если после остывания пруток невозможно оторвать от поверхности шва, не повредив самого прутка. Пере- [c.196]
По положению в пространстве различают горизонтальные, нижние, вертикальные, потолочные и наклонные сварные швы. При изготовлении трубных деталей и при сборке их в элементы и узлы, а также при монтаже трубопроводов желательно сваривать стыки в наиболее выгодном — нижнем положении, поворачивая их вокруг оси, т. е. применять поворотные стыки. Сварка неповоротных стыков значительно труднее, чем поворотных, так как часть стыка при этом неизбежно должна выполняться в потолочном положении. [c.189]
В местах работы людей по сборке стыков, сварке их, установке арматуры и т. д. траншеи с вертикальными стенками и без креплений должны иметь местные откосы или местные крепления. [c.292]
Кольцевые стыки труб сваривают в раструб заливным швом. Для этого один конец трубы развальцовывают оправкой. К нему пристыковывают конец второй трубы, кромки которой для плотного прилегания предварительно скашивают. Трубы со стенками толщиной 5 мм и более также сваривают в стык. Сварку производят в нижнем положении с поворотом трубы. [c.157]
Наклеивание материала выполняется в следующей последовательности нанесение и сушка грунтовок, послойное наклеивание материалов, герметизация стыков (сварка или склейка), сушка (выдержка) оклеечного покрытия. Система покрытия (вид наклеиваемого и клеящего материалов, количество наносимых слоев) регламентируется ППР. [c.182]
Для возможности проверки качества сварных соединений трубопроводов, подлежащих приемке органами Госгортехнадзора или газовой технической инспекцией, каждый сварщик одновременно со сваркой трубопровода обязан сварить контрольный стык. Сварка контрольных стыков должна производиться в условиях, одинаковых со сваркой трубопровода, с применением тех же материалов и в том же положении, в котором выполняются сварщиком стыки свариваемого трубопровода. Сварка контрольных стыков должна производиться также в том случае, когда в процессе работы сварщику приходится менять марку стали труб или марку электродов. [c.722]
Аргонно-дуговая сварка алюминия неплавящимся (вольфрамовым) электродом. Для образования правильного шва должны применяться металлические подкладки с канавкой по линии стыка. Сварка производится переменным током высокой частоты. [c.86]
Заварку первого слоя шва неповоротных стыков также выполняют газоэлектрической сваркой, автоматами и полуавтоматами. В зависимости от зазора в стыке сварку ведут сверху вниз или снизу вверх. [c.179]
Для контроля качества сварных соединений трубопроводов и его деталей одновременно со сваркой каждый сварщик обязан сварить контрольные стыки в количестве 1 % Для углеродистых и низколегированных марок сталей и 2% для аустенитных марок сталей от общего числа сваренных 1Ш однотипных стыков, но не менее одного стыка. Сварка контрольных стыков осуществляется в условиях, тождественных с условиями сварки трубопровода. [c.189]
В комплекс работ по монтажу блоков входят устройство подмостей разбивка осей трубопроводов строповка подъем и установка блоков в проектное положение временное крепление блоков расстроповка сборка монтажных стыков сварка [c. 176]
В комплекс работ по монтажу блоков входят устройство подмостей разбивка осей трубопроводов строповка подъем и установка блоков в проектное положение временное крепление блоков расстроповка сборка монтажных стыков сварка стыков испытание и приемка трубопроводов заделка стыков теплоизоляции. [c.186]
Стыки с выявленными при контроле дефектами могут быть исправлены, если их суммарная длина не превышает 10 % периметра. Стыки с трещинами ремонту не подлежат и должны быть вырезаны. Выполнять ремонт стыков сваркой изнутри труб не допускается.-Дефектное место шва удаляют абразивным инструментом или газовым резаком с после- дующей обработкой поверхности реза до металлического блеска шлифмашинкой. Заваривают ремонтные участки шва электродами с основным покрьггием диаметром 2,5 — 3,25 мм в соответствии с табл. 18. Предварительный подогрев при этом выполняют до 150 °С при любой температуре окружающего воздуха. Контроль отремонтированных участков стыков производят после термообработки радиографическим методом и замерами твердости. Повторный ремонт сварных швов не допускается. [c.74]
При давлении в аппарате менее 10 МПа цилиндрические обечайки выполняют из пластичных материалов, в основном из листов вальцовкой с последующим соедннеинем стыков преимущественно сваркой. Прн соединении стыков пз медных и латуршых листов применяют также и найку. После соединения стыка сваркой или пайкой цилиндрические обечайки подвергают технологической правке (калибровке). [c.142]
Свальцованные из листов цилиндрические обечайки после соединения стыка сваркой или пайкой иро одят технологическую правку (калибровку). Наружная и внутренняя поверхности обечаек на станке обычно не,обрабатываются. [c.329]
Контроль температуры подогрева под сварку при ремонте в зимних условиях (Гвоздпомощью термопар и потенциометров с записью термического режима стыка. Сварку в летних условиях (7 возд 0°С) можно проводить с контролем температуры стыка посредством термощупов и термокарандашей. [c.74]
Х5, Х5ВФ, Х5М, 1Х8ВФ невозможно проводить термическую обработку сварных стыков, сварку рекомендуется выполнять аустенитными электродами марки ОЗЛ-12 [2, 3]. [c.159]
Цилиндрические обечайки из стали, цветных металлов и их сплавов, винипласта при давлении среды в аппарате до 10 Мн1м изготовляются преимущественно из вальцованных листов с последующей сваркой стыков. Сварка продольных и поперечных швов обечайки должна производиться только стыковой. Стыки цилиндрических обечаек из медных и латунных сплавов, кроме [c.46]
Как выполняется сварка неповоротных стыков труб – пошаговое руководство
Технология сварки неповоротных стыков труб подбирается в соответствии с тем, как расположены трубы и с каким наклоном.
В связи с этим выделяют несколько видов сварных соединений:
- Вертикальное.
- Горизонтальное.
- С уклоном в 450.
Кроме того, способ сварки во многом зависит от толщины стенок трубных изделий. К примеру, соединение трубных изделий, имеющих стенки толщиной 12 миллиметров, выполняется методом наложения трех слоев. При этом толщина каждого слоя не должна превышать 4 мм. Сварка неповоротных стыков труб имеет множество особенностей, определяющие наклон электродов, которые следует знать.
Блок: 1/7 | Кол-во символов: 632
Источник: https://trubaspec.com/soedinenie-trub/kak-vypolnyaetsya-svarka-nepovorotnykh-stykov-trub-poshagovoe-rukovodstvo.html
Правила техники безопасности
Приступая к соединению поворотных стыков труб или неповоротных аналогов, нужно знать, что работы такого типа имеют высокий уровень опасности. Поэтому необходимо выполнять определенные требования.
Соединение трубных изделий встык посредством газовой или электрической сварки необходимо выполнять на специально оборудованных площадках, которые имеют специальное оснащение, включая различные средства защиты от электрической дуги. Эти элементы распределяются так, чтобы присутствующие поблизости люди были полностью изолированы.
Для соединения трубных изделий, имеющих большое диаметральное сечение и вес свыше 20 кг, рекомендуется использовать специальные подъемники. Вход на площадку требуется освободить, его ширина не может быть менее 1 м. Рабочие температурные значения в помещении должны поддерживаться в пределах +160С. Обязательным условием считается наличие вентиляционной системы и свободное пространство.
Согласно технологии осуществления работ, предполагающих использование сварочного оборудования, все металлические детали и элементы должны быть заземленными (про «Виды технологий сварки труб – преимущества и недостатки способов»). Аналогичные требования предъявляются для корпуса трансформатора и рабочего места. Применение сварочного устройства допускается только с изолированными проводами и кабелем.
Как уже говорилось выше, соединение неповоротных стыков трубы выполняется несколькими способами, которые напрямую зависят от того, как расположена труба.
Блок: 2/7 | Кол-во символов: 1541
Источник: https://trubaspec. com/soedinenie-trub/kak-vypolnyaetsya-svarka-nepovorotnykh-stykov-trub-poshagovoe-rukovodstvo.html
Содержание
Сварка неповоротных стыков трубопроводов, при толщине стенки 12мм, происходит с выполнением трёх слоёв шва. Высота каждого слоя не превышает 4мм, а ширина валика равна 2-3 диаметрам сварочного электрода.
Стыки труб с диаметром более 300мм сваривают обратно-ступенчатым способом. Рекомендуемая длина каждого участка составляет 150-300мм. Порядок их сваривания показан на схеме ниже. Цифрами указана последовательность сварки участков по слоям, а стрелками — направление сварки.
Блок: 2/4 | Кол-во символов: 519
Источник: https://taina-svarki.ru/svarka-razlichnyh-konstruktsyi/svarka-truboprovodov/svarka-nepovorotnyh-stykov-trub.php
Методика работы с горизонтальным стыком
Методика действий с неповоротными стыками трубопровода в горизонтальном положении отличается тем, что разделывать кромки полностью не обязательно. Осуществлять эти действия необходимо средней дуговой сваркой. Можно сохранить лишь несущественную разделку в 10 градусов. Такие действия обеспечивают улучшение процесса соединения металлических частей и сохранности их качества на прежнем уровне. Варить горизонтальные стыки трубопровода лучше обособленными неширокими слоями. Первым валиком проваривается корень шва, при этом используются электроды 4 миллиметра в диаметре. Лимит силы по закону Ома должен быть установлен в диапазоне от 160 до 190 А. Электрод получает движение характерное возвратно-поступательному, в то время как внутри стыка должен появиться нитевидный валик 1-1,5 мм высотой. Покрытие прослойки №1 подлежит тщательной зачистке. Прослойка №2 проделывается таким образом, чтобы он закрывал предыдущую прослойку, когда электрод движется возвратно поступательным образом и когда происходит его практически незаметное покачивание между краями верхней и нижней кромок.
Таблица соотношения сварочных токов в зависимости от различных показателей
Направление второго слоя не отличается от первого. Перед выполнением третьего слоя силу тока необходимо увеличить до 250-300 А. Чтобы сделать процесс соединения металлических элементов более производительным, нужно использовать электроды диаметром 5 миллиметров. Направление варки третьего слоя осуществляется противоположно направлениям предыдущих двух слоев. Третий валик рекомендуется выполнять на более высоких режимах. Скорость нужно выбрать такую, чтобы валик был выпуклым. Варить необходимо под «углом назад» или под прямым углом. Третий валик должен заполнять две трети ширины валика №2.
Выполнение четвертого валика следует вести на режимах, используемых при выполнении третьего. Угол наклонения электрода — 80-90 градусов от поверхности трубы, которая расположена по вертикали. Направление четвертого валика остается прежним.
Технология выполнения электросварки с горизонтальными стыками при наличии более 3-х прослоек имеет свою особенность: третья прослойка со всеми последующими выполняются в направлениях, каждый из которых противоположен предыдущему. Трубы, достигающие диаметра в 200 мм, как правило, подлежат сварке сплошными швами. Обратно-ступенчатый способ характерен для сварочного процесса стыков трубопровода диаметром более 200 мм. Каждому участку рекомендуется быть примерно 150-300 мм длиной.
Блок: 3/5 | Кол-во символов: 2512
Источник: https://svarkaed.ru/svarka/izdeliya-i-konstruktsii/svarka-nepovorotnyh-stykov-trub-osnovnye-tehnologii.html
Правила заполнения заделки труб
Начинать заполнение заделки нужно с низа кромки, которая является площадкой. Это необходимо для выбора оптимального способа сварки. Валик горизонтального расположения следует выполнять в повышенном режиме. Также метод сварки определяется расположением шлака, «угол назад» или « под прямой угол».
Для получения валика необходимо усиление или «горбинка», образующаяся при сварке в положении снизу для создания полки, благодаря которой выполняется сварка следующего валика при повышенном режиме. Вторая обработка должна проводиться аккуратными движениями, придерживаясь нижнего края.
Перед началом сварки третьего валика определяют уровень его полноты. При этом важно, чтобы разделка, незаполненная между соединительным швом и верхней кромкой, была не очень большой для четвертого валика и не очень узкой для двух валиков. Третий валик по верхнему краю должен иметь наименьшее значение ширины до верхней кромки. Оптимальный размер может совпадать с диаметром электрода.
Заполнение разделки проводится при формировании еще 3 валиков, которые позволяют заполнить основу сварного шва и укрепить стык. При проведении работ важно держать прямой угол, а разделку заполнять при высокой скорости сварки. Только так можно добиться прочного скрепления слоев между собой.
Блок: 4/7 | Кол-во символов: 1329
Источник: https://trubaspec.com/soedinenie-trub/kak-vypolnyaetsya-svarka-nepovorotnykh-stykov-trub-poshagovoe-rukovodstvo.html
Видео: сварка неповоротного стыка. Замок на сварку
Дополнительные материалы по теме:
Блок: 4/4 | Кол-во символов: 93
Источник: https://taina-svarki.ru/svarka-razlichnyh-konstruktsyi/svarka-truboprovodov/svarka-nepovorotnyh-stykov-trub.php
Выполнение замков
Этап выполнения замков предполагает окончательные работы по формированию валиков. При этом сварка каждого валика сопровождается заступом на основной шов величиной 2 мм. Готовый замок представляет исходную точку валика, со смещением по отношению к предыдущему слою на 5 мм.
Декоративный шов завершает сварку труб в неповоротном положении. Выполняя наплавку в горизонтальном положении, формируют узкие валики. Последний из них должен быть абсолютно плоским. Сваривание выполняется в высокоскоростном режиме.
При полном сваривании стыка должен учитываться весь периметр без обрыва. Допускается смещение замков относительно друг друга не больше, чем на 50 мм.
Многопроходной вид сварки поворотных и неповоротных труб, имеющих толстые стенки, предполагает спиралевидное ведение. В этом случае сокращается количество замков и, как следствие, уменьшается число дефектов. Сварку следует прекращать на расстоянии около 20 мм от начала валика, чтобы выровнять сварные швы по высоте. Больший валик можно подрубить, а также сточить.
Подрубить валик можно практическим способом, позволяющим снизить количество замков и выполнить более качественное соединение. Такой способ берет начало от кромки валика, которая подплавляется задержкой дуги. Затем делают заход на валик с действующей электродугой и переходят на следующий слой, учитывая предыдущий. В результате окончание одного слоя становится продолжение другого валика.
Блок: 5/7 | Кол-во символов: 1473
Источник: https://trubaspec.com/soedinenie-trub/kak-vypolnyaetsya-svarka-nepovorotnykh-stykov-trub-poshagovoe-rukovodstvo.html
Горизонтальная наплавка
Сварка неповоротных стыковых труб горизонтального расположения считается достаточно сложной технологией. Выполнить такую работу может только профессиональный сварщик, имеющий определенные навыки и опыт. Наиболее трудным можно назвать постоянное регулирование электрода для изменения угла наклона.
Сварка выполняется в трех последовательных позициях:
- Потолочная.
- Вертикальная.
- Нижняя.
Каждый шов выполняется с индивидуальным значением величины тока. Потолочная позиция предусматривает сварку на высоком уровне мощности. Все этапы предполагают безотрывную сварку, в ее начале лучше всего использовать метод «углом назад», а завершать работу — «углом вперед».
Блок: 6/7 | Кол-во символов: 706
Источник: https://trubaspec.com/soedinenie-trub/kak-vypolnyaetsya-svarka-nepovorotnykh-stykov-trub-poshagovoe-rukovodstvo.html
Количество использованных доноров: 3
Информация по каждому донору:
- https://trubaspec.com/soedinenie-trub/kak-vypolnyaetsya-svarka-nepovorotnykh-stykov-trub-poshagovoe-rukovodstvo.html: использовано 5 блоков из 7, кол-во символов 5681 (53%)
- https://svarkaed.ru/svarka/izdeliya-i-konstruktsii/svarka-nepovorotnyh-stykov-trub-osnovnye-tehnologii.html: использовано 2 блоков из 5, кол-во символов 4376 (41%)
- https://taina-svarki.ru/svarka-razlichnyh-konstruktsyi/svarka-truboprovodov/svarka-nepovorotnyh-stykov-trub.php: использовано 2 блоков из 4, кол-во символов 612 (6%)
Техномор Архангельск тел. 473-473 — Сварка труб
Общая информация. При производстве трубопровода сварной стык трубы может быть горизонтальным, поворотным и неповоротным (рис. 106).
Трубы, перед сваркой и сборкой, должны быть проверены на соответствие техническим условиям и требованиям, по которым сооружается весь трубопровод. Основными требованиями и техническими условиями проекта являются: соответствие механических свойств и химического состава металла труб требованиям технических условий или ГОСТов, наличие сертификатов труб; отсутствие разностенности труб; отсутствие эллипсности.
Во время подготовки стыков труб для сварки проверяют перпендикулярность плоскостей реза и оси трубы, угол раскрытия шва и величину притупления. Величина притупления должна составлять 2 — 2,5 мм, а угол раскрытия шва 60 — 70° (рис. 107). С торцов труб фаски снимают газовой резкой, механическим способом или другим способом, обеспечивающим требуемый размер, форму и качество обрабатываемой кромки.
Разница толщины стенок свариваемых стыков труб и смещение кромок должно быть не более 10% толщины стенки, но не превышать 3 мм. Необходимо обеспечивать равномерный зазор между кромками стыкуемых труб, примерно 2—3 мм.
Перед сваркой стыкуемые кромки труб и прилегающие к ним наружные и внутренние поверхности очищают от ржавчины, окалины, масла и грязи на длине 15 — 20 мм.
Прихватки являются частью сварного шва и выполняются тем же сварщиком, который будет сваривать стык, и теми же электродами.
При сборке труб диаметром не больше 300 мм прихватки выполняются по окружности равномерно в четырёх местах швом длиной 50 мм, а высотой 3 — 4 мм каждая. При сборке труб диаметром свыше 300 мм прихватки выполняют по всей окружности стыка равномерно через 250 — 300 мм.
При сборке трубопровода необходимо стремиться, по возможности, к тому, чтобы большее количество стыков варилось в поворотном положении. Трубы с толщиной стенки 12 мм свариваются в три прохода. Первый проход делает провар в корне шва и надежно сплавляет кромки. При этом наплавленный металл образовывает внутри трубы равномерный валик высотой 1 — 2 мм, распределенный по всей окружности. Что бы получить качественный провар без грата и сосулек необходимо осуществлять возвратно-поступательные движения электрода с непродолжительной задержкой на сварочной ванночке, незначительные поперечные колебания между кромками и образование в вершине угла скоса кромок небольшого отверстия. Это отверстие появляется при проплавлении металла эл. дугой. Его размер должен быть не больше зазора между трубами и не превышать 2 мм.
Сварка поворотного стыка. Первый слой сваривают электродом диаметром 2 — 3 мм, а высота шва 3 — 4 мм. Второй слой наплавляются при повышенном токе электродами большего диаметра.
Первый и второй слой выполняют одним из способов:
1. Стык делится на четыре участка. Сначала обваривают участки 1 — 2, затем трубу переворачивают на 180° и обваривают участки 3 и 4 (рис 108). На следующем этапе трубу переворачивают еще на 90° и обваривают участки 5 — 6, затем опять переворачивают на 180° и обваривают участки 7 — 8.
2. Стык делится на четыре участка. Сначала обваривают участки 1 — 2, переворачивают трубу на 90° и обваривают участки 3 — 4 (рис. 109). После первого слоя трубу переворачивают на 90° и обваривают участки 5 — 6, затем переворачивают трубу на 90° и обваривают участки 7 — 8.
3. При сварке трубы диаметром более 500 мм стык делится на несколько участков. Сварка ведётся отдельными участками обратно-ступенчатым способом (рис. 110). Длина каждого из участков шва 1 – 8 зависит от диаметра трубопровода и может составлят от 150 до 300 мм.
Третий слой накладывают в рассмотренных выше способах при вращении трубы в одном направлении. На трубе диаметром до 200 мм стык не делится на участки, а сваривается сплошным швом и поворотом трубы во время сварки (рис. 111). Второй и третий слои выполняют так же, как и первый, но в противоположном направлении. В любом случае каждый следующий слой должен перекрываться предыдущим на 10—15 мм.
Сварка неповоротных стыков. Неповоротный стык трубы при толщине стенки до 12 мм сваривается в три слоя. Высота каждого слоя должна быть не более 4 мм, а ширина валика, примерно, равна 2-3 диаметрам электрода.
Стык трубы диаметром более 300 мм сваривается обратно-ступенчатым методом. Длина участка должна быть 150 — 300 мм, а очерёдность наложения показан на (рис. 112).
Первый слой получается при возвратном-поступательном движении электрода с задержкой на сварочной ванночке. Величину тока устанавливают в пределах от 140 до 170А. Это позволяет проплавлять кромку стыка и образовывать ниточный узкий валик высотой 1 — 2 мм на внутренней стороне. При этом сварка должна быть выполнена без прожогов, а на свариваемые кромки не должно попадать крупных брызг расплавленного металла. Для этого необходимо дугу держать короткой, а отрывая ее от ванны, удалять не более чем на 1- 2 мм. Перекрытие смежных слоёв должно составлять около 20 — 25 мм.
Для сварки второго слоя применяется тот же метод, что и для первого слоя. При сварке второго слоя электрод перемещают поперечно от края одной кромки до края другой кромки.
При сварке каждого слоя поверхность шва может быть вогнутой или немного выпуклой. Повышенная выпуклость шва в основном при потолочной сварке часто является причиной плохого провара.
Для улучшения наблюдения в зоне сварки последнего слоя, в области кромок предпоследний слой накладывается так, чтобы его поверхность была на 1 — 2 мм ниже свариваемых кромок. Последний слой выполняется шириной на 2—3 мм больше, чем ширина разделанных кромок и с усилением 2 —3 мм. Слой должен иметь плавный переход от наплавленного к основному металлу.
`
Сварка труб — технология, методы, способы
В сварке труб используются промышленные способы для малоуглеродистых и низколегированных сталей: электродуговая, газовая, аргонная или полуавтоматическая. На практике чаще всего применяется ручная дуговая, многие профессионалы советуют именно этот способ, который позволят сделать тройной шов. Но прежде чем приступить к сварочным работам требуется предварительно произвести шлифовку трубы, выровнять стыки, нарезку кромок и прогрев свариваемой поверхности.Особенности сварки труб разного диаметраСварка труб разного диаметра считается одним из сложных видов сварочных работ. Первый этап – подготовительный, кромка очищается от грязи и смазочного материал. Трубы заводского производства изготавливаются под углом в 30 градусов, поэтому если скоса нет, то фаска снимается режущим инструментом. Затем обе кромки совмещаются и привариваются ровным швом длинной не мене 80 м. Если диаметр трубы до 300 мм, то промежутки между прихватами – 300 мм. Электроды для прихвата используются такие же, как и для сварки стыков.Как рассчитать цену за стык
Цена сварочных работ рассчитывается индивидуально и зависит от таких факторов как:
- • какой расходный материал (электроды) используется;
- • объем трудозатрат, сюда входит стоимость 1 часа работы конкретного мастера, а также учитывается сложность конструкции и метод сварки;
- • амортизация оборудования;
- • сроки выполнения работ;
- • подготовительные мероприятия: очистка, обезжиривание и прочее.
Из расчета того какой вид энергии используется различают 3 способа сварочных работ:
- • термический. Для нее характерные такие методы сварки – дуговая, газовая, плазменная;
- • термомеханический – контактная и диффузионная сварка;
- • механический – холодная, ультразвуковая и методом взрыва.
Стальные трубы варят аппаратами MIG/MAG/TIG. Перед началом работ трубы в обязательном порядке предварительно очищают от ржавчины и окисления. Затем с трубы снимается фаска, а сварочный шов заливают расплавленным металлом, чтобы конструкция была прочной и герметичной. Самый востребованный способ соединения стальных труб – ручная дуговая сварка. Ручная сварка практические ничем не уступает электродной. Для сварки стали используют электроды для углеродистой стали, благодаря тому, что большинство металлоконструкций выполнены из углеродистой стали.
Сварные соединения — обзор
12.7 Структурный анализ стелларатора
Начнем с того, что отметим, что структурный анализ токамаков и стеллараторов концептуально, логически и алгоритмически схож. Это заставляет нас еще больше сосредоточиться на конкретных вопросах, связанных в основном с опытом проектирования стеллараторов W7-X.
Многие характеристики, необходимые для расчетов прочности и жесткости, приведены приблизительно. Поэтому параметрический анализ широко используется при проектировании MFR, особенно его нелинейных несущих и опорных конструкций.Коэффициенты безопасности для номинальных, ожидаемых и экстремальных индивидуальных параметров выбираются на основе опыта работы с аналогичными конструкциями, а также всестороннего анализа неопределенностей. В конструкции W7-X эти коэффициенты безопасности были приняты равными 1,2, 1,1 и 1,0 соответственно. Такой выбор позволил учесть изменчивость конструктивных и функциональных свойств материалов, коэффициентов трения, степени затяжки зазоров между элементами крепления, смещения деталей друг относительно друга и т. Д.
Как и в случае с токамаками, пондеромоторные силы в стеллараторах вызывают распределенные нагрузки, действующие на катушки. Тороидально направленные силы стремятся сплющить катушки и переворачивать их вокруг радиальной оси. Эти силы воспринимаются стальными корпусами катушек, центральной несущей конструкцией и опорами между катушками.
Для стеллараторов проблема магнитоупругой устойчивости не является критической, в отличие от токамаков, поскольку стеллараторы подвергаются гораздо более слабым пондеромоторным силам, а их трехмерные катушки не подвержены потенциально дестабилизирующим деформациям.Хотя пондеромоторные силы играют доминирующую роль в развитии напряженного состояния, другие составляющие напряжения, такие как вес и давление охлаждающей жидкости, учитываются в конструкции. Эти факторы имеют фундаментальное значение для анализа прочности на этапах сборки и испытаний машины. В стеллараторах распределенные механические нагрузки меньше, чем в токамаках, при той же величине магнитного поля вдоль оси плазменного столба из-за большего количества катушек и, следовательно, меньших сечений обмоток и токов катушек.
Анализу прочности и жесткости MS должна предшествовать физико-механическая «гомогенизация» обмотки, необходимая для определения их ортотропных «эффективных» свойств. Отличительной особенностью стелларатора является то, что области наибольшей интенсивности / деформации напряжений в обмотках расположены на границе раздела «усредненного» материала и внешней изоляции корпуса катушки. Поэтому при моделировании стеллараторного МС используется субмоделирование вместо стандартного подхода «обратного прохода», распространенного в конструкции токамака.Смещения, определенные при анализе глобальной модели, используются в качестве граничных условий для уточненной подмодели в интересующей области.
Для математического моделирования МС удобно выделить регулярную часть конструкции. В стеллараторах обычная часть является либо 72-градусной (в машинах на основе конфигурации Helias с пятью периодами поля, например W7-AS и W7-X), либо 90-градусной (в четырехпериодной машине, такой как TJ- II и HSX) азимутальный сектор, содержащий от 8 до 12 витков.
Конструкция сверхпроводящего МС должна учитывать ухудшение физических и механических свойств материалов при криогенных температурах. Важную проблему представляет явление «прерывистой пластификации», которое прогрессирует в зависимости от скорости нагружения [12]. Из-за потенциальной потери производительности из-за этого эффекта пластические деформации не допускаются конструктивными стандартами для многих типов криогенного оборудования.
Анализ механической прочности конструкционных элементов стелларатора W7-X MS, нагруженных в упруго-пластическом диапазоне, основывался на следующем постулате: эти элементы соответствуют заданному критерию статической прочности даже в том случае, если локальные пластические деформации на некоторых участках превышают 1%, если их гипотетически заменить конструкционными материалами, характеристики которых задаются только при комнатной температуре, несущая способность которых достаточна согласно упругопластическим расчетам.Единственным исключением являются криогенные трубопроводы, для которых допустимая деформация выбирается с учетом криогенной защиты материала.
На вакуумную камеру стелларатора действует меньший диапазон пондеромоторных сил по сравнению с ВВ токамака. Нарастание и разрядка тока катушки в стеллараторе происходит медленнее, чем в токамаке. Обрыв тока и переход проводников катушки из сверхпроводящего в резистивное состояние маловероятны. Гало-токи и вертикальные смещения плазмы незначительны.Основными источниками пондеромоторных сил, которые необходимо учитывать при анализе конструкции и долговечности ВВ и компонентов внутри корпуса, являются вихревые токи, индуцируемые во время разрядки тока катушки, скачок плазменного и диамагнитного тока, а также ток, текущий из ВВ. к электропроводящим компонентам в емкости.
Нормы расчета прочности и жесткости стеллараторов еще не определены. Вот почему процесс проектирования W7-X регулировался руководящими принципами проектирования ИТЭР.Последние предназначены для гораздо более тяжелых условий эксплуатации, например, для увеличения количества рабочих циклов в десятки раз, и были несколько модифицированы (смягчены) для W7-X. Такое послабление стандартов проектирования не может распространяться на стеллараторы на основе топливного цикла DT. Исключение также распространяется на сварочные процессы W7-X и испытания сварных соединений. Смягченные стандарты проектирования W7-X допускают следующее:
- •
Пластификация конструкционных материалов MS — в той степени, в которой желаемая несущая способность конструкции подтверждается расчетами, учитывающими низкотемпературную деградацию материалов.
- •
Контролируемое разрушение — в той степени, в которой количественный анализ роста трещины указывает на более чем 10-кратный запас по критическому количеству циклов нагружения.
- •
Местное отслоение изоляции обмотки — до такой степени, что численный анализ не выявляет никакого распространения потери прочности. Износ изоляции вблизи области отслоения из-за микродислокаций соседних слоев изоляции относительно друг друга практически маловероятен из-за небольшого количества рабочих циклов.
- •
Локальное пластическое течение в элементах конструкции МС, так как позволяет повысить допустимый уровень деформации.
Кроме того, критерии прочности сварных соединений для W7-X менее требовательны. Как известно, качество сварки измеряется коэффициентом прочности соединения, то есть отношением сварного соединения к показателям прочности основного металла. Коэффициент прочности соединения установлен как один из нормативов проектирования. В проекте W7-X указано следующее:
- •
Каждое сварное соединение рассматривалось как несущий конструкционный элемент с коэффициентом прочности 0.85. Для проведения необходимых оценок использовалось упруго-пластическое приближение.
- •
Сварные конструкции имеют двухуровневую систему управления избыточным давлением, предотвращающую повышение давления выше 1,2 атм. В нормативном контексте это позволяет рассматривать конструкцию как ВВ с «ослабленными» требованиями к прочности сварных соединений.
- •
Критерии и соотношения ИТЭР использовались для оценки сопротивления соединений циклическим напряжениям.
- •
В математических моделях сварных соединений длиннее 5 мм радиус кривизны шва принимался равным 2 мм. Для более коротких соединений радиус кривизны был прямо пропорционален длине соединения.
«Ослабленные» стандарты и адекватность этих исключений подтверждены в ходе многочисленных тестов и сравнений между теоретическими и экспериментальными данными.
В любом случае высшая квалификация сварщика является одним из важнейших «стандартов проектирования» для любого MFR.
Подготовка стыков под орбитальную сварку: подготовка концов труб и подгонка
Сварка труб и трубопроводов делится на множество миров. С одной стороны, суровый мир субподрядчиков по сварке собственников / операторов. Эти сварщики носят сварочные маски в виде блинов, водят грузовики с хорошо установленными источниками питания для сварки труб сзади и, по-видимому, имеют бесконечный запас сварочных стержней, спрятанных вокруг их людей и транспортных средств. На другом конце — гораздо более точный и требовательный мир орбитальной сварки.На первый взгляд, последнее имеет примерно столько же общего с первым, как ракетостроение, анализ ДНК и другие профессии, связанные с лабораторными халатами. При более внимательном рассмотрении выясняется, что это неправда.
На самом деле, независимо от того, свариваются ли трубы вручную или с помощью автоматизированного оборудования, основы сварки труб не так уж и отличаются. Подготовка стыков под орбитальную сварку начинается так же, как и подготовка стыков под сварку труб методом SMAW или MIG: с помощью боковой шлифовальной машины. Однако подготовка стыков труб под орбитальную сварку становится и сложнее, и проще.
Подготовка основных сварных швов трубНезависимо от используемого процесса сварка труб — и вся сварка в этом отношении — начинается с удаления краски, ржавчины, смазки, анодирования, фрезерного покрытия и любых других посторонних материалов, которые могут повредить сварной шов с поверхностей, подлежащих обработке. сварной. Чаще всего для этого используют болгарку. Он может легко и быстро удалить с трубы посторонние загрязнения и покрытия, оставив для сварки только оголенную металлическую поверхность.Струя воздушного компрессора или быстро испаряющийся растворитель может удалить металлические фрагменты и пыль, оставленные шлифовальным кругом.
При начальной подготовке стыка следует соблюдать осторожность, чтобы не повредить трубу. Слишком длительное шлифование может привести к получению очень чистой и гладкой поверхности, но также может удалить слишком много материала и, как следствие, изменить диаметр и размеры трубы. Слишком долгая шлифовка в одном месте также может привести к перегреву и обесцвечиванию трубы.Изменение размеров трубы или ее механических свойств из-за перегрева влияет на общую целостность секции трубы, что делает ее непригодной для использования в трубопроводе. После первоначальной подготовки следует провести базовый визуальный осмотр, чтобы убедиться, что подготовка не повредила трубу. После очистки и осмотра конец трубы готов к механической обработке.
Обработка концов труб для базовой подготовки стыков под орбитальную сваркуСварные швы должны проходить на всем протяжении стыка и превращать два металлических куска в одно сплошное изделие.При работе с толстыми кусками металла необходимо создать канавку, чтобы сварочная головка могла проникать в глубину стыка и чтобы можно было уложить непрерывный сварной шов от внутреннего края трубы к внешней поверхности. Эта канавка создается путем прорезания угла на торце трубы с обеих сторон соединения. В любом типе трубы с толщиной стенки более 1/8 дюйма (около трех миллиметров (мм)) можно предположить, что потребуется некоторый скос, чтобы сварной шов мог проникнуть на всю толщину трубы. стенка трубы.
Типичная сварная фаска, приваренная вручную, состоит из трех отдельных плоскостей, врезанных в конец трубы, как показано на схеме ниже:
- Фаска: Плоская плоскость, отклоненная от внутреннего диаметра трубы и от стыка. Фаска открывает шов, так что внутренний диаметр открыт для сварки.
- Сторона: Плоская поверхность, перпендикулярная трубе, рядом с внутренним диаметром трубы. Он также отражается перпендикулярной поверхностью на конце трубы, к которому она будет присоединяться.
- Зенковка: Опциональная дополнительная фаска на внутреннем диаметре трубы, которая помогает довести ширину лицевой поверхности до свариваемых размеров или обеспечивает место для сварки трубы внутреннего диаметра.
Тип фаски, показанный на диаграмме выше, называется V-образной канавкой. Общий внешний угол сварного шва от внешнего края каждой фаски составляет от 60 до 75 градусов (37,5 градусов на каждую сторону очень распространено в промышленности, как показано на фото ниже).Его можно рассматривать как стандартную подготовку концов трубы и использовать при толщине стенки трубы от примерно 3/16 дюйма или примерно 4,76 мм до 1,5 дюйма или 38 мм. Таким образом можно подготовить большинство стыковых соединений концов труб перед сваркой.
Еще одним важным параметром для подготовки и монтажа трубы является корневой зазор, который представляет собой расстояние между противоположными поверхностями трубы. В большинстве случаев орбитальной сварки предпочтительно, чтобы не было корневого зазора, а грани стыкуются вместе в конфигурации «стыкового соединения».
Множество различных передовых методов сварки труб дают точную специфику и детали, чтобы помочь сварщикам определить правильный угол скоса, толщину лицевой поверхности, глубину и угол зенковки, а также общую геометрию подготовки концов трубы. Эти рекомендации должны быть включены в график производства сварочных работ, и перед сваркой подготовленные концы труб следует сверять с графиком, чтобы убедиться в их правильности.
Несмотря на то, что подготовка швов с одним V-образным пазом является обычным явлением, это не единственный способ подготовки сварных швов.С учетом более толстых материалов, которые часто используются при орбитальной сварке, механизированные процессы сварки труб часто требуют других типов подготовки стыков.
Обработка концов трубы для орбитальной сварки с узкими канавкамиПри толщине стенки трубы около одного дюйма общая ширина стыка от внешнего края каждой фаски в одной фаске с V-образной канавкой становится непрактичной для заполнения с точки зрения как времени, так и необходимого материала.
Подготовка одного конца трубы, которая может уменьшить объем необходимого материала, — это подготовка J-образной канавки.Он имеет дополнительное преимущество, так как обеспечивает более плоское гнездо для корневого прохода и делает возможным более узкий зазор между поверхностями труб. Этот тип подготовки трубы получил свое название от небольшого изгиба у основания фаски. Профиль подготовки конца трубы с J-образной канавкой следующий:
J-образная канавка также может быть выполнена с двумя углами, что называется составной фаской, как показано ниже:
Тип подготовки концов трубы и точные углы сильно зависят от требований проекта, толщины материалов и типа процесса орбитальной сварки.Сегодняшние строгие стандарты и высокое давление также означают, что эти фаски должны быть точными, чтобы избежать растрескивания и других проблем. После того, как концы труб будут обработаны, их необходимо будет проверить, чтобы убедиться, что углы скоса правильные, а поверхность имеет точно правильную ширину.
В идеале обработка концов труб должна производиться специальными режущими и обрабатывающими инструментами. Результаты значительно точнее, чем при использовании боковой шлифовальной машины, и на них потребуется гораздо меньше времени. Как и сам процесс орбитальной сварки, экономия времени и повышение качества, связанные с использованием правильных инструментов для работы, окупаются дополнительных затрат на необходимое специализированное оборудование.То же самое и с фитингами труб.
Сборка труб и орбитальная сварка стыковВ полевых условиях секции труб часто свисают с вилок фронтального погрузчика, и используются тросы, чтобы тянуть каждую секцию трубы на место, где они выравниваются с помощью зажимных стержней. К счастью, более сложные методы значительно ускоряют и упрощают монтаж труб и позволяют работать с более длинными участками труб.
Если подготовка стыка орбитальной сваркой была выполнена правильно, орбитальная сварка трубы проста.Операция устанавливает направляющую на трубе, прикрепляет сварочную головку к направляющей, выполняет проверку орбитального сварочного аппарата, чтобы убедиться, что сварочная головка и другое оборудование находятся в хорошем рабочем состоянии, а в контроллер загружается надлежащий график сварки, затем запускается Сварочная головка вращается вокруг трубы, чтобы убедиться, что все в порядке.
Для сварки стыков труб можно использовать различные автоматизированные процессы сварки труб, но сварка вольфрамовым электродом в среде инертного газа (TIG) или дуговой сваркой вольфрамовым электродом (GTAW) позволяет получить самые точные и высококачественные сварные швы.Автоматическая орбитальная сварка открывает возможность изготавливать непрерывные стыки толстых труб полностью из высококачественной сварки GTAW. Точная подготовка сварных швов под орбитальную сварку и непрерывная орбитальная сварка GTAW с подачей проволоки в узкие канавки обеспечивают точные технические требования, предъявляемые к промышленным трубопроводам.
Arc Machines, Inc. предоставляет промышленное оборудование для орбитальной сварки GTAW, способное выполнять сварные швы толщиной до 12 дюймов. Головки для орбитальной сварки и источники питания Arc Machines — лучшие варианты для выполнения сложных проектов орбитальной сварки.По вопросам, касающимся продуктов, обращайтесь по адресу [email protected] . По вопросам обслуживания обращайтесь по адресу [email protected] . Arc Machines приветствует возможность обсудить ваши конкретные потребности. Свяжитесь с нами , чтобы договориться о встрече.
Сварка труб встык — Copier Machinery
Если трубы необходимо сварить друг с другом, перед началом сварки необходимо прижать два скошенных конца трубы друг к другу.Когда сварка сделана, сварка называется сваркой стыкового соединения.
Другое название сварки стыковых соединений — паз под квадрат. Когда трубы должны быть приварены к каждому, оба конца трубы должны быть сначала обработаны на станке для снятия фасок.
Наша стационарная машина для снятия фаски с труб Beaver S-serie подходит для этой работы.
В крупных проектах трубопроводов во многих случаях необходимо выполнить много стыковых сварных швов , и снятие фаски — это один шаг до того, как можно будет выполнить сварку трубы.Распространенными методами сварки труб являются TIG-сварка и MIG-сварка . Стыковые швы — это сварные швы, при которых две части металла привариваются к одной и той же высокой или плоской поверхности.
Свяжитесь с нами для получения дополнительной информации о нашей серии Beaver S или наших станках для чистовой обработки труб с ЧПУ.
Если у вас есть вопросы, свяжитесь с нами по адресу [email protected] или позвоните нам по телефону +31 (0) 183441313 в рабочее время.
J Prep
«J Prep» или «J-подготовка» в процессе снятия фаски означает, что сварочная кромка имеет форму буквы J.J-образная подготовка — это способ сварки с узким зазором, что означает, что на меньше сварочного материала, и меньше сварочной проволоки необходимо использовать в процессе сварки, зазор или пространство меньше, чем при сварке с V-образной фаской, что приводит к тому, что Подготовительная сварка J выполняется быстрее и требует меньше времени. Сварка J-образного препарирования труднее из-за множества различных сварных швов и потому, что этот метод чаще используется для труб с толстыми стенками.
Когда мы предлагаем оборудование для снятия фаски и заказчику требуется J-образная препаровка, важно выяснить, каков радиус J-образной препарирования и каков угол J-образной препарирования.
Если у нас есть эта информация, мы можем посоветовать, какой тип станка и какой набор инструментов использовать. Если вам необходимо выполнить стыковую сварку с использованием J preps, свяжитесь с нами, чтобы получить решение для снятия фаски на трубах. Просто отправьте нам письмо по адресу [email protected].
I во многих случаях требуется датчик внутреннего диаметра для корня на J-образной препарировании, который должен быть точным по всей длине трубы. Устройство отслеживания внутреннего диаметра или так называемая система копирования ID отслеживает внутренний диаметр трубы при подготовке J-образной формы, таким образом отслеживая овальность трубы и формируя скос с более жесткими допусками.
J-образная фаска
J-образная фаска или J-образная фаска абсолютно одинаковы.
Поскольку есть также v-образный скос, x-образный скос и j-образный скос, буква в сочетании со словом bevel поясняет подготовку. V-образные и J-образные скосы при сварке известны как V-образные и J-образные соединения.
Кажется, что слово J bevel более распространено в европейских странах. World J Prep больше используется в Соединенном Королевстве, Соединенных Штатах Америки и Австралии.В нефтегазовой промышленности используются термины J-скашивание и J-подготовка.
Более подробную информацию о нашей компании вы найдете на нашем сайте Copier Bevelmachines.
Соединение труб стыковой сваркой
Что такое стыковая сварка?
Стыковой сварной шов — это тип сварного шва, при котором «стыковой конец» заготовки (трубы или трубки в нашем бизнесе) приваривается к другой в той же плоскости по окружности. Стыковая сварка — это наиболее распространенный тип соединения, который используется в системах трубопроводов.Этот тип сварки обычно используется для соединений труб, не требующих сборки или замены, например, для магистральных или подземных трубопроводов.
Как подготовить трубы к стыковой сварке?
Трубы должны иметь гладкие или скошенные концы, чтобы можно было выполнять сварку стыковых соединений. На кромке выполняется скос, чтобы освободить место для сварочной горелки, поэтому трубу можно сваривать встык на всю толщину стенки. Толщина и диаметр труб должны быть одинаковыми.Кроме того, качество фаски является определяющим фактором качества сварного шва, поскольку сварочные операции необходимо выполнять с внешней стороны труб. В то время как наиболее распространенными формами фаски трубы для стыковой сварки являются V-образная и J-образная фаска, стыковой шов может выполняться с любой формой фаски трубы. Вместо формы скоса сварка на кромке делает его стыковым сварным швом.
V-образный или J-образный скос: что лучше для стыковой сварки?
Несмотря на то, что почти все виды фасок можно сваривать встык, они имеют свои преимущества и недостатки.Как уже упоминалось, V-образная кромка и J-образная кромка являются наиболее распространенными формами фасок труб для стыковой сварки, поэтому мы обсудим основные различия между ними.
Угол J-образной фаски обычно меньше, чем угол V-образной фаски, что означает, что с помощью J-образной фаски можно создать меньше места для сварочной горелки. Это усложняет сварщику сварочный процесс. Хотя это проблема для J-образной фаски, общий объем сварного шва будет меньше из-за ограниченного пространства, создаваемого J-образной фаской.Это означает, что для сварки требуется меньше материала (сварочной проволоки) и времени, что снижает производственные затраты.
Для труб с небольшой толщиной стенки зазор всегда будет небольшим, поэтому нет существенной разницы между количеством материала или временем сварки. Тогда V-образная фаска обычно является лучшим вариантом. Если толщина стенки увеличится, влияние разницы в объеме будет значительным. Вот почему использование J-образной фаски более распространено на трубах с большой толщиной стенки, чем на трубах с меньшей толщиной.
Еще один способ уменьшить объем сварки труб с большой толщиной стенки — использовать составную фаску. Это можно сделать для V-образной фаски и для J-образной фаски, но чаще используется для V-образной фаски. Первая часть фаски будет стандартной фаской 30 ° / 37,5 °, но после 19 мм внутренней поверхности земли (или корня) она изменится на 10 °.
Что мы предлагаем
Наши стационарные станки для снятия фаски с труб серии Beaver могут создавать идеально скошенные концы желаемой формы, чтобы подготовить трубы для стыковой сварки.Мы предлагаем полный спектр станков для снятия фасок с ручным, автоматическим и ЧПУ для металлических труб от 3 до 56 дюймов.
Как мы все знаем, SAW — это очень эффективный процесс для быстрого заполнения открытых стыковых швов в толстостенных трубопроводах и намотках. Rotoweld 3.0 с опцией SAW — это универсальное и мощное оборудование. В дополнение к уникальному полностью автоматизированному корневому проходу MIG без дефектов, он предлагает широкий выбор опций для проходов заполнения, а именно: MIG распылением, сердечник из флюса и SAW.Независимо от того, является ли ваш объем работ углеродистой или нержавеющей сталью, стандартной стенкой или толстой стенкой, Rotoweld значительно увеличит (в 4-8 раз) вашу производительность и обеспечит 100% воспроизводимость качества сварных швов.
Свяжитесь с нами для получения дополнительной информации о возможностях наших станков для снятия фасок и Rotoweld.
(PDF) Разрушение сварных соединений между трубой из углеродистой стали и коленами из нержавеющей стали 304
Разрушение сварных соединений между трубой из углеродистой стали и
коленами из нержавеющей стали 304
Анвар Уль-Хамид
*
, Хани М.Таванси, Нуреддин М. Аббас
Лаборатория характеристик материалов, Научно-исследовательский институт, Университет нефти и полезных ископаемых имени короля Фахда, P.O. Box 1073,
Dhahran 31261, Саудовская Аравия
Получено 2 июля 2004 г .; принято 3 июля 2004 г.
Доступно онлайн 12 сентября 2004 г.
Реферат
В нескольких сварных швах между трубой из углеродистой стали (CS) и коленами из нержавеющей стали (SS) типа 304, составляющих систему газопровода
нефтехимической установки, образовались трещины после относительно короткого периода использования, что приводит к утечке.Газ
, протекающий по трубе, был богат водородом при температуре 45 ° C и давлении 16 кг / см
2
. Для определения наиболее вероятной причины отказа использовались светооптическая металлография
и сканирующая электронная микроскопия в сочетании с энергодисперсионной рентгеновской спектроскопией, индуктивно связанной плазмой
и испытания на микротвердость. Анализ
показал, что трещины возникли на границе раздела между трубой CS и корневым швом SS.Узкая полоса между трубой CS
и сварным швом из нержавеющей стали продемонстрировала твердость C 60 по Роквеллу, что свидетельствует об образовании мартенсита из-за сегрегации C при температуре сварки
и последующей закалке во время охлаждения. Ферритная область CS, прилегающая к сварному шву, была обезуглерожена на
и не содержала перлита; подтверждающий рассуждение. Область сварного шва была разбавлена, включая в основном
Fe с небольшими количествами Cr и Ni. Считается, что растрескивание началось в затвердевшей области.Однако отказу
могли способствовать среда, богатая водородом, и область мягкого обедненного углеродом феррита.
Ó2004 Elsevier Ltd. Все права защищены.
Ключевые слова: трещины; Анализ отказов; Зона воздействия тепла; Повреждение водородом; Сварные швы
1. Введение
В данной статье сообщается об исследовании разрушения сварных соединений разнородных металлов в системе трубопроводов на нефтехимическом заводе
. Процесс включал реформированный газ, который проходил через водоохладитель, с последующим сжатием
в трехступенчатом центробежном компрессоре синтез-газа.Выпускной трубопровод всасывающего барабана
1350-6307 / $ — см. Анкету №2004 ООО «Эльзевьер». Все права защищены.
doi: 10.1016 / j.engfailanal.2004.07.003
*
Автор для переписки. Тел .: +966 3 860 2017; факс: +966 3 860 4442.
Адрес электронной почты: [email protected] (А. Уль-Хамид).
Анализ технических неисправностей 12 (2005) 181–191
www.elsevier.com/locate/engfailanal
Поддержание чистоты труб и стыков труб при сварке
Home / Поддержание чистоты стыков труб и труб при сваркеHuntingdon Fusion Techniques HFT может удалять воздух из области сварного шва изнутри и снаружи одновременно, используя защитный экран для сварки снаружи и надувную систему продувки труб изнутри.
Сравнение сварного шва без продувки (слева) и без продувки (справа). При сварке труб и стыков труб из нержавеющей стали и титана важно, чтобы сварные швы без оксидов были окрашены как внутри, так и снаружи. Окисленные сварные швы влекут за собой штраф для изготовителя, который должен гарантировать, что окисление и изменение цвета полностью удалены механическими или химическими средствами.
Легкий подвижный экран для наружных сварных швов труб от Huntingdon Fusion Techniques HFT легко переносится сварщиком, перемещающим горелку по шву.Когда стороны сливаются вместе, горячий металл на очень короткое время защищается инертным газом аргоном, текущим через сварочную горелку и выходящим из керамической газовой чашки. В это время скользящий экран (подключенный к источнику аргона) берет на себя и защищает горячий металл до тех пор, пока его температура не упадет ниже уровня окисления и не останется идеально чистый сварной шов.
При сварке труб из нержавеющей стали и титана, а также стыков труб важно, чтобы сварные швы без окислов изнутри и снаружи были нулевого цвета.Для достижения условий нулевого цвета или отсутствия оксидов сварных швов необходимо удалить воздух вокруг шва до уровня, при котором процентное содержание кислорода составляет от 5 до 50 частей на миллион, в зависимости от металла и, в некоторой степени, , приложение. Удаление воздуха из области сварного шва изнутри и снаружи должно выполняться одновременно, и это лучше всего выполнять снаружи с помощью приспособления, называемого Weld Trailing Shield®, а изнутри — с помощью системы продувки надувных труб от Huntingdon Fusion Techniques. HFT® (Берри-Порт, Уэльс).
Подвижные экраны легкие и легко переносятся сварщиком при перемещении горелки по шву. Поскольку стороны сплавлены вместе, горячий металл на очень короткое время защищен инертным газом аргоном, текущим через сварочную горелку и из керамической газовой чашки. В это время Trailing Shield, который также был подключен к источнику аргона, берет на себя и защищает горячий металл до тех пор, пока его температура не упадет ниже уровня окисления, оставляя таким образом идеально чистый сварной шов.Между тем, внутри трубы две надувные дамбы плотно закрывают полость примерно в 10 дюймов (250 мм) с каждой стороны от стыка. Подача газа аргона выталкивает воздух наружу, и он выходит через Weld Purge Monitor®, который показывает, когда в воздухе достигнут уровень кислорода ниже 50 ppm или любой другой уровень, требуемый WPS (технологическая карта сварки). В это время сварщик начинает свой процесс.
Без таких принадлежностей сварка выполняется в окисленной среде, что приводит к потере коррозионной стойкости и приводит к металлургическим дефектам соединения.Окисленные сварные швы влекут за собой штраф для изготовителя, который должен гарантировать, что окисление и изменение цвета полностью удалены механическими или химическими средствами. Такая дополнительная работа может повлиять на рентабельность и сроки доставки. Обратите внимание на сверхчистую внешнюю поверхность сварного шва на видео ниже.
COB Industries Inc., PO Box 36-1175, Melbourne, FL 32936-1175, 321-723-3200, www.cob-industries.ком .
Показатели напряжений для кольцевых сварных соединений, включая радиальную усадку сварного шва, несоответствие и переходы конической стенки (Технический отчет)
Родабо, Э. С., и Мур, С. Э. Индексы напряжения для кольцевых сварных соединений, включая радиальную усадку сварного шва, рассогласование и переходы с конической стенкой . США: Н. П., 1978.
Интернет. DOI: 10,2172 / 6518357.
Родабо, Э.C., & Moore, S.E. Индексы напряжения для кольцевых сварных соединений, включая радиальную усадку сварного шва, несоответствие и переходы конической стенки . Соединенные Штаты. https://doi.org/10.2172/6518357
Родабо, Э. К., и Мур, С. Э. Пт.
«Показатели напряжений кольцевых сварных швов, включая радиальную усадку шва, рассогласование и переходы конической стенки». Соединенные Штаты.https://doi.org/10.2172/6518357. https://www.osti.gov/servlets/purl/6518357.
@article {osti_6518357,
title = {Индексы напряжений для кольцевых сварных соединений, включая радиальную усадку сварного шва, несоответствие и переходы между коническими стенками},
author = {Родабо, Э. К. и Мур, С. Э.},
abstractNote = {Представлен обзор индексов напряжения B, C и K, используемых в Кодексе ASME для атомных электростанций для кольцевых стыковых швов и кольцевых угловых швов.Теоретические нагрузки представлены, чтобы помочь в оценке C-индексов. Данные испытаний на усталость представлены для помощи в оценке K-индексов и CK-продуктов. Представлена теория предельной нагрузки для помощи в оценке B-индексов. В результате этого обзора сделаны рекомендации по внесению изменений в Кодекс ASME. Основная часть этого состоит из определения определений кольцевых сварных соединений и переходов, а также соответствующих индексов напряжений для этих соединений.},
doi = {10.2172 / 6518357},
url = {https: // www.osti.gov/biblio/6518357},
journal = {},
number =,
объем =,
place = {United States},
год = {1978},
месяц = {9}
}