Технология ручной дуговой сварки
Среди различных способов сваривания деталей распространена технология ручной дуговой сварки посредством электродов. Эта универсальная технология используется на производствах различного масштаба. Данный способ позволяет без замены оборудования и сварочного инструмента (при условии правильного выбора режима) делать швы разного типа и назначения. Ручная дуговая сварка позволяет соединять детали в любом пространственном положении. Можно организовать сваривание в труднодоступных местах.
Технология ручной дуговой сварки при помощи электрической дуги прямого действия отличается простой интеграцией в любое производство. Устойчивый сварочный процесс обеспечивается благодаря непрерывной подаче конца электродного элемента в область горения дуги. Не происходит значительных отклонений по длине дуги.
Окисление электродного металла и увеличение разбрызгивания усиливаются при длинной дуге. При этом сокращается глубина провара, получается сварное соединение с включением оксидов.
Возбуждение дуги происходит в условиях кратковременного замыкания электрической цепи. Сварщик прикасается к металлу концом электрода и отводит его на 2-4-милиметровое расстояние. В результате появляется электрическая дуга. Ее горение поддерживается благодаря поступательному движению электрода.
Возбуждение дуги может производиться скользящим движением части электрода по поверхности металла. После касания необходим быстрый отвод электродного элемента на нужное расстояние. Это позволяет соблюсти технологию и получать качественное соединение.
В ходе сварки электрод перемещается:
- вдоль соединения;
- по направлению к детали по мере плавления;
- поперек соединения с целью получения необходимого сечения и формы шва.
При сваривании покрытым электродом происходит плавление покрытия и стержня. При расплавлении покрытия образуется шлак, выделяются газы. Шлак полностью обволакивает капли металла, которые появляются при плавлении проволоки.
При всплытии на поверхность шлаковой ванны шлак очищает расплавленный металл. Выделяемые газы оттесняют воздушные массы из реакционной области (зоны дуги). Это способствует созданию и поддержанию лучших условий защиты. Специальное покрытие электрода способствует газошлаковой защите материала сварного соединения.
Посредством покрытых электродов сваривают цветные/черные металлы, сплавы различной толщины. Подобные электроды активно применяются при наплавке. Технология ручной дуговой сварки достаточно универсальна. При небольших затратах на ее интеграцию в производственный цикл сокращается период окупаемости сварочного оборудования благодаря увеличению производительности труда, объемов выпуска сварных деталей.
Возврат к списку
Технология ручной дуговой сварки — виды электродуговых аппаратов, электрические процессы, способы сварщиков
12НояСодержание статьи
- Общая информация
- Ручная электродуговая сварка – что это такое
- Этапы процедуры
- Принцип работы и технология ручной дуговой сварки
- Безопасность при MMA способе
- Используемые электроды при процессе электродуговой сварки
- Виды ручной дуговой сварки
- Преимущества и недостатки
- Что влияет на качество и размеры сварного соединения
- Способы электродуговой сварки в разных положениях
- Дуга электросварки
- Влияние режима на шов
- Обучение основам мастерства
Металлоконструкции отличаются прочностью и износостойкостью. При плохом соединении металлических элементов конструкция из металла просто не выдержит нагрузку. Самые прочные – цельноштампованные изделия, но они очень дорогостоящие. В целях снижения стоимости и ускорения работы придумали ручную дуговую электрическую сварку (РДС), а что это такое – расскажем в нашей статье.
Общая информация
У этого метода есть дополнительные международные названия, аббревиатуры широко используются при изготовлении комплектующих. Можно встретить – MMA (Manual Metal Arc – дословный перевод нашего термина), российское сокращение РДС, или короче – РД. Метод придуман отечественным инженером Николаем Бернардосом, который впоследствии совершенствует свой прибор и создает разновидности. Патент на изобретение был куплен и внедрен в производство металлоконструкций во всем мире. Классический материал – угольный электрод, но есть новые изобретения, способы, задействующие плавящиеся стержни.
Ручная электродуговая сварка – что это такое
Это тип соединения двух и более элементов металлической конструкции с помощью образования электрической дуги и расплавления металла. Шов образуется между самой поверхностью и нижней частью проводника, состоящего из проволоки и защитного покрытия. Сейчас часто станки заменяются на заводах автоматическими аппаратами и моделями типа «полуавтомат». РДС применяется в домашних условиях из-за простоты оборудования доступной стоимости. Посмотрим видео-обзор с теоретическими знаниями:
Этапы процедуры
Все профессиональные сварщики и любители действуют по алгоритму:
- Подготовка предполагает тщательное очищение всех поверхностей и закрепление заготовки на рабочем месте.
- Появление дуги. Чтобы она образовалась, необходимо подать напряжение и 2-3 раза быстрыми движениями прикоснуться наконечником к металлу.
- Проведение шва – скорость и угол варьируется в зависимости от физических характеристик материала.
- Финальная обработка – следует снять неровности, убрать лишнюю окалину, зачистить соединение.
Иногда требуются дополнительные операции, например, предварительный нагрев заготовки или подача защитного газа. Однако основные элементы алгоритма отражены верно.
Принцип работы и технология ручной дуговой сварки
От источника питания на электродержатель подается переменный или постоянный ток (встречаются оба варианта). Напряжение позволяет создать электродугу, которая нагревает две поверхности металла. При движении ручки позади от проводника образуется сварочная ванна. В этой области происходит диффузионное соединение расплавленных сплавов. После их остывания, вещество кристаллизуется и снова превращается в твердый элемент – уже монолитный. Чтобы шов не окислялся под воздействием кислорода проволока в электроде покрыта специальным составом, который при плавлении выделяет инертный газ, вытесняющий О2.
Как делается РДС
Электрическая дуга поддерживается подаваемым током. При этом возможны различные полярности. Классический вариант – подается минус, а на заготовке поддерживается плюс, но встречается ситуация с противоположной подачей напряжения. Длина электродуги – расстояние между сварочной ванной и электродом. Она зависит от скорости проведения электродержателя. Помимо газа от покрытия проводника в области плавки железа образуются шлаки, они способствуют:
- увеличению скорости металлообработки;
- более долгому поддержанию высокой температуры;
- хорошему, ровному сварному соединению;
- защите от кислорода и окисления.
Как зажечь дугу для дуговой электросварки
Необходимо 2-3 раза легким движением прикоснуться концом вертикально направленного электрода к заготовке. Если быстро не отвести руку, произойдет залипание, поверхность будет испорчена. Второй метод – провести концом материала вдоль будущего шва. Посмотрим обучающее видео:
youtube.com/embed/frVuytuqFxg» frameborder=»0″ allowfullscreen=»»/>Как правильно перемещать сварку
Можно варить углом «назад» и «вперед», то есть к себе и от себя. В первом случае сильнее прогрев сплава, а во втором меньше. То есть следует сделать выбор в зависимости от материала. Угол наклона выбирается в соответствии с образованной сварочной ванной. Длина электродуги должна быть постоянно одинаковой – около 2-3 мм. В зависимости от необходимой прочности конструкции, используемого сплава, можно выбрать один из видов движения электродуговой сварки, схемы которых представлены в статье.
Безопасность при MMA способе
Всегда надевайте защитный костюм, обувь с прочными носами и массивной подошвой. Никогда не приступайте к работе в шлепках, с открытыми частями тела. Также следует надевать специальные сварочные перчатки – достаточно чувствительные к движениям, но хорошо защищающие. Будьте внимательны к глазам, всегда надевайте очки для сварки или используйте щиток. Тщательно подготовьте рабочее место, уберите легко воспламеняющиеся предметы. Вблизи всегда имейте огнетушитель и аптечку, так как деятельность связана с рисками.
Используемые электроды при процессе электродуговой сварки
Все проводники в продаже можно поделить на:
- Плавкие. Их сердцевина плавится и добавляется к расплавленному металлу двух заготовок, остается в шве. Она обмазана эффективным для создания газовой атмосферы флюсовым порошком.
- Неплавкие. Изготовлены из вольфрама и служат исключительно для подачи тока. Газ для ванны подается специальным шлангом.
Еще одно различие – диаметр сечения. Чем он больше, тем выше сила тока и шире максимальный шов. Подробнее в видео:
Присадочная проволока – что это
Еще одна разновидность. По сути, это крупный моток материала (алюминия, меди), который выполняет такие же функции, как и плавкий электрод, то есть проводит ток и одновременно является материалом для образования соединения между элементами конструкций. Отличие – отсутствие обсыпки, поэтому газ необходимо подавать извне. Второй вариант – посыпать флюсовый порошок вдоль образования шва.
Виды ручной дуговой сварки
Сразу скажем о «старшем брате» РДС – полуавтомате. Сейчас используется чаще, так как работа с аппаратурой быстрее и эффективнее. РД различают по:
- типу тока – переменный и постоянный;
- используемому проводнику – плавкий и неплавкий;
- необходимости дополнительного нагревания.
В целом процесс одинаковый, особенности только в том, какое оборудование используется и с каким металлом происходит работа – его температура плавления.
Преимущества и недостатки
Плюсы:
- удобство в использовании, не обязательно закреплять деталь на полу, можно даже работать на весу;
- установка не занимает много места;
- есть возможность соединять различные сплавы;
- можно перенести на другое место, взять с собой в машину;
- простота применения – можно легко обучить основам технологии электродуговой сварки.
Минусы:
- Контакт с газом и яркие вспышки света негативно влияют на здоровье сварщика.
- Хороший ровный шов получится только после длительного опыта и умения работать с различными материалами.
- Достаточно трудоемкий и долгий процесс.
Сделаем вывод – РДС больше применим в домашних условиях и на малых производствах.
Что влияет на качество и размеры сварного соединения
Факторы, влияющие на результат:
- Сила тока. Увеличение показателя приводит к значительному провару.
- Диаметр электрода.
- Напряжение.
- Постоянный или переменный ток. Первый дает узкий шов, второй – широкий.
Мы вспомнили, для чего нужен шлак и как он образуется. Чем качественнее обсыпка проводника и лучше само изделие, с точки зрения химического состава, тем лучше, аккуратнее получится шов.
Способы электродуговой сварки в разных положениях
Это одно из самых крупных преимуществ установки РДС – сварщик может находиться в любом отношении со свариваемыми поверхностями. Получится хорошее соединение, если придерживаться определенных технических норм.
Нижнее расположение
Наиболее привычное. Заготовка лежит на полу или невысоком столе, человек находится сверху. Хорошо закрепите детали и следите за плавным и равномерным образованием ванны.
Вертикальное
Из-за притяжения расплавленный металл будет стремиться стечь, могут образовываться подтеки. Легче работать сверху вниз, но лучше наоборот, так как капли раскаленного материала будут покрывать уже готовый, затвердевший шов.
Потолочное
Работу необходимо вести очень медленно, делая периодические интервалы. Так сплав будет успевать остывать и кристаллизоваться, чтобы не капать вниз. Также это способствует дополнительному прогреву.
Дуга электросварки
Этим термином называют длительный разряд тока, создающий высокую температуры. Фактически это горение газов, которые при обычных условиях не так интенсивно передают электроны и ионы. Его запускает электронная эмиссия – высвобождение отрицательно заряженной частицы в момент соприкосновения электрода и металла.
Влияние дуги на качество шва
Чем меньше расстояние, тем ровнее соединение – без капель, подтеков. Но держать несколько миллиметров очень трудно. Также короткая электродуга при правильном процессе ручной дуговой сварки приводит к:
- равномерному расплавлению обсыпки;
- ровному пучку искр;
- достаточной глубине проплавления;
- отсутствию окисления.
Параметр можно определять по звучанию – если оно равномерное, без щелчков и сбоев, то нужно стремиться поддерживать это расстояние.
Влияние режима на шов
При работе с различными поверхностям следует по-разному располагать элементы и сваривать торцы, ровные отрезы, сечения и прочее. Но это не должно заставлять вас менять параметры аппаратуры. Выбор режима зависит исключительно от того, какой ширины и глубины проплав вам необходим. Для выбора вам поможет таблица:
Толщина металла, мм | Сила тока, А | Диаметр электрода, мм |
3 | 175 — 185 | 3 |
5 | 200 — 225 | 4 |
7 | 250 — 270 | 5 |
10 | 300 — 330 | 6 |
Воздействие тока
Чем показатель больше, тем глубже плавится металл, прочнее соединение. Но одновременно с этим уменьшается его широта. Также имеет значение разновидность используемого оборудования, работает оно на переменном или постоянном электричестве. В первом случае соединительный участок будет более узким.
Обучение основам мастерства
Чтобы стать профессиональным сварщиком ручной дуговой сварки, необходимо проходить обучение в техникуме. Профессиональный работник имеет разряд, характеризующий его умение работать с различными материалами и сложными конструкциями. Но для домашнего использования достаточно почитать нашу статью и посмотреть видео:
Чтобы уточнить интересующую вас информацию, свяжитесь с нашими менеджерами по телефонам 8 (908) 135-59-82; (473) 239-65-79; 8 (800) 707-53-38. Они ответят на все ваши вопросы.
Технология ручной электродуговой сварки, электроды
Технология ручной электродуговой сварки, электроды
Ручная электродуговая сварка с помощью металлических электродов с защитной обмазкой является наиболее распространенным способом сварки при изготовлении трубопроводов с условным проходом более 80 мм
Сущность способа заключается в следующем. Тепло, необходимое для разогрева кромок металла, получается при горении электрической дуги, образуемой между свариваемым металлом и металлическим электродом. Электрическая дуга оплавляет основной металл и расплавляет металлический стержень электрода (температура дуги достигает 3500°С и выше). Расплавленный металл заполняет зазор между кромками свариваемых деталей и при застывании соединяет их в одно целое.
В зависимости от толщины стенки трубы сварку стыков выполняют в один или несколько слоев (проходов). Число слоев шва при ручной дуговой сварке зависит от толщины стенки трубы:
Толщина стенки трубы, мм | ДоЗ | 4—5 | 6—9 | 10—12 | 13—15 |
Число слоев шва | 1 | 2 | 3 | 4 | 5 |
На рабочем месте сварщика (сварочный пост) должны находиться все необходимые принадлежности и инструменты (электрододержатель, ящик для хранения электродов, переносный металлический ящик для огарков, щитки и шлемы, молоток, зубило, металлическая щетка, а также комплект шаблонов и щупов). Сварщик должен иметь также гибкий, хорошо изолированный провод необходимой длины и требуемого сечения (сварочный кабель).
Щитки и шлемы служат для защиты глаз и кожи лица от вредного действия излучения сварочной дуги. Изготовляют их из фибры или специально обработанной фанеры; весят они не более 0,6 кг. Для наблюдения за дугой в лицевой части щитка и шлеме имеется прямоугольный вырез размером 120×60
Основным инструментом электросварщика является электрододержатель, который должен удовлетворять следующим требованиям: весить не более 500 г; иметь надежную изоляцию от тока; обеспечивать возможность быстрого закрепления электрода под любым углом, не перегреваться при длительной эксплуатации.
Выпускаются различные типы электрододержателей: щипцовый, с пружинящими кольцами, вилочный. Наибольшее применение в последние годы получают электрододержатели щипцового типа.
При ручной электродуговой сварке трубопроводов очень важно правильно подобрать тип и марку электродов. Технологические свойства и прочностные характеристики электродов во многом определяют производительность сварки, а также герметичность, прочность и долговечность сварных соединений трубопроводов. Стальные электроды для дуговой сварки сталей разделяются на классы: для сварки углеродистых и легированных конструкционных сталей, легированных теплоустойчивых, высоколегированных и других сталей. Кроме того, электроды разделяются на типы: Э42, Э42А, Э46, Э50 и т. д. Цифра обозначает среднее значение временного сопротивления металла шва на разрыв в
Таблица 12 | |||||
Электроды металлические для электродуговой сварки труб | |||||
Тип электрода | Марка электрода | Коэффициент наплавки, г/ct’H | Механичесские свойства | Род и полярность тока | |
временное сопротивление кгс/мм2 | |||||
Э42 | ВЦС-1 | 9,5-13,5 | 42 | 18 | Переменный и постоянный |
Э42 | ОММ-5 | 8,5-9 | 44—50 | 18 | То же |
Э46 | МР-3 | 7,25 | 46-57 | 22,1 | » |
Э42А | УОНИ-13/45 | 9,8 | 43-45 | 28—32 | Постоянный, обратная полярность |
Э42А | см-п | 9,5-10,5 | 46—53 | 25-34 | Переменный и постоянный, обратная полярность |
Э42А | УП-1/45 | 9,9—10,3 | 28—33 | То же | |
Э46 | всп-з | 11,8 | 46—51 | 18—31 | » |
Э50А | УОНИ-13/55 | 8 | 50—55 | 25-30 | Постоянный, обратная полярность |
Э50А | ВСК-50 | 11 | 50 | 28 | Переменный и постоянный, обратная полярность |
Э50А | УП-1/55 | 10 | 54—56 | 28 | То же |
Э60А | УОНИ-13/65 | 8 | 60—65 | 20-25 | Постоянный, обратная полярность |
Э70 | К-70 | 7,8 | 70 | 12 | То же |
Э85 | УОНИ-13/85 | 9,8 | 85___ 90 | 15—20 | |
Э85 | ЦЛ-18 | в!б5 | 85,9 | 13,3 | » |
Э100 | ЦЛ-19 | 9 | 107,6 | 12,6 | » |
10—11 | |||||
ЭА1 | УОНИ-13/НЖ | 60—70 | 35—50 | » | |
ЭА1 | ЭНТУ-3* | — | 59-65 | 32-45 | » |
Примечания:
1. Для марок электродов, отмеченных звездочкой, механические свойства указаны после термообработки.
2. Указанные типы электродов обеспечивают сварку в любом пространственном положении.
Указанные в таблице электроды Э42, Э46 и Э42А предназначены для сварки малоуглеродистых и низколегированных сталей, Э50А — для сварки среднеуглеродистых и низколегированных сталей, электроды, Э60А, Э70, Э85 и Э100 — для сварки легированных сталей повышенной прочности,-ЭА1—для сварки высоколегированных теплоустойчивых сталей.
Покрытия электродов очень гигроскопичны, т. е. способны увлажняться в процессе их хранения и транспортирования. Поэтому перед производством сварочных работ их рекомендуется высушить. Для этого электроды помещают на 1—2 ч в специальные переносные сушильные печи, где температура достигает 150—300° С.
Одной из важных характеристик электродов, в значительной степени определяющей производительность сварки, является коэффициент наплавки αН Коэффициент наплавки определяют по формуле:
где: qН— вес наплавленного электродного металла, г;
I — сварочный ток, а;
t — время, ч.
Коэффициент наплавки характеризует удельную производительность сварки. Чем больше величина αН, тем больше производительность сварки.
1. В чем преимущества ручной электродуговой сварки перед газовой?
2. В чем сущность ручной электродуговой сварки?
3. Когда применяют многослойную сварку?
4. Какие основные инструменты и приспособления применяют при ручной электродуговой сварке?
5. Назовите основные типы или классы электродов. Как их обозначают и как расшифровывают эти обозначения?
6. Какие основные марки электродов применяют для сварки трубопроводов из углеродистой стали?
7. Какие основные марки электродов используют для сварки легированных сталей?
4. Что такое коэффициенты наплавки?
Все материалы раздела «Сварка труб» :
● Способы сварки трубопроводов и виды сварных соединений
● Подготовка труб под сварку
● Технология газовой сварки и резки
● Кислородно-флюсовая и дуговая резка
● Технология ручной электродуговой сварки, электроды
● Источники питания сварочной дуги
● Автоматическая и полуавтоматическая сварка под флюсом
● Автоматическая и полуавтоматическая сварка в защитных газах
● Сварка трубопроводов из легированной стали
● Сварка трубопроводов высокого давления, термообработка сварных соединений
● Сварка трубопроводов из алюминия и его сплавов, из меди и ее сплавов
● Пайка трубопроводов, дефекты сварных швов
● Контроль качества сварных швов
● Виды сварки и применяемое оборудование
● Сварка и склеивание винипластовых труб
● Сварка полиэтиленовых трубопроводов
● Правила техники безопасности при резке и сварке трубопроводов
Электродуговая сварка – особенности, как выполняется + Видео
Электродуговая сварка – это наиболее популярный способ выполнения сварочных работ, при которых используется электрическая дуга.
1 Технология электродуговой сварки
Для данного вида сварочных работ требуется сильноточный источник питания с малым напряжением. К одному из зажимов такого аппарата подсоединяют электрод для сварки, к другому – свариваемое изделие. Расплавление кромок деталей, которые необходимо соединить, осуществляется дуговым электрическим разрядом. При этом указанная электродуга имеет температуру более 5 тысячи градусов, что выше температуры, при которой плавятся любые известные человечеству металлы.
Задача дуги состоит в том, чтобы преобразовать в теплоту электроэнергию. Под влиянием полученной теплоты происходит расплавление электродного металла и свариваемых поверхностей. Это приводит к формированию сварочной ванны, где металл сварочного стержня взаимодействует с металлом детали. А образующийся при таком процессе шлак уходит на поверхность, создавая пленку, выполняющую защитную функцию. После того как металл затвердевает, получается прочное и качественное соединение.
Для сварки электродугой применяют электроды двух видов:
- неплавящиеся;
- плавящиеся.
Если используется неплавящийся сварочный стержень, сварной шов создается за счет расплавления специальных прутков (проволоки), которые называют присадочными и вводят в саму ванну. Плавящийся электрод не требует применения такой присадки.
В некоторых случаях в электроды добавляют натрий, калий, другие элементы, характеризуемые легкостью ионизации. Делается это для того, чтобы сварочная дуга обладала большей устойчивостью. Сварной шов от окисления может предохраняться газами с защитными функциями:
- углекислым;
- гелием;
- полностью инертным аргоном.
Защитные газы подают при проведении сварки из сварочной головки.
В настоящее время электросварка дугой может выполняться постоянным либо переменным током. Меньший разброс расплавленного металла (его брызг) отмечается при использовании постоянного тока, так как отсутствует смена его полярности и переход через ноль.
2 Сварочная дуга – что она собой представляет?
Под дугой, используемой для выполнения сварочных мероприятий, понимают одну из разновидностей электроразряда в газах. При этом разряде отмечается прохождение через газовый промежуток электротока под влиянием электрического поля. По сути, речь идет именно об электрической дуге. Но так как применяют ее в процессе сварки, дугу называют не иначе как сварочной.
На дуге фиксируется снижение напряжения. Она является одним из элементов сварочной электрической цепи. Электрод, подключаемый к «плюсовому» полюсу источника питания, при выполнении сварочных работ на постоянном токе именуют анодом. Если его подключают к «минусовому» полюсу – катодом. При работе на переменном токе каждый из сварочных стержней поочередно является то катодом, то анодом.
Дуговой промежуток – это расстояние между двумя электродами. Длина такого промежутка определяет длину электродуги. При малых температурах в стандартных условиях газы состоят из молекул и атомов с нейтральными характеристиками. Об их электропроводимости речи не идет. Добиться прохождения через газовую среду электротока можно исключительно тогда, когда в ней присутствуют ионы и электроны – элементы с определенным зарядом. Процесс формирования данных элементов принято называть ионизацией.
Заряженные частицы образуются в дуговом промежутке в результате того, что с поверхности катода начинается испускание электронов. Это приводит к ионизации паров и газов, находящихся в промежутке. Электрическая дуга может быть:
- сжатой;
- свободной (прямого действия).
В первом случае сечение электрической дуги могут уменьшать посредством регулирования газового потока, изменения сопла горелки сварочного аппарата, электромагнитного поля. Свободная же дуга неизменна.
3 Электродуговая сварка металлов – разновидности процесса
Для разных металлов рекомендованы различные виды осуществления сварочных работ. Для сварки изделий из чугуна, легированных сталей, некоторых цветных металлов, а также из нержавеющей стали обычно применяется ручная технология с защитой сварочной зоны. В данном случае электрод подсоединяют к электродержателю.
Конец стержня для сварки нагревается в тот момент, когда он прикасается к свариваемому изделию (наблюдается замыкание цепи тока). Нагретый электрод отводят от поверхности сварки (обычно на расстояние до 5 мм), что приводит к установлению дуги. Ток в дальнейшем поддерживается уже за счет дугового разряда.
Важнейшим условием получения качественного соединения при описываемой технологии является наличие обмазки – специального флюса густой консистенции, который окружает стержень для сварки. Обмазка предохраняет ванну и непосредственно электродугу от попадания в них газов из воздуха, обеспечивает высокую стабильность разряда, привносит раскислители, делающие сварочный металл более чистым.
По схожей схеме производится и сварка под флюсом. Правда, при ней роль электрода выполняет проволока, которую с катушки подают через пласт флюса в сварочную зону. Такой процесс можно считать практически полностью автоматическим. С его помощью несложно соединять изделия большой толщины, причем на отличном уровне производительности. Как правило, эту технологию применяют при выполнении больших объемов сварочных работ, так как предварительная подготовка изделий к соединению друг с другом требует немалого времени.
Достаточно популярной считается и технология сварки металлов в инертном газе при помощи вольфрамового неплавящегося электрода. Она предполагает защиту сварочной зоны гелием либо аргоном, которые подаются извне. При описанном способе вредные примеси из атмосферы не попадают в ванну. Чаще всего вольфрамовые стержни рекомендуются для соединения конструкций из нержавейки, никеля, алюминиевых сплавов.
Подробнее хочется рассказать о сварке плавящимися электродами по газоэлектрической технологии. По своей сути она напоминает процесс, выполняемый под слоем флюса, которым является газ, обволакивающий дугу, торец стержня и ванну. Газ подают через сварочное сопло. Целесообразность такой методики обусловлена тем, что при ней допускается получать дуговой разряд с разными параметрами, вводя смеси газов и кислород в незначительных количествах.
Газоэлектрический метод позволяет сваривать металлы с высокой химической активностью (например, медь, «нержавейку», магний и так далее). Он, кроме того, обеспечивает:
- удобство сварки в навесном и вертикальном положениях;
- высокую скорость процесса;
- визуальный контроль выполнения операции со стороны сварщика;
- отличную чистоту шва;
- возможность соединять изделия и с очень большими толщинами, и с очень малыми.
Реже сварка проводится электродами трубчатого типа. При данной операции электрический разряд формируется между трубчатым непрерывным стержнем (порошковой проволокой с флюсом) и изделием, подвергающимся сварке. Функцию присадочного материала при этом выполняет материал электрода, а сварочная ванна защищается элементами, образующимися в процессе разложения флюса.
Технология дуговой сварки. Виды электродуговой сварки.
Самый распространенный способ электродуговой сварки является способ сварки с помощью металлических электродов.
Схематический процесс электродуговой сварки и её виды изображены на рис. 1.
Виды электродуговой сварки.
Рис. 1. Виды дуговой электросварки:
а – сварка металлическим электродом:
1 – генератор; 2,3 – провод; 4 – металл; 5 – электрододержатель; 6 – электрод; 7 электрическая дуга.
б – сварка угольным электродом:
1 – электрическая дуга; 2 – электрод угольный; 3 – металл; 4 – присадочный пруток; 5 – держатель.
Технология ручной дуговой сварки.
Ток от генератора или трансформатора 1 по проводу 2 подводится к свариваемому металлу 4, а по проводу 3—к электрододержателю 5, в который зажимается электрод 6. Сварщик, приближая электрод к свариваемому металлу, замыкает цепь, возникает электрическая дуга 7. От тепла электрической дуги металл нагревается до температуры плавления и происходит слияние двух металлов. Расплавленный металл электрода служит присадочным материалом. Оказывать механические усилия на свариваемые детали при этом способе электросварки не требуется.
Преимущества и недостатки сварки постоянным и переменным током.
Электродуговая сварка выполняется как при переменном, так и постоянном токе.
Преимущества и недостатки постоянного тока.
Постоянный ток дает более устойчивую электрическую дугу и, благодаря неодинаковому выделению тепла на положительном и отрицательном полюсах, допускает более гибкую регулировку распределения тепла, применяя прямую (отрицательный полюс на электроде) или обратную (отрицательный полюс на детали) полярности. Это имеет большое значение при сварке цветных металлов, тонких листов металлов и некоторых марок специальных сталей. Оборудование для сварки на постоянном токе в 1,5 раза дороже оборудования для сварки на переменном токе.
Преимущества переменного тока.
Преимуществом сварки на переменном токе служат небольшие габариты, малый вес и сравнительно невысокая стоимость электросварочных трансформаторов, а также простота их эксплуатации и значительная экономичность.
Недостатки переменного тока.
К недостаткам сварки на переменном токе относятся трудность выполнения потолочной и вертикальной сварки и необходимость употребления более дорогих обмазных электродов. Качество сварки при использовании переменного и постоянного тока равноценно.
Сварка угольным электродом.
Другим способом электросварки является сварка угольным электродом.
Процесс сварки угольным электродом.
Процесс электросварки угольными электродами следующий (см. рис. 1, б). При сварке электрическая дуга 1 возникает между угольным или графитовым электродом 2 и свариваемой деталью 3. Шов получается при плавлении прутка 4, который называется присадочным прутком, он вводится со стороны в электрическую дугу. Для начала сварки электроды графитовые или угольные зажимаются в держатель 5. Одновременно происходит плавление электрической дугой кромок свариваемого металла. Такой способ сварки в промышленности применяется очень редко.
Значит, для угольного электрода присадочным материалом для заполнения шва будет пруток, который вводится со стороны в электрическую дугу, а при сварке металлическим электродом присадочным материалом будет металл самого электрода.
Преимущества электродуговой сварки перед газовой заключаются в том, что она в три-четыре раза дешевле газовой и безопасна от взрыва горючих газов.
Технология и способы ручной дуговой сварки покрытыми электродами
Само происхождение сварки напрямую связано с появлением металлорежущей индустрии и обработки всевозможных разновидностей материала. В особенности она процветала там, где находились залегания железной и цветных руд металла.
Первым способом сварки, который «увидел свет», была сварка ковкой или, другими словами, «кузнечная сварка». О свойствах и первые способы обработки металлов, были известно еще 3 тыс. лет назад.
Но далее, с расширением потребности в более качественной и совершенной продукции из различных железных и металлических материалов, усовершенствовались как металлургические, так и сварочно-соединительные процессы.
Продолжая свой путь, «в ногу» с технологическим развитием, сварка, с изобретением электричества, получила способ соединительного процесса, с помощью электрической дуги.
Уже с начала XIX века о сварке начинают идти публикации. Василий Петров, русский ученый, в 1809 году написал статью о своих экспериментах с электрической дугой. Также два независимых друг от друга учёных-изобретателя Бенардос Н.Н и Славянов Н.Г. разрабатывали в 1881-1882 гг различные способы сварки, чтобы соединить две металлические части в одну единую конструкцию.
Электрическая дуга, получаемая с помощью трехфазного тока, стала новым вариантом сварки. Новый тип сварочного соединения был предложен в 1905 году русским ученым Миткевичем В.Ф. А вот способ использования переменного тока принадлежит разработчику Holslag C. J, который его предложил в 1919 году. Усовершенствования вариантов сварочных работ в XIX веке продолжали такие учёные, как Эдмунд Дэви и Элиу Томпсон и многие другие учёные и изобретатели.
Способ сварки в космическом пространстве был изобретен советскими учеными и применен в 1969 году 16 октября. Сварка была произведена в условиях глубокого вакуума на космическом корабле «Союз-6».
На сегодня уже разработано и используется более 150 вариантов сварки. Также варианты имеют свои квалификации.
Сварка – это технология высокотемпературного процесса для соединения двух и более частей в одну неразъемную конструкцию путём установления межатомных связей, общего или местного нагрева. Существует также процесс сварки путем пластической деформации. Может также производиться в сочетании двух вышеперечисленных процессов вместе. Сварка представляет собой межмолекулярное соединение сцепляемых между собой деталей и установление молекулярной связи в пограничном слое, что будет характеризовать непрерывность структуры сварной конструкции.
Ручная дуговая сварка покрытыми электродами
Ручная дуговая сварка покрытыми электродами — один из самых распространённых вариантов сварочных работ, применяемых в различных сферах деятельности и индустрии. Для нее характерно:
- Простота технологии сварочного процесса, удобный и относительно лёгкий сварной агрегат, возможность сварки в сложно доступных местах и в любой пространственной комбинации положений.
- Правильный выбор специальных приспособлений, правильных параметров технологии «варения» и другие факторы правильных сварных швов на изготовляемой конструкции.
Качество сварных швов может зависеть не только от выбора технологии сварочного соединения, но также и от следующих важных факторов, таких как:
- Состав порошкового покрытия электрода и его качество,
- Общее состояние поверхности, на которой будет проводиться сварочно-соединительный процесс
- Общая подготовка к проведению данной операции по сварочной работе — это самый основной фактор качества.
Сам процесс включает в себя работу со сварочным штучным электродом и оборудованием, подающим на стержень постоянный либо переменный ток. Процесс расплавления происходит с помощью электрической дуги. В коротком временном контакте (чирканье) электрода и рабочей поверхности сварочной детали появляется электрическая дуга, при которой происходит плавление напыления, находящееся на металлическом стержне электрода и основного металла свариваемой конструкции. Именно эти компоненты в расплавленном состоянии создают шов сварки. В процессе высоких температур в зоне ванны происходит соединение металла стержня и детали, которую нужно сварить. При этом все ненужные шлаки вытесняются наружу. После чего нужно отвести электрод на пару мм от участка сварки, и далее дуга с помощью поступательного тока под действием высоких температур будет плавить порошковое напыление и металл электрода.
Металл, из которого состоит электрод, контактируя с металлом деталей сварки, имеет свойства перемешиваться, вытесняя шлаки и газы из зоны сварки. Образованные шлаки несут защитную функцию от взаимодействия сварной конструкции с азотом и кислородом воздуха. К тому же сам металл очищается при выходе шлака наружу.
Способы увеличения производительности дуговой сварки
Основной минус дуговой сварки — это её малая производительность. Поэтому было разработано несколько вариантов для улучшения производительности этого сварочного соединения.
- Самым распространенным вариантом дуговой сварки является нанесение на электрод специального железного порошка. Электрод с порошковым железным покрытием порядком повышает коэффициент наплавки до 18 г / А, что значительно повышает производительность дуговой сварки относительно эксплуатации обычных электродов без специального напыления. Производительность сварочного процесса увеличивается благодаря дополнительному железному напылению на электроде, который также участвует в создании шва сварки.
- Следующий не менее эффективный способ, также нашедший обширное применение в данной сфере, это когда происходит глубокое проплавление сварочного изделия.
Для этого способа используют электроды с более утолщённым покрытием. Особенность этого способа заключается в том, что более толстое напыленное покрытие плавится медленнее, чем сам металлический стержень электрода. Так на конце электрода образуется некая втулка, в которой будет находиться сварная дуга. Кромки свариваемого материала опираются на образовавшуюся втулку. При этом глубина проплавления становится больше. Также при том, что плавление металла электрода по отношению к его напылению протекает медленнее, то в сварочном шве его меньше, чем сварного материала. Это один из моментов, который повышает производительность дуговой сварки.
- Следующий на очереди вариант производительности дуговой сварки, который можно отметить, это трёхфазное «варение» при использовании переменного тока, а точнее, его трёх фаз. Производится путём подведения к сварному материалу двух электродов. При сварочном соединении образуются три дуги, которые будут действовать попеременно. Одна дуга будет между электродами, а две другие — между электродами и основным материалом.
При данном варианте отмечается, что производительность повышается, как и тепло, которого выделяется при сварочной работе в два, три раза больше, чем при варке однофазной дугой.
- А еще, во время «варения», с целью повышения производительности, также пользуются методом «наклонного электрода». Для наклонного расположения электрода применяют специальное приспособление, в конструкцию которого входит штанга, которая должна быть изолированной от электрических воздействий свариваемого материала. А ещё в приспособление входит обойма, которая подключена к электрическому источнику сварочной дуги. При этом обойма должна иметь свободное скольжение по штанге. Электрод фиксируется в обойме под наклоном к сварным кромкам. В свободном скольжении обойма с наклонно установленным электродом будет двигаться по штанге по мере плавления электрода. При этом направление сварочной дуги производится в сторону штанги, этим самым образуется сварной шов.
- Метод лежачего электрода. Для этих работ используют специальные электроды с плавящим покрытием, которые намного толще, чем стандартные электроды для дуговой сварки и длиной в 1.
5-2 метра. Вдоль сварных кромок выкладывается электрод. Для его фиксации поверх кладут прокладку и прижимают тяжёлым брусом из меди. Создают дугу путём замыкания угольным стержнем свободного конца электрода, так как на другой его конец накинут специальный зажим с тоководом. Таким образом, при устойчивом горении дуги происходит плавление электрода и сварного материала, образуя сварной шов. Этот способ имеет широкое применение в труднодоступных местах, для обычной сварки.
Соединяя различные конструкции сварочным способом в зависимости от их положения в пространстве, существует несколько вариантов расположения сварочных швов:
- Потолочные
- Нижние
- Горизонтально и вертикально в вертикальной плоскости.
Плюсы и минусы дуговой сварки
Если рассматривать положительные и отрицательные стороны этого вида сварочных работ, то можно отметить такие положительные моменты
Плюсы:
- Простота сварочного оборудования в эксплуатации соединительных работ различных конструкций.
- Сам сварочный аппарат весит относительно немного и оснащён дополнительно передвигающимися роликами, что упрощает его перемещение.
- Сварочные манипуляции можно проводить во всех пространственных вариантах расположения сварных конструкций, а именно: потолочном, нижнем, горизонтальном и вертикальном в вертикальной плоскости.
- Существует возможность варить конструкции в труднодоступных или же, для некоторых вариантов сварочного оборудования, вообще недоступных местах,
- Возможность производить сварочно-соединительные работы различного рода материала, не только касающихся железных и металлических конструкций, но также работу по сцепке деталей с цветными материалами.
- В отличие от других вариантов сварочного оборудования, именно на этом быстрее всего происходит переход на работу с другим видом материала.
- В ручной дуговой сварке присутствует самый большой и исчерпывающий ассортимент всевозможных типов свариваемых материалов.
Имея множество положительных моментов и достоинств, все же существуют и весомые отрицательные нюансы, которые не позволяют поставить этот тип сварки, на самый высокий уровень в сварочной индустрии.
Минусы дуговой сварки:
- Предварительная подготовка перед работой занимает много времени и финансовых затрат.
- Относительно субъективным фактором определяется качество сварных работ и свойства этого оборудования.
- Общая пониженная производительность по отношению к другим вариантам сварного оборудования.
- Условия, в которых обычно проводятся ручные сварочные работы, определяются как весьма вредные и относительно тяжёлые для общего состояния здоровья.
- Этот вид сварочных работ неприемлем, без присутствия человека.
- 0,0762 s
- ©2020 Все права защищены
Ручная дуговая сварка покрытыми электродами
Существуют различные методики получения неразъемных соединений. Сварка ручная дуговая считается наиболее рациональной и универсальной. Соответствует ли это действительности, как она ведется покрытыми электродами, особенности технологии, способы повышения ее эффективности – все это станет предметом разговора.
Когда лучше использовать
- При частой смене положения электрода. С помощью дуговой сварки можно получить качественный шов в различных направлениях – горизонтальном, вертикальном, под любым углом.
- Когда работы ведутся в сложных условиях, в том числе, труднодоступных местах.
- Если необходимо создать неразъемное соединение между разнородными металлами (сплавами), или быстро переориентироваться с одного на другой, что часто и бывает в процессе монтажа.
- Для получения швов небольшой протяженности.
Технология дуговой сварки
Любой покрытый электрод – металлический стержень, внешний слой которого (обсыпка силикатная, флюсовая, стеклянная) при сгорании образует или газовой облако, или шлак. Именно они и являются защитной средой, препятствующей проникновению в рабочую зону воздуха.
Классификация компонентов покрытия
По типу образующихся газов
- Ионизирующие.
- Защитные.
По виду шлаков
- Легирующие.
- Рафинирующие.
- Раскислители.
- Защитные, создающие «корку».
В зависимости от типа электродов шлаки также могут быть пластифицирующими и связывающими.
Существует несколько видов сварки – током постоянным, импульсным (в/ч), переменным. При подаче напряжения он идет по цепи «электрод – обрабатываемая заготовка», но только в момент касания детали. Это приводит к образованию дуги. В зоне высокой температуры (до 6 800 – 7 000 ºС) плавятся и кромки образца, и стержень. В результате дальнейшей кристаллизации металлов, которая происходит при ее снижении (так как электрод перемещается вдоль намеченной линии), получается шов.
В ручном режиме сварка ведется током переменным или постоянным. Профессионалы предпочитают последний вариант, причем с прямой полярностью. В результате электрод остается холодным, а нагревается металл в рабочей зоне.
Что учесть? Для разных видов сварки применяются свои электроды, для «=» или «~» тока.
Условия качественного ведения дуговой сварки
- Сухие срезы образцов и электрод.
- Бесперебойная подача тока.
- Целостность изоляции заземлителя. Ее дефекты нередко вызывают порчу шва, «залипание» электрода в рабочей зоне из-за «утечки» тока.
Необходимое оборудование
- Балансный реостат. С его помощью, меняя силу тока, можно выполнять не только сварочные работы, но и ряд других – резку, наплавку, стягивание.
- Кабель-заземлитель. Он является элементом эл/цепи и образует замкнутый контур, по которому протекает ток.
- «Держак».
Техника выполнения дуговой сварки
Зажигание дуги
Сила тока устанавливается, исходя из типа шва, его пространственной ориентации, марки покрытого электрода, вида металла и ряда других особенностей работы. В таблице указаны наиболее применяемые значения.
Способы «розжига»
№1 – легкое касание металла с последующим подъемом электрода на 20 – 25 мм.
№2 – применяется при обрыве дуги. Касание впереди кратера, с отведением в обратном направлении, до зоны наплава. Одновременно происходит удаление из него шлаков.
Рекомендация
Оптимальным считается диаметр дуги, лежащий в пределах 0,7 – 1,0 от сечения металлического стержня электрода. В процессе сварочных работ желательно выдерживать этот параметр в указанных рамках. Тогда шов получится качественный и ровный.
Положение покрытого электрода
Зависит от пространственной ориентации шва: потолочное, вертикальное или горизонтальное, нижнее. При накладке вертикальных швов электрод может перемещаться в обоих направлениях, как удобнее сварщику. При нижнем положении – наклон в направлении сварки. Движение – или «от себя», «или на себя».
Характеристики швов
Ширина валика зависит от специфики выполняемой операции и соотносится с диаметром покрытого электрода.
- От 0,8 до 1,5 d – «ниточный» (узкий) шов накладывается, если он первичный в многослойном. Также применяется, если толщина свариваемых образцов сравнительно небольшая (тонкий прокат).
- 2,2 – 4,0 d – самый распространенный (средний) шов. Наиболее практикуемые (но не единственно возможные) движения электрода показаны на рисунке.
Длина – зависит от специфики ведения сварки. Швы: короткие – до 30 см, средние – от 0,35 до 1 м и длинные – более 100 см.
Толщина – зависит от глубины «разделки». Исходя из этого, швы делаются одно- или многопроходными, в несколько слоев или в один.
Что лучше?
На получение шва, сделанного за 1 проходку, времени тратится меньше. Следовательно, повышается производительность. Существенный минус – недостаточная эластичность соединения, возможный перегрев металла на отдельных участках.
Многослойный шов получается более прочным, так как при повторной проходке нижележащий уровень подвергается дополнительному термическому воздействию. Структура соединения становится однородной, что напрямую сказывается на его надежности. При такой технологии сварки швы делаются разными способами: «горкой», «каскадами», последовательным наложением каждого очередного слоя по всей протяженности линии стыка. Последний вариант наиболее распространен, а два первых применяются в основном при сварке образцов большой толщины (или при глубоких разделах).
Качество нижнего слоя – гарантия прочности всего соединения. Именно первой проходке должно быть уделено повышенное внимание.
Полезные советы
- Овладевать технологией дуговой сварки желательно на том же типе аппарата, с которым предполагается работать в дальнейшем.
- Защитные фильтры имеют разные номера. Для конкретного сварщика он подбирается индивидуально, с учетом особенностей его зрения (диоптрии, чувствительность). Критерий один – сварочную ванну работник должен видеть четко.
- От правильно выбранного зазора деталь – электрод зависит качество соединения.
Если он слишком мал, то получится выпуклый шов, так как прогрев металла будет недостаточным. При его величине, большей рекомендуемой, укладка расплава будет неравномерной из-за того, что дуга станет «прыгать» (отклоняться от линии сварки).
Основные правила ТБ
- При дуговой ручной сварке запрещается прокладка заземлителя по сырой основе, тем более лужам, подтаявшему снегу и тому подобное.
- Все операции проводятся только в резиновых перчатках. Перед началом работы в обязательном порядке проверяется их целостность.
- Лицо мастера должно быть защищено от раскаленных брызг металла, а глаза – еще и от яркого света.
Если перчатки всего лишь прорезиненные, то они должны быть абсолютно сухими. В противном случае в момент смены электрода есть риск поражения током по цепи: реостат – «держак» – работник – земля.
Остается добавить, что в статье даны лишь «азы» технологии и способов дуговой ручной сварки. Все ее преимущества могут быть реализованы лишь при условии, если работник обладает необходимыми знаниями и практическими навыками. Только в этом случае будет обеспечено высокое качество шовного соединения.
Успехов вам в овладении навыками сварщика!
Изучение новейших сварочных технологий в Вирджиния-Бич
Сварщики используют ручное или компьютерное оборудование для соединения или резки металлических деталей, заполнения отверстий и сглаживания швов в металлических изделиях. Много лет назад, когда кто-то думал о карьере сварщика, они думали о работе на производственной линии, но это намного больше.
Когда большинство людей думают о сварке, они редко думают о ней как о высокотехнологичной отрасли, но многие сварочные работы являются именно такими! Благодаря технологическому прогрессу сварщики теперь имеют повышенную точность, более высокое качество продукции и большую универсальность.
Существует 30 различных типов сварки, от кислородных до высокотехнологичных, таких как использование лазерных лучей. Сегодня из-за различных типов сварки и связанных с ними опасностей, таких как искры и огонь, как никогда важно иметь надлежащую подготовку в аккредитованной школе, если вы хотите продолжить карьеру сварщика.
Достижения в области сварки
Сегодня у сварщиков есть много разных областей, на которых они могут сосредоточиться, некоторые из наиболее распространенных видов сварки включают:
- MIG — газовая дуговая сварка металла (GMAW)
- TIG — газовая дуговая сварка вольфрамом (GTAW)
- Stick — Дуговая сварка защищенного металла (SMAW)
- Дуговая сварка порошковой проволокой (FCAW)
- Энергетическая лучевая сварка (EBW)
- Сварка атомарным водородом (AHW)
- Газовая вольфрамо-дуговая сварка
- Плазменно-дуговая сварка
- Морская сварка… и многие другие.
Постоянно внедряются новые технологии, чтобы предоставить сварщикам новейшие инструменты, методы и технологии, которые помогут им выполнять свою работу и продвигаться по карьерной лестнице.
Морская сварка
Морская сварка стала очень востребованной нишей в сварочной промышленности, особенно в районах, расположенных близко к водоемам. Морская дипломная программа предоставит студентам подготовку в области строительства и ремонта оборудования стальных конструкций и труб.
Студенты должны научиться сваривать трубы в различных положениях как в классе, так и в лаборатории, а также узнают, как оставаться в безопасности при работе на верфях и различных ремонтных предприятиях. По завершении студенты могут быть готовы искать работу в качестве сварщиков конструкций и труб.
Район Hampton Roads предлагает множество возможностей для морских сварщиков
Если вы находитесь в районе Хэмптон-Роудс в Вирджиния-Бич, вы в нескольких минутах ходьбы от рек Джеймс, Нансемонд и Элизабет, Чесапикский залив и Атлантический океан находятся в непосредственной близости, что делает этот район желанным для морских сварщиков. Доступ ко всей воде в этом районе, это идеальная среда для тех, кто занимается бизнесом в водоемах и вокруг них.
Получение степени в области морской сварки с менеджментом услуг в Институте передовых технологий
Advanced Technology Institute (ATI) предлагает широкий спектр сварочных программ, включая морскую сварку с сервисным менеджментом. Если вы хотите сделать карьеру в области морской сварки, дипломная программа ATI может стать для вас правильным выбором.По завершении вы получите степень младшего специалиста в области технологий морской сварки.
Если вы подумываете о карьере сварщика на море, вам необходимо связаться с ATI, чтобы узнать больше об их различных сварочных программах и выбрать лучшую для вас. Обратитесь сегодня к одному из консультантов ATI по приемным комиссиям, который может предоставить дополнительную информацию о карьере сварщика на море.
Сварочное оборудование | Общественный колледж Нью-Ривер
КУРСЫ ПО СВАРКИ NRCC:
Не знаете, какие курсы вам нужно пройти? Поговорите с академическим консультантом за помощью или посетите каталог и выберите свою программу обучения.
Посетите сайт приемной комиссии, чтобы зарегистрироваться в классы
Сварочные процессы
Дуговая сварка защищенного металла
Дуговая сварка защищенного металла — наиболее распространенный метод соединения металлов. Сварка «палкой», как ее обычно называют, представляет собой процесс дуговой сварки с дугой между покрытым электродом и сварочной ванной. SMAW использует защиту от разложения покрытия электрода и присадочный металл от электрода.Используя процесс SMAW, сварщик может быстро выполнять высококачественные сварные швы на различных типах металлов с различной толщиной во всех положениях с отличной однородностью.
Газовая дуговая сварка металла
Этот процесс, также известный как сварка MIG, является чрезвычайно быстрым и экономичным, поскольку в нем используется дуга между непрерывной присадочной проволокой и сварочной ванной. GMAW часто используется в производственной работе из-за его скорости, универсальности и простоты использования. Этот процесс используется с защитой от поступающего извне газа и используется для сварки металла различной толщины от тонкого металла до толстого листового металла в любом положении.
Газовая дуговая сварка вольфрамом
Газовая вольфрамовая дуговая сварка, часто называемая сваркой TIG, может использоваться практически для любого металла. Дуга между неплавящимся электродом (вольфрамом) и сварочной ванной дает высококачественные сварные швы, которые не требуют дополнительной обработки после сварки. В этом процессе для защиты сварочной ванны используется защитный газ.
Дуговая сварка порошковой проволокой
Процесс дуговой сварки порошковой проволокой аналогичен процессу GMAW и использует тот же тип оборудования, что и GMAW.FCAW также использует дугу между непрерывной присадочной проволокой и сварочной ванной. Этот процесс используется с защитным газом от флюса, содержащегося внутри трубчатого электрода, а также может использовать газ, подаваемый извне (провод с двойным экраном).
Углеродно-дуговая резка на воздухе
В процессе резки с воздушной угольной дугой (CAC-A) металл удаляется физически путем строжки или резки. Между деталью и угольным электродом возникает дуга, в результате чего происходит интенсивное нагревание, которое плавит намеченную область детали.Во время резки воздух проходит через дугу и диспергирует расплавленный материал. Процесс воздушной угольной дуги может выдалбливать или резать металлы, что невозможно при использовании кислородно-топливных методов. Этот метод чаще всего используется для обработки углеродистой стали, нержавеющей стали, многих медных сплавов и чугуна.
История сварки: хронология и информация
Что касается металлообработки, то история сварки сравнительно недавняя, начиная примерно с 1000 г. до н. Э.
История начинается с открытия и обработки металлов в древних цивилизациях, начиная с меди, бронзы, серебра, золота и железа.Затем металлообработка перешла к стали. Первые сваренные детали считаются золотыми украшениями.
Технологии оставались практически неизменными до промышленной революции 1700-1918 годов.
В это время была разработана технология кузнечной сварки, в которой для соединения двух частей друг с другом используется нагретый металл. Это было похоже на знакомую кузницу.
В начале 19 века был открыт ацетилен, который стал контролируемым источником тепла для сварки.
Современная сварка не началась до повсеместного распространения электричества в начале 20 века.
Потребность в сварке военного назначения во время Первой и Второй мировых войн ускорила технологию и методы сварки.
До Первой мировой войны сварка не использовалась для соединения металлов в критических объектах, таких как корабли, из-за трещин.
На временной шкале истории сварки ниже подробно описано, как развивалась технология.
Хронология металлообработки и сварки
Сварка Б.С.
Первым в истории сварки металлом считается медь, поскольку ее можно ковать и гнуть.
4000 г. до н.э. .
Считается, что история сварки началась в Египте в 4000 г. до н. Э. В общем, цивилизации начинались с меди, а затем прогрессировали до бронзы, серебра, золота и железа.
3500 до н. Э.
Открытие олова
3000 — 2000 до н. Э.
Люди начали работать с бронзой между 3000 и 2000 гг. До н.э.C. В период бронзового века маленькие круглые золотые коробочки изготавливались сваркой внахлест под давлением.
В этот период из металла делают украшения, столовую посуду и оружие.
3000 до н. Э.
Шумеры делали мечи твердой пайкой.
Египтяне используют тепло, выделяемое древесным углем, для превращения железной руды в губчатое железо. Произведенные частицы сколачиваются вместе, в результате чего получается первая сварка давлением (также называемая твердой фазой)
Гробница царицы Пу-аби содержит золотую чашу с ручкой, припаянную к стене чаши.Золотой кубок также обнаружил, что на внешней стороне кубка есть припой.
2250 г. до н. Э.
Кобальт, используемый персами для окрашивания стекла.
Это пример пайки в 2600 году до нашей эры. в Месопотамии (Ирак) с использованием металла, сочетающего серебро и золото1500 до н.э.
Открытие Меркурия.
Пример плавки железа (становится более распространенным в 1200 г. до н. Э.).
1475 г. до н. Э.
В гробнице визиря Рех-ми-ре обнаружено изображение пайки.
1330 до н. Э.
В 1330 году до нашей эры египтяне паяли и выдували трубы. для пайки металлов.
Египетская пайка — 1330 г. до н. Э. — Золотая маска смерти Тут-Энч-АмонаЖурнал сварки и резки 2005
1000 г. до н. Э.
Производство железа началось в 1000 г. до н.э., когда металл изгибался в печах для производства мечей и наконечников копий. (один вид называется каталонской печью)
Золотые сундуки, найденные в Ирландии, были изготовлены путем штамповки притертых швов (форма сварки давлением).
с 900 по 850 г.
до н. Э.
Египтяне начали производство металлических орудий в 900–850 годах до нашей эры. В эту эпоху популярность железа медленно росла из-за того, что бронза и медь стали широко использоваться и стали широко использоваться.
Было найдено железное оружие, которое восходит к вавилонянам примерно в 900 году до нашей эры.
589 до н. Э.
Китайцы во времена династии Суй развили способность превращать кованое железо в сталь в 589 году нашей эры.Японцы производили сталь путем сварки и ковки для производства самурайских мечей.
A.D. История сварки
60 г. н.э.
Впервые в истории сварки процесс пайки золотом был описан Плинием. Он описывает, как соли действовали как флюс и как цвет металла определяет сложность пайки (цвет указывает на присутствие оксидов).
Железный столб Дели изготовлен из железных заготовок. Кузнецы сварили конструкцию высотой примерно 25 футов и весом 6 тонн310 н.э.
Сварка использовалась в железном столбе в Дели, Индия, около 310 г. н.э., весом 5 г / г.4 метрических тонны. (на фото выше). Другие строения подобной конструкции найдены в Англии, Скандинавии и Риме. Источником железа были метеоры.
1000 — 1099 г. н.э. (11 век)
В рукописи, написанной монахом Феофилом, есть описание смешивающего флюса для пайки серебра. Он указывает на использование хлорида натрия и тарпата калия. Металлы на 66 процентов состоят из серебра и меди.
1375
Открытие металлического цинка.
Средневековье (с 5 по 15 век) стало периодом в истории сварки, когда кузнечная сварка была в центре внимания. Кузнецы кололи горячий металл до тех пор, пока он не застыл.
Визуальная история сварки, с 14 по 17 века
1540
Vannoccio Biringuccio выпустил De la pirotechnia с описанием операции ковки.
Мастера эпохи Возрождения приобрели опыт в этом процессе, и сварка продолжала развиваться в течение следующих столетий.
1568
Бенвентуто Челлини, итальянский ювелир, пишет о пайке сплава серебра и меди с использованием процесса пайки
1599
Первый экземпляр корня слова weld (изначально хорошо)
16 век: изготовлена первая чугунная пушка
18 век
Большинство нововведений за это время в истории сварки использовались в доменных печах. Т
его небольшой постепенный прогресс продолжался до середины 18 века и до начала промышленной революции.Уже тогда прогресс был больше в том, как выполнялась работа.
Вместо того, чтобы один человек выполнял весь проект, работа была разделена на более мелкие части и поручена работникам средней квалификации.
1735
Доказательства того, что платина использовалась доколумбовыми индейцами в Эквадоре
1751
Чистый никель, созданный шведским химиком Акселем Ф. Кронштедтом с использованием немецкой руды.
1766
Свойства газообразного водорода, описанные Генри Кавендишем, английским химиком и физиком
1774
Открытие кислорода
1776
Принципы кислородной резки, установленные Лавуазье (французский язык).
19 век
1800
Сэр Хамфри Дэви изобрел электрическую дугу. Дуга создавалась между двумя угольными электродами, которые питались от батареи.
Аллесандро Вольта открыл гальванический элемент, который позволяет соединить два разных металла и стать проводником во влажном состоянии.
1808-1827
Старший Хамфри Дэви доказывает, что алюминий существует. На самом деле он был обнаружен Фридрихом Велером в 1827 году.
1828
Губчатая платина сваривается между собой холодным прессованием и затем молотком в горячем состоянии.
1836
Ацетилен был открыт в 1836 году Эдмундом Дэви, но не применялся в сварке до 1900 года, когда была разработана подходящая паяльная лампа.
1838
Патент, выданный Юджину Десбассайрсу де Ричмону на сварку плавлением
1839
Открытие генерации напряжения с помощью униполярного устройства Майклом Фарадеем.
1841
Воздушно-водородная выдувная трубка, разработанная немцем Х. Россье для пайки свинцом.
1846
Ключевой момент в истории сварки с существенным улучшением процесса кузнечной сварки.
Джеймс Нэсмит, работая в британском адмиралтействе, обнаружил, что при подготовке сварочных поверхностей со слегка выпуклой поверхностью из стыка выдавливаются стружка и флюс. Это улучшает прочность сустава.
1850-х годов
Работоспособные и практичные электрические генерирующие устройства были изобретены и разработаны к 1850 году. Заслуга Ампера, Эрстеда, Уитстона, Фарадея Ома и Генри за успехи в исследованиях электрического тока.
К середине 19 века уже были доступны работающие электрогенерирующие устройства.
1856
Джеймс Джоуль сварил пучок проводов, используя электрический ток и внутреннее сопротивление для создания тепла. Позже Элиху Томсон усовершенствовал процесс контактной сварки.
1860
Wilde разрабатывает электросварку. В 1865 году выдан технологический патент.
1862
Фридрих Велер использует карбид кальция для создания газообразного ацетилена
1876
Компания Отто Бернца разрабатывает и продает бензиновые фонари.
1881
Первое задокументированное использование сварки плавлением было в 1881 году Огюстом де Меритеном, когда он сварил пластины свинцовой батареи вместе с угольным электродом.
Сварка проводилась в боксе с неподвижным электродом.
Оригинальный аппарат Benardos с углеродным электродом — 1885Успехи в сварке продолжились с изобретением металлического электрода русским Николаем Славяновым и американцем К. Гроб в конце 1800-х годов. Они не знали о работе друг друга.
Кредит также принадлежит Эли Уитни, который изобрел идею взаимозаменяемых деталей. Это привело к производству металлических штампов и форм.
1882
Открытие сварки металлическими электродами было признано в Европе в 1892 году.
Введен в 1888 г. Н.Г. Slavianoff. Большинство историков приписывают Славянову открытие использования неизолированных металлических электродов для дуговой сварки.
1885
Два ученика Огеста де Меритенса, Н. Бенардос и С.Ольшевский продолжил свою работу, и в 1887/88 году ему был выдан патент на сварочный процесс, в котором использовались угольные электроды (угольная дуговая сварка) и источник электроэнергии.
При дуговой сварке угольным электродом используется дуга между угольным электродом и сварочной ванной. Процесс используется с экранированием или без приложения давления или без него. Основным заявленным использованием была ремонтная сварка.
В патенте, выданном в 1885 году Огесту и Н. Бенардосам, отмечается, что процесс углеродной сварки можно использовать для сварки двух металлов, резки металлов и пробивания отверстий в металле.В патенте описаны как твердый углеродный электрод, так и полый электрод, который будет заполнен порошкообразными металлами.
Поскольку они предназначались для того, чтобы порошок плавился и подтекал к сварному шву, некоторые считают, что они изобрели металлическую дуговую сварку. В конечном счете, из-за ограниченности этого подхода большинство историков не приписывают им это достижение.
1886
Элиху Томсон подал заявку на получение 2 патентов на процесс «Аппарат для электросварки».
Изобретение контактной сварки (RW) с первыми патентами, полученными Элиу Томпсоном в 1885 году. Он добился успехов в течение следующих 15 лет.
1888
Выдан патент Ольчевскому и Бернардосу на сварку угольной дугой.
1889–1892
C.L. Гроб считается пионером сварки в США:
- 1889: получен патент на оборудование и процесс для стыковой сварки оплавлением
- 1890: 2 патента на точечную сварку. Получен первый патент на металлические электроды.
- 1892: получен патент на процесс дуговой сварки металлическим электродом
1890
Первый известный случай использования «факела» для взлома банковского хранилища.
1892
Технический ацетилен производится в Северной Каролине путем смешивания воды и карбида кальция.
Локомотив Болдуина начинает использовать углеродную дуговую сварку для ремонта локомотивов.
1895
Горение ацетилена и кислорода, обнаруженное Анри Ле Шателье.
Аргон, открытый сэром Уильямом Рэмси и лордом Рейли.
1897
Kleinschmidt ввел использование медных электродов.
Сварка 20 века
1900
Foresche и Charles Picard разработали первую коммерческую горелку для кислородно-ацетиленовой сварки.Процесс используется без приложения давления (AWS).
Примерно в 1900 году А. П. Штроменгер разработал в Великобритании металлический электрод с покрытием, имевший более стабильную дугу.
1901
Кислородное копье, изобретенное Эрнстом Менне
1903
Изобретена термитная сварка, другой процесс, кислородно-топливная сварка, также получил широкое признание в качестве коммерческого процесса.
Первая машина для контактной стыковой сварки после слияния компаний Allgemeine Elektricitats-Gesellschaft (AEG) и Union-Elektricitats-Gesellschaft (UEG).
1906
Выпуск первых аппаратов для контактной точечной сварки. К 1910 г. было произведено около 367 аппаратов для точечной и шовной сварки.
Представлен метод сварки LaGrange-Hobo. В этом методе один конец подсоединяется к токопроизводителю, а другой конец погружается под воду.
Ток, протекающий через деталь, вызывает образование частично ионизированного газа в воде.
Сопротивление детали электрическому потоку и газу, создающему энергию, которая создает тепло в сварном соединении.
Когда свариваемая деталь попадала на сварочный нагрев, ее вынимали из водяной бани и сваривали.
1907–1908
Оскар Кьельберг получил патент на процесс нанесения электродного покрытия, называемый дуговой сваркой в защищенном металлическом корпусе. Покрытие помогло стабилизировать дугу, обеспечивая более качественные сварные швы, чем неизолированные электроды.
При дуговой сварке защищенным металлом используется дуга между покрытым электродом и сварочной ванной. Процесс используется с защитой от осаждения электродного покрытия без приложения давления и с присадочным металлом от электрода.
Индустрия дуговой сварки в США начинается с двух компаний: Siemund-Wienzell Electric Welding Co., созданная в США, запатентовала метод дуговой сварки металла. Открывается вторая компания, также созданная немецкими основателями, под названием Enderlien Electric Welding Co.
Lincoln Electric производит первый сварочный аппарат постоянного тока с переменным напряжением.
1908
Бернардос запатентовал процесс электрошлака, который позволил сварщику сваривать толстые листы за один проход. Обрисованный им процесс популярен сегодня.
1909
- Система плазменной дуги, использующая газовый вихрь для стабилизации дуги, была изобретена Шоннером во время работы в компании BASF.
- A.P. Strohmenger изобретает квазидуговой электрод, который обматывают асбестовой пряжей.
1910
- Чарльз Хайд получил патент на пайку стальных труб.
1911
- Первый трубопровод, созданный методом кислородно-ацетиленовой сварки. Происходит за пределами Филадельфии.
- Matters разрабатывает плазменную горелку для нагрева печи для плавления металлов.
1912
- Kjellberg получил второй патент на электрод с более толстым покрытием из асбеста и связующим из силиката натрия.
- Lincoln Electric представляет первые коммерческие сварочные аппараты
- Первый автомобильный кузов, сваренный E.G. Budd с использованием точечной сварки
- Металлические электроды с покрытием, представленные А.П. Строменгером. Покрытия были сделаны из глины или извести. Также получил патент на электрод, покрытый синим асбестом и связующим из силиката натрия.Впервые электрод произвел сварной шов без примесей.
1919
- Сварка переменным током была изобретена К.Дж. Холслагом, но не стала популярной в течение следующего десятилетия. Электродуговая сварка была методом, используемым в Соединенных Штатах до 1920 года. Проблема с этим методом заключалась в том, что сварочная дуга была нестабильной, а сварные швы не были такими прочными, как свариваемый металл. Сначала кислородная сварка была более популярным методом сварки. за счет портативности и относительно невысокой стоимости.По мере развития 20-го века он потерял популярность в промышленности и был в значительной степени заменен дуговой сваркой, поскольку продолжалась разработка металлических покрытий (известных как флюс) для электрода, которые стабилизируют дугу и защищают основной материал от примесей.
Сварка кораблей была ненадежной из-за трещин до Первой мировой войны Первая мировая война вызвала значительный всплеск использования сварочных процессов, и различные военные державы пытались определить, какой из нескольких новых сварочных процессов было бы лучше всего.
1917
- Дефицит газа в Англии привел к тому, что промышленность обратилась к электродуговой сварке для производства бомб и мин.
1919
- Президент Вильсон создает Комитет по сварке в военное время в Корпорации аварийного флота США.
- Создание Американского общества сварщиков
- Разработка электрода с бумажным покрытием компанией Reuben Smith
1920-е годы
В 1920-е годы в технологии сварки были достигнуты большие успехи, включая введение в 1920 году автоматической сварки, при которой электродная проволока подавалась непрерывно.
Защитный газ стал предметом пристального внимания, поскольку ученые пытались защитить сварные швы от воздействия кислорода и азота в атмосфере.
Пористость и хрупкость были основными проблемами, и разработанные решения включали использование водорода, аргона и гелия в качестве сварочной атмосферы.
Процесс сварки штучной сваркой стал быстро развиваться благодаря усовершенствованию покрытия сердечника проволоки и электродов. Рентгеновская технология позволила проверить прочность сварного шва.
- Исследования электродов с покрытием привели к лучшему сердечнику проволоки и улучшенному покрытию электродов.
- Британцы в основном использовали дуговую сварку и даже построили корабль Fulagar с полностью сварным корпусом. В какой-то момент корабль сел на мель и остался целым, потому что он был сварным, а не клепанным.
- Американцы сомневались, но начали осознавать преимущества дуговой сварки, когда этот процесс позволил им быстро отремонтировать свои корабли после нападения немцев в гавани Нью-Йорка в начале войны.
- Дуговая сварка была впервые применена к самолетам во время войны, так как фюзеляжи некоторых немецких самолетов были построены с использованием этого процесса.
- Немцы применяли электродуговую сварку на самолетах
- Немецкий торговый флот диверсировал свои корабли в гавани Нью-Йорка, прежде чем бежать. Успешно применялись сварочные ремонты, это поставило сварку на карту.
- В автомобильной промышленности начали использовать автоматическую сварку.
- Сотрудник General Electric П.О. Компания Nobel разработала автоматическую сварку постоянным током.
- До 1920 года сварка производилась постоянным током, вырабатываемым батареями. В конце 1920 — начале 1930-х годов стали популярны сварочные аппараты переменного тока.
В течение следующего десятилетия дальнейшие достижения позволили сварку химически активных металлов, таких как алюминий и магний. Это, в сочетании с разработками в области автоматической сварки, переменного тока и флюсов, привело к значительному развитию дуговой сварки в 1930-х годах, а затем во время Второй мировой войны.
1923
- Создание института инженеров сварки
1924
- Первые все сварные дома постройки У.
С. Бойлер
1926
- П.К. Деверс и Х. Сварка Хобарта с использованием гелия и аргона в качестве защитного газа.
- Военно-морская научно-исследовательская лаборатория выпускает документ об использовании рентгеновских лучей для проверки сварных швов.
1927
- A.O. Сотрудник компании Smith, Джон Дж. Чайл патентует первый экструдированный титановый электрод, который позже получил название E6010.
1928
- Первый сварной железнодорожный мост, созданный Westinghouse для транспортировки больших генераторов.
1929
- Lincoln Electric производит электрод Fleetwood 5 с тяжелым покрытием.
- Американское общество сварки устанавливает символы сварки.
1930
- Патент, выданный H.O. Хобарт для дуговой сварки, и процесс, который стал GMAW (газовая дуговая сварка металла).
- Сварка под флюсом, разработанная National Tube Company
- Создано цельносварное торговое судно
- Выпуск шпильки под приварку, которая вскоре стала популярной в судостроении и строительстве.
В том же году была изобретена дуговая сварка под флюсом, и она продолжает оставаться популярной сегодня. К 1930 году дуговая сварка была дешевле, чем клепка и газовая сварка.
- Деверс и Хобарт выдан патент на использование электрической дуги в атмосфере инертного газа. Не очень хорошо воспринимается сварочной промышленностью из-за высокой стоимости газа (гелий и аргон) и неподходящей доступности горелки.
1931
- Сварка нержавеющей стали (первоначально называемая дробеструйной сваркой) E.G.Будд Производство
В середине века было изобретено много новых методов сварки.
1934
- Регулятор времени для контактной сварки разработан Westinghouse (первоначально назывался Ignitron).
1935
- Введен процесс сварки под флюсом с использованием непрерывной подачи проволоки и гранулированного флюса. Первоначально процесс назывался Union Melt. Установлен британский стандарт на сварочные электроды
- и выпущен твердый экструдированный электрод.
1936
- Первый сварочный аппарат переменного тока, представленный Miller Electric Manufacturing. Метод отличался высокой скоростью наплавки металла (отношение веса наплавленного металла к весу нетто израсходованных электродов без учета шлейфов) и отсутствием дуги (отклонение электрической дуги от нормального пути из-за магнитных сил. ).
1937
- Применение сварки подтверждено стандартом BS 538 в зданиях из конструкционной стали (дуговая сварка металлом низкоуглеродистой стали).
1938
- Сварка самотеком, представленная К.К. Мадсен
- Немцы сваривают корабли, чтобы уменьшить вес и создать более крупные суда
1939
- Использование точечной сварки алюминия в авиации
1940-1941
- Газовая дуговая сварка вольфрамом (GTAW) после десятилетий разработки была окончательно доведена до совершенства в 1941 году (патент выдан в 1942 году).
Изобрел Рассел Мередит. Разработано компанией Linde.Также называется HELIARC или TIG. Горелка с водяным охлаждением была способна работать с большим током. При газовой вольфрамовой дуговой сварке используется дуга между неплавящимся вольфрамовым электродом и сварочной ванной. Процесс используется с защитным газом и без приложения давления.
- Army находит применение нержавеющей стали, алюминия и магния в таком оборудовании, как истребители.
- Создание Канадской ассоциации сварщиков.
- Технология пайки погружением, разработанная для печати монтажных плат.Первый процесс массовой пайки.
1942
- Георгию Хафергуту выдан патент на сварочный процесс в форме хлопушки.
1943
- Газовая дуговая сварка металлическим электродом (GMAW) изобретена К. Б. Волдрихом, П. Дж. Риппелем и Ховардом Б. Кэри. Разработано в корпорациях Dow и Northrup, а затем передано по лицензии Linde Corporation.
- Компания sciaky начинает продажу трехфазного сварочного аппарата сопротивлением.
1945
- Разработка экспериментального ручного пистолета MIG в Мемориальном институте Баттеля (Колумбус, Огайо)
- Сварка заменила клепку в качестве основного метода сборки для судов с 5 171 судном, построенными до 1945 года.
1948
- В 1948 году последовала газовая дуговая сварка металлическим электродом (GMAW заменила прежние термины «инертный газ для металла» (MIG) и «металлический газ» (MAG)), что позволило выполнять быструю сварку цветных металлов, но требовало использования дорогостоящих защитных газов. «Процесс дуги металлической дуги в защитном газе был представлен компанией Air Reduction на выставке AWS в Филадельфии. При дуговой сварке металлическим газом используется дуга между сплошным присадочным электродом (расходным материалом) и сварочной ванной. Процесс используется с защитой от поступающего извне газа и без приложения давления.
- В Университете штата Огайо открылся первый факультет техники сварки.
- Процесс сварки металлической дуги в инертном газе (MIG) разработан компанией Air Reduction. Сварка
- SIGMA (дуговая сварка металла в среде защитного газа) разработана для сварки толстых листов.
1949
- Westinghouse представляет сварочные аппараты с селеновым выпрямителем.
1950-е годы
- Экранированная дуговая сварка металлом была разработана в 1950-х годах с использованием расходуемого электрода и атмосферы двуокиси углерода в качестве защитного газа, и быстро стала самым популярным процессом дуговой сварки металлическим электродом.
- A.C. — Выпрямительные сварочные аппараты постоянного тока со встроенной частотой для сварки TIG. Miller Electric разработала управляемую Миллером волну переменного тока. Сварщик, который использовался для критических сварных швов на ракетах и самолетах.
- Процесс электронно-лучевой сварки, запущенный A.J. Stohr
- Выпущена пайка волной припоя печатных плат.
- E.O. Институт сварки им. Патона занимается разработкой электростаговой сварки (ЭШС).
1951
- DryRod Electrode печь для контроля уровня влажности в электродах.
1954 -1957
- Дебютировал процесс дуговой сварки порошковой проволокой (FCAW), в котором самозащитный проволочный электрод можно было использовать с автоматическим оборудованием, что привело к значительному увеличению скорости сварки, и в том же году была изобретена плазменная сварка. Запатентовано в 1957 году компанией National Cylinder Gas Company.
1956
- Процесс сварки трением, внедренный Россией
1958–1959
- Электрошлаковая сварка была выпущена в 1958 году, а в 1961 году последовала ее родственница — электрогазовая сварка.
- Среди других недавних достижений в области сварки — прорыв в области электронно-лучевой сварки в 1958 году, который сделал возможной глубокую и узкую сварку за счет концентрированного источника тепла.
- Представлен процесс короткой дуги. В процессе используются провода небольшого диаметра и усовершенствованный блок питания.
1960
- После изобретения лазера в 1960 году лазерная сварка появилась несколько десятилетий спустя и оказалась особенно полезной при высокоскоростной автоматической сварке.Однако оба эти процесса по-прежнему довольно дороги из-за высокой стоимости необходимого оборудования, что ограничивает их применение.
- Введен процесс сварки взрывом.
1962
- Sciaky сварные швы Капсула Mercury Space (созданная с внешней и внутренней титановой оболочкой).
Из-за небольшого размера каждого титанового листа металл необходимо было сваривать тройным листом, а затем сваривать с другими листами.Процесс TIG использовался без присадочного металла. Источник: Руководство НАСА, Процедуры сварки титана и титановых сплавов
.1963
- Отмечено разработками в области испытаний сварных швов.
Тест Varestraint определяет, можно ли сваривать основной металл, а также жизнеспособность различных сварочных процессов.
- Wall-Colmony представляет горелку Fusewelder Torch.
Устройство для сварки плавкими вставками — это кислородно-ацетиленовая горелка, которая часто используется, когда необходимо нарастить сварной шов и завершить сварку твердой наплавки.
1965-1967
- Сварка и резка лазером СО2
- В Великобритании начинается гравитационная сварка
1969
- Россияне сваривают в космосе СОЮЗ-6.
1970
- Представлены новые технологии пайки для поддержки электронной миниатюризации:
— паровая фаза
— инфракрасный
— горячий газ
Современная сварка
Сегодня существует более 90 сварочных процессов с постоянным исследованием новых металлов, используемых в атомной, космической и судостроительной отраслях. Многие изменения произошли в 1980-х и 1990-х годах, когда сварка перешла от искусства к науке.
- Роботизированная сварка
- Бортовые компьютеры
- Современные электроды
- Экзотические газовые смеси
1991
- Сварка трением с перемешиванием, представленная TWI.
1999
- Институт Эдисона разрабатывает метод, позволяющий увеличить проникновение флюса в сварной шов на 300%.
2000
- Введение в магнитно-импульсную сварку.
- Рентгеновский снимок используется для сварки композита металл / матрица
- Использование диодной лазерной сварки расширенных металлов, таких как титановая фольга из нержавеющей стали.
2008
- Разработка гибридной лазерно-дуговой сварки
2013
- Разработка газовой дуговой сварки-пайки металла, процесса сварки стали, используемой в автомобилях. В процессе используется присадочный металл, состоящий из кремния с медным сплавом.
- Сварка низкоуглеродистой стали и алюминия внахлест по лазерной технологии.
Будущие тенденции в области сварки
- Сварочные операции необходимо более полно интегрировать в гибкие производственные процессы и схемы управления процессами.
Сварка будет становиться все более автоматизированной, поскольку она интегрируется во все производственные конструкции и координируется с улучшенными информационными системами. - Продукция будущего, требующая сварных соединений, будет состоять из материалов, предназначенных для сваривания, таких как высокопрочные стали, которые также являются интеллектуальными материалами, содержащими встроенные компьютерные микросхемы для контроля характеристик жизненного цикла сварной конструкции.Такие материалы могут открыть новые возможности для использования сварки в качестве метода соединения в ближайшие десятилетия.
- В будущем моделирование сварки будет частью нового акцента на интеграции сварки на протяжении всего производственного цикла.
- Инженеры по сварке и материалам будут разрабатывать новые материалы и адаптировать существующие материалы, которые специально предназначены для сварки в готовые изделия мирового класса.
- Разработка материалов, снижающих потребность в энергии.
Дуговая сварка под флюсом: технология, улучшающаяся с возрастом
Технологии производства сегодня очень сильно отличаются от методов и процессов, использовавшихся в начале 20 века. Однако в случае дуговой сварки под флюсом (SAW), уникального безопасного и последовательного метода сварки, который используется с 1930-х годов, новые технологии не уменьшили его значимости для производства деталей, подвергнутых механической обработке. Фактически, автоматизированная сварочная технология гарантирует, что ПАВ остается важной частью наших производственных процессов здесь, в Allis Roller.
Что такое дуговая сварка под флюсом?
Сварка под флюсом (SAW) была впервые запатентована в 1935 году и наиболее широко использовалась при производстве танков во время Второй мировой войны. Те же элементы, которые сделали SAW идеальным процессом для сварки деталей резервуаров, также делают его идеальным для продольных и кольцевых стыковых швов, необходимых сегодня для трубопроводных труб и сосудов под давлением. SAW использует порошковый флюс, который действует как проводник между сварочным электродом и заготовкой и предотвращает выход искр, дыма и брызг во время процесса.В результате отпадает необходимость в защитном экране во время процесса сварки, а большое количество металла может быть наплавлено за короткое время, что делает SAW отличным выбором для сварки тяжелых элементов оборудования.
Преимущества использования SAW для безопасной и эффективной сварки тяжелых деталей — вот почему Allis Roller продолжает использовать ее на собственном предприятии при производстве тяжелых деталей со сложной механической обработкой для сельскохозяйственной, строительной и горнодобывающей промышленности.
Будущее SAW в мире автоматизированного производства
В Allis Roller большая часть наших процессов обработки и производства включает использование компьютеризированного оборудования, которым управляет один из наших квалифицированных специалистов, и наше применение SAW ничем не отличается. Во время механизированного или автоматизированного процесса SAW программа ЧПУ вращает деталь с заданной скоростью, контролируя при этом температуру и скорость сварки, чтобы гарантировать оптимальное качество и стабильность детали. В отличие от ранней технологии SAW, использовавшейся во время Второй мировой войны, автоматическая SAW стала более быстрой, экономичной и точной.
В дополнение к включению как традиционных, так и автоматизированных процессов SAW по требованию заказчика наши инженеры продолжают совершенствовать наши собственные системы для производства более крупных деталей.Мы чаще всего используем SAW для изготовления структурных поперечных труб длиной три фута в тракторных погрузчиках CNH, но прямо сейчас Allis Roller работает над созданием гораздо большего приводного вала — 7 дюймов в диаметре на 5 футов в длину — для размещения SAW даже более тяжелое оборудование. Allis Roller также обновила наш сварочный аппарат до MillerDC650 и добавила новую горелку / устройство подачи, чтобы увеличить нашу производительность и приспособить сварочную проволоку большего диаметра. Каждое из этих обновлений помогает нам максимально использовать потенциал исторически актуальных сварочных технологий в производстве более крупных и качественно обработанных деталей.
Allis Roller являются экспертами в области инноваций и совершенствования методов сварки под флюсом в интересах наших клиентов. Каждый проект, который проходит через наши двери, тщательно проверяется, и выбираются лучшие машины для работы, чтобы обеспечить точное и экономичное изготовление деталей для наших клиентов. Для получения дополнительной информации об использовании SAW в Allis Roller свяжитесь с одним из членов нашей команды через страницу контактов.
Вам понравился этот пост? Поделись:
Сварка: ARC — Forsyth Tech
Сварка: ARC
Это курс продолжительностью один семестр, предназначенный для обучения студентов основным принципам дуговой сварки. Студенты будут работать на сварочных аппаратах трансформаторного типа AC-DC. Исследования будут включать диапазоны нагрева, полярность и использование сварочных электродов с флюсовым покрытием. Сварка будет выполняться на низкоуглеродистой стали в плоском, горизонтальном и вертикальном положениях. При использовании инструментов и оборудования на протяжении всего курса особое внимание уделяется безопасности. Требуются защитные очки.
Описание занятия
Ожидается, что сварщик произведет следующие ремонты:
- Ремонт и установка трубопроводных систем
- Ремонт механических систем
- Ремонт и строительство различных металлоконструкций
Дополнительная информация
Развитие экономических кадров: технические стандарты сварки
Вакансии
Сварщиков нанимают сварочные подрядчики, ремонтные предприятия, больницы, фабрики и другие сервисные компании.
Профессиональный прогноз
Цели обучения
Основные темы:
- Принципы дуговой сварки
- Аппарат для сварки трансформаторов переменного и постоянного тока
- Диапазон нагрева и полярность, необходимые для сварки различных металлов
- Типы сварочных стержней, используемых для каждого свариваемого материала
- Сварочные позиции; потолочные, горизонтальные, вертикальные
- Безопасность магазина
Посредством лекций в аудитории и практических занятий в лаборатории студент узнает о безопасном и практическом применении дуговой сварки. Учебные занятия проводятся в лаборатории / классе по сварке технических навыков. Лаборатория оснащена необходимыми принадлежностями и инструментами для преподавания этого курса и ознакомления студентов с принципами дуговой сварки.
Рекомендуемые курсы и навыки
Предварительных условий нет, но очень важна сильная механическая способность.
Полезные личные качества
Должен уметь работать в команде, быть организованным, ориентированным на детали и решать проблемы.
Расписание курсов
Даты | дней | раз | Местоположение | Стоимость | Единицы | Код курса |
---|---|---|---|---|---|---|
06.07.2021 — 29.07.2021 | вт, чт | 17:30 — 20:30 | Stokes Trade Shop Bldg 105 | $ 80.![]() | 2,40 | 143387 |
Контактная информация по программе
Для получения дополнительной информации обратитесь в службу поддержки клиентов по телефону 336.734.7023.
Исследование: Сварщики предпочитают полуавтоматическое оборудование для дуговой сварки
Мировые продажи оборудования для дуговой сварки достигли ~ 1 600 000 (единиц) в 2018 году, говорится в последнем отчете о рынке оборудования для дуговой сварки.Согласно анализу исследования, на мировом рынке оборудования для дуговой сварки прогнозируется среднегодовой темп роста ~ 6% в течение прогнозируемого периода 2019 и 2029 годов. Растущий спрос на продукцию для дуговой сварки в нескольких отраслях конечного использования, таких как автомобилестроение и транспорт, энергетика и Согласно оценкам, строительство будет стимулировать рост рынка оборудования для дуговой сварки в прогнозируемом периоде.
Согласно всестороннему исследованию и углубленному изучению, ожидается, что рост числа жилищных и инфраструктурных проектов и улучшение объектов общественного транспорта, в том числе железных и автомобильных дорог, приведут к значительному росту рынка дуговой сварки во всем мире.В автомобильной промышленности широко используются различные технологии дуговой сварки, такие как газовая дуговая сварка (GMAW) и газо-вольфрамовая дуговая сварка (GTAW). Ожидается, что дальнейший рост рынка будет обусловлен развитием конструкции автомобилей, требующей применения конкурентоспособных процедур дуговой сварки, а также растущим спросом на автомобили.
Кроме того, ожидается, что несколько крупномасштабных инфраструктурных проектов, запущенных в рамках правительственных программ развития, станут основными движущими силами роста рынка оборудования для дуговой сварки на международном рынке.По оценкам, в 2019 году мировой рынок оборудования для дуговой сварки достигнет выручки в размере ~ 5 млрд долларов США, а к концу 2029 года ожидается впечатляющий рост.
Основные отрасли промышленности остаются основными каналами получения доходов
Ожидается, что увеличение капитальных затрат на строительство в сочетании с планируемыми в ближайшем будущем мега инфраструктурными проектами в развивающихся регионах приведет к увеличению продаж оборудования для дуговой сварки в течение расчетного периода.Ожидается, что безудержные инвестиции в основные промышленные секторы будут стимулировать спрос на оборудование для дуговой сварки и газы в течение всего прогнозируемого периода.
Несмотря на то, что дуговая сварка металлическим электродом в защитных оболочках (SMAW) или более известная как технология дуговой сварки, является самым старым методом дуговой сварки на рынке, она, как ни удивительно, занимает наибольшую долю рынка, несмотря на другие технологии дуговой сварки, разработанные для различных применений. За пятами следуют и другие сварочные технологии: порошковая сварка (FCAW), плазменная сварка (PAW) и дуговая сварка металлическим электродом в газе (GMAW). Сварочные операции с высокой степенью индивидуализации и специфики требуют дуговой сварки вольфрамовым электродом (GTAW), для которой требуется профессиональный опытный персонал по дуговой сварке, поскольку ее нелегко автоматизировать.
Сварщики считают полуавтоматическое оборудование для дуговой сварки более экономичным и эффективным по сравнению с оборудованием для ручной и автоматической дуговой сварки. Таким образом, рост спроса на полуавтоматическую дуговую сварку, по оценкам, будет стимулировать рост мирового рынка оборудования для дуговой сварки. Полуавтоматическое оборудование для дуговой сварки, такое как TIG (вольфрамовый инертный газ), MIG (металлический инертный газ), и оборудование для дуговой сварки с флюсовой сердцевиной, набирает обороты на рынке Ближнего Востока и Африки благодаря росту отраслей конечного использования, таких как как строительство, энергетика, автомобилестроение, нефть и газ.
Тенденции развивающихся рынков, обусловленные использованием технологий и газа
Использование гелия для защиты при дуговой сварке могло быть плодотворным, но его высокая цена и дефицит привели к его неравномерному использованию в различных экономиках по всему миру. Использование гелия особенно распространено в странах с изобилием природного газа, что приводит к резкому снижению отпускных цен. США, Катар и Алжир являются одними из крупнейших стран, которые производят около 75% от общего мирового производства гелия.Гелий в таких странах продается по цене около 30 000 долларов США за тонну, в то время как отпускная цена в других странах может доходить до 75 000 долларов США за тонну. Недавняя инфляция цен на гелий также стала тревожным фактором, поскольку цены на сырой гелий выросли на 135% в годовом исчислении на недавно завершившемся аукционе правительства США.
Когда дело доходит до выбора защитного газа для сварки металлов дуговой технологией, инертные газы занимают первое место по сравнению с другими газами. Гелий и аргон являются двумя наиболее распространенными инертными газами, используемыми в технологии дуговой сварки, но высокая цена гелия вынуждает операторов сварки выбирать аргон для защиты.Его низкая цена в сочетании с выгодными защитными свойствами, вероятно, повлияет на преобладание аргона в оборудовании для дуговой сварки и на рынке газа в текущем сценарии, а также в будущем.
Рынок оборудования для дуговой сварки: Vendor Insights
Анализ исследования также подчеркивает находчивые взгляды на конкурентную структуру рынка оборудования для дуговой сварки и типичные подходы известных игроков рынка. По оценкам, мировой рынок оборудования для дуговой сварки достаточно фрагментирован, и на долю ведущих игроков приходится менее 43% от общего объема рынка.Некоторые из ключевых игроков, определенных на глобальном конкурентном рынке, — это Daihen Corporation, The Lincoln Electric Company, Colfax Corporation, Obara Group, Inc., Illinois Tool Works Inc, Hyundai Welding Co. Ltd, Fronius International GmbH, Panasonic Corporation и Kemppi Oy. .
В этом исследовании освещаются ключевые возможности рынка оборудования для дуговой сварки и делается вывод, что в течение прогнозируемого периода этот рынок будет демонстрировать среднегодовой темп роста ~ 6%.
Эти выводы основаны на отчете «Рынок оборудования для дуговой сварки », подготовленном Persistence Market Research.
Аппараты для дуговой сварки | Краткое описание процесса сварки
Газовая дуговая сварка металлом
Дуговая сварка — это тип сварки, при котором используется источник сварочного тока для создания электрической дуги между электродом и основным материалом для плавления металлов в точке сварки. Они могут использовать как постоянный (DC), так и переменный (AC) ток, а также расходуемые или неплавящиеся электроды. Область сварки обычно защищена каким-либо защитным газом, паром и / или шлаком.
Для обеспечения электрической энергией, необходимой для процессов дуговой сварки, можно использовать несколько различных источников питания. Наиболее распространенная классификация — источники питания постоянного тока и источники питания постоянного напряжения. При дуговой сварке напряжение напрямую связано с длиной дуги, а сила тока связана с количеством подводимого тепла. Источники питания постоянного тока чаще всего используются для процессов ручной сварки, таких как дуговая сварка газом вольфрамовым электродом и дуговая сварка в среде защитного металла, поскольку они поддерживают относительно постоянный ток даже при изменении напряжения.Это важно, потому что при ручной сварке может быть трудно удерживать электрод идеально устойчивым, и в результате длина дуги и, следовательно, напряжение имеют тенденцию колебаться. Источники питания с постоянным напряжением поддерживают постоянное напряжение и изменяют ток, поэтому они чаще всего используются для автоматизированных сварочных процессов, таких как газовая дуговая сварка, дуговая сварка порошковой проволокой и сварка под флюсом. В этих процессах длина дуги остается постоянной, так как любые колебания расстояния между проволокой и основным материалом быстро устраняются за счет большого изменения тока.Например, если проволока и основной материал подойдут слишком близко, ток будет быстро увеличиваться, что, в свою очередь, приведет к увеличению тепла и плавлению кончика проволоки, возвращая его на исходное расстояние разделения.
Направление тока, используемого при дуговой сварке, также играет важную роль при сварке. В процессах с плавящимся электродом, таких как дуговая сварка в защитном металлическом корпусе и газовая дуговая сварка, обычно используется постоянный ток, но электрод может заряжаться как положительно, так и отрицательно.При сварке положительно заряженный анод будет иметь более высокую концентрацию тепла, и в результате изменение полярности электрода влияет на свойства сварного шва. Если электрод заряжен положительно, он будет плавиться быстрее, увеличивая проплавление и скорость сварки. В качестве альтернативы, отрицательно заряженный электрод приводит к более мелким сварным швам. В процессах с использованием неплавких электродов, таких как сварка газовой вольфрамовой дугой, можно использовать как постоянный ток (DC), так и переменный ток (AC).Однако при постоянном токе, поскольку электрод создает только дугу и не обеспечивает присадочный материал, положительно заряженный электрод вызывает неглубокие сварные швы, а отрицательно заряженный электрод — более глубокие сварные швы. Между ними быстро проходит переменный ток, что приводит к сварным швам со средней проплавкой. Один из недостатков переменного тока, тот факт, что дуга должна повторно зажигаться после каждого перехода через ноль, был устранен с помощью изобретения специальных блоков питания, которые создают прямоугольную диаграмму направленности вместо нормальной синусоидальной волны, устраняя время низкого напряжения после нулевые переходы и минимизация последствий проблемы.
Lincoln Electric и ESAB являются лишь двумя из многих производителей оборудования для дуговой сварки.
Методы расходных электродов
Одним из наиболее распространенных видов дуговой сварки является дуговая сварка в защитном металлическом корпусе (SMAW), также известная как ручная дуговая сварка металлическим электродом (MMAW) или сварка стержнем. Электрический ток используется для зажигания дуги между основным материалом и расходуемым электродным стержнем или «стержнем». Электродный стержень изготовлен из материала, совместимого с основным свариваемым материалом, и покрыт флюсом, который выделяет пары, которые служат в качестве защитного газа и образуют слой шлака, оба из которых защищают зону сварки от атмосферного загрязнения. .Сам сердечник электрода действует как присадочный материал, поэтому отдельный наполнитель не нужен. Этот процесс очень универсален, требует небольшого обучения операторов и недорогого оборудования. Однако время сварки довольно велико, поскольку расходные электроды необходимо часто заменять, а шлак, остатки флюса, необходимо удалять после сварки. Кроме того, процесс обычно ограничивается сваркой черных металлов, хотя специальные электроды сделали возможной сварку чугуна, никеля, алюминия, меди и других металлов.Универсальность метода делает его популярным в ряде приложений, включая ремонтные работы и строительство.
Газовая дуговая сварка металлическим электродом (GMAW), обычно называемая MIG (Metal Inert Gas), представляет собой полуавтоматический или автоматический процесс сварки, при котором непрерывно поданная расходная проволока действует как электрод и присадочный металл, а также инертная или полуинертная защита. газ обтекал проволоку, чтобы защитить место сварки от загрязнения. Источник постоянного напряжения постоянного тока чаще всего используется с GMAW, но также используется постоянный переменный ток.При непрерывной подаче присадочных электродов GMAW обеспечивает относительно высокие скорости сварки, однако более сложное оборудование снижает удобство и универсальность по сравнению с процессом SMAW. Первоначально разработанный для сварки алюминия и других цветных металлов в 1940-х годах, GMAW вскоре стал экономично применяться для стали. Сегодня GMAW широко используется в таких отраслях, как автомобильная промышленность, благодаря своему качеству, универсальности и скорости. Из-за необходимости поддерживать стабильную оболочку из защитного газа вокруг места сварки, может быть проблематичным использование процесса GMAW в областях с сильным движением воздуха, например на открытом воздухе.
Дуговая сварка порошковой проволокой (FCAW) — это разновидность метода GMAW. Проволока FCAW представляет собой тонкую металлическую трубку, заполненную порошкообразным флюсом. Иногда используется защитный газ, подаваемый извне, но часто сам флюс используется для создания необходимой защиты от атмосферы. Этот процесс широко используется в строительстве из-за высокой скорости сварки и портативности.
Сварка под флюсом (SAW) — это высокопроизводительный сварочный процесс, при котором дуга зажигается под покровным слоем гранулированного флюса.Это увеличивает качество дуги, поскольку загрязняющие вещества в атмосфере блокируются флюсом. Шлак, образующийся на сварном шве, обычно снимается сам по себе, и в сочетании с использованием непрерывной подачи проволоки скорость наплавки высока. Рабочие условия значительно улучшаются по сравнению с другими процессами дуговой сварки, поскольку флюс скрывает дугу и не образуется дыма. Этот процесс обычно используется в промышленности, особенно для крупногабаритных изделий [9]. Поскольку дуга не видна, она обычно автоматизирована. Пила возможна только в положениях 1F (плоская кромка), 2F (горизонтальная кромка) и 1G (плоская канавка).
Методы использования неплавящихся электродов
Газовая вольфрамовая дуговая сварка (GTAW) или сварка TIG (вольфрам в инертном газе) — это процесс ручной сварки, в котором используется неплавящийся электрод, изготовленный из вольфрама, смеси инертного или полуинертного газа и отдельного присадочного материала. Этот метод, особенно полезный для сварки тонких материалов, характеризуется стабильной дугой и высококачественными сварными швами, но требует значительных навыков оператора и может выполняться только на относительно низких скоростях. Его можно использовать практически для всех свариваемых металлов, хотя чаще всего применяется для нержавеющей стали и легких металлов.Он часто используется, когда качество сварных швов чрезвычайно важно, например, в велосипедах, самолетах и на море. В родственном процессе, плазменной сварке, также используется вольфрамовый электрод, но для создания дуги используется плазменный газ. Дуга более концентрированная, чем дуга GTAW, что делает поперечный контроль более критичным и, таким образом, в целом ограничивает технику механизированным процессом. Благодаря стабильному току, этот метод может использоваться для материалов более широкого диапазона толщин, чем процесс GTAW, и он намного быстрее.Его можно применять ко всем тем же материалам, что и GTAW, за исключением магния; Автоматическая сварка нержавеющей стали — одно из важных применений этого процесса. Разновидностью процесса является плазменная резка, эффективный процесс резки стали.
Другие процессы дуговой сварки включают атомарно-водородную сварку, углеродную дугу, электрошлаковую сварку, электрогазовую сварку и дуговую сварку шпилек.
Проблемы с коррозией
Некоторые материалы, особенно высокопрочные стали, алюминий и титановые сплавы, чувствительны к водородной хрупкости.Если электроды, используемые для сварки, содержат следы влаги, вода разлагается под действием тепла дуги и выделяющийся водород попадает в решетку материала, вызывая его хрупкость. Электроды для таких материалов со специальным низководородным покрытием поставляются в герметичной влагонепроницаемой упаковке. Новые электроды можно использовать прямо из банки, но при подозрении на поглощение влаги их необходимо высушить путем запекания (обычно при температуре от 800 до 1000 ° F (425–550 ° C)) в сушильном шкафу.Используемый флюс также должен быть сухим.
Некоторые аустенитные нержавеющие стали и сплавы на основе никеля склонны к межкристаллитной коррозии. Под воздействием температур около 700 ° C (1300 ° F) в течение слишком длительного времени хром вступает в реакцию с углеродом в материале, образуя карбид хрома и истощая края кристаллов хрома, ухудшая их коррозионную стойкость в процессе, называемом сенсибилизацией. Такая сенсибилизированная сталь подвергается коррозии в областях вблизи сварных швов, где температура и время были благоприятными для образования карбида.Этот вид коррозии часто называют распадом сварного шва.
Knifeline attack (KLA) — еще один вид коррозии сварных швов, поражающих стали, стабилизированные ниобием. Карбид ниобия и ниобия растворяется в стали при очень высоких температурах. При некоторых режимах охлаждения карбид ниобия не осаждается, и тогда сталь ведет себя как нестабилизированная сталь, вместо этого образуя карбид хрома. Это затрагивает только тонкую зону шириной несколько миллиметров в непосредственной близости от сварного шва, что затрудняет обнаружение и увеличивает скорость коррозии.Конструкции из таких сталей должны быть нагреты в целом до примерно 1950 ° F (1070 ° C), когда карбид хрома растворяется и образуется карбид ниобия. Скорость охлаждения после такой обработки не имеет значения.
Присадочный металл (материал электродов), неправильно подобранный для условий окружающей среды, также может сделать их чувствительными к коррозии. Также возникают проблемы гальванической коррозии, если состав электрода достаточно отличается от свариваемых материалов или сами материалы не похожи.Даже между разными марками нержавеющих сталей на основе никеля коррозия сварных соединений может быть серьезной, несмотря на то, что они редко подвергаются гальванической коррозии при механическом соединении.
История
Основные статьи: Кузнечная сварка, Контактная сварка, Кислородная сварка и дуговая сварка вольфрамовым электродом
Хотя примеры кузнечной сварки восходят к эпохе бронзы и железного века, дуговая сварка стала применяться гораздо позже. В 1802 году Василий Петров открыл непрерывную электрическую дугу и впоследствии предложил ее возможные практические применения, включая сварку.Французский изобретатель электротехники Огюст де Меритенс создал первую угольную дуговую горелку, запатентованную в 1881 году, которая успешно использовалась для сварки свинца при производстве свинцово-кислотных аккумуляторов. В 1881–1882 годах русский изобретатель Николай Бернардос создал метод электродуговой сварки стали, известный как углеродная дуга, с использованием углеродных электродов. Достижения в области дуговой сварки продолжились с изобретением металлических электродов в конце 19 века русским Николаем Славяновым (1888 г.) и американцем К.Л. Гроб. Около 1900 г. А. П. Штроменгер выпустил в Великобритании металлический электрод с покрытием, который давал более стабильную дугу. В 1905 году русский ученый Владимир Миткевич предложил использовать для сварки трехфазную электрическую дугу. В 1919 году сварка на переменном токе была изобретена К.Дж. Холслагом, но не стала популярной еще десять лет.
Конкурирующие сварочные процессы, такие как контактная сварка и кислородно-топливная сварка, также были разработаны в это время; но оба, особенно последняя, столкнулись с жесткой конкуренцией со стороны дуговой сварки, особенно после нанесения металлического покрытия (известного как флюс) на электрод, чтобы стабилизировать дугу и защитить основной материал от примесей, разработка продолжается.
Во время Первой мировой войны в судостроении Великобритании начали использовать сварку вместо клепаных стальных листов. Американцы также стали более восприимчивыми к новой технологии, когда процесс позволил им быстро отремонтировать свои корабли после нападения Германии в гавани Нью-Йорка в начале войны. Впервые дуговая сварка была применена к самолетам во время войны, и фюзеляжи некоторых немецких самолетов были построены с использованием этого процесса. В 1919 году британский кораблестроитель Каммелл Лэрд начал строительство торгового судна Fullagar с полностью сварным корпусом; она была спущена на воду в 1921 году.
В 1920-е годы в технологии сварки были достигнуты значительные успехи, включая введение в 1920 году автоматической сварки, при которой электродная проволока подавалась непрерывно. Защитный газ стал предметом пристального внимания, поскольку ученые пытались защитить сварные швы от воздействия кислорода и азота в атмосфере. Пористость и хрупкость были основными проблемами, и разработанные решения включали использование водорода, аргона и гелия в качестве сварочной атмосферы. В течение следующего десятилетия дальнейшие достижения позволили сварку химически активных металлов, таких как алюминий и магний.Это, в сочетании с разработками в области автоматической сварки, переменного тока и флюсов, привело к значительному развитию дуговой сварки в 1930-х годах, а затем во время Второй мировой войны.
В середине века было изобретено много новых методов сварки. Сварка под флюсом была изобретена в 1930 году и продолжает оставаться популярной сегодня. В 1932 году россиянин Константин Хренов успешно осуществил первую подводную электродуговую сварку. Газовая вольфрамовая дуговая сварка после десятилетий развития была окончательно доведена до совершенства в 1941 году, а в 1948 году последовала газовая дуговая сварка металлическим электродом, которая позволила быстро сваривать цветные материалы, но требовала дорогостоящих защитных газов.Использование расходуемого электрода и атмосферы двуокиси углерода в качестве защитного газа быстро сделало его самым популярным процессом дуговой сварки металла. В 1957 году дебютировал процесс дуговой сварки порошковой проволокой, в котором самозащитный проволочный электрод можно было использовать с автоматическим оборудованием, что привело к значительному увеличению скорости сварки. В том же году была изобретена плазменная сварка. Электрошлаковая сварка была выпущена в 1958 году, а в 1961 году последовала ее родственница — электрогазовая сварка.
Хотите поговорить с нашей командой?
Может быть, вы не уверены, какой сварочный аппарат вам подходит? Наши специалисты по продажам будут рады обсудить ваши требования к сварке.
Обладая обширными знаниями обо ВСЕХ марках и моделях, они могут предложить наиболее подходящую машину для вашего применения и бюджета.
В период с понедельника по пятницу в течение рабочего дня с 8:00 до 17:00 по Гринвичу мы постараемся ответить на ваш запрос в течение 2 часов с момента получения вашего электронного письма.
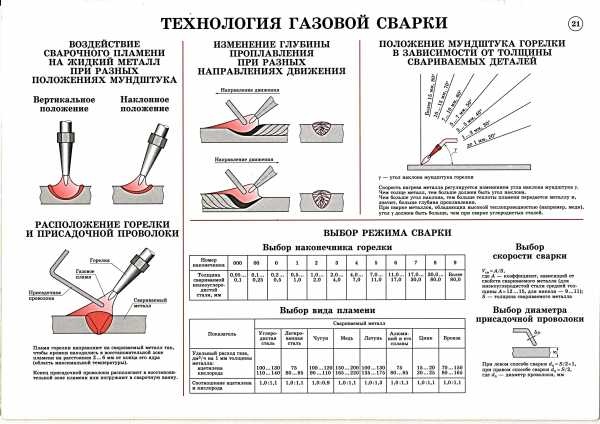