Услуги по термообработки сварных швов
Местная термообработка сварных соединений, наряду со сваркой, является одной из основных технологических процессов при монтаже и ремонте трубопроводов и сосудов давления в различных отраслях промышленности (газовой, нефтяной, нефтеперерабатывающей, тепловой энергетике и прочее), положительно влияет на надежность сварных конструкций, повышает их работоспособность.
Три последовательных этапа процесса термообработки:
— нагрев до определенной температуры с заданной скоростью;— выдержка при этой температуре в течение определенного времени;
— охлаждение с заданной скоростью.
Режим термообработки сварных швов выбирается в зависимости от марки свариваемой стали. Его можно посмотреть в регламентирующих документах, таких как СТО, РД, РТМ, ОСТ в зависимости в какой области будет применяться свариваемое изделие.
В результате термической обработки снижается уровень сварочных напряжений, улучшается структура и свойства металла соединения, снижается содержание водорода.
В связи с применением новых марок сталей, увеличением диаметров и толщин стенок трубопроводов и сосудов давления , возрастает требование к качеству термической обработки. Неправильное выполнение- может стать причиной разрушения сварных соединений .
Опытные специалисты нашего предприятия, аттестованные операторы- термисты, предлагают вам свои услуги по термической обработке сварных соединений как на территории нашего предприятия, так и по месту нахождения вашего объекта. Все работы осуществляются на установках индукционного или резистивного нагрева собственного производства.
Для заказа услуги по термообработки сварных швов Вам необходимо предоставить следующую информацию:
— марка стали;
— диаметр трубы и толщина стенки;
— вид сварного шва;
— вид и режим процесса термообработки;
— количество стыков;
— предполагаемое место работы.
Термообработка сварных швов трубопроводов
Способов высокотемпературной обработки металла существует очень много.
Термообработка сварных швов – этапы
Термообработка сварных швов заключается в нагреве металла в местах соединения для снятия напряжения, которое образовалось в швах во время сварки. Термообработка сварных швов состоит из трех этапов:
- Подготовительный этап – нагрев изделия перед началом сварочных работ. Производится для придания металлу эластичности.
- Промежуточная термообработка – постоянный нагрев изделия в процессе произведения сварочных работ. Производится для достижения максимальной эластичности металла, вследствие чего образуется минимальное напряжение.
- Термообработка сварных швов – нагрев изделия непосредственно после проведения всех сварочных работ. Производится для максимального избавления изделия от остаточного напряжения металла в местах соединения.
Термообработка сварных швов трубопроводов – это отличный способ защитить уязвимые места изделия от коррозии и повысить уровень прочности труб, продляя их срок эксплуатации.
Термообработка сварных швов – достоинства нагрева ТВЧ
Нагрев ТВЧ обладает широким рядом преимуществ, что и позволило ему отвести все альтернативные виды нагрева на второй план.
- Термообработка сварных швов получается равномерной, что позволяет максимально разгладить напряжение металла.
- Тепло образуется непосредственно в металле без воздействия внешних раздражителей на изделие.
- Индукционный нагрев может повторить любую среду, так же может производиться в вакуумной среде для защиты металла от окисления.
- Нагрев ТВЧ позволяет экономить значительную часть производственных ресурсов, что положительно сказывается на бюджете предприятия.
- Индукционная установка обладает компактными размерами, и может легко перевозиться на место проведения работ, если возникнет такая необходимость.
Термообработка сварных швов при помощи индукционного оборудования стала простым процессом, позволяющим улучшить качество трубопроводов из нержавеющей стали.
Термообработка сварных швов
Сварные соединения, выполненные дуговыми способами, непосредственно после процесса сварки характеризуются неоднородностью структуры и свойств сварного шва, зоны термического влияния, а также наличием в них сварочных напряжений.
Неоднородность структуры и свойств металла зависят главным образом от неравномерности нагрева при сварке. Металл шва в процессе сварки в расплавленном состоянии имеет температуру свыше 2000°С, в то время, как соседние слои металла находятся в твердом состоянии при намного более низких температурах. Вдоль сварного шва возникает область металла, которая при сварке нагревается до очень высокой температуры, а потом охлаждается до комнатной. Эта область называется зоной термического влияния (ЗТВ).
Все металлы сжимаются при снижении температуры. Этому процессу в области сварки препятствуют окружающие холодные слои металла и как следствие в области сварного шва и в ЗТВ возникают остаточные сварочные напряжения. Сварочные напряжения могут достигать значительных величин, близких к пределу текучести (250-350 МПа). Сварочные напряжения опасны тем, что могут вызвать появление трещин в сварных соединениях, особенно выполненных из легированных сталей. Кроме того, эти стали в производственных условиях при сварке быстро остывают, что приводит к образованию закалочных структур в сварном шве и ЗТВ, также способствующих образованию трещин. При больших остаточных напряжениях в присутствии определённых химических веществ могут происходить особый вид разрушения – коррозионное растрескивание.
Ещё одна проблема – водород. Если в зоне сварки окажется вода, она может попасть под электрическую дугу. Под воздействием электричества вода будет разложена на кислород и водород, который, в свою очередь, попадет в расплав. Присутствие водорода может привести к серьезным проблемам при сварке.
Одним из основных средств решения этих проблем и повышения надежности сварных соединений является нагрев или термическая обработка, в результате которой снижается уровень сварочных напряжений, улучшается структура и свойства металла соединения, удаляется водород.
- Предварительный подогрев перед сваркой;
- Сопутствующий подогрев во время сварки;
- Послесварочный нагрев.
- Термический отдых;
- Высокий отпуск;
- Нормализация;
- Стабилизирующий отжиг;
- Аустенизация.
Термообработка сварных швов является важной стадией технологического процесса. Неправильно проведенная послесварочная термообработка сварных соединений может свести на «нет» все предыдущие усилия.
В зависимости от размера и вида обрабатываемого изделия, марки стали, вида термообработки, а также количества сварных швов на изделии экономически и технически целесообразным могут быть разные виды термообработки: местная (пошовная, локальная) термообработка отдельных сварных швов или объемная (внепечная) термообработка всего изделия.
Термообработка сварных соединений
Главная / Термообработка сварных соединенийСварные соединения, непосредственно после процесса сварки, характеризуются неоднородностью структуры и свойств сварного шва, зоны термического влияния и наличием в них сварочных напряжений.
Термическая обработка — один из основных способов решения этих проблем и повышения надежности сварных соединений. Результат – снижение уровня сварочных напряжений, улучшение структуры и свойств металла соединения, удаление водорода.
Термообработка сварных швов широко применяется в различных отраслях: нефтеперерабатывающей, энергетической, химической. ООО «Южгазстрой» проводит местную термическую обработку труб (нагрев касается непосредственно шва). Процесс термообработки состоит из трех последовательных этапов: нагрев до определенной температуры с заданной скоростью, выдержка при этой температуре в течение определенного времени и последующее охлаждение с заданной скоростью. Соблюдение регламентирующих значений этих параметров имеет большое значение для качества термообработки.
Режимы термической обработки выбираются согласно режимам, установленным для свариваемой стали. Контроль пригодности того или иного режима термообработки ведется с учетом механических свойств и микроструктуры металла сварного соединения. В случаях, когда металл шва отличается по химическому составу от основного металла, наши специалисты вводят необходимые корректировки в режимы термообработки.
После термообработки сварное соединение становится равноценным основному металлу по всему комплексу физико-химических свойств при условии, что химический состав металла шва и свариваемой стали был одинаковым. В ряде случаев, при одинаковых с основным металлом химическом составе и термообработке, металл шва может иметь механические свойства, превышающие свойства основного металла.
ООО «Южгазстрой» проведет согласно Вашему заказу любой процесс местной термической обработки сварных соединений на месте мобильными нагревательными установками.
<a href=»https://www.olark.com/site/6954-889-10-9802/contact» mce_href=»https://www.olark.com/site/6954-889-10-9802/contact» title=»Contact us» target=»_blank»>Questions? Feedback?</a> powered by <a href=»http://www.olark.com?welcome» mce_href=»http://www.olark.com?welcome» title=»Olark live chat software»>Olark live chat software</a>Обработка сварных швов после сварки: виды термообработки
Автор admin На чтение 3 мин. Просмотров 857 Опубликовано
Для того чтобы качество металла, формирующего сварной шов, соответствовало определенным требованиям по прочности, стойкости к коррозии применяют различные технологические процессы.
При этом обработка сварного шва может осуществляться как в процессе выполнения сварки, так и по ее завершению.
Виды обработки
В общем можно выделить несколько технологических приемов, по которым выполняется обработка сварных швов, при этом каждый из них преследует определенную цель:
- Термическая обработка позволяет снять остаточные напряжения в металле, возникающие при выполнении сварочных работ. Она является одним из основных методов, применяемых при работе с различными сталями и металлами (начиная от чугуна, заканчиваю нержавейкой и высоколегированными сталями).
Специалисты выделяют два вида термической обработки сварного шва — местный (прогреву и охлаждению подвергается только сам шов) и общий (нагревается вся деталь). - Механическая обработка сварных швов после сварки позволяет удалить оставшийся шлак и убедиться в качестве соединения. Всем приходилось видеть, как исполнитель обстукивает шов молотком или выполняет его зачистку. Оставшийся шлак может стать причиной возникновения коррозионных процессов.
- Нанесение различных защитных покрытий на сварочный шов так же помогает бороться с появлением коррозии. Простейшим способом является нанесение грунтующей краски, в качестве примера можно обратить внимание на металлоконструкции, на которых четко видно появление ржавчины в местах сварных соединений. Это говорит о том, что в этом случае не была выполнена качественная обработка шва после сварки.
Более подробно следует остановиться на термической обработке, позволяющей существенно повысить именно качество металла, формирующего сварочный шов.
Термическая обработка
Итак, вот что позволяет достичь термическая обработка сварных швов:
- Снижение остаточных напряжений, возникающих при выполнении сварочных работ.
- Улучшение структуры материала и самого шва, и околошовных зон.
- Улучшение физических и эксплуатационных свойств металла (устойчивость к коррозии, жаропрочность и многое другое).
При выполнении термической обработки выполняется нагрев сварного шва или всего изделия до определенной температуры и выдержка в таком состоянии определенный период времени. Охлаждение осуществляется тоже по определенной схеме. Чаще всего для нагрева применяется индукционное оборудование, но могут использоваться и другие технологические схемы, в том числе и комбинированные (муфельные печи, нагрев с применением газоплазменных установок, гибкие нагреватели сопротивления).
К основным видам термообработки сварных швов относят:
- Высокий отпуск — его принцип заключается в нагреве стали до 650-750 градусов (режим зависит от марки материала) и выдержке при такой температуре до 5 часов. Такая термообработка позволяет снять до 80% напряжений, повысить ударную вязкость, улучшить пластичность, снизить твердость металла.
- Для углеродистой, а также низколегированной стали применяется нормализация. Такая термообработка сварного шва заключается в нагреве до 950 градусов и выше, после чего осуществляется выдержка (нескольких минут) и охлаждении в условиях атмосферного воздуха. Данная процедура позволяет снизить размер зерна металла, формирующего сварной шов, снизить напряжения, повысить прочность соединения.
- Для выполнения закалки на аустенит (аустенизации) необходимо нагреть шов до температуры не менее 1075 градусов. В таком состоянии изделие выдерживается не менее часа, после чего осуществляется быстрое охлаждение. Данная технология применяется для аустенитовых сталей и позволяет увеличить пластичность сварного шва.
- Стабилизирующий отжиг отличается от аустенизации только температурой нагрева (970 градусов) и меньшим временем выдержки.
Выбор вида термической обработки сварного соединения должен основываться на химических и физических свойствах материала (марке стали).
При этом особое внимание необходимо уделять соблюдению температурного режима, любое отклонение от него может привести к ухудшению качества сварного шва.
Термообработка сварных швов — Сварка, пайка, металлообработка
Виды термической обработки
При сборке различных металлоконструкций применяют два основных способа соединения деталей – разборные конструкции и скрепленные между собой. Последний тип соединения комплектующих в основном выполняется при помощи их сваривания. При этом в местах сварных швов возникают напряжения металла, которые негативно влияют на качество соединений и в целом на сваренную металлоконструкцию.
В связи с этим в местах сварочных швов понижается расчетная прочность, они в большей степени подвержены коррозии.
Для устранения этих недостатков применяются некоторые способы, при помощи которых сварные соединения приобретают необходимые технологические и конструктивные свойства — термообработка сварных швов.
Типы обработки сварных швов и соединений
На практике для обработки сварных соединений используют несколько приемов, которые выполняются как при проведении сварочных работ, так и по их завершении. Все эти способы применяют для защиты сварных швов, но применяют их в разных условиях.
Механическая обработка. Используют этот прием для удаления шлаковых отложений и контроля качества выполнения сварочных работ. Остатки шлака способствуют развитию коррозии соединений.
Обработка защитными составами. Этот способ применяют после выполнения сварочных операций.
Соединения обрабатывают грунтовочными красками, которые защищают швы от коррозии.
Термическая обработка. Применяется для разгрузки сварочных швов от остаточных напряжений металла. Этот метод обработки наиболее распространенный, так как позволяет обработать любые сварочные соединения.
Его можно проводить как во время сварочных работ, так и после их окончания.
Задачи и виды термообработки сварочных швов
При проведении сварочных работ, в соединениях сопрягаемых металлов под влиянием высоких температур происходят различные химические изменения структуры металла. При этом возникают напряжения различного рода.
причина возникновения напряжений и изменение структуры в зоне проваренного шва – это разница температур, в местах сварки металла, имеет жидкое состояние, а сама деталь, менее нагретая, имеет кристаллическое строение. Вследствие этого, в соединениях возникают напряжения, которые отрицательно влияют на его прочность.
При резком охлаждении происходит закаливание сварочного шва, особенно часто это наблюдается при сварке легированных сталей, в связи с этим в местах сварочных сопряжений образуются трещины.
Дополнительная термическая обработка сварных швов до определенной температуры и установленной скорости нагрева, приводит к нормализации сваренных металлов, и снимает внутренние напряжения, образуемые при их сварке.
Термообработка (отжиг) сварных соединений выполняется несколькими способами, которые применяются в зависимости от условий проведения сварочных работ и марки свариваемого металла. Производят нагрев как самого сварочного шва (местный нагрев) так и всей сваренной конструкции.Для проведения термообработки металла применяют – газопламенные установки, муфельные печи, гибкие нагревательные сопротивления. Наиболее часто для термической нормализации сварных швов используют индукционные нагреватели.
В зависимости от типа тепловой обработки сваренных деталей применяют следующие виды их термообработки:
Предварительный нагрев.
Применяется как перед началом сварочных работ, так и непосредственно при сваривании изделий. Этот вид термообработки применяется для сварки труб из низкоуглеродистой стали, соединения которых прогревают до температуры 150–200 °C, что препятствует их быстрому остыванию.
Термический отдых.
Сваренное соединение деталей нагревают до температуры 250–300 °C и производят их выдержку при этой температуре в течение определенного времени. При этом в сварочном шве уменьшается количество диффузионного водорода, и снижаются внутренние напряжения.
Высокий отпуск.
Этот способ предусматривает нагрев сваренных конструкций до температуры 650–750 °C, в зависимости от свариваемых металлов, выдержкой их в этих условиях в течение 5 часов, с последующим медленным охлаждением. При таких условиях происходит снижение внутренних напряжений в сварных швах на 80–90%. Применяется для сталей, содержащих средний процент углерода.
Нормализация.
Применяется для высокоуглеродистых легированных сталей. Сварные швы нагревают до 950-1050 градусов, производят выдержку при этой температуре в течение нескольких минут и дают остыть деталям на открытом воздухе.
Для термообработки сварных швов также применяют аустенизацию, нормализацию с отпуском и стабилизирующий отжиг.
Все эти виды тепловой обработки сварных швов и соединений применяются исходя из физико-химических свойств металлов.
выделите фрагмент текста и нажмите Ctrl+Enter
Источник: https://xn--h2afsf5c.xn--p1ai/%D1%81%D1%82%D0%B0%D1%82%D1%8C%D0%B8/%D1%82%D0%B5%D1%80%D0%BC%D0%BE%D0%BE%D0%B1%D1%80%D0%B0%D0%B1%D0%BE%D1%82%D0%BA%D0%B0-%D1%81%D0%B2%D0%B0%D1%80%D0%BD%D1%8B%D1%85-%D1%88%D0%B2%D0%BE%D0%B2-%D0%B8-%D1%81%D0%BE%D0%B5%D0%B4%D0%B8%D0%BD%D0%B5%D0%BD%D0%B8%D0%B9
Рд 34.17.310-96 сварка, термообработка и контроль при ремонте сварных соединений трубных систем котлов и паропроводов в период эксплуатации — скачать бесплатно
ВСЕРОССИЙСКИЙ ДВАЖДЫ ОРДЕНА ТРУДОВОГО КРАСНОГО ЗНАМЕНИ ТЕПЛОТЕХНИЧЕСКИЙ НАУЧНО-ИССЛЕДОВАТЕЛЬСКИЙ ИНСТИТУТ
(ВТИ)
РОССИЙСКОЕ АКЦИОНЕРНОЕ ОБЩЕСТВО
(РАО) «ЕЭС РОССИИ»
ФЕДЕРАЛЬНЫЙ ГОРНЫЙ И ПРОМЫШЛЕННЫЙ НАДЗОР РОССИИ
(ГОСГОРТЕХНАДЗОР РОССИИ)
УТВЕРЖДЕН РАО «ЕЭС России» 20 марта 1996 г. | УТВЕРЖДЕН Госгортехнадзором России 11 апреля 1996 г. |
РУКОВОДЯЩИЙ ДОКУМЕНТ
РД 34 . 17.310-96
СВАРКА, ТЕРМООБРАБОТКА И КОНТРОЛЬ ПРИ РЕМОНТЕ СВАРНЫХ СОЕДИНЕНИЙ ТРУБНЫХ СИСТЕМ КОТЛОВ И ПАРОПРОВОДОВ В
ПЕРИОД ЭКСПЛУАТАЦИИ
Обязателен для всех министерств, ведомств,
предприятий и организаций
Москва НПО ОБТ
1997
Разработчики:
Всероссийский теплотехнический научно-исследовательский институт (ВТИ), РАО «ЕЭС России», Госгортехнадзор России
Составители:
Ф.А. Хромченко (докт. техн. наук) — ответственный исполнитель, В.А. Лаппа, В.Ф. Злепко (канд. техн. наук), А.П. Берсенев, В.В. Гусев, Н.А. Хапонен, А.А. Шельпяков
Настоящий отраслевой руководящий документ устанавливает требования к технологическим процессам ремонта с применением ручной дуговой сварки и термообработки стыковых, штуцерных и тройниковых сварных соединений паропроводов и коллекторов котлов тепловых электростанций и котельных, повреждающихся в ходе эксплуатации, а также требования к качеству сварных соединений после ремонта, к оборудованию и материалам, применяемым при сварке.
РД предназначен для организаций, связанных с эксплуатацией, ремонтом и монтажом оборудования тепловых электростанций.
Предисловие
Настоящий отраслевой руководящий документ распространяется на:
трубопроводы пара I категории 1-, 2- и 3-й групп;
трубопроводы пара в пределах котла и турбины с температурой эксплуатации свыше 450 °С независимо от давления;
коллекторы (камеры) и приваренные к ним трубы (штуцера) с температурой пара свыше 450 ºС независимо от давления, изготовленные из теплоустойчивых хромомолибденованадиевых сталей 12Х1МФ, 15Х1М1Ф, 20ХМФЛ, 15Х1М1ФЛ.
Настоящий руководящий документ не распространяется на элементы центробежнолитых труб из стали 15Х1М1Ф-ЦЛ.
С момента введения в действие настоящего отраслевого руководящего документа утрачивает юридическую силу РД 34 17.205-90 «Инструкция по приварке штуцеров к коллекторам из стали 12X1МФ аустенитными электродами без термической обработки».
Требования настоящего отраслевого нормативного документа обязательны для применения всеми расположенными на территории Российской Федерации предприятиями и объединениями предприятий, имеющими в своем составе (структуре) тепловые электростанции и котельные, независимо от форм собственности и подчинения.
1. ОБЩИЕ ПОЛОЖЕНИЯ
1.1. Технологические процессы сварки, термообработки и контроля сварных соединений (далее — ремонтная технология), установленные настоящим руководящим документом, применяют в условиях действующих электростанций непосредственно по месту трассировки паропроводов, ремонтируемых котлов или в специальных помещениях — рабочих площадках на отдельных трубных блоках.
1.2. Работы по ремонтной технологии проводят специализированные организации (электростанции, ремонтные предприятия или другие организации), имеющие разрешение (лицензию) на эти работы органов Госгортехнадзора России.
1.3. Ремонтную технологию выбирают после определения причин повреждения элементов оборудования, при этом должны быть учтены:
результаты обследования поврежденного сварного соединения;
конструкция сварного соединения;
технология изготовления сварного соединения;
условия эксплуатации сварного соединения;
статистика аналогичных повреждений на электростанции;
планируемый срок дальнейшей эксплуатации оборудования.
При необходимости проводят поверочный расчет сварного соединения на прочность с учетом действия статических изгибающих или циклических нагрузок.
1.4. Техническую консультацию по применению технологии ремонта осуществляет ВТИ по запросу электростанции.
При необходимости ВТИ разрабатывает ремонтную технологию с учетом конкретного характера повреждения, конструкции сварных деталей (изделий) и условий эксплуатации и оценки остаточного ресурса отремонтированных сварных соединений.
1.5. Технологические операции проводят при положительной температуре окружающего воздуха, отсутствии сквозняков, ветра и атмосферных осадков, а также исключении возможности попадания золы, воды, нефтепродуктов в зону нагрева при сварке и термической обработке.
Ремонтируемое сварное соединение должно быть освобождено от недопустимых защемлений, изгибающих и растягивающих нагрузок.
Источник: http://www.gosthelp.ru/text/rd341731096svarkatermoobr.html
Нормализация сварных соединений — Энциклопедия по машиностроению XXL
Термообработка сварных швов. Индукционный нагрев широко используется для термообработки (отпуска или нормализации) сварных соединений. Кольцевые сварные швы на трубах и аппаратах нагревают одновременным способом в кольцевых разъемных или неразъемных индукторах промышленной или средней частоты. Температуры зависят от марки стали и цели обработки и колеблются в пределах 600—1200 °С. Часто термообработку приходится проводить во время монтажа. При этом используются гибкие индукторы из специального кабеля с естественным или водяным охлаждением, которые накладываются на слой теплоизоляции. Выпускаются специальные стационарные и переносные установки для термообработки кольцевых швов, состоящие из источника питания, индукторов пли гибкого кабеля-индуктора, аппаратуры управления И конденсаторной батареи. Мощности установок составляют десятки, реже сотни киловатт.
Нормализация сварных соединений не приводит к изменению их предела усталости, изменяется только место разрушения. Это связано с тем, что нормализация повышает прочностные свойства металла, но в то же время снижает упрочнение сварного стыка, полученное при сварке вследствие значительной пластической деформации при высоких температурах. [c.189]
Нормализация сварных соединений и зон термического влия ния осуществляется при температуре 850—900° С в зависимости от марки стали. [c.28]
Высокий отпуск является основным видом термической обработки в монтажных условиях, он позволяет на 70—90 % снизить уровень остаточных сварочных напряжений. При высоком отпуске применяют медленную скорость охлаждения после окончания выдержки (300— 400°С/ч) до 300 °С, что достигается охлаждением сварных соединений под слоем теплоизоляции, после чего допускается охлаждение на воздухе. Основным отличием нормализации сварных соединений от этого вида термической обработки является охлаждение под слоем теплоизоляции после окончания выдержки, что гарантирует высокую пластичность металла сварных соединений. Термический отдых применяют для сварных соединений, металл которых имеет повышенную склонность к образованию трещин. Сварные соединения для этого нагревают до 250—300 °С и затем подвергают выдержке в течение нескольких часов. При термическом отдыхе в сварных соединениях уменьшается содержание водорода и несколько снижается уровень остаточных сварочных напряжений.
[c.206]
Восстановить структуру и механические свойства углеродистых сталей на указанном участке можно только последующей нормализацией сварного соединения. [c.272]
В случае необходимости производится нормализация сварного соединения с нагревом той же горелкой [c.365]
За истекшие годы, казалось бы, вполне устоялись наши представления о возможностях электрошлаковой сварки толстого металла. Немало было сделано в нашей стране и за рубежом, в частности в Великобритании, для устранения основного препятствия на пути этого прогрессивного способа сварки — необходимости нормализации сварного соединения. К сожалению, будучи довольно эффективными в применении к нелегированным сталям, все эти средства оказались недостаточными в случае легированных сталей, для которых неизбежное разупрочнение металла околошовной зоны требует восстановления его свойств высокотемпературной термообработкой.
[c.25]
В последние годы разработаны и находят применение более экономичные, по сравнению с полной нормализацией, приемы повышения ударной вязкости сварного соединения, выполненного электрошлаковой сваркой. К их числу относится сварка с пониженной погонной энергией и сопутствующей нормализацией металла сравнительно небольшой толщины (до 40 мм). Эта нормализация состоит в том, что на участке сварного соединения, остывшем примерно до температуры 500° С, устанавливают дополнительные нагреватели (горелки, индукторы и др. ). Перемещаясь со скоростью сварки, они нагревают металл сварного соединения до телшературы нормализации. Находит также применение нормализация сварного соединения в интервале более низких температур (Лсз—АС]).
[c.486]
После электрошлаковой сварки низкоуглеродистой стали толщиной более 80—100 мм требуется высокотемпературная термическая обработка — нормализация сварного соединения. [c.143]
Нормализация сварных соединений может обеспечить некоторое улучшение свойств вследствие перекристаллизации и измельчения зерна, поэтому термообработка рациональна при однослойной сварке под флюсом металла большой толщины, при 174 [c.174]
До —70 при любой толщине и условии нормализации сварных соединений [c.197]
К недостаткам электрошлаковой сварки следует отнести образование крупного зерна в шве и околошовной зоне вследствие замедленного нагрева и охлаждения. После сварки необходима термическая обработка (отжиг или нормализация) для измельчения зерна в металле сварного соединения.
[c.202]
Для обеспечения равнопрочности сварного соединения после сварки производят полную термообработку изделия, которая заключается в закалке и последующем высоком отпуске или в нормализации. [c.125]
Термическая обработка для снятия сварочных напряжений — отпуск 630—650° С для получения пластичного сварного соединения и выравнивания «механических свойств — закалка с отпуском для сварных соединений, выполненных ЭШС, — нормализация, а выполненных КТС — отпуск. [c.139]
Термическая обработка путем нормализации и улучшения не позволяет повысить предел усталости сварных соединений до уровня прочности основного металла в том же состоянии термической обработки. При сварке трением в зоне сварного стыка происходит нарушение волокнистой структуры, которую имеет основной металл. Это нарушение структуры металла снижает его сопротивляемость циклическим нагрузкам. Снижение предела усталости нормализованных и улучшенных сварных соединений по сравнению с основным металлом, имеющим волокнистую структуру и аналогично термообработанным, характеризуется следующим соотношением
[c.189]
Механические свойства сварного соединения, выполненного из стали 25Л, 35Л пластинчатыми электродами из стали ЮХСНД (ГОСТ 5058—65) и прошедшего до сварки высокий отпуск, а после сварки нормализацию и высокий отпуск, значительно превышают свойства основного металла. Механические свойства различных зон сварного соединения из стали МСт.5, выполненного пластинчатыми электродами из стали ЮХСНД после сварки и термической обработки, приведены в табл. 57. [c.523]
Для получения оптимальных механических свойств сварное соединение должно подвергаться термической обработке, устраняющей перегрев околошовной зоны и измельчение первичной структуры металла шва. Термическая обработка сварного изделия заключается в нормализации или закалке с последующим отпуском по режиму стали.
[c.524]
В настоящее время имеется достаточно технических оснований для применения системы унификации и нормализации узлов трубопроводов. С введением межотраслевых нормалей устранены допускавшиеся в трубопроводах излишние запасы прочности, установлен единый ограничительный ассортимент труб для технологических трубопроводов, унифицированы номенклатура, конструкции и нормализованы типоразмеры деталей трубопроводов, марки стали, применяемые для их изготовления, и обеспечено широкое внедрение сварных соединений тру- [c.18]
При применении в связи с эксплуатационной необходимостью металлов с пониженной свариваемостью проектировать конструкции следует с учетом этого свойства. Для сведения к минимуму неблагоприятных изменений свойств металла сварного соединения и исключения в нем дефектов необходимо применять виды и режимы сварки, оказывающие минимальное термическое и другие воздействия на металл, и проводить технологические мероприятия (подогрев, искусственное охлаждение и др. ), снижающие влияние на него сварочных воздействий. Термическая обработка после сварки (нормализация, закалка с отпуском и др.) может в значительной степени устранять неоднородность свойств в сварных заготовках. Прочность зоны сварного соединения может быть повышена механической обработкой после сварки прокаткой, проковкой и др.
[c.288]
Св-ОЗГА ГОСТ 2246—60 16ГС (ЗН) и 16ГТ(ЗЫ) двухслойной стали АН-348А или ОСЦ-45 по ГОСТ 9087—59, или им Для рабочей температуры стенки от —30 до+ 450 С. Д.ая рабочей температуры стенки от —31 до—40″С при толщине метал.ча не более 24 мм. Для рабочей температуры стенки от —31 до — 40 С и любой толщине металла при условии нормализации сварных соединений [c.352]
Г2С(М) равноценных Для рабочей температуры стенкп от — 30 до 4- 475 С. Для рабочей температуры стенки от — 31 до — 40 С при толщине металла )ie более 24. ii.ii. Для рабочей температуры стенки от — 31 до — 70 С и любой толщине металла при условии нормализации сварных соединений
[c. 352]
Г2С1(МК) Для рабочей температуры стенки от — 41 до — 70°С и любой толщине металла при условии нормализации сварных соединений [c.353]
Сталь 20ХМФ сваривается с предварительным и сопутствующим подогревом изделий до температуры 250—300° С. После сварки изделие подвергают высокому отпуску помещают в печь при температуре не более 200° С, нагревают до 700° С со скоростью 40— 50 град/час, выдерживают при 700° С от 2 до 5 час., охлаждают до 200° С со скоростью 40—50 град час. Нормализация сварных соединений при температуре 920—940° С не рекомендуется, так как при этом наблюдается резкое разупрочнение металла шва. [c.223]
Термической обработке (отжигу или нормализации) сварные соединения подвергают с целью снятия внутренних термических напряжений, предупреждения образования трещин, а также для восстановления нормальной структуры металла. Режимы термообработки зависят от марки свариваемой стали и обычно указыва-
[c. 425]
В табл. 10-5 приведены типичные режимы сварки низколегированной стали с пониженным содержанием углерода (например 09Г2ДТ). Сварку такой стали на приведенных режимах также можно выполнять без нормализации сварных соединений. [c.523]
Применение стыковой сварки оплавлением заставляет использовать нетехнологичные штамповки с удлиненным хвостовиком, припуск на оплавление составляет 6—7 мм на сторону. При этом наличие видманштетовой структуры в зоне перегрева требует нормализации сварного соединения, а сварочные дес рмации вынуждают применять расточку ушков после сварки. Сварка трением позволяет обходиться без последующей термообработки, припуск на осадку составляет всего 3—4 мм на сторону. Кроме того, сварка трением дает возможность сваривать детали 1, окончательно обработанные в соответствии с чертежом, с деталями 2 и выдерживать указанные выше требования чертежа. [c.339]
Св.-ОЗГА То же То же 16ГС 09Г2С Для рабочей температуры стенки от —30 до -1-450°. Для рабочей температуры стенки от —31 до —40° прн любой толщине металла при условии нормализации сварных соединений Для рабочей температуры стеики от —30 до -Ь475°.
[c.98]
Г2С талла свыше 24 мм при отсутствии нормализации сва 1-ных соединений Для рабочей температуры стенки от —41 до —70 при отсутствии нормализации сварных соединений [c.98]
В сварных соединениях зону перекристаллизации разделяют на два участка зону перегрева с относительно крупным зерном (Гмакс 1273 К) и зону нормализации с мелким зерном (7 тах[c.513]
Восстановительная термообработка проводилась индукционным способом со ступенчатым перемещением индуктора. Термической обработке подвергались прямые и гнутые трубы и их сварные соединения без демонтажа паропровода. И проводилось по двум режимам одинарная нормализация с отпуском и двойная нормализация с отпуском. Исследование структуры всех труб паропроводов и кратковременных и длительных свойств пробных гибов 0 273×32 мм и 0 325×38 мм после термообработки показало следующее
[c. 259]
Низкоуглеродистая сталь с содержанием до 0,25%С Среднеуглеродистая сталь с содержанием 0,26 — 0,45%С Высокоуглеродистая сталь с содержанием 0.46 — 0.759Й С 120—150°С — на многослойных швах при сварке больших толшин (40 ММ) 150 — 300°С 300 — 450°С Отпуск при 640 — 670°С для снятия сварочных напряжений, выравнивания структуры и механических свойств. В некоторых случаях (Например, ЭШС) нормализация при 920—940 С с последующим отпуском. Для получения требуемых механических свойств сварного соединения при сварке среднелегированной стали применяется закалка с последующим отпуском [c.137]
Прочность сварных соединений стали Х15Н9Ю может быть повышена до а = = ПОн-130 кПмм путем их нормализации при 950—975° С, обработки холодом при —70° С с выдержкой 2 ч или при температурах —50 или —60° С с выдержкой 4 ч и последующей рихтовкой и старением при 400 10° С с выдержкой I ч, охлаждение на воздухе. [c.142]
Нами было исследовано влияние таких видов термической обработки, как отжиг, нормализация и улучшение на усталостную прочность соединений, выполненных сВ аркой трением из сталей 45 и 40Х. Результаты испытаний показали, что отжиг снижает усталостную прочность сварных соединений. По сравнению со сварными соединениями без термической обработки предел усталости снижается на 357о. Разрушение при испытаниях происходит по сварному стыку. Таким образом, отжиг отрицательно влияет на усталостную прочность оварных соединений из-за общего понижения прочностных свойств металла и металла зоны сварки.
[c.189]
При автоматической многослойной сварке (больше одного слоя) после наложения каждого слоя поверхность шва тщательно очищают от шлака. Для поддержания устойчивой дуги сварку производят с применением флюса. Сварку выполняют только качественными (толстообмазанными) электродами, состав электродной проволоки подбирают так, чтобы основной металл и металл сварного соединения были бы равнопрочны. В процессе сварки обечайка деформируется. Для придания ей цилиндрической формы обечайку калибруют путем обкатки в листогибочных вальцах в горячем состоянии. Последнее используется также для нормализации, в процессе которой сварные швы и околошовная зона освобождаются от сварочных напряжений. На рис. 15-5 показана электрошлаковая сварка применительно к продольному шву барабана. Для выполнения сварочных работ барабан располагают в вертикальном положении неподвижно. На кромки стыкуемой обечайки накладывают медные ползуны — кристаллизаторы, перемещаемые в процессе сварки снизу вверх, а расстояние между кромками устанавливается дистанционной планкой. В образовавшийся объем, ограниченный кромками обечайки, ползунами н дистанционной планкой, вводят электродную проволоку и возбуждают сварочную дугу под слоем флюса, который при разогреве расплавляется. Расплавленный флюс обладает электропроводностью.
[c.171]
После сварки соединение подверглось нормализации при 950° С, затем отпуску при 620° С и охлаждению со скоростью V = 50° С/ч (рис. 16, б). Предел выносливости равен 12,5 кгс/мм . Образцы испытывались со снятым усилением шва. Усталостные изломы, так же как и в сварном соединении стали 0Х12НДЛ со сталью 15Г2ВЛ, происходили по зоне сплавления металла электрода со сталью 0Х12НДЛ.
[c.35]
Термическая обработка сварных соединений
Хотя термообработка является своевременной и дорогостоящей операцией, она является обязательной во многих прикладных кодексах и стандартах.
Существует множество терминов, которые используются для описания диапазона термической обработки, которая может применяться к сварному соединению, каждый из которых имеет очень специфическое значение…
Обработка раствора
Разработан для приема в раствор элементов и соединений, которые затем удерживаются в растворе за счет быстрого охлаждения от высокой температуры обработки раствора.Повышает устойчивость к коррозии, а также может снижать прочность соединения. Может сопровождаться термообработкой при более низкой температуре для контролируемого преобразования выделений (старение или дисперсионное твердение) в некоторых сплавах.
Отжиг
Включает нагрев металла до высокой температуры, при котором происходит рекристаллизация и / или фазовое превращение, а затем его медленно охлаждают, часто в печи для термообработки. Этот процесс выполняется для размягчения металла после того, как он был закален, на примере холодной обработки, когда полный отжиг дает очень мягкую микроструктуру.Часто отмечается снижение текучести и прочности на разрыв, а в случае ферритных сталей — обычно снижение вязкости.
Нормализация
Выполняется только на ферритных сталях и включает нагрев стали на 30-50 ° C выше верхней температуры превращения, а затем охлаждение на неподвижном воздухе. Этот процесс термообработки приводит к уменьшению размера зерна с улучшением прочности и ударной вязкости.
Закалка
Эта термообработка требует быстрого охлаждения от высокой температуры.Ферритная сталь должна быть нагрета до температуры выше верхней температуры превращения, а затем закаляться в воде, масле или воздушной струе. Получение мелкозернистого мартенсита очень высокой прочности. Стали всегда отпускаются после процесса закалки и никогда не используются в закаленном состоянии.
Закалка
Выполняется при относительно низкой температуре, ниже более низкой температуры превращения в ферритных сталях. Этот процесс снижает твердость, снижает предел прочности и улучшает ударную вязкость и пластичность.Большинство нормализованных сталей подвергаются отпуску перед сваркой, при этом все закаленные стали используются в закаленном и отпущенном состоянии.
Отверждение от старения или осаждения
Еще одна низкотемпературная термообработка, предназначенная для получения выделений правильного размера и распределения, что увеличивает текучесть и предел прочности. Эта термообработка обычно следует за термообработкой на твердый раствор. Более продолжительное время и / или высокие температуры приводят к увеличению размера осадка и снижению как твердости, так и прочности.
Снятие напряжения
Как следует из названия, этот процесс предназначен для уменьшения остаточных напряжений, возникающих при усадке сварного шва. При повышении температуры металла предел текучести уменьшается, что позволяет перераспределять остаточные напряжения за счет ползучести сварного шва и основного металла. Охлаждение от температуры снятия напряжения контролируется, чтобы предотвратить возникновение вредных температурных градиентов.
Пост-нагрев
Осуществляется сразу после завершения сварки. Это низкотемпературная термообработка, при которой предварительный нагрев увеличивается на 100 ° C и выдерживается в течение примерно 3-4 часов.Таким образом, содействие диффузии любого водорода в сварном шве или HAZ (зона теплового воздействия) из стыка снижает риск образования холодных трещин, вызванных водородом. Используется только там, где водородное холодное растрескивание является серьезной проблемой — ферритные стали, которые очень чувствительны к трещинам, очень толстые соединения и т. Д.
Термическая обработка после сварки
Есть три основных причины, по которым проводится термообработка после сварки:
- Для достижения стабильности размеров с целью сохранения допусков во время операций механической обработки или во время перетряски
- Для изготовления специальных металлургических конструкций с целью достижения требуемых механических свойств
- Для снижения риска возникновения проблем в процессе эксплуатации, таких как коррозия под напряжением или хрупкое разрушение, за счет уменьшения остаточного напряжения в сварном элементе.
Снятие напряжений — одна из основных термических обработок для достижения вышеуказанных целей.
Это дорогостоящая операция, требующая полного или частичного нагрева сварной детали до высокой температуры. Это может вызвать нежелательные эффекты в некоторых сплавах.
Однако высокое остаточное напряжение, зафиксированное в сварном соединении, может вызвать деформацию, выходящую за рамки допустимых параметров, когда изделие подвергается механической обработке или вводится в эксплуатацию. Высокие остаточные напряжения в углеродистых и низколегированных сталях могут увеличить риск хрупкого разрушения, создавая движущую силу для распространения трещин.Остаточные напряжения вызовут коррозионное растрескивание под напряжением в правильной среде.
Чтобы снизить этот уровень остаточного напряжения, компонент повторно нагревают до достаточно высокой температуры. При повышении температуры предел текучести падает, что позволяет деформироваться и остаточному напряжению уменьшаться до тех пор, пока не будет достигнут приемлемый уровень. Компонент будет выдерживаться при этой температуре, известной как замачивание, в течение некоторого времени, пока не будет достигнуто стабильное состояние, а затем снова охладиться до комнатной температуры.Остаточное напряжение, остающееся в соединении, равно пределу текучести при температуре выдержки.
Для получения дополнительной информации см. Полную статью TWI здесь или узнайте больше о применении и управлении термообработкой от TWI.
Westermans имеет на складе большое количество продуктов для термообработки и снятия напряжения, нажмите здесь, чтобы увидеть машины от AEC и Cooperheat, в качестве альтернативы, если у вас есть оборудование для термообработки, которое вам больше не требуется, мы всегда заинтересованы в покупке для наших клиентов по всему миру, отправьте подробности Питеру Вестерману сюда или по электронной почте peter @ westermans.com.
Термическая обработка сварных соединений — часть 1
Термическая обработка — это трудоемкая и дорогостоящая операция. Это может повлиять на прочность и ударную вязкость сварного соединения, его коррозионную стойкость и уровень остаточного напряжения, но также является обязательной операцией, указанной во многих прикладных нормах и стандартах. Кроме того, это важная переменная в квалификационных требованиях к процедуре сварки.
Прежде чем обсуждать диапазон термических обработок, которым может подвергаться металл, необходимо четко определить, что означают различные термины, используемые для описания диапазона термических обработок, которые могут применяться к сварному соединению. Такие термины часто используются неправильно, особенно неспециалистами; для металлурга они имеют очень точное значение.
Обработка раствора
Осуществляется при высокой температуре и предназначен для приема в раствор элементов и соединений, которые затем остаются в растворе за счет быстрого охлаждения от температуры обработки раствора. Это может быть сделано для уменьшения прочности соединения или повышения его коррозионной стойкости. В случае некоторых сплавов за ней может последовать термообработка при более низкой температуре для контролируемого преобразования выделений (старение или дисперсионное твердение).
Отжиг
Он заключается в нагревании металла до высокой температуры, при котором происходит рекристаллизация и / или фазовое превращение, а затем в медленном охлаждении, часто в печи для термообработки. Это часто выполняется для смягчения металла после того, как он был закален, например, путем холодной обработки; полный отжиг, дающий самую мягкую микроструктуру.Это также приводит к снижению как текучести, так и предела прочности, а в случае ферритных сталей, как правило, к снижению ударной вязкости.
Нормализация
Это термообработка, которая проводится только для ферритных сталей. Он включает нагрев стали примерно на 30-50 ° C выше верхней температуры превращения (для стали с содержанием углерода 0,20% это будет около 910 ° C) и охлаждение на неподвижном воздухе. Это приводит к уменьшению размера зерна и повышению прочности и ударной вязкости.
Закалка
Это быстрое охлаждение от высокой температуры. Ферритную сталь следует нагреть до температуры, превышающей верхнюю температуру превращения, и закалить ее в воде, масле или воздушной струе, чтобы получить очень прочный мелкозернистый мартенсит. Стали никогда не используются в закаленном состоянии, они всегда отпускаются после операции закалки.
Закалка
Термическая обработка ферритных сталей при относительно низкой температуре, ниже более низкой температуры превращения; в обычной конструкционной углеродистой стали это значение будет в диапазоне 600-650 ° C.Он снижает твердость, снижает прочность на разрыв и улучшает пластичность и вязкость. Большинство нормализованных сталей подвергаются отпуску перед сваркой, все закаленные стали используются в закаленном и отпущенном состоянии.
Отверждение от старения или осадков
Низкотемпературная термообработка, предназначенная для получения осадков правильного размера и распределения, тем самым увеличивая текучесть и предел прочности. Обычно ему предшествует термообработка на твердый раствор. Для стали температура может быть где-то между 450-740 ° C, алюминиевый сплав будет выдерживаться при температуре 100-200 ° C.Более продолжительное время и / или более высокие температуры приводят к увеличению размера осадка и снижению как твердости, так и прочности.
Снятие напряжений
Как следует из названия, это термообработка, предназначенная для снижения остаточных напряжений, возникающих при усадке сварного шва. Он основан на том факте, что при повышении температуры металла предел текучести уменьшается, что позволяет перераспределить остаточные напряжения за счет ползучести сварного шва и основного металла.Охлаждение от температуры снятия напряжения контролируется, чтобы не возникало вредных температурных градиентов.
Пост-нагрев
Низкотемпературная термообработка, проводимая сразу после завершения сварки путем увеличения предварительного нагрева примерно на 100 ° C и поддержания этой температуры в течение 3 или 4 часов. Это способствует диффузии водорода в зонах сварного шва или термического влияния из стыка и снижает риск образования холодных трещин, вызванных водородом. Он используется только для ферритных сталей, где водородное холодное растрескивание является серьезной проблемой. I.е. стали с очень высокой трещиностойкостью, очень толстыми соединениями и т. д.
Термическая обработка после сварки (PWHT)
Итак, что означает термин «термообработка после сварки»? Для некоторых инженеров это довольно расплывчатый термин, который используется для описания любой термической обработки, проводимой после завершения сварки. Однако для других, особенно тех, кто работает в соответствии с нормами для сосудов высокого давления, такими как BS PD 5500, EN 13445 или ASME VIII, он имеет очень точное значение. Поэтому, когда инженер говорит о послесварочной термообработке, отжиге, отпуске или снятии напряжений, это рекомендуется.
Термическая обработка после сварки может выполняться по одной или более из трех основных причин:
- для достижения стабильности размеров с целью сохранения допусков во время операций механической обработки или во время встряски при эксплуатации
- для изготовления специальных металлургических конструкций с целью достижения требуемых механических свойств
- для снижения риска возникновения проблем в процессе эксплуатации, таких как коррозия под напряжением или хрупкое разрушение, за счет снижения остаточного напряжения в сварном элементе.
Диапазон термообработки для достижения одной или нескольких из этих трех целей в диапазоне свариваемых черных и цветных металлов и сплавов, очевидно, слишком обширен, чтобы подробно описать их в этих кратких статьях о работе.Акцент в следующем разделе будет сделан на PWHT углеродистых и низколегированных сталей в соответствии с требованиями стандартов, хотя кратко будут упомянуты другие формы термообработки, с которыми инженер-сварщик может столкнуться в черных сплавах. Здесь задействованы два основных механизма: во-первых, снятие напряжения и, во-вторых, микроструктурные модификации или отпуск.
Устройство снятия напряжения
Почему необходимо снимать напряжение? Это дорогостоящая операция, требующая, чтобы часть или все сварное изделие было нагрето до высокой температуры, и она может вызвать нежелательные металлургические изменения в некоторых сплавах.Как упоминалось выше, может быть одна или несколько причин. Высокие остаточные напряжения, зафиксированные в сварном соединении, могут вызвать деформацию, выходящую за пределы допустимых размеров, когда изделие обрабатывается или вводится в эксплуатацию. Высокие остаточные напряжения в углеродистых и низколегированных сталях могут увеличить риск хрупкого разрушения, создавая движущую силу для распространения трещин. Остаточные напряжения вызовут коррозионное растрескивание под напряжением в подходящей среде, например, в углеродистой и низколегированной стали при щелочной среде или нержавеющей стали, подверженной воздействию хлоридов.
Что вызывает эти высокие остаточные напряжения? Сварка включает осаждение расплавленного металла между двумя по существу холодными поверхностями основного металла. По мере охлаждения стыка металл сварного шва сжимается, но сдерживается холодным металлом с обеих сторон; поэтому остаточное напряжение в соединении увеличивается с понижением температуры. Когда напряжение достигает достаточно высокого значения (предел текучести или предел текучести при этой температуре), металл пластически деформируется с помощью механизма ползучести, так что напряжение в соединении соответствует пределу текучести.По мере того как температура продолжает падать, предел текучести увеличивается, препятствуя деформации, так что при температуре окружающей среды остаточное напряжение часто равно пределу текучести (рис. 1).
Чтобы снизить этот высокий уровень остаточного напряжения, компонент повторно нагревается до достаточно высокой температуры. При повышении температуры предел текучести падает, что позволяет деформироваться и остаточному напряжению уменьшаться до тех пор, пока не будет достигнут приемлемый уровень. Компонент будет выдерживаться при этой температуре (замачиваться) в течение определенного периода времени до достижения стабильного состояния, а затем снова охлаждаться до комнатной температуры.Остаточное напряжение, остающееся в соединении, равно пределу текучести при температуре выдержки.
На рис. 1 показано, что остаточное напряжение в углеродистой марганцевой стали достаточно устойчиво падает от температуры окружающей среды до примерно 600 ° C, но что для высокопрочных сталей, устойчивых к ползучести, температура должна быть выше 400 ° C, прежде чем остаточное напряжение начнет падать. Нержавеющая сталь практически не подвергается воздействию до тех пор, пока температура не превысит 500 ° C. Следовательно, существует диапазон температур выдержки для различных сплавов для достижения приемлемого снижения остаточного напряжения без отрицательного воздействия на механические свойства соединения.В углеродисто-марганцевых сталях эта температура будет составлять 550-620 ° C, в жаропрочных сталях — 650-750 ° C, а в нержавеющих сталях — 800-850 ° C.
Следующая статья будет посвящена отпуску ферритных сталей, а за ней последует дополнительная информация о других сплавах и методах применения и контроля термообработки.
Для получения дополнительной информации свяжитесь с нами.
Термическая обработка сварных соединений — Часть 2
Часть 1 этой серии статей дает определения некоторых термических обработок, которые могут применяться к сварному соединению, и касается операции снятия напряжений в сборке из ферритной стали.Температурный диапазон, в котором происходит снятие напряжения, также вызовет отпуск тех областей в ЗТВ, где могли образоваться твердые структуры.
Закалка
Закалка — это термообработка, которая применима только к сталям и проводится для размягчения любых твердых микроструктур, которые могли образоваться во время предыдущих термообработок, улучшения пластичности и вязкости. Отпуск также позволяет образовываться осадкам и контролировать их размер для обеспечения требуемых механических свойств.Это особенно важно для хромомолибденовых сталей, устойчивых к ползучести. Отпуск включает нагрев стали до температуры ниже нижней критической температуры; на эту температуру влияют любые легирующие элементы, добавленные в сталь, так что для углеродисто-марганцевой стали температура составляет около 650 ° C, для стали 2¼CrMo — 760 ° C. Закаленные стали всегда отпускаются. Нормализованные стали также обычно поставляются в отпущенном состоянии, хотя иногда низкоуглеродистую углеродисто-марганцевую сталь можно сваривать только в нормализованном состоянии, причем отпуск достигается во время PWHT.Отожженные стали в отпущенном состоянии не поставляются.
Отпуск инструментальных сталей может выполняться при температурах до 150 ° C, но для конструкционных сталей, которыми занимается инженер-сварщик, температура отпуска обычно составляет где-то между 550-760 ° C, в зависимости от состава стали. .
Термическая обработка после сварки (PWHT)
Как упоминалось в Части 1, PWHT — это особый термин, который охватывает как снятие напряжений, так и отпуск, и его не следует путать с термообработкой после сварки.Такая обработка может включать старение алюминиевых сплавов, обработку аустенитной нержавеющей стали на твердый раствор, выделение водорода и т. Д. PWHT является обязательным требованием во многих нормах и спецификациях при соблюдении определенных критериев. Он снижает риск хрупкого разрушения за счет снижения остаточного напряжения и повышения ударной вязкости, а также снижает риск коррозионного растрескивания под напряжением. Однако он оказывает небольшое положительное влияние на усталостные характеристики, если только напряжения не являются в основном сжимающими.
Это важная переменная во всех квалификационных спецификациях процедуры сварки, таких как ISO 15614 Часть 1 и ASME IX.Добавление или исключение PWHT или термообработки вне установленных временных и / или температурных диапазонов требует повторной аттестации процедур сварки. Температуры PWHT для сварных швов, выполненных в соответствии с требованиями EN 13445, ASME VIII и BS PD 5500, приведены ниже в таблице 1.
Таблица 1: Температуры PWHT из технических характеристик сосудов под давлением
Марка стали | BS EN 13445 | ASME VIII | BS PD 5500 |
---|---|---|---|
| Нормальная температура выдержки ° C | Диапазон температур ° C | |
C Сталь | 550-600 | 593 | 580-620 |
C 1/2 Пн | 550-620 | 593 | 630-670 |
1Cr 1/2 Mo | 630-680 | 593 | 630-700 |
2 1/4 Cr / Mo | 670-720 | 677 | 630-750 |
5CrMo | 700-750 | 677 | 710-750 |
3 1/2 Ni | 530-580 | 593 | 580-620 |
Обратите внимание на таблицу 1, что ASME VIII определяет минимальную температуру выдержки, а не диапазон температур, как в спецификациях BS и EN.
Как упоминалось выше, PWHT является обязательным требованием при соблюдении определенных критериев, главным из которых является толщина. BS EN 13445 и BSPD 5500 требуют, чтобы швы толщиной более 35 мм были PWHT, а ASME VII — более 19 мм. Если, однако, сосуд должен быть введен в эксплуатацию, где возможна коррозия под напряжением, PWHT является обязательной, независимо от толщины. Время выдержки также зависит от толщины. Как правило, это один час на каждые 25 мм толщины; для обеспечения точности следует обращаться к соответствующей спецификации.
Эти различные требования в рамках спецификаций означают, что необходимо проявлять большую осторожность, если необходимо провести квалификационное испытание процедуры, которое предназначено для соответствия более чем одной спецификации. Еще одним важным моментом является то, что температура PWHT не должна быть выше исходной температуры отпуска, поскольку существует риск снижения прочности ниже указанного минимума для стали. Термоструйная термообработка при температуре выше отпуска возможна только в том случае, если механические испытания проводят, чтобы показать, что сталь имеет адекватные механические свойства. Очевидно, что испытания должны проводиться на реальном материале в новых условиях термообработки.
Максимальная и минимальная скорости нагрева и охлаждения выше 350-400 ° C также указаны в кодах приложений. Слишком высокая скорость нагрева или охлаждения может привести к неприемлемым деформациям из-за неравномерного нагрева или охлаждения, а в очень жестких компонентах может вызвать образование трещин под напряжением во время нагрева.
Применение PWHT
Метод PWHT зависит от ряда факторов; Какое оборудование имеется, каковы размеры и конфигурация компонента, какая температура выдержки должна быть достигнута, может ли оборудование обеспечить равномерный нагрев при требуемой скорости нагрева? Лучший способ — использовать печь.Это может быть постоянная стационарная печь или временная печь, возведенная вокруг компонента, причем последняя особенно полезна для больших громоздких конструкций или для термообработки больших компонентов на месте. Постоянные печи могут быть загружены тележкой со станиной на колесах, на которой размещается компонент, или топочной печью, в которой используется неподвижный под и съемная крышка. Как правило, печь, предназначенная для термической обработки сосуда высокого давления на 150 тонн, имеет размеры около 20 м в длину, дверь 5×5 м и потребляет около 900 кубических метров газа в час.
Печи можно нагревать с помощью электричества, резистивного или индукционного нагрева, природного газа или масла. При использовании ископаемого топлива следует позаботиться о том, чтобы топливо не содержало таких элементов, как сера, которые могут вызвать проблемы с растрескиванием некоторых сплавов, особенно если это аустенитные стали или никелевые стали, например коррозионно-стойкая оболочка. Какое бы топливо ни использовалось, атмосферу в печи следует тщательно контролировать, чтобы не происходило чрезмерного окисления, образования накипи или науглероживания из-за несгоревшего углерода в атмосфере печи.Если печь работает на газе или жидком топливе, пламя не должно касаться компонента или термопар для контроля температуры; это приведет либо к локальному перегреву, либо к недостижению температуры PWHT.
Очень важно контролировать температуру компонента во время термообработки. В большинстве современных печей используется зональный контроль с помощью термопар, измеряющих и контролирующих температуру областей внутри печи, причем управление осуществляется автоматически с помощью компьютерного программного обеспечения. Зональный контроль особенно полезен для управления скоростью нагрева при PWHT-обработке деталей из стали различной толщины.Однако не рекомендуется использовать мониторинг температуры печи, так как это доказывает, что в компоненте достигнуты правильные температуры. Поэтому термопары обычно прикрепляются к поверхности компонента через определенные промежутки времени, и именно они используются для автоматического регулирования скорости нагрева и охлаждения, а также температуры выдержки для достижения однородной температуры. Нет никаких жестких правил относительно количества и расположения термопар, каждый элемент нужно оценивать отдельно.
Как упоминалось ранее, предел текучести снижается при повышении температуры, и компонент может быть не в состоянии выдерживать свой собственный вес при температуре PWHT. Таким образом, существует реальная возможность чрезмерного искажения. Важно, чтобы компонент имел надлежащую опору во время термообработки, а козлы, форма которых соответствовала компоненту, должны быть размещены через равные промежутки времени. Расстояние между ними будет зависеть от формы, диаметра и толщины предмета. Внутренние опоры могут потребоваться внутри цилиндра, такого как сосуд высокого давления; в этом случае опоры должны быть из аналогичного материала, чтобы коэффициенты теплового расширения были согласованы.
Хотя термическая обработка сосуда высокого давления за одну операцию в печи, достаточно большой, чтобы вместить весь сосуд, является предпочтительным методом, это не всегда возможно. В этом случае нормы применения сосуда высокого давления разрешают термическую обработку готового сосуда по частям в печи. Необходимо перекрывать нагретые участки — ширина перекрытия обычно связана с толщиной сосуда. BS EN 13445, например, определяет перекрытие 5√Re, где R = внутренний диаметр и e = толщина; ASME VIII определяет перекрытие 1. 5 метров. Следует помнить, что если это будет сделано, в резервуаре будет область (которая может содержать сварные швы), которая испытала два цикла PWHT, и это необходимо учитывать при квалификационных испытаниях процедуры сварки. Также вызывает беспокойство область между нагретой зоной внутри печи и холодной зоной вне печи. Температурный градиент должен контролироваться путем соответствующей изоляции емкости теплоизолирующим одеялом, а требования приведены в прикладных кодах.
Конечно, возможно собрать и послать сосуд секциями, а затем провести локальную термообработку последнего шва закрытия. Местная PWHT будет обсуждаться в следующей части этой серии, посвященной термообработке.
В следующей статье будет представлена дополнительная информация о других сплавах и методах применения и управления термообработкой.
Для получения дополнительной информации свяжитесь с нами.
Термическая обработка после сварки (PWHT)
Сварка является неотъемлемой частью эксплуатации и технического обслуживания активов в нефтяной (добывающей, промежуточной, перерабатывающей) и химической промышленности. Хотя он имеет множество полезных применений, сварочный процесс может непреднамеренно ослабить оборудование, создавая остаточные напряжения в материале, что приведет к ухудшению свойств материала.
Чтобы обеспечить сохранение прочности материала детали после сварки, регулярно выполняется процесс, известный как Термическая обработка после сварки (PWHT) . PWHT может использоваться для снижения остаточных напряжений, как метод контроля твердости или даже для повышения прочности материала.
Если PWHT выполняется неправильно или полностью игнорируется, остаточные напряжения могут в сочетании с нагрузочными напряжениями превысить конструктивные ограничения материала.Это может привести к разрушениям сварных швов, более высокому потенциалу растрескивания и повышенной восприимчивости к хрупкому разрушению .
PWHT включает в себя множество различных типов потенциальных обработок; два наиболее распространенных типа — последующий нагрев и снятие напряжения:
- Пост-нагрев:
- Растрескивание, вызванное водородом (HIC) , часто возникает, когда во время сварки в материал попадает много водорода из окружающей среды.
Нагревая материал после сварки, можно рассеивать водород из зоны сварки, предотвращая таким образом HIC.Этот процесс известен как пост-нагрев и должен начинаться сразу после завершения сварки. Вместо того, чтобы дать возможность остыть, материал необходимо нагреть до определенной температуры в зависимости от типа и толщины материала. При этой температуре его следует выдержать в течение нескольких часов в зависимости от толщины материала.
- Снятие напряжения:
- К моменту завершения сварочный процесс может вызвать большое количество остаточных напряжений в материале, что может привести к повышенному потенциалу коррозии под напряжением и растрескивания, вызванного водородом.PWHT может использоваться для снятия этих остаточных напряжений и снижения этого потенциала. Этот процесс включает нагрев материала до определенной температуры с последующим его постепенным охлаждением.
Должен ли материал подвергаться PWHT, зависит от ряда факторов, включая такие вещи, как его система легирования или подвергалась ли он ранее термообработке. Некоторые материалы действительно могут быть повреждены PWHT, в то время как другие почти всегда требуют этого.
Как правило, чем выше содержание углерода в материале, тем больше вероятность того, что после проведения сварочных работ потребуется PWHT.Точно так же, чем выше содержание сплава и толщина поперечного сечения, тем больше вероятность того, что материалу потребуется PWHT.
Список литературы- Фундерберк, Р. Скотт, 1998. «Ключевые концепции: термообработка после сварки». Инновации в сварке Том XV, № 2.
- Ахмед Халил, Кришан Дж., 2002. «Термическая обработка после сварки — примеры из практики», Информационный бюллетень BARC, специальный выпуск ко Дню основателя, стр. 111-115.
Это определение неполное? Вы можете помочь, внося свой вклад.
Связанные темы
Инструменты тем
Поделиться темой
Внести свой вклад в определение
Мы приветствуем обновления этого определения Integripedia от сообщества Inspectioneering. Щелкните значок
ссылку ниже, чтобы открыть форму, которая позволит вам внести изменения в определение и отправить
их инспекционному составу.
Местная термообработка сварных швов труб среднего диаметра током высокой частоты
Хага, Х., Аоки, К., Сато, Т., Механизмы образования дефектов сварных швов при высокочастотной контактной сварке сопротивлением, J. Weld. , 1981, т. 60, нет. 6. С. 104–109.
Google ученый
Такатоши О., Юкинори И., Сатоши И., Технология высокой надежности зоны сварки высокочастотной электросварочной линии труб, JFE Tech. Отчетность .2015. 20. С. 12–132.
Google ученый
Shin, M.H., Han, J.M., Lee, Y.S. и Kang, H.W., Исследование механизмов образования дефектов в ERW для стали API , Proc. 10-й Int. Pipeline Conference IPC – 2014, 29 сентября — 3 октября 2014 г., Калгари, Канада, 2014 г.
Google ученый
Головин Г.Ф. А., Зимин Н.В., Технология термической обработки металлов с применением индукционного нагрева, , Ленинград: Машиностроение, 1990.
Google ученый
Ян, П., Гюнгёр, О.Е., Тибо, П., Либехерр, М., и Бхадешия, HKDH, Решение проблемы ударной вязкости стальных труб, полученных с помощью высокочастотной индукционной сварки и термической обработки J. Mater. Sci. Англ. А , 2011, т. 528, ном. 29–30, с. 8492–8499.
Артикул Google ученый
Ткачук М.А., Багмет О.А. Определение оптимальной температуры нагрева при локальной термообработке сварного шва трубы токами высокой частоты // Завод.Лаборатория. Диаг. Mater. , 2015, т. 81, нет. 5. С. 39–43.
Google ученый
Прохоров Н.Н., Галиченко Е.Н., Медведев А.П. и др. Патент РФ 2096485, Бюлл. Изобрет. , 1997, нет. 15.
Ламухин А.М. Ю., Дубинин И.В. Запуск литейно-прокатного комплекса и освоение производства высококачественного проката для электросварных труб // Металлург . 2010. Т.54, нет. 1. С. 19–27.
Артикул Google ученый
Кислица В.В., Ламухин А.М., Исаев О.Б. и др. Литейно-прокатный комплекс: новые технологии производства трубных валков, Черн. Металл. .2013. 4. С. 50–56.
Google ученый
Энгель Л. и Клингеле Х., Rasterelektronenmikroskopische Untersuchungen von Metallschäden , Leipzig: Hanser, 1982.
Google ученый
Лин А.Ф., Механика и механизмы разрушения: Введение , Materials Park, OH: ASTM Int., 2005.
Google ученый
У вас недостаточно прав для чтения этого закона в настоящее время
У вас недостаточно прав для чтения этого закона в настоящее время Логотип Public.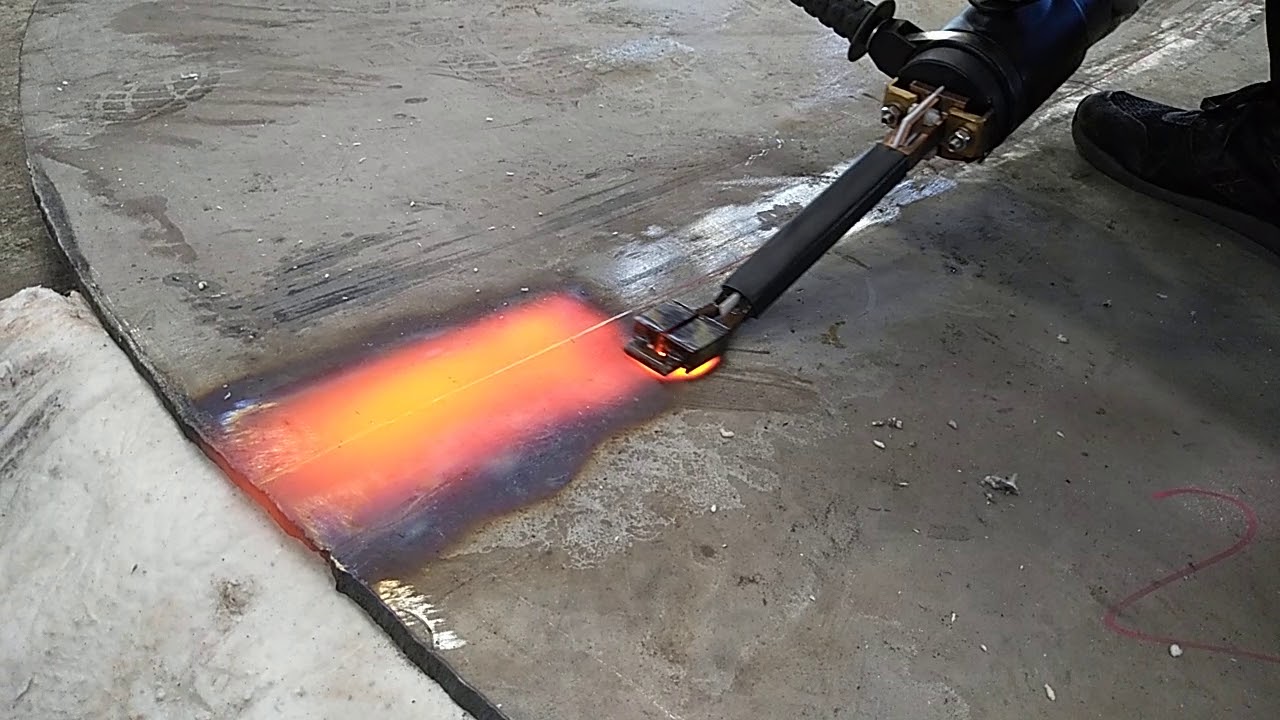
Public.Resource.Org
Хилдсбург, Калифорния, 95448
США
В настоящее время этот документ недоступен для вас!
Уважаемый гражданин:
В настоящее время вам временно отказано в доступе к этому документу.
Public Resource ведет судебный процесс за ваше право читать и говорить о законах. Для получения дополнительной информации см. Досье по рассматриваемому судебному делу:
Американское общество испытаний и материалов (ASTM), Национальная ассоциация противопожарной защиты (NFPA), и Американское общество инженеров по отоплению, охлаждению и кондиционированию воздуха (ASHRAE) против Public.
Resource.Org (общедоступный ресурс), DCD 1: 13-cv-01215, Объединенный окружной суд округа Колумбия [1]
Ваш доступ к этому документу, который является законом Соединенных Штатов Америки, был временно отключен, пока мы боремся за ваше право читать и говорить о законах, по которым мы решаем управлять собой как демократическим обществом.
Чтобы подать заявку на получение лицензии на чтение этого закона, обратитесь к Своду федеральных нормативных актов или применимым законам и постановлениям штата на имя и адрес продавца. Для получения дополнительной информации о постановлениях правительства и ваших правах гражданина в соответствии с нормами закона , пожалуйста, прочтите мое свидетельство перед Конгрессом Соединенных Штатов. Вы можете найти более подробную информацию о нашей деятельности на публичном ресурсе. в нашем реестре деятельности за 2015 год. [2] [3]
Спасибо за ваш интерес к чтению закона.Информированные граждане — это фундаментальное требование для работы нашей демократии. Благодарим вас за усилия и приносим извинения за возможные неудобства.
С уважением,
Карл Маламуд
Public.Resource.Org
7 ноября 2015 г.
Банкноты
[1] http://www.archive.org/download/gov.uscourts.dcd.161410/gov.uscourts.dcd.161410.docket.html
[2] https://public.resource.org/edicts/
[3] https://public.resource.org/pro.docket.2015.html
Термическая обработка трубы, сваренной прямым швом высокой частоты после сварки
Ключевые слова: Термическая обработка трубы, сваренной прямым швом высокой частоты после сварки
После сварки труб с прямым швом высокой частоты после сварки термическая обработка представляет собой новую технологию устранения остаточных напряжений. Перед сваркой материал предварительно нагревается до температуры пост-термообработки, а сварной шов постоянно нагревается в процессе сварки для поддержания этой температуры.После завершения сварки его нагревают теплоизоляционной ватой для медленного охлаждения.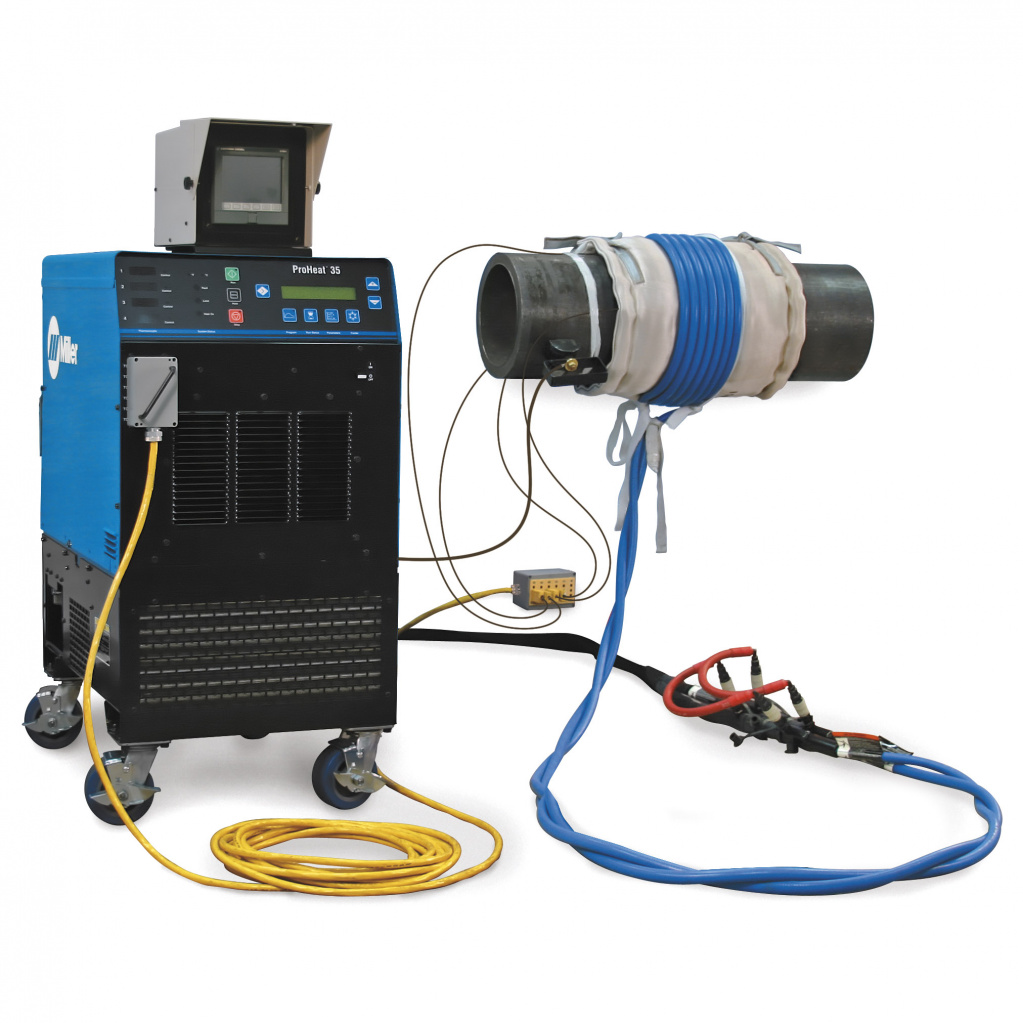
Неразрушающий контроль сварного шва трубопровода в проекте водоснабжения представляет собой большую стальную трубу, особенно стальную трубу толщиной t = 30 мм, используемую в качестве моста для труб, необходимо выдерживать давление воды, но также выдерживают вес стальной трубы и изгибающий момент воды, поэтому требования к качеству сварки особенно высоки.Для стальной трубы большого диаметра толщиной t = 30 мм продольный шов и кольцевые соединения относятся к классу сварных швов, требующих 100% рентгеновского контроля и 100% ультразвукового контроля; и толщиной t = 24 мм заглубленная стальная труба, продольный шов — это класс сварки, 20% — рентгеновский контроль пленки и 50% — ультразвуковой контроль.
После сварки термообработка может эффективно снизить остаточное напряжение сварки, и чем выше температура термообработки, тем лучше эффект устранения остаточного напряжения.