Лазерная сварка титана, алюминия и других металлов – особенности технологии и оборудования
Лазерная сварка — это технология, в которой основным элементом воздействия на материалы является лазер. Главное достоинство лазера – способность концентрировать большую мощность излучения на единицу площади (1-10МВт/см2), что обеспечивает сварку различных материалов толщиной от нескольких микрон до сантиметров.
Действие лазера
Суть сварки лазером заключается в том, что излучение, проходя через фокусирующую систему, концентрируется в определенной точке. Все, что попадает в эту точку, подвергается сильнейшему термическому воздействию.
Похожие процессы происходят при разжигании огня с помощью лупы. Так как лазерное излучение монохромное и когерентное (с постоянной разностью фаз в пространстве или времени), то используя обычную оптическую линзу можно получить высокую концентрацию энергии на очень маленькой площади.
В месте концентрации луча металл быстро расплавляется. Для формирования сварного шва достаточно убрать лазер или расфокусировать его. Благодаря маленькой области термического воздействия в свариваемом материале практически отсутствуют деформации. Шов получается тонким и не требует дальнейшей обработки.
Типы сварочных аппаратов
Лазерный сварочный аппарат использует импульсное или непрерывное излучение, и может делать швы любого типа. Так как мощность излучателя рассчитана на максимальную толщину свариваемого металла, то при сварке тонких листов (0,05-1 мм) применяется расфокусировка луча.
По типу активного тела лазерное сварочное оборудование бывает с:
- твердотельным лазером;
- газовым;
- газодинамическим лазером.
Импульсный лазерный аппарат производит сварку точечно. Для создания сплошного шва сварные точки наносятся с перекрытием.
Частота импульсов у разных моделей разная, обычно в пределах 4-20 Гц. Скорость сварки доходит до 20 м/час.
Твердотельные лазеры
Основным элементом твердотельного прибора является стержень из рубина или стекла с неодимом, который находится в осветительной камере. Когда в камеру с определенной частотой подается свет большой мощности, то в кристалле (активном теле) происходит возбуждение атомов, что приводит к излучению света одной длины волны.
Торцы стержня из рубина представляют собой отражающие зеркала, одно из них частично прозрачное. Через него происходит выход энергии в виде лазерного излучения.
В стационарных установках кроме собственно лазера и оптической системы фокусировки луча аппарат имеет систему газовой защиты, систему перемещения головки и свариваемого изделия.
Твердотельные приборы имеют относительно небольшую мощность от 1 до 6 кВт. Они применяются в основном в микроэлектронике, приборостроении и ювелирном деле, где приходится приваривать выводы микрочипов толщиной несколько микрон, катоды кинескопов электронно-лучевых трубок или сваривать мелкие элементы на ювелирных изделиях. Используется как точечная сварка.
Газовые лазеры
В газовых лазерных устройствах для сварки активным телом является смесь углекислого газа, азота и гелия.
Газовая смесь из баллонов с помощью насоса продувается через газоразрядную трубку, где с помощью электрических разрядов происходит возбуждение газа. Газогазрядная труба имеет отражающее и прозрачное зеркало по торцам, весь процесс происходит, как в твердотельном лазере.
По сравнению с твердотельными газовые лазеры мощнее, их мощность может превышать 20 кВт. Имеют систему водяного охлаждения. Сварочные аппараты с газовым лазером могут варить толстый металл до 2 см со скоростью 1 м/мин.
Газодинамические лазеры
Газодинамические лазерные устройства самые мощные. Активным телом является окись углерода, нагретая до 3000 ⁰K и пропущенная через сопло Лаваля. На выходе из сопла происходит резкое падение давления и, соответственно, охлаждение газа.
При этом процессе молекулы окиси углерода испускают монохромное излучение. Для повышения мощности в качестве источника накачки применяются дополнительные лазеры.
Такой способ позволяет развивать мощность газодинамического лазера до 100 кВт и более, что позволяет варить металлы толщиной 35 мм со скоростью 200 м/час. Такая производительность недоступна другим видам сварки.
Лазерно-дуговая технология
Гибридная технология совмещает в себе преимущества дуговой и лазерной сварки. Когда нужно сваривать толстые листы металла с большой скоростью и минимальным подводом тепла к сварочной зоне в автоматическом режиме, то для этого потребуется оборудование с лазерно-дуговой сваркой.
За счет быстрого разогрева лазером сварочной ванны улучшается качество шва, его глубина. Это уменьшает напряжения и деформации от возникновения соединительного шва.
Кроме этого приводит к большой скорости сварки, появляется возможность провести сваривание в один проход. Нет жестких требований к соединяемым кромкам. В комбинации с дуговой сваркой обычно используется твердотельный лазер.
Особенности процесса
Благодаря возможности концентрировать огромную энергию на маленькой площади лазерная сварка титана, а также алюминия, нержавейки и других металлов не представляет трудностей.
Для лазерной сварки не требуются особые условия. Она может производиться в окружении обычной атмосферы. Как и при дуговой электросварке требуется защита деталей в точке соединения от влияния воздуха. Для этого применяют инертные газы.
Из-за высокой мощности лазерного луча металл в сварочной ванне начинает кипеть. Пары ионизируются и рассеивают луч лазера. Для борьбы с этой проблемой в зону сваривания стали направлять струю газа подавляющего плазму.
Его роль выполняет гелий, который не рассеивает луч благодаря своей легкости и прозрачности. При одновременной подаче защитного и подавляющего плазму газов струя направляется так, что сдувает плазму с рабочей зоны.
Преимущества и недостатки
Главным достоинством лазерной сварки является регулировка количества энергии в конкретной точке на очень маленькой площади. Это позволяет получать прочные и надежные соединения при работе с мелкими изделиями. Поэтому ее применяют высокоточные производства.
Лазерная сварка может использоваться удаленно от оператора. Известна установка для ремонта стальных трубопроводов находящихся на дне водоема. С помощью вращающихся зеркал лазерный луч доставляется на место назначения, где происходит сварка.
Мощные лазеры могут проваривать толстые металлы при узком шве и минимальном термическом воздействии на соседние слои. Имеют высокую степень автоматизации работ, высокую скорость сварки и отличное качество шва.
Главным недостатком лазерной сварки является высокая стоимость оборудования. Установки имеют низкий КПД (не более 2 %), соответственно высокую стоимость сварочных работ.
Меры безопасности
При работе с лазерной сваркой использование очков обязательно. В стационарных установках должны быть защитные экраны, не позволяющие оператору попасть в рабочую зону лазера. Предусматриваются системы блокировки работы лазера при нарушении рабочей зоны персоналом.
Стены помещения покрываются матовой краской имеющей минимальную отражающую способность. В автоматических системах пульты управления и контроля находятся за пределами рабочего помещения.
Оптоволоконный лазерный сварочный аппарат XTW-750 XTLASER (Китай)
Аппараты ручной лазерной сварки с оптоволоконными лазерными излучателями — новейшая разработка в области сварочных технологий, пришедшая на смену аргонодуговой сварке. Используются при сварке таких металлов, как нержавеющая сталь, железо, алюминий и других металлов. Характеризуются большой глубиной сварки, прочностью сварных швов, подходят для сварки любой сложности.
Установки для лазерной сварки генерируют излучение в импульсном и непрерывном режимах. Технология включает в себя точечное и шовное сварные соединения. Для шовного применяется непрерывный режим генерации или импульсный с перекрытием, для точечного — только импульсный. Точечный метод дает минимальные деформации и используется для соединения изделий небольшой толщины. При шовной сварке происходит формирование глубокого сварочного канала. Метод обладает высокой эффективностью при обработке сталей, титана, меди и алюминия. Луч высокой плотностью мощности разрушает поверхностные оксидные пленки и препятствует образованию новых и не требует применять защитные инертные газы. Сваривание элементов небольшой толщины производится с расфокусировкой луча, это позволяет исключить сквозное прожигание изделия. Для получения прочного шва аппарату лазерной сварки необходимо оснащение источником излучения достаточной мощности.
Используются при производстве кухонной утвари, сантехники, бытовой техники, металлической мебели, окон и дверей, автозапчастей, в рекламном производстве и во многих других сферах.
Сварной шов гладкий и красивый
Отсутствует деформация поверхности, не требует последующего шлифования, отсутствует необходимость чистовой обработки сварного шва.
Равномерность сварки
Достигается равномерным распределением точечной энергии лазерного сварочного аппарата.
Высокая скорость сварки
Скорость лазерной сварки в 2-10 раз выше, чем скорость традиционной сварки.
Точное позиционирование
Точное позиционирование благодаря системе красный луч.
Универсальность
Гибкие настройки позволяют производить шовную и точечную сварку.
Удобство эксплуатации
С помощью ручного пистолета можно сваривать длинные отрезки (отсутствует ограничение длины сварки длиной рабочего поля). Возможность сваривать труднодоступные зоны и осуществлять сварку под любым углом.
Простота эксплуатации
Гибкий ручной режим работы легок в освоении, не требует специального обучения.
Экономия в обслуживании
Отсутствие расходных материалов, низкое электропотребление, стабильность работы и длительный срок службы снизят затраты на обслуживание.
Экологичность
Надежная и экологически чистая технология без загрязнения окружающей среды.
Компактность
Легкий вес и компактность позволяют использовать установку в любых производственных условиях.
Устойчивость к коррозии и высокая термостойкость
Лазерная сварка металлов: сферы применения, виды, типы лазеров для сварки
Лазерная сварка металла — один из самых новых методов создания неразъемных соединений. Он отличается исключительной точностью, производительностью и высоким качеством сварного шва.
Нагрев и плавление металла в рабочей зоне проводится лазерным лучом. Метод позволяет сваривать разнородные материалы. Несмотря на высокую стоимость и сложность оборудования, популярность этого метода постоянно растет.
Для домашних мастерских становятся доступны аппараты бытового уровня.
Лазерная сварка
Технология лазерной сварки
Световой поток, генерируемый лазером, отличается монохромностью. Все волны потока, в отличие от солнечного спектра, имеют равные длины волн. Это облегчает управление потоком с помощью фокусировки линзами и отклонения призмами. В лазере возникает явление волнового резонанса, что многократно увеличивает мощность пуска.
Принцип действия лазерной сварки базируется на поглощении энергии пучка лазера металлом в рабочей зоне. При этом происходит сильный локальный нагрев.
Технология сварки лазером напоминает технологию газовой сварки. Подготовительные операции заключаются в механической обработке и химическом обезжиривании зоны соединения. Далее луч лазера направляется в начало шва, происходит нагрев металла, его плавление и образование сварочной ванны. Луч перемещается вдоль линии шва, за ним движется сварочная ванна и зона кристаллизации.
Схема лазерной сварки
После кристаллизации шов проводится зачистка шва от окалины и шлаков.
Лазерная сварка позволяет получить однородный, прочный и долговечный шов.
Условия и методы проведения процесса
Для достижения высокой мощности луча необходима его фокусировка. Она проводится в ходе серии последовательных отражений от переднего и заднего полусферических зеркал. Когда интенсивность пучка превышает пороговое значение, он проходит через центр переднего зеркала и далее, через систему направляющих призм, к рабочей зоне.
Лазерная сварка металлов может проводиться при различном взаиморасположении соединяемых заготовок. Глубину проплавления металла в рабочей зоне можно регулировать в широком диапазоне — от поверхностного до сквозного. Работу также можно вести непрерывным лучом или прерывистыми импульсами.
Способ позволяет сваривать как детали из тонкого листового проката, так и сложные профили и детали большой толщины.
Различают следующие виды процесса:
- В стык. Проводится без присадочных материалов и флюсовых порошков в защитной газовой атмосфере.
- Внахлест. Свариваемые кромки накладываются одна на другую. Требуется обеспечить прижим заготовок друг к другу.
Лазерная сварка в стык
Компактные аппараты бытового класса позволяют проводить лазерную сварку своими руками.
Аппараты лазерной сварки металлов
Для проведения точечной или сплошной лазерной сварки необходимо:
- лазер с источником питания ;
- блок оптической фокусировки;
- механизм перемещения луча в рабочей зоне;
- приспособления для подачи инертных газов для защиты рабочей области.
По конструкции активного излучателя все аппараты лазерной сварки разделяют на два типа:
Аппарат для лазерной сварки ЛТА4-1Аппарат для лазерной сварки ЛТСК435-20
Оба типа могут работать как в импульсном, так и в непрерывном режиме.
Лазеры с твердым активным элементом
Такие установки могут излучать световой поток как непрерывно, так и дискретными импульсами. Активный излучатель делают из розового искусственного рубина, смешивая оксид алюминия и ионы хрома. Торцы стрежня полируют, создавая на них зеркальные поверхности, отражающие свет. Ионы хрома, облучаемые излучением лампы накачки, переизлучает свет на частоте работы лазера.
Функционирование их проходит следующим способом:
- Стержнеобразный активный элемент помещен вместе с лампой накачки внутри рабочего корпуса.
- Энергия периодических вспышек лампы накапливается в активном элементе, фокусируясь и отражаясь от торцевых зеркал.
- По достижении порогового значения интенсивности светового пучка он проходит излучение рабочего импульса.
Лазер с твердым активным элементом
Аппараты с твердым активным телом работают на волне длиной 0,69 микрон. Мощность их достигает нескольких сотен ватт.
Аппараты с элементами на основе газовой среды
Установки с газообразным активным телом потребляют более высокое напряжение, и позволяет развивать большую мощность — до десятков киловатт. Лампа накачки облучает в таких приборах не твердотельный стержень, а газовую смесь в колбе. Для смеси используют углекислый газ, азот и гелий.
Она находится под давлением в несколько атмосфер. Два (или более) электрода периодически инициируют электрический разряд в газовой смеси. Импульс так же усиливается многократным отражением от торцевых зеркал.
Когда интенсивность достигает порогового значения, когерентный импульс проходит через полупроницаемое зеркало и сквозь оптическую систему направляется в рабочую зону.
Схема аппарата с элементом на основе газовой среды
Газовые установки работают с длинами волны около 10 микрон. Практический коэффициент полезного действия доходит до 15%
Особенности работы с тонкостенным металлом
При сваривании заготовок средней и большой толщины необходимо проплавление материала на всю толщину. Для этого используют излучение высокой интенсивности. Особенностью сварки лазером тонкостенных металлов является высокий риск прожигания листа. Чтобы избежать этого, необходимо строго контролировать следующие характеристики:
- мощность излучения;
- скорость движения луча;
- фокусировка рабочего пятна.
Сваривание тонкостенных заготовок проводят на минимальной мощности. При непрерывном режиме повышают скорость движения рабочего пятна. В импульсном режиме сокращают длительность импульса и повышают их скважность.
Лазерная сварка тонкостенных металлов
Если же на минимальной мощности плотность потока все равно слишком высока — используют преднамеренную расфокусировку луча. Это снижает КПД, но исключает прожигание листа и разбрызгивание металла.
Различия в технологии для разных металлов
Существуют отличия в технологическом процессе для различных металлов и их сплавов.
При сваривании заготовок из стали требуется провести механическую зачистку от ржавчины и других загрязнений. Детали должны быть тщательно обезжирены и высушены. Присутствие в зоне шва влаги может привести к повышенной гидратации материала шва и снижению его прочности и долговечности.
Аналогичная механическая подготовка и обезжиривание требуется для большинства цветных металлов и сплавов.
Нержавеющие сплавы сваривать допускается только встык. Нахлест может привести к возникновению тепловых напряжений в материале.
Благодаря высокой скорости ведения луча в рабочей области не успевают образоваться окислы. Это позволяет сваривать нержавеющие и титановые сплавы без применения флюсовых порошков и атмосферы защитных газов. Эта уникальная способность делает лазерный метод незаменимым при сваривании особо ответственных конструкций атомной, аэрокосмической и оборонной индустрии.
Ручная сварка
Технический прогресс последних лет позволил создать компактный аппарат для ручной лазерной сварки. На рынке представлено множество моделей с различными параметрами и функциональностью.
Они позволяют провести:
- починку малогабаритных и миниатюрных конструкций;
- точечную сварку;
- наплавочные операции;
- ремонт небольших пресс-форм;
- пайку электронных компонентов;
- дезинфекцию медицинских изделий.
Ручная сварка
Стоимость таких аппаратов все еще значительная. Окупится он при условии большого объема работ.
Применение сварки лазером
Метод применяется для соединения особо ответственных конструкций либо в том случае, когда другими методами соединить заготовки не удается. Наиболее распространен метод в таких областях, как:
- Устройства высокой точности.
- Изделия из легких цветных металлов.
- Соединение чугунных заготовок.
- Сваривание пластика.
- Весьма важная область применения лазерной сварки — оборонная промышленность
- Основные достоинства метода следующие:
- ограниченная зона нагрева снижает риск коробления материала;
- при использовании гибких световодов возможна работа в узкостях и труднодоступных местах;
- сварочный аппарат без дополнительных модификаций применим для резки конструкций и раскроя листового металла;
- исключительное качество и долговечность швов;
- высокая производительность;
- отсутствие расходных материалов.
Минусы, как и у любой действующей технологии, также присутствуют:
- высокая стоимость аппарата;
- малый коэффициент полезного действия;
- высокие требования к образованию и опыту работника.
В конечном счете, сопоставляя преимущества и недостатки сварки лазером, все больше предприятий и даже небольших мастерских принимают решение о переходе на новую технологию.
Используемое оборудование
Несмотря на различные габариты и мощность, оборудование для лазерной сварки относится к одному из основных типов: с твердым или с газообразным рабочим телом. Они различаются лишь методом возбуждения светового излучения. С металлом оба типа станков лазерной сварки работают одинаково.
Твердотельные установки
Такие приборы чаще используются в режиме непрерывного излучения. Они характеризуются более высокими рабочими частотами и ограниченным КПД и мощностью. Твердотельные агрегаты чаще используют для сваривания малогабаритных и тонкостенных изделий.
Импульсный твердотельный лазер
Газовые аппараты
Если требуется соединять заготовки большой толщины, применяют устройства с газообразным рабочим телом. Излучение возбуждается в газовой среде электрическим разрядом. Такие аппараты сваривают детали до 20 миллиметров. Такой способ позволяет достичь высоких мощностей в луче и более высоких значений КПД. Однако устройство прибора более сложное, в нем используется хрупкая стеклянная колба.
Газовый лазер
Гибридные установки
Для сложных конфигураций свариваемых деталей и листов большой толщины были разработаны гибридные сварочные установки. Рядом с лазерной головкой в них располагается горелка электродугового полуавтомата.
Гибридный лазерно-дуговой процесс сварки в среде защитного газа
Проволока используется в качестве присадочного материала и заполняет сварочный зазор, участвуя в формировании шовного материала.
Источник: https://stankiexpert.ru/spravochnik/svarka/lazernaya-svarka-metalla.html
Лазерная сварка металлов: сферы применения, виды, типы лазеров для сварки
Итак, сферы применения таковы:
- производство приборов и прочих точных механизмов;
- производство сложных изделий на основе легкоплавких металлов;
- изготовление деталей из чугуна;
- изготовление пластмассовых изделий.
Такая технология в промышленности стала применяться всего порядка 20 лет назад, и если есть возможность, то можно купить станки для только стационарного типа, но и ручные для сварки в домашних условиях.
Плюсы и минусы
Лазерное соединение металлов имеет свои плюсы и минусы. Что касается преимуществ, то они следующие:
- площадь металла нагревается незначительно, что сильно сокращает его коробление во время работы;
- лазерный луч передается по волоконной оптике, благодаря чему он попадается даже в труднодоступные места;
- лазерное оборудование можно использовать не только для сварки металла, но и его резки;
- оно обеспечивает высокое качество сварных швов;
- процесс сваривания обеспечивает хорошую производительность, его легко контролировать.
Но имеет технология и свои недостатки:
- оборудование очень дорогое;
- сварочный аппарат обладает низким КПД;
- оператор установки должен иметь высокую квалификацию.
Но, несмотря на недостатки, лазер — это единственный вариант для обеспечения точной сварочной операции или соединения легкоплавких материалов.
Виды сварки
Лазерная сварка бывает двух видов:
- Стыковая — в этом случае не используют присадки и флюс. Между металлами допускается минимальный стык, не больше 0,2 мм. Такое же значение является максимальным для фокусировки лазерного луча на стык. Сварку проводят посредством «кинжального» проплавления металла на всю толщину с интенсивностью лазерного излучения до 1 мВт/см2. Шов в этом случае нужно предохранять от окисления аргоном или азотом, а гелий защитит его от пробоя лазерного излучения;
- Нахлесточная — металлические листы накладываются друг на друга, они соединяются посредством мощного излучения. Сварка проводится с локальным прижимом деталей. Максимально допустимый зазор между поверхностями металлов при работе — 0,2 мм. В случае необходимости повышения качества соединяемых деталей используется двойной шов.
- При сваривании металлов применяют лазеры двух типов:
- Тот или иной тип лазера подбирается в зависимости от цели использования оборудования.
Твердотельный
В данном случае активным телом выступает рубиновый стержень со стеклом и примесью неодима или же алюмо-иттриевого граната, который легирован неодимом или иттербием. Стержень располагается в осветительной камере. Чтобы возбудить атомы активного тела, применяют лампу накачки, которая создает мощные световые вспышки.
На торцах активного тела находятся два зеркала:
- частично прозрачное;
- отражающее.
Лазерный луч будет выходить сквозь частично прозрачное зеркало, заранее оно многократно отражается в рубиновом стержне и усиливается. Твердотельные лазеры не слишком мощны, их мощность составляет от 1 до 6 кВт.
С помощью данных лазеров свариваются только мелкие и не толстые детали, чаще всего — это объекты микроэлектроники, например, тонкие проволочные выводы с диаметром 0,01−0,1 мм на основе нихрома, золота или тантала. Допускается и точечная сварка изделий на основе фольги с диаметром точки порядка 0,5−0,9 мм. Таким же способом выполняется герметичный катодный шов на кинескопах современных телевизоров.
Катод — это трубка с длиной в 2 мм, диаметром 1,8 мм и толщиной стенки 0,04 мм. К такой трубке приваривают дно толщиной в 0,12 мм на основе хромоникелевого сплава. Такие мелкие изделия варят благодаря высокой степени фокусировки луча, а также точной дозировке энергии посредством регулирования длительности импульса в определенных рамках.
Газовый
Газовые лазеры — более мощные, активным телом в них выступает газовая смесь. Газ прокачивается из баллонов с помощью насоса посредством газоразрядной трубы. Энергетическое возбуждение газа происходит за счет электрического разряда между электродами. По торцам газоразрядной трубы находятся зеркала. Электроды подключают к источнику питания, а сам лазер охлаждается с помощью водяной системы.
Основной минус оборудования с продольной прокачкой газа — это его габариты. А вот лазеры с поперечной прокачкой газа более компактные. Общая мощность может составлять от 20 кВт и больше, благодаря чему можно соединять металлы с толщиной до 20 мм на большой скорости — порядка 60 м/ч.
Самые мощные конструкции — газодинамические. В них для работы применяют газы, которые нагреваются до температуры от 1000 до 3000 К. Газ в них быстро истекает через сопло Лавля, в итоге происходит адиабатическое расширение, а затем газ охлаждается в зоне резонатора.
При охлаждении возбужденные молекулы переходят на более низкий энергетический уровень, при этом испускается когерентное излучение. Накачка может происходить с применением другого лазера или прочих мощных энергетических источников.
Мощные конструкции позволяют сваривать на скорости около 200 м/ч стали толщиной в 35 мм.
Поэтому в условиях применения высокомощного оборудования в зону сварки, кроме защитного газа, также подают и плазмоподавляющий газ.
Им обычно выступает гелий, который намного легче аргона и не будет рассеивать луч. Чтобы упростить процесс нужно, использовать специальные газовые смеси, обладающие плазмоподавляющей и защитной функцией.
В таком случае горелка должна подавать газ так, чтобы он мог сдувать ионизированный пар.
Во время работы луч медленно углубляется в деталь и оттесняет жидкий металл сварочной ванны на заднюю стенку кратера. Это обеспечивает «кинжальное» проплавление при условии большой глубины и малой ширине шва.
Большая концентрация энергии в луче позволяет достичь высокой скорости работы, а также обеспечивает хороший термический цикл и высокую прочность металла шва.
Станки для сварки лазером
Для данного вида сварочных работ применяется оборудование как мобильного, так и компактного типа, также может использоваться полноразмерное оборудование для соединения крупногабаритных деталей.
Часто в промышленных целях используют такие модели станков, как:
- ЛАТ-С — он применяется для самой лазерной сварки, а также наплавки металлов.
Обладает высокой мощностью, благодаря чему можно добиться высоких показателей в плане производительности. Может быть оснащен автоматическими координатными столами, благодаря чему можно обрабатывать сложные конструкции на высокой скорости. Станок включает в себя два модуля. В первом находится источник питания и устройство для охлаждения лазера, а второй модуль — это такой подвижный каркас, где находится лазерный излучатель. Два модуля легко двигаются благодаря наличию колес в основании. Для стационарной работы со станком неподвижность обеспечивается за счет специального механического блокиратора;
- МУЛ-1 — этот станок малогабаритный, используется для лазерной сварки и наплавки металлов. Также с его помощью можно паять золото и серебро. Варить ювелирные изделия данным станком можно легко и с соблюдением высокой точности. Часто оборудование используют для ремонта и производства ювелирных изделий. Металлические части небольшого размера можно сварить без сильного нагрева, допускается даже соединение оправ для очков. Устройство удобное тем, что для работы достаточно напряжения в 220 В. В зависимости от выбранного режима, мощность прибора составляет от 1,9 до 2, 5 кВт;
- ЛАТ-400 — применяется для соединения крупногабаритных изделий. Система включает в себя мощный твердотелый лазер, устройство питания и охлаждения. Лазер обладает высокой мощностью и производительностью, благодаря чему даже сложные работы можно осуществлять на высокой скорости. Оборудование подключается за счет трехфазной сети в 380 В. При пиковой нагрузке мощность аппарата составляет порядка 13 кВт. Установка оснащена механизированной системой, которая приводится в движение за счет двигателя постоянного тока. Это позволяет легко передвигать лазерную головку в трех плоскостях.
Ручная лазерная сварка проводится с применением таких аппаратов:
- WELD-WF — портативное устройство, благодаря которому можно выполнять работы даже в труднодоступных местах. Оно включает в себя манипулятор, соединяемый с волокном.
Сгенерированное лазерное излучение передается по волокну. Поскольку есть наличие обратной связи, с помощью аппарата можно получить максимально качественный шов по сравнению с оборудованием, в котором нет подобных опций. Аппарат имеет мощность всего 1,5 кВт и работает от сети в 220 В. Он подходит для разных ремонтных работ, когда выполнить демонтаж сложно или требует много времени;
- CLW120 — ручной аппарат с невысокой мощностью, который отлично подходит для работ, требующих ювелирной точности, а также точечной лазерной сварки. Кроме этого, с его помощью можно соединять цветные и черные металлы, нержавеющую сталь или же титановые сплавы. Мощность оборудования — 10 кВт, требования к сети — 220 В.
- Почти все перечисленные аппараты оснащены бинокуляром, который защищает зрение от негативного воздействия лазерного луча и вместе с тем помогает в несколько раз увеличить объект обработки, чтобы работа была выполнена качественно и точно.
Источник: https://tokar.guru/svarka/lazernaya-svarka-metallov-i-ee-osobennosti.html
Что такое лазерная сварка? Преимущества и недостатки
Лазерная импульсная сварка — нечасто встречающийся, но все же заслуживающий внимания метод соединения металлов и стекла. С помощью такого метода возможна быстрая, качественная и эстетичная лазерная сварка нержавейки, лазерная сварка алюминия и даже сварка серебра.
Весь процесс проходит в автоматическом или полуавтоматическом режиме, поэтому шов всегда получается прочным и долговечным, ведь вероятность человеческого фактора невелика. В этой статье мы кратко расскажем, что из себя представляет лазерная сварка, какие преимущества и недостатки есть у этой технологии.
Общая информация
Лазерная сварка металлов осуществляется с помощью специального оборудования.
Как мы писали выше, оно может быть полуавтоматическим (работать под контролем мастера) и автоматическим, вплоть до роботизированных моделей, осуществляющих работу без присутствия человека.
Суть сварки с помощью такого оборудования проста: металл нагревается и плавится за счет лазерного луча, поэтому такой метод часто называют просто «сварка лазерным лучом».
У лазерного луча есть ряд очень важных характеристик, которые как раз и позволяют сваривать детали. Например, пучок луча концентрируется строго в одной точке и не рассеивается. Благодаря такой особенности на одном небольшом участке концентрируется большой поток энергии, за счет которой и плавится металл. Этой энергии достаточно для быстрой и качественной сварки даже толстых металлов.
Одна из самых универсальных лазерных установок — это «Квант 15». Такое оборудование часто используется для сварки однородных и разнородных металлов толщиной до 3 миллиметров. Так, например, такой лазерный сварочник широко применяется в стоматологии при создании протезов. Также с его помощью возможна лазерная сварка нержавейки.
Все лазерные установки делятся на два типа: твердотельные и газовые. Также существует лазерно-дуговая сварка.
Это гибрид из лазерной и дуговой сварки, который обладает всеми преимуществами и того, и другого метода соединения металлов.
Лазерно-дуговая сварка очень технологична и редко применяется в домашних мастерских или на небольших заводах, так что остановимся подробнее на первых двух типах лазерной сварки.
Применение твердотельного лазера
Твердотельный лазер используется в связке со специальными электродами. Электроды могут быть рубиновыми, стеклянными, с примесями неодимов.
Схема стандартного твердотельного лазера изображен на картинке ниже. Мощность таких лазерных установок крайне мала и не превышает 6 кВт.
Поэтому твердотельные лазеры используют для сварки деталей малых толщин. Например, детали, которые необходимы в микроэлектронике.
Таким лазером можно сварить детали из золота, нихрома или тантала. Можно расплавить проволоку диаметром менее 1 миллиметра. Также можно точечно сварить фольгированные детали.
Применение лазера с газом
Газовые лазеры более мощные по сравнению с твердотельными, поэтому сфера их применения гораздо шире. Здесь вместо электродов используется защитный инертный газ, зачастую аргон. Схему газового лазера вы можете видеть на картинке ниже.
Единственный недостаток газовых лазеров — это их немалый размер и вес. Но он вполне оправдан, ведь за громоздким тяжелым корпусом скрывается большая мощность, достигающая 20 кВт. А это значит, что с помощью такого оборудования можно соединить даже самые толстые детали, не сбавляя скорости (средняя скорость сварки газовым лазером — 60 метров в час).
Но самые впечатляющие, конечно, газодинамические лазеры. Для их работы требуется нагреть газ до очень высоких температур. Сам лазер выдает до 100 кВт и сваривает металл со скоростью 200 метров в час. Конечно, такие установки используются только на очень крупных производствах.
С помощью газовой установки любой мощности становится возможна лазерная сварка алюминиевых сплавов, лазерная сварка кузова автомобиля, лазерная сварка нержавеющей стали и даже лазерная сварка стекла. Так что сфера применения действительно обширна.
Также есть один нюанс, который нужно учесть. Не важно, что вам предстоит: лазерная сварка алюминиевых сплавов, нержавейки или стекла, в любом случае сварочная зона нуждается в защите от кислорода.
Здесь все так же, как и при обычной ручной дуговой сварке. Сварочная зона может сильно пострадать от кислорода, шов получится некачественным.
Мы уже писали выше, что при газовой сварке лазером используется аргон, но порой этого недостаточно.
Если установка слишком мощная, луч лазера может быстро рассеиваться из-за стремительного испарения металла. Чтобы этого избежать помимо аргона нужно подавать газ, подавляющий плазму.
Для этих целей зачастую используют гелий, поскольку он не препятствует аргону и при этом не дает лучу рассеиваться.
Опытные мастера используют в работе равную смесь аргона и гелия, обеспечивая сразу две функции: защитную и плазмоподавляющую.
Преимущества и недостатки
Преимущества лазерной сварки можно описать одним словом — точность. Лазерные установки никогда не ошибаются, с их помощью можно направить луч в конкретную точку и вероятность ошибки будет минимальна. Даже при работе с очень мелкими деталями. При этом качество соединения всегда очень хорошее.
Мощные лазеры, использующие в работе газ, довольно глубоко проваривают деталь, оставляя узкий шов. За счет этого преимущества детали не деформируются даже при воздействии очень высоких температур, поскольку зона повышенного термического напряжения сфокусирована в одной точке.
Следующий плюс просто невозможен для большинства типов сварки. Луч лазера можно направить с довольно большого расстояния, что крайне удобно в труднодоступных местах.
К примеру, существует лазерный аппарат, способный ремонтировать подводные трубопроводы. Это становится возможным за счет использования зеркал. Луч прямой, но его всегда можно отразить в любую необходимую сторону.
Все это позволяет выполнять лазерную сварку в самых неожиданных местах.
Верх мастерства — сварка двух и более деталей одновременно, используя для этого всего одну установку. Для этого используется призма, которая расщепляет луч и направляет его сразу в несколько сторон. С помощью такого метода можно снизить себестоимость сварки и увеличить производительность.
Единственный недостаток — большая цена лазерных установок и их технологическая сложность. Не каждый сварщик оценит преимущества лазерной сварки и пожелает получить соответствующую квалификацию.
Вместо заключения
Электросварка лазером — это по-настоящему современная технология, которой стоит обучиться, если вы желаете улучшить свои профессиональные навыки.
С помощью лазерного сварочника вы без труда соедините металлы больших и малых толщин, вам станет доступна быстрая и качественная лазерная сварка алюминиевых сплавов и нержавеющей стали.
Желаем удачи в работе!
Источник: https://svarkaed. ru/svarka/vidy-i-sposoby-svarki/chto-takoe-lazernaya-svarka-preimushhestva-i-nedostatki.html
Лазерная сварка металлов: как работает аппарат и оборудование для сварки меди лазером
Лазерная сварка – один из современных методов, позволяющих соединять и разрезать металлические детали.
Ее работа основывается на использовании сфокусированного лазерного луча, благодаря чему появляется возможность выполнения швов на очень тонком металле.
Технология лазерной сварки
Соединение деталей из нержавейки с легкостью осуществляется аргоновой сваркой или полуавтоматами. Однако в задачах формирования швов на достаточно тонком металле отмеченные методы оказываются малоэффективными. Высокая температура, возникающая в аргоновой сварке, способна попросту расплавить изделие или же деформировать его.
В данном случае наиболее эффективной является лазерная сварка металлов. С ее помощью удается сформировать тонкий шов, а дефекты, связанные с действием температуры, будут минимальны.
Итак, каков же принцип работы и в чем преимущества лазерной технологии?
Суть метода заключается в расплавлении тонких кромок металла с помощью лазера. Он формируется посредством испускания фотонов атомами. Такое явление называется индуцированным излучением.
Полученный световой поток позволяет плавить кромки материала и соединять их между собой. Кроме того свечение можно подавать в зону сварки импульсно с высокой энергией или же постоянно с меньшей силой воздействия.
В гибридных версиях сварки присадочная проволока может также создавать дугу, расплавляющую ее кончик. Световой пучок, в свою очередь, будет укладывать расплавленный присадочный материал в шов.
Обычно сварочную ванну защищают инертным газом. В этих целях применяется гелий или аргон. Однако тут есть и некоторые особенности. Взаимодействие лазера с металлом приводит к его нагреву и испарению. В результате луч может экранироваться и преломляться.
Избежать подобной ситуации позволяет гелий. Газ принудительно поступает к сварному соединению, снижая испарение металла.
Технология лазерной сварки.
Данная технология нашла широкое применение в различных отраслях промышленности и производства. Она используется для соединения изделий из алюминия, титана, меди лазером. Сфокусированный луч позволяет расплавлять кромки деталей толщиной от 0,1 мм до 10 мм.
Благодаря возможности формирования тонких аккуратных швов эта технология получила широкое распространение в ремонте ювелирных изделий и оправ очков. В этих целях используются специальные малогабаритные настольные установки.
Место воздействия пучка в оборудовании отмечено точкой, под которую мастер подносит соединяемые детали и включает прибор. В результате происходит точечная сварка.
В случае необходимости создания шва на круглых изделиях, они вращаются с помощью специального оборудования во время сварки.
Данная технология сварки имеет ряд преимуществ. Благодаря им она выделяется на фоне других методов.
К основным достоинствам следует отнести следующие:
- возможность получения узкого и высокого шва, чего невозможно добиться полуавтоматами;
- глубокий провар без наплывов с другой стороны изделия;
- маленькая область взаимодействия света с деталью позволяет ей не перегреваться во время сварки, что исключает появления дефектов, связанных с термическим воздействием;
- высокая скорость работы и производительность;
- возможность соединения тонких деталей;
- безопасность;
- простота использования.
К недостаткам метода следует отнести его высокую стоимость. В связи с этим данная технология оказывается наиболее эффективной на производстве, где она достаточно быстро окупается.
Оборудование для проведения лазерной сварки
Схема устройства лазерного сварочного аппарата.
Существует две разновидности приборов для лазерной сварки: твердотельные и газовые аппараты. Чтобы сделать правильный выбор подобного устройства необходимо знать особенности каждого из них.
Как уже отмечалось ранее аппарат лазерной сварки может работать импульсно или постоянно. Ручная твердотельная лазерная установка относится к устройствам функционирующим по второму принципу. В основе таких приборов находится твердый стержень, наиболее часто используется розовый рубин.
На внешний контур и лампу подаются токи. Лампа генерирует высокочастотные, кратковременные импульсы света. В результате описанных процессов внутри стержня формируется ионизированный лазерный пучок. Под действием магнитного поля он высвобождается в нужном направлении.
Указанная технология формирования лазера отличается невысокой мощностью. В связи с этим она применяется для небольших изделий, позволяя формировать качественные швы. Широкое распространение этот метод получил в микроэлектронике.
Аппараты с элементами на основе газовой среды
Газовое оборудование лазерной сварки более мощное по сравнению с твердотельными аналогами. Такие установки работают с использованием высоковольтных источников. Поддерживаются оба типа режимов источников: импульсный и постоянный.
Ручной лазерный аппарат подобного типа характеризуется более длинными волнами, а также высокой рабочей мощностью. Самыми распространенными являются газодинамические приборы. В качестве активной среды тут используются газы, температура которых может достигать трех тысяч градусов.
Мощность газовых установок позволяет сваривать металлические листы толщиной до двадцати миллиметров. Стоит отметить, что в этом случае также формируются аккуратные качественные швы, а за счет локализации термического воздействия изделия не деформируются после сварки.
Принцип работы устройств похож на твердотельные, однако вместо стержня лампа облучает газовую смесь, находящуюся под давлением в несколько атмосфер. Электроды периодически вызывают электрический разряд в смеси.
После многократных отражений от торцевых зеркал когерентный луч проходит через оптическую систему и облучает рабочую область.
Особенности сварки лазером тонкостенных металлов
Основное преимущество лазерной сварки – ее разнообразие. Каждому виду работы можно подобрать соответствующее оборудование. В зависимости от типа поставленных задач и материалов, которые предстоит сваривать, можно подобрать наиболее оптимальные устройства.
Так, например, соединение деталей маленькой и большой толщины необходимо осуществлять разными установками. Как уже было отмечено выше, в одном случае лучше воспользоваться твердотельным лазером, а в другом – аппаратами на основе газа.
Схема сварки лазерным лучом.
Особенно эффективной данная технология оказывается в сварке тонкостенных металлов. Использование других методов влечет за собой ряд рисков, связанных с прожиганием материала, а также с появлением различных термических дефектов.
Лазерная сварка позволяет избежать указанных проблем, однако для этого необходимо точно контролировать мощность излучения, скорость движения луча, а также фокусировку рабочего пятна.
Соединение тонкостенных деталей осуществляют на минимальной мощности. Если сваривание проводится в импульсном режиме, тогда повышают скважность импульса и сокращают его длительность. А в непрерывном режиме скорость движения лазера повышают.
Если установка не позволяет понизить мощность до необходимого уровня, тогда луч следует расфокусировать. Это уменьшит производительность сваривания, зато исключит вероятность прожигания изделия.
Отличия в технологии сваривания деталей из разных металлов
Различные металлы сваривают в соответствии с различными технологическими нормами. Работа с заготовками из стали требует предварительной зачистки от загрязнений, включая ржавчину. Также изделие должно быть тщательно обезжирено и высушено.
Технология сварки металла большой толщины.
Наличие влаги в области соединения деталей может привести к повышенной гидратации и, как следствие, к снижению его прочности и долговечности.
Благодаря высокой скорости движения луча, станки лазерной сварки позволяют формировать шов без окислов. В результате становится возможным осуществлять соединение нержавеющих и титановых сплавов без флюса и инертных газов.
Эта уникальная способность делает подобные установки незаменимыми при сваривании особенно ответственных конструкций.
Развитие технологий за последние годы позволило создать компактный прибор для ручной лазерной сварки. На сегодняшний момент существует множество моделей, представленных в магазинах. Все они могут похвастаться различными параметрами и функциональностью.
Итог
Лазерная сварка металла – уникальная технология, позволяющая соединять тонкие материалы, нержавеющие и титановые сплавы. Главной особенностью данной технологии является формирование качественного, аккуратного шва без каких-либо дефектов, связанных с деформациями деталей.
Благодаря указанным преимуществам такой тип сварки получил широкое распространение на различных производствах.
Источник: https://tutsvarka.ru/vidy/lazernaya-svarka
Лазерная сварка
Содержание:
Сферы применения лазерной сварки
Широкий диапазон режимов лазерного излучения обеспечивает возможность сварки любых металлов и сплавов с высокой точностью, а также позволяет сваривать разнородные материалы в одно изделие. При лазерной сварке не используются припои и флюс, следовательно, сварной шов не отличается по составу от основного изделия и поэтому отсутствует необходимость в последующей очистке и доработке готовой детали. За счет особенностей технологии, в лазерных сварных швах практически отсутствует пористость, а их прочность составляет порядка 95 % от прочности цельного металла.
Высокая точность и качество даже очень тонкого сварного шва обеспечивают технологии лазерной сварки металлов. Лазерная сварка получила широкое применение в областях микроэлектронной, ювелирной, рекламной и других промышленностях.
В частности, на станках с числовым программным управлением (ЧПУ) для лазерной сварки от компании SEKIRUS возможно изготовление объемных букв для рекламных конструкций, сварка конструкций из нержавеющей стали для пищевой промышленности, сварка металлических корпусов электронных компонентов, ремонт ювелирных изделий, очков, часовых механизмов, сварка медицинских инструментов, изготовление зубных протезов и многое другое.
Большинство установок имеют средние и малые габаритные размеры и питаются от сети 220 В, поэтому они достаточно мобильны и не требуют специальных производственных условий.
Полуавтоматический режим работы станка с одной стороны обеспечивает высокую производительность за счет использования специальных программ обработки и гибкой настройки параметров лазерного излучения, а с другой стороны – предоставляет оператору полный и удобный контроль процесса сварки с помощью микроскопа (в станках для ювелирной сварки и пайки) или CCD-монитора (в универсальных станках для лазерной сварки).
Преимущества и недостатки ручной лазерной сварки
В отличии от традиционной сварки лазерная ручная сварка имеет целый ряд преимуществ:
- Высокая скорость сварки, в 2-10 раз превышающих традиционную сварку
- Простота эксплуатации, Не требуется высокая квалификация оператора. Одна машина может заменить не менее двух сварщиков в год.
- Отпадает необходимость в шлифовке шва, за редким исключением,
- Отсутствие копоти, дыма и неприятных запахов в сравнении с обычной сваркой, Можно использовать в закрытых помещениях с вытяжкой
- Нет расходных материалов, кроме азота, электричества и замены линзы в сварочном пистолете,
- Долгий срок службы,
- Безопасность,
- Экологичность,
- Низких расход материалов для микропайки.
Единственный недостаток таких аппаратов – это их стоимость, но она зависит от выбранного лазерного источника и компенсируется отсутствием расходных материалов при эксплуатации, а также более высокой скоростью сварки.
Мощность таких лазеров составляет 500-1500 Вт. С помощью аппаратов ручной сварки изготавливаются:
- кухонные раковины
- лестничные лифты
- различные полки
- духовки
- перила из нержавеющей стали для дверей и окон
- распределительные коробки
- мебель и многие другие детали
Микропайка
Лазерный луч может выполнять точечную, стыковую, пакетную сварки, сварку сварным швом и т. д.
После фокусировки можно получить небольшое пятно, которое точно позиционируется и используется в групповой сварке заготовок микро и небольших размеров для массового производства, в основном для сварки тонкостенных материалов и прецизионных деталей.
Высокий коэффициент сжатия, малые ширина сварного шва, зона термического влияния, деформация, быстрая скорость сварки дают возможность не обрабатывать детали после сварки.
Сравнение с традиционными методами сварки
Параметр | Традиционная сварка | Лазерная сварка |
Подвод тепла к заготовке (тепловой эффект) | Очень высокий нагрев | Низкий нагрев |
Деформация заготовки | Высокая | Низкая |
Прочность соединения с основным материалом | Обычная | Очень высокая |
Дополнительная обработка, пост-обработка | Шлифование, зачистка | Не требуется или требуется в редких случаях |
Скорость сварки | Обычная | В 2-5 раз выше |
Свариваемые материалы | Нержавеющая сталь, углеродистая сталь, алюминий | Нержавеющая сталь, углеродистая сталь, алюминий, оцинкованная сталь, медные сплавы, титан |
Расходные материалы | Много | Мало |
Сложность обработки и работы оператора | Высокая | Простая |
Безопасность оператора | Безопасно | Безопасно |
Воздействие на окружающую среду | Высокое загрязнение | Не влияет, очень низкое воздействие |
Отказоустойчивость | Хорошая | Хорошая |
Сварка колебанием луча | Нет | Да |
Регулировка ширины пятна | Нет | Да |
Качество сварного шва | Обычное (зависит от уровня оператора) | Преимущественно высокое |
Перейти в раздел можно по этой ссылке.
Источник: https://lasergu.ru/novosti-akcii/lazernaya_svarka/
Аппарат лазерной сварки XT-Laser LW-1000 Raycus
Лазерная сварка XT-Laser
Аппараты ручной лазерной сварки с оптоволоконными лазерными излучателями — новейшая разработка в области сварочных технологий, пришедшая на смену аргонодуговой сварке. Используются при сварке таких металлов, как нержавеющая сталь, железо, алюминий и других металлов. Характеризуются большой глубиной сварки, прочностью сварных швов, подходят для сварки любой сложности.
Установки для лазерной сварки генерируют излучение в импульсном и непрерывном режимах. Технология включает в себя точечное и шовное сварные соединения. Для шовного применяется непрерывный режим генерации или импульсный с перекрытием, для точечного – только импульсный. Точечный метод дает минимальные деформации и используется для соединения изделий небольшой толщины. При шовной сварке происходит формирование глубокого сварочного канала. Метод обладает высокой эффективностью при обработке сталей, титана, меди и алюминия. Луч высокой плотностью мощности разрушает поверхностные оксидные пленки и препятствует образованию новых и не требует применять защитные инертные газы. Сваривание элементов небольшой толщины производится с расфокусировкой луча, это позволяет исключить сквозное прожигание изделия. Для получения прочного шва аппарату лазерной сварки необходимо оснащение источником излучения достаточной мощности.
Преимущества
Сварной шов гладкий и красивый
Отсутствует деформация поверхности, не требует последующего шлифования, отсутствует необходимость чистовой обработки сварного шва.
Равномерность сварки
Достигается равномерным распределением точечной энергии лазерного сварочного аппарата.
Высокая скорость сварки
Скорость лазерной сварки в 2-10 раз выше, чем скорость традиционной сварки.
Точное позиционирование
Точное позиционирование благодаря системе красный луч.
Универсальность
Гибкие настройки позволяют производить шовную и точечную сварку.
Простота эксплуатации
Гибкий ручной режим работы легок в освоении, не требует специального обучения.
Лазерная сварка металлов, ювелирных изделий
В современном производстве сваривание металлов является одним из важнейших технологических процессов. Такой способ, как лазерная сварка, подразумевает использование в качестве источника энергии лазер. В последние годы этот метод приобрел достаточно большую популярность, поскольку обладает рядом весомых преимуществ и позволяет производить соединения, в том числе разнородных металлов. Рассмотрим эти вопросы подробнее.
Виды и сфера применения
Лазерная сварка – это высокотехнологичный способ создания сварных конструкций. Для него не требуется проведение сварочных работ в вакууме или газовая камера. Установка лазерной сварки производит луч лазера, который является мощным источником энергии. Это достигается за счет фокусировке всей энергии в одной точке, диаметр которой не превышает нескольких сантиметров.
Применяются непрерывные и импульсные лазеры. Лазерная сварка металлов чаще всего бывает импульсной, так как при точечном воздействии достигаются лучшие результаты. В данном случае происходит накопление значительного объема энергии, который далее оказывает кратковременное воздействие на металл. Так как зона воздействие мала, то на нее оказывается максимальное воздействие энергии. Импульсный метод применяется при сваривании легко деформируемых видов металла, так как его глубина незначительна.
При необходимости формирования шва применяется непрерывный тип сваривания лазером. Технология сходна с элетродуговым методом и характеризуется выделением СО2. Выделение газового канала дает возможность варить металлы даже большой толщины при узком шве.
Существуют две основные разновидности сварочных аппаратов, осуществляющих работу лазером:
- Твердотельное устройство дает короткие волны более слабой мощности.
Возможна сварка импульсным или непрерывным режимом. Устройство данных аппаратов предполагает выход лазерного излучения из стеклянной головки с включением рубина и неодима. Световые вспышки создаются лампой накачки, которая помещена в специальную камеру.
Данные аппараты имеют сферу применения в точечной сварке электронных приборов, в частности кинескопов для телевизоров.
- Газовое устройство также может работать в режиме импульса или непрерывно. Этот аппарат представляется устройство более высокой мощности с источниками тока высоких вольт. Данные аппараты отличаются достаточно высокой стоимостью.
Область применения данного метода сваривания достаточно разнообразна:
- Производство сложных приборов, требующих электронных схем и высокой точности;
- Лазерная сварка кузова автомобиля;
- Сваривание маленьких деталей вместо пайки.
Преимущества
Лазерная сварка по сравнению с другими сварочными технологиями имеет ряд отличительных особенностей и преимуществ:
- Процесс отличается высокими показателями производительности и скорости;
- Минимальные размеры термического воздействия позволяют получать швы малых размеров;
- Аппараты легки в управлении и имеют возможность перепрограммирования;
- Данный вид сваривания полностью экологичен;
- Соединение элементов отличается высокой надежностью и качеством;
- Лазер позволяет производить работу в труднодоступных местах.
Особенности
Для лазерной сварки толстых металлов, которые требуют глубокого расплавления, необходимо создание газового канала. Это в корне отличается от процесса сваривания тонких металлов. Параметрами, от которых зависит глубина расплавления, являются:
- Мощность лазера;
- Скорость проведения сварки;
- Варианты фокусировки лазерного луча;
- Расходимость лазерного луча.
Выбор мощности лазера производится исходя из того, что при минимальном значении должно происходить проплавление в минимальной ширине, а при максимальном получаемый шов будет без дефектов. Размер фокуса лазерного луча составляет не более 1 мм, а наиболее качественная работа производится со скоростью около 30 мм/с.
Сварка стали
Низкоуглеродистые стали достаточно распространены в сфере изготовления сварочных конструкций. Перед свариванием металл зачищается от ржавчины, грязи и влаги. Применение данного метода целесообразно при необходимости точной подгонки деталей без большого их нахлеста. Этим объясняется широкое обращение к свариванию лазером при изготовлении кузовов для автомобилей.
В данном случае рекомендуется применяться режим высокой скорости до 40 мм/с. Процесс происходит в среде защитных газов на автоматических или полуавтоматических линиях.
Ручная сварка лазером
В настоящее время существуют лазерные сварочные аппараты, которые настроены на сварку своими руками с некоторыми программируемыми настройками аппарата. Такое оборудование позволяет:
- Выполнять точечную сварку «стык встык»;
- Осуществлять лазерную наплавку, ремонтировать пресс-формы без потери их качества;
- Производить обработку деталей различного медицинского оборудования;
- Производить сваривание миниатюрных деталей, например ювелирных украшений;
- Проводить сварочные работы в области микроэлектроники.
Лазерная сварка ювелирных изделий в последние годы практически полностью вытеснила пайку, так как позволяет создавать изделия без видимых швов. Это достигается тем свойством этого метода, который заключается в минимальном размере места воздействия лазера.
Пользуется популярность лазерная сварка очков, в том числе оправ не только из металла, но и пластика. При этом соединение сплавляемых деталей получается очень прочным и не подвержено разрушению.
Подведем итоги
Сваривание деталей при помощи лазера является современным и востребованным методом сплавления различных элементов, таких как металл, пластик. Ряд отличительных преимуществ вывели этот способ в лидеры в таких областях, как создание высокоточных приборов с электрическими микросхемами, автомобильных кузовов, ремонт и создание ювелирных изделий.
Лазерные аппараты отличаются высокой стоимостью, однако эти затраты полностью окупаются высочайшим качеством получаемых соединений.
Лазерная сварка и наплавка — важное для нашей компании направление деятельности. Мы много лет специализируемся на разработке и производстве оборудования для лазерной сварки и наплавки различных металлов и их сплавов, а также вспомогательных устройств, делающих процесс лазерной сварки удобнее и производительнее. Нашими клиентами являются как крупные предприятия, так и небольшие фирмы и мастерские по все России и территории ближнего зарубежья. География продаж и клиенты. Установки, аппараты, станки для лазерной сварки металлов для различных областей примененияНаши лазерные установки могут применяться для ремонта и восстановления пресс-форм, штампов и различной оснастки, ремонта и производства инструментов, в том числе медицинских, ювелирных изделий, производстве зубных протезов, герметизации радиоэлектронной аппаратуры, сварки сильфонов, теплообменников, датчиков и фильтров, а также для других работ по сварке и наплавке. Ручная и автоматизированная лазерная сварка различных металловНаше оборудование позволяет осуществлять точечную и шовную сварку и наплавку в ручном и автоматизированном режиме методами для сварки материалов малых толщин, а также сварку с глубоким проплавлением. Шовная сварка может производиться как прямолинейными и кольцевыми, так и сложными по форме сварными швами. Технология лазерной сварки и наплавки может применяться для изделий из черной и нержавеющей стали, титана, ковара, вольфрама, алюминия, серебра, золота, меди, манганина, а также других металлов и сплавов. Простота и индивидуальный подходКонструкция нашего оборудования может легко адаптироваться к различным особенностям производства заказчика. Мы обладаем большим опытом по встраиванию нашего оборудования в производственные линии. Мы можем разработать и изготовить оснастку для перемещения деталей и изделий (вращатели и т.п.), системы перемещения лазерной сварочной головки для сварки в труднодоступных местах или сварки сложных деталей по требованиям заказчика. Гид по оборудованию для лазерной сварки и наплавки (по сериям и моделям)
Гид по оборудованию для лазерной сварки и наплавки (по сферам применения)
Больше информации о нашем оборудовании и лазерной сваркеВ разделе «Системы перемещения и автоматизация» представлено вспомогательное оборудование (координатные столы, вращатели и т.п.), делающее процесс лазерной сварки удобнее и производительнее. В разделе «Технология лазерной сварки» представлена постоянно пополняемая подборка материалов о лазерной сварке и наплавке.
Подборка видео о лазерной сварке и нашем оборудовании Все видео о нашем оборудовании и лазерной сварке можно посмотреть на нашем канале YouTube здесь. |
Лазерная сварка | Аппараты лазерной сварки Sekirus
Сварка металла лазером – это один из методов обработки материала, предназначенный для изготовления деталей из нескольких частей и заготовок различных габаритов. Преимущество технологии заключается в абсолютной индифферентности к размерам соединяемых деталей. Такая особенность поспособствовала широкому распространению установок лазерной сварки во всех отраслях точного машиностроения, автомобилестроения, создания авиационного и космического транспорта, ювелирном деле, медицине и прочее.
Принцип работы приборов заключается в нагревании соприкасающихся поверхностей материала с целью их соединения. Металл под действием лазерного пучка плавится равномерно и на всю толщину, что позволяет создавать идеальные швы. Сварочный шов формируется при охлаждении поверхности до момента кристаллизации. В результате образовывается прочное соединение по всей площади детали.
Лазерные сварочные аппараты: разновидности, преимущества, стоимость
Лазерные сварочные аппараты делятся на стационарные, ручные и роботизированные. Разница между ними только в способе использования и мощности лазерного источника, в то время как качество обработки одинаково высокое. При этом ручной аппарат более практичный: удобное переносное устройство, способно повысить эффективность работы сотрудников, и увеличить производительность предприятия.
Преимуществами лазерных сварочных устройств являются:
- Универсальность – возможность работы с большим ассортиментом материалов и их сочетаниями.
- Высокий КПД – минимум энергозатрат и максимум результата.
- Минимальное количество брака – лазерный луч аккуратно воздействует на все типы материалов и не деформирует термочувствительные детали, трещина на металле не образовывается, а сам материал не теряет своих характеристик.
- Идеальные швы – концентрация энергии лазера в одной точке позволяет получить ультратонкие соединения без наплывов материала по сторонам.
- Высокая скорость работы – заготовка нагревается быстро и равномерно, что экономит драгоценное время.
- Простота и безопасность использования – для работы с лазерным агрегатом не требуется создание особых производственных условий, но очень важно соблюдать технику безопасности при работе с лазерным оборудованием.
Приобрести компактный и производительный сварочный лазерный аппарат – это отличное капиталовложение, которое с первого дня использования начнет окупаться.
Высокое качество по доступной цене
Надежные аппараты для лазерной сварки можно найти в нашем каталоге.
В нашем интернет-магазине представлено несколько конфигураций сварочных аппаратов SEKIRUS:
- автоматические станки на основе газовых трубок;
- автоматические устройства на основе волоконного излучателя IPG/Raycus;
- ручные сварочные аппараты для обработки металлических заготовок толщиной до 4 миллиметров.
- роботизированные сварочные комплексы
Наша компания реализует только проверенные аппараты от известного производителя. Специалисты всегда готовы помочь консультацией, предложат оптимальные варианты по доступной цене. При необходимости мастера продемонстрируют работу станков в нашем демозале, произведут пусконаладочные работы, обучат персонал. Если у вас возникли вопросы или вы уже готовы приобрести высококачественное лазерное сварочное оборудование, то звоните по телефону +7 (812) 309-80-44 .
Следует ли перейти с точечной сварки на лазерную сварку с замочной скважиной?
Применение лазерной сварки с замочной скважиной может привести к тому, что процесс сварки будет в три-четыре раза быстрее по сравнению с точечной контактной сваркой — для повышения производительности и эффективности — при одновременном повышении качества и повторяемости сварных швов.
Большинство производителей ищут способы сэкономить деньги и повысить эффективность без ущерба для качества.Производственные операции, в которых используется точечная контактная сварка, могут значительно повысить производительность и качество в некоторых случаях за счет перехода на лазерную сварку с замочной скважиной.
Применение лазерной сварки со спайкой может привести к тому, что процесс сварки будет в три-четыре раза быстрее по сравнению с точечной контактной сваркой, а также повысит качество и повторяемость сварки. Однако лазерная сварка с замочной скважиной может не подходить для каждой работы.
Помните о нескольких факторах, решая, является ли лазерная сварка с замочной скважиной лучшим выбором для вашей области применения.
Основы точечной сварки
Точечная сварка сопротивлением может использоваться, когда необходимо сварить вместе два куска материала толщиной до 3 мм, уложенных друг на друга. Этот процесс часто используется в отраслях транспорта и формовки листового металла для таких применений, как изготовление деталей кузова и рамы автомобилей, а также для сварки офисной мебели и ящиков с инструментами.
В процессе точечной сварки используются два электрода: один расположен внизу основного материала, а другой — вверху. Между двумя электродами прикладывается давление, которое сдвигает две металлические части вместе. Ток проходит между электродами, образует сварной шов и соединяет две поверхности вместе.
Одна из проблем точечной сварки заключается в том, что, когда два электрода высвобождаются, они оставляют вмятину на основном металле. В сварочных операциях, где важны эстетические требования, для удаления этих вмятин на материале требуется шлифовка после сварки и часто окраска, что увеличивает время и затраты на процесс.
Точечная сварка обычно выполняется вручную; его сложно и дорого автоматизировать, особенно в приложениях с низким и средним объемом. Также сложно установить предсказуемый процесс при использовании автоматической точечной сварки, потому что электроды быстро изнашиваются, а это означает, что параметры процесса и подгонка постоянно меняются. Это также может повлиять на воспроизводимость качества детали при точечной сварке. Кроме того, робот, необходимый для выполнения автоматической точечной сварки, довольно тяжелый и может быть громоздким, что является недостатком реализации для многих операций.
Как показывает практика, для эффективной автоматизации точечной сварки требуется очень большой объем детали. Примером этого является производство автомобильных деталей, в котором часто используется точечная сварка. Точечная сварка лучше всего подходит в случаях, когда сборка деталей неудовлетворительна и требуется что-то, чтобы сжать две детали вместе для сварки. Точечная сварка также имеет более дешевую точку входа; для этого необходимо приобрести только ручной аппарат для точечной сварки.
Основы лазерной сварки с замочной скважиной
В некоторых случаях, когда требуется контактная точечная сварка листового металла, автоматизированный процесс лазерной сварки с замочной скважиной может сэкономить время и улучшить качество сварки.Этот процесс хорошо подходит для сварки некоторых разнородных металлов, которые может быть трудно правильно сваривать контактной точечной сваркой из-за различий в физических, химических и механических свойствах основных металлов.
Лазерная сварка с замочной скважиной использует мощный лазерный луч для сварки двух заготовок. Лазер с высокой плотностью энергии поражает небольшое точечное пятно на материале. Когда свет попадает на верхнюю поверхность, он плавится и испаряет металл. Давление пара металла толкает жидкий металл вниз и в сторону, образуя замочную скважину.Когда лазерный луч перемещается по поверхности, замочная скважина следует за лучом и создает сварной шов, который обычно бывает глубоким и узким.
Одно из соображений, которое следует учитывать при точечной сварке, заключается в том, что она оставляет вмятину на основном металле. В сварочных операциях, где важны эстетические требования, избавление материала от этих вмятин требует шлифовки после сварки и часто окраски, что увеличивает время и затраты на процесс.
В подходящих областях применения лазерная сварка с замочной скважиной предлагает:
- Точный контроль глубины проплавления, что исключает любую деформацию или вмятины на задней стороне нижней части.Это сокращает время и деньги, затрачиваемые на шлифовку или подкраску после сварки.
- Очень маленький размер луча — менее 1 мм, что приводит к небольшой зоне термического влияния. Это дает преимущества при сварке тонких материалов или металлов, в которых важен контроль тепловложения.
- Чрезвычайно быстрый процесс, который обычно в три-четыре раза быстрее, чем ручная точечная контактная сварка.
- Стабильность и предсказуемость, которые позволяют получить высококачественные готовые сварные швы, а также сократить время и деньги, затрачиваемые на доработку.
Рекомендации по преобразованию
Переход с точечной контактной сварки на лазерную сварку с замочной скважиной требует учета нескольких ключевых факторов, чтобы определить, является ли это правильным выбором для работы и применения.
- Стоимость: Поскольку лазерная сварка — это автоматизированный процесс, он требует инвестиций в роботизированную сварочную систему.
Для небольших предприятий, которые не производят много деталей с высокой повторяемостью, этот тип инвестиций может оказаться невыполнимым или обеспечить необходимый возврат инвестиций (ROI), чтобы оправдать покупку.
- Окно допуска для материала: Правильная оснастка и крепление имеют решающее значение для успеха при лазерной сварке. Две свариваемые детали должны быть прижаты друг к другу без зазора для получения высококачественного лазерного шва. Это делает правильное соединение и представление материала важным, поэтому операция должна поддерживать правильную настройку и сборку детали.
- Повторение: Лазерная сварка с замочной скважиной лучше всего подходит для повторяющегося процесса, в котором производится много деталей, даже если это означает большое количество деталей с меньшими объемами каждой детали.Из-за необходимых инвестиций в настройку системы, приложения с частым повторением или большим объемом деталей обычно обеспечивают лучшую окупаемость инвестиций при лазерной сварке.
Учет этих факторов может помочь вам определить, подходит ли лазерная сварка с замочной скважиной для вашей работы.
Лазерная сварка с замочной скважиной предлагает множество преимуществ в правильных применениях, включая точный контроль глубины проплавления, очень маленький размер луча для небольшой зоны термического влияния, большую стабильность и чрезвычайно быстрый процесс.
Традиционная сварка по сравнению с лазерной сваркой
Лазерная и традиционная сварка все еще конкурируют с
С гораздо более высокой скоростью обработки и более высоким качеством можно подумать, что лазерная сварка быстро захватит сферу применения. Но традиционная сварка сохраняется. И в зависимости от того, кого вы спросите и какие приложения вы рассматриваете, он может никогда не исчезнуть. Итак, каковы плюсы и минусы каждого метода, которые продолжают приводить к смешанному рынку?
Линия Fusion Line от Trumpf оснащена лазером с проволокой для придания большей массы сварному шву, перекрывая зазоры шириной до 1 мм.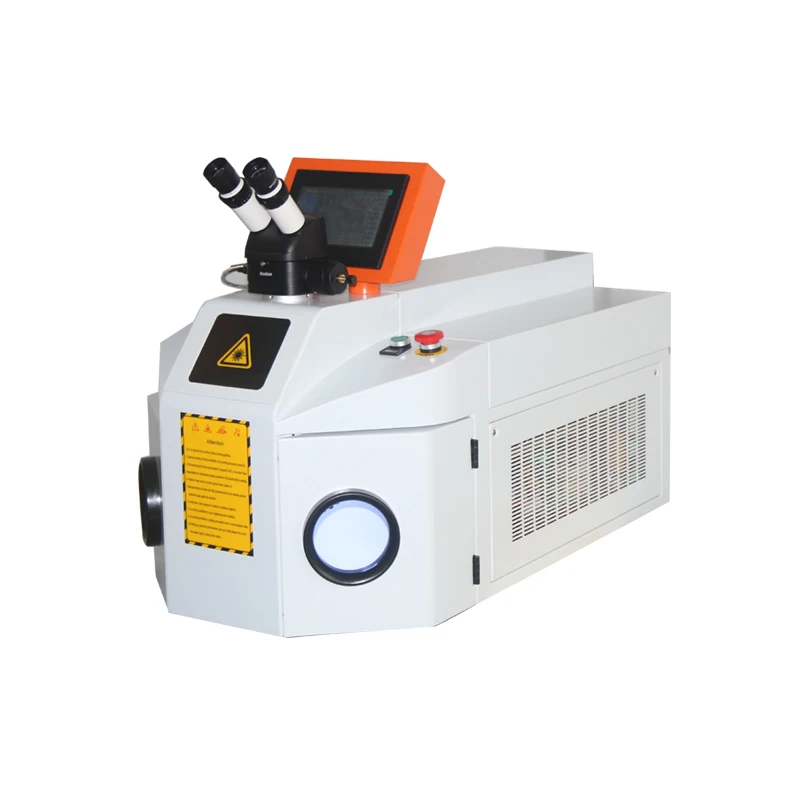
Традиционные методы сварки остаются популярными. Вообще говоря, в промышленности используются три типа традиционной сварки: MIG (металлический инертный газ), TIG (вольфрамовый инертный газ) и точечная сварка. При контактной точечной сварке два электрода прижимают детали, которые необходимо соединить между собой, через это пятно пропускается большой ток, а электрическое сопротивление материала детали генерирует тепло, которое сваривает детали вместе. По словам Эрика Миллера, менеджера по развитию бизнеса лазерной группы Miller Electric Mfg LLC в Аплтоне, штат Висконсин, это быстрый метод., это основной метод, используемый в автомобилестроении, особенно для кузовов. Но, добавил он, самый большой рынок для лазерной сварки — это замена точечной контактной сварки. И наоборот, Миллер не видел «какой-либо лавины» в использовании лазеров, заменяющих TIG или MIG. И даже в группе автоматизации компании около 90 процентов проектов выполняются в MIG.
Big на MIG
Чем объясняется непреходящая популярность MIG? «Расходный материал — это проволока с непрерывной подачей», — сказал Миллер. «Таким образом, он добавляет материал и усиливает сварной шов, что делает его идеальным для углового шва [в котором детали перпендикулярны].«Автогенный лазер объединяет два основных материала вместе. По словам Миллера, лазер может выполнять угловой шов, но точность деталей и всего остального должна быть на порядок выше.
«При сварке MIG на угловом соединении допуск составляет не менее плюс-минус половина диаметра проволоки, а в целом даже больше», — сказал он. Точно так же технологическое окно MIG для других типов сварных швов намного больше, чем у лазера. Другими словами, детали не должны быть такими точными, а приспособления не должны обеспечивать почти идеальную посадку, как в случае с аутогенным лазером.
Темная область под сварным швом слева показывает глубокое проплавление и полное сплавление хорошего сварного шва MIG. На изображении справа показан лазерный сварной шов с полным сплавлением, но с очень неглубоким проплавлением, что уменьшает смешивание наполнителя и основы.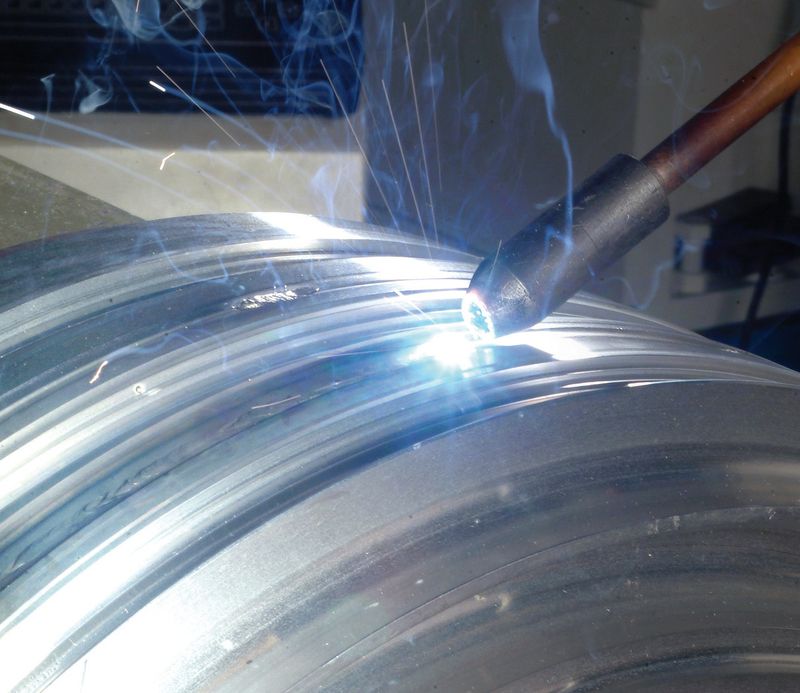
MIG также проще автоматизировать. По словам Миллера, единственными факторами, которые вам нужно контролировать, являются скорость движения, напряжение, сила тока, угол резака и рабочий угол, и «если вы сделаете пять из десяти вещей правильно, вы все равно получите хороший сварной шов». Для автоматизации лазерной сварки требуется робот с превосходной точностью траектории и повторяемостью, а в процессе сварки нужно контролировать больше факторов.В этом отношении TIG аналогичен.
Нельзя сказать, что автоматизировать сварку MIG настолько просто, что это может сделать каждый. По-прежнему требуется эксперт для программирования и диагностики проблем. Эд Хансен, директор по глобальному управлению продуктами и гибкой автоматизации ESAB Welding & Cutting Products, Дентон, Техас, сказал, что это еще один плюс для MIG.
«После многих лет эмпирических и научных данных традиционная сварка хорошо известна. Мы знаем, что нужно для того, чтобы получить предсказуемый результат, обеспечивающий соединение, которое требуется конструкции.И даже несмотря на то, что мы говорим о нехватке квалифицированной рабочей силы, что является реальной проблемой для отрасли, все еще существует большой пул опытных сварщиков, техников и инженеров, которые все знакомы с управлением этими традиционными процессами ». Для большинства продуктов это простое и недорогое решение, обеспечивающее приемлемые результаты.
Темная область под сварным швом слева показывает глубокое проплавление и полное сплавление хорошего сварного шва MIG. На изображении справа показан лазерный сварной шов с полным сплавлением, но с очень неглубоким проплавлением, что уменьшает смешивание наполнителя и основы. Это случай, когда первоначальная стоимость системы MIG или TIG меньше, чем стоимость лазерной системы. Однако стоимость лазеров снижается и будет продолжать снижаться. «Стоимость лазера составляет от трети до половины стоимости системы лазерной сварки, — сказал Хансен, — а стоимость в зависимости от возможностей сварки снижается на 10-15 процентов в год».
Миллер также отметил, что «лазерная технологическая головка дороже, чем традиционные головки, волокно доставки дороже, и защита лазерной ячейки также дороже.Например, лазерная ячейка должна быть «светонепроницаемой» со стенками толщиной 4 дюйма (101,6 мм), чтобы выдерживать прямое попадание в течение 10 минут без прожига. (Лазер не будет в фокусе более 4 дюймов [101,6 мм]. ] на большую глубину.) Системы TIG и MIG могут быть экранированы недорогим листовым металлом, который оставляет зазоры.
С другой стороны, если учесть разницу в производительности и стоимости детали, лазер, как мы увидим, часто выигрывает. Это особенно верно для TIG, который является очень медленным процессом, требующим высокой квалификации, что делает его дорогостоящим в использовании.По этой причине Миллер сказал, что TIG в основном ограничивается производством промышленного пищевого оборудования и бытовой техники, а также некоторыми прецизионными компонентами. «Люди выбирают TIG для пищевого оборудования, потому что сварной шов не имеет пористой поверхности — он очень гладкий», — сказал он. Но если эти детали необходимо производить в больших объемах, рентабельность инвестиций в лазерную систему «взорвет двери» TIG, поэтому, естественно, в таких случаях она берет верх.
Масуд Харуни, менеджер по продукции по лазерной сварке компании Trumpf Inc., Хоффман Эстейтс, Иллинойс, сказал, что даже TIG не может обеспечить полностью удовлетворительную поверхность для пищевой промышленности и других приложений, где внешний вид имеет решающее значение.«Это не так плохо, как MIG, но поверхность TIG определенно требует шлифовки после обработки, в которой нет необходимости при использовании лазера», — сказал Харуни. «Кроме того, скорость лазерной сварки видимых швов в два-три раза выше, чем у TIG. Если вы видите хороший радиус на холодильнике или аналогичной детали, значит, он был отшлифован или сварен лазером ».
Последний голос за традиционную сварку: за исключением нескольких специализированных случаев, лазерная сварка должна быть автоматизирована из соображений безопасности. И это оставляет много работы сварщикам, как объяснил Хансен.«Робот не может взбираться на леса или залезать в трюм корабля. Мы можем мечтать о таких супер-роботах, но с практической точки зрения в ближайшем будущем их здесь не будет ».
Тенденции принятия лазерных решений
По мнению Миллера, производство в США обычно консервативно, и «если нет проблемы, которую нужно решить, будет выбрано самое дешевое, надежное и проверенное решение. Таким образом, люди начинают смотреть в сторону лазера только тогда, когда сварка MIG не работает или сварка TIG идет слишком медленно.”
Объемная сварка TIG либо уже переехала за границу, либо была заменена лазером, так где же лазер может бросить вызов MIG?
Одной из основных проблем является повреждение — металлургическое или конструктивное — потенциально вызванное относительно длительной и широко распространенной теплопередачей MIG в деталь с последующим длительным циклом охлаждения. И наоборот, лазер передает тепловую энергию очень маленьким лучом, плавя только локализованную область. Общее количество подводимого тепла намного меньше, чем при сварке MIG, и деталь остывает очень быстро, сводя к минимуму деформацию и металлургические эффекты.
Харуни предложил полезную аналогию: «Представьте себе бутылку воды на песчаном пляже в сравнении с иглой. Если вы положите на бутылку пятифунтовую гирю, она не пробьет песок. Но если вы нанесете на иглу всего несколько унций, это произойдет. Думайте о весе, которое вы прикладываете, как о нагреве, о бутылке как о MIG, а об игле как о лазере ».
Хансен из ESAB сказал, что лазер снижает тепловложение примерно на 85 процентов по сравнению с MIG, и «остаточное напряжение в сварном шве прямо пропорционально тепловложению.Чем больше тепла вы поместите в него, тем больше остаточного напряжения вы создадите. А это означает коробление, деформацию, усадку и все эти вещи, которые вызывают кошмар, когда вы берете эту деталь и делаете из нее сборку или вставляете ее в конструкцию или транспортное средство ».
Чем больше деталь, тем больше мелких индивидуальных остаточных напряжений становятся макро-прогибами, которые очень дорого исправить, и их трудно исправить позже, добавил он. И это главное соображение для клиентов, которые пытаются «облегчить» свою продукцию.Более того, по его словам, «некоторые сплавы расслаиваются или изменяют свойства при нагревании, или структура зерен растет нежелательным образом. У многих из этих материалов зернистая структура и микроструктура будут другими, если сварной шов расплавить, а затем охладить ».
С расположенным на расстоянии источником тепла и высококонцентрированной областью расплава внизу лазерная сварка кажется волшебством, как показано здесь в системе Miller Electric.Миллер из Miller Electric отметил, что последнее поколение высокопрочных сталей «приобретает большую прочность благодаря сложным процессам термообработки.Когда вы расплавляете и затвердеваете при низкой скорости охлаждения (как при сварке MIG), все эти сильные стороны исчезают. Лазер может помочь сохранить исходную прочность материала ».
В другом примере Миллер сказал, что сварка титана методом MIG затруднена из-за «проблемы с плавающим катодом». Дуга нестабильна. Так что лазер — идеальный выбор ». С алюминием серии 6000 проблема заключается в горячем растрескивании. «Горячее растрескивание — это функция силицида магния, мигрирующего к границе зерен. Поэтому, если вы можете нагреть материал, расплавить его и охладить до того, как силицид магния переместится, тогда вы сможете создать сварной шов без трещин », — сказал он.«Лазер может сделать это, используя новейшие методы сканирования, при которых мы перемещаем луч вперед и назад с помощью зеркала».
Превосходная пропускная способностьLaser
С точки зрения Миллера, большинство применений лазера связано с трудносвариваемыми материалами. С точки зрения Харуни, лазер настолько быстрее, что даже проекты из листового металла переходят на лазер. Насколько быстрее? Харуни из Trumpf сказал, что сварка MIG обычно происходит со скоростью 20-30 дюймов (508-762 мм) в минуту — максимум 40 дюймов (1016 мм) в минуту. Лазер, по словам Харуни, может сваривать со скоростью почти 200 дюймов (508 см) в минуту, поэтому сам процесс соединения уже намного быстрее. Второе преимущество — сокращение постобработки. Харуни заметил, что если внешний вид сварного шва ухудшится. Важно то, что после сварки MIG вам потребуется длительный цикл шлифовки, в котором нет необходимости после лазерной сварки.
«Вот почему, — добавил он, — обычно случается, что деталь, изготовленная с помощью сварки MIG по цене 25 долларов, будет стоить всего 15 долларов за лазерную сварку, даже с учетом более высоких первоначальных вложений в лазерную сварку.Например, Харуни рассказал о недавнем проекте, в котором Трампф сократил время цикла сварки большой двери с десяти часов до 35 минут. Другой заказчик столкнулся с трудностями при сварке MIG алюминиевого электрического корпуса. Сушилки были частой проблемой, и общее время цикла составляло четыре часа. Харуни сказал, что Trumpf сократил это время до 18 минут с помощью лазерной сварки.
Хансен добавил, что способность лазера глубоко проникать в материал многократно увеличивает его преимущество перед традиционной сваркой. Поскольку лазер не только в три-десять раз быстрее, чем MIG (и даже быстрее по сравнению с TIG), он может сваривать относительно толстые швы, которые потребуют нескольких проходов с помощью MIG или TIG.
«Традиционные методы также требуют очистки и шлифования между проходами, что еще больше увеличивает общее время цикла», — пояснил Хансен. «Лазер может выполнять однопроходную сварку примерно на полдюйма по сравнению с примерно пятью проходами для сварки MIG, в зависимости от используемого процессора. Более полудюйма для лазерной сварки потребовалось бы заранее вырезать или отшлифовать скос до кромки, но это гораздо меньший скос, чем фаски всего соединения, необходимые для сварки MIG ».
Таким образом, для материала толщиной в полдюйма лазерная сварка будет в 15-50 раз быстрее, чем MIG, только по скорости сварки — и даже быстрее, если учесть дополнительную постобработку, необходимую для MIG.
Сравнение методов: несварное соединение внизу, сварка MAG чуть выше, сварка Trumpf Fusion Line (которая сочетает в себе проволоку и лазер) выше, и вверху автогенная лазерная сварка после перепроектирования соединения для этого процесса.Конечно, при такой высокой производительности вам потребуется много сварочных работ, чтобы питать лазерную систему и максимизировать рентабельность инвестиций. Как сказал Хансен, «обычно лазер может производить от трех до пяти систем дуговой сварки, например, при сварке листов. Чтобы запитать пять систем дополнительной дуги, потребуется много работы.”
Новые технологии в сочетании со старыми
Поскольку для автогенной лазерной сварки требуется плотная посадка между соединяемыми деталями, во многих случаях лучше всего изменить расположение стыков, чтобы представить лазеру перекрывающиеся поверхности (чтобы использовать его прокалывающую способность). Все больше производителей готовы вкладывать средства в более совершенные процессы и инструменты для разведки и добычи, чтобы воспользоваться преимуществами более высокой производительности лазера.
Но для тех, кто устойчив к таким изменениям или в ситуациях, когда промежутки неизбежны, существуют гибридные системы, сочетающие в себе технологию лазера и подачи проволоки, а также другие новые разработки, расширяющие область применения лазера.Одна простая концепция (упомянутая ранее в отношении решения проблемы горячего растрескивания) — это раскачивание лазерного пятна. Миллер сказал, что это старая концепция, которая в последнее время стала намного более экономичной. Он предложил пример перемещения пятна диаметром 1,2 мм вперед и назад по площади 3 мм с высокой скоростью, эффективно захватывая большую площадь и при этом обеспечивая хороший сварной шов.
Хансен сказал, что гибридные системы сочетают в себе процесс MIG и лазерный луч. «Мы действительно используем лазер для проникновения.Обычно, если вы хотите повлиять на проплавление сварного шва MIG, вам нужно увеличить силу тока. Используя лазер для проплавления, мы можем уменьшить силу тока на MIG и использовать сварной шов наименьшего диаметра, который позволяет наша конструкция для инженерных целей. Таким образом, лазер позволяет нам оптимизировать MIG ». Также существует синергия между процессами благодаря стабилизации дуги лазерным лучом. «Мы можем путешествовать по дуге намного быстрее, чем если бы у нас не было лазерного луча. Вот почему мы можем так быстро реализовать гибридный процесс », — сказал он.
Комплект больших шестиосных лазерных порталов ESAB для сварки пассажирских вагонов. Линия Fusion LineTrumpf, которую Харуни описал как «технологический лазер с добавлением проволоки для увеличения массы зазоров», может перекрывать зазоры шириной до 1 мм.
Со своей стороны, ЭСАБ разработал адаптивную технологию сварки, которая определяет состояние деталей и изменяет параметры процесса в соответствии с ними. В системе используется камера, которая «рисует лазерную полосу на детали, а затем смотрит на нее под углом параллакса, чтобы увидеть форму соединения, примерно на 20-40 мм впереди процесса», — сказал Хансен.Лазерная когерентная визуализация используется для измерения замочной скважины, прорезанной лазером в металле. «Мы можем измерить глубину проникновения и форму замочной скважины и использовать эту информацию либо в качестве меры качества, либо в замкнутом контуре для управления процессом», — сказал он.
Система автоматически регулирует проникновение лазера, мощность лазера, параметры газовой металлической дуги, скорость подачи проволоки, напряжение, поток газа и скорость перемещения по мере того, как сварочная головка обрабатывает деталь. Гол, которым руководил У.Требования S. Navy заключаются в том, чтобы обеспечить преимущества лазерной сварки с низким тепловложением «деталей, подготовленных традиционным способом» (то есть деталей, которые не были обработаны с жесткими допусками для стандартной лазерной сварки). Хансен сообщил, что это расширяет технологическое окно для гибридной сварки в пять раз по сравнению с тем, что было бы возможно при стационарном управлении.
Лазерная сварка остается относительно новой для многих пользователей, и Харуни подчеркнул приверженность Trumpf обучению и поддержке с самого начала, а также преимущества автономного программирования их систем после установки.
Trumpf также предлагает TeachLine, новую сенсорную систему на основе камеры, которая определяет местоположение свариваемого шва. «Заказчики не хотят прерывать производство, чтобы запрограммировать новую деталь, или вносить изменения в свое программирование, поэтому они могут использовать это автономное программирование и загрузить деталь, запрограммировать ее и доставить в ячейку. С TeachLine им не нужно настраивать его. TeachLine увидит деталь и откорректирует созданную вами программу в автономном режиме. Комбинация автономного программирования и TeachLine помогает нашим клиентам быстро вносить изменения в производство.”
ЭСАБ также внедряет новый пакет «цифровых решений», который объединяет огромное количество информации, охватывающей весь процесс сварки, включая присадочный материал, основной материал и газ, чтобы упростить использование систем. Как сказал Хансен: «Сложную систему легко создать. Очень сложно сделать сложную систему простой. И вот к чему мы идем с нашими цифровыми решениями. Мы используем наши знания о процессе, чтобы принимать разумные решения по управлению процессом, чтобы оператору не нужно было быть таким же опытным или знающим, как в прошлом.”
ЭСАБ также работает над тем, чтобы сделать свое оборудование способным оценивать качество производимого сварного шва и, в идеале, не допускать возникновения дефектов или разрывов.
Наконец, традиционная сварка также претерпела улучшения, такие как усовершенствованные формы волны и концепция ActiveWire Miller Electric, которая непрерывно подает проволоку MIG вперед и назад, чтобы уменьшить разбрызгивание и тепловложение. Такой подход расширяет возможности автоматизации сварки MIG и делает MIG жизнеспособным решением даже для сварки некоторых сверхтонких материалов.
A Грунтовка для лазерной сварки | Блог по интеграции роботов Genesis
Относительно высокая скорость обработки, низкое тепловложение, низкая зона термического влияния и минимальная деформация делают лазерную сварку идеальным решением для многих сварочных работ. Типы высокоточной сварки классифицируются в зависимости от интенсивности импульса, продолжительности луча и того, перемещается ли луч при подаче напряжения.
Лазерная точечная сварка
Бесконтактный процесс создает единый точечный сварной шов, соединяющий два металла.Сфокусированный лазерный луч поглощается подложкой, и металл плавится. Этот жидкий металл течет, затвердевает и образует точечный сварной шов. Небольшие точечные сварные швы чрезвычайно полезны, когда производителям необходимо избежать теплового повреждения материалов или электрических компонентов вблизи зоны сварки.
Главное преимущество лазерной точечной сварки — скорость. Весь процесс занимает всего миллисекунды. А лазерную точечную сварку можно повторить, чтобы обеспечить надлежащее соединение с металлами разной толщины. Несколько точек можно сваривать одновременно как для скорости, так и для правильного выравнивания компонентов.Лазерная точечная сварка часто используется для деталей авиакосмической отрасли, медицинских устройств и электроники.
Электропроводная сварка
Процесс кондуктивной сварки аналогичен точечной сварке, но лазерный луч перемещается после образования ванны расплава. Модулированные или импульсные лазеры создают сварные швы, которые могут быть структурно герметичными. С помощью лазера можно получить гладкий закругленный шов, не требующий дополнительной шлифовки или отделки.
Электропроводящие швы часто используются при глубине проплавления менее 2 мм.Электропроводность соединяемых материалов ограничивает максимальную глубину сварного шва. Ширина токопроводящего шва всегда больше его глубины. Детали автомобильного кузова, аккумуляторные батареи и герметичные уплотнения являются обычными применениями для кондуктивной сварки.
Сварка глубоким проникновением
Для создания лазерного шва с глубоким проплавлением используются чрезвычайно высокие плотности энергии. Используемый высокоэнергетический сфокусированный лазерный луч плавит и испаряет подложку. Давление пара вытесняет расплавленный металл.Это создает глубокую и узкую «замочную скважину». Лазерный луч перемещается, расплавленный металл обтекает замочную скважину, а затем затвердевает в глубоком и узком шве вдоль пути лазера.
Сварку с глубоким проплавлением можно использовать для самых толстых металлов. Даже некоторые металлы с высокой отражательной способностью можно сваривать толщиной до 15 мм благодаря длине волны лазера в ближнем инфракрасном диапазоне. Яркость мощных волоконных лазеров позволяет использовать линзы с большим фокусным расстоянием. Меньшая чувствительность упрощает создание высококачественных сварных швов.Сварные швы с глубоким проплавлением используются в таких областях, как компоненты трансмиссии и сталь толстого сечения для судов и трубопроводов.
Лазерная сварка может помочь вашему бизнесу
Лазерная сварка повышает скорость и производительность во многих отраслях промышленности. Узнайте, как решения для роботизированной сварки от Genesis Systems могут способствовать росту вашего бизнеса.
Лазерная сварка обеспечивает оптимальную эффективность
Дэн Белз из компании Amada предлагает очень простое уравнение для случая, когда изготовителю следует рассмотреть установку для лазерной сварки: «Если от 40 до 80 процентов выполняемой вами работы выполняется сварщиком, то вам нужно серьезно взглянуть на нее. технология лазерной сварки », — сказал он.Здесь мы видим лазерный сварочный аппарат FLW ENSIS в действии. Изображение любезно предоставлено Amada.Хотя лазерная сварка существует уже несколько лет, кажется, что только сейчас она приближается к критической рыночной стадии, когда ее внедрение будет ускоряться здесь, в Северной Америке.
«Похоже, на рынке существует выжидательная позиция, как если бы люди не были уверены, что технология зарекомендовала себя на рынке», — сказал Масуд Харуни, менеджер по продукции по лазерной сварке в TRUMPF North. Америка.«Тем не менее, сколько деталей в автомобилях, которые мы водим, производятся с использованием лазерной сварки каждый день?»
«За последние несколько лет количество различных типов транспортных средств, оснащенных более широким спектром силовых установок, выросло», — сказал Майк Шарп, менеджер по развитию лазерного бизнеса FANUC Robotics Ltd. «В отрасли есть много разных производителей, предлагающих разные модели, но их поставщики обслуживают еще более широкий рынок. Этот более широкий ассортимент продукции означает, что необходимо выполнить больше работы с добавленной стоимостью.Лазеры способствуют этому ».
Нерешительность среди мастерских, конечно, понятна — крупные инвестиции в технологию, которая меняет подход цеха как к сварке, так и к процессам проектирования, могут быть пугающими, особенно если цех обычно работает по проектам своих клиентов.
Но как только клиенты осознают ценность использования лазерной сварки, они могут довольно быстро адаптироваться. Дэн Белз, менеджер по продуктам компании Amada FLW, был свидетелем того, как работа мастерской помогла изменить точку зрения клиента.
«Как только они увидели качество деталей, которые они получали с помощью лазерной сварки, заказчик фактически предоставил цеху карт-бланш на проектирование детали, однако она будет лучше всего работать на аппарате для лазерной сварки», — сказал Белз. «Они в основном сказали:« Это то, что должна делать часть; спроектируйте ее так, чтобы она лучше всего подходила для лазерной сварки ».
Чисто законченные работы
Преимущества лазерной сварки довольно очевидны, когда вы видите деталь прямо из машины.Используя кондуктивную сварку, система лазерной сварки с присадочным материалом состоит из двух частей и по существу плавит материал, соединяя две поверхности вместе. Такие детали часто встречаются в автомобильных кузовных сборках, требующих высокого качества и гладких сварных соединений, поэтому их сложно сварить вручную. Но с правильным приспособлением лазерная сварка такой детали занимает мало времени и создает более чистый и точный готовый продукт.
В тяжелой промышленности, тем временем, выигрыш от использования техники сварки с глубоким проплавлением (замочной скважиной) можно сравнить с дуговой сваркой металлическим газом.Тепло полностью проникает через переднюю кромку расплавленного металла шва. По мере развития источника тепла расплавленный металл заполняет его за ним, образуя сварной шов. С помощью этой технологии в цехах можно добиться более прочного сварного шва (нагрузка на площадь сварного шва). А поскольку тепловложение в заготовку намного ниже, чем при GMAW, сварной шов менее подвержен таким проблемам, как растрескивание. Меньший нагрев также означает меньшую деформацию детали.
Бывают случаи, когда в стыках образуется щель, и ее можно устранить с помощью системы подачи проволоки на станке.Эта система вводит больше материала в стык, что помогает расплавить и устранить зазор.
«Используя приспособления из листового металла, наш заказчик смог сократить время производства детали с четырех часов до 18 минут», — сказал Масуд Харуни из TRUMPF. «Мы видим, как многие из наших клиентов возвращают нам креативные решения по ремонту, после того, как начинают думать иначе». Здесь мы видим пример фиксации в действии в сварочной ячейке. Изображение предоставлено TRUMPF.
Шарп призывает людей думать о лазерной сварке просто как о «еще одном методе, еще одном источнике энергии для выполнения работ, которые раньше, возможно, выполнялись вручную, или как об инструменте, который может улучшить или заменить существующие процессы». Его уникальность заключается в том, насколько быстрее он может выполнять определенные работы.
Но доказательство, как говорится, в пудинге.
«Мы завершили установку в январе на предприятии, которое занимается сваркой исключительно низкоуглеродистой стали», — сказал Белз. «Этот магазин производит чехлы трех разных размеров, от 1 до 2 футов.и 4 на 4 фута. Они разработали универсальное приспособление для этой работы и сваривают около 350 крышек каждую неделю. На их сварку у них уходило четыре дня, по два сварщика в первую и вторую смену каждый день. Теперь им требуется один день, две смены и два оператора, чтобы их сварить. Между тем, после сварки, раньше они касались каждой из этих частей, зачищали брызги, шлифовали сварные швы, которые в этом нуждались, и подкрашивали отверстия. Теперь 335 или более из этих 350 деталей отправляются прямо в окрасочную камеру, полностью минуя отделку.Теперь покрасочная камера стала их узким местом ».
Второй заказчик Belz, производитель оригинального оборудования, находился в процессе разработки нового продукта для лазерной сварки. Компания тратит время на то, чтобы настроить и усовершенствовать дизайн для лучшей установки, но как только это произойдет, машина будет занята выпуском крупных партий продукции. Хотя редизайн внешнего интерфейса может быть более сложным, долгосрочная экономия времени будет существенной.
Поддержка бесперебойного производства
Важно, чтобы производители не понимали, что лазерная сварка так же проста в применении, как лазерная резка на плоской станине.
TRUMPF предлагает учебные курсы по технологии, в первую очередь ориентированные на крепление и эксплуатацию, но также помогает клиентам с дизайнерскими идеями плавно переходить к производству.
Крепление рассматривается как препятствие для многих, рассматривающих эту технологию, но, как объясняет Харуни, «большинство приспособлений, которые мы помогаем спроектировать и использовать, очень легко построить. Поскольку деформация намного меньше по сравнению с традиционной сваркой, приспособления могут быть изготовлены из листового металла, который легче и дешевле по сравнению с механически обработанными прочными металлическими приспособлениями.”
После создания приспособления повторяемость создает свои преимущества.
И как только производитель привык к тому, как работает оборудование, Харуни и Белз заявили, что они заметили, что клиенты стали более изобретательными. В качестве хорошего примера компания Belz привела регулируемое приспособление одного покупателя. Пример Харуни не так уж и примечателен.
Майк Шарп из FANUC Robotics призывает людей думать о лазерной сварке просто как о «еще одном методе, еще одном источнике энергии для выполнения работ, которые раньше, возможно, выполнялись вручную, или как об инструменте, который может улучшить или заменить существующие процессы.«Уникальность этого метода заключается в том, насколько быстрее он может выполнять определенные работы. Изображение любезно предоставлено FANUC Robotics.
«Используя приспособления из листового металла, наш заказчик смог сократить время производства детали с четырех часов до 18 минут», — сказал Харуни. «Мы видим, как многие из наших клиентов возвращают нам креативные решения по ремонту, после того, как начинают думать иначе».
Другой образ мышления, который должен измениться, когда производитель начинает путь к лазерной сварке, — это трюизм «больше изгибов, меньше сварных швов».Если деталь закреплена для очень быстрого процесса сварки, дополнительные изгибы иногда могут быть контрпродуктивными.
«Во многих случаях использование вашего листа снижается, если вы режете деталь для большего количества изгибов», — сказал Харуни. «Теперь, если вы, скажем, строите коробку, может быть более целесообразным, чтобы две концевые детали представляли собой отдельные прямоугольные детали, которые можно приваривать со скоростью 120 дюймов в минуту к более простому изгибному профилю. Дело в том, что использование лазерной сварки изменяет оптимальную конструкцию многих деталей, и это способствует использованию листов при резке, поскольку каждая деталь имеет прямоугольную форму.»
Belz предлагает очень простое уравнение для случая, когда изготовителю следует рассмотреть установку для лазерной сварки:« Если от 40 до 80 процентов выполняемой вами работы выполняется сварщиком, то вам нужно серьезно взглянуть на технология лазерной сварки », — сказал он.
Обновление производственного инструмента
Каждый производитель постоянно модернизирует свою линейку продуктов, чтобы облегчить лазерную сварку для своих клиентов. Например, TRUMPF теперь имеет свою автономную систему программирования TruTops Weld, которая позволяет цехам программировать детали для сварки в ячейке лазерной сварки, в то время как другие детали работают, поэтому нет необходимости проходить процесс обучения робота с помощью подвески и терять драгоценное время работы сварочной ячейки.
«Самой важной частью этой программы на самом деле является наш датчик TeachLine, который интегрирован в программу», — сказал Харуни. «Обычно, когда вы берете программу и вводите ее в реальный мир, ее необходимо настроить. Однако эта сенсорная технология определяет точное положение компонента на машине и автоматически адаптирует программу. Опять же, это сокращает время на повторное обучение ».
Amada, тем временем, имеет свой аппарат FLW-ENSIS, который был модернизирован новой системой подачи проволоки, которая включает выпрямитель проволоки и двухтактный двигатель, поэтому можно имитировать действия ручного оператора при сварке MIG.
«Линейная система для проволоки также была модернизирована, — сказал Белз. «Эта комбинация, наряду с нашей вращающейся линзой, которая позволяет вам легче закрывать зазоры в материале, дает вам гораздо больше возможностей при выборе способа обработки шва.
«У нас есть клиенты, которые могут приваривать дюймовую скобу к другому куску формованного материала, и посадка может быть неправильной. Но вместо того, чтобы возиться со своим креплением, они просто бросают провод, чтобы заполнить его, потому что знают, что это даст им нужный результат.Подача проволоки делает процесс более щадящим. Мы потратили так много времени на продвижение оборудования и приспособлений, но клиенты понимают, что им нужно и когда им это нужно, поэтому те, кто обучен этому процессу, теперь делают выбор, исходя из своих потребностей ». Это еще один пример клиентов, которые теперь понимают, как меняются технологии, и делятся своими знаниями с производителями машин.
Преимущества лазерной сварки довольно очевидны, если вы видите деталь прямо из машины.Скорость и точность сварки в сочетании с сокращением или полным отказом от постобработки позволяют значительно сэкономить время и трудозатраты. Изображения любезно предоставлены Amada.
FANUC имеет большой опыт как в области робототехники, так и в области лазерной техники. На FABTECH Atlanta 2018 компания продемонстрировала то, что она назвала своей системой волоконно-лазерной сварки FF3000, в которой робот загружал купоны в машину, сваривал два куска материала вместе, а затем наносил на них лазерную маркировку.Система демонстрирует простоту использования благодаря прямому управлению с подвесного пульта обучения роботов, позволяя лазеру и роботам действовать как одно целое, упрощая приложение и увеличивая время безотказной работы.
«У нас есть технология выбора волоконного лазера, которая позволяет нам иметь несколько выходных волокон от одного лазерного источника, что позволяет нам, например, сваривать и резать одну сборку, что дорого, но удовлетворяет потребности некоторых объектов». — сказал Шарп. Но Шарп видит особую силу FANUC в технологии управления, которая хорошо известна многим в отрасли.
«Движение робота и функции лазера объединяются на одной шине управления, что упрощает настройку и позволяет легко собирать обширные диагностические данные», — сказал он. Диагностика оборудования FANUC означает доступ к технологии управления системами Zero Down Time (ZDT), которая позволяет оператору узнать, когда какая-либо часть узла нуждается в обслуживании или замене. «Это позволит проверить определенные тенденции и сообщить вам, когда, например, ваш покровный слайд пачкается, или если вы получаете слишком много рассеянного света или слишком большое обратное отражение на вашем лазере.Дело в том, чтобы избежать незапланированного обслуживания, и это поможет вам в этом ».
Все, включая оптику, управляется непосредственно с обучающего пульта, что опять же означает, что пользователь, скорее всего, узнает элементы управления.
Как и другие компании, FANUC разработала технологию, которая позволяет лучше управлять волоконным лазером на детали, чтобы перекрыть более широкие зазоры в материале. Это известно как управляемый роботом воблер луча. Производитель разработал свою модель с помощью LaserMech.
«Наша технология позволяет направлять луч примерно по 50-миллиметровому шаблону на рабочей поверхности», — сказал Шарп. «Поскольку и движение робота, и лазер управляются одним и тем же контроллером, вы можете получить очень быструю реакцию для выполнения очень специфических функций, включая плетение, C-образные зажимы, зигзаги и прямолинейные стежки на шве. Я также могу писать в режиме низкого энергопотребления, который встроен во все наши лазеры для маркировки деталей. Между тем, плетение луча включает в себя фактическое перемещение робота во время движения луча.Это то, что позволяет нам закрывать зазоры в сварочных материалах и дает нам более широкие возможности для процесса, поскольку движение жестко контролируется с помощью серводвигателей. Точность всех составляющих элементов означает, что можно получить очень точное позиционирование пути ».
Шарп поднял важный вопрос, когда упомянул элементы управления, движение и сбор данных. Он видит силу своей компании в ее способности сочетать знания в области лазеров, движения, сбора данных и искусственного интеллекта.Хотя это может быть правдой, также верно и то, что совместное применение всех этих вещей на разных уровнях производственной операции меняет характер цеха. Проблема для многих состоит в том, чтобы адаптировать свой подход к новым технологиям, которые теперь доступны для использования. Те, кто применил волоконную лазерную сварку, похоже, извлекают выгоду из своих новых инвестиций. Просто это немного другое мышление.
Belz видит, что изменения происходят быстро.
«Похоже, мы достигли переломного момента.В этом году наши продажи увеличились вдвое по сравнению с предыдущим годом. Я ожидаю, что то же самое произойдет в следующем году ».
Хотя он по-прежнему считает, что необходимо провести много обучения на местах, Харуни также убежден, что внедрение технологии ускорится, и не только в OEM-производителях.
Преимущества лазерной сварки довольно очевидны, если вы видите деталь прямо из машины. Скорость и точность сварки в сочетании с сокращением или полным отказом от постобработки позволяют значительно сэкономить время и трудозатраты.Изображения любезно предоставлены Amada.
«Помимо производителей оригинального оборудования, увеличение заказов показывает, что мастерские охотно используют эту технологию для производства деталей более высокого качества и с меньшими затратами», — сказал он.
С редактором Робертом Колманом можно связаться по адресу [email protected].
Amada Inc., www.amada.com
FANUC America Inc., www.fanucamerica.com
TRUMPF Inc., us.trumpf.com
Основы лазерной сварки — Laser Chirp
Джефф Шеннон
Введение
Этот документ представляет собой очень краткий обзор ключевых аспектов лазерной сварки и соображений, касающихся текущих производственных процессов.Пользователи всегда должны сотрудничать с компаниями, разбирающимися в тонкостях лазерной сварки, чтобы обеспечить производственное решение, оптимизированное для конкретных производственных требований.
Механизм лазерной сварки
Режим проводимости — Выполняется при низкой плотности энергии, образуя мелкий и широкий сварной шов. Обычно используется для обеспечения очень гладкого и эстетичного внешнего вида, а также для герметизации сварных швов аккумуляторных батарей, чтобы гарантировать, что никакие частицы не могут попасть в аккумулятор.Лазеры фокусируют всю мощность света или фотоны до очень малого диаметра, что создает очень высокую концентрацию мощности (плотность мощности), которая быстро нагревает металлы. Существует три типа режимов сварки, в зависимости от плотности мощности, содержащейся в пределах размера фокусного пятна: режим проводимости, переходный режим «замочной скважины» и режим проплавления / «замочной скважины» (см. Рисунок 1).
Переходный режим — Возникает при средней плотности мощности и приводит к большему проникновению с отношением ширины к глубине около 1-1.5, и используется во многих приложениях для микросварки.
Замочная скважина / режим проникновения — Дальнейшее увеличение пиковой плотности мощности создает испаренный элемент, известный как замочная скважина. Замочная скважина имеет низкую оптическую плотность и поэтому действует как канал для подачи лазерной энергии вглубь детали. В этом режиме отношение ширины к глубине> 5.
Конструкция детали для лазерной сварки
Перед сваркой любых деталей необходимо выполнить анализ свариваемости, включая выбор материала, конструкцию соединения, допуски на сборку и требуемые функциональные возможности сварки.В таблице 1 приведены сведения о свариваемости наиболее часто используемых материалов.
Также важно провести анализ при сварке разнородных материалов, потому что многие желательные комбинации разнородных материалов создают интерметаллические области, которые могут вызвать хрупкость. В таблице 2 приведены общие рекомендации по выбору разнородных материалов.
Таблица 2. Рекомендации по выбору разнородных материаловПри микросварке материала покрытия толщина и метод покрытия могут иметь значительное влияние на процесс сварки.Никелирование предпочтительно с использованием метода электролитического покрытия. Сварка внахлест оцинкованной стали широко используется в автомобильной промышленности. Для выполнения такой сварки необходимо обеспечить отвод цинка с низкой температурой кипения.
Можно сваривать стыки различной геометрии. Наиболее распространенные конструкции сварных швов показаны на рисунке 2.
Рис. 2. Три конструкции шва с нормативным допуском сварного зазораСтыковой шов — проплавление шва происходит непосредственно по границе стыка, очень эффективное использование мощности для достижения прочности сварного шва.Однако требуется выравнивание лазера по стыковому соединению, и по мере того, как толщина материала уменьшается ниже 0,02 дюйма, сборка деталей таким образом, чтобы они были близко друг к другу, становится проблемой.
Угловой шов — Провар под углом к стыку стыка; Прочность сварного шва — это баланс ширины сварного шва и проплавления. Для толщины верхнего листа менее 0,04 дюйма лазер можно направить вертикально вниз для облегчения движения.
Сварка внахлест — При наложении двух частей внахлест необходимо проплавить верхний лист, чтобы добраться до границы раздела.Прочность создается шириной сварного шва на границе раздела, а не глубиной проплавления. Однако здесь нет интерфейса для выравнивания, поэтому этот режим очень удобен для размещения лазера на детали. Как правило, такая геометрия соединения требует простейшего инструмента.
Импульсная лазерная сварка
Импульсные Nd: YAG и волоконные лазеры в основном используются для тонкой сварки микросварок. Пиковая мощность (используется для контроля проплавления) и ширина импульса (параметр точной настройки, используемый для регулировки проплавления и ширины сварного шва) являются ключевыми параметрами, которые необходимо оптимизировать.Оптимальная пиковая мощность определяется как пиковая мощность, которая обеспечивает наиболее глубокое проникновение без выброса материала. Типичные значения пиковой мощности могут находиться в диапазоне 0,25–3 кВт с шириной импульса 0,1–5 мс.
Для шовной сварки, которая фактически представляет собой серию перекрывающихся точечных швов, частота следования импульсов или частота импульсов регулируют нагрев детали. При выполнении шовной сварки важно поддерживать постоянное перекрытие точек вокруг детали, чтобы избежать появления горячих точек. Следовательно, следует синхронизировать положение лазера на детали и срабатывание лазера; эта операция известна как стрельба по положению.На рисунке 3 показаны примеры многих материалов и деталей, которые можно сваривать с помощью импульсного лазера.
Рис. 3. Примеры импульсной лазерной сварки Непрерывная лазерная сварка
Лазер, который может оставаться включенным до выключения, известен как непрерывный (CW) лазер. Для непрерывной сварки можно использовать волоконный, дисковый, CO 2 или диодный лазер. Лазеры непрерывного действия обычно используются для сварки отверстий и проплавления. Рассматриваемые параметры лазера — это размер оптического пятна, качество луча и мощность.Типичные уровни мощности для непрерывной сварки составляют от 1 до 6 кВт, обеспечивая глубину проплавления до и более 0,25 дюйма (6 мм) в стали и алюминии.
Качество луча, или M 2 , является относительно новым параметром, который показывает, насколько близок профиль мощности лазера к идеальному профилю мощности по Гауссу. Лазер, близкий к гауссову, называется одномодовым; лазер, расположенный дальше от гауссова, называется многомодовым. Качество луча нужно выбирать с умом.
На рисунке 4 показан (а) сварной шов одномодовым волоконным лазером мощностью 500 Вт со значением M 2 , равным 1.2 при 300 дюйм / мин (IPM) с размером 30 микропятно; (b) многомодовый лазерный сварной шов мощностью 700 Вт со значением M 2 , равным 15, при 100 IPM с размером пятна 150 мкм; и (c) сварка многомодовым волоконным лазером мощностью 1 кВт со значением M 2 , равным 15, при 80 IPM с размером пятна 250 мкм. Например, при выборе лазера для стыковой или угловой сварки нельзя выбрать одномодовый лазер, поскольку выравнивание лазера по границе раздела нецелесообразно. Однако его можно использовать для сварки внахлест.
Рис. 4. Влияние качества луча на сварной шов для одномодового и многомодового лазера. Одним из интересных аспектов непрерывного одномодового волоконного лазера является чрезвычайно высокая плотность мощности, которую они могут обеспечить, что может использоваться для сварки материалов с высокой отражающей способностью (например, алюминий и медь) с относительно низкими средними мощностями.На рис. 5 показаны различные примеры непрерывной лазерной сварки.
Рис. 5. Примеры непрерывной лазерной сварки Роль вспомогательного газа в лазерной сварке
Вспомогательный газ может использоваться при лазерной сварке для создания инертной среды, которая помогает предотвратить окисление сварных швов и просто для получения эстетичных блестящих сварных швов, особенно при микросварке это предпочитают многие конечные пользователи; уменьшить блокировку луча сверхмелкозернистыми частицами, образующимися при образовании замочной скважины; и для защиты лучевой оптики путем перенаправления дыма от фокусирующей головки.Аргон и азот — наиболее часто используемые газы; гелий иногда используется для сварных швов с критическим проплавлением.
При сварке проплавлением дополнительная поперечная струя и воздушный нож также используются для облегчения удаления сверхмелкозернистых частиц при сварке волоконным и дисковым лазерами, при этом воздушный нож находится под покровным скользящим элементом фокусирующей оптики для предотвращения попадания пыли и минимум помощи в уменьшении разбрызгивания. Обратите внимание, что лучшей защитой от чрезмерного разбрызгивания при сварке с проплавлением является использование фокусирующей оптики с фокусным расстоянием не менее 8 дюймов (200 мм), чтобы физическое расстояние до сварного шва уменьшало разбрызгивание.
Элементы системы лазерной сварки
Каждая система лазерной сварки состоит из пяти одинаковых элементов: лазера, доставки лазера на рабочую станцию, фокусировки лазера, движения и инструментов.
Для всех лазеров (кроме лазера CO 2 ) лазер может быть доставлен на рабочую станцию с помощью гибкого кабеля, что обеспечивает очень удобное подключение лазера непосредственно к фокусирующей головке. Головка фокусировки позволяет сфокусировать лазер в точную точку, обычно между 0.004-0,02 дюйма. Затем используется подходящее движение, которое выбирается в зависимости от конкретной детали. Движение может перемещать лазер, деталь или и то, и другое. Лазер — это очень гибкий инструмент, обеспечивающий широкий спектр производственных решений. Оснастка — это последний важный элемент системы лазерной сварки. Его важность нельзя недооценивать. Инструмент должен быть спроектирован таким образом, чтобы минимизировать допуски на сборку.
Доктор Джефф Шеннон — менеджер по передовым технологиям в Amada Miyachi America.
Традиционная сварка vs.Лазерная сварка
Сварка — это процесс изготовления, в котором используется тепло для соединения двух или более отдельных деталей. В настоящее время профессионалы отрасли используют в своей работе как традиционные методы дуговой сварки, точечной сварки, так и лазерной сварки. Оба варианта процесса обладают уникальными характеристиками, которые делают их пригодными для различных случаев. Например, традиционная сварка обеспечивает менее точную подгонку детали, в то время как лазерная сварка обеспечивает большую скорость обработки и меньший риск термической деформации.
В следующей статье резюмируются различия между традиционными сварочными услугами и услугами лазерной сварки, в том числе описывается их процесс, основные преимущества и типичные области применения.
Традиционные процессы сварки
Сегодня существует несколько традиционных методов сварки, в том числе:
- Сварка вольфрамовым электродом в среде инертного газа (TIG) . В этом методе дуговой сварки используется неплавящийся вольфрамовый электрод для нагрева заготовки и плавления присадки (при ее наличии) для получения сварного шва.
- Сварка металла в среде инертного газа (MIG). В этом методе дуговой сварки для получения сварного шва используется элемент расходуемой проволоки, служащий электродом и присадочным материалом.
- Точечная сварка. В этом методе сварки используется пара электродов для зажима деталей вместе и пропускания электрического тока между ними для создания сварного шва.
Процесс сварки в режиме лазерной проводимости
Сварка в режиме лазерной проводимости — это передовая технология соединения металлов, в которой используется сфокусированный лазерный луч с заданным размером пятна.Во время сварочных операций лазерный расплав локализует участки детали и, если присутствует, присадочный материал, чтобы сформировать точные сварные швы. Titanova предлагает как автогенные (без присадочного материала), так и неавтогенные варианты с использованием лазерной сварки горячей проволокой или лазерной сварки холодной проволокой. В зависимости от геометрии детали, соединения и общих требований к конструкции, лазеры могут использоваться вместо традиционного процесса сварки.
<Подробнее о лазерной сварке с подачей горячей и холодной проволоки.>
Преимущества традиционной сварки
Лазерная сварка имеет ряд преимуществ по сравнению с традиционными методами сварки. Однако традиционные сварочные процессы остаются надежным производственным решением для многих отраслей по следующим причинам:
- Они понятны производственному сообществу благодаря унаследованным операциям.
- Они предназначены для менее точной сборки деталей.
- Их проще автоматизировать.
- Они имеют более низкие начальные инвестиционные затраты.
- Их можно реализовать вручную.
Преимущества лазерной сварки
По сравнению с традиционными методами сварки, лазерная сварка имеет следующие преимущества:
- Меньше тепла. При лазерной сварке зона термического влияния (HAZ) намного меньше, а общее тепловложение намного ниже, чем при традиционных сварочных операциях.
- Сниженный риск макро-прогибов и перекосов. Вышеупомянутые качества также позволяют снизить искажения, вызванные тепловым воздействием.Меньше тепла означает меньшее тепловое напряжение, что приводит к меньшему повреждению заготовки.
- Более быстрое время обработки. Несмотря на более высокие первоначальные вложения в инструмент, лазерная сварка часто оказывается более рентабельной, чем традиционная сварка из-за более высокой скорости обработки. Более высокие скорости производства также означают более высокие производственные мощности, что приводит к более быстрому производственному циклу.
- Лучше подходит для тонких металлов. Благодаря регулируемому размеру пятна лазерная сварка является отличным методом соединения тонких или хрупких металлических деталей.Размер пятна может быть специально разработан таким образом, чтобы расплавить только необходимое количество металла для получения сварного шва, тем самым сводя к минимуму возникновение тепловых внутренних напряжений, деформаций и дефектов.
Применение лазерной сварки
Более высокая точность, управляемость и эффективность, обеспечиваемые процессом лазерной сварки, делают его подходящим для производства следующего:
- Детали гидравлики и управления жидкостью
- Узлы с тонкой оболочкой, критичные к искажениям
- Пленки
- Топливная рейка
- Медицинские инструменты
- Теплообменники из нержавеющей стали
- Ящики металлические тонкие
- Тонкие детали манометра
- Тонкая трубка
Свяжитесь со специалистами по лазерной сварке Titanova Today
Хотя традиционные методы сварки имеют свои преимущества, лазерная сварка стала популярным вариантом соединения металлов из-за ее точности, контроля и способности сваривать деликатные или тонкие металлические детали.Если вам нужна лазерная сварка или другие услуги по лазерной обработке материалов, рассмотрите вариант Titanova. У нас более 30 лет опыта в этой области. Чтобы получить информацию о наших возможностях лазерной сварки, посетите нашу страницу возможностей лазерной сварки или свяжитесь с нами сегодня.
Размер пятна, качество лазера и производительность сварки
Влияние размера пятна и качества лазерного луча на характеристики сварки при использовании мощных непрерывных твердотельных лазеровГерт Верхаге и Пол Хилтон, TWI Ltd
Доклад, представленный на ICALEO 2005, 24-м Международном конгрессе по применению лазеров и электрооптики, 31 октября — 4 ноября 2005 г., Майами, Флорида, США.Документ № 511.
Аннотация
Для сварки, резки и обработки поверхностей использование мощных волоконных лучей твердотельных лазеров дает множество преимуществ. Всего 10 лет назад единственным доступным лазерным источником этого типа был Nd: YAG-лазер с ламповой накачкой — лазер со скромным качеством луча. Несмотря на такое скромное качество луча, эти лазерные источники широко используются для сварки, особенно в автомобильной промышленности. Однако сегодня диапазон лазерных лучей непрерывного действия (CW), доставляемых по волокну, значительно увеличился, равно как и качество лазерного луча.Выбор источника лазера для конкретного приложения уже не очевиден. В этой статье рассматривается вопрос о том, как качество лазерного луча лазеров с непрерывной подачей волокна влияет на производительность сварки, путем сравнения серии сварных швов, выполненных на тонких и толстых сечениях алюминия и стали, с использованием постоянной мощности лазера от лазерных источников с различным качеством луча.
Введение
Всего несколько лет назад любому, кто хотел использовать преимущества волоконно-оптической доставки луча от лазерного источника, нужно было учитывать капитальные затраты, эксплуатационные расходы, надежность и способность лазера выполнять требуемый процесс.В то время не нужно было рассматривать тип лазерного источника, поскольку единственным доступным лазерным источником с непрерывной подачей волокна был стержневой Nd: YAG-лазер с ламповой накачкой. Сегодняшний пользователь лазерной энергии с оптоволоконной доставкой должен теперь добавить к приведенному выше списку тип технологии, используемой для генерации лазерного луча. Это связано с быстрым прогрессом, достигнутым за последние несколько лет в создании лазерных источников непрерывного инфракрасного излучения с длинами волн, подходящими для передачи по оптическому волокну.Стержневые Nd: YAG-лазеры с диодной накачкой, Yb-волоконные лазеры и Yb: YAG-лазеры с тонкими дисками в настоящее время коммерчески доступны с мощностью не менее 4 кВт.
Пользователи лазератеперь также сталкиваются с дополнительными вопросами качества и яркости лазерного луча, так как оригинальные стержневые лазеры CW Nd: YAG с ламповой накачкой могли достигать произведения параметров луча только около 20-25 мм.мрад при 4 кВт, в то время как некоторые из них Упомянутая выше передовая лазерная технология может работать при мощности 4 кВт при минимальных параметрах луча 2 мм.мрад.
Следствием высокого качества лазерного луча, то есть низкого значения произведения параметров луча, является то, что луч может быть сфокусирован в оптическое волокно малого диаметра. На стороне обработки это означает, что фокусирующая оптика заданного диаметра обеспечивает лучшую фокусируемость лазерного луча до минимального диаметра перетяжки луча (размера пятна). Или, для данного размера пятна и фокусирующей оптики данного диаметра, более высокое качество луча приведет к более высокой яркости (определяемой как отношение плотности мощности в перетяжке луча и телесного угла, образованного фокусирующим конусом луча).Для данного размера пятна более высокое качество луча приведет к большей глубине фокуса в перетяжке луча. Высокое качество луча также позволит увеличить расстояние между фокусирующей линзой и деталью, что дает практическое преимущество в виде минимизации повреждения оптической системы разбрызгиванием.
Каждая из упомянутых выше передовых лазерных технологий имеет свои преимущества, а в некоторых случаях и недостатки. Целью данной статьи не является комментирование в этой области, а, скорее, исследование возможностей процесса сварки ряда источников непрерывного лазерного излучения с волоконной подачей и систем фокусировки луча с произведениями параметров луча от 23 до 4 мм.мрад в контролируемой серии экспериментов с алюминием и сталью для определения глубины проплавления как функции скорости сварки при постоянной мощности лазера 4 кВт.
Общие сварочные характеристики стержневых лазеров CW Nd: YAG с мощностью детали до 10 кВт были описаны Расселом и Хилтоном. [1] Verhaeghe и Hilton [2] сообщили о сварочных характеристиках Yb-лазера мощностью 7 кВт, а Weberpals, Russ, Dausinger и Hügel [3] сообщили о сварочных характеристиках Yb мощностью 4 кВт: YAG-лазер с тонкими дисками.Hügel [4] сообщил о сварочных характеристиках стержневого лазера на Nd: YAG с диодной накачкой. В некоторых работах также сравниваются характеристики различных лазерных источников, например Bartel, Pathe, Roatzsch и Weick [5] , которые обсуждают влияние качества луча при сварке с Nd: YAG и CO 2 лазерами и Ream [6] , который сравнил эффективность сварки Nd: YAG, дискового и волоконного лазеров. Verhaeghe и Hilton [2] также сравнили результаты волоконного лазера с данными CO 2 и Nd: YAG.Общая проблема со сравнениями в [2, 5] и [6] , однако, заключается в том, что данные получены за разные (иногда длительные) периоды времени, на немного разных выборках, с разными размерами пятен и в разные полномочия, что в совокупности затрудняет делать краткие выводы. В работе, представленной здесь, все эксперименты проводились на одних и тех же материалах, мощность всех лазеров измерялась одним и тем же измерителем мощности, и оптические системы были выбраны для получения, а также для получения « наименьшего » диаметра пятна, диаметра пятна как близко к 0.4 мм для каждого используемого лазерного источника. Целью данной работы было исследование характеристик источников непрерывного лазерного излучения с волоконной подачей для сварки алюминия и стали, для различных параметров лазерного луча и размеров сфокусированного пятна.
Программа экспериментальных работ
Характеристики лазеров, использованных в этих экспериментах, и их систем доставки пучка приведены в таблице . Четыре различных лазера с произведением параметров луча от 23 до 4 мм.мрад.
Таблица 1 Характеристики лазеров и систем доставки пучка, использованных в экспериментах
Лазер | Лазер 1 | Лазер 2 | Лазер 3 | Лазер 4 | |||||
---|---|---|---|---|---|---|---|---|---|
905 Nd: YAG6 905 Yb: Fib re | Yb: YAG диск | ||||||||
Диаметр выходного волокна (мм) | 0.6 | 0,3 | 0,1 | 0,2 | |||||
Фокусное расстояние коллимирующей линзы (мм) | 200 | 120 | 120 | 150 | 200 | ||||
Фокусное расстояние фокусирующей линзы (мм) | 200 | 150 | 160 | 500 | 160 | 280 | 200 | ||
Номинальная ширина тали (мм) | 0,60 | 0,45 | 0.40 | 0,42 | 0,13 | 0,37 | 0,20 | ||
Измеренная перетяжка балки (86% точек) (мм) | 0,61 | 0,44 | 0,39 | 0,40 | 0,14 | 0,34 | 0,20 | ||
Продукт параметра луча * (мм.мрад) | 23 | 22 | 18 | 4 | 4 | 7 | 7 | ||
Длина Рэлея * (мм) | 4.0 | 2,5 | 2,1 | 9,9 | 1,2 | 4,0 | 1,1 | ||
Мощность лазера на заготовке | 4000 | 4000 | 4000 | 4000 | 4000 | 4000 | 4000 | ||
Плотность мощности на перетяжке балки для 4000 Вт (кВт / мм 2 ) | 13,7 | 26,6 | 33,8 | 31,5 | 264,4 | 45.1 | 134,2 | ||
Яркость (при 4000 Вт) (10 5 Вт / мм 2 . Стерадиан) | 2,79 | 3,04 | 5,96 | 54,25 | 46,60 | 18,01 | 27,34 | ||
* На основе данных о каустике балки |
с | P = мощность, измеренная на заготовке, Вт F = фокусное расстояние фокусирующей линзы, мм ω0 = радиус перетяжки луча, мм D = апертура лазерного луча, мм |
Из точек данных в Рис. 8 также можно увидеть, например, что для скорости сварки 1 м / мин для достижения глубины проплавления 8 мм нет необходимости использовать лазерная система с яркостью более 10 6 Вт / мм 2 .стерадиан. То же самое верно для глубины проплавления чуть менее 4 мм при скорости сварки 5 м / мин, а также для глубины проплавления 2 мм при скорости сварки 15 м / мин.
Рисунок 8 показывает тот же график, что и в Рисунок 7 , но для сварки стали вместо алюминия. В случае стали может показаться, что оптимальная яркость для достижения наибольшей глубины проплавления немного отличается в зависимости от скорости сварки, то есть от 32 до 38 x 10 5 Вт / мм 2 .стерадиан для скоростей сварки 1 и 15 м / мин соответственно.
Причины такой оптимальной яркости и ее очевидной независимости от скорости сварки и материала на момент написания этой статьи не были полностью поняты.
Рис. 8. График зависимости глубины проплавления стали от яркости сфокусированного лазерного пятна для скоростей сварки 1, 5 и 15 м / мин. Линии — это путеводитель для глаз.
Рисунки 9 и 10 демонстрируют улучшение рабочих характеристик для алюминия и стали соответственно, достигнутое в этом эксперименте, с использованием системы с наименьшим произведением параметра луча и размером пятна, т.е.е. 4 мм.мрад и 0,14 мм, по сравнению с системой с наибольшим произведением параметра луча и размером пятна, то есть 23 мм.мрад и 0,61 мм. Это показывает, что выбор источника лазера с параметром ближнего луча и небольшим размером пятна может улучшить характеристики сварки как стали, так и алюминия.
Рис. 9. Глубина проплавления алюминия в зависимости от скорости сварки для двух крайних значений: размера сфокусированного пятна и произведения параметров луча, использованных в экспериментах.
Рис.10. Глубина проплавления стали в зависимости от скорости сварки для двух крайних значений: размера сфокусированного пятна и произведения параметров луча, использованных в экспериментах.
Выбор системы лазерной сварки
Результаты, представленные на рис. 5 , показывают, что при выборе оптимальной сварочной системы с возможностью обработки в диапазоне скоростей сварки и толщины материала не будет никакой реальной пользы от использования сфокусированного пятна меньше 0,3 мм. в диаметре.Сочетание этого показателя с «оптимальным» показателем яркости 33×10 5 Вт / мм 2 . Стерадиан указывает на то, что этого можно достичь с помощью объектива с фокусным расстоянием около 350 мм для системы фокусировки с апертурой 50 мм. , например. Если числовая апертура волокна для доставки луча составляет порядка 0,2, то для достижения размера пятна 0,3 мм с коллимирующей линзой с фокусным расстоянием 175 мм потребуется волокно для доставки с диаметром около 0,15 мм.Чтобы использовать такое волокно, произведение параметров луча лазера должно составлять от 5 до 7 мм · рад.
Выводы
Производительность серии непрерывных лазерных систем с волоконной подачей была оценена при мощности лазера 4000 Вт, измеренной на заготовке, для сварки алюминия и стали. В работе исследовались размеры пятна от 0,61 до 0,14 мм и произведения параметров пучка от 23 до 4 мм · рад. Работа позволила сделать следующие выводы:
- Для данного качества лазерного луча меньшее пятно обычно обеспечивает либо более высокую скорость сварки для данной глубины проплавления, либо увеличение глубины проплавления для данной скорости сварки.Чем меньше уменьшение размера пятна, тем меньше усиление.
- Для лазера с фиксированным произведением параметра луча, равным 4 мм.мрад, увеличение глубины проплавления при переходе от диаметра пятна 0,4 мм к диаметру пятна 0,14 мм невелико для скоростей сварки менее 7,5 м / мин, но тогда линейно увеличивается выше этой скорости.
- Для заданного диаметра пятна 0,4 мм лазер с лучшим качеством луча обычно обеспечивает либо более высокую скорость сварки при заданной глубине проплавления, либо увеличение глубины проплавления при заданной скорости сварки.
- Небольшое увеличение глубины проникновения можно увидеть при любом качестве луча для диаметров пятна менее 0,3 мм.
- График зависимости глубины проплавления от яркости лазерного луча показывает, что для скоростей сварки от 15 до 1 м / мин существует «оптимальная» яркость для увеличения глубины проплавления как алюминия, так и стали. Эта оптимальная яркость составляет от 32 до 38 x10 5 Вт / мм 2 .steradian, независимо от скорости сварки или материала.
Благодарности
Авторы хотели бы поблагодарить Энтони Эллиотта, Пола Фенвика и Харви Уитмора из TWI за их помощь в проведении испытаний сварки. Авторы также благодарны коллегам из Trumpf и IPG за помощь в выполнении некоторых работ, описанных в этой статье. Это исследование стало возможным благодаря участию Агентства регионального развития Йоркшира и Хамбера.
Список литературы
- Рассел, Дж.Д., Хилтон, П.А. (2001) Разработка установки для лазера Nd: YAG мощностью 10 кВт, в материалах 7 -й Международной конференции по сварке : Высокопроизводительные процессы соединения: основы, прикладное оборудование, Аахен, Германия, том 1, 299-310.
- Verhaeghe, G., Hilton, PA, (2005) Битва источников — использование высокомощного Yb-волоконного лазера для сварки стали и алюминия, in Proceedings of the 3 rd International WLT Conference of Lasers in Manufacturing, Мюнхен, Германия , 33-38.
- Weberpals, J., Russ, A., Dausinger, F. Hügel, H. (2005) Влияние диаметра фокуса при лазерной сварке тонким дисковым лазером, в материалах 3 rd International WLT Conference of Lasers in Manufacturing , Мюнхен, Германия, 39-42.
- Хюгель, Х. (2000) Новые твердотельные лазеры и возможности их применения, в Оптике и лазерах в технике, том 34, 213-229.
- Bartel, W., Pathe, D., Roatzsch, R., Weick, JM (1997) Влияние качества луча при сварке лазерами Nd: YAG и CO 2 , Труды конференции «Лазеры в обработке материалов», Мюнхен , Германия, т.3097, 147-156.
- Ream, S.L. (2005) Диск и оптоволокно становятся все популярнее, Industrial Laser Solutions, февраль 2005 г., 15-19.
- Greses J, Hilton P A, Barlow C. Y, Steen W. M (2002) Затухание шлейфа при высокомощной лазерной сварке Nd: YAG, в Proceedings of ICALEO 2002, Скоттсдейл, Аризона, США, том 94, 10 стр.
- Оливье С. А., Хилтон П. А., Рассел Дж. Д. (1999) Обработка материалов с помощью лазерной установки на Nd: YAG мощностью 10 кВт, в Proceedings of ICALEO 1999, Сан-Диего, Калифорния, США, раздел D, 233-241.
Герт Верхаеге — механик (MSc) и европейский инженер по сварке (EWE), который начал свою карьеру в 1994 году в OCAS, бельгийском научно-исследовательском центре Arcelor, работая над индивидуально сваренными заготовками для ULSAB (Ultra Light Steel Auto Body) проект.С 1996 года он был старшим руководителем проектов в TWI Ltd, где он руководил множеством проектов по различным дуговым и лазерным процессам и приложениям. Его особый опыт связан с сваркой алюминия, гибридной лазерно-дуговой сваркой и, в последнее время, обработкой волоконным лазером.
Пол Хилтон — менеджер по технологиям в TWI, где он отвечает за стратегическое развитие лазерной обработки материалов.