Контроль визуальный — Энциклопедия по машиностроению XXL
Дефектоскопия. Неразрушающие методы и средства контроля. Визуальный и измерительный контроль [c.173]Система оптико-электронного сканирования для магнитно-люминесцентного и люминесцентного контроля (Англия). В капиллярной дефектоскопии механизированные полуавтоматические линии действуют уже более 20 лет, Основной источник низкой надежности контроля — визуальный осмотр объектов контроля. Прежние попытки автоматизировать осмотр были неудачными из-за влияния фона и невозможности учета общей визуальной информации об объекте контроля. Данная система не только фиксирует, но интерпретирует индикаторные следы дефектов по размерам, форме и положению, принимая решение о годности объекта. [c.180]
Были рассмотрены все возможные комбинации использования четырех выше указанных способов, дл5 каждой из которых определялись значения параметров, характеризующих эффективность системы контроля, г строился обобщенный показатель качества контроля функция желательности.
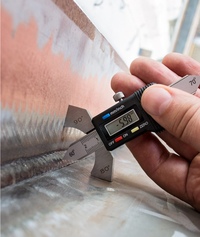
Методы производства контроля (визуальный, инструментальный или лабораторный) устанавливаются в каждом конкретном случае а зависимости от специфики объектов контроля. [c.186]
Различают следующие виды контроля визуальный контроль изделий после покрытия (цвет, блеск, шероховатость поверхности) определение пористости и толщины слоя покрытий испытание на коррозионную стойкость определение механических и физических свойств покрытий (пластичности, стойкости к высоким температурам и др.).
Контроль объектов или стадий процесса производства может быть летучим — срок проведения его не регламентирован периодическим — проводится через определенный промежуток времени (часы, сутки, месяцы) непрерывным — ведется непрерывно (постоянно). В зависимости от средств контроля различают контроль визуальный, когда
[c.95]
При автоматических методах сварки и допустимости контроля визуальным осмотром обратной стороны допускается применение устройств для местной защиты.
Визуальные МНК применяются не только для армированных пластиков. Использование композитов в Сандвичевых конструкциях вызывает необходимость и в этом случае применять такие методы контроля. Визуальный осмотр непосредственно после отверждения еще не остывших сотовых сандвичевых конструкций позволяет обнаружить пузыри, непроклеенные участки или расслоенные участки. Эти пузыри могут исчезнуть после охлаждения конструкции при пониженном давлении. Когда необходимо определить визуально наличие или отсутствие открытых пор в слоистых пластиках, желательно использовать специальные световые установки, которые могут помочь увидеть дефекты в структуре. Однако таким способом в основном могут наблюдаться только большие дефекты.
Методика выявления дефектов уплотнительных поверхностей и деталей разъемных соединений включает методы контроля (визуальный и инструментальный) контролируемые параметры уплотнительных поверхностей и деталей узла уплотнения (отклонение формы уплотнительных поверхностей — некруглость, прямолинейность образующей уплотнительной поверхности, угол наклона уплотнительной поверхности к оси сосуда, трещины на уплотнительных поверхностях и на резьбовой и гладкой частях крепежных шпилек, дефекты уплотнительных поверхностей механического и коррозионного происхождения резьба шпилек и гаек основного крепежа — размеры, механические повреждения, коррозия, шероховатость) методы проведения и средства измерений контролируемых параметров деталей разъемных соединений.
По виду проверяемых параметров качества применяются следующие методы контроля визуальный (внешний осмотр), геометрический (контроль размеров и форм изделий), качественный (качество металлов и материалов), химический,, физический и др.

Контроль (визуальный, пыжом) Укупорка [c.25]
Производственный контроль. У заготовок перед зубообработкой на специальных приспособлениях контролируют поверхности, которые используют в качестве установочных баз на зубообрабатывающих операциях и контроле. Визуально проверяют наличие забоин и заусенцев на установочных поверхностях. [c.417]
Отливки должны подвергаться следующим видам контроля визуально с измерениями основных размеров контролю химического состава (поплавочно) контролю механических свойств (включая твердость) гидравлическому испытанию неразрушающему контролю сплошности металла отливок (МПД радиусных переходов и рентгенопросвечивание или гаммаграфия концов присоединительных патрубков).
Таким образом, в описанном случае измерительное устройство работает на полуавтоматическом цикле управление подачей приспособления осуществляется автоматически, процесс контроля — визуально. Однако данная конструкция измерительного приспособления легко может быть переведена на автоматический цикл рабо-218
[c.218]
Кроме того, отливки должны проходить следующие виды контроля визуальный с измерениями основных размеров химического состава (по плавкам) механических свойств (включая твердость) гидравлические испытания неразрушающий контроль сплошности металла отливок (МПД радиусных переходов и рентгенопросвечивание или гаммаграфия концов присоединительных патрубков).
Контроль отливок прежде всего осуществляют визуально для выявления брака или отливок, подлежащих исправлению. Правильность конфигурации и размеров проверяют разметкой, плотность металла отливки — гидравлическими испытаниями под давлением воды до 200 МПа. Внутренние дефекты выявляют в специализированных лабораториях. Технический контроль возложен на отдел технического контроля завода. [c.180]
К механическим устройствам относятся главным образом трехконтактные индикаторные скобы, предназначенные для визуального контроля.
На линии выполняются следующие операции I — полная токарная обработка наружного кольца 2 — черновая токарная обработка внутреннего кольца 3 — чистовая токарная обработка внутреннего кольца 4 — клеймение 5 — магазины задела 5 и 7 — термическая обработка наружного и внутреннего колец 8 — визуальный контроль 9 — плоское шлифование наружного и внутреннего колец (поочередно) а — базового торца б — противоположной поверхности 10 — бесцентровое шлифование наружной поверхности наружного кольца 11 — черновое бесцентровое шлифование дорожки качения наружного кольца 12 — чистовое бесцентровое шлифование дорожки качения наружного кольца 13 — бесцентровая доводка дорожки качения наружного кольца 14 — снятие наката 15 — визуальный контроль 16 — промывка и сушка наружного кольца 17 — автома-
465]
Здесь на позиции 10 нижний пуансон приподнимает балку до упора в верхний пуансон, создавая прогиб кромок банджо примерно на 2°. Затем на позиции 11 подающее устройство захватывает балку и выносит ее из линии для визуального контроля на позиции 11а. Контролер осматривает швы и, ес 1и картер требует подварки, нажимает кнопку Дефект . По этой команде подающее устройство опускает балку на склиз, направляя ее на под-варку, а из накопителя забирает ранее подваренную балку и подает ее в линию. При качественных швах контролер нажимает
Все сварные соединения сосудов и их элементов подлежат визуальному и измерительному контролю с целью выявления в них следующих дефектов [c.49]
Активными методами являются визуальный и измерительный контроль, ультразвуковая дефектоскопия, магнитные, радиографические капиллярные, метод вихревых токов, электрический.
Визуальный и измерительный контроль (ВИК)
[c. 179]
Визуальный осмотр и при необходимости выполнения текущего контроля измерениями являются необходимыми и обязательными условиями контроля качества как при изготовлении, так и при эксплуатации технологического оборудования, работающего под внутренним давлением. [c.179]
В 10—30-х годах текущего столетия были опробованы методы микроскопического анализа изучение под микроскопом поперечного шлифа электролитически покрытой поверхности, измерение под микроскопом неровностей поверхности по репликам из желатина и т. д. Предпринимали попытки косвенной оценки неровностей поверхности по потерям энергии маятника при торможении его неровностями поверхности во время качания, по разности размеров деталей до и после доводки, по предельному углу регулярного отражения света, по теневой картине поверхности на экране с увеличенными изображениями поверхностных дефектов, по расходу воздуха через участок контакта сопла с испытуемой поверхностью, по четкости изображения растра на испытуемой поверхности или на экране после отражения от нее светового пучка, по электрической емкости контактирующей пары испытуемая поверхность — диэлектрик с нанесенным слоем серебра , по нагрузке на индентер при определенном его сближении с испытуемой поверхностью, по изображению мест плотного соприкосновения призмы с неровностями поверхности и т.
Светорассеивающее (молочное) МС13 Пластинка стекла толщиной 2 мм должна иметь коэффициент пропускания То для источника света А не менее 50+3%, определяемый на фотометрической установке при отсутствии света, проходящего прямо через стекло. Отступление от нейтральности 40%. Глушение стекла равномерное. Контроль визуальный Прессованные диаметром не больше 120 мм, по ГОСТ 3514-57 [c.729]
Размеры коррозионньЕх повреждений определяются неразрушающими методами контроля (визуальный, ультразвуковой, вихретоковый, рентгеновский и др. ). Остаточная прочность силовых элементов с коррозионными повреждениями должна быть определена, как правило, на основе экспериментальных исследований. Приближенная оценка может быть сделана по величине коэффшщента интенсивности напряжений К = К = ). При этом, зона коррозионного повреждения представляется в виде усталостной трещины соответствующего размера.
[c.423]
Гидравлические системы. Визуальным методом выявляют места возможной утечки. Преимуществом метода является то, что система заполнена рабочей жидкостью, испытания совмещаются с опрессовкой и проверкой функционирования. Недостаток метода — невозможность контроля визуально недоступных мест утечки, низкая чувствительность и субъективность. Критерии оценки образование подтеков без каплепадения, подтекания с каплеобразованием, капельные утечки. Соответствующий диапазон утечек для масел и нефтепродуктов 0,025… 10 mmV(m ). Визуальный метод контроля со сбором утечек на фильтровальную бумагу несколько точ-
[c. 52]
В системе УСП существует два вида контроля, определяющего пригодность компоновки к зксплуатации контроль визуальный и контроль с помощью мерительных средств. Под визуальным контролем подразумевается внешний осмотр приспособления, который должен определить правильность его конструкции. Оценивается, правильно ли сделан выбор типа конструкции, удачно ли расположение на базовой плоскости всех входящих в компановку узлов, посадоч1ных мест, крепежно-прижимных устройств и установочно-направляющих элементов и, наконец, пол1ож0ние самой обрабатываемой детали в приспособлении. [c.163]
Цвет можно контролировать путем визуального сравнения образца со стандартными цветными эталонами. Можно доказывать, что в конечном счете глаз является единственным справедливым арбитром, но возникает много вопросов, из которых самым трудным, вероятно, является Чей глаз Помимо генетических аномалий, которые рассматривались выще, известно, что цветовосприятие изменяется с возрастом из-за возникновения в глазах желтой пятноподобной пигментации, и что стандартный наблюдатель — это статистическая абстракция. Все это — сильные аргументы в пользу контроля цвета путем физических измерений. Эти измерения и их интерпретация должны быть тесно связаны с визуальным восприятием наблюдателя. На практике имеется два вида цветового контроля — визуальный и инструментальный.
[c.450]
Диагностика технологических коммуникаций и оборудования ГРС осуществляется при помощи комплекса измерительных средств и методов неразрушающего контроля визуально-оптический вибродиагностический акустико-эмиссионный метод измеритель твердости ультразвуковая дефектоскопия толщинометрия термографический магнитный. 49 [c.49]
Затем балка снова возвращается к сборщику для визуального контроля и подварки в случае необходимости, после чего он освобождает балку от закрепления п приспособлении, и автоопера- [c.104]
После визуального контроля технологических швов и приварки технологических планок трубы поступают на сварку йнутренних рабочих швов. Сварку осуществляют трехдуговым аппаратом А-1448, слежение за направлением электродов по стыку производится автоматически или визуально путем совмещения иертикаль-ной линии креста на экране телевизора с риской на внутренней
[c. 298]
Auto AD обладает широкими возможностями отображения различных видов рисунка. Предусмотрены команды, которые позволяют при редактировании рисунка быстро перемещаться от одного его фрагмента к другому для визуального контроля внесенных изменений. Можно производить зумирование, изменяя экранное увеличение выводимого изображения, или панорамирование, перемещая рисунок по видовому экрану сохранять выбранный вид, а затем восстанавливать его для вывода на печать или просмотра. Допускается также одновременный просмотр различных участков изображения при разделении области рисунка на несколько неперекрывающихся видовых экранов. [c.184]
Экспертное обследование предполагает получение информации о фактическом состоянии элементов длительно проработавшего оборудования, наличия в нем повреждений, выявления причин и механизмов возникновения повреждений. Оно должно проводиться в соответствии с программой, разработанной на основе анализа технической документации, а также данных функциональной диагностики и должно включать визуальный (внешний и внутр)енний) контроль измерение геометрических параметров и толщины стенок замер твердости и определения механических характеристик, металлографические исследования основного металла и сварных соединений определение химического состава дефектоскопический контроль (вид и объем которого устанавливаются с учетом требований полноты и достаточности выявления дефектов и повреждений) испытания на прочность и герметичность и др.
[c.166]
Визуальные методы неразрушающего контроля — Энциклопедия по машиностроению XXL
Визуальные методы неразрушающего контроля [c.468]Основной комплекс работ по контролю коррозионного состояния бурового оборудования проводят в период демонтажа его при ремонтных работах. Наиболее широко применяют визуальный осмотр, методы неразрушающего контроля (ультразвуковой, радиографический) и химический контроль буровых растворов и других технологических сред на содержание продуктов коррозии. Эти методы контроля коррозии в сочетании с металлографическим методом и методом выборочного определения изменения механических свойств конструкционных материалов оборудования после эксплуатации являются одной из основных мер профилактики отказов работы оборудования. [c.111]
Продольные и поперечные швы в обечайках, трубах, а также швы приварки днищ, штуцеров, люков и т.
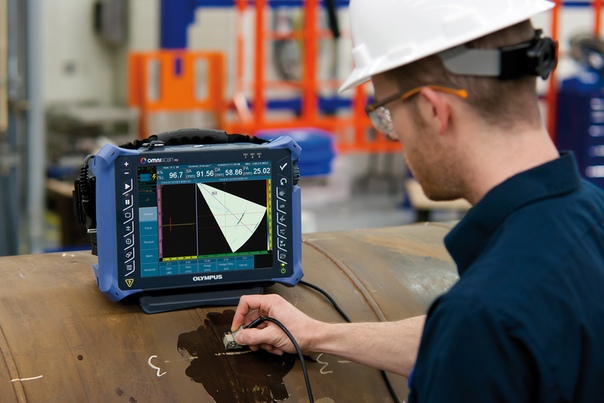
Контроль течеисканием. Назначение метода — определить герметичность сварного или паяного соединения. Обнаружение дефекта каким-либо из рассмотренных ранее методов неразрушающего контроля не позволяет, за некоторым исключением (например, определенные визуально сквозные свищи или трещины), сделать вывод о плотности соединения. Поэтому необходимо проводить испытания на герметичность, которые назначаются, как правило, наряду с другим каким-либо контролем. [c.552]
В калибровочных цехах, как правило, качество поверхности прутков проверяют визуально. Поэтому контролем качество занимается большое число работников цехов и отделов технического контроля, что не исключают в некоторых случаях возможности отгрузки потребителям прутков с поверхностными дефектами. В связи с этим внедрение методов неразрушающего контроля качества прутков имеет важное значение.
[c.310]
Капиллярные методы неразрушающего контроля основаны на капиллярном проникновении индикаторных жидкостей (пенетрантов) в полости поверхностных и сквозных несплошностей материала объектов контроля и регистрации образующихся индикаторных следов визуальным способом или с помощью преобразователя. [c.563]
Применение метода неразрушающего контроля на экзаменационном образце. Он состоит из следующих шагов a) для уровня II — выбор способа контроля и определения условий контроля b) подготовка (состояние поверхности) и визуальный контроль экзаменационного образца ) калибровка образца (1) выполнение контроля е) завершение контроля 35 20 [c.453]
Дефектоскопия. Неразрушающие методы и средства контроля. Визуальный и измерительный контроль [c.173]
Контроль качества паяных соединений обычно осуществляют неразрушающими методами (по параметрам режимов пайки, визуальным методом, испытанием на герметичность, методами дефекте- и рентгеноскопии).
[c.922]
К неразрушающим методам диагностики, применяемым для оценки состояния сварных соединений паропроводов отечественных энергетических установок, относятся визуальный и измерительный контроль, измерение твердости, стилоскопирование, ультразвуковая и магнитопорошковая дефектоскопия, цветная дефектоскопия с проникающим излучением, вихретоковый метод, дефектоскопия аммиачным откликом, метод магнитной памяти металла и металлографический анализ с реплик (и/или срезов металла) и с помощью переносного микроскопа. Большинство этих методов применяется для диагностирования сварных соединений по месту их расположения на коллекторах котлов и трассах паропроводов в соответствии с требованиями по НТД и ПТД [3, 15, 18, 42, 53]. [c.146]
На основании анализа различных неразрушающих методов дефектоскопии, приведенных в табл. 11, видно, что наиболее высокой эффективностью обладают импульсный акустический, СВЧ и инфракрасный методы контроля.

На основании анализа технической документации, данных визуального и измерительного контроля, а также контроля элементов сосуда неразрушающими методами принимается решение о необходимости определения химического состава, структуры и механических свойств металла. Такая необходимость возникает, например, при диагностировании сосудов, установленных на открытом воздухе, которые в холодное время года подвергаются воздействию низких температур, в результате чего температура стенки может стать ниже, чем минимальная разрешенная температура применения стали, что может привести к снижению пластических свойств металла и опасности возникновения и развития хрупких трещин. Это относится в первую очередь к сосудам, изготовленным из углеродистых и некоторых низколегированных сталей. Эти работы выполняются обязательно при выявлении аномальных зон с наличием микротрещин или твердостью металла, выходящей за допускаемые пределы. По возможности работы выполняют без вырезки массивных образцов неразрушающим способом путем отбора малых проб (микропроб).
[c.254]
К неразрушающим методам контроля качества сварных и паяных соединений относят визуальный и измерительный контроль контроль на непроницаемость (герметичность) конструкций контроль для обнаружения внутренних дефектов. [c.248]
Есть возможность проконтролировать этим методом и наиболее нагруженные участки трубопроводов ГРС тройники, задвижки, отводы и другие элементы, которые также иногда разрушаются. Применение в этом случае известных методов наружного неразрушающего контроля, таких как визуальный осмотр, ультразвуковой, радиографический и магнитный методы, также проблематично. [c.110]
В качестве неразрушающих методов контроля нри обследовании применяются визуальный осмотр поверхностная дефектоскопия (цветная, люминесцентная, магнитная и др. ) ультразвуковая дефектоскопия просвечивание проникающим излучением и др.
[c.240]
Неразрушающие методы контроля можно подразделить на визуальные (оптические, проникающие жидкости, лазерная голография) термические (с использованием инфракрасного излучения и жидких кристаллов) методы проникающего излучения (рентгеновские, изотопные) электромагнитные методы (вихретоковые, микроволновые, диэлектрические) и акустические методы (ультразвуковой, акустическая интерферометрия, акустическое излучение). [c.257]
Контролю подлежат следующие детали, работающие при температуре выше 450 С корпуса клапанов автоматического затвора, корпуса регулирующих клапанов, сопловые коробки, корпус цилиндра турбины, ротор, рабочие лопатки, диафрагмы, паровпускные и перепускные трубы, шпильки и гайки, сварные швы. Для контроля применяют как разрушающие (спектральный анализ, исследование микроструктуры и механических свойств на вырезанных образцах), так и неразрушающие методы. Из неразрушающих наибольшее применение наряду с визуальным осмотром находят капиллярные, магнитные, акустические и радиационные методы контроля.
[c.386]
Здесь размеры трещин величиной 0,5 мм соответствуют размерам начальных производственных дефектов 5 мм — надежно обнаруживаемым размерам трещин с помощью неразрушающих методов контроля на ремонтных заводах 25 — 75 мм — надежно обнаруживаемым размерам трещин при целенаправленном визуальном контроле в эксплуатации. [c.420]
По массовости применения методов неразрушающего контроля сварных конструкций помимо визуально измерительного метода, который применяется для всех конструкций как первая стадия контроля, выделяются два метода — радиационный и ультразвуковой. Дaшdыe методы используются для обнаружения и оценки внутренних дефектов в объектах различгшй толщины. [c.218]
Завышенная деформация, оплавление и смещение деталей хорошо выявляются при визуальном контроле и измерениях размеров детали. Трещины и непровары, а также негерметичность сварных соединений выявляются известными методами неразрушающего контроля ульт-.развуком, капиллярными и магнитными методами, течеискателями, гидро- и пневмоиспытаниями. Небольшие локальные непровары и склейки поверхностей без образования сварного соединения неразрушающими методами контроля не выявляются. Для предупреждения появления этих дефектов необходимо тщательно контролировать качество подготовки соединяемых поверхностей к сварке, а также соблюдать выбранные и проверенные параметры режима сварки. В массовом производстве можно осуществлять разрушающий контроль нескольких товарных деталей из партии, выявляя непровары и склейки в изломе деталей и изменяя в случае необходимости параметры режима.
[c.279]
Дефекты ухудшают физико-механические свойства металлов, например прочность, пластичность, плотность, электропроводность, магнитную проницаемость и т.д. Их часто разделяют на явные и скрытые. Первые обнаруживают при визуальном способе контроля или при помощи инструментальных средств и методов, которые приведены в нормативной документации. Если дефекты с большой вероятностью выяв тяются с по.мошью соответствующих инструментальных методов неразрушающего контроля, но не обнаруживаются визуальной, то их тоже относят к явным. Скрытый дефект нельзя обнаружить предусмотренным методом и аппаратурой.
[c.85]
Техническое состояние оборудования определяется числом дефектов и степенью их опасности. Дефектом называют каждое отдельное несоответствие детали или технической системы требованиям, установленным технической документацией. По расположению дефекты подразделяют на наружные и внутренние (скрытые). Наружные дефекты чаще всего обнаруживают визуально, скрытые — посредством различных методов неразрушающего контроля. По форме дефекты бывают объемные и плоскостные. Объемные пpoявляюf я в виде изменения (искажения) начальной формы или размеров объекта, плоскостные — в виде трещин или полос скольжения. По происхождению дефекты подразделяют на производственные и эксплуатационные. Производственные дефекты могут быть металлургически-
[c. 5]
Визуальный и измерительный контроль металлоконструкций, механизмов и оборудования выполняют в соответствии с типовыми картами осмотра установок. При необходимости применяют различные методы неразрушающего контроля. В качестве одного из основных предусматривается использование метода акустической эмиссии, позволяющего выявить в металлоконструкциях зарождающиеся и развивающиеся дефекты типа усталостных трещин. Акустикоэмиссионная диагностика осуществляется совместно со статическими испытаниями установки под нагрузкой. [c.258]
Наибольшую опасность могут вызывать случаи разрушения червяка. Визуальный осмотр разрушенных червяков подтверждает усталостный характер их разрушения, начинающийся у корня зуба. Характер разрушения свидетельствует о постоянном развитии и накоплении трещин в результате нескольких последовательных этапов, протекающих с различными скоростями. Это обстоятельст. во свидетельствует о возможности предварительного обнаружения трещин на начальной стадии ее образования с помощью методов неразрушающего контроля магнитной дефектоскопии, рентгеноскопии, применения ультразвукового контроля. Применение этих традиционных методов требует предварительной разборки редукторов, что делает их малоэффективными в условиях эксплуатации.
[c.222]
Данные стандарты по приемке косоются определения допустимости дефектов такого размера и типо, которые могут быть выявлены с помощью родиог-рофической дефектоскопии и других методов неразрушающего контроля, а том числе и визуального. Эти стандарты служат для оценки профессионального мастерство при выполнении сварных швов а соответствии с требованиями технических условий, прошедших квалификационные испытания. Примечание а отношении дефектов, расположенных на внутренней стороне сварных швов в трубопроводах, предназначенных дпя сероводородных сред, могут быть приняты дополнительные ограничения. [c.121]
Диагностика технологических коммуникаций и оборудования ГРС осуществляется при помощи комплекса измерительных средств и методов неразрушающего контроля визуально-оптический вибродиагностический акустико-эмиссионный метод измеритель твердости ультразвуковая дефектоскопия толщинометрия термографический магнитный. 49
[c.49]
Определение необходимых для оценки технического состояния и остаточного ресурса технологических элементов ГРС параметров проводится при помощи комплекса средств (приборов) и методов неразрушающего контроля, таких как визуально-оптический в ибро диагностический магнитный [c.137]
Для остальных дефектов, по крайней мере, максимальных из них, необходимо уточнить местоположение и размеры, используя шурфование и методы неразрушающего контроля, включая визуальные. Как показывает практика, это важный этап, что связано с погрешностью приборов и несовершенством дeтoдoв дешифровки сигналов. Однако ясно, что размеры и формы всего массива локальных дефектов уточнить не представляется возможным. Следовательно, построенная расчетная схема должна давать заниженное значение несущей способности участка с дефектом, что идет в запас прочности (дефект-аналог должен быть несколько опаснее дефекта-оригинала). [c.25]
Более того оптимизация всех факторов, влияющих на точность и трудоемкость дискретного алгоритма реконструкции, требует формирования такого обобщенного технико-экономического критерия качества реконструкции, который бы выходил за рамки проблем метрологии и аппаратурной реализации цифровой обработки и в большей степени учитывал влияние величины и характера возникающих ошибок на конечный результат неразрушающего контроля методом ПРВТ с учетом процесса визуальной расшифровки томограмм и возможных альтернативных технических решений.
[c.404]
Выполненные расчеты длительности роста трещины по зависимости расстояния мезолиний от длины трещины показали, что ее развитие в тяге происходило длительное время в течение около 8600 полетов. К моменту разрушения в эксплуатации тяга наработала 4772 ч, после последнего ремонта ее наработка составила 255 ч. Из условия средней продолжительности полета вертолета 30 мин указанные периоды в полетах составляют соответственно около 9544 и 510. Выполненный расчет показывает, что трещина была пропущена в ремонте. Это объясняется тем, что, по условиям ремонта, с тяги не смывается краска, а неразрушающие методы ее контроля не применяются. Визуально же выявить трещину не было возможности потому, что ее развитие происходи.по квазихрупко с едва заметным раскрытием берегов трещины в принороговой области скоростей роста трещины. В этом случае только специально настроенная аппаратура может быть эффективна в выявлении усталостных трещин. Причем под слоем краски такие трещины не выявляются даже ею, если не проведено специальной оценки чувствительности аппаратуры и ее настройки, как это имело место с контролем панели крыла ВС в эксплуатации, когда трещины не были выявлены, а после снятия краски их размер оказался в несколько сотен миллиметров [1].
[c.749]
К неразрушающим методам контроля относят визуальный осмотр, простукивание, тепловой, оптический, электрический, радиоволновый, радиационный, контроль проникающими веществами, ультразвуковой контроль. Наибольшее распространение получил последний метод, основанный на измерении длины волны, амплитуды, частоты или скорости распространения ультразвуковых колебаний в клеевом шве. По способу выявления дефектов среди методов ультразвукового контроля выделяют теневой, эхо-импульсный, импедансный, резонансный, велосимметрический, метод акустической эмиссии. Для реализации этих методов разработана соответствующая аппаратура (см. раздел 8). При контроле клееных сотовых конструкций с сотами из алюминиевого сплава и обшивками из ПКМ целесообразно применять несколько методов [100]. Акустический метод, например, с использованием импедансных дефектоскопов ИД-91М и АД-42И с частотной и амплитудной регистрацией колебаний соответственно эффективен для обнаружения отслоений сотового заполнителя от обшивки, а радиографический — для выявления повреждений сотового заполнителя и обшивки, а также для фиксирования мест заливки в соты пасты.
[c.537]
При диагностировании технического состояния длительно проработавших аппаратов измерение толщины всех стенок конструктивных элементов аппарата (обечаек корпуса, днища, патрубков штуцеров, горловины люков-лазов и др.) производится ультразвуковыми приборами, отвечающими требованиям ГОСТ 28702 Контроль неразрушающий. Общие технические требования . Разметку точек замера толщины стенки рекомендуется производить краской или мелом по образующей обечаек корпуса, начиная от верхней или нижней образующей. Расположение и количество точек замера толщины стенки уточняется при разметке по результатам визуального осмотра конкретного аппарата. Участки с повышенным коррозионным износом, наиболее теплонапряженные места аппарата должны подвергаться контролю этим методом в о(5язательном порядке для определения степени коррозионно- [c.199]
Большинству отливок из суперсплавов принадлежит решающая роль в конструкции двигателя. Поэтому средства неразрушающего обнаружения дефектов этих отливок очень важны, затраты на них, включая потери по отбраковке и переработке лома, могут достигать 20 % стоимости отливки. Помимо визуального контроля и проверки размеров наиболее популярны сегодня такие методы инспекции, как фотоавторадиографи-ческая и люминесцентная дефектоскопия. Последние усовершенствования в прямой радиометрической дефектоскопии придали ей чувствительность, фактически не уступающую чувствительности пленочных методов. Инспекция стала экономически выгодной благодаря усовершенствованию средств визуализации (различные выдеокамеры, экраны и другие средства) и использованию компьютерных методов.
[c.191]
К неразрушающим методам контроля относятся измерение размеров и шероховатости поверхности отливки, визуальный осмотр их поверхности, а также специальные виды контроля (рентгеновский, гамма-дефектоскопия, ультразвуковой, цветная дефектоско- [c.491]
Размеры коррозионньЕх повреждений определяются неразрушающими методами контроля (визуальный, ультразвуковой, вихретоковый, рентгеновский и др.). Остаточная прочность силовых элементов с коррозионными повреждениями должна быть определена, как правило, на основе экспериментальных исследований. Приближенная оценка может быть сделана по величине коэффшщента интенсивности напряжений К = К = ). При этом, зона коррозионного повреждения представляется в виде усталостной трещины соответствующего размера.
[c.423]
В 1999-2001 гг. НПП СибЭРА прошло аккредитацию в Системе экспертизы промышленной безопасности Госгортехнадзора России, имеет аттестованную лабораторию неразрушающих методов контроля, в том числе по ультразвуковому, акустико-эмиссионному, магнитному проникающим веществам, визуально-измерительному, вибродиагностическо-му, вихретоковому, оптическому, радиационному контролю. [c.335]
Визуально измерительный контроль (ВИК) качества сварных соединений и трубопроводов
- Главная
- Услуги
- Визуально-Измерительный Контроль
Наше Производственное Объединение «ВЗРК» предоставляет услуги по визуально-измерительному контролю сварных соединений. Специалисты предприятия имеют большой опыт в обследованиях такого рода, они фиксируют полученные данные и предоставляют заказчику.
Не рискуйте качеством и репутацией своих изделий и конструкций – вовремя проверяйте качество сварных соединений.
Все параметры сварных соединений должны контролироваться в процессе выполнения сварочных работ, при подготовке к процессу сварки, после выполнения сварочных работ, а также кроме самого сварного шва требуется требуется наблюдение за поверхностями свариваемых металлов и всех доступных плоскостей, участвующих в процессе сваривания. Качество шва напрямую влияет на прочность и деформационные характеристики всей металлоконструкции или металлического изделия.
Наиболее простой способ проверки качества сварных швов — визуально-измерительный контроль (ВИК). Порядок и критерии применения данного метода определены ГОСТ 23479-79.
Для визуального контроля качества сварных соединений не требуется применение крупногабаритных сложных установок, что повышает мобильность данного обследования. Однако точность и достоверность результатов в таком обследование напрямую зависит от квалифицированности сотрудника, который его проводит.
Ограничения визуально-измерительного метода не позволяют использовать его в качестве единственного метода контроля.
Методом визуального и измерительного контроля сварных соединений проверяют трубопроводы, бункеры, резервуары, вышки, молниеприемники – любые металлические изделия, соединения в которых производятся посредствам сварки.
Внешний осмотр и требования к сварным швам
ВИК контроль сварных соединений рекомендуется проводить на стационарных (неподвижных) участках с плоской ровной поверхностью, где возрастает возможность получения достоверных результатов.
Визуальный и измерительный контроль качествапри проведении сварки в условиях монтажа конструкции, строительстве, ремонте или другое, должен проводиться на месте производства этих работ.
При осмотре стоит обеспечить для обследователя безопасное проведение работ, оборудовать место осмотра дополнительными источниками света, предоставить как можно больший угол обзора для осмотра поверхности.
Сварные швы должны соответствовать основным требованиям, предъявляемым к соединениям такого типа. Габаритные размеры валика должны находиться в заданных пределах, структура должна быть однородной и ровной без излишних выпуклостей и впадин. Необходимо удалить, если это возможно, с поверхности ржавчину. Желательно должна отсутствовать пористость, трещины различных видов, сколы и т.п.
Преимущества метода
- ВИК контроль с применением измерительных инструментов обладает рядом преимуществ перед другими методами:
- Простота осуществления требуемых процедур;
- Отсутствие особых требований к квалификации специалиста;
- Низкая стоимость инструментов;
- Невысокая стоимость самой услуги;
- Хороший предварительный метод исследования для определения основного метода обследования;
- Небольшие затраты времени.
Недостатки визуально-измерительного метода
Есть и недостатки у метода визуального-измерительного контроля сварных швов:
- Значительные ограничения по размеру изъянов: 0,1-0,2 мм;
- Невысокая точность измерений;
- Возможность обнаружения только видимых с внешней стороны дефектов и подозрения на возможные повреждения внутри;
- Субъективность в оценке многих видов дефектов.
Однако очевидные преимущества настолько велики, что этот метод используется практически везде с дополнением другими способами контроля, позволяющими исключить имеющиеся недостатки.
Как упоминалось ранее, стоимость приборов для проведения такого рода обследования невысокая, также все инструменты являются малогабаритными. Несмотря на низкую стоимость, для данного метода существует один из самых широких перечней оборудования.
Для визуального контроля сварных швов и выполнения измерений дефектов сварных соединений применяются метрологические средства:
- Штангенциркуль, линейки металлические и деревянные, толщиномер, микрометр — для измерения линейных параметров;
- Шаблоны, щупы, угломеры с нониусом, микрометрические и индикаторные нутрономеры — для замеров линейных и угловых величин.
- Лупа, микроскоп, бороскоп, эндоскоп — для увеличения оптических возможностей глаза.
- Поверочные плиты.
- Шаблоны специальные и универсальные резьбовые, радиусные и т.п.
Применение оптических приборов, помогает увеличить точность исследования, так как такие приборы могут увеличивать видимую глазу поверхность в 10-20 раз.
Для фиксации некоторых видов дефектов, выявленных при визуальном осмотре сварных соединений, и регистрации результатов, в современной практике часто используется видео- и фотосъёмка с применением измерительных средств, в качестве эталонов. В этом случае,есть возможность визуализировать полученные результаты.
Допустимые погрешности в измерениях при проведении обследования
Измеряемая величина, мм |
Допустимая погрешность измерения, мм |
|
---|---|---|
≤ 0,5 |
0,1 |
|
≥ 0,5 |
≤ 1,0 |
0,2 |
≥ 1,0 |
≤ 1,5 |
0,3 |
≥ 1,5 |
≤ 2,5 |
0,4 |
≥ 2,5 |
≤ 4,0 |
0,5 |
≥ 4,0 |
≤ 6,0 |
0,6 |
≥ 6,0 |
≤ 10 |
0,8 |
≥ 10 |
1,0 |
Визуальный контроль поэтапно
- Проводится первичный осмотр шва на обнаружение коррозирующих участков, инородных вкраплений или других повреждений.
- Соединение очищается от шлака, грязи, пыли и др. Также делаются замеры толщины и ширины шва.
- Проводится исследование качества всего сварного соединения и выписывается акт о предварительном осмотре.
- Проводится более детальное обследование с применением инструментов, делаются конкретные замеры поверхности шва и его дефектов, если такие обнаружены.
- Выдается заключение об осмотре с рекомендацией второго неразрушающего метода контроля (если необходимо).
Перед проведением неразрушающего контроля ВИК, все лица, участвующие в обследовании, должны пройти специальный инструктаж по технике безопасности и отразить это в специальном журнале.
Документы о проведении обследования
Все результаты неразрушающего контроля ВИК фиксируются в журнал учета работ по визуальному и измерительному контролю. В виде отчетной документации выдаются заказчику протоколы, акты или заключения.
В отдельных случаях результатом осмотра также является клеймо, поставленное на изделие в случае подтверждения положительных результатов обследования.
Визуальный контроль соединения перед сваркой
На данном этапе материалы для сварки осматривают для выявления окалин, вмятин, элементов коррозии, инородных вкраплений и т.п. Также тщательно проверяются кромки под сварку и сборку заготовок.
Состоянию кромки уделяется особое внимание, так как от качества кромок зависит качество всего соединения и его пригодности к эксплуатации.
Специалист, проводящий надзор за подготовкой, осматривает зазор между кромками, степень их затупленности, величину нахлестки и зазора между листами (внахлест), для угловых соединений контролируется угол между свариваемыми элементами и зазор между ними.
Визуальный контроль во время сварки
Наблюдатель обязан контролировать режим сварки на этом этапе, силу подачи тока и напряжения, скорость сварки и т.д.
Необходимо тщательно осматривать первый слой сварки, нанесенный дугой, так как от его качества зависит качество всего шва. Нередко, специалисты пользуются специальными увеличивающими приборами (например, лупа), чтобы осматривать первый слой на наличие дефектов. Если таковых не обнаруживается, то каждый последующий слой не требует такого досконального осмотра.
Перед и во время сварочной процедуры производится оценка исправности сварочной аппаратуры и оборудования.
ВИК сварных швов
Хотя ВИК сварки является достаточно простой процедурой, ее высокая эффективность в обнаружении дефектов впечатляет.
После сварки материалов или деталей, специалист можетобнаружить трещины, вкрапления, кратеры, наплывы, бугры и т.п. увидев их глазами, а также сравнив с эталонными образцами.
После визуального осмотра, при обнаружении дефектов, необходимо выделить эти места с помощью мела или другим способом, провести замеры дефекта, охарактеризовать повреждение и провести его анализ, если это возможно и занести результаты в журнал и протокол.
Преимущества «ВЗРК»в оказании услуги по визуальному контролю качества
- Налаженная система проведения визуально-измерительного контроля.
- Квалифицированные и сертифицированные на проведение такого рода обследования сотрудники.
- Возможность проведения в любой точке государства.
- Невысокая стоимость.
- Индивидуальный подход.
- Возможность проведения других методов обследования.
Стоимость визуально-измерительного контроля сварных соединений
Стоимость такой услуги для каждого заказчика формируется индивидуально, в зависимости от ряда факторов: расположения объекта для обследования, общее количество обследуемых соединений, необходимость применения конкретных инструментов и др.
Мы сделаем все, что необходимо для исследования и удовлетворения любой спецификации Ваших объектов.
Заказать услуги Производственного Объединения «ВЗРК»
Для заказа услуги ВИК контроля сварных соединений Вы можете связаться с нами по телефонам, указанным в шапке сайта или с помощью онлайн формы. Наши сотрудники более подробно расскажут о процессе обследования, дадут консультацию по интересующих Вас вопросам.
Наше предприятие досконально подходит к каждому заказчику и предоставляет качественную услугу.
3. Оптические методы, визуальный и измерительный контроль
3.1. Классификация оптических методов контроля
Оптический неразрушающий контроль основан на взаимодействии электромагнитного излучения с контролируемым объектом и регистрации результатов этого взаимодействия. Методы, относящиеся к оптическому НК по ГОСТ 24521—80, различаются длиной волны излучения или их комбинацией, способами регистрации и обработки результатов взаимодействия излучения с объектом. Общим для всех методов является диапазон длин волн электромагнитного излучения, который составляет 10-9…10-3 м (3 x 1О18…3 x1010 Гц) и охватывает диапазоны ультрафиолетового (УФ), видимого (ВИ) ((3,8…7,8) x 10-7 м) и инфракрасного (ИК) излучения, а также информационные параметры оптического излучения, которыми являются пространственно-временное распределение его амплитуды, частоты, фазы, поляризации и степени когерентности. Изменение этих параметров при взаимодействии с объектом контроля в соответствии с основными физическими явлениями (интерференции, поляризации, дифракции, преломления, отражения, рассеяния, поглощения и дисперсии излучения), а также изменения характеристик самого объекта в результате эффектов люминесценции, фотоупругости, фотохромизма и др. используют для получения дефектоскопической информации. Оптическое излучение — это электромагнитное излучение, возникновение которого связано с движением электрически заряженных частиц, переходом их с более высокого уровня энергии на более низкий. При этом происходит испускание световых фотонов.
Основными количественными показателями, характеризующими оптическое излучение, являются следующие параметры:
• скорость распространения оптического излучения в вакууме v0 = 299792,5 км/с. В оптически прозрачных средах излучение распространяется со скоростью
Где n – показатель преломления среды, зависящий от ее проницаемости; и — длина волны оптического излучения соответственно в вакууме и оптической среде; f – частота излучения, Гц;
— мощность потока излучения, Вт,
Где Q – излучаемая энергия, Дж; t – время, с;
— сила излучения, Вт/ср,
,
Где — телесный угол, в котором распространяется поток Ф, ср;
— плотность тока излучения (освещенность), Вт/м2
,
где S — площадь излучения, м2.
Оптические методы НК разделяют на три группы. В первую группу входят визуальный и визуально-измерительный методы, которые являются наиболее простыми и доступными, имеют наибольшее распространение и обязательны для применения при диагностировании технических устройств и объектов всех типов. Ко второй группе относятся фотометрический, денсиметрический, спектральный и телевизионный методы, которые основаны на результатах измерений с использованием электронных приборов. К третьей группе относятся интерферометрический, дифракционный, фазово-контрастный, рефрактометрический, нефелометрический, поляризационный, стробоскопический и голографический методы, использующие волновые свойства света и отличающиеся наивысшей точностью измерения — с точностью до десятых долей длины волны излучения, — но сложностью в реализации.
Выбор условий контроля должен сводиться к обеспечению нормальных условий освещенности контролируемого объекта, установлению требуемого режима работы и взаимного расположения объекта контроля и аппаратуры.
Схемы испытаний методами оптического вида контроля по ГОСТ 23479-79 приведены в табл. 3.1.
Визуальный и измерительный контроль ВИК
Поиск дефектов промышленного, технологического и иного оборудования, а также различных зданий и сооружений в некоторых случаях осуществляется путем их визуального осмотра или же осмотра с использованием специальных приборов. Проведение ВИК (визуально-измерительного контроля) позволяет выявить повреждения и деформации объекта, не прибегая к его разборке или выведению из эксплуатации. В процессе обследования могут применяться разнообразные приборы, увеличивающие изображение (лупы, линзы, эндоскопы и микроскопы). Также используются различные измерительные инструменты и приспособления: шаблоны, щупы, глубино- и угломеры.
Содержание:
«Аттестационный региональный центр специалистов неразрушающего контроля» осуществляет подготовку персонала и выполняет диагностику различных объектов. Визуальное исследование оборудования и конструкций — начальный этап комплексной дефектоскопии. При проведении измерительного контроля учитывается ограниченность данного метода, обеспечивающего осмотр только видимой части оборудования или конструкции.
Основная цель мероприятий, проводимых в рамках визуально-измерительного контроля, состоит в выявлении дефектов на внешних поверхностях объектов и в их полостях. Кроме того, данная методика исследования позволяет установить отклонение геометрических показателей от заданных требований. В ходе наружного осмотра также определяются признаки усталости материалов, которые могут привести к разрушению конструкции.
Когда проводится визуально-измерительный контроль?
Неразрушающие способы исследований объектов широко распространены во всех отраслях промышленности, на транспорте и в других сферах. Наш «Центр» оказывает услуги ВИК предприятиям и организациям по разовым заявкам или на основе постоянно действующих договоров в следующих целях:
- Для обнаружения поверхностных дефектов, которые различимы невооруженным глазом. Это могут быть раковины, поры, трещины, расслоения, заусеницы и другие повреждения, выявляемые в ходе визуального осмотра деталей, узлов и конструкций невооруженным глазом. Микротрещины и иные микроскопические нарушения структуры материала определяются с использованием специальных методов дефектоскопии и рентгенографии.
- Для исследования характера повреждений и установления вида поверхностных дефектов деталей, обнаруженных с использованием иных способов дефектоскопии (капиллярного, акустического, магнитопорошкового и других).
- Изучение сварных соединений в металлоконструкциях на соответствие требованиям нормативной документации.
Измерительные и визуальные методы исследования заготовок деталей, промышленных полуфабрикатов и сварных соединений в узлах конструкций осуществляются в ходе всего технологического процесса. Они включают в себя входной контроль материалов и изделий, а также их проверку во время изготовления сборочных единиц. ВИК производится при подготовке деталей к соединению сваркой и сборке их в узлы. Также визуальное наблюдение ведется в процессе сварочных работ, а по их завершении производится устранение дефектов в стыках. На завершающем этапе изготовления изделий, а также в процессе эксплуатации проводится оценка качества соединений, материалов и конструкций.
Методология и ограничения на области применения
Визуально-измерительный контроль осуществляется в соответствии с требованиями национальных и международных стандартов. В частности, исследования сварных соединений выполняются согласно методике, утвержденной ГОСТ Р ИСО 17637-2014 и инструкцией РД 03-606-03. Непосредственно работы выполняют специалисты ВИК-лаборатории, оснащенной современными приборами и измерительными средствами.
Важно то, что применение методов визуального контроля и измерений ограничено только видимыми участками объектов. Возможно также исследование полостей при помощи гибких или жестких эндоскопов.
Специалисты «АРЦ НК» используют передовые способы неразрушающего исследования объектов. Мы осуществляем визуальный и измерительный контроль (ВИК) по доступной стоимости.
Визуально-оптический метод
При исследовании объектов специалистами применяются простейшие оптические средства (лупы и зеркала). Такой визуальный контроль (цена его проведения определяется согласно прейскуранту), называется визуально-оптическим. Данный метод изучения физико-механических свойств объекта предполагает использование минимального перечня инструментов и приборов и предусматривает, в первую очередь, тщательный осмотр его поверхностей.
Для обследования скрытых полостей и труднодоступных частей котлов, теплообменников, различных механизмов или технологических сооружений используют различные виды эндоскопических систем. Визуально-оптический контроль осуществляется на основе правильно подобранного подхода и по заранее разработанному плану. Исходя из решаемых задач, определяется перечень необходимого оборудования.
По окончании исследования специалисты неразрушающего контроля осуществляют обработку результатов дефектоскопии и оформляют их документально. Объективность и точность данных, полученных с использованием методов ВИК, обеспечивается высокой квалификацией сотрудников. Необходимый уровень профессионализма эксперта достигается в процессе обучения и приобретается с опытом.
Измерительный контроль
Измерительный контроль — одна из основных составных частей упомянутых способов неразрушающих испытаний. Цель его состоит в определении физических размеров обследуемой строительной конструкции, сооружения, узла или отдельной детали.
В процессе выбора метода измерительного контроля специалисты руководствуются требованиями нормативов, которые определяют необходимые метрологические характеристики применяемых приборов:
- цена деления,
- диапазон и пределы измерений,
- значение допустимых погрешностей измерительных средств.
Данный метод позволяет определять размеры объектов или поверхностных дефектов, выявляемых при помощи органов зрения. Минимальная величина измеряемых предметов находится в пределах от 0,1 до 0,2 мм.
Перечень и стоимость услуг
Компания «Аттестационный региональный центр неразрушающего контроля» производит визуальный и измерительный контроль по . Перечень предоставляемых услуг включает следующие разновидности ВИК (ВОК):
- Исследования сварных швов трубопроводов диаметром до 1220 мм, а также технологического и промышленного оборудования.
- Входной контроль заготовок из разных материалов на предприятиях.
- Исследования готовой продукции на наличие поверхностных дефектов.
- Контроль подготовки и сборки деталей под сварку.
- Контроль сварных конструкций после их изготовления, а также на стадии эксплуатации при техническом диагностировании.
Стоимость исследований определяется согласно действующим тарифам и зависит от трудозатрат, используемого оборудования и объемов работ.
Порядок проведения ВИК
Визуально-измерительный (визуально-оптический) контроль осуществляется специалистами соответствующего профиля в строгом соответствии с установленными нормативами. В частности, контроль сварных соединений производится согласно инструкции РД 03-606-03, утвержденной постановлением Гостехнадзора № 92 от 11 июня 2003 года. Порядок проведения работ следующий:
- Получение технического задания на исследование сварного шва с указанием его типа, номера, местоположения и основных характеристик.
- Изучение технологической инструкции и операционной карты, а также конструкции узла и документации на изделие.
- Визуальное исследование сварного шва на предмет наличия маркировки, личного клейма специалиста или бригады сварщиков.
- Тщательный осмотр объекта на наличие всех видов трещин вне зависимости от их направления.
- Проверка шва на отсутствие отслоений, посторонних включений, пор сквозных или частичных, свищей и прожогов, чешуйчатости, раковин и брызг расплава.
- Обследование качества зачистки шва и прилегающих участков, а также определение основных технических параметров.
По завершении контроля принимается решение об использовании иных методов неразрушающего контроля. По результатам проведенных работ составляется акт, который подписывается специалистом. Последовательность операций для исследования иных объектов аналогична описанной, но может иметь некоторые особенности.
Инструменты и оборудование для визуально-измерительного контроля
Для исследования различных объектов применяются специальные средства наблюдения и измерения. Выбор того или иного прибора визуально-оптического контроля определяется необходимостью работы в цеху или в полевых условиях.
Традиционные методы ВИК основаны на применении следующих видов оптических приборов:
- Лупы и микроскопы. Предназначены для исследования объектов, удаленных от глаз специалиста не более чем на 250 мм. Эти приборы позволяют выявлять трещины, очаги коррозии и различные дефекты покрытий, а также проводить их измерения.
- Оптические и видеоэндоскопы, бороскопы. Необходимы для изучения полостей и труднодоступных узлов конструкций различного назначения. Приборы позволяют проводить дефектацию деталей механизмов без их предварительной разборки.
Что касается измерительных приборов, в обязательный набор специалиста входят:
- штангенциркули,
- угломеры,
- угольники,
- измерительные линейки,
- щупы,
- шаблоны,
- рулетки и другие приспособления.
Специалисты нашего «Центра» имеют большой опыт проведения ВИК с использованием всех названных приборов, что обеспечивает высокую достоверность наблюдений и надлежащую точность измерений.
Преимущества визуального и измерительного метода контроля
Методы визуального и измерительного контроля имеют несколько преимуществ перед иными способами исследований:
- В ходе диагностики объект не подвергается разрушению и деформации.
- Невысокие временные и трудовые затраты на проведение ВИК.
- Широкая сфера применения описываемых технологий.
Визуальный и измерительный контроль дает возможность выявлять такие разнообразные дефекты на доступных для наблюдения частях деталей, а также в полостях:
- раковины, очаги эрозии и коррозии, следы износа и истирания, забоины и другие повреждения;
- трещины крупные (более 0,5 мм) и мелкие (не более 0,1 мм), зоны остаточной деформации деталей и разрушения узлов, разнообразные загрязнения всех возможных видов;
- наличие в полостях посторонних предметов и включений, мест утечек жидкостей и газов, а также следов высокотемпературных воздействий на материалы.
В дальнейшем обнаруженные дефекты могут быть дополнительно исследованы при помощи иных методов дефектоскопии: вихретоковой, цветной или ультразвуковой. Они позволят уточнить масштабы повреждений.
Более подробную информацию по техническим и финансовым вопросам проведения визуально-измерительного контроля можно получить в офисе компании (г. Томск) или по указанному на сайте номеру телефона.
Лицензии и свидетельства
Свидетельство об аккредитации НОАП
Свидетельство об аккредитации НОАЛ
Удостоверение ТУО
Лицензия на осуществление образовательной деятельности
Свидетельство об аттестации ЛНК
Свидетельство об аккредитации ЛНК
Свидетельство об аккредитации лаборатории разрушающих и других видов испытаний
Свидетельство СРО
Лицензия на использование ионизирующих источников излучения
Санитарно-эпидемиологическое заключение на помещения и оборудование
Санитарно-эпидемиологическое заключение по работе с ИИИ
Перечень центров по подготовке и аттестации Газпром
Сертификат соответствия СМК
Уведомление Минтруда по охране труда
Аттестат соответсвия ЦОК
Область деятельности ЦОК
Свидетельство Гемма
Подборка по базе: Практическое задание 1.1.1_ Основные понятия, термины и определе, ПР9 Исследование методов сварки оптоволоконных линий.docx, Лучевые методы в диагностике туберкулеза А.docx, СОВРЕМЕННЫЕ ИНСТРУМЕНТАЛЬНЫЕ МЕТОДЫ В ПОЧВОВЕДЕНИИ.pdf, Назначение и основные возможности графического редактора.ppt, Математические методы расчета установившихся режимов работы элек, 16301 соц методы в админ пр.doc, Лекция Методы определения порядка реакции.ppt, План-график контроля производственных факторов.docx, Инструкция по работе в системе модульно-рейтингового контроля.do |
% PDF-1.5 % 272 0 объект> endobj xref 272 89 0000000016 00000 н. 0000002577 00000 н. 0000002076 00000 н. 0000002682 00000 н. 0000003020 00000 н. 0000003334 00000 н. 0000003404 00000 н. 0000004033 00000 н. 0000004662 00000 н. 0000004723 00000 н. 0000005197 00000 н. 0000011437 00000 п. 0000011492 00000 п. 0000011990 00000 п. 0000012066 00000 п. 0000012135 00000 п. 0000018277 00000 п. 0000019152 00000 п. 0000019934 00000 п. 0000020655 00000 п. 0000020725 00000 п. 0000023914 00000 п. 0000024216 00000 п. 0000026478 00000 п. 0000026754 00000 п. 0000027248 00000 н. 0000027781 00000 п. 0000028666 00000 п. 0000029499 00000 н. 0000029552 00000 п. 0000029730 00000 п. 0000030124 00000 п. 0000030946 00000 п. 0000031021 00000 п. 0000031482 00000 п. 0000031932 00000 п. 0000032062 00000 н. 0000032207 00000 п. 0000032313 00000 п. 0000055681 00000 п. 0000055988 00000 п. 0000056397 00000 п. 0000056695 00000 п. 0000057084 00000 п. 0000057279 00000 н. 0000057691 00000 п. 0000057765 00000 п. 0000058071 00000 п. 0000081549 00000 п. 0000112854 00000 п. 0000112939 00000 н. 0000113001 00000 п. 0000113080 00000 н. 0000113125 00000 н. 0000113733 00000 н. 0000113752 00000 н. 0000113775 00000 п. 0000113798 00000 н. 0000113820 00000 н. 0000113843 00000 н. 0000113866 00000 н. 0000113904 00000 н. 0000113927 00000 н. 0000114002 00000 н. 0000114077 00000 н. 0000114152 00000 н. 0000114226 00000 п. 0000114260 00000 н. 0000114283 00000 н. 0000114317 00000 н. 0000114340 00000 н. 0000114374 00000 н. 0000114397 00000 н. 0000114431 00000 н. 0000114454 00000 н. 0000114480 00000 н. 0000114514 00000 н. 0000114548 00000 н. 0000114629 00000 н. 0000114710 00000 н. 0000114809 00000 н. 0000114858 00000 н. 0000114890 00000 н. 0000114916 00000 н. 0000115015 00000 н. 0000115064 00000 н. 0000115096 00000 н. 0000115122 00000 н. 0000115239 00000 н. трейлер ] >> startxref 0 %% EOF 274 0 obj> поток xb`Pe`he`g`? €
Оценка визуального осмотра парентеральных препаратов
Расчеты для анализа результатов осмотра
После завершения трех испытаний визуального осмотра тремя инспекторами и записи наблюдений в Таблицу 2, следующие данные используются для начала анализа результатов:
- Общее количество проверок = Общее количество проверенных флаконов (100) × Число проверок (3) × Число проверяющих (3) = 100 × 3 × 3 = Всего 900 проверок
- Общее количество проверенных хороших виал = Количество хороших флаконов (80) × Количество проверок (3) × Количество инспекторов (3) = 80 × 3 × 3 = 720 проверенных хороших виал
- Общее количество проверенных плохих виал = Количество плохих виал (20) × Количество проверок (180) × Количество инспекторов (30) = 20 × 3 × 3 = 180 проверенных плохих пузырьков
На основе этих данных выполняется несколько вычислений.Эти расчеты и результаты представлены в таблице 3.
Расчет | Уравнение | Значения | % |
---|---|---|---|
Общая точность | (\ (\ frac {Всего \; число \; \; проверок \; которые \; соответствуют \; \; стандартам} {Всего \; число \; \; проверок} \)) x 100 | (\ (\ frac {862} {900} \)) x 100 | 95.8 |
Общая частота ошибок | (\ (\ frac {Общее \; число \; \; проверок \; которые \; не \; не \; соответствуют \; \; стандартам} {Общее \; число \; \; проверок} \) ) х 100 | (\ (\ frac {38} {900} \)) x 100 | 4,2 |
Хорошие агрегаты оценены как плохие | (\ (\ frac {Всего \; число \; \; хороших \; единиц \; оценено \; как \; плохо} {Всего \; количество \; из \; хороших \; единиц \; проверено} \) ) х 100 | (\ (\ frac {33} {720} \)) x 100 | 4.6 |
Плохие агрегаты оценены как хорошие | (\ (\ frac {Всего \; количество \; \; плохих \; единиц \; оценено \; как \; хорошо} {Всего \; количество \; из \; плохих \; единиц \; проверено} \) ) х 100 | (\ (\ frac {5} {180} \)) x 100 | 2,8 |
Точность инспектора | (\ (\ frac {Число \; из \; правильно \; соответствует \; по \; \; инспектору} {Количество \; из \; инспекций \; выполнено \; по \; \; инспектору} \) ) х 100 | ||
Пример для инспектора 1 | (\ (\ frac {280} {300} \)) x 100 | 93.3 | |
Частота ошибок для конкретного устройства | (\ (\ frac {Number \; of \; incorrent \; соответствует \; на \; \; конкретном \; блоке} {Number \; of \; проверок \; выполнено \; на \; \; определенном \; unit} \)) x 100 | ||
Пример для флакона 11 | (\ (\ frac {8} {9} \)) x 100 | 88,9 | |
Хорошие агрегаты, оцененные инспектором как плохие | (\ (\ frac {Число \; из \; хороших \; единиц \; оценено \; как \; плохо \; \; \; инспектор} {Число \; из \; хороших \; единиц \; проверенных \; by \; the \; инспектор} \)) x 100 | ||
Пример для инспектора 1 | (\ (\ frac {17} {240} \)) x 100 | 7.1 |
Используя эти расчеты, мы можем затем определить верхнюю и нижнюю границы доверительных интервалов для показателей точности инспектора на хороших объектах с 95% доверительным интервалом (α = 0,05):
Значение нижней границы = $$ \ frac {1} {1+ \ frac {n-x + 1} {x} F_ {2 (x + 1), 2x, \ alpha / 2}} $$
Значение верхней границы = $$ \ frac {\ frac {x + 1} {nx} F_ {2 (x + 1), 2x, \ alpha / 2}} {1+ \ frac {x + 1} {nx} F_ {2 (x + 1), 2x, \ alpha / 2}} $$
где
x = количество правильных совпадений с хорошими юнитами инспектором
n = общее количество хороших единиц, проверенных инспектором
F v1, v2, α = значение таблицы распределения F со степенями свободы v1 и v2 на уровне достоверности альфа (95%)
Пример для инспектора 1:
Значение нижней границы = $$ \ left (\ frac {1} {1+ \ frac {240-223 + 1} {223} F_ {2 (240-223 + 1), (2×223), 0.05/2}} \ справа) x 100 $$
= 88,9%
Значение верхней границы = $$ \ left (\ frac {\ frac {223 + 1} {240-223} F_ {2 (223 + 1), 2 (240-223), 0,05 / 2}} {1+ \ гидроразрыв {223 + 1} {240-223} F_ {2 (223 + 1), 2 (240-223), 0,05 / 2}} \ вправо) x 100 $$
= 95,8%
Примечание. Для расчета точного доверительного интервала лучше всего использовать статистическое программное обеспечение, поскольку формулы сложны. Для ручного расчета можно использовать относительно простой метод нормальной аппроксимации. Формулы следующие:
формула $$ \ left (p \ pm Z_ {1 — (\ alpha / 2} \ sqrt {\ frac {p (1-p)} {n}} \ right) x 100 $$
где
P = \ (\ frac {Число \; из \; правильных \; совпадает \; с \; хорошими \; единицами \; по \; \; инспектор} {Общее \; количество \; из \; хороших \; единиц \; проверено \; \; \; инспектором} \)
Z 1- (α / 2) = 1.96 для 95% ДИ
n = общее количество хороших единиц, проверенных инспектором
Графические инструменты для интерпретации данных испытаний
Данные, полученные в ходе инспекционных испытаний, можно проиллюстрировать графически с помощью приложения для работы с электронными таблицами или имеющегося в продаже статистического программного обеспечения.
Первый отчет (рисунок 1) показывает общую точность процесса визуального контроля (95,8%). Весь процесс соответствует минимальной приемлемости для точности 95% (допустимый предел).
На Рисунке 1 также сравнивается индивидуальная точность трех инспекторов. Инспектор 1 имел степень точности 93,3%, что ниже предела точности приемки. Следовательно, инспектора 1 необходимо переучить.
Проблемой, связанной с «показателем ошибочной классификации» на Рисунке 1, является наличие дефектных единиц, оцененных как хорошие (плохие, оцененные как хорошие). Единицы, ошибочно классифицированные как хорошие, могут представлять опасность для здоровья пациентов и поэтому неприемлемы с точки зрения GMP. Ошибки в классификации могли быть связаны с ошибками конкретного инспектора или же являлись пограничными случаями, в которых любому инспектору трудно отличить хорошие от плохих единиц.
Рисунок 2 может быть полезен для интерпретации коэффициентов ошибочной классификации. Низкий уровень точности в целом и среди всех инспекторов указывает на необходимость повышения эффективности процедур, мероприятий или обучения визуальных инспекций.
Визуальный осмотр подводных железобетонных конструкций — ограничения и инструменты
Визуальный осмотр является наиболее широко используемым методом контроля подводных железобетонных конструкций. Этот метод экономичен, не требует больших затрат времени и дорогостоящего и большого количества оборудования.
Визуальный осмотр используется не только для выявления повреждений на поверхности конструкции, но также для определения и обнаружения серьезно поврежденных позиций конструкции.
При оценке подводной железобетонной конструкции могут быть задействованы такие методы, как фотография, видео и взгляд инспекторов, ныряющих под водой.
Визуальная оценка подводных бетонных конструкций, ограничения техники и необходимые инструменты, используемые в этом методе, обсуждаются в следующих разделах.
Рис.1: Визуальный осмотр подводных железобетонных конструкций
Визуальный осмотр подводных железобетонных конструкций
При визуальном осмотре подводных конструкций ПКР обсуждаются следующие пункты:
- Инструменты для визуального контроля
- Измерительное оборудование для визуального контроля под водой
- Ограничение метода визуального контроля
- Тактильная оценка подводной железобетонной конструкции
Инструменты для визуального осмотра Подводные железобетонные конструкции
Для визуального осмотра подводных железобетонных конструкций используются различные инструменты и оборудование.Такие инструменты могут включать монтировки, молотки, измерительные стержни, которые могут потребоваться для проведения зондирования бетона, и кирки.
В этой технике обычно наблюдаются расслоения и пустоты, поэтому оборудование для скалывания имеет большое значение для откола части бетона и определения степени проникновения повреждений в бетон.
Тип оценки, полученный с помощью этих инструментов, следует использовать в качестве руководства для дальнейшей оценки и анализа.
Вспышки и маска из прозрачной воды очень важны для улучшения видимости и достижения лучших результатов подводного осмотра.Это связано с тем, что такие устройства могут улучшить видимость под водой, что важно при проведении подводного осмотра.
Сообщается, что лампы с йодистым таллием и йодистым кварцем успешно использовались в процессе подводного контроля.
Измерительное оборудование для визуального контроля подводных конструкций ПКР
Есть несколько простых инструментов, которые используются дайверами для получения ограниченного количества данных в процессе обследования подводных железобетонных конструкций.
Это оборудование недорогое и может быть легко использовано, не затрачивая много времени. Их способность определять степень разрушения значительно ограничена.
Измерительные инструменты можно разделить на различные группы, включая линейные измерения, круговые измерения и глубину выкрашивания или деформации.
Линейные измерения для визуального контроля
Приборы, применяемые для линейных измерений при обследовании подводных железобетонных конструкций, представлены в таблице-1.
Таблица-1: Инструменты линейных измерений, их применение и точность
Типы устройств | Применение прибора | Точность измерений |
Линейка, фигура-2 | Измерьте длину трещины, ширину и длину скола | +/- 0,5 мм |
Метчик, фигура 3 | Используется для измерений до 100 м | +/- 5 мм |
Магнитная лента | Используется для круговых измерений и максимум 3 м | +/- 1 мм |
Весы | Используется в сочетании с фотографией | +/- 5 мм |
Компаратор | Измерьте ширину трещины | +/- 0.025 мм для сухих условий, но под водой точность снижена |
Рис.2: Линейка
Рис.3: Рулетка
Круговые измерения
Приборы, используемые для получения круговых измерений при визуальном осмотре подводной железобетонной конструкции, представлены в таблице-2.
Таблица 2: Инструменты для круговых измерений, их применение и точность
Типы устройств | Применение прибора | Точность измерений |
Суппорт, фигура 4 | Измерения диаметром до 2 м | +/- 0.5 мм |
Специальные приспособления | Измерьте овальность члена | +/- 5 мм |
Рис.4: Штангенциркуль
Измерения глубины деформации или выкрашивания
Существует ряд устройств, используемых при подводном контроле для измерения деформации или глубины выкрашивания, и эти инструменты представлены в таблице 3.
Таблица-3: Деформация устройств измерения глубины откола, их применение и точность
Типы устройств | Применение прибора | Точность измерений |
Калибр профиля | Используется для записи зеркального отображения дефектов на бетонных элементах | +/- 0.5 мм |
Натянутый провод | Используются для больших деформаций или участков скола, в дополнение к измерению отклонения стержней от вертикали | +/- 5 мм |
Отливки | Применяется для получения зеркального изображения o |
Визуальный осмотр поверхности самолета с использованием дистанционно настраиваемого робота-альпиниста и усовершенствованной техники глубокого обучения
Осмотр поверхности самолета включает обнаружение дефектов поверхности, вызванных коррозией, а также трещин и пятен от разлива нефти, жир, отложения грязи и т. д.В обычном процессе осмотра поверхности воздушного судна выполняется визуальный осмотр человека, который занимает много времени и неэффективен, тогда как роботы с бортовыми системами технического зрения могут безопасно, быстро и точно осмотреть обшивку самолета. В этой работе предлагается модель обнаружения дефектов и пятен на поверхности самолета с использованием реконфигурируемого альпинистского робота и усовершенствованного алгоритма глубокого обучения. Реконфигурируемый дистанционно управляемый робот, названный «Kiropter», предназначен для захвата изображений поверхности самолета с помощью встроенной камеры RGB.Для обнаружения пятен и дефектов по этим изображениям предлагается усовершенствованная платформа SSD MobileNet. В структуру глубокого обучения SSD MobileNet включен фильтр обнаружения периодических образов на основе самофильтрации, позволяющий улучшить обнаружение пятен и дефектов на изображениях обшивки самолета. Модель была протестирована с использованием реальных изображений поверхности самолета, полученных с Boeing 737, и поверхности компактного самолета с помощью дистанционно управляемого робота. Результаты экспериментов доказывают, что усовершенствованная платформа SSD MobileNet обеспечивает повышенную точность обнаружения поверхностных дефектов и пятен самолета по сравнению с традиционными моделями.
1. Введение
Осмотр обшивки самолета важен в рамках Программы предотвращения и контроля коррозии (CPCP) для обеспечения структурной целостности самолета [1]. Согласно CPCP, самолет должен содержаться в полной чистоте от отложений, содержащих загрязняющие вещества, такие как масло, смазка, грязь и другие органические или инородные материалы, чтобы предотвратить потенциальный риск коррозии, разрушения уплотнений и пластмассовых деталей самолета. Кроме того, после плановой очистки самолета его следует тщательно осмотреть на предмет выявления неочищенных участков (обычно пятен) и дефектов поверхности.Во время очистки чистящее средство может нарастить эти дефекты, что может увеличить причиненный ущерб [1, 2].
Визуальный осмотр человека на сегодняшний день является наиболее широко используемым методом проверки поверхности самолетов [3, 4] согласно CPCP. Однако существующая практика попадания на корпус самолета для проведения наземного осмотра вызывает у инспекторов вопросы безопасности. Это также требует много времени и временами бывает неэффективным из-за усталости инспектора или скуки. Автоматизированные системы проверки обшивки самолета, основанные на методах компьютерного зрения, могут позволить инспектору безопасно, быстро и точно выполнить необходимый визуальный осмотр [3, 5, 6].Роботизированная помощь для осмотра обшивки самолета исследовалась в [4, 7–9]. Этим системам требуется гибкая роботизированная платформа с дистанционным управлением с различными возможностями передвижения для доступа к поверхности самолета и оптимальный алгоритм обнаружения для автоматического обнаружения пятен и дефектов на обшивке самолета.
Разработка роботизированной инспекционной платформы с хорошей адгезией, мобильностью и гибкостью является ключевой задачей. Обычно для проверки самолетов используются альпинистские роботы фиксированной морфологии.Они используют магнитные устройства, вакуумные присоски или силу пропеллера, чтобы удерживаться и подниматься по поверхности самолета [8, 10–12]. Однако эти альпинистские роботы сталкиваются с трудностями при доступе к замкнутым пространствам из-за их менее гибкой конструкции [8, 9, 13]. Им также трудно преодолевать стыки и фюзеляж, перекрывающиеся друг с другом, что снижает их охват [9]. Реконфигурируемые роботизированные платформы могут получать доступ к замкнутым пространствам, пересеченной местности и труднопроходимым поверхностям за счет динамического изменения их формы и функциональности.В последнее время реконфигурируемая роботизированная платформа была широко разработана и развернута в различных приложениях, включая инспекции [14, 15], ремонт [16], уборку [17, 18] и космические приложения [19]. Kwon et al. [20] разработал реконфигурируемый робот для проверки внутренних трубопроводов и осмотра канализационных трубопроводов. В [14] авторы разработали реконфигурируемый робот для осмотра мостов. Реконфигурируемые изменяющие форму роботы, основанные на алгоритме укладки тромино и тетромино, также были разработаны для мытья полов [21, 22].Робот для уборки пола обеспечивает лучшее покрытие площади пола, чем роботы с фиксированной морфологией.
Еще одним ограничением для метода визуального осмотра самолета является разработка алгоритма обнаружения для автоматического распознавания пятен и дефектов. В последнее десятилетие различные алгоритмы визуального осмотра применялись в области осмотра самолетов и обнаружения поверхностных дефектов. Эти алгоритмы визуального контроля подразделяются на два типа: традиционный визуальный контроль на основе обработки изображений [5, 23–25] и методы машинного обучения [26–31].Обычно традиционные алгоритмы используют элементарные характеристики, такие как границы, яркость, гистограмма и спектральные характеристики для обнаружения и сегментации дефектов [28]. Однако эти методы обработки изображений хорошо работают только в контролируемых средах и часто не работают в сложных реальных сценариях из-за шума и сложного фона. Более того, для различных дефектов пороговые значения, часто используемые в этих алгоритмах, необходимо отрегулировать, или может даже потребоваться переработка алгоритмов [28]. Алгоритмы на основе CNN были успешно реализованы в приложениях для обнаружения и проверки дефектов, включая обнаружение поверхностных трещин и дефектов [26–28, 30, 32], проверку солнечных панелей [33] и проверку очистки [34].Ча и Чой предложили использовать CNN [32] и метод Faster RCNN [29] для лучшего обнаружения трещин в бетонных и металлических поверхностях. Автор предлагает использовать Faster RCNN, который имеет более оптимизированную ограничивающую рамку для локализации трещин. Далее автор также предлагает систему БПЛА для маркировки и локализации трещин в бетоне [35, 36].
Как правило, ключевой проблемой алгоритмов глубокого обучения для этого приложения является требование большого объема данных изображения и оптимального алгоритма предварительной обработки.Предварительная обработка играет жизненно важную роль, помогая сети распознавать малоконтрастные объекты и различать объекты со схожими характеристиками, такими как грязь, пятна и царапины на поверхности самолета, и все это при небольших затратах, которые ничтожны по сравнению с увеличением сложность архитектуры CNN [26]. Ли и др. включил алгоритм предварительной обработки с SSD MobileNet в приложение для обнаружения поверхностных дефектов. Здесь авторы используют гауссову фильтрацию, обнаружение краев и алгоритмы обнаружения Хафа по кругу, чтобы улучшить качество краев и отфильтровать шум из изображения [26].В [37] использовалась информация о границах для повышения точности обнаружения Faster RCNN в приложении для обнаружения дорожных знаков. Автор доказал, что информация о краях улучшила точность обнаружения и скорость отзыва Faster RCNN. Брендель и Бетге разработали модель CNN, названную BagNets, которая использует функцию локального изображения для достижения лучшего коэффициента обнаружения и хорошей чувствительности функции [38]. В [28] Tao et al. доказывают, что их компактные CNN обеспечивают лучшее обнаружение в обученной сети на основе текстур, чем изображение контента.
Чтобы преодолеть недостатки, упомянутые ранее, в этой статье предлагается реконфигурируемый робот на основе всасывания под названием «Kiropter» для проверки самолетов вместе с улучшенной платформой глубокого обучения SSD MobileNet для распознавания и классификации пятен и дефектов на поверхности самолета. Реконфигурируемый робот способен получать доступ к ограниченным областям, перекрывающимся стыкам и фюзеляжу на корпусе самолета, динамически изменяя его форму и функциональность. Фильтр обнаружения периодических образов на основе самофильтрации принят, как и в случае с платформой глубокого обучения SSD MobileNet, для эффективного улучшения результатов распознавания в малоконтрастных пятнах и дефектных областях на изображении кожи самолета.Эта статья организована следующим образом: соответствующая работа описана в Разделе 2. Раздел 3 описывает архитектуру и функциональность робота. Усовершенствованная модель проверки на основе глубокого обучения описана в разделе 4. Результаты экспериментов представлены в разделе 5. Наконец, в разделе 6 представлены выводы и будущие работы.
2. Сопутствующие исследования
Очень мало работ по обшивке самолетов осмотр есть в литературе. Некоторые из этих работ посвящены разработке роботизированной платформы для проверки, а другие — алгоритму обнаружения.Сигель и Гунатилэйк [39] разработали модель осмотра поверхности самолета, основанную на мобильной платформе осмотра короны (CIMP), которая фиксирует изображения корпуса самолета и использует алгоритм компьютерного визуального осмотра для распознавания дефектов на поверхности. Визуальный алгоритм состоит из схемы улучшения изображения на основе вейвлетов для выделения трещин и трехуровневой нейронной сети с прямой связью, состоящей из десяти входов, тридцати скрытых слоев и двух выходов для классификации трещин и коррозии.Улучшенный удаленный визуальный осмотр обшивки самолета на основе роботизированной системы CIMP с использованием улучшенного алгоритма NN предложен Alberts et al. [40]. Здесь автор проектирует трехуровневую сеть (входной, скрытый и выходной слои) с 169 входными сетевыми узлами на основе узлов для различения здоровых и потрескавшихся участков поверхности самолета. Об автоматизированном визуальном осмотре самолета сообщает Rice et al. [24], где авторы используют камеру глубины, установленную на крыше, для сканирования поверхности самолета. Затем следует алгоритм подбора контура для визуализации дефектов, имеющихся на самолете.Mumtaz et al. [23] исследовали три алгоритма обработки изображений, чтобы различать трещины и царапины на обшивке самолета. Авторы протестировали нейронную сеть, контурное преобразование (CT) с классификатором скалярного произведения (DPC) и дискретное косинусное преобразование (DCT) с DPC и комбинацией DCT и CT с DPC. Среди трех DCT CT с комбинированными схемами DPC обеспечивает более высокую скорость распознавания. Jovacevíc et al. [5] разработали автоматизированную модель внешнего осмотра самолета для автономного мобильного коллаборативного робота (кобота) с использованием методов обработки 2D-изображений.Авторы используют маску ядра для удаления шума и улучшения текстуры на участках поверхности самолета. Алгоритмы преобразования Хафа (HT) и круга обнаружения краев (EDC) ar
Методы визуального контроля — Большая химическая энциклопедия
Лазерные системы контроля стволов предназначены для расширения и, возможно, в конечном итоге, для замены трудоемких, отнимающих много времени и субъективных методов визуального контроля, которые в настоящее время используются на этих объектах.[Стр.1066]Степень износа может быть измерена одним или несколькими из следующих методов: визуальный осмотр, изменение веса, изменение свойств при растяжении. Визуальный осмотр в первую очередь зависел от испытаний A-5 … [Стр.1068]
Визуальный осмотр и измерение Абрамчук считает это настолько важным, что должно стать логической прелюдией к большинству других методов контроля. Правильно выполненный визуальный осмотр может … [Pg.1142]
Введение жестких процедур личной безопасности и визуального или рентгеновского досмотра ручной клади во всех внутренних и международных аэропортах в 1972 г. привело к почти полному устранению инциденты скайджекинга в США.Эта ситуация, скорее всего, прервала или задержала дальнейшую разработку методов автоматического неразрушающего контроля багажа на терминалах авиакомпаний … [Pg.387]
После завершения этих оценок эффективность проверки машины следует сравнить с метод визуального осмотра. [Pg.320]
Положительное давление / погружение Вакуум / погружение Проникновение красителя Испытание на утечку пара / частиц Визуальные методы проверки Испытания на пропускание света … [Pg.655]
Другие подходы к представлению информации для облегчения визуализации значимых структур для быстрого принятия решения задействовать приложения, связанные с комбинаторной химией.Например, методы анализа образцов, полученных из комбинаторной химии, обеспечивают визуальное представление 96-луночного планшета (рис. 5.5) (Yates et al., 2001). После анализа ЖХ / МС выполняется автоматический анализ в соответствии с заранее установленными пороговыми значениями для поиска протонированной молекулы иона аналита. Если ион обнаружен, то визуальное представление соответствующей лунки отмечается отличительной цветовой схемой. Таким образом, ученый быстро проверяет визуальное представление, чтобы принять решение.[Стр.58]
На самом деле идентификация одной или нескольких форм коррозии требует визуального наблюдения, методов неразрушающего контроля, оптического микроскопического исследования, а иногда и электронной сканирующей микроскопии и т. Д. Первое исследование коррозионного внешнего вида корпуса должно разделить коррозию на равномерную и локальную. Локальную коррозию можно далее идентифицировать как макроскопическую или микроскопическую локальную коррозию. Микроскопическая атака — это небольшое количество растворенного металла, сопровождающееся значительным повреждением, прежде чем явление станет видимым невооруженным глазом.[Pg.338]
Наиболее часто используемым методом инвентаризации является метод визуального контроля. Этот метод требует, чтобы фармацевт или другой назначенный персонал визуально проверяли количество предметов, оставшихся на полке. Затем по этому количеству человек определяет, есть ли в наличии адекватный инвентарь или следует разместить заказ. Человек может использовать ROP и EOQ, чтобы определить, следует ли размещать заказ, и количество заказов. Это система повторного заказа с фиксированным количеством, в которой дата повторного заказа меняется, но количество остается прежним.[Pg.179]
В Сиднее проводится серия исследований, направленных на выявление маркеров раннего заболевания с использованием как визуального осмотра, так и метода SCS. Визуальный осмотр данных MRS показал в 11% случаев, что стандартная гистопатология была неправильной из-за неполного исследования образца ткани. Как следствие, патология этих и еще 15% случаев была рассмотрена вслепую. Ткани, исследованные с помощью MRS, были серийно разрезаны, и срезы исследовались каждые 100 мкм.Была подчеркнута неточность рутинных процедур госпитальной патологии, где исследуются участки в 17:00 только на двух или трех уровнях. [Pg.97]
Физические методы Визуальный контроль Цельное зерно, только качественный … [Pg.174]
Визуальный контроль клеев проводится как на неотвержденных, так и на неотвержденных образцах. Неотвержденные материалы проверяются на однородность распределения наполнителя, консистенцию и клеевое покрытие. Методы проверки определены в пунктах 3.4.1 и 3.8.3 метода 5011.4 стандарта MIL-STD-883F. … [Pg.353]
Общий контроль, предотвращение и мониторинг коррозии следует планировать с самого начала. Для обнаружения и мониторинга коррозии необходимо использовать различные методы, в то время как защита от коррозии будет осуществляться путем добавления ингибирования и использования защитных покрытий [5]. Визуальный осмотр, лазерные методы, метод испытания проникновения жидкости с помощью репликационной микроскопии, испытание магнитными частицами, метод вихретокового контроля, метод акустической эмиссии, термические методы контроля и неразрушающие методы — это различные методы, которые следует использовать при мониторинге коррозии трубопроводов [5] .[Pg.658]
Спектры могут стать довольно сложными, когда ядерное квадрупольное взаимодействие заметно, как для оксида азота (NO), введенного в цеолит Na-A, обсуждаемого в главе 6. Также известно, что NO имеет тенденцию к димеризации, образуя 5 = 1 вид в этих условиях [39]. Комплекс в триплетном состоянии образуется при взаимодействии с одним или несколькими ядрами Na в цеолите [40]. Спектр, полученный после преобразования трехимпульсного сигнала ESEEM на рис. 2.22, трудно анализировать визуально.Методы получения сверхтонкой и квадрупольной связи путем моделирования описаны в главе 3. [Pg.56]
Для калибровки, если совокупный объем жидкости больше 1 мкл, предлагается метод объемного взвешивания. Но для калибровки объема одной капли метод визуального контроля проще. [Pg.2734]
PVB и катионный PVB смешивали с поли (виниуденфторидом) (PVDF). Эти смеси были использованы для изготовления мембран для гидрофильтрации (32). Для изучения смешиваемости смесей применяли метод визуального контроля и метод температуры стеклования.PVDF не смешивается с PVB, но частично смешивается с катионным PVB. [Стр.56]
Требования и методы проверки должны быть определены для TBS. Осмотру способствует прозрачность расплавленных солей, но все же его необходимо проводить при повышенной температуре. Предполагается, что визуальный осмотр возможен с использованием активно охлаждаемых погружных камер с сапфировыми смотровыми окнами. Другие методы контроля также могут быть адаптированы к TBS, но еще не прошли оценку. Здесь предполагается, что коррозия материалов на углеродной основе (особенно колец C / C 0) будет достаточно медленной, поэтому проверка гибких уплотнений C / C между блоками не потребуется в течение срока службы TBS.[Стр.28]
Kruse et al. (1983) исследовали цинковые трубы и образцы стальных труб с различным цинковым покрытием. Все образцы подверглись коррозии в водопроводной воде Дортмунда в 11 испытательных линиях, содержащих горячую воду с температурой около 60 ° C и холодную воду, причем как с прерывистым, так и с непрерывным потоком, в некоторых испытаниях периодически добавлялись полифосфаты или ортофосфаты. Одна тестовая линия работала на теплой воде от водонагревателя с катодной защитой резервуара по методу Гульдагера.Визуальный осмотр, а также … [Pg.297]
Самым распространенным методом осмотра ЛЭП является визуальная оценка, проводимая с места пешим патрулированием или с воздуха при штатном воздушном (вертолетном) наблюдении . Это очень эффективный метод, но он должен использоваться в сочетании с инструментальными, химическими, биологическими, электрическими и электрохимическими методами с последующим лабораторным анализом отказов, чтобы получить истинную картину состояния человека. [Pg.723]
DOT и TC заявляют, что результаты требуемых периодических проверок цилиндра должны регистрироваться, а копия должна храниться у владельца или уполномоченного агента владельца либо до истечения периода повторных испытаний, либо до тех пор, пока цилиндр не будет повторный осмотр или повторное тестирование, в зависимости от того, что произойдет раньше [1, 2].Также баллон, прошедший процедуру переквалификации, должен иметь постоянную печать на баллоне в установленном порядке. Примечание. После даты (месяца и года) следует буква E, когда разрешается повторная аттестация методом визуального внешнего осмотра вместо повторного гидростатического испытания. [Стр.173]
Тест на протирание используется для обнаружения загрязнений на визуально недоступных участках в качестве вспомогательного средства в дополнение к вышеуказанным визуальным проверкам. Поверхность слегка протирают чистой белой бумагой или безворсовой тканью, которую затем исследуют в белом и ультрафиолетовом свете.Область не следует тереть достаточно сильно, чтобы удалить оксидную пленку, поскольку это можно принять за фактическое загрязнение поверхности. Осматриваемый элемент необходимо повторно очистить, если этим методом проверки будет обнаружено неприемлемое количество постороннего материала. [Pg.215]
Существуют компьютерные методы визуального контроля, называемые автоматическим оптическим контролем (AOl). Оборудование AOI сравнивает плату или ее внутренние слои с ожидаемыми данными и / или конструктивными элементами, которые были запрограммированы в управляющий компьютер.Они могут быть общими … [Pg.851]
Метод визуального осмотра с использованием «темного поля …
Технические статьи
, Ёсихиро Сатаке, инженер по продажам — Nacacue Corporation Опубликовано 12.09.2018
Для освещения для визуального осмотра традиционно широко использовалось светлое поле.
Чтобы наблюдать аномалию состояния в ярком поле, аномалия становится темнее, чем окружающая среда.
Поле зрения и проверяемый объект становятся максимально яркими, и если есть отклонения от нормы, отклоняется ненормальный отраженный свет, так что согласно теории отклонение от нормы кажется темнее, чем окружающее.
С другой стороны, в случае темного поля (и коллимации) аномалия становится ярче, чем окружающая среда.
Держите поле зрения темным (не смотрите на освещение), держите проверяемый объект над лучом. В это время коллимированный световой луч идет прямо и отражается при ненормальном попадании.Поскольку этот аномально отраженный свет достигает глаз, логично предположить, что аномалия выглядит яркой в темноте.
В ярком поле, из-за способа наблюдения, световые лучи, отличные от аномально отраженного света, также достигают глаза, поэтому их было трудно проверить.
В этом отношении, если это коллимация темного поля, будет виден (только) аномально отраженный свет, что упрощает проверку.
Вместо того, чтобы улавливать ненормальный отраженный свет в ярко-конденсированном состоянии, легче оставаться в глазу, если аномалия радостно светится в темноте.
Например, даже если образец, имеющий такое свойство, что световые лучи отражаются вокруг, например призма или светоделитель, применяется коллимированное освещение темного поля, видимые световые лучи (аномально отраженный свет) достигают глаза, за исключением лишние лучи, осмотр становится легким.
Кроме того, он совместим с осмотром в проходящем свете и исследованием в отраженном свете, и можно также сказать, что отраженный свет можно использовать для наблюдения за состоянием поверхности зеркала или для наблюдения за внутренним состоянием линзы в проходящем свете.
Другими словами, он широко доступен для визуального осмотра.
Кроме того, он может излучать не только белый свет, но и зеленый, поэтому он может быть использован в качестве исследования.
.