Плазморез своими руками из инвертора, подробности изготовления, видео
Домашние мастера, занимающиеся обработкой металла, сталкиваются с необходимостью раскраивать металлические заготовки. Это можно сделать при помощи угловой шлифовальной машины (болгарки), кислородного резака или плазмореза.
- Болгарка. Качество среза очень высокого уровня. Однако выполнить фигурный раскрой невозможно, особенно если это касается внутренних отверстий с изогнутыми краями. К тому же есть ограничения по толщине металла. Тонкие листы резать болгаркой невозможно. Главное преимущество – ценовая доступность;
- Кислородный резак. Может вырезать отверстие любой конфигурации. Но добиться ровного среза невозможно в принципе. Края получаются рваными, с каплями оплавленного металла. Тяжело режется толщина более 5 мм. Приспособление не слишком дорогое, но требуется иметь большой запас кислорода для работы;
- Плазморез. Доступным этот прибор не зазовешь, но высокая стоимость оправдана качеством среза.
Учитывая неподъемную для большинства домашних мастеров цену – многие умельцы «кулибины» изготавливают плазменный резак своими руками.
Способов несколько – можно создать конструкцию полностью «с нуля», или использовать готовые приспособления. Например – из сварочного аппарата, несколько модернизированного под новые задачи.
Изготовить плазморез своими руками реальная задача, но сначала необходимо понять, как он работает.
Общая схема изображена на иллюстрации:
Устройство плазмореза
Блок питания.
Он может быть сконструирован по-разному. Трансформатор имеет большие габариты и массу, но позволяет резать более толстые заготовки.
Потребление электроэнергии выше, это необходимо учитывать при выборе точки подключения. Такие блоки питания мало чувствительны к перепадам входного напряжения.
Инверторы экономичны, у них выше КПД. Дуга, полученная с помощью такого источника питания, горит стабильнее, что положительно влияет на качество реза.
Инвертор легче, и занимает меньше места в сравнение с трансформатором. Это делает прибор мобильным, что позволяет работать в труднодоступных местах.
Однако есть и недостатки. Толщина разрезаемой заготовки ограничена.
Плазмотрон.
Рабочая головка, с помощью которой производится резка.
Схема плазменного резака:
На электрод подается напряжение от инвертора для возбуждения плазменной дуги. Выбирается тугоплавкий металл, с образованием прочного окисла.
Например, цирконий, гафний или бериллий. Сопло служит для формирования плазменной струи. В зону образования плазмы подается сжатый воздух, который одновременно придает форму плазменной струе и охлаждает электрод.
Параметры сопла определяют характеристики реза. От диаметра зависит скорость разреза заготовки и размер прожигаемой щели. Величина отверстия на типовом резаке обычно равняется 3 мм. От длины напрямую зависит качество обработки. Однако слишком длинное сопло сильно нагревается и быстро изнашивается.
Охладитель (он же изолятор) частично отводит тепло от сопла, продлевая его ресурс. В рабочем режиме плазма достигает температуры более 25000°.
Поскольку плазма состоит не только из потока заряженных частиц, а еще и из воздуха – он должен подаваться в больших количествах. Этим вопросом заведует компрессор. Если рабочий ток не превышает пары сотен ампер, используется обычный воздух из атмосферы. Толщина разрезаемого металла менее 5 см.
В промышленных резаках выше сила тока и применяются различные газы: аргон, гелий, азот и даже кислород с водородом.
По управляющему комплекту шланг-кабель поступает как электрический ток, так и сжатый воздух (газ).
Подробное описание как сделать плазмотрон для плазмореза в этом видео.
Как работает плазморез
После нажатия управляющей клавиши, ток большой величины и частоты зажигает (в буквальном смысле) электрическую дугу между соплом и электродом.
Когда дежурная дуга заполняет все сопло, подается сжатый воздух (газ). От воздействия высокой температуры газ ионизируется, и становится проводником. Фактически возникает короткое замыкание через воздух, который превращается в газообразный электрод.
В этот момент из сопла вырывается сформированная конусом плазма с температурой более 20000° С. При таких условиях электропроводность раскаленного воздуха внутри плазменного потока, равна проводимости металла.
При соприкосновении плазмы с металлом заготовки, возникает классическая дуга, как при электродной сварке. В роли электрода выступает плазма. Дуга моментально нагревает металл в точке соприкосновения. Размер пятна равен диаметру сопла. Превратившийся в жидкость металл, моментально выдувается под напором сжатого воздуха. Происходит резка заготовки.
Важно! При работе с плазморезом требуется определенная сноровка. Двигаться необходимо равномерно, с правильно заданной скоростью.
Если головку вести слишком медленно – рез получится не таким ровным, и будет слишком широким. Нагревшиеся края металла станут корявыми. Быстрое перемещение не позволит качественно выдувать расплавленный металл, и рез потеряет непрерывность.
Этого недостатка лишены станки плазморезы, в которых сопло управляется механически.
Однако стоимость таких устройств слишком высока. Самостоятельное изготовление затруднено, по причине дороговизны комплектующих. Мы рассмотрим возможность изготовления ручного плазменного резака со средними параметрами.
Плазморез своими руками из инвертора
Основная сложность – изготовление собственно плазмотрона. Точнее – режущего сопла.
Металлы, из которых вытачиваются наконечники, к доступным не относятся. Поэтому есть смысл приобрести готовое сопло. Патрубок для подключения шланга, работающего под давлением – должен быть установлен промышленным путем.
Рабочая область имеет температуру в несколько тысяч градусов, поэтому любой доступный в домашних условиях способ сварки, не подойдет.
Также необходимо всегда иметь запас расходных материалов. Сопло, из какого бы прочного металла оно не было сделано, изнашивается довольно быстро. Поэтому комплект из 5-10 насадок и катодов не помешает. К тому же лучше иметь несколько различных диаметров сопла, для работы с разными металлами.
Токопроводящий кабель от инвертора объединяют со шлангом для подачи сжатого воздуха. Вся конструкция должна составлять единое целое, иначе можно просто запутаться в шлангах во время работы.
В качестве корпуса для сопла хорошо использовать керамические втулки. Это и диэлектрик, и охладитель, неплохо рассеивающий лишнее тепло.
Самодельный плазморез, в отличие от обычного сварочника нуждается в управлении поджигом дежурной плазмы. Для этого в конструкцию готового инвертора встраивается осциллятор, который дает первичную искру для запала.
После появления рабочей плазмы его необходимо отключать. Для этого используется схема, работающая при помощи реле. Как только ток достигает рабочей величины – осциллятор выключается и дуга работает от основного (нагрузочного) выхода инвертора.
В остальном инвертор остается без изменений. Мощности хватает для обеспечения горелки при толщине металла до 20 мм. Обычно большую толщину в домашних условиях не обрабатывают.
Самодельный плазморез не может обойтись без компрессора. Для образования стабильной рабочей плазмы достаточно давления 2-2,5 атмосферы. Такую величину обеспечит даже обычный автомобильный компрессор.
Вся проблема в том, что во время работы расходуется огромное количество воздуха, и компрессор не может восполнить его с нужной скоростью. Если давление упадет – рабочая плазменная дуга разрушится, и резать металл будет невозможно.
Вопрос решается установкой воздушного ресивера. Он служит аккумулятором для накопления давления. Кратковременные интервалы работы резака не успевают снизить давление, а во время перерывов компрессор пополняет запас сжатого воздуха.
Можно использовать баллоны тормозной системы от грузовиков. Например – от «Камаза». Однако более практичным будет приобретение стандартного комплекта компрессора с ресивером.
Только обязательно оснастите комплект редуктором. Необходимо иметь возможность выставлять и поддерживать постоянное давление. Покупка компрессора не будет обременительной для бюджета, если использовать его для других целей. Например, для покраски с помощью краскопульта.
С помощью подобной самоделки можно резать как тонкую жесть толщиной 1 мм, так и толстые стальные пластины. Если работать по шаблону – можно вырезать качественные заготовки не хуже станка с ЧПУ.
В этом видео подробности сборки самодельного плазмореза.
About sposport
View all posts by sposport
Как сделать аппарат плазменной сварки своими руками?
Соединение поверхностей при сварке плазмой! Плазменная сварка – способ, кардинально отличный от всех существующих традиционных сварочных технологий.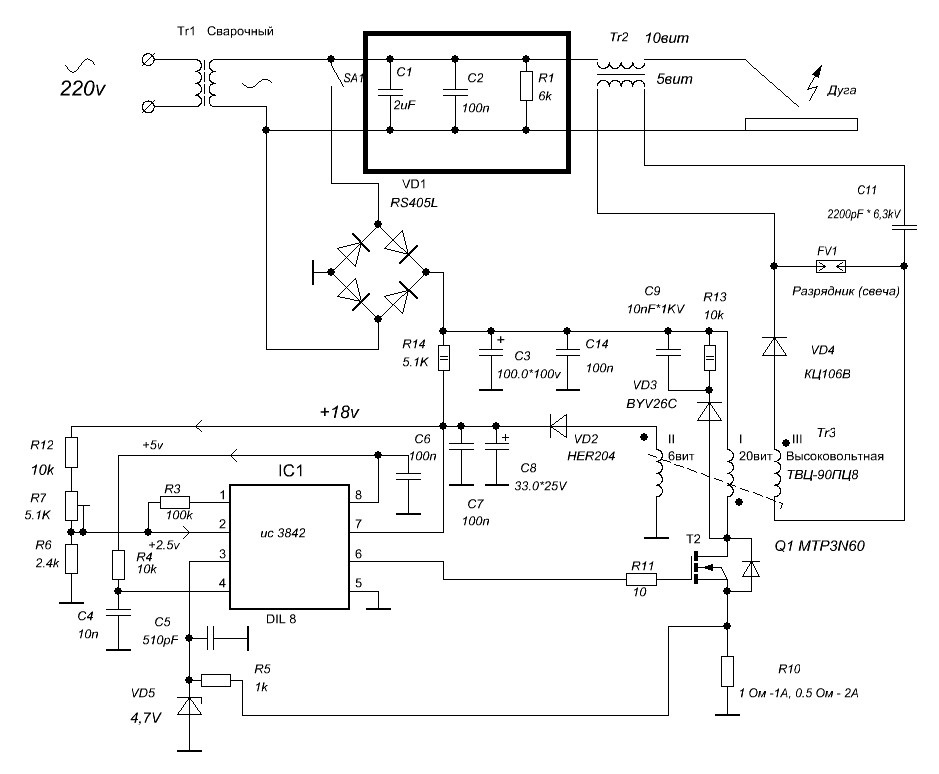
Аппарат плазменной сварки
Проявляется это в существующих преимуществах плазменной сварки:
- Безопасность процесса для сварщика;
- Уникальная возможность экономии электричества;
- Высокий уровень производительности, которым характеризуется соответствующий сварочный аппарат;
- Обеспечение высококачественного результата сварки либо резки.
По своей сути плазменная сварка представляет собой инновационный процесс соединения металлических плоскостей. На сегодня данная разновидность активно применяется в отдельных отраслях производства: машиностроении, приборостроении, на авиационных предприятиях и др.
Используется плазменная сварка при необходимости получения шва высокой прочности. Характерно, что оборудование для плазменной сварки не требует кислородных баллонов.
Технология является экологически чистой, так как в ходе сваривания металла не происходит выделения вредных веществ и газов. Кроме того, посредством плазменного оборудования возможна не только сварка, но и резка металлов и сплавов (достаточно лишь обзавестись соответствующим резаком).
Подробнее о процессе сварки
Для верного представления о технологии сварочного процесса важно детально вникнуть в саму его суть. С точки зрения физики при плазменной сварке ионизированный газ (т.е. плазма) посредством сопла направляется на поверхность свариваемых деталей. Для образования плазмы необходимо обеспечить нагрев рабочего газа до высокой температуры. Достигается это за счет сильного электротока.
Процесс работы плазмой
Применять соответствующий аппарат можно для соединения:
- Тонкостенных труб;
- Различного рода тонких емкостей;
- Деталей, изготовленных из фольги;
- Отдельных элементов ювелирных изделий.
Самостоятельная сборка сварочного аппарата
Аппарат для плазменной сварки, а также резки металлов для своего функционирования нуждается лишь в сжатом воздухе и электричестве. В тех случаях, когда применяется компрессорное оборудование, аппарат потребует только электричества. В результате при осуществлении сварки требуется замена электродов, а также сопла плазмотрона.
Самостоятельное конструирование аппарата плазменной сварки требует кропотливой работы.
Прежде всего, необходимо заняться разработкой схемы блока питания. Именно от такого блока и зависит полноценное функционирование аппарата.
Для проведения работ понадобятся:
- Дроссель от обычного аппарата сварки. Этот элемент необходим для стабилизации напряжения. Если не обеспечить стабильность, то скачки напряжения будут гасить плазму, так необходимую для сварки и резки;
- Тиристорный трехфазный выпрямитель. Его включение в схему объясняется потребностью в ограничении тока в области 50 ампер;
- Обычный стартер автомобиля. Эта деталь нужна для обеспечения автоматического поджога. Впрочем, возможно и применение обычного трамблера. Все это избавит от необходимости ручного поджога.
При создании плазменного сварочного аппарата особо пристальное внимание, безусловно, нужно уделить корпусу. При наличии всех необходимых материалов и неплохих металлообрабатывающих станков самостоятельное изготовление всех основных элементов не вызовет трудностей.
Шов после соединения деталей плазменной сваркой
Для полноценного представления о том, как выглядит собираемый аппарат сварки и резки, предлагаем изучить в интернете большое изобилие схем.
Ключевым элементом для сварки и резки является плазменная горелка. Конструкция ее такова, что это, по сути, удобная рукоятка, в которой расположены анод и катод.
Анод, будучи одновременно и соплом, изготавливается из меди. В ходе сварочного процесса происходит его охлаждение водой. В качестве катода же применяется вольфрам (в том числе и лантанированный).
Эти два элемента не контактируют, поскольку изолированы при помощи спецматериалов. Как правило, посредством асбеста.
Для возникновения плазменной дуги между анодом и катодом применяется постоянный ток, имеющий напряжение в 100 В. Именно такая дуга позволяет нагреть до необходимой высокой температуры газ. Сварка начинает работать: возникает поток плазмы, в котором и размещаются свариваемые детали (либо осуществляется резка металлов).
Таким образом, самостоятельное конструирование аппарата для проведения плазменной сварки вполне реально. Результатом станет возможность качественного соединения различных металлических деталей. Собственноручно собранный аппарат пригодится для многих случаев, особенно удобной плазменная сварка своими руками будет при ремонте личного авто.
Плазменная резка своими руками — Строительство саун и бань
Плазменная резка представляет собой способ резки металлов с применением вместо резца в качестве режущего инструмента струи плазмы. Между электродом иПлазменная резка представляет собой способ резки металлов с применением вместо резца в качестве режущего инструмента струи плазмы. Между электродом и соплом аппарата или поверхностью разрезаемого металла зажигается электрическая дуга. В сопло аппарата в свою очередь подается под давлением газ, который превращается в плазму под воздействием электрической. Плазма нагревается до 5 — 30 тысяч градусов, а скорость работы составляет пределах 500-1 500 метров в секунду.
Содержание:
- Понятие плазменной резки
- Достоинства плазменной резки
- Принцип работы аппарата плазменной резки
- Выбор аппарата плазменной резки
- Использование аппарата плазменной резки
Понятие плазменной резки
Различают поверхностную и разделительную плазменную резку металла. Широкое распространение на практике нашла именно вторая методика. Сама резка может осуществляться двумя способами: плазменной струей или дугой. При резке металла плазменной дугой включается разрезаемый металл в электрическую цепь. Дуга образуется между изделием и вольфрамовым электродом. При резке плазменной струей в электрическую цепь изделие не включается. Дуга в резаке возникает между двумя электродами.
Обычно плазменную резку проводят в атмосфере. Резка при применении дополнительной среды выступает дальнейшим усовершенствованием — при помощи такой среды ограничивается длина дуги. При толщине металлического листа в пару миллиметров и использовании кислорода как параллельность обработанных поверхностей сопоставима с данным параметром при лазерной резке. Получение параллельных поверхностей возможно при резке листов, которые имеют толщину вплоть до 10 миллиметров.
При плазменной резке низколегированных и мягких сталей предпочтительнее использовать в качестве режущего газа кислород. Расплавленное железо отличается пониженную вязкость, поэтому разжиженный материал из паза легче удаляется. В результате кромки образуются практически без заусенцев. Ещё одним преимуществом применения кислорода является уменьшенное содержание в обработанных кромках азота.
Как режущий газ иногда используется азот. При этом для резки аналогичной толщины листа требуется меньшая сила электротока и тратятся меньшие термические нагрузки на электроды, срок службы которых существенно увеличивается. Если не уменьшать нагрузки, то возможно возрастание содержания азота в кромке, что отрицательно сказывается при выполнении дальнейшей работы. Иногда как более дешевый газ используется воздух, но он уменьшает срок службы сопел и электродов, а также повышает содержание на порезанных кромках азота по сравнению кислородом.
Достоинства плазменной резки
С помощью оборудования для плазменной резки вы можете обрабатывать почти любые металлы – черные и цветные, а также тугоплавкие. Посредством плазменной резки можно обрабатывать металлы в несколько раз быстрее газовой резки. Технология плазменной резки позволяет получать заготовки без каких-то ограничений по геометрической форме. Возможен и процесс сложной фигурной резки.
Подобная технология позволяет разрезать металл точно и быстро, причем процедура эффективна при работе с металлом разной толщины — близко 0,5 — 50 миллиметров. Методика плазменной резки в отличие от кислородной технологии резки позволяет разрезать железосодержащие материалы и материалы, что железа не содержат. Применение плазменной технологии для резки металла, не содержащего железа, является более быстрой, безопасной и эффективной альтернативой механической резке.
Плазменная резка металла по техническим характеристикам и скорости резки является особенно эффективной для прямых резов, к примеру, для резания листов и зачистки кромок, для обработки профилей. Серьёзным преимуществом по сравнению с лазерной резкой является возможность обработки более широких листов металла, резки листов под углом для будущей сварки и получения деталей с небольшими дефектами на поверхности, окалинах и загрязнениях.
При плазменной резке получаются намного меньшие затраты на метр длины металла. Поэтому данная методика в последнее время получила широкое распространение на крупных производствах. При использовании дополнительной среды плазменная резка может применяться на воздухе и даже под водой. Именно вода, попадающая между соплом и плазмой, выступает дополнительной средой при резке алюминия и легированных сталей, обработке низколегированных и мягких сталей.
Принцип работы аппарата плазменной резки
Аппарат для плазменной резки предназначается для высокотемпературного местного нагрева струей плазмы поверхностей материалов, которые имеют малую толщину, в процессе термической обработки. Применение аппарата плазменной резки — резка электропроводного и неэлектропроводного материала, пайка и сварка высокотемпературными припоями, поверхностная термообработка (закалка, местный отжиг, огневая зачистка), сварка черного и цветного металла и другие работы, которые связаны с высокотемпературным местным нагревом.
Реализуется в плазменной горелке технология получения из водяного пара плазмы. Принцип плазменной резки металла в общих чертах можно описать так: в узком канале сопла зажигается электрическая дуга, через этот канал продувается водяной пар, интенсивно охлаждая дугу. Водяной пар при этом ионизируется, и в результате чего создается плазменная струя, которая имеет температуру порядка 6000 градусов.
В процессе резки металла плазма не нагревает обширные участки металла. Материал, который разрезается плазменным резаком, способен охлаждать намного быстрее, чем металл, что разрезан кислородной резкой. Функция пара рабочей жидкости сведена к охлаждению самых нагруженных частей горелки – катода и сопла, стабилизации столба разряда и выдуванию из сопла дуги. Система подачи пара действует по «открытой схеме»: из резервуара самотеком пар попадает по каналам охлаждения в разрядную камеру и выбрасывается через сопло в атмосферу.
Стабилизация дуги относительно оси центра сопла обеспечивается соосношением сопла и катода специальной конструкции и спирального потока пара при помощи тангенциальной подачи в камеру. В резервуаре горелки размещен запас рабочей жидкости. В резервуаре горелки находится капиллярно-пористый влаговпитывающий материал, который служит для транспортировки рабочей жидкости к поверхности нагревателя с помощью капиллярного эффекта. Источник питания на катоде имеет отрицательный потенциал и на сопле положительный.
Выбор аппарата плазменной резки
Если вы решили прикупить такое оборудование, для начала стоит тщательно проанализировать некие параметры, которые будут влиять на качество работы аппарата плазменной резки. Есть опции, которые являются принципиально важными для резака, есть – дополнительные, которые в ваших условиях работы могут попросту не понадобиться.
Виды аппаратов плазменной резки
Аппараты плазменной резки делятся на две разновидности: инверторные и трансформаторные.
К достоинствам инверторных аппаратов плазменной резки металла относят такие параметры, как компактность, малое потребление энергии, привлекательный дизайн и небольшой вес. К недостаткам причисляют невысокую продолжительность включения особенно на большом токе и ограничение по максимальной мощности — не больше 70 Ампер. Но главным недостатком выступает то, что инверторные плазморезы являются очень чувствительными к перепадам напряжения.
К достоинствам трансформаторных аппаратов плазменной резки относят высокое продолжение включения и значительную надежность. К тому же при падении напряжения поломки аппарата не происходит, только уменьшается его мощность. Установки с продолжением включения больше 70% можно применять для автоматической резки, где длительность непрерывной работы плазмотрона намного больше, чем при ручной резке. К недостаткам относят размеры и вес, который является значительно большим, чем у плазменных инверторов, а также высшее энергопотребление.
Мощность аппарата
Подбирать номинальную мощность аппарата необходимо зависимо от толщины и вида разрезаемого металла. Толщину металла определяет тип газового потока (азот, воздух) и диаметр сопла. Определите, какой вы будете резать металл, и проверьте мощность вашего оборудования. К примеру, аппарат, который имеет входную мощность 60 или 90 Ампер, способен резать металл, что отличается толщиной до 30 миллиметров.
Аппарат подобного типа предназначен для использования в разных отраслях промышленности, при проведении работ в автомобильных ремонтных и домашних мастерских. Если вы желаете резать толстый металл, то стоит выбрать аппарат с номинальной мощностью 90 или 170 Ампер, как на фото плазменной резки металла на нашем сайте. Используя данный аппарат, вы сможете порезать металл, который имеет толщину до 50 миллиметров.
Обязательно стоит проверить первичное напряжение и силу тока, что необходима для источника питания. Также стоит определить, нужен ли вам универсальный аппарат, что способен работать с разным током и напряжением. Некоторые аппараты могут работать только с напряжением 380 или 220 Вольт, однофазным или трехфазным током питания. В некоторых аппаратах зарубежного производства предусмотрена функция Auto-Line, что позволяет подсоединять оборудование к любой электрической сети.
Скорость и время резки
Перед покупкой аппарата сварочной резки нужно проверить скорость резки данного оборудования. Обычно этот показатель измеряется сантиметрами в минуту. Некоторые аппараты могут перерезать металл, который имеет толщину 30 миллиметров, на протяжении 5 минут, другие – за одну минуту. Скорость резки является очень важной характеристикой, особенно когда нужно уменьшать расходы времени.
При покупке аппарата плазменной резки нужно обратить внимание на продолжительность его работы — время, на протяжении которого аппарат может работать без перегрева. Если длительность работы составляет 60 %, то аппарат может работать без перерыва 6 минут, а в течение 4 минут ему нужно охлаждаться. Очень важна высокая продолжительность для выполнения длинных разрезов или использования аппарата при повышенной температуре.
Продолжительность работы указывается, как правило, для максимальной мощности аппарата. Если вы будете использовать оборудование с меньшей мощностью, то продолжительность его работы соответственно увеличится. Температура среды, где эксплуатируется аппарат плазменной резки, также влияет на этот показатель.
Плазменная горелка
Выбирать плазматрон необходимо в зависимости от особенностей продуктов или материалов, которые вы будете резать. Плазменная горелка всегда должна иметь достаточную мощность для обеспечения качественной резки в тяжелых условиях и быть стойкой к ударам при интенсивной эксплуатации. Вы можете использовать плазматроны различной конструкции.
Плазматроны с медным соплом являются более прочными, чем аппараты с керамическим соплом, практически не бьются, имеют воздушное охлаждение. Рукоятки могут комплектоваться дополнительными элементами, что крепятся к плазматрону и поддерживают наконечники на необходимом расстоянии от рабочей поверхности — 1,6-3 миллиметра. Посмотрите видео о плазменной резке металла — это существенно облегчает работу оператора.
Длина дополнительного элемента, то есть расстояние между плазменной горелкой и рабочей поверхностью, зависит от необходимой силы тока и толщины разрезаемого металла. При использовании малых токов можно прикоснуться соплом к поверхности металла. При использовании большого тока (больше 60 Ампер) расстояние между поверхностью металла и плазматроном должно быть минимум 1,6-4,5 миллиметров.
При выборе плазменной горелки рекомендуется выяснить, для какой цели она будет служить, потому что возможны разные конструкционные решения. Если горелка будет использоваться только в пределах малых токов и разрезать исключительно тонкие листы металла, то защитный газ для охлаждения плазматрона не требуется, и в горелку будет подаваться только воздух, что необходим для резки. Если вы используете плазматрон для резки толстого листового металла, то нужен больший ток, и желательно в плазматрон подавать азот, а не воздух.
Внешние параметры аппарата
Для плазменной резки необходим сжатый воздух и другие комплектующие – электроды для резки и сопло горелки. Поврежденные и изношенные запчасти влияют на качество резки. Низкий уровень квалификации оператора, высокая влажность воздуха, процесс резки толстого листа металла с применением интенсивного режима ускоряют износ таких комплектующих частей. Посмотрите видео о ручной плазменной резке металла — оптимального качества резки можно достичь только при одновременной замене электрода и сопла.
Если вам нужен переносной аппарат, очень важными факторами выступают его размеры и вес. Можно купить небольшой переносный агрегат, который весит меньше 40 килограмм. Также в продаже имеются мощные аппараты, которые весят больше, они служат стационарными постами резки и способны качественно выполнять резку металлов, что отличаются толщиной до 50 миллиметров.
Использование аппарата плазменной резки
Ручную плазменную резку металла при помощи специального оборудования может проводить даже человек без сварочного опыта. Имея аппарат плазменной резки в домашнем обиходе, вы можете осуществлять резку металла и других материалов — пластика, древесины, керамической плитки. Но иногда не по карману купить готовый аппарат, потому что его стоимость, а поэтому и цена плазменной резки слишком высока. В этом случае можно изготовить плазменный резак самостоятельно, купив блок питания и сопло.
Плазменные резаки, созданные своими руками, не уступают по мощности заводским. В качестве рабочего материала для плазмы используют в самодельных аппаратах воздух. Для охлаждения применена жидкая система: полость анодного блока принято заполнять тосолом или обычной водой. Дугу в сопле можно получить при помощи вольфрамового стержня, для изготовления которого берут кусочек электрода. Остальные части продаются в магазинах в качестве комплектующих. Остается только собрать их воедино.
Работая с аппаратами плазменной резки, нужно строго придерживаться правил безопасности, потому что при этой работе имеет место большое число факторов, которые представляют опасность для человека: температура, высокое напряжение, расплавленный металл и ультрафиолетовое излучение. Рекомендуется носить одежду сварщика и под рукой иметь сварочный щиток с затемненными стеклами.
Перед началом процесса плазменной резки металла своими руками необходимо осмотреть защитный щиток, электрод и сопло! Нельзя начинать работу, если электрод или сопло недостаточно закреплены. Не желательно стучать плазматроном для удаления брызг металла, потому что можно его повредить. Для экономии материалов нужно избегать обрыва и частого зажигания плазменной дуги.
При подготовке к работе аппарата плазменной резки в него подается сжатый воздух. Можно выбрать один из трех источников сжатого воздуха: подключение к системе сжатого воздуха, которая имеется на заводе, баллоны сжатого воздуха или воздушный компрессор. Львиная доля аппаратов имеют регулятор, который необходим для подачи и распределения воздуха в системе.
При расчете определенного тока и скорости резки рекомендуется выполнить несколько пробных разрезов при высоком токе. При необходимости, зависимо от скорости резки, вы можете уменьшать ток. Если он является слишком высоким или скорость резки выступает маленькой, разрезаемый металл будет перегреваться и может возникать окалина. Правильно определив ток и скорость резки, вы сможете получить чистый разрез, на котором практически не возникает окалины, а разрезаемый металл не деформируется.
Плазменную резку листового металла принято начинать, размещая горелку близко к краю разрезаемого металла. Дальше нужно нажать кнопку выключателя горелки, после этого зажжется дежурная дуга, а потом режущая дуга. После того, как режущая дуга зажглась, нужно медленно двигать горелку вдоль желаемой линии разреза. Регулировать скорость движения необходимо так, чтобы искры виднелись с обратной стороны листового металла. Дугу направляется под прямым углом к металлу и вниз.
Если на обратной стороне металла не заметно искр, то металл насквозь не прорезался. Это может совершаться из-за чрезмерно большой скорости движения, малого тока или направления струи плазмы к поверхности металла не под углом 90 градусов. По окончании резки горелку следует слегка наклонить в сторону конца разреза или остановится на время, чтобы закончить процесс резки. После того, как была отпущена кнопка выключателя на горелке, воздух для охлаждения горелки некоторое время подаваться ещё будет.
Проплавить отверстие в металле получится, если угол наклона горелки достигнет 40 градусов. Необходимо нажать кнопку выключателя горелки аппарата плазменной резки. Когда загорелась режущая дуга, следует наклонить горелку таким способом, чтобы угол ее наклона достигал 90 градусов. Только тогда дуга сможет насквозь проплавить основной металл. Рекомендуется руководствоваться следующим правилом: данным способом вы сможете проплавить металл толщиной не больше самой высокой толщины разрезаемого металла, что указана в паспорте аппарата плазменной резки.
Таким образом, если нужно раскроить металл или сделать отверстие в цельном металлическом изделии, лучшим вариантом для проведения подобных работ является по технологии и стоимости плазменная резка металла. Для осуществления данной процедуры необходим специальный резак, отличительная особенность которого кроется в том, что резка происходит не благодаря электрической дуге, а за счет образования потока раскаленной плазмы.
Изучаем виды сварочных аппаратов и их особенности
Технология соединения металлов с помощью сварки была изобретена более ста лет назад. Метод, основанный на заполнении швов расплавленными металлами, начиная с дуговой электросварки совершенствовался.
Современные сварочные технологии позволяют надежно соединять разные металлыи сплавы. Технологии сварки используют как электрический ток, так и смеси газов, комбинирование разных источников энергии и новейшие достижения технической мысли.
К сварочным аппаратам, работающим от электросети относятся:
Рассмотрим каждый вид оборудования более подробно.
Трансформаторы
Именно с них началась история сварочного соединения металлов. Для получения тока сварки в аппаратах этого типа используются трансформаторы, понижающие напряжение питающей сети до необходимых параметров с возможностью регулирования рабочего тока.
Для этого в большинстве моделей используется способ, основанный на изменении расстояния между обмотками. Классические сварочные трансформаторники рассчитаны на работу со сталью. Чтобы сваривать цветные металлы или сплавы конструкция дополняется элементами, занимающими немалое место в корпусе аппарата.
КПД у сварочных трансформаторов очень высок и достигает девяноста процентов. Однако часть этой энергии просто нагревает сам аппарат. Учитывая большую массу корпуса и внутреннего оборудования, для эффективного охлаждения требуется довольно мощная система принудительной вентиляции.
В последнее время этот вид сварочных аппаратов применяется все меньше, но, благодаря стоимости и надежности, пользуется некоторым спросом. Основными сферами их применения являются производства, технологические процессы которых требуют выполнения сварки стальных конструкция в больших объемах.
Выпрямители
Основным отличием сварочных выпрямителей от обычных трансформаторных аппаратов является то, что рабочим током в них служит не переменный, а постоянный. Можно сказать, что это тот же аппарат с понижающим трансформатором, в конструкцию которого добавлены:
выпрямительный мост из диодов;
регулирующее ток устройство;
схемы пуска и защиты.
Основным преимуществом сварочных выпрямителей является стабильность тока сварки и более устойчивое горение сварочной дуги.
Трансформаторы и выпрямители имеют одинаковые недостатки, вытекающие из похожести конструкций. Во-первых – большой вес, основу которого составляет понижающий трансформатор. Во-вторых – сильные скачки напряжения в питающей сети при выполнении операции сварки.
Инверторы
Благодаря современным знаниям в области электротехники инженерам и конструкторам удалось создать новые модели сварочных аппаратов, удачно заменивших громоздкие трансформаторы и выпрямители. Эти устройства были названы инверторами.
Особенность этих приборов в том, что они работают на стабилизированным постоянном токе и обладают рядом неоспоримых достоинств:
устойчивостью к перепадам напряжения сети;
устойчивой электрической дугой;
минимальным разбрызгиванием расплавленного металла.
В этом их отличие от старых моделей, понижающие трансформаторы которых работают на переменном токе сети, имеют грубые регулировки и потому не могут «похвастать» подобными эксплуатационными свойствами. Классический инвертор состоит из нескольких функциональных узлов.
Наименование | Устройство | Предназначение |
Блок питания |
Обеспечение сварки электрическим током нужного напряжения. |
|
Контактный конвертер |
|
Главный узел, обеспечивает работу устройства. |
Блок управления |
Управляет вентиляторами, обеспечивает необходимую температуру в устройстве, координирует функции всех элементов. |
Инверторные сварочные аппараты потребляют мало электроэнергии. Например, при работе электродом, диаметр которого равен 3 мм, потребляется столько же электричества, сколько от двух электрочайников. Поэтому подобные устройства могут работать и от автономных источников питания – генераторов, дизельных станций и т.д.
Аргонодуговой аппарат
Цветные металлы и легированная сталь «не по зубам» обычной сварке. Это объясняется воздействием на поверхность стыков атмосферного кислорода. При нагревании на них образуется тонкий слой окиси, препятствующий надежному соединению, и металл начинает гореть.
Наиболее простым и действенным способом борьбы с негативным воздействием кислорода является его вытеснение из рабочей зоны каким-либо инертным газом. Широкое применение получил аргон, обладающей более высокой плотностью по сравнению с кислородом.
В аргонно-дуговых сварочных аппаратах поступление газа должно быть отрегулировано так, чтобы к моменту возникновения дуги в ее зоне не осталось атомов кислорода. Поэтому подача аргона начинается за 20-30 сек. до начала самой сварки.
Для работы в среде инертного газа могут быть использованы как плавящиеся электроды в виде проволоки из алюминия, так и неплавящиеся, выполненные из вольфрама.
В первом случае шов между соединяемыми деталями заполняется расплавленным металлом самого электрода, во втором материал заготовок в месте соединения нагревается до температуры плавления и заполняет место соединения.
Аппарат для точечной сварки
Точечная или контактная сварка применяется для соединения деталей из листового металла небольшой толщины или имеющих малую площадь соприкосновения.
В производстве этот метод широко применяется при необходимости выполнения многочисленных, однотипных соединений. Например, в автомобильной промышленности для соединения деталей кузовов, на заводах металлоконструкций, производящих различные виды сеток для ограждений.
Как работает
В аппаратах контактной сварки для создания дуги используется электрический ток большой силы. В отличие от электросварки с использованием плавящихся электродов при точечном способе используется металл самих деталей.
В простейшей модели аппарата точечной сварки трансформатор имеет особую конструкцию, понижающую напряжение сети в 220 V и, одновременно, повышающий силу тока в десятки раз. Соединяемые детали закрепляются между двумя электродами, к которым подводится преобразованный и накопленный в блоке конденсаторов ток.
Время воздействия тока на детали составляет не более 1,5 с. Благодаря такому импульсу и одновременному сжатию заготовок в точке соприкосновения деталей происходит кратковременное плавление металла. После остывания элементы надежно соединены.
Аппарат для газовой резки и сварки
Кроме электрических устройств для сварки и резки металлов используются аппараты, в которых для получения высоких температур применяются смеси горючих газов с кислородом. В современных устройствах может использоваться ацетилен и пропан.
Первый газ вырабатывается в специальных установках в результате реакции воды с карбидом кальция. Выделяемый при этом газ подается по специальному шлангу к ручной горелке.
В отличие от ацетилена, который получают непосредственно на месте в специальных генераторах, пропан находится в баллонах под высоким давлением. Для его подачи так же используются шланги.
Дополнительно применяется сжиженный кислород, закачанный в баллоны. Он подводится к горелке по отдельному шлангу и играет роль окислителя.
Обедняя или обогащая рабочую смесь газов кислородом, сварщик добивается разной температуры пламени, размеров факела и рабочего участка. При правильно подобранном соотношении возможно перерезать толстый лист металла. При этом ширина реза может быть не более нескольких миллиметров.
Обязательным атрибутом оборудования для газосварочного оборудования является редуктор, устанавливаемый на всех типах баллонов. Это устройство имеет вентили и манометры, позволяющие контролировать давление как в самом баллоне, так и в шлангах.
Плазменная сварка
Температуры и мощности электрической дуги бывает недостаточно для некоторых металлов и условий работы. Для увеличения этих параметров применяются установки, называемые плазмотронами, в которых происходит сильное сжатие дугового факела
Для дополнительного увеличения мощности плазмы в ее зону вводится специальный газ с плазмообразующими свойствами. В результате установка для плазменной сварки создает дугу температурой 30 0000С, что в несколько раз выше показателей обычных сварочных аппаратов.
Плазменная дуга обеспечивает более глубокий прогрев металла при малом распространении тепла в объеме материала; позволяет сваривать детали большой толщины при относительно невысокой ширине шва.
плазмотрон — Мир науки,техники,медицины и образования © первая научно-техническая коммерческая социальная сеть
Принцип действия большинства плазматронов мощностью от нескольких кВт до нескольких мегаватт, практически один и тот же.
Между катодом, выполненным из тугоплавкого материала, и интенсивно охлаждаемым анодом, горит электрическая дуга. Через эту дугу продувается рабочее тело (РТ) — плазмообразующий газ, которым может быть воздух, водяной пар, или что другое. Происходит ионизация РТ, и в результате на выходе получаем четвертое агрегатное состояние вещества, называемое плазмой.
В мощных аппаратах вдоль сопла ставится катушка эл.магнита, он служит для стабилизации потока плазмы по оси и уменьшения износа анода.
Наша первая модель не имела активного охлаждения анода. В качестве рабочего тела использовался водяной пар из специально сооруженного электрического парогенератора — герметичный котел с двумя титановыми пластинками, погруженными в воду и включенными в сеть 220V. Катодом плазматрона служил вольфрамовый электрод диаметром 2 мм который быстро отгорал. Диаметр отверстия сопла анода был 1.2 мм, и оно постоянно засорялось. Получить стабильную плазму не удалось, но проблески все же были, и это стимулировало к продолжению экспериментов.
В данном плазмогенераторе в качестве рабочего тела испытывались пароводяная смесь и воздух. Выход плазмы получился интенсивнее с водяным паром, но для устойчивой работы его необходимо перегревать до температуры в не одну сотню градусов, чтобы не конденсировался на охлажденных узлах плазматрона. Такой нагреватель еще не сделан, поэтому эксперименты пока что продолжаются только с воздухом.
Фотографии внутренностей плазматрона:
Анод выполнен из меди, диаметр отверстия сопла от 1.8 до 2 мм. Анодный блок сделан из бронзы, и состоит из двух герметично спаянных деталей, между которыми существует полость для прокачки охлаждающей жидкости — воды или тосола.
Катодом служит слегка заостренный вольфрамовый стержень диаметром 4 мм, полученный из сварочного электрода. Он дополнительно охлаждается потоком рабочего тела, подаваемого под давлением от 0.5 до 1.5 атм.
Вот и полностью разобранный плазматрон:
Электропитание подводится к аноду через трубки системы охлаждения, а к катоду — через провод, прицепленный его держателю.
Запуск, т.е. зажигание дуги, производится закручиванием ручки подачи катода до момента соприкосновения с анодом. Затем катод надо сразу же отвести на расстояние 2..4 мм от анода (пара оборотов ручки), и между ними продолжает гореть дуга.
Электропитание, подключение шлангов подачи воздуха от компрессора и системы охлаждения — на следующей схеме:
В качестве балластного резистора можно использовать любой подходящий электронагревательный прибор мощностью от 3 до 5 кВт, например подобрать несколько кипятильников, соединенных параллельно.
Дроссель выпрямителя должен быть рассчитан на ток до 20 A, наш экземпляр содержит около сотни витков толстой медной проволоки.
Диоды подойдут любые, рассчитанные на ток от 50 А и выше, и напряжение от 500 V.
ОСТОРОЖНО! ЭТОТ ПРИБОР ИСПОЛЬЗУЕТ
БЕСТРАНСФОРМАТОРНОЕ ПИТАНИЕ ОТ СЕТИ!
Воздушный компрессор для подачи рабочего тела взят автомобильный, а для прокачки охлаждающей жидкости по замкнутому контуру используется автомобильный омыватель стекол. Электропитание к ним подводится от отдельного 12-вольтового трансформатора с выпрямителем.
Как показала практика, и эта конструкция тоже оказалась экспериментальная. Наконец-то получена стабильная работа в течение 5 — 10 минут. Но до полного совершенства еще далеко.
Сменные аноды постепенно выгорают, а делать их из меди, да еще с резьбой, затруднительно, уж лучше бы без резьбы. Система охлаждения не имеет прямого контакта жидкости со сменным анодом, и из-за этого теплообмен оставляет желать лучшего. Более удачным был бы вариант с прямым охлаждением.
Детали выточены из имевшихся под рукой полуфабрикатов, конструкция в целом слишком сложна для повторения.
Также необходимо найти мощный развязывающий трансформатор, без него пользоваться плазматроном опасно.
Снимки плазматрона при разрезании проволоки и стальных пластинок. Искры летят почти на метр.
Как сделать плазморез из сварочного аппарата
Отслужившие детали различных машины и инструментов отлично подходят для изготовления полезных в домашнем хозяйстве устройств своими руками. Если есть в наличии ненужный сварочный инвертор, то из него можно сделать самодельный плазморез.
О том, каким образом превратить прибор для сваривания металла в устройство, которое способно разрезать прочный материал, будет подробно рассказано в этой статье.
Преимущество плазмореза перед газовым резаком
Одним из самых простых устройств для резки металла является газовый резак. Такой прибор стоит небольших денег и расходные материалы к нему также недороги. Но при выполнении газосварочных работ происходит нагрев слишком большой площади металла.
По этой причине материалы, обладающие большой теплопроводностью могут покоробиться и изменить цвет. Как в месте плавления металла, так и на значительном удалении от термического воздействия пламени горелки.
Преимущество плазмореза заключается в том, что удаётся получить очень тонкую струю раскалённого газа, которая будет воздействовать на небольшую площадь поверхности, что позволит значительно уменьшить нагрев детали.
Принцип работы плазмореза
Изготовить плазморез самостоятельно, не разбираясь в принципе работы этого устройства практически невозможно.
Процесс образования плазмы происходит в результате:
- Подачи электрического тока в горелку.
- Между электродами (катод и анод) горелки возникает электрическая дуга.
- Воздух под давлением подаётся в горелку и «выдувает» дугу наружу, при этом значительно увеличивая её температуру.
- К разрезаемому металлу подключается кабель «массы», поэтому ионизируемое пламя как бы замыкает о поверхность материала.
В результате получается высокоэффективное устройство для разрезания различных металлов. В том числе тех, которые обладают повышенными показателями теплопроводности.
Смотрите видео, где в доступной форме показано что такое плазменная резка и как она работает:
Детали для самодельного устройства
Плазморез из сварочного инвертора своими руками изготавливается из следующих деталей.
1. Плазмотрон. Эта деталь в конструкции плазмореза является наиболее важной.
Даже при наличии необходимого по силе электрического тока и давления газа, дугу не удастся получить, если внутренние электроды будут неправильно расположены. А отверстие для подачи воздуха будет иметь неподходящий диаметр.
Стоит такая деталь довольно дорого, поэтому домашние мастера предпочитают изготавливать горелки самостоятельно из подручных деталей.
2. Источник тока. В самодельном плазморезе источником тока будет сварочный инвертор.
3. Компрессор. Чтобы обеспечить длительную подачу сжатого воздуха в плазмотрон необходимо приобрести компрессор средней мощности.
Узнайте из этого видео, как выбрать компрессор для плазменной резки:
Также потребуются для самодельного плазмореза купить достаточное количество медных проводов большого диаметра. Для подключения «массы» к разрезаемой детали и обеспечения плазмотрона необходимым количеством электроэнергии.
Самостоятельное изготовление плазмотрона
Горелка или плазмотрон может быть изготовлена из подручных материалов. Чтобы собрать этот элемент самодельного плазмореза понадобятся:
- ручка;
- кнопка пуска;
- специальный электрод;
- сопло;
- изолятор.
Для изготовления самодельного плазмотрона идеально подойдёт ручка от мощного паяльника. Как правило, такая деталь имеет серединное отверстие, через которое и будут подводиться электрический ток и сжатый воздух.
Кнопку лучше использовать достаточно большую, чтобы во время работы пользоваться устройством было максимально комфортно.
Электроды потребуется приобрести в магазине. Для самостоятельного изготовления плазмотрона лучше выбирать изделия, изготовленные из гафния.
Для работы с металлами различной толщины потребуется также купить набор сопл.
Изготавливается плазмотрон в такой последовательности:
- Сразу за ручкой помещается металлическая трубка, покрытая изнутри фторопластом.
- Внутри трубки размещается электрод, который почти по всей длине закрыт высокотемпературной изоляцией.
- За электродом устанавливается с помощью резьбового соединения сопло подходящего диаметра.
Плазмотрон готов к использованию. Ещё для работы устройства потребуется подключить для подачи воздуха шланг от компрессора и электрический провод от инвертора.
Посмотрите видео, где человек рассказывает, как он пытался сделать плазмотрон:
Источник тока
В качестве источника электроэнергии можно использовать сварочный инвертор со следующими показателями:
- напряжение питания – 220 В;
- мощность – от 4 кВт;
- возможность регулировки тока от 20 – 40 А.
Сборка плазмореза
Когда отдельные детали плазмореза будут готовы, можно приступить к сборке. Чтобы работать с самодельным устройством было максимально комфортно, необходимо свести к минимуму количество тянущихся за ручкой проводов и шлангов.
Для более компактного размещения рабочего провода его помещают внутри шланга, по которому производится подача сжатого воздуха. Провод надёжно подсоединяется к электроду, при этом шланг также должен быть подключён к горелке без образования зазоров.
Другой контакт от инвертора будет подключаться к разрезаемой детали в качестве «массы» поэтому его следует оборудовать клеммой типа «крокодил».
Из этого видео вы узнаете, как самому сделать шланг пакет, шлейф для плазмореза:
Процесс разрезания металла с помощью плазменного резака очень прост. После подачи электричества образуется электрическая дуга. Момент образования запала регулируется кнопкой, которая была ранее установлена на ручке плазмотрона. Воздух подаётся от компрессора по шлангу и раздувает дугу, тем самым увеличивая её температуру, которая может достигать 8000ºС.
Для того чтобы затушить дугу достаточно отпустить кнопку на ручке. Таким образом горелка будет работать только в тот момент, когда необходимо разрезать металл, что сведёт к минимуму эффект перегрева, к которому самодельные изделия очень чувствительны.
Интересное видео про плазморез своими руками и из чего он состоит:
Советы и рекомендации
Важно не только знать, как переделать инвертор в плазморез, но и как сделать работу такого устройства максимально эффективной и безопасной.
Далее будут приведены несколько рекомендаций. Придерживаясь которых можно избежать наиболее распространённых ошибок при изготовлении и использовании самодельного устройства:
- Перед тем как приступить к изготовлению из сварочного инвертора устройства для резки металлов, следует наметить на бумаге основные элементы такой системы. Самостоятельно изготовленные чертежи и схемы позволят в процессе работы не допустить досадных ошибок, которые наиболее часто бывают вызваны обычной невнимательностью.
- Несмотря на то, что плазменный резак имеет очень узкое пламя, которое не слишком разогревает даже металлы обладающие повышенной теплопроводностью, рекомендуется при работе с алюминиевыми изделиями использовать в качестве распыляющего газа неон или аргон, которые не позволят окислиться поверхности, подвергнувшейся воздействию высокой температуры.
- Чтобы максимально сократить время на изготовление плазмореза рекомендуется приобрести готовую горелку для газового резака. Такое изделие позволит максимально эффективно и безопасно работать с металлом.
- При использовании самодельного плазмореза необходимо придерживаться основных правил техники безопасности. Прежде всего, следует обеспечить защиту от воздействия электричества и брызг расплавленного металла. Для этой цели используются специальная обувь, перчатки и фартук. Также необходимо надевать защитные очки, которые позволят предохранить зрение от воздействия ультрафиолетовых лучей. В процессе резки металла выделяется большое количество вредных для здоровья веществ, поэтому рекомендуется защищать органы дыхания с помощью респиратора.
О том, как из инвертора сделать плазморез своими руками подробно рассказано в этой статье. Перед началом изготовления плазменного резака рекомендуется проверить работоспособность инвертора.
В отличие от сварочного трансформатора, инвертор отличается компактностью, малым весом и высоким КПД, что объясняет его популярность в домашних мастерских, небольших гаражах и цехах.
Он позволяет закрывать большинство потребностей в сварочных работах, но для качественной резки требуется лазерный аппарат или плазморез.
Универсальный аппарат для сварки
Лазерное оборудование очень дорогое, плазморез тоже стоит недешево. Плазменная резка и сварка металла небольшой толщины имеет прекрасные характеристики, недостижимые при использовании электросварки. При этом силовой блок у плазмореза и сварочного аппарата для электродуговой сварки во многом имеют одинаковые характеристики.
Возникает желание сэкономить, и при небольшой доработке использовать его и для плазменной резки. Оказалось, что это возможно, и можно встретить много способов переделки сварочных аппаратов, в том числе инверторных, в плазморезы.
Аппарат плазменной резки представляет собой тот же сварочный инвертор с осциллятором и плазмотроном, кабелем массы с зажимом и внешним или внутренним компрессором. Часто компрессор используется внешний и в комплект поставки не входит.
Если у владельца сварочного инвертора имеется еще и компрессор, то можно получить самодельный плазморез, приобретя плазмотрон и сделав осциллятор. В итоге получится универсальный сварочный аппарат.
Принцип работы горелки
Работа аппарата плазменной сварки и резки (плазмореза) основана на использовании в качестве режущего или сваривающего инструмента плазмы, четвертого состояния вещества.
Для ее получения требуется высокая температура и газ под высоким давлением. При создании между анодом и катодом горелки электрической дуги в ней поддерживается температура в несколько тысяч градусов.
Образование плазмы
Если пропустить при таких условиях через дугу струю газа, то он ионизируется, расширится в объеме в несколько сотен раз и нагреется до температуры в 20-30 тысяч °C, превращаясь в плазму. Высокая температура почти мгновенно расплавляет любой металл.
В отличие от кумулятивного снаряда процесс образования плазмы в плазмотроне регулируемый.
Анод и катод в резаке плазмореза находятся на расстоянии нескольких миллиметров друг от друга. Осциллятор вырабатывает импульсный ток большой величины и частоты, пропускает его между анодом и катодом, что приводит к возникновению электрической дуги.
После этого через дугу пропускается газ, который ионизируется. Так как все происходит в замкнутой камере с одним выходным отверстием, то получившаяся плазма с огромной скоростью вырывается наружу.
На выходе горелки плазмореза она достигает температуры 30000 ° и плавит любой металл. Перед началом работ к заготовке с помощью мощного зажима подсоединяется провод массы.
Когда плазма достигает заготовки, то электрический ток начинает течь через кабель массы и плазма достигает максимальной мощности. Ток доходит до 200-250 А. Цепь анод – катод разрывается с помощью реле.
Резка
При пропадании основной дуги плазмореза, эта цепь опять включается, не давая исчезнуть плазме. Плазма играет роль электрода в электродуговой сварке, она проводит ток, а благодаря своим свойствам создает в области соприкосновения с металлом область с высокой температурой.
Площадь соприкосновения струи плазмы и металла маленькая, температура высокая, нагрев происходит очень быстро, поэтому практически отсутствуют напряжения и деформации заготовки.
Срез получается ровный, тонкий не требующий последующей обработки. Под напором сжатого воздуха, который используется в качестве рабочего тела плазмы, жидкий металл выдувается и получается рез высокого качества.
При использовании инертных газов с помощью плазмореза можно проводить качественную сварку без вредного воздействия водорода.
Плазмотрон своими руками
При изготовлении плазмореза из сварочного инвертора своими руками самой сложной частью работ является производство качественной режущей головки (плазмотрона).
Инструменты и материалы
Если делать плазменный резак своими руками, то легче использовать в качестве рабочего тела воздух. Для изготовления понадобятся:
- рукоятка, в которой должны поместиться кабель и трубка для подачи воздуха;
- пусковая кнопка горелки плазмореза;
- изолирующая втулка;
- электрод горелки плазмореза;
- устройство завихрения воздушного потока;
- набор сопел различного диаметра для резки металлов различного вида и толщины;
- защитный наконечник от брызг жидкого металла;
- ограничительная пружина для поддержания одинакового зазора между соплом горелки плазмореза и разрезаемым металлом;
- насадки для снятия фасок.
Расходные материалы плазмореза в виде сопел, электрода стоит купить в магазине сварочного оборудования. Они в процессе резки и сварки выгорают, поэтому имеет смысл приобретать по несколько штук на каждый диаметр сопла.
Чем тоньше металл для резки, тем меньше должно быть отверстие сопла горелки плазмореза. Чем толще металл, тем больше отверстие сопла. Наиболее часто используется сопло с диаметром 3 мм, оно перекрывает большой диапазон толщин и видов металлов.
Сборка
Сопла горелки плазмореза прикрепляются прижимной гайкой. Непосредственно за ним располагается электрод и изолирующая втулка, которая не позволяет возникнуть дуге в ненужном месте устройства.
Затем расположен завихритель потока, который направляет его в нужную точку. Вся конструкция помещается во фторопластовый и металлический корпус. К выходу трубки на ручке горелки плазмореза приваривается патрубок для подсоединения воздушного шланга.
Электроды и кабель
Для плазмотрона требуется специальный электрод из тугоплавкого материала. Обычно их изготавливают из тория, бериллия, гафния и циркония. Их применяют из-за образования при нагреве тугоплавких окислов на поверхности электрода, что увеличивает длительность его работы.
При использовании в домашних условиях предпочтительней применение электродов из гафния и циркония. При резке металла они не вырабатывают токсичных веществ в отличие от тория и бериллия.
Кабель от инвертора и шланг от компрессора к горелке плазмореза нужно прокладывать в одной гофрированной трубе или шланге, что обеспечит охлаждение кабеля в случае его нагрева и удобство в работе.
Сечение медного провода нужно выбрать не менее 5-6 мм2. Зажим на конце провода должен обеспечивать надежный контакт с металлической деталью, в противном случае дуга с дежурной не перекинется на основную дугу.
Компрессор на выходе должен иметь редуктор для получения нормированного давления на плазмотроне.
Варианты прямого и косвенного действия
Конструкция горелки плазмореза довольно сложная, выполнить в домашних условиях даже при наличии различных станков и инструментов сложно без высокой квалификации работника. Поэтому изготовление деталей плазмотрона нужно поручить специалистам, а еще лучше приобрести в магазине. Выше была описана горелка плазмотрона прямого действия, она может резать только металлы.
Существуют плазморезы с головками косвенного действия. Они способны резать и неметаллические материалы. В них роль анода выполняет сопло, и электрическая дуга находится внутри горелки плазмореза, наружу под давлением выходит только плазменная струя.
При простоте конструкции устройство требует очень точных настроек, в самодеятельном изготовлении практически не применяется.
Доработка инвертора
Для использования инверторного источника питания для плазмореза его нужно доработать. К нему нужно подключить осциллятор с блоком управления, который будет выполнять функцию пускателя, поджигающего дугу.
Схем осцилляторов встречается довольно много, но принцип действия один. При запуске осциллятора между анодом и катодом проходят высоковольтные импульсы, которые ионизируют воздух между контактами. Это приводит к снижению сопротивления и вызывает возникновение электрической дуги.
Затем включается газовый электроклапан и под давлением воздух начинает проходить между анодом и катодом через электрическую дугу. Превращаясь в плазму и достигая металлической заготовки, струя замыкает цепь через нее и кабель массы.
Основной ток величиной примерно 200 А начинает течь по новой электрической цепи. Это вызывает срабатывание датчика тока, что приводит к отключению осциллятора. Функциональная схема осциллятора изображена на рисунке.
Функциональная схема осциллятора
В случае отсутствия опыта работы с электрическими схемами можно воспользоваться осциллятором заводского производства типа ВСД-02. В зависимости от инструкции по подключению они присоединяются последовательно или параллельно в схему питания плазмотрона.
Перед изготовлением плазмореза, необходимо определить предварительно с какими металлами, и какой толщины хотите работать. Для работы с черным металлом достаточно компрессора.
Для резки цветных металлов потребуется азот, высоколегированной стали нужен аргон. В связи с этим, возможно, потребуется тележка для перевозки газовых баллонов и понижающие редукторы.
Как любое оборудование и инструмент, сварочный аппарат с плазменной головкой требует определенной сноровки от пользователя. Движение резака должно быть равномерным, скорость зависит от толщины металла и его вида.
Медленное движение приводит к образованию широкого реза с неровными краями. Быстрое перемещение приведет к тому, что металл прорезается не во всех местах. При должной сноровке можно получить качественный и ровный срез.
Плазменные резаки активно используются в мастерских и предприятиях, связанных с цветными металлами. Большинство небольших предприятий применяют в работе плазменный резак, изготовленный своими руками.
Плазменный резак хорошо себя показывает при разрезе цветных металлов, поскольку позволяет локально прогревать изделия и не деформировать их. Самостоятельное производство резаков обусловлено высокой стоимостью профессионального оборудования.
В процессе изготовления подобного инструмента используются комплектующие от других электроприборов.
Особенности и назначение плазменного резака
Инвертор плазменной резки используется для выполнения работ как в домашних, так и в промышленных условиях. Существует несколько видов плазморезов для работы с различными типами металлов.
- Плазморезы, работающие в среде инертных газов, например, аргона, гелия или азота.
- Инструменты, работающие в среде окислителей, например, кислорода.
- Аппаратура, предназначенная для работы со смешанными атмосферами.
- Резаки, работающие в газожидкостных стабилизаторах.
- Устройства, работающие с водной или магнитной стабилизацией. Это самый редкий вид резаков, который практически невозможно найти в свободной продаже.
Плазменный резак или плазматрон – это основная часть плазменной резки, отвечающая за непосредственную нарезку металла.
Большинство инверторных плазменных резаков состоят из:
- форсунки;
- электрода;
- защитного колпачка;
- сопла;
- шланга;
- головки резака;
- ручки;
- роликового упора.
Принцип действия простого полуавтоматического плазмореза состоит в следующем: рабочий газ вокруг плазмотрона прогревается до очень высоких температур, при которых происходит возникновение плазмы, проводящей электричество.
Затем, ток, идущий через ионизированный газ, разрезает металл путем локального плавления. После этого струя плазмы снимает остатки расплавленного металла и получается аккуратный срез.
По виду воздействия на металл различают такие виды плазматронов:
- Аппараты косвенного действия.
Данный вид плазматронов не пропускает через себя ток и пригоден лишь в одном случае – для резки неметаллических изделий. - Плазменная резка прямого действия.
Применяется для разрезки металлов путем образования плазменной струи.
Конструкция плазменного резака и рекомендации по работе с ним серьезно разнятся в зависимости от типа устройства.
Делаем плазменный резак своими руками
Плазменная резка своими руками может быть изготовлена в домашних условиях. Неподъемная стоимость на профессиональное оборудование и ограниченное количество представленных на рынке моделей вынуждают умельцев собирать плазморез из сварочного инвертора своими руками.
Самодельный плазморез можно выполнить при условии наличия всех необходимых компонентов.
Перед тем как сделать плазморежущую установку, необходимо подготовить следующие комплектующие:
- Компрессор.
Деталь необходима для подачи воздушного потока под давлением. - Плазмотрон.
Изделие используется при непосредственной резке металла. - Электроды.
Применяются для розжига дуги и создания плазмы. - Изолятор.
Предохраняет электроды от перегрева при выполнении плазменной резки металла. - Сопло.
Деталь, размер которой определяет возможности всего плазмореза, собранного своими руками из инвертора. - Сварочный инвертор.
Источник постоянного тока для установки. Может быть заменен сварочным трансформатором.
Трансформаторные источники постоянного тока характеризуются следующими недостатками:
- высокое потребление электрической энергии;
- большие габариты;
- труднодоступность.
К преимуществам такого источника питания можно отнести:
- низкую чувствительность к перепадам напряжения;
- большую мощность;
- высокую надежность.
Инверторы, в качестве блока питания плазмореза можно использовать, если необходимо:
- сконструировать небольшой аппарат;
- собрать качественный плазморез с высоким коэффициентом полезного действия и стабильной дугой.
Благодаря доступности и легкости инверторного блока питания плазморезы на его основе могут быть сконструированы в домашних условиях. К недостаткам инвертора можно отнести лишь сравнительно малую мощность струи. Из-за этого толщина металлической заготовки, разрезаемой инверторным плазморезом, серьезно ограничена.
Одной из главнейших частей плазмореза является ручной резак.
Сборка данного элемента аппаратуры для резки металла осуществляется из таких компонентов:
- рукоять с пропилами для прокладки проводов;
- кнопка запуска горелки на основе газовой плазмы;
- электроды;
- система завихрения потоков;
- наконечник, защищающий оператора от брызг расплавленного металла;
- пружина для обеспечения необходимого расстояния между соплом и металлом;
- насадки для снятия окалин и нагара.
Резка металла различной толщины осуществляется путем смены сопел в плазмотроне. В большинстве конструкций плазмотрона, сопла закрепляются специальной гайкой, с диаметром, позволяющим пропустить конусный наконечник и зажать широкую часть элемента.
После сопла располагаются электроды и изоляция. Для получения возможности усиления дуги при необходимости в конструкцию плазматрона включают завихритель воздушных потоков.
Сделанные своими руками плазморезы на основе инверторного источника питания являются достаточно мобильными. Благодаря малым габаритам такую аппаратуру можно использовать даже в самых труднодоступных местах.
Чертежи
В глобальной сети интернет имеется множество различных чертежей плазменного резака. Проще всего изготовить плазморез в домашних условиях, используя инверторный источник постоянного тока.
Наиболее ходовой технический чертеж резака на основе плазменной дуги включает следующие компоненты:
- Электрод.
На данный элемент подается напряжение от источника питания для осуществления ионизации окружающего газа. Как правило, в качестве электрода используются тугоплавкие металлы, образующие прочный окисел. В большинстве случаев конструкторы сварочных аппаратов используют гафний, цирконий или титан. Лучшим выбором материала электрода для домашнего использования является гафний. - Сопло.
Компонент автоматического плазменный сварочного аппарата формирует струю из ионизированного газа и пропускает воздух, охлаждающий электрод. - Охладитель.
Элемент используется для отвода тепла от сопла, поскольку при работе температура плазмы может достигать 30 000 градусов Цельсия.
Большинство схем аппарата плазменной резки подразумевают такой алгоритм работы резака на основе струи ионизированного газа:
- Первое нажатие на кнопку пуск включает реле, подающее питание на блок управления аппаратом.
- Второе реле подает ток на инвертор и подключает электрический клапан продувки горелки.
- Мощный поток воздуха попадает в камеру горелки и очищает ее.
- Через определенный промежуток времени, задаваемый резисторами, срабатывает третье реле и подает питание на электроды установки.
- Запускается осциллятор, благодаря которому производится ионизация рабочего газа, находящегося между катодом и анодом. На данном этапе возникает дежурная дуга.
- При поднесении дуги к металлической детали зажигается дуга между плазмотроном и поверхностью, называющаяся рабочей.
- Отключение подачи тока для розжига дуги при помощи специального геркона.
- Проведение резальных или сварочных работ. В случае пропажи дуги, реле геркона вновь включает ток и разжигает дежурную струю плазмы.
- При завершении работ после отключения дуги, четвертое реле запускает компрессор, воздух которого охлаждает сопло и удаляет остатки сгоревшего металла.
Что нам понадобится?
Для создания аппарата плазменной сварки необходимо обзавестись:
- источником постоянного тока;
- плазмотроном.
В состав последнего входят:
- сопло;
- электроды;
- изолятор;
- компрессор мощностью 2-2.5 атмосферы.
Большинство современных мастеров изготавливают плазменную сварку, подключаемую к инверторному блоку питания. Сконструированный при помощи данных компонентов плазмотрон для ручной воздушной резки работает следующим образом: нажатие на управляющую кнопку зажигает электрическую дугу между соплом и электродом.
Сборка инвертора
В случае, если фабричного инвертора нет в наличии, можно собрать самодельный.
Инверторы для резаков на основе газовой плазмы, как правило, имеют в строении такие комплектующие:
- блок питания;
- драйвера силовых ключей;
- силовой блок.
Сборка инвертора для плазморезов или сварочного оборудования не может обойтись без необходимых инструментов в виде:
- набора отверток;
- паяльника;
- ножа;
- ножовки по металлу;
- крепежных элементов резьбового типа;
- медных проводов;
- текстолита;
- слюды.
Блок питания самодельного инвертора для плазменной резки собирается на базе ферритового сердечника и должен иметь четыре обмотки:
- первичную, состоящую из 100 витков проволоки, толщиной 0.3 миллиметра;
- первая вторичная из 15 витков кабеля с толщиной 1 миллиметр;
- вторая вторичная из 15 витков проволоки 0.
2 миллиметра;
- третья вторичная из 20 витков 0.3 миллиметровой проволоки.
Силовой блок самодельного инвертора должен состоять из специального трансформатора. Для создания данного элемента следует подобрать два сердечника и намотать на них медную проволоку толщиной 0.25 миллиметров.
Отдельного упоминания стоит система охлаждения, без которой инверторный блок питания плазмотрона может быстро выйти из строя.
Рекомендации по работе
При работе на аппарате плазменной резки для достижения наилучших результатов нужно соблюдать рекомендации:
- регулярно проверять правильность направления струи газовой плазмы;
- проверять правильность выбора аппаратуры в соответствии с толщиной металлического изделия;
- следить за состоянием расходных деталей плазмотрона;
- следить за соблюдением расстояния между плазменной струей и обрабатываемым изделием;
- всегда проверять используемую скорость резки, чтобы избежать возникновения окалин;
- время от времени диагностировать состояние системы подвода рабочего газа;
- исключить вибрацию электрического плазмотрона;
- поддерживать чистоту и аккуратность на рабочем месте.
Заключение
Аппаратура для плазменной резки – это незаменимый инструмент для аккуратной нарезки металлических изделий. Благодаря продуманной конструкции плазмотроны обеспечивают быстрый, ровный и качественный порез металлических листов без необходимости последующей обработки поверхностей.
Большинство рукоделов из небольших мастерских предпочитают своими руками собирать мини резаки для работы с не толстым металлом. Как правило, самостоятельно сделанный плазморез по характеристикам и качеству работы не отличается от заводских моделей.
Define Plasma — ознакомьтесь с программным обеспечением для плазменной резки и плазменной резки
Компоненты плазменной системы
Базовая система плазменной резки включает следующие компоненты:
- Источник питания — Источник постоянного тока постоянного тока. Напряжение холостого хода обычно находится в диапазоне от 240 до 400 В постоянного тока.
Выходной ток (сила тока) и общая мощность источника питания в киловаттах определяют скорость и толщину резки системы. Основная функция источника питания — обеспечение необходимой энергии для поддержания плазменной дуги после ионизации.
- Схема зажигания дуги — В большинстве горелок с жидкостным охлаждением на 130 ампер и выше это схема высокочастотного генератора, вырабатывающая переменное напряжение от 5000 до 10000 вольт на частоте примерно 2 МГц. Это напряжение создает внутри горелки дугу высокой интенсивности для ионизации газа и образования плазмы. Вместо схемы пуска с высокой частотой, описанной выше, в плазменных горелках обычно используется движущийся электрод или технология «обратного пуска» для ионизации газа.
- Горелка — служит держателем для расходуемого сопла и электрода и обеспечивает охлаждение (газ или вода) этих деталей.Сопло и электрод сужают и удерживают плазменную струю.
Программное обеспечение для плазменной резки
Для механизированной резки используется программное обеспечение плазменной резки для программирования станка. В некоторых случаях программное обеспечение ЧПУ может использоваться для программирования отдельных деталей или небольших серий, но большинство изготовителей и производителей полагаются на программное обеспечение, обычно называемое программным обеспечением для раскроя CAD / CAM, которое предлагает гораздо более широкие функции и возможности.
Некоторые типы программного обеспечения CAD / CAM для плазменной резки могут контролировать и автоматически настраивать практически все аспекты операции плазменной резки.Например, Hypertherm ProNest ® поддерживает такие параметры, как ток дуги, напряжение, предварительный поток газа, настройки потока резки, скорости резки, высоту резки, типы прожига, высоту прожига и другие. Все это предназначено для упрощения работы оператора станка и повышения производительности.
Другие функции, часто встречающиеся в программном обеспечении плазменной резки:
- Предотвращение столкновений
- Цепная резка
- Мостовик
- Обрезка общей линии
- Многоголовочная резка
- Разрез скелета
И в некоторых случаях программное обеспечение может помочь достичь оптимальных результатов, например:
- Повышенное качество отверстий
- Более простая установка фаски
- Более короткое время цикла
Типовые области применения и отрасли
Плазма используется как в ручных, так и в механизированных системах для резки широкого спектра проводящих материалов, включая низкоуглеродистую сталь, углеродистую сталь, нержавеющую сталь, алюминий, медь, латунь и другие металлы.
Применения для резки включают:
Отрасли и рынки включают:
- Сельское хозяйство и животноводство
- Судостроение
- Горное дело
- Энергия
- ОВК и механическое производство
- Сервисные металлоцентры
- Строительное оборудование
- Ремонт автомобилей
- Произведения искусства, вывески и украшения
- Трубы и трубопроводы
- Общее строительство
- Гражданское строительство
- Общие производственные и ремонтные мастерские
Не знаете, какой процесс или метод использовать?
Здесь вы найдете полезную информацию:
Системы плазменной резки — проблемы с запуском, отказ горелки
ПРЕДУПРЕЖДЕНИЕ. Техническое обслуживание и ремонт системы плазменной резки должны выполняться только специалистами в области поиска и устранения электрических неисправностей.В системах плазменной резки используется электричество высокого напряжения и постоянного тока. Поражение электрическим током может повредить или убить.
Признак
Резак не может инициировать режущую дугу, когда все остальные условия нормальной работы выполнены правильно — источник питания включен, соблюдены предохранительные блокировки и блокировки на месте, предварительная подача газа в резак и резак в пределах расстояния передачи.
Последовательность операций для типичной системы плазменной резки следующая: сигнал пуска-резки отправляется на источник питания для подачи питания на систему.Открывается соленоид, позволяя газу течь к горелке. Реле контрольной дуги фиксируется, активируя напряжение холостого хода (OCV) между соплом (+) и электродом (-). Высокочастотная (ВЧ) искра (см. Рисунок 1) подается на горелку от генератора высокого напряжения с выходным напряжением 3000–10 000 В переменного тока. Генератор высокой частоты обычно включает высоковольтный трансформатор, конденсаторы, узел искрового разрядника и катушку.
Высокочастотная искра ионизирует газ, проходящий через резак, делая его электропроводным. Ионизированный газ позволяет току течь между электродом и соплом. Этот ток ограничивается контрольным резистором до 20-40 А постоянного тока. Дуга выходит из отверстия и снова присоединяется к лицевой стороне сопла, образуя вспомогательную дугу (см. Иллюстрацию 2) .
Пилотная дуга образует электрический путь к заготовке. Если горелка находится в пределах расстояния переноса, обычно 0,25-0,50 дюйма от материала, вспомогательная дуга переместится на пластину, поскольку пластина подключена к положительному полюсу цепи постоянного тока и не ограничивается резистором (см. Рисунок 3 ) .Схема измерения тока определяет перенос дуги, отключает высокочастотный генератор и размыкает реле вспомогательной дуги.
Проще говоря, горелке необходимы три компонента для образования пилотной дуги: плазменный газ, мощность постоянного тока и высокочастотный переменный ток. Если какой-либо из этих ингредиентов отсутствует, резак не будет стрелять, перемещать или резать.
Иллюстрация 1
Рисунок 2
Рисунок 3
Устранение неполадок при запуске
При возникновении проблем с запуском оператор должен сначала оценить вспомогательную дугу. Он поднимает резак на несколько дюймов над материалом, чтобы обеспечить хороший и четкий обзор резака. Затем он подает сигнал факелу на огонь. После нескольких секунд подачи газа на горелке должна образоваться вспомогательная дуга. Здоровая пилотная дуга будет держаться в воздухе несколько секунд. Он ищет дугу яркого бело-голубого цвета, которая выступает на 0,25-0,50 дюйма от конца сопла. Дуга не должна шипеть, шипеть или скрипеть; он должен быть ровным и устойчивым. Он должен несколько раз проверить пилотную дугу в воздухе, чтобы убедиться, что условие повторяется.
Проблема 1: Жесткий запуск
Если вспомогательная дуга извергается и вспыхивает, но зажигается с перерывами, проблема может заключаться в трудном запуске. Жесткий пуск происходит, когда HF пытается разрушить барьер высокого давления между электродом и соплом. Это может быть вызвано недостаточной HF или избыточным давлением газа. Вот четыре шага, чтобы исправить затрудненный запуск.
Проверить давление и расход газа. Давление плазмообразующего газа или настройка расхода не должны превышать рекомендуемые заводом-изготовителем настройки.Избыточное давление в плазменной камере затрудняет прохождение высокочастотной искры зазора, так что вспомогательная дуга эффективно гаснет до того, как она полностью установится. Высокое давление газа является причиной большинства проблем с жестким запуском, и его часто упускают из виду — усердный специалист по устранению неполадок может заменить каждый компонент в контуре управления только для того, чтобы обнаружить, что давление воздуха было слишком высоким.
Очистите шланги и провода, по которым подается газ и питание к резаку, и осмотрите их на предмет видимых повреждений или ослабленных соединений.Если экран покрыт грязью, металлической пылью или влагой, высокочастотная энергия может рассеиваться. Обдуйте провода воздушным шлангом или протрите их чистой тканью. Удалите все катушки в выводах — они могут вызвать большую индуктивность. Изолируйте провода от режущего устройства.
Осмотрите, очистите и повторно закройте узел искрового разрядника. Высокая частота от генератора высокого напряжения обычно отправляется на конденсаторы, которые разряжают электричество через узел искрового разрядника. Со временем электроды искрового разрядника могут изнашиваться или загрязняться металлической пылью и грязью.Очистите электроды и снова установите зазоры в соответствии со спецификациями производителя. Зазор должен составлять от 0,015 до 0,030 дюйма, в зависимости от системы.
При использовании горелки с водяным охлаждением проверьте удельное сопротивление охлаждающей жидкости. Для большинства систем оно должно быть меньше 10 кОм / см или 10 микромос.
Проблема 2: Слабая синяя искра в горелке
Если на горелке есть видимая искра, но это маленькая синяя искра, которая похожа на искру в точках искрового промежутка, то пилотная дуга имеет высокую частоту, но не имеет постоянного тока.Наиболее вероятными причинами потери постоянного тока в вспомогательной дуге являются изношенные контакты или неисправная катушка в реле вспомогательной дуги; или неисправный пилотный резистор.
Проблема 3: На горелке или на искровом промежутке нет искры
Нет питания переменного тока к генератору высокого напряжения; неисправный высоковольтный генератор; неисправные конденсаторы; закорочен или поврежден узел искрового разрядника.
Проблема 4: Нет искры в горелке, искра в искровом промежутке, тяжелый запуск
См. Проблему 1; короткое замыкание или разрыв провода резака; короткое замыкание или разрыв соединения в корпусе резака.
Плазменный резак
Я давно хотел плазменный резак, но он очень дорогой, а из более дешевых можно только резать
довольно тонкий металл. Идея заключалась в том, чтобы построить плазменный резак со стороны источника питания и заставить его работать с дешевым
Китайский фонарик купил на Ebay. По сути, нужен источник питания, способный выдавать несколько сотен вольт постоянного тока.
разомкнутая цепь, но при нагрузке обеспечивает постоянный ток где-то в районе 40-60 ампер.Также необходимо включить
высокочастотная цепь для зажигания дуги и различные другие детали, чтобы резак резал.
Все изображения на этой странице — версии с низким разрешением. Щелкните их, чтобы увидеть более крупные версии (может потребоваться некоторое время загрузить)
Самой важной частью источника питания плазменной резки является трансформатор. На самом деле это было шесть трансформаторы для микроволновых печей с перемотанными вторичными обмотками. Все трансформаторы были от микроволн мощностью 800 или 850 Вт и следовательно, они рассчитаны на мощность около 1 кВт каждая (обычно заявленная мощность микроволновой печи — микроволновая печь). выходная мощность, а не вход в трансформатор).Сварные швы, скрепляющие пластинки E-I, были прорезаны сняли ножовку и вторичную обмотку высокого напряжения.
Новые вторичные обмотки представляли собой 35-40 витков эмалированной медной проволоки диаметром 2 мм, намотанной на самодельные картонные бобины.
Магнитные шунты были оставлены в трансформаторах, чтобы помочь ограничить ток. Трансформаторы тогда были
зажаты вместе, протестированы (с помощью нескольких футов толстой стальной проволоки на выходе в качестве сильноточной нагрузки), а затем
дуговая сварка обратно вместе.
Затем шесть трансформаторов были приварены к отрезку стального коробчатого сечения, который затем был прикреплен болтами к верхней половине 25 литровая бочка с ацетоном, которая была разрезана пополам примерно на 2/3 высоты. Затем мы подключили вторичные обмотки последовательно, а первичные обмотки параллельно перед сборкой барабана с трансформаторами внутри и соединением, заделанным мягким припоем. Затем барабан и трансформаторы были тщательно высушены, и барабан был заполнен примерно 22 литрами ASDA smart-price. моторное масло (трансформаторное было бы лучше, но намного дороже).Масло обеспечивает как охлаждение, так и изоляцию для трансформаторов.
На второй из двух картинок выше показан барабан трансформатора, теперь заполненный маслом и установленный на деревянной тележке. В
в какой-то момент в будущем будут добавлены более совершенные колеса, которые позволят плазменной резке перемещаться по неровной поверхности. Также
виден еще один перемотанный микроволновый трансформатор и выпрямитель, который подает 12 В постоянного тока. к различным битам схемы управления,
выключатель-предохранитель в металлическом корпусе, который контролирует входящую мощность, и самодельный соленоидный выключатель, который переключает выход
трансформаторы.
На фотографиях ниже показаны выпрямители, выходной переключатель и цепь плавного пуска. Четыре мостовых выпрямителя на 35 А
установлен на двух восьмиугольных алюминиевых радиаторах. Подключения к ним имеют одинаковое сопротивление, чтобы
разрешить распределение нагрузки между ними. Выход трансформатора достигает их через выходной переключатель и дроссель балласта переменного тока, который
ограничивает ток на регулируемую величину (регулировка осуществляется изменением воздушного зазора). Дроссель намотан на другой
Сердечник трансформатора СВЧ с использованием того же провода, что и для обмоток трансформатора.Выходной переключатель состоит из двух
бронзовые контакты, немного гибкой сильноточной оплетки и соленоид от стартера. Контакты в солоноиде стартера
не использовались, поскольку они не предназначены для размыкания цепи с таким напряжением и могут легко вызвать дугу при размыкании. В
самодельный выключатель разделяет контакты на гораздо большее расстояние, чтобы дуга гасла быстро.
Также выше видны сглаживающие конденсаторы для основного выхода с резисторами утечки, выпрямитель для цепи управления 12 В. цепи и цепи плавного пуска, которая замыкает большое реле через несколько секунд после включения, замыкая нагреватель элементы, используемые для ограничения начального пускового тока.
Продолжение следует …
Схема запуска плазменной горелки
ПРЕДПОСЫЛКИ СОЗДАНИЯ ИЗОБРЕТЕНИЯНастоящее изобретение относится к плазменным горелкам, в частности направляется на плазменную горелку с улучшенным генератором вспомогательной дуги. схема.
Плазменные горелки, также известные как дуговые горелки, известны в
искусство для выполнения операций, таких как резка, сварка и т. д., на
детали и работают, направляя плазму, состоящую из ионизированного газа
частицы к заготовке.Пример обычного одиночного газа
плазменная горелка проиллюстрирована в патенте США No. № 3,813,510, переданный
правопреемник здесь. Как показано в последнем патенте, газ должен быть
ионизированный, например азот, подается через каналы в механизме горелки.
таким образом, чтобы кружиться перед концом отрицательно заряженного
электрод. Сварочный наконечник, примыкающий к концу электрода, имеет
достаточно высокое напряжение, приложенное к нему, чтобы вызвать скачок искрового промежутка
между электродом и сварочным наконечником, тем самым нагревая газ и
вызывая его ионизацию.Пилотное напряжение постоянного тока между электродом и
сварочный наконечник поддерживает вспомогательную дугу. Ионизированный газ в зазоре выглядит как
пламя и распространяется за пределы наконечника, где его можно увидеть
оператор. Расширение пилотной дуги и пламени, которое для
практические цели могут рассматриваться как общие, в зависимости от
мощность в зазоре, т. е. ток дуги, а также давление
газ попадает в зазор и выходит из факела. Пилотная дуга обеспечивает
источник света, который позволяет оператору видеть правильное положение для
горелку перед началом сварки или резки.
Фактически
На практике, когда горит пилотная дуга, дуга в форме петли выходит из
факел можно увидеть. Когда головка резака опускается к
заготовке, пилотная дуга перескакивает с электрода на заготовку из-за
тот факт, что полное сопротивление пути тока детали ниже, чем
сопротивление пути тока сварочного наконечника.
Обычные плазменные горелки с одним газом включают цепи вспомогательной дуги, которые обеспечить 20-40 ампер. ток вспомогательной дуги при 100-200 вольт через зазор между наконечником электрода, в результате чего дуга увеличивается примерно на 1 / 4-1 / 2 дюйма мимо сварочного наконечника.Как следствие, факел должен быть в пределах 1 / 4-1 / 2 дюйма от заготовки до скачка дуги переноса к заготовке. Это создает трудности при начале резки или сварочные работы.
Кроме того, в цепи обычного плазмотрона зажигается вспомогательная дуга.
высокочастотным сигналом, который генерируется в блоке питания и
проходит по относительно длинному кабелю к плазменной горелке. Этот
приводит к рассеянию энергии. Кроме того, радиочастотный шум, создаваемый
обычная схема генерации искрового промежутка может дублировать другие
электрические системы, подключенные к горелке, такие как числовое программное обеспечение
машина для управления узорчатым движением резака и мешает
с работой этих машин.
Таким образом, целью настоящего изобретения является создание плазменной горелка с цепью вспомогательной дуги, которая не страдает от вышеупомянутые проблемы.
Объект изобретения, а также другие преимущества обеспечивает
Схема вспомогательной дуги плазменной горелки, которая создает вспомогательную дугу, имеющую низкий
рабочий цикл. Схема предназначена для периодического зажигания вспомогательной дуги.
В предпочтительном варианте пилотная дуга гасится электрически.
практически сразу после зажигания.В другом варианте осуществления
пилотная дуга гасится механически за счет продувки
газ под высоким давлением между электродом и сварочным наконечником. Низкая пошлина
цикл вспомогательной дуги позволяет схеме генерировать большое количество
мощность дуги, не сталкиваясь с недостатками, которые
обычно сопровождают пусковую дугу большой мощности. С другой стороны, большой
мощность в вспомогательной дуге создает большую длину вспомогательной дуги, тем самым
необходимо увеличить допустимое расстояние между горелкой и деталью
для создания передаточной дуги.
В предпочтительном варианте осуществления изобретения полуволновой выпрямленный постоянный ток напряжение подается между электродом и сварочным наконечником через пилотную дугу постоянного тока схема. Пусковые импульсы подаются на пусковую цепь для зажигания. пилотная дуга при выбранных углах полуволнового выпрямленного напряжения.
Другие цели, преимущества и особенности данного изобретения:
обеспечивается схемой зажигания вспомогательной дуги, в которой блок искрового разрядника,
блокирующий конденсатор и дроссельная катушка исключены, и в них нет радиочастотного перемещения
длина подводящей линии между блоком питания и горелкой
сборка. В настоящем изобретении используется автотрансформатор, который
выполняет три функции, необходимые для цепи зажигания вспомогательной дуги. В
автотрансформатор генерирует импульсы высокого напряжения для ионизации газа между
электрод горелки и сварочная головка. Он действует как дроссельная катушка для предотвращения
высокая частота в зазоре горелки из-за образовавшейся искры
в нем, от возвращения в выводы постоянного тока. Наконец, он действует как DC
выводная линия для пропускания пилотного постоянного тока, который может достигать 100 ампер.,
между сварочным наконечником и электродом.
Первичная обмотка автотрансформатора включена в цепь с зарядным устройством.
конденсатор и средство переключения с электронным управлением, такое как кремний
управляемый выпрямитель. Зарядный конденсатор заряжается мощностью
блок питания, после чего включается переключатель с электронным управлением.
на. Когда происходит последнее, все напряжение на конденсаторе
мгновенно появляется на первичной обмотке автотрансформатора. Из-за
большое повышающее отношение витков между вторичной и первичной обмотками
автотрансформатор, напряжение на вторичной обмотке автотрансформатора
становится очень высоким, в результате чего искра проскакивает зазор между
электрод горелки и сварочный наконечник.Схема, включая авто
трансформатор, размещается на конце кабеля узла горелки, а не
на конце кабеля питания.
РИС. 1 представляет собой схематическое изображение системы плазменной горелки предшествующего уровня техники. включая схему зажигания вспомогательной дуги.
РИС. 2 представляет собой схематический чертеж одного предпочтительного варианта осуществления предмета. изобретение.
РИС. 3 — второй предпочтительный вариант осуществления изобретения.
РИС. 4 — диаграмма форм сигналов напряжения, появляющихся в выбранных местах схема, показанная на фиг.3.
ПОДРОБНОЕ ОПИСАНИЕ ПРЕДПОЧТИТЕЛЬНОГО ВАРИАНТА ОСУЩЕСТВЛЕНИЯ Теперь обратимся к фиг. 1, который показывает систему плазменной горелки предшествующего уровня техники,
Узел горелки в общем обозначен позицией 10 как включающий электрод 36.
и сварочный наконечник 38, между которыми проходит поток газа, обозначенный значком
стрелки 40. Это должно быть понятно любому специалисту в данной области.
что факел, на самом деле, намного сложнее, чем показано на
рисунок, но упрощенной иллюстрации достаточно для
объяснение проблем предшествующего уровня техники, а также улучшения
предмета изобретения.Пример конкретного резака можно найти в
вышеупомянутый патент Hatch в США. ИНЖИР. 1 также указывает на заготовку
показан, как правило, 12, блок питания 14 и кабель 16.
простираясь между блоком питания и горелкой. Кабель в некоторых устройствах
может быть приблизительно 50 футов в длину. Как и в случае с фонариком
Сама по себе, только часть силового агрегата 14 показана, насколько это необходимо
для понимания предшествующего уровня техники и настоящего изобретения. Как показано,
Блок питания 14 включает в себя 60-тактный источник 18, силовой трансформатор 20,
элемент искрового разрядника 22, источник постоянного тока 34, блокировочный конденсатор постоянного тока 24, дроссель переменного тока
катушка 26, переключатель 28 и полное сопротивление пути 30 и 32.
При работе блок питания 60 циклов обеспечивает мощность 60 циклов через
первичная обмотка трансформатора 20, который затем переключается на
вторичная обмотка трансформатора с мощностью, достаточной для создания искры на
искровой разрядник 22. Трансформатор 20 представляет собой типичную неоновую вывеску.
трансформатор. Искровой разрядник 22 создает, по сути, радиочастотный шум; но в
В этом случае часть этого РЧ-шума используется для создания вспомогательной дуги. В
радиочастотный сигнал, создаваемый искровым разрядником, проходит длину
кабель 16 и проходит между электродом 36 и сварочным наконечником 38.В
энергии через зазор достаточно, чтобы искра перепрыгнула через зазор,
тем самым ионизируя газ, протекающий между ними. Это приводит к первоначальному
пилотная дуга обозначена как 42a. Пилотная дуга поддерживается постоянным током.
что обычно составляет 20-40 ампер. и обеспечивается блоком питания постоянного тока 34
через те же провода, по которым передается РЧ-сигнал. Блокирующий конденсатор 24
необходимо для предотвращения подачи сигнала постоянного тока от блока 34 питания обратно в
система переменного тока, а дроссельная катушка 26 необходима для предотвращения высокочастотного
входящие в цепь питания постоянного тока.Следует отметить, что во время этого
время, переключатель 28 замкнут, чтобы обеспечить замкнутый контур постоянного тока управляющего сигнала,
Включает положительный вывод источника 34 постоянного тока, резистор 32, резистор 30,
нормально замкнутый переключатель 28, дроссельная катушка 26, электрод 36, вспомогательная дуга 42a,
сварочный наконечник 38 и отрицательный вывод источника постоянного тока 34.
Из-за потока газа, обозначенного цифрой 40, пилотная дуга будет замкнута как
обозначено как 42b. Петля будет проходить ниже сварочного наконечника и может быть
видно оператору даже в сварочной маске.Как факел
При приближении к заготовке 12 дуга перескакивает с 42b на 42c. Так и будет
Следует отметить, что путь полного сопротивления цепи постоянного тока, включая обрабатываемую деталь
12 ниже, чем полное сопротивление цепи постоянного тока, включая сварку
наконечник 38 из-за наличия импеданса 30 на последнем пути. Так и будет
также следует отметить, что небольшой ток будет продолжать течь в цепи постоянного тока.
цепь, которая включает сварочный наконечник до тех пор, пока переключатель 28 не будет
открывается с помощью блока переключения ножного или ручного управления или автоматически
реле измерения тока, которое размыкает переключатель 28, как только течет ток
через заготовку 12.
Как указывалось ранее, вспомогательная дуга 42b простирается примерно на 1 / 4-1 / 2 дюйма мимо сварочного наконечника, а это, в свою очередь, означает, что горелка должна быть поднесено так близко к заготовке, чтобы дуга перешла на заготовку что встречаются трудности.
Хотя длину вспомогательной дуги можно увеличить за счет увеличения вспомогательной дуги.
В настоящее время это обычно создает больше проблем, чем решает.
Во-первых, сварочный наконечник будет разрушаться намного быстрее, поэтому
значительно сокращает срок службы сварочного наконечника.Во-вторых, компоненты в
цепь вспомогательной дуги, например, резисторы, конденсаторы, диоды, провода, будут
должны быть больше, что увеличивает объем и стоимость вспомогательной дуги. схема.
Другой недостаток системы, показанной на фиг. 1 заключается в том, что радиочастотный сигнал проходит по длинному кабелю 16. Это увеличивает радиочастотный шум в системе. и может мешать правильной работе другого электрического оборудования подключен к фонарику. Например, система горелки часто используется с и управляется станком с числовым программным управлением — i.э., компьютер — который движется резак в соответствии с запрограммированным вводом, чтобы получить желаемый рез или приварить шаблон на заготовке. Если радиочастотный шум возвращается в компьютер, он может нанести ущерб желаемому образцу. Наконец, применение RF вниз по относительно длинной ведущей линии приводит к значительной потере высокочастотная мощность.
Следует отметить, что описанная выше система была стандартной в
искусство в течение многих лет, несмотря на упомянутые проблемы. Также следует отметить
что высокочастотный сигнал, генерируемый искровым разрядником 22, не просто
обеспечивается, потому что только радиочастотный сигнал может зажечь вспомогательную дугу. На
Напротив, мощность в 60 циклов может вызвать прямое зажигание электрической дуги. В
Причина, по которой последнее нецелесообразно, заключается в том, что пилотный ток
необходимо для управления вспомогательной дугой, и если мощность 60 циклов была
вместо ВЧ-мощности для зажигания вспомогательной дуги
требуется непрактично большая дроссельная катушка для разделения цикла 60
питание от цепи питания пилота постоянного тока.
Следует отметить, что в нескольких случаях одни и те же цифры используются на фиг.
1, 2 и 3. Эти цифры обозначают части, которые во всех отношениях идентичны.
три фигуры.Признаки фиг. 2, которые отличаются от предшествующего уровня техники на фиг.
1 в основном представляют собой схему 50 на конце узла горелки
кабель 16 и немного изменений в блоке питания 14. Блок питания
блок 14 включает генератор 66 импульсов, а источник 34 постоянного тока включает
третий терминал, обозначенный символом ++, функция которого
будет описано ниже. Клемма + источника постоянного тока 34 является
подключен через шунтирующий резистор 32 к заготовке 12, как в случае
предшествующий уровень техники. Также, как и в случае предшествующего уровня техники, постоянный пилотный ток
путь, который включает электрод 36 и сварочный наконечник 38, кроме того
включает переключатель 28 и средство 30 сопротивления. Четыре выводные линии
от блока питания, входящего в кабель 16, обозначены значком
цифры 1, 2, 3 и 4 в кружке. Это означает, что соответствие
между подводящими линиями, входящими в кабель 16 со стороны источника питания, и теми
выходящий из кабеля 16 на конце кабеля 16 узла горелки.
генератор импульсов 66 выдает периодические импульсы, которые могут, например, иметь
частота десять импульсов в секунду.Точная частота не
критически важны для работы изобретения.
Схема 50 включает автотрансформатор 52, имеющий первичную обмотку 56 и
вторичная 54, зарядный конденсатор 58, диод 60 и кремниевый управляемый
выпрямитель 62. Вторичная обмотка 54 автотрансформатора 52 подключена
непосредственно к сварочному наконечнику 38. Проведите линию 4 от кабеля 16, который является
подводящая линия, подключенная к отрицательной клемме источника питания постоянного тока 34, является
подключен непосредственно к электроду 36. В конкретном описанном примере
здесь предполагается, что источник 34 постоянного тока обеспечивает 200 вольт постоянного тока между
терминал показал «-», а терминал показал «+».Это дальше
предполагается, что блок 34 питания постоянного тока обеспечивает 500 вольт постоянного тока между
терминал обозначен «+», а терминал — «++». Следовательно, в
цепь 50, 500 В постоянного тока существует между подводящими линиями 2 и 3. Из-за
полярность диода 60 и состояние отсечки SCR 62, конденсатор 58
заряжается до 500 вольт постоянного тока.
Когда импульс от генератора 66 импульсов появляется на выводе 64 затвора SCR
62, последнее устройство становится проводящим диодом. Параллельное сочетание
SCR 62 и диода 60 по существу становится коротким замыканием, потому что каждый
устройство может проводить ток в одном направлении.Следовательно, все 500
напряжение на конденсаторе 58 также должно появляться на первичной обмотке 56
трансформатор 52. В конкретном примере, описанном здесь, отношение витков
между первичной и вторичной — 1:30. Следовательно, напряжение
на вторичной обмотке будет 15000 вольт, и этого будет достаточно, чтобы
вызвать проскакивание искры между электродом 36 и сварочным наконечником 38. Это будет
отметил, что когда SCR 62 включен, схема, включающая SCR 62, диод
60, конденсатор 58 и первичная обмотка 56 действуют как цепь вызывного сигнала, имеющая
частота зависит от значения индуктивности первичной обмотки 56 и
значение емкости конденсатора 58.В конкретном примере, если это
Предполагается, что конденсатор представляет собой конденсатор емкостью 0,25 мкФ, катушка представляет собой
катушка из ферритового стержня, имеющая 225 витков с отношением витков приблизительно
1:30, а кремниевый управляемый выпрямитель — модель 40 RCS 60 производства
International Rectifier Company, схема катания будет иметь частоту
150 килоциклов. Однако следует отметить, что цепь вызывного сигнала будет
затухает почти мгновенно из-за рассеивания энергии через
зазор горелки между электродом 36 и сварочным наконечником 38.
Автотрансформатор не только обеспечивает необходимое повышение напряжения до
инициировать искру, необходимую для вспомогательной дуги, она также обеспечивает путь
для пилотного питания постоянного тока. Весь тракт питания пилота постоянного тока включает в себя «+»
клемма от блока питания 34, резисторы 30, 32, выключатель 28 замкнут, вывод
линия 3, трансформатор 52, сварочный наконечник 38, вспомогательная дуга 42a, электрод 36, вывод
линию 4 и клемму «-» источника постоянного тока 34. Катушка, конечно, действует как
практически нулевое сопротивление постоянному току.Однако отмечается
те самые стандартные катушки, которые способны обеспечить тип
повышающее напряжение, необходимое для зажигания плазменной дуги, не сможет
также переносят относительно большой пилотный ток постоянного тока, потому что они не будут
предназначен для этой цели.
Автотрансформатор также действует как дроссельная катушка для предотвращения генерирования радиочастотных помех. путем создания промежутка между резаком и источником постоянного тока.
На практике последняя схема приведет к появлению вспомогательной дуги, показанной позицией 42a.
который затем будет задут до пилотной дуги контура, показанной позицией 42b. Обычно
в резаке, который предназначен для использования в качестве резака, а не
сварочной горелки давление потока газа будет достаточно большим, чтобы
через короткий промежуток времени, например, около миллисекунды, вспомогательная дуга
будет полностью взорван. Таким образом, с момента включения пилотной дуги
инициируется до тех пор, пока цепь вспомогательной дуги не будет отключена, после
передача дуги на заготовку, вспомогательная дуга прерывистая.
Иначе говоря, рабочий цикл вспомогательной дуги составляет менее 100%, что
он находится в схеме фиг.1. На самом деле это существенно меньше, чем
100%. В результате мгновенная мощность может быть увеличена выше
используются в уровне техники, в то же время снижая среднюю мощность
ниже того, что используется в известном уровне техники. Компоненты схемы можно выбрать,
например, чтобы обеспечить ток вспомогательной дуги около 100 ампер. Это будет
приведет к получению гораздо более длинной дуги и уменьшит проблему, упомянутую выше.
Следует отметить, что в этом варианте осуществления желаемый низкий рабочий цикл
зависит от газа, задувшего дугу между импульсными зажиганиями.
Этот
не может быть удовлетворительным способом сокращения рабочего цикла для некоторых
ситуации. Это особенно актуально, когда плазменный резак используется для
сварка, при которой давление газа может быть слишком низким, чтобы сдуть пилотный
дуга. Предпочтительная схема как для периодического включения, так и для электрического
гашение вспомогательной дуги показано на фиг. 3 и будет описано
впоследствии.
Следует отметить, что хотя схема 50 на фиг. 2 предпочтительно размещенный на конце кабеля 16 горелки, можно было бы Поместите цепь 50 на конец кабеля 16 источника питания.Однако делая что может затруднить предоставление необходимой мощности для инициирования зазор горелки, потому что значительная часть энергии создается за счет разряда конденсатор 58 через первичную обмотку автотрансформатора будет рассеивается нагрузкой на длинном проводе 16.
Хотя блок 14 питания на фиг. 2 обозначен как обеспечивающий
отдельные генераторы постоянного тока и импульсы, это будет хорошо понятно любому из
обычный специалист в данной области техники, что и мощность постоянного тока, и импульсы могут быть
полученные по обычной схеме от базового блока питания переменного тока. Кроме того, схема 50 может работать от выпрямленных импульсов переменного тока, а не
чем стандартный источник питания постоянного тока. Эта альтернатива проиллюстрирована на фиг.
3.
Схема по фиг. 3 отличается от фиг. 2 в том, что вспомогательная дуга гаснет электрически. Это достигается заменой пилота постоянного тока. напряжение, приложенное к зазору горелки с полуволновым выпрямленным переменным током напряжение, а также синхронизируя запускающие импульсы с желаемым угол полуволнового выпрямленного напряжения.
На ФИГ.4 формы сигналов a, b, c и d представляют формы сигналов напряжения. возникающий в схеме фиг. 3 в точках, обозначенных как проход d соответственно.
Части 10, 50 и 16 на фиг. 3, как на фиг. 2. Кроме того,
Схема 34 питания постоянного тока обеспечивает постоянное напряжение между электродом и
заготовка. Источник 70 переменного тока подключен через переключатель 28 к первичному
трансформатора 71. Источник переменного тока обеспечивает напряжение, показанное в форме волны a
фиг. 4 из 50 или 60 Гц, как правило.Трансформатор включает в себя пару
вторичные обмотки 73 и 74. Диод 76 полуволна выпрямляет напряжение
через вторичную обмотку 74, в результате чего форма сигнала напряжения c, показанная на фиг. 4.
последнее напряжение подается на зазор горелки через выводы 3 и 4 кабеля.
16. Полуволна диода 75 выпрямляет напряжение на вторичной обмотке 73,
приводя к форме сигнала напряжения b на фиг. 4. Подается последнее напряжение.
через выводы 2 и 3 кабеля 16 к цепи 50 зажигания вспомогательной дуги.
В частности, последнее напряжение заряжает конденсатор 58 до пикового значения
форма волны напряжения.
Форма волны напряжения на вторичной обмотке 74 также применяется к обычному
схема генерации синхронных импульсов для создания импульсов d по фиг. 4 что
подключены через выводы 1 и 3 кабеля 16 между затвором и катодом
SCR 62. Таким образом, как можно понять из форм сигналов на фиг. 4, когда
триггерный импульс d подается на SCR 62, конденсатор 58 будет полностью
заряжен достаточным напряжением для зажигания стартовой дуги таким же образом
как описано выше в связи с фиг. 2. Также в это время
напряжение c на промежутке будет максимальным. Четверть цикла спустя,
напряжение c снизится до нуля. Незадолго до этого напряжение c
опустится ниже того уровня, при котором будет выдерживаться вспомогательная дуга, а последняя
погаснет.
Рабочий цикл для конкретных форм сигналов, показанных на фиг. 4 будет меньше 25%. Рабочий цикл можно дополнительно уменьшить, задерживая импульсы d относительно пика формы сигнала c, или уменьшив частоту сигнала импульсы d или оба.
Уилкинс, Раймонд Г.
НАСТОЯЩИЙ ПАТЕНТ СООТВЕТСТВУЕТ ДАННЫМ ПАТЕНТАМ:Патент | Приоритет | Правопреемник | Название |
4517439, | 07 мая 1984 года | Источник питания AC-DC | |
4678888, | 21 января 1983 г. | PLASMA ENERGY CORPORATION, CORP OF NORTH CAROLINA | Аппарат силовой цепи для зажигания и работы плазменной дуги |
4818916, | 06 марта 1987 | ООО «Перкин Элмер» | Система питания для плазменной горелки с индуктивной связью |
5349605, | 15 июня 1990 | СИДНЕЙСКИЙ УНИВЕРСИТЕТ; ЭЛЕКТРОКОМИССИЯ НОВОГО ЮЖНОГО УЭЛЬСА, | Источник питания дуговой горелки постоянного тока |
5399957, | 15 мая 1990 | Сиднейский университет Комиссия по электричеству Нового Южного Уэльса | Источник питания горелки с коммутацией постоянного тока |
5416297, | 30 марта 1993 г.![]() | HYPERTHERM, INC | Схема и метод зажигания плазменной горелки |
5548097, | 30 марта 1993 г. | Hypertherm, Inc. | Схема зажигания плазменной резки и способ, обеспечивающий функцию принудительного переноса дуги |
5961855, | 28 января 1998 | Victor Equipment Company | Низковольтная электрическая система монтажа деталей на месте (PIP) для горелки контактного пуска |
59 | 12 марта 1998 | Victor Equipment Company | Схема пилотной дуги плазменной горелки |
6084196, | 25 февраля 1998 | Компания Дженерал Электрик | Плазменная дуговая сварка при повышенных температурах изделий из жаропрочных сплавов на основе никеля |
6133543, | 06 ноября 1998 | HYPERTHERM, INC | Система и метод двойного порогового измерения в плазменной горелке ARC |
6215088, | 04 мая 1998 | Inocon Technologie Gesellschaft m.![]() | Метод частичного слияния предметов |
6350960, | 28 ноября 2000 | Victor Equipment Company | Схема безопасного сброса с заменой деталей и метод контактного пуска плазменной горелки |
6359251, | 10 апреля 2000 | HYPERTHERM, INC | Архитектура централизованного управления системой плазменной дуги |
6365867, | 01 ноя 2000 | National Technology & Engineering Solutions of Sandia, LLC | Плазменная горелка с коаксиальной подачей проволоки |
6475215, | 12 октября 2000 г. | Хирургическое устройство и метод квантовой энергии | |
6622058, | 10 апреля 2000 | HYPERTHERM, INC | Архитектура централизованного управления системой плазменной дуги |
6772040, | 10 апреля 2000 | HYPERTHERM, INC | Архитектура централизованного управления системой плазменной дуги |
6780184, | 12 октября 2000 г.![]() | Хирургическое устройство и метод квантовой энергии | |
68, | 10 апреля 2000 | Hypertherm, Inc. | Архитектура централизованного управления системой плазменной дуги |
6947802, | 10 апреля 2000 | Hypertherm, Inc. | Архитектура централизованного управления для системы лазерной обработки материалов |
7022935, | 08 декабря 2003 | Illinois Tool Works Inc .; Illinois Tool Works Inc | Плазменный резак со встроенным высокочастотным пускателем |
7186947, | 31 марта 2003 г. | Hypertherm, Inc. | Монитор процесса лазерной и плазменной обработки материалов |
7982159, | 25 сентября 2007 | Lincoln Global, Inc | Зажигание плазменной дуги однополярным импульсом |
8541710, | 27 января 2005 г.![]() | Hypertherm, Inc. | Способ и устройство автоматического регулирования газа для плазменной горелки |
8809728, | 27 января 2005 г. | Hypertherm, Inc. | Способ и устройство автоматического регулирования газа для плазменной горелки |
81, | 19 августа 2011 | Illinois Tool Works Inc | Плазменная горелка и подвижный электрод |
9833860, | 22 июля 2016 | Lincoln Global, Inc. | Система и способ переноса плазменной дуги для плазменной резки |
9855620, | 7 февраля 2005 г. | Lincoln Global, Inc.; Lincoln Global, Inc | Сварочная система и способ сварки |
9956639, | 7 февраля 2005 г. | Lincoln Global, Inc | Модульный источник питания для электродуговой сварки и выходной прерыватель |
Дата | События платы за обслуживание |
Дата | График технического обслуживания |
30 сентября 1983 года | Открыто окно оплаты комиссии за 4 года |
30 марта 1984 года | Начало льготного периода 6 месяцев (с доплатой) |
30 сентября 1984 | Истечение срока действия патента (на 4 год) |
30 сентября 1986 | 2 года на возрождение непреднамеренно заброшенного конца.![]() |
30 сентября 1987 | Открыто окно оплаты пошлин 8 лет |
30 марта 1988 | Начало льготного периода 6 месяцев (с доплатой) |
30 сентября 1988 | Истечение срока действия патента ( за год 8) |
30 сен 1990 | 2 года на возрождение непреднамеренно брошенного конца. (за год 8) |
30 сентября 1991 | Открыто окно оплаты 12 лет |
30 марта 1992 | Начало льготного периода 6 месяцев (w доплата) |
30 сентября 1992 | истечение срока действия патента ( за год 12) |
30 сентября 1994 | 2 года на возрождение непреднамеренно брошенного конца.(на 12 год) |
Как работает плазменная резка?
В процессе плазменной резки, который используется при резке электропроводящих металлов, этот электропроводящий газ используется для передачи энергии от источника электроэнергии через плазменный резак к разрезаемому материалу.
Базовая система плазменной резки состоит из источника питания, цепи зажигания дуги и резака. Эти системные компоненты обеспечивают электрическую энергию, способность к ионизации и управление процессом, которые необходимы для получения высококачественных и высокопроизводительных резов на различных материалах.
Источник питания представляет собой источник постоянного тока постоянного тока. Напряжение холостого хода обычно находится в диапазоне от 240 до 400 В постоянного тока. Выходной ток (сила тока) источника питания определяет скорость и толщину резки системы. Основная функция источника питания — обеспечение необходимой энергии для поддержания плазменной дуги после ионизации.
Схема зажигания дуги может иметь конструкцию с обратным воздушным потоком, которая используется в сериях Hypertherm Powermax, или схему высокочастотного генератора, которая вырабатывает переменное напряжение от 5000 до 10000 вольт при частоте около 2 мегагерц.Это напряжение используется для создания дуги высокой интенсивности внутри горелки для ионизации газа и образования плазмы.
Горелка служит держателем расходуемого сопла и электрода и обеспечивает охлаждение (газ или вода) этих частей. Сопло и электрод сужают и удерживают плазменную струю.
Последовательность работы с плазменным резаком
Источник питания и цепь зажигания дуги подключаются к горелке через соединительные провода и кабели.Эти выводы и кабели обеспечивают необходимый поток газа, электрический ток и высокую частоту в горелку для запуска и поддержания процесса.
ШАГ 1: Входной сигнал запуска отправляется на источник питания. Это одновременно активирует напряжение холостого хода и подачу газа к горелке (см. Рисунок 2). Напряжение холостого хода можно измерить от электрода (-) до сопла (+). Обратите внимание, что сопло подключается к плюсу источника питания через резистор и реле (реле вспомогательной дуги), а разрезаемый металл (заготовка) подключается непосредственно к плюсу.Газ проходит через сопло и выходит через отверстие. В это время дуги нет, так как нет пути тока для постоянного напряжения.
ШАГ 2: После стабилизации потока газа активируется высокочастотный контур. Высокая частота прерывается между электродом и соплом внутри горелки таким образом, что газ должен пройти через эту дугу, прежде чем выйти из сопла. Энергия, передаваемая от высокочастотной дуги к газу, вызывает ионизацию газа и, следовательно, электропроводность.Этот электропроводящий газ создает путь тока между электродом и соплом, в результате чего образуется плазменная дуга. Поток газа проталкивает эту дугу через отверстие сопла, создавая вспомогательную дугу.
ШАГ 3: Предполагая, что сопло находится в непосредственной близости от заготовки, вспомогательная дуга будет прикрепляться к заготовке, так как путь тока к положительному положению (в источнике питания) не ограничивается сопротивлением, как положительный подключение форсунки есть.Ток, протекающий к заготовке, измеряется электроникой на источнике питания. При обнаружении этого протекания тока высокая частота отключается, и реле вспомогательной дуги размыкается. Ионизация газа поддерживается за счет энергии основной дуги постоянного тока.
ШАГ 4: Температура плазменной дуги плавит металл, протыкает заготовку, а высокоскоростной поток газа удаляет расплавленный материал из нижней части пропила. В это время инициируется движение резака и начинается процесс резки.
Варианты процесса плазменной резки
Обычная плазменная резкаВ этом процессе обычно используется один газ (обычно воздух или азот), который охлаждает и производит плазму. Большинство этих систем рассчитаны на ток менее 100 А для резки материалов толщиной менее 5/8 ″. В основном используется в портативных приложениях.
Двойная газовая плазменная резка В процессе плазменной резки с использованием двух газов (кислородно-топливной) используются два газа; один для плазмы и один в качестве защитного газа. Защитный газ используется для защиты зоны разреза от атмосферы, обеспечивая более чистую кромку разреза. Это, вероятно, самый популярный вариант, так как можно использовать множество различных комбинаций газов для получения наилучшего качества резки для данного материала.
Water Shield Plasma Cutting — это разновидность процесса с двумя газами, в котором защитный газ заменяется водой. Он обеспечивает улучшенное охлаждение сопла и заготовки, а также лучшее качество резки нержавеющей стали.Этот процесс предназначен только для механизированных приложений.
Плазменная резка с впрыском воды Плазменная резка с впрыском воды использует один газ для плазменной резки и воду, вводимую либо радиально, либо вихревой непосредственно в дугу, чтобы значительно улучшить сужение дуги, поэтому плотность дуги и температура увеличиваются. Этот процесс используется при токах от 260 до 750 ампер для высококачественной резки различных материалов и различной толщины. Этот процесс предназначен только для механизированных приложений.
Precision Plasma Cutting обеспечивает превосходное качество резки более тонких материалов (менее 1/2 дюйма) на более низких скоростях. Это улучшенное качество является результатом использования новейших технологий для сверхсужения дуги, что значительно увеличивает плотность энергии. Более низкие скорости требуются, чтобы устройство движения могло более точно формировать контур. Этот процесс предназначен только для механизированных приложений.
Подготовка к установке системы | Плазменные системы Victory CNC
Размещено by victorycnc & подано в раздел «Системы плазменной резки».
При добавлении системы плазменной резки к вашему производству важно учитывать логистические факторы до установки системы. Вам нужно будет разработать план до того, как появится ваша новая система, чтобы у вас была простая установка и плавный запуск.
1. Желаемое расположение стола
Перед установкой системы убедитесь в наличии необходимого пространства и рассмотрите расположение компонентов системы плазменной резки. К ним относятся стол для резки, источник питания плазменного резака, сжатый воздух / газ и контроллер ЧПУ.Ваш поставщик оборудования для плазменной резки сможет помочь вам определить схему, которая оптимизирует рабочий процесс и операционные требования. Режущие поверхности должны быть на фут шире и на три фута длиннее, чем зона резки, чтобы можно было использовать погрузку и стоянку на портале. Дополнительные параметры могут изменить эту площадь.2. Требуемый источник питания
Убедитесь, что у вас правильное входное напряжение для питания всей системы плазменной резки. Это будет зависеть от типа устройства плазменной резки, которое вы выбрали для своей системы: для некоторых устройств плазменной резки требуется однофазное питание, но для большинства требуется трехфазное питание.Перед установкой системы сообщите своему торговому представителю, какой тип питания у вас установлен, поскольку входное напряжение установлено на заводе.
3. Сжатый воздух
Системы требуют стабильной подачи сухого сжатого воздуха 15 куб. Фут / мин при 130 фунт / кв. Дюйм с регулятором 150 фунт / кв. Дюйм и манометром на машине. Подача сжатого воздуха никогда не может упасть ниже 120 фунтов на квадратный дюйм. Мы рекомендуем специальный воздушный компрессор, так как система подачи воздуха на заводе часто падает ниже 120 фунтов на кв.4. Необходимая вентиляция
Тип необходимой вентиляции будет зависеть от того, есть ли у вас уровень грунтовых вод или нисходящий поток. Водные слои контролируют дым и пыль, поэтому вытяжной вентилятор не требуется. Однако для систем с нисходящим потоком потребуется коллектор дыма и пыли для очистки выхлопных газов и возврата очищенного воздуха в рабочую зону. Перед установкой системы рассмотрите дополнительные требования к выхлопной системе и ее расположение.5. Надлежащее заземление для плазменной системы определенного типа
Транзитное напряжение или высокочастотный электрический шум от источника питания плазменной резки потенциально может мешать работе контроллера ЧПУ и кабелей управления, что приводит к неисправности системы.
6. Необходимое программное обеспечение для рисования САПР
Если чертежи САПР еще не являются частью вашего бизнеса, вам нужно будет выбрать и приобрести программу. Облегченные программы САПР, включенные в программное обеспечение контроллера, на самом деле бесполезны, за исключением легкого редактирования.Программное обеспечение контроллера включает в себя «Библиотеку форм», поэтому у вас будет доступ к пятидесяти распространенным формам. Для этих форм потребуется ввести размер до резки. Есть несколько очень хороших программных пакетов САПР, доступных за несколько сотен долларов, поэтому вам не придется платить тысячи, чтобы получить программу, равную AutoCAD. Чтобы вырезать деталь, вам потребуется чертеж САПР, сохраненный в файле DWG или DXF. Если у вас есть готовые файлы DXF с деталями, которые вы хотите вырезать, вы сможете сразу приступить к резке.Чтобы быстро освоить CAD, обратитесь в местную среднюю школу или техническое училище, многие из которых сейчас преподают CAD. Студенты, заинтересованные в работе неполный рабочий день, могут помочь вашим людям изучить САПР или сделать это за вас.
7. Очистка подземных вод
При установке потребуется достаточное количество водоподготовки, например Plasma Quench 44, для предотвращения ржавчины и роста бактерий на столе.8. Wi-Fi
Перед установкой системы вы должны установить WiFi-маршрутизатор (подключенный к вашей сети) и поместить его в пределах досягаемости контроллера машины.Качественные системы ЧПУ будут включать Wi-Fi, чтобы соединить вашу систему с производителем для обновления программного обеспечения, помощи оператора и диагностики. Хотя Wi-Fi можно использовать для передачи вырезанных файлов из офиса на машину, рекомендуется использовать USB-накопители, чтобы WiFi можно было отключить, когда он не нужен.
9. Расходные материалы для резака
Расходные материалы, необходимые для плазменной резки, различаются в зависимости от системы.Ваш плазменный резак будет доставлен с ограниченным количеством расходных материалов для резака. Желательно заказать дополнительную партию расходных материалов — производитель сможет вам помочь.10. Требуемое обучение для работы
Определите, кто будет основным оператором (-ами) до прибытия вашей плазменной системы. Это важно, поскольку обучение системы обычно происходит при установке, и лучше всего обучать операторов напрямую. Это позволяет операторам задавать вопросы и получать ответы на них от самых знающих специалистов в области плазменной резки.Всегда хорошо, когда стабильный член руководства также учится управлять системой. Плазменный резак— Gizmosmith
В Интернете есть несколько планов установки плазменной резки своими руками. Большинство из них — это салфетки-наброски, которые кто-то отсканировал и выложил на форум, чтобы опытные сварщики могли их побелить.
У этого есть несколько проблем. Основная из них заключается в том, что он не изолирован должным образом от сети переменного тока. Изолирующий трансформатор может обеспечить эту изоляцию и может быть импровизирован из двух идентичных трансформаторов, соединенных спина к спине, с их вторичными обмотками.Он будет действовать как трансформатор 1: 1, но вместо того, чтобы иметь токопроводящий путь от входа к выходу, мощность передается по индукции.
Я делаю плазменный резак с парой изолирующих трансформаторов, сделанных из трансформаторов СВЧ. Я выбрал трансформаторы для микроволновых печей, потому что я могу получить их дешево или бесплатно, и они могут выдерживать большую мощность.
После того, как я подключу свой вариак, я собираюсь протестировать блок питания. Если с тестом все пройдет хорошо, я подумаю о том, чтобы получить плазменную головку с Ebay или от Harbour Freight, и закончу сборку с помощью заимствованного или импровизированного воздушного компрессора.
Этим вечером я добавил радиаторы к паре выпрямителей, которые планирую использовать в блоке питания самодельного плазменного резака. Каждый выпрямитель будет обрабатывать половину силовой нагрузки устройства, поэтому у меня есть мощные выпрямители на 35 А / 600 В. Каждый выпрямитель имеет квадратный металлический корпус с отверстием посередине, поэтому я просверлил и проткнул отверстие в центре пары радиаторов процессора и прикрутил выпрямители к радиаторам. Этот рисунок может помочь прояснить сборку.
Я возлагал большие надежды на оригинальные вентиляторы, которые были на этих радиаторах, но смазка, которая была в них, превратилась в жевательную резинку, и они не вращались.Новые вентиляторы от ноутбуков, работают от 5В.
Я планирую получить 5 В от низковольтных обмоток накала трансформаторов для микроволновых печей, которые я использую для развязывающего трансформатора источника питания. Есть два набора из двух трансформаторов, соединенных «спина к спине», чтобы действовать как изолирующие трансформаторы.