Краткий обзор основных IGBT-технологий
Для опытных инженеров, которые давно занимаются разработкой электроприводов, эта статья о биполярных транзисторах с изолированным затвором (insulated-gate bipolar transistor, IGBT) — обобщение известных истин. Однако для новичков, которые только недавно начали проектировать электроприводы, используют IGBT в других приложениях и не вполне знакомы с основными технологиями и соответствующей терминологией, этот перевод статьи может стать кратким справочным пособием.
Информация, изложенная на страницах этой статьи, в первую очередь может оказаться полезной при выборе IGBT-транзисторов для нового проекта, т.к. те некоторые сведения, которые требуется знать о разных типах IGBT, не упоминаются в технических описаниях. Кроме того, во многих справочных руководствах отсутствует информация о технологиях изготовления IGBT. Понимание различий между этими техпроцессами позволяет найти современную замену устройствам IGBT, которые используются в уже существующих приложениях.
CРАВНЕНИЕ IGBT C MOSFET
По сравнению с MOSFET-транзисторами, процессы обработки поверхности IGBT имеют много схожего, но основные различия в динамических характеристиках этих устройств обусловлены разными структурами нижней поверхности полупроводниковых пластин. Хорошо известные n-канальные транзисторы MOSFET, работающие в режиме обогащения, делятся на планарные и выполненные по технологии Trench. Электрическое поле, созданное приложенным между затвором и истоком положительным напряжением значительной величины, вынуждает большое количество носителей дрейфовать от имплантированной n-зоны к имплантированной p-зоне.
В MOSFET планарного типа большая часть пути тока приходится на боковой дрейф, а меньшая — на отрезок между поворотом на 90° и стоком (см. рис. 1). Чем длиннее общий путь, включая небольшой отрезок канала, где проводимость модулируется металлическим затвором, тем больше сопротивление Rds(0n> на единицу площади (при том же напряжении VDSS и шаге между ячейками).
В транзисторах Trench MOSFET канал дрейфующих к стоку носителей полностью вертикален, а проводимость модулируется в намного большей степени за счет большей площади металлического затвора, расположенного по сторонам канала. В результате сопротивление Rds(0N) у транзисторов этого типа меньше по сравнению с планарными устройствами. В обоих случаях электроны дрейфуют от истока по n- и p-каналам в подложку n-типа, обеспечивая т.н. открытое состояние транзистора.
Как известно, в n-канальном MOSFET, работающем в режиме обогащения, имеется внутренняя npn-структура. Работа этого устройства редко вызывает проблемы благодаря тому, что его переход база-эмиттер практически закорочен металлизированным покрытием электрода истока. Если напряжение между стоком и истоком устройства достаточно быстро увеличивается при протекании заряда в биполярный транзистор от обратной емкости CRSS, он может включиться, а затвор — потерять способность к управлению. И хотя защелкивания не происходит, т.к. прекращается управление только биполярным транзистором, последствия могут быть катастрофичными. Большинство приложений нечувствительно к этому режиму работы из-за паразитных элементов, которые ограничивают скорость нарастания фронта VDS.
IGBT-транзистор работает схожим образом, но за счет слоя р+ на нижней поверхности полупроводниковой пластины. Кристаллы IGBT, выполненные по технологии PT (punch-through), имеют достаточно большую толщину — порядка 200 мкм у 600-В устройств. Главным образом, это обусловлено очень толстым эпитаксиальным слоем p+ (около 100 мкм), нанесенным на заднюю поверхность подложки n-типа. Эти устройства также имеют буферный слой n+, который нанесен непосредственно поверх слоя p+. Именно благодаря этому слою n+ возник термин punch-through (смыкание р-n-перехода). С этой точки зрения, это устройство очень напоминает по строению планарный MOSFET.
Для объяснения работы механизма punch-through следует принять два допущения, учитывая ограниченный объем этой статьи. Вывод коллектора IGBT фактически представляет собой эмиттер внутреннего биполярного рnр-транзистора. Следует учитывать динамические характеристики этого устройства.
В случае сильнолегированных n- и р-каналов перехода база-эмиттер обеспечивается более высокий коэффициент усиления по току в схеме с общим эмиттером и меньшее напряжение VCE(SAT), чем при использовании слаболегированной зоны n+. Чем указанный коэффициент усиления выше, тем ниже VCEO относительно VCBO биполярного транзистора. (Опытные инженеры могут по этому случаю вспомнить, как в свое время выбирали биполярные транзисторы с небольшим коэффициентом усиления по току для импульсных источников питания, а затем пропорциональный управляющий сигнал для базы, чтобы вывести транзисторы из насыщения).
IGBT-транзисторы, выполненные по технологии PT, преодолевают эти асимптотические пределы. Как только IGBT начинает выключаться, напряжение VCBO pnp-транзистора блокирует напряжение. Следует заметить, что переход коллектор-база pnp-транзистора находится рядом с верхней поверхностью этого устройства. Между pnp-коллектором верхней части IGBT (эмиттером устройства) и переходом база-эмиттер с рекомбинирующими носителями начинает появляться высокое напряжение. Оно приводит к возникновению электрического поля, которое убывает по мере удаления от верхней части устройства к внутреннему граничному слою n-/n+. Если поле достаточно велико у этого граничного слоя, переход коллектор-база распространяется в буферный слой n+. В результате переход база-эмиттер внутреннего pnp-транзистора очень быстро закрывается, «хвост» тока становится короче по сравнению с «хвостом» в устройствах типа NPT (non-punch-through), у которых этот буферный слой отсутствует.
IGBT, выполненные по технологии PT, например транзисторы 4-го поколения от компании International Rectifier, имеют отрицательный температурный коэффициент. Это значит, что напряжение VCE уменьшается с увеличением температуры, что затрудняет возможность параллельного соединения устройств и вынуждает тщательно подбирать соответствующее значение VCE. Расчетное время короткого замыкания, как правило, невелико и не устанавливается. Это обусловлено относительно высоким коэффициентом усиления по току биполярного транзистора и неспособностью точно управлять крутизной n-канального MOSFET, чтобы ограничить максимальный ток и, как следствие, максимальную рассеиваемую мощность.
NPT-УСТРОЙСТВА
В отличие от PT IGBT, NPT-транзисторы, например 4-го поколения от компании International Rectifier, имеют легированную зону p+ на нижней стороне подложки n-типа. Поскольку эта зона сравнительно небольшой толщины, обработка подложки обходится дешевле. Буферный слой n+ отсутствует. Несмотря на внешнее сходство, разница между этими двумя структурами устройств значительная. Состояние включения и выключения реализуются схожим образом, но в NPT-транзисторах отсутствует эффект смыкания, что позволяет сократить время накопления заряда и побуждает рекомбинировать носители в переходе база-эмиттер собственной pnp-структуры. В результате «хвост» коллекторного тока при выключении NPT-транзисторов немного длиннее, чем у PT-устройств, а остальные характеристики идентичны.
Из-за меньшего коэффициента усиления по току в собственной pnp-структуре напряжение VCE(SAT) PT-транзисторов несколько выше, чем у NPT, благодаря чему легче управлять максимальным током pnp-транзистора с меньшим коэффициентом усиления с помощью собственного n-канального MOSFET. Это значит, что длительность короткого замыкания NPT-устройства хорошо определяется и контролируется. Значение этого параметра у NPT IGBT-транзисторов находится в диапазоне до 10 мкс.
Наконец, характеристики n-канального MOSFET превалируют над NPT IGBT. Это значит, что напряжение VCE(SAT) увеличивается с ростом температуры, позволяя соединять эти устройства параллельно друг другу.
FIELD-STOP IGBT
Рассмотрим совершенно новое устройство из семейства IGBT — очень эффективные IGBT-транзисторы семейства Field Stop. Сама по себе эта технология позволяет уменьшить напряжение насыщения за счет намного меньшей толщины подложки. В этом случае относительно тонкий слой n-обедняется при закрытии перехода коллектор-база и смыкается с тонким хорошо управляемым слоем n+, в котором рост электрического поля прекращается. Транзисторы, выполненные по технологии Field-Stop, имеют очень малую толщину по сравнению с устройствами NPT и PT. Благодаря использованию слоя n+, прекращающего дальнейшее распространение электрического поля, Field-Stop IGBT можно отнести к семейству PT-устройства. Однако транзисторы Field-Stop намного лучше управляются, чем их предшественники PT.
IGBT-транзисторы, появившиеся на базе технологии MOSFET, относятся к Trench-устройствам, как например транзисторы IR 7-го поколения. Как уже упоминалось, технология Trench позволяет с помощью затворного напряжения той же величины модулировать намного большую область дрейфа, увеличивая коэффициент усиления n-канального MOSFET, уменьшая расстояние до стока и величину сопротивления в открытом состоянии. Траектория прохождения тока в этом случае представляет собой вертикальную прямую линию, идущую от коллектора к эмиттеру. Меньшее значение Rds(0N) MOSFET наряду с более высоким коэффициентом усиления биполярного транзистора за счет тонкого буферного слоя n+ обеспечивает меньшее напряжение VCE(SAT).
Комбинация технологий Trench и Field-Stop при создании, например, 1200-В семейств транзисторов IR 6- и 7-го поколений, обеспечивает меньшее значение RDS(ON) и толщину устройства, больший коэффициент усиления канала и наличие зоны n+ Field-Stop, благодаря чему появляется возможность использовать устройство в параллельных конфигурациях при минимальном времени накопления заряда и большей устойчивости к намного более высоким температурам. Из-за тонкого перехода база-коллектор в собственном pnp-транзисторе при значительном токе может возникнуть нехватка носителей и состояние ненасыщения. Поскольку максимальный ток короткого замыкания ограничен, упрощается механизм противодействия возникновению этих условий.
У всех этих устройств — общий механизм отказа. У MOSFET, который мы рассмотрели выше, имеется внутренний npn-транзистор, расположенный параллельно выводам стока и истока. Переход база-эмиттер этого npn-транзистора закорочен металлизированным покрытием истока вдоль n- и p-каналов. В IGBT имеется дополнительный p-слой на обратной стороне устройства, благодаря которому тиристор формируется из этого паразитного npn-транзистора (npnp). В отличие от MOSFET, который может пропустить большой импульс тока коммутации через емкость CRSS, транзистор IGBT в этих условиях полностью защелкивается. Коэффициенты усиления этих переходов тщательно контролируются, но при нарушении установленных режимов IGBT защелкивается.
ЧЕГО НЕТ В ТЕХНИЧЕСКИХ ОПИСАНИЯХ
При поиске подходящего устройства для конкретного приложения используются руководства по выбору, с помощью которых выясняются требуемые характеристики — напряжение, ток, частота коммутации и другие параметры. В одних случаях эти руководства хорошо справляются со своей задачей, в других имеются досадные ограничения.
Как правило, информация о рассмотренных выше технологиях не предоставляется в технических описаниях несмотря на то, что эти материалы широко используются на семинарах, производстве и при обсуждении характеристик устройств. Может быть, настало время дополнить технические описания необходимой информацией?
Очевидно, что при выборе списка материалов, например для силового преобразователя или его замены современным устройством, знание о технологии его построения окажет разработчику неоценимую услугу.
Предположим, необходимо создать емкостной регулятор яркости, управляемый несфазированным полным мостом ZVT (Zero Volt Switching — коммутация при нулевом напряжении). При этом следует понять, подойдет ли с этой целью резонансная топология? Ответ на этот вопрос положителен в тех случаях, когда ток нагрузки достаточно велик, чтобы в первичной индуктивности рассеяния накопилась энергия примерно той же величины, что и в емкости COSS противоположного IGBT в полумостовых схемах. В иных случаях выбирается жесткая коммутация. Таким образом, используется и мягкая, и жесткая коммутация. Однако ни одно руководство по выбору не дает ответа на этот важный вопрос.
При разработке электропривода возникают и другие вопросы, на которые не найти ответа в руководстве по выбору. Нужна ли в схеме защита от короткого замыкания? Как правило, нет, т.к. у привода отсутствуют незащищенные выводы и потому вероятность их замыкания нулевая. В рассматриваемом примере разработчику следует обеспечить малые значения COSS (выходная емкость), QG (заряд затвора), CRSS (емкость обратного смещения), EOFF (энергия выключения) и QRR (заряд обратного восстановления диода). Этот набор параметров реализуется с помо- щью любой технологии — PT, NPT или Field-Stop/Trench — в зависимости от частоты коммутации.
Для выбора оптимального устройства следует обсуждать эти приложения с инженерами по применению и производителями. Следует также выбрать диод, соответствующий конкретной IGBT-технологии. Как правило, предпочтителен выбор диодов с малым значением QRR. Высокие значения IRR, QRR и tRR могут стать причинами большого шума.
Итак, этот краткий обзор IGBT-технологий можно рассматривать как пособие для проектирования не только стандартных, но и новых приложений, в отношении которых наблюдается нехватка важной информации.
схема и преимущество использования в сварке
Применение высоковольтных мощных полупроводников позволило создавать компактные производительные сварочные инверторы. Последним словом в этой области после MOSFET инверторов стали сварочные аппараты на IGBT транзисторах.
Полевые полупроводники
Используемые в инверторах полупроводники по MOSFET технологии – это полевые силовые транзисторы с изолированным затвором. Управление полупроводником осуществляется напряжением, в отличие от биполярных транзисторов, управляемых током. Канал ключа имеет высокую проводимость 1 мОм. В закрытом виде у них огромное входное сопротивление.
Изначально полевые полупроводники использовались и до сих пор применяются как ключи. В схемах импульсных источников питания применяются полевики с индуцированным затвором. В таком исполнении при нулевом напряжении на затвор-исток канал закрыт.
Для открытия ключа требуется подать потенциал определенной полярности. Для управления ключом не требуется силовых источников. Данные полупроводники часто используются в источниках питания и инверторах.
Биполярный прибор
IGBT – это биполярный транзистор с изолированным затвором, применяемый в инверторе. Фактически он состоит из двух транзисторов на одной подложке. Биполярный прибор образует силовой канал, а полевой является каналом управления.
Соединение полупроводников двух видов позволяет совместить в одном устройстве преимущества полевых и биполярных приборов. Комбинированный прибор может, как биполярный, работать с высокими потенциалами, проводимость канала обратно пропорциональна току, а не его квадрату, как в полевом транзисторе.
При этом IGBT транзистор имеет экономичное управление полевого прибора. Силовые электроды называются, как в биполярном, а управляющий получил название затвора, как в МОП приборе.
IGBT транзисторы для сварочных инверторов и силовых приводов, где приходится работать при высоких напряжениях, стали использовать, как только отладили технологию их производства. Они сократили габариты, увеличили производительность и мощность инверторов. Иногда они заменяют даже тиристоры.
В IGBT инверторе для обеспечения работы мощных переключателей применяются драйверы – микросхемы, усиливающие управляющий сигнал и ускоряющие быструю зарядку затвора.
Некоторые модели IGBT транзисторов работают с напряжением от 100 В до 10 кВ и токами от 20 до 1200 А. Поэтому их больше применяют в силовых электроприводах, сварочных аппаратах.
Полевые транзисторы больше применяют в импульсных источниках и однофазных сварочных инверторах. При токовых параметрах 400-500 В и 30-40 А они имеют лучшие рабочие характеристики. Но так как IGBT приборы могут применяться в более тяжелых условиях, их все чаще применяют в сварочных инверторах.
Применение в сварке
Затем инвертор преобразует постоянное напряжение в переменное, но уже высокой частоты (от 30 кГц до 120 кГц). Проходя через понижающий высокочастотный трансформатор (преобразователь), напряжение понижается до нескольких десятков вольт. Потом этот ток преобразуется обратно в постоянный.
Все преобразования необходимы для уменьшения габаритов сварочного аппарата. Традиционная схема сварочного инвертора получалась надежной, но имела очень большие габариты и вес. Кроме этого, характеристики сварочного тока с традиционным источником питания были значительно хуже, чем у инвертора.
Передача электроэнергии на высокой частоте позволяет использовать малогабаритные трансформаторы. Для получения высокой частоты постоянный ток преобразуется с помощью высоковольтных, мощных силовых транзисторов в переменный частотой 50-80 кГц.
Для работы мощных транзисторов напряжение 220 В выпрямляется, проходя через мостовую схему и фильтр из конденсаторов, который уменьшает пульсации. На управляющий электрод полупроводника подается переменный сигнал с генератора прямоугольных импульсов, который открывает/закрывает электронные ключи.
Выходы силовых транзисторов подключаются к первичной обмотке понижающего трансформатора. Благодаря тому, что они работают на большой частоте, их габариты уменьшаются в несколько раз.
Силовой инверторный блок
Переменное напряжение 220 В – это некоторое усредненное значение, которое показывает, что оно имеет такую же энергию, как и постоянный ток в 220 В. Фактически амплитуда равна 310 В. Из-за этого в фильтрах используются емкости на 400 В.
Мостовая выпрямительная сборка монтируется на радиатор. Требуется охлаждение диодов, поскольку через них протекают большие токи. Для защиты диодов от перегрева на радиаторе имеется предохранитель, при достижении критической температуры он отключает мост от сети.
В качестве фильтра используются электролитические конденсаторы, емкостью от 470 мкФ и рабочим напряжением 400 В. После фильтра напряжение поступает на инвертор.
Во время переключения ключей происходят броски импульсного тока вызывающие высокочастотные помехи. Чтобы они не проникали в сеть и не портили ее качество, сеть защищают фильтром электромагнитной совместимости. Он представляет собой набор конденсаторов и дросселя.
Сам инвертор собирается по мостовой схеме. В качестве ключевых элементов применяются IGBT транзисторы на напряжения от 600 В и токи соответствующие данному инвертору.
Они тоже с помощью специальной термопасты монтируются на радиаторы. При переключениях этих транзисторов возникают броски напряжения. Чтобы их погасить применяются RC фильтры.
Полученный на выходе электронных ключей переменный ток поступает на первичную обмотку высокочастотного понижающего трансформатора. На выходе вторичной обмотки получается переменный ток напряжением 50-60 В.
Под нагрузкой, когда идет сварка, он может выдавать ток до нескольких сотен ампер. Вторичная обмотка обычно выполняется ленточным проводом для уменьшения габаритов.
На выходе трансформатора стоит еще один мощный диодный мост. С него уже снимается необходимый сварочный ток. Здесь используются быстродействующие силовые диоды, другие использовать нельзя, потому что они сильно греются и выходят из строя. Для защиты от импульсных бросков напряжения используются дополнительные RC цепи.
Мягкий пуск
Для питания блока управления инвертора применяется стабилизатор на микросхеме с радиатором. Напряжение питания поступает с главного выпрямителя через резистивный делитель.
При включении сварочного инвертора конденсаторы начинают заряжаться. Токи достигают таких больших величин, что могут сжечь диоды. Чтобы этого не произошло, используется схема ограничения заряда.
В момент пуска ток проходит через мощный резистор, который ограничивает пусковой ток. После зарядки конденсаторов резистор с помощью реле отключается, шунтируется.
Блок управления и драйвер
Управление инвертором осуществляет микросхема широтно-импульсного модулятора. Она подает высокочастотный сигнал на управляющий электрод биполярного транзистора с изолированным затвором. Для защиты силовых транзисторов от перегрузок дополнительно устанавливаются стабилитроны между затвором и эмиттером.
Для контроля напряжения сети и выходного тока используется операционный усилитель, на нем происходит суммирование значений контролируемых параметров. При превышении или понижении от допустимых значений срабатывает компаратор, который отключает аппарат.
Для ручной регулировки сварочного тока предусмотрен переменный резистор, регулировочная ручка которого выводится на панель управления.
Сварочное оборудование на IGBT транзисторах имеет наилучшие характеристики по надежности. По сравнению с полевыми ключами биполярные транзисторы с изолированными затворами имеют преимущество больше 1000 В и 200 А.
При использовании в бытовых приборах и сварочных инверторах для домашнего пользования первое место до недавнего времени оставалось за сварочным оборудованием с MOSFET полупроводниками. Эта технология давно используется и хорошо отработана. Но у нее нет перспектив роста, в отличие от оборудования на IGBT транзисторах.
Новые модели уже ничем не уступают устройствам с полевыми приборами и на малых напряжениях. Только по цене первенство остается за аппаратами с полевыми транзисторами с индуцированным затвором.
Технологии производства IGBT-модулей АО «Протон-Электротекс»
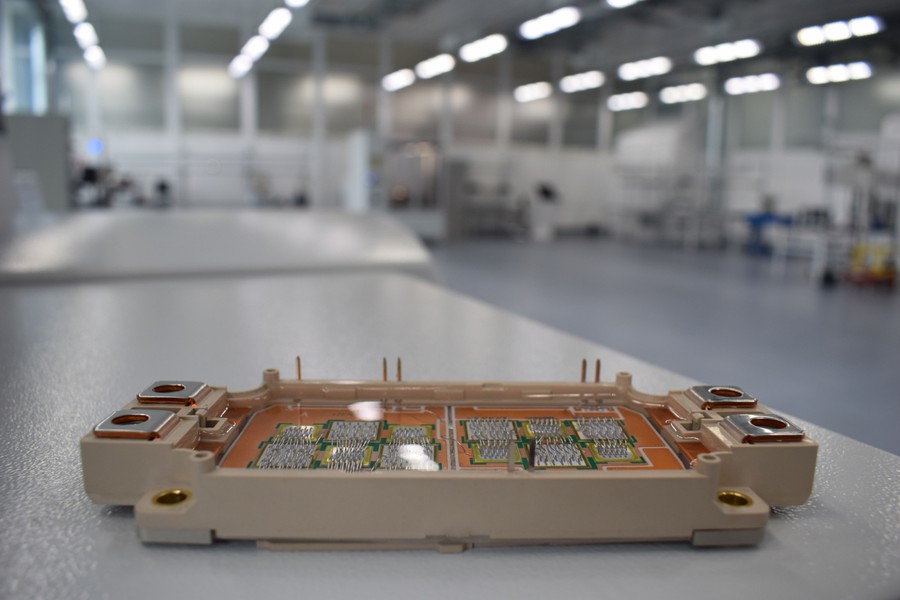
Введение
Мир стремительно меняется. Заметнее всего эти изменения отражает потребительская электроника: любой сможет отличить современный мобильный телефон или телевизор от аппарата 2000 года выпуска. Прошедшие полтора десятилетия навсегда изменили наши привычки, график нашего рабочего времени и методы нашей работы. Изменилось восприятие информации мозгом и фундаментальная структура занятости в развитых странах. Теперь изменения в компонентной базе, исследование свойств материалов и развитие технологии готовят человечеству новый рывок — изменение уклада в энергетике, который в конечном итоге должен привести к революционному по своему значению отказу от ископаемого топлива, как когда-то человечество отказалось от паровозов и печного отопления. В соответствии с отчетом IEA (международное агентство по энергетике), первичная выработка энергии из возобновляемых источников в 2012 составила 13,2% мирового энергобаланса, а в 2013 г. — уже 22%. В эту долю входят ветро- и гидроэлектростанции, а также солнечная энергетика всех типов. Такой бурный рост использования «чистой» энергии в совокупности с постоянной борьбой за снижение удельной энергоёмкости в промышленности и домашнем хозяйстве подтолкнули огромный спрос на системы преобразования энергии и их составные части, прежде всего IGBT-модули. Они нашли свое применение в промышленных приводах и управляемых инверторах, оборудовании солнечных, приливных и ветряных станций, электротранспорте. Дальнейшее развитие альтернативных, энергосберегающих и высокоэффективных источников электроэнергии позволяет уверенно снижать долю ископаемых видов топлива и гарантирует рост компаниям, которые работают в сфере производства компонентов «новой энергетики». Разумеется, рынок оставит на сцене только производителей, гарантирующих стабильность поставок и качество своих продуктов, поскольку отказы приборов и систем энергоснабжения несут огромные риски.
![]() | Ставцев Александр. Технический директор АО «ПРОТОН-ЭЛЕКТРОТЕКС» www.proton-electrotex.com «Процесс непрерывного развития лежит в основе успеха |
Важно отметить, что огромные нагрузки и тяжелые режимы работы конечных устройств требуют от производителей силовой электроники (в т.ч., IGBT-модулей) современного парка оборудования и квалифицированного персонала. А тотальная интеграция производителей современной электроники в международные цепочки поставок комплектующих, проекты и рынки должны поддерживаться должным уровнем представительства таких компаний в основных регионах сбыта. Всем этим требованиям соответствует лидер отечественной силовой электроники, АО «ПРОТОН-ЭЛЕКТРОТЕКС» (г. Орел). За последние три года предприятие провело полную модернизацию собственного производства IGBT-модулей, внедрило современную систему управления предприятием и разработало новое поколение приборов. Модули, выпускаемые АО «ПРОТОН-ЭЛЕКТРОТЕКС», находят применение в десятках стран мира благодаря тщательно выстроенной системе представительств и совместным проектам с мировыми лидерами отрасли. Присутствие компании на основных выставках и научных конференциях позволяет АО «ПРОТОН-ЭЛЕКТРОТЕКС» следить за мировыми тенденциями в области силовых полупроводников и поставлять на рынок продукцию, качество которой гарантировано внедренными на производстве стандартами серии ISO 9001.
На предприятии АО «ПРОТОН-ЭЛЕКТРОТЕКС» реализована полная производственная линия, соответствующая всем современным стандартам и расположенная в едином помещении с испытательным комплексом. Такая организация позволила улучшить ритмичность внутренней логистики и сократить цикл сборки приборов. Помещение было заново оснащено климатическим оборудованием, которое позволяет добиться температуры, влажности и давления, заданных стандартами для чистых помещений. Промышленный воздух соответствует DIN ISO 8573-1 класс чистоты 2.4.1 (Рис. 1).
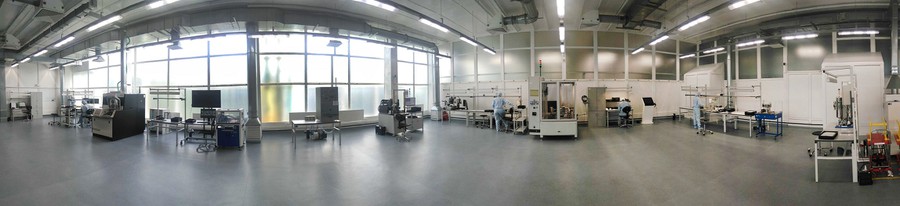
![]() | Сергей Валев Директор ООО «Ай Ви Тек Электроникс» www.ivtec.ru «Есть заказчики, для которых я чувствую своим долгом пойти на шаг |
Первой фазой проекта развития АО «ПРОТОН-ЭЛЕКТРОТЕКС» стало освоение в 2015-2016 гг. производства IGBT-модулей «классической» конструкции. После изобретения принципа работы IGBT в 1968 г. и появления первых опытных образцов в начале 1980-х годов, усилиями крупных игроков (Infineon, IR, IXYS, ABB, Toshiba и пр.) постепенно сложился «стандартный ряд» габаритных размеров и типов этих приборов. В своем нынешнем виде IGBT-модули появились на мировом рынке более 15-ти лет назад, но до сих пор не потеряли своей актуальности благодаря огромному количеству стандартизированных посадочных мест и габаритов конечных устройств (выпрямителей, преобразователей) в которых они являются компонентом. Аналогично любым стандартизированным промышленным изделиям, IGBT-модули будут оставаться в своем нынешнем внешнем виде еще как минимум 15 лет. Рынок благосклонно воспринял появление новых игроков, предлагающих стандартные «семейства» этих приборов по конкурентной цене, и АО «ПРОТОН-ЭЛЕКТРОТЕКС» занял там свое достойное место. Внешний вид модулей классической конструкции представлен на рисунке 2.
![]() | ![]() | |
Рисунок 2. Модули классической конструкции производства АО «ПРОТОН-ЭЛЕКТРОТЕКС» в корпусах с шириной основания: а — 62мм; б — 34мм. |
Однако, как и во всем остальном, внешний вид не определяет наполнение. Несмотря на то, что классические габаритные размеры модулей сложились давно, их «начинка» непрерывно совершенствуется и оптимизируется с целью улучшения основных параметров прибора, снижения его себестоимости и повышения качества и ресурса.
Если сравнить передовую технологию производства модулей классической конструкции 15 лет назад и в наши дни, то можно выделить ряд важных отличий и нововведений на каждом шаге технологической цепочки. Общими принципами развития можно считать следующие:
- уменьшение числа технологических операций,
- минимизация ручного труда и трудоемкости на единицу продукции,
- исключение и сокращение расхода промежуточных реагентов и материалов (флюса, рабочего инструмента, оснастки)
- повышение воспроизводимости и контролируемости процесса,
- увеличение технологического окна («робастности») процесса.
Результатом развития технологии должно стать дальнейшее повышение потребительских качеств приборов при снижении их себестоимости.
Далее в статье проанализированы решения, реализованные АО «ПРОТОН-ЭЛЕКТРОТЕКС» в своем производстве и поддерживающие заданный вектор развития предприятия.
Вакуумная пайка
Качество конечного изделия закладывается с первого же технологического процесса. Первый шаг в процессе производства IGBT модулей — это пайка. Паяный шов обеспечивает механическое соединение компонентов, требуемую электро- и теплопроводность, устойчивость к термоциклированию и в конечном итоге, играет немаловажную роль в надежности изделия.
Классическая конвекционная пайка и пайка в паровой фазе с использованием паяльной пасты повсеместно уступают место вакуумной пайке. Причина этой тенденции — неравномерность прогрева массивных теплопроводящих элементов при парофазной и конвекционной пайке. Существуют также риски локального перегрева и высокий градиент температур при пайке крупных изделий в силу разницы теплоемкости элементов их конструкции. Соединение после конвекционной пайки, как правило, получается неоднородным и содержит дефекты. Использование в процессе пайки паяльной пасты или иных веществ-активаторов вынуждает прибегать к дополнительной влажной очистке, так как флюсы, содержащиеся в пасте, химически активны, и их остатки могут негативно сказаться на надежности прибора. Сложность подбора припоев с требуемой эластичностью и устойчивостью к термоциклированию также приводит к снижению ресурса модуля.
Командой АО «ПРОТОН-ЭЛЕКТРОТЕКС» этот процесс реализован другим, более современным методом — бесфлюсовой пайкой в вакууме с использованием преформ, кондуктивным нагревом и активацией поверхности в парах муравьиной кислоты.
Данный подход применяется практически всеми известными производителями силовой электроники в России и мире, позволяет реализовать весь заложенный конструктивный ресурс и повысить надежность прибора за счет следующих особенностей:
- Пайка всего изделия за один подход, следовательно, меньший тепловой стресс для чувствительных к перегреву компонентов;
- Возможность выбора большой номенклатуры припоев из различных материалов с требуемой эластичностью и температурой плавления;
- Высокая химическая чистота преформ в сравнении с пастой;
- Отсутствие необходимости последующей влажной отмывки;
- Высокое качество паяного шва, благодаря вакууму и, как следствие, малое количество каверн и пустот в соединении;
- Кондуктивный прогрев, при котором в первую очередь прогреваются компоненты с большой теплоемкостью — теплоотвод-основание и DCB, и лишь в последнюю — хрупкие кристаллы. Как результат — минимальное воздействие высоких температур на полупроводниковую часть прибора;
- Крайне гибкая настройка температурного профиля пайки и высокая повторяемость воспроизводимость — что важно для бессвинцовых технологий;
- Высокое качество соединения в металлургическом плане — более равномерная рекристаллизация припоя, с общей площадью дефектов, включая «холодную пайку», расслоения и каверны (менее <3%).
Все вышеописанные особенности позволяют добиться низкого процента дефектов пайки IGBT-модулей, что является большим конкурентным преимуществом АО «ПРОТОН-ЭЛЕКТРОТЕКС». При выборе печи, как и всего остального оборудования первой фазы своего проекта, АО «ПРОТОН-ЭЛЕКТРОТЕКС» ориентировался на предпочтения лидеров отрасли и выбрал среднюю по производительности двухкамерную вакуумную печь VADU 200XL производства PINK GmbH Thermosysteme (Германия). По общему мнению на рынке, она обладает рядом преимуществ по сравнению с другими системами.
Запатентованная технология создания динамического зазора при нагреве и многокамерная конструкция с отдельной камерой принудительного охлаждения позволяют добиваться отличных результатов пайки за минимально-возможное время. Уровень вакуума в ходе выполнения процесса в печи VADU также регулируемый, и обеспечивает стабильный и повторяемый процесс, отсутствие всплесков и брызг припоя независимо от начальных условий и термической массы загруженных изделий. Вакуум, плавно подаваемый непосредственно в момент образования жидкой фазы, практически полностью выводит пузыри из паяного соединения.
Применение динамически-регулируемого зазора, плавной регулировки вакуума и принудительного охлаждения позволяют выполнять термические профили по стандартам IPC / JEDEC, а также подстраивать их в широком технологическом коридоре под требования производителей силовых модулей.
Технические преимущества печей серии VADU довольно широко известны, и нет смысла подробно останавливаться на них. Важно, что кроме конструктивных технологических преимуществ, процесс пайки в АО «ПРОТОН-ЭЛЕКТРОТЕКС» проводится с применением оптимальной для силовых модулей оснастки. Вопрос оснастки и размещения изделий в камере является ключевым, а некоторые производители бывают вынуждены подстраиваться под габариты вакуумной камеры, причем низкая тепловая мощность печей не позволяет им применять тару и оснастку надлежащего типа.
Оснастка, разработанная VADU, недорога и стандартна, а ее конструкция связана со сложившимся рядом типоразмеров модулей. То есть, АО «ПРОТОН-ЭЛЕКТРОТЕКС» получил рабочее решение процесса и сразу же приступил к работе без долгой фазы прикидок и отработки режимов. Такой подход отражает высокую вовлеченность PINK в работу с производителями силовой электроники и изначальное понимание нужд заказчика.
Плазменная очистка
Еще одним важным технологическим процессом, реализованным АО «ПРОТОН-ЭЛЕКТРОТЕКС» с самого начала работы является использование аргонно-кислородной плазмы для микро-очистки и активации поверхностей. Это эффективный способ, который позволяет избежать использования опасных и ядовитых растворителей и стабилизировать параметры сварки, пайки и нанесения покрытий. Суть процесса в том, что молекулы ионизированного газа в наведенном поле тока высокой частоты и условиях разрежения (при давлении порядка 0,1 Атм.) действуют на физическом и химическом микроуровне, и «счищают» загрязнения и очаги окисления с поверхности деталей, а также возбуждают атомы верхних слоев деталей поверхности, делая их более восприимчивыми к соединению с другими деталями, т.е., увеличивают адгезионные свойства очищаемых поверхностей. Этот эффект подтверждается улучшением смачиваемости поверхности (уменьшением силы поверхностного натяжения при контакте), см. рис 3.
С помощью плазменной очистки АО «ПРОТОН-ЭЛЕКТРОТЕКС» удалось быстро оптимизировать параметры ультразвуковой сварки и улучшить качество заливки модуля компаундом.
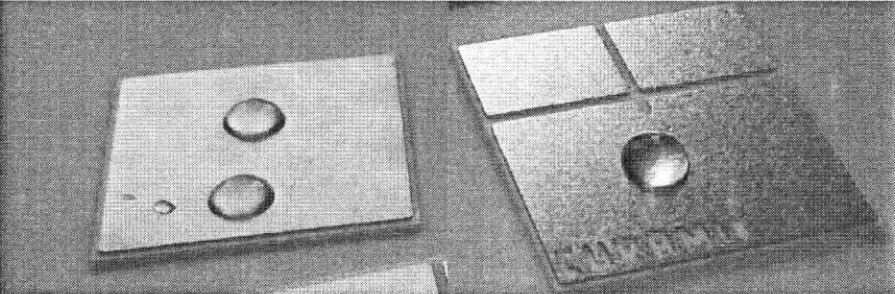
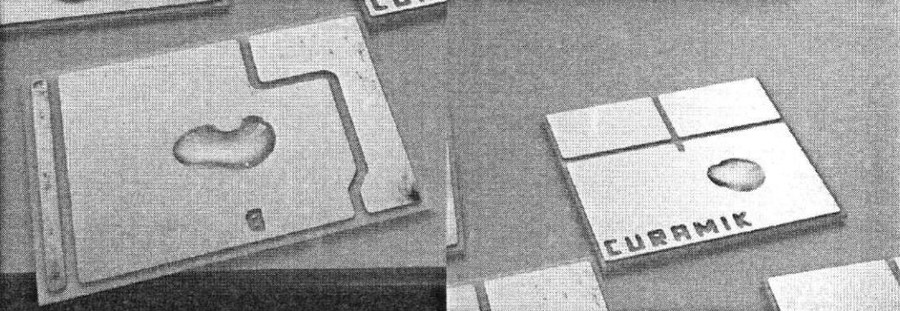
Рисунок 3. Смачиваемость до очистки (а) и после (б)
При выборе оборудования АО «ПРОТОН-ЭЛЕКТРОТЕКС» также принял осознанное решение, продиктованное характером продукции. Оборудование плазменной очистки исторически пришло в сборочную технологию из полупроводникового производства. Там оно обычно применяется в агрессивных по отношению к поверхности операциях травления или снятия фоторезиста, и поэтому использует частоты 13,56 МГц или 2,54 ГГц для генерации высокоэнергетической плазмы. Соответственно, энергия, передаваемая плазме на такой частоте, может привести к перегреву поверхности и повлиять на физические характеристики поверхности, способствовать паразитным химическим реакциям и повредить чувствительные элементы полупроводниковых кристаллов. Поэтому в установке, выбранной АО «ПРОТОН-ЭЛЕКТРОТЕКС» используется плазма, генерируемая при низкой частоте (40-50 кГц), которая имеет следующие преимущества:
- Более высокая плотность ионов. Низкочастотная плазма обеспечивает большую плотность энергии на квадратный сантиметр, чем высокочастотная очистка. Хотя это может показаться нелогичным, высокочастотные системы плазменной очистки фактически теряют значительную энергию за счет потерь тепла. Потери энергии плазмы частотой 13,56 МГц в 850 раз выше, чем при использовании системы частотой 40 кГц.
- Повышенная эффективность. Эффективность плазменной системы рассчитывается из отношения энергии, используемой при производстве плазмы, к энергии, рассеиваемой в тепло. Низкочастотная плазменная система действует как идеальный конденсатор с бесконечным емкостным сопротивлением или нулевой утечкой тока в режиме ожидания.
- Лучшая однородность. За счет ламинарного, а не факельного потока плазмы, низкочастотные системы обеспечивают гораздо более равномерную обработку поверхности, а за счет горизонтальной подачи плазмы они не имеют «затенения», которое происходит, когда образцы на верхних полках образуют преграду для обработки образцов на нижних полках.
На производстве АО «ПРОТОН-ЭЛЕКТРОТЕКС» задействована установка плазменной очистки G1000E компании Yield Engineering Systems, универсальная и популярная у производителей СВЧ-приборов, светодиодов и многокристальных модулей единица оборудования.
Ультразвуковое сканирование
Еще одним решением, позволившим быстро выйти на заданный уровень качества и сократить время отработки техпроцесса было введение процесса проверки методом ультразвукового сканирования. Ультразвуковое сканирование — незаменимый при работе с массивными деталями метод неразрушающего контроля и применяется как после процесса пайки, так и на других этапах производства модуля, таких как ультразвуковая сварка выводов.
![]() | Ernst Eggelaar Генеральный директор Microtronic GmbH microtronic.de «…инициативная и целеустремленная команда с отличным пониманием |
Сканирование позволяет выявить брак на ранних этапах производства, обнаружить расслоения и дефекты, невидимые для любого иного метода контроля и позволяет оперативно указать на причину дефектов в самом начале работы участка, не теряя таким образом ценных компонентов и времени.
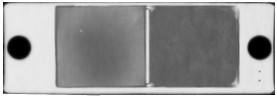
АО «ПРОТОН-ЭЛЕКТРОТЕКС» остановило свой выбор на установке ультразвуковой дефектоскопии и томографии SONIX ECHO™. Этот недорогой и хорошо известный в отрасли сканирующий акустический микроскоп является универсальным инструментом контроля для разработки, производства и анализа отказов полупроводниковых приборов. Микроскоп способен обнаруживать воздушные прослойки толщиной от 0,05 мкм и определять дефекты линейными габаритами от 10 мкм. Особенно важно отметить возможность распознавания микротрещин в керамике, которые могут являться результатом производственного брака у производителя DBC подложек, не распознанными в ходе выходного контроля.
Ультразвуковая сварка
Ультразвуковая сварка силовых выводов, управляющих выводов и соединений полупроводниковых кристаллов — критически-важный процесс, пришедший на смену прижимным и паяным конструкциям. Современный подход к технологии производства IGBT модулей классической конструкции состоит в минимизации количества сварных и паяных соединений, что уже привело к почти полному вытеснению пайки силовых выводов. Оборудование ультразвуковой сварки в АО «ПРОТОН-ЭЛЕКТРОТЕКС» позволяет гибко подходить к конструированию траверс корпусов, применять проволоку, ленту, алюминиевые и медные проводники разного сечения для получения полной гаммы высококачественных приборов, способных конкурировать с аналогами от мировых лидеров.
![]() | Jan Fritzges Руководитель отдела оборудования специального назначения Schunk Sonosystems GmbH http://www.schunk-sonosystems.com/en/ «Протон-Электротекс» успешно использует наши системы |
В текущем производстве нашли применение сразу несколько установок ультразвуковой сварки: от полуавтоматов серии F&S Bondtec 5650 и автоматов F&K Delvotec G5 66000 до систем Schunk DS20/35, покрывающих все возможные потребности предприятия. Благодаря ультразвуковой сварке модули производства АО «ПРОТОН-ЭЛЕКТРОТЕКС» не имеют ограничения срока службы, связанного с деградацией контактных (прижимных) и паяных соединений проводников внутри прибора, характерных для конструкции IGBT-модулей ранних серий.
Возможно, упоминание УЗ-сварки как инновации выглядит странно, поскольку в традиционных дискретных приборах и интегральных схемах ее применение было единственным методом получения электрического соединения начиная с 1960-х годов. Однако, в силовой электронике УЗ сварка получила свое распространение относительно недавно, а ряд приборов до сих пор выпускаются с применением пайки, прижима или иного контактного соединения компонентов.
Ультразвуковая сварка силовых выводов
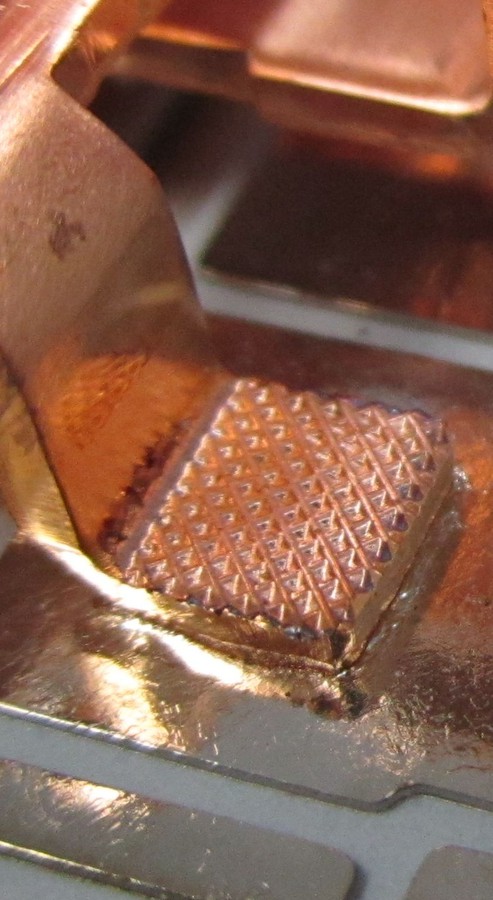
Хотелось бы особенно подчеркнуть, что методом УЗ-сварки АО «ПРОТОН-ЭЛЕКТРОТЕКС» пользуется и для присоединения мощных токовыводов сечением в несколько квадратных миллиметров. С точки зрения энергозатрат, чистоты процесса и снижения рисков возникновения дефектов, такая УЗ-сварка имеет ряд преимуществ. Наиболее важными из них, по нашему мнению, является отсутствие промежуточных и вспомогательных слоев припоя. Кроме того, этот процесс чист и менее затратен. Так как при сварке не применяются флюсы, не требуется и очистка после процесса. При УЗ-сварке отсутствует неизбежный при пайке термический стресс, поскольку УЗ-сварка, в отличие от пайки, происходит методом наклепа (холодной нагартовки) без достижения температуры плавления металла. Это позволяет снизить термические нагрузки на прибор в целом и на порядок повысить надежность соединения за счет прочной гальванической связи без паразитных реактивных сопротивлений и с диффузией материалов токовывода и подложки «медь‑в‑медь».
УЗ-сварка токовыводов позволяет увеличить токонесущую способность и уменьшить потери проводимости. Это достигается отсутствием дополнительного слоя металла припоя, который имеет другое значение проводимости. В качестве индикатора такой повышенной надежности можно привести данные об отсутствии отказов соединений токовыводов после термоциклирования, то есть полностью исключает эффект «ползучести» под постоянной нагрузкой при электротермоциклировании, который часто происходит в паяных конструкциях.
Ультразвуковая разварка проволокой
![]() | Stefan Berger Руководитель по продажам F&S Bondtec GmbH http://fsbondtec.com «Наша фирма F&S Bondtec — поставщик настольных установок |
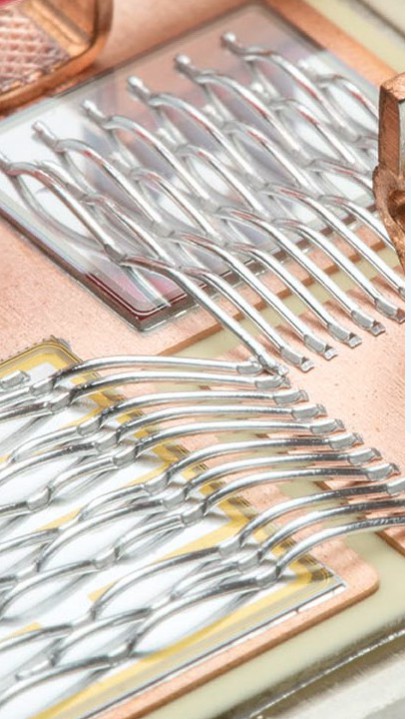
УЗ-сварке соединений кристаллов микропроволокой и лентой в АО «ПРОТОН-ЭЛЕКТРОТЕКС» также уделяется достойное внимание. Дело в том, что IGBT-модули в основном, применяются в тяжелых условиях и подвержены экстремальным температурным, вибрационным и комбинированным нагрузкам. В сравнении со сталью, у которой кривая усталости имеет явный перегиб для меди и алюминия, основных металлов, применяемых в силовой электронике, нет такого выраженного предела (на рис. 7 показаны кривые усталости стали и алюминия). Иными словами, сталь не разрушается, если не превышен ее предел напряжений, а медь и алюминий разрушаются под воздействием сколь угодно малых циклических нагрузок после определенного количества колебаний. Тестирование по ускоренному профилю в соответствии со стандартом IEC 60068-2-64 показывает, что силовые выводы способны выдержать лишь около 100 часов вибронагрузкок с частотой от 10 до 2000 Гц, и качество УЗ-соединений имеет определяющую роль в обеспечении надежности изделия.
![]() | Paul Gruber Руководитель по продажам, Европейский регион F&K Delvotec Bondtechnik GmbH http://www.fkdelvotec.com «Мы оцениваем своё партнерство с „Протон-Электротекс“ за последние |
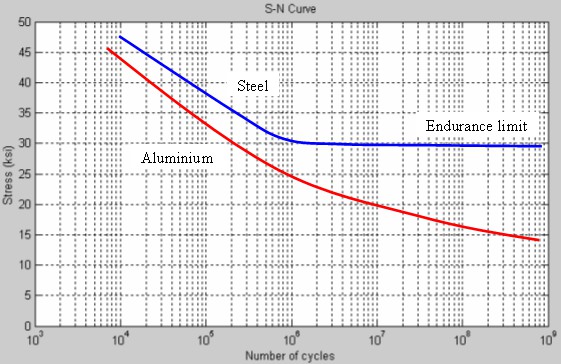
Установки УЗ сварки F&S Bondtec 5650 и F&K Delvotec G5 66000, в силу своих конструктивных особенностей, позволяют реализовать максимальную надежность соединений . Обе установки имеют богатые возможности по настройке и контролю параметров. Благодаря высокому уровню автоматизации они снижают влияние оператора на производственный процесс. Помимо всех прочих преимуществ в автоматических установках УЗ-сварки реализована обратная связь для контроля протекающих во время сварки процессов в реальном времени, элементы самодиагностики и самокалибровки, документирование процесса сварки, сбор и контроль статистических данных.
Важно отметить, что производительность установок применительно к толстой проволоке силовых модулей не является решающим фактором: предел производительности был достигнут много лет назад, и связан с физическим временем, необходимым для образования диффузного соединения металлов. Поэтому преимущества установок сварки и критерии выбора системы в основном, связаны с качеством и прогнозируемостью этого процесса. УЗ-сварка на установках F&S и F&K показала высокую воспроизводимость и широкое «окно» технологических параметров. Тесты в АО «ПРОТОН-ЭЛЕКТРОТЕКС» показали, что процесс сварки толстой алюминиевой проволокой на установках F&K Delvotec хорошо контролируется благодаря возможности тонкой настройки параметров сварки и геометрии петли.
В общей сложности система управления G5 контролирует около 200 параметров сварки: больше, чем в какой-либо иной установке. При этом, в большинстве случаев создание программы и работа оператора проходят интуитивно и вовлекают минимум величин. Но в пограничных случаях F&K Delvotec всегда предлагает более тонкую настройку, что важно в условиях опытного и многономенклатурного производства АО «ПРОТОН-ЭЛЕКТРОТЕКС».
Благодаря работе системы BPC нового поколения, служащей для активного управления мощностью и длительностью импульсов сварки с использованием обратной связи в реальном времени, мы убедились в устойчивости управляющей системы установок к изменению свойств исходных компонентов, гибкой и требующей минимального вмешательства операторов благодаря интеллектуальной системе машинного зрения.
- Прочность на срез соединения, полученного УЗ-сваркой, (среднее значение) составляет 18,9 Н;
- Все силовые токовыводы и соединения между кристаллами имеют нулевую дефектность по эффектам «ползучести» и отслаиваний при термоциклировании.
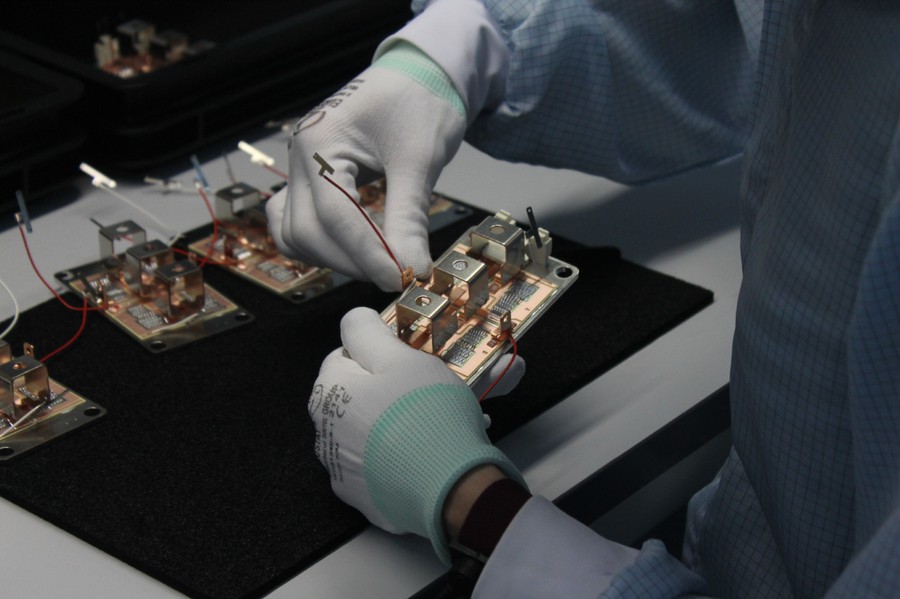
Контроль качества и испытания модулей на надежность
Огромное внимание при оснащении нового производства было уделено формализации и гармонизации методик испытаний и тестирования IGBT-модулей для отечественных и зарубежных заказчиков. Особенно важно, помимо приемо-сдаточных испытаний и исключения поставки дефектной продукции, обеспечить надежную и долговременную работу IGBT-модулей у заказчика. Поэтому командой разработчиков и технологов АО «ПРОТОН-ЭЛЕКТРОТЕКС» был разработан комплекс оборудования, который позволяет проводить 100% измерений параметров изделий при комнатной и повышенной температурах.
Все IGBT-модули АО «ПРОТОН-ЭЛЕКТРОТЕКС» проходят периодические и квалификационные испытания, соответствующие ГОСТ 24461-80 и международному стандарту IEC 60747-9. При этом для контроля статических и динамических электрических параметров продукции в производстве используются индивидуально спроектированные по техническому заданию АО «ПРОТОН-ЭЛЕКТРОТЕКС» комплексы Schuster на основе измерителей TPS 625 и DTS 758. Подобные комплексы применяют практически все производители силовой электроники в мире, что упрощает кооперацию и обсуждение наших задач с зарубежными заказчиками и партнерами.
В ходе запуска технологической и испытательной линии в АО «ПРОТОН-ЭЛЕКТРОТЕКС» тщательно изучались и испытывались опытные образцы модулей в сравнении с аналогами, предлагаемыми на рынках России и Европы. Результаты испытаний и тестов в заводских и независимых лабораториях доказали правильность выбора оборудования и технологических параметров, а также высокую квалификацию и уровень подготовки инженерного и производственного персонала, поскольку параметры модулей производства АО «ПРОТОН-ЭЛЕКТРОТЕКС» не уступают зарубежным аналогам.
- Основание модуля изолировано от токопроводящих элементов и выдерживает 4000 В;
- Результаты электротермоциклирования дают результат около 40000 циклов, при ∆Т = 100°С. И в этом наши показатели ТЦ и ЭТЦ не уступают показателям ведущих европейских производителей.
- Модули проходят высокотемпературное хранение в течении не менее 1000 часов при температуре 180°С с последующей проверкой изоляции;
- Испытания на ждущий режим в течении 1000 часов подтверждают сохранение блокирующих характеристик и тока утечки IGES в пределах нормы.
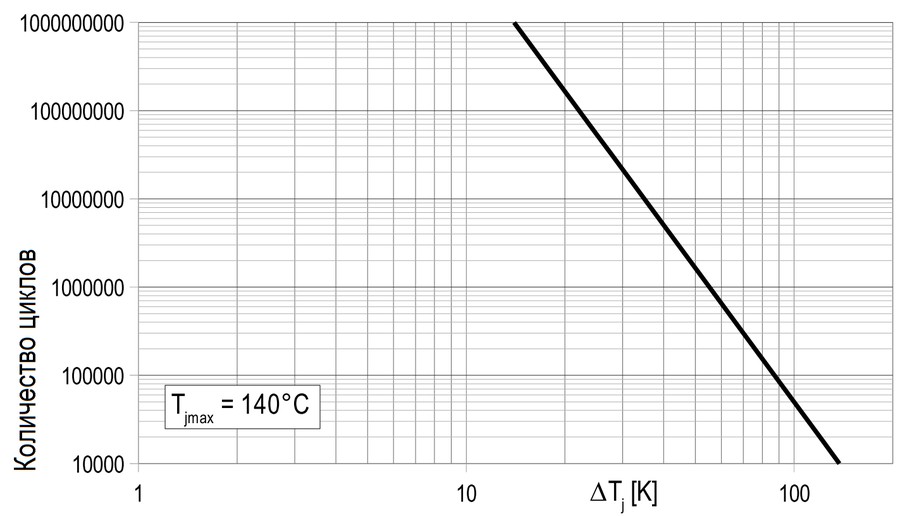
Заключение
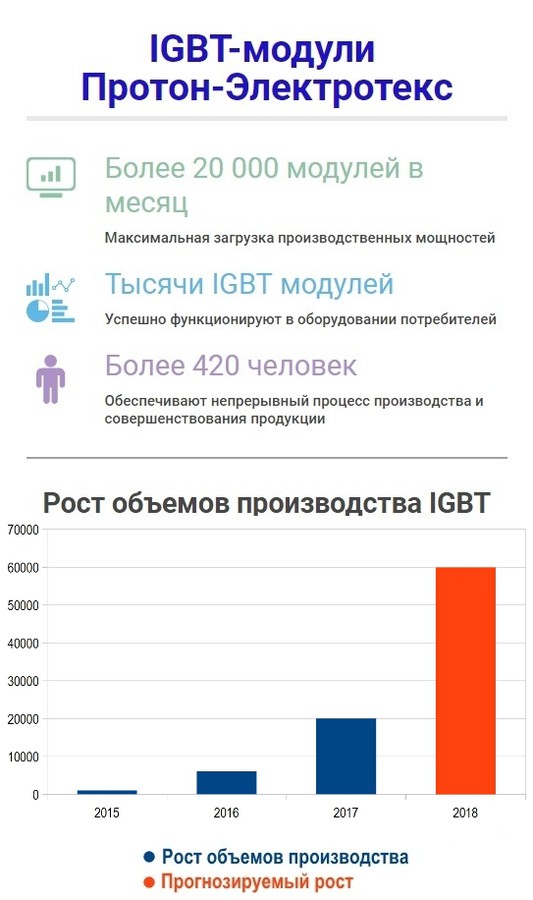
Уже более 20 лет АО «ПРОТОН-ЭЛЕКТРОТЕКС» занимается разработкой и производством силовых полупроводниковых приборов (тиристоров, диодов и модулей). Накопленный за эти годы опыт позволил предприятию открыть для себя такую область, как производство IGBT.
По результатам выполнения первой фазы перспективного плана развития АО «ПРОТОН-ЭЛЕКТРОТЕКС» можно констатировать, что проект удался. На предприятии отработаны действительно универсальные технологические процессы с применением лучшего на сегодняшний день комплекта оборудования, создан важный кадровый ресурс, налажен серийный выпуск продукции на конкурентном внешнем и внутреннем рынках. Взятый руководством компании курс на открытость и реальную конкурентоспособность, построение современной системы производства и маркетинга, постепенно выводит АО «ПРОТОН-ЭЛЕКТРОТЕКС» на позиции полноценного игрока отрасли. Производство уже работает в соответствии с мировыми стандартами и соответствует всем тенденциям развития силовой полупроводниковой техники. На предприятии создан конструкторский центр, позволяющий проектировать и производить модули, конкурирующие с лучшими аналогами.
Кроме всего вышесказанного АО «ПРОТОН-ЭЛЕКТРОТЕКС» постоянно стремится к повышению качества выпускаемой продукции. Исследуются и развиваются такие направления как синтеринг и улучшение тепловых свойств модулей.
Однако, помимо техники наш проект имеет в основе человеческую составляющую. Задача, выполненная компанией всего за два года, имеет прочный фундамент отношений, доверия и честности с поставщиками и специалистами отрасли. Мы рады, что на пути выполнения наших задач получили и получаем искреннюю поддержку со стороны производителей оборудования и их представительств в России.
АО «ПРОТОН-ЭЛЕКТРОТЕКС»:
Болыдрев А. Ю., Ставцев А.В.
ООО «АЙ ВИ ТЕК ЭЛЕКТРОНИКС»:
Валев С.Н.
всё, что вам нужно знать
Время чтения: 6 минут
За последние 100 лет технология сварки претерпела значительные изменения. Классические сварочные аппараты были усовершенствованы, а в продаже появились совершенно новые устройства. Наибольший вклад в развитие домашней и любительской сварки внесло изобретение инверторного сварочного аппарата. Его электронная «начинка» позволяет внедрить функции, которые недоступны классическому трансформатору или выпрямителю.
А если в сварочном аппарате применяется электроника, значит, используются и транзисторы. В этой статье мы подробно расскажем, что такое транзистор, какие транзисторы используются в сварочных инверторах и чем отличаются транзисторы IGBT в сварочном аппарате от транзисторов MOSFET.
Содержание статьи
Общая информация
Транзисторы — что это такое? Наверняка каждый, кто хоть раз сталкивался с ремонтом или банальной разборкой радиоэлектроники, слышал этот термин. Говоря простыми словами, транзистор — это электронная деталь с выводами, изготовленная из полупроводникового материала. Основная функция транзистора — это усиление или генерирование электрических сигналов, поступающих извне. Также с помощью транзисторов выполняется коммутация.
На данный момент транзисторы есть в любом электронном приборе и являются один из важнейших компонентов. В середине прошлого века сразу несколько ученых получили Нобелевскую премию за изобретение транзистора. И с тех пор это небольшое приспособление кардинально изменило мир электроники.
Транзисторы очень маленькие и компактные. Они экономичны, их производство стоит недорого. Несмотря на свой скромный размер, транзистор устойчив к механическому воздействию и долговечен. Также транзисторы способны исправно работать при низком напряжении и при высоких значениях тока. Именно благодаря этим достоинствам к концу 20-го века транзисторы стали неотъемлемой частью каждого электронного прибора. В том числе, у инверторных сварочных аппаратов.
Читайте также: Инструкция по эксплуатации сварочного инвертора для новичков
С помощью транзисторов удалось собрать компактную схему и внедрить ее в инвертор. Таким образом, существенно снизились размеры и вес сварочного аппарата. На данный момент производители предлагают инверторы весом до 5 кг, которые можно положить в рюкзак и взять с собой на выездные работы. Также такие аппараты незаменимы при сварке на высоте или в труднодоступных местах.
В сравнении с обычным трансформатором, который использовался раньше для сварки, инверторы намного проще в освоении. А наличие дополнительных функций (например, функции горячего старта или антизалипания) помогает новичкам как можно скорее приступить к работе. И все это заслуга транзисторов.
Транзисторы в инверторах
Транзистор — это один из главных компонентов современного сварочного инвертора. Без него инвертор в принципе не будет так называться. И, поскольку сварочные инверторы уже прочно вошли в нашу жизнь, то нелишним будет узнать немного больше об их электронной «начинке». Эта информация будет полезна не столько мастерам по ремонту сварочных аппаратов, сколько самим сварщикам. Для лучшего понимая сути используемого вами оборудования.
Итак, на данный момент чаще всего в сварочных инверторах применяются транзисторы двух типов: IGBT и MOSFET. Именно благодаря им удается добиться достойного качества работ, внедрения новых функций и уменьшению габаритов аппарата.
Подробнее про IGBT
Мы решили заострить ваше внимание на IGBT транзисторах, поскольку они считаются самыми технологичными. IGBT представляет собой стандартный биполярный транзистор с изолированным затвором. Усиливает и генерирует электрические колебания. Часто применяется в инверторе. От полевого транзистора отличается тем, что генерирует силовой канал, а не управляет им. Представляет собой 2 транзистора на подложке.
Именно благодаря IGBT транзисторам удалось развить производство современных сварочных инверторов. Поскольку именно данный тип транзисторов способен работать при высоком напряжении. Очень скоро производителям стало ясно, что применение IGBT транзисторов способно вывести производство инверторов на новый уровень. Удалось значительно уменьшить размеры аппаратов и увеличить их производительность. Порой стандартный IGBT транзистор способен заменить даже тиристор.
Иногда в IGBT инверторы внедряют специальные микросхемы, которые усиливают управляющий электрический сигнал и ускоряют зарядку затворов. Это необходимо для исправного функционирования мощных переключателей.
IGBT или MOSFET?
Выше мы уже упомянули, что помимо транзисторов типа IGBT существуют еще и транзисторы MOSFET. И многие сварщики любят спорить на форумах, какие транзисторы лучше, а какие хуже. Что мы думаем по этому поводу? Сейчас узнаете.
IGBT — это биполярные транзисторы. А MOSFET — полевые. И отличий у них больше, чем многим кажется на первый взгляд. Основное отличие — максимальная мощность, которую способен выдержать транзистор. У IGBT этот показатель выше, поэтому стоят они дороже, чем MOSFET. А это значит, что управляющая схема тоже стоит дороже.
На практике, сварщик практически не заметит разницы при работе с инверторам на IGBT или MOSFET. В характеристиках разница есть, но на практике она ощущается слабо. К тому же, на IGBt инверторы сложнее найти запчасти и вообще грамотного мастера по ремонту. И расходники стоят дороже.
Если вы используете недорогой инвертор для домашней сварки, то разницу между IGBT и MOSFET вы точно не заметите. Все преимущества IGBT раскрываются только в профессиональном оборудовании, предназначенном для высоковольтного подключения. В таком случае больший диапазон мощностей действительно играет важную роль и стоит предпочесть IGBT инвертор. В остальных же случаях не важно, какие транзисторы установлены. Вы, как любитель, разницу не почувствуете.
Словом, если вы новичок, то приобретайте инвертор на любых транзисторах. Инвертор на MOSFET будет стоить дешевле, вы сможете проще и быстрее его отремонтировать. А если вы выбираете инвертор для профессиональной сварки, то лучше выбрать аппарат на IGBT транзисторах. Они позволят использовать больше мощности. Но и их обслуживание обойдется дороже.
Вместо заключения
Не важно, какие именно силовые транзисторы для сварочных инверторов вы выберите. В любом случае, современный инвертор предоставит вам множество удобных плюсов. Вы сможете брать его с собой, поскольку вес и размеры незначительны. Вы сможете выполнять мелкий ремонт, даже если варите впервые, поскольку дополнительные функции упростят вашу работу. А благодаря технологичным транзисторам электронная схема будет работать еще стабильнее и дольше.
Да, инверторные аппараты куда сложнее по своему строению как раз за счет применения электроники. Вы не сможете починить инвертор «на коленке», как это можно сделать с трансформатором. Но преимуществ слишком много, чтобы отказываться от нововведений. А что вы думаете по этому поводу? Поделитесь своим мнением в комментариях ниже. Желаем удачи в работе!
[Всего: 3 Средний: 2/5]Что выбрать: MOSFET или IGBT -инвертор?
Не нужно на 100% разбираться в премудростях электротехники, чтобы высказать мнение по теме. Заголовок « MOSFET или IGBT?» напоминает старое соревнование форматов: VHS или DVD? Кто же победит? И пусть скажут, сравнение не корректное. Но, DVD формат великолепный, качество звука и изображения замечательные, а мы все так привыкли к старому доброму VHS…
Для тех, кто не понимает о чем идет речь, поясним.На сегодняшний день существует две технологии изготовления сварочных инверторов,
- первая основа на базе полевых транзисторов с изолированным затвором (MOSFET) и пользуется успехом на правах «старого, работающего и проверенного варианта»
- вторая — на базе биполярных транзисторов с изолированным затвором (IGBT). Это инновационная технология, новое поколение и тому подобное.
Возникает закономерный вопрос: что же выбрать старое, проверенное время, или относительно новое, но более технологичное?
Попробуем пару доводов и, как говорится, ближе к «телу»…
Что не говори, а IGBT занимают меньший объем и при этом позволяют получить более высокую силу тока на выходе, они меньше нагреваются.Разве это не аргумент в пользу IGBT? Возражения же заключаются в том, что схемы IGBT покамест не идеально продуманы и т.д., разработчикам не было времени на это и они звучат «натянуто».
Конечно, если покупать инвертор для бытовой сварки, то не так уж важно, какие у него транзисторы внутри. Вообще не важно, что внутри. Главное, чтобы электрод поджигался нормально, дуга не прыгала туда-сюда, чтобы электрод не залипал. Так же, желательно, чтобы инвертор работал при пониженном напряжении в сети, не боялся забросов напряжения, чтобы желтая лампа перегрева редко зажигалась.
Если речь идет о небольших объемах бытовых работ, практически любой инвертор в этом станет надежным другом и товарищем, та же Ресанта или Сварог, или Фубаг, или отечественный Форсаж и т.д. и т.п.
Но что, если нужен профессиональный аппарат, когда варить придется целый день. Наше мнение, здесь лучше IGBT. Почему? Возьмем для примера сварочный аппарат РICO 180 — это же прелесть, а не сварочник! Приведем в качестве примера его систему охлаждения. Она интеллектуальная и включается только тогда, когда транзисторы нагреваются.А в РICO даже после 15 и более минут сварки на небольших токах вентилятор не шелохнется. Это значит, что схемы холодные, корпус аппарата холодный. И все это IGBT, они менее интенсивно, чем MOSFET и на более высоких токах. Ну и что мне с этого, скажете Вы? Очень просто. Чем меньше работает вентилятор, тем лучше! Особенно если Вы работаете в запыленных помещениях. Основной враг инвертора — это пыль. Она является основной причиной досрочного выхода инверторов из строя. Соответственно, чем меньше пыли затягивается в сварочный аппарат, тем лучше! А это значит, чем дольше не включаются кулеры, тем лучше! Получить это можно только с IGBT.
Несомненный плюс так же состоит в том, что достигается высокая мощность при еще более малом весе. Каждый грамм играет роль, если приходится целый день носить инвертор на плече.
Минус в свое время был в дороговизне ремонта IGBT и невозможности подчас найти запчасти. Но время идет, техника совершенствуется, а то, что раньше было дорогим и недоступным, становится обыденным и легкозаменяемым! Так что наше мнение, будущее за новыми технологиями. А Вы как думаете? Стоит с этим согласиться?
Сегодня уже ни для кого не секрет кто выиграл в битве «VHS или DVD».
.
MOSFET или IGBT?
Сначала рассмотрим различия в целом. В настоящий момент все производители инверторов (ММА) выпускаются по полупроводниковым технологиям IGBT и MOSFET. Не буду вдаваться в подробности, скажу только то, что в схемотехнике этих аппаратов используются разные полупроводниковые транзисторы IGBT и MOSFET. Основое различие между этими транзисторами — различный ток коммутации. Большим током обладают транзисторы IGBT.
Для изготовления стандартного инвертора понадобится 2–4 транзистора IGBT (в зависимости от рабочего цикла), MOSFET — 10–12, т.к. они могут не пропускать через себя большие токи, поэтому их приходится делить на такое большое количество транзисторов. Вот собственно в чем и отличие.
Тонкость в том, что транзисторы очень сильно греются и их необходимо установить на мощные алюминиевые радиаторы. Чем больше радиатор, тем больше съем тепла с него, а, следовательно, его охлаждающая способность. Чем больше транзисторов, тем больше радиаторов охлаждения необходимо установить, следовательно, увеличиваются габариты, вес и т.д. MOSFET здесь однозначно проигрывает.
На практике схемотехника MOSFET не позволяет создать аппарат на одной плате: т.е аппараты, которые сейчас есть в продаже, собраны в основном на трех платах. IGBT-аппараты всегда идут на одной плате.
Основные недостатки MOSFET
- соединение трех плат;
- худший теплообмен;
- каскадный выход транзисторов из строя при неисправности одного транзистора;
- меньший КПД (относительно IGBT).
Проще говоря, IGBT более современная технология, чем MOSFET.
Недостатки MOSFET
Что лучше MOSFET или IGBT?
Некоторые компании идут в ногу со временем и при производстве сварочных инверторов используют IGBT транзисторы американской фирмы «Fairchaild», частота переключения составляет 50 кГц, т. е. 50000 раз в секунду. IGBT использует режим неспроста, ведь рабочий диапазон температур у них с сохранением гораздо больше, чем у MOSFET, т.е. при нагреве у MOSFETa падают качественные характеристики.
В конструкции САИ (Ресанта) используется одна маленькая плата, которая устанавливается вертикально, а также работают 4 транзистора IGBT (обособленно друг от друга, т. Е. Не выгорают все, если выгорел один как на MOSFET) и 6 диодов-выпрямителей ( а не 12 как у MOSFET), соответственно отказоустойчивость ниже. Это ещё один «плюс» IGBT.
Можно напомнить покупателю о том, что в современных сварочных инверторов используется только 4 обособленных транзистора, а не 12 каскаднозависимых, как у MOSFET.Всякое в жизни бывает, но, чтобы не произошло выхода из строя одного транзистора (если не гарантийный случай), замена покупателю обойдется где-то в районе 400 р., А не 12 × 110 р. = 1320 р. Думаю, что разница приличная.
Как отличить: Визуально аппараты IGBT в большинстве своём от MOSFET вертикальным расположением силовых разъёмов, т. к. плата одна и обычно устанавливается вертикально. У MOSFET аппаратов выходы обычно расположены горизонтально, т. к. платы в конструкции горизонтально закреплены.Нельзя точно утверждать, что это верно на 100%. Точнее можно сказать, сняв кожух с аппарата.
Многие компании пытаются «выиграть баллы» на транзисторах. Так, например, компания «Aiken» в настоящий момент выпустила на рынок аппаратов (по технологии MOSFET) с наклейками на боковых панелях «Используются транзисторы TOSHIBA» а также «Используются транзисторы Mitsubishi». Пытаются выползти на громких и знакомых брендах. На практике это не подтвердилось. Так на крупнейшей инструментальной выставке России Московская международная выставка инструментов (MITEX-2011), которая проходила в ноябре 2011г.в «Экспоцентре» (г. Москва), я попросил представителей стенда компании разобрать их САИ с наклейкой «Используются транзисторы Mitsubishi» и предположить данные транзисторы. В итоге сварочные инверторы разобрали, но данных транзисторов не встретили. Сами компании сотрудники «Айкен» были в шоке, обнаружив безымянные транзисторы.
.схема и преимущество использования в сварке
Применение высоковольтных мощных полупроводников создают компактные производительные сварочные инверторы. Последним словом в этой области после MOSFET инверторов стали сварочные аппараты на транзисторах IGBT.
Полевые полупроводники
Используемые в инверторах полупроводники по технологии MOSFET — это полевые силовые транзисторы с изолированным затвором. Управление полупроводником осуществляется напряжением, в отличие от биполярных транзисторов, управляемых током.Канал ключа имеет высокую проводимость 1 мОм. В закрытом виде у них огромное входное сопротивление.
Изначально полевые полупроводники использовались и до сих пор применяются как ключи. В схемах импульсных источников питания применяются полевики с индуцированным затвором. В таком исполнении при нулевом напряжении на затвор-исток канал закрыт.
Для открытия ключа требуется подать этот потенциал полярности. Для управления ключом не требуется силовых источников.Данные полупроводники часто используются в источниках питания и инверторах.
Биполярный прибор
IGBT — это биполярный транзистор с изолированным затвором, применяемый в инверторе. Фактически он состоит из двух транзисторов на одной подложке. Биполярный прибор образует силовой канал, а полевой каналом управления.
Соединение полупроводников двух видов позволяет совместить в одном устройстве преимущества полевых и биполярных приборов. Комбинированный прибор может, как биполярный, работать с высокими возможностями, проводимость канала обратно пропорциональна току, а не его квадрату, как в полевом транзисторе.
При этом транзистор IGBT имеет экономичное управление полевого прибора. Силовые электроды называются, как в биполярном, а управляющий получил название затвора, как в МОП приборе.
IGBT транзисторы для сварочных инверторов и силовых приводов, где приходится работать при высоких напряжениях, стали использовать, как только отладили их производства. Они сократили габариты, увеличили производительность и мощность инверторов. Иногда они заменяют даже тиристоры.
В инверторе IGBT для обеспечения работы мощных переключателей применяются драйверы — микросхемы, усиливающие управляющий сигнал и ускоряющие быструю зарядку затвора.
Некоторые модели транзисторов IGBT работают с напряжением от 100 В до 10 кВ и токами от 20 до 1200 А. Поэтому их больше применяют в силовых электроприводах, сварочных аппаратов.
Полевые транзисторы больше применяют в импульсных источниках и однофазных сварочных инверторах. При токовых параметров 400-500 В и 30-40 А они имеют лучшие рабочие характеристики. Так как IGBT приборы в более тяжелых условиях, их все чаще применяют в сварочных инверторах.
Применение в сварке
Простой сварочный инвертор представляет собой импульсный источник питания. В однофазном инверторном источнике питания переменный ток напряжением 220 В или 60 Гц выпрямляется с помощью мощных диодов, схема включения мостовая.
Затем инвертор преобразует постоянное напряжение в переменное, но уже высокой частоты (от 30 кГц до 120 кГц). Проходя через понижающий высокочастотный трансформатор (преобразователь), понижается до нескольких десятков вольт.Потом этот ток преобразуется обратно в постоянный.
Все преобразовать необходимые для уменьшения габаритов сварочного аппарата. Традиционная схема сварочного инвертора получалась надежной, но очень большие габариты и вес. Кроме этого, характеристики сварочного тока с традиционным питанием были значительно хуже, чем у инвертора.
Передача электроэнергии на высокой частоте позволяет использовать малогабаритные трансформаторы. Для получения высокой частоты постоянный ток преобразуется с помощью высоковольтных, мощных силовых транзисторов в переменный диапазон 50-80 кГц.
Для работы мощных транзисторов напряжение 220 В выпрямляется, проходя через мостовую схему и фильтр из конденсаторов, который уменьшает пульсацию. Направляющий электрод полупроводника переменный сигнал с генератора прямоугольных управлясов, открывает / закрывает электронные ключи.
Выходы силовых транзисторов подключаются к первичной обмотке нижнего трансформатора. Благодаря тому, что они работают на большие частоты, их габариты уменьшаются в несколько раз.
Силовой инверторный блок
Переменное напряжение 220 В — это некоторое усредненное значение, которое показывает такую же энергию, как и постоянный ток в 220 В. Фактически амплитуда равна 310 В. Из-за этого в фильтрах используются емкости на 400 В.
Мостовая выпрямительная сборка монтируется на радиатор. Требуется охлаждение диодов, через них протекают большие токи. Для защиты от перегрева на радиаторе имеется предохранитель, при достижении критической температуры он отключает мост от сети.
В качестве фильтра используются электролитические конденсаторы, емкостью от 470 мкФ и рабочим напряжением 400 В. После фильтра напряжение поступает на инвертор.
Во время переключения ключей броски импульсного тока вызывающие высокочастотные помехи. Чтобы они не проникали в сеть и не портили ее качество, сеть защищают фильтром электромагнитной совместимости. Он представляет собой набор конденсаторов и дросселя.
Сам инвертор собирается по мостовой схеме.В качестве ключевых элементов используются IGBT-транзисторы на напряжение от 600 В и токи соответствующему инвертору.
Они тоже с помощью специальной термопасты монтируются на радиаторы. При переключениях этих транзисторов возникают броски напряжения. Чтобы их погасить применяются RC фильтры.
Полученный на выходе электронного ключа переменный ток поступает на первичную обмотку высокочастотного понижающего трансформатора. На выходе вторичной обмотки получается переменный ток напряжением 50-60 В.
Под нагрузкой, когда идет сварка, он может выдавать ток до нескольких сотен ампер. Вторичная обмотка обычно выполняется ленточным проводом для уменьшения габаритов.
На выходе трансформатора стоит еще один мощный диодный мост. С него уже снимается необходимый сварочный ток. Здесь используются быстродействующие силовые диоды, другие использовать нельзя, потому что они сильно греются и выходят из строя. Для защиты от импульсных бросков напряжения используются дополнительные RC цепи.
Мягкий пуск
Для питания блока управления инвертора применяется стабилизатор микросхеме с радиатором. Напряжение питания поступает с главного выпрямителя через резистивный делитель.
При включении сварочного инвертора конденсаторы начинают заряжаться. Токи достигают таких больших величин, что могут сжечь диоды. Чтобы этого не произошло, используется схема ограничения заряда.
В момент пуска ток проходит через мощный резистор, который ограничивает пусковой ток.После зарядки конденсаторов резистор с помощью реле отключается, шунтируется.
Блок управления и драйвер
Управление инвертором микросхема широтно-импульсного модулятора. Она подает высокочастотный сигнал на управляющий электрод биполярного транзистора с изолированным затвором. Для силовых транзисторов от перегрузок устанавливаются стабилитроны между затвором и эмиттером.
Для контроля напряжения сети и выходного тока используется операционный усилитель, на нем происходит суммирование контролируемых параметров.При превышении или понижении от допустимых значений срабатывает компаратор, который отключает.
Для ручной регулировки сварочного тока предусмотрен переменный резистор, регулировочная ручка которого выводится на панель управления .
Сварочное оборудование на транзисторах IGBT имеет наилучшие характеристики по надежности. По сравнению с полевыми ключами биполярные транзисторы с изолированными затворами имеют преимущество больше 1000 В и 200 А.
При использовании в бытовых приборах и сварочных инверторах для домашнего использования первое место до недавнего времени оставалось за сварочным оборудованием с полупроводниками MOSFET.Эта технология давно используется и хорошо отработана. Отличное от оборудования на транзисторах IGBT.
Новые модели уже ничем не уступают устройствам с полевыми приборами и на малых напряжениях. Только по цене первенство остается за аппаратами с полевыми транзисторами с индуцированным затвором.
.Особенности применения биполярных транзисторов с изолированным затвором
Современные силовые устройства преобразования параметров электроэнергии строятся на силовых полупроводниковых ключах, отличающихся от биполярных транзисторов. Особое место них занимают рассматриваемые в статье IGBT технологии, то есть устройство с использованием БТИЗ транзисторов (биполярных транзисторов с изолированным затвором) или в английской аббревиатуре IGBT (биполярные транзисторы с изолированным затвором) транзисторов.Применение этих технологий расширяет возможности силовых электротехнических устройств.
Биполярные транзисторы с изолированным затвором
Различают две технологии реализации транзисторов IGBT, которые поясняются эквивалентными схемами, приведенными на рис.1а, б, а для маломощных транзисторов — на рис.1, в [2]. Как следует из рис.1 , IGBT транзисторы имеют три электрода: эмиттер (э), коллектор (к) и затвор (з).
Рис.1 Технологии реализации IGBT транзисторов |
Сочетание двух полупроводниковых приборов в одной структуре обеспечивает объединить преимущества полевых и биполярных транзисторов: высокое входное сопротивление и малое сопротивление между силовыми электродами во включенном состоянии.
Обратим внимание на то, что на эквивалентных схемах у силового транзистора в том месте, где обозначен эмиттер, написано «коллектор», а где обозначен коллектор написано «эмиттер».Это общепринятое обозначение по принципу управления, указывающее, что входной сигнал управления подается между затвором и эмиттером.
Кратко охарактеризуем историю создания и развития IGBT транзисторов, являющихся продуктом развития технологий силовых транзисторов. Эта история насчитывает несколько десятилетий. С 80-х годов прошлого века и по нынешнему времени созданы четыре поколения этих приборов: первое поколение — с 1985 года, когда были достигнуты максимальные значения напряжения U макс = 1000В, ток I макс ≈ 25А и минимальное время переключения t пер.мин ≈1мкс второе — с 1990 года, когда были достигнуты максимальные значения U макс = 1600В, I макс ≈ 50А и минимальное значение времени переключения t пер.мин ≈0.5мкс третье — с 1994 года, когда были достигнуты максимальные значения напряжения U макс = 3500В тока I макс ≈ 100А и максимальное значение времени переключения t пер.мин ≈0.25мкс и, наконец, четвертое поколение — с 1998 года, для которого характерны следующие достижения: U макс = 4500В, I макс ≈ 150А, время переключения t пер.мин ≈0.2мкс
Для входного пробивного напряжения U вх.пр современных IGBT транзисторов в справочных данных практически всех фирм-производителей транзисторов значение, равное U вх.пр = ± 20В, таким образом при работе с этим приборами необходимо следить, чтобы напряжение затвор-эмиттер не превышало указанное значение напряжения. Далее, напряжение на затворе IGBT транзистор, при входной МОП и выходной биполярный транзистор начинает отпираться, составляет от 3,5 до 6,0 В, и гарантированное напряжение, при котором транзистор полностью открыт, то есть может пропускать максимально допустимый ток через коллектор- эмиттерный переход, составляет от 8 до предельного значения 20 В.
Максимальные токи, которые могут коммутировать современные транзисторы IGBT, находятся в пределах от 7 до 150 А, а их допустимый импульсный ток, как правило, в 2,5 — 3,0 раза максимальный максимальный. Для больших мощностей выпускаются составленные из нескольких транзисторов модули с предельными значениями тока до 1000 А. Пробивные напряжения IGBT транзисторов находятся в пределах от 400 до 4500 В.
Основные параметры некоторых транзисторов IGBT в табл.1 , а модулей, выпускаемых по технологии Trench или NPT, — в табл. 2 [1].
Табл.1 | ||||||||||||
Тип элемента | U кэ В | В | I к при А | I к при | Р | |||||||
IRG4BC30FD | 600 | 1,6 | 31 9 0003 | 17 | 100 | |||||||
IRGBC30MD2 | 600 | 3,9 | 26 | 16 | 100276 IRG4PC30FD | 600 | 1,6 | 31 | 17 | 100 | ||
IRG4PC40FD | 600 | 27 | 160 | |||||||||
IRG4PC50FD | 600 | 1,5 | 70 | 39 | 200 | |||||||
IRGPC40MD2 | 600 | 4,0 | 40 | 24 | 160 | 160 | 160 IRGPC50MD2 | 600 | 3,0 | 59 | 35 | 200 |
IRGPh402694 03 | 31200 | 31200 0315 9 100 | ||||||||||
IRGPh50FD2 | 1200 | 4,3 | 9 0094 29 | 17 | 160 | |||||||
IRGPh50MD2 | 1200 | 4,4 | 31 | 0 18 | IRGPH50FD2 | 1200 | 3,9 | 45 | 25 | 200 | ||
IRGPH50MD2 | 42 | 23 | 200 | |||||||||
OM6516SC | 1000 | 4,0 | 900 8725 | 125 | ||||||||
OM6520SC | 1000 | 4,0 | — | 25 | 12527 | 12527 |
Табл.2 | |||||
Тип модуля | U кэ В | U кэн 4 к при А | I к при А | Р Вт | |
IRGDDN300M06 | 600 | 3,0 | 399 | 159 | 1563 9 0026 |
IRGDDN400M06 | 600 | 3,0 | 599 | 239 | 1984 |
04 IRGD3600M06 | 04 IRGD3600M06 , 7 | 799 | 319 | 2604 | |
IRGRDN300M06 | 600 | 3,0 | 399 | 1563 | |
IRGRDN400M06 | 600 | 3,0 | 599 | 239 | 900 87|
IRGRDN600M06 | 600 | 3,7 | 799 | 319 | 2604 |
3 7 4 | 3,0 | 299 | 119 | 1000 | |
IRGTDN300M06 | 600 | 3,0 | 399 4 3,0 | 399 4 900 | 1316 |
Где:
- U кэ — Напряжение коллектор-эмиттер
- U кэн — Напряжение коллектор-эмиттер открытого транзистора
- I к — Постоянный ток коллектора
- Р — Максимальная рассеиваемая мощность
Напряжение коллектор-эмиттерного перехода открытого транзистора находится в пределах от 1,5 до 4,0 В (в зависимости от типа, значений тока и предельного напряжения IGBT) транзистора) в одинаковых режимах работы.Для различных типов приборов напряжение на переходе открытого транзистора тем выше, чем выше значение пробивного напряжения и скорость переключения.
Вследствие низкого коэффициента усиления выходного биполярного транзистора в целом, транзистор IGBT защищен от вторичного пробоя и прямоугольную область безопасной работы.
С ростом температуры на напряжение коллектор-эмиттерном переходе транзистора несколько увеличивается, что дает возможность дополнительные приборы на общую нагрузку и увеличивать суммарный выходной ток.
Также как МОП транзисторы, транзисторы IGBT имеют емкости затвор-коллектор, затвор-эмиттер, коллектор-эмиттер. Величины этихкостей обычно в 2 — 5 раз ниже, чем у МОП транзисторов с аналогичными предельными потребностями. Это связано с тем, что у IGBT транзисторов на входе размещен маломощный МОП транзистор. Для управления им в динамических режимах нужна меньшая мощность.
Время нарастания или спада напряжения на силовых электродах IGBT транзисторов при оптимальном управлении составляет около 50 — 200 нс и определяется в основном расходом или разряда емкости затвор-коллектор от схемы управления.
Существенным преимуществом транзисторов IGBT по сравнению с биполярными транзисторами является то, что биполярные транзисторы в структуре IGBT не насыщаются и, следовательно, у них отсутствует время рассасывания. Однако после уменьшения напряжения на затворе ток через силовые электроды протекает в течение от 80 до 200 нс до единиц мкс в зависимости от типа прибора. Уменьшить эти временные параметры невозможно, так как база p-n-p транзистора недоступна.
Технологические методы уменьшения времени спада ведут к увеличению напряжения насыщения коллектор-эмиттерного перехода.Поэтому чем более быстродействующим транзистор, тем выше напряжение насыщения.
БТИЗ транзисторы по сравнению с МОП транзисторами обладают преимуществами преимуществ:
- Экономичностью управления, имеющей меньшее значение затвора и, соответственно, меньшими динамическими потерями на управление.
- Высокой плотностью тока в переходе эмиттер-коллектор — такой же, как и у биполярных транзисторов.
- Меньшие потери в режимах импульсных токов.
- Практически прямоугольной областью безопасной работы.
- Возможности параллельного соединения транзисторов для работы на общую нагрузку.
- Динамическими характеристиками транзисторов, выпущенных за последние годы, приближающимися к характеристикам МОП транзисторов.
Основным недостатком транзисторов IGBT является сравнительно большое время выключения, что ограничивает частоту переключения до 20–100 кГц даже у самых быстродействующих транзисторов.Кроме того, с увеличением частоты необходимо уменьшать ток коллектора. Например, из зависимости тока коллектора IGBT транзистора от частоты для транзистора IRGPC50UD2, приведенной на рис. 2 , следует, что при частотах работы транзисторов, превышающих 10 кГц, приходится уменьшать ток коллектора более чем в два раза. Увеличить производительность паразитных индуктивностей монтажа.
Рис.2 Зависимость тока коллектора IGBT транзистора от частоты |
Процесс включения IGBT транзистора делится на два этапа. При подаче положительного напряжения между затвором и истоком открывается полевой транзистор, и далее движение зарядов из области в области p приводит к открыванию биполярного транзистора, то есть к появлению тока между эмиттером и коллектором.Таким образом, полевой транзистор управляет биполярным.
У IGBT с максимальным значением напряжения в пределах 500 — 1200 Падение напряжения в насыщенном состоянии транзисторов находится в диапазоне 1,2 — 3,5 В, то есть оно приблизительно такое же, как и у биполярных транзисторов. Однако эти значения напряжения намного меньшие по сравнению со значениями падения силовых МОП транзисторах в проводящем состоянии с аналогичными функциями.
С другой стороны, МОП транзисторы с максимальными значениями напряжения, не превышающими 200 В, имеют меньшие значения напряжения между силовыми электродами во включенном состоянии, чем транзисторы IGBT.В связи с этим применением МОП транзисторов является предпочтительным в области низких рабочих напряжений и коммутируемых токов до 70 А.
По быстродействию IGBT транзисторы превосходят биполярные транзисторы, однако уступают МОП транзисторам. Значения времен рассасывания накопленного заряда и спада тока при выключении IGBT транзисторов находятся в пределах 0,2 — 0,4 мкс.
Область безопасной работы IGBT транзисторов позволяет обеспечить надежную работу этих устройств без усложнений цепями ускорения переключения при частотах от 10 до 20 кГц.Этого не могут обеспечить биполярные транзисторы.
IBGT транзисторы к приборам силовой электроники, и выпускаемые промышленностью на сегодняшний день реальные приборы имеют предпочтение в их использовании в диапазоне мощностей киловатт до единиц мегаватт. Дальнейшее совершенствование IGBT транзисторов проводится по пути повышения быстродействия, предельных коммутируемых токов и напряжений.
Управление МОП и IGBT транзисторамиМОП и IGBT транзисторы являются полупроводниковыми приборами, управляемыми напряжением.Из обширного круга вопросов, относящихся к проблеме управления этими приборами, представляет собой наиболее сложный случай управления, который имеет самое место в мостовой или полумостовой схеме включения с индуктивной погрузкой.
Отметим, что управление транзисторами инверторов можно осуществлять через импульсные высокочастотные трансформаторы, хотя такое управление усложняет конструкцию и принципиальную схему инвертора. Отсутствие тока потребления на управление в статических режимах и низкое общее потребление мощности затворами транзисторов позволяют отказаться от трансформаторных схем питания.
Компаниями-производителями силовых полупников выпускается ряд драйверов управления, которые согласовывают маломощную схему управления с выходными транзисторами верхнего и нижнего плеча силового инвертора. Выходные каскады этих драйверов выполняются, как правило, в виде двухтактных усилителей на полевых транзисторах, обеспечивающих импульсный выходной ток до 2 А. Организация питания верхнего инвертора осуществляется по схеме зарядного «насоса», показанной на рис.3.
Рис.3 Схема питания верхнего плеча инвертора |
Схема формирования, гальваническая развязка и усилитель нижнего плеча источника получает питание от низковольтного вспомогательного источника питания U н . При включении транзистора нижнего плеча VT2 (в первом полупериоде работы) диод VD1 открывается и заряжает накопительный конденсатор С1, в дальнейшем питающий усилитель верхнего плеча.В каждом полупериоде при открытом транзисторе VT2 конденсатор C1 подзаряжается, а при открытом транзисторе VT1 питается выходной усилитель верхнего плеча.
В последнее время фирмы-производители полупниковых приборов начали выпускать драйверы отдельных транзисторов полумостовых и мостовых схем, выдерживающие напряжение до 600 В. В качестве приведенной ниже модели драйверов [3]:
- IR2125 — драйвер верхнего плеча;
- IR2110, Н1Р25001Р, PWR 200 / 201– драйверы полумостового инвертора;
- IR2130 — драйвер трехфазной мостовой схемы;
- IR2155 — драйвер полумостового инвертора с автогенератором.
Эти драйверы надежно работают и обеспечивают оптимальные параметры в работе с МОП и IGBT транзисторами. К тому же их стоимость небольшая, а схемы инверторов требуют установки всего лишь одного драйвера и нескольких внешних компонентов.
Переключение больших токов с высокими скоростями переключения сопряжено с рядом трудностей. Использование специальных мер обеспечения значительного количества энергии в силовых шинах тока и нежелательных переключений силовых ключей, всплески высокого напряжения, дополнительной мощности рассеяния силовых транзисторов, ложные срабатывания и т.д.
Микросхема драйвера IR2110 является одной из многих применяемых для полумостовых высоковольтных инверторов. Полумостовой инвертор на IGBT транзисторах показан на рис. 4 . Резисторы R2 и R3 для уменьшения скорости переключения силовых транзисторов. Дело в том, что управление затворами мощных IGBT или МОП транзисторов непосредственно от драйвера IR2110 или ему аналогичного может привести к нежелательно высоким скоростям переключения.
Реалистичная инвертора обладает конечными значениями величин индуктивная конструкция соединений, которые выделяются всплески напряжений при установке плеч, причем чем меньше переключения, больше амплитуда переключателей.Величины резисторов R2 и R3 выбираются таким образом, чтобы фронты переключателей не порождали значительных потерь и больших импульсных амплитуд, нарушающих работу инвертора.
Рис.4 Схема полумостового инвертора на транзисторах IGBT |
На входы 10 и 12 должны поступать две импульсные системы, причем вход 10 управляет транзистором VT1, а вход 12 — транзистором VT2. Вход 11 включает или выключает инвертор и может выключить защиту, то есть при подаче напряжения на вход 11 работа преобразователя прекращается.
Драйвер IR2155, позволяющий получить самую простую схему полумостового преобразователя, представляет собой монолитную интегральную схему, способную управлять двумя транзисторами в полумостовом преобразователе. Они могут работать при напряжениях питания до 600 В, имеют четкие формы выходных импульсов с элементами заполнения от 0 до 99%.
Функциональная схема драйвера IR 2151 на рис. 5.
Рис.5 Функциональная схема драйвера IR 2151 |
Драйвер содержит входную часть на операционных усилителях, которая может работать в автогенераторном режиме. Частота определяется дополнительными навесными элементами, подключаемыми к выводам C1, R1. Генераторы паузы на нуле задержки во включении выходного транзистора на 1 мкс после закрытия транзистора. В канале верхнего плеча осуществляется гальваническая развязка, далее напряжение усиливается усилителем мощности на полевых транзисторах и выходное напряжение с выхода HO (7) поступает на затвор силового транзистора.Нижнее плечо работает от задающего генератора через генератор паузы на нуле и задержки устройства.
Для обеспечения стабильности работы драйвера внутри имеется стабилитрон, ограничивающий напряжение Vcc (1) на уровне 15 В.
Литература
- Краткий каталог International Rectifier. Дайджест продукции.
- В.И. Сенько и др. Электроника и микросхемотехника (на укр. Яз.). Том 1. — К .: Обереги, 2000.
- М.Браун. Источники питания. Расчет и конструирование. Пер. с англ. — К .: МК-Прогрес, 2007.
- Микросхемы для импульсных источников питания — 3. — М .: Изд. дом «Додека — ХХI», 2002.