Капиллярный контроль сварных соединений оборудования и конструкций
Мы проводим капиллярный контроль сварных соединений оборудования и конструкций для обнаружения наружных (сквозных и поверхностных) дефектов в сварных швах.
Метод капиллярного контроля позволяет выявлять:
- Непровары
- Горячие и холодные трещины
- Поры
- Раковины
Также этот метод работает для определения расположение и величину деффекта при сварки как чёрных металлов, так и цветных металлов и сплавов.
Метод капиллярного контроля выстраивается на способности индикаторной жидкости проникать в полости дефектов, оставляя индикаторные следы, которые легко идентифицируются при осмотре или с помощью преобразователя. Порядок проведение данного контроля регулируется стандартами ГОСТ 18442 и EN 1289
Этапы проведения капиллярного контроля:
- Подготовка и предварительная очистка
- Нанесение индикаторной жидкости
- Промежуточная очистка
- Выявление сварочных деффектов
- Составление протокола с результатами
- Окончательная очистка поверхности
Капиллярный метод контроля сварных соединений очень простой, при этом экономически выгодный и вполне эффективный. Поэтому данный метод контроля качества используется повсеместно. Вы наверняка встретите баллончик с пенетрантом как в цеху крупного завода, так и в гараже у домашнего мастера.
Конечно, с помощью такого метода можно обнаружить далеко не все возможные дефекты, скрытые от глаз сварщика. Но если вы в полевых условиях или высокое качество шва не так уж важно, то можно ограничиться и капиллярным контролем.
Стоимость работ:
Капиллярный контроль сварных соединений оборудования и конструкций, положение сварного соединения вертикальное и горизонтальное с одной стороны | 1м2 | 3686 |
Капиллярный контроль сварных соединений оборудования и конструкций, положение сварного соединения потолочное с одной стороны | 1м2 | 6053 |
где и как применяется, особенности, плюсы и минусы
Контроль качества сварочных соединений это важная стадия для создания хорошей работы.
Выполняется он за счет применения специального оборудования или химикатов. Этод вид контроля называется дефектоскопией. Сейчас мы разберём метод дефектоскопии, на который у вас не уйдёт много денег, называется он капиллярным контролем.
Капиллярный контроль имеет свои положительные стороны. Одно из них состоит в том, что он не меняет качество металлической поверхности детали и не разъедает его своим воздействием. Ещё один плюс это простота метода.
Его можно изучить даже малообразованным сотрудникам. Но простота в работе с ним не значит, что можно браться за него без всяких знаний.
Полезно будет изучить все детали, чтобы правильно применять этот контроль качества. Об этих деталях и об их технологии мы и поговорим.
Содержание статьиПоказать
Основные данные
Для капиллярного контроля соединений применяются специальные жидкости, на этом и основывается весь метод. У этих жидкостей есть и другие названия.
Например, индикаторы или пенетранты. У них есть свои особенности, которые вы должны знать. Одна из таких особенностей это проникание внутрь самых маленьких дефектов и оставление яркого следа после себя.
Этот след можно заметить без какого-либо оборедования, поэтому рабочий может легко вычислить расположение дефектов. При маленьком размере дефекта, иногда используют увеличительную лупу.
Как можно заметить, ничего сложного в применении капиллярного метода нет.
Капиллярным методом вы можете найти много разных дефектов, не просто трещинки, но и прожоги, непроваренные участки.
Все изъяны можно распознать не приобретая при этом дорогие аппараты. Также вы сможете вычислить величину дефектов, и где они точно расположены на всём протяжении соединения.
При этом вы можете проводить контроль разного вида заготовок. Например, металлических, стеклянных или керамических деталей, а также заготовок из искусственного полимера.
Поэтому с таким контролем можно работать в нескольких отраслях и это хорошее качество для производства.
Виды
Работа с капиллярным контролем может пойти двумя путями. Первый называется основным и состоит в том, что при работе вы применяете только один метод.
Второй путь называют комбинированным, в нём, как не сложно догадаться, используется несколько видов проверки дефектов. При работе с капиллярным, вы пользуетесь и радиографическим методом.
Эти два вида также имеют свои ответвления. При использовании первого, можно столкнуться с выбором: работать со специальным раствором или выбрать способ, при котором нужна фильтрующая суспензия.
А для выявления результатов проверки существует ещё четыре способа. Ваш выбор может упасть в сторону хроматического или ахроматического способа, а может, вы остановитесь на люминесцентном или люминесцентно-хроматическом методе.
И это всё только о первом виде капиллярного контроля.
В комбинированный метод входит наличие капиллярного контроля, а в связке с ним, могут применять множество других видов проверки. Например, использование магнитного, индукционного, радиографического и других методов.
При любом из этих способов необходимо работать с химическими жидкостями.
А чтобы обнаружить результаты, для каждого отдельного способа нужно применять оборудование, которое подходит под вид применяемого контроля. Для радиографического контроля используют рентгеновское оборудование.
При такой проверке нужно провести капиллярный контроль, а затем пропустить деталь через рентгеновский аппарат и сделать снимок, чтобы найти расположение всех дефектов.
Работа
Последовательность действий при капиллярном контроле очень проста. Теперь мы расскажем всё подробнее, и вы сможете самостоятельно убедиться в лёгкости этого способа проверки.
Первым этапом будет очистка поверхности соединения. Для этого можно использовать растворитель. Необходимо убрать с наружной стороны шва всю грязь, остатки краски и масла.
После этого нужно просушить заготовку. Сушка можно осуществить естественно, поместив деталь на свежий воздух. Желательно провести чистку металла наждачной бумагой, чтобы точно убрать всю грязь и не нужные частицы.
При использовании наждачной бумаги, металл должен быть неровным или пористым. Если поверхность гладкая, то прибегать к наждачке не обязательно. Если чистить гладкий металл, вы можете затереть дефект, из-за чего его будет сложнее обнаружить.
Следующим шагом будет нанесение пенетранта. Наносить его можно по-разному, но об этом мы расскажем попозже. Один из простых методов заключается в нанесении пенетранта, используя баллончик.
Также можно использовать кисть, или погружать заготовку в пенетрант целиком. При погружении, нахождение детали в ёмкости с веществом не должно быть меньше пяти минут. После этого необходимо отчистить деталь от остатков вещества.
Далее нужно снова высушить заготовку. После этого на швы нужно нанести вещество, которое проявляет дефекты. На этом вся работа закончена. Для контроля вам понадобятся пенетрант и проявитель.
Закупив эти вещества, вы спокойно можете опробовать метод в своём гараже. Даже если вы уверены в идеальности своей сварки, такой контроль качества нужно провести, чтобы получить точную оценку своей работе.
Когда вы придете в магазин за нужными веществами для капиллярного метода, важно быть очень внимательным при выборе. На полках магазинов можно встретить кучу веществ, которые могут приглянуться ценой.
Однако зачастую они не могут дать положительный итог, а иногда и вовсе могут подвергнуть ваше здоровье опасности. На пенетранте экономить не стоит, вы всё равно уже экономите, используя этот метод, поэтому лучше выбрать хорошее вещество.
Наши рекомендации остановятся на жидкости в баллончике. Это очень удобно, так как распыление идёт равномерно по всему металлу.
Также проверку можно осуществить, используя флуоресцентные пенетранты. Этот вид светится в тёмных помещениях. Для того чтобы заметить результат, вам не нужно надевать никаких специальных очков, достаточно просто смотреть на заготовку в темной зоне.
Из этой зоны заранее нужно убрать все отсвечивающие предметы.
При использовании обычных пенетрантов, вы можете осматривать деталь как под солнечным светом, так и под яркой лампой. Хотя наши рекомендации всё же остановятся на втором.
Как наносить жидкость
Мы уже говорили, что нанесение жидкости при капиллярном контроле может происходить, используя баллончик или кисть. Эти способы являются самыми простыми. При работе с баллончиком и кистью, вещество само проникает внутрь швов.
Ещё можно использовать один знакомый метод: погружение детали в резервуар с веществом. Температурный режим пенетратов от пяти до пятидесяти градусов. Поэтому нанесение можно делать в уличных условиях.
Ещё один метод нанесения пенетранта называется вакуумным. Он гораздо дороже, но при этом эффективней. Заготовку размещают в вакуумной камере, а затем выкачивают воздух. На участках с дефектами понижается уровень давления.
Затем запускается вещество, которое выделяет нужные вам места. Этот метод используется, когда необходима качественная проверка на дефекты, но применить другой метод невозможно.
Последний способ включает в себя использование звуковых и ультразвуковых волн. Они воздействуют на жидкость и вгоняют её в соединения. Однако при применении такого способа, дефект может деформироваться.
Как проводить очистку
После нанесения пенетрантового вещества, нужно провести очистку от лишних частиц. Для этого вам понадобится тряпка или губка. Можно взять те, которые вы используете, когда моете посуду.
Смочите тряпку и протрите все участки соединения. Этот метод очистки самый простой и мало затратный, но эффективности в нём не много.
Также можно воспользоваться растворителем, это будет эффективней обычной воды. Для того, чтобы применить растворитель, нужно сначала хорошо высушить деталь.
Хотя растворитель использовать эффективней, чем воду, есть способы ещё лучше.
Первое, что приходит в голову – это соединить два предыдущих метода. Сначала использовать воду, а затем применить растворитель. Но если вы хотите максимальной эффективности, вы можете купить очиститель в баллончике.
С ним вы точно проведете качественную очистку. После очистительных процедур, необходимо опять провести сушку заготовки. При большом объёме лишнего времени, можете оставить её на улице, чтобы она высохла естественным путём.
Главное чтобы солнце не попадало на неё. При маленьком количестве времени и недостатке нужного оборудования, можно провести сушку, используя тряпку без ворса. Также можно использовать фен, это самый простой способ.
Как наносить проявляющее вещество
youtube.com/embed/1KBaP8sZa4o?feature=oembed» frameborder=»0″ allow=»accelerometer; autoplay; encrypted-media; gyroscope; picture-in-picture» allowfullscreen=»»/>Теперь вам известно, как наносить пенетрантовое вещество и проводить очистку детали. Осталось подробнее разобраться с самым последним этапом – нанесение проявителя.
Этот этап самый важный, так как он оказывает большое влияние на результаты контроля. Каким способом вы будете наносить проявитель, не сильно важно. Важным моментом здесь является выбор правильного вещества.
Существует несколько видов проявителей. И каждый предназначен для отдельных ситуаций. Например, сухой проявитель применяют в соединении с флуоресцентным пенетрантом. Этот вид довольно дорогой.
Применяют его не так часто. Однако результаты проверки очень хорошие.
Также существуют жидкие вещества для проявления. Они изготавливаются на различных основах. У наиболее популярных за основу берут водную суспензию.
Для нанесения можно использовать как баллончики для распыления, так и полностью погружать деталь в ёмкость с проявителем. При использовании ёмкости, погружать, надолго не стоит. После этого необходимо снова просушить деталь, используя специальный фен.
Ещё один вид жидких проявителей бывает на веществах, которые похожи на растворители своими свойствами. Низкая цена и высокая эффективность. Для нанесения пользуются распылителями.
На проявление уходит от десяти до двадцати минут. Если вы не достигли нужного вам результата, увеличьте это время ещё на десять минут.
Повторная проверка
При капиллярном контроле возможна ситуация, когда результаты проверки на дефекты вас не устраивают. Это может произойти, если вы продержали деталь в ёмкости с пенетрантным веществом недостаточное время.
Это может случиться не из-за вас, но результат уже будет испорчен.
Также возможны случайные ошибки в проведении проверки на всех этапах при капиллярном контроле. В таких ситуациях начинающие работники приходят к вопросу: «Возможна ли повторная проверка на дефекты?».
Мы ответим на это положительно.
Главное при повторном контроле провести тщательную очистку детали от всех ранее использованных веществ. Использовать необходимо те же вещества, того же производства, с которыми вы работали при первичном контроле, искать новые не обязательно.
Достаточно просто в точности соблюдать все правила из этой статьи, и повторная проверка может выйти гораздо лучше.
Финальная часть
При капиллярном методе контроля вы не столкнётесь с какими-то непреодолимыми сложностями и не потратите много денег.
Из-за своей доступности этим методом пользуются на многих предприятиях. Встретить знакомые пенетрантовые и проявляющие вещества вы можете, как в мастерской у домашних работников, так и на крупном производстве.
Если сравнивать с другими методами контроля, некоторые некачественные участки можно пропустить, используя капиллярный способ проверки. Но, если вы не можете использовать специальное оборудование, этот выбор будет самым надёжным.
Если вы работаете на дому, и у вас нет огромных бюджетов, это также хорошая возможность проверить вашу работу на дефекты.
Приходилось ли вам сталкиваться с капиллярным контролем сварных соединений? Поделитесь своим опытом, он будет полезен для начинающих. Продуктивности в работе!
используемые методы, порядок проведения и необходимые материалы
Для определения качества сварного шва проводится его контроль. Капиллярный контроль является одним из основных контрольных методов, которые на сегодняшний день активно применяются для проверки швов.
Что такое капиллярный контроль
Данный метод относится к группе неразрушающих и предполагает наличие множества способов его проведения с применением различных расходных материалов.
С помощью такого метода выявляются наружные и внутренние недостатки шва. Описываемый метод позволяет определить практически все дефекты: непровары, поры, трещины и т. д. Капиллярный контроль позволяет определить местонахождение дефекта, его ориентацию к поверхности детали, а также его размеры.
Данный метод применяется для проверки любых металлов (чёрных и цветных), а также для контроля соединения стекла, пластмасс, керамики и т. д. Капиллярный метод получил широкую область применения при определении недостатков сварочных швов.
Суть процесса проверки состоит в том, что на полученное соединение наносятся специальные индикаторы в виде жидкости. Они с лёгкостью проникают в любой материал, если в нём имеются пустоты, проходят даже через самые маленькие трещины и возникают на обратной стороне от места их распыления. Где проявляется цветной индикатор, там и находится дефект.
Используемые методы
Существует две группы способов проведения капиллярного контроля: основные и комбинированные.
Основные
Основные методы предполагают использование исключительно капиллярной проверки с жидкими индикаторами.
Основные методы контроля:
- По видам используемых растворов:
- проникающие растворы;
- фильтрующие суспензии.
- По способу получения результата:
- яркостный;
- люминесцентный;
- люминесцентно-цветной;
- цветной.
Комбинированные
Комбинированные способы подразумевают применение ряда способов проверки неразрушающего характера, одним из которых является капиллярный.
Комбинированные способы:
- магнитный;
- электростатический;
- радиационный способ излучения или поглощения;
- электроиндукционный.
Перечисленные методы различаются в зависимости от их технологии воздействия на поверхность, поддающуюся проверке.
Процесс проведения капиллярного контроля
Перед началом проверки необходимо зачистить и просушить участок, который будет проверяться. Далее наносится индикаторная жидкость, часть которой проникает в поры и трещины, а остатки нужно тщательно удалить. После этого для вытягивания жидкости применяется проявитель. Индикатор проявляется на поверхности соединения в виде цветных пятен, которые и обозначат местонахождение изъяна, его размер и форму.
Материалы для капиллярной дефектоскопии
Необходимый перечень материалов для проведения капиллярного контроля:
- Индикаторная жидкость:
- флуоресцентная жидкость;
- цветная жидкость.
- Промежуточные очистители:
- растворитель или вода;
- водочувствительный эмульгатор;
- растворимый жидкий очиститель.
- Проявители:
- жидкий проявитель на водной основе;
- жидкий проявитель на основе растворителя;
- водный растворитель в виде суспензии.
Подготовка металла к проверке
Перед началом нужно провести зачистку поверхности сварочного шва. Рекомендуется использовать комбинацию механического и химического способов.
Сперва проводят механическую обработку металлической щёткой. Но не стоит сильно усердствовать: при интенсивном воздействии затираются поверхностные недостатки, и индикаторная жидкость не сможет проникнуть вглубь металла. Это приведёт к ошибочным суждениям о качестве шва.
Химическая обработка обычно проводится спиртом или растворителем. Нужно помнить, что химикаты могут вступать в реакцию с индикаторами, поэтому нужно их тщательно смывать водой или специальными реагентами. Важно, чтобы проверяемый участок был хорошо просушен, иначе результаты проверок будут неточными.
Нанесение индикатора
Индикаторная жидкость может наноситься различными способами:
- Стандартный капиллярный способ – при таком методе жидкость сама проникает в сварочный шов без специального вмешательства. Нанесение проводится путём смачивания, нанесения струёй погружения детали в жидкость.
- Ультразвуковой способ – заполнение пустот пор и трещин проводится посредством ультразвукового эффекта.
- Вакуумный – детали помещаются в вакуумную установку, с помощью которой из внутренних полостей откачивается воздух. Давление в этих пустотах ниже, чем атмосферное. Поэтому нанесённая жидкость легко проникает в них.
- Компрессионный – способ, при котором на индикаторную жидкость воздействуют высоким давлением, и она заполняет пустоты, выталкивая воздух.
- Деформационный – индикатор проникает внутрь сварочного шва при помощи воздействия звуковых волн, но при этом увеличивается размер выявленного дефекта.
Промежуточная очистка поверхности
Проводить очистку поверхности шва нужно аккуратно, чтобы не удалить индикатор с поверхностных недостатков. Очищать можно:
- Обычной водой, при помощи губки или тряпки. Температура воды не должна превышать +50оС.
- Эмульгаторами на основе масел. Вначале поверхность металла промывается водой, затем наносится эмульгатор, который также смывается водой.
- Растворителями. Поверхность шва просушивается, а затем протирается тканью, пропитанной растворителем.
- Комбинированный способ – сначала проверяемый участок промывается водой, а затем вытирается губкой, смоченной растворителем.
- После промежуточной очистки необходимо хорошо просушить сварочный шов.
Нанесение проявителя
Сразу после просушки на проверяемый участок равномерным тонким слоем наносится проявитель. Разновидности проявителей:
- Сухой.
Его использование возможно только в комплексе с флуоресцентными индикаторами. Наносится равномерным слоем при помощи обычного напыления.
- Жидкий на основе растворителя. Такой проявитель наносится методом равномерного распыления, чтобы образовалась тонкая и однородная плёнка.
- Жидкий на основе водной суспензии или водного раствора. Наносится методом распыления или способом замачивания свариваемых деталей в жидком проявителе. Однако после погружения в жидкость заготовки нужно быстро достать и тщательно просушить.
Стандартно время проявления занимает от 10 до 30 мин. в зависимости от используемого растворителя.
Капиллярный контроль сварных соединений — Все о сварке
Дефектоскопия сварных швов — обязательный этап после любой коммерческой сварки. Для тех, кто не знает, поясним. Дефектоскопия — поиск в сварном шве скрытых от глаз дефектов с применением специальных приборов или жидкостей. Один из недорогих способов дефектоскопии — капиллярный контроль сварных соединений.
Главное преимущество капиллярного контроля — он не разрушает металл и не изменяет его качественные характеристики. К тому же, такой контроль не требует дополнительного обучения сотрудников, поскольку он очень прост в применении и расшифровке. Но, несмотря на это, у капиллярного контроля есть свои особенности, которые нужно учитывать. О них мы и расскажем в этой статье. Также вы узнаете, какова сущность и технология капиллярного контроля.
Содержание статьи
- Общая информация
- Разновидности капиллярного контроля
- Технология
- Способы нанесения жидкостей
- Способы очистки
- Способы нанесения проявителя
- Повторный контроль
- Вместо заключения
Общая информация
Капиллярный контроль сварных швов — метод контроля качества, суть которого заключается в применении специальных жидкостей. Их еще называют индикаторами или пенетрантами. Такие жидкости обладают особыми свойствами. Они способны проникать в самые мелкие трещинки, оставляя при этом следы яркого цвета. Следы хорошо заметны невооруженным глазом, так что сварщик без труда может определить точное местоположение дефекта. Если дефекты очень маленькие, то можно использовать увеличительные лупы. Подобные методы контроля сварных швов эффективны и просты в использовании.
Используя капиллярный метод контроля можно обнаружить многие дефекты: начиная от трещин и пор, заканчивая прожогами и непроварами. Словом, все основные дефекты можно увидеть, не используя при этом дорогостоящего оборудования. Также можно узнать физические размеры дефекта и его точное местоположение.
Читайте также: Визуально-измертельный контроль качества
Капиллярный контроль применим ко многим материалам, будь то черный или цветной металл, различные искусственные полимеры (например, пластмасса или полипропилен), стекло и даже керамика. Так что область применения действительно большая, капиллярный контроль может найти себе применение во многих отраслях.
Разновидности капиллярного контроля
Существует две разновидности капиллярного контроля: основной и комбинированный. Основной метод заключается в том, что вы используете только технологию капиллярного контроля и ничего более. А при комбинированном методе капиллярный контроль может использоваться до любого другого контроля. Например, радиографического.
Эти методы в свою очередь имеют свои разновидности. В основном методе капиллярного контроля можно использовать либо специальный раствор, либо фильтрующую суспензию. А чтобы обнаружить результаты контроля, можно использовать хроматический, ахроматический, люминесцентный или люминесцентно-хроматический способ. Все этого относится к основному методу.
В комбинированном методе всегда используется капиллярный контроль, а также магнитный, индукционный, радиографический или любой другой метод контроля качества. Во всех этих способах нужно применять специальные жидкости, но для обнаружения результатов контроля используются приборы, характерный для каждого отдельного типа контроля качества. Например, в радиографическом методе таким прибором будет рентгеновский аппарат. В таком случае деталь сначала подвергают капиллярному контролю, а затем делают рентгеновский снимок, чтобы точно обнаружить, где располагаются дефекты.
Технология
Выше мы писали, что метод капиллярного контроля очень простой, и это правда. Сейчас мы вам подробно расскажем, как провести такой контроль. Вы сможете повторить его самостоятельно.
Для начала очистите поверхность шва. Это можно сделать с помощью любого растворителя. На поверхности не должны быть грязи, пятен от краски или от масла. Также просушите деталь, можно сделать это естественным образом на свежем воздухе. Также рекомендуем зачистить металл металлической щеткой или наждачкой. Так вы точно удалите все загрязнения и лишние вкрапления.
Но здесь есть один нюанс. Использовать щетку или наждачку нужно только в том случае, если поверхность металла неровная или пористая. Если металл относительно ровный и гладкий, то лучше ограничиться растворителем. В противном случае вы просто затрете наружные дефекты и не сможете потом обнаружить их при проведении контроля.
Далее нужно нанести пенетрант на поверхность шва. Есть несколько методов нанесения, о них мы поговорим позже. Скажем лишь, что самый простой метод — нанесение прямо из баллончика, с помощью кисти и погружение детали в емкость с пенетрантом. В последнем случае деталь нужно выдержать в жидкости от 5 минут и выше. Затем нужно удалить с поверхности излишки пенетранта. О том, как это сделать, мы тоже подробно рассказываем далее.
После того, как мы нанесли пенетрант, а затем убрали его излишки, нужно деталь просушить. После просушки нанесите на поверхность металла проявитель. Все готово. Согласитесь, ничего сложного. Так что можете приобрести баллончики с пенетрантом и проявителем, чтобы поэкспериментировать у себя в гараже. Поверьте, результата вас приятно удивит. Возможно, вы всегда считала свою сварку идеальной. Но только благодаря контролю получите по-настоящему объективную картину.
Обращаем ваше внимание, что к покупке пенетрантов нужно отнестись серьезно. Сейчас в магазинах появилось много дешевых жидкостей от неизвестных производителей, которые в лучше случае просто не дают должного результата, а в худшем — могут быть взрывоопасными или опасными для здоровья. Не экономьте на жидкостях для капиллярного контроля, они и так стоят не очень дорого по сравнению с другими способами контроля качества. Самый удобный формат жидкости — это, конечно, в баллончиках. Они равномерно распыляются на поверхность металла, что очень удобно. Рекомендуем новичкам именно жидкости в баллончиках.
Также капиллярная дефектоскопия может проводиться с помощью флуоресцентных пенетрантов. Это пенетранты, которые светятся в темноте. Для наблюдения за результатом не нужно использовать специальные очки, достаточно просто осмотреть деталь в затемненном помещении. При этом нужно использовать ультрафиолетовые лампы. В самом помещении не должно быть никаких посторонних предметов, которые могут отсвечивать.
Если используются обычные цветные пенетранты, то можно проводить осмотр детали и при дневном свете. Но мы все же рекомендуем использовать специальные яркие лампы.
Способы нанесения жидкостей
Выше мы упоминали, что пенетранты можно наносить с помощью аэрозольного баллончика или кисти. Это, пожалуй, самый примитивный и простой способ нанесения жидкости на контролируемую поверхность металла. В таких случаях жидкость сама распределяется по вглубь металла. Чтобы добиться лучших результатов можно погрузить деталь в емкость, наполненную пенетрантом. Температура пенетранта может быть от 5 до 50 градусов по Цельсию, так что можно проводить контроль даже на улице.
Но это не единственные методы нанесения жидкостей. Существуют и более продвинутые. Например, компрессионный метод, когда пенетрант подается на шов под определенным давлением. Благодаря давлению жидкость быстрее и эффективнее проникает вглубь металла. А сам контроль дает лучшие результаты по сравнению с простыми методами нанесения.
Также существует абсолютно противоположный способ нанесения жидкостей — вакуумный. Этот способ дорогостоящий, но очень эффективный. Деталь нужно поместить в вакуумную камеру и лишают ее воздуха. В результате в местах, где есть скрытые дефекты, давление сильно падает. Далее наносится жидкость, которая тут же заполняет все дефектные полости. Способ не из простых и дешевых, так что применяется в случаях, когда нужно добиться высокого качества шва и нет возможности использовать другие методы контроля.
Также можно использовать звуковые или ультразвуковые волны, которые будут воздействовать на жидкости, вгоняя их глубоко в металл. Но нужно учитывать, что такой метод деформирует дефекты, так что применяется он крайне редко.
Способы очистки
Как вы помните из технологии, после нанесения пенетранта и его выдержки нужно удалить излишки. Самый простой способ сделать это — смочить теплой водой мягкую тряпку или губку для мытья посуды и протереть ею поверхность шва. Такой способ самый экономный, не очень эффективный.
Вместо воды можно использовать растворитель. Но перед этим поверхность детали нужно как следует просушить. Этот способ очистки куда лучше тряпки с водой, но все равно недостаточно эффективен. Мы рекомендуем комбинировать протирание водой и протирание растворителем. Если вы готовы потратиться, то можете использовать специальные очистители в баллончиках. Они отлично справляются со своей задачей.
После очистки деталь нужно снова высушить. Если время позволяет, то оставьте деталь на свежем воздухе на некоторое время. Но не оставляйте на солнцепеке. Если времени мало и нет никаких приборов, то можно просто хорошо протереть тряпкой без ворса. Если в вашем распоряжении есть фен, то можете удалить влагу таким способом. Он самый эффективный и быстрый.
Способы нанесения проявителя
Итак, мы разобрались, как правильно наносить пенетрант и очищать деталь от ее излишков. Но что насчет проявителя? Ведь от него во многом зависит конечный результат. Здесь метод нанесения не так важен, как в случае с пенетрантом. Важнее выбрать подходящий тип проявителя и нанести его на очищенную и высушенную поверхность.
Проявители бывают разные. Есть сухие, их не очень удобно наносить, они используются только в сочетании с флуоресцентными пенетрантами. Стоят недешево. Используются редко, понятно, по каким причинам. Но результат контроля отличный.
Второй вид — жидкий проявитель. Может быть изготовлен с применением разных основ. Самый популярный — жидкий на основе водной суспензии. Можно наносить разными способами: и распылять, и замачивать в емкости. Если решите использовать емкость, то погружение должно быть кратковременным. За ним должна следовать просушка с применением специального фена.
Также есть жидкий проявитель на основе веществ, сходных по свойствам с растворителями. Недорогие и вполне эффективные, наносятся равномерным слоем с помощью распыления. Больше нечего добавить.
Проявлять нужно около 10-20 минут. Если результат не достигнут, то можно добавить еще минут 10 к основному времени.
Повторный контроль
В процессе капиллярного контроля могут произойти многие ситуации, из-за которых результат контроля будет неудовлетворительным. Например, вы решили погрузить деталь в емкость с пенетрантом, но выдержали меньше времени, чем должны были. И произошло это не по вашей вине. Или же вы случайно допустили ошибку при выполнении технологии капиллярного контроля. В таких случаях новички часто спрашивают: «Можно ли провести повторный контроль?». Наш ответ: да, можно.
Самое главное — хорошо очистить металл от остатков пенетранта и проявителя. Также используете те же жидкости, не нужно брать жидкости другого производителя. Соблюдая эти простые правила, вы сможете провести повторный контроль, который может оказаться куда успешнее предыдущего.
Вместо заключения
Капиллярный метод контроля сварных соединений очень простой, при этом экономически выгодный и вполне эффективный. Поэтому данный метод контроля качества используется повсеместно. Вы наверняка встретите баллончик с пенетрантом как в цеху крупного завода, так и в гараже у домашнего мастера.
Конечно, с помощью такого метода можно обнаружить далеко не все возможные дефекты, скрытые от глаз сварщика. Но если вы в полевых условиях или высокое качество шва не так уж важно, то можно ограничиться и капиллярным контролем. Также капиллярный контроль незаменим в маленьких частных мастерских, где прибыль небольшая и экономическая сторона вопроса играет главную роль. А вы использовали в своей практике капиллярный метод контроля качества швов? Расскажите об этом в комментариях ниже. Не забывайте делиться этой статьей в социальных сетях. Желаем удачи в работе!
Watch this video on YouTube
Капиллярный контроль сварных соединений
К одним из наиболее популярных методик неразрушающего контроля относится капиллярная дефектоскопия. Она позволяет выявить сквозные и неглубокие дефекты в сварных швах, определить точное месторасположение, направленность и размер трещин, несплавлений и непроваров.
Суть методики цветной дефектоскопии заключается в использовании индикаторной жидкости капиллярно-проникающего действия, предназначенной для смачивания исследуемой поверхности. В дальнейшем дефектоскопист регистрирует полученные индикаторные следы. Капиллярный контроль сварных соединений производится в соответствии с ГОСТ 18442-80.
Капиллярный контроль: основные этапы
1. Исследуемая поверхность очищается.
Для лучшего проникновения красящих веществ в изъяны поверхность изделия предварительно обрабатывается с использованием воды либо органического очистителя. Исследуемый участок должен быть тщательно очищен от загрязнителей (масляного и коррозийного налета), металлических и лакокрасочных покрытий. В ходе сушки с дефектов удаляются остатки воды (очистителя).
2. На материал наносится пенетрант.
Для полного покрытия пенетрантом, изделие полностью помещается в ванну с температурой от 5 до 50 °С. Для глубокой пропитки достаточно 5-30 минут. В некоторых случаях пенетрант распыляется либо наносится на поверхность изделия кистью.
3. Излишки пенетранта удаляются.
Для снятия лишнего пенетранта пригодится салфетка, проточная вода либо очиститель. Излишки вещества снимаются исключительно с окружающих поверхностей, но не из дефектных углублений. Для сушки используется салфетка без ворса либо воздушный поток.
4. На объект контроля наносится проявитель.
Высушив поверхность, специалист наносит на нее легкий и гладкий слой белого проявителя.
5. Проводится контроль.
Опытные и сертифицированные дефектоскописты специализируются на изготовлении операционно-технологических карт ПВК, выявлении дефектов сварных соединений, выдаче заключений со схемами исследуемых швов и указанием точного расположения обнаруженных дефектов.
Капиллярный контроль, цветная дефектоскопия | ООО «Квалитест»
Проведение капиллярного метода контроля: особенности, назначение, применение
Одним из наиболее распространенных методов диагностики качества деталей и оборудования без нарушения их целостности является капиллярный контроль (цветная дефектоскопия). Данный метод позволяет выявить и охарактеризовать дефекты, расположенные на поверхности изделия, либо сквозные повреждения (коррозия, трещины, свищи, полости, непровары и другие). Для качественной покраски и избежания появления подобных дефектов мы советуем пользоваться специальными аппаратами для электростатического распыление краски.
Наиболее целесообразен капиллярный метод контроля для обнаружения предельно малых повреждений, которые невозможно заметить при осмотре невооруженным глазом и путем применения увеличительных приборов. Как правило, дефект недостаточно контрастирует с общим фоном материала, поэтому даже использование лупы или микроскопа не позволяет его обнаружить.
Для проведения капиллярного метода неразрушающего контроля может быть использовано оборудование разных производителей. Сегодня на рынке одними из наиболее востребованных являются наборы для капиллярной дефектоскопии Magnaflux: линии, установка, ультрафиолетовые лампы.
Как реализуется капиллярный метод контроля?
При проведении капиллярного неразрушающего контроля изделия на его поверхность наносится специальное вещество — пенетрант. Но перед этим исследуемую поверхность следует тщательно очистить от жира, ржавчины, пыли и загрязнений, а затем — просушить. После этого на поверхность обрабатывается пенетрантом для капиллярного контроля (например Magnaflux SKL-SP2), который проникает в существующие дефекты. Излишки пенетранта удаляются с поверхности, таким образом, остается только вещество в полостях дефектов.
Для того чтобы извлечь пенетрант, заполнивший дефект, на поверхность, используется проявитель (например Magnaflux SKD-S2). Результат (наличие дефекта) может быть оценен визуально либо (при использовании люминесцентного пенетранта) путем просвечивания в темном помещении. Для этой цели используется ультрафиолетовый светильник с длиной волны 365 нм, а повреждения проявляются в виде светящихся точек или линий.
Капиллярный неразрушающий контроль: разновидности
В зависимости от способа получения результата, различают следующие виды капиллярного контроля:
- цветная дефектоскопия;
- люминесцентная дефектоскопия;
- люминесцентно-цветная дефектоскопия.
Капиллярный контроль: востребованность и применение
Диагностика с помощью капиллярного метода контроля дает возможность исследовать объекты разных размеров, форм, изготовленные из разных материалов, в том числе металла (например, капиллярный контроль сварных соединений и сварных швов), пластмассы, стекла, чугуна и других. Применяется капиллярный метод в ракетостроении, машиностроении, электротехнике, медицине, атомной энергетике и других отраслях промышленности.
Купить оборудование для цветной дефектоскопии или люминесцентной дефектоскопии вы можете в компании Квалитест в Москве, Санкт-Петербурге и других городах России.
Капиллярный контроль сварных соединений: методы и особенности
Одним из наиболее часто используемых в сварном деле вариантов дефектоскопии служит капиллярный контроль сварных соединений. Применяемый способ относится к контролю с помощью неразрушающих исследований. Этим методом можно обнаружить трещины, прожоги, раковины, пустоты, поры и подобные дефекты на сварных швах, их размеры и месторасположение. Преимуществами являются простота и отсутствие необходимости в дорогостоящем оборудовании. Капиллярный контроль можно объединять с другими методами проверки.
Суть метода
Капиллярный контроль сварных швов предполагает применение специальных жидкостей, называемых индикаторами или иначе пенетрантами. Используется их способность проникать внутрь металла по капиллярам. При попадании в трещинки и пустоты остаются следы насыщенного цвета.
По ним легко определить наличие и расположение дефектов. Рассмотреть их можно визуально или прибегнув к помощи лупы.
Технология контроля
Капиллярная дефектоскопия сварных швов проходит в несколько этапов. Перед началом процесса необходимо провести подготовку. Она заключается в очистке поверхности от грязи механическим или химическим способом. Для этого используются растворитель и наждачная бумага. Металл перед проверкой должен быть хорошо высушен.
Нанесение индикатора
Возможно применение нескольких способов:
- Обычный.
Пенетрант наносится на поверхность смачиванием с помощью кисточки, распылением из баллончика, погружением в емкость с индикаторной жидкостью.
- Компрессионный. Индикатор подается под давлением.
- Вакуумный. Требуется наличие вакуумной установки.
- Вибрационный. На нанесенный индикатор воздействуют ультразвуковыми волнами.
Нанесение индикатора требует соблюдения температурного диапазона. Он должен быть не менее 10 и не более 50°С. Детали следует устанавливать в такое положение, чтобы предотвратить стекание индикатора.
Очистка
После нанесения индикатора необходимо произвести очистку поверхности от его излишков. Это можно сделать теплой водой с помощью мягкой тряпки, салфетки или губки. Возможно использование какого-либо вида очистителя. Поверхность затем должна быть хорошо просушена.
Нанесение проявителя
Используются разные виды проявителей:
- сухой;
- водный раствор;
- жидкие на основе суспензии или растворителя.
Время проявления — минут 10-20. Затем можно начинать анализ наличия дефектов.
Повторный контроль
Если не удалось произвести качественное исследование, то контроль повторяют. Поверхность предварительно очищают от следов нанесения индикатора и проявителя. При этом следует использовать индикаторы такой же марки, как и в первый раз.
Преимущества
Достоинствами капиллярного метода контроля сварных швов являются:
- Простота проведения.
- Низкая стоимость.
- Возможность использования в качестве индикатора керосина.
- Быстрота.
- Высокая эффективность.
Способ капиллярного контроля является безопасным и не наносит урона здоровью исполнителя. Применим для исследования швов на поверхности различных металлов.
Интересное видео
Азбука неразрушающего контроля сварных швов
Азбука неразрушающего контроля сварных швовNDTnet 1998 Июнь, Том 3 №6 Понимание преимуществ и недостатков каждой формы неразрушающего обследование может помочь вам выбрать лучший метод для вашего заявления
ЧАРЛЬЗ ХЕЙС *
Выражение признательности: Статья была впервые опубликована в журнале Welding Journal в мае 1997 г. ![]() опубликована Американским обществом сварщиков, 550 NW LeJeune Road, Miami, FL 33126. | ЧАРЛЬЗ ХЕЙС — менеджер по международным продажам / поддержке, Линкольн Электрик Ко., Кливленд, Огайо. Он имеет сертификат NDT Level III от Американское общество неразрушающего контроля и является членом подкомитета AWS D1D по инспекциям. |
Введение
- Философия, которой часто руководствуются при изготовлении сварных узлов и конструкций, заключается в «обеспечении качества сварки». Однако термин «качество сварного шва» относителен. Приложение определяет, что хорошо, а что плохо.Как правило, любой сварной шов имеет хорошее качество, если он соответствует требованиям внешнего вида и будет
бесконечно продолжать выполнять работу, для которой он предназначен.
Первый шаг к обеспечению сварного шва
качество заключается в определении степени, требуемой приложением. Стандарт должен быть установлен на основе требований к услуге.
«Каким бы ни был стандарт
качество, все сварные швы должны быть
проинспектирован «.![]() |
Неразрушающий контроль (NDE) методы контроля позволяют на постоянной основе проверять соответствие стандартам, исследуя поверхность и подповерхностные слои сварной шов и окружающий основной материал.Пять основных методов: обычно используется для проверки готовых сварных швов: визуальный, жидкий пенетрант, магнитная частица, ультразвуковой и рентгенографический (рентген).
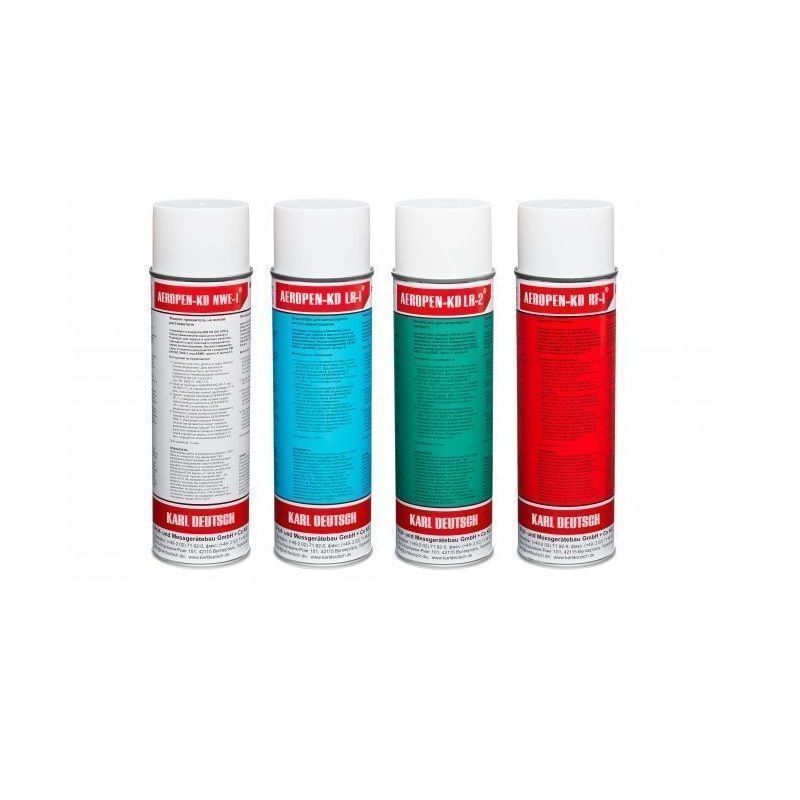
Визуальный осмотр (VT)
- Визуальный осмотр часто является наиболее экономичным методом, но он должен проводиться до, во время и после сварки. Многие стандарты требуют его использования перед другими методами, потому что нет смысла подвергать явно плохой сварной шов сложным методам контроля. В стандарте ANSI / AWS D1.1, Нормы сварки конструкций для стали, говорится: «Сварные швы, подлежащие неразрушающему контролю, должны быть признаны приемлемыми при визуальном осмотре». Для визуального осмотра требуется небольшое оборудование.Помимо хорошего зрения и достаточного освещения, все, что требуется, — это карманная линейка и размер сварного шва.
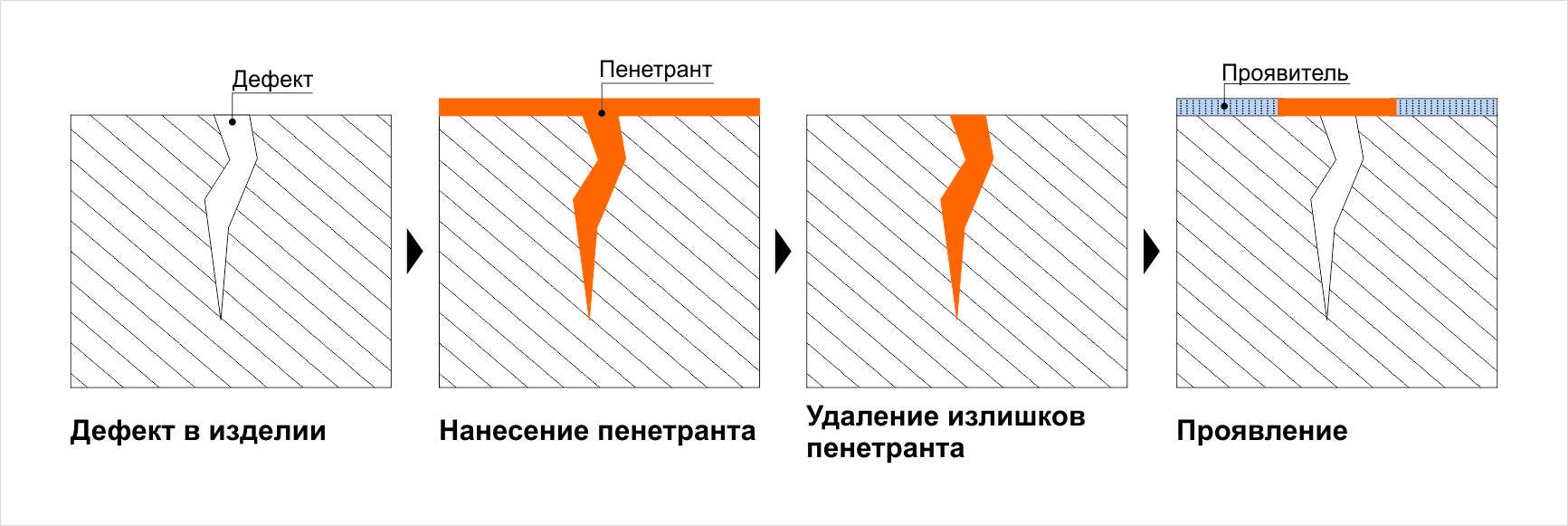
«Визуальный осмотр — лучшее купить в ОСО, но это необходимо место до, во время и после сварки ». |
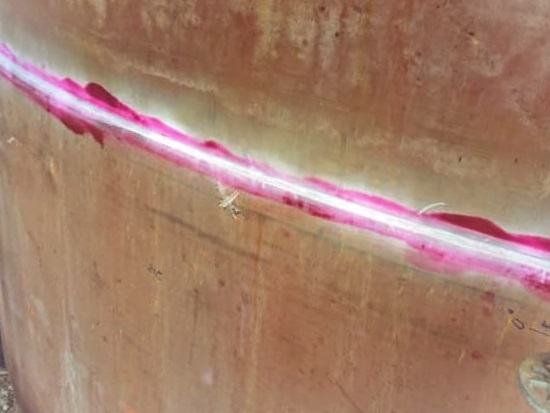
Во время изготовления визуальный осмотр сварного шва и кратера на конце может выявить такие проблемы, как трещины, недостаточное проникновение и включения газа или шлака.Среди обнаруживаемых визуально сварных швов обнаруживаются трещины, поверхностный шлак во включениях, поверхностная пористость и поднутрения.
На простых сварных швах может быть достаточно осмотра в начале каждой операции и периодически в процессе работы. Где больше одного слоя наполнителя
металл осаждается, однако, может быть желательно проверить каждый слой перед нанесением следующего. Корневой проход многопроходного сварного шва является наиболее важным для прочности сварного шва. Он особенно подвержен растрескиванию и, поскольку он быстро затвердевает, может задерживать газ и шлак.При последующих проходах условия, вызванные формой сварного шва или изменениями в конфигурации соединения, могут вызвать дальнейшее растрескивание, а также подрезы и улавливание шлака. Затраты на ремонт можно свести к минимуму, если визуальный осмотр обнаружит эти дефекты до начала сварки.
Визуальный контроль на ранней стадии производства также может предотвратить недосварку и переварку. Использование сварных швов меньшего размера, чем указано в технических характеристиках, недопустимо. Слишком большие бусины излишне увеличивают стоимость и могут вызвать деформацию из-за дополнительной усадки.
После сварки визуальный осмотр может выявить различные дефекты поверхности, включая трещины, пористость и незаполненные кратеры, независимо от последующих процедур проверки. Можно оценить отклонения размеров, коробление и дефекты внешнего вида, а также характеристики размера сварного шва.
Перед проверкой поверхностных дефектов сварные швы необходимо очистить от шлака. Перед осмотром не следует проводить дробеструйную очистку, так как ударная закалка может закрыть мелкие трещины и сделать их невидимыми. AWS D1.1 Кодекс по сварке конструкций , например, не допускает упрочнение «корня или поверхностного слоя сварного шва или основного металла по краям сварного шва».
Визуальный осмотр позволяет обнаружить только дефекты на поверхности сварного шва. Спецификации или применимые нормы могут требовать, чтобы также была исследована внутренняя часть сварного шва и прилегающие металлические зоны. Неразрушающие исследования могут использоваться для определения наличия дефекта, но они не могут измерить его влияние на работоспособность продукта, если только они не основаны на корреляции между дефектом и некоторыми характеристиками, влияющими на служба.В противном случае разрушающие испытания — единственный надежный способ определить работоспособность сварного шва.
Радиографический контроль (RT)
- Рентгенография (рентген) — один из самых важных, универсальных и широко применяемых методов неразрушающего контроля — рис.1.
Рис. 1 — Рентгенография — один из наиболее важных, универсальных и широко распространенных методов обследования.![]() | Рис.2 — Более толстые области образца, подвергаемого рентгеновскому облучению, или материал с более высокой плотностью поглощает больше излучения, и соответствующие области на рентгенограмме будут светлее |
Рентген используется для определения внутренней прочности сварных швов.Период, термин «Качество рентгеновского снимка», широко используется для обозначения благодаря этому методу контроля обеспечивается высокое качество сварных швов.
Радиография основана на способности рентгеновских лучей и гамма-лучей проходить через металл и другие материалы, непрозрачные для обычного света, и производить фотографические записи передаваемой лучистой энергии. Все материалы будут поглощать известное количество этой лучистой энергии, и, следовательно, рентгеновские лучи и гамма-лучи могут использоваться для выявления разрывов и включений внутри непрозрачного материала. Постоянная запись на пленку внутренних условий покажет основную информацию, по которой можно определить прочность сварного шва.
«Рентгенография — одна из наиболее широко распространенные околосмертные переживания методы «. |
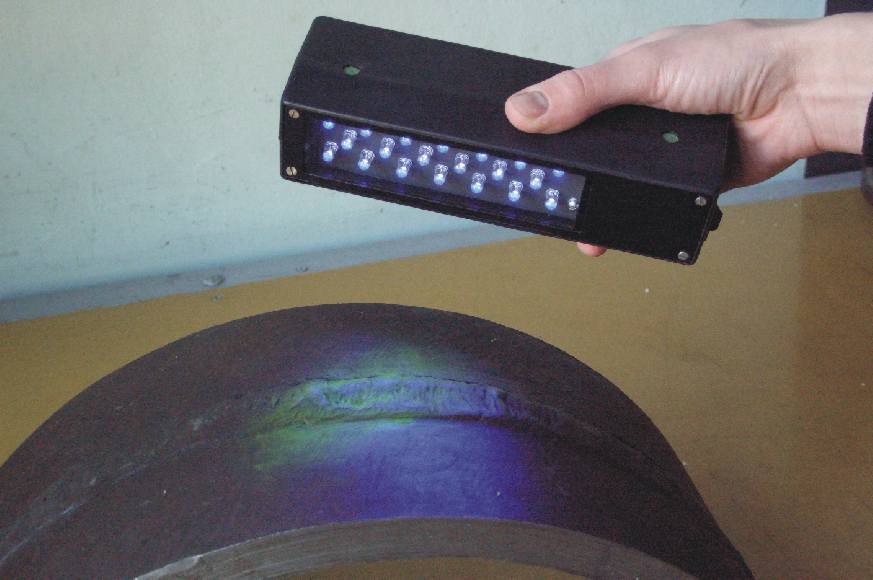
Когда рентгеновские лучи или гамма-лучи направляются на участок сварной конструкции, не все излучение проходит через металл. Различные материалы, в зависимости от их плотности, толщины и атомного номера, будут поглощать лучистую энергию разной длины.
Степень, в которой различные материалы поглощают эти лучи, определяет интенсивность лучей, проникающих через материал.Когда регистрируются вариации этих лучей, становится доступным средство заглянуть внутрь материала. Изображение на проявленной светочувствительной пленке называется рентгенограммой. Непрозрачный материал поглощает определенное количество излучения, но там, где есть тонкий участок или пустота (шлаковые включения или пористость), поглощение меньше. Эти области будут на рентгенограмме выглядят темнее. Заросли области образца или более высокая плотность материал (включение вольфрама), будут поглощать больше излучения, и соответствующие им области на рентгенограмме будут светлее — Рис.2.
Будь то в магазине или в полевых условиях, надежность и интерпретирующая ценность рентгенографических изображений зависят от их резкости. и контраст. Способность наблюдателя обнаружить дефект зависит от резкости его изображения и его контраста с
фон. Чтобы быть уверенным, что рентгенографическое облучение дает приемлемые результаты, на деталь помещают датчик, известный как индикатор качества изображения (IQI), чтобы его изображение было воспроизведено на рентгенограмме.
IQls, используемые для определения качества рентгенографии, также называются пенетраметрами.Стандартный дырочный пенетраметр представляет собой прямоугольный кусок металла с тремя просверленными отверстиями заданного диаметра. Толщина куска металла — это процент от толщины исследуемого образца. Диаметр каждого отверстия разный и кратен толщине пенетраметра. Пенетраметры проволочного типа также широко используются, особенно за пределами США. Они состоят из нескольких отрезков проволоки разного диаметра. Чувствительность определяется наименьшим диаметром проволоки, который хорошо виден на рентгенограмме.
Пенетраметр не является индикатором или прибором для измерения размера несплошности или минимального обнаруживаемого размера дефекта. Это является показателем качества рентгенографической техники.
Рентгенографические изображения не всегда легко интерпретировать. Следы и полосы, потемнения и пятна, вызванные обработкой пленки, могут затруднить выявление дефектов. Такие пленочные артефакты могут маскировать несплошности сварного шва.
Поверхностные дефекты будут видны на пленке и должны быть распознаны.Поскольку угол экспонирования также влияет на рентгенограмму, оценить угловые швы этим методом сложно или невозможно. Поскольку рентгенограмма сжимает все дефекты, возникающие по всей толщине сварного шва, в одну плоскость, она имеет тенденцию создавать преувеличенное впечатление о дефектах рассеянного типа, таких как пористость или включения.
Рентгеновское изображение внутренней части сварного шва можно просматривать на флуоресцентном экране, а также на проявленной пленке. Это позволяет осматривать детали быстрее и с меньшими затратами, но при этом сохраняется четкость изображения.
но разрешение изображения
Можно преодолеть многие недостатки радиографической визуализации, связав флуоресцентный экран с видеокамерой. Вместо того, чтобы ждать проявления пленки, можно просматривать изображения.
в реальном времени. Это может улучшить качество
и снизить затраты на производство
такие приложения, как сварка труб, где проблему можно быстро выявить и устранить.
Оцифровывая изображение и загружая его в компьютер, изображение может быть улучшено и проанализировано до невозможной ранее степени. Можно наложить несколько изображений. Значения пикселей можно отрегулировать, чтобы изменить оттенки и контраст, выявив мелкие дефекты и неоднородности, которые не проявятся на пленке.Цвета могут быть назначены различным оттенкам серого, чтобы еще больше улучшить изображение и выделить недостатки. Процесс оцифровки изображения, снятого с флуоресцентного экрана, — когда компьютер обрабатывает изображения и передает его на монитор для просмотра — занимает всего несколько секунд. Однако из-за временной задержки мы больше не можем рассматривать это «реальное время». Это называется «радиоскопические снимки».
Существующие пленки можно оцифровать для достижения тех же результатов и улучшения процесса анализа. Еще одним преимуществом является возможность архивировать изображения на лазерных оптических дисках, которые занимают гораздо меньше места, чем хранилища старых пленок, и их гораздо легче вспомнить, когда это необходимо.
Таким образом, промышленная радиография — это метод контроля, использующий
Рентгеновские лучи и гамма-лучи в качестве проникающей среды и уплотненная пленка в качестве носителя записи для получения фотографической записи внутреннего качества. Как правило, дефекты сварных швов состоят либо из пустот в самом металле шва, либо из включений, плотность которых отличается от окружающего металла шва.
Радиографическое оборудование производит радиацию, которая может быть вредной для тканей тела в чрезмерных количествах, поэтому следует строго соблюдать все меры безопасности. Для достижения удовлетворительных результатов необходимо тщательно выполнять все инструкции. Только персонал, обученный радиационной безопасности и квалифицированный как промышленный рентгенолог, должен иметь право проводить радиографические исследования.
Контроль магнитных частиц (MT)
Рис. 3 — Применения для испытания магнитными частицами включают проверку кромок пластин перед сваркой, в процессе контроля каждого сварного прохода или слоя, оценку после сварки и ремонт. |
Этот метод может использоваться для проверки кромок листа перед сваркой, при проверке процесса каждого прохода или слоя сварного шва, оценке после сварки и для проверки ремонта — Рис.3.
Это хороший метод для обнаружения поверхностных трещин любого размера как в сварном шве, так и в прилегающем основном металле, подповерхностных трещинах, неполном сплавлении, поднутрении и недостаточном проплавлении сварного шва, а также дефектов на отремонтированных краях основного металла. Хотя испытание с помощью магнитных частиц не должно заменять рентгенографию или ультразвуковое исследование для оценки геологической среды, оно может иметь преимущество перед их методами при обнаружении плотных трещин и неоднородностей поверхности.
При использовании этого метода зонды обычно размещаются с каждой стороны проверяемой области, и между ними пропускается большая сила тока через рабочее место.Магнитный поток создается под ночным углом к потоку тока — рис. 3. Когда эти силовые линии сталкиваются с разрывом, например, с продольной трещиной. они отклоняются и просачиваются через поверхность, создавая магнитные полюса или точки притяжения. А магнитный присыпанный к поверхности порошок будет прилипать к месту течи цепче чем где-либо еще, формируя указание на разрыв.
Чтобы это указание проявилось, несплошность должна быть расположена под углом к магнитным силовым линиям.Таким образом, при продольном пропускании тока через заготовку будут видны только продольные дефекты. Укладываем заготовку Внутри катушки соленоида образуются продольные силовые линии (рис. 3), которые заставляют поперечные и угловые трещины становиться видимыми при нанесении магнитного порошка.
Хотя метод магнитных частиц намного проще в использовании, чем радиографический контроль, он ограничен использованием ферромагнитных материалов и не может использоваться с аустенитными сталями. Соединение основного металла и металла шва с разными магнитными характеристиками создает неоднородности магнитного поля, которые могут быть ошибочно интерпретированы как ненадежные.С другой стороны, истинный дефект может быть скрыт порошком, прилипшим к безвредной магнитной неоднородности. Чувствительность уменьшается с увеличением размера дефекта, а также с круглыми формами, такими как газовые карманы. Он лучше всего подходит для удлиненных форм, таких как трещины, и ограничивается поверхностными дефектами и некоторыми подповерхностными дефектами, в основном на более тонких материалах.
Поскольку поле должно быть достаточно искажено, чтобы создать внешнюю утечку, необходимую для выявления дефектов, мелкие удлиненные неоднородности, такие как микротрещины, швы или включения, параллельные магнитному полю, не будут обнаружены. Они могут
развиваться путем изменения направления поля, и рекомендуется применять поле с двух направлений, предпочтительно под прямым углом друг к другу.
Магнитные порошки можно наносить сухим или влажным способом. Метод сухого порошка популярен для проверки тяжелых сварных деталей, тогда как мокрый метод часто используется для проверки компонентов самолетов. Сухой порошок равномерно рассыпается по поверхности с помощью краскопульта, мешка для пыли или распылителя. Мелкодисперсные магнитные частицы имеют покрытие для увеличения их подвижности и доступны в сером, черном и красном цветах для улучшения видимости.В мокром методе очень мелкие красные или черные частицы взвешиваются в воде или легком нефтяном дистилляте. Его можно растекать или распылять, либо деталь можно окунуть в жидкость. Влажный метод более чувствителен, чем сухой метод, поскольку он позволяет использовать более мелкие частицы, которые могут обнаруживать очень мелкие дефекты. Флуоресцентные порошки могут использоваться для повышения чувствительности и особенно полезны для определения несплошностей в углах, шпоночных пазах, шлицах и глубоких отверстиях.
«МТ может иметь преимущество через RT и UT при обнаружении плотные трещины и поверхность сбивает с толку.» |
Жидкий пенетрант Инспекция (PT)
Рис. 4 — Пенетрантный контроль красителя аналогичен проникающему контролю, за исключением того, что используются ярко окрашенные красители, видимые при обычном свете. |
Жидкостный проникающий контроль часто называют расширением метода визуального контроля. Многие стандарты, такие как Кодекс AWS D1. 1, гласят, что «сварные швы, подлежащие испытанию на проникающую способность … должны оцениваться на основе требований к визуальному контролю».
Используются два типа проникающих жидкостей — флуоресцентные и видимые красители. При флуоресцентном проникающем контроле на поверхность исследуемой детали наносится сильно флуоресцентная жидкость с хорошими проникающими свойствами.Капиллярное действие втягивает жидкость в отверстия на поверхности, а затем удаляется излишек. «Проявитель» используется для нанесения пенетранта на поверхность, и полученная индикация просматривается в ультрафиолетовом (черном) свете. Высокий контраст между флуоресцентным материалом и объектом позволяет обнаруживать мельчайшие следы пенетранта, указывающие на дефекты поверхности.
Инспекция красителей аналогична, за исключением того, что используются ярко окрашенные красители, видимые при обычном свете — рис.Обычно с пенетрантами красителя используется белый проявитель, который создает резко контрастирующий фон с ярким цветом красителя. это обеспечивает большую мобильность, устраняя необходимость в ультрафиолетовом свете.
Проверяемая деталь должна быть чистой и сухой, потому что любые посторонние предметы могут закрыть трещины или отверстия и исключить проникновение пенетранта. Пенетранты можно наносить окунанием, распылением или кистью, но должно быть достаточно времени, чтобы жидкость полностью впиталась в неровности.Это может занять час или больше при очень сложной работе.
Жидкостный проникающий контроль широко используется для обнаружения утечек. Обычная процедура — нанести флуоресцентный материал на одну сторону сустава и подождать достаточное время для капиллярного действия.
чтобы занять место, а затем просмотрите другую сторону в ультрафиолетовом свете. В тонкостенных сосудах этот метод позволяет выявить утечки, которые обычно не обнаруживаются с помощью обычного испытания воздухом с давлением 5-20 фунтов / дюйм 2 . Когда толщина стенки превышает 1/4 дюйма.однако чувствительность проверки на герметичность снижается.
Ультразвуковой контроль (UT)
Рис. 5 — Ультразвуковой контроль обнаруживает неоднородности как на поверхности сварного шва, так и под ней. Компактное портативное оборудование позволяет легко использовать его в полевых условиях. |
Поверхностные и подповерхностные дефекты в металлах могут быть обнаружены, локализованы и измерены с помощью ультразвукового контроля, включая дефекты, слишком малые для обнаружения другими методами.
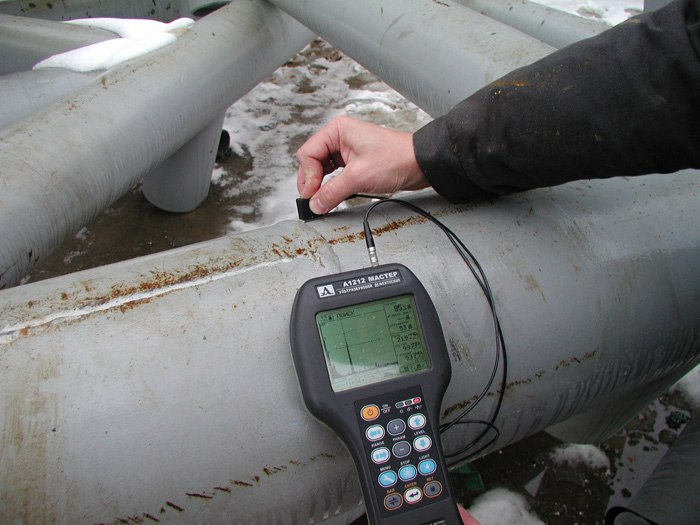
Ультразвуковой блок содержит кристалл кварца или другого пьезоэлектрического материала, заключенный в датчик или зонд.При приложении напряжения кристалл быстро вибрирует. Когда ультразвуковой преобразователь прижимается к проверяемому металлу, он передает механические колебания той же частоты, что и кристалл, через соединительный материал в основной металл и сварной шов. Эти колебательные волны распространяются через материал, пока не достигнут разрыв или изменение плотности. В этих точках часть вибрационной энергии отражается обратно. Поскольку ток, вызывающий вибрацию, отключается и включается с частотой 60-1000 раз в секунду, кристалл кварца периодически действует как приемник, улавливающий отраженные колебания.Они вызывают давление на кристалл и генерируют электрический ток. Подаваемый на видеоэкран, этот ток вызывает вертикальные отклонения на горизонтальной базовой линии. Полученный узор на лицевой стороне трубки представляет отраженный сигнал и разрыв. Компактное портативное ультразвуковое оборудование доступно для полевого осмотра и обычно используется при мостовых и строительных работах.
Ультразвуковой контроль менее пригоден для определения пористости сварных швов, чем другие методы неразрушающего контроля, поскольку круглые газовые поры реагируют на ультразвуковые испытания как серию одноточечных отражателей.Это приводит к низкоамплитудным характеристикам, которые легко спутать с «шумом базовой линии», присущим параметрам тестирования. Однако это предпочтительный метод испытаний для обнаружения несплошностей и расслоений более простого типа.
Переносное ультразвуковое оборудование доступно с цифровым управлением и микропроцессорным управлением. Эти инструменты могут иметь встроенную память и обеспечивать распечатку бумажных копий или видеонаблюдение и запись. Они могут быть связаны с компьютерами, что позволяет проводить дальнейший анализ, документирование и архивирование, как и с радиографическими данными.Ультразвуковое исследование требует квалифицированной интерпретации высококвалифицированного и хорошо обученного персонала.
Таблица 1 — Справочное руководство по основным методам неразрушающего контроля сварных швов | |||||
Инспекция Метод | Необходимое оборудование | Включает детектирования из | Преимущества | Ограничения | Замечания |
Визуальный | Увеличительное стекло Калибр сварного шва Карманная линейка Прямая кромка Стандарты качества | Дефекты поверхности — трещины, пористость, незаполненные кратеры, включения шлака коробление, недосварка, переварка, плохо сформированные валики, перекосы, неправильная подгонка | Бюджетный.![]() Может применяться в процессе работы, позволяя устранять неисправности. Указывает на неправильные процедуры. | Применимо только к дефектам поверхности. Не обеспечивает постоянной записи. | Всегда должен быть основным методом проверки, независимо от того, какие другие методы требуются. — единственный «продуктивный» вид обследования. Является необходимой функцией каждого, кто каким-либо образом участвует в сварке. |
Рентгенографический | Коммерческие рентгеновские или гамма-приборы, специально разработанные для контроля сварных швов, отливок и поковок. Пленочные и технологические установки. Оборудование для рентгеноскопии. | Внутренние макроскопические дефекты — трещины, пористость, выбоины, неметаллические включения, неполное проникновение корней, подрезание, сосульки, прожоги. | Когда показания записаны на пленку, дает постоянную запись.![]() При просмотре на рентгеноскопическом экране недорогой метод внутреннего осмотра. | Требуется умение выбирать углы экспозиции, работать с оборудованием и интерпретировать показания. Требуются меры безопасности. Обычно не подходит для контроля угловых швов. | Рентгеновский контроль требуется по многим нормам и спецификациям. Пригоден для аттестации сварщиков и сварщиков. Из-за стоимости его использование должно быть ограничено теми областями, где другие методы не обеспечивают требуемой уверенности. |
Магнитная Частица | Специальное торговое оборудование. Магнитные порошки — сухая или влажная форма; может быть флуоресцентным для просмотра в ультрафиолетовом свете. | Отлично подходит для обнаружения неровностей поверхности — , особенно поверхностных трещин. | Более простой в использовании, чем радиографический контроль.![]() Позволяет контролировать чувствительность. Относительно недорогой метод. | Применимо только к ферромагнитным материалам. Требуется умение интерпретировать показания и распознавать нерелевантные шаблоны. Трудно использовать на неровных поверхностях. | Удлиненные дефекты, параллельные магнитному полю, могут не давать рисунка; по этой причине поле следует прикладывать с двух направлений под прямым или близким углом друг к другу. |
Жидкость Пенетрант | Коммерческие наборы, содержащие флуоресцентные пенетранты или красители и проявители. Прикладное оборудование для разработчика. Источник ультрафиолетового излучения — при использовании флуоресцентного метода. | Трещины на поверхности, которые не видны невооруженным глазом. Отлично подходит для обнаружения утечек в сварных деталях. | Применимо к магнитным и немагнитным материалам.![]() | Обнаруживаются только дефекты поверхности. Не может эффективно использоваться на горячих сборках. | В тонкостенных сосудах выявляются утечки, которые обычно не обнаруживаются обычными воздушными испытаниями. нерелевантные состояния поверхности (дым, шлак) могут давать неверные показания. |
Ультразвуковой | Специальное торговое оборудование, эхо-импульсного или передающего типа. Стандартные эталонные шаблоны для интерпретации RF или видео шаблонов. | Поверхностные и подземные дефекты, в том числе слишком мелкие, чтобы их можно было обнаружить другими методами. Специально для обнаружения дефектов подповерхностного слоя. | Очень чувствительный. Позволяет зондировать суставы, недоступные для рентгенографии. | Требуется высокий уровень навыков в интерпретации шаблонов эхо-импульса.![]() | Эхо-импульсное оборудование широко используется для контроля сварных швов. Оборудование передаточного типа упрощает интерпретацию образов, где это применимо. |
Выбор контроля качества
- Хорошая программа проверки неразрушающего контроля должна признавать ограничения, присущие каждому процессу.Например, и рентгенография, и ультразвук имеют разные факторы ориентации, которые могут определять выбор того, какой процесс использовать для конкретной работы. Их сильные и слабые стороны дополняют друг друга. В то время как рентгенография не может надежно обнаружить дефекты, похожие на ламинацию, ультразвук в этом лучше. С другой стороны, ультразвук плохо подходит для обнаружения рассеянной пористости, в то время как рентгенография очень хороша.
- Выбор процесса. Процесс должен соответствовать работе.
- Подготовка. Конфигурация стыка должна быть правильной и совместимой с процессом сварки.
- Процедуры. Процедуры должны быть подробно описаны и строго соблюдаться во время сварки.
- Предварительное тестирование. Полномасштабные макеты или смоделированные образцы должны использоваться, чтобы доказать, что процесс и процедуры обеспечивают желаемый стандарт качества.
- Персонал. К работе должны быть привлечены квалифицированные специалисты.
Какие бы методы контроля ни использовались, уделение внимания «пяти принципам» качества сварки поможет свести последующий контроль к рутинной проверке. Затем правильное использование методов неразрушающего контроля будет служить проверкой, чтобы поддерживать соответствие переменных и качество сварки в пределах стандартов.
Пять П являются |
Авторские права © NDT.net, [email protected] 1. Июнь 1998 г. / DB: Article / DT: tutor / SO: AWS / AU: HAYES_CHARLES / CN: US / CT: NDT / CT: weld / ED: 1998-06
ОДИНОЧНЫЙ ПИК
Неразрушающий контроль
Неразрушающий контроль (NDT) — это процесс проверки, тестирования или оценки материалов, компонентов или узлов на предмет разрывов или различий в характеристиках без нарушения работоспособности детали или системы. Другими словами, когда проверка или испытание завершены, деталь все еще можно использовать.
В рамках неразрушающего контроля мы предоставляем следующие услуги:
- Инфракрасное тепловидение (термография)
- Проверка проникновения красителя
- Рентгенография
- Испытание на твердость по Бринеллю
- Бороскопия
- Тестирование магнитных частиц
- Ультразвуковой контроль
- Обнаружение утечек
- Контроль низкоскоростных подшипников
- Электрический разряд
- Дефектоскоп
- Измерение расхода
Инфракрасное тепловидение (термография):
Это метод удаленного мониторинга состояния, который обнаруживает аномалии температуры поверхности и определяет их характеристики для использования в профилактическом обслуживании на вашем предприятии.
Инспекция проникновения красителя:
Это метод, который используется для выявления дефектов поверхности путем вытекания окрашенного или флуоресцентного красителя из дефекта. Метод основан на способности жидкости втягиваться в «чистую» поверхность, разрушая дефект капиллярным действием. После периода времени, называемого «выдержкой», избыток пенетранта с поверхности удаляется и наносится проявитель. Это действует как промокашка. Он извлекает пенетрант из дефекта, чтобы выявить его наличие.
Рентгенография:
Используется для обнаружения неоднородностей во внутренней структуре сварных швов. Очевидным преимуществом обоих этих методов тестирования является их способность помочь установить внутреннюю целостность сварного шва без разрушения сварного компонента.
Испытание на твердость по Бринеллю:
Тест на твердость по Бринеллю — это тест на твердость вдавливанием, который может предоставить полезную информацию о металлических материалах. Эта информация может коррелировать с прочностью на разрыв, износостойкостью, пластичностью или другими физическими характеристиками металлических материалов и может быть полезна при контроле качества и выборе материалов.
Бороскопия:
Осмотр внутренней поверхности трубопроводов и сварных соединений. В настоящее время фармацевтическая промышленность применяет бороскоп для документирования сварных стыков с целью проверки.
Контроль магнитных частиц (MPI):
MPI использует магнитные поля и мелкие магнитные частицы (т.е.е. железные опилки) для выявления дефектов в компонентах. Единственное требование с точки зрения возможности проверки — проверяемый компонент должен быть изготовлен из ферромагнитного материала, такого как железо, никель, кобальт или некоторые из их сплавов. Ферромагнитные материалы — это материалы, которые могут быть намагничены до уровня, при котором контроль будет эффективным.
Ультразвуковой контроль (UT):
Он использует высокочастотную звуковую энергию для проведения исследований и измерений.Ультразвуковой контроль может использоваться для обнаружения / оценки дефектов, измерения размеров, определения характеристик материала и т. Д. Для иллюстрации общего принципа проверки
Сегодня современные методы неразрушающего контроля используются при производстве, изготовлении и инспекциях в процессе эксплуатации, чтобы гарантировать целостность и надежность продукции, контролировать производственные процессы, снизить производственные затраты и поддерживать единый уровень качества. Во время строительства неразрушающий контроль используется для обеспечения качества материалов и процессов соединения на этапах изготовления и монтажа, а контроль неразрушающего контроля в процессе эксплуатации используется для обеспечения целостности используемых продуктов, необходимых для обеспечения их полезности и безопасности. публики.
процедур испытания сварки алюминия | Warco Engineering
28 мая 2018Алюминий — прочный, но легкий металл. Затем интеллектуально обработанные формы сплава добавляют материалу желаемые механические и физические свойства, такие как способность противостоять коррозии. Теперь, присмотревшись внимательнее, мы рассмотрим соединения, которые крепят алюминиевые детали. В частности, мы собираемся углубиться в процедуры тестирования сварки алюминия.Присмотритесь еще раз, в сварном шве есть крошечные дырочки?
Пористость Слабость
Когда сварочное оборудование не защищает стык достаточным количеством инертного газа, алюминий приобретает пористую структуру. Проблема иногда видна невооруженным глазом, обычно в виде кратеров и точечных отверстий, но самая большая часть этого дефекта материала, вероятно, находится внутри сварного шва. Газовая пористость обычно настолько тонко встроена в сварной шов, что ее можно обнаружить только с помощью процедуры ультразвукового или радиографического контроля.
Испытание дефектов открытой поверхности
Вернувшись к точечным отверстиям и кратерам, работа выглядит дилетантской, и, возможно, придется внести запись в досье сварщика, чтобы он мог пройти переподготовку. Между тем, насколько глубоко проникает эффект обскуры? Аэрозольные красители, видимые или флуоресцентные, извлекаются из набора инструментов инспектора сварки. Цветной спрей ищет невидимые неровности. По мере того, как жидкий пенетрант впитывается в сварной шов, капиллярное действие выделяет ямки, выявляет трещины и добавляет четкости линиям плавления.Недорогой и простой в применении, все же требуется умение интерпретировать результаты этого визуально ориентированного испытания сварного шва.
Использование электронного оборудования
Визуальный осмотр и жидкие пенетранты обнаруживают микротрещины, проколы и проблемы с пористостью. Однако единственный способ заглянуть внутрь сварного шва алюминия — это использовать инструментальную процедуру испытания. Анализ магнитных частиц отсутствует, потому что этот метод предназначен для ферромагнитных металлов.Приведенный в эксплуатацию закаленный корпус устройства для рентгенографических испытаний приступает к работе. В качестве альтернативы, прицел и переносной наконечник ультразвукового инструмента отражают звук в сварном шве. Зная о теплопроводности этой популярной группы сплавов, инспектор по сварке добросовестно выявляет и регистрирует несплошности сварного шва.
Помните, алюминиевые сварные швы успешно применяются каждый час и каждый день. Однако металл чувствителен к теплу и окружающей атмосфере.Он быстро сжимается, поэтому растрескивание при сжатии является проблемой. Кроме того, необходимо заняться водородной пористостью, примером загрязнения конденсата. Если ток оборудования, скорость нанесения и газовая зона достаточны, сварной шов, вероятно, будет формироваться должным образом. Однако одного «вероятно» недостаточно для инспектора по сварке, поэтому инструменты этого профессионального эксперта по сварке всегда в пределах досягаемости, равно как и правильные процедуры тестирования и сфокусированный на лазере ум.
Оптимизировано: Netwizard SEO
центровка | Расположение компонентов машины таким образом, чтобы они были предварительно настроены в соответствии с требованиями проекта.Центровка проверяется при визуальном осмотре. |
Американский институт нефти | API. Некоммерческая организация, регулирующая промышленные стандарты для нефтяной и газовой промышленности. Коды Американского института нефти используются для сварочных работ на нефтепроводах или связанных с ними материалах. |
Американское общество инженеров-механиков | ASME.Организация, издающая технические материалы и устанавливающая промышленные и производственные стандарты. Коды Американского общества инженеров-механиков используются для проектов, связанных со сваркой трубопроводов высокого давления.![]() |
Американское общество сварки | AWS. Профессиональная организация, которая поддерживает и продвигает сварочную промышленность и связанные с ней процессы. Американское сварочное общество составляет множество сварочных кодексов. |
AWS | Американское сварочное общество. Профессиональная организация, которая поддерживает и продвигает сварочную промышленность и связанные с ней процессы. AWS пишет множество сварочных кодов. |
основной металл | Один или несколько металлов, которые нужно сварить вместе для образования соединения.Свойства основного металла должны быть совместимы со свойствами металла, образующего соединение. |
коричневый | Алмазный индентор конической формы, используемый при испытаниях на твердость по Роквеллу.![]() |
стыков стыковых | Тип сварного шва с разделкой кромок, который соединяет две параллельные части без перекрытия.Стыковые сварные соединения можно испытывать в ходе испытаний на управляемый изгиб и испытания на поперечное растяжение. |
капиллярное действие | Способность вещества тянуть жидкость вверх против силы тяжести. Капиллярное действие притягивает пенетрант к поверхности детали при тестировании на пенетрант. |
углерод | Обычный неметаллический элемент, встречающийся во всех типах стали.Углерод является основным упрочняющим элементом стали. |
Сертифицированные инспекторы по сварке | CWI.![]() |
прочность на сжатие | Способность материала противостоять силам, которые пытаются его сжать или раздавить.Прочность на сжатие — это величина сжимающего напряжения, которое материал может выдержать до разрушения. |
коррозионная стойкость | Способность материала противостоять разрушению и химическому разрушению из-за воздействия на поверхность в определенных условиях. Коррозионную стойкость стали можно улучшить за счет присутствия хрома. |
контактная смазка | Вещество, обычно масло, которым покрывается испытуемый образец при ультразвуковом контроле.![]() |
поперечное сечение | Внутренняя часть поверхности, которая обнажается прямым разрезом. Поперечные сечения часто подвергаются испытанию и контролю сварных швов для обеспечения качества сварки. |
Кристалл кварца | Устройство для ультразвукового контроля, преобразующее электрическую энергию в механическую.Кристаллический кварц посылает вибрации в образец для поиска дефектов. |
Шкала C | Шкала испытания твердости по Роквеллу, в которой используется индентор Брайля и нагрузка 150 кг для проверки твердости. Шкала C является наиболее распространенной шкалой, которая используется для твердых сталей и металлов.![]() |
CWI | Сертифицированный инспектор по сварке.Лицо, сертифицированное Американским сварочным обществом для проведения визуального контроля сварных швов. CWI должен уметь выявлять возможные нарушения непрерывности и дефекты сварки, использовать измерительные приборы и контролировать любой ремонт. |
дефект | Поверхностный или структурный дефект, который может привести к браку детали. Дефекты можно обнаружить посредством визуального осмотра или других форм неразрушающего контроля. |
дефекты | Поверхностный или структурный дефект, который может привести к браку сварной детали. Дефекты сварного шва могут включать непровар и трещины. |
разрушающие испытания | Метод тестирования, при котором материалы подвергаются суровым условиям, которые приводят к выходу продукта из строя.![]() |
разработчик | Вещество, которое помогает притягивать пенетрант к поверхности детали при испытании на проникновение. Проявитель делает дефекты детали видимыми за счет капиллярного воздействия. |
разрывов | Неравномерность сварной детали, которая может потребовать, а может и не потребовать фиксации или удаления сварной детали.Нарушения целостности можно обнаружить при визуальном осмотре. |
разрыв | Неравномерность сварной детали, которая может потребовать, а может и не потребовать фиксации или удаления сварной детали. Нарушения целостности можно обнаружить при визуальном осмотре.![]() |
пластичность | Мера способности материала вытягиваться, растягиваться или формироваться без разрушения.Пластичность — это механическое свойство. |
время ожидания | Время, в течение которого индентор под нагрузкой прижимается к исследуемому материалу во время испытания на твердость. Время выдержки помогает обеспечить точные показания твердости. |
время ожидания | Время, в течение которого жидкость или проникающий краситель впитывается поверхностью детали и просачивается в дефекты.Время выдержки зависит от ряда различных переменных, включая тип металла и область применения. |
Электропроводность | Способность материала действовать как средство передачи электричества.![]() |
Сертификация электродов | Процесс обеспечения соответствия электродов спецификациям, требуемым для проекта.Сертификация электродов требует от сварщиков проведения испытаний на твердость. |
электромагнит | Магнит, образованный электрическим током. Электромагнит обычно формируется путем наматывания проволоки на железный сердечник и его электрического заряда. |
ярмо электромагнитное | Переносное оборудование, которое создает магнитное поле для обнаружения поверхностных и подповерхностных дефектов на определенном участке испытательного образца.Электромагнитные ярмы питаются от переменного или постоянного тока.![]() |
кратер на конце | Углубление на поверхности сварного шва. Кратеры на концах считаются дефектами, если они выходят за пределы допусков сварочных норм. |
черные металлы | Металл, в котором железо является основным ингредиентом.Черные металлы могут подвергаться испытаниям на магнитные частицы, поскольку они обладают высокими магнитными свойствами. |
черные металлы | Металл, содержащий железо. Черные металлы можно классифицировать с помощью искрового испытания. |
файл | Стальной инструмент с известным уровнем твердости, используемый при испытании на твердость от царапин.При испытании на твердость от царапин файл перемещается по поверхности образца для оценки твердости. |
файл скретч-тест | Тест на твердость, который показывает способность материала сопротивляться царапинам. Тесты на царапины на файлах выполняются с использованием стальных файлов. |
Испытание на разрыв углового шва | Разрушающее испытание, при котором ломается одна сторона образца углового шва.Испытания на разрыв углового шва могут предоставить инспектору полезную информацию о качестве сварного шва. |
Испытание на разрыв углового шва | Разрушающее испытание, при котором разрушается одна сторона испытательного образца углового шва. При испытании на разрыв углового сварного шва возрастающая нагрузка прикладывается к несваренной стороне углового шва до тех пор, пока сварной шов не разрушится. |
угловых швов | Тип сварного шва треугольной формы, соединяющий две поверхности под прямым углом друг к другу внахлест, Т-образное соединение или угловое соединение.Угловые швы нельзя проверить с помощью радиографических исследований. |
плоскостность | Допуск, описывающий допустимую изменчивость формы и внешнего вида поверхности. Плоскостность сварной детали можно проверить при визуальном осмотре. |
люминесцентный | Излучение вещества, поглощенного светом.Флуоресцентные жидкости, используемые в тестах на пенетрант, требуют использования ультрафиолетового света, чтобы дефекты были видны. |
рентгеноскопический экран | Экран, освещенный сзади люминесцентными лампами, на котором отображается рентгеновский снимок. Рентгеноскопические экраны позволяют немедленно просматривать рентгеновские лучи. |
гамма-лучи | Высокочастотное электромагнитное излучение с короткими длинами волн.Гамма-лучи имеют большую глубину проникновения, чем рентгеновские лучи. |
шлифовальный круг | Абразивный инструмент в форме круга, который изнашивает металл от заготовки. Шлифовальные круги используются при искровых испытаниях, чтобы помочь определить тип металла. |
швов с разделкой кромок | Тип сварного шва, который состоит из отверстия между двумя поверхностями, которое обеспечивает пространство для размещения металла шва.Сварные швы с разделкой кромок часто испытывают с использованием испытаний на поперечное растяжение. |
управляемое испытание на изгиб | Разрушающий тест на изгиб сварного шва для оценки пластичности и прочности. При испытаниях на управляемый изгиб образец образца подвергают трехточечному изгибу. |
управляемое испытание на изгиб | Разрушающий тест на изгиб сварного шва для оценки пластичности и прочности.В ходе испытаний на управляемый изгиб образец образца подвергается трехточечному изгибу. |
твердость | Способность материала сопротивляться проникновению, вдавливанию и царапинам. Уровни твердости проверяются с помощью испытаний на твердость при вдавливании. |
испытания на твердость | Тест, который определяет, как материал реагирует на внешние силы, которые пытаются поцарапать, проникнуть или вдавить его.Большинство испытаний на твердость включают вдавливание образца материала и определение значения твердости на основе размера вдавливания. |
испытания на твердость | Тесты, которые определяют, как материал реагирует на внешние силы, которые пытаются поцарапать, проникнуть или вдавить его. Большинство испытаний на твердость включают вдавливание образца и определение значения твердости в зависимости от размера отпечатка. |
ЗТ | Зона термического влияния. Часть основного металла, которая не была расплавлена, но все еще имеет измененные механические свойства из-за тепла от сварки. ЗТВ может содержать изменения магнитных свойств. |
зона термического влияния | HAZ.Часть основного металла, которая не была расплавлена, но все еще имеет измененные механические свойства из-за тепла от сварки. Зона термического влияния может содержать изменения магнитных свойств. |
высокоуглеродистая сталь | Сталь, содержащая от 0,45% до 0,50% углерода. Высокоуглеродистые стали чрезвычайно прочные и твердые. |
соляная кислота | Кислотное высококоррозионное химическое соединение.Соляная кислота иногда используется в тестах на макротравление для улучшения обзора поперечного сечения. |
неполный сплав | Нарушение сплошности сварного шва, при котором металл сварного шва и основной металл или прилегающие сварные швы не полностью сплавлены. Неполный сплав значительно ухудшает целостность сварного шва. |
неполное проникновение | Сварной шов, который не проходит по толщине соединяемого материала.Неполное проникновение можно исправить, если оно обнаружено достаточно рано в процессе. |
непрямое намагничивание | Создание сильного магнитного поля внутри детали для поиска дефектов. Косвенное намагничивание может быть достигнуто с помощью регулируемых переносных устройств. |
стык | Край или точка соединения двух или более металлических частей.Соединения могут содержать расплавленный основной металл, а также присадочный металл. |
подготовка швов | Подготовка основного металла перед сваркой. Совместная подготовка может включать предварительный нагрев и резку. |
Тест Кнупа | Испытание на микротвердость с использованием небольшого алмазного индентора пирамидальной формы и относительно легких нагрузок от 10 граммов до 1 килограмма.Тест на твердость по Кнупу длится около 10-15 секунд. |
кругов | Нарушение сплошности основного металла, которое может образоваться в процессе производства стали. Перехлесты приводят к небольшим зазорам в стали. |
стали низколегированные | Сталь, содержащая небольшое количество намеренно добавленных материалов, изменяющих свойства металла.Низколегированная сталь обладает сильными магнитными свойствами. |
Макротравление | Разрушающий тест, включающий полировку и травление небольшого поперечного сечения сварного шва с использованием слабокислой смеси. Испытания на макротравление позволяют исследовать внутреннюю структуру сварного шва. |
Макротравление | Разрушающий тест, включающий полировку и травление небольших поперечных сечений сварного соединения с использованием слабокислой смеси.Испытания на макротравление позволяют исследовать внутреннюю структуру сварного шва. |
магнитное поле | Сила притяжения, окружающая магниты и проводники с током. Магнитное поле используется для выявления дефектов при магнитопорошковом контроле. |
Магнитопорошковый контроль | Тип неразрушающего контроля, при котором обнаруживаются несплошности на сварном изделии с помощью магнитного порошка и магнитных сил.При магнитопорошковом контроле для исследования сварного изделия используются магнитные поля и электрические токи. |
испытания магнитных частиц | Неразрушающий контроль, при котором используется магнитный порошок или жидкость для выявления дефектов в детали. При испытаниях магнитных частиц магнитный порошок будет группироваться вокруг поверхностного дефекта. |
магнитные испытания | Простой тест, используемый для определения типа используемого металла, прижимая магнит к заготовке и наблюдая за реакцией.Магнитные тесты не так точны, как химический анализ. |
магнетизм | Сила притяжения и отталкивания материалов. Чаще всего магнетизм возникает между металлами. |
механические свойства | Характеристика, описывающая, как материал реагирует на воздействие силы, которая пытается растянуть, сжать, согнуть, вмять, поцарапать или сломать его.Механические свойства могут быть проверены методами разрушающего контроля. |
метанол | Ядовитый жидкий спирт, который можно использовать в качестве растворителя при испытании на макротравление. Метанол поможет образцу высохнуть быстрее в тесте на макротравление. |
испытание на микротвердость | Тип испытания на твердость, предназначенный для испытания очень мелких или хрупких материалов.Испытания на микротвердость, также известные как испытания на микротвердость, включают очень легкие нагрузки. |
NDT | Неразрушающий контроль. Метод тестирования, используемый для оценки конкретных свойств материала без повреждения или необратимого изменения материала. Методы неразрушающего контроля включают визуальный осмотр и рентгеновский контроль. |
никель | Серебристо-белый металл, с которым легко работать.Никель часто используется в сплавах. |
неразрушающий контроль | NDT. Метод тестирования, используемый для оценки конкретных свойств материала без повреждения или необратимого изменения материала. Методы неразрушающего контроля включают визуальный осмотр и рентгеновский контроль. |
перелив | Сварные швы слишком велики для технических характеристик.Переполнение обходится дорого и может вызвать искажения в будущем. |
пенетрантный тест | Тип неразрушающего контроля, при котором используется флуоресцентная жидкость или краситель для обнаружения поверхностных дефектов. Пенетрантные тесты можно использовать, когда нельзя использовать магнитные тесты. |
пенетрантные тесты | Неразрушающий тест, при котором используется краситель или флуоресцентная жидкость для обнаружения дефектов на материале путем втягивания жидкости в крохотные отверстия на поверхности детали.Пенетрантные тесты можно использовать там, где тестирование магнитными частицами неэффективно. |
физические свойства | Характеристика, которая описывает объемные, тепловые, электрические и магнитные свойства материала. Физические свойства можно проверить до, во время и после процесса сварки. |
точечные отверстия | Сварочный дефект, вызванный высокой температурой сварки, в результате которого на сварном шве образуются маленькие пузырьки.Точечные отверстия — еще одно название небольшой пористости. |
пористость | Несплошность, характеризующаяся появлением крошечных пустот или пузырьков на сварном шве в результате захвата газов в материале. Чрезмерная пористость может ослабить сварной шов и привести к браку детали, если она не соответствует техническим требованиям. |
Тепло после сварки | Нагревание основного металла после завершения процесса сварки.Нагрев после сварки снижает остаточное напряжение, возникающее в металле во время сварки. |
драгоценные металлы | Редкий, встречающийся в природе химический элемент. Драгоценные металлы включают золото и серебро. |
предварительный нагрев | Нагревание основного металла для поддержания определенной температуры во время сварки.Предварительный нагрев может потребоваться, чтобы избежать растрескивания металла шва и прилегающих зон сварного шва. |
недвижимость | Физические и механические характеристики материала, которые отличают его от других материалов. Свойства определяют поведение и характеристики материала, в том числе то, как материал будет реагировать при большой нагрузке или при резких перепадах температуры. |
прототипы | Предварительная модель продукта, испытанная для оценки характеристик конструкции.Прототипы обычно проходят разрушающее тестирование, чтобы предоставить информацию о потенциальном успехе или неудаче соединительного материала в конкретной среде. |
Эхо-импульсное оборудование | Оборудование для ультразвукового контроля, которое использует высокочастотные звуковые волны для обнаружения дефектов или неровностей в детали. Оборудование для импульсного эха часто работает от батарей и переносится. |
излучение | Потенциально вредная энергия, излучаемая в виде частиц или волн.Во время рентгенологического исследования испускается излучение. |
рентгенограмма | Изображение, выводимое на чувствительный экран или пленку с помощью рентгеновских или гамма-лучей. Рентгенограммы позволяют увидеть сварной шов изнутри. |
радиографический контроль | Широко используемый неразрушающий контроль, который использует рентгеновские или гамма-лучи для получения изображения внутренней структуры материала.При рентгенографическом исследовании дефекты или неровности материала проявляются в виде темных пятен. |
Испытание на твердость по Роквеллу | Испытание на твердость, при котором измеряется степень проникновения в материал шарикового или алмазного индентора, приложенного под максимальной нагрузкой 150 кг в течение 10 секунд. Испытания на твердость по Роквеллу используют разные шкалы для разных групп материалов. |
Проникновение корня | Глубина проникновения присадочного металла в корень сварного шва. Неполное проникновение корня ослабляет сустав. |
прочность на сдвиг | Способность материала противостоять силам, которые пытаются заставить его внутреннюю структуру скользить по себе и разделяться.Прочность на сдвиг — это величина напряжения сдвига, которую материал может выдержать до разрушения. |
шлаковые включения | Флюс, который расплавился в сварном шве и застрял в расплавленном металле. Включения шлака обычно классифицируются как дефекты. |
промывочный растворитель | Вещество, используемое в коммерческих испытаниях на проникновение жидкости для очистки деталей от посторонних предметов.Промывка растворителем может потребоваться в некоторых коммерческих пенетрантах для красителей. |
звуковые волны | Колебания на очень высоких частотах. Звуковые волны, используемые при ультразвуковом контроле, выходят за рамки обычного человеческого слуха. |
искровые испытания | Метод определения типа металла путем удерживания металла на шлифовальном круге и наблюдения за искрами.Искровые испытания обычно используются только для черных металлов и не могут заменить химический анализ. |
квадрат | Металлический инструмент, состоящий из двух прямых кромок, установленных под прямым углом друг к другу. Квадраты используются при визуальном осмотре для проверки точности прямых углов или в качестве ориентира для рисования линий на материале. |
нержавеющая сталь | Тип стали, содержащей более 11% хрома и обладающей отличной твердостью и коррозионной стойкостью.Нержавеющую сталь можно сваривать с помощью множества различных способов сварки. |
статические нагрузки | Внешняя сила, которая применяется и удерживается в фиксированном положении в течение определенного времени. Статические нагрузки — важный компонент стандартизированных испытаний на твердость. |
прямая | Плоский прямоугольный ручной инструмент с дюймами или метрами, который можно использовать для рисования прямых линий, определения прямолинейности линии или проведения измерений.При визуальном осмотре используется линейка. |
прямолинейность | Допуск, описывающий допустимую изменчивость формы и внешнего вида линии. Прямолинейность сварной детали можно проверить при визуальном осмотре. |
сила | Способность материала противостоять силам, которые пытаются его сломать или деформировать.Конкретные типы прочности включают предел прочности на разрыв, предел текучести и прочность на сжатие. |
разрыв при растяжении | Когда материал ломается или разрушается при растяжении или растяжении. Разрушение при растяжении может происходить в металле с высокими твердыми свойствами в зоне термического влияния. |
прочность на разрыв | Способность материала противостоять силам, которые пытаются его разорвать или растянуть.Прочность на растяжение — это величина растягивающего напряжения, которое материал может выдержать до разрушения. |
испытательные пластины | Образец сварного шва, изготовленный в соответствии со стандартами сварки, который используется для проверки или подтверждения процедуры сварки, свойств материала и квалификации сварщика. Испытательные пластины, также называемые пробными купонами, свариваются в соответствии со стандартами сварки для проекта. |
образцов для испытаний | Часть испытательной пластины, которая подвергается испытанию материала и проверке.Результаты испытаний образцов заносятся в протокол аттестации процедуры сварки. |
теплопроводность | Физическое свойство, указывающее, насколько хорошо тепловая энергия передается через материал. Стальные сплавы, медь и алюминий обладают высокими свойствами теплопроводности. |
допуски | Приемлемое отклонение от желаемого размера, которое все еще соответствует спецификациям детали.Допуски указывают допустимую разницу между физическим элементом и его предполагаемой конструкцией. |
поперечный | Линия, перпендикулярная заготовке или сварной конструкции. При испытании на разрыв углового шва нагрузка прикладывается поперек свариваемой стороны. |
испытание на поперечное растяжение | Разрушающий тест, при котором сварная деталь растягивается до разрыва.Испытания на поперечное растяжение обычно требуются как часть механических испытаний сварных швов с разделкой кромок. |
испытание на поперечное растяжение | Разрушающий тест, при котором сварная деталь растягивается до разрыва. Испытания на поперечное растяжение обычно требуются как часть механических испытаний сварных швов с разделкой кромок. |
ультразвуковой | Частота выше диапазона человеческого слуха.Ультразвуковые частоты используются при неразрушающем ультразвуковом контроле сварных швов. |
ультразвуковой контроль | Неразрушающий контроль, при котором используются ультразвуковые волны для обнаружения внутренних дефектов. При ультразвуковом контроле неоднородность или изменение плотности детали будет действовать как отражатель для высокочастотных вибраций. |
ультразвуковой датчик | Устройство, излучающее звуковые волны, используемое при ультразвуковом контроле.Ультразвуковые датчики имеют наконечник из кристаллического кварца. |
ультразвуковые испытания | Метод неразрушающего контроля, при котором высокочастотная звуковая волна проходит через деталь. При ультразвуковом испытании изменения сигнала обычно указывают на дефекты материала. |
ультрафиолет | УФ-свет.Свет, невидимый невооруженным глазом, потому что он состоит из очень коротких волн. Ультрафиолетовый свет необходим для просмотра результатов флуоресцентного пенетрантного теста. |
выточка | Сварочный дефект, который ослабляет сварной шов и проявляется в виде канавки в основном металле по краю сварного шва. Подрезка может привести к тому, что деталь не будет проверяться визуально. |
выточка | Сварочный дефект, который ослабляет сварной шов и проявляется в виде канавки в основном металле по краю сварного шва.Подрезы — это дефект, который может сильно ослабить сварной шов. |
подрезка | Сварочный дефект, который ослабляет сварной шов и проявляется в виде канавки в основном металле по краю сварного шва. Поднутрение нелегко обнаружить при визуальном осмотре, но его можно обнаружить с помощью рентгенологического исследования. |
под сварку | Наплавленный валик меньше, чем требуется в технических характеристиках.Недосварку можно обнаружить и исправить при визуальном осмотре. |
Универсальная испытательная машина | Машина для испытания материалов, используемая для оценки прочности материалов на растяжение и сжатие. Универсальные испытательные машины могут выполнять множество стандартных разрушающих испытаний, включая испытания на поперечное растяжение и управляемый изгиб. |
УФ свет | Ультрафиолетовый свет.Свет, невидимый невооруженным глазом, потому что он состоит из очень коротких волн. Ультрафиолетовый свет необходим для обнаружения мелких дефектов при испытании на магнитные частицы. |
Тест Виккерса | Испытание на твердость, при котором алмаз пирамидальной формы прижимается к материалу в течение стандартного времени выдержки 10-15 секунд и при максимальной нагрузке 120 кг для создания вмятины.В испытании на твердость по Виккерсу размер вмятины определяет значение твердости. |
частота видеосигнала | Частота сигнала, передающего изображения и импульсы. Частота обычно измеряется в герцах (Гц) или циклах в секунду. |
визуальный контроль | VT.Оценка, при которой инспектор должен внимательно изучить сварную деталь на предмет поверхностных дефектов или дефектов. Визуальный контроль также известен как визуальный осмотр. |
сварной шов | Сварной присадочный металл, проходящий по стыку. Проверка сварного шва может выявить дефекты, которые могут повлиять на характеристики сварного шва. |
Анализ процедуры сварки | Результат теста или процедуры, выполняемой для оценки процесса изготовления.Анализ процедуры сварки может проводиться путем проведения разрушающих испытаний. |
код сварки | Стандарт, используемый для управления сварочными процессами и обеспечения безопасных методов сварки и высококачественной сварной продукции. Многие сварочные нормы написаны Американским сварочным обществом. |
Аттестационное испытание сварочных работ | Тест, проводимый сварщиком для определения способности сварщика выполнять определенную сварку или положение.Квалификационные испытания сварочных характеристик относятся к WPS. |
Квалификационная запись процедуры сварки | Письменная запись результатов сварного шва, который прошел испытания и проверку материала. Квалификационные записи процедуры сварки относятся к WPS. |
Спецификация процедуры сварки | WPS.Письменный документ, содержащий всю необходимую и конкретную информацию о применении сварочного проекта. Перед использованием спецификации процедуры сварки должны быть утверждены и протестированы. |
сварная деталь | Сварной шов. Сварные детали проверяются на наличие дефектов и разрывов. |
размер сварного шва | Металлический инструмент, который измеряет элемент детали или сварной шов, чтобы определить, находится ли элемент в пределах указанного предела или допуска.Измеритель размера сварного шва — один из основных инструментов, используемых при визуальном контроле. |
WPS | Спецификация технологии сварки. Письменный документ, содержащий всю необходимую и конкретную информацию о применении сварочного проекта. WPS должен быть одобрен и протестирован, прежде чем его можно будет использовать. |
Рентгеновский снимок | Электромагнитная волна с высокой частотой и низкой длиной волны, используемая в радиографических испытаниях.Рентгеновские лучи используются для осмотра твердых предметов внутри во время рентгенологического исследования. |
Рентгенологические исследования | Метод неразрушающего контроля, использующий электромагнитные волны для обнаружения дефектов в материале. Рентгеновские тесты используются для просмотра внутренних поверхностей твердых объектов. |
предел текучести | Способность материала выдерживать постепенное, прогрессирующее усилие без остаточной деформации.Предел текучести — это сила, которую материал может выдержать до разрушения. |
цинк | Голубовато-белый металл, устойчивый к коррозии и имеющий относительно низкую температуру плавления. Алюминиево-цинковые сплавы обычно плохо свариваются. |
Расширенные методы соединения для современного автомобиля
Эта статья впервые появилась в ноябрьском выпуске ABRN за 2014 год.
Когда друзья и семья думают о машинах прошлых лет, они часто говорят мне: «Они не строят их так, как раньше». Я говорю им, вы даже не представляете, насколько вы правы. Сегодняшние автомобили на световые годы опережают то, что было всего несколько лет назад. Мы обсуждаем уже не автомобили будущего, а уже существующие на дорогах автомобили, и некоторые из них ремонтируются, как будто ничего не изменилось. В связи с серьезными изменениями в конструкции транспортных средств, отрасли ремонта столкновений потребуется изучить некоторые передовые методы крепления и новый образ мышления.Давайте рассмотрим некоторые передовые методы крепления, необходимые для ремонта транспортных средств, которые сегодня находятся в дороге.
Пайка МИГ
ПайкаMIG используется по разным причинам. Его можно использовать для выполнения непрерывных сварных швов на панелях, где возникает проблема коробления или перегрева термочувствительных материалов. MIG-пайка также используется для выполнения щелевых сварных швов при соединении термочувствительных материалов и там, где это рекомендовано в информации о ремонте автопроизводителя. Большинство паяных соединений MIG используются для крепления стальной детали с более низкой прочностью к стальной детали с более высокой прочностью, чувствительной к нагреванию.Еще одним преимуществом пайки MIG является то, что она мягче стали, что упрощает формовку и обработку. (См. Рисунок 1 Рисунок 1 Правка шариков из силиконовой бронзы не дает искр при шлифовании.)
Предел прочности при растяжении проволоки для припоя MIG составляет приблизительно 275–350 МПа, но при правильном выполнении паяное соединение MIG может быть прочнее из-за толщины валика на тыльной стороне.
Присадочный металл, обычно кремнистая бронза, плавится при более низкой температуре, чем основной металл стали.(Кстати, пайка MIG не может использоваться для алюминиевых панелей, потому что кремниевая бронза плавится при более высокой температуре, чем алюминий.) Расплавленный присадочный металл втягивается в соединение за счет капиллярного действия. Для успешного ремонта при пайке MIG требуется капиллярное действие для прочного соединения. Капиллярное действие — это процесс, при котором расплавленный присадочный металл растекается по задней стороне ремонтного шва. Затем присадочный металл связывается с основным металлом.
При выполнении паяных соединений MIG попробуйте использовать ручную строчку для контроля зоны теплового воздействия (HAZ).Этот метод хорошо работает при использовании сварочного аппарата GMA (MIG), в котором вместо стальной проволоки используется проволока из кремнистой бронзы. Некоторые машины имеют предварительно запрограммированные настройки для пайки MIG. Эти машины также могут регулировать размер электрода, толщину материала и сплав электрода. Цель открытого стыкового соединения состоит в том, чтобы создать сварной шов на задней стороне, который почти не отличим от переднего борта. (См. Рис. 2 Без правильного корневого зазора капиллярное действие не будет.)
Естественная тенденция, когда кто-то начинает пайку MIG, — это включить сварщика, чтобы валик выглядел так же, как при сварке GMA (MIG).Это и ненужно, и вредно для ремонтного шва. Это резко увеличит ЗТВ, но при этом может не обеспечить должного капиллярного действия.
Еще одна важная часть пайки MIG — поддержание правильного корневого зазора для обеспечения прочности паяного соединения. Если корневой промежуток слишком мал, капиллярное действие не будет достаточным. Когда передняя сторона стачивается, сварной шов на обратной стороне — единственное, что обеспечивает прочность ремонтного шва.
Как и в случае сварных швов GMA (MIG), вы должны визуально осматривать и разрушать рабочие швы. При проверке практических сварных швов ищите трещины вокруг паяного соединения так же, как при проверке сварных швов GMA (MIG). Еще один разрушительный тест, который следует провести, — это разрушающий тест на измельчение. Для проверки сделайте сварной шов и отшлифуйте лицевую сторону на уровне поверхности. Затем деструктивно проверьте сварной шов. Этот тест подтвердит, что сустав обладает достаточным капиллярным действием.
Сварка алюминия
Теперь давайте рассмотрим сварку алюминия GMA (MIG).Для некоторых предприятий по ремонту автомобилей класса люкс в сварке алюминия нет ничего нового, но для многих она практически неизвестна. Первое, что необходимо, — это подходящее оборудование. Большинству производителей автомобилей требуется сварщик, способный выполнять сварку в импульсном режиме. (Подробную информацию можно узнать у каждого производителя транспортных средств.) (См. Рис. 3 Этот аппарат импульсной сварки создает качественный сварной шов.)
Следующее, что потребуется, — это обучение и практика. Сварка алюминия гораздо менее щадящая, чем традиционная сварка стали.При сварке алюминия подготовка поверхности абсолютно необходима для успешной сварки. После контакта с воздухом алюминий почти мгновенно образует слой оксида алюминия. Этот непроводящий слой оксида алюминия чрезвычайно твердый, имеет более высокую температуру плавления, чем алюминий, и вызывает очень плохие сварные швы из-за пористости. (См. Рис. 4. При сварке алюминия необходимо использовать метод проталкивания для создания прочного сварного шва.)
Если есть какие-либо недостатки в технике сварки, сварка алюминия покажет это в виде плохого сварного шва.Вот где обучение и практика будут ключевыми. При сварке стали GMA (MIG) вы можете толкать или тянуть сварочную ванну и добиваться определенного успеха в любом методе. Но с алюминием вы должны подтолкнуть сварочную ванну. Это приведет к предварительному нагреву панели перед сваркой, что сохранит стабильную дугу и позволит защитному газу защитить зону сварки от внешних загрязнений.
Заклепка
Последний метод крепления, который мы рассмотрим, — это склеивание заклепками, при этом основное внимание уделяется скреплению самопробивающими заклепками (SPR).Это снова не новость для тех, кто ремонтирует стальные и алюминиевые автомобили класса люкс. Но для остальной отрасли это новая концепция. Хорошая новость заключается в том, что с новым оборудованием и некоторыми тренировками вы получите то, что вам нужно. При склеивании заклепками есть некоторые общие черты со склеиванием контактной точечной сваркой сжатием (STRSW), которые будут вам знакомы.
Сходство заключается в том, что сборка панели и подготовка фланца должны быть главными приоритетами для успешного ремонта. Зажимы точечного сварочного аппарата не исправят перекос панели, как и пистолет SPR.Если панели не выровнять, это приведет к некачественному ремонту. Кроме того, подготовка фланца имеет решающее значение, чтобы клей мог правильно прикрепить панели. И, как всегда, не забудьте подготовить картридж с клеем, следуя инструкциям производителя продукта, чтобы обеспечить надлежащее отверждение клея. (См. Рис. 5 Этот пистолет SPR устанавливает запасные заклепки.)
Теперь давайте посмотрим на необходимое оборудование; основным инструментом, который понадобится, является пистолет SPR. Типы автомобилей, которые вы ремонтируете, помогут определить, какое оружие необходимо, типы (глухие заклепки часто используются вместе с SPR) и размер SPR, а также любые аксессуары, необходимые для пистолета SPR.(Для получения более подробной информации см. Информацию о ремонте производителя транспортного средства). На губках пистолета SPR потребуется несколько различных наборов штампов, некоторые из них используются для извлечения ранее установленных SPR, а некоторые — для установки новых SPR. (См. Рис. 6. Это один из многих доступных комплектов пистолетов SPR.)
Последняя часть этой головоломки — выбор правильного размера и типа заклепки. Длина SPR или глухой заклепки должна соответствовать толщине соединяемых панелей.Слишком длинный SPR не сформируется правильно и может оставить отверстие на задней стороне панели, в то время как слишком короткий SPR не сформируется правильно, создав слабое место при ремонте и может вызвать сбой при ремонте. Лучший способ определить, какой SPR требуется, — это следовать инструкциям по ремонту автопроизводителя.
Заключение
Ремонт современных сложных автомобилей — это не ремонт прошлых лет. Обширные комбинации материалов и методов соединения у производителей транспортных средств требуют, чтобы индустрия ремонта столкновений обновила свои инструменты, оборудование, методы, обучение и мыслительный процесс.Если промышленность не адаптируется к этому новому миру, полный и безопасный ремонт также станет частью прошлого.
Связанные курсы I-CAR
Курс Теория сварки алюминия GMA
Курс Введение в пайку MIG
Курс Введение в соединение заклепками
Разрушающий контроль сварных швов
Разрушающий контроль сварных швов, как следует из названия, включает в себя физическое разрушение готового сварного шва для оценки его характеристик.Этот метод тестирования часто используется для ряда приложений. Некоторые из этих приложений включают аттестацию процедуры сварки и аттестационные испытания сварщиков, выборочный контроль производственных сварных швов, исследовательский контроль и работы по анализу отказов. Для определения целостности или рабочих характеристик сварного шва используется ряд методов разрушающего контроля сварных швов. Обычно они включают разрезание и / или разрыв сварного элемента и оценку различных механических и / или физических характеристик.Мы кратко рассмотрим некоторые из наиболее распространенных методов этого типа контроля сварки. Мы рассмотрим испытание на макротравление, испытание на разрыв углового шва, испытание на поперечное растяжение и испытание на управляемый изгиб. Мы рассмотрим, как они используются и для определения характеристик каких типов сварных швов они предназначены. Мы рассмотрим их преимущества перед другими методами контроля и их ограничения.
Макро-травление — Этот метод тестирования обычно включает удаление небольших образцов сварного соединения.Эти образцы полируются по их поперечному сечению, а затем протравливаются с использованием некоторого типа смеси слабых кислот, в зависимости от используемого основного материала. Кислотное травление обеспечивает четкий внешний вид внутренней структуры сварного шва. Особый интерес часто проявляется к линии сплавления, являющейся переходом между сварным швом и основным материалом. Такие параметры, как глубина проникновения, отсутствие плавления, недостаточное проникновение корня, внутренняя пористость, трещины и включения могут быть обнаружены во время осмотра протравленного образца.Этот тип контроля, очевидно, является моментальным снимком общего качества длины сварного шва, когда используется для выборочного контроля производственных сварных швов. Этот тип испытаний часто чрезвычайно успешно используется для выявления проблем сварки, таких как возникновение трещин, при анализе отказов.
Испытание на разрыв углового сварного шва — Этот тип испытаний включает разрыв образца углового сварного шва, сваренного только с одной стороны. Образец имеет нагрузку, приложенную к его несваренной стороне, поперек сварного шва и направленную к его несваренной стороне (обычно в прессе).Нагрузка увеличивается до тех пор, пока сварной шов не разрушится. Затем неисправный образец проверяется, чтобы установить наличие и степень нарушений сплошности сварки. Этот тест даст хорошее представление о степени несплошностей на всей длине испытанного сварного шва (обычно от 6 до 12 дюймов), а не о появлении точек в поперечном сечении, как при испытании на макротравление. Этот тип контроля сварных швов позволяет выявить такие элементы, как отсутствие плавления, внутреннюю пористость и включения шлака. Этот метод тестирования часто используется вместе с тестом на макротравление.Эти два метода тестирования дополняют друг друга, предоставляя информацию об аналогичных характеристиках с различной детализацией и разными способами.
Испытание на поперечное растяжение — Поскольку большая часть конструкции основана на свойствах растяжения сварного соединения, важно, чтобы свойства растяжения основного металла, металла сварного шва, связи между основанием и сварным швом , и зона термического влияния соответствуют проектным требованиям. Предел прочности сварного соединения получают путем вытягивания образцов до разрушения.Прочность на растяжение определяется делением максимальной нагрузки, необходимой во время испытания, на площадь поперечного сечения. Результат будет в единицах натяжения на площадь поперечного сечения. Это испытание почти всегда требуется как часть механических испытаний при оценке технических требований к процедуре сварки для швов с разделкой кромок.
Управляемое испытание на изгиб — это метод испытания, при котором образец изгибается до заданного радиуса изгиба. Для оценки пластичности и прочности сварных соединений используются различные виды испытаний на изгиб.Испытания на управляемый изгиб обычно проводятся поперек оси сварного шва, и их можно проводить в испытательных машинах плунжерного типа или в испытательных приспособлениях для испытания на изгиб по периметру. Испытания на изгиб торца проводят при растяжении торца шва, а испытания на изгиб корня шва — при растяжении корня шва. При испытании толстых листов на изгиб образцы для испытаний на боковой изгиб обычно вырезают из сварного соединения и изгибают с поперечным сечением шва при растяжении. Испытание на управляемый изгиб наиболее часто используется при испытаниях процедуры сварки и аттестации сварщиков.Этот тип испытаний особенно хорош при обнаружении дефектов плавления гильзы, которые часто открываются на поверхности пластины во время процедуры испытания.
TP316L скважинная капиллярная ГНКТ, Капиллярная НКТ, Китай, Производитель
TP316L ГНКТ с капиллярами для забоя скважин
опыта
Нефтегазовый сектор представляет собой один из основных рынков MEILONG TUBE для поставки широкого спектра форм и материалов для коррозионностойких капиллярных трубок.Наша продукция для насосно-компрессорных труб успешно используется в некоторых из самых агрессивных подводных и скважинных условий, и у нас есть многолетний проверенный опыт поставок продукции, отвечающей строгим требованиям к качеству в нефтегазовой и геотермальной энергетике.
Усовершенствования в технологии расширенной эксплуатации нефтяных и газовых месторождений все чаще требовали использования длинных непрерывных труб из нержавеющей стали и никелевых сплавов для гидравлического управления, контрольно-измерительной аппаратуры, закачки химикатов, шлангокабелей и трубопроводов управления.Преимущества этой трубной технологии привели к снижению эксплуатационных расходов, улучшенным методам добычи и уменьшению капитальных затрат за счет подключения скважинных клапанов и закачки химикатов с удаленными и вспомогательными скважинами к стационарной или плавучей центральной станции
опыта
Нефтегазовый сектор представляет собой один из основных рынков сбыта MEILONG TUBE для поставки широкого спектра форм и материалов для коррозионностойких капиллярных трубок.Наша продукция для насосно-компрессорных труб успешно использовалась в некоторых из самых агрессивных подводных и скважинных проектов , и у нас есть многолетний проверенный опыт поставки продукции, которая соответствует строгим требованиям к качеству в нефтегазовой и геотермальной энергетике.
Совершенствование технологии усовершенствованной эксплуатации нефтяных и газовых месторождений все чаще требует использования длинных непрерывных труб из нержавеющей стали и никелевых сплавов для гидравлического управления, контрольно-измерительной аппаратуры, закачки химреагентов, шлангокабелей и трубопроводов для контроля трубопроводов.Преимущества этой трубчатой технологии привели к снижению эксплуатационных расходов, улучшенных методов добычи и уменьшению капитальных затрат за счет подключения скважинных клапанов и закачки химикатов с удаленными и вспомогательными скважинами к стационарной или плавучей центральной операционной платформе.
Диапазон производства
Гибкие НКТ доступны в различных формах продукции в зависимости от требований заказчика. Мы производим сварные и перетянутые швом, сварные швы, перетянутые и бесшовные трубные изделия.Стандартные марки — 316L, сплав 825 и сплав 625. Другие марки нержавеющей стали в дуплексном и супердуплексном исполнении, а также никелевый сплав доступны по запросу. НКТ могут поставляться в отожженном или холоднодеформированном состоянии.
• Сварные и тянутые трубы.
• Диаметр от 3 мм (0,118 ’’) до 25,4 мм (1,00 ’’).
• Толщина стенки от 0,5 мм (0,020 ’’) до 3 мм (0,118 ’’).
• Типичные размеры: 1/4 ’’ x 0,035 ’’, 1/4 ’’ x 0.049 ’’, 1/4 ’’ x 0,065 ’’, 3/8 ’’ x 0,035 ’’, 3/8 ’’ x 0,049 ’’, 3/8 ’’ x 0,065 ’’.
• Допуск на внешний диаметр +/- 0,005 ’’ (0,13 мм) и +/- 10% толщины стенки. Другие допуски доступны по запросу.
• Длина рулона до 13 500 м (45 000 футов) без орбитальных соединений в зависимости от размеров продукта.
• Герметичные трубки с покрытием из ПВХ или неизолированные.
• Доступны на деревянных или стальных катушках.
Материалы
• Аустенитная сталь 316L (UNS S31603)
• Дуплекс 2205 (UNS S32205 и S31803)
• Супер дуплекс 2507 (UNS S32750)
• Инколой 825 (UNS N08825)
• Inco nel 625 (UNS N06625)
Приложения
Компания MEILONG предлагает линию coiled co ntrol из нержавеющей стали и никелевых сплавов.
Наши продукты используются в следующих областях:
• Скважинные гидравлические трубопроводы нтр.
• Скважинный химический завод нитролин.
• Subsea co ntrol линии для гидроэнергетики и закачки химреагентов.
• Smoothbore co ntrol линии, используемые в волоконно-оптических системах.
Вопросы качества
При выборе типа капиллярной гибкой трубы для конкретной среды следует учитывать несколько факторов.Наиболее важные критерии, влияющие на это решение, — это устойчивость к давлению и риск коррозии. Бесшовная труба, прошедшая холодную обработку и отожженную, имеет полностью однородную кристаллическую деформируемую структуру. Ленточный материал, используемый для изготовления сварной трубы, имеет ту же форму, но в месте сварного шва он становится литой структурой, которая может подвергаться коррозии преимущественно окружающей трубе. Благодаря сочетанию холодной обработки и последующего отжига сварной шов me tal можно перекристаллизовать, преобразовав эту область в деформированную структуру, в результате чего получится однородное поперечное сечение с равным потенциалом коррозии по всей трубе, как у бесшовной трубы.Опускание имеет большое значение для достижения рекристаллизации литой структуры сварного шва в частично гомогенизированную отожженную структуру. Дополнительная работа в зоне сварного шва, создаваемая проходами процесса волочения, обеспечивает полную перекристаллизацию.
Теоретически стойкость к давлению труб, изготовленных методом сварки и отжига, должна быть одинаковой, но в правилах проектирования обычной практикой является уменьшение сварных труб из-за риска несовершенного сварного шва, ведущего к ослаблению. Деформации, возникающие при последующей операции перерисовки, определят качество сварного шва, а любые слабые места на центральной линии будут обнаружены визуальным осмотром и / или испытанием под давлением.Поэтому бесшовные сварные и утопленные, сварные и утопленные / вытянутые с заглушкой трубы имеют такое же номинальное давление, которое выше, чем у сварных труб.
Другие соображения, которые могут повлиять на тип указанной трубки, включают шероховатость поверхности, совместимость с компрессионными фитингами, допуски, концентричность, длину и, конечно же, цену. Сварные трубки имеют гладкую внешнюю и внутреннюю поверхность, за исключением буртика, который может выступать в зоне сварки. Это может вызвать проблемы с компрессионными фитингами.Сварные и утопленные трубки имеют гладкую поверхность наружного диаметра, что делает их пригодными для использования с компрессионными фитингами, но имеет несколько более грубое отверстие из-за утопления и выступающий сварной шов pro только на внутреннем диаметре. Сварные, протянутые с помощью пробок и бесшовные трубы имеют гладкую поверхность с наружным диаметром и однородную поверхность отверстия без выступающего сварного шва.
Трубы, изготовленные сваркой из ленты, обычно более центричны, чем бесшовные трубы, где однородность толщины стенок зависит от центричности со первой прошивки в полую форму.Однако бесшовные трубы будут соответствовать стандартным коммерческим допускам, таким как те, что указаны в ASTM A269.
Обычно с помощью шовной сварки полосы можно получить менее длины, чем можно получить путем вытягивания из бесшовных пустот. Эти длины могут быть увеличены путем утопления или вытяжки. Где очень длинные отрезки без сварных швов.
Преимущества перерисовки сварной трубы
Длинные отрезки можно изготавливать с помощью шовной сварки сформированной полосы, но такие трубки имеют неплотность OD и ID disco и могут иметь локальные проблемы механической прочности или коррозии.Сварная и утопленная труба улучшает эти аспекты и за несколько десятилетий доказала свою надежность в эксплуатации на морских платформах. Несмотря на то, что они дороже, чем сварные или однотонные трубы , сварные и перемотанные трубы все же относительно недороги по сравнению с бесшовными.
Бесшовные трубы имеют однородное поперечное сечение , однако это самый дорогой метод изготовления, имеющий ограничение в непрерывной длине, которая может быть получена между соединениями. За небольшую надбавку по сравнению с ценой на сварные и заглубленные трубы, трубы могут изготавливаться методом сварки и вытяжки с плавающей пробкой, в результате чего получается продукт, внешний вид которого аналогичен бесшовному, но со значительным преимуществом в виде гораздо меньшего количества непрерывных длин мм и значительного снижения затрат.
Обеспечение качества
Контроль за процессом и качеством продукции MEILONG TUBE имеет решающее значение для постоянного достижения высочайших стандартов в критически важных нефтегазовых областях. Co ntrol строгого качества применяется на каждом этапе технологических операций. Индивидуальные планы качества, разработанные с учетом требований клиентов к проектам, также могут быть включены в качество нашей продукции.
Линия co ntrol имеет 100% габариты , окончательно проверена и испытана на вихревые токи в соответствии с международными стандартами ASTM или DIN .Перед выпуском и сертификацией все линии проходят 100% гидравлические испытания под давлением.
У нас есть одобрения BS EN ISO 9001 и BS EN ISO 14001, а также одобрения отдельных клиентов.
Co Давление в трубопроводе ntrol
Рабочее давление трубки зависит от условий эксплуатации каждого конкретного применения и требуемого запаса прочности. Это может быть определено или только заказчиком и выражено как пропорция либо давления текучести, либо номинального давления разрыва трубы.Это значения, которые повышают напряжение до теоретического предела текучести или предела прочности материала на растяжение.
В соответствии с традицией безопасное рабочее давление окончательно выражается как пропорция либо прочности на разрыв, либо предела текучести капиллярной трубки. В разных отраслях промышленности и в нормативных документах для сосудов высокого давления применяются разные методы.
Qua lity assurance
Качество нашей продукции для линии co ntrol в нефтегазовом секторе гарантируется не только во время контролируемого производственного процесса co , но и путем тестирования готовой продукции.Типичные тесты включают:
• Неразрушающие испытания
• Гидростатические испытания
• Контроль качества поверхности
• Измерения точности Dimensio
• Факельные и совместные испытания ning
• Испытания на механические и химические свойства.