технологии нанесения, свойства, состав, характеристики
Полимерный металл — металлическая деталь, на поверхность которой с помощью специального оборудования наносится защитное покрытие. После нанесения образуется прочный слой на основе полимеров, который защищает металлические поверхности от воздействия влаги, агрессивных факторов.
Состав:
- коллеры, пигменты;
- связующие вещества;
- разные добавки для улучшения свойств.
Металлы с полимерным покрытием отличаются устойчивостью к воздействию химических веществ, влаги, перепадам температуры.
Сферы применения:
Из отдельных деталей изготавливаются металлоконструкции, которые будут устанавливаться в воде или местах с повышенным уровнем влажности.
Полимерный металл в машиностроении (Instagram / bazz_linser)Обработка проводится для улучшения свойств материала. Возможные изменения:
- Изменение вида, шероховатости поверхностей.
- Повышение электро- и теплопроводности.
- Понижение коэффициента трения.
- Снижение газо- и паропроницаемости.
- Снижение проницаемости ионизирующего излучения.
Добиться подобных свойств можно при внесении дополнительных компонентов к основному составу.
Виды полимерного слоя
Разновидности:
- ПВДФ (поливинилденфторид). Преимущества — устойчивостью к выцветанию и механическим повреждениям, придание блеска поверхностям, увеличение срока службы металлических деталей.
- Пурал. Изготавливается на основе полиуретана. Преимущества — стойкость к сильному нагреванию, воздействию ультрафиолета и химикатов. Недостаток — восприимчивость к пластичному деформированию.
- Полиэстер. Преимущества — стойкость к воздействию ультрафиолета, влаги, химических веществ. Состав имеет высокую гибкость, выдерживает перепады температуры.
- Пластизоль. После проведения работ образуется слой большой толщины. Имеет самую высокую устойчивость к механическим повреждениям, перепадам температуры.
Положительные стороны:
- Высокий уровень адгезии. Если правильно подготовить металлические поверхности, между ними и полимером образуется связь на молекулярном уровне.
- Стойкость к воздействию влаги. Полимерные покрытия наносятся на металлоконструкции, расположенные в воде, ими покрывают днища лодок. Даже при активной эксплуатации защитный слой сохраняет целостность, не пропускает влагу.
- Высокая износоустойчивость, механическая прочность. Поврежденный слой легко восстановить.
- Стойкость к воздействию ультрафиолета. Многие краски по металлу быстро выцветают на солнце. Полимерный слой не подвержен данной проблеме. Он может постоянно находиться под солнечными лучами без потери свойств.
- Стойкость к перепадам температуры.
- Долговечность. При нормальных условиях покрытие прослужит около 50 лет
- Стойкость к воздействию химических веществ. Для проверки этого свойства можно покрыть металлическую деталь полимером и погрузить ее в растворитель.
Защитный слой сохранит целостность, свойства.
Недостатки:
- Из-за высокой адгезии покрытие сложно удалить.
- Защитные составы подходят только для работы с металлом.
- Для нанесения полимеров нужно использовать специальное оборудование.
Автомобиль из полимерного металла (Instagram / pokraska_diskov_astana)Полимерные покрытия выдерживают воздействие открытого пламени. Это связано с технологией нанесения.
Нанесение полимерного слоя
Нанесение полимерного слоя происходит с помощью специального оборудования в промышленных камерах.
Условия нанесения полимера
Особенности проведения работ:
- Уровень влажность в зоне обработки не должен превышать 60%.
- Выполнять работы нужно в герметичной камере.
- Нужно заранее освободить рабочую зону от посторонних предметов.
- Деталь должна быть закреплена.
Нельзя наносить защитное покрытие на улице, в грязных помещениях с большим количеством пыли, мусора.
Подготовка металла
Чтобы увеличить адгезию пластика с металлом, поверхности нужно правильно подготовить. Их нужно очистить от загрязнений, протереть растворителем, чтобы смыть жировые пятна. Обработку для удаления налета можно выполнять химическим, термическим или механическим способами. Важно сделать поверхности ровными, убрать грязь.
Смешивание и применение полимерного состава
Полимерный состав может смешиваться с коллерами для изменения цвета. Нанесение покрытия:
- В герметичной камере включается освещение. Мастер одевается в костюм химзащиты.
- Детали подвешиваются на крюки или зажимаются в специальных креплениях.
- На заготовки навешивается минусовой кабель, называемый массой.
- Камера с мастером закрывается, он наносит краску.
Процесс нанесения должен проходить медленно. Важно равномерно нанести покрытие на поверхности, чтобы не образовалось неровностей.
Нанесение полимерного покрытия (Instagram / ilber.aktobe)Тепловая стабилизация полимерного металла
После нанесения краски выполняется медленного нагревание детали для изменения свойств и характеристик материала. Заготовки погружаются в специальную камеру, которая нагревается до 200°С. Длительность тепловой стабилизации — 60 минут. После этого нужно отключить печь, оставить ее остывать до 100°С. Когда она остынет, можно открывать камеру. Если попытаться охладить детали принудительно, произойдет растрескивание защитного слоя.
Советы по применению полимерных покрытий для металла:
- Перед нанесением полимера нужно подготовить рабочую камеру — установить эффективное освещение, удалить лишние предметы.
- При проведении работ нужно использовать костюм химической защиты, дыхательную маску, защитные очки.
- Нанесение покрытия повторяют 3 раза.
Красить можно одновременно несколько деталей, но для этого нужна просторная покрасочная камера, печь для тепловой стабилизации.
Полимерный слой на металле надежно защищает материал от образования ржавчины, выравнивает поверхности, делает их прочнее. Эффект зависит от правильности подготовки рабочих поверхностей, нанесения полимерного слоя.
Обрезинивание валов, роликов, колес. Гуммирование.
Наша компания оказывает услуги по обрезиниванию, гуммированию металлических поверхностей. Мы предлагаем восстановление изношенного и нанесение нового покрытия из резины, силикона, полиуретана на:
- колеса
- ролики
- валы
В зависимости от технического требования Заказчика обрезинивание производится методом горячего крепления (с использованием формы и без использования формы) или методом холодного крепления.
- Изделия поставляются Заказчику в окончательно обработанном виде.
- На изделия предоставляется гарантия.
- Возможен выезд наших специалистов на предприятия Заказчика.
- Имеем возможность забирать изделия на обработку (обрезинивание) и доставлять готовые изделия Заказчику.
- Подбор покрытия для изделия производится индивидуально по требованию Заказчика.
- Различные цвета и стойкость покрытия к агрессивным средам.
- Твердость покрытия от 25 до 95 ед. по Шору А. Рабочая температура от -60 º до 250º С.
- Широкие технические возможности.
- Обрезинивание валов диаметром до 600 мм.
Качественное обрезинивание — это сложный технологический процесс, который должен проводиться профессионалами.
Работы по обрезиниванию выполняются двумя основными способами:
- Обрезинивание методом горячего крепления (с использованием формы и без использования формы).
Сырую резиновую смесь соединяют с металлической поверхностью в процессе вулканизации. Применяются высококачественные резиновые и силиконовые смеси.
Особого внимания заслуживает обрезинивание валов и роликов методом экструдирования. При выполнении работ данным методом резина наносится методом экструзии непосредственно на заготовку. При этом получается покрытие без включения пузырьков воздуха, сцентрированное по отношению к валу и небольшим припуском на последующую обработку. Данный метод обеспечивает наивысшее качество и значительно увеличивает срок службы валов.
Технические возможности обрезинивания валов данным методом таковы:
- Длина покрываемой поверхности вала до 2200 мм.
- Диаметр вала от 10 до 230 мм.
- Толщина покрытия от 5 до 25 мм.
Метод экструзии незаменим при выполнении таких работ, как обрезинивание полиграфических валов или обрезинивание валов ламинатора.
Гуммирование валов формовым методом или методом намотки позволяют наносить покрытие на
- валы диаметром до 600 мм.
При обрезинивании колес мы в основном используем формовой метод.
- Обрезинивание методом холодного крепления
Вулканизованную резину крепят адгезивами (клеями) к металлической поверхности.
Обрезинивание валов, роликов, колес – услуга, актуальная практически для всех отраслей промышленности.
Как защитить металл от коррозии или механического истирания?
Гуммирование – это нанесение резинового покрытия на металлические изделия с целью защиты их от коррозии и других вредных воздействий.
Гуммирование считается одним из лучших способов защиты к действию агрессивных сред. Срок службы гуммированных покрытий зависит от температуры и характера окружающей агрессивной среды. В благоприятных условиях покрытия сохраняют свои защитные свойства до 7 лет. Гуммирование – один из лучших способов защиты химической аппаратуры.
Гуммирование, как метод защиты оборудования от коррозии имеет множество преимуществ:
- высокая водо- и химическая стойкость;
- устойчивость к абразивному износу;
- устойчивость к переменным динамическим нагрузкам;
- устойчивость к резким колебаниям температуры;
- очень низкая водо- и газопроницаемость.
Несколько слов о гуммировании валов.
Эти работы выполняются двумя основными способами:
- Гуммирование валов методом горячего крепления (с использованием формы и без использования формы).
- Гуммирование валов методом холодного крепления.
Особого внимания заслуживает гуммирование валов методом экструдирования. Данный метод обеспечивает наивысшее качество и значительно увеличивает срок службы валов. Подробнее об этом и других методах гуммирования валов рассказано выше.
Гуммирующий материал подбирается индивидуально.
При гуммировании применяются высококачественные резиновые и силиконовые смеси.
Процесс гуммирования может быть произведен нашими специалистами как на предприятии Заказчика, так и в специальной мастерской на нашей производственной базе. Гуммирование крупногабаритного оборудования производится по месту его установки.
По вопросам, связанным с ремонтом, восстановлением покрытия валов,
роликов, колес обращайтесь по телефонам:
(496) 547-77-22; (496) 547-77-21; (926) 541-05-77
Как сделать обрезинивание металла
Обрезинивание позволяет сделать любую твердую поверхность не скользящей, более теплой и приятной на ощупь.
Материалы:
- самоклеющаяся сетка серпянка;
- малярный скотч;
- герметик;
- растворитель.
Как выполнить прорезинивание на металле
Поверхность для обрезинивания необходимо обезжирить растворителем. Если это металл склонный к образованию ржавчины, то его нужно также прогрунтовать, чтобы на нем под резиной не началась коррозия от контакта с компонентами герметика.
После обезжиривания на поверхность наклеивается стеклосетка. Если нужно обрезинивать торцы и боковые стороны предмета, то серпянка клеится с перегибом и на них. Желательно наложить 2 слоя сетки, чтобы толщина обрезинивания была хотя бы 1 мм.
Если обрезинивание выполняется частично, то по его границе приклеивается малярная лента.
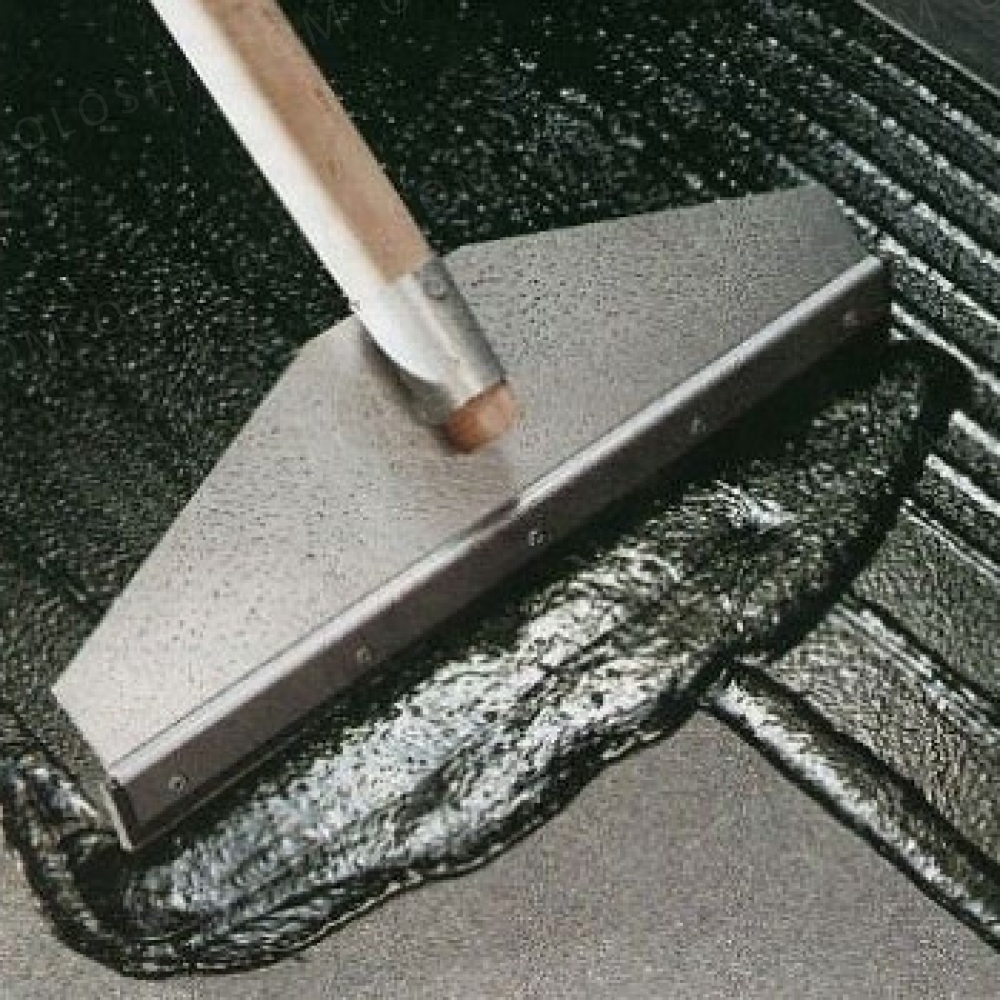
Далее на сетку наносится герметик. Он может быть силиконовым, полиуретановым, акриловый или любым другим. Выбор герметика зависит только от нужных рабочих качеств обрезиненного слоя, которые нужно получить.
Шпателем или пластиковой картой состав втирается в сетку до заполнения всех ячеек. После этого герметик просушивается феном.
Как только на герметике появится присохшая корка, наносится второй слой.
Он также разглаживается и просушивается феном.
На этот раз состава уйдет меньше, только чтобы частично загладить углубления в ячейках сетки.
Чтобы окончательно убрать неровности и создать матовую поверхность, укладывается третий тонкий слой герметика.
Он разглаживается в одном направлении губкой для мытья посуды.
Выровняв герметик нужно придать ему матовость. Она создается легкими касательными движениями губки.
Далее нужно сделать паузу до полного высыхания герметика.

Обрезинивание с использования малярной стеклосетки позволяет точно контролировать толщину слоя герметика. Серпянка армирует покрытие, увеличивает его прочность и стойкость к трению. Данным способом можно покрывать металл, дерево и прочие материалы, совместимые с применяемым видом герметика.
Смотрите видео
Защитные покрытия: виды, функции, особенности
Уникальной разновидностью неметаллических защитных покрытий являются антифрикционные материалы. По внешнему виду они напоминают краски, однако вместо пигментов содержат частицы твердых смазочных веществ, которые равномерно распределены в смеси связующих компонентов и растворителей.
В противокоррозионной практике для изоляции металла от воздействия агрессивных сред используются специальные защитные покрытия. Все они подразделяются на металлические и неметаллические.
Металлические – анодные и катодные – покрытия наносятся на поверхности методами газотермического напыления, окунания, гальванизации, плакирования или диффузии.
К неметаллическим защитным покрытиям относятся лакокрасочные составы, полимерные пленки, силикатные эмали, резины, оксиды металлов, соединения фосфора, хрома и др.
Рассмотрим все виды покрытий подробнее.
Металлические защитные покрытия
В качестве анодных металлических покрытий выступают металлы, электрохимический потенциал которых меньше, чем у обрабатываемых материалов. У катодных он, наоборот, выше.
Анодные покрытия обеспечивают электрохимическую защиту металлических поверхностей и выполняют свои функции даже при нарушении целостности слоя.
Катодные покрытия препятствуют проникновению агрессивных сред к основному металлу благодаря образованию механического барьера. Они лучше защищают поверхности от негативных воздействий, но только в случае неповрежденности.
В зависимости от способа нанесения металлические покрытия подразделяются на следующие виды.
Гальванические покрытия
Гальванизация – это электрохимический метод нанесения металлического защитного покрытия для защиты поверхностей от коррозии и окисления, улучшения их прочности и износостойкости, придания эстетичного внешнего вида.
Гальванические покрытия применяются в авиа- и машиностроении, радиотехнике, электронике, строительстве.
В зависимости от назначения конкретных деталей на них наносятся защитные, защитно-декоративные и специальные гальванические покрытия.
Защитные служат для изоляции металлических деталей от воздействия агрессивных сред и предотвращения механических повреждений. Защитно-декоративные предназначены для придания деталям эстетичного внешнего вида и их защиты от разрушительных внешних воздействий.
Специальные гальванические покрытия улучшают характеристики обрабатываемых поверхностей, повышают их прочность, износостойкость, электроизоляционные свойства и т.д.
Разновидностями гальванических покрытий являются меднение, хромирование, цинкование, железнение, никелирование, латунирование, родирование, золочение, серебрение и пр.
Газотермическое напыление
Представляет собой перенос расплавленных частиц материала на обрабатываемую поверхность газового или плазменным потоком. Покрытия, образованные таким методом, отличаются термо- и износостойкостью, хорошими антикоррозионными, антифрикционными и противозадирными свойствами, электроизоляционной или электропроводной способностью. В качестве напыляемого материала выступают проволоки, шнуры, порошки из металлов, керамики и металлокерамики.
Выделяют следующие методы газотермическогого напыления:
- Газопламенное напыление: самый простой и недорогой метод, применяемый для защиты крупных площадей поверхности от коррозии и восстановления геометрии деталей
- Высокоскоростное газопламенное напыление: используется для образования плотных металлокерамических и металлических покрытий
- Детонационное напыление: применяется для нанесения защитных покрытий, восстановления небольших поврежденных участков поверхности
- Плазменное напыление: используется для создания тугоплавких керамических покрытий
- Электродуговая металлизация: для нанесения антикоррозионных металлических покрытий на большие площади поверхности
- Напыление с оплавлением: применяется тогда, когда риск деформации деталей отсутствует или он оправдан
Погружение в расплав
При использовании этого метода обрабатываемые детали окунаются в расплавленный металл (олово, цинк, алюминий, свинец). Перед погружением поверхности обрабатываются смесью хлорида аммония (52-56 %), глицерина (5-6 %) и хлорида покрываемого металла. Это позволяет защитить расплав от окисления, а также удалить оксидные и солевые пленки.
Данный метод нельзя назвать экономичным, так как наносимый металл расходуется в больших количествах. При этом толщина покрытия неравномерна, а наносить расплав в узкие зазоры и отверстия, например, на резьбу, не представляется возможным.
Термодиффузионное покрытие
Данное покрытие, материалом для которого выступает цинк, обеспечивает высокую электрохимическую защиту стали и черных металлов. Оно обладает высокой адгезией, стойкостью к коррозии, механическим нагрузкам и деформации.
Слой термодиффузионного покрытия имеет одинаковую толщину даже на деталях сложных форм и не отслаивается в процессе эксплуатации.
Плакирование
Метод представляет собой нанесение металла термомеханическим способом: путем пластичной деформации и сильного сжатия. Чаще всего таким образом создаются защитные, контактные или декоративные покрытия на деталях из стали, алюминия, меди и их сплавов.
Плакирование осуществляется в процессе горячей прокатки, прессования, экструзии, штамповки или сваривания взрывом.
Виды и особенности неметаллических покрытий
Неметаллические покрытия подразделяются на органические и неорганические. Они создают на обрабатываемых поверхностях тонкую, инертную по отношению к агрессивным веществам пленку, которая предохраняет детали от негативных воздействий окружающей среды.
Лакокрасочные защитные покрытия
В состав таких покрытий входят пленкообразующие вещества, наполнители, пигменты, пластификаторы, растворители и катализаторы. Варьирование состава позволяет получать материалы со специфическими свойствами (токопроводящие, декоративные, особопрочные, жаростойкие и т.п.). Они не только защищают изделия в различных условиях, но и придают им эстетичный внешний вид.
В группу лакокрасочных покрытий входят лаки, краски, грунтовки, олифы, шпаклевки.
Силикатные эмали
Применяются для изделий, работающих при высоких температурах в химически агрессивных средах.
Эмалевое защитное покрытие формируется с помощью порошка или пасты. Процесс проходит в несколько этапов. Сначала на изделие наносится грунтовая эмаль – она улучшает адгезию, уменьшает термические и механические напряжения.
Затем, после спекания первого слоя при температуре +880… + 920 °С, накладывается покровная эмаль, после чего изделие снова подвергается нагреванию до +840… +860 °С.
Если требуется нанести несколько слоев силикатной эмали, вышеописанные операции проводят поочередно несколько раз. Изделия из чугуна, к примеру, обрабатывают в 2-3 подхода.
Застывшая эмаль представляет собой тонкое, похожее на стекло, покрытие. Его основным недостатком является сравнительно низкая прочность – под воздействием ударных нагрузок эмаль может растрескиваться или скалываться.
Полимерные защитные покрытия
В число наиболее распространенных полимеров, применяющихся для защиты металлов от коррозии, входят полистирол, полиэтилен, полипропилен, полиизобутилен, фторопласты, эпоксидные смолы и др.
Полимерное покрытие осуществляется методами окунания, газотермического или вихревого напыления, обычной кистью. Остывая, оно образует на поверхности сплошную защитную пленку толщиной несколько миллиметров.
Разновидностью полимерных являются антифрикционные твердосмазочные покрытия. Внешне эти материалы похожи на краски, однако вместо пигментов они содержат высокодисперсные частицы твердых смазочных веществ, которые равномерно распределены в смеси связующих компонентов и растворителей.
Основу покрытий могут составлять дисульфид молибдена, графит, политетрафторэтилен (ПТФЭ) и прочие твердые смазки. В качестве связующих применяются акриловые, фенольные, полиамид-имидные, эпоксидные смолы, титанат, полиуретан и некоторые другие специальные компоненты.
Антифрикционные твердосмазочные покрытия, а также специальные растворители и очистители для предварительной подготовки поверхностей разрабатывает российская компания «Моденжи».
Материалы MODENGY применяются в средне- и тяжелонагруженных узлах трения скольжения (направляющих, зубчатых передачах, подшипниках и т.д.), на деталях двигателей внутреннего сгорания (юбках поршней, вкладышах валов, дроссельной заслонке), в резьбовом крепеже, трубопроводной арматуре, пластиковых и металлических элементах автомобилей (замках, петлях, пружинах, скобах, механизмах регулировки и т.д.), а также в других парах трения металл-металл, металл-резина, полимер-полимер, металл-полимер.
Покрытия MODENGY наносятся однократно на весь срок службы деталей. С их помощью создаются узлы трения, не требующие дальнейшего обслуживания и применения традиционных смазочных материалов.
Антифрикционные покрытия MODENGY отличаются:
- Высокой несущей способностью
- Работоспособностью в запыленной среде
- Низким коэффициентом трения
- Широким диапазоном рабочих температур
- Высокой износостойкостью
- Противозадирными и антикоррозионными свойствами
- Стойкостью к воздействию кислот, щелочей, растворителей и других химикатов
- Работоспособность в условиях радиации и вакуума
Покрытия ложатся тонким слоем, поэтому практически не меняют исходные размеры деталей, зато обеспечивают им необходимый комплекс триботехнических и защитных свойств.
Применение материалов MODENGY позволяет эффективно управлять трением, повышать ресурс и энергоэффективность оборудования.
Оксидные защитные пленки
Оксидирование – это окислительно-восстановительная реакция металлов, которая возникает благодаря их взаимодействию с кислородом, электролитом или специальными кислотно-щелочными составами. В результате этого процесса на металлических поверхностях образуется защитная пленка, которая увеличивает их твердость, снижает риск образования задиров, улучшает приработку деталей и повышает срок их службы.
Оксидирование используется для получения защитных и декоративных покрытий, а также для формирования диэлектрических слоев. Различают химические, анодные (электрохимические), термические, плазменные и лазерные методы этой обработки.
Резиновые защитные покрытия
Гуммирование, или создание защитных покрытий из резины или эбонита, помогает защитить трубопроводы, химические аппараты, резервуары для перевозки и хранения химических веществ от воздействия агрессивных сред.
Защитное покрытие может быть сформировано из мягкой или твердой резины. Консистенция контролируется добавками серы: мягкая содержит от 2 до 4 % этого вещества, твердая – от 30 до 50 %.
Покрытие наносится на предварительно очищенные и обезжиренные поверхности. Скопившийся после обработки воздух выдавливается валиком. В качестве заключительного этапа гуммирования проводится вулканизация изделий.
Резиновые покрытия являются хорошими диэлектриками, обладают стойкостью ко многим кислотам и щелочам (но не к сильным окислителям). Из существенных недостатков резиновых покрытий можно выделить их старение со временем.
Смазки и пасты
При длительном хранении и перевозке металлоизделий в качестве защитных покрытий могут использоваться специальные смазки и пасты – они препятствуют попаданию на поверхности влаги, пыли и различных газообразных веществ, наносятся кистью или методом распыления.
Консервационные материалы изготавливаются на основе минеральных масел (вазелинового, машинного) и воскообразных веществ (воска, парафина, мыла). Очень популярны смазки, в состав которых входит 5 % парафина и 95 % петролатума (смеси парафинов, масел и минеральных восков – церезинов).
Главный недостаток паст и смазок, применяющихся в качестве защитных покрытий, состоит в том, что целостность образовавшейся пленки легко нарушить. Именно поэтому лучшей альтернативой пластичных составов являются антифрикционные твердосмазочные покрытия.
Снижение трения и износа в парах «резина-металл» с технологией твердой смазки
Применение покрытий MODENGY, реализующих технологию твердой смазки, позволяет максимально снизить потери на трение и повысить срок эксплуатации резино-металлических уплотнительных устройств.
Наиболее распространенными уплотнительными устройствами в машиностроении являются манжетные и кольцевые уплотнения. Они широко используются в трубопроводной арматуре, погружных насосах, на валах, в подшипниках и других узлах с парами трения «резина-металл». Конструкция многих винтовых насосов также предусматривает металлический ротор, который при вращении контактирует с резиновой оболочкой.
Упругость и эластичность конструкционных материалов позволяет таким уплотнениям плотно прилегать к металлическим поверхностям и обеспечивать хорошую герметизацию. В то же время при взаимном перемещении элементов большое количество энергии уходит на преодоление сил трения. Это явление приводит к повышенному износу и деформациям резиновых элементов, нарушению герметичности сопряжений и снижению ресурса оборудования в целом.
При проектировании и изготовлении уплотнительных устройств используются современные технологичные материалы. Это позволяет решить две противоречивые, на первый взгляд, задачи – обеспечить их максимальную эффективность и одновременно снизить потери на трение.
Механизм трения в парах «резина-металл»
Одной из проблем, возникающих при работе резиновых уплотнений, является прилипание резины к сопряженным металлическим поверхностям. В состоянии покоя коэффициент трения резины по металлу достигает огромных значений – f=1,0…1,2. Для страгивания деталей в этом случае необходимо преодолеть силу трения и приложить к уплотнению значительные усилия. При этом резина выдавливается в зазоры, и на поверхности уплотнения часто образуются характерные повреждения (илл. 1). В дальнейшем они могут привести к разрыву материала и разгерметизации узла.
Илл. 1. Внешний вид повреждений резиновой детали, вызванных прилипанием к металлической поверхности
Величина силы трения резины по металлу прямо пропорциональна коэффициенту трения, который, согласно молекулярно-механической теории, имеет механическую и молекулярную составляющие. Механическая возникает вследствие взаимного перемещения и деформации контактирующих поверхностей, имеющих миконеровности. Молекулярная составляющая обусловлена силами притяжения молекул конструкционных материалов.
В резино-металлических парах преобладает механическое трение. Снизить его можно путем шлифования, полирования или других методов финишной обработки металлической поверхности. Сглаживание микронеровностей увеличивает площадь площадь контакта деталей, однако в этом случае начинает преобладать молекулярное трение.
Таким образом, снижение трения в парах «резина-металл» является сложной инженерной задачей. Для ее решения существует современная технология твердой смазки, которую реализуют антифрикционные твердосмазочные покрытия MODENGY.
Принцип работы покрытий
Антифрикционные твердосмазочные покрытия формируют на поверхности металлической детали композиционный слой толщиной около 15-25 мкм. Связующее вещество прочно сцепляется с основой и образует полимерную матрицу, ячейки которой заполнены частицами твердых смазочных материалов – дисульфида молибдена, политетрафторэтилена, графита и др.
При нанесении покрытия микронеровности поверхности заполняются и выравниваются, увеличивается ее опорная площадь (илл. 2). Слоистая структура материала обеспечивает малое сопротивление сдвигу. При этом снижается механическая составляющая коэффициента трения.
Илл. 2. Покрытие на поверхности детали
Образовавшийся защитный слой препятствует прилипанию резины к металлу и выполняет разделительную функцию. Это снижает молекулярную составляющую коэффициента трения.
Антифрикционные твердосмазочные покрытия MODENGY во многих случаях полностью заменяют другие виды смазочных материалов. В отличие от пластичных смазок или масел покрытия выдерживают очень высокие нагрузки, не выдавливаются из зоны трения, инертны по отношению к различным химическим веществам и устойчивы к агрессивным факторам.
Выбор покрытия для пар трения «резина-металл»
Задачу снижения трения в парах «резина-металл» успешно решают покрытия MODENGY 1006, MODENGY 1010, MODENGY 1011, MODENGY 1014. Инженеры компании «Моденжи» реализовали десятки проектов, основанных на применении данных покрытий на:
- Внутренних цилиндрических поверхностях пневмо- и гидроцилиндров (илл. 3)
- Вращающихся валах, контактирующих с резиновыми манжетными уплотнениями
- Штоках трубопроводной арматуры
- Металлических деталях насосов – роторах и подшипниках скольжения
- Элементах торцовых уплотнений
Илл. 3. Элементы гильзы пневоцилиндра до и после нанесения покрытия MODENGY 1014
Покрытия MODENGY для пар трения «резина-металл» обладают следующими параметрами и характеристиками.
MODENGY 1006 с дисульфидом молибдена и графитом имеет серо-черный матовый цвет. Диапазон его рабочих температур -70…+315 °С, несущая способность (машина трения SRV) – 1800 МПа, коэффициент трения при контактном давлении 1300 МПа – 0,05.
Черное глянцевое покрытие MODENGY 1010 с ПТФЭ в качестве твердосмазочного компонента работает при температурах от -70 до +250 °С. Его несущая способность по методу Falex составляет 2300 H, а степень защиты от коррозии – более 300 часов в соляном тумане.
MODENGY 1011 на основе ПТФЭ после нанесения и полимеризации образует серебристый защитный слой, выдерживающий температуры от -70 до +250 °С. Данное покрытие обладает такое же несущей способностью, как и MODENGY 1010, однако от коррозии оно защищает дольше – в течение 500 часов.
MODENGY 1014 с дисульфидом молибдена и ПТФЭ имеет серый матовый цвет. Диапазон его рабочих температур составляет -75…+255 °С. Покрытие имеет самые высокие показатели несущей способности (2800 МПа) и антикоррозионных свойств (более 672 часов в соляном тумане) среди всех перечисленных материалов.
Все покрытия наносятся на предварительно подготовленную (очищенную и обезжиренную) поверхность методом распыления. Уже через 10 минут жидкий состав высыхает и набирает начальную прочность, при которой детали можно транспортировать без риска повреждения покрытия. Полноценная эксплуатация деталей возможна только после полной полимеризации слоя.
Преимущества покрытий MODENGY
Покрытия MODENGY предотвращают скачкообразное движение и прилипание резины к металлу при страгивании с места, за счет чего плавность хода деталей и ресурс механизма в целом повышаются.
За счет заполнения впадин и выравнивания микронеровностей улучшается герметичность конструкции.
Покрытия MODENGY обеспечивают отличную антикоррозионную защиту металла, что в ряде случаев позволяет отказаться от применения нержавеющих сталей и заменить их более дешевыми конструкционными материалами.
Поверхности под нанесение покрытий не требуют сложной финишной обработки. При условии предварительной очистки и обезжиривания достаточно шероховатости 0,8 мкм. Это снижает стоимость изготовления деталей.
Благодаря снижению трения в уплотнительных устройствах повышается КПД механизмов.
На сухой защитный слой не налипают абразивные частицы, что обеспечивает возможность работы в условиях запыленности.
Антифрикционные твердосмазочные покрытия MODENGY разработаны с учетом всех триботехнических процессов, протекающих в парах трения «резина-металл». Именно поэтому они позволяют максимально снизить потери на трение и повысить срок эксплуатации резино-металлических уплотнительных устройств.
Антифрикционные покрытия. Их преимущества перед пластичными смазками
В статье рассмотрены преимущества антифрикционных покрытий MODENGY, приведены типичные примеры их применения.
Для снижения трения в подвижных узлах любого оборудования требуется их своевременное смазывание. Выбор вида и способа смазки производится с учетом конструкции и условий эксплуатации пары трения.
Механизм действия традиционных жидких и пластичных смазочных материалов состоит в образовании разделительной смазочной пленки между движущимися поверхностями при определенном сочетании нагрузки и скорости, необходимом для установления гидродинамического или полужидкостного режима трения.
Однако реальные условия работы механизмов далеки от идеальных. Некоторые из механизмов (например, оборудование кирпичного производства) предназначены для постоянной эксплуатации в пыльной среде под воздействием высоких температур, нагрузок. Узлы большинства машин и оборудования в отдельные моменты времени или в течение всей эксплуатации также работают в режиме, при котором происходят локальные нарушения смазочной пленки, приводящие к повышенному трению, изнашиванию и образованию задиров. В таком режиме находятся не только тяжелонагруженные тихоходные узлы, но и все механизмы в моменты пуска, останова, реверсирования движения и в процессе приработки. Наиболее очевидным подтверждением этого факта является износ, который сопровождает работу всех машин.
В последние годы получил распространение новый вид смазочных материалов – антифрикционные покрытия. Они существенно снижают износ, значительно повышают надежность работы и ресурс узлов и механизмов.
Антифрикционные твердосмазочные покрытия (АТСП) – это смазочные материалы, подобные краскам, но содержащие вместо красящего пигмента высокодисперсные частицы твердых смазочных веществ, равномерно распределенных в смеси связующих веществ и растворителей.
Твердые сухие смазки обладают стабильным низким коэффициентом трения и обеспечивают хороший смазочный эффект.
В зависимости от того, какая несущая способность требуется от покрытия, в качестве сухих смазочных веществ применяют:
- Для высоких нагрузок – дисульфид молибдена MoS2 и/или поляризованный графит
- Для средних нагрузок – политетрафторэтилен (тефлон, PTFE, ПТФЭ) и/или другие полимеры
Связующие элементы обеспечивают адгезию к субстрату, химическую стойкость и защиту от коррозии. В качестве связующих используют эпоксидные смолы, титанаты, полиуретаны, акриловые, фенольные, полиамид-имидные и специальные компоненты.
При использовании органических связующих элементов термостойкость антифрикционных покрытий достигает +250 °С, а неорганические системы позволяют покрытиям работать при экстремально высоких температурах — вплоть до +600 °С.
Растворители предназначены для переноса и распределения твердых смазок и связующих на субстрате, а также для обеспечения нужной вязкости антифрикционного покрытия путем разбавления перед нанесением.
Для улучшения необходимых свойств, а также для модификации и придания антифрикционным покрытиям новых свойств в них добавляют присадки.
Антифрикционные покрытия наносятся на поверхность с помощью обычных технологий окрашивания, таких как распыление, трафаретная печать, окунание, нанесение кистью. После нанесения покрытия и сушки растворитель испаряется, а связующие вещества полимеризуются и обеспечивают надежное сцепление с основой. Выбор конкретного способа нанесения антифрикционных покрытий зависит от геометрии покрываемых деталей и желаемого результата с точки зрения равномерности и долговечности покрытий.
При нанесении покрытия на одну из деталей пары трения в процессе работы происходит частичный перенос твердых смазок на сопряженную поверхность. Таким образом, в процессе трения под нагрузкой формируются плотные и очень гладкие антифрикционные пленки, закрывающие неровности материала основы. В результате при работе пары трения скорость изнашивания покрытия сводится к минимуму.
Эти процессы иллюстрирует фотография, полученная с помощью сканирующего электронного микроскопа при увеличении 1000 раз. На левой части показано покрытие сразу после отверждения, а на правой – после приработки и формирования гладкой пленки из твердых смазок.
Преимущества антифрикционных покрытий перед другими видами смазочных материалов
Применение антифрикционных покрытий на сегодняшний день является самым перспективным способом решения многих проблем, связанных с потерями на трение в движущихся узлах.
В отличие от сухих смазок в виде натертых пленок частицы твердых веществ антифрикционных покрытий прочно удерживаются на поверхности с помощью связующего компонента.
По сравнению с применением традиционных смазочных материалов – пластичных и жидких смазок – антифрикционные покрытия имеют ряд преимуществ.
После нанесения антифрикционного покрытия образовавшаяся тонкая сухая смазочная пленка предотвращает налипание абразивной пыли и грязи на поверхность.
Благодаря тому, что твердые смазочные вещества удерживаются на поверхности связующими, антифрикционные покрытия в большинстве случаев обеспечивают смазку на весь срок службы. Сухие смазки в составе АТСП обладают исключительной термической стабильностью и химической инертностью, стойкостью к окислению и влаге. Они не стареют и не испаряются, способны эффективно работать в условиях радиации и вакуума даже после продолжительного простоя узла.
Толщина покрытия легко контролируется и может составлять от 5 до 20 мкм, что практически не влияет на исходную точность размеров детали. Возможно локальное нанесение антифрикционных покрытий на определенные участки поверхности. Обладая высокими противоизносными и антикоррозионными свойствами, АТСП могут заменить хромирование, цинкование и другие виды обработки.
Сравнение основных видов твердых смазок
Результаты испытаний антифрикционных покрытий MODENGY показали их способность снижать трение до минимальных значений (см. рисунок 1).
Рис. 1. Результаты испытаний АТСП на машине трения Falex LFW1 в соответствии с ASTM D2714
При применении покрытий на основе дисульфида молибдена коэффициент трения с ростом нагрузки снижается и стабилизируется на значении несколько сотых. Такое трение без применения антифрикционных покрытий возможно только в режиме жидкостной смазки, когда движущиеся поверхности полностью разделены слоем масла и не контактируют напрямую друг с другом.
Другие характеристики антифрикционных покрытий также значительно различаются в зависимости от имеющихся в составе сухих смазок.
Существенным недостатком графита, ограничивающим сферу его применения по сравнению с дисульфидом молибдена, является его недостаточная адгезия к металлическим поверхностям. Его молекулы неполярны и проявляют смазочные свойства лишь в присутствии влаги.
Этот недостаток можно устранить путем внедрения в слоистую структуру графита поляризующих агентов. Высокая адгезия поляризованного графита к металлическим поверхностям, наряду с термической стабильностью, делают его одним из наиболее перспективных инновационных смазочных материалов.
Поляризованный графит начала применять компания «Моденжи», создавшая уникальную линейку АТСП.
Типичные применения АТСП MODENGY
Линейка продуктов MODENGY включает антифрикционные покрытия на основе различных видов твердых смазок, в том числе дисульфида молибдена, графита, политетрафторэтилена (тефлона), а также специальных композиций.
Связующее вещество в составе покрытия определяет его защитные свойства, химическую стойкость, а также тип отверждения (температуру полимеризации).
Выбор конкретного материала производится с учетом конструкции узла трения, условий его работы и желаемого способа нанесения.
Антифрикционные покрытия MODENGY способны работать в широком температурном диапазоне, что позволяет предлагать решения для самых различных, в том числе экстремальных условий.
MODENGY 1005 на основе дисульфида молибдена характеризуется повышенной несущей способностью. Рабочие температуры: от -70 до +255 °С. Сферы применения:
- Подшипники скольжения
- Направляющие скольжения
- Шлицевые и шпоночные соединения
- Зубчатые передачи
- Другие узлы с парами трения металл-металл
- Подшипники скольжения
- Направляющие скольжения
- Шлицевые и шпоночные соединения
- Зубчатые передачи
- Другие узлы с парами трения металл-металл
- Подшипники скольжения
- Направляющие скольжения
- Зубчатые передачи
- Резьбовые соединения
- Шлицевые и шпоночные соединения
- Другие узлы с парами трения металл-металл
- Подшипники скольжения
- Направляющие скольжения
- Зубчатые передачи
- Резьбовые соединения
- Шлицевые и шпоночные соединения
- Другие узлы с парами трения металл-металл
MODENGY 1001 на основе дисульфида молибдена и графита выдерживает температуры от -180 до +440 °С. Наносится на:
- Подшипники скольжения
- Направляющие скольжения
- Открытые зубчатые передачи
- Закрытые зубчатые передачи
- Цепные передачи
- Шлицевые и шпоночные соединения
- Резьбовые соединения
- Гибкие валы в оболочках
- Сопряжения с посадками с натягом
- Регулировочные клинья
- Электрические контакты
- Ходовые винты
- Тросы управления в оболочках
- Другие узлы с парами трения металл-металл
- Подшипники скольжения
- Направляющие скольжения
- Зубчатые передачи
- Резьбовые соединения
- Шлицевые и шпоночные соединения
- Другие узлы с парами трения металл-металл
- Подшипники скольжения
- Резьбовые соединения
- Подвижные уплотнения
- Другие узлы с парами трения металл-пластик, металл-резина
- Уплотнительные устройства
- Направляющие скольжения
- Подшипники скольжения
- Гибкие валы
- Резьбовые соединения
- Зубчатые передачи
- Другие узлы с парами трения металл-пластик, пластик-пластик, кожа-пластик, кожа-металл, дерево-кожа, металл-резина, металл-металл
Дополняя пластичные смазки и масла, а часто полностью заменяя их, антифрикционные покрытия MODENGY надежно защищают от износа металлические и пластиковые поверхности в самых экстремальных условиях эксплуатации, часто используются в качестве аварийной смазки.
Производители автокомпонентов применяют антифрикционные покрытия MODENGY при массовом выпуске поршней, нанося их методом трафаретной печати.
Перед нанесением АТСП требуется тщательно очищать и обезжиривать поверхности — в целях лучшего сцепления покрытия с ними.
Качество и долговечность покрытий MODENGY гарантирует только их применение в комплексе со вспомогательными средствами для очищения и финишной подготовки поверхностей.
Для быстрой очистки и обезжиривания металлических деталей, рабочих поверхностей тормозных систем, цепных передач, фрикционных муфт, электрических контактов предназначен Очиститель металла MODENGY. Его многокомпонентная формула обеспечивает эффективное удаление загрязнений различной химической природы: нефтепродуктов, силиконовых масел, консервационных составов, адсорбированных пленок газов, влаги и др. Состав испаряется быстро и без остатка, не вызывает коррозии металлов.
В качестве финального шага перед нанесением АТСП специалисты настоятельно рекомендуют использовать Специальный очиститель — активатор MODENGY. Он обеспечивает дополнительное обезжиривание поверхностей и способствует высокой адгезии антифрикционного покрытия.
Пошаговую инструкцию по нанесению аэрозольного антифрикционного покрытия на примере MODENGY Для деталей ДВС смотрите ниже.
Наука о адгезии — соединение резины с металлом
Адгезия резина к металлу
Исторически сложилось так, что в резиновой промышленности использовалось несколько методов соединения, чтобы добиться надежного и прочного соединения резины с металлом. В современных клеевых технологиях используются как однослойные, так и двухслойные клеевые составы, причем предпочтение отдается в зависимости от требований обслуживания склеиваемого узла. Например, двухслойная система будет предпочтительнее для применений, связанных с воздействием суровых условий окружающей среды, таких как автомобильная промышленность.В данной статье основное внимание будет уделено двухслойным системам.
Двухслойные клеевые системы состоят из грунтовочного слоя и адгезионного верхнего покрытия. Грунтовка обеспечивает надежную адгезию к металлической подложке, обеспечивая при этом необходимую реактивность с адгезивным верхним покрытием. Грунтовка также обеспечивает термостойкость и устойчивость к коррозии, которые желательны для применений в суровых условиях окружающей среды. Типичная грунтовка состоит из пленкообразующих полимеров, сшиваемых смол, наполнителей и системы носителя на основе растворителя или воды.
Рисунок 1 — Узел, соединенный между резиной и металлом
На высохшую грунтовку наносится адгезивное финишное покрытие. Верхнее покрытие обеспечивает средство реакции с ненасыщенностью в основной цепи эластомера, как правило, во время процесса формования. Верхнее покрытие также должно реагировать со слоем грунтовки, чтобы обеспечить межслойную адгезию клея и грунтовки. Типичное адгезионное верхнее покрытие может состоять из отвердителей, пленкообразующих полимеров, наполнителей и системы носителя.
Внутри связанного узла на каждом из интерфейсов происходят различные взаимодействия, так что достигается общая адгезия. Интерфейс грунтовки к металлу включает адсорбцию и / или хелатирование компонентов грунтовки на поверхности металла. Граница раздела грунтовка-клей обеспечивает межслойную адгезию за счет адсорбции и / или диффузии соответствующих компонентов внутри слоев. Перекрестное соединение химического состава реактивного верхнего покрытия с грунтовкой и эластомером также происходит на каждой из границ раздела этих соответствующих слоев.Внутри адгезионного и грунтовочного слоев также происходит внутреннее сшивание полимерных систем.
Слои компонентов в связанном узле расположены таким образом, что они постепенно уменьшаются по модулю от грунтовки к эластомеру. Это можно увидеть в связанном узле, показанном на рисунке 1. Причина такого расположения состоит в том, чтобы обеспечить градиент изменения жесткости между подложкой и эластомером, устраняя резкую границу раздела.
Процесс соединения резины с металлом
Последовательное производство прочных узлов, соединенных резиной и металлом, включает рассмотрение пяти основных концепций: тип эластомера, подготовка поверхности, подготовка грунтовки / клея, и литье.Каждый шаг равнозначен с точки зрения важности, и каждый из них требует высокого уровня внимания на этапе проектирования и разработки процесса. Надежный план управления технологическим процессом также приведет к производству прочных сборных узлов. В следующих разделах более подробно рассматриваются все основы.
Для получения дополнительной информации о принципах склеивания эластомеров и выборе правильной комбинации эластомер / клей щелкните здесь.
Эластомер ТипПервое, что нужно учитывать при выборе подходящей адгезивной системы, — это тип эластомера, который будет использоваться.Считается, что некоторые эластомеры легче связывать, чем другие, из-за более высокой степени полярности и более высокого уровня ненасыщенности. Это можно рассматривать как показатель склеиваемости, который показан на рисунке 2. Существуют различные рецептуры клея, предназначенные для склеивания различных типов эластомеров общего и специального назначения.
Следует также учитывать, что компаундирование играет важную роль в связываемости эластомеров. Что касается уровней наполнителя, то тип и количество наполнителя играет роль в сцепляемости.Например, соединения с менее чем 40 p.h.r. (частей на сотню каучука) сажу обычно сложнее связывать, чем сажи с более высоким содержанием. Кроме того, включение в состав глины и кремнезема способствует склеиванию. Уровень серы в соединении также играет важную роль в способности связывания, поскольку соединения с небольшим содержанием серы или без нее могут быть трудно связывать. Минимум 1 час. было обнаружено, что сера в составе способствует связыванию. Также необходимо обратить внимание на связывающее действие различных ускорителей, масел, наполнителей и антиразложений, которые используются в составе.
Подготовка поверхностиСледующим важным этапом в процессе склеивания является подготовка поверхности металлической подложки. Правильно подготовленная металлическая поверхность — важный шаг для получения оптимального сцепления. Первое действие при подготовке металлической поверхности — удаление с поверхности всех технологических масел и смазок. Это может быть достигнуто за счет использования методов обезжиривания растворителем или процесса щелочной очистки. Нерастворимые материалы, такие как ржавчина, также необходимо удалить с поверхности металла.Это может быть достигнуто с помощью методов механической обработки, таких как струйная обработка стальной или алюминиевой абразивной дробью, шлифовка или механическая обработка.
Часто для работы с деталями требуется воздействие суровых условий окружающей среды. В таких случаях может потребоваться химическая обработка металла для предотвращения окисления. Химическая обработка металла обычно осуществляется в форме фосфата цинка или железа для стали, кислотного травления для нержавеющей стали и процессов хроматного алодирования или анодирования алюминия.Эта химическая обработка металла также служит для защиты целостности соединения. После подготовки металлических частей рекомендуется как можно скорее нанести грунтовку. Если необходимо сделать перерыв между подготовкой и грунтовкой, важно предотвратить загрязнение металлической поверхности.
Подготовка грунтовки / клеяСледующим шагом в процессе склеивания является подготовка грунтовки и клея к использованию. При подготовке клеевой системы к использованию в первую очередь необходимо довести материалы до предполагаемой рабочей температуры.Это важно, так как температура влияет на вязкость продукта. Также чрезвычайно важно правильно перемешать грунтовку и клей до и во время использования. Это позволяет равномерно распределить осевшие ингредиенты по продукту во время нанесения. Перемешивание материалов на основе растворителей может происходить путем перемешивания или встряхивания; Системы на водной основе следует смешивать только с низкой скоростью (20-30 об / мин), чтобы предотвратить пенообразование. Системы на водной основе никогда не следует встряхивать по той же причине.Системы на основе растворителей следует смешивать на взрывозащищенном оборудовании со скоростью 40-60 об / мин. В таблице 1 приведены типовые рекомендации по смешиванию клеевых систем на основе растворителей.
Наконец, в зависимости от выбранного метода нанесения может возникнуть необходимость разбавить адгезивную систему рекомендованным разбавителем. Разбавление продукта до соответствующей вязкости имеет решающее значение для установления контролируемого процесса, в котором достигается соответствующая толщина пленки. При разбавлении грунтовки или клея важно добавлять разбавители медленно, чтобы предотвратить образование материала.Это может привести к необратимому гелеобразованию или разделению фаз материала.
Нанесение грунтовки / клеяСледующим обсуждаемым аспектом процесса склеивания является нанесение грунтовочно-клеевой системы. Можно использовать несколько методов нанесения грунтовки и финишного покрытия; к ним относятся распыление, окунание, чистка щеткой и прокатка. Независимо от выбранного метода, важно использовать метод, позволяющий достичь оптимальной рекомендуемой толщины сухой пленки системы.Обычно рекомендуемая толщина сухой пленки для оптимального склеивания составляет 0,005–0,010 мм для грунтовок и 0,015–0,020 мм для клея. Увеличенная толщина сухой пленки верхнего покрытия (0,02-0,038 мм) рекомендуется для склеивания после вулканизации.
Стандартная операция по нанесению адгезивной системы на основе растворителя заключается в нанесении грунтовки на подготовленный металл, сушке грунтовки, нанесении адгезионного верхнего покрытия и сушке верхнего покрытия. Системы на водной основе требуют предварительного нагрева металла перед нанесением; заданная температура поверхности металла 322 ° С.15-333,15К рекомендуется. Сушку этих материалов можно проводить при комнатной температуре или ее можно ускорить за счет использования печи с циркуляцией воздуха при температурах 338,15-366,15 К. Важно не допускать, чтобы температура поверхности детали превышала 393,15K, поскольку это может привести к преждевременному склеиванию. Схема типичного распыления клея на основе растворителя показана на рисунке 3.
После нанесения адгезивной системы важно соблюдать осторожность при обращении с покрытыми деталями, чтобы не загрязнять клеящую поверхность.По этой причине при работе с деталями следует использовать хлопчатобумажные перчатки. Также важно отформовать детали как можно скорее после нанесения покрытия. Однако в случае необходимости замены детали следует хранить в запечатанных контейнерах, чтобы они не подвергались воздействию загрязняющих веществ и ультрафиолетового излучения. Следует связаться с производителями клея для получения информации о максимальном времени перерыва покрытых деталей.
БагетДетали из резины по металлу обычно производятся с использованием процессов литья под давлением, литья под давлением или прессования.Автоклавирование и паровое формование без давления также используются в некоторых специализированных приложениях. В процессе формования необходимо тщательно определять параметры, чтобы вулканизация эластомера и отверждение клея происходили одновременно. Кроме того, во время цикла формования обязательно должен быть достигнут тесный контакт эластомера и клея. Это достигается за счет оптимизации давления формования и вязкости эластомера; это обеспечивает надлежащее смачивание эластомера на клейкой поверхности.Также необходимо обеспечить поддержание однородной температуры в каждой полости формы на протяжении всего цикла формования. Колебания температуры могут привести к потенциальному отказу от облигаций.
Другой важный аспект процесса формования включает нагрев деталей с покрытием, когда они загружаются в полости формы; это называется предварительным запеканием. Важно оптимизировать условия предварительного обжига деталей с покрытием для процесса формования. В некоторых случаях чрезмерное нагревание может привести к преждевременному отверждению клеевой системы.В других случаях отсутствие предварительного обжига может препятствовать активации клея во время цикла формования. Использование загрузочных досок может помочь гарантировать, что все детали в формах с несколькими гнездами будут предварительно обожжены в течение одного и того же времени.
Этап формования имеет решающее значение для получения качественного соединения, поскольку и эластомер, и адгезивная система зависят от этого этапа для отверждения / вулканизации вместе друг с другом. Отсутствие переменного контроля на этом этапе может привести к спорадическим сбоям облигаций на местах.
Для получения дополнительной информации о принципах склеивания эластомеров и выборе правильной комбинации эластомер / клей щелкните здесь.
Тестирование / поиск неисправностей
Испытания на сцепление резины с металлом обычно проводятся в соответствии с рекомендациями ASTM D 429-14. Этот метод испытаний описывает восемь типов испытательных образцов и методов (методы от A до H), которые можно использовать для оценки склеивания. В методе испытаний также определены средства определения типа нарушений адгезии.«R» обозначает разрушение резины; это желательный режим отказа для связанных узлов, поскольку он указывает на то, что отказ произошел в слое резины. «RC» указывает, что отказ произошел на границе раздела резина-цемент (клей). «CP» — это разрушение на границе раздела цемента (адгезива) и грунтовки, а «CM» — разрушение на границе раздела цемента (адгезива) и металла или раздела металла с грунтовкой. Примеры этих типов отказов показаны на Рисунке 4.
Рисунок 4Использование этой номенклатуры для режима отказа позволяет техническому персоналу выполнить более целенаправленную оценку устранения неисправностей и определить вероятную основную причину.Было обнаружено, что более 50% разрывов связки — это разрушение RC, примерно 30% — разрушение CM, а оставшаяся часть представляет собой комбинацию CP и когезионного разрушения (когезионное разрушение — это разрыв внутри грунтовочного или клеевого слоя). Следует отметить, что подавляющее большинство неисправностей в полевых условиях связано с недостаточной толщиной сухой пленки грунтовки и / или верхнего покрытия. Это указывает на важность контроля толщины клеевой пленки на данной детали.
Для получения дополнительной информации о принципах связывания эластомеров и испытании связи резина-металл щелкните здесь.
Сводка
Адгезивные системы между резиной и металлом традиционно представляют собой двухслойные системы, включающие грунтовку и верхнее покрытие / клей, которые можно использовать для приклеивания широкого спектра эластомеров к субстратам (обычно металлическим). Механизм адгезии основан на различных взаимодействиях, которые происходят между поверхностями раздела металла, грунтовки, клея и эластомера. Чтобы клеевая система выполняла свою функцию, ее необходимо правильно использовать. Это включает рассмотрение пяти основных аспектов адгезии резины к металлу: тип эластомера, метод подготовки металла, подготовка грунтовки / клея, нанесение грунтовки / клея и операция формования.Внимание к деталям, касающимся каждого из этих аспектов процесса соединения резины с металлом, позволит обеспечить надежную операцию соединения и надежную готовую деталь.
Для получения дополнительной информации о принципах склеивания эластомеров и выборе правильной комбинации эластомер / клей щелкните здесь.
Проблемы с приклеиванием резины к металлу
60000 тем вопросов и ответов — образование, алоха и развлечениятема 10157
Обсуждение началось в 2001, но продолжаться до 2020 года
2001 г.В.Сэр,
У меня проблемы с приклеиванием металла к резине с помощью:
1. Связующие вещества cil.
2. Связующие вещества Megum.
3. Связующие вещества Chemlock.
Я занимаюсь производством резиновых рулонов для промышленного использования. Старая резина удаляется из стального корпуса. Стальная поверхность подвергается пескоструйной очистке, тщательно очищается растворителем (нафтой). Наносится связующий агент, когда он высыхает, листы нитриловой резины оборачиваются ручным давлением вокруг стального корпуса.Хлопковая лента и веревка плотно обматываются. Собранный корпус вулканизируется в автоклаве с открытым паром с использованием ступенчатого отверждения. Разрушение чаще всего происходит от стальной поверхности.
Посоветуйте, пожалуйста, решение.
Мухаммад Азим— Лахор, Пенджаб, Пакистан
2001 г.
A. Уважаемый господин Азим:
Почти все производители шин решают эту проблему, покрывая стальную проволоку бронзой перед вулканизацией. Они считают, что это лучше всего остального. Единственная проблема в том, что если вы производитель рулонов, вам нужен цех по нанесению бронзы, чтобы работать на вас, или вам нужно оборудование для нанесения щеточного покрытия, чтобы сделать это самостоятельно в своем магазине.
Удачи,
Гильермо МарруфоМонтеррей, Нидерланды, Мексика
2001
A. Попробуйте нанести тонкий слой (1–5 десятых мил) 70/30 Cu / Zn (латунь) перед склеиванием.
Tom Pullizzi
Falls Township, Пенсильвания
2001
A. Покрытие валков химическим никелем. Несколько лет назад кто-то покрыл несколько форм шин, думая, что это поможет отсоединить их. Это произошло наоборот, и форма так и не распалась. Чтобы вызвать это явление, должна быть настоящая резина.
Дэн Уивер— Токкоа, Джорджия
2001
А.В авиастроении выполняется значительное количество соединений резины с металлами. Основным правилом подготовки поверхности является получение и поддержание поверхности, «свободной от воды». По моему опыту, продукты на нефтяной основе никогда не имели такой чистой поверхности.
Алан Купер— Даллас, Техас
2001
A. Я не уверен, что следует выбирать бронзовый (Cu / Sn) сплав, а использовать латунное покрытие (Cu / Zn). Обычно альфа-латунь дает хорошее сцепление. Возможно, бронза подойдет, но обычно используется латунь.
Per Moller— Дания
2001 г.
A. Следующие вещи важны.
1. Обработка поверхности и чистота поверхности.
2. Поверхность не окисляется.
3. Толщина грунтовки.
4. Толщина клея.
5. Температура застывания. (<350 ° F)
— Шарлотт, Северная Каролина
2002
A. Используете ли вы двухкомпонентный агент, то есть грунтовочный слой, а затем связующий агент, такой как Chemisol? Дробеструйная очистка с последующим обезжириванием должна дать достаточно хорошую поверхность для сцепления грунтовки.Попробуйте разные обезжириватели. Учтите, что ЛЮБЫЕ масла, попадающие на связующее, препятствуют приклеиванию резины. Достаточно прикоснуться к агенту руками без перчаток.
Возможно, происходит предварительное отверждение связующего. Вы используете тепло для сушки?
Рэй Галлахер— Ирландия
2007
A. 1-очистка поверхности хлористым метиленом или обработка металлического вала на токарном станке
2-нанесение связующего грунта
3-нанесение связующего или верхнего слоя
4-температура отверждения не менее 150 ° C ступенчато
5-если в этом случае возникнут какие-либо проблемы, резиновая смесь имеет чрезмерные ускорители и должна быть сведена к минимуму, а смазочное масло несовместимо с резиной и связующим.
-10-й день месяца Рамадан — Египет
Как приклеить резиновую прокладку к стальному тренажеру?
2007 — эта запись добавлена к этой теме редактором вместо создания дублирующейся темы В. Я разработал тренажерный зал; Есть две стойки из стали, на которых сидит гантель. Я использую резиновую прокладку, чтобы смягчить вес. Мне нужно, чтобы резина постоянно прилипала к стали.
Какой клей / связующее мне следует использовать?
дизайнер продукта — Бока Ратон, Флорида
17 марта 2010 г.
А.Кажется, виновата подготовка металла. Процедура должна быть:
1. Пескоструйная очистка с использованием острых железных крошек для стали (может быть, 350 микрон) и оксида алюминия для цветных металлов. Если используется новая оправка, ее необходимо обезжирить как перед пескоструйной очисткой, так и после нее.
2. Обезжирьте, используя чистый растворитель (затем используйте чистые перчатки).
3. Нанесите тонкий слой и высушите на воздухе в чистой среде (обычно кистью наносят на маленькие валики). Некоторые каучуки (например, NBR, VMQ, FKM) можно связать одним связующим, для других требуется верхнее покрытие (которое сцепляется с первым слоем и резиной).
4. Плотно оберните резиновые полоски, особенно на концах, чтобы не допустить попадания пара вдоль линии склеивания. N.B. некоторые пористые металлы (например, алюминий) могут нуждаться в первом обжиге покрытия, чтобы предотвратить проникновение пара снизу.
5. Поэтапное отверждение зависит от вулканизации резины и обычно не влияет на адгезию NBR. NBR сжимается на оправке и добавляет сжимающее усилие к линии соединения. Некоторые каучуки, которые требуют ступенчатого отверждения для выделения отходящих газов, включают силикон, FKM, vamac.
Будьте осторожны, не склеивайте в пыльной среде или там, где используются разделительные средства.
Надеюсь, это поможет.
Грег Роулинсон— Манчестер, Великобритания
Приклеивание эпоксидной смолы к стали с помощью RTV
22 августа 2012 г. В. Сразу после сушки стальной детали мы склеиваем магнит с эпоксидным покрытием, используя 1 часть силиконового каучука RTV. Высушенная стальная поверхность должна иметь чистоту 40 дин / см (без разрывов воды) или лучше для обеспечения желаемой прочности сцепления. Может кто-нибудь посоветовать подходящее химическое вещество и концентрацию ??
Спасибо.
— Элкхарт, Индиана, США
24 августа 2012 г.
А.Воздействие воздуха или кислородной плазмы на полимеры, такие как резина и ПВХ, увеличивает поверхностную энергию этих материалов. Считается, что это происходит из-за сшивки полимерных цепей. Эффект легко проверить, капнув каплю воды на необработанную поверхность. Он остается каплей, а на обработанной плазмой поверхности легко растекается, т.е. смачивает поверхность. Это свойство помогает значительно улучшить сцепление.
Х. Р. Прабхакара — консультантbangaloreplasmatek.com — Бангалор, Карнатака, Индия
27 августа 2012 г.
В.Приношу извинения за то, что я случайно пропустил ключевую информацию в моем первоначальном вопросе:
* Мы моем и ополаскиваем стальные детали ультразвуком.
* Они устраняют ржавчину с помощью системы сушки поставщика.
* Поставщик не удаляет капли воды так быстро и энергично, как центрифуга.
* Мы без проблем используем центрифуги.
* Мы хотим использовать полностью автоматизированную систему поставщика (с сушилкой) на нашем производственном участке. Если нам необходимо установить центрифугу на производственном участке, это преимущество автоматизации будет потеряно.
* Нам нужны сухие, нержавеющие стальные детали с чистотой не менее 40 дин / см, поэтому мы можем приклеить силиконовую резину RTV 1 часть к магнитам с эпоксидным покрытием.
Какое химическое вещество / метод / концентрация добавки к воде для ополаскивания DI лучше всего обеспечивает желаемый результат?
Спасибо за вашу помощь.
— Элкхарт, Индиана, США
19 сентября 2012 г.
A. Отец:
Когда я работал в одном отделе компании, другой отдел (отдел оборудования для выкапывания картофеля) спросил меня о приклеивании резины к стали.Я не знал ответа, но я видел резину, приклеенную к стали в машине для копания картофеля.
С уважением,
Доктор Томас Х. Кук Консультант по цинкованию— Хот-Спрингс, Южная Дакота, США
20 сентября 2012 г.
A. Один метод, который часто используется для приклеивания арматурной проволоки в шинах, заключается в том, чтобы сначала покрыть сталь латунной пластиной.
Джеффри Холмс, CEF
Спартанбург, Южная Каролина
Услуги компаний по склеиванию резины и металла
Список компаний, занимающихся склеиванием резины и металла
Применения
Склеивание резины и металла предлагает производителям способ создания более сложных деталей, как малых, так и большой, для применения в самых разных отраслях промышленности.Общие области применения включают гашение вибрации, амортизацию, уплотнение, рассеяние трения, шумоизоляцию, комфортный захват и многое другое.
Обычно металло-резиновые изделия, изготовленные с помощью этого процесса, используются в таких отраслях, как аэрокосмическая, автомобильная, строительная, электрическая, промышленное машиностроение, медицина, сантехника, прокат резиновых изделий и гасители вибрации.
Произведенная продукция
Применения резины, приклеенной к металлическим деталям, многочисленны и разнообразны.Примеры обычных приклеенных к металлической резине деталей и продуктов включают уплотнения, прокладки, поверхности колодок, педали, подшипники и т.п.
В аэрокосмической и автомобильной промышленности они помогают при установке и функционировании ножных педалей, бамперов, рулевых колес, усиленных шин, опор двигателя и т. Д. В строительстве и производстве процессы соединения резины с металлом помогают создавать компоненты продукта, включая конвейерные ленты, прокладки, подшипники, ролики с резиновым покрытием и многое другое.Они также служат для медицинской промышленности с деталями на силиконовой связке, такими как ручки хирургических инструментов. Кроме того, они встречаются в компонентах электрических кабелей, заглушках, трубах и резервуарах с резиновым покрытием.
Соединение резины с металлом — Colorado Molded Products Co.
История
Производители впервые начали использовать натуральный каучук в качестве клея еще в 1830 году. Всего девять лет спустя Чарльз Гудиер открыл процесс вулканизации; то есть он обнаружил, что может сделать резину эластичной, смешав ее с серой и затем нагревая.Примерно 20 лет спустя, в 1862 году, Чарльз Сандерсон получил британский патент на процесс электроосаждения латуни на металлическую основу. Его цель, которую он выполнил, заключалась в том, чтобы сделать соединение резины с металлом более успешным, сделав металл более приспособленным для удержания этой связи.
В начале 20 века производители автомобилей обнаружили, что в их новых продуктах будут использоваться резиновые амортизаторы. Чтобы приспособиться к этому, им нужно было разработать методы для более прочного соединения резины с металлом.Их первым решением была обработка кристаллизованного каучука кислотами. Таким образом они могли создавать резиновые цементы на основе растворителей. Эти цементы были именно тем материалом, который им нужен для лучшего сцепления резины с металлом. К концу 1920-х годов резиновые цементы на основе растворителей были стандартными связующими веществами в автомобильной промышленности.
Спустя много лет после того, как производители начали использовать связующие на основе растворителей, они поняли, что эти клеи вредны для окружающей среды. Поэтому они перешли на клеи на водной основе, которые намного более экологичны.Кроме того, когда только началось соединение резины с металлом, производители чаще всего использовали сталь всех марок.
Сегодня производители выполняют склеивание резины с металлом, используя широкий спектр процессов склеивания, адгезионных материалов и металлов.
Материалы
Процесс склеивания резины включает три основных компонента: металлическую основу, резиновый материал и связующие вещества.
Металлические материалы
Основное требование, которому должна соответствовать металлическая подложка (металлическая поверхность, которую необходимо склеить), — это способность выдерживать высокое давление и высокую температуру, возникающую в процессе.Однако то, что материал можно использовать для склеивания резины, не означает, что он всегда будет хорошо работать. Скорее, результаты связывания резины со сплавом зависят от состава сплава.
Типы склеиваемого металла весьма разнообразны. Самый популярный — алюминий. Другие распространенные металлы, используемые для резиновой склейки, включают сталь, латунь, бериллий и медь. Склеивание резины также может выполняться с неметаллическими материалами, такими как ткань, стекло и различные пластмассы.
Сталь — это железный сплав, известный своей высокой прочностью на растяжение, долговечностью, пластичностью и свариваемостью.
Алюминиевые сплавы стали наиболее популярным металлом для склеивания, поскольку он менее дорогой и более легкий, чем сталь, но он не снижает прочности или качества уплотнения.
Латунные сплавы в целом привлекательны и легки. Они также не образуют искр и антимикробны и хорошо работают в условиях низкого трения.Они плохо работают в условиях высокой температуры, так как имеют низкую температуру плавления.
Бериллий — это медный сплав с некоторыми превосходными качествами, такими как высокая электропроводность, пластичность, способность к термообработке, стабильность, коррозионная стойкость и низкая ползучесть.
Медь — это природный элемент, известный как металл за его электропроводность, теплопроводность, коррозионную стойкость, антимикробные свойства, пластичность, мягкость, пластичность, немагнетизм и способность к соединению.
Резиновые материалы
Что касается каучука и резиновых эластомеров (резиноподобных материалов), производители могут использовать любой тип, при условии, что он может течь в форму, не вызывая заметного уровня сшивки, и до тех пор, пока материалы, из которых состоит резина, не будут слишком быстро вытекать на поверхность неотвержденной массы.
Типы каучука и резиновых эластомеров, которые производители обычно используют в процессе склеивания, включают нитрил, неопрен, силикон и ряд других синтетических и натуральных каучуковых материалов.
Нитриловый каучук — это резиновый материал с отличной адгезией, отличной стойкостью к истиранию, хорошей стойкостью к разрыву, хорошей или отличной маслостойкостью и хорошей или отличной стойкостью к растворителям. Этот эластомер — отличный выбор для связывания резины с металлом, помимо создания связанных продуктов, которые будут в присутствии высокополярных, таких как ацетон или хлорированных углеводородов.
Неопрен — чрезвычайно популярный синтетический каучуковый материал. Он обладает высокой прочностью на разрыв, отличными атмосферостойкостью, хорошей устойчивостью к разрыву и отличной стойкостью к истиранию.При приклеивании к металлу он обычно используется в автомобильной промышленности, строительстве, производстве проводов и кабелей, а также в общественном транспорте.
Силиконовый каучук известен своей превосходной термостойкостью, высокой прочностью на разрыв и разрывом, а также отличными атмосферостойкостью. Чаще всего производители прикрепляют его к металлу для создания уплотнений, уплотнительных колец и прокладок для использования в HVAC, электротехнике, машиностроении и общественном транспорте.
Связующее вещество
Связующее вещество — это растворы на основе воды или растворителя, на которые нанесено грунтовочное покрытие, состоящее из смол фенольного типа, и верхнее покрытие из различных материалов, включая полимеры.Большинство решений запатентованы и доступны для стандартной покупки. По большому счету, производители теперь используют клеи на водной основе в качестве связующих веществ, в отличие от клеев на основе растворителей.
Клеи на водной основе гораздо более экологически безопасны, чем клеи на основе растворителей. Кроме того, было обнаружено, что они столь же долговечны и обеспечивают одинаково безопасные и надежные уплотнения.
Подробности процесса
После выбора подложки, резинового материала и связующего клея процесс склеивания следует довольно универсальной процедуре.Он начинается со стандартного процесса формования резины, в ходе которого производители создают формованную резиновую поверхность. Затем он продолжается обработкой металлической поверхности и поверхности резины и заканчивается нанесением связующего вещества на эти поверхности.
1. Грунтовка резины
Во-первых, производители должны нанести на резину серый грунтовочный слой с помощью распылительной машины большого объема с низким давлением. Обратите внимание, что производители должны следить за тем, чтобы площадь распыления была немного шире, чем площадь, занимаемая черным финишным слоем, подлежащим нанесению.
2. Очистка подложки
Затем, прежде чем они смогут покрыть подложку клеем, производители тщательно ее очищают; они не могут оставить после себя никаких масел или грязи в процессе изготовления. Для этого они могут использовать химическую очистку, пескоструйные аппараты или обезжириватели.
3. Формование резины
Следующий этап, процесс формования резины, является наиболее важной частью процесса склеивания резины. Для этого производители сначала помещают металлический компонент в форму.После этого обычно вводят нагретую, почти расплавленную, неотвержденную резину. Это называется резиной для литья под давлением. На этом этапе процесса формования производители могут добавлять или не добавлять плакированные вставки для дополнительной прочности сцепления. Они также могут добавлять вставки для дополнительной устойчивости. Пластинчатые вставки изготавливаются из металлических материалов, таких как сталь. Производители изготавливают вставки самых разных форм и размеров. Если они включают в себя вставки в процессе формования, они называют процесс формования вставкой или литьем под давлением.
4. Отверждение резины
После помещения резины в форму производители оставляют резину для высыхания и отверждения. После полного высыхания деталь считается готовой, и ее вынимают из формы. Иногда форма сохнет так, что она немного больше поверхности металла, поэтому вокруг металла образуется тонкий слой резины. В других случаях форма и основа сильно отличаются друг от друга из-за сложной конструкции резиновых деталей.
Конструкция
При разработке детали, соединенной резиной с металлом, производители учитывают детали применения, такие как окружающая среда, в которой она будет находиться, как часто она будет использоваться, тип нагрузки (и) на нее. должен поддерживать или выдерживать любые применимые стандартные требования.
На основе этих данных производители принимают решение о типе связующего, а также о способах склеивания и формования. Обычно производители выбирают резиновый материал в зависимости от изготавливаемой детали или используемого металла. Производители выбирают необходимое количество покрытий в зависимости от вида воздействия, которому подвергнется деталь. Если деталь не будет подвергаться воздействию высокой влажности, давления или тепла, производители могут успешно склеить ее с помощью только одного слоя адгезива.Точно так же толщина связующего слоя зависит от природы резинового материала, на который он нанесен.
Варианты и аналогичные процессы
Некоторые из процессов отверждения резины, которые производители используют для связывания резины с металлом, включают химическое отверждение, отверждение выхлопным паром, отверждение вулканизатора и индукционный нагрев.
Химическое отверждение начинается, когда производители наносят связующее на подкладку, а затем оставляют ее при комнатной температуре в течение нескольких дней.Это позволяет химическому веществу полностью проникнуть в подкладку. Если они захотят, производители могут ускорить процесс, добавив тепла. Эту практику они часто используют на судах или резервуарах с полевой футеровкой, нуждающихся в ремонте.
Отверждение отработанным паром включает заглушку емкости с субстратом, чтобы пар просачивался внутрь и отверждал его. Производители обычно заглушают основание, набивая на него острый пар или заглушая отбортовку, чтобы пар мог проникнуть внутрь. Отверждение отработанным паром — это щадящий метод, который предотвращает ослабление или повреждение связующего и связывающего клея.
Отверждение вулканизатора довольно просто. Производители осуществляют это, помещая связанный резиной металл в вулканизатор с острым паром. Там он лечит под давлением. Отверждение вулканизатора создает самую прочную связь резины с металлом.
Индукционный нагрев — это энергоэффективный бесконтактный метод отверждения, в котором для отверждения продуктов используется замкнутый цикл индукционного нагрева. Производители часто используют его как часть поточного производства, потому что он очень быстрый, точный и надежный, а также потому, что он обеспечивает точное отверждение крошечных пространств.
Преимущества
Соединение резины с металлом дает множество преимуществ тем, кто использует склеенные продукты и детали. Во-первых, склеивание создает одно из самых прочных клеевых соединений. Во-вторых, соединение резины с металлом универсально; производители могут отливать резину в металлические подложки с любым дизайном. Еще один аспект универсальности соединения резины с металлом — это температурный диапазон. Поскольку производители могут использовать в этом процессе очень много различных резиновых материалов, а также связующих и отвердителей, они могут создавать продукты, которые работают в чрезвычайно широком диапазоне температур.Наконец, поскольку производители могут использовать адгезивные материалы на водной основе и резину, не содержащую свинца, соединение резины с металлом более экологически безвредно, чем многие другие процессы соединения.
Выбор подходящего производителя
Чтобы помочь вам в поиске поставщика высококачественных услуг по склеиванию резины и металла, мы перечислили некоторых из лучших известных нам производителей в индустрии склеивания. Прежде чем вы их изучите, мы рекомендуем вам потратить некоторое время на то, чтобы записать спецификации вашего приложения, такие как ваш бюджет, срок, объем вашего запроса, ваши стандартные требования и предпочтения по доставке.Таким образом, когда придет время определять подходящего производителя, у вас будет контрольный список квалификаций.
Когда будете готовы, взгляните на те компании, которые мы перечислили на этой странице. Вы найдете их зажатыми между нашими информационными параграфами. В зависимости от ваших требований выберите трех или четырех человек, с которыми вы хотите подробно поговорить, а затем обратитесь к каждому из них. Используя свой список спецификаций в качестве руководства, обсудите свое приложение и их услуги. После того, как вы поговорите с каждым производителем, сравните и сопоставьте их услуги, их цены и общее обслуживание клиентов и выберите наиболее подходящий для вас.Удачи!
Информационное видео по соединению резины с металлом
Услуги компаний по соединению резины с металлом
бизнес Отраслевая информация
Соединение резины и металла
Каучук обладает способностью связываться с металлами всех видов. Связанная резина прочнее, чем в исходном состоянии. Производители во многих отраслях промышленности полагаются на соединение резина-металл для своих компонентов.Резину можно использовать для объединения нескольких частей в единую конструкцию, а также она обеспечивает очень прочное сцепление с металлом.
Процесс соединения резины с металлом — это средство, с помощью которого резина механически связывается с металлической вставкой в процессе формования . Продукты, изготовленные с помощью услуг по склеиванию резины и металла, используются в различных областях промышленности, торговли и медицины.
Соединение резины с металлом — Britech Industries | Соединение резины с металлом — Da / Pro Rubber, Inc. | Соединение резины и металла — Accurate Products, Inc. |
Соединение резины с металлом — RD Rubber Technology Corporation | Соединение резины с металлом — Accurate Products, Inc. | Соединение резины с металлом — Accurate Products, Inc. |
Применения для соединения резины с металлом
Металлическое соединениеиспользуется для изготовления изделий для различных областей применения в автомобильной, аэрокосмической, строительной, сантехнической, электрической, промышленной технике, глушителях и в медицинской промышленности, а также в производстве резиновых валиков на заказ.
В автомобилестроении используется большое количество металлических деталей, связанных резиной. Рулевое колесо соединено с рулевой колонкой с помощью различных резиновых деталей. Ножные педали и бамперы являются примерами обычных предметов, которые имеют характеристики резины / металла.
Изделия для соединения резины с металлом
К изделиям, изготовленным из соединения резины и металла, относятся:
Материалы для соединения резины с металлом:
Производство металлических и резиновых изделий заключается в приклеивании резины к металлу с помощью различных клеев.В процессе соединения резины с металлом есть три основных компонента:
- Резиновый материал — можно использовать любой тип бутадиен-стирольного силиконового каучука при условии, что материал может течь в форму без развития значительного уровня сшивки, а вещества, составляющие резиновый материал, не будут быстро вытекать на поверхность неотвержденного запаса.
- Металлическая основа (покрытие) — Металлическое соединение — это металлическое вещество, которым может быть алюминий, латунь, медь, сталь или многие другие металлы, которые используются в процессе соединения резины и металла; разные металлы используются в зависимости от требований приложения.
- Связующие агенты — состоят из:
- Растворы на основе растворителя или воды
- Грунтовка на основе фенольных смол
- Покрытие из полимеров и других материалов
Традиционным металлом, используемым при склеивании резиновых металлов, является сталь во всех ее формах и сортах. Однако все большее количество изделий изготавливается из алюминиевых сплавов и полиамидов, поскольку они менее дороги и легче по весу без ущерба для качества или долговечности.
Пошаговое описание процесса склеивания
Принимая важные меры, начиная с проектирования детали и заканчивая тестированием, изготовитель резины и производитель могут гарантировать, что соединение достаточно прочное для применения и условий эксплуатации.
- Оцените конструкцию и геометрию детали на предмет технологичности.
- Определите резину и связующие вещества в зависимости от назначения.
- Определите, как металлическая поверхность будет реагировать на резину.
- Приобретите вставку. После того, как все стороны согласятся выбрать правильный материал для вставки, производитель или формовщик может закупить формовку вставки в соответствии с окончательными спецификациями. Поручая формовщику закупать вставку, производитель может сэкономить время и полагаться на отношения с поставщиками формовочной фирмы для обеспечения качества.
- Подготовьте деталь. Способность формовочной фирмы подготовить деталь к максимальной прочности сцепления имеет решающее значение. Сложная химия взаимодействия металла и резины, а также влияние самого процесса формования резины должны быть учтены путем подготовки вставки.Подготовка включает в себя один или все следующие шаги:
- Перед тем, как на основу можно будет нанести клей, ее необходимо хорошо очистить от пыли, грязи и масел, оставшихся в процессе изготовления.
- Вставки (резиновые) сначала подготавливаются к производству с использованием системы обезжиривания , чтобы очистить детали от любых загрязнений перед нанесением клеевого соединения.
- Нанесение термоактивированной грунтовки и адгезионных систем, таких как фенольная смола, окунанием, распылением или вручную с помощью кистей художника.
- Маскировка части вставки, чтобы покрыть все, кроме определенной области, где должна склеиваться резина.
- Обжиг загрунтованной вставки , чтобы убедиться, что она высохла и подготовлена к формованию.
- Связующие вещества наносятся на поверхность слоями. Нанесение связующих веществ обычно требует распыления серого грунтовочного покрытия на несколько более широкую площадь, чем черный верхний слой, с использованием распылительной машины большого объема с низким давлением.
- Если деталь не будет подвергаться воздействию высокой температуры, влажности или давления, иногда можно нанести один слой адгезива. Конкретный тип клеевого материала определяется несколькими различными факторами; условия эксплуатации готовой детали и выбранные в качестве материалов резина и металл.
- Большинство адгезивов разбавлено химически чистым растворителем, таким как метанол, что облегчает нанесение клея или окунание. Очень важно разработать правильное соотношение смеси клея и метанола, чтобы гарантировать, что толщина клея и процент твердого вещества достаточны для обеспечения прочного соединения.Если смесь слишком вязкая, это может привести к тому, что клей не схватится должным образом из-за отверждения кожи или сметания со вставки из-за протекания резины под высоким давлением в полость. Хорошая формовочная фирма будет проводить испытания, чтобы гарантировать надлежащий процент твердых частиц и толщину клея при каждом производственном цикле.
- После того, как основание было изготовлено, его необходимо очистить от пыли, мусора, грязи и масла с помощью пескоструйной машины, химикатов и обезжиривающих средств.
- Иногда для большей прочности добавляют пластины с покрытием.Оставляют резину затвердеть, и когда она полностью высохнет, деталь готова.
- Иногда сама форма немного больше, чем подложка, и резина образует тонкое покрытие вокруг металла, в то время как для других изделий требуются сложные конструкции резиновых деталей, которые сильно отличаются от размеров подложки.
- Процесс формования резины считается самым важным и сложным этапом в процессе склеивания. Металлический компонент помещается в форму, в которую, скорее всего, впрыскивается неотвержденная резина, нагретая и почти расплавленная.
- Компрессионное формование — предварительное формование неотвержденной резины заданного веса и формы, помещаемой в полость формы. Когда форма закрыта, две пластины давят на эластомер, который затем заполняет полость. Эластомер выдерживают под давлением и нагревают, пока резина не затвердеет, что позволяет детали сохранять свою форму.
- Трансферное формование — начинается с предварительно сформированной неотвержденной резины, которая помещается в передаточную ванну замкнутой системы формования.Затем шток / плунжер распределяет резину по полостям для придания формы детали, которая затем отверждается путем приложения давления и тепла в течение определенного периода времени.
- После завершения процесса формования резины типичные вторичные операции включают снятие заусенцев для удаления излишков резины, последующее отверждение, очистку и специальную упаковку.
- На протяжении всего процесса формования резины важно соблюдать правила обращения с деталями и их хранения, как после подготовки вставки, когда были нанесены клеи, так и после формования детали, чтобы избежать загрязнения.Резиновые детали и вставки должны быть сухими, очищенными от пыли и грязи, и обращаться с ними должны только операторы в перчатках.
- После того, как деталь будет готова, ее следует хранить при комнатной температуре вдали от прямых солнечных лучей. Кроме того, деталь следует держать вдали от сварочных работ, которые выделяют озон, который может повредить резину.
Методы, используемые для соединения резины с металлом
Отверждение вулканизатора — это метод соединения резины с металлом, при котором металлическое изделие с резиновым покрытием помещается в вулканизатор с острым паром и отверждается под давлением.Метод вулканизации обеспечивает наивысшую адгезию резины к металлу и самую высокую плотность для агрессивных сред.
Химическое отверждение — это метод, при котором агент наносится на поверхность футеровки и пропускается через футеровку в течение нескольких дней при комнатной температуре. Процесс химического отверждения, который может быть ускорен за счет применения тепла, обычно используется при ремонте резервуаров или больших емкостей с полевой футеровкой.
Индукционный нагрев обеспечивает надежный, повторяемый, бесконтактный и энергоэффективный нагрев за минимальное время на очень небольших площадях с точными производственными допусками без нарушения индивидуальных металлургических характеристик.Регулирование индукционного нагрева с обратной связью обеспечивает повторяемые, быстрые и точные циклы нагрева, что делает его идеальным для поточных производственных процессов.
Отверждение отработанным паром — это метод, при котором емкость закрывается глухими фланцами или покрывается тентом, в который впускается острый пар. Метод отработанного пара поддерживает целостность и сцепление футеровки и часто используется для резервуаров с футеровкой в полевых условиях, которые слишком велики для транспортировки.
Варианты процесса
Практически любой материал может быть связан с резиной, если он выдерживает нагрев и давление в процессе формования резины.Однако результаты связывания резины со сплавами, такими как бронза и латунь, в значительной степени зависят от состава сплавов. Факторы окружающей среды также изменили связующий материал. Первоначально использовались клеи на основе растворителей, но сегодня они в основном были заменены клеями на водной основе, экологически чистой альтернативой, которая, как было доказано, обеспечивает те же герметизирующие свойства, которые способны выдерживать те же условия и так же долго.
Склеивание резины может происходить с материалами, отличными от металла, хотя склеенный металл является наиболее известным, поскольку все марки стали, алюминия, меди, бериллия и латуни прилипают к связанной резине.Однако металл должен выдерживать высокую температуру и давление, возникающие в процессе склеивания. Также используются стекло, ткань и различные пластмассы. Каучуковый материал может быть натуральным или синтетическим и включать кремний, неопрен и нитрил.
Что следует учитывать при выборе производителя
Из-за большого разнообразия используемых сегодня деталей, состоящих из соединенной резины с металлом, большинство цехов, специализирующихся на производстве этих деталей, являются специализированными цехами, которые работают с клиентами от уровня проектирования до производства.
Найдите лучшие изделия на связке между резиной и металлом для оказания услуг, которые являются экономически эффективными и будут учитывать все производственные цели, включая быстрое выполнение работ и высококачественные резиновые изделия при выборе производителя.
IQS Directory реализует подробный список компаний, производящих склеивание резины с металлом . Воспользуйтесь нашим списком, чтобы изучить и отсортировать лучшие компании, производящие соединения резины с металлом, с предварительным просмотром рекламы и подробным описанием каждого продукта. Любая компания, производящая соединение резины с металлом, может спроектировать, спроектировать и обеспечить соединение резины с металлом в соответствии со спецификой компании.
На нашем веб-сайте можно легко связаться с компаниями, производящими склеивание резины и металла, с помощью формы быстрого запроса предложения. Информация о компании включает ссылки на веб-сайты, профиль компании, адреса, телефон, видеоролики о продуктах и информацию о продуктах. Доступны отзывы клиентов и новостные статьи по конкретным продуктам. Этот источник подходит вам, будь то приклеивание к металлической резине, приклеивание к металлическим изделиям или приклеивание клея для металлической резины.
Типы соединения резины с металлом
- Алюминиевая связка — это особый металлический материал, используемый в резиновой и металлической связке; Алюминий — очень популярный выбор, поскольку он прочен и устойчив к коррозии, а также имеет низкую стоимость и очень легкий вес.
- Связанный металл может представлять собой множество различных металлических веществ или их сплавов, которые связаны с резиной для производства определенных продуктов, таких как автомобильные шины, промышленные детали, такие как прокладки или медицинские принадлежности.
- Связанный каучук может быть синтетическим или натуральным каучуком, который связывается посредством тепла и адгезива с металлом, тканью или стеклом для создания специализированных продуктов с особыми характеристиками, такими как прочность и гибкость.
- Приклеивание резины к металлу — это процесс, который требует приклеивания резины к металлу, подвергнутого пескоструйной очистке, или формования.
- Приклеивание резины к металлу относится к адгезивам, используемым в процессе соединения резины с металлом, что позволяет создавать различные продукты в различных отраслях промышленности, включая автомобильную промышленность и медицину.
- соток
из резины или силикона и уплотнения вращающихся или скользящих валов. Кольца круглые ,
часто изготавливаются с резиновым покрытием на металле, используются в приложениях
такие как амортизаторы и дифференциалы.
- иногда бывает
склеивается резиной, когда требуется более высокая изоляция трубопровода
и поглотитель вибрации.
- представляет собой нетепловой или химический способ соединения резины с металлом, который включает
приклеивание предварительно сформованной резиновой детали к металлу через
заранее определенная канавка или пространство и мягкий адгезивный агент.
- Резина, приклеенная к металлу придает металлическому материалу эластичность и демпфирующие свойства.
- — это производственный процесс, при котором резина приклеивается к различным материалам для придания им эластичных свойств.
- это обычные устройства, изготовленные путем приклеивания резины к металлу. Резиновые втулки
используются в процессе прессования экрана, при подъеме флага и
другие приложения, в которых требуется проушина для прохождения лески. Их можно найти в предложении здесь .
- Изделия из резины — изделия из натуральных и синтетических каучуков.
- Резиновые ролики используются для выдавливания воды из целлюлозы при производстве бумаги.
Рулон имеет металлический сердечник, но для более эффективной работы сердечник
выложенный
с резиной. Вы можете удобно найти производителей роликов здесь, в IQS Directory .
- общие
виды продукции, изготовленные по технологии резинового склеивания. Пломбы ар
часто используется в качестве запорных элементов в гидравлическом оборудовании.
- Силиконовое соединение — это процесс соединения резиной, в частности, с использованием силикона, который особенно широко используется в области медицины в качестве хирургических инструментов.
Условия соединения резины с металлом
—
Химические вещества, которые добавляют в каучуки для ускорения вулканизации.
Резина без ускорителей полимеризуется в 20-30 раз дольше.
— Добавлены химикаты
резине, чтобы активировать отверждение.
— Склонность
резина для приклеивания к контактной поверхности.
— Материал, который может
использоваться для приклеивания одной поверхности к другой.
— Соединение одинаковых
или различные типы материалов с помощью клея, создающего позитивное вещество
сцепление по всей поверхности стыка.
— Удельная нагрузка,
применяется при растяжении, сжатии, изгибе, отслаивании, ударе, расколе или
сдвиг, необходимый для разрушения клеевого узла при возникновении разрушения
в плоскости связи или рядом с ней. Резина и металл Прочность сцепления измеряется в фунтах.
на квадратный дюйм (psi).
— Требуется сила
привести в действие скольжение. Высокое значение пробоя указывает на развитие
адгезия.
— Равномерный слой
химические грунтовки или клеи, которые используются для химической связи
между резиной и подложкой.
— Адгезия
вулканизированного каучукового материала на контактную поверхность с помощью подходящего
контактные цементы.
— Давление
наносится на сборку для достижения склеивания контактных клеев.
— Также известна как «вулканизация»,
это постоянное изменение, которое резина претерпевает во время формования.
— Любой материал,
при растяжении более чем в два раза его длина может вернуться к исходному состоянию
форма.
— Тенденция
некоторых резиновых металлических связующих материалов растрескиваться в результате многократного изгиба или напряжения
в той же точке.
— Сырая резина
полученные из органических источников, например овощей.
— Также упоминается как
«Буна-Н», это наиболее часто используемый эластомер для уплотнительных колец,
благодаря широкому диапазону температур, стойкости к нефтяным жидкостям и
хорошие физические свойства.
— Используемый общий термин
для описания всех каучуков и пластмасс, участвующих в соединении резины и металла. Полимер — это также химический термин
это относится ко всем органическим материалам, которые образованы из цепочек повторяющихся
химические единицы.
— Химический материал, который
улучшает сцепление герметика с основанием.
— Также называется «постоянным»
набор, «это степень, в которой резина не полностью восстанавливается до
его первоначальная форма после длительной деформации.
— Любая поверхность, на которую
наносится покрытие или герметик.
— Образована связь
между эластомером и загрунтованной поверхностью за счет использования тепла и
давление. Эластомер вулканизируется одновременно с связкой.
Информационное видео по соединению резины с металлом
Новый клей для приклеивания резины к металлу: GMK 2410 Контактный клей для резины и металла
Переключить меню- Добро пожаловать в Swift Supplies!
- 07 3180 8824
- войти в систему или зарегистрируйтесь
- Сравнить
- Корзина
- Клеи и герметики
- Все клеи и герметики
- Акриловые клеи и ММА
- Все акриловые клеи и ММА
- Easy-Mix PE-PP 45
- Easy-Mix RK-7000
- Easy-Mix RK-7300
- Пластиковая связь
- Акриловый клей RK-1300
- Клей акриловый РК-1500
- Клейкие принадлежности и оборудование
- Все аксессуары и оборудование для клея
- Адгезивные наполнители, волокна и добавки
- Адгезионные грунтовки и усилители
- Раздаточное оборудование и аксессуары
- Контактный и вулканизующий клей
- Все контактные и вулканизирующие клеи
- Клей 3M Scotch-Weld 1300L
- Контактный клей GMK 2410
- Контактный клей GMK 2510
- Цемент холодной вулканизации SC2000
- Эластичные клеи и герметики
- Все эластичные клеи и герметики
- Эластичные клеи — MS-полимеры
- Полиуретановые клеи и герметики
- Силиконовые клеи и герметики
- Клеи и герметики Viton
- Эпоксидные клеи, покрытия и компаунды
- Все эпоксидные клеи, покрытия и компаунды
- Палочки для ремонта эпоксидной смолы
- Жидкие эпоксидные клеи и покрытия
- Пластиковые металлические системы на основе эпоксидной смолы
- Полиуретановые клеи и литейные смеси
- Все полиуретановые клеи и литейные смеси
- Полиуретановые литейные смеси
- Легко смешивающиеся полиуретановые структурные клеи
- Полиуретановые эластичные клеи и герметики
- Клеи-распылители
- Супер клеи (цианоакрилатные клеи)
- Все суперклеи (цианоакрилатные клеи)
- Наборы и пакеты супер клея
- Грунтовки, наполнители и аксессуары Super Glue
- VA 100 Супер клей
- VA 250 Супер клей черный
- VA 30 Супер клей черный
- VA 8312 Супер клей
- VA 8406 Супер клей
- VA Contact Gel Super Glue
- ВМ 120 Супер клей
- Фиксаторы резьбы
- Все фиксаторы резьбы
- Клеи для уплотнения фланцев и прокладок
- Удерживающие клеи
- Клеи для резьбовых труб и фитингов
- Клеи для фиксации резьбы
- Противозадирные и промышленные смазочные материалы
- Все противозадирные и промышленные смазочные материалы
- Монтажные пасты и спреи против заклинивания
- Все монтажные пасты и спреи против заклинивания
- Anti-Seize High Tech
- Стандарт Anti-Seize
- Медный противозадирный
- Высокоэффективные консистентные смазки и смазочные материалы
- Все высокоэффективные консистентные смазки и смазочные материалы
- Пищевая смазка AL-F
- Смазка AL-W морского класса
- Смазка для резки масла Bio-Cut
- Силиконовая смазка
- Химия, спреи и жидкости
- Все химические вещества, спреи и жидкости
- Клейкая смазка и спреи для консистентной смазки
- Адгезивные спреи
- Антикоррозионные спреи и жидкости для покрытия поверхностей
- Все спреи и жидкости для защиты от коррозии и покрытия поверхностей
- Алюминиевые спреи и покрытия
- Латунные спреи и покрытия
- Спреи и покрытия из хромированного серебра
- Медные аэрозоли и покрытия
- Защита от коррозии, съемный
- Золотые спреи и покрытия
- Защита от ржавчины 2000 Plus
- Спреи и покрытия из нержавеющей стали
- Цинковые спреи и покрытия Cold-Gal
- Спреи и жидкости для ухода и защиты
- Все спреи и жидкости для ухода и защиты
- Распыление на кокпит
- Защитная пена для рук
- Металлическая жидкость NSF
- Уход за нержавеющей сталью
- Спреи и жидкости для очистки и обезжиривания
- Все чистящие и обезжиривающие спреи и жидкости
- 3M 300 HIPA Чистый
- Очиститель клея 3M 700
- Очиститель тормозов
- Очиститель горелки
- Очиститель цитрусовых
- Чистящие средства
- Электро контактный очиститель
- Быстрый очиститель NSF
- Пенный очиститель NSF
- Промышленный очиститель NSF
- Очиститель форм
- Пенный очиститель
- Очиститель деталей и сборок
- Пластиковый очиститель
- Очиститель экрана
- Очиститель поверхностей
- Очиститель козырька
- Мастерская Очиститель
- Смазочные и многофункциональные спреи и жидкости
- Все смазочные и многофункциональные спреи и жидкости
- Смазка AT-44 с ПТФЭ
- Смазочные жидкости с сухой пленкой из ПТФЭ
- Средство для разрыхления ржавчины и контактные жидкости
- Силиконовые смазочные спреи и жидкости
- W44T Универсальные жидкости
- Растворители и разделительные агенты, спреи и жидкости
- Все растворители и разделительные агенты, спреи и жидкости
- Защита алюминия от шлифования
- Масло для резки Bio-Cut
- Средства для удаления жевательной резинки
- Средства для удаления этикеток
- Средства для удаления плесени
- Конвертеры ржавчины
- Средство для разрыхления ржавчины и контактные жидкости
- Спрей от ржавчины
- Спреи специального назначения и специальные жидкости
- Все специальные спреи и специализированные жидкости
- Универсальный уплотнительный спрей
- Защита от шлифования алюминия
- Спреи и жидкости против брызг
- Спреи для испытаний на трещины
- Лаки для воздушной сушки Elmotherm
- Вспомогательные средства для стартера двигателя
- Глиптал 1201 Красная эмаль
- Спреи и жидкости для обнаружения утечек
- Спреи для проверки дымовых извещателей
- Электроизоляция, проводники и инструменты
- Вся электрическая изоляция, проводники и инструменты
- Кабель и провод
- Все кабели и провода
- Силовой кабель
- Кабельные наконечники, перемычки и клеммы
- Все кабельные наконечники, перемычки и клеммы
- Кабельные вводы
- Кабельные ссылки
- Кабельные наконечники
- Кабельный органайзер
- Все кабельные системы
- Защита кабеля
- Кабельные стяжки
- Электроизоляционные и защитные ленты
- Все электроизоляционные ленты и защитные ленты
- Тканевая лента
- Экранирующая лента EMI
- Лента из стекловолокна
- Пленка
- Другая специализированная электрическая лента
- Бумажная лента
- Резиновая лента
- Лента виниловая и ПВХ
- Лаки и составы для электротехники
- Все электрические лаки и составы
- Лаки и отделочные материалы для электрических покрытий
- Электрические смолы и герметики
- Эпоксидные замазки и электрические компаунды
- Электроинструменты
- Все электрические рабочие инструменты
- Устройства для зачистки кабелей и проводов
- Инструменты для обжима кабеля
- Инструменты для резки кабеля
- Инструменты для кабельных стяжек
- Принадлежности и запасные части для электроинструментов
- Гибкие электроизоляционные листы и материалы
- Все гибкие электроизоляционные листы и материалы
- Изоляционные ткани
- Изоляционные пленки и пластмассы
- Изоляционные бумаги
- Термоусадочные и электрические рукава
- Все термоусадочные и электрические рукава
- Электроизоляционная оболочка (без усадки)
- Термоусадка и холодная усадка
- Прочие электрические детали и аксессуары
- Все прочие электрические детали и аксессуары
- Гибкие щелевые клинья
- Клеммные колодки двигателя
- Другие электрические продукты и решения
- Изоляторы StandOff
- Жесткие электроизоляционные листы и материалы
- Все жесткие электроизоляционные листы и материалы
- Бакелит
- Эпоксидное стекло
- Слюда
- Полиэфирное стекло
- Прокладки и уплотнения
- Все прокладки и уплотнения
- Пробковые уплотнительные материалы
- Все материалы для пробкового уплотнения
- Листы пробковых прокладок
- Войлок
- Все войлок
- Войлочные уплотнительные ленты
- Лист войлока промышленной инженерии
- Клеи для прокладок и уплотнений
- Комплекты прокладок и уплотнений
- Все комплекты прокладок и уплотнений
- Комплекты для изоляции фланца
- Комплекты уплотнительных колец
- Прокладки и уплотнительные ленты
- Все прокладки и уплотнительные ленты
- Ленты с мгновенным уплотнением фланца
- Ленты для ремонта труб
- Самоамальгамирующиеся герметизирующие ленты
- Твердая резиновая уплотнительная лента и полоса
- Губчатые уплотнительные ленты
- Резьбовой шнур и лента
- Инструменты для прокладок
- Все инструменты для прокладок
Конверсионное покрытие и предварительная обработка | Pioneer Metal Finishing
Конверсионное алюминиевое покрытие
Конверсионные алюминиевые покрытия — это недекоративные покрытия, наносимые на алюминиевые детали для получения тонкого электропроводящего покрытия, обеспечивающего коррозионную стойкость.Эти покрытия также являются отличным базовым покрытием для алюминиевых деталей, требующих окраски, поскольку они значительно улучшают адгезию краски к алюминию.
Посмотреть все отделочные покрытия
Фосфат марганца
Фосфат марганца — это обработка, в которой используются соль марганца, фосфорная кислота и ускоритель, и все они применяются при очень высоких температурах.Этот процесс конверсионного покрытия включает растворение основного металла и впоследствии является частью фактического покрытия, обеспечивая превосходную износостойкость.
Процесс производства фосфата марганца компании Pioneer широко используется в приложениях с частичным контактом, например, в зубчатых колесах, а также в приложениях, в которых используются экстремальные значения крутящего момента или требуются многократные износы, например, болты. Это связано с природной кристаллической структурой марганца, которая очень прочна и не трескается. Благодаря такой структуре фосфат марганца также является идеальным покрытием для прерывания технологических процессов.
Стандартные характеристики
PS8890 — Метод A
GM4277M
Соответствие RoHs, REACH, ELV и WEEE
Повышение производительности
Коррозионная стойкость
Чрезвычайно прочный при частичном контакте
Поддерживает экстремальные значения крутящего момента
Превосходен в многократных применениях
Обеспечивает основу для последующих покрытий
Восприимчивые металлы
Сталь
Мойка деталей
Промывка деталей — это процесс, с помощью которого можно удалить ржавчину, фрезерные масла и смазочные масла с помощью различных методов.Обычно детали, которые в конечном итоге подвергаются дробеструйной очистке, необходимо мыть перед обработкой, чтобы предотвратить загрязнение струйной среды. Собственное оборудование Pioneer предназначено для мытья любых деталей, от хрупких до прочных.
Повышение производительности
Тщательно очищает поверхность перед дополнительными процессами
Пассивация
Пассивация — это неэлектролитический финишный процесс, который делает нержавеющую сталь более устойчивой к ржавчине.В процессе пассивации обычно используется азотная или лимонная кислота для удаления свободного железа с поверхности. Это приводит к образованию инертного защитного оксидного слоя, который с меньшей вероятностью вступит в химическую реакцию с воздухом и вызовет коррозию.
За счет химического удаления нелегированного железа с поверхности нержавеющей стали процесс пассивации позволяет формировать тонкую оксидную «пленку» на чистой поверхности. Когда поверхностное железо удаляется, другие компоненты сплава (в первую очередь хром, а также часто и никель) остаются в виде поверхностного слоя над лежащей ниже сталью.При контакте с воздухом эти элементы вступают в реакцию с кислородом с образованием оксидного слоя, который защищает остальную часть стали от коррозии.
Стандартные спецификации
ASTM A380 (коды F, I и J)
ASTM A967 (NITRIC 2 и 5)
QQ-P-35 (ТИП VI)
Соответствие RoHs, REACH, ELV и WEEE
Повышение эффективности
Коррозионная стойкость
Адгезия к краске
Восприимчивые металлы
Нержавеющая сталь
Макс.размер детали
132 ″ x 48 ″ x 28 ″
20 ″ x 30 ″ x 9 ″
Рассол и масло
Pickle & Oil — это обработка поверхности металла, используемая для удаления загрязнений, таких как пятна, ржавчина или окалина, с черных металлов.Связки разламываются, части разделяются, а затем погружаются в раствор, содержащий сильные кислоты, используемые для удаления поверхностных примесей. Он обычно используется для удаления окалины или очистки стали в различных процессах производства стали. После травления наносится легкое водорастворимое средство для защиты от ржавчины, чтобы замедлить скорость образования ржавчины.
Преимущества в производительности
Обеспечивает чистую и более гладкую поверхность, чем дробеструйная обработка
Обеспечивает качественное нанесение краски и внешний вид
Превосходное нанесение на поверхность для E-Coat и Powder Coat
Косметическая консистенция чистой поверхности
Восприимчивые металлы
Сталь
Фосфат цинка
Фосфат цинка — это процесс, который широко используется для улучшения коррозионной стойкости и адгезии краски к стали и чугуну.Плотность покрытия, наносимого погружением, от 150 мг / кв.фут до 1200 мг / кв.фут может быть легко достигнута. Хотя получаемая кристаллическая структура обычно используется в качестве основы для адгезии краски, она также может служить кратковременным ингибитором коррозии, улучшая при этом внешний вид основы.
Стандартные характеристики
PS-80
TES1000
TES1007
PS119.0
Соответствие RoHs, REACH, ELV и WEEE
Повышение производительности
Коррозионная стойкость
Обеспечивает основу для последующих покрытий
Восприимчивые металлы
Сталь