Требования к сварным швам металлоконструкций
В процессе производства и монтажа металлических конструкций часто возникает необходимость в использовании сварных соединений. Сварочные работы проводятся в соответствии с проектной документацией или технологическим процессом. Эта документация содержит стандартные или специальные инструкции, которых нужно беспрекословно придерживаться, чтобы добиться наилучшего качества шовных соединений. Сварные швы металлоконструкций должны обладать высокими показателями прочности и долговечности. Их эксплуатационные характеристики и уровень качества обозначены в ГОСТ 23118-12.
Каким требованиям должен соответствовать металл шва?
Металл, из которого производятся шовные соединения, должен соответствовать ряду стандартных норм. Перечислим основные требования к сварным швам металлоконструкций:
- величина относительного удлинения материала должна составлять 16 % и более;
- ударная вязкость металла должна составлять более 24 Дж/см2, этот показатель замеряют при среднесуточной температуре воздуха в наиболее холодный 5-дневный период;
- металл, из которого изготовлены сварные соединения и швы металлоконструкций, должен иметь такие же (или более высокие) характеристики временного сопротивления разрыву, как и у основного металла, из которого состоят свариваемые изделия;
- если металлоизделия свариваются в заводских условиях, необходимо следить за тем, чтобы коэффициент твердости металла шовного соединения составлял менее 350 HV для металлических конструкций 1-й группы и до 400 HV для изделий других групп, описанных в СНиП II-23-81;
- если сварочные работы проводятся непосредственно в процессе монтажа и сборки конструкций, коэффициент твердости шовного металла не должен превышать значение 400 HV.
Соблюдение всех перечисленных требований и тщательный контроль сварных швов металлоконструкций позволят обеспечить надежность и долговечность сварных соединений, предотвратить преждевременную потерю прочности и избежать аварийного разрушения металлических изделий.
Классификация швов по уровню качества
Шовные соединения по уровню качества условно делятся на три основных категории.
I категория. В первую категорию относят шовные соединения с наиболее высокими эксплуатационными характеристиками (прочностью, долговечностью, стойкостью к разрывам и пр.) В частности, к таковым относятся следующие типы швов:
- поперечные стыковые соединения, подвергающиеся сильным растягивающим напряжениям;
- нахлесточные, тавровые и угловые шовные соединения, которые работают на отрыв при растягивающих напряжениях;
- швы в металлических изделиях, которые согласно СНиП II-23-81 отнесены к 1-й группе (или ко 2-й группе при условии, что температура воздуха в месте возведения металлической конструкции опускается ниже отметки -45 °С).
II категория. Во вторую категорию входят швы со средними показателями качества. К таким сварным соединениям относятся:
- продольные стыковые элементы, на которые воздействует напряжение сдвига;
- связующие угловые швы в металлоизделиях 2-й и 3-й группы, подвергающиеся растягивающим напряжениям;
- швы в углах и стыках, предназначенные для соединения фасонок со сжатыми деталями металлоизделий.
III категория. К данной категории относятся шовные сварные соединения низкого качества, среди которых:
- поперечные соединения в стыках, подверженные сжимающим напряжениям;
- продольные швы в стыках, а также связующие соединения в углах, используемые в сжатых элементах конструкций;
- швы в стыках и углах, применяемые во вспомогательных деталях металлоизделий.
УЗК-контроль сварных швов. Рассматриваем во всех подробностях
В отраслях машиностроения, строительства и других разделах промышленности без сварочных процессов не обойтись. Сварка, как элемент прочного и надежного соединения деталей и узлов, занимает ведущее место в хозяйственной деятельности человека. Без нее невозможно благоустроить быт, проложить коммуникации, дать воду, газ. Главным условием длительной эксплуатации сварных элементов является качество сварки. Определить визуально это почти невозможно, но способ есть.
Ультразвуковая дефектоскопия
В начале 30-х годов прошлого века ученые разработали новый метод контроля сварных швов ультразвуком – ультразвуковая дефектоскопия. Он основан на свойстве высокочастотных колебаний проникать в структуру металлического изделия и отражаться от неровностей и пустот с разной звуковой проницаемостью. Эта особенность акустических волн положена в основу метода ультразвуковой дефектоскопии. Акустические волны представлены упругими колебаниями материальных частиц в диапазоне от 20 кГц до 500 мГц.
Технология проведения узк-контроля сварных швов заключается в следующем. Специальным устройством искусственно создается ультразвуковая волна, затем она направляется в точку исследования. Попадая в проверяемый шов она отражается. В случае неудовлетворительной сварки ультразвуковая волна преломляется и отклоняется от обычного вектора. Оператор узк-оборудования видит на мониторе отклонение и дает определение дефекту. Этот способ дефектоскопии получил название «узк метод неразрушающего контроля». Суть отражения, преломления волн и другой специфики разберет лишь оператор-дефектоскопист. Все измерения производятся согласно установленному ГОСТу.
Применять способ диагностики сварных швов ультразвуком можно для различных типов металлов:
- высоколегированные стали;
- чугун;
- алюминий, медь, бронза, латунь и другие сплавы;
- слабо проводящие ультразвук металлы.
Узк-контроль и области его использования
Узк-контроль металла применяется в большинстве областей промышленности и народного хозяйства. Незаменима дефектоскопия на объектах, связанных с повышенной опасностью: газопроводы, нефтепроводы, теплосети.
- в энергетике;
- в химической и нефтегазовой отраслях;
- для определения износа труб в магистральных трубопроводных сетях;
- для обнаружения изъянов сварных швов в изделиях, подверженных воздействию повышенных температур и давления;
- в изделиях, эксплуатация которых проходит в активных средах.
- в гидравлических и водопроводных системах;
- узк-контроль деталей с нестандартной геометрической формой;
- в индивидуальных случаях при реконструкции зданий и помещений.
В большинстве отраслях машиностроения не обойтись без ультразвукового контроля узлов и агрегатов. Компактность оборудования позволяет проводить узк-контроль труб и других изделий в полевых условиях.
Положительные стороны узк-контроля
Работы по ультразвуковому контролю сварных швов имеют ряд преимуществ:
- высокая точность проверки качества швов за малый промежуток времени;
- диагностика в полевых условиях;
- при выполнении работ по узк-контролю изделие не подвергается деформации;
- при проведении диагностики не требуется выведение объекта из эксплуатации;
- работы безопасны для окружающих;
- приемлемая стоимость.
Положительным аспектом являются параметры проведения работ по ультразвуковому контролю. Оператор-дефектоскопист, используя специальное оборудование, осуществляет диагностику сварных швов изделия на глубине до 10 метров. Практика доказывает, что узк-контроль деталей может быть одинаково эффективен для проверки любых типов сварных соединений, имеющих толщину шва от 4 до 800 мм.
Какие дефекты можно выявить, используя метод узк-диагностики?
Основанный на методе ультразвуковой дефектоскопии, данный способ позволяет четко определить брак в сварном шве. Правильно проведенная диагностика места сварки дает полное представление о специфике дефекта. Специфическими задачами метода служит выявление следующих недостатков:
- определение трещин в зоне около сварных швов;
- выявление пор и зон объекта, пораженных коррозией;
- поиск участков сварного шва с дефектами;
- шовные расслоения металла;
- определение участков объекта с несоответствующим химическим составом, искаженным геометрическим размером;
- провисание наплавленного метала в нижней части шва.
Услуги по узк-контролю сварных швов от компании «ДСН»
Многие организации в целях экономии средств или своей некомпетентности обходят стороной работы по выполнению узк-контроля или обращают на него внимание непосредственно перед вводом промышленного объекта в эксплуатацию. Это приводит к дополнительным расходам, а иногда и к аварийным ситуациям и техногенным катастрофам в процессе использования. Для исключения подобных моментов важно вовремя проводить ультразвуковую дефектоскопию.
Узк-контроль сварных швов выполняется согласно ГОСТ 24507-80 и ГОСТ 21120-75. Компания «ДСН» предоставляет полный спектр услуг по ультразвуковой диагностике сварных швов с полной классификацией выявленных дефектов по типам и размерам. В список работ предприятия включена ультразвуковая толщинометрия, необходимая при экспертизе промышленной безопасности, главной задачей которой является распознавание соответствия толщины металла согласно входящим паспортным данным.
Цена услуг узк-контроля зависит от габаритных размеров и геометрии объекта, шероховатости, количества и других факторов. Менеджеры помогут рассчитать стоимость диагностики любого изделия, а специалисты компании «ДСН» выполнят работы по узк-контролю качественно и быстро в соответствии с требованиями и нормами.
Сварные металлоконструкции
Сварными конструкциями называют самые разные изделия из листового металла, при изготовлении которых использовалась технология сварки. Как правило, такие элементы становятся основой для строительства быстровозводимых зданий хозяйственного или технического назначения.
Основные преимущества:
- позволяют экономить металл, так как рабочие сечения элементов в соединительных узлах металлоконструкций задействованы полностью;
- позволяют придать металлическим элементам наиболее подходящую под эксплуатационные нагрузки форму;
- позволяют снизить вес соединительных элементов в узлах сварки;
- позволяют применять тонкостенные конструкции, благодаря чему уменьшается расход металла и вероятность получения брака.
- дают возможность снизить трудозатраты на производство и сборку металлоконструкций, одновременно с этим позволяя использовать конструкции различных типов сечений.
Кроме того, технология сварки дает возможность снизить металлоемкость производимых изделий.
При производстве сварных металлоконструкций необходимо учесть множество факторов: назначение и условия эксплуатации изделий, нагрузка на сварные соединения и узлы, обеспечение необходимой эффективности сварочного процесса, подготовка оборудования, разработка элементов нужной конфигурации, способных выдержать высокие нагрузки.
Технология сварки металлоконструкций используется при создании ферм, балок, двутавров и других элементов. Их высота может составлять 3-4 м и более, а длина может быть неограниченной. Сварка позволяет производить балки с толстыми поясами значительной ширины, но при этом с тонкими высокими стенками. Благодаря этому можно экономить на строительных работах, уменьшив расход металла.
При сварке необходимо полностью соблюдать технологию для того, чтобы швы были сформированы правильно, без малейших отклонений и дефектов. Х–образная разделка кромок позволят уменьшить количество наплавленного металла практически в два раза и обеспечить наилучшее формирование сварочного шва. В этом случае деформация после сварки будет минимальной, а надежность шва — соответствующая всем необходимым требованиям. Перед осуществлением сварочных работ металлоконструкции больших габаритов собирают так, как это предусмотрено проектными чертежами. Все сопряжения при этом следует временно закрепить. При сборке связей металлических ферм элементы крепятся на болтах, чтобы конструкция была правильной конфигурации. При сварке детали плотно сжимают с помощью разнообразных конструкций: тисков, струбцин, систем пазов и др.
- сварка автоматическая под слоем флюса;
- сварка в защитных газах.
При этом отмечается, что ручная сварка постепенно вытесняется механизированной сваркой с использованием порошковых проволок небольшого диаметра в защитных газовых смесях. Такой вид сварки особенно часто применяется для обработки стыковых соединений в потолочном или вертикальном положении. Кроме того, механизированная сварка оправдана при создании угловых швов в коробчатых элементах. Если необходимо сделать шов при обработке деталей из металла значительной толщины, прибегают к многослойной сварке в узкую разделку и с применением порошка. Для всего этого цехи оснащаются сварочными аппаратами нового поколения. Как правило, это портативные малогабаритные и многоэлектронные установки, полностью автоматизированные.
Производство сварочных работ в заводских условиях требует соблюдения нескольких правил, соблюдение которых позволит получить шов требуемого качества и с минимальными дефектами. Сварка должна производиться при температуре окружающей среды или металла не ниже –18°C. При значительных отклонениях от этой температуры необходимо прогреть металл на расстоянии, равном его толщине.
ГОСТ 8713–79 и ГОСТ.11533–75 — для швов, выполненных автоматической и полуавтоматической сваркой под флюсом.
ГОСТ 14771–76 — для швов, выполняемых сваркой в защитных газах.
ГОСТ 5264–80, ГОСТ 11534–75 — для швов, выполняемых ручной дуговой сваркой.
ГОСТ 15164–78 — для швов, образованных с помощью электрошлаковой сварки.
ГОСТ 15878–79 и ГОСТ 14776–79 — для контактной и дуговой точечной сварки.
Сварные швы нестандартные гост
Сварные швы нестандартные гост
Скачать гост 2. 312-72 единая система конструкторской.
Обозначение сварных соединений.
Обозначение сварных соединений и сварных швов на чертежах.
3.

Нестандартный сварной шов по гост 2. 312-72 ескд youtube.
Обозначение сварного шва разработка и оформление.
Гост 2. 312-72 ескд. Условные изображения и обозначения. Обозначение сварных швов | сварка и сварщик. Гост 23518-79 дуговая сварка в защитных газах. Соединения. Гост 2. 312-72 | текст. Методика создания обозначений сварных швов 15. 05. 2015. Гост 2. 312-72 ескд условные изображения и обозначения.Гост.
Обозначение сварки на чертежах по гост.Гост 2. 312-72 единая система конструкторской документации.
Примеры условных обозначений стандартных швов.
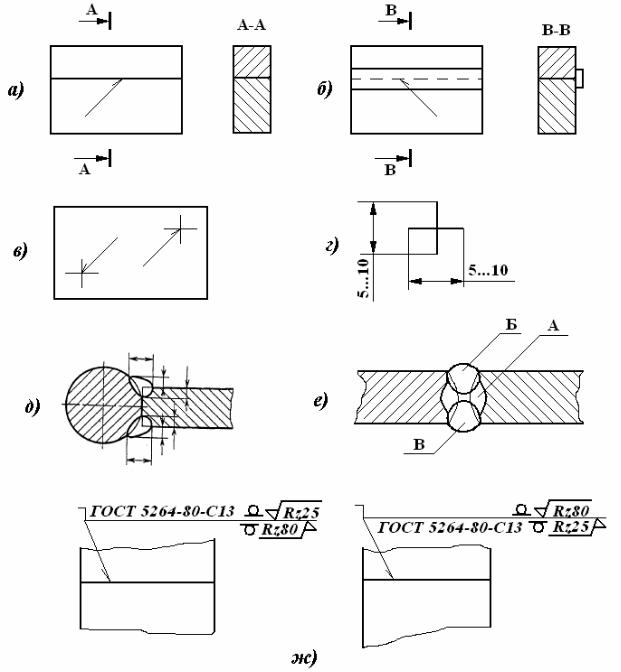
Сварные швы в creo parametric 3. 0 птс официальный.
Условные изображения и обозначения швов сварных соединений.Гост 2. 312-72*. Ескд. Условные изображения и обозначения.
Craftbook скачать для minecraft Скачать la noire через торрент Приказ 157н последняя редакция Робин гуд принц воров скачать Песня скачать кто ты такойКатегории сварных швов гост допустимые дефекты. Дефекты и контроль качества сварных соединений
Нарушение требований, установленных нормативными документами, при сварке плавлением приводит к образованию брака. Дефекты сварных соединений ГОСТ 30242-97 разделяет на шесть групп. Их нужно знать так же хорошо, как и то, правильно.
Трещины: разновидности, причины их образования
Трещиной называют несплошность, которая вызывается резким охлаждением или воздействием нагрузок. Разновидность этого дефекта, которую можно обнаружить только оптическими приборами с увеличением, не менее пятидесятикратного, называют микротрещиной.
Продольные трещины располагаются вдоль сварного соединения и могут располагаться:
- в металле шва;
- в основном материале;
- на границе сплавления;
- в области температурного влияния.
Трещины в основном металле, причиной которых являются высокие напряжения, называют скрытыми. Внешне они напоминают ступеньки. Этот дефект присущ сварным соединениям значительной толщины. Высокие напряжения вызываются слишком жесткими соединениями или некорректным выбором сварочной технологии. Уменьшение сварочных напряжений снижает вероятность образования скрытых продольных трещин.
Конфигурация продольных трещин определяется линиями сплавления шва и основного металла.
Эти трещины разделяют на:
- горячие, их причиной является высокотемпературная хрупкость сплавов;
- холодные – возникают при медленном разрушении металла.
Поперечные трещины ориентированы перпендикулярно оси сварного шва. Они могут возникать, как в основном материале и металле сварного соединения, так и в зоне температурного влияния.
Радиальные трещины расходятся из одной точки и иначе называются звездообразными. Места их расположения аналогичны локализациям поперечных трещин. Причины образования поперечных и радиальных трещин такие же, как и у продольных.
В месте отрыва дуги на поверхности шва образуется углубление. Дефекты, которые возникают в этом месте, называют трещинами в кратере. Они разделяются на продольные, поперечные, звездоподобные. Конфигурацию этого дефекта определяют: микроструктура зоны сварного соединения, фазовые, термические и механические напряжения.
Если возникает группа не связанных друг с другом трещин, то они называются раздельными. Места и причины их возникновения аналогичны этим характеристикам поперечных и радиальных трещин.
Если из одной трещины образуется группа трещин, то такой брак носит название разветвленных трещин. Места их расположения – основной материал, металл шва, область термического влияния. Причины возникновения такие же, как и у продольных трещин.
Поры: их форма, места расположения и причины появления
Дефекты сварных соединений и соединений в виде полостей в сварном соединении называют порами. Эти полости заполнены газом, который не успел выделиться наружу.
Различают следующие разновидности пор:
- Газовая полость – это образование произвольной формы, не имеющее углов, причиной появления которого явились газы, не успевшие покинуть расплавленный материал.
- Газовой порой называют газовую полость, имеющую сферическую форму.
- Группа газовых пор, которая располагается в металле сварного соединения, называется равномерно распределенной пористостью.
- Скопление пор – это три или более газовых полостей, расположенных кучно на расстоянии между собой, не превышающем тройной диаметр максимальной поры.
- Цепочкой пор называют ряд газовых полостей, которые располагаются линией вдоль сварного соединения с расстоянием между ними, не превышающем трех диаметров наибольшей из пор.
- Если дефектом является несплошность, вытянутая вдоль оси сварного шва и имеющая высоту, которая гораздо меньше длины, то она называется продолговатой полостью.
- Свищом называют трубчатую полость, которая располагается в металле сварного шва. Свищ вызывается выделением газа. Его форма и положение определяются источником газа и режимом твердения. Как правило, свищи образуют скопления в форме елочек.
- Газовая полость, нарушающая целостность поверхности сварного соединения, называется поверхностной порой.
- Если во время затвердевания вследствие усадки образуется полость – она носит название усадочной раковины. А усадочная раковина, расположенная в конце валика и не заваренная при последующих проходах, называется кратером.
Поры – дефекты сварных соединений, фото которых приведено ниже, появляются из-за наличия вредных примесей, как в основном металле, так и в присадочном. Поры могут образовываться из-за ржавчины и прочих загрязнений, которые не были удалены перед проведением сварки с кромок материала, повышенного содержания углерода, высокой скорости сварочного процесса, нарушений защиты сварочной ванны. Самой частой причиной возникновения пор является отсыревшее покрытие плавящегося электрода.
Наличие одиночных пор не представляет опасности, а вот их цепочка может негативно сказаться на прочностных характеристиках сварного соединения. Участок сварочного шва, пораженный этими дефектами, переваривают, предварительно механически его зачистив. Поры и шлаковые включения
Виды твердых включений в сварном шве
Твердые инородные включения, как металлического, так и неметаллического характера, имеющие в своей конфигурации хотя бы один острый угол, являются недопустимым дефектами в сварном соединении, поскольку играют роль концентраторов напряжений. Дополнительная опасность этих дефектов заключается в том, что они не видимы снаружи. Обнаружить их можно только методами неразрушающего контроля.
Шлаковые включения в сварном соединении
Твердые включения разделяются на следующие виды:
- Шлаковые включения – это шлаки, попавшие в сварочный шов. В зависимости от того, в каких условиях они были образованы, они бывают линейными, разобщенными, прочими. Причины их образования – большие скорости сварочного процесса, загрязненные кромки, многослойная сварка, если швы между слоями очищены некачественно. Форма этих бракованных включений очень разнообразна, поэтому они могут быть гораздо опаснее округлых пор.
- Флюсы, служащие для защиты металла от окисления, являются причиной образования флюсовых включений. Также, как и шлаковые, флюсовые включения делят на линейные, разобщенные и прочие.
- Причинами образования оксидных включений могут быть: недостаточно чистая поверхность основного или присадочного металлов, вытаскивание горячего сварочного прутка из области защиты, неправильная подготовка кромок – слишком сильное их затупление.
- Частицы сторонних металлов – вольфрама, меди или других образуют металлические включения. Причиной их образования может стать эрозия вольфрамового электрода или случайное попадание металлических частиц снаружи, а также при использовании для поджига медной стружки.
Несплавление и непровар: причины возникновения
Непровар и несплавлениеДефекты – несплавление и непровар – это отсутствие соединения основного материала и металла сварного соединения.
Несплавление возникает при высоких скоростях сварочного процесса и силе тока более 15000С. Для предотвращения несплавлений необходимо уменьшить скорость сварки, снизить временной разрыв между образованием и заполнением канавки, тщательно очищать сварочную зону от масел и загрязнений. Несплавления могут располагаться:
- в корне сварного шва;
- на боковой стороне;
- между валиками.
Непровар возникает по причине невозможности расплавленного металла достичь корня шва. Причин непровара может быть несколько:
- недостаточный сварочный ток;
- слишком высокая скорость перемещения электрода;
- увеличенная длина дуги;
- слишком маленький угол скоса кромок;
- перекос свариваемых кромок;
- недостаточный зазор между кромками;
- неправильно выбранный – увеличенный – диаметр электрода.
- попадание шлака в зазоры между кромками;
- неадекватный выбор полярности для данного типа электродов.
Непровар – очень опасный и недопустимый сварочный дефект.
Виды отклонений формы наружной поверхности шва от заданных значений
К нарушениям формы сварочного шва относят следующие дефекты:
- Подрезы непрерывные – представляют собой непрерывные углубления, расположенные на наружной части валика шва. Если подрезы располагаются со стороны корня одностороннего шва и образуются по причине усадки вдоль границы, их называют усадочными канавками. Подрезы являются широко распространенными поверхностными дефектами, которые возникают из-за слишком высокого напряжения дуги при сваривании угловых швов или по причине неточного ведения электрода. В этом случае одна из кромок проплавлена более глубоко, что приводит к стеканию металла на находящуюся в горизонтальном положении деталь. Для заполнения канавки металла не хватает. При сварке стыковых швов подрезы образуются редко.
При слишком высоких значениях скорости сварки и напряжения дуги, как правило, возникают двухсторонние подрезы. Такого же типа дефект получается и при автоматической сварке в случае повышения угла разделки.
- Превышения выпуклостей стыкового или углового шва представляют собой избыток наплавленного металла с лицевой стороны швов сверх положенного значения.
- Если избыток наплавленного металла сверх установленного значения располагается на обратной стороне стыкового шва, то такой дефект называют превышением проплава. Разновидность – местный избыточный проплав.
- Если избыток наплавляемого металла натекает на основной металл, но не сплавляется с ним, то такой дефект называют наплавом.
- Линейное смещение возникает, если свариваемые поверхности расположены параллельно, но не на одном уровне.
- Угловым называют смещение между двумя поверхностями при их расположении под углом, который отличается от необходимого.
- Натек образуется из металла сварного шва который оседает под воздействием силы тяжести.
Натек образуется при горизонтальном, потолочном, нижнем положениях сварки, в угловом соединении и шве нахлесточного соединения.
- При прожоге металл сварочной ванны вытекает, образуя сквозное отверстие. Причинами прожога могут стать загрязненность поверхности основного металла или электрода.
- Неполное заполнение разделки кромок возникает из-за недостаточного количества присадочного материала.
- Если в угловом соединении один катет значительно превышает другой, то возникает дефект чрезмерной асимметрии.
- Неравномерная ширина сварного шва.
- Неровная поверхность – это неравномерность формы усиления шва по его протяженности.
- Вогнутость корня шва представляет собой неглубокую канавку со стороны корня шва, которая образовалась по причине усадки.
- Из-за возникновения пузырьков в период затвердевания металла образуется пористость в корне шва.
- Возобновление. Этот дефект представляет собой местную неровность поверхности в зоне возобновления сварочного процесса.
Наплыв и подрез
Прочие дефекты сварных швов
Все дефекты сварных швов и соединений, которые не были перечислены выше, относятся к категории “прочие”. К ним принадлежат следующие типы дефектов:
- Случайная дуга. В результате возникновения случайного горения дуги возникает местное повреждение поверхностного слоя основного металла, который примыкает к области сварного шва.
- Брызги металла – капли, которые образовались от наплавляемого или присадочного металла во время сварочного процесса. Они прилипают к поверхности остывшего металла сварного шва или основного металла, расположенного в околошовной области.
- Вольфрамовые брызги – создаются частицами вольфрама, выброшенного из расплавленного электрода на основной металл или на сварной шов.
- Поверхностные задиры – это дефекты, которые возникают из-за удаления временно приваренного приспособления.
- Утонение металла образуется при механической обработке. При этом толщина металла имеет значение, которое меньше допустимой величины.
Допустимые дефекты сварных соединений – это отклонения, наличие которых не снижает эксплуатационные свойства сварного соединения и их присутствие разрешено нормативной документацией. Все остальные дефекты, как правило, исправляются с помощью подварки. Исправлять качество сварки более двух раз не разрешается, так как может произойти перегрев или пережог металла.
Сегодня сварка используется повсеместно для соединения различных металлических деталей. Она успешно используется как в промышленности, так и в частных бытовых условиях. называется неразъемное соединение деталей посредством сварки. В результате этого формируются различные участки, которые характеризуются определенным набором свойств. Все зависит от степени нагрева. Они могут различаться по физическим, химическим и механическим свойствам. Основные дефекты сварных соединений известны достаточно давно. Их следует избегать в процессе выполнения работы.
Сварка используется для соединения металлических деталей в промышленности и бытовых условиях.
Характеристика и виды сварных соединений
Перед тем как начать разговор о дефектах сварных соединений, стоит подробнее поговорить об их основных видах и характеристиках. Принцип сварки достаточно прост. Расплавленный металл образует шов, который кристаллизуется. Тот материал, который частично оплавляется, составляет зону сплавления. Рядом с этой зоной образуется та, в которой нагретый металл испытывает дополнительные напряжения. Ее называют зоной термического влияния. После этого идет основной металл. Его структура и свойства в процессе проведения работ никак не изменяются.
Классификация сварных швов по положению в пространстве.
Существует несколько основных видов сварных соединений. Наиболее распространенными среди них являются встык, внахлест, тавровые и угловые. Все они различаются между собой установкой основных материалов, расположением шва. На качества шва напрямую влияет множество самых разнообразных факторов. Могут образовываться и внутренние дефекты, и наружные. На качество швов напрямую влияет степень загрязненности металлов, которые подлежат соединению.
Здесь могут присутствовать самые разнообразные окислы, жировые пленки и так далее. Именно поэтому свариваемые поверхности обязательно нужно очищать перед проведением работ. Кстати, в процессе их проведения нужно бороться с окислами, образующимися на поверхности. В любом случае прочность конечного соединения напрямую зависит от отсутствия дефектов. Шов иногда может иметь точно такую же прочность, что и основной материал, но этого достаточно сложно достичь.
О дефектах сварных соединений
Как уже отмечалось ранее, дефекты сварных соединений могут носить самый разнообразный характер. О них обязательно нужно помнить в процессе проведения работ. Если человек имеет багаж знаний по ним, то он сможет сваривать детали, у которых будут идеальные швы. Именно к этому и нужно стремиться.
Таблица основных видов сварных соединений.
- Подрез. Это один из видов дефектов сварных соединений.
Представляет собой канавку, которая образуется в месте сплавления основного металла и шва. Чаще всего такие дефекты появляются тогда, когда есть большие сварочные ванны. Имеется в виду, что расплавляется большое количество металла вследствие использования больших показателей тока.
- Наплав. Этот дефект характеризуется тем, что происходит натекание материала шва на основной металл. Очень неприятный недостаток.
- Непровар. Такой дефект сварных соединений может иметь место в тех случаях, когда образуется недостаточная расплавленность основного металла в местах соединений конструктивных элементов. Это место чаще всего заполняется шлаком, который, ввиду своей структуры, образует пористости и пустоты во швах. Это недопустимо. Конструкция сразу теряет свои свойства. Когда используется дуговая сварка, то непровар может образоваться из-за использования недостаточной силы тока. Это один из самых опасных дефектов. Связано это прежде всего с тем что в этом месте начинают образовываться дополнительные напряжения в ходе последующей эксплуатации конструкции.
Это очень часто приводит к скорому ее разрушению. От этого дефекта можно избавиться. Для этого непровар выявляют, а затем производят наплавку в сложных участках.
- Трещины. Это частичное разрушение материала на шве или в зоне, которая расположена около него. Они могут образовываться по нескольким причинам. Если говорить о процессе, когда металл еще горячий, то трещины появляются в результате кристаллизации металла. В твердом состоянии с ним могут также происходить самые разнообразные структурные превращения. Это вторая причина появления подобных дефектов.
Дефекты сварных швов: несплавления, неравномерная форма, наплыв, трещины, свищи, перегрев.
Механизм образования горячих трещин достаточно прост. В ходе выполнения сварочных работ происходит нагрев металла. После того как источник тепла устраняется, он начинает постепенно охлаждаться. Разумеется, начинают образовываться и зоны кристаллизации. Они начинают плавать среди еще расплавленного металла. Если бы не было микрозон, которые позволяют осуществлять взаимодействие горячего и холодного материала, то все сварные соединения содержали бы дефекты. Однако этого не происходит. Таким образом, можно считать, что чем выше интервал кристаллизации, тем более возможно появление горячих трещин. Углерод напрямую влияет на этот показатель. Здесь прямая зависимость. Чем больше в стали углерода, тем шире становится интервал кристаллизации.
Холодные трещины могут образовываться в месте шва. Они появляются при охлаждении материала до температуры приблизительно в 200-300 градусов по Цельсию. Они могут появляться не сразу, что делает их более опасными. Связано появление холодных трещин с тем, что в материале начинают возникать различные структурные превращения вследствие тех или иных химических превращений. Здесь существует прямая зависимость от количества в материале углерода. Чем его больше, тем больше вероятность того, что появятся холодные трещины. Эта склонность к образованию холодных и горячих трещин определяет такой параметр, как свариваемость металлов. Этот параметр характеризует способность получения свариваемого соединения, ничем не отличающегося от основных материалов.
Поры и неметаллические включения
Дефекты сварных швов: кратеры, подрезы, поры, непровар, шлак, прожог.
Поры. Эти дефекты сварных соединений встречаются достаточно часто. Поры представляют собой пустоты, которые заполняются газом. Они могут иметь микроскопические размеры, а могут образовывать в структуре дефекты размером в несколько миллиметров. При этом образуются они чаще всего в местах соединения шва с основным материалом. На этот дефект оказывает влияние множество самых разнообразных параметров.
Самым главным из них является концентрация газа в варочной ванне. Газ выделяется из металла в процессе его плавления. Этот процесс никак нельзя предотвратить. Угарный газ не способен растворяться в железе, соответственно, он выделяется в виде пузырьков.
Неметаллические включения. Эти дефекты самих сварных соединений связаны с попаданием инородных включений в структуру шва в результате проведения работ.
Трещины в сварном соединении.
Существует огромное разнообразие таких включений. Шлаковые, к примеру, могут образовываться в результате недостаточной очистки материалов, которые подлежат соединению.
Их причиной может стать недостаточно полное удаление шлака при многослойной сварке. При работе, которая производится за счет плавления, образуется во шве материал, который по физическим и химическим свойствам отличается от основного металла. В связи с этим также могут образовываться подобные дефекты. Инородные включения могут носить самый разнообразный характер.
Изучение дефектов
Дефект сварки – поры, это заполнение пустот газами.
Разумеется, если есть дефекты различных сварных соединений, то их обязательно нужно изучать. Для этого достаточно часто используется макроанализ. Он заключается в том, что структура металла изучается с помощью невооруженного глаза или лупы. В отличие от микроскопического анализа, макроанализ не позволяет в должной мере изучить структуру материала. Его основная задача – это контроль качества соединяемых деталей в процессе сварки. Он позволяет определить тип излома, волокнистое строение, нарушения сплошной структуры и так далее. Для того чтобы провести такой анализ, необходимо изучаемую часть подвергнуть травлению специальными элементами и обработке на шлифовальных машинах. Этот образец носит название макрошлифа. На его поверхности не должно быть никаких неровностей или инородных включений, в том числе и масляных.
Все те дефекты, которые были описаны выше, вполне могут изучаться и выявляться с помощью макроанализа.
Чтобы выявить структуру материала, чаще всего используются методы поверхностного травления.
Виды наплывов в швах.
Такой подход самым лучшим образом подходит для низкоуглеродистых и среднеуглеродистых сталей. Макрошлиф, который подготовлен заранее, нужно погрузить в реактив той частью, которая подвергается анализу. При этом его поверхность обязательно должна быть зачищена с помощью спирта. В результате взаимодействия элементов происходит химическая реакция. Она позволяет вытеснять медь из раствора. Происходит замещение материалов. Медь в результате осаждается на поверхности пробника. Те места, где на основной материал медь легла не полностью, подвергаются травлению. Эти места и содержат какие-либо дефекты. После этого образец изымается из водного раствора, сушится и очищается. Все эти действия нужно проделывать максимально быстро, чтобы не произошло реакции окисления. В результате этого можно выявить те участки, где присутствует большое количество углерода, серы и других материалов.
Травление участков, которые содержат эти материалы происходит не одинаково. Там, где присутствует большая концентрация углерода и фосфора, медь на поверхности выделяется неинтенсивно. Здесь минимальная степень защиты металла. Вследствие этого данные места подвергаются самому большому травлению. В результате проведения реакции эти участки окрашиваются в более темный цвет. Лучше использовать этот метод для сталей, которые содержат минимальное количество углерода. Если его будет очень много, то медь с поверхности образца будет весьма проблематично удалить.
Виды подрезов в швах.
Есть и другие методы макроанализа структуры материалов при сварном соединении. К примеру, часто для определения количества серы используется метод фотоотпечатков. Фотобумагу при этом смачивают и держат на свету какое-то время. После этого она просушивается между листами фольгированной бумаги. Раствор, в который она изначально помещается, содержит определенное количество серной кислоты. Затем, разумеется, эта бумага ровным слоем укладывается на макрошлиф.
Она должна разглаживаться с помощью валика, чтобы полностью были исключены все ее деформации. Все пузырьки воздуха, которые могут оставаться между фотобумагой и металлом, должны быть полностью удалены. Только в этом случае исследование будет носить объективный характер. Ее нужно удерживать в таком положении приблизительно 3-10 минут. Время зависит от того, какова изначальная толщина пробника, а также от других факторов.
Виды непроваров.
Включения серы, которые располагаются в наплавленном металле, обязательно вступят в реакцию с кислотой, которая была нанесена на поверхность фотобумаги. В очагах выделения сероводорода будет образовываться такое вещество, которое носит название фотоэмульсия. Участки сернистого серебра, которые будут образовываться в результате реакции, наглядно показывают распределение серы в металле.
Разумеется, эти участки будут наблюдаться на бумаге. Фотобумага, которая была использована для проведения опыта, подлежит мытью, а затем выдерживанию в растворе гипосульфита. После этого ее еще раз промывают в жидкости и сушат. В том случае если в сварном шве будут присутствовать фтористые включения, они обязательно выделятся наружу в виде участков темного цвета.
Подведение итогов
Таким образом, в настоящее время существует множество методов выявления дефектов сварных соединений. Все они имеют определенную цель. Каждый способ позволяет выяснить, сколько в структуре шва содержится того или иного материала, который может пагубно влиять на его структуру.
Помимо методов макроанализа, в последнее время достаточно часто внедряются методы микроанализа. Они имеют то же самое предназначение, что и предыдущие. Однако дополнительно позволяют изучить структуру материала. Здесь работа ведется на молекулярном уровне строения кристаллической решетки.
Все отклонения от технологических параметров, вызванные небрежностью в работе, нарушением режимов и внешними причинами, часто не зависящими от сварщика, могут привести к возникновению дефектов в сварочном шве и околшовной зоне, попадающей в область термического воздействия. К дефектам приводит и нарушение технологических приемов как самого процесса сварки, так и некачественная подготовка, неисправность оборудования, отклонения от норм качества сварочных материалов, влияние погодных условий, низкая квалификация сварщика.
Возникновение дефектов часто связано с металлургическими и тепловыми явлениями, возникающими в процессе образования сварочной ванны и ее кристаллизации (горячие и холодные трещины, поры, шлаковые включения и т. д.; Эти дефекты снижают прочность и надежность сварного соединения, его герметичность и коррозионную стойкость. Все это может оказать значительное влияние на эксплуатационные возможности всей конструкции и даже вызвать ее разрушение.
Дефекты сварочных швов могут быть наружными и внутренними.
Наружные дефекты сварочных швов
К наружным дефектам сварных швов (рис.1) относят нарушение размеров и формы шва, подрезы и другие отклонения, которые могут быть обнаружены при внешнем осмотре сварного соединения.
Нарушение формы и размеров сварного шва чаще всего вызваны колебаниями напряжения в электрической сети, небрежностью в работе или низкой квалификацией сварщика, проявляющейся в неправильном выборе режимов, неточном направлении электрода и методике его перемещения. Дефекты проявляются в неодинаковой ширине сварочного шва по его длине, в неравномерности катета угловых швов, чрезмерной выпуклости и резких переходах от основного металла к наплавленному. Отклонения от размеров и формы сварного соединения, проявляющиеся в угловых швах, связаны с неправильной подготовкой кромок, неравномерной скоростью сварки, а также с несвоевременным контрольным обмером шва. При автоматической и полуавтоматической сварке эти дефекты чаще всего связаны с колебаниями напряжения, проскальзыванием проволоки в подающих роликах, нарушениями режимов сварки.
Непровар — местное отсутствие сплавления между свариваемыми элементами, между основным и наплавленным металлом или отдельными слоями шва при многослойной сварке. Причинами непровара являются некачественная подготовка свариваемых кромок (окалина, ржавчина, малый зазор, излишнее притупление и т.д.), большая скорость сварки, смещение электрода с оси стыка, недостаточная сила тока. В результате непровара снижается сечение шва и возникает местная концентрация напряжений, что в конечном итоге снижает прочность сварного соединения. При вибрационных нагрузках даже мелкие непровары могут снижать прочность соединения до 40%. Большие непровары корня шва могут снизить прочность до 70%. Поэтому если непровар превышает допустимую величину, участок шва подлежит удалению с последующей переваркой.
Подрез — дефект, наиболее часто встречающийся при сварке. Он выражен в виде углубления по линии сплавления сварного шва с основным металлом. В результате подреза происходит местное уменьшение толщины основного металла, что приводит к снижению прочности. Особенно опасен подрез в случаях, когда он расположен перпендикулярно действующим рабочим напряжениям. Подрез возникает обычно при повышенном напряжении дуги с завышенной скоростью сварки, когда одна из кромок проплавляется глубже, жидкий металл стекает на горизонтальную плоскость и его не хватает для заполнения канавки. При сварке угловых швов подрезы возникают в основном из-за смещения электрода в сторону вертикальной стенки, что вызывает значительный разогрев, плавление и стекание металла на горизонтальную полку. В стыковых швах подрезы образуются при сварке на больших токах и при неправильном положении присадочного материала. К подрезу могут привести увеличенные углы разделки кромок. Этот дефект обнаруживается визуально и при отклонениях выше установленной нормы полежит переварке с предварительной зачисткой.
Подрезы небольшой протяженности, ослабляющие сечение шва не более чем на 5% в конструкциях, работающих под действием статических нагрузок можно считать допустимыми. В конструкциях, работающих на выносливость, подрезы недопустимы.
Наплыв — проявляется в виде натекания металла шва на поверхность основного металла без сплавления с ним. Наплывы резко изменяют очертания швов и тем самым снижают выносливость констукции. Причиной этого дефекта может стать пониженное напряжение дуги, наличие окалины на свариваемых кромках, медленная сварка, когда появляются излишки расплавленного присадочного металла. Чаще всего наплывы возникают при сварке горизонтальных швов на вертикальной плоскости. При сварке кольцевых поворотных стыков наплывы могут возникать при неправильном расположении электрода относительно оси шва. Наплывы большой протяженности недопустимы.
Прожог — сквозное проплавление обычно возникает из-за большого тока при малой скорости сварки. Проявляется он в виде сквозного отверстия в сварочном шве, которое возникает в результате утечки сварочной ванны. При многослойной сварке прожог возникает в процессе выполнения первого прохода шва. Причинами прожога могут стать — завышенный зазор между свариваемыми кромками, недостаточная толщина подкладки или неплотное ее прилегание к основному металлу, что создает предпосылку для утечки сварочной ванны. Прожог может образоваться при внезапной остановке подачи защитного газа. При сварке поворотных кольцевых стыков прожоги вызываются неправильным расположением электрода относительно зенита. Дефект обнаруживается визуально и переваривается после предварительной зачистки. Ожоги вызываются попаданием жидкого металла на участки, которые находятся вне сварного шва.
Незаваренный кратер — дефект сварного шва, который образуется в виде углублений в местах резкого отрыва дуги в конце сварки. В углублениях кратера могут появляться усадочные рыхлости, часто переходящие в трещины. Кратеры обычно появляются в результате неправильных действий сварщика. При автоматической сварке кратер может появляться в местах выводных планок, где обрывается сварочный шов. Кратеры часто являются причиной начала развития трещин и поэтому недопустимы. Их зачищают и заваривают.
Поверхностное окисление — окалина или пленка оксидов на поверхности сварного соединения. Поверхностное окисление зависит от плохой защиты сварочной ванны, качества подготовки свариваемых кромок, неправильной регулировки подачи защитного газа, его составом, большим вылетом электрода.
Свищ — воронкообразное углубление в сварочном шве, развивающееся из раковины или большой поры. Причиной развития свища чаще всего является некачественная подготовка поверхности и присадочной проволоки под сварку. Дефект обнаруживается визуально и подлежит переварке.
Внутренние дефекты сварочных швов
Трещины бывают холодные и горячие (рис. 2). Трещины могут быть как наружными, так и внутренними. Это самые опасные дефекты сварного соединения, часто приводящие к его разрушению. Проявляются они в виде разрыва в сварном шве или в прилегающих к нему зонах. Сначала трещины образуются с очень малым раскрытием, но под действием напряжений их распространение может быть соизмеримо со скоростью звука, в результате чего происходит разрушение конструкции. Причинами образования трещин являются большие напряжения, возникающие при сварке. Чаще всего трещины проявляются при сварке высокоуглеродистых и легированных сталей в результате быстрого охлаждения сварочной ванны. Вероятность появления трещин увеличивается при жестком закреплении свариваемых деталей.
Горячие трещины — появляются в процессе кристаллизации металла при температурах 1100 -1300°С вследствие резкого снижения пластических свойств и развития растягивающих деформаций. Появляются горячие трещины на границах зерен кристаллической решетки. Появлению горячих трещин способствует повышенное содержание в металле шва углерода, кремния, водорода, никеля, серы и фосфора. Горячие трещины могут возникать как в массиве шва, так и в зоне термического влияния. Распространяться горячие трещины могут как вдоль, так и поперек шва. Они могут быть внутренними или выходить на поверхность.
Холодные трещины — возникают при температурах ниже 120°С, то есть сразу после остывания сварочного шва. Кроме того, холодные трещины могут возникнуть и через длительный промежуток времени. Причиной появления холодных трещин являются сварочные напряжения, возникающие во время фазовых превращений, приводящих к снижению прочностных свойств металла. Причиной появления холодных трещин может стать растворенный атомарный водород, не успевший выделиться во время сварки. Причинами попадания водорода могут служить непросушенные швы или сварочные материалы, нарушения защиты сварочной ванны.
Поры — представляют собой полости внутри шва, заполненные не успевшим выделиться газом (в первую очередь водородом). Они могут быть округлой или вытянутой формы, а их размеры зависят от размеров пузырьков образовавшихся газов. Поры могут быть одиночными или развиваться целой цепочкой вдоль сварочного шва. Основными причинами появления пор являются: присутствие вредных примесей в основном или присадочном металлах, ржавчина или другие загрязнения, не удаленные со свариваемых кромок перед сваркой. Повышенное содержание углерода также способствует появлению пор. Поры могут появляться при нарушениях защиты сварочной ванны, повышенной скорости сварки. Основной причиной появления пор при сварке плавящимся электродом является отсыревшее покрытие. Одиночные поры не опасны, но их цепочка влияет на прочность сварного соединения. Участок сварочного шва, в котором присутствуют поры, подлежит переварке предварительной механической зачисткой.
Шлаковые включения — это дефекты сварного шва, выраженные в наличии полостей, заполненных не успевшим всплыть шлаком. Образование шлаковых включений происходит при некачественной подготовке свариваемых кромок и присадочного материала, завышенной скорости сварки или плохой защите ванны. При сварке в защитных газах шлаковые включения встречаются редко. Шлаковые включения могут иметь размер до нескольких десятков миллиметров и поэтому являются очень опасными. Участок шва, на котором шлаковые включения превышают допустимые нормы, подлежит вырубке переварке.
Вольфрамовые включения — возникают при нарушении защиты сварочной ванны при сварке неплавящимся вольфрамовым электродом. Кроме этого вольфрамовые включения возникают при коротких замыканиях или завышенной плотности тока. Особенно часто встречаются вольфрамовые включения при сварке алюминия и его сплавов, в которых вольфрам нерастворим.
Оксидные включения — образуются в результате образования труднорастворимых тугоплавких пленок. Чаще всего они возникают вследствие значительных поверхностных загрязнений или при нарушениях защиты сварочной ванны. Являясь прослойкой в массиве шва, оксидные включения резко снижают прочность сварного соединения могут привести к его разрушению под приложенной в процессе эксплуатации нагрузкой.
В ходе сварных работ, как и при любых других способах обработки металлов не исключены дефекты сварочных швов, образующихся по целому ряду причин.
Перечень факторов, влияющих на качество сварного соединения очень обширен, однако основной причиной дефектов являются неуправляемые химические процессы, происходящие в пограничных областях зоны сварки.
Причиной деффектов может быть кристаллизация металла, его химическая неоднородность, а также взаимодействие расплавленной массы с твердым материалом заготовок или с окружающими газами и шлаками. Ещё одной нуждающейся в учёте причиной появления дефектов (трещин, в частности) являются нежелательные напряжения в зоне сварки.
Характер отклонений сварных соединений от нормы (дефектов) зависит от . Это объясняется технологическими особенностями того или иного процесса.
Различие достаточно отчётливо проявляется во всех основных её видах, а именно – при электродуговой обработке металлов, контактном сваривании листовых заготовок и, наконец, в газовой сварке.
Электродуговой метод
К основным причинам образования дефектов при можно отнести два основных фактора. Это химические реакции, приводящие к нарушению структуры швов, а также серьёзные отклонения от существующих технологий.
Сварочные дефекты, возникающие во втором случае, чаще всего проявляются в виде прожогов, непроваров и нарушений геометрических размеров шва или трещин, возникающих после остывания материала.
Процесс образования холодных трещин при сварке объясняется недопустимыми механическими нагрузками на шовное соединение. Такие отклонения от нормальной структуры шва чаще всего наблюдаются при сваривании углеродистых (легированных) сталей, а также большинства чугунных изделий.
Вообще же в теории электродуговой сварки рассматриваются самые различные нарушения структуры сварного соединения. Помимо так называемого «холодного» растрескивания к таким дефектам причисляют «горячие», макроскопические и микротрещины.
Все перечисленные отклонения от нормы со временем приводят к расширению зоны действия дефекта и аварийным разрушениям некачественно проваренной конструкции. По этой причине исследованию качества образующихся при дуговой сварке швов уделяется повышенное внимание.
Газосварка
Основные причины дефектов, проявляющихся при газовой сварке, чаще всего те же, что и в перечисленных ранее случаях, касающихся других категорий сварочных работ.
Это те же нарушения в технологии подготовки заготовок перед сплавлением и ошибки, допущенные во время формирования шва (по причине использования нестандартных расходных материалов, например).
Вот почему с целью предупреждения дефектов газосварки особое внимание уделяется грамотному выбору правильного режима сваривания, а также уровню квалификации самого исполнителя работ.
По доступности выявления нарушений при газосварке все известные дефекты делятся на поверхностные и скрытые. К первой категории относятся типовые непровары, значительные по размеру наплывы, а также вогнутости, прорезы, кратеры, образующиеся на основании (в корне шва).
Сюда же следует отнести недопустимое смещение линии стыка (неправильная их разделка), резкие перепады по толщине и поверхностные трещины.
К скрытым и, как правило, трудно выявляемым дефектам газовой сварки относятся внутренние пористые образования, микроскопические газовые каналы, а также шлаковые и оксидные вкрапления.
Этот список может быть продолжен такими нередко возникающими нарушениями структуры свариваемых заготовок, как малозаметные непровары между слоями и внутренние микротрещины.
Точечный контактный метод
К дефектам контактного сваривания принято относить следующие визуально различимые (наружные) нарушения в структуре соединений:
- наблюдаемые невооружённым глазом трещины;
- точечные прожоги;
- наружные выплески;
- разрывы металла с поверхностным проявлением структуры;
- нарушения формы контакта и многие другие.
Основными причинами появления таких отклонений в структуре контакта являются неправильное выставление параметров (амплитуды или длительности) импульсного тока, недостаточное усилие при сжатии электродов.
К дефектам приводит некачественная подготовка обрабатываемых поверхностей перед сваркой, близкое расположение контактной точки к краю точечного соединения.
Среди других причин – недостаточная величина нахлеста заготовок, недопустимый перекос сочленяемых деталей, износ электродов и многое другое.
Основным скрытым дефектом при сварке контактными методами является «слипание» листовых заготовок, при котором между ними образуется лишь кажущийся, чисто внешний контакт. Данный дефект может проявляться не только при сварке под давлением, но и при других известных видах точечного сваривания.
Обнаружить визуально этот вид дефектного образования обычными методами физического контроля практически невозможно
. Предупредить его удаётся только путём строгого соблюдения технологии и поддержания в норме основных параметров сварочного процесса (амплитуды и длительности импульсного тока, а также необходимого усилия сжатия).
Исправление и предотвращение
Наличие дефектов при любом типе сварки не всегда приводит к непоправимому результату и выбраковке заготовки. Существует определённый набор нарушений техпроцесса или отклонений от нормы, которые могут быть исправлены сразу же по завершении процесса.
Простейшим и кардинальным способом исправления любого огреха при сварке является вырубка забракованного участка и повторное его заваривание (с учётом обнаруженной неисправности, конечно). Для исключения или исправления ряда дефектов вполне достаточно скорректировать положение рабочего инструмента с электродом.
При использовании этого приёма следует помнить о том, что сварка методом «на подъём» способствует перераспределению расплавленного металла в зоне ванны, а работа по способу «углом вперед» позволяет снизить глубину проплавления.
Поскольку на исправление брака потребуются дополнительные расходы – желательно так организовать сварочный процесс, чтобы исключить необходимость повторных работ.
Один из наиболее эффективных способов предотвращения дефектов – это добавление одного из компонентов при сварке в защитной среде, что позволяет увеличить коэффициент заполняемости шва и предотвращает возможные подрезы.
Для повышения текучести жидкого металла, обеспечивающей заполнение корневой части шва, достаточно нагреть предварительно место сварки до определённой температуры посредством специальных добавок (флюсов).
Достичь требуемого эффекта нередко удаётся и за счёт увеличением силы тока. При этом тщательная зачистка сварных кромок и удаление с их поверхности окисных плёнок также снижают вероятность нарушения режима сварки.
Разделка трещин
Для устранения холодных трещин применяется способ их повторной сварки с ограничением расширения области дефекта по обе стороны (подготовку специальных «уловителей»).
Такие уловители выполняются в виде небольших отверстий, просверленных на удалении порядка 1,5 см от краёв образования, способных замедлить или полностью прекратить его рост.
Ремонт трещин предполагает определенный порядок операций, учитывающий необходимость тщательной подготовки к повторному свариванию. На этом этапе подготавливаемые к восстановлению кромки сначала разделываются под углом 60 °.
Для проведения этой операции используется либо обычное зубило, либо специальный разделочный электрод, посредством которого края реза полностью очищают от всех мешающих сплавлению образований и неровностей.
Просверленные ранее ограничивающие отверстия-ловушки удалять совсем необязательно.
Наличие дефектов сварки, как правило, приводит к снижению прочностных показателей подготавливаемого соединения, и, как следствие – к нарушению работоспособности конструкции (её повышенной аварийности). Именно поэтому вопросу обнаружения и исправления дефектов всегда уделяется особое внимание.
Время чтения: ≈12 минут
Не важно, какую технологию вы выбрали для выполнения сварочных работ. Дефекты могут возникнуть в любом случае, что при , что при сварке . Появление дефектов связано либо с неопытностью сварщика, либо с неправильно выбранным режимом сварки, либо с недостаточно тщательным контролем качества.
Поэтому важно предотвращать дефекты и контроль качества сварных соединений должен проводится после выполнения каждой сварочной операции. В этой статье мы подробно расскажем, какие существуют распространенные дефекты сварных швов. И какие методы контроля можно использовать, чтобы обнаружить их.
Любой опытный сварщик скажет вам, что существуют многочисленные виды дефектов сварных швов. Их можно разделить на две категории — наружные и внутренние. Наружные дефекты сварных швов можно обнаружить прямо на поверхности шва с помощью специального инструмента (например, лупы) или хорошего зрения. Внутренние дефекты сварных швов визуально не видны и для их обнаружения нужно использовать особые методики контроля качества. О них мы расскажем ближе к концу. А пока дефекты.
В рамках этой статьи мы не будем перечислять все возможные дефекты, а расскажем только о самых распространенных. Итак, ниже наша краткая классификация дефектов сварных швов.
Непровар
Непровар в сварном шве — один из самых часто встречающихся дефектов у новичков. Представляет собой небольшой участок с недостаточно проваренным металлом. Основные причины образования непроваров — слишком длинная сварочная дуга, недостаточная сила тока или обе ошибки одновременно.
У новичков непровары образуются в том случае, если была выполнена неправильная или если сварка велась слишком быстро. Как не трудно догадаться, чтобы предотвратить непровар сварного шва нужно подобрать оптимальный режим сварки, варить не слишком быстро и на короткой дуге.
Подрез
Если вы когда-либо варили тавровый или нахлесточный шов, то наверняка могли заметить небольшие углубления вдоль сторон сварного валика. Это и есть подрезы. Частая причина образования подрезов — слишком быстрая сварка или неправильно подобранное напряжение сварочной дуги. Также подрезы порой возникают из-за слишком длинной дуги.
Некоторые новички спрашивают: «Допускаются ли подрезы сварных швов?». Да, но только в очень сложных конструкциях, где подрезов не избежать. В подобных ситуациях подрезы называют просто «допустимые дефекты сварных швов». В остальных случаях это недопустимые дефекты.
Наплыв
Наплыв в сварном шве в 95% случаев свидетельствует о том, что вы неправильно настроили или недостаточно тщательно зачистили кромки. Очевидно, что для предотвращения образования дефекта нужно правильно настроить силу сварочного тока и немного повысить напряжение дуги.
Прожог
Прожог сварного шва — это сквозное отверстие в сварном соединении, которое вы можете обнаружить невооруженным глазом. Прожоги образуются из-за медленной сварки. В одном месте концентрируется слишком большая температура и металл плавится больше, чем должен. Главная опасность прожогов — существенное снижение прочности шва.
Понизьте сварочный ток и ускорьте формирование шва. Только так вы сможете предотвратить появление прожогов. Уделите особое внимание, если варите алюминий. У него очень высокая теплопроводность, при этом низкая температура плавления. Так что получить прожог на алюминиевой заготовке проще простого.
Кратер
Кратер — это воронка небольшого размера, расположенная прямо на валике шва. Чаще всего в самом его конце. Образуется из-за резкого обрыва дуги. Ведите дугу плавно и оканчивайте сварку постепенно. Если на вашем сварочном аппарате есть специальный режим предотвращения образования кратеров, то включите его.
Горячая или холодная трещина
Трещины в сварных швах — также один из самых часто встречающихся дефектов. Трещины бывают холодными и горячими. Горячие образуются во время сварки, а холодные — после. Горячие трещины образовываются при несовместимости электрода/присадочной проволоки и свариваемого металла. Иногда трещины могут образоваться при попытке заварить кратер, о котором мы говорили выше. Проверяйте, чтобы состав присадочного материала и металла был идентичен.
С холодными трещинами все проще. Они образовываются только в том случае, если шов слишком хрупкий и не выдерживает механической нагрузки. Единственный способ предотвратить появление холодных трещин — соблюдать технологию сварки и работать профессионально. Горячие и холодные трещины могут быть как внутренними (скрытыми от глаз), так и наружными.
Поры
Что такое пора в сварке? Пора (а чаще всего поры) — это небольшие углубления в структуре шва. Могут быть поверхностными или внутренними. Представьте муравейник, который пронизывают множественные ходы. Вот то же самое происходит и со швом. Поры без сомнения можно назвать самым частым дефектом из всех возможных.
Если в ходе процесса образовались поры в сварном шве, значит вы с самого начала все делали неправильно. Скорее всего, вы недостаточно тщательно зачистили кромки и не защитили шов от попадания кислорода. А подобные ошибки совершают только те, кто только-только начал свое знакомство со сваркой. На работайте на сквозняке и проверяйте качество электродов/исправность горелки/исправность системы подачи газа.
Методы контроля качества
Что ж, теперь вы знаете самые распространенные дефекты сварных соединений и причины их возникновения. Теперь давайте поговорим о . Мы расскажем вам о самых часто применяемых и эффективных. Это визуально-измерительный контроль, радиационный и ультразвуковой контроль.
Визуально-измерительный контроль
(ВИК) — это самый простой и самый старый способ оценки качества сварного соединения. Из названия понятно, что в ходе этого контроля используется визуальное наблюдение и измерительные приборы. Под визуальным наблюдением подразумевается простой осмотр шва невооруженным глазом или с помощью лупы. В отдельных случаях используют микроскопы. А в качестве измерительных инструментов чаще всего применяют обычные линейки. Это самый доступный и недорогой метод контроля, поскольку инструменты стоят недорого и такому контролю можно обучить самого сварщика, выполняющего работу. Предприятию даже не нужно нанимать отдельных специалистов для проведения этого контроля.
Сейчас в магазинах продаются специальные наборы со всеми необходимыми инструментами и даже подробно инструкцией, как проводить контроль. Вам достаточно один раз прочесть брошюру, все запомнить и вы уже можете провести такой контроль самостоятельно. Но, несмотря на все плюсы, есть у ВИК большой недостаток — значительное влияние человеческого фактора на результат контроля. Вся ответственность ложится на плечи человека. И если он в силу объективных или субъективных причин не сможет выполнить контроль качественно, то есть вероятность брака.
Радиационный контроль
(его также называют радиографическим) — очень интересный метод контроля, который основан на применение рентгеновских лучей. Да, как при рентген-диагностике в поликлинике. Деталь повещается в специальный аппарат (или аппарат устанавливается на деталь), затем сквозь металл пропускают рентгеновское излучение и на выходе получают снимок, на котором видны все дефекты сварки. Эта технология наверняка известна вам давно.
Нетрудно догадаться, что подобная диагностика крайне эффективна. На снимке видны малейшие дефекты, которые невозможно обнаружить любым другим способом. Особенно, если снимок выполняется с применением компьютера, на котором потом можно детально рассмотреть все изъяны сварки. Но при работе с рентгенографом необходимо соблюдать повышенную технику безопасности. Частицы радиации могут заражать воздух, из-за чего он становится токопроводимым. А о возможном вреде для здоровья и говорить не приходится. Так что к выполнению радиационного контроля должны быть допущены только хорошо обученные сотрудники.
Ультразвуковой контроль
Ультразвуковая дефектоскопия сварных швов (он же ультразвуковой контроль качества или просто УЗК сварных швов) — метод контроля, который во многом схож с выше описанным радиационным. Только вот вместо рентгеновских лучей здесь используются ультразвуковые волны. Для фиксации результата используется ультразвуковой дефектоскоп для контроля сварных соединений.
Суть его работы проста. На поверхность шва посылаются ультразвуковые волны, которые проходят сквозь металл. Проходят не полностью, часть лучей отражается и возвращается обратно. Если у шва есть какой-либо дефект, то отразившиеся и вернувшиеся назад волны будут ослаблены и искажены. Проще говоря, они будут отличаться от тех, что были пущены вначале проведения контроля. Все эти изменения как раз и фиксирует дефектоскоп.
Ультразвуковой контроль используется очень часто. Для его проведения можно установить большой стационарный дефектоскоп в отдельном кабинете, а можно приобрести компактную модель для выездной диагностики. И эта компактная модель сможет дать вполне объективный результата. С помощью дефектоскопа можно не только узнать местонахождение дефекта, но и его размеры. Но нужно учитывать, что дефектоскопы стоят дорого и для работы с ними нужно дополнительно обучать персонал. Или искать специалиста «на стороне».
Вместо заключения
Дефекты сварных швов и соединений бывают разными, но суть всегда одна — они так или иначе нарушают эксплуатационные характеристики готового изделия. Чтобы их избежать необходимо как можно больше практиковаться, правильно настраивать режим сварки и не забывать о контроле качества. Проведение ультразвукового контроля занимает считанные минуты, а в результате вы получаете объективную картину и можете трезво оценить качество своей работы.
% PDF-1.7
%
116 0 объект
>
endobj
xref
116 79
0000000016 00000 н.
0000002472 00000 н.
0000002692 00000 н.
0000002750 00000 н.
0000002786 00000 н.
0000003387 00000 н.
0000003536 00000 н.
0000003668 00000 н.
0000003937 00000 н.
0000004467 00000 н.
0000004939 00000 н.
0000005512 00000 н.
0000005761 00000 н.
0000006342 00000 п.
0000006379 00000 п.
0000006406 00000 н.
0000006520 00000 н.
0000006632 00000 н.
0000007265 00000 н.
0000008685 00000 н.
0000009114 00000 п.
0000009572 00000 н.
0000009657 00000 н.
0000010030 00000 н.
0000010515 00000 п.
0000011629 00000 п.
0000012276 00000 п.
0000012431 00000 п.
0000013036 00000 п.
0000013711 00000 п.
0000014920 00000 п.
0000015998 00000 н.
0000017027 00000 п.
0000018100 00000 п.
0000018406 00000 п.
0000018684 00000 п.
0000019761 00000 п. 0000020803 00000 п.
0000023453 00000 п.
0000023523 00000 п.
0000023632 00000 п.
0000054169 00000 п.
0000054432 00000 п.
0000054930 00000 п.
0000059742 00000 п.
0000068913 00000 п.
0000069160 00000 п.
0000085835 00000 п.
0000114019 00000 н.
0000122529 00000 н.
0000154707 00000 н.
0000154772 00000 н.
0000154865 00000 н.
0000158185 00000 н.
0000158478 00000 н.
0000158780 00000 н.
0000158807 00000 н.
0000159240 00000 н.
0000181429 00000 н.
0000181685 00000 н.
0000182202 00000 н.
0000211661 00000 н.
0000211700 00000 н.
0000221042 00000 н.
0000221292 00000 н.
0000221687 00000 н.
0000222069 00000 н.
0000222563 00000 н.
0000223054 00000 н.
0000245528 00000 н.
0000245803 00000 н.
0000246188 00000 п.
0000246586 00000 н.
0000246980 00000 н.
0000283336 00000 н.
0000283375 00000 н.
0000287234 00000 н.
0000454314 00000 н.
0000001876 00000 н.
трейлер
] / Назад 1420596 >>
startxref
0
%% EOF
194 0 объект
> поток
hb«a`b`c`? ̀
% PDF-1. 5
%
4101 0 объект>
endobj
xref
4101 209
0000000016 00000 н.
0000008336 00000 н.
0000004476 00000 н.
0000008493 00000 п.
0000008632 00000 н.
0000009077 00000 н.
0000010152 00000 п.
0000010190 00000 п.
0000010243 00000 п.
0000010861 00000 п.
0000011300 00000 п.
0000016576 00000 п.
0000017300 00000 п.
0000017415 00000 п.
0000019176 00000 п.
0000020702 00000 п.
0000022497 00000 п.
0000024425 00000 п.
0000026412 00000 п.
0000028379 00000 п.
0000028496 00000 п.
0000030375 00000 п.
0000032190 00000 п.
0000422047 00000 н.
0000422187 00000 н.
0000422731 00000 н.
0000422786 00000 н.
0000422878 00000 н.
0000423484 00000 н.
0000423620 00000 н.
0000423717 00000 н.
0000423969 00000 н.
0000424248 00000 н.
0000424336 00000 н.
0000424666 00000 н.
0000424945 00000 н.
0000425587 00000 н.
0000425723 00000 н.
0000425824 00000 н.
0000426076 00000 н.
0000426338 00000 н.
0000426426 00000 н.
0000426756 00000 н.
0000427035 00000 п.
0000427673 00000 н.
0000427809 00000 н.
0000427908 00000 н.
0000428104 00000 п.
0000428363 00000 п.
0000428451 00000 п.
0000428787 00000 н.
0000429068 00000 н.
0000429651 00000 п.
0000429787 00000 н.
0000429882 00000 н.
0000430134 00000 п.
0000430415 00000 н.
0000430503 00000 н.
0000430841 00000 п.
0000431121 00000 н.
0000478669 00000 н.
0000478806 00000 н.
0000479024 00000 н.
0000482591 00000 н.
0000482679 00000 н.
0000483010 00000 н.
00004
00000 н. 00004
00000 н. 00004 00000 н. 00004
00000 н. 00004 00000 н. 00004
00000 н. 00004
00000 н. 00004 00000 н. 0000400000 н. 00004
00000 н. 00004
00000 н. 00004
00000 н. 00004
00000 н. 00004
00000 п. 00004
00000 н. 00004 00000 н.
00004
00000 н.
00004
00000 н. 00004
00000 п. 00004
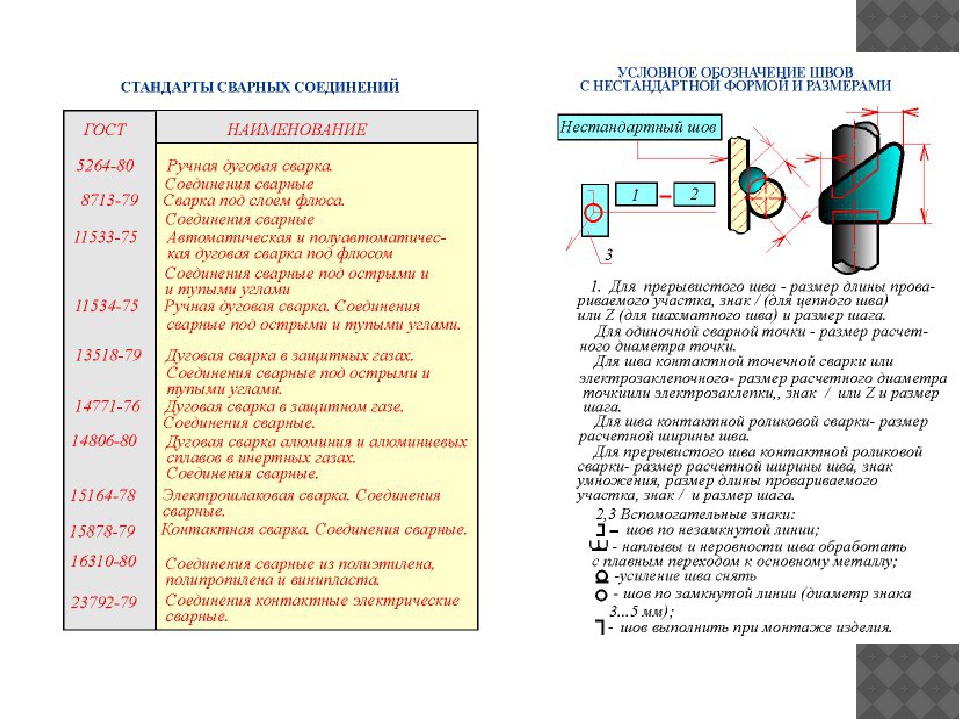
00000 н. 00004
00000 н. 00004 00000 н. 00004 00000 н. 00004
00000 н. 00004
00000 н. 00004 00000 п. 00004
00000 н. 00004
00000 н. 0000494789 00000 н. 0000494834 00000 н. 0000494913 00000 н. 0000494990 00000 н. 0000495035 00000 н. 0000495080 00000 н. 0000495125 00000 н. 0000495170 00000 н. 0000495270 00000 н. 0000495315 00000 н. 0000495415 00000 н. 0000495460 00000 н. 0000495555 00000 н. 0000495600 00000 н. 0000495691 00000 п. 0000495736 00000 н. 0000495781 00000 п. 0000495826 00000 н. 0000495926 00000 н. 0000495971 00000 п. 0000496079 00000 п. 0000496124 00000 н. 0000496212 00000 н. 0000496257 00000 н. 0000496355 00000 н. 0000496400 00000 н. 0000496499 00000 н.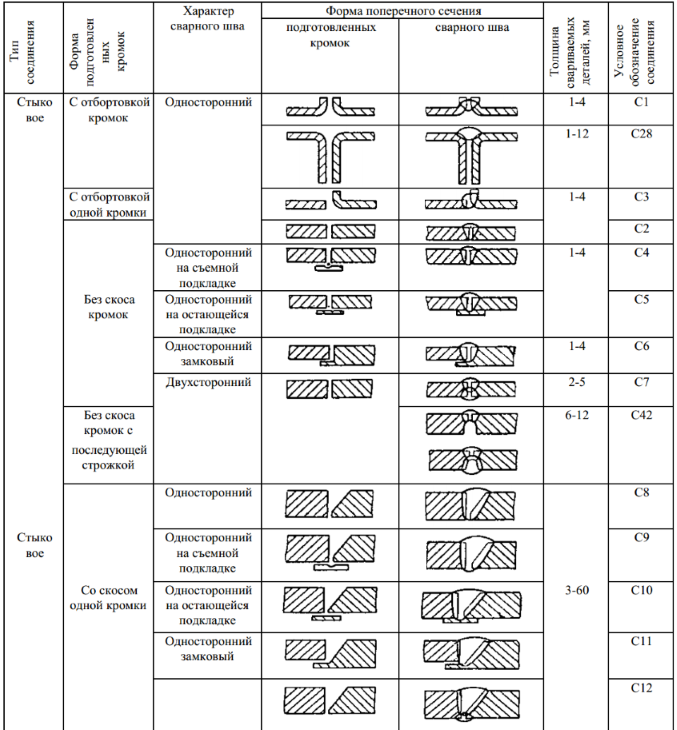

Оценка прочности и микроструктуры сварных труб с ламинацией стенок
Основные моменты
- •
Сварка металла с прослоями приводит к неравномерной нагрузке на сварные соединения.
- •
Неравномерная нагрузка приводит к послойному разрушению дефектных участков.
- •
Применение магнитного контроля неэффективно для обнаружения расслоений ниже 100 мкм.
- •
Необходимо выполнить ультразвуковой контроль толщины стенки по всему периметру трубы.
Реферат
Представленное исследование было проведено с целью изучения причин развития трещины на заводском кольцевом сварном шве, выполненном контактной сваркой с использованием высокочастотных токов.Трещина появилась в подземном магистральном газопроводе. Исследование включало визуальный и размерный контроль объекта, ультразвуковые испытания толщины стенки трубы, химический анализ, оптическое и электронно-микроскопическое исследование, измерение микротвердости сварных швов и зон термического влияния, испытания на статическое растяжение и фрактографический анализ. Исследование показало, что в металле одной из сварных труб имеются прослои. Были исследованы структура и морфология сварного шва и металла в прилегающих частях трубы, а также проанализировано влияние включений на структуру сварного шва.Важным результатом исследования было то, что ламинаты были неоднородными, имели многослойную структуру и образовывались под действием ряда производственных факторов. Их совместный эффект привел к некачественному сварному шву и дальнейшему развитию трещин в процессе эксплуатации. При поточном контроле магнитным дефектоскопом ни трещины, ни расслоения стенки трубы не обнаружено.
Ключевые слова
Ламинирование
Сварка
Диаграмма деформирования
Дефекты проката
Металлография
Рекомендуемые статьиЦитирующие статьи (0)
Полный текст© 2021 Elsevier Ltd.Все права защищены.
Рекомендуемые артикулы
Ссылки на статьи
Качество сварных швов ГОСТ 3242 79. Методы неразрушающего контроля
ГОСТ 3242-79
МЕЖГОСУДАРСТВЕННЫЙ СТАНДАРТ
СОЕДИНЕНИЯ СВАРНЫЕ
МЕТОДЫ КОНТРОЛЯ КАЧЕСТВА
ИПК ИЗДАТЕЛЬСКИЙ СТАНДАРТ
Москва
МЕЖДУНАРОДНЫЙ СТАНДАРТ
Постановление Госкомитета СССР по стандартам от 2 августа 1979 г.2930, срок действия установлен
от 01. 01.81
Ограничение срока действия снято постановлением Госстандарта от 21.10.92 № 1434
1. Настоящий стандарт устанавливает методы контроля качества и их объем для выявления дефектов сварных соединений металлов и сплавов, выполненных методами сварки, указанными в ГОСТ 19521-74.
2. Применение метода или комплекса методов контроля для выявления дефектов сварных соединений при техническом контроле конструкций на всех этапах их изготовления, ремонта и модернизации зависит от требований к сварным соединениям в технической документации на конструкцию.
Методы контроля должны соответствовать приведенным в таблице и указаны в технической (конструкторской и технологической) документации на сооружение.
3. Допустимость использования методов, не указанных в настоящем стандарте, должна быть предусмотрена в технической документации на проектирование. Технология контроля сварных швов любым методом должна быть установлена в нормативно-технической документации на контроль.
Неразрушающие методы контроля качества сварных соединений
Тип управления | Метод контроля | Характеристика метода | Область применения | Обозначение стандарта метода контроля | ||||
Обнаружены дефекты | Чувствительность | Особенности метода | ||||||
Технический осмотр | Внешний осмотр и измерение | Дефекты поверхности | Несплошности, отклонения размеров и формы сварного шва от заданных значений более 0.1 мм, а также поверхностное окисление сварного шва | Метод позволяет обнаруживать дефекты минимально обнаруживаемого размера при осмотре и измерении сварного соединения оптическими приборами с увеличением до 10 ´ и средства измерения | Не ограничено | |||
Капилляр | Цвет Люминесцентный Люминесцентный цвет | Дефекты поверхности (несплошности) | ГОСТ 18442-80 | Чувствительность и надежность метода зависят от качества подготовки поверхности стыка к контролю. | Не ограничено | |||
Радиация | Радиографический Радиоскопический Радиометрический | Внутренние и поверхностные дефекты (несплошности), а также дефекты формы стыка | от 0,5 до 5,0% контролируемой толщины металла От 3 до 8% контролируемой толщины металла 0.От 3 до 10% контролируемой толщины металла | Обнаружение дефектов по ГОСТ 7512-82. Чувствительность зависит от характеристик испытуемого сварного соединения и средств контроля | ||||
Акустический | Ультразвуковой | Внутренние и поверхностные дефекты (несплошности) | Толщина сварного шва, мм | Предел чувствительности, мм 2 | Размер, количество и характер дефектов определяются условно по ГОСТ 14782-86 .![]() | |||
от 1.От 5 до 10 включительно ул. 10 до 50 « «50» 150 « «150» 400 « «400» 2000 « | 0,5 — 2,5 2,0 — 7,0 3,5 — 15,0 10,0 — 80,0 35,0 — 200,0 | |||||||
Магнитный | Магнетоферрозон | Уровни условной чувствительности по ГОСТ 21104-75 | Метод обеспечивает обнаружение: внутренних несплошностей, расположенных на глубине 10 мм от поверхности стыка; | |||||
Магнитный | Магнетоферрозон | Поверхностные и подземные неоднородности | Уровни условной чувствительности по ГОСТ 21104-80 | разнонаправленных дефекта. Чувствительность и надежность метода зависит от качества приготовления контрольного соединения. | ||||
Магнитная частица | Поверхностные и подземные неоднородности | Уровни условной чувствительности по ГОСТ 21105-87 | Метод позволяет выявить внутренние несплошности, расположенные от поверхности стыка на глубине до 2 мм включительно.Чувствительность и надежность метода зависят от качества приготовления соединения для контроля. | |||||
Магнитографический | Поверхностные, подземные и внутренние неоднородности | от 2 до 7% толщины контролируемого металла | Надежность контроля снижается при наличии неровностей на исследуемой поверхности стыка размером более 1 мм. | Соединения стыковые, сварные газовой дугой, ферромагнитные конструкции. Контролируемая толщина не более 25 мм | ||||
Обнаружение утечек | Радиация | Сквозные дефекты | Для криптона 85 (85 кг) — от 1 · 10 -9 до 1 · 10-14 мм 3 МПа / с | Радиоактивная опасность | Обнаружение утечек в сварных соединениях, работающих под давлением, закрытых конструкциях атомной энергетики, а также закрытых конструкциях, когда невозможно использовать другие методы обнаружения утечек. | |||
Обнаружение утечек | ||||||||
Масс-спектрометрия | Сквозные дефекты | По дороге: накопление при атмосферном давлении — до 1 · 10-6 мм 3 МПа / с откачка от 1 · 10-7 до 1 · 10-4 мм 3 МПа / с зонд — до 1 · 10-5 мм 3 МПа / с | Условия эксплуатации течеискателя: температура окружающей среды 10-35 ° С, максимальная относительная влажность воздуха 80% | Способ накопления давления заключается в определении общей степени негерметичности закрытых конструкций. Метод вакуумирования — определение суммарной утечки закрытых и открытых конструкций. Зондовый метод — обнаружение локальных утечек в сварных соединениях крупногабаритных конструкций. Контролируемая толщина не ограничена | ||||
Калибр | Сквозные дефекты | По дороге: перепад давления — от 1 · 10-3 до 7 · 10-3 мм 3 МПа / с манометр дифференциального давления — до 1 · 10-8 мм 3 МПа / с | Чувствительность метода снижается при обследовании конструкций большого объема. Продолжительность испытания, испытательный газ и температура окружающей среды, а также атмосферное давление влияют на точность испытания | Сварные соединения закрытых конструкций, работающих под давлением: метод перепада давления — для определения суммы общих утечек; Метод манометра дифференциального давления — для локального обнаружения утечек. Контролируемая толщина не ограничена | ||||
Обнаружение утечек | Галоген | Сквозные дефекты | Фреон 12: атмосферный зонд — до 5 · 10-4 мм 3 МПа / с Вакуумный зонд— до 1 · 10-6 мм 3 МПа / с | Надежность и чувствительность контроля снижается, если контролируемая поверхность имеет неровности (провисания, вмятины), препятствующие приближению иглы к контролируемой поверхности | Обнаружение места и величины локальных утечек в сварных соединениях закрытых конструкций, работающих под давлением.Контролируемая толщина не ограничена | |||
Газоаналитический | С по дефекты | Для фреона 12 (90%) в смеси с воздухом от 2 · 10 -4 до 4 · 10 -4 мм 3 МПа / с | Надежность контроля снижается при наличии в окружающей атмосфере различных паров и газов, в том числе растворителей для подготовки поверхности испытуемого стыка, табачного дыма и газов, образующихся при сварке | Локализация локальных утечек в сварных соединениях закрытых конструкций, работающих под давлением. | ||||
Химический кий | Сквозные дефекты | Для аммиака — до 6,65´ ´ 10-4 мм 3 МПа / с Для аммиака — от 1 · 10 -1 до 1 мм 3 МПа / с | Соблюдение правил пожарной безопасности и правил работы с опасными химическими веществами | Обнаружение локальных утечек в сварных соединениях открытых и закрытых конструкций, работающих под давлением или предназначенных для хранения жидкостей.Контролируемая толщина не ограничена | ||||
Обнаружение утечек | Акустический | Сквозные дефекты | Не менее 1 · 10 -2 мм 3 МПа / с | Контроль осуществляется при отсутствии шумовых помех. | Обнаружение утечек в сварных стыках подземных водопроводов и газопроводов высокого давления… Контролируемая толщина не ограничена | |||
Капилляр | Сквозные дефекты | Люминесцентный — от 1 · 10 -2 до 5 · 10 -2 мм 3 МПа / с Цвет люминесценции — от 1 · 10 -2 до 5 · 10 -2 мм 3 МПа / с Люминесцентно-гидравлический — 1 · 10-4 до 5 10-4 мм 3 МПа / с Смачивание керосином — до 7 · 10 -3 мм 3 МПа / с | Требуется тщательная очистка контролируемой поверхности.Чувствительность метода снижается при контроле больших толщин и при контроле сварных соединений, расположенных во всех пространственных положениях, кроме нижнего. При смачивании керосином — высокая пожароопасность | Обнаружение утечек в сварных соединениях открытых и закрытых конструкций: люминесцентные и люминесцентные — сварные соединения конструкций, рабочее тело которых — газ или жидкость; люминесцентно-гидравлическое и керосиновое смачивание — сварные соединения конструкций, рабочим телом которых является жидкость. | ||||
Обнаружение утечек | Литье воды под давлением | Сквозные дефекты | От 3 · 10-4 до 2 · 10-2 мм 3 МПа / с | Обнаружение локальных утечек в сварных соединениях закрытых конструкций, работающих под давлением. Контролируемая толщина не ограничена | ||||
Лить водой без давления | Сквозные дефекты | Не более 1 · 10 -3 мм 3 МПа / с | При осмотре сварных соединений большой мощности необходимо обеспечить жесткость конструкции | Нормативно-техническая документация, утвержденная в установленном порядке | ||||
Полив высокого давления | Сквозные дефекты | Чувствительность метода возрастает при нанесении на исследуемую поверхность люминесцентно-индикаторного покрытия. | Обнаружение локальных утечек в сварных соединениях открытых конструкций. Контролируемая толщина не ограничена | Нормативно-техническая документация, утвержденная в установленном порядке | ||||
Полив рассеянной струей воды | Сквозные дефекты | Не более 1 · 10 -1 мм 3 МПа / с | Чувствительность метода возрастает при нанесении на исследуемую поверхность люминесцентно-индикаторного покрытия.Контроль осуществляется перед установкой оборудования | Обнаружение локальных утечек в сварных соединениях открытых конструкций. Контролируемая толщина не ограничена | Нормативно-техническая документация, утвержденная в установленном порядке | |||
Обнаружение утечек | Пузырь | Сквозные дефекты | Пневматический: дутьевой воздух — от 7 · 10-4 до 1 · 10-3 мм 3 МПа / с обдув струей сжатого воздуха — до 1 · 10 -2 мм 3 МПа / с Пневмогидравлический: аквариум — до 1 · 10 -3 мм 3 МПа / с бароаквариум — от 5 · 10 -4 до 1 · 10 -5 мм 3 МПа / с Вакуум (с использованием вакуумных камер) — до 1 · 10 -2 мм 3 МПа / с | Управление осуществляется сжатым воздухом. Состав пенообразователя зависит от температуры воздуха при испытании пневматическим и вакуумным методами. | Локальное обнаружение утечек. Пневматический метод: продувка воздухом — сварные соединения закрытых конструкций, рабочее тело которых — газ или жидкость; | Нормативно-техническая документация, утвержденная в установленном порядке | ||
обдув струей сжатого воздуха — сварные швы открытых крупногабаритных конструкций. Пневмогидравлические методы для аквариумов и бароаквариумов: сварных стыков малых закрытых конструкций, работающих под давлением. Вакуумный метод — с односторонним подходом к контролируемым соединениям. Контролируемая толщина не ограничена | ||||||||
Обнаружение утечек | Открытие | Внутренние дефекты | Выявлены макроскопические дефекты | Раскрытие производится штамповкой, сверлением, газовой или воздушно-дуговой строжкой, шлифованием, а также вырезанием участка сварного соединения с последующим послойным изготовлением из него тонких шлифов. | Сварные соединения, не прошедшие термическую обработку или недоступные для радиационного и акустического контроля. Контролируемая толщина не ограничена | |||
Технологический тест | Внутренние и поверхностные дефекты | Выявленные макроскопические и микроскопические дефекты | Контрольная проба выполняется по тому же технологическому процессу и тем же сварщиком (а), что и контрольные сварные соединения | Не ограничено |
СВАРНЫЕ СОЕДИНЕНИЯ
МЕТОДЫ КОНТРОЛЯ КАЧЕСТВА
ИПК ИЗДАТЕЛЬСКИЕ СТАНДАРТЫ
Москва
МЕЖГОСУДАРСТВЕННЫЙ СТАНДАРТ
Постановлением Государственного комитета СССР по стандартам от 2 августа 1979 г. 2930, срок действия установлен
от 01.01.81
Ограничение срока действия снято постановлением Госстандарта от 21.10.92 № 1434
1. Настоящий стандарт устанавливает методы контроля качества и их объем для выявления дефектов сварных соединений металлов и сплавов, выполненных методами сварки, указанными в ГОСТ 19521-74.
2. Применение метода или комплекса методов контроля для выявления дефектов сварных соединений при техническом контроле конструкций на всех этапах их изготовления, ремонта и модернизации зависит от требований к сварным соединениям в технической документации на конструкцию.
Методы контроля должны соответствовать приведенным в таблице и указаны в технической (конструкторской и технологической) документации на сооружение.
3. Допустимость использования методов, не указанных в настоящем стандарте, должна быть предусмотрена в технической документации на проектирование. Технология контроля сварных швов любым методом должна быть установлена в нормативно-технической документации на контроль.
Неразрушающие методы контроля качества сварных соединений
Тип управления | Метод контроля | Характеристика метода | Область применения | Обозначение стандарта метода контроля | ||||
Обнаружены дефекты | Чувствительность | Особенности метода | ||||||
Технический осмотр | Внешний осмотр и измерение | Дефекты поверхности | Несплошности, отклонения размеров и формы сварного шва от заданных значений более 0.1 мм, а также поверхностное окисление сварного шва | Метод позволяет обнаруживать дефекты минимально обнаруживаемого размера при контроле и измерении сварного шва с помощью оптических приборов с увеличением до 10 ´ и измерительных приборов. | Не ограничено | |||
Капилляр | Люминесцентный Люминесцентный цвет | Дефекты поверхности (несплошности) | ГОСТ 18442-80 | Чувствительность и надежность метода зависят от качества подготовки поверхности стыка к контролю. | Не ограничено | |||
Радиация | Радиографический Радиоскопический Радиометрический | Внутренние и поверхностные дефекты (несплошности), а также дефекты формы стыка | от 0,5 до 5,0% контролируемой толщины металла От 3 до 8% контролируемой толщины металла 0. | |||||
Акустический | Ультразвуковой | Внутренние и поверхностные дефекты (несплошности) | Толщина сварного шва, мм | Предел чувствительности, мм 2 | Размер, количество и характер дефектов определяются условно по ГОСТ 14782-86 . | |||
от 1.От 5 до 10 включительно ул. 10 до 50 « «150» 400 « «400» 2000 « | ||||||||
Магнитный | Магнетоферрозон | Уровни условной чувствительности по ГОСТ 21104-75 | Метод обеспечивает обнаружение: внутренних несплошностей, расположенных на глубине 10 мм от поверхности стыка; | |||||
Магнитный | Магнетоферрозон | Поверхностные и подземные неоднородности | Уровни условной чувствительности по ГОСТ 21104-80 | разнонаправленных дефекта. Чувствительность и надежность метода зависит от качества приготовления контрольного соединения. | ||||
Магнитная частица | Поверхностные и подземные неоднородности | Уровни условной чувствительности по ГОСТ 21105-87 | Метод позволяет выявить внутренние несплошности, расположенные от поверхности стыка на глубине до 2 мм включительно.Чувствительность и надежность метода зависят от качества приготовления соединения для контроля. | |||||
Магнитографический | Поверхностные, подземные и внутренние неоднородности | от 2 до 7% толщины контролируемого металла | Надежность контроля снижается при наличии неровностей на исследуемой поверхности стыка размером более 1 мм. | Соединения стыковые, сварные газовой дугой, ферромагнитные конструкции. Контролируемая толщина не более 25 мм | ||||
Обнаружение утечек | Радиация | Сквозные дефекты | Для криптона 85 (85 кг) — от 1 · 10 -9 до 1 · 10-14 мм 3 МПа / с | Радиоактивная опасность | Обнаружение утечек в сварных соединениях, работающих под давлением, закрытых конструкциях атомной энергетики, а также закрытых конструкциях, когда невозможно использовать другие методы обнаружения утечек. | |||
Обнаружение утечек | ||||||||
Масс-спектрометрия | Сквозные дефекты | По дороге: накопление при атмосферном давлении — до 1 · 10-6 мм 3 МПа / с откачка от 1 · 10-7 до 1 · 10-4 мм 3 МПа / с зонд — до 1 · 10-5 мм 3 МПа / с | Условия эксплуатации течеискателя: температура окружающей среды 10-35 ° С, максимальная относительная влажность 80% | Способ накопления давления заключается в определении общей степени негерметичности закрытых конструкций. Метод вакуумирования — определение суммарной утечки закрытых и открытых конструкций. Зондовый метод — обнаружение локальных утечек в сварных соединениях крупногабаритных конструкций. Контролируемая толщина не ограничена | ||||
Калибр | Сквозные дефекты | По дороге: перепад давления — от 1 · 10-3 до 7 · 10-3 мм 3 МПа / с манометр дифференциального давления — до 1 · 10-8 мм 3 МПа / с | Чувствительность метода снижается при обследовании конструкций большого объема. Продолжительность испытания, испытательный газ и температура окружающей среды, а также атмосферное давление влияют на точность испытания | Сварные соединения закрытых конструкций, работающих под давлением: метод перепада давления — для определения суммы общих утечек; Метод манометра дифференциального давления — для локального обнаружения утечек. Контролируемая толщина не ограничена | ||||
Обнаружение утечек | Галоген | Сквозные дефекты | Фреон 12: атмосферный зонд — до 5 · 10-4 мм 3 МПа / с Вакуумный зонд— до 1 · 10-6 мм 3 МПа / с | Надежность и чувствительность контроля снижается, если контролируемая поверхность имеет неровности (провисания, вмятины), препятствующие приближению иглы к контролируемой поверхности | Обнаружение места и величины локальных утечек в сварных соединениях закрытых конструкций, работающих под давлением.Контролируемая толщина не ограничена | |||
Газоаналитический | С по | Для фреона 12 (90%) в смеси с воздухом от 2 · 10 -4 до 4 · 10 -4 мм 3 МПа / с | Надежность контроля снижается при наличии в окружающей атмосфере различных паров и газов, в том числе растворителей для подготовки поверхности испытуемого стыка, табачного дыма и газов, образующихся при сварке | Локализация локальных утечек в сварных соединениях закрытых конструкций, работающих под давлением. | ||||
Химическая промышленность | Сквозные дефекты | Аммиак — до 6,65 ´ ´ 10 -4 мм 3 МПа / с Для аммиака — от 1 · 10 -1 до 1 мм 3 МПа / с | Соблюдение правил пожарной безопасности и правил работы с опасными химическими веществами | Обнаружение локальных утечек в сварных соединениях открытых и закрытых конструкций, работающих под давлением или предназначенных для хранения жидкостей.Контролируемая толщина не ограничена | ||||
Обнаружение утечек | Акустический | Сквозные дефекты | Не менее 1 · 10 -2 мм 3 МПа / с | Контроль осуществляется при отсутствии шумовых помех. | Обнаружение утечек в сварных стыках подземных водо- и газопроводов высокого давления.Контролируемая толщина не ограничена | |||
Капилляр | Сквозные дефекты | Люминесцентный — от 1 · 10 -2 до 5 · 10 -2 мм 3 МПа / с Цвет люминесценции — от 1 · 10 -2 до 5 · 10 -2 мм 3 МПа / с Люминесцентно-гидравлический — 1 · 10-4 до 5 10-4 мм 3 МПа / с Смачивание керосином — до 7 · 10 -3 мм 3 МПа / с | Требуется тщательная очистка контролируемой поверхности.Чувствительность метода снижается при контроле больших толщин и при контроле сварных соединений, расположенных во всех пространственных положениях, кроме нижнего. При смачивании керосином — высокая пожароопасность | Обнаружение утечек в сварных соединениях открытых и закрытых конструкций: люминесцентные и люминесцентные — сварные соединения конструкций, рабочее тело которых — газ или жидкость; люминесцентно-гидравлическое и керосиновое смачивание — сварные соединения конструкций, рабочим телом которых является жидкость. | ||||
Обнаружение утечек | Литье воды под давлением | Сквозные дефекты | От 3 · 10-4 до 2 · 10-2 мм 3 МПа / с | Обнаружение локальных утечек в сварных соединениях закрытых конструкций, работающих под давлением. Контролируемая толщина не ограничена | ||||
Лить водой без давления | Сквозные дефекты | Не более 1 · 10 -3 мм 3 МПа / с | При осмотре сварных соединений большой мощности необходимо обеспечить жесткость конструкции | Нормативно-техническая документация, утвержденная в установленном порядке | ||||
Полив высокого давления | Сквозные дефекты | Чувствительность метода возрастает при нанесении на исследуемую поверхность люминесцентно-индикаторного покрытия. | Обнаружение локальных утечек в сварных соединениях открытых конструкций. Контролируемая толщина не ограничена | Нормативно-техническая документация, утвержденная в установленном порядке | ||||
Полив рассеянной струей воды | Сквозные дефекты | Не более 1 · 10 -1 мм 3 МПа / с | Чувствительность метода возрастает при нанесении на исследуемую поверхность люминесцентно-индикаторного покрытия.Контроль осуществляется перед установкой оборудования | Обнаружение локальных утечек в сварных соединениях открытых конструкций. Контролируемая толщина не ограничена | Нормативно-техническая документация, утвержденная в установленном порядке | |||
Обнаружение утечек | Пузырь | Сквозные дефекты | Пневматический: дутьевой воздух — от 7 · 10-4 до 1 · 10-3 мм 3 МПа / с обдув струей сжатого воздуха — до 1 · 10 -2 мм 3 МПа / с Пневмогидравлический: аквариум — до 1 · 10 -3 мм 3 МПа / с бароаквариум — от 5 · 10 -4 до 1 · 10 -5 мм 3 МПа / с Вакуум (с использованием вакуумных камер) — до 1 · 10 -2 мм 3 МПа / с | Управление осуществляется сжатым воздухом. Состав пенообразователя зависит от температуры воздуха при испытании пневматическим и вакуумным методами. | Локальное обнаружение утечек. Пневматический метод: продувка воздухом — сварные соединения закрытых конструкций, рабочее тело которых — газ или жидкость; | Нормативно-техническая документация, утвержденная в установленном порядке | ||
обдув струей сжатого воздуха — сварные швы открытых крупногабаритных конструкций. Пневмогидравлические методы для аквариумов и бароаквариумов: сварных стыков малых закрытых конструкций, работающих под давлением. Вакуумный метод — с односторонним подходом к контролируемым соединениям. Контролируемая толщина не ограничена | ||||||||
Обнаружение утечек | Открытие | Внутренние дефекты | Выявлены макроскопические дефекты | Раскрытие производится штамповкой, сверлением, газовой или воздушно-дуговой строжкой, шлифованием, а также вырезанием участка сварного соединения с последующим послойным изготовлением из него тонких шлифов. | Сварные соединения, не прошедшие термическую обработку или недоступные для радиационного и акустического контроля. Контролируемая толщина не ограничена | |||
Технологический тест | Внутренние и поверхностные дефекты | Выявленные макроскопические и микроскопические дефекты | Контрольная проба выполняется по тому же технологическому процессу и теми же сварщиками, что и контрольные сварные соединения | Не ограничено |
МЕЖГОСУДАРСТВЕННЫЙ СТАНДАРТ
СВАРНЫЕ СОЕДИНЕНИЯ
МЕТОДЫ КОНТРОЛЯ КАЧЕСТВА
Официальное издание
ИЗДАТЕЛЬСКИЕ СТАНДАРТЫ ИПК
УДК 621. 791.052: 658.562: 006.354 Группа B09
МЕЖГОСУДАРСТВЕННЫЙ СТАНДАРТ
СВАРНЫЕ СОЕДИНЕНИЯ Методы контроля качества
Соединения сварные. Методы контроля качества
ГОСТ 3242-69
Постановлением Государственного комитета СССР по стандартам от 2 августа 1979 г. № 2930 срок действия установлен
Ограничение срока действия снято постановлением Госстандарта от 21.10.92 № 1434
1. Настоящий стандарт устанавливает методы контроля качества и их объем для выявления дефектов сварных соединений металлов и сплавов, выполненных методами сварки, указанными в ГОСТ 19521-74.
2. Применение метода или комплекса методов контроля для выявления дефектов сварных соединений при техническом контроле конструкций на всех этапах их изготовления, ремонта и модернизации зависит от требований к сварным соединениям в технической документации на конструкцию.
Методы контроля должны соответствовать приведенным в таблице и указаны в технической (конструкторской и технологической) документации на сооружение.
3. Допустимость использования методов, не указанных в настоящем стандарте, должна быть предусмотрена в технической документации на проектирование.Технология контроля сварных швов любым методом должна быть установлена в нормативно-технической документации на контроль.
Официальное издание
Перепечатка запрещена
Переиздание. Май 2002
© Издательство стандартов, 1979 © ИПК Издательство стандартов, 2002
Тип управления | Метод контроля | Характеристика метода | Область применения | ||||
Выявлено | Чувствительность | Особенности метода | |||||
Технический осмотр | Внешний осмотр и измерение | Дефекты поверхности | Несплошности, отклонения размеров и формы сварного шва от заданных значений более 0. | Метод позволяет обнаруживать дефекты минимально обнаруживаемого размера при контроле и измерении сварного шва с помощью оптических приборов с увеличением до 10х и средств измерений. | Не ограничено | ||
центно-цвет | Дефекты поверхности (несплошности) | Условные уровни материальности по ГОСТ 18442-80 | Чувствительность и надежность метода зависят от качества подготовки поверхности стыка к контролю. | Не ограничено | ГОСТ 18442-80 | ||
Радиограмма физический Радиоскоп — Радиометрия | Внутренние и поверхностные дефекты (неисправности), а также дефекты формы стыка | от 0,5 до 5,0% от контролируемой толщины металла от 3 до 8% от контролируемой толщины металла от 0,3 до 10% от контролируемой толщины металла | Выявленные ^ дефекты по ГОСТ 7512-82. | ГОСТ 20426-82 | ГОСТ 7512-82 | ||
УЗИ | Внутренние и поверхностные дефекты (несогласованность) | Толщина сварного шва, мм | Предел чувствительности, мм 2 | Размер, количество и характер дефектов определяются условно по ГОСТ 14782-86 . | ГОСТ 14782-86 | ГОСТ 14782-88 | |
1.5-10 клавиш. ул. 10 до 50 « | 2,0- 7,0 3,5-15,0 10,0- 80,0 35,0-200,0 | ||||||
феррозонд- | Поверхностные и подземные неоднородности | Условные уровни паритета по ГОСТ 21104-75 | Метод обеспечивает идентификацию: внутренних несплошностей, расположенных на глубине 10 мм от поверхности стыка; | ГОСТ 21104-75 | ГОСТ 21104-75 |
2 ГОСТ 3242-79
Тип управления
Метод контроля
Характеристика метода
Выявлено
Чувствительность
Особенности метода
Область применения
Обозначение стандарта метода контроля
феррозонд-
Уровни условной чувствительности по ГОСТ 21104-80
недр, а не
разнонаправленный
дефектов,
Чувствительность и надежность метода зависит от качества
ГОСТ 21104-75
ГОСТ 21104-75
контроль
порошок
Уровни условной чувствительности по ГОСТ 21105-87
недр без
Метод обеспечивает: внутренние несплошности, расположенные от поверхности стыка на глубине до 2 мм включительно, Чувствительность и надежность метода зависят от качества подготовки стыка к контролю_
ГОСТ 21105-87
ГОСТ 21105-87
графический
Наземные, подземные и внутренние, кроме
от 2 до 7% толщины контролируемого металла
Надежность контроля снижается при наличии неровностей на исследуемой поверхности стыка размером более 1 мм. Чувствительность снижается с увеличением глубины
Сварные соединения
газо-дуговая сварка ферросплавов
риала, контролируемая толщина не более 25 мм
Спо
Для криптона 85 (85 кг) — от ■ Ю-9 до МО — «4 мм 3 МПа / с
Радиоактивная опасность
Обнаружение утечек при сварке
работает под
закладные конструкции атомной энергетики
закрытые конструкции, когда невозможно использовать другие
ГОСТ 3242-79 С.
Тип управления | Метод контроля | Характеристика метода | Область применения | Обозначение | ||
Выявлено | Чувствительность | Особенности метода | стандартный метод контроля | |||
спектрометр рицикл | С по | По дороге: накопление при атмосферном давлении — до Н (Н мм 3 МПа / с лакировка от М0 “7 до МО -4 мм 3 МПа / с зонд — до МО -5 мм 3 МПа / с | Условия эксплуатации течеискателя: температура окружающей среды 10-35 ° С, максимальная относительная влажность 80% | Способ накопления давления — определение общей степени герметичности между конструкциями, Метод вакуумирования — определение общей степени герметичности закрытых и открытых конструкций, Зондовый метод — определение локальных утечек в сварных соединениях крупногабаритных конструкций, Контролируемая толщина не ограничена | ||
рицикл | С по | По дороге: перепад давления — от МО-3 до 7-10 ~ 3 мм 3 МПа / с манометр дифференциального давления — до Н (Н мм 3 МПа / с | Чувствительность метода снижается при обследовании конструкций больших объемов. | Сварные соединения закрытых конструкций, работающих под давлением: метод перепада давления — да для определения величины полной утечки; метод манометра дифференциального давления — да, локальное обнаружение утечек, Контролируемая толщина не ограничена |
4 ГОСТ 3242-79
Тип управления | Метод контроля | Характеристика метода | Область применения | Обозначение стандарта метода контроля | ||
Выявлено | Чувствительность | Особенности метода | ||||
С по | Для фреона 12: атмосферный зонд — до 5-10-4 мм 3 МПа / с вакуумный зонд — до M0 “6 мм 3 МПа / с | Надежность и чувствительность контроля снижается, если контролируемая поверхность имеет неровности (провисания, вмятины), препятствующие приближению иглы к контролируемой поверхности | Обнаружение места и величины локальных утечек в сварных соединениях закрытых конструкций, работающих под давлением, контролируемая толщина не ограничена | |||
литический | С по | Для фреона 12 (90%) в смеси с воздухом от 2 «10» 4 до 4-10 «4 мм 3 МПа / с | Надежность контроля снижается при наличии в окружающей атмосфере различных паров и газов, включая растворители и подготовку поверхности испытуемого соединения, табачный дым и газы, образующиеся при сварке | Определение места локальных утечек в сварных соединениях закрытых конструкций, работающих под давлением, контролируемая толщина не ограничена | ||
С по | Аммиак-до 6. | Соблюдение правил пожарной безопасности и правил работы с опасными химическими веществами | Обнаружение локальных утечек в сварных соединениях открытых и закрытых конструкций, работающих под давлением или предназначенных для хранения жидкостей, контролируемая толщина не ограничена |
ГОСТ 3242-79
Продолжение P a
Тип управления | Метод контроля | Характеристика метода | Область применения | Обозначение | ||
Выявлено | Чувствительность | Особенности метода | SshpDsfsh с MCI UD контроль | |||
С по | Не менее МО -2 мм 3 МПа / с | Управление осуществляется при отсутствии шумовых помех, возможно дистанционное управление | Обнаружение утечек в сварных стыках подземных водопроводов и газопроводов высокого давления, контролируемая толщина не ограничена | |||
Капилляр | С по | Люминесцентный — от NO -2 до 5-10 -2 мм 3 МПа / с Люминесцентно-цветной — от MO -2 до MO “2 мм 3 МПа / с Люминесцентно-гидравлический-MO -4 до M0“ 4 мм 3 МПа / s Смачивание керосином — до 7 «10» 3 мм 3 МПа / с | Требуется тщательная очистка контролируемой поверхности. При смачивании керосином — высокая пожароопасность | Обнаружение течей в сварных соединениях открытых и закрытых конструкций: люминесцентные и люминесцентные — сварные соединения конструкций, рабочим телом которых является газ или жидкость; люминесцентно-гидравлические и смачивание керосином — сварные соединения конструкций, рабочим веществом которых является жидкость, контролируемая толщина не ограничена |
Тип управления | Метод контроля | Характеристика метода | Область применения | Обозначение стандарта метода контроля | ||
Выявлено | Чувствительность | Особенности метода | ||||
Литье воды под давлением | С по | От 3-10-4 до NO «2 мм 3 МПа / с | Обнаружение локальных утечек в сварных соединениях закрытых конструкций, работающих под давлением. | |||
Лить водой без давления | С по | Не более МО «3 мм 3 МПа / с | При осмотре сварных соединений большой мощности необходимо обеспечить жесткость конструкции | Нормативно-техническая документация утверждена в установленном порядке | ||
Полив высокого давления | С по | Не более МО «1 мм 3 МПа / с | Чувствительность метода возрастает с увеличением люминесцентно-индикаторного покрытия исследуемой поверхности.Контроль осуществляется перед установкой оборудования | Обнаружение локальных утечек в сварных соединениях открытых конструкций. Контролируемая толщина не ограничена | Нормативно-техническая документация, утвержденная в установленном порядке | |
Полив рассеянной струей воды | С по | Не более МО «1 мм 3 МПа / с | Чувствительность метода возрастает при нанесении люминесцентно-индикаторного покрытия исследуемой поверхности. | Обнаружение локальных утечек в сварных соединениях открытых конструкций. Контролируемая толщина не ограничена | Нормативно-техническая документация, утвержденная в установленном порядке |
ГОСТ 3242-79 С.
Тип управления
Характеристика метода
контроль
Область применения
Обозначение стандарта метода контроля
Выявлено
Чувствительность
Особенности метода
Через
Пневматический: надувной — от 7-10-4 до МО- 3 мм 3 МПа / с надувом сжатым воздухом — до МО -2 мм 3 МПа / с Пневмогидравлический: аквариумный — до М0 “3 мм 3 МПа / с баро -аквариум — от MO -4 до MO -5 мм 3 МПа / с Вакуум (с использованием вакуумных камер) -до M0 “2 мм 3 МПа / с
Контроль осуществляется сжатым воздухом, состав пенообразующих смесей зависит от температуры воздуха при испытании пневматическим и вакуумным методами контроля
Обнаружение
Пневматический способ: обдувом — сварные соединения закрытых конструкций, рабочее тело которых
Нормативно-техническая документация, утвержденная в установленном порядке
обдув струей сжатого воздуха — сварные швы открытых крупногабаритных конструкций,
Пневмогидравлические методы для аквариумов и бароаквариумов: сварные соединения малых закрытых конструкций, работающих под давлением,
Вакуумный метод — с односторонним подходом к контролируемым швам, контролируемая толщина не ограничена
8 ГОСТ 3242-79
Тип управления | Метод контроля | Характеристика метода | Область применения | Обозначение | ||
Выявлено | Чувствительность | Особенности метода | стандартный метод контроля | |||
Открытие | Внутренние дефекты | Выявлены макроскопические дефекты | Раскрытие производится штамповкой, сверлением, газовой или воздушно-дуговой строжкой, шлифованием, а также вырезанием участка сварного шва с последующим изготовлением: после осмотра требуется сварка оголенного участка сварного шва | Сварные соединения, не прошедшие термообработку или недоступные для радиационного и акустического контроля, контролируемая толщина не ограничена | ||
Технологический тест | Внутренние и поверхностные дефекты | Выявленные макроскопические и микроскопические дефекты | Контрольная проба выполняется по тому же технологическому процессу и теми же сварщиками, что и контрольные сварные соединения | Не ограничено |
Редактор Т. П.Шашина Технический редактор Л.А. Гусева Корректор В.И. Баренцева Компьютерный макет И.А. Налейкина
Ed. человек. № 02354 от 14.07.2000г. Сдан в комплект 01.07.2002. Подписано в печать 18 июля 2002 г. Уэл. печать l. 1.40. Учебно-издательский дом 0.80.
Тираж 124 экз. С 6617. Зак. 604.
Издательство Стандарты ИПК, 107076 Москва, Колодезный пер., 14. e-mail: Верстка в ИД на ПК
Филиал ИПК Издательство стандартов — тип.«Московский типограф», 103062 г. Москва, Лялин пер., 6.
ГОСТ 3242-79
Группа В09
МЕЖГОСУДАРСТВЕННЫЙ СТАНДАРТ
СОЕДИНЕНИЯ СВАРНЫЕ
Методы контроля качества
Соединения сварные. Методы контроля качества
Дата введения 01.01.81
Постановлением Государственного комитета СССР по стандартам от 2 августа 1979 г. N 2930 срок действия установлен с 01.01.81
Ограничение срока действия исключен постановлением Госстандарта России от 10.21.92 N 1434
ВЗАМЕН ГОСТ 3242-69
РЕСПУБЛИКАЦИЯ. Май 2002 г.
1. Настоящий стандарт устанавливает методы контроля качества и область их применения при обнаружении дефектов сварных соединений металлов и сплавов, выполненных способами сварки, указанными в ГОСТ 19521-74.
Стандарт соответствует рекомендациям СЭВ по стандартизации PC 5246-73 *, PC 4099-73, PC 789-67 и международному стандарту ISO 2437-72.
________________
* Доступ к международным и иностранным документам, упомянутым здесь и далее по тексту, можно получить, перейдя по ссылке
2.Применение метода или комплекса методов контроля для выявления дефектов сварных соединений при техническом контроле конструкций на всех этапах их изготовления, ремонта и модернизации зависит от требований к сварным соединениям в технической документации на конструкцию.
Методы контроля должны соответствовать приведенным в таблице и указаны в технической (конструкторской и технологической) документации на сооружение.
3. Допустимость применения методов, не указанных в настоящем стандарте, должна быть предусмотрена в технической документации на проектирование. Технология контроля сварных швов любым методом должна быть установлена в нормативно-технической документации на контроль.
Неразрушающие методы контроля
Неразрушающие методы контроля качества сварных соединений
Тип управления | Метод контроля | Характеристика метода | Область применения | Обозначение стандарта на метод контроля | |||
Обнаруженные дефекты | Чувствительность | Особенности метода | |||||
Технический осмотр | Внешний осмотр и измерение | Дефекты поверхности | Разрывы отклонения размера и формы сварного шва от заданных значений более 0. | Способ позволяет при контроле и измерении сварного соединения обнаруживать дефекты минимально обнаруживаемого размера с помощью оптических приборов с увеличением до 10 и средств измерений | Не ограничено | ||
Капилляр | Цвет Люминесцентный Цветной люминесцентный | Дефекты поверхности (несплошности) | ГОСТ 18442-80 | Чувствительность и надежность метода зависят от качества подготовки поверхности стыка к контролю. | Не ограничено | ||
Излучение | Радиографический Радиоскопический Радиометрический | Внутренние и поверхностные дефекты (несплошности), а также дефекты формы соединения | 0,5 — 5,0% контролируемой толщины металла 3-8% контролируемой толщины металла 0,3 — 10% контролируемой толщины металла | ||||
Акустический | Ультразвуковой | Внутренние и поверхностные дефекты (несплошности) | Толщина сварного шва, мм | Предел чувствительности, мм | Размер, количество и характер дефектов определяются условно по ГОСТ 14782-86 .![]() | ||
От 1.От 5 до 10 включительно | |||||||
Ст. От 10 до 50 « | |||||||
«50» 150 « | |||||||
«150» 400 « | |||||||
«400» 2000 « | |||||||
Магнитный | Магнитная заслонка | Уровни условной чувствительности по ГОСТ 21104-80 * | Метод обеспечивает идентификацию: внутренних несплошностей, расположенных на глубине 10 мм от поверхности стыка; разнонаправленные дефекты. Чувствительность и надежность метода зависит от качества подготовки контрольного соединения. | ||||
_______________ | |||||||
Магнито | Поверхностные и подземные неоднородности | Уровни условной чувствительности по ГОСТ 21105-87 | Метод обеспечивает выявление внутренних несплошностей, расположенных от поверхности стыка на глубине до 2 мм включительно.Чувствительность и надежность метода зависят от качества приготовления соединения для контроля. | ||||
Магнито | Поверхностные, подземные и внутренние неоднородности | От 2 до 7% толщины контролируемого металла | Надежность контроля снижается при наличии неровностей на исследуемой поверхности стыка размером более 1 мм. | Соединения стыковые, сварные газовой дугой, ферромагнитные конструкции. Контролируемая толщина не более 25 мм | |||
Обнаружение утечек | Радиация | Сквозные дефекты | Криптон 85 — от 1 · 10 до 1 · 10 мм МПа / с | Радиоактивная опасность | Обнаружение утечек в сварных соединениях, работающих под давлением, в закрытых конструкциях атомной энергетики, а также в закрытых конструкциях, когда невозможно использовать другие методы обнаружения утечек. | ||
Масс-спектрометрический | Сквозные дефекты | По пути: накопление при атмосферном давлении — до 1 10 мм МПа / с откачка от 1 10 до 1 10 мм МПа / с зонд — до 1 10 мм МПа / с | Условия эксплуатации течеискателя: температура окружающей среды 10-35 ° С, максимальная относительная влажность 80% | Способ накопления давления заключается в определении общей степени негерметичности закрытых конструкций. Метод вакуумирования — определение суммарной утечки закрытых и открытых конструкций. Зондовый метод — обнаружение локальных утечек в сварных соединениях крупногабаритных конструкций Контролируемая толщина не ограничена | |||
Калибр | Сквозные дефекты | По ходовой части: Перепад давления — от 1 10 до 7 10 мм МПа / с Манометр перепада давления до 1 10 мм МПа / с | Чувствительность метода снижается при обследовании конструкций большого объема. Продолжительность испытания, температура проверочного газа и окружающей среды, а также значение атмосферного давления влияют на точность испытания. | Сварные соединения закрытых конструкций, работающих под давлением: Метод перепада давления — для определения суммы суммарных протечек; Метод манометра дифференциального давления — для определения локальных утечек. Контролируемая толщина не ограничена | |||
Галоген | Сквозные дефекты | Фреон 12: Датчик атмосферы — до 5 10 мм МПа / с Зонд вакуума — до 1 10 мм МПа / с | Надежность и чувствительность контроля снижается, если контролируемая поверхность имеет неровности (провисания, вмятины), которые не позволяют иглу приближаться к контролируемой поверхности | Определение места и величины локальных утечек в сварных соединениях закрытых конструкций, работающих под давлением. | |||
Газоаналитический | Сквозные дефекты | Для фреона 12 (90%) в смеси с воздухом от 2 · 10 до 4 · 10 мм МПа / с | Надежность контроля снижается при наличии в окружающей атмосфере различных паров и газов, в том числе растворителей для подготовки поверхности испытуемого стыка, табачного дыма и газов, образующихся при сварке | Определение места локальных утечек в сварных соединениях закрытых конструкций, работающих под давлением. | |||
Химическая промышленность | Сквозные дефекты | Для аммиака — до 6,65 10 мм МПа / с Для аммиака — от 1 10 до 1 мм МПа / с | Соблюдение правил пожарной безопасности и правил работы с опасными химическими веществами | Обнаружение локальных утечек в сварных соединениях открытых и закрытых конструкций, работающих под давлением или предназначенных для хранения жидкостей.Контролируемая толщина не ограничена | |||
Акустический | Сквозные дефекты | Не менее 1 10 мм МПа / с | Контроль осуществляется при отсутствии шумовых помех. | Обнаружение утечек в сварных стыках подземных водо- и газопроводов высокого давления. Контролируемая толщина не ограничена | |||
Капилляр | Сквозные дефекты | Люминесцентный — от 1 10 до 5 10 мм МПа / с Люминесцентный цвет — от 1 10 до 5 10 мм МПа / с Люминесцентно-гидравлический — от 1 · 10 до 5 · 10 мм МПа / с Смачивание керосином — до 7 10 мм МПа / с | Требуется тщательная очистка контролируемой поверхности.Чувствительность метода снижается при контроле больших толщин и при контроле сварных соединений, расположенных во всех пространственных положениях, кроме нижнего. При контроле смачиванием керосином — высокая пожароопасность | Обнаружение утечек в сварных соединениях открытых и закрытых конструкций: люминесцентно-люминесцентный люминесцентно-гидравлическое и керосиновое смачивание — сварные соединения конструкций, рабочим телом которых является жидкость. | |||
Подача воды под давлением | Сквозные дефекты | От 3 · 10 до 2 · 10 мм МПа / с | Обнаружение локальных утечек в сварных соединениях закрытых конструкций, работающих под давлением. Контролируемая толщина, без ограничений | ||||
Лить водой без давления | Сквозные дефекты | Не более 1 10 мм МПа / с | При контроле сварных соединений большой мощности необходимо обеспечить жесткость конструкции | Нормативно-техническая документация, утвержденная в установленном порядке | |||
Полив под высоким давлением | Сквозные дефекты | Не более 1 10 мм МПа / с | Чувствительность метода повышается при нанесении на исследуемую поверхность люминесцентно-индикаторного покрытия. | Обнаружение локальных утечек в сварных соединениях открытых конструкций. Контролируемая толщина не ограничена | Нормативно-техническая документация, утвержденная в установленном порядке | ||
Обрызгиванием рассеянной струей воды | Сквозные дефекты | Не более 1 10 мм МПа / с | Чувствительность метода повышается при нанесении люминесцентно-индикаторного покрытия контролируемой поверхности.Контроль проводится перед установкой оборудования | Обнаружение локальных утечек в сварных соединениях открытых конструкций. Контролируемая толщина не ограничена | Нормативно-техническая документация, утвержденная в установленном порядке | ||
Пузырь | Сквозные дефекты | Пневматика: продувка воздухом — от 7 10 до 1 10 мм МПа / с продувка струей сжатого воздуха — от 1 10 мм МПа / с пневмогидравлическая: аквариум — 1 10 мм МПа / с бароаквариум — от 5 10 до 1 10 мм МПа / с Вакуум (с использованием вакуумных камер) — до 1 10 мм МПа / с | Управление осуществляется сжатым воздухом. Состав пенообразователя зависит от температуры воздуха при испытании пневматическим и вакуумным методами. | Локальное обнаружение утечек. Пневматический способ: обдув струей сжатого воздуха — сварные соединения открытых крупногабаритных конструкций. Пневмогидравлические способы для аквариумов и бароаквариумов: сварные соединения малогабаритных закрытых конструкций, работающих под давлением. Вакуумный метод — с односторонним подходом к контролируемым соединениям. Контролируемая толщина не ограничена | Нормативно-техническая документация, утвержденная в установленном порядке | ||
Открытие | Внутренние дефекты | Выявлены макроскопические дефекты | Раскрытие осуществляется путем перфорации, сверления, газовой или воздушно-дуговой строжки, шлифовки, а также вырезания участка сварного соединения с последующим послойным изготовлением из него тонких участков. | Сварные соединения, не прошедшие термообработку или недоступные для радиационного и акустического контроля. Контролируемая толщина не ограничена | |||
Технологические испытания | Внутренние и поверхностные дефекты | Выявленные макроскопические и микроскопические дефекты | Контрольная проба выполняется по тому же технологическому процессу и тем же сварщиком (ами), что и контрольные сварные соединения | Не ограничено |
Электронный текст документа
подготовлен ЗАО «Кодекс» и проверен:
официальное издание
Москва: Издательство стандартов ИПК, 2002
СВАРНЫЕ СОЕДИНЕНИЯ
МЕТОДЫ КОНТРОЛЯ КАЧЕСТВА
ГОСТ 3242-79
ГОСУДАРСТВЕННЫЙ КОМИТЕТ СССР ПО СТАНДАРТАМ
ГОСУДАРСТВЕННЫЙ СТАНДАРТ СОЮЗА ССР
Постановлением Государственного комитета СССР по стандартам от 2 августа 1979 г.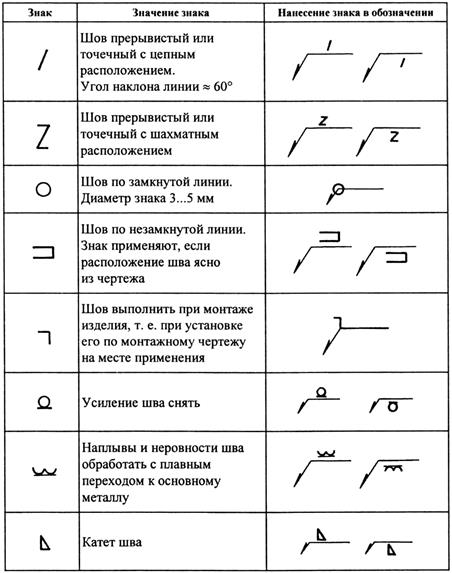
с 01.01.81
до 01.01.91
Несоблюдение стандарта преследуется по закону.
1. Настоящий стандарт устанавливает методы контроля качества и их объем для выявления дефектов сварных соединений металлов и сплавов, выполненных методами сварки, указанными в ГОСТ 19521-74. Стандарт соответствует рекомендациям СЭВ по стандартизации PC 5246-73, PC 4099-73, PC 789-67 и международному стандарту I CO 2437-72.2. Применение метода или комплекса методов контроля для выявления дефектов сварных соединений при техническом контроле конструкции на всех этапах ее изготовления, ремонта и модернизации зависит от требований к сварным соединениям в технической документации на конструкцию. Способы контроля должны соответствовать приведенным в таблице и указаны в технической (конструкторско-технологической) документации на сооружение. 3. Допустимость использования методов, не указанных в настоящем стандарте, должна быть предусмотрена в проектно-технической документации. Технология контроля сварных швов любым методом должна быть установлена в нормативно-технической документации на контроль.
Неразрушающие методы контроля качества сварных соединений
Тип управления | Метод контроля | Характеристики метода | Область применения | Обозначение стандарта метода контроля | Обнаружены дефекты | Чувствительность | Особенности метода | Технический осмотр | Внешний осмотр и измерение | Дефекты поверхности | Несплошности, отклонения размеров и формы сварного шва от заданных значений более 0.1 мм, а также поверхностное окисление сварного шва | Метод позволяет при контроле и измерении сварного соединения обнаруживать дефекты минимально обнаруживаемого размера с помощью оптических приборов с увеличением до 10 ´ и измерительных приборов.![]() | Не ограничено | Капилляр | Цветной люминесцентный люминесцентный цвет | Дефекты поверхности (несплошности) | Уровни условной чувствительности по ГОСТ 184412-80 | Чувствительность и надежность метода зависят от качества подготовки поверхности стыка к контролю. | Не ограничено | ГОСТ 18442-80 | Радиация | Радиографическая радиоскопическая радиометрия | Внутренние и поверхностные дефекты (несплошности), а также дефекты формы соединения | от 0,5 до 5,0% от контролируемой толщины металла от 3 до 8% от контролируемой толщины металла от 0,3 до 10% от контролируемой толщины металла | Обнаружение дефектов по ГОСТ 7312-76.![]() | По ГОСТ 20426-82 | ГОСТ 7512-75 | Акустический | Ультразвуковой | Внутренние и поверхностные дефекты (несплошности) | Толщина сварного шва, мм | Предел чувствительности, мм 2 | Размер, количество и характер дефектов определяются условно по ГОСТ 14782-76 | .По ГОСТ 14782-76 | ГОСТ 14782-76 | от 1.С 5 по 10 включительно ст. L0 до 50 « «150» 400 « «400» 2000 « | Магнитный | Магнетоферрозон | Уровни условной чувствительности по ГОСТ 21104-80 | Метод обеспечивает обнаружение: внутренних несплошностей, расположенных на глубине 10 мм от поверхности стыка; разнонаправленные дефекты.![]() | По ГОСТ 21104-80 | ГОСТ 21104-80 | Магнитный порошок | Поверхностные и подземные неоднородности | Уровни условной чувствительности по ГОСТ 21105-75 | Метод позволяет выявить внутренние несплошности, расположенные от поверхности стыка на глубине до 2 мм включительно. Чувствительность и надежность метода зависят от качества приготовления соединения для контроля. | По ГОСТ 21105-75 | ГОСТ 21105-75 | Магнито-графический | Поверхностные, подземные и внутренние неоднородности | от 2 до 7% толщины контролируемого металла | Надежность контроля снижается при наличии неровностей на исследуемой поверхности стыка размером более 1 мм.![]() | Соединения сварные газо-дуговые стыковые, ферромагнитные конструкции.Контролируемая толщина не более 25 мм | Обнаружение утечек | Радиация | Сквозные дефекты | Для криптона 85 (85 Kr) — от 1 × 10-9 до 1 × 10-14 мм 3 МПа / с | Радиоактивная опасность | Обнаружение утечек в сварных соединениях, работающих под давлением, закрытых конструкциях атомной энергетики, а также закрытых конструкциях, когда невозможно использовать другие методы обнаружения утечек.Контролируемая толщина не ограничена | Масс-спектрометрический | Сквозные дефекты | По методу: накопление при атмосферном давлении — до 1 × 10-6 мм 3 МПа / с откачка — от 1 × 10 -7 до 1 × 10 -4 мм Зонд 3 МПа / с — до l × 10-5 мм 3 МПа / от | Условия эксплуатации течеискателя: температура окружающей среды 10-35 ° С, максимальная относительная влажность воздуха 80% о | Способ накопления давления заключается в определении общей скорости утечки закрытой конструкции.![]() | Калибр | Сквозные дефекты | По методу: перепад давления — от 1 × 10 -3 до 7 × 10 -3 мм 3 МПа / с манометр дифференциального давления — до l × 10-8 мм 3 МПа / с | Чувствительность метода снижается при обследовании конструкций большого объема.Продолжительность испытания, температура испытательного газа и окружающей среды, а также значение атмосферного давления влияют на точность испытания. | Сварные соединения закрытых конструкций, работающих под давлением: метод перепада давления — для определения величины суммарных утечек; метод манометра дифференциального давления — для определения локальных утечек. Контролируемая толщина не ограничена | Галоген | Сквозные дефекты | Для фреона12: зонд атмосферный — до 5 × 10 -4 мм 3.![]() | Надежность и чувствительность контроля снижается, если контролируемая поверхность имеет неровности (провисания, вмятины), препятствующие приближению зонда к контролируемой поверхности | Обнаружение места и величины локальных утечек в сварных соединениях закрытых конструкций, работающих под давлением. Контролируемая толщина не ограничена | Газоаналитический | Сквозные дефекты | Фреон 12 (90%) в смеси с воздухом от 2 × 10-4 до 4 × 10-4 мм 3-МПа / с | Надежность контроля снижается при наличии в окружающей атмосфере различных паров и газов, в том числе растворителей для подготовки поверхности испытуемого стыка, табачного дыма и газов, образующихся при сварке | Определение локальных утечек в сварных соединениях закрытых конструкций, работающих под давлением.![]() | Химическая промышленность | Сквозные дефекты | Аммиак — до 6,65 × 10-4 мм 3 МПа / с Аммиак — от 1 × 10-1 до 1 мм 3 МПа / с | Соблюдение правил пожарной безопасности и правил при работе с опасными химическими веществами | Обнаружение локальных утечек в сварных соединениях открытых и закрытых конструкций, работающих под давлением или предназначенных для хранения жидкостей. Контролируемая толщина не ограничена | Акустический | Сквозные дефекты | Не менее 1 × 10-2 мм 3 МПа / с | Контроль осуществляется при отсутствии шумовых помех.Возможен удаленный мониторинг | Обнаружение утечек в сварных стыках подземных водо- и газопроводов высокого давления.![]() | Капилляр | Сквозные дефекты | Люминесцентный — от 1 × 10 -2 до 5 × 10 -2 мм 3 МПа / с Люминесцентный — от l × 10 -2 до 5 × 10 -2 мм 3 МПа / с Люминесцентно-гидравлический — от 1 × 10 — 4 до 5 × 10 -4 мм 3 МПа / с Смачивание керосином — до 7 × 10 -3 мм 3 МПа / с | Требуется тщательная очистка контролируемой поверхности.Чувствительность метода снижается при контроле больших толщин и при контроле сварных соединений, расположенных во всех пространственных положениях, кроме нижнего. При контроле смачиванием керосином — высокая пожароопасность | Обнаружение течей в сварных соединениях открытых и закрытых конструкций: люминесцентные и люминесцентные — сварные соединения конструкций, рабочим веществом которых является газ или жидкость; люминесцентно-гидравлическое и керосиновое смачивание — сварные соединения конструкций, рабочим телом которых является жидкость.![]() | Путем заливки воды под давлением | Сквозные дефекты | От 3 × 10-4 до 2 × 10-2 мм 3 МПа / с | При контроле сварных соединений большой грузоподъемности необходимо обеспечить жесткость конструкции | Обнаружение локальных утечек в сварных соединениях закрытых конструкций, работающих под давлением. Контролируемая толщина не ограничена | ГОСТ 3285-77 | Лить водой без давления | Сквозные дефекты | Не более 1 × 10 -3 мм 3 МПа / с | При осмотре сварных соединений большой грузоподъемности необходимо обеспечить жесткость конструкции | ГОСТ 3265-77 | Полив под высоким давлением | Сквозные дефекты | Не более 1 × 10 -1 мм 3 МПа / с | Чувствительность метода возрастает при нанесении люминесцентно-индикаторного покрытия исследуемой поверхности.![]() | Обнаружение локальных утечек в сварных соединениях открытых конструкций. Контролируемая толщина не ограничена | ГОСТ 3285-77 | Полив рассеянной струей воды | Сквозные дефекты | Не более 1 × 10 -1 мм 3 МПа / с | Чувствительность метода возрастает при нанесении люминесцентно-индикаторного покрытия исследуемой поверхности. Контроль перед установкой оборудования | Обнаружение локальных утечек в сварных соединениях открытых конструкций.Контролируемая толщина не ограничена | ГОСТ 3285-77 | Пузырь | Сквозные дефекты | Пневматический: надувной — от 7 × 10 -4 до 1 × 10 -3 мм 3 МПа / с обдувом сжатым воздухом — до 1 × 10 -2 мм 3 МПа / с Пневмогидравлический: аквариумный — до 1 × 10 -3 мм 3 МПа / с бароаквариум — от 5 × 10-4 до 1 × 10-5 мм 3 МПа / с Вакуум (с использованием вакуумных камер) — до 1 × 10-2 мм 3 МПа / с | Управление осуществляется сжатым воздухом.![]() | Локальное обнаружение утечек. Пневматический способ: обдувом — сварные соединения закрытых конструкций, рабочее тело которых — газ или жидкость; обдув струей сжатого воздуха — сварные швы открытых крупногабаритных конструкций. Пневмогидравлические методы для аквариумов и бароаквариумов: сварные соединения небольших закрытых конструкций, работающих под давлением. Вакуумный метод — с односторонним подходом к контролируемым соединениям.Контролируемая толщина не ограничена | ГОСТ 3285-77 | Открытие | Внутренние дефекты | Выявлены макроскопические дефекты | Раскрытие производится резкой, сверлением, газовой или воздушно-дуговой строжкой, шлифованием, а также вырезанием участка сварного соединения с последующим послойным изготовлением из него тонких участков.![]() | .Сварные соединения, не прошедшие термообработку или недоступные для радиационного и акустического контроля.Контролируемая толщина не ограничена | — | Технологический тест | Внутренние и поверхностные дефекты | Выявленные макроскопические и микроскопические дефекты | Контрольная проба выполняется по тому же технологическому процессу и тем же сварщиком (-ами), что и контрольные сварные соединения. | Без ограничений | — |
(PDF) Прочность сварных конструкций при низких климатических температурах
4 Заключение
а) Анализ технических методов выбора стали для сварных металлоконструкций, эксплуатируемых при низких климатических температурах
, и результаты испытаний сварных Образцы показали, что эти методы обеспечивают защиту
высококачественных изготовленных конструкций от возникновения хрупкого разрушения. Однако эти методы не позволяют
обосновать допустимый размер дефекта в сварных соединениях.
б) Испытания сварных образцов из полномасштабного проката с трещиноподобным концентратором
позволяют определить максимальный размер сварочного дефекта, который не начинает развиваться при воздействии эксплуатационных нагрузок
. Использование экспериментальных данных учитывает изменение свойств стали в зоне термического влияния
шва и влияние остаточных сварочных напряжений.
в) На примере крана, рассчитанного на работу при минус 55 ° С, показано, что сталь 09Г2С-15 обеспечивает работоспособность своей металлической конструкции
при условии, что она не содержит дефектов, повреждений или усталостных трещин более
размером более 14 мм.
Список литературы
1. Соколов С., Грачев А., Межд. Rev. Mech. Eng., 12 (5), 448-453 (2018)
2. G. Shi, Y. Chen, Adv. Struct. Eng., 21, 1376-1387, (2018)
3. Хрупкое разрушение. Elasticity.Toughness and Liberty Ship, Metallurgical Associates, Inc., доступно по адресу:
http://metassoc.com/?s=spring+2011
4. М.Р. Гарифуллин, А.В. Барабаш, Е.А. Наумова, О.В. Жувак, Т. Йокинен, М. Хейнисуо, Mag. Civ. Англ.
63, 53–76 (2016)
5. И.Н. Придько, В. Мущанов, Х. Бартоло, Н. Ватин, И. Рудниева, Маг. Civ. Англ. 65, 27–41 (2016)
6. Дэн Д., Матер. Des., 30 (2), 359-366 (2009)
7. Х. Дай, Дж. Фрэнсис, Х.Стоун, Х. Стоун, Х. Бхадешиа, П. Уизерс. Металл. Mater. Trans., 39A, 3070-3078
(2008)
8. Барсом М., Рольф С. Контроль разрушения и усталости конструкций. Применение механики разрушения (PTR
Prentice Hall, США, 1987)
9. Атлури С., Вычислительные методы в механике разрушения, том 2, (Elsevier Science Publishers BV,
Амстердам, 1986)
10. X Чжу, Дж. Джойс, англ. Фракция. Мех., 85, 1-46, (2012)
11.S. Dugdale, J. Mech. Phys. Solids, 8 (2), 105-108 (1960)
12. Т. Вадхольм, Исследование низкотемпературной вязкости и зарождения трещин в сварных конструкционных сталях,
Магистерская диссертация (NTNU, Trondheim, 2014)
13. S Седмак, А. Седмак, И. Камагич, Frattura integr. strutt., 12, 371-382 (2018)
14. Р. Гоял, С. Богданов, Eng. Провал. Anal., 93, 340-355 (2018)
15. S. Xu, H. Reinhardt, Int. J. Fract., 98 (2), 151-177 (1999)
16.С. Мариани, У. Перего, Int. J. Numer. Meth. Eng., 58, 103-126 (2003)
17. Р. Герцберг, Механика деформации и разрушения конструкционных материалов (Wiley, New-York, 1989)
18. J. Rice, J. Appl. Меч, 55 (1), 98-103 (1988)
19. ГОСТ 32578-2013. Краны подъемные. Стальные конструкции. Металлические конструкции. Требования к материалам.
(Стандартинформ, Москва, 2015)
20. ISO 20332: 2008 (2008) Краны — Подтверждение компетентности стальных конструкций (Международная организация по стандартизации
, Женева, Швейцария)
21.H. Murakami, Справочник факторов интенсивности стресса (Pergamon press, Oxford, 1987)
22. E. Wessel, Eng. Фракция. Мех., 1, 77-82 (1968)
23. С. Соколов. Engin. Res., 38 (3), 151–156 (2018)
MATEC Web of Conferences 245, 08001 (2018) https://doi. org/10.1051/matecconf/201824508001
EECE-2018
5
СТАНДАРТ | AWWA C 200-XX (XX: представляет год последней редакции) | |||
РАЗДЕЛ 1: ОБЩИЕ ПОЛОЖЕНИЯ | ||||
ОБЛАСТЬ ПРИМЕНЕНИЯ | Этот стандарт распространяется на трубы с прямым или спиральным швом, сваренные встык, и бесшовные трубы диаметром 6 дюймов.(150 мм) с номинальным диаметром и более для передачи и распределения воды или для использования в других объектах системы водоснабжения. | |||
ПРОВЕРКА | Все выполненные работы и материалы, поставляемые в соответствии с настоящим стандартом, могут быть проверены покупателем, но такая проверка не освобождает производителя от ответственности за предоставление материалов и выполнение работ в соответствии с настоящим стандартом. | |||
ОБЕСПЕЧЕНИЕ КАЧЕСТВА | Производитель должен поддерживать программу обеспечения качества, чтобы гарантировать соответствие минимальным стандартам. В его состав должен входить сертифицированный инспектор по сварке (AWS QC1) для проверки того, что сварщики и сварочные процедуры имеют квалификацию, соблюдаются процедуры с ограничением испытаний и выполняются функции обеспечения качества. | |||
ДЕФЕКТЫ | Готовая труба не должна иметь недопустимых дефектов. Ремонт дефектов не допускается, если глубина дефекта превышает 1/3 номинальной толщины стенки трубы и если длина той части дефекта, в которой глубина превышает 12,5%, превышает 25% внешний диаметр трубы. Каждая отремонтированная труба подлежит гидростатическим испытаниям в соответствии с требованиями стандарта. | |||
МАРКИРОВКА | Серийный номер или другое обозначение должно быть нанесено на видном месте на каждой секции трубы и каждой специальной секции. | |||
РАЗДЕЛ 2: МАТЕРИАЛЫ | ||||
ASTM | Если труба должна быть изготовлена в соответствии с требованиями одной или нескольких спецификаций ASTM, классы труб должны быть:
| |||
ИЗГОТОВЛЕННЫЙ | Когда труба должна быть изготовлена в соответствии со стандартами; пластины, листы или катушки должны быть выбраны в соответствии со следующими физическими свойствами и спецификациями. | |||
ПЛИТ
| ||||
РУЛОНКИ И ЛИСТЫ
Для листов максимально допустимое отклонение толщины должно быть 0.010« под заказанную толщину. Для листов максимально допустимые отклонения толщины должны соответствовать спецификациям ASTM A-568. | ||||
РАЗДЕЛ 3: ИЗГОТОВЛЕНИЕ ТРУБЫ | ||||
ОБЩИЕ ТРЕБОВАНИЯ | Трубы, произведенные на трубном заводе, должны пройти процедуры контроля качества AWWA C-200.Такая труба должна быть изготовлена в соответствии со стандартными требованиями ASTM A-53, A-134, A-135 и A-139. | |||
ИЗГОТОВЛЕНИЕ | Сварной шов должен иметь одинаковую ширину и высоту по всей длине трубы. По договоренности между покупателем и производителем сварка может выполняться как автоматическим, так и ручным способом. | |||
Все спиральные, продольные и кольцевые швы, используемые при изготовлении трубы, должны быть сварными стыковыми соединениями с полным проплавлением. Максимальный допуск радиального смещения пластин: Для толщины 3/8 дюйма или меньше = 0,1875 толщины или 1/16 дюйма — в зависимости от того, что больше. Для толщины 3/8 дюйма и более = 0,1875 толщины или 1/8 дюйма — в зависимости от того, что меньше. | ||||
СВАРКА | Процедуры, сварщики, а также все операторы должны иметь квалификацию в соответствии с разд. | |||
ПРОИЗВОДСТВЕННЫЕ СВАРОЧНЫЕ ИСПЫТАНИЯ | Производственные испытания сварных швов состоят из: испытания на два изгиба (внутренний и внешний), двух испытаний на растяжение с уменьшенным сечением и испытания на макротравление. Периодичность производственных испытаний сварных швов: Должен быть как минимум один комплект образцов для испытаний сварных швов, взятых каждого размера, сорта и толщины стенки в результате работы, выполняемой каждой производственной машиной и каждым оператором не менее чем на каждых 3000 футов трубы. . | |||
РАЗДЕЛ 3.4: ГИДРОСТАТИЧЕСКОЕ ИСПЫТАНИЕ | ||||
ТЕСТ | Каждая длина трубы должна быть испытана производителем на гидростатическое давление не ниже, чем определяемое по следующей формуле: P = 2St / D Где: P = минимальное давление гидростатического испытания (фунт / кв. Примечание : По соглашению между покупателем и производителем, когда диаметр и толщина стенки трубы таковы, что пропускная способность испытательного оборудования превышает эти требования, испытательные давления могут быть уменьшены или нет. могут использоваться разрушающие методы испытаний. S = напряжение в стенке трубы во время гидростатического испытания, которое должно быть в 0,75 раза больше указанного минимального предела текучести используемой стали или как указано покупателем. T = толщина стенки (дюйм) D = внешний диаметр (дюймы). Испытательное давление должно удерживаться в течение времени, достаточного для наблюдения за сварными швами. Утечек быть не должно. | |||
РАЗДЕЛ 3. 5: ДОПУСТИМЫЕ РАЗМЕРЫ ВЕСА И РАЗМЕРОВ | ||||
ТОЛЩИНА | Если покупателем не указано иное, допуски по толщине стенки и весу сварных труб должны определяться требованиями спецификаций, по которым заказываются пластины или листы. | |||
ОКРУЖЕНИЕ | Труба должна быть практически круглой. Наружная окружность трубы не должна отклоняться более чем на +/- 1%, но не более чем на » от номинальной внешней окружности на основе номинального диаметра. | |||
ПРЯМОСТЬ | Готовая труба не должна отклоняться более чем на 1/8 дюйма.от 10 футов. длинная линейка прижалась к трубе. | |||
ДЛИНА | Указанные в заказе длины труб должны поставляться с допуском +/- 2 ». | |||
ПОДГОТОВКА | Если труба имеет фаску на концах для стыковой сварки на месте, концы должны быть скошены под углом 300 с допуском +50, -00 с шириной поверхности основания 1/16 дюйма +/- 1 / 32 ». | |||
КОНЦЫ С ФЛАНЦАМИ | Концы, на которые устанавливаются фланцы, должны быть отшлифованы (продольные и спиральные сварные швы) на уровне грунта на достаточном расстоянии, чтобы обеспечить надлежащую установку фланца. | |||
ОВАЛЬНОСТЬ | Овальность концов трубы должна соответствовать диаметру и толщине стенки.Любая некруглость должна быть ограничена гладким овалом, который можно придать домкратом до круглой формы. | |||
ДИАМЕТР | Допуск на диаметр концов составляет от — 1/16 дюйма до более 1/8 дюйма указанного диаметра. -1 / 16 » равно -0,196 » по окружности, а +1 / 8 » равно + 0,393 » по окружности. | |||
ПЛОЩАДНОСТЬ | Для трубы, которая должна быть сварена встык на месте, концы секций трубы не должны отклоняться более чем на 1/8 дюйма.в любой точке от истинной плоскости, перпендикулярной оси трубы и проходящей через центр трубы на конце. | |||
СПЕЦИАЛЬНЫЕ КОНЦЫ | По соглашению между производителем и покупателем концы трубы могут поставляться с конфигурациями соединений и допусками, отличными от описанных в данном документе. В таких случаях концы труб должны соответствовать описанию подробных чертежей, предоставленных покупателем. |
Окна просмотра для оптических приложений — VACOM
Давление газа определяется путем измерения потерь тепла в зависимости от давления
Теплопроводность, зависящая от количества частиц и плотности, является еще одной характеристикой газа. Энергия передается при столкновении молекул. Эффективность переноса зависит от длины свободного пробега частиц. В определенном диапазоне давлений теплопроводность пропорциональна давлению.Однако следует учитывать такие отвлекающие эффекты, как конвекция газа, тепловое излучение, тепловые потери на контактах разъема и т. Д.
В основе концепции вакуумметра Пирани лежит тонкая проволока, нагретая до постоянной температуры, которая значительно выше температуры окружающего газа в вакууме. Проволока (типичный диаметр: 5… 25 мкм; длина от 50 до 100 мм) передает тепло газу и одновременно является частью электрической цепи, например, моста Уитстона.Температуру, зависящую от давления, можно определить по измеренному сопротивлению провода. Благодаря технической реализации в устройствах Пирани контролируется электрическая мощность, которая прямо пропорциональна сопротивлению провода.
Мост Уитстона, который используется для стабилизации температуры, также может измерять разницу между напряжением нагревателя и заданным опорным напряжением. Разница между фактическим и опорным напряжением устанавливается на ноль при значении давления, при котором теплопроводность больше не играет роли.Эта калибровка в основном устраняет нежелательные эффекты теплового излучения и теплопроводности на контактах соединителя провода.
Преимуществами вакуумметра Пирани являются широкий диапазон измерения от 10 -4 мбар до атмосферного давления, а также точность ± 10%, достаточная для большинства приложений.
Теплопроводность газа также является функцией средней скорости молекул и, следовательно, молекулярной массы частиц газа.В связи с этим вакуумметры тепловых потерь измеряют давление в зависимости от типа газа. Обычно приборы калибруются для азота и воздуха. Измерения с другими газами (например, аргоном; гелием) следует интерпретировать с осторожностью. Например, продувка камеры аргоном может вызвать небольшое избыточное давление в камере, которое не может быть отображено датчиком Пирани.
В диапазонах давления выше 10 мбар конвекция газа увеличивается, и на его движение влияют силы тяжести.