(вопрос) р6м5 закалка на первичную твердость.
спай
вопрос в следующем:
1.есть печка с температурой до 1150 гр.
2.есть опушенный кусок быстрореза
хочется понять как лучше провести ТО для клинков.
на вторичную твердость полагаю смысла калить нет ?
рад буду услышать разные варианты. идеи и мысли.
пока речь идет о эксперименте, есть 2 ненужных куска, буду на них тренироваться.
Kerogen
Вроде недавно проскакивало 880, охл. в воде, отпуск 200. Но детали расписаны не были. Думаю, что при охлаждении только в воде заготовка может пойти трещинами, я бы попробовал через воду в масло с выдержкой в воде не больше 1 секунды.
С уважением.
Termist
спайинтересный термин 😊 😊 😊 😊 Если проводить ТО по уму, то для отжига быстрореза, нужно не меньше 10 часов.
опушенный
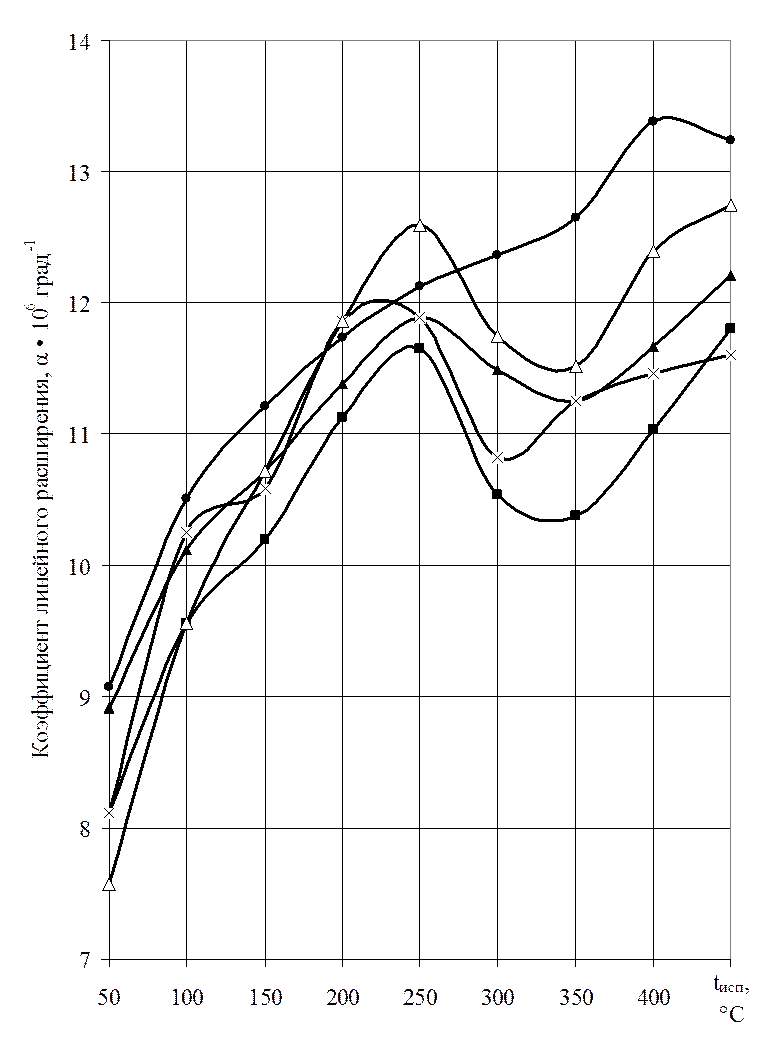
спай
))))
ну отжиг я не делал. положил в печку и подержал при 800 гр часа 2.
после чего полотно стало довольно приятно обрабатывается напильником.
назовем это процесс опусканием быстрореза )))
Просто Пух
Отдал кузнецу одну протяжку на пробу расковать,попросил просто дать остыть после на воздухе.Потом в ОТК измерил твердость 62-64 ед.На то р6м5 и называют в народе «самокалом» что он сам твердость набирает.
А год назад вытачивал насадки на сверло под евровинт из сырого «самокала»,термист потом нагрел его до малинового цвета и просто дал остыть.
Вот с чем сталкивался.Поэкспериментируйте.
Termist
Тиснул из книги:
Охлаждение при закалке быстрорежущей стали следует производить в масле. В результате медленного охлаждения с высоких температур (например, на воздухе) могут выделиться карбиды, что ухудшает режущие свойства.
Весьма хорошие результаты (в смысле уменьшения закалочной деформации) дает ступенчатое охлаждение.
Для превращения остаточного аустенита в мартенсит производят обработку холодом или отпуск.
Низкий отпуск против оптимального нагрева не вызвал способности превращения аустенита в мартенсит. На рис. 10, а белые поля — остаточный аустенит; после многократного отпуска остаточного аустенита нет
отпуск при 500
отпуск при 600
В плохо отожженной быстрорежущей стали после закалки наблюдается особый вид брака: при нормальной твердости и нормальном количестве остаточного аустенита сталь оказывается очень хрупкой, а ее излом — грубозернистый, чешуйчатый, напоминает нафталин. Этот вид брака быстрорежущей стали обычно называется нафталиновым изломом.
спай
я вот не понял, нужно её отжигать перед повторной закалкой ?
деформации она не подвергалась, до высоких температур не нагревалась.
Просто Пух
Ага.Получается пост актуален и для меня…
спай
спасибо всем.
в общем пока мне видится 2 варианта.
закалка 1100 масло. потом морозильник ))
1 кусок будет отпуск 250гр по часу 3 раза
2 кусок будет отпуск 550гр по часу 3 раза
спай
даже видимо с учётом того, что печка одна, то на 2 заготовке первый отпуск будет совместно с первой заготовкой.
250 1 час. потом 3 по 550…
Termist
ikar’eff
закалке от 1250-1280 С. Проявится ли при закалке с пониженных температур — ХЗ, но рисковать не стоит, лучше отжечь, ИМХО.
По поводу температуры закалки, при нагреве до 1150 градусов в стали будет большое количество нерастворимых карбидов; при температуре 1250 градусов будет иметь слишком большое зерно. Оптимальной температурой закалки Р6М5 является 1200 градусов.
спайСмысл ? Эффект один, что в морозилку сунуть но нужны температуры до -70, для превращения остаточного аустенита в мартенсит, что отпустить !
потом морозильник ))
Почему люди молчат, эффект от 2-х процедур практически 1
Без обработки холодом остаточный аустенит может быть превращен в мартенсит,отпуском. Для этого закаленную сталь нагревают до 560 .С, при этом из аустенита выделяются карбиды
спайпри низком отпуске аустенит не превратится в мартенсит !!! Вам подходит
1 кусок будет отпуск 250гр по часу 3 раза
спай
2 кусок будет отпуск 550гр по часу 3 раза
спай
Termist
потом морозильник ))
Смысл ? Эффект один, что в морозилку сунуть но нужны температуры до -70,
на рис 211 видно, что если температура закалки 1100 то нижняя граница мартенситного преобразования чуть меньше 0.
ikar’eff
По поводу температуры закалки, при нагреве до 1150 градусов в стали будет большое количество нерастворимых карбидов
Для обеспечения теплостойкости в 600 С, может, ЛЭ в растворе и недостаточно будет, но к ножу это мало отношения имеет 😊 А твердости там достаточно будет.
при температуре 1250 градусов будет иметь слишком большое зерно. Оптимальной температурой закалки Р6М5 является 1200 градусов.
1250-1280 С — стандартная температура закалки для Р6М5. это небольшой перегрев ради теплостойкости, но все равно зерно достаточно мелкое — номер 10-11.
спай
в общем с быстрорезом что- то нифига у меня не получилось…
1 кусок калил 1100 между 2 чугуниевыми пластинами ( 1 нет масла, 2 заготовка уже тонко сведена, боялся поведёт). в итоге нифига она не закалилась, свободно грызётся напильником.
2 кусок попробовал с 1050 в воду. ясное дело всё повело, да к тому-же и опять таки, напильник свободно грызёт.
в общем надо видимо с подогревом и со 1250 калить его.
kirsan_kaifat
с рапидом потому и работают мало. куча причин. дорогой, плохо обрабатывается, и сложная ТО(и дорогая)
спай
угу…
инженер поможет — Термическая обработка инструментов из быстрорежущей стали
Для получения высокой стойкости и производительности инструментов необходимо, чтобы их рабочие части имели соответствующую твердость и сопротивление изнашиванию. Это возможно за счет создания основной мелкозернистой мартенситной структуры, которая достигается предварительной ковкой и изотермическим отжигом до механической обработки, а после механической обработки — закалкой и отпуском. Для этих тепловых процессов характерным является следующее:
1) нагрев инструмента под ковку, отжиг и закалку не должен быть быстрым, чтобы весь материал успел равномерно прогреться; в то же время слишком медленный нагрев вызывает появление окалины;
2) выдержка инструмента в печи должна быть достаточной для структурных превращений, но во избежание выгорания углерода с поверхности инструмента и роста зерен аустеиита нельзя передерживать его при высокой температуре;
3) охлаждение инструмента нужно производить в зависимости от химического состава стали с определенной интенсивностью
.
Указанные операции термической обработки применяются для всех классов инструментальных сталей. Однако температурные режимы этих процессов во многом зависят от марки стали и от размеров инструмента. Учитывая сравнительно широкое применение быстрорежущих сталей для изготовления режущих инструментов, рассмотрим характерные особенности отдельных операций термообработки.
Быстрорежущие стали обычно поставляются в отожженном состоянии со структурой мелкозернистого (сорбитообразного) перлита с избыточными карбидами. Твердость сталей обычной производительности Р9 и Р18, согласно ГОСТ, должна составлять не более НВ = 207—255, а сталей повышенной производительности — до НВ = 269—293. При этом толщина обезуглероженного слоя на сторону для прутков диаметром 5—100 мм не должна превышать 0,45—1,3 мм.
У шлифованной стали (серебрянки) обезуглероженнын слой вообще не допускается. Пластичность поставляемой быстрорежущей стали, определяемая механическими характеристиками, при необходимости должна проверяться технологическими испытаниями образцов пробной рубкой, штамповкой, а также пробами на загиб.
Так как карбидная неоднородность в прокате диаметром свыше 50 мм обычно больше 3 баллон, то заготовки из прутков больших диаметров для уменьшения карбидной неоднородности следует подвергать дополнительной ковке. Ковке подвергаются также слитки из быстрорежущей стали. Таким образом, термообработка быстрорежущих сталей включает, кроме основных операций закалки и отпуска, также операции ковки и последующего отжига. При выборе видов и режимов термообработки следует учитывать получение необходимой зернистости, твердости (не менее HRC = 62—65), прочности и теплостойкости стали. Следует также отмстить, что изменение режимов нагрева, выдержки и охлаждения по-разному влияет на получение оптимальных величин вышеуказанных характеристик. Так, твердость закаленной стали с повышением температуры закалки сначала возрастает, а затем уменьшается. Теплостойкость же зависит только от легированное™ твердого раствора и возрастает с повышением температуры закалки, а прочность — от структурных факторов и прел<де всего от величины зерна и условий распределения карбидов.
Нагрев для ковки из-за плохой теплопроводности быстрорежущей стали должен быть замедленным. Заготовки из стали Р18 диаметром свыше 50—60 мм сначала помещают в печь с температурой 400—600° С и медленно нагревают, исходя из расчета 7— 8 минут на каждые 10 мм толщины, а затем нагревают до 780— 820° С и выдерживают при этой температуре, т. е. в области превращения перлита в аустенит, также из расчета 7—8 минут на каждые 10 мм диаметра. Более мелкие заготовки следует сразу помещать в печь с температурой 780—820° С. Дальнейший нагрев проката до температуры начала ковки /= 1140—1180° С, а слитков до /=1150—1200° С производится относительно быстро.
Изотермический отжиг быстрорежущих сталей необходим для снятия напряжений, полученных при обработке давлением, и для понижения твердости, а также создания структуры зернистого или сорбитообразного перлита, сообщающего стали относительно хорошую обрабатываемость резанием.
Изотермический отжиг быстрорежущей стали Р18 производится нагреванием до температуры 850—870° С с выдержкой не более 12 часов при этой температуре. После окончания выдержки производят охлаждение стали до температуры 720—740° С со сравнительно небольшой скоростью (40—50° в час), а затем при 720—740° С сталь снова выдерживается не менее 4 часов. Следует особо отметить, что быстрорежущие стали, содержащие молибден или кобальт и особенно чувствительные к обезуглероживанию при отжиге, целесообразно отжигать в печах с защитной атмосферой или в чугунной стружке.
При резании с большой скоростью вызывается неравномерный разогрев поверхностного слоя обрабатываемого инструмента, что является причиной создания поверхностных напряжений и образования участков с мартенситно-аустенитной структурой. В связи с этим для крупных инструментов сложной формы и большой длины, например для протяжек, после обработки резанием для снятия напряжений и подготовки стали к закалке рекомендуется производить высокий отпуск. Этот отпуск производится нагревом инструмента до температуры 650—680° С с выдержкой до 2— 3 часов и с последующим охлаждением на воздухе или в масле.
Высокая красностойкость и режущая способность быстрорежущей стали зависят не только от химического состава, исходной мелкозернистой структуры с равномерным распределением карбидов, но и от особых условий закалки и отпуска. Поэтому нагрев при закалке таких сталей до высоких температур, отстоящих недалеко от температуры плавления, является специфической особенностью термической обработки этих сталей.

Продолжительность нагрева до высоких температур, как установлено практикой, до некоторой степени пропорциональна сечению инструмента и составляет 8—9 секунд на 1 мм диаметра или толщины при нагреве в соли и 10—12 секунд для нагрева в печи.
Следует отметить, что качество закалки во многом зависит от точности установления закалочных температур, так как от незначительного изменения химического состава стали закалочная температура изменяется. При этом интервал изменения закалочных температур для определенной стали должен быть уменьшен до 10—5° С, что повышает режущую способность инструмента до 1,5 раза.
Окончательный нагрев инструментов из обычных быстрорежущих сталей наиболее целесообразно выполнять в расплавленной соли ВаС12, а из сталей, содержащих кобальт или более 1,5—2% молибдена, для лучшей защиты от обезуглероживания — в контролируемых атмосферах или в очень хорошо расплавленной соли, но с сокращенной выдержкой, используя при этом нагрев до 1100—1150° С.
Условия охлаждения нагретого до закалочной температуры инструмента следует устанавливать в зависимости от его размеров и формы. Ускоренное охлаждение до 500—400° С задерживает выделение карбидов из аустенита и способствует получению лучшей теплостойкости.
Непрерывную закалку с охлаждением в масле (30—100° С) можно применять для инструментов простой формы (резцы, сверла), имеющих диаметр (толщину) до 30—40 мм. Инструменты небольшого сечения диаметром, или толщиной, 3—5 мм можно охлаждать сжатым воздухом или непосредственно на воздухе.
Ступенчатую закалку с предварительным подстуживанием на воздухе с выдержкой 2—5 минут в горячей охлаждающей среде (калиевой селитре) при г = 450—500° С или 250—350° С, т. е. п области наибольшей устойчивости аустенита, целесообразно проводить для фасонных некрупных и не очень длинных и тонких инструментов. После окончания выдержки инструмент охлаждается непосредственно на воздухе. При отсутствии ванны с расплавленной смесью инструменты можно также охлаждать в масле до 300—450°, а затем на воздухе.
Изотермическая закалка, рекомендуемая для крупных и длинных инструментов, производится охлаждением в расплавленной соли с температурой 200—300° С с выдержкой 30—60 минут. Кроме того, для очень крупных инструментов с резкими переходами может применяться прерывистая закалка, которая осуществляется сначала в подогретом масле до 90—100° С, когда получается частичное мартенситное превращение, а затем инструменты переносятся в печь для отпуска. Заслуживает внимания также закалка под прессом. Она применяется для уменьшения деформации инструментов простой формы и весьма небольшого размера. В этом случае инструменты сначала охлаждаются в соли до 500—600° С, а затем в масле под прессом.
Несмотря на высокую температуру нагрева, правильно закаленная быстрорежущая сталь должна иметь мелкозернистую структуру, состоящую из легированного мартенсита (порядка 50%), высоколегированного остаточного аустенита (порядка 30%) и сложных карбидов (порядка 20%). Для дальнейшего перевода остаточного аустенита во вторичный, более легированный мартенсит сразу же после закалки производится многократный отпуск. Последний осуществляется для инструментов из быстрорежущих сталей нормальной производительности при температуре 560—570° С с выдержкой в течение 60—75 минут при нагреве в соляной ванне и с выдержкой 60 минут при нагреве в печи. После этого производится охлаждение инструмента на воздух
Сталь Р6М5 – легированная инструментальная сталь
Сталь марки Р6М5 – особый вид легированной инструментальной стали, предназначенный для изготовления быстрорежущих металлообрабатывающих инструментов. Сталь имеет много аналогов на мировом рынке с различными обозначениями. В таблице сведены как точные, так и ближайшие аналоги Р6М5:
США |
Германия |
Япония |
Франция |
Англия |
Евросоюз |
Италия |
Испания |
||||||||||||||
— |
DIN,WNr |
JIS |
AFNOR |
BS |
EN |
UNI |
UNE |
||||||||||||||
|
|
|
Китай |
Швеция |
Болгария |
Венгрия |
Польша |
Румыния |
Чехия |
Австрия |
Юж. Корея |
GB |
SS |
BDS |
MSZ |
PN |
STAS |
CSN |
ONORM |
KS |
Особенности упрочняющей термической обработки Р6М5
Хотя вольфрамомолибденовую сталь Р6М5 называют «самозакаливающейся», процесс закалки нельзя пускать на самотек. Соблюдение рекомендованных режимов отжига, нагревания и отпуска позволяет увеличить сроки работы резцов и фрез на 20-30%.
Закалка инструмента производится ступенчато с предварительным подогревом в соляных ваннах: по 15-30 сек. при температурах 500 и 850 °С. Продолжительность окончательного нагревания до температуры 1280°С рассчитывается по эмпирической формуле: 10 с*1 мм толщины металла. Режим отпуска – трехкратный по 1 часу каждый при Т=580-600°С.
В современном машиностроении все чаще режущий инструмент для обработки металлов выполняют с применением приваренных режущих поверхностей. При термической обработке сварного инструмента его помещают в солевой раствор таким образом, чтобы место сварки не доходило до уровня раствора на 15—20 мм.
Производство и поставки легированных инструментальных сталей
Сталь Р6М5 после розлива содержит включения карбидов различного размера, которые существенно снижает ее механические свойства. Поэтому при производстве Р6М5 необходима тщательная проковка заготовок при строгом контроле температур начала и конца ковки. Во время ковки крупные карбидные группы дробятся и равномернее распределяются по структуре металла. При недостаточной поковке возникает местное скопление карбидов, в которым прочность материала на излом много ниже.
Такая стабильность производства обеспечивается на Череповецком (ПАО «Северсталь») и Челябинском (группа МЕЧЕЛ) металлургических комбинатах.
Краткая справка о предприятиях:
Череповецкий металлургический комбинат – крупнейший стальной актив дивизиона «Российская сталь», входящего в состав «Северсталь».
Челябинский металлургический комбинат (группа МЕЧЕЛ)
ОАО «Мечел», основанное в 2003 году, является одной из ведущих мировых компаний в горнодобывающей и металлургической отраслях. В компанию входят производственные предприятия в 11 регионах России, а также в США, Литве и Украине.
«Мечел» объединяет более 20 промышленных предприятий.
Прокат стальной горячекатаный полосовой стали Р6М5 длиной 3-6 метров различного профиля по ГОСТ 4405-75 и ГОСТ 19265-73 выпускается на Ижевском металлургическом заводе, входящем в состав МЕЧЕЛ.
Цены, условия поставки и объемы реализуемой продукции указаны на официальных сайтах заводов, но для приобретения малых партий металла придется обращаться к металлотрейдерам. Заводы не отгружают 1-2 тонны металла, а средний заказ именно такой.
Среди наиболее популярных трейдеров сталь Р6М5 можно приобрести у компаний:
Сталь Р6М5 — Живучий.рф — информационный портал
Главная > edc > ножевые стали > Р6М5
Р6М5 характеристики
Сталь P6M5 — быстрорежущая инструментальная сталь. Применяется для режущих инструментов, работающих в условиях значительного нагружения и нагрева рабочих кромок. Инструмент из быстрорежущих сталей обладает высокой стабильностью свойств и хорошо подходит для изготовления кухонных, туристических или складных ножей. Сталь Р6М5 практически вытеснила похожие по своим свойствам стали Р18, Р12 и Р9 и нашла применение при обработке цветных сплавов, чугунов, углеродистых и легированных сталей, а также некоторых теплоустойчивых и коррозиестойких сталей.
Расшифровки стали Р6М5
Буква «Р» — это обозначение быстрорежущих сталей. Слово взято из транскрипции английского «rapid»», переводящегося, как «быстрый».
Цифра за буквой «Р» обозначает процентное содержание в сплаве вольфрама (6%)
Далее идет буква «М», обозначающая присутствие в сплаве молибдена (5).
Кроме Mo, быстрорежущие стали могут содержать в своей маркировке такие обозначения: «К» — кобальт, «Ф» — ванадий, «Т» — титан, «Ц» — цирконий.
Данная марка стали имеет довольно сложный состав и не простое производство. Далеко не все производители ножей могут работать со сталью Р6М5. И цена на готовое изделие выходит, как правила довольно «кусачая». Но ножи из стали Р6М5 обладают исключительными качествами. Режущая кромка ножа из этой стали долго держит заточку. Ножи обладают отличным качеством реза. При очень высокой твердости, сталь обладает хорошей пластичностью, что делает нож очень прочным.
В основном из этой стали делают ножи с фиксированным лезвием типа «финка». Из-за повышенной твердости сталь не применяют для изготовления топоров и мачете.
Ко всему прочему сталь является жаропрочной. Нож из Р6М5 можно заточить на станке без риска перекала режущей кромки.
К минусам данной стали можно отнести её слабые антикоррозийные свойства и сложность заточки.
Новичку я бы не советовал нож из стали Р6М5. Его действительно сложно точить, как правило для качественной заточки используют специальные диски из эльбора (сверхтвердый материал, по свойства приближен к алмазу). Но если Вам нужна невероятная «мощь» и надежность то это хороший выбор.
Нож из стали Р6М5 это не игрушка, это очень серьезная вещь, готовая к серьезным испытаниям.
Твердость стали Р6М5 — 62-65 RHC
Состав стали Р6М5
Углерод (С) 0,82 – 0,90 %
Марганец (Mn) 0,20 – 0,50 %
Хром (Cr) 3,8 – 4,4 %
Кремний (Si) 0,20 – 0,50 %
Молибден (Мо) 4,8 – 5,3 %
Ванадий (V) 1,7 – 2,1 %
Кобальт (Со) 0,5 %
Никель (Ni) 0,4 %
Фосфор (Р) 0,03 %
Сера (S) 0,025 %
Вольфрам (W) 5,5 – 6,5%.
Главная > edc > ножевые стали > Р6М5
Перейти в магазин «Живучий.рф»
Купить подарочный ящик для ножа Ammo Box
Руководство по термообработке
Марка сталиВыберите сталь variant005B017R026A042A047A (C45) 047Q056K057F058A061A (C60E) 123A (20MnCrMo4-2) 124D (20MoCrS4) 124Q126H (20Cr2 *) 127C136B143A145h246F146S (16NiCrS4) 146T147Q (16NiCr6-4 *) 151A152A (20NiCrMo2-2) 152B152C (20NiCrMo2-2) 152D152E152G ( 20NiCrMo2-2) 152J152K152Q152R152Y154C156B156F156T157B157C (20NiCrMo7) 157D (20NiCrMo7) 157F157G (20NiCrMo7) 157Q158Q (20NiMo9-7 *) 159B (18CrNiMo7-6) 159Q (18CrNiMo7-6) 159S (18CrNiMo7-6) 159X (18CrNiMo7-6) 192R214E214Q214X215B216A216S222A222B225A (18CrMo8 -5 *) 225C (18CrMo8-5 *) 234B234G234J234K (16MnCr5) 234S236F (20MnCr5) 236Q (20MnCr5) 242S245S (12NiCr14-6 *) 248D248Q (18CrNi8) 250RMn125Cr (18CrNi8) 250A2-5Cr (18CrNi8) 250A250Cr (18CrNi8) 250A2-5No) 253C253D (14NiCrMo13-4) 253F253G253h353L (22NiCrMo12-5 *) 253S (22NiCrMo12-5 *) 254R254S254T255G (18NiCrMo14-6) 255Q (18NiCrMo14-6) 256A256G (23NiCrMo15-5 *) 258Q (20NiMo9-7 *) 263A264Y266L267C268A275A (24NiSiMnMo7- 6-6 *) 277L (16CrMnNiMo9-5-2 *) 277Q (16CrMnNiMo9-5-2 *) 277T280E280h380M280N280P280T (19MnV6 *) 280X281B281K281P (19MnV6 *) 281T * 29MnV 4L295A295G295R296B296C297A — Hybrid55299Q299T316A316R322A (25CrMo4) 322D (25CrMo4) 322G322h422N322Q323A326C (42CrMo4) 326F326J326T327A (42CrMo4) 327B327K327N327S332K335C350A350Q355B (40NiCrMo7-3 *) 356D (34CrNiMo6) 356Q (34CrNiMo6) 357C365A375J382K (46MnVS3) 382L382M382P391X397A — Hybrid60398Q (32CrMoV12-10 *) 416A417R420F420G (24CrMo13- 6) 453C (31NiCrMo13-4) 455A (28NiCrMnMo14-6-4 *) 466A466F467A468Y473F477L (40SiCrMnMo7-6-6 *) 477T478K481C482A (38MnVS6) 495B (304-7Cr * 42MoNiCr) 495B (484-7Cr 42MoNiCr) 6) 498C498h599Q (30MoCrV20-7 *) 510A (С55) 510N510P511K513Y528A528B528E (50CrMo4) 528Q (50CrMo4) 531A591A591B591C593B (51CrV4) 593G593Q (51CrV4) 593Y593Z594Y596Y606A608A673Y674Y677B677L (66SiMnCrMo6-6-4) 677Q (66SiMnCrMo6-6-4) 696R722C722S754H755V803A (100Cr6) 803B803C803D (100Cr6) 803F (100Cr6) 803G803J (100Cr6) 803K803L803N (100Cr6) 803P (100Cr6) 803Q (100Cr6) 803T803V803X803Z (100Cr6) 804C804Q821J821L (10025Cr7) 8Cr7Mo (10025Cr7) 8Qr7Cr7 (100Cr724Mo) (100Cr7) 8Cr7 (100Cr7) 8Qr7 (100Cr7) 8Cr7 (100Cr7) 8Cr7 (100Cr7) 8Cr7 (100Cr7) 8Cr7 (100Cr7) 8Cr7 (100Cr7) 8Cr7 (100Cr7) 8Cr7) 3) 825T (100CrMo7-3) 826B (100CrMo 7-4) 826Q827B (100CrMnMoSi8-4-6) 827Q831B (100CrMnSi4-4) 832K (100CrMnSi6-6) 832T837N837R (100CrMnSi6-4) 837S (100CrMnSi6-4) (508P6001621Xy20055H300) 888P60016Hybrid 2725 (4734) 3350 (8312) 4803 (4803) 9270 (1289) 100Cr6 (5621) 100CrMnSi6-4 (5625) 14Xh4MA (4708) 159X (1270) 15MA27 (7245) 15N3MA (4707) 16MnCr 5 (4316) 16NiCrS4 (4730) 17Cr 3 (5502) 18CrNiMo7-6 (4761) 1E1671 (5463) 20NiCrMo2-2 (4548) 21CrMoV 5 7 (6130) 21HGNMA (4766) 23MnCrMo5 (5503) 24M13B (5446) 25CrMoS144 HHH JV (5504) 280 M (7266) (19MnVS6 M) 280 T (7260) 280 X (7255) 285 K (1246) 28CrS4 (5548) 30CrMoV 9 (6140) 30CrNiMo 8 (6507) 327 P (1234) 34 CrMo 4 (6048) 34CrNiMo6 (6499) (ISO 898 класс 10.9) 34CrNiMo6 M (6502) 368,6 (5478) 36CrB4 (5498) 38 MnSiV5 (7239) 38MB5 (5496) 38MnSiVS5 (7219) 40 CrMoV 4-6 (1217) 40CrMo4 (6077) 41Cr 4 MOD (55174) 42Cr82 ) 50CrV 4 (7408) 51B20 (4336) 51CrV 4 (1282) 520 МВт + (2727) 52CrMoV 4 (1284) 52CrMoV4 (7407) 52Mn5BY (5234) 5HS64CC (4722) 605M36 (5905) 60Cr3 (5740) 6150 A 655M13 (4715) 709M40 (6107) 722M24 (8310) 817M40 (6506) 826M40 (6518) 92245H (5515) 92506 МБ, (уровень A (4525) 92506 МБ. (Уровень A (4525) 92506-3 (4540) 92520 ( Уровень A) J1 (1285) 92520 (уровень B) J1 (4739) 92523 Уровень A (1288) AISI 4140 (6115) ASTM A 193 B16 (6098) ASTM A 193 B7 (6093) ASTM A 193 B7 / L7 (1272) ASTM A 320 L7 (6137) ASTM A 320 L7 (1281) BCM 311 (5465) BM 212 (5415) BM 311 (5480) C 38 MOD (7224) C 38 + N (7228) CK 45 (5081) CK 50 ( 5155) CNMO 510 (6521) CROMOBOLT (6116) HYDAX 15 (2720) HYDAX 25 (2630) IB 20 NI MOD (5460) IMACRO M (8302) IMACRO NIT (8303) IMAFORM / 5CRB4 (5450) IMANITE (6132) IMAROCK ( 5910) IMATRA C100 (5614) IMATRA CHA (5600) MC 212 (4334) OVAKO 280 P (7265) P355NH (2714) S235JR (2191) S355J0, S355J2 (27 08) S355J0.S355J2 (2708) S355J2 + M (2723) S520M / S355J2 (2722) SAE 1080 MOD (1287) SAE 4140 MOD (6139) SAE 4340 (6514) SAE 8620 (4542) SS 2230-00 (7402) STL 2244- 05 (6129) ST�L 2541 (6501) TB 1398 (4741) TS280M-LX (7252) V-1580 (5241) V-1649 MOD (5074) V-2146 (7259) V-2158-60 (4326) V -2158-70 (4324) V-2244-64 (6126) V-2250-00 MOD S (6112) V-2525-60 (4756) V-2525-70 (4757) V-2903 (7210) V-2904 (7205) V-2906-95 (1258) XC 55 MOD (5235) 11MnCrB5-3 (SB9690) 16MnCrS5 (SB9206) 20MnB4 (SB9625) 22MnB5 (SB9643) 25CrMo4 (SB9224) 27MnB4 (SB9654) 27MnCr96 (SB9654) 27MnCr96 -2 (SB9652) 27MnCrB5-2 (SB9667) 28MnB5 (SB9694) 29MnCrB5-2 (SB9667) 30MnB5 (SB9662) 30MnB5 (SB9671) 34CrNiMo6 (SB9205) 38Si7 (SB9040) 42CrMo (SB9040) 42CrMo (SB9040) 42CrMo (SB9040) 42CrMo (SB9040) 42CrMo (SB9040) 42CrMo (SB9040) 42CrMo) ) 51CrV4 (SB9292) 51CrV4 (SB9212) 51CrV4 (SB9282) 51CrV4 (SB9290) 52CrMoV4 (SB9296) 55Cr3 (SB9257) 56SiCr7 (SB9084) 61SiCr7 (SB9064) C3516 C35E (SB3645) (SB3645) C3516 C35E (SB3645) (SB3645) C45 (SB1672) C55 SBC55 (SB8665) C60E EN 10083-2: 2006, исх. (SB8680) SAE 1005SAE 1010SAE 1015SAE 1020SAE 1025SAE 1030SAE 1033SAE 1034SAE 1035SAE 1037SAE 1038SAE 1040SAE 1045SAE 1050SAE 1055SAE 1059SAE 1060SAE 1062SAE 1064SAE 1065SAE 1069SAE 1070SAE 1075SAE 1080SAE 1084SAE 1085SAE 1086SAE 1090SAE 1095SAE 1108SAE 1109SAE 1110SAE 1111SAE 1112SAE 1113SAE 1114SAE 1115SAE 1116SAE 1119SAE 1120SAE 1123SAE 1139SAE 1145SAE 1152SAE 1211SAE 1320SAE 1330SAE 1335SAE 1340SAE 1345SAE 1513SAE 1518SAE 1522SAE 1524SAE 1525SAE 1526SAE 1527SAE 1533SAE 1534SAE 1536SAE 1541SAE 1544SAE 1545SAE 1546SAE 1547SAE 1548SAE 1551SAE 1552SAE 1553SAE 1561SAE 1566SAE 1570SAE 1572SAE 1580SAE 1590SAE 15B21SAE 15B28SAE 15B30 HSAE 15B35 HSAE 15B37 HSAE 15B41 HSAE 15B48 HSAE 15B62 HSAE 2317SAE 2330SAE 2340SAE 2345SAE 2512SAE 2515SAE 2517SAE 300MSAE 3115SAE 3120SAE 3130SAE 3135SAE 3140SAE 3145SAE 3150SAE 3215SAE 3220SAE 3230SAE 3240SAE 3250SAE 3310SAE 3312SAE 3316SAE 3325SAE 3335SAE 3340SAE 3415SAE 3435SAE 3450SAE 4012SAE 4023SAE 4024SAE 4027SAE 4028SAE 4032SAE 4037SAE42SAE 4028SAE 4032SAE 4037SAE42SAE 4620SAAE11 4620SAAE11 4620SAAE11 4620SAAE11 4620SAAE11 4620SAAE11 4620SAAE11 4620SAAE11 4 SAE 4120SAE 4121SAE 4125SAE 4130SAE 4131SAE 4817SAE 4135SAE 4817SAE 4137SAE 4140SAE 4142SAE 4145SAE 4147SAE 4150SAE 4161SAE 4317SAE 4320SAE 4330 ModSAE 4337SAE 4340SAE 43BV12SAE 43BV14SAE 4419SAE 4422SAE 4427SAE 4608SAE 4615SAE 4617SAE 4621SAE 4640SAE 46B12SAE 4715SAE 4718SAE 4720SAE 4812SAE 4815SAE 4820SAE 50100SAE 5015SAE 5045SAE 5046SAE 5060SAE 50B40SAE 50B44SAE 50B46SAE 50B50SAE 50B60SAE 51100SAE 5115SAE 5117SAE 5120SAE 5130SAE 5132SAE 5135SAE 5140SAE 5145SAE 5147SAE 5150SAE 5152SAE 5155SAE 5160SAE 51B60SAE 52100SAE 6115SAE 6117SAE 6118SAE 6120SAE 6125SAE 6130SAE 6135SAE 6140SAE 6145SAE 6150SAE 6195SAE 71360SAE 71660SAE 7260SAE 8115SAE 81B45SAE 8615SAE 8617SAE 8620SAE 8622SAE 8625SAE 8627SAE 8630SAE 8632SAE 8635SAE 8637SAE 8640SAE 8641SAE 8642SAE 8645SAE 8647SAE 8650SAE 8653SAE 8655SAE 8660SAE 86B30SAE 86B45SAE 8715SAE 8717SAE 8719SAE 8720SAE 8735SAE 8740SAE 8742SAE 8745SAE 8750SAE 8822SAE 9250SAE 9254SAE 9255SAE 9259SAE 9260SAE 9340SAE 9340SAE 9261SAE 9340SAE 9340SAE 9340SAE 9261SAE 9340SAE 9261SAE 9340SAE 9261SAE 9340SAE AE 9442SAE 9445SAE 9447SAE 94B15SAE 94B17SAE 94B30SAE 94B40SAE 9747SAE 9763SAE 9840SAE 9845SAE 9850SAE 304SAE 403SAE 410SAE 414SAE 416SAE 422SAE 431SAE 440ASAE 440BSAE 440CSAE 502Ph23-8Ph27-7Maraging 200Maraging 250Maraging 300Maraging 350AISI W5AISI S1AISI S2AISI S5AISI S6AISI S7AISI O1AISI O2AISI O6AISI O7AISI A2AISI A3AISI A4AISI A6AISI A7AISI A8AISI A9AISI A10AISI A11AISI D2AISI D3AISI D4AISI D5AISI D7AISI L2AISI L6AISI h20AISI h21AISI h22AISI h23AISI h24AISI h29AISI h31AISI h32AISI h33AISI h34AISI h35AISI h36AISI h52AISI h53AISI T1AISI T2AISI T4AISI T5AISI T6AISI T8AISI T15AISI M1AISI M2AISI M4AISI M6AISI M7AISI M10AISI M30AISI M33AISI M34AISI M36AISI M41AISI M42AISI M43AISI M46AISI M47AISI M48AISI M50AISI M52AISI M62DIN C15DIN C22DIN C35DIN C40DIN C50DIN C55DIN C60DIN C67DIN 8CrMo16DIN 10CrMo9-10DIN 14NiCr10DIN 14NiCr14DIN 15Cr3DIN 15CrNi6DIN 15NiCr13DIN 16NiCr4DIN 16NiCr11DIN 16MnCr5DIN 16CrNiMo6DIN 16NiCrMo12DIN 16NiCrMo12-6DIN 17Cr3DIN 17MnB4DIN 17MnV7DIN 17CrNi6-6DIN 17NiCrMo 6-4DIN 17CrNiMo6DIN 18CrNi8DIN 18CrMo4DIN 18NiCr5-4DIN 18CrNiMo7-6DIN 18NiCrMo14-6DIN 18NiCrMo5DIN 19MnVS6DIN 19MnB4DIN 20MnB-3DIN 20MnB5DIN 20MnV6DIN 20Mn5DIN 20MnCr5DIN 20MnCrMo4-2DIN 20MnCrB5DIN 20MoCr4DIN 20NiCrMo2DIN 20NiCrMo7DIN 20NiCrMo2-2DIN 20NiMoCrS6-5DIN 21MnCr5DIN 21NiCrMo2DIN 21CrMoV5-7DIN 21CrMoV5-11DIN 22MnB4DIN 22MnB5DIN 22CrMoS3- 5DIN 23MnB4DIN 23MnNiMoCr5-4DIN 23MnNiCrMo5-2DIN 24CrMo13-6DIN 25MnB5DIN 25CrMo4DIN 27MnCrB5-2DIN 28Cr4DIN 28Mn6DIN 28NiCrMoV10DIN 30MnB5DIN 30CrNiMo8DIN 30NiCrMo2-2DIN 30CrMoV9DIN 30MnVS6DIN 31CrMoV9DIN 31CrMo12DIN 32CrB4DIN 32CrMoV12-28DIN 33CrMoV12-9DIN 34Cr4DIN 34CrMo4DIN 34CrNiMo6DIN 34CrAlNi7DIN 34CrAlMo5-10DIN 35NiCr18DIN 35NiCrMo16DIN 36Mn5DIN 36NiCr6DIN 36CrB4DIN 36NiCrMo16DIN 37Cr4DIN 37MnSi5DIN 37MnB5DIN 55Cr3DIN 38Cr4DIN 38Si7DIN 39NiCrMo3DIN 39MnCrB6-2DIN 40CrMnMo7DIN 40CrMoV-7DIN 55Cr3DIN 40CrMoV4-7DIN 40CrMoV13-9DIN 40CrMnMoS8-6DIN 40NiCrMo8DIN 40 NiCrMo 10-5DIN 40CrMnNiMo8-6-4DIN 41Cr4DIN 41CrAlMo7DIN 42MnV7DIN 42CrMo4DIN 43MnSi Mo4DIN 45SiCrV6DIN 45NiCrMo16DIN 45NiCrMoV16-6DIN 46Cr2DIN 46Si7DIN 46MnVS3DIN 50CrV4DIN 50CrMo4DIN 50CrMoV13-14DIN 51CrV4DIN 51CrMoV4DIN 52CrMoV4DIN 52SiCrNi5DIN 54SiCr6DIN 54SiCrV6DIN 54NiCrMoV6DIN 55Si7DIN 55NiCrMoV7DIN 56Si7DIN 56NiCrMoV7DIN 58CrV4DIN 60Cr3DIN 60MnSiCr4DIN 60SiCrV7DIN 60WCrV7DIN 60WCrV8DIN 61SiCr7DIN 62SiMnCrV4DIN 65SiCrV7DIN 70Mn4DIN 90MnCrV8DIN 95MnWCr5DIN 100Cr6DIN 100CrMo7DIN 100CrMo7-3DIN 100CrMnSi4-4DIN 100CrMnSi6-4DIN 100CrMnMoSi8- 4-6DIN 100MnCrW4DIN 115CrV3DIN X12CrMo9-1DIN X19NiCrMo4DIN X33CrS16DIN X37Cr13DIN X37CrMoV5-1DIN X37CrMoW5-1DIN X38CrMo16DIN X38CrMoV51DIN X40Cr14DIN X40CrMoV5-1DIN X45NiCrMo4DIN X50CrMoV5-1DIN X50CrMoV5-1-1DIN X82WMoCrV6-5-4DIN X91CrMoV18DIN X100CrMoV5DIN 125Cr1DIN X155CrVMo121DIN X153CrMoV12DIN X210CrW12DIN X210Cr12SS 1350SS 1370SS 1572SS 1650SS 1655SS 1672SS 1674SS 1770SS 1914SS 1922SS 2085SS 2090SS 2120SS 2127SS 2140SS 2142SS 2172SS 2216SS 2218SS 2225SS 2230SS 2234SS 2242SS 2244SS 2258SS 2260SS 2301SS 2304SS 2310SS 2312SS 2314 SS 2324SS 2333SS 2346SS 2352SS 2387SS 2541SS 2506SS 2511SS 2512SS 2523SS 2550SS 2710SS 2722SS 2912SS 2940EN 8EN 9EN 11EN 11EN 12EN 12EN 13EN 13EN 14AEN 14AEN 15EN 15EN 16EN 16EN 17EN 17EN 17EN 18EN 18EN 19EN 19EN 20AEN 20EN 20EN 21BEN 25EN 21BEN 25EN 21BEN 25EN 29AEN 29AEN 30AEN 30AEN 31EN 31EN 32EN 32EN 33EN 33EN 33EN 34EN 34EN 35EN 35EN 36AEN 36AEN 36CEN 36CEN 39AEN 39AEN 39BEN 39BEN 40AEN 40AEN 40CEN 40CEN 41AEN 41AEN 41BEN 41BEN 43AEN 111 43AEN 45EN 45EN 47EN 47EN 47EN1 35EN1 35EN3 355EN 355EN 361EN 361EN 362EN 362EN 363EN 363S10CS10CS20CS20CS30CS30CS35CS35CS40CS40CS45CS45CS50CS50CS55CS55CS60CS60CS70CS70CS75CS75CSCCrM1SCCrM1SCCrM3SCCrM3SCM 420SCM 420SCM 4404SCM 4404SCM415SCM415SCM418SCM418SCM420SCM420SCM425SCM425SCM430SCM430SCM440SCM440SCM822SCM822SCMV4SCMV4SCr415SCr415SCr420SCr420SCr430SCr430SCr440SCr440SCr445SCr445SCM1SCM1SCM2SCM2SCM3SCM3SCM5SCM5SCMnCr2SCMnCr2SCMnCr3SCMnCr3SCMnCr4SCMnCr4SCMnCrM2SCMnCrM2S CMnCrM3SCMnCrM3SCMnM3SCMnM3SCMQ4ESCMQ4ESCMQ4VSCMQ4VSCMQ5VSCMQ5VSCMV1SCMV1SCMV2SCMV2SCMV3SCMV3SCMV4SCMV4SCMV5SCMV5SCMV6SCMV6SCNCrM2SCNCrM2SCSiMn2SCSiMn2SK70SK70SK80SK80SK90SK90SK120SK120SKh3SKh3SKh4SKh4SKh5SKh5SKh20SKh20SKH50SKH50SKH51SKH51SKH52SKH52SKH53SKH53SKH54SKH54SKH55SKH55SKH56SKH56SKH57SKH57SKH58SKH58SKH59SKH59SKS2SKS2SKS3SKS3SKS4SKS4SKS7SKS7SKS8SKS8SKS11SKS11SKS21SKS21SKS31SKS31SKS41SKS41SKS43SKS43SKS44SKS44SKS55SKS55SKS51SKS51SKS81SKS81SKS93SKS93SKS94SKS94SKS95SKS95SKT3SKT3SKT4SKT4
Страница не найдена — электронагревательные
- MyOvenOnline
- Войти
- Английский
- Шведский
- Английский
- Компания
- Карьера
- Реселлеры
- Список литературы
- Продукты
- Промышленные печи и печи
- Вакуумные печи
- Камерные печи и печи
- Климатические камеры и климатические камеры
- Технологические линии термообработки
- Конвейерные печи
- Временные печи и печи
- Печи с выдвижным подом 9000 9000 Стандартные печи с выдвижным подом 9000 9000 Верхние печи 9000 оборудование
- Печи с шагающими балками
- Колокольня печь — СИСТЕМА 250/251
- Запасные части печи
- Промышленные печи и печи
- Оборудование для термообработки (PWHT)
- Мобильные установки для термообработки
- Регистраторы
- Нагреватели с керамической подкладкой
- Кабели и разветвители Разъемы
- Инструменты для измерения и калибровки
- Изоляция для высоких температур
- Контроллеры
- Принадлежности
- 20 Дополнительное оборудование
- 20 Дополнительное оборудование
- Печи для прутковой сварки
- Портативный нагреватель сварочного стержня — HP7
- Шкаф для сухого хранения — SD220
- (S) Печь для повторной сушки стержня — SDO400
- (M) Печь для повторной сушки стержня — EDO400
- (L) Печь для повторной сушки стержня — EDO535
- Запасные части
- Промышленные печи б / у
- Воздухонагреватели и нагревательные батареи
- Воздухонагреватель — FHU 36
- Мобильный отопительный агрегат — HA 27
- Тепловентиляторный агрегат
- Мобильный отопительный агрегат — HA 33
- Батареи электрического обогревателя
Цифровой контроллер и регистратор - Операторские интерфейсы — HMI
- Цифровой регистратор
- Системы терморегулирования
- ISOPAD® — Решения для электрического отопления
- Нагревательные кабели и ленты
- Гибкие нагревательные панели
- Нагревательные рубашки
- Шланги с подогревом
- Барабанные нагреватели
- Нагреватели для газовых баллонов
- Принадлежности
- Изоляционные и жаропрочные материалы
- Superwool® — Теплоизоляционные одеяла
- Высокотемпературные ткани
- Услуги
- Термическая обработка
- Обработка металлов
- Электрооборудование
- Техническое обслуживание и ремонт
- Модернизация и реконструкция
- Обучение
- Услуги по аренде
- Служба персонала
- Термическая обработка
- Проектов
- Контакт
Проектирование охлаждающих устройств для термообработки
1.Введение
Микроструктура и природа зерен, размер зерна и состав определяют общее механическое поведение стали. Термическая обработка обеспечивает эффективный способ управления свойствами стали за счет управления скоростью охлаждения. Способ термической обработки зависит от многих аспектов. Один из важнейших параметров — объем производства. Еще один важный параметр — это размер изделий. Мы специализируемся на крупном производстве, таком как охлаждение межклетьевых [1] и выходных столов горячекатаной полосы, охлаждение выходных столов листов и листов, охлаждение сортового проката на выходе из прокатного стана, охлаждение рельсов, труб. и специальные профили [2], линии непрерывной закалки и термообработки стальных полос.Такая обработка называется поточной термообработкой материалов и часто используется на установках горячей прокатки. Этот метод позволяет получить требуемую структуру материала без необходимости повторного нагрева. Поточная термообработка характеризуется пропусканием горячего материала через секцию охлаждения. Однако многие из обсуждаемых тем можно применить и к более мелким продуктам.
Процедура проектирования охлаждающих секций для получения требуемой структуры и механических свойств представляет собой итеративное исследование, включающее несколько важных этапов.Начнем с диаграммы преобразования непрерывного охлаждения (CCT) для выбранного материала. Далее следует численное моделирование охлаждения, чтобы найти подходящую интенсивность охлаждения и его продолжительность. Зная желаемую интенсивность охлаждения, новая секция охлаждения спроектирована и испытана в лабораторных условиях [3]. Граничные условия получены из лабораторных экспериментов и протестированы с использованием численной модели. Когда найдено лучшее решение, оно проверяется на реальном образце и изучается структура результата.В большинстве случаев процесс необходимо повторить, поскольку диаграмма CCT нацелена на другой размер образца, а скорость охлаждения в рассчитанном участке непостоянна.
2. Стратегия проектирования
При разработке проекта системы охлаждения для непрерывной термообработки мы должны знать оптимальный режим охлаждения для материала и продукта. Любой непрерывный процесс термообработки должен со временем изменять интенсивность охлаждения. Более того, практика показала, что результаты, полученные при использовании небольших образцов (обычно для диаграммы CCT), обычно отличаются от результатов, полученных при использовании реальных изделий большого поперечного сечения, поскольку невозможно достичь идентичных температурных режимов в весь объем из-за низкого коэффициента диффузии.Мы не можем ожидать от продукта того же поведения, что и для небольшой выборки.
Далее рассмотрим технические средства, которые могут быть использованы для достижения требуемого температурного режима. Существуют разновидности технических приемов горячего охлаждения стали; в одном из них используется распылительное охлаждение. Секция охлаждения должна обеспечивать достижение требуемой температурной предыстории в охлаждаемой детали, предписанной металлургами. Применяемые форсунки позволяют регулировать охлаждение в широком диапазоне. Интенсивность охлаждения групп форсунок необходимо измерить, а затем полученные результаты можно использовать в численной модели температурного поля в охлаждаемом материале.
2.1. Эффект Лейденфроста и его влияние
Следует понимать, что интенсивность охлаждения сильно зависит от температуры поверхности. Так называемый эффект Лейденфроста может наблюдаться выше определенной температуры. Во время этого эффекта жидкость, которая находится рядом с гораздо более горячим объектом, чем точка кипения жидкости, создает слой пара, который изолирует жидкость от горячего объекта и предохраняет эту жидкость от быстрого кипения. Это связано с тем, что при температурах выше точки Лейденфроста часть воды, которая находится около горячей поверхности, сразу испаряется при контакте с горячей пластиной, а образовавшийся газ удерживает остальную жидкую воду, предотвращая дальнейшее прямой контакт между жидкой водой и плитой.Температуру, при которой начинает проявляться эффект Лейденфроста, предсказать непросто. Это зависит от многих аспектов. Одно из них — скорость и размер капель. По приблизительным оценкам, точка Лейденфроста может возникнуть при довольно низких температурах, например, 200 ° C. С другой стороны, при высокой скорости воды точка Лейденфроста может быть даже выше 1000 ° C. На рис. 1 показаны измеренные коэффициенты теплопередачи (HTC) для сопла водяного тумана. На графике показаны три измерения для одного и того же сопла при различных параметрах воды и воздуха.Можно найти три режима. Первый — для низких температур, когда HTC относительно высок и медленно понижается. Эта часть находится ниже точки Лейденфроста. С определенной температуры HTC стремительно падает. Это переходный режим, при котором некоторые капли находятся выше точки Лейденфроста, а некоторые — ниже этой точки. Для последнего режима HTC относительно низка и постоянна или может увеличиваться из-за увеличения излучения с увеличением температуры поверхности. Разработанная секция охлаждения должна работать в первом режиме при низких температурах или в третьем режиме при практически постоянном HTC.Настоятельно рекомендуется избегать второго переходного режима, поскольку температура поверхности продукта обычно не является однородной. Из-за сильной зависимости HTC от температуры поверхности достигается неоднородное охлаждение, вызывающее деформацию продукта.
Рисунок 1.
Перемещение точки Лейденфроста для сопла водяного тумана и различных условий воды и воздуха.
2.2. Типы форсунок и их управляемость
Форсунка обычно производит один из трех типичных распылителей: плоскоструйный, полноконусный и твердоструйный (см.рис.2). Однако могут быть и другие формы, такие как полый конус, квадрат, спираль и т. Д. Важным параметром является управляемость секции охлаждения и интенсивность охлаждения. Форсунки водяного тумана могут использоваться для мягкого охлаждения и широкого диапазона управляемости (см. Рис. 3). HTC может варьироваться от нескольких сотен Вт / м².K до нескольких тысяч Вт / м².K. Сопла водяного тумана не самые дешевые, а сжатый воздух дорог с точки зрения энергопотребления. Форсунки, работающие только на воде, часто могут обеспечить более дешевое решение.Маленькие полноконусные форсунки с высоким давлением и большим расстоянием от поверхности также могут обеспечить очень мягкое охлаждение. С другой стороны, при использовании плоскоструйных или твердоструйных сопел высокого давления на малых расстояниях можно получить HTC более 50000 Вт / м².К даже при высоких температурах поверхности (см. Рис. 4). Это приводит к огромному тепловому потоку, превышающему 50 МВт / м². В данном случае для плоскоструйных сопел очень важно расстояние от поверхности формы сопла, потому что для 100 мм HTC может быть 50000 Вт / м².K, но для 1000 мм он может быть похож на сопло водяного тумана.В заключение можно сказать, что для мягкого охлаждения воздушным туманом или полноконусной водой можно использовать только форсунки, а для жесткого охлаждения — плоские форсунки с небольшими расстояниями. В некоторых случаях твердоструйные форсунки используются для жесткого охлаждения, но часто возникают две основные проблемы: большое количество воды создает слой воды на продукте, а пятно распыления небольшое, что вызывает неоднородное охлаждение. С другой стороны, для твердоструйных форсунок засорение не представляет большой проблемы.
Рисунок 2.
Плоскоструйные, полноконусные и твердоструйные форсунки с расчетным распределением воды по плоской поверхности
Рисунок 3.
Регулируемость сопла водяного тумана при температуре поверхности 1000 ° C
2.3. Влияние скорости продукта на коэффициент теплопередачи
Три измерения сравниваются, когда единственным различным параметром является скорость разливки. Первый эксперимент был стационарным без движения, второй эксперимент использовал скорость 2 м / с, а последний эксперимент проводился со скоростью 5 м / с. В этих трех экспериментах использовалось идентичное сопло водяного тумана, и во всех экспериментах использовались одинаковые настройки давления — давление воды 2 бара, давление воздуха 2 бара.На рис. 5 показано распределение коэффициента теплоотдачи в экспериментальной группе при изменении скорости. HTC для стационарного корпуса (в мельнице невозможно) симметричный, козырек узкий. Интенсивность охлаждения уменьшается с увеличением скорости. Распределение коэффициента теплопередачи становится более несимметричным при увеличении скорости продукта. Наблюдаемый эффект вызван потоком на поверхности и различными условиями парообразования перед и за падающей струей.
Рисунок 4.
Распределение HTC под распылением для плоскоструйных форсунок высокого давления при температуре поверхности 1000 ° C.
3. Интенсивность охлаждения и численные модели
Чтобы спроектировать секцию охлаждения, необходимо знать интенсивность охлаждения для группы форсунок и коллекторов форсунок. Точное знание коэффициента теплопередачи как функции параметров распыления и температуры поверхности является ключевой проблемой для любых проектных работ. Интенсивность охлаждения зависит от нескольких параметров, в основном от типа сопла, выбранного давления и расхода, температуры поверхности материала и скорости движения материала во время распыления.Отсутствует функция, описывающая интенсивность охлаждения с использованием всех упомянутых параметров. Это причина, по которой настоящее измерение абсолютно необходимо.
3.1. Методика эксперимента
Во время поточной термообработки продукт движется, поэтому наш испытательный образец также должен проходить через секцию охлаждения. На рис. 6 схематически показан подходящий эксперимент, используемый для получения граничных условий для численного моделирования. Горячий образец движется с заданной скоростью, близкой к реальным условиям.Образец проходит под распылением, которое охлаждает горячий образец. Для пластин простой формы рекомендуется изолировать все поверхности, кроме той, на которой исследуется интенсивность охлаждения. Одна или несколько термопар встроены в образец и измеряют температуру во время эксперимента. Установленные термопары не должны беспокоить охлаждаемую поверхность. По этой причине их следует устанавливать внутри образца, а не на исследуемой поверхности. В принципе, когда все поверхности изолированы, кроме исследуемой, достаточно одной термопары.Однако эта термопара должна находиться как можно ближе к исследуемой поверхности. В противном случае разрешение описания граничных условий будет ухудшено. После измерения используется обратный алгоритм для вычисления граничных условий на исследуемой поверхности на основе измеренной температурной истории внутри образца. Пример записанной температурной истории показан на рис. 7.
Рисунок 5.
Влияние скорости на коэффициент теплопередачи.
Рисунок 6.
Движущийся образец со встроенными термопарами, охлаждаемыми водяным спреем
Рисунок 7.
Пример зарегистрированной температурной истории одной термопарой внутри образца, вычисленная температура поверхности над установленной термопарой, зарегистрированное положение термопары в секции охлаждения и расчетный коэффициент теплопередачи. Секция охлаждения оснащена пятью рядами плоскоструйных форсунок.
Рисунок 8.
Стенд для испытаний теплопередачи
Рисунок 9.
Примеры измерения граничных условий на стальном листе, рельсе и трубе.
Стенд для испытания теплопередачи, представленный в [4], спроектирован таким образом, что он позволяет перемещать образцы массой до 50 кг с плавно регулируемой скоростью от 0,1 до 6 м / с (см. Рис. 7). На опорной раме есть тележка для перемещения, на котором закреплен образец при рассмотрении со встроенными датчиками температуры и измерительной системой (см. 9). Движение каретки обеспечивается протяжным канатом через ведущий шкив и двигателем с редуктором.Электродвигатель питается от преобразователя частоты с возможностью плавного изменения скорости. Направление каретки можно изменить, а проходы повторять в необходимом количестве. Весь цикл программируется и контролируется с помощью главного компьютера. В центральном секторе есть участок напыления, где можно расположить форсунки произвольной конфигурации, когда необходимо измерить распределение коэффициентов теплопередачи или тепловых потоков. Образец снабжен термопарами, подключенными к регистратору данных.Термопары калибруются перед использованием, и результаты калибровки используются для устранения динамической ошибки при измерении высокотемпературных тепловых процессов. Перед фактическим экспериментом тележка с образцом устанавливается на электронагреватель и нагревается до необходимой температуры внутри печи. После стабилизации температуры в образце нагревательное устройство снимается, подставка переводится в положение для распыления, включается насос для воды и каретка проходит через секцию охлаждения.Положение охлаждаемой поверхности может быть горизонтальным с опрыскиванием верхней или нижней поверхности или вертикальным. Сигналы с датчиков считываются регистратором данных, который перемещается вместе с образцом. При этом также записывается сигнал, указывающий фактическое положение каретки. После выполнения необходимого количества проходов через зону охлаждения данные экспортируются из внутренней памяти регистратора данных в компьютер для дальнейшей обработки.
3.2. Обратное вычисление граничных условий и численные модели
Информация из температурных историй на определенной глубине под исследуемой поверхностью используется в качестве входных параметров для обратной задачи теплопроводности.Выходными данными обратной задачи являются истории температуры поверхности, тепловые потоки и коэффициенты теплопередачи (HTC) как функции времени и положения. Чаще всего в математических моделях используется граничное условие типа 3’d, где тепловой поток задается значением HTC и температурой охлаждающей воды.
Если граничные условия твердого тела должны быть определены из измерений переходной температуры в одном или нескольких внутренних точках, это обратная задача теплопроводности (IHCP), во время которой необходимо найти рассеянный импульс на границе.IHCP решить гораздо сложнее, чем прямую проблему. Такие проблемы чрезвычайно чувствительны к ошибкам измерения. Существует ряд процедур, разработанных для решения некорректно поставленных задач в целом. Тихонов ввел метод регуляризации [5], чтобы снизить чувствительность некорректно поставленных задач к ошибкам измерения. Математические методы решения наборов плохо обусловленных алгебраических уравнений, называемые методами однозначной декомпозиции, также могут использоваться для IHCP [6].Подходы к IHCP были очень разными. Сюда входит использование теоремы Дюамеля (или интеграла свертки), которая ограничивается линейными задачами [7]. Численные процедуры, такие как конечные разности [8] [9] [10] и конечные элементы [11], также использовались из-за присущей им способности решать нелинейные задачи. Методы точного решения были предложены Бурггафом [12], Имбером и Ханом [13], Лэнгфордом [14] и другими. В некоторых методах используются преобразования Лапласа, но они ограничены линейными случаями [15].Комбинированный подход также описан в [16]. Улучшение искусственного интеллекта привело к появлению новых подходов, таких как генетический алгоритм [17] и нейронные сети [18] [19] [20].
Все указанные алгоритмы требуют точной математической модели испытуемого образца для решения прямой задачи теплопроводности. В некоторых случаях аналитические методы могут использоваться для точного математического решения проблем проводимости. Эти решения были получены для многих упрощенных геометрий и граничных условий и хорошо описаны в литературе [21] [22] [23].Однако чаще всего геометрия и граничные условия исключают такое решение. В этих случаях лучшей альтернативой является использование численного метода. В ситуациях, когда нет аналитического решения, можно использовать численный метод. В настоящее время существует несколько методов, позволяющих численно решать основные уравнения задач теплопередачи. К ним относятся: метод конечных разностей (FDM), метод конечных объемов (FVM), метод конечных элементов (FEM), метод граничных элементов (BEM) и другие.Для одномерной модели с постоянными свойствами материала существует приятное сходство. Все FDM, FVM и FEM с уравнениями весовой функции палатки могут быть представлены в аналогичной форме:
ddt (β T1 + γ T2) = — αΔx2 (T1 − T2) + q1 (t) ρ c ΔxE1
ddt (γ Tj − 1 + 2 β Tj + γ Tj + 1) = — αΔx2 (Tj − Tj + 1) + αΔx2 (Tj − 1 + Tj) E2
ddt (γ TN − 1 + β TN) = — αΔx2 (TN − 1 − TN) + qN (t) ρ c ΔxE3
где β и γ имеют значения, указанные в Табл. 1. Уравнения (1–3) ограничены тепловыми свойствами, не зависящими от температуры, но эти концепции могут быть расширены на случаи T-переменной.В целом для многомерных моделей и свойств материалов, зависящих от температуры, самые простые уравнения получаются для FDM, в то время как сложность уравнений для FVM и FEM в несколько раз выше.
β | γ | β + γ | |||||
FDM | 1/2 | 1/2 | FVM | 3/8 | 1/8 | 1/2 | |
FEM | 2/6 | 1/6 | 1/2 |
Таблица 1.
Значения β и γ уравнения. (1–3)
3.3. Реализация фазового перехода
Физические процессы, такие как превращения твердого тела в жидкое и твердое состояние, включают фазовые изменения. Численное рассмотрение этого нелинейного явления связано со многими проблемами. В методах решения фазового перехода обычно используются общая энтальпия H, кажущийся удельный коэффициент теплоемкости cA или источник тепла q˙.
Природа фазового перехода затвердевания может принимать различные формы. Классификация основана на веществе в области фазового перехода.Ниже приведены наиболее распространенные случаи:
Отличный : Область фазового перехода состоит из твердой и жидкой фаз, разделенных плавным непрерывным фронтом — замерзание воды или быстрое затвердевание чистого металла.
Сплав : Область фазового перехода имеет кристаллическую структуру, состоящую из зерен, а граница раздела твердое тело / жидкость имеет сложную форму — большинство металлических сплавов.
Непрерывный : Жидкая и твердая фазы полностью диспергированы по всей области фазового перехода, и нет четкой границы раздела между твердой и жидкой фазами — полимерами или стеклами.
При отчетливом изменении фазы состояние характеризуется положением интерфейса. В таких случаях обычно используется класс так называемых методов слежения за линией фронта . Однако в случаях b) и c) в моделях используется фазовая доля.
Процесс фазового перехода можно описать одним уравнением энтальпии
∂H∂t + ∇⋅ (gdHdsd + glHlsl) = ∇⋅ (k∇T) E4
где g — объемная доля фазы, s — фазовая скорость, индексы d и l относятся к твердой и жидкой фазам (или структуре A и структуре B) соответственно [24].K представляет собой (в данном случае) проводимость смеси, определяемую как
k = gdkd + glklE5
, а His — энтальпия смесиH = gs∫TrefTρdcddT + gl∫TrefTρlcldT + ρlclLE6
, где Tref — произвольная эталонная температура. Чтобы преодолеть проблему нелинейного (неоднородного) коэффициента теплоемкости, используется нелинейный источник. Член ∂H / ∂t может быть разложен как
∂H∂t = cvol∂T∂t + δH∂gl∂tE7
Пренебрегая эффектами конвекции в уравнении. (4) и подставив уравнение. (7) дает
cvol∂T∂t = ∇⋅ (k∇T) + q˙E8
, где
q˙ = −δH∂gl∂tE9
Ур.Уравнение (4) является нелинейным и содержит две связанные, но неизвестные переменные Hand T. Это уравнение удобно переформулировать в терминах одной неизвестной переменной с нелинейной скрытой теплотой. Сонг [25] и [26] Комини использует так называемую кажущуюся теплоемкость. Кажущуюся удельную теплоемкость можно определить как
cA = dHdT = cvol + δHdgldTE10
, где
cvol = gdρdcd + glρlclδH = ∫TrefT (ρlcl − ρdcd) dT + ρlL.E11
, подставив в Eg. (4) дает уравнение кажущейся теплоемкости
cA∂T∂t = ∇⋅ (k∇T) E12
Другой подход — полная энтальпия.Из уравнения. (6) можно записать
∇T = H / cvol − δH∇gl / cvolE13
Подстановка в уравнении. (4) приведет к уравнению полной энтальпии
∂H∂t = ∇⋅ (kcvol∇H) + ∇⋅ (kcvolδH∇gl) E14
3.4. Обратный метод последовательной идентификации
Для измерений, когда термопара, установленная внутри исследуемого тела, также вызывает возмущение температуры поверхности, так как она очень близка к исследуемой поверхности, HTC необходимо вычислять непосредственно обратным методом. Классическая и очень эффективная последовательная оценка, предложенная Беком [27], которая вычисляет тепловой поток вместо HTC, имеет несколько ограничений.Таким образом, Поганка разработала новый метод последовательной идентификации для решения подобных обратных задач. Основной принцип определения зависящих от времени граничных условий (тепловой поток, HTC и температура поверхности) из истории измеренных переходных температур основан на охлаждении (или нагреве) нагретого (или холодного) образца с установленной внутри термопарой (см. Рис.6). . Предположим для простоты одномерную обратную задачу с трехмерной моделью с установленной термопарой:
Известные размеры образца.
Известные термические свойства материала образца, зависящие от температуры.
Известный температурный профиль в начале охлаждения (обычно постоянный).
Все поверхности утеплены, кроме охлаждаемой.
HTC не зависит от позиции.
Образец нагревается перед началом измерения. Охлаждение применяется к одной поверхности и регистрируется температурный отклик внутри образца.Граничные условия, зависящие от времени, вычисляются с использованием обратного метода на основе измеренной температурной истории (см. Рис. 7). Охлаждение большего количества поверхностей также может быть исследовано при использовании большего количества термопар.
Этот новый предложенный подход вычисляет шаг за шагом (шаг по времени) коэффициенты теплопередачи (HTC) на исследуемой поверхности с использованием измеренной температурной истории внутри охлаждаемого или нагретого твердого тела. Однако этот метод можно очень легко изменить для вычисления любых граничных условий, например.грамм. Тепловой поток. Метод использует последовательную оценку изменяющихся во времени граничных условий и использует данные будущих временных шагов для стабилизации некорректной обратной задачи [28]. Чтобы определить неизвестную поверхность HTC в текущий момент времени tm, измеренные температурные отклики Tm * сравниваются с вычисленной температурой Tm от прямого решателя с использованием n шагов будущего времени
SSE = ∑i = m + 1m + n (Ti * −Ti) 2E15
Может использоваться любой прямой решатель e. грамм. метод конечных объемов, описанный Патанкаром [29].Вычислительная модель должна включать просверленное отверстие, всю внутреннюю структуру встроенной термопары и свойства материала, зависящие от температуры.
В то время, когда в образце присутствует нулевая однородная температура, предполагается, что тепловой поток равен нулю, и, следовательно, нулевой HTC на всех поверхностях. В противном случае не может быть однородной температуры. Это можно сделать e. грамм. нагреванием в печи по прошествии достаточно длительного времени. Если начальная температура неоднородна, то на первом временном шаге необходимо изменить алгоритм.
Алгоритм запускается с нулевого временного индекса, когда HTC равен нулю (см. Рис. 10). Алгоритм использует прямой решатель и вычисляет температурный отклик в положении термопары для линейного изменения (увеличения или уменьшения) HTC (см. HTC1 и T1, вычисленные на рис. 10) за несколько временных шагов. Эти временные шаги называются будущими временными шагами n, и пять из них используются на Рис. 10 – Рис. 11. Определение минимального количества необходимых будущих временных шагов для стабилизации последовательного алгоритма описано в [28].Вычисленные и измеренные истории температуры сравниваются с использованием уравнения. (15) тот же, что и для последовательного подхода Бека. Наклон линейно изменяющейся HTC, определяемой как
v = ∂h∂tE16
, должен изменяться до минимума функции SSE в уравнении. (15) найдено. Такой минимум говорит о том, что рассчитанная температурная история соответствует измеренной температурной истории, что лучше всего подходит для использования линейно изменяющейся HTC в течение n будущих временных шагов.
Рисунок 10.
История измеренных температур и две рассчитанные истории температуры с использованием двух разных наклонов HTC для будущих временных шагов.
Рисунок 11.
Реальный HTC и шесть оптимальных линейно изменяющихся HTC.
Когда найден лучший наклон HTC, прямой решатель используется для вычисления температурного поля на следующем временном шаге с использованием вычисленных граничных условий. Алгоритм повторяется для следующих временных шагов, пока не будет достигнут конец записанной истории температуры (см. Рис. 11). Для n измеренных временных шагов можно вычислить только k − n временных шагов благодаря использованию будущих данных. Этот метод отлично работает, когда реальный HTC почти линейен во времени.При резком изменении наклона расчетная кривая HTC получается немного более гладкой, чем реальная; чем больше используется будущих временных шагов, тем более гладкой будет вычисленная кривая HTC (большая разница между вычисленным и реальным HTC), но алгоритм последовательной обратной идентификации более стабилен.
Функция SSE, описанная уравнением. (15) имеет только один минимум и зависит только от одной переменной — наклона HTC (см. Уравнение 16). Более того, функция очень близка к параболической функции вблизи искомого минимума, потому что она представляет собой сумму квадратов разностей температур.Метод оптимизации Брента [30], в котором используется обратная параболическая интерполяция, является идеальным кандидатом для нахождения минимума функции SSE в уравнении. (15).
Метод оптимизации Brent основан на параболической интерполяции и золотом сечении. Искомый минимум должен находиться между двумя заданными точками 1 и 2 (см. Рис. 12). Сходимость к минимуму достигается за счет обратной параболической интерполяции. Значения функции SSE вычисляются только в нескольких точках. Парабола (пунктирная линия) проводится через три исходные точки 1, 3, 2 на функции SSE (сплошная линия).Функция оценивается по минимуму параболы, 4, который заменяет точку 1. Новая парабола (пунктирная линия) проводится через точки 3, 4, 2. Алгоритм повторяется до тех пор, пока не будет найден минимум с желаемой точностью. Если три точки лежат на одной прямой, вместо параболической интерполяции используется золотое сечение [30].
Рисунок 12.
Сходимость к минимуму с помощью обратной параболической интерполяции.
3.5. Оценка граничных условий
Для демонстрации процедуры используется реальное измерение.Секция охлаждения состоит из пяти рядов плоскоструйных сопел. Нагретый образец многократно проходит под распылительными форсунками. Несколько термопар в один ряд, перпендикулярный направлению движения образца, были установлены в образце, чтобы иметь возможность исследовать также однородность охлаждения по образцу. Для простоты мы сосредоточимся только на одной термопаре, однако легко проделать процедуру для всех термопар. Запись температуры в результате такого измерения показана на рис. 7. Также показано записанное положение (зигзагообразная линия) термопары, демонстрирующее многократные проходы через секцию охлаждения.Обратным методом были вычислены граничные условия: температура поверхности и HTC. Все показанные строки являются функцией времени; однако для численного моделирования нам понадобится HTC как функция положения и температуры поверхности. Начнем с измерения температуры поверхности. См. Рис. 13, где температура поверхности показана зеленой линией в зависимости от положения. Зеленые линии представляют температуру поверхности, через которую проходит пластина во время эксперимента. В том месте, где показана зеленая линия, мы также знаем HTC по измерениям.Значения HTC показаны с помощью цветовой шкалы. Значения HTC между зелеными линиями интерполируются. Эта диаграмма показывает распределение HTC в зависимости от температуры поверхности и положения и является ключевым моментом для точного численного моделирования. Значения HTC над самой верхней зеленой линией экстраполируются и не являются точными, так как данные измерений недоступны. Мы должны избегать использования этих значений при численном моделировании.
Рисунок 13.
Граничные условия, подготовленные для численного моделирования на основе измерений, показанных на рис.7. График показывает HTC как функцию в зависимости от положения в секции охлаждения в направлении движения образца и от температуры поверхности охлаждаемого образца.
3.6. Численное моделирование
Подготовив граничные условия, можно провести численное моделирование охлаждения изделий из различных материалов и различной толщины. Повторяя граничные условия, мы можем моделировать длинную секцию охлаждения с большим количеством рядов охлаждающих сопел. Пример такого моделирования показан на рис.14 и нарисовано в CCT. Вы можете увидеть вычисленную температуру на поверхности и в центре материала. Очевидно, что скорость охлаждения для температуры поверхности выше, чем в центре. Результаты представлены на диаграмме CCT, однако не следует, что скорость охлаждения далека от постоянной. Это очень важно, потому что диаграмма CCT является только информативной, и окончательная структура должна быть проверена экспериментальным измерением. Скорость охлаждения непостоянна по трем основным причинам.Одна из них вызвана пропусканием продукта под отдельным рядом форсунок. Проходы очевидны из кривой Т-поверхности на рис. 14. Вы можете видеть перепады температуры, когда продукт проходит под распылением с последующим повторным нагревом из-за внутренней емкости тепла в продукте. Вторая причина — упомянутая точка Лейденфроста. Вы можете видеть низкую скорость охлаждения в центре до 20 с, так как температура поверхности выше точки Лейденфроста, а после этого скорость охлаждения увеличивается и достигает максимума, который почти втрое превышает значение выше точки Лейденфроста.Снижение скорости охлаждения наблюдается по мере приближения температуры поверхности к температуре воды. Третья причина — низкий коэффициент диффузии для больших продуктов. Продукт нельзя охладить с той же скоростью охлаждения на поверхности, что и в центре. Чем ниже коэффициент диффузии и чем больше продукт, тем больше разница между скоростью охлаждения на поверхности и в центре.
Рисунок 14.
Моделирование охлаждения на диаграмме CCT.
4. Проверка на пилотном испытательном стенде
Важно понимать, что скорость охлаждения в секции охлаждения в промышленном применении далека от постоянного значения, на основе которого строятся диаграммы CCT.Функциональность проверки вновь спроектированной системы охлаждения до ее внедрения на заводе имеет важное значение. Конструкция, полученная с помощью численной модели, должна быть проверена и доработана с помощью дальнейших натурных испытаний на охлаждение. Кусочки трубы, рельса, проволоки или пластины реальных размеров с установленными термопарами испытываются в проектируемой секции охлаждения. Длина лабораторного испытательного стенда, показанного на рисунках 8 и 9, ограничена, поэтому образец должен быть ускорен перед входом в секцию охлаждения до скорости, обычно используемой в установке, и после прохождения через секцию охлаждения направление движения движение обратное.Таким образом, образец несколько раз проходит под секциями охлаждения. Этот процесс охлаждения контролируется компьютером для моделирования работы в длинной секции охлаждения, обычно используемой на заводе. Сопла, давления и конфигурации коллектора проверены. Конструкция охлаждения и используемые давления модифицируются до тех пор, пока не будет получен требуемый температурный режим и окончательная структура. Затем полномасштабные образцы материалов вырезаются для испытаний свойств и структуры материала.
Когда термическая обработка выполняется на более крупном продукте, таком как рельс, в основном на его головке, невозможно достичь одинаковой скорости охлаждения на поверхности и в центре головки рельса.Скорость охлаждения вблизи поверхности намного выше, и может появиться еще больший повторный нагрев, который может привести к очень различным свойствам материала (см. Рис. 15). По мере того, как головка рельса проходила под струей спрея, температура поверхности быстро падала, после чего происходил повторный нагрев из-за тепла, накопленного внутри головки. Повторный нагрев вызвал более низкую твердость у поверхности, как показано на рис. 14. Центр головки более твердый, потому что на большей глубине повторного нагрева не происходило. Чтобы избежать этой проблемы, секцию охлаждения следует модифицировать.Одним из решений является использование большего количества насадок с меньшим шагом рядов, а также насадок с меньшим HTC. Это может быть достигнуто за счет меньшего давления или меньших форсунок. Также можно рассмотреть возможность замены плоскоструйного сопла на полноконусные. Также следует учитывать температуру Лейденфроста. Мы должны быть выше или ниже температуры Лейденфроста, но определенно не рядом, чтобы избежать больших различий в скорости охлаждения при небольших изменениях температуры поверхности.
Рис. 15.
Измеренные графики температуры в головке рельса на двух глубинах и измеренная микротвердость в головке рельса после термообработки.
Термическая обработка — это метод, используемый для изменения физических, а иногда и химических свойств материала. Чаще всего применяется в металлургии. Термическая обработка также используется при производстве многих других материалов, таких как стекло. Термическая обработка включает использование нагрева или охлаждения, обычно до экстремальных температур, для достижения желаемого результата, такого как отверждение или размягчение материала. Методы термообработки включают отжиг, цементирование, дисперсионное упрочнение, отпуск и закалку.Примечательно, что хотя термин термическая обработка применяется только к процессам, в которых нагрев и охлаждение выполняются с конкретной целью намеренного изменения свойств, нагрев и охлаждение часто происходят как побочные фазы других производственных процессов, таких как горячая штамповка или сварка. Рекомендуемые дополнительные знанияТермическая обработка металлов и сплавовМеталлические материалы состоят из микроструктуры мелких кристаллов, называемых «зернами» или кристаллитами.Природа зерен (то есть размер и состав зерна) определяет общее механическое поведение металла. Термическая обработка обеспечивает эффективный способ управления свойствами металла, контролируя скорость диффузии и скорость охлаждения внутри микроструктуры. Отжиг
Отжиг — это метод, используемый для восстановления холодной обработки и снятия напряжений в металле. Отжиг обычно приводит к получению мягкого пластичного металла.Когда отожженной детали дают остыть в печи, это называется термообработкой «полный отжиг». Когда отожженная деталь вынимается из печи и охлаждается на воздухе, это называется «нормализующей» термообработкой. Во время отжига мелкие зерна рекристаллизуются с образованием более крупных зерен. В сплавах с дисперсионным твердением частицы растворяются в матрице, «растворяя» сплав. Закалка и отпуск (закалка и отпуск)Для закалки металл (обычно сталь или чугун) необходимо нагреть до состояния аустенитного кристалла и затем быстро охладить.В зависимости от сплава и других соображений (например, соображений максимальной твердости по сравнению с растрескиванием и деформацией) охлаждение может осуществляться принудительным воздухом или другим газом (например, азотом), маслом, полимером, растворенным в воде, или рассолом. При быстром охлаждении аустентит превращается в мартенсит, твердую хрупкую кристаллическую структуру. Незакаленный мартенсит, хотя и очень твердый и прочный, слишком хрупкий, чтобы его можно было использовать в большинстве случаев. Метод, позволяющий решить эту проблему, называется закалкой.В большинстве случаев требуется, чтобы закаленные детали были отпущены (термообработка при низкой температуре, часто триста градусов по Фаренгейту или сто пятьдесят градусов по Цельсию) для придания некоторой прочности. Более высокие температуры отпуска (могут достигать тридцати тысяч градусов по Фаренгейту, в зависимости от сплава и применения) иногда используются для придания дополнительной пластичности, хотя некоторая прочность теряется. Металлурги часто разрабатывают сложные схемы термической обработки для оптимизации механических свойств сплава.В аэрокосмической промышленности суперсплав может подвергаться пяти или более различным операциям термической обработки для достижения желаемых свойств. Это может привести к проблемам с качеством в зависимости от точности контроля температуры печи и таймера. Осадочное твердение
Некоторые металлы считаются металлами с дисперсионным твердением . Примеры включают в себя алюминиевые сплавы серии 2000, 6000 и 7000, а также некоторые суперсплавы и некоторые нержавеющие стали.Если закалить дисперсионно-твердый сплав, его легирующие элементы будут захвачены раствором, что приведет к получению мягкого металла. Старение «растворенного» металла (либо при комнатной температуре — «естественное старение» — или при нескольких сотнях градусов — «искусственное старение») позволяет легирующим элементам диффундировать через микроструктуру и образовывать интерметаллические частицы. Эти интерметаллические частицы выпадают из раствора и действуют как усиливающая фаза, увеличивая прочность сплава. В некоторых случаях естественным образом стареющие сплавы могут храниться в морозильной камере для предотвращения затвердевания до тех пор, пока не будут выполнены дальнейшие операции — например, сборка заклепок может быть проще с более мягкой частью. Выборочная закалкаНекоторые методы позволяют различным областям одного объекта подвергаться различной термической обработке. Это называется дифференциальным упрочнением. Часто встречается в высококачественных ножах и мечах. Китайский цзянь — один из самых ранних известных примеров этого, а японская катана — наиболее широко известный. Другой пример — непальские хукури. См. Также
Список литературы«Основы физического металлургии».Рид-Хилл, Роберт. 3-е издание. PWS Publishing, Бостон. 1994 г.
|
8.Техническая термообработка — Скачать PDF
1 8. Техническая термообработка
2 8. Техническая термообработка 95 6 cm C 400 C C cm C температура C При сварке детали подводимое количество тепла оказывает влияние не только на сам сварной шов, но и на окружающий основной материал (HAZ).Температурное поле, которое появляется вокруг сварного шва при использовании различных процедур сварки, показано на рисунке 8.1. На рис. 8.2 показано влияние свойств материала на процесс сварки. Определяющие факторы процесса, представленные на этом рисунке, такие как температура и интервал плавления, теплоемкость, тепловыделение и т. Д., В значительной степени зависят от химического состава материала. Металлургические свойства здесь характеризуются, например, однородность, структура и текстура, физические свойства, такие как тепловое расширение, прочность на сдвиг, пластичность.Структурные изменения, вызванные подводом тепла (процесс 1, 2, 7 и 8), напрямую влияют на механические свойства сварного шва. Кроме того, на химический состав металла шва и прилегающего основного материала также влияют процессы 3–6. 6 см 4 Распределение различных методов сварки см 2 Кислородно-ацетиленовая сварка ручная дуговая сварка металлическим электродом -60 мм мм 60 br-er04 -01.cdr Рис. 8.1 Зона термического влияния при оксиацетиленовой сварке 600 CC 800 CC Расстояние от центральной линии шва C 600 C 400 CCC Зона термического влияния при ручной дуговой сварке металлическим электродом Основываясь на бинарной системе, формируются различные зоны структуры. показано на рисунке 8.3. Таким образом, зона крупного зерна возникает, например, в областях с сильно повышенной температурой аустенизации. В то же время в этих областях появляются пики твердости из-за значительного снижения критической скорости охлаждения и грубого бр-ei cdr. Рисунок Нагревание и плавление сварочного материала. Плавление частей основного материала. Реакция прохождения сварочного материала с атмосферой дуги. Реакция прошедшего сварочного материала. с расплавленным основным материалом Взаимодействие между сварочной ванной и твердым основным материалом (возможно, сварные швы). Реакция металла и флюса с атмосферой. Затвердевание сварочной ванны и шлака. Охлаждение сварного соединения до твердого состояния. Термическая обработка после сварки, если необходимо. Устойчивое изменение свойств материала тепло, температура и интервал плавления, теплота плавления, температура кипения (металл, покрытие) Удельная теплоемкость, температура и интервал плавления, теплопроводность, коэффициент теплового расширения, однородность, время Состав атмосферы, сродство, давление, температура, диссоциация, ионизация, скорость реакции Соотношения растворимости, температуры и давления под воздействием высокой температуры ce, удельный вес, флюс сварочной ванны Процессы диффузии и изменения положения, время, формирование границ, упорядоченная — неупорядоченная структура Сходство, температура, давление, время Тепло расплава, условия охлаждения, плотность и пористость шлака, интервал затвердевания Фазовые диаграммы (в зависимости от времени) , теплопроводность, коэффициент нагрева, прочность на сдвиг, пластичность Фазовые диаграммы (в зависимости от времени), текстура при теплой деформации, пластичность, модуль упругости Фазовые диаграммы, рабочая температура, механическая и химическая деформация, время Классификация процесса сварки на отдельные механизмы
3 8.Техническая термообработка 96 зерен. Эта зона сварного шва является областью, где обнаруживаются наихудшие значения ударной вязкости. На Рисунке 8.4 вы можете увидеть, насколько сильно можно повлиять на пик твердости отдельных структурных зон и зон с неблагоприятными механическими свойствами. При нанесении электрошлакового шва на лист толщиной 200 мм за один проход достигается ширина ЗТВ примерно 30 мм. Используя трехпроходную технику, ЗТВ уменьшается до 8 мм. Твердость сварного шва твердость понижение неполное плавление крупнозернистое стандартное преобразование неполная кристаллизация рекристаллизация 1 CG 800 PS При использовании различных процедур различия в формировании зон термического влияния становятся еще более четкими, как показано на рисунке зона термического влияния (видна на макросе) старение голубая хрупкость, 2 6 0,8 2,% 3 содержание углерода Эти эффекты можно активно использовать в adbr-er04-03.cdr преимущества материала, например, для корректировки расчетных механических свойств в соответствии с выбором, показанным на рис. 8.3. Зоны микроструктуры сварного шва — отношение к двоичной системе, или для устранения негативных эффектов сварки. Особенно это касается высокопрочных мелкозернистых сталей и высоколегированных материалов, которые специально оптимизированы для достижения особого качества, например Устойчивость к коррозии в определенных агрессивных средах, эта термообработка после сварки имеет большое значение. На рисунке 8.6 показаны области на диаграмме Fe-C для различных методов термообработки.Отчетливо видно, что содержание углерода (а также содержание других легирующих элементов) оказывает отчетливое влияние на уровень температуры отжига, показанный на Рисунке 8.4.
4 8. Техническая термообработка 97, например, крупнозернистая термообработка или нормализация. Также можно видеть, что начало образования мартенсита (MS-линия) смещается в сторону непрерывно снижающихся температур с увеличением содержания углерода.Это важно, например, для процессов закалки (будет объяснено позже). метастабильная система железо-углерод (частично) 100 электронно-лучевая сварка 1600 расплав + твердый раствор 1493 CCH — твердый раствор B — твердый раствор A раствор N cbc атомная решетка 1 расплав C 1400 цветов тепла 1 желтый белый диффузионная термообработка 2, светло-желтый E желтый 40 проход дуговой сварки под флюсом / закрытый проход 1000 крупнозернистых термообработка cfc атомная решетка 911 GA 2 800M 769 CP 723 феррит COS (твердый раствор) рекристаллизационная термообработка 600 cbc атомная решетка нормализация + закалка (- мишкристалл) рекристаллизационная термообработка QA см мягкий отжиг для снятия напряжений + вторичный цементит (Fe3C) 1000 желтый красный светлый красный 800 K вишнево-красный темно-красный коричневый красный 600 темно-коричневый 12 дуговая сварка в газовой среде, 5 0,8 1 1,5 2 Fe Содержание углерода в% по массе 0 5 закалка отпуск доэвтектоидная сталь эвтектоидная сталь заэвтектоидная сталь MS Содержание цементита в% по массе br-er04-05.cdr br-er04-06.cdr Развитие зоны теплового воздействия при электродуговом, субдуговом и MIG-MAG-сварке Металлургическое исследование методов термообработки Рис. 8.5 Поскольку эта диаграмма не охватывает влияние времени, можно использовать только постоянные конечные температуры. Прочтите, прогнозы относительно скорости нагрева и охлаждения невозможны. Таким образом, ниже будут объяснены индивидуальные методы термообработки в зависимости от их температурно-временного поведения. C-феррит + br-ei cdr Рисунок 8.6 0,4 0,8% C-Content интенсивный нагрев Крупнозернистая термообработка длительное время несколько часов Рисунок 8.7
5 8. Техническая термообработка 98 На рис. 8.7 подробно показан процесс Тt термической обработки крупнозернистого сплава, содержащего 0,4% С. Термическая обработка крупного зерна применяется для создания зерна размером до можно улучшить механические свойства. В случае сварки крупное зерно нежелательно, хотя и неизбежно вследствие цикла сварки.Из рисунка 8.7 видно, что существует два метода термообработки крупного зерна. Первый способ — выдержать температуру, близкую к выше, в течение пары часов с последующим медленным охлаждением. Второй способ очень важен для сварочного процесса. Здесь крупное зерно образуется при значительно более высокой температуре с относительно короткими периодами. На рис. 8.8 схематично показано поведение температуры и времени на ТТТ-диаграмме. (Примечание: кривые объясняют механизмы работающей структуры, их нельзя использовать в качестве примеров для чтения.Для определения t 8/5, значений твердости или распределения микроструктуры всегда используются TTT-диаграммы, которые всегда считываются непрерывно или изотермически. Смешанные типы, такие как кривые 3–6, для этой цели не допускаются!). C, 1 MS br-ei cdr Рисунок 8.8 Линия феррита ² s 10³ TTT-диаграмма с процессами термообработки феррит-бейнитный мартенсит 1: нормализация 2: простая закалка 3: прерывистая закалка 4: горячая закалка 5: бейнитный отжиг 6: патентование (изотермический отжиг) Наиболее важные методы термообработки можно разделить на части отжига, закалки и отпуска, и эти отдельные процессы можно использовать по отдельности или вместе.Процесс нормализации показан на рисунке 8.9. Он используется для получения однородной ферритной структуры. Для этого сталь подвергается термообработке примерно на 30 ° C выше Ас 3 до образования однородной массы. Это состояние является отправной точкой для последующей закалки и / или закалки и отпуска. В случае заэвтектоидных сталей аустенизация происходит выше температуры. Нагрев должен быть быстрым, чтобы зерно оставалось как можно более мелким (см. ТТА-диаграмму, глава 2). Затем следует воздушное охлаждение, обычно приводящее к переходу в состояние феррита (см. Рисунок 8.8, строка 1; образование феррита и нормированной микроструктуры).
6 8. Техническая термообработка 99 Рисунок 8.9 Феррит C + br-ei cdr Для упрочнения материала аустенизация и гомогенизация также проводятся при температуре на 30 ° C выше A C3. Также в этом случае нужно следить, чтобы зерна оставались как можно более мелкими. Чтобы обеспечить полное превращение в мартенсит, следует последующая закалка до тех пор, пока температура не станет намного ниже Ms-температуры. Рис. кривая 2 на рисунке 8.8). Такие процессы закалки создают очень высокие термические напряжения, которые могут разрушить заготовку во время закалки. Таким образом, существуют вариации этого процесса, при которых образование подавляется, но из-за меньшего температурного градиента термические напряжения остаются на некритическом уровне (кривые 3 и 4 на рисунке 8.8). На практике это может быть достигнуто, например, путем остановки процесса закалки в воде при определенной температуре и продолжения охлаждения более мягкой охлаждающей средой (маслом). При более длительной выдержке при повышенном уровне температуры превращения могут происходить и в области бейнита (кривые 5 и 6).0,4 0,8% C-Content Нормализация превращения и гомогенизации твердого раствора (30-60 мин) при 30 ° C выше AC 3 феррит + br-ei cdr Рис. 8.10 быстрое нагревание на воздухе, охлаждение, начало образования мартенсита 0,4 0 , 8% C-Content Закалка на 30 ° C выше закалки в воде Начало образования мартенсита
7 8. Техническая термообработка 100 На рисунке 8.11 показана процедура закалки и отпуска.За закалкой следует еще одна термообработка ниже A c1. Во время этого процесса отпуска происходит разрушение мартенситного феррита C + br-ei cdr, рис. 8.11. Образуются феррит и цементит. Поскольку это изменение вызывает очень тонкую микроструктуру, эта термообработка приводит к очень хорошим механическим свойствам, например сила и стойкость. На рисунке 8.12 показана процедура мягкого отжига. Здесь мы стремимся настроить мягкую и подходящую микроструктуру для обработки. Такая структура характеризуется большей частью шаровидными частицами цементита, в то время как пластинчатая структура решена (на Рисунке 8.12, отмеченные кружками, слева: до, справа: после мягкого отжига). Для доэвтектических сталей эта сфероидизация цементита достигается термической обработкой, близкой к указанной ниже. В этих сталях часть углерода, связанного с цементитом, растворяется во время термообработки близко ниже, оставшиеся пластинки цементита со временем превращаются в шарики, а более крупные растут за счет более мелких (преобразование осуществляется, потому что площадь поверхности это сильно редуцированное термодинамически более благоприятное состояние).Заэвтектические стали помимо пластинчатой структуры имеют цементитную сетку на границах зерен. 0,4 0,8% C-содержание примерно на 30 C выше Закалка и отпуск Закалка и отпуск C-феррит + br-ei cdr закалка медленное охлаждение 0,4 0,8% C-содержание Мягкий Время отжига зависит от заготовки от 10 до 20 C ниже или отжиг цементита колебаниями + / — 20 градусов вокруг Рисунок 8.12
8 8.Техническая термообработка 101 Сфероидизация цементита достигается за счет использования процессов трансформации во время колебаний. При превышении степени превращения феррита в происходит одновременное растворение определенного количества углерода в соответствии с бинарной системой Fe C феррит + br-ei cdr Рисунок 4 0,8% C-Content Время снятия напряжения в зависимости от детали между 450 и 650 ° C. Когда температура снова падает ниже и поддерживается ниже примерно на 20 ° C до завершения превращения, происходит повторное осаждение цементита на существующих зародышах.Повторение этого процесса приводит к ступенчатой сфероидизации цементита, а частое преобразование позволяет избежать укрупнения зерна. Микроструктура после мягкого отжига часто представляет состояние материала при поставке. На рисунке 8.13 показан принцип термической обработки для снятия напряжения. Эта термообработка используется для устранения дислокаций, вызванных сваркой, деформацией, трансформацией и т. Д., С целью повышения ударной вязкости детали. Снятие напряжения работает только в том случае, если имеющиеся дислокации могут двигаться, т.е.е. деформации пластической конструкции должны выполняться в микродиапазоне. Повышение температуры — это обычно используемый метод, чтобы сделать возможными такие деформации, поскольку предел текучести уменьшается с повышением температуры. Термическая обработка для снятия напряжения не должна вызывать каких-либо других изменений свойств, так что отпускаемые стали термообработаны при температуре ниже отпуска. Снятие напряжения Нормализация Закалка (закалка) Закалка и отпуск Раствор или закалка термообработка Закалка br-ei cdr Рис. 8.14 Термическая обработка при температуре ниже нижней точки перехода, в основном от 600 до 650 ° C, с последующим медленным охлаждением для снятия внутренних напряжений; нет существенного изменения нынешних свойств. Нагрев до температуры немного выше верхней точки перехода (заэвтектоидные стали выше нижней точки перехода) с последующим охлаждением в спокойной атмосфере. Охлаждение от температуры выше точки перехода или с такой скоростью, что наблюдается явное увеличение твердости на поверхности или по всему поперечному сечению, обычно из-за развития мартенсита.Термическая обработка для достижения высокой пластичности с определенным растягивающим напряжением путем закалки и последующего отпуска (в основном при более высокой температуре. Быстрое охлаждение заготовки. Также быстрое охлаждение аустенитных сталей от высокой температуры (в большинстве случаев выше 1000 ° C) для получения почти однородной микроклимата). -конструкция с высокой пластичностью называется «закалочной термообработкой». Нагрев после предыдущей закалки, холодной обработки или сварки до температуры между комнатной температурой и нижней точкой превращения A1; остановка при этой температуре и последующее целенаправленное охлаждение.Вид и назначение термической обработки
9 8. Техническая термообработка 102 На рис. 8.14 показан обзор термообработок, которые важны для сварки, а также их цели. местный предварительный нагрев отжиг простой предварительный нагрев. Это ограничено только размерами / формой заготовки или возникающими затратами. Самая важная часть диаграммы — это вид термической обработки, сопровождающей сварку.Ниже описаны наиболее важные процессы. предварительный нагрев повышение рабочей температуры предварительный нагрев всей детали br-ei cdr Рис. 8.15 термообработка перед сваркой снятие напряжения простая ступенчатая сварка с постоянной рабочей температурой изотермическая сварка Типы термообработки, связанные со сваркой, сопровождающая комбинацию термообработки, чистая ступенчатая закалка сварка, снятие напряжения комбинированная модифицированная ступенчатая закалка сварка термообработка всей детали термообработка после сварки (послесварочная термообработка) отжиг закалка закалка и отпуск последующий нагрев (послесварочная термообработка) местная термообработка термообработка в сочетании со сварочным раствором отпускная термообработка 800 C 600 Рисунок 8.15 показывает в основном термическую обработку в связи со сваркой. Процессы термообработки делятся на: до, во время и после сварки. Обычно перед сваркой применяется термообработка для снятия напряжений или нормализационная термообработка, чтобы отрегулировать надлежащее состояние материала для сварки. После сварки можно проводить практически любую возможную термообработку. На рис. 8.16 показано влияние различных сопутствующих термообработок во время сварки, представленных на диаграмме TTT. Наиболее быстрое охлаждение достигается при сварке без предварительного нагрева, с добавлением небольшой доли бейнита, в основном образуется мартенсит (кривая 1, аналогичная рисунку 8.8, закалка). Простой нагрев перед сваркой без дополнительного времени остановки снижает скорость охлаждения в соответствии с кривой 2. Доля мартенсита в формирующейся структуре уменьшается, а также T br-er04-16.cdr MSTA (1) (2) (3 ) s 10 5 t H (1): Сварка без предварительного нагрева, (2): Сварка с предварительным нагревом до 380 C, без времени остановки (3): Сварка с предварительным нагревом до 380 C и около 10 мин. время остановки T A: температура остановки, t H: время выдержки Рисунок 8.16 TTT-диаграмма для различных условий сварки
10 8.Техническая термообработка 103 степени упрочнения. Если во время сварки материал выдерживается при температуре выше M S (кривая 3), то образование мартенсита будет полностью подавлено (см. Рис. 8.8, кривые 4 и 5). Чтобы объяснить поведение температуры-времени, используемое ниже, на рис. 8.17 показано наложение всех индивидуальных влияний на материалы, а также результирующий T-T-образный ход в HAZ. В качестве примера выбрана сварка с простым предварительным нагревом. Пластина предварительно нагревается в течение периода t V.После удаления источника тепла начинается охлаждение заготовки. Когда достигается t S, начинается сварка, и ее пик температуры перекрывает кривую охлаждения основного материала. По окончании сварки начинается период охлаждения t A. Сплошная линия представляет результирующее поведение температуры и времени ЗТВ. TTSTV начало шва, конец t V t S t ATV: Температура предварительного нагрева, TS: Температура плавления материала, t V: Время предварительного нагрева, t S: Время сварки, t A: Время охлаждения (комнатная температура), MS: Начальная температура мартенсита: Верхняя температура превращения,: Нижний диапазон температуры превращения Диапазон преобразования результирующей температуры в области зоны термического влияния основного материала.распределение предварительным нагревом, ход температуры при сварке. br-er04-17.cdr Изменение температуры во время сварки с простым предварительным нагревом показано на рисунке Рисунок Распределение во время сварки с предварительным нагревом TTVTA t V t S t ATV: температура предварительного нагрева, TA: рабочая температура, t V: время предварительного нагрева, t S : Время сварки, t: Время охлаждения (комнатная температура) A br-ei cdr Рисунок 8.18 заготовки, точки сварного шва Сварка с простым предварительным нагревом В течение времени сварки t S происходит падение рабочей температуры TA.Обычно осуществляется дополнительное воздушное охлаждение, однако скорость охлаждения также можно снизить, покрывая теплоизоляционными материалами. Другой вариант сварки с предварительным подогревом — это сварка при постоянной рабочей температуре. Это
11 8. Техническая термообработка 104 T T V br-ei cdr Рис. 8.19: t H = 0 достигается за счет дальнейшего нагрева во время сварки, чтобы избежать падения рабочей температуры.На рис. 8.19 показан этот случай (пунктирная линия, TA не должно быть выше MS), а также частный случай изотермической сварки. При изотермической сварке заготовка нагревается до рабочей температуры выше MS (начало образования мартенсита) и также удерживается там после сварки до завершения преобразования аустенитизированных участков. Целью изотермической сварки является охлаждение в соответствии с кривой 3 на рисунке 8.16 и, таким образом, подавление образования мартенсита. TA t S t V t H t ATV: Температура предварительного нагрева, TA: Рабочая температура, t: Время предварительного нагрева, V Сварка с предварительным нагревом и остановкой при рабочем MS t S: Время сварки, t A: Время охлаждения (комнатная температура), t: Время выдержки H Рисунок 8.20 показан ход Т-Т во время сварки с последующим нагревом (последующая термообработка, см. Рисунок 8.15). Такая обработка может быть проведена очень легко, для местного предварительного нагрева обычно используется газовая сварочная горелка. Таким образом, характеристики ударной вязкости некоторых сталей могут быть значительно улучшены. На нижнем рисунке показана комбинация предварительной и последующей обработки. Такая обработка применяется к сталям, которые имеют такую сильную тенденцию к закалке, что невозможно избежать растрескивания, несмотря на простой предварительный нагрев перед сваркой, если они охлаждаются непосредственно с рабочей температуры.Такие материалы подвергаются термообработке сразу после сварки при температуре от 600 до C, так что формируется TTTN br-er04-20.cdr 1. Последующий нагрев TNTV Рисунок 8.20 t S t N t A 2. Предварительный и последующий нагрев TA t V t S t R t N t ATV: температура предварительного нагрева, t S: время сварки, TA: рабочая температура, t A: время охлаждения (комнатная температура), TN: температура последующего нагрева, t N: время последующего нагрева t V: предварительный нагрев time, t: Время остановки R Сварка с предварительным и последующим нагревом
12 8.Исключается техническая термообработка 105 мартенсита и одновременно устраняются остаточные напряжения при сварке. Цели модифицированной ступенчатой закалочной сварки T Ha не следует здесь обсуждать, рисунок. Такие виды обработки используются для преобразования M S в инертные материалы. Цель T Anl t S рисунка — показать, насколько сложна термообработка t HTA: рабочая температура, T Anl: температура отпуска, T: температура закалки, Hä t A t HT St: температура шага, t A: время охлаждения, t: Время закалки, Ab t Ha t Ab t Anl: Время отпуска, t H: Время выдержки, t: Время сварки S t Anl t A заготовки, точки сварки может стать для материала в сочетании со сваркой.br-ei cdr Модифицированное ступенчатое упрочнение сварного шва На рис. 8.21 представлен Т-образный ход точки в ЗТВ за первый проход. Корневой проход был сварен без предварительного нагрева. Последующие проходы сваривали без охлаждения до определенной температуры. В результате рабочая температура увеличивается с увеличением количества проходов. Второй проход сваривается при температуре предварительного нагрева, которая уже выше температуры начала мартенсита. Тепло, которое остается в заготовке, предварительно нагревает верхние слои сварного шва, корневой проход подвергается последующей термообработке за счет того же эффекта.Во время сварки последнего прохода температура предварительного нагрева достигла такого высокого уровня, что критическая скорость охлаждения не будет превышена. Благоприятным эффектом многопроходной сварки является нагрев HAZ каждого предыдущего прохода выше температуры рекристаллизации с соответствующей кристаллизацией. TTV: температура предварительного нагрева, TS: температура плавления материала, t V: время предварительного нагрева, t S: время сварки t A: Время охлаждения (комнатная температура),: Верхняя температура превращения, M: Начальная температура мартенсита S Рисунок 8.22 показано распределение температуры при многопроходной сварке. Сплошная линия сварного шва T S T V br-er04-22.cdr Рис. 8.22 t S t V t Зона термического влияния 4 3 сварных прохода 2 1 наблюдаемая точка — Распределение во время многопроходной сварки M S ISF 2004
13 8. Техническая термообработка 106 эффектов в ЗТВ. Зона крупного зерна с неблагоприятными механическими свойствами присутствует только в ЗТВ последнего слоя.Для достижения оптимальных механических характеристик сварка не выполняется согласно рисунку. Как правило, одинаковые условия сварки должны применяться для всех проходов и должны соблюдаться предписанные t 8/5 раз, сварка следующего прохода не будет выполняться до предыдущий проход охладился до определенной температуры (сохраняя температуру промежуточного прохода). Кроме того, заготовка не будет нагреваться до чрезмерно высоких температур. На рисунке 8.23 показана номограмма, на которой можно интерпретировать рабочую температуру, а также минимальное и максимальное тепловложение для некоторых сталей в зависимости от углеродного эквивалента и толщины стенки.Если, например, закаленная и отпущенная в воде мелкозернистая конструкционная сталь S690QL с толщиной стенки 40 мм является сварной, можно найти следующие данные: — минимальное тепловложение от 5,5 до 6 кДж / см — максимальное тепловложение около 22 кДж / см — предварительный нагрев до около 160 C — после сварки, снятие остаточного напряжения между 530 и 600 C. Стали, помещенные в заштрихованную область, называемую зоной выдержки, должны быть обработаны водородным отжигом. Выше этой области необходимо провести отжиг для снятия напряжения. Ниже этой области термообработка после сварки не требуется.Рисунок 8.23
Изменения микроструктуры и улучшение механических свойств литого сплава AlSi7MgCu0,5, вызванное термообработкой и РКУП при комнатной температуре
Изменения микроструктуры и улучшение механических свойств литого сплава AlSi7MgCu0,5, вызванные термической обработкой и методом равноканального углового прессования (РКУП).Для повышения пластичности сплава требовалась термообработка сплава после литья, выполняемая до применения технологии РКУП. Поэтому образцы проанализированных сплавов были отожжены на раствор при оптимизированной температуре 823 К в течение 4 часов для растворения частиц интерметаллической фазы π (Al 8 FeMg 3 Si 6 ) и образования сфероидальных частиц Si. Впоследствии закалка в воде и искусственное старение при оптимизированной температуре 573 К в течение 5 часов использовались для получения сплава с излишним состоянием.Микроструктура сплава состояла из твердого раствора α (Al), эвтектических частиц Si и интерметаллида β (Mg 2 Si), Q-Al 4 Mg 5 Si 4 Cu, α -Al 12 (Fe, Mn) 3 Si и / или α -Al 15 (Fe, Mn) 3 Si 2 частиц фазы. Кристаллическая структура настоящих фаз была подтверждена дифракцией жестких рентгеновских лучей в Deutsches Elektronen-Synchrotron (DESY) в Гамбурге и дифракцией электронов в выбранной области (SAED), выполненной внутри просвечивающего электронного микроскопа (TEM).Термообработанный сплав был обработан методом РКУП при комнатной температуре по маршруту А. Повторная РКУП сплава гомогенизировала неоднородную микроструктуру после литья и сформировала ультрамелкую микроструктуру субзерен с удлиненными субзеренами шириной 0,2 мкм и м и 0,65 мкм мкм. по длине и высокой плотности дислокаций. Микроструктурные изменения в сплаве, вызванные как термообработкой, так и РКУП, привели к высокому деформационному упрочнению сплава, что проявилось в улучшении прочности, пластичности и микротвердости сплава по сравнению с литым состоянием сплава.
1. Введение
Доэвтектические алюминиево-кремниевые сплавы — хорошо известные литейные материалы, используемые в автомобильной промышленности благодаря их отличной литейной способности, высокому соотношению прочности к массе, хорошим механическим свойствам при повышенной температуре, хорошей износостойкости и низкой термической стойкости. -коэффициент расширения [1]. Однако низкая ударная вязкость и пластичность этих сплавов ограничивают их более широкое применение, особенно в машиностроении. Эти ограничения являются результатом гетерогенной структуры сплавов, состоящей из α -твердого раствора, эвтектических частиц Si и частиц интерметаллической фазы, богатых Fe и Mn, с нежелательной морфологией, размером и распределением, которые рассматриваются как примеси [2 ].
Добавление Mg и Cu к сплавам Al-Si и оптимизированная термообработка могут улучшить механические свойства этих сплавов. Эти добавленные элементы обеспечивают их твердорастворное и дисперсионное твердение. Термическая обработка, включая отжиг на твердый раствор, закалку и старение, является наиболее широко используемым методом улучшения прочностных свойств этих сплавов из-за образования выделений из перенасыщенного твердого раствора во время применяемого естественного или искусственного старения [3]. На начальном этапе искусственного старения прочность и твердость сплавов повышаются до максимального значения.Это результат образования когерентных и / или полукогерентных частиц упрочняющей фазы. Снижение прочности сплавов после продолжительного старения и / или при высокой температуре старения сопровождается повышением их пластичности за счет образования некогерентных частиц упрочняющей фазы и их укрупнения [4].
Помимо термической обработки сплавов Al-Si-Mg-Cu, выполняемой для повышения их прочности и пластичности, в последние десятилетия часто использовались методы интенсивной пластической деформации (SPD).Эти методы используют механизм деформации для измельчения и гомогенизации микроструктуры и упрочнения по размеру зерна, а также деформационного или деформационного упрочнения этих сплавов. Среди всех методов ИПД РКУП широко используется при исследовании алюминиевых сплавов, особенно в связи с получением ультрамелкозернистых (УМЗ) структур сплавов и заготовок подходящего размера для различных структурных приложений [5, 6]. Преимущество и уникальность этого метода по сравнению с другими методами ИПД состоит в том, что прессованные заготовки имеют одинаковый начальный и конечный размер поперечного сечения.В углу пресс-формы для РКУП УМЗ-структура сильно деформированных сплавов формируется простым сдвигом. Более того, в случае сплавов с неоднородным химическим составом и микроструктурой происходит гомогенизация материала. Однако окончательные результаты этого метода зависят, прежде всего, от геометрии штампа, маршрута обработки, количества проходов и температуры обработки [7].
Целью данной работы является исследование влияния повторяющейся обработки РКУП при комнатной температуре на микроструктуру и механические свойства изношенного литейного сплава AlSi7MgCu0.5 сплав.
2. Материалы и методы
Для исследования использовалась отливка из промышленного сплава AlSi7MgCu0,5 с химическим составом, указанным в таблице 1. Оптимальный характер литой структуры был достигнут путем модификации расплава Sr и модифицирования промышленным измельчителем зерна Al-Ti-B. В качестве исходного литого состояния использовали образцы, вырезанные с поверхности отливки на глубину 10 мм. Цилиндрические заготовки из сплава в литом состоянии с размерами 10 мм в диаметре и 100 мм длиной были отожжены на раствор при 823 K в течение 4 часов, затем закалены в воде и искусственно состарены при 573 K в течение 5 часов для получения изношенного состояния сплава. .После этой термообработки до РКУП экспериментальные заготовки были сильно деформированы методом РКУП при комнатной температуре за 4 прохода через матрицу с углом между каналами Φ = 90 ° и углом на внешнем углу матрицы Ψ = 37 °. Заготовки обрабатывались с использованием маршрута А в матрице ECAP, где заготовки не вращались между отдельными проходами. Повторяющиеся заготовки, проходящие по этому маршруту, являются наиболее эффективными для измельчения и гомогенизации литой структуры сплавов Al-Si [8].
|
Микроструктуру литого, изношенного и ECAP-состояния сплава наблюдали с помощью светового микроскопа (LM) и сканирующего электронного микроскопа (SEM). Металлографические образцы готовили шлифовкой, полировкой, травлением в растворе 0,5% HF в дистиллированной воде и / или глубоким травлением в растворе 7% соляной кислоты, 13% азотной кислоты и 80% уксусной кислоты.После обработки методом РКУП микроструктура и субструктура сплава были изучены в плоскости X (перпендикулярно направлению прессования), как показано на рисунке 1. Субструктура сплава наблюдалась с помощью просвечивающей электронной микроскопии (ПЭМ) на окончательно утоненные фольги в растворе 33% азотной кислоты и 67% метанола при температуре 238 К и напряжении 16 В. Фазовый анализ состояний сплавов проводился методом жесткой дифракции рентгеновских лучей (XRD) на канале P02.1 при Накопительное кольцо PETRA III в Deutsches Elektronen-Synchrotron (DESY) в Гамбурге.Испытание состояний сплава на растяжение проводилось на коротких цилиндрических образцах при начальной скорости деформации 2,5 · 10 −4 · с −1 при комнатной температуре. Толщина коротких образцов диаметром 5 мм составляла 10 мм. Характеристики прочности на разрыв ( R p0.2 : предел текучести; R м : предел прочности при растяжении) и характеристики пластичности ( A : удлинение при растяжении; A г : равномерное удлинение при растяжении; Z : уменьшение площади).Измерения микротвердости по Виккерсу проводили на плоскости X образцов при нагрузке 200 г и времени нагружения 30 секунд.
3. Результаты
3.1. Микроструктура сплава в литом состоянии
Микроструктура сплава AlSi7MgCu0,5 в литом состоянии (рис. 2 (а)) была дендритной и неоднородной. Он состоит из дендритов твердого раствора α (Al), междендритных сетей частиц эвтектического кремния и α -твердого раствора и частиц интерметаллических фаз.На рис. 2 (б) показаны частицы эвтектической и интерметаллической фаз в микроструктуре глубоко травленого сплава. Морфология эвтектических частиц Si была волокнистой и коралловидной. Частицы интерметаллических фаз имели стержневидную форму и неправильную морфологию шрифта. Фазовый анализ методом жесткого XRD показал, что твердый раствор α (Al) и частицы эвтектического кремния были преобладающими фазами в литом состоянии сплава (рис. 3 (а)). Наличие π (Al 8 FeMg 3 Si 6 ), β (Mg 2 Si), Q-Al 4 Mg 8 Si 7 Cu 2 и α -Al 12 (Fe, Mn) 3 Si и / или α -Al 15 (Fe, Mn) 3 Si 2 фазы также были обнаружены с помощью дифракционного анализа ( Рисунок 3 (б)).Положения α -Al 12 (Fe, Mn) 3 Si и α -Al 15 (Fe, Mn) 3 Si 2 максимальные интенсивности соответствовали одному и тому же углу 2θ в сравнение дифрактограмм с измеренными дифракционными данными с небольшими отклонениями. Возможно присутствие фазы с обеими стехиометриями в литом состоянии сплава.
3.2. Микроструктура состояния сплава с усредненным содержанием
Микроструктура состояния сплава, прошедшего термообработку до РКУП (после отжига на твердый раствор, закалки и искусственного старения), показана на рисунке 4 (а).Морфология отдельных фаз в микроструктуре сплава видна на рисунке 4 (б). Применение термической обработки не изменило неоднородную микроструктуру сплава и дендритный характер твердого раствора α (Al). Однако во время отжига в растворе происходит частичная сфероидизация и укрупнение эвтектических частиц Si и α -Al 12 (Fe, Mn) 3 Si и / или α -Al 15 (Fe, Mn) 3 Si 2 частиц.Присутствие основных фаз, твердого раствора α, (Al) и эвтектических Si-частиц, в состоянии изношенного сплава было подтверждено рентгеноструктурным анализом, как показано на рисунке 5 (а). Сравнение дифрактограмм, полученных для этого состояния сплава (рис. 5 (b)), с картинами состояния сплава после литья (рис. 3 (b)) показало, что интерметаллид π (Al 8 FeMg 3 Si 6 ) частицы фазы растворялись во время обработки раствора. Напротив, интенсивность α -Al 12 (Fe, Mn) 3 Si и / или α -Al 15 (Fe, Mn) 3 Si 2 фазы была незначительно выросла.И наконец, интенсивность интерметаллической фазы Q-Al 4 Mg 8 Si 7 Cu 2 фазы значительно увеличилась, а интенсивность фазы β (Mg 2 Si) увеличилась незначительно. Присутствие этих интерметаллических частиц в микроструктуре изношенного сплава было также подтверждено SAED. Также было обнаружено, что при искусственном старении происходит выделение некогерентных частиц фазы β (Mg 2 Si), Q-Al 4 Mg 5 Si 4 фазы Cu, Al x Fe y Si z фаза, и возникли Si-частицы из твердого раствора α (Al) (рис. 6 (б)).Частицы выпавших фаз были распределены в твердом растворе сплава однородно, как показано на рисунке 6 (а).
3.3. Микроструктура сплава после обработки РКУП
Обработка РКУП привела к значительному изменению микроструктуры состояния термообработанного сплава AlSi7MgCu0,5. Микроструктура этого состояния после 4 проходов заготовки через равный канал при комнатной температуре в плоскостях X , Y и Z показана на рисунках 7 (a), 7 (c) и 7 (e).
Сравнение микроструктуры усредненного (рис. 4 (а)) и ECAP (рис. 7 (а)) сплава показывает, что дендритная структура сплава эффективно гомогенизируется за счет фрагментации и перераспределения эвтектических частиц Si, частиц интерметаллических фаз и выпадает в осадок. После применения метода РКУП изменения морфологии эвтектических Si-частиц не произошло; однако их неравномерное расположение в твердом растворе было изменено на линию в плоскостях X и Y прессованной заготовки.В плоскости Z гомогенизация частиц Si, распределение в матрице было незначительным из-за характера деформации прессованных заготовок по маршруту А.
Фрагментация частиц, присутствующих в структуре сплава, была подтверждена оценкой их среднего значения. размер ( d ) и количество на единицу площади ( n ) в плоскости X прессованной заготовки, как показано в Таблице 2. ECAP привело к уменьшению среднего размера и увеличению количества на единицу площади Частицы Si, частицы интерметаллической фазы и выделения в микроструктуре сплава по сравнению с недеформированным и усредненным состоянием сплава.
|
Идентификация фаз ECAPed AlSi7MgCu0.5 методом РФА показал наличие в его структуре основных и второстепенных фаз. Он является результатом дифрактограмм сплава на рисунках 8 (а) и 8 (b). Твердый раствор алюминия и частицы Si были основными фазами в анализируемом состоянии сплава, и Q-Al 4 Mg 8 Si 7 Cu 2 , β (Mg 2 Si), α -Al 12 (Fe, Mn) 3 Si и / или α -Al 15 (Fe, Mn) 3 Si 2 были второстепенными фазами, а также в изношенном сплаве состояние (рисунок 5).На рис. 9 показана зависимость между интенсивностью рефлекса (111) твердого раствора α (Al) сплава РКУП и азимутальным углом кольца Дебая – Шеррера. Можно наблюдать сильную преимущественную ориентацию зерен твердого раствора.
Обработка сплава AlSi7MgCu0,5 методом РКУП привела к образованию ультрамелких зерен твердого раствора. Субструктура 4-кратно спрессованного сплава состояла из удлиненных зерен и / или субзерен с неравновесными, волнистыми и искривленными границами и высокой плотностью дислокаций как внутри субзерен, так и в зоне границ субзерен, как показано на рисунках 7 (b). и 7 (d).Средняя ширина зерен и / или субзерен в плоскости X твердого раствора прессованной заготовки составляла 0,2 мкм м, а длина составляла 0,65 мкм мкм. SAED (рисунки 7 (b), 7 (d) и 7 (f)) показали, что удлиненные зерна и / или субзерен с предпочтительной ориентацией (текстурой) разделены малоугловыми границами зерен (LAGB) и / или высокоугловыми зернами.