Разделка кромок под сварку: виды, ГОСТ, формы, углы
Прежде, чем сваривать заготовки, их кромкам придают определенную форму. Такая операция называется «разделка». Ее выполняют на изделиях средней и большой толщины для того, чтобы:
- дать инструментам сварщика удобный доступ к коренной области шва;
- обеспечить качественную проварку по всей толщине соединяемых деталей.


Разделка кромок увеличивает зону шва и, соответственно, расход сварочных материалов. Наименьший расход наблюдается в том случае, когда кромки не разделывается вовсе. Сварка идет без разделочной подготовки. При малых толщинах применяют отбортовку. При подготовке к сварке делают фаски различной формы, одно- и двухсторонние. Прямолинейные односторонние скосы легче всего заваривать. Фаски сложной формы требуют доступа сварщика к лицевой и изнаночной сторонам конструкции.
Для чего выполняется, цель подготовки и зачистки
Перед выполнением подготовки торцы подлежат обязательной зачистке. Зачистка разделяется на две стадии:
- Механическая. Проводится для удаления слоя окислов, ржавчины, окалины и других механических загрязнений. Выполняется проволочными щетками или абразивными дисками различной зернистости и формы. Небольшие детали могут зачищаться вручную, для более крупных используют угловые шлифмашины (УШМ), в обиходе называемые «болгарками».
- Химическая. Выполняется для обезжиривания области шва и удаления из нее других видов химических загрязнений. Используются органические растворители. Некоторые сплавы пред сваркой протравливают кислотами.
Если проводить сварочные работы без предварительной зачистки, то загрязнения, попавшие в шовный материал, существенно снизят его прочность и долговечность.
После зачистки поверхности можно приступать к разделке кромок под сварку. Она проводится для того, чтобы дать электроду или горелке доступ ко всей сварочной зоне. Особенно это важно для толстостенных конструкций, которые приходится проваривать в несколько проходов. Основная цель разделочных операций — обеспечение глубокого и полного провара по всей глубине и длине шва.
Различают несколько разновидностей подготовительных работ:
- Ручная правка. Проводится на правильных плитах, применяется ручной молоток.
- Механическая правка. Используется пресс или прокатка в правильных вальцах. С заготовки снимаются зоны кривизны (вздутия и впадины) и коробления.
- Разметка. Суть операции заключается в переносе линейных и угловых размеров будущего изделия с чертежа на поверхности заготовки. Обозначаются также места сверления отверстий. Разметка выполняется острыми чертилками или контрастными маркерами. Необходимо также не забывать о припуске, оставляемом для операций механической обработки. Разметка выполняется для уникальных и мелкосерийных изделий. Серийные и массовые изделия не размечаются, а обрабатываются по шаблонам.
- Термообработка. Нагрев до относительно невысоких температур используется для повышения пластичности и обрабатываемости металла.
- Раскрой. Резка листового проката под необходимый размер заготовки проводится механическими ножницами, линейными или роликовыми. Раскрой высокоуглеродистых сплавов осуществляют с помощью установок газовой или плазменной резки. Высоколегированные сплавы разрезают лазерными резаками либо применяют кислородные резаки под флюсом.
- Гибка. Проводится для изгиба заготовок согласно чертежей. Выполняется на гибочных станках в холодном или нагретом состояниях.
После проведения комплекса подготовительных операций приступают к собственно разделке кромок.
Различают следующие виды разделки кромок:
- односторонние;
- двухсторонние.
По форме скоса выделяют такие типы разделки кромок под сварку, как:
- V-образная;
- X-образная;
- U-образная.
Правильно выполненная подготовка под сварку помогает сформировать сварочную ванну наилучшей формы, обеспечит плавное соединение двух заготовок, минимизирует возникающие после кристаллизации внутренние напряжения.
Важно отметить, что скосы не должны заканчиваться острой кромкой. В этом случае возникает вероятность локальных непроваров или прожогов.
На последних 2-3 миллиметрах кромку делаю плоской, формируя так называемое притупление.
Оборудование для механической разделки
В ходе механической обработке стыков чаще других используются следующие операции:
- строгание;
- фрезерование;
- долбление;
- абразивное резание.
Для каждой группы операций применяется свое специализированное оборудование.


Сенсорно-механическое устройство для подготовки кромок
Для подготовки прямых стыков используются строгальные станки. Резец из высокопрочной инструментальной стали устанавливается под необходимым углом и совершает возвратно- поступательный движения вдоль торца, снимая за каждый проход небольшой слой металла. Механизированная система подачи резца перемешает его немного ниже перед началом очередного прохода. Станки отличаются простотой устройства, надежностью и низкой себестоимостью операции.
Если же линия шва криволинейная, приходится применять специализированные фрезеровальные станки. Фреза, закрепленная в шпинделе под углом, движется под управлением рабочей программы вдоль линии шва, снимая необходимую фаску. Эту операцию также можно выполнить и на универсальном обрабатывающем центре, но тогда себестоимость ее заметно возрастет.
Для разделки кромок при сварке заготовок, которые по своим размерам не помещаются на станок, а также для обработки стыков труб для магистральных трубопроводов, используют мобильные кромкоскалыватели. Они закрепляются на заготовке и работают методом долбления. По качеству поверхности и точности соблюдения размеров фаски получаются гораздо хуже, чем на стационарных станках. Им требуется дополнительная доводка.
Абразивная обработка используется при подготовке относительно небольших заготовок, а также для дополнительной доводки после фрезерования и скалывания. Обязательной шлифовке подлежат детали из нержавеющих и алюминиевых сплавов.
Скос под сварку труб трубопроводов
Сварка труб необходима в самых разных отраслях. Это и производство, и транспорт, и строительство. Отдельно стоят магистральные трубопроводы и жилищно — коммунальное хозяйство. Люди применяют в своей жизни большое количество типоразмеров труб, сделанных из разных материалов и эксплуатируемых в разных условиях. Различаются и требования по подготовке кромок. Иногда без нее можно обойтись, а иногда — это неотъемлемое требование для обеспечения качества и безопасности эксплуатации.
Государственный стандарт 16037-80 регламентирует способы и параметры подготовки к сварке стальных труб для различных видов и сочетаний свариваемых конструктивных элементов и их сочетаний. Стандарт предусматривает такие типы соединений, как:
- в стык;
- угловое;
- внахлест.
Нормы, закрепленные в стандарте, являются обязательными к исполнению. Без их соблюдения нельзя говорить о качественной сварке и распространяются на электродуговую и газовую ее разновидность, включая применение флюсов и атмосферы защитных газов.


Виды соединения труб при сварке трубопровода
Предписывается в стандарте и механическая, и химическая зачистка поверхности перед сваркой.
Река труб большого диаметра должна осуществляться специализированным оборудованием. В случае применения ручного инструмента (УШМ) резать трубу следует по секторам, соблюдая требования правил безопасной работы.
Под отводы
Это вид соединения, позволяющего разделить поток в трубе (или соединить два потока). При подготовке сварки отвода с основной деталью делают скос одной или двух кромок под 45° к продольной оси. Если отвод присоединяется в стык, то заготовки должны быть равной толщины. Угловые присоединения допускается выполнять без фаски.
Под штуцеры
Это патрубок меньшего по отношению к основной трубе диаметра. Он вваривается в основную трубу и отводит из нее поток. Их также используют в качестве средства присоединения к основной трубе гибких шлангов. Штуцер соединяют с трубопроводом такими приемами:
- угловым швом для ответвления;
- внахлест для промежуточной установки.
Оба приема предусматривают односторонний не разделанный шов. Фаски формируются мехобработкой или газовым резаком.
Для сосудов и резервуаров
Металлические резервуары и сосуды представляют собой объекты повышенной опасности. Содержимое может быть химически активным, находиться под давлением или иметь высокую температуру. Из-за этого высококачественному соединению их деталей и формированию кромок труб под сварку всегда уделяется повышенное внимание.
Стандарт предписывает следующим условиям:
- Для стенок толщиной 3-25 мм используют V- либо X- образную фаску.
- 26-60 мм — используют U-образный.
- Для стенок большей толщины применяют специальные формы разделки и технологии сварочных работ.
Стыкового соединения
В этом случае детали лежат в одной плоскости, а торцы их разделяет небольшой промежуток. В этом случае формируется прочный и долговечный шов, заготовки после сваривания практически становятся единым куском металла. Сваривание встык применяется для конструкций, к которым предъявляются высокие требования. Так выполняется, например, сварка труб при сборке плетей под магистральные трубопроводы.
Для заготовок толщиной до 3 мм достаточно выполнить отбортовку кромок. Если толщина 3-25 мм — делают фаску с одной стороны. При толщине от 26 до 60 мм потребуется двухсторонняя фаска на обеих деталях.


Угловое соединение
Угловых соединений
Это соединения, для которых угол между поверхностями более 30°. Угол разделки кромок зависит от угла между поверхностями.
Для них стандарт предусматривает следующие требования, исходя из толщины:
- до 1 мм разделка углов по краям заготовок не требуется;
- 1-3 мм – достаточно отбортовать;
- 3-20 мм –фаска с одной стороны.
При толщинах 20-50 мм выполняют двустороннюю фаску обеих кромок.
Для двутавровой балки
Это металлический профиль, в сечении похожий на букву H Он обладает повышенной устойчивостью к изгибным напряжениям и является часто применяемым несущим элементом в машиностроении и строительстве. Соединяется с другими элементами с применением таврового шва. Разделка под сварку также зависит от толщины профиля:
- 4-25 мм – односторонняя фаска;
- 26-60 мм – фаска делается с двух сторон;
Прокат большей толщины встречается редко, для него предусмотрены особые формы разделки и технологии сварочных работ.
Виды, типы, формы скосов для швов при ручной дуговой сварке
В ходе ручной электродуговой сварки используются следующие типы:
V-образная
прямая фаска с одной стороны используется для листового проката от 3 до 26 мм. Угол скоса определяется числом разделанных кромок:
- одна — 50°;
- две — 60°.
X-образная
скашиваются две стороны листа 12-60 мм. Угол фаски – 60°.


V- и X-образное соединения
U-образная
Криволинейная фаска на одной из сторон рекомендуется для заготовок от 20 до 60 мм. Эффективен при ручной электродуговой сварке. В этом случае достигается существенная экономия сварочных материалов за счет формирования сварочной ванны оптимальной формы. Повышается также и скорость сварки. Все это положительно влияет на себестоимость сварочных операций.
Обозначения
Геометрические параметры разделки определяются конструктивными характеристиками соединяемых деталей. Влияет на них и диаметр электрода или сварочной проволоки. Угол скоса должен давать возможность доступа инструмента к корню шва.
Основными параметрами являются:
- Зазор b. Наименьшее расстояние между торцами заготовок. Обычно его делают не больше 2-3 мм. Если конструктивные или технологические условия требуют большего зазора, то соединение выполняют с большим количеством присадочного материала, а также с использованием специальных траекторий движения горелки. Используют также метод нескольких проходов.
- Притупление C. Не скашиваемая нижняя часть торца. Оставляется для обеспечения заданной формы шовного материала. Служит также для снижения риска корневых прожогов. Если притупление по конструктивным или технологическим условиям оставляется менышим 1 мм или вовсе не делается, следует прибегать к специальным мерам.
- Угол скоса β. Острый угол, образуемый торцом заготовки и плоскостью кромки. Бывает от 10 до 30°. В случае одностороннего скоса может достигать 45°.
- Угол разделки α. Угол, образуемый плоскостями фасок обеих заготовок. Его назначение – обеспечение доступа электрода к корню шва. Равен удвоенному значению β.
Для предотвращения прожога при малых (или нулевых) значениях притупления принимают следующие меры:
- сварочные подкладки, исключающие прожог и вытекание расплава;
- подушка из флюса;
- выполнение предварительной подварки;
- формирование замкового шва.
Конструкторы и технологи должны стремиться к соблюдению нормативных значений зазора и притупления. Применение любых дополнительных операций и специальных методов ведет к росту трудоемкости, снижению производительности и повышенному расходу сварочных материалов. Все это негативно влияет на производительность и себестоимость сварочных операций.
Способы разделки кромок
В ходе подготовительных работ применяются такие способы разделки кромок:
- Газовым резаком. Метод не отличается высокой точностью и качеством поверхности. Обязательно требуется дополнительная механическая обработка для выравнивания фаски и его шлифовки.
- Механическая резка. При обработке строганием или фрезерование дополнительной обработки не требуется. После долбежки нужна такая же доработка, как и после газовой резки.


Способы разделки кромок под сварку
На заготовках, имеющих форму тел вращения, удобно формировать фаски на токарно — расточных станках.
Для криволинейных швов применяются специализированные фрезеровальные станки или универсальные обрабатывающие центры. Применение специализированного оборудования позволяет снизить себестоимость операции.
Для прямолинейных кромок доступен самый широкий выбор оборудования. Наиболее производительными и экономичными являются строгальные станки. Доступна также обработка фрезерованием и пневмошлифовка.
Дополнительная механическая обработка для выравнивания поверхности может проводиться вручную, с применением УШМ. Сохранилась также и доработка с применением зубила и напильника. К механизированным способам относят пескоструйную и дробеструйную обработку.
Правила подготовки изделий
Для любого метода сварки необходим комплекс подготовительных операций, направленных на выравнивание поверхности заготовки и ее очистку от слоя окислов, шлаков, окалины, ржавчины и других механических и химических загрязнений. В них входят:
- правка;
- зачистка;
- разметка;
- раскрой.
Химическая очистка проводится для полного обезжиривания и удаления следов посторонних химических веществ в околошовной области, как минимум на 30 мм в каждую сторону от линии шва.
В качестве дополнительной операции по указаниям технологов может проводиться локальная или общая термообработка. Она предназначена для снятия внутренних напряжений, возникших на предыдущих стадиях обработки. Термообработка также может использоваться для улучшения таких характеристик материала, как прочность, упругость, пластичность и свариваемость.
Тщательное проведение подготовительных операций позволяет получить прочное, бездефектное и долговечное сварное соединение.
Разделку кромок, как правило, проводят после завершения комплекса подготовительных операций. Правильно выполненная разделка позволяет рассчитывать на качественный шов. Электрод (или проволока) должен иметь доступ к корневой области шва и выполнить глубокий и полный провар.


Зачистка металла
Кромки свариваемых заготовок проходят предсварочную подготовку одним из трех способов:
- Без разделки. Допускается для материалов тоньше 1 миллиметра. Достаточное качество шва может быть обеспечено и без формирования фасок.
- Отбортовка. Торцы заготовок прокатываются на специальном оборудовании и становятся тоньше. Односторонняя делается для стыковых и угловых швов. Двусторонняя – при сварке встык.
- Формирование скосов.
Если деталь перемещалась или хранилась, то после разделки следует выполнить повторное обезжиривание непосредственно пред началом сварочных работ.
В случае длительного хранения потребуется повторить и механическую зачистку для удаления окисной пленки, успевшей образоваться на поверхности.
Требования к готовым поверхностям
К поверхностям, подготовленным для сварки, предъявляются следующие требования:
- Выровненная поверхность. Должны быть исключены искривления, коробление, поверхностные дефекты.
- Чистота. Должны быть удалены окисные пленки, ржавчина, окалина, пыль и стружка, лакокрасочные покрытия и смазка.
- Точность разделки кромок. Недопустимы перепады угла скоса и притупления.
Скачать ГОСТ 5264-80
Четкое выполнение этих требований дает возможность выполнить качественный, прочный и долговечный шов.
Под каким углом
Угол скоса измеряется между плоскостями скошенной кромки и торцом. Он определяется такими параметрами:
- Метод сварки. Для газовой рекомендовано 40-45°, высота притупления от полумиллиметра до миллиметра. Для электросварки – 30-35°.
- Диаметр сварочного материала. Электрод или проволока должны свободно достигать корневой области.
- Толщина материала. С увеличением толщины угол должен становиться более тупым.
Особенности методов резки также влияют на величину угла.
Оборудование и инструмент
Для выполнения подготовительного блока операций доступно большое разнообразие оборудования:
- Ручная правка. Правильные столы, молот.
- Механическая правка. Прессы, вальцы.
- Зачистка. УШМ с дисками или проволочными щетками. Органические растворители для обезжиривания.
- Термообработка. Прогрев газовыми горелками и индукционным методом.
- Раскрой. Газовый резак, роликовые ножницы, установки плазменной и лазерной резки.
- Гибка. Ручным инструментом или на гибочных установках.


Гибочный станок
Станки для обработки кромок
Для этой операции применяют как универсальные инструменты, так и специализированное оборудование. Выбор типа зависит от объема работ.
В качестве универсальных инструментов используются угловые шлифмашины, напильники, другой ручной слесарный инвентарь.
Представлены на рынке и специальные устройства — кромкорезы и фаскосниматели. Их применение экономически оправдано при подготовке больших объемах однотипных швов.


Станок для обработки кромок под сварку
Технология разделки кромок
Основа технологического процесса разделки кромок — это удаление части материала из зоны шва для обеспечения его однородности, прочности и долговечности. Металл удаляется механической обработкой или газовой резкой под определенным углом.
Если после обработки качество поверхности неудовлетворительное, то проводится дополнительная мехобработка.
В большинстве случаев скос не доходит до нижней кромки заготовки. Там оставляют притупление. Его назначение — снизить риск прожога металла и вытекания расплава из шва.
Мехобработка для заготовок, имеющих форму тел вращения, проводится на токарных станках.
Прямолинейные фаски снимают на строгальных или фрезеровальных станках. Применяются и установки для пневмошлифовки и долбежные станки. В отдельных случаях используются установки водяной резки под высоким давлением.
В условиях небольших мастерских поверхности под сварку обрабатывают ручным слесарным инструментом и дорабатывают напильником.
Кроме газовой резки, используются плазменные и лазерные установки. Они позволяют добиться высокой точности обработки и качества поверхности, формируя К-, V-, и Х-профили скоса.
Разделка трещин в металле перед сваркой
При ремонте трещин в изделиях также требуется их разделать. Обрабатывают их обязательно на всю глубину и по всей протяженности. Сквозные трещины разделывают с двух сторон, чтобы снизить потери металла и расход сварочных материалов для наплавки. Выполняют операцию одним из двух способов:
- Механический. Вырубают зубилом или шлифуют абразивами.
- Термический. Применяют газовый резак.
Углы трещины следует засверлить, чтобы снять внутренние механические напряжения и остановить дальнейшее распространение.


Разделка трещин в металле перед сваркой
Для деталей различной толщины
Для заготовок, различающихся по толщине, даются такие рекомендации:
- до 1 мм разделка кромок не требуется;
- от 1 до 3 мм достаточно провести отбортовку;
- от 3 до 25 формируется односторонний скос;
- от 26 до 60 рекомендован двусторонний скос.
Рекомендации сохраняют свою силу для заготовок разной формы и для разных видов швов.
для чего выполняется подготовка скоса шва под сваривание труб, трубопроводов, листового металла; виды, формы, способы, правила
Перед выполнением сварочных работ следует произвести этапы подготовки рабочего изделия. Одной из подобных процедур является разделка кромок. Суть данного процесса заключается в придании кромкам, подлежащих свариванию, необходимых размеров и формы.
Разделку следует проводить при сваривании изделий, толщина которых превышает 5 мм. при осуществлении односторонней сварки и 8 мм. – при двусторонней.
Разделка кромок изделий разной конфигурации осуществляется в соответствии с определенными правилами. Необходимость получения соединения конкретного типа также подразумевает некоторые нюансы. Именно грамотной разделке кромок разнообразных заготовок будет посвящена статья.
Для чего выполняется: цель подготовки и зачистки
Прежде чем приступать к разделке кромок, необходимо произвести очистку поверхности
- осуществление провара по всей толщине свариваемых изделий;
- обеспечение доступа к корню шва сварочного инструмента.
Подготовка свариваемых поверхностей
Предварительная подготовка свариваемых металлических поверхностей включает выполнение нескольких процедур:

Вальцы
Правка может выполняться вручную на специальных правильных плитах из стали или чугуна с помощью пресса или посредством ударов молотка. Механическая правка производится на листоправильных вальцах. Правка осуществляется с целью избавления от дефектов и кривизны.
Предварительная зачистка. В процессе подготовки металл необходимо очистить от масел, красок и лаков с помощью бензина или любого растворителя. Грязь и ржавчина удаляются кордщеткой, абразивными кругами или болгаркой. Изделия из высоколегированных сталей необходимо вычищать до блеска.

Кордщетки, насадки на болгарку
Разметка позволяет определить формы и размеры будущего изделия. Выполнять разметку нужно внимательно, так как даже небольшая неточность приведет к дефекту. Важно помнить о припуске на обработку.
Небольшой подогрев деталей.
Механическая резка металлических листов осуществляется с помощью роликовых ножниц, которые оборудованы ножами. Резка деталей из углеродистых сталей проводится плазменно-дуговой или газокислородной технологиями, легированные стали – кислородно-флюсовый и плазменно-дуговой методы.
При необходимости изделия подвергаются гибке.
После выполнения данных процедур, можно приступать к разделке кромок. Грамотно выполненный скос обеспечивает плавность перехода между свариваемыми заготовками, снизит возможное напряжение на область шва. О том, как правильно это сделать расскажем далее.
Важно! Общая информация для всех видов соединений. Обязательно нужно оставлять притупление. Величина притупления – 2,0-2,5 мм, зазор – 0-4 мм. Отсутствие притупления может привести к прожогам, а отсутствие зазора – к непровару.
Скос под сварку труб, трубопроводов
Сваривание труб осуществляется в различных сферах деятельности: в быту и промышленности, на производстве. Потребность в соединении труб возникает и при первоначальной прокладке и при ремонтных работах. Поэтому важно знать, в каких случаях следует осуществлять разделку, а когда можно обойтись без этой процедуры.
[ads-pc-2][ads-mob-2]
Под отводы
Отвод представляет собой фитинг, использующийся для изменения направления потока жидкости, газа или пара в трубопроводе. Для получения качественного стыкового соединения отвода с трубой, исполнителю необходимо выполнить односторонний скос одной или двух кромок под углом в 45 градусов относительно оси трубы.
Важно! При стыковом соединении детали должны иметь одинаковую толщину.
Кроме этого, сварщик может сделать угловое соединение, которое осуществляется без скоса.
Под штуцеры
Штуцер – это патрубок (небольшое отрезок трубы), привариваемый к любой конструкции и служащий для подключения к ней трубопровода с целью отвода жидкости, газа или пара.
Штуцер с трубопроводом может соединяться следующими способами:
- угловое соединение ответвительного штуцера с трубой односторонним швом без скоса кромок;
- нахлесточное соединение промежуточного штуцера с трубой односторонним швом без скоса кромок.
Скосы с торцов труб можно снимать с помощью механической обработки или газовой резкой.
Для сосудов и резервуаров
При разделке кромок под сварку различного рода сосудов и резервуаров следует следовать следующим рекомендациям:
- если толщина стенок изделия составляет 3-26 мм., то следует применять V-образный или X-образный скос;
- при толщине стенок, не превышающей 60 мм., следует выполнить U-образный скос кромок.
Стыкового соединения
Стыковое соединение (сварка встык) – тип соединения, при котором заготовки расположены в одной плоскости и примыкают друг к другу торцами. Такой тип соединения обеспечивает высокие прочностные характеристики, поэтому применяется при работе с ответственными конструкциями.
Изделия толщиной 1,0-3,0 мм. свариваются встык после отбортовки кромок.
Для деталей с толщиной стенок до 26 мм. следует выполнить односторонний скос одной или обеих кромок, с толщиной до 60 мм. – двухсторонний скос каждой кромки.
Угловых соединений
Угловое соединение – тип соединения, в котором угол между рабочими поверхностями двух заготовок в месте примыкания кромок превышает 30 градусов.
При толщине стенок изделия до 3 мм. рекомендуется выполнять отбортовку кромок.
При работе с большими толщинами (до 20 мм.) необходимо проводить односторонний скос одной кромки, значительные толщины требуют двухстороннего скоса.[ads-pc-3][ads-mob-3]
Под сварку двутавра (двутавровой балки)

Сварка деталей, толщина которых от 4 до 26 мм. осуществляется с односторонним скосом, толстостенные изделия (до 60 мм.) варятся после проведения двухстороннего скоса.
Виды (типы, формы) скосов для швов при РДС (ручной дуговой сварке)
Различают несколько типов скосов, каждый из которых следует использовать при работе с определенными изделиями и при особых требованиях к сварочному соединению.
V-образная
V-образный скос – односторонний прямолинейный скос одной или двух кромок. Данный тип применяется при работе с листовым металлом, толщина которого варьируется в диапазоне от 3 до 26 мм. Угол разделки двух кромок – 60 градусов; одной кромки – 50 градусов.
X-образная
X-образный скос – двухсторонний прямолинейный скос двух кромок, который используется при сварке изделий толщиной 12-60 мм. Угол разделки – 60 градусов.
U-образная
Также иногда выделяют K-образный скос, который применяется, когда одно из одна из кромок имеет двухсторонний скос, а другая – односторонний.
Обозначения
При ознакомлении с чертежами сварных соединений можно встретить буквенные обозначения. Каждому исполнителю необходимо знать их значение.
Элементы, встречающие на чертежах по подготовке кромок для сварки:
- в – ширина шва;
- h – высота шва;
- β – угол скоса кромки;
- α – угол раскрытия кромок;
- К – катет шва – наиболее короткое расстояние от плоскости соединяемой первой заготовки до границы углового соединения, которое расположено на плоскости второй заготовки;
- b – величина зазора – расстояние между заготовками, стандартный диапазон величин 1,5-2,0 мм.;
- С – величина притупления – нескошенная часть торца кромки, обычно составляет 1-3 мм.
Способы выполнения обработки (разделки кромок)
Как уже было сказано ранее существует несколько способов выполнения разделки кромок:
- газовая резка требует последующей механической или ручной обработки;
- механическая резка осуществляется на ножницах, после необходимо произвести механическую или ручную доработку.
Для тел вращения механическая обработка проводится на расточном станке; для прямолинейных элементов предназначена фрезерная обработка, механическая строжка, использование метода пневмошлифовки, угловой шлифовальной машинки (болгарки).
Ручная обработка подразумевает рубку зубилом или доработку напильником.
Правила подготовки изделий
Подготовка изделий для последующего проведения сварки – один из важнейших этапов, независимо от используемого метода.
Обязательно проведение нескольких процедур: правка, зачистка, разметка, резка. Проведение каждого процесса гарантирует исключение различного вида дефектов заготовок.
В зависимости от типа обрабатываемых изделий и их толщины возможен нагрев деталей, который обеспечит более качественное соединение.[ads-pc-4][ads-mob-4]
Требования к готовым поверхностям
Перед выполнением сварки кромки должны соответствовать следующим требованиям:
- очищены от различных загрязнений: пыль, грязь, ржавчина, краски, лаки, масла;
- иметь ровную поверхность, без кривизны;
- не должно быть перепадов или изменения угла скоса.
Под каким углом
Угол скоса – острый угол между плоскостью скоса кромки и торца.
Угол скоса зависит от следующих факторов:
- от вида применяемого вида сварки: газовая сварка – 40-45 градусов, притупление – 0,5-1,0 мм.; электродуговая – 30-35 градусов и такая же величина притупления;
- от диаметра электрода или другого расходного материала, размеры кромки должны обеспечивать доступ стержня к корню шва;
- от толщины заготовок, чем она больше, тем больше должен быть угол открытия кромок.
Оборудование и инструмент
Исполнителям предлагается широкий выбор ручных инструментов и автоматического оборудования для подготовки изделия к сварке.
Ручная правка осуществляется на правильных машинах ударами молотка, механическая – на листоправильных вальцах.
Зачистка может выполняться с помощью специальных растворителей, абразивными кругами, болгаркой.
Подогрев осуществляется газовой горелкой.
Для резки металла можно использовать газовую горелку, роликовые ножницы.
Ручная гибка осуществляется кувалдами, молотками, тисками или наковальнями, роликовые гибочные станки обеспечивают механическую обработку.
Станки для обработки кромок
Для обработки кромок могут использоваться стандартные инструменты, имеющие широкий диапазон сфер применения: болгарка или напильник. Кроме этого, исполнителям предлагается специализированное оборудование – кромкорезы (на картинке). Производители сварочного оборудования выпускают различные модели фаскоснимателей. Подробная информация представлена в отдельной статье.
Видео
Технология (разделки кромок)
Сущность технологии разделки кромок состоит в снятии части металла под определенным углом (углом скоса) с изделия, который в последствии будет подвергаться свариванию.
При снятии необходимо оставить притупление. Оно нужно для того, чтобы во время процессов прихватки и сварки расплавляющиеся кромки не создавали щель, которую будет сложно заварить.
Разделка трещин в металле перед сваркой
Трещины обязательно разделывать полностью, чтобы имелась возможность проварить их на всю глубину. Разделка осуществляется строго по всей длине трещины, с одной или с двух сторон, в зависимости от толщины детали и удобства проведения процесса.
Разделка может проводиться следующими способами:
- механические: вырубка или шлифовка;
- термические: дуговая или кислородная строжка или резка.

Разделка трещины на лопнувшем топоре для ремонта
После разделки углы трещины необходимо засверлить по краям, чтобы предотвратить появление подобных дефектов.
Для элементов различной толщины

стыковое соединение с отбортовкой кромок (для тонкого металла)
Различные конструкции и элементы имеют разную толщину стенок:
- при работе с тонкостенными изделиями (до 5 мм.) разделка кромок не требуется;
- наличие отбортовки кромок также не требует их разделки;
- если толщина стенок деталей составляет от 5 до 20 мм. рекомендуется осуществлять односторонний скос;
- при толщине изделий от 20 до 60 мм. следует производить двухстороннюю разделку.
Данные правила являются стандартными для разных деталей и для различных типов соединений.
всё, что вы хотели знать
Что такое разделка кромок? Для чего выполняется разделка кромок при сварке? Эти вопросы часто задают многие новички. Многие не понимают, зачем вообще тратить время на разделку кромок. Неужели качество шва будет заметно лучше? Наш ответ: да. Любое металлическое изделие требует предварительной подготовки перед сваркой. Разделка кромок — это подготовительный этап, включающий в себя придание кромкам определенной формы.
Нужно ли выполнять разделку кромок в любом случае? Мы не рекомендуем это делать. Разделка нужна для деталей, где толщина металла минимум 5 миллиметров и выше. Если толщина детали менее 5 миллиметров, что разделка кромок свариваемых изделий не принесет желаемого результата. Это лишь один из множества нюансов, которые стоит учитывать при разделке. О них мы и расскажем в этой статье.
Содержание статьи
Перед разделкой
Разделка под сварку выполняется для общего улучшения качества шва, поскольку металл хорошо проваривается и у сварщика есть прямой доступ к корню сварного соединения. Но есть один главный нюанс, который вы должны учесть, чтобы добиться хорошего качества работ. Это подготовка металла под разделку. Без подготовки вся ваша работа потеряет смысл. И речь идет не о простой очистке поверхности от грязи и масла. Речь идет о полноценной подготовке металла.
Если вы будете варить листовой металл, то первое, что нужно сделать — это пропустить его через вальцы. Вальцы — это два металлическим валика, между которыми пропускается листовой металл. Такой процесс также называется правкой металла. Правку можно выполнять и вручную с помощью молотов, но это не лучший способ добиться ровной поверхности. Ведь в результате вы должны избавиться от искривлений металла.
Дальше нужно металл как следует зачистить. Удалите всю грязь, пятна от масла и краски. Это можно сделать с помощью любого растворителя, мы в своей работе используем уайт спирит. Въевшуюся грязь и признаки коррозии можно удалить с помощью кордщетки, болгарки или абразивного круга. Если деталь сделана из нержавеющей стали, то ее нужно начистить до зеркального блеска.
Далее нужно детали немного прогреть. Делается это с помощью специальных электрических печей или газовых горелок. Если деталь еще только на чертежах, то сделайте на металле разметку и вырежьте детали с помощью роликовых ножниц по металлу. Также можно использовать методы плазменной и газовой резки.
Все, теперь деталь можно подвергать разделке. Только при соблюдении всех этих процедур вы можете добиться качественного результата при разделке кромок. Но это только начало, ведь дальше нужно правильно выполнить скосы кромок, чтобы снизить напряжение у шва и улучшить его качество. Далее мы расскажем о формах скосов и о том, как правильно выполнять разделку.
Формы скосов кромок
Существуют разные виды разделки кромок под сварку. Но корректнее называть их видами формы скосов кромок. Каждая форма имеет свои характерные особенности, поэтому форма подбирается индивидуально для каждой детали. Нельзя бездумно выбирать произвольную форму просто потому, что вы научились делать только ее. Обучитесь выполнять скосы всех форм, чтобы расширить свои возможности. Итак, существуют следующие формы скосов кромок.
V-образная форма
V-образный скос кромок под сварку — самый популярный тип скоса, поскольку делается проще всего и широко применяется в большом диапазоне толщин. Выполняется с двух или с одной стороны. Рекомендуемый угол скоса должен составлять около 60 градусов, если скосов два с обеих сторон. Если скос выполняется только для одной кромки под сварку, то рекомендуем угол в 50 градусов.
X-образная форма
X-образный скос — выполняется с двух сторон, применяется при разделке толстых металлов. Рекомендуемый угол скосов — 60 градусов.
U-образная форма
U-образный скос — самый сложно выполнимый для многих новичков за счет непростой формы. Выполняется с двух сторон, подходит для сварки толстых металлов от 20 миллиметров. Зачастую кромки разделывают таким образом, когда нужно выполнить РДС сварку. Это связано с тем, что при такой форме скосов металл меньше наплавляется и электроды расходуются медленнее.
Это основные формы скосов. Бывают и другие (например, К-образный скос), но они применяются в редких случаях.
Разделка кромок
Теперь поговорим непосредственно о разделке кромок. Существует несколько основных способов разделки. Это газовая резка, механическая резка и ручная резка. Газовая резка применяется редко, поскольку требует использования баллонов с газом, а это не всегда удобно. К тому же, после газовой резки вам в любом случае придется доработать скос механическим или ручным способом. Так что давайте остановимся на них поподробнее.
Механическая разделка кромок самая популярная. Ее можно выполнить в любых условиях и без особо опыта. Выполняется с помощью различных приспособлений. Например, ножниц по металлу с последующей ручной доработкой, расточного станка, фрезеровочного станка или болгарки. Болгарка (она же угловая шлифовальная машинка) — самый недорогой способ механической обработки кромок. Применяется повсеместно.
Что касается ручной разделки кромок, то этот метод используется нечасто. И скорее для доработки уже готовой кромки, которую разделали механическим методом. Для ручной разделки можно использовать напильник или метод рубки металла зубилом.
Обратите внимание, что существует допустимое смещение кромок при сварке. Допустимое смещение кромок — это тема для отдельной статьи, поскольку информации много. Так что мы не будем подробно расписывать здесь все нормы. Вы можете прочесть их в ГОСТах или любых других нормативных документах.
Просто держите в голове, что кромки не должны быть идеально симметричными и параллельными друг другу. Также учитывайте, что при разделке разных изделий могут быть свои нюансы. Например, разделка кромок под сварку трубопроводов требует особой точности.
Вместо заключения
Теперь вы знаете, с какой целью выполняют разделку и какие существуют типы разделки кромок под сварку. Да, в рамках одной небольшой статьи трудно раскрыть все особенности и нюансы, рассказать обо всех углах скосов и предостеречь от ошибок. Но это основная информация, которая поможет вам на начальном этапе. Опытные мастера могут поделиться своим опытом разделки кромок в комментариях ниже, чтобы начинающие сварщики могли узнать для себя что-то новое. Желаем удачи в работе!
соединения стальных трубопроводов, кольцевые стыки, швы – Определенных деталей и элементов на Svarka.guru
Ручная дуговая сварка труб остается одним из самых распространенных способов монтажа трубопроводных систем, являющихся как самостоятельными транспортно-распределительными сетями, так и компонентами технологического оборудования. Высокое качество стыков трубопроводных комплексов — это залог их безопасного функционирования.
Способы сварки, типы стыков, геометрические параметры и типовые размеры, а также способы разделки кромок — все это регламентировано в ГОСТ 16037-80 ручная дуговая сварка соединения сварные. Строгое соблюдение требований стандарта при проектировании, формировании технологического процесса и выполнении сварки стальных трубопроводов обеспечивает должный уровень качества.
Условные обозначения соединений
В стандарте описаны три типа сварных соединений трубопроводов:
- стыковые, обозначаются литерой С
- угловые, литерой У
- нахлесточные, обозначаются литерой Н.
Внутри каждого типа актуальный стандарт детализирует множество подтипов в зависимости от:
- вида сварного шва;
- числа сторон проварки;
- конфигурации подкладки;
- ее съемности;
- без скоса, со скосом одной или двух кромок;
- формы сечения кромок
- формы сечения шовного материала
- способа сварки;
- толщины стенок;
- диаметра трубы.
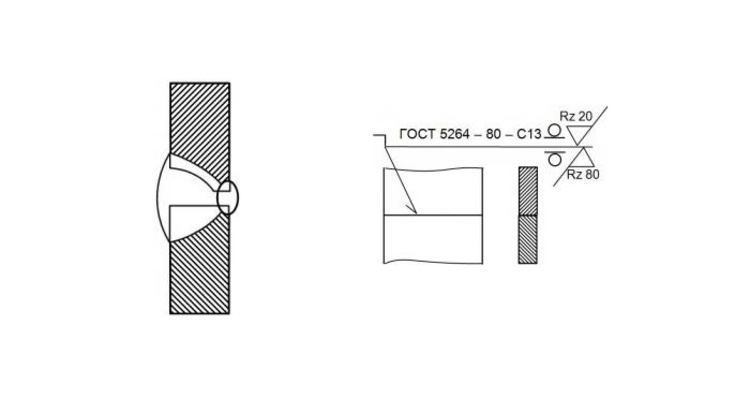
В условное обозначение, кроме типа, входит признак замкнутости линии, способ сварки, параметры катета и вспомогательные символы. В соответствии с ГОСТ 16037 80 используется сварка аргоном, под флюсом и газом. Работа в атмосфере защитных газов может выполняться как плавким, так и неплавким электродом. Обычно трубы выполняют из углеродистой стали. Для работы в агрессивных средах применяют нержавеющие сплавы. Реже используются сплавы цветных металлов.
Конструктивные элементы и размеры кромок заготовок и шва
Сварка труб ГОСТ 16037-80 подразумевает следующие основные элементы:
- s: толщина заготовки;
- b: расстояние между кромками заготовок;
- e: ширина шва;
- g: его выпуклость;
- а –общая толщина шва;
- с -притупление кромки;
- В –глубина нахлеста;
- K — катет углового шва;
- Dn – общий диаметр трубы;
- f – размер фланцевой фаски.


Для ряда швов актуальными являются только часть указанных параметров. Значения размеров приведены в стандарте в зависимости от метода трубной сварки, регламентируемой ГОСТ.
Типы сварных швов
Стыковые швы используются при сварке кольцевых стыков труб в соответствии с ГОСТ. Такие соединения обозначаются С1-С53
Они выполняются одно- и двухсторонними, с прямолинейным и закругленным скосом кромок и с расточкой.
В односторонних швах может быть предусмотрена съемная или остающаяся подкладка, а также расплавляемая вставка.
Соединения секторов на повороте трубопровода выполняется со скосом кромок и обозначаются С54-С55.
Соединения фланца и трубопровода обозначается как С56

Угловые швы обозначаются У5-У21, нахлесточные Н1-Н4
Таблица размеров катета шва
Значения катетов шва в зависимости от типа шва, расстояния между кромками, сварочного метода и размера фланцевой фаски сведены в таблицы для каждого типа отдельно.
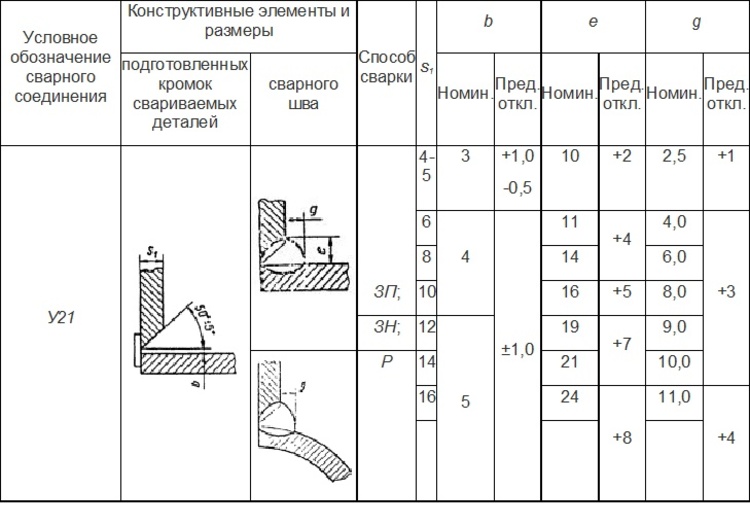
Разделка труб под сварку
ГОСТ регулирует виды и характеристики подготовки к сварным работам для различных типов соединений:
- стыковых;
- угловых;
- нахлесточных.
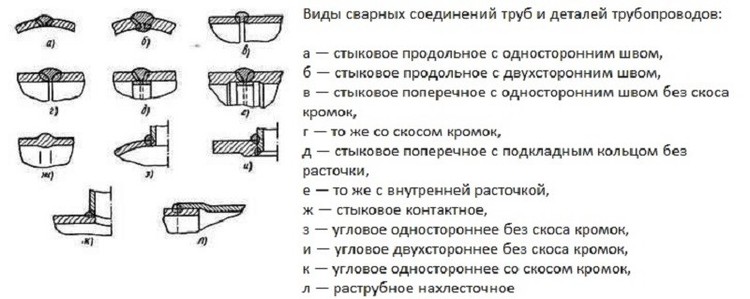
Перед началом сварочных работ необходимо проводить подготовку. В нее входит:
- механическая зачистка, выполняется с целью удаления пыли, следов коррозии, оксидной пленки;
- химическая обработка, для удаления масложировых пятен и окисной пленки;
- разделка кромок.
Разделка проводится с помощью механической обработки кромки. При монтаже трубопроводов она выполняется специальными машинами. Во время ремонтных работ допускается выполнение разделки с помощью угловых шлифмашин.
Разделка кромок выполняется при толщине заготовок от 4 мм.
Для угловых соединений под отводы выполняют скашивание одной или обеих кромок под углом 45о.
Стыки на трубопроводах подразделяются на поворотные и неповоротные.
Сварка стальных трубопроводов ГОСТ 16037 рекомендует применять по возможности поворотные стыки. Они варятся в наиболее удобном и выгодном нижнем сварочном положении, разделка кромок для него выполняется одинаково по всему периметру стыка.
Неповоротный стык приходится варить во всех сварочных положениях, переходящих одно в другое по мере продвижения по шву вокруг трубы.
Разница между толщиной стенок соединяемых встык труб не должна быть более 10% и не превышать трех миллиметров. При этом ширина зазора должна быть постоянной по всему стыку и находиться в переделах от 2 до 3 мм.


До того, как начать монтаж, необходимо обработать кромки и околошовную зону на 20-30мм, очистив ее от механических загрязнений, следов коррозии и масложировых пятен.
Перед основной электродуговой сваркой торцы труб прихватывают друг к другу:
- трубы до 300 мм в диаметре: 4 прихватки;
- свыше 300 мм- равномерно через каждые 200-300 мм.
Трубы с толщиной стенок 12 мм и более проваривают в три приема. На первом этапе формируют корень шва в виде валика с возвышением 1,5-3 мм, равномерно распределенного по длине стыка. Электрод при этом следует вести возвратно-поступательно.
Фаски под сварку
При соединении толстых трубных заготовок сформированный шов следует делать толще, чем сама деталь. Для формирования соединения с заданными геометрическими параметрами требуется выполнить разделку кромок, сняв фаску. После этого электроду будет обеспечен доступ для качественной проварки шва на всю глубину.
Основными параметрами фаски являются:
- Зазор b. расстояние меду заготовками, до 2-3 мм.
- Притупление C. Не скошенная часть кромки. ее оставляют, чтобы снизить вероятность прожога корня шва..
- Угол скоса β. При двусторонней разделке острый угол принимает значения 15-30 о, при односторонней- до 45о.
- Угол разделки α. Тупой угол равен двойному значению угла скоса, обеспечивает должный доступ к корню шва для сварочного оборудования.
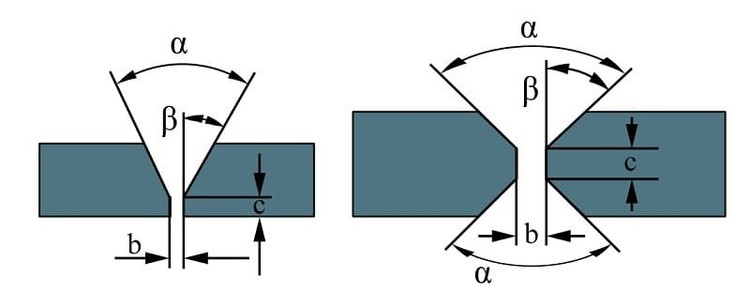
Если значение притупления невелико или его вовсе нет, то прожог предотвращают такими методами, как:
- использование подкладок, препятствующих вытеканию расплавленного металла;
- сварка на флюсовой подушке;
- предварительное подваривание;
- выполнение замка.
Технологам следует обращать особое внимание на корректный расчет и соблюдение оптимальных значений параметров разделки. Это позволяет снизить трудоемкость, экономно расходовать материалы и сохранять контроль над себестоимостью.
При подготовке стыковых соединений вид фаски зависит от толщины деталей:
- 3-25мм: одностороння фаска;
- 26-60мм: двухсторонняя;
Для угловых устанавливаются следующие границы:
- 3-20мм: одностороння;
- 21-50 мм: двухстороння.
Исходя из геометрической формы профиля поперечного сечения, выделяют такие типы разделки:
- обычный скос, профиль представляет собой трапецию,
- Х-образная, два скоса сделаны навстречу друг другу таким образом, что профиль поперечного сечения двусторонней разделки визуально напоминает очертания буквы Х;
- U-образная, профиль поперечного сечения криволинейный и напоминает очертания буквы U.
ГОСТ на сварку труб рекомендует применять U-образную разделку при больших толщинах заготовок, с целью снизить площадь сечения шва и, следовательно, снизить расход материалов и повысить скорость работы.
Форму разделки выбирают, руководствуясь толщиной труб:
- 3-25мм: Х-образная или V–образная;
- 26-60мм- U–образная;
- более 60 мм- специальные формы.
Они представляют собой:
- уступы;
- сложные криволинейные профили, призванные сохранить доступ электрода к корню шва и понизить площадь поперечного сечения.
Для разделки используются следующие способы:
- Газовый резак. Характеризуется низкой точностью и недостаточным качеством поверхности. Требует дополнительной обработки механическими способами.
- Мехобработка. Строгальная или фрезерная обработка дает достаточную чистоту и форму поверхности. Долбежная обработка также требует финишной мехобработки.
При разделке кромок труб большого диаметра используются специальные торцовочные аппараты. Во время ремонтных работ на магистралях отопления разделка часто выполняется вручную шлифмашинами.
Заключение
ГОСТ на сварку трубопроводов – важный регламентирующий документ, устанавливающий условия на подготовку и проведение работ. Он определяет методы сварки, типы соединений, статус разделки и конструктивные параметры для каждого из них. Трубопровод служит не один год. Он также должен выдерживать давление жидкости или газа. Строгое соблюдение требований гост 16037 на сварку трубопроводов необходимо для обеспечения прочности, долговечности и герметичности сварных соединений.
Конструктивные элементы подготовки кромок и размеры швов
Форму разделки кромок и их сборку под сварку характеризуют четыре основных конструктивных элемента: зазор b, притупление с, угол скоса кромки beta и угол разделки кромок alfa, равный beta или 2 beta
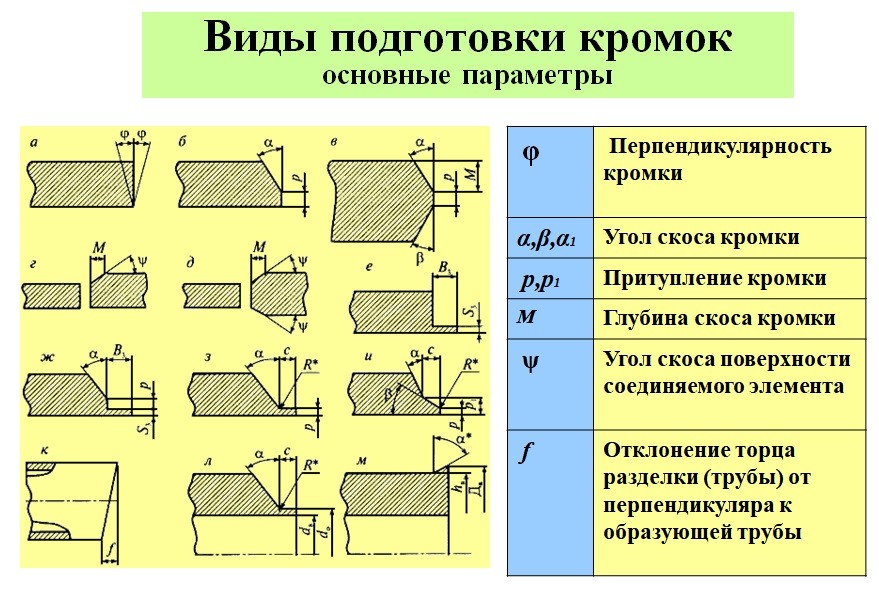
Существующие способы дуговой сварки без разделки кромок позволяют сваривать металл ограниченной толщины при односторонней сварке ручной — до 4 мм,механизированной под флюсом — до 18 мм). Поэтому при сварке металла большой толщины необходимо разделывать кромки. Угол скоса кромки обеспечивает определенную величину угла разделки кромок, что необходимо для доступа дуги вглубь соединения и полного проплавления кромок на всю их толщину.
Читайте также: Классификация сварных соединений
Стандартный угол разделки кромок в зависимости от способа варки и типа соединения изменяется в пределах от 60 ± 5 до 20 ± 5 градусов. Тип разделки и величина угла разделки кромок определяют количество необходимого дополнительного металла для заполнения разделки, а значит, производительность сварки. Так, например, Х-образная разделка кромок по сравнению с V-образной позволяет уменьшить объем наплавленного металла в 1,6- 1,7 раза. Уменьшается время на обработку кромок. Правда, в этом случае возникает необходимость вести сварку с одной стороны шва в неудобном потолочном положении или кантовать свариваемое изделия.
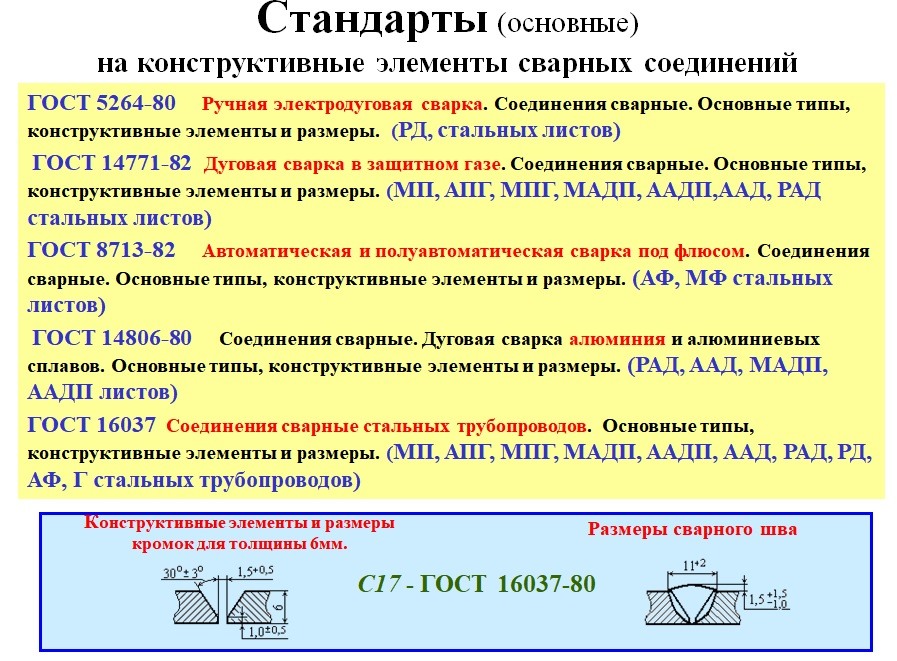
Стандарты на конструктивные элементы сварных соединений по способам сварки
Притупление с обычно составляет 2 ± 1 мм. Его назначение -обеспечить правильное формирование и предотвратить прожоги в вершине шва. Зазор b обычно равен 1,5-2мм, так как при принятых углах разделки кромок наличие зазора необходимо для провара вершины шва, но в отдельных случаях при той или иной технологии зазор может быть равным нулю или достигать 8-10 мм и более.
Для всех типов швов важны полный провар кромок соединяемых элементов и внешняя форма шва как с лицевой стороны (так называемое усиление шва), так и с обратной стороны, т. е. форма так называемого обратного валика. В стыковых,особенно односторонних швах трудно проваривать кромки притупления на всю их толщину без специальных приемов, предупреждающих прожог и обеспечивающих хорошее формирование обратного валика.
Важное значение также имеет образование плавного перехода металла лицевого и обратного валиков к основному металлу, так как это обеспечивает высокую прочность соединения при динамических нагрузках. В угловых швах также бывает трудно проварить корень шва на всю его толщину, особенно при сварке наклонным электродом. Для этих швов рекомендуется вогнутая форма поперечного сечения шва с плавным переходом к основному металлу, что снижает концентрацию напряжений в месте перехода и повышает прочность соединения при динамических нагрузках.
Читайте также: Обозначения сварных соединений на чертежах
Подготовка кромок технологических трубопроводов (НГДО4,12, ОХНВП16, МО2, ГДО)
Отклонение от перпендикулярности торца трубы относительно образующей:
05мм. для Dу до 65мм.; 1,0мм. для Dу св.65мм. до 125мм.; 1,5мм для Dу свыше 125мм. до 500мм.; 2,0 мм для Dу свыше 500мм.(п. 7.1.18. ПБ 03-585-03)
Кромки труб (элементов) и прилегающие к ним участки по внутренней и наружной поверхностям шириной не менее 20 мм. должны быть очищены от ржавчины и загрязнений до металлического блеска и обезжирены (п. 7.1.19. ПБ 03-585-03)
Газовую, воздушно-дуговую или плазменную резку труб из закаливающихся теплоустойчивых сталей необходимо производить с предварительным подогревом 200-250 С и медленным охлаждением. После резки кромки должны быть проконтролированы капиллярной или порошковой дефектоскопией. Обнаруженные трещины удаляются механической зачисткой по всей кромке. (п.п. 7.1.16., 7.1.17 ПБ 03-585-03)
После термической резки кромки труб из закаливающихся сталей должны быть зачищены на глубину не менее 3 мм., а из углеродистых и аустенитных сталей на глубину не менее 0,5 мм. от наибольшей впадины реза (п.п. 18.20,18.21 РД 38.13.004)
Подготовка кромок трубопроводов котельного оборудования (КО1,2)
Концы труб из углеродистых и низколегированных сталей разрешается обрабатывать кислородной, плазменно-дуговой или воздушно-дуговой резкой с последующей зачисткой кромок режущим или абразивным инструментом до удаления следов огневой резки.Подготовленные к сборке кромки должны быть без вырывов, заусенцев, резких переходов и острых углов.
Кромки и прилегающие к ним участки поверхностей деталей должны быть зачищены до металлического блеска и обезжирены на ширину: по наружной поверхности не менее чем на 20 мм. от кромки разделки, –по внутренней не менее 10 мм. При установке штуцера поверхность со стороны наложения шва должна быть зачищена на ширину 15-20 мм. от отверстия, а поверхность очка на всю глубину. (п. 6.2.4. РД 153-34.1-003)
Кислородную резку труб из хромо молибденовых и хромо ванадиевых сталей с толщиной стенки более 12 мм. при температуре воздуха ниже 0 С необходимо производить с предварительным подогревом 200 С и медленным охлаждением. (п. 6.1.5. РД 153-34.1-003)
При термической резке высоколегированных сталей (мартенситного мартенситно-ферритного и аустенитного классов)должен быть предусмотрен припуск не менее 1 мм. на последующую механическую обработку (п. 6.1.4. РД 153-34.1-003)
Подготовка кромок строительных конструкций
Непосредственно перед сваркой кромки и прилегающие к ним участки на ширину 20 мм. при ручной или механизированной дуговой сварке и не менее 50 мм. для автоматической, а также места примыкания начальных и выводных планок должны быть тщательно очищены от окалины грязи, краски, масла, ржавчины,влаги, снега и льда. (п. 5.6. РД 3415.132, п.1.4.2 ОСТ 36-58, п. 6.5 ОСТ 36-60)
Огневую резку кромок деталей из стали С345 и более прочных при температуре окружающего воздуха ниже минус 15 С нужно проводить с предварительным подогревом металла в зоне реза до 100 С. (п. 5.5. РД 3415.132)
После термической (кислородной, воздушно-дуговой, плазменной) резки поверхности реза должны быть механически обработаны:
- на элементах из сталей С235 до С285 – до удаления следов резки
- на элементах из сталей С345 до С375 – с удалением слоя толщиной не менее 1 мм.
- на элементах из сталей С390 до С440 — с удалением слоя толщиной не менее 2 мм.
При обработке абразивным инструментом следы зачистки должны быть направлены вдоль кромок (п. 5.3. РД 34 15.132).
Подготовка кромок трубопроводов газового оборудования (ГО 1,2)
Типы конструктивные элементы и размеры сварных соединений должны соответствовать ГОСТ 16037 (п.7.49. СП 42-102)
Подготовка кромок под стандартную разделку выполняется механической обработкой или газовой резкой с последующей зачисткой шлиф машинкой (п. 7.51. СП 42-102)
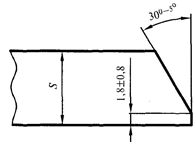
Подготовка кромок трубопроводов газового оборудования
Кромки труб (элементов) и прилегающие к ним участки по внутренней и наружной поверхностям шириной не менее 10 мм. должны быть очищены до металлического блеска (п. 7.52. СП 42-102)
Подготовка кромок магистральных и промысловых газопроводов (СТО Газпром 2-2.2-136)
Геометрические параметры торцов труб, СДТ, ЗРА должны соответствовать ТР-1 – ТР-23 Таблица А8
Свариваемые кромки и прилегающие к ним внутренние и наружные поверхности свариваемых элементов должны быть зачищены механическим способом шлиф машинкой на ширину не менее 15 мм.
(п 10.2.13)
Допускается производить резку труб, в т.ч. для выполнения
специальных сварных соединений (захлестов и др.), с применением оборудования механизированной орбитальной газовой или воздушно-плазменной резки с последующей механической обработкой торцов труб станком подготовки кромок или шлиф машинками до требуемой разделки при этом, металл должен быть сошлифован на глубину от 0,5 до 1,0 мм, а внутреннее усиление заводского шва должно быть сошлифовано «заподлицо» с внутренней поверхностью трубы (п.10.2.7)
Подготовка кромок сосудов, работающих под давлением (ГОСТ Р 52630-2007) (КО 3, ОХНВП 1,2)
Форма подготовки кромок должна соответствовать требованиям технической документации или проекта.
Кромки подготовленных под сварку элементов сосудов должны быть зачищены на ширину не менее 20 мм, Кромки не должны иметь следов ржавчины, окалины, масла и прочих загрязнений. Кромки должны проходить визуальный осмотр для выявления пороков металла. Не допускаются расслоения, закаты, трещины, а для двухслойной стали — также и отслоения коррозионно-стойкого слоя.
При толщине листового проката более 36 мм зону, прилегающую к кромкам, дополнительно следует контролировать ультразвуковым методом на ширине не менее 50 мм для выявления трещин, расслоений и т.д.
Технологические особенности подготовки под сварку и сварки стыковых, угловых, тавровых и нахлесточных соединений одно- и двухсторонних, со скосами и без скоса кромок, на весу и на подкладках.
При стыковом шве в верхнем диапазоне толщины листа должна быть проведена подготовка корня шва с обратной стороны. Это рекомендуется и для предотвращения возникновения дефектов и при всех случаях сваривания подварочных слоев и при двустороннем свариванииX-образных и двойных Y-образных швов в верхнем диапазоне толщины листа. УV-образных швов и швов HV фаза корня может быть несколько ломаной, высота притупления Y-образного шва зависит от используемой силы тока. U- образные швы и двусторонние U-образные швы по экономическим соображениям используются прежде всего при сваривании листов большой толщины, так как из-за небольшого угла раскрытия заполняемый объем шва меньше, чем при V-образных, Y- образных,X-образных и двойных Y-образных швах. У угловых швов зазор между кромками должен быть как можно меньшим, чтобы в него не мог попасть шлак. Это касается в первую очередь Т-образных соединений, соединений внахлестку и угловых швов.
Разделка сварных кромок у нелегированных и низколегированных сталей производится, как правило, газовыми автогенными резаками. Высоколегированные стали и металлы, подвергаемые ручной сварке, могут разрезаться плазменной струей. Удаление возникающей при термической резке оксидной пленки требуется, как правило, только в исключительных случаях. При наличии особенных требований в отношении соблюдения небольших допусков рекомендуется механическая доработка кромок. В особенности это относится к кольцевым швам. Современные технологии резки электронным или лазерным лучом чаще используются в механизированном производстве и являются скорее исключением при ручной сварке стержневым электродом.
Факторы, влияющие на выбор типа сварного соединения
При выборе типа сварного соединения учитывают:
- условия нагружения сварной конструкции при эксплуатации (статические или динамические нагрузки постоянные,переменные и др.)
- способ и условия изготовления сварной конструкции (ручная сварка, автоматическая в заводских или монтажных условиях)
- удобства и возможности при сборке и сварке, достигаемую экономию основного металла, электродов и др.
Читайте также: Положения при сварке
Если вы нашли ошибку, пожалуйста, выделите фрагмент текста и нажмите Ctrl+Enter.
обработка стыковых соединений для качественного сварного шва
Проплавление металла толщиной 5 мм и более довольно трудная задача при использовании ручной дуговой сварки. Получение качественного шва в этих условиях затруднительно даже для опытных сварщиков.
По этой причине ГОСТами и другими руководящими документами предписывается формировать соответствующим образом кромки заготовок. Разделка кромок под сварку делается при выполнении практически всех угловых и стыковых соединений.
Обязательная подготовка
Единственной задачей разделки кромок является желание получить качественный надежный шов. Разделку проводят так, чтобы электрод легко мог достать до нижних слоев и проварить изделие по всей толщине.
Подготовка кромок перед сваркой проводится в любом случае. Она может быть:
- без разделки;
- с отбортовкой;
- с разделкой.
Обязательный подготовительный этап заключается в очистке торцовой и прилегающей области от всевозможных механических и жировых загрязнений, оксидных пленок, ржавчины на расстояние не менее 20 мм в соответствии с ГОСТ.
Зачистка стыков под сварку может производиться вручную с использованием наждачки, щетки с металлической щетиной, напильника, шлифовальной машинки или с применением химических реагентов.
После того как детали собраны в узел, который предстоит варить, и зафиксированы, правильно обработать кромки уже не получится.
Подготовку стыков рекомендуется делать при толщине стенок свариваемых деталей 5 мм и более. Односторонняя отбортовка выполняется при сварке стыковых и угловых соединений.
Двухсторонняя отбортовка производится при стыковой сварке. В целом разделка заключается в придании кромкам определенной формы, в результате чего они становятся тоньше.
Скосы
Стыки с разделкой кромок бывают с односторонним скосом одной или двух кромок и с двусторонним скосом одного или двух стыков. Скосы могут быть прямолинейными или криволинейными, с притуплением или без него.
При односторонней сварке разделку стыков делают в виде буквы V или U. При сварке с обеих сторон реализуется K или X-образные разделки. Разделка для односторонней сварки более трудоемка, чем при сваривании с двух сторон.
Выбор скосов кромок под сварку определяется конструкцией свариваемых изделий, толщиной металла и диаметром электрода. Форму разделки определяет угол и форма скоса, а также высота притупления.
Притуплением называют нескошенную часть стыка. Оно нужно для правильного образования сварного шва и предотвращения прожога. Притупление бывает толщиной от 1 до 3 мм.
Иногда обходятся совсем без него. Тогда предусматриваются специальные мероприятия предотвращающие прожог сварного шва. Сваривание производят на подкладке, основе из флюса или используют замковое соединение.
При использовании ручной электродуговой сварки подготовку кромок у металла толщиной менее 5 мм не делают. Если изделие более толстое, то обычно используют одностороннюю симметричную разделку с углом в 60 °-80 °и притуплением 1-3 мм.
Для соединений в стык с К-, V-, и Х-образной обработкой кромки, совокупный угол скоса равен 45 °-55 °, а при сваривании с подкладкой – 10 °-12 °. Эти параметры влияют на свойства шва и прямо определяют его характеристики.
Методы резки
Разделка кромки заключается в том, что с торца детали снимают часть металлы под углом. Угол определяют между плоскостью торца и образовавшегося скоса.
Разделку можно провести механическим способом и термическим. Впоследствии, в зависимости от качества образованной поверхности, проводится механизированная или ручная доработка.
Механизированная доработка осуществляется на расточном оборудовании для тел вращения. Для прямолинейных поверхностей используются фрезерные станки или пневматические шлифовальные машины.
Если специального оборудования нет, то поверхность под сварку можно доработать вручную с помощью зубила и напильника.
Термические методы разделки кромок – это газовая (при помощи кислорода), плазменная и лазерная резка. При терморезке можно получить К-, V-, и Х-образные скосы кромок. К механическим методам относятся фрезеровка, строгание, резка абразивом и долбежными устройствами.
Особенности методов резки
При газовой кислородной резке легированных сталей свободный углерод образует карбиды, удалить которые очень трудно. Поэтому подготовку таких сплавов, как хромированная нержавейка, например, проводят другими способами. Газовую разделку кромок применяют в основном к углеродистым сталям.
Качество термической резки, проведенной вручную, почти всегда оставляет желать лучшего, поэтому требуется дополнительно обрабатывать срез абразивом. К тому же изменяется состав и свойства верхнего слоя, что приводит к деформации изделий.
Плазменная резка позволяет получить качественный срез практически любых металлов. В роли плазмообразующего газа применяют воздух. Переносные устройства терморезки оснащаются газовыми и плазменными горелками. При установке трех горелок можно делать скосы кромок К-образной формы.
При машинной термической резке, качество кромок получается высоким, и удовлетворяет требованиям ГОСТов. Лазерная разделка кромок используется, когда ее нечем заменить, стоит она очень дорого.
Механическая резка обеспечивает получение качественных скосов кромок. К достоинствам относится создание скосов сложной формы. Но есть и существенные недостатки, среди которых невысокая производительность и трудность формирования кромок на крупных заготовках.
При формировании двусторонних скосов механическим методом требуется кантовка заготовок. Резка стыков абразивами является вредным производством и требует много ручного труда. Элементы абразива вызывают трещины.
Оборудование для механической разделки
Основные механические способы подготовки стыков – это фрезеровка, строжка, долбежка и резка абразивом.
Кромкострогальные станки используются при разделке стыков прямолинейных заготовок и позволяют получать любые виды разделки кромок. Кромкофрезерное оборудование может работать с криволинейными заготовками.
Переносные устройства используют, чтобы подготавливать стыки трубопроводов. Кромкоскалывающее оборудование работает на высокой скорости, но кромки требуют дальнейшей доводки.
Для доводки стыков абразивом применяют шлифовальные машинки. Данная обработка используется после фрезеровки изделий из нержавейки и алюминия.
Все методы разделки кромок имеют свои полюсы и минусы, все зависит от конкретики, вида обрабатываемых заготовок, условий работы и требуемой точности обработки.
Сборка стыков труб | Сварка и сварщик
При сборке стыков с односторонней разделкой кромок и свариваемых без подкладных колец и подварки корня шва смешение внутренних кромок не должно быть выше, чем установлено технической документацией на трубопровод.
Подготовленные кромки и прилегающие к ним участки должны был, зачищены механическим способом до металлического блеска и обезжирены на ширину не менее 20 мм с наружной и не менее 10 мм с внутренней стороны.
При сборке стыков труб под сварку следует пользоваться центровочными приспособлениями, предпочтительно инвентарными, непривариваемыми к трубам.
Прямолинейность труб в стыке (отсутствие переломов) и смещение кромок проверяют линейкой длиной 400 мм, прикладывая ее в трехчетырех местах но окружности стыка.
В правильно собранном стыке просвет между концом линейки и поверхностью трубы должен быть не более 1,5 мм, а в сваренном стыке — не более 3 мм.
При сборке труб и других элементов, имеющих продольные и спиральные швы. последние должны быть смещены один относительно другого. Смещение — не менее трехкратной толщины стенки свариваемых труб, но не менее 100 мм.
Последовательность сборки стыка с подкладным кольцом:
- устанавливают кольцо в одну из труб с зазором между ним и внутренней поверхностью трубы не более 1 мм;
- делают прихватку кольца с наружной стороны трубы в двух местах, а затем приваривают его к трубе ни точным швом с катетом не более 4 мм;
- зачищают ниточный шов от шлака и брызг;
- надвигают на выступающую часть подкладного кольца стыкуемую трубу;
- устанаваливают зазор 4-5 мм между ниточным швом и стыкуемой трубой;
- проверяют правильность сборки;
- приваривают подкладное кольцо ниточным швом к стыкуемой трубе.
Приварка подкладного кольца
Корневой шов сваривают электродами диаметром 2,5-3,0 мм. Размеры подкладного кольца: ширина 20-25 мм, толщина 3-4 мм.
Перед прихваткой и началом сварки качество сборки должен проверять сварщик. Качество сборки стыков трубопроводов под давление выше 2,2 MПа или диаметром более 600 мм независимо от рабочего давления проверяет мастер или контролер. При контроле качества сборки стыков паропроводов с рабочей температурой 450°С и выше необходимо убедиться в наличии заводского номера плавки, номера трубы.
Конструкция стыков трубных элементов по РД 153-34.1-003-01
Подготовленные кромки свариваемых деталей | Способ сварки | Наружный диаметр, мм | Конструктивные размеры | |||
S, мм | a, мм | b, мм | α, град | |||
Разделка без скоса кромок и без подкладного кольца | РД | ≤ 159 | 2 — 3 | 0,5 — 1,5 | — | — |
РАД | ≤ 100 | 1 — 3 | ≤ 0,3; (0,5 — 1,5) | — | — | |
Г | ≤ 100 | 1 — 3 | 0,5 — 1,5 | — | — | |
ААД | ≤ 159 | ≤ 4 | ≤ 0,3 | — | — | |
АФ | ≥ 200 | 4 — 8 | 1,5 — 2,0 | — | — | |
V-образная разделка без подкладного кольца | РД, МП | любой | 3 — 5 | 1,0 — 1,5 | 0,5 — 1,5 | 30±3; (25 — 45) |
РД, МП | любой | 6 — 14 | 1,0 — 2,0 | 0,5 — 1,5 | 30±3; (25 — 45) | |
АФ | ≥ 200 | 15 — 25 | 2,0 — 2,5 | 0,5 — 1,5 | 30±3; (25 — 45) | |
КСС | ≥ 32 | 4 — 25 | ≤ 0,5;(1 -2) | 0,5 — 1,5 | 30±3; (25 — 45) | |
РАД, АДД | ≤ 630 | 2 — 10 | ≤ 0,5; (1 — 2) | 0,5 — 1,5 | 30±3; (25 — 45) | |
Г | ≤ 159 | 3 — 8 | 1 — 2 | 0,5 — 1,5 | 30±3; (25 — 45) | |
V-образная разделка с подкладным кольцом | РД | >100 | £ 16 | 7 — 9 | — | 15 ±2 |
РД | > 100 | £ 16 | 7 — 9 | — | 7 ±1 | |
РД | >100 | £5 | 2,5 — 3,5 | — | 30+3; (25 — 45) | |
МП | >100 | >5 | 8 — 9 | — | 30±3; (25 — 45) | |
МП | ≥ 133 | 2 10 . | 8 — 9 | — | 15 ± 2 | |
АФ | >200 | 4 — 5 | 4 — 5 | — | 15 ± 2 | |
АФ | >200 | >5 | 6 — 7 | — | 15 ± 2 | |
Двухскосная разделка без подкладного кольца | Зазор a без скобок — при выполнении корневого слоя аргонодуговой сваркой без присадочной проволоки, в скобках — с присадочной Углы скоса кромок α в скобках — предельно допустимые | |||||
МП | ≥ 133 | ≥ 16 | 1,5 — 2,5 | 1,5 — 2,0 | 10 ± 2 | |
КСС | ≥133 | ≥ 10 | ≤ 0,5; (1 — 2) | 1,5 — 2,0 | 10 ± 2 | |
Чашеобразная разделка без подкладного кольца | КСС | ≥ 108 | ≥5 | ≤ 0,5; (1 -2) | 3 ±0,2 | 15 ± 2 |
РД — ручная дуговая сварка |
Допустимые смещения (несовпадения) внутренних диаметров стыкуемых трубных элементов по РД 153-34.1-003-01
Характер отклонения и эскиз стыкуемых элементов | Толщина стенки, мм | Давление рабочей среды, кгс/см2 (МПа) | Диаметр, мм | Допустимое отклонение, мм |
S ≤ 4 | Р < 22 (2,2) | Dн>200 | n1≤0,2S | |
S > 4 | Р < 22 (2,2) | Dн>200 | 0,15S< n1 ≤2 | |
Не нормирована | Р ≥ 22 (2,2) | Не нормирован | (0,02S+0,4) ≤ n1 ≤ 1 | |
Не нормирована | Не нормировано | Dp2-Dp1 ≤ 2 | n1 ≤ 1 | |
Не нормирована | Не нормировано | Не нормирован | При n ≤ 6 фигурное подкладное кольцо размером n1≤1 |
Правила выполнения прихваток
Прихватки ставят всегда только с наружной стороны трубы и тщательно зачищают. Нельзя ставить прихватки в местах пересечения торца трубы и продольных швов. В процессе сварки прихватки нужно полностью переплавить или удалить механическим способом.
Прихватка собранных под сварку элементов трубопровода должна ставиться с использованием тех же сварочных материалов, которые приготовлены и для сварки. Рекомендуется тот же способ сварки, что и для корневого шва. Если для него выбрана автоматическая или механизированная сварка, то прихватки следует ставить ручным дуговым или ручным аргонодуговым способом. Это делает сварщик, допущенный к сварке стыков труб соответствующей марки стали, который и будет сваривать данный стык.
Прихватки располагают равномерно по периметру стыка:
Диаметр труб, мм | Число прихваток | Протяженность прихваток, мм | |
До 50 | 1 -2 | 5-20 | |
Св. 50 до 100 | 1 -3 | 20-30 | |
Св. 100 до 400 | 3-4 | 30-40 | |
Св. 400 | Через 300-400 мм | 40-60 |
Высота прихваток
S, мм | Вид ручной сварки | ||
Покрытым электродом | Аргонодуговая | ||
1-3 | h = S | h = S | |
3-10 | h = (0,6-0,7)S | h = b + 0,5 мм | |
Св. 10 | 5-6 мм | h = b + 1,5 мм |
К качеству прихваток предъявляются те же требования, что и к основному шву. Прихватки с недопустимыми дефектами, обнаруженными визуально, удаляют механическим способом и ставят новые.
Подготовка кромок и конструкция стыков
Сварка алюминия и его сплавов
Есть несколько более важных решений, влияющих на успех сварки, чем правильная конструкция соединения. Проблемы с качеством или производительностью сварного шва часто можно объяснить неправильной подготовкой кромок. Конструкция соединения определяется требованиями к прочности, сплавом, толщиной материала, типом и расположением соединения, доступом для сварки и используемым процессом сварки.
Существует три основных вида сварного шва: стыковой, угловой и краевой, показанные на рис. 5.3, из которых можно разработать шесть основных типов соединений. Это стыковое, тройниковое, угловое, крестообразное, краевое и нахлесточное соединения, показанные на рис. 5.4.
Статическая прочность на растяжение этих типов сварных швов определяется толщиной шва (рис. 5.5). Размер стыкового сварного шва с полным проплавлением определяется толщиной наплавленного металла шва в плоскости листа или
.5.3 Стыковые, угловые и кромочные швы. |
5.4 Типы стыков, полученные при стыковой, угловой и торцевой сварке. |
(в)
5.6 Толщина горловины углового сварного шва: (а) угловой шов; (б) угловой шов под углом и выпуклый. |
5.5 Толщина стыкового шва при стыковом шве: (a) стыковой сварной шов полностью; (б) частичный стыковой сварной шов; (c) Т-образный стыковой шов.
труба, 12 на рис. 5.5. При расчете допустимого статического расчетного напряжения стыкового или углового сварного шва для избыточного металла сварного шва кредит не принимается, т.е. е. что над поверхностью основного металла для стыка или за пределами равнобедренного треугольника углового шва, как указано в (t2 — t2).
■ Равная длина колена 45 °, выпуклая поверхность правильного равнобедренного треугольника Избыток металла сварного шва не влияет на прочность.Плоский носок
Филе неравной длины ноги |
вогнутая поверхность уменьшенная толщина горловины, если судить по длине ноги |
1,7 Наклон под углом, выпуклый, вогнутый и неравной длины ножек.
Для углового шва форма сварного шва и степень проникновения в корень будут влиять на толщину шва.На рис. 5.6 эффективная толщина горловины равна tj. Размер углового шва должен быть определен проектировщиком и должен быть достаточным, чтобы выдерживать нагрузку. Поэтому горловина может полностью отличаться от толщины материала.
Угловой шов можно также описать как угловой, вогнутый или выпуклый. Кроме того, угловой сварной шов может иметь неодинаковые отрезки длины. Эти четыре типа углового шва показаны на рис. 5.7.
5.5.1 Сварка встык
Стыковой шов, типичные формы которого показаны на рис.5.8, представляет собой простой и легко спроектированный стык, в котором используется минимальное количество материала. На рис. 5.8 также приведены определения некоторых характеристик подготовки под сварку, таких как «поверхность корня», «угол скоса» и «прилегающий угол». Стыковые швы, как показано на рис. 5.5, также можно классифицировать как полный провар или частичный провар.
При обычных процессах сварки плавлением, таких как TIG и MIG, проникновение металла шва в поверхность плоской пластины из прохода валика по пластине обычно составляет 3 мм и 6 мм соответственно.Для достижения стыкового сварного шва с полным проплавлением при толщинах, превышающих эти, необходимо, чтобы две близко расположенные стыковые кромки были скошены, хотя оставление небольшого зазора между кромками увеличивает провар. Типичные приготовления к сварке для различных процессов можно найти в соответствующей главе о процессах. Стыковые соединения могут быть односторонними или двухсторонними — если они двухсторонние, часто необходимо зарезать или зашлифовать первую свариваемую сторону, чтобы получить соединение без каких-либо непроваров.
Одноместный — V
Двойной — V
Одинарный скос
Двухместный — V
Одноместный — V
1,8 Различные формы стыкового шва.
5.9 Предлагаемая конструкция для соединения листов разной толщины. |
Эффективный размер стыкового сварного шва с полным проплавлением равен расчетной толщине горловины, по сути, толщине пластины / трубы более тонкого компонента.Как упоминалось в другом месте, высота металлического шва или глубина проплавления корня не принимаются во внимание. Хотя это не часто используется в производстве алюминия из-за необходимости согласования прочности соединения и прочности основного металла, в соединениях с малой нагрузкой соединение с частичным проваром (рис. 5.5b) может быть приемлемым. Частичное проплавление может быть достигнуто за счет использования стыкового стыка с закрытым квадратным сечением или толстой корневой поверхности. Соединение с частичным проплавлением дает экономическую выгоду, так как подготовка кромок практически не требуется, она экономична по присадочному металлу и ее легко собрать, поскольку не нужно контролировать корневой зазор.Ограничения заключаются в том, что рентгенографическая интерпретация затруднена из-за отсутствия проникновения, снижается усталостная долговечность и снижается статическая механическая прочность. Эффективный размер в случае шва с частичным проплавлением — это ширина сварного шва за вычетом высоты крышки.
Если необходимо сварить две секции неравной толщины, задача сварщика будет облегчена, и лучшие свойства, в частности усталостные, будут достигнуты, если более толстая из двух частей будет иметь фаску или конус для соответствия более тонкой.Для достижения этого конус на более толстом компоненте должен быть в диапазоне от 4 до 1, чтобы уменьшить эффект повышения напряжения при резком изменении толщины (рис. 5.9).
Форма подготовки сварного шва может быть выбрана так, чтобы обеспечить проплавление корня и прочное основание, чтобы обеспечить требуемую последовательность проходов или контролировать разбавление металла шва от основного металла. Процесс MIG может, но с трудом, использоваться для получения прочного, бездефектного проплавленного валика — для прочного соединения необходимо использовать либо подкладную планку, либо полосу, либо сварной шов необходимо обрезать и сделать второй боковой сварной шов. .Эти методы более подробно рассматриваются в другом месте. Процесс TIG можно использовать для получения прочного, полностью пропитанного корневого валика без обрезки или подкладки. «Спущенный» конический шов (рис. 5.10) разработан для обеспечения высочайшего качества корневого проплавления с использованием процесса TIG. Это используется в таких приложениях, как стыковая сварка труб, когда сварные швы должны быть односторонними и иметь гладкий корневой валик, который не будет препятствовать потоку в трубе.
Для сварки AC-TIG земля должна быть 4.Мин. 5 мм, для сварки TIG и MIG на постоянном токе земля должна быть не менее 2 мм |
Прочность прочного, бездефектного стыкового шва обычно соответствует прочности присадочного металла или прочности основного металла после отжига, как обсуждается в главе 2. Стыковое соединение является наилучшим в условиях динамической нагрузки, особенно если превышение металл шва зачищается заподлицо. Для достижения наилучших свойств две составляющие части требуют точного совмещения, что подразумевает соответствующие прихваты, сборку и фиксацию.
5.5.2 Опорные стержни и подкладные ленты
Несмотря на то, что на обратной стороне стыкового сварного шва можно нанести герметизирующий слой без задних канавок, нельзя полагаться на то, что он даст прочный, бездефектный сварной шов. Односторонние соединения можно сваривать методом TIG для получения надежного корневого прохода, но для обычного (неимпульсного) процесса MIG часто требуется постоянная или временная подкладка для нанесения корневого прохода MIG. Назначение подкладки или полосы — поддерживать корневой проход в тех местах, где условия затрудняют контроль борта.Обычно опорная полоса является временной и может быть снята сразу после завершения сварки, а опорная полоса является постоянной частью соединения. Несущий стержень или планка могут значительно упростить задачу установки соединения — например, легко справляются с изменениями корневого зазора, и соединения могут быть самозажимными, может быть достигнут хороший внешний вид корневого валика и могут быть снижены затраты.
Рифленая временная опорная планка обеспечивает хорошую форму проплавленного валика, причем канавка используется в качестве формы для расплавленного металла сварного шва.Это обеспечит лучшие динамические характеристики, чем постоянная подкладка. Резервное пруткового материала может быть недорогой мягкой стали, но более длительный срок службы может быть получена из бара с меньшим риском загрязнения, если используется нержавеющая сталь. Также можно использовать керамическую основу в виде гибкой полосы плитки или клейкой ленты. Следует избегать использования меди или медных сплавов, потому что
5.11 Типичные самовыжимные профили. Предоставлено ALCAN. |
риска заражения.Несущий стержень без канавок потребует, чтобы корневой проход был заземлен и, возможно, был нанесен герметизирующий проход для создания прочного шва. При сварке TIG с использованием подкладного стержня шов следует выполнять без корневого зазора. Это необходимо для предотвращения прямого воздействия дуги TIG на материал основы и, возможно, его плавления.
Несъемная несущая полоса вплавляется в корневой проход, и необходимо тщательно выбирать сплав, совместимый с основным металлом и наполнителем. Полоса должна быть примерно 4-6 мм толщиной и закреплена на месте.Однако многие профили из алюминия могут изготавливаться со встроенной подкладной полосой, и таким образом упрощается сборка стыков. Можно спроектировать выдавленных как с опорной полосы и построенной в такой форме, что соединение само-отсадки, как показано на рис. 5.11.
Щели, связанные с постоянными подкладными полосами, приводят к локальным концентрациям напряжений. Это может снизить сопротивление удару и усталости, если корень находится в зоне сильной нагрузки. Щель также может вызвать локальную коррозию, хотя даже в морской среде это не было зарегистрировано как серьезная проблема при выборе правильного сплава.Несмотря на эти потенциальные недостатки, постоянные подкладные полосы являются общей чертой многих конструкций, используемых в сложных условиях.
Основа из инертного газа может использоваться для критических применений, таких как пищевая или фармацевтическая промышленность, трубопроводы или сосуды, и очень полезна, когда нет доступа к задней части сварного шва для создания задней строжки и уплотнения. Продувка аргоном предотвратит окисление корневого валика и оксидных пленок, вплавленных в стык, обеспечивая гладкую, ровную корневую валику TIG.Типовые конструкции опорных стержней и лент приведены на рис. 5.12.
Временная опорная планка для листа толщиной более 3 мм (TIG) или 6 мм (MIG) |
Сварка алюминия и его сплавов Толщина t »- |
Похожего дизайн временной подложки бара для пластины или труб менее 6 мм толщины |
Корневой зазор заданный | Г л | |
А | ||
А 4 | Ø | illWv |
Конструкция с постоянной подкладкой для толстых и тонких листов |
Предлагаемая подготовка к сварке и подкладочная лента для горизонтально-вертикального (ПК) положения сварки |
5.5.3 Тройник Как следует из названия, Т-образное соединение (рис. 5.4b) — это соединение, в котором один элемент расположен примерно под прямым углом к своему партнеру, при этом наиболее обычными применениями являются соединения пластины с пластиной или ответвления. Стойка T может быть соединена стыковым сварным швом, угловым сварным швом или сварными швами или комбинацией |
два типа сварного шва (рис. 5.5c). Тройник — это простой сварной шов, который легко спроектировать, который, за исключением Т-образного стыка, требует небольшой подготовки кромок или совсем не требует ее.Точность подгонки в значительной степени зависит от точности, с которой подготовлен край стойки T. Неправильный разрез даст переменный зазор, что может привести к недостаточной толщине горловины, как показано на рис. 5.13.
Угловой сварной шов может вызвать трудности с достижением полного проникновения в корень, в результате чего в углу образуется пустота. Это считается нежелательным, особенно в критических случаях, поскольку отсутствие плавления приводит к увеличению напряжения в корне и также уменьшает толщину горловины.Сварщик должен знать об этой проблеме, так как основная причина — неправильная техника сварки.
Если Т-образный стык представляет собой фланцевое соединение, необходимо оставить достаточно металла, чтобы сварной шов не оплавил угол фланца и не допустил изменений в подгонке. Как показывает практика, достаточной считается длина ветви углового сварного шва в 2,5–3 раза (рис. 5.14). Это не может предотвратить коробление кромки фланца из-за деформации под воздействием тепла сварки, особенно когда размер галтеля велик по сравнению с толщиной фланца.
Прочность тройникового шва, выполненного угловым сварным швом, определяется прочностью на сдвиг углового сварного шва или сварных швов, прочность тройникового шва — прочностью металла шва или ЗТВ. Если соединение подвергается поперечным сдвигающим нагрузкам, изгибающие напряжения в соединении могут привести к преждевременному выходу из строя, особенно если соединение выполнено угловой сваркой только с одной стороны. Угловые сварные швы с обеих сторон или Т-образное стыковое соединение с полным проплавлением позволят существенно увеличить нагрузки до разрушения (рис.5.15). Плохие динамические характеристики тройников: изменение сечения с горизонтального на вертикальное
5.15 Модернизация угловых сварных швов с боковой нагрузкой для повышения производительности. |
вызывает высокие напряжения на носках сварных швов, резко сокращая усталостный ресурс.
5.5.4 Угловой шарнир
Угловое соединение может рассматриваться как стыковое соединение и используется для соединения двух пластин под прямым углом друг к другу (рис.5.4f). Может быть сложно собрать и поддерживать правильное выравнивание, особенно в тонких гибких листах. Корень одностороннего сварного шва при растягивающей нагрузке очень слаб, и для достижения максимальной прочности угловое соединение необходимо сваривать с обеих сторон. Односторонний сварной шов может также иметь складку, содержащую оксиды, вдоль центральной линии проплавленного валика, что дополнительно снижает прочность сварного шва. Было обнаружено, что импульсная сварка на переменном токе AC-TIG эффективна для уменьшения вероятности появления этой особенности.Угловое соединение чаще всего встречается в приложениях с низкой нагрузкой и при обработке листового металла.
5.5.5 Кромочный стык
Краевое соединение (рис. 5.4e) легко собрать и удерживать во время сварки. Как и угловой сварной шов, он является слабым в ситуациях нагружения, которые вызывают растяжение корня, и редко используется в конструкциях, ограничиваясь ненесущими приложениями в тонких листах. Оплавление углов соединяемых кромок может быть проблемой и может привести к неглубокому сварному шву с небольшой толщиной шва.
5.5.6 Внахлестку
Соединение внахлест, пожалуй, самое простое в сборке соединение. Он состоит из двух перекрывающихся пластин, соединенных угловым швом (рис. 5.4c). Различия в размерах компонентов легко адаптируются, и подготовка кромок не требуется, хотя скос, как на рис. 5.16, можно использовать для гарантии полного сращивания корня.
Соединение неэкономично с точки зрения материала, так как материал перекрытия является ненужным. Перекрытие должно быть как минимум в три раза больше толщины более тонкой пластины.Также необходимо следить за тем, чтобы сварной шов не расплавил угол верхней пластины, поскольку это приводит к уменьшению эффективной толщины горловины галтеля.
Прочность соединения определяется прочностью на сдвиг углового шва. Размер и длина сварных швов должны быть указаны проектировщиком, чтобы гарантировать соответствующую несущую способность.
5.5.7 Точечная, электрозаклепочная и щелевая сварка
Скошенная кромка пластины, как указано выше, помогает достичь полного проникновения в корень |
Квадратный край, как показано выше, может затруднить полное проникновение в корень, что приведет к отсутствию дефекта сплавления и уменьшению толщины горловины. |
5.16 Срезание кромки листа внахлест для улучшения проплавления. |
Электродуговая сварка и точечная сварка показаны на рис. 5.17. Процессы TIG и MIG способны полностью проплавить 2-3 мм через верхний лист соединения внахлест, чтобы обеспечить приемлемый сварной шов. Лазер и
5.17 Электрозаклепка и точечная сварка с использованием сварки TIG или MIG. |
может выполнять точечную сварку и сварку «штырями» на листах значительной толщины, в случае электронно-лучевой сварки — до 200 мм.
СваркаTIG обычно ограничивается тонкими листами толщиной менее 2 мм и находит лишь очень ограниченное применение в производстве. Основная часть точечной сварки выполняется с использованием сварки MIG и более подробно рассматривается в главе 7. Однако проектировщик должен знать о переменном качестве точечной сварки, что приводит к низкой прочности и плохим усталостным характеристикам. Высокая сдержанность, присущая этой форме сварного шва, почти всегда приводит к деформации, особенно когда сварные швы имеют небольшой шаг, и может привести к образованию горячих трещин в ЗТВ.Эти особенности ограничивают возможности точечной сварки.
Сварка электрозаклепкой аналогична точечной сварке, за исключением того, что верхняя пластина разрезается, образуя отверстие, которое либо полностью заполняется металлом шва, либо сваривается угловой сваркой вокруг его обода. Этот тип сварного шва страдает теми же проблемами, что и точечная сварка, с переменным качеством и недостаточной прочностью. Их обоих обычно избегают, когда требуется структурная целостность.
Щелевой сварной шов более полезен в конструкционных целях, чем точечная сварка или сварка электрозаклепкой, поскольку требуется наплавка достаточной длины сварного шва.Это позволяет создать стабильную сварочную ванну и выполнить прочный шов. Сварной шов может быть однопроходным, полностью заполняя щель, или угловым швом с обеих сторон. Для обеспечения наилучшего качества позиции запуска и остановки должны находиться на верхней пластине, вне паза. Пазы под угловую сварку предпочтительнее, если толщина листа превышает 5 мм. Прочность щелевого шва определяется сопротивлением сдвигу наплавленного металла.
Таблица A.4 BS EN BS EN Старая версия BS / DTD Температура (° C) числовое химическое число обозначение обозначение Liquidus Solidus IVIdUng диапазон Al 99.99 1 660 660 0 AW-1080A Al 99,8 1A AW-1070A…
Таблица A.3 Цифровое обозначение BS EN Химическое обозначение BS EN Старый номер BS Обозначение ANSI Температура (° C) Ликвидус Солидус Диапазон плавления Al 99,5 LM0 640 658 18 AC -46100 Al Si10Cu2Fe…
Таблица A.2 Свойства Алюминий Железо Никель Медь Титан Кристаллическая структура FCC BCC FCC FCC HCP Плотность (г / см3) 2,7 7,85 8,9 8,93 4,5 Точка плавления (° C) 660 1536 1455 1083 1670…
.Skelp подготовка кромок для изготовления труб ERW
Для получения качественного сварного шва необходимо начинать с хороших кромок.
При производстве труб и труб, сваренных сопротивлением (ВСВ), это очень важно. Идеальные кромки практически невозможно получить постоянно с помощью вращающейся боковой обрезки рулонов одинарной ширины или боковой обрезки и продольной резки мастер-рулонов.
При боковой обрезке горячекатаных рулонов одинарной ширины, продольной и боковой обрезке эталонного рулона на несколько прядей критически важно удалять материал одинаково с каждой стороны рулона, оставляя стренгу желаемой ширины для формовка, сварка и калибровка.
Есть три фундаментальных, но критических процесса, которые необходимо контролировать при производстве труб и трубок для ВПВ, над которыми оператор стана имеет запас контроля — подготовка кромок скелпа, формирование поддонов и ВПВ.
В этой статье рассматриваются три аспекта подготовки кромок скелпа:
1. Потребность в самых чистых, гладких и твердых кромках, которые могут быть получены от вращающихся ножниц, чтобы можно было сделать шов ВПВ самого высокого качества.
2. Базовый Механика роторных ножниц
3.Стандарты качества, которым должна соответствовать кромка со срезанной кромкой, чтобы оператор стана мог произвести сварной шов наилучшего возможного качества. Хотя в этой статье речь идет не о высокочастотной сварке, необходимо изучить характеристики протекания тока в этом процессе сварки.
Глубина радиатора (проникновения) в кромки перед завершением сварки «V» для сварочного аппарата 450 000 циклов в секунду (сПс) составляет примерно 1/32 дюйма. Стрингеры сдвига, шероховатая поверхность или любые неровности на поверхности разделения, которые достигают 1/32 дюйма, могут привести к дефектам сварки.Высокочастотный ток также легко перескакивает на поверхности с острыми краями и остриями.
Хотя неровности кромок проходят через оребренные проходные валки, они могут отрываться от лицевой поверхности при нагревании, потому что они очень горячие. Эти неровности могут окисляться с обеих сторон и вызывать дефект сварного шва, обычно называемый черным пятном. Движение этих неровностей поверхности вызывается нагревательными и магнитными силами при сварке «V».
Когда формованная банка выходит из последней стойки оребрения, она проходит под кольцевой катушкой или скользящими контактами.Края будут нагреваться одинаково, если они параллельны друг другу в вертикальной и горизонтальной плоскостях. Если нижние края расположены ближе друг к другу, чем верхние, а это обычно так, ближайшие друг к другу края станут наиболее горячими.
Если сварщику предъявляются чистые, гладкие, твердые кромки, единственные недомогания или дефекты сварного шва являются результатом слишком горячего или слишком холодного нагрева.
Если установленная мощность сварки при постоянной скорости сварки настолько высока, что возникает состояние горячей сварки, это может привести к появлению таких дефектов, как выскакивание и проплавление.Если настройка мощности сварки при постоянной скорости сварки настолько низка, что возникает состояние холодной сварки, возникают такие дефекты, как непрозрачные сварные швы, швы холодной сварки или полное отсутствие сварки.
Механика ротационной резки
Рисунок 1: Режущее действие между двумя смещенными дисковыми ножами. |
Основными соображениями при использовании роторных ножниц для удаления или разделения материала являются:
1.Требуемая сила и мощность.
2. Производительность оснастки.
3. Влияние технологического процесса на физические свойства материала.
4. Состояние поверхности разделения.
Оператор не может контролировать форму скелпа. Форма скелпа, хорошая или плохая, отражает контур поперечного сечения материала.
Проблемы, вызывающие плохую форму, включают краевую волну, торцевой крюк, выпуклость, центральную пряжку или консервирование. Skelp может быть приемлемым для процесса производства труб и труб из ВПВ, даже если он имеет некоторые из этих проблем формы.
Когда скелп обрабатывается роторным режущим устройством, материал проталкивается между парами дисковых ножей, установленных в смещенном или шахматном положении и установленных на параллельных валах. Лезвия перекрывают друг друга, вызывая срезание, которое разделяет материал (см. Рисунок 1 ).
Лезвия только частично разрезают материал сверху и снизу. Остальное сломано или сломано. Именно эта изломанная поверхность создает нежелательное состояние кромки в процессе изготовления труб и труб из ВПВ.
Прежде чем исследовать срезанные кромки скелпа, производитель должен подумать о целях, которых он хочет достичь при подготовке кромок к сварке.
Рисунок 2: (A) показывает теоретически идеальную обрезанную и разрезанную прядь скелпа. (B) — теоретическое сечение горячекатаного рулона. (C) показывает форму отдельных прядей, когда катушка разрезана. |
Поперечное сечение в Рис. 2A показывает обрезанную и разрезанную прядь скелпа, которая теоретически идеальна.Его края чистые, прочные, без заусенцев и идеально прямоугольные.
Если бы такую кромку можно было изготовить, это значительно уменьшило бы проблемы сварки, возникающие в процессе производства труб. Однако это невозможно из-за материала, с которого производители начинают. На рисунке 2B показано теоретическое поперечное сечение горячекатаного рулона. На рис. 2C показана форма отдельных жил при разрезании катушки.
Отношение резания к глубине излома зависит от химического состава и твердости скелпа, а также от боковых зазоров между верхним и нижним лезвиями.Этот боковой зазор в первую очередь определяется толщиной скелпа и качеством обрезанного края. Цель состоит в том, чтобы получить как можно большую поверхность среза без полного ущерба для срока службы лезвия.
Исследование под микроскопом срезанной кромки показало бы, что кромка образуется за счет комбинации переворачивания, глубины резания, излома и образования заусенцев.
Окончательное состояние кромки будет в первую очередь определяться боковым зазором лезвий. От того, острые ли лезвия или хорошо ли они используются, также зависит окончательное состояние кромок.
По мере увеличения пластической деформации начинается опрокидывание кромки по мере продолжения проникновения лезвия. Опрокидывание кромки — это пластический поток, вызванный комбинацией сжимающей силы, пары сил, создаваемой давлением сдвига, и боковым зазором между лезвиями. (см. Рисунок 3 ).
Рисунок 3: Эти рисунки иллюстрируют эффекты опрокидывания кромки, вызванные сжимающей силой, силой, создаваемой срезанием, и боковым зазором между лезвиями. |
По мере увеличения глубины проникновения лезвия образуется полированная поверхность. Эта поверхность относительно плоская, гладкая и твердая и обычно составляет небольшую часть толщины скелпа. По мере протягивания скелпа через лезвия проникновение увеличивается до тех пор, пока не будет превышен предел прочности скелпа. Затем происходит разрушение.
Поверхность трещины выглядит зернистой и составляет большую часть толщины скелпа по глубине.
Далее идет фреза. Он присутствует почти всегда и является результатом смещения при сжатии, образованного радиусом (тупой частью) лопастей.
Состояние кромки после продольной резки
Было бы неуместно обсуждать стандарты качества для обрезанной кромки при производстве труб и труб для ВПВ, не глядя на то, что определяет общее качество скелпа.
Операторы трубных заводов ERW понимают, что операция продольной резки рулонов и боковой обрезки может вызвать проблемы с качеством, которых не было у поступающих рулонов. Продольная резка и боковая обрезка не влияют на такие свойства, как химический состав или твердость скелпа, но они могут влиять на внешний вид поверхности, размер ширины, плоскостность, выпуклость и волнистость края.Это может повлиять на окончательное качество и пригодность трубы или трубки.
Рисунок 4: На этом рисунке показаны поверхности кромок, образованные различными зазорами лезвий. |
Если скелп не удерживается поперечно опорными роликами на всю ширину и верхними прижимными роликами на входной и выходной сторонах продольно-резательного / бокового триммера, он будет изгибаться ближе к центру, и ширина обрезки будет быть больше, чем ожидалось.Особенно это касается скелпа для большой трубы.
Важными характеристиками качества скелпа для производства приемлемых труб и трубок для ВПВ являются:
1. Внешний вид поверхности.
2. Физическая форма.
3. Точность размеров.
4. Постоянство физической прочности.
5. Обработка кромочной поверхности.
Наиболее распространенным элементом управления технологическим процессом, который, по-видимому, оказывает наибольшее влияние на состояние обработки кромочной поверхности, является зазор лезвия. На рисунке 4 показаны поверхности кромок, образованные различными зазорами между лезвиями.
Зазор между ножами всегда рассчитывается как процент от толщины скелпа. На рисунке 4 показаны два типа ребер и перечислены данные для пяти типов ребер.
Данные из такой таблицы, которую оператор комбината должен собирать с течением времени, являются хорошей отправной точкой для разработки статистического управления процессом (SPC). Доступно несколько устройств для электронного измерения качества поверхности в микродюймах.
Самый простой метод определения состояния срезанной кромки — это визуальное сравнение срезанной кромки с приемлемым стандартом. Этим стандартом может быть механически обработанная поверхность, представляющая собой хорошо срезанную кромку.
Другие элементы производства трубных заводов, которые влияют на качество стружки для изготовления труб и труб из ВПВ, включают оборудование, инструменты, техническое обслуживание и рабочие процедуры.
Хотя некоторые неровности кромки скатываются на лицевую поверхность скелпа и могут вызывать некоторые проблемы при сварке, другие настолько прочные, что сопротивляются скатыванию на лицевую поверхность и сглаживанию.
Доступны по крайней мере два различных типа оборудования для улучшения поверхности отделения скелпа после ротационной боковой обрезки или продольной резки. Более старый из этих двух — строгальный станок, иногда называемый зигзагом. Другой тип — кромкофрезер.
Кромкофрезерный станок может использоваться вместе с существующим устройством боковой обрезки или может использоваться исключительно для подготовки кромки фрезерования рулонов. Обычно кромкофрезерный станок может снимать от 10 до 15 миллиметров с каждой стороны при стандартной производительности.При пониженной производительности кромкофрезерный станок может снимать 1-1 / 2 дюйма (37,5 мм) с каждой стороны.
Резюме
В условиях жесткой конкуренции на рынке, требующей продуктов высочайшего качества и надежности, производители труб и трубок должны выполнять все процессы в полной мере. Ничто меньшее не удовлетворит клиента.
Производители труб и труб должны разработать сравнительный метод, который предупредит их о типе срезанной кромки, перемещающейся в трубный стан. Исходя из этого, они могут разрабатывать диаграммы SPC на пути к производству прецизионных кромок скелпа.Эти диаграммы могут даже указывать на то, что существующего оборудования недостаточно для изготовления кромок, которые позволяют улучшить сварку.
.Документ не найден — PTC.com
PTC.com- Магазин
- EN
- Войти
- Почему PTC
- Преимущества PTC
- Что мы делаем
- Истории клиентов
- Информация о компании
- История
- Быстрые факты
- Управленческая команда
- Карьера
- Корпоративная ответственность
- Офисы по всему миру
- Свяжитесь с нами
- Пресса и СМИ
- Новости
- Связи с инвесторами
- Каталог социальных сетей
- Преимущества PTC
- Решения
- Общие проблемы
- Интернет вещей
- корпоративных приложений
- Управление жизненным циклом продукта
- Компьютерное проектирование
- Управление жизненным циклом услуг
- Общие проблемы
- Продукты
- Семейства продуктов
- PTC Creo
- PTC Windchill
- PTC Arbortext
- PTC Mathcad
- Целостность PTC
- PTC Servigistics
- ThingWorx
- Все товары
- Ключевые темы
- Работа в среде с несколькими САПР
- 3D CAD
- Визуализация
- PLM для розничной торговли
- Управление производственными процессами
- Глобальная разработка продуктов
- Качество продукции в мире
- Гибкое моделирование
- Ресурсы для продукта
- Бесплатные загрузки
- Как купить
- Обучение
- Академическая программа PTC
- Истории клиентов PTC Creo
- Бесплатная 30-дневная пробная версия PTC Creo
- Справочные центры PTC
- Семейства продуктов
- Услуги
- Услуги
- Услуги обучения
- Стратегические услуги
- Услуги по развертыванию
- Обучение и усыновление
- Услуги по оптимизации
- Облачные службы
- Услуги по обновлению Windchill 11
- Услуги
- Сообщества
- Сети
- Сообщество PTC
- Партнеры
- Академическая программа PTC
- Каталог социальных сетей
- Блоги
- Истории жизненного цикла продукта
- PTC Creo
- PTC Mathcad
- Руководитель службы
- События
- LiveWorx
- Интернет-трансляции и семинары
- Сети
- Поддержка
- Техническая поддержка
- Портал электронной поддержки
- Загрузки программного обеспечения
- Обновления безопасности PTC
- Сообщить об уязвимости системы безопасности
- Глобальная служба поддержки
- Изучить решения для поддержки
- Центр обслуживания клиентов
- Техническая поддержка
Документ не найден — PTC.com
PTC.com- Магазин
- EN
- Войти
- Почему PTC
- Преимущества PTC
- Что мы делаем
- Истории клиентов
- Информация о компании
- История
- Быстрые факты
- Управленческая команда
- Карьера
- Корпоративная ответственность
- Офисы по всему миру
- Свяжитесь с нами
- Пресса и СМИ
- Новости
- Связи с инвесторами
- Каталог социальных сетей
- Преимущества PTC
- Решения
- Общие проблемы
- Интернет вещей
- корпоративных приложений
- Управление жизненным циклом продукта
- Компьютерное проектирование
- Управление жизненным циклом услуг
- Общие проблемы
- Продукты
- Семейства продуктов
- PTC Creo
- PTC Windchill
- PTC Arbortext
- PTC Mathcad
- Целостность PTC
- PTC Servigistics
- ThingWorx
- Все товары
- Ключевые темы
- Работа в среде с несколькими САПР
- 3D CAD
- Визуализация
- PLM для розничной торговли
- Управление производственными процессами
- Глобальная разработка продуктов
- Качество продукции в мире
- Гибкое моделирование
- Ресурсы для продукта
- Бесплатные загрузки
- Как купить
- Обучение
- Академическая программа PTC
- Истории клиентов PTC Creo
- Бесплатная 30-дневная пробная версия PTC Creo
- Справочные центры PTC
- Семейства продуктов
- Услуги
- Услуги
- Услуги обучения
- Стратегические услуги
- Услуги по развертыванию
- Обучение и усыновление
- Услуги по оптимизации
- Облачные службы
- Услуги по обновлению Windchill 11
- Услуги
- Сообщества
- Сети
- Сообщество PTC
- Партнеры
- Академическая программа PTC
- Каталог социальных сетей
- Блоги
- Истории жизненного цикла продукта
- PTC Creo
- PTC Mathcad
- Руководитель службы
- События
- LiveWorx
- Интернет-трансляции и семинары
- Сети
- Поддержка
- Техническая поддержка
- Портал электронной поддержки
- Загрузки программного обеспечения
- Обновления безопасности PTC
- Сообщить об уязвимости системы безопасности
- Глобальная служба поддержки
- Изучить решения для поддержки
- Центр обслуживания клиентов
- Техническая поддержка