РД 26.260.15-2001 Стилоскопирование основных и сварочных материалов и готовой продукции
РД 26.260.15-2001
Дата введения 2002-11-22
ЛИСТ УТВЕРЖДЕНИЯ
РД 26.260.15-2001
СТИЛОСКОПИРОВАНИЕ ОСНОВНЫХ И СВАРОЧНЫХ МАТЕРИАЛОВ И
ГОТОВОЙ ПРОДУКЦИИ
Генеральный
директор ОАО «ВНИИПТхимнефтеаппаратуры» | В.А.Панов |
Заместитель
генерального директора ОАО «ВНИИПТхимнефтеаппаратуры» | В.Л.Мирочник |
Заведующий
отделом стандартизации | В.Н.Заруцкий |
Заведующий
отделом N 29 | С. |
Заведующий
лабораторией N 56 | Л.В.Овчаренко |
Разработчик,
старший научный сотрудник | Л.В.Гурьева |
Зав. сектором стандартизации | Т.В.Мухина |
СОГЛАСОВАНО | |
Заместитель
генерального директора по научно-производственной деятельности | В.В.Раков |
УТВЕРЖДЕНО
Председатель ТК 260
«Оборудование химическое и нефтегазоперерабатывающее» В.А.Заваров 2001
1
РАЗРАБОТАН ОАО «Волгоградский научно-исследовательский и проектный
институт технологии химического и нефтяного аппаратостроения» (ОАО
«ВНИИПТхимнефтеаппаратуры) по заданию Госгортехнадзора России.
Коллектив авторов:
Курдюмова A.M., Гурьева Л.В., Мирочник В.Л., Хапонен Н.А.
2
УТВЕРЖДЕН И ВВЕДЕН В ДЕЙСТВИЕ Техническим комитетом N 260
«Оборудование химическое и нефтегазоперерабатывающее» Листом
Утверждения от 20.12.2001
3
СОГЛАСОВАН письмом Госгортехнадзора России N 12-06/959 от
22.11.2002
4
ВЗАМЕН «Инструкции по стилоскопированию основных и сварочных
материалов и готовой продукции», согласованной с ГГТН РФ письмом N
12-6/1108 от 10.12.96
1 ОБЛАСТЬ ПРИМЕНЕНИЯ
Настоящий руководящий
документ является переработанным и расширенным продолжением
«Инструкции по стилоскопированию основных и сварочных материалов и
готовой продукции» согласованной с ГГТН РФ письмом от N 12-6/1108
от 10.12.96 и распространяется на сосуды, аппараты, все детали
аппаратов (обечайки, днища, патрубки, сварные соединения и др.), а
также на исходные материалы в виде проката, сварочных проволок,
промежуточных деталей на различных этапах технологического процесса
и т.
Настоящий руководящий документ предусматривает определение химического состава вышеназванных объектов методом стилоскопирования с целью установления соответствия типа использованной стали и сварочных материалов чертежам и РД по сварке, отраслевым стандартам и руководящим документам с помощью стационарных и переносных стилоскопов.
РД охватывает марки сталей, наиболее распространенные в нефтяном, химическом и газовом аппаратостроении, к числу которых относятся стали низколегированные 15ХМ, 40ХМФА, 35Х, 10Х2ГНМ, 30ХМА, 16ГС, 09Г2С, легированные 15Х5М, 15Х5ВФ, 12Х8ВФ, 20Х13 и высоколегированные 12Х18Н9, 04Х18Н10, 08Х17Н13М2Т, 10Х17Н13МЗТ, 20Х25Н20С2, ХН32Т, 06ХН28МДТ и др.
2 НОРМАТИВНЫЕ ССЫЛКИ
В
настоящем руководящем документе использованы ссылки на следующие
стандарты, правила и другие источники:
ГОСТ
495-92* Листы и полосы медные. Технические условия
________________
*
На территории Российской Федерации действует ГОСТ
1173-2006.
ГОСТ
1012-72 Бензины авиационные. Технические условия
ГОСТ
1435-90* Прутки, полосы и мотки из инструментальной нелегированной
стали. Общие технические условия
________________
*
На территории Российской Федерации действует ГОСТ
1435-99. Здесь и далее. — Примечание изготовителя базы
данных.
ГОСТ
2424-83 Круги шлифовальные. Технические условия
ГОСТ
12.1.005-88 ССБТ. Общие санитарно-гигиенические требования к
воздуху рабочей зоны
ГОСТ
12.2.007.0-75 ССБТ. Изделия электротехнические. Общие требования
безопасности
ОСТ 26-291-94 Сосуды и аппараты стальные сварные. Общие технические условия
СН 245-71 Санитарные нормы проектирования промышленных предприятий
СНиП 3.05.05-84 Технологическое оборудование и технологические трубопроводы
ПБ 03-108-96* Правила устройства и безопасной эксплуатации технологических трубопроводов
________________
* На территории Российской Федерации действуют ПБ 03-585-03.
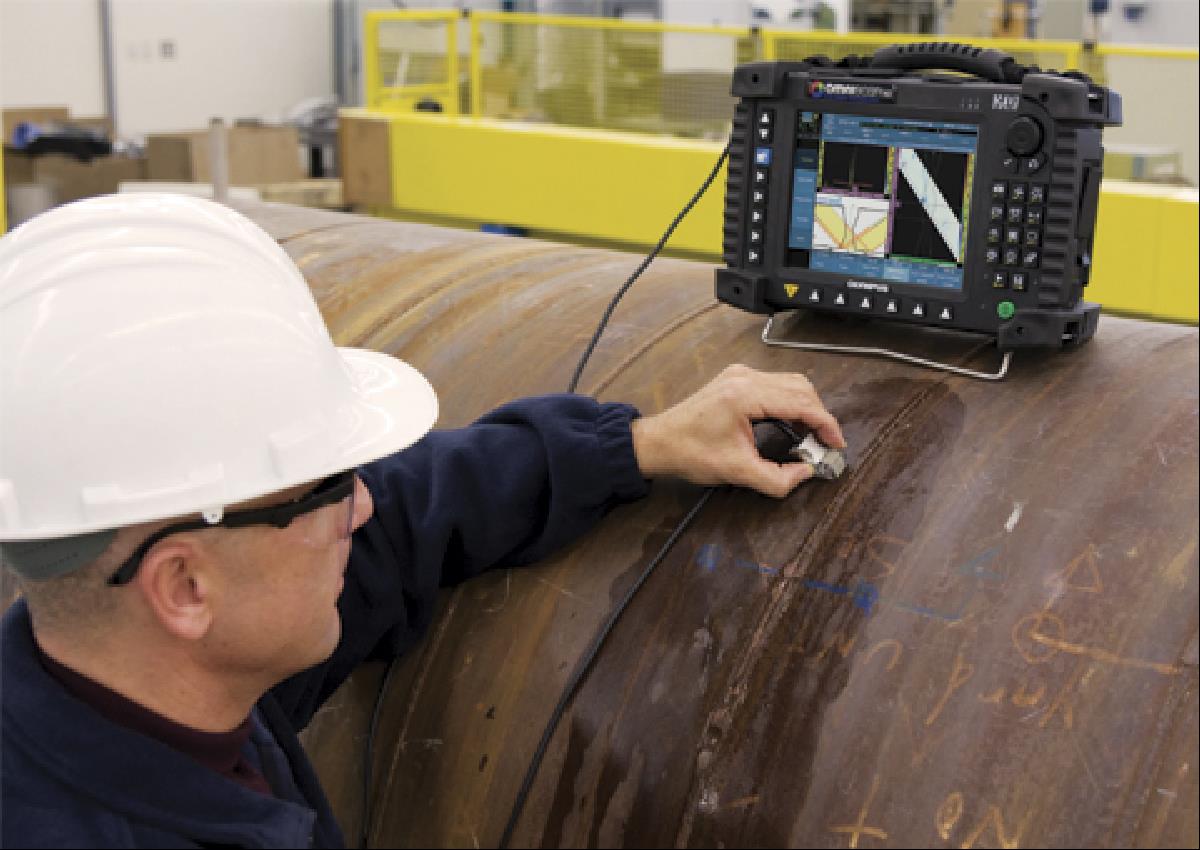
ПБ 09-170-97* Общие правила взрывобезопасности для взрывопожароопасных химических, нефтехимических и нефтеперерабатывающих производств
* На территории Российской Федерации действуют Правила безопасной эксплуатации и охраны труда для нефтеперерабатывающих производств. — Примечание изготовителя базы данных.
ПБ 10-115-96* Правила устройства и безопасной эксплуатации сосудов, работающих под давлением
______________
* На территории Российской Федерации действуют ПБ 03-576-03. — Примечание изготовителя базы данных.
Правила по устройству и содержанию лаборатории и пунктов спектрального анализа, обязательные для всех министерств, ведомств и учреждений
РД 009-364-00 Типовая инструкция по организации безопасного проведения огневых работ на взрывоопасных и взрывопожарных объектах
ТУ 48-19-102-82 Молибденовые стержни для переносных стилоскопов
ТУ 48-19-57-73 Вольфрамовые стержни для переносных стилоскопов
Типовая инструкция по организации безопасного проведения газоопасных работ / Утв.
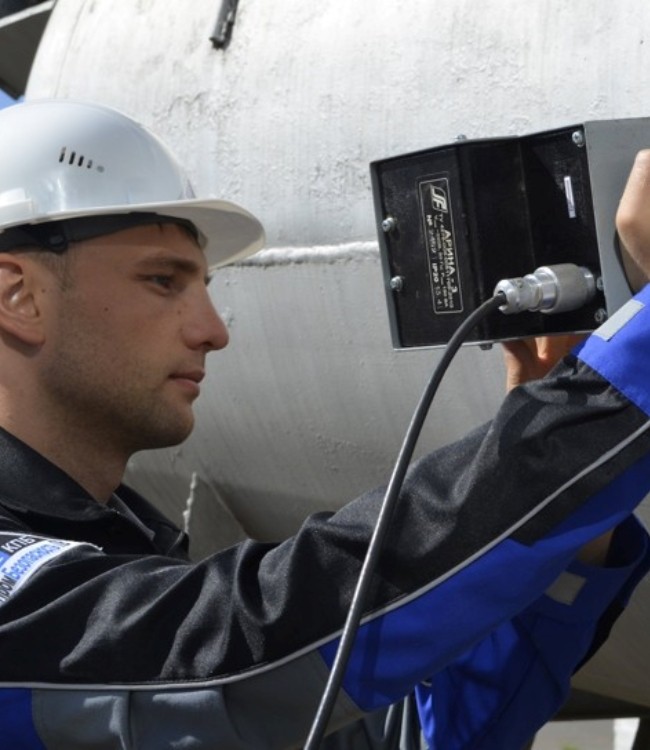
Правила
технической эксплуатации электроустановок потребителей / Утв.
Госэнергонадзор РФ 31.03.92
ПОТ
РО-14000-005-98 Положение. Работы с повышенной опасностью.
Организация проведения.
Правила
техники безопасности при эксплуатации электроустановок
потребителей* / Утв. Госэнергонадзор РФ
* На территории Российской Федерации действуют «Межотраслевые правила по охране труда (правила безопасности) при эксплуатации электроустановок» (ПОТ Р М-016-2001, РД 153-34.0-03.150-00). Здесь и далее. — Примечание изготовителя базы данных.
Общеминистерские нормы
обслуживания для вспомогательных рабочих цехов основного и
вспомогательных производств Министерства химического и нефтяного
машиностроения СССР. — М., 1977. — c.41-51
ВСН
21-77 Инструкция по проектированию отопления и вентиляции
нефтеперерабатывающих и нефтехимических предприятий
3 ОБЩИЕ ПОЛОЖЕНИЯ
3.
3.2 Стилоскопирование
металла свариваемых деталей и металла шва производится с целью
установления соответствия марки использованных для сварки
материалов требованиям соответствующих НТД и ТУ на изготовление
изделия.
Обязательному
стилоскопированию должны подвергаться в изготовленном сосуде детали
корпуса, находящегося под давлением (обечайки, днища, патрубки,
фланцы) из низко-, средне- и высоколегированных марок сталей, а
также соединяющие их сварные швы в объеме и местах, установленных
заводами-изготовителями.
Стилоскопирование следует производить на зачищенных до блеска участках (площадках) поверхности.
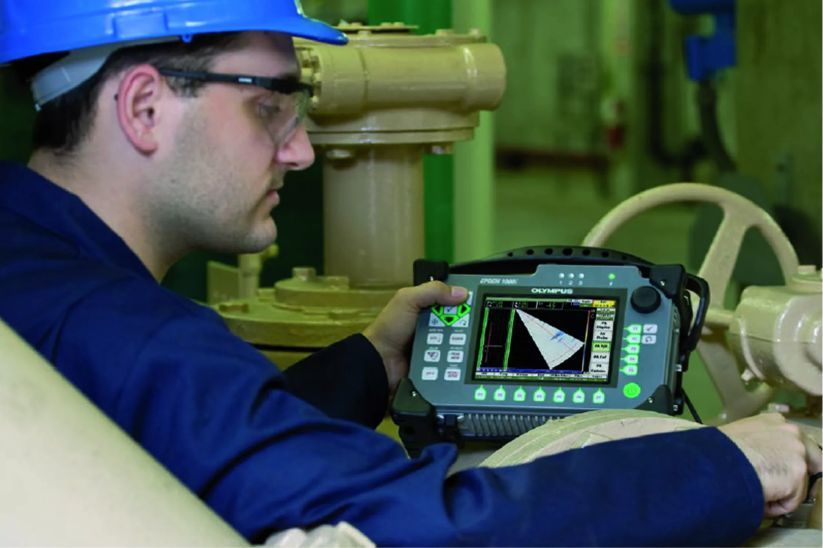
Выполнение стилоскопирования металла свариваемых деталей и металла сварного шва следует осуществлять с помощью переносных стилоскопов. На сварных соединениях, выполнявшихся одновременно двумя сварщиками, стилоскопированию должны подвергаться два диаметрально противоположных участка шва. В остальных случаях стилоскопирование может производиться на одном участке.
В случае неудовлетворительных результатов производится повторное стилоскопирование металла свариваемых деталей и металла шва в 3-х различных участках.
При выявлении несоответствия марки используемой стали или сварного соединения хотя бы на одной детали, проверенных в неполном объеме, стилоскопированию должны быть подвергнуты все однотипные детали, сварные соединения, узлы.
Результаты стилоскопирования на соответствие марки стали использованных материалов требованиям технических условий на изготовление изделия должны быть зафиксированы в специальном журнале с выдачей соответствующих протоколов.
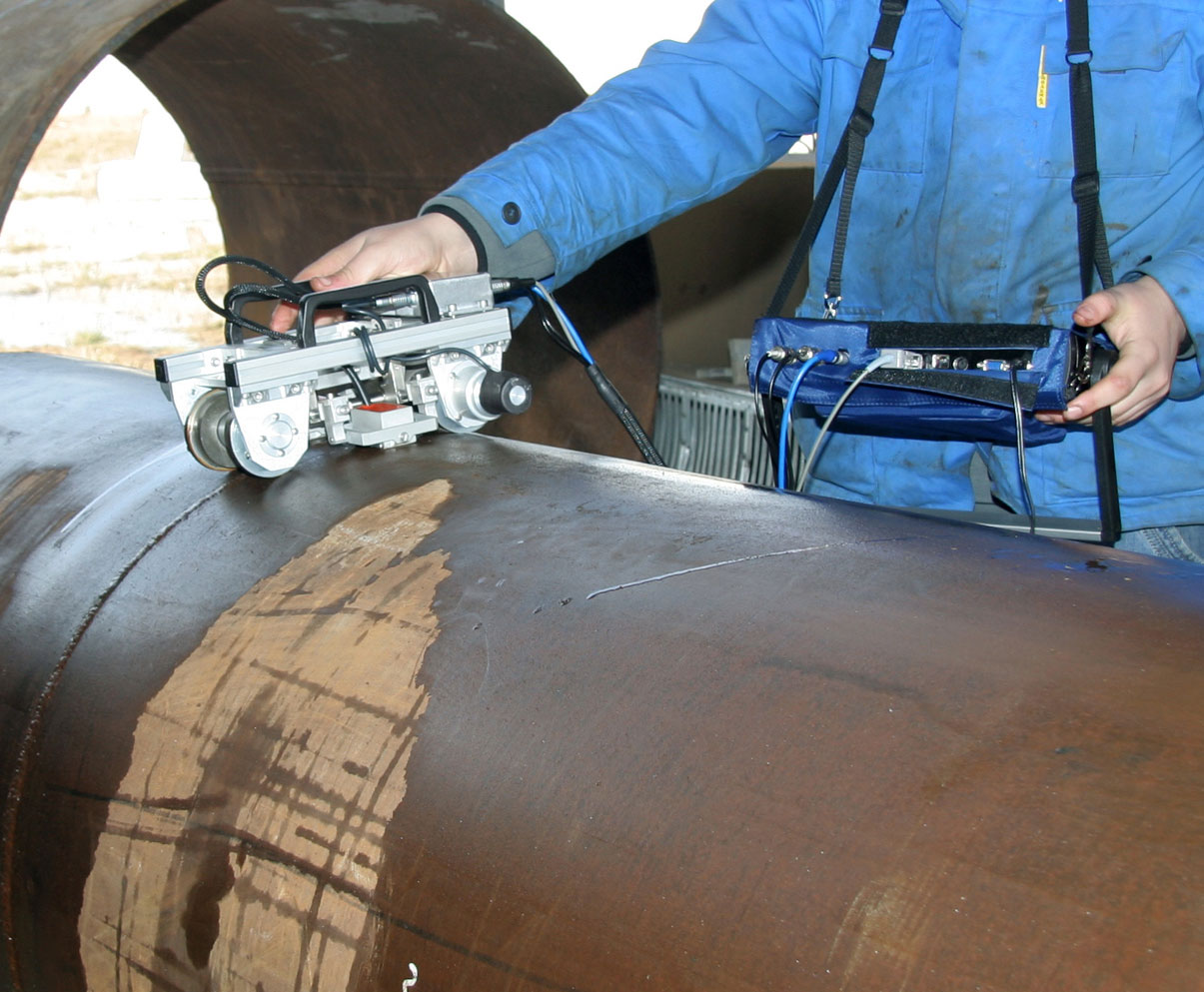
Контроль стилоскопированием не производится:
— при невозможности осуществления контроля вследствие недоступности сварных швов;
— по условиям техники безопасности.
4 СТИЛОСКОПИЧЕСКИЙ КОНТРОЛЬ ХИМИЧЕСКОГО СОСТАВА СТАЛЕЙ, СВАРНЫХ СОЕДИНЕНИЙ
4.1 Сущность работы на стилоскопе
Полуколичественный анализ
при помощи стилоскопа производится следующим образом: между
образцом и вспомогательным или «постоянным» электродом зажигается
дуговой разряд. Его излучение направляется на входную щель
стилоскопа. Горение дуги сопровождается переносом вещества
электрода с одного полюса на другой. Поэтому заточку постоянного
электрода необходимо производить перед каждым новым анализом.
Для установления
количественного содержания элемента в сплаве пользуются оценкой
относительной интенсивности анализируемой линии и линии
сравнения.
Однако возможности глаза
как измерительного прибора ограничены. Глаз не может достаточно
точно определить отношение интенсивностей двух спектральных линий. Но он очень чувствителен к установлению равенства или неравенства
интенсивностей двух световых линий (двух спектральных линий). На
этом принципе и основан метод количественного анализа с помощью
стилоскопа.
4.2 Приборы и материалы. Вспомогательное оборудование
4.2.1 Приборы
Все виды стационарных
стилоскопов, выпускаемые в СССР ранее и в настоящее время в РФ, к
числу которых относятся СЛ-10, СЛ-11, «Спектр», а также переносные
типа СЛП-1, СЛП-3, СЛП-4, СЛУ-1 (в двух вариантах — стационарном и
переносном) и «Метаскоп» фирмы Крауткремер производства ФРГ.
4.2.2 Материалы
Медные дисковые электроды
для стационарных стилоскопов, изготовленные из меди марки М2
(ГОСТ
495), стальные из стали У7 (ГОСТ
1435). Молибденовые и вольфрамовые стержни для переносных
стилоскопов (ТУ 48-19-102 и ТУ 48-19-57 соответственно), размеры и
форма которых рекомендованы в описании к прибору; комплекты
эталонов различных марок сталей, выпускаемых ВНИИСО, необходимые
для проверки и разработки стилоскопических признаков оценки
содержания легирующих элементов.
4.2.3 Вспомогательное
оборудование
Круги шлифовальные
(ГОСТ
2424) из электрокорундовых материалов для заточки поверхности
проб при работе на стационарных стилоскопах, набор напильников для
заточки анализируемой поверхности изделий при приведении
стилоскопического контроля химического состава с применением
переносных стилоскопов.
4.3 Подготовка к анализу
4.3.1 Подготовка
электродов и образцов
Подготовка электродов
включает в себя заточку электродов с помощью токарного станка
(медные, железные стержневые электроды для стационарных
стилоскопов), заточку с помощью круга молибденовых и вольфрамовых
электродов для переносных стилоскопов. Дисковые медные электроды
затачиваются по периметру напильником.
При заточке электродов не
требуется строгого сохранения форм, но необходимо, по возможности,
придерживаться единообразия в их подготовке. Новая форма заточки
влечет за собой необходимость проверки стилоскопических признаков
по образцам с известным химическим составом.
Перед началом работы
анализируемая поверхность образца должна быть тщательно зачищена.
Проба, анализируемая на стационарных стилоскопах, может быть
заточена на токарном, фрезерном станках, наждачном круге или
напильником.
В
образце для заточки при обработке поверхности напильником или на
наждачном круге выбирается небольшой плоский участок. Зачищенная
поверхность должна быть не менее 20х20 мм. Окалина,
антикоррозионные покрытия, ржавчина, жировые и прочие загрязнения,
а также дефекты в виде пор, шлаковых включений, трещин, раковин и
других пороков поверхности подлежат удалению. Если анализируемый
образец проходил травление или химическую обработку, то при
зачистке этот слой необходимо снять вышеописанным способом.
Анализ готовых изделий,
крупных заготовок и прочих объектов, не подлежащих транспортировке
в лабораторию, выполняется переносными стилоскопами. В этом случае
поверхность пробы зачищается напильником.
4.3.2 Подготовка прибора
к работе
После выполнения работ по
2.2.1 при проведении стилоскопического контроля на стационарных
стилоскопах типа «Спектр» произвести установку пробы и в
зависимости от аналитических задач установить один из режимов
источников возбуждения спектра.
Включить прибор.
Готовность прибора к работе, порядок работы указаны в техническом
описании и инструкции по эксплуатации прибора.
Убедившись в правильности
выполненных операций, нажать кнопку «пуск», зажечь дугу или искру,
отыскать нужную группу линий и после соответствующего
рекомендованного для данного элемента времени обыскривания
произвести оценку содержания его в пробе (таблица 1).
Стилоскопические признаки определения содержания
легирующих элементов
Марка
сталей | Группа
линий | Область
спектра | Признаки
сравнения | Пределы
опреде- | Условия | Допол- | Комплект
эталонов ВНИИСО для проверки приз- | |
1 | 2 | 3 | 4 | 5 | 6 | 7 | 8 | |
ОПРЕДЕЛЕНИЕ
ХРОМА | ||||||||
35Х, 15ХМ,
30ХМ | Cr | 1Cr<7 | до 0,2 | дуга
постоянного тока, ток 3 А, фаза поджига 90°, количество импульсов
100 в секунду, время предвари- | Мо, Ni, V,
W | 20, 21, 22, 34, 29 и др. | ||
1Cr=7 | 0,3-0,4 | |||||||
2Cr=7 | 0,6-0,8 | |||||||
1Cr=6 | 1,0 | |||||||
1Cr>6 1Cr5 | 1,5 | |||||||
2Cr=6 | 2,0-2,5 | |||||||
15Х5М, 15Х5, 20Х13М, 20Х13 | Cr | 4Cr<3 1Cr — видна слабо | 3,0-4,0 | то же | Mo, Ni, V, W,
Ti | 14, 36, 93 и
др. | ||
4Cr<3 1Cr — видна отчетливо | 6,0 | |||||||
4Cr=3 | 8,0 | |||||||
4Cr>3 1Cr<2 | 10,0-12,0 | |||||||
4Cr>>3 1Cr=2 | 15,0 | |||||||
1Cr>2 | 18,0 | |||||||
12Х18Н10Т, 04Х18Н9, 06ХН28МДТ, 20Х25Н20С2, 08Х17Н13М2Т | Cr | 1Cr=2 | 16,0 | дуга
постоянного тока, ток 3 А, фаза поджига 90°, количество импульсов
100 в секунду, время предвари- | Мо, Ni, V, W,
Ti | 9, 27, 45, 64,
31 | ||
1Cr>2 1Cr<3 | 20,0 | |||||||
1Cr>3 | 25,0 | |||||||
стилоскопирование и анализ состава металла в Санкт-Петербурге
Анализ качества выполненных сварочных работ (или тест на состав металла в сплавах) проводится по-разному. В ряде случаев производится срез сварного шва, или его подвергают воздействию давлением, чтобы определить его сопротивления усилию. Но наиболее подходящим для решения данной задачи считается стилоскопирование, один из методов неразрушающего контроля, направленный на анализ состава и количества легирующих примесей и дающий определенное представление о качестве и надежности сварного шва. Считается, что проверить состав металла именно таким способом будет гораздо эффективнее и проще, чем прибегнуть к разрушающим методам контроля.
Данная проверка состава и структуры металла основывается на свойстве каждого легирующего элемента создавать свой уникальный спектр, в процессе пропуска его паров от электрической дуги через призму, с определенной широтой и яркостью отдельных линий (в луче из семи цветов). Для оценки результатов разработаны специальные тематические атласы, которые содержат спектры всех основных веществ. Осуществляющий стилоскопирование специалист сопоставляет показания в окуляре стилоскопа с известными элементами в атласе. Преобладание того или иного спектра говорит о характере и количестве вещества, входящего в состав стали.
Стилоскопирование, или спектральный анализ металла производится и в стационарных условиях, с помощью больших аппаратов, и на выезде, посредством компактных моделей.
Более подробно принцип действия стилоскопирования выглядит следующим образом:
- В процессе анализа, между двумя электродами (один электрод установлен на приборе, второй – это анализируемая проба) возбуждается, путем нагревания, импульсный электрический разряд.
- Излучение элементов, возбужденных в разряде атомов и входящих в состав пробы, улавливается полихроматором с вогнутой дифракционной решеткой и раскладывается в спектр.
- Благодаря тому, что каждый химический элемент имеет свою совокупность спектральных линий, обусловленную концентрацией элемента в пробе, удается установить характер, состав и количество того или иного элемента в металле.
- Полученный в ходе успешного анализа спектр расшифровывают с помощью специально разработанных таблиц и атласов спектров.
- Чтобы провести количественный анализ пробы, из спектра выделяют одну или несколько аналитических линий анализируемого элемента. Рассчитывается данная величина с помощью следующей формулы:
J(l ) = а × сb, где J – это интенсивность спектральной линии, l – длина, с — концентрацией элемента в пробе, а и b — величины, зависящие от условий анализа.
Методы контроля сосудов и аппаратов ГОСТ 34347-2017
Главная / Проектировщику / Справочная информация – ГОСТ СНИП ПБ / ГОСТ 34347-2017 /Версия для печати7.1 Общие требования
7.1.1 Геометрические размеры и форму поверхностей необходимо измерять с помощью средств, обеспечивающих погрешность не более 30 % установленного допуска на изготовление.
Габаритные размеры сосудов необходимо определять путем суммирования размеров входящих в них сборочных единиц и деталей.
7.1.2 Контроль качества поверхностей на отсутствие плен, закатов, расслоений, грубых рисок, трещин, снижающих качество и ухудшающих товарный вид. необходимо проводить путем визуального и измерительного контроля.
На поверхности сосуда не допускаются риски, царапины, вмятины и другие дефекты, превышающие требования стандартов или технических условий на поставку основного материала.Недопустимые дефекты исправляют в соответствии с 5.6.5.
7.1.3 Обязательную проверку наличия, содержания, мест расположения клейм на сварных швах и маркировки на готовом сосуде (самостоятельно поставляемых сборочных единицах и деталях) необходимо осуществлять визуальным осмотром.
7.1.4 Контроль качества сварных соединений необходимо проводить:
а) визуальным и измерительным контролем;
б) механическими испытаниями;
в) испытанием на стойкость к межкристаллитной коррозии;
г) металлографическими исследованиями;
д) стилосколированием сварных швов;
е) ультразвуковым контролем;
ж) радиографическим контролем;
и) капиллярным или магнитопорошковым контролем;
к) другими методами (акустической эмиссией, люминесцентным контролем, определением содержания ферритной фазы и др.), если необходимо.
7.1.5 Окончательный контроль качества сварных соединений сосудов, подвергаемых термической обработке, необходимо проводить после термической обработки.
Для сварных соединений сосуда из низколегированных марганцовистых и марганцево-кремнистых сталей или двухслойных сталей с основным слоем из этих сталей, подвергаемых в процессе изготовления нормализации или закалке с отпуском, механические испытания и металлографические исследования допускается проводить до окончательной термической обработки (высокого отпуска).
При этом полученные положительные результаты механических испытаний необходимо считать окончательными.
7.1.6 Контроль комплектности, консервации, окраски, упаковки необходимо проводить путем сопоставления объема и качества выполненных работ с требованиями настоящего стандарта и технических условий.
7.1.7 Предприятие-изготовитель негабаритных сосудов, транспортируемых частями, должно провести контрольную сборку.
Допускается вместо сборки проводить контрольную проверку размеров стыкуемых частей при условии, что предприятие-изготовитель гарантирует собираемость сосуда.
7.1.8 В процессе изготовления сборочных единиц и деталей необходимо проверять на соответствие требованиям стандартов (технических условий) и проектной документации:
- состояние и качество свариваемых сборочных единиц и деталей и сварочных материалов;
- качество подготовки кромок и сборки под сварку;
- соблюдение технологического процесса сварки и термической обработки.
7.2 Визуальный и измерительный контроль сварных соединений
7.2.1 визуальный контроль и измерение сварных швов необходимо проводить после очистки швов и прилегающих к ним поверхностей основного металла от шлака, брызг и других загрязнений.
7.2.2 Обязательному визуальному и измерительному контролю подлежат все сварные швы в соответствии с действующей НТД и ГОСТ 3242 для выявления дефектов, выходящих на поверхность шва и не допустимых в соответствии с требованиями настоящего стандарта. Визуальный и измерительный контроль необходимо проводить в доступных местах с двух сторон по всей протяженности шва.
7.3 Механические испытания
7.3.1 Механическим испытаниям необходимо подвергать стыковые сварные соединения, определяющие прочность сосуда. К стыковым соединениям, определяющим прочность сосуда, следует относить продольные швы обечаек, хордовые и меридиональные швы выпуклых днищ. Механические испытания необходимо проводить на контрольных стыковых сварных соединениях в объеме, указанном в таблице 17.
7.3.2 Измерению твердости необходимо подвергать металл шва сварных соединений сосудов (работающих под давлением деталей) из сталей, указанных в таблице 14. и металл шва коррозионно-стойкого слоя в сварных соединениях из двухслойных сталей.
7.3.3 Допускается проводить измерение твердости металла шва на контрольных образцах, если невозможно его осуществить на готовом сосуде (детали). Твердость необходимо проверять не менее чем в трех точках поперек сварного соединения.
При получении неудовлетворительных результатов по какому-либо виду механических испытаний допускается проведение повторного испытания на удвоенном количестве образцов, вырезанных из того же контрольного сварного соединения, по тому виду механических испытаний, которые показали неудовлетворительные результаты. Если при повторном испытании получены неудовлетворительные результаты хотя бы на одном образце, сварное соединение считают непригодным.
Таблица 17. Объем механических испытаний контрольных сварных соединений
Вид испытания | Группа сосуда | Количество образцов | Примечание |
---|---|---|---|
Растяжение при температуре 20 °С | 1—5 |
Две образца типов XII, XIII, XIV или XV по ГОСТ 6996 |
Испытание на растяжение отдельных образцов из сварных трубных стыков можно заменить испытанием на растяжение целых стыков со снятым усилием |
Изгиб при температуре 20 °С |
1—5 |
Два образца типов XXVII. XXVIII по ГОСТ 6996 |
Испытание сварных образцов труб внутренним диаметром до 100 мм и толщиной стенки до 12 мм может быть заменено испытанием на сплющивание по ГОСТ 6996 (образцы типов XXIX. XXX) |
Ударная вязкость на об- разцах KCV или KCU (при толщине металла не менее 12 мм) при температуре 20°С |
1—5 из сталей, склонных к тер- мическому воз- действию (12МХ, 12ХМ, 15Х5М и др.) |
Три образца типа VI или IX по ГОСТ 6996 с над- резом по оси шва |
Испытание на ударный изгиб зоны термического влияния проводят на сварных соединениях, выполненных электрошлакоеой сваркой без последующей нормализации, а также при наличии требований в технических условиях* или проектной документации |
Ударная вязкость на об- разцах KCV или KCU (при толщине металла не менее 12 мм) при температуре 20 °С |
1—3 при давлении более 5 МПа. 1—2 при темпера- туре св. 450°С |
Три образца типа VI или IX по ГОСТ 6996 с над- резом по оси шва |
Испытание на ударный изгиб зоны термического влияния проводят на сварных соедине |
Спектральный анализ сварных соединений
Рекомендуем приобрести:
Установки для автоматической сварки продольных швов обечаек — в наличии на складе!
Высокая производительность, удобство, простота в управлении и надежность в эксплуатации.
Сварочные экраны и защитные шторки — в наличии на складе!
Защита от излучения при сварке и резке. Большой выбор.
Доставка по всей России!
Спектральный анализ (стилоскопирование) является одним из методов контроля без разрушения изделий.
Его проводят для установления марки используемых сварочных материалов, определения состава наплавленного металла и свариваемых деталей.
С помощью спектрального анализа за 15—20 мин можно провести: анализ легированной стали и определить содержание таких элементов, как Cr, Mo, Ti, Ni, V, Si, Mg, Mn, С, P; анализ алюминиевых сплавов на Mg, Mn, Si, Fe, Cu, Zn, Ti и бронз на Ni, Al, Fe, Mn.
Спектральный анализ проводят с помощью стилоскопов. В монтажных условиях нашли применение переносные стилоскопы типа СЛП-1, СЛП-2.
Стилоскоп СЛП-1 применяют для быстрого визуального качественного и полуколичественного анализа легированных и низколегированных сталей, а также цветных металлов. По принципу действия переносной стилоскоп аналогичен стилоскопам стационарных конструкций.
Спектральный аппарат стилоскопа СЛП-1 представляет собой автоколлимационный спектроскоп (рис. 95). Лучи, полученные при дуговом разряде между контролируемым изделием и электродом, проходят через защитные светофильтры и направляются призмой на конденсатор, который концентрирует лучи на щель спектроскопа. С помощью объектива расходящиеся лучи превращаются в параллельные, а специальными призмами разлагаются в спектр. Катет одной из этих призм посеребрен, за счет чего происходит отражение лучей в обратном направлении. Попадая снова в объектив, пучок лучей превращается уже в сходящийся, который в свою очередь через систему призм идет в окуляр, где и рассматривают спектр.
Для возбуждения дуги в стилоскопе СЛП-1 используется генератор типа ПГД-1 (рис. 96), работающий от сети переменного тока напряжением 110 или 220 в.
При включении генератора в электрическую сеть переменный ток с входной панели Ш1 через замкнутые блокировочные контакторы В3, предохранители Пр1 и Пр2, переходные колодки Ш4 и Ш5 подается на первичную обмотку разделительного трансформатора Tp1.
Нажатием кнопки на рукоятке стилоскопа заставляют срабатывать магнитный пускатель Р, включая генератор. С вторичной обмотки разделительного трансформатора через ограничительные сопротивления R1 и R2, пакетный переключатель В2, контакты магнитного пускателя Р, вторичную обмотку высокочастотного трансформатора Тр3 напряжение подводится к электроду стилоскопа. Одновременно от одной из секций вторичной обмотки Tp1 через R1 и контакторы магнитного пускателя Р напряжение (около 90 в) подается на первичную обмотку повышающего трансформатора Тр2. С повышающего трансформатора напряжение в 1800 в подводится к искровому колебательному контуру, состоящему из емкостей С7—С10, индуктивности (обмотка трансформатора) и искрового разрядника РИ.
Конденсаторы колебательного контура заряжаются от трансф
Стилоскопирование для определения содержания легирующих элементов
Стилоскопирование – качественный спектральный анализ на наличие легирующих элементов, основанный на получении с помощью электрической дуги раскаленных паров металлов на поверхности объекта контроля с последующим анализом их спектра. Стилоскопирование используется для контроля элементов котлов и трубопроводов, изготовленных из легированной стали, а также наплавленного металла сварных соединений. Метод позволяет производить оценку марочного соответствия применяемых сварочных материалов, контроль на наличие легирующих элементов в сплавах и металле. Преимуществами данного анализа являются возможность узнать состав изделия, не разрушая его, безопасность и компактность используемых аппаратов.
ООО «АРЦ НК» проводит повышение квалификации (предаттестационную подготовку) по стилоскопированию. После прохождения обучения специалист получает знания и навыки по контролю металла и сварных соединений методом стилоскопирования.
Повышение квалификации по стилоскопированию осуществляется в очной, очно-заочной и дистанционной формах. По окончанию обучения специалисту выдаются документы установленного образца.
Повышение квалификации направлено на получение практических навыков и помогает успешно сдать экзамены при аттестации персонала испытательных лабораторий по СДА-24-2009. При необходимости у обучающегося по завершению курса имеется возможность пройти аттестацию и получить удостоверение специалиста РИ. Подготовка по разрушающим и другим методам испытаний осуществляется по мере набора группы не реже одного раза в квартал.
Лицензии и свидетельства
Свидетельство об аккредитации НОАП
Свидетельство об аккредитации НОАЛ
Удостоверение ТУО
Лицензия на осуществление образовательной деятельности
Свидетельство об аттестации ЛНК
Свидетельство об аккредитации ЛНК
Свидетельство об аккредитации лаборатории разрушающих и других видов испытаний
Свидетельство СРО
Лицензия на использование ионизирующих источников излучения
Санитарно-эпидемиологическое заключение на помещения и оборудование
Санитарно-эпидемиологическое заключение по работе с ИИИ
Перечень центров по подготовке и аттестации Газпром
Сертификат соответствия СМК
Уведомление Минтруда по охране труда
Аттестат соответсвия ЦОК
Область деятельности ЦОК
Свидетельство Гемма
все, что вы хотели знать
Дефектоскопия сварных швов — обязательный этап после любой коммерческой сварки. Для тех, кто не знает, поясним. Дефектоскопия — поиск в сварном шве скрытых от глаз дефектов с применением специальных приборов или жидкостей. Один из недорогих способов дефектоскопии — капиллярный контроль сварных соединений.
Главное преимущество капиллярного контроля — он не разрушает металл и не изменяет его качественные характеристики. К тому же, такой контроль не требует дополнительного обучения сотрудников, поскольку он очень прост в применении и расшифровке. Но, несмотря на это, у капиллярного контроля есть свои особенности, которые нужно учитывать. О них мы и расскажем в этой статье. Также вы узнаете, какова сущность и технология капиллярного контроля.
Содержание статьи
Общая информация
Капиллярный контроль сварных швов — метод контроля качества, суть которого заключается в применении специальных жидкостей. Их еще называют индикаторами или пенетрантами. Такие жидкости обладают особыми свойствами. Они способны проникать в самые мелкие трещинки, оставляя при этом следы яркого цвета. Следы хорошо заметны невооруженным глазом, так что сварщик без труда может определить точное местоположение дефекта. Если дефекты очень маленькие, то можно использовать увеличительные лупы. Подобные методы контроля сварных швов эффективны и просты в использовании.
Используя капиллярный метод контроля можно обнаружить многие дефекты: начиная от трещин и пор, заканчивая прожогами и непроварами. Словом, все основные дефекты можно увидеть, не используя при этом дорогостоящего оборудования. Также можно узнать физические размеры дефекта и его точное местоположение.
Читайте также: Визуально-измертельный контроль качества
Капиллярный контроль применим ко многим материалам, будь то черный или цветной металл, различные искусственные полимеры (например, пластмасса или полипропилен), стекло и даже керамика. Так что область применения действительно большая, капиллярный контроль может найти себе применение во многих отраслях.
Разновидности капиллярного контроля
Существует две разновидности капиллярного контроля: основной и комбинированный. Основной метод заключается в том, что вы используете только технологию капиллярного контроля и ничего более. А при комбинированном методе капиллярный контроль может использоваться до любого другого контроля. Например, радиографического.
Эти методы в свою очередь имеют свои разновидности. В основном методе капиллярного контроля можно использовать либо специальный раствор, либо фильтрующую суспензию. А чтобы обнаружить результаты контроля, можно использовать хроматический, ахроматический, люминесцентный или люминесцентно-хроматический способ. Все этого относится к основному методу.
В комбинированном методе всегда используется капиллярный контроль, а также магнитный, индукционный, радиографический или любой другой метод контроля качества. Во всех этих способах нужно применять специальные жидкости, но для обнаружения результатов контроля используются приборы, характерный для каждого отдельного типа контроля качества. Например, в радиографическом методе таким прибором будет рентгеновский аппарат. В таком случае деталь сначала подвергают капиллярному контролю, а затем делают рентгеновский снимок, чтобы точно обнаружить, где располагаются дефекты.
Технология
Выше мы писали, что метод капиллярного контроля очень простой, и это правда. Сейчас мы вам подробно расскажем, как провести такой контроль. Вы сможете повторить его самостоятельно.
Для начала очистите поверхность шва. Это можно сделать с помощью любого растворителя. На поверхности не должны быть грязи, пятен от краски или от масла. Также просушите деталь, можно сделать это естественным образом на свежем воздухе. Также рекомендуем зачистить металл металлической щеткой или наждачкой. Так вы точно удалите все загрязнения и лишние вкрапления.
Но здесь есть один нюанс. Использовать щетку или наждачку нужно только в том случае, если поверхность металла неровная или пористая. Если металл относительно ровный и гладкий, то лучше ограничиться растворителем. В противном случае вы просто затрете наружные дефекты и не сможете потом обнаружить их при проведении контроля.
Далее нужно нанести пенетрант на поверхность шва. Есть несколько методов нанесения, о них мы поговорим позже. Скажем лишь, что самый простой метод — нанесение прямо из баллончика, с помощью кисти и погружение детали в емкость с пенетрантом. В последнем случае деталь нужно выдержать в жидкости от 5 минут и выше. Затем нужно удалить с поверхности излишки пенетранта. О том, как это сделать, мы тоже подробно рассказываем далее.
После того, как мы нанесли пенетрант, а затем убрали его излишки, нужно деталь просушить. После просушки нанесите на поверхность металла проявитель. Все готово. Согласитесь, ничего сложного. Так что можете приобрести баллончики с пенетрантом и проявителем, чтобы поэкспериментировать у себя в гараже. Поверьте, результата вас приятно удивит. Возможно, вы всегда считала свою сварку идеальной. Но только благодаря контролю получите по-настоящему объективную картину.
Обращаем ваше внимание, что к покупке пенетрантов нужно отнестись серьезно. Сейчас в магазинах появилось много дешевых жидкостей от неизвестных производителей, которые в лучше случае просто не дают должного результата, а в худшем — могут быть взрывоопасными или опасными для здоровья. Не экономьте на жидкостях для капиллярного контроля, они и так стоят не очень дорого по сравнению с другими способами контроля качества. Самый удобный формат жидкости — это, конечно, в баллончиках. Они равномерно распыляются на поверхность металла, что очень удобно. Рекомендуем новичкам именно жидкости в баллончиках.
Также капиллярная дефектоскопия может проводиться с помощью флуоресцентных пенетрантов. Это пенетранты, которые светятся в темноте. Для наблюдения за результатом не нужно использовать специальные очки, достаточно просто осмотреть деталь в затемненном помещении. При этом нужно использовать ультрафиолетовые лампы. В самом помещении не должно быть никаких посторонних предметов, которые могут отсвечивать.
Если используются обычные цветные пенетранты, то можно проводить осмотр детали и при дневном свете. Но мы все же рекомендуем использовать специальные яркие лампы.
Способы нанесения жидкостей
Выше мы упоминали, что пенетранты можно наносить с помощью аэрозольного баллончика или кисти. Это, пожалуй, самый примитивный и простой способ нанесения жидкости на контролируемую поверхность металла. В таких случаях жидкость сама распределяется по вглубь металла. Чтобы добиться лучших результатов можно погрузить деталь в емкость, наполненную пенетрантом. Температура пенетранта может быть от 5 до 50 градусов по Цельсию, так что можно проводить контроль даже на улице.
Но это не единственные методы нанесения жидкостей. Существуют и более продвинутые. Например, компрессионный метод, когда пенетрант подается на шов под определенным давлением. Благодаря давлению жидкость быстрее и эффективнее проникает вглубь металла. А сам контроль дает лучшие результаты по сравнению с простыми методами нанесения.
Также существует абсолютно противоположный способ нанесения жидкостей — вакуумный. Этот способ дорогостоящий, но очень эффективный. Деталь нужно поместить в вакуумную камеру и лишают ее воздуха. В результате в местах, где есть скрытые дефекты, давление сильно падает. Далее наносится жидкость, которая тут же заполняет все дефектные полости. Способ не из простых и дешевых, так что применяется в случаях, когда нужно добиться высокого качества шва и нет возможности использовать другие методы контроля.
Также можно использовать звуковые или ультразвуковые волны, которые будут воздействовать на жидкости, вгоняя их глубоко в металл. Но нужно учитывать, что такой метод деформирует дефекты, так что применяется он крайне редко.
Способы очистки
Как вы помните из технологии, после нанесения пенетранта и его выдержки нужно удалить излишки. Самый простой способ сделать это — смочить теплой водой мягкую тряпку или губку для мытья посуды и протереть ею поверхность шва. Такой способ самый экономный, не очень эффективный.
Вместо воды можно использовать растворитель. Но перед этим поверхность детали нужно как следует просушить. Этот способ очистки куда лучше тряпки с водой, но все равно недостаточно эффективен. Мы рекомендуем комбинировать протирание водой и протирание растворителем. Если вы готовы потратиться, то можете использовать специальные очистители в баллончиках. Они отлично справляются со своей задачей.
После очистки деталь нужно снова высушить. Если время позволяет, то оставьте деталь на свежем воздухе на некоторое время. Но не оставляйте на солнцепеке. Если времени мало и нет никаких приборов, то можно просто хорошо протереть тряпкой без ворса. Если в вашем распоряжении есть фен, то можете удалить влагу таким способом. Он самый эффективный и быстрый.
Способы нанесения проявителя
Итак, мы разобрались, как правильно наносить пенетрант и очищать деталь от ее излишков. Но что насчет проявителя? Ведь от него во многом зависит конечный результат. Здесь метод нанесения не так важен, как в случае с пенетрантом. Важнее выбрать подходящий тип проявителя и нанести его на очищенную и высушенную поверхность.
Проявители бывают разные. Есть сухие, их не очень удобно наносить, они используются только в сочетании с флуоресцентными пенетрантами. Стоят недешево. Используются редко, понятно, по каким причинам. Но результат контроля отличный.
Второй вид — жидкий проявитель. Может быть изготовлен с применением разных основ. Самый популярный — жидкий на основе водной суспензии. Можно наносить разными способами: и распылять, и замачивать в емкости. Если решите использовать емкость, то погружение должно быть кратковременным. За ним должна следовать просушка с применением специального фена.
Также есть жидкий проявитель на основе веществ, сходных по свойствам с растворителями. Недорогие и вполне эффективные, наносятся равномерным слоем с помощью распыления. Больше нечего добавить.
Проявлять нужно около 10-20 минут. Если результат не достигнут, то можно добавить еще минут 10 к основному времени.
Повторный контроль
В процессе капиллярного контроля могут произойти многие ситуации, из-за которых результат контроля будет неудовлетворительным. Например, вы решили погрузить деталь в емкость с пенетрантом, но выдержали меньше времени, чем должны были. И произошло это не по вашей вине. Или же вы случайно допустили ошибку при выполнении технологии капиллярного контроля. В таких случаях новички часто спрашивают: «Можно ли провести повторный контроль?». Наш ответ: да, можно.
Самое главное — хорошо очистить металл от остатков пенетранта и проявителя. Также используете те же жидкости, не нужно брать жидкости другого производителя. Соблюдая эти простые правила, вы сможете провести повторный контроль, который может оказаться куда успешнее предыдущего.
Вместо заключения
Капиллярный метод контроля сварных соединений очень простой, при этом экономически выгодный и вполне эффективный. Поэтому данный метод контроля качества используется повсеместно. Вы наверняка встретите баллончик с пенетрантом как в цеху крупного завода, так и в гараже у домашнего мастера.
Конечно, с помощью такого метода можно обнаружить далеко не все возможные дефекты, скрытые от глаз сварщика. Но если вы в полевых условиях или высокое качество шва не так уж важно, то можно ограничиться и капиллярным контролем. Также капиллярный контроль незаменим в маленьких частных мастерских, где прибыль небольшая и экономическая сторона вопроса играет главную роль. А вы использовали в своей практике капиллярный метод контроля качества швов? Расскажите об этом в комментариях ниже. Не забывайте делиться этой статьей в социальных сетях. Желаем удачи в работе!
Многоосная циклическая деформация и малоцикловая усталость образцов из низкоуглеродистой стали и родственных сварных металлических образцов
Эксперименты на малоцикловую усталость малоуглеродистой стали Q235B и связанных с ней образцов сварного металла проводят при одноосных, синфазных и Условия нагрузки не в фазе 90 °. Значительное дополнительное циклическое упрочнение при несинфазном нагружении на 90 ° наблюдается как для основного металла, так и для связанного с ним сварного шва. Кроме того, процесс сварки дает дополнительное дополнительное упрочнение при тех же условиях нагружения по сравнению с основным металлом.Многоосная малоцикловая усталостная прочность при несинфазном нагружении на 90 ° значительно снижается как для образцов основного металла, так и для образцов сварного металла. Сварная деталь имеет меньшую усталостную долговечность, чем основной металл при заданных условиях нагружения, и уменьшение усталостной долговечности сварной детали увеличивается с увеличением амплитуды деформации. Параметры критической плоскости KBM, FS и MKBM оцениваются для полученных данных по усталости. Установлено, что параметры FS и MKBM лучше коррелируют с усталостной долговечностью как для образцов основного металла, так и для образцов сварного металла.
1. Введение
Технические компоненты всегда подвергаются сложным циклическим нагрузкам в течение периода обслуживания, и в конечном итоге отказ происходит из-за накопленных усталостных повреждений [1]. В инженерных приложениях усталостные разрушения происходят в локальных областях, где концентрации напряжений создают многоосные состояния напряжения / деформации [2]. Многоосные состояния напряжения / деформации обычно возникают из-за разнонаправленных внешних нагрузок, эффектов надрезов и сложных геометрических особенностей, которые действительно влияют на усталостную прочность инженерных компонентов [3].
Понимание многоосной усталостной прочности металлических материалов всегда основывается на экспериментальных наблюдениях на тонкостенных трубчатых образцах при осевом крутильном нагружении. В течение длительного периода испытания на многоосную усталость в основном сосредоточены на основном металле. Обзор экспериментов на многоосную усталость металлических материалов можно найти в [4, 5]. В последнее десятилетие Chen et al. [6] исследовали многоосную прочность нержавеющей стали типа 304 при последовательном двухосном нагружении.Gao et al. [7, 8] испытывали многоосную усталостную прочность стали 16MnR и алюминиевого сплава 7075-Т651 при различных траекториях многоосного нагружения. Шанг и Ван [9] провели усталостные испытания горячекатаной среднеуглеродистой стали 45 при осевом крутильном нагружении с использованием синусоидальной формы волны. Многоосное циклическое деформирование и усталостное поведение нержавеющей стали типа 304 и среднеуглеродистой стали 1050 изучены Шамсаи [10]. Гладский и Шукаев [11] провели сравнительный анализ одноосной и многоосной малоцикловой усталостной прочности титанового сплава типа ВТ1-0.
Для сварных стальных конструкций остаточные напряжения, дефекты сварки, неоднородность материала в зоне сварного шва и т.д., вызванные процессом сварки, могут значительно снизить усталостную прочность сварных соединений [12–14]. В настоящее время расчет сварных соединений на усталость основывается в основном на кривых сопротивления усталости S-N , полученных на основе статистического анализа результатов испытаний на одноосную усталость классифицированных сварных деталей конструкций [15–17]. Однако многоосная усталость сварных соединений исследуется редко.Chen et al. [18] провели эксперименты по малоцикловой усталости на нержавеющей стали 1Cr-18Ni-9Ti и соответствующем металле шва при осевой, крутильной и противофазной нагрузке на 90 °. Усталость свариваемых деталей при изгибно-крутильных и непропорциональных нагрузках исследована в [19].
Многоосная усталость металлических материалов привлекала широкое внимание в последние десятилетия. Исследования многоосной усталости часто проводят с использованием эквивалентного параметра, который позволяет сравнивать многоосное нагружение с одноосным [20].Затем методы анализа усталости, разработанные для одноосного случая, могут быть использованы для решения задач многоосной усталости. Хорошо известный критерий Мэнсона-Коффина, который широко используется в анализе одноосной малоцикловой усталости, модифицирован для условий многоосного нагружения. В последние десятилетия критерий Мэнсона-Коффина с точки зрения параметров критической плоскости, таких как параметры KBM и FS, играет важную роль в оценке многоосных усталостных повреждений (подробнее см. [21, 22]).
Для изучения многоцикловой деформации и малоцикловой усталости сварных соединений из низкоуглеродистого сплава Q235B, которые все более широко используются в стальных конструкциях в Китае, проводятся усталостные эксперименты со сталью Q235B и ее сварными деталями с использованием тонкослойной стали. трубчатые образцы со стенками при полностью обращенных условиях нагружения с контролируемой деформацией с одноосным, синфазным и противофазным нагружением на 90 °. Параметры критической плоскости KBM, FS и MKBM оцениваются на основе экспериментальных данных, собранных в этом исследовании.
2. Методика эксперимента
2.1. Материалы и образцы
Материалом, исследуемым в настоящем исследовании, является конструкционная сталь с низким содержанием углерода Q235B, которая широко используется в стальных конструкциях Китая. Исследуемая сталь Q235B имеет модуль Юнга 204 ГПа, предел текучести 270 МПа, предел прочности 390 МПа, коэффициент Пуассона 0,3 и относительное удлинение 36,9%. Химический состав стали Q235B представлен в таблице 1.
|
Образец из основного металла имеет трубчатую геометрию с внешним и внутренним диаметрами 18 мм и 14 мм соответственно. Толщина стенки в измерительном сечении 2 мм. Геометрия образца основного металла показана на рисунке 1.
Сваренный образец изготовлен вручную методом сварки в среде защитного газа CO 2 .Используется сварочная проволока МГ70С-6 диаметром 2 мм. Химический состав сварочной проволоки представлен в таблице 2.
|
Изготовление сварного металлического образца сопровождается [18]. Хорошо спроектированный надрез сначала обрабатывается в центре стержня основного металла, а затем надрез заполняется металлом сварного шва. Наконец, сварной металлический образец обрабатывается до формы, соответствующей образцу основного металла. Изготовленный сварной металлический образец имеет зону сварки длиной 18 мм в центре калибровочной длины.Геометрия испытанного сварного тонкостенного трубчатого образца идентична базовой (см. Рис. 2).
Монотонные механические свойства образцов основного металла и сварного металла перечислены в таблице 3.
| |||||||||||||||||||||||||||||||||||||||||||||||||||||
Испытания на усталость в условиях одноосного, синфазного и несинфазного нагружения под углом 90 ° проводятся при полностью обращенном нагружении с контролируемой деформацией и постоянной амплитудой.Применяемые формы сигналов как для основного металла, так и для сварного металла являются синусоидальными. Три пути деформации при испытании показаны на рисунке 3. По горизонтальной оси отложена осевая деформация, а по вертикальной оси — деформация сдвига. Корреляция горизонтальной оси и вертикальной оси выводится из критерия фон Мизеса, в котором эквивалентная деформация фон Мизеса.
Испытания на усталость проводились на машине растяжения-кручения MTS при контролируемой нагрузке с использованием экстензометра деформации растяжения-кручения с измерительной длиной 25 мм, который установлен в центре наружной части измерительной секции образца для измерения механической нагрузки. реакции напряжения.Частота нагрузки для испытаний с постоянной амплитудой составляет 1,0 Гц. Предполагается, что усталостная долговечность — это количество циклов, в течение которых наблюдается снижение на 30% по сравнению с максимальным напряжением растяжения или сдвига при одноосном испытании.
3. Результаты и обсуждение
Стабильные петли гистерезиса образцов основного металла и сварного металла при одноосном, синфазном и противофазном нагружении на 90 ° при разной амплитуде деформации представлены на рисунках 4–6. соответственно. Можно заметить, что поведение деформации многоосного цикла для условия синфазного нагружения в основном такое же, как и для одноосного, в то время как поведение деформации многоосного цикла для условия несинфазного нагружения значительно изменилось.Максимальные отклики на сдвиг и осевое напряжение, а также сдвиговые и осевые деформации являются одновременными в условиях синфазного нагружения как для основного металла, так и для образца сварного металла. Однако максимальные значения реакции на циклическое напряжение и деформацию не всегда возникают одновременно при несинфазном нагружении на 90 °, что указывает на то, что пластическая текучесть металла при несинфазном нагружении на 90 ° различна. от того под одноосным.
Прочность металлов и сплавов (ICSMA 7)
перейти к содержанию- О Эльзевире
- О нас
- Elsevier Connect
- Карьера
- Продукты и решения
- Решения НИОКР
- Клинические решения
- Исследовательские платформы
- Исследовательский интеллект
- Образование
- Все решения
- Сервисы
- Авторы
- Редакторы
- Рецензенты
- Библиотекарей
Механическое поведение сварных швов из дисперсионно-упрочненных алюминиевых сплавов
1.Введение
Благодаря своей относительно низкой плотности и высокой прочности, алюминиевые сплавы серий 2 xxx , 6 xxx и 7 xxx широко используются в транспортной промышленности для производства структурных каркасов и компонентов. Эти сплавы находят применение в условиях искусственного старения, что позволяет получить высокие механические свойства, т.е. предел текучести алюминиевого сплава 7075-Т651 до 500 МПа. Однако, когда сварочные процессы используются для выполнения соединения, большое количество подводимого тепла рассеивается за счет теплопроводности через основной материал вблизи сварочного валика.Это рассеяние тепла приводит к образованию локализованных изотермических участков, на которых температурный градиент оказывает важное и пагубное влияние на микроструктуру и, следовательно, на механические свойства сварного соединения (образование мягкой зоны). Это изменение микроструктуры влияет на эксплуатационные характеристики сварных соединений, поскольку механические свойства резко ухудшаются по сравнению с основным материалом.
В этой главе представлена информация о механическом поведении сварных соединений алюминиевых сплавов с точки зрения свойств, определяемых испытаниями на растяжение, вдавливание и усталость, а также об условиях роста усталостной трещины в различных зонах сварных соединений.
1.1. Осаждение и механические свойства алюминиевых сплавов
Процесс дисперсионного твердения требует, чтобы второй компонент в алюминиевом сплаве был достаточно растворим, чтобы обеспечить широкое растворение при повышенной температуре (температура солюбилизационной обработки) и чтобы растворимость значительно снижалась при более низких температурах. так обстоит дело с сплавами Al-Cu (рис. 1) [1].
Согласно рисунку 1, чтобы вызвать дисперсионное твердение, сплав нагревают до температуры, превышающей температуру сольвуса, для получения гомогенного твердого раствора α, позволяющего растворить вторую фазу θ и устраняя сегрегацию сплава.Как только температура солюбилизации достигается, сплав охлаждается с высокой скоростью, чтобы ограничить процесс диффузии атомов в направлении потенциальных центров зародышеобразования. Наконец, перенасыщенный твердый раствор α ss нагревают до температуры ниже температуры сольвуса. При этой температуре атомы обладают способностью диффундировать на короткие расстояния. Поскольку фаза α ss нестабильна, атомы Cu диффундируют в нескольких местах зарождения, и может образоваться контрольное преципитация.Осадочное упрочнение металлов выполняется для получения дисперсии частиц вторых фаз и создания препятствий для движения дислокаций. Степень упрочнения зависит от металлической системы, объемной доли и размера частиц, а также от взаимодействия частиц с дислокациями. Взаимодействие осевших частиц с дислокациями очень важно с точки зрения величины упрочнения. Были установлены некоторые механизмы, включающие обход частиц с помощью петли Орована, обходное скольжение или сдвиг частиц.На рис. 2 показаны силы, действующие на подвижную дислокацию в напряженном металле, содержащем дисперсию частиц второй фазы.
Рисунок 1.
Фазовая диаграмма алюминия и меди с высоким содержанием алюминия, показывающая процесс солюбилизации и осаждения [1].
Рисунок 2.
Баланс сил, действующих при сопротивлении частицы движению дислокации [1].
Рассматривая силы равновесия между линейным натяжением T дислокации и силой сопротивления частицы второй фазы F , получаем:
По мере увеличения F увеличивается изгиб дислокаций, i .е. θ увеличивается. Величина F важна для управления последовательностью событий. Сила натяжения линии дислокации максимальна при θ = 90 º. Если частица твердая, например, F может быть больше 2 T , то дислокации будут обходить частицу либо за счет петли Орована, либо за счет поперечного скольжения, и частица останется неизменной, то есть недеформированной (Рисунок 3).
Рисунок 3.
Дислокация встречается с твердыми недеформируемыми частицами второй фазы: высвобождение дислокации при более высоких напряжениях может происходить за счет образования петель Орована или поперечного скольжения [1].
Фактическая сила частицы в этом случае становится несущественной, поскольку операция обхода становится зависимой только от расстояния между частицами. Если, однако, сила частицы такова, что максимальная сила сопротивления достигается до sin θ = 1, тогда частицы будут раздвигаться, и дислокация пройдет через частицу (рис. 4).
Рисунок 4.
Движение дислокации может продолжаться через частицы второй фазы (разрезание частиц).
Следовательно, из этого следует, что при заданном расстоянии между частицами (заданная объемная доля и размер частиц) твердые частицы будут давать максимальное дисперсионное твердение, и это условие определяет максимально достижимую степень твердения.Мягкие частицы дают меньшую степень затвердевания. Рассмотрение зависимости между приложенным напряжением и изгибом дислокации, следуя Оровану [2], приводит к уравнению Орована:
, где Δ τ y — увеличение предела текучести из-за частиц, G модуль сдвига матрицы, b вектор Бюргерса дислокации и L расстояние между частицами. L в уравнении Орована обычно считается расстоянием между частицами, расположенными на квадратной сетке в плоскости скольжения.
Эшби [3] развил свое уравнение, чтобы учесть расстояние между частицами и эффекты статистически распределенных частиц. Соотношение Эшби-Орована имеет вид:
Δτy = 0,84 (1,2Gb2πL) ln (x2b) E3Применение фактора Тейлора для поликристаллических материалов, выражающее микроструктурные параметры в терминах объемной доли и реального диаметра и преобразуя напряжение сдвига в растягивающее напряжение, урожайность [4]:
Δσy = (0,538Gbf1 / 2X) ln (X2b) E4, где Δ σ y — увеличение предела текучести (МПа), G — модуль сдвига (МПа), b — вектор Бюргерса (мм), f — объемная доля частиц, а X — реальный (пространственный) диаметр частиц (мм).В таблице I представлен эффект упрочнения с точки зрения предела текучести для некоторых алюминиевых сплавов в отожженном (O) и в условиях искусственного старения (T6).
Предел текучести (МПа) | |||||||||||||||||||||||||||||||||||||||||||||||||||||||||||||||
Сплав | Отожженное состояние (O) | Разница в возрасте 6) 9032 9032 9032 | |||||||||||||||||||||||||||||||||||||||||||||||||||||||||||||
2014 | 97 | 417 | 320 | ||||||||||||||||||||||||||||||||||||||||||||||||||||||||||||
6061 | 55 | 276 | 221 | ||||||||||||||||||||||||||||||||||||||||||||||||||||||||||||
7075 | 103 | 503 | 400 |
Материал | EIIT (ГПа) | σy (МПа) | n | P0 (N) | P0 (Н) 98.6 | 266 | 0,46 | 0,015 | | ||||||||||||||||||||||||||||||||||||||||||||||||||||||
Сварной металл | 78,0 | 133 | 0,48 | 0,022 | |||||||||||||||||||||||||||||||||||||||||||||||||||||||||||
HAZ | 87,4 | 106 | 0,46 | 2.
Материал | E (МПа) a | σy (МПа) | ε (%) c | H (МПа) d | n d | |||||||
6061-T6 | 68 | 279 | 27 | 14.0 | 408 | 0,08 | ||||||
6061-T6 (сварной металл, ER4043) | 68 | 151 | 226 | 4,00 | 464 | 0,20 | ||||||
6061-T6 (HAZ, мягкая зона) ) | 68 | 120 | 183 | 13,0 | 300 | 0,16 | ||||||
7075-T651 | 72 | 530 | 568 | 8,00 | 794 | 0,08 T651 (сварное соединение, ER5356) | 68 | 165 | 260 | 2.80 | 677 | 0,25 |
Таблица 3.
Механические свойства при растяжении сварных швов алюминиевых сплавов 6061-T6 и 7075-T651 (GMAW).
a Лучшее линейное соответствие из кривых среднего напряжения-деформации; b Получено из σ = PA0; c , полученное из ε = lf-l0l, d , полученное с помощью уравнения Рамбера-Осгуда.
2.3. Усталость сварных швов из алюминиевых сплавов
Усталостное или усталостное повреждение — это последовательное изменение свойств материалов по отношению к приложению циклического напряжения, которое может привести к разрушению.В условиях одноосного циклического нагружения можно выделить соотношение напряжений R , определяемое максимальным и минимальным напряжением, следующим образом:
как функция σ max и σ min , мы можем получить постоянную составляющую напряжения (амплитудное напряжение σ a ) и среднее значение напряжения (среднее напряжение σ м ) при различных условиях нагружения (Рисунок 17).
Некоторые практические приложения включают циклическую нагрузку с постоянной амплитудой, но часто встречаются нерегулярные нагрузки как функция времени. В этом случае мы обсудим некоторые результаты в терминах нагрузки постоянной амплитуды. Простейшее испытание на усталость состоит в подвергании образца циклической нагрузке (различные уровни амплитуды напряжения σ a ) с постоянной частотой и измерения количества циклов до разрушения N f .Представление уровня напряжения как функции от N f дает кривую S — N или кривую Велера. Схематическое изображение кривой Велера показано на рисунке 18.
Рисунок 17.
Требуемое нагружение при одноосной усталости, a) полностью обратное напряжение (σm = 0), b) асимметричное повторяющееся напряжение (σm ≠ 0) и c ) от нуля до напряжения растяжения (σmin = 0).
Рисунок 18.
Представление кривой Велера и различных областей усталости [21].
На рисунке 18 можно выделить различные области: (i) Малоцикловая усталость. В этом случае к образцу прилагается высокий уровень напряжения (обычно выше предела текучести материала). Из-за высокой деформации во время испытания количество циклов до разрушения обычно ниже (от 10 2 до 10 4 ). (ii) Высокая циклическая усталость. Это связано с упругим поведением образца на макроуровне, то есть уровень напряжения не превышает предел текучести материала.Отказ ожидается при большом количестве циклов, например более 10 5 . Фактически, граница между мало- и многоцикловой усталостью четко не определяется конкретным числом циклов. Наиболее важным отличием является то, что низкая циклическая усталость связана с макропластической деформацией при каждом цикле нагружения. Когда применяется уровень напряжения при многоцикловой усталости, отображается предел усталости или предел выносливости, который представлен асимптотой на кривой Велера. В некоторых металлических материалах это может быть получено при количестве циклов порядка от 10 6 до 10 7 .(iii) Гигацикл усталости. Эта область соответствует очень большому количеству циклов, и было замечено, что предел выносливости имеет тенденцию уменьшаться, когда количество циклов увеличивается.
Хорошо известно, что усталостное повреждение является поверхностным явлением, на что указывает Форсайт [22], который определил наличие рельефов, связанных с образованием полос локализационной деформации, названных стойкими полосами. Топография поверхности определяется образованием интрузий и выдавливаний, как схематично показано на Рисунке 19.
Рис. 19.
Формирование внедрений и выдавливаний на свободной поверхности из-за переменного скольжения, зарождения микротрещин и образования основных трещин из микротрещин [21].
При испытании на одноосное растяжение эти полосы приводят к образованию микротрещин (состояние I на рисунке 19), которые ориентированы под углом 45 градусов по отношению к оси тяги. Эти полосы влияют только на определенные зерна. Устойчивая ориентация полос и образование трещин в состоянии I важны в случае одноосного и многоосного нагружения.Браун и Миллер [23, 24] ввели полезные обозначения в мультиаксиальном нагружении для фасетов A и B, которые схематически изображены на рисунке 20.
Рисунок 20.
Направленный аспект усталостного повреждения. Важность ориентации поля напряжений относительно поверхности планов и свободной поверхности материала (зон штриховки) [23, 24].
Фасеты типа B обеспечивают вектор сдвига, который проникает в материал, и они более опасны, чем фасеты типа A, от которых вектор сдвига касается свободной поверхности образца.Образование внедрений и выдавливаний, связанных с устойчивыми к скольжению полосами, а также микропространство трещин в состоянии I представляют интерес на расстоянии от размера зерна (небольшие усталостные трещины). Таким образом, с учетом того, что микротрещины связаны с кристаллографическим аспектом, как только трещина встречает первую границу зерна, она начинает раздваиваться в соответствии с состоянием II, и достигается распространение в перпендикулярном направлении главного напряжения.
В дополнение к упомянутому ранее механизму усталостного разрушения в случае сварки особое значение имеет коэффициент концентрации напряжений, обусловленный геометрией сварного валика.В этом смысле Амбриз и др. В [20] было количественно оценено влияние сварочного профиля, созданного методом модифицированной непрямой электрической дуги (MIEA), на усталостную долговечность алюминиевого сплава 6061-T6. Для определения коэффициента концентрации напряжений K t в сварных швах MIEA был измерен характерный профиль сварки, как указано на рисунке 21.
Рисунок 21.
Точки концентрации напряжений в сварных швах MIEA и их соответствующие размеры. α = угол, образованный усилением сварного шва пластинами, r = радиус надреза, t = высота усиления сварного шва, w = ширина сварочного профиля и h = толщина пластин.
Затем было проведено испытание на одноосную усталость с циклическим нагружением с синусоидальной формой волны на частоте 35 Гц и соотношении нагрузки R = 0,1 в атмосферном воздухе при комнатной температуре. Предел выносливости (77 МПа) был рассчитан с использованием метода Локати, а кривая Велера (рисунок 22) была построена между 77 и 110 МПа.
Рис. 22.
Кривая Велера для сварных швов алюминиевого сплава 6061-T6, выполненная MIEA, и данные из литературы [25] для соединения с одной V-образной канавкой.
На рисунке 22 показано максимальное напряжение σ max в зависимости от числа циклов до разрушения N f , полученное в результате испытания сварных соединений на усталость.Экспериментальные результаты были подогнаны согласно следующему выражению:
, где A, и b — экспериментальные значения, определенные с помощью аппроксимирующей кривой.
Что касается геометрии сварочного профиля, сравнение усталостных характеристик сварных швов MIEA с результатами, приведенными в литературе [25] для конфигурации с одним V-образным соединением для того же алюминиевого сплава, показывает значительное улучшение усталостной долговечности для MIEA. сварные образцы. Влияние K t на зарождение трещины и разрушение показано на рисунке 23.
Рисунок 23.
Типичный макрос усталостного разрушения сварных швов MIEA.
Учитывая, что если условия нагружения способствуют образованию основной трещины (Рисунок 19), она будет расти в соответствии с областью степенного закона, как схематически показано на Рисунке 24.
Рисунок 24.
Режимы роста усталостной трещины как функция ΔK.
Скорость роста усталостной трещины d a / d N в зависимости от диапазона коэффициента интенсивности напряжений Δ K в различных зонах сварного соединения (основной металл, металл шва и ЗТВ) изучалась ранее [26 , 27].Результаты были проведены на образцах компактного типа (КТ) с приложением постоянной амплитуды циклической нагрузки с синусоидальной формой волны на частоте 20 Гц, коэффициентом нагрузки R 0,1 и диапазоном нагрузок 2,5 кН в атмосферном воздухе при комнатной температуре. . Δ K был вычислен с помощью следующего уравнения:
ΔK = ΔP (2 + aW) BW1 / 2 (1-aW) 3/2 [0,886 + 4,64aW-13,32 (aW) 2 + 14,72 (aW) 3−5.6 (aW) 4] E13, где a — длина трещины в образце (начальная трещина 8 мм), W — ширина распространения трещины и B — толщина образца (5 мм в данном случае).
Учитывая область устойчивого роста трещины, показанную на рисунке 24, экспериментальные результаты для a были нанесены на графики d a / d N в зависимости от Δ K согласно следующему выражению:
где C и м — константы, полученные из аппроксимирующей кривой. В таблице IV приведены наиболее подходящие значения для C и м , а также их коэффициент корреляции.
Материал | C | м | R2 |
6061-T6 (подвижный) | 5.00 × 10 -7 | 2.426 | 0,89 |
6061-T6 (поперечный) | 3,97 × 10 -8 | 3,320 | 0,97 |
Сварной металл | 2,63 × 10 -14 | 8,550 | 0,92 |
HAZ | 3,77 × 10 -9 | 6,650 | 0,89 |
Таблица 4.
Константы подгонки, полученные из экспериментальных значений (рисунок 25) [27 ].
На рис. 25 показан рост усталостной трещины основного металла (6061-T6) при прокатке и поперек направления прокатки.
Рис. 25.
Скорость роста усталостной трещины в зависимости от ΔK: a) основной металл 6061-T6, b) металл шва и c) HAZ.
Этот график показывает, что микроструктурные характеристики (анизотропия) не оказывают существенного влияния на рост усталостных трещин, как можно было бы ожидать, учитывая, что предел текучести в направлении прокатки выше, чем в поперечном направлении.Однако это не относится к металлу сварного шва и ЗТВ (рисунки 25b и c), в которых трещина имеет тенденцию распространяться быстрее, чем в основном металле. В случае металла шва (рис. 25b) более высокая скорость роста трещины по сравнению с основным металлом связана с низкой ударной вязкостью из-за высокого содержания кремния (~ 5,5 мас.%), Обеспечиваемого присадочным металлом во время сварки. Аналогичным образом, для HAZ можно наблюдать, что трещины растут быстрее, чем основной металл, аспект, который объясняется микроструктурным преобразованием тонких игольчатых выделений β ’’ в выделения крупнозернистой формы брусков β ’, образованных тепловым эффектом.
Международная промышленная выставка «Металл-Экспо»
А.Г. Романов
Председатель оргкомитета «Металл-Экспо»
Форум производителей стали, который в этом году отмечает свое 25 -летие, является уникальным событием не только для черной металлургии, но и для мировой экономики в целом. За последние несколько лет выставка стала ведущей деловой площадкой для сталелитейных компаний, производителей труб, производителей проволочной сетки, производителей алюминиевого проката и сплавов, трейдеров стали, сервисных центров металлопродукции, а также ключевых потребителей металлопродукции: строителей, инженеры, нефтегазовые компании, транспортно-логистические компании и др.
Металл-Экспо — территория с особой атмосферой. Все эти годы выставка была стартовой площадкой для новых масштабных проектов, стартапов и новых профессиональных инициатив. Выставка, без преувеличения, как зеркало отражает всю новую историю российской черной металлургии и основные тенденции мирового производства стали.
Форум стал обязательным для всех крупнейших мировых сталелитейных и металлургических компаний. Экспозиция и количество участников растут с каждым годом, демонстрируя весь спектр современных материалов, оборудования и решений для сталелитейной промышленности, металлообработки и металлопотребления.В этом году «Металл-Экспо’2019» демонстрирует множество инновационных решений для металлургической отрасли.
Приглашаем участников и посетителей юбилейной «Металл-Экспо» принять участие в насыщенных мероприятиях, посвященных всем ключевым аспектам черной металлургии, включая металлообработку, тяжелое машиностроение, а также наиболее актуальным проблемам экономики, маркетинга и т.д. дискуссии и конкурсы образуют Неделю металла в Москве.
Кроме того, форум — прекрасная возможность для установления новых деловых контактов, поиска новых ниш и направлений развития бизнеса.
Желаем всем участникам и посетителям Металл-Экспо’2019 успехов, хорошей работы, новых бизнес-идей и хороших деловых партнеров. Пусть выставка зарядит вас энергией успеха!
Услуги по прядению, формовке и сварке металла
Прядение металла, также называемое формованием, представляет собой процесс металлообработки, с помощью которого создаются высокопроизводительные осесимметричные детали. В отличие от других процессов формования металла, которые разрезают и удаляют материал для получения желаемой формы, прядение металла преобразует металлический диск или трубу, вращая диск или трубу и превращая ее в оправку, зажимая ее на горизонтальном или вертикальном токарном станке и создавая коническую , тороидальной или другой круглой формы.Процесс может быть горячим или холодным, в зависимости от конкретного пряденного материала.
Процесс прядения металла осуществляется посредством автоматического прядения с ЧПУ или ручного прядения. Наиболее подходящий тип прядения металла выбирается с учетом объема производства и требуемой сложности получаемых деталей.
Преимущества прядения металла
Прядение металла предлагает ряд преимуществ тем, кто ищет универсальный и оптимизированный процесс, в том числе:
По сравнению с инструментами, используемыми в альтернативных методах формования, инструменты для прядения металла обычно составляют 10% от стоимости.
Процесс прядения металла позволяет значительно сократить время выполнения работ — инструменты и детали могут быть доступны в течение недель, а не месяцев.
- Максимальная гибкость конструкции
Инструменты для прядения металла можно быстро и легко заменить в соответствии с изменяющимся дизайном продукции, обеспечивая гибкость, когда это больше всего необходимо.
- Бесшовная высококачественная конструкция
Прядение металла позволяет получать гладкие, прочные изделия без швов и сварных швов, поскольку детали требуют особой прочности и великолепного внешнего вида.
Совместимые металлы
Прядение металлов совместимо с широким спектром металлов, каждый из которых дает уникальный набор преимуществ. Предполагаемое применение и требования проекта влияют на выбор материала. Несколько распространенных материалов для прядения металла включают:
Высокая коррозионная и термостойкость, а также отличное соотношение прочности к весу нержавеющей стали, особенно серии 300 и 400, делают ее одним из наиболее распространенных материалов, используемых при прядении металла, и идеальным выбором для промышленных деталей и оборудование, посуда, высокоточные инструменты, декоративные детали и многое другое.Нержавеющая сталь проста в изготовлении и является одним из самых экономически эффективных металлов.
Углеродистая стальочень популярна для изготовления жестких деталей, ее легко красить и покрывать. Он не имеет минимальных требований к хрому, никелю, титану, вольфраму, молибдену и другим элементам. Чем больше добавлено углерода, тем выше долговечность получаемого материала. При прядении металла совместимы как холоднокатаная, так и горячекатаная углеродистая сталь — горячекатаный прокат имеет тенденцию быть более пластичным и гибким.Прядильная обработка углеродистой стали приводит к получению прочных, однородных и экономичных продуктов, которые также можно полностью перерабатывать.
Когда при выборе материала в первую очередь учитываются вес продукта и стоимость, присущие алюминию свойства делают его идеальным выбором. Его чрезвычайно низкая плотность, пластичность и высокая коррозионная стойкость используются в строительстве, на транспорте и в аэрокосмической промышленности. Обычно производится прядение алюминия серий 2000, 3000, 5000, 6000 и 7000.
Медь, немагнитный металл, используется для изготовления как твердых, так и эстетически привлекательных металлических формующих деталей — идеально подходит для приложений, требующих функциональности, красоты или отличного баланса обоих. Его устойчивость к потускнению и коррозии, а также высокая пластичность и технологичность делают его лучшим выбором для прядения металла. Кроме того, медь обладает прекрасной теплопроводностью и электропроводностью, а также естественными антимикробными свойствами.
Другие металлы, которые можно использовать при прядении металла:
Инконель, также известный как высокопрочная сталь, содержит железо и хром (с более высоким содержанием хрома).Поскольку существуют различные серии сплавов Inconel, наиболее подходящий тип необходимо выбирать в соответствии с требованиями приложения. Высокая прочность, превосходная стойкость к коррозии и окислению, а также устойчивость к воздействию высоких температур и высоких давлений являются отличительными качествами Inconel.
Экзотический металлический сплав, обладающий высокой устойчивостью к коррозии, хастеллой очень хорошо работает в средах с высокими нагрузками, которые другие традиционные металлы могут не выдержать. Хастеллой состоит из более чем 22 элементов в различных соотношениях, включая, помимо прочего, хром, железо, кобальт, медь, молибден и марганец.
Подобно алюминию, титан отличается впечатляющим соотношением прочности и веса, низкой плотностью и высокой коррозионной стойкостью. Его прочность на разрыв часто лучше, чем у стали, хотя, как правило, при более высоких затратах. Долговечность и легкий вес титана используются для изготовления деталей и применений в аэрокосмической отрасли, которые зависят от стабильной и долговечной работы.
Бронза, известная своей эстетической ценностью и механической прочностью, является еще одним металлом с высокой коррозионной стойкостью, используемым при прядении металла.Бронза, металл примерно на 10% тяжелее стали, обладает уникальным набором характеристик благодаря сочетанию сплавов — меди и олова. Применения, требующие более высокой прочности материала, чем одна только медь, могут выиграть от долговечных свойств бронзы. Он также известен своей теплопроводностью и электропроводностью, устойчивостью к коррозии и способностью выдерживать высокие температуры и высокое трение. Бронза предназначена для бесшовной обработки и сварки.
Большая часть меди по теплопроводности, обрабатываемости, антимикробности и коррозионной стойкости также проявляется в латуни, сплаве, обычно состоящем из меди и цинка.Однако она прочнее чистой меди, и все разновидности бронзы обладают пластичностью, пластичностью и низким коэффициентом трения. Эстетическая привлекательность — это заметное преимущество при выборе латуни.
Применения для прядения металла
Прядение металла представляет собой экономичную и универсальную возможность для широкого спектра коммерческих и промышленных применений, в том числе:
- Детали самолетов
- Оборудование для общепита
- Архитектура и освещение
- Посуда
- Газовые баллоны и сосуды под давлением
- Компоненты тяжелой промышленности для масел, автомобилей и наземного транспорта
- Музыкальные инструменты
Услуги по прядению металла и оснастка в Helander
Helander создает металлические компоненты, изготовленные методом фильерного производства, в соответствии со спецификациями наших клиентов.Мы прядем детали размером до 60 дюймов между центрами, а наше оборудование обрабатывает детали диаметром до 100 дюймов. Мы также можем работать с материалами различной толщины, в том числе:
- Нержавеющая сталь от 0,018 дюйма до 0,375 дюйма
- Углеродистая сталь от 0,018 до 0,375 дюйма
- Алюминий от 0,018 дюйма до 2,00 дюйма
Помимо формования металла, Helander также предлагает инструменты собственного производства, сварку, абразивную полировку и гидроформование, что помогает снизить ваши расходы и оптимизировать производство.Более быстрое время выполнения работ и более низкие затраты — два наиболее привлекательных преимущества прядения металла. Возможность формовать компоненты очень большой толщины и большого диаметра с однородностью и высоким качеством при малых и больших количествах — более привлекательные причины для рассмотрения формования металла.
Чтобы узнать, будет ли прядение металла полезным для вашей области применения или конечного продукта, свяжитесь с нами сегодня.
(Нажмите на картинку, чтобы увеличить)Вместимость
До 0.250 «Нержавеющая сталь
До 0,375″ Углеродистая сталь
До 0,750 «Алюминий
Ручное прядение (ручное прядение)
Прядение с ЧПУ
Формование на двухвалковых ножницах
Закрывание концов труб (горячее прядение)