7.Стыковые сварные соединения. Расчет и конструирование.
Стыковые — соединяются торцами (а). Имеют наименьшую концентрацию напряжений при передаче усилий, экономичны. Толщина элементов не ограничена. Соединение = прямым или косым швом.
Усиливают накладками – комбинир. (б).
Стыковые наиболее рациональны, но требуют дополнительной разделки кромок.
Работа и расчет стыковых швов
Прочность при растяжении или сжатии зависит от характеристик металла и шва.
При действии N
распределение напряжений по длине шва
принимается равномерным, рабочая
толщина шва = меньшей из толщин элементов.
Напряжение в шве (а)
Rсв
— расчетное сопротивление сварного
стыкового соединения сжатию или
растяжению, у — коэффициент условий
работы элемента.
Расчетное сопротивление стыкового соединения при сжатии соединения Rсв=R.
При Rсв ≤ Rосновного металла то шов делают косым (с проверкой) (б). Рассчёт косых швов: перпендикулярно шву
вдоль шва
а и б — на продольную силу; в — на изгиб
При действии изгибающего момента (в)
где — момент сопротивления шва.
Соединения встык, работающие на нормальные напряжения и срез, проверяют
8.Сварные соединения с угловыми швами. Расчет и конструирование.
Угловые — элементы расположены под углом (г).
Фланговые — параллельно осевому усилию.
Лобовые — перпендикулярно усилию (рассчитывают условно).
Работа и расчет соединений, выполненных угловыми швами
— соединения
внахлестку.
Фланговые работают на срез и изгиб. Разрушение может происходить по металлу шва, по осн. металлу на границе его сплавления с металлом шва.
Велики напряжения в корне шва.
Рассматриваем возможность разрушения шва от условного среза:
По металлу шва
По границе сплавления с металлом шва
βш и βс — коэфф. глубины проплавления — в зависимости от вида сварки
Lш =L-10мм, RВш—расчетное сопротивление срезу металла шва;
Rувс—расчетное сопротивление срезу (условному) металла границы сплавления.
Удобнее определять необходимую длину швов, задаваясь их толщиной kш: kш = меньшей из толщин элементов,
Толщина шва исходя из его возможной расчетной длины:
Напряжения от силы сдвига и момента:
По металлу шва
По металлу границы сплавления
Площади швов
должны быть
распределены обратно пропорционально
расстояниям от шва до оси элемента.
при общей требуемой площади швов —
Площадь большего шва на «обушке» уголка
Площадь меньшего шва на «пере» уголка
9.Достоинства и недостатки болтовых соединений. Виды болтов, применяемые в строительных мк. Разновидности болтовых соединений.
Болтовые = раньше сварных. Простота и надежность в работе.
Они более металлоемки, имеют накладки, ослабляют отверстиями.
Болты грубой и нормальной точности — отклонения диаметра 1 мм и 0,52 мм (для болтов d≤30 мм). Они = из углеродистой стали. Класс прочности болтов (5.6). Первое число = 50 = временное сопротивление (σв кгс/мм2), а 5*6=30 — предел текучести материала (σт кгс/мм2).
Отверстия на 2—3
мм больше диаметра болта — облегчает
посадку болтов (преимущество). Но это
повышает деформативность соединения
при работе на сдвиг. Эти болты = крепежные.
Болты повышенной точности — из углеродистой стали. d отверстия = +0,3 мм от диаметра болта.
Болты сидят плотно и хорошо воспринимают сдвигающие силы. Сложность изготовления и постановки болтов = применяются редко.
Высокопрочные болты — из легированной стали, термически обрабатывают. Они = нормальной точности, отверстия большего диаметра, но гайки затягивают спец-ключом. Силы трения препятствуют сдвигу элементов относительно друг друга. Высокопрочный болт работает на осевое растяжение.
Необходима одинаковая толщина элементов, а то несущая способность болта резко уменьшается.
Применяют клееболтовое. Преимущества — простота устройства; По качеству — не уступают сварке, но уступают ей по расходу металла.
Самонарезающие
болты —
наличие резьбы. Материал — сталь
термоупрочненная. d=6 мм для прикрепления
профилированного настила к прогонам и
элементам фахверка. Преимущество —
доступ к конструкции только с одной
стороны.
Фундаментные (анкерные) болты — передачи растягивающих усилий с колонн на фундамент. Материал — стали марок ВСтЗкп2, 09Г2С и 10Г2С1.
Сварные соединения | Сварочное производство при изготовлении трансформаторов и электрических машин
Страница 2 из 8
Соединения деталей и узлов конструкции, образуемые с помощью сварки, называют сварными соединениями, а часть сварного соединения, образуемую
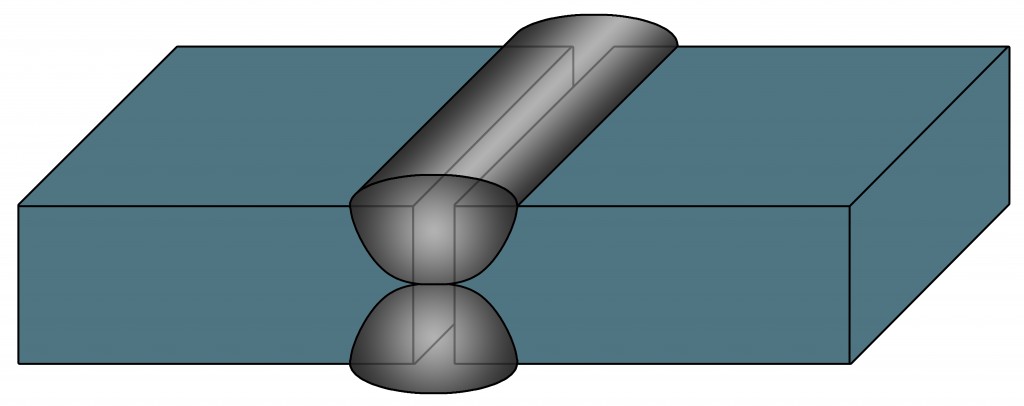
Рис. 1. Сварные швы и соединения.
а — виды сварных швов в зависимости от их положения в пространстве; б — виды сварных соединений в зависимости от взаимного расположения свариваемых деталей.
В зависимости от положения в пространстве сварные швы бывают нижние, горизонтальные, вертикальные и потолочные (рис. 1, а). Самый простой для выполнения нижний шов, так как при сварке этим швом капли расплавленного металла стекают вниз, в сварочную ванну. Наиболее трудным для выполнения является потолочный шов.
Р и с. 2. Стыковые швы.
а — шов без скоса кромок, односторонний; б — У-образный шов со скосом кромок, односторонний; в — Х-образный с двумя симметричными скосами двух кромок; г — U-образный с криволинейными скосами двух кромок, двусторонний; д — К-образный с двумя симметричными скосами одной кромки.
В зависимости от взаимного расположения свариваемых деталей различают следующие наиболее распространенные виды сварных соединений: стыковое, внахлест, тавровое, угловое, торцовое и отбортованное (рис. 1,б). В зависимости от протяженности различают прерывистые и непрерывистые (сплошные) швы. Соединения, где не требуется герметичность сварных швов, выполняют прерывистым швом, получаемым при полуавтоматической или ручной сварке.
Элементы подготовки кромок под сварку и размеры сварных швов указываются в стандартах и разделяются по видам сварки: сварка под флюсом, полуавтоматическая сварка в среде углекислого газа и ручная дуговая сварка.
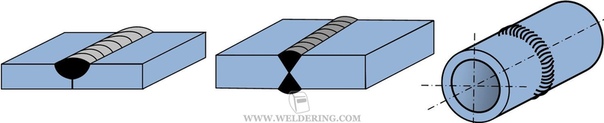
Рис. 3. Схема наложения сварных швов:
а — обратноступенчатый способ; б — метод уравновешивания деформаций. Цифры обозначают порядок нанесения швов.
При сварке почти всегда возникают остаточные сварочные напряжении, как правило, растягивающие напряжения в шве и сжимающие в основном металле. Для уменьшения остаточных сварочных напряжений прн создании сварных конструкций и разработке рабочей технологии сборки и сварки узлов необходимо избегать применения пересекающихся швов, располагать швы симметрично, не применять швов с излишними размерами катетов и усилений, применять, где это возможно, прерывистые швы, при наложении длинных швов (свыше 1 м) использовать обратноступенчатый способ наложения швов от середины к концам (рис. 3,а), сварку конструкций с симметричным расположением швов веста по методу уравновешивания деформаций (рис. 3,б).
В готовых узлах уменьшение сварочных напряжений достигается высоким отпуском (при температуре 550— 680 °С) в течение нескольких часов, прокаткой, проковкой сварных швов и околошовной зоны.
Технологический процесс изготовления сварных металлоконструкций машин и трансформаторов состоит из следующих основных операций: резки заготовок из листового и профильного проката, изготовления из заготовок деталей, подготовки поверхности в зоне шва, сборки узлов с предварительной прихваткой, сварки, зачистки швов и поверхностей от шлака и грата, снятия внутренних напряжений, испытания на прочность и плотность сварных швов, отделки и окраски изготовленных металлоконструкций.
Для изготовления металлоконструкций применяются различные виды малоуглеродистых сталей из профильносортового проката.
Материалы для изготовления сварных стальных конструкций необходимо выбирать не только по эксплуатационным требованиям, но и с учетом возможности высококачественной сварки. Например, малоуглеродистые стали лучше свариваются (не образуют трещин и т. п.), чем высокоуглеродистые и легированные. Поэтому одним из основных критериев качества сталей для сварки является их свариваемость.
МК — Глава 5. СВАРНЫЕ СОЕДИНЕНИЯ
1. Виды сварных соединений
Различают следующие виды сварных соединений: стыковые, внахлестку, угловые и тавровые (впритык).
Стыковыми
называют соединения, в которых
элементы соединяются торцами
или кромками и один элемент
является продолжением другого.
Стыковые соединения наиболее
рациональны, так как имеют
наименьшую концентрацию
напряжений при передаче
усилий, отличаются
экономичностью и удобны для
контроля. Толщина свариваемых
элементов в соединениях такого
вида почти не ограничена.
Стыковое соединение листового
металла может быть сделано
прямым или косым швом. Стыковые
соединения профильного
металла применяются реже, так
как затруднена обработка их
кромок под сварку.
Соединениями
внахлестку называются такие, в
которых поверхности
свариваемых элементов
частично находят друг на друга.
Эти соединения широко
применяют при сварке листовых
конструкций из стали небольшой
толщины (2-5 мм), в решетчатых и
некоторых других видах
конструкций. Разновидностью
соединений внахлестку
являются соединения с
накладками, которые применяют
для соединения элементов из
профильного металла и для
усиления стыков.
Иногда стыковое соединение профильного металла усиливают накладками, и тогда оно называется комбинированным.
Соединения внахлестку и с накладками отличаются простотой обработки элементов под сварку, но по расходу металла они менее экономичны, чем стыковые. Кроме того, эти соединения вызывают резкую концентрацию напряжений, из-за чего они нежелательны в конструкциях, подвергающихся действию переменных или динамических нагрузок и работающих при низкой температуре.
Угловыми называют соединения, в которых свариваемые элементы расположены под углом.
Тавровые
соединения (соединения
впритык) отличаются от угловых
тем, что в них торец одного
элемента приваривается к
поверхности другого элемента.
Угловые и тавровые соединения
выполняются угловыми швами,
широко применяются в
конструкциях и отличаются
простотой исполнения, высокой
прочностью и экономичностью.
В ответственных конструкциях, в тавровых соединениях (например, в швах присоединения верхнего пояса подкрановой балки к стенке) желательно полное проплавление соединяемых элементов.
2. Сварные швы
Сварные швы классифицируют по конструктивному признаку, назначению, положению, протяженности и внешней форме.
По
конструктивному признаку швы
разделяют на стыковые и
угловые (валиковые). В табл. 5.2
показаны виды швов и
необходимая форма разделки
кромок соединяемых элементов
различной толщины для
обеспечения качественного
соединения при
автоматизированной и ручной
сварке.
Стыковые швы наиболее рациональны, так как имеют наименьшую концентрацию напряжений, но они требуют дополнительной разделки кромок. При сварке элементов толщиной больше 8 мм для проплавления металла по всей толщине сечения необходимы зазоры и обработка кромок изделия. В соответствии с формой разделки кромок швы бывают V, U, X и К-образные. Для V- и U-образных швов, свариваемых с одной стороны, обязательна подварка корня шва с другой стороны для устранения возможных непроваров, являющихся источником концентрации напряжений.
Начало и конец шва
имеют непровар и кратер,
являются дефектными и их
желательно выводить на
технологические планки за
пределы рабочего сечения шва, а
затем отрезать.
При автоматической сварке принимаются меньшие размеры разделки кромок швов вследствие большего проплавления соединяемых элементов (табл. 5.2). Чтобы обеспечить полный провар шва, односторонняя автоматическая сварка часто выполняется на флюсовой подушке, на медной подкладке или на стальной остающейся подкладке..
При электрошлаковой сварке разделка кромок листов не требуется, но зазор в стыке принимают не менее 14 мм.
Угловые (валиковые) швы наваривают в угол, образованный» элементами, расположенными в разных плоскостях. Применяющаяся при этом разделка кромок изделия показана в табл. 5.2.
Угловые швы,
расположенные параллельно
действующему осевому усилию,
называют фланговыми, а
перпендикулярно усилию -
лобовыми.
Швы могут быть
рабочими или связующими
(конструктивными), сплошными
или прерывистыми (шпоночными).
По положению в пространстве во
время их выполнения они бывают
нижними, вертикальными,
горизонтальными и потолочными.
Сварка нижних швов наиболее
удобна, легко поддается
механизации, дает лучшее
качество шва, а потому при
проектировании следует
предусматривать возможность
выполнения большинства швов в
нижнем положении.
Вертикальные, горизонтальные и
потолочные швы в большинстве
своем выполняются при монтаже.
Они плохо поддаются
механизации, выполнить их
вручную трудно, качество шва
получается хуже, а потому
применение их в конструкциях
следует по возможности
ограничивать.
3. Температурные напряжения и деформации при сварке
Причины
возникновения и
характеристика сварочных
напряжений и деформаций.
Неравномерный разогрев
изделия при сварке порождает
неравномерную температурную
деформацию его. Монолитность
материала изделия
препятствует свободной
температурной деформации
отдельных частей его, в
результате чего во время
сварки образуются напряжения и
пластическая деформация части
металла соединения, а после
охлаждения в изделии остаются
сварочные напряжения и
деформации. Оставшиеся после
сварки напряжения и деформации
называются термическими
сварочными. Эти напряжения, не
связанные с действием внешних
сил, являются внутренними,
собственными напряжениями
первого рода,
уравновешиваемыми в объеме
элемента и вызывающими его
деформацию. Помимо термических
сварочных напряжений в
соединении могут существовать
напряжения структурные,
получающиеся в результате
быстрого охлаждения
соединения и появления
переохлажденных структур, не
свойственных данному
температурному состоянию
изделия, например мартенсита.
Структурные напряжения сильно
зависят от свойств материала и
технологии сварки, термические
сварочные напряжения и
деформации — от
конструктивного решения и
технологии сварки.
Сварочные
напряжения и деформации при
наплавке валика на кромку
листа. Лист при наплавке
валика на кромку разогревается
неравномерно по ширине и
распределение температуры
поперек листа имеет вид
убывающей кривой е — е.
Если бы рассматриваемый лист состоял из отдельных узких, продольных полос, не связанных друг с другом по краям, то каждая такая полоса удлинялась бы пропорционально своей температуре на
Сварочные
напряжения и деформации при
соединении листов встык. При
сварке двух листов встык
возникают как продольные, так и
поперечные сварочные
напряжения и деформации. Эпюры
этих напряжений должны быть
уравновешенными, и в
результате сварки двух листов
встык получаются эпюры
напряжений. Сварочные
напряжения существенно
увеличиваются при сварке встык
деталей, закрепленных от
свободных перемещений по
краям. В этом случае детали при
нагревании расширяются в
сторону шва и в гаком
сближенном состоянии
свариваются. При остывании шва
невозможность свободной
деформации закрепленного по
краям изделия вызывает большие
растягивающие напряжения в
нем, которые могут привести к
разрушению.
Возникновение в стыковом шве и в околошовной зоне растягивающих сварочных напряжений двух направлений создает плоско напряженное состояние этой зоны, что может привести к хрупкому разрушению.
Сварочные
напряжения и деформации при
соединении угловыми швами. В
угловых швах также возникают
сварочные напряжения, так как
жесткость соединяемых
элементов препятствует
свободному сокращению шва при
остывании. Остаточные
сварочные напряжения вызывают
продольную и поперечную усадку
швов и деформацию элементов.
Усадка происходит всегда к
центру шва. Наиболее
неблагоприятна поперечная
усадка, которая примерно в 10
раз больше продольной.
Снизить сварочные деформации можно рядом технологических мероприятий, в том числе закреплением или даже выгибом изделия в сторону, обратную его усадке, однако в этом случае увеличиваются сварочные напряжения.
Влияние
сварочных напряжений на
прочность соединения.
Сварочные напряжения
линейного характера не влияют
на прочность изделия при
наличии в соединении от
внешних усилий тоже линейного
напряженного состояния,
совпадающего по направлению с
первым. В силу
уравновешенности сварочных
напряжений они будут
увеличивать и уменьшать
напряжения от внешней
нагрузки, но не будут нарушать
равновесия внешних сил,
действующих на изделие.
Сварочные напряжения,
совпадающие по знаку с
напряжениями от нагрузки,
могут вызвать преждевременное
появление местной текучести в
изделии, выравнивающей
неравномерное распределение
напряжений. Пластическая
работа материала в этом случае
уменьшает сварочные
напряжения, и после первой же
разгрузки конструкция
работает упруго.
При плоском
однозначном поле сварочных
напряжений (например, средняя
зона двух листов, сваренных
встык, испытывающая растяжение
в двух направлениях) они
препятствуют развитию
пластичности при суммировании
сварочных и силовых напряжений
и могут вызвать хрупкое
разрушение изделия. Их
неблагоприятное воздействие
усиливается источниками
концентрации напряжений
вследствие дефектов сварного
шва. Особенно опасны сварочные
напряжения, появляющиеся при
сварке толстых изделий, так как
в этом случае распределение
остаточных напряжений носит
объемный характер, еще более
затрудняющий влияние
пластичности материала на
выравнивание напряжения.
[ | | | ]
Что такое стыковая сварка?
Сварка может понравиться многим. Установите металлы, опустите козырек, зажгите дугу и приступайте к делу. То, что несколько часов назад могло быть просто грудой металлических деталей, появилось бы из ослепляющего белого каления как нечто практичное и полезное. Но понимание стыковых швов важно для того, чтобы это произошло.
Так что же такое стыковой шов? Стыковой шов — это наиболее распространенный тип соединения, который используется при изготовлении конструкций и систем трубопроводов.Это кольцевой сварной шов, на который вокруг шва наносится расплавленный металл.
Способность формировать и формировать новое ценное оборудование или целые конструкции из нескольких случайных кусков металла может быть воодушевляющей, и это одна из причин, по которой многие люди присоединяются к этой профессии. Это не просто жизнь, а страсть сварщиков.
Что такое стыковой шов?
Как производители металла, мы можем распиливать, резать, шлифовать, гнуть, пробивать, надрезать и полировать сложные конструкции.Сварка — вот где происходит настоящее волшебство. Обычные части комбинируются и соединяются вместе, чтобы создать ворота и заборы вокруг вашей собственности, расширения рам для транспортных средств и дополнительных приспособлений для техники.
Выполнение сварных швов хорошего качества требует знаний и практики, особенно в отношении сварных швов. Существует только два основных типа непрерывных сварных швов: угловой шов и стыковой шов . Некоторые сварщики заметят, что их больше, но, по сути, все они представляют собой модификации углового или стыкового шва.
Две детали из недрагоценных металлов собираются вместе и закрепляются на верстаке или на креплениях. Обычно между металлами остается зазор примерно 1/8 дюйма (3 мм). Сварщик зажигает дугу и вводит наполнитель в зазор, образуя лужу расплавленного металла. Затем бассейн перемещается по длине стыка с добавлением дополнительного наполнителя непрерывным потоком.
Между металлами остается зазор, чтобы расплавленный металл проникал глубоко внутрь соединяемых деталей.Если оставить зазор между металлами слишком мал, металл может проникнуть недостаточно глубоко. Если вы оставите слишком большой промежуток, у вас получится большой шов на противоположной стороне деталей.
Толщина металла также влияет на уровень проплавления. Если ваши металлические детали имеют размер более 3/16 дюйма, фаска обычно применяется на одном или обоих верхних краях. Это может сделать зазор шире и позволить металлу более эффективно стекать на всю толщину металла. И наоборот, если металлические детали слишком тонкие, может вообще не понадобиться оставлять зазор между деталями.
Виды стыковых сварных соединений
Стыковые швы выполняются разными способами, и каждый из них служит для разных целей. Типичные примеры стыковых сварных соединений включают следующее:
Src: https://www.twi-global.comКвадратный шов встык
Квадратный стыковой сварной шов в основном используется в проектах, где толщина металла составляет 3/16 дюйма или меньше. Квадратное стыковое сварное соединение достаточно прочное, но его не рекомендуется использовать в тех случаях, когда готовая конструкция будет подвергаться ударным нагрузкам или усталости при длительной эксплуатации.
Подготовить стык не составляет труда, так как для этого нужно соединить только края металлических пластин. Однако для достижения наилучшего результата важно точно подогнать металлы друг к другу по всей длине соединения. Также необходимо оставить достаточно корневого отверстия для шва, чтобы наполнитель мог проникнуть глубоко внутрь.
Стыковая сварка с канавкой
Если вы хотите сваривать металлы толщиной более 3/16 дюйма, вам, вероятно, понадобится стыковое соединение с рифлением. Целью проточки металлических пластин является придание стыку необходимой прочности. Более толстые металлы имеют больше места для нанесения наполнителя, а проточка листов обеспечивает более прочное соединение.
Если вы применяете сварной шов с канавкой для своего проекта, очень важно сохранить угол канавки, достаточный для того, чтобы электрод мог вливаться в стык. Если канавка слишком узкая, наполнитель не проникнет достаточно глубоко и через некоторое время потрескается. Однако вам также необходимо избегать чрезмерного снятия фаски на металлическом листе, потому что это может привести к потере металла шва и времени, не дав вам необходимой выгоды.
Стыковое сварное соединение с разделкой кромок может быть либо с одной канавкой только с одной стороны, либо с двумя канавками, с канавками с обеих сторон. Это в основном зависит от толщины металла и типа сварных швов, которые вам нужно сделать. На более толстых металлах можно делать канавки с обеих сторон, а на тонких листах — только с одной стороны. Если вы работаете над множеством проектов, вам, вероятно, придется использовать оба, поэтому лучше изучить оба стиля.
В под сварку встык
Одинарный V-образный стыковой шов чаще встречается на рамах толщиной от 1/4 до 3/4 дюйма.Угол скоса соединения составляет около 60 градусов для плиты и 75 градусов для трубы в целом. Подготовить металл можно с помощью специального станка для снятия фасок или резака. Подготовка V-образного шва обходится дороже, чем квадратного стыкового соединения. Для этого сварного шва вам также потребуется больше присадочного материала, чем для квадратного стыка.
Преимущество в том, что этот сварной шов прочнее, чем стыковое соединение квадратного сечения. Однако не рекомендуется, если готовая конструкция изогнута в корне сварного шва.
Двойной V-образный сварной шов
Двойной V-образный стыковой сварной шов отлично подходит для различных проектов. Его основное преимущество заключается в том, что металлы толщиной более 3/4 дюйма могут иметь желобки с обеих сторон. Однако его можно использовать на более тонких металлических пластинах, где критична нагрузка.
Подготовка двойного V-образного шва занимает больше времени, чем одинарного V-образного шва. Требуется меньшее количество присадочного материала; однако, поскольку пространство между двумя канавками уже, чем было бы для одной V-образной канавки, только с одной стороны.
Поскольку сварочный аппарат выделяет много тепла во время производства, вам следует чередовать сварочные швы для двойного V-образного соединения. Проведите сварщиком по всей длине металла с одной стороны и дайте ему остыть, прежде чем приступить к работе с другой стороны. Это помогает создать более симметричный шов и сводит к минимуму вероятность коробления.
Преимущества стыковой сварки
Многие сварщики предпочитают использовать стыковой сварной шов в своих проектах, потому что он создает достаточно прочный сварной шов, и его легко применять в различных ситуациях.Он предлагает пользователям следующие преимущества.
- Множественные стыковые сварные швы могут быть выполнены на всей площади стыка с различными размерами и формами сечения. Например, стыковые сварные швы используются везде, от ободов велосипедных колес до железнодорожных рельсов. Вам нужно убедиться, что соединяемые секции должны точно совпадать. Вы также можете создавать косые стыки с помощью стыковой сварки, такие как те, которые вы, возможно, видели в сварных металлических оконных рамах.
- Сварку можно выполнять для самых разных материалов, таких как сталь, алюминий, нержавеющая сталь, никелевые сплавы, титан и т. Д.
- Сварной шов создает сплошное фазовое соединение. Расплавленный металл и загрязнения, образующиеся в месте удара, выдавливаются в осадку в процессе нагрева. Это гарантирует, что затвердевание, пористость и растрескивание не будут проблемой.
- Процесс сварки может быть завершен в автоматическом или полуавтоматическом режиме без попадания дуги под другим углом. Вы можете контролировать соединение после каждого удара, чтобы определить качество сварки.
- Стыковое сварное соединение прочное и надежно герметичное.
- Идеально подходит для непрерывной стальной конструкции в трубах, так как соединения между фитингами и трубами в системе трубопроводов имеют хорошую прочность.
- Стыковые сварные швы обычно имеют гладкую поверхность, так как в канавку наносится наполнитель.
- Фитинги, приваренные встык, отличаются невысокой стоимостью.
- Стыковые сварные швы занимают меньше места в конструкции.
Присадочный материал для стыковых швов
Стальные стержни следует зажать с усилием, чтобы свести их вместе для стыковой сварки.В большинстве случаев для сварки металла вы будете использовать медь 3 класса. Это хороший проводник, обеспечивающий хороший механический износ, прочность и долговечность.
Стальной заусенец или выпуклость, которые могут образоваться во время стыковой сварки, следует удалить. Вы можете сделать это вручную или кусачками.
Связанные вопросы
В чем разница между сваркой враструб и стыковой сваркой? Между сваркой с раструбом и стыковой сваркой существует несколько различий. Например, у них разные шов и канавка, другое обнаружение, другое применение и они имеют разные затраты.Подробнее о различиях вы можете прочитать здесь.
Что такое сварка тройников? Тройники используются для сварки двух пластин или сегментов с поверхностями, расположенными в стыке под углом примерно 90 градусов друг к другу. Однако поверхность одной пластины или детали не находится в той же плоскости, что и вывод другой поверхности.
Каковы стандарты сварочной фаски? Во многих случаях, например, при снятии фаски на трубе, нормальным является фаска 37.Угол 5 градусов. Ключевой момент, о котором следует помнить, заключается в следующем: независимо от уровня, способность поддерживать этот угол в пределах допустимого уровня — лишь один из важнейших ключей к фантастическому скосу.
Подобные сообщения:
Что такое стыковая сварка?
Стыковой сварной шов — один из самых простых и универсальных типов конструкций сварных швов. Соединение формируется простым размещением двух металлических частей встык, а затем сваркой вдоль соединения. Важно отметить, что при стыковом соединении поверхности соединяемых деталей находятся в одной плоскости, а металл сварного шва остается в плоскостях поверхностей.Таким образом, детали почти параллельны и не перекрываются, например, в отличие от соединений внахлест.
Схема стыковой сварки
В зависимости от толщины металлических деталей могут быть выполнены различные типы канавок. Подготовка канавок также называется подготовкой кромок сварных швов и необходима для более толстых металлов. Примерами типов канавок в зависимости от их формы являются V-образная канавка, J-образная канавка и U-образная канавка. Конструкция канавки изменяется в зависимости от требований к сварному шву с полным или частичным проплавлением.Струбциновая сварка может выполняться с использованием различных видов сварки — ручных, механизированных или автоматизированных. Тонкие листы обычно сваривают без какой-либо подготовки кромок шва, такие соединения называются квадратными стыковыми соединениями.
Стыковые соединения можно сваривать дуговой сваркой, контактной сваркой и сваркой пучком высоких энергий, и это даже может быть частью операции пайки.
Вначале сварные детали можно удерживать вместе с помощью прихваточного шва, который представляет собой временное соединение, которое обеспечивает правильное выравнивание компонентов при выполнении стыковой сварки.Для соединения деталей в области стыкового соединения может потребоваться предварительный нагрев.
Стыковая сварка обычно применяется в различных отраслях промышленности, от трубопроводных систем, автомобилестроения, энергетики, энергетики и т. Д.
Типы стыковых сварных соединений
Как упоминалось ранее, различные типы стыковых сварных соединений названы в честь их конкретной формы. Различные типы соединений включают одинарные V-образные, двойные V-образные, одинарные и двойные скосы, одинарные и двойные U-образные, одинарные и двойные J-образные соединения, квадратные стыковые соединения и даже их комбинации. Самый простой из них с точки зрения центровки — это квадратный стыковой шов.
Во всех случаях сварные швы выполняются встык с толщиной основного металла. Чтобы контролировать деформацию сварной сборки, важно контролировать проплавление сварного шва, используя конструкцию соединения двойного проплавления.
Для стыковых швов, в зависимости от различных факторов, между деталями обычно имеется зазор от 2 до 3 мм (1/8 дюйма), который называется корневым зазором. Зазор нужен для того, чтобы присадочный металл полностью проникал в стык.Если зазор слишком мал или слишком велик, это приведет к дефектам сварного шва.
Преимущества
Стыковые швы дают несколько преимуществ, в том числе:
- Высокая прочность, полное сплавление
- Легко обрабатывается
- Контроль искажений
- Легко проверить
Недостатки
Есть некоторые недостатки, такие как:
- Геометрия сварки может ограничивать область применения
- Может потребоваться крепление или опора
- Чувствительность к плохим поверхностям
стыковой сварной шов против углового шва
Основное различие между стыковым и угловым сварным швом — это угол между соединяемыми деталями. Если соединяемые поверхности находятся в одной плоскости, то это стыковой шов. Если поверхности перпендикулярны (под углом 90 °), то их обычно соединяют угловым швом. Для угловых швов подготовка сварных швов не требуется, как для стыковых.
В угловом сварном шве присадочный металл наносится на стык в треугольном сечении, так что он образует угол 45 ° с обеими соединяемыми деталями. Для достижения необходимой толщины сварного шва сварку проводят в несколько проходов.
Деформация угловых и стыковых швов возникает в результате усадки при остывании присадочного металла. Этого можно избежать путем предварительного нагрева и / или выполнения последовательных проходов на противоположных сторонах стыка.
Заключение
Стыковая сварка — это часто используемая конструкция соединения для множества применений в различных отраслях промышленности из-за своей простоты. Этот базовый метод включает несколько различных форм сварных швов, подходящих для различной толщины сварного шва.
TWI может дать совет по всем аспектам материалов и соединения. Здесь вы можете узнать больше о наших консультационных услугах по сварке.
Часто задаваемые вопросы по теме (FAQ)
Что такое стыковая сварка или стыковые соединения?
Неважно, хотите ли вы заниматься сваркой только для хобби или для выбора профессии, вам рано или поздно придется изучить сварочные соединения. Это основная основа сварки, с которой вы будете сталкиваться ежедневно. По данным Американского общества сварщиков, существует пять различных типов сварных соединений.К ним относятся угловые соединения , стыковые, нахлесточные, краевые и тройники .
Знакомство с пятью соединениями звучит легко, но для каждого из них есть множество различных типов сварных швов, обозначений сварки, требований и т. Д. В этом руководстве мы сосредоточимся на одном из наиболее распространенных — стыковом соединении .
Что такое стыковые соединения?
Стыковое соединение просто означает, когда два компонента соединены вместе, но находятся в одной плоскости. Как я уже упоминал ранее, это одно из самых распространенных соединений, с которыми вы будете сталкиваться в своей карьере сварщика.Одна из причин, по которой стыковое соединение является более распространенным, заключается в том, что он дает множество преимуществ. К ним относятся:
- Можно автоматизировать или вручную.
- Экономически выгодно, особенно на заводах, где стыковое соединение может сэкономить время и деньги.
- Подготовка стыкового соединения проста.
- Простой сустав для изучения и выполнения.
- Если все сделано правильно, стыковое соединение представляет собой очень прочный сварной шов.
Однако, как и все в жизни, стыковое соединение не идеально и имеет некоторые недостатки.К ним относятся:
- Склонен к образованию избыточных полостей в сварном шве или пористости.
- Улавливание и растрескивание шлака могут быть более распространенными.
Различные типы стыковых сварных швов
Если следовать определению, которое мы дали ранее, стыковые соединения могут показаться довольно простой сваркой. Однако все становится немного сложнее, когда вы начинаете изучать все различные типы сварных швов, которые имеет стыковое соединение.
Термин Американского национального института стандартов (ANSI) для этих сварных швов — Groove Welds .Вы также можете услышать, что они называются стыковых сварных швов , что является термином Международной организации по стандартизации (ISO). Иногда их даже можно назвать Bevel Butt Weld . Независимо от того, как вы их называете, все они имеют одинаковые сварные швы.
Как видно из рисунка выше, есть немало сварных швов с разделкой кромок, которые вам нужно запомнить. Но прежде чем вы начнете, вам необходимо знать основы сварки с разделкой кромок и что такое скос.
Что такое сварной шов с разделкой кромкой?
Сварка с разделкой кромок или стыковая сварка просто относится к типу сварного шва, используемого в стыковом соединении.В зависимости от глубины проплавления сварного шва с разделкой кромок его можно разделить на две категории. К ним относятся:
Полное проникновение в стык (CJP) — Материал сварного шва полностью проходит до корневого отверстия и заполняет зазор.
Частичное проникновение в стык (PJP) — Материал сварного шва не достигает корневого отверстия, а лишь частично заполняет зазор.
Что такое скос?
Если вам нужен более глубокий провар для сварного шва с разделкой кромок, вам понадобится скос. Для тех, кто не знаком, скос означает просто наклонную кромку объекта или конструкции. Снятие фаски на краях компонента уменьшит толщину металла, но при этом позволит получить прочное соединение.
Угол и глубина фаски чрезвычайно важны для определения прочности соединения. Не уходя слишком далеко от темы, вот несколько важных вещей, о которых следует помнить относительно угла и глубины:
- Угол обычно составляет около 45 градусов, но может варьироваться.
- Угол должен быть достаточно широким, чтобы можно было удобно положить первую бусину.
- Угол не может быть углом 90 градусов.
- Глубина должна быть достаточно большой, чтобы обеспечить почти полное проникновение. Будьте осторожны, не заходите слишком глубоко, иначе во время сварки вы можете пробить дно.
Если вы хотите узнать больше о том, как скашивать кромку металла, мы перечислили видео ниже, которое должно быть полезным.
Сварной шов с квадратной канавкой
Теперь, когда мы закончили с основами, мы можем перейти к изучению первого сварного шва с канавкой, сварного шва с квадратной канавкой.К счастью, это один из самых простых в освоении стыковых суставов.
Начнем с того, что этот шов обычно выполняется на более тонких металлах, толщиной до 4,5 мм или 0,1772 дюйма. Так как это выполняется только на тонких металлах, нет необходимости скашивать кромки металла или изменять его вообще.
Как сварить стыковое соединение с квадратной канавкой
Сварной шов со скосом с канавкой
Итак, теперь, когда вы знаете, какое стыковое соединение использовать для более тонких металлов, что, если металл, который вы используете, слишком толстый? Здесь пригодится скос.Это также подводит нас к следующему стыковому соединению Bevel Groove Weld .
Как вы можете видеть на изображении выше, сварка со скосом с канавкой имеет два основных варианта. К ним относятся:
Сварной шов с одной кромкой и канавкой — Соединение, в котором один из свариваемых металлов скошен с одной стороны. Толщина листа: 3⁄16–3⁄8 дюйма (4,76–9,53 мм)
Двойной сварной шов со скосом под кромку — Соединение, в котором один из свариваемых металлов скошен с обеих сторон. Толщина пластины: более 3⁄8 дюйма (9.53 мм)
Как выполнить сварку стыкового соединения со скосом канавки
Сварной шов с V-образной канавкой
Так же, как и сварной шов с конической канавкой, для сварного шва с V-образной канавкой требуется скошенная кромка. Однако вместо того, чтобы только один из металлов имел скошенную кромку, оба металла имеют скошенный край. Скосы вместе образуют V-образную форму, отсюда и название соединения.
У вас есть выбор между двумя вариантами сварного шва с V-образной канавкой, которые вы можете найти ниже:
Сварной шов с одинарной V-образной канавкой — Кромки обоих металлов скошены, образуя букву «V».Толщина листа: до 3⁄4 дюйма (19,05 мм)
Сварной шов с двойной V-образной канавкой — Кромки с обеих сторон металлов скошены, образуя букву «V» с обеих сторон. Толщина листа: более 3⁄4 дюйма (19,05 мм)
Как приварить стыковое соединение с V-образной канавкой
Сварной шов с J-образной канавкой
Сварной шов с J-образной канавкой — это другой тип стыкового шва, в котором не использует скошенную кромку . В нем используется паз в форме буквы «J». Несмотря на то, что у него нет фаски, как у предыдущих сварных швов, у J-образной канавки есть те же два разных типа на выбор: одинарный и двойной.
Сварной шов с одинарной J-образной канавкой — Этот сварной шов требует, чтобы один из металлов имел кромку J-образной канавки, а другой металл имел правильную квадратную кромку. Толщина листа: 1⁄2–3⁄4 дюйма (12,70–19,05 мм)
Сварной шов с двойной J-образной канавкой — Для этого сварного шва один из металлов имеет J-образную канавку с обеих сторон кромки, а другой металл также имеет правильную квадратную кромку. Толщина листа: более 3⁄4 дюйма (19,05 мм)
Сварной шов с U-образной канавкой
Точно так же, как V-образная канавка похожа на скошенную канавку, U-образная канавка похожа на J-образную канавку.С U-образной канавкой вы будете делать такую же J-образную канавку, но вместо того, чтобы иметь только один из металлов с J-образной канавкой, он будет у обоих металлов. Именно здесь сварной шов получил свое название, поскольку эта канавка имеет U-образную форму.
Вы, наверное, уже догадались, что существует два разных типа сварных швов с U-образной канавкой.
Сварной шов с одинарной U-образной канавкой — Кромки обоих металлов имеют J-образную канавку, которая при соединении образует U-образную канавку. Толщина пластины: до 3⁄4 дюйма (19.05 мм)
Сварной шов с двойной U-образной канавкой — Кромки на обоих металлах с обеих сторон имеют J-образную канавку, образующую две U-образные канавки. Толщина листа: более 3⁄4 дюйма (19,05 мм)
Полезные ссылки и источники
Безопасность при сварке
Как и в каждой из наших статей или руководств, мы почти уделяем первоочередное внимание напоминанию людям об опасностях при сварке. Любой опытный сварщик скажет, как глупо не принимать это всерьез. Чтобы должным образом защитить себя, тоже не нужно много времени.
Один из самых простых способов защитить себя от множества опасностей — это сварочный шлем. Сварочная маска защитит вас от вспышки сварщика, ожогов от УФ-излучения и даже случайного попадания мусора. Некоторые другие простые способы защиты от других опасностей включают использование подходящих сварочных перчаток и обеспечение надлежащей вентиляции.
Welding — SteelConstruction.info
Сварка — это основной вид деятельности на заводе-изготовителе, которым занимаются опытные квалифицированные специалисты, работающие в системе управления качеством сварки под контролем ответственного координатора сварки. Он используется для подготовки стыков к подключению в магазине и на месте, а также для крепления других приспособлений и фурнитуры. На заводе-изготовителе для разных видов деятельности используются разные методы сварки.
По сути, в процессе сварки используется электрическая дуга для выработки тепла для плавления основного материала в соединении. Отдельный присадочный материал, поставляемый в качестве расходуемого электрода, также плавится и соединяется с основным материалом, образуя расплавленную сварочную ванну. По мере того, как сварка продолжается вдоль соединения, сварочная ванна затвердевает, сплавляя основной металл и металл сварного шва.Для заполнения стыка или нарастания сварного шва до проектного размера может потребоваться несколько проходов или проходов.
Сварка
(Изображение любезно предоставлено William Haley Engineering Ltd.)
[вверх] Принципы дуговой сварки металлом
Терминология области сварного шва
Сварка — это сложное взаимодействие физических и химических наук. Правильное определение металлургических требований и разумное практическое применение являются предпосылкой для успешной сварки плавлением.
В процессе дуговой сварки металлическим электродом используется электрическая дуга для выработки тепла для плавления основного материала в соединении. Отдельный присадочный материал, поставляемый в качестве расходуемого электрода, также плавится и соединяется с основным материалом, образуя расплавленную сварочную ванну. Сварочная ванна подвержена атмосферному загрязнению и, следовательно, нуждается в защите во время критической фазы замерзания жидкости и твердого тела.Защита достигается либо за счет использования защитного газа, за счет покрытия бассейна инертным шлаком, либо за счет комбинации обоих действий.
В процессах с защитным газом от удаленного источника поступает газ, который подается на сварочную дугу через горелку или горелку. Газ окружает дугу и эффективно исключает атмосферу. Точный контроль необходим для поддержания подачи газа с подходящей скоростью потока, так как слишком большое количество может вызвать турбулентность и засасывать воздух, а может быть настолько же вредным, насколько и слишком маленьким.
В некоторых процессах используется флюс, который плавится в дуге для образования шлакового покрытия, которое, в свою очередь, покрывает сварочную ванну и защищает ее во время замерзания. Шлак также затвердевает и самораспускается или легко удаляется легким сколом. Действие плавления флюса также создает газовый экран для защиты.
По мере сварки вдоль стыка сварочная ванна затвердевает, сплавляя основной металл и металл шва. Для заполнения стыка или нарастания сварного шва до проектного размера может потребоваться несколько проходов или проходов.
Тепло от сварки вызывает металлургические изменения в основном материале, непосредственно примыкающем к границе или линии плавления. Эта область изменения известна как зона термического влияния (HAZ). Общая терминология, используемая в области сварного шва, показана справа вверху.
Сварочные операции требуют надлежащего технологического контроля со стороны компетентных сварщиков, чтобы гарантировать достижение проектных характеристик, минимизировать риск дефектных соединений, вызванных низким качеством сварки, и предотвратить образование склонных к образованию трещин микроструктур в ЗТВ.
[вверх] Виды сварных соединений
Большинство конструкционных сварных соединений выполняется на заводе-изготовителе и описывается как стыковые или угловые швы. Сварка на месте также возможна, и руководство по вопросам сварки на месте доступно в GN 7.01.
[вверх] Стыковые швы
Макрос клиновидного стыкового шва
(Изображение любезно предоставлено Mabey Bridge Ltd.)
Стыковые сварные швы обычно представляют собой стыковые соединения в прокатных профилях или стыковые соединения листов на стенках и фланцах, чтобы приспособиться к изменению толщины или восполнить доступный материал по длине.Положения этих стыковых швов допускаются при проектировании, хотя ограничения доступности материалов или схема монтажа могут потребовать согласования различных или дополнительных сварных швов. Тройники, приваренные встык, могут потребоваться, если при поперечных соединениях возникают значительные нагрузки или усталость.
Стыковые швы — это сварные швы с полным или частичным проплавлением, выполняемые между материалами со скошенными или скошенными кромками. Стыковые швы с полным проплавлением предназначены для передачи всей прочности сечения.Как правило, эти соединения можно сваривать с одной стороны, но по мере увеличения толщины материала желательна сварка с обеих сторон, чтобы уравновесить эффекты деформации, с операцией обратной строжки и / или шлифования в процессе для обеспечения целостности корень шва. Односторонние стыковые сварные швы с подкладными полосами из керамической или прочной стали обычно используются для соединения больших площадей пластин (например, стальных пластин настила) и там, где есть закрытые коробчатые секции, трубы или элементы жесткости, доступ к которым для сварки возможен только с одного сторона.Расчетная толщина горловины определяет глубину проплавления, необходимую для швов с частичным проплавлением. Обратите внимание, что соображения усталости могут ограничивать использование сварных швов с частичным проплавлением, особенно на мостах. Руководство по подготовке к сварке доступно в GN 5.01.
Следует приложить все усилия, чтобы избежать стыковой сварки приспособлений из-за затрат, связанных с подготовкой, временем сварки, более высоким уровнем квалификации сварщиков и более строгими и трудоемкими требованиями к испытаниям. Кроме того, стыковые швы имеют тенденцию иметь большие объемы наплавленного металла шва; это увеличивает эффект усадки сварного шва и приводит к более высокому уровню остаточного напряжения в соединении.Чтобы уравновесить усадку и распределить остаточное напряжение, минимизируя таким образом деформацию, необходима тщательная последовательность сварочных операций.
Иногда бывает необходимо обработать стыковые сварные швы заподлицо по причинам усталости, или для улучшения дренажа стальных балок, устойчивых к атмосферным воздействиям, или для улучшения режима испытаний. Следует избегать зачистки заподлицо только по эстетическим соображениям, потому что трудно обработать поверхность, чтобы она соответствовала смежной поверхности после прокатки, и результат часто более визуально заметен, чем исходный сварной шов. Кроме того, шлифование представляет собой дополнительную опасность для здоровья и безопасности, которую следует избегать по возможности. Правка стыковых швов до гладкой поверхности обычно не требуется для строительных стальных конструкций, поскольку обычно они не подвержены усталости.
- Пример обработанного стыкового шва с гладкой поверхностью и сливными пластинами
(изображения любезно предоставлены Mabey Bridge Ltd.)
[вверх] Угловые швы
Макрос однопроходного углового шва
(Изображение любезно предоставлено Mabey Bridge Ltd.)
В большинстве сварных соединений в зданиях и мостах используются угловые швы, обычно в форме тройника. Обычно они включают в себя концевую пластину, ребро жесткости, подшипниковые и распорные соединения с прокатными секциями или плоскими балками, а также соединения стенки с фланцем на самих пластинчатых балках. Их относительно просто подготовить, сварить и испытать в обычных конфигурациях, при этом главным соображением является сборка стыков.
В S275 полная прочность стали также развивается в угловых сварных швах и сварных швах с частичным проплавлением с вышележащими угловыми швами при условии, что такие сварные швы симметричны, выполнены с использованием правильных расходных материалов и сумма сварных швов равна толщине элемента, который сварные швы стыкуются.
Размеры сварных швов должны быть указаны на чертежах проекта вместе с любыми специальными требованиями по классификации усталости. BS EN ISO 22553 [1] предписывает правила использования символов для детализации сварных соединений на чертежах.
Обращается внимание на тот факт, что в традиционной практике Великобритании для определения размера углового сварного шва обычно используется длина ветви, но это не универсально: в европейской практике используется толщина горловины, а в стандарте BS EN 1993-1-8 [2] дает требования относительно размера горла, а не длины ноги. Проектировщик должен следить за тем, чтобы было ясно, какой размер указан, и что все стороны должны знать, что было указано.
[вверх] Процессы
Важными факторами, которые подрядчик по изготовлению металлоконструкций должен учитывать при выборе процесса сварки, являются способность выполнять проектные требования и, с точки зрения производительности, скорость наплавки, которая может быть достигнута, а также рабочий цикл или эффективность процесса. (Эффективность — это отношение фактического времени сварки или дуги к общему времени, в течение которого сварщик или оператор занят выполнением сварочного задания.Общее время включает настройку оборудования, чистку и проверку выполненного шва.)
Ниже описаны четыре основных процесса сварки, которые регулярно используются при производстве стальных конструкций в Великобритании. Номера процессов определены в BS EN ISO 4063 [3] . Разновидности этих процессов были разработаны с учетом практики и оборудования отдельных производителей, и другие процессы также имеют место для конкретных приложений, но выходят за рамки данной статьи.
[вверх] Металлоактивная газовая сварка (MAG), процесс 135
Сварка MAG
(Изображение любезно предоставлено Kiernan Structural Steel Ltd.)
MAG-сварка сплошным проволочным электродом — это наиболее широко используемый процесс с ручным управлением для заводских производственных работ; это иногда называют полуавтоматической сваркой или сваркой CO 2 . Сплошной проволочный электрод из сплошной проволоки пропускается через устройство подачи проволоки к «пистолету», который обычно удерживается и управляется оператором. Питание подается от источника выпрямителя или инвертора по соединительным кабелям к устройству подачи проволоки и кабелю горелки; электрическое подключение к проводу осуществляется через контактный наконечник на конце пистолета.Дуга защищена защитным газом, который направляется в зону сварного шва через кожух или сопло, окружающее контактный наконечник. Защитные газы обычно представляют собой смесь аргона, диоксида углерода и, возможно, кислорода или гелия.
Хорошая производительность наплавки и рабочий цикл можно ожидать от процесса, который также можно механизировать с помощью простых моторизованных кареток. Газовая защита может быть сдувана сквозняками, что может вызвать пористость и возможные вредные металлургические изменения в металле сварного шва.Таким образом, этот процесс лучше подходит для заводского производства, хотя он используется на месте, где могут быть предусмотрены эффективные укрытия. Он также более эффективен в плоском и горизонтальном положениях; Сварные швы в других положениях наплавляются с более низкими параметрами напряжения и силы тока и более подвержены дефектам плавления.
Металлоактивная газовая сварка (МАГ), процесс 135
Металлоактивная газовая сварка (MAG), процесс 135
MAG-сварка электродом с флюсовой сердцевиной, процесс 136 представляет собой разновидность, в которой используется то же оборудование, что и MAG-сварка, за исключением того, что плавящийся проволочный электрод имеет форму трубки малого диаметра, заполненной флюсом. Преимущество использования этих проволок состоит в том, что можно использовать более высокие скорости наплавки, особенно при сварке в вертикальном положении (между двумя вертикальными поверхностями) или в верхнем положении. Наличие тонкого шлака помогает преодолевать силу тяжести и позволяет наносить сварные швы в местах с относительно высокими током и напряжением, тем самым снижая вероятность дефектов плавления. Добавки флюса также влияют на химию сварного шва и, таким образом, улучшают механические свойства соединения.
[вверху] Ручная дуговая сварка металлом (MMA), процесс 111
Этот процесс остается наиболее универсальным из всех сварочных процессов, но его использование в современной мастерской ограничено.Трансформаторы переменного тока, выпрямители постоянного тока или инверторы подают электроэнергию по кабелю на электрододержатель или клещи. Проволочный электрод с флюсовым покрытием (или «стержень») вставляется в держатель, и сварочная дуга возникает на конце электрода, когда он ударяется о заготовку. На острие электрода плавится, образуя ванну расплава, которая сплавляется с основным материалом, образуя сварной шов. Флюс также плавится, образуя защитный шлак и создавая газовый экран, предотвращающий загрязнение сварочной ванны по мере ее затвердевания.Добавки флюса и сердечник электрода используются для влияния на химический состав и механические свойства сварного шва.
Обычно используются электроды с основным покрытием, контролируемым водородом. Эти электроды необходимо хранить и обращаться с ними в соответствии с рекомендациями производителя расходных материалов, чтобы сохранить их низкие водородные характеристики. Это достигается либо путем использования сушильных шкафов и подогреваемых колчанов для хранения и обработки продукта, либо путем покупки электродов в герметичных упаковках, специально разработанных для поддержания низкого уровня водорода.
Недостатками процесса являются относительно низкая скорость наплавки и высокий уровень отходов, связанных с непригодными для использования концевыми штырями электродов. Тем не менее, он остается основным процессом для сварки на стройплощадке и для труднодоступных мест, где громоздкое оборудование не подходит.
Ручная дуговая сварка металлом (MMA), процесс 111
Ручная дуговая сварка металлом (MMA), процесс 111
[вверх] Дуговая сварка под флюсом (SAW), процесс 121
Оперативная сварка под флюсом
(Изображение любезно предоставлено Mabey Bridge Ltd.)
Это, вероятно, наиболее широко используемый процесс для сварки угловых швов перемычки между стенкой и фланцем и стыковых сварных швов на линии толстой пластины для получения отрезков длины фланца и стенки. В процессе процесса непрерывный провод подается через контактный наконечник, где он устанавливает электрический контакт с мощностью от выпрямителя, в зону сварки, где он изгибается и образует ванну расплава. Сварочная ванна заполняется флюсом, подаваемым из бункера. Флюс, непосредственно покрывающий расплавленную сварочную ванну, плавится, образуя шлак и защищая сварной шов во время затвердевания; избыточный флюс собирается и повторно используется.По мере охлаждения шва шлак замерзает и отслаивается, оставляя высококачественные профильные швы.
Этот процесс по своей сути более безопасен, чем другие процессы, поскольку дуга полностью покрывается во время сварки, отсюда и термин дуга под флюсом. Это также означает, что требования к личной защите меньше. Высокая производительность наплавки — особенность процесса, поскольку он обычно механизируется на портальных мостах, тракторах или другом специализированном оборудовании. Это позволяет контролировать параметры и дает рекомендации по точному размещению сварных швов.
Сварка под флюсом (SAW), процесс 121
Сварка под флюсом (SAW), процесс 121
[вверх] Приварка шпилек методом вытяжной дуги 783
Композитные мосты требуют приваривания соединителей со срезными шпильками к верхнему фланцу пластинчатых или коробчатых балок и в других местах, где требуется композитное воздействие стали на бетон, например.грамм. на интегральных абатментах. В зданиях композитные балки требуют приваривания соединителей срезных шпилек к элементам либо непосредственно к верхнему фланцу, либо чаще через постоянный настил из оцинкованной стали на композитных полах, где верхний фланец балки остается неокрашенным.
Сварной шов на балке моста
(Изображение любезно предоставлено Mabey Bridge Ltd.)
Приварка шпилек через настил
(Изображение любезно предоставлено Structural Metal Decks Ltd.)
Метод приварки шпилек известен как процесс с натянутой дугой, и требуется специальное оборудование в виде мощного выпрямителя и специального пистолета. Шпильки загружаются в пистолет, и при электрическом контакте с изделием концевые дуги сгибаются и плавятся. Продолжительность дуги рассчитывается так, чтобы между концом шпильки и основным материалом установилось расплавленное состояние. В нужный момент пистолет погружает шпильку в сварочную ванну.Керамическая манжета окружает шпильку для защиты и поддержки сварочной ванны, стабилизации дуги и формовки смещенной сварочной ванны для формирования сварной манжеты. Когда сварной шов затвердевает, наконечник отслаивается. У удовлетворительных сварных швов обычно есть правильная, яркая и чистая втулка, полностью окружающая шпильку.
Приварка шпилек методом вытяжной дуги 783
[вверху] Технические требования к процедуре сварки
Чертежи детализируют конструктивную форму, выбор материала и указывают сварные соединения. Подрядчик по изготовлению металлоконструкций выбирает методы сварки каждой конфигурации стыка, обеспечивающие требуемые характеристики. Прочность, вязкость разрушения, пластичность и усталость — важные металлургические и механические свойства, которые необходимо учитывать. Тип соединения, положение сварки, производительность и требования к ресурсам влияют на выбор подходящего процесса сварки.
Выбранный метод представлен в спецификации процедуры сварки (WPS), в которой подробно описана информация, необходимая для инструктирования и руководства сварщиками, чтобы обеспечить повторяемость характеристик для каждой конфигурации соединения.Пример формата WPS показан в Приложении A стандарта BS EN ISO 15609-1 [4] . Подрядчики по изготовлению металлоконструкций могут иметь свой собственный корпоративный шаблон, но все они включают важную информацию, позволяющую передать сварщику надлежащие инструкции.
Необходимо подкрепить WPS свидетельством удовлетворительных испытаний процедуры в виде протокола аттестации процедуры сварки (WPQR), подготовленного в соответствии с BS EN ISO 15614-1 [5] . Введение этого стандарта гласит, что испытания процедуры сварки, проведенные в соответствии с прежними национальными стандартами и спецификациями, не аннулируются при условии их технической эквивалентности; Для этого могут потребоваться дополнительные тесты.Основные подрядчики по изготовлению металлоконструкций в Великобритании прошли предварительную квалификацию сварочных работ, позволяющих производить удовлетворительные сварные швы в большинстве конфигураций стыков, которые могут встретиться в сталелитейном строительстве и мостовой промышленности.
В случаях, когда данные предыдущих испытаний не имеют отношения к делу, необходимо провести испытание процедуры сварки, чтобы установить и подтвердить пригодность предлагаемого WPS.
Руководство по стандартным спецификациям процедуры сварки для стальных конструкций доступно в публикации BCSA No.58/18.
[вверх] Процедура испытаний
BS EN ISO 15614-1 [5] описывает условия для проведения испытаний процедуры сварки и пределы действия в пределах квалификационных диапазонов, указанных в стандарте. Координатор сварки готовит предварительную спецификацию процедуры сварки (pWPS), которая является первоначальным предложением для проведения испытания процедуры. Для каждой конфигурации стыка, будь то стыковой или угловой шов, учитывается марка и толщина материала, а также ожидаемые допуски посадки, которые могут быть достигнуты на практике.Выбор процесса определяется методом сборки, положением сварки и тем, является ли механизация жизнеспособным предложением для повышения производительности и обеспечения постоянного качества сварки. Размеры подготовки швов зависят от выбора процесса, любых ограничений доступа и толщины материала.
Расходные материалы выбираются из соображений совместимости с марками материалов и достижения заданных механических свойств, в первую очередь с точки зрения прочности и ударной вязкости. Для сталей марки S355 и выше используются продукты с водородным контролем.
Риск водородного растрескивания, пластинчатого разрыва, растрескивания при затвердевании или любой другой потенциальной проблемы оценивается не только с целью проведения испытания, но и для предполагаемого применения процедуры сварки в проекте. Соответствующие меры, такие как введение предварительного или последующего нагрева, включены в pWPS.
Контроль искажений обеспечивается правильной последовательностью сварки. При необходимости вводятся обратная строжка и / или обратное шлифование для достижения целостности корневого шва.
Указаны диапазоны сварочного напряжения, тока и скорости для определения оптимальных условий сварки.
Допустимые диапазоны групп материалов, толщины и типа соединения в пределах спецификации тщательно рассматриваются, чтобы максимально использовать pWPS. Подготавливаются испытательные пластины достаточного размера для извлечения образцов для механических испытаний, включая образцы для любых дополнительных испытаний, указанных или необходимых для повышения применимости процедуры.
Пластины и pWPS передаются сварщику; испытание проводится в присутствии эксперта (обычно из независимого проверяющего органа), и ведется запись фактических параметров сварки вместе с любыми необходимыми изменениями процедуры.
Завершенные испытания передаются независимому эксперту для визуального осмотра и неразрушающего контроля в соответствии с таблицей 1 Стандарта. Удовлетворительные испытательные пластины затем отправляются на разрушающий контроль, опять же в соответствии с таблицей 1. Неразрушающие методы контроля, как правило, включают ультразвуковой контроль для объемного контроля и контроль магнитных частиц для выявления дефектов поверхности.
Пример испытательного образца процедуры сварки
(Изображение любезно предоставлено Mabey Bridge Ltd.)
Существует ряд дополнительных стандартов, детализирующих подготовку, обработку и испытания всех типов образцов для разрушающих испытаний. Обычно специализированные лаборатории организуют подготовку образцов для испытаний и проводят фактические механические испытания и составление отчетов. Типичные образцы для стыкового сварного шва пластины включают испытания на поперечное растяжение, испытания на поперечный изгиб, испытания на удар и образец для макроэкспертизы, на котором проводится испытание на твердость. Для испытаний на удар минимальные требования к поглощению энергии и температура испытания обычно такие же, как и для основного материала в соединении. Целесообразно проверить все сварочные процедуры до предела возможного применения, чтобы избежать повторения подобных испытаний в будущем.
Завершенные результаты испытаний заносятся в протокол аттестации процедуры сварки (WPQR), утверждаемый экспертом. Типичный формат показан в Приложении B стандарта BS EN ISO 15614-1 [5] .
Существует дополнительное общее требование, касающееся испытаний процедуры сварки, согласно которому в случаях, когда грунтовки краски должны быть нанесены на работу до изготовления, они наносятся на образец материала, использованного для испытаний. На практике требуется тщательный контроль толщины краски, чтобы избежать дефектов сварки.
BS EN ISO 14555 [6] описывает метод испытаний для соединителей шпилек, приваренных дуговой сваркой. Стандарт включает требования к испытаниям, необходимым для подтверждения целостности сварных швов шпилек, а также устанавливает требования к производственным испытаниям для контроля приваривания шпилек в процессе. Допускается также квалификация, основанная на предыдущем опыте, и большинство подрядчиков по производству стальных конструкций могут предоставить доказательства, подтверждающие это.
Дополнительное руководство по испытаниям процедуры сварки доступно в GN 4.02.
[вверх] Водородный крекинг
Растрескивание может привести к хрупкому разрушению соединения с потенциально катастрофическими последствиями. Водородное (или холодное) растрескивание может происходить в области основного металла, прилегающей к границе плавления сварного шва, известной как зона термического влияния (HAZ).Разрушение металла сварного шва также может быть вызвано определенными условиями. Механизмы, вызывающие отказ, сложны и подробно описаны в специальных текстах.
Рекомендуемые методы предотвращения растрескивания водородом / HAZ описаны в BS EN 1011-2 [7] , приложение C. Эти методы определяют уровень предварительного нагрева для изменения скорости охлаждения, что дает время водороду для миграции на поверхность. и ускользнуть (особенно если поддерживается в виде пост-нагрева после завершения соединения) вместо того, чтобы оставаться в жестких, напряженных зонах.Предварительный нагрев не препятствует образованию микроструктур, подверженных образованию трещин; он просто снижает один из факторов, водород, так что растрескивания не происходит. Предварительный нагрев также снижает термический шок.
Подкладки предварительного нагрева
(Изображение предоставлено Mabey Bridge Ltd.)
Одним из параметров, необходимых для расчета предварительного нагрева, является погонная энергия. Заметным изменением в стандарте является отказ от термина «энергия дуги» в пользу тепловложения для описания энергии, вводимой в сварной шов на единицу длины прогона.Расчет подводимого тепла основан на сварочном напряжении, токе и скорости движения и включает коэффициент теплового КПД; формула подробно описана в BS EN 1011-1 [8] .
Высокая устойчивость и повышенные значения углеродного эквивалента, связанные с более толстыми листами и более высокими марками стали, могут потребовать более строгого контроля процедур. Опытные подрядчики по изготовлению металлоконструкций могут выполнить эту дополнительную операцию и соответственно учесть ее.
BS EN 1011-2 [7] подтверждает, что наиболее эффективной гарантией предотвращения водородного растрескивания является снижение поступления водорода в металл шва из сварочных материалов.Процессы с изначально низким водородным потенциалом эффективны как часть стратегии, так же как и принятие строгих процедур хранения и обращения с водородными электродами. Данные и рекомендации поставщиков расходных материалов служат руководством для обеспечения минимально возможных уровней водорода для типа продукта, выбранного в процедуре.
Дополнительные информативные приложения к BS EN 1011-2 [7] описывают влияние условий сварки на ударную вязкость и твердость в ЗТВ и дают полезные советы по предотвращению растрескивания при затвердевании и разрыва пластин.
Дополнительное руководство по крекингу водородом / HAZ доступно в GN 6.04.
[вверх] Квалификация сварщика
Квалифицированный сварщик
(Изображение любезно предоставлено Mabey Bridge Ltd.)
BS EN 1090-2 [9] требует, чтобы сварщики имели квалификацию в соответствии с BS EN ISO 9606-1 [10] . Этот стандарт предписывает испытания для аттестации сварщиков в зависимости от процесса, расходных материалов, типа соединения, положения сварки и материала.Сварщики, успешно прошедшие испытания процедуры, получают автоматическое одобрение в пределах квалификационных диапазонов, указанных в стандарте. Сварщики должны быть аттестованы в соответствии с BS EN ISO 14732 [11] , когда сварка полностью механизирована или автоматизирована. В этом стандарте особое внимание уделяется проверке способности оператора настраивать и регулировать оборудование до и во время сварки.
Квалификация сварщика ограничена по времени и требует подтверждения действительности в зависимости от продолжительности работы, участия в работе соответствующего технического характера и удовлетворительной работы.Продление квалификации сварщика зависит от зарегистрированных подтверждающих свидетельств, демонстрирующих продолжающуюся удовлетворительную работу в пределах исходного диапазона испытаний, и доказательства должны включать либо объемные разрушающие испытания, либо разрушающие испытания. Успех всех сварочных операций зависит от персонала, имеющего соответствующую подготовку и регулярного контроля компетентности посредством инспекций и испытаний.
[вверх] Проверка и испытания
BS EN 1090-2 [9] устанавливает объем проверки до, во время и после сварки и дает критерии приемки, связанные с классом исполнения.Большинство испытаний неразрушающие; Разрушающие испытания проводятся только на отводных плитах.
[вверх] Неразрушающий контроль
Магнитный контроль частиц (MPI) сварного шва
(Изображение любезно предоставлено Mabey Bridge Ltd. )
Неразрушающий контроль проводится в соответствии с принципами BS EN ISO 17635 [12] . Для стальных конструкций основными методами являются визуальный осмотр после сварки (см. GN 6.06), магнитопорошковый контроль (обычно сокращенно MPI или MT) для поверхностного контроля сварных швов (см. GN 6.02) и ультразвуковой контроль (UT) для подповерхностного контроля сварных швов (см. GN 6.03). Радиографические испытания также упоминаются в BS EN 1090-2 [9] . Радиография требует строгого контроля за здоровьем и безопасностью; это относительно медленно и требует специального оборудования. Использование этого метода в стальных конструкциях снизилось по сравнению с более безопасным и портативным оборудованием, используемым в UT.Безопасные запретные зоны необходимы на производстве и на месте во время рентгенографии. Однако рентгенографию можно использовать для уточнения природы, размеров или степени множественных внутренних дефектов, обнаруженных ультразвуком.
Технические специалисты с признанной подготовкой и квалификацией в соответствии с BS EN ISO 9712 [13] требуются для всех методов неразрушающего контроля.
BS EN 1090-2 [9] требует, чтобы все сварные швы подвергались визуальному контролю по всей их длине.С практической точки зрения сварные швы следует визуально осматривать сразу после сварки, чтобы гарантировать своевременное устранение очевидных дефектов поверхности.
Дальнейшие требования к неразрушающему контролю основаны на эксплуатационных методах и требуют более строгого исследования первых пяти соединений новых технических требований к процедуре сварки, чтобы установить, что эта процедура способна производить сварные швы соответствующего качества при внедрении в производство. Затем указываются дополнительные неразрушающие испытания, основанные на типах соединений, а не на конкретных критических соединениях.Цель состоит в том, чтобы опробовать различные сварные швы в зависимости от типа соединения, марки материала, сварочного оборудования и работы сварщиков и, таким образом, поддерживать общий мониторинг производительности.
Если указано частичное или процентное обследование, руководство по выбору продолжительности испытания дано в BS EN ISO 17635 [12] ; При обнаружении недопустимых разрывов площадь исследования соответственно увеличивается.
BS EN 1090-2 [9] также включает в таблицу минимальное время выдержки перед дополнительным неразрушающим контролем в зависимости от размера сварного шва, подводимой теплоты и марки материала.
Признавая, что там, где требования к усталостной прочности более обременительны и требуется более строгая проверка, BS EN 1090-2 [9] действительно предусматривает спецификацию выполнения проекта для определения конкретных соединений для более высокого уровня проверки вместе с объемом и метод тестирования.
Для класса EXC3 критерием приемлемости дефектов сварного шва является уровень качества B согласно BS EN ISO 5817 [14] . Там, где необходимо достичь повышенного уровня качества для удовлетворения конкретных требований к усталостной прочности, BS EN 1090-2 [9] дает дополнительные критерии приемлемости с точки зрения категории деталей в BS EN 1993-1-9 [15] для расположения сварного шва.
Как правило, дополнительные критерии приемки практически не достижимы при обычном производстве. Стандартные испытания процедуры сварки и квалификационные испытания сварщиков не оцениваются по требованиям этого уровня. Если необходимо достичь такого уровня качества, требования должны быть сосредоточены на соответствующих деталях соединения, чтобы подрядчик имел возможность подготовить спецификации процедуры сварки, квалифицировать сварщиков и разработать соответствующие методы контроля и испытаний.
Неразрушающий контроль
[вверх] Разрушающее испытание
В стандарте BS EN 1090-2 [9] нет требований о проведении разрушающих испытаний поперечных соединений в натяжных фланцах. Тем не менее, объем для определения конкретных соединений для проверки позволит в спецификации проекта испытать, например, образцы от «стекающих» пластин, прикрепленных к встроенным стыковым сварным швам. Дополнительно производственные испытания могут быть указаны для: марок стали выше S460; угловые швы, в которых используются характеристики глубокого проплавления сварочного процесса; для мостовидных ортотропных настилов, где требуется макросъемка для проверки проплавления сварного шва; и на соединениях ребер жесткости с соединительными пластинами.
[вверх] Производственные испытания приварки шпилек
Испытание на изгиб приварной шпильки
(Изображение любезно предоставлено Mabey Bridge Ltd.)
Сварные шпильки для соединителей, работающих на сдвиг, исследуются и испытываются в соответствии с BS EN ISO 14555 [6] . В стандарте подчеркивается необходимость контроля процесса до, во время и после сварки. Предпроизводственные испытания используются для подтверждения процедуры сварки и, в зависимости от области применения, включают испытания на изгиб, испытания на растяжение, испытания на крутящий момент, макросъемку и радиографическое обследование.
Производственные испытания сварных швов также необходимы для приварки шпилек с дугой протяжки. Они должны выполняться производителем до начала сварочных работ на конструкции или группе аналогичных конструкций и / или после определенного количества сварных швов. Каждое испытание должно состоять как минимум из 10 сварных шпилек и быть испытано / оценено в соответствии с требованиями BS EN ISO 14555 [6] . Количество необходимых тестов должно быть указано в спецификации контракта.
[вверх] Качество сварки
Влияние дефектов на характеристики сварных соединений зависит от приложенной нагрузки и свойств материала.Эффект также может зависеть от точного расположения и ориентации дефекта, а также от таких факторов, как рабочая среда и температура. Основное влияние дефектов сварного шва на эксплуатационные характеристики стальных конструкций заключается в повышении риска разрушения из-за усталости или хрупкого разрушения.
Типы дефектов сварки можно разделить на одну из нескольких общих рубрик:
- Трещины.
- Плоские дефекты, кроме трещин, например непробиваемость, отсутствие плавления.
- Включения шлака.
- Пористость, поры.
- Поднутрения или дефекты профиля.
Трещины или плоские дефекты, проникающие через поверхность, потенциально являются наиболее серьезными. Включения вкрапленного шлака и пористость вряд ли станут причиной разрушения, если только они не будут чрезмерными. Подрезы обычно не представляют серьезной проблемы, если не существуют значительные растягивающие напряжения поперек стыка.
При выборе класса исполнения в BS EN 1090-2 [9] устанавливаются критерии приемки, при превышении которых дефект считается дефектом.
Если дефекты обнаружены в результате осмотра и испытаний во время производства, вероятно, потребуется обработка после сварки (см. GN 5.02) или другие меры по исправлению положения, хотя во многих случаях конкретный дефект может быть оценен по концепции « пригодность для цели ». Такое принятие зависит от фактических уровней напряжения и значимости усталости на месте. Это вопрос быстрой консультации между подрядчиком по изготовлению металлоконструкций и проектировщиком, поскольку, если это приемлемо, можно избежать дорогостоящего ремонта (и возможности появления дополнительных дефектов или деформации).
Руководство по контролю качества сварных швов и контролю сварных швов доступно в BCSA № 54/12 и GN 6.01.
[вверх] Список литературы
- ↑ BS EN ISO 22553: 2019, Сварка и родственные процессы. Символическое изображение на чертежах. Сварные соединения. BSI.
- ↑ BS EN 1993-1-8: 2005, Еврокод 3. Проектирование стальных конструкций. Дизайн стыков, BSI
- ↑ BS EN ISO 4063: 2010, Сварка и родственные процессы. Номенклатура процессов и ссылочные номера, BSI
- ↑ BS EN ISO 15609-1: 2019, Технические требования и аттестация процедур сварки металлических материалов.Спецификация процедуры сварки. Дуговая сварка, BSI
- ↑ 5,0 5,1 5,2 BS EN ISO 15614-1: 2017 + A1: 2019, Технические требования и квалификация процедур сварки металлических материалов.
Проверка процедуры сварки. Дуговая и газовая сварка сталей и дуговая сварка никеля и никелевых сплавов, BSI
- ↑ 6,0 6,1 6,2 BS EN ISO 14555: 2017, Сварка. Дуговая сварка металлических материалов, BSI
- ↑ 7.0 7,1 7,2 BS EN 1011-2: 2001, Сварка. Рекомендации по сварке металлических материалов. Дуговая сварка ферритных сталей, BSI
- ↑ BS EN 1011-1: 2009, Сварка. Рекомендации по сварке металлических материалов. Общее руководство по дуговой сварке, BSI
- ↑ 9,0 9,1 9,2 9,3 9,4 9,5 9,6 9,7 9,8 BS EN 1090-2: 2018, Изготовление металлоконструкций и алюминиевых конструкций.Технические требования к стальным конструкциям, BSI
- ↑ BS EN ISO 9606-1: 2017 Квалификационные испытания сварщиков. Сварка плавлением. Стали, BSI
- ↑ BS EN ISO 14732: 2013.
Сварочный персонал. Квалификационные испытания сварщиков и наладчиков механизированной и автоматической сварки металлических материалов BSI
- ↑ 12,0 12,1 BS EN ISO 17635: 2016, Неразрушающий контроль сварных швов. Общие правила для металлических материалов, BSI
- ↑ BS EN ISO 9712: 2012.Неразрушающий контроль. Квалификация и сертификация персонала по неразрушающему контролю, BSI
- ↑ BS EN ISO 5817: 2014, Сварка. Соединения, сваренные плавлением стали, никеля, титана и их сплавов (за исключением лучевой сварки). Уровни качества для выявления недостатков, BSI
- ↑ BS EN 1993-1-9: 2005, Еврокод 3. Проектирование стальных конструкций. Усталость, BSI
[вверх] Ресурсы
- Стальные здания, 2003 г. (Публикация № 35/03), BCSA
- Стальные мосты: практический подход к проектированию для эффективного изготовления и строительства, 2010 г. (Публикация №51/10), BCSA
- Национальные технические условия на стальные конструкции (7-е издание), 2020 г.
(Публикация № 62/20), BCSA
- Типовые спецификации процедуры сварки для металлоконструкций — Второе издание, 2018 г. (Публикация № 58/18), BCSA
- Высокопрочные стали для применения в конструкциях: Руководство по производству и сварке, 2020 г. (Публикация № 62/20), BCSA
- Руководство по контролю сварных швов для металлоконструкций, 2012 г. (Публикация № 54/12), BCSA
- Хенди, К.Р.; Ильес, округ Колумбия (2015) Steel Bridge Group: Рекомендации по передовой практике в строительстве стальных мостов (6-й выпуск). (P185). SCI
[вверх] Дополнительная литература
- Руководство проектировщика металлоконструкций (7-е издание), 2011 г., глава 26 — Сварные швы и проектирование для сварки, Институт стальных конструкций.
[вверху] См. Также
Welding — SteelConstruction.info
Сварка — это основной вид деятельности на заводе-изготовителе, которым занимаются опытные квалифицированные специалисты, работающие в системе управления качеством сварки под контролем ответственного координатора сварки. Он используется для подготовки стыков к подключению в магазине и на месте, а также для крепления других приспособлений и фурнитуры. На заводе-изготовителе для разных видов деятельности используются разные методы сварки.
По сути, в процессе сварки используется электрическая дуга для выработки тепла для плавления основного материала в соединении. Отдельный присадочный материал, поставляемый в качестве расходуемого электрода, также плавится и соединяется с основным материалом, образуя расплавленную сварочную ванну. По мере того, как сварка продолжается вдоль соединения, сварочная ванна затвердевает, сплавляя основной металл и металл сварного шва.Для заполнения стыка или нарастания сварного шва до проектного размера может потребоваться несколько проходов или проходов.
Сварка
(Изображение любезно предоставлено William Haley Engineering Ltd.)
[вверх] Принципы дуговой сварки металлом
Терминология области сварного шва
Сварка — это сложное взаимодействие физических и химических наук. Правильное определение металлургических требований и разумное практическое применение являются предпосылкой для успешной сварки плавлением.
В процессе дуговой сварки металлическим электродом используется электрическая дуга для выработки тепла для плавления основного материала в соединении. Отдельный присадочный материал, поставляемый в качестве расходуемого электрода, также плавится и соединяется с основным материалом, образуя расплавленную сварочную ванну. Сварочная ванна подвержена атмосферному загрязнению и, следовательно, нуждается в защите во время критической фазы замерзания жидкости и твердого тела.Защита достигается либо за счет использования защитного газа, за счет покрытия бассейна инертным шлаком, либо за счет комбинации обоих действий.
В процессах с защитным газом от удаленного источника поступает газ, который подается на сварочную дугу через горелку или горелку. Газ окружает дугу и эффективно исключает атмосферу. Точный контроль необходим для поддержания подачи газа с подходящей скоростью потока, так как слишком большое количество может вызвать турбулентность и засасывать воздух, а может быть настолько же вредным, насколько и слишком маленьким.
В некоторых процессах используется флюс, который плавится в дуге для образования шлакового покрытия, которое, в свою очередь, покрывает сварочную ванну и защищает ее во время замерзания. Шлак также затвердевает и самораспускается или легко удаляется легким сколом. Действие плавления флюса также создает газовый экран для защиты.
По мере сварки вдоль стыка сварочная ванна затвердевает, сплавляя основной металл и металл шва. Для заполнения стыка или нарастания сварного шва до проектного размера может потребоваться несколько проходов или проходов.
Тепло от сварки вызывает металлургические изменения в основном материале, непосредственно примыкающем к границе или линии плавления. Эта область изменения известна как зона термического влияния (HAZ). Общая терминология, используемая в области сварного шва, показана справа вверху.
Сварочные операции требуют надлежащего технологического контроля со стороны компетентных сварщиков, чтобы гарантировать достижение проектных характеристик, минимизировать риск дефектных соединений, вызванных низким качеством сварки, и предотвратить образование склонных к образованию трещин микроструктур в ЗТВ.
[вверх] Виды сварных соединений
Большинство конструкционных сварных соединений выполняется на заводе-изготовителе и описывается как стыковые или угловые швы. Сварка на месте также возможна, и руководство по вопросам сварки на месте доступно в GN 7.01.
[вверх] Стыковые швы
Макрос клиновидного стыкового шва
(Изображение любезно предоставлено Mabey Bridge Ltd.)
Стыковые сварные швы обычно представляют собой стыковые соединения в прокатных профилях или стыковые соединения листов на стенках и фланцах, чтобы приспособиться к изменению толщины или восполнить доступный материал по длине.Положения этих стыковых швов допускаются при проектировании, хотя ограничения доступности материалов или схема монтажа могут потребовать согласования различных или дополнительных сварных швов. Тройники, приваренные встык, могут потребоваться, если при поперечных соединениях возникают значительные нагрузки или усталость.
Стыковые швы — это сварные швы с полным или частичным проплавлением, выполняемые между материалами со скошенными или скошенными кромками. Стыковые швы с полным проплавлением предназначены для передачи всей прочности сечения.Как правило, эти соединения можно сваривать с одной стороны, но по мере увеличения толщины материала желательна сварка с обеих сторон, чтобы уравновесить эффекты деформации, с операцией обратной строжки и / или шлифования в процессе для обеспечения целостности корень шва. Односторонние стыковые сварные швы с подкладными полосами из керамической или прочной стали обычно используются для соединения больших площадей пластин (например, стальных пластин настила) и там, где есть закрытые коробчатые секции, трубы или элементы жесткости, доступ к которым для сварки возможен только с одного сторона.Расчетная толщина горловины определяет глубину проплавления, необходимую для швов с частичным проплавлением. Обратите внимание, что соображения усталости могут ограничивать использование сварных швов с частичным проплавлением, особенно на мостах. Руководство по подготовке к сварке доступно в GN 5.01.
Следует приложить все усилия, чтобы избежать стыковой сварки приспособлений из-за затрат, связанных с подготовкой, временем сварки, более высоким уровнем квалификации сварщиков и более строгими и трудоемкими требованиями к испытаниям. Кроме того, стыковые швы имеют тенденцию иметь большие объемы наплавленного металла шва; это увеличивает эффект усадки сварного шва и приводит к более высокому уровню остаточного напряжения в соединении.Чтобы уравновесить усадку и распределить остаточное напряжение, минимизируя таким образом деформацию, необходима тщательная последовательность сварочных операций.
Иногда бывает необходимо обработать стыковые сварные швы заподлицо по причинам усталости, или для улучшения дренажа стальных балок, устойчивых к атмосферным воздействиям, или для улучшения режима испытаний. Следует избегать зачистки заподлицо только по эстетическим соображениям, потому что трудно обработать поверхность, чтобы она соответствовала смежной поверхности после прокатки, и результат часто более визуально заметен, чем исходный сварной шов. Кроме того, шлифование представляет собой дополнительную опасность для здоровья и безопасности, которую следует избегать по возможности. Правка стыковых швов до гладкой поверхности обычно не требуется для строительных стальных конструкций, поскольку обычно они не подвержены усталости.
- Пример обработанного стыкового шва с гладкой поверхностью и сливными пластинами
(изображения любезно предоставлены Mabey Bridge Ltd.)
[вверх] Угловые швы
Макрос однопроходного углового шва
(Изображение любезно предоставлено Mabey Bridge Ltd.)
В большинстве сварных соединений в зданиях и мостах используются угловые швы, обычно в форме тройника. Обычно они включают в себя концевую пластину, ребро жесткости, подшипниковые и распорные соединения с прокатными секциями или плоскими балками, а также соединения стенки с фланцем на самих пластинчатых балках. Их относительно просто подготовить, сварить и испытать в обычных конфигурациях, при этом главным соображением является сборка стыков.
В S275 полная прочность стали также развивается в угловых сварных швах и сварных швах с частичным проплавлением с вышележащими угловыми швами при условии, что такие сварные швы симметричны, выполнены с использованием правильных расходных материалов и сумма сварных швов равна толщине элемента, который сварные швы стыкуются.
Размеры сварных швов должны быть указаны на чертежах проекта вместе с любыми специальными требованиями по классификации усталости. BS EN ISO 22553 [1] предписывает правила использования символов для детализации сварных соединений на чертежах.
Обращается внимание на тот факт, что в традиционной практике Великобритании для определения размера углового сварного шва обычно используется длина ветви, но это не универсально: в европейской практике используется толщина горловины, а в стандарте BS EN 1993-1-8 [2] дает требования относительно размера горла, а не длины ноги. Проектировщик должен следить за тем, чтобы было ясно, какой размер указан, и что все стороны должны знать, что было указано.
[вверх] Процессы
Важными факторами, которые подрядчик по изготовлению металлоконструкций должен учитывать при выборе процесса сварки, являются способность выполнять проектные требования и, с точки зрения производительности, скорость наплавки, которая может быть достигнута, а также рабочий цикл или эффективность процесса. (Эффективность — это отношение фактического времени сварки или дуги к общему времени, в течение которого сварщик или оператор занят выполнением сварочного задания.Общее время включает настройку оборудования, чистку и проверку выполненного шва.)
Ниже описаны четыре основных процесса сварки, которые регулярно используются при производстве стальных конструкций в Великобритании. Номера процессов определены в BS EN ISO 4063 [3] . Разновидности этих процессов были разработаны с учетом практики и оборудования отдельных производителей, и другие процессы также имеют место для конкретных приложений, но выходят за рамки данной статьи.
[вверх] Металлоактивная газовая сварка (MAG), процесс 135
Сварка MAG
(Изображение любезно предоставлено Kiernan Structural Steel Ltd.)
MAG-сварка сплошным проволочным электродом — это наиболее широко используемый процесс с ручным управлением для заводских производственных работ; это иногда называют полуавтоматической сваркой или сваркой CO 2 . Сплошной проволочный электрод из сплошной проволоки пропускается через устройство подачи проволоки к «пистолету», который обычно удерживается и управляется оператором. Питание подается от источника выпрямителя или инвертора по соединительным кабелям к устройству подачи проволоки и кабелю горелки; электрическое подключение к проводу осуществляется через контактный наконечник на конце пистолета.Дуга защищена защитным газом, который направляется в зону сварного шва через кожух или сопло, окружающее контактный наконечник. Защитные газы обычно представляют собой смесь аргона, диоксида углерода и, возможно, кислорода или гелия.
Хорошая производительность наплавки и рабочий цикл можно ожидать от процесса, который также можно механизировать с помощью простых моторизованных кареток. Газовая защита может быть сдувана сквозняками, что может вызвать пористость и возможные вредные металлургические изменения в металле сварного шва.Таким образом, этот процесс лучше подходит для заводского производства, хотя он используется на месте, где могут быть предусмотрены эффективные укрытия. Он также более эффективен в плоском и горизонтальном положениях; Сварные швы в других положениях наплавляются с более низкими параметрами напряжения и силы тока и более подвержены дефектам плавления.
Металлоактивная газовая сварка (МАГ), процесс 135
Металлоактивная газовая сварка (MAG), процесс 135
MAG-сварка электродом с флюсовой сердцевиной, процесс 136 представляет собой разновидность, в которой используется то же оборудование, что и MAG-сварка, за исключением того, что плавящийся проволочный электрод имеет форму трубки малого диаметра, заполненной флюсом. Преимущество использования этих проволок состоит в том, что можно использовать более высокие скорости наплавки, особенно при сварке в вертикальном положении (между двумя вертикальными поверхностями) или в верхнем положении. Наличие тонкого шлака помогает преодолевать силу тяжести и позволяет наносить сварные швы в местах с относительно высокими током и напряжением, тем самым снижая вероятность дефектов плавления. Добавки флюса также влияют на химию сварного шва и, таким образом, улучшают механические свойства соединения.
[вверху] Ручная дуговая сварка металлом (MMA), процесс 111
Этот процесс остается наиболее универсальным из всех сварочных процессов, но его использование в современной мастерской ограничено.Трансформаторы переменного тока, выпрямители постоянного тока или инверторы подают электроэнергию по кабелю на электрододержатель или клещи. Проволочный электрод с флюсовым покрытием (или «стержень») вставляется в держатель, и сварочная дуга возникает на конце электрода, когда он ударяется о заготовку. На острие электрода плавится, образуя ванну расплава, которая сплавляется с основным материалом, образуя сварной шов. Флюс также плавится, образуя защитный шлак и создавая газовый экран, предотвращающий загрязнение сварочной ванны по мере ее затвердевания.Добавки флюса и сердечник электрода используются для влияния на химический состав и механические свойства сварного шва.
Обычно используются электроды с основным покрытием, контролируемым водородом. Эти электроды необходимо хранить и обращаться с ними в соответствии с рекомендациями производителя расходных материалов, чтобы сохранить их низкие водородные характеристики. Это достигается либо путем использования сушильных шкафов и подогреваемых колчанов для хранения и обработки продукта, либо путем покупки электродов в герметичных упаковках, специально разработанных для поддержания низкого уровня водорода.
Недостатками процесса являются относительно низкая скорость наплавки и высокий уровень отходов, связанных с непригодными для использования концевыми штырями электродов. Тем не менее, он остается основным процессом для сварки на стройплощадке и для труднодоступных мест, где громоздкое оборудование не подходит.
Ручная дуговая сварка металлом (MMA), процесс 111
Ручная дуговая сварка металлом (MMA), процесс 111
[вверх] Дуговая сварка под флюсом (SAW), процесс 121
Оперативная сварка под флюсом
(Изображение любезно предоставлено Mabey Bridge Ltd.)
Это, вероятно, наиболее широко используемый процесс для сварки угловых швов перемычки между стенкой и фланцем и стыковых сварных швов на линии толстой пластины для получения отрезков длины фланца и стенки. В процессе процесса непрерывный провод подается через контактный наконечник, где он устанавливает электрический контакт с мощностью от выпрямителя, в зону сварки, где он изгибается и образует ванну расплава. Сварочная ванна заполняется флюсом, подаваемым из бункера. Флюс, непосредственно покрывающий расплавленную сварочную ванну, плавится, образуя шлак и защищая сварной шов во время затвердевания; избыточный флюс собирается и повторно используется.По мере охлаждения шва шлак замерзает и отслаивается, оставляя высококачественные профильные швы.
Этот процесс по своей сути более безопасен, чем другие процессы, поскольку дуга полностью покрывается во время сварки, отсюда и термин дуга под флюсом. Это также означает, что требования к личной защите меньше. Высокая производительность наплавки — особенность процесса, поскольку он обычно механизируется на портальных мостах, тракторах или другом специализированном оборудовании. Это позволяет контролировать параметры и дает рекомендации по точному размещению сварных швов.
Сварка под флюсом (SAW), процесс 121
Сварка под флюсом (SAW), процесс 121
[вверх] Приварка шпилек методом вытяжной дуги 783
Композитные мосты требуют приваривания соединителей со срезными шпильками к верхнему фланцу пластинчатых или коробчатых балок и в других местах, где требуется композитное воздействие стали на бетон, например.грамм. на интегральных абатментах. В зданиях композитные балки требуют приваривания соединителей срезных шпилек к элементам либо непосредственно к верхнему фланцу, либо чаще через постоянный настил из оцинкованной стали на композитных полах, где верхний фланец балки остается неокрашенным.
Сварной шов на балке моста
(Изображение любезно предоставлено Mabey Bridge Ltd.)
Приварка шпилек через настил
(Изображение любезно предоставлено Structural Metal Decks Ltd.)
Метод приварки шпилек известен как процесс с натянутой дугой, и требуется специальное оборудование в виде мощного выпрямителя и специального пистолета. Шпильки загружаются в пистолет, и при электрическом контакте с изделием концевые дуги сгибаются и плавятся. Продолжительность дуги рассчитывается так, чтобы между концом шпильки и основным материалом установилось расплавленное состояние. В нужный момент пистолет погружает шпильку в сварочную ванну.Керамическая манжета окружает шпильку для защиты и поддержки сварочной ванны, стабилизации дуги и формовки смещенной сварочной ванны для формирования сварной манжеты. Когда сварной шов затвердевает, наконечник отслаивается. У удовлетворительных сварных швов обычно есть правильная, яркая и чистая втулка, полностью окружающая шпильку.
Приварка шпилек методом вытяжной дуги 783
[вверху] Технические требования к процедуре сварки
Чертежи детализируют конструктивную форму, выбор материала и указывают сварные соединения. Подрядчик по изготовлению металлоконструкций выбирает методы сварки каждой конфигурации стыка, обеспечивающие требуемые характеристики. Прочность, вязкость разрушения, пластичность и усталость — важные металлургические и механические свойства, которые необходимо учитывать. Тип соединения, положение сварки, производительность и требования к ресурсам влияют на выбор подходящего процесса сварки.
Выбранный метод представлен в спецификации процедуры сварки (WPS), в которой подробно описана информация, необходимая для инструктирования и руководства сварщиками, чтобы обеспечить повторяемость характеристик для каждой конфигурации соединения.Пример формата WPS показан в Приложении A стандарта BS EN ISO 15609-1 [4] . Подрядчики по изготовлению металлоконструкций могут иметь свой собственный корпоративный шаблон, но все они включают важную информацию, позволяющую передать сварщику надлежащие инструкции.
Необходимо подкрепить WPS свидетельством удовлетворительных испытаний процедуры в виде протокола аттестации процедуры сварки (WPQR), подготовленного в соответствии с BS EN ISO 15614-1 [5] . Введение этого стандарта гласит, что испытания процедуры сварки, проведенные в соответствии с прежними национальными стандартами и спецификациями, не аннулируются при условии их технической эквивалентности; Для этого могут потребоваться дополнительные тесты.Основные подрядчики по изготовлению металлоконструкций в Великобритании прошли предварительную квалификацию сварочных работ, позволяющих производить удовлетворительные сварные швы в большинстве конфигураций стыков, которые могут встретиться в сталелитейном строительстве и мостовой промышленности.
В случаях, когда данные предыдущих испытаний не имеют отношения к делу, необходимо провести испытание процедуры сварки, чтобы установить и подтвердить пригодность предлагаемого WPS.
Руководство по стандартным спецификациям процедуры сварки для стальных конструкций доступно в публикации BCSA No.58/18.
[вверх] Процедура испытаний
BS EN ISO 15614-1 [5] описывает условия для проведения испытаний процедуры сварки и пределы действия в пределах квалификационных диапазонов, указанных в стандарте. Координатор сварки готовит предварительную спецификацию процедуры сварки (pWPS), которая является первоначальным предложением для проведения испытания процедуры. Для каждой конфигурации стыка, будь то стыковой или угловой шов, учитывается марка и толщина материала, а также ожидаемые допуски посадки, которые могут быть достигнуты на практике.Выбор процесса определяется методом сборки, положением сварки и тем, является ли механизация жизнеспособным предложением для повышения производительности и обеспечения постоянного качества сварки. Размеры подготовки швов зависят от выбора процесса, любых ограничений доступа и толщины материала.
Расходные материалы выбираются из соображений совместимости с марками материалов и достижения заданных механических свойств, в первую очередь с точки зрения прочности и ударной вязкости. Для сталей марки S355 и выше используются продукты с водородным контролем.
Риск водородного растрескивания, пластинчатого разрыва, растрескивания при затвердевании или любой другой потенциальной проблемы оценивается не только с целью проведения испытания, но и для предполагаемого применения процедуры сварки в проекте. Соответствующие меры, такие как введение предварительного или последующего нагрева, включены в pWPS.
Контроль искажений обеспечивается правильной последовательностью сварки. При необходимости вводятся обратная строжка и / или обратное шлифование для достижения целостности корневого шва.
Указаны диапазоны сварочного напряжения, тока и скорости для определения оптимальных условий сварки.
Допустимые диапазоны групп материалов, толщины и типа соединения в пределах спецификации тщательно рассматриваются, чтобы максимально использовать pWPS. Подготавливаются испытательные пластины достаточного размера для извлечения образцов для механических испытаний, включая образцы для любых дополнительных испытаний, указанных или необходимых для повышения применимости процедуры.
Пластины и pWPS передаются сварщику; испытание проводится в присутствии эксперта (обычно из независимого проверяющего органа), и ведется запись фактических параметров сварки вместе с любыми необходимыми изменениями процедуры.
Завершенные испытания передаются независимому эксперту для визуального осмотра и неразрушающего контроля в соответствии с таблицей 1 Стандарта. Удовлетворительные испытательные пластины затем отправляются на разрушающий контроль, опять же в соответствии с таблицей 1. Неразрушающие методы контроля, как правило, включают ультразвуковой контроль для объемного контроля и контроль магнитных частиц для выявления дефектов поверхности.
Пример испытательного образца процедуры сварки
(Изображение любезно предоставлено Mabey Bridge Ltd.)
Существует ряд дополнительных стандартов, детализирующих подготовку, обработку и испытания всех типов образцов для разрушающих испытаний. Обычно специализированные лаборатории организуют подготовку образцов для испытаний и проводят фактические механические испытания и составление отчетов. Типичные образцы для стыкового сварного шва пластины включают испытания на поперечное растяжение, испытания на поперечный изгиб, испытания на удар и образец для макроэкспертизы, на котором проводится испытание на твердость. Для испытаний на удар минимальные требования к поглощению энергии и температура испытания обычно такие же, как и для основного материала в соединении. Целесообразно проверить все сварочные процедуры до предела возможного применения, чтобы избежать повторения подобных испытаний в будущем.
Завершенные результаты испытаний заносятся в протокол аттестации процедуры сварки (WPQR), утверждаемый экспертом. Типичный формат показан в Приложении B стандарта BS EN ISO 15614-1 [5] .
Существует дополнительное общее требование, касающееся испытаний процедуры сварки, согласно которому в случаях, когда грунтовки краски должны быть нанесены на работу до изготовления, они наносятся на образец материала, использованного для испытаний. На практике требуется тщательный контроль толщины краски, чтобы избежать дефектов сварки.
BS EN ISO 14555 [6] описывает метод испытаний для соединителей шпилек, приваренных дуговой сваркой. Стандарт включает требования к испытаниям, необходимым для подтверждения целостности сварных швов шпилек, а также устанавливает требования к производственным испытаниям для контроля приваривания шпилек в процессе. Допускается также квалификация, основанная на предыдущем опыте, и большинство подрядчиков по производству стальных конструкций могут предоставить доказательства, подтверждающие это.
Дополнительное руководство по испытаниям процедуры сварки доступно в GN 4.02.
[вверх] Водородный крекинг
Растрескивание может привести к хрупкому разрушению соединения с потенциально катастрофическими последствиями. Водородное (или холодное) растрескивание может происходить в области основного металла, прилегающей к границе плавления сварного шва, известной как зона термического влияния (HAZ).Разрушение металла сварного шва также может быть вызвано определенными условиями. Механизмы, вызывающие отказ, сложны и подробно описаны в специальных текстах.
Рекомендуемые методы предотвращения растрескивания водородом / HAZ описаны в BS EN 1011-2 [7] , приложение C. Эти методы определяют уровень предварительного нагрева для изменения скорости охлаждения, что дает время водороду для миграции на поверхность. и ускользнуть (особенно если поддерживается в виде пост-нагрева после завершения соединения) вместо того, чтобы оставаться в жестких, напряженных зонах.Предварительный нагрев не препятствует образованию микроструктур, подверженных образованию трещин; он просто снижает один из факторов, водород, так что растрескивания не происходит. Предварительный нагрев также снижает термический шок.
Подкладки предварительного нагрева
(Изображение предоставлено Mabey Bridge Ltd.)
Одним из параметров, необходимых для расчета предварительного нагрева, является погонная энергия. Заметным изменением в стандарте является отказ от термина «энергия дуги» в пользу тепловложения для описания энергии, вводимой в сварной шов на единицу длины прогона.Расчет подводимого тепла основан на сварочном напряжении, токе и скорости движения и включает коэффициент теплового КПД; формула подробно описана в BS EN 1011-1 [8] .
Высокая устойчивость и повышенные значения углеродного эквивалента, связанные с более толстыми листами и более высокими марками стали, могут потребовать более строгого контроля процедур. Опытные подрядчики по изготовлению металлоконструкций могут выполнить эту дополнительную операцию и соответственно учесть ее.
BS EN 1011-2 [7] подтверждает, что наиболее эффективной гарантией предотвращения водородного растрескивания является снижение поступления водорода в металл шва из сварочных материалов.Процессы с изначально низким водородным потенциалом эффективны как часть стратегии, так же как и принятие строгих процедур хранения и обращения с водородными электродами. Данные и рекомендации поставщиков расходных материалов служат руководством для обеспечения минимально возможных уровней водорода для типа продукта, выбранного в процедуре.
Дополнительные информативные приложения к BS EN 1011-2 [7] описывают влияние условий сварки на ударную вязкость и твердость в ЗТВ и дают полезные советы по предотвращению растрескивания при затвердевании и разрыва пластин.
Дополнительное руководство по крекингу водородом / HAZ доступно в GN 6.04.
[вверх] Квалификация сварщика
Квалифицированный сварщик
(Изображение любезно предоставлено Mabey Bridge Ltd.)
BS EN 1090-2 [9] требует, чтобы сварщики имели квалификацию в соответствии с BS EN ISO 9606-1 [10] . Этот стандарт предписывает испытания для аттестации сварщиков в зависимости от процесса, расходных материалов, типа соединения, положения сварки и материала.Сварщики, успешно прошедшие испытания процедуры, получают автоматическое одобрение в пределах квалификационных диапазонов, указанных в стандарте. Сварщики должны быть аттестованы в соответствии с BS EN ISO 14732 [11] , когда сварка полностью механизирована или автоматизирована. В этом стандарте особое внимание уделяется проверке способности оператора настраивать и регулировать оборудование до и во время сварки.
Квалификация сварщика ограничена по времени и требует подтверждения действительности в зависимости от продолжительности работы, участия в работе соответствующего технического характера и удовлетворительной работы.Продление квалификации сварщика зависит от зарегистрированных подтверждающих свидетельств, демонстрирующих продолжающуюся удовлетворительную работу в пределах исходного диапазона испытаний, и доказательства должны включать либо объемные разрушающие испытания, либо разрушающие испытания. Успех всех сварочных операций зависит от персонала, имеющего соответствующую подготовку и регулярного контроля компетентности посредством инспекций и испытаний.
[вверх] Проверка и испытания
BS EN 1090-2 [9] устанавливает объем проверки до, во время и после сварки и дает критерии приемки, связанные с классом исполнения.Большинство испытаний неразрушающие; Разрушающие испытания проводятся только на отводных плитах.
[вверх] Неразрушающий контроль
Магнитный контроль частиц (MPI) сварного шва
(Изображение любезно предоставлено Mabey Bridge Ltd. )
Неразрушающий контроль проводится в соответствии с принципами BS EN ISO 17635 [12] . Для стальных конструкций основными методами являются визуальный осмотр после сварки (см. GN 6.06), магнитопорошковый контроль (обычно сокращенно MPI или MT) для поверхностного контроля сварных швов (см. GN 6.02) и ультразвуковой контроль (UT) для подповерхностного контроля сварных швов (см. GN 6.03). Радиографические испытания также упоминаются в BS EN 1090-2 [9] . Радиография требует строгого контроля за здоровьем и безопасностью; это относительно медленно и требует специального оборудования. Использование этого метода в стальных конструкциях снизилось по сравнению с более безопасным и портативным оборудованием, используемым в UT.Безопасные запретные зоны необходимы на производстве и на месте во время рентгенографии. Однако рентгенографию можно использовать для уточнения природы, размеров или степени множественных внутренних дефектов, обнаруженных ультразвуком.
Технические специалисты с признанной подготовкой и квалификацией в соответствии с BS EN ISO 9712 [13] требуются для всех методов неразрушающего контроля.
BS EN 1090-2 [9] требует, чтобы все сварные швы подвергались визуальному контролю по всей их длине.С практической точки зрения сварные швы следует визуально осматривать сразу после сварки, чтобы гарантировать своевременное устранение очевидных дефектов поверхности.
Дальнейшие требования к неразрушающему контролю основаны на эксплуатационных методах и требуют более строгого исследования первых пяти соединений новых технических требований к процедуре сварки, чтобы установить, что эта процедура способна производить сварные швы соответствующего качества при внедрении в производство. Затем указываются дополнительные неразрушающие испытания, основанные на типах соединений, а не на конкретных критических соединениях.Цель состоит в том, чтобы опробовать различные сварные швы в зависимости от типа соединения, марки материала, сварочного оборудования и работы сварщиков и, таким образом, поддерживать общий мониторинг производительности.
Если указано частичное или процентное обследование, руководство по выбору продолжительности испытания дано в BS EN ISO 17635 [12] ; При обнаружении недопустимых разрывов площадь исследования соответственно увеличивается.
BS EN 1090-2 [9] также включает в таблицу минимальное время выдержки перед дополнительным неразрушающим контролем в зависимости от размера сварного шва, подводимой теплоты и марки материала.
Признавая, что там, где требования к усталостной прочности более обременительны и требуется более строгая проверка, BS EN 1090-2 [9] действительно предусматривает спецификацию выполнения проекта для определения конкретных соединений для более высокого уровня проверки вместе с объемом и метод тестирования.
Для класса EXC3 критерием приемлемости дефектов сварного шва является уровень качества B согласно BS EN ISO 5817 [14] . Там, где необходимо достичь повышенного уровня качества для удовлетворения конкретных требований к усталостной прочности, BS EN 1090-2 [9] дает дополнительные критерии приемлемости с точки зрения категории деталей в BS EN 1993-1-9 [15] для расположения сварного шва.
Как правило, дополнительные критерии приемки практически не достижимы при обычном производстве. Стандартные испытания процедуры сварки и квалификационные испытания сварщиков не оцениваются по требованиям этого уровня. Если необходимо достичь такого уровня качества, требования должны быть сосредоточены на соответствующих деталях соединения, чтобы подрядчик имел возможность подготовить спецификации процедуры сварки, квалифицировать сварщиков и разработать соответствующие методы контроля и испытаний.
Неразрушающий контроль
[вверх] Разрушающее испытание
В стандарте BS EN 1090-2 [9] нет требований о проведении разрушающих испытаний поперечных соединений в натяжных фланцах. Тем не менее, объем для определения конкретных соединений для проверки позволит в спецификации проекта испытать, например, образцы от «стекающих» пластин, прикрепленных к встроенным стыковым сварным швам. Дополнительно производственные испытания могут быть указаны для: марок стали выше S460; угловые швы, в которых используются характеристики глубокого проплавления сварочного процесса; для мостовидных ортотропных настилов, где требуется макросъемка для проверки проплавления сварного шва; и на соединениях ребер жесткости с соединительными пластинами.
[вверх] Производственные испытания приварки шпилек
Испытание на изгиб приварной шпильки
(Изображение любезно предоставлено Mabey Bridge Ltd.)
Сварные шпильки для соединителей, работающих на сдвиг, исследуются и испытываются в соответствии с BS EN ISO 14555 [6] . В стандарте подчеркивается необходимость контроля процесса до, во время и после сварки. Предпроизводственные испытания используются для подтверждения процедуры сварки и, в зависимости от области применения, включают испытания на изгиб, испытания на растяжение, испытания на крутящий момент, макросъемку и радиографическое обследование.
Производственные испытания сварных швов также необходимы для приварки шпилек с дугой протяжки. Они должны выполняться производителем до начала сварочных работ на конструкции или группе аналогичных конструкций и / или после определенного количества сварных швов. Каждое испытание должно состоять как минимум из 10 сварных шпилек и быть испытано / оценено в соответствии с требованиями BS EN ISO 14555 [6] . Количество необходимых тестов должно быть указано в спецификации контракта.
[вверх] Качество сварки
Влияние дефектов на характеристики сварных соединений зависит от приложенной нагрузки и свойств материала.Эффект также может зависеть от точного расположения и ориентации дефекта, а также от таких факторов, как рабочая среда и температура. Основное влияние дефектов сварного шва на эксплуатационные характеристики стальных конструкций заключается в повышении риска разрушения из-за усталости или хрупкого разрушения.
Типы дефектов сварки можно разделить на одну из нескольких общих рубрик:
- Трещины.
- Плоские дефекты, кроме трещин, например непробиваемость, отсутствие плавления.
- Включения шлака.
- Пористость, поры.
- Поднутрения или дефекты профиля.
Трещины или плоские дефекты, проникающие через поверхность, потенциально являются наиболее серьезными. Включения вкрапленного шлака и пористость вряд ли станут причиной разрушения, если только они не будут чрезмерными. Подрезы обычно не представляют серьезной проблемы, если не существуют значительные растягивающие напряжения поперек стыка.
При выборе класса исполнения в BS EN 1090-2 [9] устанавливаются критерии приемки, при превышении которых дефект считается дефектом.
Если дефекты обнаружены в результате осмотра и испытаний во время производства, вероятно, потребуется обработка после сварки (см. GN 5.02) или другие меры по исправлению положения, хотя во многих случаях конкретный дефект может быть оценен по концепции « пригодность для цели ». Такое принятие зависит от фактических уровней напряжения и значимости усталости на месте. Это вопрос быстрой консультации между подрядчиком по изготовлению металлоконструкций и проектировщиком, поскольку, если это приемлемо, можно избежать дорогостоящего ремонта (и возможности появления дополнительных дефектов или деформации).
Руководство по контролю качества сварных швов и контролю сварных швов доступно в BCSA № 54/12 и GN 6.01.
[вверх] Список литературы
- ↑ BS EN ISO 22553: 2019, Сварка и родственные процессы. Символическое изображение на чертежах. Сварные соединения. BSI.
- ↑ BS EN 1993-1-8: 2005, Еврокод 3. Проектирование стальных конструкций. Дизайн стыков, BSI
- ↑ BS EN ISO 4063: 2010, Сварка и родственные процессы. Номенклатура процессов и ссылочные номера, BSI
- ↑ BS EN ISO 15609-1: 2019, Технические требования и аттестация процедур сварки металлических материалов.Спецификация процедуры сварки. Дуговая сварка, BSI
- ↑ 5,0 5,1 5,2 BS EN ISO 15614-1: 2017 + A1: 2019, Технические требования и квалификация процедур сварки металлических материалов.
Проверка процедуры сварки. Дуговая и газовая сварка сталей и дуговая сварка никеля и никелевых сплавов, BSI
- ↑ 6,0 6,1 6,2 BS EN ISO 14555: 2017, Сварка. Дуговая сварка металлических материалов, BSI
- ↑ 7.0 7,1 7,2 BS EN 1011-2: 2001, Сварка. Рекомендации по сварке металлических материалов. Дуговая сварка ферритных сталей, BSI
- ↑ BS EN 1011-1: 2009, Сварка. Рекомендации по сварке металлических материалов. Общее руководство по дуговой сварке, BSI
- ↑ 9,0 9,1 9,2 9,3 9,4 9,5 9,6 9,7 9,8 BS EN 1090-2: 2018, Изготовление металлоконструкций и алюминиевых конструкций.Технические требования к стальным конструкциям, BSI
- ↑ BS EN ISO 9606-1: 2017 Квалификационные испытания сварщиков. Сварка плавлением. Стали, BSI
- ↑ BS EN ISO 14732: 2013.
Сварочный персонал. Квалификационные испытания сварщиков и наладчиков механизированной и автоматической сварки металлических материалов BSI
- ↑ 12,0 12,1 BS EN ISO 17635: 2016, Неразрушающий контроль сварных швов. Общие правила для металлических материалов, BSI
- ↑ BS EN ISO 9712: 2012.Неразрушающий контроль. Квалификация и сертификация персонала по неразрушающему контролю, BSI
- ↑ BS EN ISO 5817: 2014, Сварка. Соединения, сваренные плавлением стали, никеля, титана и их сплавов (за исключением лучевой сварки). Уровни качества для выявления недостатков, BSI
- ↑ BS EN 1993-1-9: 2005, Еврокод 3. Проектирование стальных конструкций. Усталость, BSI
[вверх] Ресурсы
- Стальные здания, 2003 г. (Публикация № 35/03), BCSA
- Стальные мосты: практический подход к проектированию для эффективного изготовления и строительства, 2010 г. (Публикация №51/10), BCSA
- Национальные технические условия на стальные конструкции (7-е издание), 2020 г. (Публикация № 62/20), BCSA
- Типовые спецификации процедуры сварки для металлоконструкций — Второе издание, 2018 г. (Публикация № 58/18), BCSA
- Высокопрочные стали для применения в конструкциях: Руководство по производству и сварке, 2020 г. (Публикация № 62/20), BCSA
- Руководство по контролю сварных швов для металлоконструкций, 2012 г. (Публикация № 54/12), BCSA
- Хенди, К.Р.; Ильес, округ Колумбия (2015) Steel Bridge Group: Рекомендации по передовой практике в строительстве стальных мостов (6-й выпуск). (P185). SCI
[вверх] Дополнительная литература
- Руководство проектировщика металлоконструкций (7-е издание), 2011 г., глава 26 — Сварные швы и проектирование для сварки, Институт стальных конструкций.
[вверху] См. Также
Welding — SteelConstruction.info
Сварка — это основной вид деятельности на заводе-изготовителе, которым занимаются опытные квалифицированные специалисты, работающие в системе управления качеством сварки под контролем ответственного координатора сварки.Он используется для подготовки стыков к подключению в магазине и на месте, а также для крепления других приспособлений и фурнитуры. На заводе-изготовителе для разных видов деятельности используются разные методы сварки.
По сути, в процессе сварки используется электрическая дуга для выработки тепла для плавления основного материала в соединении. Отдельный присадочный материал, поставляемый в качестве расходуемого электрода, также плавится и соединяется с основным материалом, образуя расплавленную сварочную ванну. По мере того, как сварка продолжается вдоль соединения, сварочная ванна затвердевает, сплавляя основной металл и металл сварного шва.Для заполнения стыка или нарастания сварного шва до проектного размера может потребоваться несколько проходов или проходов.
Сварка
(Изображение любезно предоставлено William Haley Engineering Ltd.)
[вверх] Принципы дуговой сварки металлом
Терминология области сварного шва
Сварка — это сложное взаимодействие физических и химических наук.Правильное определение металлургических требований и разумное практическое применение являются предпосылкой для успешной сварки плавлением.
В процессе дуговой сварки металлическим электродом используется электрическая дуга для выработки тепла для плавления основного материала в соединении. Отдельный присадочный материал, поставляемый в качестве расходуемого электрода, также плавится и соединяется с основным материалом, образуя расплавленную сварочную ванну. Сварочная ванна подвержена атмосферному загрязнению и, следовательно, нуждается в защите во время критической фазы замерзания жидкости и твердого тела.Защита достигается либо за счет использования защитного газа, за счет покрытия бассейна инертным шлаком, либо за счет комбинации обоих действий.
В процессах с защитным газом от удаленного источника поступает газ, который подается на сварочную дугу через горелку или горелку. Газ окружает дугу и эффективно исключает атмосферу. Точный контроль необходим для поддержания подачи газа с подходящей скоростью потока, так как слишком большое количество может вызвать турбулентность и засасывать воздух, а может быть настолько же вредным, насколько и слишком маленьким.
В некоторых процессах используется флюс, который плавится в дуге для образования шлакового покрытия, которое, в свою очередь, покрывает сварочную ванну и защищает ее во время замерзания. Шлак также затвердевает и самораспускается или легко удаляется легким сколом. Действие плавления флюса также создает газовый экран для защиты.
По мере сварки вдоль стыка сварочная ванна затвердевает, сплавляя основной металл и металл шва. Для заполнения стыка или нарастания сварного шва до проектного размера может потребоваться несколько проходов или проходов.
Тепло от сварки вызывает металлургические изменения в основном материале, непосредственно примыкающем к границе или линии плавления. Эта область изменения известна как зона термического влияния (HAZ). Общая терминология, используемая в области сварного шва, показана справа вверху.
Сварочные операции требуют надлежащего технологического контроля со стороны компетентных сварщиков, чтобы гарантировать достижение проектных характеристик, минимизировать риск дефектных соединений, вызванных низким качеством сварки, и предотвратить образование склонных к образованию трещин микроструктур в ЗТВ.
[вверх] Виды сварных соединений
Большинство конструкционных сварных соединений выполняется на заводе-изготовителе и описывается как стыковые или угловые швы. Сварка на месте также возможна, и руководство по вопросам сварки на месте доступно в GN 7.01.
[вверх] Стыковые швы
Макрос клиновидного стыкового шва
(Изображение любезно предоставлено Mabey Bridge Ltd.)
Стыковые сварные швы обычно представляют собой стыковые соединения в прокатных профилях или стыковые соединения листов на стенках и фланцах, чтобы приспособиться к изменению толщины или восполнить доступный материал по длине.Положения этих стыковых швов допускаются при проектировании, хотя ограничения доступности материалов или схема монтажа могут потребовать согласования различных или дополнительных сварных швов. Тройники, приваренные встык, могут потребоваться, если при поперечных соединениях возникают значительные нагрузки или усталость.
Стыковые швы — это сварные швы с полным или частичным проплавлением, выполняемые между материалами со скошенными или скошенными кромками. Стыковые швы с полным проплавлением предназначены для передачи всей прочности сечения.Как правило, эти соединения можно сваривать с одной стороны, но по мере увеличения толщины материала желательна сварка с обеих сторон, чтобы уравновесить эффекты деформации, с операцией обратной строжки и / или шлифования в процессе для обеспечения целостности корень шва. Односторонние стыковые сварные швы с подкладными полосами из керамической или прочной стали обычно используются для соединения больших площадей пластин (например, стальных пластин настила) и там, где есть закрытые коробчатые секции, трубы или элементы жесткости, доступ к которым для сварки возможен только с одного сторона.Расчетная толщина горловины определяет глубину проплавления, необходимую для швов с частичным проплавлением. Обратите внимание, что соображения усталости могут ограничивать использование сварных швов с частичным проплавлением, особенно на мостах. Руководство по подготовке к сварке доступно в GN 5.01.
Следует приложить все усилия, чтобы избежать стыковой сварки приспособлений из-за затрат, связанных с подготовкой, временем сварки, более высоким уровнем квалификации сварщиков и более строгими и трудоемкими требованиями к испытаниям. Кроме того, стыковые швы имеют тенденцию иметь большие объемы наплавленного металла шва; это увеличивает эффект усадки сварного шва и приводит к более высокому уровню остаточного напряжения в соединении.Чтобы уравновесить усадку и распределить остаточное напряжение, минимизируя таким образом деформацию, необходима тщательная последовательность сварочных операций.
Иногда бывает необходимо обработать стыковые сварные швы заподлицо по причинам усталости, или для улучшения дренажа стальных балок, устойчивых к атмосферным воздействиям, или для улучшения режима испытаний. Следует избегать зачистки заподлицо только по эстетическим соображениям, потому что трудно обработать поверхность, чтобы она соответствовала смежной поверхности после прокатки, и результат часто более визуально заметен, чем исходный сварной шов.Кроме того, шлифование представляет собой дополнительную опасность для здоровья и безопасности, которую следует избегать по возможности. Правка стыковых швов до гладкой поверхности обычно не требуется для строительных стальных конструкций, поскольку обычно они не подвержены усталости.
- Пример обработанного стыкового шва с гладкой поверхностью и сливными пластинами
(изображения любезно предоставлены Mabey Bridge Ltd.)
[вверх] Угловые швы
Макрос однопроходного углового шва
(Изображение любезно предоставлено Mabey Bridge Ltd.)
В большинстве сварных соединений в зданиях и мостах используются угловые швы, обычно в форме тройника. Обычно они включают в себя концевую пластину, ребро жесткости, подшипниковые и распорные соединения с прокатными секциями или плоскими балками, а также соединения стенки с фланцем на самих пластинчатых балках. Их относительно просто подготовить, сварить и испытать в обычных конфигурациях, при этом главным соображением является сборка стыков.
В S275 полная прочность стали также развивается в угловых сварных швах и сварных швах с частичным проплавлением с вышележащими угловыми швами при условии, что такие сварные швы симметричны, выполнены с использованием правильных расходных материалов и сумма сварных швов равна толщине элемента, который сварные швы стыкуются.
Размеры сварных швов должны быть указаны на чертежах проекта вместе с любыми специальными требованиями по классификации усталости. BS EN ISO 22553 [1] предписывает правила использования символов для детализации сварных соединений на чертежах.
Обращается внимание на тот факт, что в традиционной практике Великобритании для определения размера углового сварного шва обычно используется длина ветви, но это не универсально: в европейской практике используется толщина горловины, а в стандарте BS EN 1993-1-8 [2] дает требования относительно размера горла, а не длины ноги.Проектировщик должен следить за тем, чтобы было ясно, какой размер указан, и что все стороны должны знать, что было указано.
[вверх] Процессы
Важными факторами, которые подрядчик по изготовлению металлоконструкций должен учитывать при выборе процесса сварки, являются способность выполнять проектные требования и, с точки зрения производительности, скорость наплавки, которая может быть достигнута, а также рабочий цикл или эффективность процесса. (Эффективность — это отношение фактического времени сварки или дуги к общему времени, в течение которого сварщик или оператор занят выполнением сварочного задания.Общее время включает настройку оборудования, чистку и проверку выполненного шва.)
Ниже описаны четыре основных процесса сварки, которые регулярно используются при производстве стальных конструкций в Великобритании. Номера процессов определены в BS EN ISO 4063 [3] . Разновидности этих процессов были разработаны с учетом практики и оборудования отдельных производителей, и другие процессы также имеют место для конкретных приложений, но выходят за рамки данной статьи.
[вверх] Металлоактивная газовая сварка (MAG), процесс 135
Сварка MAG
(Изображение любезно предоставлено Kiernan Structural Steel Ltd.)
MAG-сварка сплошным проволочным электродом — это наиболее широко используемый процесс с ручным управлением для заводских производственных работ; это иногда называют полуавтоматической сваркой или сваркой CO 2 . Сплошной проволочный электрод из сплошной проволоки пропускается через устройство подачи проволоки к «пистолету», который обычно удерживается и управляется оператором. Питание подается от источника выпрямителя или инвертора по соединительным кабелям к устройству подачи проволоки и кабелю горелки; электрическое подключение к проводу осуществляется через контактный наконечник на конце пистолета.Дуга защищена защитным газом, который направляется в зону сварного шва через кожух или сопло, окружающее контактный наконечник. Защитные газы обычно представляют собой смесь аргона, диоксида углерода и, возможно, кислорода или гелия.
Хорошая производительность наплавки и рабочий цикл можно ожидать от процесса, который также можно механизировать с помощью простых моторизованных кареток. Газовая защита может быть сдувана сквозняками, что может вызвать пористость и возможные вредные металлургические изменения в металле сварного шва.Таким образом, этот процесс лучше подходит для заводского производства, хотя он используется на месте, где могут быть предусмотрены эффективные укрытия. Он также более эффективен в плоском и горизонтальном положениях; Сварные швы в других положениях наплавляются с более низкими параметрами напряжения и силы тока и более подвержены дефектам плавления.
Металлоактивная газовая сварка (МАГ), процесс 135
Металлоактивная газовая сварка (MAG), процесс 135
MAG-сварка электродом с флюсовой сердцевиной, процесс 136 представляет собой разновидность, в которой используется то же оборудование, что и MAG-сварка, за исключением того, что плавящийся проволочный электрод имеет форму трубки малого диаметра, заполненной флюсом.Преимущество использования этих проволок состоит в том, что можно использовать более высокие скорости наплавки, особенно при сварке в вертикальном положении (между двумя вертикальными поверхностями) или в верхнем положении. Наличие тонкого шлака помогает преодолевать силу тяжести и позволяет наносить сварные швы в местах с относительно высокими током и напряжением, тем самым снижая вероятность дефектов плавления. Добавки флюса также влияют на химию сварного шва и, таким образом, улучшают механические свойства соединения.
[вверху] Ручная дуговая сварка металлом (MMA), процесс 111
Этот процесс остается наиболее универсальным из всех сварочных процессов, но его использование в современной мастерской ограничено.Трансформаторы переменного тока, выпрямители постоянного тока или инверторы подают электроэнергию по кабелю на электрододержатель или клещи. Проволочный электрод с флюсовым покрытием (или «стержень») вставляется в держатель, и сварочная дуга возникает на конце электрода, когда он ударяется о заготовку. На острие электрода плавится, образуя ванну расплава, которая сплавляется с основным материалом, образуя сварной шов. Флюс также плавится, образуя защитный шлак и создавая газовый экран, предотвращающий загрязнение сварочной ванны по мере ее затвердевания.Добавки флюса и сердечник электрода используются для влияния на химический состав и механические свойства сварного шва.
Обычно используются электроды с основным покрытием, контролируемым водородом. Эти электроды необходимо хранить и обращаться с ними в соответствии с рекомендациями производителя расходных материалов, чтобы сохранить их низкие водородные характеристики. Это достигается либо путем использования сушильных шкафов и подогреваемых колчанов для хранения и обработки продукта, либо путем покупки электродов в герметичных упаковках, специально разработанных для поддержания низкого уровня водорода.
Недостатками процесса являются относительно низкая скорость наплавки и высокий уровень отходов, связанных с непригодными для использования концевыми штырями электродов. Тем не менее, он остается основным процессом для сварки на стройплощадке и для труднодоступных мест, где громоздкое оборудование не подходит.
Ручная дуговая сварка металлом (MMA), процесс 111
Ручная дуговая сварка металлом (MMA), процесс 111
[вверх] Дуговая сварка под флюсом (SAW), процесс 121
Оперативная сварка под флюсом
(Изображение любезно предоставлено Mabey Bridge Ltd.)
Это, вероятно, наиболее широко используемый процесс для сварки угловых швов перемычки между стенкой и фланцем и стыковых сварных швов на линии толстой пластины для получения отрезков длины фланца и стенки. В процессе процесса непрерывный провод подается через контактный наконечник, где он устанавливает электрический контакт с мощностью от выпрямителя, в зону сварки, где он изгибается и образует ванну расплава. Сварочная ванна заполняется флюсом, подаваемым из бункера. Флюс, непосредственно покрывающий расплавленную сварочную ванну, плавится, образуя шлак и защищая сварной шов во время затвердевания; избыточный флюс собирается и повторно используется.По мере охлаждения шва шлак замерзает и отслаивается, оставляя высококачественные профильные швы.
Этот процесс по своей сути более безопасен, чем другие процессы, поскольку дуга полностью покрывается во время сварки, отсюда и термин дуга под флюсом. Это также означает, что требования к личной защите меньше. Высокая производительность наплавки — особенность процесса, поскольку он обычно механизируется на портальных мостах, тракторах или другом специализированном оборудовании. Это позволяет контролировать параметры и дает рекомендации по точному размещению сварных швов.
Сварка под флюсом (SAW), процесс 121
Сварка под флюсом (SAW), процесс 121
[вверх] Приварка шпилек методом вытяжной дуги 783
Композитные мосты требуют приваривания соединителей со срезными шпильками к верхнему фланцу пластинчатых или коробчатых балок и в других местах, где требуется композитное воздействие стали на бетон, например.грамм. на интегральных абатментах. В зданиях композитные балки требуют приваривания соединителей срезных шпилек к элементам либо непосредственно к верхнему фланцу, либо чаще через постоянный настил из оцинкованной стали на композитных полах, где верхний фланец балки остается неокрашенным.
Сварной шов на балке моста
(Изображение любезно предоставлено Mabey Bridge Ltd.)Приварка шпилек через настил
(Изображение любезно предоставлено Structural Metal Decks Ltd.)
Метод приварки шпилек известен как процесс с натянутой дугой, и требуется специальное оборудование в виде мощного выпрямителя и специального пистолета. Шпильки загружаются в пистолет, и при электрическом контакте с изделием концевые дуги сгибаются и плавятся. Продолжительность дуги рассчитывается так, чтобы между концом шпильки и основным материалом установилось расплавленное состояние. В нужный момент пистолет погружает шпильку в сварочную ванну.Керамическая манжета окружает шпильку для защиты и поддержки сварочной ванны, стабилизации дуги и формовки смещенной сварочной ванны для формирования сварной манжеты. Когда сварной шов затвердевает, наконечник отслаивается. У удовлетворительных сварных швов обычно есть правильная, яркая и чистая втулка, полностью окружающая шпильку.
Приварка шпилек методом вытяжной дуги 783
[вверху] Технические требования к процедуре сварки
Чертежи детализируют конструктивную форму, выбор материала и указывают сварные соединения.Подрядчик по изготовлению металлоконструкций выбирает методы сварки каждой конфигурации стыка, обеспечивающие требуемые характеристики. Прочность, вязкость разрушения, пластичность и усталость — важные металлургические и механические свойства, которые необходимо учитывать. Тип соединения, положение сварки, производительность и требования к ресурсам влияют на выбор подходящего процесса сварки.
Выбранный метод представлен в спецификации процедуры сварки (WPS), в которой подробно описана информация, необходимая для инструктирования и руководства сварщиками, чтобы обеспечить повторяемость характеристик для каждой конфигурации соединения.Пример формата WPS показан в Приложении A стандарта BS EN ISO 15609-1 [4] . Подрядчики по изготовлению металлоконструкций могут иметь свой собственный корпоративный шаблон, но все они включают важную информацию, позволяющую передать сварщику надлежащие инструкции.
Необходимо подкрепить WPS свидетельством удовлетворительных испытаний процедуры в виде протокола аттестации процедуры сварки (WPQR), подготовленного в соответствии с BS EN ISO 15614-1 [5] . Введение этого стандарта гласит, что испытания процедуры сварки, проведенные в соответствии с прежними национальными стандартами и спецификациями, не аннулируются при условии их технической эквивалентности; Для этого могут потребоваться дополнительные тесты.Основные подрядчики по изготовлению металлоконструкций в Великобритании прошли предварительную квалификацию сварочных работ, позволяющих производить удовлетворительные сварные швы в большинстве конфигураций стыков, которые могут встретиться в сталелитейном строительстве и мостовой промышленности.
В случаях, когда данные предыдущих испытаний не имеют отношения к делу, необходимо провести испытание процедуры сварки, чтобы установить и подтвердить пригодность предлагаемого WPS.
Руководство по стандартным спецификациям процедуры сварки для стальных конструкций доступно в публикации BCSA No.58/18.
[вверх] Процедура испытаний
BS EN ISO 15614-1 [5] описывает условия для проведения испытаний процедуры сварки и пределы действия в пределах квалификационных диапазонов, указанных в стандарте. Координатор сварки готовит предварительную спецификацию процедуры сварки (pWPS), которая является первоначальным предложением для проведения испытания процедуры. Для каждой конфигурации стыка, будь то стыковой или угловой шов, учитывается марка и толщина материала, а также ожидаемые допуски посадки, которые могут быть достигнуты на практике.Выбор процесса определяется методом сборки, положением сварки и тем, является ли механизация жизнеспособным предложением для повышения производительности и обеспечения постоянного качества сварки. Размеры подготовки швов зависят от выбора процесса, любых ограничений доступа и толщины материала.
Расходные материалы выбираются из соображений совместимости с марками материалов и достижения заданных механических свойств, в первую очередь с точки зрения прочности и ударной вязкости. Для сталей марки S355 и выше используются продукты с водородным контролем.
Риск водородного растрескивания, пластинчатого разрыва, растрескивания при затвердевании или любой другой потенциальной проблемы оценивается не только с целью проведения испытания, но и для предполагаемого применения процедуры сварки в проекте. Соответствующие меры, такие как введение предварительного или последующего нагрева, включены в pWPS.
Контроль искажений обеспечивается правильной последовательностью сварки. При необходимости вводятся обратная строжка и / или обратное шлифование для достижения целостности корневого шва.
Указаны диапазоны сварочного напряжения, тока и скорости для определения оптимальных условий сварки.
Допустимые диапазоны групп материалов, толщины и типа соединения в пределах спецификации тщательно рассматриваются, чтобы максимально использовать pWPS. Подготавливаются испытательные пластины достаточного размера для извлечения образцов для механических испытаний, включая образцы для любых дополнительных испытаний, указанных или необходимых для повышения применимости процедуры.
Пластины и pWPS передаются сварщику; испытание проводится в присутствии эксперта (обычно из независимого проверяющего органа), и ведется запись фактических параметров сварки вместе с любыми необходимыми изменениями процедуры.
Завершенные испытания передаются независимому эксперту для визуального осмотра и неразрушающего контроля в соответствии с таблицей 1 Стандарта. Удовлетворительные испытательные пластины затем отправляются на разрушающий контроль, опять же в соответствии с таблицей 1. Неразрушающие методы контроля, как правило, включают ультразвуковой контроль для объемного контроля и контроль магнитных частиц для выявления дефектов поверхности.
Пример испытательного образца процедуры сварки
(Изображение любезно предоставлено Mabey Bridge Ltd.)
Существует ряд дополнительных стандартов, детализирующих подготовку, обработку и испытания всех типов образцов для разрушающих испытаний. Обычно специализированные лаборатории организуют подготовку образцов для испытаний и проводят фактические механические испытания и составление отчетов. Типичные образцы для стыкового сварного шва пластины включают испытания на поперечное растяжение, испытания на поперечный изгиб, испытания на удар и образец для макроэкспертизы, на котором проводится испытание на твердость.Для испытаний на удар минимальные требования к поглощению энергии и температура испытания обычно такие же, как и для основного материала в соединении. Целесообразно проверить все сварочные процедуры до предела возможного применения, чтобы избежать повторения подобных испытаний в будущем.
Завершенные результаты испытаний заносятся в протокол аттестации процедуры сварки (WPQR), утверждаемый экспертом. Типичный формат показан в Приложении B стандарта BS EN ISO 15614-1 [5] .
Существует дополнительное общее требование, касающееся испытаний процедуры сварки, согласно которому в случаях, когда грунтовки краски должны быть нанесены на работу до изготовления, они наносятся на образец материала, использованного для испытаний. На практике требуется тщательный контроль толщины краски, чтобы избежать дефектов сварки.
BS EN ISO 14555 [6] описывает метод испытаний для соединителей шпилек, приваренных дуговой сваркой. Стандарт включает требования к испытаниям, необходимым для подтверждения целостности сварных швов шпилек, а также устанавливает требования к производственным испытаниям для контроля приваривания шпилек в процессе.Допускается также квалификация, основанная на предыдущем опыте, и большинство подрядчиков по производству стальных конструкций могут предоставить доказательства, подтверждающие это.
Дополнительное руководство по испытаниям процедуры сварки доступно в GN 4.02.
[вверх] Водородный крекинг
Растрескивание может привести к хрупкому разрушению соединения с потенциально катастрофическими последствиями. Водородное (или холодное) растрескивание может происходить в области основного металла, прилегающей к границе плавления сварного шва, известной как зона термического влияния (HAZ).Разрушение металла сварного шва также может быть вызвано определенными условиями. Механизмы, вызывающие отказ, сложны и подробно описаны в специальных текстах.
Рекомендуемые методы предотвращения растрескивания водородом / HAZ описаны в BS EN 1011-2 [7] , приложение C. Эти методы определяют уровень предварительного нагрева для изменения скорости охлаждения, что дает время водороду для миграции на поверхность. и ускользнуть (особенно если поддерживается в виде пост-нагрева после завершения соединения) вместо того, чтобы оставаться в жестких, напряженных зонах.Предварительный нагрев не препятствует образованию микроструктур, подверженных образованию трещин; он просто снижает один из факторов, водород, так что растрескивания не происходит. Предварительный нагрев также снижает термический шок.
Подкладки предварительного нагрева
(Изображение предоставлено Mabey Bridge Ltd.)
Одним из параметров, необходимых для расчета предварительного нагрева, является погонная энергия. Заметным изменением в стандарте является отказ от термина «энергия дуги» в пользу тепловложения для описания энергии, вводимой в сварной шов на единицу длины прогона.Расчет подводимого тепла основан на сварочном напряжении, токе и скорости движения и включает коэффициент теплового КПД; формула подробно описана в BS EN 1011-1 [8] .
Высокая устойчивость и повышенные значения углеродного эквивалента, связанные с более толстыми листами и более высокими марками стали, могут потребовать более строгого контроля процедур. Опытные подрядчики по изготовлению металлоконструкций могут выполнить эту дополнительную операцию и соответственно учесть ее.
BS EN 1011-2 [7] подтверждает, что наиболее эффективной гарантией предотвращения водородного растрескивания является снижение поступления водорода в металл шва из сварочных материалов.Процессы с изначально низким водородным потенциалом эффективны как часть стратегии, так же как и принятие строгих процедур хранения и обращения с водородными электродами. Данные и рекомендации поставщиков расходных материалов служат руководством для обеспечения минимально возможных уровней водорода для типа продукта, выбранного в процедуре.
Дополнительные информативные приложения к BS EN 1011-2 [7] описывают влияние условий сварки на ударную вязкость и твердость в ЗТВ и дают полезные советы по предотвращению растрескивания при затвердевании и разрыва пластин.
Дополнительное руководство по крекингу водородом / HAZ доступно в GN 6.04.
[вверх] Квалификация сварщика
Квалифицированный сварщик
(Изображение любезно предоставлено Mabey Bridge Ltd.)
BS EN 1090-2 [9] требует, чтобы сварщики имели квалификацию в соответствии с BS EN ISO 9606-1 [10] . Этот стандарт предписывает испытания для аттестации сварщиков в зависимости от процесса, расходных материалов, типа соединения, положения сварки и материала.Сварщики, успешно прошедшие испытания процедуры, получают автоматическое одобрение в пределах квалификационных диапазонов, указанных в стандарте. Сварщики должны быть аттестованы в соответствии с BS EN ISO 14732 [11] , когда сварка полностью механизирована или автоматизирована. В этом стандарте особое внимание уделяется проверке способности оператора настраивать и регулировать оборудование до и во время сварки.
Квалификация сварщика ограничена по времени и требует подтверждения действительности в зависимости от продолжительности работы, участия в работе соответствующего технического характера и удовлетворительной работы.Продление квалификации сварщика зависит от зарегистрированных подтверждающих свидетельств, демонстрирующих продолжающуюся удовлетворительную работу в пределах исходного диапазона испытаний, и доказательства должны включать либо объемные разрушающие испытания, либо разрушающие испытания. Успех всех сварочных операций зависит от персонала, имеющего соответствующую подготовку и регулярного контроля компетентности посредством инспекций и испытаний.
[вверх] Проверка и испытания
BS EN 1090-2 [9] устанавливает объем проверки до, во время и после сварки и дает критерии приемки, связанные с классом исполнения.Большинство испытаний неразрушающие; Разрушающие испытания проводятся только на отводных плитах.
[вверх] Неразрушающий контроль
Магнитный контроль частиц (MPI) сварного шва
(Изображение любезно предоставлено Mabey Bridge Ltd.)
Неразрушающий контроль проводится в соответствии с принципами BS EN ISO 17635 [12] . Для стальных конструкций основными методами являются визуальный осмотр после сварки (см. GN 6.06), магнитопорошковый контроль (обычно сокращенно MPI или MT) для поверхностного контроля сварных швов (см. GN 6.02) и ультразвуковой контроль (UT) для подповерхностного контроля сварных швов (см. GN 6.03). Радиографические испытания также упоминаются в BS EN 1090-2 [9] . Радиография требует строгого контроля за здоровьем и безопасностью; это относительно медленно и требует специального оборудования. Использование этого метода в стальных конструкциях снизилось по сравнению с более безопасным и портативным оборудованием, используемым в UT.Безопасные запретные зоны необходимы на производстве и на месте во время рентгенографии. Однако рентгенографию можно использовать для уточнения природы, размеров или степени множественных внутренних дефектов, обнаруженных ультразвуком.
Технические специалисты с признанной подготовкой и квалификацией в соответствии с BS EN ISO 9712 [13] требуются для всех методов неразрушающего контроля.
BS EN 1090-2 [9] требует, чтобы все сварные швы подвергались визуальному контролю по всей их длине.С практической точки зрения сварные швы следует визуально осматривать сразу после сварки, чтобы гарантировать своевременное устранение очевидных дефектов поверхности.
Дальнейшие требования к неразрушающему контролю основаны на эксплуатационных методах и требуют более строгого исследования первых пяти соединений новых технических требований к процедуре сварки, чтобы установить, что эта процедура способна производить сварные швы соответствующего качества при внедрении в производство. Затем указываются дополнительные неразрушающие испытания, основанные на типах соединений, а не на конкретных критических соединениях.Цель состоит в том, чтобы опробовать различные сварные швы в зависимости от типа соединения, марки материала, сварочного оборудования и работы сварщиков и, таким образом, поддерживать общий мониторинг производительности.
Если указано частичное или процентное обследование, руководство по выбору продолжительности испытания дано в BS EN ISO 17635 [12] ; При обнаружении недопустимых разрывов площадь исследования соответственно увеличивается.
BS EN 1090-2 [9] также включает в таблицу минимальное время выдержки перед дополнительным неразрушающим контролем в зависимости от размера сварного шва, подводимой теплоты и марки материала.
Признавая, что там, где требования к усталостной прочности более обременительны и требуется более строгая проверка, BS EN 1090-2 [9] действительно предусматривает спецификацию выполнения проекта для определения конкретных соединений для более высокого уровня проверки вместе с объемом и метод тестирования.
Для класса EXC3 критерием приемлемости дефектов сварного шва является уровень качества B согласно BS EN ISO 5817 [14] . Там, где необходимо достичь повышенного уровня качества для удовлетворения конкретных требований к усталостной прочности, BS EN 1090-2 [9] дает дополнительные критерии приемлемости с точки зрения категории деталей в BS EN 1993-1-9 [15] для расположения сварного шва.
Как правило, дополнительные критерии приемки практически не достижимы при обычном производстве. Стандартные испытания процедуры сварки и квалификационные испытания сварщиков не оцениваются по требованиям этого уровня. Если необходимо достичь такого уровня качества, требования должны быть сосредоточены на соответствующих деталях соединения, чтобы подрядчик имел возможность подготовить спецификации процедуры сварки, квалифицировать сварщиков и разработать соответствующие методы контроля и испытаний.
Неразрушающий контроль
[вверх] Разрушающее испытание
В стандарте BS EN 1090-2 [9] нет требований о проведении разрушающих испытаний поперечных соединений в натяжных фланцах. Тем не менее, объем для определения конкретных соединений для проверки позволит в спецификации проекта испытать, например, образцы от «стекающих» пластин, прикрепленных к встроенным стыковым сварным швам. Дополнительно производственные испытания могут быть указаны для: марок стали выше S460; угловые швы, в которых используются характеристики глубокого проплавления сварочного процесса; для мостовидных ортотропных настилов, где требуется макросъемка для проверки проплавления сварного шва; и на соединениях ребер жесткости с соединительными пластинами.
[вверх] Производственные испытания приварки шпилек
Испытание на изгиб приварной шпильки
(Изображение любезно предоставлено Mabey Bridge Ltd.)
Сварные шпильки для соединителей, работающих на сдвиг, исследуются и испытываются в соответствии с BS EN ISO 14555 [6] . В стандарте подчеркивается необходимость контроля процесса до, во время и после сварки. Предпроизводственные испытания используются для подтверждения процедуры сварки и, в зависимости от области применения, включают испытания на изгиб, испытания на растяжение, испытания на крутящий момент, макросъемку и радиографическое обследование.
Производственные испытания сварных швов также необходимы для приварки шпилек с дугой протяжки. Они должны выполняться производителем до начала сварочных работ на конструкции или группе аналогичных конструкций и / или после определенного количества сварных швов. Каждое испытание должно состоять как минимум из 10 сварных шпилек и быть испытано / оценено в соответствии с требованиями BS EN ISO 14555 [6] . Количество необходимых тестов должно быть указано в спецификации контракта.
[вверх] Качество сварки
Влияние дефектов на характеристики сварных соединений зависит от приложенной нагрузки и свойств материала.Эффект также может зависеть от точного расположения и ориентации дефекта, а также от таких факторов, как рабочая среда и температура. Основное влияние дефектов сварного шва на эксплуатационные характеристики стальных конструкций заключается в повышении риска разрушения из-за усталости или хрупкого разрушения.
Типы дефектов сварки можно разделить на одну из нескольких общих рубрик:
- Трещины.
- Плоские дефекты, кроме трещин, например непробиваемость, отсутствие плавления.
- Включения шлака.
- Пористость, поры.
- Поднутрения или дефекты профиля.
Трещины или плоские дефекты, проникающие через поверхность, потенциально являются наиболее серьезными. Включения вкрапленного шлака и пористость вряд ли станут причиной разрушения, если только они не будут чрезмерными. Подрезы обычно не представляют серьезной проблемы, если не существуют значительные растягивающие напряжения поперек стыка.
При выборе класса исполнения в BS EN 1090-2 [9] устанавливаются критерии приемки, при превышении которых дефект считается дефектом.
Если дефекты обнаружены в результате осмотра и испытаний во время производства, вероятно, потребуется обработка после сварки (см. GN 5.02) или другие меры по исправлению положения, хотя во многих случаях конкретный дефект может быть оценен по концепции « пригодность для цели ». Такое принятие зависит от фактических уровней напряжения и значимости усталости на месте. Это вопрос быстрой консультации между подрядчиком по изготовлению металлоконструкций и проектировщиком, поскольку, если это приемлемо, можно избежать дорогостоящего ремонта (и возможности появления дополнительных дефектов или деформации).
Руководство по контролю качества сварных швов и контролю сварных швов доступно в BCSA № 54/12 и GN 6.01.
[вверх] Список литературы
- ↑ BS EN ISO 22553: 2019, Сварка и родственные процессы. Символическое изображение на чертежах. Сварные соединения. BSI.
- ↑ BS EN 1993-1-8: 2005, Еврокод 3. Проектирование стальных конструкций. Дизайн стыков, BSI
- ↑ BS EN ISO 4063: 2010, Сварка и родственные процессы. Номенклатура процессов и ссылочные номера, BSI
- ↑ BS EN ISO 15609-1: 2019, Технические требования и аттестация процедур сварки металлических материалов.Спецификация процедуры сварки. Дуговая сварка, BSI
- ↑ 5,0 5,1 5,2 BS EN ISO 15614-1: 2017 + A1: 2019, Технические требования и квалификация процедур сварки металлических материалов. Проверка процедуры сварки. Дуговая и газовая сварка сталей и дуговая сварка никеля и никелевых сплавов, BSI
- ↑ 6,0 6,1 6,2 BS EN ISO 14555: 2017, Сварка. Дуговая сварка металлических материалов, BSI
- ↑ 7.0 7,1 7,2 BS EN 1011-2: 2001, Сварка. Рекомендации по сварке металлических материалов. Дуговая сварка ферритных сталей, BSI
- ↑ BS EN 1011-1: 2009, Сварка. Рекомендации по сварке металлических материалов. Общее руководство по дуговой сварке, BSI
- ↑ 9,0 9,1 9,2 9,3 9,4 9,5 9,6 9,7 9,8 BS EN 1090-2: 2018, Изготовление металлоконструкций и алюминиевых конструкций.Технические требования к стальным конструкциям, BSI
- ↑ BS EN ISO 9606-1: 2017 Квалификационные испытания сварщиков. Сварка плавлением. Стали, BSI
- ↑ BS EN ISO 14732: 2013. Сварочный персонал. Квалификационные испытания сварщиков и наладчиков механизированной и автоматической сварки металлических материалов BSI
- ↑ 12,0 12,1 BS EN ISO 17635: 2016, Неразрушающий контроль сварных швов. Общие правила для металлических материалов, BSI
- ↑ BS EN ISO 9712: 2012.Неразрушающий контроль. Квалификация и сертификация персонала по неразрушающему контролю, BSI
- ↑ BS EN ISO 5817: 2014, Сварка. Соединения, сваренные плавлением стали, никеля, титана и их сплавов (за исключением лучевой сварки). Уровни качества для выявления недостатков, BSI
- ↑ BS EN 1993-1-9: 2005, Еврокод 3. Проектирование стальных конструкций. Усталость, BSI
[вверх] Ресурсы
- Стальные здания, 2003 г. (Публикация № 35/03), BCSA
- Стальные мосты: практический подход к проектированию для эффективного изготовления и строительства, 2010 г. (Публикация №51/10), BCSA
- Национальные технические условия на стальные конструкции (7-е издание), 2020 г. (Публикация № 62/20), BCSA
- Типовые спецификации процедуры сварки для металлоконструкций — Второе издание, 2018 г. (Публикация № 58/18), BCSA
- Высокопрочные стали для применения в конструкциях: Руководство по производству и сварке, 2020 г. (Публикация № 62/20), BCSA
- Руководство по контролю сварных швов для металлоконструкций, 2012 г. (Публикация № 54/12), BCSA
- Хенди, К.Р.; Ильес, округ Колумбия (2015) Steel Bridge Group: Рекомендации по передовой практике в строительстве стальных мостов (6-й выпуск). (P185). SCI
[вверх] Дополнительная литература
- Руководство проектировщика металлоконструкций (7-е издание), 2011 г., глава 26 — Сварные швы и проектирование для сварки, Институт стальных конструкций.
[вверху] См. Также
В чем смысл стыковой сварки?
Дата : 六 23, 2016 Категории : Новости рынка / Просмотры новостей : 6,115 просмотров
Стыковая сварка — это один из способов сварки.В процессе стыковой сварки две части материала соединяются параллельно вдоль кромки в одну линию. Стыковые сварные соединения могут выполняться на большом аппарате непрерывно или на переносном сварочном аппарате, управляемом сварщиком. Стыковое сварное соединение является экономичным и надежным. метод соединения материалов без дополнительных компонентов. (Что такое фитинги для стыковой сварки?)
Труба стыковая сварочная
Процесс стыковой сварки может использоваться как для металла, так и для пластика. Когда два стальных листа уложены бок о бок и свариваются вместе вдоль линии, это типичный пример стыкового сварного соединения.
пластина с V-образной канавкой для стыковой сварки
Если толщина материала мала, квадратная и гладкая кромка материала подходит для стыкового сварного шва. Если материал более толстый для сварки, края должны быть скошены, чтобы образовать одиночную V-образную канавку или двойную V-образную канавку, двойную V-образная канавка используется для самой толстой толщины, это означает, что материал скошен с обеих сторон.