Резка металла: способы, инструменты для резания
Резка металла представляет собой процесс разделения материала на части. Таким способом производится раскрой металлических листов или отрезка сортового проката. Воздействием режущего инструмента на металл создаются заготовки для дальнейшей обработки. По разработанным чертежам формируется конфигурация поверхности. Для обработки металла резанием необходимо оборудование. Это могут быть ручные инструменты, механические станки или приспособления, обеспечивающие нагрев материала.

Способы резки
Существует несколько способов разделения материала. Технология зависит от оборудования, применяемого в процессе работы. Выделяют следующие виды резки металла:
Ручная резка металла
Ручное резание металла не является высокоэффективным и в промышленных масштабах не используется. При ручной резке используются следующие инструменты:
Гидроабразивная резка металла
Гидроабразивный способ резки основан на воздействии струи воды, смешанной с абразивными частицами, на обрабатываемую заготовку. Давление подаваемой жидкости составляет 5000 атм. К преимуществу такой резки металла относится возможность получения разнообразных линий. Обработке подвергаются сплавы определенной марки с небольшой толщиной листа.
Термическая резка металла
Резание металлов горячим способом основано на отсутствии контакта между инструментом и заготовкой. Горячая струя расплавляет и разделяет материал в нужном месте.
К видам термической резки относятся:
Газокислородная резка
Газокислородная резка состоит из 2 этапов:
- В место реза направляется струя пламени, которая выходит из резака. В качестве горючего материала используется ацетилен.
- После разогрева идет подача кислорода, который прорезает размягченную металлическую поверхность. Параллельно удаляются окислы.
В процессе работы расстояние от нижней точки резака до поверхности изделия должно оставаться постоянным. От этого зависит качество реза.
Для этой цели используются лазерные резаки. Процесс основан на подаче лазерного луча в точку поверхности. Происходит фокусирование тепловой энергии. Ведется прогрев участка, расплавление материала и последующее его испарение. При перемещении луч разрезает поверхность.
К недостаткам способа относится возможность работы с изделиями низкой теплопроводности и небольшой толщины.

Плазменная
В качестве оборудования для плазменной резки используется плазматрон. Через имеющееся в нем сопло под высоким давлением выходит кислород. Его температура составляет до 20 тыс. градусов. Ширина пучка 3 мм. Происходит нагрев участка поверхности, его частичное выгорание и выдувание расплава.
К преимуществу метода относится высокая скорость реза и возможность работать с заготовками до 150 мм толщины.
Механическая резка металла
Механическая резка металла осуществляется с помощью воздействия специальной стали с высокой степенью закалки. За счет большой твердости инструмент разрезает изделие.
При резке используются такие виды оборудования:
Резка ленточной пилой
Ленточная пила представляет собой полотно, которое закрепляется в специальном оборудовании. Материал инструмента такой же, как и у ручного изделия. На одной стороне расположены зубцы. В процессе работы двигателя станка идет вращение шкивов, благодаря которому происходит непрерывное движение ленты.
В процессе работы наблюдается небольшой отход, потому что ширина полотна составляет 1,5 мм. Возможна резка как листового металла, так и круглых заготовок.
Ударная резка металла на гильотине
Гильотинная резка металла используется для подготовки заготовок из листовой стали при штамповочных операциях. Разрезаемое полотно располагается на горизонтальной поверхности, подается до упора и разрезается гильотинными ножницами по всей ширине одним ударом.
Важно то, что ножи прикасаются к листу не по всей длине поверхности. Верхний инструмент располагается под углом. Соприкосновение с металлом идет в 1 точке, которая перемещается по всей длине реза. Процесс напоминает работу обыкновенных ножниц.
Резка на дисковом станке
В качестве рабочего инструмента используется диск. По его наружной поверхности располагаются зубья. Сверху стоит защитный кожух. В качестве привода используется электродвигатель, который приводит во вращение диск. Получается срез высокого качества.
По такому же принципу устроены труборезы, которыми разрезаются трубы. В процессе работы идет постоянный поворот заготовки на 360 градусов. Есть возможность делать срезы под разными углами.
Инструменты для резки
При работе в домашних условиях важно знать, чем режется металл. Чаще всего используются ручные ножницы или ножовка. Для промышленности требуются станки, с установленной на них пилой или гильотиной. Это связано с большими объемами производства и необходимостью выдержки точности размеров.

Ручные ножницы
Ручными ножницами можно разрезать материал, толщиной до 3 мм. Они имеют несколько видов резцов по металлу:
- Резцы для прямого реза.
- Для криволинейного.
- Пальцевые. Бывают прямого вида и зеркального. С их помощью вырезаются сложные фигуры.
- С одним подвижным лезвием, а вторым фиксированным, закрепленным в верстак.
Пилы
Пилы часто используются для резки металла. Они бывают нескольких видов:
- Ручные. Вставляются в специальную раму, имеющую С-образный вид.
- Дисковые. В качестве привода используется электродвигатель или ручное приспособление.
- Ленточные. Применяются только в промышленных целях.
- Торцевые. Имеют возможность совершать рез под разными углами.
- Маятниковые. Отличительной особенностью является наличие на торцевой части твердосплавной напайки.
- Циркулярные. Торец изготавливается из абразивных или твердосплавных напаек.
Углошлифовальная машина
В качестве станка для резки используется углошлифовальная машина. Другое ее название — болгарка. Она обладает следующими преимуществами:
- Благодаря небольшому весу и малым габаритам приспособление удобно в работе.
- Возможность резки изделий разной толщины.
- Большой выбор вариантов сменных дисков.
Благодаря процессу обработки металлов резанием, есть возможность получения любого вида изделий. Для этого существует разнообразный инструмент, с помощью которого ведется не только распил в прямом направлении, но и выпиливаются сложные фигуры.
Типы резки металла: как выбрать наиболее подходящий
Вопросы, рассмотренные в материале:
- Какие существуют типы резки металла
- Как осуществляется холодная резка металла
- Каковы преимущества термической резки металла
- Как правильно выбрать нужный тип резки металла
Резание металла – один из основных технологических процессов металлообработки. Используется он при необходимости разделения на несколько частей листовой или сортовой заготовки. В современном производстве применяются высокоточные и экономичные типы резки металла, позволяющие быстро и с минимальными потерями материала получить изделия необходимой конфигурации.
Основные типы резки металла
Существуют следующие типы резки металла:
1. Холодный (механический). Резка происходит за счет механического воздействия на металл специальным режущим инструментом, изготовленным из материала с твердостью, намного большей, чем жесткость обрабатываемого изделия. Применяются следующие инструменты:
- гильотина;
- ленточнопильный станок;
- дисковая (циркулярная) пила и «болгарка».
2. Горячий (термический). Обрабатываемая заготовка расплавляется по линии разреза, а остатки металла удаляются газом. Горячий тип резки металла подразделяется на следующие виды резания:
- газокислородный;
- лазерный;
- плазменный.
Но не все типы резки металла – как холодной, так и горячей – позволяют получить изделие заданной чистоты. Остановимся более подробно на каждом из вышеперечисленных способов.
Холодные типы резки металла
Резка металла механическим способом
Резка с помощью гильотины.
При таком способе резания используются специальные механические инструменты – ножницы и ножи по металлу. Заготовка устанавливается на рабочий стол и закрепляется прижимной балкой. Затем с помощью специального лезвия производится резка. В результате получается идеально ровный край, без лишних кромок, заусенцев и зазубрин. Режут материал сразу по всей ширине листа, поэтому кривизна среза нулевая.
В настоящее время используются следующие виды гильотин для рубки металла:
- ручные;
- гидравлические;
- пневматические»
- электромеханические.
Они не отличаются друг от друга по принципу действия, но последние три вида дополнены электроникой, обеспечивающей точность и безопасность резки. Также есть станки, которые могут резать металл не только поперек, но и вдоль. Чаще всего гильотинный тип обработки применяют при заготовительных работах.
Недостатки данного способа:
- Может применяться не для всех типов металлов и имеет ограничения по толщине заготовки. Например, гидравлические станки предназначены для металла толщиной до 6 мм.
- Полученные в результате резки заготовки часто не соответствуют нужному размеру, так как точность обработки зависит от квалификации оператора.
- Невозможно осуществить фигурную резку.
Рекомендовано к прочтению
Ленточнопильная резка.
В настоящее время этот тип резки металла очень популярен по причине невысокой стоимости оборудования, хорошей производительности и несложного обслуживания. Режущим инструментом является ленточная пила, натянутая на шкивах.
Современные ленточнопильные станки (ЛПС) дополняются разнообразным оборудованием и электроникой, благодаря которым агрегат легко встраивается в конкретную производственную линию. Скорость резки подобной машины в среднем составляет около 100 мм/мин и выше.
Способ резки на ЛПС позволяет добиваться точного соответствия заданным параметрам, а место разреза не нужно дополнительно обрабатывать. Метод хорош для высокоточных изделий и деталей с гладкой поверхностью. ЛПС подходит для любого металла, а ширина реза составляет всего 1,5 мм.
При таком типе резке металла важно соблюдать ряд условий:
- точный выбор шага зубьев режущего полотна в соответствии с сечением распиливаемого профиля с помощью специальных таблиц;
- скорость подачи;
- скорость резки.
ЛПС позволяет резать металлическую заготовку под углом, что является большим преимуществом по сравнению с гильотиной.
К недостаткам этого типа резки металлов относятся невозможность получить фигурный рез и ограничение размера заготовок в зависимости от возможностей станка.
Резка металла циркулярной пилой и «болгаркой».
С помощью циркулярной пилы делают точные разрезы хорошего качества. Этот инструмент позволяет контролировать угол разреза.
К недостаткам такого типа резки относят большое количество отходов, невысокую скорость и маленькую глубину разрезания.
Для резки профильного проката можно использовать болгарку. На месте среза не остается окалины и окислов, мало отходов.
Но низкая производительность при таком типе резки металла является его главным недостатком по сравнению с другими способами.
Горячая резка металла
Современное промышленное производство требует высокопроизводительных способов металлообработки, позволяющих выпускать максимально возможное количество заготовок заданного качества в минимальные сроки. Этим требованиям отвечают горячие типы резки металла.
Газокислородная резка.
Принцип работы основан на том, что в чистом кислороде при температуре выше +1000 °C металл плавится и выгорает. Место реза предварительно разогревается до температуры воспламенения материала. В качестве разогревающего газа обычно используется ацетилен. На время прогрева влияют толщина металла, его марка и состояние поверхности заготовки.
После того как место разреза прогревается, в сопло резака подается струя горящего кислорода. Она прорезает заготовку по всей толщине, плавно перемещаясь вдоль линии реза. В процессе горения кислорода также удаляются окислы, образующиеся на поверхности полуфабриката.
Для того чтобы разрез получился качественным, важно соблюдать одинаковое расстояние между резаком и заготовкой во время обработки. Это нелегкая задача при использовании ручного газокислородного резака. В случае автоматизации процесса резание происходит на большой скорости кислородом высокого давления, в результате производительность работы и качество среза значительно возрастают.
Уникальность способа заключается в возможности:
- разрезания заготовок большой ширины;
- обработки изделий из титана.
- невозможность использования при резке цветных металлов (меди, алюминия), хромоникелевых и высокоуглеродистых сталей;
- большая ширина реза, образование окислов, наплывов, невысокое качество;
- невозможность обработки криволинейных поверхностей;
- изменение физических свойств материала в области разреза в результате высокотемпературного воздействия.
Плазменная резка металла.
Тип резки при помощи плазмы основан на принципе интенсивного расплавления металла по линии разреза за счет теплового воздействия сжатой электрической дуги и последующего его испарения. Под воздействием электрической дуги образуется полностью или частично ионизированный газ, или плазма. Температура внутри газоплазменного потока достигает +15 000…+20 000°С, что позволяет в разы увеличить производительность процесса по сравнению с газокислородной резкой, а также избавиться от недостатков последней.
Из всех перечисленных типов резки металла в настоящее время благодаря своим преимуществам плазменная обработка является оптимальным выбором для современных металлообрабатывающих производств:
- плазменный рез высокоточен и не оставляет наплывов;
- позволяет резать по кривым линиям;
- исключается изменение физических свойств металла (перекаливания) за счет узконаправленного нагрева участка резки;
- оборудование не имеет баллонов с взрывоопасным газом, соответственно, не требует заправки и доставки этих емкостей;
- не требуется особого режима соблюдения мер пожарной безопасности;
- отсутствует подготовительный этап очистки, потому что высокотемпературное воздействие эффективно удаляет посторонние примеси (в виде ржавчины, грязи, краски), качество разреза остается неизменным;
- не нужны специальные присадки для цветных металлов, используется дешевая электроэнергия и воздух, расходные материалы – только сопла и электроды, поэтому плазменная резка металлов – экономически выгодный технологический процесс.
Недостатки данного типа резки металла:
- Из-за воздействия высоких температур изменяются свойства кромок заготовки. Они становятся более твердыми, часть материала теряется, поэтому нужны дополнительные затраты на обработку края. В любом случае качество кромок после плазменной резки значительно лучше, чем после газокислородной: нет окалины, ширина зоны с цветами побежалости в пять раз меньше.
Лазерная резка металла.
Данный тип относится к инновационным технологическим процессам. Суть его – в интенсивном воздействии на металл узкого лазерного луча, обладающего стабильной частотой и длиной волны. Он может фокусироваться на небольшом участке поверхности с помощью оптики, управляемой специальной компьютерной программой. Благодаря такому технологическому решению лазерная резка имеет непревзойденные параметры точности.
Высокая плотность энергии, характерная для направленного и узко концентрированного лазерного излучения, позволяет нагреть и испарить строго определенный участок металлической заготовки.
Лазерная резка происходит следующим образом:
- нагревание до температуры плавления по линии реза;
- расплавление металла;
- погружение в толщу разрезаемого материала.
При погружении лазерного луча внутрь металла происходит повышение температуры, в результате чего материал расплавляется и закипает. Этот процесс потребляет много энергии, поэтому для ее экономии в зону разреза подается вспомогательный газ, с помощью которого происходит плазменная резка. В зависимости от теплотехнических свойств материала заготовки, вспомогательными газами могут быть обычный воздух, азот, кислород, инертный газ.
Достоинства лазерного типа резки металла:
- максимально узкие резы;
- отсутствие деформации при резании тонких листов стали и мягких полуфабрикатов;
- возможность точного раскроя по сложным контурам;
- минимальное количество неровностей;
- маленькая площадь термического воздействия;
- универсальность метода – подходит к любым сплавам;
- несложное управление станком лазерной резки.
Единственный недостаток лазерной резки – небольшая допустимая толщина металла.
Чем хороша гидроабразивная резка металла
Гидроабразивная резка металла – принципиально иной по сравнению с остальными метод металлообработки. Он отличается от способов горячей резки тем, что не изменяет физико-механические свойства материала заготовки. При таком типе резки металла отсутствует деформация краев – их оплавление и сваривание.
Технологический процесс основан на использовании насоса сверхвысокого давления – до 6 000 бар, который через сопло диаметром 0,1 мм подает воду со специальным абразивом, образующую узконаправленную струю, способную разрезать сталь толщиной до 30 см. Скорость резки листа толщиной 1 мм на гидроабразивной установке может достигать 2,7 м/мин.
Основные достоинства лазерного типа резки металлов:
- Обрабатываемая поверхность не нагревается, потому что подаваемая струя воды моментально охлаждает рабочую область.
- Гидроабразивная резка справляется с самыми сложными конфигурациями и профилями любых заданных параметров.
- Не требуется дополнительных работ по обработке края в виде шлифования, качество разреза получается очень высоким.
- Ручные установки для гидроабразивного типа резки пригодны для использования под водой, глубина работ может достигать нескольких сот метров. Один насос высокого давления способен подавать воду одновременно на две-три установки.
- Экономичность – даже по сравнению с плазменной гидроабразивная резка выигрывает, при этом скорость разрезания может достигать 30 000 мм/мин без ухудшения качества разреза.
- Безопасность – станки для гидроабразивной резки идеально использовать в цехах с повышенной взрывоопасностью, а также с использованием легковоспламеняющихся материалов, так как гарантируют отсутствие искры, нагревания поверхности.
Основными недостатками гидроабразивных станков являются высокие эксплуатационные расходы и шумовой фон во время применения.
Самые последние технологические разработки в области резки металла предоставляют новые возможности для резания заготовок большой толщины. Это оборудование для ультразвуковой, криогенной и электроимпульсной обработки. Пока на нашем рынке оно не получило широкого распространения из-за высокой стоимости и сложности управления.
Какой тип резки металла выбрать
Выбирая тип резки металла для производства, прислушайтесь к советам профессионалов.
Технологи по металлообработке советуют обратить внимание на 10 признаков идеального способа резания:
- Увеличение скорости обработки со стабильным качеством.
- Чистый срез без остаточных следов и деформаций.
- Возможность резки металлов разной толщины.
- Износостойкость режущего инструмента.
- Возможность обработки поверхностей с посторонними загрязнениями.
- Возможность фигурной резки.
- Вариативность профиля разреза.
- Возможность совмещения с другими технологическими операциями (например, со снятием фаски).
- Простая управляемость.
- Экономичный раскрой.
Просто выберите технологический процесс, который будет совмещать максимальное количество рекомендуемых признаков для конкретного случая.
Почему следует обращаться именно к нам
Мы с уважением относимся ко всем клиентам и одинаково скрупулезно выполняем задания любого объема.
Наши производственные мощности позволяют обрабатывать различные материалы:
- цветные металлы;
- чугун;
- нержавеющую сталь.
При выполнении заказа наши специалисты применяют все известные способы механической обработки металла. Современное оборудование последнего поколения дает возможность добиваться максимального соответствия изначальным чертежам.
Для того чтобы приблизить заготовку к предъявленному заказчиком эскизу, наши специалисты используют универсальное оборудование, предназначенное для ювелирной заточки инструмента для особо сложных операций. В наших производственных цехах металл становится пластичным материалом, из которого можно выполнить любую заготовку.
Преимуществом обращения к нашим специалистам является соблюдение ими ГОСТа и всех технологических нормативов. На каждом этапе работы ведется жесткий контроль качества, поэтому мы гарантируем клиентам добросовестно выполненный продукт.
Благодаря опыту наших мастеров на выходе получается образцовое изделие, отвечающее самым взыскательным требованиям. При этом мы отталкиваемся от мощной материальной базы и ориентируемся на инновационные технологические наработки.
Мы работаем с заказчиками со всех регионов России. Если вы хотите сделать заказ на металлообработку, наши менеджеры готовы выслушать все условия. В случае необходимости клиенту предоставляется бесплатная профильная консультация.
Резка металла
пер.Каштановый 8/14 51100 пгт.Магдалиновка
Nikolaenko Dmitrij
Резка металла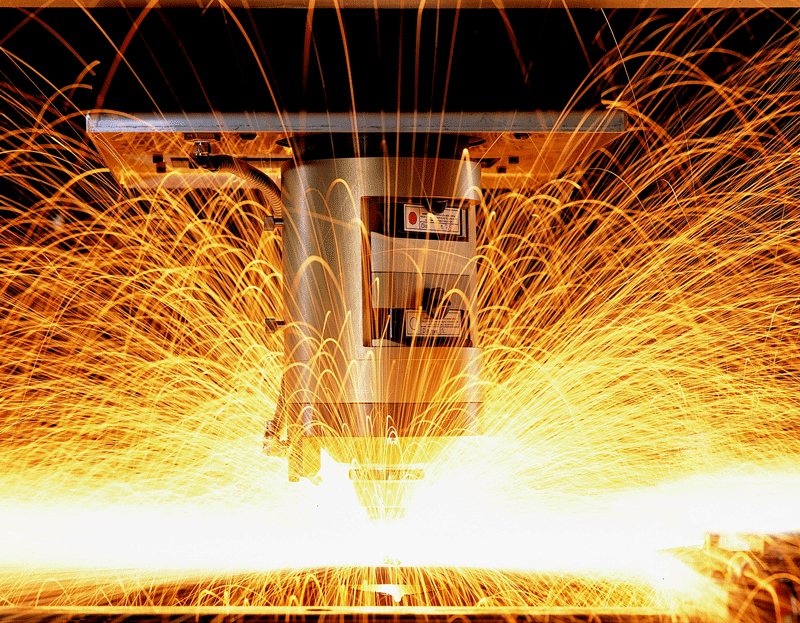
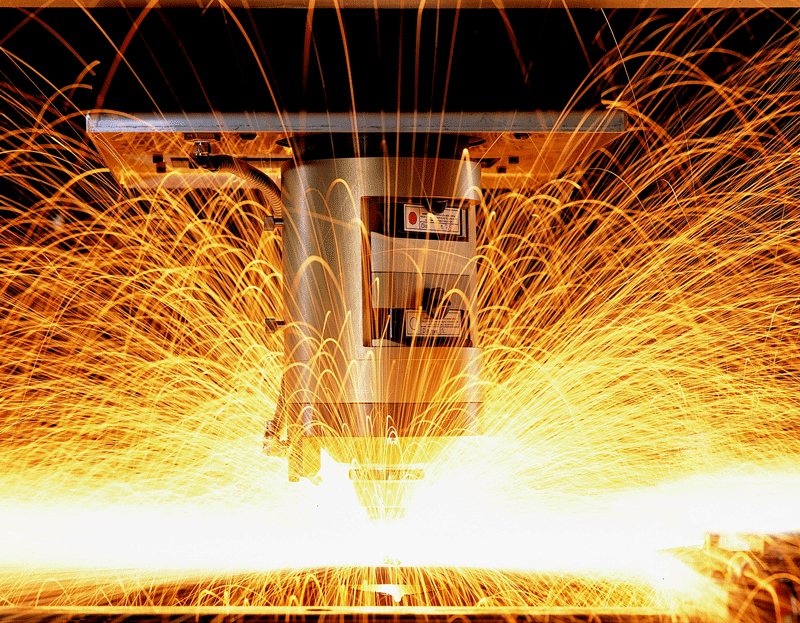
- 5
- 4
- 3
- 2
- 1
Резка металла – это процесс отделения частей или заготовок от сортового, литого и листового металла. Этот процесс является основой всей металлообрабатывающей отрасли. И не исключением стали работы по ремонту или строительству зданий. Различные типы резки обязательным образом применяются также в ремонте и обслуживании любой механической и даже электронной техники. На сегодняшний день резка металла представлена несколькими методами с применением специального оборудования. Каждый из вариантов отличается своими особенными качествами и свойствами, и применение того или иного метода обработки металла требует некоторых знаний данных методик.
Особенности резки металлов
Основные характеристики, по которым определяют какой именно тип и инструмент для резки металла применять, можно выделить в следующий список:
- температура резки, главное условие – минимальный нагрев разрезаемого материала;
- скорость;
- качество срезов и граней, особенно высокие требования предъявляются деталям, которые применяются в движущихся механизмах или лицевым сторонам конструкций в сооружениях;
- стоимость использования данного инструмента;
- безопасность работы на определенном участке строительства или месте работы.
Mетоды резки металла, которые представлены в приведенном выше списке, позволяют подбирать лучший вариант для каждого отдельного условия. В некоторых случаях, например при выполнении работы в жилых массивах, учитывается также фактор шумового, светового и пылевого загрязнений. Особенности резки металлов важно учитывать, так как это основной залог успеха в работе и экономии, как времени, так и денег. Правильно выбираемый тип резки гарантирует сохранение технических характеристик заготовки и детали. На выбор современным мастерам предлагается следующий список основных и самых доступных типов резки металла:
- лазерная резка;
- плазменная резка;
- газовая резка;
- Резка электродуговой сваркой;
- резка аргонодуговой сваркой;
- механическая резка;
- гидроабразивная резка.
Подбор типа резки может изменяться в зависимости от рода металла, который нужно обрабатывать. Для этого стоит знать главные особенности резки металлов каждым из представленных типов инструмента.
Лазерная резка
Рабочим инструментом выступает лазер, твердотельного или газового типов. Метод считается одним из лучших среди современных предложений. Минимальная ширина реза лазера составляет всего 0,1 мм, поэтому инструмент применяется даже при высокоточном производстве. Точность размеров заготовок представляется с погрешностью +/- 0,01 мм. Кроме того, лазерная резка металла отличается высокой продуктивностью работы, скорость реза 0,167 м/с, позволяет выполнять большие объемы работы при времени стандартной рабочей смены. В зависимости от мощности установки, максимальная толщина разрезаемой стали может достигать 20 мм.
Плазменная резка
Технология резки плазмой основывается на интенсивном разогреве металла под воздействием электрической дуги и с дальнейшим удалением расплавленного материала с помощью высокоскоростного плазменного потока. Температура плазмы достигает 15 000 – 20 000 С0. Производительность работы плазменной резки значительно выше, чем кислородной или электродуговой. Плазменная резка металла позволяет выполнять резы любой сложности и конфигурации, при этом не требуется заправки баллонов воздухом или сжатым воздухом. Этот вид обработки металла считается одним из самых доступных в экономическом плане. Толщина листа может достигать 50 мм.
Газовая резка
Газовая резка металла на сегодняшний день является одним из самых популярных методов обработки металла. Простота в работе и обслуживании установки делает свое дело. Принцип работы основан на разогреве металла в месте реза и удалении жидкого материала под воздействием высокого давления подаваемого кислорода, который одновременно служит и разогревающим средством. Однако газовая резка подходит далеко не для всех металлов и сплавов. Алюминий не удастся разрезать по нужным контурам, так как его температура горения всего 900 С0, а при газовой резке нужно прогревать достаточный участок материала. Рез таким оборудованием получается значительной ширины, на котором остаются окислы, наплывы и шлаки. В результате получаются далеко неточные контуры деталей.
Резка сварочным инвертором
Резка металла сварочным инвертором требует расходования электродов и не может обеспечить точных контуров вырезаемых деталей. Не все металлы могут обрабатываться таким инструментом.
Аргонодуговая резка
Аргонодуговая резка и сварка выполняются в среде инертного газа аргона. Выполняется с применением электродов. Инструмент применяется для обработки цветных металлов и углеродистых сталей.
Механическая резка
Механическая резка выполняется различным инструментом в зависимости от толщины обрабатываемого материала и требований к получаемой детали. Применяются ленточнопильные станки, болгарки, ручные пилы, ножницы и гильотины. Этот метод является одним из самых распространенных среди населения. Качество срезов и толщина обрабатываемого металла зависят от применяемого инструмента.
Гидроабразивная резка
Уникальная в своем роде гидроабразивная резка отличается настоящей универсальностью и многозадачностью. Основной недостаток – дороговизна оборудования. Обрабатываемый материал не поддается воздействию температуры. Скорость и точность резов на высоком уровне, поэтому используется при изготовлении сложных механизмов и точных деталей машин. Толщина разрезаемого материала (обрабатываются практически любые материалы: керамика, пластик, металл) может достигать 300мм и больше.
На страницах этого сайта можно найти всю необходимую для пользователей инструмента информацию. В отдельном разделе представлена подборка, где резка металла резаком и другим инструментом, представлена в видео.
способы резки металла, чем можно резать
Существует большое количство различных способов резки металла. В связи с этим, вопросы: чем режут металл, чем можно резать металл и чем резать толстый металл, не утрачивают своей актуальности.
Для максимального удовлетворения потребительского спроса, на смену морально устаревшим, классическим методам обработки, пришло достаточно много альтернативных вариаций.
СОДЕРЖАНИЕ СТАТЬИ
Так чем же лучше резать металл и чем вообще режут металл? Чем можно разрезать толстый металл? Ответ на этот вопрос достаточно многогранен, в связи с тем, что процесс резки применяется не только в промышленных масштабах, но и в домашних условиях.
Существует несколько основных способов резки металла, о которых мы расскажем ниже.РЕЗКА МЕТАЛЛА ЛАЗЕРОМ
Эта, одна из самых передовых технологий, приобретает все большую популярность благодаря своей исключительной точности и высокой производительности. Суть лазерной резки металла заключается в точечном, направленном воздействии лазерного луча на металл. Воздействие лазером позволяет производить детали любой геометрической сложности контура, с сохранением максимальной точности, практически идеальной ровности кромок, при этом не теряя производительности.
Управление установкой производится оператором станка ЧПУ. Полная автоматизация процесса сводит вероятность ошибки, и, как следствие, выбраковки деталей, к минимуму.
Процесс работы такого станка разделен на три этапа:- Создание чертежного изображения разрабатываемой детали;
- Загрузка чертежей в файловом изображении в программу ЧПУ;
- Обработка данных и запуск выполнения.
- Источник излучения (рабочая среда).
- Источник энергии.
- Оптический зеркальный резонатор.
В зависимости от типа источника энергии, установки для резки металла делят на:
Газовые
В них действующая сила это сочетание воздействия луча и смесей газа.
Твердотопливные
Действие происходит за счет многомерного зеркального усиления газоразрядной лампы.
Газодинамические
В данном случае лазерный луч усиливает нагретый углекислый газ.
По технологическому способу действия лазерного луча, проводится разделение на:- Метод плавления. Такой тип обработки оправдан при работах с любыми заготовками, в том числе, толстостенными и изготовленными из меди и алюминия. Суть метода заключается в плавлении места среза направленным лучом, сочетающимся с подачей струи сжатого газа, отводящей расплавленный металл вниз и охлаждающей кромки.
- Метод испарения. Этот метод заключается в нагреве металла, который проводит его через три стадии:плавления, кипения и испарения.
ВИДЕО ЛАЗЕРНОЙ РЕЗКИ МЕТАЛЛА
Преимущества лазерной резки
К основным положительным качествам обработки лазером принято относить:- Универсальность;
- Технологическую безопасность;
- Высочайшую скорость и производительность;
- Чистоту процесса;
- Сверхточное выполнение сложных контуров.
ПЛАЗМЕННАЯ РЕЗКА ТОЛСТОГО МЕТАЛЛА
В вопросе «чем резать тостый металл«, плазменная резка — лучший вариант. В данном случае, воздействие на металл производит струйная подача плазмы. По своей сути плазма является ионизированным газом, разогретым до сверхвысоких температур.
Различают два типа воздействия:- Плазменно-дуговой рез. Суть метода соответствует названию. Между режущим инструментом и изделием, пропускают электрическую дугу. Электрод внедряют в корпус, оснащенный отводом. Подающийся под большим давлением газ, минуя электрод, разогревается до высоких температурных отметок и подвергается ионизации. Наличие отвода в корпусе, обеспечивает высокую скорость потока. Созданная электрическая дуга оплавляет металл, подаваемый газ удаляет из высокотемпературного воздействия.
- Косвенно воздействующий механизм. В данном случае, воздействующая электроискра находится непосредственно внутри режущего элемента и воздействие происходит только за счет плазмы.
ВИДЕО ПЛАЗМЕННОЙ РЕЗКИ МЕТАЛЛА
Преимущества плазменной резки металла
К преимуществам обработки металла плазмой относят:
- Универсальность в отношении любых видов материала;
- Высокую скорость процесса при минимальных повреждениях и деформациях;
- Гладкость мест разреза;
- Техническая безопасность;
- Возможность обработки сложных контуров.
- Возможность резать толстый металл.
РЕЗКА МЕТАЛЛА ГАЗОВЫМ РЕЗАКОМ
В вопросе «чем режут металл» — данный способ является одним из самых простых с технической точки зрения. Его суть заключается в разогреве места резки металла до состояния горения и последующей подачей очищенного кислорода для завершения действия.
Весь процесс делится на три этапа:- Разогрев до предельных температур;
- Окисление кислородом;
- Удаление шлаковых образований выдуванием и отвердение мест среза.
Из чего состоит оборудование для газовой резки металла
Оборудование газовой резки состоит из:- Газовый баллон.
- Шланги для подключения.
- Режущий элемент.
- Мундштук с регулируемыми размерами.
- Система регуляции.
- Плавность ведения резака;
- Соблюдение угла наклона на 6 градусов против движения;
- Разогрев не менее чем до отметки в 1000 градусов.
Преимущества
К преимуществам резки металла газовым резаком следует отнести:- Возможность резки толстого металла с сохранением ровных и качественных швов;
- Автономность и мобильность;
- Универсальность и скорость процесса;
- Экономическая выгода.
КИСЛОРОДНАЯ РЕЗКА МЕТАЛЛА
В процессе кислородной резки металла происходит процесс горения металла в кислороде, который идет потоком в виде струи, удаляющей оксиды. Самое главное, что в данной процедуре металл не плавится — он лишь горит, при этом сохраняя свою твердость и прочность, а рамки реза выходят ровными.
Существуют некоторые подвиды кислородной резки металла, о которых мы расскажем ниже:
Кислородно-флюсовая резка
При кислородно-флююсовой резке металла используют порошковый плюс, который подается в место реза, из-за чего процедура облегчается, так как флюс на место реза оказывает 3-ное действие: абразивное, химическое и термическое.
Кислородно-копьевая резка
Кислородно-копьевая резка металла подразумевает собой высокий температурный режим, поддерживаемый из-за сгорания кислородного «копья», которое представляет собой трубку из стали, через которую в область реза подается кислород.ГАЗОЭЛЕКТРИЧЕСКАЯ РЕЗКА МЕТАЛЛА
Для газоэлектрической резки, исходя из названия, необходим источник электричества. Газоэлектрическая металлорезка бувает двух разновидностей:Воздушно-дуговая газоэлектрическая резка
Металл, который расплавился, удаляют при помощи мощной воздушной струи, движущейся под высоким давлением.
Кислородно-дуговая резка
При этом виде газоэлектрической резки металла осуществляется движение кислородной струи, которая вызывает горение накаленного электродугой металла, и удаление оксидов из области реза.
Основной минус газоэлектрического способа резки металла — начало науглероживания металла в области реза. Обычно, такой вид металлорезки применяют в случае, если необходимо избавиться от дефектов сварных швов.
ПРЕИМУЩЕСТВА И НЕДОСТАТКИ ГАЗОВЫХ СПОСОБОВ РЕЗКИ МЕТАЛЛА
Основные плюсы, которые можно выделить из способов газовой металлорезки:- Доступная цена;
- Процессы понятны и не вызывают сложностей;
- Возможно резать толстый металл;
Из недостатков можно выделить следующее:
- Неидеальная точность резки;
- Высокий расход материала;
- Небольшая скорость резки;
- Необходима доп. обработка по краям реза;
- Возможна термическая деформация металлоизделий;
ГИДРОАБРАЗИВНАЯ РЕЗКА МЕТАЛЛА
Гидроабразивная резка – современный способ резки металла, позволяющий высокоточно производить раскрой листового металла по линиям любой кривизны и сложности и резать толстые металлические изделия толщиной до 200 миллиметров. В данной технологии обработки металла используется очень тонкая струя водного раствора, смешанного с абразивными частицами. Жидкость подается под высоким давлением порядка 4 тысяч атмосфер через специальное узкое сопло, имеющее диаметр до 0,5 миллиметров.
Скорость, с которой раствор взаимодействует с металлом, сравнима со скоростью звука, зачастую даже выше, что, в свою очередь, позволяет производить резку металла с высокой скоростью и очень гладкую поверхность реза, сравнимую с методом лазерной резки металла.
Преимущества
Гидроабразивная резка металла является, на сегодняшний день, одним из лучших способов резки металла, так как она обеспечивает возможность резать толстый металл, сложные детали нестандартной формы легко поддаются обработке, расход металла минимален вследствие маленькой ширины реза, а низкий температурный режим в зоне реза обеспечивает защиту от деформации и плавления.
Гидроабразивная резка используется, в основном, в декоративной и художественной резке, где требуется высочайшая точность реза и минимальный расход металла.
МЕХАНИЧЕСКИЕ СПОСОБЫ РЕЗКИ МЕТАЛЛА
Механические способы резки металла в промышленных масштабах используются все реже. В данном методе часто встает вопрос: какой станок по металлу лучше выбрать, однако обычно для этих целей используют ленточные, дисковые и гильотинные станки по металлу. Минус такого оборудования в его ограниченных возможностях и достаточно высокой трудоемкости процесса.Резка металла на ленточном станке
Данный станок это фиксированное режущее полотно с зубцами на одной стороне. Благодаря работе мотора происходит непрерывное вращение ленты.
Гильотинное
оборудование
Обрабатываемый металлический материал фиксируется в горизонтальном положении и подвергается рубящему удару станка резака-гильотины.
Резка металла дисковым станком
Суть действия схожа с работой ленточного станка. Отличие состоит только в возможности вращения металлической заготовки на 360 градусов.
ЧЕМ РЕЖУТ МЕТАЛЛ В ДОМАШНИХ УСЛОВИЯХ
Резка металла в домашних условиях производится при помощи механических устройств. К ним можно отнести как не промышленные модели станков, так и подручный инструмент. К наиболее часто используемым приспособлениям для резки металла в домашних условиях можно отнести:
Ручные ножницы для резки металла
Ручные ножницы позволяют резать металл толщиной до 3 миллиметров.
Пилы различного типа для резки
Пилы ручные, дисковые, торцевые, ленточные и маятниковые.
Болгарка для резки металлоизделий
Болгарка достаточно популярна и универсальна в домашних условиях.
ПОДРОБНЕЕ О ВИДАХ РУЧНЫХ НОЖНИЦ ДЛЯ РЕЗКИ МЕТАЛЛА
Существует несколько видо ручных ножниц для резки металла, каждый из которых обладает своими особенностями, преимуществами и недостатками. Рассмотрим их ниже.
Гильотинные ножницы
Преимуществами такого вида ручных ножниц для резки металла является: При разделке металла такими ножницами обеспечивается:- Не остается каких-либо механических дефектов;
- Наружное покрытие металла, который режут, сохраняется в прекрасном качестве;
- Высокий показатель точности резки;
Особенность гильотинных ножниц заключается в том, что в их строении предусмотрен нож, который движется строго в одной плоскости, что прекрасно подходит для разрезания металлических листов. Если изменять угол наклона ножа, то существенно снижается необходимое усилие руки, однако, при этом страдает показатель качества резки. Гильотинные ножницы бывают как ручные, так и механические, либо с гидроприводным модулем.
Ручными ножницами практически невозможно разрезать металл средней толщины, а вот гильотинные ножницы с гидроприводом очень здорово себя показыают в показателях точности резки, так как они зачастую имеют ЧПУ-модуль, позволяющий «запоминать» типовые операции.
Шлицевые ножницы по металлу
Шлицевые ножницы позволяют резать металл по прямым и кривым произвольным линиям, благодаря чему, возможно выполнить качественную декоративную или фигурную резку металла. Работают такие ножницы от электродвигателя.
РАЗНОВИДНОСТИ ПИЛ ДЛЯ РЕЗКИ МЕТАЛЛА
Как и с ручными ножницами, существует несколько видов пил для металлорезки, которые обладают своими плюсами и минусами:
Дисковая пила
Самая легкая в работе пила. В дисковой пиле используются качественные диски из высокоустойчивых твердых сплавов или быстрорежущая специальная сталь, не подверженная температурному режиму. Основное ее применение — распил тонких металлических листов и листов средней толщины. Обычно один из факторов ценообразования на дисковую пилу — это ее распиловочный круг, ведь в зависимости от его диаметра, пила расширяет свой возможный спектр задач.
Из минусов можно отметить то, что хорошие дисковые пилы редко стоят дешево и имеют крупные габариты, что не всегда удобно.
Сабельная пила
Сабельная пила по своему образу схожа с электродрелью с удлиненной пилой, а по принципу работы — с электролобзиком. Существует 2 варианта сабельных пил: аккумуляторные и с зарядкой от сети.
Многообразие пильных полотен позволяет выполнять сабельной пилой различные задачи по резке металла. С сабельной пилой сложнее управляться, нежели с дисковой — для нее надо иметь правильные навыки и отличный глазомер.
Углошлифовальная машина
За этим серьезным названием скрывается знакомая всем болгарка. Интересно то, что изначально она разрабатывалась как инструмент для шлифования, однако теперь по функциональным качествам заменят сабельную и дисковую пилы.
Универсальность углошлифовальной машины позволяет проводить резку, шлифовку и полировку металлических изделий — для этого стоит просто купить необходимые материалы и комплектующие.
СРАВНЕНИЕ СПОСОБОВ РЕЗКИ МЕТАЛЛА
При сравнении основных способов резки металла лучшими видами для промышленных масштабов признаны лазерная и плазменная резка металла.
- Доступна резка по любым кривым линиям;
- Возможность резать толстый металл практически любой толщины;
- Благодаря точности резки металла данными способами обеспечивается высокая точность;
- Универсальность выбора металла: возможность резки алюминия, оцинковки, нержавейки, титана, черных металлов и т.д. одним оборудованием;
- Экономия времени на этап подготовки металла к резке: благодаря высокой температуре лазерная и плазменная резка легко справляется с инородними примесями;
- Затраты на электроэнергию и воздух — достаточно низкие, как и на расходные материалы.
Что касается выбора наилучшего способа резки металла в домашних условиях, то здесь наибольшую популярность имеет углошлифовальная машина (болгарка). Ее многофункциональность и относительно невысокая цена являются несомненными преимуществами в вопросе: «чем лучше резать металл дома».
ИТОГ: ЧЕМ ЛУЧШЕ РЕЗАТЬ МЕТАЛЛ
Отвечая на вопросы: «Чем режут металл» и «чем резать толстый металл«, стоит отметить, что несмотря на доступность многих из перечисленных вариантов обработки, качество зависит не только от сложности оборудования, но и от профессионализма специалистов на нем работающих. Компания «Металик» имеет в своем арсенале оборудование для проведения всех видов резки металла любой толщины и конфигурации. Получить консультацию и оставить заказ вы можете на нашем сайте, или связавшись с нами по телефону.
Особенности резки металла: обзор популярных способов
Вопросы, рассмотренные в материале:
- Особенности лазерной резки металла
- Особенности механической резки металла
- Особенности гидроабразивной резки металла
- Особенности плазменной резки металла
При изготовлении металлических деталей или заготовок необходимо учитывать особенности резки металла. От типа оборудования для раскроя и материала будет зависеть не только скорость и качество выполнения работ, но и их стоимость. А в условиях производства цена обработки является одним из ключевых параметров.
Существует большое количество способов, которым можно раскроить металл, и подробно описать их в рамках одной статьи будет затруднительно. Поэтому мы остановимся на самых популярных методах резки, расскажем об их особенностях и преимуществах.
Особенности лазерной резки металла
В основе данного метода лежит тепловое влияние лазера на металл, в ходе которого материал последовательно нагревается, затем закипает и испаряется. Резка лазером происходит с высокими энергозатратами, именно поэтому ее в основном применяют для обработки тонкого листового металла.
Сравнительно толстые листы материала режут в ходе их плавления. Для облегчения процесса он сопровождается подачей газа (кислорода, азота, гелия, аргона или воздуха), который убирает из зоны реза плавящийся металл, отходы горения, способствует воспламенению материала и охлаждает поверхность вокруг расплава. Самым эффективным считается кислород, поскольку он повышает скорость работы и глубину реза.
Скорость, с которой происходит резка, зависит он нескольких параметров: мощности устройства (лазера), толщины материала, а также его теплопроводности. Высокий показатель проводимости тепла приводит к большим энергозатратам, поскольку тепло быстрее отводится из рабочей зоны. Примером могут служить особенности лазерной резки различных видов металла лазером мощностью 600 Вт. Обработка таким образом титана или черного металла идет достаточно легко, в то время как медь и алюминий режутся значительно сложнее из-за их высокой теплопроводности.
В таблице ниже собраны усредненные параметры для резки разных материалов:
Малоуглеродистая сталь |
Инструментальная сталь |
Нержавеющая сталь |
Титан |
|||||||
Толщина, мм |
1,0 |
1,2 |
2,2 |
3,0 |
1,0 |
1,3 |
2,5 |
3,2 |
0,6 |
1,0 |
Мощность лазера, Вт |
100 |
400 |
850 |
400 |
100 |
400 |
400 |
400 |
250 |
600 |
Скорость резания, м/мин |
1,6 |
4,6 |
1,8 |
1,7 |
0,94 |
4,6 |
1,27 |
1,15 |
0,2 |
1,5 |
Виды лазерной резки
Оборудование для лазерной резки имеет три основные части:
- Источник излучения (рабочую среду).
- Источник получения энергии (систему накачки), с помощью которого создается условие для начала электромагнитного излучения.
- Резонатор (зеркала) для усиления излучения лазера.
Рекомендовано к прочтению
Существует три вида лазеров, предназначенных для резки, в зависимости от типа источника излучения:
- Твердотельные.
- Газовые.
- Газодинамические.
Твердотельные. Основная часть данного агрегата – осветительная камера. В нее помещены источник энергии – газоразрядная лампа-вспышка, обладающая большой мощностью, а также рабочее твердое тело. Последнее может быть стержнем из алюмо-иттриевого граната, который легировали иттербием или неодимом, а также из рубина или из неодимового стекла. С двух торцов стержня расположены полупрозрачное и отражающее зеркала. В них много раз отражается лазерный луч из рабочего тела, усиливаясь и выходя сквозь полупрозрачное зеркало.
Еще одним представителем твердотельных лазеров является волоконный. Благодаря стекловолокну внутри агрегата происходит усиление излучения, поступающего из полупроводникового лазера.
Рассмотрим пример работы лазера с рабочим телом из гранатового стержня, который легирован неодимом. Активным центром при этом будут ионы последнего. Они возбуждаются под воздействием излучения, поступающего из газоразрядной лампы. Это значит, что у них возникает переизбыток энергии.
Постепенно возвращаясь в нормальное состояние, ионы, отдавая энергию, испускают фотоны, которые являются потоком света. Они же, в свою очередь, побуждают иные возбужденные ионы вернуться в исходное состояние. Итогом является быстро возрастающий, практически лавинообразно, процесс. Зеркала направляют движение луча. Отражая, они возвращают фотоны внутрь рабочего тела вновь и вновь, способствуя тем самым возникновению новых фотонов, а также возрастанию излучения. Основными его характеристиками являются повышенная концентрация энергии и низкая расходимость лазерного луча.
Газовые. Рабочее тело данного агрегата – двуокись углерода. Также им может стать смесь двуокиси углерода с гелием и азотом. Насос перекачивает газ сквозь газоразрядную трубку. Электроразряды возбуждают летучее вещество. Усилителями излучения служат полупрозрачное и отражающее зеркала. Существуют три типа таких лазеров: щелевые, с поперечной или продольной прокачкой. Различаются они особенностями конструкции.
Газодинамические. Данный вид лазеров считается самым мощным. Рабочее тело данных устройств – двуокись углерода, которая нагревается до температуры от 1 000 до 3 000 °К или от +726 до +2 726 °С. Возбуждается он вспомогательным лазером малой мощности. Углекислый газ пропускается сквозь сопло Лаваля (канал посередине специально заужен), затем он быстро расширяется и остывает. Результатом такого процесса становится переход атомов газа в спокойное состояние из возбужденного и излучение, испускаемое им.
Особенности механической резки металла
Резка – это технологический процесс, с помощью которого происходит разделение материала на части или изготовление изделия определенной формы. Механическая обработка подразумевает использование токарных, фрезерных станков и специализированного оборудования для резки металла.
Данный технологический процесс проводится с учетом следующих моментов:
- При механической обработке обязательно происходит нагрев металла, в результате чего меняются основные свойства, снижается прочность, увеличивается пластичность материала. Для получения среза высокого качества необходимо полностью исключить нагрев заготовки.
- Некоторые сплавы металлов нужно предварительно разогревать. Это труднообрабатываемые сплавы. Разрезать их можно только при нагреве, проведенном заранее.
- Необходимо внимательно отнестись к следующим качествам обрабатываемой заготовки: твердости, теплопроводности, свариваемости.
Сталь и иные сплавы чаще всего режутся непосредственно в ходе подготовки их к последующей обработке, при изготовлении конечного продукта, а также для изменения формы, размеров готового изделия в ходе монтажа конструкций. Способов резки металлов много, и все они имеют свои свойства.
Механическая обработка, не использующая предварительный нагрев металла, достаточно распространена. Она включает следующие технологические процессы:
- Рубка. Режущим инструментом при этом является специализированные ножи и ножницы. Важными преимуществами рубки считаются низкая себестоимость, высокая производительность, а также точность разделения материала на части. Впрочем, данный метод можно применять не ко всем заготовкам. Например, им нельзя резать изделия сложной формы. Ограничения также касаются и толщины листов металла.
- Резка с использованием дисковой пилы. Данный метод используется уже много лет, подходит для производства изделий сложной формы без ограничений в толщине металла. Режущий инструмент – армированный круг с абразивом. Профессиональное оборудование позволяет получить достаточно чистый срез высокого качества. Однако есть и недостаток – достаточно низкая скорость работы.
- Ленточная резка может проводиться исключительно на специализированном оборудовании. Станки, оборудованные ленточными пилами, используются для работы с трубным и сортовым металлическим прокатом, прутками разного диаметра. Основными преимуществами метода считаются высокая производительность, а также срез отличного качества.
Впрочем, механическая обработка подходит не для всех видов материалов. Некоторым требуется термическая обработка, имеющая свои особенности резки металла.
Особенности гидроабразивной резки металла
Гидроабразивная резка металла применяет истирающий (эрозийный) способ влияния на заготовку водяной струи и абразивного вещества. Их твердые частицы, двигаясь с высокой скоростью, переносят энергию. Ударяясь о заготовку, они отрывают ее частицы и убирают их из реза. Скорость, с которой проходит обработка, зависит от свойств материала заготовки, массы воздействующих частиц, их формы, твердости, кинетической энергии и угла удара.
Насос нагнетает сверхвысокое давление воды (до 1 000 – 6 000 атм), после чего она поступает на режущую головку. Через дюзу (узкое сопло), имеющее диаметр от 0,08 мм до 0,5 мм, вода на большой скорости (от 0,9 до 1,2 км/с и более) попадает в смесительную камеру. Там она смешивается с абразивным веществом. Это может быть карбид кремния, гранатовый песок, зерна электрокорунда или иной материал, имеющий повышенную твердость. После чего смесь вырывается из трубки, имеющей диаметр от 0,5 до 1,5 мм, и режет металл. Остатки ее энергии гасятся в воде, слой которой имеет толщину от 0,7 до 1 м.
Абразивом выступают материалы, имеющие по Моосу твердость не менее 6,5. Выбирают его в зависимости от того, насколько твердой является заготовка. При этом нельзя забывать, что при использовании твердого абразивного вещества происходит ускоренный износ режущей головки.
В ходе гидроабразивной обработки металла резка идет в основном абразивным материалом, вода же доставляет его к рабочему месту. Абразивные частицы должны иметь размер от 10 до 30 % от диаметра режущей струи. Тогда она будет стабильно течь и эффективно воздействовать на металл.
Размер зерен, как правило, составляет от 0,15 до 0,25 мм или от 150 до 250 мкм. Если же необходим срез с минимальной шероховатостью, то берут зерна размером от 0,075 до 0,1 мм или 75–100 мкм. Специалисты полагают, что оптимальным является размер менее вычисляемой величины: (dс.т.– dв.с.)/2, в которой dс.т. и dв.с.– внутренние диаметры смесительной трубки и водяного сопла соответственно.
Особенности плазменной резки металла
Данный вид резки является одной из разновидностей термического разреза, который проводится плазменной струей. Последняя, в свою очередь, представляет собой поток ионизированного и сильно нагретого газа. Не погружаясь в терминологию, можно сказать, что плазма – это источник тепловой энергии с максимальной температурой до +30 000 °С. Такой нагрев дает возможность резать металлы, обработка которых не под силу кислородной горелке.
Плазменная резка имеет ряд преимуществ:
- Универсальность. Может применяться при работе с цветными и черными металлами и их сплавами, сталями (легированными, углеродистыми и иными). Подходит для использования с заготовками, деталями, трубами, листами и профилями.
- Высокая скорость работ – в 25 раз быстрее, чем резка заготовок той же толщины (до 5 см) при газопламенной резке.
- Качество. Помимо самой резки, плазма удаляет из рабочей зоны излишки расплава. Нагрев имеет локальный характер и не деформирует материал вокруг.
- Высокая точность. Профессиональная аппаратура позволяет делать как прямые, так и прямолинейные разрезы, создавать сложные формы и отверстия разного диаметра.
- Экономическая выгода. На стоимость резки значительное влияние оказывает используемый газ. А для большей части изделий из металла применяется простой и бесплатный воздух.
Генератором плазмы является плазмотрон, он создает плазменную дугу или струю, имеющую высокую температуру и значительную скорость. В начале идет формирование электрической дуги с температурой +5 000 °С. После чего в сопло начинает поступать газ, который ионизируется при контакте с электродугой, а затем происходит процесс преобразования его в плазму, имеющую температуру +30 000 °С. Скорость плазменного потока может быть от 0,5 до 1,5 км/с. Такая струя прекрасно режет материал до 20 см толщины.
Плазменная резка обладает не только эффективностью, но и высоким качеством. На краях реза нет наплава и окалины, поскольку поток просто выдувает остатки расплава из рабочей зоны. Кроме того, происходит исключительно локальный нагрев металла, поскольку плазма обладает высокой концентрацией. Следовательно, близлежащая территория не испытывает воздействия и не деформируется.
Почему следует обращаться именно к нам
Мы с уважением относимся ко всем клиентам и одинаково скрупулезно выполняем задания любого объема.
Наши производственные мощности позволяют обрабатывать различные материалы:
- цветные металлы;
- чугун;
- нержавеющую сталь.
При выполнении заказа наши специалисты применяют все известные способы механической обработки металла. Современное оборудование последнего поколения дает возможность добиваться максимального соответствия изначальным чертежам.
Для того чтобы приблизить заготовку к предъявленному заказчиком эскизу, наши специалисты используют универсальное оборудование, предназначенное для ювелирной заточки инструмента для особо сложных операций. В наших производственных цехах металл становится пластичным материалом, из которого можно выполнить любую заготовку.
Преимуществом обращения к нашим специалистам является соблюдение ими ГОСТа и всех технологических нормативов. На каждом этапе работы ведется жесткий контроль качества, поэтому мы гарантируем клиентам добросовестно выполненный продукт.
Благодаря опыту наших мастеров на выходе получается образцовое изделие, отвечающее самым взыскательным требованиям. При этом мы отталкиваемся от мощной материальной базы и ориентируемся на инновационные технологические наработки.
Мы работаем с заказчиками со всех регионов России. Если вы хотите сделать заказ на металлообработку, наши менеджеры готовы выслушать все условия. В случае необходимости клиенту предоставляется бесплатная профильная консультация.
Основные способы резки металла: как выбрать подходящий
Вопросы, рассмотренные в материале:
- Основные способы резки металла
- Механические способы резки металла
- Термические способы резки металла
- Ручные способы резки металла
- Гидроабразивный способ резки металла
- От чего зависит стоимость резки металла в специализированной фирме
На сегодняшний день существует множество способов резки металла. Причем каждый из них имеет как свои достоинства, так и недостатки. Чтобы выбрать наиболее эффективный в той или иной ситуации метод, нужно принять во внимание множество факторов: толщину заготовки, размер листа, свойства металла и т. д.
Только подобрав «правильный» способ резки металла, можно рассчитывать на высокую скорость операций, качество получаемых на выходе изделий и, что немаловажно, адекватную стоимость производимых работ.
Основные способы резки металла
Рассечение заготовок в соответствии с заданными чертежами требует пошагового выполнения определенных операций и точного соблюдения технологии. Высокое качество изделий обеспечивается вниманием к деталям процесса. При выполнении раскройных работ учитывается комплекс характеристик материала: его твердость, устойчивость к деформациям, химический состав и степень электропроводимости.
Существует несколько способов раскроя: одни – универсальные, другие – специализированные. Каждый из них показывает наиболее высокий результат при работе с тем или иным материалом. Большинство способов резки металла используется в заготовительном производстве. Они отличаются повышенной производительностью, высокой точностью и возможностью работы со сложными материалами.
Но есть и такие варианты резки, которые легко можно реализовать в гаражной мастерской и даже с выездом на объект.
Все многообразие способов резки листового металла, известных на сегодняшний день, условно можно объединить в следующие группы: ручные, механические и термические. Каждая из них включает ряд приемов, позволяющих работать с заготовками того или иного вида.
Так, группа ручных методов включает резку ножницами для металла, использование пилы или углошлифовальной машины (болгарки). Механические подразумевают применение гильотины, дискового станка или ленточной пилы. Термические – лазерную, плазменную и газокислородную резку.
Механические способы резки металла
Для механического раскроя заготовки используются инструменты из специальной закаленной стали – это гарантирует их прочность и способность рассекать металл. Резка осуществляется с помощью гильотины, ленточной пилы или дискового станка.
- Резка метала с помощью гильотины.
Гильотинная обработка чаще всего применяется при штамповочных операциях, когда необходимо получить большое количество типовых изделий. Прокатный лист укладывается на горизонтальную рабочую поверхность, а специальный резак рассекает его по всей ширине. Примечательно, что такой способ резки чем-то напоминает ножницы – соприкосновение ножа и заготовки происходит под углом в одной точке, которая перемещается по мере его движения.
- Резка металла ленточной пилой.
Такая обработка металлических заготовок очень напоминает способ резки металла без электричества – классической пилой. Только в этом случае металлическое полотно с зубцами закрепляется на шкивах, которые обеспечивают его непрерывное движение. Такой метод нельзя назвать безотходным, потому что ширина режущего механизма составляет 1,5 мм, из-за этого образуется стружка. Стоит отметить, что на таких агрегатах можно разрезать не только плоские листы, но и трубы любого диаметра.
- Резка металла с помощью дискового станка.
Инструмент для работы представляет собой режущий диск с зубьями по внешнему контуру. Его приводит в движение электромотор, а защитный кожух предохраняет мастера от производственных травм. Дисковый станок во многом напоминает труборез. Кромки на нем получаются качественными, а срез точным. Последний при необходимости можно выполнить под углом.
Термические способы резки металла
Существуют следующие виды терморезки: газокислородная, лазерная и плазменная. Их еще можно назвать бесконтактными, поскольку они выполняют срез при помощи струи газа, плазмы или лазерного луча, не касаясь заготовки непосредственно оборудованием.
- Газокислородный метод.
Он основан на том, что под воздействием кислорода, нагретого до +1000 °C и более, металл начинает плавиться, а его окалины попросту выгорать. Таким образом формируется чистый срез.
Способ резки металла газом включает в себя два этапа. На первом предполагаемая линия раскроя нагревается до температуры воспламенения металла. Делают это, как правило, ацетиленом, который дает достаточно горячее пламя. Кислород на данном этапе резки не применяют. Время нагрева зависит от толщины листа и его химического состава.
Когда заготовка нагревается до нужного состояния, к процессу подключается кислород. Направленный огненный поток рассекает прокат по намеченной линии. Преимущество использования этого газа заключается не только в его способности легко прорезать листы железа, но и в том, что он выжигает все окалины и окислы, оставляя кромку чистой.
Рекомендовано к прочтению
Важным условием того, чтобы линия среза всегда получалась ровной, является одинаковое расстояние между соплом и заготовкой на протяжении всей операции. С ручными аппаратами, которые часто используются для резки металла в домашних условиях, добиться такой постоянности очень сложно. В промышленных же цехах установлено профессиональное автоматизированное скоростное оборудование. На таком легко получить качественные изделия, к тому же оно имеет большую производительность.
К плюсам такого способа относят:
- возможность резки толстых заготовок;
- большую мощность, которая позволяет обрабатывать даже титановые прокаты.
Минусы следующие:
- под воздействием температур физические свойства заготовки изменяются;
- при раскройке таким способом в месте среза снимается большое количество материала, кромка невысокого качества, по краям образуются наплывы и окислы;
- нет возможности выполнить фигурную резку;
- нет условий для обработки цветных металлов (алюминия, высокоуглеродистой и хромоникелевой стали, меди).
- Лазерный метод.
Лазерный способ резки металла заключается в воздействии на заготовку направленного луча. Его температура настолько высока, что материал в зоне работы тоже нагревается, закипает и испаряется. Тот факт, что луч очень тонкий, обеспечивает четкий срез.
Направленный поток нагревает заготовку не полностью, а только вдоль линии резки, поэтому такой способ хорошо подходит и для работы с тонкими листами, изделиями с низкой теплопроводностью, алюминием, медью, сталью (в т. ч. нержавеющей), с трубами.
К преимуществам этого способа относят возможность обработки практически любых материалов и сплавов.
К недостаткам лазерной резки относится то, что она требует больших энергозатрат. Кроме того, обработку могут проводить только мастера-профессионалы, а высокое качество изделий достигается только при работе с тонкими исходниками.
- Плазменный метод.
Эту технологию еще называют дуговым способом резки металла, поскольку образование плазмы происходит при непосредственном нагревании электрической дуги. Ионизированный газ, доведенный до состояния плазмы, расплавляет материал по линии среза и сдувает остатки с кромки. Устройство, которое используется для таких работ, называется плазмотроном или плазморезом.
Преимущества резки в этой технике следующие: высокая производительность, безопасность мастера, незначительный нагрев поверхности заготовки.
К недостаткам использования плазмотрона относятся: высокая стоимость оборудования и его обслуживания, необходимость квалифицированных знаний оператора, ограниченность максимально допустимой толщины изделия и шумность производства.
Ручные способы резки металла
Разрезание металла с помощью специальных инструментов позволяет получить изделия различной конфигурации. Работая в малой гаражной мастерской, важно подобрать подходящий способ сечения. Если в промышленных масштабах для этого применяют мощные станки, то привычным способом резки металла в домашних условиях часто является работа ножницами, ножовкой или болгаркой. В данной ситуации далеко не всегда важна предельная точность – зачастую навыков мастера достаточно.
- Углошлифовальная машина (болгарка).
Ее можно назвать домашним станком для резки, поскольку она обладает относительно высокой производительностью. Помимо этого, такая техника имеет следующие преимущества:
- компактность – благодаря малым размерам агрегат можно применить почти в любом помещении;
- неограниченность заготовок по толщине;
- возможность выбрать режущий диск, подходящий к каждому конкретному случаю.
- Ручные ножницы.
Несмотря на то, что ими можно обработать прокаты толщиной до 3 мм, они имеют целый ряд разновидностей, позволяющих подобрать лучший из них для комфортной работы:
- ножницы для прямого среза;
- ножницы для криволинейного среза;
- пальцевые ножницы для работы с изделиями сложной геометрии – они могут быть прямые или зеркальные;
- вариант, когда один режущий конец зафиксирован в тисках, а другой остается подвижным.
Их часто применяют как один из способов резки металла. Сегодня на рынке представлены следующие вариации этого инструмента:
- Дисковые – зубья расположены по окружности диска. В движение такой инструмент может приводить электрический или ручной привод.
- Ленточные – их часто можно встретить в промышленных цехах.
- Маятниковые – имеют твердосплавную напайку в торцевой части.
- Ручные – закрепляются в специальной С-образной раме.
- Торцевые – благодаря особой конструкции могут выполнять срез под углом.
- Циркулярные –их торцевая часть покрыта абразивами нужной жесткости, имеются твердосплавные напайки.
Гидроабразивный способ резки металла
Отличающаяся от других методов раскройка с помощью водореза способна обрабатывать материал, толщина которого доходит до 300 мм (этот показатель характерен для стали).
Ключевым элементом агрегата для гидроабразивной обработки является сверхмощный мотор. Некоторые модели способны подавать воду под давлением 6 000 бар. Жидкость рассекает практически любой вид материала не только благодаря такому напору, но и за счет высокой интенсивности. Так, проходя через алмазное, рубиновое или сапфировое сопло, струя достигает скорости, которая в 3 раза превосходит скорость звука.
Мощность такого способа резки металла можно изменять по необходимости. Так, мягкие материалы рассекают чистой водой, а для твердых в нее добавляют гранатовый песок – так увеличивается абразивность струи.
Для выявления максимально производительного способа рубки за границей проводили эксперимент. Было выявлено, что наиболее «опасный соперник» для водоструйной резки – это лазер. Затем оба типа установок раскраивали пакеты металлопроката (толщина каждой пластины составляла 0,3 мм). Оказалось, что при работе с заготовками до 6 мм наиболее эффективен лазер. Он показывает высокую скорость и качество при относительно небольших расходах энергии. Но при раскрое пластин толщиной свыше 6 мм победу по этим показателям одержал гидроабразив.
Водоструйный способ обработки имеет множество плюсов. Мы остановимся на главных из них. Во-первых, при работе заготовка совершено не нагревается. Это означает сохранение всех ее прочностных характеристик. Во-вторых, толщина «ножа» в этой технологии сопоставима с толщиной волоса, что гарантирует высокое качество кромок и минимальные потери материала.
Мы рассмотрели множество способов резки металла, их преимущества и недостатки, поэтому знаем, что для работы лазером необходимо, чтобы отражение материала было минимальным – иначе сила луча уйдет в пустую. Для плазмореза ключевую роль играет электропроводимость заготовки. В отличие от них, водорезке такие нюансы нипочем. Однако не стоит применять ее в случаях, когда намокание нежелательно, например, при склонности изделия к коррозии.
Если говорить о недостатках такого способа, то стоит отметить его высокую цену. Она обусловлена работой на большом давлении – детали изнашиваются и требуют частой замены.
От чего зависит стоимость резки металла в специализированной фирме
На цену работы влияют:
- выбранный способ резки;
- производительность станков;
- характеристики материала заготовок;
- объем работ;
- сложность резки;
- требования к качеству кромок.
Если предстоит работа с большим количеством заготовок, цена может быть снижена благодаря экономии энергии работы оборудования.
При заказе малых партий стоимость, как правило, обговаривается в каждом случае индивидуально. Если обычно счет выставляется путем умножения цены расчетной единицы (килограмма, метра и др.) на количество, то здесь необходимо принять во внимание затраты на переналадку агрегата.
Несмотря на растущее предложение услуг по обработке металла современный потребитель всегда предпочтет сервис, мастера которого все работы выполняют качественно и вовремя. Большое значение при выборе имеет и наличие сопутствующих предложений, например, по доставке готовых изделий.
Почему следует обращаться именно к нам
Мы с уважением относимся ко всем клиентам и одинаково скрупулезно выполняем задания любого объема.
Наши производственные мощности позволяют обрабатывать различные материалы:
- цветные металлы;
- чугун;
- нержавеющую сталь.
При выполнении заказа наши специалисты применяют все известные способы механической обработки металла. Современное оборудование последнего поколения дает возможность добиваться максимального соответствия изначальным чертежам.
Для того чтобы приблизить заготовку к предъявленному заказчиком эскизу, наши специалисты используют универсальное оборудование, предназначенное для ювелирной заточки инструмента для особо сложных операций. В наших производственных цехах металл становится пластичным материалом, из которого можно выполнить любую заготовку.
Преимуществом обращения к нашим специалистам является соблюдение ими ГОСТа и всех технологических нормативов. На каждом этапе работы ведется жесткий контроль качества, поэтому мы гарантируем клиентам добросовестно выполненный продукт.
Благодаря опыту наших мастеров на выходе получается образцовое изделие, отвечающее самым взыскательным требованиям. При этом мы отталкиваемся от мощной материальной базы и ориентируемся на инновационные технологические наработки.
Мы работаем с заказчиками со всех регионов России. Если вы хотите сделать заказ на металлообработку, наши менеджеры готовы выслушать все условия. В случае необходимости клиенту предоставляется бесплатная профильная консультация.
Виды и способы резки металла
Любые промышленные предприятия и частные мастера нуждаются в специальном станке для резки металла. Значением имеет его соответствие техническим требованиям и параметрам. Известно несколько способов обработки изделий. Металл обрабатывается методом ручной резки, лазером, плазмой или под давлением. Выбор конкретного вида резки металла зависит от стоимости, эффективности работ и их итогового результата.
Обработка металла холодным и горячим приемами
Резка металла осуществляется холодным (механическим) и горячим приемами. Первый характеризуется механическим воздействием на обрабатываемое изделие. Значение имеет твердость режущего инструмента. Резка осуществляется инструментом, значительно превосходящим по твердости обрабатываемую деталь. При данном способе применяются инструменты:
Горячая резка деталей подразумевает термическое воздействие на них. Они расплавляются в нужном месте, а остатки расплава удаляются газом. Горячий способом включает в себя виды резки:
- газокислородную;
- лазерную;
- плазменную.
Не всегда холодная металлообработка позволяет добиться необходимой чистоты конечного изделия. Такая проблема возникает при кислородной и воздушно-дуговой резке. Указанные методы применяются только в качестве подготовительных работ.

Схемы воздушно-дуговой резки
Разновидности холодной резки
Указанный прием имеет ряд достоинств, среди которых:
- высокая точность результата;
- экономичность;
- ровность краев разреза.
Основной недостаток заключается в изготовлении только прямолинейных разрезов.
Резка металла циркулярной пилой позволяет делать качественные и точные разрезы с возможностью контролировать их угол. Главный недостаток инструмента в оставлении после себя большого количества отходов. Пила работает при сравнительно небольшой скорости. Она не позволяет резать детали на значительную глубину.
Нарезание элементов при помощи болгарки используется для профильного проката. Болгарка не оставляет на обработанном материале окислов и окалин. После металлообработки остается мало отходов. Данный способ обладает низкой производительностью по сравнению с другими вариантами.
Рубка гильотиной имеет ряд ограничений касательно деталей со сложной конфигурацией, но считается самым недорогим и эффективным методом металлообработки.

Конструкция гильотинного станка
Использование ленточнопильного станка считается наиболее универсальным вариантом для обработки любых металлических деталей. Аппарат позволяет проводить работы под любым углом, избегая серьезных потерь тепла. В результате конечный продукт имеет идеальные кромки. Станок используется только для изделий с определенными размерами.

Конструкция ленточнопильного станка
Газокислородная резка
Нарезать металл методом кислородной металлообработки допустимо при соблюдении целого ряда условий:
- металлический элемент содержит незначительное количество легированных компонентов;
- для изделия характерна невысокая теплопроводность;
- обрабатываемый материал имеет температуру плавления больше, чем температуру горения.
Кислородную резку не рекомендуется использовать в качестве основного приема металлообработки. После нее на материале остаются окислы, влияющие на все его качество.
Лазерная металлообработка
Лазерное разрезание изделий является прогрессивным приемом. Суть его в воздействии на прокат узконаправленного светового луча, разогревающего деталь в месте контакта до высоких температур. Под действием луча металлоизделие расплавляется, а остатки расплава сдуваются с его поверхности специальным газом.
При лазерном методе отсутствует деформация металлоизделия, удается получить высокоточный результат без необходимости дополнительной обработки краев.

Схема и общий вид установки
При всех достоинствах указанные виды разрезания металлоизделий имеют несколько недостатков:
- применение только для тонколистового материала толщиной до 20 мм;
- невозможность обработки алюминиевых сплавов, металлоизделий из нержавеющей стали из-за их высокой отражаемости световых лучей.
Разрезание плазменным методом
Разрезание металлоизделия плазмой подразумевает воздействие на его определенный участок газовой смеси под высоким давлением. Плазменный поток представляет собой сильно нагретый и подвергшийся ионизации газ. Температура потока составляет 150000С.

Резка плазменной дугой и плазменной струей
В месте воздействия плазмы на деталь происходит ее выгорание и плавление. Части расплавленного металла выдуваются газовой смесью. Метод можно использовать для резки любых типов изделий.
Нарезание металлоизделий плазмой превосходит по производительности все другие способы. Она в 10 раз быстрее любых механических методов резки металлоизделий. Плазменное разрезание в 4 раза быстрее лазерного метода.
Плюс метода в том, что им осуществляют разрезание металлических изделий различной толщины (до 150 мм).
Имеются минусы у данного способа:
- требуется металлообработка краев деталей;
- края после обработки имеют небольшой наклон на 40;
- не рекомендуется применять для разрезания титана и других металлоизделий большой толщины.
Гидроабразивный метод
Разрезание изделий гидроабразивным методом имеет следующее определение: раскрой материала путем воздействия на него смеси песка и воды, подаваемых под давлением через узконаправленное сопло. Песок в сочетании с водой способны разрезать металлоизделия, имеющие толщину 30 см.
Способ относится к числу инновационных. После раскроя детали нет необходимости в дополнительной обработке ее краев.
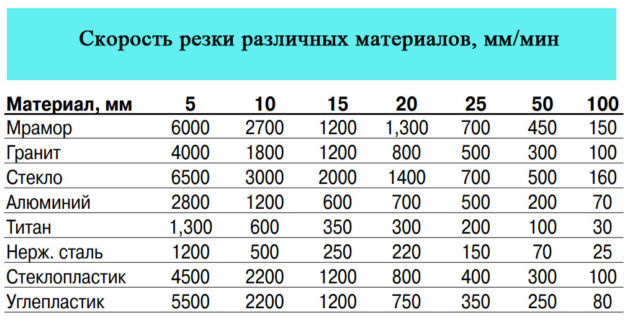
Скорость гидроабразивной резки
Указанный способ не относится к горячему методу разрезания металлоизделий, поскольку при нем отсутствует термическое воздействие на обрабатываемую деталь. Благодаря этому разрезание может быть выполнено без деформации изделия.
Главным недостатком гидроабразивного метода является невозможность резки металлов, подверженных коррозии. Применяемое оборудование имеет высокую стоимость и не всегда доступно для частных нужд.
Видео по теме: Станок гидроабразивной резки WTJ
Сравнение механической обработки и резки металлических труб для прецизионных применений
Metal Cutting всегда находится в поиске последних инноваций в инструментах, которые мы используем для швейцарской обработки с ЧПУ, точного шлифования, массовой чистовой обработки и даже услуг притирки, которые мы предлагаем. Тем не менее, эти методы обработки не позволяют понять, что такое Metal Cutting Corporation.
Тип настоящей резки металла, в котором мы преуспеваем, — например, отрезание тонкостенных стальных трубок для медицинских устройств и других прецизионных применений — на самом деле довольно уникален.Для этих очень точных и больших объемов наши методы резки металлических труб находятся в центре внимания по сравнению с обработкой труб или другими доступными методами резки труб.
Для подкожных трубок и других очень маленьких трубок, которые обычно ищут наши клиенты, проблема заключается в том, что — в зависимости от того, как выполняется процесс — некоторые процессы резки могут вызывать проблемы, такие как:
- Засорение внутреннего диаметра (ID)
- Сгибание концов трубы
- Разрушение всей трубы
Однако Metal Cutting — одна из немногих компаний, которые могут успешно разрезать трубы этого типа, независимо от того, насколько мал диаметр трубы или насколько тонка стенка трубки.
Существуют способы лазерной резки трубок мелких деталей, например медицинских стентов. Однако лазеры не могут разрезать соты или совокупность деталей; трубы необходимо разрезать индивидуально, что является медленным и дорогостоящим процессом.
Metal Cutting позволяет резать большое количество тонкостенных стальных труб одновременно, причем делать это экономично и без каких-либо вышеупомянутых проблем. Фактически, мы любим говорить, что если трубку можно протянуть, мы можем ее разрезать.
Например, мы можем разрезать трубки из нержавеющей стали с внутренним диаметром всего 25 мкм (0.001 ”) и наружным диаметром (OD) всего 75 мкм (0,003 дюйма) — другими словами, трубка размером с человеческий волос. Большая часть этих очень тонкостенных стальных труб используется в:
- Медицинские приборы, например, для глазной хирургии или аналогичных методов лечения
- Научные инструменты, в которых необходимо измерять и / или распределять небольшие точные количества жидкости
Другие преимущества резки трубок для мелких деталей
Скорость и стоимость — не единственные преимущества методов Metal Cutting для резки металлических труб.Например, помимо возможности разрезать пучок небольших трубок, при необходимости мы можем разрезать вращающиеся трубки — прорезая только стенку трубки, исключая дополнительное время хода и втягивание колеса.
Еще одно важное отличие — неизбежный тепловой эффект лазерной резки металла. Из личного опыта я знаю, что предотвращение нагрева лазера может быть критической проблемой даже в хирургии человека.
Для процедуры, которая мне понадобилась несколько лет назад для удаления полипа из голосовых связок, меня попросили найти хирурга, который умел бы использовать холодный нож, а не лазер.Это потому, что тепло, выделяемое лазером, может вызвать необратимые рубцы на голосовых связках.
Естественно, я пошел с экспертом по холодному ножу, и я рад сказать, что моя операция прошла успешно, а мой голос как новенький. Аналогичным образом, при использовании методов Metal Cutting для работы с тонкостенными трубами не возникает зоны термического влияния и возникающих в результате деформации или изменения цвета деталей, как при лазерной резке.
Конечно, само собой разумеется, что лазерная резка отлично подходит для получения чрезвычайно сложных форм, которые намного превосходят возможности Metal Cutting.Для тех областей применения, где требуется такая сложность, сравнение наших методов резки и лазерной резки означает сравнение яблок и апельсинов.
В этих случаях «компромисс» между несколько меньшей скоростью и определенно более высокой стоимостью — это просто часть необходимой цены для достижения надлежащих результатов.
Гибкость при поиске мелких деталей НКТ
Хотя мы являемся экспертами в области резки металлических труб, мы не производим их. Тем не менее, Metal Cutting по-прежнему приносит пользу нашим клиентам благодаря взаимоотношениям с поставщиками.
Это дает нам возможность закупать материалы у всех без исключения лучших поставщиков тонкостенных труб из нержавеющей стали, таких как 316, 304,
.5 вещей, которые следует учитывать при термической обработке металла
Мы уже говорили в другом месте о том, как тепловое расширение может быть фактором при принятии решения о том, насколько точными должны быть размеры металлической детали.
А именно, если даже небольшая разница в допуске, вызванная тепловым расширением, повлияет на работу детали, то разумно избегать указания очень жесткого допуска, когда существует риск изменения температуры окружающей среды. А это означает вариации на любом этапе процесса, от обрезки детали и проверки до сборки и конечного использования.
Но что насчет того, если вы намеренно обрабатываете металлы как обычную часть производственного процесса? Что в таком случае нужно учитывать при создании спецификаций для небольших обрезанных металлических деталей, таких как те, которые мы производим здесь, в Metal Cutting Corporation?
Почему металлы подвергаются термической обработке? Есть много важных причин. Но в основном процесс термической обработки металлов включает контролируемое приложение тепла для изменения физических, а иногда и химических свойств материала.
Несмотря на то, что мы не занимаемся термической обработкой металлов в рамках наших услуг в Metal Cutting, мы учитываем его потенциальные эффекты изменения размеров . Но прежде чем мы исследуем непреднамеренные последствия для размеров металлических деталей, давайте обсудим некоторые преимущества термической обработки и отжига.
В зависимости от используемого метода термически обработанные металлы становятся тверже или мягче, более или менее хрупкими, прочнее или слабее. Исходя из желаемых конечных результатов, метод может включать:
- Использование нескольких процедур
- Изменение температуры термообработки металла
- Изменение продолжительности воздействия тепла
- Контроль скорости или скорости охлаждения материала
Способ применения и отвода тепла при термообработке металла влияет как на предел текучести, так и на твердость конечного продукта.
Например, нержавеющая сталь обычно подвергается термообработке для повышения ее твердости; с другой стороны, он также может стать более хрупким.
И наоборот, нержавеющая сталь может подвергаться термообработке для повышения ее пластичности, что помогает минимизировать растрескивание и повысить обрабатываемость. Однако этот процесс также может снизить твердость стали.
Следовательно, для получения металла с желаемыми характеристиками — например, нержавеющей стали с высоким пределом прочности на разрыв, но относительно низкой хрупкостью — может потребоваться несколько обработок при разных температурах и разное время.
Часто используется взаимозаменяемо с термином термическая обработка. , отжиг. — это особый метод, используемый для смягчения металлов с целью повышения их пластичности и уменьшения хрупкости.
Отжиг может также использоваться для увеличения однородности металлов, а также для восстановления их пластичности перед дальнейшей обработкой. Например, при обработке нержавеющей стали 316 она может приобретать нежелательные магнитные свойства; однако отжиг нержавеющей стали может восстановить ее первоначальное немагнитное состояние (или очень близко к нему).
Отжиг осуществляется в специализированных печах, в которых жестко контролируются условия. Металл нагревается до высокой температуры — обычно немного выше температуры рекристаллизации.
Материал выдерживают при высокой температуре от нескольких часов до нескольких дней, а затем дают остыть (в случае стали и других черных металлов — очень медленно).
При термообработке металла также важна атмосфера, в которой происходит процесс, потому что она влияет на поверхность и прочность материала.
Например, если вы термообрабатываете вольфрам в нормальной атмосфере, это приведет к окислению, которое сделает поверхность пористой. Однако работа в контролируемой среде — такой как вакуум или герметичная атмосфера азота, аргона или водорода — позволяет термически обрабатывать металл без окисления.
Низкоуглеродистая стальможет подвергаться отжигу в среде, богатой углеродом, для цементирования стали с поверхностным слоем с высоким содержанием углерода, который обладает хорошей усталостной и износостойкостью. Этот метод используется для повышения твердости и долговечности таких изделий, как проволочные пружины и поковки из углеродистой стали.
Однако, если «науглероживание» не является желательным признаком, отжиг следует проводить в среде с низким содержанием углерода или без него.
Иногда поиск правильной «формулы» как для состава сплава, так и для метода термообработки металла имеет важное значение для достижения желаемых конечных свойств. Отличным примером является свойство памяти формы никель-титанового сплава , также известного как NiTi или нитинол .
Этот «упругий» материал впервые широко использовался для изготовления оправ для очков, которые могут сгибаться и, казалось бы, волшебным образом возвращаться к своей первоначальной форме.Сегодня NiTi широко используется для изготовления трубок медицинских устройств, таких как проводники для катетеров, стенты и иглы для микрохирургии.
Свойство памяти формы NiTi зависит от термической обработки. Это то, что позволяет NiTi претерпевать деформацию при одной температуре, а затем восстанавливать свою первоначальную, недеформированную форму при нагревании выше так называемой температуры превращения.
Тем не менее, NiTi, как известно, трудно сделать как из-за высокой реакционной способности титана, так и из-за того факта, что даже небольшие изменения в составе могут повлиять на температуру превращения.
Например, если атомы титана соединяются с кислородом или углеродом, кристаллическая структура NiTi может потерять титан, что приведет к снижению температуры превращения. Если никеля слишком мало и материал выдерживается слишком долго, температура превращения повышается.
Какой бы метод ни использовался для термообработки металлов, жизненно важно указать этот процесс в спецификациях на отрезанные металлические детали. Примечательно, что термообработка металла может изменить одни размеры тщательно обработанных деталей и не повлиять на другие параметры.
Например, если у вас есть спецификация прямолинейности, вы должны подумать, повлияет ли термообработка и возникающее в результате расширение металла на размеры ваших вырезанных деталей и, в конечном итоге, на то, насколько хорошо они будут работать — и если да, то вы может потребоваться соответствующая корректировка допусков.
Кроме того, важно убедиться, что термообработанные металлические детали будут правильно упакованы, чтобы избежать деформации или повреждения ранее вырезанных деталей во время их транспортировки.
Например, в отделе Metal Cutting мы всегда хотим знать, будут ли вырезанные детали отправлены третьей стороне для термической обработки или отжига. Поскольку детали становятся более податливыми в результате отжига, неправильная упаковка может привести к деформации отожженных деталей, когда они будут переупакованы и отправлены вам (или отправлены обратно нам для дополнительной обработки).
Такие детали, как стержни, могут деформироваться, если они расширяются и не упаковываются должным образом после термообработки металла. Другие детали могут начать тереться друг о друга и поцарапать поверхность, если упаковка больше не удерживает термообработанные металлические детали надежно.
Еще одна причина для тщательных спецификаций
Суть в том, что в случае термически обработанного металла методы и эффекты должны быть рассмотрены и предоставлены вашим партнерам по производству, когда вы создаете спецификации для ваших требований к мелким деталям. Это поможет оптимизировать технологичность и получить желаемые результаты.
.Услуги по резке металла на заказ
Услуги по резке металла на заказ
С момента своего основания в 1967 году компания Metal Cutting совершенствовала искусство и науку в сфере услуг по резке металла на заказ. Наша высококвалифицированная, квалифицированная и опытная команда специалистов по прецизионной резке металла ежедневно производит десятки тысяч деталей, соблюдая не только сжатые сроки, но и жесткие допуски, требуемые производителями высокотехнологичного оборудования. С нашим набором современного оборудования в сочетании с нашим внутренним инвентарем различных специальных металлических труб, стержней и проволоки, мы готовы выполнять даже самые строгие спецификации и производственные графики.
Прецизионная резка
Среди наших услуг по резке металла по индивидуальному заказу наши навыки точной резки позволяют нам выдерживать очень жесткие допуски на резку с самыми высокими значениями Cpk / Ppk. Имея в своем распоряжении более 45 патентованных абразивно-отрезных станков и электроэрозионных станков на наших двух заводах, мы предлагаем непревзойденный объем и точность размеров для производства отрезанных металлических деталей без заусенцев.
Узнать больше
Шлифовка и доводка
Предлагая полный спектр услуг по шлифованию и притирке, Metal Cutting предлагает широкий спектр поверхностей с ЧПУ, профильных, врезных, конических, двухдисковых и бесцентрового шлифования.Наша притирка, шлифование поверхностей и двухдисковое шлифование позволяет нам создавать особую отделку поверхности, включая высокополированную, и чрезвычайно жесткие допуски по длине с исключительной плоскостностью. Наши бесцентрово-шлифовальные станки с ЧПУ и подачей позволяют нам создавать самые сложные и индивидуальные конические и конические детали для наших клиентов с диаметром от 0,002 дюйма (0,05 мм) и длиной от 12 футов (4 м) до 0,080 дюйма. «(2 мм).
Узнать больше
Полировка
Наши услуги по резке металла по индивидуальному заказу выводят полировку металла за рамки традиционных возможностей.Наши тщательно разработанные уникальные рецепты механической полировки сочетают в себе полный спектр абразивов, действия, жидкостей, температуры и времени, чтобы обеспечить однородную поверхность металла с гладкостью до Ra 0,010 мкм в объемах от нескольких частей до десятков миллионов.
Узнать больше
Обработка
Для современной обработки наши опытные и высококвалифицированные механики и универсальные токарные автоматы швейцарского типа и многоосевые станки с ЧПУ идеально оснащены для быстрой и эффективной токарной, фрезерной и сверлильной обработки сложных и мелких прецизионных металлических деталей. .
Узнать больше
Чистовая
В дополнение к полировке поверхности до гладкости Ra 0,010 мкм, Metal Cutting выполняет широкий спектр индивидуальных услуг по финишной обработке металлов, включая окончательную подготовку деталей после резки. Наша прецизионная обработка радиуса металла представляет собой более дешевую альтернативу индивидуальной обработке фасок. Мы предлагаем маскированную и немаскированную пескоструйную очистку для контролируемого истирания металлических поверхностей. Мы также занимаемся пассивацией на собственном предприятии, предлагаем методы с использованием лимонной и азотной кислоты в соответствии с последним стандартом ASTM A967.
Узнать больше
.5 фактов, которые нужно знать о концентричности по внешнему / внутреннему диаметру
Как избежать требований к концентричности по внешнему / внутреннему диаметру при поиске труб
Подобно кругу в спирали, как колесо внутри колеса, измерения внешнего диаметра (OD) и внутреннего диаметра (ID) трубы с соблюдением требований по концентричности могут составить одну большую головную боль.
Все мы знаем, что поиск мелких деталей — не идеальный мир. (Черт возьми, именно поэтому допуски существуют в первую очередь!) Тем не менее, иногда чертеж показывает, что требуется концентричность — а идеальную концентричность измерить почти так же сложно, как и достичь.
Но, почему ?
1. Определение концентричности
Что такое соосность? В геометрических размерах и допусках (GD&T) концентричность представляет собой сложный допуск — своего рода «круговую симметрию», используемую для определения зоны допуска для средних точек цилиндрической или сферической детали.
В чем разница между цилиндричностью и соосностью? В то время как цилиндричность является индикатором округлости и прямолинейности по всей оси трехмерной детали, концентричность сравнивает внешний и внутренний диаметр или округлость в двух разных точках.
Иногда называется соосность, GD & T концентричности «управляет центральной оси ссылочного элемента, к оси базовой точки» в соответствии с веб-сайта GD & T Basics.
Проще говоря, вы можете определить концентричность как меру постоянства толщины стенки трубы, трубы или другого цилиндра. Таким образом, концентричность определяет центральную ось, которая получается из средних точек детали, измеренных в поперечных сечениях.
Это означает, что если бы концентричность была «идеальной», то толщина стенки между наружным и внутренним диаметром была бы одинаковой в каждом поперечном сечении, в каждой точке вокруг диаметра трубы.
Что делает концентричность такой сложной?
Что делает концентричность НКТ такой сложной характеристикой? Он основан на измерениях от производной оси, а не от осязаемой поверхности, создавая теоретическую цилиндрическую зону допуска 3D, в которую должны попадать все производные средние точки трубы.
Именно поэтому концентричность обычно резервируется для высокоточных деталей, где критически важно контролировать эти средние точки.
Что такое эксцентриситет vs.концентричность?
При изменении толщины стенки трубы у вас есть эксцентрическая труба , в которой центр окружности, образованной наружным диаметром, находится в точке, отличной от центра окружности, образованной внутренним диаметром. (Другими словами, две окружности не концентрические .)
Эксцентриситет измеряется путем взгляда на поперечное сечение для определения минимального и максимального размеров стенки трубы, а затем вычисления разницы между минимальной и максимальной толщиной и деления полученного значения пополам.
2. Обозначения концентричности OD / ID
Требования к внешнему и внутреннему диаметру трубок могут быть указаны на чертеже несколькими способами, в том числе:
- Знак концентричности GD&T, представляющий собой круг внутри круга
- Процент эксцентриситета
- TIR (общее показание индикатора)
- Письменные утверждения, такие как «OD и ID должны быть концентрическими в пределах 0,00X дюйма»
Иногда используется другой термин если говорить о соосности, это биение стены , что то же самое, что и TIR.Биение стенок рассчитывается путем установки индикатора на деталь, когда она вращается вокруг своей оси, которая измеряет не только концентричность, но и округлость детали.
Биение стенки определяется эксцентриситетом трубы и описывает изменение толщины стенки по сравнению с указанной номинальной стенкой — также указывается как максимальная толщина стенки минус минимальная толщина стенки. Биение стены также можно выразить как «эксцентриситет, умноженный на два».
В тех случаях, когда эти (и другие) термины используются на чертежах для описания требований к соосности, поставщики материалов и цеха прецизионной резки металла сталкиваются с проблемой определения не только того, какой машинный процесс использовать, но и того, как измерить соосность, чтобы она соответствовала спецификации .
Типичное обозначение концентричности3. Проблемы измерения концентричности
Это подводит нас к трудностям, как измерить концентричность и определить, достигаются ли указанные OD и ID. Неконцентричность является одним из самых сложных GD & T черты, чтобы измерить, из-за трудностей в создании (теоретически) центральную ось, которая служит в качестве опорной точки (опорная ось).
Измерение концентричности также требует выполнения множества измерений в серии поперечных сечений, а также точного картирования поверхности и определения средних точек этих поперечных сечений.Затем эти серии точек должны быть нанесены на график, чтобы увидеть, попадают ли они в цилиндрическую зону допуска.
Эта задача может быть выполнена только на координатно-измерительной машине (CMM) или другом компьютерном измерительном приборе и требует очень много времени. А это, конечно, означает добавленную стоимость.
Еще одна проблема заключается в том, что с сегодняшней моделью для микрообработки детали, которые необходимо измерить, часто меньше, чем когда-либо прежде. Например, в случае крошечных прецизионных трубок, используемых в качестве компонентов в медицинских устройствах, проблема заключается в том, как проверить концентричность двух диаметров в очень и очень маленьких трубках.
4. Когда требуется концентричность
При всей этой сложности, концентричность обычно используется только для деталей, требующих очень высокой степени точности для правильного функционирования.
Критичность концентричности зависит от конечного использования, например, от того, должен ли какой-то физический объект с собственным внешним диаметром вписаться в трубку. Например:
- В общем, если труба должна войти внутрь отверстия, а другая часть должна соответствовать внутреннему диаметру трубки, тогда внешний диаметр, внутренний диаметр и концентричность могут быть согласованы, чтобы все эти части работали вместе.
- Однако, если приложение требует, чтобы жидкость или газ проходили через трубку, концентричность может вообще не иметь значения, поскольку несоосность трубки не препятствует прохождению потока.
Но даже там, где концентричность не критична, может быть важно знать, насколько далеко может быть концентрический OD / ID. Например, если жидкость или газ будет течь через трубку под давлением, вам может потребоваться указать минимально допустимую толщину стенки , чтобы гарантировать, что давление не вызовет разрыва в тонком месте на неконцентрической стенке трубки. .
В некоторой степени выбор материала может также зависеть от соосности или минимальной / максимальной толщины стенки. Например, если вы решили использовать сварную трубу, которая будет подвергаться шлифовке для формирования детали, вы можете указать минимальную толщину, чтобы предотвратить слишком тонкую шлифовку стенки трубы и вызвать разрыв сварного шва.
Аналогичным образом, если ваше конечное приложение будет использовать трубку для перемещения жидкости под высоким давлением, бесшовные вытяжной материал, а не сварной, может быть лучшим выбором, чтобы минимизировать риск поломки.Но опять же, если трубка просто будет выпускать воздух в окружающую среду, то использование бесшовных трубок будет явлением чрезмерной инженерии.
5. Альтернатива: биение и биение
В некоторых случаях вы можете избежать затрат времени и средств на проверку соосности, заменив требования по концентричности на биение , которое легче измерить и легче достижимо.
Опять же, концентричность показывает, насколько хорошо цилиндрический элемент центрирован на теоретической оси, а биение — насколько элемент отклоняется от идеальной окружности, которая идеально центрирована на оси вращения.Другими словами, биение — это комбинация соосности и округлости — и если деталь идеально круглая, биение будет равно соосности.
Хотя концентричность и биение — это не одно и то же, их часто можно использовать взаимозаменяемо для достижения одного и того же основного конечного результата.
Большая разница в том, что при биении вы можете физически прикоснуться к поверхности детали и измерить ее. Контроль биения также будет контролировать концентричность, хотя, по общему признанию, не в той же степени, как при применении концентричности самостоятельно.
Разработка трубок с учетом достижимых допусков
Помните, возможность изготовления деталей с допустимыми допусками является критически важным фактором при создании чертежей. Вот почему большинство механиков, специалистов по измерениям и инженеров-конструкторов рекомендуют по возможности избегать концентричности OD / ID.
Вместо этого вы можете использовать другие применимые геометрические обозначения GD&T в чертежах и конструкциях трубок, чтобы избежать ошибок, связанных с концентричностью внешнего и внутреннего диаметров, не встраивая его в детали.
Чтобы узнать больше о том, как указание характеристик и допусков GD&T влияет на качество изготовления деталей, загрузите нашу бесплатную статью Как настроить запрос предложения с максимальной выгодой: часто задаваемые вопросы при поиске мелких деталей.
.