Диффузионная сварка, технология и оборудование.
Диффузионная сварка — сварка за счёт взаимной диффузии на атомарном уровне свариваемых поверхностей деталей. Диффузионная сварки применяется в частности при производстве компенсаторов шинных медных пластинчатых КШМ для получения монолитной однородной контактной площадки из тонких медных пластин.
Определения и сущность диффузной сварки описаны в ГОСТ 26011-74. Диффузионная сварка производится воздействием давления и нагревом свариваемых деталей в защитной среде. Перед сваркой поверхность детали обрабатывают по 6 классу шероховатости и промывают для обезжиривания ацетоном.
Температура нагрева составляет 0,5 – 0,7 от температуры расплавления металла свариваемых деталей. Высокая температура обеспечивает большую скорость диффузии и большую пластичность деформирования металла. При недостаточной диффузии в сварке используют металлические прокладки (фольга из припоя ВПр7 толщиной 0,1 – 0,06 мм.) или порошок (фтористый аммоний), прокладываемые в месте сварки. Перед сваркой фольгу приваривают к поверхности одной из деталей с помощью контактной сварки. В процессе сварки прокладка расплавляется.
Процесс сварки осуществляется с использованием разных источников нагрева. В основном применяют индукционный, радиационный, электронно-лучевой нагрев, нагрев проходящим током, тлеющим разрядом или в расплаве солей
Сварка протекает при давление в камере – 10−2 мм. рт. ст. или в атмосфере инертного газа (иногда водорода). Вакуум или защитная атмосфера предохраняет свариваемые поверхности от загрязнения.
Сварка производится сжатием деталей с давлением 1 – 4 кгс/мм2. Давление, применяемое при способах сварки без расплавления материалов, способствует разрушению и удалению окисных пленок и загрязнений на поверхности металла, сближению свариваемых поверхностей до физического контакта и эффективного атомного взаимодействия, обеспечению активации поверхностей для протекания диффузии и рекристаллизации. Различается сварка с высокоинтенсивным силовым воздействием (свыше 20 МПа) и сварка с низкоинтенсивным силовым воздействием (до 2 МПа).
Диффузионная сварка проходит в две стадии:
- Сжатие свариваемых поверхностей, при котором все точки соединяемых материалов сближаются на расстоянии межатомных взаимодействий.
- Формирование структуры сварного соединения под влиянием процессов релаксации.
В отличие от традиционных способов сварки расплавлением, где к основному металлу вводится дополнительный металл в шве, диффузионная сварка позволяет получить однородный шов без серьезных изменений в физико-механическом составе места соединения.
Соединения обладают следующими показателями:
- наличие сплошного шва без пор и образований раковин;
- отсутствие окисных включений в соединении;
- стабильность механических свойств.
Благодаря тому, что диффузия – это естественный процесс проникновения одного вещества в другое, в зоне соприкосновения не нарушается кристаллическая решетка материалов, а следовательно, отсутствует хрупкость шва.
Недостатки технологии диффузионной сварки
- необходимость вакуумирования рабочей камеры;
- тщательная подготовка и очистка свариваемых поверхностей.
Преимущества технологии диффузионной сварки
- диффузионная сварка не требует сварочных припоев, электродов;
- не нужна дополнительная механическая обработка свариваемых поверхностей;
- высокое качество сварного соединения;
- малый расход затрачиваемой энергии;
- широкий диапазон толщин свариваемых деталей – от долей мкм, до нескольких метров.
Применение диффузионной сварки
К преимуществам данной технологии относят возможность диффузионной сварки разнородных материалов с получением равнопрочного шва без существенных изменений в физико-химических характеристиках, высокий уровень защиты и отсутствие необходимости в присадочном металле. Такая сварка позволяет создание прочных конструкций как из однородных металлов со сплавами, так материалов разного рода, в том числе резко отличающихся своими характеристиками, например пористых составов со слоистыми. Это не растворимые друг в друге, тугоплавкие или малопластичные металлы и сплавы, соединение которых довольно затруднительно. А применение диффузионного способа позволяет получать сварные конструкции даже из таких пар металлов и сплавов, которые практически невозможно соединить с помощью других видов сварки. Примером этого может служить диффузионная сварка титана со сталью, стойкой к коррозии, молибдена с медью или ниобия с вольфрамом, силикатов (кварц, стекло) с металлами, жестких углеводородов (графит и сапфир) со сплавами, стекла с ферритами и металлами.
Оборудование
Для проведения диффузионной сварки выпускается оборудование, различаемое по степени вакуумирования: с низким вакуумом (до 10-2 мм рт. ст.), со средним вакуумом (10-3…10-5 мм рт. ст.), с высоким вакуумом (свыше 10-5 мм рт. ст.), с защитным газом разной степени давления.
Для нагрева деталей применяют индукционный нагрев токами высокой частоты, электроконтактный нагрев током, радиационный нагрев электронагревателем.
В установках используют гидравлические или механические системы давления. Установки бывают с ручным управлением, полуавтоматические и автоматические с программным управлением. Автоматы применяются в крупносерийном или массовом производстве.
По теме
Компенсаторы шинные медные КШМ
Подключение трансформатора к шинопроводу
Популярные товары
Шины медные плетеные
Шины изолированные гибкие и твердые
Шинодержатели
Изоляторы
Индикаторы наличия напряжения
схема, особенности и области применения
Диффузия — это процесс, во время которого при тесном контакте между поверхностями молекулы и атомы разных элементов начинают смешиваться и проникать друг в друга. В естественных условиях данный процесс протекает достаточно медленно, поэтому он не приемлем для производственных условий.
Но в 1953 году советский физик Николай Федорович Казаков смог добиться повышения скорости взаимного проникновения молекул и атомов друг в друга. Он поместил соединяемые заготовки в вакуум, повысил температурные показатели и оказал на них усиленное давление. Так и появилась диффузионная сварка, которая позволяет соединять детали из разных видов металлов.
Характеристика диффузионной сварки
Во время диффузионной сварки металлов используются специальные сварочные стенды. На их поверхности размещаются элементы, затем стенды с ними помещаются в камеру с вакуумом. На соединяемую зону оказывается давление, если потребуется, она может подвергаться температурному воздействию.
В соответствии с основными особенностями сварочного процесса, он может длиться от нескольких минут до часов. В результате изделие приобретает характеристики, которые невозможно получить при проведении других видов сварок.
Чтобы при проведении диффузной сварки удалось получить прочный и качественный шов стоит обратить внимание на несколько важных условий:
- При помощи специальной установки требуется создать вакуум. Чем выше будет разряжение внутри, тем быстрее и эффективнее будет протекать сварочный процесс. Чтобы получить физический вакуум в обычных условиях требуются большие затраты. По этой причине приходиться применять небольшое разряжение, которое редко может превышать 10-5 мм рт.ст.. Но даже этого показателя достаточно для получения отличных результатов.
- Во время сварки необходимо нагревать соединяемые детали. Иногда процесс может протекать при комнатной температуре, но тогда на формирование шва может потребоваться много времени. При увеличении температуры повышается текучесть металлов и ускоряется диффузия. Нагревание может выполнять разными способами — индукционным, электроконтактным, радиационным.
- После достижения требуемой температуры в область соединения подается необходимое давление. Оно может быть разных типов — длительное или кратковременное, локальное или одновременно распределенное. Это требуется для ускорения взаимного проникновения частиц вещества.
- Для повышения прочности сварного соединения требуется применять тонкую медную, золотую, платиновую, никелевую фольгу. Ее толщина должна составлять несколько микрон. Также области стыков заготовок рекомендуется обрабатывать химическими веществами.
- Каждая готовая деталь подвергается дефектоскопии. Обычно вакуумная сварка требуется для применения радиации и ультразвука.
Области применения
Диффузионная сварка в вакууме является наиболее подходящим вариантом для сваривания разнородных металлов в различных сочетаниях, к примеру, стали и бронзы, стали и керамики и многое другое.
Данный вид сваривания наиболее подходящий для получения прочного и монолитного соединения. После проведения процесса шов получается ровным, без дефектов, неровностей. Обычно он применяется в ситуациях, когда нет возможности применять стандартные виды фиксирования металлических элементов.
Сварка в вакууме часто используется для изготовления следующих металлических конструкций и заготовок:
- гильз двигательных цилиндров. Этот вид сварки часто используют в производстве авиатехники;
- тормозных колодок и дисков;
- основных компонентов турбокомпрессоров;
- штампов с повышенным показателем твердости;
- изделий с металлокерамической основой;
- для производства сложных композитов разных типов — из стекла и меди, металлов с графитом, кварцем, сапфиром;
- этот вид сварки часто используют при соединении труднообрабатываемых стальных и титановых сплавов с высоким показателем жаростойкости;
- для создания полупроводниковых компонентов.
Важно! Главная сфера применения диффузионного сварочного процесса — область высоких технологий (авиационной, космической, другие виды машиностроения). Кроме этого этот метод позволяет создавать микроскопические элементы из сферы сложной электроники.
Достоинства
Диффузионная сварка титана и других видов металлов в вакууме обладает целым рядом преимуществ, которые обязательно требуется учитывать при проведении данного процесса:
- Во время сварки не нужно применять разные расходные материалы — электроды, флюсовые смеси.
- Этот процесс экологически чистый. Во время него не происходит горения и выделения в воздух вредных веществ, паров.
- Метод обладает небольшой энергоемкостью. Это позволяет значительно снизить финансовые затраты.
- Имеет возможность соединять сразу нескольких заготовок. В итоге это позволит получить многослойные конструкции с уникальными качествами.
- При помощи этого метода можно осуществлять соединение поверхностей с разными размерами и формами. При этом показатели толщины заготовок могут быть любыми. Данные условия имеют важное значение для микроэлектроники.
- Сварка позволяет получить качественный и прочный шов, с которым не способна сравниться другие виды сварочных процессов.
Стоит отметить! Этот вид сварки имеет еще одно важное преимущество — он постоянно совершенствуется и улучшается. Раньше в камере был только вакуум, а сейчас дополнительно закачиваются инертные газы. Это позволяет производить соединение металлов, пластика, стекла, керамики и других сложных композитных смесей.
Ниже на картинке имеется схема диффузионной сварки, она достаточно простая.
Недостатки
Не стоит забывать, что у диффузионного сварочного процесса имеются отрицательные качества:
- оборудование для диффузионной сварки имеет высокую стоимость. Также они нуждаются в постоянном квалифицированном обслуживании, которые могут предоставить только специально обученные люди;
- для сваривания больших деталей требуется использование больших вакуумных камер. Но они стоят достаточно дорого;
- обязательным условием для проведения сварки является проведение чистки и обработки поверхностей деталей.
Заключение
Проведение диффузионного сварочного процесса позволяет получить качественные и прочные конструкции из разных видов металла и композитного материала. Это безопасный метод, которые не представляет угрозы для окружающей среды и человека. Но все же перед тем как его проводить стоит рассмотреть его важные особенности и нюансы.
Интересное видео
Диффузионная сварка: преимущества и недостатки
Атомы веществ находятся в постоянном движении, вот почему жидкости и газы могут смешиваться. Твердые тела тоже имеют подвижные элементарные частицы, но у них более жесткая кристаллическая решетка. И все же, если два твердых тела сблизить на расстояние взаимодействия атомных сил, то в месте контакта частицы одного вещества будут проникать в другое и наоборот. Такое взаимное проникновение веществ получило название диффузии, а эффект был положен в основу одного из методов соединения металлов. Он так и называется — диффузионная сварка металлов.
Что можно соединять диффузионной сваркой
Диффузионная сварка в вакууме имеет огромные технологические возможности. С ее помощью можно соединять:
- Металлы однородной и неоднородной структуры, а также их сплавы. Тугоплавкие металлические вещества типа тантала, ниобия и вольфрама.
- Вещества неметаллического характера с металлами: графит со сталью, медь со стеклом.
- Материалы конструкционные на основе из металла, керамику, кварц, ферриты, стекло, полупроводниковые структуры (однородные и неоднородные), графиты и сапфир.
- Материалы композиционные, пористые с сохранением их свойств и текстуры.
- Полимерные вещества.
Касаемо конфигурации и размера заготовок — они могут быть разными. В зависимости от величины рабочей камеры, можно работать с деталями от нескольких микрон (полупроводниковые элементы) до нескольких метров (сложные слоистые структуры).
Как устроена диффузионная установка
Комплекс для сварки диффузионным методом включает следующие основные элементы:
- Рабочую камеру. Она изготовлена из металла и предназначена для ограничения рабочей среды, в которой создается вакуум.
- Станину – шлифованную подставку. На нее опирается рабочая камера, вдоль которой она может перемещаться.
- Вакуумный уплотнитель. Является прокладкой между камерой и подставкой.
- Роликовый механизм и прижимной винт. С их помощью осуществляется перемещение камеры вдоль направляющих и фиксация ее на подставке.
- Насос вакуумный. Создает безвоздушное пространство в рабочей зоне.
- Генератор с индуктором. Выступают системой нагрева свариваемых деталей.
- Пуансоны жаропрочные, цилиндры гидравлические и насос масляный представляют механизм сжатия деталей под заданным давлением.
В зависимости от модификации установки диффузионной сварки могут отличаться формой камер и способом их герметизации. Также разными бывают методы разогрева деталей. Могут использоваться радиационные нагреватели, генераторы высоких токов, установки тлеющего разряда, электронно-лучевые нагреватели.
Диффузионные процессы при сварке
Если взять шлифованные металлические пластины, соединить их и положить под груз, то через несколько десятков лет будет заметен эффект обоюдного проникновения металлов друг в друга. Причем глубина проникновения будет в пределах миллиметра. Все дело в том, что скорость диффузии зависит от температуры соединяемых материалов, расстояния между элементарными частицами веществ, а также от состояния контактирующих поверхностей (отсутствия загрязнений и окислений). Вот почему в естественных условиях ее процесс протекает так медленно.
В промышленности для быстрого получения соединения процесс диффузии ускоряют, учитывая все эти условия. В рабочей камере:
- Создают вакуум с остаточным уровнем давления до 10-5 мм ртутного столба либо наполняют среду инертным газом. Таким образом детали не подвержены воздействию кислорода, который является окислителем любого металла.
- Материалы разогревают температурой в 50-70% от температуры плавления заготовок. Этим добиваются увеличения пластичности деталей за счет более подвижного состояния их элементарных частиц.
- На заготовки оказывают воздействие механическим давлением в пределах 0,30-10,00 кг/мм2, сближая межатомные расстояния до размеров, позволяющих установить общие связи и взаимно проникнуть в близлежащие слои.
Требования к подготовке материалов
Перед тем как поместить заготовки свариваемых элементов в диффузионную установку, их подвергают предварительной обработке. Основная цель обработки контактирующих частей заготовок направлена на получение более гладких, ровных и однородных поверхностей, а также удаление из зоны соединения невидимых маслянистых образований и грязи. Обработка заготовок бывает:
- химической;
- механической;
- электролитической.
Пленки окислов, как правило, не влияют на процесс диффузии, так как они самоликвидируются в процессе нагревания в вакуумной среде.
Когда диффузионная сварка протекает недостаточно эффективно между веществами, у которых неодинаковый температурный коэффициент расширения, либо образуется хрупкий шов, используют так называемые буферные прокладки. Ими может служить фольга различных металлов. Так, медная фольга применяется при диффузионной сварке заготовок из кварца.
Характеристики получаемых соединений
В отличие от традиционных способов сварки расплавлением, где к основному металлу вводится дополнительный металл в шве, диффузионная сварка позволяет получить однородный шов без серьезных изменений в физико-механическом составе места соединения. Готовый стык обладает следующими показателями:
- наличие сплошного шва без пор и образований раковин;
- отсутствие окисных включений в соединении;
- стабильность механических свойств.
Благодаря тому что диффузия — это естественный процесс проникновения одного вещества в другое, в зоне соприкосновения не нарушается кристаллическая решетка материалов, а следовательно, отсутствует хрупкость шва.
Соединение деталей из титана
Диффузионная сварка титана и его сплавов характеризуется получением качественного соединения при высокой экономической эффективности. Она широко применима в медицине для изготовления деталей протезов, а также в других областях.
Детали подвергают нагреву до температур на 50º – 100º ниже, чем температура, при которой происходит полиморфное превращение. При этом на материалы оказывают небольшое давление в 0,05–0,15 кгс/мм².
Химический состав титанового сплава не влияет на крепость соединения элементов таким способом сварки.
Преимущества метода
При диффузионной сварке возможно:
- соединять однородные и неоднородные твердые вещества;
- избегать деформации деталей;
- не использовать расходники в виде припоев и флюсов;
- получать безотходное производство;
- не применять сложные системы приточно-вытяжной вентиляции, так как в процессе не образуется вредных паров;
- получать любую площадь зоны контактного соединения, ограниченную только возможностью оборудования;
- обеспечить надежный электрический контакт.
К этому следует добавить отличный эстетический вид готовой детали, которая не требует применения дополнительных операций обработки, таких как удаление сварной окалины, например.
Недостатки технологии
Диффузионная сварка является сложным технологическим процессом, к ее основным недостаткам можно отнести:
- необходимость применения специфического дорогостоящего оборудования;
- потребность в наличии производственных площадей, установка имеет немалые габариты;
- требование иметь специальные знания, навыки и понимание процесса работы;
- затраты времени на тщательную предварительную обработку заготовок;
- содержание вакуумной установки в предельной чистоте, иначе невидимая пыль может оседать на свариваемых элементах и приводить к браку соединения;
- трудность проверки качества шва без необходимости его разрушения.
Учитывая все это, а также специфику использования вакуумных установок, диффузионная сварка востребована только в условиях предприятий, а не частного использования.
Промышленное оборудование для диффузионной сварки
Существует несколько типов промышленного оборудования, разработанных для диффузионной сварки. Они в основном отличаются друг от друга спецификой свариваемых материалов и применением разных систем нагрева деталей.
Установка типа МДВС предназначена для производства гибких медных шин, контактных групп выключателей высоковольтных из меди и керрита, деталей газлифтных клапанов насосов скважинных, выполненных из нержавейки и твердых сплавов металлов. В системе применим эффект электроконтактного нагрева.
Сварочный комплекс типа УДВМ-201. Выполняет соединение методом диффузионной сварки материалов из стекла разных марок. Нагрев рабочей поверхности осуществляется методом радиационного излучения.
Оборудование сварочное УСДВ-630. Установка индукционного нагрева для сварки материалов композитных на основе титана и меди. Такие системы позволяют нагревать большие по площади детали.
Машина МДВС-302 для диффузионной сварки с применением высокочастотного нагрева деталей. Характеризуется наличием малогабаритного генератора на транзисторной схеме.
Сварка неплавящимся электродом в среде защитного инертного газа: технология процесса, оборудование
При сваривании неплавящимся электродом дуга возникает между электродом, находящимся в горелке, из которой подается защитный газ, и изделием. Для образования шва при этом в сварочную ванну подается присадочный материал. Если сварка ручная, то присадка подается непосредственно сварщиком, если автоматическая, процесс происходит без его участия.
Данный способ сваривания используется для сваривания неферромагнитных материалов, среди которых: магний, алюминий, цирконий, никель, титан, бронза, медь, нержавеющая сталь и другие. Этот метод сварки позволяет сварщику тонко чувствовать глубину проплавления металлов, что способствует хорошему качеству шва. При ручной сварке специалист сам управляет горелкой и присадочным материалом, что избавляет изделие от непроваров и других дефектов сварочного шва.
Область применения метода
Этот метод применяется в основном для сваривания тонкостенных цветных металлов. Он используется в производстве велосипедов, изготовлении различных заготовок. С его помощью изготавливаются различные предметы интерьера из нержавеющей стали и других материалов. Последующая обработка шва делает его практически незаметным.
Неплавящиеся электроды и их типы
На сегодняшний день при изготовлении металлоконструкций с помощью описываемого способа используются такие виды электродов:
- вольфрамовые. Наиболее распространенный вид, используемый при сварке неплавящимся электродом. Представляет собой стержень диаметром 1-4 мм. Вольфрам имеет очень высокую температуру плавления, что позволяет применять этот материал для изготовления электродов. Делятся на стандартные, иттрированные, лантанированные, торированные;
- угольные. Часто применяются для сварки изделий из цветных металлов и сталей, имеющих малую толщину стенок и для воздушно-дуговой резки металлов. Используются как с присадкой, так и без, могут складываться по линии сварки или подаваться непосредственно в сварочную ванну. Сварочный процесс при использовании этих материалов проводится на токе величиной не больше 580 А;
- графитовые. Особенно активно эти электроды применяются при работе с кабелями из меди. Отлично приспособлены к обработке, устойчивы к температурному воздействию и не подвержены быстрому износу. Благодаря всем этим качествам, весьма распространены на отечественном рынке.

Технология, особенности и оборудование необходимое для сварки
Способ сваривания неплавящимся электродом чаще всего применяют для соединения металлов с толщиной не более 5-6 мм, но это не значит, что его нельзя использовать для сваривания более толстостенных металлов. При сварке без применения присадки шов формируют, оплавляя кромки металла, при использовании присадки она подается в место формирования шва по тому же принципу, что и сварочная проволока при газосварке.
Оборудование, необходимое для сварки неплавящимся электродом, включает в себя:
- источник сварочного тока, на котором расположен регулятор силы тока, и вольтметр с амперметром для контроля процесса регулирования;
- TIG-горелку и рукав, которые подсоединяются к сварочному источнику. По рукаву на горелку подается защитный газ, в случае с использованием водяного охлаждения подается также охлаждающая жидкость;
- газовый баллон с защитным газом, подсоединенный с помощью рукава к источнику сварочного тока и оборудованный регулятором расхода и расходомером газа;
- обратный кабель для соединения изделия с источником сварочного тока.
При автоматической сварке используются автоматизированные системы для подачи изделий и управления инструментами для сварки.
Аргонная сварка неплавящимся электродом выполнятся переменным (TIG-AC) и постоянным (TIG-DC) токами. При сварке постоянным током может применяться обратная и прямая полярности. Если электрод подключен к плюсовому полюсу источника сварочного тока, то полярность является обратной, и в таком случае для сваривания применяются электроды большего диаметра, чем при прямой. Сваркой на переменном токе пользуются в основном для соединения беррилия, магния и алюминия, имея при этом не такую хорошую стабильность дуги, как на прямом токе, что, впрочем, исправляется наличием режима импульсной сварки на некоторых сварочных аппаратах.
В процессе сваривания длина дуги должна составлять 1,5-3 мм, её напряжение — 22-34 В. Размер вылета неплавящегося электрода не должен быть больше 3-5 мм, а в случае со стыковыми и угловыми швами — не более 5-7 мм.
В роли защитного газа чаще всего используются аргон или смесь аргона с гелием, они немного ухудшают стабильность сварочной дуги, но при этом усиливают её энергию, тем самым увеличивая скорость сварки. Для сваривания изделия толщиной до 10 мм применяют левый тип положения горелки для того, чтобы защитный газ имел прямой доступ к месту формирования шва. Для сварки более толстостенных материалов способ меняют на правый.
Недостатки и преимущества
Среди достоинств данного метода соединения следует указать:
- высокую скорость сварки;
- по окончании сварочных работ шов не требует дополнительной обработки;
- простота освоения техники сваривания при этом методе;
- прочность соединения, благодаря использованию аргона в качестве защитного газа;
- металл не деформируется при сварке, так как прогревается на минимальной площади;
- большое количество свариваемых металлов.
Из недостатков можно отметить:
- неудобство сваривания деталей под острым углом из-за формы сварочной горелки;
- затрудняется выполнение работы при сквозняках или на улице при ветреной погоде, так как нарушается правильная подача защитного газа в зону формирования шва;
- металл перед процессом сварки требует тщательной подготовки.
Дуговая сварка плавящимся электродом в защитных газах: оборудование и технология процесса
Дуговая сварка плавящимся электродом — это метод, при котором между свариваемым изделием и концом электрода возникает электрическая дуга, под действием которой основной металл и электрод начинают плавиться, образуя сварочную ванну, а обмазочный материал электрода при этом создает газовую защитную среду, необходимую для качественного шва.
Плюсы и минусы метода
Плюсами этого способа сваривания всегда считались:
- простота эксплуатации и низкая цена оборудования для сварного процесса;
- возможность сваривания большого количества разновидностей металлов при широком спектре выбора электродного материала;
- возможность выполнять сварные работы в труднодоступных местах;
- уместно сваривание в любых пространственных положениях.
Из недостатков стоит выделить:
- в процессе выделяется большое количество веществ, вредных как для самого сварщика, так и для окружающих;
- качество сварного шва во многом зависит от опыта и квалификации сварщика;
- скорость выполнения работ зачастую ниже, чем при иных методах;
- при выполнении сварки на постоянном токе магнитные поля сильно влияют на отклонение дуги, что затрудняет процесс.
Оборудование для ручной дуговой сварки
Оборудование, необходимое для ручного дугового сваривания, состоит:
- из источника питания, который может быть как переносным, так и стационарным в зависимости от вида выполняемых сварщиком работ;
- из кабеля с электродержателем, в котором фиксируется покрытый специальной обмазкой электрод;
- из кабеля обратного заземления для соединения свариваемого изделия с источником питания.
Также не стоит забывать о дополнительных средствах, таких, как: защитная маска, перчатки сварщика, разнообразные приспособления для удаления шлака и другие вещи, необходимые для удобства специалиста.
Перенос электродного металла: виды и характеристики
Перенос электродного металла делится на три типа:
- крупнокапельный перенос. Случается, если процесс происходит с высоким напряжением на электрической дуге и невысокими параметрами тока при сваривании. Размер капель плавящегося электрода при этом имеет диаметр больше сечения самого электрода. Процесс сварки в таком случае возможен только в вертикальном пространственном положении, так как сварочная ванна при таком переносе имеет большие размеры и её становится сложно контролировать.
- мелкокапельный перенос. При данном виде переноса металла капли расплавленного электродного материала равны или меньше по диаметру, чем сам электрод. Процесс сварки проходит с высоким напряжением на дуге и высокими параметрами тока. При мелкокапельном переносе увеличивается скорость выполнения работ, шов имеет более аккуратный вид. Такой тип переноса наиболее подходит для сваривания толстостенных металлов.
- струйный перенос. Струйный перенос металла обычно происходит при высокой силе тока и использовании электрода с прямой полярностью. При данном переносе очень мелкие капли металла идут одна за другой непрерывной цепочкой, обеспечивая ровную и гладкую на ощупь поверхность шва. Этот же тип переноса характерен для полуавтоматической сварки в среде защитного газа.
Сварочный процесс
От источника сварочного тока к электроду поступает электроэнергия. Во время контакта электрода со свариваемым металлом образуется электрическая дуга, которая расплавляет изделие и электрод, вследствие чего возникает сварочная ванна. Электродный материал, поступая в эту ванну, сплавляет кромки металла, который нужно сварить, а обмазка обеспечивает защиту в области формирования шва и образует защитный слой по окончании процесса сваривания.

Сварка плавящимся электродом в защитных газах
Этот тип сварки подразумевает собой сварку с помощью автоматических или полуавтоматических сварочных аппаратов, в процессе сварочная проволока подается в зону формирования шва. В роли защитного газа чаще всего выступают аргон либо углекислый газ, которые подаются в зону действия электрической дуги для обеспечения хорошего соединения металлов и отсутствия дефектов сварочного шва. Высокие сварочные токи и малый диаметр сварочной проволоки делают необходимой большую скорость подачи проволоки в сварочную ванну, скорость сваривания при этом составляет 15-80 м/ч.
Этот способ отличается высокой производительностью и большой скоростью процесса, что способствует его распространению в сфере промышленного производства металлоконструкций, машиностроении.
Из-за отсутствия шлаковых включений и возможности аккуратного выполнения сварки при очень малых толщинах материала данный метод получил широкое распространение на разнообразных СТО и других предприятиях по обслуживанию и ремонту автомобилей.
Пошаговая последовательность получения надежного и безопасного соединения медных проводов методом сварки
Среди различных способов соединения медных носителей тока лучше всего зарекомендовал себя метод сварки. Соединенные сваркой жилы образуют равномерную массу с максимальной проводимостью. Это не допускает внутреннего разогрева, сохраняет пожарную безопасность и бесперебойную работу сетевых электроустановок.
Какое оборудование потребуется для сварки медных проводов
Для сваривания подготовленных медных кабелей понадобится инвертор, электроды.
Особенности меди: текучесть, высокая теплопроводность, способность поглощать газы — требуют от исполнителя опыта и мастерства.
Применяемые электроды
Для сварки медных проводов применяют две разновидности электродов: угольные или графитовые с покрытием из медного напыления:
- температура разрушения материала электрода — более 3800ºС, а у меди плавление при 1080ºС, что допускает их многократное использование;
- быстрый разогрев материала стержня до температуры разжижения меди;
- во время сварки углеродный стержень не прилипает к проводам;
- 5-10 А — достаточный, хотя и небольшой ток для устойчивого разряда дуги.
Особенности использования угольных электродов
Электроды изготавливаются из прессованного в форме стержня электротехнического угля черного цвета. Концы его имеют скос. Даже при совсем небольшой силе сварочного тока на кончике электрода возникает высокая температура.
Угольный электрод используется, когда графитовым элементом сварить не удается. Работать нужно очень внимательно, чтобы не допустить перегрева изоляции. Угольные электроды обычно используются в сварочных устройствах малой мощности.
При работе с электродами из угля надо учитывать следующие особенности:
- место сварки обладает хрупкостью, может окисляться и иметь пористую структуру;
- из-за высокой температуры дуги электрод быстрее расходуется;
- угольным стержневым электродом работать сложнее, чем графитовым, требуются практические навыки.

Сварочные электроды из графита
Стержни-электроды из графита имеют серый цвет с небольшим металлическим оттенком. Кристаллическая структура углерода не подвержена окислению. При сварке кристаллический графит образует устойчивое к коррозии и температуре соединение. Эти электроды выгодны в использовании, они дешевле угольных. Стержни не растрескиваются, служат долго.
При необходимости возможна замена на подручные изделия из графита — щетки от коллекторных двигателей, стержни разобранных батареек. В случае использования подручной графитовой замены без омеднения вместо обычного держателя применяют зажим «крокодил».

Графитовые электроды чаще используются с инверторами, регулирующими сварочный ток.
Инверторы
Для сварки подойдет прибор постоянного или переменного тока с напряжением в диапазоне 12-36 В, регулировка тока обязательна.
Выбор модели исходит из предполагаемых режимов использования прибора: от получасовой работы без перерыва до многочасового интенсива.
Если прибор будет использоваться нечасто, то подойдет модель, обеспечивающая максимальный сварочный ток 150 А мощностью порядка 500 Вт. Этого достаточно для сварки скруток-жгутов сечением 20-25 мм².

Рекомендованные режимы сварочного тока для разных проводников
Величина сварочного тока зависит от размера сечения и количества жил в скрутке: чем толще скрученный жгут, тем большее значение силы тока нужно выставить на сварочном аппарате:
- 2 жилы, сечение каждой 1,5 мм² — 70 А;
- 3 жилы, сечение каждой 1,5 мм² — 80-90 А;
- 2-3 жилы, сечение каждой 2,5 мм² — 80-100 А;
- 3-4 жилы, сечение каждой 2,5 мм² — 100-120 А.
Указанные режимы сварочного тока являются ориентировочными. У разных производителей провода отличаются по химическому составу и заявленному сечению, сварочные приборы также отличаются своими характеристиками. Поэтому величину сварочного тока лучше подбирать практически на небольшом отрезке того же провода. Оптимальным при подборе режима опытным путем будет тот, когда дуга устойчива, а кончик электрода не клеится к месту сварки.
У современных аппаратов инверторного типа:
- устойчивый сварочный разряд, обеспечивающий качественное выполнение сварочных работ;
- при сварке жидкий металл не разбрызгивается;
- дуга не ослепляет сварщика из-за невысокой точки плавления меди;
- инверторы нетяжелые, их габариты небольшие, что позволяет переносить их к месту монтажа на ремне.
Подготовительные работы
Перед началом работы с проводами нужно еще раз проверить отсутствие на них напряжения.
Для дальнейшей работы понадобятся нож или специальные разделочные приспособления, наждачная шкурка, растворитель, плоскогубцы или пассатижи, изоляционная лента или термоусадочная трубка. Если для изоляции применяется термоусадочная трубка, очень удобно использовать фен, дающий плотное облегание пленкой.
Для получения качественного соединения проводится подготовительная работа в такой последовательности:
- с жилы бережно снимают участок изоляционного покрытия не менее 7 см для жилы сечением 1,5 мм². Если провода толще, то на каждые 0,5 мм² диаметра жилы убавляют 5 мм изоляции. Разделку проводят вдоль проводника ножом или специальным инструментом — стриппером;
- оголенные участки провода зачищают наждачной шкуркой;
- поверхность проводников обезжиривают ацетоном или уайт-спиритом;
- аккуратно, чтобы не повредить провода, скручивают их в жгутик руками или плоскогубцами, стараясь обеспечить их плотное прилегание друг к другу;
- кусачками или монтажными ножницами отрезают кончик жгута для выравнивания жил.
Алгоритм сварки проводов
Для безопасной работы понадобятся рукавицы, защитные сварочные очки, спецодежда. Нужно еще раз проверить, что под местом сварки нет легковоспламеняющихся предметов. Убедившись в полной безопасности, можно начинать сварку:
- на скрутку возле изоляции ставят зажим-радиатор для отвода избыточного тепла от медного проводника и защиты изоляционного покрытия от оплавления;
- туда же крепится «масса» сварочного инвертора;
- к сварочному аппарату подключают питание от сети;
- держатель с электродом подносят к концу скрутки;
- дуга расплавляет медь, на конце жгута-скрутки образуется наплыв в виде капли;
- процесс сварки происходит 1-2 секунды.
После того как сварка остынет, скрутку помещают в термоусадочную трубку или обматывают изоляционной лентой.
подготовка, необходимые материалы, технология процесса
Сварка лежачим электродом – это разновидность дуговой сварки, при которой электрод укладывается между деталями вдоль линии соединения, после чего зажигается дуга, и сварка происходит в автоматическом режиме.
Нюансы технологии и преимущества метода
Сверху и снизу будущего шва укладываются медные накладки – нижняя не дает стечь расплавленному электроду, а верхняя формирует ровную поверхность на стыке деталей и делает дугу закрытой. Электродов может быть несколько.
К преимуществам сварки лежачим электродом относят:
- отсутствие открытой дуги;
- уменьшение разбрызгивания окалины;
- возможность сварки трех или четырех деталей друг с другом одновременно;
- автоматизация процесса сварки.
Данный метод не требует ручного направления электрода и позволяет осуществлять сваривание сразу несколько групп деталей одним работником на одном сварочном агрегате, имеющим несколько держателей электродов.
Подготовка и материалы
Сварщику потребуются:
- несколько электродов с обмазкой;
- медные и стальные подкладки;
- фиксаторы для деталей;
- штангенциркуль;
- сварочный аппарат.
Лучше использовать электроды, разработанные специально для данного вида сварки – марки ОСЗ-12, ОСЗ-15Н и ОСЗ-17Н. Из стандартных подойдет электрод марки Э-46. Диаметр электрода выбирается в зависимости от толщины свариваемых деталей и особенностей материала – от 4 до 10 мм. Сварочный ток возрастает с увеличением диаметра электрода и варьируется в пределах 220-620 ампер.

Стальная прокладка сверху медной выполняет роль груза, препятствующего скидыванию медной накладки парами сгораемой обмазки электродов. Толщина медных подкладок и накладок – от 2 до 5 мм.
Вместо меди допустимо использовать кирпичи с гладкой поверхностью или любой другой негорючий тяжелый материал с гладкой поверхностью.
Штангенциркуль нужен для отмеривания одинаковой ширины нижнего зазора с двух концов свариваемых деталей – размер зазора важен при использовании неплотно прилегающих подкладок из кирпича, чтобы электрод не растекся под деталями при расплавлении.
Описание процесса сварки
Процедура сварки включает следующие шаги:
- Зачистка поверхностей деталей.
- Установка нижней подкладки.
- Установка деталей на подкладке.
- Выставление ширины зазора и фиксация деталей неподвижно.
- Укладывание электродов между деталями.
- Установка защитной прокладки, медной и стальной накладок.
- Пуск сварочной дуги.
- Остывание и зачистка сварного шва.
Сначала электроды устанавливаются в держатель, потом укладываются между деталями – масса подключается к нижней подкладке. Максимальная длина свариваемого в один прием шва – 1,2 метра, так как при большей длине возникнет преждевременный перегрев остатка электрода.
Сварка лежачим электродом используется в основном для формирования прямых швов, но допустимо сгибать электрод по форме будущего шва не более, чем на угол в 30 градусов, так как перегиб приведет к осыпанию обмазки и обрыву электрода при сварке в месте обсыпания. По этой же причине нельзя использовать несколько стыкующихся электродов вместо одного длинного.
Прокладка из бумаги между медной накладкой и деталями используется для предотвращения преждевременного износа прокладки, при этом важно следить, чтобы края прокладки не выступали наружу, так как они могут самовозгораться при сварке и стать причиной пожара.
Запуск дуги можно осуществить двумя способами:
- другим электродом, подключенным к этому же аппарату;
- куском металла.
Если используется стационарный сварочный агрегат, лучше запускать дугу другим электродом, установленным в держателе, при этом важно закрепить держатель, в котором зажаты лежачие электроды, так как притяжение, возникающее при образовании дуги, может вытянуть лежачие электроды из-под подкладки. Для пуска дуги отрезком металла нужно соединить таким отрезком край свариваемой детали и конец электрода. Держать металлический отрезок нужно в электроизолирующих рукавицах.
Несмотря на то что сварочная дуга скрыта под поверхностью медной накладки, сварщику нужно использовать защищающую глаза маску, так как излучение дуги видно в начале и в конце сварки. Кроме того, существует риск откидывания недостаточно тяжелой накладки в процессе сварки и открытия дуги.
Располагать детали можно как в одной плоскости, так и под углом друг к другу, в этом случае зазор между деталями не устанавливается, а накладка подгоняется по форме усеченного уголка в разрезе.
Вместо медной накладки может использоваться сыпучий флюс, электроды в таком случае берутся без обмазки. Использование флюса в сварке лежачим электродом позволяет не ограничивать длину сварного соединения, формируемого за одну процедуру. Кроме того, электрод без обмазки можно изгибать на больший угол при сварке деталей с изгибами.
Когда нужно сварить три или четыре детали вокруг одного центрального шва, такие детали нужно расположить в следующем порядке:
- Вниз укладывается самая массивная деталь.
- По бокам – близкие по форме детали.
- Поверх лежачего электрода укладывается наиболее легкая деталь.
Верхняя деталь должна покрывать лежачие электроды полностью и прижиматься грузом (обычно используют кирпичи). Для сварки более двух деталей лучше использовать пучок из трех или семи электродов.
С помощью лежачего электрода можно формировать не только стыковые соединения, но и сваривать плоские металлические листы, расположенные внахлест. Для этого верхняя накладка изготавливается в виде продольного металлического бруска, в котором проделана канавка для электродов. Накладка кладется на закрепленные внахлест листы канавкой с электродом вниз, при этом листы проплавляются насквозь, если их толщина до 8 мм, или насквозь проплавляется только верхний лист, если нижний достаточно толстый.
Если требуется сварить много однотипных пар деталей, то подобрать оптимальную толщину электрода, величину сварочного тока и ширину зазора можно опытным путем. Для этого нужно сваривать парные обрезки деталей лежачим электродом, после чего разрезать их поперек сварного шва и оценивать его качество – при выраженной границе шов-деталь нужно увеличить сварной ток, при наличии впадин – уменьшить ширину зазора, утолщать электрод или использовать пучок электродов.
Электродинамический громкоговоритель | Статья об электродинамическом громкоговорителе от The Free Dictionary
громкоговоритель, в котором взаимодействие между магнитным полем постоянного магнита и током в движущейся катушке, подключенной к источнику электрических колебаний, используется для преобразования электрических колебаний на звуковых частотах. механическим колебаниям.
Катушка, которая расположена в воздушном зазоре магнита, диафрагма, жестко прикрепленная к катушке, и магнитная система составляют динамик (см. Рисунок 1).Взаимодействие тока и магнитного поля производит механические колебания диафрагмы, которые сопровождаются излучением звуковых волн либо непосредственно, как в прямой радиатора громкоговоритель, или через рога, как в роговой громкоговоритель. Для обеспечения надежности работы и высококачественного звука динамик размещается в деревянном, пластиковом или металлическом корпусе.
Рисунок 1 . Схема электродинамического громкоговорителя с прямым излучателем: (М) магнит, (MD) подвижная диафрагма, (VC) звуковая катушка
Электродинамические громкоговорители используются в радиоприемниках, проигрывателях и магнитофонах.Номинальная мощность громкоговорителя, которая меняется в зависимости от предполагаемого использования громкоговорителя, составляет от 0,05 Вт до 100 Вт. КПД громкоговорителей с прямым излучателем обычно не превышает 1–3%. Электродинамические громкоговорители могут воспроизводить звук в относительно узком частотном диапазоне, например от 300 Гц (Гц) до 5000 Гц, или в широком диапазоне, например от 40 Гц до 15000 Гц. Однако сложность широкополосных громкоговорителей затрудняет их производство, и в электродинамических громкоговорителях часто используются системы, состоящие из нескольких громкоговорителей, каждый из которых воспроизводит звук в определенной части частотного диапазона.
СПИСОК ЛИТЕРАТУРЫ
Римский-Корсаков, А.В. Электроакустика . М., 1973.Эфрусси, М. М. Громкоговорители и их применение , 2-е изд. Москва, 1976.
Н. Т. М ОЛОДАЯ и Л. З. П АПЕРНОВ
Большая Советская Энциклопедия, 3-е издание (1970-1979). © 2010 The Gale Group, Inc. Все права защищены.
.FCAW (Дуговая сварка с флюсовым сердечником) Определение, процесс и машина
Дуговая сварка с флюсовым сердечником (FCAW) — это Сварочная дуговая электрическая проволока с флюсом (центральный защитный сердечник). FCAW — это комбинация процессов сварки GMAW, SMAW и SAW. В этом источнике сварочной энергии FCAW используется электрический ток постоянного или переменного тока, поступающий от электростанций или через трансформатор или выпрямитель.
Сварка FCAW — это один из видов электросварки, при котором сварочные электроды с присадочной проволокой непрерывно или механически непрерывно вводятся в электрическую дугу.Сварочная проволока или электроды, используемые для сварки FCAW, изготовлены из тонкого металлического цилиндрического проката, затем он заполняется флюсом в зависимости от его полезности.
Определение сварки FCAW, процесс и классификация проволоки:
Процесс сварки FCAW такой же, как и сварка GMAW, но разница заключается в сварочной проволоке или трубчатом электроде, содержащем флюс, в то время как GMAW Solid. По способам защиты сварку FCAW можно разделить на две части.
FCAW Процесс:
- FCAW SS (самозащитный).
Процесс защиты металла шва плавится с использованием газа, образующегося при испарении или реакции флюса сердечника. - FCAW G (газовая защита).
Это защита с двойным газом, которая защищает металл шва от плавления с использованием собственного газа, а также с добавлением защитного газа, который поступает извне. Вышеупомянутые два метода вместе для получения сварочного шлака из флюса в сварочной проволоке, который служит для защиты металла шва в процессе замораживания. Однако отличие заключается в способе использования указанной выше системы дополнительной подачи газа и использовании сварочной горелки (сварочного пистолета).


Сварка FCAW по принципу действия делится на два:
- Автоматический (автомат автоматический).
- Полуавтомат (полуавтомат).
Основные характеристики (Основные характеристики) блока, принадлежащего FCAW в процессе сварки:
- FCAW Сварка металлургии имеет характер, которым можно управлять с помощью выбора флюса.
- FCAW имеет высокую производительность, поскольку может поставлять электроды для непрерывной сварки.
- При образовании валиков или выступов расплавленный сварочный шлак можно защитить толстой сваркой FCAW, как правило, с использованием газа CO2 или его смесей с аргоном в качестве защитного газа. Но во избежание попадания загрязненного металла наружу или во избежание пористости, он должен быть избирательно-содержащим флюсом, обладающим свойствами связывания кислорода или раскислителем.
FCAW Характер машина и процесс:
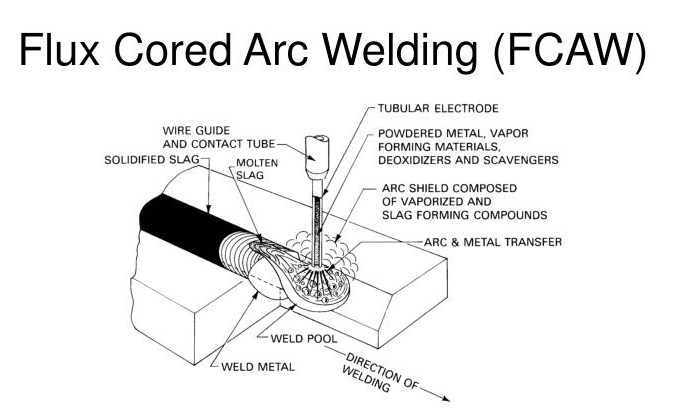
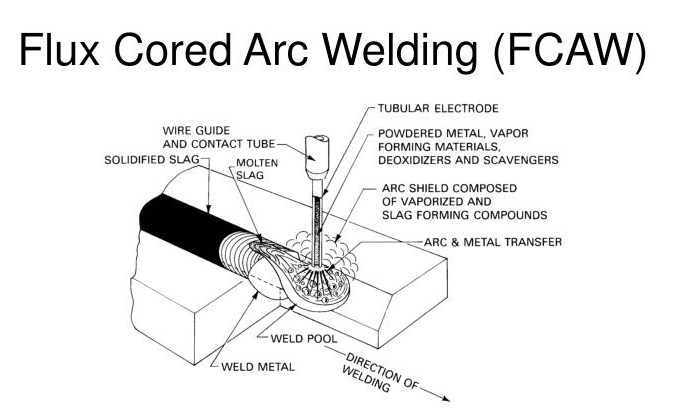
FCAW Сварочный аппарат в зависимости от силы тока делится на три вида, а именно: сварочный аппарат постоянного или постоянного тока (DC), сварочный аппарат переменного или переменного тока. (AC) и сварочный аппарат, который является двойным сварочным аппаратом, который может использоваться для сварки постоянным током (DC) и сварки на переменном токе (AC).Сварочный ток постоянного тока можно использовать двумя способами: прямой и обратной полярностью.
Сварочный аппарат постоянного тока с прямой полярностью (DC-) используется, когда точка плавления основного материала высокой и большой емкости, к держателям электродов, подключенных к отрицательному полюсу и металлическому стержню, подключена к положительному полюсу, в то время как Сварочный аппарат с обратной полярностью постоянного тока (DC +) используется, когда нижний стержень и небольшая емкость для материалов с температурой плавления, к держателям наполнителя, подключаются к положительному полюсу, а металлический стержень — к отрицательному полюсу.Выбор при использовании отрицательной или положительной полярности постоянного тока определяется в первую очередь используемым электродом. Некоторые наполнители FCAW предназначены для использования только DC- или DC +. Другие наполнители могут использоваться как в DC-, так и в DC +.
См .: Определение сварки и история
Области применения FCAW:
- Углеродистая сталь.
- Стальная наплавка и оболочка.
- Нержавеющая сталь.
- Чугун.
- Сталь низколегированная углеродистая.
- Точечная сварка листовой стали
Сварка FCAW Проволока Классификация :
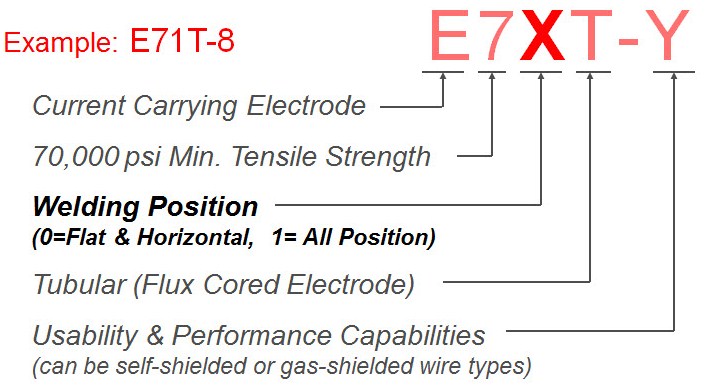
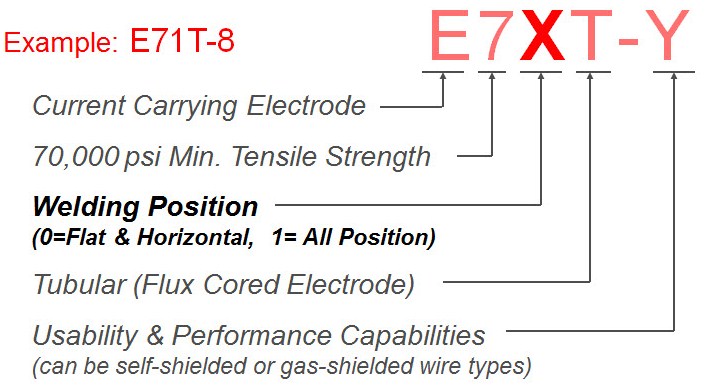
При сварке углеродистой и низколегированной стали широко используется электрод с флюсовой сердцевиной, который широко используется Т-1 (кислый шлак), Т-2 (однопроходная сварка) и Т-5 (основной шлак).
- Электрод Т-1 обладает хорошими сварочными свойствами, но не помогает сохранить кислотный шлак в металле сварного шва с низким содержанием водорода, если он специально не изготовлен. Только определенное количество порошкового электрода может иметь низкое содержание водорода, и это наиболее широко доступный электрод типа T-1. №
- Электрод типа Т-2 предназначен для однопроходной сварки ржавых металлов и имеет раскислитель Mn и Si выше. Электроды T-2 никогда не должны использоваться для многопроходной сварки из-за увеличения Mn и Si, так как прочность на растяжение не растворенного металла шва будет увеличиваться в размере, вызывая проблемы с трещинами при сварке или использовании кислых условий эксплуатации. .
- Электрод 5 типа Т имеет основной шлак, содержащий низкое содержание водорода в металле сварного шва и повышающий ударные свойства и удовлетворительное сопротивление растрескиванию. Преимущества и недостатки
Преимущества FCAW:
- Процесс FCAW-g имеет преимущество более глубокого проникновения и более высокой скорости зарядки, чем процесс SMAW. Таким образом, сварочный процесс становится более экономичным в сварочных цехах.
- Наполнитель FCAW-SS устраняет необходимость во внешнем защитном газе и выдерживает более сильный ветер, не вызывая пористости.
Недостатки FCAW:
- FCAW-G и FCAW-SS образуют слой шлака, который разрушается между слоями сварного шва.
- Процесс FCAW-g дает больше дыма, чем сплошная проволока GMAW. Проволока FCAW-SS даже вызывает больше дыма, поэтому для работы в сварочных цехах требуется соответствующая вентиляция, а иногда требуются специальные инструменты для вывода дыма в сварочную горелку.
В приведенной выше статье о процессе сварки FCAW и ее определении вы можете посмотреть классификацию проволоки FCAW и получить дополнительную информацию.Для FCAW Welder то же самое, что и GMAW, но если сертификат сварщика FCAW не может использоваться для сварки GMAW или других процессов. Поскольку стандарт или код в ASME, другой процесс должен выполнить повторную аттестацию.
.Аппарат для холодной сварки, Аппарат для электроискровой сварки (аппарат для сварки электростатическим разрядом), Аппарат для сварки серого чугуна, Сварочное оборудование для серого чугуна, Сварочное оборудование для алюминия, Сварочный аппарат для меди, Аппарат для ремонта металла, Аппарат для сварки дефектов пористости, Аппарат для сварки дефектов отливки
AWE-19US (новый)
ВЫСОКОСКОРОСТНАЯ УЛЬТРАЗВУКОВАЯ МАШИНА ДЛЯ ХОЛОДНОЙ СВАРКИ
Ультразвуковые вибрационные высокочастотные разряды со скоростью более 20000 в секунду позволяют AWE-19US устранять различные дефекты литья с высокой скоростью и высоким качеством.
Используется для сварки дефектов отливки / Сварка дефектов бывшего в употреблении оборудования / Ремонт стальных форм / Упрочнение поверхности из вольфрамовой стали и т. Д.
Qingdao Atom Welding Equipments Co., Ltd. (Китай) — ведущая в мире компания по исследованию технологий холодной сварки и производству оборудования.
У нас более 10 лет опыта в этой области, и мы постоянно обновляем нашу технологию холодной сварки и улучшаем характеристики оборудования.
Производство аппаратов для холодной сварки (аппаратов для электроискровой сварки ESD) и интеллектуальных прецизионных сварочных аппаратов (аппаратов для сварки тонкой нержавеющей стали, аппаратов для сварки канальных букв и знаков) достигло международного уровня отраслевой специализации.
в основном используется для ремонта всех видов дефектов литья, таких как дефекты песчаных отверстий, дефекты вздутия, дефекты пористости штифта, небольшие дефекты усадки, дефекты трещин и т. Д., Подходит для ковкого чугуна, серого чугуна, алюминия, стали, меди. Широко используется в автомобильной промышленности; промышленность по производству электроприборов; медицинское оборудование; строительство; промышленность стальных конструкций; мостостроение и другие отрасли.
Интеллектуальный прецизионный сварочный аппарат в основном используется для сварки тонкой нержавеющей стали, с очень блестящей сварочной поверхностью, без черной кромки, без полировки.
Ключевые слова: Аппарат для холодной сварки, Аппарат для электроискровой сварки, Аппарат для аргонодуговой сварки, Аппарат для сварки дефектов отливки, Аппарат для сварки дефектов из ковкого чугуна (SG-чугуна), Аппарат для сварки дефектов серого чугуна, Аппарат для сварки дефектов алюминиевого литья, Сварка медного литья. Машина, Сварочный аппарат из нержавеющей стали, Сварочный аппарат для дефектов дырки, Сварочный аппарат для дефектов песочных отверстий, Аппарат для термоусадочной сварки, сварочный аппарат, сварочный пистолет, сварочный электрод, аппарат для холодной сварки, сварочные принадлежности, Сварка дефектов насоса, Сварка дефектов автозапчастей
.