Неразрушающий контроль | Сварка и сварщик
ГОСТ 18353-79 «Контроль неразрушающий. Классификация видов и методов» в зависимости от физических явлений, положенных в основу неразрушающего контроля подразделяет его на виды:
— оптический;
— радиационный;
— акустический;
— магнитный;
— вихретоковый;
— электрический;
— радиоволновой;
— тепловой;
— проникающими веществами.
Вид контроля – это условная группировка методов неразрушающего контроля, объединенная общностью физических принципов, на которых они основаны. Методы каждого вида неразрушающего контроля классифицируются по определенным признакам:
— характеру взаимодействия физических полей с объектом;
— первичным информативным параметрам;
— способам получения первичной информации.
Методы контроля качества сварных соединений устанавливает ГОСТ 3242-79.
Применение метода или комплекса методов контроля для обнаружения дефектов сварных соединений при контроле конструкций при ее изготовлении, ремонте и реконструкции зависит от требований, предъявляемых к сварным соединениям в технической документации на конструкцию. Технология контроля сварных швов любым методом должна быть установлена в нормативно-технической документации на контроль.
Методы неразрушающего контроля качества сварных соединений
Визуальный контроль и измерения
Визуально-оптический контроль – это один из методов неразрушающего контроля оптического вида. Он основан на получении первичной информации об объекте при визуальном наблюдении или с помощью оптических приборов. Это органолептический контроль, т.е. воспринимаемый органами чувств (органами зрения) ГОСТ 23479-79 «Контроль неразрушающий. Методы оптического вида» устанавливает требования к методам контроля оптического вида. Визуальный метод контроля позволяет обнаруживать несплошности, отклонения размера и формы от заданных более 0,1 мм при использовании приборов с увеличением до 10х. Визуальный контроль, как правило, производится невооруженным глазом или с использованием увеличительных луп 2х до 7х. В сомнительных случаях и при техдиагностировании допускается увеличение до 20х.
Визуальный контроль выполняется до проведения других методов контроля. Дефекты, обнаруженные при визуальном контроле, должны быть исправлены до проведения контроля другими методами.
Радиографический контроль
Радиационный вид неразрушающего контроля в соответствии с ГОСТ 18353-79 делится на методы: радиографический, радиоскопический, радиометрический. Радиографический метод контроля основан на преобразовании радиационного изображения контролируемого объекта в радиографический снимок. Требования к радиографическому контролю регламентированы ГОСТ 7512-82 «Контроль неразрушающий. Сварные соединения. Радиографический метод».
Схема просвечивания рентгеновскими лучами:
1 – рентгеновская трубка; 2 – кассета; 3 – фотопленка; 4 – экраны.
Метод ультразвуковой дефектоскопии
Данный метод относится к акустическому виду неразрушающего контроля (ГОСТ 3242-79), применяется при толщине металла шва не менее 4 мм. Он основан на использовании ультразвуковых волн, представляющих собой упругие колебания материальной среды с частотой выше 0,5-0,25 МГц (выше той, которую способны воспринимать слуховые органы человека). В этом методе контроля (ГОСТ 14782-86) используется способность ультразвуковых волн отражаться от границы раздела двух сред, обладающих разными акустическими свойствами. Когда при прохождении через сварной шов ультразвуковые волны встречают на своем пути дефекты (трещины, поры, шлаковые включения, расслоения и т. д.), они отражаются от границы раздела металл–дефект и могут быть зафиксированы при помощи специального ультразвукового дефектоскопа.
Магнитные методы контроля
Магнитные методы контроля основаны на принципе использования магнитного рассеяния, возникающего над дефектом при намагничивании контролируемого изделия. Например, если сварной шов не имеет дефектов, то магнитные силовые линии по сечению шва распределяются равномерно. При наличии дефекта в шве вследствие меньшей магнитной проницаемости дефекта магнитный силовой поток будет огибать дефект, создавая магнитные потоки рассеяния.
Прохождение магнитного силового потока по сварочному шву:
а – без дефекта; б – с дефектом
В соответствии с ГОСТ 18353-79 в зависимости от способа регистрации потоков рассеяния различают три магнитных метода контроля: магнитопорошковый, индукционный, магнитографический. Наиболее распространен магнитопорошковый метод или магнитопорошковая дефектоскопия (МПД).
Вихретоковый контроль
Методы вихретокового контроля основаны на регистрации изменения электромагнитного поля вихревых токов, наводимых возбуждающей катушкой в электропроводящем объекте контроля. Вихревые токи – это замкнутые токи, индуктированные в проводящей среде изменяющимся магнитным полем. Если через катушку пропускать ток определенной частоты, то магнитное поле этой катушки меняет свой знак с той же частотой. Интенсивность и распределение вихревых токов в объекте зависят от его геометрических, электромагнитных параметров и от взаимного расположения измерительного вихретокового преобразователя (ВТП) и объекта. В качестве преобразователя используют обычно индуктивные катушки (одну или несколько). Синусоидальный или импульсный ток, действующий в катушках ВТП, создает электромагнитное поле, которое возбуждает вихревые токи в электропроводящем объекте. Электромагнитное поле вихревых токов воздействует на катушки преобразователя, наводя в них ЭДС или изменяя их полное сопротивление. Регистрируя напряжение на зажимах катушки (трансформаторный вихретоковый метод) или ее сопротивление (параметрический вихретоковый метод) получают информацию о свойствах объекта и о положении преобразователя относительно него.
Методы контроля проникающими веществами
Капиллярная дефектоскопия
Капиллярные методы НК предназначены для обнаружения открытых дефектов, выходящих на поверхность: трещин, пор, раковин, непроваров и других несплошностей поверхности изделий без их разрушения. Различают два основные метода капиллярной дефектоскопии: цветной и люминесцентный. Этими методами контролируют детали различной формы из аустенитных, титановых, алюминиевых, медных и других немагнитных материалов. Эти методы позволяют выявлять:
— трещины сварочные, термические, усталостные;
— пористость, непровары и другие дефекты типа открытых несплошностей различной локализации и протяженности, невидимые невооруженным глазом и лежащие в пределах чувствительности и надежности дефектоскопических средств.
Течеискание
Пузырьковый метод с использованием вакуумных камер
Вакуумный контроль сварных швов применяют в тех случаях, когда применение других способов почему-либо исключено. В частности, этот метод широко применяется при контроле сварных днищ резервуаров, газгольдеров, цистерн, гидроизоляционных ящиков. Он позволяет обнаружить отдельные поры диаметром до 0,004 0,005 мм, а производительность при его использовании достигает 40 – 60 м сварных швов в час. Вакуум создают при помощи переносной вакуум-камеры, которую устанавливают на наиболее доступной стороне проверяемого участка шва, предварительно обильно смоченной мыльным раствором. В результате разности давлений по обеим сторонам шва воздух будет проникать в камеру при наличии неплотностей в сварном соединении. В местах трещин, непроваров, газовых пор образуются стойкие мыльные пузырьки, хорошо видимые через прозрачный верх камеры. Отметив расположение дефектов мелом, цветным карандашом или краской, впускают атмосферный воздух, камеру снимают и сделанные отметки переносят на сварной шов.
Контроль швов газоэлектрическими течеискателями
В настоящее время применяют два вида газоэлектрических течеискателей: гелиевые и галоидные. Чувствительность газоэлектрических течеискателей к выявлению неплотностей в швах очень высока, но ввиду сложности конструкции и значительной стоимости изготовления их применяют только для контроля особо ответственных сварных конструкций.
Принцип работы гелиевого течеискателя основан на высокой способности гелия при определенном вакууме проходить сквозь неплотности сварных швов. При контроле сварные швы снаружи испытуемой емкости обдувают из резинового шланга тонкой струёй гелия, находящегося под небольшим давлением в специальном сосуде — газометре. При наличии неплотностей в швах гелий или его смесь с воздухом попадает из емкости в масс-спектрометрическую камеру, в которой поддерживается высокий вакуум. При попадании гелия в масс-спектрометрическую камеру в ней возникает ионный ток, который подается на индикаторы — миллиамперметр и сирену. Величина отклонения стрелки миллиамперметра позволяет судить о размерах дефекта.
Испытания плотности сварных швов
Испытаниям на плотность подвергают емкости для горючего, масла, воды, трубопроводы, газгольдеры, паровые котлы и др. Существуют несколько методов контроля плотности сварных швов: гидравлическое испытание, испытание водой без давления или наливом, испытание струей воды или поливом, пневматическое испытание, испытание аммиаком, испытание керосином.
Неразрушающий контроль сварных соединений: методы и технология проведения
Прочность сварных конструкций зависит от качества швов, которое невозможно объективно оценить после визуального осмотра. Поэтому были разработаны другие методы неразрушающего контроля сварных соединений. При проведении не нарушается целостность элементов конструкции. Неразрушающим контролем сварного соединения обнаруживают внешние и скрытые изъяны, их размеры, расположение. Полученные данные позволяют с высокой точностью определять качество швов. На предприятиях неразрушающему контролю сварных соединений подвергают всю продукцию.
Основные дефекты
Наружные и внутренние дефекты образуются в основном из-за нарушения технологии. Методами неразрушающего контроля сварных швов выявляют:
- Подрезы, которые образуются, если завышен ток или держится длинная дуга.
- Непровары, возникающие при работе с заниженными сварочными токами, завышенной скоростью ведения электрода, недостаточным зазором между кромками заготовок.
- Прожоги образуются, если сварку выполняют завышенным током с малой скоростью.
- Появление пор внутри соединения. Они образуются из-за быстрого охлаждения, от влаги, попадающей в расплавленный металл с непросушенных электродов или плохо очищенных кромок.
- Кратеры появляются при обрыве дуги или неправильном завершении шва.
- Трещины снаружи и скрытые образуются при неравномерном остывании объема расплавленной зоны. Для предотвращения этого явления основной металл предварительно подогревают.
- Кусочки шлака остаются внутри, не успев всплыть при быстром охлаждении шва, если работа выполнялась с повышенной скоростью малым током.
Методы неразрушающего контроля сварных соединений
Способы проверки качества швов и требования, предъявляемые к ним, приведены в ГОСТ 3242-79. Методы объединены в группы по принципу действия. Выбор вида неразрушающего контроля сварных соединений зависит от возможностей и условий проведения.
Визуально-измерительный
Этим методом при внешнем осмотре, используя эталоны, шаблоны, лупу, линейку, выявляют наружные изъяны размером от 0,1 мм. Перед проверкой шов и рядом расположенные поверхности очищают от шлака, брызг металла. К достоинствам относится доступность и отсутствие сложного оборудования. На предприятиях сварщики после обучения самостоятельно проводят проверку соединений на наличие изъянов. Недостатком считают субъективность оценки качества. Работник может не заметить дефект из-за невнимательности, усталости или недомогания. Другие способы контроля применяют после проведения визуального осмотра и устранения выявленных изъянов.
Ультразвуковой
Метод основан на способности звуковых волн высокой частоты, посылаемых излучателем, отражаться от границы раздела сред с разной плотностью. Вернувшийся ультразвук улавливается датчиком дефектоскопа, после преобразования выводится на дисплей. По степени ослабления и углу отражения сигнала оператор определяет расположение, величину дефектов. Мобильный вариант ультразвукового дефектоскопа удобен для проверки качества сварных соединений при монтаже магистральных трубопроводов или больших конструкций.
Из достоинств отмечают простоту проверки и быстрое получение результатов. Однако для расшифровки отраженных сигналов требуется оператор с профессиональной подготовкой. Высокая цена аппаратуры не окупается на мелких предприятиях.
Капиллярный
Этим способом выявляют наружные и сквозные дефекты, которые не видны невооруженным глазом. Принцип действия основан на способности жидкостей (индикаторов) с высокой текучестью проникать в мельчайшие полости, которые наносят на соединение. Через 0,5 — 30 минут, когда индикатор заполнит дефекты, излишки удаляют. Для определения размеров изъянов поверхность обрабатывают реагентом (проявителем), который в местах контакта с индикатором меняет цвет.
На производстве диагностику проводят горячим минеральным маслом и раствором извести, на которой после высыхания проявляются контуры дефектов. Вместо них также применяют пару краска ― бензол. Для улучшения контрастности в качестве проявителя берут флуоресцирующий реагент. Метод недорогой, но не выявляет скрытые дефекты.
Магнитный
Суть метода состоит в наведении на диагностируемом участке магнитного поля. Если изъянов нет, силовые линии остаются ровными, если есть ― изгибаются в местах нарушения структуры металла. На практике магнитные неразрушающие методы контроля выполняют двумя способами:
- графическим с регистрацией искажений специальным прибором;
- с помощью железного порошка, который после высыпания на проверяемый участок начинает скапливаться в местах расположения изъянов.
Радиографический
Этим способом диагностируют швы на особо ответственных конструкциях. Суть заключается в просвечивании металла рентгеновскими лучами или гамма-излучением с фиксацией результата на фотопленке. По изображению на снимке определяют размеры пустот или посторонних включений. Диагностику проводят стационарными и компактными аппаратами для работы в полевых условиях.
К достоинствам радиографии относятся точность результатов, быстрое проведение диагностики. Основным минусом считается повышение уровня радиации рядом с работающим прибором. Поэтому необходимо обеспечение безопасности персонала. Высокая цена аппаратуры и расходных материалов также не радует.
Заключение
Некоторые методы неразрушающего контроля сварных соединений успешно применяют в домашних мастерских. Поскольку требования к самодельным конструкциям невысоки, их проверяют визуально-измерительным неразрушающим контролем сварных соединений. Для освоения технологии покупают специальный кейс с набором инструментов и инструкцией по применению. При проверке швов на герметичность предпочтение отдают капиллярному неразрушающему контролю сварных соединений. В качестве индикатора берут керосин, проявителя ― раствор мела.
Виды и методы неразрушающего контроля сварных соединений
Под поверхностью внешне красивого и аккуратного сварного шва могут скрываться. Недопустимо, чтобы из-за подобных дефектов ответственная деталь развалилась в самый неподходящий момент. Эта проблема остро стоит перед разработчиками самой разной продукции.
В машиностроении, для которого особенно важна способность конструкций противостоять динамическим нагрузкам. Не вышедшие на орбиту спутники, разбившиеся самолеты, попавшие в аварию автомобили или затонувшие корабли – вполне возможно, что все это результат некачественно выполненной сварки.
В строительстве, где преобладают статические нагрузки. Многоэтажные небоскребы, пролеты мостов или большие по площади перекрытия простоят много лет лишь в том случае, если надежно соединить их металлические конструкции и арматуру. Причиной обрушения может стать даже незначительная трещина.
В массовом производстве, когда идет речь о десятках и сотнях тысяч сварных соединений. Падение спроса на продукцию из-за ее низкого качества приводит к большим финансовым потерям. Ради того, чтобы подобного не произошло, стоит пойти на дополнительные траты и организовать пост контроля качества сварных швов.
При изготовлении штучной продукции и опытных образцов. Результаты научного эксперимента могут оказаться не точны, а время, потраченное на проведение замеров, будет потрачено впустую, если не соблюсти точных параметров сварного соединения при изготовлении ответственного оборудования. Уникальное изделие, созданное для того, чтобы прослужить десятки лет, не проработает и малой части расчетного срока. А все из-за того, что вовремя не была проведена дефектоскопия.
Повсюду соединительные швы должны быть надежны. Важно, чтобы они были равномерны, герметичны, прочны и по всей площади полностью соответствовали предъявляемым требованиям.
Применяемые методы проверки
Чтобы повысить качество продукции и своевременно выявить опасный брак, ученые разработали методы неразрушающего контроля сварных соединений. Для этого они использовали процессы, в основе которых лежат различные физические явления. На сегодняшний день наибольшее распространение получили следующие способы обнаружения дефектов:
Визуально-оптический. Используя оптические приборы, можно во всех подробностях разглядеть поверхность детали и обнаружить пропуски и трещины, невидимые невооруженным глазом. В большинстве случаев для этого используют устройства с увеличением до десяти крат. Но если у контролера возникнут сомнения, допускается двадцатикратное увеличение. Заглянуть при этом под поверхность шва все равно не получится, а потому этот метод контроля – первичный. Он не дает полной и объективной картины
Радиографический, при котором используют гамма-лучи, проходящие сквозь контролируемую деталь. Полученное таким способом изображение фиксируется на пленке. Эта методика довольно эффективна, но позволяет получить представление лишь об ограниченном участке шва. Скорость подобного обследования невелика и технология плохо подходит для массового производства.
Радиоскопический. В этом случае также применяется источник гамма-излучение, но изображение не фиксируется на пленке, а выводится на экран специального устройства. Появляется возможность контроля в реальном времени, что важно при постоянном обследовании больших партий продукции. С учетом этого можно закрыть глаза даже на относительно высокую стоимость оборудования.
Радиометрический. Изображения на экране или пленке невозможно перевести в цифры, а визуальная оценка не всегда бывает объективна. Измеряя интенсивность гамма-излучения при его прохождении через сварное соединение, и сравнивая полученные результаты с результатами, полученными при обследовании эталонных образцов, удается значительно повысить стандарты контроля качества.
Ультразвуковой. Это самый эффективный из методов акустической дефектоскопии. Его целесообразно использовать в тех случаях, когда толщина сварного шва превышает 4 мм. Известно, что ультразвуковые волны отражаются от границы между разными средами. Анализируя характер прохождения этих волн через структуру материала, можно составить точное представление о ее однородности.
Магнитографический. Намагничивая контролируемые детали и регистрируя изменение магнитных полей, полученные результаты фиксируют на прижимаемом к шву специальном носителе. Полученные данные точны, и по ним можно судить не только о внешних, но и о внутренних дефектах. Основной недостаток очевиден – как и радиография, такой способ контроля требует определенного времени.
Магнитопорошковый. С помощью суспензии на основе смешанного с керосином флюоресцирующего порошка, частицы которого намагничены, удается обнаружить малые, шириной в один и более микрон, трещины. Под воздействием созданного переменного магнитного поля частицы скапливаются в местах дефектов и повторяют их форму. Это можно хорошо рассмотреть, подсветив их кварцевой лампой. При всей своей относительной простоте магнитопорошковый метод показывает достаточную эффективность в основном при контроле уже зачищенных швов.
Индукционный. С помощью искателя, конструкция которого может быть различна, можно проверить однородность магнитного поля, создаваемого на ограниченном, до 300 мм длиной, участке шва. Таким образом, регистрируются потоки рассеивания, возникающие в местах дефектов. Обследование не занимает много времени. Но это лишь предварительный метод диагностики, требующий обследования места обнаруженного повреждения более точными способами.
Вихретоковый. Основанный на взаимодействии специального преобразователя с создаваемыми внутри контролируемого участка вихревыми токами, этот метод неразрушающего контроля сварных соединений не получил широкого распространения. Дело в том, что на результаты измерений оказывает сильное влияние однородность материала, создавая трудности для точного выявления места дефекта. Его просто не видно на фоне возникающих помех.
Капиллярный. Этот метод дефектоскопии был известен еще в Средние века. Однако, и сегодня он не потерял своей актуальности. Его суть в том, что на обследуемую деталь наносят проникающую жидкость – ее называют пенетрант – и по следам ее проникновения выявляют трещины и другие повреждения. Чтобы облегчить процесс, пенетрант часто окрашивают во флюоресцирующие цвета. Понятно, что таким образом удается выявить лишь внешние повреждения. Зато он подходит для обследования ферромагнитных материалов.
Пузырьковый, с использованием вакуумных камер. Нанеся на поверхность детали мыльный раствор, и создав разряжение с помощью вакуумной камеры, удается с достаточно высокой точностью обнаружить место, где сварной шов негерметичен. Этот специфический способ можно использовать при проверке таких конструкций, как цистерны, гидроизоляционные ящики или газгольдеры. Однако установка вакуумной камеры – непростая задача. Высокая стоимость оборудования и трудности при его использовании ограничивают применение эффективной методики.
Контроль сварных швов с помощью газоэлектрических течеискателей. Наибольшее распространение получили устройства, в которых в качестве рабочего тела используется гелий. С одной стороны проверяемой поверхности устанавливают вакуумную камеру, оборудованную масс-спектрометром. С другой – обдувают сварное соединение гелем, находящимся под небольшим давлением. Если шов негерметичен, то вещество проникает внутрь камеры. По регистрируемым показаниям можно судить о размерах повреждения. Из-за сложности оборудования этот метод оправдывает себя лишь при проверке особо ответственных деталей.
Существуют и другие технологии, по разным причинам применяемые лишь ограниченно, или считающиеся неэффективными.
Выбор технологии
Желая наладить контроль сварных швов, нужно осознавать, что выбор конкретной методики зависит от множества факторов.
Объемов выпуска продукции. Сколь бы ни были точны полученные данные, использовать при крупносерийном производстве способы проверки, отнимающие много времени, попросту нерентабельно. С его помощью возможен лишь выборочный контроль, а он не всегда дает объективную картину. В то же время, при опытном, штучном или мелкосерийном производстве, скорость контроля не имеет решающего значения. Когда стоимость конечного продукта высока, а его качество имеет решающее значение, имеет смысл потратить время на самое тщательное обследование.
Необходимой точности замеров. Для изделий, где герметичность сварного соединения не имеет значения, и не испытывающих высоких нагрузок, достаточно получить информацию общего характера. Это касается бытовой техники, простых строительных конструкций или изделий легкой промышленности. В случае, когда важна герметичность шва, следует отдать предпочтение способам, выявляющим даже малейшие неплотности в соединениях. Для обследования деталей, испытывающих высокие нагрузки, придется использовать технологии, способные дать максимально полное представление о внутренней структуре сварного шва. Ведь скрытые дефекты, проявившиеся спустя какое-то время, часто становятся причиной серьезных техногенных катастроф. В связи с этим отдельную проблему представляет неразрушающий контроль сварных соединений трубопроводов. Тысячи километров магистралей, по которым течет вода, движется жидкое или газообразное топливо могут быть выведены из эксплуатации из-за невидимой глазу трещины. Разрыв труб, по которым в производственных цехах перекачиваются химически агрессивные вещества, недопустим, так как вполне способен привести к человеческим жертвам.
Особенностей производства. При анализе сварных соединений электронных компонентов, нагрев которых недопустим, а размер деталей которых мал, приходится отказываться от многих эффективных методов дефектоскопии в пользу пусть и не столь надежных, но лучше подходящих для решения задачи. Иные проблемы приходится решать там, где длина швов составляет многие сотни метров. При прокладке газопроводов или строительстве судов не получится использовать оборудование, с успехом работающее в научной лаборатории.
Применяемые материалы. В современном производстве используются различные детали и сплавы. Все они имеют свои особенности, отличаясь по внутренней структуре, магнитным свойствам, реакции на температурный нагрев или воздействие давлением. Все это следует учитывать при выборе способа контроля. Ведь методика, хорошо зарекомендовавшая себя при проверке качества сварных швов изделий, выполнены из стали, может оказаться неэффективна для дефектоскопии деталей, изготовленных из алюминия.
Вникая в суть процесса
Важно не только правильно определиться с технологией проведения замеров. Многое зависит от того, насколько хорошо используемое оборудование будет освоено персоналом. Применяемые в современном производстве способы автоматизации не отменяют человеческого фактора. Ведь обслуживают автоматику все равно люди. А потому необходимо, чтобы персонал не просто бездумно нажимал кнопки и реагировал на сигналы, подаваемые чувствительной аппаратурой. Подобный подход ошибочен, хотя и выглядит для многих организаторов производств привлекательно. Лишь понимая суть происходящих процессов, можно дать объективную оценку данным, полученным при неразрушающем контроле сварных соединений.
Поделись с друзьями
0
0
0
0
Неразрушающий контроль сварных соединений: виды, методы, особенности
Существующие в электрическом деле методы неразрушающего контроля сварных соединений полностью соответствуют требованиям, изложенным в ГОСТе 3242. Особенностью всех методов является то, что дефекты выявляются косвенно, без механических повреждений и не разрушают сварные соединения.
Универсального способа, при применении которого можно было бы выявить все существующие дефекты, не существуют. Поэтому используется их совокупность.
Существующие дефекты
Неразрушающий контроль соединений, выполненных сварным способом, позволяет выявить как внешние, так и внутренние дефекты.
Внешние — это прожоги, трещины, царапины, сколы, надрезы, плохо проваренные участки. Их легко увидеть при визуальном осмотре. Другое дело — внутренние. Для их определения понадобится специальное оборудование.
Виды контроля
Выбор оптимального варианта зависит от толщины шва, состояния поверхности, характеристик металла. Виды неразрушающего контроля сварных соединений основываются на различных физических явлениях: оптических, акустических, радиационных, магнитных, тепловых.
Визуально-измерительный
Наружные дефекты можно без особых проблем выявить внешним осмотром. В качестве дополнительного приспособления используется лупа, имеющая сильное увеличение. Для измерения размера дефекта применяется линейка или другой мерительный инструмент. Такой метод контроля обязателен для всех соединений с помощью сварки. Он может применяться как подготовка к другим методам.
Ультразвуковая дефектоскопия
Суть способа — способность ультразвуковых волн проникать через металл и отражение их от шлаков и включений неметаллического характера. Приборы для этого метода называются ультразвуковыми дефектоскопами.
На экране осциллографа отображаются волны, отраженные от сварного шва. Информация, которую получает контролер, содержит сведения о размере и местоположении дефектов.
Магнитная дефектоскопия
В методе используется явление электромагнетизма. Магнитные волны проходят через соединение сваркой. На месте дефектов образуются рассеянные магнитные потоки, имеющие искривления. Примером использования является неразрушающий контроль сварных соединений трубопроводов.
При наличии раковин или трещин меняется величина магнитного потока, что регистрируется прибором.
Радиографический контроль
Называется также рентгенографическим. Основан на свойстве рентгеновских лучей в различных материалах распространяться по-разному, что важно, когда они встречают включения шлаков или пустоты в металле.
На месте шва устанавливают специальный аппарат, который делает снимки на пленке. Если имеются дефекты, то это будет отражено на снимках. Неразрушающий контроль сварных соединений, выполненный таким способом, является одним из самых точных.
Капиллярный контроль
Для этого метода необходимы индикаторы — жидкости, обладающие свойством глубоко проникать в материал, оставляя следы яркого цвета. При наличии пустот индикаторы просачиваются сквозь них.
Такой неразрушающий контроль сварных швов выполняется следующим образом. Поверхность шва тщательно очищается и высушивается. На нее наносят индикатор, который по капиллярам проникает глубоко в металл. После очищения от излишков на это место наносят проявитель, задача которого вытянуть жидкость из материала. О дефектах можно судить по образовавшемуся рисунку.
Где производится контроль
Местом осуществления контроля может служить лаборатория неразрушающего контроля сварных соединений, где имеется все необходимое оборудование. В лаборатории используются все главные методы, применяемые для контроля качества выполненных сварных швов. Исследования проводят с соблюдением требований, указанных в соответствующих нормативных документах.
Преимущества неразрушающего контроля
К достоинствам применения таких методов относятся:
- Сохранение целостности изделия. После анализа и устранения дефектов можно сразу начинать их эксплуатацию.
- Исследования можно проводить без привязки к постоянному месту.
- Быстрое получение результата.
- Привлечение к исследованиям специальных лабораторий.
- Невысокая стоимость.
Возможно применение сразу нескольких способов контроля.
Интересное видео
Неразрушающий контроль сварных соединений: методы и технологии проведения
Неразрушающие испытания предназначены для оценки тех или иных физических свойств изделия, характеризующих надежность или прочность соединения. Эти свойства имеют связь с наличием в испытываемом образце дефектов.
Для чего нужен
Методы неразрушающего контроля сварных соединений применяют для обнаружения дефектов на поверхности и в толще проверяемого изделия, а также для определения их пространственного положения, размеров и формы. При этом целостность изделий не нарушается.
По термодинамическому признаку неразрушающие способы дефектоскопии подразделяются на виды:
- связанные с применением передачи энергии;
- использующие движение вещества.
Методы и технологии
Согласно ГОСТ 3242-79, к перечню неразрушающих методов контроля сварных соединений относятся:
- внешний осмотр;
- капиллярный;
- радиационный;
- ультразвуковой;
- магнитный.
К преимуществам неразрушающего контроля относятся:
- проведение испытаний проводится непосредственно на изделиях;
- применяется комплекс методов, выявляющий разные свойства соединения или вещества;
- исследование можно проводить на установке без прекращения ее работы.
Внешний осмотр
Предназначен для обнаружения поверхностных дефектов:
- трещин;
- наплывов;
- непроваров;
- прожогов;
- подрезов.
Также выявляет смещение деталей и несоответствие размеров. Применение оптических приборов позволяет обнаружить дефекты минимального размера.
Перед осмотром выполняется подготовка:
- очистка шва и прилегающих поверхностей от шлака, окалины, металлических брызг;
- при необходимости – травление.
Оценка внешнего вида проводится с использованием специальных эталонов. Геометрические параметры сверяют с помощью шаблонов и измерительных инструментов.
Капиллярный
Суть метода состоит в капиллярной диффузии индикаторной жидкости в полости материала внешней поверхности исследуемой детали с целью выявления дефектов в виде индикаторных следов визуальным способом или с использованием преобразователя.
Способ предназначен для выявления в контрольных образцах поверхностных и сквозных дефектов, определения их ориентации по поверхности и расположения. Для трещин и других протяженных дефектов определяется протяженность.
Капиллярный контроль распространяется на объекты:
- любого размера и формы;
- из черного и цветного металла и их сплавы, пластмассы, керамики, стекла, твердых неферромагнитных материалов.
Условия выявления дефектов сварки капиллярным методом:
- наличие полостей, очищенных от загрязнений и прочих веществ;
- свободный выход на поверхность исследуемого образца;
- глубина распространения, превышающая ширину раскрытия полостей.
Капиллярные методы классифицируют на основные и комбинированные.
Основные способы подразделяются на виды:
- жидкостный;
- проникающих растворов;
- фильтрующих суспензий;
- люминесцентный;
- цветной;
- люминесцентно-цветной;
- яркостный.
Комбинированные способы бывают капиллярно-:
- электростатический;
- электроиндуктивный;
- магнитопорошковый;
- радиационный (излучения и поглощения).
Исследование выполняется с помощью капиллярного дефектоскопа.
Радиационный
Суть метода состоит в способности рентгеновских лучей и гамма-излучения просвечивать непрозрачные предметы и оказывать действие на индикаторы.
Цель:
- выявление внутренних и внешних дефектов;
- достаточно точное определение местоположения дефектов без разрушения образца.
Радиационный контроль в зависимости от способа регистрации выявленных результатов и типа индикатора подразделяется на виды:
- радиографический;
- радиометрический;
- радиоскопический.
Радиографический метод, включающий рентгенографическое и гамма-графическое исследование, имеет наибольшее практическое использование. Способ заключается в фиксации изображения на специальной бумаге (пленке).
Радиоскопический способ (радиационная интроскопия) предполагает получение изображения внутренней структуры исследуемого образца на экране. При радиометрическом методе информация о внутреннем состоянии контрольного предмета поступает в виде регистрируемых электрических сигналов.
Каждый из методов радиационного неразрушающего контроля предполагает использование:
- источника ионизирующего излучения;
- детектора – регистратора информации;
- контролируемого объекта.
Ультразвуковой
Метод основан на использовании явления отражения ультразвуковых волн от линии раздела двух сред, имеющих различные акустические свойства. Ультразвук – это упругие колебания материальной среды, частота которых выше 20 кГц.
Ультразвуковой контроль сварных швов предполагает использование частот в интервале 0.5-5.0 мГц. Для получения ультразвуковых колебаний используют несколько способов, самым распространенным из которых является метод, основанный на пьезоэлектрическом эффекте кристаллов сегнетовой соли или кварца.
Ультразвуковой контроль сварного шва производится с помощью пьезоэлектрического преобразователя. С помощью метода в сварных швах можно обнаружить:
- шлаковые включения;
- поры;
- непровары;
- расслоения;
- трещины.
Ультразвуковой контроль требует высокой квалификации и опыта работы оператора.
Магнитный
Метод заключается в фиксации изменений связи электромагнитного поля с контролируемыми образцом и эталоном. Магнитный контроль предполагает использование электромагнитных явлений постоянного и переменного электрических и магнитных полей, диапазона частот, пределы которых отвечают уравнениям Максвелла.
Различают следующие способы неразрушающего магнитного контроля:
- Магнитоферрозондовый. Предназначен для выявления внутренних несплошностей, находящихся на глубине до 10 мм от внешней поверхности изделия, и разнонаправленных дефектов.
- Магнито-порошковый. Цель – обнаружение дефектов на глубине до 2 мм.
- Магнито-графический. Для исследования дефектов сварных стыковых соединений дуговой газовой сварки и конструкций из ферромагнитного материала. Толщина – менее 25 мм.
Неразрушающие методы контроля качества сварных швов и соединений
Когда образуется сварочный шов, то по его внешнему виду не всегда можно сказать, насколько качественно он сделан. Стоит сразу отметить, что какое бы соединение не было, в сварной конструкции оно становится самым уязвимым местом, которое в первую очередь ломается от нагрузок. Поэтому, к его созданию следует подходить с особой ответственностью, особенно, если изделие с ним будет применяться в опасных зонах, в которых возлагаются большие нагрузки. Чтобы не произошло ни каких опасных ситуаций, перед вводом в эксплуатации подобного изделия его подвергают разнообразным проверкам.

Неразрушающие методы контроля сварных швов и соединений
Существует разрушающий и неразрушающий контроль сварных соединений, который помогает выявить наличие дефектов в шве. В первом случае образцы после прохождения контроля, как правило, ломаются вследствие деформации. Этот способ помогает не только выявить дефекты, но и проверить характеристики. Он больше подходит для серийных выпусков. Более популярным оказывается неразрушающий контроль сварных швов, так как он оставляет изделие в целостности и помогает определить место расположения дефекта, его характер и размеры.

Контроль сварных соединений
Такие методы проводятся уже после того как изделие остыло и место соединение было обработано. В зависимости от наличия того или иного прибора, а также прочих технических возможностей, подбирают способ, каким именно будет проводиться анализ. К каждому изделию может подбираться как один способ контроля, так и несколько, так как далеко не все из них универсальны. Неразрушающий контроль сварных швов проходит по ГОСТ 18442-80.
Преимущества
- Неразрушающий контроль сварного шва помогает сохранить изделие в целостности и после анализов вводить его в эксплуатацию;
- Некоторые его разновидности позволяют проводить мобильные исследования, не привязываясь к стационарному месту;
- Результат можно получить достаточно быстро, без длительного времени ожидания;
- Стоимость проведения контроля является относительно небольшой;
- Осмотр в несколько этапов позволяет сделать данные более точными.
Недостатки
- Невозможно определить какими именно характеристиками будет обладать изделия без прикладывания предельных нагрузок;
- Некоторые из способов оказываются вредными для здоровья человека.
Дефекты, образование и анализ
Дефекты в местах соединения во время сварки являются достаточно распространенным делом, так как на их образование воздействует много факторов. Неразрушающие методы контроля сварных швов помогают выявить все из них и определить, насколько они опасны во время использования. Может возникнуть непроварка определенной области, которая сделает более низкий уровень крепления двух заготовок. Это может возникать из-за неправильного выбора режима или периодического затухания дуги во время процесса.
Раковины образуются из-за попадания в сварочную ванну кислорода или влаги во время соединения. Она делает шов более хрупким. Как правило, это скрытый дефект, который невозможно увидеть невооруженным глазом. Это может случиться по причине использования влажных электродов или недостаточного уровня защиты обмазки.
Поры получаются при мелких вкраплениях посторонних веществ и недостаточном уровне защиты. Они не являются существенным дефектом. Но при наличии большого количества делают соединение менее крепким.
Трещины и микротрещины получаются при резком остывании шва и неправильном температурном режиме. Иногда требуется предварительный подогрев основного металла, а также подобная процедура на завершающей стадии, что поможет избежать подобных моментов.
Виды неразрушающего контроля сварных соединений
- Визуальный;
- Капиллярный;
- Магнитный;
- Ультразвуковой;
- Радиационный.
Особенности выбора
Рассматривая, какие методы включает неразрушающий контроль сварных соединений, следует определиться с тем, какие из них лучше всего применять для конкретного случая. Ведь применение всех их будет нецелесообразным, так как это выйдет слишком дорого и долго. Среди всего разнообразия можно подобрать подходящий вариант. В профессиональной сфере чаще всего применяют ультразвуковой метод, так как он отличается простотой. Аппараты для проведения диагностики являются универсальными, так что могут подходить для любого типа соединения.

Ультразвуковой контроль качества сварных соединений и швов
Если необходимо проверить особо ответственные швы, то здесь не обойтись без радиационного метода, так как он позволяет точно определить внутреннюю структуру. Данный метод наиболее дорогостоящий и сложный в исполнении, так что в небольших мастерских и в частной сфере он практически не применяется. В отличие от него, визуальный осмотр оказывается всегда полезным и даже если используются более сложные и точные способы, он все равно применяется.
«Важно!
При работе с радиационным методом необходимо использовать средства защиты, чтобы не получить дозу облучения.»
Методы неразрушающего контроля сварных соединений
Визуальный. Самый простой и обязательный при любых процедурах осмотра. Он проводится в то время, когда шов остыл и был очищен от шлака. Иногда поверхность дополнительно обрабатывается, если высота наплавленного металла оказалась слишком большой, и только после этого осматривается специалистами. Практически все дефекты, находящиеся на наружной поверхности можно рассмотреть невооруженным глазом или при помощи лупы. Здесь же проверяется правильность геометрии полученного соединения. Помимо простоты, это еще и самый дешевый способ.

Визуальный контроль сварных швов и соединений
Капиллярный контроль требует использования жидкостей с высоким уровнем текучести. Зачастую в этой роли выступает керосин. Неразрушающие методы контроля сварных соединений такого типа называют еще цветными, так как на поверхность металла, с обратной стороны которой должен выступить керосин, наносят реагент, что меняет цвет при контакте с выступающей жидкостью. Это помогает определить насколько герметичным получился шов, так как при наличии микротрещин нельзя использовать подобные швы. Это универсальный способ, который подходит для всех изделий и разновидностей металла.

Капиллярный контроль сварных швов и соединений
Магнитный способ. Здесь применяется принцип электромагнетизма. На участок сварного шва воздействует устройство, которое образует магнитное поле. Линии данного поля проходят сквозь основной металл и через шов. Если структура металла однородна, то линии остаются ровными, но при наличии дефектов они искривляются. Для фиксации искажения применяют графический и порошковый метод. Первый ловит искажения специальным прибором, а во втором случае высыпается порошок, который скапливается в том месте, где имеется дефект.

Магнитный контроль сварных швов и соединений
Ультразвуковая дефектоскопия сварных швов проводится при помощи специального ультразвукового устройства. Здесь используется принцип отражения волн звука от границ поверхностей с различной плотностью. Таким образом, если при прохождении через металл шва будут возвращаться волны, то значит, что в них располагаются воздушные поры. Для фиксации дефектов необходимо использовать специальный датчик. Существуют мобильные модели устройства, что обеспечили ему столь широкую популярность. Способ сложно осуществляет проверку крупнозернистых металлов, а также далеко не каждый человек сможет расшифровать полученные данные, так как тут нужно специальное образование.

Ультразвуковая дефектоскопия сварных швов
Рентгенографический контроль сварных соединений основан на свойствах проникновения гамма излучения и рентгеновских лучей сквозь металлическую поверхность. Дефекты фиксируются на фотопленке. Но это достаточно дорогостоящий способ. Также это самый вредный для здоровья человека способ.
Неразрушающий контроль качества сварных соединений трубопроводов
На чтение 8 мин. Обновлено
Как контролировать сварные соединения у трубопровода узнаем в данной статье. Чтобы получить представление о реальном состоянии металла в местах соединений, применяется так называемый неразрушающий контроль сварных соединений трубопроводов. Безопасность вместе с надёжностью конструкции часто определяется качественным уровнем швов.
Стандарты в законодательстве создают строгие нормативы для процесса. Его проводят только профессионалы, обладающие соответствующими навыками.
Контроль качества сварных соединений и необходимость его проведения
Когда проводятся сварочные работы на трубопроводах, появления дефектов не избежать. В свою очередь, эти недостатки оказывают негативное влияние на внешний вид сварных соединений, их технические характеристики вместе с надёжностью. Всего выделяют две разновидности повреждений: формирования шва и дефекты металлургического типа.
Формирование структурного шва приводит к появлению металлургических изъянов. Они обычно появляются, пока материал охлаждается или нагревается. Вторая группа повреждений вызвана несоблюдением норм во время проведения работ.
Заранее требуется выявлять следующие разновидности недостатков. Они все негативно влияют на качество всего трубопровода в итоге.
- Нарушения в металлической микроструктуре. Приводят к тому, что повышается содержание оксидов, появляется крупная зернистость, зёрна с окисленными краями.
- Наличие газовых включений или пор. Бывают групповыми или единичными, иногда выглядят как мостики. Или выходят на поверхность. Тогда их называют свищами.
- Примеси со шлаками внутри швов. Из-за них изделие теряет первоначальную прочность.
- Возникновение трещин разных типов характерно для участков со швами, околошовного пространства. Отличия кроются в размерах.
- Группа непроваров. Это название для локальных участков шва, в котором нет сцепления с основным материалом.
- Прожоги или отверстия в сварных швах, которые появляются при вытекании расплава, когда проходит сварка.
- Подрезы. Название для канавок в продольной плоскости на границах со швами, поверхности основного металла.
- Нарушения в формах и размерах швов.
Только в случае выявления каждого из дефектов можно гарантировать надёжность трубопровода на максимальном уровне.
Необходимо провести тщательную оценку того, как подобные изъяны влияют на конструкцию. Иначе невозможно исправить положение до того, как начинается эксплуатация трубопровода.
По каким принципам проводится неразрушающий контроль качества?
Всего существует два метода, на основании которых проводится контроль качества сварных соединений трубопроводов.
- Когда целостность соединения не нарушают.
- С нарушениями.
Чтобы оценить состояние всех сварных швов, применяют неразрушающий способ проверки качества. Такой контроль необходимо проводить как во время сварочных работ, так и после их завершения.
Это нужно для того, чтобы обезопасить конструкцию ещё до того, как начнётся непосредственная эксплуатация. В свою очередь, существуют свои методы для проведения неразрушающей оценки качества.
- По проницаемости.
- Магнитный, рентгенографический контроль.
- Метод с применением ультразвука.
- Капиллярная, радиационная дефектоскопия.
- Измерения и проведения внешнего осмотра.
Что касается разрушающих методов, то их проводят на образцах изделия, которые уже вырезаны из своей первоначальной позиции.
Правила внешнего и технического осмотра
Любую проверку качества трубопровода начинают проведением внешнего осмотра. Он бывает не только чисто визуальным, но и предполагает использование измерительных и других видов технических инструментов. Это позволит выявить проблемы во внешних факторах, соответствие текущего состояния нормативам и требованиям законодательства.
Видео
Обнаружение даже небольших трещин в сварных соединениях не составит труда, если очистить небольшой участок на шве, а потом обработать его при помощи спирта, кислотного слабого раствора.
Геометрические размеры не определить без линейки и штангенциркуля. Хорошее освещение сделает проверки более эффективными. Как и использование лупы, поддерживающей увеличение в 8-10 раз.
Капиллярные методики контроля сварных соединений: о сути
Этот контроль качества сварных соединений трубопроводов предполагает использование контрастных жидкостей, которые просачиваются внутрь металла через мельчайшие повреждения, если они обнаружены на поверхности. Так называемые пенетранты используются чаще всего.
Когда такие вещества используются, дефекты просто окрашиваются в определённый цвет.
Пенетранты могут состоять из разных основ:
- Трансформаторное масло.
- Бензол.
- Скипидар.
- Керосин.
Кроме того, и сами составы делятся на несколько разновидностей.
- С красителями, которые наблюдаются при дневном цвете. Чаще всего используется ярко-красный оттенок.
- С люминесцирующими компонентами. Недостатки проявляются, если использовать ультрафиолетовые лучи.
Метод обладает чувствительностью в 0,1-0,5 мкм. Она может достигать 500 мкм, если поддерживается верхний предел.
Видео
Проверка сварного соединения трубопровода с помощью керосина считается одним из наиболее простых способов. Важно – наличие высоких свойств по проникновению у состава. У таких испытаний имеется свой отдельный порядок. Водную смесь с каолином или мелом наносят на соединительные участки. После чего всё подсушивают, пока не образуется плёнка белого цвета.
Керосин должен обильно смочить обратную сторону шва, на протяжении минимум получаса. Даже если есть только микроскопические трещины – керосин пройдёт сквозь поверхность. После чего он становится заметным с обратной стороны. Визуально дефекты выделить не составит труда.
Как проверяют проницаемость?
Когда сваривают ёмкости, трубопроводы и так далее, необходимостью становится именно оценка того, какой является герметичность. Такой контроль качества так же проводится с использованием различных методов и инструментов:
- Испытания по гидравлике и пневматике.
- Пузырьковым методом.
- Течеиспускание.
И так далее. Пневматические испытания – это когда внутрь трубопровода запускают воду или газ в больших количествах. Пенообразующий состав наносят на поверхность снаружи. Если появляются пенистые пузырьки – значит, герметичность была нарушена.
Видео
Как правильно выбрать метод неразрушающего контроля соединений трубопровода?
Выбор оптимального способа проверки соединений трубопровода не составит труда. Нужно учесть всего лишь следующие факторы.
- Показатели экономии и технических свойств.
- Особенности изготовления сварной конструкции.
- Состояние, в котором находится поверхность.
- Сварное соединение по толщине и типу.
- Сам металл с определением физических свойств.
Видео
Главное – помнить, что при использовании неразрушающих методов дефекты выявляются лишь косвенно.
Неразрушающий контроль сварных соединений с помощью ультразвука
В основе метода – акустические изменения, которые происходят, когда сквозь исследуемое соединение проводят звуковые колебания, со сверхвысокой частотой. Степень ослабления обратного сигнала и скорость распространения становятся самыми важными свойствами звука для данного исследования.
Ультразвуковая дефектоскопия проводится на основе следующих принципов.
- Источник ультразвука генерирует звуковые волны. Они точно проходят через зону, которая и требует диагностики. Потом отражаются от тех мест, где вероятнее всего появление недостатков.
- Звуковая волна обязательно должна отражаться от чего-либо, иначе выявление изъянов будет невозможным. Угловая искательная головка – специальное приспособление, которое обеспечивает появление должного эффекта.
- Звуковая волна не только отражается от участка с изъяном, он способствует изменению в угле преломления. О величине внутренних дефектов судят по тому, насколько большими оказались подобные изменения.
Результат: устранение дефектов
Устранения требуют любые недочеты, не соответствующие начальным техническим условиям. Если это невозможно, то изделие просто считается бракованным.
Видео
Плазменно – дуговая резка в обычной ситуации помогает справиться с проблемами. Для этого же проводят проверку, с последующей обработкой с применением абразивных кругов.
После отпуска сварных изделий исправляют дефекты, которые допускают проведение тепловой обработке. Главное – соблюдать определённые правила.
- Участки с недочетами должны оставаться меньшими по сравнению с удаляемыми участками по длине, с каждой из сторон.
- Разделка так же требует особой выборки. Двойная ширина швов до процедуры должна оставаться примерно такой же, как и после.
- Обязательно сохранение надёжности проваров.
- Наличие плавных очертаний без разрывов обязательно для поверхности при каждой выборке. Наличие острых заусенцев вместе с углублениями так же недопустимо.
Участок необходимо полностью очистить после того, как ремонтные работы завершатся. Переходы к основному металлу от дефектных участков должны быть плавными.
Видео
Допустимо применение только механического метода, если речь идёт об алюминиевых, титановых сплавов. Применение шлифовки требует абразивов.
Устраняя недостатки, берут те же материалы с технологиями, что использовались для наложения основного шва. После чего становится обязательным проведение повторного контроля.
Как определить, в каких объёмах требуется контроль качества соединений?
Это индивидуальная черта в каждом методе. Обычно опираются на нормативные документы, действующие в той или иной сфере. Объёмы контроля устанавливаются в процентах от общей протяжённости самих сварных соединений.
Обязательно надо учитывать, к какой категории относится то или иное сварное соединение трубопровода. А так же назначение вместе с условиями эксплуатации. И последствиями, к которым может привести разрушение на тех или иных участках.
Требуется отдельно указать определённые участки, если объём контроля составляет меньше ста процентов. Рекомендуется составлять максимально подробные схемы.
Применение методов неразрушающего контроля стало привычным для многих отраслей промышленности. Причина того, что неразрушающий контроль сварных соединений трубопроводов стал таким популярным – в полном соответствии требованиям, которые предъявляются к самим методам контроля.
А таких требований тоже существует немало. Хорошо, если удаётся полностью автоматизировать контроль соединений. И использовать приборы, обладающие максимальной надёжностью.
Главное – чтобы они были доступными в условиях производства. Упрощёнными должны быть сами методики. А средства контроля нужно создавать так, чтобы они выдерживали продолжительную эксплуатацию.
Что такое неразрушающий контроль (NDT)? Методы и определение
Неразрушающий контроль (NDT) — это метод испытаний и анализа, используемый в промышленности для оценки свойств материала, компонента, конструкции или системы на предмет характерных различий или сварочных дефектов и неоднородностей без повреждения оригинальной детали. НК также известен как неразрушающий контроль (NDE), неразрушающий контроль (NDI) и неразрушающий контроль (NDE).
Этот часто задаваемый вопрос был создан для того, чтобы предоставить подробное описание того, что такое неразрушающий контроль, введение в каждый из методов, разницу между неразрушающим контролем и разрушающим контролем и преимущества использования этого метода анализа.
Если у вас есть вопросы или вам нужна помощь, напишите нам, чтобы получить консультацию специалиста:
Содержание
Щелкните ссылки ниже, чтобы перейти к разделу руководства:
Текущие методы испытаний неразрушающего контроля включают:
Испытание на акустическую эмиссию (AE)
Это пассивный метод неразрушающего контроля, который основан на обнаружении коротких импульсов ультразвука, излучаемого активными трещинами под нагрузкой. Датчики, рассредоточенные по поверхности конструкции, обнаруживают АЭ.Можно даже обнаружить АЭ от пластификации в сильно нагруженных областях до образования трещины. Часто метод для использования во время контрольных испытаний сосуда под давлением, AE-тестирование также является методом непрерывного мониторинга состояния конструкций (SHM), например, на мостах. Источниками АЭ также являются утечки и активная коррозия.
Узнать больше
Электромагнитные испытания (ET)
В этом методе тестирования используется электрический ток или магнитное поле, пропускаемое через проводящую часть.Существует три типа электромагнитных испытаний, включая вихретоковые испытания, измерение поля переменного тока (ACFM) и дистанционные полевые испытания (RFT).
Вихретоковый контроль использует катушку переменного тока для индукции электромагнитного поля в испытуемом образце, при измерении поля переменного тока и удаленном полевом испытании используется зонд для введения магнитного поля, а RFT обычно используется для испытания труб.
Наземный радар (GPR)
Этот геофизический метод неразрушающего контроля направляет радиолокационные импульсы через поверхность материала или подповерхностную структуру, такую как скала, лед, вода или почва.Волны отражаются или преломляются, когда они сталкиваются с заглубленным предметом или границей материала с различными электромагнитными свойствами.
Методы лазерных испытаний (LM)
Лазерные испытания делятся на три категории, включая голографические испытания, лазерную профилометрию и лазерную ширографию.
В голографическом тестировании используется лазер для обнаружения изменений на поверхности материала, который подвергался нагрузкам, таким как нагревание, давление или вибрация. Затем результаты сравниваются с неповрежденным эталонным образцом для выявления дефектов.
В лазерной профилометрии используется высокоскоростной вращающийся лазерный источник света и миниатюрная оптика для обнаружения коррозии, точечной коррозии, эрозии и трещин путем обнаружения изменений поверхности с помощью трехмерного изображения, созданного на основе топографии поверхности.
Лазерная ширография использует лазерный свет для создания изображения до того, как поверхность подвергнется напряжению и будет создано новое изображение. Эти изображения сравниваются друг с другом, чтобы определить наличие каких-либо дефектов.
Испытание на утечку (LT)
Испытание на герметичность можно разделить на четыре различных метода — испытание на утечку пузырьками, испытание изменением давления, испытание галогенных диодов и испытание масс-спектрометром.
При испытании на утечку пузырьками используется резервуар с жидкостью или мыльный раствор для больших деталей для обнаружения утечки газа (обычно воздуха) из образца в виде пузырьков.
Используется только в закрытых системах. Испытания на изменение давления используют давление или вакуум для контроля образца. Потеря давления или вакуума в течение установленного периода времени покажет, что в системе есть утечка.
При тестировании галогенных диодов также используется давление для поиска утечек, за исключением того, что в этом случае воздух и индикаторный газ на основе галогена смешиваются вместе, и для обнаружения любых утечек используется блок обнаружения галогенных диодов (или «детектор»).
При тестировании масс-спектрометромиспользуется гелий или смесь гелия и воздуха внутри испытательной камеры с «детектором» для обнаружения любых изменений в пробе воздуха, которые могут указывать на утечку. В качестве альтернативы можно использовать вакуум, и в этом случае масс-спектрометр будет отбирать образцы из вакуумной камеры для обнаружения ионизированного гелия, что покажет, что произошла утечка.
Утечка магнитного потока (MFL)
В этом методе используется мощный магнит для создания магнитных полей, которые насыщают стальные конструкции, такие как трубопроводы и резервуары для хранения.Затем используется датчик для обнаружения изменений плотности магнитного потока, которые показывают любое уменьшение материала из-за точечной коррозии, эрозии или коррозии.
Испытания в микроволновой печи
Этот метод ограничен использованием диэлектрических материалов и использует микроволновые частоты, передаваемые и принимаемые испытательным датчиком. Испытательный зонд обнаруживает изменения диэлектрических свойств, таких как усадочные полости, поры, посторонние материалы или трещины, и отображает результаты в виде сканирования B или C.
Испытания на проникновение жидкости (PT)
Испытание на проникновение жидкости включает нанесение жидкости с низкой вязкостью на испытываемый материал.Эта жидкость просачивается в любые дефекты, такие как трещины или пористость, до нанесения проявителя, что позволяет проникающей жидкости просачиваться вверх и создавать видимые признаки дефекта. Испытания на проникновение жидкости могут проводиться с использованием пенетрантов, удаляемых растворителем, смываемых водой пенетрантов или постэмульгируемых пенетрантов.
Тестирование магнитных частиц (MT)
В этом процессе неразрушающего контроля магнитные поля используются для поиска неоднородностей на поверхности или вблизи поверхности ферромагнитных материалов. Магнитное поле можно создать с помощью постоянного магнита или электромагнита, для которого требуется приложить ток.
Магнитное поле будет выделять любые неоднородности, поскольку линии магнитного потока создают утечку, что можно увидеть, используя магнитные частицы, которые втягиваются в несплошность.
Нейтронно-радиографический контроль (NR)
Нейтронная радиография использует пучок нейтронов низкой энергии для проникновения в заготовку. Хотя луч прозрачен в металлических материалах, большинство органических материалов позволяют видеть луч, что позволяет просматривать и исследовать структурные и внутренние компоненты для обнаружения дефектов.
Радиографические исследования (RT)
Радиографический контроль использует излучение, прошедшее через образец для обнаружения дефектов. Рентгеновские лучи обычно используются для тонких или менее плотных материалов, а гамма-лучи — для более толстых или более плотных предметов. Результаты можно обработать с помощью пленочной рентгенографии, компьютерной рентгенографии, компьютерной томографии или цифровой рентгенографии. Какой бы метод не использовался, излучение будет показывать неоднородности материала из-за силы излучения.
Узнать больше
Тепловое / инфракрасное тестирование (IRT)
При инфракрасном тестировании или термографии используются датчики для определения длины волны инфракрасного света, излучаемого поверхностью объекта, который может использоваться для оценки его состояния.
В пассивной термографии используются датчики для измерения длины волны испускаемого излучения, и, если коэффициент излучения известен или может быть оценен, температуру можно рассчитать и отобразить как цифровое значение или как изображение в ложных цветах.Это полезно для обнаружения перегрева подшипников, двигателей или электрических компонентов и широко используется для мониторинга потерь тепла из зданий.
Активная термография создает температурный градиент через структуру. Элементы внутри него, которые влияют на тепловой поток, приводят к колебаниям температуры поверхности, которые можно проанализировать для определения состояния компонента. Часто используется для обнаружения приповерхностных отслоений или дефектов соединения в композитах.
Узнать больше
Ультразвуковой контроль (UT)
Ультразвуковой контроль влечет за собой передачу высокочастотного звука в материал для взаимодействия с элементами материала, которые отражают или ослабляют его.Ультразвуковой контроль в общих чертах делится на импульсное эхо (PE), сквозное прохождение (TT) и времяпролетную дифракцию (ToFD).
Узнать больше
Инспекция импульсного эхо-сигнала
Этот метод вводит звуковой луч на поверхность исследуемого материала. Звук будет проходить через деталь, достигая задней стенки материала и затем возвращаясь к датчику, или возвращаясь раньше, когда отражается от неоднородности внутри детали. Если скорость звука известна, записанный интервал времени используется для определения пройденного расстояния в материале.
Проверка передачи
TT использует отдельные преобразователи для излучения и приема звука. Передающий зонд расположен с одной стороны тестового образца, а приемный преобразователь — с другой стороны. По мере того, как звук проходит через компонент, он ослабляется внутренними элементами, такими как пористость. Измерение толщины с помощью этого метода обычно невозможно.
Время пролета дифракции (ToFD)
Дифракция — это процесс изменения длины волны звука при взаимодействии с неоднородностью материала.Этот механизм используется в ситуациях, когда невозможно получить истинное отражение, но возникает достаточная дифракция, чтобы изменить время пролета звука в устройстве захвата высоты тона. Этот метод используется для обнаружения кончика дефекта, расположенного перпендикулярно контактной поверхности зонда. ToFD также используется для проверки задней стенки на предмет коррозии.
Испытания на погружение
Требование влажного сопряжения ультразвукового датчика с деталью может быть проблемой для больших или сложных геометрических образцов.Для удобства эти части погружаются в воду — обычно в погружной бак. Этот метод обычно дополняется исполнительными механизмами, которые перемещают деталь и / или датчик внутри резервуара во время ультразвукового контроля.
Узнать больше
Испытания с воздушной парой
Определенные проверки и материалы не допускают применения мокрого сопряжения, поэтому при определенных обстоятельствах может быть проведено ультразвуковое испытание с воздушным сопряжением. Это влечет за собой применение звука через воздушный зазор.Обычно это влечет за собой использование проверки с более низкой частотой.
Испытание электромагнитного акустического преобразователя (ЭМАП)
EMAT Testing — это метод бесконтактного контроля, в котором используется генерация и прием электромагнитного звука без непосредственного контакта или мокрой связи с деталью. ЭМАП особенно подходят для чрезмерно жарких, холодных, чистых или сухих сред. Как и в случае с обычным ультразвуком, ЭМАП могут генерировать нормальные и наклонные лучи, а также другие режимы, такие как направленные волны.
Волноводные испытания (GW)
Идеально подходит для испытания труб на большие расстояния. При испытании с помощью направленной волны используются формы ультразвуковых волн для отражения изменений в стенке трубы, которые затем отправляются в компьютер для контроля и анализа. Волноводные испытания могут проводиться с использованием средних или длинных диапазонов испытаний — волноводных ультразвуковых испытаний среднего диапазона (GW MRUT) и управляемых волновых ультразвуковых испытаний на больших расстояниях (GW LRUT). Методы GW MRUT охватывают площадь от 25 мм до 3000 мм, в то время как GW LRUT покрывает расстояния, превышающие это значение, и может использоваться для проверки площадей на сотни метров из одного места.
Усовершенствованные ультразвуковые методы
Автоматизированная проверка
Преимущество автоматизации достигается за счет интеграции датчиков неразрушающего контроля со стандартными коммерчески доступными промышленными роботами, а также с совместными роботами, также известными как «коботы». Специально написанное программное обеспечение для сбора и визуализации данных создает беспроблемный и интуитивно понятный пользовательский интерфейс, который можно адаптировать к конкретным потребностям.
TWI разработала несколько высокопроизводительных автоматизированных систем контроля, подходящих как для исследовательских и опытно-конструкторских работ, так и для контроля производства.
Ультразвуковой контроль фазированных решеток (PAUT)
ДатчикиPAUT отличаются от обычных UT-датчиков тем, что они состоят из набора отдельных элементов, которые могут генерировать импульс независимо. Управляя временем срабатывания каждого элемента, можно фокусировать или направлять звуковые лучи. Путем поворота луча по диапазону углов или глубин можно получить виды в поперечном сечении с использованием одного зонда, где при обычном УЗИ может потребоваться несколько комбинаций зонда и клина.Виртуальный зонд может быть создан из ряда элементов, и он может быть проиндексирован электронным способом по длине массива, чтобы создать широкое сканирование кисти.
Узнать больше
Захват полной матрицы (FMC)
FMC является развитием метода PAUT и использует те же датчики. Его главное преимущество состоит в том, что нет необходимости фокусировать или направлять луч, так как вся интересующая область находится в фокусе. Он также относительно устойчив к дефектам смещения и структурному шуму. Это упрощает настройку и использование.Недостатком является то, что размеры файлов очень большие, а скорость сбора данных может быть ниже, чем при PAUT.
Узнать больше
Виртуальная апертура источника (VSA)
VSA — это разновидность FMC, которая сохраняет большинство преимуществ превосходного качества изображения, но со значительно уменьшенными размерами файлов и скоростью сбора данных, которые могут превышать скорость PAUT.
Анализ вибрации (VA)
В этом процессе используются датчики для измерения сигнатур вибрации от вращающегося оборудования, чтобы оценить его состояние.Типы используемых датчиков включают датчики перемещения, датчики скорости и акселерометры.
Узнать больше
Визуальное тестирование (VT)
Визуальный контроль, также известный как визуальный осмотр, является одним из наиболее распространенных методов, при котором оператор смотрит на образец. Этому может способствовать использование оптических инструментов, таких как увеличительные стекла или компьютерные системы (известные как «удаленный просмотр»).
Этот метод позволяет обнаруживать коррозию, несоосность, повреждения, трещины и многое другое.Визуальное тестирование присуще большинству других типов неразрушающего контроля, поскольку они обычно требуют от оператора поиска дефектов.
TWI предлагает широкий спектр услуг по неразрушающему контролю в промышленности.
Узнайте, в каких областях мы можем вам помочь, посетив наши страницы обслуживания ниже, или напишите нам, чтобы узнать, как мы можем помочь:
.Неразрушающий контроль — Ультразвуковой контроль
Что такое ультразвуковой контроль?
Ультразвуковой неразрушающий контроль, также известный как ультразвуковой неразрушающий контроль или просто УЗ, представляет собой метод определения толщины или внутренней структуры испытуемого образца с помощью высокочастотных звуковых волн. Частоты или высота тона, используемые для ультразвукового контроля, во много раз превышают предел человеческого слуха, чаще всего в диапазоне от 500 кГц до 20 МГц.
Какие материалы можно тестировать?
В промышленных приложениях ультразвуковой контроль широко используется для металлов, пластмасс, композитов и керамики.Единственными распространенными инженерными материалами, которые не подходят для ультразвукового контроля с помощью обычного оборудования, являются изделия из дерева и бумаги. Ультразвуковая технология также широко используется в биомедицинской области для диагностической визуализации и медицинских исследований.
Принцип ультразвукового контроля.
СЛЕВА: зонд посылает звуковую волну в исследуемый материал. Есть два показания, одно от начального импульса зонда, а второе от эхо-сигнала от задней стенки.
ВПРАВО: Дефект создает третью индикацию и одновременно уменьшает амплитуду индикации задней стенки.
Как это работает?
Высокочастотные звуковые волны очень направленные, и они будут проходить через среду (например, кусок стали или пластика), пока не встретят границу с другой средой (например, воздухом), после чего они отражаются обратно к своему источнику. Анализируя эти отражения, можно измерить толщину испытательного образца или найти признаки трещин или других скрытых внутренних дефектов.
При ультразвуковом контроле ультразвуковой преобразователь, подключенный к диагностическому аппарату, проходит над проверяемым объектом.Преобразователь обычно отделяется от объекта испытаний связующим веществом (например, маслом) или водой, как при испытании иммерсией.
Есть два метода приема ультразвуковой волны: отражение и затухание.
В режиме отражения (или эхо-импульса) преобразователь выполняет как отправку, так и прием импульсных волн, поскольку «звук» отражается обратно в устройство. Отраженный ультразвук исходит от поверхности раздела, например, от задней стенки объекта или от дефекта внутри объекта.Диагностическая машина отображает эти результаты в виде сигнала с амплитудой, представляющей интенсивность отражения, и расстояние, представляющее время прибытия отражения.
В режиме затухания (или сквозной передачи) передатчик посылает ультразвук через одну поверхность, а отдельный приемник определяет количество, достигшее его на другой поверхности после прохождения через среду. Дефекты или другие условия в пространстве между передатчиком и приемником уменьшают количество передаваемого звука, таким образом обнаруживая их присутствие.Использование связующего увеличивает эффективность процесса за счет уменьшения потерь энергии ультразвуковой волны из-за разделения между поверхностями.
Контроль труб с помощью ультразвукового дефектоскопа
Каковы преимущества ультразвукового контроля?
Ультразвуковой контроль полностью неразрушающий. Образец для испытаний не нужно разрезать, разрезать или подвергать воздействию вредных химикатов. Требуется доступ только к одной стороне, в отличие от измерения с помощью механических инструментов для измерения толщины, таких как штангенциркуль и микрометры.В отличие от рентгенографии, ультразвуковые исследования не представляют потенциальной опасности для здоровья. Когда тест настроен должным образом, результаты очень надежны и воспроизводимы.
Каковы потенциальные ограничения ультразвукового контроля?
Для ультразвуковой дефектоскопии требуется обученный оператор, который может настроить испытание с помощью соответствующих эталонов и правильно интерпретировать результаты. Проверка некоторых сложных геометрических форм может быть сложной задачей. Ультразвуковые толщиномеры должны быть откалиброваны в соответствии с измеряемым материалом, а приложения, требующие измерения широкого диапазона толщин или измерения акустически различных материалов, могут потребовать нескольких настроек.Ультразвуковые толщиномеры дороже механических.
На строительной площадке техник проверяет сварной шов трубопровода на предмет дефектов с помощью ультразвукового прибора с фазированной решеткой. Сканер, состоящий из рамы с магнитными колесами, удерживает датчик в контакте с трубой с помощью пружины. Влажная зона — это ультразвуковая связка, которая позволяет звуку проходить в стенку трубы.
Ультразвуковой контроль сварных швов
Одной из наиболее полезных характеристик ультразвукового контроля является его способность определять точное положение несплошности в сварном шве.Этот метод тестирования требует высокого уровня подготовки и компетентности оператора и зависит от создания и применения подходящих процедур тестирования. Этот метод тестирования может использоваться для черных и цветных металлов, часто подходит для тестирования более толстых участков, доступных только с одной стороны, и часто может обнаруживать более тонкие линии или более простые дефекты, которые не так легко обнаружить с помощью радиографического тестирования.
Стандарты
Международная организация по стандартизации (ISO)
- ISO 7963, Неразрушающий контроль. Ультразвуковой контроль. Спецификация калибровочного блока No.2
- ISO / DIS 11666, Неразрушающий контроль сварных швов. Ультразвуковой контроль сварных соединений. Уровни приемки .
- ISO / DIS 17640, Неразрушающий контроль сварных швов. Ультразвуковой контроль сварных соединений
- ISO 22825, Неразрушающий контроль сварных швов. Ультразвуковой контроль. Испытание сварных швов аустенитных сталей и сплавов на никелевой основе.
Европейский комитет по стандартизации (CEN)
- EN 583, Неразрушающий контроль — Ультразвуковой контроль
- EN 1330-4, Неразрушающий контроль — Терминология — Часть 4: Термины, используемые в ультразвуковом контроле
- EN 1712, Неразрушающий контроль сварных швов — Ультразвуковой контроль сварных соединений — Уровни приемки
- EN 1713, Неразрушающий контроль сварных швов — Ультразвуковой контроль — Определение характеристик сварных швов
- EN 1714, Неразрушающий контроль сварных швов — Ультразвуковой контроль сварных соединений
- EN 12223, Неразрушающий контроль — Ультразвуковой контроль — Спецификация калибровочного блока №1
- EN 12668-1, Неразрушающий контроль. Характеристики и проверка оборудования для ультразвукового исследования. Часть 1. Инструменты.
- EN 12668-2, Неразрушающий контроль. Характеристики и проверка оборудования для ультразвукового исследования. Часть 2: Зонды .
- EN 12668-3, Неразрушающий контроль — Характеристики и проверка оборудования для ультразвукового исследования — Часть 3: Комбинированное оборудование
- EN 12680, Основание — Ультразвуковое исследование
- EN 14127, Неразрушающий контроль — Ультразвуковое измерение толщины
Часто задаваемые вопросы по ультразвуковому контролю
- Что такое ультразвуковой преобразователь?
Преобразователь — это любое устройство, преобразующее одну форму энергии в другую.Ультразвуковой преобразователь преобразует электрическую энергию в механические колебания (звуковые волны), а звуковые волны в электрическую энергию. Как правило, это небольшие портативные сборки, которые бывают самых разных частот и стилей для удовлетворения конкретных потребностей тестирования. - Что такое ультразвуковой толщиномер?
Ультразвуковой толщиномер — это прибор, который генерирует звуковые импульсы в испытуемом образце и очень точно измеряет временной интервал до получения эхо-сигнала.Запрограммированный на скорость звука в исследуемом материале, прибор использует эту информацию о скорости звука и измеренный временной интервал для вычисления толщины с помощью простого соотношения [расстояние] равно [скорость], умноженное на [время]. - Насколько точен ультразвуковой толщиномер?
При оптимальных условиях коммерческие ультразвуковые датчики могут достигать точности до +/- 0,001 мм, с точностью +/- 0,025 мм или выше, возможной для большинства распространенных технических материалов.Факторы, влияющие на точность, включают однородность скорости звука в исследуемом материале, степень рассеяния или поглощения звука, состояние поверхности, а также точность и осторожность, с которыми инструмент был откалиброван для конкретного применения. - Кто пользуется ультразвуковыми датчиками?
Основное применение ультразвуковых датчиков — измерение остаточной толщины стенок корродированных труб и резервуаров. Измерение может быть выполнено быстро и легко без необходимости доступа внутрь или необходимости опорожнения трубы или резервуара.Другие важные приложения включают измерение толщины формованных пластиковых бутылок и аналогичных контейнеров, лопаток турбин и других прецизионных обработанных или литых деталей, медицинских трубок малого диаметра, резиновых шин и конвейерных лент, корпусов лодок из стекловолокна и даже контактных линз. - Что такое ультразвуковой дефектоскоп?
Звуковые волны, проходящие через материал, будут предсказуемым образом отражаться от дефектов, таких как трещины и пустоты. Ультразвуковой дефектоскоп — это инструмент, который генерирует и обрабатывает ультразвуковые сигналы для создания отображения формы волны, которую может использовать обученный оператор для выявления скрытых дефектов в испытательном образце.Оператор определяет характерный образец отражения от хорошей детали, а затем ищет изменения в этом образе отражения, которые могут указывать на дефекты. - Какие недостатки вы можете найти в нем?
С помощью ультразвуковых дефектоскопов можно обнаружить и измерить широкий спектр трещин, пустот, отслоений, включений и подобных проблем, влияющих на структурную целостность. Минимальный размер обнаруживаемого дефекта в данном приложении будет зависеть от типа испытываемого материала и типа рассматриваемого дефекта. - Кто пользуется ультразвуковыми дефектоскопами?
Ультразвуковые дефектоскопы широко используются в критических областях, связанных с безопасностью и качеством, включая сварные швы, стальные балки, поковки, трубопроводы и резервуары, авиационные двигатели и рамы, автомобильные рамы, железнодорожные рельсы, силовые турбины и другую тяжелую технику, корабли корпуса, отливки и многие другие важные приложения. - Какие другие типы инструментов доступны?
Ультразвуковые системы визуализации используются для создания высокодетализированных изображений, похожих на рентгеновские лучи, отображающих внутреннюю структуру детали с помощью звуковых волн.Технология фазированных решеток, первоначально разработанная для медицинской диагностической визуализации, используется в промышленных условиях для создания изображений поперечного сечения. Крупные системы сканирования используются в авиакосмической промышленности и поставщиками металлообработки для проверки на наличие скрытых дефектов как в сырье, так и в готовых деталях. Ультразвуковые генераторы / приемники и анализаторы сигналов используются во множестве приложений для исследования материалов.
Ссылки: www.olympus-ims.com и Welding and Cutting United States
.Полное руководство по неразрушающему контролю
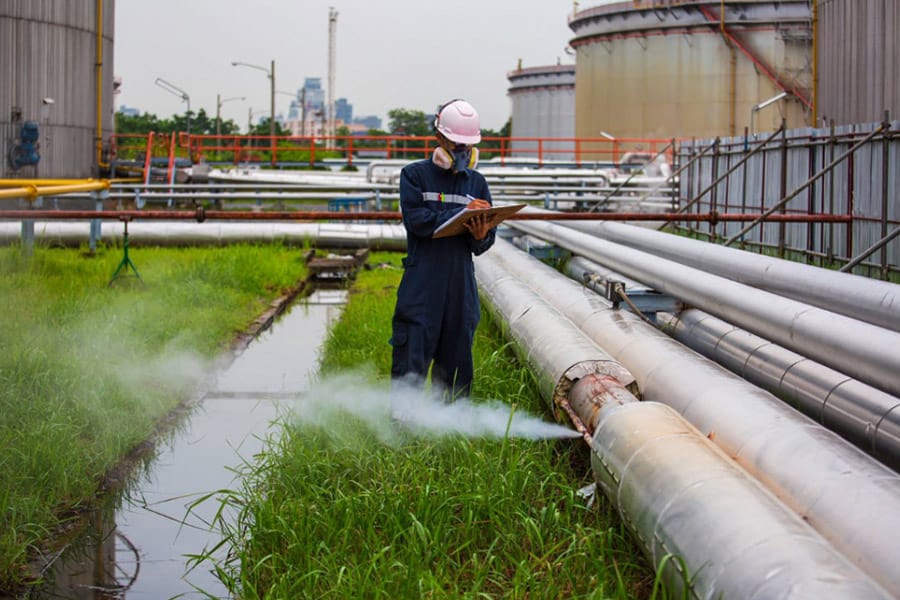
Введение в неразрушающий контроль
Мы живем в сконструированном мире, окруженном большими конструкциями, зависящими от сложных машин. Наша жизнь и средства к существованию неразрывно связаны с надлежащим функционированием нашей инфраструктуры и оборудования. Чтобы это было безопасно, мы должны быть абсолютно уверены в технологиях, на которые мы полагаемся. Неразрушающий контроль обеспечивает эту уверенность.
Во многих отраслях промышленности по всему миру неразрушающий контроль требуется по закону.Там, где это не так, он остается неотразимым и убедительным передовым опытом. Освоение этого сложного предмета занимает десятилетия и является делом тех, кто посвящает свою жизнь этой профессии. Это требует значительного обучения и практического опыта в широком диапазоне сценариев. Даже после 30 лет тестирования все еще можно увидеть что-то совершенно новое.
Тем не менее, из-за отсутствия многолетнего опыта менеджеры компаний или государственных органов часто вынуждены принимать решения относительно своих программ неразрушающего контроля.Чтобы сделать правильный выбор, важно хорошо понимать цель, области применения, требования и различные методы неразрушающего контроля. Этот обзор предназначен для использования в качестве руководства по предмету, предоставляя основную информацию по каждому аспекту неразрушающего контроля, в том числе:
Определение неразрушающего контроля
Во-первых, что такое неразрушающий контроль? Неразрушающий контроль (NDT), как его обычно понимают, относится к любым средствам определения прочности и целостности объекта без разрушения объекта.Другие ярлыки, такие как неразрушающий контроль (NDI), неразрушающий контроль (NDE) и неразрушающий контроль (NDE), используются взаимозаменяемо. Различные этикетки чаще используются в разных географических регионах или разными производителями.
Какой бы ярлык ни использовался, NDT описывает категорию исследования, а не конкретный метод тестирования. Некоторые из наиболее распространенных типов неразрушающего контроля включают ультразвуковой контроль, вихретоковый контроль, жидкостный проникающий контроль, испытание магнитными частицами, радиографию, лазерное испытание и визуальный контроль.
На каждой этикетке обозначены средства тестирования — например, ультразвуковые испытания используют высокочастотные звуковые волны. Есть еще несколько видов неразрушающего контроля, которые будут рассмотрены позже в этом обзоре. За исключением визуального тестирования (широкий термин, используемый для описания всевозможных проверок с использованием основных органов чувств: зрительного, слухового, тактильного и обонятельного), каждый метод тестирования требует специального устройства, предназначенного для этой цели. Понимание сильных и слабых сторон каждого метода помогает компаниям удовлетворить свои потребности в тестировании наиболее эффективным способом.Технологии создали современный мир; неразрушающий контроль делает его безопасным в использовании.
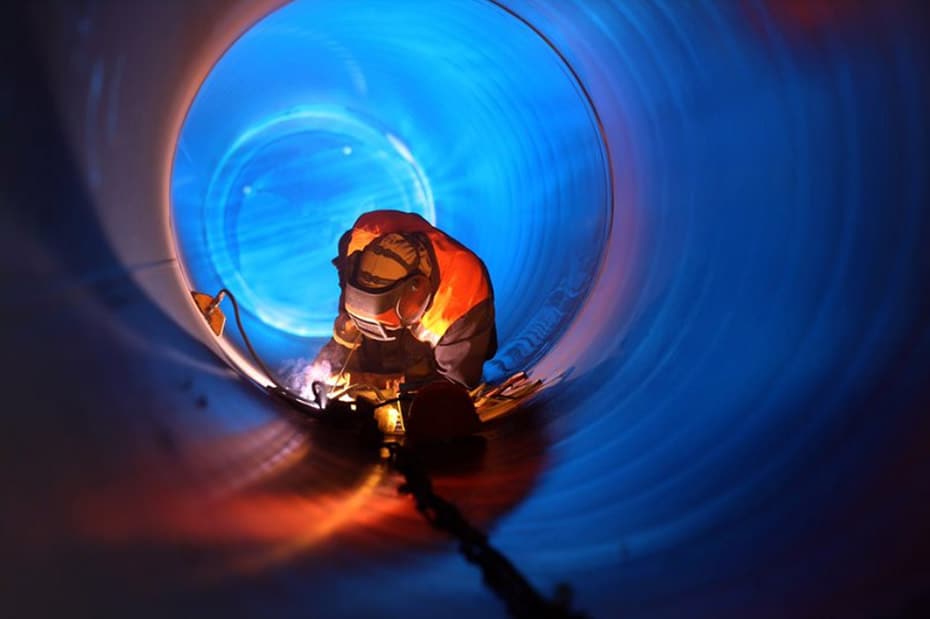
Цель неразрушающего контроля
Основная цель неразрушающего контроля — оценка качества объекта без его разрушения. Основная причина этого — управление рисками. Хотя неразрушающий контроль не устраняет риск, он может значительно снизить или уменьшить его.
Неразрушающий контроль контрастирует и сочетается с разрушающим контролем.НК позволяет проводить испытания фактически находящихся в эксплуатации объектов и оборудования. И наоборот, после того, как объект был разрушен, его нельзя вернуть в сервис. Таким образом, цель неразрушающего контроля по сравнению с разрушающим испытанием — снизить риск повреждения важного оборудования или инфраструктуры в полевых условиях.
Эти два служат взаимосвязанным целям. Разрушающее тестирование дает точную оценку того, что нужно для разрушения объекта. Зная пределы, установленные разрушающим испытанием в лаборатории, технические специалисты проводят неразрушающий контроль в полевых условиях, чтобы определить, насколько близок объект к достижению этих пределов.Если объект находится слишком близко к пределу, неразрушающий контроль позволяет безопасно отремонтировать или заменить его до того, как будет нанесен какой-либо ущерб.
Все объекты нужно тестировать? Нет. Неразрушающий контроль имеет смысл, когда риск выхода объекта из строя превышает затраты на его тестирование. К объектам повышенного риска относятся объекты, которые в случае отказа представляют опасность для жизни окружающих, например пассажирские самолеты или ядерные реакторы. К объектам высокого риска также относятся те, которые могут нанести серьезный финансовый или экологический ущерб, например нефтепроводы.Стоимость тестирования зависит от стоимости оборудования и времени сотрудников; рабочее время включает как обучение, так и фактическое тестирование.
К счастью, компаниям не нужно гадать, какое оборудование или инфраструктуру тестировать — многие требования к неразрушающему контролю продиктованы национальными правительствами. Правительства часто основывают свои юридические требования на информации, опубликованной международными органами по стандартизации, такими как ASTM или ISO. Таким образом, производной — хотя, тем не менее, важной — целью неразрушающего контроля является обеспечение соответствия нормативным требованиям.Пренебрежение требованиями неразрушающего контроля может привести к более высоким штрафам и штрафам, чем простое их соблюдение.
Отрасли промышленности, использующие неразрушающий контроль
Неразрушающий контроль широко используется во многих важных отраслях промышленности мира. Любая промышленность с большим физическим оборудованием или инфраструктурой, вероятно, будет использовать какой-либо неразрушающий контроль. Кроме того, в каждой отрасли обычно практикуются несколько методов неразрушающего контроля. Например, авиакомпании будут использовать ультразвуковой контроль для проверки лопастей вентилятора турбины и вихретоковый контроль для поиска поверхностных или подповерхностных дефектов в многослойных конструкциях.
Отрасли, в которых обычно практикуют неразрушающий контроль:
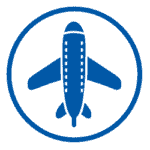
Авиация
Производители авиакосмической отрасли, авиакомпании и ремонтные службы обязаны по закону проводить различные периодические проверки неразрушающего контроля. Практически все аспекты самолета или вертолета должны проверяться через определенные промежутки времени. Также необходимо инспектировать космические корабли и дроны. В авиации и космонавтике используется множество различных методов неразрушающего контроля, включая ультразвуковые, вихретоковые и другие.
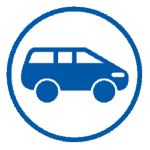
Автомобильная промышленность
Хотя владельцы транспортных средств не обязаны проводить неразрушающий контроль, производители обязаны. Чтобы предотвратить выход материала из строя на дороге, производители должны проверять компоненты автомобиля на наличие трещин и дефектов, проблем, возникающих из-за неправильной термообработки и недопустимого смешения материалов.
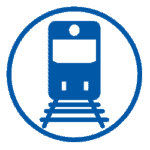
Железная дорога
Как поезда, так и их пути требуют неразрушающего контроля, как и многие связанные с ними интермодальные складские и логистические системы. Необходимо проверять колеса, оси, тормоза и гидравлические системы вагонов поезда, а также рельсы и их крестовины.Краны, стояки и сборные резервуары требуют периодических проверок безопасности, особенно сборные резервуары, в которых хранятся опасные материалы.
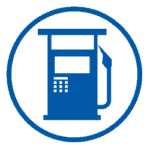
Нефть и газ
Отвечая за тысячи миль и триллионы долларов инфраструктуры и оборудования, все подразделения нефтегазовой отрасли полагаются на неразрушающий контроль для предотвращения несчастных случаев и защиты своих инвестиций. На буровых площадках, трубопроводах и нефтеперерабатывающих заводах бригады неразрушающего контроля постоянно проводят инспекции сварных швов, труб, стояков, резервуаров и больших поковок.Огромный объем инспекций, проводимых нефтегазовой отраслью, позволяет получить эффективное портативное оборудование для неразрушающего контроля.

Power Generation
Большие электростанции имеют нулевую устойчивость к сбоям и строгие требования к испытаниям. Атомные станции, в частности, доверяют своим решениям по неразрушающему контролю для обеспечения безопасной эксплуатации. Но угольные, нефтяные и газовые заводы полагаются на неразрушающий контроль при обнаружении дефектов в своих турбинах, трубопроводах и связанных с ними системах. Возобновляемые электростанции, включая гидроэлектростанции и ветряные электростанции, также проверяют целостность своего оборудования и систем.
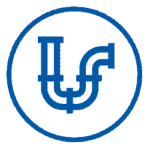
Производство
Компании тяжелой промышленности обычно используют неразрушающий контроль для обеспечения качества продукции перед поставкой. Производители труб, стали и трубок проверяют целостность материалов и сварных швов. Производители турбин, крупных судов и кораблей также доверяют неразрушающему контролю определение соответствия своей продукции соответствующим спецификациям. Производители специальных композитов могут обнаруживать пустоты, расслоение, колебания плотности, пористость, напряжения, повреждения и инородные материалы, присутствующие в их продуктах.НК в производстве гарантирует не только безопасность продукции, но и репутацию компании.
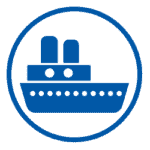
Морские суда
Большие и малые морские суда зависят от неразрушающего контроля для предотвращения разрушения материалов в море. Металлические и композитные корпуса проверяются производителями, а также периодически в процессе эксплуатации. Лопасти гребных винтов, турбины и внутреннее оборудование, такое как сборные резервуары или котлы, также должны регулярно проверяться. Суда с ядерными двигателями должны испытывать свои системы так же тщательно, как и парогенераторы на суше.Из-за трудностей морского права режимы морского неразрушающего контроля часто являются в первую очередь прерогативой судовладельцев и производителей, хотя и осведомленных в соответствии с международными стандартами.
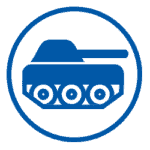
Военные
Военные полагаются на аэрокосмические, военно-морские и ядерные технологии и должны тщательно проверять находящееся в их ведении оборудование, чтобы гарантировать надежность своей миссии. Военные автомобили, боеприпасы и сооружения также обычно требуют проведения неразрушающего контроля.
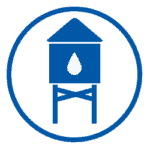
Коммунальные предприятия
Энергокомпании и водоканалы используют неразрушающий контроль, чтобы их инфраструктура оставалась безопасной и эффективной.Например, очистные сооружения проверяют целостность резервуаров, прудов и труб.
Независимо от отрасли, наиболее частым применением неразрушающего контроля является проверка целостности конструкционных материалов. Эти материалы включают металлы различного состава и толщины, композитные материалы, волокна и пластмассы. Потребность в неразрушающем контроле для данного приложения определяется вероятностью и последствиями сбоя приложения.
Требования к неразрушающему контролю
Определенные минимальные стандарты неразрушающего контроля предписаны законом.Разные страны или органы следуют разным стандартам, поэтому компаниям, работающим в разных странах, могут потребоваться разные требования к тестированию или отчетности для одного и того же приложения. Компании, в отношении которых действуют частично совпадающие ограничения, должны соблюдать самые строгие из них.
Авиакомпании, нефтегазовые компании и производители больше всего подвержены сложным и частично совпадающим нормативным требованиям. Программы неразрушающего контроля должны разрабатываться в консультации с соответствующими экспертами или юрисконсультом, чтобы обеспечить полное соблюдение требований.
Большинство государственных стандартов по неразрушающему контролю основаны на рекомендациях независимых международных организаций, включая ISO и ASTM. Эти организации частично основывают свои стандарты на исследованиях производителей и нескольких национальных и международных торговых ассоциаций. Эти торговые ассоциации включают Международный комитет неразрушающего контроля, Американское общество неразрушающего контроля и Ассоциацию управления неразрушающим контролем.
Правилапо неразрушающему контролю могут определять детали, подлежащие испытанию, используемые методы, периодичность испытаний, минимальные значения приемлемости и стандарты ведения документации.Производители неразрушающего контроля используют эти стандарты в качестве справочных при разработке контрольно-измерительного оборудования и решений. Стандарты и оборудование развиваются вместе, с появлением более эффективных решений, отвечающих более строгим требованиям. Производители должны иметь возможность продемонстрировать, насколько их продукты соответствуют нормативным требованиям для любого приложения, которое они продают.
Обучение и сертификация по неразрушающему контролю
Для успешной эксплуатации технологии неразрушающего контроля требуется соответствующая подготовка и опыт.В некоторых случаях, когда сертификация персонала по неразрушающему контролю требуется стандартами, кодексами или правилами, многие сертифицируют свой персонал в соответствии с международным стандартом ISO 9712. Однако, поскольку неразрушающий контроль подпадает под действие различных регулирующих режимов, сертификация и обучение тоже подпадает под действие различных режимов регулирования. Хотя не существует единого центрального, окончательного органа по обучению НК, варианты обучения, тем не менее, остаются доступными. Учебные курсы проводятся производителями продукции, сторонними организациями и самими работодателями.Работодатели имеют право по своему усмотрению устанавливать требования к обучению сотрудников неразрушающему контролю.
ОбучениеNDT обычно делится на три уровня, примерно соответствующих уровню знаний ученика, подмастерья и мастера. В отрасли они известны как сертификаты уровня I, уровня II и уровня III.
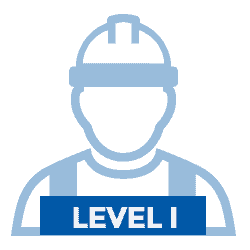
На самом базовом уровне специалисты по неразрушающему контролю должны продемонстрировать квалификацию в одном или нескольких ограниченных типах оценки, то есть в ультразвуковом обнаружении трещин в сварных швах.Они должны иметь возможность определять, прошло ли приложение оценку или нет, и задокументировать результаты. Технические специалисты также должны иметь возможность настраивать, калибровать, хранить и соблюдать меры безопасности для одного или нескольких типов оборудования неразрушающего контроля. Техников уровня 1 должны контролировать техники более высокого уровня.
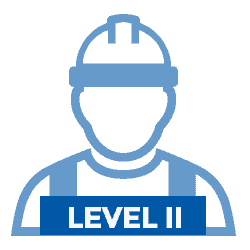
Специалисты по неразрушающему контролю среднего уровня должны продемонстрировать глубокое понимание возможностей и слабых сторон своих методов неразрушающего контроля. Они должны быть знакомы с взаимосвязью между стандартами и методами испытаний, а также внутренними и внешними нормами и правилами.Технические специалисты уровня II могут настраивать и калибровать оборудование, а также интерпретировать результаты. Они могут руководить командой технических специалистов уровня I и составлять отчеты для презентации.
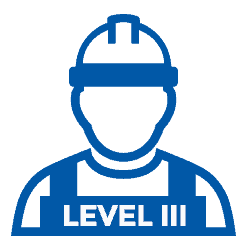
Специалисты-эксперты по неразрушающему контролю разрабатывают стратегии неразрушающего контроля, которые реализуют техники уровня I и II. Они превращают внешние правила во внутренние передовые практики. Они определяют методы и стандарты испытаний и могут нести ответственность за выбор или рекомендацию оборудования. При отсутствии установленных стандартов технические специалисты уровня III должны иметь средства для разработки собственных стандартов.Технические специалисты уровня III контролируют и проверяют техников уровня I и II.
Для успешной оценки неразрушающего контроля требуются как теоретические, так и прикладные знания. Опыт также является незаменимым учителем. В рамках своих требований к сертификации технические специалисты по неразрушающему контролю должны подтвердить свою квалификацию в письменных и практических экзаменах, в то время как минимальные требования к опыту гарантируют, что важные проверки находятся в надежных руках.
Виды неразрушающего контроля
На протяжении столетий было разработано множество различных типов неразрушающего контроля, от простейших визуальных проверок и испытаний на герметичность до передовых ультразвуковых или радиографических методов.Каждый исследуемый материал имеет разные свойства, некоторые из которых более подходят для одного типа неразрушающего контроля, чем для другого. Методы неразрушающего контроля различаются в зависимости от средств тестирования, необходимого оборудования, скорости и охвата, которые они обеспечивают, и, в некоторых случаях, необходимых мер безопасности.
Не существует универсального «лучшего» метода неразрушающего контроля. Лучший метод в любом сценарии — тот, который наиболее точно отвечает потребностям организации, использующей его. В современной промышленности скорость, простота использования и диапазон применения часто являются предпочтительными качествами решений неразрушающего контроля.
Щелкните здесь, чтобы перейти к конкретному методу неразрушающего контроля:
Ультразвуковой контроль | Вихретоковый контроль | Визуальное тестирование | Ультразвуковой контроль на больших расстояниях | Утечка магнитного потока | Лазерное тестирование | Радиографические исследования | Тестирование магнитных частиц | Акустическая эмиссия | Тепловое / инфракрасное тестирование | Анализ вибрации | Тестирование на проникновение жидкости | Проверка на герметичность
Ультразвуковой контроль (UT)
Ультразвуковой контроль зарекомендовал себя как один из самых эффективных методов современного неразрушающего контроля.Этот метод работает путем наведения высокочастотных звуковых волн на твердые объекты, как правило, металл или композит. На распространение звуковых волн влияют такие неоднородности, как колебания плотности, трещины, пустоты, соты или посторонние предметы. Собирая и интерпретируя возвращенные звуковые волны, оборудование для ультразвукового тестирования может отображать внутреннюю часть многих твердых объектов. В зависимости от используемого оборудования и требований приложения, волны могут быть собраны, когда они отражаются назад или проходят через сканируемый материал.
Ультразвуковой контроль основан на использовании преобразователей для преобразования электрической энергии в ультразвуковые волны. В то время как в старых методах использовался один датчик за раз, в современном оборудовании для ультразвукового контроля с фазированной решеткой (PAUT) используется несколько датчиков, работающих в тандеме. Этот метод значительно увеличивает скорость проверки, зону охвата и специфичность.
Недавно в усовершенствованные приборы PAUT были добавлены более высокие характеристики, включая времяпролетную дифракцию (TOFD) и метод полной фокусировки (TFM).Эти новые методы идеально подходят для проведения более сложных проверок.
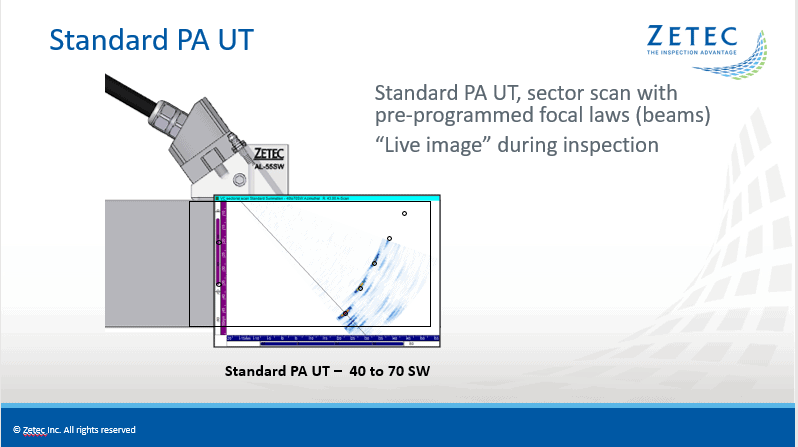
Ультразвуковое оборудование повсеместно используется для объемных испытаний в различных отраслях промышленности из-за его ряда преимуществ. PAUT обеспечивает быстрые и точные показания без необходимости настройки. Само оборудование может быть легким и портативным для полевых операций, но при этом достаточно прочным, чтобы работать в неблагоприятных условиях. Диапазон применений для тестирования ультразвуковых покрытий делает эту технологию привлекательной для крупных организаций, поскольку она упрощает закупку оборудования и схемы обучения.
Как и все методы неразрушающего контроля, ультразвуковой контроль подходит не для всех областей применения. Материалы с более крупными зернами, такие как железо, мешают передаче волн. Нечетная геометрия, включая изогнутые поверхности, иногда может создавать трудности при покрытии без определенной передовой техники или полного решения. Кроме того, качество зонда существенно влияет на глубину проникновения и качество изображения.
Подробнее о Современное ультразвуковое испытательное оборудование и программное обеспечение
Вихретоковый контроль (ECT)
Вихретоковый контроль использует магнитные поля для формирования изображений проводящих материалов.Изменения свойств материала создают неоднородности в поле, подобно тому, как горные породы создают водовороты в ручьях. Эти изменения указывают на коррозию, трещины, пустоты, соты, расслоение и потерю толщины.
Вихретоковая технология находит регулярное применение в промышленности благодаря своей портативности, скорости и точности. Одним из наиболее важных применений вихретокового контроля является электроэнергетика. Вихретоковая технология доказала свою эффективность и экономичность для проверки труб теплообменника и охладителя.Портативное вихретоковое оборудование позволяет проводить проверки на месте, сокращая время простоя, необходимое для выполнения проверок.
Недавнее нововведение в вихретоковом контроле — это технология вихретоковой матрицы (ECA), которая идеально подходит для наземных и приповерхностных карт в различных отраслях промышленности, включая аэрокосмическую, железнодорожную, промышленную, нефтегазовую. ECA — это чрезвычайно быстрый, экономичный и простой в использовании метод, обеспечивающий очень точные результаты.
Хотя вихретоковая технология может проникать через тонкие непроводящие покрытия, такие как цинк на оцинкованной стали, в остальном ее использование ограничено проводящими материалами.Кроме того, вихревые токи могут иметь трудности со сложной геометрией или большими площадями. Хотя они ограничивают диапазон вихретокового оборудования, оно остается очень эффективным инструментом в пределах своих параметров.
Подробнее о Вихретоковый неразрушающий контроль
Визуальное тестирование (VT)
Самый старый вид неразрушающего контроля — это визуальный контроль. Он использует маломощное оборудование, включая бороскопы и фиброскопы, для контроля дефектов.Быстрые, недорогие и прямые визуальные испытания могут стать первым инструментом для выявления проблем с активами и инфраструктурой, от трещин до коррозии. Тем не менее, визуальное тестирование неадекватно при попытке идентифицировать множество различных типов отказа материала на достаточно раннем этапе, чтобы безопасно отремонтировать или заменить оборудование. Когда зрение не видно, или дефекты небольшие или внутренние, визуальный осмотр не выполняется. Фактически, различные недостатки визуального контроля создали необходимость во всех других формах неразрушающего контроля.
Ультразвуковой контроль на большом расстоянии (LRUT)
УЗИ на большие расстояния — это метод ультразвукового контроля, используемый специально для трубопроводов.Ультразвуковые преобразователи или катушки встроены в кольцо, которое перемещается по трубе. Преобразователи излучают волны, которые обеспечивают изображение внутренней части стенки трубы. Неровности и изменения толщины изменяют волны, открываясь техническим специалистам. Этот метод не требует жидкой связи между датчиками и поверхностью.
Утечка магнитного потока (MFL)
Утечка магнитного потока — это эффективный метод полевых испытаний, который в основном используется для проверки больших труб, труб и дна резервуаров.Мощный магнит используется для насыщения материала магнитным полем. Датчик обнаруживает колебания магнитного поля, вызванные различиями в свойствах материала, такими как коррозия, точечная коррозия, потеря толщины или трещины. Трубы можно сканировать, не снимая изоляции, с помощью магнита и датчика, перемещающегося по длине цилиндра. Полы резервуаров необходимо сканировать с помощью генераторов поля, расположенных последовательно. Эта технология хороша для черных металлов и способна обнаруживать недостатки в крупной инфраструктуре.
Методы лазерных испытаний (LM)
Преобладают три типа лазерного неразрушающего контроля — профилометрия, ширография и голографические испытания. В профилометрии используется вращающийся лазер для визуализации внешней поверхности труб и трубок, обнаружения трещин, эрозии или точечной коррозии.
Ширография — это высокоточный метод обнаружения дефектов материала «до и после». Лазер записывает изображение материала до и после приложения напряжения и использует обнаруженные различия для вывода внутренних структур.
Голография использует аналогичный метод «до и после» для определения дефектов в масштабе микрометров. Эти два метода различаются оборудованием и программным обеспечением, используемым для получения результатов. Ширография предпочтительна для больших поверхностей; голография для маленьких.
Радиографические исследования (RT)
Радиографические исследования вошли в воображение общественности благодаря рентгеновским аппаратам. Метод проникает через объект и носитель записи излучением. Более темные области на носителе записи указывают на большее количество излучения, прошедшего через эту область объекта, указывая на трещины, пустоты или изменение плотности.Рентгеновские лучи обычно используются для более тонких материалов; гамма-лучи для более толстых. Пленочные или компьютеризированные датчики могут использоваться в качестве носителей информации. Радиографическое обследование требует значительного оборудования и опыта, а также мер безопасности для предотвращения чрезмерного воздействия радиации.
Нейтронно-радиографические испытания используют концентрированный луч нейтронов для проникновения в объекты, а не рентгеновские или гамма-лучи. Для генерации нейтронных пучков необходимо использовать линейный ускоритель или бетатрон. Нейтроны проходят через металлы, но не через большинство органических материалов.В сочетании со стандартной рентгенографией это дает более подробную картину интерьера объектов. Эта технология используется только в лабораторных условиях.
Тестирование магнитных частиц (MT)
При испытании с помощью магнитных частиц используется движение индикаторных частиц для подтверждения внутренних неоднородностей в ферромагнитных материалах. Испытуемая деталь должна быть покрыта окрашенными магнитными частицами в виде сухого порошка или жидкой суспензии. Магнит индуцирует электромагнитное поле в испытуемом материале.Поле заставляет магнитные частицы двигаться к любым неоднородностям, поперечным направлению магнитного поля, обеспечивая визуальную индикацию дефектов.
Тестирование магнитных частиц — это обширная дисциплина, и для создания магнитных полей можно использовать множество методов. Испытание на магнитные частицы требует значительной настройки и очистки и не может быть легко использовано в полевых условиях.
Испытание на акустическую эмиссию (AET)
Испытание на акустическую эмиссию основано на аналогичном принципе ультразвукового контроля — передаче акустических волн через твердые объекты.Однако распространение и измерение волн выполняются разными способами. Волны вызываются резким приложением силы к объекту, например ударом молотка или другой механической нагрузкой. Изменения температуры и давления также могут вызывать соответствующие волны.
Вместо того, чтобы прислушиваться к изменениям волновых характеристик и картированию на их основе, тестирование акустической эмиссии обнаруживает физическое движение самой среды. Изменения или несоответствия в материале объекта, такие как пустота, можно обнаружить по различиям в движениях, обнаруживаемых отдельными датчиками.Хотя испытания на акустическую эмиссию эффективны для пластмасс и других материалов, они менее распространены и требуют больших затрат на оборудование, чем другие методы неразрушающего контроля. Эта технология чаще всего встречается в лабораторных условиях.
Тепловое / инфракрасное тестирование (IRT)
При тепловых испытаниях используется захваченное инфракрасное излучение, исходящее от объекта, для получения изображения поверхности объекта. Тепловидение может указать на коррозию, пустоты, посторонние предметы или расслоение. Сканируемые области должны быть открыты, чтобы обеспечить прямую видимость инфракрасной камеры.Хотя тепловые испытания могут быть эффективными, обнаруженные им дефекты также могут быть обнаружены другими методами, которые требуют гораздо менее обширной настройки.
Анализ вибрации (VA)
Анализ вибраций превосходно подходит для проверки целостности вращающихся частей, включая турбины, шестерни, валы и подшипники. Обычно используются три типа анализа вибраций: акселерометры, датчики скорости и датчики вихретокового смещения.
Акселерометрынаиболее эффективны для высокоскоростных приложений, поскольку они чувствительны к высоким частотам.Датчики скорости используют магнит для создания электрического поля от вращающейся части, что позволяет эффективно измерять детали, движущиеся с низкой или умеренной скоростью.
Датчики смещения вихревых токов измеряют физическое движение вращающейся части по нежелательным горизонтальным или вертикальным осям. Они могут обнаруживать изменения зазора или движения вала, указывающие на необходимость ремонта.
Испытания на проникновение жидкости (PT)
Испытание на проникновение жидкости обеспечивает визуальную индикацию трещин или других дефектов, которые соединяются с поверхностью материалов.Жидкий пенетрант в первую очередь полезен для непористых материалов, поскольку пористые материалы скрывают признаки дефектов. Этот метод тестирования покрывает или пропитывает материалы индикаторной жидкостью. Эта жидкость поступает в отверстия на поверхности материала. Когда жидкость, оставшаяся на поверхности, удаляется, жидкость возвращается из трещин. Везде, где всплывает жидкость, обнаруживается дефект; чем больше жидкости, тем больше дефект.
Без канала, соединяющего дефект с поверхностью, жидкость не может попасть в него.Таким образом, необходимо использовать другие методы для обнаружения закрытых пустот или сот. Поверхность материала также должна быть чистой, поскольку масла и другие остатки не могут повлиять на способность жидкости проникать в трещины. Кроме того, пенетрант требует значительного оборудования, настройки и очистки для обработки самой жидкости. Хотя этот метод можно использовать эффективно, он часто более медленный и громоздкий, чем другие методы неразрушающего контроля.
Тестирование на герметичность (LT)
Проверка герметичности — это категория неразрушающего контроля, относящаяся к нескольким методам определения наличия утечек в герметичных сосудах.Существует четыре распространенных метода обнаружения утечек газа, хотя некоторые из них похожи. Испытания на изменение давления либо повышают давление, либо создают вакуум в герметичном сосуде. Потеря давления или вакуума указывает на утечку. Тестирование пузырьков также зависит от индикатора давления. Детали подвергаются давлению, а затем погружаются в жидкость. Наличие пузырьков указывает на место утечки.
Тестирование галогенных диодови масс-спектрометров схоже, оба используют газ-идентификатор для обнаружения утечки.В сосуд под давлением вводят галоген или гелий (часто смешанный с воздухом). Детектор с галогеновыми диодами или масс-спектрометр, расположенный за пределами зоны повышенного давления, предупреждает технических специалистов о присутствии галогена или гелия, указывая на утечку.
Некоторые пузырьковые тесты могут быть выполнены на месте с использованием специального оборудования для создания герметичных участков на больших и / или плоских поверхностях. Однако испытание на наличие пузырьков и другие методы проверки на герметичность отнимают много времени и требуют громоздкого оборудования и настройки.Лучше всего их выполнять в лабораторных условиях.
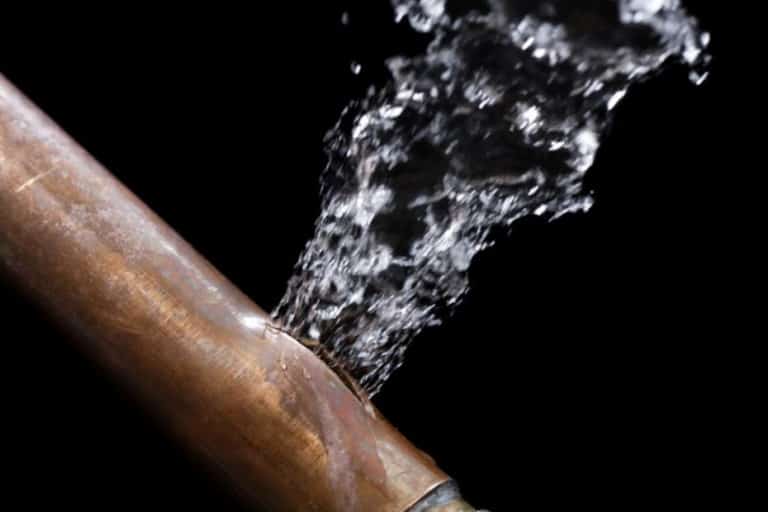
Сравнение методов неразрушающего контроля
Сравнение различных типов неразрушающего контроля может быть затруднено; каждый уникален и предназначен для своего назначения. Это также означает, что в зависимости от приложения, вероятно, потребуется или предпочтителен один определенный тип неразрушающего контроля. Тем не менее, когда выбор неясен, важно понимать относительные достоинства каждого метода неразрушающего контроля, чтобы принять правильное решение относительно оборудования.
В таблице ниже представлено общее сравнение различных типов неразрушающего контроля, материалы, для которых они обычно используются, а также практические соображения, такие как скорость, требования к настройке и опасности.
Материалы | Скорость | Пределы | Опасности | Установка | |
Ультразвуковой | Сталь, сплавы, прочие металлы и композиты | Быстро | Грубые, грубые или слишком толстые материалы | Нет | Быстро |
Вихретоковый | Тонкие проводящие материалы | Быстро | Только токопроводящие материалы | Нет | Быстро |
Визуальный | Все материалы | Быстро | Невозможность обнаружения мелких или скрытых дефектов | Нет | Быстро |
UT большого радиуса действия | Трубопровод | Быстро | Только трубопровод | Нет | Значительное |
Магнитный поток | Трубы, трубки, днища резервуаров | Быстро | Доступ | Нет | Умеренное |
Лазерное тестирование | Металлы, пластмассы, композиты, трубопроводы | Быстро | Доступ | Повреждение глаз | Умеренное |
Рентгенография | Большинство материалов | Быстро | Крупное оборудование и требования безопасности | Радиация | Умеренное |
Магнитная частица | Материалы ферромагнитные | Быстро | Только ферромагнитные материалы | Локализация твердых частиц и жидкостей | Медленная |
Акустическая эмиссия | Пластмассы, композиты, металлы | Умеренное | Требуется несколько датчиков | Нет | Умеренное |
Тепловизор | Металл, пластик, композит | Умеренная | Доступ | Нет | Умеренное |
Вибрация | Вращающиеся объекты | Умеренное | Доступ | Близость к вращающимся частям | Умеренная |
Жидкий пенетрант | Непористые материалы | Медленная | Доступ, транспортировка жидкостей | Контейнер для жидкости | Медленная |
Проверка на герметичность | Запечатанные сосуды | Медленная | Требуется напорная камера | Давление или вакуум | Медленная |
Выбор подходящего неразрушающего контроля для вашего приложения
Во многих случаях правильный метод неразрушающего контроля для конкретного приложения — это тот, который требуется по закону.Если никакие применимые законы не определяют метод тестирования, руководство все равно можно найти, изучив передовой опыт, опубликованный международными организациями по стандартизации. Точно так же производитель рассматриваемой детали может также публиковать стандарты и передовой опыт неразрушающего контроля со своей стороны. Если ни один из вышеперечисленных ответов не дает ответа, проконсультируйтесь с техником по неразрушающему контролю уровня III, который может порекомендовать наилучшие следующие шаги. Вообще говоря, полевые работы с металлами и композитами, вероятно, могут быть выполнены с использованием ультразвукового оборудования и оборудования для вихретокового контроля, либо их обоих.
Не все оборудование неразрушающего контроля одинаково. Некоторые инструменты предназначены для лабораторных работ; другие для тяжелой работы в поле. Выбор подходящего производителя неразрушающего контроля так же важен, как и выбор правильного метода. Производители могут предоставить не только оборудование, но и обучение, поддержку и консультации. Те, у кого есть большой опыт работы в отрасли, обладают институциональными знаниями и опытом, необходимыми для решения новых или сложных вопросов проверки. Партнерство с проверенным производителем неразрушающего контроля может обеспечить не только эффективное оборудование неразрушающего контроля, но и бесценное спокойствие.
Zetec уже несколько десятилетий является ведущим поставщиком решений неразрушающего контроля. Чтобы узнать больше о нашем оборудовании для ультразвукового и вихретокового неразрушающего контроля, свяжитесь с нами сегодня!
.Безопасность при неразрушающем контроле (NDT)
Безопасность в неразрушающем контролеНЕОБХОДИМОСТЬ НК
Визуальные наблюдения, даже с увеличением, не могут обнаружить все мелкие дефекты под поверхностью в отливке, кованых металлах или металлах сварных швов, например, в сосудах высокого давления, котлах и компонентах ядерной энергетики. Правильный NDT , однако, обнаружит все такие показания без повреждения компонентов.
Методы неразрушающего контроля
ВИДЫ НК
- Магнитная частица.
- Пенетрант.
- Ультразвуковой.
- Электромагнитный.
- Радиографический.
Испытание магнитных частиц при неразрушающем контроле
Контрольный тестMP является наиболее распространенным методом неразрушающего контроля для поковок. Он использует магнетизм для притяжения и удержания очень мелких магнитных частиц прямо на самой детали. Если дефект присутствует, он прерывает магнитное поле, что четко видно по рисунку, нанесенному частицами.
Деталь намагничивается в подходящем направлении линейным напряжением постоянного тока, преобразованным в низкое напряжение (от 4 до 18 вольт) переменного тока большой силы, полуволновой ток или трехфазный полнополупериодный ток.
НАЖМИТЕ ЗДЕСЬ? БЕЗОПАСНОСТЬ ИСПЫТАНИЙ ГИДРО
МЕРЫ ПРЕДОСТОРОЖНОСТИ Испытание магнитными частицами :
- Все электрические цепи должны быть установлены и заземлены в соответствии с Национальным электрическим кодексом или любым другим подходящим кодом.
- Необходимо обеспечить местную вытяжку для контроля частиц пыли, используемых для испытаний.
- Если локальная вытяжка невозможна, оператор должен носить средства защиты органов дыхания.
- Оператор должен носить средства защиты глаз для защиты от раздражающего воздействия частиц пыли и искрения.
- Необходимо использовать средства индивидуальной защиты для защиты от возможного раздражения кожи порошком.
НАЖМИТЕ ЗДЕСЬ? СИЗ В ДЕТАЛЯХ
НАЖМИТЕ ЗДЕСЬ? ВСЕ СИЗ — КОД
Пенетрантный контроль (DP) при неразрушающем контроле:
ИспытанияDP используются для обнаружения трещин, пор и подобных признаков, которые открываются на поверхности в металлах или других твердых материалах.
Сначала проверяемая деталь очищается, затем на поверхность наносится пенетрант, который в течение нескольких минут втягивается в дефекты за счет капиллярного действия. Пенетрант удаляется с поверхности, но остается в отверстии поверхности, пока не будет удален проявителем.
МЕРЫ ПРЕДОСТОРОЖНОСТИ в Инспекция проникновения (DP)
- Большинство пенетрантов — это органические соединения, которые могут вызывать дерматит.
- Следует избегать контакта с кожей и строго соблюдать правила личной гигиены.
- Курение, материалы для курения, продукты питания и напитки не должны храниться или использоваться в зоне испытаний.
- Открытые участки кожи следует промыть перед курением, едой или питьем.
Ультразвуковые испытания (UT) в неразрушающем контроле:
Ультразвуковые волны (выше слышимого диапазона 20000 Гц создаются электронным генератором, который подает высокочастотное напряжение на пьезоэлектрический кристалл.
Разработаны три основных ультразвуковых метода.Метод отражения, метод сквозной передачи и метод резонансной частоты.
МЕРЫ ПРЕДОСТОРОЖНОСТИ в Ультразвуковые испытания (UT)
- Оборудование должно быть отключено от источника питания, а
- Конденсаторы разряжаются всякий раз, когда электронно-лучевая трубка должна быть отрегулирована или снята.
Электромагнитные методы неразрушающего контроля в неразрушающем контроле:
В настоящее время используются два типа электромагнитных испытаний: магнитоиндуктивный и вихретоковый.
Магнитоиндуктивный метод использует вариации проницаемости магнитных материалов для создания вариаций в измерительной катушке или зонде.
Вихревой ток использует переменный ток в катушке или датчике для индукции вихревого тока в проверяемой детали. Дефекты и отклонения в свойствах или геометрии вызывают изменения силы и распределения вихревого тока.
Показание отображается на электронно-лучевой трубке, на измерителе, с помощью подходящего или видимого сигнала тревоги, или с помощью комбинации этих методов.
МЕРЫ ПРЕДОСТОРОЖНОСТИ:
- В некоторых установках для частотного тестирования считывателей операторы получали внутреннее ожог, когда они проходили между объектом и испытательным устройством. Следует сформулировать и обеспечить соблюдение специальных правил.
- Необходимо установить заграждения для предотвращения доступа операторов и других лиц в такие зоны.
- Следует четко соблюдать рекомендации производителя оборудования.
Рентгенологические исследования при неразрушающем контроле:
Радиография использует рентгеновское и гамма-излучение.Рентгеновские лучи однонаправлены, и их длины волн могут варьироваться в определенных пределах, чтобы соответствовать условиям. Гамма-радиография отличается от рентгеновской радиографии тем, что гамма-лучи являются разнонаправленными, а их длины волн, характерные для источника, не регулируются.
НАЖМИТЕ ЗДЕСЬ? ПОРЯДОК РАДИОГРАФИЧЕСКОГО ОБСЛЕДОВАНИЯ
НАЖМИТЕ ЗДЕСЬ? ДЕТАЛИ РАДИАЦИОННОЙ БЕЗОПАСНОСТИ
НАЖМИТЕ ЗДЕСЬ? Правила радиационной защиты
МЕРЫ ПРЕДОСТОРОЖНОСТИ Рентгенологические исследования:
- Все источники ионизирующего излучения потенциально опасны. Их следует хранить и обращаться с ними в соответствии с инструкциями поставщика источника.
- Воздействие излучения на операторов следует регулярно контролировать в соответствии с инструкциями поставщика.
- К работе должен допускаться только обученный и сертифицированный оператор.
- Прилегающая территория должна быть эффективно оцеплена и исключена возможность проникновения в нее людей.
- По возможности, работа должна выполняться в подходящем закрытом помещении, построенном в соответствии с требованиями поставщика источника.
- Все операторы должны проходить медицинский осмотр с частотой, рекомендованной поставщиком источника.
- По окончании работ, источник должен храниться в соответствии с инструкцией поставщика источника.
Прочтите также это:
Теперь ваша очередь:
Вы читаете на сайте rlshumancare.com. Не забывайте название RLS HUMAN CARE. Пожалуйста, поделитесь с друзьями и помогите RLS HUMAN CARE. Благодарю вас!!
.