Новые технологии в сварке
В лазерном центре Санкт-Петербургского ЦНИИ РТК ведутся исследования в области новых технологий сварки металлов. Ученые исследуют процесс, представляющий собой взаимодействие двух тепловых источников нагрева: лазера и плазменного пучка. Связав эти два процесса, можно получить новую эффективную и относительно недорогую технологию сварки. Область ее возможного применения простирается от автомобилестроения до строительства магистральных трубопроводов.
Технологический макет представленного на видео роботизированного комплекса предназначен для исследований, проводимых в области гибридной лазерно-дуговой сварки – новые технологии в сварке .
Рассмотрен процесс, представляющий собой взаимодействие двух тепловых источников нагрева. Первый источник- это источник лазерного высококонцентрированного излучения, а второй источник – это источник плазмы, который дает более широкие характеристики и более дешевый вид энергии для тепловложения, но имеет ряд недостатков с точки зрения качества получаемого сварного соединения.
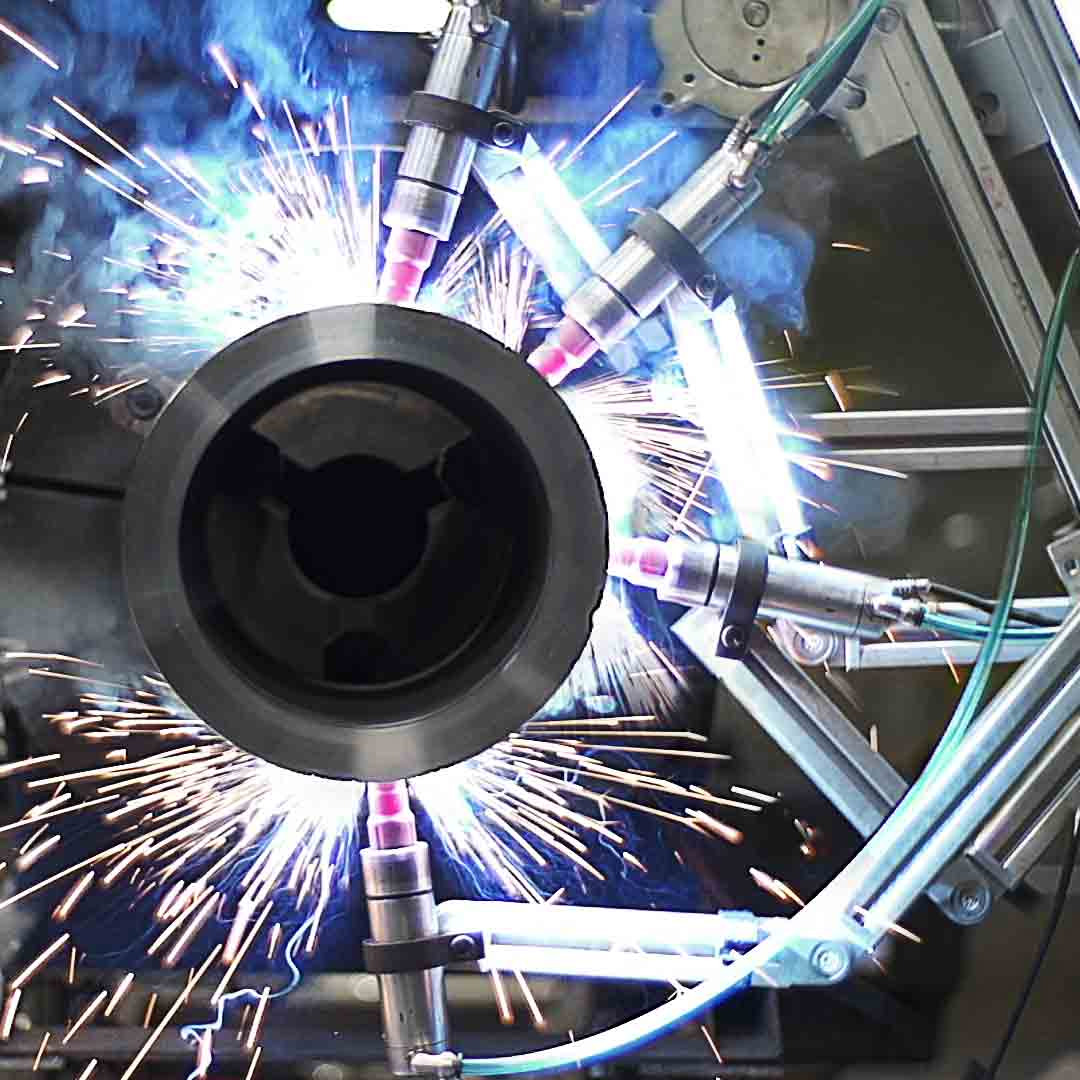
Идея скомбинировать — не нова. Комбинируют сейчас многое, не только плазму с лазером. Размешать дорогой лазер с дешевым теплом, например световым, индукционным – это сегодня одно из основных перспективных направлений в мире. Предварительно этот процесс был промоделирован математически, и одной из задач исследований явилась и проверка математической модели на адекватность, на точность воспроизведения процесса.
Актуальность данной работы основана на ряде проблем, которые существуют в судостроении и автомобилестроении. Например, проблема необходимости деформации тонколистовой стали после сваривания. Это характерно для кузовных деталей автомобилей. После сварки им должна быть придана определенная форма. Должна быть определенная пластичность сваренной заготовки.
Комплекс использовался для совместных прикладных исследований с Центром перспективных исследований АвтоВАЗа для производства сталей кузовных частей автомобилей ВАЗ.
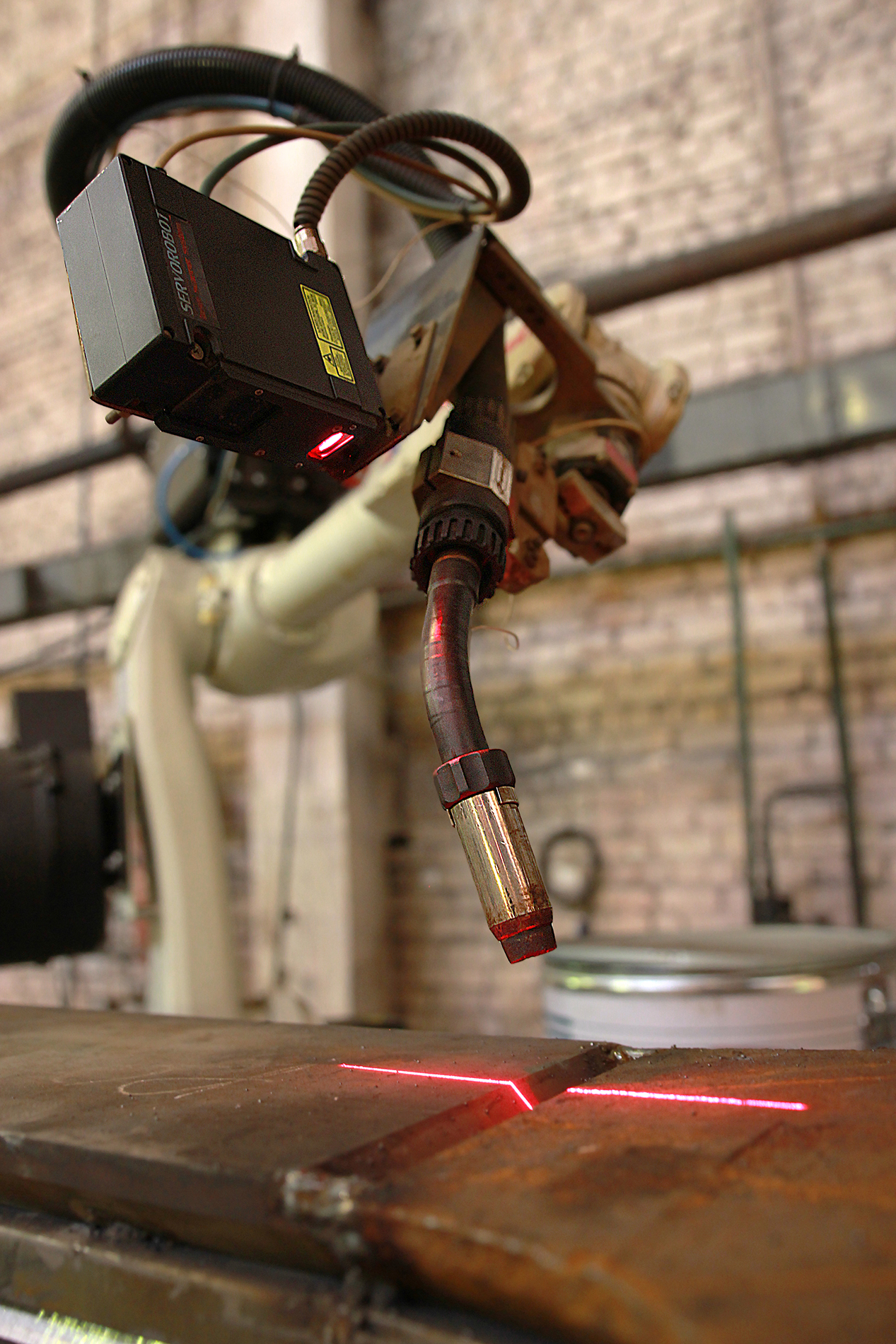
Программное обеспечение, основанное на математической модели, которая легла в основу этого процесса, является уже сейчас востребованным с точки зрения коммерциализации.
Кроме статьи «Новые технологии в сварке» смотрите также:
ИННОВАЦИОННЫЕ ТЕХНОЛОГИИ В СВАРОЧНОМ ПРОИЗВОДСТВЕ, ТАКИЕ КАК ПЛАЗМЕННАЯ СВАРКА.
Барминова Т.Н.
Георгиевский филиал Невинномысский государственный
Гуманитарно- технический институт
ИННОВАЦИОННЫЕ ТЕХНОЛОГИИ В СВАРОЧНОМ ПРОИЗВОДСТВЕ, ТАКИЕ КАК ПЛАЗМЕННАЯ СВАРКА.
Основу любой современной техники, в том числе, колёсной и гусеничной, составляют изделия из металла. А металл, каким бы прочным он не был, всё равно не вечен. При этом он не только ржавеет, но и гнётся, и даёт трещины. Основным способом ремонта металла была и остаётся его резка и сварка. Где-где, а здесь, казалось бы, особенно, в области сварки металлов, уже вряд ли можно придумать что-то новое. Разве что, усовершенствовать какую-то давно работающую технологию, которую её изобретатели, их последователи или другие энтузиасты, пытаются улучшить, внося туда какие-то новшества с оглядкой на требования сегодняшнего дня.
Одним из важнейших свойств металлов является их способность подвергаться той или иной обработке. Можно говорить о способности металлов пластически деформироваться в холодном или горячем состоянии, обрабатываться резанием, изменять свои свойства под влиянием термической обработки и т. д.. Очевидно, можно и необходимо говорить о способности металлов соединяться в процессе сварки и пайки — об их свариваемости и паяемости.
Технологические сложности и низкая экономическая эффективность традиционных видов сварки при производстве деталей и изделий привели к необходимости разработки принципиально нового метода.
Очевидно, что при определении понятия свариваемости металлов необходимо исходить из физической сущности сварки и отношения к ней металлов. Сварку целесообразно рассматривать как сочетание нескольких одновременно протекающих; процессов: взаимная кристаллизация металлов, тепловое воздействие на металл в околошовных участках и плавление, металлургическая обработка и кристаллизация металла шва. Под свариваемостью, следовательно, необходимо понимать отношение металлов к этим основным процессам.
Плазменная сварка – это сварка плавлением, при которой нагрев проводится направленным потоком дуговой плазмы (плазменной струей). Процесс осуществляется по схеме прямого действия. Плазменный способ является продолжением развития сварки в среде аргона вольфрамовым электродом и отличается следующими процессами: принудительное вдувание в дугу плазмообразующего газа и сжатие дуги за счет размещения ее в специальном плазмотроне.
Плазменная дуга отличается от обычной электродуги высокой концентрацией энергии и широкими возможностями ее регулирования. Отсюда вытекают преимущества плазменной дуговой сварки, которые следует выделить особо.
Высокая концентрация дуги – это минимальная зона теплового воздействия (ЗТВ), меньшее коробление изделия.
Плазменная дуга цилиндрической формы – отсюда меньшая критичность к изменению длины дуги, высокая стабильность проплавления и геометрии сварного шва.
Вольфрамовый электрод защищен соплом – значит, нет включений вольфрама в шве.
Высокое качество сварочных швов, не требующих дополнительной обработки.
Высокая скорость сварки – от 10 до 50 м/ч.
Отличное качество сварки при автоматизации процесса.
Качество сварочных соединений сравнимо с качеством швов, получаемых при электронно-лучевой сварке. Но та сложнее в обеспечении, т.к. обладает вредным рентгеновским излучением. Неслучайно более «прирученная» плазменная сварка, показывая почти те же результаты, нашла применение в авиастроении и ракетной технике. А там, как известно, к технологиям – особые требования. Впрочем, плазменные методы обработки охотно взяли на вооружение и автомобилестроение, электронное, электротехническое, химическое машиностроение, пищевая промышленность и др.
Но я хочу, отдельно остановится на точечной сварке. Ведь именно в этой сфере плазма стала наиболее востребованной в промышленности, найдя применение даже на автоматизированных комплексах, что может свидетельствовать только о высокой степени доверия к самой технологии.
Плазменная точечная сварка, в отличие от контактной, является односторонней. Благодаря этому возможна приварка листов к объемным конструкциям, а также сварка в труднодоступных местах, что касается и угловых соединений снаружи, и тавровых соединений внутри металлоконструкций.
Кроме того, плазменная сварка проводится бесконтактно. Значит, отсутствуют деформации, обеспечивается отличное качество видовой (лицевой) стороны. Достигается высокая стабильность и воспроизводимость (повторяемость) точек.
Для сварки применяются различные типы плазменных горелок (плазмотронов). Выбор зависит от вида и способа сварки (ручной или автоматический), а также от толщины свариваемых изделий. Металлический наконечник плазмотрона – съемный, что позволяет производить одной горелкой точечную сварку изделий различной конфигурации и толщины.
Процессы сварки могут быть смоделированы и запрограммированы.
Электронное регулирование подачи плазмообразующего газа, управление продувкой защитных газов, автоматический контроль за установкой охлаждения, сигнализация с индикацией на дисплее появившихся неисправностей существенно облегчает автоматизацию сварочного процесса. При настройке сварочных параметров имеется возможность точечной сварки в режиме многочисленных различных по величине и частоте коротких импульсов. Это позволяет ограничить нагрузку на плазменную горелку и улучшить оптику точечного соединения.
Плазмообразующая среда
В этом качестве, как уже говорилось выше, применяют различные газы (аргон, гелий, азот, водород и их смеси между собой или с воздухом). Механизм образования плазмы этих газов различен. Низкие энергетические характеристики аргоновой плазмы несколько ограничивают ее возможности. Гелий обладает более высокими энергетическими показателями, но из-за высокой стоимости и дефицитности не может иметь широкого применения. Азот по сравнению с аргоном имеет лучшие энергетические и экономические плазменные показатели, но при нагреве до высоких температур оказывает вредное влияние на окружающую среду.
Воздушная плазма является самой экономичной, высоко энергетической и доступной. Однако образующиеся нитриды и озон значительно ухудшают санитарно-гигиенические условия труда. Водород имеет отличные теплофизические свойства. Он позволяет достигнуть напряженности электрического поля в 2–3 раза выше, чем в аргоновой дуге, и повысить энергетический потенциал сжатой дуги за счет высокой теплопроводности и энтальпии. Наличие водорода в плазменной струе благоприятно сказывается на качестве сварного соединения, поскольку водород предохраняет расплавленный металл от действия окружающей среды. Но, как нетрудно догадаться, недостатками плазменной водородной среды являются взрывоопасность и пониженный ресурс работы сопла плазмотрона. Высокая теплопроводность снижает тепло- и электроизоляцию сопла от плазменной струи.
Между тем, в последнее время появились аппараты, в которых плазмообразующей средой выступает водяной пар. В такой роли он просто идеален, т.к. представляет собой удачное и дешевое сочетание водорода с кислородом.
При образовании плазмы воды (ионизации) образуется два объема ионов водорода и один объем ионов кислорода. Диссоциация водяного пара на водород и кислород начинается при температуре 1500К и при температуре 2300К составляет 1,8%. Основная масса водяного пара диссоциируется при температуре 4000К. Дальнейшее повышение температуры способствует ионизации водорода с поглощением значительного количества тепла. Соответственно при рекомбинации в области анода (изделия) высвобождается большое количество энергии, способствующей интенсификации процесса плавления металла. При высоких температурах, которые дает плазменная струя, водяной пар может также диссоциировать на водород и гидроксил (ОН). Последний, являясь высокоустойчивым соединением, не растворяется в металле, способствуя тем самым улучшению поверхности расплавленного металла (поверхность характеризуется металлическим блеском).
Большие перспективы использования водяного пара в качестве плазмообразующей среды вызывали желание разработчиков плазмотронов искать технические решения, позволяющие создать такие приборы. Однако сложности разработки и изготовления подобных аппаратов долго не давали возможности говорить об их широком применении, тем более промышленном. Но прорыв в этом направлении совершен, причем в России.
Инновационная разработка российской оборонной промышленности в использовании возможностей плазмы была удостоена золотых медалей на международных салонах изобретений в Брюсселе, Женеве и Софии. Их универсальность и многофункциональность заключаются в следующем: резка косвенной и прямой дугой; сварка – плазменная и плазменно-дуговая; пайка твердым и мягким припоем.
Устройство состоит из блока-инвертора и плазменно-водяной горелки. Последняя выполнена в форме пистолета и включает в себя разрядную камеру, конструктивно объединенную с устройством для парообразования. Такое решение позволило создать эффективную систему охлаждения электродов горелки за счет использования тепловой энергии, выделяемой на электродах для парообразования. Получилась по сути саморегулируемая система охлаждения (чем больше мощность, выделяемая на электродах горелки, тем больше количество вырабатываемого плазмообразующего пара).
Сварка возможна для «черных» и низколегированных сталей, в т. ч. некоторых сортов нержавеющих. Свариваются и сплавы алюминия, металлы медной группы, чугуны и т.д. А практика показывает, что путем подбора соответствующих присадочных материалов и флюсов большинство задач удается успешно решить. Такое возможно только при применении инновационных технологий, таких как плазменная сварка или сварочные инверторы. Если использовать этот способ сварки, металл не просто разогревается плазменной струей, но и подвергается газодинамическому воздействию. За счет этого работы проводятся быстро, и за короткий промежуток времени можно создать огромное количество сварочных швов. Производительность труда повышается, а стоимость сварки, наоборот, падает почти в 6 раз. Надежды на эту технологию огромны, но, к сожалению, сегодня ее применяют не так часто, как можно было бы. Пока использовать плазменную сварку повсеместно мешает дороговизна ее оборудования. И при этом технология нуждается в доработке. Сейчас работать с этой технологией могут только высококвалифицированные специалисты.
Идеальной плазмообразующей средой – экологически чистой, взрывобезопасной и безотходной, является водяной пар. К тому же, он не оказывает негативного влияния на санитарно-гигиенические условия труда.
СВАРКА И РОДСТВЕННЫЕ ТЕХНОЛОГИИ В ОСВОЕНИИ КОСМОСА И МИРОВОГО ОКЕАНА. XXI ВЕК
Ученый с мировым именем, организатор науки Борис Евгеньевич Патон вот уже 47 лет возглавляет Научно-исследовательский институт электросварки им. Е. О. Патона в Киеве. Под его руководством здесь развиваются научные основы и техника сварки, создаются и внедряются в промышленность новые, прогрессивные сварочные технологии. Много раз Б. Е. Патон, бессменный член редакционного совета «Науки и жизни», выступал на страницах журнала со статьями о путях развития науки и научно-технического прогресса (см. «Наука и жизнь» № 5, 1969 г.; № 10, 1972 г.; № 9, 1974 г.; № 7, 1976 г.; № 4, 1977 г.; № 10, 1981 г.; № 5, 1986 г.; № 1, 1988 г.).Борис Евгеньевич Патон.
Грузовая стрела-манипулятор транспортирует космонавта-оператора и оборудование к месту проведения работ на внешней поверхности станции «Мир».
Схема прокладки сварного газопровода по дну Черного моря между Джубгой (Россия) и Самсуном (Турция).
Орбитальная станция «Мир» полной конфигурации, на которой из года в год проводятся эксперименты по космическим технологиям.
Летчики-космонавты СССР В. Н. Кубасов и Г. С. Шонин.
Наука и жизнь // Иллюстрации
Подводная механизированная сварка при ремонте трубопровода на дне Волги.
Так в перспективе будут выглядеть сборка и сварка трубопроводов на дне океана.
‹
›
Сегодня ученый обращает взгляд в будущее и размышляет о том, какие проблемы придется решать сварочной науке в XXI веке и какое место займут сварочные технологии в освоении космоса и Мирового океана.
Президент Национальной академии наук Украины, академик Российской академии наук Б. ПАТОН, директор Института электросварки им. Е. О. Патона (Киев).
В преддверии нового века возникает естественное желание поразмышлять над тем, что нас ожидает впереди, куда мы идем, какими путями. Это в полной мере относится к научно-техническому прогрессу, к сварочной науке и технике, без которых просто невозможно представить себе современное производство и строительство.
БУДУЩЕЕ СВАРОЧНЫХ ТЕХНОЛОГИЙ
В соответствии с терминологией, предложенной Европейской сварочной федерацией, термин «сварка» означает соединение, резку и обработку поверхности материалов всех типов с использованием таких процессов, как сварка, пайка (твердая и мягкая), термическая резка, газотермическое напыление, адгезионное сцепление, микросоединение. Этот перечень включает и управление, обеспечение качества, неразрушающий контроль, гигиену труда и охрану здоровья персонала.
Основная задача сварочного производства — проектирование и изготовление сварных конструкций. Сварными в наше время делают конструкции из стали, цветных металлов и сплавов. Все глубже проникает сварка в производство изделий из синтетических материалов, создаются технологии сварки разнородных металлов и сплавов, освоена сварка композиционных материалов. Наиболее ответственные гражданские и военные машины и инженерные сооружения изготовляются в сварном исполнении. Год от года растут требования к качеству сварных конструкций, повышаются их надежность и долговечность.
О масштабах применения сварки можно судить по данным статистики: примерно 70% всего выпускаемого в мире стального проката используется в сварных конструкциях; годовой объем мирового производства сварочных материалов и оборудования достигнет в нынешнем году в денежном выражении 40 миллиардов долларов. В разных странах мира в сварочном производстве заняты миллионы сварщиков, резчиков, дефектоскопистов и других специалистов.
Конечно, все это относится к производству и строительству в земных условиях. Однако на всех этапах развития человечества его привлекали Вселенная (ближний и дальний космос) и гидросфера (Мировой океан). Во все века люди стремились овладеть небесным и водным пространствами.
Эпохой активного вторжения человека в космос, в глубины океанов и морей стала вторая половина XX века. И это естественно и закономерно. Вместе с тем благодаря достижениям научно-технического прогресса появилась иллюзорная надежда на то, что человек обретет безграничную власть над окружающей средой, над природой. Такая философия очень опасна. Она может привести к глобальной катастрофе. Мы должны всегда помнить об этом.
Несомненно, в наступающем XXI веке будут интенсивно развиваться космические исследования, направленные на решение земных проблем, продолжатся глубокие фундаментальные исследования происхождения жизни на планете и эволюции человека. Дальнейшее проникновение человека в космос позволит создать такие новые жизненно важные отрасли, как глобальная информационная система, добыча внеземных ресурсов, космическая биотехнология, космическая энергетика, технология производства полупроводниковых монокристаллов, и другие.
Сейчас на орбите объединенными усилиями космических держав сооружается международная космическая станция. Реально рассматривается задача освоения Луны, ее минеральных и энергетических ресурсов. Продолжается штурм Марса. Чтобы осуществить эти грандиозные планы, нужно строить совершенно новые сооружения, создавать принципиально новые материалы. При этом решающую роль будут играть микрогравитация и вакуум, наличием которых определяются характеристики различных конструкций. Принципиально изменятся условия и методы труда человека.
Новую космическую технику будут создавать как в земных, так и в орбитальных условиях. И здесь очень важная роль отводится сварке и связанным с ней совершенно новым процессам и технологиям.
Говоря о гидросфере, прежде всего стоит вспомнить, что три четверти поверхности нашей планеты составляют океаны, моря, озера, реки. Они всегда привлекали людей своими необъятными просторами и глубинами. И хотя складывались легенды об ихтиандрах, до недавнего времени человек мог проникнуть лишь в верхние, мелководные зоны Мирового океана.
Практическое освоение континентального шельфа началось во второй половине нашего столетия. Сегодня в крупных промышленных масштабах добывают нефть и газ. Согласно прогнозу, в 2004 году мировая добыча нефти составит 3150 миллионов тонн, из них 32% будет получено со дна морей и океанов. Примерно такую же долю составит объем добытого на шельфе природного газа. Развитие этой отрасли было бы невозможно без строительства мощных буровых и эксплуатационных платформ, терминалов, обустройства подводных месторождений. Кроме этого создана современная технология укладки мощных подводных трубопроводов. Так, в Северном море сооружен газопровод «Zip Pipe» диаметром до 1220 миллиметров, протяженностью более 1000 километров.
Пока все эти объекты построены на шельфе, глубина которого, как правило, не превышает 300 метров, правда, газопровод из Алжира в Европу уложен на глубине 600 метров. И это, конечно, не предел. Россия уже приступила к осуществлению грандиозного проекта — прокладке газопровода протяженностью около 400 километров на глубине свыше 2000 метров по дну Черного моря.
Сейчас разрабатывается технология строительства и эксплуатации на дне морей и океанов газоперекачивающих и нефтяных насосных станций без непосредственного участия человека. В этой связи возникают чрезвычайно сложные задачи диагностики и ремонта всех подводных сооружений топливно-энергетического комплекса. Нужно заметить, что пока самые квалифицированные водолазы могут действовать на глубине лишь до 300 метров.
Грандиозный шаг вперед сделала Япония. Здесь на сравнительно мелководном шельфе строятся целые города. При этом широко используются сварные сваи, опоры, платформы, трубопроводы.
В глубинах океанов таятся огромные запасы минеральных ресурсов. Их добыча, в частности марганцевых конкреций, пока нерентабельна. Но по мере исчерпания этих полезных ископаемых на суше и дальнейшего мощного развития научно-технического прогресса человечество неизбежно придет к добыче минеральных ресурсов со дна океанов и морей, глубины которых достигают 5000 метров.
Самостоятельную задачу представляет подъем затонувших кораблей и других конструкций. Эти огромные «запасы» металла, веками скапливавшиеся на дне морей и океанов, могут и должны быть введены в процесс рециклинга.
Совершенно очевидно, что проблемы освоения гидросферы, так же как и космического пространства, не могут быть решены без широкого применения разнообразных процессов и технологий сварки, резки, нанесения покрытий. Водная среда и громадные гидростатические давления — очень сложные условия для практического применения сварочных и сопутствующих им технологий, поэтому для их создания понадобятся дорогие и трудоемкие исследования.
Подводя итог вышесказанному, можно утверждать, что в наступающем XXI веке нас ожидают большие, чрезвычайной сложности работы в космосе и в глубинах Мирового океана. При этом громадное значение будут иметь сварочные технологии, используемые для создания сложного оборудования и аппаратуры в земных условиях. Частично они уже существуют, но для дальнейшего освоения космоса и гидросферы необходимо разрабатывать новые процессы сварки, резки, пайки и нанесения различных покрытий. В XXI веке появятся новые, экзотические материалы. Для их обработки и соединения опять-таки понадобятся совершенно новые технологии. К выполнению этих работ сварочная наука и техника достаточно подготовлены.
Иначе обстоит дело с созданием материалов и технологий их обработки непосредственно в космосе и гидросфере, где условия необычайно сложны и принципиально отличаются от земных. И те и другие технологии объединяет то, что они заведомо должны быть ориентированы на экстремальные условия. Для космоса характерны не только микрогравитация и вакуум, но и термоциклирование, неизбежное при работах на орбите. В гидросфере же приходится иметь дело с непрерывной водной средой и со все большими и большими гидростатическими давлениями. При этом, в отличие от космоса, в глубинах мирового океана всегда сохраняется постоянная положительная температура. Обитание и, главное, работа человека в таких экстремальных условиях связаны с громадными трудностями, а иногда и просто невозможны. В обоих случаях нужны скафандры и высоконадежные системы жизнеобеспечения. Скафандры для работы в открытом космосе уже многократно проверены в деле, они существуют около 40 лет. Водолазные скафандры позволяют работать на глубине только до 300 метров. Погружение на большую глубину пока неосуществимо, и связано это в том числе с физиологическими особенностями организма человека.
И в космосе, и в гидросфере возникают трудности со снабжением электроэнергией, особенно если речь идет об ее длительном потреблении. Чтобы вырабатывать электроэнергию в космических условиях, понадобятся огромные солнечные батареи и мощные аккумуляторы. Полагаю, в дальнейшем будут использоваться и другие источники, в частности ядерные. Они могут функционировать на автономной необитаемой орбитальной станции-платформе, а излучаемый поток энергии будут принимать на обитаемой станции.
Ряд технологических операций в космосе может выполняться только при дистанционном управлении рабочими процессами с применением всевозможных роботов и манипуляторов. Некоторые образцы таких устройств уже действуют на американских шаттлах и на российской орбитальной станции «Мир». В большинстве случаев в их работу может вмешиваться оператор-космонавт, в том числе и в открытом космосе.
Немалые трудности представляет снабжение электроэнергией оборудования, работающего в подводных условиях на больших глубинах. Чтобы передать значительное количество электроэнергии с надводного корабля на глубину, нужны специальные кабели достаточно большого сечения. Потери электроэнергии в них окажутся весьма существенными, и будет относительно трудно добиться жестких вольт-амперных нагрузочных характеристик. Видимо, предпочтение следует отдать аккумуляторным батареям, которые можно снабдить соответствующими преобразователями энергии. Вполне реально использовать в будущем сверхпроводниковые кабельные линии, соединяющие мощный источник питания на надводном корабле с приемной подстанцией на дне. Здесь предстоит искать оптимальные решения.
Что касается роботов и всевозможных манипуляторов, то их применение для глубоководных работ исключает возможность непосредственного вмешательства оператора. Человек будет управлять рабочими процессами дистанционно, из глубоководного обитаемого подводного судна (батискафа). Подводные суда можно оборудовать достаточно мощными подъемно-транспортными устройствами, оснастить телевизионными камерами и различными сенсорами. Батискафы будут использовать как для визуального наблюдения, так и для инструментального контроля за состоянием подводных трубопроводов и другого оборудования.
Сварка в космосе и гидросфере сможет получить серьезное распространение только в том случае, если удастся разработать весьма совершенные методы неразрушающего контроля сварных соединений, методологию технической диагностики сварных конструкций. Для этого потребуются мощные банки данных и компьютерное моделирование. Режимы сварки в широком понимании этого термина будут выбираться с помощью компьютеров. В целом без компьютеризации создать новые технологии сварки и применить их в космосе и гидросфере просто невозможно.
Как видим, строительно-монтажные и ремонтные работы в космосе и гидросфере очень сложны и кардинально отличаются от таковых в наших земных условиях. Остановимся несколько подробнее на собственно сварочных и сопутствующих технологиях.
КОСМОС
Сначала несколько слов о наиболее распространенной в земных условиях дуговой сварке. В космосе, где вакуум и микрогравитация оказывают существенное влияние на процессы сварки, резки, пайки и напыления, очень трудно обеспечить устойчивое горение дуги и стабильное протекание процесса сварки. Особенно это относится к сварке плавящимся электродом. Еще в шестидесятых годах в Институте электросварки им. Е. О. Патона Национальной академии наук Украины (сокращенно ИЭС НАНУ) были проведены опыты, включающие реальную сварку в космических условиях. Они показали, что дуговая сварка в открытом космосе не имеет больших перспектив.
Не дает положительных результатов и плазменная сварка, также опробованная в космосе. Тем не менее в дальнейшем дуговая и плазменная сварка и резка все же смогут найти применение в космосе, например при сооружении различных объектов на Луне. Совершенствовать и тот и другой вид сварки, а также электродуговую металлизацию, безусловно, необходимо. Для этого потребуются серьезные исследования физики дуги и металлургических процессов, протекающих при дуговой сварке в вакууме, в условиях микрогравитации.
Тем не менее сварка плавлением нужна в космосе уже сейчас при сооружении крупных орбитальных станций и платформ, а также при ремонтных операциях. Самый оптимальный процесс — электронно-лучевая сварка, поскольку необходимый для нее вакуум присутствует в космосе постоянно, а микрогравитация не составляет непреодолимых трудностей. В ИЭС созданы оборудование и технология, позволившие еще в 1984 году совместно с НПО «Энергия» осуществить электронно-лучевую сварку, резку, пайку и напыление различных металлов в открытом космосе. Эти работы превосходно выполнили космонавты С. Е. Савицкая и В. А. Джанибеков. В 1986 году в расширенном виде опыты повторили. Их провели в открытом космосе космонавты В. А. Соловьев и Л. Д. Кизим.
В девяностых годах специалисты ИЭС создали новое оборудование для применения электронно-лучевой технологии в космосе. Это установка «Универсал», снабженная сменным инструментом для сварки, резки, пайки и напыления. Она питается электроэнергией от бортовой сети космической станции. «Универсал» можно либо использовать как ручной инструмент, либо встраивать в механизированные дистанционно управляемые установки, применяемые в основном для восстановления деградировавших поверхностей теплозащитных экранов, антенн и других объектов на космических станциях. Установка «Универсал» прошла весь комплекс предполетных испытаний, сертифицирована и готова к проведению серии запланированных натурных экспериментов на орбитальной станции «Мир». Во время подготовки к полету установку «Универсал» осваивала группа американских астронавтов, прошли также «горячие» тренировки несколько российских экипажей, которым предстоит проводить сварочные эксперименты в космосе.
Работы, связанные с применением электронно-лучевой технологии в космосе, продолжаются: совершенствуется оборудование, увеличивается его мощность. Все это позволит сваривать и резать металл практически любой толщины.
Весьма интересна для применения в открытом космосе лазерная технология. От электронно-лучевой ее отличают по крайней мере два существенных преимущества: во-первых, нет высокого ускоряющего напряжения и, во-вторых, может быть применена волоконная оптика. Это значит, что можно установить лазер стационарно и транспортировать световой луч в любую точку орбитальной станции снаружи (в открытом космосе), а также внутри ее. Присущие лазерной технологии недостатки — низкий, по сравнению с электронным лучом, кпд процесса и сравнительно большие масса и габариты установки — устранимы, но над этим нужно работать. В недалеком будущем лазерная технология, видимо, найдет применение на космических орбитах. Особые надежды мы возлагаем на диодные лазеры.
Нет препятствий и для применения в открытом космосе контактной сварки (в частности, точечная сварка была проверена еще в шестидесятых годах). Это относится и к шовной (роликовой) сварке. Нужно создать своего рода установку «Универсал» со сменным инструментом для точечной и роликовой сварки, а также с устройствами, защищающими оператора от возможных выплесков металла. Контактную сварку можно будет использовать в космосе при сооружении различных конструкций из тонколистовых материалов и для их ремонта. Она может найти применение при сооружении объектов на Луне.
Представляют интерес различные сварные трансформируемые конструкции, изготовленные на Земле. Их можно доставлять на орбитальную станцию либо на Луну в компактном виде. Оболочечные металлоконструкции способны «раздуваться» с помощью небольшого избыточного внутреннего давления и приобретать заданную форму и габариты. Соединяя с помощью сварки отдельные преобразуемые элементы, можно собирать в космосе более сложные и крупные сооружения. Найдут применение и трансформируемые раздвигающиеся и складывающиеся конструкции, состоящие из унифицированных узлов. Их можно использовать как на орбитальных космических станциях, так и на Луне.
Словом, сварочные технологии в космосе — это не научная фантастика. Думаю, они будут востребованы уже в начале XXI века, по мере развития работ на международной орбитальной космической станции.
ГИДРОСФЕРА
Существуют «мокрая» и «сухая» технологии подводной сварки. В первом случае сварка (это же касается и резки) осуществляется непосредственно в воде, во втором — сварка и резка проводятся в локальных и крупногабаритных камерах, где можно создать либо газовую атмосферу, либо вакуум.
Конечно, весьма интересна и перспективна «мокрая» сварка, например, при сооружении в гидросфере крупных сварных конструкций и их ремонте. Такая технология применяется в наше время на глубине до 100 метров, при этом, как правило, в работе участвует оператор-водолаз. Однако в перспективе будут освоены глубины порядка сотен и тысяч метров, где работа оператора невозможна. Сварка и резка в таких экстремальных условиях должны быть полностью автоматическими.
Задача несколько облегчается благодаря тому, что за процессом сварки можно наблюдать и частично управлять им из находящегося поблизости батискафа. Решающую роль в работе сварочного оборудования должны играть подводные роботы и дистанционно управляемые манипуляторы. Но, как видим, на пути подготовки и сборки изделий под сварку и в процессе собственно сварки возникают громадные трудности.
Наибольший интерес для гидросферы представляет дуговая сварка. Однако следует иметь в виду, что на больших глубинах, где гидростатические давления достигают нескольких сотен атмосфер, свойства дуги и протекание металлургических процессов совершенно не изучены. В этом направлении нужны серьезные и длительные исследования, результаты которых сегодня трудно предсказать. Но постановка таких исследований крайне необходима.
Речь может и должна идти также о применении в гидросфере других способов сварки и резки. Определенную перспективу представляют различные варианты контактной сварки. Собственно точечная сварка, в том числе металлов больших толщин, видимо, возможна. Но для этого предстоит разработать такие конструкции и их сварные узлы, в которых точечные соединения будут иметь необходимый комплекс свойств.
Несколько сложнее обстоит дело с контактной стыковой сваркой. Получить качественные соединения, выполненные «мокрой» стыковой сваркой оплавлением, не удастся. Значит, необходимо развивать «сухую» сварку. То же самое относится к стыковой сварке сопротивлением.
В гидросфере может быть применена взрывная технология. Прежде всего это касается резки взрывом, используемой при ремонтных работах. Примером может служить вырезка дефектного участка подводного трубопровода либо резка трубчатых свай, на которых установлены исчерпавшие ресурс буровые или эксплуатационные платформы. Разработанные в ИЭС технологии резки взрывом безопасны для окружающей водной среды и ее обитателей. Опыт использования этой технологии на глубинах в несколько десятков метров позволяет предположить, что «резать» взрывом можно и на большей глубине. Но для этого необходимы серьезные исследования.
Возможно использование и лазерной технологии с применением твердотельного лазера и волоконной оптики. Лазер можно установить на надводном корабле, а световой луч транспортировать по волоконному световоду. Другой вариант — опустить лазер в герметичном корпусе на дно или поместить в батискаф, из которого «выпускается» световод с «горелкой». Словом, заставить работать под водой световой луч лазера в наших силах. Однако получить качественное сварное соединение очень трудно. Первые опыты по лазерной сварке под водой уже проводятся, но опять-таки необходимы серьезные эксперименты в гипербарических камерах. Видимо, предстоят длительные исследования, в том числе связанные с созданием новых присадочных материалов. Таким образом, при всей заманчивости «мокрой» сварки и резки, чтобы использовать их при строительстве и ремонте различных конструкций и сооружений под водой на больших глубинах, нужны очень серьезные, длительные и дорогие исследования и опытно-конструкторские работы.
Что касается «сухой» сварки, то выполнить ее в вакуумной камере под водой очень сложно. Ведь речь идет о том, чтобы поместить в крупногабаритную камеру либо всю сооружаемую конструкцию, либо ее узлы. Создать в такой камере вакуум при давлениях в окружающей водной среде в несколько десятков и даже сотен атмосфер чрезвычайно трудно. Полагаю, что разработки в этой области малоперспективны.
Реально можно осуществить сварку на больших глубинах в локальных камерах, которые устанавливаются в зоне сварки. В них подается газ под давлением, несколько превышающим гидростатическое давление окружающей среды. Вода вытесняется, и создается контролируемая газовая среда. Нужны только насосы высокого давления и достаточный запас газа. Необходимо следить за тем, чтобы плотность посадки камеры в зоне сварки была максимальной. В противном случае существенно возрастает расход газа, и это вызывает дополнительные трудности. Полагаю, что пока можно говорить лишь о необитаемых камерах.
Процесс сварки (резки) в камерах под водой должен быть автоматизирован. Управлять им и вести наблюдение можно только дистанционно — из батискафа либо из надводного корабля. Для этого в камере надо установить телевизионные мониторы и различные сенсоры. Информация от них будет выводиться на центральный пульт в батискафе или надводном корабле. Если батискаф оборудовать механической рукой и другими манипуляторами, то оператор сможет вмешиваться в работу при сооружении и сварке конструкции.
В случае необходимости в такой камере можно проводить антикоррозионное напыление различных конструкций. Это, например, газотермическое и плазменно-дуговое напыление, а также электродуговая металлизация. Однако о целесообразности использования этих процессов говорить пока рано. У нас нет опыта применения технологий, основанных на использовании электрической дуги при столь высоких давлениях. В этом направлении также предстоят серьезные длительные исследования в гипербарических камерах.
В камерах с контролируемой газовой атмосферой можно применять лазерный луч. Но и в этом случае предстоит добиться стабильного качества сварных соединений, создать новые присадочные материалы и технологии собственно сварки. Нужна также технология лазерной резки в условиях высокого давления газовой среды в камерах.
Все процессы сварки в камерах должен сопровождать неразрушающий контроль качества сварных швов — ультразвуковой, магнитный или рентгеновский. Естественно, процессы контроля тоже должны быть автоматизированы.
Электроснабжение сварочных и сопутствующих технологических процессов на больших глубинах представляет самостоятельную и достаточно сложную задачу. Видимо, оптимальными, как уже было сказано, будут источники энергии, состоящие из аккумуляторной батареи и преобразователей, прежде всего инверторов. Источники питания можно поместить в герметичные кожухи с устройствами для теплообмена, опустить на дно, а после окончания работ поднять на надводный корабль либо «захоронить» на дне. Выбор варианта будет определяться экономическими соображениями. Можно разместить источники питания и в батискафе. В обоих случаях потребители электроэнергии подключаются к ним дистанционно с помощью манипуляторов, размещенных на батискафе, либо роботов.
Чрезвычайно сложная и актуальная задача — ремонт на больших глубинах сварных конструкций. Для него нужны дистанционно управляемые сборочные стапели, кондукторы и манипуляторы. Оказалось, что ремонтные работы значительно сложнее сварочных. Сегодня ремонт одного сварного стыка подводного трубопровода на глубине 100 метров и более стоит несколько миллионов долларов. Поэтому строители всегда стремятся выполнить максимальный объем сборки и сварки на берегу. Очень сложным будет неразрушающий контроль качества сварных соединений.
Огромное значение приобретает техническая диагностика сварных подводных сооружений. Эта задача решается сегодня во многих промышленно развитых странах. Систематический контроль, в том числе ультразвуковой контроль за эксплуатационным состоянием сварных соединений, ведется на сотнях морских буровых скважин на весьма больших глубинах.
Таким образом, сварка, резка, напыление и пайка в гидросфере представляют собой очень сложную комплексную задачу. Особенно, когда речь идет о больших глубинах, которые, несомненно, будут осваиваться в XXI веке.
Ученым и специалистам в области сварочной науки и техники предстоит выполнить сложнейшие исследования и опытно-конструкторские разработки, без них просто невозможно создать и освоить технологии соединения металлов, нанесения покрытий и сооружения уникальных конструкций в открытом космосе и гидросфере. При этом возникают огромные проблемы и в области экологии. Словом, нам предстоит решать чрезвычайно увлекательную научную и инженерную задачу.
Масштабность и комплексный характер всех этих проблем заставляют говорить об интеграции мировой сварочной науки и техники, это особенно важно, когда национальные ассигнования на науку сокращаются. Необходимо общими усилиями создавать крупные международные проекты, которые будут реализовываться на основе специализации и кооперации многих сварочных и других научных центров ведущих стран мира.
Новейшие сварочные технологии могут сэкономить время и деньги
Новейшие сварочные технологии могут сэкономить время и деньги Меню- Оборудование
- Сварщики
- Механизмы подачи проволоки
- Сварочный интеллект
- Автоматизация
- Плазменные резаки
- Газовое оборудование
- Газовый контроль
4 величайших новых технологии, которые меняют сварку сегодня ~ Vietnam Welder
Сварка развивается и развивается быстрее, чем когда-либо прежде.Новые технологические достижения сделали сварку более точной, эффективной и экономичной. Вот как они совершают революцию в сварке! Вы также можете прочитать:
Новая технология автомобильной сварки, как ожидается, создаст гораздо более прочную связь
1. Процесс передачи поверхностного натяжения
Процесс передачи поверхностного натяжения (STT), разработанный и запатентованный Lincoln Electric, предназначен для повышения производительности за счет замены таких старых методов сварки, как дуговая сварка металлическим электродом в газе и дуговая сварка вольфрамовым электродом в среде газа.Преимущества этого процесса: сокращение сварочного дыма и типичных брызг, сокращение времени, затрачиваемого на обучение кого-либо сварочной технике, и увеличение скорости. Сварка STT идеальна при работе с нержавеющими сталями и оцинкованной сталью.2. Сварка трением с перемешиванием
Автопроизводители во всем мире постоянно ищут новые способы снижения производственных затрат без ущерба для качества и безопасности автомобилей. Такие компании, как Honda Motor, сделали ставку на алюминий как на более дешевый материал, и, чтобы обеспечить простой и безопасный процесс соединения алюминия и стали, они разработали новые формы сварки трением с перемешиванием.Этот новый метод помогает создать более стабильную и надежную связь между двумя материалами за счет перемещения вращающегося инструмента по верхней части алюминия, который затем приклеивается к стали. Инженеры
Honda также разработали технологию сборочного конвейера, которая помогает в массовом производстве автомобилей, использующих сварку трением с перемешиванием, например, шестиосевого робота. По словам менеджера по сборке, заменив обычный стальной подрамник на подрамник из алюминия и стали, инженеры Honda могут снизить массу кузова на 25%.Этот высокоэффективный метод также помог снизить до 50% затрат на электроэнергию во время процесса сварки.
НАСА, известнейшее имя в технологии запуска, применило эту инновационную технологию сварки для разработки самого большого в мире сварочного инструмента. Подробнее здесь .
3. Лазерная сварка
Лазерная сварка — довольно новая технология, которая включает преобразование световой энергии в тепловую. Излучение, испускаемое при лазерной сварке, позволяет лучам преодолевать большие расстояния со значительной потерей качества.Хотя первоначальные затраты на лазерную сварку выше, чем у традиционных методов точечной сварки, значительное сокращение времени цикла в конечном итоге делает лазерную сварку более эффективным вариантом.
4. Точечная контактная сварка
Устойчивая точечная сварка связана с прямым приложением противоположных сил с использованием электродов с острым концом. General Motors воспользовалась этой технологией для производства более легких и более экономичных автомобилей из алюминия. Избавившись от примерно 2 фунтов заклепок на капоте, дверях и подъемных воротах автомобиля, инженеры могут при необходимости использовать этот излишек веса на других участках автомобиля.Благодаря технологии контактной точечной сварки алюминиевые детали можно напрямую сваривать, используя куполообразный электрод с несколькими кольцами.
Будьте в курсе изменений в сварочной технике
В свете стремительного развития новых сварочных технологий для сварщиков как никогда важно быть в курсе последних изменений в технологии. Особенно важна точечная контактная сварка и сварка трением с перемешиванием, поскольку они знакомы с STT. Компания Vietnam Manpower Service and Trading Company обеспечит вашу компанию сварщиками, которые хотят учиться и быть в курсе современных технологий.По любым вопросам, не стесняйтесь обращаться к нам: (+84) 949 594 116 I [email protected]Новые технологии сварки труб
Прокладка газопровода через обозначенные водно-болотные угодья Миссисипи и Алабамы может оказаться сложной задачей для любого подрядчика, но толстостенная труба, указанная в проекте Gulfstream, создала новые проблемы при сварке для подрядчика Sunland Construction Inc., потому что длина трубы в два раза больше Таким образом, Sunland использует инновационные методы сварки, чтобы уменьшить количество необходимых сварочных проходов и, что наиболее важно, обеспечить стабильное качество сварных швов и качество рентгеновских лучей.
КомпанияSunland Construction Inc. со штаб-квартирой в Юнис, штат Луизиана, обратилась к системе автоматической орбитальной сварки труб Autoweld® от Lincoln Electric Company для заполнения и заглушки проходов, а также к процессу STT® (Surface Tension Transfer®) для прокладки критического корневого прохода. Внедрив эти новые технологии сварки, Sunland смогла убрать один проход электрода из процесса корневого прохода, а также полностью исключить шлифовку на этом этапе. Благодаря системе Autoweld компания сократила время, необходимое для заполнения и заполнения проходов.
«С момента использования новых сварочных систем Lincoln мы добились значительных улучшений как в повышении качества, так и в экономии времени, — сказал Джо Рэтклифф, руководитель проекта Sunland Construction Inc. — Наши сварщики гордятся новым оборудованием. этой работы выполняются гладко «.
Проект Гольфстрим
Проект Gulfstream — это газопровод, который берет начало недалеко от Паскагулы, штат Миссисипи, и пересекает Мексиканский залив до округа Манати во Флориде.Будучи на берегу, трубопровод тянется через южную и центральную часть Флориды до округа Палм-Бич. Этот газопровод будет обслуживать коммунальные предприятия и объекты энергетики Флориды, производя 1,1 миллиарда кубических футов в день дополнительного природного газа — этого достаточно для обеспечения электроэнергией 4,5 миллиона домов.
Участок трубопровода компанииSunland Construction Inc. включает установку 6,1 миль трубы диаметром 36 дюймов в округе Джексон, штат Миссисипи, и 9 миль в округе Мобил, штат Алабама.
Sunland, 27-летняя компания с пятью подразделениями, выиграла вакансию в компании Gulfstream на конкурсной основе.В этом проекте задействовано более 250 сотрудников, на выполнение которого уходит в общей сложности семь месяцев. Sunland ожидает, что ее часть проекта Gulfstream будет завершена в начале 2002 года.
По словам Рэтклиффа, подготовка к установке труб на этой работе — непростая задача. «Прежде чем мы сможем даже начать сварку, мы должны сначала очистить землю, подготовить полосу отвода, установить сваи на некоторых участках, возвести строительные мосты и внести дополнительный грунт там, где это необходимо. Из-за условий заболоченных территорий все сварочные работы бригады должны работать на больших 4 футах.х 20 футов. деревянные коврики. Эти маты, иногда укладываемые в несколько слоев, обеспечивают стабильную и сухую рабочую поверхность. После завершения работ на участке Sunland Construction Inc. также несет ответственность за восстановление прилегающих территорий до их первоначального состояния.
«Сварка для этой работы выполняется тремя бригадами, одна сварка идет сразу за другой, — отметил Рэтклифф. «Первая бригада устанавливает корневой шов, вторая бригада немедленно следует за ним, используя сварку штангой, чтобы выполнить проход горячего наполнителя, а затем бригада Autoweld завершает процесс сварки, выполняя заливку и заглушку.«
Из-за экстремальных условий на площадке процесс Autoweld выполняется внутри сварочного «дома» или модульного агрегата, который поднимается и перемещается каждые 40 футов (от стыка к стыку) с помощью Caterpillar Challenger с боковой стрелой.
Труба
Труба для наземной части проекта Gulfstream предоставлена Berg Steel Pipe Corporation из Панама-Сити, Флорида, и ее материнской компанией Europipe GmbH из Германии. Труба X70 имеет толщину стенки от 0 до 0 мм.635 до 1,22. Эта толстостенная труба была рассчитана таким образом, чтобы трубопровод мог выдерживать диапазон давлений системы Gulfstream. Труба покрыта эпоксидной смолой Fusion Bond (FBE) как внутри, так и снаружи, и большая часть трубы также имеет бетонное покрытие для контроля плавучести.
Корневой проход
Sunland Construction Inc. использовала процесс STT из-за его преимуществ.
STT — это модифицированный процесс MIG, в котором используется технология высокочастотного инвертора с усовершенствованным контролем формы волны для получения высококачественных сварных швов, а также значительного уменьшения брызг и дыма.Технология STT позволяет контролировать нагрев сварочной ванны независимо от скорости подачи проволоки — это позволяет сварщику лучше контролировать сварочную ванну и дает возможность регулировать подвод тепла для достижения желаемого профиля корневого валика. Сварщик просто помещает дугу в переднюю часть сварочной ванны и следует за ней по трубе вертикально вниз.
С помощью этой системы сварщики Sunland могут добиться равномерного зазора, используя внутренний пневматический зажим для выравнивания и разнесения трубы для точной сварки.
В частности, для проекта Gulfstream компания STT может выполнить качественный сварной шов и позволяет разместить большее количество сварочного металла на толстостенной трубе для повышения устойчивости к растрескиванию. При использовании STT компании Sunland требуется всего один проход для корневого валика по сравнению с двумя проходами плюс время шлифования палкой.
«Поскольку корневой проход является основой для остальной части сварного шва, получение высококачественного, прочного и однородного шва для нас очень важно», — сказал Ратклифф.«Мы очень довольны STT. Это позволило нам сэкономить время, и это простая система для обучения наших сварщиков. Процесс STT очень щадящий, что означает, что он помогает компенсировать перекосы, если и когда это необходимо».
Две машины STT на стройплощадке Gulfstream используются в сочетании с проволокой Lincoln .045 L-56 ™ SuperArc® и 100% защитным газом CO2. По сравнению со смешанными газами CO2 обеспечивает лучшее проникновение и дешевле.
«STT может наносить корневой валик с большой консистенцией при самых разных состояниях шва», — пояснил Рэтклифф.
Пасс для горячего розлива
После завершения корневого прохода следующая бригада сварщиков следует за ним, чтобы сварить проход горячего присадочного материала. Из-за толщины трубы при выполнении этой работы компания Sunland Construction Inc. решила нанести один проход горячего наполнителя вниз по корню с помощью процесса прилипания вниз с низким содержанием водорода. «Добавленный присадочный металл, который мы нанесли на этом этапе, дает нам дополнительную основу для укладки первого присадочного материала для проволоки и означает, что нам не нужно делать такое количество проходов с системой Autoweld», — отметил Ратклифф.
Для выполнения этого промежуточного этапа Sunland использует стержень Lincoln LH-D 80 с обычным сварочным аппаратом Lincoln с ременным приводом на 300 ампер.
Заполнение и крышка
Для проекта Gulfstream компания Sunland Construction Inc. решила инвестировать в автоматизированный процесс сварки переходов заливки и крышки. Ранее компания Sunland выполняла проходы для заполнения и заглушки с помощью стержневого электрода 70+, привариваемого вертикально вниз и требующего множества проходов.
«Нам нужен автоматический метод для повышения эффективности и снижения общих затрат», — сказал Рэтклифф.«Для нас также было важно найти систему, которая могла бы обеспечить качественный продукт, но при этом была бы простой в эксплуатации.
В своем поиске компания связалась с рядом производителей, чтобы выяснить, какая система лучше всего работает в этом приложении. «Мы сузили круг выбора и посетили несколько производителей, чтобы опробовать их системы, в том числе Lincoln Electric», — отметил Рэтклифф. «Наша команда поехала в штаб-квартиру Lincoln в Кливленде, где у нас была возможность провести наши процедуры на реальной установке Autoweld.После того, как мы вернулись, мы перечислили плюсы и минусы каждой системы, и Lincoln’s Autoweld оказалась на первом месте. Важным фактором в нашем решении стал объем технической поддержки, которую Lincoln может нам предоставить ».
Система Autoweld размещена в помещении, поэтому сварку можно производить вне помещений. Эти дома перемещаются с помощью боковых стрел (Challenger) с одного отрезка трубы на другой. Sunland использует шесть Caterpillar Challenger с генераторами с приводом от вала отбора мощности для выработки 100 ампер при 460 вольт, необходимых для работы Autoweld и принадлежностей.
Lincoln используется специально разработанная легкая сварочная головка для перемещения по окружности трубы. Кроме того, в установке используется внешняя гусеничная лента, размещенная на трубе с одной стороны от фаски сварного шва. Две работающие одновременно машины завершают сварку вертикально вверх: одна машина начинает снизу, а другая — сбоку. Как только машина, запущенная сбоку, достигает вершины, она позиционируется так, чтобы начать работу снизу, чтобы закончить свою сторону трубы.Использование процесса вертикальной сварки вверх — это отход от традиционной сварки вертикально вниз, обычно применяемой для труб.
Каждая толщина стенки трубы требует различных настроек станка для каждого конкретного прохода. Эти настройки представлены в виде таблицы и могут быть легко установлены на машине. В системе Autoweld используется проволока с сердечником из флюса 0,052 дюйма и защитный газ из 25 CO2 / 75 аргона.
С помощью Autoweld Sunland Construction Inc. постоянно добивается стабильных сварных швов рентгеновского качества. «Autoweld делает наплавку металла очень стабильной, однородной и точно контролируемой», — отмечает Рэтклифф.«Сварной шов обладает высокой прочностью на разрыв и хорошими показателями Шарпи в зонах нагрева сварного шва и трубы. Кроме того, машина очень прочна и надежна».
Система AutoweldSunland питается от Invertec® V350-PRO, чрезвычайно легкого инвертора, способного обрабатывать многопроцессорные приложения. Отличительной чертой этого источника питания является чрезвычайно плавная дуга благодаря передовой инверторной технологии.
«Мы считаем, что V-350 — это самое современное сварочное оборудование, он дает вам возможность поддерживать точные настройки и характеристики дуги», — заявил Ратклифф.«Даже после долгих часов использования на нашей строительной площадке машина оставалась надежной».
Контроль качества
Все сварные швы после завершения визуально проверяются, а затем просвечиваются с помощью внутреннего гусеничного тележки. Все сварные швы должны соответствовать требованиям API 1104, раздел 9.
Сервис
КомпанияSunland Construction Inc. была чрезвычайно довольна услугами, которые ей оказывала компания Lincoln. «Поддержка на месте, оказанная командой Lincoln Electric Mobile, состоящей из Троя Гуркина и Стивена Брауна, была превосходной, — сказал Рэтклифф.«Мы также получили огромную поддержку со стороны группы Autoweld из Кливленда, включая Эрика Стюарта, технического специалиста Autoweld, который был на месте для большей части проекта. Lincoln изо всех сил старался помочь нам внедрить наши новые процессы и предложить новые технологии, когда это необходимо. »
Sunland также воспользовалась программами обучения Lincoln на месте и в Кливленде. «Перед Lincoln стояла задача взять сварщиков с разным уровнем подготовки и поработать с ними, чтобы научиться понимать систему Autoweld и работать с ней.Это была огромная тренировочная работа, которая потребовала от Линкольна немало времени. Мы ценим все, что они сделали, чтобы эта работа прошла гладко «.
Будущее
Sunland Construction Inc. уже планирует, как новые станки STT и Autoweld можно будет использовать в будущих работах для повышения эффективности.
Современная упрощенная технология сварки, разработанная для повышения эффективности сварки
Рисунок 1
Некоторые источники сварочного тока рассчитаны на простую настройку всего за несколько шагов.Благодаря доступным технологиям операторы могут просто ввести толщину свариваемого материала, и аппарат автоматически установит правильное напряжение и скорость подачи проволоки.
Источники сварочного тока эволюционируют от тяжелых аналоговых аппаратов с ручками для набора номера, которые раньше преобладали в промышленной сфере. Сегодняшние источники питания — это более легкие и мощные машины с цифровыми экранами. Благодаря таким функциям, как упрощенные интерфейсы и автоматическая настройка параметров, операторы становятся проще, чем когда-либо, в использовании.
Это хорошая новость, поскольку отрасль борется с нехваткой квалифицированных сварщиков, и многие компании ищут способы повысить производительность и добиться большего с меньшим количеством рабочих. Когда источник питания обеспечивает большую простоту использования и улучшенное управление дугой, сварщикам с разным уровнем подготовки становится проще производить высококачественные сварные швы и уменьшать количество ошибок.
По мере того, как машины становятся проще в использовании снаружи, их упрощенные интерфейсы и улучшенное качество дуги обусловлены все более совершенными технологиями внутри.Инвестиции в источники питания, призванные помочь сварщикам легко устанавливать правильные параметры, могут помочь компаниям сэкономить время и деньги на обучении и доработке.
Развитие технологий сварки
По мере развития всех технологий — от сотовых телефонов до телевизоров — источники сварочного тока также развиваются, поскольку инновации приводят к созданию более интеллектуального оборудования с расширенными возможностями. Во многих случаях эти источники питания даже обеспечивают более широкие возможности в меньших и более легких корпусах. Эти достижения в области сварочных технологий помогают решить несколько задач отрасли:
Опытные сварщики покидают штат .По мере того как более опытные сварщики достигают пенсионного возраста, их место занимают более молодые сварщики, и у них другие ожидания в отношении своей рабочей среды. Они рассчитывают использовать источники сварочного тока, которые в большей степени отражают окружающую их технологию, например смартфоны. Производственные цеха, использующие эту передовую сварочную технологию, могут заинтересовать молодых сварщиков и научить их работать быстрее, чем сварщики предыдущего поколения, которым приходилось полагаться на свои собственные навыки, а не на технологии.
Стремление к повышению производительности продолжается . Усиление конкуренции подталкивает многие компании к увеличению объемов производства и производительности при сохранении или снижении затрат. Вот почему передовые процессы, такие как сварка металлическим электродом в импульсном газе (GMAW-P), все чаще используются. GMAW-P — это модифицированный процесс распыления, при котором источник питания переключается между высоким пиковым током или напряжением и низким фоновым током или напряжением от 30 до 400 раз в секунду. Во время этого переключения пиковый ток сжимает каплю проволоки и толкает ее к сварному шву.В то же время фоновый ток поддерживает дугу, но производит настолько низкое тепловложение, что передача металла невозможна, что позволяет сварочной ванне слегка замерзнуть и помогает предотвратить прожог. Это действие отличается от традиционного процесса распыления, при котором крошечные капельки расплавленного металла непрерывно переносятся в сварное соединение. Из-за активности дуги GMAW-P снижает потребность в очистке после сварки по сравнению с более традиционным GMAW с постоянным напряжением.
Старые источники сварочного тока часто требуют дополнительных действий и усилий для настройки импульсной сварки; новые аппараты предназначены для упрощения импульсного процесса сварки.Это позволяет большему количеству компаний внедрять передовые процессы даже с менее опытными сварщиками.
Другие производители работают с тонкими материалами . В различных отраслях промышленности многие производители переходят на использование более легких и тонких материалов, которые по-прежнему обеспечивают необходимую прочность. Это еще один фактор, побуждающий все больше компаний использовать передовые процессы, такие как импульсная сварка, которые вводят меньше тепла в материал, уменьшая вероятность прожога и деформации более тонких металлов.
Что означает «упрощенное»?
Одно дело сказать, что современный источник сварочного тока «упрощен» по сравнению со старой технологией, но что это на самом деле означает? Давай пройдемся через это.
Настройка машины . Некоторые производители предоставляют все оборудование и аксессуары, необходимые для начала сварки, включая источник питания, механизм подачи проволоки, сварочные и контрольные кабели, регулятор потока газа и пистолет GMAW, в одном пакете, чтобы значительно сократить время настройки. Иногда большая часть оборудования также предварительно собрана.Это упрощает подготовку аппарата к сварке.
Рисунок 2
Многие новые источники сварочного тока используют цифровые экраны с простыми кнопками. Это экономит время на настройку и регулировку процессов и упрощает установку необходимых параметров для получения высококачественных сварных швов.
Взаимодействие с машиной . Новые источники сварочного тока часто предназначены для простой настройки, выполняемой всего за несколько шагов. При использовании некоторых технологий операторы могут просто выбирать толщину свариваемого материала, а все остальные параметры устанавливаются автоматически.Если один из параметров регулируется, машина автоматически настраивает и другие. Устранение необходимости вручную настраивать напряжение и скорость подачи проволоки помогает ускорить настройку и упростить работу. С точки зрения контроля качества это гарантирует использование правильных параметров.
Обычно при использовании сложных процессов сварщик должен вводить больше информации для получения хорошей дуги. На некоторых источниках питания можно настроить десятки параметров для точной настройки качества дуги и управления лужей при импульсной сварке.Это усложняет процесс.
Возьмем, к примеру, процесс GMAW-P. Большинство новичков в этом процессе предполагают, что длина дуги равна напряжению. Однако при этом процессе длина дуги зависит от напряжения, но фактическое число может быть произвольным. Источник питания может иметь шкалу от -10 до 10, а 0 — это отправная точка, обычно для сварщика, чтобы сделать настройки. Если сварщик хочет отрегулировать мощность, он настраивает регулятор ниже 0 для меньшей мощности и выше 0 для большей мощности.Этой регулировки избегают современные источники питания, которые принимают решение за сварщика; программа GMAW-P предоставляет определенные атрибуты с помощью простой настройки управления.
Упрощенный интерфейс помогает устранить подобные сложности при использовании расширенных процессов. Когда в интерфейсе используется всего несколько кнопок и нет скрытых меню, менее опытным сварщикам легче вводить дополнительные параметры, необходимые для достижения успеха.
Ускорение связи .Импульсная сварка не нова, но со временем она стала более надежной и простой в использовании по мере развития процесса и используемых для него источников энергии.
Одной из причин этого является технология, используемая для соединения источника питания и механизма подачи проволоки. Предыдущая аналоговая технология, которая позволяла сварщику и подающему устройству обмениваться данными, была ограниченной и медленной, а современные процессы требуют высокоскоростной связи. Импульсная сварочная дуга измеряется в миллисекундах, поскольку она реагирует и регулируется в зависимости от того, как оператор выполняет сварку, и условий сварного шва.Медленная связь между источником питания и питателем ограничивает качество импульсной дуги.
Высокоскоростная цифровая связь в современных источниках питания обеспечивает улучшенное качество дуги, поскольку обмен данными происходит почти мгновенно и дугу можно быстро изменить. Некоторые источники питания также имеют ручку управления дугой, позволяющую операторам точно настраивать дугу в соответствии со своими предпочтениями без изменения основных параметров.
Более быстрая цифровая связь также позволяет оператору контролировать параметры и получать обратную связь от механизма подачи проволоки — вместо того, чтобы возвращаться к источнику питания — для повышения производительности и качества сварки.
Кроме того, технологические усовершенствования привели к появлению более совершенных типов процессов импульсной сварки, которые обеспечивают более щадящую дугу и более широкий рабочий диапазон, чем традиционные сварочные сварочные аппараты с постоянным напряжением. Это облегчает сварщикам любого уровня подготовки выполнение высококачественных сварных швов.
Цифровой мониторинг сварного шва . Мониторинг сварочных данных также становится проще с новыми сварочными технологиями. Возможность собирать информацию в цифровом виде, а не вручную, помогает компаниям отслеживать и измерять производительность, качество и затраты.
Интеллектуальные инструменты сварки помогают выявлять потенциальные проблемы при сварке. Они могут повысить производительность и качество за счет подробного анализа времени горения дуги и обнаружения пропущенных или дефектных сварных швов. В результате сокращается количество доработок в сварочном цехе, и большее количество деталей быстрее выходит из дверей.
По мере того, как источники сварочного тока с годами упрощались, возможности оборудования расширились. Эта комбинация особенно полезна, поскольку помогает менее опытным сварщикам выполнять высококачественные сварные швы — даже при использовании передовых процессов, таких как импульсная сварка, — чтобы их можно было обучить и быстрее приступить к работе.
Брайан Хаммерс — технический менеджер, Miller Electric Mfg. Co., 1635 W. Spencer St., P.O. Box 1079, Appleton, WI 54912-1079, 920-734-9821, www.millerwelds.com.
Wise Welding Technology & Engineering Co., Ltd
1. Краткое введение
Мы, компания Wise Welding Technology & Engineering Co., Ltd., (WTEC), организована и работает как современная корпоративная система, специализирующаяся на поставках решений автоматизации для многих отраслей, таких как нефтехимическая, морская, строительная, особенно в производстве котлов и сосудов под давлением. .В частности, наша деятельность охватывает широкий спектр услуг по проектированию, производству, установке, обучению, ноу-хау и послепродажному обслуживанию.
Наша компания была основана в 1984 году, производственные мощности расположены в Пекине, Китай.
2. Часть нашего артикула
В число наших клиентов входят многие всемирно известные производители котлов, такие как:
АЛЬСТОМ (КИТАЙ)
ПЕРЕДНИЙ КОЛЕСО (КИТАЙ)
FERROLI (КИТАЙ)
ФУЛТОН (КИТАЙ)
ОШАЦ (КИТАЙ, ТУРЦИЯ)
BABCOCK & WILCOXCOMPANY (США)
BABCOCK-HITACHIINC (ФИЛИППИНЫ)
ОТДЕЛЕНИЕ BABCOCK-HITACHI KURE (ЯПОНИЯ)
ISHIKAWAJIMA-HARIMA HEAVY INDUSTRIES CO., ООО (IHI JAPAN)
DP CLEAN TECH (ПОЛЬША)
BHARAT HEAVY ELECTRICALS LIMITED (БХЕЛ, ИНДИЯ),
L & T-MHI BOILERS PRIVATE LIMITED (ИНДИЯ)
MAPNA BOILER CO. (ИРАН)
BANGKOK INDUSTRIAL BOLLERS CO., LTD (ТАИЛАНД)
3. Основные преимущества
1) Богатый опыт
Имея 30-летний опыт работы в производстве котлов, наши установки, машины, услуги и технологические ноу-хау широко используются производителями котлов по всему миру.В Китае мы занимаем более 70% рынка автоматического сварочного оборудования для мембранных панелей и более 90% рынка оборудования для сварки седловых отверстий. Для нас большая честь поделиться своим опытом с нашими клиентами.
2) Сильная конструкция
Возможности WTEC в области проектирования прочно поддерживаются командой специалистов-исследователей, в которую входят профессора, доктора, аспиранты и инженеры-конструкторы. Кроме того, у нас есть сварочная лаборатория для разработки передовых методов сварки и внедрения новейших технологий в нашу продукцию.Исходя из этого, WTEC может удовлетворить все требования клиентов в области сварочной техники и автоматизации производства.
3) Современные сварочные технологии
WTEC продолжает приспосабливаться к последним мировым технологическим тенденциям; мы можем интегрировать в наши машины самые современные сварочные технологии.