ГОСТ 1585-85 Чугун антифрикционный для отливок. Марки (с Изменением N 1), ГОСТ от 19 сентября 1985 года №1585-85
ГОСТ 1585-85
Группа В11
МКС 77.080.10
ОКП 41 1150
Дата введения 1987-01-01
1. РАЗРАБОТАН И ВНЕСЕН Министерством энергетического машиностроения СССР
2. УТВЕРЖДЕН И ВВЕДЕН В ДЕЙСТВИЕ Постановлением Государственного комитета СССР по стандартам от 19.09.85 N 2943
3. ВЗАМЕН ГОСТ 1585-79 в части марок чугуна
4. ССЫЛОЧНЫЕ НОРМАТИВНО-ТЕХНИЧЕСКИЕ ДОКУМЕНТЫ
5. Ограничение срока действия снято по протоколу N 7-95 Межгосударственного Совета по стандартизации, метрологии и сертификации (ИУС N 11-95)
6. ИЗДАНИЕ с Изменением N 1, утвержденным в августе 1989 г. (ИУС 12-89)
Настоящий стандарт распространяется на антифрикционный чугун для отливок, работающих в узлах трения со смазкой, и устанавливает марки, определяемые химическим составом, микроструктурой и твердостью.
1. МАРКИ
1.1. Марки чугуна, его химический состав, микроструктура и твердость должны соответствовать нормам, указанным в табл.1-3.
Таблица 1
Марка чугуна* | Массовая доля элемента, % | ||||||||||||
С | Si | Mn | Сr | Ni | Тi | Сu | Sb | Pb | Al | Mg | P | S | |
АЧС-1 | 3,2-3,6 | 1,3-2,0 | 0,6-1,2 | 0,2-0,5 | — | — | 0,8-1,6 | — | — | — | — | 0,15-0,40 | Не |
АЧС-2 | 3,0-3,8 | 1,4-2,2 | 0,3-1,0 | 0,2-0,5 | 0,2-0,5 | 0,03-0,10 | 0,2-0,5 | — | — | — | — | 0,15-0,40 | Не |
АЧС-3 | 3,2-3,8 | 1,7-2,6 | 0,3-0,7 | Не более 0,3 | Не более 0,3 | 0,03-0,10 | 0,2-0,5 | — | — | — | — | 0,15-0,40 | Не |
АЧС-4 | 3,0-3,5 | 1,4-2,2 | 0,4-0,8 | — | — | — | — | 0,04- | — | — | — | Не | 0,12- |
АЧС-5 | 3,5-4,3 | 2,5-3,5 | 7,5-12,5 | — | — | — | — | — | — | 0,4- | — | Не | Не |
АЧС-6 | 2,2-2,8 | 3,0-4,0 | 0,2-0,6 | — | — | — | — | — | 0,5-1,0 | — | — | 0,5-1,0 | Не |
АЧВ-1 | 2,8-3,5 | 1,8-2,7 | 0,6-1,2 | — | — | — | Не более 0,7 | — | — | — | 0,03-0,08 | Не | Не |
АЧВ-2 | 2,8-3,5 | 2,2-2,7 | 0,4-0,8 | — | — | — | — | — | — | — | 0,03-0,08 | Не | Не |
АЧК-1 | 2,3-3,0 | 0,5-1,0 | 0,6-1,2 | — | — | — | 1,0-1,5 | — | — | — | — | Не | Не |
АЧК-2 | 2,6-3,0 | 0,8-1,3 | 0,2-0,6 | — | — | — | — | — | — | — | — | Не | Не |
________________
* В обозначении марки: АЧ — антифрикционный чугун; С — серый с пластинчатым графитом; В — высокопрочный с шаровидным графитом; К — ковкий с компактным графитом; цифра — порядковый номер марки.
Таблица 2
Марка чугуна | Графит | Перлит* | Фосфидная эвтектика (характер распре- деления) | Прочие составляющие | |||
Форма | Размер | Распре- деление | Занимаемая площадь | Дисперс- | |||
АЧС-1 | ПГф1, | ПГд15- | ПГр1- | П-П70 | ПД0,3- | ФЭр1, | Цементит не допускается |
АЧС-2 | |||||||
АЧС-3 | П85, П70 | ||||||
АЧС-4 | П-П85 | ||||||
АЧС-5 | Аустенит: после закалки — не менее 80% поля шлифа, в литом состоянии — не менее 45% поля шлифа. | ||||||
АЧС-6 | П-П85 | ПД0,3- | ФЭр2, | Цементит не допускается | |||
АЧВ-1 | ШГф2, ШГф4, ШГф5 | ШГд15- | П96-П45 | ПД0,3- | ФЭр1, | Не более 5% цементита | |
АЧВ-2 | П70-П45 | ||||||
АЧК-1 | КГф2, КГф3 | КГд15- | П-П85 | Цементит не допускается | |||
АЧК-2 | П70-П45 |
________________
* Для всех марок чугуна структура металлической основы вида ПТ1.
Таблица 3
Марка чугуна | Твердость по Бринеллю (НВ) |
АЧС-1 | 180-241 |
АЧС-2 | 180-229 |
АЧС-3 | 160-190 |
АЧС-4 | 180-229 |
АЧС-5 | 180-290 |
140-180* | |
АЧС-6 | 100-120 |
АЧВ-1 | 210-260 |
АЧВ-2 | 167-197 |
АЧК-1 | 187-229 |
АЧК-2 | 167-197 |
________________
* После нагрева до температуры 950-1000 °С, выдержки и закалки.
Назначение и условия применения чугуна приведены в приложениях 1 и 2.
Массовая доля марганца в чугуне марки АЧС-5 приведена в приложении 3.
(Измененная редакция, Изм. N 1).
2. МЕТОДЫ ИСПЫТАНИЙ
2.1. Химический состав чугуна определяют по ГОСТ 28473, ГОСТ 2604.1 — ГОСТ 2604.6, ГОСТ 2604.8 — ГОСТ 2604.10, ГОСТ 2604.13, ГОСТ 22536.0 — ГОСТ 22536.12, ГОСТ 27809.
Допускается применение физических методов определения химического состава.
Содержание сурьмы, свинца и магния определяют по методикам, согласованным между изготовителем и потребителем.
Отбор проб для определения химического состава производят по ГОСТ 7565.
(Измененная редакция, Изм. N 1).
2.2. Микроструктуру чугуна определяют по ГОСТ 3443.
2.3. Определение твердости проводят по ГОСТ 27208. Количество образцов для определения твердости устанавливают в нормативно-технической документации.
ПРИЛОЖЕНИЕ 1 (справочное). НАЗНАЧЕНИЕ АНТИФРИКЦИОННОГО ЧУГУНА
ПРИЛОЖЕНИЕ 1
Справочное
Марка чугуна | Назначение |
АЧС-1 | Для работы в паре с закаленным или нормализованным валом |
АЧС-2 | То же |
АЧС-3 | Для работы в паре с закаленным или нормализованным валом или валом, не подвергающимся термической обработке |
АЧС-4 | Для работы в паре с закаленным или нормализованным валом |
АЧС-5 | Для работы в особо нагруженных узлах трения в паре с закаленным или нормализованным валом |
АЧС-6 | Для работы в узлах трения при температуре до 300 °С в паре с валом, не подвергающимся термической обработке |
АЧВ-1 | Для работы в узлах трения с повышенными окружными скоростями в паре с закаленным или нормализованным валом |
АЧВ-2 | Для работы в условиях трения с повышенными окружными скоростями в паре с валом, не подвергающимся термической обработке |
АЧК-1 | Для работы в паре с закаленным или нормализованным валом |
АЧК-2 | Для работы в паре с валом, не подвергающимся термической обработке |
ПРИЛОЖЕНИЕ 2 (справочное).
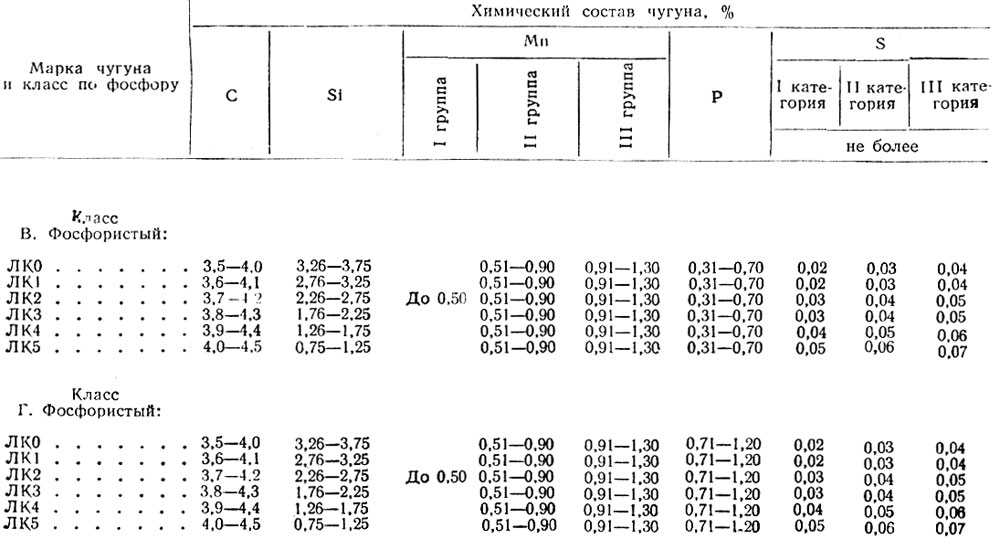
ПРИЛОЖЕНИЕ 2
Справочное
1. Применение отливок из антифрикционного чугуна в узлах трения требует соблюдения условий, указанных ниже.
Тщательный монтаж, обеспечивающий точное сопряжение трущихся поверхностей и отсутствие перекоса.
Непрерывная смазка, не допускающая искрений или значительного нагрева узла трения.
Повышение зазоров по сравнению с установленными для бронзы на 15-30%, при наличии значительного нагрева узла трения в работе — до 50%.
Приработка на холостом ходу и постепенное повышение рабочих нагрузок.
2. Режимы работы деталей из антифрикционного чугуна в узлах трения должны соответствовать нормам, указанным в таблице.
Марка чугуна | Давление , МПа | Скорость | , МПа·м/с |
Не более | |||
АЧС-1 | 5,0 | 5,0 | 12,0 |
14,0 | 0,3 | 2,5 | |
АЧС-2 | 10,0 | 0,3 | 2,5 |
0,1 | 3,0 | 0,3 | |
АЧС-3 | 6,0 | 1,0 | 5,0 |
АЧС-4 | 15,0 | 5,0 | 40,0 |
АЧС-5 | 20,0 | 1,0 | 20,0 |
30,0 | 0,4 | 12,5 | |
АЧС-6 | 9,0 | 4,0 | 9,0 |
АЧВ-1 | 1,5 | 10,0 | 12,0 |
20,0 | 1,0 | 20,0 | |
АЧВ-2 | 1,0 | 5,0 | 3,0 |
12,0 | 1,0 | 12,0 | |
АЧК-1 | 20,0 | 2,0 | 20,0 |
АЧК-2 | 0,5 | 5,0 | 2,5 |
12,0 | 1,0 | 12,0 |
Примечание. Проводимые для некоторых марок чугуна два предельных значения для и, соответственно, для указывают допустимые сочетания значений каждого из этих показателей.
ПРИЛОЖЕНИЕ 3 (справочное). СОДЕРЖАНИЕ МАРГАНЦА В ЧУГУНЕ МАРКИ АЧС-5
ПРИЛОЖЕНИЕ 3
Справочное
Толщина стенки отливки, мм | Массовая доля марганца, % |
От 5 до 10 | От 7,5 до 8,5 |
Св. 10 » 20 | Св. 8,5 » 9,5 |
» 20 » 30 | » 9,5 » 10,5 |
» 10,5 » 11,5 | |
» 40 » 60 | » 11,5 » 12,5 |
Текст документа сверен по:
официальное издание
Чугун. Марки. Технические условия.
Методы анализа: Сб. ГОСТОв. —
М.: ИПК Издательство стандартов, 2004
Механизм влияния качества литейного кокса на химический состав чугуна Текст научной статьи по специальности «Технологии материалов»
УДК 669.1:921.74
Вдовин К.Н., Иванова В.А., Феоктистов Н.А.
МЕХАНИЗМ ВЛИЯНИЯ КАЧЕСТВА ЛИТЕЙНОГО КОКСА НА ХИМИЧЕСКИЙ СОСТАВ ЧУГУНА
Аннотация. Рассмотрен механизм влияния качества литейного кокса, применяющегося в вагранке, на химический состав чугуна и его основные механические характеристики (твердость, структура). Ключевые слова: кокс, вагранка, качество, углерод, кремний, фосфор, зольность.
Литейный кокс имеет сложный химический состав, который влияет на газовый и шлаковый режимы плавки в вагранке, а также на состав металлической фазы. Ее химический состав формируется постепенно при стекании по шихте и коксовой насадке. При этом происходят различные химические реакции между составляющими кокса и элементами формирующегося чугуна.
На содержание углерода в чугуне оказывает влияние содержание его в коксе. Из литературы известно, что степень науглероживания чугуна зависит от расхода кокса (табл. 1), который в свою очередь зависит от зольности: чем больше золы в нем, тем меньше углерода содержится в чугуне (10% золы — 3,2-3,3% углерода; 15% золы — 3% углерода; 20% золы — 2,8% углерода) [1-3].
Таблица 1
Зависимость коэффициента науглероживания К от расхода кокса
Расход кокса от металлозавалки, % Удельный расход воздуха, м3/м2-мин
100-120 140-160 180-200
9 1,3 1,1 0,9
10 1,4 1,2 1,0
12 1,5 1,3 1,1
15 1,7 1,5 1,3
20 1,9 1,7 1,5
На содержание углерода в чугуне влияют не только зольность кокса, но и влажность, и выход летучих веществ. Количество углерода в разных условиях работы вагранки может значительно меняться в зависимости от состава шихты. Если шихта содержит незначительное количество стального лома, то насыщение углеродом будет минимальным, если же шихта содержит высокий процент стального лома, то количество углерода в чугуне существенно возрастет.
Процессы перехода серы и углерода в чугун происходят и в горне [3, 4]. Кроме того, в нем протекают реакции восстановления железа, марганца, кремния шлака и диоксида углерода. Процесс восстановления оксидов металлов в горне идет настолько эффективно, что при достаточной высоте горна весь металл, окислившийся в зонах подогрева, плавления и перегрева, может быть восстановлен [5]. В основе механизма перехода углерода в чугун в горне лежит молекулярная диффузия углерода в чугун, науглероживание которого увеличивается при повышении коэффициента диффузии, времени пребывания чугуна в контакте с коксом, а также увеличение поверхности соприкосновения раскаленного кокса с расплавленным чугуном. Науглероживание неподвижной жидкой массы чугуна в горне вагранки протекает значительно медленнее, и содержание углерода здесь дополнительно повышается на 0,3 — 0,5 % [1 — 3].
Механизм восстановления кремния из кокса
Кремний является трудновосстановимым оксидом с высокой теплотой диссоциации, т.е. протекает при высоких температурах и сопровождается значительным расходом тепла. В вагранке наиболее благоприятные условия для восстановления кремния наблюдаются в зоне перегрева чуть выше уровня фурм. В этой зоне температура продуктов плавки может достигать 1500-16700С [6, 7].
Ранее проведенные исследования процессов, происходящих в коксе при термообработке, показали, что они сопровождаются газификацией диоксида кремния золы по реакции [8]
SiO2 золы + Скокса = ^Ю} + {СО}. Ю} + [С] = ВД + {СО};
— исследование восстановления кремния из кокса через соединение SiC по реакции [10]
SiCкокса — №] + [С].
Исследования проводили на металлургическом коксе (Кд) и спецкоксах (К1, К2), полученных на базе некоксующихся углей и отличающихся высокой реакционной способностью, что позволило установить влияние свойств кокса на содержание кремния в чугуне.
Технический и химический анализы золы кокса приведены в табл. 1. Необходимость использования спецкокса в исследованиях была продиктована, с одной стороны, интересом к спецкоксу, как к перспективному и менее дефицитному топливу, с другой стороны, возможностью выявления влияния реакционной способности и зольности на процессы восстановления кремния непосредственно из кокса.
В табл. 2 и 3 приведены результаты исследований по восстановлению кремния из его газообразного оксида по реакции. При этом было учтено, что в условиях эксперимента значительная часть выделившегося оксида кремния из кокса выдувалась из реакционного пространства печи струей аргона. Как видно из данных табл. 2 и 3, с ростом зольности кокса увеличивается количество выделяющегося в газовую фазу оксида кремния по реакции. Соответственно растет и переход кремния из газовой фазы в расплав. С увеличением же реакционной способности кокса содержание кремния понижается, что связано с расходованием оксида кремния на карбидообразование по реакции.
Кроме того, с повышением зольности кокса количество кремния, восстановленного из кокса, при фильтрации чугуна также увеличивается. Это связано с повышением интенсивности карбидообразования на поверхности кокса, что способствует росту содержания кремния в чугуне.
Проведенные расчеты по определению количества диоксида кремния золы кокса, израсходованной на восстановление кремния из карбида кремния SiC по реакции и из газовой фазы SiO, приведены в табл. 4.
Таблица 2
Характеристика доменного кокса и спецкокса
Показатели Кд К1 К2
Технический анализ, %
Wa 0,30 1,20 1,60
А» 14,00 14,20 19,30
1,58 3,29 2,98
0,58 0,38 0,32
Пористость, % 45,80 33,00 24,40
Реакционная способность [37], мл/г с 0,62 8,40 9,10
Структурная прочность, % 82,00 70,00 69,70
Содержание в золе, %
SiO2 50,50 5 7,01 53,48
М2О3 26,32 21,25 22,05
Fe2Oз 11,60 7,24 7,83
СаО 4,40 2,76 2,68
МдО 1,80 1,77 1,84
Таблица 3
Экспериментальные данные по восстановлению кремния из кокса в синтетический сплав Fe-C [9]
Кокс А», % Реакционная способность, мл/г с Прирост кремния в сплаве Fe-C, %
Кд 14,00 0,62 0,241
К1 14,28 8,40 0,165
К2 19,30 9,10 0,210
Таблица 4
Анализ восстановления кремния из кокса в передельный чугун по схемам ^Ю}— р] и SiC0к—>[Si]
Кокс т$ю2 кокса, г Расход SiЮ2 кокса на восстановление кремния по схеме SiC0к—[Si] (реакция (28)), мас. Ю}—р] (реакция (27)), мас.%
Кд 2,524 41,6 (1,05) 33,95 (0,857)
К1 3,659 40,99 (1,50) 31,15 (1,140)
К2 4,781 50,20 (2,40) 30,52 (1,459)
Из данных табл. 4 видно, что примерно 50% всего диоксида кремния золы кокса расходуется на восстановление кремния через SiC и лишь около 30% -через газовую фазу SiO. Так как процессы восстановления кремния в реальных условиях протекают одновременно, они вносят свою долю в суммарное содержание кремния в чугуне.
По данным работы [7] угар кремния при выплавке чугуна в коксовой вагранке составляет 10-25% при холодном дутье и 15-25% при горячем дутье (кислый процесс). Вероятно, угар кремния в действительности превышает эти значения за счет процессов восстановления кремния из золы кокса.
Механизм восстановления фосфора при плавке чугуна
Традиционно считается, что фосфор — это вредная примесь, которая способствует появлению брака в отливках. В то же время он является графитизирующим элементом и оказывает влияние на литейные свойства чугуна (снижает кинематическую вязкость и поверхностное натяжение с увеличением жидкотекучести) [11]. Кроме того, фосфор оказывает влияние и на химический состав выплавляемого чугуна. Присутствие фосфора замедляет переход кремния из газовой фазы в жидкий металл [9]. Наиболее существенно влияние начальных концентраций фосфора до 0,35 мас.%.
Из опыта ведения доменной плавки известно, что фосфор, как и кремний, способствует снижению углерода в чугуне. Влияние фосфора на растворимость углерода в железоуглеродистых расплавах можно оценить по уравнению (при Ыр>0,04)
АМ£ =-0,84 МР,
где Np — атомная концентрация фосфора в железе; АМ£ — изменение атомной концентрации углерода в присутствии фосфора. О)4 и его содержание зависит от месторождения. Мел и мрамор имеют состав идентичный известняку, доломит содержит ~ 0,023 % Р2О5.
Исследования химического состава чугунов ваграночной плавки Ярославского электровозоремонт-ного завода (ЯЭМЗ) филиала «Желдорреммаш» (табл. 5), соответствующих требованиям ГОСТ 28186-89 и ОСТ 32.194-2002, позволили установить наличие тесной корреляционной связи между содержанием фосфора и углерода в чугуне (рис. 1 и 2).
Для объяснения полученной зависимости рассмотрим возможный механизм восстановления фосфора при плавке чугуна.
Таблица 5
Средние арифметические значения содержания фосфора, кремния и углерода в чугуне
Чугун Содержание в чугуне, %
фосфора углерода
По ГОСТ 28186-89 (тип колодки Ф [174]) 1,29 3,12
По ОСТ 32.194-2002 (тип колодки С [175]) 0,43 3,46
В вагранке во взаимодействии находятся фазы: металл (чугун), шлак, газ и кокс. Поэтому конечный состав чугуна по фосфору будет зависеть от реакций взаимодействия между этими фазами (рис. 3).
Рис. 1. Зависимость содержания углерода от содержания фосфора в чугуне, соответствующего требованиям ГОСТ 28186-89
Рис. 2. Зависимость содержания углерода от содержания фосфора в чугуне, соответствующего требованиям ОСТ 32.194-2002
Рис. 3. Схема взаимодействия между фазами в вагранке (цифры в скобках соответствуют химическим реакциям)
Фосфиды ^е2Р и FeP) железа металлической части шихты растворяются в процессе плавки в металле, а фосфаты железа (Реэ(РО4)2) могут восстанавливаться уже при 800-900°С по реакциям [17]:
2Feз(PO4)2+16CO=3Fe2P+P+16CO2, 2Feз(PO4)2+16C=3Fe2P+P+16CO.
Газификация фосфатов кальция (Саз(РО4)2) и алюминия из золы кокса возможна уже при 500 0С. Поэтому восстановление фосфора из кокса в чугун будет происходить через газовую фазу. Возможный механизм газификации фосфатов кальция в присутствии кремнезема в золе кокса будет происходить как с участием углерода кокса, так и с участием углерода, растворенного в чугуне. Кроме того, фосфиды кальция, содержащиеся во флюсах, при нагреве могут разлагаться с образованием газообразных реагентов РО и РО2, которые затем реагируют с углеродом кокса [17].
В процессе плавки в шлак фосфор попадает главным образом из флюсов. При пересчете на Р2О5 в шлаке содержится 0,1-0,5% фосфора [2]. Таким образом, источниками фосфора при плавке чугуна в вагранке могут быть все составляющие шихты. Поскольку фосфор является поверхностно-активным элементом, то реакции восстановления происходят через поверхность металла с участием газообразной фазы. Восстановление фосфора в чугун приводит к снижению его содержания в металле.
Исследование влияния характеристик качества литейного кокса на структуру и механические свойства чугуна
В связи с развитием комплексного управления жизненным циклом изделия, актуальной является проблема наследственности в металлических сплавах и, в частности, в чугуне и стали. Выявление связи между свойствами исходных материалов и готовых изделий позволит осуществить эффективное управление технологическими процессами, интенсифицировать производство, повысить качество выпускаемой продукции.
Под понятием наследственности в чугунах традиционно понимают связь между свойствами исходных шихтовых материалов и свойствами отливок. Например, известно, что углерод кокса в процессе плавки является одним из источников центров кристаллизации [18, 19]. Поскольку в настоящее время еще много серого чугуна для литейного производства выплавляют в вагранках, а в качестве топлива, как правило, применяют литейный кокс [20], в задачу исследований входило установление влияния свойств литейного кокса, как одной из составляющей шихты, на качество отливок.
Исследования проведены на примере технологического процесса изготовления отливок колодки тормозной вагонной из серого чугуна в соответствии с требованиями ГОСТ 28186-89 ((ЯЭМЗ). Непосредственная заливка расплава из вагранки в литейную
форму позволила установить влияние свойств кокса на характеристики чугуна при условии стабильности технологического процесса.
Для исследований были выбраны образцы серого чугуна, выплавленного с использованием в шихте литейного каменноугольного кокса марки КЛ-1. Причем кокс 1-й, 2-й и 3-й партий соответствовал требованиям ГОСТ 3340-88, а кокс 4-й партии — ТУ 0761027-00187852-10.
Литейный кокс 1-й партии отличается наибольшей зольностью и наименьшей прочностью, кокс 3-й партии содержит наименьшее количество серы и влаги, кокс 4-й партии — наиболее прочный и низкозольный, но содержит максимальное количество серы (табл. 6). Средние значения химического состава и твердости чугуна представлены в табл. 7.
Как видно из данных табл. 6 и 7, с уменьшением зольности (с увеличением доли углерода) литейного кокса наблюдается повышение содержания углерода в чугуне. Кроме того, в 4-й партии литейного кокса, как и в чугуне, выплавленном с использованием в шихте этого кокса, массовая доля серы является наибольшей. Чугун, выплавленный с применением литейного кокса 3-й партии, содержит наименьшее количество кремния и марганца, однако обладает максимальной твердостью. Данные химического состава этого чугуна не согласуются с его твердостью, что может быть обусловлено различиями в структуре. % Зольность, А», % Массовая доля общей серы, Std, % Показатель прочности, М40, %
1 4,8 12,0 0,48 73,2 5,9
2 4,8 11,8 0,48 73,3 5,9
3 4,5 11,7 0,44 73,3 5,9
4 4,8 11,6 0,60 73,8 5,8
*Данные сертификатов качества на партии литейного кокса.
Таблица 7
Химический состав и твердость чугуна
Обозначение партии кокса Массовая доля элементов в чугуне, % Твердость, НВ
С Si Мп Р S
1 2,89 1,74 0,61 1,43 0,07 241-55
2 2,90 1,92 0,70 1,23 0,07 229-241
3 2,98 1,30 0,45 1,40 0,07 255-269
4 3,12 1,90 0,62 1,12 0,08 229-241
Графитные включения структуры чугуна, выплавленного с применением различных партий литейного кокса, оценивали в соответствии с требовани-
ями ГОСТ 3443-87 (рис. 4). Статистические данные были получены при исследовании 16 образцов серого чугуна (по четыре образца чугуна соответственно для каждой партии литейного кокса) по десяти изображениям каждого микрошлифа. Результаты статистического анализа оценки характеристик графитных включений приведены в табл. 8.
Обозна-
чение Размеры включений Количество
партии графита, мкм включений графита, %
кокса
1 ПГд45 (преобладает), ПГд90 ПГ6, ПГ10 (преобладает)
2 ПГд45, ПГд90 ПГ10 (преобладает), ПГ12
3 ПГд45 ПГ6 (преобладает), ПГ10
4 ПГд90 ПГ12 (преобладает), ПГ10
Статистические данные результатов количественного анализа характеристик включений графита приведены в табл. 9.
Данные табл. 8 и 9 свидетельствуют о наличии связи между свойствами литейного кокса и химическим составом чугуна. Например, большим содержанием углерода и серы отличается чугун, выплавленный на 4-й партии литейного кокса, что согласуется с пониженной зольностью и повышенным содержанием серы этого кокса.
Таблица 9
Результаты количественного анализа включений графита
Партия литейного кокса Число колоний* Удельный вес ядер в колониях Wя , % як Содержание графита Г, %
1 13 17,6-23,5 7,1-10,3
2 13 16,8-19,7 9,5-12,1
3 12 24,9-26,7 6,7-8,9
4 15 12,6-19,3 10,9-13,2
б
Рис. 4. Микрошлифы серых чугунов, выплавленныхс использованием в шихте различных партий литейного кокса: а — 1-я партия; б — 2-я партия; в — 3-я партия; г — 4-я партия (х100)
Таблица 8
Размеры и количество включений графита в структуре чугуна
Для более точного определения количества и формы включений графита в чугуне были реализованы планиметрический и точечный методы количественного анализа. Эти методы позволили оценить размеры колоний и ядер включений графита, а также удельный вес ядра в колонии. Метод проверки статистической гипотезы о равенстве значений в соответствии с требованиями ГОСТ Р 50779.23-2005 подтвердил несущественность расхождения между значениями, полученными этими методами.
* Округленное до целого среднеарифметического число колоний по 10 изображениям для каждого образца.
Результаты оценки формы и размеров включений графита в образцах чугуна свидетельствуют о том, что для всех образцов характерно наличие завихренного пластинчатого графита (ПГф2) небольшой длины от 45 до 90 мкм, который распределен колониями (ПГр3). Наибольшее количество включений графита наибольшей длины содержит чугун, выплавленный также на 4-й партии литейного кокса (рис. 4, г), для которого характерна пониженная зольность (наибольшее содержание углерода) (табл. 7).
Результаты планиметрического и точечного методов количественного анализа свидетельствуют о том, что наибольшие различия по включениям графита имеют образцы, плавка которых осуществлялась на 3-й и 4-й партиях литейного кокса.
Структура чугуна, выплавленного на 3-й партии литейного кокса (рис. 4, в), характеризуется наименьшим числом колоний с большим удельным весом ядер в них, а также меньшим содержанием графита и относительно небольшим количеством мелких включений графита. Подобная структура чугуна обеспечила наибольшую его твердость (см. табл. 7), несмотря на пониженное содержание кремния, марганца, повышенное содержание фосфора и относительно невысокое содержание углерода по сравнению с другими образцами чугуна. Кокс 3-й партии отличается пониженной влажностью и содержанием серы, то есть имеет более высокое качество как ваграночное топливо по сравнению с коксом других партий.
Чугун, выплавленный на 4-й партии кокса, имеет большее число колоний с наименьшим удельным весом ядер в них (удельный вес ядер в структуре , %, во
всех образцах составил 1,9), что может свидетельствовать о появлении дополнительного числа центров при
г
кристаллизации. В качестве зародышей при кристаллизации могли выступать как не растворившиеся графитные включения в расплаве, перешедшие из кокса, так и сульфиды (в 4-й партии кокса массовая доля серы имеет наибольшее значение).
По характеристикам графитных включений образцы чугуна, выплавленного на 1-й и 2-й партиях кокса, занимают промежуточное положение между указанными образцами чугуна.
Фосфидная эвтектика (ФЭ) во всех образцах чугуна имеет одинаковое строение (ФЭ3) и занимает одну и ту же площадь микрошлифа (ФЭп 2000). Ее параметры оотносятся с содержанием фосфора в чугуне. В чугуне, выплавленном на 4-й партии кокса, массовая доля фосфора имеет наименьшее значение, а в чугунах, выплавленных на 1-й и 2-й партиях кокса, — наибольшее. Фосфидная эвтектика представлена в виде разорванной сетки с наименьшим из представленных образцов значением среднего диаметра ячеек сетки для 4-й партии литейного кокса, а для 1-й и 2-й партий кокса — с наибольшим значением. Меньшее содержание фосфора в чугуне, содержащем большее количество углерода, согласуется с повышенным содержанием углерода в литейном коксе.
Таким образом, анализ структуры чугуна, полученного при плавке с использованием в шихте различных партий литейного кокса, позволил выявить его влияние не только на химический состав чугуна, но и на структуру. Были выявлены свойства литейного кокса, влияющие на форму и размеры включений графита в чугуне: содержание золы (Ла, %), массовая доля общей серы %), массовая доля общей влаги в рабочем состоянии %).
Список литературы
1. Воздвиженский В.М., Грачев В.А., Спасский В.В. Литейные сплавы и технология их плавки в машиностроении: учеб. пособие для машиностроительных вузов по специальности
«Машины и технология литейного производства». М.: Машиностроение, 1984. 432 с.
2. Леви М.А., Мариенбах Л.М. Основы теории металлургических процессов и технология плавки литейных сплавов. М.: Машиностроение, 1970. 496 с.
3. Ващенко К.И., Шумихин В.С. Плавка и внепечная обработка чугуна для отливок: учеб. пособие. К.: Вища школа, 1992. 246 с.
4. Липницкий А.М. Плавка чугуна и сплавов цветных металлов. Л.: Машиностроение, 1973. 192 с.
5. Грачев В.А., Черный А.А. Современные методы плавки чугуна. Саратов: Приволжское кн. изд-во, 1973. 342 с.
6. Сухарчук Ю.С., Юдкин А.К. Плавка чугуна в вагранках: учебник для профессионального обучения рабочих на производстве. 2-е изд., перераб. и доп. М.: Машиностроение, 1989. 176 с.
7. Ким В.А., Иванова В.А., Печегузова Л.Н. Газификация SiO2 и изменение фазового состава золы кокса при термической обработке // Комплексное использование минерального сырья. 1994. № 5. С.41-45.
8. Иванова В.А., Ким В.А., Епархин О.М. Исследование восстановления кремния из SiO-газа при выплавке фосфористого чугуна // Изв. вузов. Черная металлургия. 1999. № 9. С. 9-11.
9. Иванова В.А., Файбышев Н.Е., Ким В.А. Восстановление кремния из кокса // Металлургия машиностроения: международный научно-технический журнал. 2002. № 4 (7). С. 2-3.
10. Иванова В.А., Ким В.А., Епархин О.М. Восстановление кремния при фильтрации // Изв. вузов. Черная металлургия. 2000. № 4. С. 5-7.
11. Григорьев В.П., Вишкарев А.Ф., Королев В.Г. Влияние фосфора и марганца на поверхностное натяжение железоуглеродистых расплавов // Изв. вузов. Черная металлургия. 1960. № 4. С. 55-65.
12. Балапанов М.К. Реологические и поверхностные свойства расплавов доменной плавки глиноземсодержащих железных руд: дис. … канд. техн. наук. Караганда, 1985. С. 123.
13. Ващенко К.И., Рудой А.П. Зависимость поверхностного натяжения чугуна от химического состава // Изв. вузов. Черная металлургия. 1966. № 7. С. 26-33.
14. Волков С.Е., Левенец Н.П., Самарин А.М. Поверхностное натяжение расплавов Fe-P-O // Поверхностные явления в расплавах и возникающих из них твердых фазах. Нальчик, 1965. С. 411-415.
15. Паулинг Л. Природа химической связи. Л., 1947. 440 с.
16. Никольский Б.П. Справочник химика. Т.1. Изд. 2-е. М.: Химия, 1963. 1071 с.
17. Популях Л.А. Исследование поведения фосфора в доменной печи с целью получения чугунов с пониженным содержанием примесных элементов: дис. … канд. техн. наук: 05.16.02 / Популях Лариса Алексевна. М., 2009. 145 с.
18. Никитин В.И., Никитин К.В. Наследственность в литых сплавах. 2-е изд., перераб. и доп. М.: Машиностроение, 2005. 476 с.
19. Писаренко Л.В., Лукашевич С.Ф. О наследственности чугунов // Литье и металлургия. 2002. №2. С. 55-57.
20. Кульбовский, И.К., Поддубный А.Н., Богданов Р.А. Образование центров кристаллизации графита в расплаве промышленного чугуна // Литейное производство. 2008. № 6. С. 11-14.
Сведения об авторах
Вдовин Константин Николаевич — д-р техн. наук, проф., зав. кафедрой технологии металлургии и литейного производства, ФГБОУ ВО «Магнитогорский государственный технический университет им. Г.И. Носова», Магнитогорск, Россия. E-mail: [email protected]
Иванова Валерия Анатольевна — канд. техн. наук, доц., зав. кафедрой технологии материалов, стандартизации и метрологии, ФГБОУ ВО «Ярославский государственный технический университет», Ярославль, Россия. E-mail: [email protected].
Феоктистов Николай Алексеевич — канд. техн. наук, доц., ФГБОУ ВО «Магнитогорский государственный технический университет им. Г.И. Носова», Магнитогорск, Россия.
INFORMATION ABOUT THE PAPER IN ENGLISH
MECHANISM OF INFLUENCE OF QUALITY FOUNDRY COKE ON THE CHEMICAL COMPOSITION OF IRON
Vdovin Konstantin Nikolaevich — D.Sc. (Eng.), Professor, Head of the department of Materials Science and foundry, Nosov Magnitogorsk State Technical University. Magnitogorsk, Russia. E-mail: [email protected].
Ivanova Valerya Anatolievna — Ph. D. (Eng.), Associate Profeessor, Head of the department Head . the Department of Materials Technology , Standardization and Metrology. Jaroslavl State Technical University. Jaroslavl, Russia. E-mail: [email protected].
Feoktistov Nikolai Aleksandrovich — Ph. D (Eng), Assistent Professor, Nosov Magnitogorsk State Technical University. Magnitogorsk, Russia. E-mail: [email protected].
Abstract. The mechanism of influence of quality foundry coke in a cupola being applied on the chemical composition of the iron core and its mechanical characteristics (hardness, structure).
Keywords : coke cupola , quality, carbon, silicon , phosphorus and ash .
♦ ♦ ♦
18.01.2018 18:12 Сталь и чугун – это одни из наиболее популярных видов литейных материалов, применяющихся в промышленности. По своим свойствам они довольно схожи, понять, чем отличается сталь от чугуна, можно разными способами. Некоторые из методов можно использовать только в заводских условиях с помощью высокоточного оборудования, другие подходят для применения в быту. Основное отличие чугуна от стали заключается в составе металлов. Сталь представляет собой сплав железа (45%) с углеродом (не более 2%) и легирующими примесями, в качестве которых могут выступать такие вещества, как никель, молибден либо другие. Этот металл отличается высокой прочностью, пластичностью, легкостью обработки. В состав чугуна также входит железо с углеродом, но последнего должно быть от 2% и больше. В качестве легирующих добавок обычно выступает кремний, фосфор, марганец или другие компоненты. Различия физико-химических характеристикОсновная разница в качествах этих металлов заключается в следующем:
Можно ли отличить чугун от стали визуально?Если речь идет о фрагментах или заготовках, обработка которых не нанесет вреда, можно посмотреть на визуальные отличия металлов. На сломе изделия из чугуна появляется темно-серый матовый оттенок, стальная поверхность более светлая, имеет глянцевую текстуру. Внешний вид зависит от содержания углеродистых компонентов, различить их можно по типу трещин: на высокоуглеродистых стальных поверхностях они похожи на дефект в виде раскола, на изделии из низкоуглеродистого сплава железа трещины выглядят как разрыв пластичного типа. На вопрос о том, можно ли отличить готовые изделия по оттенку или текстуре, можно дать однозначный ответ: предметы из стали более светлые, практически всегда имеют глянцевый оттенок, изделия из чугуна – темные и матовые. Как отличить чугун от стали?Чтобы отличать эти металлы друг от друга, можно использовать следующие способы:
Методы механического воздействия могут применяться в бытовых условиях, когда нужно определить, чугун или сталь перед вами, без применения специального оборудования. В лаборатории может использоваться современная техника, с помощью которой проводится спектральный или микроскопический анализ свойств металлов. Эти методы обеспечивают результат высокой точности, но используются преимущественно в промышленных целях, на производстве и в научно-технической отрасли ввиду сложности и дороговизны оборудования. |
Химический состав чугуна и стали
Чугун начали применять много десятилетий назад. Этот материал обладает особыми эксплуатационными характеристиками, которые отличаются от свойственных стали. Производство чугуна, несмотря на появление большого количества различных сплавов, налажено во многих странах. Для того чтобы определить свойства чугуна, следует рассмотреть особенности его химического состава, от чего зависят те или иные физические качества.
Химический состав чугуна является важным фактором, который во многом определяет механические свойства получаемых отливок. Кроме этого, на многие свойства оказывает влияние механизмы первичной и вторичной кристаллизации.
Содержание углерода в чугуне может варьироваться в пределах от 2,14 до 6,67 процентов. Современные технологии производства позволяют с высокой точностью контролировать концентрацию всех элементов в составе, за счет чего снижается показатель хрупкости и увеличиваются другие эксплуатационные характеристики.
Рассматривая химический состав чугуна следует отметить, что в него, кроме железа и углерода, обязательно входят следующие элементы:
- Кремний (концентрация не более 4,3%). Данный элемент оказывает благоприятное воздействие на чугун, делая его более мягким и улучшая его литейные свойства. Однако слишком высокая концентрация может сделать материал более восприимчивым к пластичной деформации.
- Марганец (не более 2%). За счет добавления этого элемента в состав существенно увеличивается прочность материала. Однако слишком большая концентрация может стать причиной хрупкости структуры.
- Сера относится к вредным примесям, который могут существенно ухудшать эксплуатационные качества материала. Как правило, концентрация серы в составе чугуна не превышает показателя 0,07%. Сера становится причиной появления трещин при нагреве состава.
- Фосфор содержится в составе в концентрации менее 1,2%. Повышение концентрации фосфора в составе становится причиной появления трещин при охлаждении состава. Кроме этого, данный элемент становится причиной ухудшения других механических качеств.
Как и во многих других составах, наиболее важным из химических элементов чугуна является углерод. От его концентрации и вида зависит разновидность материала. Структура чугуна может существенно различаться в зависимости от применяемой технологии производства.
Физический свойства
Чугун получил широкое распространение благодаря привлекательным физическим качествам:
- Стоимость материала существенно ниже стоимости других сплавов. Именно поэтому его применяют для создания самых различных изделий.
- Рассматривая плотность чугуна, отметим, что данный показатель существенно ниже, чем у стали, за счет чего материал становится намного легче.
- Температура плавления чугуна может несколько различаться в зависимости от его структуры, в большинстве случаев составляет 1 200 градусов Цельсия. За счет включения в состав различных добавок температура плавления чугуна может существенно повышаться или уменьшаться.
- При выборе материала многие уделяют внимание тому, что цвет чугуна может несколько отличаться в зависимости от структуры и химического состава.
Температура кипения чугуна также во многом зависит от химического состава. Для того, чтобы рассмотреть физические свойства материала, следует уделить внимание каждой его разновидности. Иная структура и химический состав становятся причиной придания иных физико-механических качеств.
Технология производства
Выплавка чугуна проводится на протяжении нескольких десятилетий, что связано с его уникальными эксплуатационными качествами. Большое количество разновидностей сплавов определяет применение особых правил маркировки. Маркировка чугунов проводится следующим образом:
- Литейные обозначаются буквой Л.
- Серый получил широкое распространение, для его обозначения применяется сочетание букв «СЧ».
- Ковкий обозначают КЧ.
- Предельный или белый обозначают буквой П.
- Антифрикционный или серый обозначают АЧС.
- Легированные чугуны могут обладать самым различным химическим составом и обозначаются буквой «Ч».
Технология производства чугуна предусматривает проведение нескольких этапов, которые позволяют получить требуемую структуру. Рассматривая процесс получения чугуна, отметим следующие моменты:
- Производство проводится в специальных доменных печах.
- Легированный и жаростойкий чугун могут получаться при использовании в качестве сырья железной руды.
- Технология представлена в восстановлении оксидов железа руды. В результате перестроения кристаллической решетки и изменения структуры на выходе получается материал, который называют чугуном.
- Рассматривая способы производства, отметим, что особенности технологии также заключаются в применяемых материалах – коксах. Под коксом подразумевают природный газ или термоантрацит, выступающие в качестве топлива.
- Изготовление чугуна предусматривает отпуск железа в твердой форме при применении специальной печи. На данном этапе получается жидкий чугун.
Оборудование для производства чугуна может существенно отличаться. Кроме этого, применяемая технология производства во многом определяет то, какой будет получен материал. Примером можно назвать производство ВЧШГ, которое связано с приданием структуре необычную форму.
Разновидности чугуна
Существует довольно большое количество разновидностей рассматриваемого материала. Классификация чугунов во многом зависит от структуры и химического состава. Выделяют следующие виды чугуна:
- Серый. Эта разновидность материала характеризуется низкой пластичностью и высокой вязкостью, а также хорошей обрабатываемостью резанием. В составе углерод содержится в виде графита. Область применения – машиностроение; производство деталей, работающих на износ. Как показывает практика, концентрация фосфора может варьироваться в достаточно большом диапазоне: от 0,3 до 1,2%. За счет особого химического состава материал обладает высокой текучестью и часто применяется в художественном литье. Антифрикционный чугун обходится в относительно невысокую стоимость, что также определяет его широкое распространение.
- Белый. За счет того, что в этом составе углерод представлен в качестве цементита, структура характеризуется чрезвычайной хрупкостью и повышенной твердостью, а также низкими литейными свойствами и плохой обрабатываемостью резанием. Стоит учитывать, что белый чугун применяется для переделки в сталь или изготовлении ковкого. Очень часто его называют предельным.
- Половинчатый характеризуется повышенной устойчивостью к износу, что связано с распределением углерода на цементитную и свободную основу. Часто эта разновидность материала применяется в машиностроении и станкостроении.
- Легированный. Для того чтобы придать особые свойства чугуну также проводится его легирование. Легированный чугун обладает повышенной износостойкостью, коррозионной стойкостью за счет включения в состав никеля и хрома, а также меди. Подобные варианты исполнения чугуна получают свое название в зависимости от того, как легирующий элемент использовался при их изготовлении.
- Высокопрочный чугун производится путем введения в состав жидкого серого чугуна различных элементов, к примеру, магния и кальция. В результате легирования меняется форма графита – он напоминает шар и при этом не меняет кристаллическую решетку. Стоит учитывать, что по своим свойствам этот металл напоминает углеродистую сталь, применяется, в основном, при изготовлении различных износостойких деталей.
- Ковкий. Получают его при переплавке белого чугуна, который следует нагреть до высокой температуры и выдерживать в подобном состоянии. В некоторых случаях для придания составу особых качеств проводится добавление легирующих элементов. Основными свойствами можно назвать высокую вязкость и повышенную степень пластичности. Получил широкое распространение в машиностроительной промышленности.
- Специальный. Представляет собой сплав, в который входит большое количество марганца и кремния. Зачастую применяется для удаления кислорода из стали при его производстве или переплавке, за счет чего понижается температура плавления.
Каждая разновидность чугуна обладает своей особой структурой и химическим составом, которые и определяют область применения.
Применение
Из-за особых физико-механических качеств применение чугуна стало возможно в самых различных сферах:
- Для производства различных деталей в машиностроительной отрасли. На протяжении многих лет именно этот сплав применяется при изготовлении самых различных деталей для двигателя внутреннего сгорания. При этом автопроизводители проводят изменение основных свойств материала путем его легирования, что необходимо для достижения уникальных качеств. Кроме этого, большое распространение получили тормозные колодки из данного сплава.
- Изделия из чугуна могут выдерживать воздействие низкой температуры. Поэтому материал применяется при производстве техники и инструментов, которые эксплуатируются в жестких климатических условиях.
- Ценится чугун в металлургической области. Это связано с невысокой стоимостью, которая во многом зависит от концентрации углерода и особенностей получаемой структуры. Высокие литейные качества также делают материал более привлекательным. Получаемые изделия характеризуются высокой прочностью и износостойкостью.
- На протяжении нескольких последних десятилетий рассматриваемый сплав широко применяется при изготовлении сантехнического оборудования. Это связано с высокими антикоррозионными способностями, а также возможностью получения изделий самой различной формы. Примером можно назвать чугунные ванны и радиаторы, различные трубы, батареи и мойки. Несмотря на появление материалов, которые могли бы заменить чугун, подобные изделия пользуются большой популярностью. Это связано с тем, что они сохраняют первозданный вид на протяжении длительного периода эксплуатации.
- Применяется сплав и для изготовления различных декоративных элементов, что связано с высокими литейными качествами. Примером можно назвать решетку для перил, различные статуэтки и многое другое.
Кроме этого, область применения зависит от нижеприведенных свойств рассматриваемого материала:
- Некоторые марки обладают высокой прочностью, которая характерна для стали. Именно поэтому материал применяется даже после появления современных сплавов.
- Чугунные изделия могут на протяжении длительного периода сохранять тепло. При этом тепловая энергия может равномерно распространяться по материалу. Эти качества стали использоваться при изготовлении отопительных радиаторов или других подобных изделий.
- Принято считать, что чугун – экологически чистый материал. Именно поэтому его часто применяют при изготовлении различной посуды, к примеру, казана.
- Высокая стойкость к воздействию кислотно-щелочной среды.
- Высокая гигиеничность, так как все загрязняющие вещества могут легко удаляться с поверхности.
- Рассматриваемый материал характеризуется достаточно длительным сроком службы при условии соблюдения рекомендаций по эксплуатации.
- Входящие в состав химические вещества не могут нанести вреда здоровью.
В заключение отметим, что давно открытая технология производства рассматриваемого материала на протяжении многих лет оставалась практически неизменной. Это связано с тем, что при относительно невысоких затратах можно было получить большой объем расплавленного сплава. На сегодняшний день часто проводится производство материала из лома, что позволяет еще в большой степени снизить себестоимость получаемого продукта.
Если вы нашли ошибку, пожалуйста, выделите фрагмент текста и нажмите Ctrl+Enter.
Чугун — это сплав железа с углеродом. По процентному содержанию железа содержится более 90%. Количество углерода колеблется в пределах 2,14- 6,67%. Благодаря этому элементу материал имеет высокую твердость, но появляется хрупкость. Это влечет ухудшение ковкости и пластичности. В некоторые виды для улучшения характеристики добавляются легирующие элементы: алюминий, хром, ванадий, никель.
Характеристика видов углеродистого металла
Диаграмма железо-углерод показывает, из чего состоит чугун. Кроме железа, присутствует углерод в виде графита и цементита.
Состав сплава чугуна имеет разновидности:
- Белый. Присутствующий здесь углерод находится в химически связанном состоянии. Металл прочный, но хрупкий, поэтому плохо поддается механической обработке. В промышленности используется в виде отливок. Свойство материала позволяют вести его обработку абразивным кругом. Сложность вызывает процесс сварки, поскольку есть вероятность появления трещин из-за неоднородности структуры. Применение нашел в областях, связанных с сухим трением. Обладает повышенной жаростойкостью и износостойкостью.
- Половинчатый. Обладает повышенной хрупкостью, поэтому не нашел широкого применения.
- Серый. ГОСТ 1412–85 указывает, какой процент примесей содержит в своем составе этот металл: 3,5% углерода, 0,8% марганца, 0,3% фосфора, 0,12% серы и до 2,5% кремния. Присутствующий в пластинчатой форме углерод создает низкую ударную вязкость. Характеристика вида указывает, что на сжатие материал работает лучше, чем на растяжение. При достаточном нагреве обладает неплохой свариваемостью.
- Ковкий. Ферритовая основа такого вида обеспечивает ему высокую пластичность. В изломе имеет черный, бархатистый цвет. Получается из белого, который томится длительное время при температуре 800−950 градусов.
- Высокопрочный. Отличие от других видов заключается в присутствии графита шаровидной формы. Получается из серого после добавления в него магния.
Индивидуальные свойства металла
Материал характеризуется определенными характеристиками. К ним относятся:
- Физические. Такие величины, как удельный вес или коэффициент расширения зависят от того, сколько составляет в металле содержание углерода. Материал тяжелый, поэтому из него можно делать чугунные ванны.
- Тепловые. Теплопроводность позволяет аккумулировать тепло и удерживать, распространяя его равномерно во все стороны. Это используется при изготовлении сковородок или батарей для отопления.
- Механические. Эти характеристики меняются в зависимости от графитовой основы. Наиболее прочный — серый чугун, имеющий перлитовую основу. Материал с ферритовой составляющей более ковкий.
В зависимости от наличия примесей появляется разница в свойствах материала.
К таким элементам относятся сера, фосфор, кремний, марганец:
- Сера уменьшает текучесть металла.
- Фосфор понижает прочность, но позволяет изготавливать изделия сложной формы.
- Кремний увеличивает текучесть материала, снижая его температуру плавления.
- Марганец дает прочность, но понижает текучесть.
Различия между чугуном и сталью
Чтобы понять, чем отличается сталь от чугуна, нужно рассмотреть их характеристики. Отличительной особенностью чугуна является количество углерода. Минимальное содержание его составляет 2,14%. Это основной показатель, по которому можно отличить этот материал от стали.
Содержание железа в стали составляет 45%, а процентное содержание углерода до 2. Для определения различий на глаз нужно обратить внимание на цвет. Сталь имеет светлый оттенок, а чугун темный.
Определить же процентное содержание примесей может только химический анализ. Если сравнивать температуру плавления чугуна и стали, то у чугуна она ниже и составляет 1150−1250 градусов. У стали — в районе 1500.
Чтобы отличить материал, нужно провести следующие действия:
- Изделие опускается в воду и определяется объем вытесненной воды. У чугуна плотность меньше. Она составляет 7,2г/см3. У стали — 7,7−7,9 г / см3 .
- К поверхности прикладывается магнит, который к стали притягивается лучше.
- При помощи шлифовальной машинки или напильника натирается стружка. Затем она собирается в бумагу и вытирается об нее. Сталь не оставит следов.
Плюсы и минусы материала
Как и любой материал, чугун имеет положительные и отрицательнее стороны. К положительным качествам относятся:
- большая разновидность состояний.
- некоторые виды обладают высокой прочностью;
- возможность длительное время сохранять температуру;
- экологическая чистота, что позволяет изготавливать из него посуду;
- стойкость к кислотно-щелочной среде;
- высокая гигиеничность;
- длительный срок эксплуатации и долговечность;
- безвредность материала.
Однако и минусы тоже присутствуют. К ним относятся:
- при длительном нахождении в воде поверхность покрывается ржавчиной;
- высокая стоимость материала;
- низкая пластичность серого вида чугуна;
- хрупкость.
Чугун — это металл, который характеризуется высоким содержанием углерода. Благодаря этому у него присутствуют качества, которые бывают необходимы для промышленных и бытовых целей.
Чугун |
---|
Фазы железоуглеродистых сплавов |
Структуры железоуглеродистых сплавов |
Виды чугуна
Чугун это сплав железа с углеродом, а так же как правило с кремнием, марганцем, фосфором и серой, при этом в составе чугуна количество углерода находится в диапазоне от 2,14 до 6,67% (в стали углерод находится в количестве до 2,14%).
По своим техническим характеристкикам чугун представляет собой достаточно хрупкий материал.
Углерод в чугуне находится либо в виде центита (Fe3C), либо в виде графита, в зависимости от количества содержания в чугуне этих соединений выделяют следующие виды чугуна:
— серый;
— белый;
— половинчатый;
— ковкий;
— высокопрочный.
Теперь давайте немного поподробней остановимся на каждом из них.
Серый чугун.
В данном виде чугуна большая часть углерода, либо вообще весь находится в виде графита. Цвет излом чугуна – серый (от сюда и название). Данный вид чугуна имеет высокие литейные свойства, в связи с этим используется для литья, хорошо поддаётся металлопобработке.
Белый чугун
В отличии от серого чугуна, данный вид чугуна плохо поддаётся металлообработке. Углерод содержащийся в нём находится исключительно в цементите. Цвет излома – светлый. Белый чугун характеризуется высокой твёрдость, что не позволяет обрабатывать его режущим инстурментм. Используют белый чугун, как правило полупродукта, для получения ковкого чугуна.
Ковкий чугун
Данный вид чугуна получают от отливки и термической обработки белого чугуна, в процессе которой образуется хлопьевидный графит.
Основной сферой использования ковкого чугуна является производство автомобилей и сельхоз технике.
Половинчатый чугун
В данном виде чугуна углерод находится как в виде цементита, так и в виде графита.
Используется половинчатый чугун, как фрикционный материал в условиях сухого трения. Из данного вида чугуна производят детали с повышенной износоустойчивостью.
Высокопрочный чугун
Высокопрочный чугун содержит углерод в виде шаровидного графита, который образуется в процессе кристаллизации. Как правило данный вид чугуна используют для производства важных деталей в машиностроении, а так же для производства высокопрочных труб для газопроводов, нефтепроводов, а так же водоснабжения.
Главной особенностью всех чугунов является их плохая свариваемость.
Читайте так же:
Газовая цементация, общие вопросы
Сравнение чугунной и стальной дроби
Состав и формы графита в чугунах
Состав и формы графита в чугунах
Варьируя химический состав, скорость затвердевания и режимы термической обработки, можно в значительной степени управлять свойствами чугуна. Одним из наиболее важных процессов, определяющих свойства чугуна, является его графитизация. Графитная фаза придает чугуну ряд свойств, которые невозможно встретить в других сплавах.
Чугунами принято называть сплавы железа с углеродом, которые содержат в структуре эвтектику. Помимо углерода и кремния чугуны содержат и другие элементы. Эти примеси разделяют на две группы: 1) технологические или обычные примеси, попадающие в состав чугуна в процессе производства; 2) легирующие и модифицирующие – специально вводимые элементы для регулирования структурообразования и свойств чугуна. К обычным примесям относят фосфор, серу, марганец, газы (водород, азот, кислород). Нелегированным считают чугун, содержащий до 3,5–4,0 % Si, до 1,5-2,0 % Mn, до 0,3 % P, до 0,2-0,3 % S и менее 0,1 % Cr, Ni Cu. Содержание основного компонента – углерода,– составляет около 4 %, и его оптимальное значение зависит от содержания других элементов. Количество фосфора может доходить до 0,8 % при производстве отливок специального назначения, например, для художественного литья (каслинское литье). Возможное содержание газов зависит от способа выплавки чугуна и может изменяться от 10,6 (вагранка) до 7,1 см3/100 г (индукционная печь). Наиболее распространенными легирующими элементами являются хром, никель, алюминий, медь, титан, вольфрам и др. Обычные примеси (марганец, кремний) могут быть легирующими элементами при повышенном их содержании. В качестве модифицирующих добавок в чугуны вводят магний, кальций, церий, лантан, сурьму, висмут и другие элементы. Такие чугуны называют модифицированными.
Для анализа процессов структурообразования в чугунах используют обычно двойную диаграмму состояния Fe – C. Из диаграммы следует, что в двойных сплавах область чугунов начинается для С > 2,03–2,06 %. По содержанию углерода для двойной диаграммы чугуны разделяют на доэвтектические (C 4,3 %). Для затвердевания доэвтектического чугуна характерно то, что кристаллизация начинается с появления дендритов первичного аустенита. При затвердевании же заэвтектического чугуна процесс кристаллизации начинается с появления графитных или цементитных частиц.
Система железо – цементит является термодинамически менее стабильной по сравнению с системой железо — графит. Поэтому выделившийся цементит в определенных условиях, например, при нагреве, распадается с образованием графита. Этот процесс называют графитизацией. Обратное превращение (графит -> цементит) в закристаллизовавшемся чугуне не происходит. По степени графитизации чугун подразделяют на белый (практически не графитизированный), отбеленный или половинчатый (частично графитизированный) и серый (в значительной степени или полностью графитизированный).
Деление чугунов на до–, за– и эвтектические по содержанию углерода достаточно условно. Однако для практики литейного производства эвтектичность имеет особое значение – чугуны эвтектического состава обладают лучшими технологическими свойствами. Они имеют меньшую усадку и максимальную жидкотекучесть (из всех сплавов температура кристаллизации эвтектики минимальна, отсутствует интервал кристаллизации – твердо-жидкого состояния). Поэтому для оценки эвтектичности промышленных чугунов вводят показатели углеродного эквивалента или степени эвтектичности.
Углеродный эквивалент учитывает смещение фигуративной точки сплава на двойной диаграмме железо–углерод под влиянием примесей, чаще всего, кремния и фосфора:
Степень эвтектичности показывает относительное содержание эвтектики в чугуне и определяется как:
Чем ближе Сэкв к 4,3 %, тем ближе структура чугуна к эвтектической, тем меньше избыточной фазы (аустенита, графита или цементита). Этому же соответствует Sэвт=1,0. Влияние остальных элементов в указанных выше количествах несущественно. Необходимо учитывать, что углеродный эквивалент и степень эвтектичности являются скорее литейными, чем металлографическими характеристиками. При содержании углерода более 4,3 % Sэвт становится больше 1,0 (100 %), хотя доля эвтектики в сплаве падает. В легированных чугунах углеродный эквивалент будет более сложным образом зависеть от содержания других элементов. Например, многие высокоуглеродистые среднелегированные инструментальные стали по структурному типу являются чугунами (имеют в структуре эвтектику).
В рамках стандартов ведущих промышленных стран мира имеется несколько системных методик, которые позволяют описывать основные градации формы графита по типам. В зависимости от формы графита различают следующие основные типы конструкционного чугуна (рис.1.1): серый чугун с пластинчатым графитом (СЧ), высокопрочный чугун с шаровидным графитом (ВЧШГ), чугун с вермикулярным графитом (промежуточные формы между компактными пластинчатыми формами)(ЧВГ), ковкий чугун (КЧ). При этом структура металлической матрицы может быть различной — от ферритной до аустенитной.
Рисунок 1.1 – Схемы микроструктур чугуна: а – серый чугун на ферритной основе; б – чугун с вермикулярным графитом; в – серый феррито-перлитный чугун; г – серый чугун на перлитной основе; д – высокопрочный феррито-перлитный чугун; е –высокопрочный перлитный чугун; ж – белый чугун (доэвтектический; графит отжига (хлопьевидный).
Включения графита в сером и высокопрочном чугунах обычно окружены небольшой оторочкой металлической основы, обогащенной кремнием. Обычно именно здесь и выделяется в первую очередь структурно-свободный феррит. Небольшое количество такого феррита в сером и высокопрочном чугунах бывает даже полезным для механических свойств металла, так как в этом случае хрупкая фаза (графит) оказывается окаймленной пластичной и вязкой, которая оказывает дополнительное сопротивление к возникновению и распространению микро- и макротрещин при нагружении металла.
Для серых чугунов характерен большой диапазон изменения размеров, формы и количества графитных включений, а также степени их распределения в металлической основе. Согласно ГОСТ 3443-87 «Отливки из чугуна с различной формой графита. Методы определения структуры», графит в структуре чугуна эталонирован по форме (Гф1-Гф5, к серым чугунам при этом относятся ПГф1-ПГф4), размерам включений (ПГд15-ПГд1000, цифра обозначает длину или диаметр включения, видимого на шлифе), характеру распределения только серого чугуна (ПГр1-ПГр9), по количеству (ПГ2-ПГ12, где ПГ2 соответствует содержанию графита до 3% площади шлифа, а ПГ12 — свыше 12%). Аналогичные международные стандарты по контролю структуры чугуна – ASTM A 247-67, DIN EN ISO 945, 1994.
Многие эксплутационные свойства серого чугуна зависят от размеров и количества графитных включений. Очевидно, что сравнительно мелкие включения с завихренными пластинами при их равномерном распределении обеспечивают более высокие эксплутационные свойства чугуна. Крупные пластины графита с относительно прямыми заостренными кромками служат источниками образования трещин, приводя в конечном итоге к разрушению детали или изделия в целом. Во многих крупноразмерных включениях графита наблюдаются характерные внутренние трещины в виде продольных разрывов сплошности, вызванных ростовыми напряжениями. Значительный уровень ростовых напряжений служит также причиной сильно выраженного рыхлого пакетного строения холмиков роста.
Одним из факторов, обеспечивающих управление процессом формообразования графита, является скорость охлаждения металла при затвердевании. Чем она выше, тем больше величина переохлаждения металла и, следовательно, больше возникает центров кристаллизации аустенитной фазы. Однако, при значительном увеличении скорости охлаждения чугуна в результате неравномерного распределения углерода и примесей в отдельных микрообъемах жидкой фазы может начаться образование цементитной эвтектики, что существенно изменяет свойства отливки.
Шаровидный графит в промышленных отливках не имеет идеальной сферической формы. Поверхность шаровидного графита состоит из множества тонколепестковых выступов. Эти лепестки правильной полигональной и неправильной округленной формы в совокупности образуют структуру чередующихся волнообразных гряд. Исследование ионотравленных срезов шаровидного графита позволило выявить следующие типы слоистой структуры: дендритную, дендритно-концентрическую, зигзагообразную и концентрическую. Получение того или иного типа слоистой структуры обычно связывают с условиями охлаждения и химическим составом модификатора.
Литературные данные о химическом и фазовом составе неметаллических включений в шаровидном графите далеко не однозначны. Вместе с тем, по этим данным представляется возможным сделать вывод о том, что роль неметаллических включений в образовании конечных форм роста графита второстепенна. Неметаллические включения, встречающиеся в пластинчатом и шаровидном графите, не содержат углерода и в равной степени встречаются в центральных и периферийных участках. В магниевом чугуне с шаровидным графитом они содержат магний, кремний, кальций, серу и железо. В промышленном магнийцериевом чугуне с шаровидным графитом в центральной части графитовых включений обнаружены частицы диаметром 2…5 мкм переменного состава, содержащие преимущественно оксиды цезия, магния и железа.
В целом же чугун с шаровидным графитом является весьма перспективным конструкционным материалом. Как показывает практика последних десятилетий, чугун с шаровидным графитом, обладая высокими служебными свойствами и высокой экономичностью, вытеснил большое количество изделий из чугуна с пластинчатым графитом и стали. В большинстве промышленно развитых стран мира среди литых железоуглеродистых сплавов чугун с шаровидным графитом занимает второе место по массе выпускаемых отливок после серого чугуна.
Использование чугуна с вермикулярной формой графита в качестве самостоятельного конструкционного материала предложено в середине 50-х годов, а само название «чугун с вермикулярным графитом» впервые встречается у Р. Шелленга. Вермикулярный графит, подобно обычному пластинчатому графиту, формируется посредством ветвления в пределах эвтектической аустенитно-графитной колонии. На первых стадиях затвердевания формируется графит шаровидной формы, который затем трансформируется в вермикулярный. В ряде работ показано, что кончики включений вермикулярного графита в течение всего процесса кристаллизации остаются в контакте с жидким металлом.
Специфика анизотропного микростроения вермикулярного графита заключается в периодическом сочетании микрозон слоисто-блочной структуры, подобной структуре пластинчатого графита, и слоисто-концентрической, характерной для шаровидного графита. При этом кристаллографическая ориентировка слоев роста смежных микрокристаллитов каждого лепестка вермикулярного графита, как правило, сильно различается. Видимо, механизм формирования вермикулярного графита состоит в автономном образовании и послойном зародышевом разрастании составляющих графит микрокристаллитов.
Особое строение и форма вермикулярного графита являются основной причиной более высокого уровня упругих свойств по сравнению с чугуном с пластинчатым графитом. Это объясняется тем, что модуль упругости Е сильно зависит от скорости деформации графитовых включений и, следовательно, от размера и пространственной формы графита. Например, при приблизительно одинаковом химическом составе чугуна модуль упругости в зависимости от формы графита составляет 80*103 Н/мм2 у чугуна с пластинчатым графитом, 157*103 Н/мм2 у чугуна с вермикулярным графитом и 170*103 Н/мм2 у чугуна с шаровидным графитом. Влияние матрицы (ферритная – перлитная) менее существенно.
Не останавливаясь на комплексном рассмотрении основных преимуществ, которые могут быть достигнуты в случае использования в отливках чугуна с вермикулярным графитом по сравнению с чугуном с пластинчатым и шаровидным графитом, отметим лишь, что чугун с вермикулярным графитом высоко экономичен. Это позволяет рекомендовать его для широкого круга отливок сложной конфигурации с различной толщиной стенки и регламентацией по механическим свойствам.
Помимо рассмотренных форм графита в структуре чугунов с шаровидным и вермикулярным графитом встречаются различные вырожденные формы, среди которых наибольший практический интерес представляют графит переохлаждения и шаровидный разорванный (звездообразный). Графит переохлаждения на поверхности шлифа в оптическом микроскопе имеет вид россыпи мелких и мельчайших изолированных обломков. Причины образования и реальная морфология этого графита изучены достаточно слабо. Эта вырожденная форма тонко дифференцированного графита часто встречается в тепловых узлах отливок в условиях модифицирования цериевым мишметаллом.
Разорванный (звездообразный) шаровидный графит соответствует эталону ШГф10 и ШГф11 (ГОСТ 3443-87). Наличие подобного графита также значительно снижает прочностные свойства чугуна с шаровидным и вермикулярным графитом. Разорванный шаровидный графит представляет собой незаполненную секториально-дендритную форму роста. Основной причиной характерной недостроенности такого типа шаровидного графита служит избыток примесей, в том числе сфероидизирующих, на фронте роста призматических плоскостей кристаллической решетки, вызывающий в определенный момент времени углеродо-непроницаемость диффузионного пограничного слоя расплава у этих плоскостей. Характерно, что по размеру разорванный шаровидный графит в 2-3 раза превышает полностью застроенный шаровидный графит.
В целом же комплексные данные о различных формах графита в чугуне способствуют расширению научных представлений о генезисе формообразования графита в процессе затвердевания отливки. Это, в конечном счете, позволит в максимальной степени стимулировать развитие тенденции улучшения качества промышленных отливок, обладающих более высокими эксплуатационными характеристиками при существенном снижении их массы, что, соответственно, повысит конкурентоспособность литых чугунных изделий за счет уменьшения металлоемкости выпускаемой продукции при гарантированном повышении качества.
Формирование структуры чугуна в реальных отливках происходит в неравновесных условиях и зависит от множества факторов, которые не учитываются равновесными двойными диаграммами состояния. Поэтому для определения структуры чугунных отливок и их механических свойств обычно используются различные эмпирические диаграммы и номограммы, широко рассмотренные во многих работах.
На процессы структурообразования чугуна в первую очередь влияют углерод и кремний. В сером чугуне они определяются изменением не только содержания графита, но и структуры матрицы. В целом повышение содержания углерода в чугуне уменьшает прочность, модуль упругости и твердость и увеличивает пластичность и циклическую вязкость. Однако при низком содержании углерода наблюдается сначала некоторая анормальность (повышение прочности и твердости) с увеличением содержания углерода, что, вероятно, является следствием устранения междендритного графита и сопровождающего его феррита.
Различие влияния кремния и углерода заключается в том, что кремний образует твердый раствор с ферритом, тем самым повышает его прочность и твердость и понижает его плотность и вязкость. В серых чугунах к легирующему влиянию кремния добавляется еще и графитизирующее, что может резко изменить те или иные механические свойства. Только в малоуглеродистом и малокремнистом чугуне наблюдается сначала некоторое увеличение прочности вследствие устранения междендритного графита. Однако при содержании кремния сверх определенного количества уменьшается пластичность серого чугуна, что является следствием преобладающего влияния силикоферрита, которое проявляется, несмотря на ферритизацию структуры. Твердость серого чугуна кремний изменяет в противоположном направлении, понижая ее сначала в результате графитизации и увеличивая ее затем вследствие образования силикоферрита.
Достаточно часто влияние углерода и кремния на механические свойства чугуна рассматривают совместно, используя для этого функцию углеродного эквивалента или эвтектичности (см. выше), хотя относительное влияние этих элементов на положение эвтектической точки далеко не всегда соответствует их влиянию на механические свойства.
Влияние марганца проявляется благодаря легированию феррита, измельчению перлита, торможению графитизации, образованию свободных карбидов и некоторому улучшению формы пластинчатого графита. В соответствии с этим, даже в небольших пределах 1-2%, марганец заметно повышает твердость чугуна. Более сильно влияние марганца проявляется при больших его концентрациях, порядка 5-7 %. Прочность, пластичность и вязкость серого чугуна сначала повышаются при увеличении содержания марганца, а затем падают вследствие увеличения неоднородности структуры. Так, падение пластичности и вязкости обычно начинается уже при концентрациях 0,3-0,5 % Mn, а прочности — при 0,8-1,2 % Mn.
По вопросу влияния серы на механические свойства чугуна существуют достаточно противоречивые мнения. С высокой степенью достоверности можно утверждать, что сера и сульфиды железа оказывают весьма неблагоприятное влияние на прочность и пластичность чугуна при одной и той же структуре матрицы, что объясняется ослаблением границ зерен эвтектикой Fe-FeS. Помимо этого, сера способствует перлитизации структуры и может также повысить прочность и твердость ферритного или феррито-перлитного серого чугуна. Вредное влияние серы подавляется марганцем, который в соединении с серой дает сернистый марганец, представляющий собой тугоплавкое соединение, всплывающее в шлак и частично остающееся в отливках в виде неметаллических включений. Обычно, учитывая вредное влияние серы, в практике литейного производства стремятся регламентировать содержание серы на весьма низких уровнях.
Влияние фосфора на механические свойства чугуна следует признать отрицательным с точки зрения изменения его прочностных характеристик. Вследствие наличия фосфора в чугуне происходит легирование феррита, размельчение эвтектического зерна и образование включений фосфидной эвтектики. При этом значительно повышается твердость и понижается пластичность и вязкость чугуна. Общая закономерность изменения прочности чугуна заключается в следующем: сначала происходит возрастание прочностных показателей по мере повышения содержания фосфора, а затем при выделении фосфидной эвтектики они начинают понижаться. Следует дополнительно отметить, что влияние фосфора снижается с увеличением содержания кремния в чугуне.
В практике литейного производства фосфор считается графитизатором. Это — следствие косвенного влияния фосфора на перераспределение элементов в аустените и жидкой фазе и образования тройной эвтектики с очень низкой температурой плавления. Значительное увеличение интервала затвердевания фосфористого чугуна в присутствии участков жидкой фазы до температуры 950 оС способствует повышению количества графита.
В ряде случаев для изменения механических и физических свойств чугун легируют. Обычно при легировании чугуна используются те же химические элементы, что и при легировании стали. К элементам, оказывающим положительное влияние на графитизацию, относят алюминий, кремний, никель, медь, кобальт и т.п. Противодействуют выделению графита такие элементы, как хром, ванадий, вольфрам и молибден. Сравнивая имеющиеся в литературе данные, необходимо отметить, что существует определенная аналогия между склонностью чугуна, содержащего хром, молибден и марганец, к отбелу, а также к повышению температуры начала его графитизации. Легирующие элементы, воздействуя на структуру чугуна, оказывают решающее влияние на его механические и эксплутационные свойства. Влияние легирующих элементов в низколегированных чугунах с пластинчатым графитом на структуру приведено в табл.1.1.
Таблица 1.1 — Влияние основных легирующих элементов на структуру чугуна
ПАО «Магнитогорский металлургический комбинат»
Новые возможности обновленного стана 2500 горячей прокатка Расширение сортамента, повышение качества, наращивание мощностей Инвестиционное лидерство Целевые инвестиции в высококачественные активы и высокорентабельные проекты
Социальная ответственность Соблюдение интересов работников, партнеров
Интернет-магазин Продажа продукции производства ПАО «ММК» в режиме онлайн
ИНДУСТРИЯ-4.0 ММК продолжает реализацию Ключевым элементом Стратегии развития Группы ММК до 2025 года является Социальная ответственность Соблюдение интересов работников, партнеров
Интернет-магазин Продажа продукции производства ПАО «ММК» в режиме онлайн
|
Чугун на самом деле представляет собой сплав железо-углерод-кремний, содержащий от 3 до 5,5 процентов углерода, от 1 до 3 процентов кремний, а также следы других элементов, таких как сера, магний и калий в сумме около 0,5 процента. Напротив, стали содержат менее 2 процентов углерода. Согласно матовой базе сайта, главные преимущества чугуна — невысокая цена и возможность формования сложных форм за один этап производства.Чугун — это черный металл, но он достаточно сильная устойчивость к ржавчине Характеристики Прочие типы Технические материалы Сплавы Функция ГЛАВНАЯ | БЛОГ Кастинга | СВЯЗАТЬСЯ С НАМИ |
В чем разница между чугунным и кованым железом?
Люди могут подумать, что термин «чугун» относится ко всем ранним изделиям из железа, или что ранние изделия из железа всегда были «коваными», или что и то, и другое может быть правдой. Они будут неправы. На самом деле, основное различие между ними простое:
Чугун — это железо, которое было расплавлено, вылито в форму и оставлено для охлаждения.
Кованое железо — это железо, которое нагревали и затем обрабатывали инструментами. Фактически, термин «обработанный» произошел от причастия прошедшего времени слова «работал».
Но давайте углубимся в подробности.
Чугун
«Чугун» — это общий термин, который относится к ряду сплавов железа, но обычно ассоциируется с наиболее распространенным серым чугуном. Хотя чугун может звучать как литая форма чистого железа, на самом деле это сплав, содержащий от 2 до 4% углерода, плюс меньшее количество кремния и марганца.Другие примеси, такие как сера и фосфор, также обычны.
Чугун получают путем плавки железной руды или чугуна (продукт добычи железной руды) и смешивания с ломом металлов и другими сплавами. Жидкую смесь разливают в формы и дают ей остыть и затвердеть. Из-за более высокого содержания углерода чугун затвердевает как гетерогенный сплав, поэтому он содержит несколько материалов в разных фазах в своей микроструктуре, что влияет на его физические свойства.
Например, в микроструктуре чугуна есть частицы углерода, которые при охлаждении металла образуют удлиненные чешуйки графита. Графит имеет низкую плотность и твердость, но высокую смазывающую способность. Таким образом, он предлагает немного структурных преимуществ, но он действительно ставит под угрозу окружающую железную матрицу, создавая точки внутреннего напряжения, которые могут привести к трещинам.
По сравнению с кованым чугуном или сталью чугун хрупкий, твердый и не ковкий. Его нельзя сгибать, растягивать или придавать форму молотком.Его слабая прочность на разрыв означает, что он сломается, прежде чем согнется или деформируется. Однако он обладает хорошей прочностью на сжатие и широко использовался в строительстве до появления сталелитейной промышленности в начале 20 века.
По сравнению со сталью чугун имеет более низкую температуру плавления, более текуч и менее реагирует с материалами форм, что делает его хорошо подходящим для литья. Это значительно менее трудоемкий процесс, чем изготовление изделий из кованого железа, поэтому он был заметной формой производства на протяжении 18 и 19 веков.В строительной отрасли чугун в значительной степени был заменен сталью, но он все еще используется во многих отраслях промышленности.
Кованое железо
Кованое железо состоит в основном из железа с добавлением 1-2% шлака, побочного продукта плавки железной руды — обычно смеси оксидов кремния, серы, фосфора и алюминия. Во время изготовления утюг снимают с огня и обрабатывают молотком, пока он еще горячий, чтобы придать ему окончательную форму.
Кованое железо часто имеет волокнистый вид, но оно также мягче и пластичнее, чем чугун.Кованое железо очень ковкое, то есть его можно нагревать, повторно нагревать и обрабатывать в различных формах. На самом деле, чем больше работает, тем сильнее он становится.
Кованое железо имеет гораздо более высокий предел прочности на разрыв, чем чугун, что делает его более подходящим для использования в строительстве горизонтальных балок. В целом сильно противостоит переутомлению. Он деформируется без сбоев, если он не перегружен намного выше допустимой нагрузки или не деформируется из-за воздействия сильного тепла (например, из-за огня).
Он широко использовался в строительстве зданий в XIX веке, но в XX веке был заменен сталью.Сегодня кованое железо используется в основном в декоративных целях.
Коррозия
Чугун и кованое железо подвержены коррозии, когда голые поверхности подвергаются воздействию кислорода в присутствии влаги. В отличие от других металлов, которые образуют защитное окислительное покрытие, железо со временем ржавеет и полностью отслаивается. Это может быть непросто для наружных сред, где могут продолжаться осадки и влажность.
Во избежание ржавчины изделия из железа следует покрывать защитным покрытием.Краска обычно используется для защиты голого металла. Порошковые покрытия — это еще один метод, который хорошо подходит для уличной мебели, подверженной износу в местах с интенсивным движением. Порошковые покрытия очень долговечны и не выгорают, не трескаются и не трескаются в течение длительного времени.
Брэд Доне, вице-президент
Reliance Foundry Co. Ltd., Британская Колумбия, Канада
Ищете запчасти? Зайдите в SourceESB.
Свойства серого чугуна и химический состав
Свойства серого чугуна и химический состав | Литье в песчаные формы, литье по выплавляемым моделям и обработка с ЧПУ в Китае30 июля 2010 г.
Серый чугун (отливки из серого чугуна) называют так из-за цвета поверхности излома.Он содержит 1,5-4,3% углерода и 0,3-5% кремния, а также марганец, серу и фосфор. Он хрупкий, имеет низкую прочность на разрыв, но его легко отлить.
Все данные в этом документе относятся к китайскому стандарту GB / T 9439-1988. Qingdao Casting Quality напишите все материалы из справочника.
www.castingquality.com
Наши услуги
Качество литья с упором на промышленность металлических деталей, мы предоставляем профессиональные услуги в области литья металлов.
Песочное литье — это популярный метод формования металлов, подходит для всех материалов, таких как серый чугун, ковкий чугун, ковкий чугун, углеродистая сталь, нержавеющая сталь, алюминий и бронза.
Просмотров: 1847
также называют прецизионным литьем по выплавляемым моделям, в основном подходит для деталей из углеродистой и нержавеющей стали. Мы также производим детали из серого и высокопрочного чугуна, алюминия и бронзы методом литья по выплавляемым моделям. Он может достичь наилучшего внешнего вида с хорошей переносимостью
Просмотров: 1847
Метод раковинного литья — хороший вариант для замены литья по выплавляемым моделям и литья в песчаные формы.качество лучше, чем детали для литья в песчаные формы, пригодные для массового производства.
Просмотров: 1847
Фрезерование с ЧПУ, токарная обработка с ЧПУ с центром с ЧПУ 5 xix, мы обеспечиваем прецизионную обработку всех отливок на основе проектных чертежей клиентов.
Просмотров: 1847
Служба механического проектирования, основанная на требованиях клиентов, наше программное обеспечение — Solidworks и AutoCAD.
Просмотров: 1847
Проектирование и производство пресс-форм будет обслуживать промышленность литья металлов и литья пластмасс.Основываясь на нашем более чем 10-летнем опыте, мы поставляем профессиональные формы для наших клиентов в Европе и Северной Америке.
Просмотров: 1847
Свойство серого чугуна
Предел прочности при растяжении образцов отливки для серого чугуна
Серый чугун марки | Отдельный образец Предел прочности при растяжении | Отливки из серого чугуна | |
Толщина стенки / мм | Предел прочности при растяжении σb≥ / МПа | ||
HT100 | 100 | > 2.5 ~ 10 > 10 ~ 20 > 20 ~ 30 > 30 ~ 40 | 130 100 90 80 |
HT150 | 150 | > 2,5 ~ 10 > 10 ~ 20 > 20 ~ 30 > 30 ~ 40 | 175 145 130 120 |
HT200 | 200 | > 2,5 ~ 10 > 10 ~ 20 > 20 ~ 30 > 30 ~ 40 | 220 195 170 160 |
HT250 | 250 | > 4.0 ~ 10 > 10 ~ 20 > 20 ~ 30 > 30 ~ 50 | 270 240 220 200 |
HT300 | 300 | > 10 ~ 20 > 20 ~ 30 > 30 ~ 50 | 290 250 230 |
HT350 | 350 | > 10 ~ 20 > 20 ~ 30 > 30 ~ 50 | 340 290 260 |
www.castingquality.com
.com
Свойство прочности на разрыв прикрепленных образцов отливок
Серый чугун марки | Толщина стенки / мм | Предел прочности при растяжении σb≥ / МПа | Предел прочности при растяжении (для справки) σb≥ / МПа | |||
Прилагаемый тестовый купон | Прикрепленный испытательный блок | |||||
φ30 мм | φ50 мм | R15 мм | R25 мм | |||
HT150 | > 20 ~ 40 > 40 ~ 80 > 80 ~ 150 > 150 ~ 300 | 130 115 — — | — (115) 105 100 | 120 110 — — | — — 100 90 | 120 105 90 80 |
HT200 | > 20 ~ 40 > 40 ~ 80 > 80 ~ 150 > 150 ~ 300 | 180 160 — — | — (155) 145 135 | 170 150 — — | — — 140 130 | 165 145 130 120 |
HT250 | > 20 ~ 40 > 40 ~ 80 > 80 ~ 150 > 150 ~ 300 | 220 200 — — | — (190) 180 165 | (210) 190 — — | — — 170 160 | 205 180 165 150 |
HT300 | > 20 ~ 40 > 40 ~ 80 > 80 ~ 150 > 150 ~ 300 | 260 235 — — | — (230) 210 195 | (250) 225 — — | — — 200 185 | 245 215 195 180 |
HT350 | > 20 ~ 40 > 40 ~ 80 > 80 ~ 150 > 150 ~ 300 | 300 270 — — | — (265) 240 215 | (290) 260 — — | — — 230 210 | 285 255 225 205 |
Прочие механические свойства отливок из серого чугуна
Марка | Прочность на сжатие σbc / МПа | Прочность на сдвиг τb / МПа | Испытание на удар αKV / (Дж / см2) | Безопасный диапазон напряжений σ-1 / МПа | Модуль упругости Ε / ГПа |
HT150 | 500 ~ 700 | 150 ~ 250 | – | 60 ~ 90 | 70 ~ 90 |
HT200 | 600 ~ 800 | 200 ~ 300 | 2 ~ 5 | 80 ~ 90 | 80 ~ 110 |
HT250 | 800 ~ 1000 | 250 ~ 350 | 4 ~ 8 | 100 ~ 140 | 100 ~ 130 |
HT300 | 1000 ~ 1200 | 300 ~ 450 | 7 ~ 10 | 120 ~ 160 | 120 ~ 140 |
HT350 | 1100 ~ 1300 | 350 ~ 500 | 9 ~ 11 | 140 ~ 180 | 130 ~ 160 |
Твердость отливок из серого чугуна
Серый чугун марки | Класс твердости | Диапазон твердости HBS | Металлография |
HT100 | х 245 | ≤170 | Феррит |
HT150 | h275 | 150 ~ 200 | Феррит + Перлит |
HT200 | х295 | 170 ~ 220 | Перлит |
HT250 | h315 | 190 ~ 240 | Перлит |
HT300 | h335 | 210 ~ 260 | Перлит (модифицированный чугун) |
HT350 | h355 | 230 ~ 280 | Перлит (модифицированный чугун) |
Термическая обработка отливок из серого чугуна
Масса отливки кг | Начальная температура / οC | Скорость нагрева / (οC / ч) | Температура хранения / οC | Время сохранения тепла / ч | Скорость охлаждения / (οC / ч) | Конечная температура / οC | |
Чугун | Низколегированный чугун | ||||||
Простые отливки | |||||||
<200 | ≤200 | ≤100 | 500 ~ 550 | 550 ~ 570 | 4 ~ 6 | 30 | 200 |
200 ~ 2500 | ≤200 | ≤80 | 500 ~ 550 | 550 ~ 570 | 6 ~ 8 | 30 | 200 |
> 2500 | ≤200 | ≤60 | 500 ~ 550 | 550 ~ 570 | 8 | 30 | 200 |
Прецизионные отливки | |||||||
<200 | ≤200 | ≤100 | 500 ~ 550 | 550 ~ 570 | 4 ~ 6 | 20 | 200 |
200 ~ 2500 | ≤200 | ≤80 | 500 ~ 550 | 550 ~ 570 | 6 ~ 8 | 20 | 200 |
Отливка из серого чугуна, химический состав не упоминается ни в одном стандарте, поэтому мы предлагаем только следующий химический состав на основе фактического производства.
Марка | Толщина стенки / мм | С | Si | Mn | пол ≤ | S ≤ |
HT100 | – | 3,4 ~ 3,9 | 2,1 ~ 2,6 | 0,5 ~ 0,8 | 0,3 | 0,15 |
HT150 | <30 30 ~ 50 > 50 | 3,3 ~ 3,5 3,2 ~ 3,5 3,2 ~ 3,5 | 2,0 ~ 2,4 1.9 ~ 2,3 1,8 ~ 2,2 | 0,5 ~ 0,8 0,5 ~ 0,8 0,6 ~ 0,9 | 0,2 0,2 0,2 | 0,12 0,12 0,12 |
HT200 | <30 30 ~ 50 > 50 | 3,2 ~ 3,5 3,1 ~ 3,4 3,0 ~ 3,3 | 1,6 ~ 2,0 1,5 ~ 1,8 1,4 ~ 1,6 | 1,7 ~ 0,9 0,8 ~ 1,0 0,8 ~ 1,0 | 0,15 0,15 0,15 | 0,12 0,12 0,12 |
HT250 | <30 30 ~ 50 > 50 | 3.0 ~ 3,3 2,9 ~ 3,2 2,8 ~ 3,1 | 1,4 ~ 1,7 1,3 ~ 1,6 1,2 ~ 1,5 | 0,8 ~ 1,0 0,9 ~ 1,1 1,0 ~ 1,2 | 0,15 0,15 0,15 | 0,12 0,12 0,12 |
HT300 | <30 30 ~ 50 > 50 | 2,9 ~ 3,2 2,9 ~ 3,2 2,8 ~ 3,1 | 1,4 ~ 1,7 1,2 ~ 1,5 1,1 ~ 1,4 | 0,8 ~ 1,0 0,9 ~ 1,1 1,0 ~ 1,2 | 0,15 0,15 0,15 | 0.10 0,10 0,10 |
Серый чугун Сравнить
Индекс | Страна | Серый чугун марки | ||||||
1 | Китай | – | HT350 | HT300 | HT250 | HT200 | HT150 | HT100 |
2 | Японский | – | FC350 | FC300 | FC250 | FC200 | FC150 | FC100 |
3 | США | №60 | № 50 | № 45 | №35 / №40 | № 30 | № 25 | № 20 |
4 | Россия | СЧ40 | CЧ35 | CЧ30 | CЧ24 / CЧ25 | CЧ18 / CЧ20 / CЧ21 | CЧ15 | CЧ10 |
5 | Германия | GG40 | GG35 | GG30 | GG25 | GG20 | GG15 | GG10 |
6 | Италия | – | G35 | G30 | G25 | G20 | G15 | G10 |
7 | Франция | FGL400 | FGL350 | FGL300 | FGL250 | FGL200 | FGL150 | – |
8 | Англия | 400 | 350 | 300 | 260 | 180/220 | 150 | 100 |
9 | Польша | Z140 | Z135 | Z130 | Z125 | Z120 | Z115 | – |
10 | Индия | FG400 | FG350 | FG300 | FG260 | FG200 | FG150 | – |
11 | Румыния | FC400 | FC350 | FC300 | FC250 | FC200 | FC150 | – |
12 | Испанский | – | FG35 | FG30 | FG25 | FG20 | FG15 | – |
13 | Бельгия | FGG40 | FGG35 | FGG30 | FGG25 | FGG20 | FGG15 | FGG10 |
14 | Австралия | T400 | Т350 | Т300 | T260 | T220 | Т150 | – |
15 | Швеция | O140 | O135 | O130 | O125 | O120 | O115 | O110 |
16 | Венгрия | OV40 | OV35 | OV30 | OV25 | OV20 | OV15 | – |
17 | Болгария | – | Вч45 | Вч40 | Вч35 | Вч30 | Вч25 | – |
18 | ISO | – | 350 | 300 | 250 | 200 | 150 | 100 |
19 | КОПАНТ | FG400 | FG350 | FG300 | FG250 | FG200 | FG150 | FG100 |
20 | Тайвань (Китай) | – | – | FC300 | FC250 | FC200 | FC150 | FC100 |
21 | Голландия | – | GG35 | GG30 | GG25 | GG20 | GG15 | – |
22 | Люксембург | FGG40 | FGG35 | FGG30 | FGG25 | FGG20 | FGG15 | – |
23 | Австрия | – | GG35 | GG30 | GG25 | GG20 | GG15 | – |
24 | Europa-Norm | EN-GJL-350 | EN-GJL-300 | EN-GJL-250 | EN-GJL-200 | EN-GJL-150 |
Отливки из серого чугуна
Чугунные колеса были изготовлены методом литья в песчаные формы, они также называются направляющими роликами или гусеничными роликами для железных дорог, опорными колесами с фланцами, опорными роликами с фланцами, промышленными опорными колесами, стальными рельсовыми колесами.
Корпус шпинделя из ковкого чугуна
Корпус шпинделя для вала, штока или подшипника. Производство: литье в песчаные формы. Материал: литье из высокопрочного чугуна GGG40, GGG50, GGG60, GGG70, GGG80 Качество отливки Промышленная поставка Обработка с ЧПУ для отливок корпуса шпинделя в Китае. Просмотров: 279
Чугунные гильзы цилиндров
Метод литья: литье в песчаные формы или центробежное литье. Прецизионная обработка: токарная обработка и шлифование. Материал: серый чугун HT250; GG20; Гильза цилиндра FC25 — центральная рабочая часть Просмотров: 331
Запасные части для направляющих устройств и насосов
Процесс литья в песчаные формы с ЧПУ; Серый чугун (серый чугун), материал HT200 / GG20 / GG25; Фитинги направляющего устройства насоса со статическим балансом, с защитой от краски Просмотров: 70
Чугун Отливки рабочего колеса водяных насосов.Основным материалом является чугун GG20 / HT200 / HT300. Метод литья в песчаные формы с ЧПУ и статической балансировкой. Просмотров: 79
Фитинги из ковкого чугуна, материал ниппеля — ковкий чугун 300-6. Черная поверхность или горячая поверхность (белая). Литье в песчаные формы, горячее погружение с резьбой Механическая обработка. Стандарт: EN 10242, DIN 2950 Просмотров: 87
Просмотров: 1847
15 апреля 2019 г.,error: Alert: Спасибо за интерес, но статья защищена! Вы можете нажать на верхний правый адрес электронной почты!
Чугун — tec-science
Введение
До сих пор фазовая диаграмма железо-углерод рассматривалась только до содержания углерода 2.06%. Если это содержание углерода превышено, происходят дальнейшие фазовые превращения. В основном это тоже связано с другой микроструктурой. Железные материалы с содержанием углерода менее 2,06% состоят из микроструктуры на основе эвтектоидов (перлит , ) и более 2,06% микроструктуры на основе эвтектики (ледебурит).
В принципе, это также приводит к другим свойствам материала. Эта разница также отражается в подразделении на стали и чугун .Например, черные металлы с содержанием углерода ниже 2,06% называются сталью , а черные материалы с содержанием углерода более 2,06% — чугун .
Рисунок: Классификация сталей и чугуна на фазовой диаграмме железо-углеродСталь имеет микроструктуру на основе перлитной (эвтектоидной) основы, а чугун — микроструктуры на основе ледебурита (эвтектики)!
Эта статья предназначена для предоставления более подробной информации об этой новой микроструктуре чугуна.
Чугун
Фазовая диаграмма ниже показывает полную фазовую диаграмму железо-углерод метастабильной системы, в которой углерод присутствует в микроструктуре в форме цементита. Таким образом, микроструктура метастабильной системы может состоять максимум на 100% из цементита. Поскольку содержание углерода в цементите (\ (Fe_3C \)) составляет 6,67%, метастабильная фазовая диаграмма железо-углерод заканчивается на этой концентрации.
Рисунок: Полная диаграмма железо-углерод метастабильной системыЕсли только диапазон фазовой диаграммы выше, чем содержание углерода 2.06%, то становится очевидным принципиальное различие между сталями , и чугуном в процессе затвердевания.
При концентрации углерода менее 2,06% сталь первоначально затвердевала в виде твердого раствора (однородная микроструктура аустенита) в пределах типичного диапазона кристаллизации в форме линзы на диаграмме состояний.
В области чугуна, однако, фазовая диаграмма больше не показывает эту линзовидную область затвердевания, а показывает типичный горизонтальный «K» кристаллической смеси.Состав эвтектики составляет 4,3% углерода, где встречаются две линии ликвидуса, падающие слева и справа.
В зависимости от того, затвердевает ли соединение железо-углерод в виде твердого раствора (содержание углерода <2,06%) или в виде смеси кристаллов (содержание углерода> 2,06%), другие механические свойства материала также возникают при комнатной температуре. Сплавы, затвердевшие в виде кристаллической смеси, обычно более подходят для процессов литья (так называемые литейные сплавы). Однако по сравнению с этим затвердевший твердый раствор может быть сформирован намного лучше и поэтому особенно подходит для различных процессов формования, таких как гибка, ковка, прокатка, глубокая вытяжка и т. Д.(так называемые деформируемые сплавы).
По этим причинам производственной обработки выделяют соединения железа с углеродом с содержанием углерода ниже или выше 2,06%. Этот материал с содержанием углерода менее 2,06% называется сталью . С другой стороны, содержание углерода выше 2,06% означает чугун , так как он особенно подходит для процессов литья. В отличие от этого, стали могут обрабатываться намного лучше и, следовательно, поддаются ковке, в отличие от чугуна. Обратите внимание, что переходы в механических свойствах на уровне 2.Ограничение 06% всегда гладко!
Стали сначала кристаллизуются в виде твердых растворов, а чугун — в виде смесей кристаллов.
По сравнению со сталью, чугун имеет микроструктуру на основе эвтектики! Причина того, что сталь не образует эвтектики, в конечном итоге заключается в том, что сталь уже затвердела до того, как остаточный расплав мог достичь эвтектического состава. Так же, как стали можно разделить на доэвтектоидные и заэвтектоидные стали, чугун можно разделить на доэвтектоидные и заэвтектоидные стали соответственно.
В то время как стали обычно затвердевают в соответствии с метастабильной системой из-за относительно низкого содержания углерода, чугун может кристаллизоваться как в метастабильной форме (белый чугун , ), так и в стабильной форме (серый чугун ). Подавляющее большинство чугуна затвердевает в соответствии со стабильной системой из-за относительно высокого содержания углерода. Вместо осаждения цементита чугун затем подвергается осаждению графита во время затвердевания или охлаждения.
Выделение графита вместо цементита влияет на температуры превращения на фазовой диаграмме. Соответственно, необходимо различать стабильную и метастабильную фазовую диаграмму железо-углерод. На диаграмме ниже сравниваются метастабильная фазовая диаграмма (синяя) и стабильная фазовая диаграмма (дополненная красным).
Белый чугун
В белом чугуне чугун затвердевает в метастабильной форме и, таким образом, подвержен образованию цементита.Цементит заставляет поверхность излома чугуна казаться блестящей белой, к чему относится термин «белый» чугун.
В зависимости от содержания углерода белый чугун можно разделить на эвтектических чугун (4,3% C), доэвтектических чугун (<4,3% C) и заэвтектических чугун (> 4,3% C). Формирование и преобразование микроструктуры во время затвердевания и охлаждения таких типов чугуна более подробно объясняется ниже.
Эвтектический чугун
Если чугун имеет эвтектический состав 4,3% углерода, расплав обычно затвердевает при термической остановке. Из-за сильного переохлаждения образуется тонкая смесь аустенита и цементита. Эта эвтектическая микроструктура мелкодисперсного аустенита и цементита также называется ледебурит-I сразу после затвердевания.
Эвтектическая фазовая смесь аустенита и цементита сразу после затвердевания называется ледебурит-I!
Обратите внимание, что в левой части фазовой диаграммы чугуна (на 2.06%) применяется аустенитная фаза, а с правой стороны (6,67%) цементитная фаза. Эти фазы аустенит и цементит, таким образом, в конечном итоге являются компонентами системы сплавов A / B (A ≙ «аустенит») и (B «цементит»).
Сразу после затвердевания кристаллы аустенита, присутствующие в ледебурите, полностью насыщаются углеродом при 1147 ° C, т.е. они показывают максимально возможную концентрацию углерода, растворимого в аустените. Поскольку растворимость непрерывно уменьшается в соответствии с пределом растворимости (линия сольвуса) во время дальнейшего охлаждения, кристаллы аустенита постоянно осаждают цементит.
Наконец, при 723 ° C из аустенита выделяется столько углерода, что он достигает эвтектоидного состава 0,8% углерода. Теперь кристаллы аустенита в эвтектике ледебурита-I начинают превращаться в перлит при постоянной температуре. Таким образом, бывшие кристаллы аустенита превратились в перлит. Эта эвтектическая фазовая смесь перлита и цементита теперь называется ледебурит-II из-за измененной микроструктуры.
Эвтектическая фазовая смесь перлита и цементита, присутствующая при комнатной температуре, называется ледебурит-II!
Доэвтектический чугун
В случае доэвтектического чугуна при достижении линии ликвидуса из расплава выделяются только первичные кристаллы аустенита.Это увеличивает содержание углерода в остаточном расплаве. Как только содержание углерода наконец повысится до 4,3% при 1147 ° C, остаточный расплав кристаллизуется при постоянной температуре с образованием эвтектики (ледебурит-I). Сразу после затвердевания микроструктура состоит из эвтектики и ранее осажденных кристаллов аустенита.
Как первичный аустенит, так и кристаллы аустенита, содержащиеся в ледебурите-I, осаждают цементит по мере охлаждения из-за уменьшения растворимости углерода.Следовательно, микроструктура в этом состоянии состоит из ледебурита-I и включенного в него первичного аустенита, а также осажденного цементита. При 723 ° C окончательно достигается эвтектоидный состав кристаллов аустенита (как в первичных кристаллах, так и в эвтектике).
В то время как ледебурит-I превращается в ледебурит-II, первичные зерна аустенита превращаются в зерна перлита. Следовательно, микроструктура доэвтектического чугуна состоит из ледебурита-II с включенными в него перлитными зернами и цементитом, предварительно выделенным из кристаллов аустенита.
На микрофотографии ниже показан образец доэвтектического чугуна с 2,7% углерода. Видны твердые растворы \ (\ gamma \), которые изначально росли дендритно, а затем превратились в перлит (темные пятна). В качестве примера на рисунке показан дендрит, разрезанный микрофотографией в плоскости. Как правило, эта микроструктура перлита состоит из феррита и пластинчатого цементита. Между ветвями перлитных дендритов находится эвтектика, которая также подверглась превращению \ (\ gamma \) — \ (\ alpha \) — и, таким образом, наконец, присутствует в микроструктуре в виде лидебурита-II (темные пятнистые области).
Рисунок: Микрофотография доэвтектического чугуна с содержанием углерода 2,7%.Для сравнения, следующая микроструктура показывает доэвтектический чугун с более высоким содержанием углерода 3,8%. Обращает на себя внимание значительно большая доля эвтектической матрицы по сравнению с перлитом. В этом случае очень тонкий пластинчатый цементит больше не может быть растворен в перлите с помощью световой микроскопии — поэтому он выглядит темным как единая поверхность!
Рисунок: Микрофотография доэвтектического чугуна с содержанием углерода 3.85%.Заэвтектический чугун
В заэвтектическом чугуне только первичный цементит с полосообразной структурой сначала кристаллизуется во время затвердевания. Из-за связанного с этим осаждения углерода из остаточного расплава содержание углерода в нем снижается. Когда в остаточном расплаве наконец достигается эвтектический состав 4,3% углерода при 1147 ° C, он затвердевает до эвтектического ледебурита-I.
Сразу после затвердевания микроструктура состоит из первичного осажденного полосового цементита, который внедряется в окружающий ледебурит-I.Аустенит, содержащийся в эвтектике, наконец, подвергается осаждению цементита при понижении температуры. Если содержание углерода в аустените упало до 0,8% при 723 ° C, он начинает превращаться в перлит. Таким образом, эвтектический ледебурит-I становится ледебурит-II.
Таким образом, микроструктура охлажденного заэвтектического чугуна состоит при комнатной температуре из преимущественно осажденных полос цементита, которые залегают в эвтектике ледебурита-II.
На микрофотографии ниже показан заэвтектический чугун с 5.5% углерода. Эвтектический ледебурит-II (с мелким рисунком) и преимущественно осажденные иглы цементита, которые из-за травления во время изготовления образца выглядят как белые удлиненные полосы.
Рисунок: Микрофотография заэвтектического чугуна с содержанием углерода 5,5%Серый чугун
Чугун с пластинчатым графитом (серый чугун)
Без какой-либо серьезной обработки расплава графит обычно кристаллизуется в пластинчатой форме. Это известно как отливка из пластинчатого графита .Так как это «нормальный» тип чугуна, он просто обозначается как серый чугун .
На микрофотографии ниже показан серый чугун с 3,5% углерода. Виден пластинчатый графит (темные большие области), окруженный микроструктурой на основе перлита (темные мелкие полосы).
Рисунок: Микроструктура чугуна с пластинчатым графитом (серый чугун)Чугун с пластинчатым графитом обладает отличными литейными свойствами и поэтому предлагает широкий спектр применений.Кроме того, отливка из пластинчатого графита показывает очень хорошую обрабатываемость, поскольку графит также служит твердой смазкой. Кроме того, графитовые пластинки в литой конструкции обладают особым эффектом гашения колебаний. Вот почему отливка из пластинчатого графита используется, среди прочего, в качестве материала для компонентов, подверженных высоким вибрационным нагрузкам, таких как станины машин или судовые дизельные двигатели.
Однако графитовые пластинки оказывают неблагоприятное влияние на предел прочности на разрыв, поскольку они действуют как выемки («заданные точки разрыва») в структуре отливки.Поэтому отливки из пластинчатого графита следует подвергать не растяжению, а давлению. Прочность на сжатие составляет ок. В 4 раза выше прочности на разрыв!
Однако во многих случаях литейный материал должен выдерживать высокие растягивающие нагрузки. Поскольку пластинки графита, очевидно, оказывают мешающее воздействие, осаждение пластинчатого графита необходимо специально предотвращать во время процесса затвердевания или охлаждения. Альтернативой литью из пластинчатого графита является литье из шаровидного графита, как описано ниже.
Чугун с шаровидным графитом (чугун с шаровидным графитом)
Чтобы графит в сером чугуне выпадал в осадок не в виде пластинок, а сферически, расплав перед затвердеванием необходимо специально обработать такими добавками, как алюминий. Осадок графита в сферической форме тогда называется чугун с шаровидным графитом или чугун с шаровидным графитом .
На микрофотографии ниже показана микроструктура чугуна с шаровидным графитом с 3.6% углерода. Можно увидеть сферически осажденный графит (темные, округлые области), который сократился от непосредственно прилегающих областей. Окружающие участки состоят из почти безуглеродного железа (феррита), поэтому оно кажется белым.
Рисунок: Микроструктура чугуна с шаровидным графитом (чугун с шаровидным графитом, высокопрочный чугун)Эффект выемки шаровидного графита значительно снижен за счет округлой формы по сравнению с пластинчатым графитом. Следовательно, прочность на растяжение чугуна с шаровидным графитом значительно лучше.Поскольку чугун с шаровидным графитом более пластичен, чем «нормальный» серый чугун, этот тип чугуна также называют чугун с шаровидным графитом .
Чугун с вермикулярным графитом (чугун с компактным графитом)
Чугун с вермикулярным графитом предлагает (также называемый чугун с компактным графитом ) компромисс по свойствам между чугуном с пластинчатым и шаровидным графитом. Графит осаждается как червяк, в результате чего сферический графит также может в определенной степени образовываться в микроструктуре.
На микрофотографии (к сожалению, еще нет!) Показан чугун с вермикулярным графитом. Виден графит (черный), который осаждается как червяк, часть которого все еще осаждается в сферической форме. Углерод был удален с окружающих участков, которые выглядели белыми (феррит).
Отливка из вермикулярного графита благодаря своей хорошей термостойкости особенно подходит для изготовления двигателей.
Чугун с чешуйчатым графитом (ковкий чугун)
В так называемом чугуне с чешуйчатым графитом (или ковком чугуне ) углерод образует отдельные чешуйки графита.Чтобы получить эту хлопьевидную микроструктуру, на предварительной стадии ковкий чугун сначала затвердевает без графита. Таким образом, микроструктура этого так называемого белого чугуна содержит только цементит вместо графита. Только после последующей термообработки, отжига , метастабильный цементит распадается на свою окончательную форму чешуйчатого графита и затем относится к группе серого чугуна.
На микрофотографии ниже показан ковкий чугун с 2.7% углерода. Виден графит, осажденный хлопьями (черные области). Вокруг чешуек часто образуются участки, не содержащие углерода (феррит), поэтому они выглядят белыми. Там углерод из решетки скопился в чешуйчатую структуру.
Рисунок: Микроструктура чугуна с чешуйчатым графитом (ковкого чугуна)Преимущество ковкого чугуна заключается в его хорошей литейной способности и аналогичных свойствам стали, таких как хорошая ударная вязкость и прочность. Ковкий чугун используется для изготовления тонкостенных деталей, тормозных барабанов, арматуры и т. Д.
Процесс, состав, различия и преимущества.
Чугун по существу представляет собой сплав железа с углеродом. Процент углерода в чугуне превышает 2%. В зависимости от требований к литью в чугун могут быть добавлены другие важные элементы, такие как кремний, марганец, сера, фосфор и т. Д., Которые заметно изменяют структуру и свойства получаемого сплава.
Отливка из высокопрочного чугуна — это процесс, в котором магний / церий (как сплав магния / церия) добавляют в чугун.Он вступает в реакцию с серой и кислородом в расплавленном чугуне и изменяет способ образования графита. Ковкий чугун (также называемый чугун с шаровидным графитом или чугун с шаровидным графитом) широко используется в качестве основного промышленного материала вместо высококачественного чугуна. В то время как большинство разновидностей чугуна сравнительно хрупкие, отливки из высокопрочного чугуна гораздо более пластичны из-за включения графита с шаровидным графитом. Затвердевшие отливки из высокопрочного чугуна содержат почти идеальные сферы графита. Благодаря добавлению к графиту незначительного процента магния или церия, высокопрочный чугун имеет меньше неоднородностей в структуре сплава.Ковкий чугун — процесс
Базовый чугун, используемый для высокопрочного чугуна, обычно имеет высокое значение углеродного эквивалента. В жидкое железо добавлено около 0,04% магния. Поскольку магний кипит при относительно низкой температуре, происходит бурная реакция из-за высокого давления пара магния при температуре обработки. Это вызывает сильное взбалтывание жидкого железа. Значительное количество магния также теряется в виде пара. При этом в железе также образуются оксиды и сульфиды, что приводит к образованию окалины на поверхности металла.Перед разливкой чугуна необходимо как можно полнее удалить окалину. Также уместно отметить, что после обработки остаточный магний в жидком чугуне непрерывно окисляется на поверхности металла, вызывая потерю магния, которая может повлиять на сфероиды графита. Поэтому важно выбирать производителя чугуна с шаровидным графитом, заботящегося о качестве, чтобы сохранить его свойства. Как только процесс добавления магния завершен должным образом, чугун инокулируют и разливают.Затем графит осаждается в виде сфероидов. При литье высокопрочного чугуна очень важно не допускать попадания примесей. Кислород и сера реагируют с магнием, влияя на сфероидальную форму молекул. Существуют различные стандарты ASTM / DIN и другие международные стандарты для литья высокопрочного чугуна. Эти различные сорта получают путем манипулирования микрокристаллической структурой вокруг сфероида графита.
Состав отливок из высокопрочного чугуна
Литой или серый чугун — это сплав, характеризующийся относительно высоким содержанием углеродных чешуек (от 2% до 4%).Напротив, углерод в высокопрочном чугуне имеет форму сферических узелков. Формирование таких конкреций достигается добавлением в расплав отливок «нодулизаторов», таких как магний или церий. Благодаря присущим им свойствам, такие конкреции препятствуют образованию трещин и увеличивают пластичность. Именно поэтому этот процесс называется литьем из высокопрочного чугуна. В литом состоянии матрица будет состоять из различных пропорций перлита и феррита, и по мере увеличения количества перлита прочность и твердость железа также увеличиваются.Пластичность и ударные свойства в основном определяются соотношением феррита и перлита в матрице.
Механические свойства высокопрочного чугуна контролируются наличием графитовых включений. Отливки из высокопрочного чугуна различных марок производятся путем получения в чугуне различной микроструктуры матрицы. Для улучшения литейных свойств высокопрочного чугуна могут быть добавлены легирующие элементы. В некоторых особых случаях для достижения различных свойств может применяться термическая обработка.Марки отливок из высокопрочного чугуна основаны на механических свойствах отливки.
Различия в литье ковкого и серого чугуна
Есть два важных различия в характеристиках литья серого и ковкого чугуна. В отличие от серого чугуна высокопрочный чугун представляет собой сплав, образующий окалину. Остаточный магний, необходимый для образования шаровидного графита, быстро окисляется всякий раз, когда жидкий металл подвергается воздействию воздуха. Если не соблюдать осторожность, образуется окалина силиката магния, которая может вызвать дефекты на поверхности отливки или чуть ниже, обычно на верхних поверхностях отливок.Поэтому обычная практика — фильтровать кожухи из ковкого чугуна через керамические фильтры. Второе отличие от серого чугуна — это необходимость подачи отливок из высокопрочного чугуна для обеспечения минимальных усадочных дефектов. Ковкий чугун всегда имеет высокий углеродный эквивалент, поэтому объем затвердевания осажденного графита должен обеспечивать полностью прочное сечение. Только самые прочные формы (например, формы на связке из силиката натрия или формы с потерянной пеной) выдерживают давление, возникающее в результате осаждения графита.
Преимущества высокопрочного чугуна
- Ковкий чугун, поскольку он ковкий, повышает безопасность и надежность технологического оборудования. Улучшенные механические свойства ковкого чугуна также делают его устойчивым к коррозии. В общем, чугун с шаровидным графитом по многим свойствам превосходит или не уступает чугуну и даже стальному литью. Стоимость чугуна примерно на 30-35% ниже, чем стального литья. Он также имеет лучшую износостойкость и гашение вибрации по сравнению с литой сталью.Кроме того, из-за более высокой концентрации свободного углерода и более высокого содержания кремния графитовый чугун (серый и ковкий) имеет наибольшую текучесть и наименьшую усадку по сравнению с любым черным металлом.
- Для производства высококачественного высокопрочного чугуна необходимы опыт и развитая инфраструктура. Очень немногие компании в Индии обладают такой инфраструктурой. Qualitas Exports — один из таких производителей высокопрочного чугуна и механически обработанных компонентов.
- По оценкам, производство ковкого чугуна составляет от 35 до 40% всех отливок из чугуна в таких странах, как США, Индия, Германия, Великобритания, Франция, Китай и т. Д.
- Ковкий чугун находит применение в коленчатых валах, тормозных суппортах, ступицах, телах, водопроводных трубах, фитингах и других деталях, где требуется гибкость.
Модель из чугуна | FLOW-3D CAST
Одной из основных проблем инженера-литейщика является чрезмерная усадочная пористость, которая может образоваться во время затвердевания. Большинство объемных изменений в чугунах происходит во время охлаждения жидкого сплава от температуры разливки до состояния солидуса и, что более важно, во время эвтектического затвердевания, когда образуются гамма-железо, графит и карбид.Размещение стояков (или стояков ) обеспечивает дополнительный металл для подпитки усадки. Оптимальный подступенок важен для получения отливок хорошего качества при минимальных затратах. Степень усадки также можно контролировать путем правильного легирования и охлаждения металла. Модель чугуна FLOW-3D CAST учитывает все эти факторы для прогнозирования образования пористости и развития фаз во время эвтектического затвердевания.
Обзор модели чугуна
Чугун — это почти эвтектический чугун, легированный углеродом и кремнием.Углерод обычно присутствует в диапазоне от 2,5 до 4,5 мас.%, А кремний в диапазоне от 1 до 3 мас.%. Кремний добавляется для стабилизации графита и уменьшения склонности к «охлаждению» (т.е. образованию карбидного железа). Другие элементы и соединения присутствуют в следовых количествах и обычно либо контролируют форму графита (например, магний в ковком чугуне), действуют как дополнительные раскислители (например, фосфор), либо служат модификаторами графита (например, ферросилиция).
FLOW-3D CAST модель чугуна учитывает объемные изменения, происходящие от температуры разливки до солидуса: усадка при охлаждении в жидком состоянии; дальнейшая усадка при образовании доэвтектического гамма-железа; последующая усадка или расширение во время эвтектической реакции; и вторичная усадка от окончания эвтектической реакции до солидуса.Поскольку чугун обычно содержит фазы, отличные от железа, которые могут влиять на образование карбида, эвристический допуск — в форме параметра восприимчивости к охлаждению — сделан для влияния этих фаз на плотность затвердевшего металла.
Скрытое тепловыделение в модели кристаллизации чугуна рассчитывается как функция температуры (так называемый путь замерзания), определенной из фазовой диаграммы Fe-C [1], с использованием концентрации углерода и кремния в начальное плавление.Модель может использоваться вместе с общей моделью затвердевания с потоком или без него. Однако изменения объема, связанные с образованием различных фаз, связаны только с упрощенной моделью усадки, которая не включает поток.
Эффект движения стенки кристаллизатора во время расширения чугуна в данной модели не учитывается. Любое увеличение объема нетто, которое не может быть покрыто доступным пространством в форме, игнорируется.
В области эвтектики скорость эвтектического фронта используется для вычисления локальной тенденции к охлаждению и, следовательно, местного количества карбида, поэтому возможно моделирование зон охлаждения возле стенок формы.Не предпринимается никаких попыток отслеживать дальнейшие переходы эвтектических фаз во время твердотельного эвтектоидного превращения, то есть окончательная микроструктура в литом состоянии не прогнозируется.
Для гиперэвтектических чугунов предполагается, что только графит образуется на начальной доэвтектической стадии затвердевания, как в серых чугунах и чугунах с шаровидным графитом. Другими словами, модель не включает затвердевание гиперэвтектического белого чугуна во время доэвтектической стадии, на которой в основном образуется карбид.
Чугунный путь замораживания
Чугунный путь замораживания выполнен из эвтектического сплава. Его можно охарактеризовать температурой ликвидуса, температурой эвтектики, твердыми фракциями начала и конца эвтектики и температурой солидуса. Все, кроме двух последних величин, вычисляются из равновесной тройной фазовой диаграммы Fe-C-Si [1].
Растворимость углерода в гамма-фазе зависит от содержания Si в мас.% Согласно:
(1) $ latex \ displaystyle {{C} _ {{\ gamma, mx}}} = 2.07-0.098Si, $
, что близко соответствует растворимости, сообщенной Стефанеску [2]. Температура ликвидуса сплава в градусах Цельсия следует из гипоэвтектической плоскости ликвидуса:
(2) $ latex \ displaystyle {{T} _ {i}} = 1636-113 \ left ({C + 0,25 Si} \ right) $
или плоскость гиперэвтектического ликвидуса [2]:
(3) $ latex \ displaystyle {{T} _ {i}} = — 505,8 + 389,1 \ left ({C + 0,31 Si} \ right), $
, а эвтектические составы и температуры даны пересечением этих плоскостей:
(4) $ latex \ displaystyle {{C} _ {e}} = 4.26-0,296Si, $ $ latex \ displaystyle {{T} _ {e}} = 1154,6 + 5.2Si $
Начало эвтектической реакции — это производная величина, определяемая правилом рычага:
(5) $ latex \ displaystyle {{f} _ {e}} = \ frac {{c — {{c} _ {\ varepsilon}}}} {{{{c} _ {{\ gamma, mx}}} — {{c } _ {\ varepsilon}}}}. $
Измерения в [3] показывают, что это приближение подходит для ряда чугунов.
Конец реакции графитовой эвтектики, f ee и солидус T s , оставлены как определяемые пользователем величины.Если учесть положительную сегрегацию фосфора в жидкости, фактическая температура солидуса ниже температуры графитовой эвтектики и составляет всего 1100 ° C. В этом случае предполагается, что осаждение графита завершается до окончания замораживания, и что последняя фракция замораживаемого металла, 1- f ee , имеет плотность ρ ei , отличную от плотность эвтектики.
Изменения плотности
Обычно перегрев в чугунных отливках велик, и усадка во время охлаждения значительна еще до того, как начнется затвердевание.Температурная зависимость плотности жидкого железа моделируется либо в линейной форме:
(6) $ latex \ displaystyle \ rho \ left (T \ right) = {{\ rho} _ {0}} \ left [{1 — \ alpha \ left ({T — {{T} _ {0}}} \ right)} \ right] $
или путем определения функции ρ (T) в табличной форме.
Находясь в диапазоне замерзания, гамма-железо образуется до тех пор, пока не будет достигнута твердая фракция f e . Плотность этой фазы ϒ составляет 7,2 г / см 3 [4,5,6].При достижении твердой фракции f e начинается эвтектическая реакция, во время которой регулярная (белая) эвтектика и нерегулярная серая эвтектика конкурируют друг с другом. При высоких скоростях замерзания и высоких скоростях фронта эвтектики замерзания белая эвтектика стабильна отчасти из-за более мелких градиентов концентрации углерода перед фронтом эвтектики. При более низких скоростях эвтектического фронта серая эвтектика устойчива.
Для учета образования холода используется простой подход. В диапазоне скоростей фронта эвтектического замерзания
(7) $ latex \ displaystyle {{\ nu} _ {e}} \ in \ left [{\ frac {{\ nu -}} {{{{X} _ {{eut}}}}}, \ frac {{\ nu +}} {{{{X} _ {{eut}}}}} \ right] $
количество образовавшегося холода варьируется от нуля до максимально допустимый для данного состава углерода.Параметры ν- = 30 мк / мс и ν + = 60 мк / мс и X eut — это критерий восприимчивости к холоду, параметр, определяемый пользователем, со значениями в диапазоне от 0,0 до 1.0 со значением по умолчанию один. Для хорошо модифицированного железа или для серой эвтектики с высокой удельной поверхностью X eut близко к нулю, и холода не образуется. С другой стороны, если в утюг нет прививки, значение по умолчанию, равное единице, должно быть более подходящим.Фактическое значение X eut должно быть определено экспериментальным путем, например, с помощью теста с охлаждающим клином ASTM (рис. 1.).
Обрабатываемость чугуна | Современное литье
Саймон Н. Леках и фон Л. Ричардс, Миссурийский университет науки и технологий, Ролла, штат Миссури
(Нажмите здесь, чтобы увидеть историю в январском выпуске Modern Casting.)
Существуют различные способы улучшения обрабатываемости отливок.Влияние естественного старения на обрабатываемость чугуна различается в зависимости от его легирующих элементов, которыми являются нитридообразующие (титан), карбидообразующие (хром) и модификаторы подвижности азота (марганец). Взаимосвязь между старением чугуна и обрабатываемостью отливок была подтверждена в ходе многочисленных лабораторных и промышленных испытаний в отношении таких параметров, как сила резания, износ инструмента, качество поверхности и точность размеров. Недавнее подтверждающее испытание подтвердило оптимальное время старения для определенного состава с целью улучшения обрабатываемости серого чугуна.
Чугун Естественное старениеПонимание того, как старение влияет на обрабатываемость, позволяет производителям планировать оптимальное окно для обработки. Явление старения при комнатной температуре было задокументировано для различных типов черных сплавов, включая чугуны и стали. В сером чугуне прочность на разрыв увеличилась на 5-15% после 5-30 дней старения при комнатной температуре.
Исследования старения закаленных сплавов на основе железа показали трехступенчатый процесс осаждения.В некоторых случаях падение прочности наблюдается в начале процесса старения. Кинетика старения при повышенных температурах в чугуне выявила типичные кривые старения, полученные при различных температурах (рис. 1). График Аррениуса был построен с использованием констант скорости в зависимости от величины, обратной абсолютной температуре (рис. 2).
Влияние легирующих элементовХотя старение при повышенной температуре в меньшей степени зависит от состава сплава, химический состав чугуна сильно влияет на кинетику старения при комнатной температуре.С практической точки зрения важно влияние изменений содержания марганца и серы на скорость старения чугуна. При исследовании чугуна с содержанием марганца 0,8–0,83% старение было завершено через 25 дней, в то время как для этого процесса потребовалось всего 15 дней для чугуна с 0,51% марганца при аналогичных уровнях серы 0,04–0,06%.
Для изучения влияния легирующих элементов была оценена кинетика старения чугунов после шести плавок с вариациями содержания марганца, азота и серы. Кривые изменения силы обычно имели пик перед усилением и «долину релаксации» до достижения полного возрастного усиления.
Легирование марганцем влияет как на время предварительного упрочнения, так и на пик полного упрочнения. Чугун из плавки с 0,53% марганца имел самую высокую скорость реакции. Каждое железо с более низким содержанием марганца и особенно с более высоким содержанием марганца имело более длительное время реакции старения.
Влияние элементов, образующих карбид / нитридЕстественное возрастное упрочнение чугуна происходит в Fe-BCC (феррите) путем осаждения нитрида железа. Карбидообразующие элементы, такие как хром, способствуют уменьшению содержания свободного феррита в чугуне и уменьшают общий возможный эффект упрочнения.Изделие для испытаний на обрабатываемость в отливке, изготовленное из чугуна с 0,2% хрома, не показало улучшения обрабатываемости после старения.
Элементы, образующие нитриды, такие как титан, алюминий и бор, могут полностью подавить упрочнение выделений нитрида железа. Азот, доступный при затвердевании с образованием метастабильного твердого раствора в феррите, влияет на упрочнение чугуна при старении. Низкорастворимый азот, оставшийся после образования нитрида титана, не позволяет производить заметное упрочнение чугуна старению.Температурный диапазон перенасыщения феррита составляет от комнатной температуры до 572F (300 ° C), и за пределами этого диапазона возможность старения ограничена в соответствии с термодинамикой.
Обрабатываемость состаренного чугунаУсилие режущего инструмента: Предметы для испытаний на обрабатываемость, рекомендованные Американским литейным обществом, использовались для торцевых разрезов на токарном станке с числовым программным управлением (ЧПУ). Эти образцы для испытаний были изготовлены в лаборатории с использованием форм без обжига и на промышленных предприятиях по литью металлов с использованием форм из сырого песка.Чугуны из перлита / феррита с вариациями углеродного эквивалента от 3,9% до 4,3% были испытаны в литом состоянии и после 25 дней естественного старения. В литом состоянии или в необработанном состоянии силы резания увеличиваются с увеличением твердости в чугунах с меньшим углеродным эквивалентом, что является типичным и ожидаемым. В то же время появился обратный тип зависимости, при котором сила резания уменьшалась, когда повышение твердости происходило только за счет естественного старения каждого утюга.
Такое необычное поведение можно объяснить потребностью в энергии для формирования стружки.В чугуне без старения мягкий феррит поглощает энергию, вызывая значительную пластическую деформацию. Этот эффект приводит к нарастанию кромок на режущей кромке инструмента, что также может способствовать увеличению силы резания за счет увеличения области деформации (аналогично износу инструмента). Напротив, когда старение железа происходит в результате выделения Fe4N в феррите, это увеличивает прочность и твердость железа и позволяет образовывать стружку с меньшей степенью пластической деформации, что может снизить силу резания.
Аналогичные результаты были достигнуты в других чугунах с ферритом в металлической матрице и другой формой графита.Например, старение снижает силы резания после старения высокопрочного чугуна со сферическим графитом и значительным содержанием свободного феррита.
Однако старение не всегда улучшает обрабатываемость чугуна. Например, стареющий чугун, содержащий карбидообразующие элементы, оказывал полностью противоположное влияние на обрабатываемость отливки. Наблюдалось видимое и статистически значимое увеличение средних нормальных сил резания для старых образцов по сравнению с несозревшими образцами. Отношение пассивной силы резания к нормальной используется в качестве показателя износа инструмента, потому что по мере того, как инструмент теряет остроту, он имеет увеличивающуюся пассивную силу реакции.Это соотношение увеличивается более значительно при резке состаренного серого чугуна с содержанием карбид-промотирующих элементов. Микроструктура в этом случае была перлитной с небольшим количеством стеадита и свободного карбида, но без свободного феррита.
Чтобы проверить влияние микроструктуры на обрабатываемость чугуна, отливки из той же плавки подвергались дальнейшим испытаниям после термообработки ферритизации / разделения. Эта обработка превратила перлит в феррит и дала разрешающий эффект, что позволило повторить естественное старение.Наблюдаемый эффект был противоположен ранее обсуждавшемуся испытанию чугуна с перлитной матрицей и стеадитной фазой в том, что старение ферритированного / разрешенного серого чугуна улучшило обрабатываемость. Силы резания были уменьшены на всех исследованных скоростях резания (рис. 3). Из этих испытаний можно сделать вывод, что весь серый чугун, демонстрирующий улучшенную обрабатываемость в состаренном состоянии, содержал некоторое количество свободного феррита, в то время как серый чугун, демонстрирующий повышенные силы резания после старения, не имел свободного феррита, но был полностью перлитным с фазами цементита / стеадита.
Это различное поведение состаренных чугунов в зависимости от металлической матрицы связано с энергией стружкообразования. Хотя серый чугун является хрупким материалом при растяжении, стружка может подвергаться значительной пластической деформации, поскольку в напряженном состоянии во время обработки преобладают сжатие и сдвиг. Если предполагается, что образование стружки связано с пластической деформацией до разрушения, то изменения вязкости разрушения логически повлияют на поведение при механической обработке. Работа разрушения при испытании на растяжение оценивалась по кривой «напряжение-смещение».В перлитном чугуне работа разрушения и силы резания увеличиваются после старения.
Напротив, железо, ферритированное термической обработкой, показало уменьшение работы разрушения и сил резания из-за старения.
Измерения износа инструмента и промышленной обработкиИзнос инструмента ниже при обработке серого чугуна, состаренного при комнатной температуре, поскольку состаренный чугун требует меньших затрат труда от обрабатывающего центра для образования и дробления стружки. Уменьшение требуемой работы было продемонстрировано измерениями усилия инструмента и испытанием силы тока, потребляемой при обработке незаряженного и состаренного железа.Наименьшая мощность потребовалась для обработки отливок, выдержанных в течение 3-6 дней, по сравнению с чугуном, выдержанным на 1, 9 и 20 дней. При этом оптимальном времени старения обработанные отливки имели лучшее качество поверхности (меньшую шероховатость), но весь состаренный чугун имел лучшую чистоту поверхности, чем чугун без старения.
Другие испытания проводились с промышленной обработкой торцевых поверхностей тормозных дисков легкового автомобиля. Чрезмерный износ инструмента привел к изменению геометрии инструмента и увеличению сил резания, что способствовало упругой деформации отливки с увеличением наклона и нарушением требуемого допуска на перпендикулярность («наклон»).Данные о наклоне обработки промышленных отливок сравнивались двумя способами. Для обработки 50 отливок без старения потребовалось два изменения положения инструмента. Изменения положения инструмента не требовалось во время обработки состаренных отливок после 50 или 200 отливок, что указывает на более стабильные размеры и сокращение времени простоя для корректировки положения инструмента. На рисунке 5 показано сравнение измеренного износа инструмента для различных операций. Старение значительно снизило износ инструмента на большинстве операций.
Промышленная рекомендация по улучшению обрабатываемости чугуна путем старения
Существуют три возможных сценария изменения обрабатываемости серого чугуна во время естественного старения (Таблица 1).
Первый сценарий: старение не происходит и, следовательно, не влияет на обрабатываемость. Отсутствие эффектов старения в чугуне может быть вызвано повышенным содержанием нитридообразующих элементов (особенно титана) по сравнению с азотом. Возможно добавление азота к железу, которое может ускорить старение. Термодинамические данные могут быть применены, чтобы определить, достаточно ли «свободного азота» для старения чугуна. Упрощенный критерий может быть таким: если% N <(0,15-0,20)% Ti, старение не произойдет.
Второй сценарий: если чугун проявляет старение, это явление можно использовать для улучшения обрабатываемости отливки.Старение сопровождается уменьшением сил резания и износа инструмента. В этих утюжках достаточно свободного азота, чтобы способствовать старению.
Пониженные силы резания и улучшенные механические свойства были подтверждены на лабораторных отливках, содержащих различные углеродные эквиваленты. В этих чугунах было немного свободного феррита и не было свободного цементита или стеадита. Оптимальное время старения зависит от конкретного содержания «свободного марганца» и может быть оценено. Уменьшение времени старения для улучшения обрабатываемости может быть достигнуто за счет теплого (слегка повышенная температура) старения.
Третий сценарий: Серый чугун имеет повышенные концентрации карбидообразующих элементов, таких как хром, в дополнение к большому процентному содержанию фосфора. Эти химические комбинации с определенной скоростью охлаждения могут способствовать образованию стеадита / цементита в полностью перлитной матрице. Если в этом чугуне будет пренебрежимо мало свободного феррита, старение увеличит силы резания в этом чугуне. Эффективная модификация и химический контроль повлияют на взаимодействие обрабатываемости отливки со старением в этих чугунах.Однако в этом случае «свежие» отливки могут оказаться более поддающимися обработке.
Подтверждающий тестПять AFS 5J, 10 дюймов Образцы для испытаний диаметра разливали в формы для выпечки от одной 200 фунтов. индукционная печь тепла. Химический состав чугуна показан в таблице 2. Микроструктура была в основном перлитной с содержанием феррита примерно 5-10%. Измеренная твердость в средней части исследуемого изделия составляла 200-210HB в литом состоянии (без старения). Поверхностный слой после литья (1/8 дюйма.) был удален при предварительной механической обработке, чтобы избежать влияния структуры поверхности литья, взаимодействия кристаллизатора с металлом и отклонения геометрии на результаты испытаний. Испытуемые изделия подвергали торцевой обработке с ЧПУ в день 0, день 5, день 9, день 15 и день 22 с измерением сил резания.
Восемь резов (общее время обработки 30 мин) выполнялись с каждого диска, каждый раз с использованием новой инструментальной вставки. Толщина исследуемого изделия давала восемь повторяющихся надрезов, и каждое испытание повторялось дважды. Результаты испытаний представлены на рис.7.
Результаты этих тестов сравнивались с прогнозами в соответствии с предложенной методологией.
Шаг 1 — Оценка возможного возрастного усиления: Nfree = N-0,20Ti = 0,01-0. 2 * 0,008 = 0,0084 мас.% Или 84 частей на миллион; общее% N и% Ti позволяет ожидать приблизительно 0,14 мас. % Fe4N. Произойдет возрастное укрепление.
Этап 2 — Контрольная микроструктура: в матрице без свободного карбида / стеадита, имеющей небольшое количество свободного феррита вокруг чешуйчатого графита, упрочнение старением может улучшить обрабатываемость отливки в соответствии со вторым сценарием (таблица 1).
Шаг 3 — Время старения: Время полного старения составляет 15-17 дней, а время предварительного упрочнения — 7-9 дней. Усилие инструмента значительно упало в течение первых пяти дней и также было низким через 15 дней, что примерно соответствует ожидаемому времени для упрочнения при старении при комнатной температуре.
Прогнозы, основанные на предыдущих исследованиях, подтвердились. Значительное уменьшение силы резания и стандартные отклонения наблюдались через 9-15 дней естественного старения, что находится между прогнозируемым временем предварительного упрочнения и временем полного старения.Что касается других параметров обрабатываемости, износ инструмента зависит не только от среднего значения силы резания, но и от стабильности процесса резания, причем износ инструмента продолжал снижаться до полного времени старения.
Эти правила могут помочь в определении оптимального окна обрабатываемости для состаренного чугуна:
- Оценить свободный азот на основе общего азота и концентрации титана как% N> 0,2% Ti, но недостаточно высокий, чтобы образовалась газовая пористость для повышения прочности при старении.