Сварка в мостостроении: материалы, оборудование
Прокладывая не одну сотню тысяч километров дорог различного назначения, строители постоянно сталкивались с проблемой возведения долговечных металлических сооружений, позволяющих организовать надежный проезд различного транспорта через водные преграды и другие сложные участки рельефа. Применение для строительства мостов клепочной технологии не давало возможности обеспечить достаточно высокие прочностные параметры конструкции на протяжении длительной эксплуатации. Ведь под периодическим воздействием повышенных механических нагрузок клепаное соединение начинало постепенно терять свою несущую способность.
1 / 1
Применение сварки в мостостроении
Для решения такой проблемы строители непрерывно искали технологию, позволяющую как можно эффективнее и за короткий срок осуществлять работы по ремонту и усилению мостовых пролетов.
Дуговая сварка в мостостроении дала возможность успешно справляться с такими задачами. Однако, проведение сварочных операций при осуществлении ремонтно-восстановительных мероприятий как на крупных мостах, так и небольших мостовых сооружениях имеет существенное отличие от процессов сварки, применяемых при строительстве разнообразных зданий. Во-первых, это связано со сложной структурой пролетных металлоконструкций. Практически все ее составляющие отличаются многообразием форм и размеров. К тому же несущее сооружение многократно подвергается периодическому (циклическому) воздействию механических нагрузок, создаваемых проезжающими железнодорожными составами либо грузовым автотранспортом.
Эффективно решить проблему возведения надежных и долговечных мостов позволило открытие электрической дуги, послужившей своеобразным толчком к разработке технологии электродуговой сварки. Этим способом начали соединять металлические детали за счет сплавления их в месте соединения с помощью дуги электрического разряда. Для проведения электродугового сварочного процесса в качестве электродов используют соединяемые стальные заготовки и специальный токопроводящий проводник. Длительный электрический разряд, создаваемый между ними в особой газообразной среде, способен создавать высокотемпературный режим. Его мощности хватает даже для расплавления металла, у которых температура плавления более 3000°C.
Первоначально сварка металлических мостов производилась с применением угольных электродов. Однако для обеспечения надежности и долговечности сварного шва нужно было использовать более прогрессивные материалы. Оптимальным решением стало применение металлических электродов с флюсовым покрытием. Использование такого токопроводящего сварочного проводника позволило сразу решить две задачи. Стальной стержень выступает в роли присадочного материала для заполнения разделки в свариваемом соединении, а своеобразная флюсовая «оболочка» предоставляет возможность создавать гарантированную защиту расплавленного металла от воздействия азота и кислорода из окружающего воздуха.
Применение электродуговой сварки позволило полностью исключить технологии соединения элементов моста с помощью заклепок. Такой способ возведения несущих стальных конструкций позволил обеспечить им достаточно высокие параметры устойчивости как к статическим, так и к динамическим механическим нагрузкам на протяжении многих десятилетий. И даже при возникновении усталостных трещин в путепроводном сооружении можно очень быстро и с минимальными затратами устранить такой дефект с помощью ремонта участка электродуговой сваркой.
Мост любого назначения – это весьма ответственная конструкция. Следовательно, при его возведении требуется использовать лишь самые прогрессивные материалы и технологии.
Применение электродуговой сварки дает возможность обеспечить выполнение всех обязательных требований к металлической конструкции. Существенную роль в проведении качественного процесса сварки играет правильный подбор сварочных материалов. Именно за счет этого можно гарантировать получение сварного шва с необходимыми эксплуатационными характеристиками.
Какие материалы используются для сварки мостовых конструкций
Для возведения мостов различного назначения в основном используют низко- и среднелегированные марки стальных сплавов. Применение таких металлов дает возможность производить наиболее ответственные металлоконструкции. К их разряду специалисты относят и сооружения, возводимые для движения разнообразного транспорта через преграды на пути строительства транспортного пути.
Применение сварки в строительстве мостов и путепроводов позволяет возводить надежные и долговечные конструкции, способные гарантированно выдерживать периодические повышенные динамические нагрузки, создаваемые проезжающими разнообразными транспортными средствами.
Для обеспечения высоких прочностных характеристик в возводимых несущих сооружениях нужно правильно подбирать сварочный процесс и материалы.
Стандартно в мостостроении применяется электродуговая механизированная сварка в защитной газообразной среде, либо автоматическая сварка под слоем флюса.
Мы предлагаем использовать для строительства мостовых конструкций аппараты двух видов:
-
Сварочные установки для механизированной сварки с жесткой вольт-амперной характерисстикой. В них мы рекомендуем использовать проволоку порошковую газозащитную проволоку.
-
Аппараты автоматической сварки под флюсом, на которых напряжение на дуге регулируется автоматически (падающая вольтамперная характеристика). В зависимости от этого показателя изменяется и скорость подачи сварочной проволоки.
При выполнении работ по ремонту либо усилению пролетных сооружений мостов применяют сварочное оборудование ручной электродуговой сварки. В этом случае для получения надежного соединения стальных конструкций мы рекомендуем использовать электроды марки УОНИ-13/55. Они способны обеспечить свариваемому шву достаточно высокую ударную вязкость и прочность. За счет минимального содержания к водородав наплавленном металле, конструкции обладают прекрасной устойчивостью к возникновению трещин и знакопеременным нагрузкам.
В связи с этим, такие электроды традиционно применяют для возведения ответственных металлоконструкций, эксплуатируемых в северных широтах.
Сварка в мостостроении | Сварак
Мостовые конструкции (особенно пролетные строения железнодорожных мостов) работают в наиболее тяжелых условиях. На них воздействуют значительные переменные и динамические нагрузки, а также низкие температуры окружающей среды. В то же время мосты являются весьма ответственными сооружениями, в которых не допускается образование каких-либо трещин в процессе их эксплуатации. Как сторонникам, так и противникам сварки было совершенно очевидно, что успешное применение сварки в мостостроении позволит широко применять ее и в других металлоконструкциях.
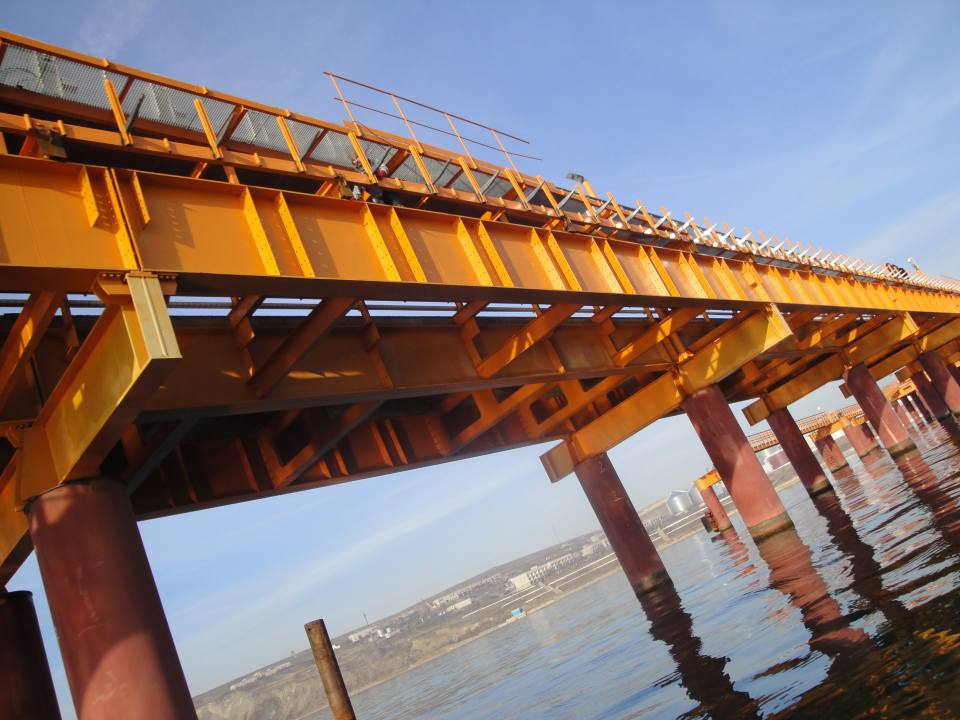

В результате первых исследований, выполненных Е. О. Патоном и его сот-рудниками, было установлено, что «стыки без накладок, неосуществимые в клепаных конструкциях, являются большим преимуществом электросварки».
- Учитывая, что временное сопротивление металла шва, наплавляемого электродами с меловой обмазкой, на 25—30% ниже, чем у стали Ст. 3, стыки узких листов рекомендовалось выполнять с помощью косых швов, а в совмещенных стыках балок двутаврового сечения — ставить стыковые накладки только в растянутом поясе.
- При этом был установлен наиболее рациональный порядок сварки [50, 101, 102].
- Экспериментальная проверка различных способов прикрепления продольных балок к поперечным показала, что при статическом и ударном нагружениях сварные прикрепления намного прочнее клепаных.
В разработанных рациональных способах сопряжений балок, на их соединение требовалось только 6— 13% массы дополнительных деталей клепаных прикреплений [50, 100].Одновременно были установлены рациональные виды сварных стержней, составленных из двух уголков [107], исследованы различные способы соединений между ветвями сжатых стержней [110], созданы мостовые опорные части в сварном исполнении [103], изучены влияние длины фланговых швов на пх прочность [108],совместная работа фланговых и лобовых швов [109], исследована возможность усиления старых клепаных пролетных строений с помощью сварки [106, 114, 124].
Многие экспериментальные исследования выполнялись путем сопоставления результатов испытаний балок и целых конструкций при статическом, ударном, а в ряде случаев п вибрационном нагружении. По сравнению с испытанием моделей или отдельных сварных швов это позволяло получить более надежные и убедительные результаты, которые сразу же использовали на практике [50].
Для усталостных испытаний была создана специальная вибрационная машина [19]. С помощью этой машины в 1931 г. были проведены первые в нашей стране сравнительные усталостные испытания двух пролетных строений мостов длиной по 12 м — одного клепаного, а другого цельносварного [19,104]. Расчетной нагрузкой для обоих мостов служила фиктивная ось в 10 т. Клепаные п сварные соединения были запроектированы равнопрочными.
Сварное пролетное строение выдержало до образования первого усталостного разрушения 215 тыс. циклов перемен напряжений, а клепаное — 40 тыс. и только после его ремонта 180 тыс. Динамические характеристики сварного моста оставались постоянными в течение всего периода испытаний. Разрушение произошло не по металлу шва, а по основному металлу в зоне соединения. Клепаные прикрепления раскосов и стоек разрушались от усталости по заклепочным отверстиям. В 1933 г. были проведены исследования по сопоставлению вибропрочности сварных и клепаных соединений и узлов [112].
На основании проведенных исследований в 1933 г. были сформулированы «Принципы проектирования сварных мостов» [111] и составлен «Альбом электросварных конструкций мостов»
[ИЗ]. Авторы этих документов указывали: «эти принципы касаются следующих вопросов: 1) метода изготовления на заводе, сварки и монтажа сварных мостов; 2) типа сечений элементов; 3) типа сварных швов; 4) конструкции узловых и стыковых соединений; 5) расположения и конструкций монтажных стыков; 6) строительного подъема; 7) допускаемых напряжений». Следует отметить, что в этих «Принципах» обсуждался вопрос о целесообразности применения стыковых швов с учетом того, что при повторных нагрузках они работают лучше, чем фланговые. Допускаемые напряжения рекомендовалось принимать такими же, что и в строительных металлических конструкциях, поскольку динамическое воздействие нагрузок учитывается высоким динамическим коэффициентом, а действительная нагрузка всегда меньше расчетной.
Проведенные исследования и разработанные «Принципы» способствовали дальнейшему развитию работ по изучению несущей способности сварных конструкций и более обоснованному их проектированию.
В этот же период в ЦИС НКПС под руководством Г. А. Николаева были проведены большие работы по испытанию сварных соединений и узлов [77, 78], изучению распределения напряжений в лобовых швах [80], усилению сваркой старых мостов [81—83], испытанию статической и вибрационной нагрузкой сварного двенадцатиметрового пролетного строения [79], изучению сварных соединений, подвергающихся воздействию динамических нагрузок [89], исследованию влияния сварки на основной металл [90], опытному про-ектированию сварных пролетных строений мостов [84, 88], составлению первых в отечественной практике технических условий на проектирование пролетных строений железнодорожных мостов [85].
- Первые мосты с применением электродуговой сварки были изготовлены во Владивостоке, где под руководством В. П. Вологдина еще в
- начале 20-х годов начали внедрять дуговую сварку в промышленность.
- Под его руководством летом 1928 г. на Эгершельде четыре сварщика за 25 дней построили сварной мост пролетом 25,8 м.
- По-видимому, это был первый сварной мост в Европе.
- В 1929 г. построен второй мост пролетом 25,04 м, а в 1931 г. сварена мостовая ферма, элементы коробчатого сечения которой были составлены из двух уголков [23].
Первый железнодорожный мост с цельносварными сквозными фермами пролетом 12 м с ездой поверху был построен в 1932 г. на Калининской железной дороге по проекту ЦИС НКПС. Конструкция пролетного строения полностью повторяла клепаную [38, 79]. Сварку выполняли электродами с меловой обмазкой. Это пролетное строение успешно эксплуатировалось 12 лет; оно было заменено в 1944 г. пролетным строением большей грузоподъемности, причем каких-либо дефектов в сварных соединениях выявлено не было.
В 1932 г. по проекту Укргипродора на заводе «Азовсталь» была построена с участием Киевского отделения Украинского автогенного треста сварная железнодорожная эстакада [52, 86].
Первые сварные железнодорожные мосты в нашей стране были построены примерно в тот же период, что и за рубежом. В Польше первое сварное пролетное строение было установлено 8имой 1928—1929 гг. на одном из железнодорожных мостов около г. Ло- вича. В Германии первый железнодорожный мост пролетом 10 м (со сплошностенчатыми фермами) был сдан’ в эксплуатацию в начале 1930 г. [24]. Несколько раньше сварные мосты были построен в США.
К 1934 г. в нашей стране, помимо упомянутых, было построено еще три сварных моста: два железнодорожных со сплошностенчатыми фермами, пролеты которых составляли 20 и 23 м, и пятипролетный автодорожный, также со сплошными фермами. 2X14 75+20+ +2X14, 75 м [38, 86].
Более широкое применение сварки в железнодорожных мостах со сквозными главными фермами относится к 1935— 1936 гг. На ЛИНИИ Уфа — Ишпмбаево в 1935 г. было установлено цельносварное пролетное строение со сквозными фермами пролетом 45 м [86, 87]. Проект выполнялся под руководством Г. А. Николаева в ЦИС НКПС. В то время это было самое крупное сварное пролетное строение. До его сооружения наибольшим по пролету (42 м) сварным железнодорожным мостом считался мост через водопад Чикопэ, сооруженный в США около Бостона.
Построенное сварное пролетное строение запроектировано идентично типовому клепаному под нагрузку Н7. Все элементы изготавливали из стали Ст. 3, сварку выполняли электродами с меловой обмазкой. Согласно специальным техническим условиям допускаемые напряжения на основной металл составляли 130 МПа, а на металл сварных соединений (допускались только валиковые швы)—80 МПа для заводской сварки и 72 МПа для швов, выполняемых на монтаже. Сварка встык не допускалась. Все стыки перекрывали накладками. Нахлесточпые прикрепления раскосов, стоек и подвесок, помимо валиковых швов, имели дополнительные прорезные швы. Основные сварочные работы выполняли на заводе в сравнительно теплое время, трещины в процессе сварки появлялись крайне редко. Монтажные работы пришлось выполнять зимой прп низких температурах (до —35° С). В процессе монтажа пролетного строения были обнаружены трещины в некоторых заводских швах, а также в основном металле поперечных балок и второстепенных элементов. Поперечные балки были заменены, а в других элементах трещины перекрыли накладками.
Созданию этого моста предшествовали большие исследовательские работы, выполненные под руководством Г. А. Николаева в ЦИС НКПС, вклю чая испытания моделей наиболее от-ветственных элементов и соединений [88—90]. Построенное пролетное строение подвергалось тщательным статическим и динамическим испытаниям. На основании заключения ЦИС НКПС мост был допущен к нормальной эксплуатации. Полагали, что это «явится сдвигом в консервативном отношении к применению сварки в мостостроении» [86].
Это пролетное строение нормально эксплуатировалось длительное время. Однако в изготовленных вслед за ним по проекту Гипротранса НКПС четырех пролетных строениях, имевших ту же схему, но несколько иную конструкцию, были обнаружены трещины в основном металле и в швах уже при приемке этих мостов в эксплуатацию. В отличие от предыдущего моста, все элементы которого были выполнены из листового проката, в главных фермах этих четырех пролетных строений применили прокатные швеллера. Они были изготовлены из импортной томасовской стали, которая, как оказалось впоследствии, не отвечала необходимым требованиям, отчего и образовались трещины [38]. В дальнейшем процесс образования трещин продолжался, поэтому все четыре пролетных строения к на-чалу 50-х годов были заменены клепаными.
Рис. 12.1. Поперечное сечение главной балки моста лейтенанта Шмидта в Ленинграде
Рис. 12.2. Монтажный стык главной балки моста лейтенанта Шмидта
Позднее установили, что из-за применения для сварных мостов сталей, не отвечающих определенным требованиям, в том числе и хладостойкости, во многих случаях образовывались трещины, а иногда имели место и аварии. В частности, широкое использование томасовской стали А-37 для изготовления автодорожных мостов в Бельгии (вплоть до 1939 г.) и недостаточно высокое качество сварочных работ вызвали образование большого числа трещин в 50 сварных пролетных строениях. После катастрофического разрушения одного из них (пролетом 74,5 м, установленного на мосту через канал Альберта у г. Хассельта) все эти пролетные строения были заменены новыми.
Дальнейшее развитие сварного мостостроения связано с переходом на сварку швов толстообмазанными электродами и под флюсом. Поскольку прочность таких швов практически равна прочности основного металла, стыки без накладок постепенно стали основным видом соединения ответственных элементов пролетных строений. Переход к стыковым соединениям не только менял конструктивное оформление отдельных узлов, но заметно повлиял и на выбор систем цельносварных мостов. Стало возможным использовать листовой прокат любой ширины и большой толщины. Поэтому наиболее целесообразными стали балочные мосты со сплошностенчатыми неразрез
ными фермами малой высоты (1/20— 1/16 пролета) или же комбинированные системы с жесткими балками. Однако переход к стыковым швам не был легким. В подтверждение этому рассмотрим в качестве примера сварку монтажных стыков автодорожиого моста им. лейтенанта Шмидта — выдающегося сварного сооружения довоенного времени.
В 1936—1938 гг. мост реконструировали по проекту Г. П. Передери я [123]. Взамен устаревших пролетных строений с чугунными арками установили два неразрезных трехпролетпых строения со сплошностенчатыми балками коробчатого сечения (рис. 12.1) общей длиной по 123 м (расчетные пролеты 35,2+41,3+44,8 м). Между ними в разводном пролете разместили два крыла, главные балки которых имели двутавровое сечение. При ширине моста 24 м в поперечном сечении имеются только две главные балки, между которыми располагается клетка из поперечных и продольных балок для поддержания монолитной железобетонной плиты. Сечения главных балок с постоянной высотой 2200 мм изменяются по длине моста только за счет увеличения толщины горизонтальных листов и добавления на отдельных участках узких полос (по две на каж-дый пояс). Толщина одиночных поясных листов доходит до 50 мм, а пакета из двух листов — до 88 мм. Поперечные и продольные балки двутаврового сечения имеют высоту соответственно
Продольные и поперечные балки были целиком выполнены в заводских цехах. В процессе их сварки серьезных трудностей не встречалось. Главные балки были изготовлены в виде монтажных блоков длиной по 9—10 м. Перед погрузкой на понтоны монтажные блоки укрупняли в плети длиной примерно по 40 м. Их собирали и сваривали на специальных подмостях, что позволило иэ 48 монтажных стыков 40 выполнить на заводе.
- Монтажные стыки главных балок (рис. 12.2) сваривали качественными электродами ТК, разработанными и изготовленными Кировским заводом.
- Сварку выполняли в зимнее время, при этом в ряде случаев швы разрушались.
- Первоначально сварку вели в такой последовательности: на половину сечения заполняли стыки поясов, затем сваривали стык наружной стенки, в послед-нюю очередь — стык внутренней стенки. Во время сварки последний шов лопнул на всю длину.
Его переварили заново, после чего приступили к доварке поясных швов, при этом пояса выпучились (см. рис. 12.2). Такие же явления происходили и на других первых стыках. Сварку прекратили и возобновили только после дополнительных исследований, выполненных с участием Н. О. Окербло- ма. Был установлен иной порядок сварки стыка с предварительным отгибом стыкуемых листов [123]. При новой технологии почти все стыки успешно заваривали с первого раза. По окон-чании сварки поверхность швов обработали пневматическим зубилом. Мост успешно эксплуатируется и в настоящее время.
В 30-х годах были построены и некоторые другие автодорожные и железнодорожные мосты [38], существенно отличающиеся от клепаных. Здесь следует отметить железнодорожный мост со сварным двухшарнирным арочным пролетным строением с ездой поверху пролетом 140 м (рис. 12.3). Это оригинальное пролетное строение, не имевшее себе равных в то время в мировой практике, было изготовлено в 1939—1940 гг. по проекту В. А. Росновского. Для поясов сквозных арок применяли металлические трубы диаметром 820 мм, заполненные бетоном. Трубы изготавливали из листового металла путем его вальцовки и сварки продольным стыковым швом.
Раскосы и стойки имеют двутавровое сечение. В процессе эксплуатации в ряде сварных узлов, которые имели конструктивные недостатки, поя вились трещины.
После усиления таких узлов пролетное строение продолжает находиться в эксплуатации и работает нормально [132].
К началу Великой Отечественной войны в нашей стране было построено около 20 сварных мостов. Кроме того, в конце 30-х годов мостовым заводом НКПС было изготовлено для железнодорожных мостов 20 цельносварных пролетных строений с ездой поверху со сплошностенчатыми двутавровыми главными балками пролетом 23 м. Они бы-
ли использованы в годы Великой Отечественной войны для восстановления
мостов. Общая масса всех сварных летных строений составляла около 5000 т, из них примерно 2000 т относились к пролетным строениям железнодорожных мостов.
Не все сварные мосты оказались удачными. В ряде пролетных строений возникали трещины как в процессе их изготовления, так и во время эксплуатации. Все сварные мосты выполнялись из обычной низкоуглеродистой стали, которую применяли и для клепаных мостов. Конструктивные формы сварных мостов мало чем отличались от клепаных. Однако на изготовление сварных мостов требовалось металла на 15— 20% (а иногда и на 25%) меньше, чем на клепаные. Были исключены трудоемкие операции по пробивке и рассвер-ловке многочисленных отверстий; уменьшился объем внутрицеховых транспортных операций по доставке металла; существенно увеличился фронт производства работ. В результате значительно уменьшилась общая трудоемкость изготовления мостов, особенно пролетных строений со сплошными балками [24].
Вместе с тем неизбежные неудачи начального периода породили у ряда ведущих специалистов предубеждение и недоверие к сварным мостам. Уже тогда высказывались опасения в отношении возможности обеспечения требуемого сопротивления усталости сварных мостов, особенно железнодорожных, подвергающихся значительному воздействию переменных напряжений. Только в последние предвоенные годы это недоверие начало интенсивно рассеиваться [24]. В зарубежных странах, особенно в Германии, в этот период развивается сварное мостостроение. Несмотря на серьезные повреждения трещинами пролетных строений автодорожных мостов Рюдерсдорф—Кальк- берге (1936 г. ) и Кайзерберг (1936 г.), а также железнодорожного путепровода Зообрюкке (1937 г.), в Германии с 1932 по 1941 г. было построено 800 сварных автодорожных мостов и 300 железнодорожных [24].
В нормах для железнодорожпых мостов большое внимание уделено учету влияния усталости. Допускаемые напряжения на основной металл предписывалось принимать в зависимости от вида сварного соединения п характеристики переменного нагружения.
Минимальные допускаемые напряжения были установлены для соединений с фланговыми и лобовыми швами. При механической обработке зоны перехода к сварным швам допускаемые напряжения на основной металл заметно повышались.
Довоенный опыт проектирования и изготовления сварных мостов, накопленный как в нашей стране, так и за рубежом, подробно обобщен в книге Б. Н. Горбунова [24]. Однако действовавшие в то время нормы, разработан-ные для железнодорожных мостов, не использовали новые результаты испытаний сварных соединений и ориентировались только на качество сварки, обусловленное применением электродов с меловой обмазкой. В этих нормах были приведены допускаемые напряжения только на срез швов. Все стыки листов рекомендовалось перекрывать наклад-ками, а швы рассчитывать по площади сечения прикрепляемых элементов [24].
Безусловно, качество сварки, зависящее от ее технологии, во многом предопределяло несущую способность мостовых конструкций. Важно было повысить производительность сварочных работ, особенно на заводе. В те годы были высказаны различные предложения по по-вышению производительности сварки — сварка наклонным и лежачим электродом, применение электродов повышенного диаметра, увеличение плотности тока и др. Однако радикально решить многие вопросы (как это понимали в ИЭС еще на заре развития сварного мостостроения) можно было только на основе механизации и автоматизации процесса сварки [105]. Большие исследования, выполненные институтом, позволили решить эту важнейшую техническую задачу в короткое время. Авто- технология сварки которой в то время матическую сварку под флюсом разра- не была отработана надлежащим обработали в 1939 г. , что впоследствии по- зом. Во многих случаях электроды изго- зволило применять ее и в сварном товляли из телеграфной проволоки и мостостроении. других некондиционных материалов.
В 1940 г. рассматривался проект но- Качество сварки почти не контролиро- вого автодорожного моста через Днепр вали. Все это отрицательно отразилось в Киеве.
ИЭС предложил для разработки 25 тем, связанных с применением сварки в мостостроении, согласовал их с Министерством путей сообщения и в короткие сроки выполнил свои обязательства [116]. В течение 1946—1947 гг. Министерству путей сообщений были переданы законченные результаты исследований по 15 темам; исследования по остальным 10 темам были завершены в 1948 г.
Среди этих работ необходимо отметить создание стали для сварных мостов [2, 41, 116, 119]. Клепаные мосты изготавливали из стали Ст. 3 мостовая (ОСТ 12535—38). Исследования, проведенные в Институте электросварки в 1946— 1947 гг., показали, что эта сталь кипя-щей выплавки не пригодна для сварных мостов ввиду склонности ее к старению и строчечного расположения в ней сульфидных включений.
Было установлено, что содержание в стали углерода не должно превышать 0,20%, а кремния — 0,25%. Сталь не должна иметь скоплений серы в виде сульфидных строчек, способствующих образованию трещин в процессе сварки. Эти условия необходимы для исключения образования трещин в швах в процессе сварки. Сталь для сварных мостов должна быть малочувствительна к надрезам при низких температурах. Исключить сульфидные строчки и повысить хладостойкость можно при использовании спокойной, а не кипящей стали.
Институт электросварки разработал основные положения технических условий на такую сталь и добился выплавки ее для изготовления опытного сварного пролетного строения (L= 77 м). Вначале эту сталь именовали Ст. 3 для сварных мостов и выплавляли по МПТУ 2321—49, затем ее назвали сталью М16С
(ГОСТ 6713—53). Теперь она имеет марку 16Д (ГОСТ 6713-75).
В этот же период были изменены химсостав и технология изготовления флюса АН-3, организован промышленный выпуск улучшенного флюса АН-348,, установлен состав электродной проволоки Св-08ГА с повышенным содержанием марганца (ГОСТ 178—48, затем ГОСТ 2246—51), разработаны режимы автоматической сварки для всех швов, применяемых в мостостроении, создана аппаратура для автоматической сварки под флюсом [56, 62, 93, 94, 97, 98, 116 и др. ].
Интересны работы по установлению зависимости между механическими свойствами металла шва и скоростью его остывания при сварке [95]. На основании этих исследований были даны практические рекомендации по сварке стали большой толщины. Одновременно разрабатывали технологию автоматической сварки отечественной низколегированной стали CXJI-2, применение которой в мостостроении позволяло дополнительно экономить металл [116].
Таким образом, в первые послевоенные годы для сварного мостостроения была создана надежная база, на основе которой оно могло быстро развиваться.
В то время в ИЭС разрабатывались многие темы по прочности и конструированию сварных мостов [116]. При этом исследовали влияние остаточных напряжений на несущую способность сварных элементов; решали, нужно ли подвергать сварные элементы мостов термической обработке; устанавливали предельно допустимую толщину листов для сварных мостов. Под руководством и при непосредственном участии Б. О. Патона вели работы по изысканию оптимальных форм цельносварных пролетных строений. В результате были созданы новые типы пролетных строений из крупных плоскостных или пространственных блоков, которые целиком собирают и сваривают па заводе и в готовом виде на железнодорожных
платформах доставляют к месту строп- Многие важные вопросы были выясне- тельства [116]. Были разработаны не- ны. Но это конечно не значит, как несколько эскизных проектов сварных однократно подчеркивал тогда Е. О. Па- пролетных строений. Позднее на основе тон, что надо ждать, пока будут решены одного из них было запроектировано все вопросы, связанные с применением опытное цельносварное пролетное сварки в мостостроении, и только после строение L = 66 м. этого приступать к постройке сварных
Впервые в практике мостостроения при монтаже этих пролетных строений применили автоматическую сварку. Каждый монтажный стык сваривали в следующем порядке: сперва сварочным трактором ТС-17М выполнялся стыковой шов нижнего пояса; затем, после подгонки вставки, аппаратом А-384 с принудительным формированием заваривали вертикальные стыки; в последнюю очередь сварочным трактором сваривали стыковые швы горизонтальной вставки верхнего пояса. Угловые швы между поясами и стенкой выполняли вручную. Качество всех швов было высокое. Из 1399 м монтажных швов в пролетном строении, выполняемом по проекту, 704 м сварены автоматами. Три мон-тажных стыка в балке жесткости и стыки «рыбок» верхних поясов продольных балок проезжей части пролетного строения, выполненного по проекту НИИ мостов, также выполнены автоматической сваркой.
Пролетные строения испытывали па статическую, выбрацпонную и динамическую нагрузки летом и зимой [154]. Оба пролетные строения успешно выдержали все испытания и нормально эксплуатируются под обращающимися поездными нагрузками по настоящее время.
В сентябре 1952 г. были успешно завершены работы по сооружению опытного цельносварного автодорожного моста через северную протоку Немана [143]. Проект разработан Киевским филиалом Союздорпроекта ГУшосдор при участии ИЭС. Монтажные элементы моста изготовлены Днепропетровским заводом им. Бабушкина. Сварку на монтаже осуществляла бригада ИЭС. Мост длиной 377 м имеет десять пролетов, пять из них перекрывает неразрезное балочное пролетное строение со сварны-ми монтажными соединениями, а остальные — перекрыты таким же сварным строением, но с клепаными монтажными стыками. Сплошностенчатые главные балки двутаврового сечения во всех пролетах имеют высоту стенки 1,8 м. Ширина нижних поясов 500 и 330 мм при толщине 30 и 20 мм. Верхние (благодаря включению в работу железобетонной плиты) имеют сечение 330X12 мм. По условиям транспортировки главные балки разделены на монтажные элементы небольшой длины (8,5 и 10,3 м), что увеличило число монтажных стыков в каждом пролетном строении до 72.
Сопоставление трудоемкости монтажных работ пролетных строений со сварными и клепаными монтажными соединениями показало, что на клепку узлов было затрачено 203, а на сварку — 225 чел.-дней. Таким образом, трудоемкость монтажной сварки не намного превышает трудоемкость клепки. Однако общая трудоемкость основных мон-тажных работ по цельносварному и сварному пролетному строению с клепаными стыками составили соответственно 840 и 630 чел.-дней. Сборка цельносварного пролетного строения — более трудоемкая операция, чем клепано-сварного, проходившего контрольную сборку на заводе. Были и другие причины, повысившие трудоемкость монтажа цельносварного строения [143].
Рис. 12.6. Цельносварное комбинированное пролетное строение системы НИИ мостов а — верхние продольные связи; б — портал; в — главные фермы; г — поперечные связи в пролете; д — нижние продольные связи; е — проезжая часть и тормозные связи
Рис. 12.7. Цельносварное комбинированное пролетное строение системы ИЭС АН УССР а — верхние продольные связи; б — главные фермы; в — поперечники; г — проезжая часть; д — нижние продольные связи
Рис. 12.9. Общий вид цельносварного моста имени Б. О. Патона
Значительные работы в этот же период были выполнены по созданию железнодорожных сварных мостов. В 1947 г. (институтом «Проектсталькон- струкция» для железнодорожных мостов были разработаны две серии стандартных клепано-сварных пролетных строений с ездой понизу пролетами от 33 до 110 м.
В 1949 —1950 гг. начали выпускать продукцию Кременчугский и Воронежский мостовые заводы. С 1950 г. Кременчугский мостовой завод при научно-технической помощи Института электросварки и НИИ мостов начал изготавливать серию цельноперевози- мых сварных пролетных строений железнодорожных мостов со сплошностенчатыми главными балками пролетом 23 и 33,6 м. При их изготовлении применяли плоскостной метод образования отдельных частей конструкции. Листовые заготовки собирали и сваривали встык автоматом на флюсовой подушке, образуя полотнища стенок и поясных листов на полную длину балок. Из этих полотнищ собирали балки двутаврового сечения и сваривали в полу- поворотном кондукторе с наложением угловых швов «в лодочку», напроход, также автоматом. Затем устанавливали и приваривали полуавтоматом ребра жесткости к стенке балки поочередно с двух сторон и фасонки связей к поясам; ручной сваркой приваривали уплотня-ющие прокладки между поясами и торцами вертикальных ребер жесткости.
После этого балки устанавливали вертикально и объединяли попарно в блоки с постановкой продольных и поперечных связей, привариваемых внахлестку к фасонкам связей ручной электродуговой сваркой. В последующем (1952—1953 гг.) конструкцию пролетных строений со сплошностенчатыми балками несколько изменили. Фасонки продольных связей стали присоединять не к поясам, а к стенкам балок в зонах с пониженным уровнем напряжений. Фасонки в растянутой зоне стенок прикрепляли вначале при помощи сварки, затем заклепками, а наминая с 70-х годов — высокопрочными болтами. Пролетные строения длппои до 45 м стали выполнять одноярусными.
В 1951—1952 гг. большую работу по проектированию цельносварных и клепано-сварных пролетных строении проделал проектный институт «Лентранс- мостпроект». В тесном сотрудничестве с Институтом электросварки, НИИ мостов и мостостроительными заводами этот институт разработал ряд индивидуальных и типовых проектов, по которым уже к 1953 г. было изготовлено свыше 12 ООО т сварных и клепано-сварных железнодорожных пролетных строений.
Значительную помощь в организации изготовления и монтажа сварных пролетных строений оказал мостостроительным заводам и строительным организациям Главмостострой МПС, большая роль в этом принадлежала Н. А. Холину.
На вновь построенных Кременчугском и Воронежском заводах Главмостостроя МПС и на заводах Минтяжстроя только за период с 1949 по 1953 г. было изготовлено 169 железнодорожных сварных пролетных строений общей массой 7700 т и свыше 15 тыс. ост», Украинский филиал Союздорпроекта при участии Института электросварки, НИИ мостов, ЦНИИС.
Так, за 7—8 лет, прошедших после выхода в 1946 г. постановления правительства о внедрении автоматической сварки в мостостроение, была проделана огромная работа. В результате была доказана возможность изготовления качественных железнодорожных и автодорожных сварных мостов.
При этом была достигнута значительная экономия металла и снижена трудоемкость изготовления пролетных строений. Только по одному Днепропетровскому.
В 1955—1956 гг. по проекту Гипро- трансмоста при участии Института электросварки Кременчугский мостовой завод изготовил из стали М16С металлоконструкции неразрезного цельносварного пролетного строения пролетом (72,6+108+72,6 м) с двутавровыми главными балками переменной высоты. Ново-Арбатский, ныне Калининский мост в Москве (рис. 12.11) сооружал в 1957—1958 гг. Мостотрест. Автоматическую сварку на монтаже выполняла бригада ИЭС им. Патона. В пролетном строении этого моста железобетонная плита проезжей части включена в совместную работу с балками. При этом следует отметить, что осуществить такое решение в сварных мостах значительно проще, чем в клепаных. Поэтому уже первые послевоенные автодорожные мосты (через северную протоку Немана, Днестр и др.) являются стале- железобетоннымп. Развитию сталежелезобетонных. мостов способствовали исследования, проведенные ЦНИИС [140].
К числу сталежелезобетонных мостов относятся: мост с балками коробчатого сечения из низколегированной стали марки 10ХСНД через канал им. Москвы в г. Химки (проект разработал Гип- ротрансмост) и мост через Сейм в Пу- тивле (проект ГПИ «Укрпроектсталь- конструкция»). В сплошностенчатых главных балках последнего моста высотой 2000 мм (1/30 пролета) благодаря применению предварительного папря-
Рис. 12.11. Общий вид Калининского моста через р. Москва в процессе строительства
жения удалось добиться рекордно малого расхода стали—всего 150 кг/м2 вместо 220 кг/м2 в типовых пролетных строениях.
Применение сварки оказалось весьма эффективным в пролетных строениях комбинированной системы со сталеже-лезобетонными балками жесткости, уси-ленными гибкими подпружными арками (например, мост через Старый Днепр в Запорожье пролетом 196 м), а также в комбинированных строениях висячей системы (русловая часть Паркового моста через Днепр в Киеве, построенного в 1957 г.).
Вместе с тем хотя в сталежелезобетонных пролетных строениях значительно снижается расход металла, масса плиты все же заметно увеличивает постоянную нагрузку. Использование сварки в автодорожных мостах позволило в дальнейшем разработать более
рациональные решения: сначала железо-бетонную плиту заменили металлической ребристой (такое решение было принято в начале 60-х годов при строительстве четырех городских мостов), а затем стали применять ортотропные плиты. (Например, мосты через реки Катунь и Арпу.) Однако более совершенные конструкции пролетных строений с ортотропными плитами появились в нашей стране позднее.
В конце 50-х годов ряд специалистов- мостовиков продолжал сомневаться в надежности цельносварных пролетных строений железнодорожных мостов. По рекомендации мостовой комиссии НТС МПС в 1958—1959 гг. НИИ мостов было проведено испытание многократно-повторной нагрузкой двух опытных моделей, имитирующих пролетные строения стержневой системы пролетом 66 м, изготовленных в половину натуральной величины, одной — клепаной, а ДРУ» гой — цельносварной. Они были изготов-лены соответственно из стали марки Ст. 3 мостовая и марки М16С (ГОСТ 6713—53). Обе модели выдержали примерно одинаковое число циклов нагружения (около 500 000) при изменении напряжений от 18,5 до 118,5 МПа [125]. Клепаная модель разрушилась по нижнему поясу фермы в районе узлового прикрепления по первому ряду заклепок, а сварная —по стыковому соединению растянутого раскоса с верхней узловой фасонкой крайней панели фермы. Характерно, что при испытании сварной модели первыми начали отделяться от фасонок приваренные к ним внахлестку нижние горизонтальные связи, выдержав только 100 000 циклов нагружения. В остальном цельносварная модель. не уступала по долговечности клепаной модели.
В те же годы по проекту Ленгииро- трансмоста под техническим руководством НИИ мостов было построено из стали М16С еще одно цельносварное железнодорожное пролетное строение пролетом 66 м стержневой системы, установленное на мосту через Десну. Верхний пояс главных ферм в нем имеет коробчатое сечение, а все остальные элементы, включая и нижний пояс,— Н-образное. Узлы ферм выполнены при помощи фасонок-вставок. Металлоконструкции были изготовлены Воронежским мостовым заводом и смонтированы трестом Мостострой № 1.
Особенностью изготовления данного пролетного строения явилось то, что все стыковые соединения узловых фасонок с вертикальными листами элементов ферм сваривали автоматом в вертикальном положении однопроходным швом с принудительным его формированием как на заводе, так и на монтаже. Кроме элементов Н-образного сечения, были изготовлены элементы коробчатого сечения с двухсторонними угловыми швами — внутренними и наружными. Существующие типы сварочных автоматов не были приспособлены для выполнения подобных работ. Осуществив модернизацию автомата ТС-17М и уменьшив его наружные габариты, удалось обеспечить наложение этим авто
матом внутренних и наружных угловых швов коробчатого элемента при положении «в лодочку». В остальном технология изготовления и монтажа пролетного строения была аналогична технологии, примененной при создании пролетных строений моста через р. Болва.
Однако технологию изготовления ко-робчатых элементов необходимо было усовершенствовать, так как требовалось восемь раз кантовать элементы для их сварки «в лодочку», а раздельное наложение всех угловых швов автоматом ТС-17М приводило к Винтообразному искривлению коробчатого элемента.
В целом же опыт постройки и испытаний указанных трех цельносварных пролетных строений железнодорожных мостов пролетами по 66 м каждое показал, что мосты подобной конструкции могут выполняться должного качества. При этом по сравнению с клепаными пролетными строениями аналогичных пролетов расход металла снижался на 30%. Недостатком конструкции указанных цельносварных пролетных строений со сквозными фермами является отсутствие в монтажных соединениях устройств, обеспечивающих быстрое и четкое фиксирование элементов и узлов в проектном положении, изменяемость заданного положения элементов в процессе сварки монтажных соединений и значительный объем ручных сборочно-сварочных работ.
В те годы были проведены дискуссии о преимуществах и недостатках открытых Н-образных сечений элементов главных ферм пролетных строений мостов и закрытых, коробчатых. В итоге было признано рациональным применение закрытых сечений. По проекту Гипротрансмоста в 1959—1960 гг. Воронежским мостовым заводом были изго-товлены из стали М16С четыре клепано-сварных пролетных строения пролетом 66 м каждое, установленное на мосту через Северный Донец; большинство сварных элементов главных ферм здесь коробчатого сечения. Учитывая,
что технология сварки коробчатых сече- стали интенсивно внедрять сборные же- ний элементов предыдущего дельно- лезобетонные конструкции. К концу сварного моста была не вполне совер- 50-х годов строительство металлических шенной, НИИ мостов изготовил на базе мостов резко сократилось, изготовление сварочного трактора ТС-17М опытные сварных пролетных строений со сквоз- образцы двухдуговых автоматов двух ными фермами практически прекрати- типов с разнесенными в сторону на пш- лось вовсе. Однако работы научно-ис- рину коробчатых элементов электрода- следовательских и проектных институ- ми: один — для одновременного наложе- тов в этот период продолжались. Так, в ния двух угловых швов внутри элемен- 1956 г. были введены новые нормы та, а другой — для наружных швов. Од- проектирования и изготовления сварновременно отрабатывалась технология ных пролетных железнодорожных мо- изготовления этих элементов [167]. стов [141], а в 1962 г. «Технические ус- Была принята следующая последова- ловия проектирования железнодорож- тельность выполнения операций: внача- ных, автомобильных и городских мостов ле собирали и сваривали внутренними и труб» [142], составленные ЦНИИС и угловыми швами элемент открытого Союздорнии.
Согласно этим нормам, L;-образного сечения, включающий все сварные соединения и прикрепле- нижний перфорированный горизонталь- ния растянутых элементов должны под- ный и два вертикальных листа, а затем вергаться механической обработке для устанавливали верхний сплошной гори- обеспечения плавности перехода швов зонтальный лист, замыкающий коробча- на основной металл, тое сечение, и попарно накладывали Большую и плодотворную работу по
остальные шесть угловых швов элемен- возрождению применения сварки в же- та указанными двухдуговыми автомата- лезнодорожных мостах провели НИИ ми. При наложении внутри замкнутого мостов, ЦНИИС, Гипротрансмост и Лен- сечения коробки угловых швов, прива- гипротрансмост при эффективной под- ривающих вертикальные листы к сило- держке Института электросварки. В ратному горизонтальному, управляли и ботах этих институтов предлагалось наблюдали за процессом сварки автома- применять в пролетных строениях мо-том через перфорации другого горизон- стов низколегированные стали повы- тального листа, расположенного при вы- шенной и высокой прочности взамен уг- полнении этих работ сверху. Монтаж- леродистых [10, 34, 57]. Предлагалось ные отверстия под заклепки получали также перейти на новые принципы в объемных кондукторах в полностью проектирования конструкций по пре- сваренных элементах после фрезеровки дельным состояниям вместо допускае- их торцов. мых напряжений [142], создавать более
При освидетельствовании данных про- прогрессивные типы сварных конструк- летных строений в эксплуатации Мосто- ций пролетных строений мостов [51]» испытательной станцией Главного уп- совершенствовать технологию их изго- равления пути МПС были выявлены за- товления и монтажа, разработать про- зоры величиной до 1 мм между поверх- грессивные методы контроля качества ностями узловой фасонки и коробчатого сварных соединений, создать специали- элемента. Причина образования подоб- зированую аппаратуру для автоматиче- ных дефектов не была установлена, но ской сварки и ультразвуковой дефекто- это несколько отразилось на примене- скопии сварных соединении и т. п. нии пролетных строений железнодорож- В основу метода расчета сварных сое- ных мостов с фермами указанного динений на усталость положены резуль- типа. таты исследований ЦНИИС [7—41»
В этот период во всех областях строп- 30-32, 71]. Применительно к мостам тельства, в том числе и в мостостроении, изыскиваются стали повышенной и вы-
сокой прочности, разрабатывается технология их сварки [34, 42, 57]. Проведенные НИИ мостов исследования позволили рекомендовать для сварных мостов низколегированные стали повышенной прочности класса С50/35 марок 15ХСНД и 10Г2СД с использованием ранее применявшихся сварочных материалов — проволоки Св-08ГА, флюса АН-348А, но при режимах сварки не выше 50 ООО Дж/см. Монтажные соединения рекомендовано выполнять при помощи высокопрочных болтов из стали 40Х, обеспечивающих при натяжении их на заданное усилие работу соединений на трение [4]. Рекомендовалось также перейти от открытых Н-образных и двутавровых типов сечений сильно нагруженных элементов главных ферм к замкнутым коробчатым с более высокой крутильной жесткостью и рацио-нальным размещением металла по сечению.
Была обоснована допустимость применения в элементах ферм соединительных угловых швов малого поперечного сечения с катетами 5—7 мм при толщине свариваемых деталей до 50 мм включительно [164]. В других частях конструкции также рекомендовалось исполь-зовать швы малого сечения при условии выполнения требований расчета [63]. Доказана возможность применения без- диафрагменных коробчатых элементов в конструкциях главных ферм пролетных строений [27], а также допустимость машинной кислородной резки без последующей механической обработки (строжки) «свободных» кромок [161] с применением нового способа резки — «смыв-процесса» [155]. Продолжалось изучение влияния конструктивно-технологических факторов на несущую способность сварных соединений и конструкций [12, 13, 33, 47, 48, 69, 70, 72, 74, 131, 144, 145, 147, 168], нестационарно- сти нагружения и учета ее при расчетах на усталость сварных мостов [ 14, 15, 35, 135, 146, 149], долговечности монтажных соединений [25, 26, 61]. Разрабатывались методы контроля и требова
ния к качеству сварных швов и соединений [22, 28,126].
Выполненные работы послужили им-пульсом для нового этапа развития сварного мостостроения, характеризуемого широким использованием низколегированных сталей и прогрессивных конструктивно-технологических решений.
В конце 60-х годов начали в плановом порядке изготовлять типовые цельносварные железнодорожные пролетные строения с ездой поверху из низколегированной стали 15ХСНД со сплошностенчатыми двутавровыми главными балками пролетом 23—33,6 м.
Постепенно расширялось производство мостовых конструкций со сплошностенчатыми главными балками из низколегированной стали 15ХСНД (как по числу изделий, так и по их размерам и форме). Из выполненных конструкций можно назвать семь пролетных строений со сплошностенчатыми главными балками пролетом по 45 м моста через Минусинскую протоку.
Проводились исследования по изучению прочности и долговечности фрикционных соединений на высокопрочных болтах [18, 134].
По проекту Ленгипротрансмоста, раз-работанному по техническому заданию НИИ мостов, в 1962—1964 гг. было построено первое в стране опытное железнодорожное болто-сварное пролетное строение из низколегированных сталей 15ХСНД и 10Г2СД со сквозными фермами пролетом 110 м с ездой понизу [122]. Оно установлено на мосту через канал Фархадской ГЭС (рис. 12.12). Верхний и нижний пояса главных ферм, все сжатые и наиболее нагруженные растянутые раскосы имеют коробчатое сечение с перфорированным нижним горизонтальным листом. Слабонагружеп- ные раскосы, стойки и подвески главных ферм Н-образного сечения; балки проезжей части — двутавровые, а элементы горизонтальных связей — таврового сечения. Изготовляли сварные конструкции пролетного строения на Воронежском мостовом заводе, монти
ровал их Мостопоезд № 451 Мосто-строительного треста № 4. Все коробчатые элементы сваривали двухдуговыми автоматами [1]. Порядок изготовления их был примерно такой, же, как и ранее применявшийся при сварке пролетных строений моста через Северный Донец [167]. При изготовлении коробчатых элементов были выполнены замеры с целью выявления характера и величины их деформации при сварке. В результате были установлены причины бочкообразного искривления поперечного сечения коробчатых элементов и приняты меры по устранению, таких деформаций [152] .
Монтажные отверстия под высокопрочные болты образовывали малого диаметра (18 мм) в листовых заготовках по разметке и накладным кондукторам. Рассверливали их на проектный диаметр (23 мм) при контрольной плоскостной сборке частей пролетного строения. Успешно был выполнен монтаж сварных металлоконструкций на высокопрочных болтах. Данное пролетное строение явилось базовым для разработки Гипротрансмостом вначале 60-х годов типовых болтосварных железнодо-рожных пролетных строений из низколе-гированной стали 15ХСНД с ездой понизу, пролетами 33,6—110 м.
Рис. 12.12. Опытное болтосварное пролетное строение моста через канал Фархадской ГЭС а — верхние продольные связи
; б — портал; в — главные фермы; г — поперечные связи в пролете; д — проезжая часть.
Однако широкое применение их сдерживалось ссылками на недостаточный опыт эксплуатации таких пролетных строений. Лишь в 1970—1971 гг. Воронежский мостовой завод приступил к серийному выпуску таких пролетных строений, сперва небольших, а затем и пролетами 88 и 110 м.
В тот же период были сооружены: автодорожный мост через Буг у Николаева по проекту Киевгипротранса. Ме-таллоконструкции пролетного < строения сварные, а монтажные соединения на высокопрочных болтах; городской мост Александра Невского через Неву в Ленинграде с цельносварным однокрылым разводным, пролетом из стали 15ХСНД длиной 55 м; городской Литейный мост через Неву в Ленинграде с неразрезными сварными пролетными ‘строениями, состоящими из шести ниток главных балок из стали 15ХСНД. Все монтажные стыки главных балок выполнены сварными.
Новый этап в развитии конструктивных форм сплошностенчатых сварных пролетных строений отражает построенный в 1969—1970 гг. по проекту Гипротрансмоста городской мост через канал им. Москвы у Химок с неразрезным
дролетным строением из низколегированной стали 10ХСНД пролетами 81+ +135+81 м. Главные балки в нем коробчатого поперечного сечения. Ширина коробок 6,0 м, высота стенок 3,6 м. Железобетонная плита проезжей части включена в совместную работу с главными балками. Все монтажные стыки балок и поперечных двухстенчатых диафрагм выполнены со вставками и сварены автоматической сваркой под флюсом. Сварные металлоконструкции изготавливал Воронежский мостовой завод, монтировал Мостоотряд № 4 Мостотреста. Активную научно-техни- ческую помощь в создании пролетного строения на стадиях проектирования, изготовления и монтажа оказывали НИИ мостов, ЦНИИС и ИЭС им. Е. О. Патона.
Новые конструктивные формы были предложены в начале 70-х годов при строительстве железнодорожного моста через р. Юганская Обь. Четыре пролетные строения в нем длиной по 66 м каждое изготовлены по проекту Гипро- трансмоста из стали 10ХСНД в виде сталежелезобетонных сварных балок ко-робчатого сечения. Монтажные стыковые соединения блоков балок, прикрепление ребристой горизонтальной плиты к нижним поясам балок и элементов поперечных связей выполнены при помощи высокопрочных болтов.
Иногда на одном и том же мосту применяют как сварные монтажные стыки, так и фрикционные соединения. В частности, на автодорожном вантовом мосту через Шексну в Череповце элементы пролетного строения с мощными главными балками коробчатого сече-ния соединены между собой на монтаже автоматической сваркой [54], а блоки эстакадной части — с помощью соединений на высокопрочных болтах.
Сравнительные данные массы п трудоемкости изготовления пролетного строении через Ангару в Иркутске в зависимости от типа монтажных соединении (по данным института «Гипротрансмост»)
В качестве примера рассмотрим монтажные стыки пролетного строения эстакады через шлюзы Днепрогэс-2 в, Запорожье. Эстакада расположена на кривой радиуса 250 м. В поперечном сечении моста имеется только одна несущая балка трапецеидального коробчатого сечения с шириной понизу 6000 мм и по верху 9000 мм с двухсторонними консолями по 6500 мм (рис. 12.14). Проезжая часть состоит из стальной ор
тотропной плиты. Монтажные стыки главных балок наиболее целесообразно выполнять цельносварными. Для сварки наклонных стенок главных балок Институт электросварки изготовил специальный автомат.
Поперечные монтажные стыки ортотропной плиты, стыкуемой из-за криво- линейности пролетного строения,— нового типа, исключающего необходимость соединения между собой отдельных ребер и позволившего полностью отказаться от ручной сварки.
В 1976—1979 гг. построено два крупнейших в нашей стране вантовых автодорожных моста через Днепр в Киеве и: через Шексну в Череповце. Московский мост через Днепр в Киеве состоит из двух частей — эстакадной и вантовой длиной 447 м. Пролетное строение вантовой части составлено из двух ниток коробчатых балок высотой 3600 мм, подвешенных к прямолинейным вантам. Балки эстакадной части имеют двутавровое сечение такой же высоты. Все монтажные стыки сварены на берегу. Цельносварные стыки двутавровых балок такой же конструкции, как и на всех предыдущих мостах,— с двумя вставками. Главные балки вантовой части состоят из четырех блоков — двух вертикальных двутаврового сечения (с такими же цельносварными стыками) и двух плоских блоков ортотропной плиты проезжей части и днища. Листовой настил верхней плиты соединен с главными балками с помощью сварки внахлестку; поперечные балки имеют стыки на высокопрочных болтах; соединения нижних плит днища с полками балок сварные.
При сварке монтажных стыков главных балок этого моста вертикальные швы впервые выполняли самозащитной порошковой проволокой с принудительным формированием. В дальнейшем для сварки вертикальных стенок большой толщины (например, 25 мм —в стыках на мосту через Шексну) применяли двухэлектродную дуговую сварку порошковой проволокой диаметром2,35 мм с принудительным формированием шва.
Крупным цельносварным сооружением из низколегированной стали 15ХСНД являются сооруженные в Москве в 1975—1977 гг. пролетные строения Рижской эстакады длиной более 4 км. Все элементы пролетных строений, изготовленные на Люберецком заводе мостового оборудования, и монтажные стыковые соединения главных балок выполнены с помощью автоматической сварки. Вертикальные стыки стенок балок сваривали автоматом также порошковой проволокой с принудительным формированием шва.
Рис. 12.14. Поперечное сечение эстакады через шлюзы ДнепроГЭСа
Рис. 12.13. Болтосварной стык главных балок со сплошной стенкон
1 — монтажные накладкп; г — высокопрочные болты; з — отверстие для высокопрочных болтов крепления накладок; 4 — монтажная накладка, закрепляемая высокопрочными болтами к выводным планкам и шоссейных дорог в северных и северо- восточных районах страны существенно возросли требования к хладостойкости конструкций. За истекшие годы стали, применяемые для мостостроения, качественно изменились. Сталь марки М16С по ГОСТ 6713-53 (с гарантией ударной вязкости при —20° С и после механического старения), сыгравшая большую роль в развитии строительства сварных мостов, перестала удовлетворять возросшим требованиям к основному материалу не только по прочности, но и по хладостойкости. Еще в начало 50-х годов в мостах стали применять низколегированную сталь марки 15ХСНД по ГОСТ 5058-57 с гарантией
по ударной вязкости при —40° С или после механического старения. С целью дальнейшего повышения надежности сварных мостов в ГОСТ 5058-65 была предусмотрена возможность заказа низколегированных сталей с двумя указанными проверками ударной вязкости.
В дальнейшем мостовые стали совер-шенствовали путем их термической об-работки. В 1965 г. ЦНИИС совместно с Орско-Халиловским металлургическим комбинатом были разработаны «Технические условия на термически обработанную сталь 15ХСНД для сварных мостов»; введены разработанные ЦНИИС и Гипротрансмостом Нормы (ВСН 145-68) по проектированию, изготовлению, монтажу и приемке сварных пролетных строений всех видов мостов северного исполнения: Нормы (ВСН 148-68), регламентирующие применение в мостах термоулучшенных сталей класса С 52/40, в том числе марки 10ХСНД в сварных пролет-ных строениях мостов различного назначения [129]; внесены соответствующие изменения главы СНиПИ-Д. 7-62*.
В 1973 г. Минчермет СССР утвердил разработанные ЦНИИС совместно с Орско-Халиловским комбинатом новые технические условия на сталь для мостостроения [129] с правом выбора заказчиком вида ее термообработки. По этим ТУ мостостроение обеспечивалось сталью до 1 июля 1978 г. Они были отменены в связи с вводом в действие ГОСТ 6713-75 на сталь углеродистую и низколегированную для мостостроения, разработанного совместно ЦНИИ МПС, ЦНИИС и НИИ мостов. В этом стандарте учтен предыдущий опыт применения известных указанных выше марок сталей как в сварных мостах, так и в других ответственных сварных конструкциях.
Следующим этапом в разработке металлов для сварных мостов явилось создание ряда марок сталей с нитридным упрочнением. ЦНИИпроектстальконструкция совместно с ЦНИИчермет
разработана нитридоупрочненная низко-легированная сталь 14Г2АФД, предназначенная для работы при пониженных температурах. В нормализованном состоянии она имеет класс прочности С 52/40. Эту сталь применили в пролетных строениях пойменной части моста через Шексну в Череповце. Институтом черной металлургии (Днепропетровск), Институтом электросварки им. Е. О. Патона и Коммунарским металлургическим заводом для сварных мостов создана низкокремнистая (полуспокойная) сталь с нитридным упрочнением 15Г2АФДпс [76]. Ее также поставляют в нормализованном состоянии, и она имеет класс прочности С 52/40. Из этой стали изготовлены пролетные строения эстакадной части Московского моста через Днепр в Киеве. Опыт сварки элементов этого моста на Ждановском заводе металлоконструкций показал, что сталь 15Г2АФДпс хорошо сваривается. По сравнению с другими сталями данного класса прочности (например, сталью 10ХСНД) она имеет не только повышенную хладостойкость и лучшую свариваемость, но и более низкую стоимость. В постановлении от 28 декабря 1971 г. Государственный комитет Совета Министров СССР по науке и технике рекомендовал применять сталь 15Г2АФДпс для изготовления сварных мостов и других ответственных конст-рукций в северном исполнении.
Из выполненных конструкций в северном исполнении следует назвать построенное в 1975 г. из термически улучшенной стали 10ХСНД неразрез- ное болтосварное пролетное строение со сквозными фермами железнодорожного моста через р. Лену с пролетами 110+132+110 м на трассе БАМ
(рис. 12.15). Технология изготовления металлоконструкций принята в основном той же, что и при изготовлении типовых болтосварных пролетных строений из низколегированной стали 15ХСНД с коробчатыми перфорированными элементами, но при этом были отработаны технология и режимы свар
ки, обеспечивающие требуемую ударную вязкость при —70°.
Эта технология позволила изготовить и смонтировать указанное неразрезное пролетное строение в сжатые сроки: за 6 месяцев.
В настоящее время пролетные строения железнодорожных мостов как со сквозными фермами пролетами до 132 м, так и со сплошностенчатыми главными балками пролетами до 66 м включительно изготовляют лишь в сварном исполнении.
Примером использования хладостойкой высокопрочной стали 14X2 ГМР класса С 70/60 может служить автодорожный мост через р. Смотрич в Каменец-Подольске. Он состоит из трехпролетного рамного металлического строе-ния общей длиной 179 м (рис. 12.16), в котором коробчатые главные балки бистальные: нижние высоконапряженные пояса выполнены из термически упрочненной стали 14Х2ГМР, а остальные элементы — из стали 14Г2. Кон-струкция ортотропной плиты также отличается от ранее применявшихся. Она составлена из продольных балок трапецеидального коробчатого сечения с шагом 600 мм и поперечных балок таврового сечения через 4000 мм. Листовой настил имеет толщину от 12 до 20 мм.
В данном пролетном строении впервые применили монтажную сварку стыков главных балок при навесном монтаже. Это стало возможным после разработки ГПИ «Укрпроектстальконструк- ция» и Киевским отделом ОКБ ГМС Минтрансстроя специальных инвентарных элементов, позволяющих фиксиро-вать навешиваемый блок с опнрапнем его снизу и закреплением тяжами сверху. Приспособление позволяет регулировать положение блока в пространстве и устанавливать необходимые зазоры между стыкуемыми кромками листов. Монтажные стыки главных балок — совмещенные, их сваривали вручную. Элементы главных балок и ортотропной цлиты проходили контрольную сборку
на заводе. Сопряженно главных балок со стенками коробчатого сечении ног выполняли с помощью ручной сварки на монтаже без переходных элементов [42,43, 49, 138].
Проект моста разработан ГПИ «Укрпроектстальконструкцпя* при участии Института электросварки. Конструкции изготовил Днепропетровский завод металлоконструкции им. И. В. Бабушкина, а монтаж осуществил Мостострой-1 Министерства транспортного строительства. Технологию заводской и монтажной сварки разрабатывал Институт электросварки.
По-видимому, в дальнейшем высокопрочные стали будут более широко применять особенно в сильнонапряженных элементах при гибкости не более 60. Что касается алюминиевых сплавов, используемых в строительстве, то, как показали исследования НИИ мостов [29, 128], из-за низкого модуля упругости и высокой стоимости в мостостроении их целесообразно применять лишь в ограниченном объеме.
Дальнейшие исследования и разработки в области сварного мостостроения связаны с изысканием новых высокопрочных п коррозионностойких сталей для изготовления пролетных строений (особенно в северном исполнении), улучшением конструктивных решений, основанных па использовании короб-чатых сеченпй и ортотропных плит, совершенствовании вантово-балочных систем [16, 17]. Эти работы направлены на снижение металлоемкости конструкций, трудоемкости изготовления и монтажа пролетных строений, повышение их надежности и сокращение эксп-луатационных расходов.
Специфические задачи по сварным мостам возникают в связи с реконструкцией сети автомобильных дорог и переводом многих из них в первую техническую категорию [39].
За прошедшие полстолетия впедрешш сварки в мостостроение в пашей стране построено сварных мостов общей массой свыше 700 тыс. т. Наиболее бурно свар
Рис. 12.15. Неразрезпое болтос парное пролет* вое строоппо 110+132+110 м моста через р. Лену
а — nepxnue продольные оппзн; б — портал; в — гдавныо фермы; а— проезжая часть, горизонталь-ные диафрагмы и шшшне продольные овлэи
Рис. 12.16. Схома поперечного соченпя моста в г. Каменец-Подольск
ное мостостроение развивалось в начальный послевоенный период и в 70-х годах, когда мостовые заводы Министерства транспортного строительства полностью переключились на изготовление сварпых мостовых конструкций взамен клепаных. В последние годы для изготовления металлических пролет- пых строений преимущественно применяют низколегированные стали класса прочности С 50/35 н С 52/40. Сварные пролетные строения устанавливают и эксплуатируют во всех районах страны, включая северные и северо-восточные,
185000
в том числе па всей трассе БАМ. Только в последние годы большие сварные мосты построены через Днепр в Киеве, Обь в Новосибирске, Ангару в Иркутске, Иртыш в Омске, Шексну в Череповце. Начато строительство мостов со сварными пролетными строениями через Даугаву в Риге, Неву под Ленинградом, Каму в Березниках и др.
Дальнейшее развитие сварного мостостроения связано с применением высокопрочных сталей и повых конструктивных решений пролетных строении. Для автодорожных мостов перспективны пролетные строения с одной-дву-мя коробчатыми балками и стальной ортотропной плитой. При таком решении достигается значительная механизация заводского изготовления элементов и выполнения монтажных соединений. Дальнейшее развитие получат вантовые автодорожные мосты, а также предвари
тельно напряженные и бнстальиые конструкции.
Ближайшим этапом в развитии металлических железнодорожных мостов явится переход на применение в пролетных строениях мостов сварных герметически замкнутых коробчатых алиментов и коррозионно-стойких сталей повышенной прочности. Уже сейчас построено и испытано опытное сварно-пролетное строение из низколегированной стали с герметичными замкнутыми коробчатыми элементами пролетом 66 м с монтажными соединениями на высокопрочных болтах, установленное па мосту через р. Ловать. Получены положительные результаты.
За истекшие 50 лет сварка в мостостроении прошла путь от единичных экспериментов до массового внедрения и стала ведущим технологическим процессом при изготовлении конструкций Металлических мостов.
Подобные статьи
SMART-роботизация сварочного производства вместе с Valk Welding
В этом видео 👆 роботизированный комплекс для сварки компонентов мостовых конструкций. Это один из последних проектов автоматизации сварочного производства с участием компании Valk Welding, из более чем 2600 реализованных. Проект реализован в Чешской Республики.
Основные компоненты роботизированного сварочного комплекса 👇
- Антропоморфный сварочный робот Panasonic TL-2000 WGh4
- Портал консольного типа перемещаемый по линейному траку
- Ротатор-позиционер с одной активной колонной, с рабочей нагрузкой до 2000 кг
- Самое главное: умные лазерные датчики и программное обеспечение
- S – Specific (Конкретный), объясняется, что именно необходимо достигнуть.
- M – Measurable (Измеримый), объясняется, в чем будет измеряться результат.
- A – Attainable, Achievable (Достижимый), объясняется, за счёт чего планируется достигнуть цели.
- R – Relevant (Релевантный), определение истинности цели. Действительно ли выполнение данной задачи позволит достичь желаемой цели? Необходимо удостовериться, что выполнение данной задачи действительно необходимо.
- T – Time-bound (Ограниченный во времени), определение временного триггера/промежутка по наступлению/окончанию которого должна быть достигнута цель (выполнена задача).
Роботизация – это процесс в котором операции ранее осуществлявшиеся человеком, передаются для исполнения роботу.
Valk Welding – это европейская компания со штаб-квартирой в Алблассердаме (Нидерланды) которая была образованная в 1961 году, как поставщик сварочных материалов, в чём они преуспели и на сегодняшний день являются одним из крупнейших в странах ЕС из независимых поставщиков сварочной проволоки, осуществляя поставки около 600 тонн/месяц.
Valk Welding также является одним из самых успешных и продвинутых интеграторов сварочных роботов в странах ЕС. Более 2600 реализованных проектов по автоматизации сварочного производства.
В 2014 году был представлен первый роботизированный комплекс сборки и сварки строительных стальных конструкций «Voortman Fabricator» 👇
Подробнее о совместном проекте «Voortman Fabricator», в статье «Металлоконструкции делать не просто, а очень просто!»
Это не единственный совместный проект Voortman и Valk Welding. Первым совместным проектом этих двух компаний, была роботизированная установка термической резки «VOORTMAN V808», которая в настоящие время превратилась в «товар массового потребления». Voortman в настоящие время отгружает своим клиентам до 3х V808 каждый месяц. 👇
Первый VOORTMAN V808 запустили осенью 2009 года, в октябре того же года, я с коллегами приехал посмотреть на это чудо техники. 👇
Это первый роботизированный комплекс компании VOORTMAN, сейчас V808 значительно изменился, повзрослел и стал намного серьёзней, умнее и симпатичнее, но и тогда, в 2009 году он казался супер продвинутым.
Для нашей компании, тогда сделали демонстрационный образец детали вырезанной из двутавра с нашим логотипом. 👇 Правда сделали ошибку в названии, но всё ровно приятно 😊
Такой сувенир из Нидерландов, вместо магнитика 👆 ))
Первая роботизированная система плазменной резки V808, фотография сделана мной 14.10.2009 👇 Современная (2017 год) машина V808, фотография приХватизирована на сайте компании VOORTMAN 👇 К сожалению, V808 и аналогичное оборудование в РФ популярностью не пользуется, основная причина того ГОСТ 23118-2012 и непробиваемые твердолобы.
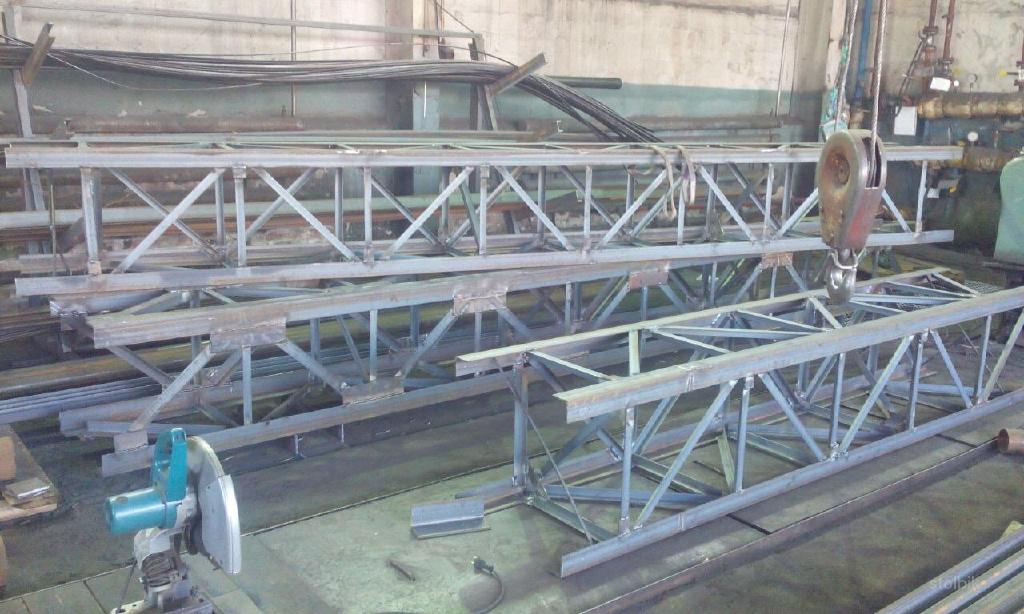
4.11.2 Образование отверстий проводят на предприятии-изготовителе сверлением или продавливанием. Продавливание отверстий не допускается в расчетных соединениях, а также оговоренных в рабочей документации.В ГОСТ 23118 нет запрета на производство отверстий методом плазменной резки. Но и не написано, что можно в расчётных узлах резать отверстия термическими методами. Вот многие и упираются твёрдым лбом, нельзя резать и всё тут. Во всём мире кроме России – режут, а в РФ нельзя! Не написано в ГОСТ, что можно, значит нельзя. Прям национальная трагедия, так как производительность болтовых отверстий, полученных методом сверления значительно ниже, чем плазменной резкой.
Но скоро эта глупость будет исправляться, с 01.07.2017, когда будет введён ГОСТ Р 57351-2016 «Конструкции стальные строительные. Общие технические условия» — идентичный европейскому стандарту EN 1090-2, где в пункте 6.6.3 «Выполнение отверстий», сказано:
Отверстия для крепежных элементов могут выполняться любым способом (сверление, пробивкой, лазерной, плазменной или другой термической резкой), при соблюдении следующих условий 👈Да здравствует торжество разума!
Возвращаемся к Valk Welding
Ещё один из последних проектов автоматизации производства на основе промышленных роботов. Посмотрите видео внимательно, проникнитесь уровнем SMART-организации производства металлических конструкций. 👇
Портал консольного типа перемещаемый по линейному траку длинной 15 метров, что позволяет быстро перестраивать роботизированный сварочный комплекс для работы с длинномерными конструкциями.
Пятнадцатиметровый трак позволяет создать две сборочно-сварочные ячейки для симультанной организации производства (параллельная сборка и сварка), пока в одной ячейки конструкция сваривается, во второй производится сборка. После завершения рабочих циклов, люди и сварочный робот меняются местами.
На видео вариант коллаборативной симультанной организации производства с тремя ячейками, которые обслуживает один сварочный робот.
В первой и третей ячейках — узлы собираются в кондукторах и обвариваются антропоморфным роботом. Во второй ячейки — узлы собираются в готовую конструкцию, с последующей сваркой.
Программирование осуществляется в «Panasonic DTPS», программное обеспечение позволяет различные варианты программирования роботов. Система может работать с CAD 3D различных форматов: WRL, XGL, ZGL, 3DXML, STL, IGES. О возможностях «Panasonic DTPS» будет отдельная публикация.
Сайт компании Valk Welding
Сайт компании Voortman
Электроды для сварки мостовых конструкций
Подробности- Подробности
- Опубликовано 30.10.2015 08:54
- Просмотров: 1630
В целях повышения надёжности стальных конструкций мостов в 2008 году в Российской Федерации были введены стандарты, ужесточившие требования к качеству сварных соединений.
Данные изменения нашли отражение в подходах к сертификации продукции со стороны НАКС, утверждена новая группа технических устройств – КСМ. Если ранее значения ударной вязкости наплавленного металла определялись при -40°С, то для группы КСМ испытания нужно проводить при -60°С. Также были повышены нормативные требования к пределу прочности сварного шва – с 490 до 530 МПа.
ООО «Северсталь-метиз: сварочные материалы» со сложной задачей разработки продукта, отвечающего жестким требованиям, справилось весьма успешно. На базе электродов УОНИ-13/55 с основным видом покрытия специально для КСМ технические специалисты компании разработали электроды УОНИ-13/55КСМ. Для оценки соответствия был проведён аудит технологического процесса производства УОНИ-13/55КСМ, по результатам которого новый СТО был одобрен научно-исследовательским центром «Мосты» (филиал ОАО «НИИ транспортного строительства»).
Завершающим и ключевым этапом разработки нового продукта стала его аттестация в НАКС по группе КСМ. Результаты испытаний, представленные в таблице 1, показывают, что электроды УОНИ-13/55КСМ производства «Северс-таль-метиз: сварочные материалы» не просто соответствуют требованиям НТД, но и значительно превосходят их. Более того, электроды УОНИ-13/55КСМ обладают уникальным свойством – самоотделением шлаковой корки, что позволяет значительно сократить время на зачистку сварных швов и повысить эффективность сварочного процесса.
Новые электроды УОНИ-13/55КСМ включены в реестр КСМ и признаны соответствующими марке электродов УОНИИ-13/55, указанной в СТО-ГК «Трансстрой»-005-2007 и СТО-ГК «Трансстрой»-012-2007. Это позволило компании «Северсталь-метиз: сварочные материалы» расширить ассортиментное предложение для строителей мостовых конструкций, в котором теперь помимо специализированной сварочной проволоки, аттестованной ранее, представлены и специализированные электроды.
Читайте также
Добавить комментарий
Применение сварки в строительстве мостов
Добавил(а): Оксана 24 марта
Сотни тысяч километров дорог связаны общей паутиной. Такое было бы немыслимо, если бы человек не научился строить долговечные сооружения, позволяющие преодолевать реки и ущелья. Мосты – совершенные конструкции, способные выдерживать огромные нагрузки при великолепных показателях долговечности. Одним из видов соединения металлических элементов мостов является сварочный шов. Сварка активно вытесняет любые другие виды соединения – все это благодаря великолепным результатам, которые достигаются только за счет монолитного приваривания металлических деталей.
Применение сварки в мостостроении
Любой мост является весьма ответственной конструкцией. А это значит, что для его возведения необходимо использовать только самые совершенные строительные материалы. В последнее время все чаще задействуется электродуговая сварка, в которой важную роль играют качественные показатели сварочных электродов. Именно они определяют, какими свойствами будет обладать сварной шов.
Только такой ответственный производитель как «СпецЭлетрод» может гарантировать, что изготавливаемые сварочные электроды будут соответствовать всем требованиям качества. Об этой компании мы расскажем чуть ниже.
Какие электроды используются для сварки
Среди большого числа производителей электродов особенно ярко выделяется отечественная компания «СпецЭлектрод», которая выпускает широкий ассортимент продукции для электродуговой сварки. В частности, уникальная в своем роде марка электрода УОНИ-13/55, изготовленная на предприятии «СпецЭлектрод», зарекомендовала себя как наилучший вариант для соединения деталей мостовых конструкций.
Любой мост испытывает динамические нагрузки. Каждый раз, когда по нему проезжает машина, проходит человек или проносится поезд, он немного отклоняется от горизонтальной оси. Основная нагрузка ложится на места соединения металлических составляющих моста. В этом случае качество сварного шва играет первостепенную роль. В частности УОНИ-13/55 отличается возможностью получения пластичного шва, стойкого к динамическим нагрузкам. Это одно из существенных преимуществ рассматриваемой нами марки электродов.
Кроме всего прочего, сварочные электроды отличаются способностью создавать швы, стойкие к образованию трещин. А предварительная обработка поверхности позволяет достигать максимальной прочности созданного соединения.
Многие строительные компании успели оценить качество электродов УОНИ-13/55. Их применяют не только в строительстве мостов, но и при проведении целого ряда ремонтных и восстановительных работ.
Помните, что ответственные работы требуют ответственного подхода!
Оцените статью: Поделитесь с друзьями!Отработка технологии сварки элементов мостовых конструкций
Технологические виды сервиса являются одним из приоритетных направлений деятельности ТЦ ТЕНА. Прежде чем принять решение о закупке того или иного оборудования, заказчику необходимо убедиться в его способности к решению поставленных производственных задач с максимальной эффективностью. Для этого в сварочной лаборатории нашего технологического центра имеется обширный набор демонстрационного оборудования, который включает в себя аппараты для ручной сварки, системы автоматизации и механизации сварочных процессов, несколько робот-ячеек, системы для ручной и автоматической плазменной резки.
Краткий видеоотчет о недавно выполненной работе по подбору технологии и параметров режима для автоматической сварки элементов мостовых конструкций представлен Вашему вниманию. Особым требованием к соединениям являлось обязательное соблюдение формы шва от умеренно ослабленного (вогнутого) до умеренно усиленного (выпуклого) с плавными галтельными переходами к основному металлу для минимизации концентрации напряжений и обеспечения надёжной работы конструкции в условиях динамического нагружения от перемещающегося по мосту транспорта и ветровых воздействий.
Задача была решена с применением сварочной платформы нового поколения TPS/i, которая даёт беспрецедентные возможности по настройке параметров режима сварки, включает в себя функции высокоскоростного регулирования и стабилизации дуги, механизм подачи с высокими динамическими характеристиками.
Для позиционирования и перемещения горелки при отработке параметров режима сварки в лабораторных условиях использовался сварочный трактор FlexTrack 45, позволяющий перемещать горелку со скоростью до 3,5 м/мин и реализовывать 3 вида поперечных колебаний с настраиваемыми параметрами.
Сварочная проволока ESAB ОК AristoRod 13.26
Неомедненная Ni-Cu легированная сварочная проволока с уникальной обработкой поверхности ASC (Advanced Surface Characteristics – поверхность с улучшенными характеристиками), предназначенная для сварки сталей стойких к атмосферной коррозии типа COR-TEN, Patinax, Dillicor. Наплавленный металл обладает повышенной стойкостью к коррозии в слабоагрессивных средах, таких как морская вода и при контакте с газами с высоким содержанием сернистых соединений. Проволока также рекомендуется для сварки мостовых конструкций и корпусов судов, изготавливаемых из низколегированных сталей повышенной прочности типа 10ХСНД и 15ХСНД, а также других низколегированных сталей с пределом текучести до 470 МПа, которые обладают повышенной стойкостью к атмосферной коррозии.
Выпускаемые диаметры: 0,8; 1,0 и 1,2 мм
Классификация |
Сертификация |
EN ISO 14341-A: G 42 0 C1 Z 3Ni1Cu |
DNV: II YMS (C1) DNV: III YMS (M21) |
Химический состав
С | Mn | Si | Ni | Cu | P | S |
0.08-0.11 | 1.25-1.55 | 0.70-0.90 | 0.80-0.90 | 0.25-0.60 | max 0.025 | max 0.025 |
Механические свойства
Предел текучести σт, Н/мм² | Предел прочности ?в, Н/мм? | Удлинение δ, % | Ударная вязкость KCV, Дж/см? |
Защитный газ — M21 (80%Ar + 20%CO2) | |||
540 | 625 | 26 | 175 при +20°С 138 при -20°С |
Строительство мостов — Сварка
Более полумиллиона мостов ежедневно перевозят легковые и грузовые автомобили через реки Соединенных Штатов. По оценкам Министерства транспорта США, каждый четвертый из этих мостов считается структурно несовершенным или функционально устаревшим. На самом деле, это неудивительно, учитывая, что большинству мостов в США от 50 до 60 лет. Большинство из них было построено в 1950-х и 60-х годах после подписания президентом Эйзенхауэром Закона о федеральных автомобильных дорогах.
Это может быть совпадение, но два самых крупных отказа мостов за последнее десятилетие произошли на мостах, построенных в то время. Мост I-35W в Миннесоте, открывшийся для движения в 1967 году после трех лет строительства, обрушился в вечерний час пик в 2007 году, в результате чего десятки автомобилей оказались в реке Миссисипи. Несмотря на то, что мост на Interstate 35 был вторым по загруженности пролетом во всей Миннесоте, и даже несмотря на то, что мост был отмечен как структурно несовершенный еще в 1990 году, строительство нового моста планировалось провести только в 2020 году.
Почти шесть лет спустя часть другого моста на другой крупной артерии, I-5 в штате Вашингтон, обрушилась после того, как негабаритный грузовик, перевозивший груз в Ванкувер, ударился о несколько потолочных опорных балок. Этот пролет, пересекающий реку Скагит и построенный в 1955 году, уже был признан функционально устаревшим из-за отсутствия избыточных несущих балок. Другими словами, инженеры осознали, что отказ только одной важной части может привести к обрушению всего моста.
Преодоление разрыва Несмотря на приведенные примеры, Федеральное управление шоссейных дорог настаивает на том, чтобы У.С. мосты безопасны. В нем говорится, что структурно несовершенные или функционально устаревшие обозначения просто означают, что мост имеет структурный дефект, требующий добавления нагрузки или ограничения движения, или, в случае функционально устаревшего моста, такого как мост через реку Скагит, имеет больший и больший трафик, чем первоначально предназначены.
Независимо от того, считают ли федеральные эксперты и эксперты штата эти мосты небезопасными или нет, все согласны, что мосты, по крайней мере, уязвимы. Хорошая новость заключается в том, что штаты работают над исправлением или заменой многих из этих более уязвимых мостов.Замена моста Таппан Зи в Нью-Йорке стоимостью 4 миллиарда долларов в настоящее время является крупнейшим мостовым проектом в Соединенных Штатах, но, конечно, не единственным. Проекты реализуются во всех 50 штатах, при этом наиболее срочные работы выполняются в северных штатах экипажами, пытающимися предотвратить приход зимы.
Две системы Hypertherm HyPerformance украшают объекты Casco Bay Steel, включая эту систему с длинными столами. Но прежде чем строительные бригады смогут что-либо сделать, им понадобится сталь. В любой год Casco Bay Steel Structures Inc.через его двери пройдет более 20 000 тонн стали. В двух местах в штате Мэн более 100 человек работают над резкой и сваркой стальных балок. И эти балки не такие уж и маленькие.
Негабаритные грузовики, вилочные погрузчики и тяжелые краны занимаются лесопилением на складе площадью 30 акров. Доставка стали, разгрузка стали, перемещение стали; начиная с раннего утра и заканчивая поздно ночью. Эта сталь поступит на один из двух заводов Casco Bay Steel по производству длинномерных материалов и, в конечном итоге, на проекты в Новой Англии, Нью-Джерси и Нью-Йорке.
Подобно рекам, которые они пересекают, каждый мост и поддерживающие их фермы разные. Некоторые из них прямые, некоторые изогнутые, а некоторые сужаются, все с переменной глубиной и длиной. Самый длинный промежуток времени, чтобы покинуть Casco Bay Steel? 172 фута, что составляет более половины длины футбольного поля. Наитяжелейший? 89 тонн.
Поскольку ни одна компания не хочет изготавливать дефектную балку, которая могла бы попасть на мост, используемый тысячами легковых и грузовых автомобилей в день, процесс изготовления Casco Bay Steel является очень дисциплинированным.От получения необработанной стали до окончательного сглаживания балки работа выполняется тщательно с несколькими контрольными точками по пути.
Хотя Casco Bay Steel меньше 20 лет, ее президент Брайон Тейт хорошо разбирается в производстве конструкционной стали. Он начал заниматься бизнесом, когда ему было 19 лет, более трех десятилетий назад. За это время Тейт увидел множество изменений в способе конструкции балок.Сегодня этот процесс стал быстрее и автоматизирован.
«Сегодняшние технологии действительно помогли нам производить больше продукции за меньшее количество часов и сохранить нашу конкурентоспособность», — говорит Тейт. «Сегодня нас меньше, чем 30 лет назад, но мы производим больше».
Одним из наиболее заметных изменений для Тейта стал переход от кислородной резки к плазменной резке. Casco Bay Steel добавила возможности плазменной резки около семи лет назад. Тейт говорит, что одно только улучшение скорости резки имело огромное значение.
Старое и новое: оригинальный мост через реку Маскома рядом с его заменой, построенный из стальных балок плазменной резки от Casco Bay Steel.
Casco Bay Steel перешла на резку 5 дюймов стали в минуту. с кислородным топливом для резки 115 дюймов стали в мин. с плазмой. В качестве дополнительного бонуса Casco Bay Steel обнаружила, что качество резки при использовании плазмы также было лучше.
«Качество резки, которое мы должны использовать в нашем процессе, на самом деле минус ноль плюс шестнадцатое», — объясняет Тейт. «У нас должны быть красивые квадратные пропилы без зазубрин, и Hypertherm дает нам это.”
Всего Casco Bay Steel использует две системы Hypertherm: HyPerformance HPR260XD и HPR400XD. Обе системы были разработаны для операций резания по оси x y, косой кромки и роботизированной резки и отличаются высокой скоростью резания, быстрой сменой технологического цикла, быстрым переключением и высокой надежностью при работе с мягкой сталью, алюминием и нержавеющей сталью. Толщина резки стали с помощью этих систем может варьироваться, хотя чаще всего толщина резки находится в диапазоне от 1/2 до 1 дюйма.
«Мы были впечатлены качеством резки Hypertherm, — говорит Тейт. «Как только мы увидели разницу, мы захотели убедиться, что все наши будущие системы будут от Hypertherm».
Среди балок Casco Bay Steel, изготовленных с помощью систем Hypertherm, есть серия стальных балок, используемых на мосту на заднем дворе Hypertherm. Департамент транспорта Нью-Гэмпшира, находящийся менее чем в четырех милях от крупного предприятия Hypertherm, заменяет мост, эксплуатируемый с 1927 года. Мост отлично прослужил, но тем не менее, почти 90 лет дорожного движения привели к потерям.Бетонные столбы, удерживающие мост через реку Маскома, рушатся. Балки и стержни заржавели и обнажились.
Когда мост был построен почти 90 лет назад, автомобильная сцена выглядела совсем иначе. По оценкам, в дороге находилось 20 миллионов автомобилей, в среднем одна машина на каждые две семьи в США. Сегодня цифры поменялись местами. Каждая американская семья владеет как минимум двумя автомобилями. В целом по дорогам США проезжает более 250 миллионов легковых и грузовых автомобилей. Примерно 17000 из них путешествуют U.S. Маршрут 4 через реку Маскома каждый день — ожидается, что к 2030 году их число почти удвоится.
«Сегодня строительство моста — это гораздо больше, чем 50 лет назад», — говорит Питер Кехо, инженер-строитель из NHDOT. «Например, есть экологические проблемы, особенно потому, что река Маскома служит источником питьевой воды для города Ливана, а также существуют проблемы с регулированием дорожного движения. По этому маршруту проходит 17000 автомобилей в день, и нам необходимо приспособиться к нему с объездами, флагами и т. Д.”
Чтобы повысить безопасность и увеличить расстояние обзора, новый мост через реку Маскома немного шире, чем первоначальный пролет 1927 года. Пять пластинчатых балок переменной глубины, длиной от 86 до 125 футов и общим весом 430 тонн, соединены фрикционным соединением для покрытия 440 футов. большой пролет. Мост спроектирован так, чтобы служить 80 лет, но Кехо считает, что прочная конструкция сохранит его в эксплуатации и в следующем столетии.
Casco Bay Steel потребовалось около шести недель, чтобы завершить процесс изготовления, а строительной бригаде — три недели, чтобы возвести и установить балки на площадке моста.
«Сейчас мы видим, что на мостах все больше используется технология плазменной резки», — говорит Кехо. «Не только балки моста, но также краны и концевые плотины к компенсаторам моста».
Первые автомобили и грузовики начали пересекать новый мост через реку Маскома в этом месяце, но работа бригады еще не закончена. Вместо этого они переезжают по соседству, чтобы начать снос старого моста. После этого мы переходим к следующему проекту, в котором, к лучшему или худшему, недостатка нет, поскольку NHDOT работает над заменой другого моста в своем списке.
Casco Bay Steel Structures Inc.
Hypertherm Inc.
Проект для строительства стального моста
Чтобы обеспечить безопасное, экономичное и надежное выполнение конструкции стального моста (изготовление, сборку и возведение), проектировщики должны знать процессы изготовления и монтажа, возможности и ограничения стальных конструкций. подрядчик и как выбор дизайна влияет на эти процессы. В этой статье содержится руководство по проектированию строительства: в ней обычно следует последовательность действий, выполняемых подрядчиком по изготовлению металлоконструкций.
Виадук Лагентиум, A1 (М) Даррингтон — Дишфорт
(изображение любезно предоставлено Mabey Bridge Ltd.)
Целями «проектирования для строительства» являются:
- Для максимальной эффективности строительства
- Свести к минимуму необходимость в уточнении и изменении
Достижение этих целей снизит затраты, сократит срок строительства, повысит качество и безопасность работ.
Деятельность подрядчика по изготовлению металлоконструкций включает планирование, заказ, моделирование, изготовление, сборку, нанесение покрытий и монтаж.
Holmfield Viaducts, A1 (M) Даррингтон — Дишфорт
(изображение любезно предоставлено Mabey Bridge Ltd. )
[вверх] Планировка
Существует два основных подхода к проектированию и строительству:
- Традиционный подход — проектировщик принимает конструктивные решения, а подрядчик по изготовлению металлоконструкций строит по чертежам.
- Участие подрядчика на раннем этапе (ECI) — Проектировщик и подрядчик по изготовлению металлоконструкций взаимодействуют на раннем этапе для оптимизации процесса строительства
[вверх] Традиционный дизайн
В соответствии с традиционными договоренностями, на стадии концепции и стадии рабочего проектирования проектировщик постоянных работ создает законченный проект, который затем передается вместе с сопроводительной технической спецификацией, обычно через главного подрядчика, подрядчику по стальным работам.Проектировщик предполагает конкретный метод возведения и принимает решения относительно подходящего проектного решения, позволяющего безопасно построить конструкцию в рамках программы и бюджета в соответствии с этим методом.
Для проектирования в соответствии с Еврокодами технические требования к стальным конструкциям описаны в BS EN 1090-2 [1] , и это относится к «основному проектному методу возведения», методу, который проектировщик использовал при разработке дизайн. Участники тендера могут предложить альтернативные методы строительства (см. GN 4.04), в зависимости от конкретного опыта или возможностей, которые они могут предложить, но какой бы метод ни был выбран, исходный или альтернативный, связь между проектированием и строительством лежит в основе эффективного и экономичного решения.
[вверх] ECI — Привлечение подрядчиков на раннем этапе
Раннее вовлечение подрядчика — это форма контракта, в которой главный подрядчик и подрядчики по производству стальных конструкций вовлекаются в процесс проектирования намного раньше. Очевидно, что существенным преимуществом этого типа контракта является то, что проектировщик может обратиться за советом к «специалистам» для помощи в разработке наиболее подходящего решения. Это может принести пользу:
- Разработка схемы
- Разработка стоимости
- Возможность сборки
[вверх] Ограничения
Быстрая установка во время закрытия дороги
Мост на Шордич-Хай-Стрит
(Изображение предоставлено Mabey Bridge Ltd.)
Каждый объект имеет различную среду и инфраструктуру, и каждый представит различные ограничения и возможности, которые проектировщик должен рассмотреть, прежде чем определять структурную форму.Участок может иметь большое влияние на конструктивную форму и способ возведения. Конкретные факторы включают:
- Расположение строения
- Ограничения сайта
- Доступ
- Сроки возведения
- Наличие и размер монтажного цеха
- Требования к быстрой установке, например: во время владения
- Работа над водой или рядом с ней
Перед тем, как выбрать конструктивную форму, важно сравнить каждый вариант с основными проблемами строительства и сравнить практические методы доставки и возведения моста.
[вверх] Стандарт на выполнение металлоконструкций
«Базовым стандартом» в Еврокодах для производства стальных конструкций является BS EN 1090-2 [1] . Этот стандарт представляет собой всеобъемлющий документ с рядом опций и альтернатив, подходящих для конкретного проекта; для британских мостов Спецификация для дорожных работ [2] будет подходящей для большинства проектов автомобильных мостов. Для железнодорожных мостов Спецификация Network Rail на стальные конструкции [3] очень похожа.
Дополнительная информация о технических характеристиках стальных конструкций моста имеется.
[наверх] Регламент МЧР
Правила CDM [4] требуют, чтобы каждый, кто участвует в проекте, выявлял опасности на раннем этапе, чтобы их можно было устранить или уменьшить на стадии проектирования. Бессмысленно сначала завершить дизайн, а потом пытаться устранить риски, связанные с дизайном. К тому времени все решения будут приняты, и любые изменения будут стоить времени и денег. Устранение опасностей из конструкции, пока это практически осуществимо, устранит связанный с этим риск и, следовательно, является лучшим вариантом.
Получение концептуального метода возведения прямо в начале проекта имеет основополагающее значение для общего успеха проекта.
[вверх] Заказ
[вверх] Материалы и компоненты
Самый экономичный способ закупить листы и профили — это на станах размеры, соответствующие проекту. Акционеры берут гораздо больше за тонну, а использование стандартных размеров потребует дополнительных стыковых швов и большего количества отходов. Поэтому важно, чтобы предоставление информации для заказа материалов соответствовало срокам выполнения заказа, требуемым предприятиями.Информация, необходимая подрядчику для подготовки заказов, следующая:
Плиты на складе подрядчиков по изготовлению металлоконструкций
(Изображение любезно предоставлено Mabey Bridge Ltd. )
Геометрия
- План расположения
- Уровни на подшипниках
- Конечный профиль верхнего фланца
- Определение окорока (если есть)
- Заглушка статическая нагрузка — всего и в разбивке
- Допуск развала (при наличии)
- Размеры сварного шва между стенкой и фланцем (на усадку и изгиб)
- Ориентация стыков и концов балок
Подкладка
- Размеры листа и профиля
- болтов — количество, тип, диаметр, покрытие
- Срезная шпилька — количество, длина, диаметр
Спецификация
Различная дополнительная информация и опции, перечисленные в BS EN 1090-2 [1] , приложение A, должны быть предоставлены проектировщиком, а руководство по этому поводу дано в Спецификации для дорожных работ [2]
[вверху] Размер болта
Соединения должны быть спроектированы с использованием болтов M24 с предварительным натягом, где это возможно, потому что их легче затянуть, чем болты M30, и с большей вероятностью они будут доступны на складе для компенсации потерь или внесения изменений в конструкцию. Следует избегать нестандартных размеров, таких как M22 и M27, потому что поставщики не хранят их на складе.
[вверху] Размер срезной шпильки
Соединители со срезной шпилькой, подходящие для мостовых работ, доступны в диаметрах 19, 22 и 25 мм, но подрядчики по изготовлению металлоконструкций предпочитают шпильки 19 мм. Все доступные размеры подходят для удовлетворительной сварки, но с увеличением размера увеличивается уровень дефектов сварного шва и износ сварочного оборудования.
[вверху] Геометрия
Первая ключевая информация, которая нужна подрядчику по изготовлению металлоконструкций, — это геометрия готовой формы, и эта информация обычно передается на чертежах.Для композитного автомобильного моста проектировщик укажет предполагаемую окончательную геометрию при завершении, но для определения изготовленной формы стальных конструкций требуется дополнительная информация, дающая допуск на остаточную деформацию, для предполагаемой последовательности возведения («проектный метод возведения» в соответствии с BS EN 1090-2 [1] ). Информация также должна четко показывать, какие элементы должны быть действительно вертикальными, какие элементы изогнутыми и, в случае соединений, какие поверхности должны совпадать и выравниваться.
[вверху] Припуски на остаточную деформацию
Постоянные деформации возникают в результате усадки во время изготовления и прогибов из-за собственного веса конструкции, наложенных статических нагрузок и усадки бетонного настила. Подрядчик стальных конструкций рассчитает допуски на изменения формы во время изготовления, поскольку они находятся под его контролем. Однако допуски на прогиб конструкции и окончательная информация о профиле должны быть указаны на чертежах и необходимы на ранней стадии для заказа материалов.Отдельные компоненты моста с простой опорой показаны ниже.
Схематическое изображение профилирования стальных балок
Примечания:
- Требуемый окончательный профиль определяет дорожный или железнодорожный инженер
- Строительный припуск рассчитывается проектировщиком с учетом прогиба собственного веса, предварительного напряжения, усадки бетона и т.
Д. Его следует разделить на собственный вес стали и другие постоянные нагрузки, чтобы можно было рассчитать уровни после завершения монтажа стальных конструкций.
- Припуск на изготовление определяется подрядчиком по изготовлению металлоконструкций и может быть в любом направлении, вверх или вниз в зависимости от деталей.
[вверху] Кривизна в плане
Кривизна в плане в балках может быть легко устранена подрядчиками по монтажу металлоконструкций. Помимо того, что они более эстетичны, чем использование балок, изогнутых рядом прямых участков, изогнутые в плане балки упростят конструкцию консолей настила по длине конструкции.
Как и кривизна на отметке, кривизна в плане должна определяться проектировщиком с использованием либо четко определенных радиусов кривизны, либо ряда координат.
На практике изогнутый в своей плоскости фланец формируется с использованием режущего оборудования с числовым программным управлением в виде ряда прямых поясов, обычно не длиннее 500 мм для радиусов до 125 м или не более 1000 мм для радиусов. более 125 м. Дизайнер обычно не указывает это.
[вверху] Информация о подшипниках
Типовая опора моста
Некоторые конструкторы считают, что, поскольку подшипники обычно поставляются производителями в течение восьми недель, им не нужно разбираться в требованиях к подшипникам раньше, чем за восемь недель до начала монтажа стальных конструкций на месте.Восьминедельный срок изготовления подшипника на самом деле является периодом производства подшипника, и если есть какие-либо особые требования к проекту (например, ограничитель подъема), производитель подшипника должен будет спроектировать подшипник и получить одобрение конструкции до этого периода производства.
Кроме того, стальные конструкции подрядчик нуждается в конических деталях подшипника пластины и ориентациях подшипников в начале своего процесса изготовления, то есть требуется информация подшипника для стальных конструкций подрядчика гораздо раньше, чем изготовитель подшипника.
Назначение подшипника и его ориентация относительно основных стальных элементов, к которым они прикреплены, также должны быть четко определены на чертежах стальных конструкций, чтобы избежать ошибок во время изготовления.
Руководство о том, как проектировщики должны рассчитывать диапазон перемещений, который должен быть указан для опор моста, с учетом как теплового изменения, так и неопределенности относительного расположения опор на под- и надстройках, доступно в SCI P406.
[наверх] Своевременное и достаточное определение
Проектировщик должен предоставить достаточную информацию, позволяющую подрядчику по изготовлению металлоконструкций провести серию перекрестных проверок и, таким образом, обеспечить точность предоставленной информации.Например, желательно показать на чертежах как основу окончательного профиля моста, так и уровни на опорах. Это позволяет независимо проверять критическую границу раздела между стальными конструкциями и основанием.
Кроме того, если на чертежах металлоконструкций на ранней стадии будет представлен необходимый уровень информации, это сведет к минимуму количество «запросов на информацию» (RFI), которые подрядчику по изготовлению металлоконструкций потребуется поднять, чтобы полностью определить требования к стальным конструкциям.Наряду с минимизацией работы как подрядчика, так и проектировщика, это, в свою очередь, сократит время между выдачей информации о стальных конструкциях и началом процесса изготовления. Чтобы планировать и выполнять свою работу эффективно, подрядчику по изготовлению стальных конструкций необходимо заполнить и согласовать всю необходимую информацию до того, как он начнет работу, и это отражено в требованиях пункта 4.1.1 стандарта BS EN 1090-2 [1 ] .
[вверх] Моделирование конструкции
После того, как требования к стальным конструкциям полностью определены, эта информация может быть использована подрядчиком по стальным конструкциям для создания двухмерной или трехмерной модели стальных конструкций с помощью программного обеспечения CADCAM.
Это программное обеспечение создаст список компонентов (стенки и фланцы балок, ребра жесткости, элементы распорки и т. Д.), Необходимых для конструкции, и создаст программы для каждой из машин, которые будут использоваться в процессе изготовления.
Модель также можно использовать в качестве «виртуального пробного монтажа» стальных конструкций, что позволяет подрядчику по стальным конструкциям смотреть на детали стальных конструкций под любым углом. Это особенно полезно при работе со сложными деталями, например, концами мостов с перемычкой, поскольку это позволяет подрядчику по изготовлению металлоконструкций проверять доступность детали в рамках разработки проекта до начала изготовления.
Моделирование CADCAM
(видео любезно предоставлено Mabey Bridge Ltd.)
Пример стальных конструкций в конце большого арочного моста показан ниже. На нем показаны внутренние соединения жесткости и болтовые соединения, а также фланцевые и перегородочные пластины.
Часть 3D-модели связанного арочного моста — некоторые внешние пластины не показаны для наглядности
(Изображение любезно предоставлено Mabey Bridge Ltd.)
[вверх] Изготовление металлоконструкций
Основными видами деятельности на заводе по изготовлению являются:
[вверху] Предварительная сборка под сварку встык
Подрядчик по изготовлению металлоконструкций обычно сваривает фланцы и пластины стенки встык на всю длину в цехе перед сборкой балки. Это означает, что такие цеховые соединения могут находиться в разных положениях на двух фланцах и не должны совпадать с каким-либо цеховым соединением в стенке. Если возможно, вся поставляемая плита (из которой будут вырезаны несколько компонентов) будет приварена встык, так как это уменьшит количество переходных / переходных пластин и минимизирует требования к испытаниям стыковой сварки.
Стыковая сварка перед сборкой
(видео любезно предоставлено Mabey Bridge Ltd.)
[вверх] Резка и сверление
Пример станка для плазменной резки, маркировки и сверления с ЧПУ
(Изображение любезно предоставлено Mabey Bridge Ltd.)
Оборудование для газовой или плазменной резки используется для резки фланцев по длине и ширине, стенок по профилю и изгибу и ребер жесткости по форме.Листы толщиной до 35 мм можно профилировать на оборудовании плазменной резки. Пластины толщиной более 35 мм обычно режут с использованием оксипропана, что безопаснее, чем использование оксиацетилена.
В дополнение к геометрическим требованиям к кривизне в плане и предварительному каркасу, определенным проектировщиком, подрядчик по изготовлению металлоконструкций также учтет допуски, необходимые для термической резки и усадки, чтобы окончательная геометрия балки соответствовала требуемой.
Некоторые станки для резки листового металла также имеют возможность отмечать позиции ребер жесткости на стенках и фланцевых плитах и сверлить отверстия под болты для стыковых соединений.В противном случае вырезанные пластины маркируются вручную и просверливаются позже. Дополнительную информацию о термической резке конструкционных сталей см. В GN 5.06.
Поддержание постоянных диаметров болтов и результирующих диаметров отверстий для болтов в конструкции позволяет избежать потенциально дорогостоящих ошибок. Если для болтового соединения или отверстия в арматуре требуется дополнительный допуск, проще и дешевле указать отверстие большего диаметра, чем отверстие с прорезью.
Подготовка планшетов
(Видео любезно предоставлено Mabey Bridge Ltd.)
[верх] Сборка
Типичная машина T&I
(Изображение любезно предоставлено Mabey Bridge Ltd. )
Способность подрядчика по изготовлению металлоконструкций использовать свое автоматизированное оборудование для изготовления стальных конструкций может значительно снизить производственные затраты и улучшить качество готовой продукции. Это, вероятно, наиболее важно при сборке плоских пластин в готовые компоненты.
В случае особо сложных конструкций проектировщик вряд ли сможет произвести наиболее рентабельную деталь без участия подрядчика по изготовлению металлоконструкций, который будет выполнять работы. Полезно иметь в виду, что разные подрядчики по производству стальных конструкций имеют разное оборудование и, следовательно, разные возможности.
У некоторых подрядчиков по изготовлению стальных конструкций есть машины T&I, которые используются для сборки плоских листов в T-образные секции, а затем в I-секции. Эти машины будут иметь ограничения по длине, высоте, ширине, весу, кривизне (в плане и по высоте) и подвешиванию балок, которые могут быть приспособлены, которые будут различаться для разных подрядчиков стальных конструкций. Более крупные машины могут производить балки глубиной до 4 м и шириной 1,5 м. Сварные швы можно налаживать за несколько проходов через машину, но сварные швы на коротких участках необходимо выполнять вручную.
Как упоминалось выше, чем больше конструкция подходит для автоматизированной сборки, тем более рентабельным будет ее изготовление. Проектирование балок в виде двутавровых балок, а не коробчатых балок, сделает их более подходящими для автоматизированной сборки. Как правило, двутавровая балка включает 85% автоматизированную сборку, при этом вручную выполняется только усиление жесткости (если не используется робототехника).Коробка с открытым верхом будет включать в себя 70% автоматизированную сборку с автоматической сваркой швов между стенками и верхними фланцами, приваркой ребер жесткости к стенкам и нижних фланцев к сформированным пластинам жесткости с помощью робота, а также сваркой нижнего фланца к стенкам осуществляется вручную. Коробка с закрытым верхом будет включать 35% автоматизированного профилирования и маркировки только пластин, а все остальные виды изготовления (сборка коробки и придание жесткости) будут выполняться вручную.
Автоматическая сборка секций
(Видео любезно предоставлено Mabey Bridge Ltd.)
[вверх] Сварка
[вверху] Доступ для сварки
Доступ для сварки
(Изображение любезно предоставлено Mabey Bridge Ltd.)
По возможности, ребра жесткости фермы должны быть подробно описаны, чтобы сварочное оборудование подрядчика по изготовлению стальных конструкций могло иметь доступ к сварным швам ребер жесткости при необходимости. Это особая проблема в местах опоры, где необходимо близкое расстояние между ребрами жесткости подшипников и домкратов.
Обычно для роботизированной сварки расстояние в свету между соседними ребрами жесткости не должно быть меньше 400 мм или ширины ребра жесткости, в зависимости от того, что больше, с учетом перекоса любых ребер жесткости.
Детализация сварных швов ребер жесткости к стенкам главной балки также должна отражать перекос необходимого ребра жесткости. Они всегда должны указываться как двусторонние угловые сварные швы до тех пор, пока угол ребра жесткости к стенке фермы не станет меньше 30 градусов, после чего следует указывать односторонний стыковой сварной шов полной прочности (примечание — НЕ стыковой сварной шов с полным проникновением).
Усиление секций
(видео любезно предоставлено Mabey Bridge Ltd.)
[вверху] Тип и размер сварного шва
У проектировщиков возникает соблазн увеличить размер сварных швов для ускорения проектирования, однако сочетание больших сварных швов жесткости и тонких стенок балки может привести к видимому искажению стенки, более известному как эффект «голодной лошади». Точно так же сварные швы с увеличенным размером на концах опорных элементов жесткости могут вызвать локальные деформации, которые затрудняют создание удовлетворительной поверхности для опорных пластин.Поэтому сварные швы ребер жесткости следует проектировать и рассчитывать по размеру в соответствии с их назначением, но не более того. Все сварные соединения должны быть детализированы таким образом, чтобы посадочная длина на 5 мм превышала длину плеча сварного шва. Это обеспечит хорошее качество сварного шва, избегая ненужной подготовки кромок листа.
Площадка для угловых швов
(Изображение любезно предоставлено Mabey Bridge Ltd.)
[вверху] Угловые отверстия в ребрах жесткости
При детализации ребер жесткости проектировщику следует подумать, как лучше всего справиться со стенкой балки и сварными швами фланца.
Традиционно для обеспечения того, чтобы элемент жесткости не касался сварного шва фермы, обычно используется выступ; тем не менее, это приводит к трудностям в обеспечении достаточной защитной обработки внутри выемки. Эта проблема еще больше усугубляется обслуживанием этих деталей на протяжении всего срока службы конструкции. Для окрашенных мостов этого можно избежать, используя «снайперский» элемент жесткости, который плотно прилегает к стенке фермы к сварному шву фланца; затем сварной шов ребра жесткости пропускают по сварному шву фермы, образуя деталь «сварной шов» без каких-либо ограниченных участков доступа для защитной обработки.
Для мостов из погодоустойчивой стали, однако, нет системы защитной обработки, но необходимо обеспечить достаточный дренаж, поэтому ребро жесткости с радиусным отверстием 50 мм предпочтительнее в месте нижнего фланца, где требуется дренаж. В мостах из атмосферостойкой стали следует избегать углов с зазубринами (под углом 45 ° поперек внутреннего угла), потому что доступ хуже, чем через сквозное отверстие, а острый угол может вызвать растрескивание сварного шва.
[вверху] Элементы из атмосферостойкой стали
Изготовленный «уголок» из атмосферостойкой стали.
(Изображение любезно предоставлено Mabey Bridge Ltd.)
Профили из погодоустойчивой стали менее доступны в Великобритании, чем профили из обычной конструкционной стали. Это особенно актуально для небольших количеств. Таким образом, проектировщикам настоятельно рекомендуется на ранней стадии согласовать с производителем доступность необходимых погодоустойчивых стальных прокатных профилей.
Потенциальное отсутствие катаных профилей из атмосферостойкой стали означает, что вторичные элементы жесткости могут быть спроектированы в виде плоских пластин, приваренных к требуемой секции, вместо катаных уголков или швеллеров.Их необходимо детализировать, чтобы у каждого сварного шва была подходящая посадочная деталь.
Болты с предварительным натягом, устойчивые к атмосферным воздействиям, используемые при строительстве мостов, обычно доступны в Великобритании (размер M24), но могут быть ситуации, когда они импортируются из Северной Америки (в британских единицах измерения, т. Е. 1 дюйм), поэтому они должны быть спроектированы как Размер M24, но расстояние между болтами должно быть таким, чтобы можно было заменить болты 1 «.
[вверху] Шлифовка заглушек под приварку
Многие клиенты считают, что стыковой сварной шов становится невидимым, когда заглушки шлифуются заподлицо с основным металлом.На практике это не так; шлифовка стыковых швов заподлицо служит только для распределения шлифованной поверхности по большей площади, прилегающей к сварному шву, и это хорошо видно даже на окрашенной конструкции. Большинство клиентов соглашаются, что после того, как они увидят появление шлифованного стыкового шва заподлицо, эстетически лучше «обработать» такие стыки (т.е. удалить брызги сварного шва и т. Д.), Чем шлифовать стыковой сварной шов заподлицо. Рекомендации по правке после сварки см. В GN 5.02.
С точки зрения проектирования, шлифованный стыковой шов заподлицо является лучшей деталью усталостной прочности, чем стыковой сварной шов, который не был отшлифован заподлицо; однако обычное присутствие поблизости ребер жесткости обычно делает это несущественным.
Несмотря на вышеизложенное, сварные швы на верхней поверхности верхних фланцев главной балки необходимо отшлифовать заподлицо, чтобы облегчить установку постоянной и консольной опалубки, а также сварные швы к верхней поверхности нижних фланцев главной балки на стальных мостах, устойчивых к атмосферным воздействиям, должны быть полностью отшлифованы. промывка грунта для облегчения стекания дождевой воды.
[вверх] Ребра жесткости и распорки
[вверху] Ребра жесткости стенки
Типичная конструкция простого элемента жесткости с одной промежуточной стенкой представляет собой плоскую пластину, приваренную к одной стороне стенки и соединенную с одним фланцем, обычно с верхним фланцем.Предпочтительны плоские ребра жесткости, поскольку они легко привариваются к пластинам стенки и полки с помощью угловых швов по всему периметру. Обычно они прикрепляются после соединения стенки с фланцами.
Придание жесткости — относительно дорогостоящая операция, и промежуточные ребра жесткости следует использовать только там, где это необходимо для прикрепления промежуточных элементов жесткости к балкам.
[вверху] Ребра жесткости подшипника
Несущие элементы жесткости на стойке из атмосферостойкой стали
(также показаны элементы жесткости поддомкрачивания и элементы жесткости стенки при изменении направления нижней полки)
Мост через реку Иден, обход Темпл-Сауэрби
Стенки плоских балок и катаных балок обычно проектируются с поперечными несущими элементами жесткости в каждой позиции опоры.Обычно балка моста размещается так, чтобы нижний фланец располагался наверху опоры, а ребра жесткости концентрично над опорой. Между верхней поверхностью подшипника и нижней стороной фланца почти всегда требуется коническая опорная плита, чтобы подшипник оставался горизонтальным.
Концы ребра жесткости подшипника должны быть надлежащим образом соединены с обоими фланцами, и обычно ребро жесткости «плотно прилегает» к фланцу, подверженному сосредоточенной нагрузке.Почти всегда это нижний фланец. Конец элемента жесткости подшипника необходимо будет отшлифовать, чтобы обеспечить выполнение этого требования.
Ребра жесткости опоры должны быть достаточно широкими, чтобы контролировать перпендикулярность главных балок в опорных позициях. На мостах с сильным перекосом могут также потребоваться дополнительные ребра жесткости рядом с несущими ребрами жесткости, чтобы контролировать прямоугольность балок.
Ребра жесткости подшипников и домкратов должны быть указаны как «подогнанные» к верхней поверхности нижнего фланца элемента, с которым они соединены.Из-за достижимых допусков на плоскостность пластины и прямоугольность балки, нецелесообразно указывать уровень подшипника для посадки обоих фланцев.
[вверх] Детализация для сборки
Сборка стальных конструкций может иметь значительное влияние на детализацию стальных конструкций. Например, болты не следует располагать ближе 100 мм от поверхности стенки балки или элемента жесткости, чтобы их можно было затянуть с использованием стандартного оборудования. Особое внимание следует уделять креплению элементов жесткости к перекошенным элементам жесткости, поскольку доступ для натяжного оборудования к задней части элемента жесткости будет ограничен.
[вверху] Вертикальность стенки и ребра жесткости
Проектировщики должны указать, что стенки балок должны быть вертикальными на опорах при возведении стальных конструкций (см. GN 7.03). Часто происходит поперечный поворот стальных балок, особенно в косых мостах, поэтому необходимо указать, на какой стадии они являются вертикальными. Фактические повороты из-за постоянных воздействий на практике иногда бывают небольшими из-за ограничений со стороны опалубки, распорок и вибрирующего бетона, но невозможно предсказать, что произойдет.
Вторичные силы, возникающие при повороте перемычек в соответствии с расчетами, обычно невелики, и им противодействует связь / диафрагма на опоре. Конструкция должна учитывать эти силы.
Ребра жесткости должны быть по возможности перпендикулярны фланцам, а не вертикально. Когда ребра жесткости вырезаются изначально, края обрезаются под прямым углом, поэтому, если концы встречаются с фланцем под углом, их обычно необходимо скошить, чтобы ограничить сварной зазор. Ребра жесткости подшипника обычно устанавливаются номинально вертикально.
[вверх] Выравнивание поверхностей
При изменении толщины полки ступенька должна быть на внутренней стороне, чтобы общая глубина балки оставалась постоянной. Полотно можно легко профилировать по форме ступеньки, когда оно вырезано из листа, а гладкая внешняя поверхность упрощает работу с автоматами для сварки балок.
В местах соединения перемычек разной толщины ступеньки выполняются с обеих сторон перемычки, чтобы перемычка находилась по центру секции балки.
[вверху] Зазоры стыков
Зазор между главными балками в болтовых соединениях не должен быть меньше 6 мм, чтобы учесть допуски на изготовленную длину основных балок и положение отверстий для болтов в соединении.
На лестничных площадках зазор между концами поперечных балок и основными балками, к которым они присоединены, не должен быть меньше 10 мм, чтобы учесть допуски на длину поперечной балки, прямолинейность основных балок, точность профилирования ребер жесткости главной балки и расположение отверстий под болты.
Зазоры в стыках главной балки
(Изображение любезно предоставлено Mabey Bridge Ltd.)Швы на поперечных балках лестничного настила
(Изображение любезно предоставлено Mabey Bridge Ltd.)
[вверху] Подключения
Заводские соединения почти всегда сварные, в то время как большинство соединений на объекте выполняется болтовым соединением по причинам, указанным ниже. Соединения следует располагать в соответствии с ограничениями транспортировки, а также в соответствии с жизнеспособным методом монтажа. Следует обратить внимание на свободный доступ для сварки, а также на место для установки и затяжки болтов с помощью электроинструмента.
[вверху] Болт
Болтовое соединение на большой пластинчатой балке
(Изображение любезно предоставлено Mabey Bridge Ltd.)
Некоторым клиентам не нравится внешний вид соединений на болтах, но следует помнить, что соединения на болтах относительно малы. Как правило, болтовые соединения предпочтительнее для соединений на объекте, поскольку они дешевле, чем сварные соединения, быстрее устанавливаются (поскольку не все болты необходимо устанавливать во время первоначального монтажа), менее зависят от погодных условий и редко требуются временные опоры. Вся абразивоструйная очистка выполняется подрядчиками по производству металлоконструкций — оцинкованные болты используются для краткосрочной защиты, чтобы избежать струйной очистки перед покраской.
Почти все болтовые соединения в мостовых сооружениях в Великобритании спроектированы как противоскользящие соединения с использованием болтов с предварительным натягом, традиционно называемых болтами с высокой прочностью на трение (HSFG). Это позволяет передавать силы от элемента к элементу за счет трения, возникающего между частями соединения внахлест. Производительность зависит от состояния поверхности интерфейсов.
Перед окончательной затяжкой и после установки необходимо проверить группу болтов, чтобы убедиться, что все интерфейсы находятся в контакте. Затем все болты полностью затягиваются выбранным способом. Доступны различные методы затяжки:
Спецификация проекта должна давать подрядчику стальных конструкций свободу использовать метод по своему выбору. У большинства компаний есть любимый метод, который они считают наиболее экономичным и надежным. Руководство по установке болтов с предварительным натягом доступно в GN 7.05.
[вверху] Сварка
Типичное укрытие для сварного соединения на месте
(Изображение любезно предоставлено Mabey Bridge Ltd.)
Сварные стыки делают линию стальной конструкции более четкой, но они все еще видны, даже если поверхность заземлена заподлицо (как упоминалось ранее). Однако сварные соединения обычно дороже, чем соединения болтов на месте, требуют больше времени для завершения и вносят элемент риска программы из-за плохой погоды и / или возможного ремонта дефектов.
Для выполнения сварного стыка требуются временные опоры или опорные планки для поддержки и выравнивания балки до завершения сварки, а также защита от атмосферных воздействий вокруг стыка.Сварные швы выполняются в запланированной последовательности, как правило, сначала фланцы, затем стенки. Все сварные швы подлежат контролю, обычно перед испытанием требуется 48 часов. По завершении сварная зона стыка потребует струйной очистки и нанесения системы покрытия. Для крупных проектов с более чем 500 соединениями сварка на месте может быть более экономичной из-за затрат на установку. Дополнительную информацию по сварке на месте см. В GN 7.01.
Сварное соединение после изготовления
(видео любезно предоставлено Mabey Bridge Ltd.)
[вверху] Срезные шпильки на накладках
Срезные шпильки на крышках болтовых соединений могут мешать затяжке болтов. Это следует учитывать проектировщику при детализации болтовых соединений. Количество срезных шпилек на накладках должно быть минимальным и располагаться на продольной центральной линии (как можно дальше от болтов). Расстояние между срезными шпильками не должно быть меньше 75 мм, в противном случае для сварочного пистолета, используемого для соединения срезных шпилек, не будет достаточно места.Расстояние между срезными штифтами ограничено максимум 800 мм согласно BS EN 1994-2 [5]
Расположение срезных шпилек на крышке
(Изображение любезно предоставлено Mabey Bridge Ltd.)
[вверху] Толщина крышки
Пример нескольких более тонких накладок
(Изображение любезно предоставлено Mabey Bridge Ltd.)
Накладки толщиной более 30 мм могут стать слишком жесткими, чтобы болты с предварительным натягом в стыковых соединениях могли правильно прилегать. Если требуются стыковые накладки толщиной более 30 мм, подрядчик по изготовлению металлоконструкций часто предлагает комбинацию более тонких пластин, которые достаточно гибки, чтобы справиться с небольшими волнами, угловыми изменениями и ступенями.
[вверху] Толщина и материал упаковочной плиты
Доступны упаковочные плиты толщиной до 1 мм.В стыках, где разница в толщине между соединительными элементами составляет менее 2 мм, уплотнительные пластины не требуются.
Толщина упаковки
Если толщина листа в месте стыка изменяется на 2 или 3 мм, как это обычно бывает в балочных стенках, требуется упаковка 1 мм на каждой поверхности, чтобы избежать смещения стенок и, как следствие, увеличения риска возникновения проблем при установке болтов во фланцах. Минимальная толщина пакета 1 мм теперь разрешена в BS EN 1090-2 [1] , охватывающем как предварительно нагруженные, так и ненагруженные соединения.
Материал упаковки
В пункте 8. 1 стандарта BS EN 1090-2 [1] говорится, что «Уплотняющие пластины должны иметь совместимую… механическую прочность с соседними пластинчатыми компонентами соединения». В этом случае «совместимый» не следует интерпретировать как «аналогичный», потому что не всегда возможно получить небольшие количества тонкого материала для пакетов в предварительно нагруженных соединениях с такими же классами, что и соединяемые элементы. Для пакетов толщиной менее 7 мм углеродистую сталь можно покупать только таких марок, как DC01 по BS EN 10130 [6] , которые не имеют гарантированных механических свойств, а прокладки из погодоустойчивой стали доступны только из стали Corten A, которая имеет более низкий предел текучести. прочность и UTS, чем у S355W согласно BS EN 10025-5 [7] и отсутствие гарантии прочности.На практике сжимающее напряжение из-за предварительной нагрузки и напряжение сдвига из-за сопротивления скольжению намного ниже, чем минимально возможный предел текучести для стального материала, и нет риска хрупкого разрушения, поэтому эти альтернативные материалы приемлемы для использования в качестве набивки в предварительно нагруженные стыки.
[вверх] Закрытые помещения
Пример отверстий для доступа в коробчатой балке
(Изображение любезно предоставлено Mabey Bridge Ltd.)
Согласно действующему законодательству о МЧР [4] , работы в «замкнутых пространствах» следует избегать, если это экономически выгодно. Коробчатые балки «с открытым верхом» создают такое ограниченное пространство после того, как плита настила будет построена, и обслуживание внутренней системы защитной обработки станет проблемой для клиента. Закрытые коробчатые балки образуют ограниченное пространство после того, как закрывающая пластина коробчатой балки была размещена во время сборки. Поэтому такие коробки также становятся проблемой для подрядчика по изготовлению металлоконструкций во время изготовления и любой начальной внутренней окраски.
Всю внутреннюю окраску можно с минимальными затратами избежать, используя погодостойкую сталь. Дополнительные затраты на сталь не полностью компенсируются отказом от внутренней окраски, но премия небольшая, особенно если принять во внимание затраты и риски, связанные с обслуживанием внутренней системы.
Производственные работы внутри коробки также должны быть максимально сведены к минимуму. Проектировщик может внести свой вклад в это, детализируя угловые сварные швы для закрывающей пластины в секции коробчатой балки как внешние сварные швы и спроектировав коробчатую балку таким образом, чтобы сварные соединения между любыми внутренними ребрами жесткости и закрывающей пластиной не требовались.
Там, где это невозможно, необходимо создать безопасную систему работы для изготовления коробчатой балки. В дополнение к достаточному удалению дыма это часто приводит к прорезанию отверстий для доступа в стенке коробчатой балки рядом с любыми стыковыми сварными швами или внутренними ребрами жесткости, которые могут быть закрыты после завершения изготовления, используя панели заполнения, которые привариваются встык к стенке балки с использованием односторонние наружные стыковые швы с внутренней подкладкой.
Все вышеперечисленное приведет к значительному увеличению затрат на изготовление любой коробчатой балки.
Нанесение покрытия на готовую балку
(Изображение любезно предоставлено Mabey Bridge Ltd.)
Защитная обработка обычно проводится после завершения всех производственных операций, но до того, как будут собраны какие-либо компоненты с болтовым соединением. Наряду со спецификацией того, что должно быть защищено, должна быть четко указана информация о том, какие поверхности не должны защищаться на данном этапе.
Защитная обработка
(видео любезно предоставлено Mabey Bridge Ltd.)
[вверх] Доступ для покраски
Проектировщики должны учитывать доступ, необходимый для применения защитной обработки ко всем участкам открытых стальных конструкций, где это необходимо. Это часто может быть проблемой на концах перекошенных мостов, где комбинация скошенных опор / ребер жесткости и квадратных концевых пластин / подъемных ребер жесткости может привести к полузамкнутым стальным конструкциям, к которым трудно получить доступ для окраски.
[вверху] Концевая защита ребра жесткости
В тех случаях, когда промежуточные ребра жесткости сокращаются за пределами нижней полки главной балки, предельная длина между нижней стороной ребра жесткости и нижней полкой, требуемая BS EN 1993-1-5 [8] , недостаточна для обеспечения защитной обработки. надлежащим образом приложен к концам, если элемент жесткости обрезан под прямым углом. Обрезка конца ребра жесткости под углом 45 ° позволит избежать этой проблемы.
Типичное ребро жесткости стенки
(Изображение любезно предоставлено Mabey Bridge Ltd.)Возврат краски на верхний фланец
(Изображение любезно предоставлено Mabey Bridge Ltd.)
[вверху] Возврат краски верхнего фланца
Возврат защитной обработки по краям верхних фланцев главной балки не должен выходить за пределы внешней поверхности срезных шпилек. В противном случае краску придется наносить кистью, потому что ее нельзя распылить без риска покрасить некоторые шпильки. Проектировщик должен учитывать это при детализации расположения опалубки и расположения срезных стоек.
[вверху] Шлифование кромок
Автоматический кромкошлифовальный станок
(Изображение любезно предоставлено Mabey Bridge Ltd.)
Исторически сложилось так, что края открытых пластин были закруглены до радиуса 3 мм. Однако при использовании современных систем защитной обработки эпоксидной смолы с процессами химического отверждения (более старые системы акрилатного каучука основывались на процессе отверждения испарением), которые можно наносить более толстыми однослойными слоями, обычно считается достаточным закруглить края до радиуса 2 мм. Это было признано Highways England в их Спецификации для дорожных работ [2] .
[вверх] Транспорт
Чтобы максимально увеличить объем работ, выполняемых в рамках производственных работ, и, таким образом, достичь высочайшего качества, стальная конструкция изготавливается из частей, размер которых может быть разумно доставлен на строительную площадку. Проектировщик должен предвидеть, как конструкция будет разделена на отдельные компоненты для доставки на площадку, особенно с учетом размеров элементов и положений стыков.Ограничения, связанные с транспортировкой сфабрикованных предметов автомобильным транспортом в пределах Великобритании, кратко изложены ниже:
Вид нагрузки | Максимальные габариты автомобиля | Требуется уведомление | |||
---|---|---|---|---|---|
Длина жесткого | Ширина | Масса | Полиция | HA | |
Нормальный | 18.![]() | 2,9 м | 44 тонны | Нет | Нет |
Ненормальное | 27,4 м | 5,0 м | 44 тонны | 2 дня | Нет |
18,65 м | 2,9 м | 80 тонн | Нет | 2 дня | |
30 м | 5,0 м | 80 тонн | 2 дня | 2 дня | |
30 м | 5.0 м | 150 тонн | 2 дня | 5 дней | |
30 м | 6,1 м | 150 тонн | 2 дня | 10 дней | |
Спецзаказ | > 30 м | > 6,1 м | > 150 тонн | 5 дней | 10 недель |
Транспортировка длинной балки
(Изображение любезно предоставлено Mabey Bridge Ltd.)
Указанные ограничения могут быть изменены, и могут применяться местные ограничения, поэтому приведенную выше таблицу следует использовать только в качестве руководства. Обратитесь к GN 7.06 за дополнительными советами.
Ограничения, установленные Highways England, относятся к перемещению грузов по основным дорогам и не принимают во внимание физические ограничения, такие как уличная мебель, крутые повороты и горбатые мосты, которые существуют рядом с производственными заводами или рядом с площадкой моста .
Доступ к строительной площадке и размещение монтажного завода должны быть спланированы и упорядочены, чтобы свести к минимуму нарушение работы смежных служб / инфраструктуры.Доступ на площадку должен быть согласован со схемой управления движением, чтобы кран и стальные конструкции могли быть доставлены на площадку и мобилизованы с минимальными нарушениями.
Проиллюстрированные здесь подвесные балки длиной 35 м были доставлены на строительную площадку в виде пары скоб для однопролетного неразъемного моста. Возможность транспортировать балки на всю длину избавляет от необходимости проектировать стыки на месте и необходимости места на месте для сборки балок на большие длины или в пары.
[вверх] Монтаж моста
Как устроен мост и как он построен, связаны между собой.Признание этой ссылки повлияет на безопасность и качество строительства. Способы возведения стальных мостовых конструкций значительно различаются от участка к объекту и от проекта к проекту. Таким образом, тема эрекции — обширная и разнообразная тема. В этом разделе рассматриваются аспекты, которые следует учитывать на этапах начального и детального проектирования.
Дополнительную информацию можно найти в Руководстве по установке стальных мостов.
[верх] Установка подшипников
Типовой подшипник
(Изображение любезно предоставлено Mabey Bridge Ltd.)
Первыми стальными конструкциями, которые будут возведены на месте, являются опоры моста. Функция опоры — переносить вес надстройки на основание. Они также могут передавать поперечные и продольные силы. Они несут большие силы, но могут быть легко повреждены из-за неправильного обращения или установки. Производители поставляют подшипники в виде целых узлов, скрепляемых транспортировочными болтами, которые предназначены в основном для транспортировки и установки. После того, как подшипник установлен и балка приземлилась, важно, чтобы шипы были освобождены, чтобы стальные конструкции могли «дышать» контролируемым образом.
подшипники могут поставляться прикреплены к балкам, но она является более общим для них, чтобы быть выровнены и выравнивают на подструктуры и прикреплены к балкам впоследствии. Конструктор должен дать четкие инструкции относительно линии, уровня и настройки подшипников, чтобы гарантировать их правильную работу при эксплуатации. Подшипники либо привинчиваются к конической пластине (в резьбовых отверстиях), либо через конусную пластину и фланец, однако последний не является предпочтительным, поскольку он отделяет позднее предоставление информации о подшипниках от изготовления балок.Поскольку в настоящее время общее требование о том, что опоры моста должны быть заменяемыми, необходимо выбирать для облегчения замены.
Конструктор должен предусмотреть безопасный доступ для точной установки подшипников. Возможно, потребуется сохранить средства доступа для обслуживания и замены подшипников.
[вверх] Монтаж с помощью кранов
Монтаж с использованием кранов считается наиболее экономичным методом возведения большинства конструкций.Однако обратите внимание, что только гусеничные краны и некоторые небольшие мобильные краны для пересеченной местности могут перемещаться по площадке с грузом. Участки площадки, прилегающие к мосту, повлияют на положение и размер крана, который можно использовать, и это повлияет на грузоподъемность и, следовательно, на выбор крана и размер детали. Площадь для предварительной сборки также влияет на размер подъемника.
Монтаж моста Порт с использованием мобильных кранов
(Изображение любезно предоставлено Mabey Bridge Ltd.)Виадук Лагентиум, A1 (М) Даррингтон — Дишфорт
(Изображение любезно предоставлено Mabey Bridge Ltd.)
Компактный и загруженный участок (вверху слева) показывает строительство моста через реку, железную дорогу и дорогу; мост находится рядом с прилегающими зданиями. Для главного моста была выбрана арка на привязи, а для пролета реки — лестничная площадка. Такой выбор позволил возвести палубы небольшими частями на временные эстакады, а арку возвести позже.Из-за доступной площади для предварительной сборки и установки кранов каждая арка была возведена в виде трех отдельных частей с максимальным весом 102 т при радиусе 35 м с использованием крана грузоподъемностью 1000 т с подъемником 200 т.
Главный участок пути Даррингтон-Дишфорт (вверху справа) потребовал подъема парных балок длиной 50 м с большим радиусом. Каждая пара балок поднималась скобами, прикрепленными к верхним фланцам. Балки должны быть проверены на наличие этой высокой местной растягивающей силы и на устойчивость при изгибе в середине пролета.Инженер по временным работам обычно устанавливает подъемные планки и проверяет устойчивость балок во время подъемных операций. От проектировщика постоянных работ обычно не требуется смотреть на это временное состояние.
Щелкните здесь, чтобы увидеть мост кряквы на дороге Уайт Роуз, Донкастер, устанавливаемый над главной линией Восточного побережья с использованием одного из крупнейших мобильных кранов в Великобритании.
Щелкните здесь, чтобы увидеть арочный лифт на Центральном мосту Линк в Мертир-Тидвиле.
[вверх] Специализированный транспорт
Транспортировка предварительно собранного настила
(Изображение любезно предоставлено Mabey Bridge Ltd.)
Если подъем в рабочее положение не подходит, например, когда нет места для крана или поблизости есть воздушные кабели, одним из вариантов является сборка стальных конструкций на низком уровне вдали от (но близко к) фактической площадки моста. . Затем собранные стальные конструкции поднимаются домкратом, чтобы позволить специальным транспортным единицам под палубой. Затем блоки используются для транспортировки деки на место.
Транспортировка является наиболее подходящей, когда весь мост можно транспортировать как единое целое.Таким образом, его можно предварительно смонтировать на временных опорах, которые не создают высоких местных сил или не блокируют напряжения, зависящие от последовательности монтажа. Предварительная сборка за пределами площадки также позволяет клиенту продолжить строительство опор и опор моста, например, без нарушения сборки стали.
Щелкните здесь, чтобы увидеть, как мост Ли-Роуд устанавливается с использованием специальных транспортных средств в Слау.
[вверх] Запуск
Монтаж металлоконструкций над дорогой или рекой включает сборку металлоконструкций, как правило, за устоями на подъезде к шоссе.Металлоконструкции монтируются на роликах с низким сопротивлением или скользящей системе на каждой опоре или временной опоре. Используется тяга и удерживающая система. Металлоконструкции требуют тщательного выравнивания конструкции для обеспечения надлежащей подгонки перед запуском и должны иметь достаточно времени в программе, чтобы это учесть. Однако сборка, как правило, проводится почти на уровне земли, с использованием гораздо меньших и менее дорогих кранов и минимальных работ на высоте.
Щелкните здесь, чтобы увидеть 15-часовой спуск моста за 70 секунд по схеме замены виадука Лугор.
[вверх] Домкрат прядильный
Подъемные домкраты обычно не используются в качестве метода возведения, так как они лучше всего подходят для подъемов больших размеров, которые нельзя выполнять краном. Временные работы по прокладке ручья обычно сложны и дороги; на разделение конструкции на возводимую часть должны влиять возможности оборудования.
Подъемный домкрат, возможно, наиболее часто используется для подъема длинных участков реки в середине пролета с баржи, но он подходит и для других случаев, таких как арка реки Уск, показанная слева.На фото показана схема поддомкрачивания троса центральной части арок пролета 190 м. Центральные части арки подняли на палубу и переместили под домкратные башни. Главный подъемник — 640 тонн. Элементы арки должны были быть спроектированы для фиксированных изгибающих напряжений из-за пролета между положениями подъемника.
[вверху] Влияние продолжительности эрекции
Продолжительность возведения обычно определяется программой клиента, особенностями участка и программой главного подрядчика.Продолжительность возведения на площадке позволяет контролировать баланс между предварительной сборкой на производственной площадке или на площадке, примыкающей к предлагаемому мосту, и элементами конструкции, которые могут быть возведены непосредственно с транспорта.
[вверх] Монтаж на новых участках
участков Greenfield позволяют свободно выбирать методы эрекции и обычно имеют достаточно времени. Стальную надстройку можно установить прямо с транспортного средства, а элементы соединить вместе на месте. Объем предварительной сборки в этой ситуации продиктован преимуществом программы площадки, заключающейся в предварительной сборке металлоконструкций на производственной площадке.На мосту ниже показан монтаж над подъездной дорогой. Это означает, что, хотя доступ для кранов был свободен, временные промежуточные опоры, возможно, были невозможны.
Строительство с нуля
M6 Toll
[вверх] Возведение во время владения
Мост на Шордич-Хай-стрит
(Изображение любезно предоставлено Mabey Bridge Ltd.)
Требование поддерживать транспортный поток, будь то автомобильный, железнодорожный или водный, может серьезно ограничить продолжительность монтажных работ. В таких случаях монтаж должен происходить в течение фиксированного или определенного периода «владения».
Работа в любой форме владения требует тщательного и точного планирования. Часто цена перебега может быть чрезмерной для обеих сторон. Если это так, может быть полезно, чтобы большая часть конструкции была предварительно собрана перед монтажом.Затем весь мост можно поднять на место с помощью большого крана, установленного рядом с площадкой.
Конструкция должна предусматривать максимально возможную сборку конструкции перед возведением, с минимальным объемом работ по размещению и фиксации после того, как мост будет установлен. В некоторых случаях строительство колоды может продолжаться после возведения, но в других случаях колода должна быть отлита заранее. Использование несъемной опалубки очень выгодно для возведения во владение, поскольку она обеспечивает безопасную рабочую платформу для завершения плиты перекрытия.
Показанный здесь арочный мост, который несет продолжение линии Ист-Лондона над Шордич-Хай-стрит, был смонтирован за одним из опор и поднят краном во время 36-часовой выдержки на дороге. Перед подъемом уложили постоянную опалубку и арматуру настила. Полная масса составила 353 т. Владение дорогой было забронировано на несколько месяцев вперед.
[вверху] Устойчивость во время монтажа
Manchester Ship Canal — Manchester Metro Link
(Изображение любезно предоставлено Mabey Bridge Ltd.)
Эффективная конструкция пластинчатых балок с рядом параллельных стальных пластинчатых балок с использованием композитной конструкции позволяет получить небольшие верхние фланцы. Это делает их склонными к продольному изгибу при кручении во время строительства, прежде чем плита затвердеет. Также существует риск нестабильности во время погрузки-разгрузки, доставки и воздействия сильного ветра. Следовательно, дизайнеры должны учитывать стройность в различных условиях монтажа.
Наиболее распространенным способом повышения устойчивости является сборка балок в пары скоб, что делает их более устойчивыми во время подъема и на месте по сравнению с одиночной балкой.Повышенная устойчивость может также снизить потребность в опорных эстакадах. Как следствие, монтаж на месте будет короче, так как большой процент болтовых соединений и окраски будет завершен до возведения конструкции. Однако транспортировка скрепленных пар увеличивает транспортные расходы.
В идеале проектировщики должны использовать любые временные распорки для обеспечения эксплуатационных характеристик и, таким образом, сделать их постоянными. Как правило, постоянные связи более экономичны и позволяют избежать опасностей, связанных с их удалением.Операция по удалению временных распорок по своей природе опасна из-за ограниченного пространства над головой после заливки настила. Это затрудняет установку подходящих средств для опускания того, что часто бывает довольно тяжелыми кусками стали. Эта опасность еще более усугубляется, если связи расположены над дорогой или железной дорогой.
[вверх] Конструкция палубы
Монтаж балок с консольными опалубками и опалубкой
(Изображение предоставлено Mabey Bridge Ltd.)
Предварительная сборка для композитной конструкции может использоваться для установки ответственных опалубок и опалубки, временных и постоянных проходов и защиты краев перед подъемом секции моста на место. Преимущество этого двоякое. Опалубку можно установить на низком уровне, что по своей природе более безопасно, а также исключает эту операцию на критическом пути. В противном случае опалубка будет установлена после завершения возведения.
Системы ложных работ, подобные показанной выше, были разработаны таким образом, чтобы их можно было прикреплять и снимать без какого-либо значительного риска повреждения защитной обработки (или загрязнения поверхности атмосферостойкой стали).Это устраняет необходимость в последующей обработке поверхности, экономя время и деньги.
[вверх] Список каталогов
- ↑ 1,0 1,1 1,2 1,3 1,4 1,5 1,6 BS EN 1090-2: 2018, Выполнение стальных и алюминиевых конструкций. Технические требования к стальным конструкциям, BSI
- ↑ 2,0 2,1 2,2 Руководство по контрактной документации на дорожные работы (MCHW).Том 1: Технические условия на дорожные работы. Конструкционные стальные конструкции серии 1800. Август 2014, TSO
- ↑ NR / L2 / CIV / 140 / 1800C Технические условия на стальные конструкции, Network Rail, июнь 2016 г.,
- ↑ 4,0 4,1 Правила строительства (проектирования и управления) (CDM) 2015
- ↑ BS EN 1994-2: 2005, Еврокод 4. Проектирование композитных стальных и бетонных конструкций. Общие правила и правила для мостов. BSI.
- ↑ BS EN 10130: 2006, Плоский прокат из холоднокатаной низкоуглеродистой стали для холодной штамповки.Технические условия поставки, BSI
- ↑ BS EN 10025-5: 2019, Технические условия поставки конструкционных сталей с повышенной стойкостью к атмосферной коррозии, BSI
- ↑ BS EN 1993-1-5: 2006 + A2: 2019, Еврокод 3. Проектирование стальных конструкций. Металлические элементы конструкции, BSI
[вверх] Ресурсы
- Стальные мосты: практический подход к проектированию для эффективного изготовления и строительства, 2010 г. (Публикация № 51/10), BCSA,
- Глава 4 Болтовые соединения
- Глава 5 Сварка
- Глава 6 Точность
- Стоимость главы 7
- Глава 8 Примеры из практики
- Хенди, К.Р.; Айлс, округ Колумбия (2015) Steel Bridge Group: Рекомендации по передовой практике в строительстве стальных мостов (6-й выпуск). (P185). SCI
- Ильес, округ Колумбия (2015) Определение проектных смещений для подшипников движения моста. (P406). SCI
- Сертификат и контрольный список передачи безопасной площадки, 2008, BCSA
- Руководство по установке стальных мостов, 2005 г. (Публикация № 38/05), BCSA
[вверху] См. Также
[вверх] Внешние ссылки
ОбновлениеWelding для Infrastruture: мост в любую точку
Сказать, что Stinger Welding Inc.уникальный, можно было бы не сказать ничего. В конце концов, сертифицированный AISC производитель мостов и их компонентов из Кулиджа, штат Аризона, гордится своей командой, чьи средства к существованию — изготовление, сборка и монтаж компонентов, которые удерживают человеческую жизнь в равновесии. А с учетом проектов, за которые взялась компания, и того, как они были реализованы, у кого хватит смелости оспорить их?
Работающая с 1996 года компания Stinger Welding зарекомендовала себя как производитель, с которым нужно считаться на Юго-Западе.По словам Гэри Гарднера, менеджера по обеспечению / контролю качества и CWI, где работает около 100 сварщиков, компания, наиболее известная своей способностью быстро выполнять проекты, добилась успеха благодаря высокому качеству своей рабочей силы и приверженности каждого отдельного человека. для Стингера.
«Одна из вещей, которые мне очень нравятся в этом месте, — это то, что у нас очень хорошая рабочая сила», — сказал Гарднер.
«Все начинается с людей, занятых производством. Если они не полностью привержены этому, то контроль качества ничего не может сделать, чтобы это исправить.Как бы тщательно вы что-то ни проверяли, вы не превратите плохое в хорошее. Он должен исходить из низов ».
Быстрая работа, поддержание качества
Приверженность Stinger быстрому завершению проектов не означает, что компания жертвует качеством. Все построено в соответствии с требованиями к качеству, указанными в кодексах и выше, объяснил Гарднер.
«У нас очень низкий процент брака в этом месте».
Отчасти причина того, что качество сварных швов было таким хорошим, по словам Гарднера, — это процессы, на которые компания в значительной степени опирается.Компания предпочитает использовать порошковую сварку, газовую сварку металлической порошковой проволокой, приварку шпилек и дуговую сварку под флюсом (SAW) для более крупных деталей. На самом деле, нередко можно увидеть сварщиков, использующих установку SAW в полевых условиях.
Как правило, изготовление мостов и дуговая сварка в экранированном металле (SMAW) идут рука об руку. Но в компании Stinger SMAW — это не процесс выбора. Вместо этого FCAW составляет от 80 до 90 процентов сварочных работ, выполняемых в цехе и на строительной площадке.
«Мы возьмем с собой генератор с постоянным напряжением и чемоданскую сварочную установку с механизмом подачи проволоки и газовыми баллонами, и поднимем их краном, где нам нужно сваривать.Я слышал, как приходят несколько ДОТов и говорят: «Мы никогда раньше не видели, чтобы кто-то делал это. Вы возводите с сердечником из флюса? Да. Вы можете подняться и провести рентгеновское обследование или ультразвуковое испытание, и оно пройдет ».
Бывают случаи, когда SMAW является очевидным выбором, объяснил Гарднер, например, в труднодоступном месте, где сварщик может согнуть электрод, чтобы дотянуться до него. По словам Гарднера, SMAW не имеет смысла для тяжелых конструкций, в которых сварные швы должны быть действительно хорошими.
«Это очень медленно и сложнее контролировать электрод.С FCAW мы почти всегда получаем действительно высококачественные сварные швы с минимальными переделками. Мы можем спать по ночам, потому что знаем, что построили что-то хорошее ».
MacArthur Maze
В 2007 году бензозаправщик перевернулся на калифорнийской межштатной автомагистрали 880, загорелся и разрушил два пролета путепровода на межштатной автомагистрали 580 недалеко от Окленда. Департамент транспорта Калифорнии (Caltrans) немедленно объявил проект реконструкции моста для участия в торгах на этот отрезок шоссе, известный как лабиринт Макартура, который обслуживает более 150 000 автомобилей в день.
«Авария с танкером имела немедленные и далеко идущие последствия для местной экономики. Транспортные потоки пришлось изменить, другие строительные проекты были отложены, а общественный транспорт был ужасно перегружен. По первоначальной оценке Caltrans, для завершения работ потребуется не менее шести месяцев. реконструкция «, — пояснил Гарднер.
Stinger Welding выиграла субподряд на поставку 12 пластинчатых балок, что позволит провести аварийный ремонт.
Опыт компании в строительстве критичных к разрушению мостовых конструкций (проекты, требующие специальной сертификации из-за несущей конструкции) помог ей выиграть тендер.
Покупатель стали у Стингера немедленно позвонил и нашел все нужные сорта стали примерно за полчаса. Поскольку это был проект, финансируемый из федерального бюджета, сталь должна была быть произведена в США.
После того, как сталь была заказана, компания наняла двух водителей грузовиков для беспосадочной перевозки материала с восточного или юго-западного побережья прямо на предприятие Stinger.
«Сталь начала поступать на следующий день после того, как мы ее заказали. Она попала прямо на стол для обжига, и мы начали резать ее на куски», — сказал Гарднер.
Соответствуя строгим стандартам AWS и Caltrans, пластинчатые балки — или структурные опоры — для лабиринта МакАртура имели высоту 42 дюйма, самая длинная — 90 футов, а самая короткая — около 60 футов. Они построены из A709 Grade 50. , высокопрочная низколегированная конструкционная сталь.
Большая часть каждой плоской балки, изготовленной на месте на заводе Stinger, была изготовлена с использованием SAW. Стингер выбрал источники питания Lincoln Electric Idealarc® DC-1000, тракторные механизмы подачи проволоки LT-7, механизмы подачи проволоки NA-3 с проволокой Lincolnweld® LA-75 и флюсом 888 ™.
Источники энергии использовались в сочетании с тремя тракторами и двумя подающими механизмами на манипуляторах, что позволило изготавливать эти балки с применением SAW. Стингер обнаружил, что комбинация проволоки и флюса, а также источника питания с тремя тракторами и механизмом подачи проволоки дает ряд преимуществ на протяжении всего производственного процесса.
Во-первых, он удовлетворил потребность в высокопрочной проволоке и флюсе с низким содержанием водорода, которые необходимы для надежной сварки мостовой стали AASHTO M270 / ASTM A709 Grade 50 в соответствии с AWS D1.5 код.
«Сварные швы, полученные в результате этой комбинации, неизменно соответствуют требованиям к механическим свойствам и обеспечивают чрезвычайно хорошую ударную вязкость при низких температурах», — сказал Гарднер.
Комбинация проволочного электрода и флюса является многоцелевой, и компания Stinger смогла использовать одну и ту же пару расходных деталей для всех применений на ПАВ, включая сварку атмосферостойкой стали. Это привело к экономии времени и средств, поскольку требовалось меньше протоколов аттестации процедур (PQR) и спецификаций процедур сварки (WPS).
Оборудование также позволяло быстро изменять конфигурацию для различных сварочных процессов, включая FCAW, газовую дуговую сварку металлическим электродом (GMAW), газовую дуговую сварку вольфрамовым электродом (GTAW) и SMAW, а также SAW, что сокращало время, затрачиваемое Stinger на периодическая калибровка в соответствии с требованиями AWS.
Работая в две смены по 10 часов, компания смогла изготовить 12 пластинчатых балок всего за восемь дней, что позволило открыть пролеты моста I-580 всего за три месяца — на шесть недель раньше лучших оценок.Изначально Caltrans рассчитывала, что для завершения реконструкции потребуется не менее шести месяцев.
«У Caltrans было шесть штатных инспекторов на месте, которые проверяли и неразрушающим образом проверяли 10 процентов сварных швов, и они почти не могли угнаться за нами. Мы никогда не видели, чтобы DOT двигался так быстро», — сказал Гарднер.
В дополнение к быстрому ремонту, внимание компании Stinger к деталям воплотилось в каждой из его 12 балок на проходящем осмотре лабиринта MacArthur Maze без каких-либо переделок на месте.
Строим мосты безопаснее и прочнее с помощью приварки строительных шпилек
Приварка шпилек — это уникальная сварочная операция, поскольку она имеет очень широкий диапазон применений, различающихся несколькими способами, включая размер, прочность и функцию сварного шва и шпильки, а также используемые материалы. Тем не менее, приварка шпилек часто считается легким игроком в сварочных процессах. Хотя это правда, что приварка шпилек очень эффективна во многих небольших приложениях, она одинаково эффективна в широком спектре крупномасштабного производства.
В каждой обрабатывающей промышленности существуют различные применения приварки шпилек, больших и малых. Когда дело доходит до конструкций и строительства зданий, приварка шпилек имеет больше применений, чем любой другой вид сварки. С помощью крепежных систем Northland вы можете найти услуги и инструменты, необходимые для любого проекта приварки строительных шпилек, независимо от масштаба.
Приварка строительных шпилек может выполняться методами приварки шпилек конденсаторным разрядом или дуговой сваркой, и это часто используется для ряда строительных проектов.Некоторые распространенные крупномасштабные применения приварки шпилек в строительной отрасли включают конструкции парковок, высотные здания, стадионы, водонапорные башни и мосты.
В частности, мосты требуют особого подхода к строительству, когда дело доходит до применения приварки шпилек.
Сварные шпильки в мостуПриварка шпилек используется на многих типах мостов. Основная функциональная роль точек приварки шпилек в подавляющем большинстве мостов — удерживать и / или укреплять соединители, работающие на сдвиг, к бетонному основанию:
- Точки подключения : Сварка шпилек используется для создания прочных соединений.Этот процесс позволяет сжиматься и расширяться при изменении температуры и ветре, влияющем на мост, без нарушения структурной целостности.
- Точки соединения пластин : Некоторые компоненты моста состоят из стальной обшивки и других подобных секций, собранных вместе, чтобы сформировать полную конструкцию моста. Эти секции часто соединяются с помощью процесса приварки шпилек к бетону. В частности, приварка шпилек часто используется для соединения стальных балок с бетонными плитами в сочетании с мощными сетками, образуя прочное и гибкое соединение.
- Шпильки противоскольжения . Эти шипы создают эффект грохота, который водители слышат при въезде и выезде с моста.
Без дополнительной прочности и необходимого учета движения в условиях непогоды и ветра, которые обеспечивает сварка шпилек, мосты не были бы такими безопасными и эффективными, как сегодня.
Найдите здесь принадлежности для сварки шпилек
Чтобы узнать больше о приварке строительных шпилек или других применениях приварки шпилек, свяжитесь с Northland Fastening Systems по телефону (651) 730-7770 или , чтобы запросить расценки сегодня.
(PDF) Усталость мостовых соединений с использованием сварных труб или стальных узловых решений
4 РЕЗЮМЕ И ВЫВОДЫ
Из интерпретации и сравнения результатов испытаний
между непосредственно сваренными и литыми стальными узлами
можно вспомнить основные моменты:
— Установлено, что сварные соединения имеют усталостную прочность
ΔσC = 86 МПа, что аналогично усталостной прочности
ΔσC = 87 МПа для кольцевых стыковых швов
с подкладными стержнями.
— Кривая усталостной прочности в горячих точках кольцевого стыка
сварных швов между отливками и элементами CHS
соответствует ΔσC = 54 МПа без подкладки
стержней и ΔσC = 87 МПа с подкладными стержнями. При расчете диапазона напряжений
необходимо учитывать коэффициент концентрации напряжений
(SCF) из-за различий в толщине
и диаметре трубчатых элементов и отливок
заглушек.
— Значительное различие в усталостных характеристиках
между сварными соединениями и литыми узлами было ob-
послужило причиной растрескивания в сварных соединениях
направлено высокой концентрацией напряжений в подошвах сварных швов, а в
— на литых узлах. вызвано в основном корнем шва
дефектами кольцевых стыковых швов на отливках.
— Узлы из литой стали особенно подходят для узлов
рядом с опорами или на них. В зоне растяжения в середине пролета
прямые сварные соединения являются лучшим решением с точки зрения усталостной надежности.
На основе численных исследований сварных узлов даны следующие
рекомендаций по снижению:
— Метод напряжений в горячих точках оказался
единственным текущим, широко принятым расчетом на усталость
Методом для сварных трубных соединений .Для определения
SCF существующие формулы руководства по проектированию
не могут быть экстраполированы на низкие значения γ, такие как
γ ≤ 12, типичные для мостов. Для этих случаев новые
SCF были получены на основе анализа FE. Результаты
показывают сильную тенденцию к уменьшению SCF при
уменьшении γ.
— Рекомендуемый минимальный SCF в критических стыках
мест в текущих проектных спецификациях,
SCF = 2,0, является серьезным недостатком, если применяется к
сварным К-образным стыкам мостов CHS.При γ ≤ 12 рекомендованный минимум
SCF можно принять как
SCF = 1,0 для K-образных соединений CHS.
На основе численных исследований узлов из литой стали
даны следующие рекомендации:
— Процедура количественного определения допустимого начального размера дефектов отливки
для обеспечения сбалансированной конструкции между
между различными потенциальными трещинами. площадки
в стальном литом узле разработан для композитного железобетонного моста тип.
.Размер дефекта
варьируется от примерно 28 до 88% от
толщины стенки в месте расположения дефекта отливки
.
— Процедуру можно упростить, выразив
SIF с постоянным поправочным коэффициентом.
ПОДТВЕРЖДЕНИЕ
Проведенное исследование является частью проекта
P591, надзор за которым осуществляет Versuchsanstalt für Stahl,
Holz und Steine при Техническом университете
000 Карлсруэ при финансовой поддержке
при финансовой поддержке ForschungsvereinigungStahlanwendung e.V. (FOSTA), Дюссельдорф, в пределах
, Stiftung Stahlanwendungsfor-
schung, Essen. Представленный здесь материал
также содержит результаты предыдущих исследований, спонсированных
Швейцарским федеральным управлением автомобильных дорог (FEDRO) и
Швейцарским национальным научным фондом (SNF).
СПРАВОЧНАЯ ИНФОРМАЦИЯ
Блэр М., Стивенс Т. Л., Справочник по стальному литью, Стальной фонд-
Американское общество и ASM International, 1995.
DNV, Анализ усталостной прочности морских стальных конструкций.
Рекомендуемая практика RP-C203. Det Norske Veritas,
2001.
Haldimann-Sturm, SC, Ermüdungsverhalten von Stahlguss-
, зарегистрированный в Брюккене на Stahlhohlprofilen, EPFL Thesis No.
3274, сварная труба
3274, Lausann, Lausann подключения, Basis
и использование положений AWS, Elsevier Science Publishers,
Amsterdam, 1992.
Милн, И., Эйнсворт, Р.А., Дауллинг, А.Р., Стюарт, А.Т., As-
Оценка целостности конструкций, содержащих дефекты,
R / H / R6 — Редакция 3, Центральный совет по производству электроэнергии,
Май 1986.
Рауль, Дж., Фотография сделана во время строительства моста Сен-Килиан
на шоссе A73, недалеко от Шлейзингена, Германия,
2005.
Шумахер А., Нуссбаумер А. Экспериментальное исследование на
усталостные характеристики сварных трубчатых К-образных соединений мостов.
Engineering Structures, Elsevier Science, 28 (5), стр. 745-
755.
Шумахер, А. Усталостное поведение сварных полых круглых отверстий
стыков секций в мостах. EPFL Thesis No. 2727, Lausanne,
2003a.
Schumacher, A., Sturm, S., Walbridge, S., Nussbaumer, A.,
Hirt, MA Расчет на усталость мостов с круглыми сварными швами
полых профилей Отчет ICOM n0 489E, ICOM / EPFL,
Lausanne , 2003б.
SIA 261, Einwirkungen auf Tragwerke, Schweizerischer Inge-
nieur- und Architektenverein, 2003.
Штурм, С., Нуссбаумер, А., Хирт, М.А., Усталостное поведение узлов из литой стали
в мостовых конструкциях, Proceed. 10-го
Внутр. Symp. по трубчатым конструкциям, стр. 357-364, Tubular
Structures X, A.A. Издательство Balkema, Мадрид, 2003.
Веселчич, М., Герион, С., Путли, Р., Литая сталь в трубчатых мостах
— новые приложения и технологии, Proceed.
10-го Межд. Symp. on Tubular Structures, pp. 135-142, Tubu-
lar Structures X, A.A. Balkema Publishers, Madrid, 2003.
Zhao, XL. Et al., Руководство по проектированию круглых и прямоугольных соединений
полых профилейпри усталостной нагрузке, CIDECT, №
8, TÜV-Verlag Rheinland, Köln, 2000
Чжао, XL, Пакер, JA, Методика расчета на усталость сварных соединений полых профилей
, Док. XIII-1804-99, XV-1035-99,
IIW, Кембридж, Абингтон, 2000.
Зданий | Бесплатный полнотекстовый | Усталостные детали в стальных мостах
1.Введение
Мосты — жизненно важная часть инфраструктуры в любом современном обществе. В Европе, как и во многих других частях индустриального мира, быстрое промышленное развитие, имевшее место в первой половине XIX века, сопровождалось огромным расширением инфраструктуры, включая мосты в количественном отношении. Сегодня многие железнодорожные и автомобильные мосты, построенные в тот период, все еще используются, несмотря на то, что их технический срок службы — во многих случаях — считается уже завершенным.Недавнее картирование возрастного профиля существующих стальных железнодорожных мостов в Европе [1] показывает, что более 70% этих мостов имеют возраст более 50 лет и около 30% из них — более 100 лет. Кроме того, этот старый парк железнодорожных и шоссейных мостов в настоящее время подвергается более строгим требованиям с точки зрения повышенной интенсивности движения и более высоких транспортных нагрузок, чтобы соответствовать требованиям более эффективных транспортных систем.Если говорить о стальных мостах, усталость часто является серьезной проблемой, ограничивающей несущую способность и остаточный срок службы существующих конструкций.Правильная идентификация подверженных усталости деталей в мосту, наряду с хорошо спланированными процедурами проверки и успешными графиками укрепления и ремонта, могут гарантировать непрерывную и удовлетворительную работу мостов в течение их срока службы. Также в новом строительстве важно избегать деталей конструкции, которые, как было показано, подвержены усталости на этапе проектирования. В результате информация об усталостных характеристиках различных деталей существующих мостов жизненно важна для менеджеров или владельцев мостов, а также является обратной связью для проектировщиков и инженеров мостов.
В исследовании, посвященном усталостным характеристикам существующих стальных и композитных мостов [2], были собраны случаи усталостных повреждений, которые были зарегистрированы для различных типов мостов и деталей. В общей сложности более 100 случаев повреждения были изучены и классифицированы в соответствии с типом деталей и / или механизмом наблюдаемого усталостного растрескивания. Результаты этого исследования показывают, что более 90% всех зарегистрированных случаев вызваны вторичными эффектами, так называемым растрескиванием, вызванным деформацией.Этот тип усталостного повреждения часто является результатом вторичных сдерживающих сил, возникающих в результате какого-либо непреднамеренного или недооцененного взаимодействия между различными элементами моста. Плохая детализация, наряду с незакрепленными зазорами и резкими изменениями жесткости в соединениях между различными элементами, также способствует усталостному растрескиванию большинства деталей. Нормы проектирования и методы оценки обычно содержат очень мало указаний о том, как следует учитывать или предотвращать такой вид усталостного повреждения.Проектировщик моста несет ответственность за то, чтобы за счет хорошей детализации избежать этих вторичных эффектов и связанных с ними усталостных повреждений. На рисунке 1 показаны собранные случаи повреждений, сгруппированные по типу деталей. Наиболее распространенные виды усталостных повреждений, вызванных деформацией, можно найти в соединениях между стрингерами и балками перекрытия, между последними и основными несущими элементами моста, а также в местах соединения диафрагм и поперечных распорок.Кроме того, довольно часто встречаются усталостные повреждения деталей ортотропных настилов и элементов мостов со скошенными концами или обрезанными фланцами в местах их соединения с другими элементами. В этой статье рассматривается ряд общих деталей мостов, подверженных усталостным повреждениям. Обсуждаются механизмы, лежащие в основе усталостного растрескивания для каждого типа деталей, и решаются проблемы, связанные с плохой детализацией и упущенным или непредвиденным поведением и воздействием нагрузки.Рисунок 1. Собраны случаи усталостных повреждений, перечисленные в соответствии с типом деталей, в которых они были обнаружены.
Рисунок 1. Собраны случаи усталостных повреждений, перечисленные в соответствии с типом деталей, в которых они были обнаружены.
2. Усталостное растрескивание от дефектов сварных швов
В целом сварные детали более подвержены усталостному растрескиванию по сравнению с болтовыми или клепанными деталями. Дефекты и неоднородности сварного шва, такие как подрезы сварного шва, застрявшие пористости и отсутствие плавления, являются концентраторами напряжений, из-за которых может инициироваться усталостное растрескивание.Неблагоприятные сварочные остаточные напряжения и концентрации напряжений из-за геометрии сварного шва и микротрещин, вызванных сваркой, являются другими факторами, которые часто ускоряют процесс усталостного повреждения деталей сварных мостов.
В очень редких случаях дефекты сварных швов вызывали усталостное повреждение деталей стальных мостов под действием первичных нагрузок. Эти случаи встречаются либо в довольно старых мостах, построенных до того, как методы контроля качества и методы неразрушающего контроля были хорошо разработаны, либо в деталях, которые рассматривались как «второстепенные» для несущей способности моста и поэтому не были включены в контроль качества такого рода.Одним из примеров последнего случая является усталостное растрескивание в балках мостов со сварными продольными ребрами жесткости. Несколько мостов в США испытали этот тип растрескивания [3,4]. Трещины возникли из-за дефектов сварного шва на пересечении угловых сварных швов, соединяющих продольные ребра жесткости со стенкой фермы, и стыковых швов, выполненных для поперечных стыков продольных ребер жесткости, см. Рис. 2. Деталь считалась второстепенной и не проверялась. пересечения сварного шва.Пересечение сварных швов также обеспечивало путь для роста трещины от ребра жесткости в стенку фермы, что в некоторых случаях приводило к хрупкому разрушению. Рисунок 2. Усталостное растрескивание мостовой балки от дефектов сварного шва в точке пересечения сварных швов (по [3]). Рисунок 2. Усталостное растрескивание мостовой балки от дефектов сварного шва в точке пересечения сварных швов (по [3]).3. Детали с изменением в разделе
Детали, которые влекут за собой изменение поперечного сечения элемента или частей элемента, довольно часто встречаются в стальных мостах.Самый простой пример можно найти в плоских балках на переходах размеров полки (ширины, толщины или того и другого). В элементарной детали такого типа хорошо известно, что усталостная прочность детали (в данном случае поперечный стыковой шов) может быть существенно увеличена путем создания плавного перехода между соединенными пластинами. Это может быть достигнуто за счет сужения или закругления соединенной пластины.
Однако существуют более сложные детали, в которых изменение поперечного сечения элемента вызывает сложное состояние напряжения, включающее дополнительные компоненты напряжения, которые могут быть достаточно высокими, чтобы вызвать усталостное повреждение детали.Эти компоненты напряжения обычно довольно трудно предсказать с помощью простого анализа, и проектировщики иногда пренебрегают ими или не обращают на них внимания.
Деталь, в которой были обнаружены многочисленные проблемы усталости в Соединенных Штатах и Японии [5,6], можно найти в мостах Гербера и в мостовых балках с уменьшенной глубиной у опор, рис. 3. Согласно теории балок, изгибающие напряжения в балки возле опоры незначительны, и балка рассчитывается в этих местах с учетом силы сдвига.Из-за уменьшения глубины балки и, как следствие, изменения поперечного сечения, деформация балки вызовет дополнительные касательные и радиальные напряжения в стенке балки и в сварных швах между полкой и стенкой вдоль кривизны выреза, см. рис. 4. Сообщалось о случаях повреждения, связанного с усталостным растрескиванием стенки балки, а также в сварных швах между полкой и стенкой. В последнем случае соединение фланца и стенки осуществлялось угловыми сварными швами. Трещины в стенке фермы могут расти либо в направлении, касательном к кривизне полки (вызванном компонентом радиального напряжения), либо в радиальном направлении (создаваемым компонентом касательного напряжения), см. Рисунок 5.На рисунке 6 показан другой случай, в котором изменение поперечного сечения подвески в арочном мосту привело к появлению дополнительных компонентов напряжения, которые не были учтены при проектировании этого элемента. В этой детали не только осевые напряжения в I-образной подвеске увеличиваются из-за изменения поперечного сечения, но и поперечные напряжения (в плоскости стенки) возникают локально в местах, где эти осевые силы во фланцах изменяются. направление. В этих местах на плите перемычки наблюдались усталостные трещины.Трещина росла вдоль углового шва параллельно направлению нормальных осевых напряжений в подвеске, что свидетельствует о том, что они были созданы компонентом напряжения, перпендикулярным сварным швам.Рисунок 3. Мостовые балки с уменьшенной высотой распространены в: ( a ) мостах Гербера; и ( b ) на опорах мостов.
Рисунок 3. Мостовые балки с уменьшенной высотой распространены в: ( a ) мостах Гербера; и ( b ) на опорах мостов.
Рисунок 4. Касательные и радиальные напряжения в балках с уменьшенной глубиной и три режима растрескивания, которые могут возникнуть в этой детали.
Рисунок 4. Касательные и радиальные напряжения в балках с уменьшенной глубиной и три режима растрескивания, которые могут возникнуть в этой детали.
Рисунок 5. Примеры радиальных и тангенциальных трещин [5]. Рисунок 5. Примеры радиальных и тангенциальных трещин [5].Рисунок 6. Усталостное растрескивание вертикальной подвески с изменением поперечного сечения вблизи ее соединения с балкой жесткости арочного моста.
Рисунок 6. Усталостное растрескивание вертикальной подвески с изменением поперечного сечения вблизи ее соединения с балкой жесткости арочного моста.
4. Усталостное растрескивание, вызванное вибрацией, в подвесах мостов
Вертикальные подвески в стальных арочных мостах обычно рассчитаны на воздействие осевых сил. Детали подвесных соединений с аркой и настилом моста, как правило, разработаны таким образом, чтобы обеспечить соединение без моментов.По этой причине часто предполагается, что подвески соединены штифтами на обоих концах.
Сообщалось о нескольких случаях, в которых наблюдались усталостные трещины в соединениях мостовых подвесов [4,7]. В большинстве случаев сочетание двух различных механизмов способствовало образованию усталостных трещин в этих деталях.Вибрация: тонкие подвески обычно имеют очень низкую жесткость на изгиб, что делает их очень чувствительными к резонансу. Кабели могут подвергаться воздействию транспортных нагрузок на мосту и / или ветровых нагрузок.
Вторичные напряжения из-за жесткости соединения: Идеальных безмоментных штифтовых соединений в действительности не существует. Даже при таком проектировании соединение всегда будет приобретать некоторую вращательную жесткость, присущую деталям или постепенно в течение срока службы моста, например, из-за коррозии (так называемого замерзания).
Колебание кабелей в сочетании с недооцененной или непредвиденной жесткостью соединения может привести к многочисленным циклам с колебаниями момента (напряжения изгиба) в подвеске рядом с ее соединениями.Даже несмотря на то, что величина этих изгибающих напряжений может быть относительно низкой, большое количество циклов нагружения, вызванное вибрацией, может привести к усталостному растрескиванию детали.
На рисунке 7 показан пример арочного моста, в котором у подвесок образовались усталостные трещины в местах их соединения со стальной аркой. Этот железнодорожный мост, построенный в 1943 году, имеет пролет 61 м и представляет собой стальную арку с двумя шпалами (балками жесткости), соединенными балками перекрытия. Подвесы были изготовлены из стальных тросов диаметром 79 мм.Деталь крепления подвески к стальной арке также показана на рисунке 7. Усталостное повреждение было обнаружено в начале 1980-х годов; некоторые вешалки треснули и полностью отсоединились от своих соединений с аркой. Растрескивание, возникшее на резьбовой части подвески, было связано с комбинацией колебаний и вторичного изгиба подвесок при их соединении со стальной аркой [7]. Те же механизмы — часто в сочетании с плохой детализацией подвесного соединения — привели к аналогичным усталостным повреждениям стальных арочных мостов в Японии [5].Пример показан на рисунке 8. Рисунок 7. Усталостное растрескивание подвесов моста через реку Скеллефте в Швеции [7]. Рисунок 7. Усталостное растрескивание подвесов моста через реку Скеллефте в Швеции [7]. Рисунок 8. Усталостное растрескивание в подвесках моста Машита в Японии [5]. Рисунок 8. Усталостное растрескивание в подвесках моста Машита в Японии [5].5. Мостовые балки и стрингеры в соединениях деревянных шпал
Во многих старых железнодорожных мостах транспортные нагрузки на мостах передаются на продольные несущие элементы (мостовые балки или стрингеры) через деревянные шпалы, опирающиеся на эти элементы и соединенные с ними посредством с помощью крючков или болтов.Сообщалось о нескольких случаях усталостного повреждения, когда стрингеры проявляли усталостное растрескивание в местах под деревянными шпалами [8,9]. В сварных балках трещины часто растут вдоль носка сварных швов, соединяющих стенку балки с верхней полкой. В старых клепанных балках трещины были обнаружены вдоль галтели одного из L-образных профилей, образующих верхнюю полку балки, см. Рис. 9.Есть два основных действия, которые могут способствовать возникновению такого типа усталостного растрескивания.
- Деформация изгиба деревянных шпал под действием вертикальных осевых нагрузок. Соответствующий поворот концов деревянной анкеры вызывает локальный изгиб полки фермы, к которой она присоединена, а также деформацию стенки балки вне плоскости, см. Рисунок 10a.
- Поперечные силы на мосту, вызывающие изгиб стенки балки вне плоскости. Этот эффект более выражен в изогнутых мостах, но он также может быть вызван различными неровностями пути в прямых мостах, см. Рисунок 10b.
Оба действия имеют очень короткие линии влияния, вызывая большое количество циклов загрузки каждый раз, когда проходит поезд.
Усталостное повреждение из-за взаимодействия между балками моста и деревянными шпалами можно в основном найти в местах вдоль балки, где деформация, возникающая в результате этого взаимодействия, локально концентрируется в гибких областях (т. Е. Там, где более глобальная деформация, как показано на рисунке 10 сдерживается). Эти места, например, находятся рядом с соединениями стрингеров с балками перекрытия (см. Рисунок 9) или рядом с диафрагмами и поперечными распорками из-за более сильного сдерживающего эффекта в этих местах.Сосредоточение деформации на очень небольших участках стенки балки или на выступе полки балки в приклепанных стрингерах приводит к высоким напряжениям изгиба в этих местах и постепенно приводит к усталостному растрескиванию. Одни и те же механизмы приводят к аналогичному усталостному растрескиванию автомобильных мостов. Деформация в этих случаях обычно вызывается поперечным изгибом бетонного настила, который действует совместно со стальными балками. Рисунок 9. Пример усталостного растрескивания стрингеров при стыках деревянных шпал [8]. Рисунок 9. Пример усталостного растрескивания стрингеров при стыках деревянных шпал [8].Рисунок 10. Схематический рисунок, показывающий деформации, возникающие в балке моста в результате: ( a ) деформации изгиба из-за эксцентриситета рельса; и ( b ) Поперечные силы.
Рисунок 10. Схема, показывающая деформации, возникающие в балке моста в результате: ( a ) деформации изгиба из-за эксцентриситета рельса; и ( b ) Поперечные силы.
6. Мембраны и поперечные связи
Диафрагмы и поперечные связи являются жизненно важными элементами, которые используются во многих типах мостов для обеспечения поперечной устойчивости конструкции моста во время строительства и / или против поперечных и скручивающих нагрузок, действующих на мост. Во многих случаях эти стабилизирующие элементы соединяются с лонжеронами моста (главными балками или стрингерами) с помощью соединительных пластин, которые привариваются, привинчиваются или приклепываются к стенке балки. В сварных мостах на протяжении многих лет обычной практикой было исключение сварных швов, соединяющих вертикальные ребра жесткости с полкой балки, чтобы избежать деталей с низкой усталостной прочностью.Вместо этого соединительную пластину либо обрезают на коротком расстоянии от фланца, либо устанавливают на фланец, либо непосредственно, либо с помощью куска стали в качестве заглушки, устанавливаемой под элементом жесткости, см. Рисунок 11b – d.Рисунок 11. Детализация соединения элементов поперечины с балками моста.
Рисунок 11. Детализация соединения элементов поперечины с балками моста.
Известно, что деталь около окончания поперечных пластин (или вертикальных ребер жесткости), используемых для соединения диафрагм или поперечных связей, является одной из наиболее критических с точки зрения усталости стальных мостов.Усталостное растрескивание здесь в основном обнаруживается в стенке фермы, начиная с конца элемента жесткости и растя почти горизонтально в направлении, параллельном нормальным напряжениям изгиба в стенке, см. Рис. 12. Об этом типе усталостного растрескивания сообщалось на обеих железных дорогах. и автомобильные мосты и могут быть найдены во многих типах мостов, включая двух- и многобалочные мосты, мосты с коробчатыми балками и мосты с фермами. Однако механизм усталостного растрескивания на соединениях диафрагмы и поперечных связей один и тот же, независимо от типа моста.Случаи нагружения, которые приводят к вторичному изгибу балок моста (в слабом направлении) и / или крутильной деформации поперечного сечения моста, вызывают неравномерный прогиб балок, которому противодействует диафрагма или элементы поперечных распорок. Следовательно, в этих элементах возникают растягивающие и сжимающие силы, действующие перпендикулярно плоскости стенки балки и вызывающие вторичные изгибающие напряжения, которые локализуются в нежесткой части стенки между фланцем балки и концом соединительной пластины, см. Рисунок 12.На железнодорожных мостах эти поперечные и скручивающие нагрузки более очевидны для изогнутых и наклонных мостов, но они также могут возникать в прямых мостах из-за возможных эксцентриситетов или неровностей пути. Те же эффекты очевидны для автомобильных мостов, где груз грузовика может занять любое положение в поперечном направлении моста, вызывая неравномерный прогиб балок моста.
Кроме того, было показано, что заклепочные соединения обсуждаемого здесь типа склонны к усталостному растрескиванию [10].В этом случае усталостное повреждение обнаруживается либо в выступе соединительного уголка, либо в заклепках, соединяющих угол со стенкой балки, см. Рисунок 13.Рисунок 12. Дифференциальный прогиб мостовых балок приводит к высоким локальным напряжениям изгиба в незажатых зазорах стенки между фланцем балки и окончанием коротких соединительных пластин.
Рисунок 12. Дифференциальный прогиб мостовых балок приводит к высоким локальным напряжениям изгиба в незажатых зазорах стенки между фланцем балки и окончанием коротких соединительных пластин.
Рисунок 13. Усталостное растрескивание в клепаном соединении элементов поперечных связей [11]. Рисунок 13. Усталостное растрескивание в клепаном соединении элементов поперечных связей [11].7. Соединения стрингера с балкой перекрытия
Во многих существующих мостах соединения стрингера с балкой перекрытия с механическим креплением выполняются с помощью двойных уголков, приклепанных или привинченных к пластинам стенки обоих элементов. Обычной инженерной практикой было проектировать эти соединения с учетом только поперечных сил (их несущая функция заключается в передаче торцевых реакций стрингера на балку перекрытия).Хотя это предположение может быть адекватным для расчета конечного предельного состояния, поведение этих соединений при умеренных нагрузках может существенно отличаться.
Соединения этого типа показали высокую уязвимость к усталостному растрескиванию. Сообщалось о большом количестве случаев повреждения, в которых были обнаружены усталостные трещины в соединительных углах [12,13]. Трещины обычно начинаются у выступающей части соединительного уголка и растут вдоль кромки уголка. На рисунке 14b показан пример такого усталостного растрескивания. Рисунок 14. Пример усталостного повреждения соединений стрингера с балкой перекрытия [12]: ( a ) в месте соединения головки заклепки и стержня; ( b ) на внешней стороне соединительного уголка. Рисунок 14. Пример усталостного повреждения соединений стрингера с балкой перекрытия [12]: ( a ) в месте соединения головки заклепки и стержня; ( b ) на внешней стороне соединительного уголка. В старых клепаных соединениях также очень распространены отказы заклепок.Здесь трещины начинаются в стыке между головкой заклепки и стержнем (вызванные поддеванием и изгибом заклепки) и, наконец, приводят к полному разъединению головки заклепки, см. Рисунок 14a. Усталостные повреждения такого типа обычно локализуются в верхней части соединения, но также сообщалось о случаях повреждений с усталостным растрескиванием и / или разрушением заклепки в нижней части соединения [12].Усталостное растрескивание в соединениях стрингера с балкой перекрытия вызывается вторичными эффектами, которые по своей природе вызваны деформацией.Здесь можно выделить два механизма.
Вращение концов стрингера связано с изгибом. Несмотря на то, что двухугловые соединения были спроектированы как простые соединения, работающие на сдвиг, обычно неизбежно, что эти соединения также приобретают некоторую жесткость при вращении, таким образом частично ограничивая вращение концов стрингеров. Следовательно, отрицательный изгибающий момент будет развиваться на концах стрингеров, подвергая крепежные детали и углы соединений нагрузкам, которые не учитываются при проектировании, см. Рисунок 15.Этот вид воздействия имеет относительно короткую линию влияния, вызывая большое количество циклов нагружения в течение срока службы моста. Игнорируемое взаимодействие между системой перекрытия (стрингеры и балки перекрытия) и основной несущей конструкцией (основной балки или основные фермы, например). Деформация изгиба основного моста фермы, например, связана с продольным смещением стыков фермы, к которым соединены балки перекрытия. Однако балки перекрытия частично сдерживаются от следования этой деформации из-за осевой жесткости стрингеров и их соединений с балками перекрытия.В результате вторичные осевые силы будут развиваться в стрингерах и их соединениях с балками перекрытия, в то время как последние будут подвергаться вторичному изгибу (по слабой оси), см. Рисунок 16. Этот вид взаимодействия имеет линию влияния, которая равна длине пролета моста, а в случае железнодорожных мостов, по сути, существует один цикл загрузки каждый раз, когда проходит поезд.Рисунок 15. Вторичный изгиб на концах стрингера из-за ограниченного вращения конца. Изгибающие и осевые напряжения в верхней части соединения стрингера с балкой перекрытия могут быть достаточно высокими, чтобы в конечном итоге привести к усталостному растрескиванию.
Рисунок 15. Вторичный изгиб на концах стрингера из-за ограниченного вращения конца. Изгибающие и осевые напряжения в верхней части соединения стрингера с балкой перекрытия могут быть достаточно высокими, чтобы в конечном итоге привести к усталостному растрескиванию.
Рисунок 16. Взаимодействие между системой перекрытия (продольные балки и балки перекрытия) и основными фермами моста приводит к появлению вторичных осевых сил и изгибающего момента в косых балках и балках перекрытия соответственно.
Рисунок 16. Взаимодействие между системой перекрытия (продольные балки и балки перекрытия) и основными фермами моста приводит к появлению вторичных осевых сил и изгибающего момента в косых балках и балках перекрытия соответственно.
Усталостные трещины в двойных углах соединений стрингера с балкой перекрытия возникают из-за изгибающих напряжений, и поэтому их довольно трудно обнаружить на ранних стадиях, то есть до того, как поверхностная трещина прорастет на толщину соединительного уголка. Однако испытания на усталость частей моста, включая клепаные двухугловые соединения, показывают, что скорость распространения этих трещин очень мала [12].Наличие этих трещин напрямую не угрожает целостности несущей функции системы пола. Тем не менее, по крайней мере, в одном случае сообщалось, что усталостное растрескивание в соединениях стрингера с балкой перекрытия привело к полному разделению стрингера — режиму отказа, который может поставить под угрозу все характеристики моста (Международный институт сварки).8. Соединения между балками перекрытия и основными несущими элементами
Подобно соединениям балок перекрытия, соединения между балками перекрытия и основными несущими элементами или системой (главная балка, основные фермы, арочные стяжки и т. Д.) также показали многочисленные проблемы с усталостью. В принципе, механизмы взаимодействия, лежащие в основе усталостного растрескивания в этих двух типах соединений, одинаковы. Вторичный изгибающий момент (в плоскости стенки балки перекрытия) может возникнуть на концах балок перекрытия в результате ограничения вращения, обеспечиваемого их соединениями с основными несущими элементами. Кроме того, взаимодействие между системой перекрытия (стрингеры и балки перекрытия) и основной несущей конструкцией может привести к вторичному изгибу балок перекрытия вне плоскости, как показано на рисунке 16.На рисунках 17 и 18 показаны два примера усталостного растрескивания, вызванного ограниченным вращением концов балок перекрытия. В соединениях с механическим креплением усталостное повреждение обычно обнаруживается в соединительных уголках или в заклепках (или болтах), соединяющих уголки с основным несущим элементом [5,14], см. Также рисунок 15. В сварных деталях, где пол балка соединена со сварной поперечной пластиной, о трещинах сообщалось в стенке главной балки (типы A и C на рис. 18) или в соединительной пластине вдоль ее углового сварного шва к стенке главной балки (тип C) [4,5, 10].Второй тип взаимодействия (поперечный изгиб балок перекрытия) также привел к усталостным повреждениям многих типов стальных мостов. Один из примеров показан на рисунке 19. В этом случае верхняя полка балки перекрытия обрезается около балки перекрытия, ведущей к соединению основной фермы, оставляя небольшой — локально гибкий — зазор в стенке балки перекрытия, где сосредоточена деформация. . В таком случае после зарождения трещины дальнейшее распространение усталостной трещины обусловлено вторичным изгибающим напряжением в балке перекрытия вблизи соединения.О таком же виде усталостного растрескивания сообщалось для автодорожных балочных мостов [4,10], мостов с фермами [5] и арочных мостов [14,15].Рисунок 17. Усталостное повреждение балки перекрытия, приклепанной к соединению главной фермы, в результате сдерживающего воздействия.
Рисунок 17. Усталостное повреждение балки перекрытия, приклепанной к соединению главной фермы, в результате сдерживающего воздействия.
Рисунок 18. Усталостное растрескивание в балке перекрытия, приваренной к соединению главной балки.
Рисунок 18. Усталостное растрескивание в балке перекрытия, приваренной к соединению главной балки.
Рисунок 19. Усталостное растрескивание в стенке балки перекрытия, вызванное деформацией поперечного изгиба, возникающей при взаимодействии между системой перекрытия и основными фермами моста.
Рисунок 19. Усталостное растрескивание в стенке балки перекрытия, вызванное деформацией поперечного изгиба, возникающей при взаимодействии между системой перекрытия и основными фермами моста.
9. Элементы со скошенными концами и обрезанными фланцами
Чтобы облегчить их соединение с другими элементами моста, диафрагмы, стрингеры и балки перекрытия часто имеют скошенные концы или обрезанные фланцы на их соединениях, см. Рисунок 20. Эти элементы часто проявляют склонность к усталостному растрескиванию [4,5,15,16]. Как правило, трещины начинаются и увеличиваются в стенке элемента в тех областях, которые ослаблены локально из-за обрезки колпачка или фланца.Рисунок 20. Примеры элементов перемычки со скошенными концами или обрезанными фланцами: ( a ) диафрагма; ( б ) балка перекрытия; и ( c ) стрингер.
Рисунок 20. Примеры элементов перемычки со скошенными концами или обрезанными фланцами: ( a ) диафрагма; ( б ) балка перекрытия; и ( c ) стрингер.
Здесь применяются те же виды вторичного эффекта, которые описаны в пунктах 6-8 выше. Кроме того, копирование или короткая обрезка фланца может способствовать более раннему усталостному растрескиванию несколькими способами.
За счет удаления частей полок балки около конца модуль сечения балки существенно уменьшается. Таким образом, вторичный изгиб из-за ограниченного торцевого вращения может привести к относительно высоким напряжениям изгиба в перемычке вблизи торцевого соединения.
Область рядом с выступом или обрезанным фланцем также является местом концентрации напряжений, что дополнительно снижает сопротивление усталости.
Иногда торцы обрабатываются пламенной резкой без дополнительной обработки, что приводит к шероховатости кромок.Остаточные напряжения, возникающие в процессе резания, также могут способствовать раннему развитию усталостных повреждений этих элементов.
10. Соединения между стыками балок
На многих длиннопролетных мостах стальные балки обычно изготавливаются в несколько сегментов из-за ограничений транспортировки и изменений секций. Следовательно, сборка сегментов стальных балок выполняется на месте посредством сварных или заклепочных соединений. При использовании сварных соединений вырезы в стенке балки делаются в местах ее пересечения с фланцами для облегчения выполнения поперечных стыковых швов и предотвращения пересечения сварных швов. В нескольких исследованиях было показано, что вырезы в перемычке, также известные как отверстия, подвержены усталостному растрескиванию [11,17,18].Часто сообщается, что место зарождения усталостной трещины находится на носках углового сварного шва углубления; где он может расти либо в стенке, либо поперек фланца, см. рисунок 22. Рисунок 22. Примеры усталостного растрескивания мостовых балок с отверстиями в отверстиях в местах сильной концентрации напряжений [11]. Рисунок 22. Примеры усталостного растрескивания мостовых балок с отверстиями в отверстиях в местах сильной концентрации напряжений [11].Механизмы, которые могут приводить к усталостному растрескиванию балок в отверстиях, можно разделить на две принципиально разные подгруппы:
Резкое введение концентраторов напряжения на фланцах.Фланцы — это самые внешние элементы стальных балок, которые, согласно теории балок, подвергаются максимальным нормальным напряжениям при изгибе. Вырезы в стенке и соответствующие сварные швы на пересечении с фланцами создают серьезные области концентрации напряжений, перпендикулярных направлению максимального напряжения.
- Вторичные напряжения из-за деформации сдвига балки. Хотя деформация сдвига жестких длиннопролетных балок обычно не учитывается при проектировании, локальные эффекты таких деформаций могут быть значительными.Как видно на Рисунке 23, в результате существующего сдвига возникает относительно небольшое смещение (δ) между секциями до и после ствола скважины. Однако, поскольку боковая опора фланца, обеспечиваемая перегородкой, больше не доступна в этом разделе, фланец подвергается дополнительной деформации. В этом случае полка аналогична балке с фиксированными обоими концами, поддерживающими дополнительный момент (M добавить ). Эта деформация вызывает напряжения, действующие на подошву сварного шва на одном конце, и уменьшает их на другом конце.
Рисунок 23. ( a ) Деформация изгиба и сдвига секции с углублением; ( b ) Распределение напряжений по толщине фланца на подошве сварного шва; ( c ) 3D конечно-элементная модель.
Рисунок 23. ( a ) Деформация изгиба и сдвига секции с углублением; ( b ) Распределение напряжений по толщине фланца на подошве сварного шва; ( c ) 3D конечно-элементная модель.
Линия влияния таких механизмов ограничена небольшой площадью и, таким образом, оказывается влияние на большое количество циклов загрузки на каждом проходе поезда.Кроме того, влияние вторичных напряжений из-за деформации сдвига становится заметным на участках, где увеличивается отношение напряжения сдвига к нормальному напряжению [19]. Поэтому на этапе проектирования следует уделять особое внимание размещению стыков в менее уязвимых местах.11. Сварные накладки
Частичные накладки приварены к фланцам стальных балок моста, чтобы увеличить моментную нагрузку и, следовательно, допустимую транспортную нагрузку и пролет моста.Однако усталостные трещины неоднократно обнаруживались на концах накладки в усиленных элементах [4,20]. Конец накладки имеет наименьшую усталостную прочность из всех деталей и рассматривается как нижняя граница усталостной прочности сварных деталей в балке моста [21]. Наиболее яркими примерами таких отказов являются большое количество обнаруженных усталостных трещин на концах накладки на мостах у пруда Yellow Mill в Коннектикуте в 1970-е годы и на Королевском мосту в Мельбурне, Австралия. Такие усталостные трещины возникают на подошве сварного шва поперечного торцевого шва накладки и начинают развиваться в стенке после того, как они распространяются по всей ширине полки, см. Рисунок 24.Основная причина такого низкого поведения концов накладки связана с быстрым изменением жесткости сечения до и после сварной накладки, что вызывает сильную концентрацию напряжений на конце пластины. Кроме того, неизбежно образующиеся микротрещины на носке шва в результате процесса сварки ускоряют усталостное разрушение. Кроме того, сообщается, что при отсутствии поперечного торцевого сварного шва усталостная прочность не улучшается [22]. Кроме того, в таких случаях в нескольких случаях наблюдались другие механизмы деградации, такие как коррозия, вызванная попаданием воды между крышкой и фланцем [11]. Рисунок 24. Усталостное растрескивание торцов накладки [11]. Рисунок 24. Усталостное растрескивание торцов накладки [11].12. Выводы
Всестороннее исследование усталостных характеристик деталей стальных мостов показывает, что большинство случаев усталостных повреждений, которые были зарегистрированы для автомобильных и железнодорожных мостов, вызваны вторичными нагрузками. В большинстве случаев непредвиденное (или иным образом упущенное) взаимодействие между различными элементами и несущими системами моста, часто в сочетании с плохой детализацией, было причиной усталостного растрескивания деталей моста.В некоторых случаях сложное напряженное состояние может также существовать в некоторых конструктивных деталях, которые часто трудно учесть при упрощенном проектировании, и проектировщик может их не заметить. Основным механизмом большинства типов усталостного растрескивания, вызванного вторичными эффектами, является приложенная деформация, которая циклически повторяется.
Общей чертой многих деталей, которые испытали этот вид усталостного растрескивания, является то, что они включают в себя какое-то резкое изменение жесткости, как правило, в незакрепленных зазорах, где сосредоточена приложенная деформация.Это часто приводит к высоким локальным напряжениям, которые в конечном итоге могут привести к усталостному растрескиванию детали. Наиболее распространенные виды усталостных повреждений, вызванных деформацией, можно найти в соединениях между стрингерами и балками перекрытия, между последними и основными несущими элементами моста, а также в местах соединения диафрагм и поперечных распорок. Кроме того, довольно часто встречается усталостное повреждение деталей ортотропных настилов и элементов мостов со скошенными концами или обрезанными фланцами в местах их соединения с другими элементами.
Сварочные сертификаты
Сварщик должен иметь Сертификат Сварки Стальных Конструкций, прежде чем приступить к работе на стыках балок и балок или других соединений конструкционной стали на транспортных конструкциях. Сварщик должен пройти квалификацию перед выполнением различных сварных швов, описанных в Стандартных спецификациях Техаса 2014 года для строительства и обслуживания автомагистралей, улиц и мостов, пункт 448.
Сертификаты на сварку стальных конструкций
Сертифицированный сварщик прошел сертификацию AWS D1.5 Квалификация Кодекса по сварке мостов изложена в Стандартных спецификациях Техаса 2014 года для строительства и обслуживания автомагистралей, улиц и мостов, статья 448.4.2.2, «Сертифицированный сварщик стальных конструкций».
Все сварочные работы для сертификации должны выполняться в присутствии персонала испытательной лаборатории. Сварщик несет ответственность за все расходы, связанные с испытаниями, необходимыми для сертификации. Сертификация остается в силе до тех пор, пока сварщик выполняет допустимую работу для TxDOT, как определено Подразделением мостов.
Квалификация по разным сваркам
Квалифицированный сварщик — это опытный сварщик, способный выполнять качественные сварные швы, но не имеющий сертификата TxDOT. Квалифицированный сварщик должен пройти испытание на соответствие требованиям к другим сварным швам на рабочем месте перед сваркой. См. Стандартные технические условия Техаса 2014 года для строительства и обслуживания автомагистралей, улиц и мостов, статья 448.4.2.1.
Испытательные лаборатории
TxDOT не ведет список утвержденных испытательных лабораторий, которые должны иметь сертифицированного инспектора по сварке (CWI) и экзаменатора уровня II Американского общества неразрушающего контроля (ASNT) для проведения тестов и интерпретации результатов.TxDOT является последней инстанцией в случае разногласий между лабораторией тестирования и TxDOT.
Отправьте все результаты тестов по указанному ниже адресу. TxDOT оставляет за собой право отказать в приеме результатов сертификационных испытаний лабораторий, которые не соответствуют стандартам AWS и ASNT. В таких случаях TxDOT может провести аудит испытательной лаборатории, чтобы определить ее приемлемость.
Контакты
Подразделение мостов TxDOT
Отдел строительства и обслуживания
125 E.11-я улица
Остин, Техас 78701
(512) 416-2824