Термическая сварка
Под термической сваркой принято понимать соединение металлов, основывающееся на расплавлении кромок металла, в результате чего образуется соответствующая ванна, в которой металл соединяется на молекулярном уровне и позволяет выполнить прочный монолитный шов. Подобные технологии благодаря своей простоте и качеству соединения металлических элементов получили широкое распространение. К такому термическому классу принято относить лазерную, плазменную, газовую, дуговую технологию. Поговорим поподробнее о преимуществах и недостатках термической сварки, а также опишем ее распространённые классы.
Из преимуществ такой термической технологии можем выделить следующее:
- Отличные показатели прочности соединения.
- Низкая трудоемкость работ.
- Невысокая себестоимость.
- Минимальный расход металла.
Если же говорить о недостатках, то можно отметить следующее:
- Неровности на поверхности заготовки и наличие оксидной пленки существенно ухудшает качество соединения.
- Термическая сварка возможна только с металлами, близкими по показателям тугоплавкости.
Термическое влияние сварки
Газовая термическая сварка подразумевает нагрев металла в зоне соединения при помощи газового пламени. Такая газовая горелка может использовать различный газ, который эффективно нагревает металл до его жидкого состояния, а после кристаллизации и затвердевания обеспечивается максимально прочное соединение. Газовые горелки позволяют оптимальным образом регулировать температуру пламени, что в свою очередь дает возможность работать с различными по тугоплавкости материалами. Газовая сварка может выполняться как по классической технологии термической обработки металлов, так и с использованием дополнительного присадочного материала. Такие электроды расправляются одновременно с соединяемыми металлами, кристаллизуются и на молекулярном уровне соединяют материалы. Следует учитывать свойства конкретных металлов, сплавы которых входят во взаимодействие друг с другом.
Из преимуществ данной технологии можем отметить простоту данной работы и отличное качество соединения. В то же время необходимо отметить, что данная технология подразумевает использование специального оборудования, в том числе баллонов со сжатым газом, поэтому к проведению такой работы с газом допускаются только сертифицированные специалисты, имеющие большой опыт работы с такими горелками на газу. Также должное внимание необходимо уделить качеству используемого оборудования.
Полуавтоматическая термическая сварка: технология
Использование данной технологии подразумевает использование специальной проволоки, которая с помощью автоматической системы аппарата подается в рабочую зону, где быстро расплавляется и позволяет обеспечить прочность соединения. В качестве защитного газа может использоваться аргон и СО2. Основное назначение такого газа — это защита сварочной ванны от воздействия воздуха, который может существенно ухудшить качество соединения металлов.
При полуавтоматической технологии используется специальное оборудование, которое позволяет быстро расплавлять кромки. При этом данная технология отличается простотой и может выполняться как профессиональными специалистами, так и обычными домовладельцами при необходимости им выполнить прочное соединение элементов. Даже обычные домовладельцы смогут с использованием таких полуавтоматических аппаратов провести сварку, обеспечив максимальное качество выполненного соединения.
Аргонодуговая сварка
Такой вид термической сварки подразумевает использование вольфрамовых электродов, которые заправляются в горелку. При выполнении соединения такой электрод с помощью автоматической системы подается в пламя горелки, расплавляется и стекает в шов, гарантируя соединение на молекулярном уровне. Для защиты сварочной ванны от негативного воздействия кислорода используется аргон, который предотвращает появление окислительной пленки. Аргон поступает из подключенного к горелке баллона со сжатым газом. Регулируют подачу аргона при помощи редуктора, выставляя его на определённое положение, в зависимости от конкретной разновидности металлических элементов.
Термитная сварка
Оборудование орбитальной сварки из Германии! Низкие цены! Наличие в России! Демонстрация у Вас.
Orbitalum Tools — Ваш надежный партнер в области резки и торцевания труб, а так же автоматической орбитальной сварки промышленных трубопроводов.
Виды сварки — Термитная сварка
Термитная сварка — процесс сварки металлических деталей жидким металлом заданного химического состава, получаемого в результате термитной (алюминотермической) реакции. Сущность термитной реакции заключается в том, что алюминий способен восстанавливать окислы металлов со значительным выделением тепла, в результате чего происходит изменение потенциального состояния энергии и рекристаллизация компонентов, участвующих в процессе:
Значительное количество тепла, выделяемого при термитной реакции, длительное время сохраняет металл в жидком перегретом состоянии и дает возможность использовать его для технологических целей.
В отличие от обычного процесса горения термитная реакция может происходить в замкнутых системах или даже в вакууме, так как реакция происходит за счет кислорода, содержащегося в окислах металлов.
Термитный процесс с железо-алюминиевым составом протекает в соответствии со следующей зависимостью:
Основным высококалорийным горючим, применяющимся в термитных Смесях, является алюминий. После кислорода и кремния алюминий является самым распространенным элементом земной коры и составляет около 8% массы Земли (железо 4,7%).
Принцип получения трудновосстанавливаемых металлов из их окислов впервые был выдвинут крупнейшим русским ученым-химиком, основоположником современной физической химии Н Н. Бекетовым. В 1865 г. в своей докторской диссертации «Исследования над явлениями вытеснения одних элементов другими» Бекетов превратил этот принцип в научную теорию, заложив основу алюминотермии. Он установил, что алюминий обладает очень большой активностью, соединяясь с кислородом, и что при определенных условиях алюминий легко восстанавливает из окислов другие металлы, стоящие правее его в таблице напряжений химических элементов.
Сварочный термит состоит из порошкообразного металлического алюминия и окислов железа в виде окалины (технологического отхода горячей обработки стали), а также различных присадок, вводимых в шихту для легирования получаемой стали.
Какие условия необходимы для начала термитной реакции?
1 Термитная шихта должна быть рассчитана так, чтобы в ходе реакции выделилось необходимое количество тепла для расплавления и перегрева конечных продуктов термитной реакции
2. Компоненты термитной шихты: алюминиевый порошок и окислы железа должны быть мелких фракций и тщательно перемешаны.
3. Для начала термитной реакции в любой точке термитной шихты необходимо создать температурный толчок не ниже 1350o. после чего термитная реакция быстро распространится на всю шихту.
В результате термитной реакции, которая в течение 15—30 сек. протекает очень активно, образуются металл (около 50% от первоначального веса термитной шихты) и шлак.
В процессе термитной реакции часть тепла расходуется на нагревание стенок тигля, лучеиспускание и т. д. Однако, несмотря на это, количество выделяющегося тепла достаточно для того, чтобы расплавить шихту и перегреть продукты реакции — жидкий металл и шлак до 2600—2700
Качество термитного металла определяется физико-химическими свойствами компонентов шихты.
Для получения металла (стали) нужного химического состава в шихту вводят в измельченном состоянии легирующие материалы: ферромарганец, ферромолибден, ферротитан, феррованадий, углерод и т. д.
Измельченная легирующая присадка закладывается в тигель вместе с термитными компонентами.
Участие легирующих элементов в термитной реакции очень многообразно: они легируют термитную сталь, раскисляют и рафинируют ее. Кроме того, они частично теряются — испаряются и переходят в шлак.
Ценные ферросплавы (ферротитан, феррованадий и др. ) повышают прочность термитной стали, так как в ходе реакции, находясь в жидком состоянии, они образуют карбидную фазу титана и ванадия. Наличие в стали перечисленных карбидов увеличивает ее мелкозернистость, повышает твердость и т. п.
Длительность термитной реакции oт момента зажигания термита до ее окончания и полного отделения металла от шлака находится в прямой зависимости от количества сжигаемого термита и колеблется от 15 до 40-50 сек.
При одновременном сжигании больших количеств термита реакция протекает с относительно небольшими потерями тепла.
Термитные смеси в зависимости от их назначения можно условно разделить на следующие группы;
1) элементарная термитная смесь — железная окалина плюс алюминиевый порошок в стехиометрическом соотношении;
2) термит для сварки рельсовых стыков. В шихту вводится стальной наполнитель — мелкие кусочки малоуглеродистой проволоки или стальная малоуглеродистая стружка, ферромарганец и порошкообразный графит,
3) термит для сварки легированных сталей. В качестве присадки используются ферротитан, феррованадий и др.;
4) термит для сварки чугуна. В присадку вводится значительное количество кремния. Марганец исключается. Высокое содержание кремния в термитном металле способствует выделению графита в сварочной и переходной зонах и обеспечивает получение достаточно прочных сварных соединений;
5) термит для сварки высокомарганцовистых сталей. В этот термит вводится увеличенное количество марганца и углерода в виде ферромарганца и чугунной стружки;
6) специальные термиты — пиротехнические, для наварки пода в металлургических печах, уменьшения усадочных раковин в слитках, вторичного дробления минералов и руд, изготовления термитных брикетов и т. п.
История развития производства термита и термитной сварки рельсов
В Москве термитную сварку впервые применили в 1915 г.. когда было сварено 126 стыков. В 1918 г. сварили еще 151 стык. С 1923 г. в трамвайных путях столицы начинают регулярно варить стыки термитом. До 1925 г. стыки сваривали импортным термитом. В 1925 г. на Московском термитно-стрелочном заводе инженером М. Л. Карасевым было налажено промышленное производство термита.
М. А. Карасев внес крупный вклад в развитие алюминотермии, организовав на базе отечественной технологии выпуск термитных смесей для народного хозяйства. Он предложил рациональные способы производства алюминиевого порошка и термита. Ему были выданы авторские свидетельства на «аппарат для получения эерноволокнистого алюминия», «шаровой мельницы для производства алюминиевого порошка», «механической нагрева-тельной печи для обжига железной обсечки и окалины при изготовлении термита» и т. п.
В последующие годы в путях московского трамвая было сварено термитом свыше 100 000 стыков.
Сварка производилась двумя способами: комбинированным и врасклинку. Ввиду того, что стыки, свариваемые последним способом, часто выходили из строя, к 1931 г. этот способ перестали применять Вместо него начали внедрять способ сварки промежуточным литьем. Одновременно начали применять способ сварки «дуплекс» (способ промежуточною литья с последующим прессованием). Однако этот способ не получил широкого распространения из-за сложности технологического процесса.
Качество сварки термитных стыков за первые 10 лет ежегодно улучшалось, и количество лопнувших (в течение года) стыков в среднем не превышало 0,8%.
Применение отечественного термита для сварки рельсовых стыков показало его превосходство перед импортировавшимся термитом. В стыках рельсов, сваренных отечественным термитом, значительно меньше процент брака. Это подтверждают результаты эксплуатации первой очереди Московского метрополитена. Так, например, каждый рельсовый стык на участке Сокольники—Парк культуры в 1938 г, выдержал 13,4 млн. ударов с грузонапряженностью 53 млн. т-км.
В 1936 г. вышло из строя 0,17% от количества эксплуатируемых в путях стыков, в 1937 и 1938 г. — по 0,5%.
Из приведенного количества выбывших из строя стыков 75% разрушились из-за наличия болтовых отверстий в зоне сварки.
В эти же годы термит стали внедрять в другие отрасли народного хозяйства. В частности, была разработана и успешно осуществлена термитная сварка стыков легированных труб первого прямоточного котла высокого давления; начали применять также термитную сварку для ремонта крупногабаритных стальных деталей: валов, колонн и т. п.
Применение термитной сварки в трамвайных хозяйствах
Сварка стыков рельсов радикально решает проблему борьбы с блуждающими токами, которые наносят значительный ущерб подземным металлическим коммуникациям.
Бесстыковой путь дает возможность уменьшить экономические затраты по текущему содержанию пути, позволяет увеличить скорость движения рельсового транспорта, уменьшает шум и удлиняет срок службы подвижного состава.
Рассматривая применяющиеся в настоящее время различные способы сварки стыков рельсов — электроконтактный, электрошлаковый, газопрессовый, ванный, электродуговой с приваркой накладок и подкладок и термитный, — нельзя не отдать предпочтение последнему, у которого такие преимущества:
1) удобство, маневренность применяющейся оснастки;
2) возможность применения без электроэнергии;
3) высокая производительность;
4) достаточная прочностная характеристика.
Термитная сварка позволила к 1953 г. в Москве и Ленинграде иметь в трамвайных путях бесстыковые соединения.
В трамвайных хозяйствах многих городов отдается предпочтение термитной сварке стыков рельсов. За последние 25—30 лет термитная сварка претерпела небольшие качественные изменения.
Из всех способов термитной сварки — кузнечного, промежуточного литья, комбинированного, «дуплекс» — получил широкое распространение способ промежуточного литья.
С 1950 г. применяется модернизированный способ промежуточного литья — «единый» способ, который хотя и не дает провара по всему сечению рельсов, но благодаря простоте всего технологического процесса позволил расширить внедрение термитной сварки в трамвайных путях.
В связи с массовым применением термитной сварки на транс порте появилась потребность как в качественном улучшении сварного стыка — получение плотного стыка с хорошим проваром и постоянством химического состава термитной стали, так и в изменении количественных характеристик — повышение производительности, уменьшение расхода материалов и т. д.
Условия, необходимые для проведения термитной реакции
Чтобы осуществить термохимическую реакцию между восстановителем и окислителем, необходимо наличие определенных условий, как то: химической чистоты компонентов термитной шихты, соответствующего измельчения их, определенного соотношения составляющих термита в шихте, доведения термитной смеси до температуры начала реакции.
В составе железо-алюминиевого термита восстановителем является алюминий в порошкообразном состоянии, а окислителем — порошок железной окалины. Химическая чистота восстановителя и окислителя необходима для обеспечения определенной активности и теплотворной способности термита, а также для качества сварки.
Окислитель — железная окалина — должен содержать минимальное количество кремния, серы и фосфора.
Кислородный баланс окалины 24,5—26% О2, что недостаточно для получения активной высококалорийной термитной реакции. Чтобы увеличить содержание кислорода в окалине, ее подвергают специальной обработке при высокой температуре в окислительной среде.
Большое влияние на ход реакции оказывает измельчение составляющих термитной шихты. Более крупные компоненты используются в реакциях с большими порциями шихты. Для небольших порций термита применяют более измельченные порошки.
Отклонение от указанных пределов в ту или иную сторону нарушает нормальные соотношения восстановителя и окислителя в термите, что приводит к снижению его калорийности, повышает в термитном металле содержание Al или насыщает металл кислородом, что отрицательно влияет на качество термитной сварки.
Чтобы осуществлялась реакция между алюминием и железной окалиной, термитная шихта должна быть нагрета до температуры воспламенения, которая для железо-алюминиевого термита при правильно выбранном соотношении составляющих достигает 1340-1360o. Это — критическая точка начала активной реакции, хотя медленно протекающие термохимические процессы уже начинаются при нормальной температуре после смешения компонентов термитной шихты.
Медленно протекающие термохимические процессы безопасны, но они снижают теплотворную способность термита, вследствие эгого длительное хранение его нежелательно.
Применение термита
Термит широко применяется в различных отраслях народного хозяйства. Он используется Для сварки крупногабаритных стальных и чугунных конструкций и арматуры железобетонных узлов. Термитом можно сваривать трубы и провода контактной сети, а также провода высоковольтных линий электропередачи.
Термитный металл обладает хорошими литейными свойствами и может употребляться для прицезионного литья.
В технической литературе освещено применение термитной сварки при:
а) производстве крупногабаритных деталей, состоящих из нескольких элементов: коленчатых валов, рулевых рам судов, приварке лопастей к гребным валам судов и пр.;
б) восстановлении цилиндров прессов, поршневых штоков, колонн кузнечных прессов, роторных валов, валков, а также ведущих реверсивных шестерен прокатных станов, всевозможных станин—клетей прокатных станов, станин прессов и главных станин ковочно-высадочных машин и пр.;
в) ремонте чугунного технологического оборудования сталелитейных цехов: изложниц, шлаковых ковшей, поддонов и т. д.
Термитную сварку крупногабаритных деталей лучше всего производить в литейном цехе, где имеется необходимое технологическое оборудование, а также грузоподъемные механизмы.
Термитная сварка крупных чугунных деталей дает большой экономический эффект, особенно для восстановления технологического оборудования металлургического производства: различных ковшей, изложениц, поддонов, а также всевозможных станин.
Приступая к термитной сварке чугунных деталей, нужно учитывать повышенную чувствительность чугуна к температурным изменениям. При нагревании чугуна выше критической точки и охлаждении со скоростью, превышающей 149o в мин., он становится хрупким.
Одним из важнейших условий успешного проведения термитной сварки чугунных деталей является предварительный подогрев. При сварке чугунных деталей, помимо местного подогрева в зоне сварки до 900o, необходимо произвести и общий подогрев всей детали до 450—500o.
Весьма эффективно применение термита для сварки стыков стержней большого диаметра непосредственно в блоках гидросооружений, где нельзя использовать стыковую сварку. При этом
повышается экономия металла, используемого на накладки или технологические изгибы сопрягаемых элементов, а также увеличивается производительность сварки по сравнению с электродуговым или ванным способом. Кроме того, облив улучшает работу арматуры в бетонных сооружениях, так как, выступая за габариты стержня, он повышает сцепляемость арматуры с бетоном.
Термитная сварка стыков арматурных стержней, как правило производится без предварительного подогрева, но с несколько большим расходом термита на стык.
При термитной сварке стыков арматурных стержней применяют универсальные огнеупоры, являющиеся одновременно и тиглем и формой.
На железнодорожном транспорте широко применяется термитная приварка электросоедимениний к рельсам. Для этого используется специальный термит, состоящий из окислов меди, сплава меди с алюминием и ферромарганца. Сжигается этот термит в тигель-форме из жаропрочного графита, способного выдерживать несколько сот плавок.
На действующих газопроводах для предохранения их от разрушения почвенной коррозией осуществляется электродренажная защита — привариваются стальные стержни, которые подключаются к источникам постоянного тока. Стальные стержни приваривают только термитом. Использование других видов сварки — электрической или газовой — недопустимо, так как в ходе сварки может произойти прожог труб, по которым подается горючий газ под давлением. Термит для приварки стержней дренажной защиты состоит из железо-алюминиевой шихты с введением в нее дополнительно магния и ферромарганца.
Для сварки стальных проводов широко применяют спрессованный в цилиндрические шашки термит, который состоит из 25% металлического магния и 75% железной окалины.
Магниевый термит применяется потому, что при сгорании он нe образует жидких шлаков.
Термитно-магниевые шашки можно использовать и при пайке. В паяльник закладывают шашку и поджигают ее обычным способом. Через несколько минут после окончания процесса горения Паяльник прогревается до нужной температуры и становится пригодным для пайки.
При строительстве электрических установок высокого напряжения часто приходится сваривать стыки многопроволочных проводов. Перед сваркой производят механическую подготовку и обезжиривание стыков, закладывают подготовленные концы проводов в цилиндрический термитный патрон и закрепляют их в сварочных клещах.
Стык проводов при поджигании термитного патрона и в процессе сварки должен быть в горизонтальном положении.
При сварке стале-алюминиевых и алюминиевых проводов со сваренного стыка необходимо удалять металлический кокиль—оболочку термитного патрона.
Термитная сварка стыков узкоколейных рельсов без предварительного подогрева может применяться в горной и лесной промышленности. Для этого используют такие же сухие формы, как и при термитной сварке арматурных стержней.
Количество термита для сварки стыка без предварительного подогрева удваивается. Это компенсируется высокой производительностью (7—10 мин.) на один стык и компактностью применяемой оснастки.
Трещины в головке, участки пробуксовки и другие дефекты рельсов устраняют термитной наплавкой.
Термитным способом можно получить термитную перегретую жидкую сталь любого состава, которая имеет высокую жидкотекучесть и хорошие литейные свойства. Это дает возможность получить из термитной стали всевозможные отливки сложной конфигурации.
Высокая жидкотекучесть термитной стали позволяет отливать из нее небольшие сложные детали, которые обычным способом из стали отлить нельзя.
Высокие литейные качества термитной антикоррозийной стали позволяют с успехом отлипать из нее любые скульптурные композиции.
Читать: «Автогенная обработка». Термитная сварка. История развития, Краткие рекомендации по технике безопасности при термитной сварке рельсовых стыков, Кузнечный способ термитной сварки
Источник: Малкин Б.В. Термитная сварка
Термитная сварка — обзор технологии и оборудования
Что делать, если нужно быстро сделать соединение деталей, да еще и в полевых условиях? Отличным выходом станет термитная сварка. О технологии подробнее.
Сварочный процесс сопряжен с тщательной подготовкой всех работ, а также с наличием различных источников питания. Да и финансовая сторона может не окупаться с применением традиционных способов варки металлов. А что делать, если нужно быстро сделать соединение деталей, да еще и в полевых условиях? Отличным выходом станет термитная сварка.
В этой статье мы поведем речь о таком быстром и относительно недорогом способе как использование термита в сварочных работах. В чем заключается такая технология и что нужно для этого?
Области использования
Как было сказано выше, термитная сварка применима в полевых условиях, или в случае невыгодных в финансовом плане других традиционных способов.
Такой способ соединения металлов нашел себе применение при ремонте железнодорожных путей, кабелей связи или электрических проводов.
Алюминотермитная сварка рельсов, в принципе, единственный способ быстро провести ремонт при минимальных затратах.
Но термитное сваривание деталей применяется и в производстве. Особенно такой способ соединения актуален при изготовлении крупных по габаритам деталей: лопасти в речных и морских судах, коленчатые валы автомобилей и других.
Также широко применяют термит при ремонте большого оборудования в металлургии и металлообработке: прокатных станов, роторных валов, кузнечных прессов и прочих.
Как это происходит в технологическом плане?
Особенности технологии
Сваривание металлических частей путем применения термита построено на плавлении кромок соединяемых деталей в процессе горения и направления расплавленного металла, полученного вследствие высоких температур.
В кузнечном деле давным-давно применялся довольно интересный способ. В емкость насыпалась сера вперемешку с окалиной. Первая поджигалась и получался расплав металла, который можно было использовать для соединения деталей. Качество, конечно, было не слишком высоким.
Конечно, современная термитная сварка более совершенна. Работает она следующим образом.
Стык соединяемых деталей проливается расплавом, полученным при сгорании термитной смеси в тигле. Температура сгорания очень большая и позволяет быстро расплавить сталь.
Запал смеси происходит электрическим способом или же, если используется порошковая сварка, подрывом пиропатрона.
Технологически термитная сварка проводится в несколько приемов:
- В стык деталей.
- Литьем в промежутки (в промежуток между свариваемыми частями).
- Комбинированный.
- Дуплекс (два приема сразу).
Как работают эти приемы
Способ термитного сваривания встык, требует тщательной подготовки соединяемых поверхностей. Потом в зазоре устанавливается термитная пленка. Отдельно от деталей в тиглях готовится расплав, который заливают встык, сами заготовки при этом сжимаются для качественного соединения.
Литье в промежуток более простой прием. Расплав готовят путем сжигания термита в отдельной форме и его льют в зазоры между деталями.
Комбинированная технология применяется при сварке железнодорожных рельсов. Торцы сначала зачищают, потом между ними укладывают стальную пластину. При заливании рельсы сжимают и получают качественные соединения.
Дуплекс предусматривает использование термитного сваривания с прессованием соединяемых частей.
Особенности сварки проводов
Термитная сварка получила большое распространение и при соединении разного рода неизолированных кабелей.
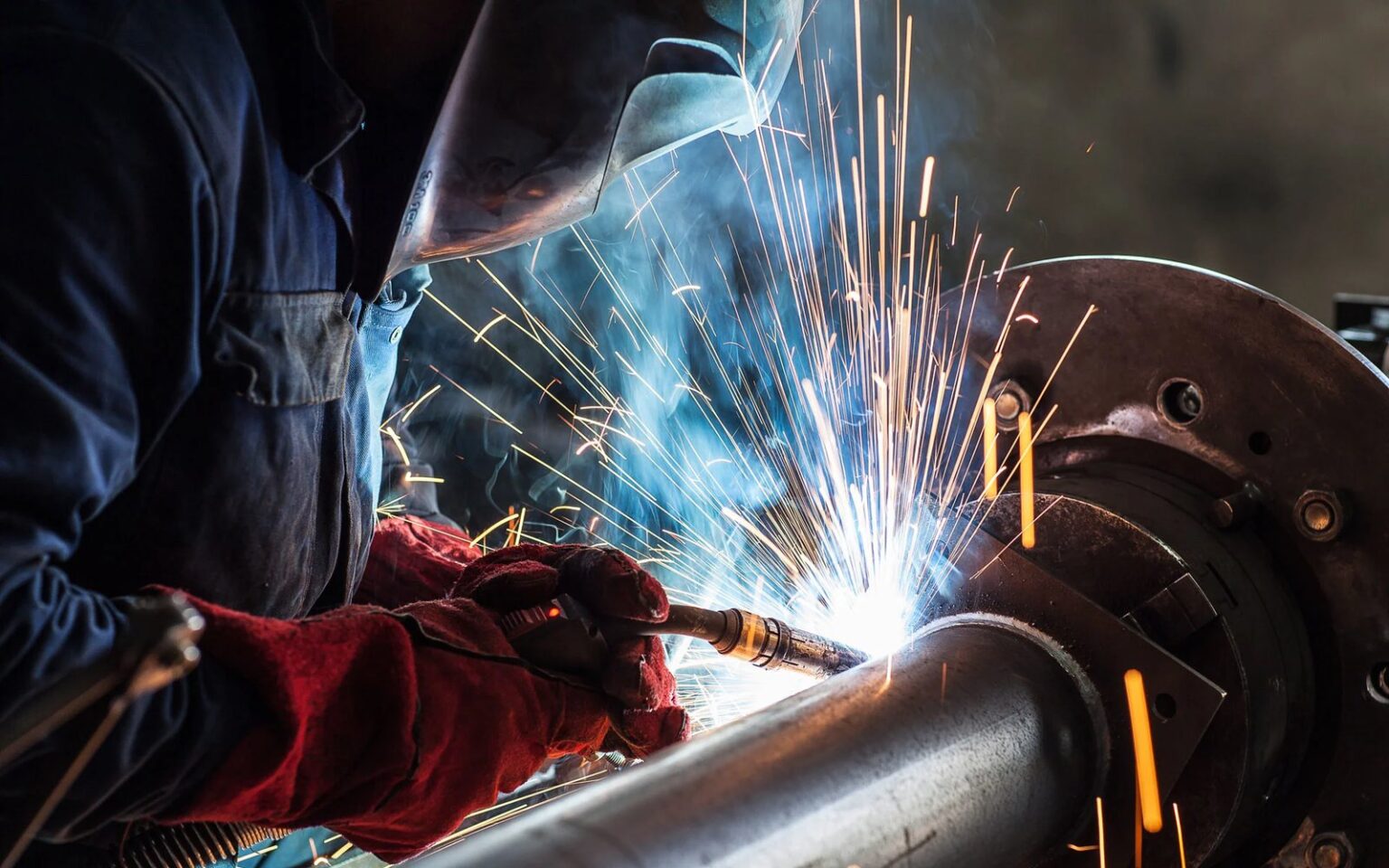
При такой технологии главное — это точный расчет и соблюдение всех правил. В месте соединения провод увеличивается сечение провода, но при этом уменьшается электрическое сопротивление.
Для сваривания используют специальный термитный патрон, состоящий из листовой меди (толщина 1,25 миллиметра), медно-фосфорных вкладышей для заполнения зазора, и собственно термитной шашки для расплавления металла с дальнейшим соединением частей.
Оборудование термитной сварке
Основное оборудование для термитной сварки — это тигель, где и будет происходит плавка и горение термита. Снизу он оборудован сливом. В зависимости от требований, он изготавливается из тугоплавких металлов или из керамики.
Технология отливки предусматривает наличие форм и матриц, позволяющих работать с расплавом. Формы бывают как одноразовыми, так и многократного использования. И, конечно же, понадобится оборудование фиксации и зажима.
Дополнительно при термитной сварке используется кислородный резак, горелка для подогрева и специальный запальник.
Термитные патроны
Термит может производиться в порошкообразном виде или же (чаще) в виде специальных патронов (карандашей).
Состоит такой карандаш из основы в виде проволоки, диаметр которой будет зависеть от толщины свариваемых деталей.
Термитный патрон
Основа покрыта термитным составом, состоящим из алюминиевых опилок и железной окалины. Соотношение состава 23% алюминия, а 77 — железо.
Также вместо алюминия в составе могут находиться и другие металлы, а их соотношение относительно окиси железа может варьироваться: магний (31%), кальций (43%), титан (31%), кремний (21%).
На конце патрона находиться затравка для поджигания.
Все патроны тщательно упаковываются и хранятся порциями необходимыми для проведения определенных работ.
Дозирование термита зависит от параметров свариваемых деталей и может колебаться от нескольких сотен грамм до десятков килограмм. Например, алюмотермитная сварка рельса стандартного профиля потребует 7-8 кг термитного состава.
Особенности применения в домашних условиях
Конечно, в бытовых условиях лучше всего воспользоваться более традиционными способами соединения металла — электродуговой или газовой сваркой. Но термит может позволить сделать мелкие ремонтные работы или использоваться для соединения строительной арматуры.
При бытовом использовании лучше всего использовать термитный состав с минимальной температурой горения в 1300 градусов, этого будет более чем достаточно.
Работы по сварке проводят, используя термитный карандаш, который при правильном соблюдении технологии позволит сделать прочное соединение.
Термитное сваривание металлов намного упрощает процесс производства и ремонта. Особенно ее применение актуально при крупногабаритных деталях, когда традиционные способы использовать затруднительно. При этом разнообразие составов позволяет добиться качества и прочности сварного шва.
Конечно, использовать такой вид в бытовых условиях просто нецелесообразно. Ведь в домашнем хозяйстве нет столь крупных конструкций, а мелкий ремонт можно провести за счет обычной электродуговой сварки. Это будет просто экономически выгодно. Да и просто безопаснее.
Безопасность при самостоятельных работах с использованием термитных патронов должна быть на очень высоком уровне. Во-первых, обязательно использование защиты для лица и открытых частей тела, а во-вторых — нужно защитить зрение, ведь горение термита сопровождается таким же ярким свечением, как и при дуговом разряде.
Часто можно увидеть видео на ютубе о самостоятельном изготовлении термита с целью резки металла. Это довольно таки бессмысленные поделки в домашнем хозяйстве не просто непрактичны (ведь обычная болгарка с отрезным кругом упрощает все операции), но и даже опасно. Использование самодельного термита чревато не просто сильным горением, а и взрывом.
А что вы думаете по этому поводу? Насколько практична термитная сварка в бытовых домашних условиях? Можно ли с помощью ее проводить ремонтные и сварочные работы? Если у Вас есть опыт такого применения, пожалуйста, поделитесь им в блоке комментариев к этой статье.
Термические процессы сварки | Строительный справочник | материалы — конструкции
Все зоны сварочного шва подвергаются термическому воздействию с определенными циклами по времени. Каждый участок сварочного шва вначале нагревается до определенной температуры, а затем охлаждается. Температурные изменения металла во время сварки называют ее термическим циклом, графическая зависимость которого отражена на рисунке. Как видно из графика, температура металла меняется в зависимости от зон сварного соединения и снижается по мере удаления от центра шва. На ширину зоны влияния накладывают отпечаток несколько факторов. В первую очередь, это толщина свариваемого металла, вид термического воздействия и его режимов. При дуговой сварке ширина этой зоны обычно находится в пределах 5—6 мм, а при газовой сварке может достигать 25 мм.
Схема изменения структуры (А), термических циклов (Б), и твёрдости (В) сварного соединения низкоуглеродистой стали при однопроходной сварке |
В зависимости от степени нагрева металла меняется и его структурное строение. Вначале в нагретом металле происходит растворение некоторых соединений, изменяющих структуру металла. Примером такого растворения может служить соединение металла с углеродом. По мере повышения температуры происходит переход низкотемпературной фазы металла в высокотемпературную (полиморфное превращение). На участках, где температура превышает точку плавления, происходит переход металла из твердой фазы в жидкую.
По мере снижения температуры, когда дуга смещается вдоль шва или гаснет, структурные изменения проходят в обратном порядке. Вначале проходит процесс кристаллизации, то есть переход жидкой фазы металла в твердую, а затем — полиморфные превращения. По мере остывания происходит выпадание из металла некоторых его фаз, например, карбидов, интерметаллидов и т.д. Температура нагрева металла меняется не только во времени, но и по мере удаления от центра шва. Поэтому структура кристаллической решетки имеет различное строение по ширине сварочного соединения.
Так, в области, где металл нагревается до температуры, превышающей точку плавления (зона плавления 1), в результате последующего процесса кристаллизации образуется сварочный шов. В этой области основной материал приобретает грубую столбчатую структуру, снижающую механическую прочность и пластичность металла.
В зоне 2, где температура ниже, проходит граница между жидкой и твердой фазой металла. На этом участке происходит частичное оплавление и рост зерен металла, накопление примесей, что приводит к снижению прочности шва. Эта зона считается самой слабой в сварочном соединении и называется зоной неполного оплавления.
В зоне 3 (зона перегрева) температура основного металла не достигает точки плавления, но все же оказывается достаточной, чтобы вызвать существенные изменения в кристаллической решетке. Основной металл в этой зоне приобретает крупнозернистую структуру, отличающуюся высокой пластичностью и ударной вязкостью. И чем шире зона перегрева, тем ярче проявляются эти свойства.
Нагрев и охлаждение на участке 4 (зона нормализации) основной металл не перегревается, что приводит к образованию мелкозернистой структуры (перекристаллизация без перегрева), обладающей высокими механическими свойствами.
На участке 5 температура основного металла не достигает величины, необходимой для полной нормализации металла (зона неполной перекристаллизации). Поэтому в данной зоне могут чередоваться между собой крупнозернистая и мелкозернистая структуры, что делает этот участок слабее по механическим качествам, чем предыдущая зона.
Изменения, происходящие в результате повышения температуры в зонах 6 и 7, зависят от предварительной обработки металла. Так, если металл перед сваркой испытал холодную деформацию (прокатку, ковку, штамповку и т.д.), то на участке 6 могут возникать процессы рекристаллизации (рост кристаллов), что приводит разупрочнению структуры. На участке 7 могут происходить процессы старения с выпаданием карбидов железа и нитридов. Это приводит к снижению механической прочности металла. Если перед сваркой металл подвергался термической обработке (отжиг), то существенных изменений в этих зонах в процессе сварки не происходит.
Экзотермическая / термитная сварка
Экзотермическая сварка — это сварка деталей расплавненным металлом, образованным в ходе химической реакции, сопровождающейся высокой температурой (большим количеством тепла). Основным компонентом этого вида сварки является термит.
Термит — это порошкообразная смесь, состоящие из двух металлов:
- Окисел второго металла с небольшой теплотой формирования (например, окисел меди или железа).
- Металл, имеющий большую теплоту окисления. Например, алюминий, который обладает очень большой активностью, соединяясь с кислородом — за счёт чего при определенных условиях он легко восстанавливает из окислов другие металлы.
Термиты применяются в вооружении — зажигательных бомбах, в металлургической промышленности — алюминотермия и для сварки металлов.
При экзотермической сварке наиболее часто применяются термиты из пары «железная окалина + алюминий» и из «медный окисел + алюминий». Эти смеси сгорают, давая металлическое железо или медь, во втором случае, и окись алюминия. Реакция сопровождается температурой более чем 3000° С.
Для проведения операции используется специальная огнеупорная форма — тигель. Порцию термита зажигают в этой форме, после чего он быстро сгорает и тигель заполняется сильно перегретым расплавом.
После небольшой отстойки расплав из-за разного веса компонентов разделяется на два слоя: снизу — жидкий металл (железо или медь), сверху — жидкий шлак, состоящий преимущественно из окиси алюминия.
Отстоявшимся расплавом заливают свариваемые изделия. При этом поверхности изделий разогреваются до сварочного жара (не расплавляя металл) и сплавляются с металлом из расплава.
Экзотермическую сварку используют для сварки железнодорожных рельс, стальных труб, при ремонте стальных, чугунных деталей, для соединения разнообразных изделий (например, заземляющего электрода и медного провода).
Для удобства примениния, созданы различные готовые комплекты, которые включают все необходимое для проведения сварочных работ.
Готовые комплекты
Экзотермическая сварка проводников
Сварка с использованием термита «медный окисел + алюминий» обеспечивает наиболее качественный контакт между двумя проводниками. Это превосходные сварные соединения, которые никогда не ослабнут, не заржавеют и чье сопротивление никогда не повысится.
Такой способ обеспечивает возможность создания связей на молекулярном уровне для разных материалов без каких-либо внешних источников энергии или тепла:
- «медь — медь»
- «медь — оцинкованная сталь»
- «медь — «чёрная» сталь»
- «медь — омеднённая сталь»
- «медь — нержавеющая сталь»
- «медь — бронза»
- «медь — латунь»
- и даже «сталь — сталь»
В тигель — графитовую форму помещаются проводник и термит (заряд). В ходе реакции в результате замещения оксида меди алюминием образуется расплав с очень высокой температурой, состоящий из меди и оксида алюминия.
Термитная сварка в домашних условиях
На чтение 31 мин. Обновлено
Сущность термитной сварки
Способ термитной сварки основан на получении тепла в процессе химической реакции, в результате свариваемые материалы нагреваются до температуры плавления и свариваются.
Для термитной сварки применяются порошкообразные горючие смеси металлов с окислами металлов, которые при сгорании выделяют большое количества тепла. Такими материалами в термитных смесях служат металлы с большой теплотой образования окислов, например алюминий и магний.
Для термитной приварки выводов ЭХЗ используется медный термит, в состав которого входят порошок алюминия, меди и из медная окалина.
Для запуска процесса сварки термитную смесь необходимо зажечь. Горение термитной смеси проходи довольно активно. Смесь сгорает за 5 — 10 сек с образованием большого количества тепла, температура может достигать 3000 градусов. Принцип термитной сварки выводов ЭХЗ основан на сжигании термитной смеси в специальной огнеупорной форме — тигле.
По окончании процесса горения продукты реакции — жидкая медь и шлак разделятся на слои в зависимости от плотности. Жидкая смесь расплавляет мембрану в тигле и выливается на свариваемый металл, оплавляя его и образуя сварное соединение. Жидкий шлак служит в качестве защиты сварного соединения и сохраняет тепло для полного завершения процесса сварки.
В термитные смеси кроме основных компонентов, добавляют различные присадки и легирующие компоненты, для улучшению технологических свойств термита и приданию сварному соединению специальных свойств.
Преимущества и недостатки
Процесс сварки термитами отличается применением особых порошковых смесей, которые в ходе сгорания выделяют большое количество тепла. Как правило, это металлические смеси, которые и называются термитами. Традиционная комбинация предусматривает использование двух компонентов – зажигающей массы и состава, из которого выделяется тепло.
В качестве окисла выступает окалина из железа, а основным активатором является термит, содержащий магний с алюминием. Кроме того, технология термитной сварки допускает использование оксидов хрома, вольфрама и никеля. Благодаря этим порошкам достигается усиление теплового воздействия. Так, если смесь из алюминия и магния обеспечивает теплоту порядка 2500 °C, то хромированные составы повышают температуру до 3500 °C.
Различаются и смеси для запала. Наиболее распространенным составом для этой задачи является комбинация магния, натрия и пероксида бария. К особенностям горящего термита можно отнести поддержание активного тепловыделения даже в условиях контакта с водой. Иными словами, смесь практически невозможно затушить случайным воздействием.
Технология произведения термитной сварки оптимальной подходит для работы с электропроводкой. Причем этот подход может использоваться и в промышленности, и в быту. В процессе осуществления работ формируется цельнометаллическое соединение окончаний проводки. При этом важно заметить, что в месте утолщения провода на участке сварки электрическое сопротивление понижается относительно остальной части материала.
Произведение сварочных операций независимо от применяемой технологии сопрягается с необходимостью довольно хлопотной организации рабочего процесса. Мастер должен подготовить оборудование, расходные материалы, а также позаботиться о технике безопасности.
При этом надо учитывать затратность мероприятия, поскольку финансовое обеспечение таких операций в регулярном режиме далеко не всегда оправдывает качество получаемого результата.
В этом плане одной из самых выгодных является термитная сварка, отличающаяся простотой выполнения, доступностью материалов и в некоторых случаях позволяет добиваться высокой прочности соединений.
Сварка при использовании термита имеет свои преимущества и недостатки.
К достоинствам данного процесса можно отнести следующее:
- Благодаря термитному веществу обеспечивается качественный шов на соединении.
Стык обладает повышенной прочностью и долговечностью. Если присутствует алюминий, то это обеспечивает минимальный риск возникновения коррозии. - Экономность.
При эксплуатации оборудования не нужно тратить большое количество электроэнергии. - Легкость.
Сваривать сталь, алюминий, чугун и другие металлы может абсолютно любой человек, даже новичок в сварочной сфере. Рабочий процесс занимает немного время, проводится компактным инструментом, с возможностью хранить его у себя в квартире либо в доме.
Недостатки термитной сварки выражаются в следующем:
- Чтобы осуществить такого рода сварку, необходимо выполнить дополнительную и подготовительную обработку изделия из металла и кабеля отдельно.
- Сварочный процесс не отслеживается, из-за чего проходится использовать бесшовное оборудование, которым умеет управляться лишь опытный профессионал, обладающий аттестацией НАКС.
Сваривание металлических частей путем применения термита построено на плавлении кромок соединяемых деталей в процессе горения и направления расплавленного металла, полученного вследствие высоких температур.
В кузнечном деле давным-давно применялся довольно интересный способ. В емкость насыпалась сера вперемешку с окалиной. Первая поджигалась и получался расплав металла, который можно было использовать для соединения деталей. Качество, конечно, было не слишком высоким.
Конечно, современная термитная сварка более совершенна. Работает она следующим образом.
Стык соединяемых деталей проливается расплавом, полученным при сгорании термитной смеси в тигле. Температура сгорания очень большая и позволяет быстро расплавить сталь.
Запал смеси происходит электрическим способом или же, если используется порошковая сварка, подрывом пиропатрона.
Технологически термитная сварка проводится в несколько приемов:
- В стык деталей.
- Литьем в промежутки (в промежуток между свариваемыми частями).
- Комбинированный.
- Дуплекс (два приема сразу).
Если говорить о главных достоинствах рассматриваемого процесса, то к ним следует отнести:
- Высокую скорость выполнения работ. Нужно отметить, что это один из наиболее быстрых методов соединения изделий из металла. К примеру, для стыковки железнодорожных рельсов требуется в среднем около 50 минут. При этом если одновременно будет работать несколько бригад, то эффективность такой работы будет лишь возрастать (всего за 2 часа три бригады могут сваривать до 12 стыков).
- Хорошее качество швов. Места стыковки деталей обладают высокой стойкостью к механическим нагрузкам и воздействию химических веществ. Кроме того, такие швы выглядят эстетически привлекательно.
- Легкость выполнения задачи. Такая технология не требует наличия особых навыков и знаний, так как справиться с ней может любой специалист при условии прохождения непродолжительного обучения. Количество задействованных работников также невелико.
- Доступность материалов. Необходимые для этого порошковые смеси и дополнительные материалы можно приобрести в специализированных магазинах, при этом их цена не будет высокой.
- Отсутствие необходимости использования дорогостоящего оборудования. В отличие от методов контактного сваривания металлических элементов, при использовании термитных смесей не обязательно использовать дорогую сварочную технику. Это особенно актуально для работы на отдаленных объектах, когда нет возможности найти источник электрического тока или транспортировать громоздкие газовые баллоны.
При этом есть и некоторые недостатки, к которым можно отнести необходимость соблюдения строгих правил по безопасности. Во-первых, сам по себе термит является легко воспламеняемым веществом, поэтому следует проявлять особую осторожность при его транспортировке и хранении. Во-вторых, во время выполнения задачи нужно позаботиться о том, чтобы вода или любые другие жидкости не попали в горящую смесь, так как это может стать причиной взрыва.
Термитная сварка получила большое распространение и при соединении разного рода неизолированных кабелей.
При такой технологии главное — это точный расчет и соблюдение всех правил. В месте соединения провод увеличивается сечение провода, но при этом уменьшается электрическое сопротивление.
Для сваривания используют специальный термитный патрон, состоящий из листовой меди (толщина 1,25 миллиметра), медно-фосфорных вкладышей для заполнения зазора, и собственно термитной шашки для расплавления металла с дальнейшим соединением частей.
Оборудование
Для термитной сварки электрохимической защиты трубопроводов используются:
- одноразовые или многоразовые тигель-формы;
- термитная смесь;
- термокарандаши;
- паяльно-сварочные стержни;
- специальные спички или устройство дистанционного зажигания.
Термитная смесь используется для сварки стальных и медных выводов ЭХЗ диаметром от 2-5 мм к стальным трубопроводам имеющим толщину стенки не менее 5 мм. Использовать термитную сварку на трубопроводах с толщиной стенки менее 5 мм запрещается, так как есть большая вероятность прожога. К хранения термитной смеси устанавливаются жесткие требования: в сухом помещении с влажностью до 80%, и температурой не более 30 градусов, вдали от нагревательных приборов.
Тигель-формы – выполняются как правило из графита и керамических материалов, имеющих высокою жаростойкостью, снабженные специальными креплениями для удержания на трубе во время сварки. Внутри тигель формы имеется мембрана отделяющая термитную смесь от свариваемой делали.
Тигель-форма для термитной сваркиТермитная смесь помещается внутрь тигель формы утрамбовывается и зажигается с помощью специальных спичек, которую вставляют в запальное отверстие крышки тигель-формы или с помощью термоподжига.
Спички для термитной сваркиСпички термитные предназначены для зажигания термитной смеси и термитных патронов.
Термоподжиг изготавливают из огнепроводного шнура замедленного горения который поджигается обычными спичками либо проводов и воспламенителя, зажигание происходит на расстоянии. Поджиг может производится на расстоянии с помощью радиопередатчика и радиоприемника-коммутатора.
Паяльно-сварочные стержни представляют собой медные термитные смеси, упакованные в цилиндрическую оболочку из ламинированной бумаги Паяльно-сварочные стержни марки ЭХЗ-1150А предназначены для приварки ЭХЗ на трубах толщиной стенки от 3,5 до 10,0 мм, ЭХЗ-1150 — на трубах толщиной стенки от 4,0 до 10,0 мм, ЭХЗ- 1152 — на трубах толщиной стенки от 10,1 до 40,0 мм, применяются для приварки всех видов электрохимической защиты на трубопроводы диаметром до 1420 мм.
Дефекты | Причины образовании дефектов | Способы устранения дефектов |
I .Низкая прочность сварного соединения, вывод отрывается от трубы при сгибании или при удалении шлака. | Некачественная зачистка поверхности трубы и конца привариваемого вывода. В формирующуюся полость тигель- формы попала термитная смесь. | Тщательно зачистить место приварки и конец вывода. Сварку повторить. Проверить плотность соединения графитовых вкладышей тигель- формы и прилегание мембраны. |
2.Форма термитного контакта неправильная, недостаточное количество наплавленного металла, в тигель- форме образуется пробка из металла и шлака. | Плохо перемешана термитная смесь, расслоение состава. Термитная смесь отсырела. | Тщательно перемешать термитную смесь перед засыпкой тигель-форму. Термитную смесь просушить. |
3. Наплавленный металл пористый. | В тигель-форму попала влага. Влага на трубе или на привариваемом конце вывода. | Просушить тигель- форму. Удалить влагу со свариваемых элементов. |
Если вы нашли ошибку, пожалуйста, выделите фрагмент текста и нажмите Ctrl Enter.
Основу оснастки составляет тигель, который обеспечивает возможность работы с термитами, в том числе по нему производится слив и расплавленной металлической массы. Данный элемент может быть выполнен из керамики или вольфрама, в зависимости от требований к температурному режиму. Отдельно подготавливаются и формы для отливки.
Специальные матрицы позволяют работать с широким спектром расплавленной основы. Также следует подготовить оборудование для термитной сварки в виде зажимных и фиксирующих приспособлений для массивных конструкций, специальный резак и технический карандаш, предназначенный специально для данного рода операций. В зависимости от условий проведения работ и требований к результату может потребоваться специальная горелка для инвертора и термометр.
Основное оборудование для термитной сварки — это тигель, где и будет происходит плавка и горение термита. Снизу он оборудован сливом. В зависимости от требований, он изготавливается из тугоплавких металлов или из керамики.
Технология отливки предусматривает наличие форм и матриц, позволяющих работать с расплавом. Формы бывают как одноразовыми, так и многократного использования. И, конечно же, понадобится оборудование фиксации и зажима.
Дополнительно при термитной сварке используется кислородный резак, горелка для подогрева и специальный запальник.
При проведении термитной сварки сварщик должен применять следующие элементы и оборудование:
- тигель из керамики или тугоплавкого металла. Он должен иметь устройство для безопасного слива расплава;
- для создания отливок потребуется применение форм и матриц. Они могут быть одноразовыми или для многократного применения;
- устройства для закрепления и сжатия деталей;
- термитный карандаш. Этот элемент применяется в домашних условиях для сваривания и резки металлов;
- комплект инструментов, которые должен иметь в составе такие элементы, как кислородный резак, газовая горелка, ножовка по металлу, полосковый термометр;
- для зачистки поверхностей стоит применять абразивный круг или металлическую щетку.
Проведение термического сварочного процесс стоит соблюдать важные особенности и правила. Несмотря на то, что он простой и не требует использования дорогого оборудования, все равно не нужно забывать про разновидности сварки и некоторые нюансы, от которых зависит прочность и внешний вид шва.
Разновидности термитной сварки
Существует четыре основных техники выполнения такой сварки – посредством промежуточного литья, комбинированная, впритык и дуплекс. В процессе выполнения операции промежуточным литьем порошкообразная смесь переходит в состояние жидкого металла, причем это не влияет на исходные характеристики активного вещества-термита.
Обычно данную методику используют для монтажа металлоконструкций, которые предварительно крепятся в нужном положении. Специально для работы с пластинчатыми изделиями, катодными и дренажными выводами применяется стыковая термитная сварка, смесь для которой предварительно обжигается в печи. Комбинированная техника предполагает сочетание литьевого метода и сварки впритык.
Области использования
Как было сказано выше, термитная сварка применима в полевых условиях, или в случае невыгодных в финансовом плане других традиционных способов.
Такой способ соединения металлов нашел себе применение при ремонте железнодорожных путей, кабелей связи или электрических проводов.
Алюминотермитная сварка рельсов, в принципе, единственный способ быстро провести ремонт при минимальных затратах.
Но термитное сваривание деталей применяется и в производстве. Особенно такой способ соединения актуален при изготовлении крупных по габаритам деталей: лопасти в речных и морских судах, коленчатые валы автомобилей и других.
Также широко применяют термит при ремонте большого оборудования в металлургии и металлообработке: прокатных станов, роторных валов, кузнечных прессов и прочих.
Как это происходит в технологическом плане?
Термитная сварка ЭХЗ
Трубопроводы, в грунте и идущие на поверхности, подвергается коррозии по по электрохимическому механизму, на поверхности металла образуются анодные и катодные зоны. Между ними образуется электрический потенциал, начинает течь ток, и происходит коррозионное разрушение.
Термитная сварка выводов ЭХЗОдин из способов защиты трубопроводов от коррозии является электрохимическая защита. Защитные покрытия наносимые на трубы не обеспечивают достаточной защиты от коррозии. Поэтому нормативно-технические документы содержать требования обеспечивать нефтяные и газовые трубопроводы средствами электрохимической защиты ЭХЗ.
Наиболее технологичным и надежным способом крепления выводов ЭХЗ – является термитная сварка. Термитная сварка выводов ЭХЗ имеет следующие преимущества перед другими способами:
- удобство, применимость в любых местах;
- мобильность, не требуется источников электроэнергии;
- высокое качество сварного соединения.
Способ термитного сваривания встык, требует тщательной подготовки соединяемых поверхностей. Потом в зазоре устанавливается термитная пленка. Отдельно от деталей в тиглях готовится расплав, который заливают встык, сами заготовки при этом сжимаются для качественного соединения.
Литье в промежуток более простой прием. Расплав готовят путем сжигания термита в отдельной форме и его льют в зазоры между деталями.
Комбинированная технология применяется при сварке железнодорожных рельсов. Торцы сначала зачищают, потом между ними укладывают стальную пластину. При заливании рельсы сжимают и получают качественные соединения.
Дуплекс предусматривает использование термитного сваривания с прессованием соединяемых частей.
Чтобы соединение при процессе сварки получилось качественным и крепким, необходимо соблюдать следующие условия:
- количество порошка термита необходимо просчитать столько, сколько нужно для заполнения металлом формы вокруг рельса;
- важно, чтобы смесь шихты была тщательно измельчена и перемешана;
- температура горения зажигательного элемента (шашка, карандаш), как катализатора поджига основной смеси, должна быть не менее 1400°C.
Несмотря на свои незначительные недостатки, термитная сварка может с успехом конкурировать по безопасности и качеству с такими сварками, как электродуговая и газовая. Например, газовая взрывоопасна, а электрическая не исключает поражение электротоком. Да и многое в этих видах сварок напрямую зависит от квалификации самого сварщика. В термитной же, большую роль играет качество смеси и сохранение технологии, а остальное получится само ― собой.
Термит может производиться в порошкообразном виде или же (чаще) в виде специальных патронов (карандашей).
Состоит такой карандаш из основы в виде проволоки, диаметр которой будет зависеть от толщины свариваемых деталей.
Термитный патрон
Основа покрыта термитным составом, состоящим из алюминиевых опилок и железной окалины. Соотношение состава 23% алюминия, а 77 — железо.
Также вместо алюминия в составе могут находиться и другие металлы, а их соотношение относительно окиси железа может варьироваться: магний (31%), кальций (43%), титан (31%), кремний (21%).
На конце патрона находиться затравка для поджигания.
Все патроны тщательно упаковываются и хранятся порциями необходимыми для проведения определенных работ.
Дозирование термита зависит от параметров свариваемых деталей и может колебаться от нескольких сотен грамм до десятков килограмм. Например, алюмотермитная сварка рельса стандартного профиля потребует 7-8 кг термитного состава.
Термитная сварка также имеет другое название – порошковая. Она подразумевает под собой подтип сварочных процессов, где источником энергии является термит. Её применяют для сварки рельс, ЭХЗ и других конструкций.
Термитом в свою очередь является смесь в виде порошка, изготовленная их металлов. Зачастую используют алюминий, магний и окалину.
После вопроса: что такое термитная сварка, необходимо разобраться в её видах и основных особенностях.
Выделяют два основных типа:
- тигельная или алюминиевотермитная;
- муфельная.
В первом типе выполняется соединение термитной сваркой для того, чтобы на поверхности создался наплавок. Таким образом, можно сваривать чугун безстычным способом. Для муфельной сварки необходим контакт, что дает возможность лишнему алюминию испариться.
Термитная сварка.
Чтобы воспользоваться вторым способом необходимо взять дополнительно накладку либо термитный патрон, который значительно облегчит задачу со сваркой проводов с одно- или многожильным типом.
Не смотря на то, что термитная сварка может показаться на первый взгляд достаточно простой, то на самом деле эта работа опасна и трудна.
Чертеж термитной сварки.
Необходимо придерживаться установленных нормативными актами правил техники безопасности при эксплуатации подобного сварочного оборудования:
- Термитное вещество необходимо хранить в теплых и проветриваемых комнатах.
- Не применяйте термит с влагой.
- При эксплуатации сварочного оборудования, находясь на улице, необходимо очистить в области половины метра поверхность от грязи, пыли и других лишних веществ и предметов.
- Не зажигайте шихту от сварочной дуги.
- Не рекомендуется начинать сварочные работы, если термометр показывает меньше 10 градусов.
- У мастера, выполняющего рабочий процесс, должен быть специальная одежда, в частности комбинезон.
- При использовании термитного инвертора необходимо во время горения засыпать термит песком, создать линию при помощи дополнительного защитного клапана для подачи кислорода и выключить перелив горючего, если горелка повредится.
В бытовом хозяйстве данная разновидность сварки спасает тех, кто не может надлежащим образом реализовать электродуговой метод или соединение газовым расплавом. Обычно в таких случаях используется термит с минимальной температурой – порядка 1300 °C. Этот режим позволяет обеспечить простейший алюминиевый состав, за счет которого можно выполнить ремонт мелких трещин в металлоконструкции, реализовать автослесарные операции или сварить строительную арматуру.
Промышленная организация процесса сварочных работ с применением термитных смесей имеет немало существенных отличий. В первую очередь, используются более эффективные металлические составы с повышенным тепловыделением. Это те же термиты с включением хрома, вольфрама и других элементов с активной функцией сгорания.
Для технической организации процесса необходимо также применение более мощного оборудования, то есть одним термитным карандашом специалисты не ограничиваются. Например, термитная сварка в электротехнической промышленности в обязательном порядке предусматривает использование инверторов, термостатов и другой аппаратуры, которая позволяет отслеживать параметры рабочего процесса.
При всей простоте выполнения данного метода сварки именно в силу специфики химических свойств термитных смесей определяются довольно жесткие правила соблюдения техники безопасности. Во-первых, предъявляются специальные требования к организации хранения металлических порошков. Следует обеспечивать хранение только в сухих и отапливаемых помещениях.
Более того, термитная сварка не допускает использования влажных порошков непосредственно в процессе поджига. Во-вторых, предъявляются особые требования и к условиям выполнения сварки. Операцию можно производить только при температуре более 10 °C. Места соединений должны быть предварительно очищены и обезжирены.
К преимуществам относят доступность материалов, несложность выполнения большинства операций и низкое энергопотребление в процессе выполнения работ. Иными словами, этот вариант подойдет и для масштабной сварки массивных строительных конструкций, и для незначительных бытовых операций. Что касается недостатков, то термитная сварка доставляет немало трудностей в работе с бесшовными соединениями.
Дело в том, что непосредственно в ходе произведения операции мастер не может в полной мере отслеживать качество формирования зазора и соединения. В итоге рассчитывать на ровное и чистое сведение частей конструкций без существенных деформаций в большинстве случаев не приходится. Но зато в плане прочности и долговечности термитные соединения считаются одними из самых лучших.
Многие часто спрашивают, что такое термитная сварка и зачем она используется? Чтобы это понять, стоит рассмотреть ее основную суть. Во время сварочного процесса применяются специальные порошковые составы, которые во время сгорания образуют большое количество тепловой энергии. Часто данные металлические смеси называют термитами.
Термическая сварка — это процедура, во время которой происходит разогревание свариваемого элемента до состояния полужидкой субстанции, но в то же время оно сплавляется в целостный состав при помощи специального порошка. Обычно применяется порошок, который состоит из железа и алюминия.
При смешивании данных элементов на основе алюмотермической реакции на области сварки образуется катализатор с высоким качеством. Основная суть этого процесса состоит в том, что во время него из соответствующего оксида химическим методом происходит полное восстановление металла.
Обратите внимание! Сварка изделий производится за счет оказания воздействия расплавленного металла из термита и сильного жара на кромки, которые начинают активно плавятся на свариваемом участке. Именно термит в данном случае выступает в качестве присадочного материала.
При термическом сварочном процессе проявляется мощный поток тепла с показателем температуры от 2400-27000С, оно выполняет функции горелки при проведении газосварки или электрода при электродуговой сварке. Главная особенность данной технологии состоит в том, что порошкообразный термит способен воспламеняться самостоятельно.
Это связано с наличием кислорода в составе порошка, который выделяется во время химической реакции из оксида железа. Именно это способы позволяет проводить термическое сваривание в среде, которая заполнена негорючими газами, к примеру, углекислым, и даже в вакууме.
Достоинства и недостатки
В первую очередь, стоит отметить, что процесс – несложный. Даже если вы не имеете большого опыта в создании швов, то соблюдая все правила и требования, можно качественно выполнить сварочную работу своими руками, к тому же процедура не отнимет много времени.
Термит для сварки способствует высокому качеству соединений, которые отличаются надежностью и долговечностью. Для работы оборудования не нужно большое количество электроэнергии.
Недостатки
Чтобы выполнить такую процедуру надо провести подготовительные работы по обработке металлических изделий и кабелей. Проследить за точностью процесса сварки просто невозможно. В связи с этим выполнить бесшовную технику могут только профессионалы.
Сферы применения
Бесстыковой путь дает возможность уменьшить экономические затраты по текущему содержанию пути, позволяет увеличить скорость движения рельсового транспорта, уменьшает шум и удлиняет срок службы подвижного состава.
1) удобство, маневренность применяющейся оснастки;2) возможность применения без электроэнергии;3) высокая производительность;4) достаточная прочностная характеристика.
Термитная сварка позволила к 1953 г. в Москве и Ленинграде иметь в трамвайных путях бесстыковые соединения.
В трамвайных хозяйствах многих городов отдается предпочтение термитной сварке стыков рельсов. За последние 25—30 лет термитная сварка претерпела небольшие качественные изменения.
Из всех способов термитной сварки — кузнечного, промежуточного литья, комбинированного, «дуплекс» — получил широкое распространение способ промежуточного литья.
С 1950 г. применяется модернизированный способ промежуточного литья — «единый» способ, который хотя и не дает провара по всему сечению рельсов, но благодаря простоте всего технологического процесса позволил расширить внедрение термитной сварки в трамвайных путях.
В связи с массовым применением термитной сварки на транс порте появилась потребность как в качественном улучшении сварного стыка — получение плотного стыка с хорошим проваром и постоянством химического состава термитной стали, так и в изменении количественных характеристик — повышение производительности, уменьшение расхода материалов и т. д.
Термитный металл обладает хорошими литейными свойствами и может употребляться для прицезионного литья.
а) производстве крупногабаритных деталей, состоящих из нескольких элементов: коленчатых валов, рулевых рам судов, приварке лопастей к гребным валам судов и пр.;б) восстановлении цилиндров прессов, поршневых штоков, колонн кузнечных прессов, роторных валов, валков, а также ведущих реверсивных шестерен прокатных станов, всевозможных станин—клетей прокатных станов, станин прессов и главных станин ковочно-высадочных машин и пр.;в) ремонте чугунного технологического оборудования сталелитейных цехов: изложниц, шлаковых ковшей, поддонов и т. д.
Термитную сварку крупногабаритных деталей лучше всего производить в литейном цехе, где имеется необходимое технологическое оборудование, а также грузоподъемные механизмы.
Термитная сварка крупных чугунных деталей дает большой экономический эффект, особенно для восстановления технологического оборудования металлургического производства: различных ковшей, изложениц, поддонов, а также всевозможных станин.
Приступая к термитной сварке чугунных деталей, нужно учитывать повышенную чувствительность чугуна к температурным изменениям. При нагревании чугуна выше критической точки и охлаждении со скоростью, превышающей 149o в мин., он становится хрупким.
Одним из важнейших условий успешного проведения термитной сварки чугунных деталей является предварительный подогрев. При сварке чугунных деталей, помимо местного подогрева в зоне сварки до 900o, необходимо произвести и общий подогрев всей детали до 450—500o.
Весьма эффективно применение термита для сварки стыков стержней большого диаметра непосредственно в блоках гидросооружений, где нельзя использовать стыковую сварку. При этом
повышается экономия металла, используемого на накладки или технологические изгибы сопрягаемых элементов, а также увеличивается производительность сварки по сравнению с электродуговым или ванным способом.
Термитная сварка стыков арматурных стержней, как правило производится без предварительного подогрева, но с несколько большим расходом термита на стык.
При термитной сварке стыков арматурных стержней применяют универсальные огнеупоры, являющиеся одновременно и тиглем и формой.
На железнодорожном транспорте широко применяется термитная приварка электросоедимениний к рельсам. Для этого используется специальный термит, состоящий из окислов меди, сплава меди с алюминием и ферромарганца. Сжигается этот термит в тигель-форме из жаропрочного графита, способного выдерживать несколько сот плавок.
На действующих газопроводах для предохранения их от разрушения почвенной коррозией осуществляется электродренажная защита — привариваются стальные стержни, которые подключаются к источникам постоянного тока. Стальные стержни приваривают только термитом. Использование других видов сварки — электрической или газовой — недопустимо, так как в ходе сварки может произойти прожог труб, по которым подается горючий газ под давлением. Термит для приварки стержней дренажной защиты состоит из железо-алюминиевой шихты с введением в нее дополнительно магния и ферромарганца.
Для сварки стальных проводов широко применяют спрессованный в цилиндрические шашки термит, который состоит из 25% металлического магния и 75% железной окалины.
Магниевый термит применяется потому, что при сгорании он нe образует жидких шлаков.
Термитно-магниевые шашки можно использовать и при пайке. В паяльник закладывают шашку и поджигают ее обычным способом. Через несколько минут после окончания процесса горения Паяльник прогревается до нужной температуры и становится пригодным для пайки.
При строительстве электрических установок высокого напряжения часто приходится сваривать стыки многопроволочных проводов. Перед сваркой производят механическую подготовку и обезжиривание стыков, закладывают подготовленные концы проводов в цилиндрический термитный патрон и закрепляют их в сварочных клещах.
Стык проводов при поджигании термитного патрона и в процессе сварки должен быть в горизонтальном положении.
При сварке стале-алюминиевых и алюминиевых проводов со сваренного стыка необходимо удалять металлический кокиль—оболочку термитного патрона.
Термитная сварка стыков узкоколейных рельсов без предварительного подогрева может применяться в горной и лесной промышленности. Для этого используют такие же сухие формы, как и при термитной сварке арматурных стержней.
Количество термита для сварки стыка без предварительного подогрева удваивается. Это компенсируется высокой производительностью (7—10 мин.) на один стык и компактностью применяемой оснастки.
Трещины в головке, участки пробуксовки и другие дефекты рельсов устраняют термитной наплавкой.
Термитным способом можно получить термитную перегретую жидкую сталь любого состава, которая имеет высокую жидкотекучесть и хорошие литейные свойства. Это дает возможность получить из термитной стали всевозможные отливки сложной конфигурации.
Высокая жидкотекучесть термитной стали позволяет отливать из нее небольшие сложные детали, которые обычным способом из стали отлить нельзя.
Высокие литейные качества термитной антикоррозийной стали позволяют с успехом отлипать из нее любые скульптурные композиции.
Читать: «Автогенная обработка». Термитная сварка. История развития, Краткие рекомендации по технике безопасности при термитной сварке рельсовых стыков, Кузнечный способ термитной сварки
При помощи термита из алюминиевой пудры выполняется наплавка на запасные части или детали. Также данная технология применяется при сваривании рельсов и чугуна, разных сплавов из хрупких металлов. Именно этот вид сваривания позволяет провести быстрый ремонт железнодорожных путей с минимальными затратами.
Термит для сварки из производных магния применяется в случаях, когда необходимо сваривать электрические коммуникации, телефонные провода и многое другое. Термитное сваривание часто используется в условиях производства. Этот способ подходит для изготовления крупных деталей — лопасти в речных и морских судах, коленчатые валы автомобилей и другие.
Термитную сварку на сегодняшний день используют для сваривания чугуна, электрических и телефонных коммуникаций, труб, частей двигателя и так далее. Особо часто термит используют для сваривания железнодорожных рельсов. Соединения получаются достаточно надёжные. Место ремонта может быть на любом участке дороги, даже в несколько сот километров от населенного пункта.
Заключение
Производители сварочного оборудования преимущественно совершенствуют аппаратуру для резки, наделяя высокими эксплуатационными качествами именно инструмент термического воздействия. Такой подход к разработке приборов себя оправдывает, но эксплуатация оборудования с повышенной мощностью закономерно требует и больших вложений в энергоснабжение.
Как показывает практика термитной сварки в быту, использование металлических порошковых смесей на основе алюминия и магния по силе резки дает тот же эффект, что и альтернативные методики. Другое дело, что содержание этих же смесей также требует немалых хлопот и затрат. Зато эти неудобства окупает универсальность технологии.
Процесс приготовления
В качестве ингредиентов обычно выступают различные металлы. Состав вещества зависит от сферы применения термита, необходимых особенностей смеси и условий использования. Производится термит как в промышленном масштабе, так и в домашних условиях.
Состав термита подбираются индивидуально, но каждая рецептура имеет общие характеристики. Главное, чтобы окислитель и горючие элементы содержались в равномерных пропорциях. Благодаря окислителю это вещество может возгораться и поддерживать горение в условиях дефицита кислорода.
Любой тип термита очень огнеопасные. Поэтому хранение и использование этого вещества требует особой подготовки и внимания. Рекомендуется приготавливать смесь непосредственно перед ее использованием.
Сфера применения
Наиболее часто термит как вещество используют в пиротехнике и для сварочных работ. В пиротехнике вещество используют для создания сигнальных огней и в качестве средств освещения.
В сварочных работах термит используется благодаря свойству горения при очень высоких температурах. Это позволяет создать шов повышенной прочности, который отличается долговечностью и высоким качеством.
Сварочный шов образуется из металлических компонентов, которые входят в состав смеси. Причем шов обладает антикоррозийными свойствами. Для выполнения сварочных работ термита недостаточно, нужно также тигельная форма с поджогом. Обычно тигельная форма производится из графита, способного выдержать высокие температуры.
Наиболее широко это вещество применяется для сварки трубопроводов.
В классический рецепт термита входят такие компоненты, как алюминий и железо. Именно такое соединение элементов наиболее широко используется при сварочных работах, строительстве и промышленности. Такой состав характеризуется высокой температурой горения.
Несмотря на то что количество железа в составе намного больше, и смесь обычно называют железной, главную роль играет алюминий. Именно этот металл определяет эффективность горения, скорость реакции и делает возможным сварочные работы.
Для использования в пиротехнике состав термита намного сложнее и включает больше химических элементов. В состав вещества традиционно входят топливные элементы и окислитель. Наиболее часто компонентами пиротехнического термита выступают хлорат калия, карбонат стронция и сера. Сера придает пламени цвет. В качестве окислителя применяется хлорат калия.
Температура пламени при горении может достигать нескольких тысяч градусов, поэтому пиротехнические работы с этим веществом выполняют только профессионалы. В такой работе очень важно соблюдение правил безопасности.
Медные смеси термит чаще всего используются для сварочных работ. Этим типом термита обслуживаются сварочные операции на газопроводах. Для повышения качества сварочного шва состав термита приготовлен так, чтобы температура горения была максимальной.
В состав обычно входит два типа меди:
- оксид меди;
- медный порошок.
Медная часть состава составляет более 80%, десятую часть составляет алюминий, а остаток — ферросилиций.
Подобная рецептура гарантирует высокое качество сварочного шва. Это достигается благодаря высокой температуре горения в процессе плавления металлов.
При производстве смеси в домашних условиях применяется классический рецепт. Нужно иметь всего лишь два компонента:
- железная окалина;
- алюминиевый порошок.
Структура компонентов должны напоминать мелкий песок. Чем мельче состояние, тем качественнее получится готовая смесь. Для производства и хранения термита в домашних условиях нужно использовать специальные емкости. Лучше всего, чтобы сосуд был изготовлен из металла, алюминия или стали.
Рецептура состава очень проста: на 3 части железа нужно добавить 4 части алюминия. Перемешивание компонентов должно производиться максимально тщательно: от этого зависит качество готового термита. В качестве катализатора можно использовать жженую марганцовку в количестве не более пятой части.
Для использования вещества необходимо подготовить рабочий сосуд, в который следует плотно утрамбовать вещество и добавить магниевую ленту. Поджег ленты провоцирует активации химической реакции. Очень важно, чтобы смесь была абсолютно сухая.
Термитная сварка подразумевает под собой наличие специального инструмента.
Тигель для термитной сварки.
Кроме этого мастеру для проведения работы потребуются:
- тигель с прикрепленным сливом;
- термитный карандаш необходим для того, чтобы выполнять сварку термитом в домашних условиях. Он не нуждается в подогреве, обжиге либо плавлении. После того, как оборудование будет подключено к сети, можно начинать работу;
- крепежные элементы для свариваемых деталей, чтобы поддержать и скрепить их;
- пила для металла, горелка для сварочного аппарата, термометр и другие предметы, которые могут понадобиться для работы.
Схема сварочной работы с термитом для рельсов, кабелей и других элементов может выглядеть следующим образом:
- дуплексом;
- впритык;
- смешано;
- с промежуточным вливанием.
Сварочный процесс при помощи термита применяется в тех случаях, когда необходимо прикрепить друг другу разные поверхности, катодные и дренажные выводы или другие схожие детали. Прежде чем начать сваривать металл, сами детали необходимо обжечь в печи.
Чтобы сварить рельсы, стрелочные механизмы и другие детали, можно воспользоваться смешанной технологией. Она соединяет в себе сварку впритык и вливанием. Прежде чем начать процесс, свариваемую часть необходимо защитить стальной пластиной с помощью пресса.
На этом месте возникнет зазор, куда и вливается термит жидкой консистенции. После того, как он застынет, шов подвергается обработке и свариванию.
История развития производства термита и термитной сварки рельсов
М. А. Карасев внес крупный вклад в развитие алюминотермии, организовав на базе отечественной технологии выпуск термитных смесей для народного хозяйства. Он предложил рациональные способы производства алюминиевого порошка и термита. Ему были выданы авторские свидетельства на «аппарат для получения эерноволокнистого алюминия», «шаровой мельницы для производства алюминиевого порошка», «механической нагрева-тельной печи для обжига железной обсечки и окалины при изготовлении термита» и т. п.
В последующие годы в путях московского трамвая было сварено термитом свыше 100 000 стыков.
Сварка производилась двумя способами: комбинированным и врасклинку. Ввиду того, что стыки, свариваемые последним способом, часто выходили из строя, к 1931 г. этот способ перестали применять Вместо него начали внедрять способ сварки промежуточным литьем. Одновременно начали применять способ сварки «дуплекс» (способ промежуточною литья с последующим прессованием). Однако этот способ не получил широкого распространения из-за сложности технологического процесса.
Качество сварки термитных стыков за первые 10 лет ежегодно улучшалось, и количество лопнувших (в течение года) стыков в среднем не превышало 0,8%.
Применение отечественного термита для сварки рельсовых стыков показало его превосходство перед импортировавшимся термитом. В стыках рельсов, сваренных отечественным термитом, значительно меньше процент брака. Это подтверждают результаты эксплуатации первой очереди Московского метрополитена. Так, например, каждый рельсовый стык на участке Сокольники—Парк культуры в 1938 г, выдержал 13,4 млн. ударов с грузонапряженностью 53 млн. т-км.
В 1936 г. вышло из строя 0,17% от количества эксплуатируемых в путях стыков, в 1937 и 1938 г. — по 0,5%.
Из приведенного количества выбывших из строя стыков 75% разрушились из-за наличия болтовых отверстий в зоне сварки.
В эти же годы термит стали внедрять в другие отрасли народного хозяйства. В частности, была разработана и успешно осуществлена термитная сварка стыков легированных труб первого прямоточного котла высокого давления; начали применять также термитную сварку для ремонта крупногабаритных стальных деталей: валов, колонн и т. п.
Изобретению термитной сварки способствовала необходимость в разработке метода соединения металлов без участия громоздкого оборудования. В то же время температура нагрева сторон должна быть достаточно высокой, чтобы проплавить толстые стороны материалов и образовать крепкое соединение.
Бекетов Н.Н. открыл явление называемое алюминотермия. Это процесс, при котором металл восстанавливается благодаря окислам алюминия. Для этого алюминиевую стружку смешивают с оксидом железа. Полученную смесь доводят до температуры 3000 градусов, вследствие чего образовывается сталь и шлак.
Ученый Гольдшмидт впервые смог воплотить эту идею на практике сваривания. Он использовал два металлических бруска, зазор между которыми заполнил горящим термитным порошком. Образовался монолитный шов приемлемого качества, а шлак всплыл на поверхность и разошёлся по сторонам. При этом его отделение было довольно свободным.
Что такое термитная сварка на деле, легко понять после ознакомления с видео. В настоящее время применяют 23% алюминиевой крошки и 77% окиси железа. Грануляция состава не превышает пол миллиметра в диаметре. Поджиг осуществляется специальным запалом. Благодаря горению происходит химическая реакция, высвобождающая большое количество тепла. При этом оксид железа преобразовывается в чистый металл, а второй компонент образует окислы и составляет шлак.
Термосварочные процессы — Большая химическая энциклопедия
Процесс термической сварки бывает двух видов: прямой и косвенный. Каждый вид термической сварки может быть дополнительно классифицирован, как показано ниже, в соответствии с методом, используемым для обеспечения тепла. [Pg.456]Другими процессами термической сварки, которые менее распространены, чем описанные выше, но все еще используются в промышленности, являются инфракрасная сварка и лазерная сварка. Они обычно используются в специальных процессах или в приложениях, которые требуют уникальных методов нагрева из-за совместной конструкции или характера конечного продукта.[Pg.462]
Термореактивные пластмассы (например, эпоксидные смолы, диуилфталатные полиэфиры, меламин, фенол и мочевина формальдегид и полиуретаны) соединяются механически или с помощью клея. Их термореактивная природа не позволяет использовать процессы сварки растворителем или термической сварки, однако они легко склеиваются с помощью многих клеев. [Pg.472]
Пожалуй, термическую сварку можно рассматривать как разновидность клеевого соединения. При термическом соединении сама основа (в расплавленном виде) действует как клей.Когда субстрат становится жидким, принципы адгезии определяют прочность и долговечность соединения. Кроме того, термические методы могут использоваться для активации термоклея, а не текстильной основы. [Pg.338]
Основная область роста клеев — термоактивируемые ленты или пленки, которые в значительной степени пересекаются с процессами термической сварки. Термическое соединение все чаще используется за счет адгезионного соединения по следующим причинам … [Pg.357]
Термическая сварка ограничивается тканями с высоким содержанием термопластичных синтетических волокон, таких как нейлон, полиэстер, полипропилен, акрил и некоторые другие материалы. смеси волокон.Как правило, свариваемые ткани должны быть изготовлены из одного и того же термопласта или быть физически и химически совместимыми друг с другом. Ткани с термопластическим покрытием (например, поливинилхлорид, полиуретан и полипропилен) также поддаются термической сварке, поскольку в этих случаях покрытие действует как клей. Свариваемость зависит от типа материала, его толщины и формы (покрытие, пленка, волокно). [Pg.357]
В некоторых отраслях промышленности, таких как автомобилестроение, часто выбирают пластмассовые материалы из-за их способности быстро соединяться.Таким образом, термопласты часто предпочтительнее термореактивных материалов, поскольку их можно соединить с помощью процессов термической сварки за несколько секунд. [Pg.509]
Термическая сварка — Большая химическая энциклопедия
Термопласты Механические крепежные детали Клеи Вращательная и вибрационная сварка Термическая сварка Ультразвуковая сварка Индукционная сварка Примечания … [Pg.548]Акрилонитрил-бутадиен-стирол (ABS). Пластмассы АБС получают из акрилонитрила, бутадиена и стирола.Материалы АБС обладают хорошим балансом физических свойств. Существует множество модификаций АБС и множество смесей АБС с другими термопластами, которые могут влиять на адгезионные свойства. Смола АБС может быть прикреплена к самой себе и к другим материалам с помощью клея, цементированием растворителем или термической сваркой. [Pg.367]
Когда сварка растворителем или термическая сварка нецелесообразны или нежелательны, можно использовать клеевые системы. Типы клея, такие как эпоксидные смолы, уретаны, термореактивные акрилы, нитрильные фенолы и цианоакрилаты, позволяют связывать АБС с самим собой и с другими субстратами.Лучшие клеи показали большую прочность, чем у ABS, однако эти клеи обеспечивают очень жесткие связи. [Pg.367]
Из-за их высокой термической стабильности и отличной устойчивости к растворителям фторуглероды не могут быть соединены цементированием растворителем, и их очень трудно соединить методами термической сварки. Из-за их инертности и низкой поверхностной энергии они, как правило, являются материалами, которые трудно соединить клеевым соединением. Обработка поверхности необходима для обеспечения любой практической прочности сцепления с фторуглеродными деталями.[Pg.370]
Из-за их превосходной химической стойкости полиолефины невозможно соединить путем склеивания растворителем. Из-за очень низкой поверхностной энергии полиолефины могут быть склеены только после обработки поверхности. Наиболее распространенный способ соединения полиолефинов — термическая сварка. [Стр.372]
Полистирол обычно связывается с самим собой цементированием растворителем, хотя использовалось обычное клеевое соединение, термическая сварка и электромагнитное соединение.Когда полистирол приклеивается к другим поверхностям, обычно используется обычное клеевое соединение. [Стр.376]
Брекчии, представляющие собой ударно сжатые агрегаты грунта (реголитовые брекчии) или термически сваренный материал (метаморфические брекчии). [Стр.84]
Полимерные клеи Механическое крепление Сварка растворителем Термическая сварка … [Стр.34]
Оболочка мембраны состоит из двух нетканых мембран и прокладок между мембранами, чтобы обеспечить открытое пространство для неограниченного дренажа пермеата.Термическая сварка на внешних режущих кромках герметизирует сэндвич мембраны (рис. 1.4). [Стр.98]
Спанбонд, с другой стороны, в основном производят из полиэтилена, полипропилена и ароматических сложных полиэфиров. Изделия с поверхностным переплетом больше похожи на бумагу, но изделия с точечным переплетом больше похожи на флис (Таблица 38-6). В этих случаях композиты из поли (этилкна) и полипропилена) свариваются методом дуговой сварки без использования клея, в результате чего получаются продукты, охватывающие всю область применения от плотной упаковочной бумаги до тонкой писчей бумаги.Поли (этиленовая) бумага может быть … [Pg.774]
С этими материалами методы склеивания растворителем или термической сварки часто являются предпочтительной альтернативой склеиванию. Однако там, где склеиваются разнородные материалы или термопласт относительно инертен к растворителям, рекомендуется склеивание. [Стр.142]
Обычно с ПММА используется цементирование в растворителе или термическая сварка. Эти методы обеспечивают более прочное соединение, чем клеевое соединение. Используемые адгезивы — это цианоакрилаты, акрилы второго поколения и эпоксидные смолы, каждый из которых обеспечивает хорошую адгезию, но плохую стойкость к термическому старению.»… [Pg.147]
При цементировании растворителем и термической сварке используется смола в самой детали в качестве фиксатора для скрепления сборки. При клеевом соединении и механическом креплении в качестве фиксатора используется другое вещество. … [Стр. 407]
Процесс термической сварки может быть двух видов, прямой и косвенный. Каждый вид термической сварки может быть дополнительно классифицирован, как показано ниже, в соответствии с методом, используемым для обеспечения тепла. [Pg.456]
Другие процессы термической сварки которые менее распространены, чем описанные выше, но все еще используются в промышленности, — это инфракрасная сварка и лазерная сварка.Они обычно используются в специальных процессах или в приложениях, которые требуют уникальных методов нагрева из-за совместной конструкции или характера конечного продукта. [Pg.462]
Когда необходимо принять решение относительно методов сборки (механическое крепление, клеевое соединение, термическая сварка или цементирование растворителем), следует учитывать особые соображения, связанные с характером основы и возможным взаимодействием с клеем. или enviroiunent. В следующих разделах рассматриваются некоторые из этих соображений и предлагаются рекомендации по различным методам сборки, которые были признаны подходящими для определенных пластиков.[Pg.463]
Современные процессы термической сварки — Большая химическая энциклопедия
Использование передовых процессов термического соединения, таких как ультразвуковая сварка. [Pg.370]Альтернативные методы, следующие за шитьем, включают склеивание, обычную термическую сварку (например, горячим воздухом и нагретым инструментом) и усовершенствованную термическую сварку (например, ультразвуковую или лазерную). Этим методам соединения и посвящена данная глава. Общее описание этих процессов вместе с применимыми материалами и приложениями представлено в Таблице 13.1. [Pg.338]
Для соединения материалов одежды был разработан ряд усовершенствованных термических процессов, отличных от процессов горячего воздуха или нагрева инструмента. Наиболее известными из них являются ультразвуковая, диэлектрическая и лазерная сварка. Из-за стоимости оборудования, необходимого уровня квалификации и относительной негибкости эти процессы используются в основном в специализированных приложениях. Однако большинство производителей одежды видят более широкое применение этих технологий в будущем, поскольку стоимость может быть оправдана предложениями о добавленной стоимости.[Pg.363]
Подобно традиционной термической сварке, эти усовершенствованные процессы нагрева могут использоваться для активации термопластичных клеев. Однако здесь основное внимание будет уделяться соединению субстратов без использования дополнительного клеящего материала. [Pg.363]
Теплофизические свойства титановых сплавов также могут способствовать трудностям, возникающим при сварке трением с перемешиванием. Некоторые численные моделирование процесса FSW показывают, что низкая температуропроводность может способствовать образованию продвигающихся боковых червоточин или туннельных дефектов в сварных швах с перемешиванием трением. Температуропроводность титановых сплавов является одной из самых низких среди всех металлов.[Pg.392]
Ares, A.E. Gatti, I.P. Gueijman, S.F. Швезов, CE (2009) Механические свойства цинк-алюминиевых сплавов в зависимости от структурных и термических параметров, Труды Международной конференции MCWASP «Моделирование процессов литья, сварки и опережающего затвердевания» — XII, Ванкувер, Канада, июнь 2009 г.… [Стр. ]
термический сварочный пистолет — это … Что такое термический сварочный пистолет?
Газовая дуговая сварка — RMD перенаправляет сюда. RMD может также относиться к минимальным распределениям, требуемым IRA.Газовая дуговая сварка… Wikipedia
Точечная сварка — вид контактной сварки, применяемый для сварки различных изделий из листового металла. Обычно листы имеют толщину 0,5–3,0 мм. В процессе используются два профилированных электрода из медного сплава для концентрации сварочного тока в небольшом пятне и…… Wikipedia
Газокислородная сварка и резка — Кислородно-ацетиленовая сварка перенаправляется сюда. Для песни см Cubanate. Сторона металла, разрезанная кислородно-пропановым резаком… Википедия
автоматика — / aw teuh may sheuhn /, n.1. техника, метод или система управления или управления процессом с помощью высокоавтоматических средств, таких как электронные устройства, сводящие к минимуму вмешательство человека. 2. механическое устройство с электронным управлением,…… Универсал
Варианты БМП-1 — это полный список вариантов и обозначений боевой машины пехоты БМП-1. Сортировка по стране происхождения. Варианты БМП бывшего СССР * БМП (Обьект 764) Оригинальный прототип БМП-1, разработанный…… Википедия
Манхэттенский проект — Эта статья о проекте атомной бомбы.Для использования в других целях, см Манхэттенский проект (значения). Район Манхэттен Манхэттенский проект создал первые ядерные бомбы. Тест Троицы… Википедия
Разрушители мифов (сезон 2006 г.) — Страна происхождения Австралия США Количество серий 28 (включая 2 специальных) Трансляция Исходный канал Discovery Channel… Wikipedia
Военная техника Турции — Военная техника Турции включает в себя широкий спектр вооружения, артиллерии, больших надводных кораблей, пушек, бронетехники, минометов, беспилотных транспортных средств и много различного оборудования.Содержание 1 Историческое развитие 1.1 Общие 1.2 1923 1950… Википедия
Пайка — Песню см. Пайка (песня). Для продукта см. Припой. Удаление контакта из провода. Пайка — это процесс, в котором два или более металлических предмета соединяются вместе путем плавления и заливки присадочного металла (припоя) в соединение,…… Wikipedia
Laser — Чтобы узнать о других значениях, см. Laser (значения). Лазерный эксперимент ВВС США… Википедия
Challenger 2 — FV 4034 Challenger 2 Challenger 2 на маневрах на равнине Солсбери Тип… Википедия
Термическая сварка Yöntemiyle Bademcik Ameliyatı
05 Ağu
Термосварка yöntemi ile bademcikler kanama olmaksızın, dikişsiz olarak çıkarılır.Thermal Welding’in en önemli avantajlarından biri dikiş kullanılmaması nedeniyle ağrının çok az olmasıdır. Термосварка ile iyileşme süreci kısalmakta ve kolaylaşmaktadır. Bu yüzden bademcik ameliyatlarında yeni bir dönem olan Thermal Welding, hastalar için ciddi kolaylık sağlamaktadır.
Bademcikler
Bademcikler, boğazımızın iki yanını kaplayan yapılardır. Bademcik enfeksiyonları kronikleşebilir. Potansiyel komplikasyon ihtimallerinden dolayı ciddiyetle ele alınmalıdır.Бу komplikasyonlar içinde, böbrek hastalıkları, kalp kapağı hastalıkları, romatizmal ateş gibi komplikasyonlar bulunmaktadır. Bademcik iltihabına bağlı uyku bozuklukları ве apneler de meydana gelebilir. Bunların ее biri ciddiye alınması gereken durumlardır.
Bademcik Ameliyatı
Hekimin tanı koyma aşamasında ayrıntılı olarak bilgilendirilmesi gerekmektedir. Bademcik iltihabı atakları ne sıklıkta gelmektedir, şiddeti nasıldır, uykuda solunum problemleri var mıdır, gibi sorular tedavi yöntemlerinin seçiminde önemli rol oynamaktadır.Bunun yanında hem muayene bulguları hem de diğer tetkikler değerlidir.
Bademcik ameliyatının ne zaman gerekli olduğu sorunsalı, hastanın hekimi bilgilendirmesi ve muayene-tetkik bulgularının değerlendirilmesi ile cevaplanabilir. Bademcikler solunum yolunu tıkıyorsa, horlama Veya uyku apnesi Gibi uykuda solunum problemleri варша, ortalama olarak yılda 4-5 Kere bademcik iltihaplanması geçiriliyorsa, romatizmal ateş, кальп kapakçık hastalığı ве Bobrek hastalığı Gibi ciddi komplikasyonlar eşlik ediyorsa bademcik ameliyatı düşünülmelidir.
Genel anesteziyle, bademciklerin kapsülü ile disksiyon yöntemi kullanılarak çıkarılması şeklinde olan bademcik ameliyatı yöntemi, klasik bademcik ameliyatıdır. Кан dolaşımının fazla olduğu bademciklerin ameliyat sırasında ве sonrasında kanama ihtimali vardır.
Thermal Welding Yöntemi ile Bademcik Ameliyatı Nedir?
Термосварка yöntemi, bademcik ameliyatlarında yeni bir yöntemdir. Тепловая сварка yöntemi hastalar için büyük kolaylık yaratır. Термосварка, ameliyat sırasında ısı enerjisi ile kanamayı kontrol altına alarak ileriki dönemde doku iyileşmesini hızlandırır.Термосварка ile bademciklerin dışında kalan dokular daha az hasar görmekte ve hasta ameliyat sonrasında sık sık su içerek ve sulu gıdalar tüketerek kısa sürede iyileşebilmektedir. Термосварка ile bademcik ameliyatı iyileşme süresi 1 haftaya inmiş ve kanama problemi ihtimali Minima çekilmiştir. Kanama problemi ihtimalinin azalmasıyla ameliyat süresi 30 dk.’ya dek indirilebilmiş aynı zamanda anestezi süresi de önemli ölçüde azalmıştır.
Термосварка yöntemi, bademcik ameliyatlarında ciddi bir проблема олан, ameliyat sonrası 10 gün kadar süren ağrıyı önemli ölçüde azaltmıştır.Tüm bu nedenlerle Thermal Welding yöntemi, сын derece etkili, son teknoloji birtonsillektomi tekniğidir.
Сварка термопластичных композитов | CompositesWorld
| 19 МИНУТ ЧТЕНИЯ
Множество методов позволяют ускорить роботизированную сварку с использованием новой технологии для увеличения объемов и больших аэроструктур.
#feature #airbus #infrastructure
Сварная индукционной сваркой оконная рама фюзеляжа TPC
Это прессованное короткое усиливающее кольцо из CF / PPS, приваренное индукционной сваркой к обшивке TenCate CF / PPS CETEX компанией KVE Composites (Den Haag, Нидерланды), демонстрирует, как оконные рамы могут быть собраны в будущих планерах TPC.
Источник | Композиты КВЭ / Фото | Имбирь Гардинер
Рис. 1. Передовые технологии сварки термопластических композитов
РИС.2 Сварка сопротивлением CF для задней перегородки
Premium AEROTEC (Аугсбург, Германия) Демонстрационный образец задней переборки под давлением Airbus A320 состоит из восьми секций CF / PPS, сваренных сопротивлением с использованием углеродного волокна в качестве резистивного элемента вместо металлической сетки.