Термообработка сварных швов трубопроводов из нержавеющей стали
Способов высокотемпературной обработки металла существует очень много. К ним можно отнести и закалку, и отпуск, и нагрев перед деформацией, и ковку, и многие другие технологичные процессы, связанные с нагревом металла. Термообработка сварных швов трубопроводов из нержавеющей стали – это один из видов высокотемпературной обработки, позволяющий получить изделие высокого качества, продлив его срок эксплуатации на максимально возможный срок.
Термообработка сварных швов – этапы
Термообработка сварных швов заключается в нагреве металла в местах соединения для снятия напряжения, которое образовалось в швах во время сварки. Термообработка сварных швов состоит из трех этапов:
- Подготовительный этап – нагрев изделия перед началом сварочных работ. Производится для придания металлу эластичности.
- Промежуточная термообработка – постоянный нагрев изделия в процессе произведения сварочных работ.
- Термообработка сварных швов – нагрев изделия непосредственно после проведения всех сварочных работ. Производится для максимального избавления изделия от остаточного напряжения металла в местах соединения.
Термообработка сварных швов трубопроводов – это отличный способ защитить уязвимые места изделия от коррозии и повысить уровень прочности труб, продляя их срок эксплуатации.
Термообработка сварных швов – достоинства нагрева ТВЧ
Нагрев ТВЧ обладает широким рядом преимуществ, что и позволило ему отвести все альтернативные виды нагрева на второй план.
- Термообработка сварных швов получается равномерной, что позволяет максимально разгладить напряжение металла.
- Тепло образуется непосредственно в металле без воздействия внешних раздражителей на изделие.
- Индукционный нагрев может повторить любую среду, так же может производиться в вакуумной среде для защиты металла от окисления.
- Нагрев ТВЧ позволяет экономить значительную часть производственных ресурсов, что положительно сказывается на бюджете предприятия.
- Индукционная установка обладает компактными размерами, и может легко перевозиться на место проведения работ, если возникнет такая необходимость.
Термообработка сварных швов при помощи индукционного оборудования стала простым процессом, позволяющим улучшить качество трубопроводов из нержавеющей стали.
Если заметили ошибку, выделите фрагмент текста и нажмите Ctrl+Enter
Термообработка сварных швов и соединений трубопроводов по ГОСТ
Практически любое воздействие на металл оказывает определенную долю влияния на его свойства. Все зависит от характера воздействия и от его интенсивности. Некоторые виды проходят практически не заметно, но другие же могут сильно менять свойства деталей. К таким воздействиям относится термическая обработка сварных соединений. Данная процедура может применяться для улучшения свойств свариваемости материала. Как правило, сюда входит три основных этапа:
- Термическая подготовка;
- Непосредственная обработка высокой температурой;
- Обработка готовой детали.
Все это требуется для того, чтобы не было резких перепадов температуры. Это может привести к деформации детали или вызывает осложнения в обработке. Это же касается и прогрева после завершения процедуры, так как не всегда можно давать остывать обработанному металлу самостоятельно. Тепловой режим подбирается по характеристикам свариваемых материалов. Прогревание должно проводиться равномерно, так как в ином случае снова возникает вероятность деформации и неправильной обработки. Если будут совершены ошибки, то возникают проблемы с последующим переносом высокой температуры, крепости изделия и прочими свойствами. Термообработка сварных соединений проводится по ОСТ 36-50-86.
Термообработка сварных швов и соединений
Преимущества
- Термообработка сварных швов помогает добавить деталям новые свойства, которые сделают их более пригодными для эксплуатации в заданных условиях;
- Процедура помогает обеспечить защиту от некоторых негативных моментов, которые возникают при сварке;
- Прогревание обеспечивает снятие внутренних напряжений, если процедура проходит по всем правилам.
Недостатки
- Зачастую термообработка сварных соединений – это необратимый процесс, так что не стоит при нем допускать ошибки;
- Для проведения операций нужно специальное оборудование;
- Высокие требования к точности режимов проведения процедур;
- Для каждого индивидуального случая нужно подбирать свои параметры обработки.
Виды термообработки
Выделяется несколько основных способов, которые пригодны для обработки сварных швов. Среди них:
- Предварительный подогрев. Это один из самых распространенных способов. Он применяется чаще всего для низколегированных и низкоуглеродистых сталей, которые относятся к перлитному классу. Подогрев осуществляется постепенно до температуры около 200 градусов Цельсия. Особенно актуально это при низкой температуре окружающей среды. Прогревание делается для предотвращения появления трещин. После окончания процедуры температура также постепенно опускается.
Предварительный подогрев сварных швов
- Высокий отпуск.
Во время данной разновидности обработке соединение металла прогревают до температуры ниже 30 градусов Цельсия, от достижения критической точки Ас1. Воздействие продолжается от 1 до 5 часов. После этого его медленно охлаждают. Сварочные напряжения спадают до 90%. Зона сваривания претерпевает различные структурные изменения. В низколегированной стали пропадает закалочная структура. Металл обретает большую пластичность и снижаются его свойства твердости. Чаще всего применяется для сталей перлитного класса.
- Нормализация. Его используют для тех сварочных соединений, которые выполнены при помощи большой погонной энергии. Как правило, в это время структура металла становится крупнозернистой и у нее сильно снижаются механические свойства, чего не стоит допускать. Соединение металла прогревают до температуры ниже 30 градусов Цельсия, чтобы не достичь критической точки Ас1. В отличие от высокого отпуска в таком состоянии деталь держат недолгое время и после этого дают остыть при обыкновенной температуре.
Чаще всего нормализация применяется для тонкостенных труб с малым диаметром из низколегированной стали. Они часто имеют пониженную пластичность и крупнозернистую структуру.
- Термический отдых. Детали нагревают до температуры в 300 градусов Цельсия. В таком состоянии ее придерживают около 3 часов. Благодаря этому снижается содержание водорода в составе шва. Это помогает снизить уровень сварных напряжений. Чаще всего отдых применяется для конструкций, сделанных из толстостенного металла, так как для них сложнее сделать высокий отпуск. Этот вид обработки еще называют дегазацией. Процедура активно применяется во время ремонта соединений трубопроводов и других предметов, контактирующих со средами с высокой коррозионной опасностью.
- Аустенизация. Во время данного процесса соединение нагревается, примерно, до температуры 1100 градусов Цельсия и выдерживается на протяжении 1,5 часов. Охлаждение происходит на воздухе. В это время внутри материала распадается феррит. Благодаря такому процессу, механические свойства стали обеспечивают снижение уровня напряжений.
Данная процедура рассчитана на материалы из высоколегированной стали.
- Стабилизирующий отжиг. Процедура применяется для аустенитных сталей, содержание легирующих элементов в которых находится на высоком уровне. В это время соединение прогревается до температуры в 860 градусов Цельсия. В таком состоянии оно выдерживается до 3 часов. В итоге получается снять около 80% сварных напряжений. Структура материала становится более стабильной. Снижается риск возникновения межкристаллической коррозии.
- Нормализация с отпуском. Это может быть восстановительная или полная термообработка. Она предназначена для изменения структуры, а соответственно и свойств, соединений различных металлов. Такая комбинация процедур предназначается для сталей, у которых повышенная устойчивость к температурному воздействию. Это помогает продлить им срок эксплуатации, особенно в сложных условиях. После проведения обработки структура металла становится более равномерной. Когда деталь охлаждается, то аустенит превращается в феррит.
После отпуска повышается пластичность и прочность соединений.
Вывод
Температура металла шва при сварке повышается до таких пределов, которые могут вызвать дефекты сварных швов, а также изменить структуру в худшую сторону. В то же время, требования к сварочным швам являются достаточно высокими в ответственных конструкциях, что часто требует дополнительной обработки. Механические испытания соединений показывают, что после правильной термической обработки свойства их значительно повышаются. В особенности это видно на трубопроводах, которые обладают тонкими стенками, но должны иметь высокий уровень герметичности и часто работают под большим давлением. Замер твердости сварного соединения после обработки показывает, насколько хорошо прошла процедура.
Термическая обработка сварных швов и соединений
Таким образом, при правильном подборе, термическая обработка станет отличным дополнением во время сварки и после нее. Для ее проведения необходимо специальное оборудование, но результаты, которые получаются в итоге, вполне оправдывают их применение. Термообработка сварных соединений технологических трубопроводов является обязательной, так как того требует технология производства. Многие детали не допускаются в эксплуатацию без проведения подобных процедур.
Виды Термической обработки (термообработки) сварных швов
Термообработка (Термическая обработка металлов)
Термообработка (Термической обработкой) называется совокупность операций нагрева метала, выдержки и охлаждения твердых металлических сплавов с целью получения заданных свойств за счет изменения внутреннего строения и структуры. Термическая обработка используется либо в качестве промежуточной операции для улучшения обрабатываемости давлением, резанием, либо как окончательная операция технологического процесса, обеспечивающая заданный уровень свойств детали.
Термическая обработка сварных соединений состоит из нагрева их с определенной скоростью до нужной температуры, выдержки при этой температуре и охлаждения также с определенной скоростью. Различают следующие виды термической обработки: термический отдых; высокий отпуск; нормализация; аустенизация; стабилизирующий отжиг; улучшение, заключающееся в нормализации с последующим высоким отпуском.
Наиболее часто в строительстве применяют высокий отпуск для углеродистых и легированных сталей с целью снижения сварочных напряжений и улучшения структуры. При этом обязательна небольшая скорость охлаждения после выдержки (300—400°С/ч) в интервале от температуры выдержки до 300 °С, после чего охлаждение на спокойном воздухе. Значительно реже применяют другие виды термообработки.
Нормализацию применяют главным образом для сварных соединений труб из легированной стали диаметром до 100 мм и небольшой толщины. Она заключается в нагреве при более высокой температуре, чем при высоком отпуске (для низколегированных сталей до 900—950 °С), выдерживании несколько минут и охлаждении в условиях утепления и предупреждения от сквозняков.
Термический отдых применяют для сварных соединений из низколегированной стали, имеющую склонность к образованию трещин вследствие выделения растворенного водорода, диффундирующего из шва в зону термического влияния. Нагрев производят до 250—300 °С и выдерживают несколько часов.
Аустенизацию применяют для получения в сварных соединениях из хромоиикелевых нержавеющих сталей однородной структуры аустенита, улучшения механических свойств (пластичности) и снижения сварочных остаточных напряжений на 70—80 %.
Стабилизирующий отжиг применяют для тех же сталей с целью снижения сварочных напряжений на 70—80%, обеспечения стабильной структуры и предупреждения появления коррозионных трещин. Улучшение относится к полной термической обработке и производится в стационарных термических печах. Оно снижает остаточные сварочные напряжения и полностью восстанавливает структуру и свойства металла, изменившиеся от сварки.
Для термической обработки применяют несколько способов нагрева:
в стационарных термических печах;
радиационный (электросопротивлением и газопламенный), индукционный; термохимический смешанный (электросопротивлением и индукционный токами промышленной частоты).
Аппаратура и технология термической обработки
Для проведения эффективной термообработки сварных соединений промышленностью и строительными ведомствами изготовляется широкий ассортимент оборудования, в комплект которого входят нагревательное устройство, источники питания и посты (пульты) управления и контроля за технологией термообработки.
Нагревательные устройства, их конструкция и технология использования должны соответствовать методам нагрева.
В строительно-монтажных организациях применяют нагревательные устройства для местной термической обработки сварных соединений, к которым относятся гибкие электронагреватели сопротивления ГЭН
Электронагреватели ГЭН состоят из набора пальцевых нагревателей, заизолированных керамическими втулками, внутри которых проходят плоские спирали из нихромовой проволоки. Подогреватель состоит из большого количества таких пальцев, гирлянда которых шириной до 160 мм достаточно гибкая для обхвата труб и корпусов конструкций диаметром от 0,1 до 5—6 м.
Большая удельная мощность ГЭН, возможность использования для нагрева спирали обычных сварочных трансформаторов и преобразователей, а также простота обслуживания и ремонта и другие качества обеспечили широкое применение этих нагревателей.
Комбинированные электронагреватели КЭН состоят из гирлянды керамических изоляторов, внутри которых проходит пучок нихромовых проволок. Как видно из 15.12,6, эта гирлянда, питаемая от одного источника (мощного сварочного трансформатора), подогревает сварное соединение за счет электронагрева нихромовой проволоки, а также наведения индукционных токов нагрева, что обеспечивает общую температуру подогрева до 1000 °С. КЭН применяют при строительстве тепловых электростанций для термической обработки стыков труб диаметром до 1620 мм.
Индукционные электроподогреватели представляют собой индукторы-соленоиды, выполненные из медной трубки или проволоки. Используют индукторы с воздушным и водяным охлаждением . При воздушном охлаждении медный неизолированный провод сечением 120—240 мм2 (при частоте 50 Гц) наматывают в один слой с зазором 15—20 мм на изделие, предварительно обмотанное теплоизоляцией. Применяют конструкцию из охлаждаемой водой латунной или медной гибкой гофрированной трубки, по наружной поверхности которой навит многожильный медный кабель, покрытый сверху гибкой асбестовой изоляцией.
Газопламенные нагреватели представляют собой горелки (многопламенные, кольцевые, трубчатые с факельным устройством и др. ), в которых в качестве горючего используются ацетилен, пропан, природный газ с добавлением кислорода или воздуха.
Для полной термообработки шаровых резервуаров и других корпусных конструкций используют специальные теплогенераторные установки с мощными факельными горелками, термообрабатывающими всю конструкцию.
Для термохимического нагрева применяют устройства, изготовленные из экзотермических смесей, в виде гибкого шнура, охватывающего стык с двух сторон, или в виде пакетов и ковриков, закрепляемых на стыке металлическими полосами. При сгорании они обеспечивают нагрев до высокого отпуска (800°С).
Источниками питания электрических нагревателей служат в основном сварочные трансформаторы, мощность которых подбирается в зависимости от величины изделия. При необходимости используют сдвоенные трансформаторы для параллельного питания нагревателей. Для индукционного нагрева кроме токов промышленной частоты, на которых работают сварочные трансформаторы, используются высокочастотные токи от машинных преобразователей повышенной частоты на 2450, 2960 и 8000 Гц и от тиристорных преобразователей на 2400 Гц.
Для термической обработки сварных соединений труб и корпусов различных аппаратов, газгольдеров и емкостей с помощью перечисленных нагревателей и источников питания комплектуются установки (посты), имеющие ручное управление процессом, ручное дистанционное управление и программное управление-Установки с дистанционным и программным управлением могут обслуживать одновременно термообработку нескольких сварных соединений. Посты для газопламенной термообработки комплектуются горелками, коллекторами для газовых баллонов или емкостями с горючим.
Рабочие-термисты, обслуживающие установки для термообработки, должны пройти обучение и получить удостоверение на право производства работ по термообработке сварных соединений на имеющемся оборудовании. Работающие с электроподогревателями сопротивления или индукционными аппаратами должны иметь группу по электробезопасности не ниже II, а электромонтажники, монтирующие эти аппараты, и руководители работ — группу не ниже III.
Для контроля температур при термообработке применяют термоэлектрические пирометры, специальные термометры, приборы, регистрирующие температуру и время (самопишущие автоматические потенциометры), термоиндикаторные карандаши и краски.
После окончания термообработки проверяют ее качество путем замеров твердости наружной поверхности сварных соединений или испытанием контрольных соединений, а в необходимых случаях — испытанием образцов, вырезанных из конструкции.
Поделиться ссылкой:
как и зачем выполняется, техника, нюансы, плюсы и минусы
Существуют области, в которых качество сварного шва имеет огромное значение, чаще всего это в производстве и при прокладке трубопроводов. Необходимо защитить шов от коррозии, деформации.
Правильно организованный рабочий процесс, опытные сварщики, точные чертежи, контроль качества, качественные комплектующие – все это необходимо.
Однако большое значение также имеют дополнительные методы обработки сварочного соединения. Одним из таких эффективных способов является термический.
Содержание статьиПоказать
Описание метода
Обработка соединений при помощи высоких температур называется термической обработкой (термообработкой) и предназначена для их защиты от коррозии, дефектов, растрескивания.
При этом повышаются механические характеристики соединения, его жаростойкость.
Метод похож на обжиг, используемый при работе с глиной, которая после этого приобретает новые свойства.
Заключается метод термообработки в нагревании соединения, удерживания его некоторое время нагретым, и затем охлаждении. Применяется при этом специальное оборудование для термообработки, о котором мы расскажем ниже.
Таких методов существует несколько, различаются они своими температурными режимами, в зависимости от обрабатываемого материала. При обработке стали, например, диапазон температур составляет от 650 до 1125 ОC. Время нагрева – от 1 до 5 часов.
После прогрева сталь охлаждается естественным способом. С помощью такого воздействия улучшаются механические характеристики, ударная вязкость, пластичность соединения.
Метод термообработки сварных соединений часто применяется при сваривании трубопроводов, где очень важны характеристики сварных швов.
Способы прогрева сварных соединений
Существует несколько способов термообработки сварных соединений. Выбор их зависит от доступности детали, ее размеров, возможности монтажа нагревательных устройств и др.
Чаще всего используются печи, нагреватели газопламенные и индукционные, специальные гибкие нагреватели.
Главные условия, которые надо учитывать при выборе способа нагрева — простота монтажа, равномерность нагрева соединения, отсутствие перепадов температур, небольшой вес устройства.
Самый несложный и недорогой метод обработки соединения – локальный, с использованием гибких нагревателей. Обычно применяется при монтаже трубопроводов.
Такие нагревательные устройства легко монтируются на трубы любого размера, их можно использовать в труднодоступных местах.
Для обработки труб малого диаметра применяются муфельные печи. При их использовании необходимо правильно установить печь. Ось вращения не должна совпадать с осью геометрической, в противном случае не удастся добиться равномерного нагрева.
Также при работе с трубопроводами широко распространены индукционные устройства, недорогие, но достаточно эффективные. Состоят они из многожильных кабелей из меди, выполняющих функцию нагревателя.
Охлаждаются эти нагреватели воздухом. При монтаже рекомендуется оставить небольшое расстояние между нагревателем и обрабатываемой деталью. Это обеспечит быстрый, равномерный разогрев шва.
Ниже вы можете увидеть таблицу со свойствами индукторов.
Еще один часто используемый метод – газопламенный, с использованием газовых горелок. Эти горелки имеют несколько каналов выхода пламени, образующегося при сгорании горючего газа и кислорода.
Такой метод обычно применяют в местах, куда сложно доставить и смонтировать другое оборудование. Минус данного способа –он требует гораздо большего времени.
Процесс термообработки
При проведении термической обработки сварного соединения необходимо учитывать длину шва, обеспечив его равномерный прогрев.
Надо правильно настроить характеристики процесса, такие как скорость, температура, время прогрева, а также скорость, время охлаждения. Начинается обработка с изоляции шва.
Например, если мы используем газовую горелку – шов изолируется асбестовым листом толщиной 2-3 см. После этого производится закрепление самой горелки. Так происходит обработка, если мы используем индукционные устройства.
Надо добиться того, чтобы сварной шов не терял тепло. Для этого надо выбирать прочные и теплостойкие изоляционные материалы.
Кроме этого, они должны быть достаточно гибкими и легкими. Ниже вы можете увидеть таблицу, где указаны самые часто используемые изоляционные материалы.
Для работ по термообработке сварных соединений необходима соответствующий опыт и навыки, специалисты в этой области предварительно обучаются. Процесс обычно контролирует старший мастер.
В его обязанности входит подбор и монтаж необходимого оборудования, контроль исправности оборудования. Также мастер должен проверить, насколько качественно проведена подготовка деталей к термообработке.
После термообработки детали надо дать остыть, затем произвести окончательную зачистку соединения от шлака.
В заключение
youtube.com/embed/KcQKiBYysDA?feature=oembed» frameborder=»0″ allow=»accelerometer; autoplay; encrypted-media; gyroscope; picture-in-picture» allowfullscreen=»»/>Если ваша первостепенная задача – добиться качественного шва, термообработка шва обязательна.
Она защитит соединение от дефектов, коррозии, трещин.
Метод достаточно прост, но эффективен, а предназначенных для этого устройств достаточно. Желаем вам успехов в работе!
Что Надо Знать термисту- практику о процессах термообработки труб?
Высокий отпуск отремонтированных сварных деталей трубопроводов (Термообработка)
Работаю термистом на передвижной установке термической обработки, вернее совмещаю основную профессию. Наше предприятие специализируется на ремонтах в энергетике. Занимаемся изготовлением, монтажом и ремонтом различных трубопроводов. Кто в теме тот должен знать, что после заварки некоторых типов труб и деталей требуется нагрев, выдержка и остывание по режиму сварных соединений или наплавок для нормализации металла и снятия внутренних напряжений.
Процесс происходит на специальном оборудовании с настраиваемыми программами режимов нагрева и остывания. Работа ответственная и требует не только теоретических знаний по настройке и процессу, но и понимания, что может пойти (или уже пошло) не так. После завершения процесса приходит дефектоскопист и замеряет основной параметр сварного стыка – твердость. Если твердость выше или ниже нормы — будем «термить» еще раз, еще много, много раз (но не более трех).
Таблица допустимых параметров твердости сварного соединения после термообработки
Возьмем пример термической обработки трубы из легированной стали 12Х1МФ. Температура нагрева и выдержки такого стыка должна быть 720-750 градусов. Допустимая твердость шва после термообработки (отпуска) должна быть в пределах 150-240 НВ (замеряется специальным прибором)
Что необходимо знать термисту- практику о тонкостях процесса термообработки?
- Если твердость, ниже (стык мягкий) значит, произошел его перегрев (выше 750 градусов)
2. Если твердость сварного шва выше нормы – то это недогрев (ниже 720 градусов)
Термист должен понимать причину отклонений от нормы и принять меры, чтобы впредь не повторять ошибки и не допустить переварки стыка. Хотя можно доказывать, что все прошло по программе и виновата машина.
Ошибки термиста при настройке термопар
- Холодный спай термопарного провода (два провода разного состава спаяны на конце) просто скручен и не обеспечено нормальное соединение.
Концы термопарного провода необходимо сваривать, желательно аргоном, без применения присадочных материалов. Иначе термопара неверно будет показывать температуру.
2. Присоединение термопарного провода к компенсационному кабелю не производится через специальные разъёмы для надежности и не свариваются аргонодуговой сваркой.
Присоединение холодного спая термопары к трубе необходимо производить с помощью контактной сварки (существуют специальные сварочные аппараты) или электросваркой через гайку с болтом.
Но, к примеру, на некоторые стали запрещено вообще приваривать, что, то временно. В таком случае термопара крепится к трубе на металлические хомуты.
крепление термопары к трубе через прихваченную электросваркой гайку
3. Необходимо строго следить за тем, чтобы провода термопары нигде не соприкасались друг с другом или корпусом.Лучше конечно применять термопары в специальной металлической оболочке,вопрос цены и качества.
Если, к примеру, термопара закреплена, верно, но концы её сомкнулись на расстоянии 10 мм от спая, получим неверные показания и при идеальной диаграмме в отчете — брак по твердости стыка при контроле.
Одна из причин неверных показаний термопары при термообработке
4. Количество установленных термопар должно быть не менее двух на стык, с возможностью переключать их для управления режимами.
Когда замечаем по приборам, что одна сторона стыка перегревается, переключаем управление нагревом на другую термопару (это если управление осуществляется по одному каналу)
Наложение нагревателей и утеплителя при термообработке
Нагреватели бывают индуктивные и радиационные (в одном случае греем за счет индукции витков, в другом за счет обычных ТЭНОВ различных конструкций). Нагреватели накладывают так, чтобы обеспечить равномерный нагрев сварного стыка. Особенно это касается ТЭНОВ. Часто нагревательные коврики (ТЭН) не получается подобрать по диаметру и остаются непрогретые участки.
Витки индуктивных нагревателей укладывают с зазором и, по возможности, между витками прокладывается асбестовый (или другой жаростойкий) шнур. Необходимо избежать замыкания на корпус. Нагревательные коврики перед установкой надо внимательно осмотреть на наличие оборванных проволок, при нагреве такие коврики, как правило, отгорают.
При наложении нагревателей нужно понимать, что расположенные рядом по схеме элементы трубопроводов большой массы (тройники, арматура и т.д.) могут забирать на себя (оттягивать) выделяемое тепло. Что бы уйти от этой проблемы можно установить дополнительные нагреватели на эти элементы или, если есть возможность, увеличить мощность на установке.
После установки нагревателей, их хорошо утеплить толстым слоем тепловой изоляции. Нельзя допускать «голых» мест, это приводит к неравномерному прогреву металла.
Процесс термообработки пошел, но как, то не так
В процессе нагрева мы можем наблюдать такие неприятности:
- Установка не может дотянуть нагрев до заданной температуры.
- Скорость нагрева либо медленней заданной, либо температура стоит на каком-то пределе и не растет.
Причина может, как я писал выше в нехватке мощности из-за оттягивания тепла на массивные детали трубопровода. Вторая причина — это сквозняк снаружи или изнутри трубы. Если есть возможность, всегда глушите трубы с двух сторон. Следите, что бы в помещении были закрыты ворота, и не гулял ветер, особенно в зимний период.
Часто, при ремонте приходится производить термообработку цеховых трубопроводов. Во время крупных ремонтов в длинной цепочке километров труб никто не может сказать, где какой участок труб открыт, а в трубе происходит тяга воздуха, мешающая прогреву стыка. В таких случаях перед заваркой стыка обязательно проверьте тягу в трубе, например зажженной спичкой. А в процессе нагрева используйте пирометр для замера температуры трубопровода до и после стыка.
Если температура, с одной стороны, заметно выше — принимайте срочные меры, ищите, откуда сквозняк, или увеличивайте мощность (это возможно при индуктивном методе термической обработки сварных стыков)
Успешной и грамотной Вам работы по термообработке. Прочтите статьи из практики термиста и какие установки стоит выбирать
Термообработка сварных стыков газопламенными горелками(резаками) · rabochiybloknot.ru
Что делать когда нет возможности провести автоматическую термообработку сварных стыков
Тема термообработки сварных стыков интересует многих начинающих специалистов производства и ремонта трубных систем и прочего оборудования. Ранее мы рассказывали какие методы бывают и практические истории из жизни термистов. Все это касалось термической обработке на специальном оборудовании. Но в трудовой жизни котельщика или ремонтника случаются ситуации, когда нет времени или отсутствует сейчас(НЕИСПРАВНО) оборудование для автоматической термообработки.
Что делать, когда при ремонте необходимо произвести отжиг после выборки трещины в труднодоступном месте? В замкнутом пространстве котла, цепочке трубопроводов или тройников большого коллектора порой нет возможности настроить индукционную или радиационную термоустановку. В таких случаях бригада, выполняющая заварку(подварку) стыков делает это с помощью газовых горелок( резаков) сразу после их (стыков)заварки.
Как провести термообработку сварных соединений газовыми горелками или резаками по правилам?
В еще советских (ныне действующих) руководящих документах по ремонту трубопроводов в энергетике, подробно описываются различные методы автоматической термообработки стыков (РД 153-34.1-003-01). Про отжиг газовыми горелками вручную сказано лишь, что допускается это делать, но строго по режиму таблиц (ссылка) и с фиксацией процесса на самописце. Ну если у нас, что-то допускается то это, что-то становится нормой жизни-а куда деваться. Вы только представьте, как на практике должен происходить процесс термообработки- нагрев стыков вручную газовой(ми) горелкой(ми). По технологии термообработка длится не менее восьми часов, то есть пару рабочих обязаны стоять (а может и лежать) с зажженными горелками восемь часов!
Как делается на практике
А на практике бывает так:
- Варится стык или выборка трещины на трубопроводе с подогревом газовой горелкой (200-300 градусов) После заварки стык и пространство в радиусе 100 мм равномерно подогревается газовыми горелками до температуры высокого отпуска (710-760 градусов) Контроль ведется с помощью пирометра или термопар с выводом на прибор.
- Здесь как правило не соблюдается скорость нагрева (не более 100-200 градусов в час). После нагрева до заданной температуры (ярко малиновый цвет) даем немного времени для равномерного прогрева участка и выдержки (обычно 10-15 минут вместо 1 часа минимум)
- Затем хорошо заматываем (укутываем) стык тепловой изоляцией, исключая сквозняки и быструю потерю тепла.
- При отсутствии сквозняков снаружи и внутри трубы (бывает и такое) стык медленно остывает, постепенно набирая заданную твердость (150-240 НВ)
- Такой способ отжига не совсем соответствует РД (руководящему документу) но после контроля дефектоскопистом, результат контроля твердости стыка соответствует норме.
Еще замечено-стыки легированной стали толстостенных труб (свыше 30 мм толщиной) можно сразу укутать изоляцией после сварки. Такие стыки по правилам свариваются с подогревом без перерыва. Потому толстый металл после окончания процесса сварки уже прогрет как русская печь до температуры отжига-остается лишь замотать стык хорошим слоем утеплителя. Но этот метод все же рассчитан на удачу, может и не прокатить.
Еще одно несоответствие технической документации такого метода-отчет в виде графика режимов термообработки.Здесь многое зависит от заказчика,который порой и не в курсе ,что необходим такой отчет. Если все же «прижмет»,то из личного опыта скажу ,что есть куча способов вручную нарисовать такие графики.
Если это самописец на бумаге,то рисуем на бумаге,если сохраненный файл программы,то всегда найдется фотошоп и прочие программы редактирования изображения.
Но повторяю еще раз все это не законно,и надо понимать на каких объектах это допустимо.По крайней мере такие исключения из правил всегда согласовываются со службой технического контроля предприятия.Там тоже не дураки сидят и им в итоге отвечать за последствия нашей работы.
Удачи вам в вашей работе!
Технологии и аппаратура ультразвукового контроля сварных соединений стальных и полиэтиленовых трубопроводов
Технологии и аппаратура ультразвукового контроля сварных соединений стальных и полиэтиленовых трубопроводов- Ультразвуковой контроль стыковых соединений ответственных стальных и полиэтиленовых трубопроводов малого диаметра (до 500 мм) с небольшой толщиной стенки традиционно считался сложной технической задачей. До сих пор во многих отраслях промышленности такие стыки контролируются только радиографическими методами, а стыковые стыки полиэтиленовых трубопроводов физическими методами не контролируются вообще.
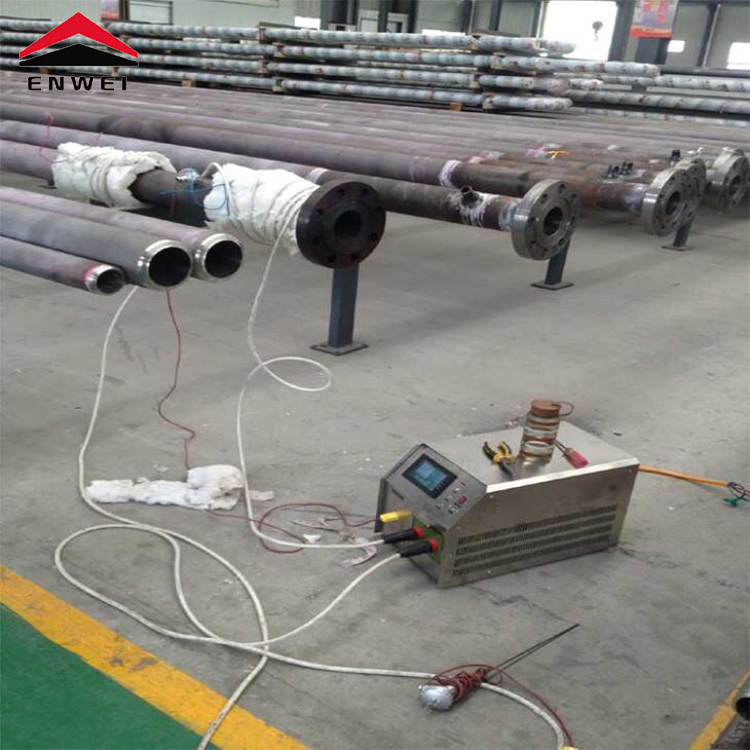
При этом трубопроводы указанного типа применяются практически во всех отраслях промышленности, включая энергетику (стальные трубопроводы различного назначения), трубопроводные транспортные системы (стальные и полиэтиленовые газонефтепроводы), химическую промышленность и др. стыки труб малых диаметров с малой толщиной стенки исчисляются миллионами штук. Поэтому проблему контроля качества таких стыков можно рассматривать как самостоятельный раздел теории и практики ультразвукового неразрушающего контроля.
Рассмотрим особенности этой задачи на примере контроля сварных соединений стальных трубопроводов. При использовании традиционных технологий ультразвукового контроля отражение ультразвуковых волн от стенок трубы и шероховатость сварного шва обычно создают настолько мощные помехи, что на их фоне можно обнаружить только дефекты значительных размеров, а также правило плоского типа. Например, при использовании одноконтурной схемы ультразвукового контроля сварных соединений труб с толщиной стенки от 4 до 6 мм в котлах уверенно выявляется неплавка , находящаяся в корне сварного шва.

Аналогичная ситуация имеет место при попытках обнаружения дефектов в стыках полиэтиленовых трубопроводов. Для них, а также для стыковой сварки оплавлением стальных труб характерно то, что все опасные дефекты имеют планарный характер и расположены крайне перпендикулярно поверхностям соединения. Подобные дефекты практически не обнаруживаются при однозондовой схеме.
Типичное экранное изображение вертикально ориентированного плоского дефекта в сварном шве, обнаруженного с помощью схемы с одним датчиком, показано на рис.1а. В этом случае отражение ультразвуковых волн от дефекта или их дифракция на его краях создают сигналы, амплитуда которых сопоставима с паразитами реверберационного характера. При этом она значительно ниже амплитуды сигналов, отраженных от шероховатости сварного шва. Поэтому обнаружение в рассматриваемых сварных соединениях как объемных, так и плоских дефектов не всегда достоверно.
Рис.![]() |
Вместе с тем существует эффективный метод ультразвукового контроля сварных соединений таких трубопроводов, описанный нами в [1].В нем используется так называемая схема контроля сварных соединений «CHORD» с раздельными функциями передачи и приема ультразвуковых волн. Основные параметры передачи и приема ультразвука (углы ввода — приема, угол между датчиком и приемником и т. Д.) Подбираются таким образом, чтобы основная энергия излучаемого луча концентрировалась в рабочем сечении сварного соединения (рис. . 1b). Благодаря этому обеспечивается обнаружение различных дефектов в любой зоне стыка в пределах толщины соединяемых труб.
Рис. 1b: |
В пределах валика усиления сварного шва (для соединений, выполненных сваркой плавким предохранителем) или вблизи зоны плавления (для соединений, выполненных стыковой сваркой) ультразвуковые волны распространяются параллельно поверхностям труб и плоскости падения (отражения) на дефект перпендикулярно отражающей поверхности плоских дефектов. Проекции лучей, достигающие дефекта (и отраженные от него), на осевой плоскости сварного соединения лежат на хорде поперечного сечения трубы — отсюда и название зондирования.
Практическая реализация схемы зондирования « аккорд » затруднена рядом эффектов, связанных с возбуждением мощных поверхностных волн вдоль исследуемой поверхности.
Таким образом, избавляясь от паразитов характера реверберации и сигналов, отраженных от неровностей стыков (усиливающий валик или заусенец сварного шва), схема « chord », вообще говоря, может порождать акустических паразитов другой природы. Это существенно ограничило применение рассмотренной схемы обследования к трубам диаметром до 100 мм.
В начале 90-х годов АО ВНИИСТ и ООО «Политест» позволили решить проблемы. Предложена новая конструкция двойных щупов типа « chord » с эластичным протектором и технология их изготовления. Данное техническое решение позволило использовать схему « хорда » для контроля сварных соединений стальных труб различных классов (в том числе — аустенитных ) диаметром от 10 до 530 мм и толщиной стенки от 2 до 10-мм. Освоено серийное производство двойного зонда типа « chord » с эластичным протектором.
Данный подход позволил решить и задачу обследования сварных стыков полиэтиленовых трубопроводов, в первую очередь — газопроводов диаметром от 63 до 315 мм с толщиной стенки от 6 до 25 мм.
Акустические характеристики стыков полиэтиленовых труб ранее не изучались. Поэтому считаем целесообразным представить в табл.1 и на рис. 2 рисунка акустических характеристик полиэтилена, из которого изготовлены такие трубы, которые мы измерили.
Марка полиэтилена | скорость продольных волн C, 10 3 м \ с | плотность. п 10 кг \ м 3 | Акустическое сопротивление, z 10 6 Па · с / м | Коэффициент затухания (f = 2,5 МГц) дБ / мм |
П-63 | 2,41 | 0,95-0,96 | 2,29-2,31 | 0,46 |
П-80 (желтый) | 2,25 | 0,94 | 2,11–2,13 | 0,62 |
П-80 (черный) | 2,32 | 0,94 | 2,18-2,19 | 0,55 |
П-100 | 2,39 | 0,96 | 2,29 | 0,44 |
Таблица 1: |
Из табл. 1 видно, что коэффициент затухания ультразвуковых волн в данном материале даже для продольных волн значительно превышает цифры, характерные для стали. Использование поперечных волн для контроля практически невозможно. Кроме того, видно, что разница в акустических характеристиках полиэтилена разных марок может достигать 10%. Это означает, что для различных марок полиэтилена изменяются параметры инспекционной оболочки, что приводит к необходимости изготовления специализированных датчиков для контроля трубопроводов из полиэтилена различных марок.
Исследования также показали, что контроль стыков полиэтиленовых труб целесообразен на частотах, не превышающих 2,5 МГц (рис. 2).
Рис 2: |
Накопленный опыт использования зондов типа «хорд» показал, что можно обеспечить соотношение сигнал / шум не менее +20 дБ для стальных труб и +12 дБ для полиэтиленовых труб. Под термином «сигнал» здесь понимается амплитуда сигнала, отраженного от контрольного отражателя калиброванного размера в стандарта , а под термином «шум» — амплитуда шума любой природы в зоне нахождения этого сигнала или вблизи эта зона. В качестве контрольного отражателя для работы с зондами типа «хорд» обычно используется отверстие с плоским дном, оси которого параллельны стенке трубы.
Нормативные диаметры контрольных отражателей (диафрагмы с плоским дном), действующих сейчас в некоторых отраслях промышленности, приведены в таблице 2:
Диаметр трубы, мм | толщина a толщины стенки трубы мм. | материал трубы | диаметр отверстия с плоским дном, мм | нормативный документ |
10-51 | 2,0-3,0 | Сталь | 0,9 | [2,3] |
18–114 | 3,0-4,0 | Сталь | 1,0 | [2,3] |
32-219 | 4,0-6,0 | Сталь | 1,2 | [2,3] |
114-325 | 6,0-9,0 | Сталь | 1,5 | [2,3] |
32-51 | 3,0-5,0 | Сталь | 1,1 | [4] |
57-76 | 3,0-5,0 | Сталь | 1,3 | [4] |
89-102 | 4,0-6,0 | Сталь | 1,4 | [4] |
108-159 | 4,0-8,0 | Сталь | 1,5 | [4] |
168-529 | 5,0-9,0 |
Изучение и объяснение термической обработки после сварки
Сварные швы
часто подвергаются термообработке после сварки. (PWHT) Есть разные причины
для этого и различные методы термообработки после сварки. Есть также определенные
риски, связанные с PWHT. На этой веб-странице мы рассмотрим использование PWHT.
Во первых
мы рассмотрим различные виды термической обработки, а затем соотнесем
их при сварке.
The WelderDestiny Compass: еженедельная подписка на электронный журнал
Вы можете посмотреть предыдущие выпуски «The WelderDestiny Compass», щелкнув здесь.
Виды термической обработки
Два
различные материалы при воздействии одного и того же термического цикла потенциально могут
имеют существенно разные результаты по материалам. Термические обработки
поэтому обычно описывается с точки зрения воздействия, которое они окажут на
материал, а не тепловой цикл. Однако есть исключения из этого
правило.

Ниже
список типичных термических обработок:
- Отжиг: Обычно это относится к обработке, необходимой для получения материала мягкое и безударное состояние. Для большинства материалов, например углеродистой стали, это будет означать очень высокую температуру, а затем очень сильное охлаждение. медленно до комнатной температуры.
- Закалка Anneal: Здесь снова делается намерение добиться «мягкой» структуры, но медленной круто будет вредно для материала. Типичным для этого является 300 серия нержавеющих сталей. (Также называемые аустенитными нержавеющими сталями.) нержавеющие стали не претерпевают существенных фазовых превращений в большая часть материала во время цикла термообработки, но может привести к образованию локально вредных фаз или частиц, когда он хранится в каком-то промежуточном температурные диапазоны в течение длительных периодов времени.Чтобы этого не случилось, материал быстро охлаждается (закаливается) от высокой температуры. (Обычно 1050 ° C) Это сокращает время, в течение которого материал остается при температуре. диапазон 500 — 850 ° C, где может наблюдаться образование границ зерен карбиды, которые серьезно снижают коррозионную стойкость материала. Этот пагубный процесс называется сенсибилизацией.
- Решение Обработка: Основная цель этой термообработки — убедиться, что все различные легирующие элементы равномерно распределены по материалу, и «Растворяется» в материале, насколько это возможно.Это часто выполняется на отливки, потому что процесс затвердевания во время отливки имеет тенденцию приводить к материал, имеющий относительно большие различия в некоторых легирующих элементах в разных частях конструкции. Обычно бывают области с высоким концентрация одних элементов и низкие концентрации других элементов. От повышение температуры до точки, при которой происходит большая диффузия, эти неравномерные концентрации легирующих элементов выровняются. Определенные фазы (например, карбиды) также будут «растворяться» (переходить в раствор) материалом при эти высокие температуры.Чтобы сохранить как можно больше легирующих элементов в раствора, некоторые материалы обычно закаливают после обработки раствором. Это очень похоже на закалочный отжиг, описанный выше.
- Закалка Закалка: Для достижения высокой твердости некоторых материалов, таких как углеродистые стали и низколегированные стали, материал можно нагревать до температуры, выше которой фаза трансформации происходят в материале. (Обычно 950 ° C для углеродистой стали.) затем материал быстро охлаждается (закаливается) с образованием некоторых метастабильных фаз (для например, мартенсит), что обеспечивает высокий уровень твердости материала.Когда материалы подвергаются закалке, они также обычно становятся хрупкими.
- Закалка: Для смягчения материала, который уже затвердел в результате предыдущего нагрева. цикла (например, закалка), вы можете снова увеличить температуру материал до точки, ниже которой он начинает испытывать объемную фазу превращений (обычно нагревают до 650-700 ° C) и выдерживают там в течение период времени. Во время этого цикла отпуска затвердевший мартенсит превращается в закаленный мартенсит, не такой твердый и хрупкий, как закаленный мартенсит, но по-прежнему очень сильный и жесткий.
- Закалка и Temper: Это комбинация двух описанных циклов термообработки. над.
- Напряжение Разгрузка: При пластической деформации пластичных металлов они заканчиваются. с большим количеством остаточных напряжений в материале. Сварка также приводит к эти остаточные напряжения вокруг сварного шва. Увеличивая температуру металла предел текучести металла снижается. (Предел текучести — это напряжение, при котором материал начинает пластически деформироваться.) Когда доходность прочность снижается из-за высокой температуры ниже уровня остаточного напряжения, тогда материал «расслабится». Это снимает стресс, который был захвачены в материале в результате деформационных или сварочных работ. Углерод Стали обычно снимают напряжение при температуре около 600 ° C. На это температура, остаточное напряжение обычно снижается примерно до 30% от текучести прочность материала при комнатной температуре. Основная причина стресса облегчение обработки состоит в том, что она улучшает вязкость разрушения компонентов.Это также снижает вероятность определенных механизмов коррозии, таких как стресс. Коррозионное растрескивание. (SCC)
- Нормализация: Обычно это выполняется с углеродистой сталью, чтобы обеспечить отсутствие напряжений и зернистая структура. Это достигается за счет взятия температуры выше температура, при которой происходит фазовое превращение в объеме материала, (обычно температура около 950 ° C), а затем дать ему остыть на неподвижном воздухе. От применяя эту обработку к обычным углеродистым / углеродистым марганцевым сталям, они будут разработать структуру, которая является очень хорошим компромиссом между прочностью и жесткостью.Это очень типичная термическая обработка стальных отливок, поковок и другие стали для получения мелкозернистой структуры.
- Осадки Отверждение: В некоторых материалах образуются очень мелкие частицы. внутри их структуры, если их температура повышена и поддерживается там в течение время. Эти маленькие частицы называются осадками. Наличие этих мелкие частицы укрепляют материал. Типичные осадки Цикл отверждения следующий: Температура материала доводится до точка, где будет проводиться «обработка раствора».Тогда материал «Закаливают», чтобы не образовывался осадок. Далее температура снова повышается (но до температуры ниже температуры раствора) который затем способствует образованию осадков. Это называется «старением». лечение. Важно отметить, что если температура слишком высока или слишком долго в течение этой части цикла, материал будет «Старше возраста». Престарелый материал будет иметь меньшую твердость и прочность, чем тот, который был должным образом выдержан.К тому же, если температура или время старения слишком низко, то материал будет «не выдержанным», что снова приведет к меньшая твердость и прочность. Недостаточное старение — меньшая проблема, потому что вы можете просто увеличьте температуру снова, чтобы продолжить старение до оптимального результат достигнут. Старение — гораздо более серьезная проблема, потому что это может быть только исправлено повторным выполнением всего цикла. (Из раствора лечения.)
- Термомеханически Контролируемый процесс: (TMCP) Строго говоря, термическая обработка такие, но я думаю, что это хорошее место, чтобы обсудить это в ближайшее время.В TMCP сталь деформируется (например, прокатывается), одновременно испытывая температуры, которые недостаточно высоки, чтобы вызвать полные фазовые превращения и рекристаллизации, но не настолько низко, чтобы приводить к чисто холодной штамповке. Каждый сталелитейный завод имеет свою собственную последовательность температур и деформация для получения прочного материала, легко свариваемого. Стали TMCP имеют тенденцию иметь низкоуглеродные аналоги, оставаясь при этом очень прочными и выносливыми.
Есть
некоторые другие более специализированные термические обработки, которые иногда используются
при очень особых обстоятельствах, но для наших целей перечисленные выше
будут основными видами термической обработки, на которые следует обратить внимание.
Влияние сварки на материалы
Fusion
Сварка связана с достаточно высокими температурами, чтобы расплавить материалы,
присоединился. Таким образом, они вводят тепловой цикл, который приводит к
материалы, близкие к сварному шву, нагреваются до температур, близких к температуре плавления
точки, а материалы, находящиеся далеко от сварного шва, почти не увеличивают
температура.Другими словами, существует температурный градиент, испытываемый
материалы, которые варьируются от температуры окружающей среды до температуры плавления.
часть основного металла, структура которого изменилась под воздействием тепла сварки
известна как зона термического влияния (HAZ) сварного шва. Материал, где
температура была недостаточно высокой, чтобы существенно повлиять на
материал просто называют основным материалом. Участок, оплавленный из-за
операция сварки называется наплавленным металлом.
структура металла сварного шва будет зависеть от состава основного металла,
состав присадочного металла и эффекты, вызванные тепловым циклом. Как
общее правило: мы можем выбрать присадочный металл, чтобы получить желаемый результат в пределах
металл шва. Однако мы не можем ничего сделать с точки зрения композиции, чтобы
зона термического влияния. (HAZ) Единственный эффект, который мы имеем в управлении
Структура ЗТВ предназначена для управления тепловым циклом.
Это
также должно быть очевидно, что тепловой цикл в ЗТВ будет иметь
значительное влияние на термическую обработку материала перед сваркой
операция.Например, некоторая часть ЗТВ основного металла углеродистой стали
будет повышена до температуры, выше которой происходят фазовые превращения в
стали. (Это называется критической температурой, и для обычных углеродистых сталей
это около 720 ° C.)
Когда
в последующем его охлаждают, снова будут фазовые превращения. Если
скорость охлаждения достаточно высокая, тогда мы можем испытать некоторую закалку
упрочнение в этой области, в результате чего получается жесткая хрупкая структура. Если охлаждение
достаточно медленный, то мы испытаем тепловой цикл, похожий на
нормализующая термическая обработка.Если скорость охлаждения очень низкая, то тепловая
Цикл будет напоминать цикл отжига стали.
Это
означает, что за счет изменения количества энергии, используемой при сварке, (также называемой
подводимого тепла) наряду с предварительным нагревом и последующим нагревом могут быть
достигается как в металле шва, так и в зоне термического влияния сварного шва.
Некоторые
материалы, такие как низколегированные стали, почти всегда приводят к закалке
структура внутри ЗТВ при сварке. Затем им требуется дополнительный нагрев после сварки.
Лечение (PWHT) для достижения желаемого результата.В случае нашего примера с
низколегированной стали, они почти всегда нуждаются в закалке для достижения
подходящая прочная и жесткая микроструктура.
Некоторые
материалы достигают значительной прочности в результате холодной обработки.
Под холодной обработкой понимается пластическая деформация металла при температуре
ниже которого деформированные зерна металла будут рекристаллизоваться. Это лечение
приводит к увеличению прочности холоднодеформированного материала.
Когда
сварка холоднодеформированного (также называемого деформационным упрочнением) материала, части
ЗТВ будет испытывать достаточно высокие температуры, чтобы вызвать перекристаллизацию и
фазовые изменения.Это устранит холодную работу и потенциально уменьшит
прочность материала в ЗТВ значительно. Обратите внимание, что термообработка после сварки не может
обратить этот эффект вспять.
Это
разупрочнение часто наблюдается при сварке упрочненных алюминиевых сплавов. В
ЗТВ всегда будет значительно слабее, чем холодно обработанный основной металл. В
единственный способ эффективно справиться с этим эффектом — спроектировать компонент в
таким образом, чтобы сварной шов находился в области с меньшим напряжением, или основание
металл в зоне сварного шва делается толще, чем требуется, чтобы компенсировать
потеря силы.
Другой способ упрочнения алюминиевых сплавов — это
осадочное твердение. Опять же, термический цикл сварки вводит
область в ЗТВ, которая не выдерживается, (Температура была достаточно высокой, чтобы вернуться
осаждается в раствор, после чего следует гашение из-за высокой скорости охлаждения
обычно связаны со сваркой.) и области, которая изношена. (Температура
был выше, чем требуется для оптимального старения, но недостаточно для возврата осадков
в раствор.) Таким образом сварка дисперсионно-твердой (также называемая состаренной)
материалы приведут к снижению прочности ЗТВ. Для небольших компонентов это
возможно подвергнуть весь компонент дисперсионному твердению
цикл, но в большинстве случаев, как правило, ничего нельзя сделать
для исправления этого снижения прочности в ЗТВ осажденного твердого
материал.
Типичная термообработка после сварки (PWHT)
Пока
теоретически возможно выполнение любой из описанных термических обработок
ранее как термообработка после сварки (PWHT) практически не использовалась
кейс. Типичные термические обработки после сварки следующие:
- Напряжение Relieve: Сварка вызывает высокие остаточные напряжения в металлах в регионе вокруг сварного шва. Это может привести к снижению характеристик вязкости разрушения и восприимчивость к механизмам коррозии, таким как коррозионное растрескивание под напряжением.(SCC) Снятие напряжения, вероятно, является наиболее часто выполняемой термообработкой после сварки, особенно на углеродистые стали и углеродистые марганцевые стали. Снятие стресса — это обычно код требование для оборудования, работающего под давлением, более определенной толщины. (Каждый код имеет различные правила для определения того, когда требуется снятие напряжения.) Для углерода стали, снятие напряжений обычно составляет около 580 ° C — 650 ° C. Обратите внимание, что лечение для снятия стресса в более высоком диапазоне может уменьшить прочность стали TMCP.Если для сталей TMCP требуется термообработка после сварки, она должна предпочтительно делать на нижнем конце диапазона.
- Характер: Для низколегированных сталей и других материалов, которые естественно твердеют при сварке, a почти всегда требуется характер. Температуры отпуска могут широко варьироваться, но для низколегированных сталей обычно составляет около 700–750 ° C. (Некоторые закаленные и закаленные микролегированные стали могут иметь значительно более низкий отпуск Обратите внимание на то, что при использовании температуры отпуска после термообработки выше этой основного металла ослабит основной металл.Поэтому отпуск после термообработки шва Рекомендуется быть примерно на 30 ° C ниже, чем состояние основного металла.
- Нормализация: Наиболее крупные конструкции сложной формы не подлежат нормированию. PWHT. Причина в том, что материал становится настолько слабым при замачивании. температура (обычно 950 ° C для углеродистой стали), что он не может поддерживать конструкции и приводит к катастрофическому короблению и деформации. Нормализационная термообработка после сварки поэтому выполняется только на довольно простых компонентах, которые можно легко поддерживается.Типичным примером может быть сварной выпуклый конец для сосуда высокого давления, перед приваркой к самому сосуду.
Риски, связанные с термообработкой после сварки
Сообщение
Термическая обработка сварного шва (PWHT) сопряжена с риском. Ниже приведен список потенциальных
проблемы, которые могут возникнуть при выполнении термообработки после сварки.
- Убыток прочности: Чрезмерное время или слишком высокая температура для снятия напряжения после сварки термообработка может привести к снижению прочности материала.Закалка также может привести к снижению прочности закаленных и закаленные материалы. Поэтому время и температура должны быть хорошими. контролируется.
- Искажение или коллапс: Температура снятия напряжения или отпуска приводит к образованию материала что значительно снижает прочность при повышенных температурах. Если элемент конструкции испытывает некоторую нагрузку на него, то в процессе послесварочной термообработки цикл может искривляться или деформироваться. Это могло иметь катастрофические и высокие затраты последствия.Поэтому важно убедиться, что все конструкции подверженные воздействию высоких температур, должным образом поддерживаются. Кроме того, если один часть конструкции испытывает значительно более высокие температуры, чем других разделах разница в тепловом расширении также может привести к серьезным искажения конструкции. Такая ситуация обычно возникает, когда кожухотрубные теплообменники подвергаются термообработке для снятия напряжений после сварки, когда температура оболочки повышается и понижается намного быстрее, чем трубки.Важно следить за тем, чтобы не было чрезмерной температуры. градиенты или различия во время операции термообработки после сварки. Для этого необходимо иметь достаточное количество термопар, прикрепленных к компонентам, чтобы гарантировать недопустимость температурных градиентов не бывает. В некоторых печах также могло быть потенциальное попадание пламени в некоторые участки на судне. Это могло, это может локально увеличить температуру до значений выше фазового превращения температура (более низкая критическая температура), что приводит к неожиданным фазовым изменениям а также изменения громкости.Они могут не только снизить механические свойства, но и привести к деформации. Чтобы этого не произошло, там должны быть эскизы загрузки печи, показывающие, каким будет влияние пламени предотвращены, а также должны быть размещены термопары в местах ближе всего к горелкам газовых или мазутных печей.
- Охрупчивание или растрескивание: Некоторые плавки материал может содержать микроэлементы, которые делают его восприимчивым к «закалке». охрупчивание ». (Обычно хром) Во время операции термообработки после сварки некоторое количество интерметаллических могут образовываться очень хрупкие фазы, приводящие к значительному и потенциально катастрофическое охрупчивание компонента или конструкции.Для обеспечения что этого не произойдет, материалы следует покупать с испытанием на образцы, которые были подвергнуты моделированию цикла термообработки после сварки. Некоторые стальные компоненты могут также иметь некоторое количество остаточного аустенита в своих структурах из-за их предыдущие термические обработки. После термообработки шва этот остаточный аустенит может превратиться в мартенситоподобная структура, хрупкая. Коды обычно требуют, чтобы окончательный контроль и неразрушающий контроль (NDT) должны быть выполнены после термообработки после сварки операции, чтобы обнаружить любые дефекты, которые образовались во время операции PWHT.Твердость Испытания после термообработки после сварки также позволяют определить, не произошло ли затвердевания. произошло во время термообработки после сварки. (Обратите внимание, что не все механизмы охрупчивания связаны с более высокой твердостью металла.)
Методы термообработки после сварки
Есть
это 3 типичных метода применения тепла для термообработки после сварки. Это следующие методы:
- Печь: При термообработке после сварки в печи весь компонент обычно помещается в печь, и температурный цикл применяется ко всему составная часть.Очевидно, это означает, что компонент или структура не должны быть такими. большой, что не помещается в топку. Также компонент необходимо переместить в где находится топка. Для работ по техническому обслуживанию или для длинных и громоздких компонентов, это часто непрактично. Основное преимущество этого вида термообработки после сварки это переменное расширение, вызванное чрезмерными температурными градиентами (разные температуры в различных частях компонента) можно свести к минимуму. Чтобы при этом важны скорости нагрева и охлаждения, так как более толстые секции будут обычно требуется больше времени для нагрева или охлаждения, чем для более тонких секций.
- Внутренний обжиг: В этом методе компонент изолирован снаружи, а тепло вводится внутрь компонента, пока весь компонент не нагреется до необходимой температуры. Тепло обычно вводится газовыми горелками. горелки. Очевидно, это подходит только для компонентов «полого» типа, таких как сосуды под давлением. К тому же это довольно дорогой вариант, связанный с рисками. с соответствующей изоляцией и защитой от пламени горелок.
- Местное внешнее нагревание: Этот метод термообработки после сварки подходит для удлиненных деталей, которым требуется только нагревание на определенных участках, а не весь компонент.Это типично для кольцевых сварных швов на трубопроводы или закрывающие сварные швы на длинных сосудах высокого давления. В этом методе какой-то элемент вводит тепло снаружи компонента (иногда элементы размещены внутри и снаружи для обеспечения равномерного нагрева) обычно в обвязка по всей окружности компонента. Подходящая изоляция сохраняет тепло от поверхности за счет конвекции и излучения. Однако тепло теряется из-за проводимости к неотапливаемым частям составная часть.Поэтому важно контролировать температурные градиенты от области, испытывающие PWHT, до областей, которые все еще остаются «холодными». Если это не так Если все сделано аккуратно, переменное тепловое расширение может привести к напряжения в зонах, прилегающих к зоне термообработки после сварки, которые может просто переместить проблему из одного места в другое.
Источники тепла для термообработки после сварки
В зависимости
Что касается метода применения тепла во время термообработки после сварки, существует ряд различных терминов.
источники.Типичные источники тепла:
- Газ или нефть Горелки: Обычно используются в больших печах или при выполнении внутренний обжиг компонента. Основная проблема в том, что горелки потенциально может задеть компоненты, что приведет к возникновению «горячих точек», где температура слишком высока по сравнению с остальным компонентом. Печь поэтому планировку необходимо тщательно спланировать, чтобы убедиться, что это не случиться. Как правило, в цепи используются дополнительные термопары. области, где возможно попадание пламени во время термообработки после сварки.
- Электрооборудование Нагревательные элементы сопротивления: Они часто используются для местной термообработки после сварки составные части. Они имеют форму матов, имеющих электрическое сопротивление. проволоки «вплетены» в керамические бусины. Эти «тепловые шарики» затем прикрепляются к поверхность, подлежащую послесварочной термообработке. Часто их просто держат на месте при помощи стальной проволоки. При использовании этих нагревательных элементов элементы размещается на поверхности металла, а вокруг снаружи, чтобы сохранить тепло.
Симптомы и лечение гипермобильности суставов — Болезни и состояния
Перейти к основному содержанию Перейти к программе чтения с экранаПоиск
Меню
Поиск: Поиск
- Дом
- Болезни и состояния
- Симптомы и самопомощь
- Тесты и лечение
- Здоровая жизнь
- Забота, поддержка и права