Способ закалки в инертных газах
Изобретение относится к области машиностроения, в частности к термообработке, преимущественно закалке, деталей из конструкционных и инструментальных легированных деталей. Задача изобретения — расширить возможности применения инертных газов аргона и гелия для светлой закалки стальных деталей. Применяют смесь состава 20% гелия, остальное аргон. Технический результат — расширяются технологические возможности применения инертных газов для светлой закалки, реализуются преимущества малодеформационной закалки инструмента в муфельных печах, процесс экологически чистый и позволяет встраивать подобные термические установки в пролетах цехов по механической обработке, охлаждающая способность в 2 раза повышается, если к аргону добавлять 20% гелия. 2 ил.
Изобретение относится к области машиностроения и может использоваться при термообработке, преимущественно закалке, деталей из конструктивных и инструментальных легированных сталей с критической скоростью закалки не более 30 град/с.

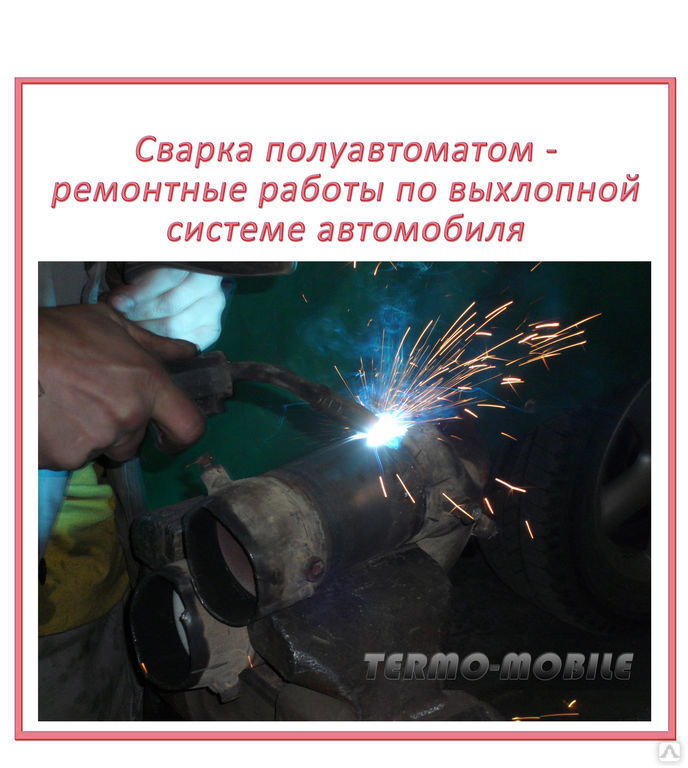

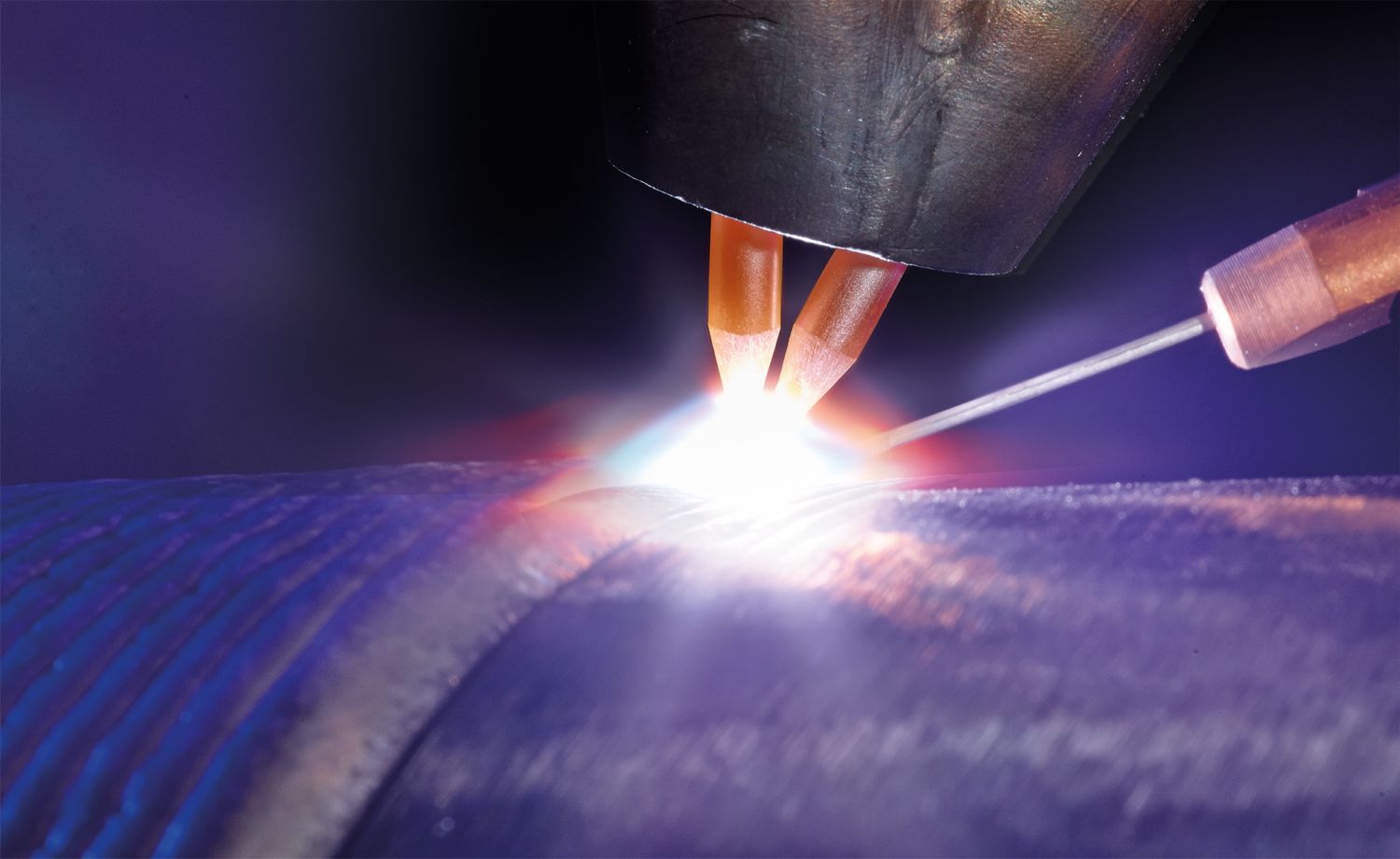
РИСУНКИ
Рисунок 1, Рисунок 2Закалка светлая — Энциклопедия по машиностроению XXL
Закалка светлая Нагрев в защитной атмосфере и охлаждение в расплавленной щелочи Для предупреждения обезуглероживания, окисления и сохранения чистоты поверхности Образование аустенита или аустенита и карбидов с последующим превращением аустенита в мартенсит Отпущенный мартенсит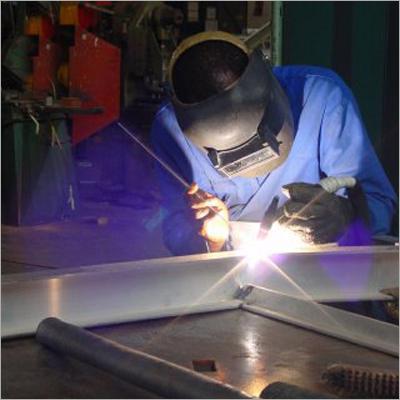
Закалка светлая i чистая [c.599]
Светлая и чистая закалка, светлый отжиг и нормализация, газовая цементация [c.151]
Светлая закалка, светлый отжиг, газовая цементация, газовое цианирование [c.151]
Материалы изделий Светлый отжиг Светлая нормализация Светлая или чистая закалка Светлое старение и светлый низкий отжиг Светлый отпуск и подогрев до 700° С [c.304]
Закалка чистая соответствует закалке светлой, но при приме- [c.542]
В. По условиям воздействия внешних факторов закалка светлая— закалка чистая — 3,, закалка под давлением — 3 . [c.118]
Закалка светлая Нагрев в защитной атмосфере и охлаждение в расплавленной щелочи [c.57]
H i рис. 450 приведены типичные микроструктуры алюминиевых бронз.
Ярко выраженная ликвация определяется с помощью реактива 50, причем богатая алюминием осевая полоса кажется светлой, а богатое цинком оставшееся поле —темным. Закаленные и состаренные сплавы с дисперсными выделениями хорошо травятся реактивом 44 (продолжительность травления 5—7 с) и 42 (травление в течение 5—7 с) при этом раствор 44 выявляет образующийся при закалке слой между смежными плоскостями скольжения. Выделения, субструктура и линии скольжения выступают только при тщательно отполированной поверхности образца. Поэтому необходимо проводить чередование травления и полировки.
Размеры и микротвердость слоев при одинаковых режимах обработки зависят от содержания углерода в углеродистых сталях. С увеличением содержания углерода в этих сталях наблюдается значительный рост микротвердости в ЗТВ луча ОКГ (рис. 4). Так, при Е = 2,06 Дж, г = 1,5 мс, / = 43,2 мм, в малоуглеродистой доэвтектоидной стали 20, структура которой состоит из феррита и перлита, микротвердость первого слоя ЗТВ луча ОКГ составляет 750—770 кгс/мм , а при обычной закалке цементированной стали 20 достигается микротвердость 300—350 кгс/мм Высокая твердость первого слоя ЗТВ свидетельствует о том, что в процессе охлаждения после воздействия луча ОКГ в нем происходили мартенситные превращения, т. е. нетравящаяся светлая полоса представляет собой малоуглеродистый мелкодисперсный мартенсит. Температура нагрева этого слоя изменялась от температуры плавления стали до точки Лсз.
В зависимости от конечных условий взаимодействия со сталью контролируемые атмосферы разделяются на а) защитные от окисления и обезуглероживания, применяемые при светлом отжиге, нормализации, светлой и чистой закалке б) науглероживающие, применяемые при газовой цементации (газо-
[c. 559]
Светлая и чистая закалка, 1. Камерные В зависимости от герметичности печи 10—20 м час [c.574]
В СВЯЗИ С широким развитием разработки природных газов в СССР, а также рациональным использованием твёрдых сортов топлива при их газификации система сжигания газообразного топлива в термических печах непрерывно улучшается. Наиболее совершенными являются системы поверхностного и диффузионного сжигания. Поверхностное сжигание обеспечивает получение максимально возможных температур в малом объёме камеры сжигания, особенно при применении катализаторов (активированный шамот, дунит и т. п.). Применение современных керамических горелок поверхностного сжигания позволяет получать тепловое напряжение до 400,0 млн. ккал м и температуры свыше 1600° С. Диффузионное сжигание даёт возможность применять радиационные трубчатые нагреватели, получившие широкое распространение в печах для светлого отжига, светлой закалки и газовой цементации.
[c.586]
Светлая и чистая закалка [c.146]
Светлая и чистая закалка сталей, светлый отжиг и нормализация, лайка медью [c.151]
Эидогаз 40 20 светлый отжиг, твердая пайка Защита от обезуглероживания, светлая закалка, спекание, светлый отжиг, твердая пайка Цементация, светлая закалка, светлый отжиг Наполнитель при азотировании и деазотироваиии [c.527]
Газовая цементация без закалки, светлый отжиг или среднетемпе-ратурный отпуск [c.566]
Закалка светлая проводится с использованием защитной атмосферы в процессе нагрева, выдержки и светлокалящего масла при охлаждении с целью предохранения поверхности изделия от окисления и обезуглероживания. [c.629]
Закалка светлая применяется для пружин, зубчатых колес, валов и других деталей, работающих в условиях переменной нагрузки с целью зандиты от окисления и обезуглероживания, а также получения высоких значений предела выносливости.
[c.542]
В современных печах с защитной атмосферой можно получать после отжига или закалки светлые и чистые детали. В печах последних конструкций детали совершенно не соприкасаются с воздухом. Закалочные печи строят, например, с опрокидывающимся подом или внутренним конвейером, так что закалка производится без выдачи детпли на воздух. [c.205]
На фиг. 120 показана структура стали с 0,4% С после закалки с 860° в масле. Темные участки по границам зерен — троостит закалки, светлые участки —. apт н ит. [c.145]
Закалка светлая Зсе) — при любой разновидности процесса закалки — осуществляется с применением защитных атмосфер при нагреве и охлаждением в светлокалящем масле. [c.69]
Охлаждение в расплавах едких щелочей, если предварительно детали нагревали в жидких солях (т, е. солях, fk вызывающих окисления), позволяет получить чистую ио1 срхиость светло-серого цвета. Закалку 1ю этому способу назьшакгг с в е г л о й.
[c.215]
Алюминиевые бронзы обладают высокими механическими свойствами, повышенной жаропрочностью и антикоррозионной стойкостью. Упрочняющая термическая обработка состоит из закалки с 850— 900° С в воде и последующего отпуска при 400—600°С в течение 1,5 ч. На рис. 16.12 показана микроструктура бронзы Бр.АЖМц10-3-1,5, состоящая из зерен а-кристаллов (светлая составляющая) и а-МЗ-эвтек-тоида (темная составляющая). [c.299]
Детали, закаленные на мартенсит, упрочняют обработкой на белый слой точением твердосплавными резцами с большим отрицательным передним углом (до 45°) без смазочно-охлаждающих жидкостей при скорости резания 60 — 80 м/мин. Поверхностный слой при этом подвергается своего рода термомеханической обработке, представляющей собой совмещение процессов высокотемпературной деформации и вторичной закалки. На поверхности образуется светлая нетравящаяся корка толщиной 0,1—0,2 мм, обладающая высокой твердостью НУ 1000—1300 При исходной твердости материала НУ 600—700) и состоящая из мелкозернистого (размер зерна 0,05—0,1 мкм) тонкоигольчатого мартенсита втюричной закалки с высокодисперсными карбидными включениями. В зоне белого слоя возникают чрезвычайно высокие сжимающие напряжения (до 500 кгс/мм ), обусловливающие резкое повыщение циклической прочности. Усталостно-коррозионная стойкость повышается примерно в 10 раз п6 сравнению с исходной. Хорошие результаты получаются только йрн условии сплошности белого слоя. В противном случае на участках разрыва слоя возникают скачки напряжений, снижаюНтие циклическую прочность. Чистовую обработку белого слоя производят микрошлифованием, полированием и суперфинишированием.
[c.323]
Как было показано выше, появление в структуре сплава фаз или сегрегаций легирующих элементов (или примесных атомов), обладающих более отрицательным потенциалом, чем матрица, приводит после нарушения пассивности к созданию более отрицательного компромиссного потенциала и усилению анодного тока. Скорость репассивации активной поверхности замедляется. Пример этого—сплав ВТ5-1, состаренный при 500°С в течение 10—100 ч.
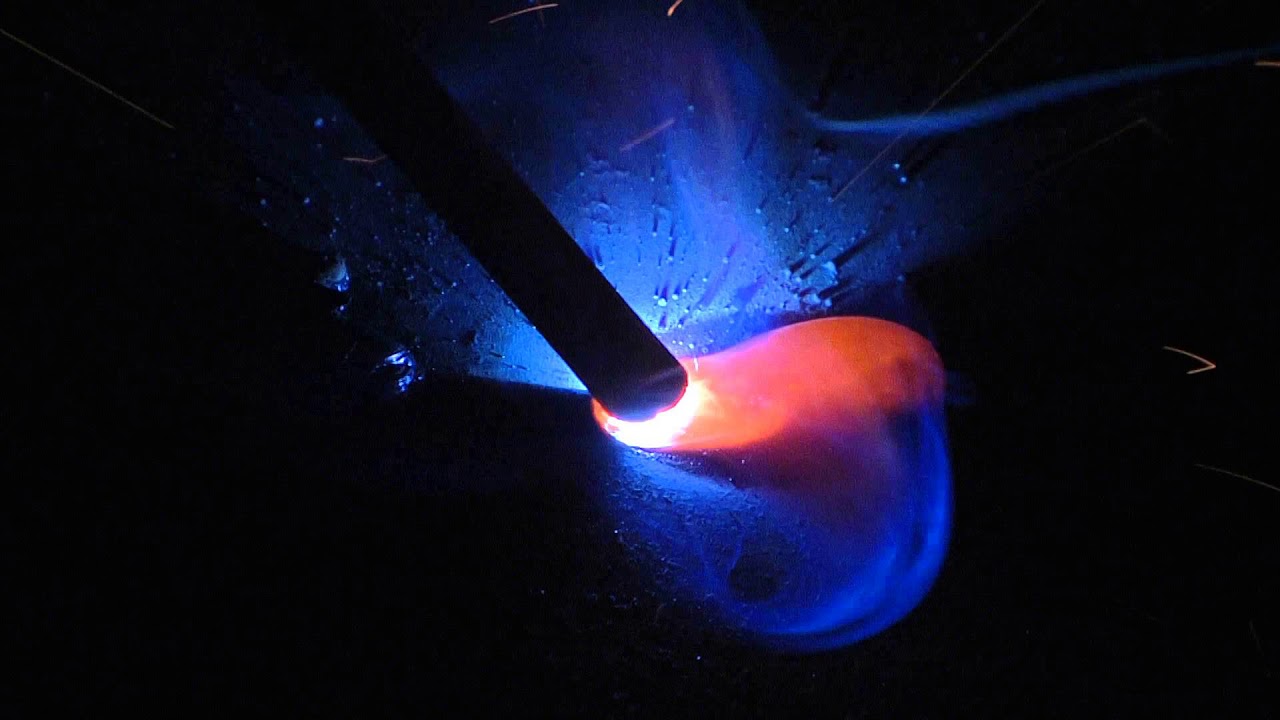
В 1935 г. в лаборатории В. П. Вологдина в Ленинградском электротехническом институте был разработан метод высокочастотной поверхностной закалки в условиях производства. Инженер Г. И. Бабат предложил новый способ высокочастотной закалки с применением электронной аппаратуры (был внедрен на заводе имени Орджоникидзе). В 1936 г. на заводе Светлана была выпуш,ена первая серия ламповых высокочастотных генераторов промышленного назначения для индукционного нагрева.
[c.118]
Некоторые виды цементита, например третичный цементит или цементит, распределенный в структуре сталей после закалки, выявляются этим травителем лучше, чем с помощью травителей, после обработки которыми карбид железа выглядит темным на фоне окружающей светлой матрицы. Клемм применял его для выявления цементита и у-фазы в закаленных структурах. Для травления не требуется удалять деформированный слой феррит-ной матрицы. Изображение структуры получается более качественным, если сульфидный осадок на всей поверхности феррита одинаково ориентирован. Очень хорошо выявляли цементит с помощью тиосульфата натрия не только в незакалеиных, но и в закаленных и отпущенных сталях [42]. Этот метод позволяет наблюдать за развитием коагуляции цементита, выделяющегося в процессе отпуска. Естественно, для изучения небольшого числа мельчайших частиц цементита важное значение имеет оптическое разрешение.
[c.90]
Подобный способ травления, примененный для сплава, содержащего 12,8% Мп и 0,46% С (термообработка нагрев 1250° С, 12 ч, аргон + закалка + нагрев, 640° С, 150 ч + закалка), позволил выявить серые аустенитные кристаллы с четкими полосами скольжения при этом феррит выглядит светлым, а карбиды темными. При травлении пикратом натрия темнеет только карбид. После одновременного травления реактивом 4 и раствором, в котором вместо пикриновой кислоты применялся паранитрофенол, Глузанов и Петак [9] в белом чугуне с 4% Мп наблюдали в первичных иглах цементита среднюю зону с измененной окраской, в то время как подобный тип цементита в чугуне с 14% Мп выглядит гомогенным. Авторы считают, что сложный железомарганцевый карбид в точке превращения (точка Кюри) цементита распадается на две фазы, так как а-карбид железа может содержать в твердом растворе лишь небольшое количество марганца. Цементит в марганцовистом чугуне с 14% Мп остается гомогенным, поскольку уже при 8% Мп точка превращения расположена при 0° С и с ростом концентрации марганца температура точки превращения снижается.
[c.111]
В настоящее время электронагрев токами высокой частоты (т. в. ч.) стал превалирующим, на некоторых заводах он применяется для 40—60% поверхностно упрочняемых деталей. Основоположником исследований и применения индукционного электронагрева является В. П. Вологдин, именем которого назван специально созданный для этих целей в Ленинграде научно-исследовательский институт (НИИТВЧ). В 30-х годах в Ленинградском электротехническом институте им. В. И. Ленина под руководством В. П. Вологдина начались исследования по применению индукционного электро-нагрева в процессах термической обработки металлов и сплавов [50—52]. Тогда же в лаборатории Ленинградского завода Светлана были начаты работы по проектированию ламповых генераторов [14, 121, 122], на Москов- ском автозаводе началось внедрение процесса поверхностной закалки с электронагревом т. в. ч. шеек коленчатых валов автомобильного двигателя, а на XT S — внедрение процесса закалки поперечного бруса трактора.
[c.148]
Закалка Средне- и высокоуглеродистая сталь. ……… Средне- и высокоуглеродистая легированная сталь. . . Быстрорежущая сталь. . . 760 980 760—985 980—1350 Светлый или чистый То же Я КГУ-1000 КГУ-Г1СО-0,6 с добавкой исходного газа ГГ-1200 ГГО КГУ-1СОО КГУ ПСО-0,6 и ПСО-1,0 с дсб вкой исходного газа h ГУ-1000 КГУ [c.

Закалочными средами служат 5—10/о-ный водный раствор каустической соды при температуре 15—30 С вода при температуре 15—30° С минеральные и растите льные масла при температуре 20—80 С светлокалящие масла (при светлой закалке) водные эмульсии и коллоидные растворы при температуре 15—30° С расплавленные соли при температуре 160- 250 С (ступенчатая и изотермическая закалка) воздушная или паро-воздуш-ная струя и др. (см стр. 628). [c.610]
31603402862 Камерная эл.печь под закалку в среде аргона СНЗ 6.12.5/12И2 (622560)
Размещение завершено
Участники и результаты
Камерная эл.печь под закалку в среде аргона СНЗ 6.12.5/12И2
Публичное акционерное общество «Нижегородский Авиастроительный Завод «Сокол»
ИНН 5259008341 КПП 525901001
- Место поставки
-
603035, Россия, Нижегородская обл.
, г. Нижний Новгород, ул. Чаадаева, д. 1
Преимущества
Участниками закупки могут быть только субъекты малого и среднего предпринимательства
Требования к участникам
Требование к отсутствию участников закупки в реестре недобросовестных поставщиков
Участник | Цена, ₽ | Рассмотрение заявок |
---|---|---|
Победитель
ЗАО «Накал» — Промышленные печи» |
░ ░░░ ░░░░░░ | ░░░░░ |
░░░ ░░░░░░░░░░░░░░░░░░ |
░ ░░░ ░░░░░░ | ░░░░░ |
Внешний вид | Модель | Максимальная t, °С | Рабочие размеры, мм | Мощность, кВт |
И2 – закрытые нагреватели в рабочей камере;
|
ПЕЧИ СЕРИЙНОГО ПРОИЗВОДСТВА БОРТЕК™ | |||
Параметры печей могут меняться по дополнительному согласованию с Заказчиком | ||||
Лабораторные печи с защитной атмосферой СНЗЛ | ||||
СНЗЛ – 1,6.2,5.1/11 И2 Гк | 1100 | 160 × 250 × 100 | 2,5 | |
СНЗЛ – 1,6.2,5.1/12 И2 Гк | 1200 | 160 × 250 × 100 | 3 | |
Камерные печи с защитной атмосферой СНЗ | ||||
СНЗ – 2,5.![]() с вентилятором |
1250 | 250 × 500 × 250 | 8 | |
СНЗ – 3.4.2,5/12 Гк | 1200 | 300 × 400 × 250 | 10 | |
СНЗ – 3.6.2/12,5 Гк | 1250 | 300 × 600 × 200 | 10 | |
СНЗ – 4.5.4/12,5 Гк | 1250 | 400 × 500 × 400 | 13 | |
СНЗ – 4.6.4/12,5 Гк | 1250 | 400 × 600 × 400 | 22 | |
СНЗ – 4.10.2,5/12 Гк | 1200 | 400 × 1000 × 250 | 18 | |
СНЗ – 5.5.4/12,5 Гк | 1250 | 500 × 500 × 500 | 18 | |
СНЗ – 5.5.5/12 Гк |
1200 |
500 × 500 × 500 |
26 |
|
СНЗ – 5.![]() |
1250 | 500 × 1000 × 600 | 41 | |
СНЗ – 6.6.6/8,5 Гк | 850 | 600 × 600 × 600 | 27 | |
СНЗ – 6.8.4/12,5 Гк | 1250 | 600 × 800 × 400 | 42 | |
СНЗ – 6.8.4/12,5 Гк с вентилятором |
1250 | 600 × 800 × 400 | 32 | |
СНЗ – 7.6.6/12,5 Гк | 850 | 700 × 600 × 600 | 30 | |
СНЗ – 7.12.5/12 Гк | 1200 | 700 × 1200 × 500 | 45 | |
СНЗ – 8.10.7/12 Гк | 1200 | 800 × 1000 × 700 | 66 | |
СНЗ – 8,5.10,5.7,5/12 Гк | 1200 | 850 × 1050 × 750 | 70 | |
Шахтные печи с защитной атмосферой СШЗ | ||||
СШЗЛ – 2.![]() |
1200 | Ø 400 × 600 | 24 | |
СШЗ – 4.6/12,5 с вентилятором |
1250 | Ø 400 × 600 | 40 | |
СШЗ – 4,5.12,5/11 з вентилятором |
1100 | Ø 450 × 1250 | 40 | |
СШЗ – 6.6/7 | 700 | Ø 600 × 600 | 41 | |
СШЗ – 6.8/10 | 1000 | Ø 600 × 800 | 50 | |
СШЗ – 6.9/11 | 1100 | Ø 600 × 900 | 38 | |
СШЗ – 6.12/11 | 1000 | Ø 600 × 1200 | 54 | |
СШЗ – 8.15/12,5 | 1250 | Ø 800 × 1500 | 58 | |
СШЗМ – 9.14/7 (вакуумная реторта) |
700 | Ø 900 × 1400 | 120 | |
СШЗ – 10.![]() |
1250 | Ø 1000 × 2500 | 105 | |
СШЗ – 11.22/12 |
1100 |
Ø 1100 × 2200 |
154 |
|
СШЗ – 12.15/11 с вентилятором |
1200 | Ø 1200 × 1500 | 100 | |
Колпаковые печи с защитной атмосферой СГЗ | ||||
СГЗ – 6.6.8/13 | 1300 | 600 × 600 × 800 | 30 | |
СГЗА – 10.10.6,5/7 | 700 | 1000 × 1000 × 650 | 28 | |
СГЗ – 10.10.10/12 | 1200 | 1000 × 1000 × 1000 | 78 | |
СГЗ – 10.16/8,5 |
850 |
Ø 1000 × 1600 |
120 |
|
СГЗ – 10.![]() |
850 | Ø 1000 × 1750 | 190 | |
СГЗ – 10.20/8,5 | 850 | Ø 1000 × 2000 | 200 | |
СГЗ – 10.21/8 | 800 | Ø 1000 × 2100 | 105 | |
СГЗ – 14.15.14/11 | 1100 | 1400 × 1500 × 1400 | 155 | |
СГЗ – 17.30/9 | 900 | Ø 1700 × 3000 | 120 | |
СГЗА – 30.20.10/11 | 1100 | 3000 × 2000 × 1000 | 170 | |
Комплектующие | ||||
Сварной поддон 3 мм, с ребрами жесткости | жаропрочная сталь 20Х23Н18 | |||
Сварной поддон 5 мм, с ребрами жесткости | жаропрочная сталь 20Х23Н18 | |||
Сварной поддон 8 мм, с ребрами жесткости | жаропрочная сталь 20Х23Н18 | |||
Сварной поддон 10 мм, с ребрами жесткости | жаропрочная сталь 20Х23Н18 | |||
Реторта сварная, 8 мм | жаропрочная сталь 20Х23Н18 | |||
Реторта сварная, 10 мм | жаропрочная сталь 20Х23Н18 | |||
Все электропечи разработаны компанией ООО «Бортек» и изготовленны в Украине.![]() |
Отжиг, закалка, отпуск, ТВЧ | Санкт-Петербургский Металлообрабатывающий завод
Термическая обработка в вакуумной печи, ТВЧ
Термическая обработка – это получение заданных свойств металла за счет изменения его внутренней структуры посредством нагрева, выдержки и охлаждения.
Наш термический цех оснащен вакуумной печью
«Ipsen» со следующими параметрами:
- Тип термообработки: отжиг, закалка, отпуск
- Максимальный вес загрузки: 800 кг
- Размеры рабочей камеры: 610x610x910 мм
- Максимальная рабочая температура нагрева: 1320 ºC
- Равномерность распределения температуры: ±5 ºC
- Рабочий вакуум: 4х10-2 мбар (3,7х 10-2 мм.рт.ст)
- Охлаждающая среда: Азот «особо чистый» (99,999%)
- Максимальное давление охлаждающего газа в печи: 12 бар
Мы предоставляем следующие услуги по термообработке:
Отжиг —нагревание металла, а затем медленное охлаждение.
Отжиг бывает разных видов (вид отжига зависит от температуры нагрева, скорости охлаждения металла).
Закалка — термическая обработка, основанная на перекристаллизации стали (сплавов) при нагреве до температуры выше критической; после достаточной выдержки при критической температуре для завершения термической обработки следует быстрое охлаждение. Закаленная сталь (сплав) имеет неравновесную структуру, поэтому применим другой вид термообработки — отпуск.
Отпуск — термическая обработка (термообработка) стали, сплавов, проводимая после закалки для уменьшения или снятия остаточных напряжений в стали и сплавах, повышающая вязкость, уменьшающая твердость и хрупкость металла.
Нормализация —термообработка, схожая с отжигом.
Различия этих термообработок (нормализации и отжига) состоит в том, что при нормализации сталь охлаждается на воздухе (при отжиге — в печи).
- Дополнительные услуги
• закалка ТВЧ; • цементация; • азотирование.
Процесс работы
Анализ запроса
Наши технологи проанализируют Ваш запрос и сформируют коммерческое предложение
Согласование и запуск
После согласования стоимости и сроков — Ваш запрос отправится на изготовление
Закалка стали У8: технология и температура
Углеродистая инструментальная сталь У8 ГОСТ 1435 – популярный материал для изготовления рабочих деталей штампов для холодной листовой штамповки высокопластичных металлов, упоров, фиксаторов, отрезных ножей холодновысадочных автоматов. Кроме того, из данной стали производят некоторые виды металлорежущей оснастки, в частности, метчики и плашки. Ручной инструмент – напильники, зубила, крейцмейсели и т.п. – также могут изготавливаться из стали У8.
Характерные особенности и свойства
Имея в своём химическом составе 0,75…0,85% углерода, а также незначительное количество иных элементов – кремния, марганца, хрома, никеля и меди – сталь У8 является эктектоидной. При пониженном содержании марганца и кремния критическая скорость охлаждения всегда увеличивается. Поэтому практически сталь У8 используют лишь для изготовления металлообрабатывающего инструмента с небольшими габаритными размерами. Закалка стали такого типа допускает применение весьма жёстких охлаждающих сред (воды или водных растворов солей). Таким образом, данная сталь не относится к прокаливаемым: сердцевина остаётся вязкой, а твёрдость, полученная в результате предварительного отжига заготовок, практически такой же и остаётся.
Схема структурных превращений У8
Закалка в воду имеет и другие отрицательные последствия – при росте скорости охлаждения структура стали остаётся крупнозернистой. При дальнейшей обработке (например, ковке) эта особенность может вызвать растрескивание поковки, особенно при значительных степенях деформации. Часто при закалке в воду изделие теряет свои размеры и коробится, что вынуждает дополнительно производить калибровку инструмента.
Необходимо отметить, что эвтектика для стали У8 представляет собой уже при 723 °С чистый аустенит без всяких признаков феррита. Все это влияет на оптимальный выбор режимов термической обработки.
Температура критических точек стали У8 составляет:
- Начало аустенитного превращения, от исходного перлита при нагреве – 720 °С.
- Окончание аустенитного превращения — 740 °С.
- Температуры начала и окончания превращения аустенита в перлит при охлаждении совпадают, и находятся в пределах 700 °С.
- Мартенситное превращение, начинаясь при 810 °С, заканчивается при 245 °С.
Скачать ГОСТ 1435-99 «Прутки, полосы и мотки из инструментальной нелегированной стали»
Твердость стали после термообработки
Общая характеристика прокаливаемости
Фактор прокаливаемости для нелегированных инструментальных сталей считается весьма важным. Большие скорости работы инструмента, начиная от пресс-автоматов, которые функционируют в непрерывном цикле, и заканчивая резьбонарезным инструментом, требуют сочетания высокой поверхностной твёрдости с достаточной вязкостью сердцевины. Иначе рабочие кромки инструментальной оснастки быстро выкрашиваются, а инструмент теряет свою точность.
Интенсивность прокаливаемости зависит от общего числа примесей, которые для стали У8 не должны превышать следующих граничных значений:
- по фосфору 0,25%;
- по сере – 0,03%;
- по меди 0,02%.
Поэтому при приобретении больших партий стали У8 всегда обращают внимание на наличие и содержание сертификатов соответствия, в которых обязательно требуется привести данные по вредным примесям.
Температура заготовки в зависимости от цвета при нагреве
Процентное содержание углерода также оказывает значительное влияние на степень вязкости сердцевины нелегированной стали, и, следовательно, на износостойкость поверхностного слоя. С этой точки зрения сталь У8 относится к вязким. Поэтому особых требований к точности соблюдения режимов термической обработки здесь не требуется.
Изготовление инструментальной оснастки из стали У8 (даже малоразмерной) затрудняется изначально небольшой пластичностью материала.
В исходном состоянии сталь марки У8 может поставляться в следующих видах сортамента по ГОСТ 5210:
- катаной широкой полосы. Ширина полосы составляет 12…48 мм, при толщине 3…10 мм;
- круглого прутка диаметром 4…18 мм;
- квадратного профиля с размером стороны от 4×4 до 18×18 мм;
- специальных профилей.
Отжиг для металла из указанного ассортимента не производится. Для остальных видов поставки, а также при горячей ковке слитков необходим отжиг.
Технология производства отжига
Режим отжига стали У8 определяется следующими факторами:
- способом укладки заготовок на под термической печи;
- соотношением высоты и толщины заготовок;
- температурой нагрева;
- типом нагревательной печи.
График отжига
Экспериментально установлено, что наиболее эффективным режимом отжига является укладка заготовок в один слой на теплоизоляционных подставках из асбеста, при расстоянии между смежными заготовками не менее 3D (под D следует понимать максимальный габаритный размер сечения в плане). Тогда для нагрева до нужной температуры (1000…1200 °С) потребуется:
- для сечения до 20 мм – 5…6 мин;
- для сечения до 30 мм – 8…10 мин;
- для сечения до 40 мм – 9…12 мин;
- для сечения до 50 мм – 12…15 мин;
- для сечения до 75 мм – 15…18 мин;
- для сечения до 100 мм – 19…25 мин;
Поскольку с увеличением продолжительности нагрева возникает опасность поверхностного науглероживания, то отжиг обычно ведут в печах с контролируемой атмосферой, либо в среде инертных газов (двуокиси углерода или даже аргона).
При иных способах укладки скорость нагрева уменьшается на 15…20%.
Лучшее качество отжига получается, если его проводить поэтапно. Вначале выполняется предварительный нагрев, для чего заготовки помещают в печь, которая уже имеет температуру в рабочей зоне до 500…550 °С, а потом постепенно нагревают изделия до требуемой температуры, не допуская скорости нагрева большей, чем 100 °С в час. По достижении требуемого температурного диапазона, отжигаемую продукцию выдерживают в печи не менее 30% от общей продолжительности операции, а потом отключают печь.
Для снятия наклёпа холоднодеформированных изделий из стали У8 их подвергают рекристаллизационному отжигу с охлаждением в расплавах солей (для мелкого инструмента), и в водном растворе поваренной соли – для более крупного. В результате улучшается механическая обрабатываемость, снижаются остаточные деформации (особенно для длинных и тонких прутков и полос), а также оптимизируется структура стали. Температура такого вида отжига составляет 670…700 °С пр выдержке в печи не более часа. При отжиге происходит полная перекристаллизация металла структура получается мелкозернистой, при равномерном распределении зёрен перлита. После отжига твёрдость стали У8 должна быть не более 190 НВ.
Закалка
Если технология закалки соблюдена, то конечная твёрдость изделий после термообработки должна находиться в пределах 59…62 HRC. Для выполнения такого условия, и сохранения необходимой структуры (мартенсит+аустенит) необходимо придерживаться следующих рекомендаций:
- Закалочные процессы протекают в полном объёме, если они начинаются при 800…820 °С.
- Соотношение времени предварительного и окончательного подогрева инструмента под закалку должно быть одинаковым, и находиться в температурном диапазоне значений 400…500 °С.
- Точное время нагрева обычно рассчитывается в зависимости от площади поверхности инструмента и его объёма. Особенно это важно при нагреве заготовок в расплавах солей: для расплавов это должно быть 8…14 мин, для водных растворов – 15…30 мин (увеличенные нормативы применяются для инструмента с резко отличающимися продольными и поперечными размерами).
- Охлаждение инструмента после закалки проводят в воде, температура которой (независимо от времени года и температуры в термическом отделении) должна находиться в пределах 18…25 °С. При более низких температурах возрастает риск растрескивания изделий, а при более высоких твёрдость инструмента получается неравномерной. Тот же дефект возможен в том случае, когда закалочная среда загрязнена минеральными и органическими остатками.
- Закалка стали У8 на воздухе невозможна.
После закалки производится отпуск изделий. При этом мартенситное превращение происходит в полной мере, внутренне напряжения снижаются, а вязкость сердцевины возрастает. Температура отпуска стали У8 после закалки составляет 140…200 °С: именно после таких температур конечная продукция сохранит достаточную твёрдость, и будет обладать достаточно вязкой сердцевиной. Время выдержки принимают в пределах 120…200 с, для измерительного инструмента температура может быть дополнительно снижена на 20…50 °С.
Иногда после заточки и шлифования инструмента из стали У8 (в основном, мерительного) проводят дополнительный отпуск. При этом температура составляет 300…350 °С, а время выдержки — 1,5…2 часа, с последующим охлаждением детали на воздухе.
Глава 5.6 / 5.6.1. Нагрев заготовок
Состояние поверхности металла при нагреве зависит от нагревательных сред, которые подразделяются на активные, обычные и защитные.
Активные среды применяют при выполнении химико-термической обработки, они были рассмотрены выше (см. подразд. 5.5.1).
К обычным средам относится воздух — атмосфера электропечей и продукты сгорания газов — атмосфера газовых печей. При нагреве в этих средах происходят реакции металла с печной атмосферой. Окисление стали начинается при 200 °С (при этом появляются цвета побежалости). Повышение температуры усиливает окисление и вызывает появление окалины — на стальных заготовках образуются рыхлые, слабо связанные с основным металлом оксиды железа. При температуре свыше 700 °С начинается обезуглероживание поверхности стальных заготовок. Эти процессы развиваются тем интенсивнее, чем выше температура и больше продолжительность выдержки. Поэтому при нагреве в печах с обычной атмосферой целесообразно уменьшать время нахождения металла при высоких температурах.
Защитные среды предохраняют стали от окисления, образования окалины и обезуглероживания. В промышленности используют газовые и жидкие среды.
Газовые эндотермические и экзотермические атмосферы получают сжиганием природного газа при определенном соотношении с воздухом. Эти атмосферы позволяют выполнять термическую обработку при температурах 650… 1 100 °С, сохраняя светлую поверхность заготовок. Однако они не являются универсальными, потому что одни операции термической обработки выполняются при более низких температурах (например, отпуск сталей), а другие, напротив, при более высоких.
Идеальной защитной средой является атмосфера, состоящая из инертных газов — аргона, гелия. Однако из-за высокой стоимости они не нашли широкого применения.
В промышленности достаточно широко используют нагрев в вакууме, который не только обеспечивает надежную защиту от окисления и обезуглероживания, но также способствует дегазации металла.
В газовых средах выполняется нагрев для осуществления практически всех видов термической обработки: отжига и нормализации, закалки и отпуска.
Жидкие среды используют в качестве нагревающих и охлаждающих. Их применяют для нагрева под закалку, отпуска, а также для охлаждения при закалке, например при проведении изотермической закалки (см. рис. 5.15). Приведем некоторые составы с различными интервалами температур применения, которые с одной стороны ограничены температурой плавления, с другой — температурой кипения, и, таким образом, используются для проведения различных операций термической обработки.
Так, смесь, состоящая из 45 % NaN03 и 55 % KN03 работоспособна в интервале температур 160… 650 °С, который охватывает температуры отпусков всех видов (низкого, среднего и высокого).
Закалочные смеси охватывают весьма широкий интервал температур, их использование позволяет выполнить закалку практически любой стали. Например, от 750…850 °С выполняется закалка углеродистых доэвтектоидных и заэвтектоидных сталей; от температуры свыше 1200 °С — закалка быстрорежущих сталей.
Состав и рабочие температуры закалочных смесей приведены ниже:
Выбор времени нагрева. Общее время нахождения деталей в печи складывается из времени нагрева до заданной температуры Н и времени выдержки при этой температуре В.
Время выдержки В достаточно регламентировано, оно определяется структурными превращениями, которые должны пройти во всем объеме заготовок (например, полное превращение перлита в аустенит), поэтому сильно изменять эту составляющую общего времени не удается.
Временем нагрева до заданной температуры Н варьировать можно, эта составляющая общего времени зависит от многих факторов.
Прежде всего скорость нагрева металла можно изменять, используя разные технологии. Самая высокая скорость обеспечивается при нагреве ТВЧ до 1000 °С/с. Скорость нагрева в жидких средах (расплавах солей) составляет около 10 °С/с, а в печах с воздушной (газовой) атмосферой она значительно ниже — примерно 1 °С/с. Однако не все способы нагрева являются универсальными, поэтому они не взаимозаменяемы.
Наибольшую скорость обеспечивают технологии поверхностного нагрева. Однако их применение ограничено применением главным образом для поверхностной закалки. Также не универсальны жидкие среды, в основном их используют для закалки и отпуска. Наиболее универсальным является оборудование с газовыми (вакуумной) средами — печи, в которых проводят все виды термической обработки.
При использовании защитных атмосфер увеличение общего времени нагрева не столь существенно. Напротив, при нагреве в печах с обычной атмосферой оно должно быть минимальным для того, чтобы снизить негативные явления (окисление, обезуглероживание и др.). Однако произвольно увеличивать скорость нагрева нельзя, необходимо учитывать целый ряд факторов: химический состав стали, габариты и конструкцию деталей и т. п.
Прежде всего следует помнить о теплопроводности стали, которая зависит от ее химического состава. Быстрый нагрев сталей с низкой теплопроводностью вызовет появление напряжений из-за объемных изменений поверхности и сердцевины детали, проходящих неодновременно. Поэтому углеродистые стали, обладающие большей теплопроводностью, чем легированные, можно нагревать быстрее.
Кроме того, скорость нагрева определяется конструкцией детали. Детали простой формы можно нагревать быстро, при этом перепад температур по сечению небольшой. Быстрее можно также нагревать детали из сталей с более однородной структурой.
Скорость нагрева зависит также от массы одновременно нагреваемого металла (садки) и расположения заготовок в печи. Это связано с тем, что перепад температур по объему печи может быть значительным — быстрее нагреваются детали, расположенные ближе к нагревателям.
В практике термической обработки используют режимы, обеспечивающие различную скорость нагрева заготовок.
Медленный нагрев деталей вместе с печью (детали загружают в холодную печь) применяют для крупногабаритных отливок и поковок из легированных сталей. Чем сложнее конфигурация заготовок, тем медленнее следует осуществлять нагрев. При такой технологии продолжительность нагрева наибольшая.
Ускорение нагрева достигается разными способами. Заготовки помещают в уже нагретую до необходимой температуры печь. Время нагрева при этом уменьшается, но увеличивается перепад температур по сечению заготовки и термические напряжения. Еще быстрее произойдет нагрев до заданной температуры, если заготовки загрузить в печь, температура которой значительно превышает необходимую по технологии. Заготовки при этом не перегреваются, так как при их помещении в печь температура резко падает. После этого нагрев до заданной температуры происходит быстро, но растет перепад температур по сечению заготовок, следовательно, увеличиваются термические напряжения.
Для уменьшения перепада температур применяют нагрев с предварительным подогревом. Для этого используют две печи. Температура первой печи ниже необходимой — в ней осуществляют подогрев, после чего заготовки переносят во вторую печь для окончательного нагрева. Этот прием применяют и при использовании жидких нагревающих сред. Так, в частности, выполняют закалочный нагрев инструментов из быстрорежущих сталей с высокой температурой закалки (свыше 120СГС). Предварительный подогрев необходим для предотвращения деформаций, которые возникают, если инструменты сразу, без подогрева, поместить в ванну с такой высокой температурой.
Система закалки в вакуумной печи: роль закалки в газе при термообработке
Используя газообразные закалочные среды, в секторе термообработки появляются новые и улучшенные модели охлаждения. Однако на эту роль подойдет не любое старое облако газа. Во-первых, обязательно наличие инертного элемента. На синтетическую атмосферу не может повлиять тепло, а заготовка из сплава не может быть каким-либо образом изменена газообразным веществом, по крайней мере, не сверх желаемых эффектов процедуры термообработки.
Основные свойства сред газового тушения
Если инертная газовая атмосфера оказывает какое-либо воздействие на пропитанную нагреванием металлическую деталь, она должна быть плотной и толстой. Обычно рассматриваемый газ поставляется в виде массы высокого давления. Это вещество, называемое закалкой в газе под высоким давлением, подается в печь с вакуумным уплотнением. Отсюда конвекционные токи и законы теплопередачи быстро охлаждают закаленный металлический предмет. Прежде чем продолжить, стоит упомянуть об этих инертных газообразных средах.Это, в порядке предпочтения, азот, гелий, аргон и водород. Аргон дает плохие результаты тушения, в то время как водород воспламеняется при контакте с кислородом.
Преимущества газового тушения
Итак, водород представляет угрозу безопасности. Аргон тоже не лучший вариант. Прилипая к потоку азота или гелия под высоким давлением, вакуумная печь, снабженная камерой закалки, получает поток закалочного газа с заданной скоростью. Здесь большое преимущество заключается в том, что газовое охлаждение не приводит к деформации металла или изменению размеров.Кстати, это особенность, которую закалка жидкостью не может повторить. Кроме того, процесс значительно ускоряется, поэтому закаленная заготовка получает более отзывчивый профиль охлаждения. Системы газового охлаждения высокого давления, снабженные точно рассчитанными по времени закалочными пазами, более управляемы, чем их аналоги для закалки с использованием масла или воды.
Решение проблемы обработки без мартенсита
Мартенситные стали, используемые в промышленности, считаются конструктивно желательными сплавами.Эти сверхтвердые сплавы используются в автомобильных компонентах, пальцах кранов и во всех областях сортировки, где требуются прочные основы. К сожалению, аустенитная сталь нелегко превращается в мартенсит, если только термообработанный сплав не подвергается быстрой закалке. Вот и все, что вам нужно для мощной системы газового охлаждения под высоким давлением.
На стальной детали с газовым охлаждением нет стекания засохшей жидкости, поэтому нет никаких посторонних покрытий, которые нужно счищать после завершения процесса.Детали, подвергнутые закалке жидкостью, имеют тенденцию к образованию остатков, поэтому они не выходят из вакуумной печи чистыми. При использовании систем газовой закалки чистая стальная деталь без изменений размеров выдвигается из печи после завершения термообработки. Никакой деформации материала не происходит, и после этого не остается никаких непонятных покрытий. Лучше всего то, что газовый эффект быстрого охлаждения превращает нагретые аустенитные структуры в закаленный мартенсит, который является сверхтвердым и устойчивым к коррозии.
Тушение азотом — Что такое гашение газом
Закалка — очень распространенный метод термической обработки стали.Процесс гашения помогает предотвратить низкотемпературные процессы, такие как фазовое превращение, за счет сокращения термодинамических и кинетических окон для этих реакций.
Закалка часто используется для увеличения твердости объекта за счет уменьшения размера кристаллического зерна пластмассовых и металлических материалов.
Что такое газовое тушение?
Закалка газом — это форма закалки, при которой в качестве закалочной среды используется газ, а не жидкость. При газовой закалке обычно используется газообразный азот, гелий, аргон, водород или их смесь / смесь для быстрого охлаждения деталей от их критической температуры.Закаливаемые металлические детали могут быть из сплавов или черных металлов.
Газовая закалка имеет ряд преимуществ.
- Закаленные газом материалы более чистые и не имеют остатков на поверхности (это исключает необходимость промывки и утилизации жидких закалочных средств).
- Закалка в газе способствует более равномерному охлаждению и вызывает меньшие искажения, чем закалка в жидкости.
- Для закалки в газе может использоваться среда, которую легко производить на месте, например газообразный азот, производимый местной системой производства азота.
Тушение азотом
Тушение азотом — это тип гашения инертным газом, в котором используется экономичная среда, которая может быть произведена на месте. PSA и мембранные генераторы азота могут использоваться для промышленного производства газообразного азота, устраняя необходимость в транспортировке и хранении баллонов со сжатым газом.
Коэффициент теплопередачи азота
Из-за размера и веса молекул азота по сравнению с другими газовыми средами, такими как водород и гелий, газообразный азот имеет меньший коэффициент теплопередачи.Однако увеличение давления охлаждающей газовой среды улучшит коэффициент теплопередачи вашей газовой закалочной системы. Это повышение давления в сочетании с рентабельным производством газообразного азота делает его подходящей средой для процесса газового охлаждения.
Процесс закалки азотом
Единственным механизмом охлаждения в процессе закалки азотом является конвекция. Конструкция печи, расположение каждой заготовки в печи и размер закаленных заготовок — все это влияет на процесс закалки газообразным азотом.
Во многих приложениях используется закалка газом под высоким давлением, поскольку увеличение давления азота также увеличивает его коэффициент теплопередачи. Увеличение скорости газообразного азота, вводимого в печь, также увеличит коэффициент теплопередачи. Однако включение нагнетателя для увеличения скорости намного дороже, чем использование дожимного компрессора азота для увеличения давления.
После термообработки ваших деталей охлаждающий вентилятор вводит в печь газообразный азот, быстро охлаждая детали от их критической температуры.
GENERON предлагает газовые решения, которые вам нужны
GENERON® — надежный поставщик, специализирующийся на разработке, производстве, проектировании и обслуживании индивидуальных решений для разделения и сжатия технологического воздуха и газа. Мы поставляем технологические пакеты более 50 лет и располагаем более чем 100 запатентованными технологиями для поддержки ваших производственных потребностей.
Свяжитесь с нами онлайн сегодня , чтобы получить ценовое предложение на генератор газообразного азота или дополнительную информацию о том, как наши решения с технологическим газом могут удовлетворить ваши потребности в закалке азота.
Произошла ошибка при настройке пользовательского файла cookie
Этот сайт использует файлы cookie для повышения производительности. Если ваш браузер не принимает файлы cookie, вы не можете просматривать этот сайт.
Настройка вашего браузера для приема файлов cookie
Существует множество причин, по которым cookie не может быть установлен правильно. Ниже приведены наиболее частые причины:
- В вашем браузере отключены файлы cookie. Вам необходимо сбросить настройки вашего браузера, чтобы он принимал файлы cookie, или чтобы спросить вас, хотите ли вы принимать файлы cookie.
- Ваш браузер спрашивает вас, хотите ли вы принимать файлы cookie, и вы отказались. Чтобы принять файлы cookie с этого сайта, нажмите кнопку «Назад» и примите файлы cookie.
- Ваш браузер не поддерживает файлы cookie. Если вы подозреваете это, попробуйте другой браузер.
- Дата на вашем компьютере в прошлом. Если часы вашего компьютера показывают дату до 1 января 1970 г., браузер автоматически забудет файл cookie. Чтобы исправить это, установите правильное время и дату на своем компьютере.
- Вы установили приложение, которое отслеживает или блокирует установку файлов cookie. Вы должны отключить приложение при входе в систему или проконсультироваться с системным администратором.
Почему этому сайту требуются файлы cookie?
Этот сайт использует файлы cookie для повышения производительности, запоминая, что вы вошли в систему, когда переходите со страницы на страницу. Чтобы предоставить доступ без файлов cookie потребует, чтобы сайт создавал новый сеанс для каждой посещаемой страницы, что замедляет работу системы до неприемлемого уровня.
Что сохраняется в файле cookie?
Этот сайт не хранит ничего, кроме автоматически сгенерированного идентификатора сеанса в cookie; никакая другая информация не фиксируется.
Как правило, в файлах cookie может храниться только информация, которую вы предоставляете, или выбор, который вы делаете при посещении веб-сайта. Например, сайт не может определить ваше имя электронной почты, пока вы не введете его. Разрешение веб-сайту создавать файлы cookie не дает этому или любому другому сайту доступа к остальной части вашего компьютера, и только сайт, который создал файл cookie, может его прочитать.
Газовая закалка гелием (Журнальная статья)
Холобофф, Р., Л'Хот, Б., Спери, Р. и Делькур, О. Закалка в газе гелием . США: Н. П., 1993.
Интернет.
Холобофф, Р., Л'Хот, Б., Спери, Р. и Делькур, О. Закалка в газе гелием . Соединенные Штаты.
Холобофф, Р., L'Hote, Б.
, Спери, Р., и Делькур, О. Пн.
«Газовая закалка гелием». Соединенные Штаты.
@article {osti_6465169,
title = {Закалка газа гелием},
author = {Holoboff, R and L'Hote, B and Speri, R and Delcourt, O},
abstractNote = {Соображения безопасности и защиты окружающей среды делают закалку газом привлекательной альтернативой традиционным жидкостным закалочным реакторам.Детали, закаленные газом, чистые и светлые и не требуют дополнительной очистки. Также отсутствуют проблемы утилизации, связанные с газовым охлаждением. Недостаток более медленных скоростей охлаждения можно преодолеть, используя гелий или гелийсодержащие газовые смеси в качестве альтернативы азоту или аргону. Преимущества использования гелия при газовой закалке в вакуумных печах в основном обусловлены его высокой теплопроводностью (среди газов уступает только горючему водороду, уступает только горючему водороду) и низкой плотности (меньше, чем у азота). или аргон).В зависимости от давления в печи скорость охлаждения можно увеличить, просто переключив газы. А поскольку вентиляторам требуется меньше энергии для циркуляции гелия, можно оптимизировать как давление в печи, так и скорость газа (скорость вентилятора). Повышение давления и / или скорости вентилятора также может увеличить скорость охлаждения. Тип газового потока вокруг деталей определяет лучшую гелиевую смесь для использования. Однако, поскольку картина может быть неочевидной, рекомендуется проводить испытания в производственных печах. В Air Liquide дорабатывается компьютерная модель газового потока и теплопередачи как функции давления и скорости.Это будет полезно для прогнозирования воздействия различных газов и газовых смесей.},
doi = {},
url = {https://www.osti.gov/biblio/6465169},
journal = {Современные материалы и процессы; (США)},
issn = {0882-7958},
число =,
объем = 143: 2,
place = {United States},
год = {1993},
месяц = {2}
}
Закалка газом при вакуумной пайке — есть ли опасность?
Дэн Кей
Сегодня ряд паяльных цехов комбинируют пайку и термообработку в своих вакуумных печах для соединения компонентов вместе, а затем для получения определенных требуемых свойств основного металла в этих паяных компонентах посредством быстрого охлаждения (закалки) сразу после пайки и перед компонентами. вынимаются из печи.Таким образом, один и тот же цикл пайки в вакуумной печи сочетает в себе пайку и термообработку, в результате чего получаются чистые паяные компоненты с особыми свойствами основного металла, отвечающими уникальным условиям конечного использования.
Типовая вертикальная вакуумная печь |
Вакуумные печи сегодня предлагают ряд возможностей, касающихся введения и использования циркулирующих газов в горячей зоне печи во время процессов пайки.Газы, обычно вводимые в вакуумную печь, представляют собой аргон или азот, но ряд цехов также добились успеха с газами водородом и гелием. Часто газы объединяют, а не используют только один газ. Водород / азот и гелий / азот — типичные комбинации, используемые в некоторых паяльных цехах.
Литература по термообработке предлагает много ценной информации о методах и эффектах термообработки металлов в зависимости от используемой газовой атмосферы, а также о скоростях охлаждения / закалки, используемых для достижения желаемых свойств конечного использования.
Чего мне не хватает в книгах или статьях о сочетании пайки с термообработкой, так это указаний относительно того, когда действительно следует начинать закалку во время цикла печи. Позвольте мне предложить в этой статье несколько предложений, основанных на том, что я много раз видел при индукционной пайке и пайке горелкой, когда закалка плохо сказывалась на паяном соединении при неправильном использовании.
Я всегда рекомендую людям (при отсутствии других знаний или опыта) выполнять пайку при температуре примерно на 100F (50C) выше опубликованной температуры ликвидуса используемого припоя.Такое количество «перегрева» должно позволить BFM хорошо протекать в паяемое соединение и через него, а также эффективно диффундировать в соединяемые поверхности основного металла (сцепляться с ними).
Затем, после процесса пайки, следует дать расплавленному BFM остыть на месте до полного затвердевания. ОЧЕНЬ важно, чтобы этот расплавленный присадочный металл НЕ нарушался во время охлаждения, так как любые такие нарушения могут привести к появлению трещин и пустот в охлаждающей BFM, что приведет к плохому сцеплению и ослаблению паяных соединений, которые могут протекать (если предполагается, что соединение находится под давлением — герметичны или герметичны) или выходят из строя под воздействием тепловых или механических нагрузок любого типа.
Я наблюдал это недавно, когда паяльный цех использовал индукционную пайку для соединения цилиндрических фитингов вместе, и, с целью ускорения производства, обработал соединение индукционной пайки быстрой струей газообразного аргона в тот момент, когда индукционная пайка была завершена. (BFM в стыке все еще был явно расплавленным). Меня привели в их магазин, чтобы помочь им определить, почему именно эта сборка имеет очень высокий уровень утечек в этом паяном соединении. Как только я увидел, что они делают с гасящим газом, я понял, в чем их проблема.Я посоветовал им подождать всего несколько секунд, пока оператор не увидит, что BFM полностью затвердел в стыке, прежде чем подавать охлаждающий газ на компонент. Проблема с утечкой исчезла.
Мои рекомендации при совмещении пайки в печи и HT:
1. Паяльные присадочные металлы (BFM) должны иметь возможность спокойно остыть из расплавленного состояния до тех пор, пока их температура не станет ниже температуры солидуса этой BFM.
Таким образом, BFM нельзя закаливать, пока они еще расплавлены, во время любой операции пайки (будь то пайка в горелке, индукционная пайка или пайка в печи).Просто никогда нельзя закаливать BFM, пока они еще расплавлены, поскольку такое быстрое охлаждение любого расплавленного BFM может нарушить процесс затвердевания, заставляя BFM перемещаться и смещаться при попытке затвердеть, что приводит к чрезмерным пустотам, растрескиванию и т. Д. В стыке. паяется.
2. Поэкспериментируйте с циклами печи, чтобы определить наилучшее время для начала быстрого охлаждения / закалки, чтобы обеспечить непрерывное затвердевание BFM.
Вы можете обнаружить, что из-за обычных задержек в работе контрольно-измерительных приборов вашей печи расплавленный BFM мог полностью затвердеть до того, как охлаждающие газы действительно попали на паяемые детали.Если так, то хорошо. Но если ваши возможности закалки таковы, что охлаждающий газ может попасть в эти детали, пока BFM еще расплавлен, вам может потребоваться немного отрегулировать время цикла охлаждения до того, как будет введен газ.
Залог успеха: Ни в коем случае не трогайте стык, пока расплав BFM находится в жидком состоянии и начинает остывать. Дайте ему полностью затвердеть, прежде чем гасить или перемещать. Тщательное соблюдение этого принципа предотвратит множество потенциальных проблем при пайке.
СЕМИНАРЫ DAN KAY BRAZING: 3-дневные семинары предусматривают интенсивное обучение «Основам пайки», охватывающее пайку материалов от алюминия до титана и керамики! УЗНАТЬ БОЛЬШЕ
Дэн Кей — Тел: 860-651-5595: — Дэн Кей управляет собственной консалтинговой / обучающей компанией по пайке и занимается твердой пайкой уже 40 лет. Дэн регулярно консультирует по вопросам пайки в вакууме и атмосфере, а также пайки горелкой (пламенем) и индукционной пайки.Его семинары по пайке, проводимые несколько раз в год, помогают людям научиться применять основы пайки для повышения производительности и снижения затрат. Контактную информацию для Дэна Кея (электронная почта, телефон, факс и т. Д.), можно найти, посетив веб-сайт его компании: http://www.kaybrazing.com/
Просмотреть список всех Статьи Дэна, пожалуйста, нажмите здесь
Прочтите биографию Дэна Кея
© Copyright Dan Kay 2015
Типы засыпки, парциального давления и охлаждающих газов для вакуумной термообработки
Вакуумные печи (рис.1) может использовать множество различных газов во время технологического цикла при работе с парциальным давлением, для обратной засыпки до атмосферного давления в конце технологического цикла и для охлаждения / закалки. Наиболее распространенными из этих газов (в порядке частоты использования) являются азот, аргон, водород и гелий (см. Таблицы №№ 1–4). Другие распространенные газы включают различные углеводороды и аммиак (для вакуумной науглероживания / нитроцементации) и специальные газы, такие как неон (для определенных приложений электроники).
Примечания:
[a] Исходя из минимального объема потребления 2830 кубических метров (100 000 кубических футов) в месяц.
[b] Все газы по сравнению с азотом, относительная стоимость которого равна единице.
[c] На основе подачи жидкости.
Примечания:
1. Всегда следует соблюдать соответствующие меры безопасности и здоровья. Свяжитесь с вашим поставщиком газа для получения более подробной информации о безопасном обращении и использовании любых газов, присутствующих на заводе.
2. Обратитесь к разделу ИДЕНТИФИКАЦИЯ ОПАСНОСТИ Паспорта безопасности материала (MSDS) для рассматриваемого газа.
3. Инертные газы, например, все удушающие. Водород легко воспламеняется, а также обладает удушающим действием. Давление газа также является потенциальной проблемой.
Азот (N 2 )
При вакуумной термообработке азот используется в основном для охлаждения / закалки, в качестве газа с парциальным давлением и для засыпки до атмосферного давления в конце цикла термообработки. Однако распространено заблуждение, что газообразный азот — это настоящий инертный газ. Это не так, и при неправильных обстоятельствах он может вступить в реакцию с поверхностью термообрабатываемого материала с пагубными последствиями.
Азот имеет удельный вес по газу 0,967 и, как таковой, немного легче воздуха (с удельным весом 1,0) и имеет точку кипения -195 ° C (–320,5 ° F) при атмосферном давлении.Он бесцветный, без запаха и вкуса. В промышленных масштабах азот производится с помощью различных процессов разделения воздуха, включая криогенное сжижение и дистилляцию, адсорбционное разделение и мембранное разделение (особое примечание: технология мембранного разделения обычно не дает газа с достаточно высокой чистотой для использования в вакууме).
Азот, используемый в большинстве вакуумных систем, поставляется как промышленный газ. Типичные уровни примесей составляют 10 ppm кислорода (максимум) и минимальная точка росы -68 ° C (-90 ° F) или ниже (3.4 частей на миллион по объему). Фактические полученные значения обычно находятся в диапазоне 2 ppm как для кислорода, так и для водяного пара. Часто бывает, что в трубопроводе к оборудованию «накапливается» больше примесей, чем в самом поставляемом продукте, в первую очередь из-за утечек. Также доступны другие сорта азота (включая электронный).
Азот является наиболее распространенным газом для обратной засыпки (рис. 2), используемым при вакуумной термообработке, в значительной степени из-за соображений стоимости и того факта, что он, как правило, не реагирует со многими материалами.Однако в зависимости от температуры азот реагирует с некоторыми материалами, особенно сплавами, содержащими хром, молибден и титан. Он обычно используется в качестве газа с парциальным давлением в диапазоне от 0,67 до 6,67 мбар (500-5000 микрон) или в конвекционном нагреве с положительным давлением, где он оказался эффективным для сокращения времени нагрева / цикла. В большинстве случаев он не перерабатывается.
Аргон (Ar)
Аргон действительно химически инертный газ, составляющий чуть менее 1% воздуха (по объему).Его удельный вес составляет 1,38, поэтому он тяжелее воздуха, а его температура кипения при атмосферном давлении составляет -185,9 ° C (-302,6 ° F). Аргон не имеет цвета, запаха и вкуса, некоррозионный, негорючий и нетоксичный. Товарный аргон является продуктом криогенного разделения воздуха, в котором процессы сжижения и дистилляции используются для получения неочищенного аргона низкой чистоты, который затем очищается до товарного продукта.
Рисунок 2 — Типичная криогенная система хранения азота (фотография любезно предоставлена компанией ALD Thermal Treatment) Аргон используется в первую очередь из-за своих свойств в качестве инертного газа, особенно там, где это важно для предотвращения водородного охрупчивания таких материалов, как титан, тантал, ниобий и цирконий. .Аргон используется в качестве газа с парциальным давлением в диапазоне от 0,67 до 6,67 мбар (500-5000 микрон) во время пайки для минимизации улетучивания, а также в качестве продувочного или продувочного газа (из-за большого размера молекулы аргона), например, двойной насос. методы пуха, используемые до начала нагрева.
Водород (H)
Водород — самый легкий из всех газов, имеющий удельный вес 0,0695 и точку кипения -252,8 ° C (-423 ° F) при атмосферном давлении. Это бесцветный, без запаха, без вкуса, легковоспламеняющийся газ, концентрация которого составляет около 0.0001% в воздухе (по объему). Водород получают несколькими способами, включая риформинг паром / метаном, диссоциацию аммиака, электролиз и извлечение из потоков побочных продуктов во время химического производства и риформинга нефти. Водород хранится и транспортируется в виде газа или криогенной жидкости.
Рисунок 3 5 — Третичная диаграмма для водорода, кислорода и азота (с диапазоном воспламеняемости для условий окружающей среды) Водород используется при термообработке, прежде всего, из-за его свойств как восстановительного газа.Водород обычно используется в качестве газа с парциальным давлением в диапазоне от 0,67 до 6,67 мбар (500-5000 микрон) во многих областях, включая пайку (например, восстановление оксидов), гидрирование (например, титан, тантал), спекание и даже во время нагрева. часть цикла при низком давлении науглероживания в вакууме, где он действует как очищающий (восстанавливающий) агент и сокращает время нагрева. Еще одно распространенное использование водорода — это циклы очистки, включающие либо печь, либо корзины / решетки / приспособления. Несколько компаний сообщают, что используют водород с избыточным давлением (+0.5 фунтов на квадратный дюйм) для таких применений, как спекание металлического порошка для облегчения удаления смазки.
Водород также может использоваться в системах газовой закалки под высоким давлением из-за его высоких свойств теплопередачи. Тем не менее, существуют проблемы безопасности, и необходимо соблюдать особые меры предосторожности (Особое примечание: использование водорода в любом типе печи может быть чрезвычайно опасным. Следует проконсультироваться с производителем оригинального оборудования (OEM), а конечный пользователь должен соблюдать все соответствующие федеральные нормы. , государственные, местные и корпоративные кодексы, правила и положения, прежде чем пытаться это сделать (например,грамм. NFPA 86, последнее издание). См. Ссылку 1 для получения дополнительных сведений об использовании водорода при вакуумной термообработке).
Полная третичная диаграмма (рис. 3) для водорода, кислорода и азота включает диапазон воспламеняемости для условий окружающей среды. Смеси внутри конверта легко воспламеняются. Температурные поправки (рис. 4) были определены, исходя из предположения, что кислород является загрязняющим веществом. Наконец, некоторые металлы (например, титан, тантал) имеют неблагоприятные реакции охрупчивания в присутствии водорода.
Гелий (He)
Гелий также химически инертен и является вторым по легкости газом (после водорода). Гелий имеет удельный вес 0,138. Это бесцветный газ без запаха и вкуса с температурой кипения -268,9 ° C (-452,1 ° F) при атмосферном давлении. Гелий присутствует в воздухе в концентрации всего 0,0005% (по объему). Основным источником поставок являются месторождения природного газа, где неочищенный гелий извлекается из потока природного газа и затем очищается. Гелий может храниться и транспортироваться в виде сжатого газа или криогенной жидкости.
Гелий используется в основном из-за своих свойств в качестве инертного газа. Из-за высокой стоимости гелий необходимо утилизировать. Компоненты системы регенерации газообразного гелия включают:
- Воздуходувка низкого давления
- Хранение низкого давления
- Повторное сжатие
- Хранение высокого давления
- Фильтрация
- Очистка
- Анализ газов
- Интерфейс с подачей газа в вакуумную печь
Гелий используется в газовой закалке под высоким давлением благодаря своим свойствам теплопередачи в диапазоне от 2 до 20 бар для увеличения скорости охлаждения груза во время закалки.В некоторых сталях это позволяет осуществить надлежащее преобразование. В других случаях, например, в случае очень больших толстых деталей или очень плотных грузов, это позволяет сократить общее время цикла.
Углеводороды
Различные углеводородные газы, такие как ацетилен (C 2 H 2 ), циклогексан (C 6 H 12 ), этилен (C 2 H 4 ), метан (CH 4 ), пропан C 3 H 8 ) и пропилен (C 3 H 6 ) используются в качестве источника углерода в таких процессах, как вакуумная науглероживание при низком давлении и нитроцементация (в сочетании с аммиаком, Nh4) или плазменная науглероживание. / азотирование.Все они легковоспламеняемы, и большинство из них имеет заметный запах.
Специальные газы
Газовые смеси могут использоваться для закалки под высоким давлением газа. К ним относятся:
1. Азот / водород
Один из методов, используемых в термической промышленности для увеличения скорости охлаждения (т. Е. Коэффициента теплопередачи) азота, заключается в добавлении небольшого процента водорода в газ. Обычно добавляется 3% водорода, чтобы смесь была негорючей, но, как сообщается, было использовано до 12% водорода (с соответствующими мерами безопасности) для улучшения результатов с маргинальными материалами.Например, цементация SAE 8620 в вакууме может быть закалена газом при более низких давлениях (в зависимости от толщины сечения детали) в смесях азота / водорода для достижения результатов, эквивалентных результатам, получаемым при закалке в масле или более высоких давлениях газообразного азота (например, твердость корпуса, поверхность и сердцевина твердость, микроструктура).
2. Аргон / гелий или аргон / водород
Охлаждающие свойства аргона можно улучшить добавлением гелия или водорода.Смеси аргона и гелия в диапазоне от 50% гелия / 50% аргона до 95% гелия / 5% аргона использовались для увеличения скорости охлаждения в зависимости от давления и материала. Сообщалось, что смеси в диапазоне от 10% водорода / 90% аргона до 40% водорода / 60% аргона улучшают твердость маргинальных материалов. Опять же, необходимо соблюдать все соответствующие меры безопасности. Дополнительным преимуществом использования газовых смесей гелия или водорода является то, что требуются менее мощные охлаждающие вентиляторы (из-за пониженной плотности газа) и потребляется меньшая мощность (Таблица 5).
Подведение итогов
Выбор засыпного газа или газа под парциальным давлением для конкретной системы вакуумной печи остается важным фактором как с металлургической, так и с финансовой точки зрения. Для обеспечения надлежащей целостности и производительности системы рекомендуется правильно подобрать размер, установить и протестировать на герметичность трубопровод для засыпного газа и расширительные (накопительные) резервуары.
Список литературы
- Херринг, Дэниел Х., Вакуумная термообработка, BNP Media Group II, 2012.
- Г-н Дон Боу, «Спросите экспертов», Air Products and Chemicals, Inc. (www.airproducts.com), частная переписка.
- Linde (www.lindeus.com)
- Г-н Тревор Джонс, Солнечные атмосферы (www.solaratm.com), личная переписка.
- Дуайер-младший, Джон, Джеймс Г. Хансель и Том Филипс, Влияние температуры на пределы воспламеняемости в атмосфере термической обработки, Air Products and Chemicals, Inc., 2003.
- Г-н Роберт Хилл, Солнечные атмосферы (www.solaratm.com)
- Airgas (www.airgas.com)
Работа GEM с высоким коэффициентом усиления в чистом аргоне
Работа GEM с высоким коэффициентом усиления в чистом аргонеРабота GEM с высоким коэффициентом усиления в чистом аргоне
А.Брессан а , А.Бузулуцков b * , Л.Ропелевский а , Ф. Саули а , Л.Шехтман10 9383
a
CERN, Женева, Швейцарияб
Институт ядерной физики им. Будкера, Новосибирск, РоссияАннотация
Мы изучаем работу газового электронного умножителя (GEM) в чистом Ar по сравнению с работой в смеси Ar-CO2.В чистом Ar были получены высокие коэффициенты усиления GEM, превышающие 700 и 3000 для одиночных и двойных структур GEM соответственно. Замечено, что на эффективное усиление GEM и его зарядку сильно влияют значения электрического поля выше и ниже GEM. Обсуждаются приложения к созданию нестареющих газовых фотоумножителей.
1. Введение
Принято считать, что газовые устройства не могут должным образом работать в режиме умножения в благородных газах, если не добавлено некоторое количество гасящего газа (в основном органического).Действительно, много лет назад было признано, что максимальное увеличение газового потока, достижимое в чистых благородных газах, довольно невелико из-за очень раннего начала вторичных лавинных процессов [1]. В частности, в чистом Ar коэффициент газового усиления не превышает нескольких сотен в пропорциональных счетчиках [2,3] и нескольких десятков в камерах с параллельными пластинами [4,5].
Плохие гасящие свойства молекулы благородного газа связаны с тем, что она одноатомная. Эта характеристика, однако, очень полезна, если кто-то интересуется детекторами, не подверженными старению: в отличие от молекулярных газов в одноатомных газах ничто не может разлагаться и, таким образом, вызывать старение.Нестареющие газовые наполнители имеют первостепенное значение для разработки газовых фотоумножителей [5-8], где даже небольшое количество химически активных молекул, образовавшихся в результате лавины, может разрушить чувствительный слой фотокатода. В частности, стабильность фотодиодов, заполненных Ar, была доказана при использовании очень большого их количества при воспроизведении звуковой пленки [4].
В течение последних двух лет интенсивно разрабатывается новое газовое устройство с внутренним усилением: газовый электронный умножитель (GEM) [9-13].GEM представляет собой тонкую каптоновую фольгу, покрытую металлом с обеих сторон и перфорированную высокой плотностью микроотверстий, внутри которых происходит усиление газа. Недавно было высказано предположение [13], что GEM может эффективно работать в чистых благородных газах, поскольку гасящие свойства заполняющего газа менее важны по сравнению с другими устройствами газового усиления. Более того, было показано, что работа GEM в чистом Xe практически не отличается от работы в Xe-CO2.
Возможная причина — эффект лавинного удержания в микроотверстиях GEM [13].Один аспект эффекта очевиден: GEM — это, по сути, многосегментное устройство с подавленными обратными связями между дырами. Второй аспект заключается в том, что из-за сильного дипольного поля, сформированного внутри отверстия [10], лавина гасится извне, когда развивается слишком далеко от оси отверстия. Следовательно, независимо от того, какой газ используется, лавина будет ограничена небольшим пространством размером в несколько десятков микрон даже при высоких коэффициентах усиления, предотвращая развитие разряда. В настоящей работе мы изучаем работу GEM в чистом Ar и сравниваем с таковой в смеси Ar-CO2.Показано, что достаточно высокие выигрыши достигаются как для одиночных, так и для двойных структур GEM. Мы также исследуем влияние электрического поля над и под GEM на его эффективное усиление и зарядку.
2. Экспериментальная установка и методика
Рис. 1 Схема сборки одинарного и двойного GEM с соответствующими обозначениями.
Все исследованные устройства GEM имели аналогичную базовую структуру: 5-миллиметровые медные электроды были нанесены на 50 мкм каптон; диаметры отверстий на металле и центре каптона составляли 80 и 50 мкм соответственно; шаг 140 м; активная площадь составляла 10´ 10 см2.Либо одинарная, либо двойная структура GEM была соединена с печатной платой (PCB) с рисунком из полос с шагом 200 мкм, который использовался в качестве элемента считывания (Рис.1). Для одиночной сборки GEM верхний и нижний зазоры составляли 4 и 2 мм соответственно. Для сборки с двойным GEM расстояние между GEM составляло 2 мм, а верхний и нижний зазоры составляли 4 и 1 мм соответственно. Детектор промывали при атмосферном давлении чистым Ar или Ar-CO2 (70-30).
В зависимости от выполняемого измерения печатная плата заземлялась через вход пикоамперметра или усилителя.Высокое напряжение подавалось на электроды ГЭУ через резистивный делитель напряжения. Для одиночного GEM электрическое поле под GEM, ELOW, было пропорционально напряжению, приложенному к GEM (напряжение GEM, VGEM): ELOW = (4, 5 или 10 кВ / см) ´ (VGEM / 400V). Электрическое поле над GEM, EUP, было зафиксировано.
В симметричном режиме работы двойного GEM, VGEM1 = VGEM2 = VGEM и электрические поля под каждым GEM были равны: ELOW1 = ELOW2 = (4кВ / см) ´ (VGEM / 400V). В асимметричном режиме работы напряжение на первом GEM было фиксированным, нижнее поле второго GEM было таким же, как и раньше, в то время как поле между GEM было слабее, варьировалось в пределах 2.4 и 3,4 кВ / см.
Детектор облучали рентгеновским пучком 8 кэВ на площади ~ 40 см2 со скоростью в диапазоне от 101 до 104 мм-2с-1. При измерении амплитуды импульса открытая площадь была уменьшена до 2 мм2 для предотвращения перегрузки усилителя.
Эффективное усиление GEM было определено измерением либо амплитуды импульса с помощью чувствительного к заряду предусилителя (время интегрирования 300 нс), либо измерения тока от печатной платы. Оба метода дали похожие результаты.Калибровка абсолютного усиления была выполнена в точке, где и ток, и скорость счета могли регистрироваться одновременно, предполагая, что начальный заряд в верхнем зазоре, созданный при преобразовании рентгеновских лучей, хорошо известен. Максимальное усиление определяется как усиление при максимальном напряжении, при котором все еще отсутствуют микроразряды в течение как минимум 1 мин. Точность измеренных значений абсолютного усиления оценивается в 20%.
3. Результаты
В одной сборке GEM был обнаружен большой сигнал в чистом Ar, при этом не было замечено никаких остаточных импульсов даже при самых высоких коэффициентах усиления.Фиг.2 показывает усиление GEM как функцию напряжения GEM, измеренного в Ar-CO2 и в чистом Ar с разными скоростями; последние точки соответствуют максимальному безопасному приросту, полученному при заданной скорости. Наборы данных были измерены в оптимизированных верхних полях EUP и в различных нижних полях ELOW.
Можно видеть, что максимальное достижимое усиление в чистом Ar составляет около 700 при скорости 102 мм-2с-1 и большой площади экспонирования. Максимальный коэффициент усиления падает до 500 при увеличении скорости на порядок. С другой стороны, он может приближаться к 1000, уменьшая площадь воздействия и немного увеличивая нижнее поле, от (4 до 5 кВ / см) ´ (VGEM / 400V).Это следует сравнить с 3000, максимальным значением усиления, полученным в Ar-CO2 при аналогичном соотношении более низкого поля к полю GEM.
Рис. 2 Зависимость эффективного коэффициента усиления одиночного GEM от напряжения GEM, измеренного в Ar-
.CO2 и в чистом Ar с разными скоростями и разным ELOW. Выставленная площадь
, размер детектора 40 см2, за исключением двух последних точек данных на графике Ar (крест
символов), где она была уменьшена до 2 мм2.
Рисунок 3 Относительное усиление одиночного GEM в чистом Ar как функция электрического поля в
верхний зазор.
Недавно стало понятно [10,11], что значения верхнего и нижнего электрических полей играют решающую роль в эффективном усилении GEM, то есть в распределении между зарядом, захваченным в дырки GEM, и зарядом, перенесенным после усиления, к нижнему зазору. Эта доля является функцией соотношений EUP / EGEM и ELOW / EGEM (здесь EGEM — среднее поле в отверстиях GEM), диффузии электронов и геометрической прозрачности GEM. Действительно, чем выше отношение ELOW / EGEM, тем большая часть заряда передается от дырок в нижний зазор.И наоборот, чем выше отношение EUP / EGEM, тем большая часть заряда теряется из-за прекращения силовых линий на верхнем электроде GEM.
Последняя точка проиллюстрирована на рисунке 3, где показано относительное усиление как функция верхнего поля: в чистом Ar оптимальное значение EUP ниже 0,5 кВ / см. В Ar-CO2 максимальное значение EUP значительно больше: около 1,5 кВ / см [10]. Разницу можно объяснить более низким рабочим напряжением GEM и, вероятно, большей диффузией электронов в чистом Ar.
Рис. 4 Эффект загрузки GEM в чистом Ar. Показан прирост GEM как функция
времени, измеренного при тех же напряжениях GEM, но в разных электрических полях в
нижний зазор. Открытая площадь составляет 2 мм2.
При слишком высоких значениях нижнего поля нижний зазор начинает работать в режиме усиления с параллельными пластинами. Хотя режим параллельных пластин и обеспечивает дополнительное усиление, он приводит к двум отрицательным эффектам: неравномерному усилению по площади и увеличению заряда GEM.Последний вызван накоплением положительного заряда на нижней, голой стороне каптона из-за ионной обратной связи. Зарядка проявляется в увеличении усиления на низких скоростях из-за увеличения локального поля в отверстиях GEM и в уменьшении усиления на высоких скоростях из-за уменьшения более низкого поля.
Это показано на рис.2. При ELOW (5 кВ / см) ´ (VGEM / 400V), ниже умножения с параллельными пластинами, нет зависимости усиления от скорости как для Ar-CO2, так и для Ar. Однако это не тот случай, когда нижнее поле увеличивается в 2 раза (см. График Ar-CO2): из-за вклада режима параллельных пластин падение усиления может достигать 50% со скоростью 104 по сравнению с этим. 102 мм-2 с-1.
Рисунок 5 Эффективное усиление двойного GEM в симметричном (VGEM1 = VGEM2) и
несимметричный (VGEM1 фиксированный) режим работы в зависимости от напряжения
— второй GEM, измеренный в Ar-CO2 и в чистом Ar. Выставленная площадь
2 мм2; Скорострельность — 103 мм-2 с-1. Верхние поля 1 и 0,4 кВ / см для Ar-
.CO2 и чистый Ar, соответственно
Мы наблюдали эффект зарядки в чистом Ar, когда абсолютное значение нижнего поля достигало 4.9 кВ / см, значение, при котором начинается лавинное размножение в Ar [14,15]. На рис.4 показана стабильность усиления, исследованная при тех же напряжениях GEM, но при разных более низких полях. Видно, что если при ELOW = 3,95 кВ / см коэффициент усиления стабильный, то при ELOW = 4,94 кВ / см он растет со временем до искры. Искровой разряд нейтрализует положительный заряд, накопленный на GEM, и инициирует следующий цикл зарядки.
Рис.6 Спектры амплитуды импульса в двойной GEM для рентгеновского излучения 8 кэВ, измеренные в Ar-CO2
и чистый Ar с эффективными усилениями около 8000 и 2000 соответственно.
Остальные условия такие же, как на рис. 5.
Дальнейшее увеличение максимального усиления было получено в двойной структуре GEM (см. Рис.5). В симметричном режиме работы максимальный выигрыш в чистом Ar составил около 3000, что следует сравнить со значением 20000, полученным в Ar-CO2. Еще более высокие коэффициенты усиления, превышающие 4000, достигаются, если работать в асимметричном режиме, когда напряжение на втором GEM выше, чем на первом.
Достаточно удовлетворительное энергетическое разрешение как в одиночном, так и в двойном GEM было получено в чистом Ar.Например, на рисунке 6 показаны амплитудно-амплитудные спектры рентгеновского излучения с энергией 8 кэВ, измеренные с помощью двойного GEM. Его энергетическое разрешение в Ar (FWHM = 23%) соответствует разрешению в Ar-CO2.
4. Резюме
В заключение, мы продемонстрировали, что довольно большой выигрыш GEM, выше 700, может быть получен в чистом Ar в одном GEM, и очень большой выигрыш, выше 3000, в двойном GEM, с разумным энергетическим разрешением. Это исключение для пропорционального счетчика и, вероятно, является следствием лавинного удержания в микроотверстиях GEM.
Следует отметить, что электроды GEM, использованные в настоящем исследовании, ранее использовались в систематическом исследовании пределов разряда и могут быть здесь слегка повреждены. Следовательно, можно было бы ожидать, что для нетронутого GEM номинальный максимальный выигрыш в Ar может быть даже выше, предположительно в 2-3 раза.
Мы также ожидаем, что дальнейшее увеличение усиления возможно в Xe при условии, что аналогичная тенденция будет наблюдаться в его смесях с CO2.
Важным наблюдением является то, что оптимальные электрические поля в Ar значительно ниже, чем в Ar-CO2.Во избежание потерь заряда и зарядки электрические поля должны быть менее 0,5 кВ / см и 4,9 кВ / см выше и ниже GEM соответственно. Это результат более низкого рабочего напряжения GEM и более раннего начала вклада режима параллельных пластин.
Полученные результаты могут найти применение в основном в области нестареющих газовых устройств. В чистых благородных газах скорость дрейфа электронов относительно мала, а диффузия велика. Следовательно, устройства, заполненные аргоном, нельзя применять для отслеживания обнаружения с высокой скоростью из-за большого времени сбора заряда.Однако они могут иметь отношение к разработке газового фотоумножителя, в котором отсутствует параллакс точки преобразования заряда. В частности, газовый детектор фотонов, состоящий из серии GEM, связанных с твердым фотокатодом и работающих в чистом Ar, Kr или Xe, мог бы быть герметичным, иметь очень длительный срок службы и не подвергаться старению. Срок службы таких газовых фотоумножителей может даже превышать срок службы обычных вакуумных фототрубок из-за более низкой энергии ионов в газовой среде по сравнению с вакуумом и, следовательно, меньшего эффекта ионной бомбардировки фотокатода.
Список литературы
[1] Э. Фюнферт и Х. Нойерт, Zahlrohre und Szintillationszähler, (Verlag, Karlsruhe,
1959) и ссылки в нем.
[2] L.Colli, N.Facchini, E.Gatti, Phys. Ред. 80 (1950) 92.
[3] Саули Ф. Принцип действия многопроволочных пропорциональных и дрейфовых камер, в:
.Экспериментальные методы в физике высоких энергий, под ред. Т.Фербель, (Аддисон-
Wesley, 1987) и ссылки в нем.
[4] A.H.Sommer, Photoemissive Materials, (Krieger, Huntington, 1980), и ссылки
.в нем.
[5] Г.Чарпак, В.Доминик, Ф.Саули и С.Маевски, IEEE Trans. Nucl. Sci.
30 (1983) 134.
[6] В. Песков, Э. Силин, Nucl. Instr. Meth. А 367 (1995) 347.
[7] Бузулуцков А., Шефер Э., Брескин А., Чечик Р., Прагер М., Nucl. Instr. Meth. A
400 (1997) 173.
[8] Э.Шефер, А.Брескин, А.Бузулуцков, Р.Чечик, М.Prager, композит
фотокатодов для визуализации видимых фотонов с помощью газовых фотоумножителей,
Препринт WIS-98/7 / Apr.-DPP, представлен на Vienna Wire Chamber Conf.’98,
для публикации в Nucl. Instr. Meth. А.
[9] Саули Ф., Nucl. Instr. Meth. А 386 (1997) 531.
[10] Р. Буклиер, В. Доминик, М. Хоч, Дж. К. Лаббе, Г. Миллион, Л. Ропелевски, Ф. Саули,
А. Шарма, Г. Манзин, Nucl. Instr. Meth. А 396 (1997) 50.
[11] Дж.Бенллох, А. Брессан, М. Капеа нс, М. Груве, М. Хох, Дж. К. Лаббе, А. Плаччи,
Л. Ропелевски и Ф. Саули, Дальнейшие разработки Gas Electron
Multiplier (GEM), препринт CERN-EP / 98-50, представленный на выставке Vienna Wire
Chamber Conf.’98, будет опубликовано в Nucl. Instr. Meth. А.
[12] Р.